DOI:
10.1039/D2RA06785D
(Paper)
RSC Adv., 2022,
12, 32249-32261
Enhancement of CO gas sensing performance by Mn-doped porous ZnSnO3 microspheres†
Received
27th October 2022
, Accepted 27th October 2022
First published on 10th November 2022
Abstract
This work reports the synthesis of Mn-doped ZnSnO3 microspheres (Zn1−xMnxSnO3) using a simple co-precipitation method with (x = 0 to 0.15) and characterized for structural, morphological, surface area, and sensing properties. X-ray diffraction (XRD) analysis revealed the face-centered cubic structure of Mn-doped ZnSnO3 samples. Brunauer–Emmett–Teller (BET) analysis demonstrated the variation in surface area from 15.229 m2 g−1 to 42.999 m2 g−1 with x = 0 to 0.15 in Zn1−xMnxSnO3. XPS indicates the change in the defect levels by Mn doping, which plays a crucial role in chemical sensors. Indeed a significant increase (≈311.37%) in CO gas sensing response was observed in the x = 0.10 sample compared to pure ZnSnO3 with a simultaneous reduction in operating temperature from 250 to 200 °C. Moreover, remarkable enhancements in response/recovery times (≈6.6/34.1 s) were obtained in the x = 0.10 sample. The Mn-doped ZnSnO3 could be a promising candidate for CO gas sensing devices used for maintaining air quality.
1 Introduction
Rapid industrialization and urbanization adversely affect the environment and human health, resulting in acid rain, ozone depletion, downgraded air quality, global warming, and the emission of various harmful gases.1 Among different hazardous gases, carbon monoxide (CO) is the most critical air pollutant, which is generated from the incomplete combustion process of fossil fuels, wood, charcoal, petroleum products, and the burnout of electrical appliances.2 The detection of CO is equally tricky owing to its colorless and odorless properties.3 It can cause death by forming carboxyhemoglobin by mixing with blood during breathing.4 Note that the exposure limit for CO is 50 ppm; hence precise monitoring is essential to reduce disastrous effects.
Metal oxide semiconductor (MOS) based gas sensors of chemiresistive-type have been extensively studied for detecting various harmful gases owing to their diversified features such as excellent sensitivity, fast response, low maintenance cost, and suitability for portable instruments.5 The working principle of MOS is based on the change in resistance of the sensing material. However, the high operating temperature and imperfect selectivity limit their practical applications. In this regard, ternary ABO3 perovskite6,7 structured MOS sensors have attracted the scientific community over the binary MOS sensors due to the presence of multiple cation sites for doping materials and exhibiting more potential for enhancing the device performance in gas sensing applications. Out of various choices, the zinc stannate (ZnSnO3) ternary compound (n-type MOS) is a potential candidate due to its high electron mobility, conductivity, good stability, and attractive physical and chemical properties8 compared to binary counterparts ZnO and SnO2. These properties enable this material to be employed in various applications such as Li-ion batteries,9 solar cells,10 photocatalysts,11 gas sensing, etc.12
Several studies have been reported on gas sensing properties of porous ZnSnO3 material, especially on volatile organic compounds (VOCs) such as acetone,13 ethanol,14 butanol,15 propanol,16 formaldehyde,17 and triethylamine.18 However, very few studies are available on the detection of gases except H2S12 and H2.19 Pure ZnSnO3 material usually suffers a requirement barrier due to low sensitivity, poor selectivity, and high operating temperature for the detection of gases other than VOCs. It is known that doping ternary MOS materials with transition metals can significantly enhance the gas sensing performance as it can change the interaction between the gases, oxygen molecules, and the surface electron due to an increase in porosity and large specific surface areas. Despite this, the available studies to improve the gas sensing properties on ZnSnO3 doped with transition metals are significantly fewer. For instance, Fe,20 Al,21 Mg,22 and Pd23 have been doped in ZnSnO3 for performance improvement.
I. Karaduman et al.24 and E. Della Gaspera et al.25 have reported the doping of transition metal Mn to ZnO compounds where improvement of CO sensing was ascribed to the multiple oxidation states of Mn, preferred adsorption of CO molecules at the transition metal dopant sites and then their migration from Mn or Cu sites to Zn sites, and large specific surface area with increased oxygen adsorption and its reactivity with CO molecules.
In correspondence to the above discussion, we decided to figure out the sensing capabilities of ZnSnO3 doped with different concentrations of Mn. This article presents a simple and economical technique for the synthesis of ZnSnO3 with different loadings of Mn (Zn1−xMnxSnO3, x = 0 to 0.15) using co-precipitation method and systematic investigation of structural and morphological properties. Then, the prepared material was used to fabricate the gas sensor device based on the resistance change model. The sensing material was exposed to different interfering gases such as ammonia, carbon dioxide, ethanol, and CO to test the selective sensing properties. Among these, CO turned out to be highly selectively sensed by (Zn1−xMnxSnO3, x = 0 to 0.15). Being highly sensitive to CO among these gases, sensing measurements of Mn-doped ZnSnO3 samples were achieved for different concentrations of CO. The best-performing device was subjected to long-term stability and reproducibility tests for repeated cycles. Finally, the plausible gas-sensing mechanism is discussed to postulate the influence of Mn doping in the ZnSnO3 perovskite microstructure.
2 Experimental section
2.1 Materials
Zinc sulfate heptahydrate (ZnSO4·7H2O, >99.5%), sodium stannate trihydrate (Na2SnO3·3H2O, >99%), manganese sulfate monohydrate (MnSO4·H2O, >99%), and ammonia solution (NH3, ∼25%) were of analytical grade and purchased from Sigma-Aldrich Co. Ltd. All the reagents were used without any further purification.
2.2 Synthesis of pure and Mn-doped ZnSnO3 microspheres
Pure and Mn-doped ZnSnO3 microspheres were synthesized by a simple co-precipitation method. In a typical experiment, 0.1 M of zinc sulfate heptahydrate was dissolved in 50 mL of deionized water. The solution was strenuously stirred at room temperature until the clear transparent solution was accomplished. Likewise, 0.1 M of sodium stannate trihydrate was added to 50 mL of deionized water and stirred. Then, under perpetual stirring, appropriate aqueous ammonia solution was poured dropwise continuously into the ZnSO4 solution to maintain a pH ∼ 10. In the next step, a certain amount of MnSO4·H2O was dissolved in the above ZnSO4 solution. Then, the sodium stannate solution was added to the above solution ([Zn]/[Sn] = 1
:
1), and the aftermath mixed solution was stirred strenuously for 2 h at 60 °C. Finally, after the chemical reaction between the precursors, the precipitates were cumulated by centrifugation at 5000 rpm and repeatedly rinsed with deionized water to remove any product contamination. Ultimately, the final products were then kept for drying in a hot oven at 100 °C for 10 h. The as-prepared pure and Mn-doped ZnSn(OH)6 were subjected to heat treatment at 500 °C for 4 h in a muffle furnace to get the pure and Mn-doped ZnSnO3 spherical particles. The final products with calculated Mn content of 0, 2.5, 5, 7.5, 10, and 15 atomic (at)% were named as ZSO, Z0.975Mn0.025SO, Z0.95Mn0.05SO, Z0.925Mn0.075SO, Z0.9Mn0.1SO, and Z0.85Mn0.15SO, respectively.
