DOI:
10.1039/D2RA02861A
(Review Article)
RSC Adv., 2022,
12, 23973-23988
Diverse utilization of surfactants in coal-floatation for the sustainable development of clean coal production and environmental safety: a review
Received
6th May 2022
, Accepted 9th August 2022
First published on 24th August 2022
Abstract
The rapidly increasing modern industrial world demands a huge uninterrupted energy supply, where high-quality coal (HQC) is one of the major sources of the required energy. In this regard, a gigantic amount of solid waste including ash and toxic chemicals, such as heavy metals, nitrate and sulphur, gases including NOx and SOx are emitted during the direct incineration process of low-rank coal. About 10 Gt of CO2 and about one-fifth of total greenhouse gases in the world are emitted each year due to coal combustion in power plants, making it the single largest cause of climate change. The UN proposed that OECD countries stop producing electricity from coal by 2030 and the rest of the world by 2040. Herein, we discuss the development of modern technologies that can convert low-quality coal (LQC) into high-quality coal (HQC) to minimize the impact of fossil fuel burn, climate change, premature death of animals and all other related environmental hazards. Amongst the many established technologies, flotation pre-treatment is the most common and effective method used worldwide due to its lower energy input than other methods. In this review, we attempt to present an up-to-date understanding of the applications and utilities of surfactants in coal floating. We also demonstrate the possible modernization of this surfactant chemistry and its prospects.
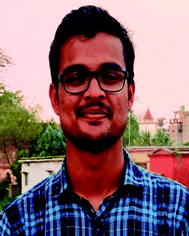 Biplab Kumar | Biplab Kumar was born in West Bengal, India. He is pursuing his MSc from The University of Burdwan, WB, India. He is also a project student in the Bioremediation Laboratory under the supervision of Prof. Bidyut Saha. |
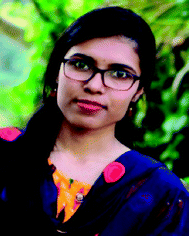 Bidisha Das | Bidisha Das was born in West Bengal, India. She is pursuing her MSc from The University of Burdwan, WB, India. She is also a project student in the Bioremediation Laboratory under the supervision of Prof. Bidyut Saha. |
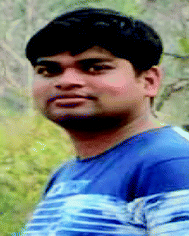 Amit Garain | Amit Garain was born in Birbhum, WB, India. He obtained his MSc from Jadavpur University India. He has published scientific articles on surfactant chemistry in reputed journals. He was a project student at Chemical Sciences Laboratory, GGDC-Singur under the supervision of Dr Monohar Hossain Mondal. |
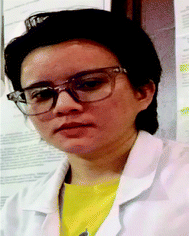 Summi Rai | Summi Rai was born in Bhojpur, Nepal. She is currently an MSc student of Mahendra Morang Adarsh Multiple Campus, Tribhuvan University, Biratnagar, Nepal. She has published some international peer-reviewed scientific articles on surfactant chemistry. |
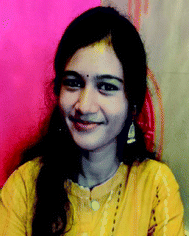 Wasefa Begum | Wasefa Begum was born in Burdwan, India. She pursued her MSc from Presidency University, Kolkata, India and is currently working as a JRF at the Department of Chemistry, Burdwan University, WB, India. |
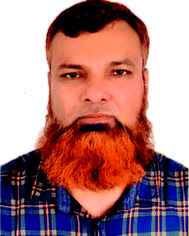 Md. Inamuddin | Dr Inamuddin is working as Assistant Professor at the Department of Applied Chemistry, Aligarh Muslim University, Aligarh, India. He has published 177 research articles in international journals of repute and nineteen book chapters in knowledge-based book editions published by renowned international publishers. He has published 115 edited books with Springer (U.K.), Elsevier, Nova Science Publishers, Inc. (USA), CRC Press Taylor & Francis Asia Pacific, Trans Tech Publications Ltd (Switzerland), IntechOpen Limited (UK), Wiley-Scrivener, (USA) and Materials Research Forum LLC (USA). He is a member of the editorial board of various journals. Currently, he is also serving as an Associate Editor for various journals (Environmental Chemistry Letter, Applied Water Science and Euro-Mediterranean Journal for Environmental Integration, Springer-Nature), Frontiers Section Editor (Current Analytical Chemistry, Bentham Science Publishers), Editorial Board Member (Scientific Reports-Nature), Editor (Eurasian Journal of Analytical Chemistry), and Review Editor (Frontiers in Chemistry, Frontiers, UK). |
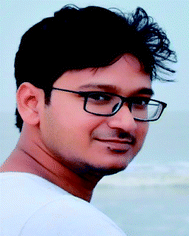 Monohar Hossain Mondal | Dr. Monohar Hossain Mondal was born in West Bengal, India. He has completed his PhD from The University of Burdwan in 2017 at the Bioremediation Laboratory (The University of Burdwan). He is an Education Service Officer of the Government of West Bengal and is presently working as an Assistant Professor in Chemistry at Govt. General Degree College Singur, WB, India. His area of interest is the bioremediation of toxic metals, surface studies and natural surfactants. He has published many international peer reviewed scientific articles on surfactant chemistry. |
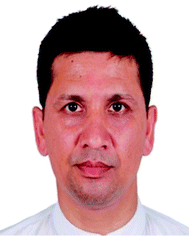 Ajaya Bhattarai | Prof. Ajaya Bhattarai was born in Jhapa, Nepal in 1974. He obtained his PhD from the University of North Bengal, India in 2010. He was a Post-doctoral Fellow under Erasmus Mundus European Commission between 2012-2013 in the Department of Chemistry, University of Warsaw, Poland. He also conducted post-doctorate research at Boston College, USA under a Fulbright Fellowship between 2018-2019. Presently, Dr Bhattarai is working as a Professor in the Department of Chemistry, Mahendra Morang Adarsh Multiple Campus, Tribhuvan University, Biratnagar, Nepal. His area of interest is polymer chemistry, surfactant chemistry, nanomaterials, and crystallography. He has published more than 150 articles in reputed journals and book chapters. |
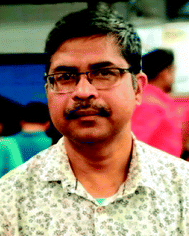 Bidyut Saha | Prof. Bidyut Saha was born in Birbhum, WB, India in 1975. He obtained his PhD from Visva Bharati University, India in 2007. He was a visiting scientist between 2009–2010 in the Department of Chemistry, UBC, Vancouver, Canada. Presently, Dr Saha is working as the HoD and Professor in the Department of Chemistry, The University of Burdwan, India. His area of interest is the bioremediation of toxic metals, micellar catalysis and inorganic reaction mechanisms. He has published more than 140 articles and book chapters in international journals. |
1. Introduction
In coal-based thermal power stations, the most important input is good-quality coal to generate electricity. Worldwide, a total of about 8500 coal power stations with over 2000 gigawatt (GW) capacity are producing one-third of the world's total consumed electricity.1 Coal is a combustible black or dark brown sedimentary organic rock, which consists of more than 50% weight carbonaceous material. Due to earthquakes and other natural calamities, organic materials accumulated in swamps and peat underground over millions of years and decomposed to coal due to geological heat and pressure.2 Coal formed in swamps is considered to be in situ formed in origin, while some peat or coal may be reworked, redeposited or even derived from the original accumulation of driftwood, which is recognized as allochthonous or drifted in origin. Based on the amount of carbon, oxygen and hydrogen present in coal, it is divided into four parts, which also reflect the four stages of coal formation, viz., peat, lignite, bituminous and anthracite, depending on the conditions in which the organic material, generally plant matter, remain. The other components include nitrogen, sulphur and other undesirable inorganic materials such as ash, which generally consist of chlorine, silica, sodium, aluminum, and different heavy metals.3 The greater the pressure and heat, the denser the organic content with less moisture and gases, leading to a higher heat value and becoming higher-ranking coal. Alternatively, lower-ranking coal contains more water and ash content, and thus is heavier than higher-rank coal (Table 1).
