Green and sustainable synthesis of poly(δ-valerolactone) with a TBD catalyzed ring-opening polymerization reaction†
Received
2nd October 2021
, Accepted 28th October 2021
First published on 29th October 2021
Abstract
Ring-opening polymerization (ROP) of lactones catalyzed by 1,5,7-triazabicyclo[4,4,0]decane-5-ene (TBD) is a highly efficient method for synthesizing aliphatic polyester materials. In order to create a green and sustainable synthetic route for poly(δ-valerolactone) with a narrow molecular weight distribution, we propose CO2 as the terminator instead of conventional organic acids, which are difficult to remove from the production solution. A flow ROP reactor for δ-valerolactone is employed to enhance the mass transfer of CO2 and implement the ROP reaction continuously. In addition to the quenching method, n-hexane is proposed as the antisolvent of the production solution to precipitate poly(δ-valerolactone) from toluene instead of normally used methanol, which works as an initiator of ROP that influences the molecular weight of polyesters as an impurity of the reaction solution. Owing to the strong hydrophobicity and volatility of n-hexane, the anhydrous toluene and residual δ-valerolactone have strong potential to be recycled via distillation separation.
Introduction
Aliphatic polyesters are versatile polymer materials, and have excellent biocompatibility and degradability. They have been more preferred in recent years in biomedical applications, such as tissue engineering1,2 and drug delivery.3,4 The ring-opening polymerization (ROP) of cyclic esters is a crucial method for obtaining aliphatic polyesters with narrow molecular weight distributions and versatile blocking structures.5–7 One of the key points of ROP is the catalyst, such as metal ions,8,9 small organic molecules,10,11 and enzymes,12,13 for promoting the ring opening of the monomer. For different kinds of catalysts, the organic catalysts have drawn increasing attention for the free of metal residue and ease to be obtained from industry.
The hydrogen bond mediated catalyst 1,5,7-triazabicyclo[4,4,0]decane-5-ene (TBD) is a widely used organic catalyst for ROP reactions due to its high catalytic activity.14–17 Different from the composite catalysts composed by hydrogen bond donors and acceptors,6,18 TBD is a bifunctional catalyst, which activates both the hydroxy group in the alcohol initiator and the carbonyl group in the cyclic ester in an anhydrous solution environment,19 as shown in Scheme 1. Since the hydroxy group is preserved at the end of the polymer chain, the ROP reaction is in fact a living polymerization. Due to the compact active sites in the TBD molecule, the ROP reaction is a fast reaction for the cyclic esters with six-membered rings, such as δ-valerolactone and lactide.20,21 Therefore, it has great potential to be used in industrial practice.
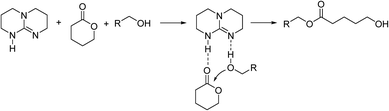 |
| Scheme 1 δ-Valerolactone ROP reaction catalyzed by TBD. | |
In contrast to the advantage in the reaction rate, the drawback of TBD is its ability of catalysing the transesterification reaction of polyester molecules,14,18 which broadens the molecular weight distribution of polyester products at a high monomer conversion. Therefore, it is necessary to precisely quench the TBD catalyzed ROP reaction before the monomer is completely converted to meet the requirement of narrow molecular weight distribution. Organic acids, such as benzoic acid, are the most used terminators, and can neutralize the alkaline active sites of TBD.11,22,23 They are usually excessively used to ensure the termination, but difficult to remove from the reaction solution, causing the anhydrous solvent and unreacted monomer to be difficult to reuse. In addition, some organic acids are also, at a certain degree, harmful to the human body for causing metabolic acidosis, convulsion, and hyperpnea.24,25 Therefore, it is significant to develop a new terminator for the TBD catalyzed ROP reaction for high quality aliphatic polyester synthesis.
Not only the improvement of the quenching process is necessary, but also recycling the solvent and unreacted monomer from the production solution is crucial for the synthesis of aliphatic polyesters. In previous studies, methanol was the most commonly used antisolvent to precipitate the polymers.22,26 Although it is good at precipitating polymers, the application of methanol also makes it difficult to recycle the chemicals, because its residue will work as an initiator for the following ROP reaction. Due to the strict molecular weight requirement for aliphatic polyesters, the uncontrolled molar ratio of monomer to initiator will strongly influence the quality of polyester products.27 Therefore, it is also desirable to develop a sustainable separation method for the products of the TBD catalyzed ROP reaction.
Based on those critical requirements for the green synthesis of aliphatic polyesters, we come up with the idea of applying carbon dioxide to quench the TBD catalyzed ROP reaction. The ROP of δ-valerolactone in anhydrous toluene is employed as a representative reaction in this research, whose product poly(δ-valerolactone) (PVL) is a useful aliphatic polyester material.26 In addition to traditional batch operation, the ROP and quenching reactions are also carried out via a continuous flow reactor, where the synthesis of PVL is operated with high mixing and mass transfer efficiencies. An antisolvent n-hexane is proposed to precipitate PVL from the CO2 quenched reaction solution to help recycle the anhydrous toluene and unreacted δ-valerolactone.
