DOI:
10.1039/D2GC03474C
(Tutorial Review)
Green Chem., 2023,
25, 453-466
Review of high-performance sustainable polymers in additive manufacturing
Received
14th September 2022
, Accepted 29th November 2022
First published on 9th December 2022
Abstract
Additive manufacturing (AM), commonly referred to as 3D printing, is viewed as a method of rapid prototyping and an alternative to traditional manufacturing. Recently, there has been increasing interest on sustainability of AM approaches and the materials that can be used. Advances in both AM technologies and polymer chemistry present multiple pathways for AM to become more sustainable, such as raw material sourcing, green synthesis, and end-of-life processing. This review provides a brief overview of AM techniques for polymers, sustainable sourcing of polymers in AM, and the advances of degradable/recyclable polymers in AM. It also provides a perspective of the potential role of AM in economic and chemical circularity, as well as opportunities for digital manufacturing for the future. Biodegradable materials for medical or other biological applications are beyond the scope of this review.
Introduction
Our world today is full of incredible advancements in science and technology, but the unintended consequences of these advances threaten our future. Synthetic polymers, which have only been manufactured widely since the 1950s, offer one of the most explicit and severe examples. Although synthetic polymers have many benefits, their durability has led to a global plastic pollution problem that now presents one of the most pervasive and extensive challenges to the health and future of our planet and its inhabitants.
Polymeric products constitute about 9% of the $12T manufacturing market sector, and 30% of that is comprised of injection molded products.1 Recent advances demonstrate that 3D printing is poised to make the jump from a “prototyping only” $8B industry to replace injection molding techniques—a $330B industry—in many areas.2 This transition in technology represents a unique moment in time to pre-emptively put polymer additive manufacturing (AM) on a sustainable trajectory. A “benign by design” strategy represents a critical step in this exciting trajectory, focusing a sustainability lens on next-generation materials for next-generation advanced manufacturing platforms.
AM is an increasingly attractive option for both rapid prototyping and manufacturing objects with complex geometries, and it's often viewed as an environmentally sustainable manufacturing option because of its intrinsic potential to leverage on-site production that minimizes both production waste and emissions from transporting manufactured goods from factory to facility. AM integrates polymer synthesis and part fabrication into a single process step, leading to chemical process intensification. This potential to go from basic feedstock resins to a final product without intermediate isolation, reprocessing, or large-scale capital allocation for reactors reduces risk for product development and drives innovation. In addition, some have predicted that AM can reduce CO2 emissions by 130.5–525.5 million tons and energy demands by up to 9.30 × 1018 J by 2025.3 Nevertheless, there are additional motivations to design for minimal environmental impacts as AM scales.
AM has spawned the demand for highly customizable, uniquely functional, and high-performance objects, which results in a rapid increase in products created by AM. However, many of these products are not designed to be recycled. There is a need to develop high-performance materials and a way to recycle the materials. Alongside material properties, high-performance products can be further enhanced with geometrical structures. Lattice geometries enabled by AM have gained special interest because of the unique strength-to-weight ratio, as well as the ability to obtain excellent mechanical properties while reducing the amount of material wasted in production (buy-to-fly ratio4) and used in the final part. Indeed, AM is driving the “de-materialization” of products in ways not possible with injection molding using latticed geometries not achievable via injection molding. Architected structures allow objects created from a single material to have a range of mechanical properties. When looking at high-performance use-cases such as an automobile, many different materials—nearly 40 different polymers developed ad hoc over decades, as opposed to being designed with a sustainability-first co-design approach— are used in a complex assembly to achieve the range of mechanical properties needed in each part of the automobile. The sheer diversity of materials that are required in an automobile makes materials recovery and recycling very challenging. However, we believe that it may be possible to substitute the overabundance of polymer types with a much smaller subset of polymer compounds, all chemically recyclable, in which the limitations in material selection can be overcome by tailoring the geometry of a mesoscale 3D-printed structure, or lattice, to achieve similar or better diversity in functionality.
In addition to tuning the geometry for high performance products, materials selection of polymers is of particular interest because of their characteristic ability to retain desirable properties when exposed to extreme conditions such as high temperature, pressure or stress, or corrosive chemicals. Polymeric materials can be designed to withstand extreme conditions for extended periods of time, making them excellent choices for many industries such as aerospace, automotive, or construction. However, the resistance to heat, chemicals, and/or mechanical stress also means that high performance polymers are difficult to remanufacture and cannot be recycled easily. The same properties that are tailored for performance conflict with the chemical properties for depolymerization.
Over 50% of polymers in AM and almost 20% of all plastics produced in the world are thermoset polymers which are crosslinked to have high resistance to chemicals and heat.5,6 While AM has the potential to reduce waste production, energy consumption, and CO2 emissions compared to traditional manufacturing, it does not inherently solve the issues of unsustainable production. Our evolving understanding of the adverse impacts of technological advancement on the environment makes it imperative that the design of high-performance materials must also include a vision for end-of-life treatment and re-use or re-cycling. Despite the many positive opportunities for AM to support the tenets of sustainability, there is a great need to ensure that AM materials themselves are chemically recyclable or compostable.
Herein, we will focus on sustainable, high-performance polymers for AM. Biodegradable materials for medical or other biological applications are beyond the scope of this review. This publication reviews the current methods of additive manufacturing, current degradable polymers used in each of the following AM methods with a focus on high-performance polymers, followed by a discussion on the impact these materials will have on society.
Current methods of additive manufacturing
The earliest recording of 3D printing through an additive process was in 1981 by Japanese inventor Hideo Kodama, who developed a method of fabricating 3D models by curing photosensitive resins layer-by-layer with UV light.7 In the field of AM materials, polymers remain the most commonly used material because early 3D printers, such as the one designed by 3D Systems Inc. in 1986,8 used polymers for rapid prototyping.9–11 In more recent years, materials for AM have spanned a wide range: ceramics,12–15 metals,16–19 hydrogels,20,21 nanomaterials,22–24 pharmaceuticals,25–27 and even biological materials such as cells and tissue.28–30 However, polymers remain the most popular material for AM due to their ease of printing, well-established technology, versatile thermomechanical performance, and chemical inertness.31 One of the key patents for 3D printing expired in 2004, and since then, numerous research articles have been published and new patents have been filed on the expansion of the AM technology. There are now four main polymer AM process modalities: material extrusion, vat photopolymerization (VP), binder jetting, and powder bed fusion, as shown in Fig. 1.32 For each type of AM, the materials properties needed, and the challenges associated with each method are briefly summarized below.
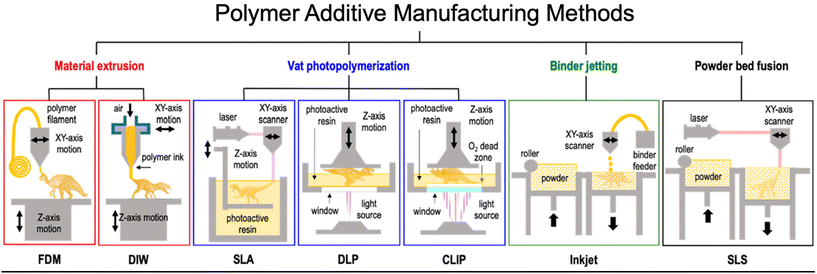 |
| Fig. 1 Description of polymer additive manufacturing methods. Reproduced from ref. 32 with permission from American Chemical Society, 2021. | |
Material extrusion
Extrusion-based AM involves the deposition of material to build an object “layer-by-layer”. Examples of extrusion-based AM include Fused Filament Fabrication (FFF)33,34 and Direct Ink Write (DIW).35,36 These processes construct a three-dimensional object by extruding a thermoplastic filament through a heated nozzle (FFF) or a viscous paste/gel/photopolymer (DIW) onto a build platform. In FFF and DIW, the polymer filament melt (FFF) or ink (DIW) must have a proper viscosity to be extruded through the printhead (typically a shear thinning behavior), and high zero shear viscosity, yield stress behavior, and/or rapid gel time once deposited to avoid flow and part slumping upon deposition. Due to the high melt viscosity of performance polymers, large FFF extrusion nozzles are typically required, which limits process resolution and results in a poor surface finish due to the “staircase” effect from the layered deposition. While these extrusion systems are inexpensive, they have a very low throughput due to the need to raster the extrusion nozzle to build each layer and have limited resolution, and feature capability results from the challenges in start/stop extrusion of viscous materials. FFF systems also feature significant anisotropy due to poor interlayer bonding caused by rapid cooling and solidification of the extrudate.
Binder jetting
Binder jetting is a method of AM where droplets of material are selectively jetted and photocured to build an object. In binder jetting, the starting material must have a very low viscosity (<0.1 Pa s) and tuned surface tension to enable jetting of picoliter droplets that can form well-defined primitives on the build surface. While jetting enables precise spatial control (∼50 μm) over multiple resins in a single build, the rheological constraints imposed by jetting significantly limit the material selection to low viscosity, low molecular weight precursors. The comparison of rheological constraints for various AM methods is shown in Fig. 2.
