DOI:
10.1039/D3PY00724C
(Paper)
Polym. Chem., 2023,
14, 3686-3694
Sulfur-rich polymers with heating/UV light-responsive shape memory and temperature-modulated self-healing†
Received
21st June 2023
, Accepted 17th July 2023
First published on 25th July 2023
Abstract
Inverse vulcanized polymers from elemental sulfur with blended mono-/di-olefins have the advantages of simple production and high atom economy, allowing them to adhere to the principles of green and sustainable chemistry. The ternary co-polymer presented herein has an adjustable glass and topological transition temperature due to the S–S dynamic network and the different feed ratios of mono-/di-olefins in the copolymerization process, together with a shape memory and self-healing capacity at different temperatures, with the lowest at 30 °C. A series of interesting properties and performances of the obtained polymers in terms of elasticity, plasticity, complex heating/ultraviolet light stimulated shape memory properties, and temperature-modulated self-healing ability have been revealed, responding to the fracture and re-bonding of the S–S bond to reconstruct the cross-linked network. The strategy could be used in the manufacture of complex three-dimensional (3D) structures for biological applications, and also has potential in shape storage devices and self-healing materials.
Introduction
Elemental sulfur, a by-product of desulfurization from the petrol and gas industry, is generated in millions of tons annually with only a portion being consumed for the production of sulfuric acid-related industrial products. A significant quantity of excess sulfur is stockpiled each year as waste, causing environmental concerns.1–3 In 2013, Pyun and colleagues first reported the inverse vulcanization (IV) involving elemental sulfur and unsaturated carbon–carbon bonds to generate a new family of organic polymers, providing a potential way to solve the problem of waste sulfur.4 Thus, molten sulfur acted as both reactant and the reaction solvent upon heating to its polymerization temperature of 159 °C or above. The generally stable form of sulfur, S8 rings, are broken during the heating and melting process to form a sulfur chain with terminal free radicals or ions, which will cross-link with the olefins.5,6 Significant improvement has been achieved for the development of both IV reaction and applications of resultant polymers in the last decade.7–9 The crosslinkers applied have been expanded extensively, including olefins,10–13 alkynes,14,15 maleimide,16 benzoxazine,17,18 as well as those economical and environmentally friendly abundant natural products, such as vegetable oils and terpenes.19,20
The applications of the resultant polymers, based on their unique properties arising from their high sulfur content, have been investigated in many aspects: the high refractive index and infrared light transmittance of infrared light has been utilised as camera lenses and thermal imaging applications;21–23 the adsorption of metal ions has been explored for the adsorption and purification of metal ions in waste water;24,25 the high performance with a theoretical energy density of up to 2600 W h kg−1 has been explored in lithium–sulfur batteries;26,27 the property of antibacterial ability facilitated its application as antibacterial materials;28,29 the reversibility of dynamic S–S bonds in the resultant polymers also has great potential in shape memory and self-healing materials. However, there is still huge space for the exploration of the applications of these S-rich polymers comparing to the ubiquitous carbon-based counterparts. We sought to develop a type of smart sulfur copolymers with heating/UV light-responsive shape memory and temperature-modulated self-healing ability.
Shape memory polymers are a specific set of functional materials that have the capability to restore their original form by simple operation with heating or light after the initial shape has been changed by an external force.30 In general, shape memory polymers have a network structure with chemical crosslinking or physical crosslinking,31 containing dynamic reversible bonds, such as dynamic disulfide,32 silicone-based exchange,33 imino exchange,34 carbamylated,35 a urethane exchange,36etc., and adaptable shape memory polymer has obtained increasing attentions for its satisfying the multiple shape changing demanding as well as its recyclability. Thus, IV polymers have been investigated for the design of shape memory materials. For example, Liu and co-authors synthesized a polysulfide through the solution polycondensation of elemental sulfur and pentaerythritol tetra(3-mercaptopropionate) with the IV process, and examined their shape memory properties.37 Recently, Yan et al. demonstrated that IV polymers synthesized from elemental sulfur and hydroxyl-containing mono-olefins with a further cross-linking by difunctional isocyanate have an attractive, vitrimer-like ability for being reshaped and recycled.38 Meanwhile, IV polymers combined with the unique dynamic property of S–S bonds exhibit self-healing ability despite their crosslinked structures. For example, Zhang and co-authors reported using elemental sulfur to achieve nano-dispersed liquid metals (LMs) in bulk polymers, producing multifunctional LM-based materials with excellent thermal-/solvent-process ability and recyclability.39 Liu and co-authors reported that polysulfides from sulfur and monoterpenes were introduced as a functional crosslinker for epoxy thermosets, and endow the epoxy material potential self-healing ability.40 Chalker et al. reported that two surfaces of these sulfur polymers can be chemically joined at room temperature through a phosphine or amine-catalyzed exchange of the S–S bonds in the polymer.20 Given the unique dynamic property of S–S bonds in S-rich polymers, the rational design of S-rich copolymers with well-modulated shape memory and self-healing ability still remains a challenge.41–43 Herein, a new type of dynamic polysulfide network polymers was synthesized through the one-pot IV reaction of sulfur with blended mono-olefins and diolefins. The S–S bond number and Tg of the dynamic polysulfide network varies with the different ratios of mono-olefin/di-olefin/sulfur for the polymerization process (Scheme 1). While re-programmable shape memory effects have previously been reported for inverse vulcanised polymers, this is the first time their physical properties, shape memory, and self-healing features have been shown to be tunable by using a combination of mono- and di-olefins, and adjusting their ratio.
