DOI:
10.1039/D2RA01493A
(Paper)
RSC Adv., 2022,
12, 20747-20754
Potential application of carbohydrate biomass in hydrometallurgy: one-pot reduction of metal oxides/salts under mild hydrothermal conditions†
Received
7th March 2022
, Accepted 13th July 2022
First published on 20th July 2022
Abstract
Carbohydrate biomass can be employed as a reductant for metallic material preparation due to it possessing diverse reducing functional groups. The reported studies focused on reduction of metal ions in acidic solution with the aid of biomass. However, we found alkali hydrothermal conditions are favorable to metal compound reduction, even direct conversion of metal oxides to metals. Based on our previous research on direct reduction of CuO and NiO into the corresponding metals, herein, conversion of other metal oxides (Fe2O3, MnO2, Co3O4, PbO2) with glucose was investigated to illustrate the universal applicability of direct reduction of metal oxides with carbohydrates under alkali hydrothermal conditions. Furthermore, metal salt reduction by carbohydrates was studied and the reduction performance of glucose and cellulose with and without alkali was compared. The results showed an alkaline hydrothermal environment is more conducive to metal reduction. Unlike the complete reduction of CuO and NiO, oxides of Fe(III), Mn(IV), Co(III) and Pb(IV) can only be partially reduced under the experimental conditions. Not only carbohydrates but also decomposed intermediates can reduce metal oxides or salts. In addition, due to the formation of stable complexes between the anions of salts and the decomposition products of carbohydrates, the reduction effects of various copper salts are significantly different. This study may provide an alternative approach to metal preparation in hydrometallurgy.
1. Introduction
Biomass utilization has attracted considerable attention as a vital strategy to alleviate the excessive dependence on fossil fuels and to reduce carbon emissions.1–3 An expected approach to biomass utilization should adapt to the molecular properties of functionalized biomass molecules to improve the efficiency and reduce the cost of application.4,5 Leaching of metal ions from ores and reduction to elementary substances is a well-known hydrometallurgical process. The target metal can be extracted from ores either by reduction roasting followed by acid leaching or directly by reductive acid leaching using various reducing agents, which generally involves methanol, dimethyl sulfoxide, oxalic acid and aqueous sulfur dioxide.6 These reductants are mainly from fossil energy and easily cause secondary pollution during operation. Many efforts have been devoted to developing green and cost-effective reducing agents.7
Glucose and cellulose which represent the basic compositions of carbohydrate biomass are the most abundant monosaccharide and polysaccharide on Earth. In fact, cellulose is a linear polymer of D-glucose with β-1,4-glycosidic bonds, and thus both possess similar reducing functional group such as hydroxyl and hemiacetal. Glucose is soluble in water but cellulose is insoluble at room temperature due to the robust crystal structure. However, cellulose can be easily decomposed to oligosaccharides and monosaccharides in high temperature water (HTW) due to the combination of cleavage of hydrogen bonds within the cellulose crystal and decrease of hydrogen linkage among water molecules, as well as partially attributed to the hydrolysis reaction in HTW.8,9 Obviously, HTW enhances the reducing ability of cellulose. Hence, the nontoxic, cheap and abundant carbohydrate biomass may be employed as an alternative and environmentally friendly reducing agent in the hydrometallurgical process.
Almost all reported studies focused on reduction of Ag(I),10,11 Au(III),12–14 Cu(II),15–18 and Mn(IV)7,19–22 in acidic solution with the aid of carbohydrate biomass. The corresponding elemental metals (e.g. Ag, Au, Cu) or low valent metal ions (e.g. Mn(II)) were obtained by reductive acid leaching process. Although researchers believe that carbohydrates act as reducing agents, detail reduction process is not involved. Some studies just mentioned biomass eventually oxidized to CO2. Obviously, biomass was not completely oxidized under mild hydrothermal conditions. In our research on hydrothermal conversion of carbohydrates into value-added chemicals, we found carbohydrates were favorable to selective oxidation to low molecular weight organic acids such as acetic acid and formic acid in alkali solution.3,23,24 Further studies demonstrated not only metal ions but also metal oxides can be directly reduced under mild alkali hydrothermal conditions.25–27 Although one-pot reduction of CuO and NiO into Cu and Ni were achieved respectively with glucose and cellulose, the different performance between glucose and cellulose with and without alkali are ambiguous, and the feasibility to other metal oxides reduction need to be examined. In this paper, reduction of other metal oxides (Fe2O3, MnO2, Co3O4, PbO2) with glucose were investigated. Furthermore, we compared the reduction ability of glucose and cellulose under alkali hydrothermal conditions and studied their performance on metal salts reduction.
