DOI:
10.1039/D2RA01976K
(Paper)
RSC Adv., 2022,
12, 18084-18092
Production of 2,5-furandicarboxylic acid via oxidation of 5-hydroxymethylfurfural over Pt/C in a continuous packed bed reactor
Received
27th March 2022
, Accepted 7th June 2022
First published on 20th June 2022
Abstract
2,5-Furandicarboxylic acid (FDCA) is a monomer that can be used to produce bioplastic, which has gained increasing interest worldwide. The production of FDCA from catalytic oxidation of 5-hydroxymethylfurfural (5-HMF) is regarded as the major route of the utilization of 5-HMF. In this work, FDCA was produced in a tubular reactor packed with Pt/C. The effects of operating parameters including reaction temperature, molar ratio of 5-HMF/NaOH, volumetric flow rate of oxygen, pressure, and catalyst amount on the yield of product were investigated. High oxygen supply provided by high pressure or high oxygen flow rate effectively decreased the yield of FDCA. The optimal conditions were at the reaction temperature of 90 °C, the molar ratio between 5-HMF and NaOH of 1
:
8, the oxygen flow rate of 33.9 mL min−1 and atmospheric pressure, providing the yield of FDCA of 86.4% and full conversion of 5-HMF. The productivity of 0.1266 kgFDCA kgcat.−1 h−1 was achieved with the residence time of 0.285 s, which was considerably shorter than the reaction times reported in the literature. These results can be used as a foundation for further investigation and for developing a compact processing unit for the production of FDCA.
Introduction
The synthesis of bio-based chemicals and polymers from renewable biomass is the sustainable alternative choice to reduce dependence on fossil-fuel resources. Biomass-derived 2,5-furandicaboxylic acid (FDCA) is a high value-added chemical that can be used to substitute the petrochemical-derived PTA (pure terephthalic acid), a principal precursor to polyethylene terephthalate (PET).1 FDCA can be used for the production of polyethylene furanoate (PEF).2,3 It can be synthesized from the oxidation of 5-hydroxymethylfurfural (5-HMF) which is derived from dehydration of carbohydrate.4,5 Catalytic oxidation of 5-HMF to produce FDCA is a complex reaction involving several intermediate molecules such as 5-hydroxymethyl-2-furancarboxylic acid (HMFCA), 2,5-diformylfuran (DFF) and 5-formyl-2-furancarboxylic acid (FFCA) in the system.6–8
The synthesis of FDCA has been performed in the conventional batch process.1,9–13 Davis et al. investigated the oxidation of 5-HMF over supported Pt, Pd, and Au catalysts in the semi-batch reactor.10 The selectivity of FDCA was 79% and 71% over Pt and Pd, respectively, at 22 °C, 690 kPa O2 with the reaction time of 6 h. The selectivity of FDCA was about 31% and 72% over Au catalyst when the reaction time was 6 h and 22 h, respectively. Schade et al. studied the oxidation of 5-HMF using supported gold- and silver-based catalysts in an autoclave as a batch reactor.13 The yield of FDCA of approximately 75% was obtained over Au/ZrO2 at 100 °C, under a pressure of 10 bar with the reaction time of 5 h. Similarly, Casanova et al. reported the FDCA yield of 78% with the reaction time of 24 h for Au/C catalyst at the reaction temperature of 65 °C and the pressure of 10 bar.14 Although the full conversion of HMF has often been reported in the literature, improving the reaction time and the yield of FDCA still requires further development. Long reaction time was due to the gas–liquid film resistance in the system. Davis et al. mentioned that the flux of O2 through the gas–liquid film was the limiting step.10
In order to improve the productivity, the development of a continuous system for the production of FDCA is necessary. Recently, a continuous electrochemical oxidation of 5-HMF to produce FDCA using Ni/NiOOH foam electrodes was demonstrated. A two-step process was required to achieve full conversion of 5-HMF, providing the yield of FDCA of 82–90%.15 However, scaling up the production to the industrial capacity can be a challenge. Packed-bed reactor can also be applied for the production of FDCA as a continuous process; however, no literature data is available. Based on the development using batch processing, it is possible to shorten the time required for the chemical reactions using a flow reactor, as the mixing is not the major effect. For instance, Chueluecha et al. shortened the reaction time from 4–8 h for batch reactor to 15 min for biodiesel production in a packed microchannel reactor.16 Sonsiam et al. drastically shortened the reaction time (residence time) for the dehydration of fructose to 5-HMF in a continuous flow reactor compared to the batch reactor.17
The synthesis of FDCA can be performed using either homogeneous or heterogeneous catalysts. Partenheimer and Grushin demonstrated the synthesis of FDCA from 5-HMF using metal/bromide catalysts, achieving 60% of FDCA yield in a batch system at 125 °C and 3 h of reaction time.18 Although the use homogeneous catalyst is possible, the separation and recycling of catalyst can be difficult. Heterogeneous catalysts have been developed for this process to avoid the separation of catalyst and product. Among heterogeneous catalysts, noble metal catalysts such as Pt, Pd and Au on various supports have been used in many studies for the synthesis of FDCA, providing good activity under mild conditions.1,10,12 Sahu and Dhepe achieved 96% of FDCA yield under normal oxygen pressure using Pt/γ-Al2O3 as catalyst at the optimal reaction conditions of a stepwise increase in the temperature (75 and 140 °C for 12 h each).19
Therefore, in this contribution, we developed a continuous system to enhance the productivity for the production of FDCA via partial oxidation of 5-HMF in a packed-bed reactor. Pt supported on activated carbon (Pt/C) was used as catalyst to improve the production of FDCA. The conversion of HMF, yield of FDCA and reaction time were monitored to evaluate the reactor performance. The effects of liquid and gas flow rates, the ratio of HMF/NaOH, temperature and pressure were investigated. The performance of our system was also compared to that of the conventional batch and semi-batch reactors.
