DOI:
10.1039/D1TC02105B
(Review Article)
J. Mater. Chem. C, 2022,
10, 805-818
Magnetic cellulose: does extending cellulose versatility with magnetic functionality facilitate its use in devices?
Received
6th May 2021
, Accepted 22nd November 2021
First published on 22nd December 2021
Abstract
Magnetism is certainly one of the most intriguing properties of materials. It provides a means for manipulating macroscopic and microscopic positioning and alignment of materials and is a characteristic that is essential for the creation of numerous devices and appliances. Cellulose is a renewable resource that encompasses a diverse portfolio of material hierarchies: the cellulose molecule, molecular clusters, fibrils, fibers, films, and wood products. Cellulose is exploited in materials due to its impressive intrinsic properties of non-toxicity, low density, and low cost as well as due to the extraordinary material properties of thermal stability and strength. However, many devices operate on electrical or magnetic signals, a functionality that cellulose lacks. To exploit cellulose in such applications, cellulose is often modified by ferromagnetic particles. Ferromagnetic cellulose fibers are not only demonstrated for separation of biomolecules and environmental accumulations but also in electrical textiles, loudspeakers, magnetic shielding, and optical and medical devices. This review focuses on presenting the current selection of methods for rendering cellulose magnetic; its demonstrated use in devices; and an outlook on the challenges, application, and gaps in knowledge of creating the requisite materials.
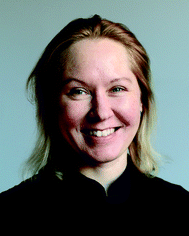
Tiina Nypelö
| Tiina Nypelö received doctorate in forest products surface chemistry from Aalto University, Finland 2012. She stayed for postdoctoral research periods in North Carolina State University,USA, and in University of Natural Resources and Life Sciences in Vienna, Austria. From 2017 she has been at Chalmers University of Technology and at Wallenberg Wood Science Center, and is Associate professor working on the topic of bio-based materials. Her research interests involve cellulose, hemicelluloses and lignins with emphasis on surface, interface, and intermolecular interactions. |
Introduction
Cellulose is a marvelous material available in nature; it comes in various formats, either natural or human-made. Much effort has been directed to functionalize cellulose to enable its use in active materials and applications that require a prompt stimuli-response. Cellulose is a material with much to offer to materials science. Cellulose fibers are a non-toxic, inexpensive (e.g., bleached hardwood kraft pulp price approximately 980 USD per metric tonnes1) and abundant (e.g., 190 million tons of wood pulp produced annually2) material for paper, textiles, and packaging, to name just a few fields of use. In addition to the “dry” forms, its hygroscopic nature makes nanosized cellulose an appealing material for hydrogels potential for medical uses. Cellulose does not melt until the onset of degradation at 240 °C,3 and cellulose particles and fibers are frequently used to reinforce polymer matrixes4–7 that benefit from its high elastic modulus and aspect ratio. In engineered materials, cellulose is often used as a substrate and carrier material and has also been demonstrated as a carrier for magnetic moieties and magnetic materials.
The aim of this review is to present the aspects related to the intrinsic magnetic properties of cellulose and the synthesis of (ferro) magnetic cellulose hybrids, their properties, and applications. The outlook provides a discussion on the limitations of current preparation methods and the uses of magnetic cellulose.
Both cellulose that exhibits the backbone structure of β-1,4-linked anhydroglucose units (AGU) and hydroxyl functionality as well as modifications that introduce a functionality but preserve the cellulose hierarchy are included here. This review focuses on cellulose from forest resources, its various hierarchical structures, and its use in devices that require magnetic functionality. Forest-based cellulose materials are available from the pulp and paper sector and may be considered abundant and currently a more widely available commodity than, for example, cellulose synthetized by bacteria. Bacterial cellulose-magnetic materials have been reviewed by Sriplai et al.8 and Hu et al.9 but these are excluded from this review.
In demonstrations where cellulose has been carbonized, separation and enzyme immobilization with magnetic cellulose,10 and magnetic acid catalysis for cellulose hydrolysis are largely excluded. The focus is on the literature published between 2010 and 2021.
Characteristics of supramolecular cellulose
The continuous motivation toward fundamentals and developing cellulose-based materials may be influenced by two aspects. First, cellulose is a polysaccharide with a high degree of polymerization. It consists of cyclic monosaccharides, linked via glycosidic bonds, thereby resulting in a linear macromolecule with backbone stiffness that, along with intrachain hydrogen bonding (Fig. 1), contributes to making cellulose dissolution behavior complex and intriguing. Second, the cellulose chains form structures beyond a single polymer chain and the resulting supramolecular structures provide an immense number of structural building blocks for purposes related to chemistry, physics, and materials science.
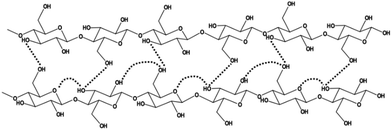 |
| Fig. 1 Structure of cellulose and inter and intrachain hydrogen bonding (dashed line). | |
Hierarchical structure of cellulose
Every other AGU is flipped over and glycosidic bonded (Fig. 1) forming a high molecular weight macromolecule that is at the lowest level of material hierarchy of cellulose considered here (Table 1). In plants, these cellulose chains are synthetized into fibrils, which are the structural units that constitute the cell wall of plant fiber. The fibers are often the targeted material from plant tissue for engineering purposes. The liberation of cellulose from wood via pulping11 is a voluminous industrial process, which provides fibers for paper, textiles, and packaging materials. Exposing the wood fibers into further chemical and mechanical treatments liberates the fibers and fibrils into nanofibers and particles. These materials are called nanocelluloses. The main engineering grades of nanocelluloses are cellulose nanofibers (CNFs) and cellulose nanocrystals (CNCs) (Fig. 2). CNFs are characterized by longer length and lower crystallinity than CNCs, which are rod-like particles produced typically via acid hydrolysis (Table 1). CNFs are excellent film-forming materials with good barrier properties.12 Furthermore, CNCs are a remarkable cellulose grade of lyotropic colloidal nanoparticles13 and have tremendous potential to revolutionize nanotechnology.14–16 CNCs self-assemble into a cholesteric liquid crystal order, in which they form a chiral organization. A nematic liquid crystal order where CNCs orient almost unidirectionally can be facilitated by applying shear force to a suspension.15
Table 1 Cellulose hierarchies available from wood for engineering, for example, magnetic cellulose materials
Structure |
Hierarchy |
Size |
Cellulose macromolecule19 |
Molecular |
Å |
Cellulose nanocrystals (CNCs), also called whiskers13,20,21 |
Molecular to nano |
d 3–5 nm |
L 100–300 nm |
Cellulose nanofibers (CNFs)22–25 |
Molecular to micro |
d 7–170 nm |
L few μms |
Native fibers (macrofibres)26,27 |
Molecular to macro |
d 20–35 μm |
L 1–3 mm |
Regenerated cellulose fibers and filaments (macrofibres)17,28 |
Molecular to macro |
d tens of μm |
Papers, membranes, textiles |
Molecular to macro |
Diverse |
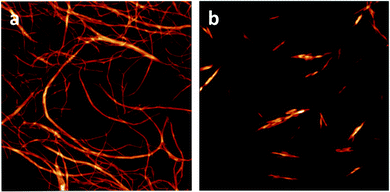 |
| Fig. 2 Atomic force microscopy visualization of cellulose nanofibers (a) and cellulose nanocrystals (b). The frame size is 3 × 3 μm. | |
Cellulose can be dissolved into solvents such as N-methylmorpholine-N-oxide17 and ionic liquids18 that enable the formation of films and fibers into solutions. Such regenerated fibers are the basis of modern textile manufacturing. They have greater homogeneity compared to native fibers and can be spun in a continuous process into filaments. The filaments are further processed into staple fibers and threads for garment and technical textiles.17 Indeed, cellulose is a family of materials that spans from molecular to macroscopic hierarchies (Table 1).
The magnetic properties of materials
Magnetism is caused by the movement and spin of electrons. The number of unpaired electrons and the size of the atom define the magnitude of magnetism. The magnetic character is divided into ferromagnetic, ferrimagnetic, antiferromagnetic, paramagnetic, superparamagnetic, and diamagnetic behavior (some of which are illustrated in Fig. 3). Ferromagnetic materials have the highest magnetic susceptibility, as all the molecular magnetic dipoles permanently align in the same direction (even without an external magnetic field, H, H = 0). In antiferromagnetic (and ferrimagnetic) materials, the dipoles align into opposite directions, thereby reducing magnetic susceptibility. Paramagnetic atoms and molecules have a magnetic moment and are weakly affected and attracted by a magnet; however, they cannot form a permanent magnet. Furthermore, superparamagnetism is a property of small particles, where magnetization can flip direction under the influence of temperature. Diamagnetic materials do not have a magnetic moment, but the magnetic field creates more induced magnetic fields in the opposite direction of the main field.
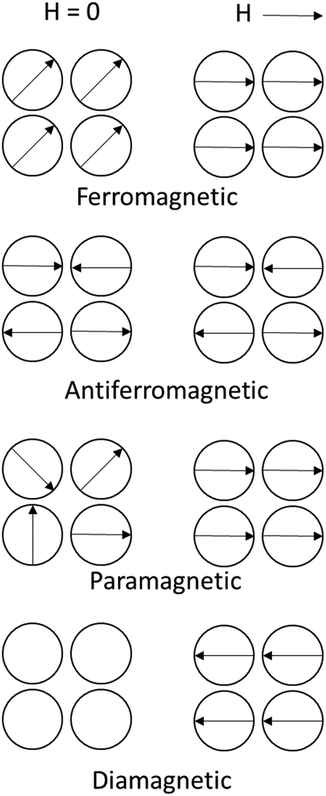 |
| Fig. 3 Illustration of the magnetic dipole moments in magnetic materials with and without an external magnetic field (H). | |
Ferromagnetism
The most familiar form of magnetic materials are ferromagnetic materials that form permanent magnets. Iron (Fe), cobalt (Co), and nickel (Ni) are the main ferromagnetic substances and 3d-block elements in the fourth period. Their electron configuration has five 3d orbitals, each of which can include two electrons. Moreover, according to Hund's rule, orbitals of similar energy levels are occupied first with parallel spins rather than paired ones (Fig. 4). For example, for iron (3d6), the ground state consists of one fully occupied d-orbital (with paired electrons) and four unpaired (Fig. 4) ones. Iron, cobalt, and nickel with their 4, 3, and 2 unpaired electrons, respectively, are ferromagnetic materials.