2. Experimental section
2.1 Materials
All metal oxides (200-mesh), salts and glucose were analytical grade and obtained from Sinopharm Chemical Reagent Co., Ltd. α-Cellulose (powder) and standard substances were purchased from Sigma-Aldrich. All reagents were used as received without further purification.
2.2 Experimental procedure
The experiments were carried out in a Teflon-lined stainless-steel batch reactor with an inner volume of 30 mL. Typically, 0.24 M metal oxide and 0.4 M carbohydrate (glucose or cellulose) were added into the alkali solution (0.1–5 M) and stirred with a magnetic blender for several minutes. The certain concentrations of metal oxide and carbohydrate were referred to our previous study.29–31 Then, the mixture was put into a rotating reactor with a speed of 30 rpm and heated in the oven which had been preheated to the given temperature for several hours. After the reaction, the reactor was taken out of oven and cooled naturally to room temperature. The liquid products were filtered with a 0.22 μm filter membrane for chromatographic measurements. The precipitate was washed with distilled water and absolute ethanol several times to remove impurities and subject to further analysis.
2.3 Product analyses
The solid samples analyses were determined by X-ray diffraction (XRD) on the Bruker D8 Advance XRD equipped with Cu Kα radiation. The scanning rate of 0.1° s−1 and 2θ range from 20° to 90° were set with 40 kV accelerating voltage and 30 mA flux. The diffraction patterns were compared with reference data of ICDD PDF-2. Notably, the reduction rate of metal oxides was calculated by the XRD quantitative analyses using software TOPAS 4.2.28 This software is based on the fundamental parameter approach (FPA), which considers the geometric and unit-specific parameters, and widely used in facile quantitative analysis of solid polycrystalline mixture.29
The liquid samples were analyzed by high-performance liquid chromatography (HPLC) measurement on Agilent 1260 serials equipped with UV-vis detector. Two Shodex RSpak KC-811 columns were used in series and mobile phase was 2 mM HClO4 with a flow rate of 1 mL min−1. Liquid samples determination were also analyzed by gas chromatography-mass spectrometry (GC-MS) on Agilent 7890A GC system with a 5795C inert MSD. A HP-INNOWax capillary column with dimensions of 30 m × 250 μm × 0.25 μm was used for separation of samples.
3. Results and discussion
3.1 Reduction of metal oxides
3.1.1 Complete reduction of CuO and NiO. The reduction of CuO and NiO performance on carbohydrates were compared initially. As illustrated in Fig. S1–S4,† the XRD patterns showed not only glucose but also cellulose can directly reduce CuO and NiO to the corresponding elemental metal powders under alkali hydrothermal conditions. The optimized reaction parameters were listed in Table 1. For cellulose, the crystal structure of cellulose is first destroyed in HTW and then dissolved in water, followed by hydrolysis to monosaccharides, whereas water soluble glucose can directly react with metal oxides or salts. Therefore, the reduction efficiency of glucose is higher than that of cellulose at a lower concentration of alkali (e.g. 0.1 M NaOH).29 Interestingly, a higher concentration of alkali (e.g. 0.4 M NaOH) can enhance the CuO reduction with cellulose and significantly shorten the reaction time. The possible reason is that higher concentration of alkali can promote the decomposition of cellulose and the formation of reducing decomposition products (e.g. lactic acid).30,31 As for reduction of NiO, the reaction needs higher concentration of alkali and longer reaction time than that of CuO. It is probably due to lower leaching of Ni and higher value of ΔGred (Gibbs free energy for reduction of metal oxide).32 As to the size of obtained Cu and Ni powder, both measurements from laser particle size analyzer and SEM indicated the size of obtained particles were much smaller than that of the initial particles.26,27 For example, the average particle sizes of the initial CuO and the Cu after reaction were 6.19 μm and 2.41 μm, respectively. The size distribution of the obtained Cu particle was narrower than that of CuO, indicating that the size of Cu obtained was more uniform.
