DOI:
10.1039/D3IM00036B
(Perspective)
Ind. Chem. Mater., 2023,
1, 332-342
Ammonia as a carbon-free hydrogen carrier for fuel cells: a perspective
Received
20th March 2023
, Accepted 28th June 2023
First published on 28th June 2023
Abstract
Driven by the growing need to decarbonize, hydrogen energy is considered a potential alternative to fossil fuels. However, due to the problems associated with energy storage and transportation for portable applications, the scalable utilization of hydrogen is not fully developed. In this perspective, the potential of utilizing ammonia as a hydrogen carrier for on-site power generation via ammonia decomposition is systematically discussed. Firstly, an analysis of the chemical properties of ammonia and the limitations of this product for hydrogen production are presented. Secondly, some existing worldwide industrial projects that present the current development status are summarized. Then, recent advances in target engineering of efficient catalysts via various strategies are provided. Finally, different types of structured reactors to date for ammonia decomposition are explored. This perspective aims to shed light on the potential of ammonia as a promising alternative to traditional hydrogen storage methods and highlights the challenges and opportunities that lie ahead in this exciting field of research.
Keywords: Ammonia decomposition; Hydrogen carrier; On-site generation; Heterogeneous catalysts; Reactor.
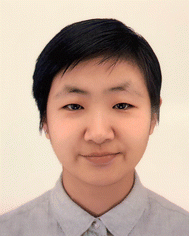 Lingling Zhai | Lingling Zhai currently works at the School of Chemical Engineering at Beijing University of Chemical Technology (BUCT). She received her Ph.D. from the Hong Kong Polytechnic University in 2021. Her research interests include ammonia–hydrogen conversional coupling and operando characterization for heterogeneous processes. |
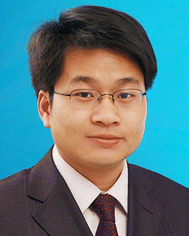 Zhonghua Xiang | Zhonghua Xiang is a Professor and Director of the Molecular Energy Materials R&D Center at BUCT. He received his Ph.D. in 2013 at BUCT and was a postdoctoral researcher at Case Western Reserve University in 2014. His current research focuses on the design and synthesis of molecular energy materials, including covalent organic polymers for fuel cells and flow batteries. |
1 Introduction
As the world grapples with pressing environmental and energy problems such as climate change, pollution, and depletion of resources due to the dependence on fossil fuels, the search for alternative clean and renewable energy solutions has never been more urgent.1 Among which, hydrogen (H2) is emerging as a leading contender in the energy sector for both stationary and mobile applications, as the only product of its combustion is water. Fuel cells powered by hydrogen can provide a steady and continuous supply of electricity. However, the commercial utilization of hydrogen fuel cells is hindered by the challenges of handling and transporting hydrogen due to its low volumetric energy density.2,3 Although hydrogen has a high energy density by mass (120 MJ kg−1),4 which is almost 3 times higher than that of gasoline (46 MJ kg−1),5 the volumetric energy density is only 0.01 MJ L−1 under ambient conditions.6 To increase mass capacity, hydrogen is often stored as a compressed gas at pressures as high as 70 MPa (ref. 7) or as a liquid at −253 °C,8 which requires intensive energy consumption. In recent years, new methods have been developed to make it easier to manage and transport. One kind is physisorption storage in porous materials, such as metal organic frameworks (MOFs)9 and porous organic polymers (POPs).10 Another rising way is storage in metal hydrides, such as LiBH411 and MgH2.12,13 However, mature technology with moderate energy consumption and an easy releasing method is still rare. On the other hand, energy storage in chemical hydrides, such as ammonia (NH3),14 methanol (CH3OH),15 and other liquid organic hydrogen carriers (LOHCs),16,17 has the potential to overcome these shortcomings since these hydrogen carriers have higher energy densities and mature transportation networks, which offers a promising solution to the challenges of hydrogen storage and transport.
Among these carriers, ammonia has emerged as a promising candidate due to its high hydrogen content (17.6 wt%) and potential economic benefits for energy production. When used as a fuel, it produces only nitrogen and water as by-products, making it a carbon-free alternative to traditional fossil fuels. It can liquefy at a low pressure of 0.86 MPa at 25 °C, providing a high volumetric energy density of 10.5 MJ L−1, which is twice that of compressed hydrogen at 70 MPa (5 MJ L−1).18 Being the second most produced inorganic chemical in the world with a global capacity of ∼230 Mt per year,19 ammonia is also well-established in terms of production, easy handling, and transportation infrastructures. There has been growing interest in the utilization of ammonia as an energy vector. Multiple industrial reports respecting safety and infrastructure aspects have been released,20–23 and a growing portfolio of ammonia-based power generation projects have been demonstrated or approved.24–26 However, challenges remain, such as safety concerns regarding ammonia's toxicity and corrosivity, and additional steps required to release H2 from NH3, which can reduce the overall efficiency. Fortunately, there are ongoing research and development efforts focused on optimizing the use of ammonia as a hydrogen carrier, which could help to overcome these obstructions.
This perspective therefore aims to discuss the potential of ammonia as a carbon-free hydrogen carrier for fuel cells. The chemical properties along with recent projects or chemical plants are addressed. Furthermore, the rational design of catalysts and reactors are illustrated, as well as their benefits and drawbacks.
2 Ammonia as a hydrogen energy carrier
2.1 Characteristics of ammonia
As mentioned, storing renewable energy in the form of chemical fuels is deemed a pragmatic approach for both short- and long-term storage, especially in the transportation sector. In this regard, NH3 has been recommended as a more technically feasible option than CH3OH due to its advantageous chemical properties. As indicated in Table 1, the gravimetric H2 content of NH3 is 40% higher than that of CH3OH, while maintaining a comparable volumetric energy density. Moreover, ammonia can be conveniently liquefied at ambient temperature and a pressure of 0.86 MPa, or at atmospheric pressure with a cooled-down temperature of −33.4 °C. With a volumetric energy density of 12.7 MJ L−1, NH3 vastly outperforms liquid hydrogen (8.49 MJ L−1) and compressed gas (4.5 MJ L−1 at 69 MPa and 25 °C).27,28 Additionally, for carbon-based fuels, obtaining pure carbon dioxide streams from industrial emissions may not be a viable long-term solution, and the expense for directly capturing carbon dioxide from the air is high.
Table 1 Comparison of chemical properties of NH3, CH3OH and H2
Properties |
NH3 |
CH3OH |
H2 |
Liquid for ammonia and methanol; compressed gas for hydrogen.
At 25 °C.
