DOI:
10.1039/D3GC00859B
(Paper)
Green Chem., 2023,
25, 4350-4361
Environmental, cost, and chemical hazards of using alternative green solvents for fullerene (C60) purification†
Received
14th March 2023
, Accepted 9th May 2023
First published on 11th May 2023
Abstract
C60 is a nanomaterial produced from the pyrolysis of hydrocarbons that needs to be extracted and purified to obtain the desired properties. Previous studies reported purification as the environmental hotspot of the C60 production process. However, no study has evaluated existing C60 purification methods and proposed alternatives based on environmental, cost, and chemical hazards. Here we used life cycle assessment (LCA) and evaluated the most common existing C60 purification methods (chromatography-crystallization, crystallization, & complexation) and identified selective complexation with 1,8-diazabicyclo[5.4.0]undec-7-ene (DBU) as the greenest existing C60 purification technique that has less environmental (70% from chromatography-crystallization & 50% from crystallization), cost (70% from chromatography-crystallization & 80% from crystallization), and chemical (30% from chromatography-crystallization & crystallization) hazards. The solvent (1,2,4-trymethylbenzene (TMB)) was identified as the environmental hotspot contributing to more than 95% of the cumulative energy demand (CED) of the complexation process. We employed green chemistry principles and an iterative approach to assess the performance of potential replacements (linseed oil, olive oil, toluene, & xylene) for TMB. Although we evaluated solvents that are expected to be greener than petroleum-based solvents, we determined toluene as the greenest alternative. Compared to the baseline complexation method, using toluene reduced the environmental impact by 59%, cost by 85%, and chemical hazards by 42%. Identifying toluene as the alternative green solvent for C60 purification can reduce the carbon footprint of C60-containing products used for various emerging applications, such as solar cells, hydrogen storage, biofuels, etc., which aligns with current decarbonization strategies.
 Seyed M. Heidari | Dr Seyed Mohammadreza Heidari is a Postdoctoral Research Fellow at the University of Michigan working on Circular Material Economy. He received his Ph.D. in Environmental Engineering under the supervision of Professor Annick Anctil at Michigan State University, where they conducted this study. Contact email: seyedmheidari[at]gmail.com. |
 Eunsang Lee | Dr Eunsang Lee is an environmental scientist focusing on life cycle assessment (LCA), sustainability, and corporate carbon management. After completing his Ph.D. dissertation in 2018 under the supervision of Dr Annick Anctil at Michigan State University, he joined the Institute for Environmental Science and Policy at the University of Illinois at Chicago, where he worked as a post-doctoral research associate. His Ph.D. work was centered on assessing organic photovoltaic materials by utilization of LCA and green chemistry, and his current research interests range from sustainable semiconductor technologies to corporate carbon management. |
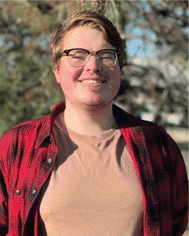 Ben Cecil | Benjamin J. Cecil received his BSc. in Chemistry at Northern Kentucky University and performed graduate work in Sustainability at Michigan State University. He now works as a Project Scientist at Nitto Avecia supporting the development and manufacture of Oligonucleotides used to treat a variety of diseases through genetic medicine platforms. |
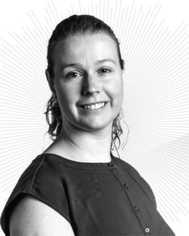 Annick Anctil | Dr Annick Anctil is an Associate Professor in Civil and Environmental Engineering at Michigan State University, where she leads research on Sustainable Energy Systems. She holds a BE and MS in Materials Engineering and a PhD in Sustainability. She uses proactive sustainability assessment to reduce the environmental impact of new technologies. At MSU, she teaches classes on sustainability and life cycle assessment of energy. |
1. Introduction
Nanomaterials such as C60 require a large volume of solvents and are usually energy intensive to produce.1 C60 is comprised of 60 carbon atoms forming a closed cage carbon molecule, and it has the most stable structure among fullerenes (C60, C70, and C>70).2 C60 has been used in various emerging applications, including solar cells,3 biofuels,4 hydrogen storage,5 drug delivery,6 photodynamic therapy,7 cosmetic products,8 and human supplement.9 The global fullerene market is expected to increase from about 490 million US dollars in 2020 to more than 730 million US dollars by 2027.10,11 C60 is typically synthesized, at an industrial scale, from combusting hydrocarbons at a high temperature and low pressure to produce fullerene-containing soot (Fig. S1 in ESI†).2 During the separation stage, the fullerene mix that contains C60 and higher fullerenes is separated from soot. Finally, purification is necessary to extract C60 from the fullerene mix. In a previous study, our group identified purification as the environmental hotspot of C60 production due to the quantity of hazardous solvents and energy required to produce high-purity material.12
Existing C60 purification methods require a large amount of energy and hazardous solvents. There are various methods to purify C60, and the most commons are chromatography, crystallization, and complexation.13 For chromatography, the difference in chemical affinity of C60, higher fullerenes, and the stationary phase allows the separation of about 50% of C60 with 99% purity from higher fullerenes.14,15 This technique requires a large amount of stationary and mobile phase (e.g., hazardous solvents like hexane), increasing the cost and the risk of hazardous exposure to the environment and workplace.13,16 For crystallization, the different solubility of C60 and higher fullerenes at specific temperatures (e.g., maximum C60 solubility at 110 °C for the C60-containing solution and −16 °C for the C70-containing solution) can yield 67% separation of C60 with 99% purity.17,18 The main drawback of the crystallization method is a large amount of energy necessary to cool down or warm up the solution, which does not follow the “design for energy efficiency” green chemistry principle. A 99% purity cannot be achieved in a single step, so the crystallization process must be repeated.18 For complexation, due to the higher electron affinity of C70 and higher fullerenes compared to C60, a bicyclic amidine, typically 1,8-diazabicyclo[5.4.0]undec-7-ene (DBU), can selectively form a complex with C70 and higher fullerenes sooner than C60, resulting in separating about 76% of C60 with 99% purity.19,20 However, similar to the other purification methods, this process needs a large volume of hazardous solvents, which can increase the cost and the carbon footprint of C60-containing products.