Table 1 Optimal reaction conditions for complete reductiona of CuO and NiO
Feedstock |
CuO |
NiO |
Complete reduction means a 100% conversion rate of metal oxides to metal. Both the concentration of glucose and cellulose were 0.4 M in this study. |
Glucoseb |
250 °C, 3 h, 0.1 M NaOH, 0.4 M glucose, 0.24 M CuO29 |
250 °C, 4 h, 5 M NaOH, 0.4 M cellulose, 0.2 M NiO |
Cellulosea |
250 °C, 1.5 h, 0.4 M NaOH, 0.4 M cellulose, 0.24 M CuO |
250 °C, 4.5 h, 5 M NaOH, 0.4 M cellulose, 0.2 M NiO31 |
While metal oxides were reduced to metals, glucose and cellulose was oxidized to low molecular weight (<C3) organics. The liquid samples were tested by GC-MS and HPLC as shown in Fig. S5–S12.† No matter reduction of CuO or NiO with glucose or cellulose, organic acids such as acetic acid, acrylic acid and formic acid and cyclopentanone derivatives formed after hydrothermal treatment. The obvious difference between glucose and cellulose as reductant is dihydric alcohols significant formation with cellulose, especially for NiO reduction. Furthermore, as shown in Fig. S11,† the peaks of ethylene glycol (EG) and propylene glycol (PG) decreased significantly in the presence of NiO. The quantity analysis of EG showed that the amounts of EG were 365 and 973 mg L−1 with and without NiO, respectively.31 The EG amount change indicated its important role in the metal oxides reduction and experimental results will be discussed in the Possible Pathway study section.
3.1.2 Partial reduction of Fe(III), Mn(IV), Co(III), Pb(IV) compounds. To examine the feasibility to reduction of metal oxides with carbohydrates, we newly conducted a series of experiments with other general metal oxides and glucose under optimal conditions referred to reduction of CuO and NiO. First, several iron oxides and hydroxides, Fe2O3, Fe3O4, Fe(OH)2 and FeO were reacted with glucose in the absence and presence of alkali. The results showed 70.6% of Fe2O3 was reduced to Fe3O4 with 2.5 M NaOH at 250 °C for 6 h (Fig. 1). However, no matter increasing the reaction time or alkali concentration, Fe(II) compounds cannot further reduce to elemental Fe. In our group previous work, iron oxides can be reduced completely to elemental iron by glycerol in the presence of alkali,33 however, complete reduction was not achieved in the mixed solution of glycerol and water. The reaction medium may play an important role in metal oxides reduction. If the metal is unstable in alkaline HTW, the reduced metal will be oxidized by water. Further experimental results will be demonstrated in the following section of metal stability study. Although no Fe formed with glucose, Fe3O4 obtained is benefit for magnetic separation and has potential application in separating associated metals in hydrometallurgy process.
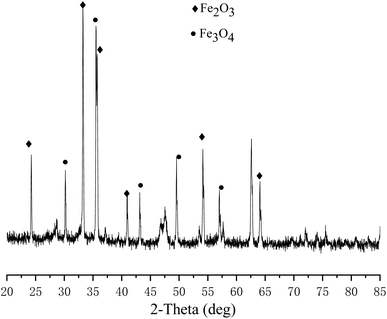 |
| Fig. 1 XRD patterns of solid product after Fe2O3 reduction with glucose (250 °C, 6 h, 2.5 M NaOH, 0.4 M glucose, 0.2 M Fe2O3). | |
Subsequently, alkali hydrothermal reduction of MnO2 was investigated. As illustrated in Fig. 2, main product was Mn3O4 after the reaction with NaOH at 250 °C for 3 h. The following research on Co3O4 reduction showed almost all Co3O4 was reduced to CoO after 6 h with 1 M NaOH, indicating reduction of Co(III) is easier than that of Mn(IV) and Fe(III) in alkali solution (Fig. 3). For PbO2 reduction with glucose, as seen in Fig. S13,† several Pb(II) compounds were obtained with 1 M NaOH for 6 h. These results demonstrated a possibility of selective reduction of mixed metal oxides by facile adjusting the alkali concentration and magnetic separation. Experiments with actual metal oxides ores containing mixed metals such as Fe, Ni, Cu, Co and Mn are in progress.