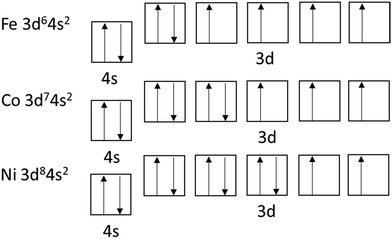 |
| Fig. 4 Ground-state electron configuration of iron, cobalt, and nickel. | |
Furthermore, paramagnetism also originates from unpaired electrons. However, the magnetism is not maintained when the magnetic field is removed. Diamagnetic materials have only paired electrons and in a magnetic field, align in the direction opposite to that of the field. Magnetic materials in engineering are typically alloys of iron, aluminum, nickel, cobalt, and rare earth elements, such as samarium, dysprosium, and neodymium. Iron can form magnetite (Fe3O4), hematite/maghemite (Fe2O3), limonite (Fe2O3 × H2O), and siderite (FeCO3) from which magnetite (Fe3O4) and maghemite (γ-Fe2O3) are common in nanoparticle forms.
Intrinsic magnetic moment of cellulose
Cellulose is a diamagnetic substance. The combination of anisotropy (Table 1) and diamagnetic polarizability makes it susceptible to a certain extent, to manipulation in a magnetic field because the diamagnetic material tends to exclude magnetic flux and the anisotropic particles orient to axis with the most diamagnetic susceptibility perpendicular to the field.29 Frka-Petesic et al.30 quantified the diamagnetic anisotropy of CNCs by optical birefringence measurements in Cotton–Mouton experiments and confirmed a negative sign of the diamagnetic anisotropy and a diamagnetic susceptibility of −0.95 × 10−6. They further confirmed that the rod-like CNCs tended to orient themselves perpendicular to a strong magnetic field.
Indeed, exposure of the elongated CNCs above a critical concentration to a high magnetic field has been demonstrated to result in alignment of the CNCs.31 Moreover, the control of CNC orientation is interesting for liquid crystal materials where, in case of CNCs, either a cholesteric or nematic order is to be manipulated. It has been suggested that cholesteric structure formation is unaffected by the magnetic field, but the pitch (the magnitude of total rotation in the cholesteric order) can be increased and is due to alignment of the individual crystals in the liquid crystal order.32 Drying a CNC film in the presence of a 0.2 T external magnetic field increases the pitch, but the resulting structure is also affected by the drying process.32
Furthermore, the unidirectional alignment of cellulose is interesting for creating anisotropic materials that exhibit piezoelectricity33 and for control over thermal expansion34 and strength35 owing to the increase in order. The potential of the aligning cellulose using magnetic fields has been proven mostly in water, but is also found in solvents of higher dielectric permittivity.31 A field of 7 T was required to align tunicin CNCs in a film that was prepared in a magnetic field.36 The tunicin CNCs are characterized by a length that is greater by a factor of 10 than that of wood CNC varieties.37 The length and rigidity that arises from the supramolecular order make it appealing in applications that benefit from the rod-like particle alignment. However, the magnetic field of 7 T is high. To put this in perspective, we may consider that the typical magnetic resonance imaging (MRI) magnets are 1.5–3 T and the strongest ones currently available exceed 10 T.38
Mao et al.39 revealed that the nematic phase of CNCs was aligned by applying a magnetic field of 0.5 T, while the isotropic phase was not. A field of 1.2 T applied to cellulose nanowhiskers (i.e., CNCs) in a cellulose matrix resulted in pronounced orientation of the nanowhiskers in certain domains, while in other areas the random orientation remained.40 A similar field strength, 1.2 T, was used to align cellulose nanowhiskers in a pulp matrix. They found that exposure to the magnetic field aligned the particles, while the wood pulp fibers remained unaligned.41 The orientation increased the storage modulus along the direction perpendicular to the magnetic field. It has actually been shown that the effect of the magnetic field on the simple shear and viscoelastic properties is more significant at a lower concentration of cellulose particles, thereby demonstrating that the interacting particles may hinder the orientation.42 However, using dilute systems is not practical most of the time for engineering materials that are designed to be solid (dry) and this is a limiting factor for using dilute systems.
Furthermore, in addition to the demand for high field strength, time is a limitation for using the intrinsic diamagnetic property of cellulose for alignment purposes: for example, 0.7 T and 20 h has been found to be required for achieving alignment.31 On the other hand, 0.56 T was reported to reach almost perfect alignment in CNC water suspension in less than 200 min.43 However, these are still long-time scales, considering the typically required magnetic response time; for example, in devices. A combination of electric and magnetic fields may facilitate shorter times. In fact, to facilitate alignment in a magnetic field (5 T), an electric field (50 V cm−1 at 100 Hz) was applied to wet-spun cellulose fibers.44 Either electric and magnetic fields alone or applied simultaneously induced alignment of CNFs. However, the issue of the long time duration required for alignment remains to be resolved.
Synthesis of magnetic cellulose
It may be that the most feasible method for introducing a magnetic property to cellulose is combining it with ferromagnetic nanoparticles. The main methods of preparation of ferromagnetic cellulose hybrid materials are presented in this chapter and summarized in Table 2.
Table 2 Approaches to render cellulose magnetic
Magnetic moiety |
In situ incorporation |
Ex situ incorporation |
Iron oxide |
Co-precipitation in cellulose matrix: cellulose suspension,47,48,51 cellulose solution49,50,56–58 |
Preformed particles: added to cellulose solution;49,52–55,59–62 surface modification of cellulose prior;63 using a retention aid71 |
Hydrothermal methods68 |
Ferrite |
Co-precipitation: in suspension,73,74,77,78,81 |
Preformed particles added to cellulose suspension72 |
solution,75 in swollen cellulose marix76 |
Hydrothermal method in suspension79,81 |
Solvothermal method80 |
Nickel |
Nanoparticles precipitated and immobilized in cellulose solution82 |
|
Iron oxide particles
Magnetite particles are by far the most utilized particles for preparing magnetic cellulose materials. Iron oxide particles and their magnetite phase are typically prepared by co-precipation45,46 using iron salt solutions—for example, precursor mixture iron(II), chloride FeCl2, and iron(III) chloride (FeCl3). Magnetite particle–cellulose hybrids have been synthetized by dissolving the salts of FeCl2 and FeCl3 into a cellulose particle suspension and initiating particle precipitation by changing pH to alkaline through the addition of a base.47–49 Maghemite particles have also been incorporated into cellulose hydrogels using the immersion of preformed hydrogel into iron salts, followed by particle initiation by a shift in the pH level.50 The structure of the formed particles via co-precipitation is determined by nucleation and molecular growth events. Nucleation begins by the formation of molecule clusters that function as precipitation points for further development into particles. The particle growth is influenced by mixing and temperature also plays a role; for example, at room temperature, a diameter of 6.5–12.5 nm was reported for total iron concentration ranging from 0.04 to 0.8 mol l−1, synthesized in a cellulose matrix, while increase in temperature affected the size distribution and dispersion.51
The co-precipitation has been mostly performed in a matrix of various cellulose material hierarchies (Table 1), thereby producing hybrid particles comprising organic cellulose and inorganic iron oxide phases. The same method has been applied to produce magnetic cellulose in solution by first dissolving the cellulose in, for example, NaOH/urea at low temperature and combining the cellulose solution with pre-formed magnetic particles52–55 or dropwise addition of a solution of FeCl3 and FeCl2 into the solution.56,57 Cellulose xanthate, that is a soluble intermediate in viscose production and can be regenerated to cellulose, was functionalized with iron oxide particles by adding premade particles as well as in a one-step synthesis by adding an iron source into the xanthate solution.49
Furthermore, ionic liquids are a rather new class of cellulose solvents, which are already being used in preparing magnetically functional cellulose: ionic liquids have been used to dissolve the cellulose and iron salts for co-precipation,58 mixing together,59–62 or grafting63 the cellulose and magnetic component. Ionic liquids were also used as a solvent for dissolution and regeneration in the sol–gel transition method to produce cellulose–chitosan magnetic composites.64,65
While co-precipitation is a widely used method, there are also other chemical methods, including hydrothermal methods.66 Hydrothermal methods for preparing cellulose composite films with Fe3O4 have been established using FeCl3, trisodium citrate dihydrate, and sodium acetate trihydrate dissolved in ethylene glycol and autoclaved at 200 °C, thereby leading to spherical particles of diameter 243 ± 72 nm.67 CNC–Fe3O4 hybrids were prepared via hydrothermal decomposition of iron(III) acetylacetonate. This was added to a mixture of oleic acid, 1-octadecene, and benzyl ether and heated to form Fe3O4 nanoparticles.68
The majority of iron oxide particles are spherical. However, the synthesis of platelike Fe2O3 nanoparticles with a size of 48 nm and a thickness of 9 nm in a cellulose matrix with weak ferromagnetic properties and magnetic anisotropy has been reported.69
The primary method of affecting the load of particles in the cellulose matrix is by varying the synthesis conditions and the reagent concentrations and ratios. However, the loading can also be adjusted by affecting the accessibility of the selected cellulose hierarchy. The modification of native macrofibres (instead of nanofibrils and regenerated macrofibres) has the likelihood of extending the modification from the surface to the fiber lumen and cell wall. An ultrasound treatment of cellulose fibers increases the amount of iron oxide particles that could be introduced via co-precipitation.70 The reasoning for this is the improved accessibility and opening of the nanoscale voids of the cellulose matrix. In addition, the ultrasound synthesis was deemed effective to control the size (10–100 nm) and the particle distribution of the magnetic iron oxide in the magnetic cellulose composite.70 The ultrasound treatment increased the mass of detected iron in the material. The so-called Lumen loading has also been facilitated for iron oxide particles to be incorporated within cellulose fibers by swelling the fibers and using polyethyleneimine (PEI) as a retention aid.71
Ferrite particles
Ferrites are formed in the reaction of iron oxide with another metal (e.g., cobalt, nickel, copper, aluminum, and manganese). Cobalt ferrite (CoFe2O4) particles are commonly used to prepare magnetic cellulose via co-precipitation.72 They can be synthetized using iron(II) sulfate (FeSO4) and cobalt(II) chloride (CoCl2)73,74 or FeCl2 and CoCl2.75 CoFe2O4 particles were synthetized in a cellulose aerogel via co-precipitation in a swollen cellulose network followed by freeze drying, which led to the production of particles of diameter 98.5 nm.76 An impressive 95% loading has been achieved by co-precipitation of cobalt ferrite in a CNF matrix. The CNFs acted as templates for the non-agglomerated growth of ferromagnetic nanoparticles (diameter, 40–120 nm).77 The same procedure has been demonstrated in CNC hybrid materials, but with a lower loading of 7 wt%.78 Electron microscopy visualization of the stages of cellulose (CNC) prior and after treatment with cobalt and iron precursor salts, after precipitation and purification are presented in Fig. 5a, b, c and f, respectively. Purification via magnetic decanting is visualized in Fig. 5d and e. The homogenous formation of magnetic particles in the cellulose matrix is evident (Fig. 5f).