Results and discussion
Quenching TBD catalyzed ROP by CO2
Like tertiary amines used to capture CO2 from industrial exhausts,28 TBD is good at absorbing CO2.29,30 A zwitterionic adduct TBD–CO2 will be generated from the reaction of TBD and CO2 as shown in Scheme 2.31 In this research, we observed that white powders quickly precipitated from the TBD toluene solutions as CO2 was fed into the reactor at 30 °C, indicating that the reaction was rapid. The solids and the remaining solutions were carefully detected by elemental and 1H-NMR analyses after centrifugal separation, and the results are shown in Table 1 and Fig. S9 and S10 in the ESI.† The mass percentages of the elements in Table 1 show that each TBD molecule combines with CO2 with the TBD concentration ranging from 0.03 to 0.15 mol L−1, in accordance with the previous literature.29–31 Besides, the results also indicate that equimolar equivalent H2O co-precipitated with TBD and CO2. Thus, the precipitate was in fact the bicarbonate of TBD.31 Because all the solutions in the experiment were prepared in a glove box with nearly anhydrous toluene (<20 mg L−1 H2O), we believe that the bicarbonate was generated by the contact of moist air and the TBD–CO2 adduct in the separation and storage of the samples. The 1H-NMR result shows that the precipitate has almost the same spectrum as TBD. Only the peaks of toluene appear in the solution, indicating that TBD was fully precipitated. Furthermore, as we raised the temperature of the TBD bicarbonate suspension from 30 to 70 °C, we found that the solid disappeared in 30 min. The remaining solution is confirmed to be the TBD solution by 1H-NMR, as shown in Fig. S11 in the ESI,† which demonstrated that the reaction of TBD and CO2 is reversible at high temperature.
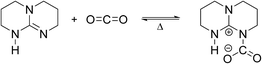 |
| Scheme 2 Reaction between TBD and CO2. | |
Table 1 Elemental analysis of the precipitates from the reaction of TBD and CO2
[TBD] (mol L−1) |
C (wt%) |
H (wt%) |
N (wt%) |
O (wt%) |
C/N |
N/O |
0.03 |
47.6 |
7.6 |
20.7 |
24.1 |
2.68 |
0.98 |
0.06 |
47.6 |
7.7 |
20.7 |
24.0 |
2.68 |
0.99 |
0.09 |
47.6 |
7.7 |
20.7 |
24.0 |
2.68 |
0.99 |
0.12 |
47.6 |
7.7 |
20.7 |
24.0 |
2.68 |
0.99 |
0.15 |
47.6 |
7.8 |
20.7 |
23.9 |
2.68 |
0.99 |
Inspired by the high reaction rate of TBD and CO2, we further investigated the quenching ability of CO2 to the TBD catalyzed ROP of δ-valerolactone in small bottle reactors. The reactions were quenched by injecting benzoic acid toluene solutions into the reaction solutions or bubbling CO2 into the solutions via needles at 30 °C, respectively. Fig. 1(a) shows the comparison of the conversions of δ-valerolactone in 6 min, which indicates that CO2 works well for quenching the ROP. According to the polydispersity indices (PDIs) of PVL from the control group experiment, shown in Fig. S4 in ESI,† the transesterification reaction will become active as the δ-valerolactone conversion is >95%. Fig. 1(b) shows that the PDIs are below 1.1 in all the quenching experiments, indicating that CO2 works the same as benzoic acid in neutralizing TBD. In contrast to the above experiments with the CO2 and TBD toluene solution only, there was no precipitate formed from the quenching solution. A possible reason for this phenomenon is that the polarity of the toluene, δ-valerolactone, and PVL mixture is higher than that of toluene, which helps to dissolve the TBD–CO2 adduct. In addition to the ability of quenching the ROP reaction, we also tested the on–off performance of CO2 for the ROP reaction because of the reversibility of the reaction between TBD and CO2. When we heated the quenched reaction solution from 30 to 70 °C, the δ-valerolactone conversion increased from 47% to 97% in 10 min, which showed that the ROP was restarted when CO2 was desorbed.
