DOI:
10.1039/D1RA06758C
(Paper)
RSC Adv., 2022,
12, 17182-17189
Manganese oxide nanorod catalysts for low-temperature selective catalytic reduction of NO with NH3
Received
8th September 2021
, Accepted 31st March 2022
First published on 9th June 2022
Abstract
MnOx nanorod catalysts were successfully synthesized by two different preparation methods using porous SiO2 nanorods as the template and investigated for the low-temperature selective catalytic reduction (SCR) of NO with NH3. The catalysts were characterized by scanning electron microscopy, transmission electron microscopy, nitrogen adsorption, X-ray diffraction, X-ray photoelectron spectroscopy, and NH3 temperature-programmed desorption. The results show that the obtained MnOx-P nanorod catalyst prepared by redox precipitation method exhibits higher NO removal activity than that prepared by the solvent evaporation method in the low temperature range of 100–180 °C, where about 98% NO conversion is achieved over MnOx(0.36)-P nanorods. The reason is mainly attributed to MnOx(0.36)-P nanorods possessing unique flower-like morphology and mesoporous structures with high pore volume, which facilitates the exposure of more active sites of MnOx and the adsorption of reactant gas molecules. Furthermore, there is a lower crystallinity of MnOx, higher percentage of Mn4+ species and a large amount of strong acid sites on the surface. These factors contribute to the excellent low-temperature SCR activity of MnOx(0.36)-P nanorods.
1. Introduction
Nitrogen oxides (NOx) are considered to be one of the main air pollutants, which can cause great harm to the ecological environment and human health. Therefore, it is urgent to control the emissions of NOx. The selective catalytic reduction (SCR) of NO with NH3 has been proven to be the most effective technology for the removal of NOx. Commercial SCR catalysts, V2O5–WO3/TiO2 and V2O5–MoO3/TiO2 catalysts have shown high activity of NO removal, and these catalysts must be used in the temperature range of 350–450 °C.1,2 To satisfy the high operating temperature, the SCR unit needs to be placed upstream of the electrostatic precipitator and desulfurization devices, resulting in the deactivation of catalysts because of high concentration of dust and SO2 in the flue gases. In order to overcome the disadvantages of these V2O5/TiO2 based catalysts, researchers have paid much attentions on developing efficient low-temperature SCR catalysts, which can be placed downstream of the desulfurizer and electrostatic precipitators without the need for reheating of flue gases.3–5
Various transition metal oxide catalysts have been found to be active in the NH3-SCR reaction. Among them, manganese oxide (MnOx) catalysts exhibit excellent low temperature-SCR activities due to their variable valence states and high redox properties.6,7 In addition, it has been demonstrated that the specific surface area and crystallinity of MnOx have also great influence on their SCR activities.8 Furthermore, it has been reported that the morphologies of the catalysts significantly influence their properties and catalytic performance.9–11 Recently, mesoporous materials have attracted extensive attention owing to their large specific surface area, highly ordered mesoporous structure, which are advantageous to the generation of abundant active sites and mass transport of gas molecules. In particular, mesoporous metal oxides combine the advantages of both metal oxides and mesoporous structure in comparison with nanoparticles, which have found applications in various fields, such as electrode materials, gas sensors and adsorption, catalysis, etc.12–14 For instance, Gao et al.15 reported a three-dimensional (3D) mesoporous MnO2 prepared using KIT-6 as a template, which showed much higher SCR activity than mesoporous MnO2 templated from SBA-15 or MCM-41, maintaining NO conversion of 100% in the temperature range of 75–275 °C, because of the special 3D mesostructure. Tian et al.16 studied MnO2 nanorods exhibited higher NO conversion than MnO2 nanotubes and nanoparticles, and found that the higher SCR activity of MnO2 nanorods may be mainly attributed to lower crystallinity, more lattice oxygen, higher reducibility, and more amount of strong acid sites. Therefore, controlled synthesis of MnOx catalysts with different morphologies is very effective way to improve their SCR activities. However, there are still many challenges.
In this work, we synthesized a series of MnOx nanorods catalysts using porous SiO2 nanorods as template through two different preparation methods. The activities of these MnOx nanorods catalysts for SCR of NO at low temperatures were evaluated. The effect of Mn loading on SCR activities of MnOx nanorods catalysts at different temperatures were also investigated. The catalysts were characterized to understand the structure and morphologies of MnOx nanorods catalysts as well as their relationship with catalytic activity. The results are of importance for better understanding of low temperature SCR reaction on nanostructured MnOx catalysts and beneficial to promote the development of NO removal technology from flue gases.