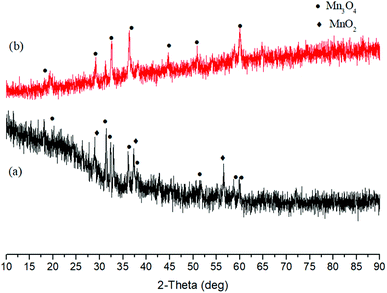 |
| Fig. 2 XRD patterns of solid products after reactions of 0.4 M glucose and 0.2 M MnO2 without (a) and with (b) 2.5 M NaOH (250 °C, 3 h). | |
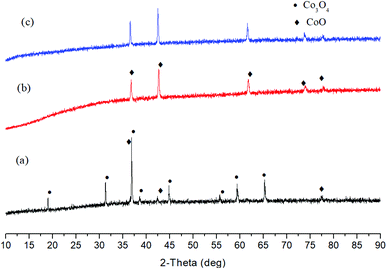 |
| Fig. 3 XRD patterns of solid products before (a) and after reactions of 0.4 M glucose and 0.2 M Co3O4 for 6 h (b) and 12 h (c) (250 °C, 1 M NaOH). | |
3.2 Reduction of metal salts
To examine the reduction performance of carbohydrate without alkali, salts of Cu, Ni and Fe were tested in the following experiments. Four copper salts, CuSO4, CuCl2, Cu(NO3)2 and Cu2P2O7 were first studied with glucose at 160 °C and 250 °C. The selection of temperature is based on the previous study of metal oxide reduction and considering the heat resistance of Teflon reactor lining. As shown in Fig. 4 and 5, Cu2P2O7 can be completely reduced to Cu at both temperatures. For CuSO4, the lower temperature (160 °C) is favorable to CuSO4 complete reduction. When the reaction temperature increased to 250 °C, a small amount of Cu2S (4.4%) appeared with Cu (87.9%) and Cu2O (7.9%). Cu2S is considered as the product of decomposition and reduction of CuSO4. On the contrary, a higher temperature (250 °C) benefits the reduction of Cu(NO3)2, which reduced products consist of Cu (89.7%) and Cu2O (10.3%). At a lower temperature of 160 °C, a significant amount of CuC2O4 (44.6%) was obtained. Further liquid samples analyses (Fig. S16 and S17†) showed there was oxalic acid after the reaction of Cu(NO3)2 with glucose. It is likely the CuC2O4 formation at lower temperatures prevents the complete reduction of Cu(NO3)2. The reason why formed copper oxalate is not conducive to reduction may be that the steric hindrance of oxalate ligand prevents the formation of hydroxyl copper complex between copper and carbohydrate, leading to difficulty in the coordination reduction reaction. At a higher temperature of 250 °C, there is no CuC2O4 in the products because thermally unstable CuC2O4 decomposed easily to CuO,34 followed by further reduction. An unexpected find is little reduction for CuCl2 under these conditions. At the experimental temperatures, the solid products were only Cu2Cl(OH)3. Obviously, the formation of copper hydroxychloride hinders the reduction of copper. This may be because copper hydroxychloride is more stable than hydroxyl copper complexes which are the key intermediates during the coordination–reduction process.35
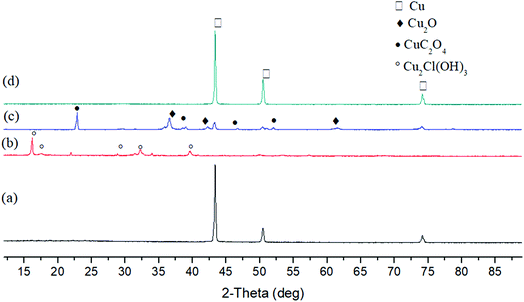 |
| Fig. 4 XRD patterns of solid products after the reduction of CuSO4 (a), CuCl2 (b), Cu(NO3)2 (c) and Cu2P2O7 (d) by glucose without NaOH (160 °C, 6 h). | |
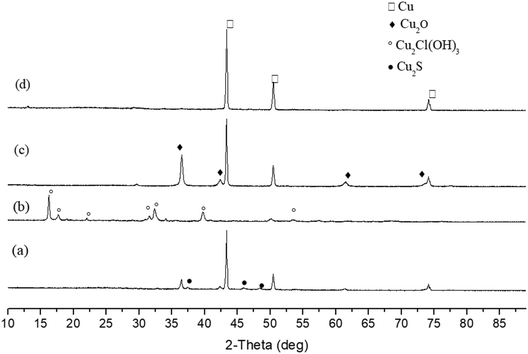 |
| Fig. 5 XRD patterns of solid products after the reduction of CuSO4 (a), CuCl2 (b), Cu(NO3)2 (c) and Cu2P2O7 (d) by glucose without NaOH (250 °C, 3 h). | |
Subsequently, copper salts (CuSO4, CuCl2 and Cu(NO3)2) reduction by cellulose were investigated. Considering the difficulty of cellulose decomposition at low temperature, 250 °C was adopted in this study. As illustrated in Fig. 6, Cu(NO3)2 was reduced completely to Cu, and CuSO4 also was mainly converted to Cu (91.4%). For CuCl2, the performance of cellulose was similar with glucose and only Cu2Cl(OH)3 was obtained in the solid sample. It can be seen that anions have significant effect on the reduction of copper salts by carbohydrates. Further liquid samples analyses (Fig. S18 and S19†) showed there were mainly cyclopentene derivatives, which were also found in the liquid products of glucose reducing copper salts.