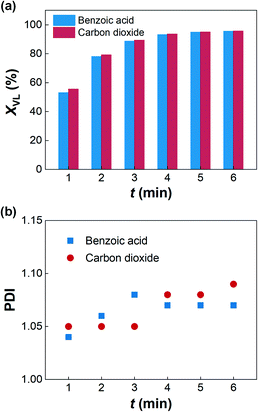 |
| Fig. 1 Quenching experiments of the TBD catalyzed ROP reaction of δ-valerolactone. (a) A comparison of δ-valerolactone conversions (xVL) for the experiments that employed benzoic acid and CO2. (b) PDIs of prepared PVL in the quenching experiments. The experiments were carried out at 30 °C with the original concentrations of δ-valerolactone, TBD, and benzyl alcohol (initiator) as [VL]0 = 2.0 mol L−1, [TBD]0 = 0.04 mol L−1, and [BnOH]0 = 0.04 mol L−1. The quenching solution with benzoic acid had a concentration of [BA]0 = 0.4 mol L−1 and the molar ratio of benzoic acid to TBD was 1.2. CO2 was bubbled for 2 min in each test at a gauge pressure of 10 kPa. | |
Continuous ROP and CO2 quenching with a flow reactor
To implement of the ROP and CO2 quenching reactions with high efficiencies, innovation of reaction equipment is important. As a heterogeneous terminator, CO2 needs to be dissolved in the reaction solution before interacting with TBD. In the above tests, excessive CO2 was injected into the solutions in batch reactors to promote CO2 dissolution. However, it is better to operate the quenching reaction via a more efficient method to reduce CO2 consumption. Recently, the flow chemistry method employing a small tubular reactor as the mass transfer enhancing equipment32–34 has been regarded as an advanced method to implement the absorption of CO2.35,36 Owing to the large specific surface area of bubbles, CO2 dissolves quickly.37,38 In addition to mass transfer enhancement, the flow reaction can also turn traditional batch processes into a continuous process,39,40 which is also one of the most important developing directions of ROP technologies.22,41 Therefore, we developed a continuous flow ROP reaction with TBD as the catalyst and CO2 as the terminator in this research.
Fig. 2 shows a schematic diagram of the flow ROP system. In this system, both the solutions of δ-valerolactone (VL) and the TBD + BnOH mixture with toluene as the solvent were fed with syringe pumps with the same volumetric flow rates. The solutions met at a Y-junction tube connector, and mixed in a screw tube mixer,42 which had been proved to have an excellent mixing ability to investigate the ROP kinetics of δ-valerolactone.20 Connected with the screw tube mixer, a 3 mL reaction tube was employed to provide a residence time (tR) from 4 to 13 min. Another flow of toluene switched with a three-way valve was used to remove air and moisture from the reactor. The reaction was carried out only at 30 °C because temperature had little influence on the ROP of δ-valerolactone due to the very low activation energy of the reaction.20 Following the reaction tube, the other Y-junction connector was used to disperse CO2 into the solution. The flow rate of CO2 at standard temperature and pressure was equal to the flow rate of the reaction solution (molar flow rate of CO2/TBD = 2.2), which was controlled by a mass flow controller (MFC). A gas–liquid Taylor flow was generated in the 1 mL quenching tube as shown in the photo in Fig. 2. A photo of the reaction platform is shown in Fig. S2 in the ESI.†
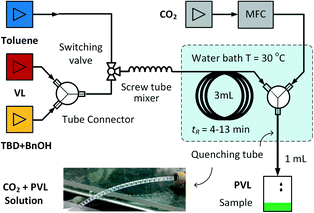 |
| Fig. 2 Schematic of the flow ROP reaction system. The main components and chemicals have been labelled in the figure. VL represents δ-valerolactone and MFC represents the mass flow controller. A photo of the CO2 Taylor flow in the quenching tube is shown. | |
The typical results of the flow ROP experiments are shown in Fig. 3 and Table 2. The −ln(1 − XVL) and the residence time tR have a linear relationship as shown in Fig. 3, exhibiting the first-order kinetics of δ-valerolactone, which is in accordance with previous research on the kinetic laws of the ROP of δ-valerolactone.20 This relationship also indicates that the δ-valerolactone conversion can be precisely controlled by the flow rate of the reactants as the quenching process is highly efficient. Table 2 shows the average molecular weights of PVL from the flow ROP reaction. Both Mn,th and Mn,NMR calculated from different methods show the number average molecular weights of PVL of 5000–9900 g mol−1. The molecular weight distribution of PVL is also exhibited in Table 2. The PDIs in all the experiments are below 1.20, indicating the efficient quenching of ROP with CO2.