2. Experimental
2.1 Catalyst preparation
All the chemical reagents used were analytical grade. MnOx nanorods catalysts were prepared by two-step process. Firstly, the porous SiO2 nanorods template was synthesized according to the previously reported procedure.17 Secondly, MnOx nanorods catalysts were prepared by two different methods using the porous SiO2 nanorods as template. Detailed preparation methods were the following:
2.1.1 Redox precipitation method (P). A series of MnOx nanorods catalysts were synthesized by the redox precipitation method using KMnO4 as oxidant and manganese acetate as reductant, respectively. In a typical synthesis, a certain amount of the as-synthesized porous SiO2 nanorods was initially dispersed in 50 mL deionized water by ultrasonic treatment, subsequently appropriate amount of manganese acetate was slowly added to the above solution. After stirring for 6 h, the solution of KMnO4 containing 40 mL deionized water was slowly added to the above mixture, and continuously stirred for 12 h. The main reaction between Mn(CH3COO)2 and KMnO4 is expressed by the following equation: (3Mn2+ + 2MnO4− + 2H2O → 5MnO2 + 4H+). Then, the obtained product was collected by filtration, and washing several times with deionized water, and then drying at 110 °C for 12 h. Finally, the SiO2@MnOx was treated with 2 M NaOH solution at 80 °C to remove the SiO2 nanorods template, followed by centrifugation and washing with deionized water several times, drying at 110 °C for 12 h. The resultant catalysts are labeled as MnOx(y)-P nanorods, where y represents the mass ratio of Mn to SiO2 nanorods template, and P represents the redox precipitation method.
2.1.2 Solvent evaporation method (E). For comparison, the MnOx nanorods catalysts were also synthesized by the solvent evaporation method using manganese acetate as the precursor. A certain amount of the as-synthesized porous SiO2 nanorods was initially dispersed in 40 mL ethanol by ultrasonic treatment. Subsequently, appropriate amount of manganese acetate was slowly added to the above solution, and stirred for 2 h. Then, the mixture was heated up to 50 °C to evaporate the ethanol. The obtained product was dried at 80 °C for 12 h, followed by calcination at 400 °C for 3 h in air atmosphere. Finally, the SiO2 nanorods template was removed with 2 M NaOH solution at 80 °C, then centrifugation, washing with deionized water several times and drying at 110 °C for 12 h. The resultant catalysts are labeled as MnOx(y)-E nanorods, where y represents the mass ratio of Mn to SiO2 nanorods template, and E represents the solvent evaporation method.
2.2 Activity test
NO removal activity tests were carried out in a fixed-bed reactor with a diameter of 8 mm. The gas mixture consisted of 500 ppm NO, 500 ppm NH3, 5.0 vol% O2 and balance N2. In all experiments, the total gas flow rate was maintained at 500 mL min−1, corresponding to a gas hourly space velocity (GHSV) of 62
000 h−1. The reaction temperatures were controlled regulated from 100 to 300 °C. The concentrations of NO and O2 in the inlet and outlet gases were continually measured on-line by a flue gas analyzer (MRU VARIO PLUS, Germany).
2.3 Characterization
The morphologies and microstructures of the samples were examined using scanning electron microscope (SEM, FEI Nova NanoSEM 450) and transmission electron microscopy (TEM, JEOL JEM-2100F). The pore structure was measured at 77 K using a Quadrasorb SI analyzer (Quantachrome Instrument Crop) and the corresponding pore size distribution was obtained by the density functional theory (DFT model). X-ray diffraction (XRD) measurements were recorded on a Rigaku D/max 2550 diffractometer using Cu Kα radiation. X-ray photoelectron spectroscopy (XPS) measurements were carried out on an Axis Ultra DLD spectrometer with Al Kα radiation. NH3-temperature programmed desorption (NH3-TPD) was performed on a TP-5080 adsorption analyzer (Xianquan Co.) with a thermal conductivity detector (TCD). Before the NH3-TPD experiment, 0.1 g sample was pretreated in He flow at 300 °C for 30 min, followed by cooling down to 100 °C. Afterwards, the He flow was switched to a stream containing 5 vol% NH3/He to adsorb NH3 for 60 min at 100 °C and then purged with He at the same temperature. Finally, the temperature was increased to 800 °C in He flow at a heating rate of 10 °C min−1.
3. Results and discussion
3.1 Morphological characterization
Fig. 1 shows SEM images of the porous SiO2 nanorods. As can be observed in Fig. 1, the obtained SiO2 nanorods shows one-dimensional rod-like structure. These nanorods are nearly uniform with lengths in the range of 300–400 nm and diameters of about 100–200 nm. Furthermore, all SiO2 nanorods are almost monodispersed without aggregation.