2.3 Characterization and measurements
The crystal structure, composition, and phase of the powder samples were identified using the X-ray diffraction (XRD, Empyrean, Malvern Panalytical X-ray diffractometer) method with Cu-Kα radiation (λ = 1.54 Å) in the 2θ range of 10°–80°. The surface morphology of the powder samples was observed by field emission scanning electron microscopy (FESEM, JEOL, JSM-7610F plus) equipped with EDX (energy dispersive X-ray) system to perform the elemental mapping and energy-dispersive spectrum (EDS) characterization. Thermogravimetric and differential thermogravimetric analysis of the as-prepared powder samples were investigated using TGA-DSC (PerkinElmer, STA8000) at a heating rate of 5 °C min−1 up to 1000 °C in an N2 atmosphere. The FTIR (Fourier transform infrared) spectra were recorded by a BRUKER TENSOR 27 spectrometer in the range of 4000–400 cm−1. The specific BET surface area and porosity were figured out from N2 adsorption–desorption measurements, which were recorded on a Quantachrome ASiQwin analyzer, taking place at ∼77 K at liquid nitrogen temperature. X-ray photoelectron spectroscopy (XPS) measurements were carried out using a Kratos AXIS spectrometer with an Al Kα source (hυ = 1486.6 eV).
2.4 Fabrication of the sensing device and measurements
The pure ZSO and Mn-doped ZSO samples in the powder forms were pressed into pellets of 10 mm diameter (shown in Fig. S1†) by using the hand operated hydraulic press machine under a constant load of 14 tons and then the pellet was used for CO sensing. The ohmic contacts were designed on the pellet to fabricate the sensing element equipping it with two thin parallel silver electrodes maintaining a gap of 1 mm. A home-built setup was used to conduct the gas sensing measurements. The sensors were kept in a chamber, and silver electrode contacts were connected to a Keithley Sourcemeter directly linked to a computer PC by LabVIEW™ (National Instruments) for recording the resistance signal with respect to time. The digital mass flow controllers of Dakota Instruments were used to control the flow of dry pure target gas and zero air in the required concentration. A dynamic–static flow-through technique was used to carry out the gas sensing measurement. The performance of the gas sensing device is expressed in terms of various sensing parameters. The gas sensing response (S%) is defined as: |
S (%) = (Ra − Rg)/Rg × 100
| (1) |
where, Ra and Rg are the resistance values of the gas sensing materials in the presence of air and target gas atmosphere, respectively.26 Response time (tres) can be described as the time attained by a gas sensor for the maximum change in resistance when exposed to the environment of the target gas. Recovery time (trec) is the time required by a gas sensor to recover its resistance value up to 90% of its original baseline resistance value after the target gas is removed from the sensing chamber.
3 Results and discussion
3.1 Structural characterization (XRD)
The effect of the concentration of Mn doping on the crystal structure of ZSO spherical particles was analyzed by X-ray diffraction (XRD) characterization. The XRD patterns of as-prepared pure and Mn-doped ZnSn(OH)6 precursor are depicted in Fig. 1a, which agrees well with the available JCPDS card no. 20-1455. The diffraction peaks in the pattern can be indexed to a pure fcc-phase ZnSn(OH)6 (space group: Pn
), which is in good agreement with the Rietveld refinement, as shown in Fig. 1b. The crystallites are preferentially oriented along the x-axis, [200] direction. Lattice parameters of the pure and Mn-doped precursors were calculated by the Rietveld refinement using the Full Prof software. The obtained lattice parameters are shown in Table 1, which depicts the minor increase in lattice parameters with the increase in Mn-doping concentration. The characteristic peaks of any other phases such as ZnO, SnO2, and other phases of ZnSnO3 or ZnSn(OH)6 were not observed, which indicates the facile substitution of Mn in ZnSn(OH)6, probably due to akin ionic radius of Mn2+ ion (0.67 Å) with Zn2+ (0.74 Å).
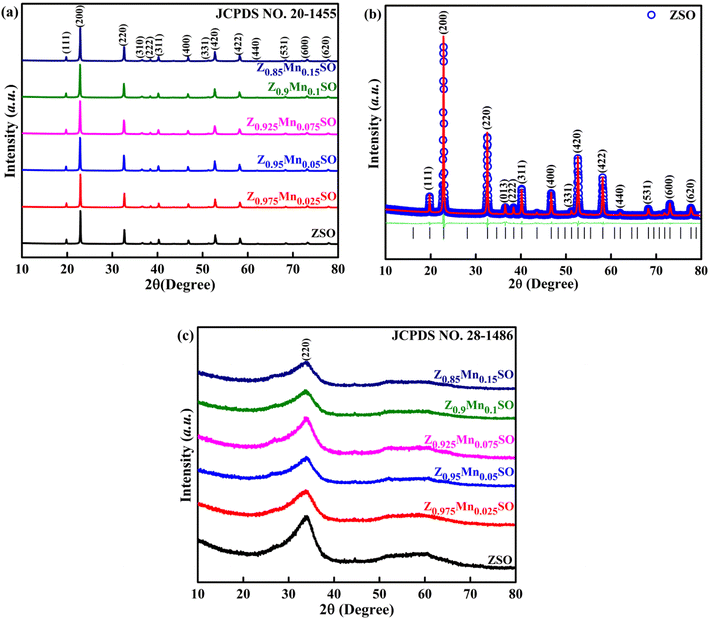 |
| Fig. 1 (a) XRD patterns of as-synthesized Zn1−xMnxSn(OH)6 samples (b) Rietveld refinement of the as-synthesized ZnSn(OH)6 sample. (c) XRD patterns of Zn1−xMnxSnO3 samples after annealing at 500 °C. | |
Table 1 Lattice parameters of the samples calculated by the Rietveld refinement
Zn1−xMnxSn(OH)6 |
Lattice constant (Å) a = b = c |
x = 0 |
7.751 ± 0.004 |
x = 0.025 |
7.754 ± 0.002 |
x = 0.05 |
7.755 ± 0.001 |
x = 0.075 |
7.755 ± 0.006 |
x = 0.1 |
7.757 ± 0.003 |
x = 0.15 |
7.761 ± 0.003 |
Fig. 1c presents the XRD characterization patterns of single phase Zn1−xMnxSnO3 samples after annealing at 500 °C. Only one broad peak was observed in all diffraction peaks related to the amorphous ZnSnO3 (JCPDS no. 28-1486). This indicates that all the pure and Mn-doped ZnSn(OH)6 precursors were converted into the final product of the pure and Mn-doped ZnSnO3 phase.