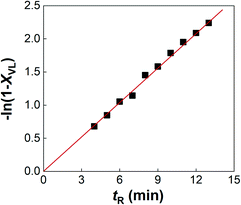 |
| Fig. 3 First-order reaction kinetics of δ-valerolactone in the flow ROP reaction. The initial concentrations of δ-valerolactone, TBD, and benzyl alcohol in the reaction solution were [VL]0 = 1 mol L−1, [TBD]0 = 0.02 mol L−1, and [BnOH]0 = 0.01 mol L−1. | |
Table 2 δ-Valerolactone conversions and the molecular weights of PVL
t
R (min) |
X
VL (%) |
M
n,th (g mol−1) |
M
n,NMR (g mol−1) |
PDI |
4 |
49.3 |
5042 |
5600 |
1.096 |
5 |
57.2 |
5825 |
6351 |
1.140 |
6 |
65.2 |
6624 |
7023 |
1.135 |
7 |
68.2 |
6924 |
7809 |
1.148 |
8 |
76.6 |
7772 |
7567 |
1.151 |
9 |
79.5 |
8058 |
8356 |
1.146 |
10 |
83.3 |
8434 |
8772 |
1.167 |
11 |
85.8 |
8689 |
8732 |
1.150 |
12 |
87.6 |
8870 |
9047 |
1.163 |
13 |
89.4 |
9045 |
9839 |
1.186 |
PVL separation and chemical recycling
Apart from the green termination of ROP, we also developed a precipitation method to separate PVL from the reaction solution. In many reported ROP reactions and the above experiments, PVL was precipitated by mixing the reaction solution with cold methanol,19 which acted as an antisolvent of toluene. However, this method would make toluene and δ-valerolactone difficult to recycle if methanol cannot be totally removed from the mixture. To overcome these shortcomings, we selected a different way to separate PVL by employing n-hexane as a new antisolvent. The dielectric constant of n-hexane is 2.02,43 which is smaller than that of toluene (2.4). Although their dielectric constants are not far from each other, the experimental results showed that PVL and the TBD–CO2 adduct can be fully precipitated from the reaction solutions at 25 °C as four times the volume of n-hexane was mixed with the CO2 quenched solution. Fig. S12 in the ESI† shows the 1H-NMR spectrum of the precipitate from the experiment with 94% δ-valerolactone conversion, indicating that the solid is composed of PVL and TBD. Fig. S13† shows the 1H-NMR spectrum of the residual solution after the centrifugal separation of the solids. Only the characteristic peaks of toluene, δ-valerolactone, and n-hexane are observed, indicating that PVL and TBD are fully separated. The efficient precipitation of PVL and TBD was achieved in the experiments with [VL]0 = 1–2 mol L−1 and [TBD]0 = 0.02–0.04 mol L−1, where the Mn,NMR of PVL ranged from 3000 to 10
000 g mol−1. The precipitated PVL can be further purified by water washing, as the 1H-NMR spectrum shows in Fig. S14,† because TBD–CO2 is very soluble in water31 and PVL is insoluble.
Another advantage of employing n-hexane as the antisolvent is its strong hydrophobicity, which prevents the adsorption of water into the reaction system. This is important for simplifying the PVL precipitation and solvent recycling. Since the residual solution after solid separation only contained n-hexane, toluene and δ-valerolactone, we further tried to separate the n-hexane from the mixture by distillation, due to its low boiling point at 69 °C (boiling points of toluene and δ-valerolactone at 0.1 MPa are 110 and 230 °C, respectively). However, the distillation in the lab failed to obtain highly concentrated n-hexane from the solution. Multistage distillation was thus necessary to separate n-hexane. Here, we used Aspen Plus to simulate the distillation of n-hexane. Setting a nine-stage column with a reflux ratio of 3, as shown in Fig. S3 in the ESI,† we simulated the concentration distributions of n-hexane, toluene, and δ-valerolactone in a 0.1 MPa column. A mixture of 0.73 wt% δ-valerolactone, 24.1 wt% toluene, and 75.2 wt% n-hexane was used as the inlet solution based on the above PVL precipitation experiment, which was fed into the column from the 5th stage with a temperature of 90 °C. Fig. 4 shows that the mixture can be well separated. 98.2 wt% n-hexane with 1.8 wt% toluene was found in the top condenser, and 96.2 wt% toluene with 3.1 wt% δ-valerolactone was found in the bottom reboiler, which showed that the recovery of n-hexane was 99.8%. The residual n-hexane in the mixture of toluene and δ-valerolactone was only 0.7 wt%, which did not affect the ROP reaction, according to a control experiment employing a solvent with 1% n-hexane and 99% toluene ([VL]0 = 2.0 mol L−1, [TBD]0 = 0.04 mol L−1, and [BnOH]0 = 0.04 mol L−1). Therefore, the mixture of toluene, δ-valerolactone, and n-hexane after distillation has the potential to be reused in the TBD catalyzed ROP reaction. Since CO2 can be easily evaporated, which had been discussed in the above section for the on–off performance of the CO2 quenching reaction, its separation was not considered in the simulation. Due to the little amount of TBD used in the experiment, it was not recovered in this research either.
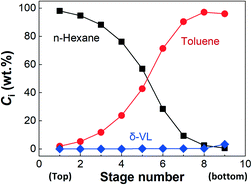 |
| Fig. 4 Substance concentration distributions in the distillation simulation. Ci is the mass percentage of the different chemicals in the system. | |
Improvement of the TBD catalyzed ROP
At the end of this article, we make a simple comparison of the classical ROP methods in recent literature and the new method created in this study. The ROP reactions with similar monomers are selected, as shown in Table 3. Due to the high solubility of polyesters in halogenated hydrocarbons, dichloromethane and chloroform are also usually used in the ROP reactions.14,44 The advantage of these solvents is their high volatility, which means they can be easily vaporized from the product solution without using an antisolvent. However, halogenated hydrocarbons are not environment friendly and they also easily absorb water in the air. In contrast to halogenated hydrocarbons, toluene was used in this study, which was also applied by other research groups.22,45 Considering the higher boiling point of toluene, it is better to use an antisolvent to precipitate the polyesters. In this study, we selected n-hexane, which is a low boiling point solvent, instead of methanol aiming to recycle toluene and residual δ-valerolactone. Because the transesterification reaction does not stop even as the lactone conversion reaches 100%, a terminator is necessary for the TBD catalyzed ROP reaction. Table 3 shows that organic acids are more used, but we demonstrate that CO2 also worked well for quenching the ROP process by neutralizing TBD, and the formed TBD–CO2 adduct can be fully precipitated from the mixture of toluene and n-hexane. Other advantages of CO2 are its low price and easy separation from the solution system. Table 3 also shows the lactone conversions and molecular weight information. Like the results in Fig. S4,† the PDIs are far from 1.2 if the lactones are fully converted into polyesters. Only Zhu et al.22 showed narrow molecular weight distributions of all polyesters with a maximum conversion of 90%. The antisolvent n-hexane and the distillation technology thus have strong potential to recycle the anhydrous toluene and to promote the utilization of δ-valerolactone in industrial processes, which are beneficial for increasing the economical and environmental friendliness of ROP reactions.