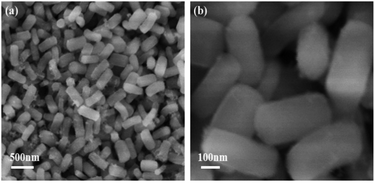 |
| Fig. 1 SEM images of the porous SiO2 nanorods. | |
The morphologies and microstructures of MnOx nanorods catalysts prepared by different methods are characterized by SEM. The results in Fig. 2 indicate the different morphology can be clearly observed over MnOx(0.36)-E and MnOx(0.36)-P nanorods. After the loading of MnOx and etching by the NaOH solution, the morphology of MnOx(0.36)-E nanorods is mainly one-dimensional rod-like structure, which does not change much compared with that of SiO2 nanorods. These indicate that MnOx is uniformly distributed in the rod-like structure, favorable to the enhancement of SCR activity. Additionally, a small amount of nanoparticles and nanosheets MnOx are observable on the surface of the rod-like structure, which may be caused by the unloaded MnOx on the SiO2 nanorods because of the precipitation and crystallization of partial manganese precursor during the solvent evaporation process. The SEM image of MnOx(0.36)-P nanorods is clearly different from that of MnOx(0.36)-E nanorods. Flower-like structure is observed, which is assembled by numerous manganese oxide nanosheets (Fig. 2c and d). After the careful observation, it is found that a certain amount of loose macroporous structure is also formed on the surface of the catalyst, due to the accumulation of MnOx nanosheets. These macroporous structure could facilitate the adsorption and desorption of reactant gas molecules on the active sites of catalyst surface, which is advantageous to NH3-SCR reaction.
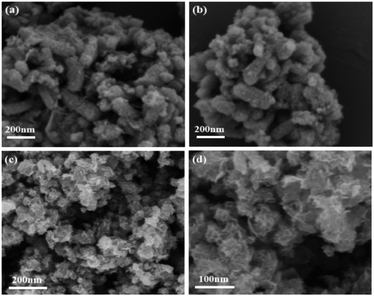 |
| Fig. 2 SEM images of (a and b) MnOx(0.36)-E and (c and d) MnOx(0.36)-P nanorods catalysts. | |
The detailed morphologies and microstructures of MnOx nanorods catalysts obtained by different methods are further characterized by TEM. From Fig. 3a, it is observed that MnOx(0.36)-E nanorods still maintains one-dimensional rod-like structure, agreeing well with the SEM results. It is worth noting that the inter center of MnOx(0.36)-E nanorods is not completely hollow structure. Since the porous SiO2 nanorods has abundant mesoporous structures, it is reasonable to expect the manganese precursor easily fills the mesoporous template including the edge and inner pores of SiO2 nanorods during the MnOx impregnation process. Thus, the inner partially hollow structure is formed after the further etching of SiO2. In addition, there exists unloaded nanoparticles and nanosheets MnOx near the rod-like structure, in accordance with the SEM results (Fig. 2a and b). Compared to TEM image of MnOx(0.36)-E nanorods, MnOx(0.36)-P nanorods is mainly composed of nanorods, with a diameter about 100–200 nm and length about 300–500 nm (Fig. 3c), which is similar with the size of the SiO2 nanorods. And it can also be seen that MnOx nanosheets are deposited on the surface of the nanorods, suggesting that the flower-like MnOx is assembled by these MnOx nanosheets. Meanwhile, many porous structures in the inner space of nanorods are also observed, which is explained because the MnOx nanosheets are self-assembled randomly and not parallel to each other, leading to the formation of the porous structure. Such results are good agreement with the SEM observation (Fig. 2c and d).
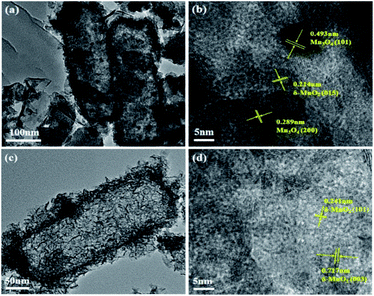 |
| Fig. 3 TEM and HRTEM images of (a and b) MnOx(0.36)-E and (c and d) MnOx(0.36)-P nanorods. | |
The HRTEM images of the two catalysts are shown in Fig. 3b and d. The HRTEM image of MnOx(0.36)-E nanorods reveals the visible lattice fringes with an interplanar spacing of 0.214, 0.289 and 0.493 nm, which can be assigned to the (015) plane of birnessite-type MnO2 (δ-MnO2), (200) and (101) planes of Mn3O4, respectively. These data suggests that Mn3O4 and δ-MnO2 coexist on the surface of MnOx(0.36)-E nanorods. However, for MnOx(0.36)-P nanorods, the lattice fringes with an interplanar spacing of 0.241 and 0.717 nm can be observed, which can be assigned to the (101) and (003) crystal planes of δ-MnO2, respectively.
3.2 NO removal activities
Fig. 4 exhibits the NO removal activities of MnOx nanorods catalysts obtained by the two different methods. It can be seen that the catalysts preparation method has significant effect on the NO removal activity. As shown in Fig. 4a, MnOx(0.36)-P and MnOx(0.72)-P nanorods catalysts exhibit higher NO removal activity, above 94% of NO conversions can be achieved at temperatures of 100–200 °C. Especially in the low temperature range of 100–180 °C, they maintain about 98% NO conversions. For MnOx(0.18)-P nanorods, it shows relatively low NO removal activity, but the maximum NO conversion is still up to 92% at 160 °C. From Fig. 4b, it can be observed that MnOx(0.18)-E and MnOx(0.36)-E nanorods catalysts exhibit relatively high NO removal activity. NO conversions of the two catalysts at 100 °C is approximately 70%, and they reach more than 90% in the temperature range of 140–240 °C. For MnOx(0.72)-E nanorods, it shows relatively low NO removal activity below 200 °C, but it reaches a maximum value (above 90%) at 240 °C. For all MnOx nanorods, NO conversions decline at relative higher temperatures, which might be explained that partial NH3 reductant is oxidized into NO.18 Fig. 4c and d compare the NO removal activities over the MnOx nanorods catalysts obtained by the two different methods. Compared with MnOx(0.36)-E nanorods, MnOx(0.36)-P nanorods exhibits higher NO conversion in the low temperature range of 100–160 °C. For the catalyst with higher Mn loading, NO conversion of MnOx(0.72)-P nanorods at low temperatures of 100–180 °C is significantly higher than that of MnOx(0.72)-E nanorods. These results clearly indicate that the catalyst prepared by redox precipitation method shows much higher NO removal activity at the low temperature range (below 200 °C) than that prepared by solvent evaporation method, which may result from the unique morphology of MnOx-P nanorods.