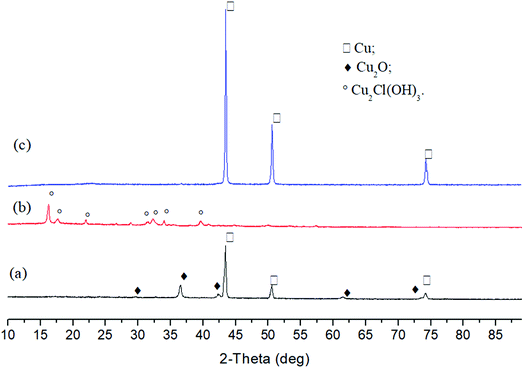 |
| Fig. 6 XRD patterns of solid products after reactions of cellulose with CuSO4 (a), CuCl2 (b) and Cu(NO3)2 (c) (250 °C, 3 h). | |
In the following experiments of nickel salts (NiCl2, NiSO4 and Ni(Ac)2) reduction by glucose or cellulose, no obvious Ni or Ni compounds peaks occurred in XRD patterns, indicating glucose or cellulose cannot direct reduce nickel salts. For Fe salts reduction, no matter Fe(NO3)3 or FeCl3, the major solid phase was Fe3O4 which was partially reduced product (Fig. 7). These results demonstrated the reduction performance of carbohydrate to metal salts without alkali is universally weaker than that to metal oxide with alkali under hydrothermal conditions. It is probably because of higher reducing ability of carbohydrate under alkaline environment.
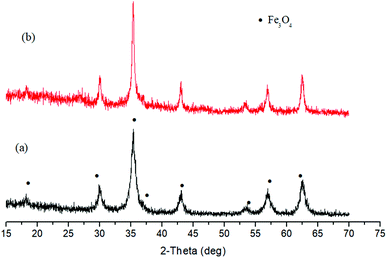 |
| Fig. 7 XRD patterns of solid products after reduction of Fe(NO3)3 (a) and FeCl3 (b) by glucose, respectively (250 °C, 3 h). | |
3.3 Possible pathway of metal oxides/salts reduction
3.3.1 Metal stability under alkali hydrothermal conditions. As mentioned above, we previously reported Fe2O3 was reduced completed to Fe by glycerol.35 However, only Fe3O4 was obtained by glucose reduction in HTW. In addition to the different reduction ability of glycerol and glucose, the influence of reaction medium should be paid attention. HTW may enhance the oxidation of metal, especially in the presence of alkali. In the study on CuO reduction with carbohydrates, we found excessively high concentration (>1 M) of alkali is unfavorable to CuO complete reduction. The reason is probably that Cu is unstable in the hot alkali HTW. To verify this conjecture, we examined the stability of Cu, Ni, Fe and Mn under alkali hydrothermal conditions. As shown in Fig. 8a, Cu is stable with 0.4 M NaOH at 250 °C for 1.5 h. However, as the NaOH concentration increased to 1 M, Cu2O (12.5 wt%) and CuO (3.7 wt%) were obtained (Fig. 8b). Cu oxides formation may attribute to Cu react with alkali, followed by dehydration. Unlike Cu, Ni phase was not changed with NaOH no matter 0.4 M or 5 M (Fig. S20†). Fe displayed unstable even without alkali at 250 °C and a 30.4 wt% yield of Fe3O4 was obtained. As addition of 1 M NaOH, Fe oxidation rose sharply and Fe3O4 yield increased to 84.1 wt% (Fig. 9). Mn is also unstable in alkaline HTW among the tested materials. As illustrated in Fig. 10, almost all Mn transformed to Mn3O4 without alkali and MnO2 with 2.5 M NaOH, respectively. The results of metal stability tests showed suitable concentration of alkali is crucial to metal oxides complete oxidation in HTW.
