DOI:
10.1039/D2RA01320G
(Paper)
RSC Adv., 2022,
12, 12152-12159
Theoretical analysis and evaluation of reaction routes by “three-parameter difference” †
Received
27th February 2022
, Accepted 4th April 2022
First published on 21st April 2022
Abstract
How to choose a high-efficiency, green and inherent safety synthetic route is an important issue for the development of the chemical industry. “Three-parameter difference” is a complex parameter with the calculation of Gibbs free energy, atom utilization and inherent safety index, and can be used to comprehensively evaluate the thermodynamic feasibility, greenness and safety of chemical reactions. This parameter has been proposed and established, but the reliability has not been determined. In this study, the parameter has been corrected to make it more universal. It was calculated and studied in the synthesis of dimethyl carbonate and toluene diisocyanate, separately. The results showed that the reaction pathways for synthesizing dimethyl carbonate from the gas-phase oxidative carbonylation of methanol by a one-step process, and toluene diisocyanate from dimethyl carbonate-ionic liquid hydroxylamine have obvious advantages and future research prospects. They are consistent with the existing actual research, which can prove the reliability of the “three-parameter difference”. More importantly, the parameter provides a theoretical basis and has an adequate practical guidance significance to design and evaluate a new synthesis route.
1. Introduction
At present, the chemical industry is developing from the early single technical and economic index to the goal of paying equal attention to the triple indexes of engineering economy, environment-friendly and process safety.1 The “three-parameter difference” parameter has been proposed and defined by our research group based on Gibbs free energy, atom utilization and inherent safety index as the theoretical basis for evaluating the thermodynamic feasibility, greenness and safety of chemical reactions.2 However, there is a little introduction on the use of this parameter. In this study, the synthesis pathways of dimethyl carbonate and toluene diisocyanate, covering various of phase states and types of reaction routes, were comprehensively analyzed by using this parameter, and hence the optimal reaction route was designed. By comparing with the existing research results, the reliability of the “three-parameter difference” was verified, which provides examples for the synthesis of the chemical products, particularly the proposal of new processes.
2. Definition and correction of “three-parameter difference”
We defined the difference ΔRi between the three parameters (
, yAUi,
) of the chemical reaction i and the three parameters (−1, 1, 0) of the ideal chemical reaction as the “three-parameter difference”, as shown in the following formula. That is, the degree of proximity to the ideal reaction was used to characterize the comprehensive performance of the reaction, and this was used as a criterion to provide a basis for the selection of the chemical reaction path. The smaller the ΔRi value is, the closer to the ideal chemical reaction; ΔRi = 0, which represents the ideal chemical reaction.
where
is the ratio of the Gibbs free energy of reaction i to the absolute value of the minimum Gibbs free energy for all reactions,
; yAUi is the atom utilization of reaction i;
is the ratio of the inherent safety index of reaction i to the maximum inherent safety index of all reactions,
.
Detailed calculations of Gibbs free energy, atomic utilization and inherent safety index mentioned above are provided in the ESI.†
On this basis, the following provisions are recommended.
(1) The selection rules of reaction conditions are as follows: the reaction conditions of the industrialized process are actual reaction conditions. Due to the uncertainty and research goal for each reaction condition in the basic research, the reaction temperature was selected as 70–150 °C; the reaction pressure as 5–25 bar; the reaction yield as 90–99%.
(2) For a multi-step reaction system, the ΔRi of the total reaction is the average value of the steps. However, the reactions with smaller or larger of ΔRi should be paid more attention.
