DOI:
10.1039/D3CC01555F
(Feature Article)
Chem. Commun., 2023,
59, 9929-9951
Deriving high value products from depolymerized lignin oil, aided by (bio)catalytic funneling strategies
Received
30th March 2023
, Accepted 10th July 2023
First published on 26th July 2023
Abstract
Lignin holds tremendous and versatile possibilities to produce value-added chemicals and high performing polymeric materials. Over the years, different cutting-edge lignin depolymerization methodologies have been developed, mainly focusing on achieving excellent yields of mono-phenolic products, some even approaching the theoretical maximum. However, due to lignin's inherent heterogeneity and recalcitrance, its depolymerization leads to relatively complex product streams, also containing dimers, and higher molecular weight fragments in substantial quantities. The subsequent chemo-catalytic valorization of these higher molecular weight streams, containing difficult-to-break, mainly C–C covalent bonds, is tremendously challenging, and has consequently received much less attention. In this minireview, we present an overview of recent advances on the development of sustainable biorefinery strategies aimed at the production of well-defined chemicals and polymeric materials, the prime focus being on depolymerized lignin oils, containing high molecular weight fractions. The key central unit operation to achieve this is (bio)catalytic funneling, which holds great potential to overcome separation and purification challenges.
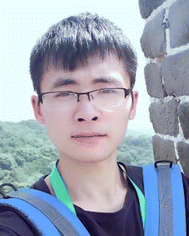
Xianyuan Wu
| Dr Xianyuan Wu was born in Anhui, China. He received his bachelor's degree in 2010 from Huaibei Normal University. Then he moved to Zhejiang University of Technology to pursue his Master degree, with the research focusing on the continuous upgrading of ethanol to butanol over supported metal catalysts. In 2018, he worked as a PhD candidate under the direction of Prof. Katalin Barta at the University of Groningen, with the research topic of catalytic transformation of lignocellulosic biomass into well-defined chemicals and polymeric materials. He has been visiting researcher at the University of Graz with a specialization of recyclable bio-based polymers. He has recently started his post-doctoral work at Massachusetts Institute of Technology, on catalytic plastic waste recycling and upcycling. |

Mario De bruyn
| Dr Ir. Mario De bruyn received his PhD in 2004 from the Centre for Surface Science and Catalysis at the Catholic University of Leuven (Belgium), work done on the selective hydrogenation of α,b-unsaturated ketones to allylic alcohols using heterogeneous catalysts, under the supervision of Prof. P. A. Jacobs and Prof. D. E. De Vos. From 2004 to 2007 he worked as an Aron Zandman postdoctoral fellow at the Weizmann Institute of Science in Israel on oxidative dehydrogenation under the guidance of Prof. Ronny Neumann. Moving into the industrial direction he then engaged in cosmetic materials research work for LVMH and Merck KgaA in France. In 2010 he took on a research associate position at the Green Chemistry Centre of Excellence, in the group of Prof. James Clark, at the University of York (UK). There he worked on various academic/industrial research assignments in the broad sphere of green- and sustainable chemistry. In 2017 he received a Marie Curie Global Fellowship to do research on sustainable heterogeneous catalysis in the groups of Prof. James Dumesic (UW-Madison), Prof. George Huber (UW-Madison) and Prof. Bert Weckhuysen (Utrecht University). Since 2020 he is a senior university assistent in the group of Prof. Katalin Barta at the Institute of Chemistry of the Karl-Franzens University Graz (Austria). |

Katalin Barta
| Katalin Barta is full professor at the University of Graz in Austria since 2019, leading the Sustainable catalysis unit at the Institute for Chemistry. Reflecting her international background, she received her master's degree in the group of Prof. István T. Horváth at ELTE Budapest (Hungary) and her PhD at RWTH Aachen, under the direction of Walter Leitner in asymmetric catalysis and ligand design. Between 2008–2010, she worked on the transformation of lignocellulosic biomass into value-added chemicals and liquid transportation fuels, as a postdoctoral fellow in the group of Prof. Peter C. Ford at the University of California, Santa Barbara. Afterwards, she was post-doctoral researcher and Associate Research Scientist (2010–2012) at Yale University, the Center for Green Chemistry and Engineering with Prof. P. T. Anastas and Prof. Julie B Zimmerman. In 2013 she joined the Stratingh Institute for chemistry, University of Groningen to start her independent research career where she was promoted Associate Professor in 2017. |
1. Introduction
Society's growing dependence on chemicals and performing polymeric materials, most of which being (still) derived from non-renewable petroleum, natural gas and coal, has led to an increased demand for the development of more sustainable chemical (manufacturing) routes, these preferentially being based on the use of renewable resources such as lignocellulosic biomass.1,2 Lignocellulosic waste generated from forestry and agriculture, representing an abundantly available non-food-competitive resource, has been projected as a promising alternative to petroleum resources for the production of bio-fuels, (drop-in) chemicals, and bio-derived polymers.3–14 Currently, the industrial biorefinery scene (e.g., sulfite pulping industry) mainly focuses on the valorization of the (hemi)cellulose fraction of lignocellulose, predominately converting it to paper. Through this process also a large amount of lignosulfonate is created; This is a valuable side-product with known applicability in the construction and plasticizer industry. In a further advancement, a range of other high value-added and sugar-derived chemicals (e.g. ethanol, ethylene glycol and 5-HMF) have also been produced.15–27 However, the potential of lignin remains largely underexploited due to its inherent structural complexity, heterogeneity, and recalcitrance.28–30 This constitutes however a missed opportunity as lignin represents ∼30% of the lignocellulosic biomass and is a rich and unique source of bio-aromatics, thus holding great potential as a source of chemicals.3–14,31,32
Over the past few decades, much progress has been achieved regarding the alkaline and oxidative depolymerization of lignin, process being related to pulping industry.33–36 More recently, reductive catalytic fractionation (RCF) of lignin have surfaced as elegant and promising techniques to turn lignin into valuable monomers.37–41 Concurrently, also thermal lignin depolymerization processes (e.g., pyrolysis) have been a focus point of development.42–44 Furthermore, very recent advances in the field have also seen a revival of oxidative lignin depolymerization methodologies, the alternative target being aromatic monomers.45 Of note to most of these technologies is the simultaneous production of oligomeric and polymeric saccharide/lignin fractions (Fig. 1). Present day, a large body of research works and reviews can be found on the downstream transformation of lignin-derived platform molecules to added-value compounds and fuels.3–14 With these approaches often focusing on the transformation of model monophenolic compounds, using a range of (classic) chemical tools, the direct use of real lignin-derived bio-oils containing dimeric and oligomeric product streams featuring difficult-to-break covalent bonds (e.g., C–C) has been markedly less explored. This relates mainly to high complexity of raw lignin-derived bio-oils, the often-low yields of single target products, and the required use of tedious multistage separation strategies and the lack of robust catalysts.46–49 In marked contrast, state-of-the-art chemical methodologies capable of dealing with the inherent complexities of lignin-derived bio-oils, allowing to produce valuable compounds from lignin in higher yields have been described. In this minireview, we summarize the latest advances on these novel chemical technologies.
 |
| Fig. 1 Comprehensive overview of the three main lignin depolymerization strategies, their commonly encountered operating conditions, and their most important chemical outcomes. | |
1.1 Oxidative depolymerization
Oxidative depolymerization of lignin is a well-developed methodology implemented at an industrial scale by the Borrrgaard company, primarily for vanillin production from lignosulphonates, main side-products generated from sulfite pulping processes. The process is typically performed at high temperature and pressure and is run in the presence of a Cu2+ catalyst, a suitable oxidant (most typically O2) and strongly alkaline conditions (Fig. 2A).33–36 Depolymerization of softwood lignosulphonates has been achieved with heterogeneous catalysts in the presence of oxygen and yields vanillin as the major product. Typical yields of vanillin from softwood sources are on the order of 5–7 wt% on lignin basis, leaving much room for improvement.50,51 Recent years have seen numerous attempts to increase the vanillin yield through the development of new more performing oxidative catalytic systems such as through the use of Pd/CeO2, CuO, LaFeO3, La/SBA-15 (See Table 1).52–61 To date, and to the best of our knowledge, the highest vanillin yield of ∼25 wt% on a lignin basis was obtained from pine lignocellulose in the presence of catalytic CuO and a NaOH aqueous solution (160 °C, 10 bar O2).62
 |
| Fig. 2 An overview of the production of vanillin from lignin and its subsequent valorizations. (A) Borregaard process of oxidative depolymerization of lignosulfonate to vanillin. (B) Downstream processing methodologies of vanillin into chemicals, polymers, and surfactants. | |
Table 1 Representative overview of the outcome of oxidative depolymerization processes on soft- and hardwood lignins
Entry |
Feedstock |
Catalyst |
Reaction conditions |
Yield of main products (wt%)a |
Ref. |
T (°C) |
P (bar) |
T (min) |
Vanillin |
Syringaldehyde |
4-Hydroxy benzylaldehyde |
Yield calculated based on lignin content in each wood.
Softwood lignosulfonate was provided by Borregaard, Norway.
The origins and types of wood were not mentioned.
Pine wood was provided from Idaho National lab.
Pinus silvestris pine.
Cryptomeria japonica cedar.
Eucalyptus was provided from South China.
Eucalyptus globulus were supplied by Caima-Industria de Celulose SA (Constancia, Portugal).
Beech wood was provided from Yunnan, China.
Eucalyptus globulus from Portuguese bleached kraft pulp plant.
Poplar was raised at the University of Wisconsin Arlington, provided by the Great Lakes Bioenergy research Concenter.
Microwave Irradiation.
