DOI:
10.1039/D3NA00211J
(Paper)
Nanoscale Adv., 2023,
5, 3671-3683
Biomass-derived carbon deposited TiO2 nanotube photocatalysts for enhanced hydrogen production
Received
2nd April 2023
, Accepted 22nd May 2023
First published on 23rd June 2023
Abstract
In this study, titanium oxide nanotubes (TiO2NTs) were deposited on the surface of activated carbon (AC) by varying the wt% of AC. The physicochemical properties of synthesized TiO2NTs–AC nanocomposites were analysed by various characterization techniques such as XRD, FT-IR, Raman, DRUV-vis, HR-TEM, XPS, PL, and N2 physisorption. The FT-IR, EDX, and XPS analyses proved the existence of interaction between AC and TiO2NTs. This study found that as the content of AC increases, the surface area and pore volume increase while the energy bandgap decreases. The TiO2NTs–AC nanocomposite with 40% AC exhibited a surface area of 291 m2 g−1, pore volume of 0.045 cm3 g−1 and half pore width = 8.4 Å and had a wide band gap energy (3.15 eV). In addition, the photocatalytic application of the prepared nanocomposites for photocatalytic H2 production was investigated. The H2 was produced via photo-reforming in the presence of a sacrificial agent (methanol) under sunlight irradiation. It was found that the prepared TiO2NTs–AC nanocomposite with 40% AC acted as an efficient photocatalyst for aqueous-methanol reforming under various optimization conditions. Approximately 18
000 μmol−1 hydrogen gas was produced via aqueous-methanol reforming under optimized conditions (catalyst dose = 100 mg, temperature = 25 °C, time = 12 hours, vol. of methanol = 20% (v/v), and pH = 7). The reusability of the TiO2NTs–AC nanocomposite was also investigated for 5 consecutive cycles, and the results suggested only a slight decline in efficiency even after the fifth cycle. This study demonstrates the ability of an activated carbon deposited TiO2NT catalyst to produce hydrogen effectively under sunlight.
1. Introduction
Along with increasing energy demand, the fossil fuel industry is also growing at an alarming rate. Developed industries release large amounts of emissions, such as greenhouse gases (GHGs) and other air pollutants, into the atmosphere.1 GHG emissions mainly contain toxic gases such as CO2, NO, NO2, and SO2, which are fatal for humans and the environment.1,2 Because of this condition, many efforts are being made immediately to reduce fossil fuel production and consumption considerably, although it seems a little far from possible.3
At this juncture, hydrogen (H2) is emerging as an alternative to fossil fuels, which can be used as an excellent carbon-free fuel.4 H2 fuel cells are presently under use for automobiles as H2 burning with O2 generates only water as a by-product, proving to be a better fuel option.5,6 Although H2 is a clean and green energy source, its production on a large industrial scale is still un-affordable.7 The significant aspects which are considered while developing the technology for H2 production are: (i) avoiding the generation of GHGs mainly COx, (ii) long-term supply, and (iii) an economically viable process.1,2
Thermal,8 chemical,9 biological,10 electrolytic,11 photo-electrolytic12 and photocatalytic processes13 have been used for H2 production. Most of the H2 these days is produced through the steam reforming of natural gases, such as methane, following the water gas shift process.5,6 However, conventional H2 production processes require high temperatures and pressure, which does not make these processes sustainable and efficient.5 Among various processes, H2 production via water splitting can be recognized as the most prominent method.14,15 The first reported suitable technology to produce H2via water splitting was the photo-assisted electrochemical method. However, it needs sophisticated instrumentations.15 Recently, H2 production occurred on the surface of various semiconductors (photocatalysts) via water splitting under light irradiation at ambient temperature, proving to be a better and more sustainable technique.5,16 The most commonly used photocatalyst is titanium oxide, TiO2 (non-toxic, cheap, and chemically stable).17 However, due to the wide band gap and fast e−–h+ recombination, its use could not have been practical for H2 production.5
Notably, the criteria to obtain an environmentally friendly and efficient photocatalyst are: (i) efficient absorption of solar light, (ii) stability under working conditions, and (iii) cost-effectiveness to split water into H2 efficiently.5–7 These criteria can be achieved by tuning the structure of the photocatalyst to have (a) charge carrier (e− and h+) separation, (b) delayed e− and h+ recombination and their migration to surface reactive centers, (c) correct alignment of band edges, and (d) avoiding the use of expensive raw materials,5 although practically this seems less possible as these criteria can only be achieved by doping the photocatalyst with expensive metals such as platinum, palladium, silver, etc.16,18,19 TiO2 has also been used to produce H2 by doping different metal species.16 Other heterogeneous materials have also been made with TiO2, although they also did not prove to be very relevant, as their cost was high.20,21 It should be noted that to make the process more efficient, a sacrificial agent such as methanol, ethanol, lactic acid, etc., has also been used.5,22 Since the sacrificial agent acts as a source of protons in the water splitting process, the H2 production rate increases substantially in the presence of the sacrificial agent.5,23,24 Although semiconductors help produce H2 through water splitting with sacrificial agents, low-cost and fast production rates under solar light irradiation are still rare.
It is found that the use of AC with semiconductors can be a good step.25 AC is fairly cheap, providing a good surface that can easily be decorated with semiconductors.26 It has also been proven from the previous literature that AC combined with semiconductors helps in charge separation (or prevention of e− and h+ recombination) for photocatalysts.25–27 Therefore, the merging of AC with semiconductors can be a practical option. However, there is hardly any reported study on H2 production by combining AC with TiO2. Therefore, in this study TiO2NTs–AC nanocomposites were synthesized and utilized for H2 production under solar light with sacrificial agent, methanol. This can be a great effort for energy production. This is the first study that has not been reported before. Hence, the objectives of this study could be described as (a) synthesis of AC, (b) synthesis of TiO2NTs, (c) synthesis of TiO2NTs–AC, (d) characterization of TiO2NTs–AC composites, (e) H2 production investigation, (f) optimization of H2 production, and (g) reusability of TiO2NTs–AC.
2. Experimental
2.1. Chemicals
Titanium(IV) isopropoxide (TTIP) (Ti[OCH(CH3)2]4 – 97%), sodium hydroxide (NaOH – 98%), potassium hydroxide (KOH – 99.95%), and methanol (CH3OH – 99.9%) are analytical research grade reagents and were obtained from Sigma Aldrich, UK. The reagents were used as received. In addition, walnut shells were collected from the local market. Deionized water was used for the preparation and activity tests.
2.2. Synthesis of materials
2.2.1. Preparation of walnut shell-derived activated carbon (AC).
AC was synthesized using walnut shells, a biomass as a raw material.28 In brief, the walnut shells were cleaned and dried under sunlight and then dried in an oven at 100 °C for 10 h. Then, 100 g of walnut shells were crushed well and pulverized. The pulverized shells were taken in a silica crucible and pre-carbonized at 450 °C for 3 h in a muffle furnace. Then, the crucible was allowed to cool to room temperature to obtain a black solid. Next, the product was collected and ground well with a pestle and mortar. To activate the black carbon powder, it was treated with 12% KOH solution for 5 h at 90 °C. Then, the obtained activated carbon slurry was filtered and placed in the open air for 12 h and subsequently transferred into a silica crucible to be thermally treated at 800 °C for 3 h. Next, the AC was washed with dil. HCl (5%) and double-distilled water until the pH of the filtered solution became neutral. Finally, the washed cake was dried at 100 °C for 5 h to remove the moisture and ground into fine AC powder using a pestle and mortar.