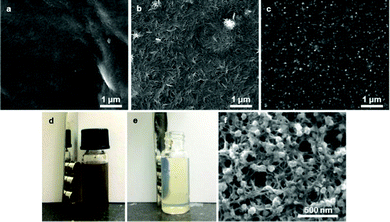 |
| Fig. 5 Electron microscopy images of CNCs (a), precursor salt-treated CNCs (b), and magnetic CNCs (c) deposited on silicon substrates. The magnetic CNC phase (d) was subjected to magnetic separation with NdFeB magnets (e) and imaged (f). Image reprinted by permission from Nypelö et al.78 | |
Copper cobalt ferrite (Cu0.5Co0.5Fe2O4) has been synthesized in situ by controlled hydrothermal chemistry and immobilized on CNCs.79 In addition, positive electric charge manganese ferrite particles (MnFe2O4) have been prepared using the solvothermal method using FeCl3 and MnCl2.80 The precipitation of zinc ferrite (ZnFe2O4) nanoparticles onto the surface of cellulose fibers has also been established.81
Nickel-containing particles
Nickel nanoparticle–cellulose-grafted graphite oxide nanocomposites have been proposed for applications in biosensors and biocatalysts.82 Moreover, the sputtering of nickel nanoparticles on carbonized cotton has also been reported.83
Properties of cellulose-magnetic particle hybrid materials
Cellulose-magnetic hybrid materials represent the possibility of cellulose functionalization with a magnetic property. The magnetic particles are primarily responsible for the ferromagnetic character that is introduced into the cellulose material.
Magnetic properties
The magnetic properties of a material are characterized by magnetization (that is, the magnetic moment per volume or mass (emu g−1)) and the response of the material to the magnetic field, known as magnetic induction (Tesla). Magnetic properties are measured and presented as magnetization versus the applied magnetic field. In ferromagnetic materials, the magnetization becomes saturated (reaches a plateau) above a certain applied field and is quantified by a saturation magnetization (i.e., a magnetic field that leads to maximum magnetization). Coercivity characterizes the ability of a ferromagnetic material to withstand an external magnetic field without demagnetization. Superparamagnetism is a property of small particles where magnetization can flip direction. The decrease in the domain size leads to a decrease in coercivity.29 Moreover, the type of magnetism sought depends on the application. In data storage applications, the particles need to have a switchable magnetic state that is not affected by temperature fluctuations. Typically, large coercivity is sought.29 For biomedical applications, superparamagnetism at room temperature is a prerequisite, along with high magnetization, to be directed into the body.84 The materials also need to be (colloidally) stable in water and in physiological conditions, with the ability to diffuse in tissue. For in vivo applications, a biocompatible surface is required, and magnetite and maghemite are commonly used in vivo. Cobalt and nickel, being toxic, are less preferred.
In a hybrid material of CNC–CoFe2O4, a maximum magnetization saturation of 12.96 emu g−1 has been obtained,85 while the CoFe2O4 alone was discussed to reach a saturation magnetization of 60 emu g−1. Furthermore, CNF saturation magnetization of 14.17 emu g−1, with 20% loading of Fe3O4 nanoparticles has been reported.86 Fe2O3 as synthetized in a cellulose matrix exhibited a saturation magnetization of 98.39 emu g−1 and the coercivity was 32.68 Oe.87 In addition, cellulose macrofibers modified with cobalt ferrite particles presented a saturation magnetization of approximately 8.0 emu g−1 and a coercivity higher than 200 Oe.72 It was indicated that the properties are adequate for magnetic recording applications.
What is the benefit of cellulose in magnetic hybrid structures?
Perhaps the most important asset of cellulose in magnetic materials is the diversity of the available natural and human-made particles and fiber forms (Table 1). In addition to the pulp fibers and regenerated fiber filaments,88 the cellulose hierarchy that has recently become popular in magnetic demonstrations are the nanocelluloses. One of the benefits of using nanocelluloses for magnetic hybrids includes the fact that the nanocelluloses can be formed into transparent films.89 The nanocellulose films resemble plastic films, and it is easy to understand the excitement generated by this potential development: it has the ability to replace synthetic plastics with natural materials. Consequently, nanocellulose films with magnetic particles are also transparent (up to a certain loading). A transparency of 86% and a tensile strength of 170 MPa was reported with 5% of Fe3O4-particle loading.86
The challenge of nanoparticles (of any kind) in materials engineering is their dispersion in a manner that allows aggregation to be controlled. An asset of using, for example, CNFs as the templates for growing particles78 is the ability to prevent the subsequent free migration of particles as well as the evident aggregation.
Nanoscale cellulose fibers used to carry magnetic moieties in hybrid materials have been created by transferring cellulose solutions into fibers via electrospinning. Electrospinning of CNC–Fe3O4 particles in a poly(3-hydroxybutyrate-co-3-hydroxyvalerate) and polyethylene glycol matrix47 as well as cobalt ferrite particles in a polyvinyl alcohol matrix78 has been used to prepare continuous nanofibers with a smaller diameter than pulp or textile fibers. Nanofibers with a small diameter are often sought in biomedical applications in which a high surface area is advantageous for interactions with tissue and cells. Another emerging field of fiber spinning is the wet spinning of suspensions containing nanocelluloses into filaments, which also involves the opportunity to incorporate magnetic particles into these filaments.90
In addition to the hierarchies listed in Table 1, there are a few additional human-made formats that have been popular in magnetic cellulose endeavors. Cellulose beads or spheres are often prepared via the dissolution of cellulose and their magnetic property is created by the incorporation of iron oxide particles in the beads.51,91–96 Cellulose has been combined with other hydrophilic polysaccharides and polymers in the creation of cellulose–hydroxyapatite magnetic beads97 and in cellulose–chitosan microspheres.98 The beads are mostly used in protein detection96 or in encapsulation and separation applications. Moreover, CNCs are used in microbead formation (or oil stabilization99) due to their specific property of assembling at an oil–water interface and functioning as a Pickering stabilizer to form a shell around the bead.100,101
Cellulose-magnetic hydrogels are a large material group used for separation and immobilization of biomolecules.102 A rather straightforward approach of preparation is the dissolution of cellulose followed by crosslinking into a gel and incorporation of iron oxide particles into the hydrogel.103 Cellulose along with other hydrophilic polymers (polyvinylalcohol and chitosan) have been demonstrated to form gels that also enclose magnetic particles104,105 and are used for the removal of heavy metals, like lead (Pb), by using the carboxylate groups of cellulose as an active site for Pb retention.106 Magnetic beta-cyclodextrin–cellulose hydrogels have been prepared by epoxidation of cellulose with cyclodextrin, followed by dispersing Fe3O4 particles in the mixture and finally coagulating the system in a CaCl2 bath into hydrogel microbeads.107 Quaternized xylan and CNCs were used to create a network via ionic crosslinking and formed a hydrogel, where magnetic functionality was incorporated via Fe3O4 synthesis within the reinforced hydrogel matrix.108
Alignment in magnetic cellulose materials
Aligned magnetic nanoparticles in a cellulose matrix were prepared by embedding a cellulose solution with Fe3O4 nanoparticles subjected to magnetic orientation, regeneration to cellulose, and stretching the composite to magnify the alignment.109 CNCs were aligned in a polymer matrix by first aligning them in the precursor system followed by curing using polymerization.110 Tunicate-CNCs were demonstrated as a filler for rubber to produce rubber composites with an alignment and magnetic functionality.111 The preparation procedure is simple exposure of the system to a magnetic field and then curing. Overall alignment is attained by the alignment of the anisotropic cellulose particles that carry iron oxide particles. A simple approach for aligning macrofibers decorated with magnetic particles has been demonstrated using permanent magnets in a flow cell.112
Furthermore, Yoshitake et al.113 demonstrated that films where the CNCs and magnetite (Fe3O4) particles are oriented can be directed by an external magnet. Rectangular strips of films assembled the draw direction vector parallel to the field vector. The manipulation of magnetically modified cellulose with a magnetic field is more instantaneous than the manipulation of neat cellulose and requires, in general, magnets with lower strength—Yoshitake et al.113 used a 0.15 T bar magnet to move the hybrid materials.