3. Analysis of the reaction route for the synthesis of dimethyl carbonate
Dimethyl carbonate (DMC) has excellent reactivity because there are various functional groups in the molecule, such as methyl, methoxy, and carbonyl group. Therefore, it can replace highly toxic phosgene and dimethyl sulphate as the carbonylation or methylation agent. At present, with the rapid development of the electric vehicle industry, the market demand of DMC in electrolytes is huge. Since the 1980s, numerous synthetic routes of DMC have been developed, mainly including phosgene process,3 transesterification method,4–6 gas-phase oxidative carbonylation of methanol (one-step process,7,8 two-step process9), methanol-urea alcoholysis method,10,11 methanol-CO2 method12 and methanol-propylene oxide-CO2 method.13,14 In this section, the “three-parameter difference” was first applied to the analysis and comparison of the reaction route for the “synthesis of DMC with methanol as the initial raw material”, and then, the similar reaction paths with different raw materials were analyzed and compared to predict and evaluate the advantages and disadvantages. The material safety index (Table S1†) and the process safety index (Table S2†) of each reaction for the synthesis of DMC are shown in the ESI.†
3.1. Reaction route for DMC synthesis from methanol as the initial raw material
The reaction equations are as follows: |
 | (R1) |
|
 | (R2) |
|
 | (R3) |
|
 | (R4) |
|
 | (R5) |
According to the Gibbs free energy, atom utilization and inherent safety index (Table S3†) of each reaction for the DMC synthesis obtained above, ΔRi was calculated, and the results are shown in Table 1. It can be seen that the order of the OSI′ is R2 > R1 = R5 > R3 > R4, indicating that the methanol-CO2 method (R4) is the safest with the lowest inherent safety index. However, the Gibbs free energy of this method is greater than 0 (Fig. S1†) in the temperature range (298–1000 K), that is, it cannot proceed spontaneously in thermodynamics, so ΔR4 is relatively large. The gas-phase oxidative carbonylation of methanol by the one-step process (R2) is less than 0, and the atom utilization rate is high, and ΔR2 (1.014) is the minimum, indicating that it is the most favorable. Moreover, this method has certain advantages, such as easily available raw materials, low toxicity, simple process and low cost. It is a promising method, which is consistent with the existing research status.7,8
Table 1 “Three parameter difference” of reactions for DMC synthesis from methanol as the initial raw material
Reactions |
ΔGo298/(kJ mol−1) |
Atom utilization |
OSI′ |
ΔRi |
R1 |
−113.57 |
0.553 |
16 |
1.105 |
R2 |
−219.17 |
0.833 |
18 |
1.014 |
R3 |
−2.36 |
0.726 |
13 |
1.255 |
R4 |
38.04 |
0.833 |
11 |
1.334 |
R5 |
0.41 |
0.542 |
16 |
1.415 |
3.2. Implementation path analysis
3.2.1. Comparison of transesterification with different epoxides as raw materials. Dimethyl carbonate was synthesized by the transesterification of ethylene oxide,13 propylene oxide15,16 and cyclohexane oxide17 as raw materials, respectively. The reaction equations are as follows: |
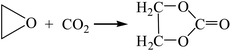 | (R6-1) |
|
 | (R6-2) |
|
 | (R7-1) |
|
 | (R7-2) |
|
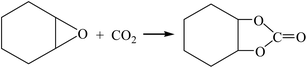 | (R8-1) |
|
 | (R8-2) |
The Gibbs free energy, atom utilization and inherent safety index (Table S4†) of the above-mentioned reactions were calculated, and the “three-parameter difference” ΔRi of each reaction are shown in Table 2. It can be seen that the transesterification (cyclohexenyl carbonate) (R8-2) is the most prone to occur thermodynamically, and the ΔR8-2 (0.860) is the smallest. However, the Gibbs free energy of cyclohexene oxide-CO2 (R8-1) is greater than 0 (Fig. S2†) within the temperature range, and the ΔR8-1 (3.639) is the largest. The average of the three-parameter difference of the two-step reaction is significantly larger than the other two reaction paths. The intrinsic safety index OSI′ of transesterification (propylene carbonate) (R7-2) is the lowest and the intrinsic safety is the highest. Considering comprehensively, the ΔR7 (1.303) of transesterification (propylene oxide) is relatively small, which indicates that the reaction route for synthesizing DMC from propylene oxide as the raw material is the most favorable.
