DOI:
10.1039/D1RA07338A
(Review Article)
RSC Adv., 2022,
12, 1604-1627
Sustainable biodiesel generation through catalytic transesterification of waste sources: a literature review and bibliometric survey
Received
2nd October 2021
, Accepted 21st December 2021
First published on 10th January 2022
Abstract
Sustainable renewable energy production is being intensely disputed worldwide because fossil fuel resources are declining gradually. One solution is biodiesel production via the transesterification process, which is environmentally feasible due to its low-emission diesel substitute. Significant issues arising with biodiesel production are the cost of the processes, which has stuck its sustainability and the applicability of different resources. In this article, the common biodiesel feedstock such as edible and non-edible vegetable oils, waste oil and animal fats and their advantages and disadvantages were reviewed according to the Web of Science (WOS) database over the timeframe of 1970–2020. The biodiesel feedstock has water or free fatty acid, but it will produce soap by reacting free fatty acids with an alkali catalyst when they present in high portion. This reaction is unfavourable and decreases the biodiesel product yield. This issue can be solved by designing multiple transesterification stages or by employing acidic catalysts to prevent saponification. The second solution is cheaper than the first one and even more applicable because of the abundant source of catalytic materials from a waste product such as rice husk ash, chicken eggshells, fly ash, red mud, steel slag, and coconut shell and lime mud. The overview of the advantages and disadvantages of different homogeneous and heterogeneous catalysts is summarized, and the catalyst promoters and prospects of biodiesel production are also suggested. This research provides beneficial ideas for catalyst synthesis from waste for the transesterification process economically, environmentally and industrially.
1 Introduction
Worldwide energy demand is rising rapidly because of the fast industrialization and population growth, influencing fossil fuel use. The price of mineral-based fuels, such as diesel, natural gas, and petroleum, has increased since the 1970s because of the rapid consumption and reduction of these fossil fuels.1 Substitute fuel has attracted significant attention because of global greenhouse gas emissions and the depletion of fossil fuels. There is an increasing interest in using new knowledge and employing diverse biofuels to convert bio-energy in many industrialized nations that are cost-effective compared to fossil fuels.2 In this respect, fatty acid methyl esters (biodiesel fuel) originating from animal fat and vegetable oil transesterification reaction (edible and non-edible plant oils, fungi and animal fats) have received considerable attention in recent years as sustainable, biodegradable, sulfur- and aromatic-free and harmless fuels.3
Biodiesel is a renewable and clean energy source and a mixture of alkyl esters got through the transesterification of several renewable resources such as animal fats and edible vegetable oils such as palm oil, sunflower oil, rapeseed oil, cottonseed oil, soybean oil and algal oil. It has qualities that are almost identical to petro-derived diesel and may thus be used in diesel engines with minor modifications. It's also biodegradable, non-toxic, and emits fewer hazardous pollutants than traditional petro-diesel. Nevertheless, the high cost of resources accounts for about 88% of the total biodiesel generation cost.4 Hence, non-edible oil feedstock for biodiesel generation, such as waste cooking oil, natural fat, jatropha oil, waste grease and micro-algae, has gained a significant interest in recent years.5 These feedstocks are difficult to handle because they mainly have water and high free fatty acid (FFA) contents, which require pretreatment for commercially acceptable conversion efficiency6 in the presence of a suitable catalyst.7 Another vital phase in the transesterification process is the selection of the catalyst that defines the cost of production, leading to the economic obstacle. The catalyst is the kingpin in the transesterification reaction and as seen in Fig. 1, from 1970 to 2021, there were 2260 articles published in the WoS journals using biodiesel and catalyst in the title search. The number of publications and citations is growing rapidly from 2003, and the total link strength, which specifies the total strength of the co-authorship links of a given country with other countries, was also provided. It can be seen that the top ten most active countries with the highest total link strength in sequence are Malaysia, Saudi Arabia, India, Pakistan, China, Australia, Vietnam, Nigeria, Taiwan, and Thailand.
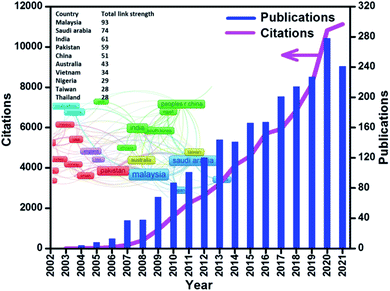 |
| Fig. 1 WoS citation, publication reports, and countries' co-occurrence network for the title search of “biodiesel” and “catalyst” in the period of 1970 to 2021. | |
Alcoholysis or transesterification reactions with a base, acid, enzyme, and other catalysts were used for biodiesel production.8 Biocatalysts and chemical catalysts are being examined, and both have their benefits and drawbacks. These catalysts are reported to be environmentally friendly and budget-friendly materials in industrial uses.9 Chemical catalysts comprise homogeneous factors (acid or alkali), heterogeneous agents (solid alkali or acid catalyst), supercritical fluids (SCFs) and heterogeneous nanostructured catalysts.9 Homogeneous catalysts can cause complications in biodiesel production, such as saponification of the feedstock by which vast quantity of by-products such as undesirable soap was produced by the reaction of the catalyst with the FFA, which then prevents the splitting of the FAME and glycerol and reduces the catalyst.7 Although transesterification with homogeneous catalysts is easy and quick, it has drawbacks in catalyst separation, reusability, and renewable resources.10
The context knowledge shows the growing significance of biodiesel processing, and the literature review below reveals the scarcity of scientometric research in this exciting field (see Table 1). The current research aims to summarize the feasibility and the challenges of biodiesel production using various heterogeneous and homogeneous catalytic processes from different waste feedstocks. The Web of Science (WOS) database was used to conduct the bibliometric study. Catalyst promoters' importance and contribution to biodiesel generation have not been adequately examined yet. There was no match for the four words of biodiesel, catalyst, promoter and review at the topic search of the WOS website. Built upon the favorable properties of catalysts and the importance of non-noble metal promoters in the transesterification process, this study also aims to gather information on synthesizing non-noble promoters supported on various organic and inorganic metal oxides to get a high biodiesel yield.
Table 1
Summary of some previously published reviews (1970–2021) in the WOS database by employing the title search of keywords such as biodiesel, transesterification, catalyst, and review
No. |
Year |
Main focus |
Ref. |
1 |
2009 |
“Review of recent developments in solid acid, base, and enzyme catalysts (heterogeneous) for biodiesel production via transesterification” |
11 |
● Impact of solid catalysts on different oil sources for fuel production |
● Heterogeneous catalysts for biodiesel production |
2012 |
“Recent developments on heterogeneous catalysts for biodiesel production by oil esterification and transesterification reactions: a review” |
12 |
● Heterogeneous catalysts application |
2 |
2013 |
“Recent developments for biodiesel production by ultrasonic assist transesterification using different heterogeneous catalyst: a review” |
13 |
● Raw materials used for biodiesel production |
● Heterogeneous catalytic transesterification |
● Ultrasonic assisted transesterification |
3 |
2016 |
“A review on biodiesel production by transesterification catalyzed by ionic liquid catalysts” |
14 |
● Solid material supported ionic liquid catalyst |
● Feasibility of using ionic liquids as the catalyst |
4 |
2017 |
“A review of ionic liquids as catalysts for transesterification reactions of biodiesel and glycerol carbonate production” |
15 |
● Role of cation and anion in ionic liquids as catalyst |
● Ionic liquid costs |
● Environmental fate of ionic liquids |
5 |
2018 |
“Advancement in catalysts for transesterification in the production of biodiesel: a review” |
16 |
● Kinetics of transesterification reaction |
● Base catalyzed transesterification |
● Homogenous and heterogeneous catalyst |
6 |
2021 |
“A review on the efficient catalysts for algae transesterification to biodiesel” |
17 |
● Energy conversion processes from algae |
● Efficient transesterification catalyst |
7 |
2021 |
“Sustainable biodiesel generation through catalytic transesterification of waste sources: a literature review and bibliometric survey” |
Current review |
● Bibliometric studies |
● Applications of biodiesel |
● Sources for biodiesel |
● Catalysts employed to produce biodiesel |
● Homogeneous, heterogeneous and catalysts promoters |
● Challenges and future work |
2 Biodiesel and its application
Biodiesel is a monoalkyl ester of long-chain fatty acid oil derivative made from sustainable lipid sources such as animal fats and vegetable oils18 by a chemical modification process called transesterification. The pure type of biodiesel can be utilized as a car engine fuel. It is typically employed as an additive to diesel to decrease hydrocarbons, carbon monoxide, and particulates from diesel fuel cars.19 The first attempts of biofuels engine operation (peanut oil engine run by Rudolf Diesel in 1900 and vegetable oil run engines in 1930s) as well the first industrial biofuels were based on food crops.20 Subsequently, a diversity of source materials was examined and developed universally. Currently, over 350 herbs have been recognized as biodiesel sources.21,22
The application of biodiesel has been noticeably increasing during the last decades. As seen in Fig. 2, biodiesel applications had risen from 7.3 million tonnes of oil equivalent (mtoe) in 1990 to 87.1 mtoe in 2020. The Renewable Fuel Standard, which was included in the Energy Policy Act of 2005, was the first to mandate the use of specific biofuel amounts. The goal was to use 4 billion gallons of renewables in transportation fuels in 2006 to increase their percentage over time. The lessening of the country's reliance on oil has been the driving concept of biofuel programmes. The Energy Independence and Security Act of 2007 set a goal of reducing gasoline usage by 20% over the following ten years. The 2008 Biomass Program has two essential purposes. The first is, by 2030, to reduce gasoline use by 30% as compared to 2004 levels. Second, corn-derived ethanol is used to generate cellulosic ethanol.23 Algal biomass has been used as food and feed supplements for humans and animals, fertilisers in agriculture, nutritional supplements and medication in the pharmaceutical industry, and phycocolloids in the phycocolloid industry.24,25 Higher prices for animal feeds have resulted from the growing use of agricultural commodities for biofuels; nevertheless, the more significant substitution of co-products for conventional feedstuffs in feed rations mitigates the input cost increases experienced by livestock and poultry farmers. In the next ten years, growth in agricultural commodities for biofuels is likely to continue. However, at a slower pace in major producing nations, government-imposed grain usage restrictions for biofuels are achieved, and new non-agricultural feedstocks are commercialised.26 A previous work,27 which examines renewable portfolio standards in the electricity sector and can be extended to transportation fuels, provides a detailed explanation of how such factors affect energy price. As a result, domestic fuel consumption may fall, offsetting the rise in global fuel consumption. The presence of biofuel subsidies mitigates the impact of any increases in domestic fuel prices.28 The replacement of feedstocks should be explored to reduce biofuel synthesis or operating costs. Waste cooking oil and waste animal fat, for example, are viewed as preferable feedstocks for biodiesel production compared to edible vegetable oil since they are both inexpensive and plentiful. Furthermore, as seen in Fig. 3, biodiesel has been used in an inclusive variety of applications such as bus29,30 and rail31,32 transportations, commercial steamships,33–35 heavy trucks,36,37 power systems such as generators,38–40 agricultural machinery,41–43 heating oil in domestic44–46 and commercial47–49 boilers, and aircraft.50–52 Thus, biodiesel has been gaining more attention as a resource for the growing demand from several industrial sections because of its numerous advantages over fossil fuels.
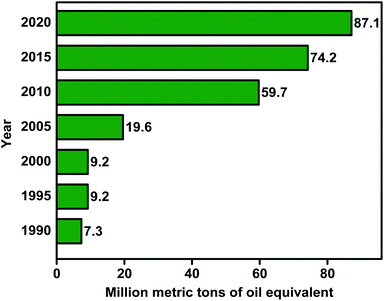 |
| Fig. 2 Universal consumption of biofuel (adapted from Statista 2020). | |
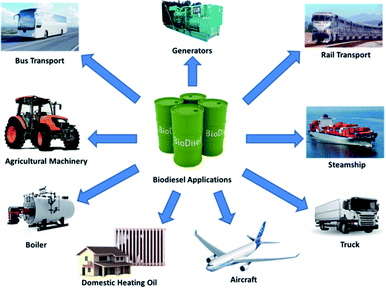 |
| Fig. 3 Biodiesel applications in different sectors. | |
3 Sources of biodiesel
One of the essential aspects of biodiesel generation, which is related to 75% of the entire cost, is choosing suitable feedstock for the process.53–55 Furthermore, biodiesel fuel quality also hinges on resource use, generation process, and origin country.56 As seen in Fig. 4, we could categorize renewable biodiesel resources into four major categories, namely edible and nonedible vegetable oils, waste oil and animal fats.18,55,57 These feedstocks comprise a combination of fatty acid alkyl esters, which will be changed into biodiesel after the transesterification and esterification processes.58,59
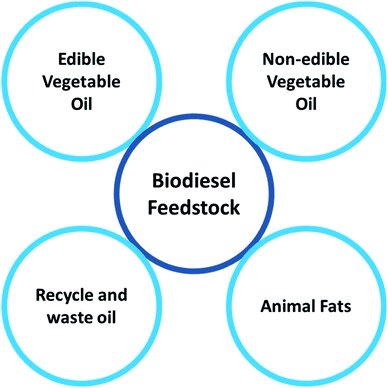 |
| Fig. 4 Biodiesel feedstocks. | |
3.1 Edible vegetable oil
One of the eco-friendly workable biodiesel feedstocks which can be formed regionally is edible vegetable oil. Edible vegetable oils like groundnut,60,61 wheat,62,63 barley,64,65 sesame seed,66,67 safflower,68,69 canola,70,71 coconut,72,73 rapeseed,74,75 rice bran,76,77 sunflower,78,79 olive,80,81 soybean,82,83 palm,84,85 peanut86,87 and corn88,89 have been employed for the generation of biodiesel and are useful as a diesel alternate. Meanwhile, most biodiesel is manufactured from eatable oils; there are several statements that many obstacles might occur.90 The disadvantage of edible oils for the source of biodiesel is the decrease of food resources, which results in the food crisis.91 Besides, the harmful effect of biodiesel generation from edible oils on the earth is ecosystem destruction and deforestation.90 Most important is the high cost of the biodiesel generation from the edible oils which makes it not economically feasible and not suitable for long-term usage. These issues can be handled by employing alternative or greener, lower-cost and reliable oil resources such as animal fats, inedible and waste cooking oil for biodiesel generation.
3.2 Non-edible vegetable oil
A large diversity of plants that create non-edible oil can be regarded for biodiesel generation. Non-edible oils contain toxic compounds, which make them not suitable for human utilization.92 Numerous oils obtained from grains or seeds of inedible plants are possible resources for biodiesel generation. These sorts of feedstocks are inexpensively obtainable and mostly labeled as non-edible oil, dominating any food competition. Studies have used numerous non-edible oils for biodiesel production such as linseed,93,94 tobacco seed,95,96 cottonseed,97,98 rubber seed,99,100 neem,101,102 moringa,103,104 pongamia,105,106 algae,107,108 jatropha,109,110 Karanja,111,112 mahua,113,114 jojoba,115,116 cumaru117–119 and camellia.120,121 The considerable interest for transforming inedible oil to biodiesel is continuously related to the high contents of free fatty acids (FFAs),92 which inhibits the separation of glycerin and ester by produced soap after reaction with an alkaline catalyst. This issue can be solved by designing multiple transesterification stages. Over the use of multiple transesterification processes, the nonedible oils will prove to be a more efficient and environmentally friendly substitute in biodiesel production.
