DOI:
10.1039/D3GC01150J
(Paper)
Green Chem., 2023,
25, 5899-5906
Rapid, room-temperature, solvent-free mechanochemical oxidation of elemental gold into organosoluble gold salts†
Received
9th April 2023
, Accepted 12th May 2023
First published on 19th May 2023
Abstract
Gold is highly valued for a wide range of commercial and technological applications but is processed exclusively through highly aggressive and toxic solvents and/or reagents, ultimately yielding water-soluble salts that are difficult to separate from inorganic reaction byproducts. As a result, development of safer, cleaner processes that would enable gold processing in non-aqueous, organic solvent is an attractive technological goal. Here, we describe a methodology that simultaneously avoids aggressive reagents and enables gold extraction into a safe organic solvent. The methodology is based on solventless, mechanochemical oxidation of metallic gold with Oxone® in the presence of tetraalkylammonium halide salts, to directly, rapidly (within 30–60 minutes) and at room temperature convert gold metal into solid salts that are immediately soluble in pure organic solvents and aqueous alcoholic media. The organosoluble gold salts are easily separated from sulfate byproducts by direct extraction into the benign solvent ethyl acetate, which is also easily recycled for re-use, providing a strategy for gold activation and dissolution without any additional reagents for purification, such as cation exchange resins, salts, or chelating agents. Besides enabling direct extraction of gold into an organic solvent, the mechanochemically obtained organosoluble gold salts can also be readily used for further syntheses, as shown here by a two-step one-pot route to prepare air- and moisture-resistant Au(I) salts, and an improved synthesis of gold nanoparticles from bulk gold.
Introduction
The development of efficient, safer and environmentally-friendly routes for the extraction and processing of rare elements is a major sustainability and technological challenge.1,2 Among rare metals, gold is notable for its commercial and technological applications, as well as fascinating chemical properties.3–9 The outstanding resistance to chemical attack means that gold processing and recycling rely on particularly aggressive and toxic techniques, requiring specialised equipment, safety precautions, and waste management.10–12 As a result, gold mining and processing is a major cause of environmental damage,13–18 as methods for gold processing range from hot aqua regia (a 3
:
1 by volume mixture of concentrated hydrochloric or hydrobromic acid with nitric acid)19 and amalgamation with mercury at research and small manufacturing scales (e.g. artisanal and small-scale gold mining),20,21 to alkali metal fusions, alkaline cyanidation, and high-temperature chlorine gas oxidation at larger scales.22–24 All these methods eventually produce water-soluble gold species such as tetrachloroaurate(III) (AuCl4−) salts that are further processed. Besides reagent toxicity, other hindrances in processing of such salts are the low volatility of water and the difficulty to separate gold salts from excess water-soluble reagents and reaction byproducts. As a result, there is much interest in new gold extraction strategies, including selective precipitation,25–27 chelating with macrocyclic hosts,28–30 or the use of 3D-printed scavenger filters.31 An important part of this effort is direct dissolution of gold into non-aqueous media,32–40e.g. “organic aqua regia” (mixtures of thionyl chloride with pyridine or other organic bases),41 solutions of elementary halogens, nitrosonium salts, ionic liquids, or deep eutectic solvents.42–51 A methodology that simultaneously avoids aggressive reagents and enables gold extraction into a safe organic solvent has, however, remained out of reach.
We have previously shown that mechanochemistry, i.e. the use of mechanical agitation in the form of grinding or shearing, to conduct chemical reactions,52–61 offers a simple method to convert noble metals into water-soluble salts by using Oxone® (2 KHSO5·KHSO4·K2SO4) oxidant.62 While avoiding toxic reagents, this methodology, however, did not resolve the difficulty of separating the water-soluble noble metal salts and byproducts.
We now present a straightforward mechanochemical method that directly converts metallic gold into [AuX4]− derivatives that are soluble in organic solvents, permitting simple, one-step separation of gold salts from water-soluble oxidation by-products by extraction into a green solvent such as ethyl acetate (EtOAc) (Fig. 1a–c). The presented strategy rests on using tetraalkylammonium salts as halide sources, yielding organo-soluble salts that can immediately and in high yield (>90% in a single pass) be extracted into EtOAc. This permits the simple separation of the resulting gold salts from the sulphate-based oxidation by-products, without having to rely on any additional cation exchange or chelation strategies that would require additional solvents and/or reagents that would ultimately complicate handling of the wastewater stream or the purification of the gold salts. The ability to directly use tetraalkylammonium halides as reagents for gold activation is enabled by the mild nature of the mechanochemical process, compared to traditional gold activation strategies that are too harsh to permit the use of such organic reagents. The resulting organoammonium tetrahaloaurate(III) salts are simply isolated by evaporation of the organic solvent, which is also readily recycled for reuse. The solid tetraalkylammonium haloaurates(III) can be directly redissolved in either pure organic media or aqueous ethanol (EtOH), making them suitable for diverse subsequent processing approaches, while remaining useful as precursors to more complex gold-based materials. The latter is evidenced through a one-pot mechanochemical process for the preparation of air- and moisture-resistant Au(I) derivatives, as well as a simplified route to gold nanoparticles (AuNPs).