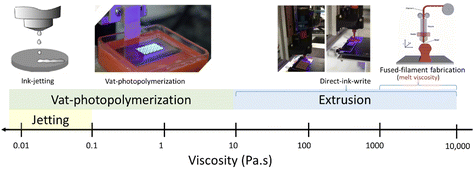 |
| Fig. 2 Rheological considerations of polymer additive manufacturing processes. (PBF is not included here as viscosity alone is not the right framework for assessing a sintering process). | |
Polymer powder bed fusion (P-PBF)
Powder bed fusion techniques involve the selective fusion of powdered polymers through the use of a scanning laser (traditionally referred to as Selective Laser Sintering (SLS)37) or overhead IR heating of a selectively doped powder bed (e.g., HP's MultiJet Fusion process,38 VoxelJet's High Speed Sintering.39 When using powders as starting material, careful consideration must be taken to ensure that the polydispersity of the particle sizes is narrow to achieve homogenous fusion and high resolution. Producing 30–50 μm powders from high-performance polymers has proven challenging and wasteful.40 Furthermore, the thermal stability and hence recyclability of the powder is often limited, leading to high amounts of waste. While P-PBF has been used to make end-use components, it has (1) a limited selection of processable materials, (2) limited throughput due to long heating/cooling cycles, (3) arduous post-processing (depowdering), (4) energy intensive processing, (5) significant waste generation (due to polymer molecular weight growth and/or oxidative degradation from thermal cycling), and (6) an inability to process multiple materials simultaneously.
Vat photopolymerization (VP)
UV curable liquid resin-based AM can broadly be divided into three generations of vat photopolymerization and material jetting. In first-generation vat photopolymerization (VP), also known as stereolithography (SLA),41 a bath containing a single liquid resin is photocured spatio-selectively by a scanning laser point source. Second generation VP, referred to as digital light projection (DLP),42 uses a rapid sequence of projected UV images that span the entire X–Y plane of a bath containing a liquid resin in a single exposure. In third-generation VP, known as continuous liquid interface production (CLIP, Fig. 3), a layer of oxygen-rich liquid resin is continuously renewed at the build surface to provide a polymerization-inhibiting liquid interface (deadzone) between growing parts and a UV-transparent window.43–45 CLIP, achievable with multiple patterns of platform movement and UV exposure46 along with different window configurations,47 enables printing at speeds up to 3000 mm h−1, 25 to 100 times higher than traditional AM methods. While to date CLIP has been limited to relatively low viscosity resins (commercially available resins from Carbon, Inc. have viscosities up to roughly 2500 cP),48 CLIP produces isotropic parts, unlike conventional 3D printing methods like fused filament fabrication (FFF) and powder bed fusion (PBF), and has proven suitable for manufacturing at high volumes and at high resolution for e.g. biomedical devices.49,50
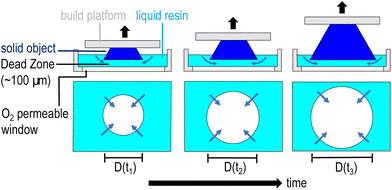 |
| Fig. 3 The CLIP process involves the creation of a polymerization dead-zone, allowing high-speed printing. | |
Sustainability of AM polymers
New materials are typically created to surpass current materials used for specific applications, often looking to improve materials properties such as strength, stiffness, and heat and chemical resistance, or even to offer essentially the same or similar material by corporate competitors. This focus on meeting materials criteria for specific applications, or building an alternative material portfolio for competitive business resins, has led to the development of excellent materials for high-performance use cases, but has also resulted in an immense global pollution challenge compounded by a significant proliferation of a large number of different materials that make processes for collection, separation and recycling difficult. Going forward, materials scientists, engineers, and policy makers must consider the whole picture of materials development in addition to what is needed during the lifetime of a material.
The key aspects of holistically sustainable materials development that have been explored include: (1) reagents and feedstocks (such as the sourcing of raw materials from renewable resources) and (2) the intentional design and incorporation of degradability or re-processability in new polymeric materials to prevent materials from entering landfills and waterways. This “whole picture” view of materials development can be captured by the framework of a circular economy.
A circular economy is defined by Geissdoerfer et al. as “a regenerative system in which resource input and waste, emission, and energy leakage are minimized by slowing, closing, and narrowing material and energy loops.51 This can be achieved through long-lasting design, maintenance, repair, reuse, remanufacturing, refurbishing, and recycling”. In short, a circular economy is an environmentally conscious and systemic design for economic development that minimizes waste and loss of value for materials. In this model, all produced goods can be recovered, recycled, and reused to keep the constituent materials in use for as long as possible. Resource input, material waste, and carbon emissions are reduced while also extending value for materials that would normally be discarded.
The idea of a circular economy is not new: the concept dates as far back as 1966 in a famous essay by Kenneth Boulding that states society must transition to a “spaceman” economy where all systems of production are cyclical such as that of a spaceship.52 Later, the term “circular economy” appeared in “The Economics of Natural Resources” by Allen Kneese.53 Over 50 years later and numerous advances in manufacturing, we still have not reached a circular economy, and we are still far from it. However, as Geissdoerfer describes, we can achieve a circular economy through design. Within materials for AM, the concept of a circular economy is being used to guide design of new materials and methods for reuse and recycling. Triggered degradation, in particular, is a very useful tool for achieving a chemically circular society: any polymeric material that is produced can be collected and broken down to its components for re-production of parts. This will extend the value of raw materials far beyond initial manufacturing and aid in progress towards a circular economy.
Design for degradability and recyclability
Degradability has been demonstrated via multiple pathways that can be summarized in two main categories: passive degradation and triggered degradation. Passive degradation occurs when a material can degrade in a naturally occurring environment and does not require very specific chemicals to trigger its degradation. It may occur in vivo, such as with sutures that naturally break down when in contact with the body, or in an outside environment such as in a landfill with sufficient UV exposure from sunlight and oxygen in the atmosphere.54 Passive degradation is an attractive field for polymer development because it has the potential to solve the plastic pollution problem while bypassing the current lack of recycling infrastructure. This suggests that a passive compostable degradation is favorable so that AM materials can degrade even when they are not properly sorted and collected to the proper waste management facility. However, even polymers that are designed to be passively degradable or compostable may not actually break down because of insufficient water or oxygen within landfills.55 Another main challenge with passive degradation is balancing the maintenance of good mechanical properties and chemical inertness for the intended period use but still achieving a reasonable timeframe for natural and safe degradation. It is assumed that the conditions in which passive degradation occurs is different than the conditions in which the polymer is in use. Thus, passively degradable materials may lack the necessary properties of thermal, mechanical, or chemical resistance for long-term high-performance applications.
Alternatively, polymers that degrade by triggered reactions may provide the necessary properties and lifetimes required by different use-cases. Triggered degradation involves the presence of a “switch” that can initiate the degradation or decomposition of a material in conditions orthogonal to their use environment. This may involve a change of catalysts, solvent introduction, irradiation, high temperature, or another external agent. Triggered degradation is an attractive field for the development of high-performance polymers because of the potential to create materials that can rival current polymer performance and lifetime while being fully recyclable once the material has served its purpose.56 However, the challenge associated with this field is the lack of large-scale infrastructure that can support the chemical recycling of many different polymer types. Some processes of chemical recycling may also include mechanical comminution such as shredding or milling products into more easily reprocessable fragments.57
The design for degradability in polymeric materials will now be reviewed as it pertains to each of the four main types of AM methods outlined above. A summary of the materials reviewed can be found in Table 1.