Cellulose in magnetic devices
This section presents demonstrations of devices that benefit from the combination of cellulose and magnetic substances. Here, a device is defined as a system adapted for a particular purpose.
Loudspeakers
An application of cellulose in magnetic devices that is tangible in everyday life is the demonstration of magnetic cellulose films in loudspeakers. A thin prototype loudspeaker has been proposed, where a cellulose–CoFe2O4 membrane is driven to generate music through a static coil.114 In a traditional loudspeaker, there is a membrane that is attached to the voice coil that moves in a magnetic gap and causes a membrane to vibrate and produce a sound. The setup by Galland et al.114 with a magnetic cellulose membrane was to make an external magnet unnecessary by introducing the magnetic cellulose membrane. The magnetic membrane in the loudspeaker prototype is depicted in Fig. 6. The benefit of using CNFs as the template for magnetic nanoparticles and in the membranes was that the nanoparticles attached to the fibrils ensured a homogeneous particle distribution. The membranes had an impressive strength of 100 MPa and a stiffness of 5 GPa at 60 wt% CoFe2O4 loading.114 The strength is due to the CNF matrix: CNF films have often been reported with a tensile strength of above 200 MPa.115,116
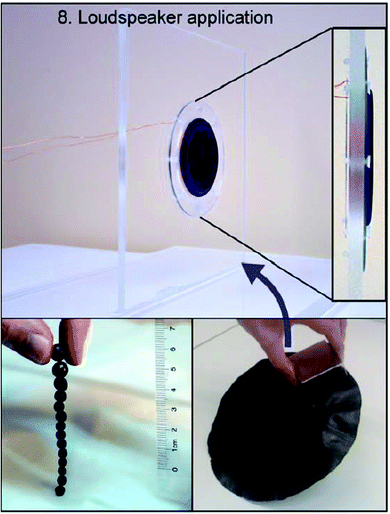 |
| Fig. 6 A magnetic membrane (bottom right) prepared by vacuum filtration of magnetic nanofibril suspension in a thin prototype loudspeaker operating without an external magnet (upper figure). Hard permanently magnetized spherical beads are shown in bottom left figure. The image has been reproduced from Galland et al.114 under CC BY-NC 3.0 license. | |
Tarres et al.117 suggested a simplified procedure for the preparation of a loudspeaker membrane, in which the in situ co-precipitation was replaced by mixing CNF and magnetite nanoparticles and using cationic starch for retention. They reported lowered strength from 80 MPa to 40 MPa with 60% loading and a Young's modulus of 5.4 GPa. The stiffness of the membranes was found to limit the use. The authors suggested consideration of plasticizers or cellulose macrofibers to improve the membrane properties.
One of the benefits of using cellulose fibers and nanofibers in membranes is that they enable the formation of films, sheets, and paper materials that are flexible, because flexible fibers form an entangled network that can be typically rolled and folded in a manner similar to paper.118 However, this flexibility is accompanied with lacking thermo-moldability and, occasionally, instability in mechanical performance that stems from humidity sensitivity. The mechanical stability of CoFe2O4-loaded nanocellulose composites has been addressed by low temperature heat treatment and impregnation with an epoxy resin, which further strengthens the nanofiber networks.119
Optical devices
The transparency of nanocellulose films with magnetic functionality is often mentioned to be beneficial for magneto-optic use.120,121 However, thus far, the optical use considerations of magnetic cellulose do not utilize the magneto-optic effect as such but rather the cellulose light-interactions combined with the magnetic character of the material. Utilizing the ability of CNCs to form cholesteric phase has inspired demonstration toward chiral photonic materials. The spacing between the rod-shaped nanoparticles as well as the chirality are essential for provoking light–cellulose interactions. The combination of magnetic functionality and optically active structure can be of interest for future magnetic cellulose materials for optical devices. Chen et al.122 incorporated iron oxide particles in CNCs via co-precipitation in the cellulose matrix. The modified particles were mixed with neat CNCs that enabled the formation of films that exhibited liquid crystalline cholesteric ordering. A field strength of 7 mT was adequate to tune the chiral nematic pitch of the cholesteric phase (Fig. 7).
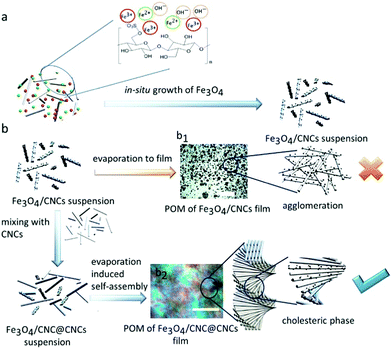 |
| Fig. 7 A schematic presentation of (a) in situ growth of Fe3O4 nanoparticles onto CNCs to form an Fe3O4/CNC suspension; (b) evaporation of Fe3O4/CNC suspensions to obtain Fe3O4/CNC film with agglomeration of cholesteric order using Fe3O4/CNC suspension or Fe3O4/CNC suspension with neat CNCs, respectively. Scale bars: 100 μm for b1 and 10 μm for b2. Reprinted with permission from Chen et al.122 Copyright (2020) American Chemical Society. | |
Using the magnetic functionality combined with optical activity has been demonstrated as proof of the concept of advanced multimodal protection of clothing against counterfeiting.123,124 The multifunctionality was obtained by modifying cellulose fibers with nanoparticles based on lanthanide-doped fluorides and magnetite that were luminescent and magnetic. As the mechanical properties were maintained, the fibers retained their applicability for use in textiles.
Magnetic hyperthermia
Magnetic hyperthermia aims to produce local heating. One of its applications is in medicine in the treatment of tumors via localized heating—that is, to facilitate the deterioration of selected malignant tissue. A cellulose hybrid material of CNCs decorated with CoFe2O4 particles has been shown to heat via the hyperthermia effect, when the aqueous dispersion was exposed to an alternating magnetic field (200 Gauss, 869 Hz).78 It is an intriguing idea in terms of not only manufacturing a new material for the magnetic hyperthermia treatment but opening consideration of the opportunities of rod-like CNCs in in vivo applications. However, the toxicological evaluation of CNCs are still in progress for their use in vivo.
Storage systems
The addition of magnetic CNC–Fe3O4 hybrids into phase change material matrices led to materials that could be used to store solar or magnetic heating energy.47 The operating temperatures between 44 and 61 °C and energy storage capacity up to 83 J g−1 were achieved and the phase change materials were demonstrated for drying agricultural products.
Magnetic shielding
There is vivid dissemination regarding the suitability of magnetic cellulose hybrid materials for magnetic shielding. Recently, electromagnetic shielding with cellulose aerogels was reviewed by Wan et al.125
Magnetic shielding refers to protecting objects from a magnetic field by the installation of another magnetic field. The magnetic field is redirected by the additional field that is generated by a ferromagnetic material. Successful magnetic shielding was achieved with iron oxide-67 and cobalt ferrite-78 decorated cellulose materials. The shielding effect can be quantified by measuring current in the film applied with and without an external magnetic field in a setup where the magnetic field-generating films are placed on a magnet.67,109 In addition, the alignment of the magnetic domains in such films allowed a specific response depending on the alignment in the film and of the magnetic field. Along the direction parallel to the magnetic orientation, the current instantly decreased from 7.4 nA to 5.1 nA when an additional magnetic field was introduced. In a perpendicular direction, the change was from 3.8 nA to 3.2 nA, thereby demonstrating that the directionality in the material modulates the magnetic shielding property.109
A combination of the chiral nematic structural features of mesoporous photonic cellulose and the magnetic properties of CoFe2O4 has also been used in electromagnetic interference shielding. The cellulose template was mesoporous and was a result of templating with cholesteric CNCs and urea-formaldehyde.126
Magnetic separation and food
Magnetic-based separation is a popular example of for magnetic cellulose hybrid materials.74,127–129 The role of the magnetism is to act as a stimulus for the collection of the target molecules. The cellulose acts as a carrier for the magnetic functionality or as the absorbent. For example, in so-called stir bar sorptive-dispersive microextraction, a magnetic stir bar is coated with magnetic (hybrid) material. Stirring results in the release of the particles into the matrix available for adsorbing the target molecules. When the stirring is stopped, the particles are collected onto the bar.73
Magnetic cellulose composite aerogels, films, and papers have been demonstrated for the adsorption of heavy metals,57,130–138 dyes,139–144 drugs,145 immobilization of enzymes and proteins,93,146–151 bacteria,54 and as carriers for drugs.152 Independent of the type of magnetic particle, the removal of heavy metals or dyes from municipal and industrial wastewater is a challenge that has been solved in numerous prior studies.153–158 Oil absorption and separation in general is one of the popular separation applications for magnetic cellulose.159–163 The release of encapsulated substances has also been demonstrated using exposure to a magnetic field and for controlled delivery of drugs for cancer treatment.164,165
Molecular imprinting and preparing cavities of a specific size and shape within a matrix has been used for preparing magnetic cellulose materials as adsorbents, for example, fluoroquinolones and artesunates.129,166–168 In addition, metal organic frameworks have been recently combined with magnetic cellulose for separation applications.169,170
Applications of magnetic cellulose materials in food are scarce perhaps because cellulose is a non-dietary fiber. Yet, an innovative approach for preparing edible coating on pineapples (and other food as well) with a nanocellulose–chitosan–iron oxide has been published to maintain human health with iron-fortified materials.171
Visualization
Imaging of soft organic matter like cellulose using electron microscopy and several scanning techniques often has the shortcoming of low contrast. This can be circumvented with sputtering and labeling. Iron is readily distinguishable within a carbon network, and energy dispersive X-ray spectroscopy mapping of iron in the cellulose matrix has been performed for the analysis of magnetic cellulose material.113,124 Another challenge of visualization of cellulose materials is that the various hierarchies of cellulose are not easily distinguished because they have the same chemical composition. Hobisch et al.172 resolved this using magnetic nanoparticles to label a certain proportion of the cellulose particles in paper and enable their visualization within the fiber matrix (Fig. 8).