Table 1 Different grades of coals with their composition and heat value
|
Dry carbon content (%) |
Moisture content before drying (%) |
Dry volatile content (%) |
Heat content (Mcal kg−1) |
Anthracite |
86–92 |
07–10![[thin space (1/6-em)]](https://www.rsc.org/images/entities/char_2009.gif) |
3–14° |
7600–7900° |
Bituminous |
70–86 |
08–38 |
14–53 |
4000–7500° |
Lignite |
65–70 |
35–55![[thin space (1/6-em)]](https://www.rsc.org/images/entities/char_2009.gif) |
53–63° |
3800–4100° |
Peat |
<60 |
75 |
63–69 |
3000° |
Analysis of coal reserve demonstrates that out of a total of 984 billion tons, about 509 billion tons is bituminous including anthracite and the remaining is sub-bituminous and lignite.4 USA possess about 25% coal, the highest coal reserve, while India has about 8%. Proximate analysis of Asian and African coal and in situ originated coal convey the facts shown in Table 2.
Table 2 Composition and heat value of Asian and African coal
Sl. No. |
Origin |
Ash |
Fixed carbon |
Total moisture |
Volatile matter |
GCV |
% |
% |
% |
% |
kcal kg−1 |
1 |
Indian |
33–36 |
29–33 |
11–13 |
22–24 |
3600–4000 |
2 |
South Africa |
12–13 |
46–50 |
9–10 |
29–30 |
6000–6300 |
3 |
Indonesia |
7–8 |
33–37 |
15–16 |
41–43 |
6000–6300 |
The price of crude coal plays the most important role in the determination of the energy charge rate (the price of 1 unit or 1 kW h−1 of electricity for domestic use), while the quality of coal determines proper combustion and operational efficiency of the boiler.5 Thus, good-quality coal is essential to avoid problems such as slagging and fouling in the boiler and increase the heat input by using less coal.2
The rapidly growing contemporary industrial world demands a huge uninterrupted energy supply, where high-quality coal (HQC) is one of the major sources of the required energy. However, despite being an abundant resource, low-rank coal cannot be utilized effectively.6–8 Specifically, huge amounts of solid waste such as ash are produced and toxic chemicals such as heavy metals, nitrate and sulphur are emitted during the direct incineration process of low-rank coal.9–13 Also, excessive harmful gases such as NOx and SOx are also released during the production of electricity from low-rank coal, resulting in a further contribution to acid rain, skin problems, etc.14–16 It is noteworthy to mention that over 10 Gt of CO2 and about one-fifth of total greenhouse gases in the world are emitted each year due to the combustion of coal in power plants across the globe, making it the single largest cause of climate change. The UN proposed that OECD countries must stop producing electricity from coal by 2030 and the rest of the world by 2040.17 The documents to date presented herein clearly demonstrate that it is necessary to develop modern technologies to convert low-quality coal (LQC) into high-quality coal (HQC) to minimize the impact of fossil fuel burn, climate change, premature death of animals and all other related environmental hazards. Currently, to achieve this goal, researchers have proposed several excellent scientific technologies for the processing of low-rank coal, such as surface modification, microwave irradiation, pyrolysis, development of high-efficient flotation reagents, and flotation pre-treatment. Amongst these technologies, flotation pre-treatment is the most common and effective method used worldwide due to its lower energy input than other methods.18–21 In this review, we attempt to focus on the modern understanding of the applications and utility of surfactants in coal floating.
2. Coal flotation: process, utility and real-time challenges
Coal flotation is a physicochemical method by which minerals are separated from coal. Coal contains two types of ashes, as follows: (i) fixed ash: mineral particles associated with coal during the coalification process and (ii) free ash: foreign materials for example carbonaceous shale, clay, sandstone, and rock that are adjacent to the coal seam.22 In addition, sulfur remains in coal as four different species, i.e., elemental, inorganic sulfate, organic and pyretic sulfur. By using the floatation process, free ash and sulfur species, especially pyretic sulphur are removed, which ultimately results in the formation of HQC with a low ash and low mineral content. Thus, the removal of ash and sulphur from coal effectively reduces the negative environmental impact by producing clean coal.23
2.1. Conventional floating technique
Presently, flotation is an efficient separation technique in with vast applications ranging from the selective separation of minerals and ions to microorganisms. Surfactants play a pivotal role in floatation especially in froth flotation due to their ability to interact with the surface of particles according to the nature of their hydrophobicity. A large number of surfactants together with auxiliary additives are used in froth flotation. Herein, we discuss the important surfactants, focusing on the mechanism by which they act in coal flotation processes. Coal and rock have different wettability, which play a key role in coal flotation. Coal, which are hydrophobic particles, get attached to air bubbles, where the other hydrophilic particles do not interact with the bubbles and remain absorbed in the pulp. Furthermore, the addition of a small number of chemicals (frothers and collectors) can enhance the selectivity.
At the beginning of the froth flotation process, the coal particles are often agitated with a flotation reagent solution in a mixer intensely, and then the mixture is moved into an specially engineered cell for the actual coal flotation process. In the cell, air is sucked and effused by a rotational impeller (Fig. 1). The hydrophobic units of the coal matter get attached to the air bubbles and float to the top of the cell, and in the next step the remaining minerals are separated via chemical treatment of the pulp, which creates a favourable condition to improve the coal particles and air bubble attachment. The specific gravity of the coal/air-combined particle is less than that of the pulp, and thus the particles float to the surface and form froth loaded with coal particles. The coal-laden froth gets skimmed off, while the undesired minerals remain in the pulp.24 In the froth flotation method, surfactants have to selectively endow the target particles with hydrophobicity to achieve productive separation. The selective adsorption of the surfactant on the mineral surface depends on a number of parameters such as the composition of the solid surface and equilibrium between the mineral-solution and surfactant solution chemistry. The basic principles associated with the flotation process and the characteristic role of surfactants in different mineral systems are presented in the following sections. Naturally, most of the minerals are hydrophilic (sulfur, talc, molybdenite, graphite, and coal are hydrophobic), and thus mineral particles can be separated by the flotation process only if hydrophobic property can be selectively imparted to the target particles to be floated. In this regard, they are treated with a surfactant, which adheres to the mineral surface, consequently imparting with it hydrophobic property. The surfactant moieties adhere with their hydrophilic head pointed towards the mineral surface and hydrophobic tail oriented towards the solution, resulting in the formation of a hydrophobic mineral surface (Scheme 1).
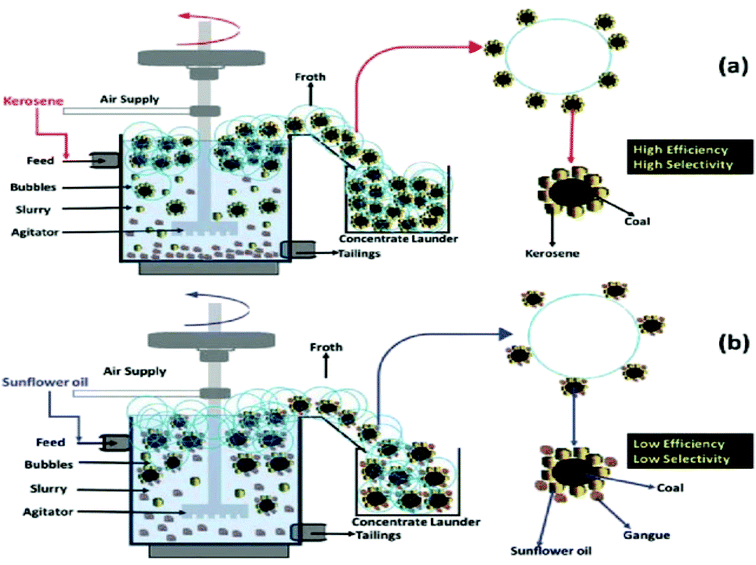 |
| Fig. 1 Mechanism of particle-oil adsorption in coal flotation with kerosene (a) and sunflower oil (b). This figure is reproduced from ref. 25 with permission from Springer-Verlag GmbH Germany, Copyright 2009. | |
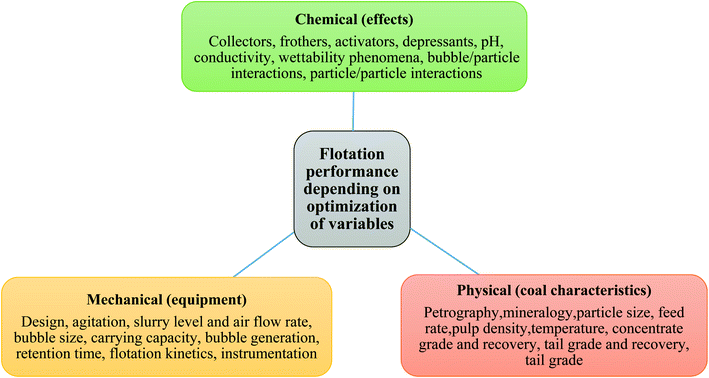 |
| Scheme 1 Flotation performance depending on the optimization of variables. | |
2.2. Reagents applied in the floatation process
To reduce the effective cost of the coal floatation process, generally the waste products from the coke oven plant or petroleum distillation products are used as reagents, which can be divided into 4 parts, i.e., non-polar oils, heteropolar reagents, inorganic electrolytes, and depressants.
