DOI:
10.1039/D2RA06381F
(Paper)
RSC Adv., 2023,
13, 10239-10248
Catalytic activity and mechanism of selective catalytic oxidation of ammonia by Ag–CeO2 under different preparation conditions
Received
10th October 2022
, Accepted 22nd February 2023
First published on 31st March 2023
Abstract
Given the problem of the high-temperature window of CeO2 catalyst activity, this study evaluated the catalytic properties of Ag/CeO2 prepared by changing the preparation methods and loadings. Our experiments showed that Ag/CeO2-IM catalysts prepared by the equal volume impregnation method could have better activity at lower temperatures. The Ag/CeO2-IM catalyst achieves 90% NH3 conversion at 200 °C, and the main reason is that the Ag/CeO2-IM catalyst has more vital redox properties, and the NH3 catalytic oxidation temperature is lower. However, its high-temperature N2 selectivity still needs to be improved and may be related to the less acidic sites on the catalyst surface. On both catalyst surfaces, the i-SCR mechanism governs the NH3-SCO reaction.
1. Introduction
In recent years, ammonia has gradually been increasingly considered as a harmful gas. Excessive emission of ammonia will not only cause a series of impacts on the environment and the decline of biodiversity,1,2 but also cause serious risks to human health. The lowest ammonia concentration that humans can perceive is 5.3 ppm,3 and the increased ammonia emissions will greatly irritate the eyes, respiratory tract, etc.4 Ammonia emissions in cities mainly come from diesel vehicle exhaust,5 as an unexpected result of introducing technology to reduce NOx emissions.6 However, after implementing China's National VI Standard, ammonia emissions have strict requirements, and the treatment of excess ammonia gas becomes necessary.
Technologies to reduce ammonia emissions include adsorption, absorption, biodegradation, catalytic oxidation, thermal decomposition, direct decomposition, and membrane separation.7–9 Ammonia selective catalytic oxidation technique (NH3-SCO) is a highly effective and eco-friendly method of treating waste gases that contain ammonia. NH3-SCO uses catalysts to oxidize NH3 to N2 and H2O under aerobic conditions selectively. Its mechanism has been extensively studied, mainly including three pathways, namely the imide mechanism (–NH mechanism), hydrazine mechanism (N2H4 mechanism), and internal selective catalytic reduction mechanism (an i-SCR mechanism). In the imide mechanism, the adsorbed NH3(ad) is dehydrogenated twice to form –NH, and –NH reacts with O to form the characteristic intermediate –HNO, after which –HNO combines with –NH to produce N2 and/or N2O;10–12 in the hydrazine mechanism, NH3(ad) removes H to become –NH2 and the two combine to form the characteristic intermediate hydrazine (NH2–NH2), and then NH2–NH2 reacts with O to produce N2 and H2O;10,13 in the i-SCR mechanism, NH3(ad) first removes H to form –NHx, which reacts with O2 to form NOx, and then is reduced to N2 and H2O by –NHx.14–16
Research on NH3–SCO catalysts has focused on catalysts made of molecular sieves, noble metals, and transition metals. The surface of molecular sieve catalysts has acidic sites, and the active centers are equally distributed, but the hydrothermal stability is poor.17–19 Noble metal catalysts are characterized by Ag, Pt, Au, Pd, and other precious elements as active components, and precious metals are usually loaded on different carriers. Generally, they have excellent low-temperature catalytic activity and can achieve a high NH3 conversion at 300 °C. But its N2 selectivity is poor, easy to sinter, and the cost is high.20–22 Transition metal catalysts mainly refer to transition metals and their oxides, characterized by low price, abundant and easy availability, and have obtained extensive attention in catalytic oxidation. However, their low-temperature catalytic capacity needs to be improved.23,24 Among them, CeO2 has apparent advantages in catalytic oxidation due to its unique physicochemical properties, oxygen storage, and release capabilities.
In our previous NH3-SCO experiments, although the CeO2 catalyst exhibits excellent redox performance, its activity at cold temperatures needs further improvement. Therefore, we use the combination of Ag and CeO2 to prepare noble metal-supported catalysts to attain high NH3 conversion at cold temperatures and evaluate the performance of Ag/CeO2 catalysts with various preparation methods and loadings. To explore the differences in NH3-SCO properties of Ag/CeO2 catalysts prepared in multiple ways, we adopted XRD, XPS, H2-TPR, and NH3-TPD characterization methods and in situ DRIFTS characterization was adopted to deduce the mechanism of the response.
2. Experimental
2.1 Catalyst synthesis
0.5 g of Ce (NO3)3·6H2O (Tianjin Comio Chemical Co., Ltd) and 0.2 g of PVP (Tianjin Hienceoptech Co., Ltd) were dissolved in 15 mL ethylene glycol, and then the above solution was slowly added to 15 mL deionized water. After continuous stirring for 30 min, the clarified liquor was transferred to a 50 mL PTFE-lined autoclave and kept at 160 °C for 8 h. After the autoclave was cooled at indoor temperature, the samples were gathered by centrifugal washing. Then, the samples were dried overnight at 110 °C in an oven. Finally, the specimens were heat treated at 500 °C for 3 h in a muffle furnace to obtain a CeO2 carrier.
2.1.1 Constant volume impregnation method. 0.0786 g of silver nitrate (Beijing Inokai Technology Co., Ltd) was weighed using an electronic balance, dissolved in deionized water, and prepared into 1 mg mL−1 of silver nitrate solution. After that, a certain amount of carrier CeO2 was weighed into the beaker, and a particular volume of silver nitrate solution was added to CeO2 drop by drop. The mixture was continuously stirred while dropping. After dropping, the mixture was mixed evenly for 30 min. Then, the specimens were kept in an air-blast drying oven and dried at 120 °C for 12 h. Eventually, the dried sample was burned in a muffle furnace at 500 °C for 3 h to obtain the catalyst, x Ag/CeO2-IM-T, where x represents the mass ratio of Ag to CeO2, and T stands for different calcination temperatures (°C).
2.1.2 Deposition–precipitation method. An appropriate amount of CeO2 was weighed using an electronic balance and then dissolved in deionized water. After stirring for 15 min, ammonium carbonate solution was added for proper alkalization. A certain amount of silver nitrate was dropped into the CeO2 solution and stirred continuously. After the dripping, the solution was allowed to stand for 30 min. The combination was aged indoors for 1 h and then washed by centrifugation with deionized water. Consequently, the material was dried at 120 °C for an entire night. Finally, the sample was placed in a quartz boat, burned in a hydrogen tube furnace, and reduced by passing a mixture of 200 mL min−1 (90% N2 and 10% H2) at 400 °C for 2 h to obtain x Ag/CeO2-DP catalyst, where x represents the mass ratio of Ag to CeO2.