There is a need to evaluate and reduce the environmental, cost, and chemical hazards of C60 purification. The only comparison of C60 purification methods used only purification yield as the indicator of “environment-friendly” process,13 which is a misleading method since (1) there is no environmental evaluation (e.g., global warming potential (GWP), cumulative energy demand (CED), & water demand (WD) impact assessment) reported for purification methods and (2) C60 production rates and solvents’ life-cycle environmental, cost, and chemical hazards are ignored while these are vital to compare purification methods, identify the greenest existing purification method, and determine greener replacements. An alternative method to evaluate chemical process sustainability was previously developed by our group and used to evaluate the existing process and help identify greener synthesis methods.21 The method combines process-based life cycle assessment (LCA) and green chemistry to evaluate the environmental, chemical hazard, and cost impacts of the existing chemical process, and the green chemistry principles are used to identify alternative processes. In this work, we used the same method to evaluate existing C60 purification methods (chromatography-crystallization, crystallization, & complexation) and identified the best initial method to be complexation (baseline). To further reduce the environmental impacts of the process of the baseline method, the iterative approach was repeated until an alternative process was identified that simultaneously reduced the environmental, cost, and chemical hazards compared to the baseline. This study shows the significance of conducting LCA to identify alternative processes, as the perceived “greener” alternatives are not always better. The proposed alternative purification process is cheaper, which can benefit C60 medical and industrial consumers, and has lower environmental impacts (e.g., GWP), which would help industry meet their GHG emission reduction targets.
2. Materials and methods
2.1. Sustainability assessment
The sustainability methodology to evaluate and guide fine chemical synthesis was developed by our group previously.21 The method combines process-based life cycle assessment (LCA) and green chemistry to evaluate the impacts of chemical synthesis and identify concerns in the production process. The functional unit is to purify one kg of C60 with 99% purity. The production process was evaluated on the basis of environmental, chemical, and cost to identify the hotspots. Green chemistry was employed to determine greener replacements for the hotspots. The iterative approach was repeated until an alternative process was identified that simultaneously reduced the environmental, cost, and chemical hazards compared to the baseline. LCA was conducted using SimaPro 9.1.0.722 to quantify the environmental impacts (GWP, CED, WD) of purifying 1 kg of C60 with 99% purity. The environmental evaluation was based on data collected from Ecoinvent 3.3, US-EI from DATA SMART, published articles (Table S2†), and experiments. E-factor, the ratio of waste mass per product mass, was also used for calculating environmental scores (eqn (1)). We considered the most common environmental impacts (GWP & CED); however, this study could be expanded by considering other ecological factors in future work. The cost and chemical hazard evaluation was conducted based on our previous paper.21 In summary, chemical hazard analysis was based on NFPA 704 standard scores, including health, flammability, reactivity, and special hazards23 (eqn (2) and (3)). Cost assessment was based on the production rate of the target substrate and the life cycle cost (LCC) of required raw materials (eqn (4)). These values were normalized using the values of the baseline process, then averaged into a single cost metric value for analysis. | 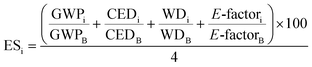 | (1) |
where ESi is the environmental score of purification processes i, and B shows the environmental impacts of the baseline process. |  | (2) |
|  | (3) |
where HSi is the chemical hazard score of the purification process i, n is the number of solvents used in the purification process i, HMj is the chemical hazard of solvent j based on NFPA 704 standard scores, AMj is the volume of solvent j, m is the number of solvents used in the baseline process, HMjB & AMjB are the chemical hazards and the volume of solvents used in the baseline. | 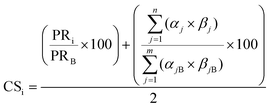 | (4) |
where CSi is the cost score of purification process i, PRi is the production rate for process i, PRB is the baseline production rate, n is the number of primary energy sources used in the process i, αj is the amount of primary energy, βj is the price per unit of primary energy, and B represents values for the baseline process.
2.1.1. Green chemistry principles.
Green chemistry principles are described in Table S1.†24 This study identified alternative solvents with high C60 solubility (to reduce the volume of required solvents – principle #5) and lower toxicity (to reduce the risk of accidental release and avoid toxifying the final products – principles #4 & #12). Plant-based solvents were also considered in this study in accordance with principle #7, which is about using renewable feedstock. We used lethal concentration 50 (LC50 – a concentration that can cause 50% death in an experimental animal population exposed to a toxicant during a predetermined period25) to indicate solvent toxicity and identify potential alternatives for the baseline solvent. LC50 can be calculated from toxicity experiments or estimated using software such as the Toxicity Estimation Software Tool (TEST, V5.1.26 TEST was developed by the U.S. Environmental Protection Agency (EPA) to allow users to estimate the LC50 of some chemicals based on molecular structures. For petroleum-based solvents (e.g., toluene and xylene), we used TEST to calculate LC50, and for plant-based solvents (olive oil and linseed oil), we used LC50 from our previous work.27
2.2. Fullerene C60 purification
2.2.1. Materials.
All chemicals were used as received. Fullerene mix (70% C60, 29% C70, and 1% higher fullerenes) was purchased from SES Research Group (Houston, TX), C60 and C70 with +99% purity from MER (Tuscan, AZ), 1,2,4-trimethylbenzene (TMB) CAS 95636 (+98%), toluene CAS 108883 (ACS reagent, +99.5%), xylenes CAS 1330207 (ACS reagent, +98.5%), linseed oil CAS 8001261 (MQ200), olive oil CAS 8001250 (MQ200, highly refined), hexane CAS 110543 (HPLC grade, +85% n-hexane), 2-propanol CAS 67630 (HPLC grade, 99.9%), 1,8-diazabicyclo[5.4.0]undec-7-ene (DBU) CAS 6674222 (puriss., +99% GC), 2-methyltetrahydrofuran CAS 96479 (+99%), were purchased from Sigma Aldrich Burlington, MA.
2.2.2. Complexation process.
The C60 purification process was based on previous studies.20,28 In summary, the fullerene mix, including C60, C70, and higher fullerenes, was dissolved in five mL of TMB using an ultrasonic bath for five min at room temperature. The complexation process started by adding 103 μl of DBU and four μl of DI water in 10 min while the solution was continuously mixed at a low speed to avoid a vortex. The complexation continued under the nitrogen atmosphere for five hours to let DBU, C70, and higher fullerenes form a solid complex. A 0.2-micron filter was used to separate the complex containing C70 and higher fullerenes from the solution containing C60. The remaining DBU was removed using 0.2 M acetic acid. Isopropanol was used to separate C60 particles from the solution via a 24-hours crystallization process. Finally, C60 particles were collected and dried to remove the residual solvent.
