DOI:
10.1039/D2QM00863G
(Research Article)
Mater. Chem. Front., 2023,
7, 145-152
Thiol for interfacial modification to improve the performance of lithium–sulfur batteries†
Received
23rd August 2022
, Accepted 8th November 2022
First published on 14th November 2022
Abstract
Lithium–sulfur (Li–S) batteries are considered as one of the most promising next-generation secondary batteries. However, the shuttle effect of soluble polysulfides in the electrolyte seriously affects the performance of Li–S batteries. In this paper, 4,4′-thiodibenzenethiol (TBBT), with two thiol functional groups, is introduced into the electrolyte as an additive to suppress the shuttle effect. TBBT captures polysulfides to form organic sulfide during the charge–discharge process, changing the existing form of active materials and effectively limiting the generation of long-chain polysulfides, leading to a long cycling life. The battery with the TBBT-containing electrolyte exhibits a high initial discharge capacity of 994.4 mA h g−1, which still maintains 752.7 mA h g−1 after cycling for 300 cycles at 0.5C. Meanwhile, a Li–S pouch cell with the TBBT additive shows a better cycling stability with a capacity retention rate of 65% after 30 cycles compared with the blank sample. In summary, this work provides an effective strategy to relieve the shuttle effect by introducing TBBT to change the existing form of active materials from long-chain polysulfides to organic sulfide during cycling.
Introduction
With the development of electric vehicles and electronic devices, current lithium-ion batteries can scarcely meet the requirement of high-energy-density batteries.1,2 Therefore, it is of great significance to develop novel high-energy-density secondary batteries. Li–S batteries show great application prospects due to their high theoretical energy density (2600 W h kg−1) and high specific capacity (1675 mA h g−1).3–5
The shuttle effect of polysulfides is one of the most serious problems, which results in a low discharge capacity, a low coulombic efficiency, severe self-discharge and lithium metal anode corrosion in Li–S batteries.6–8 Several strategies have been employed to solve this problem: surface modification of the sulfur cathode, separator decoration, the optimization of electrolyte, etc. Monoatomic doping and the introduction of polar compounds to modify the carrier materials are effective ways to adsorb the polysulfides and inhibit the shuttle effect.9–17 Moreover, introducing a multifunctional interlayer on the separator or cathode is also a valid method to prevent the shuttle effect.18–20 Although the cathode modification and separator decoration methods exhibit positive effects on suppressing the shuttle effect, the complicated process and high cost involved make it difficult to achieve large-scale application. These extra additions to the battery system could also reduce the energy density. In addition, researchers have tried to construct a stable SEI film by introducing additives in the electrolyte to prevent the continuous corrosion of the Li anode by polysulfide compounds.21–24 However, these methods that aim to fix polysulfides have limited effects since it is difficult to change the intrinsic properties of polysulfides. The key to solving this problem is optimizing the existing form of active substances during cycling, which restrains the generation of polysulfide, leading to inhibition of the shuttle effect.25,26 Recently, organic compounds with different structures have been used widely to prepare organic sulfur cathodes for improving the electrochemical performance of batteries.27–29 This organic sulfur cathode exhibits excellent reversibility and effectively reduces the effects of the polysulfide shuttle, but the preparation process is very complex. Therefore, if organic copolymers can be generated inside the battery via the introduction of additives, the cycling stability of the battery will be significantly improved and the preparation process of the organic sulfur cathode will not be needed. However, organic copolymer monomers that contain ethylenic double bonds or acetylenic bonds only show reactivity with sulfides at high temperature, so introducing them into the electrolyte as an additive cannot produce organic copolymers with sulfides during the cycling process at room temperature.30–33 Sulfhydryl functional groups are known to be reactive with sulfides at room temperature, and thus exhibit the potential to form organic copolymers.34,35 Hence, TBBT, which contains thiol functional groups, is chosen as an electrolyte additive that can react with polysulfides to form an organic copolymer during cycling, suppressing the dissolution and diffusion of polysulfides in the electrolyte. Our results show that Li–S batteries exhibit an excellent cycling performance with 0.08% decay per cycle, and the capacity retention rate reaches 75.7% after 300 cycles, showing a good cycling life in pouch cells.
Experiment
Preparation of active materials
The carbon material used in this article was manufactured using a simple template method.36 Porous carbon (C) and sublimated sulfur (S) were mixed via grinding in a ratio of 3.5
:
6.5, before being transferred to a sealed container and heated to 160 °C under an argon atmosphere for 12 hours. A slurry was then obtained by mixing the S/C complex, acetylene black, and polyvinylidene fluoride at a ratio of 7
:
2
:
1 by weight in NMP solution. The slurry was coated on an aluminum foil current collector and dried at 60 °C for 12 hours. The surface loading of the cathode is about 1–1.5 mg cm−2. The mass of TBBT is 0.15 g, and the corresponding sulfur mass is 0.0768 g. The weighed TBBT and sulfur were dissolved in 4 mL of a carbon disulfide–toluene mixed solution (1
:
1 v/v), which was stirred until the solids were completely dissolved. Then, 20 μL diethylamine was added as a catalyst and a large amount of H2S bubbles was generated immediately. The reaction solution was stirred at room temperature for 12 hours. TBBT-Sn was obtained after the reaction was completed.