2.2.2. Synthesis of anatase TiO2NTs.
The microwave hydrothermal method was used to produce TiO2NTs.29 At first, 50 mL of boiling water was used to dissolve a predetermined quantity of CTAB. To this, 90 mL of solution containing 2-propanol and TTIP was added while the mixture was being stirred for 1 hour to obtain a homogeneous suspension. To this suspension, 0.2 M NaOH solution was added dropwise to maintain pH 13. Finally, the suspension was transferred into specially designed vessels and the vessels were placed in an ETHOS microwave lab station for microwave hydrothermal treatment. The treatment was continued for 1 h at 120 °C with a microwave power of 500 W under autogenous pressure. After being filtered, the precipitate was washed repeatedly until the pH of the filtrate was near 7. Finally, the washed sample was dried in an oven at 100 °C for 4 h. After this, the substance was calcined in a muffle furnace at 450 °C for 6 h.
2.2.3. Preparation of TiO2NTs–AC nanocomposites.
To make the TiO2NTs–AC composites, a predetermined quantity of calcined TiO2NTs was dispersed in 25 mL of 2-propanol. A solution of 2-propanol containing 25 mL was stirred continuously while an unknown quantity of AC was mixed in. The treatment was continued for an additional 1 h after the AC dispersion was introduced to the TiO2NT solution while it was vigorously stirred and sonicated. After being made into TiO2NTs–AC (Scheme 1), it was filtered and then dried in a hot air oven at a temperature of 100 °C for 5 h. Four different composites were prepared by varying the wt% of AC (10, 20, 30, and 40 wt%) over a fixed amount of prepared TiO2NT powder.
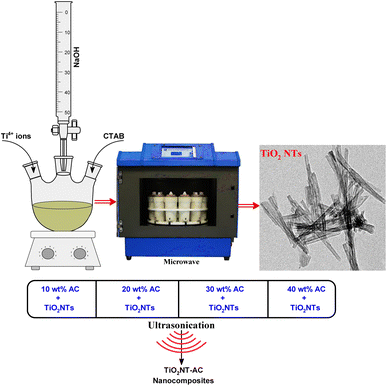 |
| Scheme 1 Synthesis of TiO2NTs and ultrasonic deposition of AC on TiO2NTs. | |
2.3. Characterization
The crystal structures of bare TiO2NTs, AC, and TiO2NTs–AC were examined using X-ray diffraction (XRD) on a D8 Advance Bruker powder X-ray diffractometer at a 2θ range of 10° to 80°. A Thermo-Fisher Scientific Nicolet iS5 FT-IR spectrometer was used to investigate surface functional groups of the prepared materials. Raman spectra were measured using a micro-Raman spectrometer and an image spectrograph, STR 500 mm Focal Length Laser Raman spectrometer, with a flat field: 27 mm (W) 14 mm (H), and resolution: 1/0.6 cm−1/pixel. A Thermo Scientific Evolution 220 diffuse reflectance UV-vis spectrophotometer (DR UV-vis) was used to investigate the optical properties of the as prepared materials in the wavelength range of 220–900 nm. The photoluminescence (PL) spectra were recorded at room temperature on a Varian Cary Eclipse Photoluminescence spectrophotometer. A high-resolution transmission electron microscope (HR-TEM) (FEI-TECNAI G2-20 TWIN with LaB6 filaments) working at 200 kV was used to analyse the morphologies of the produced nanomaterials. An Autosorb-iQ 2ST/MP, Quantachrome, nitrogen gas adsorption–desorption at 77 K was used to determine the specific surface areas of the synthesised materials. Using a Thermo-Scientific Escalab 250 Xi XPS apparatus with Al Kα X-rays having a spot size of 650 mm, the samples' X-ray photoelectron spectra were obtained.
2.4. Photocatalytic utilization of TiO2NTs–AC nanocomposites
The photocatalytic reactions were performed using a laboratory build reactor equipped with a 500 W xenon lamp with a light intensity of 800 W m−2 and photon flux of 650 lm. A double-jacket Pyrex-glass reactor (100 mL volume) was fitted with a quartz window for UV light passage. Before starting the photocatalytic activity tests, the reactor was flushed with argon gas for 20 min. Then, the UV lamp was switched on and waited for 15 minutes to reach stability (light intensity of 45 mW cm−2). The reactor is also equipped with a cold-water circulation system to keep the reaction temperature at 25 °C. To evaluate the photocatalytic efficiency of the synthesized catalysts, 20% of an aqueous methanol solution (0.15 mol methanol) and 100 mg of catalyst were used. At different time intervals, a known product sample (0.5 μL) was analysed using an Agilent gas chromatograph equipped with a TCD and Carboxen 1000 packed column.30
3. Results and discussion
3.1. XRD analysis
The XRD patterns of the synthesized samples are shown in Fig. 1. The X-ray diffraction patterns of AC and bare TiO2NT samples are compared to that of the TiO2NTs–AC NC (10–40 wt% of AC). The AC sample displayed two characteristic X-ray reflections in the XRD pattern at around 2θ values of 25° and 45° corresponding to the (002) and (101) planes that feature prominently in the cellulosic carbon framework.31 Bare TiO2NT samples displayed several characteristic XRD reflections for the anatase TiO2 phase at around 26°, 38°, 47°, 54°, 56°, 62°, 68°, 69°, and 77° accounted for the (101), (004), (200), (105), (211), (204), (116), (220), and (215) planes respectively. The XRD reflections of existing TiO2NTs matched JCPDS file (01-084-1286) of anatase TiO2 crystals and showed good agreement with the literature.32,33 The TiO2NTs–AC (10–40 wt%) composite samples also showed similar XRD peaks as bare TiO2NTs, although the intensity of AC-deposited TiO2NT samples was lower. This could be due to the excellent deposition of TiO2NTs onto the AC through several possible interactions (electrostatic and non-electrostatic). It has also been noted that no phase change was observed, irrespective of the presence of a large amount of AC. This observation indicates the existence of highly dispersed AC over the surface of the crystalline anatase structure of TiO2NTs.