Table 3 Comparison of the TBD catalyzed ROP with other methods in recent literature
|
Monomer |
Solvent |
Terminator |
Antisolvent |
Monomer conversion |
Polymer molecular weight (g mol−1) |
PDI |
The ROP was catalyzed by TBD derivatives – chiral DiPh–TBD.
|
Ref. 14 (2016) |
L-Lactide |
CH2Cl2 |
Benzoic acid |
None |
41–99%+ |
5000–38 500 |
1.18–1.8 |
Ref. 44 (2020) |
Trimethylene carbonate + δ-valerolactone |
CH2Cl2 |
Benzoic acid |
None |
97–99%+ |
15 600–40 500 |
1.17–1.88 |
Ref. 45 (2020) |
rac-Lactidea |
CH2Cl2 toluene |
Acetic acid |
Methanol |
29–99%+ |
10 900–57 400 |
1.23–2.14 |
Ref. 46 (2019) |
ε-Caprolactone |
CHCl3 |
Benzoic acid |
Methanol and water |
30–99%+ |
4200–13 600 |
1.11–1.68 |
Ref. 22 (2016) |
ε-Caprolactone/δ-valerolactone |
Toluene |
Benzoic acid |
Methanol |
9.8–90% |
1320–9120 |
1.04–1.09 |
This work |
δ-Valerolactone |
Toluene |
CO2 |
n-Hexane |
49–95% |
2800–9900 |
1.10–1.19 |
Conclusions
In this article, we propose a green terminator CO2 for the TBD catalyzed ROP reaction and a nonpolar antisolvent n-hexane for the precipitation of aliphatic polyesters and discuss its separation technology. The polymerization of δ-valerolactone is selected as the experimental system and toluene is used as the solvent to demonstrate the effectiveness of the strategy. The quenching experiment shows that the reaction between CO2 and TBD is fast, and the narrow molecular weight distribution of PVL (PDI <1.2) shows the strong quenching ability of CO2. A flow ROP reaction is created to implement the polymerization and the quenching reactions efficiently, reducing the consumption of CO2 and achieving a continuous ROP process. To separate PVL from the reaction solution, n-hexane is used as the antisolvent, which is highly hydrophobic and has a low boiling point. Both PVL and TBD can be completely precipitated, and 99.8% n-hexane could be regenerated from the residual solution via a nine-stage distillation. The terminator and antisolvent will help to build a recycling technology for TBD catalyzed ROP reactions. This work opens up an avenue for sustainable synthesis of polyvalerolactone, which can be used to synthesize other aliphatic polyesters, such as polylactic acid and polycaprolactone.
Materials and methods
Materials
All the chemicals were commercially available, including δ-valerolactone (99%, J&K), benzoic acid (99.5%, J&K), calcium hydride (CaH2 93%, J&K), TBD (>98%, TCI), benzyl alcohol (>99%), toluene (99.5%, Beijing Chemical Works), n-hexane (AR, Beijing Chemical Works), methanol (AR, Beijing Chemical Works), tetrahydrofuran (THF, 99.9+%, MREDA), CO2 (99.995%, Air Liquide), and N2 (99.999%, Air Liquide). Toluene and benzyl alcohol (BnOH) were refluxed and distilled over CaH2 for more than 3 hours with the protection of N2 before use. δ-Valerolactone was distilled over CaH2 with reduced pressure. Water contents of toluene, benzyl alcohol, and δ-valerolactone were less than 20 mg L−1. Benzoic acid and TBD were used without purification. All the anhydrous chemicals were stored in a glovebox. Deuterated chloroform used for H1-NMR analysis was provided by the Analysis Center of Tsinghua University.