Methodology
Materials
Standard chemicals including 5-hydroxymethylfurfural, 5-HMF (>99%), 5-hydroxymethyl-2-furancarboxylic acid, HMFCA (≥95%), 2,5-diformylfuran, DFF (≥96.5%), 5-formyl-2-furancarboxylic acid, FFCA (≥97%), and 2,5-furandicaboxylic acid, FDCA (97%) were purchased from Sigma-Aldrich. The solvent was prepared by dissolving NaOH (AR grade) in the ultrapure water (18.2 ohms) for all experiments. Acetonitrile (ACN) and methanol (MeOH) were HPLC grade for the analysis using HPLC. Oxygen gas (99.99%), used as the oxidizing agent, was supplied by Linde (Thailand) PLC. The platinum catalyst used was 5 wt% metal on activated carbon (Pt/C) purchased from Riogen, Inc.
Catalyst characterization
The properties of 5 wt% Pt/C was referred to the work of Makcharoen et al., who studied the deoxygenation of crude palm kernel oil over Pt/C in a continuous fixed bed reactor to produce biojet fuel.20 The surface area of catalyst was analyzed by N2 physisorption technique using 3Flex surface characterization analyzer (Micromeritics Instrument Corporation model ver. 4.04). The specific surface area was evaluated based on the Brunauer–Emmett–Teller theory (BET). The total pore volume and the average pore size were calculated by Barrett–Joyner–Halenda (BJH) method. The crystal structure of 5% wt Pt/C was examined using X-ray diffractor with an X-ray filter Cu Kβ radiation. The diffraction was recorded at 40 kV, 30 mA, a scanning rate of 1.0 deg min−1 and scanning range (2θ) of 10° to 80° with a step width of 0.01°. Catalyst surface morphology was characterized by using a scanning electron microscope (SEM, Hitachi model S-4800) at 2 kV and magnification of 1000×, 5000× and 10
000×, respectively.
Catalytic oxidation of 5-HMF
The schematic diagram of our experimental apparatus is shown in Fig. 1. In this work, a stainless-steel tubular reactor with an outer diameter of 3.18 mm was packed with 5 wt% Pt/C. For a typical experiment, the oxygen gas was supplied from a cylinder through a mass flow controller and a stream of liquid solution of 5-HMF and NaOH dissolved in ultrapure water was fed via a high-pressure syringe pump (ISCO series 260D). These two streams were combined at a T-mixer prior to entering the reactor. The multi-phase mixture flowed through the fixed-bed reactor, placed in an oil bath with internal circulation and temperature control. The oxidation of 5-HMF occurred on the catalyst surface and the reaction products diffused into the liquid stream, which flowed through a back pressure regulator installed at the end of the reactor (for the experiments at high pressure). After passing through the back pressure regulator, the mixture was separated into gas and liquid streams in a phase separator. The gas product was sent to the fume hood. During the experiment, the liquid product was collected at different times with the interval of 30 min or 1 h depending on the operating conditions (flow rates of gas and liquid). The reactor dimension and operating conditions for this system are summarized in Table 1. The performance of this reaction was addressed in terms of 5-HMF conversion, yield of FDCA and productivity, which can be calculated using eqn (1)–(3). |
 | (1) |
|
 | (2) |
|
 | (3) |
where CinHMF and CoutHMF represent the inlet and outlet concentrations of 5-HMF, respectively.