3.2 Thermal analysis (TGA-DTG)
The thermo-gravimetric analysis (TGA) was accomplished to investigate the thermal stability of as-prepared pure and Mn-doped ZnSn(OH)6 samples obtained before heat treatment, and derivative TG (DTG) curves were used to examine the thermal decomposition of the samples. As shown in Fig. 2, there is a noticeable weight loss of 17.94% up to 260 °C (2.7% from 25 °C to 130 °C and 15.24% from 130 °C to 260 °C) and only about 3% weight loss is observed from 260 °C to 1000 °C (shown in Fig. S2†). Thus, the weight loss of almost 18% up to 260 °C from the precursor samples revealed the dehydration of adsorbed water from pure and Mn-doped ZnSn(OH)6 samples and hence justifying the removal of hydroxyl (–OH) group to generate zinc stannate (ZnSnO3) and water. Further, the weight loss of almost 3% from 260 °C to 1000 °C is accredited to the dehydration of water molecules, which were trapped within the crystals and thus required more thermal energy than the adsorbed water molecules.27
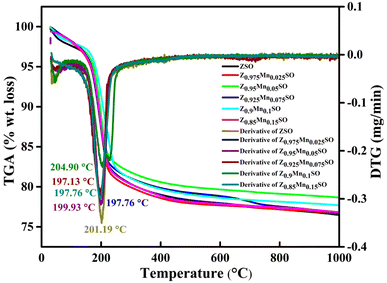 |
| Fig. 2 TG-DTG plot of the as-prepared samples of Zn1−xMnxSnO3, x = 0, 0.025, 0.05, 0.075, 0.1, 0.15. | |
The DTG curves exhibit the endothermic peaks at 201.19 °C, 197.76 °C, 199.93 °C, 197.13 °C, 204.90 °C, and 197.76 °C for ZSO, Z0.975Mn0.025SO, Z0.95Mn0.05SO, Z0.925Mn0.075SO, Z0.9Mn0.1SO, and Z0.85Mn0.15SO, respectively, that could be attributed to the evaporation of residual moisture. The overall weight loss is about 21% in the whole process, which is almost very close to the earlier reported value (21%).28 The rapid weight loss between 130 °C and 260 °C is expressed as the following chemical reaction:
|
 | (2) |
3.3 Fourier transform infrared (FTIR) spectrum analysis
The XRD results are also consistent with the FTIR analysis of both the as-prepared and annealed samples, Fig. 3, revealing relevant spectral changes in both cases. Fig. 3a illustrates the FTIR spectra of as-prepared pure and Mn-doped ZnSn(OH)6 precursors. The broad band at ∼3186 cm−1 is ascribed to the stretching vibration modes of –OH groups in water molecules. The other three peaks at 1169, 766, and 522 cm−1 are assigned to the bending and stretching vibration of M–OH or M–OH–M groups. Thus, the existence of these surface –OH groups characterizes the as-prepared samples as ZnSn(OH)6. However, Fig. 3b shows the FTIR spectra of Zn1−xMnxSnO3 samples after annealing at 500 °C where all the peaks related to –OH bond vibration disappeared, indicating the dehydration of water molecules after annealing. The strong broad absorption peak at ∼457 cm−1 could be attributed to the metal oxide (M–O) bond of Zn–O and Sn–O and the small weak band observed at 1219 to 1731 cm−1 ascribed to the stretching vibration of M–O–M bonds29,30 in ZnSnO3. Hence, the disappearance of –OH groups during annealing and the formation of the ZnSnO3 structure is clearly confirmed by the FTIR analysis.
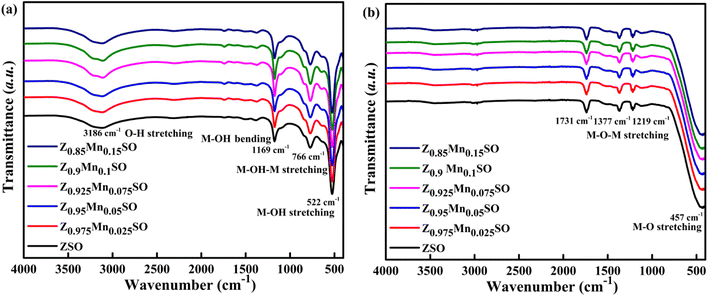 |
| Fig. 3 FT-IR spectra of (a) as-synthesized Zn1−xMnxSn(OH)6 samples, and (b) Zn1−xMnxSnO3 samples annealed at 500 °C. | |
3.4 Morphological characterization
The morphology of pure ZSO samples and with different concentrations of Mn (Zn1−xMnxSnO3, x = 0, 0.025, 0.05, 0.075, 0.1, and 0.15) after annealing at 500 °C were characterized by FE-SEM, as shown in Fig. 4. From Fig. 4a–f, it can be seen that all samples exhibit similar spherical surface morphology. It is also noted that numerous nanoparticles are stacked together to frame a porous microsphere structure. Agglomeration of particles was seen due to the high surface energy31 of the synthesized particles. The average outer diameter of spherical particles was also calculated and found to be decreasing from 900 nm to 500 nm with an increase in the concentration of Mn. Thus, Mn doping causes an increase in surface area and creates pores in microspheres. This is conducive to the quick adsorption of target gas and reaction with the materials to give better gas sensing properties.
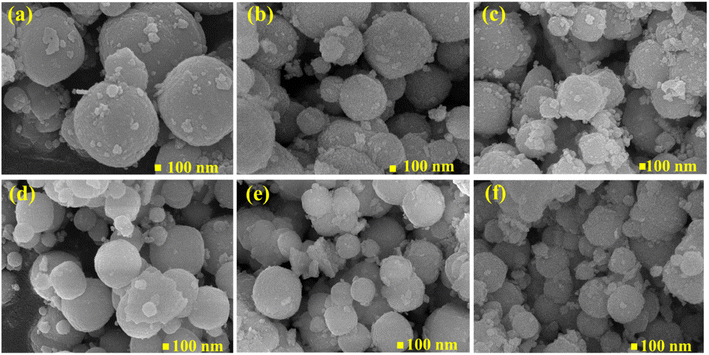 |
| Fig. 4 FESEM images of Zn1−xMnxSnO3 spherical particles, x = (a) 0, (b) 0.025, (c) 0.05, (d) 0.075, (e) 0.1, (f) 0.15. | |
EDS and SEM elemental mapping were conducted to resolve the atomic ratio and specific distribution of Zn, Sn, O, and Mn elements (Z0.9Mn0.1SO). As shown in Fig. 5c–f, the uniform distribution of Zn, Sn, O, and Mn in the selected microsphere was clearly verified. Also, according to the EDS spectrum, Fig. 5b depicts the quantitative presence of Zn, Sn, O, and Mn elements, in addition to the Au element, which is due to the Au coating used in the analysis.