Preparation of the electrolyte
1 M lithium bis(trifluoromethanesulfonyl)-imide (LiTFSI) in 1,2-dimethoxyethane (DME)/1,3-dioxolane (DOL) (v/v = 1
:
1) with 2 wt% LiNO3 prepared as the standard electrolyte. Different weights of TBBT (Bailingwei) were added to the standard electrolyte to configure the TBBT-containing electrolyte. The process of configuring the electrolyte was completed using a glove box. Sublimed sulfur (99.5%, Bailingwei) and lithium sulfide (99.9%; Bailingwei) with a molar ratio of 5
:
1 were mixed with DOL/DME (v/v = 1
:
1) with stirring to obtain the Li2S6 solution.
Electrochemical measurements
A 2025 battery was assembled using lithium foil as the negative electrode, and then electrochemical tests were carried out. The amount of electrolyte in the battery was 20 μL mg−1 S. After standing for 12 hours, the battery was cycled between 1.7 and 2.8 V using a LANDAN test system (Wuhan, China). Electrochemical impedance spectroscopy was carried out using an electrochemical workstation (Solartron 1470E). The Li2S6 solution (25 μL 100 mM Li2S6) and the mixture of the TBBT-containing electrolyte and Li2S6 solution (1 μL of 2 wt% TBBT + 25 μL of 100 mM Li2S6) as the catholyte with a sulfur-free cathode to assemble the battery respectively, which was tested under constant current conditions (0.02 mA). The cathode (area, 6.8 × 9.6 cm; S loading, 5 mg cm−2) and anode electrodes were stacked in 16 layers with PP separators to assemble the pouch cell. Under the condition that the composition remained unchanged, the dosage was reduced to 2.6 μL mg−1 S. The pouch cell was cycled between 1.7 and 2.8 V at 0.1C.
Characterization
The UV-vis absorption spectrum in the range of 250–800 nm was collected using a U-4100 spectrophotometer to characterize the reacted substance. The composition of the material was confirmed using a laser microscope confocal Raman spectrometer (inVia, Renishaw, UK). The electrode surface morphology and the elemental distribution were confirmed using scanning electron microscopy (SEM, Philips, FEI Quanta 200FEG) and energy dispersive spectroscopy (EDS). X-ray photoelectron spectroscopy (XPS, Thermo Fisher Scientific) was used to analyze differences in the electrode surface chemical composition. Fourier Transform infrared spectroscopy (FTIR; IFS66 V/S & HYPERION 3000, Bruker Optiks) was used to inspect the structure of the materials. Mass spectrometry (MS; electrospray ionization mass spectrometry) was used to analyze the charged and discharged products of the cells. The cycled cathode was immersed in a mixed solution of 20% dimethyl sulfoxide (DMSO) and 80% methanol in an Ar-filled glove box for 30 min, and 1 mL of the solution was pipetted into a UPLC-MS vial. The vial was sealed and taken out of the glove box for testing. The solvent phase of for UPLC was 100% chromatographic methanol, and 0.5 μL of the solution was tested in electrospray ionization (EIS) positive mode and a first-order mass spectrometry model was applied.