At 0.1 MPa.
|
Gravimetric H2 content wt% |
17.6 |
12.5 |
100 |
Volumetric energy densitya MJ L−1 |
12.7 |
15.5 |
4.5@69 MPa, 25 °C |
Heat of combustion kJ kg−1 |
18 603 |
22 593 |
143 000 |
Liquefaction pressureb MPa |
0.7–0.8 |
NA |
NA |
Liquefaction temperaturec °C |
−33.4 |
NA |
−253 |
Explosive limit in air vol% |
16.1–25 |
6–50 |
4–74.2 |
Global annual production Mt |
∼180 |
110 |
70 |
Carbon content wt% |
0 |
37.5 |
0 |
Flammability/toxicity |
Toxic |
Toxic |
Highly flammable |
One of the primary limitations of ammonia is its apparent toxicity, which is approximately three orders of magnitude greater than that of methanol or gasoline.27 To ensure safe use, recommended exposure limits for NH3 are set below 100 ppm.29 However, it is possible to monitor potential NH3 leaks and hazards in real-time using appropriate sensors that can sound an alarm to facilitate an immediate response. Furthermore, the human nose can detect ammonia at concentrations as low as 5 ppm in air, making it much more noticeable than odorless hydrogen.30 Meanwhile, gaseous ammonia is less dense than air at standard temperature and pressure (STP), with a density of 0.769 kg m−3 compared to air's density of 1.225 kg m−3,27 allowing it to dissipate quickly under atmospheric pressure conditions and reducing the risk of fire or explosion in the event of a leak. Additionally, the flammability range of ammonia is narrow, ranging from 15.15% to 27.35% in dry air and from 15.95% to 26.55% in 100% relative humidity air,27 as compared to hydrogen. Ammonia has a higher automatic ignition temperature of 650 °C compared to hydrogen's 520 °C, indicating a lower risk of fire.27 Therefore, it is practical to carry out appropriate hazard management measures to effectively mitigate the risk associated with ammonia exposure to both humans and the environment.
2.2 Typical types of ammonia-based fuel cells
Depending on whether the ammonia decomposition occurs separately, ammonia-based fuel cells can be classified into either direct or indirect. Normally, direct ammonia fuel cells include alkaline fuel cells (AFCs), alkaline membrane fuel cells (AMFCs) and solid oxide fuel cells (SOFCs, either proton or anion exchange membrane-based). AFCs use an aqueous hydroxide electrolyte or alkaline molten carbonate with a typical operating temperature of 50–200 °C. For this type, oxygen reacts with water at the cathode side, forming hydroxide ions. Then, these ions move to the anode through the electrolyte and react with ammonia, producing nitrogen and water. During the reaction, hydrogen is not generated and water acts as an intermediate species via the following formulas: | Anode: 4NH3 + 12OH− → 2N2 + 12H2O + 12e− | (1) |
| Cathode: 3O2 + 6H2O + 12e− → 12OH− | (2) |
| Overall: 4NH3 + 3O2 → 2N2 + 6H2O | (3) |
One main problem for AFCs is the precipitation of carbonates (K2CO3 and Na2CO3) due to the reaction of the alkaline electrolyte with CO2 in air. To this end, AMFCs were further developed with no alkaline cations. Though alkaline membranes avoid the precipitation to a certain extent, two additional drawbacks need to be considered. One is the crossover of ammonia through the membrane which may cause oxidation and decrease the open circuit potential and efficiency.31 The other is Nad poisoning over the surface of anode catalysts.32
Alternatively, SOFCs are also commonly studied for direct ammonia fuel cells. In this type, ammonia is cracked into nitrogen and hydrogen at 700–1000 °C (ref. 27) at the anode. Depending on the types of membranes, the electron transfer is based on either H+ or O2−.33 Notably, the main challenges of SOFCs include the possible nitrate formation at the anode and high temperature requirement.33,34 This means SOFCs may only be suitable for continuous stationary applications without frequent on-and-off cycles.19
On the other hand, indirect ammonia fuel cells, such as proton exchange membrane fuel cells (PEMFCs) and phosphoric acid fuel cells (PAFCs), which release hydrogen through a cracking process, realize wider possibilities for hydrogen utilization. However, ammonia is highly poisonous to the acidic electrolyte and may lead to an increase in both charge-transfer and diffusion resistances.27 The catalyst is also easy to be deactivated due to the “site-blocking effect”. Thus, the concentration is highly expected to be less than 0.1 ppm.35 Apparently, the decomposition, separation, and purification processes are energy-intensive and require further efforts to improve the total energy efficiency. Even so, the overall conversion efficiency of ammonia is calculated to be 61.0–68.5% at the point of use.19 And the energy consumption is about 15–30% of the total energy contained in hydrogen, whereas this value for methanol is 30–40% with CO2 capture apparatus.36 Additionally, the levelized cost of hydrogen transportation using ammonia is estimated to be 20% lower than that using methanol.37 All these lead to savings in facility and operating costs, improving the overall efficiency. It seems that ammonia decomposition for on-site hydrogen generation reached a closer stage for commercialization, and therefore this perspective will more focus on indirect ammonia fuel cells for practical applications.
2.3 Ammonia-based power generation projects
To apply ammonia as a power source for portable power generation systems, different technologies and projects are proposed by various research institutions and companies with powers ranging from tens of watts to several megawatts. The main application scenarios are in shipping, trucking, and material-handling equipment. For example, the Ship FC project, which is funded by the European Union,38 plans to install a 2 MW ammonia-powered SOFC system on board an offshore vessel, Viking Energy. A significant goal of this project is to establish a compelling case for long-range, high-power, and zero-emission maritime industry. Alternatively, the American technology startup company, Amogy, recently demonstrated a 100 kW ammonia-powered heavy-duty tractor in May 2022.39 Before this, they had already run a 5 kW drone based on an integrated powerpack, which had a system efficiency of appropriately 36% to 38%. Currently, Amogy is launching testing operations for a 200 kW powerpack, which will be installed on a tugboat for maritime applications in cooperation with the Sustainable Energy Catapult Center in Norway.40 In the realm of small-scale prototypes, microchannel reactors are prevalent. The joint effort of MesoSystems Technology, Inc. and Intelligent Energy, Inc. has led to the development of a compact hydrogen generation system for a fuel-cell-based power supply. The system can decompose ammonia through a microchannel reactor with an energy density of 500 W h kg−1.41 These advancements in ammonia-powered portable power generation systems represent remarkable progress in sustainable energy development.
In terms of stationary power generation applications, some companies have proposed ammonia-powered off-grid plants. In China, several domestic new energy enterprises have jointly developed a demonstration project that utilizes ammonia for on-site hydrogen production at a hydrogen fueling station. This project relies on the advanced ammonia conversion technology developed by Jiang's team from Fuzhou University, to create a zero-carbon-emission energy community.42–44 In the UK, the Science and Technology Facilities Council (STFC) also cooperated with Siemens, Ecuity, and Engie to evaluate the feasibility of centralized and decentralized cracking models and designed an ammonia cracker capable of producing hydrogen at 200 kg per day.20 Similarly, the AFC Energy company has integrated an alkaline fuel cell (240 kW) with an ammonia cracker for hydrogen production to demonstrate the feasibility of off-grid stationary electricity generators. The system had been successfully operated in the field for 18 months, highlighting its potential.45 Additionally, international organizations such as the Ammonia Energy Association (AEA),46 the International Renewable Energy Agency (IRENA),47 and the Oxford Institute for Energy Studies (OIES)21 have also made significant efforts to promote the application of ammonia as a sustainable energy commodity.