Table 1 Summary of sustainable polymers for AM with potential for use in high-performance applications
Method of AM |
Source |
Material |
Method of degradability or reprocessability |
Authors |
Year of publication |
Material extrusion |
Synthetic |
PLA |
Thermoplastic, Diels–Alder network |
Appuhamillage et al. |
2017 |
Consumer waste |
PP, PET, PS |
Thermoplastic |
Zander et al. |
2019 |
Recycled powder |
PC |
Thermoplastic |
Reich et al. |
2019 |
Wood |
PLA composite |
Thermoplastic |
Duigou et al. |
2016 |
Wood |
Wood |
Biodegradable |
Kam et al. |
2019 |
Cellulose, synthetic |
Acrylate, composite |
N/A |
Siqueira et al. |
2017 |
Lignin |
ABS, nylon composite |
N/A |
Nguyen et al. |
2018 |
Synthetic |
PEEK |
Thermoplastic |
Hu et al. |
2019 |
Industrial waste |
Geopolymer |
Crush and reuse |
Panda et al. |
2017 |
Synthetic |
Semi-crystalline thermoplastics |
Diels–Alder network |
Yang et al. |
2017 |
Synthetic |
Elastomer composite |
Diels–Alder network |
Guo et al. |
2021 |
Synthetic |
Epoxy |
Vitrimer |
Shi et al. |
2017 |
Material/binder jetting |
N/A |
N/A |
N/A |
N/A |
N/A |
Polymer powder bed fusion |
Synthetic |
Commercial polyamides, PS, PC, PEEK, etc. |
Thermoplastic |
Stansbury et al. |
2016 |
Vat photo-polymerization |
Synthetic |
Acrylates |
Thermoset – dynamic covalent bonds |
Zhang et al. |
2018 |
Synthetic |
Acrylates |
Thermoset – dynamic covalent bonds |
Rossegger et al. |
2021 |
Synthetic |
DGEBA |
Thermoset – dynamic covalent bonds |
Zhao et al. |
2021 |
Synthetic |
Epoxy |
Thermoset – dynamic covalent bonds |
Hao et al. |
2020 |
Synthetic |
Polythiourethane |
Thermoset – dynamic covalent bonds |
Cui et al. |
2022 |
Synthetic |
Thioester composite |
Thiol-thioester exchange |
Hernandez et al. |
2022 |
Synthetic |
Acrylates, polyurethane |
Degradable crosslinks |
Poelma et al. |
2019, 2021 |
Lignin |
Acrylates |
Solvent-free synthesis |
Ding et al. |
2019 |
Lignin |
Vinyl ester |
Solvent-free synthesis |
Bassett et al. |
2020 |
Soybean oil |
Epoxy |
Natural material |
Guit et al. |
2020 |
Material extrusion
Material extrusion typically relies on the extrusion of thermoplastic polymer melts, many of which are easily reprocessable. One of the most commonly used materials for FFF is poly(lactic acid) (PLA), an aliphatic polyester designed to be biodegradable and renewable. Compared to petroleum-based products, PLA has lower mechanical properties and is more expensive to produce,58 but its passive degradability by self-hydrolyzation into lactic acid has made it a popular choice as a safe and sustainable material. Since the degradation rate of PLA (as with any degradable material) depends on the conditions of its environment, there have been numerous research studies on tuning its degradability and improving its mechanical properties such that it can be used in higher performance applications. This has led to the development of different forms of PLA such as poly(L-lactic acid) (PLLA) and poly(D,L-lactic acid) (PDLLA).59 Furthermore, the combination of PLA with polyglycolic acid (PGA) formed the copolymer poly(lactic-co-glycolic acid) (PLGA) that is soluble in acetone, ethyl acetate, tetrahydrofuran, and other common solvents, and can be used to increase degradation of PLA as an AM material, as shown in Fig. 4.58,60,61
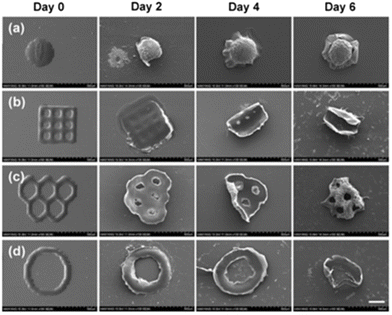 |
| Fig. 4 PLGA as a degradable material for inkjet printing. Reproduced from ref. 61 with permission from Elsevier, 2012. | |
Modifications of the PLA polymer chain allows for tunability of properties beyond degradation rate, such as improving the toughness and heat resistance of the material for higher performance use-cases. For example, poly(L-lactide-co-ε-caprolactone) (PLC) is a more elastic copolymer than PLA, has a higher degradation rate than poly(ε-caprolactone) (PCL).62 Additionally, Appuhamillage et al. found that blending PLA with a dynamic Diels–Alder functional polymer yielded a reversibly cross-linkable filament for extrusion-based printing which improved the toughness of base materials by over 200%.63 PLA blends, mixes, and composites are particularly advantageous because they allow for improvements to elastic modulus, yield strength, and maximum strain without the need for developing entirely new synthesis pathways.
Among other polymer blend filaments for FFF are materials found in packaging and consumer products such as polyolefins, polystyrene (PS), and polyethylene terephthalate (PET). The challenge of incorporating post-consumer waste into AM resins or feedstocks comes from the inhomogeneity of the polymer stream and the difficulties in recycling each type of material. For example, water absorption leads to reduction of molecular weight in PET, and shrinkage and warpage may occur during processing that makes printing difficult. Additionally, the thermal and mechanical processing cycles introduce stresses that may lead to degradation of polymer chains, and thus lower mechanical properties and performance compared to the native material.64–66 To address these challenges associated with recycling single plastics, Zander et al. processed a blend of waste polypropylene (PP), PET, and PS into filaments for 3D printing to simulate the potential to manufacture filaments from real plastic waste streams.67 The resulting filament had tensile strengths comparable to low-end commercial filaments and was thus deemed viable for extrusion-based processes. For a higher performing material, Reich et al. recycled polycarbonate (PC) powder into feedstock for a Recylebot that produced high-strength and heat-resistant filaments comparable to commercial filaments for both desktop and large-scale AM processes.68
Degradation of printed polymers can also be achieved with natural materials that are sustainably sourced, such as cellulose or lignin. There have been several studies on incorporating cellulose into AM materials to reinforce current filaments, resin, and inks. Le Duigou et al. used wood cellulose fibers to strengthen a PLA-based extrusion filament.69 Later, Kam et al. developed a method of 3D printing objects composed of 100% wood components by dispersing wood flour microparticles in a matrix of cellulose nanocrystals and xyloglucan.70 The printed wood materials exhibited similar mechanical properties as natural wood and a higher thermal insulation. In 2017, Siqueira et al. developed a sustainable cellulose-based DIW ink by suspending cellulose nanocrystals (CNCs) in a photopolymerizable monomer solution.71 The amount of CNCs added to the polymer ink determined the effect on mechanical properties: a blend of 20 wt% CNC increased the elastic modulus by 80% compared to the polymer alone. Lignin, the second most abundant raw material in nature and the most abundant aromatic polymer in nature, is polymer that can also be used as a renewable alternative to synthetic materials72–74 for higher performance applications than cellulose. Nguyen et al. found that lignin could be used to form high-performance composite polymers using ABS and nylon filament, and that lignin could replace 40–60% of the synthetic materials while enhancing stiffness and strength at room temperature.75
As science and technology evolves, more degradable materials can be synthesized or translated for AM. Recently, the additive manufacturing of polyether ether ketone (PEEK), a fully recyclable thermoplastic often used in high-performance applications such as bearings, piston parts, and compressor plate valves, was achieved by improving FDM equipment to reduce internal stress, warpage, and delamination of the polymer.76 While PEEK has been around since the 1980s, it could not be 3D printed until 2015 when FDM technology could accommodate the necessary parameters for printing high-temperature filaments.77 This is just one example of how advances in AM technologies have enabled the usage of different sustainable materials; many more advances in recycling thermosets and other polymeric materials in AM continue to be published each year.78,79
On a larger scale of material extrusion, AM of construction elements has also begun the move toward greener alternatives by replacing cement with “geopolymers”.80 Geopolymers incorporate fly ash and slag collected from industrial wastes and form covalently bonded networks of inorganic material and have been found to have sufficient mechanical properties to rival traditional cement.81 The recyclability of geopolymers have also been studied and shown promising results (fully recycled geopolymers showed 85–90% of native properties),82 but more study is required to optimize the recycling process.
Many types of materials can be recycled for AM, including the use of by-products such as wood flour and wood dust as fillers in thermosetting resins83 and converting consumer-grade thermoplastics from packaging materials into low-cost feedstock for extrusion-based AM.84 Recycling consumer products into AM filaments also provides a high-value afterlife for waste plastics, which can offset high transportation and collection costs.85 Since the current state of material extrusion depends generally on thermoplastics for prototyping, sustainable materials research for material extrusion has largely focused on cost savings, waste minimization, raw material sourcing, and incorporation of post-consumer waste rather than on development of recyclable thermosets that are more suitable for high performance applications.
A very promising advance in thermoset materials for material extrusion techniques is the use of Diels–Alder reversible thermoset (DART) process, where reversibly crosslinked polymers can be 3D printed to both improve material toughness and lower anisotropy.86 Similar to Appuhamillage's work with PLA, Guo et al. utilized Diels–Alder networks to create a re-processable and recyclable conductive elastomer that can be 3D printed.87 This printed material exhibited resistance to high humidity, brine, and ethanol, as well as thermal resistance up to 100 °C. The elastomer is also capable of retaining its mechanical properties through at least three recycling processes. Similarly, Shi et al. developed a thermosetting vitrimer epoxy ink for direct ink writing that could by recycled by dissolution in ethylene glycol at 180 °C and reused at least 4 times with nearly identical thermomechanical properties.88 The use of covalently adaptable networks is a promising path for developing vitrimer materials in AM that can be easily processed. Instead of fully degrading a polymer and repolymerizing, it is possible to incorporate re-processability in thermoset materials using heat or catalysts.
Another recent development in sustainable high-performance materials for material extrusion is the use of degradable comonomers with thermosetting poly(dicyclopentadiene) (p(DCPD)) by Davydovich et al.89 p(DCPD) is a tough and chemically resistant thermoset that is often used for automotive application such as for body panels and bumpers for trucks, buses, and construction equipment. Davydovich et al. demonstrated that the incorporation of dihydrofuran (DHF) in DCPD resins allowed the printed pDCPD to degrade into oligomeric products with product recovery around 80%. The printed material also had high ultimate strength around 35–40 MPa. Additionally, the use of frontal polymerization to cure the thermoset during printing reduces the amount of energy necessary for thermoset fabrication. This high-performance thermoset that is degradable into functional oligomers is a promising step towards a chemically circular economy.
