DOI:
10.1039/D3GC02552G
(Paper)
Green Chem., 2023,
25, 9282-9291
Towards green chemicals and edible coatings from barks and peels with near critical extraction of suberin†
Received
13th July 2023
, Accepted 2nd October 2023
First published on 19th October 2023
Abstract
Due to their complex structures, industrial suberoligneous by-products such as barks and peels remain poorly exploited. In this study, we demonstrated the efficient extraction of suberin from barks (11.3%) and peels (20.85%) via supercritical and near-supercritical transesterification without the need for catalysts. When applied in non-isocyanate polyurethane (NIPU) foams, suberinic extracts allowed the increase of the biomass content by up to 20% and facilitated the foaming process by improving pre-curing viscosity. When sprayed on fruits, the suberinic extracts effectively reduced the water loss rate by 25%, extending the shelf-life of the produce. A life cycle analysis for the latter application confirmed the competitive potential of our process against plastic sealing. This work uncovers the potential of suberoligneous biomass (SBM) to provide sustainable solutions to emerging societal challenges.
Introduction
Efficient processes to exploit agricultural, forestry and agri-food residues are essential for mitigating the environmental impact of these sectors and promoting a biomass-based economy.1 While many routes have been developed for the refining of lignocellulosic biomasses,2,3 exploitation of suberoligneous biomasses (SBM) from barks4–6 and peels of tuberous roots and tubers7–11 has remained limited and the focus has been mainly on starch, secondary metabolites, and lignin extraction or on energy production. Each year, around 190 million tons of wood bark,12 70 to 140 thousand tons of potato peels,7 and up to 40 million tons of cassava peels13 are generated. These by-products have a composition similar to wood bark but vary across species and genotypes. Currently, their primary uses for these peels include livestock feed, combustion, and residual starch extraction.7,9,11,13–16 Consequently, these by-products are poorly exploited despite being valuable sources of various polymers such as cutin and suberin.17–19 Specifically, suberin offers a potential of several million tons of biopolyesters rich in long chain polyfunctional fatty acids (Fig. S1†). Considering the stagnant growth in fatty acid production capacity20 and an anticipated steady increase of the demand (with a Compound Annual Growth Rate (CAGR) of 6%)21 in the coming years,20 extracting suberin from agricultural by-products such as peels could diversify the sustainable sources of fatty acid and associated derived compounds. However, optimal exploitation of suberin requires the development of efficient extraction methods and diversification of the few applications currently available for extracted suberin.22
Several procedures including transesterification have been described to extract suberin but none of them meets all the criteria needed to facilitate industrial implementation.22 Although transesterification is effective, adding a catalyst increases the cost, complexity and amount of effluents generated during extraction. Previous studies highlighted the possibility of autocatalyzed transesterification in supercritical methanol23–25 during vegetable oil-to-biodiesel conversions, thereby bypassing catalyst requirements. This study aims to investigate whether suberin extraction can be achieved under similar conditions (>513.4 K, 8.22 MPa) to facilitate the fractionation of SBM.
The relevance of the resulting extracts was also assessed through two innovative approaches, the first one as a bio-additive in self-blowing non-isocyanate polyurethane foams and the second one regarding the shelf-life extension of fruits.
Materials and methods
Solvents and reagents
Acetone, dichloromethane, ethanol, methanol and THF were purchased from Scharlab. Jeffamine EDR-148 was supplied by TCI. N,O-Bis(trimethylsilyl)trifluoroacetamide
:
trimethylchlorosilane (BSTFA
:
TMCS 99
:
1), trimethylpropane triglycidyl ether (TMPTE), 2,2′-(ethylenedioxy)diethanethiol, and 1,8-diazabicyclo[5.4.0]undec-7-ene (98%, DBU) were purchased from Sigma-Aldrich. All the reagents and solvents were used as provided.
Trimethylolpropane triglycidyl carbonate (TMPTC) was synthesized by organocatalyzed quantitative coupling of carbon dioxide to TMPTE as described by Monie.26
Sample preparation
Experiments were conducted on oak bark (Quercus robur), potato peels (Solanum tuberosum var. Nicola, Belgium) and cassava peels (Manihot esculenta var. Valencia, Costa Rica and var. Nase14, Rwanda). Potato and cassava were manually peeled and subjected to an enzymatic treatment as described by Schreiber27 to reduce the non-periderm fraction. Oak bark was obtained from a local sawmill. Both samples were then dried and ground to 1 mm with a Pulverisette 25 (Fritsch). The resulting samples are referred to as raw. The raw samples were successively extracted with water, ethanol and dichloromethane in a Soxhlet apparatus. The resulting samples are referred to as extracted.
Model extraction of suberin
For each suberin extraction, 1 g of dried extracted sample was suspended in methanol and heated to the desired temperature in a 75 mL Parr series 5000 reactor system (Parr Instrument Co, Illinois, USA). Supercritical (SC) and near supercritical (NSC) extractions were performed at 418, 473, 493, 518, 543 or 553 K with a volume of methanol sufficient to achieve the desired pressure (Fig. S2†). Once the temperature was achieved, the reactor was either stopped (i.e. 0 minute treatment) or maintained for the desired duration. Afterward, the reactor was air cooled to 333 K, the reaction mixture was vacuum filtered on a sintered glass disc (16 μm–40 μm porosity), and the retentate was rinsed twice with 20 mL of methanol preheated to 333 K. The filtrates were pooled and adjusted to 100 mL and are referred to as the liquid fraction, while the retentate is referred to as solid residue.
Solid residues were used for FTIR spectroscopy, Klason lignin (acid insoluble lignin and acid soluble lignin) and polysaccharide analyses.
The liquid fraction was then evaporated with a rotative evaporator (Rotavapor®, Büchi Labortechnik) and recovered successively with water, dichloromethane and acetone three times. Water fractions were pooled and used for glycerol measurement, and dichloromethane and acetone fractions were pooled together and used for FTIR and carboxylic acid measurements.