Instruments
The ROP reactions in little batch reactors were implemented in a constant-temperature magnetic stirrer (S10-3, Sile Instrument Co., Ltd.) equipped with 20 mL glass bottles as shown in Fig. S1 in the ESI.† The precipitation of PVL was also carried out with these bottle reactors. The flow ROP platform was assembled using syringe pumps (PHD ULTRA 4400, Harvard Apparatus; Fusion 6000, Chemyx; PPI, Jingyi Pump), Y-junction connectors (PEEK, polyetheretherketone, 0.5 mm, Idex Health & Science), switching valves (Xiongchuan Technology Co. Ltd.), a gas flow controller (Sevenstar Flow Co., Ltd.), a constant-temperature water bath (Hengtai Instrument Co., Ltd.), and some FEP (fluorinated ethylene propylene) tubes (Dinglifeng Tech.) for delivering fluids and carrying out reactions. The tubes applied for the ROP and quenching reactions had an inner diameter of 2.0 mm and those for fluid delivery had a 1.0 mm inner diameter. A home-made screw tube mixer was employed to enhance the mixing of the solutions as shown in Fig. S2(b) in the ESI.† The screw tube mixer was made of 1.6 mm outer-diameter FEP tube via the thermoforming method,41 which created a tubular mixing tunnel with a 0.7–1.0 mm inner diameter, 1.0 mm screw pitch, 24 mm length, and 12 μL volume. The mixer was connected to the connector of the δ-valerolactone solution and TBD + BnOH solution.
Analysis and characterization
Substance identification, δ-valerolactone conversion (XVL), and PVL molecular weight were determined by NMR (JNM-ECA600, 600 MHz, CDCl3 as the solvent) analysis.22 Fig. S5 and S6 in the ESI† show the standard 1H-NMR spectra of PVL and δ-valerolactone, respectively. Based on the areas of the characteristic peaks in the 1H-NMR spectrum of the reaction solution, the δ-valerolactone conversion was calculated as: | XVL = (F + G)/(F + G + F′) | (1) |
And the number-average molecular weight of PVL (Mn,NMR) was calculated as: | 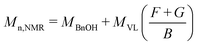 | (2) |
where F, G, B, and F′ are the peak areas in the 1H-NMR spectrum. The average molecular weight of PVL was also obtained from the δ-valerolactone conversion according to the monomer polymerization degree, as shown by Mn,th. | 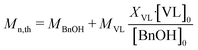 | (3) |
where MBnOH and MVL are the molecular weights of BnOH and δ-valerolactone, respectively, and [BnOH]0 and [VL]0 are the initial concentrations of BnOH and δ-valerolactone, respectively. Gel permeation chromatography (GPC, Waters Instrument included with a 2707 autosampler, 1515 HPLC pump, Styragel columns HR1-3, and 2414 refractive index detector) was used to demonstrate the consistency of the PVL molecular weight. THF was used as the mobile phase with a flow rate of 1 mL min−1. Because polystyrene was used as the standards of GPC, the average molecular weight from GPC was about 1000 g L−1 larger than that from 1H-NMR. Considering the relatively large deviation of the GPC molecular weight, only the PIDs of PVL from GPC analysis are exhibited in this paper. Elemental analysis of the solid products was carried out using an elemental analyser (Vario EL III) with 3 parallel tests.
CO2 quenching in batch reactors
To evaluate the reactivity between TBD and CO2, 0.042–0.209 g TBD was dissolved in 8.6 g toluene in stirring bottle reactors at 30 °C, and CO2 was bubbled into the bottles via needles. The gas pressure was controlled to 10 kPa via a reducing valve on the cylinder. The product solution was equally transferred into several 10 mL centrifuge tubes after the reaction. The precipitates were centrifugally separated (Anke GL-20G-C, 4000 rpm, 10 min) and dried in vacuum. The high temperature experiment was carried out by heating the bottle reactor using a magnetic stirrer under stirring conditions. For each quenching experiment in the bottle reactors, 0.084 g TBD was added to 10.58 g toluene to form a catalyst solution, and the solution was then transferred to a 20 mL glass syringe with an air sealing valve at the outlet. 0.065 g BnOH and 3.0 g δ-valerolactone were subsequently mixed in the bottle with a sealing gasket. Both the solutions were prepared in a glovebox. After moving the bottle and the syringe out of the glovebox and setting the bottle on the stirrer, the reaction was started at 30 °C by quickly injecting the catalyst solution into the bottle reactor under the protection of N2. At the set quenching time, CO2 was quickly bubbled into the bottle via the needle. Control group experiment was implemented by injecting the mixture of 0.146 g benzoic acid and 2.61 g toluene with a syringe. The product solution was partly used for NMR analysis and partly (about 10 mL) poured into 30 mL cold methanol (20 °C) to precipitate PVL. The solid was centrifugally separated and dried in vacuum before dissolving in THF for GPC analysis.
Flow ROP with the CO2 quenching reaction
In the flow ROP reaction experiment, 10 g δ-valerolactone were firstly dissolved in toluene to form a 50 mL monomer solution in each syringe. 0.122 g BnOH and 0.276 g TBD were mixed and dissolved in another 50 mL toluene solution. Both the solutions were then transferred to 50 mL stainless steel syringes with air sealing valves in the glove box. Before the experiment, the reactor was previously flushed with anhydrous toluene and high purity N2 to remove moisture and air. The δ-valerolactone and TBD + BnOH solutions were fed by the syringe pumps with equal flow rates. The total flow rates of the liquids were between 230 and 750 μL min−1. The volume flow rate of CO2 at standard temperature and pressure was set to be equal to the flow rate of the liquids. The reaction temperature of 30 °C was controlled using the water bath. After 10 to 20 min standing time, which was more than twice the substance residence time in the reaction tube, 15 mL samples were collected from the outlet. The samples were partly subjected to 1H-NMR analysis and partly poured into methanol to precipitate the PVL for GPC analysis.