2.2.1 Non-polar oils. The most suitable collectors are generally paraffinic hydrocarbon types with a high molecular weight with up to 20 carbon atoms, containing molecules such as kerosene (lamb oil), crude petroleum, fuel oil and some coal–tar distillates.26 Nonpolar collectors containing van der Waals forces between hydrocarbon molecules and covalent bonds have water repellent properties, and thus practically not involved with water dipoles. These characteristics make nonpolar oils more effective extractors of organic-rich coal particles from other particles.
2.2.2 Heteropolar reagents. Heteropolar reagents have both polar and non-polar parts such as frothers. For example, monohydric aliphatic alcohols and monocarboxylic acids contain 5–10 carbon atoms.27 Heteropolar reagents make the surface of coal more hydrophobic at low concentration due to the formation of H-bonds between their hydroxylic groups and the surface of coal, resulting in the formation of a double layer at low concentration. However, the further addition of these reagents makes the surface of coal less hydrophobic due to the formation of a second adsorption layer on the top of the first one. Thus, the use of both a frother and oily collector is desirable for most coals.
2.2.3 Inorganic electrolytes. Inorganic salts such as sea water are self-sufficient for the flotation of many natural hydrophobic mineral solutions. The electrolytes make the mineral particles hydrophobic by decreasing their surface potential at low concentrations and cause froth formation at higher concentrations. Also, the combined addition of nonpolar reagents and inorganic electrolytes sharply increases the rate of floatation for the recovery of coal.28
2.2.4 Depressants. A mixture of non-electrolyte, such as carbohydrates and tannins, complex molecules of phenols and thiosulphates and salts of inorganic acids such as sodium silicate and sodium cyanide is used as a depressant in coal flotation. Non-electrolyte is used for the dispersion of clay and shale and salt is used for the dispersion of pyrites (Fig. 2).
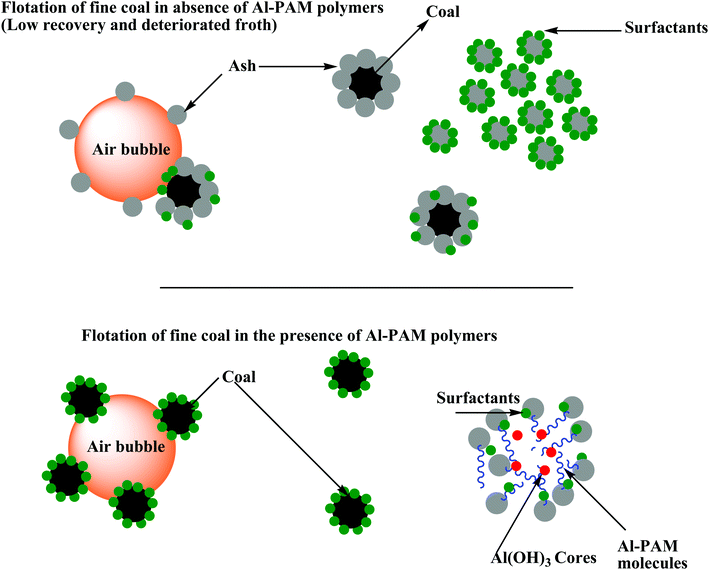 |
| Fig. 2 Flotation of fine coal in the absence and presence of polymeric surfactants. | |
2.3. Flotation pre-treatments
As discussed earlier, natural coal contains a considerable amount of impurities, which demands its physico-chemical enhancement for an improvement in its properties and reduction in the probable pollution triggered by coal combustion.29 Among the various methods, froth flotation is the most effective process for upgrading low-rank coal. Generally, this method depends on the surface properties, specifically the hydrophobicity, of the coal matter. However, this hydrophobic property of coal is altered when it is exposed to air, resulting in its oxidation. This lower grade or oxidized coal contains polar or oxygen-containing groups such as phenol groups, carbonyl groups, and hydroxyl groups, consequently increasing its hydrophilic properties by increasing the number of sites available for H-bonding with water molecules, which results in difficulties in upgrading coal by the conventional floatation technique.30 Fresh coal units having a more hydrophobic surface float easier than oxidized coal matter even with a lower quantity of floatation reagent.31 Thus, it is necessary to introduce a pre-treatment method to enhance the floatation efficiency of low-rank coal to improve its hydrophobicity. There are many pre-treatment methods available for improving the floatability of oxidized coal such as microwave treatment, thermal treatment, premixing or preconditioning, ultrasonic treatment, low temperature pyrolysis, bubble surface modification, grinding pre-treatment, attrition and direct contact mixing of new reagents such as surfactants, new collectors and regulators.32
In general, grinding pre-treatment is applied for the liberation of minerals from coal, which helps to enhance the flotation efficacy of coal by stripping its surface. The grinding process involves two main processes, that is, surface grinding and crushing. Researchers found that the oxidation layer can be removed by this method, which creates some fresh surfaces, resulting in an increase in the floatability of low-rank coal.33
It has also been found that the oxidized layer can be removed by friction occurring due to the premixing or preconditioning treatment of coal matter and also by ultrasonic treatment. Ultrasound plays a great role in eliminating the thin clay layer and oxidized layer on the surface of low-rank coal by the generating cavitation bubbles. In this regard, it should be mentioned that HIC (high intensity conditioning) only helps to remove the clay layer. However, both treatments play a vital role in increasing the flotation kinetics and recovery of combustible matter of low-rank coal.34
Before the coal flotation process, low-rank coal is sometimes preconditioned with new collectors or/and surfactants to achieve higher floatable coal matter and higher combustible matter recovery. Recently, surfactants have been widely used to modify the surface properties of oxidized coal, and in this regard, researches also reported that the blending of surfactants with oily collectors can enhance the floatation efficiency of oxidized coal due to the hydrogen bonding between the polar part of the coal matter surface and the new reagent.35
Gaseous oil collectors are also used to improve the oxidized coal flotation method. These gaseous oil molecules are so small that they can go inside the pores of coal matter and easily get adsorbed, increasing its hydrophobicity.36
A large number of pores on the surface of low-rank coal is occupied by water molecules, resulting in the formation of a hydration membrane on the surface, which interrupts the adsorption process of the collector.37 Microwave and thermal pre-treatments are used to remove the water or moisture content from the pores, in addition to the hydroxyl functional groups of oxidized coal matter. Microwave pre-treatment is carried out using a suitable microwave oven for a certain time operating at the required temperature and frequency.38
Another method of pre-treatment for the flotation of low-rank coal is the direct contact procedure. In this method, the flotation reagent and preferably a surfactant are mixed with dry coal, followed by wetting them with water for flotation, i.e., mixture of two suitable reagents for flotation is applied for the desired outcome.39 The surfactant used creates new hydrophobic sites for the flotation reagent. In this method, the formation of a microemulsion provides higher floatation selectivity.40 The presence of pores, cracks and the size distribution in coal are factors that decide the effective surface area involved with reagents during the flotation process. Given that coal flotation depends on the adsorption of the reagents in the small capillaries of coal by van der Waals forces, it mainly depends on the nature of the pore structure of coal.41
Oily collectors such as kerosene and diesel oil are traditionally used for coal flotation. The reagent consumption during flotation is low for high-rank coal because of its natural hydrophobicity. In contrast, the flotation of low-rank coal is challenging due to the abundance of oxygen-containing functional groups and pores on its surface. Consequently, the flotation performance using these traditional oily collectors is unsatisfactory, where for even the moderate recovery of low-rank coal, large dosages of reagent are required.42–44 During storage and transportation or at the mine, most of the coal undergoes oxidation by the weathering process, which leads to the formation of oxygen-containing functional groups such as phenolic, carboxylic and carbonyl on the coal surface. These groups facilitate the formation of hydrogen bonds between the coal surfaces and water, thus lowering the hydrophobicity of the coal surface and making it much more difficult to float using oily collectors (Fig. 3).43–45
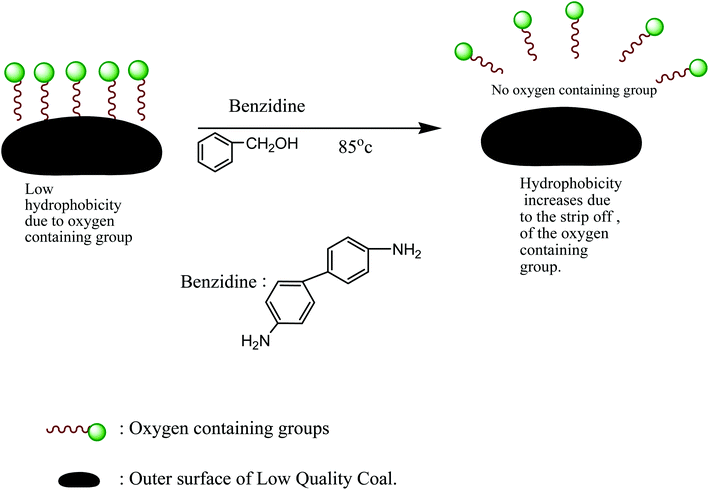 |
| Fig. 3 Chemical pre-treatment using benzidine. | |
3. Novel reagents for the modernisation of coal flotation
Despite improving the flotation efficiency, the above-mentioned methods are complicated. Thus, researchers employ novel flotation reagents to develop the flotation of low-rank coal, which can remove the oxygen-containing groups from the surface of low-rank coal.