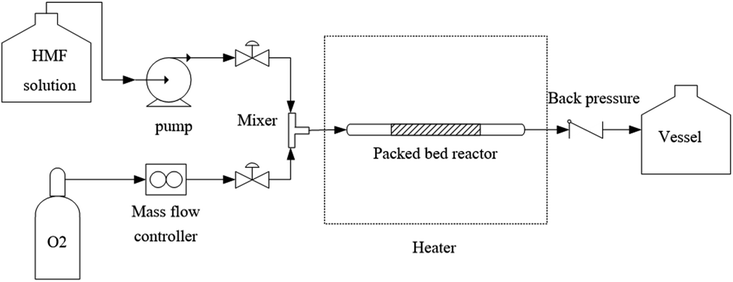 |
| Fig. 1 Schematic diagram of a continuous process for FDCA production via 5-HMF oxidation. | |
Table 1 Reactor dimension and operating parameters
Parameter |
Value |
Packed bed reactor |
Outer diameter, mm |
3.18 |
Inner diameter, mm |
2.46 |
Length, cm |
15 |
Flow rate |
Gas, mL min−1 |
33.9–90.9 |
Liquid, mL min−1 |
0.03–0.06 |
Temperature, °C |
75–90 |
Pressure, bar |
1–5.1 |
Concentration of 5-HMF, mol L−1 |
0.016 (2 g L−1) |
Amount of catalyst (5% wt Pt/C), g |
0.025–0.09 |
Product analysis
In order to quantify the yield and selectivity of product as well as the conversion of reactant (5-HMF) based on the chromatographic technique, it was necessary to have the effective separation of peaks corresponding to all species of interest (5-HMF, HMFCA, DFF, FFCA, and FDCA). We developed a method for high performance liquid chromatography (HPLC, Knauer, Germany) equipped with reversed-phase C-18 column (Supelco, 250 mm × 4.6 mm) and UV detector with the wavelength of 270 nm. The liquid samples collected from the experiments were diluted with ultrapure water and were analyzed using a mixture of ultrapure water (DI water): acetonitrile (ACN): methanol (MeOH) with 0.025 M sulfuric acid (0.025 M H2SO4) with the ratio of 90
:
5
:
5 (DI
:
ACN
:
MeOH) as mobile phase at a constant flow rate of 0.4 mL min−1. The column temperature was maintained at 50 °C and the injection volume was 10 μL. The concentration of each component was evaluated based on the calibration of standard chemicals. Fig. 2 shows that the relevant chromatographic peaks were essentially separated under the specified conditions.
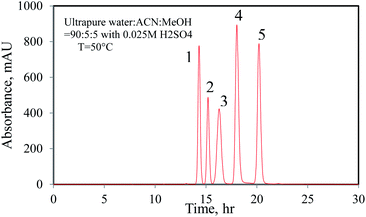 |
| Fig. 2 Chromatogram of mixed standards ((1) 5-HMF, (2) HMFCA, (3) DFF, (4) FFCA and (5) FDCA). | |
Results
Catalyst characterization
The N2 physisorption revealed that the Pt/C used in this work had the BET surface area of 1040 m2 g−1, the pore volume of 0.57 cm3 g−1 and the average pore size of 2.2 nm. It was classified as porous microparticle with high surface area and the average pore size was close to the range of meso-porous material. The XRD diffractogram of 5% Pt/C catalyst is shown in Fig. 3. The diffraction peaks locating at 2θ of 39.5, 46.05 and 67.29° were indicative of Pt crystallines, while the crystalline carbon was detected by diffraction peaks at 2θ of 24.6 and 43.4°. The average particle size of 43.8 nm was estimated from the diffraction peaks for Pt by using Scherrer's equation. The nitrogen adsorption–desorption isotherm, SEM-EDX, and NH3-TPD analysis of 5% Pt/C catalyst were previously reported by Makcharoen et al.20 The Pt particles were uniformly dispersed on the surface of carbon support.
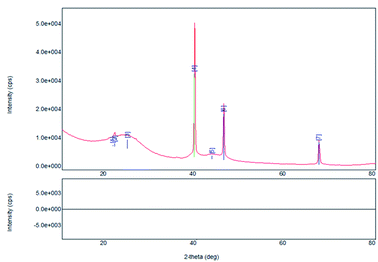 |
| Fig. 3 X-ray diffractogram of 5% wt Pt/C. | |
Preliminary experiments
The experiment was conducted for the conditions at the temperature of 75 °C, the pressure of 1 bar, the amount of the catalyst of 0.025 g, the volumetric flow rate of liquid of 0.03 mL min−1, the volumetric flow rate of gas of 33.9 mL min−1, and the concentration of 5-HMF solution of 2.0 g L−1, respectively. The molar ratio of 5-HMF/NaOH was 1
:
2. Prior to the experiment, the catalyst was reduced in situ with the hydrogen flow rate of 60 mL min−1 at the temperature of 300 °C for a period of 2 h. The product collected at the outlet of the reactor during 7 h of time-on-stream was analyzed and the results are shown in Fig. 4. Complete conversion of 5-HMF was obtained throughout the experiment and DFF was detected in trace amount (the yield was less than 0.22%), suggesting that the reaction first proceeded via the oxidation of aldehyde group of 5-HMF to produce HMFCA. Further oxidation resulted in FFCA and FDCA, respectively. Although the yield of each product was stable, the main product was FFCA. It was also noticed that the yield of FDCA gradually declined from 9.53% at 1 h to 4.66% at 7 h. Hence, the reaction condition must be adjusted to promote further oxidation in order to enhance the yield of FDCA. We varied the catalyst pretreatment conditions in terms of temperature (200 and 300 °C) and hydrogen flow rate (0, 30, and 60 mL min−1). As compared to the case of non-reduced catalyst, it was found that the pretreatment of catalyst did not cause a significant impact on the reaction performance. The difference of FDCA yield was 0.55–1.59%. Therefore, the catalyst was used without pretreatment for subsequent experiments. To shorten the time period before the liquid samples were collected (normally threefold of the residence time) for each experiment, the operating conditions were adjusted by increasing the volumetric flow rate of the liquid to 0.06 mL min−1 while the amount of catalyst was increased by twofold. The conversion of 5-HMF and the yield of each product were approximately the same as previously obtained. This set of reaction parameters was used as a basis for comparison in the next section.