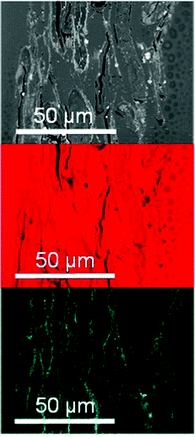 |
| Fig. 8 The cross-section of sheets containing 10% of nanoparticle-labeled materials. The elemental distribution was evaluated by energy dispersive X-rays, thereby revealing a uniform distribution of carbon (red), while the distribution of cobalt (cyan) has the form of fibrils. The image is reprinted from Hobisch et al.172 Copyright (2021), with permission from Elsevier. | |
CNC–Fe3O4 hybrids have been applied as MRI contrast agents, where the hybrid in fact showed negligible in vitro cytotoxicity and excellent contrast enhancement compared to commercial and clinical agents.68
Outlook
Most magnetic cellulose materials are prepared by co-precipitation of iron (and cobalt) salts in a cellulose suspension, which leads to the formation of magnetic particles in the cellulose matrix. It has been suggested that the interaction first develops with the precursor salts when Co2+ and Fe3+ ions are incorporated into the cellulose molecules via electrostatic attraction between the electron-rich oxygen atoms in the cellulose molecules and the electropositive metal cations (schematic presentation in Fig. 9).173 It is seen that this reduces the mobility of the metal ions, enhances the formation of, for example, CoFe2O4 nuclei, and stabilizes nanoparticles on the cellulose surface. Discussions in regard of particles formed separately and then combined with cellulose assign the interaction between cellulose and the nanoparticles to a coordinate bond between Fe3O4 and hydroxyl group of cellulose.67 The improvement in thermal stability has been considered as evidence of the interaction between hydroxyl groups and magnetic particles.48 The co-precipitation of iron oxide particles leads to strong interaction as demonstrated by the fact that the nanoparticles remained attached even under intense sonication.174 Combining preformed particles and CNCs have been reported to lead to random attachment of the magnetic nanoparticles on the cellulose due to the ionic interaction that is distributed along the cellulose.175 On the other hand, the mere immersion of biopolymers in an MnFe2O4 nanoparticle dispersion resulted in no observed interaction between the cellulose and its magnetic components.176
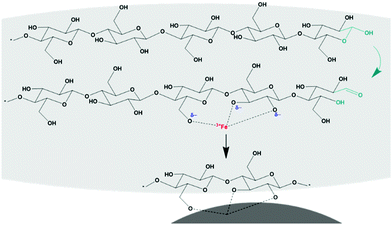 |
| Fig. 9 A scenario of coordination of a metal ion (red) with cellulose molecule or hierarchy (presented by light grey area) that. The nucleation into particles (dark grey), via co-precipitation, leads to cellulose hybrids. Reducing end group (green, the arrow indicates the two available forms, the open form and hemiacetal form) is available for modification. The asterisk (*) indicates the fact that the cellulose chain continues. | |
The question of the nature and the strength of the bond between the magnetic particles and cellulose after co-precipitation appears to have been established; however, it continues to be discussed. In the case that it indeed is an ionic interaction that guides the location of the magnetic particles on cellulose, the location of the magnetic particles cannot be controlled unless the location of the ionic interaction source on cellulose can be controlled. Furthermore, a method of deliberately depositing the particles on distinct locations of the cellulose particle could allow anisotropy created by magnetic particle location on the cellulose hierarchy rather than by the shape of the cellulose particle only. Perhaps, it actually would be easier and more effective to facilitate the directionality by controlling the location of the magnetic particles than the alignment of cellulose particles. In that case, the use of the reducing end group (Fig. 9) is an opportunity that has not been exploited yet but could provide means of controlling magnetic anisotropy.
Furthermore, the utilization of the electrostatic attraction of oppositely charged molecules has been used to further amplify combining cellulose and magnetic materials by using a cationic polyelectrolyte as an anchoring layer between CNCs and Fe3O4 nanoparticles.177 Moreover, iron oxide nanoparticle surface charge was manipulated by pH adjustment and was then used for self-assembly of the positively charged particles on the negatively charged CNCs.175 However, the utilization of the electrostatic interactions for loading cellulose materials with magnetic particles allows less control of the location of the particles than, for example, the specific modification of the reducing end of cellulose.
Covalent bonding of the nanoparticles around the cellulose particles has been established by preparing amine functionalized iron oxide particles and coupling them to carboxylic acid containing CNFs via a coupling reaction involving 1-ethyl-3-(3-dimethylaminopropyl)carbodiimide hydrochloride and N-hydroxy succinimide (EDC-NHS).178 In addition, CNC–Fe3O4 hybrids were prepared by covalently linking the cellulose with citric acid and incorporating magnetic nanoparticles in this matrix.68 A system of cellulose powder, PEI, and crosslinked magnetic nanoparticles using glutaraldehyde has been used for preparing a crosslinked material.156 Similarly, epichlorohydrin has been employed in a system of cellulose solution, PEI, and magnetic particles to create a crosslink between the cellulose and PEI.179
The application of magnetic cellulose in devices like loudspeakers indeed is becoming a reality. However, cellulose may also have negative effects on the properties of the device due to its tendency to absorb moisture, which may have an impact on the stability of the device. These issues need to be addressed in future research. Moreover, the flammability of cellulose may also be a concern. Fortunately, magnetic particles can provide flame retardancy.180,181 The presence of magnetic nanoparticles in the composite effectively increased char yield from 8% in an oxidized cellulose matrix to 25% and decreased the gas-phase products. The addition of phosphoric acid into magnetic cellulose fibers is another route to increasing the flame resistance of cellulose composites.180
The future applications of magnetic cellulose are likely to continue to concentrate on the separation of molecules and contaminants. However, there is much to explore regarding the spectacular properties of cellulose nanofibers and cellulose nanocrystals, along with the possibility to introduce a magnetic functionality. The high aspect ratio of cellulose nanofibers can provide a strong and flexible matrix for smart membranes for example. Moreover, the liquid crystalline phases of CNCs are to be used in optical devices.
Conclusions
Equipping cellulose with a magnetic functionality is motivated by the renewable, abundant, and non-toxic nature of cellulose materials, thereby making it an appealing substrate for hosting magnetic functionality. The co-precipitation of iron oxide or ferrite particles in a matrix of cellulose fibers, solution, nanofibers, and particles typically lead to a hybrid material in which the cellulose and the magnetic particles are intimately connected. The nature of the connection and, more importantly, the control of the nucleation location of the magnetic particles are ongoing discussion topics and challenges that amplify the impact of the magnetic cellulose particles in materials technology. Another future direction for research is to take advantage of the properties of cellulose nanomaterials that enable the production of innovative materials with properties that differ from those of paper but with the benefit of the same cellulose chemistry.
Author contributions
TN: conceptualization, writing, reviewing, and visualization.
Conflicts of interest
There are no conflicts to declare.
Acknowledgements
Wallenberg Wood Science Center, Area of Advance Materials at Chalmers University of Technology and Excellence Initiative Nano at Chalmers University of Technology are acknowledged for the funding provided. I am grateful to Stefan Spirk for generously sharing his knowledge regarding inorganic materials and their magnetic behavior as well as providing input on the manuscript.
Notes and references
- norexeco, https://www.norexeco.com/pulp/, (accessed Auguest 15, 2021).
- fao, http://www.fao.org/forestry/statistics/80938/en/, http://www.fao.org/forestry/statistics/80938/en/, (accessed August 15, 2021).
- W. E. Hillis, Wood Sci. Technol., 1984, 18, 281–293 CrossRef CAS.
- K.-Y. Lee, Y. Aitomäki, L. A. Berglund, K. Oksman and A. Bismarck, Compos. Sci. Technol., 2014, 105, 15–27 CrossRef CAS.
- C. Miao and W. Y. Hamad, Cellulose, 2013, 20, 2221–2262 CrossRef CAS.
-
E. C. Ramires and A. Dufresne, Advances in polymer nanocomposites, Woodhead Publishing Ltd, 2012, p. 131 Search PubMed.
- V. K. Thakur and M. K. Thakur, Carbohydr. Polym., 2014, 109, 102–117 CrossRef CAS PubMed.
- N. Sriplai and S. Pinitsoontorn, Carbohydr. Polym., 2021, 254, 117228 CrossRef CAS PubMed.
- W. Hu, S. Chen, J. Yang, Z. Li and H. Wang, Carbohydr. Polym., 2014, 101, 1043–1060 CrossRef CAS PubMed.
- A. Gennari, A. J. Fuhr, G. Volpato and C. F. Volken de Souza, Carbohydr. Polym., 2020, 246, 116646 CrossRef CAS PubMed.
-
H. Sixta, Handbook of pulp, Wiley-VCH, 2006 Search PubMed.
- A. Dufresne, Mater. Today, 2013, 16, 220–227 CrossRef CAS.
- Y. Habibi, L. A. Lucia and O. J. Rojas, Chem. Rev., 2010, 110, 3479–3500 CrossRef CAS PubMed.
- E. Kontturi, P. Laaksonen, M. B. Linder, A. H. Gröschel, O. J. Rojas and O. Ikkala, Adv. Mater., 2018, 30, 1703779 CrossRef PubMed.
- R. Kádár, M. Fazilati and T. Nypelö, Cellulose, 2020, 27, 2003–2014 CrossRef.
- R. Kádár, S. Spirk and T. Nypelö, ACS Nano, 2021, 15(5), 7931–7945 CrossRef PubMed.
-
J. Chen, Textiles and Fashion, Elsevier, 2015, pp. 79–95 Search PubMed.
- A. Michud, M. Tanttu, S. Asaadi, Y. Ma, E. Netti, P. Kääriäinen, A. Persson, A. Berntsson, M. Hummel and H. Sixta, Text. Res. J., 2016, 86, 543–552 CrossRef CAS.