Table 2 “Three-parameter difference” of transesterification with different epoxides as raw materialsa
Reactions |
ΔGo298/(kJ mol−1) |
Atom utilization |
OSI′ |
ΔRi |

|
is the average value of stepwise reaction ΔRi. The same as below. |
R6 |
R6-1 |
−2.40 |
1 |
20 |
1.405 |
1.387 |
R6-2 |
−19.56 |
0.592 |
19 |
1.368 |
R7 |
R7-1 |
−34.33 |
1 |
20 |
1.291 |
1.303 |
R7-2 |
23.74 |
0.542 |
10 |
1.315 |
R8 |
R8-1 |
484.63 |
1 |
13 |
3.639 |
2.250 |
R8-2 |
−187.82 |
0.437 |
13 |
0.860 |
3.2.2. Comparison of the two-step process and the one-step process for the gas-phase oxidative carbonylation of methanol. The reaction equations for the synthesis of DMC by the gas-phase oxidative carbonylation of methanol are as follows: |
 | (R9-1) |
|
 | (R9-2) |
|
 | (R2) |
According to the Gibbs free energy, atom utilization and inherent safety index (Table S5†) of the above-mentioned reactions, ΔRi was calculated, and the results are shown in Table 3. It can be seen that the ΔR2 (0.962) of the gas-phase oxidative carbonylation of methanol by the one-step process is smaller than that of two-step process ΔR9 (1.160), and the Gibbs free energy is lower in the investigated temperature range, making it easier to proceed thermodynamically (Fig. S3†). The ΔRi of the multi-step reaction is positively correlated with the number of reaction steps, that is, the more reaction steps, the greater is the mean value. Integrating multiple reactions can reduce the reaction steps, thereby decreasing the ΔRi, which is the target direction of developing the reaction path.
Table 3 “Three-parameter difference” of the gas-phase oxidative carbonylation of methanol to DMC
Reactions |
ΔGo298/(kJ mol−1) |
Atom utilization |
OSI′ |
ΔRi |

|
R9 |
R9-1 |
−90.94 |
0.872 |
19 |
1.166 |
1.160 |
R9-2 |
−128.24 |
0.600 |
19 |
1.154 |
R2 |
R2 |
−219.17 |
0.833 |
18 |
0.962 |
0.962 |
3.2.3. Comparison of the two-step method with propylene glycol as a recycling agent and methanol-urea alcoholysis. The reaction equations for the synthesis of DMC by the two-step method with propylene glycol as the circulating agent18 and the methanol-urea alcoholysis method are as follows: |
 | (R10-1) |
|
 | (R7-2) |
|
 | (R3) |
The Gibbs free energy, atom utilization and inherent safety index (Table S6†) of the above-mentioned reactions were calculated, and the “three-parameter difference” ΔRi of each reaction are shown in Table 4. It can be seen that the methanol-urea alcoholysis method ΔR3 (1.379) is smaller than the two-step method with propylene glycol as the circulating agent. It is verified again that the ΔRi of the multi-step reaction is positively correlated with the number of reaction steps. Transesterification (propylene carbonate) (R7-2) has the lowest OSI′ and the highest intrinsic safety, but it is not feasible in thermodynamics within the temperature range investigated (Fig. S4†), that is why ΔR7-2 (2.109) is larger.
Table 4 “Three-parameter difference” of reactions for DMC synthesis
Reactions |
ΔGo298/(kJ mol−1) |
Atom utilization |
OSI′ |
ΔRi |

|
R10 |
R10-1 |
−26.10 |
0.750 |
12 |
0.956 |
1.533 |
R7-2 |
23.74 |
0.542 |
10 |
2.109 |
R3 |
R3 |
−2.36 |
0.726 |
13 |
1.379 |
1.379 |
4. Analysis of the reaction route for the synthesis of toluene diisocyanate from toluene as the initial raw material
Toluene diisocyanate (TDI) is an important organic intermediate used in the manufacturing of polyurethane foams. Polyurethane produced by TDI has excellent properties, such as wear resistance, low temperature resistance, oil resistance and ozone resistance, and is widely used in foam plastics, elastomer wear-resistant materials and coatings.19,20 The industrial production methods of TDI mainly include: phosgene process,21 reduction carbonylation method,22 oxidative carbonylation method,23 carbon dioxide method,24 dimethyl carbonate method25–27 and urea method.28 On this basis, we proposed the dimethyl carbonate-ionic liquid hydroxylamine method. The specific reaction equations are as follows. The material safety index (Table S7†) and the process safety index (Table S8†) are shown in the ESI.†
(1) Phosgene process (R11–R13).