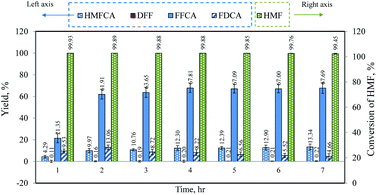 |
| Fig. 4 Time-profile of yield and conversion (operating conditions: T = 75 °C, P = 1 bar, catalyst = 0.025 g, C5-HMF = 2 g L−1, 5-HMF/NaOH = 1 : 2. L = 0.03 mL min−1, g = 33.9 mL min−1). | |
Effect of temperature
In this section, the effect of reaction temperature was studied at 75 °C and 90 °C, while other parameters were kept constant with the catalyst amount of 0.05 g, the liquid flow rate of liquid of 0.06 mL min−1, the oxygen flow rate of 33.9 mL min−1, pressure of 1 bar, and the molar ratio of 5-HMF/NaOH of 1
:
2. At both temperatures, full conversion of 5-HMF was achieved. Fig. 5 shows the yield of HMFCA, FFCA, and FDCA as time profiles. The yield of HMFCA was slightly affected upon increasing the temperature from 75 °C to 90 °C. On the contrary, the yield of FFCA dropped by approximately 20%. This was due to the accelerated rate of oxidation reaction (increased Arrhenius constants). The reaction pathway can be proposed as shown in eqn (4). The first step involved two reactions including the reversible hydration of aldehyde side-chain of 5-HMF followed by dehydrogenation. The product of this step was HMFCA. Then, the activation of C–H bond in the alcohol side-chain of HMFCA on the catalyst surface in the presence of hydroxide ions resulted in the formation of 5-formyl-2-furancarboxylic or FFCA.11 Similar to the first step, the carbonyl group of HMFCA was converted into the carboxylic group in the last step. According to our results, the effect of temperature on the reaction rate was relatively greater for the 3rd step compared to the 2nd step, resulting in a higher yield of FDCA. However, the yield of FDCA was quite small compared to the related literature. We did not increase the reaction temperature further to avoid the complex flow behavior as a result of boiling of water. |
 | (4) |
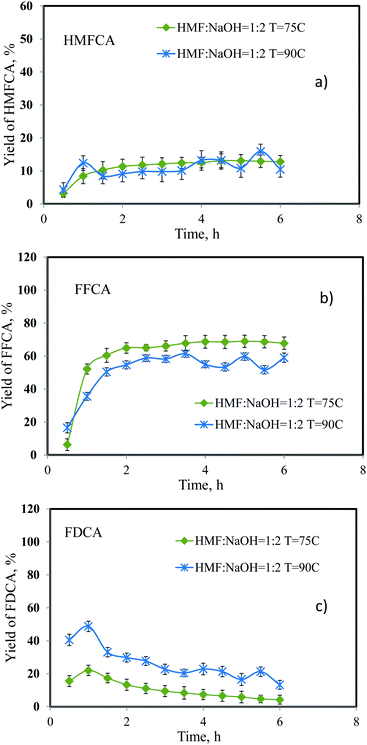 |
| Fig. 5 Effect of reaction temperature on the yield of (a) HMFCA, (b) FFCA and (c) FDCA. | |
Effect of the ratio of 5-HMF/NaOH
The presence of NaOH in the reacting mixture for the oxidation of 5-HMF can be related to the mass transfer characteristics, indirectly affecting the overall production rate of FDCA.13 Shade et al. reported that increasing the basicity of the solution improved desorption of FDCA from the catalyst surface. In other words, increasing the solubility of FDCA prevents the precipitation of the product onto catalyst surfaces. Since the reactor system employed in this work was significantly different from the autoclave reactor used in many previous studies, due to the fact that the moving front of reacting mixture is not greatly affected by the back-mixing, we studied the effect of molar ratio of 5-HMF/NaOH from 1
:
2 to 1
:
12. Other operating parameters were kept constant as 0.05 g of catalyst, reaction temperature of 90 °C, flow rate of oxygen of 33.9 mL min−1, and flow rate of 5-HMF solution of 0.06 mL min−1. The results are shown in Fig. 6. All ratios provided full conversion of 5-HMF throughout the experiment. Fig. 6a shows that increasing the basicity enhanced the yield of HMFCA and FDCA. This effect was pronounced when the ratio was changed from 1
:
4 to 1
:
8. On the contrary, only trace amount of FFCA was detected, suggesting that mass transfer was significantly improved and the conversion of HMFCA into FFCA was rate-limiting (step 2). It was possible that the desorption of FDCA from catalyst was facilitated, allowing effective conversion of FFCA to FDCA. As the ratio was further increased from 1
:
8 to 1
:
12, the yield of FDCA slightly decreased, possibly due to the degradation of FDCA and other products.19 Hence, with the yield of FDCA of 66.6%, the molar ratio between 5-HMF and NaOH of 1
:
8 was used for further studies.