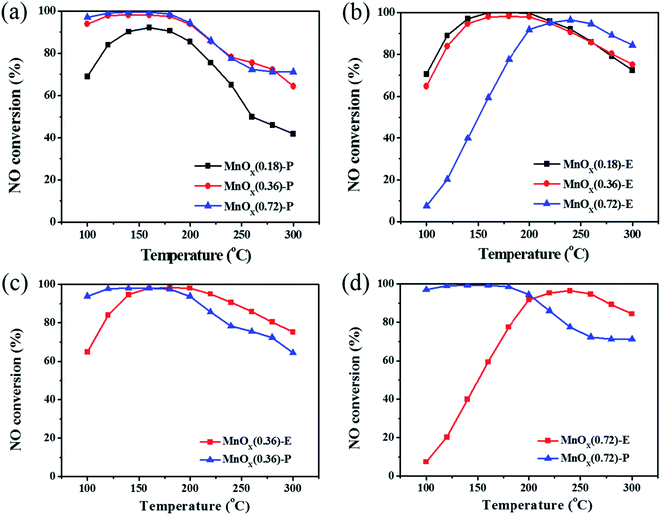 |
| Fig. 4 NO conversions over the MnOx nanorods catalysts prepared by different methods. (a) MnOx-P nanorods, (b) MnOx-E nanorods, (c) MnOx(0.36)-P and MnOx(0.36)-E nanorods, (d) MnOx(0.72)-P and MnOx(0.72)-E nanorods. | |
3.3 XRD
To further investigate the crystal phase composition of MnOx nanorods catalysts obtained by different methods, XRD patterns were characterized, and the results are shown in Fig. 5. The XRD pattern of MnOx(0.36)-E nanorods displays the characteristic diffraction peaks located at 2θ = 18.0°, 28.9°, 32.4°, 36°, 44.4°, 58.5°, 59.9° and 64.7°, which can be indexed as the (101), (112), (103), (211), (220), (321), (224) and (400) crystal planes of Mn3O4 with a spinel structure (JCPDS card no. 24-0734), respectively.19 And it can also be observed that the diffraction peaks at 12.3°, 24.8°, 36.9° and 42.2° are ascribed to the (003), (006), (101), and (015) crystal planes of δ-MnO2 (JCPDS card no. 52-0556), respectively.20 For MnOx(0.36)-P nanorods, the diffraction peaks at 12.3°, 24.8°, 36.9°, 42.2°, and 66.3° are assigned to the (003), (006), (101), (015), and (113) planes of δ-MnO2 crystalline phase. These data is consistent with the observation using HRTEM. It is worth noting that the diffraction peaks of MnOx on MnOx(0.36)-P nanorods become broader and the intensities of the peaks become much weaker than those of MnOx(0.36)-E nanorods, suggesting the smaller size of crystal particle and lower crystallinity of MnOx. It has been widely demonstrated that amorphous phase of manganese oxides usually exhibits higher catalytic activity for SCR of NO than crystal manganese oxides.21 Based on these results, it can be concluded that the improved dispersion of MnOx species is obtained by the redox precipitation method, which contributes to the excellent SCR activity of MnOx(0.36)-P nanorods, as evidenced by the results of activity evaluation presented in Fig. 4.