2.2 Catalyst characterization
X-ray powder diffraction (XRD) characterization test was performed in a d8-Focus Type X-ray diffractometer produced by Germany Brock AXS Co., Ltd, using Cu target Kα ray (λ = 0.1540598 nm), and Jade 6.5 was used for XRD data analysis.
X-ray photoelectron spectroscopy (XPS) uses ESCALAB 250Xi X-ray photoelectron spectroscopy (USA), with a limit energy resolution of 0.43 eV, a ray source of Al Kα (1486.6 eV, power 150 W, 500 μm beam spots), and the resulting XPS spectrogram uses C 1s (284.8 eV) for charge correction for standard peaks and peak fitting using XPS Peak software.
NH3-temperature-programmed desorption (NH3-TPD) uses AutoChem II 2920 and Chembet TPDTPR-type chemosorbents. 100 mg of the sample was put in an N2 atmosphere at a 10 °C min−1 heating rate to 300 °C, thermostatic pretreatment was 1 h, and was cooled to 50 °C after completion. Then, 500 ppm NH3 is passed for 1 h until adsorption saturation. After that, the flow of NH3 is stopped and purged with N2 for 30 min. After the signal is stabilized, it is heated from 50 °C to 900 °C at 10 °C min−1 in an N2 atmosphere while the NH3 concentration is continuously recorded and output with a TCD signal.
H2-temperature-programmed reduction (H2-TPR) is performed on AutoChem II 2920 and Chemobelt TPDTPR-type chemosorption instruments. 100 mg of sample is placed in an N2 atmosphere at a 10 °C min−1 heating rate to 300 °C and pretreated at a constant temperature for 1 h. The samples were cooled to 50 °C after pretreatment. At the end of the cooling, a 10% H2/Ar gas mixture is introduced, and the temperature rises to 900 °C at a rate of 10 °C min−1. During this process, the H2 consumption is recorded by the TCD detector.
In situ diffuse filter infrared spectroscopy (in situ DRIFTS) was performed using the German Bruker company Tensor II Fourier transform infrared spectrometer, supporting the MCT (Mercury Cadmium Telluride) detector, and the accessory is connected to the in situ diffuse reflection reaction cell. The adsorption, transient, and steady-state reaction experiments of the catalyst surface reaction species involved in this study were performed in this instrument, with a scanning range of 400–4000 cm−1, a diaphragm of 6 mm, a resolution of 4 cm−1, and several scans (64 times).
2.3 Activity testing
The NH3-SCO activity analyses in this study were operated in the laboratory-made fixed-bed quartz reaction device for all catalysts. The composition and concentration of the inlet reaction gas were as follows: [O2] = 10 vol, [NH3] = 500 ppm, N2 was the equilibrium gas, and 300 mL min−1 was the overall gas flow rate. The reaction temperature range of this study was 90–400 °C, and every temperature was constant for 30 min, controlled by a tubular reactor thermostat and a thermocouple. The exhaust gas detection system uses the German Bruker Tensor II infrared spectrometer to detect the concentration of NH3, N2O, NO2, and NO in import and export and uses computer supporting software for data analysis.
The evaluation indexes of NH3-SCO catalyst performance are NH3 conversion and N2 selectivity, which are determined by applying eqn (1) and (2), respectively:
|
 | (1) |
|
 | (2) |
3. Findings and analysis
3.1 Catalytic effectiveness
Different preparation methods have a huge effect on NH3-SCO activity, so we adopted the constant volume impregnation method and deposition–precipitation method to prepare Ag-based catalysts, and the NH3-SCO activities for catalysts with different methods are shown in Fig. 1. Fig. 1a shows the NH3 conversion results, and the T50 of NH3 conversion is 250 °C on the Ag/CeO2-DP catalyst, which is 50 °C lower than the CeO2 support. Still, the T90 of NH3 conversion is above 400 °C on the Ag/CeO2-DP catalyst, higher than the CeO2 support (T90 = 400 °C). The NH3 conversion of Ag/CeO2-IM catalyst reaches 90% at 200 °C, and the T90 is lower at 200 °C than the Ag/CeO2-DP catalyst and has a more excellent ammonia oxidation activity. The results of N2 selectivity are shown in Fig. 1b. The N2 selectivity of the Ag/CeO2-IM catalyst begins to decrease at 125 °C, and the N2 selectivity is 70% at 200 °C, which then continues to decline with the increase in temperature. The Ag/CeO2-DP catalyst's N2 selectivity is marginally higher than that of the Ag/CeO2-IM catalyst, and the N2 selectivity starts to decrease at 150 °C, still higher than 90% at 200 °C, but the N2 selectivity is less than 60% at 400 °C. The graphic shows that the CeO2 has better N2 selectivity than Ag/CeO2-DP catalyst and Ag/CeO2-IM catalyst from 100 °C to 300 °C, but the N2 selectivity declined sharply from 300 °C to 30% at 400 °C. We have compared the catalytic performance of this work with other catalysts in recent years listed in Table 1, and it can be found that the Ag/CeO2-IM catalyst in this study exhibits a high rate of ammonia oxidation over a wide temperature window. While other catalysts with good low-temperature activity have a narrow temperature window and catalysts with good high-temperature ammonia oxidation performance are less active in the low-temperature region, the Ag/CeO2-IM catalyst maintains a more balanced ammonia oxidation performance with an ammonia conversion rate greater than 90% within a wider temperature window from low-temperature 200 °C to high-temperature 400 °C. Overall, catalysts prepared by equal volume impregnation with better NH3 conversion were preferred for further exploration.