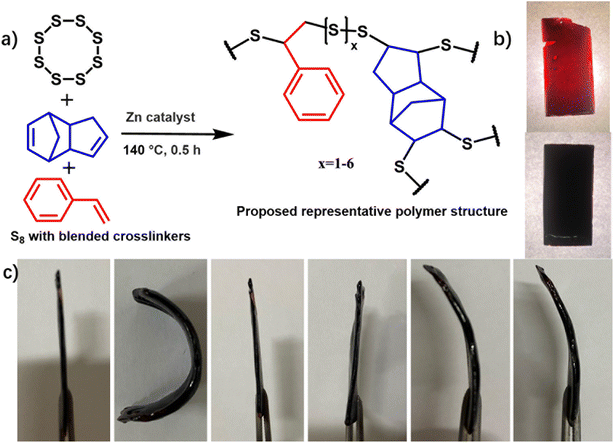 |
| Scheme 1 Inverse vulcanization of elemental sulfur (S8) with blended crosslinkers and the resultant polymers. Representative reaction scheme (a). Representative resultant polymers (b). Representative thermal/light responsible shape-memory property (c). | |
Of important note is that the resultant polymers network has elasticity and plasticity, as well as the complex thermal/ultraviolet stimulating shape memory properties, presumably due to the dynamic S–S bonding within the resultant polymers. It also attributed to the fact that heating/ultraviolet light will reorganize and restore the shape of the S–S bond structure/break the S–S bond and recombine them to rebuild the transparent cross-linked network.44–46 Self-healing ability is an inherent property of inverse vulcanized polymers ensured by the exchange of dynamic S–S bonds existing in some of the resultant polymers. In general, higher temperature is essential for the self-healing process of the majority of polymers reported in the literature,47 however, these poly(S-monoolefin-diolefin) polymers generated with this new protocol have the ability of self-healing rapidly at the temperatures as low as 30–60 °C, demonstrating, to the best of our knowledge, the first examples of reverse vulcanized polymers achieved self-healing ability at such low temperature.
Results and discussion
The IV reaction of elemental sulfur with dicyclopentadiene (DCPD) and styrene (St) in the presence of zinc dihexyldithioformate catalyst was conducted for the preparation of the materials (Scheme 1). Therefore, elemental sulfur and zinc dihexyl dithioformate were added to a round-bottom flask and heated/melted at 140 °C with stirring. Then DCPD and styrene were added into the reaction mixture to react for another 30 minutes at the same temperature. The mixture was then poured out to a silicone mould when the mould is still hot, placed in a pre-heated oven, and cured at 130 °C for 12 h. After cooling down to room temperature, the polymers were taken out of the oven, washed with distilled water, and dried in the air to afford the final product as a transparent, red-coloured, soft solid. The H2S gas was detected with smaller amounts for catalysed reactions than uncatalyzed ones (Fig. S1†). Decomposition of DCPD into cyclopentadiene (CPD) is possible with heating over 140 °C, and so some reacted CPD may also be present in the resultant polymers. However, NMR monitoring of the reaction process did not detect CPD during the polymerization (Fig. S2–S4†), so the degree of CPD inclusion is unlikely to be high. The resultant polymers were fully characterized by FTIR, NMR, PXRD, elemental analysis (Fig. 1, Table 1, and ESI†). As shown in Fig. 1a, the 1H NMR of poly(S-St-DCPD)2 (from here on, the polymer samples will be referred to by the following abbreviation system: poly(S-St-DCPD)x, where S is the elemental sulfur, St refers to styrene, and x is the series number of the resulted polymer with different ratios of styrene and DCPD. As an example, the mass ratio of S8
:
St
:
DCPD at 2.5
:
1.2
:
0.3 feed ratio, synthesized at 140 °C would have the following abbreviation: poly(S-St-DCPD)2) demonstrated negligible peaks for double bonds at 5.0–6.0 ppm of both starting reactants DCPD and styrene along with new broad peaks at 0.75, 3.6, 4.3, 4.7 ppm for the resultant polymers, evidencing the completion of the polymerization and the generation of the desired product. Furthermore, a series of polymers of poly(S-St-DCPD)1–5 were obtained with monomers and crosslinkers at different ratios. Fig. 1b revealed that the characteristic peak of C
C bond at around 3100 cm−1 diminished with a new peak appearing at about 500 cm−1, presumably attributed to the newly formed C–S bonds in the resultant polymers, while the aromatic ring from styrene is still present at around 1500–1600 cm−1. The X-ray powder diffraction (PXRD, Fig. S6c†) supported the conclusion that an amorphous polysulfide structure was present in the polymer with no obvious characteristic diffraction peaks of crystalline octatomic S8 present. Moreover, the gel content of resultant polymers was investigated (Table S1†) and their partially crosslinking network was confirmed. As shown in Table S1,† the gel amount of polymer increased from 10.85% to 42.45% by the increasement of the proportion of dicyclopentadiene in the diolefin, resulting in a gradual increase in the degree of crosslinking of the polymer. It worth pointing out that the gel content of poly(S-St) and poly(S-DCPD) are 0% and 75.80%, respectively. This result indicated the possible explanation to the low gel content for the sample poly(S-St-DCPD)1. Notably, the more crosslinkers DCPD, the higher Tg of the resultant polymers, echoing the gradual increase of Tg value measured in Fig. 1c. The Tg for poly(S-DCPD) generated under the same reaction conditions was 55 °C, much higher than all the samples with blended monomers poly(S-St-DCPD)1–5 (Fig. S5†). There is no Tg for poly(S-St) with unreacted S8 present, presumably due to the linear polymers generated with styrene. As shown by the tensile modulus in Table 1, the stiffness of these polymers is also increased in proportion to the ratio of increasing DCPD, which corresponds to the proportion of crosslinked networks generated in the polymers. Poly(S-St-DCPD)2 has the lowest modulus, and therefore highest ductility, with its low Tg below the testing temperature, making it in the rubber phase.