|
1 |
Softwood |
CuSO4 5H2O |
160 |
O2, 11–12 atm |
∼30 |
∼6.8 |
— |
— |
51
|
Lignosulfonateb |
NaOH |
2 |
Pinec |
NaOH |
160 |
O2, 10 bar |
160 |
21.1 |
— |
— |
53
|
3 |
Pined |
LaMn0.8Cu0.2O3 |
175 |
O2, 5 bar |
10 |
17.3 |
— |
— |
55
|
NaOH |
He, 15 bar |
4 |
Pine |
CuSO4 5H2O |
160 |
O2, 30 bar |
25 |
18.6 |
— |
— |
58
|
Lignine |
NaOH |
5 |
Japanese Cedarf |
Bu4NOH·30H2O |
120 |
Atmospheric |
2580 |
16.6 |
— |
— |
59
|
Air |
6 |
Organosolv |
Pd/CeO2 |
185 |
O2, 10 bar |
1440 |
5.2 |
— |
— |
60
|
Ligninc |
7 |
Pinec |
CuO |
160 |
O2, 10 bar |
120 |
25 |
— |
— |
62
|
NaOH |
8 |
Eucalyptusc |
NaOH |
160 |
O2, 10 bar |
60 |
8.2 |
20.4 |
— |
53
|
9 |
Bagassec |
CuO |
165 |
O2, 10 bar |
60 |
8.9 |
12.9 |
5.2 |
62
|
NaOH |
10 |
Eucalyptusg |
CuCl |
160 |
Air, 5 bar, |
60 |
7.5 |
24 |
— |
57
|
NaOH |
11 |
Eucalyptus Lignosulfonateh |
CuSO4 |
150 |
O2, 10 bar |
20 |
4.5 |
16.1 |
— |
70
|
NaOH |
12 |
Cornstalk |
LaCoCO3 |
120 |
O2, 5 bar |
50 |
5.0 |
10.0 |
— |
71
|
Ligninc |
NaOH |
13 |
Beech woodi |
La/SBA-15 |
MIl 200 W |
H2O2 |
10 |
9.6 |
15.7 |
— |
72
|
Lignin |
NaOH |
14 |
Mixed hardwood |
CuSO4 [mmim][Me2PO4] |
175 |
O2, 25 bar |
90 |
14.3 |
8.5 |
6.9 |
73
|
Lignin |
15 |
Eucalyptus |
NaOH |
120 |
O2, 3 bar |
120 |
4.4 |
10.3 |
— |
74
|
Ligninj |
16 |
Cornstalk |
LaFeO3 |
120 |
O2, 5 bar |
30 |
4.0 |
9.0 |
1.0 |
75
|
Ligninc |
17 |
Poplar |
CuSO4 |
160 |
Air, 25 bar |
45 |
6.5 |
13.3 |
3.8 |
76
|
Lignink |
NaOH |
18 |
Eucalyptusc |
CuO |
160 |
O2,10 bar |
60 |
10.5 |
29.2 |
— |
62
|
NaOH |
Presently, vanillin is the only commercially available lignin derivative, its uses mainly residing to flavoring and fragrance applications in the food and cosmetic industries.63,64 It is estimated that ∼3000 tons of lignosulfonate is converted to bio-based vanillin per year, accounting for ∼15% of the total production of vanillin, and this near exclusively by the Norwegian company Borregaard.63,64 Due to the presence of two reactive moieties in vanillin, an aldehyde and a phenol, vast potential exists for its use towards the production of valuable derivatives (e.g., vanillyl alcohol) as well as high-performing polymers (Fig. 2B).65–69 By extension, significant efforts have also been devoted to the oxidative depolymerization of hardwood lignin and hardwood lignosulfonates. Generally, this results in a higher overall yield of monophenolics, these typically comprising syringaldehyde, vanillin and 4-hydroxybenzaldehyde.53,57,62,70–76 A comprehensive set of results are available from Table 1. Exemplary are (a) the depolymerization of hardwood lignosulfonate in the presence of CuSO4 and NaOH, yielding vanillin and syringaldehyde in respectively 4.5 and 16.1% yields on a lignin basis;70 and (b) the ionic liquid aided oxidative depolymerization of lignin, which gives a mixture of syringaldehyde, vanillin, 4-hydroxybenzyl aldehyde, in respectively 8.5, 14.3 and 6.9 wt% on a lignin basis.73 More recently, Zhu et al. reported a very high yield of syringaldehyde (29.2 wt%) and vanillin (10.5 wt%) as obtained from the oxidative depolymerization of Eucalyptus and this using an aqueous NaOH solution and CuO as the catalyst (10 bar O2).62
Separation of said aldehydes can be achieved following a multi-step purification protocol based on the use of sodium bisulfite (Na2SO3). The latter reagent reacts with the aldehyde groups to form charged bisulfite adducts, compounds which can be separated from one another by electrophoresis but which can also be separated from other neutral compounds by liquid–liquid extraction.77,78 Recovery of the original aldehydes can then be achieved by acidification or basification63,64 Alternatively, and more recently, the Stahl group introduced the use of centrifugal partition chromatography to isolate individual aromatic chemicals obtained from the oxidative alkaline depolymerization of hardwood.76
1.2 Reductive catalytic fractionation (RCF)
Reductive catalytic fractionation (RCF) of lignocellulosic biomass, has emerged as an innovative ‘’lignin first’’ biorefinery strategy, capable of deriving value from both lignin while also retaining saccharides in a largely unaltered form.37–41 Typically, RCF involves three key events, namely (1) solvolytic delignification; (2) solvolytic and catalytic lignin depolymerization and (3) stabilization of formed lignin monomers. Thereby the latter stabilization step is crucial as to avoid re-polymerization and condensation of lignin-derived monomers.79 The main side products to RCF are poly- and oligosaccharides among which cellulose and hemicellulose.37–41 Central to this methodology is the use of a heterogeneous redox catalyst, which in the presence of hydrogen gas or a hydrogen donor engages in both the catalytic depolymerization of the lignin and the stabilization of any unsaturated reactive reaction products (i.e., lignin-derived monomers with C
C bonds) released by the solvolysis process (Fig. 3A).37–41
 |
| Fig. 3 (A) A schematic representation of the RCF process. (B) RCF-based integrated lignin biorefinery process depicting both the lignin depolymerization and catalytic downstream processing aspects. | |
Over the past years, several RCF methodologies have been developed. Generally, these give good-to-excellent yields of lignin-derived (low molecular weight) monomers as well as some higher molecular weight dimers and oligomers. Typically, the product distributions and the individual product yields are highly dependent on the plant species, used catalyst, and the operation conditions.80–95Table 2 lists a range of recently published RCF methodologies, specifically detailing the feedstock, the type of catalyst, the reaction conditions and the product yields. For example, RCF of softwood lignocellulose (e.g., pine, spruce) in the presence of heterogeneous metal catalyst and hydrogen gas yields in between 10–35 wt% lignin-derived monomers on a lignin basis. Characteristically, the monomeric fraction is rich in 4-propanol guaiacol (1G) or 4-propyl guaiacol (2G), two compounds which can be isolated/separated by simple distillation (Fig. 3B). Due to their unique structural features, both 1G and 2G can serve as versatile starting materials for the construction of a wide range of well-defined chemicals, biologically active pharmaceuticals, fuels, and polymer building blocks, and this by means of already existing synthetic strategies or by the development of new selective catalytic methods, as for instance shown in Fig. 3B.32,82,96–100
Table 2 Representative work of RCF reported phenolic monomers yields
Entry |
Feedstock |
Catalyst |
Reaction conditions |
Yield of main products (wt%) |
Monomer yield (wt%)a |
Ref. |
Solvent |
T (°C) |
P (bar) |
T (h) |
Yield calculated based on lignin content in each wood.
Pinus radiata.
Pine was provided by Aveve, Belgium.
Pine was provided by local, Netherlands.
Spruce (Picea abies) was provided by Bern University of Applied Science, Switzerland).
Birch (Betula pendula) was provided by Ecobois, Ghent, Belgium).
Beech (Fagus sylvatica) sawdust was provided by Dansk Træmeland.
Poplar was provided by local, Netherlands.
The origins and types of wood were not mentioned.
Pine was provided by Ecobois, Ghent, Belgium.
Betula pendula.
Genus Populus.
Birch was provided by staatsbosbeheer, The Netherlands.
|
1 |
Pineb |
Pd/C |
Dioxane/H2O (1 : 1) |
195 |
H2 (34.5) |
24 |
1G (20.8) |
22.4 |
80
|
2 |
Pinec |
Pd/C |
Methanol |
235 |
H2 (30) |
3 |
1G (13.9) |
34.4 |
81
|
3 |
Pined |
Cu-PMO |
Methanol |
180 |
H2 (40) |
18 |
1G (8.7) |
10.0 |
82
|
4 |
Spruce lignine |
Pd/C |
Dioxane |
200 |
H2 (40) |
15 |
1G (18.3) |
20.1 |
83
|
5 |
Birchf |
Pd/C |
Methanol |
250 |
H2 (30) |
3 |
1S (35.2), 1G (9.7) |
49.3 (C-yield) |
84
|
6 |
Beechg |
Ni/C |
Methanol/H2O (3 : 2) |
200 |
H2 (60) |
5 |
1S (28.9), 1G (9.8) |
51.4 |
85
|
7 |
Poplarh |
Cu-PMO |
Methanol |
180 |
H2 (40) |
18 |
1S (15.1), 1G (10.2) |
36 |
82
|
8 |
Poplari |
Pd/C |
Methanol/H2O (7 : 3) |
200 |
H2 (20) |
3 |
1S (21.5), 1G (14.0) |
43.5 |
86
|
9 |
Eucalyptusi |
Ru/C |
Butanol/H2O (1 : 1) |
200 |
H2 (30) |
2 |
1S (35.1), 1G (6.1) |
48.8 |
87
|
10 |
Eucalyptusi |
Pt/C |
Butanol/H2O (1 : 1) |
200 |
H2 (30) |
2 |
1S (29.0), 1G (5.3) |
49.3 |
87
|
11 |
Birchf |
Ni/Al2O3 |
Methanol/H2O (7 : 3) |
250 |
H2 (30) |
3 |
1S + 1G (21.0) |
36 |
88
|
12 |
Pinei |
Pt/C |
Methanol/H2O (1 : 2) |
230 |
H2 (30) |
3 |
2G |
11.7 |
89 |
13 |
Pinej |
Ru/C |
Methanol |
235 |
H2 (30) |
3 |
2G |
14.1 |
90
|
14 |
Birchi |
Ni/C |
Methanol |
200 |
Ar (1) |
6 |
2S (36.2), 2G (11.9) |
54 |
91
|
15 |
Birchk |
Ru/C |
Methanol |
250 |
H2 (30) |
6 |
2S (30.5), 2G (10.4) |
51.5 (C-Yield) |
92
|
16 |
Poplarl |
Zn/Pd/C |
Methanol |
225 |
H2 (34.5) |
12 |
2S (29.7), 2G (24.3) |
54 |
93
|
17 |
Birchi |
NiFe/C |
Methanol |
200 |
H2 (20) |
6 |
2S (23.7), 2G (11.1) |
39.5 |
94
|
18 |
Birchm |
Pt/γ-Al2O3 |
Methanol/H2O (1 : 2) |
230 |
N2 (30) |
3 |
2S + 2G (46.1) |
49 |
95
|
When running the RCF process from hardwood (e.g., birch, beech, eucalyptus, and poplar) lignocellulose in the presence of a suitable heterogeneous metal catalyst (e.g., Pd/C, Ni/C, Cu20PMO, Ru/C, Pt/C and Ni/Al2O3), the resulting reaction product contains typically in between 36–50 wt% monomers, a high proportion of which is 4-propanol syringol (1S) and 1G (Table 2). For example, RCF of poplar wood at 200 °C/20 bar H2 in the presence of Pd/C and a methanol/water (7
:
3) solvent mixture gave a total monomer yield of 43.5% wt%, larger than 80% of which was found to be 1S (21.5 wt%) and 1G (14 wt%).86 Modifying the Pd/C catalyst with Zn and applying a somewhat higher reaction temperature (225 °C) and hydrogen pressure (34.5 bar), was found to shift the composition of the monomer fraction towards the 1S/1G hydrodeoxygenated products propanolsyringol (2S) (29.7 wt%) and 2G (24.3 wt%).93
1.3 Base-catalyzed depolymerization
Base-catalysed depolymerization of lignin is a classic delignification pre-treatment used in the paper and pulp industry to produce high quality cellulose pulp.101,102 It is traditionally performed at high reaction temperatures (240–340 °C) and high pressures (∼10 MPa). Typically, the reaction is run in the presence of homogeneous bases (e.g., NaOH, KOH, LiOH, K2CO3), that way targeting cleavage of the β-O-4, α-O-4 and 4-O-5 linkages and yielding low-molecular weight phenolics.102–105 The product distributions and selectivity are highly dependent on the applied catalysts, the used reaction conditions as well as the lignin origins. Typical product streams resulting from this depolymerization strategy constitute low-molecular weight monophenolics (e.g., phenol, guaiacol, catechol, syringol, vanillin) and some related oligomers.102–105
High temperature base-catalyzed lignin depolymerization (HBCD) has been studied by several groups. For example, Miller et al. has investigated the influence of a series of different bases in the HBCD process (290 °C).106 It was concluded that HBCD performed with stronger bases such as KOH, NaOH is much more likely to yield low-molecular weight monomers than when weaker bases (e.g. LiOH, Na2CO3) are used.106 Chornet and co-workers developed a purification protocol capable of isolating 12 valuable monomers generated in the HBCD process of steam exploded Aspen lignin. To this purpose use was made of vacuum distillation, liquid chromatography and crystallization.107 Typically, HBCD yields less than 20 wt% monomers because of the condensation of instable lignin intermediates.108,109 In this respect, Labidi's group found that the addition of phenol (as a capping agent) during the HBCD process effectively suppresses the oligo- and polymerization of instable lignin intermediates, thus yielding significantly higher amounts of monomeric phenols. Intriguingly, the use of boric acid as an alternative capping agent led to a more dominant formation of phenolic dimers.108
Recently, base-catalysed depolymerization performed at low reaction temperature (i.e., lower than 120 °C) (LBCD) has received increasing attention while it tends to yield a lower number of but more functionalized phenolics (e.g., sinapic acid, ferulic acid, p-coumaric acid and vanillic acid) than generally obtained with HBCD.103 Although the LBCD yield of monophenolics is lower than the one obtainable with HBCD, LBCD does hold significant downstream advantages. One such advantage is the fact that natural microorganisms can catabolize aromatic acids/aldehydes – a most typical feature of sinapic acid, ferulic acid, p-coumaric acid and vanillin – into biodegradable polymers and other well-defined chemicals.110–113
1.4 Pyrolysis
Pyrolysis is a thermal degradation process run at an elevated temperature and in the absence of oxygen. Through this technique lignocellulose can be transformed into a mixture of gaseous products, bio-oil and bio-char in typically unselective manner.114–116 Generally, three different types of pyrolysis are being discerned being slow pyrolysis, fast pyrolysis and flash pyrolysis. Critical changeable factors here are the heating rate, the pyrolysis temperature, and the residence time of a feed substrate. Slow pyrolysis of lignocellulose is typically performed at lower operating temperatures and long residence time, and tends to favor the formation of bio-char. In contrast, fast pyrolysis is run at temperatures between 400–600 °C and involves short residence times and high heating rates. Depending on the reactor configuration, fast pyrolysis has been shown to give liquid product yields as high as 60–80%. Typically, such a bio-oil consists of a complex mixture of aliphatics, aromatics, and phenolics (not limiting). The bio-oil yield in a fast pyrolysis process can reach up to 75 wt%. Product distributions vary on the composition of the biomass.114–116 Flash pyrolysis is an ultra-fast type of pyrolysis, featuring very rapid heating rates (>1000 °C s−1) and very high reaction temperatures on the order of 900–1300 °C. Flash pyrolysis has also been shown to afford high yields of bio-oil (∼70%).114–117
Generally, due to the complex, instable and corrosive nature of pyrolysis bio-oil, its subsequent downstream processing follows strategies different from those of milder depolymerization strategies. Pyrolysis is a much-explored methodology to convert lignocellulose into valuable hydrocarbons (e.g., BTX) and bio-fuels.118
2. Downstream processing strategies of depolymerized lignin oils
Aside the outcomes of lignin depolymerization processes, increasingly more attention is being given to the subsequent catalytic downstream processing of lignin-derived bio-oils into useful marketable products, fuels, and bio-materials.119 But while presently much literature is available on the transformation of lignin-derived model compounds into useful (often high value) compounds, this is much less the case for the further downstream transformation of real complex lignin-derived bio-oils. In this respect, the biggest challenges relate to the complexity, heterogeneity, and recalcitrance of crude lignin-derived bio-oils.