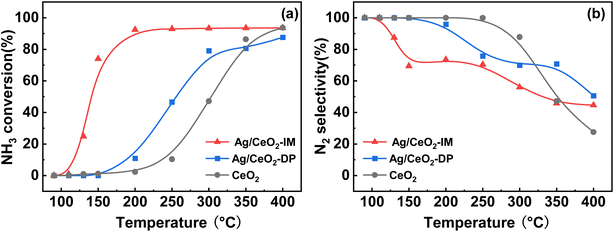 |
| Fig. 1 (a) NH3 conversion (b) N2 selectivity of CeO2, Ag/CeO2-DP, and Ag/CeO2-IM catalysts (inlet reaction gas composition: [NH3] = 500 ppm, [O2] = 10 vol%, N2 is equilibrium gas, GHSV = 60 000 h−1). | |
Table 1 Literature review of catalytic performance results related to Ag or Ce based catalysts
Catalysis |
Preparation method |
Reaction conditions |
Temperature window/°C |
NH3 conversion/% |
Ref. |
Ag/CeO2-IM |
Impregnation |
[NH3] = 500 ppm, [O2] = 10%, GHSV = 60 000 h−1 |
200–400 |
>90 |
This work |
Ag/CeO2-DP |
Deposition–precipitation |
400 |
87 |
1.75Ag/CeSnOx |
Impregnation |
[NH3] = 500 ppm, [O2] = 10%, GHSV = 100 000 h−1 |
250–400 |
100 |
14 |
Ag/Al2O3 |
Rotary evaporator |
[NH3] = 1000 ppm, [O2] = 10%, GHSV = 35 000 h−1 |
130–180 |
100 |
25 |
Ag/ZSM-5 |
110–140 |
100 |
Ag/meso-TiO2 |
Wet impregnation |
[NH3] = 5000 ppm, [O2] = 2.5% |
350–400 |
100 |
26 |
Ag/Al2O3–H2 |
Impregnation |
[NH3] = 500 ppm, [O2] = 10%, GHSV = 28 000 h−1 |
120–180 |
100 |
27 |
Ag/nano-Al2O3 |
Impregnation |
[NH3] = 500 ppm, [O2] = 10%, GHSV = 28 000 h−1 |
100–180 |
100 |
28 |
Ag/SiO2–TiO2 |
Impregnation |
[NH3] = 500 ppm, [O2] = 10%, GHSV = 28 000 h−1 |
140–240 |
100 |
29 |
CuO/CeO2-NR |
Wetness impregnation |
[NH3] = 1000 ppm, [O2] = 10%, GHSV = 40 000 h−1 |
240–250 |
100 |
30 |
CeSnOx |
Coprecipitation |
[NH3] = 500 ppm, [O2] = 10%, GHSV = 100 000 h−1 |
300–400 |
90 |
31 |
Fig. 2 depicts the impact of various Ag loading amounts on the catalytic activity of Ag/CeO2-IM. As shown in Fig. 2a, with an increase in the amount of Ag loading from 0.2 wt% to 1 wt%, T90 of NH3 conversion increased from 400 °C to 200 °C on the Ag/CeO2-IM catalysts. However, with the addition of Ag loading to 2 wt%, NH3 conversion only increased a little at the low temperature. This is because the catalytic activity rises as the number of available surface-active sites increases.32{Azadi, 2012 #48} The increased Ag loading dispersed more Ag particles on the CeO2 carrier. However, with an increase in the amount of Ag packing from 1 wt% to 2 wt%, the dispersion of Ag nanoparticles formed may not be further changed. Therefore, the number of exposed active sites no longer increases, so the NH3 conversion has not increased much. Fig. 2b shows the influence of Ag loading on the N2 selectivity of the catalyst. As Ag has a more vital oxidation capacity,33 NH3 is prone to excessive oxidation at high temperatures. Therefore, appropriate Ag loading can significantly improve NH3 conversion and maintain good N2 selectivity. When the loading reaches 1 wt%, the NH3 conversion reaches 90% at 200 °C, and the N2 selectivity of the catalyst remains above 50% at 125–400 °C, which is the optimum loading capacity for the Ag/CeO2-IM catalyst.
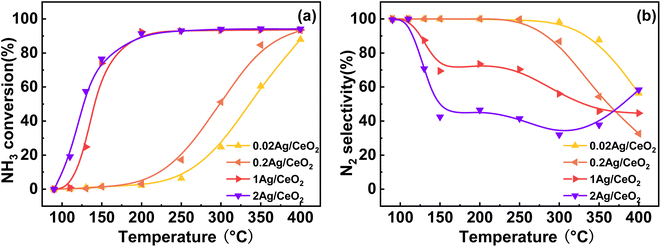 |
| Fig. 2 (a) NH3 conversion (b) N2 selectivity of Ag/CeO2-IM catalyst with different Ag loading amounts (inlet reaction gas composition: [NH3] = 500 ppm, [O2] = 10 vol%, N2 is equilibrium gas, GHSV = 60 000 h−1). | |
3.2 Catalyst phase analysis
The structure of the catalyst can be characterized by XRD. Fig. 3 displays the XRD results of Ag/CeO2 catalysts formed by various preparation methods. It can be observed that the CeO2 crystallinity increases after Ag loading, showing a typical CeO2 cubic fluorite structure diffraction pattern. It also indicates that the Ag impregnation load will not significantly change the crystal structure of CeO2 in the catalyst but also enhance the structural stability of CeO2. Notably, a slight shift in the diffraction angle towards the higher angle was observed, indicating that Ag+ had merged into the CeO2 lattice and changed the CeO2 unit cell parameters.34 In addition, the diffraction peak of Ag species was not observed, indicating that the Ag species were spread uniformly across the catalyst surface or did not reach the XRD detection limit.35
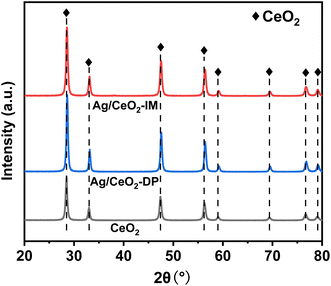 |
| Fig. 3 Results of XRD tests on the catalysts CeO2, Ag/CeO2-DP, and Ag/CeO2-IM. | |
3.3 Surface element valence and oxygen content
The XPS results for determining the state of valence and oxygen concentration of the components on the catalyst's exterior are displayed in Fig. 4 and Table 2. Fig. 4a displays the XPS Ag 3d spectra of CeO2, Ag/CeO2-DP, and Ag/CeO2-IM, where the Ag 3d5/2 core energy level binding energy appears at 367.9 and 368.4 eV. According to reports in the literature, 367.9 eV corresponds to Ag oxide,36 and 368.4 eV correlates to the metal Ag.37 The peak areas in the graph indicate that Ag/CeO2-IM catalysts have two types of Ag species on the surface: metallic Ag and Ag2O. From the deconvolution results of the peaks in Table 2, we can see that Ag/CeO2-IM has 56.02% of Ag0, which has more Ag0 acting as the active site for ammonia oxidation than Ag/CeO2-DP, so Ag/CeO2-IM has superior low-temperature ammonia oxidation performance. Fig. 4b exhibits the XPS Ce 3d spectra of Ag/CeO2-DP, Ag/CeO2-IM, and CeO2 catalysts. The markers u, u′′, and u′′′ correspond to Ce4+ of Ce 3d3/2, v, v′′ and v′′′ correspond to Ce4+ of Ce 3d5/2, while u′ and v′ correspond to Ce3+ of Ce 3d3/2 and Ce 3d5/2, respectively.38,39 The percentage Ce3+ content is shown in Table 2, with 18.30% Ce3+ on CeO2, 13.96% Ce3+ in catalyst Ag/CeO2-DP, and the least Ce3+ content of 10.8% in catalyst Ag/CeO2-IM. This is due to the redox interaction between surface Ce3+ and Ag+, which in turn produces the Ag0–CeO2 interface.40 The Ce3+ sites are involved in Ag+ reduction to form more Ag0, which also corresponds to the metal Ag content outside the catalyst.