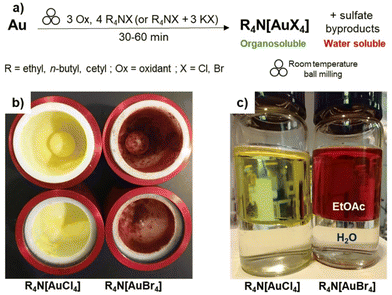 |
| Fig. 1 (a) Schematic illustration of the herein presented mechanochemical strategy for the mechanochemical conversion of gold metal into organosoluble tetrahaloaurate(III) salts. Sulfate byproducts are products of Oxone reduction, such as K2SO4 and KHSO4. Representative images of tetraalkylammonium tetrahaloaurate(III) salts obtained via the herein presented mechanochemical strategy: (b) raw products in zirconia milling jars and (c) after extraction into a mixture of EtOAc : water. Symbol for mechanochemical reactivity adapted from Rightmire and Hanusa.63 | |
Results and discussion
We first investigated the use of tetraethylammonium halides (TEAX, where X = Cl or Br) as halide sources: milling gold metal with 1.5 equivalents of Oxone© (i.e., 3 equivalents of KHSO5) and 4 equivalents of TEAX for 30 minutes yielded the corresponding [AuX4]− salts. The salts were then extracted by mixing with a 2
:
1 by volume mixture of EtOAc and water. The results were, however, poorly reproducible, most likely due to the highly hygroscopic nature of TEA+ salts (Table 1, entries 1–4) which led to water absorption and poor mixing, evident by aggregation of material on the milling media or vessel walls.
Table 1 Results of exploring TEACl and Oxone® in the oxidation of metallic gold demonstrating the effects of using commercially received or dried tetraalkylammonium salts and of milling timea
Entry |
Milling time (min) |
Conversionb (%) |
Experiments conducted using 0.1 mmol Au metal, 4 equivalents of TEACl and 3 equivalents of the oxidant (see ESI†).
Conversion based on gravimetric determination of gold after extraction in EtOAc : water mixture (2 : 1 by volume).
TEACl used as received, each entry is an individual experiment.
TEACl recrystallised and dried prior to use, experiment conducted in triplicate, with the mean value shown.
|
1c |
30 |
51 |
2c |
30 |
75 |
3c |
30 |
60 |
4c |
30 |
89 |
5c |
30 |
42 |
6c |
60 |
93 |
7c |
60 |
90 |
8d |
30 |
94 ± 2 |
9d |
60 |
92 ± 4 |
Increasing the milling time (Table 1, entries 6 and 7) or using freshly dried TEACl (Table 1, entries 8 and 9) enabled consistently high conversion. The resulting crude reaction mixtures were immediately analyzed by powder X-ray diffraction (PXRD), indicating the disappearance of Bragg reflections of gold, and the appearance of new reflections attributed to the desired tetraethylammonium haloaurate salts and potassium sulfate byproduct (Fig. 2a and also ESI Fig. S1, S2†). The conversion of gold into soluble salts was verified by reduction of the [AuX4]− species in aqueous methanol, followed by gravimetric analysis (Table S1, also ESI†).64 Analysis of the crude mechanochemical reaction products by X-ray photoelectron spectroscopy (XPS) revealed the formation of Au(III) species, evident by 4f7/2 and 4f5/2 bands centered around 87 eV and 91 eV, respectively (Fig. S16 and S17†).65 Au(I) species were also detected, as evident by 4f7/2 and 4f5/2 bands at 85 eV and 89 eV, respectively, explained by either degradation upon storage (i.e., partial photoreduction of sample stored in a clear glass vial for several days) or upon exposure to the electron beam.
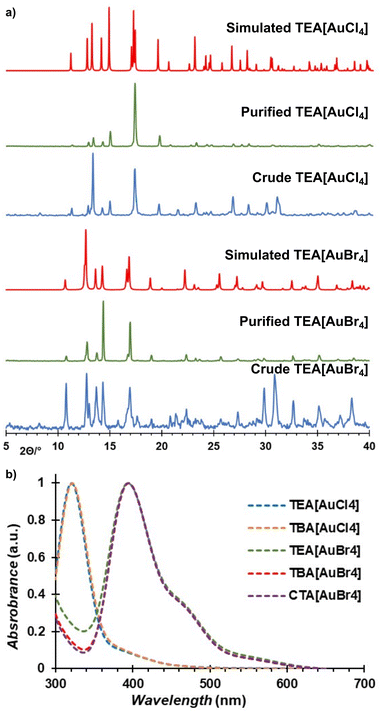 |
| Fig. 2 (a) Comparison of PXRD patterns for TEA[AuCl4] and TEA[AuBr4]. The pronounced needle-like shape of crystals indicates that the relative intensities of X-ray reflections are affected by preferred orientation effects. (b) Normalised absorption spectra for the five tetraalkylammonium tetrahaloaurate salts in this study, recorded in EtOH. | |
The pure oxidised gold compounds were readily isolated by biphasic extraction using a 1
:
2 by volume mixture of water and either EtOAc, chloroform, or dichloromethane, followed by separation and rotary evaporation of the organic phase, which allowed reuse of the organic solvent. This work-up was optimised using EtOAc as a greener solvent choice (ESI, Table S2†), demonstrating a highly efficient (ca. 90–95%) transfer of gold into the organic layer in a single extraction step.66 Overnight recrystallisation of the isolated solids from EtOAc produced diffraction-quality single crystals, and X-ray diffraction analysis confirmed the expected formula TEA[AuX4].
The PXRD patterns of the crude and isolated materials were an excellent match with those calculated from single crystal data (Fig. 2a), with the disappearance of the characteristic Bragg reflections of the K2SO4 byproduct around 30° confirming successful purification by extraction (see ESI†).