Material/binder jetting
Like material extrusion, commonly used materials in material jetting are reprocessable thermoplastics, but also include thermosetting photopolymer resins and elastomers that are more suitable for high-performance applications.90 Thermosetting resins used for material or binder jetting are typically comprised of prepolymers such as a combination of high and low molecular weight acrylates and methacrylates that can form tough materials. However, there is very little research conducted on developing specific polymers for material or binder jetting that are recyclable or sustainable. The development of degradable photopolymer chemistries beyond AM may eventually translate to material jetting, but the use of heat to lower the viscosity of materials is restricted by thermally-induced polymerization of pre-polymers.91
Polymer powder bed fusion (P-PBF)
Polymer Powder Bed Fusion (P-PBF) is a unique method of AM because it primarily uses semicrystalline thermoplastic prepolymers;92 the most commonly used material is nylon 12, but other polymers such as nylon 6, nylon 10, nylon 12, ABS, PS, and PC are commercially available.93 Selection of high-performance polymers that can be used in P-PBF is limited because of the high powder bed temperatures required for processing.
The vast majority of sustainability research for P-PBF focuses on improving the recyclability of powders and binders, rather than the recyclability of the printed material.94 Excess powders are typically collected, refined, and reused to minimize waste and cost of using virgin materials. However, reusing free powder poses its own set of challenges. The powder may contain defects from high temperature and sintering outside the print area95 and the polydispersity of particle sizes usually increases after processing, which can result in different properties from the original material.96 Even powder from the same batch that have gone through the same number of processing cycles will demonstrate varying degrees of degradation depending on how close the powder was to the parts being manufactured.97 Furthermore, the nature of PBF creates cross-contamination and powder separation challenges when printing with more than one material. To address these challenges, Kumar and Czekanski suggest that it is possible to salvage the excess waste from SLS and convert it into filament for FFF.98 By doing so, it is possible to produce filaments with better mechanical strength than current commercial filaments, reduce the waste produced by SLS, and re-use the materials without the constraints of defects and polydispersity.
Vat photopolymerization (VP)
Vat photopolymerization (VP) has been a challenging AM method for novel recyclable materials because of the common usage of thermosetting resins. Traditionally, VP relied on the polymerization of simple acrylates or epoxy monomers, but has now expanded to include many polymer systems such as aromatic polyimides, polyurethanes, and PEEK.99 Now, materials development for VP focuses on achieving end-of-life sustainability such as self-healing, reprocessability, or depolymerization for monomer recovery of thermoset materials.
For repairable thermosets, Zhang et al. developed a 3D printing re-processable thermoset (3DPRT) by mixing in zinc acetylacetone hydrate as a catalyst for transesterification reactions to occur, thereby inducing dynamic covalent bonds to form and allowing the crosslinked network to rearrange and to be reprocessed at elevated temperatures as shown in Fig. 5.100 Subsequently, Rossegger et al. applied the concept of dynamic covalent bonds in the development of an acrylate-based vitrimer for DLP that used an organic phosphate as the transesterification catalyst.101 The material could be repaired and reshaped by heating at 180 °C to fully recover the strength of the original defect-free material as shown in Fig. 6. Similarly, Zhao et al. developed an epoxy-anhydride resin using diglycidyl ether of bisphenol A (DGEBA) that can be recycled with ethylene glycol below 200 °C.102 The cured DGEBA polymers showed resistance to a range of organic solvents, including dichloromethane (DCM), dimethylformamide (DMF), 1,2,4-trichlorobenzene (TCB), xylenes, tetrahydrofuran (THF), and heptane but could be dissolved in ethylene glycol to obtain decomposed epoxy oligomers that could be reused in the preparation of a new epoxy resin with improved toughness and high chemical resistance.
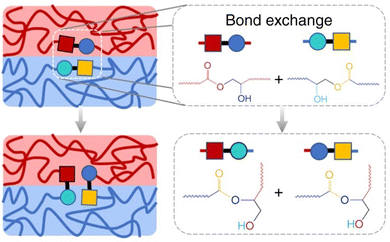 |
| Fig. 5 Illustration of bond exchange reactions (BERs) in 3D printed re-processable thermoset. Reproduced from ref. 100 with permission from Springer Nature, 2021. | |
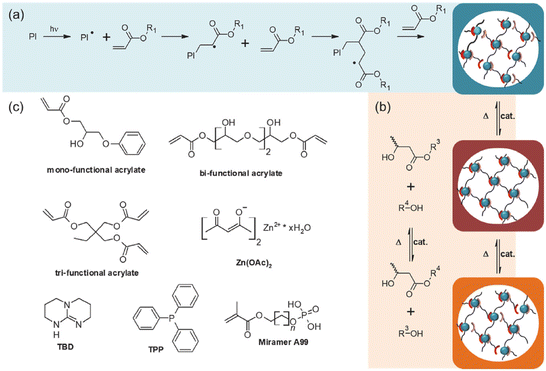 |
| Fig. 6 Illustration of photocuring and thermally reprocessable vitrimers. (a) Photocuring process; (b) thermal reprocessing via triggered exchange reactions; (c) monomers and catalysts used for the vitrimer system. Reproduced from ref. 101 with permission from Elsevier, 2021. | |
Hao et al. developed a crosslinked epoxy vitrimer network with accelerated dynamic transesterification that exhibited a Tg of 135 °C and tensile strength of 94 MPa.103 The epoxy vitrimer could be recycled into a fresh resin by grinding into a powder or degrading in an aqueous solution, and still maintain the same Tg and modulus as the original material. Similarly, Cui et al. developed a polythiourethane-based covalent adaptable network (CAN) with a Tg of 83 °C, Young's modulus of 1.2 GPa, and tensile strength of 61.9 MPa.104 Damaged and rejoined pieces of this material, as well as hot-pressed powder made from the 3D printing waste, were able to regain over 80% of the original tensile strength. Additionally, the material could be fully degraded by adding excess thiol to convert the polymer network to thiol-terminated oligomers. These vitrimer and CAN materials offer paths for full chemical recyclability and repair in AM materials.
To further drive the field of recyclable polymers for high-performance applications, Hernandez et al. demonstrated the ability to recycle 3D printed composite polymers by using thioester-containing networks. The 3D printed thioester-based composites could be degraded to recover over 90% of the composite filler, and the mass loss experiments were in agreement with a statistical model for thiol-thioester exchange.105 The capability of recycling composites makes attainable the material properties that are necessary for very durable and high-performance applications.
A recent advancement in photopolymer research beyond vitrimers and dynamic bonds is the incorporation of degradable crosslinks and bonds such that a thermoset polymer can be depolymerized to monomer or oligomer fragments to create new resins. A method of recycling thermosets resins for VP developed by Poelma et al. is to use reactive pre-polymers that can be recovered after 3D printing and reused in resins for printing new objects.57,106,107 Poelma et al. developed a method of partially recycling thermoset networks by extracting regenerable reactive prepolymers into a solvent, removing the solvent, and then collecting pre-polymers for printing as renewed resin, as shown in Fig. 7a.106 The collected pre-polymers could be used to form up to 90% of a new resin.
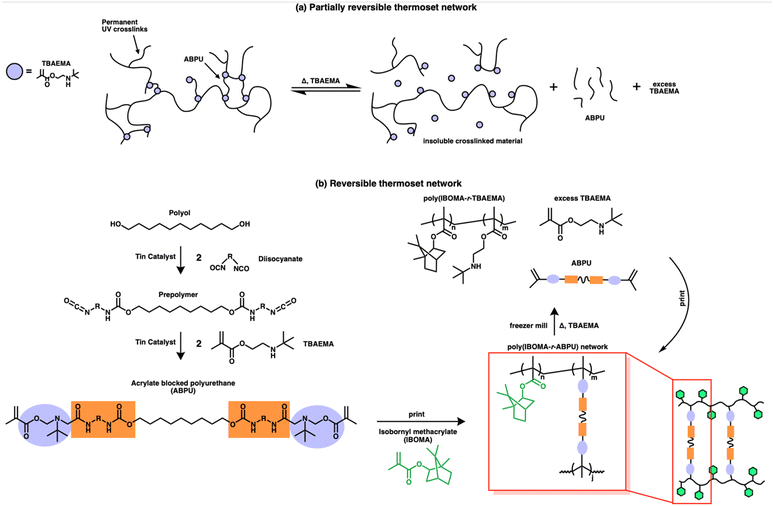 |
| Fig. 7 Illustration of reversible thermoset acrylate networks crosslinked by HUBs. (a) Partially reversible thermoset network with insoluble crosslinked materials after pre-polymer extraction; (b) reversible thermoset network with linear chains (comprised of a monofunctional monomer such as TBAEMA) and reversible crosslinks (comprised of acrylate blocked polyurethanes). The network can be degraded and recycled by comminuting the polymer via methods such as milling, then heated with the same initial reactive blocking agent (TBAEMA) to recover linear ABPUs. Reproduced from ref. 106 and 107. | |
This idea was then extended to develop a resin that can form a more reversible thermoset network, consisting of polyacrylate or polymethacrylate backbones crosslinked with acrylate-blocked polyurethanes/polyureas with hindered urea bonds (HUBs) as shown in Fig. 7b.57,107 The 3D printed object could be comminuted and heated with a reactive blocking agent (such as tert-butylaminoethyl methacrylate (TBAEMA)) to achieve a homogeneous solution or suspension for resins with up to 90% recycled pre-polymer that can be used for re-printing. This very high recovery and reuse rate for a thermoset material is an enabling step forward to achieving a fully chemically circular economy for high-performance materials.