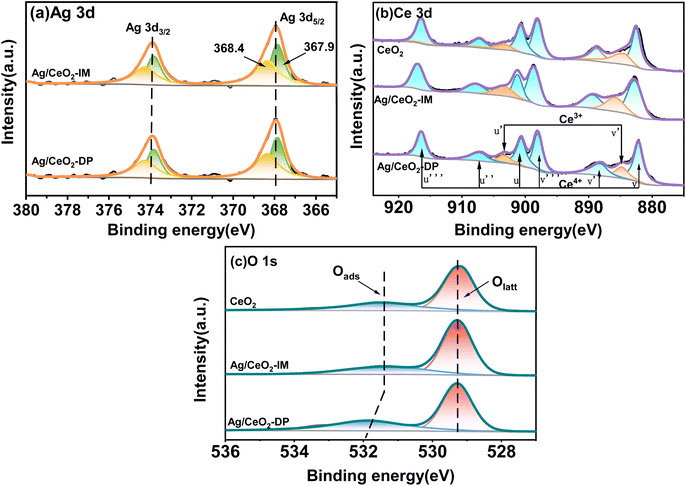 |
| Fig. 4 Results of XPS tests on the catalysts CeO2, Ag/CeO2-DP, and Ag/CeO2-IM. | |
Table 2 XPS results
Catalyst |
Actual Ag content (wt%) |
Atomic ratio (%) |
Ag0/(Ag0 + Ag+) |
Ce3+/(Ce4+ + Ce3+) |
Oads/(Oads + Olatt) |
CeO2 |
— |
— |
18.30 |
26.64 |
Ag/CeO2-DP |
1.19 |
49.83 |
13.96 |
38.15 |
Ag/CeO2-IM |
1.27 |
56.02 |
10.80 |
33.95 |
Fig. 4c exhibits the XPS O1s spectra of CeO2, Ag/CeO2-DP, and Ag/CeO2-IM. The O1s spectra may be fitted to two peaks. The binding energy is about 531 eV for surface adsorption oxygen Oads, and the surface lattice oxygen Olatt is at about 530 eV.41–43 As seen in Table 2, the catalysts obtained by both methods have higher surface adsorption of oxygen. This indicates that species of Ag present affect the ability to activate oxygen by interacting with Ce. Similar phenomena are also found in the literature.44 The Ag/CeO2-IM catalyst's surface had somewhat less adsorption oxygen Oads than the Ag/CeO2-DP catalyst due to the formation of the Ag0–CeO2 interface resulting in a slight increase in surface lattice oxygen.40
3.4 Surface acidity
Fig. 5 depicts the results characterizing the quantity and potency of acid sites across the catalyst's exterior using NH3-TPD. On the surface of the trigger, three different types of desorption peaks can be found: NH3 physically adsorbed or
species adsorbed on weak B-acid site is in charge of the temperature below 150 °C,
species adsorbed on robust B-acid site is in charge of the peak between 150 °C and 250 °C, and
species adsorbed on Lewis acid site is responsible for the peak beyond 250 °C.38,45 Fig. 5 demonstrates that the total number of acid sites is CeO2 > Ag/CeO2-DP > Ag/CeO2-IM in sequence. The Ag/CeO2-DP catalyst retains a narrow peak below 150 °C, but the Ag/CeO2-IM catalyst only has a weak peak attributed to the L-acid site. The reduction of stimulus NH3 consumption after Ag support is mainly related to the drop in acid content brought on by the presence of surface silver species,26 and Ag/CeO2-IM has a very weak acidity due to the formation of the Ag0–CeO2 interface covering more acidic sites. In addition, it has been reported that the N2 selectivity of the ammonia oxidation catalyst will be impacted by its surface acidity,46,47 which explains why the trigger with the lowest N2 selectivity is the Ag/CeO2-IM.
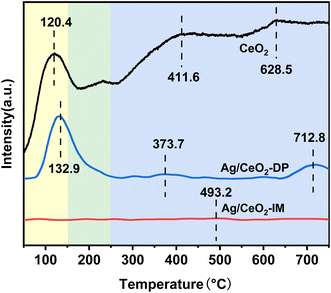 |
| Fig. 5 Test results for the NH3-TPD catalyst with CeO2, Ag/CeO2-DP, and Ag/CeO2-IM. | |
3.5 Redox performance
Fig. 6 displays the data of the H2-TPR analysis of the catalyst's redox capability. There are three reduction crests in the H2-TPR spectra of Ag/CeO2-IM, Ag/CeO2-DP, and CeO2 catalysts. The reduction of Ce4+ to Ce3+ in bulk phase CeO2 causes the peak above 750 °C. In contrast, the removal of CeO2 on the exterior causes the peak between 350 and 650 °C,48–50 and the graph shows that the catalyst's reducing peak at temperatures over 750 °C after supporting Ag is more prominent than CeO2's, and the peak between 350–650 °C disappears. The reduction of silver oxide species or the removal of oxygen on the surface of the Ag0–CeO2 interface is responsible for the appearance of new prominent peaks at temperatures below 300 °C.51,52 Moreover, Ag/CeO2-IM catalyst has a lower reduction peak temperature, which is in line with the findings of the activity test and shows Ag/CeO2-IM catalyst has a more extraordinary redox ability.
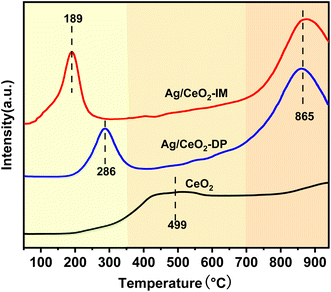 |
| Fig. 6 Test results for the H2-TPR catalyst with CeO2, Ag/CeO2-DP, and Ag/CeO2-IM. | |
3.6 Surface reaction mechanism exploration
The DRIFTS findings of NH3 + O2 co-adsorption at various temperatures were recorded to understand the surface response of NH3-SCO on multiple catalysts, as shown in Fig. 7. The infrared spectra of NH3-SCO reactions on the Ag/CeO2-IM catalyst are shown in Fig. 7a, where 965 cm−1 correspond to physically adsorbed NH3,53 1430 cm−1 can be attributed to the
species adsorbed at the Brønsted acid site,47 1320, 1591, and 1293 cm−1 infrared peaks can be credited with NH2 (ref. 47 and 54) and NH species,46 1030 cm−1 corresponds to bidentate nitrate,55 and 1222 and 1246 cm−1 correspond to bridge nitrate species.45 N2O22− species, the intermediate that gives rise to N2O, is responsible for the peak at 1010 cm−1.56,57 It can be seen from the figure that NH2 and NH species exist at 90 °C, and their peak strength is reduced to 150 °C and disappears, which indicates that some NH3 species adsorbed at low temperatures can be dehydrogenated on the surface.