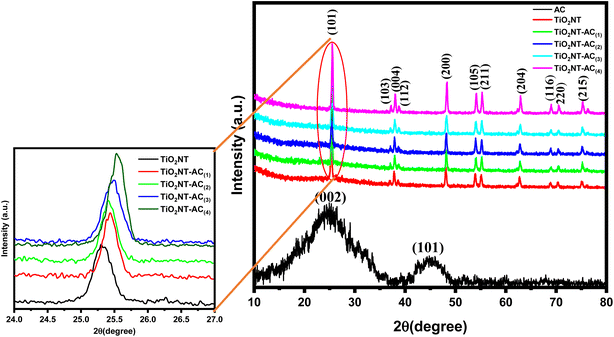 |
| Fig. 1 XRD patterns of synthesized nanocomposites. | |
The crystallite size was calculated using Scherrer's formula, i.e. {(D = Kλ/β
cos
θ) where K is a constant = 0.89, λ is the wavelength of the X-ray radiation, β is the full width at half-maximum, and θ is the diffraction angle}, which increases with an increase in AC contents (10 to 40 wt%). The larger crystallite size at higher AC content (40 wt%) resulted because the formation of larger-sized particles might be due to the coalescence of small grains via grain boundary diffusion. The change in crystallite size with an increase in AC content is presented in Table 1. Furthermore, XRD profiles did not show any reflections for other impurity phases, which suggests the high phase purity attained by the adapted synthesis method. Similar observations were reported in the previous literature.34,35
Table 1 The dependence of physiochemical properties of TiO2NTs–AC at varying AC contents
Sample |
TiO2NT crystallite size (nm) |
Surface area (m2 g−1) |
Pore volume (cm3 g−1) |
Half pore width (Å) |
Band gap (eV) |
AC |
— |
634 |
0.401 |
8.0 |
— |
Pure TiO2NTs |
9.27 |
56 |
0.014 |
13.8 |
3.12 |
TiO2NT–AC(1) |
6.31 |
127 |
0.020 |
8.4 |
3.08 |
TiO2NT–AC(2) |
6.32 |
159 |
0.023 |
8.4 |
3.08 |
TiO2NT–AC(3) |
7.49 |
204 |
0.036 |
8.4 |
3.07 |
TiO2NT–AC(4) |
15.07 |
291 |
0.045 |
8.4 |
3.01 |
3.2. Raman spectroscopy
Raman spectra of the samples were obtained for a better understanding of the structure and vibrational modes of crystalline materials. The Raman spectra of TiO2NTs and TiO2NTs–AC (10–40 wt%) are shown in Fig. 2. The Raman spectrum of bare TiO2NTs (see the black line) has shown three peaks at approximately 395.0, 515.0, and 635.0 cm−1 for B1g(1), A1g (+B1g(2)), and Eg, modes respectively. These peaks were related to the anatase phase of TiO2.28 The bands belonging to the TiO2NTs were also observed in all the Raman spectra of TiO2NT-deposited AC. In addition to TiO2NT bands, two other bands were found in the Raman spectra of TiO2NTs–AC samples (in-large inset image). These bands were assigned for the D band (sp3-defective carbon) and G band (ordered sp2-bonded carbon atoms) at approximately 1345.00 and ∼1615.00 cm−1, respectively. A slight shift in the peak position and decrease in peak intensity of the Raman peaks of TiO2NTs–AC samples confirms the formation of TiO2NTs–AC composites due to interaction between AC and TiO2NTs.34
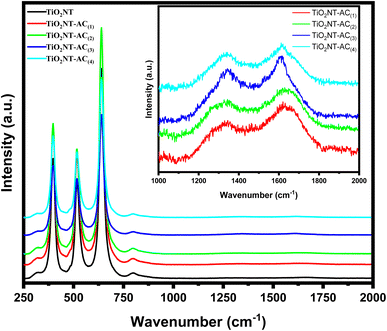 |
| Fig. 2 Raman spectra of the prepared nanocomposites. | |
3.3. FT-IR spectroscopy
To investigate the functional groups present in the synthesized materials (AC, bare TiO2NTs, and TiO2NTs–AC) and the interaction between the functional groups (of AC and TiO2NTs in TiO2NTs–AC), FT-IR spectra of the samples were collected (Fig. 3). The spectrum of the bare TiO2NT sample in the range of 4000 to 400 cm−1 (see the black line) shows an absorption peak at 600–500 cm−1 for Ti–O–Ti bond vibrations. A broad peak in the 3450–3350 cm−1 range was assigned to the water adsorbed on the surface of TiO2NTs (i.e., moisture). The existing AC also showed absorption peaks for the several functional groups in its FT-IR spectrum (see the red line). These were mainly assigned to the stretching frequency of hydroxyl groups (at nearly 3400 cm−1), alkyls (in the range of 2900–2800 cm−1), carbonyls (at 1710 cm−1), amides (at near 1650 cm−1), and some other groups such as –C–O and C
C in the range of 1400–1000 cm−1. According to previous studies, these existing functional groups in the AC can be accounted for by its carbon (cellulosic) surface. Notably, the cellulosic surface could act as a host to accommodate the hydroxylated TiO2NTs; thus, the TiO2NTs–AC nanocomposites were formed due to strong interaction between the AC and TiO2NTs. The interaction between the AC and TiO2NTs can be observed in the FT-IR spectra of the prepared NCs. The FT-IR spectra of NCs have shown all the corresponding peaks of unmodified AC and bare TiO2NTs, along with slight shifting in their peak positions. Peak intensities were also found to be reduced in the nanocomposites. The shift in the peak positions and decrease in the intensity of IR absorption peaks are due to the interaction between the AC and TiO2NTs via –OH functional groups. These observations suggest that the preparation of TiO2NTs–AC nanocomposites is successful. The strength of the interaction of TiO2NTs with AC increases with an increase in wt% of AC, which can also be confirmed by the lowering of peak intensities in their respective FT-IR spectra (20–40 wt% of AC). These results are in good agreement with previously reported research.34,35
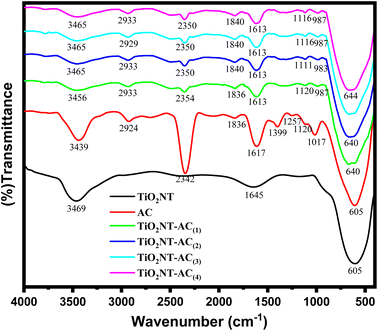 |
| Fig. 3 FTIR spectra of the prepared nanocomposites. | |
3.4. DR UV-vis spectroscopy
The solid-state diffuse reflectance UV-visible (DR UV-vis) spectra of the samples are shown in Fig. 4a. The spectrum of the bare TiO2NT sample showed a characteristic absorbance at around 320–420 nm corresponding to the absorption edge at around 380 nm. On the other hand the TiO2NTs–AC nanocomposite spectra showed two absorbance peaks centered at around 230 nm and 390 nm. This could be due to the effect of the presence of activated carbon species, which would absorb both UV and visible light. The TiO2NTs–AC composites showed extended light absorption compared with the bare TiO2NT sample. The absorption edges of TiO2NTs–AC(1), TiO2NTs–AC(2), TiO2NTs–AC(3) and TiO2NTs–AC(4) are found to be 428, 426, 422, and 415 nm respectively. The extended absorption for the synthesized composite samples is due to strong chemical interaction between the AC and TiO2NTs. The bandgap energy of semiconducting materials plays an important role in photocatalytic applications. Narrow energy bandgap materials may be involved in light absorption's electronic excitation (valence bands to conduction bands). These excitations lead to hole formation and free electrons that reach the catalytic surface and are responsible for the photocatalytic properties. The bandgap energy can be tuned by altering the orientation of materials. In this study, the energy bandgap was measured for bare TiO2NTs and TiO2NTs–AC (10–40 wt%) samples using the data obtained from DR UV-vis analysis. The Tauc plots for the synthesized samples are shown in Fig. 4b–f. It was found that the energy bandgap of TiO2NTs decreased slightly with an increase in AC wt%, although the difference was found to be small. This is possibly due to the fact that there is no change in the crystal structure irrespective of deposition of AC on the surface of TiO2NTs. The lowest bandgap (with a slight difference) was found for the highest content of AC in TiO2NTs (TiO2NTs–AC (wt% 40)) (Table 1).