3 Advanced catalysts and reactors for ammonia decomposition
Currently, the primary method for hydrogen extraction from ammonia is through thermal catalytic cracking, commonly known as the ammonia decomposition reaction (ADR). This reaction represents the reverse process of industrial ammonia synthesis, which is predominantly accomplished through the Haber–Bosch process. Under thermal catalytic conditions, ammonia can be decomposed into non-toxic hydrogen and nitrogen, without producing any greenhouse gas by-products. The ADR can be represented by the following basic formula: | 2NH3(g) → 3H2(g) + N2(g); ΔH° = 92 kJ mol−1 | (4) |
Apparently, the ADR is an endothermic process, and it has been shown theoretically that the ammonia conversion can reach up to 99.99% at a temperature of 400 °C and a pressure of 1 atm.48 However, in practice, the actual energy consumption is much higher than this theoretical limit. External heat sources are typically used in ADR crackers, resulting in operation temperatures as high as 850–950 °C.48 It is important to note that the high energy consumption required for the ADR highlights the need for further research and development of more efficient and sustainable catalysts and reactors.
3.1 Ammonia decomposition catalysts
The highly endothermic nature of the ADR necessitates the utilization of catalysts to lower the activation energy and enhance reaction kinetics. Over the past few decades, considerable advancements have been made in the field of ammonia decomposition catalysts. Precious metals, including ruthenium (Ru),49 platinum (Pt),50 palladium (Pd)51 and rhodium (Rh),52 have received considerable attention toward catalytic ammonia decomposition. Notably, Ru-based catalysts exhibit superior catalytic activity.53–55 Nevertheless, due to the scarcity and high cost of Ru, alternative cost-effective catalysts, such as Ni,56 Fe,57 and carbon-based materials,58 with comparable activity have also been extensively researched. Presently, ammonia decomposition catalysts typically comprise metals and supports, some of which also contain promoters. The metals are predominantly nano-dispersed transition metal particles or clusters, and the supports are oxides, such as magnesium oxide (MgO),59 alumina (Al2O3),60 and cerium dioxide (CeO2),61 or carbon nanotubes (CNTs).62 Promoters, such as potassium chloride (KCl) and sodium nitrate (NaNO3), which are alkali metal salts,63 may also be incorporated.
The decomposition of ammonia occurs in several steps of subsequent dehydrogenation, and the prevalent use of Ru for the ADR can be mainly attributed to its adherence to the Sabatier principle in terms of its moderate adsorption/desorption energies for the reaction intermediates. Yet, if comparable activities can be achieved, the adoption of transition metals (Ni, Fe, Co, etc.)3 may be preferred due to their abundance and lower cost. In general, the catalytic activity is influenced by various factors, including crystal orientation, coordination number, particle size, and support material.
Crystal orientation plays a critical role in determining the exposed active sites. Certain metals exhibit high activity due to their exposed high-energy crystal planes, such as Ru (001) trace sites,64–66 which have a high density of active sites and low activation energy for ammonia decomposition. Recent studies have shown that the catalytic activity of ruthenium-based catalysts can be significantly improved by engineering their crystal facets to expose more high-energy crystal facets. Roldan et al.67 simulated ammonia decomposition on the Ru (001) and Ru (111) surfaces and found that the main surface species are *NH, *N, and *H, with the rate-determining step being the formation of the N2 molecule. Similarly, Mavrikakis et al.68 revealed that the decomposition of ammonia on Ru (001) is thermochemically favorable compared to that in the gas phase (ΔE = −1.59 eV), but the intermediate *NH is more stable than the products of complete decomposition. Despite Ru, the activities of different surfaces for one metal can also be variable. For instance, the Ni (110) surface is found to be much more active than Ni (111) and Ni (211) due to the lower activation energy of associative desorption of nitrogen on Ni (110) (Fig. 1a).69 The Co (111) surface has also shown much higher activity than the Fe (110) surface, which is largely due to the lower d-band center of the metal surface.70
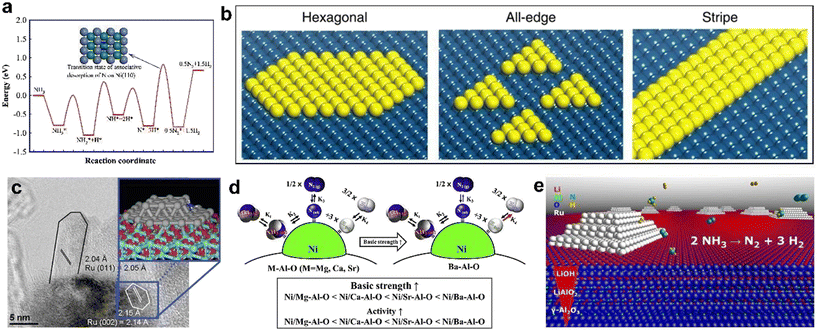 |
| Fig. 1 (a) The reaction pathway for NH3 decomposition on Ni (110). * denotes adsorbed species. The inset shows the transition state (TS) model of associative desorption of N on the Ni (110) surface (top view) (copyright 2011 Elsevier B.V.);69 (b) schematic of Ni patches on Pt (111) including hexagonal, all-edge and stripe shaped Ni clusters, consisting of (110) and (100) steps (copyright 2015 Springer Nature);72 (c) HRTEM image of the Ru/γ-Al2O3 catalyst showing an elongated rectangular particle (left) and a more isotropic particle (right) (copyright 2009 American Chemical Society);74 (d) the basic strength of the catalyst could influence the catalytic activity; the Ni/Ba–Al–O catalyst exhibits the best catalytic performance due to the strong basic properties which reduced the H2 inhibition effect (copyright 2020 Hydrogen Energy Publications LLC. Published by Elsevier Ltd.);78 (e) LiOH-modified Ru/γ-Al2O3 showed enhanced ammonia decomposition performance because of a high concentration of basic sites and partial preservation of the support porosity (copyright 2015 Elsevier B.V.).79 | |
The coordination environment is recognized as another key factor affecting the catalytic activity. Corresponding modulations can be achieved by adjusting the supports. For example, incorporating Ru into zeolite structures results in a coordination effect, and sub-nanometer Ru nanoparticles reveal high reducibility and are typically low-coordinated with short Ru–O bonds, thereby promoting strong metal–support interactions.71 Doping and hybridization are also common means to regulate the coordination environment. Studies have shown that a Ni/Pt core–shell structure demonstrates two orders of magnitude higher activity than monolayer or pure metal surfaces, as Ni terrace sites activate the N–H bond while Ni/Pt (110) edge sites accelerate N2 association (Fig. 1b).72 Another study conducted by Weidenthaler et al.73 explored the ADR performance of a series of CoAl-based catalysts, and discovered that the oxide phase of Co is reduced to the metallic phase during the reaction, with larger nanoparticle sizes showing lower activity due to their higher coordination numbers.