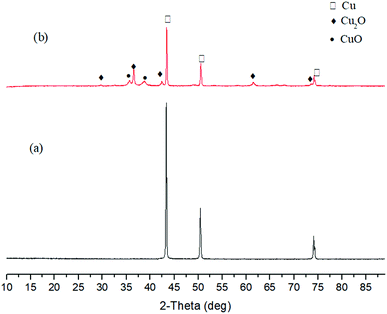 |
| Fig. 8 XRD patterns of solid products after reactions of Cu with 0.4 M (a) and 1 M (b) NaOH (250 °C, 1.5 h). | |
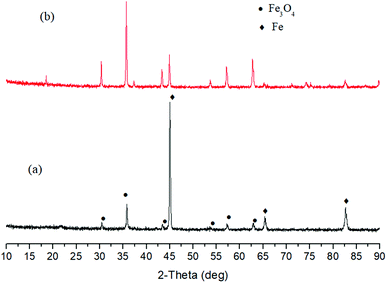 |
| Fig. 9 XRD patterns of solid products after reactions of Fe and water in the absence (a) and presence of (b) 1 M NaOH (250 °C, 6 h). | |
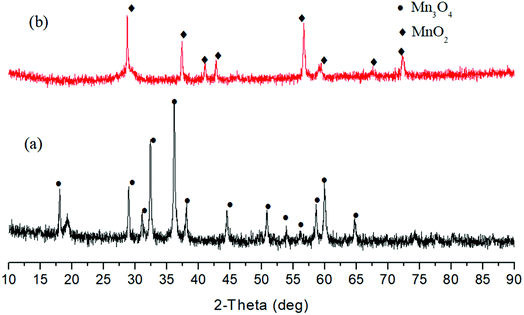 |
| Fig. 10 XRD patterns of solid products after reactions of Mn and water without (a) and with (b) 2.5 M NaOH (250 °C, 3 h). | |
3.3.2 Role of intermediates of carbohydrate decomposition. In our previous study, we found some intermediate decomposition products possess certain reduction ability. For instance, lactic acid, one of the major liquid products under alkali treatment of carbohydrates, can reduce CuO to Cu in the acid solution,26 whereas the reduction effect was limited in the alkali environment. However, NiO reduction with lactic acid cannot achieve in the acid or alkaline solution. To investigate reduction ability of other intermediates, we examined the chromatograms of the samples before and after reduction reactions. Interestingly, some dihydric alcohols, EG, PG and butylene glycol (BG) existed in the liquid samples (Fig. S7, S9 and S11†), especially with cellulose as reductant. Further experiments of these three dihydric alcohols and NiO with NaOH indicated almost all NiO was converted to Ni for 3 h at 250 °C (Fig. S21†). Analyses for liquid samples of EG experiment (Fig. S22†) showed glycolic acid formation except formic acid and lactic acid. Obviously, glycolic acid is the oxidized product of EG, also demonstrating EG engaged in the reduction.
3.3.3 Proposed pathway of metal oxides/salts reduction. The possible pathway of reduction of metal oxides/salts with carbohydrates was illustrated in Fig. 11. As to metal oxides reduction with carbohydrates, polysaccharides initially hydrolyzed to monosaccharides such as glucose and fructose in alkali hydrothermal conditions. Because a strong base in HTW can improve the solubility of metal oxides by the formation of hydroxyl complex,36,37 subsequently, dissociated metal ions from the hydroxyl complex may coordinate with adjacent hydroxyl oxygen of monosaccharide to form a five-membered heterocyclic coordination compound. The short distance between oxygen and metal ion in the coordination compound is favorable for electron transfer from the oxygen atom to metal ion, leading to the reduction of metal ion (path I). Meanwhile, monosaccharide was degraded to diols through hydrogenolysis reaction38 or lactic acid via a series of reactions such as reverse aldol and rearrangement.3 The formed diols and lactic acid also participate in the reduction of metal oxides via similar coordination–reduction process (path II & path III). Finally, metal element and organic acids (e.g. acetic acid) as the redox products were obtained.