3.3 Animal fat
The fats were demonstrated to be a feasible resource when associated with waste cooking and vegetable oils in production and economy. Synthetically, biodiesel is a combination of fatty acid alkyl ester (FAAE) derived from triglyceride molecules. Waste animal fats are considered one of the sources of triglycerides. Because the value of the feedstock is enhanced after conversion, they are a viable resource for biodiesel production.122 Moreover, leftover natural fats obtained from leather, slaughterhouses and meat process factories are a considerably probable source for biodiesel generation because of their chemical lifelessness, no corrosion, enhanced calorie level and viable feedstocks. In addition to meat processing scum, leather industry fleshing wastes have shown to be a viable source of fat for biodiesel generation when mixed with regular diesel for combustion-based applications.123,124 However, since these wastes are useless, they are thrown into the environment.125 As a result, there has been a lot of interest in using animal fat waste as a cheap source of feedstock in biodiesel synthesis. Numerous papers and studies on techniques, reactor design, applications, mixes with diesel fuel, catalysts, and operating conditions have been carried out. However, both the acid catalyst and the heterogeneous catalyst may be used to convert waste animal fats.126–128
3.4 Waste oil
Waste cooking oil is used as a low-cost feedstock all around the globe, with industrialised nations producing a million gallons of waste cooking oil each day. There is a considerable quantity of waste cooking oil being made annually all around the globe.129 The enormous mass of waste is thrown into landfills and rivers forbiddenly, producing pollution in the environment. If waste cooking oil is the operational feedstock for producing biodiesel at a lower price, a large amount of waste oil available is adequate for sustainable biodiesel production. Waste yields, i.e., lignocellulosic feedstocks and inedible unwanted oils such as waste cooking oil or vegetable scums, are the unavoidable consequence of edible oil intake as a usual ration of the human diet. Therefore, biodiesel fuel production from edible waste oil is considered a significant stage for decreasing and recycling waste oil and levies no extra cost and environmental hazard. Waste oils, however, contain small amounts of FFAs and water in a supplement to oxidized compounds, such as aldehydes, epoxides, and polymers. The large-scale generation of biodiesel fuel from unwanted eatable oils is currently achieved by a substance reaction employing alkaline catalysts. According to the quantity of produced waste cooking oils in all countries, it can be showed that diesel fuel could not utterly be substituted by biodiesel production from this source. Nevertheless, a considerable diesel fuel volume can be produced from waste cooking oils, which would partially decline the reliance on fossil fuels. Using waste cooking oils for biodiesel generation in the transesterification reaction causes the escalation of the water, FFAs and other impurities that can undesirably affect the transesterification reaction while using alkali catalysts.130–132 Besides, waste cooking oils may require a pretreatment procedure to meet proper oil properties for the transesterification reaction because their features such as specific heat and viscosity might be changed during cooking.133 Nevertheless, other options such as employing acid catalysis transesterification,134–136 supercriticality137 and enzyme catalysis133 can be used to make the production of biodiesel a more practical process.
4 Catalysts for biodiesel production
For the manufacture of biodiesel, transesterification methods are widely employed. Transesterification, as shown in Fig. 5, is a reversible reaction and is obtained by reactant combination. Strong acid or base components can be introduced to the system as catalysts. On a large scale, potassium or sodium methanolates are typically utilized. Heterogeneous catalysts are beneficial in this procedure because they are simple to remove from the result and may be reused. Solid base catalysts are advantageous in biodiesel production because they can be readily separated and reused in the process. Conversely, since it needs multiple chemical reagents and a multi-step preparation process, the available catalyst is costly, preventing future uses of this kind of catalyst.138 Materials such as CH3OK, CH3ONa, NaOH, and KOH, considered a solid alkali catalyst, are examined for biodiesel generation.9 Nevertheless, alkali metal alkoxide is found to be more effective than hydroxide.139 There are many homogeneous, enzymatic and heterogeneous catalysts that have been examined for biodiesel generation from various feedstocks. Among all, calcium oxide-based catalysts are favorable for facilitating biodiesel development and purification and reducing the cost of the biodiesel generation process because of the comprehensive variety of practical raw resources. An additional way of lowering the biodiesel cost and reducing the waste disposal obstacles is utilizing naturally calcium-rich waste substances such as animal and bird bones, mollusk and hen eggshells.9,140
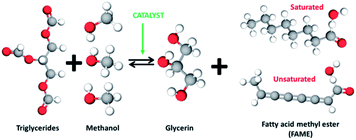 |
| Fig. 5 Transesterification of a triglyceride for biodiesel production. | |
4.1 Homogeneous catalysts
Homogeneous catalysis is a reaction when the reacting components and catalysts are mixed in a single matter state. Instances of homogeneous catalysis are basic, acid, enzymatic, and organometallic catalysis. These catalysts are being used because of the straightforward application and shorter reaction time needed to convert feedstock to the product in biodiesel industries.12 652 published works were discovered using the Web of Science data's subject search engine, including title, abstract, author keywords and keywords, plus fields inside the record and keywords like homogenous, catalyst, transesterification, and biodiesel. The minimum number of occurrences of a keyword was set at 40 and 17 keywords, respectively, to simplify the bibliometric analysis, and the findings of network visualization in Fig. 6 reveal two diverse clusters. The density of items at each node determines the size of each node in the keyword density visualization plat. Keywords with a larger circle size appear more often; keywords with a smaller circle size appear less frequently. Furthermore, the closer the things are together, the stronger their bond. The term “transesterification” had the highest total link strength, while “soybean oil” had the second-highest full link strength. During the period 1970–2020, these terms become more significant in homogeneous catalysts for biodiesel production research. Table 2 demonstrates the initial 17 keywords based on total link strength.
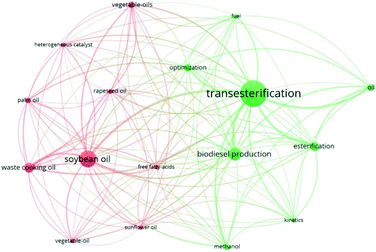 |
| Fig. 6 Co-occurrence network map of keywords based on total link strength (keywords: homogeneous, catalyst, transesterification and biodiesel). | |
Table 2 The top 17 keywords ranked according to the total link strength
Rank |
Keyword |
Total link strength |
Occurrences |
1 |
Transesterification |
2377 |
352 |
2 |
Biodiesel |
2094 |
315 |
3 |
Soybean oil |
1172 |
156 |
4 |
Biodiesel production |
928 |
140 |
5 |
Esterification |
945 |
131 |
6 |
Waste cooking oil |
825 |
108 |
7 |
Heterogeneous catalyst |
715 |
89 |
8 |
Optimization |
544 |
77 |
9 |
Oil |
357 |
63 |
10 |
Methanol |
433 |
59 |
11 |
Vegetable-oil |
473 |
59 |
12 |
Kinetics |
444 |
58 |
13 |
Palm oil |
435 |
53 |
14 |
Rapeseed oil |
398 |
49 |
15 |
Sunflower oil |
369 |
49 |
16 |
Free fatty-acids |
353 |
41 |
17 |
Fuel |
299 |
40 |
Homogeneous chemical catalysts have some merits, such as easy activity optimization, high turnover frequency and selectivity, and a high reaction rate.141,142 The most usual homogeneous catalysts used for transesterification reactions are sodium methoxide (CH3ONa), sodium (NaOH) and potassium (KOH) hydroxides. Using CH3ONa as catalysts is expensive but more applicable than KOH and NaOH compounds. CH3ONa was reported to be the best active basic catalyst, which prompted noble phase separation.143 Further, CH3ONa will help to avoid the water and soap formation.144 Two mechanisms are convoluted in the transesterification process, dependent on whether acid catalysts or basic catalysts are applied, which are discussed below.
4.2 Acidic catalysts
The transesterification reaction is catalyzed by Brønsted acids, in preference of sulfonic145–147 and sulfuric acid.148–150 According to the WOS data employing the title search by keywords such as “transesterification”, “soybean”, “acid”, and “catalyst”, 12 articles were identified and are listed in Table 3.
Table 3 Available papers in the period of 1970–2020 in WOS with the title keywords of transesterification, soybean, acid, and catalyst
Paper no. |
Paper |
Remarks |
Ref. |
1 |
“Transesterification of acid soybean oil for biodiesel production using lithium metasilicate catalyst prepared from diatomite” |
Using lithium metasilicate catalysts, the biodiesel production was over 95% in only one hour. Furthermore, wasted catalysts may be recovered and reused for at least three cycles without substantial catalysis deactivation |
151 |
2 |
“Transesterification of soybean oil to biodiesel by tin-based Brønsted–Lewis acidic ionic liquid catalysts” |
Under optimal reaction conditions, a biodiesel yield of 98.6% was obtained over the Brønsted–Lewis acidic ionic liquid catalyst with a SnCl2 loading (x) of 0.7 |
152 |
3 |
“Active acid catalyst of sulphated zinc oxide for transesterification of soybean oil with methanol to biodiesel” |
At 4 hours of reaction time, the SO42−–ZnO catalyst yielded an encouraging 80.19% FAME yield |
153 |
4 |
“SnSO4 as catalyst for simultaneous transesterification and esterification of acid soybean oil” |
After 3 hours of reaction at 100 °C, under autogenous pressure, and utilising 5 wt% SnSO4 over ethanol, the maximum biodiesel production (92%) was achieved for a model feedstock comprising 70 wt% free fatty acids (oleic acid) |
154 |
5 |
“Biodiesel production by esterification of oleic acid and transesterification of soybean oil using a new solid acid catalyst comprising 12-tungstosilicic acid and zeolite Hβ” |
For esterification of oleic acid and transesterification of soybean oil, the highest conversions were 86% and 95%, respectively. The catalyst may also be recycled up to four times losing no conversion efficiency |
155 |
6 |
“Transesterification of soybean oil to biodiesel by Brønsted-type ionic liquid acid catalysts” |
Among the IL employed in the transesterification of soybean oil, the [(CH3CH2)(3)N(CH2)(3)SO3H]HSO4 IL exhibited excellent catalytic activity and high stability, and it could be reused six times without losing activity |
156 |
7 |
“Biodiesel production via transesterification of soybean oil using acid catalyst in CO2 expanded methanol liquids” |
Complete oil conversion occurred at 10 MPa, 70 °C (reaction time 6 h) and 80 °C (reaction time 4 h) with an M/O ratio of 12 : 1 and H2SO4 content of 4%, whereas NaHSO4 catalytic reactions occurred at 10 MPa, 70 °C (reaction time 6 h) and 80 °C (reaction time 4 h) |
157 |
8 |
“Transesterification of soybean oil over WO3 supported on AlPO4 as a solid acid catalyst” |
The catalyst was shown to be stable across four transesterification cycles, losing just 4% of its activity after four uses, and may be utilized for the transesterification of low-cost oils for biodiesel generation |
158 |
9 |
“Silica-supported tin oxides as heterogeneous acid catalysts for transesterification of soybean oil with methanol” |
The heterogeneous acid catalyst was shown to have significant activity in the esterification of FFAs, and the catalysts could be recovered and reused |
159 |
10 |
“Silica-bonded N-propyl sulfamic acid used as a heterogeneous catalyst for transesterification of soybean oil with methanol” |
The catalyst exhibited activity in the esterification process of FFAs, with 95.6 percent FFA conversion at 423 K for 30 hours |
160 |
11 |
“Transesterification of soybean oil to biodiesel catalyzed by mesostructured Ta2O5-based hybrid catalysts functionalized by both alkyl-bridged organosilica moieties and Keggin-type heteropoly acid” |
The Ta2O5/Si(R)Si–H3PW12O40 hybrid materials with amounts of bridging alkyl groups showed greater reactivity toward the target reaction than the as-prepared Ta2O5/Si(R)Si–H3PW12O40 hybrid materials |
161 |
12 |
“Effect of weak acids as a catalyst on the transesterification of soybean oil in supercritical methanol” |
When the reaction temperature, pressure, methanol/oil molar ratio, and acidity of acidified soybean oil were 350 °C, 15 MPa, 40 : 1, and 15.0 mg of KOH per g, respectively, the output of biodiesel could reach 91.4 percent |
162 |
Fig. 7 illustrates the mechanisms of transesterification reactions of oil with acid catalysts for monoglycerides, and it can be extended to di- and triglyceride.163 The carbonyl group protonation of the ester results in carbocation II, which, after nucleophilic alcohol strike, creates the tetrahedral intermediate III, which reduces glycerol for the new ester IV formation and catalyst H+ regeneration. Transesterification reaction via acid catalysts is more applicable for unrefined or waste oils, but the downside is that acidic catalytic samples are suggestively less active than alkali ones.164 Moreover, the ratio of methanol to oil in the transesterification process with acid catalysts is high with a low reaction rate; therefore, these catalysts are not gaining much attention as basic catalysts.165 Even though, because of the existence of FFAs in high quantity in such oils and fat, homogeneous alkaline catalysts are not recommended. To solve this issue, free fatty acids are firstly esterified to FAME (Fig. 8) using an acid catalyst127 and thereafter, the transesterification reaction is implemented, usually by employing alkaline catalysts. In the pre-esterification technique, it is required to separate the esterified oil and the homogeneous acid catalyst, which is the principal disadvantage of this technique. This issue can be handled with the application of a heterogeneous acid catalyst.166
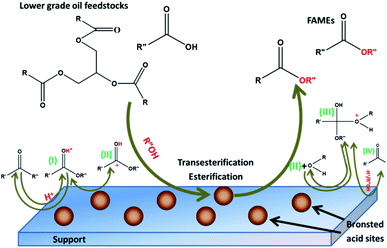 |
| Fig. 7 Acid catalyzed transesterification mechanism (adapted from ref. 167 and 168) where R′′ is ascribed as glyceride, R′ is the carbon chain of fatty acids and R is the alcohol alkyl groups. | |
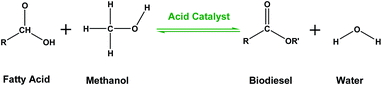 |
| Fig. 8 Esterification of FFA to fatty acid methyl ester using an acid catalyst, where R′ is ascribed as the carbon chain of fatty acid and R is the alcohol alkyl group. | |
4.3 Basic catalyst
The most often used catalysts in an industrial biodiesel production facility are base catalysts such as potassium (KOH) and sodium (NaOH) hydroxides. The following factors contribute to this: (1) cheap cost compared to heterogeneous and enzymatic catalysts, (2) market availability, and (3) ability to accelerate transesterification under moderate reaction conditions efficiently.169 Twenty-three journal articles were detected from the WOS data and are shown in Table 4 following title search using keywords such as “transesterification”, “soybean”, “base”, and “catalyst”. Basic catalysts are typically favoured to acid catalysts because of their more excellent activity and the lower process temperatures needed than acid-catalyzed transesterification. For example, reaction temperatures of 80 to 120 °C have been recorded for acid-catalyzed transesterification by H2SO4, while basic homogeneous catalysis may be successful at ambient temperatures.170 Basic catalysts have a high transesterification activity rate at low temperatures and pressures.171 Previous research has used CaO and MgO as catalysts to study the effect of catalyst basicity on the yield of products.172 They found that substantial residual oil quantity was produced because the basic centres prevented the secondary cracking. The reaction mechanism for forming fatty acid methyl esters (FAME) is described as follows in Fig. 9. Among the different catalytic systems employed in the transesterification of waste feedstock by employing the basic catalysts, it is confirmed that strong basic properties are essential to achieve this reaction. Cation-exchanged catalysts are unsuitable, whereas systems in the form of a simple oxide with a high surface area show some exciting performances. The kinetics of homogeneous basic transesterification are extremely rapid; however, there is a collateral saponification process that lowers biodiesel production efficiency.173 To avoid biodiesel production losses due to saponification processes, alcohol and oil must be dried, and the oil must have the fewest FFAs possible (less than 0.1 wt%). Furthermore, there are many disadvantages to homogeneous basic catalysis, such as its sensitivity to moisture and free fatty acid.174
Table 4 Published articles in the period of 1970–2020 in WOS with title keywords of transesterification, soybean, base, and catalyst
Paper no. |
Paper |
Remarks |
Ref. |
1 |
“Hydrogel-templated solid base catalysts for transesterification of soybean oil” |
All catalysts, except the low concentration of Ca(NO3)2, exhibiting the high activity yielding over 90% FAME after 1 hour at 65 °C, using oil to methanol molar ratio of 1 : 15 and 10 wt% of catalyst amounts |
175 |
2 |
“Transesterification of soybean oil using a novel heterogeneous base catalyst: synthesis and characterization of Na-pumice catalyst, optimization of transesterification conditions, studies on reaction kinetics and catalyst reusability” |
At optimal circumstances, the reaction kinetics followed the pseudo-first order model, with coefficients of determination and k values of 0.9862 and 0.0277 min−1, respectively |
176 |
3 |
“Transesterification of soybean oil to biodiesel by tin-based Brønsted–Lewis acidic ionic liquid catalysts” |
Under optimal reaction conditions over the Brønsted–Lewis acidic ionic liquid catalyst with SnCl2 loading (x) of 0.7, a good biodiesel yield of 98.6% was got |
177 |
4 |
“Reusability and stability tests of calcium oxide based catalyst (K2O/CaO–ZnO) for transesterification of soybean oil to biodiesel” |
The catalysts have good reusability after regeneration and excellent catalytic activity (80% fatty acid methyl ester (FAME) production after three cycles) |
178 |
5 |
“Preparation and characterization of fly ash based mesoporous catalyst for transesterification of soybean oil” |
Using produced catalyst, a maximum biodiesel production of 81.2% was achieved |
179 |
6 |
“Waste carbide slag as a solid base catalyst for effective synthesis of biodiesel via transesterification of soybean oil with methanol” |
The waste carbide slag is a potential catalyst in the manufacture of biodiesel because of its high catalytic activity, cheap cost, and large storage capacity |
180 |
7 |
“Transesterification of soybean oil to biodiesel using zeolite supported CaO as strong base catalysts” |
The supported catalyst had the capacity of water resistance and acid resistance |
181 |
8 |
