DOI:
10.1039/D2YA00202G
(Paper)
Energy Adv., 2022,
1, 935-940
Submerged comminution of lithium-ion batteries in water in inert atmosphere for safe recycling†
Received
2nd August 2022
, Accepted 5th October 2022
First published on 6th October 2022
Abstract
We would like to discuss the recycling process of lithium-ion batteries (LIBs) from the viewpoint of “safety”. We consider that comminution in water is a safer process than dry comminution as water can deactivate the negative electrode and organic electrolyte immediately. The comminution in water of relatively large fully-charged LIBs in a N2 atmosphere was carried out. However, in spite of the submerged comminution, white smoke rising from the water was observed. The hydrogen concentration above the comminution equipment reached a few percent even with N2 flow of 15–20 L min−1 (or about 4% hydrogen for a comminution of an 895 mA h cell with low N2 flow of 4.5 L min−1). Considering the high ignition properties of hydrogen–air mixtures, the submerged comminution equipment should be installed not in air but in an inert atmosphere to reduce the risk of an explosion accident.
Introduction
Lithium-ion batteries are playing a key role in climate neutrality society and their production continues to increase. At the same time, their recycling is becoming more important due to the circular economy, the safety over the lifecycle and the environmental impact of LIBs.1–4 As an example, the European Union requires the use of recycled materials at a mandatory level.5,6 The most critical point in the recycling of lithium-ion batteries is how to open the cell safely because the battery contains very active materials. The opening process can be done by a high temperature process (pyrometallurgical process), a room temperature comminution, or human hand and/or robots for direct recycling.7–9 The pyrometallurgical processes are safe and established processes,9–12 which can burn organic components as well as the batteries are opened, but they essentially consume a large amount of energy to maintain high temperature. In addition, they require a large-scale furnace and detoxification equipment for the exhaust gas including hydrogen fluoride. The direct recycling has the potential to utilize the materials from the used batteries in new batteries,13,14 but it is not practical for processing mixtures of various batteries across a wide range of ages. In recent years, a lot of room temperature comminution processes have been reported.7,15–18 However, fatal accidents have occurred due to explosions.19 It is important to ensure safety during room temperature comminution. Here we would like to discuss a safe comminution process for end-of-life LIBs at room temperature.
Lithium-ion batteries are not bombs. Explosions are presumed to be caused by air and organic gas produced by local overheating20–22 of the LIBs during comminution, or hydrogen generated by the reaction between water and the negative electrode or aluminum.23 The greatest care should be therefore taken not to mix oxygen and hydrogen, or the concentrated organic gases. The room-temperature comminution process can be classified into three types: comminution in air,24 comminution in an inert atmosphere,25,26 and comminution in water or in sprayed water.16,18,27,28Fig. 1 shows fully-charged small LIBs being cut with nippers in a N2, Ar, or CO2–Ar atmosphere. Even though the oxygen concentration in the atmosphere is low, intense flames can be observed. The cause is suspected to be an internal short circuit and the reaction of the electrolyte with the anode and cathode, etc. This is a kind of chain reaction that results in a violent exothermic reaction. Sommerville et al. stated “will not stop a fire once started”.29 Thus, even comminution in an inert atmosphere can be dangerous if the LIBs are still in a charged state. Even if LIBs in a charged state can be comminuted successfully, the crushed product taken out of the inert atmosphere into the atmospheric atmosphere is not safe. Therefore, usually the LIBs are discharged before treatment in most room-temperature comminution processes. However, damaged batteries cannot be discharged, or human error is also expected in recycling. We propose therefore “to design a process for safety based on the assumption that LIBs in a charged state may be mixed in”.
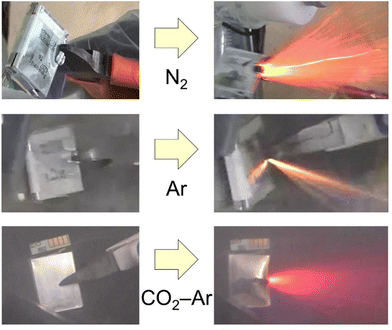 |
| Fig. 1 Photographs of fully-charged small LIBs cut with nippers in N2, Ar, or CO2–Ar atmosphere. | |
A comminution in water or in sprayed water16,18,28 can deactivate the negative electrode and dilute the organic electrolyte, and the aqueous solution works as a heatsink. If the hydrogen generated by the reaction between the water and the negative electrode can be properly treated, the process safety increases. That is, to avoid hydrogen explosion, it is strongly recommended that the comminution equipment submerged under water is installed in an inert atmosphere.