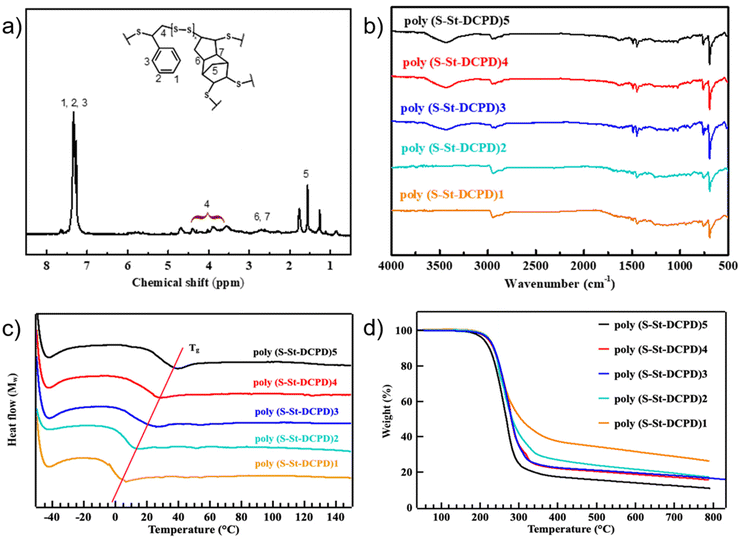 |
| Fig. 1 Representative spectra and thermal analysis of the resultant polymers: (a) Poly(S-St-DCPD)2 1H NMR, (b) poly(S-St-DCPD)1–5 FTIR, (c) poly(S-St-DCPD)1–5 DSC and (d) poly(S-St-DCPD)1–5 TGA. | |
Table 1 Summary of thermal and mechanical properties of resultant poly(S-St-DCPD)1–5 by inverse vulcanization of S8 with blended crosslinkersa
Sample name |
Proportion w% sulfur/St/DCPD |
T
g (°C) (DSC) |
T
deg, 5%/°C (N2) |
Stressmax/MPa (30 °C) |
Strainmax/% (30 °C) |
Young's modulus/MPa (30 °C) |
Reaction conditions: elemental sulfur (2.5 g) and dihexyl zinc dithioformate (25 mg, 1 wt%) were added into a round bottom flask, the mixture was then stirred at 140 °C until a homogeneous solution formed. Then DCPD + styrene (1.5 g in total, the ratio of DCPD to styrene changes across the samples from 1 (more styrene) to 5 (more DCPD) while keeping the sulfur to organic monomer ratio constant (62.5 wt% sulfur, 37.5 wt% organic comonomer)) were added and the mixture was stirred at the same temperature for 30 min. The resulted polymer poured into silica mould while it was still hot and cured in an preheated oven at 130 °C for 12 h. After cooling down to room temperature, the resulted polymer was taken out the oven, washed with distilled water, and dried in the air as the final product.
|
Poly(S-St-DCPD)1 |
62.5/33.75/3.75 |
4.6 |
122.2 |
— |
— |
|
Poly(S-St-DCPD)2 |
62.5/30/7.5 |
11.5 |
208.5 |
5.2 |
230 |
4.8 |
Poly(S-St-DCPD)3 |
62.5/25/12.5 |
22.6 |
221.5 |
7.8 |
170 |
52.6 |
Poly(S-St-DCPD)4 |
62.5/20/17.5 |
28.9 |
223.1 |
9.5 |
32 |
253.3 |
Poly(S-St-DCPD)5 |
62.5/15/22.5 |
41.6 |
224.3 |
13.3 |
5 |
725.4 |
It is worth noting that poly(S-St-DCPD)1 is not included in these tests, because the resultant polymers have such low Tg (4.6 °C) and cannot maintain a fixed shape at room temperature, indicating this polymer is not crosslinked to a sufficient degree and constitutes a thermoplastic material. Therefore, the pure copolymers of elemental sulfur with styrene or DCPD were not included in the tensile measurements as they were either not shape persistent (poly(S-St) or too brittle (poly(S-DCPD). Subsequently, hot press moulding was conducted to examine the cross-linked structure of the polymers, and the dynamic S–S bond interior the polymers.