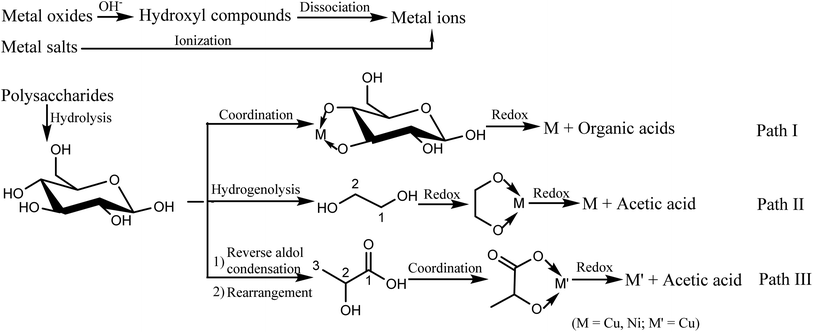 |
| Fig. 11 Proposed pathway of metal oxides/salts reduction. | |
For metal salts reduction with carbohydrates, previous reports proposed carbohydrates were oxidized to carbon dioxide and not involved detail pathway for metal ions reduction.36–38 In fact, carbohydrates were usually partially oxidized no matter in the hot acid or alkali solution. Analyses of liquid samples with copper salts (Fig. S16–S19†) showed some reductive organic intermediates such as lactic acid and oxalic acid from glucose partial oxidization were found. Hence, we believe coordination–reduction also plays a crucial role in metal salts reduction with carbohydrate as reductant. Further study of influence of pH on reduction ability of polyol compounds is ongoing.
4. Conclusions
In this study, we investigated the reduction ability of glucose and cellulose under hydrothermal conditions and compared their performance on reduction of metal oxides and metal salts. The results showed alkaline hydrothermal environment facilitates metal reduction. Unlike the complete reduction of CuO and NiO, oxides of Fe(III), Mn(IV), Co(III) and Pb(IV) can only be partially reduced under experimental conditions. Not only carbohydrates but also decomposed intermediates can reduce metal oxides or salts. In addition, due to the formation of stable complexes between the anions of salts and the decomposition products of carbohydrates, the reduction effects of various copper salts are significantly different. This study reveals carbohydrates application in metal compound reduction and may provide an alternative approach to metal preparation in hydrometallurgy.
Funding sources
Financial support from the National Key Research and Development Project (2018YFC1902103).
Conflicts of interest
The authors declare no competing financial interest.
References
- R. K. Srivastava, N. P. Shetti, K. R. Reddy, E. E. Kwon, M. N. Nadagouda and T. M. Aminabhavi, Environ. Pollut., 2021, 276, 116731 CrossRef CAS PubMed.
- M. Hamza, M. Ayoub, R. Bin Shamsuddin, A. Mukhtar, S. Saqib, I. Zahid, M. Ameen, S. Ullah, A. G. Al-Sehemi and M. Ibrahim, Environ. Technol. Innovation, 2021, 21, 101200 CrossRef CAS.
- F. M. Jin and H. Enomoto, Energy Environ. Sci., 2011, 4, 382–397 RSC.
- C. Jin, J. Nai, O. Sheng, H. Yuan, W. Zhang, X. Tao and X. W. Lou, Energy Environ. Sci., 2021, 14, 1326–1379 RSC.
- Y. Shao, K. Sun, L. Zhang, Q. Xu, Z. Zhang, Q. Li, S. Zhang, Y. Wang, Q. Liu and X. Hu, Green Chem., 2019, 21, 6634–6645 RSC.
- M. K. Jha, J.-C. Lee, M.-S. Kim, J. Jeong, B.-S. Kim and V. Kumar, Hydrometallurgy, 2013, 133, 23–32 CrossRef CAS.
- M. K. Sinha and W. Purcell, Hydrometallurgy, 2019, 187, 168–186 CrossRef CAS.
- Z. Fang, T. Minowa, R. L. Smith, T. Ogi and J. A. Kozinski, Ind. Eng. Chem. Res., 2004, 43, 2454–2463 CrossRef CAS.
- P. E. Savage and N. Akiya, Chem. Rev., 2002, 102, 2725–2750 CrossRef PubMed.
- S. Syed, Waste Manag., 2016, 50, 234–256 CrossRef CAS PubMed.
- P. Raveendran, J. Fu and S. L. Wallen, Green Chem., 2006, 8, 34–38 RSC.
- J. Tang, Y. Chen, S. Wang, D. Kong and L. Zhang, Environ. Res., 2022, 210, 112870 CrossRef CAS PubMed.
- L. Chen, J. Tang, S. Wu, S. Wang and Z. Ren, Carbohydr. Polym., 2022, 286, 119307 CrossRef CAS PubMed.
- J. C. Liu, G. W. Qin, P. Raveendran and Y. Kushima, Chem.–Eur. J., 2006, 12, 2132–2138 Search PubMed.
- L. Ramrakhiani, S. Ghosh and S. Majumdar, Clean Technol. Environ. Policy, 2022, 24, 1261–1284 CrossRef CAS.