Methods
Preparation of charged LIBs
Prismatic cells dismantled from LIBs for a hybrid electric vehicle were charged by the CC/CV (constant-current/constant-voltage) method with a potentiostat/galvanostat (Princeton Applied Research, VersaSTAT 3). In the CC charging, 0.5 A of constant current was applied to the cell. When the cell voltage reached 4.1 V, the charging was switched into CV mode with a constant cell voltage of 4.1 V. When the current was decreased to 0.005 A, the CV charging was terminated. The capacity at state of charge (SOC) = 100% is defined to be 5250 mA h. The open circuit voltage (OCV) was 2.4 V for the LIB at SOC = 0%. The cells with SOC = 25% and 50% were prepared by charging from SOC = 0% in a CC mode of 0.5 A.
Submerged comminution of LIBs
Comminution of cells submerged in lime water was performed with a biaxial crusher in a glove box under N2 flow (oxygen conc. <1%). The glove box was composed of a polycarbonate box with butyl-gloves and a lime-water tank in which the biaxial crusher (Endo Kogyo Co. Ltd, EC15-20S-J) was installed. N2 gas was extracted from compressed air by a bundle of polymer hollow fiber separation membranes (CKD Corp., NS-4L110A-N) and supplied into the hopper on the biaxial crusher. The lime water was prepared from approximate 222 L of tap water and 315.91 g of calcium hydroxide (Ca(OH)2, Nacalai Tesque, Inc.). Water temperature was measured by thermocouples above and under the biaxial crusher. The concentrations of oxygen and hydrogen were analyzed with the gas sensors (Honeywell BWTM, Max XTII) with intervals of 5 seconds. Hydrogen was sampled at a position of about 15 cm above the water level in the hopper and oxygen was sampled in the glove box. To analyze hydrogen concentration, the sampled gas was diluted by air to keep the oxygen concentration at 9–16 vol%, and the detected value of lower explosive limits (LEL) was converted by the dilution ratio. Since the gas contains a small amount of organic compounds evaporated from the LIBs, the concentration of actual hydrogen might be slightly smaller than that indicated by the LEL value. The comminution was observed from the upper side of the polycarbonate box and through a window at the side of the lime-water tank. Most of the materials of the comminuted cells were recovered from the lime water and a part was again immersed into deionized water at 10, 30, and 60 minutes after the comminution to check whether or not unreacted lithiated-carbon in the negative electrode was present. Thereafter, the recovered LIBs were dried under vacuum at room temperature for 24–72 hours and identified by X-ray diffraction (XRD, PANalytical, X’Pert-ProMPD, Cu-Kα).
Cutting of LIBs in dry atmosphere
Cutting of LIBs in dry atmosphere was performed in a glove box composed of a polycarbonate box with butyl-gloves. The atmosphere was either N2, Ar, or CO2–Ar (oxygen conc. <1%). The CO2–Ar atmosphere was prepared by flowing 5 kg of CO2 into the box (800 mm × 500 mm × 1000 mm) filled with Ar gas. The oxygen concentration was measured by gas sensors (Ichinen Jikco Co., Ltd, JKO-25 Ver. 3 or Toray Engineering D Solutions Co., Ltd, SA-25NW/LD300). The small LIB (Al casing), fully-charged with the producer's charger (895 mA h, 4.14 V), was cut with a nipper on a heat-resistant pad, board, bucket, etc. The progress of cutting the LIB was observed from the outside.
Submerged comminution of LIBs for a hybrid electric vehicle
Fig. 2 shows the schematic illustration and photographs of the equipment with the biaxial crusher for submerged comminution of LIBs in lime water. Lime water was used to avoid the corrosion of the steel of the biaxial crusher (see in Table S2, ESI†).30,31 N2 gas was extracted from compressed air through hollow fiber separation membranes.