Suberin extraction for application
For each suberin extraction, 30 g of dried raw sample (cassava or oak) was suspended in methanol and heated to 493 K for 0 minutes with 320 g of methanol in a 600 mL Parr series 5500 reactor (Parr Instrument Co, Illinois, USA) controlled by a 4848 Parr system. Once the temperature was achieved, the reactor was stopped and water-cooled to 333 K. The reaction mixtures were pooled and filtered, and the liquid fraction was dried in a rotative evaporator (Rotavapor®, Büchi Labortechnik) at 60 °C. The resulting material is referred to as a suberinic extract.
Self-blowing non-isocyanate polyurethane (NIPU) foams with suberinic extract loadings
NIPU foams were prepared as previously described.28 For each foam, 10 g of reactive mixture were prepared by successive addition of trimethylolpropane triglycidyl carbonate (TMPTC), suberinic extract, Jeffamine EDR148 (diamine), 2,2′-(ethylenedioxy)diethanethiol (dithiol), and 1,8-diazabicyclo[5.4.0]undéc-7-ène (DBU) in a beaker with the following proportion: suberinic extract + ([5CC]/[NH2]/[SH]/[DBU] = [1]/[0.75]/[0.25]/[0.05]) = 10 g of reactive mixture. (Example for 10 g of reactive mixture with 20% of suberinic extract: TMPTC = 5.0195 g; suberinic extract = 2 g; diamine = 1.9267 g; dithiol = 0.7899 g and DBU = 0.2639 g.)
The reactive mixture was stirred for 2 minutes, poured into a silicon mold and placed in an oven at the desired temperature. After 5 minutes, an additional mixing was performed and the sample was left for foaming for 5 h. Foams were cooled at room temperature in a desiccator, demolded and placed back in the desiccator for equilibration before any characterization.
Fruit coating preparation
Suberinic extracts from cassava and oak (493 K, 0 min, and 9 MPa) were dried and dissolved in ethanol with concentrations of 10 and 50 mg mL−1, respectively. The suspension was sprayed 4 times for 10 seconds on each fruit using a chromatography sprayer. A total of 10 cherry tomatoes and 5 groups of 3 blueberries were used for each condition. Mock treatment consisted in spraying only ethanol and no spraying was done on the control.
Fruits were then stored in an MLR-352H-PA growth chamber (Panasonic, Japan) at 25 °C, with 50% humidity and light step setting on 1 for 202 hours. The fruits were weighed once a day.
Characterization of suberinic extracts
Suberin mass yields.
The mass yield of suberinic extracts was calculated by weighing the residue after drying 10 mL of liquid fraction (sampled after adjustment to 100 ml) overnight at 100 °C. The results are expressed as the percentage of the initial dry weight.
FTIR spectroscopy.
Measurements were carried out on a Vertex 70 spectrometer (Bruker, Germany) equipped with a diamond attenuated total reflectance (ATR) device. 16 scans were recorded for each sample over the range of 400–4000 cm−1 with a resolution of 2 cm−1. Solid residues were ground with a mortar and pestle before analysis. For liquid fractions, a drop was placed on the diamond and air-dried before analysis.
Glycerol.
Determination of glycerol was performed by using a commercial kit (K-GCROLGK®, Megazyme, Irlande). The kit has been used in accordance with the manufacturer's instructions.
Carboxylic acids.
Samples were saponified in ethanolic KOH (0.2 M) for 1 h at boiling temperature. Determination was performed by the titration of the remaining KOH with HCl (0.04 M) compared to the control. The results were expressed in mmol of carboxylic acid function for 1 g of treated biomass.
Lignins and polysaccharides.
The structural composition was determined using well-documented techniques, namely Klason lignin and acid hydrolysis of polysaccharides, followed by derivatization.29
Partial identification of suberinic extract composition.
Liquid fractions obtained from oak (518 K, 60 min, 7.5 MPa and 493 K, 0 min, 9 MPa) and from cassava var Nase14 (493 K, 0 min, 9 MPa) were investigated for compositional analysis. First, 1 ml of sample was evaporated under nitrogen, dissolved in 300 μl of N,O-bis(trimethylsilyl)trifluoroacetamide (BSTFA)
:
trimethylchlorosilane (TMCS), 99
:
1 (Sigma-Aldrich®, Germany), and 200 μL of dichloromethane and incubated at 60 °C for 1 h. The monomers present in the derivatized samples were identified from their EI-MS spectra (70 eV, m/z 50–500) obtained with a GC-MSD Agilent 5973N (Agilent Technologies, USA) equipped with an HP-5 ms column (30 m × 0.25 mm × 0.25 μm (Agilent)). The oven program was 2 min at 80 °C, 8 °C min−1 to 210 °C, 3 °C min−1 to 280 °C, 15 °C min−1 to 320 °C, 320 °C for 15 min and He carrier gas with a flow of 1.2 ml min−1. The chromatograms were analyzed using Enhanced Chemstation D.01.02.16 (Agilent Technologies, USA) with Nist17 and Wiley275 Mass Spectral Libraries. The results were expressed as the percentage of the peak area over the total peak area.
Characterization of foams
Apparent density.
Foams were cut into 9 cubes of approximately 1 cm3 using a scalpel, measured using a caliper and weighed on an analytical scale. The results were expressed in kg per cubic meter.
Scanning electron microscopy (SEM).
Pictures were acquired with a QUANTA 600 apparatus microscope (FEI, USA). Cell size distributions were determined by measuring the diameter of all exposed cells on a foam slice using ImageJ software (v1.53k). For each sample, the areas of all exposed cells were also measured using the freehand selection tool.
Rheology.
Rheological measurements were carried out on an ARES (Advanced Rheometric Expansion System) Rheometric Scientific rheometer, equipped with two parallel plate geometries at a frequency of 1.6 Hz and a strain of 1%.
Statistical analysis
Statistical analysis was carried out using R30 version 4.1.2 (2021-11-01) with the agricolae31 package. A linear regression test and an HSD Tukey's test were performed to assess the statistically significant difference. PCA was performed with RcmdR,32 factomineR33,34 and factoextra34 packages.