- A. U. Stefanko and D. Leszczynska, J. Environ. Eng., 2021, 147, 04021069 CrossRef CAS.
- R. D. van der Weijden, J. Mahabir, A. Abbadi and M. A. Reuter, Hydrometallurgy, 2002, 64, 131–146 CrossRef CAS.
- H. Chen, J. H. Lee, Y. H. Kim, D. W. Shin, S. C. Park, X. Meng and J. B. Yoo, J. Nanosci. Nanotechnol., 2010, 10, 629–636 CrossRef CAS PubMed.
- Y. Sun, G. Fu, L. Jiang and X. Cai, Miner. Metall. Process., 2018, 35, 215–220 Search PubMed.
- J. Gan, J. Cui, X. Li, Y. Muhammad, Y. Wang and H. Su, New J. Chem., 2018, 42, 20144–20151 RSC.
- H. F. Su, Y. X. Wen, F. Wang, Y. Y. Sun and Z. F. Tong, Hydrometallurgy, 2008, 93, 136–139 CrossRef CAS.
- X. K. Tian, X. X. Wen, C. Yang, Y. J. Liang, Z. B. Pi and Y. X. Wang, Hydrometallurgy, 2010, 100, 157–160 CrossRef CAS.
- C. Wang, X. Chen, M. Qi, J. Wu, G. Gozaydin, N. Yan, H. Zhong and F. Jin, Green Chem., 2019, 21, 6089–6096 RSC.
- Y. Fang, X. Zeng, P. Yan, Z. Jing and F. Jin, Ind. Eng. Chem. Res., 2012, 51, 4759–4763 CrossRef CAS.
- F. M. Jin, G. D. Yao and Z. B. Huo, Res. Chem. Intermed., 2011, 37, 351–358 CrossRef.
- Q. Li, G. Yao, X. Zeng, Z. Jing, Z. Huo and F. Jin, Ind. Eng. Chem. Res., 2012, 51, 3129–3136 CrossRef CAS.
- G. Yao, X. Zeng, Q. Li, Y. Wang, Z. Jing and F. Jin, Ind. Eng. Chem. Res., 2012, 51, 7853–7858 CrossRef CAS.
- Bruker AXS GmbH, TOPAS V4.2, Karlsruhe, Germany, 2009 Search PubMed.
- R. W. Cheary and A. Coelho, J. Appl. Crystallogr., 1992, 25, 109–121 CrossRef CAS.
- F. Wang, Y. Wang, F. Jin, G. Yao, Z. Huo, X. Zeng and Z. Jing, Ind. Eng. Chem. Res., 2014, 53, 7939–7946 CrossRef CAS.
- Z. Ma, J. Hu, G. Yao, J. Duo, B. Jin and F. Jin, Process Saf. Environ. Prot., 2018, 115, 79–84 CrossRef CAS.
- D. Larcher and R. Patrice, J. Solid State Chem., 2000, 154, 405–411 CrossRef CAS.
- F. M. Jin, Y. Gao, Y. J. Jin, Y. L. Zhang, J. L. Cao, Z. Wei and R. L. Smith, Energy Environ. Sci., 2011, 4, 881–884 RSC.
- D. Broadbent, J. Dollimore, D. Dollimore and T. A. Evans, J. Chem. Soc., Faraday Trans., 1991, 87, 161–166 RSC.
- S. Li, M. T. Teague, G. L. Doll, E. J. Schindelholz and H. Cong, Corros. Sci., 2018, 141, 243–254 CrossRef CAS.
- H. F. Su, H. K. Liu, F. Wang, X. Y. Lu and Y. X. Wen, Chin. J. Chem. Eng., 2010, 18, 730–735 CrossRef CAS.
- M. Trifoni, L. Toro and F. Veglio, Hydrometallurgy, 2001, 59, 1–14 CrossRef CAS.
- G. Furlani, F. Pagnanelli and L. Toro, Hydrometallurgy, 2006, 81, 234–240 CrossRef CAS.
Footnote |
† Electronic supplementary information (ESI) available: XRD patterns of solid products (Fig. S1–S4, S13 and S20–S21) HPLC and GC-MS chromatograms of liquid products (Fig. S5–S12, S14–S19 and S22). See https://doi.org/10.1039/d2ra01493a |
|
This journal is © The Royal Society of Chemistry 2022 |
Click here to see how this site uses Cookies. View our privacy policy here.