Particle size is also a significant parameter influencing catalytic activity. A smaller particle size generally results in a higher catalytic activity due to an increased surface area and higher concentration of active sites. For Ru/γ-Al2O3 catalysts (Fig. 1c), it has been reported that the optimum size of elongated Ru nanoparticles is ∼7 nm with a maximum turnover frequency (TOF), whereas the optimum size for hemispherical nanoparticles is between 1.8 and 3 nm.74 The particle size can be strongly influenced by the interaction with support, and thus, porous supports with large surface areas are beneficial for the dispersion of metal nanoparticles. In addition, Zhang et al.75 examined the ammonia decomposition activities of different Ni/activated carbon (AC) catalysts and found a strong correlation between the performance and the surface area of AC. It is observed that Ni on AC with the highest surface area demonstrates the highest catalytic activity, as well as the narrowest particle size distribution and smallest averaged particle size.
The choice of support material is also an important consideration in designing effective ADR catalysts. Carbon supports are often favored due to their high specific surface area and unique electronic properties, which facilitate the dispersion of nanoparticles and electron flow. However, their stability is often limited by their susceptibility to oxidation. Metal oxides, on the other hand, possess acidity or basicity, oxygen vacancies, or redox properties that are also responsible for the catalytic activity. Basic supports are generally preferred for promoting the ADR, as the basic metal is a good electron donor, which reduces the bond energy between the metal and N, thereby promoting the desorption of the N atom.76,77 As shown in Fig. 1d, the basic properties of catalysts are affected by their alkaline earth metal ions, and strongly basic properties could reduce the H2 inhibition effect. Therefore, the Ni/Ba–Al–O catalyst reveals the best catalytic performance.78 An example of alkaline support is MgO, which donates electrons to Ru and promotes metal–support interactions through electron donation, leading to modified geometric and electronic structures of Ru nanoparticles. Despite the slightly acidic nature of the Al2O3 surface, satisfactory catalytic activity can be achieved by decorating alkaline promoters such as LiOH,79 CeO2,80 and LaOx.81,82 As indicated in Fig. 1e, the surface engineering of Ru/γ-Al2O3 with LiOH with a Li/Al ratio of 1.7 led to a 6.5 times higher activity than the unmodified catalyst. NMR and XRD characterization confirmed the in situ formation of alkali aluminates resulting in a basic modification of the support.79
3.2 Reactor design for ammonia decomposition
The design of reactors is of significance in enhancing the overall efficiency of catalytic systems. In practical applications, various reactor designs have been developed to optimize the catalytic performance, such as membrane reactors, microchannel reactors, direct Joule-heating reactors, and thermal cycling reactors.
Membrane reactors are usually applied to separate pure hydrogen from the output H2/N2 gas, as well as to eliminate the corrosion problems caused by the presence of residual NH3. Metallic palladium and its alloys are currently the most commonly used membrane materials due to their high hydrogen selectivity. Since ammonia decomposition is a volumetric expansion reaction, where increased pressure is unfavorable, thus, measures to shift the equilibrium towards hydrogen are essential. According to Wolden's study (Fig. 2a), a catalytic membrane reactor (CMR), in which a porous yttria-stabilized zirconium (Y2O3–Zr2O3) tube was impregnated with Ru and coated with a thin Pd film, achieved comparable levels of NH3 conversion to a packed-bed membrane reactor (PBMR), using an order of magnitude less Ru at a temperature lower than 120 °C.83 The combination of a Ru catalyst and Pd membrane through a porous Zr2O3 support eliminates transport resistance that limits performance in conventional PBMRs. Similarly, Jo et al.84 developed a Pd/Ta/Pd membrane reactor coupled with a Ru/La–Al2O3 catalyst (Fig. 2b). The as-prepared CMR is able to maintain a high NH3 conversion (>99%) at up to a GHSV of 3000 cm3 gcat−1 h−1 at 748 K, with more than 63% improved H2 productivity as compared with a PBR. Nevertheless, the main disadvantage of the membrane reactor is that a sweep gas on the permeate side is always required to assist the hydrogen flow through. Therefore, the hydrogen stream is diluted during the process, which is in contrast to the objective of obtaining concentrated hydrogen.
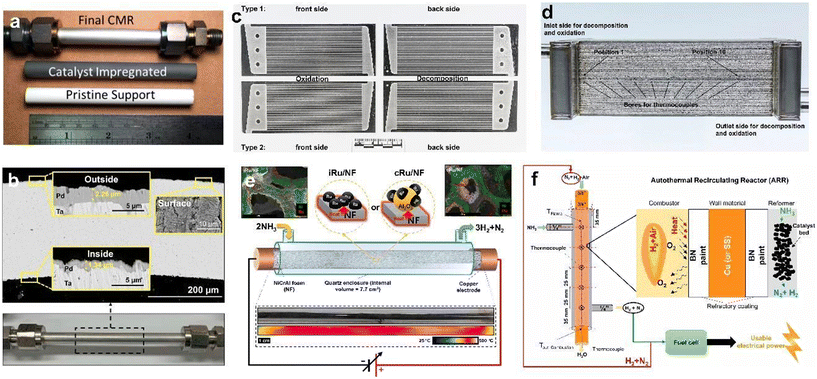 |
| Fig. 2 (a) A CMR in which an yttria-stabilized zirconium core is impregnated with Ru and deposited with a Pd film on the outside (copyright 2019 American Chemical Society);83 (b) SEM images of the cross-section and surface of the Pd/Ta/Pd composite membrane with a digital image of the membrane assembly (copyright 2020 Elsevier B.V.);84 (c) alternating microchannel plate arrangement of NH3 oxidation (left) and NH3 decomposition (right) reaction zones (copyright 2018 Elsevier B.V.);85 (d) schematic representation of the laser-welded microchannel reactor with integrated bores for ten evenly spaced thermocouples (copyright 2018 Elsevier B.V.);85 (e) schematic illustration of the Joule-heated foam reactor with impregnated Ru/NiCrAl foam (iRu/NF) or coated cRu/NF as a heating element (copyright 2021 Elsevier B.V.);86 (f) schematic illustration of the ARR for an ammonia-powered fuel cell with a combustor inside and reformer outside (copyright 2021 Elsevier B.V.).87 | |
Microchannel reactors offer improved mass transfer and heat transfer through the use of highly structured channels with high surface area-to-volume ratios. They are easy to scale up with increasing plates and elongated diffusion paths enable full NH3 conversion. Bessarabov et al.85 developed an autothermal microchannel reactor with stainless steel plates, where the NH3 decomposition occurs on the Ru side and NH3 oxidation takes place with Pt on the other side (Fig. 2c). The stack was separated by a central plate incorporating a heating block and thermocouples (Fig. 2d). The microchannel reactor demonstrates an NH3 conversion of 99.8% and an equivalent fuel cell power output of 0.71 kW. Meanwhile, due to the external heating procedure, the start-up is currently around 45 minutes, which can be further optimized for improved performance. For a wider range of microchannel reactors, the challenges regarding reactant backflow and catalyst coating fragility should also be addressed.