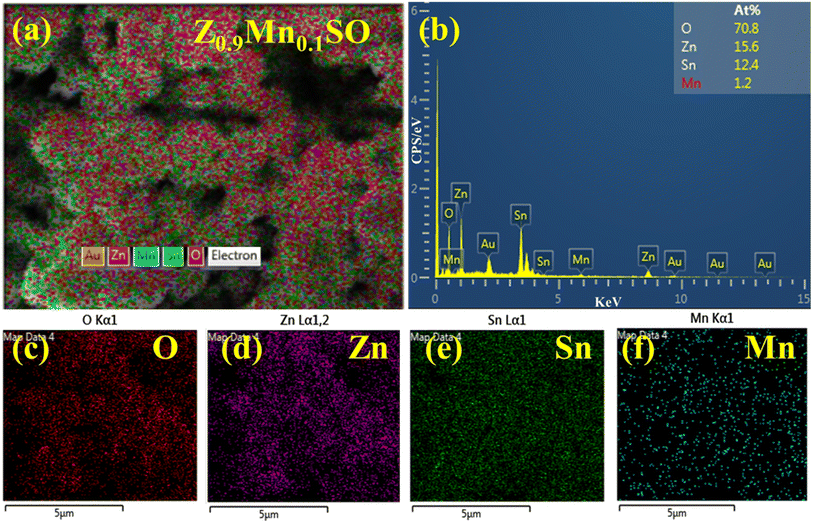 |
| Fig. 5 (a–f) EDS spectrum and elemental mapping of Zn1−xMnxSnO3 samples, x = 0.1. | |
3.5 N2 adsorption–desorption isotherm
N2 adsorption–desorption isotherm analysis is another essential technique to elucidate the properties of gas-sensing materials in terms of parameters such as specific surface area of materials, pore-size distribution, and specific pore volume. It is well affirmed that higher gas-sensing performance is achieved for materials having higher specific surface area, and thereby, more active sites contribute to the redox reaction.32 Fig. 6a–f represents the typical N2 adsorption–desorption isotherm for the Zn1−xMnxSnO3 microspheres. Based on IUPAC classification, the resulting isotherms of these six materials can be classified as type-IV isotherms along with a defined hysteresis loop. The inset of Fig. 6a–f represents the Barrett–Joyner–Halenda (BJH) pore size distribution of all these respective six materials revealing the existence of mesoporous structures. The BET surface areas and BJH pore size diameter of all these six materials are represented in Table 2. It was observed that Mn-doped ZSO materials have a higher surface area compared to that of pure ZSO material, and the increasing trend in surface area was obtained with the increase in Mn-doping concentration. Additionally, for all these six materials, the bulk of the pores lie in the region of 3–18 nm (inset of Fig. 6a–f) and very few pores lie beyond 18 nm. The average pore diameters are 3.097, 3.088, 3.075, 3.060, 3.099, and 3.091 nm, respectively, for ZSO, Z0.975Mn0.025SO, Z0.95Mn0·05SO, Z0.925Mn0.075SO, Z0.9Mn0.1SO, and Z0.85Mn0.15SO. This increased surface area with a suitable mesoporous structure is advantageous to the fast adsorption of gases, promoting surface reactions, thereby remarkably enhancing the gas sensing properties of Mn-doped ZSO materials.
 |
| Fig. 6 N2 adsorption–desorption isotherm and the corresponding BJH pore size distribution of Zn1−xMnxSnO3, x= (a) 0, (b) 0.025, (c) 0.05, (d) 0.075, (e) 0.1, (f) 0.15. | |
Table 2 Surface area, pore size, and pore volume of Zn1−xMnxSnO3 samples
Sample |
BET (m2 g−1) |
Pore size (nm) |
Pore volume (cm3 g−1) |
ZSO |
15.229 |
3.097 |
0.03279 |
Z0.975Mn0.025SO |
21.340 |
3.088 |
0.03692 |
Z0.95Mn0.05SO |
27.878 |
3.075 |
0.05281 |
Z0.925Mn0.075SO |
30.261 |
3.060 |
0.05379 |
Z0.9Mn0.1SO |
36.294 |
3.099 |
0.09990 |
Z0.85Mn0.15SO |
42.999 |
3.091 |
0.06328 |
3.6 X-ray photoelectron spectroscopy (XPS)
Gas sensing is a surface-dominant process depending on the surface state of gas sensing materials. X-ray photoelectron spectroscopy (XPS) was used to further investigate the sensing materials for the surface elemental composition and their corresponding valence state. Fig. 7a illustrates the survey spectra of ZnSnO3 (ZSO) and Z0.9Mn0.1SO samples. It indicates the existence of Zn, Sn, and O elements on the surface of ZSO samples and the presence of Zn, Sn, O, and Mn elements on the surface of Z0.9Mn0.1SO samples, which are consistent with the EDS observations. Fig. 7b presents the high-resolution spectra of Zn 2p, with two distinct peaks of Zn 2p in ZSO at binding energies of 1021.30 eV and 1044.24 eV signifying Zn 2p3/2 and Zn 2p1/2, respectively. However, the two distinct peaks of Zn 2p in Z0.9Mn0.1SO have an apparent shift to 1021.01 eV (Zn 2p3/2) and 1044.09 eV (Zn 2p1/2), respectively. Fig. 7c shows the high-resolution spectra of Sn 3d in ZSO and Z0.9Mn0.1SO. Two distinctive peaks of Sn 3d in ZSO are located at binding energies of 486.30 eV (Sn 3d5/2) and 494.71 eV (Sn 3d3/2), whereas the two distinctive peaks of Sn 3d in Z0.9Mn0.1SO are shifted to 485.84 eV (Sn 3d5/2) and 494.26 eV (Sn 3d3/2), respectively. The corresponding peaks of Zn 2p and Sn 3d demonstrate the existence of Zn2+ and Sn4+ in the samples. Deconvolution of the Mn 2p spectrum in Fig. 7d shows two distinct peaks at binding energies of 640.77 eV (Mn 2p3/2) and 654.30 eV (Mn 2p1/2) having orbital splitting energy of 13.5 eV, signifying the presence of Mn2+ in Z0.9Mn0.1SO samples. The apparent shift of the Zn 2p and Sn 3d characteristic peaks indicates the electronic interaction between the Mn2+ (dopant), Zn2+, and Sn4+ sites. Mn-doping makes the sample electron rich due to the generation of vacancy defects. To analyze the impact of oxygen vacancy defects, O 1s peaks of ZSO and Z0.9Mn0.1SO have been analyzed, as shown in Fig. 7e and f. The O 1s spectra are deconvoluted into three peaks: OL corresponding to lattice oxygen, OV caused by oxygen vacancy defect, and OC corresponding to chemisorbed oxygen. For the ZSO sample, the three peaks centered at 529.78 eV, 531.2 eV, and 532.79 eV are assigned to OL, OV, and OC, respectively. Similarly, the three distinctive peaks of O 1s in the Z0.9Mn0.1SO sample are centered at 529.05 eV, 530.11 eV, and 531.46 eV, respectively. The relative percentages of each oxygen species are depicted in Fig. 7e and f, respectively. Compared with pure ZSO, there is a significant reduction in OL concentration for Z0.9Mn0.1SO (from 40.59% to 26.70%), whereas a surge in OV (from 38.52% to 45.25%) and OC (from 20.88% to 28.05%) concentrations, suggesting the beneficial use of Mn-doping for enhancing the gas-sensing performance of ZnSnO3.