-
D. Klemm, B. Philipp, T. Heinze, U. Heinze and W. Wagenknecht, Comprehensive Cellulose Chemistry, Wiley, Weinheim, Germany, 1998 Search PubMed.
- S. Kalia, A. Dufresne, B. M. Cherian, B. Kaith, L. Avérous, J. Njuguna and E. Nassiopoulos, Int. J. Polym. Sci., 2011, 2011, 1–35 Search PubMed.
-
W. Y. Hamad, Cellulose nanocrystals: properties, production and applications, John Wiley & Sons, 2017 Search PubMed.
- T. Saito, M. Hirota, N. Tamura, S. Kimura, H. Fukuzumi, L. Heux and A. Isogai, Biomacromolecules, 2009, 10, 1992–1996 CrossRef CAS PubMed.
- Y. Qing, R. Sabo, J. Y. Zhu, U. Agarwal, Z. Cai and Y. Wu, Carbohydr. Polym., 2013, 97, 226–234 CrossRef CAS PubMed.
- C. Salas, T. Nypelö, C. Rodriguez-Abreu, C. Carrillo and O. J. Rojas, Curr. Opin. Colloid Interface Sci., 2014, 19, 383–396 CrossRef CAS.
- O. Nechyporchuk, M. N. Belgacem and J. Bras, Ind. Crops Prod., 2016, 93, 2–25 CrossRef CAS.
-
M. Ek, G. Gellerstedt and G. Henriksson, Pulping chemistry and technology, Walter de Gruyter, 2009 Search PubMed.
-
E. Sjöström, Wood chemistry: fundamentals and applications, Academic Press Inc., 1993 Search PubMed.
- G. Jiang, W. Huang, L. Li, X. Wang, F. Pang, Y. Zhang and H. Wang, Carbohydr. Polym., 2012, 87, 2012–2018 CrossRef CAS.
-
N. A. Spaldin, Magnetic materials: fundamentals and applications, Cambridge University Press, 2010 Search PubMed.
- B. Frka-Petesic, J. Sugiyama, S. Kimura, H. Chanzy and G. Maret, Macromolecules, 2015, 48, 8844–8857 CrossRef CAS.
- A. Barhoumi Meddeb, I. Chae, A. Han, S. H. Kim and Z. Ounaies, Cellulose, 2020, 27, 7901–7910 CrossRef CAS.
- J. Pan, W. Hamad and S. K. Straus, Macromolecules, 2010, 43, 3851–3858 CrossRef CAS.
- L. Csoka, I. C. Hoeger, O. J. Rojas, I. Peszlen, J. J. Pawlak and P. N. Peralta, ACS Macro Lett., 2012, 1, 867–870 CrossRef CAS.
- J. A. Diaz, X. Wu, A. Martini, J. P. Youngblood and R. J. Moon, Biomacromolecules, 2013, 14, 2900–2908 CrossRef CAS PubMed.
- A. B. Reising, R. J. Moon and J. P. Youngblood, J. Sci. Technol. For. Prod. Processes, 2012, 2, 32–41 Search PubMed.
- J. Sugiyama, H. Chanzy and G. Maret, Macromolecules, 1992, 25, 4232–4234 CrossRef CAS.
- S. Elazzouzi-Hafraoui, Y. Nishiyama, J. L. Putaux, L. Heux, F. Dubreuil and C. Rochas, Biomacromolecules, 2008, 9, 57–65 CrossRef CAS PubMed.
- A. Nowogrodzki, Nature, 2018, 563, 24–26 CrossRef CAS PubMed.
- Y. Mao, M. Bleuel, Y. Lyu, X. Zhang, D. Henderson, H. Wang and R. M. Briber, Langmuir, 2018, 34, 8042–8051 CrossRef CAS PubMed.
- T. Pullawan, A. N. Wilkinson and S. J. Eichhorn, Biomacromolecules, 2012, 13, 2528–2536 CrossRef CAS PubMed.
- D. Li, Z. Liu, M. Al-Haik, M. Tehrani, F. Murray, R. Tannenbaum and H. Garmestani, Polym. Bull., 2010, 65, 635–642 CrossRef CAS.
- D. H. Kim and Y. S. Song, Carbohydr. Polym., 2015, 126, 240–247 CrossRef CAS PubMed.
- K. J. De France, K. G. Yager, T. Hoare and E. D. Cranston, Langmuir, 2016, 32, 7564–7571 CrossRef CAS PubMed.
- H. C. Kim, J. W. Kim, L. Zhai and J. Kim, Cellulose, 2019, 26, 5821–5829 CrossRef CAS.
- H. Rashid, M. A. Mansoor, B. Haider, R. Nasir, S. B. Abd Hamid and A. Abdulrahman, Sep. Sci. Technol., 2020, 55, 1207–1215 CrossRef CAS.
- V. L. Lassalle, R. D. Zysler and M. L. Ferreira, Mater. Chem. Phys., 2011, 130, 624–634 CrossRef CAS.
- S. Y. H. Abdalkarim, Z. Ouyang, H. Y. Yu, Y. Li, C. Wang, R. A. M. Asad, Y. Lu and J. Yao, Carbohydr. Polym., 2021, 254, 117481 CrossRef CAS PubMed.
- M. Rashid, M. A. Gafur, M. K. Sharafat, H. Minami, M. A. J. Miah and H. Ahmad, Carbohydr. Polym., 2017, 170, 72–79 CrossRef CAS PubMed.
- M. H. Beyki, M. Bayat, S. Miri, F. Shemirani and H. Alijani, Ind. Eng. Chem. Res., 2014, 53, 14904–14912 CrossRef CAS.
- C. Wan and J. Li, ACS Sustainable Chem. Eng., 2015, 3, 2142–2152 CrossRef CAS.
- J. R. Correa, E. Bordallo, D. Canetti, V. León, L. C. Otero-Díaz, C. Negro, A. Gómez and R. Sáez-Puche, Mater. Res. Bull., 2010, 45, 946–953 CrossRef CAS.
- M. Anbia and F. Rahimi, J. Appl. Polym. Sci., 2017, 134, 45361 CrossRef.
- H. Y. Zhu, Y. Q. Fu, R. Jiang, J. H. Jiang, L. Xiao, G. M. Zeng, S. L. Zhao and Y. Wang, Chem. Eng. J., 2011, 173, 494–502 CrossRef CAS.
- X. Zhao, H. Li, A. Ding, G. Zhou, Y. Sun and D. Zhang, Mater. Lett., 2016, 163, 154–157 CrossRef CAS.
- H. Wu, H. Tian, S. Li, Y. Wang, Z. Ma, Z. Song and J. Wang, Cellulose, 2019, 27, 357–367 CrossRef.
- X. Yu, S. Tong, M. Ge, J. Zuo, C. Cao and W. Song, J. Mater. Chem. A, 2013, 1, 959–965 RSC.
- A. M. Donia, A. A. Atia and F. I. Abouzayed, Chem. Eng. J., 2012, 191, 22–30 CrossRef CAS.
- R. Xiong, Y. Wang, X. Zhang and C. Lu, RSC Adv., 2014, 4, 22632–22641 RSC.
- A. S. M. Wittmar, Q. Fu and M. Ulbricht, ACS Sustainable Chem. Eng., 2017, 5, 9858–9868 CrossRef CAS.
- A. S. M. Wittmar, Q. Fu and M. Ulbricht, Cellulose, 2019, 26, 4563–4578 CrossRef CAS.
- S. Peng, J. Fan and J. Chang, Adv. Mater. Res., 2013, 634–638, 913–917 Search PubMed.
- M. L. Maxim, N. Sun, H. Wang, J. R. Sterner, A. Haque and R. D. Rogers, Nanomater. Energy, 2012, 1, 225–236 CrossRef CAS.
- X. Y. Wei, J. H. Li and J. C. Chen, Adv. Mater. Res., 2013, 634–638, 2077–2080 Search PubMed.
- S. Peng, H. C. Meng, L. Zhou and J. Chang, J. Nanosci. Nanotechnol., 2014, 14, 7010–7014 CrossRef CAS PubMed.
- S. Peng, H. Meng, Y. Ouyang and J. Chang, Ind. Eng. Chem. Res., 2014, 53, 2106–2113 CrossRef CAS.
- A. Ali, M. Z. Hira Zafar, I. ul Haq, A. R. Phull, J. S. Ali and A. Hussain, Nanotechnol., Sci. Appl., 2016, 9, 49 CrossRef CAS PubMed.
- W. Yang, H. Tian, J. Liao, Y. Wang, L. Liu, L. Zhang and A. Lu, Appl. Surf. Sci., 2020, 507, 145092 CrossRef CAS.
- N. Torkashvand and N. Sarlak, Eur. Polym. J., 2019, 118, 128–136 CrossRef CAS.
- S. Liu, J. Zhou and L. Zhang, Cellulose, 2011, 18, 663–673 CrossRef CAS.
- A. M. Tang and J. K. Song, Adv. Mater. Res., 2011, 239-242, 175–181 CAS.
- W.-B. Wu, Y. Jing, M.-R. Gong, X.-F. Zhou and H.-Q. Dai, BioResources, 2011, 6, 3396–3409 CAS.
- X. Pineda, G. C. Quintana, A. P. Herrera and J. H. Sánchez, Mater. Chem. Phys., 2021, 259, 122778 CrossRef CAS.
- F. Abujaber, F. J. Guzman Bernardo and R. C. Rodriguez Martin-Doimeadios, Talanta, 2019, 201, 266–270 CrossRef CAS PubMed.
- F. Abujaber, M. Zougagh, S. Jodeh, Á. Ríos, F. J. Guzmán Bernardo and R. C. Rodríguez Martín-Doimeadios, Microchem. J., 2018, 137, 490–495 CrossRef CAS.