Results and discussion
The electrochemical performance of the Li–S batteries with TBBT as an additive was tested and the results are shown in Fig. 1. Fig. 1a displays the cycling performance of the Li–S battery with different TBBT contents. After 300 cycles at 0.5C, the battery with the 2.0 wt% TBBT-containing electrolyte exhibited the best electrochemical performance, maintaining a capacity of 752.7 mA h g−1, with a retention rate of up to 75.8%. For the battery with the 4.0 wt% TBBT-containing electrolyte, the performance dropped, which may be due to corrosion of the lithium metal anode by excessive TBBT. By contrast, the battery with the standard electrolyte had a capacity of only 636.7 mA h g−1 after 300 cycles at 0.5C, which was a capacity retention rate of 62.4%. Furthermore, the coulombic efficiency of the battery with the 2.0 wt% TBBT-containing electrolyte remained at 97.0% after 300 cycles, compared with 95.6% for the battery with the standard electrolyte. These results show that TBBT can effectively improve the coulombic efficiency and discharge capacity. Fig. S1 (ESI†) shows the charging and discharging curves during cycling. There are two discharging plateaus in the discharging curve (Fig. S1b, ESI†) and the transformation of S8 to soluble Li2S4 occurs mainly at the higher voltage plateau stage, which is the main reason for the capacity fading. The conversion process for Li2S4 to Li2S2/Li2S corresponds to the lower voltage plateau. As shown in Fig. S1 (ESI†), the charging/discharging curves of the battery with the TBBT-containing electrolyte show better consistency, indicating that the cycling stability is significantly improved after adding TBBT. Moreover, Fig. 1b compares the capacity in the higher voltage plateau for the different electrolytes. The capacity in the higher voltage plateau remains more stable after adding TBBT during cycling, with a retention rate of 87.2% after 200 cycles compared with the rapid decay with the standard electrolyte (78.3%). This further indicates that the addition of TBBT reduces the capacity loss because of the dissolution and diffusion of polysulfides. Fig. 1c displays the battery rate performance with the different electrolytes. After adding TBBT, the discharge capacity is 1157.2, 1079.7, 1021.4 and 882.5 mA h g−1 at 0.2C, 0.5C, 1C and 2C, respectively; by contrast, the discharge capacity with the standard electrolyte is only 1107.5, 975.4, 862.2 and 717.2 mA h g−1, respectively. Moreover, Fig. 1f compares the voltage polarization (as shown by the arrows in Fig. 1d and e). The voltage polarization gap for the battery before and after adding TBBT increases slowly with an increase in the cycling rate, showing favorable reaction kinetics after adding TBBT. The electrochemical impedance spectroscopy (EIS) plots of batteries with the standard and TBBT-containing electrolytes before and after cycle were tested, as shown in Fig. 1g. After 300 cycles, the battery with the TBBT-containing electrolyte exhibits a lower interfacial transfer impedance compared with the standard electrolyte, which may be attributed to the fact that the side reaction caused by shuttle effect has been suppressed. TBBT was applied for the Li–S pouch cell to further verify the application effect (Fig. S2, ESI†). The pouch cell after adding TBBT shows improved cycling stability, and remains at 6.64 A h after 30 cycles (Fig. 1h).
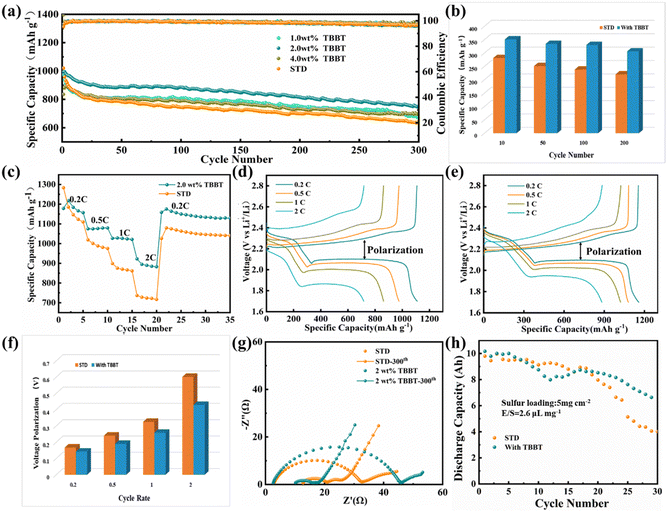 |
| Fig. 1 Electrochemical properties of Li–S batteries with a standard (STD) and a TBBT-containing electrolyte. (a) Cycling performance at 0.5C. (b) The capacity of the higher voltage plateau at different numbers of cycles at 0.5C. (c) Rate capabilities. (d and e) Charging/discharging curves, and (f) voltage polarization at different rates. (g) Electrochemical impedance spectroscopy (EIS) plots of batteries before and after cycling with and without TBBT. (h) Cycling performance of the Li–S pouch cell at 0.1C. | |
To discuss the effect of TBBT on the electrochemical performance of Li–S batteries, the reaction mechanism between TBBT and polysulfides is further discussed using Fig. 2. As shown in Fig. 2a, the color of the TBBT-containing electrolyte showed no significant change after adding Li2S6 compared with the standard electrolyte, and precipitate was deposited with increasing Li2S6 content (Fig. S3, ESI†). The precipitated sediment and the supernatant of the TBBT-containing electrolyte were separately analyzed to detected any change in the state of sulfur after the reaction. As shown in Fig. 2b, the Li2S6 peak at 280 nm disappeared, and no obvious change in TBBT peak (∼270 nm) was noted. In addition, a lead acetate test paper was used to detect the formation of H2S gas after adding Li2S6 to the TBBT-containing electrolyte (Fig. 2c). The peak around 2500 cm−1 in the FTIR results of the precipitate indicates the disappearance of thiol functional groups. The Raman spectrum also proves this (Fig. 2d and e).37 Meanwhile, the peak of the S–S bond appeared at 480 cm−1, which proves that the reacted TBBT combines with sulfur to form a new structure.38 To further verify the above conjecture, mass spectrometry was performed on the precipitate. The mass/charge ratio peak at 421.8712 matches that of the material (C6H8S8Li2) that is considered to be the newly formed product, as shown in Fig. 2f. The sulfhydryl groups promote long-chain polysulfide conversion according to the above detection results, which effectively reduces the capacity loss caused by the shuttle effect of long-chain polysulfides (eqn (1)).