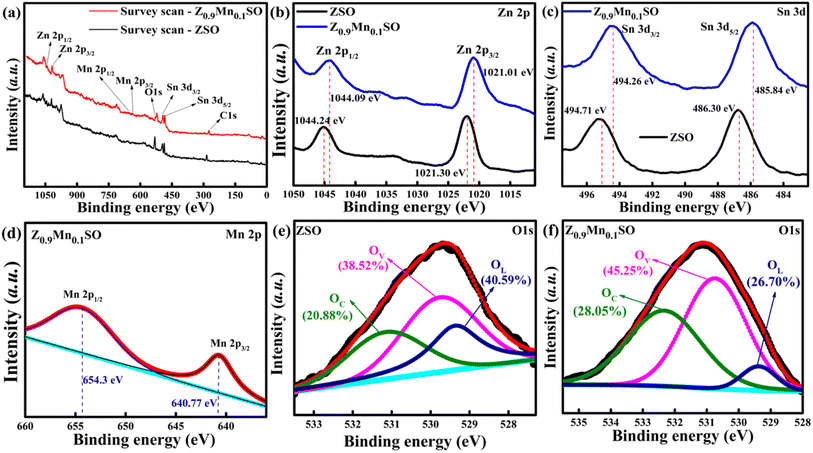 |
| Fig. 7 The XPS spectra of ZSO and Z0.9Mn0.1SO samples: (a) survey scan XPS spectra, (b) Zn 2p XPS spectra, (c) Sn 3d XPS spectra, (d) Mn 2p XPS spectra of Z0.9Mn0.1SO, (e) O 1s XPS spectra of ZSO, and (f) O 1s XPS spectra of Z0.9Mn0.1SO. | |
3.7 Gas sensing properties
The operating temperature plays an essential role in investigating the dynamic gas response of the sensor material. It significantly affects the adsorption–desorption phenomenon and reaction kinetics of the target gas with oxygen molecules on the sensor surface by improvising the activation energy in the sensing material.33 Therefore, investigations were done to test the sensing performance of Zn1−xMnxSnO3 samples by exposing to 500 ppm CO gas at various altered operating temperatures of 50–300 °C. Fig. 8a–f depicted the n-type semiconducting behaviour of all these six materials because of the decrease in resistance with the increase in operating temperature. Initially, sensors were stabilized for a constant resistance value under exposure to fresh dry air at a particular operating temperature. When the sensors were exposed to CO (reducing gas), a decrease in electrical resistance value was observed, which gets stabilized for a while and returned to the initial value after the CO supply was cut-off and re-exposed to the fresh dry air. It is obvious from Fig. 8 that Mn-doped ZSO sensors exhibit more decline in resistance value than that of pure ZSO sensors and thus exhibit higher response.
 |
| Fig. 8 Dynamic response–recovery curves of the gas sensor based on Zn1−xMnxSnO3, x = (a) 0, (b) 0.025, (c) 0.05, (d) 0.075, (e) 0.1, and (f) 0.15. | |
As shown in Fig. 9a and b, the maximum percentage change in the resistance of sensors at different operating temperatures from 50 °C to 300 °C towards 500 ppm CO was calculated and represented in terms of the response by using eqn (1). The sensing response of all the sensors was seen to follow “increase-maximum-decrease” tendency.15 Fig. 9 shows that for the pure ZSO sensor, there is a small change in response, and the maximum response is 5.79% at the operating temperature of 250 °C. However, for the entire Mn-doped ZSO sensor, the operating temperature significantly drops down to 200 °C with the remarkable enhancement in respective responses. As shown in Fig. 9a, ZSO sample doped with 10 at% Mn achieved the best response of ∼311.37% at the 200 °C operating temperature. Because Z0.9Mn0.1SO sample displays the best gas response to CO, the optimized value of Mn-doping is 0.1 (10 at%). As a result, the Z0.9Mn0.1SO sample was chosen as a propitious candidate for further studies in our work.
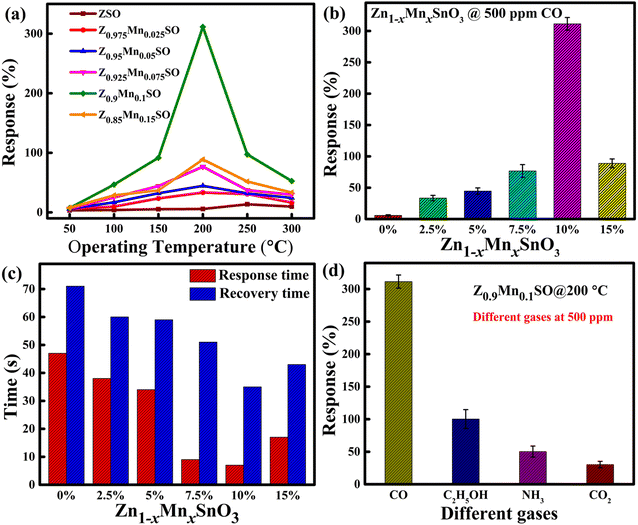 |
| Fig. 9 (a and b) Relationship between the responses of gas sensor exposed to 500 ppm CO gas and operating temperature. (c) Comparison of the response and recovery times of Zn1−xMnxSnO3 sensors upon exposure to 500 ppm CO at the operating temperature of 200 °C. (d) Selectivity study by the comparison of Z0.9Mn0.1SO sensor responses to different gases at the operating temperature of 200 °C. | |
The response time and recovery time are other essential parameters to judge the new generation gas sensor for fast detection of particular gases and speedy recovery to its ambient conditions in real application fields. The response and recovery time of the 0%, 2.5%, 5%, 7.5%, 10%, and 15% Mn-doped ZSO sensors towards 500 ppm CO at 200 °C were measured (shown in Fig. S3†) for the 90% of resistance changes and the compared results are as shown in Fig. 9c. Here, it is clearly observed that the Z0.9Mn0.1SO sensor exhibits the shortest response time of 6.6 s among all the six samples and also the accelerated desorption rate of CO on Z0.9Mn0.1SO due to the presence of Mn with the recovery time of 34.1 s.