The reduction in the amounts of raw materials needed for AM reduces the environmental impact of accessing feedstocks. However, degradable thermoset photopolymers often have high viscosities that limit their use in VP methods. The viscosity of the monomer resin needs to be low enough to flow during the printing process, either during the lift stage in techniques that use lift and retract mechanisms (SLA and DLP), or during continuous printing through the thin deadzone gap with CLIP. Currently, that viscosity limit is roughly 5 Pa s.108 While it is possible to reduce the viscosity of the resulting resin with, e.g., reactive diluents, to improve printability, these diluents can deteriorate the ultimate mechanical properties of the printed polymer part. There has been recent progress in improving the viscosity limitations of vat photopolymerizations by injecting resin to reduce the amount of time and volume of resin reflow.
In addition to diluents, solvents can help reduce viscosity of VP resins, but introduce new challenges such as post-print shrinkage and hazardous liquid wastes. To avoid solvent usage, Ding et al. developed a photocurable resin for AM by utilizing natural phenolic-based methacrylates and solvent-free thiol–ene click chemistry.109 Likewise, Bassett et al. used methacrylated vanillin, a derivative easily obtained from lignin, to create a vinyl ester resin (VER) that required no solvent for synthesis and used renewable reactants.110 The SLA-cured VER demonstrated a high Young's modulus of 4.9 GPa and Tg of 153 °C, similar to the properties of the VER when processed thermally. The ability to create resins with solvent-free synthesis introduces yet another pathway of sustainability upstream of physical manufacturing. This aids the field of AM to shift away from the use of petrochemical resources and hazardous solvents.
Among sustainable bio-based polymers, alginate, starches, oils, and proteins (such as silk fibroin) have been used to develop excellent biocompatible materials but lack the strength and thermomechanical stability to be used in extreme conditions.111–116,117 Though these bio-materials are not always suitable for high-performance applications, they do provide advancements for the challenges associated with bio-sourced AM materials such as low resolution, limited mechanical properties, and stability. For example, Shin et al. found that the inclusion of silk fibroin in poly(ethylene glycol)-tetraacrylate resins for DLP could enhance the resolution of printing.118 Additionally, Guit et al. synthesized a photopolymer resin for 3D printing using epoxidized soybean oil, and subsequently created a library of biobased methacrylates with tunable stiffness and toughness.119
Voet et al. has recently reviewed many other advances in biobased, sustainable photopolymers for 3D printing scopes including high performance application and beyond.120
Further perspectives
Sustainability, for AM and beyond, is a multifaceted goal that encompasses many approaches from material sourcing to energy consumption and waste management. In some cases, there may be trade-offs in sustainability while science continues to progress. For example, a perfectly degradable and recyclable thermoset may emerge, but it may rely on synthetic materials that are unsustainable. Likewise, a bio-based material may be sustainably sourced, but its processing may be energy intensive. Thus, it is difficult to define a single metric that can quantify the environmental impact of each development in AM. The many environmental dimensions of AM and the limited quantitative data on AM compared to traditional manufacturing have been summarized by Kellens et al.121 Here, we present further perspectives on AM and how it may impact the environment and society beyond materials development.
Waste production in AM processes
When considering the sustainability of AM materials, and their potential to realize a circular economy, it is also important to take into consideration the net waste savings, and costs, of the technology vs. traditional methods. One well-known way that AM promises to reduce material waste in manufacturing is through light-weighting of objects via latticing and topology optimization. Such lattices cannot be produced by traditional manufacturing techniques such as injection molding or subtractive manufacturing. In addition to requiring less material for part production itself, the weight-reduction of parts also lessens fuel consumption by large vehicles such as airplanes122 and automobiles.123 Nonetheless, there are still elements of AM that are wasteful themselves and require further technical advances to reduce overall footprint. For instance, the liquid waste resin from vat photopolymerization is considered a hazardous substance and must be properly stored and disposed.124 Removing some of the resin in liquid form after use is a significant overhead in printer operation and subsequently, the environmentally friendly disposal remains expensive.125 Some advances in liquid resin collection include centrifugation to remove liquid resin from printed parts so that the parts can be washed with little to no solvents, and the resin can be collected for reuse.126,127 Additionally, the support structures required for both extrusion and vat-based printing also generate single-purpose waste and consume raw materials.128 This highlights the importance of utilizing materials that are themselves degradable and reusable, even if the recovery of reusable materials or precursors is partial.106 Models are being developed to minimize scrap-to-part ratio and thus the material waste that results from excess material consumption during design and production.128,129 Ultimately, the sustainability of AM materials (and all materials) relies on first the reduction of waste production and raw material consumption, then the reuse of parts that do not need to be reprocessed, and finally the collection and recycling of materials to minimize unnecessary waste.
Opportunities for digital manufacturing
Additive manufacturing has enabled sustainable opportunities beyond materials, namely digital manufacturing. Digital manufacturing is the connection of computers and computer-aided design (CAD) models with production so that products and processes can be visualized and analyzed to improve efficiency before production begins.130 It also allows for the quantification and tracking of products so that more in-depth life cycle analyses can be performed. This capability will allow time-stamped data collection and over-the-air software upgrades to the developing tools, which will streamline their translation to commercial partners. One could also leverage the digital fabrication approaches developed to help create a future where every part made will have a unique machine-readable QR code imprinted on it that will be tied to a unique record in the cloud. In essence, every part will be “alive”, with all of its “born-on” time-stamped data (file, resin), its “in-use” and in-field performance data (i.e., an electrical connector that fails during use can be scanned by a repairman during servicing), and its death-to-recycle information to enable, perhaps for the first time, a quantitative longitudinal assessment of parts in an emerging circular economy.
For high-performance polymers that may require collection to a recycling facility to be depolymerized and recycled, a method of tracking products can give valuable insights on how much product is successfully recovered. This data can be critical for laying the foundation of new business models and practices. For example, better tracking of materials and product performances or failures can refine product recalls so that only products from the sub-section of production irregularity will need to be recalled. Additionally, this data may benefit regulatory agency confidence in additively manufactured products because it will now be possible to track adherence to product specifications and performance over the lifetime of a product.
Digital manufacturing provides the key for AM to move beyond just rapid prototyping to also provide on-demand inventory, local production of goods, flexible manufacturing plants, and access to previously impossible geometries for products. Digital manufacturing enabled by AM allows spare parts to be produced on-demand, which would eliminate the need for extra spare parts to be always held in-stock and thus also eliminate the need for their physical climate-controlled storage facilities. Additionally, the ability to access product models and manufacture a product quickly means that AM can bring more production back to local communities and avoid overseas shipping, and cut down on one of the largest air and water polluters.131 The transition to local, digital AM has contributions beyond environmental impacts: AM can bring product value back into circulation. According to UPS, over 3 percent of the world's GDP can be found in UPS delivery trucks or package cars daily.132 This huge economic value could be brought back into circulation simply by reducing the amounts of products that need to be transported.
Furthermore, production facilities that operate primarily on AM can switch production lines rapidly overnight as needed to accommodate the demands of the world. For example, a local shoe manufacturer can easily maneuver from producing sneakers to producing personal protective equipment (PPE) for emergency responders simply by changing the 3D model that is uploaded to the AM equipment. This change is nearly instantaneous and does not require a complete overhaul of the manufacturing plant, paving way for flexible manufacturing plants.
Eco-efficiency in AM
“Eco-efficiency”133 is a term used to describe efficient ecological and economical resource management, both of which can be achieved by improving materials sourcing, minimizing toxic material components, and enhancing recyclability. Often times, improving materials processing (and reprocessing) will allow for greater costs savings for companies (especially in high-cost applications such as high-performance products) in the form of reduced resource input, reduced liabilities and legal expenses, and improved relationships with all parties involved. Even if the sourcing and development of sustainable materials present a costly upfront investment, the amount of economic and ecological resources saved in the long-run will be beneficial for both public and private entities. Some examples of this include the elimination of toxic tin catalysts in polyurethane-based systems and the elimination of bisphenol-A (an endocrine disruptor) in epoxy systems. The change from the status quo to a safer, sustainable future requires a radical introduction, followed by the incremental transition to continue the step-by-step process of long-term improvement. This idea of eliminating toxic and hazardous substance usage proactively rather than cleaning up pollution reactively has been embodied in 3M's “Pollution Prevention Pays (3P)” program.134 The amount of money, time, and health saved for both public and private entities in preventing further ecological damage is often worth more than the immediate gains of continuing to use hazardous substances.