2.1 Functionalization
With oxidative depolymerization of lignocelluloses yielding complex mixtures of monophenolic aldehydes, ketones and acids,33–36,52–61 purification of these into single pure compounds is commonly perceived as uneconomical. To circumvent this problem, some strategies have been devised that can valorize such unrefined complex lignin-oils in a more direct manner. Exemplary to this methodology, Torr and co-workers have demonstrated the synthesis of some novel bio-based epoxy resins from a lignin hydrogenolysis bio-oil derived from RCF of softwood (e.g., pine), as shown in Fig. 4.120 In a typical process, native pine wood was subjected to RCF over a Pd/C catalyst (34 bar H2, 195 °C), yielding a lignin hydrogenolysis oil mainly comprised of phenolic monomers, dimers and oligomers.120 The abundant phenolics present in such lignin hydrogenolysis oil can be directly reacted with epichlorohydrin to give epoxidized lignin hydrogenolysis oil (LHEP). The resulting LHEP was blended with stoichiometric amounts of bisphenol A diglycidyl ether (BADGE) or glycerol diglycidyl ether (GDGE), and subsequently cured with diethylenetriamine (DETA) or isophorone diamine (IPDA). The so obtained bio-based epoxy resins displayed better flexural modulus (FM) and flexural strength (FS) but inferior thermal properties than achievable with the one made from pure BADGE alone. Further optimizations on glycidylation and resin formulation are still needed to produce fully bio-based epoxy resin with properties to the industry standard. Subsequent work on the preparation of similar high-performance bio-based thermoset polymers has been made from hardwood-derived lignin hydrolysis oils.121
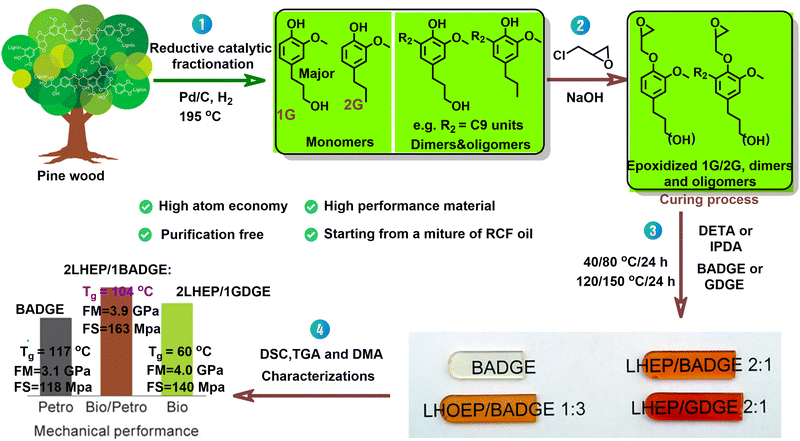 |
| Fig. 4 Overview of the synthesis of high-performance bio-based epoxy resins from lignin oil mixtures. Reproduced from ref. 120 with permission from American Chemical Society, 2020. | |
The beneficial influence of rich hydroxyl group in depolymerized lignin oil has also been explored with other industrially relevant polymer types such as polyurethanes (PUs). The latter polymer class is typically produced by the copolymerization of an isocyanate with a polyol, topping a current global production of 25 million metric tons in 2021 (i.e. 6% of the total polymer production).122–124 Furthermore, due to their tunable properties, PUs hold a remarkably wide applications, ranging from medical devices, packaging materials, water treatment systems to flame retardants and optical sensors.124–127 The synthesis of rigid bio-based PUs from softwood-derived lignin oil was reported by the Torr group and comprises two consecutive reaction steps.128 Step 1 entailed RCF of pine wood, resulting in crude lignin oil which was subjected to further purification (i.e. extraction, separation and fractionation) to provide mono- and dimer-rich phenolic lignin oil. Step 2 then concerned the co-polymerization of purified lignin oil and co-polyols with polymeric methylene diphenyl diisocyanate (pMDI), resulting in a bio-based PU foams with promising compression modulus and strength (Fig. 5). The here presented strategies that sustainably derive value from largely unrefined complex lignin oils offer great perspectives to the future commercial development of biorefineries, these not necessarily requiring the presence of extensive and expensive lignin-derived bio-oil upgrading capabilities.
 |
| Fig. 5 Schematic representation of the production of bio-based PUs from lignin hydrolysis oils (LHO) as obtainable from the RCF of pine wood. Reproduced from ref. 128 with permission from the American Chemical Society, 2021. | |
Aside epoxy resins and PUs, the technique of using largely unrefined lignin oils for direct polymerization has also been successfully demonstrated for the case of polyacrylates. Polyacrylates are commonly encountered polymers in the fields of plastics, adhesives, rubber, coating and paint formulations, a matter which largely relates to their excellent thermal and mechanical properties as well as their transparency.129–131 As an example, the Epps’ group developed a methodology to make bio-based polyacrylates (and further on high performing pressure sensitive adhesives) from a hexane-extracted lignin oil rich in 2G and 2S (Fig. 6).129 This methodology comprises three consecutive reaction steps: (1) Ru/C catalyzed RCF of poplar wood, followed by hexane extraction as a sole and minimal purification step, that way giving a 2G/2S-enriched lignin oil fraction; (2) Direct functionalization of the phenolic OH groups present in 2G and 2S with either acrylate or methacrylate groups; and (3) RAFT (reversible-addition–fragmentation chain-transfer) polymerization of (meth)acrylate modified 2G/2S, leading to poly (4pSA-co-4pGA) with promising thermal properties. In a further advancement, RAFT polymerization of pure 4pSA with n-butylacrylate to yield low dispersity triblock polymers with excellent adhesive properties.
 |
| Fig. 6 Overview of the synthesis of high-performance pressure sensitive adhesives (PSAs) from purified lignin oil. Reproduced from ref. 129 with permission from the American Chemical Society, 2018. | |
2.2 Funneling
While the above-described clever functionalization strategies can take actual advantage of multicomponent lignin oils, another interesting methodology to mitigate/reduce the complexity of lignin oils is by funneling two or more of its components to single central product. This has the added benefit that a higher nominal yield of a compound can be achieved. Typically, funneling strategies rely on partial (or even complete) defunctionalisation of the original compounds. Also, often such tailoring of the molecules also tends to lead to easier isolation/separation procedures. Below will discuss both chemical and enzymatic funneling while these two methodologies have already proven very versatile and powerful.
2.2.1 Chemocatalytic funneling.
Recent years has seen the development of a range of funneling methodologies capable of reducing the complexity of crude (or modelled) depolymerized lignin streams. Exemplary is our recent work on lignin-derived 4,4′-methylenebiscyclohexanamine (MBCA), a compound which could be created in a multicatalytic fashion from a mixture of three aromatic aldehydes, notably 4-hydroxybenzaldehyde, vanillin and syringaldehyde. Moreover, it was demonstrated that MBCA could serve the construction of fully bio-based polybenzoxazines (Fig. 7).132 In this respect it is noteworthy that MBCA is presently industrially produced by the hydrogenation of 4,4′-diaminophenylmethane (DDM) and a commonly encountered ingredient in a number of high-performance polymers.133 More specifically, the newly developed MBCA synthesis procedure comprises the following steps: (1) the selective reduction of 4-hydroxybenzaldehyde, vanillin and syringaldehyde using Pd/Al2O3 to a mixture of benzylalcohols (respectively 4-hydroxybenzylalcohol, vanillyl alcohol, syringic alcohol)– it is thereby noteworthy that the used mixture of aromatic aldehydes is readily available from the lignin-to-vanillin process; (2) Amberlyst 15 mediated electrophilic aromatic substitution of said benzylalcohols with phenol to a mixture of bisphenols; (3) demethoxylation and hydrogenation of the attained bisphenol mixture towards a mixture rich in 4,4′-methylenebiscyclohexanol (MBC) over RANEY® Nickel; (4) A RANEY® Nickel mediated near quantitative di-amination of MBC to MBCA in the presence of ammonia – a most interesting step as the RANEY® Nickel also featured as the funneling catalyst in step 3; and (5) the creation of benzoxazine monomer by Mannich condensation of MBCA diamine with naturally occurring sesamol and paraformaldehyde. (6) Thermally induced ring opening polymerization of benzoxazine monomer, yielding polybenzoxazine with desired thermal properties (Tg = 315 °C, T5% = 365 °C) comparable to bisphenol A/F based polybenzoxazines.132
 |
| Fig. 7 Turning complex lignin-derived mixtures into synthetically useful monomers (MBC-diol and MBCA-diamine) and thereof derived high-performance polyesters, polycarbonates and polybenzoxazines. | |
In a further advancement on this theme, we also explored the formation of MBC-containing polyesters such as with 2,5-furandicarboxylic acid (FDCA), terephthalic acid (TPA) and adipic acid (AA) (Fig. 7).134 Most interestingly, and building on the fact that MBC occurs as a mixture of three isomers (cis–cis, cis–trans and trans–trans), it could be shown that the use of pure MBC isomers, as well as pre-defined MBC mixtures, allowed for tailored tuning of the polyester properties. While methanolysis of these polyesters allowed for the recovery of the individual monomers, an end-of-use option was also evaluated whereby recovered MBC was converted to a set of sustainable jet fuels JF-1 and JF-2. This could be achieved by a deep hydrodeoxygenation of MBC using Ni/HZSM-5 (Fig. 7).
In addition to polyesters, also the creation of MBC-based polycarbonates (PC) was investigated and this both from isomeric pure MBC as well as MBC mixtures (PC-MBCcis–cis, PC-MBCcis–trans, PC-MBCtrans–trans and PC-MBCmixture). It was found that the stereoisomerism of MBC allows for flexible tuning of the thermal properties of these polycarbonates, and this over a remarkably wide temperature range of 117 to 174 °C.135 Importantly, these polycarbonates hold great potential as sustainable alternatives to a wide range of commercial polycarbonates (e.g., PC-BPA(bisphenol A), PC-BGA (bisguaiacol) and PC-BPF(bisphenol F). The so created MBC-based polycarbonates are generally film-forming and transparent. And due to the presence of only aliphatic cyclic structures in the polymeric backbone, they are also possibly less susceptible to degradation by UV-light (Fig. 7). This could constitute a significant advantage over aromatic BPA and other bisphenol/bisguaiacol-containing polycarbonates.
Summarizing, the here developed innovative MBC/MBCA synthesis from a mixture of three lignin-derived components has concisely demonstrated the possibility to make state-of-the-art polymers from complex mixtures using the funneling technique, a matter which will undoubtedly inspire the development of more sustainable lignocellulosic biorefinery practices.