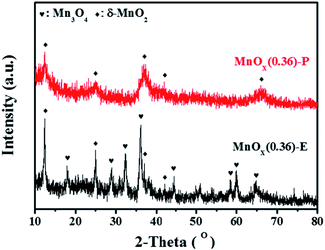 |
| Fig. 5 XRD patterns of the different samples. | |
3.4 Pore structure analysis
The pore structure characterizations of the MnOx nanorods catalysts obtained by different methods are analyzed by N2 adsorption–desorption isotherms. As presented in Fig. 6a, MnOx(0.36)-E nanorods exhibits a typical type-IV isotherm with a hysteresis loop at the relative pressure (P/P0) of 0.4–0.9, indicating the presence of mesopores. For MnOx(0.36)-P nanorods, the isotherm still belongs to the type-IV isotherm with an obvious hysteresis loop at P/P0 of 0.8–1.0, suggesting that the catalyst has characteristic of mesoporous material (Fig. 6c). Their pore sizes are further analyzed, as shown in Fig. 6b and d, respectively. The pore size distribution curve of MnOx(0.36)-E nanorods shows the coexistence of micropores and mesopores, and its pore size distributes in the range of 0.6–4 nm. MnOx(0.36)-P nanorods exhibits a wider pore size distribution and a larger number of mesopores in the range of 4–28 nm can be also observed. Moreover, the pore parameters of the samples are listed in Table 1. It can be observed that the SBET for MnOx(0.36)-P and MnOx(0.36)-E nanorods is 151 m2 g−1 and 272 m2 g−1, respectively. The SBET values of these MnOx nanorods catalysts are much larger than those of carrier-free MnOx-based catalysts as previously reported,15,22 which may result from the highly porous structure of SiO2 nanorods template and/or the accumulation of the nanoparticles. It is worth pointing out that the Vtotal of MnOx(0.36)-P nanorods (0.61 cm3 g−1) is significantly higher than that of MnOx(0.36)-E nanorods (0.31 cm3 g−1), which may be due to its flower-like structure, as demonstrated by the SEM results (Fig. 2c and d). Additionally, the pore volume of MnOx(0.36)-P nanorods at smaller pore sizes (<4 nm) decreases obviously, and the pore volume at larger pore sizes (5–28 nm) increases greatly, indicating that there exists more mesoporous structure in MnOx(0.36)-P nanorods. Thus, such rich mesoporous structure with high pore volume of MnOx(0.36)-P nanorods may be favorable for exposure of more active sites of MnOx and the adsorption of reactant molecules, leading to the excellent SCR activity at the low temperatures (below 200 °C).
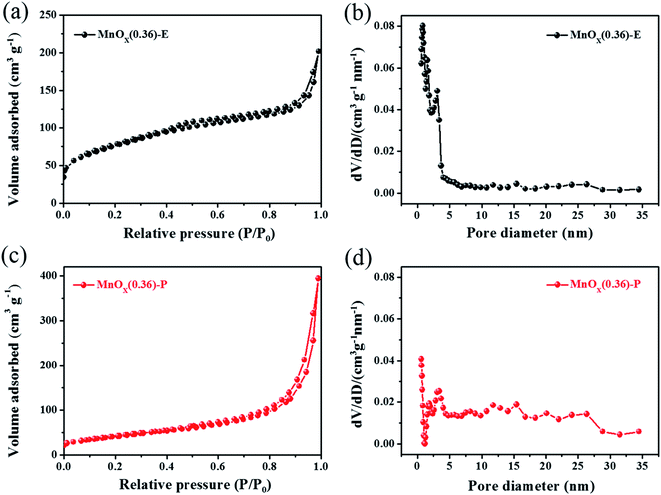 |
| Fig. 6 N2 adsorption–desorption isotherms and corresponding pore size distributions of (a and b) MnOx(0.36)-E and (c and d) MnOx(0.36)-P nanorods. | |
Table 1 Pore parameters of MnOx nanorods catalysts obtained by different methodsa
Sample |
SBET (m2 g−1) |
Vtotal (cm3 g−1) |
Average pore size (nm) |
SBET: BET specific surface area; Vtotal: total pore volume. |
MnOx(0.36)-P |
151 |
0.61 |
3.5 |
MnOx(0.36)-E |
272 |
0.31 |
4.6 |
3.5 XPS characterization
To further determine the surface chemical states of elements in MnOx nanorods catalysts, the XPS measurement was carried out and the results are presented in Fig. 7. The relative atomic ratios of Mn and O elements are summarized in Table 2. As displayed Fig. 7a, the Mn 2p spectrum of MnOx(0.36)-E nanorods exhibits two main peaks with binding energies of 653.8 eV and 642.3 eV, which represents Mn 2p1/2 and Mn 2p3/2, respectively. The Mn 2p3/2 spectrum can be fitted into three characteristic peaks at 641.0–642.0 eV, 642.2–642.5 eV and 642.9–643.7 eV, corresponding to Mn2+, Mn3+, and Mn4+, respectively.23,24 These data suggests that Mn4+, Mn3+ and Mn2+ manganese oxide phases coexist on the surface of MnOx(0.36)-E nanorods. For MnOx(0.36)-P nanorods, the binding energies of Mn 2p1/2 and Mn 2p3/2 are located at 653.9 eV and 642.2 eV, respectively. The binding energy separation between these two peaks is 11.7 eV, which is in accordance with previously reported results of MnO2,25,26 indicating that the valence of Mn element is very close to 4 in MnOx(0.36)-P nanorods. Moreover, the Mn 2p3/2 spectrum is fitted into two peaks, which are attributed to Mn3+ (642.1 eV) and Mn4+ (643.5 eV), respectively. These results further demonstrate that MnO2 is the main manganese oxide in MnOx(0.36) nanorods, which is in accordance with the XRD result. The relative ratio of different oxidation state of manganese species can be calculated by the area ratio of Mn2+, Mn3+ and Mn4+ species, as shown in Table 2. The percentage of Mn4+/Mnn+ on MnOx(0.36)-P nanorods (50.8%) is greatly higher than that on MnOx(0.36)-E nanorods (35.7%). As literature reported,27,28 manganese species with higher oxidation state are preferable for oxidation reactions over the manganese-based catalysts. It has been confirmed that Mn4+ species are beneficial to promote the low-temperature SCR activity, due to the enhancement of oxidation of NO to NO2.29,30 Therefore, the higher percentage of Mn4+ on MnOx(0.36)-P nanorods results in the increased SCR activity at the low temperatures of 100–160 °C.