Results and discussion
From supercritical (SC) to near-critical (NC) suberin extraction
SC extraction kinetics of suberin.
Model extractions were performed as described in Fig. 1A on selected suberoligneous materials (i.e. oak bark, potato peels and cassava peels), using methanol under supercritical conditions (518 K, 8.3 MPa) for 60 minutes without a catalyst. Fig. 1A also shows, after staining with Sudan red 7B, the localization of suberin in the cell walls of cassava peels, similar to oak bark35 and potato peels.35 The amount of extract from the three different materials ranged from 6.59% to 20.85% of the treated mass (Fig. 1B). Peels generated the highest extraction yield, nearly double (20.85%) the amount previously described in the literature (12.1%).17 In contrast, the bark yield was much lower (6.59%) than that previously described in the literature (39.7%).17 FTIR analysis showed the presence of a strong band between 1740 and 1700 cm−1 in both the raw material (pre-treatment) and the extract, while this band was absent in the post-treatment material (residue) (Fig. S3†). This band is typically attributed to C
O stretching from ester bonds,36,37 suggesting the suberinic composition of the extract. FTIR spectra also displayed other bands typical of suberin: symmetric stretches of methylene (C–H) and methyl (C–H, CH3) at 2850 cm−1; asymmetric stretches of methylene (C–H) at 2925 cm−1; and aromatic ring stretches at 1438, 1462, and 1469 cm−1.37 These results confirmed the technical feasibility of a one-step suberin extraction using a single solvent under SC conditions.
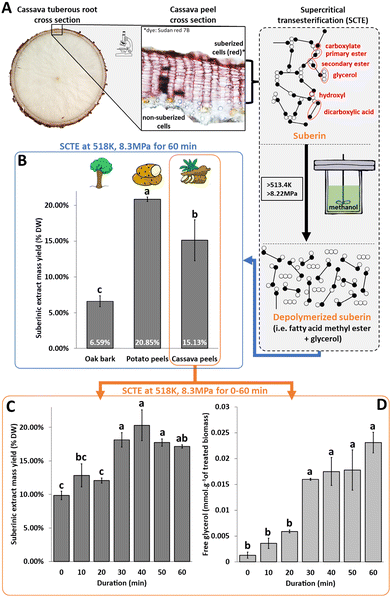 |
| Fig. 1 (A) General principle of suberoligneous SC extraction and its effect on the suberin structure (for example, cassava peel). (B) Suberinic extract mass yield obtained from Quercus robur (oak) bark, Solanum tuberosum (potato) tuber peels, and Manihot esculenta (cassava) tuberous root peels and when subjected to SC conditions (518 K, 8.3 MPa) for 60 min. (C and D) Effect of SC conditions at 518 K, 8.3 MPa, and 0–60 min on the suberinic extract mass yield and glycerol release of cassava. Different letters indicate statistically significant differences (P ≤ 0.05, Tukey HSD, n = 3); 0 min duration means that once reached, SC conditions are not maintained. | |
The impact of the extraction procedure on polysaccharide and lignin composition was determined by performing an extraction kinetic study on cassava peels between 0 and 60 minutes. The kinetic analysis (Fig. 1C) showed that 30 minutes at 518 K and 8.3 MPa was sufficient to reach the maximum level of extraction. The extraction appeared to occur in two stages. During the first phase (i.e. between 0 and 20 minutes), approximately 11.5% of suberin compounds were extracted. The extraction yield increased to 18.3% during the second phase (from 20 to 60 minutes). This result was further corroborated by the sequential release of glycerol (0–20 min, 30–50 min and 60 min) (Fig. 1D), suggesting either a preferential order between primary aliphatic esters and the different acylglycerol esters or the existence of suberin domains with contrasting resistance to transesterification. The latter hypothesis could be supported by the existence of suberan, a crystalline structure found in suberin and characterized by its resistance to saponification.38 An extended extraction duration (up to 240 minutes) confirmed that after 60 minutes, no significant modification in the suberinic extract yield or in polysaccharide and lignin content was observed (Fig. S4†), implying that these compounds were not extracted.
NC extraction of suberin.
Several extractions were performed on oak bark to investigate the effects of temperature (418–553 K), pressure (1.1–17.5 MPa) and duration (0–60 min) on the extract yield and the degree of depolymerization. The principal component analysis (Fig. 2A) highlighted that both yields and degrees of depolymerization were strongly affected by the physical state of the solvent. Under subcritical conditions, a single increase in temperature (Table S1,† treatments 2 and 7) or pressure (Table S1,† treatments 3 and 4) resulted in a decrease of the molar ratio of carboxylic acids to glycerol (i.e. higher depolymerization). Under supercritical conditions, an increase in pressure (Table S1,† treatments 11 and 12) resulted in higher extraction yields and lower depolymerization. Noticeably, higher temperatures consistently led to lower yields (Table S1,† treatments 8, 11 and 13). A longer treatment (Table S1,† treatments 3 and 5; 4 and 6; 7 and 9; 8 and 10) consistently resulted in higher yields and depolymerization of compressible liquid, while for other states of the solvent, the yield remained the same. No suberin was extracted at a temperature below 473 K (Table S1†). Importantly, this observation demonstrates that the transesterification, which occurs at a slow rate under NC conditions,39 was sufficient to extract the suberin material efficiently when a complete transesterification was not desired. This observation allows us to largely reduce the amount of energy required to extract suberin and, therefore, the cost of the process. It could also be hypothesized that suberin and suberin fragments subjected to temperature significantly higher than their reported melting temperature (between 56 and 103 °C)40 become increasingly soluble in alcohol, facilitating their migration out of the biomass.