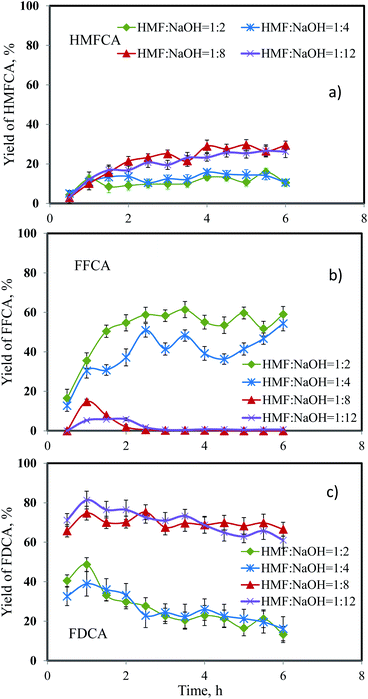 |
| Fig. 6 Effect of 5-HMF/NaOH ratio on the yield of (a) HMFCA, (b) FFCA and (c) FDCA. | |
Effect of gas flow rate
As one of the reactants for the oxidation of 5-HMF, oxygen supply is conceivably the factor affecting the yield of products. In this set of experiments, the O2 flow rate was studied at 33.9, 62.4 and 90.9 mL min−1, corresponding to gas hourly space velocity (GHSV) of 14
221, 26
177 and 38
132 h−1, respectively. The volumetric flow rate of 5-HMF solution was 0.06 mL min−1 and the amount of catalyst was 0.05 g. The reaction temperature was maintained at 90 °C and the molar ratio between 5-HMF and NaOH was 1
:
8. Results are shown in Fig. 7. The yield of FDCA and HMFCA decreased slightly when the oxygen flow rate was increased from 33.9 mL min−1 to 62.4 mL min−1. However, the amount of FFCA was negligible, indicating that the oxidation of 5-HMF to HMFCA and the oxidation of FFCA to FDCA were affected by the prevalence of oxygen and the shortened contact time of reacting mixture inside the fixed-bed reactor. This effect was more pronounced when the oxygen flow rate was further increased to 90.9 mL min−1. In this case, the yield of FDCA rapidly declined, while the opposite trend was observed for the yield of FFCA. Note that the approximately full conversion of 5-HMF was achieved for all oxygen flow rates. The yield of FFCA was almost 50% at 6 h compared to only trace amount at lower oxygen flow rates. Thus, the oxygen flow rate of 33.9 mL min−1 was used to study the effect of pressure.
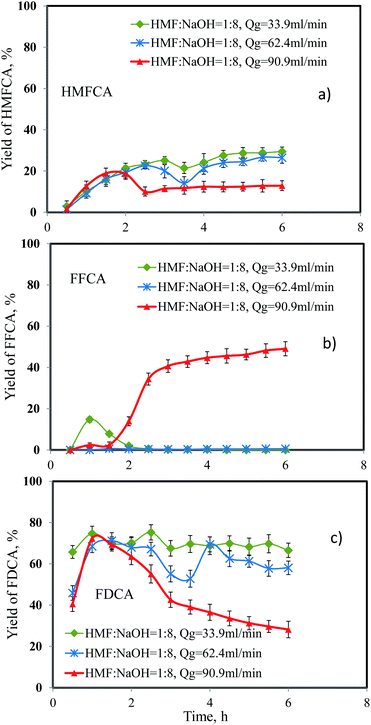 |
| Fig. 7 Effect of oxygen flow rate on the yield of (a) HMFCA, (b) FFCA and (c) FDCA. | |
Effect of pressure
For this reaction system, the oxygen supply is related to pressure of oxygen gas. The effect of pressure was studied at two levels (1 bar and 5.1 bar). For the case of atmospheric pressure, the result was taken from the previous set of experiment. For the pressure of 5.1 bar, we installed a back pressure regulator to maintain the pressure at the exit-end of the reactor. The flow rate of 5-HMF solution was 0.06 mL min−1. The oxygen flow rate was 33.9 mL min−1 and the amount of catalyst was 0.05 g. The reaction was performed at 90 °C with the molar ratio between 5-HMF and NaOH of 1
:
8. Again, complete conversion of 5-HMF was obtained for both cases. Apparently, as shown in Fig. 8, the yield of HMFCA and FDCA decreased significantly when the pressure increased from 1 bar to 5.1 bar which was in line with the work of Sahu et al.19 Although oxygen is essential for the synthesis of FDCA, oversupplying oxygen can also reduce the yield of FDCA. Conceivably, the high oxygen content on the catalyst surface (oxygen surface coverage) interferes the adsorption of other species. Therefore, the reaction rate was impeded as indicated by the markedly increase in the yield of FFCA from trace amount to approximately 80% by increasing the oxygen pressure. Under this circumstance, the oxidation of FFCA to FDCA was the rate limiting step as indicated by the elevated concentration profile of FFCA. In our system, the synthesis of FDCA under atmospheric pressure provided superior performance.