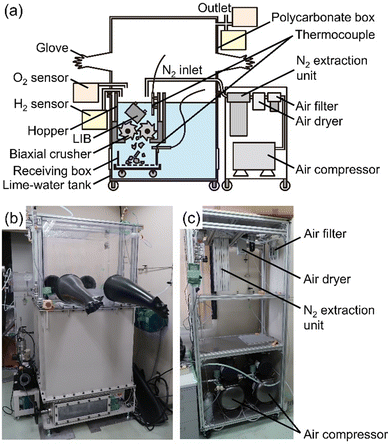 |
| Fig. 2 Equipment for submerged comminution of LIBs in lime water under N2 flow. (a) Schematic illustration. Photographs of (b) glove box with lime-water tank and (c) setup for N2 gas supply (maximum flow rate 22.0 L min−1 @ 99.9% N2, 56.4 L min−1 @ 99% N2). | |
A cell dismantled from LIBs for a hybrid electric vehicle was comminuted using the crusher immersed in lime water in a N2 glove box. Three different SOCs of the cells, 25%, 50%, and 100%, were examined, where SOC = 100% corresponds to approximately 5250 mA h (based on our measurement). The photographs of the submerged comminution and measured concentration for hydrogen above the water surface and oxygen in glove box are shown in Fig. 3(a) and (b), respectively. Movies of the comminution are given as supplemental movies (Movies S1–S3, ESI†). The comminution in water inevitably produces hydrogen gas from the reaction of water and the lithiated carbon in the negative electrode.
| LixC + xH2O → xLi+ + x/2H2 + C + xOH− | (1) |
In the submerged comminution of cells (SOC = 25% and 50%), the comminution was gently completed, generating transparent bubbles as clearly seen in the photographs. Movies S1 and S2 (ESI
†) provide clear observation of the transparent bubbles. The water temperature measured with thermocouples did not rise with comminution. The results are given in Fig. S4 in the ESI.
† After 15 seconds of comminution, hydrogen was detected in the collected gas in the hopper of the crusher, reaching a maximum of 0.7–1.2% in the case of SOC = 50 and 100%. The total amount of hydrogen evolution was larger for the higher SOC value. Since the inlet of the feed pipe of N
2 gas of flow rate 15–20 L min
−1 is located near the water surface in the hopper of the crusher, the generated hydrogen gas is rapidly diluted and its concentration is not high. The detection of hydrogen was continued for 80–120 seconds. The hydrogen concentration in the outlet tube of the glove box was detected 50–60 seconds after comminution with the maximum value of 0.3% in the experiment of SOC = 100%. This hydrogen concentration was sufficiently lower than both the lower flammability limit of 4% and the lower explosive (detonation) limits of 12–18% in air
32,33 (there seems to be discussion about these values
34), proving the safe gas-emission. In addition, the hydrogen concentration in another experiment of a small cell of 895 mA h reached about 4% above the surface of water with a low N
2 flow of 4.5 L min
−1 (see Fig. S3, ESI
†). When processing a large number of cells industrially, the dilution by nitrogen gas flow is unquestionably required to prevent hydrogen explosion.
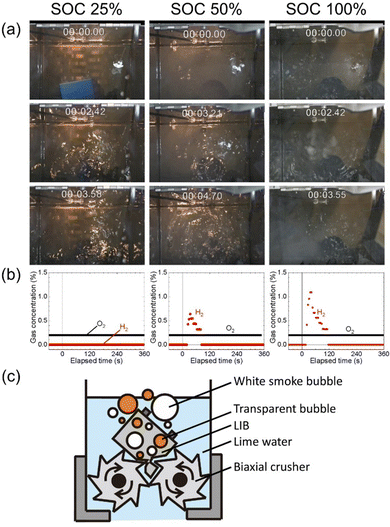 |
| Fig. 3 Observation and analysis of the submerged comminution. (a) Photographs of cell batteries being comminuted. (b) Concentration trend of hydrogen above the water surface and oxygen in the glove box. (c) Schematic illustration of the comminution in lime water for the higher SOC. | |
The crushed materials were recovered from the lime water after a certain period of time. From the products collected after 10 minutes of immersion, there was almost no gas evolution with only a slight amount of tiny bubbling observed. The deactivation of the negative electrode is mostly accomplished in a few minutes, and then gradually residual reaction proceeds. The aluminum current collector of the positive electrode remained after 60 minutes, which was confirmed by visual observation and XRD analysis.
The evolution of white smoke bubbles was a surprise and a great concern. As shown in Fig. 3(a) and (c), white smoke bubbles were observed as well as transparent bubbles during the comminution of the cell (SOC = 100%) even with the comminution in lime water in a N2 glove box; clear observation is shown in the movie (Movie S3, ESI†). The hydrogen gas pockets excluded the water and results in loss of the cooling function, and some volatile components were believed to have turned into smoke due to the local overheating. Therefore, the evolution of white smoke bubbles suggests that the risk remains even in comminution in water if the atmosphere is not inert. Fire generated by local overheating may reach the space above the water surface, like with an undersea volcanic eruption, and cause hydrogen explosion.