“The potential of using cocoa pod husks as green solid base catalysts for the transesterification of soybean oil into biodiesel: effects of biodiesel on engine performance” |
Biodiesel samples were produced using CPH/MgO-catalyzed at 60 °C and 1 wt% percent MgO doped CPH ash catalyst transesterification processes (98.7% and 91.4 percent yields for CPH/MgO and CPH ash catalysts, respectively) |
182 |
9 |
“Transesterification of soybean oil to biodiesel using cement as a solid base catalyst” |
According to the catalytic property of the cement catalyst, waste concrete catalyst was effectively utilized in the transesterification process of soybean oil |
183 |
10 |
“Mesoporous Li/ZrO2 as a solid base catalyst for biodiesel production from transesterification of soybean oil with methanol” |
The Li, K changed ZrO2 catalysts achieved high yield of biodiesel production |
184 |
11 |
“Transesterification of soybean oil on guanidine base-functionalized SBA-15 catalysts” |
The higher the functionalization extent, the higher the activity; for a 100 mol% methyl esters yield, only a few hours are required |
185 |
12 |
“Model study on transesterification of soybean oil to biodiesel with methanol using solid base catalyst” |
The activation energy range of the solid base catalyst was 9–20 kcal mol−1, which was comparable with the stated activation energy range of homogeneous catalysts |
186 |
13 |
“Effect of water on base-catalyzed transesterification of soybean oil with methanol over promoted hydrotalcite catalysts” |
N/A |
187 |
14 |
“Transesterification of soybean oil to biodiesel over heterogeneous solid base catalyst” |
The new crystal phase produced by calcinations was shown to have a positive impact on the transesterification process using XRD and DSC-TGA analysis |
188 |
15 |
“Transesterification of soybean oil to biodiesel catalyzed by mesostructured Ta2O5-based hybrid catalysts functionalized by both alkyl-bridged organosilica moieties and Keggin-type heteropoly acid” |
The as-prepared Ta2O5/Si(R)Si–H3PW12O40 hybrid materials with suitable concentrations for bridging alkyl groups exhibited higher reactivity toward the target reaction |
161 |
16 |
“CaO as a solid base catalyst for transesterification of soybean oil” |
Cal(N) was more resistant to CO2 poisoning than CaO from aragonite (Ara(N)), and the degree of poisoning was greatly dependent on the kind of precursors |
189 |
17 |
Calcium oxide as a solid base catalyst for transesterification of soybean oil and its application to biodiesel production |
The transesterification of processed waste cooking oil with an acid value of 0.3 mg-KOH per g produced FAME with a calcium content of 565 ppm |
190 |
18 |
“Calcium methoxide as a solid base catalyst for the transesterification of soybean oil to biodiesel with methanol” |
As a heterogeneous solid base catalyst, calcium methoxide possesses strong basicity and great catalytic activity, yielding 98% biodiesel in only two hours |
191 |
19 |
“Calcium ethoxide as a solid base catalyst for the transesterification of soybean oil to biodiesel” |
In these circumstances, a 95.0 percent biodiesel yield was achieved in 1.5 hours, with an activation energy of 54 149 J mol−1 |
192 |
20 |
“Transesterification of soybean oil to biodiesel using CaO as a solid base catalyst” |
The greatest results were obtained with an 8% CaO catalyst, a 65 °C reaction temperature, and a 2.03% water content in methanol, with a biodiesel yield exceeding 95% after 3 hours |
193 |
21 |
“Active phase of calcium oxide used as solid base catalyst for transesterification of soybean oil with refluxing methanol” |
The reference sample, calcium diglyceroxide, was as active as the collected catalyst in the transesterification and was air-tolerant |
194 |
22 |
“Transesterification of soybean oil to biodiesel using SrO as a solid base catalyst” |
The use of SrO as a catalyst in the transesterification of soybean oil to biodiesel is an economically feasible method to reduce biodiesel production costs |
195 |
23 |
“Transesterification of soybean oil catalyzed by potassium loaded on alumina as a solid-base catalyst” |
K2O was synthesised from KNO3 at high temperatures, and the Al–O–K groups were most likely responsible for the reaction's catalytic activity |
196 |
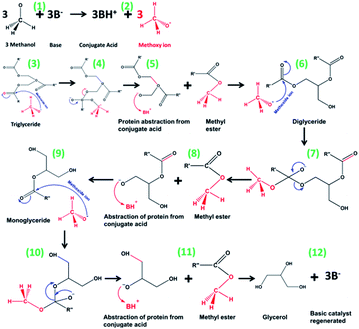 |
| Fig. 9 Mechanism of base-catalyzed transesterification.197,198 | |
The strong base (NaOH or KOH) catalysed through a homogenous transesterification process has certain constraints, such as product separation, which leads to increased biodiesel production costs.11 The method involved numbers of washings and purification stages to sustain the specified condition. It was reasonably challenging to eliminate the K/Na residues lasting in the product, and the split of glycerin also caused practical experiments. The whole process cost might be increased using a higher amount of water in the washing step.199 These factors indicate that using basic or acid heterogeneous catalysts, or better yet, a heterogeneous catalyst with acid and basic characteristics, may result in a more environmentally friendly and less expensive biodiesel manufacturing process. The triglycerides are transesterified at the basic internal sites (–O−), whereas the free fatty acids are esterified at the acid exterior sites (–H+).200
4.4 Organometallic catalysis
Organometallic catalysts are broadly employed as homogeneous catalyst phase in the forms of catalysts to enhance the rates of industrial chemical reaction and stoichiometrically in the research field. Organometallic catalysis has had a significant effect on organic synthesis during the past 50 years, allowing for the discovery of hitherto unthinkable reactions.201 Rapid advances in the research of organometallic and coordination compounds have resulted in the invention and commercialization of several catalytic processes using these compounds as catalysts.202,203 The selectivity of organometallic catalysis is a major benefit that has led to its broad use by industry.204 Transition metal compounds induce catalysis reactions that may be rationalised as a succession of stoichiometric phases connected cyclically to create a catalytic cycle. The coordination or attachment of substrate(s) to a metal core is the first step in the creation of an organometallic complex. The activated substrate(s) are then subjected to a sequence of intramolecular transformations, which may also include external groups and substrate(s) and the breakdown of the organometallic compound to provide reaction products. Platinum metal group complexes have outperformed all other organometallic catalysts in a variety of synthetic techniques. Since the beginning of the twenty-first century, it has won three Nobel awards in this field in a row.205 Tin(II) catalysts are also broadly applied on large scales to synthesise the polyesters and for polymerization of L-lactide.206 On the other hand, organotin alkoxy is widely described in transesterification reactions.207,208 Another widely generated organometallic complexes in the globe are organotin compounds.209 They are used as catalysts in a variety of industrial processes in which esters are produced via (trans)esterification, such as the synthesis of fatty acid alkyl esters (FAAEs),210 polyesters211,212 and lactones.213 The proposed transesterification mechanism of the tin based organometallic catalyst is shown in Fig. 10. This mechanism involves three necessary steps, (1) associative exchange of the alcohol onto the tin compound; (2) coordination and insertion of the carboxylic group into the Sn–O link of the tin alkoxide produced in (1); and (3) associative exchange of the intermediate. Unfortunately, we couldn't find any published article in the WOS database for a title search of two keywords of “organometallic” and “biodiesel”. However by using “organometallic” and “transesterification” words, only three papers were detected.214–216
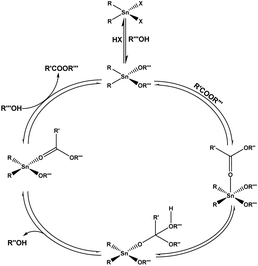 |
| Fig. 10 Diagram of the organotin(IV)-based catalytic transesterification mechanism.209 | |
4.5 Enzymatic catalysis
The enzymatic reaction is more strategic than the other systems because of its higher product quality, no wastewater production, affluent product recovery, favourable reaction situations, and no saponification. The enzyme, also named lipase, is the primary constituent in enzymatic reaction that can act as a catalyst in the extensive diversity of applications, including FFAs.217 There are fewer process stages, less wastewater and energy required for biodiesel production when enzymes are introduced as a catalyst in the system. Enzymes are recyclable and compatible with differences in the raw material variances; thus, they are hypothetically more beneficial than acid or alkaline catalysts. Additionally, they cause the increase of the separation of the products and produce a superb glycerol quality.218–220 Lipases from different sources have been investigated for their transesterification activity on other oils such as jatropha,221,222 tallow,223,224 soybean oil,225,226 sunflower oil,227,228 and waste cooking oil.229,230 Nevertheless, owing to its high cost, sluggish reaction rates, enzyme inhibition, and loss of function, enzyme transesterification is not extensively utilized.231,232
The most common method of decreasing free fatty acid of feedstocks such as oil and fat is the pre-esterification of free fatty acid by homogeneous acid catalysts before utilizing base catalyst transesterification reaction.127,129 In this technique, it is necessary to discrete the homogeneous acid catalyst from oil which is the key disadvantage of this method.233 In general, all homogeneous catalysts are linked with some other drawbacks, which might escalate the production cost because of wastewater emission and separation steps.234 The product of glycerin after transesterification reaction is low when a homogeneous catalyst is used. Then multi-stage purifications with the lengthy process are needed,79,235 which negatively affects the total costs of the transesterification process. Furthermore, the transesterification reaction via homogeneous base catalysts is not suitable for several feedstocks. Homogeneous catalysts are environmentally harmful in comparison with heterogeneous ones because they are naturally hygroscopic.236 Homogeneous catalysts are often highly selective but not particularly active or stable. On the other hand, heterogeneous catalysts are highly active (you can run them at higher temperatures because they are more robust), but they are not particularly selective.
4.6 Heterogeneous catalysts
Heterogeneous catalysts, typically in solid form, operate in a different phase in the reaction mixture of liquid compared to homogeneous catalysts. Homogeneous catalysts are corrosive, and they produce vast quantities of wastewater during the wash. Also, they give energy-intensive separation steps to separate the reaction constituents, and the catalyst cannot be effectively reused. Many results were reported to explore the activities of a range of heterogeneous materials to solve the many difficulties connected with homogeneous base and liquid acid such as alcoholysis catalysts.237 There are many advantages for heterogeneous catalyst applications over homogeneous ones, such as high glycerol purities, easier recycling and removal of the used catalysts, massive wastewater amounts, and washing section eliminations.238 Heterogeneous catalysts may also exist in distinct phases from the reactants, such as solid in liquid or aqueous reactants. As a result, heterogeneous catalysts may be suitable for excellent characteristics, including non-corrosion and easy separation.239 The primary focus of recent advancement in heterogeneous catalysis research is developing recyclable solid catalysts for the most uncomplicated biodiesel production.4 We have deliberately focused on trash assessment rather than creating renewable resources for catalytic applications in terms of material class. This is due to millions of waste disposed of as waste in a landfill without any pretreatment, which has been declared a source of organic pollution. Table 5 shows the stated production rates for a number of industrial and biological wastes discussed. Moreover, the biodiesel production cost will remarkably decrease by employing highly active waste-derived catalysts, which could also be suitable for large-scale applications. Various studies have shown the use of different waste resources such as rice husk ash,240 chicken eggshells,241 fly ash,242 red mud,243 steel slag,244 coconut shell245 and lime246 for biodiesel production. The area of the application of wastes in catalysis has attracted increasing interest in recent years.
Table 5 Production of waste for catalyst applications
Waste material |
Reported production rate |
Ref. |
Rice husk ash |
160 million tonnes per year |
247 |
Egg-shells waste |
8 million tonnes per year |
248 |
Fly ash |
800 million tonnes per year |
249 |
Red mud |
150 million tonnes per year |
250 |
Steel slag |
400 million tonnes per year |
251 |
Coconut |
23 million tonnes per year |
252 |
Lime |
120 million tonnes per year |
253 |
4.7 Rice husk ash
Rice lids 1% of the earth's surface and is a crucial food resource for many nations.254 The outer layer of paddy is called rice husk, and it makes about 20–25% of its weight. It is separated during rice milling and is mainly utilised as a source of heat in businesses and households in India. The rice husk could be an excellent solid fuel because the rice husk specific properties includes ash, volatile substance and heating value at 12.8%, 74.0% and 16.3 MJ kg−1, respectively.255 The majority of the RHA component contains silica (∼95%) and other elements such as zinc, magnesium, copper, potassium, calcium, manganese and iron.256,257 The RHA chemical composition and price point contribute to its good candidacy for industrial applications. The rice husk burning in the air always produces rice husk ash (RHA),258 which is considered an agricultural by-product in most world continents. Its low costs make it a viable and robust material as a catalyst support. RHA can also be utilized to purify the biodiesel using extracted silica from rice husk ash.259 RHA can be divided into amorphous, partial crystalline, and crystalline RHA.260 The major component of RHA (83–90%) is amorphous silica.261 Amorphous silica and carbon have potential commercial and scientific uses, and it is favoured over crystal silica because it is more reactive.262 From 1970 to 2020, only seven papers have been detected in the WOS database using “rice husk ash” and “biodiesel” keywords in the title search.256,258,263–267 These few published papers indicate a gap for catalyst development from RHA for biodiesel production studies. More particularly, there is a lot of interest in utilising silica from RHA to remove monoglyceride from crude biodiesel production since it is a by-product component of the biodiesel process that causes sedimentation in low-temperature environments.268
4.8 Eggshells
Eggshell weighs roughly 10% of the entire mass of chicken eggs; an eggshell is the substantial solid waste formed from manufacturing and food processing plants.269 The intact eggshell is around 700 nm thick and comprises two layers: an exterior microfilament-covered layer and an interior amorphous layer with a high electron density. Deteriorating eggshells, on the other hand, may reveal a middle layer with an intermediate electron density. The weight of the hen eggshell usually is 5–6 g with calcium carbonate composing 85–95% of the dry eggshell.270 Waste eggshells are produced due to the enormous consumption of eggs, posing a significant waste disposal issue, especially in overpopulated nations like China and India. The discarded eggshells may cause disposal issues as well as contamination in the environment. The use of discarded eggshells as a raw material for catalyst synthesis reduces waste while also producing a heterogeneous alkali catalyst with high cost-effectiveness. The bird eggshell is a porous bio-ceramic produced in a cell-free environment at body temperature.271 The eggshell is an entirely systematic structure with a polycrystalline organization through the solidified shell.272 There are varieties of eggshells for different birds published in the WOS, listed in Table 6 (topic search) published during 1970–2020. As seen, there are only 151 published works in total, and there is also a lack of studies on many other types of edible eggs from different birds.
Table 6 Number of papers in WOS using topic search of “eggshell”, “biodiesel”, and “bird name”
Bird |
Number of published research |
N/A |
154 |
Chicken |
51 |
Quail |
6 |
Duck |
2 |
Ostrich |
11 |
Goose |
0 |
Caviar |
0 |
Turkey |
0 |
EMU |
1 |
Hilsa |
0 |
Seagull |
0 |
Turtle |
0 |
Pheasant |
0 |
Rhea |
0 |
4.9 Fly ash
Fly ash, a solid waste produced by power stations, creates many difficulties; therefore, fly ash disposal is a critical issue273 due to a large vacant area requirement to create the dump. Although fly ash is mainly utilised for construction materials and other civil engineering projects, a part of it is nevertheless dumped in ponds or landfills. Therefore, it has become critical to develop alternate ways for fly ash disposal or appropriate use, focusing on discovering new applications and recognising new types of recycling. As a result, an effort was undertaken to create a suitable fly ash-based heterogeneous catalyst for the transesterification process to make it useful in the form of a higher value-added product. The thermal stability of fly ash is high because it includes a complex mixture with high contents of SiO2 with several metal oxides, such as CaO, MgO, Al2O3, and, particularly, Fe2O3. The mass compositions of fly ash components are shown in Fig. 11. Moreover, some minor elements such as As, Ge, Hg, Ga, and a tinge of active metals (Mn, Cu, Cr, Co, Pb, Zn, and Ni) and rare earth elements might also exist in fly ash.274 Fly ash is an appropriate substance for synthesising zeolites because of its textural, mineralogical, and chemical properties. The development of zeolites from the fly ash and their use as a catalyst for transesterification reaction eradicates the dumping obstacles. It changes waste and unwanted substances into a valuable and cheap alternative source. However, many investigations have stated the pozzolanic property of fly ash275 which has been employed in base-catalyzed reactions. Coal fly ash, for example, has been used as a precursor in the preparation of basic zeolite Na-X for biodiesel synthesis through the transesterification of sunflower oil with methanol.19 The role of fly ash as a catalyst in biodiesel generation was also explored.19,20,29 Following the WOS database and title search of “fly”, “ash”, and “biodiesel”, there are 16 published works detected and are summarized in Table 7. As seen in the table, the fly ash application for biodiesel has been started since 2012, and few publications were reported in this area. Therefore it could be beneficial to put the area of development of zeolites from fly ash waste for the transesterification process environmentally and industrially.