species (1430 cm−1) and NH2 species (1591 and 1320 cm−1) adsorbed at the Brønsted acid site appeared at 110 °C, and their peak strength first increased and disappeared after 200 °C, indicating that the Brønsted acid site was involved in the ammonia oxidation reaction. After 200 °C, bidentate nitrate (1030 cm−1), bridge nitrate (1222 and 1246 cm−1), and intermediates of N2O (1010 cm−1) appeared, and with rising temperature, their peak strength increased. The above detection results show that during the ammonia oxidation reaction of the Ag/CeO2-IM catalyst, the catalyst surface-adsorbed NH3 species underwent an ammonia oxidation process that was dehydrogenated to produce NH2 and NH. Some NHx species were over-oxidized to form NOx. Subsequently, nitrate adsorbed on the catalyst's exterior reacts with the NHx species to produce N2 and a byproduct called N2O; that is, the ammonia oxidation reaction of the Ag/CeO2-IM catalyst followed the i-SCR mechanism.
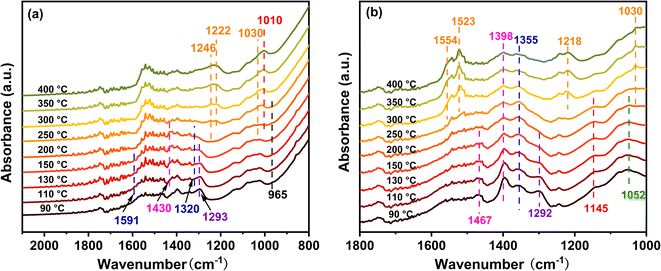 |
| Fig. 7 Ag/CeO2-IM (a) and Ag/CeO2-DP (b) catalysts acting as NH3-SCO catalysts in situ DRIFTS reactions at various temperatures. | |
The infrared spectra of the NH3-SCO reaction on the Ag/CeO2-DP catalyst are shown in Fig. 7b. Brønsted acid sites' adsorbed
species are responsible for the peaks at 1398 and 1467 cm−1,47
species adsorbed at Lewis acid sites are accountable for the peaks at 1145 and 1052 cm−145, NH2 and NH species are responsible for the peaks at 1355 and 1292 cm−1,47 and 1030, 1523, and 1554 cm−1 correspond to bidentate nitrates,55,58,59 and 1218 cm−1 is classified as bridge nitrate.45 The Ag/CeO2-DP catalyst also follows the i-SCR reaction pathway, as shown in Fig. 7b. The double-toothed nitrate and bridge nitrate species were seen outside the Ag/CeO2-DP catalyst at 300 °C. In contrast, these nitrate species were seen on the exterior of the Ag/CeO2-IM catalyst at 200 °C, indicating that the Ag/CeO2-IM catalyst had a lower NH3 ignition temperature and better NH3 oxidation capacity, which agreed with the outcomes of the two catalytic activity tests as well.
3.7 Hydrothermal stability
In practical applications, the diesel engine will undergo a stop-cooling-restart process, which will impact the catalyst's action, so we conducted a cyclic stability test on the motivation and simulated the actual situation to investigate the tolerance of the stimulus. Fig. 8 displays the Ag/CeO2-IM catalyst's stability test results over numerous cycles. During the 5 processes of the cycling test, the NH3 conversion results of the Ag/CeO2-IM catalyst remained constant, T90 was kept at 200 °C, and the N2 selectivity at 400 °C remained relatively stable at about 30%, which indicates that the Ag/CeO2-IM catalyst has good cycling stability and no major changes in the active sites during the cycling process.
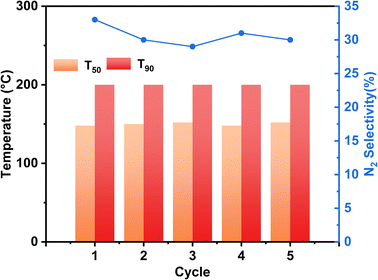 |
| Fig. 8 Comparison of T50, T90, and N2 selectivity at 400 °C for 5 cycles of stability testing of Ag/CeO2-IM catalysts (inlet reaction gas composition: [NH3] = 500 ppm, [O2] = 10 vol%, N2 is equilibrium gas, GHSV = 100 000 h−1). | |
In addition, diesel engines in practical applications usually have exhaust temperatures higher than 600 °C due to the regeneration of diesel particulate filters and contain about 10% H2O.60,61 Therefore, catalysts for diesel vehicles require high hydrothermal durability. Fig. 9 displays the Ag/CeO2-IM catalyst's activity test results before and after hydrothermal ageing at 700 °C for 12 h. Ag/CeO2-IM catalyst's hydrothermal ageing reduces NH3 conversion at low temperatures, an increase of T90 by 50 °C, and a decrease in N2 selectivity to about 50% at 200 °C, which may be due to agglutination and sintering of Ag species at 700 °C. The hydrothermal stability of the Ag/CeO2-IM catalyst needs to be improved.
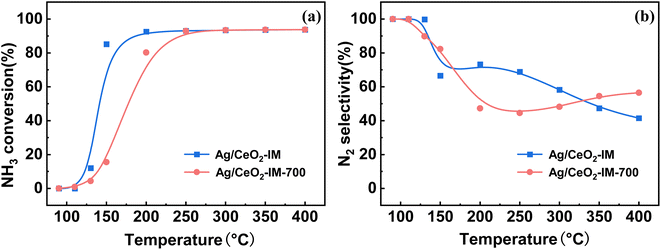 |
| Fig. 9 (a) NH3 conversion (b) N2 selectivity of Ag/CeO2-IM catalyst and Ag/CeO2-IM-700 catalyst after hydrothermal testing. | |
4. Conclusions
In this study, the deposition precipitation approach and equal volume impregnation method were used to create the Ag/CeO2 catalyst, the impact of the preparation technique and load amount on ammonia oxidation performance was discussed, and the following conclusions were drawn:
(1) The Ag/CeO2-IM catalyst prepared by the equal volume impregnation method has a better NH3 oxidation capacity than the Ag/CeO2-DP catalyst prepared by the deposition precipitation method. NH3 conversion can reach 90% at 200 °C, and T50 is below 150 °C. The Ag/CeO2-IM catalyst has good cycle stability, but its hydrothermal stability at 700 °C still needs to be improved.