After several experiments, researchers have concluded that the flotation of coal is not only dependent on its natural hydrophobicity (floating ability) but it can be improved by the use of a suitable flotation reagent. Here some of the common flotation reagents and their action on coal flotation are presented in Table 3.
Table 3 List of commonly used chemicals in coal flotation and their action and utilization46
Type |
Examples |
Functional groups |
Use |
Action |
Surface active (water-soluble) |
Aliphatic alcohols, polyglycols |
Hydroxyl nitrogenous |
Frothers |
Frothers with some collecting abilities. Also, improve the emulsification of oily collectors |
Nonpolar (water-insoluble) |
Kerosene, fuel oil |
— |
Collectors |
Selective wetting and adhesion of oil drops to coal particles |
Emulsifiers (soluble in the oily collector) |
Polyethoxylated alcohols, fatty acids, etc. |
Hydroxyl, carboxyl, nitrogenous |
Promoters |
Facilitate collector emulsification and spreading over coal |
Protective colloids |
Polymers: starch, dextrin, carboxymethyl cellulose, etc. |
Hydroxyl, carboxyl |
Depressants |
Modifiers and coal depressants |
Inorganic (water-soluble salts) |
NaCl, Na2SO4, H2SO4, Ca(OH)2 |
— |
Modifiers |
Promoter pH regulators and sulfide depressants |
Oily collectors and frothers are the two pivotal tools employed to carry out the coal flotation process. The frother is mainly used to create small bubbles and stable froth, where approximately 0.05–0.3 kg of reagent is used to create a sufficient amount of stability froth in 1 ton coal feed. The use of the oily collectors such as kerosene and diesel oil completely depends on the hydrophobic nature of the coal, and thus the quantity of reagents that are used as collectors starts at 0.2 kg per ton and ends at the amount of 2 kg per ton. A higher amount of collector is generally required for oxidised coal, which does not float easily.47 The use of a frother with oily collectors increases the efficiency of coal flotation. Frothers help to improve the emulsification by absorbing at the oil/water interface and lower the interfacial tension. Frothers also help to hold the oil droplets on the surface of coal by adsorbing at the coal/water interface (Table 4 and Scheme 2).48–50
Table 4 List of commonly used frothers in coal flotation47
Name of frother |
Chemical formula (molecular weight) |
Solubility in water |
(1) Polyglycol-type frothers |
DF1012 |
C19.9H41.8O7.3 (397.946) |
32% |
DF 250 |
C13H28O5 (264.362) |
Total |
DF-1263 |
C17H36O6 (336.469) |
Very good |
Aerofroth 65 DF 400 |
C19.5H41O7.5 (395.535) |
Total |
(2) Aliphatic alcohols |
R–OH |
|
Methyl isobutyl carbinol (MIBC) |
C6H14O (102.177) |
Low |
2,2,4-Trimethylpentanediol 1,3-monoisobutyrate (TEXANOL) |
C12H24O3 (216.321) |
Insoluble |
2-Ethyl hexanol |
C8H18O (130.231) |
Low |
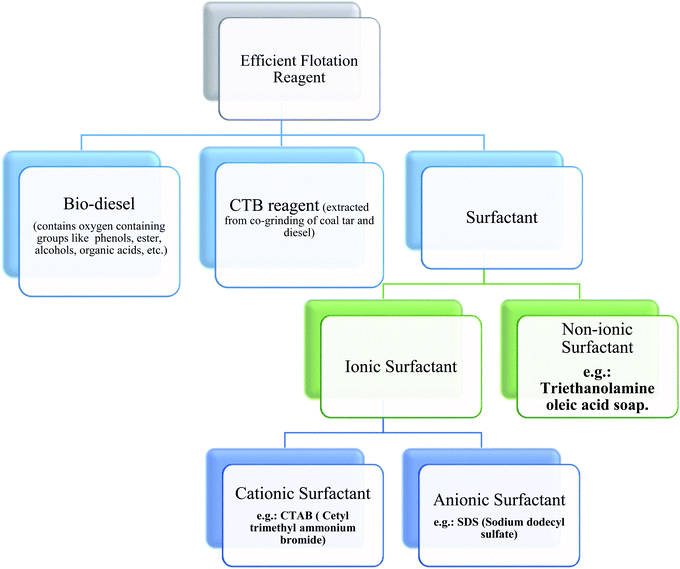 |
| Scheme 2 Different types of efficient flotation reagents used for the flotation of low-rank coal.51–55 | |
4. Surfactants as a new age all-rounder floating agent
Recently, various types of surfactants, mainly microorganism-based surfactants have been applied in different fields of coal flotation given that they are capable of making the conventional flotation process pocket friendly and eco-friendly. Surfactants show their versatility by playing different roles, such as a promoter, collector, collector efficiency enhancer, and depressant (Scheme 3).56
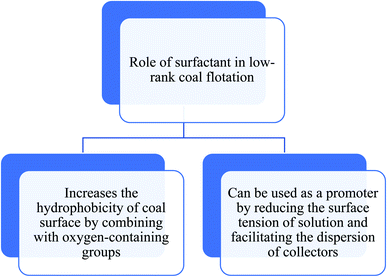 |
| Scheme 3 Role of surfactant in the flotation of low-rank coal.57 | |
The various types of surfactants and their mechanistic way of improving the flotation of low-rank coal are listed in Table 5.
Table 5 Different types of surfactants and their working process in the flotation of low-rank coal
Name of surfactant |
Nature of surfactants |
Working strategy |
Ref. |
CTAB (cetyltrimethylammonium bromide) |
Cationic |
Increases the adsorption of coal in a common oil trap by changing its zeta potential, thus enhancing the surface hydrophobicity |
54 |
SDS (sodium dodecyl sulfate) |
Anionic |
Alters the surface property and enhances the collection and selectivity of kerosene |
52 and 53 |
Triethanolamine oleic acid |
Non-ionic |
Enhances the adsorption of kerosene on the surface of coal by promoting the emulsification of kerosene |
55 |
SDBS (sodium dodecyl benzene sulfonate) |
Anionic |
Enhances the collection and selectivity of kerosene |
58 |
TX-100 |
Non-ionic |
Enhances the adsorption of kerosene on the surface of coal by promoting the emulsification of kerosene |
58 |
Tween-80 |
Non-ionic |
Enhances the adsorption of kerosene on the surface of coal by promoting the emulsification of kerosene |
59 |
Ethoxylated 2,4,7,9-tetramethyl-5-decyne-4,7-diol (Surfynol® 485) |
Gemini non-ionic surfactant |
Enhances the adsorption of n-octanol and diesel on the coal surface by promoting the emulsification of n-octanol and diesel |
59 |
Cetyltrimethylammonium chloride (CTAC) |
Cationic |
Alters the surface property, wettability, and thus promotes flotation |
60 |
Dodecyldimethylbetaine (BS-12) |
Zwitterionic |
Alters the surface property, wettability, and thus promotes flotation |
60 |
In a recent study by Gang Zhou et al. (2022),60 the influence of different types of surfactants on the froth flotation of coal was investigated using the cationic surfactant cetyltrimethylammonium chloride (CTAC) and zwitterionic surfactant dodecyldimethylbetaine (BS-12).