A Joule-heating reactor utilizes the Joule effect to generate heat by passing an electric current through a resistive material. Joule-heating reactors offer rapid and efficient heating, and are particularly suitable for direct heating applications. Then, ammonia passes through the high-temperature zone directly, and spontaneously decomposes into nitrogen and hydrogen with the assistance of catalysts. For instance, in Jo's other work,86 Ru-doped NiCrAl foam was used as both a heating element and catalyst in a microreactor (Fig. 2e) with an internal volume of 7.7 cm3. The reactor system achieved a high power density of 128 W cmreactor−3 and a reforming efficiency of 69.2%. The Joule-heating concept has a relatively simple design and reveals huge potential in scaling up for industrial applications. However, it also has certain drawbacks. The materials capable of withstanding high temperatures and corrosive environments can be expensive. Additionally, the direct heating method can cause serious volume expansion, making the mechanical stability of the heating material critical. Nonetheless, the Joule-heating concept boasts a relatively simple design and holds enormous potential for industrial-scale applications.
A thermal cycling reactor is an advanced design that utilizes recycled product gas to generate additional heat, thus enabling a self-sustained reaction without the need for external heating. Through careful design and manufacturing, this reactor has the potential to significantly improve the efficiency of ammonia decomposition. One example is an autothermal recirculating reactor (ARR)87 as indicated in Fig. 2f. It was fabricated with a Cu–BN composite as a stable heat transfer material. The ARR system achieved a maximum NH3 conversion of over 99.6% and a maximum reforming efficiency of 70.95% using a double-tube type module. Additionally, a maximum equivalent fuel cell power of 84 W was produced without the requirement of an extra heat source. This reactor demonstrated the feasibility of using self-cycled hydrogen as a prominent heat source for portable ammonia-based power generators. Meanwhile, it should be noted that the ARR system is relatively complex and requires careful design and operation, which, to some extent, may not be suitable for large-scale industrial applications.
4 Challenges and opportunities
Under the carbon neutrality goal, hydrogen is expected to play a crucial role in reducing greenhouse gas emissions and achieving a sustainable energy system. Meanwhile, the widespread adoption of hydrogen requires upgrading of infrastructure, such as the development of hydrogen fueling stations for vehicles and the integration of hydrogen into the existing natural gas grid. Apart from this upfront investment, the transportation efficiency by trailers is rather low. From this viewpoint, adopting hydrogen-containing carriers has the potential to overcome these shortcomings due to the mature transportation network and high energy density. Although methanol has attracted lots of attention recently, its utilization will inevitably increase carbon emissions in the long term, which is against the goal of carbon neutrality. Alternatively, ammonia appears to be a promising clean energy solution. As a novel energy vector, the way from ammonia to hydrogen economy is full of challenges and opportunities. As shown in Fig. 3, to apply an ammonia-based power generation system, several aspects should be considered:
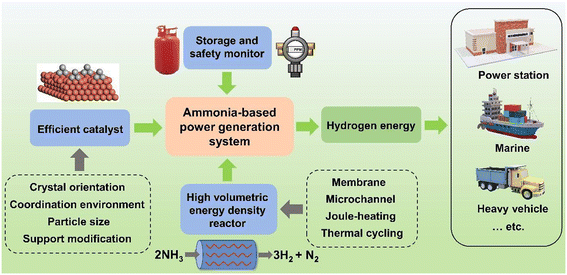 |
| Fig. 3 Areas requiring attention to build an ammonia-based power generation system. | |
1. To avoid possible leakage of ammonia, the storage tank and all connected components should use anti-corrosion materials, such as stainless steel. To ensure safety, ammonia and hydrogen gas sensors with alarming functions are required. Regular safety inspections regarding the whole system are encouraged.
2. Developing efficient and durable low-temperature (<450 °C) ammonia decomposition catalysts. Due to the scarcity and high cost of Ru, it is essential to construct highly dispersed Ru nanoparticles/nanoclusters with low content, to expose more active sites with rapid kinetics. Porous supports with layered structures tend to possess a large specific surface area which is beneficial for growing sub-nanometer particles. Nevertheless, catalysts free of precious metals with satisfying performance will be the ultimate goal.
3. Manufacturing innovative reactors with high volumetric energy density and low energy loss. For dead-end mode fuel cells, there still exists unreacted hydrogen in the outlet gas. Owing to the thermal cycling concept, the exhaust gas can be recirculated as a heating source. The co-heating method by both electricity and hydrogen combustion could be one possible direction for the development of reactors in the future.
4. Policies and regulations that incentivize the adoption of renewable energy sources can help accelerate the transition to a low-carbon economy.
5 Summary
In summary, this perspective has critically introduced ammonia as a hydrogen carrier in terms of its chemical properties, and recent plants with ammonia-based power generation, along with advances in the rational design of cracking catalysts and reactors. It is worth noting that, to realize ammonia-based hydrogen energy, not only the type of catalyst but also the type of reactor should be comprehensively considered. Fortunately, advances in the field of ammonia decomposition continue to be made, with new techniques and materials being developed to improve efficiency, selectivity, and sustainability. With the context of the above discussions, an “ammonia to hydrogen” economy may be coming for the easy and scalable use of green hydrogen in the foreseeable future.
Conflicts of interest
The authors declare no conflict of interest.
Acknowledgements
This work was supported by the National Key Research and Development Program of China (2022YFB3807500); the NSF of China (22220102003); the Beijing Natural Science Foundation (JL23003); the “Double-First-Class” construction projects (XK180301, XK1804-02); the Fundamental Research Funds for the Central Universities (buctrc202309).
References
- J. H. Montoya, L. C. Seitz, P. Chakthranont, A. Vojvodic, T. F. Jaramillo and J. K. Nørskov, Materials for solar fuels and chemicals, Nat. Mater., 2017, 16, 70–81 CrossRef PubMed.
- Y. Zhao, B. P. Setzler, J. Wang, J. Nash, T. Wang, B. Xu and Y. Yan, An efficient direct ammonia fuel cell for affordable carbon-neutral transportation, Joule, 2019, 3, 2472–2484 CrossRef CAS.
- S. Mukherjee, S. V. Devaguptapu, A. Sviripa, C. R. Lund and G. Wu, Low-temperature ammonia decomposition catalysts for hydrogen generation, Appl. Catal., B, 2018, 226, 162–181 CrossRef CAS.
- S. Atilhan, S. Park, M. M. El-Halwagi, M. Atilhan, M. Moore and R. B. Nielsen, Green hydrogen as an alternative fuel for the shipping industry, Curr. Opin. Chem. Eng., 2021, 31, 100668 CrossRef.
- A. Demirbas, Importance of biodiesel as transportation fuel, Energy Policy, 2007, 35, 4661–4670 CrossRef.
- M. R. Usman, Hydrogen storage methods: Review and current status, Renewable Sustainable Energy Rev., 2022, 167, 112743 CrossRef CAS.
- M. Li, Y. Bai, C. Zhang, Y. Song, S. Jiang, D. Grouset and M. Zhang, Review on the research of hydrogen storage system fast refueling in fuel cell vehicle, Int. J. Hydrogen Energy, 2019, 44, 10677–10693 CrossRef CAS.