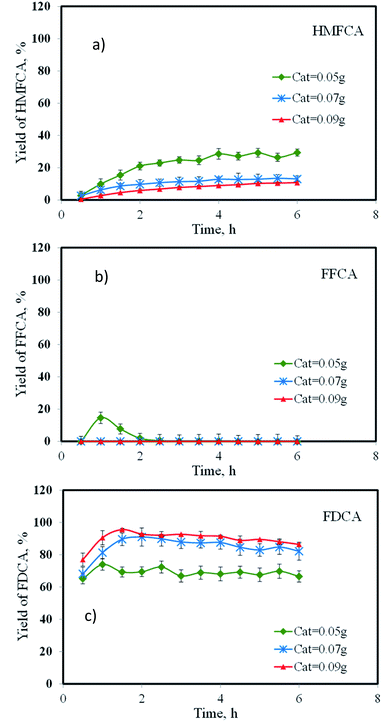 |
| Fig. 8 Effect of catalyst amount on the yield of (a) HMFCA, (b) FFCA and (c) FDCA. | |
Effect of catalyst amount
Since the previous set of experiments showed the significant amount of HMFCA in the product stream, we explored the possibility to shifting this by-product toward the formation of FDCA through further oxidation. The amount of catalyst was increased from 0.05 g to 0.09 g while other operating parameters were maintained at the reaction temperature of 90 °C, flow rate of oxygen of 33.9 mL min−1, and flow rate of 5-HMF solution of 0.06 mL min−1. As the catalyst amount increased from 0.05 to 0.07 g, the yield of HMFCA markedly decreased from 29.4% to 13.05%, corresponding to an increase in the yield of FDCA from 66.6% to 82.2% (see Fig. 9a). Note that FFCA was not present in the product indicating that the oxidation of FFCA to form FDCA was efficient. Further increasing the amount of catalyst to 0.09 g resulted in a slight change of HMFCA concentration, as the 2nd step reaction (conversion of HMFCA to FFCA) was asymptotically enhanced, suggesting an equilibrium limitation. On the contrary, FFCA was completely consumed by the 3rd reaction step, providing the FDCA yield of 86.4%.
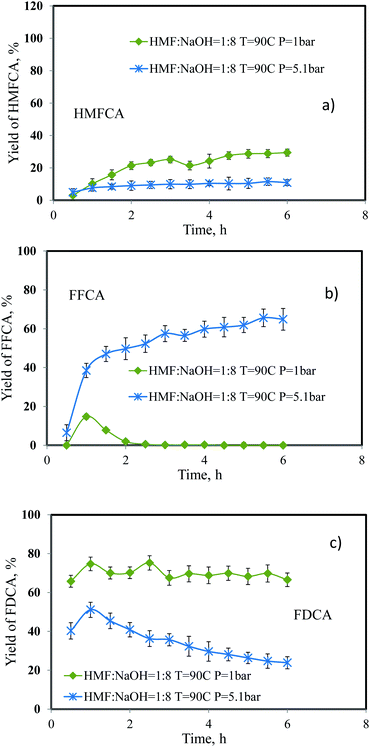 |
| Fig. 9 Effect of pressure on the yield of (a) HMFCA, (b) FFCA and (c) FDCA. | |
Comparison of reaction performance
Based on our experimental results performed for the synthesis of FDCA in a continuous fixed-bed reactor, we compared the reaction performance with those reported in related literature as summarized in Table 2. Most systems were batch processes that required elevated pressures as well as long reaction times. Note that almost full conversion was achieved in all cases. The Pt–Ni catalyst, as reported by Shen et al., provided outstanding performance in terms of yield; however, the required reaction time of 24 h and the 5-HMF-to-catalyst weight ratio of 1.5
:
1 still require further development. Our system was reasonably stable and the yield of 86.4% was relatively high compared to those obtained from other systems despite the similar productivity of 0.1266 kgFDCA kgcat.−1 h−1. Note that the exceptionally high productivity for the case of Li et al. was possibly due to the application of high pressure (40 bar). Our system offers the operation under atmospheric pressure (relatively low oxygen consumption), which can improve safety of operation and reduce the cost involved in equipment and operation at elevated pressures. It can also be further intensified by tuning the 5-HMF inlet concentration and oxygen pressure. Moreover, the residence time of 0.285 s suggested that this process could be compact and efficient compared to the batch production. This work provides the important information that can be used to further improve the performance of FDCA production. Note that only FFCA and FDCA were the main product of our system. These two components can be separated by precipitation technique due to different water solubility of FFCA and FDCA.21
Table 2 Comparison of FDCA synthesis using different systems
Type of reactor |
Catalyst |
T, °C |
P, bar |
Conversion of 5-HMF |
Reaction time, h |
Yield, % |
Productivity, kgFDCA kgcat.−1 h−1 |
Reference |
Batch |
Pt–Ni/AC (0.01 g) |
100 |
4 |
100% |
24 h |
94.2% |
0.0589 |
Shen et al., 2018 (ref. 1) |