The recrystallised tetraethylammonium tetrahaloaurates were also characterised by high-resolution mass spectrometry (HR-MS), nuclear magnetic resonance spectroscopy (NMR), Fourier-transform infrared attenuated total reflectance (FTIR-ATR), and ultraviolet-visible absorption spectroscopy (UV-Vis). Mass spectrometry confirmed the presence of Au(III) species, with [AuX4]− observed as the main ion in all cases (see ESI†). Analysis by FTIR-ATR and solution 1H-NMR spectroscopy confirmed the persistence of the NEt4+ cation in all cases (see ESI, Fig. S8, S9 and S14, S15†). Analysis by UV-Vis spectroscopy demonstrated the absence of product decomposition or formation of gold nanoparticles (AuNPs) during workup (Fig. 2b), with absorption maxima at 320 nm and 390 nm for the [AuCl4]− and [AuBr4]−, respectively, which matches the expected literature values.67 Next, we explored other tetraalkylammonium salt halide sources, such as tetrabutylammonium halides (TBAX, X = Cl, Br) that are commercially available and widely used as phase transfer agents.68 No significant change in mechanochemical reactivity was observed compared to TEA analogues, though more consistent conversions of gold were obtained without pre-drying (89 ± 2% and 94 ± 4%, for TBACl and TBABr, respectively), in agreement with the less hygroscopic nature of TBA+ salts. Additionally, in exploring the mechanochemical reactivity with TBACl, the more hygroscopic of the two herein used TBA+ salts, it was observed that adding KCl as a secondary halide source further improved the mixing efficiency while still leading to the excellent conversion (89 ± 4%) of gold metal into TBA[AuCl4] as the final product. Further optimisation of this procedure involving mixed halide sources revealed that using 1.1 equivalents of the tetraalkylammonium halide with three equivalents of KX (where X = Cl, Br) readily affords the desired product (ESI, Table S1†). Analysis by the aforementioned analytical methods confirmed the formation of the target salts TBA[AuCl4] and TBA[AuBr4] (Fig. 2b, also ESI†). X-ray diffraction-quality crystals were obtained for both compounds, revealing crystallographic parameters similar to those previously reported for TBA[AuCl4].69,70 Notably, TBA[AuBr4] (Fig. 3) is not isostructural to TBA[AuCl4], and its structure was first investigated by Johnson and coworkers in 1981, but no atomic coordinates were available due to uncertainty in the space group and TBA+ disorder.71
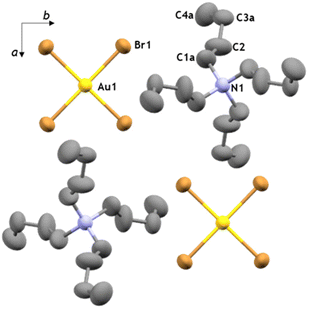 |
| Fig. 3 Thermal ellipsoid representation of the contents of the crystallographic unit cell of TBA[AuBr4], viewed down the crystallographic c-axis, with hydrogen atoms and the disorder affecting the n-butyl chains omitted for clarity. | |
With the TBA[AuCl4] and TBA[AuBr4] salts in hand, we further explored their mechanochemical reactivity. Previous reports indicated that such Au(III) salts could be selectively reduced to Au(I) analogues, allowing the preparation of air- and moisture-resistant Au(I) materials TBA[AuCl2] and TBA[AuBr2]. Specifically, Buckley et al. reported the reduction of TBA[AuCl4] to TBA[AuCl2] using sodium acetylacetonate (NaAcac) in a warm mixture of acetone and EtOH.69 Inspired by this work, we investigated the mechanochemical reduction of freshly prepared TBA[AuX4] salts by adding 1.1 equivalents of anhydrous NaAcac72 directly to the crude reaction mixture, followed by additional 30 minutes milling. The resulting two-step, one-pot mechanochemical procedure starting from metallic gold yielded pale yellow and orange-white solids for reactions containing TBACl and TBABr, respectively (Fig. 4a).
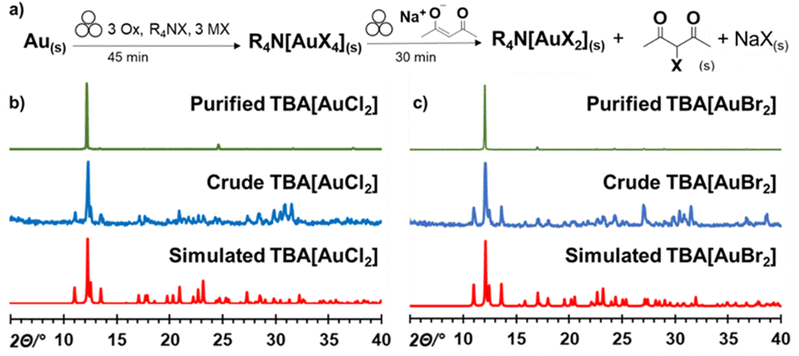 |
| Fig. 4 (a) Reaction scheme for the one pot, two-step mechanochemical preparation of Au(I) salts from gold metal through a Au(III) salt reduced with sodium acetylacetonate. Comparison of PXRD patterns for TBA[AuX2] after recrystallisation, the crude mechanochemical reaction mixture, and simulated for the corresponding crystal structures for: (b) X = Cl and (c) X = Br. The notably needle-like shape of crystals indicates that the relative intensities of X-ray reflections are affected by preferred orientation effects. | |
The PXRD patterns for the crude mechanochemical reaction mixtures (Fig. 4b and c) were a perfect match with those calculated for the TBA[AuCl2] and TBA[AuBr2] crystal structures.73 Moreover, extraction of the crude reaction mixture with CDCl3 confirmed the formation of the 3-halo-acetylacetone byproduct by 1H-NMR (Fig. 4a and ESI Fig. S13†). The TBA[AuX2] salts were isolated by extraction of the reaction mixture with EtOH/acetone, followed by recrystallisation from EtOH, resulting in yield of 75 ± 4% and 80 ± 3% for TBA[AuCl2] and TBA[AuBr2], respectively.69 Analysis of the crude milled reaction mixture by XPS also confirmed presence of Au+ in both cases (ESI, Fig. S21 and S22†).