|  | (1) |
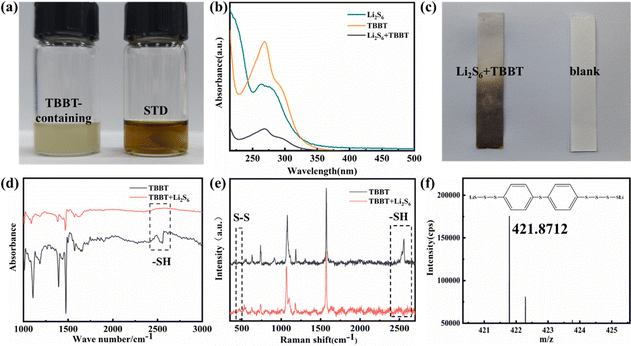 |
| Fig. 2 (a) Digital image of solutions after adding Li2S6 to the standard and TBBT-containing electrolyte, respectively. (b) UV-vis absorption of Li2S6 before and after reaction with TBBT. (c) Image for the lead acetate test paper in (a). FTIR (d) and Raman (e) spectral comparison between the precipitate and TBBT. (f) Mass spectrum (MS) of the precipitate after adding Li2S6 to the TBBT-containing electrolyte. | |
Fig. 3 demonstrates the role of TBBT in the initial discharging process. The standard electrolyte exhibits different colors at different voltages in the discharge process (Fig. 3b). Firstly, when the voltage drops to 2.2 V, the electrolyte color gradually turns brown (b and c) due to the diffusion of polysulfides. Soon after, the electrolyte color changes to green (d and e) as voltage drops to 2.0 V, which is caused by the generation of short-chain polysulfides. Nevertheless, the color of the TBBT-containing electrolyte shows no significant change during the discharging process (Fig. 3c) and remains pale yellow (g, h, i and j) because of the insoluble polysulfides. Regarding the pale yellow colour, this is more thought to be product of the reaction between TBBT and the anode, which will combine with sulfur atoms and come back to the cathode in the organic sulfide state, reducing the shuttle effect caused by long-chain polysulfides in the subsequent charging process (Fig. S4, ESI†). Therefore, TBBT effectively inhibits the shuttle effect by promoting the conversion of long-chain polysulfides.
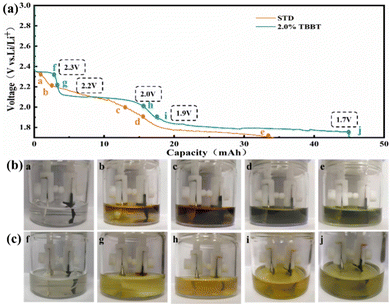 |
| Fig. 3 First cycle discharge curves of the transparent Li–S batteries with the standard and the TBBT-containing electrolyte (a), where points a–e and f–j respectively correspond to the battery photographs (b) and (c) at different discharge voltages. | |
Polysulfide shuttling during the charging process is an important factor that influences the performance of batteries. The charging process of the Li–S battery is special compared with lithium-ion batteries. The active material converts from short-chain polysulfides in an insoluble state to soluble long-chain polysulfides, and further transform to S8 deposited on the cathode surface. However, during this process, the high solubility of the long-chain polysulfides prevents them from returning to the cathode in the S8 state, resulting in a decay of battery capacity. Therefore, the effect of TBBT during the charging process was further explored. Li2S6 and a mixture of TBBT and Li2S6 (the TBBT
:
Li2S6 mole ratio is 1
:
40, consistent with that in the Li–S battery) were used as the catholyte to assemble respective batteries. The charging/discharging curves of each battery under constant current conditions are shown in Fig. 4a. After adding TBBT, the capacity loss due to the dissolution of polysulfides was effectively reduced, and the charge capacity was significantly improved. In addition, the electrolyte color change with the Li2S6 catholyte was more obvious by immersing the charged cathode into the standard electrolyte compared with the addition of TBBT (Fig. 4b), demonstrating that the content of soluble polysulfides on the cathode surface is clearly reduced with the TBBT-containing electrolyte. The charged cathode is analyzed using mass spectrometry to detect the presence of the active material. The mass/charge ratio (m/z) peaks at 559.9018 (Fig. 4c) and 623.8459 (Fig. 4d) reveal the newly formed organosulfur products C24H16S8 and C6H16S10, respectively. To further prove that the introduction of TBBT will generate organic sulfides on the cathode surface, TBBT-Sn was synthesized and tested via XPS, where the characteristic peaks were located at 163.8 and 165.0 eV (Fig. S5, ESI†).37 At the same time, when the charged cathode was tested using XPS, peaks for the organic sulfide appeared after adding TBBT (Fig. 4f), whereas these peaks did not appear in the electrode with only the Li2S6 catholyte (Fig. 4e). These results indicate that the introduction of TBBT changes the existing form of the active materials during the cycling process (eqn (2)), reducing the capacity loss caused by excessive polysulfide solubility.