Batch |
AuPd–nNiO |
90 |
10 |
95% |
6 h |
70% |
— |
Bonincontro et al., 2019 (ref. 7) |
Batch |
Au/aerosil (0.0252 g) |
90 |
10 |
>99% |
6 h |
74% |
0.1243 |
Masaud et al., 2018 (ref. 12) |
Batch |
Pt/C (0.1134 g) |
100 |
40 |
>99% |
6 h |
69% |
1.15 |
Li et al., 2016 (ref. 22) |
Batch |
Au/ZrO2 (0.098 g) |
100 |
10 |
100% |
5 h |
75% |
0.1928 |
Schade et al., 2018 (ref. 13) |
Semi-batch |
Au/C |
65 |
10 |
100% |
24 h |
78% |
— |
Casanova et al., 2009 (ref. 14) |
Batch |
Pt/γ-Al2O3 (0.10 g) |
140 |
5 |
100% |
48 h |
58% |
0.0121 |
Sahu & Dhepe, 2014 (ref. 19) |
Continuous packed bed reactor |
Pt/C (0.09 g) |
90 |
1 |
100% |
0.285 s |
86.4% |
0.1266 |
This work |
Conclusion
The synthesis of FDCA via catalytic oxidation of 5-HMF using a continuous packed-bed reactor was performed in this work. Platinum supported on activated carbon was used as catalyst. The reaction system was operated with different reaction parameters including reaction temperature (75–90 °C), molar ratio of 5-HMF/NaOH (1
:
2 to 1
:
12), volumetric flow rate of oxygen (33.9–90.9 mL min−1), pressure (1–5.1 bar) and the amount of catalyst (0.05–0.09 g). Only trace amount of DFF was detected. The system was relatively stable except for conditions with oversupply of oxygen such as high oxygen flow rate or high pressure. Under these conditions, the yield of FFCA was much higher than that of FDCA. The yield of FDCA at the optimal conditions (reaction temperature of 90 °C, molar ratio of 5-HMF/NaOH of 1
:
8, oxygen flow rate of 33.9 mL min−1, and atmospheric pressure) was 86.4%, corresponding to the productivity of 0.1266 kgFDCA kgcat.−1 h−1. The short residence time of 0.285 s and no requirements on pressurized equipment are the benefits that can be further utilized effectively for the production of FDCA.
Conflicts of interest
There are no conflicts to declare.
Acknowledgements
This research was funded by the Program Management Unit of Competitiveness, grant number C10F6.
Notes and references
- J. Shen, H. Chen, K. Chen, Y. Qin, X. Lu, P. Ouyang and J. Fu, Atomic Layer Deposition of a Pt-Skin Catalyst for Base-Free Aerobic Oxidation of 5-Hydroxymethylfurfural to 2,5-Furandicarboxylic Acid, Ind. Eng. Chem. Res., 2018, 57(8), 2811–2818 CrossRef CAS.
- K. Loos, R. Zhang, I. Pereira, B. Agostinho, H. Hu, D. Maniar, N. Sbirrazzuoli, A. J. D. Silvestre, N. Guigo and A. F. Sousa, A Perspective on PEF Synthesis, Properties, and End-Life, Front. Chem., 2020, 8, 585 CrossRef CAS PubMed.
- R. O. Rajesh, T. K. Godan, R. Sindhu, A. Pandey and P. Binod, Bioengineering advancements, innovations and challenges on green synthesis of 2, 5-furan dicarboxylic acid, Bioengineered, 2020, 11(1), 19–38 CrossRef CAS PubMed.
- H. Xia, S. Xu, H. Hu, J. An and C. Li, Efficient conversion of 5-hydroxymethylfurfural to high-value chemicals by chemo- and bio-catalysis, RSC Adv., 2018, 8(54), 30875–30886 RSC.
- A. D. K. Deshan, L. Atanda, L. Moghaddam, D. W. Rackemann, J. Beltramini and W. O. S. Doherty, Heterogeneous Catalytic Conversion of Sugars Into 2,5-Furandicarboxylic Acid, Front. Chem., 2020, 8, 659 CrossRef CAS PubMed.
- R. Cang, L.-Q. Shen, G. Yang, Z.-D. Zhang, H. Huang and Z.-G. Zhang, Highly Selective Oxidation of 5-Hydroxymethylfurfural to 5-Hydroxymethyl-2-Furancarboxylic Acid by a Robust Whole-Cell Biocatalyst, Catalysts, 2019, 9(6), 526 CrossRef.