Thermal and mechanical performance
The thermal performance of poly(S-St-DCPD) were investigated subsequently. Differential scanning calorimetry (DSC, Fig. 1c) and thermogravimetric analysis (TGA, Fig. 1d) further confirmed the generation of designed polymers. As Table 1 and Fig. 1c, 2 show, a very clear trend that the glass transition temperature (Tg) increases as the proportion of DCPD increases, as more DCPD means more crosslinks, meaning more chain immobilisation, and therefore a higher Tg (Fig. 1c, Table 1 and Fig. 2, black curve).44 This allows a tuneable physical property for the shape memory and self-healing applications. Meanwhile, an increased Tg of the polymer suggests a more crosslinked structure, as would be expected from using a higher proportion of DCPD, with two reactive C
C groups compared to styrene with one, and in agreement with the results of the gel fraction (Table S1†). The TGA traces illustrate that the similar Tdeg5% was obtained around 200 °C for all four polymer networks (Table 1 and Fig. 2, red curve). Thus, polymer networks with engineered crosslinks were successfully fabricated. Mechanical properties such as tensile strength of the materials are key factors for both shape memory and self-healing performance. As shown in Table 1 and Fig. 2, the tensile strength of these polymers is mostly between 5–13.3 MPa, similar to that of other inverse vulcanized polymers reported previously.19,20,37,41 It can be seen that the higher content of DCPD, the stronger tensile strength of the resultant polymers, whereas the poly(S-St-DCPD)5 has the greatest tensile strength of 13.3 MPa (Fig. 2).
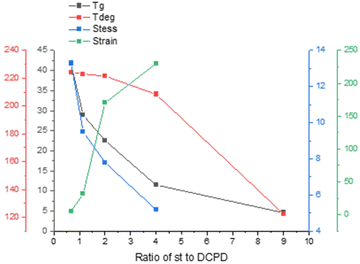 |
| Fig. 2 Trends of various properties of resultant polymer vs. ratio of styrene to DCPD. Tg (black curve and Y axis), Tdeg (red curve and Y axis), stress (blue curve and Y axis), and strain (green curve and Y axis). | |
Heat-sensitive shape memory feature
Due to the network structure of inverse-vulcanized polymers containing dynamic covalent sulfur bonds, these polysulfides should have good potential as shape memory materials. As shown in Fig. 3, the elastic shape memory behaviour of poly(S-St-DCPD)2 was conducted under thermal conditions at 30 °C, higher than its Tg of 11.6 °C. Therefore, the polysulfide film strip was bent, manually forced into a U shape prior to cool down to −40 °C first to ensure the shape recovery operation starting at a temperature way low to its Tg. Then it was treated with heating at 30 °C, an obvious shape recovery was observed in the first two minutes of heating with 80–90% return to the original shape in 30 min and fully restored in 2 h. The process can be repeated several times with negligible recovery time increase, and the higher the temperature, the quicker the shape recovers. A similar shape memory behaviour with high performance temperature requirement of 60 °C was obtained for the poly(S-St-DCPD)5 due to its’ relatively high Tg and the detailed information shown in the ESI (Fig. S7†). The dynamic covalent bond exchange in the polymers network allows both the self-healing properties, and the ability to re-set the remembered shape.38
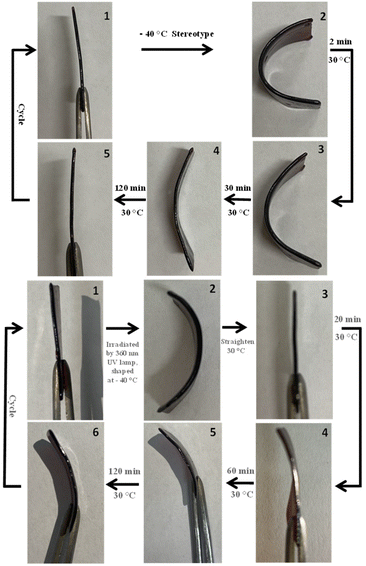 |
| Fig. 3 Shape memory feature of poly(S-St-DCPD)2 under thermal conditions (top) and ultraviolet light irradiation + thermal conditions (bottom). | |
It has been found that it is almost a linear correlation between the response temperature of shape memory and the proportion of DCPD involved in the polymers (Fig. S10†), revealing a tuneable feature of the resultant polymers for their shape memory. That is, the more diolefins involved, the higher the degree of crosslinking, and therefore the higher the Tg and response temperature for the shape memory.