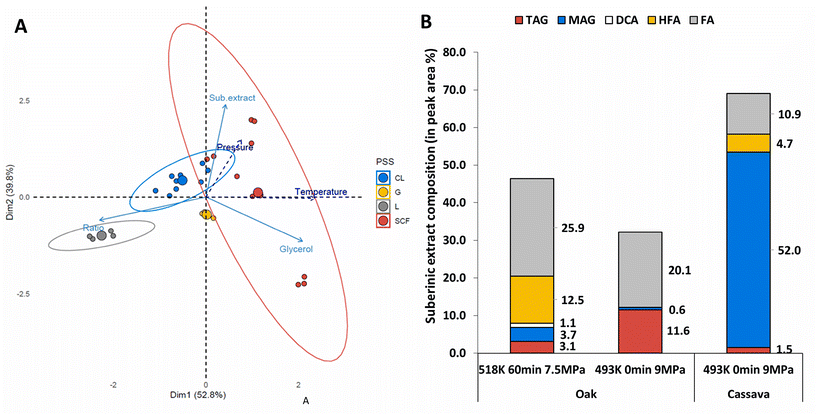 |
| Fig. 2 (A) Principal component analysis representing the impact of T (temperature), P (pressure) and PSS (physical state of solvent) on oak bark suberin extraction and depolymerization using methanol. Suberinic extract yield (Sub. extract), free glycerol (Glycerol), and molar ratio of COOH/glycerol (ratio) were used as variables. T and P are presented as illustrative variables. (B) Profiling of selected suberin extracts by gas chromatography-mass spectrometry (GC-MS) following different extraction treatments. Results are given in peak area percentage over the total peak area. | |
To assess the impact of milder extraction conditions on suberin fragmentation, two types of extractions supposedly leading to higher (518 K, 60 min, 7.5 MPa) and lower (493 K, 0 min, 9 MPa) depolymerization degrees in extracts from oak bark were analyzed by GC-MS (Fig. 2B). One extract from cassava peels (493 K, 0 min, 9 MPa) was also analyzed to assess if, for similar extraction conditions, different raw materials would produce similar extracts. Both types of extractions were in the subcritical state: gas and compressible liquid. Regarding depolymerization, GC-MS analysis revealed that the extraction conditions with the highest free glycerol content (Table S2†) also had the lowest triacylglycerol (TAG) content (3.1% against 11.6% total peak area (TPA)), which supports the hypothesis of a higher degree of depolymerization. Because the release of glycerol was similar in oak and cassava under milder extraction conditions (493 K, 0 min, 9 MPa, Table S2†), a similar GC-MS profile was expected. However, for cassava, a larger proportion of monoacylglycerols (52% TPA) was observed, compared to TAG. Overall, the profiles showed a large quantity of C16 to C19 fatty acids (Fig. 2B and Table S3†), from 10.9% to 25.9% of the total peak area (TPA). This observation suggests the occurrence of hydrolysis instead of alcoholysis (i.e. transesterification) under the conditions used for extraction. Hydrolysis of triglycerides has been previously reported as a first step in biodiesel production when subjected to supercritical water conditions.24 Such a mechanism was not expected as the aqueous phase during extraction was considered negligible because of limited residual water from the samples and from the methanol used for extraction. The molar ratio of carboxylic acids to glycerol (COOH
:
Gly) in oak (bark) and cassava (peels) extracts obtained under the same treatments revealed a higher proportion of COOH
:
Gly in oak compared to cassava (Table S2†). This observation aligned with previous studies that had reported higher levels of primary aliphatic esters in suberin from cork than in suberin from potato peels.40 Similarly, suberinic extracts from oak bark could be composed of a higher proportion of primary aliphatic esters than suberinic extracts from cassava. Given that primary and secondary esters were reported to have different susceptibilities to cleavage,41 this could explain why this extraction procedure outperformed the yields from previous studies for peels while it did not appear as efficient in extracting suberin from oak bark.
Mildly depolymerized suberin: a versatile compound
Industrial applications (i.e. foams and coatings) were assessed using oak and cassava extracts obtained under milder depolymerizing conditions (493 K, 0 min, 9 MPa). The extraction conditions were chosen as a compromise between high yield and fragmentation. Indeed, previous studies had already demonstrated that less depolymerized suberin, obtained using an ionic liquid, was naturally capable of reconstructing a network of suberin molecules.36 Suberinic extracts are typically described as waxy or oily pastes with a dark brown coloration in the literature, which was consistent with the appearance of the extracts obtained under strongly depolymerizing conditions (Fig. S5†). In our study, the suberinic extracts obtained under milder depolymerization conditions appeared as a glassy brown powder for oak (Fig. S5†) and as a brown plasticine for cassava (Fig. S6†). Such a difference may indicate a higher glass-transition temperature compared to that of suberin reported in the literature.40 Apart from their compatibility with the suberinic extracts, industrial applications were also chosen for their economic importance as well as their social and environmental relevance.
A bio-additive for self-blown non-isocyanate polyurethane foams.