Selectivity is another critical parameter to define the gas sensor's ability to differentiate a specific target gas from other interfering gases. The responses (%) of the Z0.9Mn0.1SO sample towards exposure to four different gases, carbon monoxide (CO), ammonia (NH3), ethanol (C2H5OH), and carbon dioxide (CO2) were calculated at the operating temperature of 200 °C. As demonstrated in Fig. 9d, the Z0.9Mn0.1SO sensor gives excellent responses to CO, whereas low responses to other interfering gases. Thus, the result from Fig. 9d inferred that the present Z0.9Mn0.1SO sensor has excellent selectivity towards CO.
Fig. 10a presents the changes observed in resistance values of the Z0.9Mn0.1SO sensor under the exposure of CO gas at varying concentrations in the range of 10 to 500 ppm. It clearly represents the increase in resistance value with respect to the increase in CO concentration. Moreover, the rapid response as CO gas is injected, stable value in the presence of CO environment, and then sharp recovery to the initial value when the CO gas is removed were observed at all concentrations of CO gas. The percentage change in resistance was used to compute the responses (%) and Fig. 10b depicts the increased sensor response with CO concentration. An approximate good linear correlation was observed with the CO concentration, where the linear correlation value was found to be 0.98552. The good linear response to CO allows a lower detection limit in sub-ppm level, less than 1 ppm.
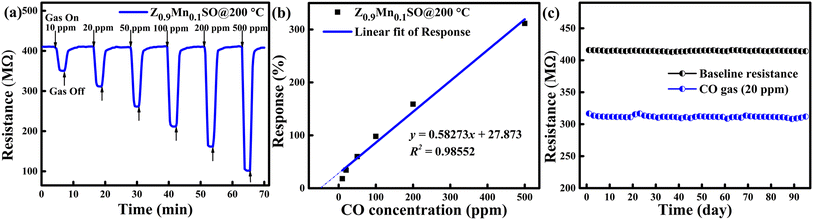 |
| Fig. 10 (a) Dynamic response–recovery curves towards different varying CO gas concentrations; (b) calibration curve at 200 °C related to Z0.9Mn0.1SO sensor. (c) Long-term stability test for the Z0.9Mn0.1SO sensor responding to 20 ppm CO gas. | |
Long-term stability test of the Z0.9Mn0.1SO sensor was also conducted over the period of 95 days at fixed 20 ppm CO and at the operating temperature of 200 °C as illustrated in Fig. 10c. It is clearly observed that the sensor shows no significant deviation in response, confirming the excellent long-term stability of the Z0.9Mn0.1SO sensor.
Table 3 illustrates the comparison of the present work with the sensing performance of other MOS based CO sensors, basically based on binary type ZnO or SnO2 or its ternary type compounds. It is worth noting that our sensor exhibited a comparatively high CO sensing performance, especially high response, low operating temperature, fast response, and recovery times.
Table 3 Comparison of recent metal oxide-based gas sensors for CO detection
Sensing material |
Operating temperature (°C) |
CO (ppm) |
Sensitivity (Ra/Rg) or response (%) |
Response/recovery times (s) |
Ref. |
ZnSnO3 |
250 |
500 |
5.79% |
30/41 |
This work |
Zn0.9Mn0.1SnO3 |
200 |
500 |
311.37% |
6.6/34.1 |
This work |
SnO2 |
310 |
200 |
7.29 |
16/28 |
34 |
SnO2 |
200 |
91 |
84.3% |
48/51 |
35 |
Ni2+-doped SnO2 |
350 |
1000 |
6.1 |
— |
36 |
TiO1.5/ZnO |
300 |
48 |
1.365 |
166/343 |
37 |
CuO-SnO2 |
200 |
100 |
3.52% |
— |
38 |
ZnO |
250 |
100 |
3.7 |
— |
39 |
ZnO/ZnCo2O4 |
300 |
10 |
17.3 |
60/50 |
40 |
Mn-ZnO |
300 |
300 |
2.5 |
40/300 |
31 |
3.8 Gas sensing mechanism
ZnSnO3 belongs to the family of n-type metal oxide semiconductors whose gas sensing mechanism is exclusively based on the alteration in the electric resistance when exposed to the gas and explained by the most accepted oxygen adsorption–desorption theory on the material surface.41 When ZnSnO3 or Zn1−xMnxSnO3-based sensors are exposed to clean air, as shown in Fig. 11a and c, oxygen molecules present in the clean air will be adsorbed on the surface of the sensing material and captivate free electrons from the surface conduction band of the sensing layer. Depending on the operating temperature, adsorbed oxygen species reacting with free electrons transform into oxygen species of ionized form, such as O2−, O−, O2− (ref. 42) As a consequence, a thick electron depletion layer (EDL) will form, causing an increase in the electric resistance of the sensor, resulting in less flow of electrons inside the sensing material. Thus, the sensor material initially exhibits high resistance in the presence of clean air. |
O2(gas) → O2(adsorbed)
| (3) |
|
O2(adsorbed) + e−(surface) → O2−(adsorbed) (<100 °C)
| (4) |
|
O2−(adsorbed) + 2e−(surface) → 2O−(adsorbed) (100–300 °C)
| (5) |
|
O−(adsorbed) + e−(surface) → O2−(adsorbed) (>300 °C)
| (6) |
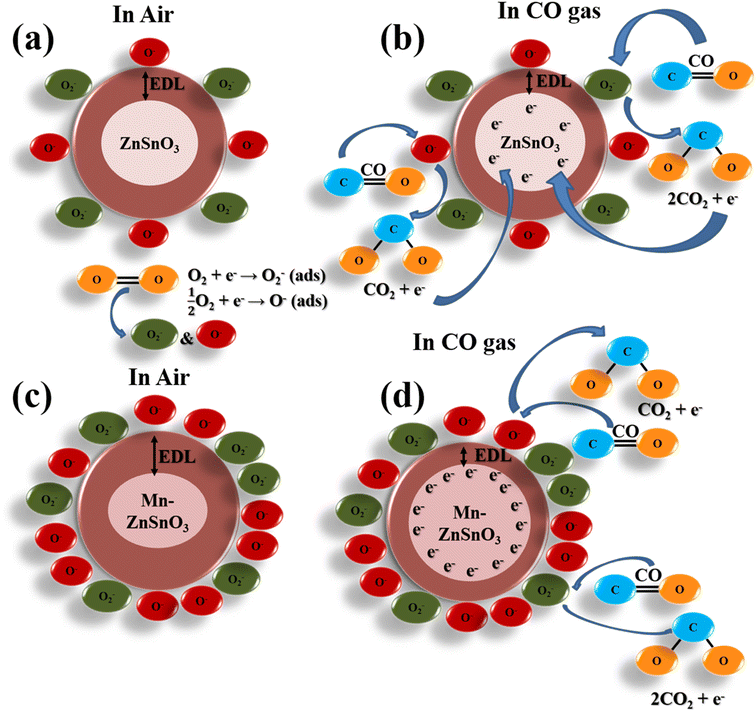 |
| Fig. 11 The schematic diagrams for CO gas sensing mechanism of pure and Mn-doped ZnSnO3 sensors in the presence of air (a) & (c) and in CO gas (b) & (d), respectively. | |
As shown in Fig. 11b and d, when the ZnSnO3 sensor material is exposed to a reducing gas such as CO, the interaction between the CO gas and the predominant chemisorbed ionized oxygen species, O−, can take place, and the electrons captivated by the chemisorbed O− are released back into the conduction band of the sensing material, as per eqn (7), and produce CO2. As a result, the thickness of the EDL layer is lessened and thus decreases the electric resistance of the sensing material, and the key redox reaction involved in the process of reaction with CO gas is as per the following equations:
|
CO(gas) + O−(adsorbed) ↔ CO2(gas) + e−
| (7) |
|
CO(gas) + O2−(adsorbed) ↔ 2CO2(gas) + e−
| (8) |
Furthermore, as the gas sensing device is re-exposed to the clean air, oxygen molecules again react with the electrons captivated from the surface conduction band of the sensing material, which again forms the thick electron depletion layer, and thus, electric resistance recovers to the initial baseline.