- X. Tang, H. Sepehri-Amin, N. Terada, A. Martin-Cid, I. Kurniawan, S. Kobayashi, Y. Kotani, H. Takeya, J. Lai and Y. Matsushita, Magnetic refrigeration material operating at a full temperature range required for hydrogen liquefaction, Nat. Commun., 2022, 13, 1817 CrossRef CAS PubMed.
- S. P. Shet, S. S. Priya, K. Sudhakar and M. Tahir, A review on current trends in potential use of metal-organic framework for hydrogen storage, Int. J. Hydrogen Energy, 2021, 46, 11782–11803 CrossRef CAS.
- Z. Chen, K. O. Kirlikovali, K. B. Idrees, M. C. Wasson and O. K. Farha, Porous materials for hydrogen storage, Chem, 2022, 8, 693–716 CAS.
- Z. Ding, H. Li and L. Shaw, New insights into the solid-state hydrogen storage of nanostructured LiBH4-MgH2 system, Chem. Eng. J., 2020, 385, 123856 CrossRef CAS.
- X. Zhang, Y. Liu, X. Zhang, J. Hu, M. Gao and H. Pan, Empowering hydrogen storage performance of MgH2 by nanoengineering and nanocatalysis, Mater. Today Nano, 2020, 9, 100064 CrossRef.
- I. Hassan, H. S. Ramadan, M. A. Saleh and D. Hissel, Hydrogen storage technologies for stationary and mobile applications: Review, analysis and perspectives, Renewable Sustainable Energy Rev., 2021, 149, 111311 CrossRef CAS.
- Z. Wan, Y. Tao, J. Shao, Y. Zhang and H. You, Ammonia as an effective hydrogen carrier and a clean fuel for solid oxide fuel cells, Energy Convers. Manage., 2021, 228, 113729 CrossRef CAS.
- L.-N. Chen, K.-P. Hou, Y.-S. Liu, Z.-Y. Qi, Q. Zheng, Y.-H. Lu, J.-Y. Chen, J.-L. Chen, C.-W. Pao and S.-B. Wang, Efficient hydrogen production from methanol using a single-site Pt1/CeO2 catalyst, J. Am. Chem. Soc., 2019, 141, 17995–17999 CrossRef CAS PubMed.
- M. Niermann, S. Drünert, M. Kaltschmitt and K. Bonhoff, Liquid organic hydrogen carriers (LOHCs)–Techno-economic analysis of LOHCs in a defined process chain, Energy Environ. Sci., 2019, 12, 290–307 RSC.
- Y. Yurko and L. Elbaz, Direct quinone fuel cells, J. Am. Chem. Soc., 2023, 145, 2653–2660 CrossRef CAS PubMed.
- F. Jiao and B. Xu, Electrochemical ammonia synthesis and ammonia fuel cells, Adv. Mater., 2019, 31, 1805173 CrossRef PubMed.
- S. Chatterjee, R. K. Parsapur and K.-W. Huang, Limitations of ammonia as a hydrogen energy carrier for the transportation sector, ACS Energy Lett., 2021, 6, 4390–4394 CrossRef CAS.
-
C. Jackson, K. Fothergill, P. Gray, F. Haroon, C. Makhloufi, N. Kezibri, A. Davey, O. LHote, M. Zarea and T. Davenne, Ammonia to green hydrogen project: Feasibility study, Siemens, Engie, STFC and Ecuity, 2019 Search PubMed.
-
A. Patonia and R. Poudineh, Global trade of hydrogen: What is the best way to transfer hydrogen over long distances, Oxford Institute for Energy Studies, Oxford, 2022 Search PubMed.
-
IRENA, https://www.irena.org/-/media/Files/IRENA/Agency/Publication/2022/May/IRENA_Innovation_Outlook_Ammonia_2022.pdf, (accessed March 2023).
-
North West Hydrogen Alliance, https://www.nwhydrogenalliance.co.uk/wp-content/uploads/2022/05/NWHA-Ammonia-International-Hydrogen-FINAL.pdf, (accessed March 2023).
-
Amogy, https://amogy.co/amogy-presents-worlds-first-ammonia-powered-zero-emission-semi-truck/, (accessed March 2023).
-
Ammonia Energy Association, https://www.ammoniaenergy.org/articles/new-ammonia-powered-vessel-designs-win-aip/, (accessed March 2023).
-
Siemens Energy, https://www.siemens-energy.com/uk/en/energy/game-changing-green-ammonia-prototype.html, (accessed March 2023).
- M. Aziz, A. T. Wijayanta and A. B. D. Nandiyanto, Ammonia as effective hydrogen storage: A review on production, storage and utilization, Energies, 2020, 13, 3062 CrossRef CAS.
- E. Rivard, M. Trudeau and K. Zaghib, Hydrogen storage for mobility: A review, Materials, 2019, 12, 1973 CrossRef CAS.
- S. Lee, E.-H. Lee and S.-W. Lee, A flexible and attachable colorimetric film sensor for the detection of gaseous ammonia, Biosensors, 2022, 12, 664 CrossRef CAS PubMed.
- X. Wang, S. Meng, M. Tebyetekerwa, W. Weng, J. Pionteck, B. Sun, Z. Qin and M. Zhu, Nanostructured polyaniline/poly (styrene-butadiene-styrene) composite fiber for use as highly sensitive and flexible ammonia sensor, Synth. Met., 2017, 233, 86–93 CrossRef CAS.
- G. Jeerh, M. Zhang and S. Tao, Recent progress in ammonia fuel cells and their potential applications, J. Mater. Chem. A, 2021, 9, 727–752 RSC.
- S. Suzuki, H. Muroyama, T. Matsui and K. Eguchi, Fundamental studies on direct ammonia fuel cell employing anion exchange membrane, J. Power Sources, 2012, 208, 257–262 CrossRef CAS.
- N. M. Adli, H. Zhang, S. Mukherjee and G. Wu, Ammonia oxidation electrocatalysis for hydrogen generation and fuel cells, J. Electrochem. Soc., 2018, 165, J3130 CrossRef CAS.
- R. Lan and S. Tao, Ammonia as a suitable fuel for fuel cells, Front. Energy Res., 2014, 2, 35 Search PubMed.
- S. Giddey, S. Badwal, C. Munnings and M. Dolan, Ammonia as a renewable energy transportation media, ACS Sustainable Chem. Eng., 2017, 5, 10231–10239 CrossRef CAS.
-
H. Blanco, Global hydrogen trade to meet the 1.5 °C climate goal: Part II—technology review of hydrogen carriers, in Global hydrogen trade to meet the 1.5° C climate goal, IRENA Abhu Dhabi, United Arab Emirates, 2022 Search PubMed.
- J. Cui and M. Aziz, Techno-economic analysis of hydrogen transportation infrastructure using ammonia and methanol, Int. J. Hydrogen Energy, 2023, 48, 15737–15747 CrossRef CAS.
-
Ship FC, https://shipfc.eu/, (accessed March 2023).