(2) The Ag/CeO2-IM catalyst has a higher content of Ag0 and stronger redox, which achieves low temperature and high NH3 conversion, but its surface acidity is less than that of Ag/CeO2-DP, which results in N2 selectivity decreasing slowly at 150–400 °C. According to the results of in situ DRIFTS, the Ag/CeO2-IM catalyst had a lower NH3 ignition temperature and better NH3 oxidation capacity, which was the main reason for the higher activities of the Ag/CeO2-IM catalyst.
(3) The mechanism of NH3-SCO on the Ag/CeO2-IM and Ag/CeO2-DP catalysts both followed the i-SCR mechanism.
Conflicts of interest
There are no conflicts to declare.
Acknowledgements
This work was supported by the National Natural Science Foundation of China (22076136), the Central Government Guides Local Science and Technology Development Fund Project (206Z3702G), and Hebei Province Major Scientific and Technological Achievement Transformation Fund Support Project (2021004012A and 22281401Z).
References
- Y. Zeng, S. Tian and Y. Pan, Revealing the Sources of Atmospheric Ammonia: a Review, Curr. Pollut. Rep., 2018, 4(3), 189–197 CrossRef.
- C. M. Clark and D. Tilman, Loss of plant species after chronic low-level nitrogen deposition to prairie grasslands, Nature, 2008, 451(7179), 712–715 CrossRef CAS PubMed.
- X. Qiang, M. Hu, B. Zhao, Y. Qin, T. Zhang, L. Zhou and J. Liang, Preparation of porous silicon/Pd-loaded WO 3 nanowires for enhancement of ammonia sensing properties at room temperature, Mater. Sci. Semicond. Process., 2018, 79, 113–118 CrossRef CAS.
- S. Gerrity, E. Clifford, C. Kennelly and G. Collins, Ammonia oxidizing bacteria and archaea in horizontal flow biofilm reactors treating ammonia-contaminated air at 10 degrees C, J. Ind. Microbiol. Biotechnol., 2016, 43(5), 651–661 CrossRef CAS PubMed.
- M. Gu, Y. Pan, W. W. Walters, Q. Sun, L. Song, Y. Wang, Y. Xue and Y. Fang, Vehicular Emissions Enhanced Ammonia Concentrations in Winter Mornings: Insights from Diurnal Nitrogen Isotopic Signatures, Environ. Sci. Technol., 2022, 56(3), 1578–1585 CrossRef CAS PubMed.
- N. J. Farren, J. Davison, R. A. Rose, R. L. Wagner and D. C. Carslaw, Underestimated Ammonia Emissions from Road Vehicles, Environ. Sci. Technol., 2020, 54(24), 15689–15697 CrossRef CAS PubMed.
- E. Liu, B. Sarkar, L. Wang and R. Naidu, Copper-complexed clay/poly-acrylic acid composites: Extremely efficient adsorbents of ammonia gas, Appl. Clay Sci., 2016, 121–122, 154–161 CrossRef CAS.
- E. Morral, D. Gabriel, A. D. Dorado and X. Gamisans, A review of biotechnologies for the abatement of ammonia emissions, Chemosphere, 2021, 273, 128606 CrossRef CAS PubMed.
- M. Saeed, M. A. Arain, M. Naveed, M. Alagawany, M. E. Abd El-Hack, Z. A. Bhutto, M. Bednarczyk, M. U. Kakar, M. Abdel-Latif and S. Chao, Yucca schidigera can mitigate ammonia emissions from manure and promote poultry health and production, Environ. Sci. Pollut. Res. Int., 2018, 25(35), 35027–35033 CrossRef CAS PubMed.
- T. Lan, Y. Zhao, J. Deng, J. Zhang, L. Shi and D. Zhang, Selective catalytic oxidation of NH(3)over noble metal-based catalysts: state of the art and future prospects, Catal. Sci. Technol., 2020, 10(17), 5792–5810 RSC.
- L. Zhang and H. He, Mechanism of selective catalytic oxidation of ammonia to nitrogen over Ag/Al2O3, J. Catal., 2009, 268(1), 18–25 CrossRef CAS.
- S. Ge, X. Liu, J. Liu, H. Liu, H. Liu, X. Chen, G. Wang, J. Chen, G. Zhang, Y. Zhang and J. Li, Synthesis of TixSn1-xO2 mixed metal oxide for copper catalysts as high-efficiency NH3 selective catalytic oxidation, Fuel, 2022, 314, 123061 CrossRef CAS.
- M. Sun, J. Liu, C. Song, Y. Ogata, H. Rao, X. Zhao, H. Xu and Y. Chen, Different Reaction Mechanisms of Ammonia Oxidation Reaction on Pt/Al2O3 and Pt/CeZrO2 with Various Pt States, ACS Appl. Mater. Interfaces, 2019, 11(26), 23102–23111 CrossRef CAS PubMed.
- Y. Zhang, M. Zhang, Y. Zang, H. Wang, C. Liu, L. Wei, Y. Wang, L. He, W. Wang, Z. Zhang, R. Han, N. Ji, C. Song, X. Lu, D. Ma, Y. Sun and Q. Liu, Elimination of NH3 by Interfacial Charge Transfer over the Ag/CeSnOx Tandem Catalyst, ACS Catal., 2023, 1449–1461 CrossRef CAS.
- H. Wang, T. Murayama, M. Lin, N. Sakaguchi, M. Haruta, H. Miura and T. Shishido, Understanding the Distinct Effects of Ag Nanoparticles and Highly Dispersed Ag Species on N-2 Selectivity in NH3-SCO Reaction, ACS Catal., 2022, 12(10), 6108–6118 CrossRef CAS.
- L. Peng, A. Guo, D. Chen, P. Liu, B. Peng, M. Fu, D. Ye and P. Chen, Ammonia Abatement via Selective Oxidation over Electron-Deficient Copper Catalysts, Environ. Sci. Technol., 2022, 56(19), 14008–14018 CrossRef CAS PubMed.
- L. Chmielarz and M. Jablonska, Advances in selective catalytic oxidation of ammonia to dinitrogen: a review, RSC Adv., 2015, 5(54), 43408–43431 RSC.
- J. Guo, Y. Peng, Y. Zhang, W. Yang, L. Gan, K. Li, J. Chen and J. Li, Comparison of NH3-SCO performance over CuOx/H-SSZ-13 and CuOx/H-SAPO-34 catalysts, Appl. Catal., A, 2019, 585, 117119 CrossRef CAS.