- X. Yu, D. Kang, Y. Hu, S. Tong, M. Ge, C. Cao and W. Song, RSC Adv., 2014, 4, 31362–31369 RSC.
- C. Wan and J. Li, Carbohydr. Polym., 2015, 134, 144–150 CrossRef CAS PubMed.
- R. T. Olsson, M. A. Azizi Samir, G. Salazar-Alvarez, L. Belova, V. Strom, L. A. Berglund, O. Ikkala, J. Nogues and U. W. Gedde, Nat. Nanotechnol., 2010, 5, 584–588 CrossRef CAS PubMed.
- T. Nypelö, C. Rodriguez-Abreu, J. Rivas, M. D. Dickey and O. J. Rojas, Cellulose, 2014, 21, 2557–2566 CrossRef.
- C. Tian, S. Fu and L. A. Lucia, Cellulose, 2015, 22, 2571–2587 CrossRef CAS.
- Q. Chen, J. Zheng, Q. Yang, Z. Dang and L. Zhang, ACS Appl. Mater. Interfaces, 2019, 11, 15478–15488 CrossRef CAS PubMed.
- K. Gupta, J. Kaur, A. Kaushik and S. Singhal, Mater. Today, 2019, 14, 417–425 CAS.
- A. Dhahri, H. Jaoua-Bahloul, M. H. V. Baouab, D. Luneau and E. Beyou, Polym. Eng. Sci., 2018, 58, 1630–1635 CrossRef CAS.
- C. Wan, Y. Jiao, X. Li, W. Tian, J. Li and Y. Wu, Nanoscale, 2020, 12, 3308–3316 RSC.
- P. Tartaj, M. del Puerto Morales, S. Veintemillas-Verdaguer, T. González-Carreño and C. J. Serna, J. Phys. D: Appl. Phys., 2003, 36, R182 CrossRef CAS.
- E. Lizundia, A. Maceiras, J. L. Vilas, P. Martins and S. Lanceros-Mendez, Carbohydr. Polym., 2017, 175, 425–432 CrossRef CAS PubMed.
- Y. Li, H. Zhu, H. Gu, H. Dai, Z. Fang, N. J. Weadock, Z. Guo and L. Hu, J. Mater. Chem. A, 2013, 1, 15278–15283 RSC.
- S. Liu, D. Tao and L. Zhang, Powder Technol., 2012, 217, 502–509 CrossRef CAS.
- M. Rubacha and J. Zieba, Fibres Text. East. Eur., 2007, 15, 64 Search PubMed.
- H. Fukuzumi, T. Saito, T. Iwata, Y. Kumamoto and A. Isogai, Biomacromolecules, 2008, 10, 162–165 CrossRef PubMed.
- A. Walther, J. V. Timonen, I. Diez, A. Laukkanen and O. Ikkala, Adv. Mater., 2011, 23, 2924–2928 CrossRef CAS PubMed.
- R. Wu and C. Hu, Cellulose, 2021, 28, 1499–1511 CrossRef CAS.
- Y. Tang, Q. Zhang, L. Wang, P. W. Pan and G. Bai, Langmuir, 2010, 26, 11266–11271 CrossRef CAS PubMed.
- P. Prikryl, J. Lenfeld, D. Horak, M. Ticha and Z. Kucerova, Appl. Biochem. Biotechnol., 2012, 168, 295–305 CrossRef CAS PubMed.
- A. Shah, M. Kuddushi, K. Mondal, M. Jain and N. Malek, J. Mol. Liq., 2020, 320, 114290 CrossRef CAS.
- J. Duan, X. He and L. Zhang, Chem. Commun., 2015, 51, 338–341 RSC.
- J. Yan, D. Horak, J. Lenfeld, M. Hammond and M. Kamali-Moghaddam, J. Biotechnol., 2013, 167, 235–240 CrossRef CAS PubMed.
- K. Du, X. Liu, S. Li, L. Qiao and H. Ai, ACS Sustainable Chem. Eng., 2018, 6, 11578–11586 CrossRef CAS.
- X. Luo, J. Zeng, S. Liu and L. Zhang, Bioresour. Technol., 2015, 194, 403–406 CrossRef CAS PubMed.
- L. E. Low, B. T. Tey, B. H. Ong, E. S. Chan and S. Y. Tang, Carbohydr. Polym., 2017, 155, 391–399 CrossRef CAS PubMed.
- W. Zhu, W. Ma, C. Li, J. Pan and X. Dai, Chem. Eng. J., 2015, 276, 249–260 CrossRef CAS.
- T. Nypelö, C. Rodriguez-Abreu, Y. V. Kolen'ko, J. Rivas and O. J. Rojas, ACS Appl. Mater. Interfaces, 2014, 6, 16851–16858 CrossRef PubMed.
- Z. Liu, D. Li, H. Dai and H. Huang, J. Mol. Liq., 2017, 232, 449–456 CrossRef CAS.
- H. Zhang, Q. Luan, H. Tang, F. Huang, M. Zheng, Q. Deng, X. Xiang, C. Yang, J. Shi, C. Zheng and Q. Zhou, Cellulose, 2016, 24, 903–914 CrossRef.
- Z. Liu, H. Wang, C. Liu, Y. Jiang, G. Yu, X. Mu and X. Wang, Chem. Commun., 2012, 48, 7350–7352 RSC.
- Z. Liu, H. Wang, B. Li, C. Liu, Y. Jiang, G. Yu and X. Mu, J. Mater. Chem., 2012, 22, 15085–15091 RSC.
- Y. Zhou, S. Fu, L. Zhang, H. Zhan and M. V. Levit, Carbohydr. Polym., 2014, 101, 75–82 CrossRef CAS PubMed.
- F. Lin, J. Zheng, W. Guo, Z. Zhu, Z. Wang, B. Dong, C. Lin, B. Huang and B. Lu, Cellulose, 2019, 26, 6861–6877 CrossRef CAS.
- J. Ren, Q. Dai, H. Zhong, X. Liu, L. Meng, X. Wang and F. Xin, Cellulose, 2018, 25, 4537–4549 CrossRef CAS.
- C. Qin, W. Yang, Y. Wang, L. Zhang and A. Lu, Cellulose, 2021, 28, 2353–2364 CrossRef CAS.
- M. Tatsumi, F. Kimura, T. Kimura, Y. Teramoto and Y. Nishio, Biomacromolecules, 2014, 15, 4579–4589 CrossRef CAS PubMed.
- L. Cao, Z. Cheng, M. Yan and Y. Chen, Chem. Eng. J., 2019, 363, 203–212 CrossRef CAS.
- M. Mashkour, M. Tajvidi, T. Kimura, F. Kimura and G. Ebrahimi, BioResources, 2011, 6, 4731–4738 CAS.
- H. Yoshitake, K. Sugimura, Y. Teramoto and Y. Nishio, Polymer, 2016, 99, 147–156 CrossRef CAS.
- S. Galland, R. L. Andersson, M. Salajková, V. Ström, R. T. Olsson and L. A. Berglund, J. Mater. Chem. C, 2013, 1, 7963–7972 RSC.
- H. Fukuzumi, T. Saito and A. Isogai, Carbohydr. Polym., 2013, 93, 172–177 CrossRef CAS PubMed.
- Y. Qing, R. Sabo, Y. Wu and Z. Cai, BioResources, 2012, 7, 3064–3075 Search PubMed.
- Q. Tarres, A. Deltell, F. X. Espinach, M. A. Pelach, M. Delgado-Aguilar and P. Mutje, Int. J. Biol. Macromol., 2017, 99, 29–36 CrossRef CAS PubMed.
- M. Zeng, A. Laromaine, W. Feng, P. A. Levkin and A. Roig, J. Mater. Chem. C, 2014, 2, 6312–6318 RSC.
- S. Galland, R. L. Andersson, V. Ström, R. T. Olsson and L. A. Berglund, ACS Appl. Mater. Interfaces, 2014, 6, 20524–20534 CrossRef CAS PubMed.
- T. Hosoya, W. Sakamoto and T. Yogo, Mater. Lett., 2014, 137, 491–494 CrossRef CAS.
- K. K. Sadasivuni, D. Ponnamma, H.-U. Ko, H. C. Kim, L. Zhai and J. Kim, Sens. Actuators, B, 2016, 233, 633–638 CrossRef CAS.
- T. Chen, Q. Zhao, X. Meng, Y. Li, H. Peng, A. K. Whittaker and S. Zhu, ACS Nano, 2020, 14, 9440–9448 CrossRef CAS PubMed.
- M. Skwierczynska, M. Runowski, S. Goderski, J. Szczytko, J. Rybusinski, P. Kulpinski and S. Lis, ACS Omega, 2018, 3, 10383–10390 CrossRef CAS PubMed.
- M. Skwierczyńska, P. Woźny, M. Runowski, M. Perzanowski, P. Kulpiński and S. Lis, J. Alloys Compd., 2020, 829, 154456 CrossRef.
- C. Wan, Y. Jiao, S. Wei, L. Zhang, Y. Wu and J. Li, Chem. Eng. J., 2019, 359, 459–475 CrossRef CAS.
- M. Giese, L. K. Blusch, M. Schlesinger, G. R. Meseck, W. Y. Hamad, M. Arjmand, U. Sundararaj and M. J. MacLachlan, Langmuir, 2016, 32, 9329–9334 CrossRef CAS PubMed.
- F. Abujaber, M. Jimenez-Moreno, F. J. Guzman Bernardo and R. C. Rodriguez Martin-Doimeadios, Mikrochim. Acta, 2019, 186, 400 CrossRef PubMed.
- T. Ahamad, M. Naushad, Ruksana, A. N. Alhabarah and S. M. Alshehri, Int. J. Biol. Macromol., 2019, 132, 1031–1038 CrossRef CAS PubMed.
- Y. F. Wang, Y. G. Wang, X. K. Ouyang and L. Y. Yang, ACS Appl. Mater. Interfaces, 2017, 9, 1759–1769 CrossRef CAS PubMed.