Next, we targeted the mechanosynthesis of a gold(III) salt that is well known in AuNP synthesis, but is rarely isolated: cetyltrimethylammonium tetrabromoaurate.74,75 The required halide source, cetyltrimethylammonium bromide (CTABr) is a cationic surfactant frequently encountered in antiseptic formulations, and extensively used in the syntheses of Au nanomaterials.76–80 The CTA[AuX4] salts have been previously noted as in situ formed precursors in AuNP synthesis upon combining an aqueous HAuCl4 solution with a saturated solution of CTABr in toluene. Ball-milling of gold, Oxone and CTABr readily afforded the target salt CTA[AuBr4] as a crystalline, bench-stable solid, with a conversion of 93 ± 2% after 30 minutes. High-quality single crystals of the salt were obtained by overnight recrystallisation from EtOAc and structural analysis revealed staggered chains of [AuBr4]− anions with short Br⋯Br contacts (3.4 Å) and layers of CTA+ with alternating hexadecyl chains (Fig. 5, also ESI†).
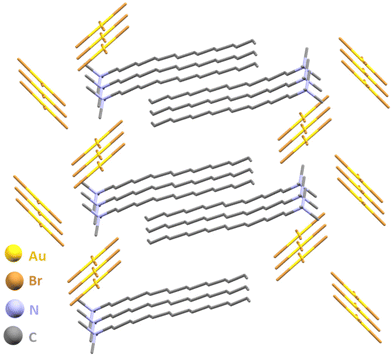 |
| Fig. 5 Fragment of the crystal structure of CTA[AuBr4], viewed along the crystallographic a-axis. | |
The direct mechanosynthesis of CTA[AuBr4] enabled a simple two-step process to convert bulk metal into CTA-stabilised AuNPs using a protocol that, in contrast to the previously reported ones which assume complete phase transfer of reagents between water and toluene, enables the use of a precise amount of gold precursor.75 Specifically, dropwise addition of aqueous NaBH4 (10 mM) to a freshly prepared toluene solution of CTABr and mechanochemically prepared CTA[AuBr4] (1.75 mM CTABr, 0.25 mM CTA[AuBr4] in 10 mL) under vigorous stirring lead to an immediate color change from red/orange to a pale yellow, followed by a progressive change to ruby red/purple, the color remaining unchanged for hours if left unattended. Comparison of the absorption profile of the initial CTA[AuBr4] solution in toluene and the final purple phase confirmed the formation of AuNPs characterised by the plasmonic band around 530 nm (Fig. 6). Dynamic light scattering (DLS) confirmed the formation of nanoparticles with an average diameter of 12 ± 2 nm (Fig. S28†).
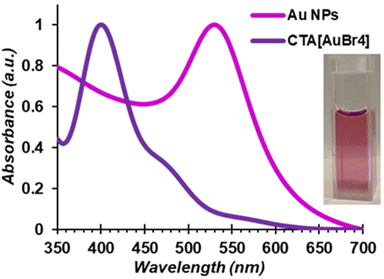 |
| Fig. 6 Normalised absorption spectra of a CTA[AuBr4] solution and of a solution of AuNPs obtained after addition of NaBH4, recorded in toluene. | |
Conclusions
In summary, we reported a straightforward, rapid, and safe conversion of elemental gold into well-defined organosoluble Au(III) salts by using tetraalkylammonium halide salts as precursors. This enabled simple isolation of the organosoluble gold derivatives from water-soluble sulfate byproducts, without relying on additional reagents and strategies that might complicate processing or purification of the desired gold-based products and associated wastestreams. This strategy eliminates the risks associated with other ways of dissolving gold in organic media, such as handling pure halogens in organic solvents, while enabling reactions taking place at room temperature over a short period of time.33 Control experiments (see ESI†) indicate that the mechanochemical halogenation of gold requires the use of ball milling, and proceeds hardly or not at all in aqueous suspension or by simple stirring. Further based on this straightforward methodology, we also introduce a promising two-step, one-pot mechanochemical methodology for the preparation of air- and moisture-stable Au(I) salts through the selective reduction of the freshly prepared Au(III) species using sodium acetylacetonate as a mild reducing agent. Finally, the use of CTABr as the bromide source in mechanochemical oxidation of gold enabled a simple, two-step procedure to transform bulk gold into AuNPs.
Overall, the work reported herein complements the widespread efforts dedicated to the synthesis and use of gold-based functional materials under mechanochemical conditions81–87 and opens the door for further development of safer and cleaner processes needed for the circular use of gold.88,89
Author contributions
Jean-Louis Do: conceptualisation, investigation, visualisation, formal analysis, writing – original draft; Thomas Auvray: conceptualisation, investigation, visualisation, formal analysis, writing – original draft; Cameron B. Lennox: investigation, formal analysis, visualisation; Hatem M. Titi: investigation, formal analysis, visualisation; Louis A. Cuccia: resources, supervision; Tomislav Friščić: conceptualisation, writing – review & editing, resources, supervision. Jean-Louis Do and Thomas Auvray contributed equally.
Conflicts of interest
There are no conflicts to declare.
Acknowledgements
We thank the support of Natural Sciences and Engineering Research Council of Canada (NSERC) Discovery Grant (RGPIN-2017-06467); John C. Polanyi Award (JCP 562908-2022); Discovery Accelerator (RGPAS 507837-17); PGS-D (to J. L. D.) and CGS-D (to C. B. L.) Scholarships. We thank the Government of Canada for Tier-1 Canada Research Chair Program (T. F.) and the Fonds de recherche du Québec – Nature et technologies (FRQNT) for a postdoctoral fellowship (T. A.). We acknowledge support of the Leverhulme Trust (Leverhulme International Professorship, LIP-2021-011) and the University of Birmingham. We thank Dr A. S. Wahba for help with MS data, Dr V. Toader for help with DLS analysis, and Dr B. G. Fiss for discussions.