-
Amogy, https://amogy.co/amogy-demonstrates-first-ammonia-powered-zero-emissions-tractor/, (accessed March 2023).
-
Amogy, https://amogy.co/amogy-launches-testing-operations-for-maritime-applications-of-ammonia-to-power-platform-in-stord-norway/, (accessed
March 2023).
-
M. Powell, A. Chellappa and T. Vencill, Compact fuel cell power supplies with safe fuel storage, Mesosystems Technology Inc Kennewick WA, 2004 Search PubMed.
- H. Fang, D. Liu, Y. Luo, Y. Zhou, S. Liang, X. Wang, B. Lin and L. Jiang, Challenges and opportunities of Ru-based catalysts toward the synthesis and utilization of ammonia, ACS Catal., 2022, 12, 3938–3954 CrossRef CAS.
- L. Jiang and X. Fu, An ammonia-hydrogen energy roadmap for carbon neutrality: Opportunity and challenges in China, Engineering, 2021, 7, 1688–1691 CrossRef.
- L. Lin, L. Zhang, Y. Luo, J. Luo, C. Chen and L. Jiang, Highly-integrated and cost-efficient ammonia-fueled fuel cell system for efficient power generation: A comprehensive system optimization and techno-economic analysis, Energy Convers. Manage., 2022, 251, 114917 CrossRef CAS.
- AFC Energy, AFC wraps ammonia to-power fuel cell generator trials, plans commercial system, Fuel Cells Bull., 2019, 2019, 11–12 Search PubMed.
-
Ammonia Energy Association, https://www.ammoniaenergy.org/, (accessed March 2023).
-
J. De Maigret, E. G. Macchi and B. Herib, Global hydrogen trade to meet the 1.5 °C climate goal: Part III–green hydrogen supply cost and potential, in Global hydrogen trade to meet the 1.5° C climate goal, IRENA Abhu Dhabi, United Arab Emirates, 2022 Search PubMed.
- I. Lucentini, X. Garcia, X. Vendrell and J. Llorca, Review of the decomposition of ammonia to generate hydrogen, Ind. Eng. Chem. Res., 2021, 60, 18560–18611 CrossRef CAS.
- C. Chen, K. Wu, H. Ren, C. Zhou, Y. Luo, L. Lin, C. Au and L. Jiang, Ru-based catalysts for ammonia decomposition: a mini-review, Energy Fuels, 2021, 35, 11693–11706 CrossRef CAS.
- D. A. Hansgen, D. G. Vlachos and J. G. Chen, Using first principles to predict bimetallic catalysts for the ammonia decomposition reaction, Nat. Chem., 2010, 2, 484–489 CrossRef CAS PubMed.
- F. He, Q. Gao, Z. Liu, M. Yang, R. Ran, G. Yang, W. Wang, W. Zhou and Z. Shao, A new Pd doped proton conducting perovskite oxide with multiple functionalities for efficient and stable power generation from ammonia at reduced temperatures, Adv. Energy Mater., 2021, 11, 2003916 CrossRef CAS.
- C. Leewis, W. Kessels, M. van de Sanden and J. Niemantsverdriet, Ammonia adsorption and decomposition on silica supported Rh nanoparticles observed by in situ attenuated total reflection infrared spectroscopy, Appl. Surf. Sci., 2006, 253, 572–580 CrossRef CAS.
- H. Fang, S. Wu, T. Ayvali, J. Zheng, J. Fellowes, P.-L. Ho, K. C. Leung, A. Large, G. Held and R. Kato, Dispersed surface Ru ensembles on MgO (111) for catalytic ammonia decomposition, Nat. Commun., 2023, 14, 647 CrossRef CAS.
- X. Zhang, L. Liu, J. Feng, X. Ju, J. Wang, T. He and P. Chen, Ru nanoparticles on Pr2O3 as an efficient catalyst for hydrogen production from ammonia decomposition, Catal. Lett., 2022, 152, 1170–1181 CrossRef CAS.
- T. A. Le, Y. Kim, H. W. Kim, S.-U. Lee, J.-R. Kim, T.-W. Kim, Y.-J. Lee and H.-J. Chae, Ru-supported lanthania-ceria composite as an efficient catalyst for COx-free H2 production from ammonia decomposition, Appl. Catal., B, 2021, 285, 119831 CrossRef CAS.
- C. Zhou, K. Wu, H. Huang, C.-F. Cao, Y. Luo, C.-Q. Chen, L. Lin, C. Au and L. Jiang, Spatial confinement of electron-rich Ni nanoparticles for efficient ammonia decomposition to hydrogen production, ACS Catal., 2021, 11, 10345–10350 CrossRef CAS.
- Y. Yi, L. Wang, Y. Guo, S. Sun and H. Guo, Plasma-assisted ammonia decomposition over Fe–Ni alloy catalysts for COx-Free hydrogen, AIChE J., 2019, 65, 691–701 CAS.
- C. Chen, Y. Chen, A. M. Ali, W. Luo, J. Wen, L. Zhang and H. Zhang, Bimetallic Ru-Fe nanoparticles supported on carbon nanotubes for ammonia decomposition and synthesis, Chem. Eng. Technol., 2020, 43, 719–730 CrossRef CAS.
- X. Ju, L. Liu, P. Yu, J. Guo, X. Zhang, T. He, G. Wu and P. Chen, Mesoporous Ru/MgO prepared by a deposition-precipitation method as highly active catalyst for producing COx-free hydrogen from ammonia decomposition, Appl. Catal., B, 2017, 211, 167–175 CrossRef CAS.
- T. Bell, H. Ménard, J.-M. G. Carballo, R. Tooze and L. Torrente-Murciano, Hydrogen production from ammonia decomposition using Co/γ-Al2O3 catalysts–insights into the effect of synthetic method, Int. J. Hydrogen Energy, 2020, 45, 27210–27220 CrossRef CAS.
- I. Lucentini, A. Casanovas and J. Llorca, Catalytic ammonia decomposition for hydrogen production on Ni, Ru and NiRu supported on CeO2, Int. J. Hydrogen Energy, 2019, 44, 12693–12707 CrossRef CAS.
- J. Chen, Z. H. Zhu, S. Wang, Q. Ma, V. Rudolph and G. Q. Lu, Effects of nitrogen doping on the structure of carbon nanotubes (CNTs) and activity of Ru/CNTs in ammonia decomposition, Chem. Eng. J., 2010, 156, 404–410 CrossRef CAS.
- K. E. Lamb, M. D. Dolan and D. F. Kennedy, Ammonia for hydrogen storage: A review of catalytic ammonia decomposition and hydrogen separation and purification, Int. J. Hydrogen Energy, 2019, 44, 3580–3593 CrossRef CAS.
- N. Gerrits and G.-J. Kroes, Curious mechanism of the dissociative chemisorption of ammonia on Ru (0001), J. Phys. Chem. C, 2019, 123, 28291–28300 CrossRef CAS.
- A. Hellman, K. Honkala, I. Remediakis, A. Logadottir, A. Carlsson, S. Dahl, C. H. Christensen and J. K. Nørskov, Ammonia synthesis and decomposition on a Ru-based catalyst modeled by first-principles, Surf. Sci., 2009, 603, 1731–1739 CrossRef CAS.