Polyurethane (PU) foams are key materials found in many daily-life products (thermal insulating panels, mattresses, shoes, protective equipment, etc.) and they represent more than 50% of the total production of PUs (24.7 million tons in 2021). Because PUs remain largely produced by the toxic isocyanate chemistry,42 greener foam production processes incorporating bio-based raw materials are urgently needed. Self-blown non-isocyanate polyurethane (NIPU) foams prepared from reactive formulations composed of a poly(cyclic carbonate), a polyamine and a (masked) thiol in the presence of a catalyst26,28,43,44 are seen as greener alternatives to conventional self-blown PUs.45 However, this process usually requires a pre-reaction step at room temperature to increase the formulation viscosity, prior to producing the blowing agent at higher temperature.43 The potential of the suberinic extract was evaluated as a bio-based viscosity modifier to facilitate foaming without requiring any pre-reaction step. The solvent-free formulation was supplemented with increasing amounts of oak extract and foamed at 80 or 100 °C for 5 h (Fig. S7†). While unfoamed NIPUs were collected at 80 °C in the absence of a bio-additive, the presence of only 1 w% of extract allowed the generation of a foam with a density of 400 kg m−3 (Fig. S8†). Increasing the loading of the extract improved the foam quality (density and pore size distribution) and a homogeneous foam was obtained at 80 °C with 20 w% oak extract (a density of about 400 kg m−3, Fig. 3). Loadings above 20 w% were detrimental to foaming at 80 °C. Cassava allowed the production of a homogeneous foam with 10 w% cassava extract with a density of 300 kg m−3 (Fig. S8†) and higher loading slightly decreased the foam density (Fig. 3). When the foaming was performed at 100 °C, a loading of 5 w% extract was sufficient to lower the foam density from 550 to 225 kg m−3 (Fig. S8†). Loadings up to 30 w% could be used at 100 °C while maintaining a foam density lower than 300 kg m−3 (Fig. S8†). Similar to foaming at 80 °C, the most homogeneous foam was obtained with 20 w% oak extract (Fig. 3). Increasing the extract loading typically resulted in smaller and more consistent pore sizes. For foaming at 80 °C with a loading of oak extract increasing from 1% to 20%, the average pore size reduced from 0.14 cm (41.6% area with pores <0.2 cm) to 0.08 cm (71.3% area with pores <0.2 cm), as shown in Fig. S9.† Similarly, at 100 °C with the loading of oak extract increasing from 1% to 30%, the average pore size dropped from 0.21 cm (9.9% area with pores <0.2 cm) to 0.12 cm (58.8% area with pores <0.2 cm), as shown in Fig. S10.† The primary beneficial effect of the suberinic extracts in NIPU foaming was attributed to the increased viscosity of the formulation (Fig. S11†), which allowed trapping the generated CO2 and thereby promoting the NIPU expansion. The increased viscosity might have resulted from suberin's higher glass-transition temperature relative to the reactive mixture, or from hydrogen bonding between the reactive mixture and suberin fragments. Although the lowest foam density achieved was slightly higher than that attainable by adding a pre-reaction step (166–207 kg m−3),43 it offered the advantage of being faster and incorporated a renewable element within the foam.
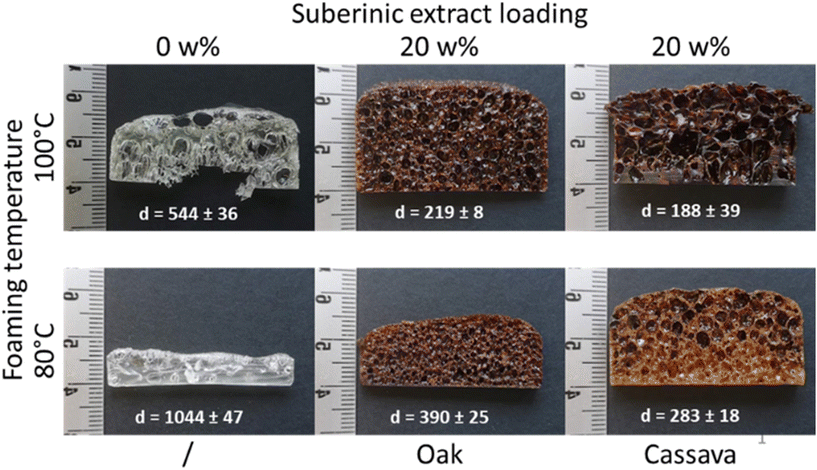 |
| Fig. 3 NIPU foams prepared with and without suberinic extracts. d = apparent density. | |
A coating to extend fruit and vegetable shelf life.
Suberin serves as a protective barrier in plants46 and the regulation of suberin biosynthesis is key in the healing and the shelf-life of crops such as potato and cassava.47,48 To investigate the potential of suberinic extracts as a biosourced coating, tests were conducted on blueberries and cherry tomatoes. The objective was to assess the capacity of suberin-based coatings to prevent water loss in fruits. An analogous application has already been successfully implemented with cutin extracts.49 The suberinic extract obtained under milder depolymerizing conditions was sprayed as an ethanolic solution at two concentrations: 10 and 50 mg mL−1. The 50 mg mL−1 concentration was chosen as it approached the solubility limit of the extract in ethanol at room temperature. The coating was not visible and thus did not alter the appearance of the fruit.
The results revealed significant differences in water loss for blueberries and cherry tomatoes treated with suberinic extracts compared to the mock treatment (Fig. 4). Blueberries showed a reduction of 25% and 20% in daily water loss when coated with 50 mg mL−1 oak and cassava extracts, respectively (Fig. S12A and C†). This meant that every 4 days, the coated fruits remained one day fresher than the untreated ones. The reduction in water loss for cherry tomatoes was 25% when coated with 10 mg mL−1 and 50 mg mL−1 cassava extracts or 10 mg mL−1 oak extract (Fig. S12B and D†). Unexpectedly, the spray with 50 mg mL−1 oak extract led to a lower protection in cherry tomatoes. The good performance of these extracts to act as a water barrier opens new opportunities for sourcing biomaterials for coating applications.
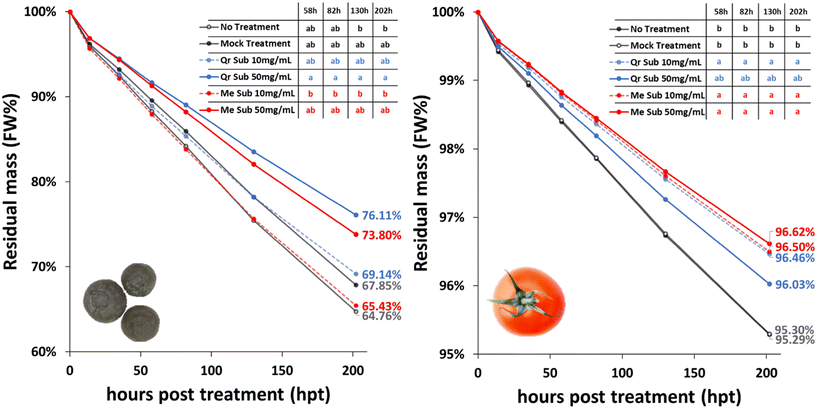 |
| Fig. 4 Residual mass of blueberry and cherry tomatoes over 202 hours with and without coatings of suberinic extract. Qr = oak; Me = cassava; Sub = suberinic extract obtained with a treatment at 493 K, 0 min, and 9 MPa. Different letters indicate statistically significant differences (P ≤ 0.05, Tukey HSD, n = 15 for blueberry and n = 10 for cherry tomatoes). | |
Suberinic extract vs. LDPE for fruit and vegetable coating.