References
-
G. Gunn, Critical Metals Handbook, John Wiley & Sons, Ltd, 2014 Search PubMed.
- T. E. Graedel, B. K. Reck and A. Miatto, Alloy information helps prioritize material criticality lists, Nat. Commun., 2022, 13, 150 CrossRef CAS PubMed.
-
H. Renner, G. Schlamp, D. Hollmann, H. M. Lüschow, P. Tews, J. Rothaut, K. Dermann, A. Knödler, C. Hecht, M. Schlott, R. Drieselmann, C. Peter and R. Schiele, Ullmann's Encyclopedia of Industrial Chemistry, 2000, pp. 93–143. DOI:10.1002/14356007.a12_499.
- A. S. Hashmi, Gold-catalyzed organic reactions, Chem. Rev., 2007, 107, 3180–3211 CrossRef CAS PubMed.
- P. Schwerdtfeger, Relativistic effects in properties of gold, Heteroat. Chem., 2002, 13, 578–584 CrossRef CAS.
- H. Schmidbaur and A. Schier, Aurophilic interactions as a subject of current research: an up-date, Chem. Soc. Rev., 2012, 41, 370–412 RSC.
- A.-V. Mudring, J. Nuss, U. Wedig and M. Jansen, Mixed Valent Gold Oxides: Syntheses, Structures, and Properties of Rb5Au3O2, Rb7Au5O2, and Cs7Au5O2, J. Solid State Chem., 2000, 155, 29–36 CrossRef CAS.
- A. Provino, S. Steinberg, V. Smetana, U. Paramanik, P. Manfrinetti, S. K. Dhar and A.-V. Mudring, Gold in the Layered Structures of R3Au7Sn3: From Relativity to Versatility, Cryst. Growth Des., 2016, 16, 5657–5668 CrossRef CAS.
- E. C. Dreaden, A. M. Alkilany, X. Huang, C. J. Murphy and M. A. El-Sayed, The golden age: gold nanoparticles for biomedicine, Chem. Soc. Rev., 2012, 41, 2740–2779 RSC.
-
R. Eisler and S. N. Wiemeyer, in Reviews of Environmental Contamination and Toxicology, ed. G. W. Ware, Springer New York, New York, NY, 2004, pp. 21–54. DOI:10.1007/978-1-4419-9100-3_2.
- A. C. Gonzalez-Valoys, J. Arrocha, T. Monteza-Destro, M. Vargas-Lombardo, J. M. Esbri, E. Garcia-Ordiales, R. Jimenez-Ballesta, F. J. Garcia-Navarro and P. Higueras, Environmental challenges related to cyanidation in Central American gold mining; the Remance mine (Panama), J. Environ. Manage., 2022, 302, 113979 CrossRef CAS PubMed.
- L. A. C. Teixeira, J. P. M. Andia, L. Yokoyama, F. V. da Fonseca Araújo and C. M. Sarmiento, Oxidation of cyanide in effluents by Caro's Acid, Miner. Eng., 2013, 45, 81–87 CrossRef CAS.
- L. J. Esdaile and J. M. Chalker, The Mercury Problem in Artisanal and Small-Scale Gold Mining, Chem. – Eur. J., 2018, 24, 6905–6916 CrossRef CAS PubMed.
- R. Eisler and S. N. Wiemeyer, Cyanide hazards to plants and animals from gold mining and related water issues, Rev. Environ. Contam. Toxicol., 2004, 183, 21–54 CAS.
- J. R. Gerson, N. Szponar, A. A. Zambrano, B. Bergquist, E. Broadbent, C. T. Driscoll, G. Erkenswick, D. C. Evers, L. E. Fernandez, H. Hsu-Kim, G. Inga, K. N. Lansdale, M. J. Marchese, A. Martinez, C. Moore, W. K. Pan, R. P. Purizaca, V. Sanchez, M. Silman, E. A. Ury, C. Vega, M. Watsa and E. S. Bernhardt, Amazon forests capture high levels of atmospheric mercury pollution from artisanal gold mining, Nat. Commun., 2022, 13, 559 CrossRef CAS PubMed.
- W. Cornwall, Illegal gold mines flood Amazon forests with toxic mercury, Science, 2022 DOI:10.1126/science.ada0701.
-
A. Bland, The Environmental Disaster That is the Gold Industry, Smithsonian Magazine, 2014, https://www.smithsonianmag.com/science-nature/environmental-disaster-gold-industry-180949762/ Search PubMed.
-
United Nations, Office on Drugs and Crime, Illegal mining and trafficking in precious metals, https://www.unodc.org/unodc/en/environment-climate/illegal-mining.html, (accessed September 2022).
-
B. P. Block, S. A. Bartkiewicz, T. Moeller, J. D. Chrisp, P. Gentile and L. O. Morgan, Inorg. Synth, 1953, vol. 4, pp. 14–17 Search PubMed.
- M. O. Fashola, V. M. Ngole-Jeme and O. O. Babalola, Heavy Metal Pollution from Gold Mines: Environmental Effects and Bacterial Strategies for Resistance, Int. J. Environ. Res. Public Health, 2016, 13, 1147 CrossRef PubMed.
-
J. Gerson, Gold Mining Is Poisoning Amazon Forests with Mercury, Scientific American, 2022, https://www.scientificamerican.com/article/gold-mining-is-poisoning-amazon-forests-with-mercury/ Search PubMed.
- M. Gökelma, A. Birich, S. Stopic and B. Friedrich, A Review on Alternative Gold Recovery Re-agents to Cyanide, J. Mater. Sci. Chem. Eng., 2016, 04, 8–17 Search PubMed.
- T. Ouchi, S. Wu and T. H. Okabe, Recycling of Gold Using Anodic Electrochemical Deposition from Molten Salt Electrolyte, J. Electrochem. Soc., 2020, 167, 123501 CrossRef CAS.