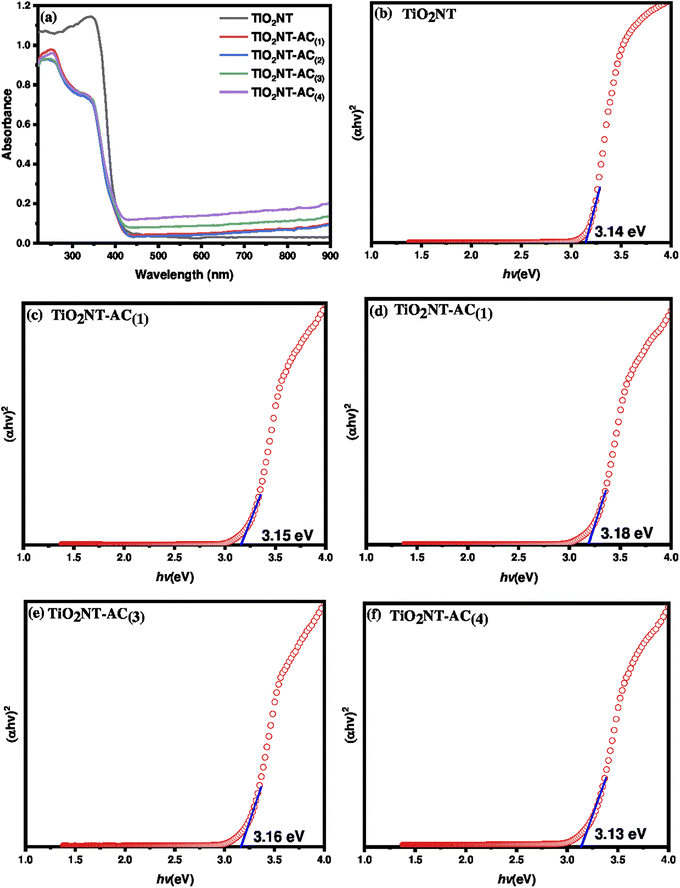 |
| Fig. 4 (a) UV-visible diffuse reflectance spectra of pure TiO2NT and TiO2NT–AC nanocomposites and (b–f) results of the Tauc plot method for band gap calculation: (b) pure TiO2NT, (c) TiO2NT–AC(1), (d) TiO2NT–AC(2), (e) TiO2NT–AC(3), and (f) TiO2NT–AC(4). | |
3.5. Photoluminescence (PL) spectroscopy
To clarify the migration and separation effectiveness of photogenerated charge carriers at the TiO2NTs–AC nanocomposite interface, photoluminescence (PL) spectra were obtained. The semiconductors' electron–hole (e−–h+) recombination is what causes the PL emission.36 As a result, it is believed that the e−–h+ recombination rate is directly proportional to the PL intensity. A lower PL intensity indicates a lower e−–h+ recombination rate, indicating the examined photocatalyst's usefulness for photocatalytic processes.36Fig. 5 displays the PL spectra for the TiO2NTs, TiO2NTs–AC (wt% = 10), and TiO2NTs–AC (wt% = 40) samples. In the visible range, the samples showed PL emission. The TiO2NT sample exhibits a higher PL intensity than the TiO2NTs–AC sample, as shown in Fig. 5. With an increase in the contents of AC (10 to 40% wt%), this intensity falls even further. Thus, it can be concluded that the e−–h+ recombination rate lowers noticeably as the AC content increases, most likely because of the synergistic interaction between the AC and TiO2NTs. This finding suggests that TiO2NTs–AC could exhibit better photocatalytic performance than pure TiO2NTs in the future. Additionally, the PL spectra offer compelling proof of the interaction between TiO2NTs and AC.34
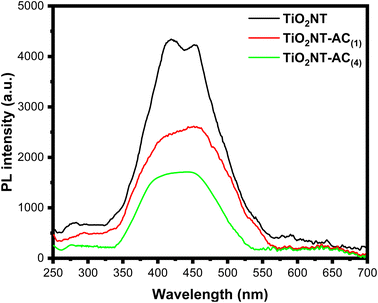 |
| Fig. 5 Photoluminescence spectra of pure TiO2NT, TiO2NT–AC(1), and TiO2NT–AC(4). | |
3.6. HRTEM analysis
The HRTEM image (Fig. 6a) analysis revealed the development of bare anatase TiO2NTs of various sizes (Table 1). The nanotubes have outer diameter around 5 and 7 nm and are 100–150 nm in length. The walls of the bare TiO2NTs consist of 2 or 3 layers with an interlayer distance of 0.6 nm. The HRTEM image (Fig. 6c) of TiO2NTs–AC suggested the presence of carbon on the surface of TiO2NTs. The size of TiO2NTs in TiO2NTs–AC was smaller than that of bare TiO2NTs, and breaking of the tubes into smaller ones could be observed. The lowering in the size of nanotubes could be due to the sonication treatment. The size of the tubes measured using TEM analysis is in agreement with the crystallite size calculated from the XRD analysis.
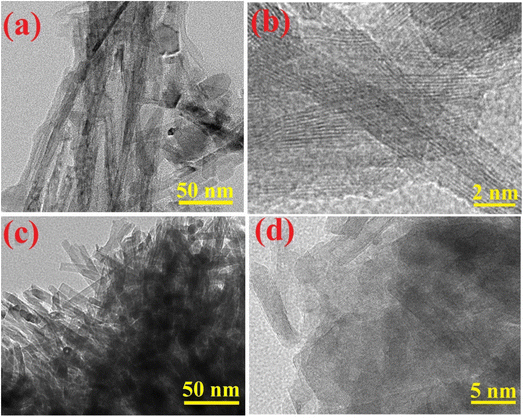 |
| Fig. 6 TEM and HRTEM images of (a and b) pure TiO2NT and (c and d) TiO2NT–AC nanocomposites. | |
3.7. XPS analysis
XPS is one of the most advanced techniques to determine the elements constituting the sample surface, its composition, and its chemical bonding state by analysing the energy of photoelectrons released upon X-ray interactions with the analysed sample. The existing sample was also subjected to the XPS analysis. The binding energy peak profile (high-resolution XPS spectrum) of the prepared sample is shown in Fig. 7. Single region binding energy profiles (such as C 1s, Ti 2p, and O 1s) for the TiO2NTs–AC nanocomposite sample are shown in Fig. 7e–g. The critical energy profile of Ti ions is shown in Fig. 7e. Fig. 7e displays the two dominant peaks at 457.2 eV and 462.9 eV belonging to the Ti 2p doublets (Ti 2p3/2 and Ti 2p1/2). These doublets accounted for Ti ions' +4-oxidation state.5 Notably, the Ti 2p3/2 binding energy peak of bare TiO2NTs was assigned at 458.0 and 463.7 eV (Fig. 7c). Therefore, the shifting in the Ti 2p3/2 peak was observed in the XPS spectrum of prepared TiO2NTs–AC.