UV light-sensitive shape memory features
The shape memory features of the resultant polymers are UV-light (360 nm) sensitive as well, particularly to those transparent polymers. With good transparency, the ultraviolet rays (360 nm of wavelength) can be transmitted through the poly(S-St-DCPD)2 film, triggering dynamic covalent S–S bond exchange. The figure shows the photo-plasticity of poly(S-St-DCPD)2 with UV-light irradiation and the combination of thermal conditions (Fig. 3, bottom). Thus, a firmly bent U shape of the polymers was formed with the UV irradiation (360 nm) towards one face of the polymers film at −40 °C for 1 h. It can be then straightened and curved by thermal treatment, indicating the similar function ability of ultraviolet irradiation with heat-sensitive processes. Therefore, the method provides a new clean and controllable method for processing network materials. Of particular note is that the shape memory features to the ultraviolet radiation limited to the mass ratio of crosslinker DCPD no greater than 0.45 to the total mass of blended styrene and DCPD in the resultant polymers. A high crosslinked network generated with high ratios of DCPD restricted the dynamic sulfur bond with the physical bond interior the polymers, providing a more stable physical bond rather than the breaking and reconnection of the dynamic S–S bond under ultraviolet light irradiation. The opaque of the resultant poly(S-St-DCPD) with great ratio of DCPD (mass ratio of DCPD > 0.45 in the total mass of blended styrene and DCPD) is another issue as the ultraviolet light could only irradiate the dynamic sulfur bonds on the surface of the polymer, with negligible effect to the ones inside the polymers.
Self-healing features at low temperature
The temperature of self-healing features could also depend on the reactant ratios applied. Thus, the self-healing of poly(S-St-DCPD)2 can be operated by hand – simply warming to body temperature (Fig. 4a and Video 1, ESI†), whilst the self-healing of the poly(S-St-DCPD)5 required a high temperature with the maximum break strength almost remained for 4 cycles of self-healing with hot process (Fig. 4b–d and Video 2, ESI†), echoing again a tuneable feature for the self-healing properties. Although there was considerable loss of the maximum breaking strength observed for all the tested polymers, there are good to excellent maximum breaking strength still remaining for the self-healing samples after cutting (Fig. 4b and Fig. S11†), with the poly(S-St-DCPD)4 keeping 62% of its original maximum break strength. This is lower than the self-healing efficiency of a related sulfur polymer system heated at 140 °C, which recovered 80% of the previous breaking strength,48 but comparable to another that recovered 61% of the breaking strength after heating at 120 °C.49
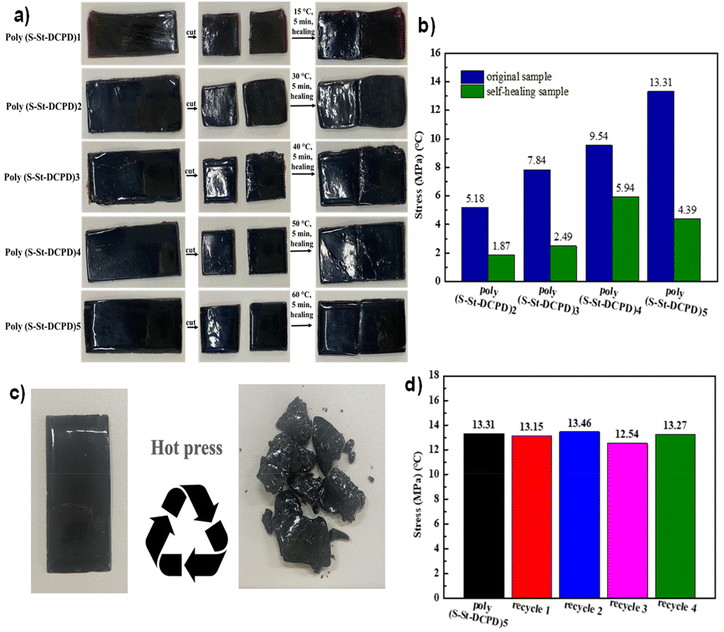 |
| Fig. 4 (a) Self-healing features of resultant poly(S-St-DCPD)1–5 at temperature of 15, 30, 40, 50, and 60 °C for 5 min, respectively. (b) Maximum break strength (MPa) of resultant original polymers and self-healing ones of the poly(S-St-DCPD)2–5. (c) Cyclic hot pressing. (d) Cycle hot pressing 5 times maximum breaking strength. | |
As aforementioned, Fig. 4a and video are the heat-based self-healing of the resultant polymers. The results show that when the cut inverse vulcanized polymers were heated at the temperature above their Tg, the dynamic covalent S–S bond inside the polymers is active, affording the self-healing ability of vulcanized polymers by the combination and reorganization of these dynamic covalent bonds reversibly. The self-healing performance of these polymers also could be recycled and reused which can improve the fatigue resistance of general polymers and prolong its service life (Fig. 4c). Moreover, the resultant polymers have excellent reprocessing and recyclable ability, for example, the poly(S-St-DCPD)5 underwent destroyed/hot-pressing cycle 4 times with negative difference of maximum breaking strength observed, demonstrating excellent reprocessing ability for the potential to be used as a new type of engineering plastic.
The shape memory and self-healing features are also feasible to the resultant polymers generated from other combined ternary systems, including S8 + α-pinene + DCPD, S8 + St + DVB, S8 + hexadecene + DCPD, with more details of their preparation, characterization, and performances presented in the ESI (Schemes S2–S4 and Fig. S12–S22†).