-
A. F. Jalbout, A. Godinez, D. F. Gervasio and H. H. Elsentriecy, US PatentUS2016068928A1, 2016 Search PubMed.
- S. Boudesocque, A. Mohamadou and L. Dupont, Efficient extraction of gold from water by liquid–liquid extraction or precipitation using hydrophobic ionic liquids, New J. Chem., 2014, 38, 5573–5581 RSC.
- L. M. M. Kinsman, B. T. Ngwenya, C. A. Morrison and J. B. Love, Tuneable separation of gold by selective precipitation using a simple and recyclable diamide, Nat. Commun., 2021, 12, 6258 CrossRef CAS PubMed.
- D. T. Sun, N. Gasilova, S. Yang, E. Oveisi and W. L. Queen, Rapid, Selective Extraction of Trace Amounts of Gold from Complex Water Mixtures with a Metal-Organic Framework (MOF)/Polymer Composite, J. Am. Chem. Soc., 2018, 140, 16697–16703 CrossRef CAS.
- A. Serpe, L. Pilia, D. Balestri, L. Marchio and P. Deplano, Characterization and Structural Insights of the Reaction Products by Direct Leaching of the Noble Metals Au, Pd and Cu with N,N’-Dimethyl-piperazine-2,3-dithione/I2 Mixtures, Molecules, 2021, 26, 4721 CrossRef CAS PubMed.
- Z. Liu, M. Frasconi, J. Lei, Z. J. Brown, Z. Zhu, D. Cao, J. Iehl, G. Liu, A. C. Fahrenbach, Y. Y. Botros, O. K. Farha, J. T. Hupp, C. A. Mirkin and J. F. Stoddart, Selective isolation of gold facilitated by second-sphere coordination with alpha-cyclodextrin, Nat. Commun., 2013, 4, 1855 CrossRef PubMed.
- W. Liu, A. G. Oliver and B. D. Smith, Macrocyclic Receptor for Precious Gold, Platinum, or Palladium Coordination Complexes, J. Am. Chem. Soc., 2018, 140, 6810–6813 CrossRef CAS PubMed.
- E. Lahtinen, M. M. Hänninen, K. Kinnunen, H. M. Tuononen, A. Väisänen, K. Rissanen and M. Haukka, Porous 3D Printed Scavenger Filters for Selective Recovery of Precious Metals from Electronic Waste, Adv. Sustainable Syst., 2018, 2, 1800048 CrossRef.
- E. Heliovaara, H. Liljeqvist, M. Muuronen, A. Eronen, K. Moslova and T. Repo, Cooperative Ligands in Dissolution of Gold, Chem. – Eur. J., 2021, 27, 8668–8672 CrossRef CAS PubMed.
- X. Li and K. Binnemans, Oxidative Dissolution of Metals in Organic Solvents, Chem. Rev., 2021, 121, 4506–4530 CrossRef CAS PubMed.
- A. Zupanc, E. Heliovaara, K. Moslova, A. Eronen, M. Kemell, C. Podlipnik, M. Jereb and T. Repo, Iodine-Catalysed Dissolution of Elemental Gold in Ethanol, Angew. Chem., Int. Ed., 2022, 61, e202117587 CAS.
- S. Raiguel, L. Gijsemans, A. Van den
Bossche, B. Onghena and K. Binnemans, Solvent Extraction of Gold(III) with Diethyl Carbonate, ACS Sustainable Chem. Eng., 2020, 8, 13713–13723 CrossRef CAS.
- J. J. M. Nelson and E. J. Schelter, Sustainable Inorganic Chemistry: Metal Separations for Recycling, Inorg. Chem., 2019, 58, 979–990 CrossRef CAS PubMed.
- A. K. Awasthi, J. Li, L. Koh and O. A. Ogunseitan, Circular economy and electronic waste, Nat. Electron., 2019, 2, 86–89 CrossRef.
- R. G. Eggert, Minerals go critical, Nat. Chem., 2011, 3, 688–691 CrossRef CAS PubMed.
- B. K. Reck and T. E. Graedel, Challenges in metal recycling, Science, 2012, 337, 690–695 CrossRef CAS PubMed.
- M. Bae, J.-C. Lee, H. Lee and S. Kim, Recovery of nitric acid and gold from gold-bearing aqua regia by tributyl-phosphate, Sep. Purif. Technol., 2020, 235, 116154 CrossRef CAS.
- W. Lin, R. W. Zhang, S. S. Jang, C. P. Wong and J. I. Hong, “Organic aqua regia”–powerful liquids for dissolving noble metals, Angew. Chem., Int. Ed., 2010, 49, 7929–7932 CrossRef CAS PubMed.
- H. Mahandra, F. Faraji and A. Ghahreman, Novel Extraction Process for Gold Recovery from Thiosulfate Solution Using Phosphonium Ionic Liquids, ACS Sustainable Chem. Eng., 2021, 9, 8179–8185 CrossRef CAS.
- G. R. T. Jenkin, D. J. Smith, A. P. Abbott, A. Z. M. Al-Bassam, D. A. Holwell and R. C. Harris, Gold and by-product recovery of critical elements from gold ores using deep eutectic solvent ionic liquids: BRIO, Appl. Earth Sci., 2016, 125, 86–87 CrossRef CAS.
- Y. Geng, Z. Xiang, C. Lv, N. Wang, Y. Wang and Y. Yang, Recovery of gold from hydrochloric medium by deep eutectic solvents based on quaternary ammonium salts, Hydrometallurgy, 2019, 188, 264–271 CrossRef CAS.
- P. Cen, K. Spahiu, M. S. Tyumentsev and M. Foreman, Metal extraction from a deep eutectic solvent, an insight into activities, Phys. Chem. Chem. Phys., 2020, 22, 11012–11024 RSC.