We used the iterative method described in 2.1 to modify the baseline process (Fig. 1). As shown in Fig. 1, the material produced from the baseline process was characterized, and screening was used based on C60 purity and yield and sustainability evaluation of potential alternative procedures with a comparable purity and yield to the baseline. The best alternative purification process was identified based on environmental, cost, and chemical hazards. High-performance liquid chromatography (HPLC-UV) was used to measure C60 purity.29–33 The column was YMC-Pack ODS-A™ (5 μm, 120 Å, 150 × 6 mm I.D.), the mobile phase was hexane/2-propanol (70/30), the flow rate was 0.7 mL min−1, the wavelength was 350 nm (0.08 AUFS), and injection was four μL.34
 |
| Fig. 1 The experimental approach to identify alternative C60 purification methods for the baseline process. | |
3. Results and discussion
3.1. Baseline selection
The first step was to select a baseline among existing methods (chromatography-crystallization,35 crystallization,36 and complexation20) based on the lowest environmental, cost, and chemical hazard scores. Fig. 2A shows the process flow diagram of the complexation and the system boundary used for sustainability assessment. Similar figures are available in the ESI† for chromatography-crystallization and crystallization methods (Fig. S2 and S3†). The environmental score of the complexation was two times lower than crystallization and three times lower than chromatography-crystallization (Fig. 2C). The GWP of the complexation was also six to ten times lower than the two other approaches. The CED to purify one kg of C60 with 99% purity was 7340 MJ for the complexation and increased to 12
900 MJ per kg-C60 for crystallization and 22
500 MJ per kg-C60 for chromatography-crystallization. The higher CED for the crystallization methods is due to the use of the large volume of solvents in the liquid chromatography for pretreatment in the chromatography-crystallization purification method. We observed a similar trend for WD. The WD of complexation was seven times lower than the crystallization and 50 times less than chromatography-crystallization. The chemical hazard scores, which vary from zero to four, were 1.0 for complexation, 1.4 for crystallization, and 1.6 for chromatography-crystallization. The purification rate was seven and 11 times higher for complexation than the other two processes. However, the complexation's Life Cycle Cost (LCC) was between the other two methods. Fig. 2C shows that complexation had the lowest environmental, chemical, and chemical hazard scores. Therefore, we identified the complexation method as the baseline.
 |
| Fig. 2 (A) The LCA system boundary for the complexation process. Grey boxes show input chemicals/energy. (B) The LCA results of existing C60 purification methods. Normalized scores (N.S.) are bold, and favorable numbers for sustainability are in orange. (C) The environmental, cost, and chemical hazards of existing C60 purification methods to determine the baseline (the process with the lowest impacts is given a score of 100%). GWP: Global Warming Potential, CED: Cumulative Energy Demand, WD: Water Demand, LCC: Life Cycle Cost, DBU: 1,8-diazabicyclo[5.4.0]undec-7-ene. | |
3.2. Baseline evaluation
The next step was to identify the environmental hotspots of the baseline. Fig. 3 shows the CED for the complexation process, which includes all processing stages to obtain 99% purity C60. The system boundary and details about the complexation process are shown in Fig. 2A. The solvent, TMB, contributed to more than 95% of the total CED of the baseline purification process since the CED of TMB is high (70 MJ kg−1) and large volume is used. Therefore, TMB was determined as the environmental hotspot, and the following steps focused on identifying alternatives to reduce the environmental burden of C60 purification.
 |
| Fig. 3 Cumulative energy demand (CED) for the purification of one kg C60 with 99% purity (cradle to gate) using complexation with DBU. | |
3.3. Alternative solvents for TMB
After identifying TMB as the environmental hotspot for the baseline, the next step was to explore alternative greener and nontoxic solvents. We used the C60 solubility and toxicity score to identify alternative solvents in accordance with the following green chemistry principles (Table S1† - #3: use substances with no or little toxicity, #4: design safer chemicals with lower environmental toxicity, #5: use less solvents, #7: use renewable feedstocks, and #12: safer substrates for accident prevention). Fig. 4 shows the toxicity scores and the solubility of C60 in various solvents. The purple area identifies solvents with a lower toxicity score than TMB and comparable C60 solubility to TMB. Two groups of solvents were selected as potential replacements: plant-based and petroleum-based solvents. Linseed and olive oil were chosen since they are nontoxic,27 have a higher solubility than TMB, and are extracted from renewable feedstocks. Xylene and toluene were selected because they are also less toxic than TMB and have comparable C60 solubility to TMB. The normalized toxicity score was 0.24 for TMB, 0.17 for xylene, 0.12 for toluene, 0.12 × 10−3 for linseed oil, and 0.38 × 10−4 for olive oil. The normalized solubility score was 0.34 for TMB, 0.18 for xylene, 0.16 for toluene, 1.0 for linseed oil, and 0.44 for olive oil. Fig. 4A presents detailed information on solvent toxicity scores and C60 solubility.
 |
| Fig. 4 (A) Solvent toxicity scores and C60 solubility. (B) The normalized toxicity and C60 solubility score of solvents are used to identify replacements for TMB. The purple area highlights potential alternative solvents. | |
Many green solvents are considered “environment-friendly” based only on the environmental impact of the solvent production stages.37 However, the environmental benefit of green solvents should also consider their performance in a specific application and the impact of recycling or disposal of the solvent. A typical example of a green solvent with varying benefits is water, which requires a large amount of energy if it needs to be removed using evaporation. In this case, linseed oil has a higher solubility and a lower toxicity score than TMB (Fig. 4B), making it a good candidate for medical applications where C60 and linseed oil can behave as drug carriers to treat target cancer cells. But for purification, where the solvent needs to be removed, the high boiling point of linseed oil is a concern. A high boiling point means more energy consumption is necessary for solvent regeneration, which might increase the products’ environmental effects. However, this depends on the overall performance of the target solvent. Therefore, this work considered both the upstream environmental impact of manufacturing the solvent and the use of the solvent for purification and compared it with TMB.