A slight odor of organic compounds was detected when recovering the crushed materials from the lime water. The exhaust gas and sampling gas to measure hydrogen concentration has such an odor, and deodorizing equipment is necessary. The comminuted LIB products are easily separated by the physical sorting process shown in Fig. 4(a) into black mass (mixture of the active materials of the electrodes), separator, Al casing, and Cu/Al foils.
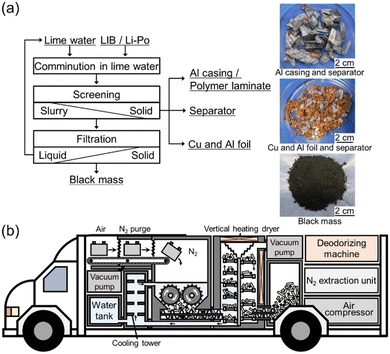 |
| Fig. 4 Overview of the recycling process of LIBs utilizing the submerged comminution. (a) Flow chart of deactivation and physical sorting process for spent LIBs by submerged comminution with lime water. (b) Schematic illustration of processing vehicle for the end-of-life LIBs. | |
Risk statement and assessment
In writing this paper, we agonized over whether the method presented here is really safe. We were concerned that those who imitated the method without understanding the essence of the process might meet with a serious accident. Therefore, we provide a list of the risks currently perceived to help readers improve safety. The following list includes those that are technically solvable and those that can be solved through education. In addition, some topics require further technological innovation. We believe that many future attempts may reveal new problems that are not currently apparent and that could be considered risks. Rather than rushing implementation, it is important to conduct basic research to better understand process safety and reaction mechanisms and share the results. This paper is one such example. We hope that each reader will take responsibility for conducting a follow-up study.
Risk identification
(1) Charged state.
In this study, experiments were conducted in a charged state, which is risky, and it is obviously better to electrically discharge the LIBs beforehand to reduce the amount of hydrogen produced.
(2) Nitrogen flow stopped.
The hydrogen gas from LIB cells is diluted by a large amount of nitrogen gas to make it safe, but if the nitrogen gas supply is interrupted, there is a risk of a hydrogen explosion or other serious accident.
(3) Sensors.
For suction type oxygen and hydrogen sensors, if water droplets or other contaminants enter the suction tube, the sensor may stop working. It is strongly recommended that multiple sensors be installed. However, most of the hydrogen sensors currently in general-use measure hydrogen concentration in air and cannot be used in an inert atmosphere such as nitrogen. Thus, it is desirable to develop inexpensive hydrogen sensors for inert atmospheres.
(4) Slow oxygen evolution.
Although not as fast as the reaction between the negative electrode and water, the positive electrode can oxidize water to cause oxygen evolution. It is important to ensure that no positive electrode material remains in the equipment, that the oxygen concentration is constantly monitored regardless of whether the equipment is operating or not, and that nitrogen flushing is continued periodically.
(5) Water temperature.
Water temperature should be monitored and care should be taken to ensure that the vapor pressure of organic materials does not increase. Also, the experiments in this paper were performed near room temperature. Unexpected reactions can be expected at higher temperatures than room temperature.
(6) Allowable concentrations.
The safe allowable concentrations in aqueous solutions of organic electrolytes and supporting electrolytes in batteries and the safe allowable concentrations of substances generated from these electrolytes must be known.
(7) Gas evolution from spent aqueous solution.
Gases are generated from the spent aqueous solution such as hydrogen gas from fine aluminum fragments that could not be collected by the filter, oxygen gas from the positive electrode material, and CO2 gas generated by the hydrolysis of carbonate. If the spent aqueous solution is stored in a sealed container, it is necessary to take precautions against hydrogen explosions and internal pressure increases.
(8) Continuous evolution of hydrogen after comminution.
It is strongly recommended that solids be dried immediately after crushing in water. Otherwise, the reaction between the aluminum and the aqueous solution may proceed continuously and slowly, resulting in the continuous evolution of hydrogen. This applies to the reaction of the positive electrode material as well.
(9) Danger of debris that has not been deactivated.
If the aluminum in certain areas, such as the edges of the battery case, is accidentally crimped and sealed during crushing, debris that has not been deactivated may remain.
(10) Safety in long-term storage and transportation.
The long-term storage of crushed materials treated with this method for more than one year and the effects of transportation have not yet been evaluated. An evaluation is needed.
(11) Processing speed: number of LIBs processed in unit time.
Industrial processing of a large number of LIBs is a future challenge. The number of pieces needs to be carefully increased.