- J. A. Whitehead, G. A. Lawrance and A. McCluskey, ‘Green’ leaching: recyclable and selective leaching of gold-bearing ore in an ionic liquid, Green Chem., 2004, 6, 313–315 RSC.
- S. Boudesocque, A. Mohamadou, A. Conreux, B. Marin and L. Dupont, The recovery and selective extraction of gold and platinum by novel ionic liquids, Sep. Purif. Technol., 2019, 210, 824–834 CrossRef CAS.
- S. Katsuta, Y. Watanabe, Y. Araki and Y. Kudo, Extraction of Gold(III) from Hydrochloric Acid into Various Ionic Liquids: Relationship between Extraction Efficiency and Aqueous Solubility of Ionic Liquids, ACS Sustainable Chem. Eng., 2015, 4, 564–571 CrossRef.
- N. Papaiconomou, G. Vite, N. Goujon, J.-M. Lévêque and I. Billard, Efficient removal of gold complexes from water by precipitation or liquid–liquid extraction using ionic liquids, Green Chem., 2012, 14, 2050–2056 RSC.
- R. Corbo, G. F. Ryan, M. A. Haghighatbin, C. F. Hogan, D. J. Wilson, M. D. Hulett, P. J. Barnard and J. L. Dutton, Access to the Parent Tetrakis(pyridine)gold(III) Trication, Facile Formation of Rare Au(III) Terminal Hydroxides, and Preliminary Studies of Biological Properties, Inorg. Chem., 2016, 55, 2830–2839 CrossRef CAS PubMed.
- M. Albayer, R. Corbo, A. F. Hill and J. L. Dutton, A simple halide and silver-free synthesis of Echavarren's catalyst directly from gold powder, Dalton Trans., 2018, 47, 1321–1324 RSC.
- T. Friščić, C. Mottillo and H. M. Titi, Mechanochemistry for Synthesis, Angew. Chem., Int. Ed., 2020, 59, 1018–1029 CrossRef.
- D. Braga, S. L. Giaffreda, F. Grepioni, A. Pettersen, L. Maini, M. Curzi and M. Polito, Mechanochemical preparation of molecular and supramolecular organometallic materials and coordination networks, Dalton Trans., 2006, 10, 1249–1263 RSC.
- P. Baláž, M. Achimovičová, M. Baláž, P. Billik, Z. Cherkezova-Zheleva, J. M. Criado, F. Delogu, E. Dutkova, E. Gaffet, F. J. Gotor, R. Kumar, I. Mitov, T. Rojac, M. Senna, A. Streletskii and K. Wieczorek-Ciurowa, Hallmarks of mechanochemistry: from nanoparticles to technology, Chem. Soc. Rev., 2013, 42, 7571–7637 RSC.
- E. Boldyreva, Mechanochemistry of inorganic and organic systems: what is similar, what is different?, Chem. Soc. Rev., 2013, 42, 7719–7738 RSC.
- C. Bolm and J. G. Hernández, Mechanochemistry of Gaseous Reactants, Angew. Chem., Int. Ed., 2019, 58, 3285–3299 CrossRef CAS PubMed.
- D. Tan and F. García, Main group mechanochemistry: from curiosity to established protocols, Chem. Soc. Rev., 2019, 48, 2274–2292 RSC.
- A. Porcheddu, E. Colacino, L. De Luca and F. Delogu, Metal-Mediated and Metal-Catalyzed Reactions Under Mechanochemical Conditions, ACS Catal., 2020, 10, 8344–8394 CrossRef CAS.
- V. Martinez, T. Stolar, B. Karadeniz, I. Brekalo and K. Užarević, Advancing mechanochemical synthesis by combining milling with different energy sources, Nat. Rev. Chem., 2022, 7, 51–65 CrossRef PubMed.
- A. A. L. Michalchuk and F. Emmerling, Time-Resolved In Situ Monitoring of Mechanochemical Reactions, Angew. Chem., Int. Ed., 2022, 61, e202117270 CrossRef CAS PubMed.
- T. Auvray and T. Friščić, Shaking Things from the Ground-Up: A Systematic Overview of the Mechanochemistry of Hard and High-Melting Inorganic Materials, Molecules, 2023, 28, 897 CrossRef CAS PubMed.
- J. L. Do, D. Tan and T. Friščić, Oxidative Mechanochemistry: Direct, Room-Temperature, Solvent-Free Conversion of Palladium and Gold Metals into Soluble Salts and Coordination Complexes, Angew. Chem., Int. Ed., 2018, 57, 2667–2671 CrossRef CAS PubMed.
- N. R. Rightmire and T. P. Hanusa, Advances in organometallic synthesis with mechanochemical methods, Dalton Trans., 2016, 45, 2352–2362 RSC.
- F. E. Beamish, J. J. Russell and J. Seath, The Determination of Gold, Ind. Eng. Chem., Anal. Ed., 2002, 9, 174–176 Search PubMed.
-
N. S. R. D. N., NIST X-ray Photoelectron Spectroscopy Database, National Institute of Standards and Technology, Gaithersburg MD, 20899, 2000, retrieved January-April 2022, DOI:10.18434/T4T88K.
- F. P. Byrne, S. Jin, G. Paggiola, T. H. M. Petchey, J. H. Clark, T. J. Farmer, A. J. Hunt, C. R. McElroy and J. Sherwood, Tools and techniques for solvent selection: green solvent selection guides, Sustainable Chem. Processes, 2016, 4, 1–24 CrossRef.
- A. K. Gangopadhayay and A. Chakravorty, Charge Transfer Spectra of some Gold(III) Complexes, J. Chem. Phys., 1961, 35, 2206–2209 CrossRef.
-
A. B. Charette, R. Chinchilla and C. Nájera, in Encyclopedia of Reagents for Organic Synthesis, 2007, DOI:10.1002/047084289X.rt011.pub2.