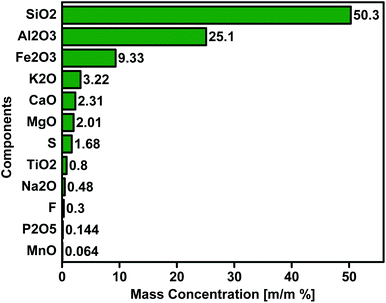 |
| Fig. 11 Fly ash mass composition.276 | |
Table 7 Published articles in the period of 1970–2020 in WOS with title keywords of fly, ash and biodiesel
Paper no. |
Paper |
Remarks |
Ref. |
1 |
“A CaO/zeolite-based catalyst obtained from waste chicken eggshell and coal fly ash for biodiesel production” |
In the methanolysis process, the CaO/FA-ZM catalyst demonstrated high activity (97.8% FAME for just 30 minutes) and stability (a minimal decrease in activity in five consecutive cycles) |
277 |
2 |
“Synthesis of hydroxy sodalite from coal fly ash for biodiesel production from waste-derived maggot oil” |
The use of a coal fly ash-derived heterogeneous HS catalyst in biodiesel synthesis from maggot oil is new, and process optimization studies show that it has the potential to improve biodiesel output and quality |
278 |
3 |
“Synthesis of pure and high surface area sodalite catalyst from waste industrial brine and coal fly ash for conversion of waste cooking oil (WCO) to biodiesel” |
The waste catalyst yielded 89.4% biodiesel, whereas the non-waste catalyst yielded 85.0%, with a high conversion of 97.0% waste cooking oil |
279 |
4 |
“Low-energy synthesis of kaliophilite catalyst from circulating fluidized bed fly ash for biodiesel production” |
The 99.2% biodiesel yield kaliophilite catalyst was readily recovered and reused for four cycles without substantial deactivation |
280 |
5 |
“Fabrication of a solid catalyst using coal fly ash and its utilization for producing biodiesel” |
Under ideal reaction conditions (2 wt% SC-Na relative to oil and 5 mL methanol per gram-oil at 50 °C for 4 h), 97.8% biodiesel conversion was accomplished. For the third round of operations, a batch operation was performed to evaluate the viability of recycling the solid catalyst, and more than 96 percent biodiesel conversion was consistently accomplished |
281 |
6 |
“Sulfated fly-ash catalyzed biodiesel production from maize acid oil feedstock: a comparative study of taguchi and box-behnken design” |
The use of an sulfated fly ash catalyst has been shown to be beneficial in the synthesis of biodiesel from feedstocks with a high free fatty acid concentration |
282 |
7 |
“Preparation of CaO/fly ash as a catalyst inhibitor for transesterification process off palm oil in biodiesel production” |
Under the conditions of oil: methanol ratio of 1 : 6, catalyst dosage of 6 wt% and temperature of 70 °C for 2 h, the biodiesel yield reaches to 71.77% |
283 |
8 |
“Microwave radiation improves biodiesel yields from waste cooking oil in the presence of modified coal fly ash” |
Under the microwave-assisted system, the modified coal fly ash catalyst improved biodiesel yields, and the maximum biodiesel yield from waste cooking oil reached 94.91% at a molar ratio of 9.67 : 1 with 3.99 wt% of modified coal fly ash catalyst (based on oil weight) at a 66.20 °C reaction temperature |
284 |
9 |
“Biodiesel production using coal fly ash-derived sodalite as a heterogeneous catalyst” |
With a 4 wt% catalyst concentration, a 12 : 1 methanol-to-oil molar ratio, and a 2 h reaction period, the synthesised sodalite was employed as a catalyst for transesterification of soy oil, yielding a maximum conversion of 95.5 wt% at 65 °C |
285 |
10 |
“Biodiesel production by using heterogeneous catalyst from fly ash and limestone” |
The B800 catalyst produced the greatest biodiesel output. The result revealed that biodiesel has characteristics that meet Indonesian National standard |
286 |
11 |
“The development of fly ash-supported CaO derived from mollusk shell of Anadara granosa and Paphia undulata as heterogeneous CaO catalyst in biodiesel synthesis” |
The yield was similar to that of biodiesel produced using a CaO catalyst generated from reagent grade CaCO3 (yield = 94%) |
287 |
12 |
“Ultrasound strengthened biodiesel production from waste cooking oil using modified coal fly ash as catalyst” |
Under ultrasonic assistance system, the modified coal fly ash catalyst improved biodiesel yields, and the highest biodiesel production from waste cooking oil reached 95.57 percent |
288 |
13 |
“Characterization, activity and process optimization with a biomass-based thermal power plant's fly ash as a potential catalyst for biodiesel production” |
The optimum yield of biodiesel achieved in a batch reactor with 5% catalyst loading was 93.9% when the temperature was 225 °C and the internal vapour pressure was 3.2 MPa |
289 |
14 |
“Evaluation of palm oil mill fly ash supported calcium oxide as a heterogeneous base catalyst in biodiesel synthesis from crude palm oil” |
Biodiesel production and FAME conversion were 79.76 percent and 97.09 percent, respectively, under transesterification conditions of 6 wt% catalyst loading, 12 : 1 methanol to oil molar ratio, 45 °C reaction temperature, 3 h reaction duration, and 700 rpm stirring speed |
290 |
15 |
Response to the comments on “novel zeolite Na-X synthesized from fly ash as a heterogeneous catalyst in biodiesel production” |
N/A |
291 |
16 |
“Novel zeolite Na-X synthesized from fly ash as a heterogeneous catalyst in biodiesel production” |
After 8 hours of reaction time, a high grade biodiesel with a yield of 83.53 percent was produced using a catalyst quantity of 3 percent (w/w) of oil and a reaction temperature of 65 °C |
292 |
4.10 Red mud
Red mud is an undesirable byproduct of the Bayer alumina production process. Around 90 million tonnes of red mud are produced globally, implying that repurposing waste from one industry and enhancing another may result in a better and more efficient environment.293 Red mud's unprotected disposal at landfill sites significantly affects the surrounding soils and groundwater due to its alkaline nature and high metallic content.294 The utilization of red mud as a catalyst for biodiesel generation delivers economical and environmentally friendly ways of reusing these sorts of wastes, expressively dropping its environmental toxicity and decreasing the biodiesel cost to make biodiesel reasonable in comparison with petroleum diesel. Only in the presence of sulphur did the red mud catalyst show acceptable activity, and the reaction product distributions were similar to those observed in the hydroliquefaction of cellulose and lignin.295 The approximate main elements of red mud are SiO2, Fe2O3, CaO, TiO2, Al2O3, and Na2O and are shown in Fig. 12, so red mud can support the preparation of catalysts. The use of the red mud catalyst for the manufacture of bio-diesel was described by Liu et al.296 The results showed that red mud is a highly active catalyst due to its inherent catalytic characteristics. Senthil et al.297 revealed that using red mud as a catalyst improves fuel properties while reducing pollution effects. However, under the title search of the WOS record, only six papers were found and are listed in Table 8, which started in 2013. Therefore, by considering the alkaline nature of red mud, the catalyst development from this waste could be highly effective in the transesterification of oil with methanol.
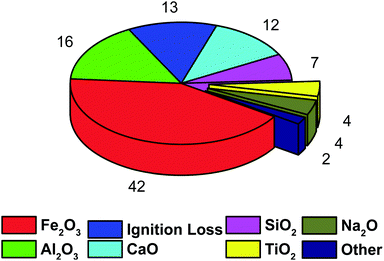 |
| Fig. 12 Approximate chemical composition (wt%) of red mud.298 | |
Table 8 Published articles in the period of 1970–2020 in WOS with title keywords of red, mud and biodiesel
Paper no. |
Paper |
Remarks |
Ref. |
1 |
“Engineered biochar composite fabricated from red mud and lipid waste and synthesis of biodiesel using the composite” |
In comparison to biodiesel synthesis using silica (92% yield at 360 °C), biochar produced an equal biodiesel yield at a considerably lower temperature (130 °C) |
299 |
2 |
“Investigations of red mud as a catalyst in Mahua oil biodiesel production and its engine performance” |
Using red mud as a catalyst not only improves the majority of the characteristics of the fuel, but it also lowers environmental stress by reducing emissions and fuel consumption |
293 |
3 |
“Biodiesel preparation from jatropha oil catalyzed by KF/red mud catalyst” |
Prepared KF/RM was an effective catalyst for biodiesel synthesis from jatropha oil through transesterification reaction, and red mud provided a suitable support for producing KF-loaded catalyst |
300 |
4 |
Effects of exhaust gas recirculation on emission characteristics of Mahua (Madhuca Indica) biodiesel using red mud as catalyst |
The use of red mud as a catalyst improves the fuel properties while lowering pollution levels |
297 |
5 |
“Biodiesel exhaust treatment with HFAC plasma supported by red mud: study on DeNOx and power consumption” |
At a specific energy of 250 J L−1, plasma treated gas increases the activity of red mud as an adsorbent/catalyst, resulting in a 60–72% NOx removal efficiency |
301 |
6 |
“Application of red mud as a basic catalyst for biodiesel production” |
The use of red mud as a catalyst in biodiesel synthesis lowers the cost of the fuel, making it competitive with petroleum diesel |
296 |
4.11 Iron and steel slag
Research on the application and improvement of solid waste elements from bulk chemical, petrochemical, metallurgical, steel and nuclear industries is significant for both enterprises and academics. Many specialists are interested in the slag recycling issue resulting from the pyrometallurgical treatment of natural materials since it offers the possibility of turning slags into valuable products while reducing waste.302 Steelmaking operations produce iron and steel by-products in two ways: iron ore-based steelmaking and scrap-based steelmaking. In all, the first one is used to create 70% of the world's steel.303 Slag materials generally consist of silica, oxides of particular metals in a given ratio that hinges on the original constitution of the element and even free metal species.304 The central chemical forms of the steel slug are presented in Fig. 13; hence it is an attractive material to develop catalysts. Other elements such as Mg, Mn, Al, Ti, and V may contribute a considerable proportion to the slag composition depending on the provenance of the iron ore.305 Therefore, attention to the industrial slag utilization in the catalyst preparation has been newly enhanced. Also, since the CaO fraction in LD-slag is high, it might be probable that it has beneficial catalytic properties for the transesterification process. Kabir et al.306 developed a zeolite from steel slag for pyrolysis of oil palm mesocarp fibres. They showed that the composition of bio-oil grew lighter and more stable, and that a large volume of metal oxides plays an essential role in the catalytic activity of steel slag. Another investigation explores that catalysts from steelmaking slags have an excellent performance in coal tar conversion to gas products.307 Unluckily, few reports have previously described the application of slag waste as a catalyst. As seen in Table 9, only six articles were published using two words of “slag” and “biodiesel” in the title search of the WOS database. Hence, the improvement of iron and steel slag catalysts in biodiesel production is an exciting subject in opinions of the appropriate waste resource deployment and its application in energy chemical production.
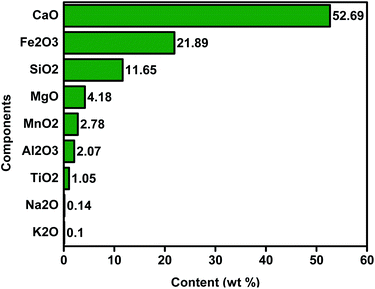 |
| Fig. 13 Steel slag's main chemical compositions.308 | |
Table 9 Published articles in the period of 1970–2020 in WOS with title keywords of slag and biodiesel
Paper no. |
Paper |
Remarks |
Ref. |
1 |
“Magnetite reduction in copper converter slag using biodiesel produced from waste cooking oil” |
Carbon monoxide, hydrogen, methane, and carbon dioxide were the primary products of biodiesel pyrolysis |
309 |
2 |
“Reduction of magnetite from copper smelting slag using petro-diesel and biodiesel” |
Biodiesel has a greater reduction impact than petro-diesel because pyrolysis of biodiesel produces more reducing gases, and its price should be considerably cheaper than petro-diesel |
310 |
3 |
“Highly stable gasified straw slag as a novel solid base catalyst for the effective synthesis of biodiesel: characteristics and performance” |
These findings suggest that the gasified straw slag catalyst has potential for biodiesel production |
311 |
4 |
“Fabrication and CO2 capture performance of magnesia-stabilized carbide slag by by-product of biodiesel during calcium looping process” |
Magnesia-stabilized carbide slag is made up of CaO–MgO grain groups, with MgO providing support for the sorbent's excellent sintering resistance |
312 |
5 |
“Waste carbide slag as a solid base catalyst for effective synthesis of biodiesel via transesterification of soybean oil with methanol” |
The connection between surface basicity and activity revealed that greater catalytic activity was caused by higher basicity |
180 |
6 |
“Catalytic effect of slags on the formation of bio-diesel fuel” |
The heat treatment of converter slag will increase the content of CaO by the decomposition reactions of Ca(OH)2 and CaCO3 |
313 |
4.12 Coconut
Coconut shell nanoparticles are selected for biodiesel additions because they are a commonly accessible agricultural waste, have a cheap cost, and have greater calorific values.314 Coconut shells are categorized as solid waste produced from agricultural activities involving a yearly generation of nearly 3.18 million tonnes.315 Coconut shells represent more than 60% of home waste quantity and present severe disposal problems for environments,316 and their chemical compositions are displayed in Fig. 14. Adding coconut shells into the brick will turn the coconut shells from waste material into potential materials that can be used to produce green building materials where large agricultural and industrial waste is discharged, and it will give twice the over benefits of decrease in the construction material cost other than disposal of wastes. It also outperforms other crushed granite aggregates in terms of impact, crushing, and abrasion resistance.317 Furthermore, the coconut shell's high carbon content, low ash level, and great strength and hardness make it ideal for catalyst development.318 Azizah et al.319 developed a catalyst via sulfonation of partially carbonized coconut shells by determined sulfuric acid and produced 88.15% biodiesel yield from palm oil. Yano et al.320 employed potassium supported on coconut-shell activated carbon to generate biodiesel from the transesterification of palm oil. They achieved 26.98% of the reaction conversion at 60 °C. Another study performed by Achanai et al.321 used potassium hydroxide supported on coconut shell activated carbon and obtained 86.3% biodiesel yield from waste cooking oil. Coconut shells, a non-degradable material and an environmental concern could be used as an effective heterogeneous catalyst for biodiesel generation, a green energy source. More interestingly, we could find only four published papers319,321–323 in the WOS title search of “biodiesel”, “coconut”, and “shell” in the period of 1970–2020. Of significance, the synthesis of new catalysts with low costs and high activity from coconut shells could play crucial roles in the environmental and industrial aspects of green and sustainable catalysts for biodiesel production.
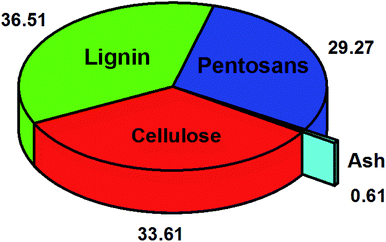 |
| Fig. 14 Coconut shells' chemical compositions (%).324 | |
4.13 Lime mud
Lime mud produced in pulp mills as a waste mainly comprises CaCO3 with residues of MgCO3 and some different ores. Lime mud is being employed as an eco-friendly and economic heterogeneous basic catalyst for the transesterification reaction. The major lime mud component, calcium carbonate, could be improved into calcium oxide throughout calcination.325 Almost 100 tonnes of lime mud is generated as a by-product of 550 tonnes of pulp production.326 The paper industry continues to produce millions of tonnes of lime mud each year, increasing with the growing demand for papers, with no efficient use anticipated. Other components in lime mud, such as silicon, magnesium, aluminium, and ferric, contribute to its alkaline nature.327 The chemical constituents of lime mud are represented in Fig. 15. So far, lime mud is principally discarded outside, resulting in a severe environmental crisis and causing land occupation. According to the title search of the WOS database, using “lime”, “mud”, and “transesterification” words, there were only five papers detected from 1970 to 2020.325,327–330 Hui et al.327 conducted the transesterification of edible peanut oil via KF supported on lime mud catalyst. They obtained 99.09% oil conversion at 64 °C, with a methanol to oil ratio of 12
:
1 and 5 wt% of catalyst. Another research was performed by Agus et al.329 employing modified lime mud base catalysts by soda–lime calcination for the transesterification of canola oil. They produced biodiesel with a yield of 99.6% at 60 °C, 4 wt% catalyst amount and a methanol to oil ratio of 12
:
1. Consequently, there is a lack of study on recycling and utilizing the lime mud for catalysis reaction, especially in the transesterification process and biodiesel production.