|  | (2) |
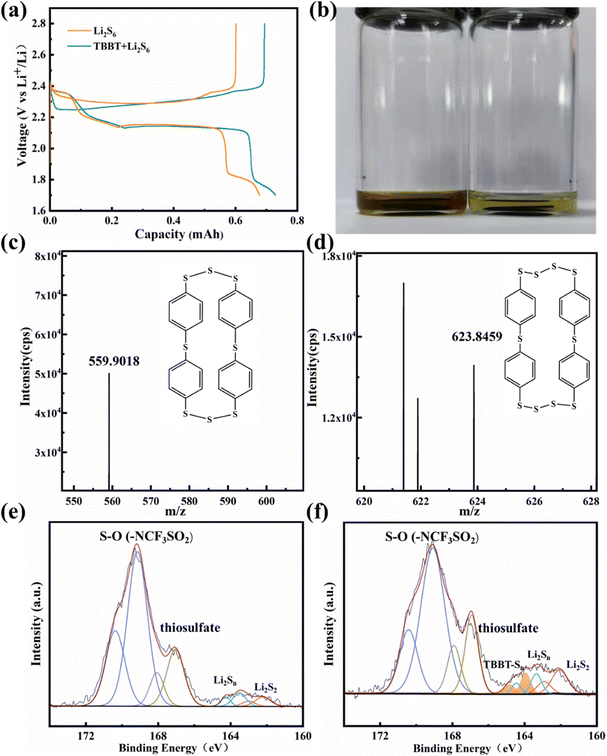 |
| Fig. 4 (a) Initial discharging and charging curves of batteries with different electrolytes (Li2S6 or a mixture of TBBT and Li2S6) as the catholyte. (b) Digital image of the cathode immersed in standard electrolyte after charging with different catholytes (left, without TBBT; right, with TBBT). (c and d) Mass spectra of the recharged products for the TBBT-containing battery. (e and f) S 2p XPS spectra of the charged cathode with Li2S6 (e) and the mixed (f) catholyte. | |
The corrosion of lithium metal anodes by polysulfides is another significant obstacle for the stable cycling performance of Li–S batteries. Fig. 5a–d show the surface morphology of the lithium metal anode after 300 cycles. The anode surface is neat and flat with the TBBT-containing electrolyte (Fig. 5a and b). By contrast, abundant moss-like, loose lithium deposits are found on the anode surface with the standard electrolyte (Fig. 5c and d), indicating that TBBT effectively alleviates polysulfide migration and reduces side reactions with the anode. To further verify the compositional variation on the anode surface with TBBT as the additive, the anode after 300 cycles was tested via XPS (Fig. 5e). The S–O (169 eV and 170.2 eV) bond of –SO2CF3 is the main component that resulting from the solution of LiTFSI. In addition, the peaks at 167.2 eV and 168.4 eV are attributed to thiosulfate. It is worth noting that Li2S2 (162.1 eV and 163.2 eV) exhibits strong signals with the standard electrolyte, which are thought to be due to the reaction between the lithium metal anode and polysulfides.39 By contrast, the signal for Li2S2 is much weaker with the TBBT-containing electrolyte, indicating that the polysulfide shuttle is suppressed. At the same time, there is no Li2S (160.3 eV and 161.5 eV) produced through side reactions on the anode surface after adding TBBT compared with the standard electrolyte, which further illustrates the protective effect of TBBT. The whole process of TBBT in the Li–S battery can be presented in the schematic diagram in Fig. 6. With the function of reducing the formation of long-chain polysulfides, introducing sulfhydryl functional groups can guarantee the stable cycling of Li–S batteries.