- R. W. Buckley, P. C. Healy and W. A. Loughlin, Reduction of [NBu4][AuCl4] to [NBu4][AuCl2] with Sodium Acetylacetonate, Aust. J. Chem., 1997, 50, 775–778 CrossRef CAS.
- C. J. Serpell, J. Cookson, D. Ozkaya and P. D. Beer, Core@shell bimetallic nanoparticle synthesis via anion coordination, Nat. Chem., 2011, 3, 478–483 CrossRef CAS PubMed.
- J. P. Johnson, H. B. Krause and E. G. Sherry, The crystal structure of tetra-n-butylammonium tetrabromoaurate(III), Acta Cryst. A, 1981, 37, C227 Search PubMed.
- R. G. Charles, Tetraacetylethane, Org. Synth., 1959, 39, 61 CrossRef CAS.
- P. Braunstein, A. Mueller and H. Boegge, Crystal structures of the tetra-n-butylammonium salts of the dichloroaurate(1-), dibromoaurate(1-), and diiodoaurate(1-) ions, Inorg. Chem., 1986, 25, 2104–2106 CrossRef CAS.
- J. Wan, J. H. Wang, T. Liu, Z. Xie, X. F. Yu and W. Li, Surface chemistry but not aspect ratio mediates the biological toxicity of gold nanorods in vitro and in vivo, Sci. Rep., 2015, 5, 11398 CrossRef CAS PubMed.
- W. Cheng, S. Dong and E. Wang, Synthesis and Self-Assembly of Cetyltrimethylammonium Bromide-Capped Gold Nanoparticles, Langmuir, 2003, 19, 9434–9439 CrossRef CAS.
- C. M. Aguirre, T. R. Kaspar, C. Radloff and N. J. Halas, CTAB Mediated Reshaping of Metallodielectric Nanoparticles, Nano Lett., 2003, 3, 1707–1711 CrossRef CAS.
- Q. Wang, Z. Wang, Z. Li, J. Xiao, H. Shan, Z. Fang and L. Qi, Controlled growth and shape-directed self-assembly of gold nanoarrows, Sci. Adv., 2017, 3, e1701183 CrossRef PubMed.
- D. K. Smith and B. A. Korgel, The importance of the CTAB surfactant on the colloidal seed-mediated synthesis of gold nanorods, Langmuir, 2008, 24, 644–649 CrossRef CAS PubMed.
- H.-Y. Wu, H.-C. Chu, T.-J. Kuo, C.-L. Kuo and M. H. Huang, Seed-Mediated Synthesis of High Aspect Ratio Gold Nanorods with Nitric Acid, Chem. Mater., 2005, 17, 6447–6451 CrossRef CAS.
- T. K. Sau and C. J. Murphy, Seeded high yield synthesis of short Au nanorods in aqueous solution, Langmuir, 2004, 20, 6414–6420 CrossRef CAS PubMed.
- C. Jobbagy, M. Molnar, P. Baranyai and A. Deak, Mechanochemical synthesis of crystalline and amorphous digold(I) helicates exhibiting anion- and phase-switchable luminescence properties, Dalton Trans., 2014, 43, 11807–11810 RSC.
- A. Beillard, X. Bantreil, T.-X. Métro, J. Martinez and F. Lamaty, Mechanochemistry for facilitated access to N,N-diaryl NHC metal complexes, New J. Chem., 2017, 41, 1057–1063 RSC.
- F. J. L. Ingner, Z. X. Giustra, S. Novosedlik, A. Orthaber, P. J. Gates, C. Dyrager and L. T. Pilarski, Mechanochemical synthesis of (hetero)aryl Au(I) complexes, Green Chem., 2020, 22, 5648–5655 RSC.
- D. Eppel, A. Eryigit, M. Rudolph, M. Bruckner, F. Rominger, A. M. Asiri and A. S. K. Hashmi, Mechanochemical Gold(III)-Carbon Bond Formation, Angew. Chem., Int. Ed., 2021, 60, 13636–13640 CrossRef CAS PubMed.
- M. J. Rak, N. K. Saadé, T. Friščić and A. Moores, Mechanosynthesis of ultra-small monodisperse amine-stabilized gold nanoparticles with controllable size, Green Chem., 2014, 16, 86–89 RSC.
- L. Yang, A. Moores, T. Friščić and N. Provatas, Thermodynamics Model for Mechanochemical Synthesis of Gold Nanoparticles: Implications for Solvent-Free Nanoparticle Production, ACS Appl. Nano Mater., 2021, 4, 1886–1897 CrossRef CAS.
- P. F. M. de Oliveira, A. A. L. Michalchuk, J. Marquardt, T. Feiler, C. Prinz, R. M. Torresi, P. H. C. Camargo and F. Emmerling, Investigating the role of reducing agents on mechanosynthesis of Au nanoparticles, CrystEngComm, 2020, 22, 6261–6267 RSC.
- Y. He and Z. Xu, Recycling gold and copper from waste printed circuit boards using chlorination process, RSC Adv., 2015, 5, 8957–8964 RSC.
- J. Ficeriová and P. Baláž, Leaching of gold from a mechanically and mechanochemically activated waste, Acta Montan. Slovaca, 2010, 15, 183–187 Search PubMed.
Footnotes |
† Electronic supplementary information (ESI) available: Material and methods, 1H NMR, ESI HR-MS, and FT-IR data, as well as details of X-ray diffraction analysis, PXRD and XPS data. CCDC 2224725 and 2224727–2224730. For ESI and crystallographic data in CIF or other electronic format see DOI: https://doi.org/10.1039/d3gc01150j |
‡ These authors contributed equally to this work. |
|
This journal is © The Royal Society of Chemistry 2023 |
Click here to see how this site uses Cookies. View our privacy policy here.