|
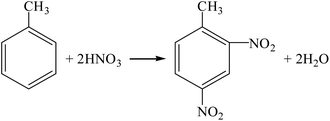 | (R11) |
|
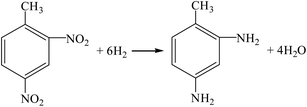 | (R12) |
|
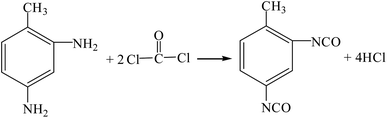 | (R13) |
(2) Reductive carbonylation one-step method (R11, R14).
|
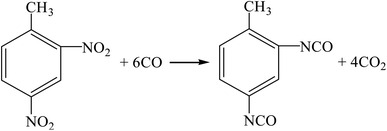 | (R14) |
(3) Reductive carbonylation two-step method (R11, R15, R16).
|
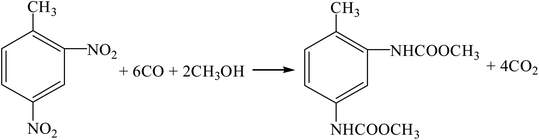 | (R15) |
|
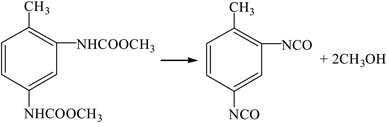 | (R16) |
(4) Oxidative carbonylation method (R11, R12, R17, R16).
|
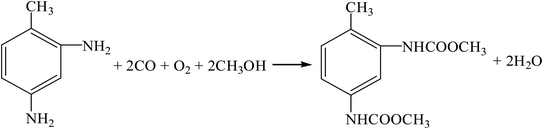 | (R17) |
(5) Carbon dioxide method (R11, R12, R18, R16).
|
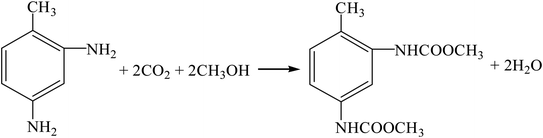 | (R18) |
(6) Dimethyl carbonate method (R11, R12, R19, R16).
|
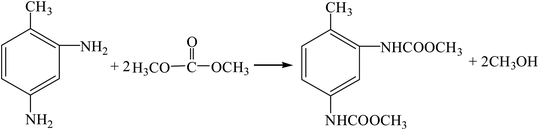 | (R19) |
(7) Urea method (R11, R12, R20, R16).
|
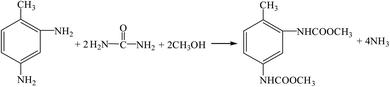 | (R20) |
(8) Dimethyl carbonate-ionic liquid hydroxylamine method (R21, R19, R16).
|
 | (R21) |
According to the Gibbs free energy, atom utilization and inherent safety index (Table S9†) of each reaction for TDI synthesis obtained above, ΔRi was calculated, and the results are shown in Table 5. It can be seen that the order of the OSI′ is R14 > R12 = R15 > R17 > R16 > R11 > R20 = R21 > R13 > R18 = R19, which indicates that the synthesis of TDI by the carbon dioxide method (R18) or dimethyl carbonate method (R19) is the safest and has the highest inherent safety. However, these two reactions cannot occur spontaneously in thermodynamics (Fig. S5†), which is the reason for the larger ΔR18 and ΔR19. Considering the overall reaction safety, the order of the OSI is RIV > RV = RVI = RVII > RIII > RI = RII > RVIII, which indicates that the synthesis of TDI by the dimethyl carbonate-ionic liquid hydroxylamine method has the highest inherent safety. And ΔR21 (0.898) is the minimum, which shows that it is the most advantageous (pre-development process) and lays a theoretical foundation for the development of a new process. The order of the ΔRi mean value is ΔRVIII > ΔRV > ΔRVII > ΔRVI > ΔRIII > ΔRII > ΔRIV > ΔRI, basically positively correlated with the number of the reaction steps. That is, by integrating multiple reactions and reducing reaction steps, the value of ΔRi can be obviously decreased, making it closer to the ideal chemical reaction. That is to say, one-step reaction not only simplifies the reaction steps, but also breaks the thermodynamic limitation, removes the safety hazards from the source, and improves the atomic economy.