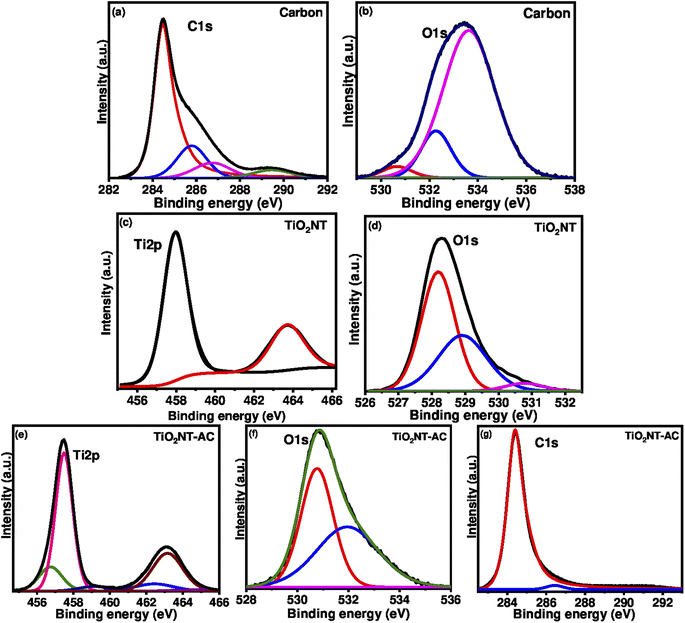 |
| Fig. 7 Deconvoluted XPS spectra of AC, pure TiO2NT, and TiO2NT–AC. | |
Fig. 7f displays the binding peak at 530.5 eV for the O 1s region (lattice oxygen) related to the TiO2NTs in the nanocomposites. It is found that the O 1s region binding energy peaks of AC (533.5 eV in Fig. 7b) and bare TiO2NTs (528.0 eV in Fig. 9d) were assigned in slightly different ranges (Fig. 7d), suggesting the shifting in the O 1s peak in the XPS spectrum of prepared TiO2NTs–AC.34Fig. 7g displays the C1 region profile related to the AC in the nanocomposites. A binding energy peak at 284.0 eV is attributed to the carbon surface.34 It should be noted that the C1 region profile related to the NC (Fig. 7g) displayed a slight difference from the C1 region profile related to the AC (Fig. 7a). These analyses, along with the shifting in the peaks, suggested the preparation of TiO2NTs–AC via interaction between the AC and TiO2NTs.
3.8. Nitrogen gas physisorption studies
The textural properties of the prepared TiO2NTs–AC were investigated using N2 physisorption analysis (Fig. 8). The N2 adsorption–desorption isotherms for TiO2NTs–AC adopt a type-III isotherm with an apparent H3 hysteresis loop as per IUPAC classification.34 The type-III adsorption–desorption isotherm reflects the adsorbate's interaction with the adsorbent's surface. The observed H3 hysteresis reflects N2 adsorption due to the capillary condensation, possibly due to the uneven distribution of aggregates in the sample with complex pore channels. The synthesized samples' pore size distribution (PSD) patterns were obtained using the NLDFT method. The results indicated the appearance of PSD peaks corresponding to macropores in TiO2NTs–AC, probably due to the aggregation between particles forming large-size voids. The analysis reflected the specific surface area of TiO2NTs–AC, which is listed in Table 1 with a pore volume and a half pore width.
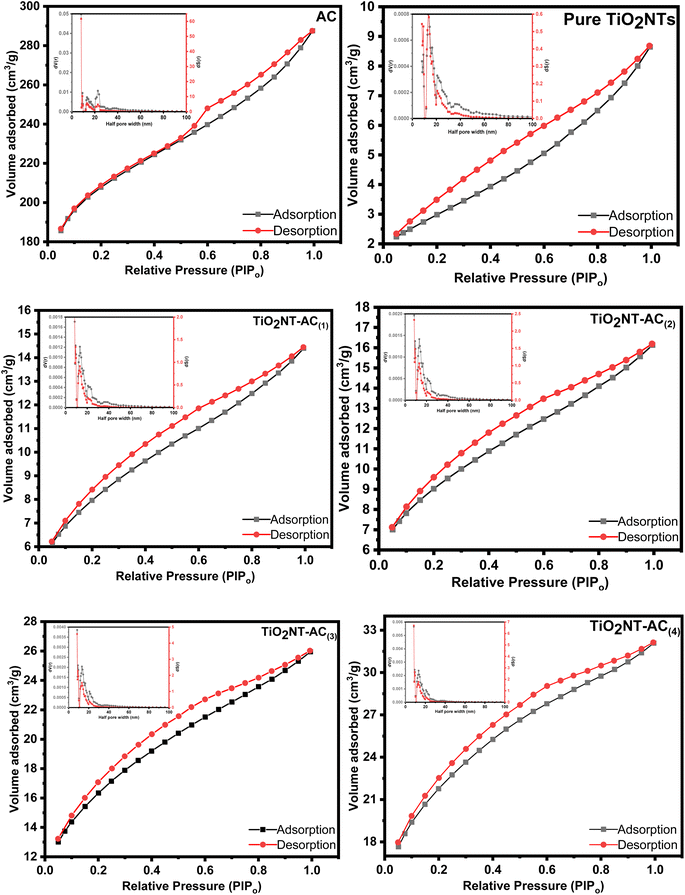 |
| Fig. 8 N2 adsorption–desorption isotherms and pore size distribution patterns (inset) of the synthesized samples. | |
3.9. Photocatalytic H2 production over TiO2NTs–AC nanocomposites
Photoreforming of aqueous-methanol was assessed for the H2 production over the prepared material. This study was carried out with 100 mg of photocatalyst in pure water with methanol under uninterrupted artificial visible light irradiation for 6 h. This study shows the efficient photocatalytic properties of the prepared material. The H2 production has been observed under different conditions such as solution (water + catalyst) pH, catalyst dosage, reaction temperature and time, and the sacrificial agent's concentration such as methanol. The photocatalytic efficiency of the composite is compared with that of bare TiO2NTs on all parameters. As can be seen, these results are shown in Fig. 9a–f. All the figures showed that the composite nanotubes showed a better hydrogen production rate under all conditions than the bare nanotubes.