Polyethylene terephthalate (PET) is one of the most widely used polyesters worldwide, with an annual production of 70 million tons.136–138 PET is industrially produced by a two-step (low and high T) copolymerization of petroleum-derived terephthalic acid (TPA) with ethylene glycol (EG). It is characterized by excellent thermal (Tg = 76 °C, Tm = 247 °C) and mechanical properties (Tensile strength: 55–75 MPa, Yong's modulus: 2800–3100 MPa).139 Recent years has seen a pronounced shift to bio-based PET whereby the central building monomer TPA were produced from lignocellulose-derived platform compounds.140–146 Only few of examples concern the synthesis of TPA from RCF oil of lignin, a feature successfully achieved by Yan's group. More specifically, they reported a three-step catalytic sequence able to convert depolymerized lignin oil into TPA (15 wt% on lignin basis) (Fig. 8). The first aspect to this strategy involved the elimination of aromatic methoxy groups by means of a MoOx/AC catalyst, yielding a mixture of 4-alkylphenols. Following, these 4-alkylphenols were carbonylated (with CO) to 4-alkylbenzoic acids, and subsequently oxidized (with O2) into terephthalic acid using a Co–Mn–Br catalyst.146
 |
| Fig. 8 Schematic representation of chemical funneling and functionalization of depolymerized lignin oil obtained from RCF of corn stover into TPA. | |
Polystyrene (PS) is another major class of synthetic polymers with vast applications in the fields of packaging and insulation.147 PS is currently produced by the polymerization of styrene, which is most commonly produced from ethylbenzene. From a bio-based perspective, the butadiene-based Diels–Alder synthesis of styrene (or ethylbenzene), which runs over the vinylcyclohexene intermediate, is probably most relevant as butadiene can be easily sourced from bioethanol.148 With though ethylbenzene being an aromatic compound, significant effort has also been devoted to its synthesis from lignin oils. Exemplary in this respect is the production of ethylbenzene from lignin oil rich in 1G and 1S obtained from Pd/C catalyzed RCF of a birch wood in the presence of RuFe/Nb2O5 catalyst as reported by the Wang group (Fig. 9).149 Central to this invention is the presence of FeOx which on the one side decreases the amount of metallic Ru0 species therewith favoring the dehydrogenative decarbonylation process of the Cpropanol–O bond, and on the other side, enhances the number of Nb4+ species and oxygen vacancies on the Nb2O5 surface, thus promoting the cleavage of the CAr–O bonds. With though an ethylbenzene yield of less than 10 wt% (on lignin basis), this strategy holds great promise but requires still significant further development and optimization.
 |
| Fig. 9 Schematic representation of the production of bio-based ethylbenzene through catalytic funneling of depolymerized lignin oil. The numbers in black reflect percentages on a lignin basis while those in blue refer to lignin oil. | |
Phenol is a very versatile and important platform chemical that has been widely used as a key intermediate to the synthesis of a broad array of polymers/resins (e.g., phenol-formaldehyde), polymer precursors (e.g., bisphenol A for epoxy resin) and pharmaceutical building blocks as in the synthesis of Aspirin.150 Currently, the main production of phenol runs over the well-known Hock process where cumene is first oxidized to cumene hydroperoxide and then further cleaved to form phenol and acetone.151 With cumene being though derived from benzene, a most hazardous compound, the route is far from sustainable.152,153 Fortunately, over the years many alternative and sustainable pathways to phenol from lignin have been developed.90,154 In this respect the Sels’ group showed that a 2S/2G lignin oil, obtained by a Ru/C mediated RCF procedure of lignocellulose, can be further transformed into phenol and propylene (Fig. 10). Central to this process sits a two-step catalytic sequence whereby first a Ni/SiO2 catalysed demethoxylation of the 2S/2G compounds occurs and in a second stage, the resulting products are dealkylated by a Z140-H zeolite to yield phenol (20 wt% on a lignin basis) and propylene (9 wt% on a lignin basis). It was further shown that any residual phenolic dimers and oligomers produced in this process could be processed into a high-quality lithographic printing ink following a three-step procedure, details of which are displayed in Fig. 10. This achievement holds significant importance as it provides an alternative for traditional lithographic inks, which tend to contain p-nonylphenol, a compound which can cause severe skin burns and eye damage, and which is also very toxic to aquatic life.155 With this proposed integrated biorefinery strategy, 78 wt% of birch lignocellulose is converted to tailored value-added chemicals, lithographic printing ink and carbohydrates, paving the way to real industrial relevance, and reduced carbon footprint.
 |
| Fig. 10 A comprehensive biorefinery strategy aimed at the production of phenol, propylene, printing ink and bioethanol from birch lignocellulose. | |
As to the valorization of the dimeric and oligomeric lignin fraction (derived from birch lignin), which tends to be void of phenolic interunit ether linkages, the Samec's group used a powerful oxidative catalytic methodology (Bobbitt's salt) to cleave the abundantly available CAr–C bonds, therewith forming and liberating 2,6-dimethoxybenzoquinone (DMBQ) in up to 18 wt% isolated yield on lignin basis (Fig. 11).156 Most interestingly, follow up work by the Barta group on the defunctionalization of DMBQ using RANEY® Nickel – a readily available industrial catalyst – provided a route to 1,4-cyclohexanediol in up to 86,5% yield. Furthermore, it was also shown that the same RANEY® Nickel catalyst could equally convert 1,4-cyclohexanediol into 1,4-cyclohexanediamine in the presence of ammonia and this in a near quantitative fashion. With both 1,4-cyclohexanediol and 1,4-cyclohexanediamine holding vast industrial relevance as monomers for polymer synthesis and as pharmaceutical building blocks, this does constitute a significant achievement.157
 |
| Fig. 11 Schematic representation of a procedure to make DMBQ, 1,4-cyclohexanediol and 1,4-cyclohexanediamine from oligomeric lignin, a typical waste lignin fraction from reductive catalytic fractionation of lignocellulosic biomass. | |
Another elegant example of chemical funneling is the RCF of beech wood lignocellulose using copper modified hydrotalcite/porous oxide (Cu20PMO) as the catalyst. At mild temperature and in the presence of H2 this has been found capable of turning lignin into a mixture of 1G and 1S. Using RANEY® Nickel and HZSM-5 in the presence of H2, these two compounds can then be elegantly funneled into 4-(3-hydroxypropyl)cyclohexan-1-ol (PC) reaching an isolated yield of 11.7 wt% on a lignin basis (Fig. 12). In the process, the other components present in the crude RCF lignin oil were converted to a range of alkanes with suitable (jet) fuel properties and reaching an actual total carbon yield of 29.5%.158 In a further advancement, the asymmetric PC diol was copolymerized with cellulose-derived methyl esters of terephthalic acid (TPA) and 2,5-furan dicarboxylic acid (FDCA) to fully bio-based polyesters [respectively poly(PC/TPA) and poly(PC/FDCA)]. Interestingly, the thermal properties of poly(PC/TPA) and poly(PC/FDCA) were found very comparable with those of polyethylene terephthalate (PET). Principally, the above-described methodology can be universally applied to lignin oils of very different origin. Overall, this approach presents a comprehensive methodology to convert lignocellulosic biomass into a range of fuel-grade alkanes and a polymer building block.159
 |
| Fig. 12 A comprehensive biorefinery strategy capable of turning lignocellulose into fuel-grade alkanes and polymeric building blocks. The latter can be used to make recyclable PET analogues. | |
Amination constitutes a great opportunity for catalytic funneling as it allows for an integrated separation of the N-containing amine products as their corresponding HCl salts. This idea features prominently in recent work by our group, namely, the RANEY® Ni catalyzed one-pot amination of a semi-fractionated RCF hardwood lignin oil in the presence of ammonia and H2. Firstly, lignin oil obtained from the RCF of birch wood [Ru/C catalyzed], was subjected to fast fractionation and distillation, that way yielding a monomeric mixture of 2G (33%) and 2S (65%). Reductive amination of the latter mixture in the presence of H2 allowed for the convergent synthesis of 4-propylcyclohexylamine (82% selectivity), an industrially relevant compound. Importantly, with the main side products of this synthetic procedure being methanol and water, this procedure holds strong green credentials. Isolation of 4-propylcyclohexylamine as its HCl salt was achieved in 6.7 wt% on a lignin basis (Fig. 13).160 Another example of catalytic funneling by means of amination concerned the amination of a softwood (pine) derived RCF lignin oil. In contrast to the above, this ran over a hydrogen borrowing methodology and gave highly pure 1G amine (as its HCl salt) in 4.6 wt% yield on a lignin basis. The latter compound is a structurally important motif to a range of pharmaceuticals such as cuspareine, capsazepine, and galipeine.161 Overall, these two examples do show the potential and capability of amination in conjunction with hydrogenation steps to obtain N-containing products from the complexity of lignin oils. Moreover, in the process, value-added primary amines are produced and this with minimal purification efforts.
 |
| Fig. 13 Process schemes of two different funneling strategies of RCF lignin oils featuring convergent amination. | |
2.3 Biological funneling
Aside chemical funneling methods, also biological funneling has been successfully explored to create tailored chemicals from lignin (Fig. 14).162–169 However, due to the heterogeneity and complexity of lignin oil, as well as the distinct presence of a range of often toxic acids, aldehydes, and phenolics therein, microbial/enzymatic catabolism of lignin oil poses significant challenges.170,171 To that end, efforts are underway to find, modify, and create microbes/enzymes with broad catabolic capabilities and a high toxicity tolerance.
 |
| Fig. 14 Lignin depolymerization and biological funneling strategy via microbial metabolism toward production of a range of value-added products for the applications of chemicals and polymers. | |
2-pyrone-4,6-dicarboxylic acid (PDC) is a potentially interesting building block that has been used to the making of polyesters, rubber, and epoxy adhesives.172–176 Different groups have described different biological methodologies capable of obtaining PDC by enzymatic catabolism of lignin-derived model compounds or directly lignin oil.177–184 Exemplary is recent work by the Noguera group where mixtures of phenolics stemming from distinct lignin depolymerization procedures were biologically funneled by the engineered bacterium Novosphingobium aromaticivorans DSM12444 to 2-pyrone-4,6-dicarboxylic acid (PDC). This methodology proved widely applicable to a range of woody biomass, yielding no less than 139 g PDC per kg poplar wood lignin. In the specific cases of maple, sorghum, and switch-grass lignin, the respective attainable PDC quantities were 88, 103 and 79 g.177 It has been proposed that the metabolic pathway of G and H aromatic units to PDC involves firstly their transformation into protocatechuic acid (PCA), which is followed by a 4,5 extradiol dioxygenase (LigAB) mediated ring opening to 4-carboxy-2-hydroxy-cis,cis-muconate-6-semialdehyde (CHMS). Oxidation of the latter compound by a dehydrogenase LigC then yields PDC (isolated as the corresponding sodium salt) (Fig. 15).178 In contrast, the metabolic route for the formation of PDC from S aromatic units is predicted to be different in the sense that syringic acid is first demethylated to 3-methylgallate (3-MGA) by means of an O-demethylase (DesA). Ring opening of 3-MGA to 4-carboxy-2-hydroxy-6-methoxy-6-oxohexa-2,4-dienoate (CHMOD) is then catalyzed by LigAB, a route which may also yield PDC as a parallel product. Alternatively, it has also been reported that CHMOD can be converted to PDC.178
 |
| Fig. 15 Schematic representation to produce PDC from depolymerized lignin oil mixture. (A) An integrated pathway combining chem-catalyzed lignin depolymerization and microbial funneling of resulting a mixture of phenolic monomers into PDC. (B) Proposed metabolic pathway toward the formation of PDC from lignin-derived monomers. Reproduced from ref. 177 with permission from the Royal Society of Chemistry, 2022. | |
Gallate (3,4,5-trihydroxybenzoic acid) is an industrially important chemical, which is widely used in the food, pharmaceutical, and cosmetic industries.185,186 Recently, Cai et.al have described a novel integrated pathway to bio-based gallate from real lignin by combining chemical lignin depolymerization with biological funneling (Fig. 16).187 More in depth, corn stover lignin was first subjected to a base-catalyzed (NaOH) depolymerization step, that way yielding a depolymerized lignin stream rich in p-coumarate, p-hydroxybenzoate, ferulate, syringate, vanillate. Secondly, it was found possible to convert a large part of this lignin oil to gallate by biological funneling. More specifically, it was shown that Rhodococcus opacus PD630-GA4 could engage in the parallel/consecutive hydroxylation, O-demethylation, and aryl side-chain oxidation of a range of lignin-derived monoaromatics to gallic acid. As a result, an excellent 63 wt% yield to gallate (0.63 g g−1 lignin) could be obtained.