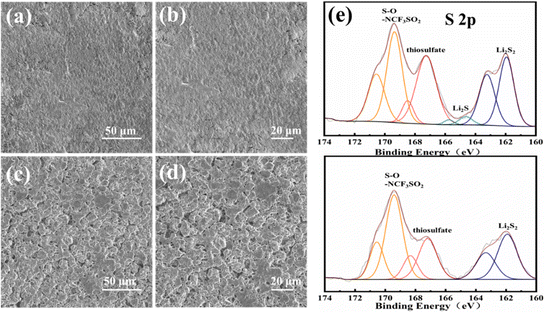 |
| Fig. 5 Surface morphology of the lithium metal anode after 300 cycles at 0.5C with the TBBT-containing electrolyte (a and b) and the standard electrolyte (c and d). (e) S 2p XPS spectra of the lithium metal anode with the standard (upper) and TBBT-containing (lower) electrolyte. | |
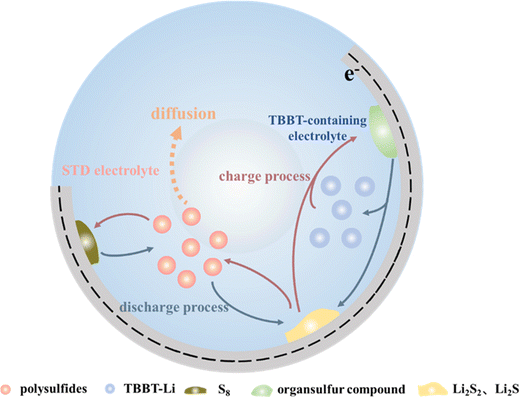 |
| Fig. 6 Schematic illustration for the Li–S battery with the TBBT-containing electrolyte. | |
Conclusion
In this work, the introduction of TBBT effectively changes the existing form of active materials by capturing polysulfides to form organic sulfide during the charge–discharge process, which can effectively limit the generation of long-chain polysulfides. Reducing these long-chain polysulfides greatly solves the capacity reduction and short cycle life that caused by polysulfide dissolution and shuttling. The battery prepared using the TBBT-containing electrolyte exhibits an excellent cycling performance, with a decay of 0.08% per cycle, and the Li–S pouch cell remains at 6.64 A h after 30 cycles. This study demonstrates that sulfhydryl functional groups can effectively improve the electrochemical performance by reducing the formation of long-chain polysulfides. In addition, selecting suitable functional additives from organosulfur copolymer monomers could be an effective method for enhancing the battery performance.
Conflicts of interest
There are no conflicts to declare.
Acknowledgements
This work is supported by the National Natural Science Foundation of China (No. 52174287 and 51904343), the National Natural Science Foundation of China (52034011), the Hunan Science and Technology innovation leading project (2020GK2074), and the Funds for Creative Research Groups of Hunan province (2020JJ1007).
References
- B. Scrosati, J. Hassoun and Y.-K. Sun, Lithium-ion batteries. A look into the future, Energy Environ. Sci., 2011, 4, 3287–3295 RSC.
- K. Xu, Electrolytes and interphases in Li-ion batteries and beyond, Chem. Rev., 2014, 114, 11503–11618 CrossRef CAS PubMed.
- A. Manthiram, Y. Fu, S. H. Chung, C. Zu and Y. S. Su, Rechargeable lithium–sulfur batteries, Chem. Rev., 2014, 114, 11751–11787 CrossRef CAS PubMed.
- B. Liu, R. Fang, D. Xie, W. Zhang, H. Huang, Y. Xia, X. Wang, X. Xia and J. Tu, Revisiting Scientific Issues for Industrial Applications of Lithium–Sulfur Batteries, Energy Environ. Mater., 2018, 1, 196–208 CrossRef.
- S. Drvarič Talian, G. Kapun, J. Moškon, A. Vizintin, A. Randon-Vitanova, R. Dominko and M. Gaberšček, Which Process Limits the Operation of a Li–S System?, Chem. Mater., 2019, 31, 9012–9023 CrossRef.
- Y. He, Z. Chang, S. Wu and H. Zhou, Effective strategies for long-cycle life lithium–sulfur batteries, J. Mater. Chem. A, 2018, 6, 6155–6182 RSC.
- D. Zheng, D. Liu, J. B. Harris, T. Ding, J. Si, S. Andrew, D. Qu, X.-Q. Yang and D. Qu, Investigation of the Li–S Battery Mechanism by Real-Time Monitoring of the Changes of Sulfur and Polysulfide Species during the Discharge and Charge, ACS Appl. Mater. Interfaces, 2016, 9, 4326–4332 CrossRef.
- S. S. Zhang, Liquid electrolyte lithium/sulfur battery: Fundamental chemistry, problems, and solutions, J. Power Sources, 2013, 231, 153–162 CrossRef CAS.
- G. Zheng, Q. Zhang, J. J. Cha, Y. Yang, W. Li, Z. W. Seh and Y. Cui, Amphiphilic surface modification of hollow carbon nanofibers for improved cycle life of lithium sulfur batteries, Nano Lett., 2013, 13, 1265–1270 CrossRef CAS PubMed.