Possible mechanism for shape memory and self-healing properties
The thermal and photosensitive shape memory and self-healing properties of these new developed S-rich polymers most likely attributed to the possible cross-linked structure of the polymers as well as the dynamic covalent S–S bonds within the polymers. As shown in Scheme S1,† the low dissociation energy of the dynamic covalent S–S bond dominated the process of hot press molding. The polymer changes from the glass state to the high elastic state when the temperature is higher than its Tg. Therefore, the shape of the polymer changes and/or merges in the high elastic state, then the polymer returns to the glass state after cooling down. The shape of the polymer in the glass state will be remained as it in the state of shape changed. UV irradiation conducts light-induced plasticity together with the S–S dynamic covalent bond activation. It was proposed that the addition of a small amount of catalyst, dihexyl zinc dithioformate, could possibly promote the generation of S free radicals. Under the irradiation of ultraviolet rays, the reversible dynamic S–S bonds within the polymer affords elastic transformation of the polymer structure by the exchange and recombination of S–S bonds, changing or healing the shape of the polymer. This method has been used to achieve light-induced plasticity in many cases.50
Conclusions
Demonstrated here are a series of ternary inverse vulcanized polymers synthesised from element sulfur blended with mono- and di-olefins. The polymers show interesting mechanical properties of re-programable shape memory and self-healing functionalities. By adjusting the different ratios of mono- and di-olefins, the shape memory and self-healing features of the resultant polymers are tunable, affording rapid self-healing performance at temperatures as low as 30 to 60 °C, which is lower than any previous reports for inverse vulcanised polymers. Low temperature self-healing reduces energy consumption, provides a relatively safe experimental environment, and offers unique and interesting potential applications. The higher the component of the mono-olefins, the lower the response temperature is for the shape memory of the resultant polymers, and the more proportion of diolefins, the higher the response temperatures. This control allows the shape response temperature to be tailored depending on the application conditions. That this control is achieved only by the use of styrene and DCPD – both low cost and common industrial monomers, produced in bulk scale, is important in its compatibility with future practical scale up and use. In addition to the thermal response ability, the polymers also showed a UV-light response ability. The protocol developed here provides not only a new method to control the shape memory and self-healing polymers at low temperatures but also expands the applications of the inverse vulcanized S-rich polymers.
Conflicts of interest
There are no conflicts to declare.
Acknowledgements
The authors gratefully acknowledge the financial support from NSFC (no. 22161040, 21564013), the Foundation of CAST (no. 2020-5) and NWNU (no. NWNU-LKZD2021-3). TH holds a Royal Society University Research Fellowship.
References
- D. A. Boyd, Sulfur and Its Role In Modern Materials Science, Angew. Chem., Int. Ed., 2016,(55), 15486–15502 CrossRef CAS PubMed.
- J. Lim, J. Pyun and K. Char, Recent Approaches for the Direct Use of Elemental Sulfur in the Synthesis and Processing of Advanced Materials, Angew. Chem., Int. Ed., 2015,(54), 3249–3258 CrossRef CAS PubMed.
- J. Lim, J. Pyun and K. Char, Neue Ansätze zur direkten Verwendung elementaren Schwefels in der Synthese und Verarbeitung moderner Werkstoffe, Angew. Chem., 2015, 127, 3298–3308 CrossRef.
- W. J. Chung, K. Char and J. Pyun, The use of elemental sulfur as an alternative feedstock for polymeric materials, Nat. Chem., 2013, 5(6), 518–524 CrossRef CAS.
- F. Zhao, Y. Li and W. Feng, Recent advances in applying vulcanization/inverse vulcanization methods to achieve high-performance sulfur-containing polymer cathode materials for Li-S batteries, Small Methods, 2018, 2(11), 1800156 CrossRef.
- S. J. Kennedy and J. C. Wheeler, Free-radical concentration in doped sulfur. Theory and experiment, J. Phys. Chem., 1983, 87(20), 3961–3966 CrossRef CAS.
- H. J. Mausle and R. Steudel, Molecular composition of liquid sulfur. 3. Quantitative-analysis in the temperature region 115–350° C, Z. Anorg. Allg. Chem., 1981, 478(7), 177–190 CrossRef.
- Y. Zhang, N. G. Pavlopoulos and T. S. Kleine,
et al., Nucleophilic activation of elemental sulfur for inverse vulcanization and dynamic covalent polymerizations, J. Polym. Sci., Part A: Polym. Chem., 2019, 57(1), 7–12 CrossRef CAS.
- X. Wu, J. A. Smith and S. Petcher,
et al., Catalytic inverse vulcanization, Nat. Commun., 2019, 10(1), 1–9 CrossRef.
- T. R. Martin, K. A. Mazzio and H. W. Hillhouse,
et al., Sulfur copolymer for the direct synthesis of ligand-free CdS nanoparticles, Chem. Commun., 2015, 51(56), 11244–11247 RSC.
- Y. hang, J. J. Griebel and P. T. Dirlam,
et al., Inverse vulcanization of elemental sulfur and styrene for polymeric cathodes in Li-S batteries, J. Polym. Sci., Part A: Polym. Chem., 2017, 55(1), 107–116 CrossRef.