Eco-efficiency and pollution prevention can serve as powerful driving forces for AM as a developing field for large-scale manufacturing. The overarching theme of achieving sustainable materials and processes pushes research and development to have foresight in finding creative solutions to problems before they happen. The linkage of business/research excellence and environmental excellence elevates the notion that a sustainable future does not come at the cost of developing fields, but rather is an investment in the field. For example, in 3M's 3P program, the proactive investment in re-engineering processes and approaches to materials research and development resulted in over 2.6 billion pounds of pollutants prevented and over 1 billion dollars saved over the course of 30 years.135 The AM field can learn from 3M's success and use eco-efficiency to drive development in early stages, rather than having to reconsider and re-engineer prior standing processes. An eco-efficient mindset can provide the opportunities for massive advantages, both ecologically and economically.
Conclusions
Additive manufacturing is in a unique position to disrupt traditional methods of manufacturing. Scientists and engineers are equipped with the wisdom of foresight to prevent a decades-long amount of waste production caused by polymers from AM. While AM has the potential to reduce the amount of material waste and CO2 emissions compared to traditional manufacturing, it does not entirely eliminate waste production. In all forms of AM (material extrusion, vat photopolymerization, powder bed fusion, etc.), high-performance polymers can be engineered to be more sustainable and still meet material properties demands. Polymer sustainability may come from how raw materials are sourced or how final materials are degraded and recycled. Degradability for recycling comes in two forms: passive degradation and triggered degradation. For high-performance use cases, triggered degradation shows the most promise in offering high toughness, strength, strain-at-failure, or thermal and chemical resistance for polymers that will have specific environmental demands. A high-performance polymer that is fully recyclable under very specific but attainable conditions can both promote waste collection and reduce the amount of raw material needed for production. Chemical degradation of thermoset polymers for recycling may be the most promising pathway for high-performance materials because it requires a reduced energy input as compared to thermal degradation. However, further research is required to obtain “green” solvents for chemical degradation so that all elements of the recycling process will be sustainable. The progress and future of polymer research lies in both new polymerization methods and in crucial depolymerization methods. Successful achievement of various depolymerization pathways for high-performance polymers will pave the path for a more sustainable world with both chemical and economic circularity.
Contributions
Gloria Chyr: Conceptualization, writing – original draft, writing – review & editing. Joseph M. DeSimone: Conceptualization, writing – original draft, writing – review & editing.
Conflicts of interest
The authors declare the following financial interests/personal relationships which may be considered as potential competing interests: Joseph M. DeSimone reports financial support to our research group was provided by Wellcome Leap Fund and startup funds provided by Stanford University School of Medicine and the School of Engineering. Gloria Chyr reports financial support was provided by the Stanford University Precourt Institute of Energy. Joseph M. DeSimone reports a relationship with Carbon that includes cofounder equity.
Acknowledgements
The authors would like to acknowledge Gabriel Lipkowitz for contributions to perspectives on waste production in AM; Anna Makar-Limanov for perspectives on figures; Crista Farrell and Dr Maria Dulay for edits and feedback during the writing process. This work was supported by the Stanford University Precourt Institute of Energy.
References
- Kearney 3D Printing, https://www.kearney.com/operations-performance-transformation/article/?/a/3d-printing-disrupting-the-12-trillion-manufacturing-sector, (accessed April 10, 2022).
- I. Campbell, D. Bourell and I. Gibson, Rapid Prototyp. J., 2012, 18, 255–258 CrossRef.
- M. Gebler, A. J. M. Schoot Uiterkamp and C. Visser, Energy Policy, 2014, 74, 158–167 CrossRef CAS.
-
P. A. Kobryn, N. R. Ontko, L. P. Perkins and J. S. Tiley, Additive Manufacturing of Aerospace Alloys for Aircraft Structures, Air Force Research Lab Wright-Patterson AFB OH Materials and Manufacturing Directorate, 2006 Search PubMed.
- E. Sanchez-Rexach, T. G. Johnston, C. Jehanno, H. Sardon and A. Nelson, Chem. Mater., 2020, 32(17), 7105–7119 CrossRef CAS.
- D. J. Fortman, J. P. Brutman, G. X. De Hoe, R. L. Snyder, W. R. Dichtel and M. A. Hillmyer, ACS Sustainable Chem. Eng., 2018, 6, 11145–11159 CrossRef CAS.
- H. Kodama, Rev. Sci. Instrum., 1981, 52, 1770–1773 CrossRef.
-
C. Hull, 3D Systems Inc., United States, US5556590A, 1996.
- B. N. Turner and S. A. Gold, Rapid Prototyp. J., 2015, 21, 250–261 CrossRef.
- T. Rayna and L. Striukova, Technol. Forecast. Soc. Change, 2016, 102, 214–224 CrossRef.
- B. Wendel, D. Rietzel, F. Kühnlein, R. Feulner, G. Hülder and E. Schmachtenberg, Macromol. Mater. Eng., 2008, 293, 799–809 CrossRef CAS.
- J. D. Cawley, Curr. Opin. Solid State Mater. Sci., 1999, 4, 483–489 CrossRef.
- P. Colombo, G. Mera, R. Riedel and G. D. Sorarù, J. Am. Ceram. Soc., 2010, 93, 1805–1837 CAS.
- M. L. Griffith and J. W. Halloran, J. Am. Ceram. Soc., 1996, 79, 2601–2608 CrossRef CAS.
- J. Deckers, J. Vleugels and J.-P. Kruth, J. Ceram. Sci. Technol., 2014, 5, 245–260 Search PubMed.
- W. E. King, A. T. Anderson, R. M. Ferencz, N. E. Hodge, C. Kamath, S. A. Khairallah and A. M. Rubenchik, Appl. Phys. Rev., 2015, 2, 041304 Search PubMed.
- G. N. Levy, R. Schindel and J. P. Kruth, CIRP Ann. Manuf. Technol., 2003, 52, 589–609 CrossRef.
- B. Vayre, F. Vignat and F. Villeneuve, Mech. Ind., 2012, 13, 89–96 CrossRef CAS.
- D. D. Gu, W. Meiners, K. Wissenbach and R. Poprawe, Int. Mater. Rev., 2012, 57, 133–164 CrossRef CAS.
- S. Hong, D. Sycks, H. F. Chan, S. Lin, G. P. Lopez, F. Guilak, K. W. Leong and X. Zhao, Adv. Mater., 2015, 27, 4035–4040 CrossRef CAS PubMed.
- C. B. Highley, C. B. Rodell and J. A. Burdick, Adv. Mater., 2015, 27, 5075–5079 CrossRef CAS PubMed.
- O. Ivanova, C. Williams and T. Campbell, Rapid Prototyp. J., 2013, 19, 353–364 CrossRef.
- W. Liu, Y. Li, J. Liu, X. Niu, Y. Wang and D. Li, J. Nanomater., 2013, 2013, e681050 Search PubMed.
- C. Zhu, T. Liu, F. Qian, W. Chen, S. Chandrasekaran, B. Yao, Y. Song, E. B. Duoss, J. D. Kuntz, C. M. Spadaccini, M. A. Worsley and Y. Li, Nano Today, 2017, 15, 107–120 CrossRef CAS.
- A. J. Capel, R. P. Rimington, M. P. Lewis and S. D. R. Christie, Nat. Rev. Chem., 2018, 2, 422–436 CrossRef.
- J. Norman, R. D. Madurawe, C. M. V. Moore, M. A. Khan and A. Khairuzzaman, Adv. Drug Delivery Rev., 2017, 108, 39–50 CrossRef CAS PubMed.
- W. Jamróz, J. Szafraniec, M. Kurek and R. Jachowicz, Pharm. Res., 2018, 35, 176 CrossRef PubMed.
- S. V. Murphy and A. Atala, Nat. Biotechnol., 2014, 32, 773–785 CrossRef CAS PubMed.
- K. Dubbin, Y. Hori, K. K. Lewis and S. C. Heilshorn, Adv. Healthcare Mater., 2016, 5, 2488–2492 CrossRef CAS PubMed.
- C. D. Lindsay, J. G. Roth, B. L. LeSavage and S. C. Heilshorn, Acta Biomater., 2019, 95, 225–235 CrossRef CAS PubMed.
- D. Bourell, J. P. Kruth, M. Leu, G. Levy, D. Rosen, A. M. Beese and A. Clare, CIRP Ann., 2017, 66, 659–681 CrossRef.
- A. Kirillova, T. R. Yeazel, D. Asheghali, S. R. Petersen, S. Dort, K. Gall and M. L. Becker, Chem. Rev., 2021, 121, 11238–11304 CrossRef CAS PubMed.
-
S. Scott Crump, Stratasys Inc., United States, US5121329A, 1992.
-
B. L. Douglass and C. R. Douglass III, Douglass InnovationsInc., United States, US20150037446A1, 2015.
- R. Merz, F. B. Prinz, K. Ramaswami, M. Terk and L. E. Weiss, Int. Solid Freeform Fab. Symp., 1994, 1–8 CAS.
- J. A. Lewis, Adv. Funct. Mater., 2006, 16, 2193–2204 CrossRef CAS.