3.4. Fullerene purification
3.4.1. Modified baseline process.
We modified the baseline process before evaluating the performance of potential TMB replacements for C60 purification. This modification was conducted to reduce the environmental impacts of the experimental starting point. The baseline purification yield was about 44%, where a considerable portion of C60 was lost due to the non-efficient filtration method. A centrifuge was used to overcome the issue and improve the yield. Centrifuges might consume more energy than pumps used in the filtration process; however, higher efficiency can save more materials for high-energy intensive materials like C60, consequently reducing the overall energy of the material production. In this modified baseline, the purification yield increased to 76%, resulting in fewer environmental, cost, and chemical hazard impacts. The modified baseline had about 43% less environmental and chemical hazard impacts and was 22% cheaper than the baseline. We conducted more experiments to reduce the modified baseline's environmental, cost, and chemical hazards.
3.4.2. Alternative plant-based solvents (P1 to P6).
After modifying the baseline, we employed potential alternative solvents for C60 purification. Linseed and olive oil were chosen as plant-based replacements for TMB because they are less toxic. This is in harmony with green chemistry principles #3: use substances with no or little toxicity, #4: design safer chemicals with lower environmental toxicity, and #12: safer substrates for accident prevention. Plus, linseed and olive oil have a higher C60 solubility than TMB, favoring green chemistry principle #5: design to use less solvents. Both oils are extracted from renewable feedstocks, following green chemistry principle #7: use renewable feedstocks (see Table S1† for the complete list of green chemistry principles).
The challenge of using linseed and olive oil for C60 purification was identifying a practical approach for dissolving C60. Various methods were evaluated to dissolve fullerenes in linseed oil and olive oil. In P1, fullerene was dissolved in olive oil, stirring for 72 h at room temperature under a nitrogen atmosphere (since C60 reacts with oxygen quickly38), as was suggested by Cataldo et al.39 C60 purification yield was lower than 5% because the fullerene-mix particles were not fully dissolved in olive oil at the beginning of the experiment, and complexation might only occur at the surface. In this situation, C70 and higher fullerenes could not form a solid complex with DBU during the complexation. As mentioned earlier, C60 is highly energy-intensive; therefore, C60 purification yield can tremendously influence the environmental impacts of C60-made products. So, it was necessary to increase the purification yield. In P2, the fullerene mix was added to olive oil at 75 °C. At the same time, the solution was stirred for two hours under a nitrogen atmosphere, as Cataldo et al.40 The purification yield was still lower than 5% since the oil might have been decomposed and reacted with C60 at a high temperature. P3 was based on a suggestion to use a sonication bath for 15 min at 50 °C to dissolve fullerenes in olive oil.41–43 The purification yield increased to 26%, which was much higher than P1 and P2 but still lower than the modified baseline purification yield. In P4, we replaced the sonication bath with an ultrasonic probe to improve the amount of dissolved C60 in olive oil before the complexation. 100 mg of the fullerene mix was dissolved in four mL of olive oil using the ultrasonic probe for three minutes while the container remained in a water bath to keep the temperature close to room temperature. This resulted in a 44% C60 purification yield. Fig. S4† shows the system boundary and process flow of P4.
Similar approaches were used to dissolve C60 in linseed oil. P5 and P6 were to identify the best purification yield for the purification method using linseed oil instead of TMB. In P5, we dissolved 100 mg of the fullerene mix in two mL of linseed oil using an ultrasonic bath for 15 min at 55 °C, as was recommended in the literature.41–43 The purification yield was 36%. P6 was based on using the ultrasonic probe for three minutes at room temperature. The purification yield increased to 61% for P6. Fig. S5† shows the system boundary and process flow of P6. We considered P3 & P4 for olive oil and P5 & P6 for linseed oil life cycle environmental assessments.
3.4.3. Alternative petroleum-based solvents (P7 & P8).
Besides the plant-based solvents (linseed & olive oil), two petroleum-based solvents (toluene and xylene) were among the potential replacements for the baseline solvent (TMB) (Fig. 4B). Toluene and xylene were selected due to their high C60 solubility (in accordance with green chemistry principle #5: design to use less solvents) and low toxicity score compared to TMB (#3: use substances with no or little toxicity, #4: design safer chemicals with lower environmental toxicity, and #12: safer substrates for accident prevention) (Fig. 4). We dissolved 100 mg of the fullerene mix in 7.5 mL of xylene in P7 and eight mL of toluene in P8. The rest of the procedures were similar to the modified baseline. The C60 purification yield was 70% for P7 and 77% for P8. Fig. S6 and S7† illustrate the process flow and the system boundary used for the life cycle environmental evaluation of P7 and P8. Fig. S8–S10† show the HPLC-UV analysis of the baseline and alternative purification processes.
3.5. Environmental, cost, and chemical hazard evaluation of potential replacements
Process-based environmental, cost, and chemical hazard assessments were needed to determine greener replacements. Selected petroleum-based solvents are more toxic than plant-based solvents and have a lower C60 solubility; however, solvent performance in the purification process can significantly affect environmental evaluations. For example, olive oil C60 solubility is higher than TMB C60 solubility, which reduces the amount of solvent needed to dissolve C60 at the beginning of purification. However, more solvent is necessary to separate C60 from C60-containing solution along the process, which can influence the purification process's overall environmental, cost, and chemical hazard burden. Therefore, it was necessary to consider a process-based LCA to quantify the environmental, cost, and chemical hazards of potential purification processes to identify greener alternative solvents.
3.5.1. Environmental impact assessment.
The C60 purification process using toluene (P8) had the lowest environmental impacts (GWP, CED, WD, and E-factor). Table 1 presents the LCA details for the baseline, the modified baseline, and alternative purification methods (P3–8). The modified baseline had about 57% less environmental impact than the baseline because a higher purification yield than the baseline resulted in using less chemicals for producing one kg of C60. C60 purification with olive oil (P3 and P4) had the highest environmental impact score, almost five times higher than the baseline and ten times higher than the modified baseline. Olive oil production requires energy, water, and chemicals, increasing associated environmental impacts. Olive oil is obtained from the fruit of olive trees, which requires irrigation at the growing stage, followed by crushing and pressing stages to produce olive paste before oil extraction,44 increasing energy consumption. Another reason is that a large quantity of solvent (e.g., heptane) is necessary to extract C60 from a C60-containing solution compared to the amount of IPA required in the baseline and the modified baseline, which increase the olive oil C60 purification's environmental burden.