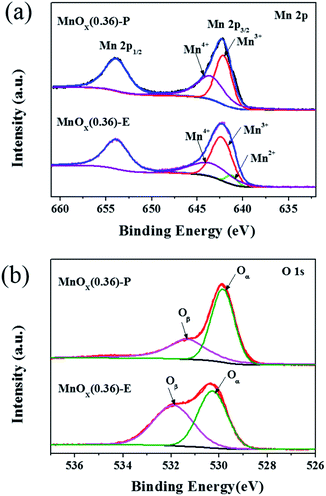 |
| Fig. 7 XPS spectra for Mn 2p (a) and O 1s (b) of the different MnOx nanorods catalysts. | |
Table 2 The relative atomic ratios of the different MnOx nanorods catalysts
Sample |
XMn (%) |
XO (%) |
Mn2+ |
Mn3+ |
Mn4+ |
Oα |
Oβ |
MnOx(0.36)-P |
0 |
49.2 |
50.8 |
61.4 |
38.6 |
MnOx(0.36)-E |
6.4 |
57.9 |
35.7 |
50.7 |
49.3 |
As shown in Fig. 7b, the O 1s XPS spectra can be fitted into two peak. The peak located at 529.5–530.2 eV can be assigned to the lattice oxygen (O2−) (denoted as Oα), while the peak located at 531.2–532.0 eV is assigned to the chemisorbed oxygen, such as O− or O22− (denoted as Oβ).31 The relative concentrations of Oα and Oβ can be determined from the area ratio of Oα/(Oα + Oβ) and Oβ/(Oα + Oβ), respectively. As illustrated by Table 2, the ratio of Oβ/(Oα + Oβ) is 49.3% and 38.6% for MnOx(0.36)-E and MnOx(0.36)-P nanorods, respectively, which is higher than the data previously reported for MnO2 nanorods (36.7%) and MnOx/TiO2-GE (19.9%).32,33 It has been widely reported that the surface chemisorbed oxygen species (Oβ) are more active than the lattice oxygen species (Oα) in oxidation reactions because of their higher mobility, which may easily exchange with oxygen in the gas phase or oxygen molecules absorbed on catalyst surface, thus acting as the supplement of lattice oxygen.34–36 Moreover, the higher concentration of Oβ is advantageous to the improvement of oxidation of NO to NO2, which facilitates the “fast SCR” reaction (4NH3 + 2NO + 2NO2 → 4N2 + 6H2O),37–39 resulting in the enhancement of catalytic activity. Thus, the relative high concentration of surface chemisorbed oxygen in MnOx(0.36)-E and MnOx(0.36)-P nanorods is favorable for achieving high SCR activity. The above XPS results demonstrate that the high concentration of Mn4+ species plays an important role in the low-temperature SCR activity of MnOx(0.36)-P nanorods.
3.6 NH3-TPD
It is generally known that the adsorption and oxidation of NH3 on the surface acid sites of catalyst are considered to be a key step in the NH3-SCR reaction. NH3-TPD experiments were performed to determine the surface acidity of the obtained catalysts, and the results are shown in Fig. 8 and Table 3. It is found that MnOx(0.36)-E nanorods exhibits two obvious desorption peaks located at the temperature range of 50–180 °C (labeled as peak 1) and 190–400 °C (labeled as peak 2). And no visible desorption peaks above 400 °C can be observed. For MnOx(0.36)-P nanorods, besides the two desorption peaks located at 50–400 °C, another desorption peak at 410–690 °C (labeled as peak 3) is also observed. The peaks 1 and 2 are ascribed to NH3 desorption from the weak acid sites, and peak 3 is assigned to the strong acid sites. It is generally accepted that the area of NH3 desorption peak is proportional to the amount of acid sites. As listed in Table 3, the desorption peak area of strong acid sites over MnOx(0.36)-P nanorods significantly enhances compared with MnOx(0.36)-E nanorods, indicating that a large amount of strong acid sites exist on its surface. Based on the above results, MnOx(0.36)-P nanorods has stronger surface acidity, especially there are more amount of strong acid sites on it, which contributes to enhancement of NH3 adsorption and oxidation on the catalyst surface, leading to the excellent low-temperature SCR activity of MnOx(0.36)-P nanorods.