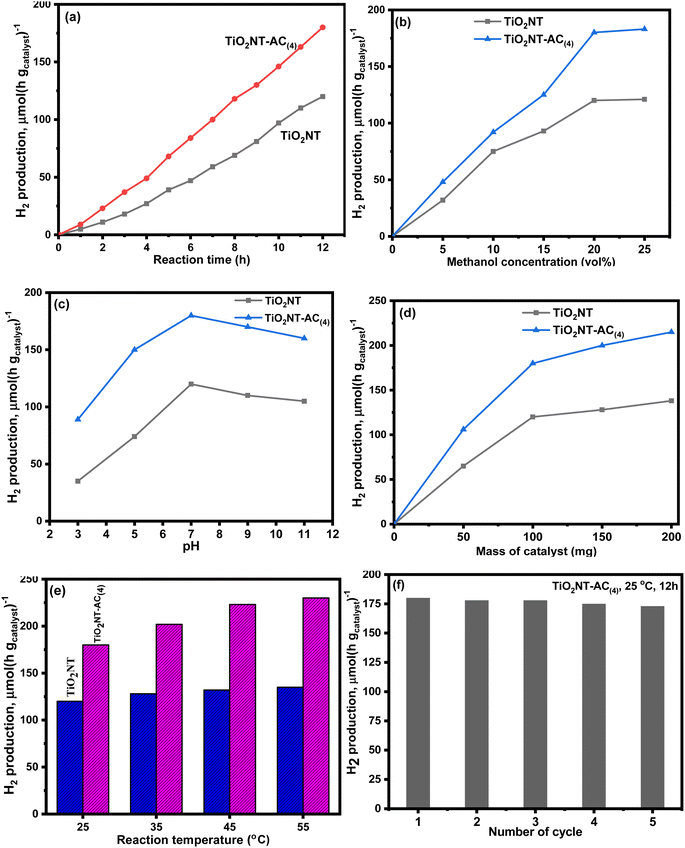 |
| Fig. 9 Photocatalytic hydrogen production over synthesized TiO2NTs and TiO2NTs–AC(4) catalysts, (a) effect of reaction time, (b) effect of concentration of methanol, (c) effect of solution pH, (d) effect of mass of catalysts, (e) effect of reaction temperature, and (f) recyclability of the TiO2NTs–AC(4) catalyst. | |
Fig. 9a clearly shows that hydrogen production increases with the increase of time. In the first 2 hours, the hydrogen production concentration was ∼1000.0 and ∼2300.0 μmol−1, over the pure NTs and composite NTs, which increased to 4600 and 8500 μmol−1 after 6 hours, respectively. On doubling the reaction time, i.e., after 12 hours, this production reached 12
000 μmol−1 and 18
000 μmol−1. It can be seen from the figure that the composite nanotubes showed much better photocatalytic properties as compared to bare TiO2NTs. Fig. 9b clearly shows that hydrogen production increases with an increase in the concentration of sacrificial agent methanol. At vol. 5% methanol, the hydrogen production concentration was ∼3100 and ∼4900 μmol−1, over the bare nanotubes and composite nanotubes, which increased to ∼11
900 and 18
000 μmol−1 using 20 vol% methanol, respectively. After this, the equilibrium was attained for both materials and no efficient change was observed with a further increase in the methanol concentration. This result might be due to the surface blocking upon methanol loading, which declines the visible light absorption. Fig. 9c shows the pH effect result, which revealed that the H2 production rate was higher at basic pH than at acidic pH. However, the best thing is that both catalysts showed the best photocatalytic activity at neutral pH (the normal pH of water). As the acidic pH was attained (towards the lower pH < 7), the hydrogen production rate decreased, and at pH = 3, the H2 production remained at only 3460 μmol−1 and 8900 μmol−1, over the pure and composite nanotubes, respectively. These rates increased with an increase in the pH and, at pH 7, reached 11
940 and 17
780 μmol−1, which was much higher than that of acidic pH. On further increasing pH (towards the higher pH > 7), the production rates decreased again, although it was almost negligible compared to acidic pH. At pH = 11, 10
420 μmol−1 and 15
950 μmol−1 H2 were produced over the pure and composite nanotubes, respectively.
The hydrogen production rate was found to be higher with increased amounts of catalysts (Fig. 9d). Over 50 mg of bare and composite nanotubes, 6400 μmol−1 and 10
625 μmol−1 hydrogen gas were produced via aqueous-methanol photoreforming, which was increased to 14
110 and 21
230 μmol−1 at 200 mg of catalysts, respectively. However, it can also be seen that the H2 production rate increases rapidly in the beginning, but as the dose increases, the production rate slows down. Therefore, a slight increase in the H2 gas production (18
000 to 21
200 μmol−1) was observed after increasing the dose from 100 mg to 200 mg. The main reason for the rate slowing down with increasing dose can be considered to be an increase in light scattering rather than light absorption with increasing dose. Hence, possibly the visible light could not reach the active sites.
The temperature effect (25–55 °C) was also observed in the present study. The hydrogen production rate was found to be higher at the increased temperature (Fig. 9d). Approximately 12
000 μmol−1 and 18
000 μmol−1 hydrogen gas were produced over pure and composite NTs at 25 °C, which reached up to 13
240 and 22
450 μmol−1 at 45 °C, respectively. At a higher temperature (45 °C), only a slight change in the H2 production was observed for both catalysts. The actual efficiency of any material depends on its reusability. Therefore, reusability also reflects the sustainability of the material. Considering this as the basis, the reusability of composite NTs was also investigated in this study. This investigation was carried out for 5 consecutive cycles (Fig. 5f). Before reusing the composite nanotubes, the material was recovered by centrifugation after each cycle; then, it was washed with deionized water and dried by passing N2 gas. After five cycles, the existing material showed only a slight decline in efficiency, which can be seen in Fig. 5f, so the existing material is useful for many processes. To investigate the structural stability of the catalyst, the XRD pattern of the spent TiO2NTs–AC(4) catalyst was compared with that of the fresh catalyst. As shown in Fig. 10, the crystal structure of the catalyst was not altered after the reaction; however a slight change in the crystallinity of the sample was observed.