They investigated the effects of two different types of surfactants on the wettability of coal using molecular dynamics simulations. After analysis of the relative concentration distribution curves of different systems, they concluded that the combination of CTAC and BS-12 improved the thickness of the adsorption layer at the water/coal interface with an increase from 21.61 Å to 27.26 Å and 32.93 Å, which is consistent with the results of the water molecular diffusion coefficient analysis. In addition, the interaction energies of CTAC and BS-12 with gas coal were −1775.18 kcal mol−1 and −1986.95 kcal mol−1, respectively, indicating the occurrence of a spontaneous adsorption process. Lastly, the contact angle experiments and X-ray photoelectron spectroscopy (XPS) analyses further verified that greater wettability occurred in case of BS-12 for gas coal compared to that of CTAC. The influence of some other types of surfactants are discussed in the later sections.
4.1. Use of surfactant as a promoter in low-rank coal flotation
The flotation of low-rank coal can be developed by using various types of surfactants as a promoter, where an amino acid surfactant named sodium cocoyl glycinate (SCG) possesses all the properties required by a promoter. SCG is mainly used in personal care products because it possesses some excellent properties, as follows:
(I) Extremely low biological toxicity.
(II) Microorganisms can easily degrade it, causing no environmental pollution.61 A milli-level SCG dosage can improve the chemical environment and promote recovery of a satisfactory amount of clean low-rank coal (Fig. 4).62
 |
| Fig. 4 Structure of SCG (sodium cocoyl glycinate). | |
4.1.1 Efficiency of SCG. (A) A small amount of SCG can increase the combustible matter recovery (CMR) of low-rank coal flotation.(B) It increases the amount of clean coal by 12% and the amount of ash content almost remains unchanged.62
Here some experimental results are presented in Table 6, which support these two efficiencies.
Table 6 Comparison of the flotation performance of low-rank coal with different additives62
Amount of kerosene (g t−1) |
Clean coal yield (%) |
Ash content (%) |
Combustible matter recovery (%) |
1000 |
<5% |
<20% |
<10% |
3000 |
15% |
<10% |
<20% |
5000 |
<25% |
>5% |
30% |
7000 |
>25% |
<10% |
>30% |
Amount of kerosene + SCG (g t−1) |
|
|
|
1000 + 20 |
|
5% |
40% |
3000 + 50 |
|
<10% |
>40% |
5000 + 20 |
30% |
|
|
5000 + 50 |
35% |
|
|
5000 + 100 |
>35% |
10% |
40% |
5000 + 1000 |
>35% |
|
|
7000 + 1000 |
|
>10% |
<40% |
Alternatively a large amount of SCG can cause some negative results due to the amphiphilic nature of SCG. The excess SCG can bind with the hydrophobic sites on the upper surface of coal and the hydrophilic sites get exposed to water and act as an inhibitor in flotation of the low-rank coal (Fig. 5).
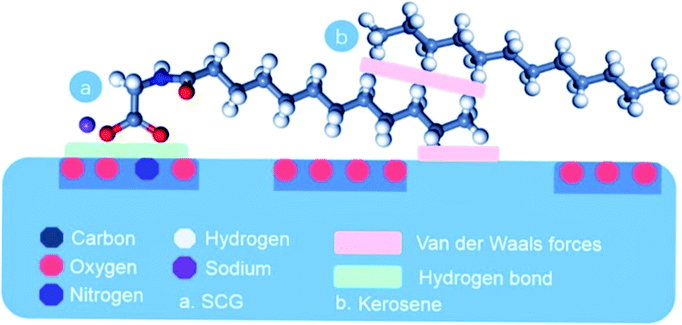 |
| Fig. 5 Adsorption of SCG and kerosene. This figure is reproduce from ref. 62 with permission from Elsevier, Copyright 2022. | |
(C) SCG binds with the hydrophilic sites on the surface of coal through its hydrophilic functional groups and exposes its hydrophobic sites towards the bubbles, this characteristic makes a significant increase in the proportion of hydrophobic sites on the coal upper surface, and it also reduces the bubble-particle attachment time (Fig. 6 and Table 7).62
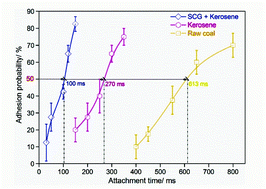 |
| Fig. 6 Graphical representation of different attachment times. This figure is reproduced from ref. 62 with permission from Elsevier, Copyright 2022. | |
Table 7 Attachment time with and without a collector62
Used collector |
Attachment time (ms) |
SCG + kerosene |
100 |
Only kerosene |
270 |
Only raw coal |
613 |
(D) The addition of SCG has a significant impact on the surface tension of a solution. The water phase captures the polar part and the oil phase captures the non-polar, which helps to reduce the oil–water interfacial tension and promote easy emulsification. This phenomenon mainly reduces the amount of collector used in flotation.
(E) SCG increases the froth layer height up to 16 cm. SCG also improves the half-life, which leads to an increase in the clean coal particles in the froth.
4.2 Use of surfactant as a collector and efficiency enhancer in low-rank coal flotation
In the process of coal mining, there are two important factors to consider, firstly, we have to prevent the hazardous drainage that forms at the time of mining, and secondly, we have to recover clean coal. The hydrophobic nature of coal can satisfy these two conditions, and by controlling this characteristic, we can optimise the overall flotation process. During coal flotation, dodecane and kerosene are commonly used as collectors, while for the removal of sulphide minerals, thiol-based collectors known as ‘xanthates’ are used. However, despite their effectiveness, they also induce some negative environmental effects.63 Biosurfactants (rhamnolipids, sophorolipids, and lipopeptides)64–67 possess lower toxicity than synthetic surfactants and can be used as a good floating agent.63 Surfactin is a lipopeptide that is produced by Bacillus subtilis, exhibiting excellent flotation properties.69 In the surfactin molecule, 7 amino acids combine to form a peptide ring, which is connected to 13 to 16 carbon-containing fatty acid chains. It forms a saddle-like shape containing two anionic residues, which forms a claw-shaped structure.66,68
4.2.1 Efficiency of surfactin. Surfactin is specifically used as an efficient collecting agent for systems that contain both sulphide minerals and coal particles.63Previously, we discussed the difficulties associated with the flotation of low-rank coal due to the presence of oxygen-containing groups on the upper surface of coal. According to several studies, it is evident that neither diesel oil nor DTAB (dodecyl trimethylammonium bromide) can efficiently recover low-rank coal alone. It was observed that a mixture of diesel oil and DTAB in a particular ratio (1
:
2) is much more effective to collect clean coal (Fig. 8).71
4.2.2 Efficiency of diesel oil and DTAB mixture. (A) A mixture of diesel oil and DTAB at a particular ratio (1
:
2) improves the clean coal yield and the ash content (Fig. 9).According to the above-mentioned results, as shown in Fig. 7(a), if diesel oil is used alone, the least amount of clean coal is obtained. Alternatively, the addition of DTAB greatly increases the amount of recovered clean coal. DTAB helps to reduce the surface tension of the floating solution and breaks the large oil drops into smaller droplets, thus forming a microemulsion of DTAB and diesel oil. This microemulsion increases the interaction between the oily collector and coal surface. DTAB also helps to indirectly increase the hydrophobicity given that the polar head group binds with the oxygen-containing sites and the long hydrophobic chain remains towards the water phase. These two factors combine to improve the hydrophobicity of low-rank coal.71 When the ratio of diesel oil and DTAB is 1
:
2, then the amount of clean coal is maximum compared to that of other ratios.