- K. Zhang, Q. Zhao, Z. Tao and J. Chen, Composite of sulfur impregnated in porous hollow carbon spheres as the cathode of Li–S batteries with high performance, Nano Res., 2012, 6, 38–46 CrossRef.
- J. Zheng, G. Guo, H. Li, L. Wang, B. Wang, H. Yu, Y. Yan, D. Yang and A. Dong, Elaborately Designed Micro–Mesoporous Graphitic Carbon Spheres as Efficient Polysulfide Reservoir for Lithium–Sulfur Batteries, ACS Energy Lett., 2017, 2, 1105–1114 CrossRef CAS.
- Q. Zhu, H.-F. Xu, K. Shen, Y.-Z. Zhang, B. Li and S.-B. Yang, Efficient polysulfides conversion on Mo2CTx MXene for high-performance lithium–sulfur batteries, Rare Met., 2021, 41, 311–318 CrossRef.
- J.-H. Zuo, P.-B. Zhai, Q.-Q. He, L. Wang, Q. Chen, X.-K. Gu, Z.-L. Yang and Y.-J. Gong,
In-situ constructed three-dimensional MoS2–MoN heterostructure as the cathode of lithium–sulfur battery, Rare Met., 2022, 41, 1743–1752 CrossRef CAS.
- X. Liang, C. Hart, Q. Pang, A. Garsuch, T. Weiss and L. F. Nazar, A highly efficient polysulfide mediator for lithium–sulfur batteries, Nat. Commun., 2015, 6, 5682 CrossRef.
- Y. Qiu, W. Li, W. Zhao, G. Li, Y. Hou, M. Liu, L. Zhou, F. Ye, H. Li, Z. Wei, S. Yang, W. Duan, Y. Ye, J. Guo and Y. Zhang, High-rate, ultralong cycle-life lithium/sulfur batteries enabled by nitrogen-doped graphene, Nano Lett., 2014, 14, 4821–4827 CrossRef CAS PubMed.
- Z. Cui, C. Zu, W. Zhou, A. Manthiram and J. B. Goodenough, Mesoporous Titanium Nitride-Enabled Highly Stable Lithium–Sulfur Batteries, Adv. Mater., 2016, 28, 6926–6931 CrossRef CAS.
- J. Liu, T. Qian, M. Wang, X. Liu, N. Xu, Y. You and C. Yan, Molecularly Imprinted Polymer Enables High-Efficiency Recognition and Trapping Lithium Polysulfides for Stable Lithium Sulfur Battery, Nano Lett., 2017, 17, 5064–5070 CrossRef CAS PubMed.
- X. Wang, S. Zhang, H. Zhang, S. Gao, S. Han, Q. Xu, J. Xu, W. Lu, X. Wu and L. Chen, 3D Porous Spherical Sulfur/Carbon Cathode Materials with in Situ Vapor-Phase Polymerized Polypyrrole Coating Layer for High-Performance Lithium–Sulfur Batteries, ACS Sustainable Chem. Eng., 2019, 7, 17491–17499 CrossRef CAS.
- V. Bharti, A. Gangadharan, T. N. Rao and C. S. Sharma, Carbon soot over layered sulfur impregnated coconut husk derived carbon: An efficient polysulfide suppressor for lithium sulfur battery, Mater. Today Commun., 2019, 22, 100717 CrossRef.
- C. Shi, B. Hong, X. Zhang, Q. Xiang, Z. Zhang, K. Zhang, J. Fang and Y. Lai,
In-situ growth poly(N-methylaniline) coating on sulfur cathode for lithium–sulfur battery, J. Electroanal. Chem., 2020, 871, 114312 CrossRef CAS.
- F. Wu, J. Qian, R. Chen, J. Lu, L. Li, H. Wu, J. Chen, T. Zhao, Y. Ye and K. Amine, An effective approach to protect lithium anode and improve cycle performance for Li–S batteries, ACS Appl. Mater. Interfaces, 2014, 6, 15542–15549 CrossRef CAS.
- S. Liu, G. R. Li and X. P. Gao, Lanthanum Nitrate As Electrolyte Additive To Stabilize the Surface Morphology of Lithium Anode for Lithium–Sulfur Battery, ACS Appl. Mater. Interfaces, 2016, 8, 7783–7789 CrossRef CAS.
- T. Yang, T. Qian, J. Liu, N. Xu, Y. Li, N. Grundish, C. Yan and J. B. Goodenough, A New Type of Electrolyte System To Suppress Polysulfide Dissolution for Lithium–Sulfur Battery, ACS Nano, 2019, 13, 9067–9073 CrossRef CAS PubMed.
- J. Liu, Y. Cao, J. Zhou, M. Wang, H. Chen, T. Yang, Y. Sun, T. Qian and C. Yan, Artificial Lithium Isopropyl-Sulfide Macromolecules as an Ion-Selective Interface for Long-Life Lithium–Sulfur Batteries, ACS Appl. Mater. Interfaces, 2020, 12, 54537–54544 CrossRef CAS PubMed.