- T. S. Kleine, N. A. Nguyen and L. E. Anderson,
et al., High refractive index copolymers with improved thermomechanical properties via the inverse vulcanization of sulfur and 1, 3, 5-triisopropenylbenzene, ACS Macro Lett., 2016, 5(10), 1152–1156 CrossRef CAS.
- P. T. Dirlam, A. G. Simmonds and R. C. Shallcross,
et al., Improving the Charge Conductance of Elemental Sulfur via Tandem Inverse Vulcanization and Electropolymerization, ACS Macro Lett., 2015, 4(1), 111–114 CrossRef CAS.
- L. Yan, D. Han and M. Xiao,
et al., Instantaneous carbonization of an acetylenic polymer into highly conductive graphene-like carbon and its application in lithium-sulfur batteries, J. Mater. Chem. A, 2017, 5(15), 7015–7025 RSC.
- P. T. Dirlam, A. G. Simmonds and T. S. Kleine,
et al., Inverse vulcanization of elemental sulfur with 1, 4-diphenylbutadiyne for cathode materials in Li-S batteries, RSC Adv., 2015, 5(31), 24718–24722 RSC.
- M. Arslan, B. Kiskan and E. C. Cengiz,
et al., Inverse vulcanization of bismaleimide and divinylbenzene by elemental sulfur for lithium sulfur batteries, Eur. Polym. J., 2016, 80, 70–77 CrossRef CAS.
- E. T. Kim, W. J. Chung and J. Lim,
et al., One-pot synthesis of PbS NP/sulfur-oleylamine copolymer nanocomposites via the copolymerization of elemental sulfur with oleylamine, Polym. Chem., 2014, 5(11), 3617–3623 RSC.
- S. Shukla, A. Ghosh and U. K. Sen,
et al., Cardanol benzoxazine-sulfur copolymers for Li-S batteries: symbiosis of sustainability and performance, ChemistrySelect, 2016, 1(3), 594–600 CrossRef CAS.
- J. A. Smith, X. Wu, N. G. Berry and T. Hasell, High Sulfur Content Polymers: The Effect of Crosslinker Structure on Inverse Vulcanization, Polym. Chem., 2018,(56), 1777–1781 CrossRef CAS PubMed.
- S. J. Tonkin, C. T. Gibson, J. A. Campbell, D. A. Lewis, A. Karton, T. Hasell and J. M. Chalker, Chemically induced repair, adhesion, and recycling of polymers made by inverse vulcanization, Chem. Sci., 2020, 11(21), 5537–5546 RSC.
- D. A. Boyd, V. Q. Nguyen and C. C. Mcclain,
et al., Optical properties of a sulfur-rich organically modified chalcogenide polymer synthesized via inverse vulcanization and containing an organometallic comonomer, ACS Macro Lett., 2019, 8(2), 113–116 CrossRef CAS PubMed.
- D. A. Boyd, C. C. Baker and J. D. Myers,
et al., ORMOCHALCs: organically modified chalcogenide polymers for infrared optics, Chem. Commun., 2017, 53(1), 259–262 RSC.
- J. J. Griebel, S. Namnabat and E. T. Kim,
et al., New infrared transmitting material via inverse vulcanization of elemental sulfur to prepare high refractive index polymers, Adv. Mater., 2014, 26(19), 3014–3018 CrossRef CAS PubMed.
- A. M. braham, S. V. Kumar and S. M. Alhassan, Porous Sulphur Copolymer for Gas-phase Mercury Removal and Thermal Insulation, Chem. Eng. J., 2018, 332, 1–7 CrossRef.
- M. P. Crockett, A. M. Evans and M. J. H. Worthington,
et al., Sulfur-limonene polysulfide: A material synthesized entirely from industrial by-products and its use in removing toxic metals from water and soil, Angew. Chem., Int. Ed., 2016, 55(5), 1714–1718 CrossRef CAS PubMed.
- A. G. Simmonds, J. J. Griebel and J. Park,
et al., Inverse vulcanization of elemental sulfur to prepare polymeric electrode materials for Li-S batteries, ACS Macro Lett., 2014, 3(3), 229–232 CrossRef CAS PubMed.
- S. H. Je, T. H. Hwang and S. N. Talapaneni,
et al., Rational sulfur cathode design for lithium–sulfur batteries: sulfur-embedded benzoxazine polymers, ACS Energy Lett., 2016, 1(3), 566–572 CrossRef CAS.
- J. A. Smith, R. Mulhall, S. Goodman, G. Fleming, H. Allison, R. Raval and T. Hasell, Investigating the Antibacterial Properties of Inverse Vulcanized Sulfur Polymers, ACS Omega, 2020, 5, 5229–5234 CrossRef CAS PubMed.
- C. Miao, X. Xun and L. J. Dodd,
et al., Inverse Vulcanization with SiO2-Embedded Elemental Sulfur for Superhydrophobic, Anticorrosion, and Antibacterial Coatings, ACS Appl. Polym. Mater., 2022, 4(7), 4901–4911 CrossRef CAS.