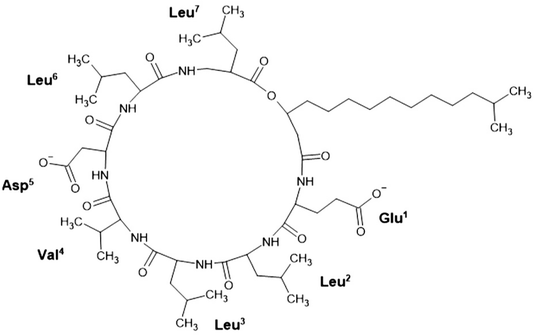 |
| Fig. 7 Structure of surfactin. This figure is reproduced from ref. 70 with permission from MDPI, Copyright 2015. | |
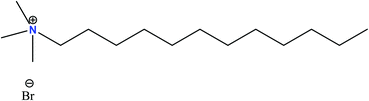 |
| Fig. 8 Structure of dodecyl trimethylammonium bromide (DTAB). This figure is reproduced from ref. 72 with permission from Springer Nature, Copyright 2019. | |
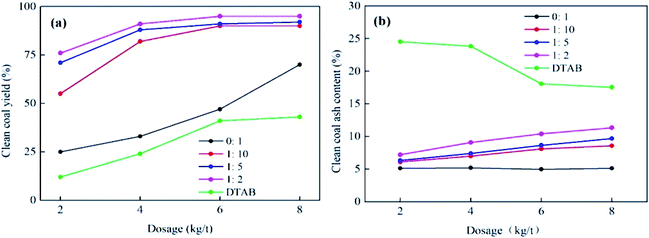 |
| Fig. 9 (a) % clean coal yield using different amounts of microemulsion dosage and (b) % ash content at different dosages of microemulsion. This figure is reproduced from ref. 71 with permission from Elsevier, Copyright 2020. | |
According to Fig. 7(b), we can see that the addition of DTAB to diesel oil also increases the amount of ash content. DTAB possesses two parts, i.e., a polar positively charged head group and non-polar carbon chain, where the positively charged head group not only comes in contact with the coal surface but also combines with the negatively charged gangue particles, which is the main reason for the increase in ash content (Fig. 10).73
 |
| Fig. 10 Interaction between mixture emulsion and low-rank coal. This figure is reproduced from ref. 71 with permission from Elsevier, Copyright 2020. | |
(B) According to the measurement of the contact angle, knowledge can be obtained the floating ability and hydrophobicity of the mineral. If the contact angle is large, the mineral possesses better hydrophobicity and floating ability. According to studies, it has been proven that the contact angle is maximum when the mixture of diesel oil and DTAB is added in a ratio of 1
:
2.71
(C) According to the measurement of the wrap angle, we can measure the adhesion probability of a bubble to a surface particle. A larger wrap angle indicates the stable attachment between bubble and particle, which indicates higher floating ability and stronger hydrophobicity. It has also been found from various experiments that the wrap angle is the highest when the diesel oil and DTAB are added in a 1
:
2 ratio.71
4.3 Use of surfactant as a depressant in reverse flotation
A non-ionic surfactant named TX-100 (Triton X-100) is widely used as a depressant in the reverse flotation process of non-coking coal (contains a lower amount of ash and has a high carbon percentage). Previously, dextrin was used as a depressant but after lots of experiments, it has been proven that the same dosage of TX-100 (5000 g t−1) will provide a lower ash content and the yield of clean coal is also reduced to some extent. The addition of TX-100 also increases the contact angle from 63.5° to 90°. With an increase in the concentration of TX-100 aqueous solution, the wettability of water increases, which makes TX-100 an efficient depressant.
According to FTIR data, it is evident that at higher concentrations, TX-100 is absorbed in a very good manner on the upper surface of raw coal, which reduces the rupturing rate at the time of bubble-coal adhesion.
TX-100 also modifies the bubble by covering its upper layer, which makes the bubble-coal particle adhesion difficult (Fig. 11).74
 |
| Fig. 11 Working strategy of Triton X-100 in reverse flotation of low-rank coal. This figure is adopted from ref. 74 with permission from Elsevier, Copyright 2021. | |
4.4 Use of surfactant as an emulsifier for the collector
The adhesion between the conventional fatty oil and oxidised coal is not very effective, and thus the percentage yield of clean coal can be improved by mixing di-propylene diamine (LDD) with kerosene and forms an emulsion, hence the contact angle increases, which indicates an increment in the hydrophobicity of the oxidised coal. LDD possesses a low surface tension, which helps to produce a more stable froth layer than conventional oil collectors. The amount of clean coal increases from 4.12% to 23.33%.75
5. Clean coal technology and environmental safety
Coal is one of the largest sources of energy in the modern scenario. However, many harmful gases such as SOx and NOx and greenhouse gases (GHG) such as CO2 are emitted due to the combustion of coal, which creates a significant disturbance in the eco-condition. The oxides of sulphur have a major impact on human health and the environment. Thus, it is necessary to improve the eco-friendly nature of coal, and also to add some more economic value. Currently, researchers are approaching clean coal technology.76 Researchers have developed several processes for desulphurization but in this section, we discuss the effect of surfactants on the desulphurization process. Mishra and co-workers used the minimum amount of Span 80 (surfactant) in a bioreactor during the desulphurization process of Turkish coal using a micro-organism (Rhodococcus erythropolis) and they achieved an excellent result by removing approximately 51.2% sulphur.77 Surfactants reduce the interfacial tension and the surface tension, which provide assistance to microbial attack and increase the probability of the bio-degradation of coal (Turkish Lignite).78 This bio-degradation takes place in both the aqueous phase and micellar phase in the presence of Span 80. Here, we present an experimental data set, which gives a clear idea about the effect of Span 80 on the desulphurization process using Leptospirillum ferriphilum (Table 8).79
Table 8 Efficiency of Span 80 in sulphur removal with varying concentrations80
Span 80 concentration (v/v) |
Initial sulphur (%) |
Final sulphur (%) |
Removed sulphur (%) |
0.02% |
7.63 ± 0.2 |
3.11 ± 0.02 |
59.2 |
0.05% |
2.97 ± 0.03 |
61.0 |
0.08% |
2.89 ± 0.09 |
62.1 |
0.1% |
2.94 ± 0.07 |
61.4 |
0.15% |
3.22 ± 0.007 |
57.7 |
0.2% |
3.44 ± 0.03 |
54.91 |
0.5% |
3.88 ± 0.04 |
49.1 |
1% |
4.63 ± 0.12 |
39.3 |
2% |
5.29 ± 0.02 |
39.3 |
No surfactant |
3.34 ± 0.08 |
56.2 |
In thermal power plants, a huge amount of coal ash gets generated as waste material, and thus it becomes necessary to utilize this huge amount of coal ash by converting it into some eco-friendly materials such as fly ash bricks (FAB), which helps to reduce the amount of ash content in the air around thermal power plants and environmental pollution to some extent. Surfactants help to reduce the ash content by improving the wettability of the solid particles, and also by reducing the viscous nature of the slurry.81 Clean coal technology (CCT) demonstrates potential to control the emission of sulfur oxides, nitrogen oxides, and particulate matter from coal-fired power stations. Clean coal plants have lower emissions of nitrogen oxides by 83%, sulfur dioxide by 98%, and particulate matter by 99.8% compared to conventional plants, according to studies done by the Department of Energy (DOE), National Energy Technology Laboratory (NETL).82 Reduced SO2 and NOx emissions result in less acid rain, which reduces lake acidification and eutrophication, as well as forest and other vegetation damage. Steel, limestone, concrete, and other materials are also less likely to be damaged. Consequently, the environmental advantages of CCT are self-evident.83
6. Future prospects and conclusions
The abundance of oxygen-containing functional groups on the surface of low-rank coal (LRC) leads to its poor surface hydrophobicity during flotation, thus there are several challenges associated with the flotation of low-rank coal. The conventionally used non-polar oily collectors such as diesel oil and kerosene cannot spread effectively on the surface of LRC, even at a high dosage, and therefore huge cost input is required. The enrichment and dewatering process of fine and ultrafine coal particles (200 μm) is much more complicated than that of a coarser size. Thus, to overcome this problem, researchers have introduced surfactants into the coal flotation process. The ratio of hydrophilic and lyophilic groups of a surfactant is termed as the HLB value (hydrophilic–lyophilic balance). Several studies on coal flotation using different surfactants having different HLB values suggested the suitable properties of reagents, which are the key to enhancing both the flotation performance and dewatering process.84 The efficiency of flotation separation was found to be the highest in the case of traditional gigantic oily collectors and surfactants having a lower HLB (lyophilic surfactants), whereas the filtration performance is best in the case of surfactants with moderate HLB values (∼10).85,86 In recent years, coal industries have made great efforts to find the best route for improving the recovery of clean coal for sustainability. To achieve this goal, mixed reagents are used (mixed surfactants, mixed collectors, oily collectors with surfactants, etc.) despite the fact that conventional individual reagents show tremendous progress in the recent coal flotation process. Surfactants enhance the separation efficiency of coal flotation by getting adsorbed selectively and quickly on the surface of coal and reduce the oil–water interfacial tension, particularly for low-rank oxidized coal particles. In this present review, we summarized the up-to-date advancement of research related to coal flotation for improving the flotation efficiency. The modern world is demanding more sustainable and greener mining reagents. In this context, the use of various bio-surfactant is a highly potent and more acceptable approach compared to conventional synthetic reagents.