- M. Agarwala, D. Bourell, J. Beaman, H. Marcus and J. Barlow, Rapid Prototyp. J., 1995, 1, 26–36 CrossRef.
-
A. S. Kabalnov, J. T. Wright and V. Kasperchik, World Intellectual Property Organization, WO2016175748A1, 2016.
-
R. Hochsmann, I. Ederer and ExOne GmbH, United States, US7807077B2, 2010.
-
C. A. Chatham, M. J. Bortner, B. N. Johnson, T. E. Long and C. B. Williams, Predicting Mechanical Property Plateau in Laser Polymer Powder Bed Fusion Additive Manufacturing via the Critical Coalescence Ratio, Social Science Research Network, Rochester, NY, 2021 Search PubMed.
- J. Huang, Q. Qin and J. Wang, Processes, 2020, 8, 1138 CrossRef CAS.
- Z. Zhao, X. Tian and X. Song, J. Mater. Chem. C, 2020, 8, 13896–13917 RSC.
- J. R. Tumbleston, D. Shirvanyants, N. Ermoshkin, R. Janusziewicz, A. R. Johnson, D. Kelly, K. Chen, R. Pinschmidt, J. P. Rolland, A. Ermoshkin, E. T. Samulski and J. M. DeSimone, Science, 2015, 347, 1349–1352 CrossRef CAS PubMed.
- R. Janusziewicz, J. R. Tumbleston, A. L. Quintanilla, S. J. Mecham and J. M. DeSimone, Proc. Natl. Acad. Sci. U. S. A., 2016, 113, 11703–11708 CrossRef CAS PubMed.
- A. R. Johnson, C. L. Caudill, J. R. Tumbleston, C. J. Bloomquist, K. A. Moga, A. Ermoshkin, D. Shirvanyants, S. J. Mecham, J. C. Luft and J. M. DeSimone, PLoS One, 2016, 11, e0162518 CrossRef PubMed.
- H. O. T. Ware and C. Sun, J. Micro Nano-Manuf., 2019, 7(3), 031001 CrossRef CAS PubMed.
- A. A. Bhanvadia, R. T. Farley, Y. Noh and T. Nishida, Commun. Mater., 2021, 2, 1–7 CrossRef.
- J. Bachmann, E. Gleis, G. Fruhmann, J. Riedelbauch, S. Schmölzer and O. Hinrichsen, Addit. Manuf., 2021, 37, 101677 CAS.
- C. L. Caudill, J. L. Perry, S. Tian, J. C. Luft and J. M. DeSimone, J. Controlled Release, 2018, 284, 122–132 CrossRef CAS PubMed.
- C. Caudill, J. L. Perry, K. Iliadis, A. T. Tessema, B. J. Lee, B. S. Mecham, S. Tian and J. M. DeSimone, Proc. Natl. Acad. Sci. U. S. A., 2021, 118, e2102595118 CrossRef CAS PubMed.
- M. Geissdoerfer, P. Savaget, N. M. P. Bocken and E. J. Hultink, J. Cleaner Prod., 2017, 143, 757–768 CrossRef.
- K. Boulding, Res. Pap. – Resour. Future, 1966, 1–14 Search PubMed.
- A. V. Kneese, Popul. Dev. Rev., 1988, 14, 281–309 CrossRef.
- N. D. Miller and D. F. Williams, Biomaterials, 1984, 5, 365–368 CrossRef CAS PubMed.
- M. J. Krause and T. G. Townsend, Environ. Sci. Technol. Lett., 2016, 3, 166–169 CrossRef CAS.
- E. M. Maines, M. K. Porwal, C. J. Ellison and T. M. Reineke, Green Chem., 2021, 23, 6863–6897 RSC.
-
J. Poelma, J. P. Rolland, R. H. N. Curvers and J. M. DeSimone, Carbon Inc., United States, US20210394399A1, 2021.
- K. J. Jem and B. Tan, Adv. Ind. Eng. Polym. Res., 2020, 3, 60–70 Search PubMed.
- T. Kitamura and A. Matsumoto, Macromolecules, 2007, 40, 509–517 CrossRef CAS.
- P. Gentile, V. Chiono, I. Carmagnola and P. V. Hatton, Int. J. Mol. Sci., 2014, 15, 3640–3659 CrossRef CAS PubMed.
- B. K. Lee, Y. H. Yun, J. S. Choi, Y. C. Choi, J. D. Kim and Y. W. Cho, Int. J. Pharm., 2012, 427, 305–310 CrossRef CAS PubMed.
- J. Korpela, A. Kokkari, H. Korhonen, M. Malin, T. Närhi and J. Seppälä, J. Biomed. Mater. Res., Part B, 2013, 101, 610–619 CrossRef PubMed.
- G. A. Appuhamillage, J. C. Reagan, S. Khorsandi, J. R. Davidson, W. Voit and R. A. Smaldone, Polym. Chem., 2017, 8, 2087–2092 RSC.
- F. A. Cruz Sanchez, H. Boudaoud, S. Hoppe and M. Camargo, Addit. Manuf., 2017, 17, 87–105 CAS.
- J. Shojaeiarani, D. S. Bajwa, C. Rehovsky, S. G. Bajwa and G. Vahidi, Polymers, 2019, 11, 58 CrossRef PubMed.
- B. Brüster, F. Addiego, F. Hassouna, D. Ruch, J.-M. Raquez and P. Dubois, Polym. Degrad. Stab., 2016, 131, 132–144 CrossRef.
- N. E. Zander, M. Gillan, Z. Burckhard and F. Gardea, Addit. Manuf., 2019, 25, 122–130 CAS.
- M. J. Reich, A. L. Woern, N. G. Tanikella and J. M. Pearce, Materials, 2019, 12, 1642 CrossRef CAS PubMed.
- A. Le Duigou, M. Castro, R. Bevan and N. Martin, Mater. Des., 2016, 96, 106–114 CrossRef.
- D. Kam, M. Layani, S. BarkaiMinerbi, D. Orbaum, S. A. BenHarush, O. Shoseyov and S. Magdassi, Adv. Mater. Technol., 2019, 4, 1900158 CrossRef CAS.
- G. Siqueira, D. Kokkinis, R. Libanori, M. K. Hausmann, A. S. Gladman, A. Neels, P. Tingaut, T. Zimmermann, J. A. Lewis and A. R. Studart, Adv. Funct. Mater., 2017, 27, 1604619 CrossRef.
- J. H. Lora and W. G. Glasser, J. Polym. Environ., 2002, 10, 39–48 CrossRef CAS.
- R. J. A. Gosselink, E. de Jong, B. Guran and A. Abächerli, Ind. Crops Prod., 2004, 20, 121–129 CrossRef CAS.
-
D. Mudgil and S. Barak, in Dietary Fiber: Properties, Recovery, and Applications, Elsevier, 2019, pp. 27–58 Search PubMed.
- N. A. Nguyen, S. H. Barnes, C. C. Bowland, K. M. Meek, K. C. Littrell, J. K. Keum and A. K. Naskar, Sci. Adv., 2018, 4(12), 4967 CrossRef PubMed.
- B. Hu, X. Duan, Z. Xing, Z. Xu, C. Du, H. Zhou, R. Chen and B. Shan, Mech. Mater., 2019, 137, 103139 CrossRef.
-
K. M. Rahman, T. Letcher and R. Reese, in Volume 2A: Advanced Manufacturing, American Society of Mechanical Engineers, Houston, Texas, USA, 2015, p. V02AT02A009 Search PubMed.
- US Patent for Reversible thermosets for additive manufacturing Patent (Patent # 11,135,744 issued October 5, 2021) – Justia Patents Search, https://patents.justia.com/patent/11135744, (accessed December 7, 2021).
- S. Saleh Alghamdi, S. John, N. Roy Choudhury and N. K. Dutta, Polymers, 2021, 13, 753 CrossRef PubMed.
- B. Panda, S. C. Paul, L. J. Hui, Y. W. D. Tay and M. J. Tan, J. Cleaner Prod., 2017, 167, 281–288 CrossRef CAS.
- J. Davidovits, J. Therm. Anal., 1991, 37, 1633–1656 CrossRef CAS.
- A. Akbarnezhad, M. Huan, S. Mesgari and A. Castel, Constr. Build. Mater., 2015, 101, 152–158 CrossRef.
-
M. Despeisse and S. Ford, in Advances in Production Management Systems: Innovative Production Management Towards Sustainable Growth, ed. S. Umeda, M. Nakano, H. Mizuyama, H. Hibino, D. Kiritsis and G. von Cieminski, Springer International Publishing, Cham, 2015, pp. 129–136 Search PubMed.
- K. Mikula, D. Skrzypczak, G. Izydorczyk, J. Warchoł, K. Moustakas, K. Chojnacka and A. Witek-Krowiak, Environ. Sci. Pollut. Res., 2021, 28, 12321–12333 CrossRef PubMed.
-
N. E. Zander, in Polymer-Based Additive Manufacturing: Recent Developments, American Chemical Society, 2019, vol. 1315, pp. 37–51 Search PubMed.