 |
| Fig. 16 Illustrative scheme of the production of bio-based gallate from lignin by the combined use of a chem-catalyzed depolymerization of lignin and a biological funneling method based on Rhodococcus opacus PD630-GA4 as a biocatalyst. Reproduced from ref. 187 with permission from the American Association for the Advancement of Science, 2019. | |
Muconic acid (MA) is a well-known platform molecule from which principally adipic acid and terephthalic acid can be produced. The latter two compounds are central building blocks to the synthesis of nylon 66 and polyethylene terephthalate (PET), respectively.188–191 Synthetically, MA can be obtained from both saccharides and lignin-derived compounds via a range of microbial metabolic pathways.192 However, as to the lignin route this has been currently mainly demonstrated for lignin-derived model compounds such as benzoate, p-coumarate, ferulate, catechol, and vanillin.193–197 And indeed few reports exist on the synthesis of MA directly from lignin or for that matter a depolymerized lignin oil stream.191,197–199 One example concerns the convergent transformation of aromatics present in an alkaline depolymerized liquor (predominately containing p-coumarate and ferulate) into cis–cis muconate (67% yield) by means of genetically engineered Pseudomonas putida KT2440-CJ103 (Fig. 17).191 Firstly, this microorganism funnels a range of lignin-derived aromatics (e.g., p-coumarate, coniferyl alcohol, vanillin, caffeate) into protocatechuate, which is subsequently decarboxylated by protocatechuate decarboxylase (AroY) to catechol. Ring-opening of the catechol to cis,cis-muconate is then achieved by CatA/CatA2 dioxygenases. Aside from the use of genetically modified Pseudomonas putida, also the natural non-engineered variant was found capable of transforming lignin-derived aromatics. More specifically, non-engineered Pseudomonas putida KT2440 was found capable of funneling aromatic monomers, dimers, and oligomers present in alkaline pretreated black liquor directly into medium chain-length polyhydroxyalkanoates (mcl-PHAs).200 This concerns an important class of polymers with a wide applicability in the plastic and adhesive industry.201–203 Mechanistically, this transformation proceeds via dioxygenase catalyzed ring cleavages of protocatechuate (and other related intermediates) (see also above), the products of which are channeled into the β-ketoadipate (β-KA) pathway to form acetyl-CoA, this being the main entry point to mcl-PHAs via fatty acid synthesis.
 |
| Fig. 17 Schematic representation of the production of bio-based muconate as well as mcl-PHAs by combined chemical depolymerization of lignin and subsequent biological funneling using (non-)engineered P. putida KT2440(-CJ103) as a biocatalyst. | |
3. Summary and outlook
Recent years have seen marked advances in lignin-first depolymerization technologies, whereby mild native lignin deconstruction allows for the valorisation of all major biomass constituents. However, the complexity and heterogeneity of crude depolymerized lignin oils pose significant challenges to further downstream-processing of all lignin-derived product fractions. Of particular concern is the multi-component nature of the obtained lignin oils, associated with purification/separation challenges, that consequently hinder economically meaningful valorisation. While the conversion of monomeric phenols is conceptually conceivable using a range of chemo-catalytic tools, this is much more difficult with the oligo- and polymeric phenolics that contain difficult-to-break covalent bonds (e.g., C–C, C–O).
In this mini review we have outlined a range of chemo- and bio-catalytic methodologies capable of reducing the complexity and heterogeneity of lignin depolymerization oils. Through the concise use of convergent (bio)chemistries, it has already been found possible to narrow down the number of components in lignin oils and even obtain well-defined compounds in encouraging isolated yields. In this respect we illustrated sustainable catalytic pathways to monophenolics or diols, that can serve as valuable polymer building blocks; the vast potential of amination strategies whereby concurrent demethoxylation of the phenolic ring erases the structural difference between soft- and hardwood derived compounds; and convergent lignin oil valorization to a range of useful compounds using (genetically modified) microbes/enzymes.
Despite encouraging successes in these areas, the main drawbacks to these methodologies have remained unaltered. For example, many of the established chemical funneling strategies still typically use high catalyst loading. This is generally required because depolymerized lignin oil tends to contain significant amounts of known and unknown impurities, which can act as catalyst poisons. Furthermore, many of the applied methodologies are hampered by a limited substrate scope. And despite the often-encouraging product yields and selectivities, the challenging downstream purification process and the use of large amounts of solvents pose question marks on industrial feasibility and the sustainability of the processes. Future progression could potentially be found in the use of more performing and robust catalysts against impurities, water contamination, strongly coordinating functional groups such as organic acids, or phenols as well as sugars that can all strongly bind to active sites. As to biological funneling, the poor solubility of the lignin oil in water forms a significant bottleneck, and then especially while it limits the attainable conversion levels. Furthermore, the toxic and recalcitrant nature of depolymerized lignin oil also tends to inhibit microbial conversion. In this respect the use of genetically engineered enzymes, yeasts or microbes may prove to be a game changer.
With an eye on the future, catalytic funnelling strategies have already shown to enable the upgrading of multicomponent lignin oils, providing access to well-defined chemical building blocks in meaningful yields, and will therefore undoubtedly gain significant attention in future research addressing sustainable biorefinery schemes. In this respect we believe that the key developments will concern increasing the robustness of (bio)catalysts to render them less susceptible to poisoning and enable higher TOF and lower metal loadings. Furthermore, an interesting research direction is the engineering of (bio)catalysts capable of cleaving of the strong C–C bonds characteristic to lignin-derived oligophenolics. With regards to the multi-component nature of the dimer/oligomer in lignin-derived bio-oils, the development of tuneable chemo- and enantioselective (bio)catalytic methodologies able to target specific enantio- and regio- isomers appears an equally intriguing future research direction with potential high relevance to lignin chemistry. Finally, the development of highly efficient separation techniques, therewith reinforcing follow up funneling strategies to industrially useful compounds whether fine chemicals, polymerizable monomers or (aviation) fuels will be crucial to the implementation of these novel research lines.
Although the tremendous progress by design of a tandem lignin-depolymerization and catalytic funneling strategies, which allowed tailoring a range of valuable products has been made in recent years, the technical and economic viability and environmental impacts of proposed integrated process should be systematically investigated and thoroughly evaluated to claim industrial feasibility. This aspect has not yet been convincingly addressed due to the comparatively early stage of the research reported here. Also, many of the reported procedures are on gram and laboratory scale, with no further scaling and optimization yet attempted. Since the transformation of lignin to target chemicals generally involves multiple catalytic reaction steps, this also requires careful reaction pathway design and process optimizations to maximize efficiency and profitability. Overall, by minimizing the loading and maximizing the recovery rate of catalyst and solvent would undoubtedly reduce operating expenses. Furthermore, the less solvent loading means smaller reactor size required that would in turn reduce the capital cost associated with high-pressure reactors. Overall, the environmental impact of the solvents used, their amount utilized, and also their recyclability will be a very crucial aspect that needs significant attention for future research and development. A reduction in solvent would significantly reduce energy consumption and GHG emissions, positively contributed to life cycle analysis. Of particular effort should be devoted to the development of more selective catalytic methodologies, aiming to maximize tailored product yield, which in turn leads to simplification of purification strategies and also consequently reducing solvent use, and overall economic advantages.
Conflicts of interest
The authors declare no competing interests.
Acknowledgements
K. B. is grateful for financial support from the European Research Council, ERC Starting Grant 2015 (CatASus) 638076 and. This work is part of the research programme Talent Scheme (Vidi) with project number 723.015.005, which is partly financed by The Netherlands Organization for Scientific Research (NWO).
References
- C. O. Tuck, Science, 2012, 338, 604 CAS.
- A. J. Ragauskas, C. K. Williams, B. H. Davison, G. Britovsek, J. Cairney, C. A. Eckert, W. J. Frederick, J. P. Hallett, D. J. Leak, C. L. Liotta, J. R. Mielenz, R. Murphy, R. Templer and T. Tschaplinski, Science, 2006, 311, 484–489 CrossRef CAS PubMed.
- Z. H. Sun, B. Fridrich, A. de Santi, S. Elangovan and K. Barta, Chem. Rev., 2018, 118, 614–678 CrossRef CAS PubMed.
- C. O. Tuck, E. Perez, I. T. Horvath, R. A. Sheldon and M. Poliakoff, Science, 2012, 337, 695–699 CrossRef CAS PubMed.
- W. Schutyser, T. Renders, S. Van den Bosch, S. F. Koelewijn, G. T. Beckham and B. F. Sels, Chem. Soc. Rev., 2018, 47, 852–908 RSC.
- Z. H. Sun, J. L. Cheng, D. S. Wang, T. Q. Yuan, G. Y. Song and K. Barta, ChemSusChem, 2020, 13, 5199–5212 CrossRef CAS PubMed.
- J. G. de Vries, Chem. Rec., 2016, 16, 2787–2800 CrossRef PubMed.
- C. Z. Li, X. C. Zhao, A. Q. Wang, G. W. Huber and T. Zhang, Chem. Rev., 2015, 115, 11559–11624 CrossRef CAS PubMed.
- J. Zakzeski, P. C. A. Bruijnincx, A. L. Jongerius and B. M. Weckhuysen, Chem. Rev., 2010, 110, 3552–3599 CrossRef CAS PubMed.
- S. S. Wong, R. Y. Shu, J. G. Zhang, H. C. Liu and N. Yan, Chem. Soc. Rev., 2020, 49, 5510–5560 RSC.
- C. P. Xu, R. A. D. Arancon, J. Labidi and R. Luque, Chem. Soc. Rev., 2014, 43, 7485–7500 RSC.
- J. C. Serrano-Ruiz, R. M. West and J. A. Durnesic, Annu. Rev. Chem. Biomol. Eng., 2010, 1, 79–100 CrossRef CAS PubMed.
- C. H. Zhou, X. Xia, C. X. Lin, D. S. Tong and J. Beltramini, Chem. Soc. Rev., 2012, 41, 8210 RSC.
- X. D. Liu, F. P. Bouxin, J. J. Fan, V. L. Budarin, C. W. Hu and J. H. Clark, ChemSusChem, 2020, 13, 4296–4317 CrossRef CAS PubMed.
- T. D. Matson, K. Barta, A. V. Iretskii and P. C. Ford, J. Am. Chem. Soc., 2011, 133, 14090–14097 CrossRef CAS PubMed.
- M. Y. Zheng, J. F. Pang, A. Q. Wang and T. Zhang, Chin. J. Catal., 2014, 35, 602–613 CrossRef CAS.
- P. F. Yang, H. Kobayashi and A. Fukuoka, Chin. J. Catal., 2011, 32, 716–722 CrossRef CAS.
- Y. Wang, H. Song, L. C. Peng, Q. S. Zhang and S. Yao, Biotechnol. Biotechnol. Equip., 2014, 28, 981–988 CrossRef PubMed.
- B. O. de Beeck, M. Dusselier, J. Geboers, J. Holsbeek, E. Morre, S. Oswald, L. Giebeler and B. F. Sels, Energy Environ. Sci., 2015, 8, 230–240 RSC.
- M. Yabushita, H. Kobayashi and A. Fukuoka, Appl. Catal., B, 2014, 145, 1–9 CrossRef CAS.
- P. L. Dhepe and R. Sahu, Green Chem., 2010, 12, 2153–2156 RSC.
- X. J. Ji, H. Huang, Z. K. Nie, L. Qu, Q. Xu and G. T. Tsao, Adv. Biochem. Eng./Biotechnol., 2012, 128, 199–224 CrossRef CAS PubMed.
- F. Delbecq, Y. T. Wang, A. Muralidhara, K. El Ouardi, G. Marlair and C. Len, Front. Chem., 2018, 6, 146 CrossRef PubMed.
- L. T. Mika, E. Csefalvay and A. Nemeth, Chem. Rev., 2018, 118, 505–613 CrossRef CAS PubMed.
- Y. Q. Zhu, C. Romain and C. K. Williams, Nature, 2016, 540, 354–362 CrossRef CAS PubMed.
- R. M. Cywar, N. A. Rorrer, C. B. Hoyt, G. T. Beckham and E. Y. X. Chen, Nat. Rev. Mater., 2022, 7, 83–103 CrossRef CAS.