Author contributions
The manuscript was prepared by Biplab Kumar and Bidisha Das; they should be treated with equal authorship. Amit Garain, Monohar Hossain Mondal, Wasefa Begum, Summi Rai, Ajaya Bhattarai, Md. Inamuddinand and Bidyut Saha edited the manuscript. It was revised several times by Monohar Hossain Mondal, Bidyut Saha and Ajaya Bhattarai.
Conflicts of interest
The authors declare no conflict of interest.
References
- F. Birol and D. Malpass, It's critical to tackle coal emissions – Analysis – IEA, [online] IEA, 2021 available at: https://www.iea.org/commentaries/it-s-critical-to-tackle-coal-emissions Search PubMed.
- A. Scott and M. Thomas, ACI Mater. J., 2007, 104(1), 62–69, DOI:10.14359/18496.
- Global Energy Review: CO2 Emissions in 2021 – Analysis – IEA, [online] available at: https://www.iea.org/reports/global-energy-review-co2-emissions-in-2021-2 Search PubMed.
- H. H. Lowry, Chemistry of Coal Utilization, John Wiley and Sons, N.Y., 1963, supp. volume Search PubMed.
- N. Manych, J. Steckel and M. Jakob, Environ. Res. Lett., 2021, 16(4), 044028, DOI:10.1088/1748-9326/abd972.
- J. Yu, A. Tahmasebi, Y. Han, F. Yin and X. Li, Fuel Process. Technol., 2013, 106, 9–20, DOI:10.1016/j.fuproc.2012.09.051.
- Q. Tu, Y. Cheng, S. Xue, T. Ren and X. Cheng, Int. J. Coal Sci. Technol., 2021, 31(4), 729–742, DOI:10.1016/j.ijmst.2021.05.009.
- K. Sun, L. Fan, Y. Xia, C. Li, J. Chen, S. Gao, B. Wu, J. Peng and Y. Ji, Int. J. Coal Sci. Technol., 2021, 8(1), 88–102, DOI:10.1007/s40789-020-00366-5.
- J. Pan, B. V. Hassas, M. Rezaee, C. Zhou and S. V. Pisupati, J. Cleaner Prod., 2021, 284, 124725, DOI:10.1016/j.jclepro.2020.124725.
- P. Hu, L. Liang, G. Xie, S. Zhou and Y. Peng, Int. J. Min. Sci. Technol., 2020, 30(6), 859–864, DOI:10.1016/j.ijmst.2020.07.008.
- S. K. Behera, H. Meena, S. Chakraborty and B. C. Meikap, Int. J. Min. Sci. Technol., 2018, 28(4), 621–629, DOI:10.1016/j.ijmst.2018.04.014.
- K. Stańczyk, A. Bajerski and M. J. Łączny, Int. J. Coal Sci. Technol., 2021, 8(1), 103–123, DOI:10.1007/s40789-020-00345-w.
- H. Dhawan, R. Kumar, S. Upadhyayula, K. K. Pant and D. K. Sharma, Int. J. Coal Sci. Technol., 2020, 7(3), 504–515, DOI:10.1007/s40789-020-00348-7.
- U. Behera, S. K. Das, D. P. Mishra, P. K. Parhi and D. Das, Int. J. Coal Prep. Util., 2021, 1–21, DOI:10.1080/19392699.2021.1995374.
- U. Behera, S. K. Das, D. P. Mishra, P. K. Parhi and D. Das, ACS Omega, 2021, 6(35), 22820–22830 CrossRef CAS PubMed.
- D. Das, S. K. Das, P. K. Parhi, A. K. Dan, S. Mishra and P. K. Misra, Energy Nexus, 2021, 4, 100025, DOI:10.1016/j.nexus.2021.100025.
- The dirtiest fossil fuel is on the back foot, The Economist, 2020, from https://www.economist.com/briefing/2020/12/03/the-dirtiest-fossil-fuel-is-on-the-back-foot Search PubMed.
- L. Tang, S. Wang, J. Guo, X. Tao, H. He, L. Feng, S. Chen and N. Xu, Fuel Process. Technol., 2017, 159, 442–447, DOI:10.1016/j.fuproc.2016.12.019.
- Y. Mao, W. Xia, Y. Peng and G. Xie, Fuel Process. Technol., 2019, 195, 106150, DOI:10.1016/j.fuproc.2019.106150.
- W. Xia, C. Niu and C. Ren, J. Cleaner Prod., 2017, 168, 1032–1038, DOI:10.1016/j.jclepro.2017.09.119.
- C. Niu, W. Xia and G. Xie, Fuel, 2017, 208, 469–475, DOI:10.1016/j.fuel.2017.07.073.
- F. Zeng, The Origin of Coal and World Reserves. Coal, Oil Shale, Natural Bitumen, Heavy Oil and Peat, Encyclopedia of Life Support Systems (EOLSS), 2009, vol. 1, p. 76, ISBN: 978-1-84826-017-7 Search PubMed.
- C. W. Angle and H. A. Hamza, Appl. Clay Sci., 1989, 4(3), 263–278, DOI:10.1016/0169-1317(89)90034-3.
- D. Kumar and D. Kumar, Wet cleaning process by major unit operations, Sustainable Management of Coal Preparation, vol. 5, Woodhead Publishing, 2018, pp. 69–114, ISBN: 9780128126325, DOI:10.1016/B978-0-12-812632-5.00005-7.
- A. Erensoy, S. Kuk and M. Ozden, Parasitol. Res., 2009, 105(2), 407–412, DOI:10.1080/15567036.2017.1356885.
- X. Bu, Y. Chen, G. Ma, Y. Sun, C. Ni and G. Xie, Adv. Powder Technol., 2019, 30(11), 2703–2711, DOI:10.1016/j.apt.2019.08.016.
- J. Mainhood and P. F. Whelan, J. Appl. Chem., 1955, 5(3), 133–144, DOI:10.1002/jctb.5010050306.
- Y. Chen, V. N. Truong, X. Bu and G. Xie, Ultrason. Sonochem., 2020, 60, 104739, DOI:10.1016/j.ultsonch.2019.104739.
- J. Cara, A. Morán, T. Carballo, F. Rozada and Á. Aller, Fuel, 2003, 82, 2065–2068 CrossRef CAS.
- C. Li, Y. Xing, X. Gui and Y. Cao, Int. J. Coal Prep. Util., 2020, 40, 553–563, DOI:10.1080/19392699.2017.1375478.
- J. Pis, G. de la Puente, E. Fuente, A. Moran and F. Rubiera, Thermochim. Acta, 1996, 279, 93–101 CrossRef CAS.
- W. Xia, J. Yang and C. Liang, Powder Technol., 2013, 237, 1–8 CrossRef CAS.
- W. Xia, J. Yang, Y. Zhao, B. Zhu and Y. Wang, Physicochem. Probl. Miner. Process., 2012, 48(2), 393–401 CAS.
- D. Feng and C. Aldrich, Chem. Eng. Commun., 2005, 192, 972–983 CrossRef CAS.
- S. Dey, Fuel Process. Technol., 2012, 94, 151–158 CrossRef CAS.
- L. Shen, F. Min, L. Liu, J. Zhu, C. Xue, C. Cai, W. Zhou and C. Wang, Fuel, 2019, 239, 446–451 CrossRef CAS.
- V. N. Petukhov, K. Y. Girevaya, D. A. Kubak and T. A. Girevoy, Coke Chem., 2013, 56, 292–298 CrossRef.
- W. Xia, J. Yang and C. Liang, Powder Technol., 2013, 233, 186–189 CrossRef CAS.
- H. A. M. Ahmed and J. Drzymala, Physicochem. Probl. Miner. Process., 2004, 38, 53–63 CAS.
- H. A. M. Ahmed and J. Drzymala, Miner. Metall. Process., 2012, 29(2), 88–96 CAS.
- A. Ping, W. Xia, Y. Peng and G. Xie, Int. J. Min. Sci. Technol., 2021, 31(2), 233–240, DOI:10.1016/j.ijmst.2020.12.026.
- Q. Feng, W. Zhao and S. Wen, Appl. Surf. Sci., 2018, 436, 823–831, DOI:10.1016/j.apsusc.2017.12.113.
- Y. Mao, X. Bu, Y. Peng, F. Tian and G. Xie, Fuel, 2020, 259, 116270, DOI:10.1016/j.fuel.2019.116270.