A Life Cycle Assessment (LCA) was conducted to analyze the environmental impact of the suberin production process (Fig. S13†). The assessment specifically focused on the use of suberin for fruit and vegetable coating. The LCA is a methodology enabling the evaluation of the environmental performances associated with a product/process/service throughout the entire life cycle, covering a wide range of environmental impact. Therefore, the primary goal of the LCA study was to assess the environmental profile of the suberin production process and to identify the key contributors to its environmental profile. To implement the LCA model, the software SIMAPRO 9.4.0.2 was utilized. The inventory data required for modelling background activities, such as electricity and chemical production, were calculated using the database Ecoinvent 3.8. The electricity consumption during the process was based on the average electricity mix for the United States, as modelled in Ecoinvent 3.8. In line with the recommendations by Piccinno et al.,50 natural gas was selected as the energy source for heating.
Subsequently, the inventory data were converted into 16 distinct environmental impact categories, using characterization factors derived from the Environmental Footprint 3.0 (EF 3.0) methodology. EF 3.0 is endorsed by the European Commission as the preferred impact assessment method to measure the life cycle environmental performances of products and processes (EU Commission Recommendation 2021/2279). For a more in-depth understanding, a thorough description of the characterization factors and environmental impact categories used in EF 3.0 is available in the report by Fazio et al.51 Additional details on the conducted LCA are provided in the ESI.†
The results indicate that the production of electricity for distillation and heat (from natural gas) are the primary contributors to the environmental impact associated with suberin production (Fig. 5A). Additionally, environmental performances of the suberin life cycle and that of LDPE with two end-of-life options were compared, as shown in Fig. 5B. This analysis revealed that the suberin life cycle has higher environmental impact for most of the considered categories. Furthermore, the sensitivity analysis in Fig 5C indicates that replacing the US electricity mix with that of Norway (which is approximately 90% hydroelectric) would lead to a better environmental performance of the suberin life cycle compared to that of the LDPE + incineration life cycle in almost all categories. Based on the LCA, it was determined that the suberin production process for food coating under the pilot extraction conditions presents higher environmental impact compared to the commonly used LDPE film. However, the environmental impact can be effectively reduced through the optimization energy and electricity use, a cleaner electricity mix, and heat recovery. Therefore, the LCA study has a future-oriented scope to provide environmental guidance to effectively improve the future environmental performances of the process. As previously discussed by Arvidsson,52 decisions made at early stages of development have far-reaching influence on future environmental consequences, compared to decisions made at later stages of development, when the possibility to alter the technology is more limited. Therefore, LCA conducted at an early stage can have a larger influence on the future development of the technology.53,54
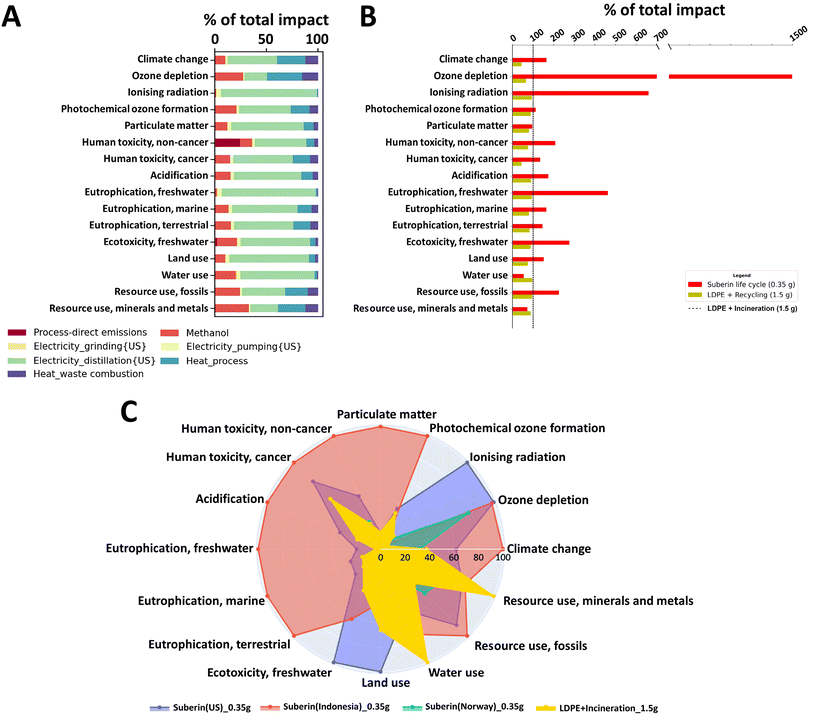 |
| Fig. 5 (A) Hotspot analysis of suberin production. Electricity for distillation and the heat process are the two main hotspots of the environmental profile of the process. (B) Comparison of suberin production for coating (0.35 g) with an equivalent amount of LDPE (1.5 g). Suberin production has higher impact compared to LDPE. Since it is edible, no end-of-life treatment is assumed for suberin. (C) Sensitivity analysis by replacing a country's electricity mix. By using the Norwegian electricity mix, the suberin production performs better than LDPE in almost all categories. | |
Given the importance of food waste caused by post-harvest losses in the tropical regions55,56 where cassava peels are available in large quantities, cassava suberinic extracts could offer affordable and sustainable coating solutions to extend the shelf life of fruits and vegetables as well as tuberous roots. This application has the potential to contribute significantly towards meeting the EU's 2030 goal of halving food spoilage.57 By extending the shelf life of perishable products using by-products from the potato industry, it promotes a circular approach to resource management.
Conclusions
We showcased a single-step, catalyst-free, and low-waste suberinic extract production. This extract offers an affordable, easy-to-apply spray coating to reduce food losses in cassava-growing regions and areas with abundant suberoligneous by-products like potato peels. Additionally, by enhancing the foam stability and viscosity in a polyurethane foam model, suberin extracts pave the way for sustainable, self-blown PHU foams.