- S. Maier, I. Stass, J. I. Cerda and M. Salmeron, Bonding of ammonia and its dehydrogenated fragments on Ru (0001), J. Phys. Chem. C, 2012, 116, 25395–25400 CrossRef CAS.
- X. Lu, J. Zhang, W.-K. Chen and A. Roldan, Kinetic and mechanistic analysis of NH3 decomposition on Ru (0001), Ru (111) and Ir (111) surfaces, Nanoscale Adv., 2021, 3, 1624–1632 RSC.
- J. A. Herron, S. Tonelli and M. Mavrikakis, Atomic and molecular adsorption on Ru (0001), Surf. Sci., 2013, 614, 64–74 CrossRef CAS.
- X. Duan, G. Qian, C. Fan, Y. Zhu, X. Zhou, D. Chen and W. Yuan, First-principles calculations of ammonia decomposition on Ni (110) surface, Surf. Sci., 2012, 606, 549–553 CrossRef CAS.
- X. Duan, J. Ji, G. Qian, C. Fan, Y. Zhu, X. Zhou, D. Chen and W. Yuan, Ammonia decomposition on Fe (110), Co (111) and Ni (111) surfaces: a density functional theory study, J. Mol. Catal. A: Chem., 2012, 357, 81–86 CrossRef CAS.
- J. Cha, T. Lee, Y.-J. Lee, H. Jeong, Y. S. Jo, Y. Kim, S. W. Nam, J. Han, K. B. Lee and C. W. Yoon, Highly monodisperse sub-nanometer and nanometer Ru particles confined in alkali-exchanged zeolite Y for ammonia decomposition, Appl. Catal., B, 2021, 283, 119627 CrossRef CAS.
- W. Guo and D. G. Vlachos, Patched bimetallic surfaces are active catalysts for ammonia decomposition, Nat. Commun., 2015, 6, 8619 CrossRef CAS.
- Y.-Q. Gu, X.-P. Fu, P.-P. Du, D. Gu, Z. Jin, Y.-Y. Huang, R. Si, L.-Q. Zheng, Q.-S. Song, C.-J. Jia and C. Weidenthaler, In situ X-ray diffraction study of Co–Al nanocomposites as catalysts for ammonia decomposition, J. Phys. Chem. C, 2015, 119, 17102–17110 CrossRef CAS.
- A. M. Karim, V. Prasad, G. Mpourmpakis, W. W. Lonergan, A. I. Frenkel, J. G. Chen and D. G. Vlachos, Correlating particle size and shape of supported Ru/γ-Al2O3 catalysts with NH3 decomposition activity, J. Am. Chem. Soc., 2009, 131, 12230–12239 CrossRef CAS.
- H. Zhang, Y. A. Alhamed, Y. Kojima, A. A. Al-Zahrani, H. Miyaoka and L. A. Petrov, Structure and catalytic properties of Ni/MWCNTs and Ni/AC catalysts for hydrogen production via ammonia decomposition, Int. J. Hydrogen Energy, 2014, 39, 277–287 CrossRef CAS.
- S. Sayas, N. Morlanés, S. P. Katikaneni, A. Harale, B. Solami and J. Gascon, High pressure ammonia decomposition on Ru–K/CaO catalysts, Catal. Sci. Technol., 2020, 10, 5027–5035 RSC.
- X. Ju, L. Liu, X. Zhang, J. Feng, T. He and P. Chen, Highly efficient Ru/MgO catalyst with surface-enriched basic sites for production of hydrogen from ammonia decomposition, ChemCatChem, 2019, 11, 4161–4170 CrossRef CAS.
- Y. Im, H. Muroyama, T. Matsui and K. Eguchi, Ammonia decomposition over nickel catalysts supported on alkaline earth metal aluminate for H2 production, Int. J. Hydrogen Energy, 2020, 45, 26979–26988 CrossRef CAS.
- S. Bajus, F. Agel, M. Kusche, N. N. Bhriain and P. Wasserscheid, Alkali hydroxide-modified Ru/γ-Al2O3 catalysts for ammonia decomposition, Appl. Catal., A, 2016, 510, 189–195 CrossRef CAS.
- Q. Meng, H. Liu, K. Xu, W. Wang and C. Jia, CeO2-x modified Ru/γ-Al2O3 catalyst for ammonia decomposition reaction, J. Rare Earths, 2023, 41, 801–809 CrossRef CAS.
- J. Cha, Y. S. Jo, H. Jeong, J. Han, S. W. Nam, K. H. Song and C. W. Yoon, Ammonia as an efficient COx-free hydrogen carrier: Fundamentals and feasibility analyses for fuel cell applications, Appl. Energy, 2018, 224, 194–204 CrossRef CAS.
- A.-R. Kim, J. Cha, J. S. Kim, C.-I. Ahn, Y. Kim, H. Jeong, S. H. Choi, S. W. Nam, C. W. Yoon and H. Sohn, Hydrogen production from ammonia decomposition over Ru-rich surface on La2O2CO3-Al2O3 catalyst beads, Catal. Today, 2022, 411, 113867 Search PubMed.
- Z. Zhang, S. Liguori, T. F. Fuerst, J. D. Way and C. A. Wolden, Efficient ammonia decomposition in a catalytic membrane reactor to enable hydrogen storage and utilization, ACS Sustainable Chem. Eng., 2019, 7, 5975–5985 CrossRef CAS.
- Y. Park, J. Cha, H.-T. Oh, T. Lee, S. H. Lee, M. G. Park, H. Jeong, Y. Kim, H. Sohn, S. W. Nam, J. Han, C. W. Yoon and Y. S. Jo, A catalytic composite membrane reactor system for hydrogen production from ammonia using steam as a sweep gas, J. Membr. Sci., 2020, 614, 118483 CrossRef CAS.
- N. Engelbrecht, S. Chiuta and D. G. Bessarabov, A highly efficient autothermal microchannel reactor for ammonia decomposition: analysis of hydrogen production in transient and steady-state regimes, J. Power Sources, 2018, 386, 47–55 CrossRef CAS.
- A. Badakhsh, Y. Kwak, Y.-J. Lee, H. Jeong, Y. Kim, H. Sohn, S. W. Nam, C. W. Yoon, C. W. Park and Y. S. Jo, A compact
catalytic foam reactor for decomposition of ammonia by the Joule-heating mechanism, Chem. Eng. J., 2021, 426, 130802 CrossRef CAS.
- A. Badakhsh, J. Cha, Y. Park, Y.-J. Lee, H. Jeong, Y. Kim, H. Sohn, S. W. Nam, C. W. Yoon and C. W. Park, Autothermal recirculating reactor (ARR) with Cu-BN composite as a stable reactor material for sustainable hydrogen release from ammonia, J. Power Sources, 2021, 506, 230081 CrossRef CAS.
|
This journal is © Institute of Process Engineering of CAS 2023 |
Click here to see how this site uses Cookies. View our privacy policy here.