- S. Chen, F. Dai, M. L. Gordin, Z. Yu, Y. Gao, J. Song and D. Wang, Functional Organosulfide Electrolyte Promotes an Alternate Reaction Pathway to Achieve High Performance in Lithium–Sulfur Batteries, Angew. Chem., Int. Ed., 2016, 55, 4231–4235 CrossRef CAS PubMed.
- J. Lian, W. Guo and Y. Fu, Isomeric Organodithiol Additives for Improving Interfacial Chemistry in Rechargeable Li–S Batteries, J. Am. Chem. Soc., 2021, 143, 11063–11071 CrossRef CAS.
- H. Kim, J. Lee, H. Ahn, O. Kim and M. J. Park, Synthesis of three-dimensionally interconnected sulfur-rich polymers for cathode materials of high-rate lithium–sulfur batteries, Nat. Commun., 2015, 6, 7278 CrossRef CAS PubMed.
- H. S. Yoo, J. H. Yoon, J. I. Kim, E. K. Koh and C. S. Hong, Unprecedented N-Inserted Disulfide Ligand Stabilized by Coordination to the Electropositive CoIIICenter, Eur. J. Inorg. Chem., 2008, 3123–3126 CrossRef CAS.
- J. Zhao, Y. Si, Z. Han, J. Li, W. Guo and Y. Fu, An Organic–Inorganic Hybrid Cathode Based on S–Se Dynamic Covalent Bonds, Angew. Chem., Int. Ed., 2020, 59, 2654–2658 CrossRef CAS PubMed.
- D. Y. Wang, Y. Si, W. Guo and Y. Fu, Long Cycle Life Organic Polysulfide Catholyte for Rechargeable Lithium Batteries, Adv. Sci., 2020, 7, 1902646 CrossRef CAS PubMed.
- D. Y. Wang, W. Guo and Y. Fu, Organosulfides: An Emerging Class of Cathode Materials for Rechargeable Lithium Batteries, Acc. Chem. Res., 2019, 52, 2290–2300 CrossRef CAS PubMed.
- J. Liu, M. Wang, N. Xu, T. Qian and C. Yan, Progress and perspective of organosulfur polymers as cathode materials for advanced lithium–sulfur batteries, Energy Storage Mater., 2018, 15, 53–64 CrossRef.
- P. T. Dirlam, A. G. Simmonds, T. S. Kleine, N. A. Nguyen, L. E. Anderson, A. O. Klever, A. Florian, P. J. Costanzo, P. Theato, M. E. Mackay, R. S. Glass, K. Char and J. Pyun, Inverse vulcanization of elemental sulfur with 1,4-diphenylbutadiyne for cathode materials in Li–S batteries, RSC Adv., 2015, 5, 24718–24722 RSC.
- H.-L. Wu, M. Shin, Y.-M. Liu, K. A. See and A. A. Gewirth, Thiol-based electrolyte additives for high-performance lithium–sulfur batteries, Nano Energy, 2017, 32, 50–58 CrossRef CAS.
- A. Bhargav, Y. Ma, K. Shashikala, Y. Cui, Y. Losovyj and Y. Fu, The unique chemistry of thiuram polysulfides enables energy dense lithium batteries, J. Mater. Chem. A, 2017, 5, 25005–25013 RSC.
- J. Li, F. Qin, L. Zhang, K. Zhang, Q. Li, Y. Lai, Z. Zhang and J. Fang, Mesoporous carbon from biomass: one-pot synthesis and application for Li–S batteries, J. Mater. Chem. A, 2014, 2, 13916–13922 RSC.
- P. Sang, Y. Si and Y. Fu, Polyphenyl polysulfide: a new polymer cathode material for Li–S batteries, Chem. Commun., 2019, 55, 4857–4860 RSC.
- J. Shen, Y. Feng, P. Wang, G. Qiu, L. Zhang, L. Lu, H. Wang, R. Wang, V. Linkov and S. Ji, Conductive Sulfur-Rich Copolymer Composites as Lithium–Sulfur Battery Electrodes with Fast Kinetics and a High Cycle Stability, ACS Sustainable Chem. Eng., 2020, 8, 10389–10401 CrossRef CAS.
- Q. Xiang, C. Shi, X. Zhang, L. Zhang, L. He, B. Hong and Y. Lai, Thiuram Vulcanization Accelerators as Polysulfide Scavengers To Suppress Shuttle Effects for High-Performance Lithium–Sulfur Batteries, ACS Appl. Mater. Interfaces, 2019, 11, 29970–29977 CrossRef CAS.
|
This journal is © the Partner Organisations 2023 |