In addition, the gas sensing performance of ZnSnO3 is greatly related to the particle size, surface area, and metal oxidation states, which can be largely influenced by the doping of transition metal elements. Transition metals are most commonly used as sensitizers to enhance the gas sensing performance of sensing materials. The doping of ZnSnO3 by the Mn element changes the particle size and increases the surface area, which results in alterations in the amount of adsorbed oxygen. It is well known that with the increase in the doping amount of Mn, the amount of oxygen molecules adsorbed increases for up to a certain concentration of Mn and then decreases.43,44 For up to 10 at% Mn, maximum number of oxygen molecules transform into ionized O− species and thus more CO molecules are involved in the reaction process. Moreover, an extra thick electron depletion layer may form at the interface with the increase in Mn concentration. Thus, when the Mn-doped ZnSnO3 sensors are exposed to the CO environment, a large number of electrons are freed and released back into the conduction band of the sensing material, ZnSnO3 microspheres, more conveniently. Also evidenced from the XPS spectra, doping with Mn generates more oxygen vacancies in the ZSO lattice and hence more free electrons, improving the gas sensing. Simultaneously, the Mn site in ZnSnO3 plays a critical role in adsorbing CO molecules at all temperatures. CO molecules are preferably adsorbed on the Mn sites to form bonds between Mn and CO. The interaction results in the donation of 5σ electrons of CO to the metal and π electrons back bonding from d-orbitals of Mn to CO. First, the CO molecules adsorb at the Mn sites and then migrate from Mn sites to Zn sites, through which Mn sites improve the CO adsorption and their interaction with oxygen species. Therefore, the doping of transition metal Mn effectively helps in intensifying the gas sensing performance of ZnSnO3 microspheres towards CO gas.
4 Conclusions
In summary, porous Mn-doped ZnSnO3 microspheres were synthesized by a simple co-precipitation method. The characterization results revealed that the Mn-doped ZnSnO3 maintains the face-centered cubic structure of pure ZnSnO3 and exhibits micro spherical morphology in the increasing order of surface area with the Mn concentration. The Mn-doping was confirmed by XPS. The BET measurements revealed an increase in surface area with an increase in Mn doping. The gas sensing performance analysis of Zn1−xMnxSnO3 chemi-resistive sensors with different Mn concentrations towards CO gas displayed enhanced sensing characteristics with respect to pure ZnSnO3 sensors. To be specific, the MOS sensor based on 10 at% Mn-doped ZnSnO3 exhibited a remarkably high response to CO gas at the reduced operating temperature of 200 °C. Moreover, the Z0.9Mn0.1SO sensor exhibit fast response and recovery times of 6.6 s and 34.1 s, respectively, with good stability and reproducibility. The enhanced gas sensing properties with respect to CO can be ascribed to the sensitization effects of Mn and porous structure. On the basis of this study, these Mn-doped porous ZnSnO3 microspheres are propitious to be applied for practical applications for monitoring CO gas in air.
Author contributions
Manish Kumar Tiwari: formal analysis, conceptualization, methodology, investigation, validation, visualizations, writing – original draft, writing – review and editing. Subhash Chand Yadav: formal analysis, visualizations, validation, writing – review, and editing. Abhishek Srivastava: writing – review and editing. Archana Kanwade: writing – review and editing. Jena Akash Kumar Satrughna: writing – review and editing. Sawanta S. Mali, Jyoti V. Patil and Chang Kook Hong: resources, writing – review and editing. Parasharam M. Shirage: formal analysis, methodology, resources, validation, writing – review and editing, supervision, project administration.
Conflicts of interest
There are no conflicts of interest to declare.
Acknowledgements
The authors are grateful to Prof. Suhas Joshi (Director, IIT Indore), Department of MEMS, IIT Indore, for providing the necessary characterization facilities to carry out the research work. The authors extend their gratitude to SIC-IIT Indore for providing the BET surface area analyzer facility. SCY thanks CSIR for providing the SRF fellowship (09/1022(0053)/2018 EMR-I), AS, AK, and JAKS thank DST for the Inspire fellowships ((IF200232), (IF200271), and (IF190546), respectively).
References
- C. Patel, B. Mandal, R. G. Jadhav, T. Ghosh, M. Dubey, A. K. Das, M. T. Htay, V. V. Atuchin and S. Mukherjee, ACS Appl. Nano Mater., 2022, 5, 2492–2500 CrossRef CAS.
- P. M. Shirage, A. K. Rana, Y. Kumar, S. Sen, S. G. Leonardi and G. Neri, RSC Adv., 2016, 6, 82733–82742 RSC.
- W. Zhang, F. Yang, J. Xu, C. Gu and K. Zhou, ACS Omega, 2020, 5, 20034–20041 CrossRef CAS PubMed.
- G. Shi, T. Yoon, S. Cha, S. Kim, M. Yousuf, N. Ahmed, D. Kim, H. W. Kang and K. S. Kim, ACS Sens., 2018, 3, 1102–1108 CrossRef CAS PubMed.
- A. Dey, Mater. Sci. Eng., B, 2018, 229, 206–217 CrossRef CAS.
- A. K. Yadav, P. Rajput, O. Alshammari, M. Khan, Anita, G. Kumar, S. Kumar, P. M. Shirage, S. Biring and S. Sen, J. Alloys Compd., 2017, 701, 619–625 CrossRef CAS.
- S. Chand Yadav, A. Srivastava, V. Manjunath, A. Kanwade, R. S. Devan and P. M. Shirage, Mater. Today Phys., 2022, 26, 100731 CrossRef CAS.
- S. S. Nalimova, A. I. Maksimov, L. B. Matyushkin and V. A. Moshnikov, Glass Phys. Chem., 2019, 45, 251–260 CrossRef CAS.