- J. G. Rosenboom, R. Langer and G. Traverso, Nat. Rev. Mater., 2022, 7, 117–137 CrossRef PubMed.
-
C. G. Yoo and A. J. Ragauskas, in Lignin Utilization Strategies: From Processing to Applications, ACS Publications, 2021, pp. 1–12 Search PubMed.
- H. L. Wang, Y. Q. Pu, A. Ragauskas and B. Yang, Bioresour. Technol., 2019, 271, 449–461 CrossRef CAS PubMed.
- S. Sethupathy, G. M. Morales, L. Gao, H. L. Wang, B. Yang, J. X. Jiang, J. Z. Sun and D. C. Zhu, Bioresour. Technol., 2022, 347, 126696 CrossRef CAS PubMed.
- A. Afanasenko and K. Barta, iScience, 2021, 24, 102211 CrossRef CAS PubMed.
- S. Elangovan, A. Afanasenko, J. Haupenthal, Z. H. Sun, Y. Z. Liu, A. K. H. Hirsch and K. Barta, ACS Cent. Sci., 2019, 5, 1707–1716 CrossRef CAS PubMed.
-
P. C. Rodrigues Pinto, E. A. Borges da Silva and A. E. Rodrigues, Biomass conversion, Springer, 2012, pp 381–420 Search PubMed.
- O. Y. Abdelaziz, S. Meier, J. Prothmann, C. Turner, A. Riisager and C. P. Hulteberg, Top. Catal., 2019, 62, 639–648 CrossRef CAS.
- C. G. Mei, C. J. Hu, Q. X. Hu, C. Sun, L. Li, X. X. Liang, Y. G. Dong and X. L. Gu, Catalysts, 2020, 10, 995 CrossRef CAS.
- R. S. Ma, M. Guo and X. Zhang, Catal. Today, 2018, 302, 50–60 CrossRef CAS.
- T. Renders, G. Van den Bossche, T. Vangeel, K. Van Aelst and B. Sels, Curr. Opin. Biotechnol, 2019, 56, 193–201 CrossRef CAS PubMed.
- M. M. Abu-Omar, K. Barta, G. T. Beckham, J. S. Luterbacher, J. Ralph, R. Rinaldi, Y. Roman-Leshkov, J. S. M. Samec, B. F. Sels and F. Wang, Energy Environ. Sci., 2021, 14, 262–292 RSC.
- T. Renders, S. Van den Bosch, S. F. Koelewijn, W. Schutyser and B. F. Sels, Energy Environ. Sci., 2017, 10, 1551–1557 RSC.
- T. I. Koranyi, B. Fridrich, A. Pineda and K. Barta, Molecules, 2020, 25, 2815 CrossRef CAS PubMed.
- S. Qiu, M. Wang, Y. M. Fang and T. W. Tan, Sustainable Energy Fuels, 2020, 4, 5588–5594 RSC.
- X. Chen, Q. Che, S. Li, Z. Liu, H. Yang, Y. Chen, X. Wang, J. Shao and H. Chen, Fuel Process. Technol., 2019, 196, 106180 CrossRef CAS.
- G. Kabir and B. H. Hameed, Renewable Sustainable Energy Rev., 2017, 70, 945–967 CrossRef CAS.
- M. Kleinert and T. Barth, Energy Fuels, 2008, 22, 1371–1379 CrossRef CAS.
- H. Luo, E. P. Weeda, M. Alherech, C. W. Anson, S. D. Karlen, Y. B. Cui, C. E. Foster and S. S. Stahl, J. Am. Chem. Soc., 2021, 143, 15462–15470 CrossRef CAS PubMed.
- M. I. F. Mota, P. C. R. Pinto, J. M. Loureiro and A. E. Rodrigues, Sep. Purif. Rev., 2016, 45, 227–259 CrossRef CAS.
- Z. Sultan, I. Graca, Y. Q. Li, S. Lima, L. G. Peeva, D. Kim, M. A. Ebrahim, R. Rinaldi and A. G. Livingston, ChemSusChem, 2019, 12, 1203–1212 CrossRef CAS PubMed.
- T. Y. Ren, Z. F. Zhang, S. P. You, W. Qi, R. X. Su and Z. M. He, Green Chem., 2022, 24, 7355–7361 RSC.
- Z. W. Cao, J. Engelhardt, M. Dierks, M. T. Clough, G. H. Wang, E. Heracleous, A. Lappas, R. Rinaldi and F. Schuth, Angew. Chem., Int. Ed., 2017, 56, 2334–2339 CrossRef CAS PubMed.
- A. W. Pacek, P. Ding, M. Garrett, G. Sheldrake and A. W. Nienow, Ind. Eng. Chem. Res., 2013, 52, 8361–8372 CrossRef CAS.
- H. R. Bjorsvik, Org. Process Res. Dev., 1999, 3, 330–340 CrossRef CAS.
- S. Rawat, P. Gupta, B. Singh, T. Bhaskar, K. Natte and A. Narani, Appl. Catal., A, 2020, 598, 117567 CrossRef CAS.
- Y. T. Zhu, Y. H. Liao, W. Lv, J. Liu, X. B. Song, L. G. Chen, C. G. Wang, B. F. Sels and L. L. Ma, ACS Sustainable Chem. Eng., 2020, 8, 2361–2374 CrossRef CAS.
- T. Hosoya, K. Kawase, Y. Hirano, M. Ikeuchi and H. Miyafuji, J. Wood Chem. Technol., 2022, 42, 1–14 CrossRef CAS.
- W. Schutyser, J. S. Kruger, A. M. Robinson, R. Katahira, D. G. Brandner, N. S. Cleveland, A. Mittal, D. J. Peterson, R. Meilan, Y. Roman-Leshkov and G. T. Beckham, Green Chem., 2018, 20, 3828–3844 RSC.
- F. Walch, O. Y. Abdelaziz, S. Meier, S. Bjelic, C. P. Hulteberg and A. Riisager, Catal. Sci. Technol., 2021, 11, 1843–1853 RSC.
- Y. Z. Hu, L. Yan, X. L. Zhao, C. U. Wang, S. Li, X. H. Zhang, L. L. Ma and Q. Zhang, Green Chem., 2021, 23, 7030–7040 RSC.
- V. E. Tarabanko, K. L. Kaygorodov, E. A. Skiba, N. Tarabanko, Y. V. Chelbina, O. V. Baybakova, B. N. Kuznetsov and L. Djakovitch, J. Wood Chem. Technol., 2017, 37, 43–51 CrossRef CAS.
- K. Yamamoto, T. Hosoya, K. Yoshioka, H. Miyafuji, H. Ohno and T. Yamada, ACS Sustainable Chem. Eng., 2017, 5, 10111–10115 CrossRef CAS.
- W. P. Deng, H. X. Zhang, X. J. Wu, R. S. Li, Q. H. Zhang and Y. Wang, Green Chem., 2015, 17, 5009–5018 RSC.
- C. Fargues, A. Mathias and A. Rodrigues, Ind. Eng. Chem. Res., 1996, 35, 28–36 CrossRef CAS.
- Y. Zhu, Y. Liao, L. Lu, W. Lv, J. Liu, X. Song, J. Wu, X. Wu, L. Li and C. Wang, ACS Catal., 2023, 13, 7929–7941 CrossRef CAS.
- M. Fache, B. Boutevin and S. Caillol, ACS Sustainable Chem. Eng., 2016, 4, 35–46 CrossRef CAS.
- M. Fache, B. Boutevin and S. Caillol, Eur. Polym. J., 2015, 68, 488–502 CrossRef CAS.
- Z. Fang, S. Nikafshar, E. L. Hegg and M. Nejad, ACS Sustainable Chem. Eng., 2020, 8, 9095–9103 CrossRef CAS.
- A. Van, K. Chiou and H. Ishida, Polymer, 2014, 55, 1443–1451 CrossRef CAS.
- L. Mialon, A. G. Pemba and S. A. Miller, Green Chem., 2010, 12, 1704–1706 RSC.
- B. G. Harvey, A. J. Guenthner, H. A. Meylemans, S. R. L. Haines, K. R. Lamison, T. J. Groshens, L. R. Cambrea, M. C. Davis and W. W. Lai, Green Chem., 2015, 17, 1249–1258 RSC.
- F. M. Ding, X. Zhou, Z. F. Wu and Z. Q. Xing, ACS Sustainable Chem. Eng., 2019, 7, 5494–5500 CrossRef CAS.
- S. G. Zhu, A. P. Marques, D. L. D. Lima, D. V. Evtuguin and V. I. Esteves, Ind. Eng. Chem. Res., 2011, 50, 291–298 CrossRef.
- H. B. Deng, L. Lin, Y. Sun, C. S. Pang, J. P. Zhuang, P. K. Ouyang, J. J. Li and S. J. Liu, Energy Fuels, 2009, 23, 19–24 CrossRef CAS.
- X. L. Gu, K. H. Cheng, M. He, Y. J. Shi and Z. Z. Li, Maderas: Cienc. Tecnol., 2012, 14, 31–42 CAS.
- S. W. Liu, Z. L. Shi, L. Li, S. T. Yu, C. X. Xie and Z. Q. Song, RSC Adv., 2013, 3, 5789–5793 RSC.
- P. C. R. Pinto, C. E. Costa and A. E. Rodrigues, Ind. Eng. Chem. Res., 2013, 52, 4421–4428 CrossRef CAS.
- J. H. Zhang, H. B. Deng and L. Lin, Molecules, 2009, 14, 2747–2757 CrossRef CAS PubMed.
- M. Alherech, S. Omolabake, C. M. Holland, G. E. Klinger, E. L. Hegg and S. S. Stahl, ACS Cent. Sci., 2021, 7, 1831–1837 CrossRef CAS PubMed.
- M. Lores, J. Vindevogel and P. Sandra, Chromatographia, 1993, 37, 451–454 CrossRef.
- M. H. Furigay, M. M. Boucher, N. A. Mizgier and C. S. Brindle, J. Visualized Exp., 2018, 2, 57639 Search PubMed.
- S. Qiu, M. Wang, Y. M. Fang and T. W. Tan, Sustainable Energy Fuels, 2020, 4, 5588–5594 RSC.
- K. M. Torr, D. J. van de Pas, E. Cazeils and I. D. Suckling, Bioresour. Technol., 2011, 102, 7608–7611 CrossRef CAS PubMed.
- K. Van Aelst, E. Van Sinay, T. Vangeel, E. Cooreman, G. Van den Bossche, T. Renders, J. Van Aelst, S. Van den Bosch and B. F. Sels, Chem. Sci., 2020, 11, 11498–11508 RSC.
- Z. H. Sun, G. Bottari, A. Afanasenko, M. C. A. Stuart, P. J. Deuss, B. Fridrich and K. Barta, Nat. Catal., 2018, 1, 82–92 CrossRef CAS.
- W. Lan, M. T. Amiri, C. M. Hunston and J. S. Luterbacher, Angew. Chem., Int. Ed., 2018, 57, 1356–1360 CrossRef CAS PubMed.
- S. Van den Bosch, W. Schutyser, S. F. Koelewijn, T. Renders, C. M. Courtin and B. F. Sels, Chem. Commun., 2015, 51, 13158–13161 RSC.
- J. Z. Chen, F. Lu, X. Q. Si, X. Nie, J. S. Chen, R. Lu and J. Xu, ChemSusChem, 2016, 9, 3353–3360 CrossRef CAS PubMed.
- T. Renders, S. Van den Bosch, T. Vangeel, T. Ennaert, S. F. Koelewijn, G. Van den Bossche, C. M. Courtin, W. Schutyser and B. F. Sels, ACS Sustainable Chem. Eng., 2016, 4, 6894–6904 CrossRef CAS.
- T. Renders, E. Cooreman, S. Van den Bosch, W. Schutyser, S. F. Koelewijn, T. Vangeel, A. Deneyer, G. Van den Bossche, C. M. Courtin and B. F. Sels, Green Chem., 2018, 20, 4607–4619 RSC.
- S. Van den Bosch, T. Renders, S. Kennis, S. F. Koelewijn, G. Van den Bossche, T. Vangeel, A. Deneyer, D. Depuydt, C. M. Courtin, J. M. Thevelein, W. Schutyser and B. F. Sels, Green Chem., 2017, 19, 3313–3326 RSC.