Table 5 “Three-parameter difference” of reactions for the TDI synthesisa
Reactions |
ΔGo298/(kJ mol−1) |
Atom utilization |
OSI′ |
ΔRi |

|
RI: phosgene process; RII: reductive carbonylation one-step method; RIII: reductive carbonylation two-step method; RIV: oxidative carbonylation method; RV: carbon dioxide method; RVI: dimethyl carbonate method; RVII: urea method; RVIII: Dimethyl carbonate-ionic liquid hydroxylamine method. |
RI |
R11 |
−213.32 |
0.835 |
14 |
1.004 |
1.015 |
R12 |
−928.75 |
0.629 |
20 |
0.947 |
R13 |
−176.11 |
0.544 |
13 |
1.095 |
RII |
R11 |
−213.32 |
0.835 |
14 |
1.004 |
1.062 |
R14 |
−973.53 |
0.497 |
23 |
1.119 |
RIII |
R11 |
−213.32 |
0.835 |
14 |
1.004 |
1.076 |
R15 |
−954.97 |
0.575 |
20 |
0.968 |
R16 |
−18.56 |
0.732 |
17 |
1.257 |
RIV |
R11 |
−213.32 |
0.835 |
14 |
1.004 |
1.054 |
R12 |
−928.75 |
0.629 |
20 |
0.947 |
R17 |
−368.76 |
0.868 |
18 |
1.008 |
R16 |
−18.56 |
0.732 |
17 |
1.257 |
RV |
R11 |
−213.32 |
0.835 |
14 |
1.004 |
1.119 |
R12 |
−928.75 |
0.629 |
20 |
0.947 |
R18 |
145.66 |
0.868 |
12 |
1.269 |
R16 |
−18.56 |
0.732 |
17 |
1.257 |
RVI |
R11 |
−213.32 |
0.835 |
14 |
1.004 |
1.105 |
R12 |
−928.75 |
0.629 |
20 |
0.947 |
R19 |
69.59 |
0.787 |
12 |
1.211 |
R16 |
−18.56 |
0.732 |
17 |
1.257 |
RVII |
R11 |
−213.32 |
0.835 |
14 |
1.004 |
1.114 |
R12 |
−928.75 |
0.629 |
20 |
0.947 |
R20 |
64.87 |
0.777 |
14 |
1.248 |
R16 |
−18.56 |
0.732 |
17 |
1.257 |
RVIII |
R21 |
−370.38 |
0.773 |
14 |
0.898 |
1.122 |
R19 |
69.59 |
0.787 |
12 |
1.211 |
R16 |
−18.56 |
0.732 |
17 |
1.257 |
5. Conclusion
The “three-parameter difference” based on Gibbs free energy, atom utilization and inherent safety index can evaluate the thermodynamic feasibility, atomic economy and inherent safety of chemical reactions comprehensively. The smaller the “three-parameter difference” is, the closer it is to the ideal reaction. In this study, the synthesis of DMC and TDI were taken as examples, and the ΔRi of each reaction was calculated and analyzed. The synthesis of DMC by the gas-phase oxidative carbonylation of methanol by a one-step process (ΔR2 = 1.104) and the synthesis of TDI by the dimethyl carbonate-ionic liquid hydroxylamine method (ΔRVIII = 1.122) had more potential. The results were consistent with the existing actual research, which proves the reliability of the “three-parameter difference”. The model has an adequate practical guidance significance to evaluate new synthesis routes.
Symbol description
Nr | NFPA reactivity rating |
Nf | Flammability |
Nt | Toxicity |
Ne | Explosiveness |
Rt | Temperature subindex |
Rp | Pressure subindex |
Ry | Yield subindex |
Rh | Heat of reaction subindex |
ICI | Individual chemical index |
IRI | Individual reaction index |
OSI′ | Individual safety index |
OCI | Overall chemical index |
ORI | Overall reaction index |
OSI | Overall safety index |
Conflicts of interest
There are no conflicts to declare.
Acknowledgements
This work was supported by the National Natural Science Foundation of China (U20A20152, 21878069) and the Central Government Guide the Development of Local Science and Technology Special Fund (206Z4002G).
References
- Y. Wang, Z. Li and S. Wang, Intrinsic Safety Catalytic Process, Chemical Industry Press, Beijing, 2018 Search PubMed.
- X. Ding, C. Wu and Y. Wang, Chin. Sci. Bull., 2020, 65, 401–409 CrossRef.