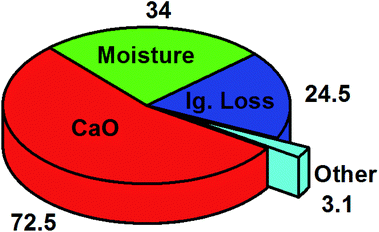 |
| Fig. 15 Lime mud chemical compositions (wt%).331 | |
4.14 Catalyst promoters
Promoters are not catalysts but mixed in small quantities with the catalysts to increase their efficiency in the reaction. At present, little interest has been shifted to applying structure promoters for CaO, providing a stable template with a high surface area, which could produce more excellent catalytic activity performance. Arsalanfar et al.332 studied the effect of Li, Cs, K, Rb and Ru promoters over the Fe–Co–Mn catalyst. They illustrated that the MgO/FeCoMn catalyst had revealed enhanced catalytic activity for converting synthesis gas into liquid fuels. Mohebbi et al.333 studied the effect of the Mo/B-ZSM-5 nano-catalyst in the free fatty acid esterification reaction. They found that the molybdenum promoter improved the crystallinity and the acid site concentration but reduced the acid site strength. Other researchers used the NiCoPt promoter over FAU zeolite for the oleic acid esterification reaction.334 They achieved 93% oleic acid conversion at 343 K. To study the catalytic activity in the partial hydrogenation of soybean oil-derived fatty acid methyl esters and enhance the oxidative stability of biodiesel, Thunyaratchatanon et al.335 employed sodium (Na), calcium (Ca), and barium (Ba) promoters for the Pd/SiO2 catalyst. The most significant turnover frequency was due to the low basic site density of Pd–Ba/SiO2. Lingmei et al.336 employed La, Ce, Zr, and Mn promoters over the Fe(II)–Zn-based catalyst for biodiesel generation from rapeseed oil. All the catalysts have comparable crystal structures, but the catalyst with 1 wt% La promoters had superior catalytic activity in the transesterification reactions. The results confirmed the high potential of the development of catalysts with promoters for industrial applications.
4.15 Biodiesel waste products
Glycerol, biodiesel washing wastewaters, methanol, and solid residues are biodiesel's most significant residues and by-products. Glycerol is the by-product that has sparked the most interest, as it can generate the most revenue for the biodiesel industry. Glycerin can be used to make various biotechnology products with high added value, such as ethanol, citric acid, 1,3 propanediol, and biosurfactants. The large amount of glycerin produced by biodiesel production worldwide means that renewable raw materials will be plentiful and inexpensive in the coming years.337 For example, in 2007, the price of refined glycerol in the United States was painfully low, around $0.30 per pound (compared to $0.70 before the expansion of biodiesel production). As a result, the price of crude glycerol fell from around $0.25 to $0.05 per pound.338 Fermentative glycerol metabolism is of particular interest due to the highly reduced nature of carbon in glycerol and the cost advantage of anaerobic processes. Low glycerol prices have a particularly negative impact on the biodiesel industry. Many now regard crude glycerol as a “waste stream” with a disposal cost associated with it, although it was once considered a desirable co-product that could contribute to the economic viability of biodiesel production.339 As a result, developing long-term techniques for exploiting this organic source material is critical. Glycerol has been converted into valuable chemicals using various techniques and procedures, including acetylation to make acetins, esterification to convert glycerol into several kinds of ester, ammoxidation to produce acrylonitrile, and gasification and steam reforming to produce synthesis gas. Pyrolysis is another advantageous process that involves heat degradation in the absence of oxygen. The formation of organic liquids, gases, and char is aided by lower process temperatures and more extended vapor residence periods. Certain researchers developed multiple strategies for using glycerol as an energy source. Jo-Han et al.340 employed microwave-assisted and carbonaceous catalytic pyrolysis of crude glycerol from biodiesel waste to generate energy for a brief period. They discovered that the fraction of product phases is most influenced by the duration spent within the quartz reactor, followed by the reaction temperature. Bühler et al.341 examined glycerol's ionic processes and pyrolysis as competing reaction routes in near- and supercritical water. They observed that the primary products of the glycerol breakdown were hydrogen, carbon dioxide, allyl alcohol, carbon monoxide, formaldehyde, ethanol, methanol, acrolein, acetaldehyde, and propionaldehyde. They suggested that the improvements and alternatives inside the ionic part of the mechanism and the additions concerning the interference of ionic and free radical reaction steps may lead to a better and more general global reaction model for the decomposition of glycerol in high-pressurized water. The conversion of waste into portable and energy profit positive products by pyrolysis makes crude glycerol a possible option for bioenergy production of bio-oil and syngas.
4.16 Prospects
The most significant factors for operative biodiesel production are the type of catalyst and feedstock. As a result, there is a clear need to find a modern and efficient method for mass production that reduces response time, manufacturing costs, and energy consumption. Feedstock selection is critical in biodiesel production, affecting various factors, including price, yield, composition, and purity. Along the way, research needs to be expedited to enhance the existing performance of biodiesel sources. Collecting waste oil, animal fat, edible and non-edible vegetable oils as a source of biodiesel and building even small factories in suburban areas to utilize these wastes to produce biodiesel is highly recommended. Additionally, attempts have been made to use waste necessity to get government's funding, such as tax relief, and enforce the collection, use, and passage of waste substances to such factories by residents and municipality. Selection and supply of suitable feedstock concentrate on maintaining non-renewable feedstocks, but it contains various parts and covers many related elements to offer assistance for current and prospective biodiesel production. Numerous applicable methods can be stated as it is logical to fulfil the associated aspects of conducting a low-cost transesterification process for biodiesel production. In the recent decade, a significant development to seize the limitations of homogeneous catalysts has been made by achieving insight into the heterogeneous catalyst synthesis from low cost and waste materials such rice husk ash, chicken eggshells, fly ash, red mud, steel slag, coconut shell and lime mud for biodiesel production. These wastes are highly desirable to consider development because of the presence of a high portion of silica, alumina, iron, calcium oxide, and many other valuable elements in their structures. However, it still lacks research on developing highly active catalysts from eggshells of birds other than chicken, such as duck, ostrich, goose, caviar, turkey, emu, hilsa, seagull turtle, pheasant, and rhea. Extension studies on the development of catalysts from red mud, iron and steel slag, coconut, lime mud, and zeolites from fly ash are desirable because of the low level of records in the WOS database. Another way of overcoming homogeneous catalyst limitations is by employing ionic liquids as a reusable and eco-friendly catalyst applicable to various feedstocks.342 Further investigations on the application of promoters such as Co, Ni, Pt, Ce, Mg, La, Zr, and Mn for heterogeneous catalyst development for transesterification reactions are recommended. The ionic liquid can be reused constantly, so it has possible application in biodiesel production. Application of biocatalysts for transesterification processes is also a novel approach and needs comprehensive investigation. It is also essential to focus on the economic analysis of the cost of biodiesel production using biological catalysts such as free lipase and traditionally immobilized lipase biocatalysts.
5. Conclusions
Worldwide demands for renewable, eco-friendly and sustainable fuels are rising rapidly because of the increasing environmental pollution from petroleum fuels and decreasing fossil fuel resources. In recent years, biodiesel, which has environmental advantages produced from renewable feedstocks, has become a more desirable fuel. Even though crude oil directly impacts the development of biodiesel technology, many biodiesel-related research initiatives are still prone to swings. Various biodiesel production approaches, including mass transfer limits, extended residence durations, scalability of the technology, and costly equipment, continue to offer hurdles. The current review studies aid in identifying beneficial developments, challenges, and opportunities in various aspects of biodiesel production. According to the literature, the main cost of biodiesel generation belongs to the feedstocks; thus, choosing a suitable source of biodiesel is significant in a cheap biodiesel production system. The search for valuable biodiesel sources must emphasise feedstock that does not affect food sources, does not lead to land-clearing, and offers greenhouse-gas declines. Biodiesel synthesis from algae and waste cooking oil is technically sound and cost-effective compared to typical vegetable oil and animal fat transesterification. From the review mentioned above, studies depict that catalysts play a crucial role in developing biodiesel. Few researchers have used homogeneous catalysts for pre-esterification and transesterification of various waste feedstocks. However, the leading disadvantage of the pre-esterification technique is the requirement of separation of the esterified oil and the homogeneous acid catalyst. This problem can be solved with the use of heterogeneous acid catalysts. However, biodiesel is presently not reasonable from an economic point of view, and more studies and technical development are required. As a suggestion, further heterogeneous catalytic development such as ionic liquids, promoters, multi-stage transesterification and associated strategies are significant to endorse biodiesel investigations and make their costs viable with other typical energy sources.
Author contributions
W. Nabgan: first author who carried out the writing parts. A. A. Jalil: took care of the bibliometric analysis and paraphrasing. B. Nabgan: took care of the bibliometric analysis and tables. Arvind H. Jadhav: writing and characterization. M. Ikram: corresponding author and english editing. A. Ul-Hamid: took the writing tasks. M. W. Ali: took the writing tasks. N. S. Hassan: helped to draw the figures and english editing.
Conflicts of interest
There are no conflicts to declare.
Acknowledgements
The principal author, Walid Nabgan, is thankful for the support from Universiti Teknologi Malaysia in the form of the Post-Doctoral Fellowship Scheme “Simultaneous heavy metals ions and organic pollutants photoredox reactions over SiO2/ZrO2 based catalysts under solar-light irradiation” (PDRU Grant number: 05E49). In addition, the authors acknowledge the financial support given for this work by Universiti Teknologi Malaysia (UTM) under the Collaborative Research Grant (CRG) number 07G61, 07G59, and 07G62.
References
- V. B. Borugadda and V. V. Goud, Renewable Sustainable Energy Rev., 2012, 16, 4763–4784 CrossRef CAS.
- J. Boro, A. J. Thakur and D. Deka, Fuel Process. Technol., 2011, 92, 2061–2067 CrossRef CAS.
- Y. Xu, W. Du, D. Liu and J. Zeng, Biotechnol. Lett., 2003, 25, 1239–1241 CrossRef CAS PubMed.
- N. Mansir, Y. H. Taufiq-Yap, U. Rashid and I. M. Lokman, Energy Convers. Manage., 2017, 141, 171–182 CrossRef CAS.
- D. Y. C. Leung, X. Wu and M. K. H. Leung, Appl. Energy, 2010, 87, 1083–1095 CrossRef CAS.
- I. Idowu, M. O. Pedrola, S. Wylie, K. H. Teng, P. Kot, D. Phipps and A. Shaw, Renew. Energy, 2019, 142, 535–542 CrossRef CAS.
- S. Boonyuen, S. M. Smith, M. Malaithong, A. Prokaew, B. Cherdhirunkorn and A. Luengnaruemitchai, J. Cleaner Prod., 2018, 177, 925–929 CrossRef CAS.
- H. C. Ong, H. H. Masjuki, T. M. I. Mahlia, A. S. Silitonga, W. T. Chong and T. Yusaf, Energy, 2014, 69, 427–445 CrossRef CAS.
- B. Thangaraj, P. R. Solomon, B. Muniyandi, S. Ranganathan and L. Lin, Clean Energy, 2019, 3, 2–23 CrossRef.
- M. Gohain, A. Devi and D. Deka, Ind. Crops Prod., 2017, 109, 8–18 CrossRef CAS.
- R. Jothiramalingam and M. K. Wang, Ind. Eng. Chem. Res., 2009, 48, 6162–6172 CrossRef CAS.
- M. E. Borges and L. Díaz, Renewable Sustainable Energy Rev., 2012, 16, 2839–2849 CrossRef CAS.
- K. Ramachandran, T. Suganya, N. Nagendra Gandhi and S. Renganathan, Renewable Sustainable Energy Rev., 2013, 22, 410–418 CrossRef CAS.
- P. Zhang, H. Liu, M. Fan, Y. Liu and J. Huang, Curr. Org. Chem., 2016, 20, 752–760 CrossRef CAS.
- Z. I. Ishak, N. A. Sairi, Y. Alias, M. K. T. Aroua and R. Yusoff, Catal. Rev., 2017, 59, 44–93 CrossRef CAS.
- A. Singh and G. Kumar, J. Biochem. Technol., 2018, 9, 17 CAS.
- E. Ghedini, S. Taghavi, F. Menegazzo and M. Signoretto, Sustainability, 2021, 13, 10479 CrossRef CAS.
- A. E. Atabani, M. M. El-Sheekh, G. Kumar and S. Shobana, in Clean Energy for Sustainable Development, ed. M. G. Rasul, A. k. Azad and S. C. Sharma, Academic Press, 2017, DOI:10.1016/b978-0-12-805423-9.00017-x, pp. 507–556.
- C. Shimasaki, in Biotechnology Entrepreneurship, Academic Press, Boston, 2014, DOI:10.1016/b978-0-12-404730-3.00009-9, pp. 113–138.
- J. R. Ziolkowska, in Biofuels for a More Sustainable Future, ed. J. Ren, A. Scipioni, A. Manzardo and H. Liang, Elsevier, 2020, DOI:10.1016/b978-0-12-815581-3.00001-4, pp. 1–19.
- E. Sadeghinezhad, S. N. Kazi, A. Badarudin, C. S. Oon, M. N. M. Zubir and M. Mehrali, Renewable Sustainable Energy Rev., 2013, 28, 410–424 CrossRef CAS.
- M. F. Othman, A. Adam, G. Najafi and R. Mamat, Renewable Sustainable Energy Rev., 2017, 80, 694–709 CrossRef.
- G. Sorda, M. Banse and C. Kemfert, Energy Policy, 2010, 38, 6977–6988 CrossRef.
- N. Gaurav, S. Sivasankari, G. S. Kiran, A. Ninawe and J. Selvin, Renewable Sustainable Energy Rev., 2017, 73, 205–214 CrossRef CAS.
- A. Neori, T. Chopin, M. Troell, A. H. Buschmann, G. P. Kraemer, C. Halling, M. Shpigel and C. Yarish, Aquaculture, 2004, 231, 361–391 CrossRef.
- J. Popp, S. Kot, Z. Lakner and J. Oláh, J. Secur. Sustain. Issues, 2018, 7, 477–493 Search PubMed.
- C. Fischer, Energy J., 2010, 31, 101–120 Search PubMed.
- D. Rajagopal, G. Hochman and D. Zilberman, Energy Policy, 2011, 39, 228–233 CrossRef.
- B. Kegl, Bioresour. Technol., 2008, 99, 863–873 CrossRef CAS PubMed.
- S. Bari, Appl. Energy, 2014, 124, 35–43 CrossRef CAS.
- Y. Zhang and A. L. Boehman, Energy Fuels, 2007, 21, 2003–2012 CrossRef CAS.
- M. Kousoulidou, G. Fontaras, L. Ntziachristos and Z. Samaras, Fuel, 2010, 89, 3442–3449 CrossRef CAS.
- Anonymous, Dyna, 2014, 89, 14–15 Search PubMed.
- P. H. Su, P. Geng, L. J. Wei, C. Y. Hou, F. Yin, G. T. Tomy, Y. F. Li and D. L. Feng, IET Intell. Transp. Syst., 2019, 13, 218–227 CrossRef.
- P. Su, Y. Hao, Z. Qian, W. Zhang, J. Chen, F. Zhang, F. Yin, D. Feng, Y. Chen and Y. Li, J. Environ. Sci., 2020, 91, 262–270 CrossRef PubMed.
- K. Na, S. Biswas, W. Robertson, K. Sahay, R. Okamoto, A. Mitchell and S. Lemieux, Atmos. Environ., 2015, 107, 307–314 CrossRef CAS.
- I. Olatunji, S. Wayne, M. Gautam, N. Clark, G. Thompson, D. McKain, P. Sindler and J. Nuszkowski, 2010.