Table 1 Environmental analysis of purification processes – from red to brown, yellow, and green: approaching environmentally benign
Methods |
CED (MJ) |
Normalized CED |
GWP (kg CO2 eq.) |
Normalized GWP |
WD (m3) |
Normalized WD |
E-factor |
Normalized E-factor |
Normalized environmental score |
Baseline |
8950 |
100 |
308 |
100 |
9.0 |
100 |
381 |
100 |
100 |
Modified baseline |
5110 |
57.1 |
176 |
57.1 |
5.0 |
56 |
217 |
57 |
57 |
P3 |
30 100 |
337 |
1790 |
581 |
94 |
1040 |
1090 |
290 |
567 |
P4 |
28 300 |
316 |
1710 |
554 |
88 |
1003 |
816 |
210 |
522 |
P5 |
15 400 |
172 |
823 |
267 |
33 |
370 |
641 |
170 |
244 |
P6 |
6770 |
75.6 |
348 |
113 |
13 |
147 |
325 |
85 |
105 |
P7 |
3180 |
35.5 |
195 |
63.3 |
9.0 |
102 |
46.5 |
12 |
53 |
P8 |
2510 |
28.0 |
151 |
49.0 |
7.0 |
78 |
39.9 |
10.0 |
41 |
C60 purification with linseed oil (P5 and P6) had lower environmental impacts than purification with olive oil but had higher environmental impacts than the modified baseline. Linseed oil C60 solubility is higher than olive oil C60 solubility, decreasing the needed solvent for C60 purification. Also, linseed oil is obtained from flax seed, which consumes less water than olive trees at the growing stages. Plus, there is no need for crushing and pressing flax seeds to obtain linseed oil, as these are necessary for olive oil production. Therefore, less energy and water are needed upstream of linseed oil C60 purification than olive oil C60 purification. Another important reason was that the C60 purification process yield was about 17% higher for linseed oil, influencing the purification environmental impacts. C60 purification with xylene (P7) had lower environmental impacts than purification with olive oil, linseed oil, the baseline, and the modified baseline. C60 purification with toluene (P8) had the lowest environmental impacts compared to the baseline, modified baseline, and other alternative methods. This is because the C60 purification process yield is highest for toluene, and toluene can be regenerated, consuming less chemicals and energy necessary for C60 purification. The environmental impact score of C60 purification with toluene was about 60% less than the baseline and 28% less than the modified baseline.
3.5.2. Cost assessment.
The C60 purification process using toluene (P8) had the lowest cost impact. Tables 2 and S3, S4† show the life cycle cost analysis and the purification rate of the baseline and alternative methods, including P3–8. It was found that the process with the highest cost metric compared to the baseline was the process that used olive oil as the purification solvent. This is due to the high-cost burden of the chemicals necessary for the olive oil process, as the production rate is comparable to that of the baseline and other processes. Due to the high-cost burden associated with using TMB in the baseline process, all studied processes had lower cost metrics than olive oil-based ones. The processes with the lowest comparative cost metric were the xylene and toluene-based, owing to their low cost of production from crude oil sources.
Table 2 Cost metric values and chemical hazard scores of processes
Method |
Cost metric value |
Hazard score for all used chemicals |
Baseline |
100 |
100 |
Modified baseline |
77.8 |
57 |
P3 (alternative using olive oil) |
162 |
190 |
P4 (alternative using olive oil) |
160.0 |
150 |
P5 (alternative using linseed oil) |
97.0 |
74 |
P6 (alternative using linseed oil) |
69.1 |
34 |
P7 (alternative using xylene) |
61.2 |
15 |
P8 (alternative using toluene) |
58.4 |
13 |
3.5.3. Chemical hazard assessment.
Chemical hazard impacts were quantified for potential alternative solvents as well as alternative purification methods. The chemical hazard score of solvents was 1.3 for TMB, 2.0 for toluene and xylene, 0.33 for linseed oil, and 0.67 for olive oil. The chemical hazard score of alternative purification processes was calculated according to the amount of chemicals used in each process. Table 2 shows normalized chemical hazard process scores to the baseline. The modified baseline chemical hazard score was 57. The highest chemical hazard score was 190 for the purification method using olive oil (P3). This is because more chemicals were necessary for C60 purification; therefore, more chemicals were counted for chemical hazard assessment. The chemical hazard score was 34 for the method using linseed oil (P6). It was almost six times lower than the chemical hazard score of P3 since less amount of solvent was required due to the higher C60 solubility of linseed oil. The chemical hazard score was even lower for the alternative methods using petroleum-based solvents mostly because toluene and xylene can be regenerated; therefore, less quantity of solvents contributed to chemical hazard evaluation. The lowest chemical hazard score was 13 for the purification process using toluene instead of TMB. Table S5† presents the detailed calculation of the solvent's chemical hazard scores.
3.6. Overall evaluation
The overall evaluation of C60 purification processes showed that the C60 purification process using toluene had the lowest scores and therefore was identified as a green replacement for C60 purification. Fig. 5 summarizes the environmental, cost, and chemical hazards evaluation of the baseline, the modified baseline, and potential alternative methods (P3–8) for C60 purification. Linseed and olive oil are nontoxic solvents with high C60 solubility extracted from renewable feedstocks, and these are in harmony with green chemistry principles #3, #4, #7, and #12. However, the process-based life cycle analysis showed that the total impacts of C60 purification were lower for toluene than linseed and olive oil. This was due to the large amount of energy, water, and chemicals necessary for producing olive oil and linseed oil. Also, the C60 purification yield was lower for purification methods using olive oil and linseed oil, which increased the amount of chemicals necessary for making one kg of C60. Another reason was that linseed and olive oil have a higher boiling point (570–590 K) compared to toluene (383 K) and xylene (417 K), which increased the energy necessary for solvent regeneration, and all linseed and olive oil were counted in process-based life cycle evaluations. Due to these reasons and overall process-based life cycle evaluations, toluene performed greener than other solvents and was determined as the green replacement for TMB for C60 purification. The purification efficiency for the baseline process (TMB) was 44%, and for the alternative process (Toluene) was 77%. Fig. S8 and S10† show the properties of C60 purified in the baseline process (TMB) and the alternative method (Toluene). Our results highlight the importance of conducting LCA to identify alternative processes, as the perceived “greener” alternatives are not always better.