- W. Zou, J. Dong, Y. Luo, Q. Zhao and T. Xie, Dynamic covalent polymer networks: from old chemistry to modern day innovations, Adv. Mater., 2017,(29), 1606100 CrossRef PubMed.
- Q. Zhang, C. Y. Shi and D. H. Qu,
et al., Exploring a naturally tailored small molecule for stretchable, self-healing, and adhesive supramolecular polymers, Sci. Adv., 2018, 4(7), eaat8192 CrossRef CAS.
- A. Takahashi, T. Ohishi, R. Goseki and H. Otsuka, Degradable epoxy resins prepared from diepoxide monomer with dynamic covalent disulfide linkage, Polymer, 2016, 82, 319–326 CrossRef CAS.
- D. Montarnal, M. Capelot and F. Tournilhac,
et al., Silica-like malleable materials from permanent organic networks, Science, 2011, 334(6058), 965–968 CrossRef CAS PubMed.
- P. Taynton, K. Yu and R. K. Shoemaker,
et al., Heat–or water–driven malleability in a highly recyclable covalent network polymer, Adv. Mater., 2014, 26(23), 3938–3942 CrossRef CAS PubMed.
- C. Yuan, M. Z. Rong and M. Q. Zhang,
et al., Self-healing of polymers via synchronous covalent bond fission/radical recombination, Chem. Mater., 2011, 23(22), 5076–5081 CrossRef CAS.
- H. Ying, Y. Zhang and J. Cheng, Dynamic urea bond for the design of reversible and self-healing polymers, Nat. Commun., 2014, 5(1), 1–9 Search PubMed.
- S. Zhang, L. Pan and L. Xia,
et al., Dynamic polysulfide shape memory networks derived from elemental sulfur and their dual thermo-/photo-induced solid-state plasticity, React. Funct. Polym., 2017,(121), 8–14 CrossRef.
- P. Yan, W. Zhao and B. Zhang,
et al., Inverse vulcanized polymers with shape memory, enhanced mechanical properties, and vitrimer behavior, Angew. Chem., Int. Ed., 2020, 59(32), 13371–13378 CrossRef CAS PubMed.
- Y. Xin, H. Peng and J. Xu,
et al., Ultrauniform embedded liquid metal in sulfur polymers for recyclable, conductive, and self–healable materials, Adv. Funct. Mater., 2019, 29(17), 1808989 CrossRef.
- L. Sun, S. Gao and X. Gui,
et al., Renewable sulfur-and monoterpenes-derived polysulfides as functional crosslinker for epoxy thermosets, Eur. Polym. J., 2020,(123), 109440 CrossRef CAS.
- H. Mutlu, E. B. Ceper and X. Li,
et al., Sulfur chemistry in polymer and materials science, Macromol. Rapid Commun., 2019, 40(1), 1800650 CrossRef PubMed.
- T. Xie, Recent advances in polymer shape memory, Polymer, 2011, 52(22), 4985–5000 CrossRef CAS.
- J. A. Smith, S. J. Green and S. Petcher,
et al., Crosslinker copolymerization for property control in inverse vulcanization, Chem. – Eur. J., 2019, 25(44), 10433–10440 CrossRef CAS PubMed.
- W. Post, A. Cohades and V. Michaud,
et al., Healing of a glass fibre reinforced composite with a disulphide containing organic-inorganic epoxy matrix, Compos. Sci. Technol., 2017,(152), 85–93 CrossRef CAS.
- L. M. Johnson, E. Ledet and N. D. Huffman,
et al., Controlled degradation of disulfide-based epoxy thermosets for extreme environments, Polymer, 2015,(64), 84–92 CrossRef CAS.
- S. J. Garcia, Effect of polymer architecture on the intrinsic self-healing character of polymers, Eur. Polym. J., 2014,(53), 118–125 CrossRef CAS.
- R. Araya-Hermosilla, G. M. R. Lima and P. Raffa,
et al., Intrinsic self-healing thermoset through covalent and hydrogen bonding interactions, Eur. Polym. J., 2016,(81), 186–197 CrossRef CAS.
- P. Yan, W. Zhao and S. J. Tonkin,
et al., Stretchable and Durable Inverse Vulcanized Polymers with Chemical and Thermal Recycling, Chem. Mater., 2022, 34(3), 1167–1178 CrossRef CAS.
- H. K. Lin and Y. L. Liu, Reactive Hybrid of Polyhedral Oligomeric Silsesquioxane (POSS) and Sulfur as a Building Block for Self-Healing Materials, Macromol. Rapid Commun., 2017, 38(10), 1700051 CrossRef PubMed.
- S. Chatani, C. J. Kloxin and C. N. Bowman, The power of light in polymer science: photochemical processes to manipulate polymer formation, structure, and properties, Polym. Chem., 2014, 5(7), 2187–2201 RSC.
Footnotes |
† Electronic supplementary information (ESI) available: Experimental section and ESI figures. See DOI: https://doi.org/10.1039/d3py00724c |
‡ These authors contributed equally to this work. |
|
This journal is © The Royal Society of Chemistry 2023 |
Click here to see how this site uses Cookies. View our privacy policy here.