- Y. Ono, Pure Appl. Chem., 1996, 68, 367–375 CrossRef CAS.
- W. Hui, M. Wang, W. Zhang, Z. Ning, W. Wei and Y. Sun, Catal. Today, 2006, 115, 107–110 CrossRef.
- D. W. Kim, C. W. Kim, J. C. Koh and D. W. Park, J. Ind. Eng. Chem., 2010, 16, 474–478 CrossRef CAS.
- Y. Watanabe and T. Tatsumi, Microporous Mesoporous Mater., 1998, 22, 399–407 CrossRef CAS.
- X. Ding, X. Dong, D. Kuang, S. Wang, X. Zhao and Y. Wang, Chem. Eng. J., 2014, 240, 221–227 CrossRef CAS.
- Y. Song, X. Ding, Y. Yan, S. Wang and Y. Wang, CIESC J., 2019, 70, 1401–1408 CAS.
- K. Nishihira, S. Yoshida and S. Tanaka, J. Clean. Prod., 1997, 5, 312 Search PubMed.
- D. Lakshmi, B. Rao and L. Nakka, Catal. Commun., 2019, 122, 1–4 CrossRef.
- M. Wang, Z. Ning, W. Wei and Y. Sun, Stud. Surf. Sci. Catal., 2004, 153, 197–200 CrossRef CAS.
- A. A. Marciniak, O. C. Alves, L. G. Appel and C. Mota, J. Catal., 2019, 371, 88–95 CrossRef CAS.
- Y. Chang, J. Tao, B. Han, Z. Liu, W. Wu, L. Gao, J. Li, H. Gao, G. Zhao and J. Huang, Appl. Catal. Gen., 2004, 263, 179–186 CrossRef CAS.
- L. A. Ming, A. Mk, C. Lnb and C. Mga, Chem. Eng. Sci., 2020, 231, 116267 Search PubMed.
- B. M. Bhanage, S. I. Fujita, Y. Ikushima, K. Torii and M. Arai, Green Chem., 2003, 5, 71–75 RSC.
- T. Wei, M. Wang, W. Wei, Y. Sun and B. Zhong, Fuel Process. Technol., 2003, 83, 175–182 CrossRef CAS.
- Q. Yang, H. Wang, X. Ding, X. Yang and Y. Wang, Res. Chem. Intermed., 2015, 41, 4101–4111 CrossRef CAS.
- T. Zhang, B. Zhang, L. Li, N. Zhao and F. Xiao, Catal. Commun., 2015, 66, 38–41 CrossRef CAS.
- A. Hassan, E. Bagherzadeh, R. G. Anthony, G. Borsinger and A. Hassan, US Pat.0005589A1, 2009 Search PubMed.
- X. Zhao, Y. Wang, F. Li, S. Wang and J. Cong, Petrochem. Technol., 1999, 9, 611–614 Search PubMed.
- S. Ozaki, J. Syn. Org. Chem. Jpn., 1972, 28, 285–295 Search PubMed.
- Y. Watanabe, Y. Tsuji, R. Takeuchi and N. Suzuki, Bull. Chem. Soc. Jpn., 1983, 56, 3343–3348 CrossRef CAS.
- F. Shi, T. L. Sima and Y. Deng, Chem. Res. Chin. Univ., 2000, 21, 1566–1568 CAS.
- A. Ion, C. V. Doorslaer, V. Parvulescu, P. Jacobs and D. Vos, Green Chem., 2008, 10, 111–116 RSC.
- G. Wang, D. Ma, X. Jia, X. Cui, X. Zhao and Y. Wang, Ind. Eng. Chem. Res., 2016, 55, 8011–8017 CrossRef CAS.
- S. Wang, G. Zhang, X. Ma and J. Gong, Ind. Eng. Chem. Res., 2007, 46, 6858–6864 CrossRef CAS.
- Y. Wang, X. Zhao, F. Li, S. Wang and J. Zhang, J. Chem. Technol. Biotechnol., 2010, 76, 857–861 CrossRef.
- X. Zhao, N. Wang, Y. Geng, H. An and Y. Wang, Ind. Eng. Chem. Res., 2011, 50, 13636–13641 CrossRef CAS.
|
This journal is © The Royal Society of Chemistry 2022 |
Click here to see how this site uses Cookies. View our privacy policy here.