- H. Bayındır, M. Z. Işık, Z. Argunhan, H. L. Yücel and H. Aydın, Energy, 2017, 123, 241–251 CrossRef.
- S. M. Krishna, P. Abdul Salam, M. Tongroon and N. Chollacoop, Appl. Therm. Eng., 2019, 155, 525–533 CrossRef CAS.
- M. R. Seraç, S. Aydın and C. Sayın, Energy Sources, Part A, 2020, 42, 2316–2331 CrossRef.
- G. Topilin, A. Yakovenko, S. Uminski and J. Nowak, TEKA Kom. Mot. Energ. Roln.-OL PAN, 2009, 9, 352–356 Search PubMed.
- G. Best, 2006.
- N. Alt and F. L. im VDMA eV, 2004.
- M. Eskiner, F. Bär, M. Rossner, A. Munack and J. Krahl, Fuel, 2015, 143, 327–333 CrossRef CAS.
- A. Macor and P. Pavanello, Energy, 2009, 34, 2025–2032 CrossRef CAS.
- J. F. González-González, A. Alkassir, J. San José, J. González and A. Gómez-Landero, Biomass Bioenergy, 2014, 60, 178–188 CrossRef.
- B. Bazooyar, A. Shariati and S. H. Hashemabadi, Energy Fuels, 2015, 29, 6804–6814 CrossRef CAS.
- L. N. Komariah, S. Arita, N. Novia, S. S. Wirawan and M. Yazid, J. Renewable Sustainable Energy, 2013, 5, 052005 CrossRef.
- M. Mansourpoor and A. Shariati, Chem. Biochem. Eng. Q., 2014, 28, 95–103 CrossRef CAS.
- P. Arkoudeas, S. Kalligeros, F. Zannikos, G. Anastopoulos, D. Karonis, D. Korres and E. Lois, Energy Convers. Manage., 2003, 44, 1013–1025 CrossRef CAS.
- D. M. Korres, D. Karonis, E. Lois, M. B. Linck and A. K. Gupta, Fuel, 2008, 87, 70–78 CrossRef CAS.
- W. E. R. Delgado, A. G. R. Meléndez, M. A. M. Betancourt, J. A. B. Páez and M. L. Gómez, Tecciencia, 2019, 14, 53–60 CrossRef.
- O. M. Ali, R. Mamat, N. R. Abdullah and A. A. Abdullah, Renew. Energy, 2016, 86, 59–67 CrossRef CAS.
- A. E. Atabani, A. S. Silitonga, I. A. Badruddin, T. M. I. Mahlia, H. H. Masjuki and S. Mekhilef, Renewable Sustainable Energy Rev., 2012, 16, 2070–2093 CrossRef.
- N. Kumar, V. Goel and S. R. Chauhan, Renewable Sustainable Energy Rev., 2013, 21, 633–658 CrossRef CAS.
- H. M. Mahmudul, F. Y. Hagos, R. Mamat, A. A. Adam, W. F. W. Ishak and R. Alenezi, Renewable Sustainable Energy Rev., 2017, 72, 497–509 CrossRef CAS.
- L. Lin, Z. Cunshan, S. Vittayapadung, S. Xiangqian and D. Mingdong, Appl. Energy, 2011, 88, 1020–1031 CrossRef.
- A. Gaurav, S. Dumas, C. T. Q. Mai and F. T. T. Ng, Green Energy Environ., 2019, 4, 328–341 CrossRef.
- A. P. Ingle, A. K. Chandel, R. Philippini, S. E. Martiniano and S. S. da Silva, Symmetry, 2020, 12, 256 CrossRef CAS.
- L. N. Okoro, S. V. Belaboh, N. R. Edoye and B. Y. Makama, Synthesis, 2011, 1, 3 Search PubMed.
- A. Ayoola, F. Hymore, C. A. Omonhinmin, O. Olawole, O. Fayomi, D. Babatunde and O. Fagbiele, Chem. Data Collect., 2019, 22, 100238 CrossRef CAS.
- H. Karlsson, S. Ahlgren, M. Sandgren, V. Passoth, O. Wallberg and P.-A. Hansson, Biotechnol. Biofuels, 2016, 9, 229 CrossRef PubMed.
- I. Ayadi, H. Belghith, A. Gargouri and M. Guerfali, BioMed Res. Int., 2019, 2019, 3213521 Search PubMed.
- S. K. Bhatia, R. Gurav, T.-R. Choi, Y. H. Han, Y.-L. Park, J. Y. Park, H.-R. Jung, S.-Y. Yang, H.-S. Song and S.-H. Kim, Bioresour. Technol., 2019, 289, 121704 CrossRef CAS PubMed.
- N. L. Boschen, M. G. P. Valenga, G. A. Maia, A. L. Gallina and P. R. P. Rodrigues, Ind. Crops Prod., 2019, 140, 111624 CrossRef CAS.
- A. Saydut, M. Z. Duz, C. Kaya, A. B. Kafadar and C. Hamamci, Bioresour. Technol., 2008, 99, 6656–6660 CrossRef CAS PubMed.
- K. A. Younis, J. L. Gardy and K. S. Barzinji, Am. J. Appl. Chem., 2014, 2, 105–111 CAS.
- U. Rashid and F. Anwar, Energy Fuels, 2008, 22, 1306–1312 CrossRef CAS.
- C. Ilkılıç, S. Aydın, R. Behcet and H. Aydin, Fuel Process. Technol., 2011, 92, 356–362 CrossRef.
- N. Dizge and B. Keskinler, Biomass Bioenergy, 2008, 32, 1274–1278 CrossRef CAS.
- A. D'Cruz, M. G. Kulkarni, L. C. Meher and A. K. Dalai, J. Am. Oil Chem. Soc., 2007, 84, 937–943 CrossRef.
- P. Nakpong and S. Wootthikanokkhan, Renew. Energy, 2010, 35, 1682–1687 CrossRef CAS.
- D. Kumar, G. Kumar and C. Singh, Ultrason. Sonochem., 2010, 17, 555–559 CrossRef CAS PubMed.
- S. Saka and D. Kusdiana, Fuel, 2001, 80, 225–231 CrossRef CAS.
- P. Šimáček, D. Kubička, G. Šebor and M. Pospíšil, Fuel, 2009, 88, 456–460 CrossRef.
- S. Zullaikah, C.-C. Lai, S. R. Vali and Y.-H. Ju, Bioresour. Technol., 2005, 96, 1889–1896 CrossRef CAS PubMed.
- S. Sinha, A. K. Agarwal and S. Garg, Energy Convers. Manage., 2008, 49, 1248–1257 CrossRef CAS.
- G. Antolın, F. Tinaut, Y. Briceno, V. Castano, C. Perez and A. Ramırez, Bioresour. Technol., 2002, 83, 111–114 CrossRef.
- M. L. Granados, M. Z. Poves, D. M. Alonso, R. Mariscal, F. C. Galisteo, R. Moreno-Tost, J. Santamaría and J. Fierro, Appl. Catal., B, 2007, 73, 317–326 CrossRef CAS.
- A. Yousuf, F. Sannino, V. Addorisio and D. Pirozzi, J. Agric. Food Chem., 2010, 58, 8630–8635 CrossRef CAS PubMed.
- F. Sanchez and P. T. Vasudevan, Appl. Biochem. Biotechnol., 2006, 135, 1–14 CrossRef CAS PubMed.
- P. Chand, C. V. Reddy, J. G. Verkade, T. Wang and D. Grewell, Energy Fuels, 2009, 23, 989–992 CrossRef CAS.
- A. Kinney and T. Clemente, Fuel Process. Technol., 2005, 86, 1137–1147 CrossRef CAS.
- M. I. Al-Widyan and A. O. Al-Shyoukh, Bioresour. Technol., 2002, 85, 253–256 CrossRef CAS PubMed.
- E. Crabbe, C. Nolasco-Hipolito, G. Kobayashi, K. Sonomoto and A. Ishizaki, Process Biochem., 2001, 37, 65–71 CrossRef CAS.
- C. Kaya, C. Hamamci, A. Baysal, O. Akba, S. Erdogan and A. Saydut, Renew. Energy, 2009, 34, 1257–1260 CrossRef CAS.
- T. Nguyen, L. Do and D. A. Sabatini, Fuel, 2010, 89, 2285–2291 CrossRef CAS.
- V. B. Veljković, M. O. Biberdžić, I. B. Banković-Ilić, I. G. Djalović, M. B. Tasić, Z. B. Nježić and O. S. Stamenković, Renewable Sustainable Energy Rev., 2018, 91, 531–548 CrossRef.
- M. Gülüm and A. Bilgin, Fuel Process. Technol., 2015, 134, 456–464 CrossRef.
- V. K. Mishra and R. Goswami, Biofuels, 2018, 9, 273–289 CrossRef CAS.
- A. Demirbas, A. Bafail, W. Ahmad and M. Sheikh, Energy
Explor. Exploit., 2016, 34, 290–318 CrossRef CAS.
- M. M. Gui, K. T. Lee and S. Bhatia, Energy, 2008, 33, 1646–1653 CrossRef CAS.
- A. Demirbas, Biomass Bioenergy, 2009, 33, 113–118 CrossRef CAS.
- R. Kumar, P. Tiwari and S. Garg, Fuel, 2013, 104, 553–560 CrossRef CAS.
- N. Usta, B. Aydoğan, A. H. Çon, E. Uğuzdoğan and S. G. Özkal, Energy Convers. Manage., 2011, 52, 2031–2039 CrossRef CAS.
- V. B. Veljković, S. H. Lakićević, O. S. Stamenković, Z. B. Todorović and M. L. Lazić, Fuel, 2006, 85, 2671–2675 CrossRef.
- D. Royon, M. Daz, G. Ellenrieder and S. Locatelli, Bioresour. Technol., 2007, 98, 648–653 CrossRef CAS PubMed.
- M. N. Nabi, M. M. Rahman and M. S. Akhter, Appl. Therm. Eng., 2009, 29, 2265–2270 CrossRef CAS.
- A. S. Ramadhas, S. Jayaraj and C. Muraleedharan, Fuel, 2005, 84, 335–340 CrossRef CAS.
- M. Morshed, K. Ferdous, M. R. Khan, M. S. I. Mazumder, M. A. Islam and M. T. Uddin, Fuel, 2011, 90, 2981–2986 CrossRef CAS.
- M. H. Ali, M. Mashud, M. R. Rubel and R. H. Ahmad, Procedia Eng., 2013, 56, 625–630 CrossRef CAS.
- A. Karmakar, S. Karmakar and S. Mukherjee, Renewable Sustainable Energy Rev., 2012, 16, 1050–1060 CrossRef CAS.
- U. Rashid, F. Anwar, B. R. Moser and G. Knothe, Bioresour. Technol., 2008, 99, 8175–8179 CrossRef CAS PubMed.
- G. Kafuku and M. Mbarawa, Appl. Energy, 2010, 87, 2561–2565 CrossRef CAS.
- L. C. Meher, V. S. S. Dharmagadda and S. N. Naik, Bioresour. Technol., 2006, 97, 1392–1397 CrossRef CAS PubMed.
- M. Naik, L. C. Meher, S. N. Naik and L. M. Das, Biomass Bioenergy, 2008, 32, 354–357 CrossRef CAS.
- A. Demirbas and M. F. Demirbas, Algae energy: algae as a new source of biodiesel, Springer Science & Business Media, 2010 Search PubMed.
- M. N. Campbell, Guelph Engineering Journal, 2008, 1, 2–7 Search PubMed.
- A. Kumar Tiwari, A. Kumar and H. Raheman, Biomass Bioenergy, 2007, 31, 569–575 CrossRef CAS.
- H. J. Berchmans and S. Hirata, Bioresour. Technol., 2008, 99, 1716–1721 CrossRef CAS PubMed.
- A. Gupta, 2004.
- Y. C. Sharma and B. Singh, Fuel, 2008, 87, 1740–1742 CrossRef CAS.
- S. V. Ghadge and H. Raheman, Biomass Bioenergy, 2005, 28, 601–605 CrossRef CAS.
- S. V. Ghadge and H. Raheman, Bioresour. Technol., 2006, 97, 379–384 CrossRef CAS PubMed.
- L. Canoira, R. Alcántara, M. Jesús García-Martínez and J. Carrasco, Biomass Bioenergy, 2006, 30, 76–81 CrossRef CAS.
- A. Sandouqa and Z. Al-Hamamre, Renew. Energy, 2019, 130, 831–842 CrossRef.
- C. W. Mohd Noor, M. M. Noor and R. Mamat, Renewable Sustainable Energy Rev., 2018, 94, 127–142 CrossRef CAS.
- P. M. F. d. Silva, E. O. Silva, M. d. S. C. Rêgo, L. M. d. R. Castro and A. I. Siqueira-Silva, Rev. Bras. Farmacogn., 2019, 29, 425–433 CrossRef CAS.
- S. Ramalingam, S. Rajendran, P. Ganesan and M. Govindasamy, Renewable Sustainable Energy Rev., 2018, 81, 775–788 CrossRef CAS.
- K.-H. Chung, J. Ind. Eng. Chem., 2010, 16, 506–509 CrossRef CAS.
- C.-Y. Lin and C.-L. Fan, Fuel, 2011, 90, 2240–2244 CrossRef CAS.
- A. A. Pollardo, H.-s. Lee, D. Lee, S. Kim and J. Kim, J. Cleaner Prod., 2018, 185, 382–388 CrossRef CAS.
- Y. Dikmen, G. Oyman and T. Sepici, 2004.
- A. Ribeiro, J. Carvalho, J. Castro, J. Araújo, C. Vilarinho and F. Castro, Mater. Sci. Forum, 2013, 730–732, 623–629 CAS.
- G. R. Srinivasan and R. Jambulingam, J. Environ. Sci. Technol., 2018, 11, 157–166 CrossRef CAS.
- S. S. Chen, T. Maneerung, D. C. W. Tsang, Y. S. Ok and C.-H. Wang, Chem. Eng. J., 2017, 328, 246–273 CrossRef CAS.
- E. Lotero, Y. Liu, D. E. Lopez, K. Suwannakarn, D. A. Bruce and J. G. Goodwin, Ind. Eng. Chem. Res., 2005, 44, 5353–5363 CrossRef CAS.
- M. Canakci and J. Van Gerpen, Trans. ASAE, 2001, 44, 1429 CAS.
- M. G. Kulkarni and A. K. Dalai, Ind. Eng. Chem. Res., 2006, 45, 2901–2913 CrossRef CAS.
- S. Marmesat, E. Rodrigues, J. Velasco and C. Dobarganes, Int. J. Food Sci. Technol., 2007, 42, 601–608 CrossRef CAS.
- M. J. Montefrio, T. Xinwen and J. P. Obbard, Appl. Energy, 2010, 87, 3155–3161 CrossRef CAS.
- S. N. Gebremariam and J. M. Marchetti, Energy Convers. Manage., 2018, 168, 74–84 CrossRef CAS.
- G. Knothe and L. F. Razon, Prog. Energy Combust. Sci., 2017, 58, 36–59 CrossRef.
- Y. Zhang, M. A. Dubé, D. D. McLean and M. Kates, Bioresour. Technol., 2003, 90, 229–240 CrossRef CAS PubMed.
- A. Gaurav, F. T. T. Ng and G. L. Rempel, Green Energy Environ., 2016, 1, 62–74 CrossRef.
- J. Mattson, N. V. Burnete, C. Depcik, D. Moldovanu and N. Burnete, Fuel, 2019, 255, 115753 CrossRef CAS.
- O. Aboelazayem, M. Gadalla and B. Saha, Renew. Energy, 2018, 124, 144–154 CrossRef CAS.
- S. M. Smith, C. Oopathum, V. Weeramongkhonlert, C. B. Smith, S. Chaveanghong, P. Ketwong and S. Boonyuen, Bioresour. Technol., 2013, 143, 686–690 CrossRef CAS PubMed.
- A. Saydut, A. Kafadar, F. Aydin, S. Erdogan, C. Kaya and C. Hamamci, 2016.
- N. Viriya-empikul, P. Krasae, B. Puttasawat, B. Yoosuk, N. Chollacoop and K. Faungnawakij, Bioresour. Technol., 2010, 101, 3765–3767 CrossRef CAS PubMed.
- F. Ma and M. A. Hanna, Bioresour. Technol., 1999, 70, 1–15 CrossRef CAS.
- V. Polshettiwar, R. Luque, A. Fihri, H. Zhu, M. Bouhrara and J.-M. Basset, Chem. Rev., 2011, 111, 3036–3075 CrossRef CAS PubMed.