(12) Dangers of fine grinding.
In our experiments, the LIB was either cut into two pieces or crushed by a biaxial crusher with a 12 mm wide blade; crushing LIB finer than this in water should be done carefully, taking care not to react too rapidly.
(13) Possibility of accelerated oxygen evolution.
If hydrogen from the negative electrode and oxygen from the positive electrode are produced at similar reaction rates, there is a danger of explosion. It is necessary to investigate whether there are factors that accelerate the rate of oxygen generation.
(14) Operator education and interlock mechanisms.
Hydrogen is transparent and colorless, and its risks are often unnoticed. It is necessary to thoroughly educate operators on hydrogen safety and install interlock mechanisms in the equipment to keep it safe.
(15) Environmental risks 1: detoxification of exhaust gases.
The exhaust gas had an odor that was presumed to be that of organic components in the battery. For the sake of the environment, it is necessary to establish a method to exclude harmful components from exhaust gases.
(16) Environmental risks 2: aqueous solution recycling.
Organic electrolytes and supporting electrolytes accumulate in the aqueous solution in a variety of forms. Those should be removed and the aqueous solution should be used repeatedly. Such studies are needed.
Conclusions and future outlook
There are still issues that need to be resolved to develop an industrializable set-up, but a social system could be established in which anyone can safely handle end-of-life LIBs anywhere; an example is shown in Fig. 4(b) in which a vehicle equipped with a submerged comminution machine in a N2 atmosphere is illustrated. As long as electricity is available, nitrogen can be inexpensively produced utilizing hollow fiber separation membranes from compressed air. Nitrogen flow reduces the risk of hydrogen explosion. Water can prevent temperature rise. However, we emphasize that any additional experiments should be performed at your own risk.
Author contributions
T. U., A. K. and Y. T. conceived the ideas. T. U., A. K. and K. Y. contributed the design of the setup, execution of the experiments, and writing the manuscript. A. K., K. Y. and Y. T. performed the analyses. All authors reviewed the manuscript.
Conflicts of interest
There are no conflicts to declare.
Acknowledgements
This work was financially supported by JST-Mirai Program Grant Number JPMJMI18C1 from Japan Science and Technology Agency (JST), and Adaptable and Seamless Technology transfer Program through Target-driven R&D (A-STEP) Grant Number JPMJTR20TF from JST. This work is conducted as a collaboration research of Laboratory of Design of Sustainable Materials and Processing, and Laboratory of Non-ferrous Extractive Metallurgy, Department of Materials Science and Engineering, Graduate School of Engineering, Kyoto University. Laboratory of Non-ferrous Extractive Metallurgy is an endowed chair by Mitsubishi Material Corp. We would like to acknowledge Prof. Takashi Nakamura at Tohoku University, Dr Satoshi Asano at Sumitomo Metal Mining Co., Ltd, and Mr Hidefumi Ishikawa at Nippon Magnetic Dressing Co., Ltd for the discussion. We also acknowledge Mr Takeo Takemura at Kyoto University for his technical assistance.
Notes and references
- W. Mrozik, M. A. Rajaeifar, O. Heidrich and P. Christensen, Energy Environ. Sci., 2021, 14, 6099–6121 RSC.
- I. Morse, Science, 2021, 372, 780–783 CrossRef PubMed.
- J. Baars, T. Domenech, R. Bleischwitz, H. E. Melin and O. Heidrich, Nat. Sustainability, 2021, 4, 71–79 CrossRef.
- P. A. Christensen, G. D. J. Harper, S. M. Lambert, W. Mrozik, M. A. Rajaeifar, M. S. Wise and O. Heidrich, Renewable Sustainable Energy Rev., 2021, 148, 111240 CrossRef.
- M. Chen, X. Ma, B. Chen, R. Arsenault, P. Karlson, N. Simon and Y. Wang, Joule, 2019, 3, 2622–2646 CrossRef CAS.
- H. E. Melin, M. A. Rajaeifar, A. Y. Ku, A. Kendall, G. Harper and O. Heidrich, Science, 2021, 373, 384–387 CrossRef CAS.
- G. Harper, R. Sommerville, E. Kendrick, L. Driscoll, P. Slater, R. Stolkin, A. Walton, P. Christensen, O. Heidrich, S. Lambert, A. Abbott, K. Ryder, L. Gaines and P. Anderson, Nature, 2019, 575, 75–86 CrossRef CAS PubMed.