- F. Wang, Y. Zhu, Z. Li, Y. Shan, W. Shan, X. Shi, Y. Yu, C. Zhang, K. Li, P. Ning, Y. Zhang and H. He, Promoting effect of acid sites on NH3-SCO activity with water vapor participation for Pt-Fe/ZSM-5 catalyst, Catal. Today, 2021, 376, 311–317 CrossRef CAS.
- T. Lan, Y. Zhao, J. Deng, J. Zhang, L. Shi and D. Zhang, Selective catalytic oxidation of NH3 over noble metal-based catalysts: state of the art and future prospects, Catal. Sci. Technol., 2020, 10(17), 5792–5810 RSC.
- H. Wang, T. Murayama, M. Lin, N. Sakaguchi, M. Haruta, H. Miura and T. Shishido, Understanding the Distinct Effects of Ag Nanoparticles and Highly Dispersed Ag Species on N2 Selectivity in NH3–SCO Reaction, ACS Catal., 2022, 6108–6118 CrossRef.
- H. Wang, M. Lin, T. Murayama, S. Feng, M. Haruta, H. Miura and T. Shishido, Selective catalytic oxidation of ammonia to nitrogen over zeolite-supported Pt-Au catalysts: Effects of alloy formation and acid sites, J. Catal., 2021, 402, 101–113 CrossRef CAS.
- H. Zhao, Z. Qu and H. Sun, Rational design of spinel CoMn2O4 with Co-enriched surface as high-activity catalysts for NH3-SCO reaction, Appl. Surf. Sci., 2020, 529, 147044 CrossRef CAS.
- W. Liu, Y. Long, X. Tong, Y. Yin, X. Li and J. Hu, Transition metals modified commercial SCR catalysts as efficient catalysts in NH3-SCO and NH3-SCR reactions, Mol. Catal., 2021, 515, 111888 CrossRef CAS.
- Z. Wang, Q. Sun, D. Wang, Z. Hong, Z. Qu and X. Li, Hollow ZSM-5 zeolite encapsulated Ag nanoparticles for SO2-resistant selective catalytic oxidation of ammonia to nitrogen, Sep. Purif. Technol., 2019, 209, 1016–1026 CrossRef CAS.
- M. Jablonska, W. Ciptonugroho, K. Gora-Marek, M. G. Al-Shaal and R. Palkovits, Preparation, characterization and catalytic performance of Ag-modified mesoporous TiO2 in low-temperature selective ammonia oxidation into nitrogen and water vapour, Microporous Mesoporous Mater., 2017, 245, 31–44 CrossRef CAS.
- F. Wang, G. He, B. Zhang, M. Chen, X. Chen, C. Zhang and H. He, Insights into the Activation Effect of H2 Pretreatment on Ag/Al2O3 Catalyst for the Selective Oxidation of Ammonia, ACS Catal., 2019, 9(2), 1437–1445 CrossRef CAS.
- F. Wang, J. Ma, G. He, M. Chen, C. Zhang and H. He, Nanosize Effect of Al2O3 in Ag/Al2O3 Catalyst for the Selective Catalytic Oxidation of Ammonia, ACS Catal., 2018, 8(4), 2670–2682 CrossRef CAS.
- F. Wang, J. Ma, G. He, M. Chen, S. Wang, C. Zhang and H. He, Synergistic Effect of TiO2–SiO2 in Ag/Si–Ti Catalyst for the Selective Catalytic Oxidation of Ammonia, Ind. Eng. Chem. Res., 2018, 57(35), 11903–11910 CrossRef CAS.
- H. Sun, H. Wang and Z. Qu, Construction of CuO/CeO2 Catalysts via the Ceria Shape Effect for Selective Catalytic Oxidation of Ammonia, ACS Catal., 2023, 1077–1088 CrossRef CAS.
- L. Zhou, M. Zhang, C. Liu, H. Wang, Y. Zhang, Y. Zang, Z. Zhang, R. Han, N. Ji, C. Song, X. Lu, W. Wang and Q. Liu, Synergistic Effect over CeSnOx Catalyst for the Selective Catalytic Oxidation of NH3, ACS Appl. Energy Mater., 2022, 5(11), 14211–14221 CrossRef CAS.
- P. Azadi, E. Afif, F. Azadi and R. Farnood, Screening of nickel catalysts for selective hydrogen production using supercritical water gasification of glucose, Green Chem., 2012, 14(6), 1766–1777 RSC.
- W. J. Liu, Y. F. Long, S. N. Liu, Y. Y. Zhou, X. Tong, Y. J. Yin, X. Y. Li, K. Hu and J. J. Hu, Promotional effect of Ce in NH3-SCO and NH3-SCR reactions over Cu-Ce/SCR catalysts, J. Ind. Eng. Chem., 2022, 107, 197–206 CrossRef CAS.
- T. Montini, M. Melchionna, M. Monai and P. Fornasiero, Fundamentals and Catalytic Applications of CeO2-Based Materials, Chem. Rev., 2016, 116(10), 5987–6041 CrossRef CAS PubMed.
- Y. Su, K. Fu, Y. Zheng, N. Ji, C. Song, D. Ma, X. Lu, R. Han and Q. Liu, Catalytic oxidation of dichloromethane over Pt-Co/HZSM-5 catalyst: Synergistic effect of single-atom Pt, Co3O4, and HZSM-5, Appl. Catal., B, 2021, 288, 119980 CrossRef CAS.
- S. Zhao, Z. Li, Z. Qu, N. Yan, W. Huang, W. Chen and H. Xu, Co-benefit of Ag and Mo for the catalytic oxidation of elemental mercury, Fuel, 2015, 158, 891–897 CrossRef CAS.
- E. Sumesh, M. S. Bootharaju and A. T. Pradeep, A practical silver nanoparticle-based adsorbent for the removal of Hg2+ from water, J. Hazard. Mater., 2011, 189(1–2), 450–457 CrossRef CAS PubMed.
- S. M. Lee, H. H. Lee and S. C. Hong, Influence of calcination temperature on Ce/TiO2 catalysis of selective catalytic oxidation of NH3 to N2, Appl. Catal., A, 2014, 470, 189–198 CrossRef CAS.
- Z. Wang, Z. Qu, X. Quan, Z. Li, H. Wang and R. Fan, Selective catalytic oxidation of ammonia to nitrogen over CuO-CeO2 mixed oxides prepared by surfactant-templated method, Appl. Catal., B, 2013, 134–135, 153–166 CrossRef CAS.
- M. V. Grabchenko, G. V. Mamontov, V. I. Zaikovskii, V. La Parola, L. F. Liotta and O. V. Vodyankina, The role of metal-support interaction in Ag/CeO2 catalysts for CO and soot oxidation, Appl. Catal., B, 2020, 260, 118148 CrossRef CAS.