The main challenge of the process is the energy required to achieve the desired temperatures (>473 K). In this study, we used a batch reactor with auto-generated pressure for the extractions. While this method may not be ideal for large-scale supercritical and near-critical extractions due to the need to heat large quantities of solvents to reach high pressure (>7 MPa), it does not render the process economically or environmentally unviable. By implementing a continuous industrial process, such as the use of a tubular reactor,39 the operational energy and equipment costs can be reduced, enhancing both the economic and environmental viability of the process. Indeed, with the LCA, we unveiled the key role played by the electricity and heat production, and the potential for suberin to have comparable, or even lower, environmental impact compared to LDPE. Though upscaling the suberinic extraction process necessitates further optimization, our work provides a seminal contribution, supporting the biomass-based economy in addressing social and industrial emerging challenges.
Conflicts of interest
There are no conflicts to declare.
Acknowledgements
H.V. acknowledges support from the University of Liège Gembloux Agro-Bio Tech and the FOSC ERA-NET Cofund on Food Systems and Climate (Project PHEALING). C.D. is FNRS Research Director and thanks the “Fonds de la Recherche Scientifique (F.R.S.-FNRS)” for funding. The authors also thank the Laboratory of Chemistry of Natural Molecules (LCNM) of the University of Liège for GC-MS analysis of the extracts.
References
- T. Keijer, V. Bakker and J. C. Slootweg, Nat. Chem., 2019, 11, 190–195 CrossRef CAS PubMed
.
- A. Patel and A. R. Shah, J. Bioresour. Bioprod., 2021, 6, 108–128 CrossRef CAS
.
- S. Takkellapati, T. Li and M. A. Gonzalez, Clean Technol. Environ. Policy, 2018, 20, 1615–1630 CrossRef CAS PubMed
.
- D. M. Neiva, S. Araújo, J. Gominho, A. de C. Carneiro and H. Pereira, Ind. Crops Prod., 2018, 123, 262–270 CrossRef CAS
.
- L.-Y. Liu, S. C. Patankar, R. P. Chandra, N. Sathitsuksanoh, J. N. Saddler and S. Renneckar, ACS Sustainable Chem. Eng., 2020, 8, 4745–4754 CrossRef CAS
.
- D. M. Neiva, J. Rencoret, G. Marques, A. Gutiérrez, J. Gominho, H. Pereira and J. C. Río, ChemSusChem, 2020, 13, 4537–4547 CrossRef CAS PubMed
.
- S. L. Sampaio, S. A. Petropoulos, A. Alexopoulos, S. A. Heleno, C. Santos-Buelga, L. Barros and I. C. F. R. Ferreira, Trends Food Sci. Technol., 2020, 103, 118–129 CrossRef CAS
.
- A. A. Fathima, M. Sanitha, L. Tripathi and S. Muiruri, Food Energy Secur., 2023, 12, e380 CrossRef
.
- G. S. Aruwajoye, Y. Sewsynker-Sukai and E. B. G. Kana, Fuel, 2020, 278, 118351 CrossRef CAS
.
- J. O. Ighalo and A. G. Adeniyi, Environ. Processes, 2021, 8, 267–285 CrossRef CAS
.
- N. A. Chohan, G. S. Aruwajoye, Y. Sewsynker-Sukai and E. B. Gueguim Kana, Renewable Energy, 2020, 146, 1031–1040 CrossRef CAS
.
- Z. Pásztory, I. R. Mohácsiné, G. Gorbacheva and Z. Börcsök, BioResources, 2016, 11, 7859–7888 Search PubMed
.
-
T. A. Amole, S. Anandan and I. Okike, A guide to the production of High-Quality Cassava Peel® mash as a feed for livestock, International Livestock Research Institute (ILRI), Nairobi, Kenya, 2019 Search PubMed
.
- A. Javed, A. Ahmad, A. Tahir, U. Shabbir, M. Nouman and A. Hameed, AIMS Agric. Food, 2019, 4, 807–823 Search PubMed
.
- C. G. Ozoegwu, C. Eze, C. O. Onwosi, C. A. Mgbemene and P. A. Ozor, Renewable Sustainable Energy Rev., 2017, 72, 625–638 CrossRef
.
- M. E. Camire, D. Violette, M. P. Dougherty and M. A. McLaughlin, J. Agric. Food Chem., 1997, 45, 1404–1408 CrossRef CAS
.
- A. Gandini, C. Pascoal Neto and A. J. D. Silvestre, Prog. Polym. Sci., 2006, 31, 878–892 CrossRef CAS
.
- N. Cordeiro, M. N. Belgacem, A. J. D. Silvestre, C. P. Neto and A. Gandini, Int. J. Biol. Macromol., 1998, 22, 71–80 Search PubMed
.
- H. De Oliveira, B. Yoon, V. Michaud, J.-D. Nam and J. Suhr, Ind. Crops Prod., 2017, 109, 843–849 CrossRef CAS
.
-
LMC
, ICIS Pan American Oleochemical Conference.
- Fatty Acid Ester Market | 2022–27 | Industry Share, Size, Growth - Mordor Intelligence, https://www.mordorintelligence.com/industry-reports/fatty-acid-ester-market, (accessed 9 May 2022).
- I. M. Aroso, A. R. Araújo, R. A. Pires and R. L. Reis, ACS Sustainable Chem. Eng., 2017, 5, 11130–11146 CrossRef CAS
.
- S. Saka and D. Kusdiana, Fuel, 2001, 80, 225–231 CrossRef CAS
.
- E. Minami and S. Saka, Fuel, 2006, 85, 2479–2483 CrossRef CAS
.
- S. Karki, N. Sanjel, J. Poudel, J. H. Choi and S. C. Oh, Appl. Sci., 2017, 7, 632 CrossRef
.
- F. Monie, B. Grignard and C. Detrembleur, ACS Macro Lett., 2022, 11, 236–242 CrossRef CAS PubMed
.