- R. A. Korus, D. S. Hoffman, N. Bam, C. L. Peterson and D. C. Drown, 1993.
- D. Bacovsky, W. Körbitz, M. Mittelbach and M. Wörgetter, IEA task, 2007, vol. 39, p. 9 Search PubMed.
- M. L. Testa, V. La Parola and A. M. Venezia, Catal. Today, 2014, 223, 115–121 CrossRef CAS.
- L. Guerreiro, J. E. Castanheiro, I. M. Fonseca, R. M. Martin-Aranda, A. M. Ramos and J. Vital, Catal. Today, 2006, 118, 166–171 CrossRef CAS.
- J. A. Melero, L. F. Bautista, G. Morales, J. Iglesias and D. Briones, Energy Fuels, 2009, 23, 539–547 CrossRef CAS.
- S. N. Gebremariam and J. M. Marchetti, Energy Convers. Manage., 2018, 174, 639–648 CrossRef CAS.
- K. A. Shah, K. C. Maheria and J. K. Parikh, Energy Sources, Part A, 2016, 38, 1470–1477 CrossRef CAS.
- K. Malins, V. Kampars and J. Brinks.
- Y. C. Chen, D. Y. Lin and B. H. Chen, J. Taiwan Inst. Chem. Eng., 2017, 79, 31–36 CrossRef CAS.
- X. X. Han, W. Yan, C. T. Hung, Y. F. He, P. H. Wu, L. L. Liu, S. J. Huang and S. B. Liu, Korean J. Chem. Eng., 2016, 33, 2063–2072 CrossRef CAS.
- I. Istadi, D. D. Anggoro, L. Buchori, D. A. Rahmawati and D. Intaningrum, in Basic Researches in the Tropical and Coastal Region Eco Developments, ed. H. Hady, H. Susanto and O. K. Radjasa, 2015, vol. 23, pp. 385–393 Search PubMed.
- C. O. Pereira, M. F. Portilho, C. A. Henriques and F. M. Z. Zotin, J. Braz. Chem. Soc., 2014, 25, 2409–2416 CAS.
- N. Narkhede and A. Patel, Ind. Eng. Chem. Res., 2013, 52, 13637–13644 CrossRef CAS.
- Y. F. He, X. X. Han, Q. Chen and L. X. Zhou, Chem. Eng. Technol., 2013, 36, 1559–1567 CrossRef.
- Z. Ma, Z. Y. Shang, E. J. Wang, J. C. Xu, Q. Q. Xu and J. Z. Yin, Ind. Eng. Chem. Res., 2012, 51, 12199–12204 CAS.
- W. L. Xie and D. Yang, Bioresour. Technol., 2012, 119, 60–65 CrossRef CAS PubMed.
- W. L. Xie, H. Y. Wang and H. Li, Ind. Eng. Chem. Res., 2012, 51, 225–231 CrossRef CAS.
- W. L. Xie and D. Yang, Bioresour. Technol., 2011, 102, 9818–9822 CrossRef CAS PubMed.
- L. L. Xu, W. Li, J. L. Hu, K. X. Li, X. Yang, F. Y. Ma, Y. N. Guo, X. D. Yu and Y. H. Guo, J. Mater. Chem., 2009, 19, 8571–8579 RSC.
- C. W. Wang, J. F. Zhou, W. Chen, W. G. Wang, Y. X. Wu, J. F. Zhang, R. A. Chi and W. Y. Ying, Energy Fuels, 2008, 22, 3479–3483 CrossRef CAS.
- W. Stoffel, F. Chu and E. H. Ahrens, Anal. Chem., 1959, 31, 307–308 CrossRef CAS.
- A. Alsalme, E. F. Kozhevnikova and I. V. Kozhevnikov, Appl. Catal., A, 2008, 349, 170–176 CrossRef CAS.
- N. U. Soriano, R. Venditti and D. S. Argyropoulos, Fuel, 2009, 88, 560–565 CrossRef CAS.
- M. Di Serio, R. Tesser, M. Dimiccoli, F. Cammarota, M. Nastasi and E. Santacesaria, J. Mol. Catal. A: Chem., 2005, 239, 111–115 CrossRef CAS.
- F. Su and Y. Guo, Green Chem., 2014, 16, 2934–2957 RSC.
- U. Schuchardt, R. Sercheli and R. M. Vargas, J. Braz. Chem. Soc., 1998, 9, 199–210 CrossRef CAS.
- M. K. Lam and K. T. Lee, in Biofuels, ed. A. Pandey, C. Larroche, S. C. Ricke, C.-G. Dussap and E. Gnansounou, Academic Press, Amsterdam, 2011, DOI:10.1016/b978-0-12-385099-7.00016-4, pp. 353–374.
- P. Morin, B. Hamad, G. Sapaly, M. G. Carneiro Rocha, P. G. Pries de Oliveira, W. A. Gonzalez, E. Andrade Sales and N. Essayem, Appl. Catal., A, 2007, 330, 69–76 CrossRef CAS.
- S. Nasreen, M. Nafees, L. A. Qureshi, M. S. Asad, A. Sadiq and S. D. Ali, Biofuels: State of Development, 2018, pp. 93–119 Search PubMed.
- R. O. Idem, S. P. R. Katikaneni and N. N. Bakhshi, Fuel Process. Technol., 1997, 51, 101–125 CrossRef CAS.
- A. Macario, G. Giordano, B. Onida, D. Cocina, A. Tagarelli and A. M. Giuffrè, Appl. Catal., A, 2010, 378, 160–168 CrossRef CAS.
- 2005.
- T. Meechai, S. Kongchamdee, W. W. Mar and E. Somsook, J. Oleo Sci., 2018, 67, 355–367 CrossRef CAS PubMed.
- M. D. G. de Luna, J. L. Cuasay, N. C. Tolosa and T.-W. Chung, Fuel, 2017, 209, 246–253 CrossRef CAS.
- X. Han, W. Yan, C.-T. Hung, Y. He, P.-H. Wu, L.-L. Liu, S.-J. Huang and S.-B. Liu, Korean J. Chem. Eng., 2016, 33, 2063–2072 CrossRef CAS.
- I. Istadi, U. Mabruro, B. A. Kalimantini, L. Buchori and D. D. Anggoro, Bull. Chem. React. Eng. Catal., 2016, 11, 34–39 CrossRef CAS.
- R. Bhandari, V. Volli and M. K. Purkait, J. Environ. Chem. Eng., 2015, 3, 906–914 CrossRef CAS.
- F.-J. Li, H.-Q. Li, L.-G. Wang and Y. Cao, Fuel Process. Technol., 2015, 131, 421–429 CrossRef CAS.
- H. Wu, J. Zhang, Q. Wei, J. Zheng and J. Zhang, Fuel Process. Technol., 2013, 109, 13–18 CrossRef CAS.
- C. Ofori-Boateng and K. T. Lee, Chem. Eng. J., 2013, 220, 395–401 CrossRef CAS.
- J.-X. Wang, K.-T. Chen, B.-Z. Wen, Y.-H. B. Liao and C.-C. Chen, J. Taiwan Inst. Chem. Eng., 2012, 43, 215–219 CrossRef CAS.
- Y. Ding, H. Sun, J. Duan, P. Chen, H. Lou and X. Zheng, Catal. Commun., 2011, 12, 606–610 CrossRef CAS.
- D. Meloni, R. Monaci, Z. Zedde, M. G. Cutrufello, S. Fiorilli and I. Ferino, Appl. Catal., B, 2011, 102, 505–514 CrossRef CAS.
- X. Liu, X. Piao, Y. Wang and S. Zhu, J. Phys. Chem. A, 2010, 114, 3750–3755 CrossRef CAS PubMed.
- A. Coker, A. Iretski, M. White, R. Hernandez and T. French, 2010.
- G. Teng, L. Gao, G. Xiao and H. Liu, Energy Fuels, 2009, 23, 4630–4634 CrossRef CAS.
- C. Fan, Z. Bin-Bin, L. Jing, Z. Guo-Yu, F. Wei-Ping and Y. Le-Fu, Acta Phys.-Chim. Sin., 2008, 24, 1817–1823 Search PubMed.
- M. Kouzu, T. Kasuno, M. Tajika, Y. Sugimoto, S. Yamanaka and J. Hidaka, Fuel, 2008, 87, 2798–2806 CrossRef CAS.
- X. Liu, X. Piao, Y. Wang, S. Zhu and H. He, Fuel, 2008, 87, 1076–1082 CrossRef CAS.
- X. Liu, X. Piao, Y. Wang and S. Zhu, Energy Fuels, 2008, 22, 1313–1317 CrossRef CAS.
- X. Liu, H. He, Y. Wang, S. Zhu and X. Piao, Fuel, 2008, 87, 216–221 CrossRef CAS.
- M. Kouzu, T. Kasuno, M. Tajika, S. Yamanaka and J. Hidaka, Appl. Catal., A, 2008, 334, 357–365 CrossRef CAS.
- X. Liu, H. He, Y. Wang and S. Zhu, Catal. Commun., 2007, 8, 1107–1111 CrossRef CAS.
- W. Xie, H. Peng and L. Chen, Appl. Catal., A, 2006, 300, 67–74 CrossRef CAS.
- T. Hiwot, Chem. Int., 2018, 4, 198–205 CAS.
- F. Ullah, L. Dong, A. Bano, Q. Peng and J. Huang, J. Energy Inst., 2016, 89, 282–292 CrossRef CAS.
- S. Semwal, A. K. Arora, R. P. Badoni and D. K. Tuli, Bioresour. Technol., 2011, 102, 2151–2161 CrossRef CAS PubMed.
- A. L. de Lima, C. M. Ronconi and C. J. A. Mota, Catal. Sci. Technol., 2016, 6, 2877–2891 RSC.
- J. Buendia, G. Grelier and P. Dauban, in Advances in Organometallic Chemistry, ed. P. J. Pérez, Academic Press, 2015, vol. 64, pp. 77–118 Search PubMed.
- G. Parshall and S. Ittel, 1992.
- B. Cornils and W. A. Herrmann, vol. 1, 245–258.
- E. V. Gusevskaya, Quim. Nova, 2003, 26, 242–248 CrossRef CAS.
- V. Terrasson and E. Guénin, in Novel Magnetic Nanostructures, ed. N. Domracheva, M. Caporali and E. Rentschler, Elsevier, 2018, DOI:10.1016/b978-0-12-813594-5.00010-2, pp. 333–371.
- A. B. Ferreira, A. Lemos Cardoso and M. J. da Silva, ISRN Renewable Energy, 2012, 2012, 142857 CrossRef.
- C.-S. Cho, D.-T. Kim, H.-J. Choi, T.-J. Kim and S.-C. Shim, Bull. Korean Chem. Soc., 2002, 23, 539–540 CrossRef CAS.
- C. E. Gonçalves, L. O. Laier and M. J. d. Silva, Catal. Lett., 2011, 141, 1111–1117 CrossRef.
- M. R. Meneghetti and S. M. P. Meneghetti, Catal. Sci. Technol., 2015, 5, 765–771 RSC.
- Y. C. Brito, D. A. C. Ferreira, D. M. d. A. Fragoso, P. R. Mendes, C. M. J. d. Oliveira, M. R. Meneghetti and S. M. P. Meneghetti, Appl. Catal., A, 2012, 443–444, 202–206 CrossRef CAS.
- G. Deshayes, F. A. G. Mercier, P. Degée, I. Verbruggen, M. Biesemans, R. Willem and P. Dubois, Chem.–Eur. J., 2003, 9, 4346–4352 CrossRef CAS PubMed.
- S. Shyamroy, B. Garnaik and S. Sivaram, J. Polym. Sci., Part A: Polym. Chem., 2005, 43, 2164–2177 CrossRef CAS.
- I. Shiina, Chem. Rev., 2007, 107, 239–273 CrossRef CAS PubMed.
- A. K. Singh, R. Prakash and D. Pandey, RSC Adv., 2012, 2, 10316–10323 RSC.
- D. R. de Mendonça, J. P. V. da Silva, R. M. de Almeida, C. R. Wolf, M. R. Meneghetti and S. M. P. Meneghetti, Appl. Catal., A, 2009, 365, 105–109 CrossRef.
- G.-H. Hu, Y.-J. Sun and M. Lambla, Die Makromolekulare Chemie, 1993, 194, 665–675 CrossRef CAS.
- B. Norjannah, H. C. Ong, H. H. Masjuki, J. C. Juan and W. T. Chong, RSC Adv., 2016, 6, 60034–60055 RSC.
- M. Kaieda, T. Samukawa, T. Matsumoto, K. Ban, A. Kondo, Y. Shimada, H. Noda, F. Nomoto, K. Ohtsuka, E. Izumoto and H. Fukuda, J. Biosci. Bioeng., 1999, 88, 627–631 CrossRef CAS PubMed.
- V. Kumari, S. Shah and M. N. Gupta, Energy Fuels, 2007, 21, 368–372 CrossRef CAS.
- L. C. Meher, D. Vidya Sagar and S. N. Naik, Renewable Sustainable Energy Rev., 2006, 10, 248–268 CrossRef CAS.
- S. Tamalampudi, M. R. Talukder, S. Hama, T. Numata, A. Kondo and H. Fukuda, Biochem. Eng. J., 2008, 39, 185–189 CrossRef CAS.
- J. Rodrigues, A. Canet, I. Rivera, N. M. Osório, G. Sandoval, F. Valero and S. Ferreira-Dias, Bioresour. Technol., 2016, 213, 88–95 CrossRef CAS PubMed.
- G. Lazar and L. Eirich, 1989.
- P. Radha, K. Prabhu, A. Jayakumar, S. AbilashKarthik and K. Ramani, Process Biochem., 2020, 95, 17–29 CrossRef CAS.
- K. V. Fernandes, E. D. C. Cavalcanti, E. P. Cipolatti, E. C. G. Aguieiras, M. C. C. Pinto, F. A. Tavares, P. R. da Silva, R. Fernandez-Lafuente, S. Arana-Peña, J. C. Pinto, C. L. B. Assunção, J. A. C. da Silva and D. M. G. Freire, Catal. Today, 2021, 362, 122–129 CrossRef CAS.
- R. C. Rial, O. N. de Freitas, C. E. D. Nazário and L. H. Viana, Renew. Energy, 2020, 149, 970–979 CrossRef CAS.
- S. J. H. Júnior, J. N. R. Ract, L. A. Gioielli and M. Vitolo, 2019.
- M. Mittelbach, J. Am. Oil Chem. Soc., 1990, 67, 168–170 CrossRef CAS.
- Y. Chen, B. Xiao, J. Chang, Y. Fu, P. Lv and X. Wang, Energy Convers. Manage., 2009, 50, 668–673 CrossRef CAS.
- N. Dizge, C. Aydiner, D. Y. Imer, M. Bayramoglu, A. Tanriseven and B. Keskinler, Bioresour. Technol., 2009, 100, 1983–1991 CrossRef CAS PubMed.
- L. P. Christopher, K. Hemanathan and V. P. Zambare, Appl. Energy, 2014, 119, 497–520 CrossRef CAS.
- L. Fjerbaek, K. V. Christensen and B. Norddahl, Biotechnol. Bioeng., 2009, 102, 1298–1315 CrossRef CAS PubMed.
- M. Di Serio, R. Tesser, L. Pengmei and E. Santacesaria, Energy Fuels, 2008, 22, 207–217 CrossRef CAS.
- A. K. Endalew, Y. Kiros and R. Zanzi, Biomass Bioenergy, 2011, 35, 3787–3809 CrossRef CAS.
- S. K. Karmee and A. Chadha, Bioresour. Technol., 2005, 96, 1425–1429 CrossRef CAS PubMed.
- A. P. S. Chouhan and A. K. Sarma, Renewable Sustainable Energy Rev., 2011, 15, 4378–4399 CrossRef CAS.
- A. Galadima and O. Muraza, Energy, 2014, 78, 72–83 CrossRef CAS.
- D. Vujicic, D. Comic, A. Zarubica, R. Micic and G. Boskovic, Fuel, 2010, 89, 2054–2061 CrossRef CAS.
- Z.-E. Tang, S. Lim, Y.-L. Pang, H.-C. Ong and K.-T. Lee, Renewable Sustainable Energy Rev., 2018, 92, 235–253 CrossRef CAS.
- V. Vinu and N. N. Binitha, Mater. Today: Proc., 2020, 25, 241–245 CAS.
- G. Anusha, Curr. Trends Biotechnol. Pharm., 2020, 14, 134–140 CrossRef CAS.