- K. Yang, J. C. Grant, P. Lamey, A. Joshi-Imre, B. R. Lund, R. A. Smaldone and W. Voit, Adv. Funct. Mater., 2017, 27, 1700318 CrossRef.
- Y. Guo, S. Chen, L. Sun, L. Yang, L. Zhang, J. Lou and Z. You, Adv. Funct. Mater., 2021, 31, 2009799 CrossRef CAS.
- Q. Shi, K. Yu, X. Kuang, X. Mu, C. K. Dunn, M. L. Dunn, T. Wang and H. J. Qi, Mater. Horiz., 2017, 4, 598–607 RSC.
- O. Davydovich, J. E. Paul, J. D. Feist, J. E. Aw, F. J. Balta Bonner, J. J. Lessard, S. Tawfick, Y. Xia, N. R. Sottos and J. S. Moore, Chem. Mater., 2022, 34, 8790–8797 CrossRef CAS.
- O. Gülcan, K. Günaydın and A. Tamer, Polymers, 2021, 13, 2829 CrossRef PubMed.
-
I. Gibson, D. Rosen, B. Stucker and M. Khorasani, in Additive Manufacturing Technologies, ed. I. Gibson, D. Rosen, B. Stucker and M. Khorasani, Springer International Publishing, Cham, 2021, pp. 203–235 Search PubMed.
- C. A. Chatham, T. E. Long and C. B. Williams, Prog. Polym. Sci., 2019, 93, 68–95 CrossRef CAS.
- J. W. Stansbury and M. J. Idacavage, Dent. Mater., 2016, 32, 54–64 CrossRef CAS PubMed.
- S. Vock, B. Klöden, A. Kirchner, T. Weißgärber and B. Kieback, Prog. Addit. Manuf., 2019, 4, 383–397 CrossRef.
- E. M. Wilts and T. E. Long, Polym. Int., 2021, 70, 958–963 CrossRef CAS.
- Y. Wang, Z. Xu, D. Wu and J. Bai, Materials, 2020, 13, 2406 CrossRef CAS PubMed.
-
R. Goodridge and S. Ziegelmeier, in Laser Additive Manufacturing, ed. M. Brandt, Woodhead Publishing, 2017, pp. 181–204 Search PubMed.
- S. Kumar and A. Czekanski, Mater. Today Commun., 2018, 15, 109–113 CrossRef CAS.
-
I. Gibson, D. Rosen, B. Stucker and M. Khorasani, Additive Manufacturing Technologies, Springer International Publishing, Cham, 2021 Search PubMed.
- B. Zhang, K. Kowsari, A. Serjouei, M. L. Dunn and Q. Ge, Nat. Commun., 2018, 9, 1831 CrossRef PubMed.
- E. Rossegger, R. Höller, D. Reisinger, M. Fleisch, J. Strasser, V. Wieser, T. Griesser and S. Schlögl, Polymer, 2021, 221, 123631 CrossRef CAS.
- W. Zhao, L. An and S. Wang, Polymers, 2021, 13, 296 CrossRef CAS PubMed.
- C. Hao, T. Liu, S. Zhang, W. Liu, Y. Shan and J. Zhang, Macromolecules, 2020, 53, 3110–3118 CrossRef CAS.
- C. Cui, L. An, Z. Zhang, M. Ji, K. Chen, Y. Yang, Q. Su, F. Wang, Y. Cheng and Y. Zhang, Adv. Funct. Mater., 2022, 32, 2203720 CrossRef CAS.
- J. J. Hernandez, A. L. Dobson, B. J. Carberry, A. S. Kuenstler, P. K. Shah, K. S. Anseth, T. J. White and C. N. Bowman, Macromolecules, 2022, 55, 1376–1385 CrossRef CAS.
-
R. H. N. J. Poelma and R. H. N. Curvers, World Intellectual Property Organization, WO2021183741A1, 2021.
-
J. Poelma, M. S. Zhang, X. Gu, J. P. Rolland and J. M. DeSimone, Carbon Inc., United States, US011299576B2, 2022.
- J. Herzberger, J. M. Sirrine, C. B. Williams and T. E. Long, Prog. Polym. Sci., 2019, 97, 101144 CrossRef CAS.
- R. Ding, Y. Du, R. B. Goncalves, L. F. Francis and T. M. Reineke, Polym. Chem., 2019, 10, 1067–1077 RSC.
- A. W. Bassett, A. E. Honnig, C. M. Breyta, I. C. Dunn, J. J. La Scala and J. F. Stanzione, ACS Sustainable Chem. Eng., 2020, 8, 5626–5635 CrossRef CAS.
- S. E. Bakarich, M. in het Panhuis, S. Beirne, G. G. Wallace and G. M. Spinks, J. Mater. Chem. B, 2013, 1, 4939–4946 RSC.
- E. Axpe and M. L. Oyen, Int. J. Mol. Sci., 2016, 17, 1976 CrossRef PubMed.
- B. Duan, L. A. Hockaday, K. H. Kang and J. T. Butcher, J. Biomed. Mater. Res., Part A, 2013, 101, 1255–1264 CrossRef PubMed.
- A. G. Tabriz, M. A. Hermida, N. R. Leslie and W. Shu, Biofabrication, 2015, 7, 045012 CrossRef PubMed.
- B. C. Maniglia, D. C. Lima, M. D. Matta Junior, P. Le-Bail, A. Le-Bail and P. E. D. Augusto, Int. J. Biol. Macromol., 2019, 138, 1087–1097 CrossRef CAS PubMed.
- J. Jia, D. J. Richards, S. Pollard, Y. Tan, J. Rodriguez, R. P. Visconti, T. C. Trusk, M. J. Yost, H. Yao, R. R. Markwald and Y. Mei, Acta Biomater., 2014, 10, 4323–4331 CrossRef CAS PubMed.
- X. Mu, V. Fitzpatrick and D. L. Kaplan, Adv. Healthcare Mater., 2020, 9, 1901552 CrossRef CAS PubMed.
- S. Shin, H. Kwak and J. Hyun, ACS Appl. Mater. Interfaces, 2018, 10, 23573–23582 CrossRef CAS PubMed.
- J. Guit, M. B. L. Tavares, J. Hul, C. Ye, K. Loos, J. Jager, R. Folkersma and V. S. D. Voet, ACS Appl. Polym. Mater., 2020, 2, 949–957 CrossRef CAS.
- V. S. D. Voet, J. Guit and K. Loos, Macromol. Rapid Commun., 2021, 42(3), 2000475 CrossRef CAS PubMed.
- K. Kellens, M. Baumers, T. G. Gutowski, W. Flanagan, R. Lifset and J. R. Duflou, J. Ind. Ecol., 2017, 21, S49–S68 CrossRef.
- S. K. Moon, Y. E. Tan, J. Hwang and Y.-J. Yoon, Int. J. Precis. Eng. Manuf. – Green Technol., 2014, 1, 223–228 CrossRef.
- S. Shanmugam, A. Naik, T. Sujan and S. Desai, INCOSE Int. Symp., 2019, 29, 394–407 CrossRef.
- Formlabs Customer Support, https://support.formlabs.com/, (accessed September 9, 2022).
- How Much Does Hazardous Waste Disposal Cost?, https://www.howmuchisit.org/hazardous-waste-disposal-cost/, (accessed March 21, 2022).
-
A. R. Day, K. J. Kwok and W. J. Tucker, World Intellectual Property Organization, WO2020069152A1, 2020.
-
R. G. Price, E. J. Sabathia Jr. and B. E. Feller, Carbon, Inc., United States, US20210237358A1, 2021.
-
R. Schmidt and N. Umetani, in ACM SIGGRAPH 2014 Studio, Association for Computing Machinery, New York, NY, USA, 2014, p. 1 Search PubMed.
- J. Jiang, X. Xu and J. Stringer, CIE48 Proceedings, 2018, 1–7 Search PubMed.
- D. Mourtzis, N. Papakostas, D. Mavrikios, S. Makris and K. Alexopoulos, Int. J. Comput. Integr. Manuf., 2015, 28, 3–24 Search PubMed.
- O. US EPA, Reducing Air Pollution from International Transportation, https://www.epa.gov/international-cooperation/reducing-air-pollution-international-transportation, (accessed December 6, 2021).
- UPS Supports The Administration To Serve The Economic And Healthcare Interests Of The Nation | About UPS, https://about.ups.com/us/en/newsroom/press-releases/customer-first/ups-supports-the-administration-to-serve-the-economic-and-healthcare-interests-of-the-nation, (accessed December 7, 2021).
-
L. D. DeSimone and F. Popoff, Eco-efficiency: The Business Link to Sustainable Development, MIT Press, 2000 Search PubMed.
-
M. G. Royston, Pollution Prevention Pays, Elsevier, 2013 Search PubMed.
- O. US EPA, 3M – Lean Six Sigma and Sustainability, https://www.epa.gov/sustainability/3m-lean-six-sigma-and-sustainability, (accessed September 7, 2022).
|
This journal is © The Royal Society of Chemistry 2023 |
Click here to see how this site uses Cookies. View our privacy policy here.