- L. Schreiber, R. Franke and K. Hartmann, Planta, 2005, 220, 520–530 CrossRef CAS PubMed
.
-
C. Detrembleur, J. M. Thomassin, B. Grignard, F. Monie and C. Jérôme, Self-Blowing Isocyanate-Free Polyurethane Foams, WO/2021/004993A1, 2021
.
- Q. Schmetz, G. Maniet, N. Jacquet, H. Teramura, C. Ogino, A. Kondo and A. Richel, Ind. Crops Prod., 2016, 94, 308–317 CrossRef CAS
.
-
Core R Team, R Foundation for Statistical Computing, 2019, 2, https://www.R-project.org Search PubMed
.
- G. H. Freeman, K. A. Gomez and A. A. Gomez, Biometrics, 1985, 41, 342 CrossRef
.
-
M. Fox and J. Bouchet-Valat, Rcmdr: R Commander. R package, 2020 Search PubMed.
- F. Lê, S. Josse and J. Husson, J. Stat. Softw., 2008, 25, 1–18 Search PubMed
.
-
A. Kassambara and F. Mundt, CRAN- R Package, 2020, 84 Search PubMed
.
- J. Graça, Front. Chem., 2015, 3, 62 Search PubMed
.
- H. Garcia, R. Ferreira, C. Martins, A. F. Sousa, C. S. R. Freire, A. J. D. Silvestre, W. Kunz, L. P. N. Rebelo and C. Silva Pereira, Biomacromolecules, 2014, 15, 1806–1813 CrossRef CAS PubMed
.
- B. Handiso, J. J. Valle-Delgado, L.-S. Johansson and M. Hughes, Ind. Crops Prod., 2021, 159, 113070 CrossRef CAS
.
- J. W. Turner, B. E. Hartman and P. G. Hatcher, Org. Geochem., 2013, 57, 41–53 CrossRef CAS
.
- P. R. S. Dos Santos, F. A. P. Voll, L. P. Ramos and M. L. Corazza, J. Supercrit. Fluids, 2017, 126, 25–36 CrossRef
.
- A. Bento, C. J. S. Moreira, V. G. Correia, R. Escórcio, R. Rodrigues, A. S. Tomé, N. Geneix, J. Petit, B. Bakan, C. Rothan, O. O. Mykhaylyk and C. Silva Pereira, ACS Sustainable Chem. Eng., 2021, 9, 15780–15792 CrossRef CAS PubMed
.
- R. Ferreira, H. Garcia, A. F. Sousa, M. Guerreiro, F. J. S. Duarte, C. S. R. Freire, M. J. Calhorda, A. J. D. Silvestre, W. Kunz, L. P. N. Rebelo and C. Silva Pereira, RSC Adv., 2014, 4, 2993–3002 RSC
.
- J. Peyrton and L. Avérous, Mater. Sci. Eng., R, 2021, 145, 100608 CrossRef
.
- F. Monie, B. Grignard, J. Thomassin, R. Mereau, T. Tassaing, C. Jerome and C. Detrembleur, Angew. Chem., Int. Ed., 2020, 59, 17033–17041 CrossRef CAS PubMed
.
-
C. Detrembleur, B. Grignard and F. Monie, Self-Blowing Isocyanate-Free Polyurethane Foams, WO/2022/128822A1, 2022
.
- F. Monie, T. Vidil, B. Grignard, H. Cramail and C. Detrembleur, Mater. Sci. Eng., R, 2021, 145, 100628 CrossRef
.
- A. E. Harman-Ware, S. Sparks, B. Addison and U. C. Kalluri, Biotechnol. Biofuels, 2021, 14, 75 CrossRef CAS PubMed
.
- Z. Wahrenburg, E. Benesch, C. Lowe, J. Jimenez, V. K. R. Vulavala, S. Lü, R. Hammerschmidt, D. Douches, W. C. Yim, P. Santos and D. K. Kosma, Plant J., 2021, 107, 77–99 CrossRef CAS PubMed
.
- H. Vanderschuren, E. Nyaboga, J. S. Poon, K. Baerenfaller, J. Grossmann, M. Hirsch-Hoffmann, N. Kirchgessner, P. Nanni and W. Gruissem, Plant Cell, 2014, 26, 1913–1924 CrossRef CAS PubMed
.
- S. Hauff, B. Chefetz, M. Shechter and W. Vetter, Phytochem. Anal., 2010, 21, 582–589 CrossRef CAS PubMed
.
- F. Piccinno, R. Hischier, S. Seeger and C. Som, J. Cleaner Prod., 2016, 135, 1085–1097 CrossRef CAS
.
-
S. Fazio, F. Biganzoli, F. De Laurentiis, L. Zampori, S. Sala and E. Diaconu, Supporting information to the characterisation factors of recommended EF Life Cycle Impact Assessment methods, 2018 Search PubMed.
- R. Arvidsson, A. M. Tillman, B. A. Sandén, M. Janssen, A. Nordelöf, D. Kushnir and S. Molander, J. Ind. Ecol., 2018, 22, 1286–1294 CrossRef CAS
.
- C. R. Hung, L. A. W. Ellingsen and G. Majeau-Bettez, J. Ind. Ecol., 2020, 24, 26–37 CrossRef CAS
.
- S. M. Moni, R. Mahmud, K. High and M. Carbajales-Dale, J. Ind. Ecol., 2020, 24, 52–63 CrossRef CAS
.
-
FAO, The State of Food and Agriculture 2019, 2019, pp. 1–182 Search PubMed
.
- I. M. Zainuddin, A. Fathoni, E. Sudarmonowati, J. R. Beeching, W. Gruissem and H. Vanderschuren, Postharvest Biol. Technol., 2018, 142, 115–123 CrossRef
.
- T. Ronzon and R. M'Barek, Sustainability, 2018, 10, 1745 CrossRef
.
|
This journal is © The Royal Society of Chemistry 2023 |
Click here to see how this site uses Cookies. View our privacy policy here.