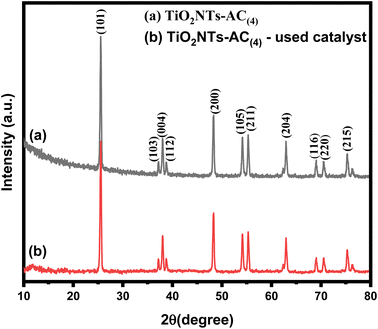 |
| Fig. 10 Comparison of XRD patterns of fresh and spent TiO2NTs–AC(4) catalysts. | |
3.10. Plausible reaction mechanism for H2 production
The whole mechanism of H2 production can be understood using Scheme 2. When simulated sun light strikes the TiO2NTs–AC composite, holes (h+) and electrons (e−) are produced. The AC traps these photogenerated e− from the CB of TiO2NTs. This results in the distribution of electric charges across the semiconductor interface, which can prevent the recombination of charge carriers. The produced e− and h+ on the surface of TiO2NTs–AC react with the water and methonal adsorbed on the surface of TiO2NTs–AC and produce the H2 gas, as shown in Scheme 2. It should be noted that the sacrificial agents may also serve as proton sources.5 Therefore, using methanol can be considered for coupling an organic substance's oxidation and proton reduction. To investigate the pathway of photocatalytic reforming of aqueous methanol over the synthesized catalysts, the gaseous products were periodically analyzed using an on-line gas chromatograph equipped with a TCD and FID. The photocatalytic reformation of aqueous methanol solution mainly produced H2 in the gas phase and minor quantities of CO, CO2 and CH4. At the end of the photocatalytic test, the liquid phase was analyzed using a gas chromatograph equipped with both the FID and MSD. It is observed that methanol undergoes oxidation up to CO2 through the formation of formaldehyde and formic acid as intermediate species. As previously reported CH3OH acts as a sacrificial agent and is oxidized by consumption of the photogenerated holes (h+) in the photocatalyst.7 The photogenerated electrons (e−) are then used in the reduction of H+ to H2. The presence of activated carbon with TiO2 decreased the recombination rate of the e−–h+ pairs, enhancing the photocatalytic activity of the catalyst. | CH3OH + H2O + 6h+ → CO2 + 6H+ | (1) |
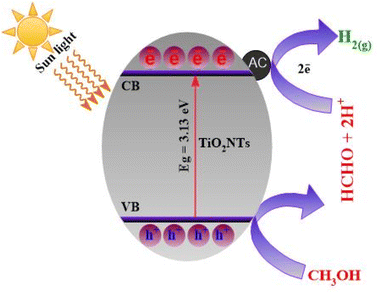 |
| Scheme 2 Plausible reaction mechanism for H2 production over the TiO2NTs–AC nanocomposite. | |
A comparison of the photocatalytic activity of the TiO2NTs–AC(4) catalyst with that of other catalysts reported in the literature is presented in Table 2. The porous TiO2NTs–AC(4) nanocomposite offered high photocatalytic H2 rates compared to other TiO2 containing catalysts such as TiO2 anatase and TiO2–AC catalysts. However, the H2 production rates are higher in the case of few other reported catalysts such as Pt–Cu/TiO2 catalysts compared to the TiO2NTs–AC(4) catalyst. It is essential to note that the presence of precious and transition metals and physicochemical characteristics of previously reported catalysts and reaction conditions are different from those of the present work. Moreover, the present research deals with deposition of activated carbon over TiO2 nanotubes via ultrasonication and utilized the synthesized materials for photocatalytic reformation of methanol to produce H2.
Table 2 Comparison of different photocatalysts reported for H2 production
S. no. |
Photocatalyst |
Sacrificial agent |
Light source |
H2 production rate |
Ref. |
1 |
TiO2/CuO |
Methanol |
Xe lamp |
8.23 mmol h−1 g−1 |
37
|
2 |
AC–TiO2 |
Glycerol |
Solar light |
20 383 μmol g−1 h−1 |
38
|
3 |
TiO2/ACS |
Glycerine |
Solar light |
203 μmol g−1 h−1 |
39
|
4 |
PtCu–TiO2 |
Methanol |
LED irradiation |
2383.9 μmol h−1 |
40
|
5 |
Pd–TiO2 |
Ethanol |
Near-UV light |
113 cm3 STP |
16
|
6 |
Pd–TiO2 |
Ethanol |
Visible light |
29 cm3 STP |
16
|
7 |
Ni/GO–TiO2 |
Methanol |
UV light |
2171 μmol h−1 g−1 |
41
|
8 |
CuO/TiO2NT |
Methanol |
Mercury lamp |
64.2–71.6 mmol h−1 g−1 |
42
|
9 |
SnS2/TiO2 |
Methanol |
Solar irradiation |
195.55 μmol g−1 |
21
|
10 |
Pt–TiO2 |
Methanol |
UV mercury lamp |
38.0 mmol g−1 h−1 |
43
|
11 |
TiO2NTs–AC |
Methanol |
Solar light |
18 000 μmol−1 g−1 h−1 |
Present work |
4. Conclusions
In this study, TiO2 nanotubes are combined with activated carbon derived from biomass to obtain TiO2NTs–AC nanocomposites. The synthesized materials showed high water-splitting efficiency, under sunlight which proved to be energy efficient for hydrogen production. The synthesized composites are porous in nature (pore volume = 0.020 cm3 g−1 and half pore width = 8.4 Å) and nanosized (crystallite size = 6.31 nm) with a high surface area (291 m2 g−1). Its band gap was measured to be 3.15 eV. The prepared material produced approximately 18
000 μmol−1 of hydrogen gas using 100 mg of catalyst at pH 7 and 25 °C under 12 hours of continuously simulated sun light irradiation. The material also showed a high reusability rate. Furthermore, the prepared nanocomposite was used for up to 5 cycles without a significant decrease, indicating its good efficiency and sustainability. Furthermore, photocatalytic activity can be influenced by the light absorption, redox nature, and mass transfer of the process, therefore, some more studies are needed to understand the influence of these factors and obtain efficient results. In addition, synthesis of activated carbon needs high energy utilization and release of air pollutants; hence, some more low cost and abundant alternatives can be searched, in the future.
Author contributions
All authors contributed to the study conception and design. Material preparation, data collection and analysis were performed by Shaeel Ahmed Althabaiti Zaheer Khan, Maqsood Ahmad Malik, Salem Mohamed Bawaked, Soad Zahir Al-Sheheri, and Mohamed Mokhtar. The first draft of the manuscript was written by Sharf Ilahi Siddiqui, Maqsood Ahmad Malik, and Katabathini Narasimharao and all authors commented on previous versions of the manuscript. All authors read and approved the final manuscript.
Conflicts of interest
There are no conflicts of interest to declare.
Acknowledgements
The authors extend their appreciation to the Deputyship for Research & Innovation, Ministry of Education in Saudi Arabia for funding this research work through the project number IFPNC-001-130-2020 and Deanship of Scientific Research (DSR), King Abdulaziz University, Jeddah, Saudi Arabia.
References
- L. Schlapbach and A. Züttel, Nature, 2001, 414, 353–358 CrossRef CAS PubMed.
- J. L. Rowsell and O. M. Yaghi, Angew. Chem., Int. Ed., 2005, 44, 4670–4679 CrossRef CAS PubMed.
- J. Yang, A. Sudik, C. Wolverton and D. J. Siegel, Chem. Soc. Rev., 2010, 39, 656–675 RSC.
- S. P. Badwal, S. Giddey and C. Munnings, Wiley Interdiscip. Rev.: Energy Environ., 2013, 2, 473–487 CAS.
- K. C. Christoforidis and P. Fornasiero, ChemCatChem, 2017, 9, 1523–1544 CrossRef CAS.
- L. Fan, Z. Tu and S. H. Chan, Energy Rep., 2021, 7, 8421–8446 CrossRef.
- J. Wen, J. Xie, X. Chen and X. Li, Appl. Surf. Sci., 2017, 391, 72–123 CrossRef CAS.