- Q. Xie, Y. Ma, X. Zhang, H. Guo, A. Lu, L. Wang, G. Yue and D. L. Peng, Electrochim. Acta, 2014, 141, 374–383 CrossRef CAS.
- S. C. Yadav, A. Sharma, R. S. Devan and P. M. Shirage, Opt. Mater., 2022, 124, 112066 CrossRef CAS.
- C. Fang, B. Geng, J. Liu and F. Zhan, Chem. Commun., 2009, 2350–2352 RSC.
- J. Xu, X. Jia, X. Lou and J. Shen, Solid. State. Electron., 2006, 50, 504–507 CrossRef CAS.
- Y. Yin, F. Li, N. Zhang, S. Ruan, H. Zhang and Y. Chen, Inorg. Chem. Front., 2018, 5, 2123–2131 RSC.
- H. Men, P. Gao, B. Zhou, Y. Chen, C. Zhu, G. Xiao, L. Wang and M. Zhang, Chem. Commun., 2010, 46, 7581–7583 RSC.
- G. Feng, Y. Che, C. Song, J. Xiao, X. Fan, S. Sun, G. Huang and Y. Ma, Ceram. Int., 2021, 47, 2471–2482 CrossRef CAS.
- L. Du, D. Wang, K. Gu and M. Zhang, Inorg. Chem. Front., 2021, 8, 787–795 RSC.
- J. Zheng, H. Hou, H. Fu, L. Gao and H. Liu, RSC Adv., 2021, 11, 20268–20277 RSC.
- B. S. Sá, C. A. Zito, T. M. Perfecto and D. P. Volanti, Sens. Actuators, B, 2021, 338, 129869 CrossRef.
- P. Wadkar, D. Bauskar and P. Patil, Talanta, 2013, 105, 327–332 CrossRef CAS PubMed.
- X. Wang, J. Ma, Q. Ren, M. Wang, Z. Yang and J. Xin, Sens. Actuators, B, 2021, 344, 130223 CrossRef CAS.
- X. Wang, T. Tao, Z. Qi, B. Leng, W. Xu, J. Ma and M. Wang, Sens. Actuators, B, 2021, 326, 129013 CrossRef CAS.
- X. Wang, H. Li, X. Zhu, M. Xia, T. Tao, B. Leng and W. Xu, Sens. Actuators, B, 2019, 297, 126745 CrossRef CAS.
- S. Bai, W. Tong, Y. Tian, H. Fu, Y. Zhao, X. Shu, R. Luo, D. Li and A. Chen, J. Mater. Sci., 2019, 54, 2025–2036 CrossRef CAS.
- I. Karaduman, M. A. Yıldırım, S. T. Yıldırım, A. Ateş, Y. A. Özdemir and S. Acar, J. Mater. Sci.: Mater. Electron., 2017, 28, 18154–18163 CrossRef CAS.
- E. Della Gaspera, M. Guglielmi, G. Perotto, S. Agnoli, G. Granozzi, M. L. Post and A. Martucci, Sens. Actuators, B, 2012, 161, 675–683 CrossRef CAS.
- P. R. Chikate, A. Sharma, S. R. Rondiya, R. W. Cross, N. Y. Dzade, P. M. Shirage and R. S. Devan, New J. Chem., 2021, 45, 1404–1414 RSC.
- A. Sharma, Y. Kumar and P. M. Shirage, J. Mater. Sci.: Mater. Electron., 2018, 29, 10769–10783 CrossRef CAS.
- R. Guo, Y. Guo, H. Duan, H. Li and H. Liu, ACS Appl. Mater. Interfaces, 2017, 9, 8271–8279 CrossRef CAS PubMed.
- Y. Chen, B. Qu, L. Mei, D. Lei, L. Chen, Q. Li and T. Wang, J. Mater. Chem., 2012, 22, 25373–25379 RSC.
- S. Paul, S. Basak and W. Ali, ACS Omega, 2019, 4, 21827–21838 CrossRef CAS PubMed.
- M. H. Darvishnejad, A. Anaraki Firooz, J. Beheshtian and A. A. Khodadadi, RSC Adv., 2016, 6, 7838–7845 RSC.
- H. Bai, H. Guo, C. Feng, J. Wang, B. Liu, Z. Xie, F. Guo, D. Chen, R. Zhang and Y. Zheng, J. Mater. Chem. C, 2022, 10, 3756–3769 RSC.
- Y. Fan, K. Li, X. Ren, W. Yan, C. Zhu, Y. Zhao, W. Zeng, Z. Chen and S. Wang, J. Mater. Chem. C, 2021, 9, 17496–17503 RSC.
- Q. Zhou, W. Chen, L. Xu, R. Kumar, Y. Gui, Z. Zhao, C. Tang and S. Zhu, Ceram. Int., 2018, 44, 4392–4399 CrossRef CAS.
- A. K. Gangwar, S. Srivastava, R. Godiwal, J. Jaiswal, P. Vashishtha, S. Pal, P. Pal, G. Gupta and P. Singh, Opt. Mater., 2022, 128, 112362 CrossRef CAS.
- L. S. Zhang and X. M. Guo, Mater. Sci. Semicond. Process., 2022, 142, 106516 CrossRef CAS.
- L. Vatandoust, A. Habibi, H. Naghshara and S. Mohammadi, Surf. Interfaces, 2022, 31, 102001 CrossRef CAS.
- S. B. Dhage, V. L. Patil, P. S. Patil, J. Ryu, D. R. Patil and Y. S. Malghe, Mater. Lett., 2021, 305, 130831 CrossRef CAS.
- A. S. Mokrushin, Y. M. Gorban, N. P. Simonenko, E. P. Simonenko, V. G. Sevastyanov and N. T. Kuznetsov, Russ. J. Inorg. Chem., 2021, 66, 1447–1454 CrossRef CAS.
- Y. V. Kaneti, N. L. Wulan Septiani, I. Saptiama, X. Jiang, B. Yuliarto, M. J. A. Shiddiky, N. Fukumitsu, Y. M. Kang, D. Golberg and Y. Yamauchi, J. Mater. Chem. A, 2019, 7, 3415–3425 RSC.
- T. Zhou, T. Zhang, R. Zhang, Z. Lou, J. Deng and L. Wang, ACS Appl. Mater. Interfaces, 2017, 9, 14525–14533 CrossRef CAS PubMed.
- X. Ma, S. Guo, J. Shen, Y. Chen, C. Chen, L. Sun, X. Zhang and S. Ruan, RSC Adv., 2016, 6, 70907–70912 RSC.
- A. Xukeer, Z. Wu, Q. Sun, F. Zhong, M. Zhang, M. Long and H. Duan, RSC Adv., 2020, 10, 30428–30438 RSC.
- Y. Bai, Y. Qin and P. Qiu, Environ. Sci.: Nano, 2021, 8, 1096–1108 RSC.
|
This journal is © The Royal Society of Chemistry 2022 |
Click here to see how this site uses Cookies. View our privacy policy here.