PVL precipitation with n-hexane as the antisolvent
The precipitation experiments with n-hexane as the antisolvent were almost the same as those using methanol as the antisolvent. About 10 mL sample was collected in 40 mL n-hexane at room temperature. The PVL was centrifugally separated and dried in vacuum.
n-Hexane distillation simulation
The distillation was simulated by Aspen Plus 8.4. A mixture of 0.73 wt% δ-valerolactone, 24.1 wt% toluene, and 75.2 wt% n-hexane was employed as the inlet solution, which had a similar composition to the residual solution after PVL precipitation, as shown in Fig. S4 in the ESI.† The inlet temperature was 90 °C and the pressure was 0.2 MPa. A RadFrac column was employed as the distillation model with a pressure of 0.1 MPa. The column had 9 theoretical stages, and the solution came from the fifth stage. The molar reflux ratio for the distillation was 3.
Author contributions
Mr. Kai Cheng did the CO2 quenching and the n-hexane precipitation experiments with little batch reactors. He also carried out the Aspen Plus simulation for n-hexane distillation. Miss Shiyao Lu did the flow ROP experiment and wrote the original draft of the paper. Prof. Kai Wang led this project, proposed the ideas of CO2 quenching and n-hexane precipitation, and revised the draft. Prof. Guangsheng Luo guided the project and provided financial support.
Conflicts of interest
There are no conflicts to declare.
Acknowledgements
We acknowledge the support from the National Natural Science Foundation of China (92034303 and 21991104) for this research.
References
- W. Zhao, J. Li, K. Jin, W. Liu, X. Qiu and C. Li, Mater. Sci. Eng., C, 2016, 59, 1181–1194 CrossRef CAS PubMed.
- Z. Terzopoulou, D. Baciu, E. Gounari, T. Steriotis, G. Charalambopoulou and D. Bikiaris, Polymer, 2018, 10, 381 Search PubMed.
- H. Yang, W. Shen, W. Liu, L. Chen, P. Zhang, C. Xiao and X. Chen, Biomacromolecules, 2018, 19, 4492–4503 CrossRef CAS PubMed.
- J. Zhao, G. Weng, J. Li, J. Zhu and J. Zhao, Mater. Sci. Eng., C, 2018, 92, 983–994 CrossRef CAS.
- R. P. Brannigan and A. P. Dove, Biomater. Sci., 2016, 5, 9–21 RSC.
- J. U. Pothupitiya, N. U. Dharmaratne, T. M. M. Jouaneh, K. V. Fastnacht, D. N. Coderre and M. K. Kiesewetter, Macromolecules, 2017, 50, 8948–8954 CrossRef CAS.
- D. K. Schneiderman and M. A. Hillmyer, Macromolecules, 2016, 49, 2419–2428 CrossRef CAS.
- N. Zhu, Z. Zhang, W. Feng, Y. Zeng, Z. Li, Z. Fang, K. Zhang, Z. Li and K. Guo, RSC Adv., 2015, 5, 31554–31557 RSC.
- N. B. Erdal, G. A. Lando, A. Yadav, R. K. Srivastava and M. Hakkarainen, Polymers, 2020, 12, 1849 CrossRef CAS.
- M. Myers, E. F. Connor, T. Glauser, A. Mock, G. Nyce and J. L. Hedrick, J. Polym. Sci., Part A: Polym. Chem., 2002, 40, 844–851 CrossRef CAS.
- C. Thomas and B. Bibal, Green Chem., 2014, 16, 1687–1699 RSC.
- Y. Yang, Y. Yu, Y. Zhang, C. Liu, W. Shi and Q. Li, Process Biochem., 2011, 46, 1900–1908 CrossRef CAS.
- A. S. Bhangale, K. L. Beers and R. A. Gross, Macromolecules, 2012, 45, 7000–7008 CrossRef CAS.
- S. A. van den Berg, H. Zuilhof and T. Wennekes, Macromolecules, 2016, 49, 2054–2062 CrossRef CAS.
- A. Bossion, R. H. Aguirresarobe, L. Irusta, D. Taton, H. Cramail, E. Grau, D. Mecerreyes, C. Su, G. Liu, A. J. Müller and H. Sardon, Macromolecules, 2018, 51, 5556–5566 CrossRef CAS.
- I. Nifant Ev, A. Shlyakhtin, V. Bagrov, B. Lozhkin, G. Zakirova, P. Ivchenko and O. Legon Kova, React. Kinet., Mech. Catal., 2016, 117, 447–476 CrossRef CAS.
- M. Hong and E. Y. X. Chen, Nat. Chem., 2016, 8, 42–49 CrossRef CAS PubMed.