- X. H. Ouyang, X. M. Huang, M. D. Boot and E. J. M. Hensen, ChemSusChem, 2020, 13, 1705–1709 CrossRef CAS PubMed.
- Y. H. Liao, S. F. Koelewijn, G. Van den Bossche, J. Van Aelst, S. Van den Bosch, T. Renders, K. Navare, T. Nicolai, K. Van Aelst, M. Maesen, H. Matsushima, J. M. Thevelein, K. Van Acker, B. Lagrain, D. Verboekend and B. F. Sels, Science, 2020, 367, 1385–1390 CrossRef CAS PubMed.
- Q. Song, F. Wang, J. Y. Cai, Y. H. Wang, J. J. Zhang, W. Q. Yu and J. Xu, Energy Environ. Sci., 2013, 6, 994–1007 RSC.
- S. Van den Bosch, W. Schutyser, R. Vanholme, T. Driessen, S. F. Koelewijn, T. Renders, B. De Meester, W. J. J. Huijgen, W. Dehaen, C. M. Courtin, B. Lagrain, W. Boerjan and B. F. Sels, Energy Environ. Sci., 2015, 8, 1748–1763 RSC.
- T. Parsell, S. Yohe, J. Degenstein, T. Jarrell, I. Klein, E. Gencer, B. Hewetson, M. Hurt, J. I. Kim, H. Choudhari, B. Saha, R. Meilan, N. Mosier, F. Ribeiro, W. N. Delgass, C. Chapple, H. I. Kenttamaa, R. Agrawal and M. M. Abu-Omar, Green Chem., 2015, 17, 1492–1499 RSC.
- Y. X. Zhai, C. Li, G. Y. Xu, Y. F. Ma, X. H. Liu and Y. Zhang, Green Chem., 2017, 19, 1895–1903 RSC.
- X. H. Ouyang, X. M. Huang, J. D. Zhu, M. D. Boot and E. J. M. Hensen, ACS Sustainable Chem. Eng., 2019, 7, 13764–13773 CrossRef CAS.
- W. Schutyser, G. Van den Bossche, A. Raaffels, S. Van den Bosch, S. F. Koelewijn, T. Renders and B. F. Sels, ACS Sustainable Chem. Eng., 2016, 4, 5336–5346 CrossRef CAS.
- J. Bomon, M. Bal, T. K. Achar, S. Sergeyev, X. Wu, B. Wambacq, F. Lemiere, B. F. Sels and B. U. W. Maes, Green Chem., 2021, 23, 1995–2009 RSC.
- W. Schutyser, S. Van den Bosch, J. Dijkmans, S. Turner, M. Meledina, G. Van Tendeloo, D. P. Debecker and B. F. Sels, ChemSusChem, 2015, 8, 1805–1818 CrossRef CAS PubMed.
- S. F. Koelewijn, S. Van den Bosch, T. Renders, W. Schutyser, B. Lagrain, M. Smet, J. Thomas, W. Dehaen, P. Van Puyvelde, H. Witters and B. F. Sels, Green Chem., 2017, 19, 2561–2570 RSC.
- S. Elangovan, A. Afanasenko, J. Haupenthal, Z. H. Sun, Y. Z. Liu, A. K. H. Hirsch and K. Barta, ACS Cent. Sci., 2019, 5, 1707–1716 CrossRef CAS PubMed.
- N. Mosier, C. Wyman, B. Dale, R. Elander, Y. Y. Lee, M. Holtzapple and M. Ladisch, Bioresour. Technol., 2005, 96, 673–686 CrossRef CAS PubMed.
- E. M. Karp, M. G. Resch, B. S. Donohoe, P. N. Ciesielski, M. H. O'Brien, J. E. Nill, A. Mittal, M. J. Biddy and G. T. Beckham, ACS Sustainable Chem. Eng., 2015, 3, 1479–1491 CrossRef CAS.
- R. Katahira, A. Mittal, K. McKinney, X. W. Chen, M. P. Tucker, D. K. Johnson and G. T. Beckham, ACS Sustainable Chem. Eng., 2016, 4, 1474–1486 CrossRef CAS.
- M. Otromke, R. J. White and J. Sauer, Carbon Resour. Convers., 2019, 2, 59–71 CrossRef CAS.
- R. Chaudhary and P. L. Dhepe, Green Chem., 2017, 19, 778–788 RSC.
- J. E. Miller, L. Evans, A. Littlewolf and D. E. Trudell, Fuel, 1999, 78, 1363–1366 CrossRef CAS.
- A. Vigneault, D. K. Johnson and E. Chornet, Can. J. Chem. Eng., 2007, 85, 906–916 CrossRef CAS.
- A. Toledano, L. Serrano and J. Labidi, Fuel, 2014, 116, 617–624 CrossRef CAS.
- T. Komatsu and T. Yokoyama, J. Wood Sci., 2021, 67, 1–12 CrossRef.
- J. G. Linger, D. R. Vardon, M. T. Guarnieri, E. M. Karp, G. B. Hunsinger, M. A. Franden, C. W. Johnson, G. Chupka, T. J. Strathmann, P. T. Pienkos and G. T. Beckham, Proc. Natl. Acad. Sci. U. S. A., 2014, 111, 12013–12018 CrossRef CAS PubMed.
- N. Kamimura, K. Takahashi, K. Mori, T. Araki, M. Fujita, Y. Higuchi and E. Masai, Environ. Microbiol. Rep., 2017, 9, 679–705 CrossRef CAS PubMed.
- H. Wang, X. D. Peng, H. Li, A. Giannis and C. He, Front. Chem., 2022, 10, 894593 CrossRef CAS PubMed.
- G. T. Beckham, C. W. Johnson, E. M. Karp, D. Salvachua and D. R. Vardon, Curr. Opin. Biotechnol, 2016, 42, 40–53 CrossRef CAS PubMed.
- K. Yogalakshmi, P. S. ivashanmugam, S. Kavitha, Y. Kannah, S. Varjani, S. AdishKumar and G. Kumar, Chemosphere, 2022, 286, 131824 CrossRef PubMed.
- G. Wang, Y. Dai, H. Yang, Q. Xiong, K. Wang, J. Zhou, Y. Li and S. Wang, Energy Fuels, 2020, 34, 15557–15578 CrossRef CAS.
- V. Dhyani and T. Bhaskar, Renewable Energy, 2018, 129, 695–716 CrossRef CAS.
- M. B. Figueiredo, I. Hita, P. J. Deuss, R. Venderbosch and H. Heeres, Green Chem., 2022, 24, 4680–4702 RSC.
-
L. Li, J. S. Rowbotham, C. H. Greenwell and P. W. Dyer, An introduction to pyrolysis and catalytic pyrolysis: versatile techniques for biomass conversion, in New and future developments in catalysis: catalytic biomass conversion, ed. S. L. Suib, Elsevier, 2013, pp. 173–208 Search PubMed.
-
F. Cherubini, G. Jungmeier, M. Mandl, C. Philips, M. Wellisch, H. Jrgensen, I. Skiadas, L. Boniface, M. Dohy and J.-C. Pouet, IEA bioenergy Task 42 on biorefineries: co-production of fuels, chemicals, power and materials from biomass, IEA bioenergy task, IEA Bioenergy Copenhagen, Denmark, 2007, pp, 1–37 Search PubMed.
- E. Feghali, D. J. van de Pas, A. J. Parrott and K. M. Torr, ACS Macro Lett., 2020, 9, 1155–1160 CrossRef CAS PubMed.
- D. J. van de Pas and K. M. Torr, Biomacromolecules, 2017, 18, 2640–2648 CrossRef CAS PubMed.
- N. V. Gama, A. Ferreira and A. Barros-Timmons, Materials, 2018, 11, 1841 CrossRef PubMed.
- R. B. Seymour and G. B. Kauffman, J. Chem. Educ., 1992, 69, 909–910 CrossRef CAS.
-
L. Fernández, Global polyurethane market volume 2015-2029.
- O. S. H. Santos, M. C. da Silva, V. R. Silva, W. N. Mussel and M. I. Yoshida, J. Hazard. Mater., 2017, 324, 406–413 CrossRef CAS PubMed.
- W. Zhou, C. Y. Bo, P. Y. Jia, Y. H. Zhou and M. Zhang, Polymers, 2019, 11, 45 CrossRef PubMed.
- V. V. Apyari, V. V. Arkhipova, M. V. Gorbunova, P. A. Volkov, A. I. Isachenko, S. G. Dmitrienko and Y. A. Zolotov, Talanta, 2016, 161, 780–788 CrossRef CAS PubMed.
- J. E. Q. Quinsaat, E. Feghali, D. J. van de Pas, R. Vendamme and K. M. Torr, ACS Appl. Polym. Mater., 2021, 3, 5845–5856 CrossRef CAS.
- S. Wang, L. Shuai, B. Saha, D. G. Vlachos and T. H. Epps, ACS Cent. Sci., 2018, 4, 701–708 CrossRef CAS PubMed.
- F. K. He, K. K. Jin, J. Sun and Q. Fang, ACS Sustainable Chem. Eng., 2018, 6, 3575–3579 CrossRef CAS.
- Y. Bao, J. Z. Ma, X. Zhang and C. H. Shi, J. Mater. Sci., 2015, 50, 6839–6863 CrossRef CAS.
- X. Y. Wu, M. V. Galkin and K. Barta, Chem Catal., 2021, 1, 1466–1479 CrossRef CAS.
- Y. W. Cao, H. Zheng, G. L. Zhu, H. H. Wu and L. He, Chin. Chem. Lett., 2021, 32, 770–774 CrossRef CAS.
- X. Y. Wu, M. De bruyn, G. Trimmel, K. Zangger and K. Barta, ACS Sustainable Chem. Eng., 2023, 11, 2819–2829 CrossRef CAS PubMed.
- X. Y. Wu, D. Xu, M. De bruyn, G. Trimmel and K. Barta, Polym. Chem., 2023, 14, 907–912 RSC.
- P. Sarda, J. C. Hanan, J. G. Lawrence and M. Allahkarami, J. Polym. Sci., 2022, 60, 7–31 CrossRef CAS.
- V. Tournier, C. M. Topham, A. Gilles, B. David, C. Folgoas, E. Moya-Leclair, E. Kamionka, M. L. Desrousseaux, H. Texier, S. Gavalda, M. Cot, E. Guemard, M. Dalibey, J. Nomme, G. Cioci, S. Barbe, M. Chateau, I. Andre, S. Duquesne and A. Marty, Nature, 2020, 580, 216–219 CrossRef CAS PubMed.
- Y. Chen, A. K. Awasthi, F. Wei, Q. Y. Tan and J. H. Li, Sci. Total Environ., 2021, 752, 141772 CrossRef CAS PubMed.
- K. Ravindranath and R. A. Mashelkar, Chem. Eng. Sci., 1986, 41, 2197–2214 CrossRef CAS.
- R. De Clercq, M. Dusselier and B. F. Sels, Green Chem., 2017, 19, 5012–5040 RSC.
- J. F. Pang, M. Y. Zheng, R. Y. Sun, A. Q. Wang, X. D. Wang and T. Zhang, Green Chem., 2016, 18, 342–359 RSC.
- J. J. Pacheco and M. E. Davis, Proc. Natl. Acad. Sci. U. S. A., 2014, 111, 8363–8367 CrossRef CAS PubMed.
- Y. T. He, Y. H. Luo, M. Y. Yang, Y. H. Zhang, L. J. Zhu, M. H. Fan and Q. X. Li, Appl. Catal., A, 2022, 630, 118440 CrossRef CAS.
- Y. Tachibana, S. Kimura and K. Kasuya, Sci. Rep., 2015, 5, 8249 CrossRef PubMed.
- M. Volanti, D. Cespi, F. Passarini, E. Neri, F. Cavani, P. Mizsey and D. Fozer, Green Chem., 2019, 21, 885–896 RSC.
- S. Song, J. G. Zhang, G. Gozaydin and N. Yan, Angew. Chem., Int. Ed., 2019, 58, 4934–4937 CrossRef CAS PubMed.
- J. L. Gurman, L. Baier and B. C. Levin, Fire Mater., 1987, 11, 109–130 CrossRef CAS.
-
https://juniperpublishers.com/rapsci/pdf/RAPSCI.MS.ID.555698.pdf
.
- L. X. Li, L. Dong, X. H. Liu, Y. Guo and Y. Q. Wang, Appl. Catal., B, 2020, 260, 118143 CrossRef CAS.