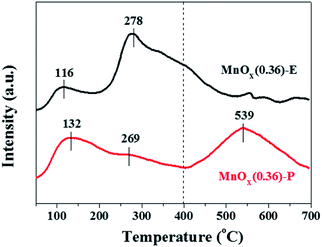 |
| Fig. 8 NH3-TPD profiles of the different MnOx nanorods catalysts. | |
Table 3 The amount of surface acids over the different catalysts
Sample |
Peak temperature (°C) |
Acid amount (a.u. g−1) |
T1a |
T2 |
T3 |
S1b |
S2 |
S3 |
The desorption peak at temperature. The area of desorption peak. |
MnOx(0.36)-P |
132 |
269 |
539 |
30.3 |
28.9 |
56.7 |
MnOx(0.36)-E |
116 |
278 |
— |
17.0 |
86.8 |
— |
4. Conclusions
A series of MnOx nanorods catalysts using porous SiO2 nanorods as template were synthesized through two different preparation methods. The obtained MnOx-P nanorods catalyst prepared by redox precipitation method exhibits higher NO removal activity at low temperatures (lower than 200 °C) in comparison to MnOx-E nanorods. About 98% NO conversion is achieved over MnOx(0.36)-P nanorods in the low temperature range of 100–180 °C. The reason is mainly attributed to its unique flower-like morphology and mesoporous structures with high pore volume. Furthermore, there are the lower crystallinity of MnOx, higher percentage of Mn4+ species and a large amount of strong acid sites on the surface of MnOx(0.36)-P nanorods. These factors result in its excellent low-temperature SCR activity.
Conflicts of interest
There are no conflicts to declare.
Acknowledgements
The authors gratefully acknowledge the financial supports from the National Natural Science Foundation of China (No. 51472086, 51002051, 22075081, 20806024), and the Natural Science Foundation of Shanghai City (12ZR1407200).
Notes and references
- S. B. Kristensen, A. J. Kunov-Kruse, A. Riisager, S. B. Rasmussen and R. Fehrmann, J. Catal., 2011, 284, 60–67 CrossRef CAS.
- P. Forzatti, Catal. Today, 2000, 62, 51–65 CrossRef CAS.
- J. W. Shi, Z. Y. Fan, C. Gao, G. Gao, B. R. Wang, Y. Wang, C. He and C. M. Niu, ChemCatChem, 2018, 10, 2833–2844 CrossRef CAS.
- J. Liu, Y. J. Wei, P. Z. Li, P. P. Zhang, W. Su, Y. Sun, R. Q. Zou and Y. L. Zhao, ACS Catal., 2018, 8, 3865–3874 CrossRef CAS.
- Y. R. Shi, X. L. Tang, H. H. Yi, F. Y. Gao, S. Z. Zhao, J. G. Wang, K. Yang and R. C. Zhang, Ind. Eng. Chem. Res., 2019, 58, 3606–3617 CrossRef CAS.
- C. Fang, D. S. Zhang, S. X. Cai, L. Zhang, L. Huang, H. R. Li, P. Maitarad, L. Y. Shi, R. H. Gao and J. P. Zhang, Nanoscale, 2013, 5, 9199–9207 RSC.
- R. H. Wang, Z. F. Hao, Y. Li, G. Q. Liu, H. Zhang, H. T. Wang, Y. G. Xia and S. H. Zhan, Appl. Catal., B, 2019, 258, 117983 CrossRef CAS.
- F. Kapteijn, L. Singoredjo, A. Andreini and J. A. Moulijn, Appl. Catal., B, 1994, 3, 173–189 CrossRef CAS.
- X. Y. Wang, K. Zhang, W. T. Zhao, Y. Y. Zhang, Z. X. Lan, T. H. Zhang, Y. H. Xiao, Y. F. Zhang, H. Z. Chang and L. L. Jiang, Ind. Eng. Chem. Res., 2017, 56, 14980–14994 CrossRef CAS.
- X. J. Yao, L. Chen, J. Cao, F. M. Yang, W. Tan and L. Dong, Ind. Eng. Chem. Res., 2018, 57, 12407–12419 CrossRef CAS.
- Z. H. Lian, W. P. Shan, Y. Zhang, M. Wang and H. He, Ind. Eng. Chem. Res., 2018, 57, 12736–12741 CrossRef CAS.
- S. H. Zhan, H. Zhang, Y. Zhang, Q. Shi, Y. Li and X. J. Li, Appl. Catal., B, 2017, 203, 199–209 CrossRef CAS PubMed.
- C. L. Xiao, X. Y. Zhang, T. Mendes, G. P. Knowles, A. Chaffee and D. R. MacFarlane, J. Phys. Chem. C, 2016, 120, 23976–23983 CrossRef CAS.
- C. Fang, L. Y. Shi, H. R. Li, L. Huang, J. P. Zhang and D. S. Zhang, RSC Adv., 2016, 6, 78727–78736 RSC.
- J. S. Gao, Y. L. Han, J. C. Mu, S. C. Wu, F. Tan, Y. Shi and X. Y. Li, J. Colloid Interface Sci., 2018, 516, 254–262 CrossRef CAS PubMed.