- S. Cui, X. Wang, X. Zhang, W. Xia, X. Tang, B. Lin, Q. Wu, X. Zhang and X. Shen, Cellulose, 2017, 25, 735–751 CrossRef.
- S. Daneshfozoun, M. A. Abdullah and B. Abdullah, Ind. Crops Prod., 2017, 105, 93–103 CrossRef CAS.
- X. Wang, S. Jiang, S. Cui, Y. Tang, Z. Pei and H. Duan, Cellulose, 2019, 26, 5051–5063 CrossRef CAS.
- A. M. Donia, A. M. Yousif, A. A. Atia and S. A. Labib, J. Dispersion Sci. Technol., 2014, 36, 898–907 CrossRef.
- X. Luo, X. Lei, N. Cai, X. Xie, Y. Xue and F. Yu, ACS Sustainable Chem. Eng., 2016, 4, 3960–3969 CrossRef CAS.
- X. Sun, L. Yang, Q. Li, J. Zhao, X. Li, X. Wang and H. Liu, Chem. Eng. J., 2014, 241, 175–183 CrossRef CAS.
- J. Lu, R. N. Jin, C. Liu, Y. F. Wang and X. K. Ouyang, Int. J. Biol. Macromol., 2016, 93, 547–556 CrossRef CAS PubMed.
- X. Luo, X. Lei, X. Xie, B. Yu, N. Cai and F. Yu, Carbohydr. Polym., 2016, 151, 640–648 CrossRef CAS PubMed.
- S. Hokkanen, E. Repo, S. Lou and M. Sillanpää, Chem. Eng. J., 2015, 260, 886–894 CrossRef CAS.
- H. Dai, Y. Huang, Y. Zhang, H. Zhang and H. Huang, Cellulose, 2019, 26, 3825–3844 CrossRef CAS.
- H. Shi, W. Li, L. Zhong and C. Xu, Ind. Eng. Chem. Res., 2014, 53, 1108–1118 CrossRef CAS.
- R. Samadder, N. Akter, A. C. Roy, M. M. Uddin, M. J. Hossen and M. S. Azam, RSC Adv., 2020, 10, 11945–11956 RSC.
- S. Peng, Y. Liu, Z. Xue, W. Yin, X. Liang, M. Li and J. Chang, Cellulose, 2017, 24, 4793–4806 CrossRef CAS.
- K. Srasri, M. Thongroj, P. Chaijiraaree, S. Thiangtham, H. Manuspiya, P. Pisitsak and S. Ummartyotin, Int. J. Biol. Macromol., 2018, 119, 662–668 CrossRef CAS PubMed.
- B. Li, Q. Zhang, Y. Pan, Y. Li, Z. Huang, M. Li and H. Xiao, Int. J. Biol. Macromol., 2020, 163, 309–316 CrossRef CAS PubMed.
- J. Sun, L. Cui, Y. Gao, Y. He, H. Liu and Z. Huang, Carbohydr. Polym., 2021, 251, 117004 CrossRef CAS PubMed.
- S. L. Cao, X. H. Li, W. Y. Lou and M. H. Zong, J. Mater. Chem. B, 2014, 2, 5522–5530 RSC.
- E. J. Cho, S. Jung, H. J. Kim, Y. G. Lee, K. C. Nam, H. J. Lee and H. J. Bae, Chem. Commun., 2012, 48, 886–888 RSC.
- K. A. Mahmoud, E. Lam, S. Hrapovic and J. H. Luong, ACS Appl. Mater. Interfaces, 2013, 5, 4978–4985 CrossRef CAS PubMed.
- H. Suo, L. Xu, Y. Xue, X. Qiu, H. Huang and Y. Hu, Carbohydr. Polym., 2020, 234, 115914 CrossRef CAS PubMed.
- H. H. Je, S. Noh, S.-G. Hong, Y. Ju, J. Kim and D. S. Hwang, Chem. Eng. J., 2017, 323, 425–433 CrossRef CAS.
- J. Zhang, X. Feng, J. Wang, G. Fang, J. Liu and S. Wang, Analyst, 2020, 145, 3407–3413 RSC.
- M. Rahimi, S. Shojaei, K. D. Safa, Z. Ghasemi, R. Salehi, B. Yousefi and V. Shafiei-Irannejad, New J. Chem., 2017, 41, 2160–2168 RSC.
- C. Wan and J. Li, ACS Sustainable Chem. Eng., 2015, 3, 2142–2152 CrossRef CAS.
- M. H. Mohamed Noor, N. Ngadi, I. Mohammed Inuwa, L. A. Opotu and M. G. Mohd Nawawi, J. Environ. Chem. Eng., 2020, 8, 104014 CrossRef CAS.
- S. Periyasamy, V. Gopalakannan and N. Viswanathan, Carbohydr. Polym., 2017, 174, 352–359 CrossRef CAS PubMed.
- A. H. Nordin, S. Wong, N. Ngadi, M. Mohammad Zainol, N. A. F. Abd Latif and W. Nabgan, J. Environ. Chem. Eng., 2021, 9, 104639 CrossRef CAS.
- E. S. Mirjavadi, R. M. A. Tehrani and A. Khadir, Environ. Sci. Pollut. Res., 2019, 26, 33478–33493 CrossRef CAS PubMed.
- Z. Zhang, H. Li, J. Li, X. Li, Z. Wang, X. Liu and L. Zhang, Chem. Phys. Lett., 2019, 731, 136573 CrossRef CAS.
- S. F. Chin, A. N. Binti Romainor and S. C. Pang, Mater. Lett., 2014, 115, 241–243 CrossRef CAS.
- Z. Xu, X. Jiang, H. Zhou and J. Li, Cellulose, 2017, 25, 1217–1227 CrossRef.
- H. Peng, H. Wang, J. Wu, G. Meng, Y. Wang, Y. Shi, Z. Liu and X. Guo, Ind. Eng. Chem. Res., 2016, 55, 832–838 CrossRef CAS.
- H. Gu, X. Zhou, S. Lyu, D. Pan, M. Dong, S. Wu, T. Ding, X. Wei, I. Seok, S. Wei and Z. Guo, J. Colloid Interface Sci., 2020, 560, 849–856 CrossRef CAS PubMed.
- X. He, T. Chen, T. Jiang, C. Wang, Y. Luan, P. Liu and Z. Liu, Carbohydr. Polym., 2021, 260, 117790 CrossRef CAS PubMed.
- L. E. Low, L. T. Tan, B. H. Goh, B. T. Tey, B. H. Ong and S. Y. Tang, Int. J. Biol. Macromol., 2019, 127, 76–84 CrossRef CAS PubMed.
- Y. Li, Y. Feng, J. Jing and F. Yang, BioResources, 2019, 14, 3615–3629 CAS.
- N. Wang, Y. F. Wang, A. M. Omer and X. K. Ouyang, Anal. Bioanal. Chem., 2017, 409, 6643–6653 CrossRef CAS PubMed.
- H. Huang, X. Wang, H. Ge and M. Xu, ACS Sustainable Chem. Eng., 2016, 4, 3334–3343 CrossRef CAS.
- Z. H. Hu, Y. F. Wang, A. M. Omer and X. K. Ouyang, Int. J. Biol. Macromol., 2018, 107, 453–462 CrossRef CAS PubMed.
- N. Wang, X.-K. Ouyang, L.-Y. Yang and A. M. Omer, ACS Sustainable Chem. Eng., 2017, 5, 10447–10458 CrossRef CAS.
- H. Lu, L. Zhang, B. Wang, Y. Long, M. Zhang, J. Ma, A. Khan, S. P. Chowdhury, X. Zhou and Y. Ni, Cellulose, 2019, 26, 4909–4920 CrossRef CAS.
- T. Ghosh, Y. Teramoto and V. Katiyar, J. Agric. Food Chem., 2019, 67, 4289–4299 CrossRef CAS PubMed.
- M. A. Hobisch, S. Zabler, S. M. Bardet, A. Zankel, T. Nypelö, R. Eckhart, W. Bauer and S. Spirk, Carbohydr. Polym., 2021, 254, 117406 CrossRef CAS PubMed.
- S. Liu, Q. Yan, D. Tao, T. Yu and X. Liu, Carbohydr. Polym., 2012, 89, 551–557 CrossRef CAS PubMed.
- P. Dhar, A. Kumar and V. Katiyar, ACS Appl. Mater. Interfaces, 2016, 8, 18393–18409 CrossRef CAS PubMed.
- Y. C. Yee, R. Hashim, A. R. Mohd Yahya and Y. Bustami, Sensors, 2019, 19, 2511 CrossRef CAS PubMed.
- N. M. Aguilar, F. Arteaga-Cardona, M. E. de Anda Reyes, J. J. Gervacio-Arciniega and U. Salazar-Kuri, Mater. Chem. Phys., 2019, 238, 121921 CrossRef CAS.
- F. Zhang, R. Wang, C. Zhen and B. Li, J. Mol. Catal. B: Enzym., 2016, 134, 164–171 CrossRef CAS.
- J. Guo, I. Filpponen, L. S. Johansson, P. Mohammadi, M. Latikka, M. B. Linder, R. H. Ras and O. J. Rojas, Biomacromolecules, 2017, 18, 898–905 CrossRef CAS PubMed.
- Y. Li, H. Zhu, C. Zhang, M. Cheng and H. He, Cellulose, 2018, 25, 4757–4769 CrossRef CAS.
- S. M. A. S. Keshk, A. A. El-Zahhar, A. M. S. Youssef and S. Bondock, Mater. Res. Express, 2019, 6, 085310 CrossRef CAS.
- S. M. A. S. Keshk, A. A. El-Zahhar, A. G. Al-Sehemi, A. Irfan and S. Bondock, Mater. Res. Express, 2018, 6, 025312 CrossRef.
|
This journal is © The Royal Society of Chemistry 2022 |
Click here to see how this site uses Cookies. View our privacy policy here.