- O. Velázquez-Martínez, J. Valio, A. Santasalo-Aarnio, M. Reuter and R. Serna-Guerrero, Batteries, 2019, 5, 68 CrossRef.
- Kelleher Environmental, Research study on reuse and recycling of batteries employed in electric vehicles: the technical, environmental, economic, energy and cost implications of reusing and recycling EV batteries, Project report for American Petroleum Institute, https://www.api.org/~/media/Files/Oil-and-Natural-Gas/Fuels/Kelleher%20Final%20EV%20Battery%20Reuse%20and%20Recycling%20Report%20to%20API%2018Sept2019%20edits%2018Dec2019.pdf, 2019.
-
D. Cheret and S. Santen, US Pat., US7169206, 2007 Search PubMed.
-
Y. Yamaguchi, Jp. Pat., JP5,657,730, 2015 Search PubMed.
-
J. J. Liotta, J. C. Onuska and R. H. Hanewald, Proceedings of the Tenth Annual Battery Conference on Applications and Advances, 1995, pp. 83–88 Search PubMed.
- E. Gies, Nature, 2015, 526, S100–S101 CrossRef CAS PubMed.
- Y. Tao, C. D. Rahn, L. A. Archer and F. You, Sci. Adv., 2021, 7, eabi7633 CrossRef CAS PubMed.
-
F. Tedjar and J.-C. Foudraz, US Pat., US7820317, 2010 Search PubMed.
-
A. Kochhar and T. G. Johnston, US Pat., US11077452, 2021 Search PubMed.
- R. Sommerville, P. Zhu, M. A. Rajaeifar, O. Heidrich, V. Goodship and E. Kendrick, Resour., Conserv. Recycl., 2021, 165, 105219 CrossRef CAS.
-
W. N. Smith and S. Swoffer, US Pat., US8616475, 2013 Search PubMed.
- National Institute of Occupational Safety and Health, Japan, Explosion accident at a machine manufacturing plant during a lithium-ion battery crushing test, Disaster Investigation Report. https://www.jniosh.johas.go.jp/publication/pdf/saigai_houkoku_2016_07.pdf#zoom=100, 2016.
- D. Lisbona and T. Snee, Process Saf. Environ. Prot., 2011, 89, 434–442 CrossRef CAS.
- X. Feng, M. Ouyang, X. Liu, L. Lu, Y. Xia and X. He, Energy Storage Mater., 2018, 10, 246–267 CrossRef.
- D. P. Abraham, E. P. Roth, R. Kostecki, K. McCarthy, S. MacLaren and D. H. Doughty, J. Power Sources, 2006, 161, 648–657 CrossRef CAS.
- Explosion at Chinese battery recycling plant kills one and injures 20, https://www.independent.co.uk/news/world/asia/explosion-blast-china-battery-fire-hunan-b1784643.html, accessed February 1, 2022.
-
J. Pudas, A. Erkkila and J. Viljamaa, US Pat., US8979006, 2015 Search PubMed.
-
T. Zenger, A. Krebs and H. J. H. V. Deutekom, Canadian Pat., CA2418527C, 2011 Search PubMed.
-
C. Hanisch, W. Haselrieder and A. Kwade, US Pat., US9780419, 2017 Search PubMed.
-
M. Kudo and S. Shimizu, Jp. Pat., JP3069306, 2000 Search PubMed.
-
M. Kudo and S. Shimizu, Jp. Pat., JP3080606, 2000 Search PubMed.
- R. Sommerville, J. Shaw-Stewart, V. Goodship, N. Rowson and E. Kendrick, Sustainable Mater. Technol., 2020, 25, e00197 CrossRef CAS.
- Y. Tsuru, Y. Tamae, Y. Nagai, T. Nakahata and K. Matsui, Effects of solution pH, sodium chloride and amino acids on the corrosion of a steel plate in lime water, J. Soc. Mater. Sci., Jpn., 2002, 51, 1197–1202 CrossRef CAS.
- V. K. Gouda, Br. Corros. J., 1970, 5, 198–203 CrossRef CAS.
- J. Van Gompel, Solid State Technol., 2005, 48, 51 CAS.
- T. Otsuka, S. Tsuge and Y. Norihiko, Sci. Technol. Energ. Mater., 2012, 73, 29–34 CAS.
- R. Kurokawa, S. Hirano, Y. Ichikawa, G. Matsuo and Y. Takefuji, Med. Gas Res., 2019, 9, 160–162 CrossRef CAS PubMed.
|
This journal is © The Royal Society of Chemistry 2022 |