 |
| Fig. 5 The environmental, cost, and chemical hazard evaluation of (A) the baseline and the modified baseline, (B) P4 (olive oil), (C) P6 (linseed oil), (D) P8 (toluene) for C60 purification. (E) A comparison of the baseline, the modified baseline, and the best alternative process (P8). (F) The details of environmental, cost, and chemical hazards of C60 purification. | |
Identifying solutions to reduce the environmental impacts of chemical production processes and, more importantly, the environmental burden of using chemicals in various applications is essential to address global environmental challenges such as climate change. The Intergovernmental Panel on Climate Change (IPCC) recently pointed out that more ambitious climate action plans are necessary to achieve the expected reduction of GHG emission goals by 2050,45 and many governments have established ambitious goals to address this issue. In the US, one example of a GHG reduction policy is the GHG Emission Reduction Plan by 2030,46 which relies on modifying current processes with high GHG emissions and developing alternatives with less and zero emissions. In this regard, chemicals can play an essential role in maximizing the environmental benefits of these replacements or, on the other side, add a new environmental burden. The GHG emissions of the chemical industry contribute to about 10% of total US manufacturing GHG emissions and have increased by 8% from 2012 to 2021 and reached more than 186 million metric tons of CO2eq.47,48 So, it is vital to carefully investigate the process-based environmental impacts of using chemicals and chemical production to reach the GHG emission reduction goals.
Chemicals can influence the environment upstream and downstream. The upstream impacts can be mainly due to chemical production, such as toluene from petroleum, olive oil from olive trees, etc. The downstream effects are due to, for instance, the use of chemicals in various applications. For example, the toluene performance in the C60 purification process to provide C60 needed for cosmetic products can generate environmental effects due to the co-chemicals necessary for C60 purification. This causes selecting green chemicals (e.g., greener solvents) more complex since, besides the chemical production procedure, the implication of chemicals in target processes can also enormously contribute to the impacts. Plus, each chemical may act and behave differently depending on the purpose of its usage. Therefore, choosing proper tools to determine greener replacements for environmental hotspots (e.g., toxic solvents) based on direct and indirect effects is vital to be more following environmental impact reduction efforts. Employing LCA and green chemistry for chemical decision-making is also emphasized for a better environmental evaluation in another published work.49 As we previously showed21 and further explained in this study, an iterative approach can help with solvent selection since green chemistry researchers can investigate using in-process monitoring to assess essential parameters such as process yields and conduct process-based sustainability evaluation to ensure the alternative “green” alternative does not create unintended environmental, cost and chemical hazards.
4. Conclusion
C60 is a highly energy-intensive material used in many emerging technologies and applications, including perovskite solar cells, hydrogen storage, biofuels, cosmetic products, and human supplement. We aimed to maximize material use efficiency and minimize environmental, cost, and chemical hazards of C60 purification to reduce the environmental burden of C60-containing products. We identified selective complexation with DBU as the greenest existing method to purify C60 with 99% purity. Our further environmental evaluations showed that the baseline solvent (TMB) was the environmental hotspot and contributed to more than 95% of the cumulative energy demand. Therefore, we identified olive oil, linseed oil, xylene, and toluene as potential alternative solvents for TMB as they were less toxic and had a comparable C60 solubility to TMB, which were in accordance with green chemistry principles.
This study showed that the performance of the potential alternative solvents for purifying C60 influenced the green solvent selection procedure. We used an iterative approach to evaluate the replacements’ performance and employed a process-based life cycle assessment to evaluate potential alternative C60 purification process sustainability. Linseed and olive oil are both nontoxic and have a higher C60 solubility than TMB, xylene, and toluene. However, plant-based oil production requires more energy, water, and chemicals than xylene and toluene at the solvent production stage and along the C60 purification process. Furthermore, some solvents require additives and process modifications to perform similarly or better than the baseline solvent. As an example, olive oil is a non-toxic solvent. Still, more heptane is necessary to separate C60 from C60-containing solution compared to what is required in the baseline, which results in a higher environmental, cost, and chemical hazard score.
This study employed green chemistry principles and process-based LCA to determine green solvents for C60 purification, which can reduce the environmental impacts (e.g., GWP, CED, WD, & E-factor) of many products containing C60. This approach can be applied to many other fine chemicals, which are more likely energy-intensive than bulk materials. Evaluating the fundamental physicochemical properties of host–guest interactions in the presence of plant-based oils was not the scope of this study; however, further research might be insightful to assess the overall performance of plant-based oils as potential green solvents in the chemical production industry.
Abbreviations & parameters
CED | Cumulative energy demand |
DBU | 1,8-Diazabicyclo[5.4.0]undec-7-ene |
GHG | Greenhouse gas |
GWP | Global warming potential |
HPLC | High-performance liquid chromatography |
IPA | Isopropyl alcohol |
IPCC | Intergovernmental panel on climate change |
LCA | Life cycle assessment |
LCC | Life cycle cost |
LC50 | Lethal concentration 50 |
NFPA | National fire protection association |
P1 | Process #1 |
Pn | Process #n |
TEST | Toxicity estimation software tool |
TMB | 1,2,4-Trymethylbenzene |
WD | Water demand |
K | Kelvin |
AMj | The volume of solvent j |
AMjB | The volume of solvents used in the baseline |
CSi | The cost score of the purification process i |
ESi | The chemical hazard score of the purification process i |
HSi | The chemical hazard score of the process i |
HMj | The chemical hazard score of solvent j |
HMjB | The chemical hazard of solvents used in the baseline |
PRi | The production rate for process i |
PRB | The baseline production rate |
αj
| The amount of primary energy |
βj
| The price/unit of primary energy |
B | Represents values for the baseline process |
Author contributions
Seyed M. Heidari: conceptualization, formal analysis, investigation, methodology, validation, visualization, writing (original draft, review & editing). Eunsang Lee: conceptualization, formal analysis for existing C60 purification methods, methodology, validation, writing (review & editing). Ben Cecil: formal analysis (LCC of alternative methods), writing (review). Annick Anctil: conceptualization, funding acquisition, resources, supervision, methodology, validation, writing (review & editing).
Conflicts of interest
There are no conflicts to declare.