- T. Shen, H. Xie, B. Gavurová, M. Sangeetha, C. Karthikeyan, T. R. Praveenkumar, C. Xia and S. Manigandan, Int. J. Hydrogen Energy, 2023, 48, 21029–21037 CrossRef CAS.
- L. Chen, H. Li, H. Wang and K. Liu, J. Cleaner Prod., 2023, 137213 CrossRef CAS.
- X. Shui, D. Jiang, Y. Li, H. Zhang, J. Yang, X. Zhang and Q. Zhang, Bioresour. Technol., 2023, 367, 128221 CrossRef CAS PubMed.
- P. Vargas-Ferrer, E. Álvarez-Miranda, C. Tenreiro and F. Jalil-Vega, J. Cleaner Prod., 2023, 409, 137110 CrossRef.
- G. Liu, H. Lu, Y. Xu, Q. Quan, H. Lv, X. Cui, J. Chen, L. Jiang and R. J. Behm, Chem. Eng. J., 2023, 455, 140875 CrossRef CAS.
- D. Aand, S. Sk, K. Kumar, U. Pal and A. K. Singh, Int. J. Hydrogen Energy, 2022, 47, 7180–7188 CrossRef CAS.
- J. Talibawo, P. I. Kyesmen, M. C. Cyulinyana and M. Diale, Nanomaterials, 2022, 12, 2961 CrossRef CAS PubMed.
- Q. Cao, S. Hao, Y. Wu, K. Pei, W. You and R. Che, Chem. Eng. J., 2021, 424, 130444 CrossRef CAS.
- B. Rusinque, S. Escobedo and H. de Lasa, Catalysts, 2021, 11, 405 CrossRef CAS.
- G. L. Chiarello, M. V. Dozzi and E. Selli, J. Energy Chem., 2017, 26, 250–258 CrossRef.
- J. Yu, L. Qi and M. Jaroniec, J. Phys. Chem. C, 2010, 114, 13118–13125 CrossRef CAS.
- R. Saravanan, D. Manoj, J. Qin, M. Naushad, F. Gracia, A. F. Lee, M. M. Khan and M. Gracia-Pinilla, Process Saf. Environ. Prot., 2018, 120, 339–347 CrossRef CAS.
- D. Xu, Y. Hai, X. Zhang, S. Zhang and R. He, Appl. Surf. Sci., 2017, 400, 530–536 CrossRef CAS.
- S. Shanmugaratnam, B. Selvaratnam, A. Baride, R. Koodali, P. Ravirajan, D. Velauthapillai and Y. Shivatharsiny, Catalysts, 2021, 11, 589 CrossRef CAS.
- H. Song, S. Luo, H. Huang, B. Deng and J. Ye, ACS Energy Lett., 2022, 7, 1043–1065 CrossRef CAS.
- A. H. Jawhari, N. Hasan, I. A. Radini, K. Narasimharao and M. A. Malik, Nanomaterials, 2022, 12, 2985 CrossRef CAS PubMed.
- S. A. Althabaiti, M. A. Malik, M. Kumar Khanna, S. M. Bawaked, K. Narasimharao, S. Z. Al-Sheheri, B. Fatima and S. I. Siddiqui, Nanomaterials, 2022, 12, 4472 CrossRef CAS PubMed.
- M. Ouzzine, A. J. Romero-Anaya, M. A. Lillo-Rodenas and A. Linares-Solano, Carbon, 2014, 67, 104–118 CrossRef CAS.
- M. Asiltürk and Ş. Şener, Chem. Eng. J., 2012, 180, 354–363 CrossRef.
- B. Mondol, A. Sarker, A. Shareque, S. C. Dey, M. T. Islam, A. K. Das, S. M. Shamsuddin, M. A. I. Molla and M. Sarker, Photochem, 2021, 1, 54–66 CrossRef.
- K. Li, H. Ruan, P. Ning, C. Wang, X. Sun, X. Song and S. Han, Res. Chem. Intermed., 2018, 44, 1209–1233 CrossRef CAS.
- L. Cui, K. Hui, K. Hui, S. Lee, W. Zhou, Z. Wan and C.-N. H. Thuc, Mater. Lett., 2012, 75, 175–178 CrossRef CAS.
- A. H. Jawhari, N. Hasan, I. A. Radini, M. A. Malik and K. Narasimharao, Fuel, 2023, 344, 127998 CrossRef CAS.
- X.-Y. Liu, M. Huang, H.-L. Ma, Z.-Q. Zhang, J.-M. Gao, Y.-L. Zhu, X.-J. Han and X.-Y. Guo, Molecules, 2010, 15, 7188–7196 CrossRef CAS PubMed.
- Z. Dong, F. Xiao, A. Zhao, L. Liu, T. Sham and Y. Song, RSC Adv., 2016, 6, 76142–76150 RSC.
- E. Ribeiro, G. Plantard, F. Teyssandier, F. Maury, N. Sadiki, D. Chaumont and V. Goetz, J. Environ. Chem. Eng., 2020, 8, 104115 CrossRef CAS.
- Y. G. Alghamdi, B. Krishnakumar, M. A. Malik and S. Alhayyani, Polymers, 2022, 14, 880 CrossRef CAS PubMed.
- S. Muthusamy and J. Charles, J. Mater. Sci.: Mater. Electron., 2021, 32, 7349–7365 CrossRef CAS.
- Y. Feng, C. Liu, J. Chen, H. Che, L. Xiao, W. Gu and W. Shi, RSC Adv., 2016, 6, 38290–38299 RSC.
- J. M. Kum, S. H. Yoo, G. Ali and S. O. Cho, Int. J. Hydrogen Energy, 2013, 38, 13541–13546 CrossRef CAS.
- N. R. Reddy, U. Bharagav, M. M. Kumari, K. Cheralathan, P. Ojha, M. Shankar and S. W. Joo, Ceram. Int., 2021, 47, 10216–10225 CrossRef.
- G. Murali, S. Gopalakrishnan, S. K. Lakhera, B. Neppolian, S. Ponnusamy, S. Harish and M. Navaneethan, Diamond Relat. Mater., 2022, 128, 109226 CrossRef CAS.
- H. Wang, H. Qi, X. Sun, S. Jia, X. Li, T. J. Miao, L. Xiong, S. Wang, X. Zhang and X. Liu, Nat. Mater., 2023, 1–8 Search PubMed.
- O. Quiroz-Cardoso, V. Suárez, S. Oros-Ruiz, M. Quintana, S. Ramírez-Rave, M. Suárez-Quezada and R. Gómez, Top. Catal., 2022, 65, 1015–1027 CrossRef CAS.
- S. Xu, A. J. Du, J. Liu, J. Ng and D. D. Sun, Int. J. Hydrogen Energy, 2011, 36, 6560–6568 CrossRef CAS.
- J. Velázquez, R. Fernández-González, L. Díaz, E. P. Melián, V. Rodríguez and P. Núñez, J. Alloys Compd., 2017, 721, 405–410 CrossRef.
|
This journal is © The Royal Society of Chemistry 2023 |
Click here to see how this site uses Cookies. View our privacy policy here.