-
M. Weber, M. Weber and M. Kleine-Boymann, Phenol. Ullmann’s Encyclopedia of Industrial Chemistry, Wiley, New York, 7th edn, 2000 Search PubMed.
- M. Weber, R. Hoffmann and M. Weber, Process Saf. Prog., 2019, 38, e12034 CAS.
- H. Babich and D. Davis, Phenol: A review of environmental and health risks, Regul. Toxicol. Pharmacol., 1981, 1(1), 90–109 CrossRef CAS PubMed.
- R. J. Schmidt, Appl. Catal., A, 2005, 280, 89–103 CrossRef CAS.
- X. M. Huang, J. M. Ludenhoff, M. Dirks, X. H. Ouyang, M. D. Boot and E. J. M. Hensen, ACS Catal., 2018, 8, 11184–11190 CrossRef CAS PubMed.
-
https://echa.europa.eu/substance-information/-/substanceinfo/100.002.909
.
- E. Subbotina, T. Rukkijakan, M. D. Marquez-Medina, X. W. Yu, M. Johnsson and J. S. M. Samec, Nat. Chem., 2021, 13, 1118 CrossRef CAS PubMed.
- X. Y. Wu, M. De Bruyn, J. M. Hulan, H. Brasil, Z. H. Sun and K. Barta, Green Chem., 2023, 25, 211–220 RSC.
- M. F. Shahriar and A. Khanal, Fuel, 2022, 325, 124905 CrossRef CAS.
- X. Y. Wu, M. V. Galkin, T. Stern, Z. H. Sun and K. Barta, Nat. Commun., 2022, 13, 3376 CrossRef CAS PubMed.
- X. Y. Wu, M. De bruyn and K. Barta, ChemSusChem, 2022, 15, e202200914 CAS.
- X. Y. Wu, M. De Bruyn and K. Barta, Catal. Sci. Technol., 2022, 12, 5908–5916 RSC.
- T. D. H. Bugg and R. Rahmanpour, Curr. Opin. Chem. Biol., 2015, 29, 10–17 CrossRef CAS PubMed.
- O. Y. Abdelaziz, D. P. Brink, J. Prothmann, K. Ravi, M. Z. Sun, J. Garcia-Hidalgo, M. Sandahl, C. P. Hulteberg, C. Turner, G. Liden and M. F. Gorwa-Grauslund, Biotechnol. Adv., 2016, 34, 1318–1346 CrossRef CAS PubMed.
- Z. X. Xu, P. Lei, R. Zhai, Z. Q. Wen and M. J. Jin, Biotechnol. Biofuels, 2019, 12, 32 CrossRef PubMed.
- Z. H. Liu, N. J. Hao, Y. Y. Wang, C. Dou, F. R. Lin, R. C. Shen, R. Bura, D. B. Hodge, B. E. Dale, A. J. Ragauskas, B. Yang and J. S. Yuan, Nat. Commun., 2021, 12, 3912 CrossRef CAS PubMed.
- Z. Chen and C. X. Wan, Renewable Sustainable Energy Rev., 2017, 73, 610–621 CrossRef CAS.
- C. W. Johnson, D. Salvachua, N. A. Rorrer, B. A. Black, D. R. Vardon, P. C. St John, N. S. Cleveland, G. Dominick, J. R. Elmore, N. Grundl, P. Khanna, C. R. Martinez, W. E. Michener, D. J. Peterson, K. J. Ramirez, P. Singh, T. A. Van der Wall, A. N. Wilson, X. N. Yi, M. J. Biddy, Y. J. Bomble, A. M. Guss and G. T. Beckham, Joule, 2019, 3, 1523–1537 CrossRef CAS.
- D. L. Gall, J. Ralph, T. J. Donohue and D. R. Noguera, Curr. Opin. Biotechnol, 2017, 45, 120–126 CrossRef CAS PubMed.
- W. H. Wu, T. Dutta, A. M. Varman, A. Eudes, B. Manalansan, D. Loque and S. Singh, Sci. Rep., 2017, 7, 8420 CrossRef PubMed.
- A. J. Borchert, W. R. Henson and G. T. Beckham, Curr. Opin. Biotechnol, 2022, 73, 1–13 CrossRef CAS PubMed.
- G. T. Beckham, C. W. Johnson, E. M. Karp, D. Salvachua and D. R. Vardon, Curr. Opin. Biotechnol, 2016, 42, 40–53 CrossRef CAS PubMed.
- K. Shikinaka, Y. Hashimoto, S. Kajita, E. Masai, Y. Katayama, M. Nakamura, Y. Otsuka, S. Ohara and K. Shigehara, Sen-I Gakkaishi, 2013, 69, 39–47 CrossRef CAS.
- M. Hishida, K. Shikinaka, M. Inazawa, Y. Katayama, S. Kajita, E. Masai, M. Nakamura, Y. Otuka, S. Ohara and K. Shigehara, Kobunshi Ronbunshu, 2009, 66, 141–146 CrossRef CAS.
- T. Michinobu, M. Hishida, M. Sato, Y. Katayama, E. Masai, M. Nakamura, Y. Otsuka, S. Ohara and K. Shigehara, Polym. J., 2008, 40, 68–75 CrossRef CAS.
- K. Shikinaka, Y. Otsuka, M. Nakamura, E. Masai and Y. Katayama, J. Oleo Sci., 2018, 67, 1059–1070 CrossRef CAS PubMed.
- Y. Suzuki, Y. Okamura-Abe, M. Nakamura, Y. Otsuka, T. Araki, H. Otsuka, R. R. Navarro, N. Kamimura, E. Masai and Y. Katayama, J. Biosci. Bioeng., 2020, 130, 71–75 CrossRef CAS PubMed.
- J. M. Perez, C. Sener, S. Misra, G. E. Umana, J. Coplien, D. Haak, Y. D. Li, C. T. Maravelias, S. D. Karlen, J. Ralph, T. J. Donohue and D. R. Noguera, Green Chem., 2022, 24, 2795–2811 RSC.
- J. M. Perez, W. S. Kontur, M. Alherech, J. Coplien, S. D. Karlen, S. S. Stahl, T. J. Donohue and D. R. Noguera, Green Chem., 2019, 21, 1340–1350 RSC.
- J. M. Perez, W. S. Kontur, C. Gehl, D. M. Gille, Y. J. Ma, A. V. Niles, G. Umana, T. J. Donohue and D. R. Noguera, Appl. Environ. Microbiol., 2021, 87, e02794–20 CrossRef CAS PubMed.
- Y. Suzuki, Y. Okamura-Abe, M. Nakamura, Y. Otsuka, T. Araki, H. Otsuka, R. R. Navarro, N. Kamimura, E. Masai and Y. Katayama, J. Biosci. Bioeng., 2020, 130, 71–75 CrossRef CAS PubMed.
- Y. Qian, Y. Otsuka, T. Sonoki, B. Mukhopadhyay, M. Nakamura, J. Jellison and B. Goodell, BioResources, 2016, 11, 6097–6109 CAS.
- K. Shikinaka, Y. Otsuka, M. Nakamura, E. Masai and Y. Katayama, J. Oleo Sci., 2018, 67, 1059–1070 CrossRef CAS PubMed.
- S. Notonier, A. Z. Werner, E. Kuatsjah, L. Dumalo, P. E. Abraham, E. A. Hatmaker, C. B. Hoyt, A. Amore, K. J. Ramirez, S. P. Woodworth, D. M. Klingeman, R. J. Giannone, A. M. Guss, R. L. Hettich, L. D. Eltis, C. W. Johnson and G. T. Beckham, Metab. Eng., 2021, 65, 111–122 CrossRef CAS PubMed.
- S. Lee, Y. J. Jung, S. J. Park, M. H. Ryu, J. E. Kim, H. M. Song, K. H. Kang, B. K. Song, B. H. Sung, Y. H. Kim, H. T. Kim and J. C. Joo, Bioresour. Technol., 2022, 352, 127106 CrossRef CAS PubMed.
- J. R. Bai, Y. S. Zhang, C. Tang, Y. Hou, X. P. Ai, X. R. Chen, Y. Zhang, X. B. Wang and X. L. Meng, Biomed. Pharmacother., 2021, 1, 110985 CrossRef PubMed.
- G. Civenni, M. G. Iodice, S. F. Nabavi, S. Habtemariam, S. M. Nabavi, C. V. Catapano and M. Daglia, RSC Adv., 2015, 5, 63800–63806 RSC.
- C. G. Cai, Z. X. Xu, H. R. Zhou, S. T. Chen and M. J. Jin, Sci. Adv., 2021, 7, eabg4585 CrossRef CAS PubMed.
- J. M. Carraher, P. Carter, R. G. Rao, M. J. Forrester, T. Pfennig, B. H. Shanks, E. W. Cochran and J. P. Tessonnier, Green Chem., 2020, 22, 6444–6454 RSC.
- I. Khalil, G. Quintens, T. Junkers and M. Dusselier, Green Chem., 2020, 22, 1517–1541 RSC.
- R. Lu, F. Lu, J. Z. Chen, W. Q. Yu, Q. Q. Huang, J. J. Zhang and J. Xu, Angew. Chem., Int. Ed., 2016, 55, 249–253 CrossRef CAS PubMed.
- D. R. Vardon, M. A. Franden, C. W. Johnson, E. M. Karp, M. T. Guarnieri, J. G. Linger, M. J. Salm, T. J. Strathmann and G. T. Beckham, Energy Environ. Sci., 2022, 15, 3534–3535 RSC.
- X. Y. Wu, M. De Bruyn and K. Barta, Chem. Ing. Tech., 2022, 94, 1808–1817 CrossRef CAS PubMed.
- A. Kaneko, Y. Ishii and K. Kirimura, Chem. Lett., 2011, 40, 381–383 CrossRef CAS.
- J. B. J. H. van Duuren, D. Wijte, B. Karge, V. A. P. M. dos Santos, Y. Yang, A. E. Mars and G. Eggink, Biotechnol. Prog., 2012, 28, 85–92 CrossRef CAS PubMed.
- T. Sonoki, M. Morooka, K. Sakamoto, Y. Otsuka, M. Nakamura, J. Jellison and B. Goodell, J. Biotechnol., 2014, 192, 71–77 CrossRef CAS PubMed.
- C. W. Johnson, P. E. Abraham, J. G. Linger, P. Khanna, R. L. Hettich and G. T. Beckham, Metab. Eng. Commun., 2017, 5, 19–25 CrossRef PubMed.
- N. Barton, L. Horbal, S. Starck, M. Kohlstedt, A. Luzhetskyy and C. Wittmann, Metab. Eng., 2018, 45, 200–210 CrossRef CAS PubMed.
- H. Almqvist, H. Veras, K. N. Li, J. G. Hidalgo, C. Hulteberg, M. Gorwa-Grauslund, N. S. Parachin and M. Carlquist, ACS Sustainable Chem. Eng., 2021, 9, 8097–8106 CrossRef CAS.
- T. Sonoki, K. Takahashi, H. Sugita, M. Hatamura, Y. Azuma, T. Sato, S. Suzuki, N. Kamimura and E. Masai, ACS Sustainable Chem. Eng., 2018, 6, 1256–1264 CrossRef CAS.
- J. G. Linger, D. R. Vardon, M. T. Guarnieri, E. M. Karp, G. B. Hunsinger, M. A. Franden, C. W. Johnson, G. Chupka, T. J. Strathmann, P. T. Pienkos and G. T. Beckham, Proc. Natl. Acad. Sci. U. S. A., 2014, 111, 12013–12018 CrossRef CAS PubMed.
- A. A. Alves, E. C. Siqueira, M. P. S. Barros, P. E. C. Silva and L. M. Houllou, Int. J. Environ. Sci. Technol., 2023, 20, 3409–3420 CrossRef CAS.
- P. K. Obulisamy and S. Mehariya, Bioresour. Technol., 2021, 325, 124653 CrossRef CAS PubMed.
- J. R. Pereira, D. Araujo, A. C. Marques, L. A. Neves, C. Grandfils, C. Sevrin, V. D. Alves, E. Fortunato, M. A. M. Reis and F. Freitas, Int. J. Biol. Macromol., 2019, 122, 1144–1151 CrossRef CAS PubMed.
|
This journal is © The Royal Society of Chemistry 2023 |
Click here to see how this site uses Cookies. View our privacy policy here.