Acknowledgements
This material is based upon work supported by National Science Foundation under Grant NSF-1511098 and NSF-1801785.
References
- H. C. Kim and V. Fthenakis, Life cycle energy and climate change implications of nanotechnologies: A Critical Review, J. Ind. Ecol., 2013, 528–541 CrossRef CAS.
- H. Takehara, M. Fujiwara, M. Arikawa, M. D. Diener and J. M. Alford, Experimental study of industrial scale fullerene production by combustion synthesis, Carbon, 2005, 43(2), 311–319 CrossRef CAS.
- T. Gatti, E. Menna, M. Meneghetti, M. Maggini, A. Petrozza and F. Lamberti, The Renaissance of fullerenes with perovskite solar cells, Nano Energy, 2017, 41, 84–100 CrossRef CAS.
- A. Y. Pulyalina, A. A. Larkina, M. V. Tataurov, L. V. Vinogradova and G. A. Polotskaya, Hybrid macromolecular stars with fullerene (C60) core included in polyphenyleneisophthalamide membranes for n-butanol dehydration, Fullerenes, Nanotubes Carbon Nanostruct., 2020, 28(1), 54–60 CrossRef CAS.
- J. Joseph, V. S. Sivasankarapillai, S. Nikazar, M. S. Shanawaz, A. Rahdar and H. Lin,
et al., Borophene and Boron Fullerene Materials in Hydrogen Storage: Opportunities and Challenges, ChemSusChem, 2020, 13(15), 3754–3765 CrossRef CAS PubMed.
- M. Kumar and K. Raza, C60-fullerenes as Drug Delivery Carriers for Anticancer Agents: Promises and Hurdles, Pharm. Nanotechnol., 2018, 5(3), 169–179 Search PubMed.
-
S. M. Heidari and M. Golsorkhi, Fullerene (C60) Evaluation for Photodynamic Therapy, NDDTE Conference Proceedings, 2020 Search PubMed.
- H. Zhou, D. Luo, D. Chen, X. Tan, X. Bai and Z. Liu,
et al., Current Advances of Nanocarrier Technology-Based Active Cosmetic Ingredients for Beauty Applications, Clin., Cosmet. Invest. Dermatol., 2021,(14), 867–887 CrossRef PubMed.
- SES Research Group, C60 in Olive oil, https://www.sesres.com/carbon-60-olive-oil/(accessed 1 Dec 2019).
- Emergen Research, Fullerene Market By Type (C60, C70, C76, Other), By Production Method (Arc Discharge Method, CVD/CCVD Process, Laser Ablation of Graphite, Others), By Shape (Nanotubes, Bucky Balls, Nano-Rods), By End-use, and By Region Forecast to 2028, https://www.emergenresearch.com/industry-report/fullerene-market (accessed 4 July 2022).
- Maximize Market Research, Global fullerene Market (2021 to 2027) – Growth, Trends, COVID-19 Impact and Forecasts, https://www.maximizemarketresearch.com/market-report/global-fullerenes-market/70582/(accessed 4 July 2022).
- A. Anctil, C. W. Babbitt, R. P. Raffaelle and B. J. Landi, Material and energy intensity of fullerene production, Environ. Sci. Technol., 2011, 45(6), 2353–2359 CrossRef CAS.
- H. Yi, G. Zeng, C. Lai, D. Huang, L. Tang and J. Gong,
et al., Environment-friendly fullerene separation methods, Chem. Eng. J., 2017, 330, 134–145 CrossRef CAS.
- P. M. Allemand, A. Koch, F. Wudl, Y. Rubin, F. Diederich and M. M. Alvarez,
et al., Two different fullerenes have the same cyclic voltammetry, J. Am. Chem. Soc., 1991, 113(4), 1050–1051 CrossRef CAS.
- H. Keypour, M. Noroozi and A. Rashidi, An improved method for the purification of fullerene from fullerene soot with activated carbon, celite, and silica gel stationary phases, J. Nanostruct. Chem., 2013, 3(1), 45 CrossRef.
- B. A. Khan, L. Cheng, A. A. Khan and H. Ahmed, Healthcare waste management in Asian developing countries: A mini review, Waste Manage. Res., 2019, 37(9), 863–875 CrossRef PubMed.
- T. Odagiri, Y. C. Chan, K. S. Kwok and K. M. Ng, A novel evaporative crystallization column for the purification of fullerene C60, AIChE J., 2007, 53(2), 531–534 CrossRef CAS.
- K. S. Kwok, Y. C. Chan, K. M. Ng and C. Wibowo, Separation of fullerenes C60 and C70 using a crystallization-based process, AIChE J., 2009, 56(7), 1801–1812 CrossRef.
- K. Nagata, E. Dejima, Y. Kikuchi and M. Hashiguchi, Kilogram-scale
[60]Fullerene Separation from a Fullerene Mixture: Selective Complexation of Fullerenes with 1,8-Diazabicyclo[5.4.0]undec-7-ene (DBU), Chem. Lett., 2005, 34(2), 178–179 CrossRef CAS.
- K. Nagata, E. Dejima, Y. Kikuchi and M. Hashiguchi, Efficient and Scalable Method for [60]Fullerene Separation from a Fullerene Mixture: Selective Complexation of Fullerenes with DBU in the Presence of Water, Org. Process Res. Dev., 2005, 9(5), 660–662 CrossRef CAS.
- E. Lee, C. J. Andrews and A. Anctil, An Iterative Approach to Evaluate and Guide Fine Chemical Processes: An Example from Chloroaluminum Phthalocyanine for Photovoltaic Applications, ACS Sustainable Chem. Eng., 2018, 6(7), 8230–8237 CrossRef CAS.
- PRé Consultants, SimaPro 9.1.0.7, Amersfoort, https://pre-sustainability.com/solutions/tools/simapro/.
-
NFP Association, NFPA 704: Standard System for the Identification of the Hazards of Materials for Emergency Response, National Fire Protection Agency, Quincy, MA, 2013 edn, 2011, Harvard Search PubMed.
-
P. G. Jessop, S. Trakhtenberg and J. Warner, The Twelve Principles of Green Chemistry, Innovations in Industrial and Engineering Chemistry, American Chemical Society, 2008, pp. 401–436 Search PubMed.