- W. Tian, H. S. Yang, X. Y. Fan and X. B. Zhang, J. Hazard. Mater., 2011, 188, 105–109 CrossRef CAS PubMed.
- W. Q. Yao, C. J. Chu, W. Z. Zheng, L. Zhan and Y. L. Wang, J. Mater. Chem. A, 2018, 6, 18191–18205 RSC.
- T. S. Park, S. K. Jeong, S. H. Hong and S. C. Hong, Ind. Eng. Chem. Res., 2001, 40, 4491–4495 CrossRef CAS.
- Y. F. Jian, M. D. Ma, C. W. Chen, C. Liu, Y. K. Yu, Z. P. Hao and C. He, Catal. Sci. Technol., 2018, 8, 3863–3875 RSC.
- G. Zhu, L. J. Deng, J. F. Wang, L. P. Kang and Z. H. Liu, Colloids Surf., A, 2013, 434, 42–48 CrossRef CAS.
- G. Gao, J. W. Shi, C. Liu, C. Gao, Z. Y. Fan and C. M. Niu, Appl. Surf. Sci., 2017, 411, 338–346 CrossRef CAS.
- S. H. Zhan, D. D. Zhu, M. Y. Qiu, H. B. Yu and Y. Li, RSC Adv., 2015, 5, 29353–29361 RSC.
- Z. Y. Fan, J. W. Shi, C. Gao, G. Gao, B. R. Wang and C. M. Niu, ACS Appl. Mater. Interfaces, 2017, 9, 16117–16127 CrossRef CAS PubMed.
- C. L. Li, X. L. Tang, H. H. Yi, L. F. Wang, X. X. Cui, C. Chu, J. Y. Li, R. C. Zhang and Q. J. Yu, Appl. Surf. Sci., 2018, 428, 924–932 CrossRef CAS.
- X. Wang, Y. Y. Zheng, Z. Xu, Y. Liu and X. L. Wang, Catal. Sci. Technol., 2014, 4, 1738–1741 RSC.
- E. Miniach, A. Sliwak, A. Moyseowicz, L. Fernández-Garcia, Z. González, M. Granda, R. Menendez and G. Gryglewicz, Electrochim. Acta, 2017, 240, 53–62 CrossRef CAS.
- X. F. Tang, Y. G. Li, X. M. Huang, Y. D. Xu, H. Q. Zhu, J. G. Wang and W. J. Shen, Appl. Catal., B, 2006, 62, 265–273 CrossRef CAS.
- Q. Shen, L. Y. Zhang, N. N. Sun, H. Wang, L. S. Zhong, C. He, W. Wei and Y. H. Sun, Chem. Eng. J., 2017, 322, 46–55 CrossRef CAS.
- B. X. Shen, Y. Y. Wang, F. M. Wang and T. Liu, Chem. Eng. J., 2014, 236, 171–180 CrossRef CAS.
- L. Zhang, D. S. Zhang, J. P. Zhang, S. X. Cai, C. Fang, L. Huang, H. R. Li, R. H. Gao and L. Y. Shi, Nanoscale, 2013, 5, 9821–9829 RSC.
- K. W. Zha, S. X. Cai, H. Hu, H. R. Li, T. T. Yan, L. Y. Shi and D. S. Zhang, J. Phys. Chem. C, 2017, 121, 25243–25254 CrossRef CAS.
- Y. Li, Y. P. Li, Y. Wan, S. H. Zhan, Q. X. Guan and Y. Tian, RSC Adv., 2016, 6, 54926–54937 RSC.
- X. N. Lu, C. Y. Song, S. H. Jia, Z. S. Tong, X. L. Tang and Y. X. Teng, Chem. Eng. J., 2015, 260, 776–784 CrossRef CAS.
- F. D. Liu, W. P. Shan, Z. H. Lian, L. J. Xie, W. W. Yang and H. He, Catal. Sci. Technol., 2013, 3, 2699–2707 RSC.
- P. Sun, R. T. Guo, S. M. Liu, S. X. Wang, W. G. Pan and M. Y. Li, Appl. Catal., A, 2017, 531, 129–138 CrossRef CAS.
- L. Chen, X. X. Wang, Q. L. Cong, H. Y. Ma, S. J. Li and W. Li, Chem. Eng. J., 2019, 369, 957–967 CrossRef CAS.
- F. D. Liu, H. He, Y. Ding and C. B. Zhang, Appl. Catal., B, 2009, 93, 194–204 CrossRef CAS.
- T. Boningari, P. R. Ettireddy, A. Somogyvari, Y. Liu, A. Vorontsov, C. A. McDonald and P. G. Smirniotis, J. Catal., 2015, 325, 145–155 CrossRef CAS.
- F. Y. Gao, X. L. Tang, H. H. Yi, J. Y. Li, S. Z. Zhao, J. G. Wang, C. Chu and C. L. Li, Chem. Eng. J., 2017, 317, 20–31 CrossRef CAS.
|
This journal is © The Royal Society of Chemistry 2022 |
Click here to see how this site uses Cookies. View our privacy policy here.