- X. Zhang, G. O. Jones, J. L. Hedrick and R. M. Waymouth, Nat. Chem., 2016, 8, 1047–1053 CrossRef CAS.
- L. Simón and J. M. Goodman, J. Org. Chem., 2007, 72, 9656–9662 CrossRef.
- S. Lu and K. Wang, React. Chem. Eng., 2019, 4, 1189–1194 RSC.
- B. Lin and R. M. Waymouth, J. Am. Chem. Soc., 2017, 139, 1645–1652 CrossRef CAS PubMed.
- N. Zhu, W. Feng, X. Hu, Z. Zhang, Z. Fang, K. Zhang, Z. Li and K. Guo, Polymer, 2016, 84, 391–397 CrossRef CAS.
- C. Tan, S. Xiong and C. Chen, Macromolecules, 2018, 51, 2048–2053 CrossRef CAS.
- M. Yu, R. Wen, L. Jiang, S. Huang, Z. Fang, B. Chen and L. Wang, Food Chem., 2018, 268, 411–415 CrossRef CAS PubMed.
- I. Timofeeva, D. Kanashina, D. Kirsanov and A. Bulatov, J. Mol. Liq., 2018, 261, 265–270 CrossRef CAS.
- S. Kan, Y. Jin, X. He, J. Chen, H. Wu, P. Ouyang, K. Guo and Z. Li, Polym. Chem., 2013, 4, 5432 RSC.
- R. C. Pratt, B. Lohmeijer, D. A. Long, R. M. Waymouth and J. L. Hedrick, J. Am. Chem. Soc., 2006, 128, 4556–4557 CrossRef CAS PubMed.
- Y. Zhang and C. Chen, Ind. Eng. Chem. Res., 2011, 50, 6436–6446 CrossRef CAS.
- N. Aoyagi, Y. Furusho, Y. Sei and T. Endo, Tetrahedron, 2013, 69, 5476–5480 CrossRef CAS.
- J. Ma, X. Zhang, N. Zhao, A. S. N. Al-Arifi, T. Aouak, Z. A. Al-Othman, F. Xiao, W. Wei and Y. Sun, J. Mol. Catal. A: Chem., 2010, 315, 76–81 CrossRef CAS.
- C. Villiers, J. Dognon, R. Pollet, P. Thuéry and M. Ephritikhine, Angew. Chem., Int. Ed., 2010, 49, 3465–3468 CrossRef CAS PubMed.
- F. M. Akwi and P. Watts, Chem. Commun., 2018, 54, 13894–13928 RSC.
- K. F. Jensen, AIChE J., 2017, 63, 858–869 CrossRef CAS.
- T. Wirth, Angew. Chem., Int. Ed., 2017, 56, 682–684 CrossRef CAS PubMed.
- S. Fransen and S. Kuhn, React. Chem. Eng., 2016, 1, 288–299 RSC.
- M. Abolhasani, A. Günther and E. Kumacheva, Angew. Chem., Int. Ed., 2014, 53, 7992–8002 CrossRef CAS PubMed.
- C. Yao, Z. Dong, Y. Zhao and G. Chen, Chem. Eng. Sci., 2015, 123, 137–145 CrossRef CAS.
- L. Yang, J. Tan, K. Wang and G. Luo, Chem. Eng. Sci., 2014, 109, 306–314 CrossRef CAS.
- P. Bana, Á. Szigetvári, J. Kóti, J. Éles and I. Greiner, React. Chem. Eng., 2019, 4, 652–657 RSC.
- D. Ott, S. Borukhova and V. Hessel, Green Chem., 2016, 18, 1096–1116 RSC.
- S. Kundu, A. S. Bhangale, W. E. Wallace, K. M. Flynn, C. M. Guttman, R. A. Gross and K. L. Beers, J. Am. Chem. Soc., 2011, 133, 6006–6011 CrossRef CAS PubMed.
- K. Wang, H. Zhang, Y. Shen, A. Adamo and K. F. Jensen, React. Chem. Eng., 2018, 3, 707–713 RSC.
-
G. Q. Liu, L. X. Ma and J. Liu, Chemistry and chemical property data manual, Chemical Industry Press, Beijing, 2002 Search PubMed.
- L. Reinisova and S. Hermanova, RSC Adv., 2020, 10, 44111–44120 RSC.
- Q. Mahmood, G. Xu, L. Zhou, X. Guo and Q. Wang, Polymers, 2020, 12, 2365 CrossRef CAS PubMed.
- A. Dzienia, P. Maksym, B. Hachula, M. Tarnacka, T. Biela, S. Golba, A. Zieba, M. Chorazewski, K. Kaminski and M. Paluch, Polym. Chem., 2019, 10, 6047–6061 RSC.
Footnotes |
† Electronic supplementary information (ESI) available: Details of the experimental set-ups, simulation model, additional results and typical 1H-NMR spectra from the experiments. See DOI: 10.1039/d1re00434d |
‡ These authors contributed equally to this paper. |
|
This journal is © The Royal Society of Chemistry 2022 |
Click here to see how this site uses Cookies. View our privacy policy here.