- M. Sun, S. Wang, Y. Li, H. Xu and Y. Chen, Promotion of catalytic performance by adding W into Pt/ZrO2 catalyst for selective catalytic oxidation of ammonia, Appl. Surf. Sci., 2017, 402, 323–329 CrossRef CAS.
- J. H. Shin, G. J. Kim and S. C. Hong, Reaction properties of ruthenium over Ru/TiO2 for selective catalytic oxidation of ammonia to nitrogen, Appl. Surf. Sci., 2020, 506, 144906 CrossRef CAS.
- Y. Wang, H. Chang, C. Shi, L. Duan, J. Li, G. Zhang, L. Guo and Y. You, Novel Fe-Ce-O mixed metal oxides catalyst prepared by hydrothermal method for Hg0 oxidation in the presence of NH3, Catal. Commun., 2017, 100, 210–213 CrossRef CAS.
- X. L. Tang, Y. Y. Zhang, Y. R. Lei, Y. Y. Liu, H. H. Yi and F. Y. Gao, Promotional catalytic activity and reaction mechanism of Ag-modified Ce0.6Zr0.4O2 catalyst for catalytic oxidation of ammonia, J. Environ. Sci., 2023, 124, 491–504 CrossRef PubMed.
- H. Wang, Q. Zhang, T. Zhang, J. Wang, G. Wei, M. Liu and P. Ning, Structural tuning and NH3-SCO performance optimization of CuO-Fe2O3 catalysts by impact of thermal treatment, Appl. Surf. Sci., 2019, 485, 81–91 CrossRef CAS.
- M. Lin, B. An, N. Niimi, Y. Jikihara, T. Nakayama, T. Honma, T. Takei, T. Shishido, T. Ishida, M. Haruta and T. Murayama, Role of the Acid Site for Selective Catalytic Oxidation of NH3 over Au/Nb2O5, ACS Catal., 2019, 9(3), 1753–1756 CrossRef CAS.
- Q. Zhang, T. Zhang, F. Xia, Y. Zhang, H. Wang and P. Ning, Promoting effects of acid enhancing on N-2 selectivity for selectivity catalytic oxidation of NH3 over RuOx/TiO2: The mechanism study, Appl. Surf. Sci., 2020, 500, 144044 CrossRef CAS.
- A. Trovarelli, Catalytic properties of ceria and CeO2-containing materials, Catal. Rev., 1996, 38(4), 439–520 CrossRef CAS.
- E. Aneggi, D. Wiater, C. de Leitenburg, J. Llorca and A. Trovarelli, Shape-Dependent Activity of Ceria in Soot Combustion, ACS Catal., 2013, 4(1), 172–181 CrossRef.
- K. Krishna, A. Bueno-López, M. Makkee and J. A. Moulijn, Potential rare-earth modified CeO2 catalysts for soot oxidation part II: Characterisation and catalytic activity with NO+O2, Appl. Catal., B, 2007, 75(3–4), 201–209 CrossRef CAS.
- L. Yu, R. Peng, L. Chen, M. Fu, J. Wu and D. Ye, Ag supported on CeO2 with different morphologies for the catalytic oxidation of HCHO, Chem. Eng. J., 2018, 334, 2480–2487 CrossRef CAS.
- G. V. Mamontov, M. V. Grabchenko, V. I. Sobolev, V. I. Zaikovskii and O. V. Vodyankina, Ethanol dehydrogenation over Ag-CeO2/SiO2 catalyst: Role of Ag-CeO2 interface, Appl. Catal., A, 2016, 528, 161–167 CrossRef CAS.
- D. M. Meng, W. C. Zhan, Y. Guo, Y. L. Guo, L. Wang and G. Z. Lu, A Highly Effective Catalyst of Sm-MnOx for the NH3-SCR of NOx at Low Temperature: Promotional Role of Sm and Its Catalytic Performance, ACS Catal., 2015, 5(10), 5973–5983 CrossRef CAS.
- Q. L. Zhang, H. M. Wang, P. Ning, Z. X. Song, X. Liu and Y. K. Duan, In situ DRIFTS studies on CuO-Fe2O3 catalysts for low temperature selective catalytic oxidation of ammonia to nitrogen, Appl. Surf. Sci., 2017, 419, 733–743 CrossRef CAS.
- S. H. Zhan, H. Zhang, Y. Zhang, Q. Shi, Y. Li and X. J. Li, Efficient NH3-SCR removal of NOx with highly ordered mesoporous WO3(chi)-CeO2 at low temperatures, Appl. Catal., B, 2017, 203, 199–209 CrossRef CAS PubMed.
- M. Q. Shen, L. L. Xu, J. Q. Wang, C. X. Li, W. L. Wang, J. Wang and Y. P. Zhai, Effect of synthesis methods on activity of V2O5/CeO2/WO3-TiO2 catalyst for selective catalytic reduction of NOx with NH3, J. Rare Earths, 2016, 34(3), 259–267 CrossRef CAS.
- Y. Liu, T. T. Gu, X. L. Weng, Y. Wang, Z. B. Wu and H. Q. Wang, DRIFT Studies on the Selectivity Promotion Mechanism of Ca-Modified Ce-Mn/TiO2 Catalysts for Low-Temperature NO Reduction with NH3, J. Phys. Chem. C, 2012, 116(31), 16582–16592 CrossRef CAS.
- M. Jablonska, A. M. Beale, M. Nocun and R. Palkovits, Ag-Cu based catalysts for the selective ammonia oxidation into nitrogen and water vapour, Appl. Catal., B, 2018, 232, 275–287 CrossRef CAS.
- L. Uran, J. Gallego, W. Ruiz, E. Bailon-Garcia, A. Bueno-Lopez and A. Santamaria, Monitoring intermediate species formation by DRIFT during the simultaneous removal of soot and NOx over LaAgMnO3 catalyst, Appl. Catal., A, 2019, 588, 117280 CrossRef CAS.
- B. Guan, R. Zhan, H. Lin and Z. Huang, Review of state of the art technologies of selective catalytic reduction of NOx from diesel engine exhaust, Appl. Therm. Eng., 2014, 66(1–2), 395–414 CrossRef CAS.
- A. Marberger, M. Elsener, R. J. G. Nuguid, D. Ferri and O. Kröcher, Thermal activation and aging of a V2O5/WO3-TiO2 catalyst for the selective catalytic reduction of NO with NH3, Appl. Catal., A, 2019, 573, 64–72 CrossRef CAS.
|
This journal is © The Royal Society of Chemistry 2023 |
Click here to see how this site uses Cookies. View our privacy policy here.