-
U.S. EPA, Fact Sheet - LC50, 2018, https://www.epa.gov/sites/default/files/2016-09/documents/ethylene-oxide.pdf (accessed 17 Octobere 2022) Search PubMed.
- US Environmental Ptotection Agency (EPA), Toxicity Estimation Software Tool (TEST), https://www.epa.gov/chemical-research/toxicity-estimation-software-tool-test.
- S. M. Heidari and A. Anctil, Identifying alternative solvents for C60 manufacturing using singular and combined toxicity assessments, J. Hazard. Mater., 2020, 393, 122337 CrossRef CAS PubMed.
- K. Nagata, E. Dejima, Y. Kikuchi and M. Hashiguchi, Kilogram-scale [60]Fullerene Separation from a Fullerene Mixture: Selective Complexation of Fullerenes with 1,8-Diazabicyclo[5.4.0]undec-7-ene (DBU), Org. Process Res. Dev., 2005, 9(5), 660–662 CrossRef CAS.
- A. Astefanei, O. Núñez and M. T. Galceran, Characterisation and determination of fullerenes: A critical review, Anal. Chim. Acta, 2015, 882, 1–21 CrossRef CAS PubMed.
- J. Wang, Q. Cai, Y. Fang, T. A. Anderson and G. P. Cobb, Determination of fullerenes (C60) in artificial sediments by liquid chromatography, Talanta, 2011, 87, 35–39 CrossRef CAS PubMed.
- J. M. Treubig and P. R. Brown, Analysis of C60 and C70 fullerenes using high-performance liquid chromatography-Fourier transform infrared spectroscopy, J. Chromatogr. A, 2002, 960, 135–142 CrossRef CAS PubMed.
- A. Carboni, E. Emke, J. R. Parsons, K. Kalbitz and P. de Voogt, An analytical method for determination of fullerenes and functionalized fullerenes in soils with high performance liquid chromatography and UV detection, Anal. Chim. Acta, 2014, 807, 159–165 CrossRef CAS PubMed.
-
J. B. Howard and J. T. McKinnon, United States Patent, 5273729, 1993 Search PubMed.
- YMC HPLC Columns Applications Notebook - WA30000, https://www.waters.com/webassets/cms/library/docs/wa30000.pdf (accessed 8 Feb 2021).
- K. S. Kwok, Y. C. Chan, K. M. Ng and C. Wibowo, Separation of fullerenes C60 and C70 using a crystallization-based process, AIChE J., 2009, 56(7), 1801–1812 CrossRef.
- Y. S. Grushko, V. P. Sedov and V. A. Shilin, Technology for manufacture of pure fullerenes C60, C70 and a concentrate of higher fullerenes, Russ. J. Appl. Chem., 2007, 80(3), 448–455 CrossRef CAS.
- P. G. Jessop, Searching for green solvents, Green Chem., 2011, 13(6), 1391 RSC.
- M. Wohlers, H. Werner, D. Herein, T. Schedel-Niedrig, A. Bauer and R. Schlögl, Reaction of C60 and C70 with molecular oxygen, Synth. Met., 1996, 77(1–3), 299–302 CrossRef CAS.
-
F. Cataldo and T. Da Ros, Medicinal Chemistry and Pharmacological Potential of Fullerenes and Carbon Nanotubes, Carbon Materials: Chemistry and Physics, 2008, vol. 1 Search PubMed.
- F. Cataldo and T. Braun, The Solubility of C60 Fullerene in Long Chain Fatty Acids Esters, Fullerenes, Nanotubes Carbon Nanostruct., 2007, 15(5), 331–339 CrossRef CAS.
-
P. Anatol'evich, P. Petrovich, B. Borisovich, M. Ehrik, R. Mikhajlovich and S. Valentinovich, et al., Fullerene Solution Prepration Method, RU2283273C2, Russia, 2006 Search PubMed.
- K. N. Semenov, N. A. Charykov, V. I. Namazbaev, N. I. Alekseyev, E. G. Gruzinskaya and V. N. Postnov,
et al., Temperature dependence of solubility of light fullerenes in some essential oils, Fullerenes, Nanotubes Carbon Nanostruct., 2011, 19(3), 225–236 CrossRef CAS.
- K. N. Semenov, N. A. Charykov, V. A. Keskinov, A. K. Piartman, A. A. Blokhin and A. A. Kopyrin, Solubility of Light Fullerenes in Organic Solvents, J. Chem. Eng. Data, 2010, 55(1), 13–36 CrossRef CAS.
-
A. Thomas, B. Matthäus and H. J. Fiebig, Fats and Fatty Oils, Ullmann's Encyclopedia of Industrial Chemistry, Wiley-VCH Verlag GmbH & Co. KGaA, Weinheim, 2015, 1–84 Search PubMed.
- The Latest IPCC Report: What is it and why does it matter?, https://www.nature.org/en-us/what-we-do/our-insights/perspectives/ipcc-report-climate-change/ (accessed 8 July 2022).
- Fact Sheet: President Biden Sets 2030 Greenhouse Gas Pollution Reduction Target Aimed at Creating Good-Paying Union Jobs and Securing U.S. Leadership on Clean Energy Technologies (Office of the Press Secretary, United States), Whitehouse.Gov, https://www.whitehouse.gov/briefing-room/statements-releases/2021/04/22/fact-sheet-president-biden-sets-2030-greenhouse-gas-pollution-reduction-target-aimed-at-creating-good-paying-union-jobs-and-securing-u-s-leadership-on-clean-energy-technologies/%0Awhi.
-
U.S. EPA, Sources of Greenhouse Gas Emissions, https://www.epa.gov/ghgemissions/sources-greenhouse-gas-emissions%0Ahttps://www.epa.gov/climatechange/ghgemissions/sources/transportation.html, (accessed 20 April 2023).
-
U.S. EPA, Greenhouse Gas reporting in the ethylene manufacturing sector, https://www.epa.gov/trinationalanalysis/greenhouse-gas-reporting-chemical-manufacturing-sector#:~:text=The chemical manufacturing sector reported, an 8%25 increase since 2012, (accessed 20 April 2023).
- K. M. D. Reyes, K. Bruce and S. Shetranjiwalla, J. Chem. Educ., 2023, 100, 209–220 CrossRef CAS.
|
This journal is © The Royal Society of Chemistry 2023 |
Click here to see how this site uses Cookies. View our privacy policy here.