- D. Bonincontro, A. Lolli, A. Villa, L. Prati, N. Dimitratos, G. M. Veith, L. E. Chinchilla, G. A. Botton, F. Cavani and S. Albonetti, AuPd-nNiO as an effective catalyst for the base-free oxidation of HMF under mild reaction conditions, Green Chem., 2019, 21(15), 4090–4099 RSC.
- M. Besson, P. Gallezot and C. Pinel, Conversion of biomass into chemicals over metal catalysts, Chem. Rev., 2014, 114(3), 1827–1870 CrossRef CAS PubMed.
- S. E. Davis, A. D. Benavidez, R. W. Gosselink, J. H. Bitter, K. P. de Jong, A. K. Datye and R. J. Davis, Kinetics and mechanism of 5-hydroxymethylfurfural oxidation and their implications for catalyst development, J. Mol. Catal. A: Chem., 2014, 388–389, 123–132 CrossRef CAS.
- S. E. Davis, L. R. Houk, E. C. Tamargo, A. K. Datye and R. J. Davis, Oxidation of 5-hydroxymethylfurfural over supported Pt, Pd and Au catalysts, Catal. Today, 2011, 160(1), 55–60 CrossRef CAS.
- S. E. Davis, B. N. Zope and R. J. Davis, On the mechanism of selective oxidation of 5-hydroxymethylfurfural to 2,5-furandicarboxylic acid over supported Pt and Au catalysts, Green Chem., 2012, 14(1), 143–147 RSC.
- N. Masoud, B. Donoeva and P. E. de Jongh, Stability of gold nanocatalysts supported on mesoporous silica for the oxidation of 5-hydroxymethyl furfural to furan-2,5-dicarboxylic acid, Appl. Catal., A, 2018, 561, 150–157 CrossRef CAS.
- O. R. Schade, K. F. Kalz, D. Neukum, W. Kleist and J.-D. Grunwaldt, Supported gold- and silver-based catalysts for the selective aerobic oxidation of 5-(hydroxymethyl)furfural to 2,5-furandicarboxylic acid and 5-hydroxymethyl-2-furancarboxylic acid, Green Chem., 2018, 20(15), 3530–3541 RSC.
- O. Casanova, S. Iborra and A. Corma, Biomass into chemicals: aerobic oxidation of 5-hydroxymethyl-2-furfural into 2,5-furandicarboxylic acid with gold nanoparticle catalysts, ChemSusChem, 2009, 2(12), 1138–1144 CrossRef CAS PubMed.
- R. Latsuzbaia, R. Bisselink, A. Anastasopol, H. van der Meer, R. van Heck, M. S. Yagüe, M. Zijlstra, M. Roelands, M. Crockatt, E. Goetheer and E. Giling, Continuous electrochemical oxidation of biomass derived 5-(hydroxymethyl)furfural into 2,5-furandicarboxylic acid, J. Appl. Electrochem., 2018, 48(6), 611–626 CrossRef CAS.
- N. Chueluecha, A. Kaewchada and A. Jaree, Biodiesel synthesis using heterogeneous catalyst in a packed-microchannel, Energy Convers. Manage., 2017, 141, 145–154 CrossRef CAS.
- C. Sonsiam, A. Kaewchada, S. pumrod and A. Jaree, Synthesis of 5-hydroxymethylfurfural (5-HMF) from fructose over cation exchange resin in a continuous flow reactor, Chem. Eng. Process., 2019, 138, 65–72 CrossRef CAS.
- W. Partenheimer and V. V. Grushin, Synthesis of 2,5-Diformylfuran and Furan-2,5-Dicarboxylic Acid by Catalytic Air-Oxidation of 5-Hydroxymethylfurfural. Unexpectedly Selective Aerobic Oxidation of Benzyl Alcohol to Benzaldehyde with Metal/Bromide Catalysts, Adv. Synth. Catal., 2001, 343, 102–111 CrossRef CAS.
- R. Sahu and P. L. Dhepe, Synthesis of 2,5-furandicarboxylic acid by the aerobic oxidation of 5-hydroxymethyl furfural over supported metal catalysts, React. Kinet., Mech. Catal., 2014, 112(1), 173–187 CrossRef CAS.
- M. Makcharoen, A. Kaewchada, N. Akkarawatkhoosith and A. Jaree, Biojet fuel production via deoxygenation of crude palm kernel oil using Pt/C as catalyst in a continuous fixed bed reactor, Energy Convers. Manage.: X, 2021, 12, 100125 CAS.
- A. A. Ghatta, J. D. E. T. Wilton-Ely and J. P. Hallett, Strategies for the Separation of the Furanic Compounds HMF, DFF, FFCA, and FDCA from Ionic Liquids, ACS Sustainable Chem. Eng., 2019, 7(19), 16483–16492 CrossRef CAS.
- S. Li, K. Su, Z. Li and B. Cheng, Selective oxidation of 5-hydroxymethylfurfural with H2O2 catalyzed by a molybdenum complex, Green Chem., 2016, 18(7), 2122–2128 RSC.
|
This journal is © The Royal Society of Chemistry 2022 |
Click here to see how this site uses Cookies. View our privacy policy here.