- A. Hidayat, A. Chafidz and B. Sutrisno, 2020.
- A. Hidayat, G. K. Roziq, F. Muhammad, W. Kurniawan and H. Hinode, 2020.
- G. Liu, J. Yang and X. Xu, Sci. Rep., 2020, 10, 10273 CrossRef CAS PubMed.
- D. Chaos-Hernández, H. Reynel-Avila, D. Mendoza-Castillo and A. Bonilla-Petriciolet, Bulg. Chem. Commun., 2019, 51, 89–92 Search PubMed.
- J. F. Puna, M. J. N. Correia, A. P. S. Dias, J. Gomes and J. Bordado, React. Kinet., Mech. Catal., 2013, 109, 405–415 CrossRef CAS.
- M. A. Mosaberpanah and S. A. Umar, Mater. Today Sustain., 2020, 7–8, 100030 CrossRef.
- G. Golakiya, University of Saskatchewan, 2020.
- M. N. A. Ahmad Zawawi, K. Muthusamy, A. P. P. Abdul Majeed, R. Muazu Musa and A. Mokhtar Albshir Budiea, J. Build. Eng., 2020, 27, 100924 CrossRef.
- W. Wang, K. Sun and H. Liu, Constr. Build. Mater., 2020, 241, 118119 CrossRef CAS.
- G. Tang, X. Liu, L. Zhou, P. Zhang, D. Deng and H. Jiang, Adv. Powder Technol., 2020, 31, 279–286 CrossRef CAS.
- O.-A. Clarence, International Development Innovation Network, 2016.
- J. Singh, Int. J. N. Innovat. Eng. Technol., 2019, 15, 61–66 Search PubMed.
- F. Nuruddin, N. Shafiq and N. M. Kamal, 2008.
- L. Armesto, A. Bahillo, K. Veijonen, A. Cabanillas and J. Otero, Biomass Bioenergy, 2002, 23, 171–179 CrossRef CAS.
- K. Bonet-Ragel, L. López-Pou, G. Tutusaus, M. D. Benaiges and F. Valero, Biocatal. Biotransform., 2018, 36, 151–158 CrossRef CAS.
- V. P. Della, I. Kühn and D. Hotza, Mater. Lett., 2002, 57, 818–821 CrossRef CAS.
- K.-T. Chen, J.-X. Wang, Y.-M. Dai, P.-H. Wang, C.-Y. Liou, C.-W. Nien, J.-S. Wu and C.-C. Chen, J. Taiwan Inst. Chem. Eng., 2013, 44, 622–629 CrossRef CAS.
- N. Saengprachum and S. Pengprecha, 2012.
- L. A.-t. Bui, C.-t. Chen, C.-l. Hwang and W.-s. Wu, Int. J. Miner. Metall. Mater., 2012, 19, 252–258 CrossRef CAS.
- R. Pode, Renewable Sustainable Energy Rev., 2016, 53, 1468–1485 CrossRef.
- G. Tufaner, A. Çalışkan, H. B. Yener and Ş. Şeref, 2019.
- E. Saputra, M. W. Nugraha, Z. Helwani, M. Olivia and S. Wang, IOP Conf. Ser.: Mater. Sci. Eng., 2018, 345, 012019 CrossRef.
- N. Saengprachum and S. Pengprecha, J. Taiwan Inst. Chem. Eng., 2016, 58, 441–450 CrossRef CAS.
- G.-Y. Chen, R. Shan, J.-F. Shi and B.-B. Yan, Fuel Process. Technol., 2015, 133, 8–13 CrossRef CAS.
- M. C. Manique, C. S. Faccini, B. Onorevoli, E. V. Benvenutti and E. B. Caramão, Fuel, 2012, 92, 56–61 CrossRef CAS.
- A. B. Soares, P. R. N. da Silva, A. M. Stumbo and J. C. C. Freitas, Quim. Nova, 2012, 35, 268–273 CrossRef CAS.
- L. Aisyah, C. Wibowo, S. Bethari, D. Ufidian and R. Anggarani, 2018.
- Z. Wei, C. Xu and B. Li, Bioresour. Technol., 2009, 100, 2883–2885 CrossRef CAS PubMed.
- Y. C. Sharma, B. Singh and J. Korstad, Energy Fuels, 2010, 24, 3223–3231 CrossRef CAS.
- M. T. Hincke, Y. Nys, J. Gautron, K. Mann, A. B. Rodriguez-Navarro and M. D. McKee, Front. Biosci., 2012, 17, 80 CrossRef PubMed.
- Y. Nys and J. Gautron, in Bioactive egg compounds, Springer, 2007, pp. 99–102 Search PubMed.
- X. Xuan, C. Yue, S. Li and Q. Yao, Fuel, 2003, 82, 575–579 CrossRef CAS.
- R. Kumar, S. Kumar and S. P. Mehrotra, Resour., Conserv. Recycl., 2007, 52, 157–179 CrossRef.
- S. K. Chaudhuri and B. Sur, J. Environ. Eng., 2000, 126, 583–594 CrossRef CAS.
- Q. V. Trinh, S. Nagy and G. Mucsi, presented in part at the MultiScience – XXXIII. microCAD International Multidisciplinary Scientific Conference, 2019 Search PubMed.
- S. M. Pavlović, D. M. Marinković, M. D. Kostić, I. M. Janković-Častvan, L. V. Mojović, M. V. Stanković and V. B. Veljković, Fuel, 2020, 267, 117171 CrossRef.
- J. Malonda Shabani, O. Babajide, O. Oyekola and L. Petrik, Catalysts, 2019, 9, 1052 CrossRef.
- T. Aniokete, M. Ozonoh and M. O. Daramola, Int. J. Renew. Energy Res., 2019, 9, 1924–1937 Search PubMed.
- P. Y. He, Y. J. Zhang, H. Chen, Z. C. Han and L. C. Liu, Fuel, 2019, 257, 116041 CrossRef CAS.
- Y. W. Go and S. H. Yeom, Environ. Eng. Res., 2019, 24, 324–330 CrossRef.
- D. R. Lathiya, D. V. Bhatt and K. C. Maheria, ChemistrySelect, 2019, 4, 4392–4397 CrossRef CAS.
- Z. Helwani, W. Fatra, E. Saputra and R. Maulana, IOP Conf. Ser.: Mater. Sci. Eng., 2018, 334, 012077 Search PubMed.
- Y. Xiang, Y. Xiang and L. Wang, J. Taibah Univ. Sci., 2017, 11, 1019–1029 CrossRef.
- M. C. Manique, L. V. Lacerda, A. K. Alves and C. P. Bergmann, Fuel, 2017, 190, 268–273 CrossRef CAS.
- H. Satriadi, A. Khaibar and M. M. Almakhi, 2017.
- H. Hadiyanto, S. P. Lestari, A. Abdullah, W. Widayat and H. Sutanto, Int. J. Energy Environ. Eng., 2016, 7, 297–305 CrossRef CAS.
- Y. Xiang, L. Wang and Y. Jiao, J. Environ. Chem. Eng., 2016, 4, 818–824 CrossRef CAS.
- P. Kumar, M. Aslam, N. Singh, S. Mittal, A. Bansal, M. K. Jha and A. K. Sarma, RSC Adv., 2015, 5, 9946–9954 RSC.
- W. W. S. Ho, H. K. Ng, S. Gan and S. H. Tan, Energy Convers. Manage., 2014, 88, 1167–1178 CrossRef CAS.
- O. Babajide, Catal. Today, 2013, 201, 210 CrossRef CAS.
- O. Babajide, N. Musyoka, L. Petrik and F. Ameer, Catal. Today, 2012, 190, 54–60 CrossRef CAS.
- M. Senthil, K. Visagavel, C. G. Saravanan and K. Rajendran, Fuel Process. Technol., 2016, 149, 7–14 CrossRef CAS.
- W. Liu, J. Yang and B. Xiao, J. Hazard. Mater., 2009, 161, 474–478 CrossRef CAS PubMed.
- H. da Silva Almeida, O. A. Corrêa, J. G. Eid, H. J. Ribeiro, D. A. R. de Castro, M. S. Pereira, L. M. Pereira, A. de Andrade Mâncio, M. C. Santos, J. A. da Silva Souza, L. E. P. Borges, N. M. Mendonça and N. T. Machado, J. Anal. Appl. Pyrolysis, 2016, 118, 20–33 CrossRef CAS.
- Q. Liu, R. Xin, C. Li, C. Xu and J. Yang, J. Environ. Sci., 2013, 25, 823–829 CrossRef CAS.
- M. Senthil, K. Visagavel and A. Avinash, Energy Sources, Part A, 2016, 38, 876–881 CrossRef CAS.
- G. Alkan, C. Schier, L. Gronen, S. Stopj and B. Friedrich, Metals, 2017, 7, 458 CrossRef.
- K. Yoon, J.-M. Jung, D.-W. Cho, D. C. W. Tsang, E. E. Kwon and H. Song, J. Hazard. Mater., 2019, 366, 293–300 CrossRef CAS PubMed.
- L. Y. Zhang, Y. Z. Wang, G. T. Wei, Z. Y. Li and H. N. Huang, Energy Sources, Part A, 2016, 38, 1713–1720 CrossRef CAS.
- A. Bhattacharyya and B. S. Rajanikanth, Energy Procedia, 2015, 75, 2371–2378 CrossRef CAS.
- Y. N. Dhoble and S. Ahmed, J. Mater. Cycles Waste Manage., 2018, 20, 1373–1382 CrossRef CAS.
- T. A. Branca, V. Colla, D. Algermissen, H. Granbom, U. Martini, A. Morillon, R. Pietruck and S. Rosendahl, Metals, 2020, 10, 345 CrossRef CAS.
- A. Galadima and O. Muraza, J. Cleaner Prod., 2020, 263, 121358 CrossRef CAS.
- F. Hildor, T. Mattisson, H. Leion, C. Linderholm and M. Rydén, Int. J. Greenhouse Gas Control, 2019, 88, 321–331 CrossRef CAS.
- G. Kabir, A. T. Mohd Din and B. H. Hameed, Bioresour. Technol., 2018, 249, 42–48 CrossRef CAS PubMed.
- R. Bakti Cahyono, A. N. Rozhan, N. Yasuda, T. Nomura, S. Hosokai, Y. Kashiwaya and T. Akiyama, Fuel, 2013, 109, 439–444 CrossRef CAS.
- Y. Zong, X. Zhang, E. Mukiza, X. Xu and F. Li, Appl. Sci., 2018, 8, 1187 CrossRef.
- H. Zhou, B. Li, Y. Wei, H. Wang, Y. Yang and A. McLean, Can. Metall. Q., 2019, 58, 187–195 CrossRef CAS.
- B. Li, Y. Wei, H. Wang and Y. Yang, ISIJ Int., 2018, 58, 1168–1174 CrossRef CAS.
- J. Wang, S. Xing, Y. Huang, P. Fan, J. Fu, G. Yang, L. Yang and P. Lv, Appl. Energy, 2017, 190, 703–712 CrossRef CAS.
- X. Ma, Y. Li, L. Shi, Z. He and Z. Wang, Appl. Energy, 2016, 168, 85–95 CrossRef CAS.
- Y. Kashiwaya, K. Toishi, Y. Kaneki and Y. Yamakoshi, ISIJ Int., 2007, 47, 1829–1831 CrossRef CAS.
- T. Siengchum, M. Isenberg and S. S. C. Chuang, Fuel, 2013, 105, 559–565 CrossRef CAS.
- A. Tharwani, A. Sablani, G. Batra, S. Tiwari, D. Reel and M. N. Gandhi, Int. J. Innov. Sci. Technol., 2017, 4, 37–41 Search PubMed.
- K. Gunasekaran, R. Annadurai and P. S. Kumar, Constr. Build. Mater., 2012, 28, 208–215 CrossRef.
- M. Kaur and M. Kaur, Int. J. Appl. Eng. Res., 2012, 7, 05–08 Search PubMed.
- A. R. Hidayu and N. Muda, Procedia Eng., 2016, 148, 106–113 CrossRef CAS.
- A. Endut, S. H. Y. S. Abdullah, N. H. M. Hanapi, S. H. A. Hamid, F. Lananan, M. K. A. Kamarudin, R. Umar, H. Juahir and H. Khatoon, Int. Biodeterior. Biodegrad., 2017, 124, 250–257 CrossRef CAS.
- Y. S. Pradana, A. Hidayat, A. Prasetya and A. Budiman, 2018.
- A. Buasri, N. Chaiyut, V. Loryuenyong, C. Rodklum, T. Chaikwan, N. Kumphan, K. Jadee, P. Klinklom and W. Wittayarounayut, Sci. Asia, 2012, 38, 283–288 CAS.
- K. Vinukumar, A. Azhagurajan, S. C. Vettivel, N. Vedaraman and A. Haiter Lenin, Fuel, 2018, 222, 180–184 CrossRef CAS.
- R. S. Pinheiro, A. M. M. Bessa, B. A. de Queiroz, A. M. S. F. Duarte, H. B. de Sant'Ana and R. S. de Santiago-Aguiar, Fluid Phase Equilib., 2014, 361, 30–36 CrossRef CAS.
- A. S. Shelke, K. R. Ninghot, P. P. Kunjekar and S. P. Gaikwad, Int. J. Civ. Eng. Res., 2014, 2278–3652 Search PubMed.
- H. Li, S. Niu, C. Lu, M. Liu and M. Huo, Sci. China: Technol. Sci., 2014, 57, 438–444 CrossRef CAS.
- J. Cheng, J. Zhou, J. Liu, X. Cao and K. Cen, Energy Fuels, 2009, 23, 2506–2516 CrossRef CAS.
- H. Li, S. Niu, C. Lu, M. Liu and M. Huo, Energy Convers. Manage., 2014, 86, 1110–1117 CrossRef CAS.
- H. Li, S.-l. Niu, C.-m. Lu and S.-q. Cheng, Energy Convers. Manage., 2015, 103, 57–65 CrossRef CAS.
- A. Wahyudi, W. Kurniawan and H. Hinode, J. Chem. Eng. Jpn., 2017, 50, 561–567 CrossRef CAS.
- R. Shan, C. Zhao, P. Lv, H. Yuan and J. Yao, Energy Convers. Manage., 2016, 127, 273–283 CrossRef CAS.
- A. Marwaha, P. Rosha, S. K. Mohapatra, S. K. Mahla and A. Dhir, Fuel Process. Technol., 2018, 181, 175–186 CrossRef CAS.
- M. Arsalanfar, A. A. Mirzaei, H. R. Bozorgzadeh, A. Samimi and R. Ghobadi, J. Ind. Eng. Chem., 2014, 20, 1313–1323 CrossRef CAS.
- S. Mohebbi, M. Rostamizadeh and D. Kahforoushan, Fuel, 2020, 266, 117063 CrossRef CAS.
- Z. T. Alismaeel, A. S. Abbas, T. M. Albayati and A. M. Doyle, Fuel, 2018, 234, 170–176 CrossRef CAS.
- C. Thunyaratchatanon, A. Luengnaruemitchai, J. Jitjamnong, N. Chollacoop, S.-Y. Chen and Y. Yoshimura, Energy Fuels, 2018, 32, 9744–9755 CrossRef CAS.
- L. M. Yang, P. M. Lv, Z. H. Yuan, W. Luo, Z. M. Wang and H. W. Li, 2011.
- R. M. M. Bühler, A. C. Dutra, F. Vendruscolo, D. E. Moritz and J. L. Ninow, Food Sci. Technol., 2013, 33, 9–13 CrossRef.
- B. J. Kerr, W. A. Dozier III and K. Bregendahl, 2007.
- S. S. Yazdani and R. Gonzalez, Curr. Opin. Biotechnol., 2007, 18, 213–219 CrossRef CAS PubMed.
- J.-H. Ng, S. K. Leong, S. S. Lam, F. N. Ani and C. T. Chong, Energy Convers. Manage., 2017, 143, 399–409 CrossRef CAS.
- W. Bühler, E. Dinjus, H. J. Ederer, A. Kruse and C. Mas, J. Supercrit. Fluids, 2002, 22, 37–53 CrossRef.
- Z. Ullah, A. S. Khan, N. Muhammad, R. Ullah, A. S. Alqahtani, S. N. Shah, O. B. Ghanem, M. A. Bustam and Z. Man, J. Mol. Liq., 2018, 266, 673–686 CrossRef CAS.
|
This journal is © The Royal Society of Chemistry 2022 |
Click here to see how this site uses Cookies. View our privacy policy here.