- J. S. Laskowski and J. D. Miller, New reagents in coal flotation. Reagents in the mineral industry, in Developments in Mineral Processing, Elsevier, 1984, pp. 145–154 Search PubMed.
- D. W. Fuerstenau, K. S. Narayanan, R. Herrera-Urbina and J. L. Diao, Int. J. Coal Sci. Technol., 1987, 11, 475–478 CAS.
- J. Laskowski, Coal flotation and fine coal utilization, Elsevier Sci., 2001, ISBN: 0-444-50537-7 Search PubMed.
- J. S. Laskowski, Surface chemistry fundamentals in fine coal processing, in The Coal Handbook: Towards Cleaner Production, vol. 1, Woodhead Publishing Series in Energy, 2013, pp. 347–421, DOI:10.1533/9780857097309.2.347.
- A. Pal, M. H. Mondal, A. Adhikari, A. Bhattarai and B. Saha, RSC Adv., 2021, 11, 33004–33016, 10.1039/D1RA04968B.
- D. W. Fuerstenau, Colloids Surf., A, 1982, 4(3), 213–227, DOI:10.1016/0166-6622(82)80019-X.
- J. D. Miller, C. L. Lin and S. S. Chang, Colloids Surf., A, 1983, 7(4), 351–355, DOI:10.1016/0166-6622(83)80061-4.
- W. Xia, J. Yang and C. Liang, Int. J. Coal Prep. Util., 2013, 33(4), 181–187, DOI:10.1080/19392699.2013.776962.
- Y. Li, W. Xia, Y. Peng and G. Xie, J. Cleaner Prod., 2020, 273, 123172, DOI:10.1016/j.jclepro.2020.123172.
- W. Li, H. Wang, X. Li, Y. Liang, Y. Wang and H. Zhang, Fuel, 2021, 289, 119886, DOI:10.1016/j.fuel.2020.119886.
- S. Chen, S. Wang, L. Li, J. Qu, X. Tao and H. He, Fuel, 2018, 227, 190–198, DOI:10.1016/j.fuel.2018.04.003.
- D. W. Fuerstenau, G. H. Harris and R. Jia, ACS Symp. Ser., 1999, 740, 230–247 CrossRef.
- M. H. Fazaelipoor, H. Khoshdast and M. Ranjbar, Korean J. Chem. Eng., 2010, 27(5), 1527–1531, DOI:10.1007/s11814-010-0223-6.
- T. Lu, Z. Li, J. Huang and H. Fu, Langmuir, 2008, 24(19), 10723–10728, DOI:10.1021/la801301v.
- F. Zhou, C. Yan, H. Wang, S. Zhou and H. Liang, Fuel, 2017, 190, 182–188 CrossRef CAS.
- X. Zhu, M. He, W. Zhang, H. Wei, X. Lyu, Q. Wang, X. You and L. Li, J. Cleaner Prod., 2020, 257, 120496, DOI:10.1016/j.jclepro.2020.120496.
- G. Zhou, M. Xing, K. Wang, Q. Wang, Z. Xu, L. Li and W. Cheng, J. Mol. Liq., 2022, 357, 118996, DOI:10.1016/j.molliq.2022.118996.
- M. Hassanzadeh, M. Kambarani, L. Tayebi and F. Yazdian, J. Surfactants Deterg., 2012, 15(5), 551–556, DOI:10.1007/s11743-012-1333-4.
- C. Niu, W. Xia, Y. Li, X. Bu, Y. Wang and G. Xie, Fuel, 2022, 307, 121810, DOI:10.1016/j.fuel.2021.121810.
- A. R. Augustyn, R. W. Pott and M. Tadie, Colloids Surf., A, 2021, 627, 127122, DOI:10.1016/j.colsurfa.2021.127122.
- H. Khoshdast, A. Sam, H. Vali and K. A. Noghabi, Int. Biodeterior. Biodegrad., 2011, 65(8), 1238–1243, DOI:10.1016/j.ibiod.2011.10.003.
- A. Pal, A. Garain, D. Chowdhury, M. H. Mondal and B. Saha, Tenside, Surfactants, Deterg., 2020, 57, 401–407 CrossRef CAS.
- A. I. Zouboulis, K. A. Matis, N. K. Lazaridis and P. N. Golyshin, Miner. Eng., 2003, 16(11), 1231–1236, DOI:10.1016/j.mineng.2003.06.013.
- B. Das, B. Kumar, W. Begum, A. Bhattarai, M. H. Mondal and B. Saha, Chem. Afr., 2022, 5, 459–480 CrossRef CAS.
- D. W. Develter and L. M. Lauryssen, Eur. J. Lipid Sci. Technol., 2010, 112(6), 628–638, DOI:10.1002/ejlt.200900153.
- M. Kowall, J. Vater, B. Kluge, T. Stein, P. Franke and D. Ziessow, J. Colloid Interface Sci., 1998, 204, 1–8, DOI:10.1006/jcis.1998.5558.
- J. F. Liu, S. M. Mbadinga, S. Z. Yang, J. D. Gu and B. Z. Mu, Int. J. Mol. Sci., 2015, 16(3), 4814–4837, DOI:10.3390/ijms16034814.
- R. Zhang, Y. Xia, F. Guo, W. Sun, H. Cheng, Y. Xing and X. Gui, Fuel, 2020, 260, 116321, DOI:10.1016/j.fuel.2019.116321.
- B. Chowdhury, M. H. Mondal, M. K. Barman and B. Saha, Res. Chem. Intermed., 2019, 45, 789–800, DOI:10.1007/s11164-018-3643-2.
- S. Jaiswal, S. K. Tripathy and P. K. Banerjee, Int. J. Miner. Process., 2015, 134, 97–110, DOI:10.1016/j.minpro.2014.11.007.
- K. Zheng, W. Xia and W. Zhang, Colloids Surf., A, 2021, 611, 125794, DOI:10.1016/j.colsurfa.2020.125794.
- Q. Zhang, C. Niu, X. Bu, M. Bilal, C. Ni and Y. Peng, Minerals, 2021, 11(11), 1271, DOI:10.3390/min11111271.
- A. S. Jatoi, S. Aziz and S. A. Soomro, Cleaner Engineering and Technology, 2021, 3, 100126, DOI:10.1016/j.clet.2021.100126.
- S. Mishra, A. Akcil, S. Panda and A. Tuncuk, Miner. Eng., 2018, 119, 183–190, DOI:10.1016/j.mineng.2018.01.032.
- Z. Sadowski, Hydrophobic Agglomeration of Fine Particles, in Mineral Processing and the Environment, Springer, Dordrecht, 1998, pp. 3–24, DOI:10.1007/978-94-017-2284-1_1.
- J. L. Li and B. H. Chen, Materials, 2009, 2, 76–94 CrossRef CAS.
- S. Mishra, A. Akcil, S. Panda and C. Erust, Hydrometallurgy, 2018, 176, 166–175, DOI:10.1016/j.hydromet.2018.01.021.
- R. K. Mohapatra, P. K. Das, D. C. Kabiraz, D. Das, A. Behera and M. Kudrat-E-Zahan, Generation, Transportation and Utilization of Indian Coal Ash, in Clean Coal Technologies, ed. R. K. Jyothi and P. K.Parhi, Springer, Cham, 2021, DOI: DOI:10.1007/978-3-030-68502-7_11.
- Clean Coal Is Crucial for American Jobs, Energy Security, and National Supply Chains, Department of Energy, https://www.energy.gov/articles/clean-coal-crucial-american-jobs-energy-security-and-national-supply-chains, accessed Apr. 11, 2022 Search PubMed.
- S. Green, PEI Power Eng. Int., 2000, 8(1), 39, DOI:10.1201/b21459-9.
- M. R. Kadagala, S. Nikkam and S. K. Tripathy, Miner. Eng., 2021, 173, 107217 CrossRef CAS.
- C. N. Mulligan, Colloid Interface Sci., 2009, 14(5), 372–378, DOI:10.1016/j.cocis.2009.06.005.
- J. E. Kostka, O. Prakash, W. A. Overholt, S. J. Green, G. Freyer, A. Canion, J. Delgardio, N. Norton, T. C. Hazen and M. Huettel, Appl. Environ. Microbiol., 2011, 77(22), 7962–7974 CrossRef CAS PubMed.
|
This journal is © The Royal Society of Chemistry 2022 |
Click here to see how this site uses Cookies. View our privacy policy here.