DOI:
10.1039/D1RA06264F
(Paper)
RSC Adv., 2022,
12, 1535-1542
High strength composites from low-value animal coproducts and industrial waste sulfur†
Received
18th August 2021
, Accepted 21st December 2021
First published on 10th January 2022
Abstract
Herein we report high strength composites prepared by reaction of sulfur, plant oils (either canola oil or sunflower oil) and brown grease. Brown grease is a high-volume, low value animal fat rendering coproduct that represents one of the most underutilized products of agricultural animal processing. Chemically, brown grease is primarily comprised of triglycerides and fatty acids. The inverse vulcanization of the unsaturated units in triglycerides/fatty acids upon their reaction with sulfur yields CanBGx or SunBGx (x = wt% sulfur, varied from 85–90%). These composites were characterized by infrared spectroscopy, dynamic mechanical analysis (DMA), mechanical test stand analysis, elemental analysis, and powder X-ray diffraction. CanBGx and SunBGx composites exhibit impressive compressive strengths (28.7–35.9 MPa) when compared to other materials such as Portland cement, for which a compressive strength of ≥17 MPa is required for residential building. Stress–strain analysis revealed high flexural strengths of 6.5–8.5 MPa for CanBGx and SunBGx composites as well, again exceeding the range of ∼2–5 MPa for ordinary Portland cements. The thermal properties of the composites were assessed by thermogravimetric analysis, revealing decomposition temperatures ranging from 223–226 °C, and by differential scanning calorimetry. These composites represent a promising new application for low value animal coproducts having limited value to be used as organic crosslinkers in the atom-efficient inverse vulcanization process to yield high sulfur-content materials that have impressive mechanical properties.
Introduction
High sulfur-content materials (HSMs) are gaining notoriety for their potential utility in several applications such as active cathode materials in Li–S batteries and optical devices, water purification, antimicrobial materials, heavy metal remediation, and in structural materials.1–37 HSMs comprise oligomeric or polymeric sulfur catenates stabilized within a crosslinked network. Catenated forms of sulfur have been underexplored largely because they are unstable with respect to the familiar orthorhombic eight-membered ring allotrope (α-sulfur) and thus the catenated forms must be confined in a network or otherwise kinetically stabilized.38 Once sulfur catenates are incorporated into a material providing such stabilization, however, the resultant HSMs exhibit some enhanced properties compared to traditional organic polymers. As a result of the thermal reversibility of S–S bond formation, for example, HSMs can often be thermally processed, thermally healed and recycled over many cycles without change to their mechanical properties. Sulfur is an attractive monomer not only by merit of the thermal processability it endows to its composite materials, but also because it is an underutilized by-product of fossil fuel refining.
Most HSMs have been prepared by inverse vulcanization (Scheme 1),1–6 although a few alternate methods for their synthesis and processing involving alternate chemical pathways have recently emerged as well.36,39–46 Inverse vulcanization relies on the reaction of olefins with thermally generated sulfur radicals. A wide range of olefins serve as viable comonomers in inverse vulcanization, including numerous bio-derived examples such as limonene, modified cellulose or lignin, finely ground peanut shells, and plant-derived terpenoid alcohols like citronellol, geraniol and farnesol.22,39,47–61
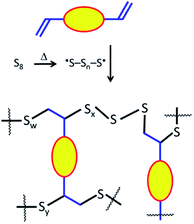 |
| Scheme 1 A general scheme for the crosslinking of unsaturated units with thermally generated sulfur radicals. | |
Although most efforts to prepare HSMs from sustainably-sourced olefins have centred on plant-derived precursors, there is a need to better utilize animal coproducts for value-added purposes as well. Full utilization of animal coproducts is especially critical from a sustainability standpoint given the greater ecological capital expended to produce animal- versus plant-derived agricultural goods. A recent application of animal-derived material to HSMs is a report of insulative HSM pressed mats including wool,62,63 in which the wool provides structural and insulative properties but may not be itself chemically integrated into the material via covalent bonds to the other components. These wool-HSM composites provide a promising route to repurpose used animal-derived wool fibre and textile goods through their combination with sulfur and canola oil. In the current context, it was of interest to incorporate a high-volume, low-value animal coproduct directly as the olefin comonomer for reaction with sulfur in an effort to obtain durable HSMs. Brown grease was identified as an ideal candidate for this purpose. Brown grease is a term broadly referring to the mixture of oils, fats, solids and detergents from food or rendering industry wastes that are captured in grease traps and it may contain partially rancidified animal fat.64–66 Because of the chemical composition and potential contaminants in brown grease, regulatory agencies do not allow brown grease to be used for animal feed and there are limited permissible uses of brown grease for ground application as a fertilizer. In the United States alone, more than 1.7 million tons of brown grease are collected every year, making brown grease, one of the most underutilize products of agricultural animal processing. Brown grease is largely comprised of naturally occurring animal fat triglycerides, significant free fatty acid content (>10% be mass) due to triglyceride hydrolysis, and usually <1% of other impurities, water and biosolids. The high concentration of free fatty acids in brown grease also hampers its use in conventional biodiesel production schemes. In previous HSM work with free fatty acids, however, sulfur and oleic acid were successfully combined to yield recyclable polymeric materials when ZnO was added as a compatibilizing agent to facilitate miscibility of the components. The resulting copolymers (ZOSx) exhibited a storage modulus of up to 400 MPa, representing an eightfold increase versus the storage modulus of sulfur.47 In another study, pure and technical grade linoleic acid were employed for polymerization with sulfur to yield ZPLSx and ZLSx, respectively. These materials had modest flexural strengths between 1.0–2.0 MPa and flexural moduli of 46–75 MPa.48 When fatty acid–sulfur HSMs were used to form composites with Pozzolan cements, the flexural moduli of these materials varied from 40–90 MPa and their compressive strengths rivaled or exceeded that of ordinary Portland cement (OPC).67 In addition to the fatty acid content of brown grease, the triglycerides present are also expected to form crosslinks with sulfur via inverse vulcanization. In the context of structural materials, HSMs made from sulfur and triglycerides have often proven to be quite mechanically strong.54,68 For example, composites made by the reaction of sulfur with canola oil (yielding CanS), sunflower oil (yielding SunS) or linseed oil (yielding LinS) had compressive strengths of 9.3, 17.9, and 22.9 MPa, respectively.68 The compressive strength of LinS represents 135% of the compressive strength required of OPC for use in residential building foundations and footers.
All of the aforementioned studies on the structural aspects of fatty acid and triglyceride-derived sulfur composites and cements suggest that analogous materials may be accessible by the reaction of sulfur with brown grease. Herein we report the use of inverse vulcanization to prepare composites CanBGx and SunBGx (Fig. 1, where x = wt% sulfur, varied from 85–90%), using as organic monomer a mixture of brown grease with either canola oil (yielding CanBGx) or sunflower oil (yielding SunBGx). The thermal, morphological and mechanical properties of these composites were characterized using differential scanning calorimetry (DSC, Fig. S1 and S2, ESI†) mechanical test stand analysis, thermogravimetric analysis (TGA, Fig. S3, ESI†), dynamic mechanical analysis (DMA, Fig. S4, ESI†) and mechanical test stand analysis, infrared spectroscopy (Fig. S5 and S6, ESI†), powder X-raw diffraction (XRD, Fig. S7 and S8, ESI†). The extent to which sulfur was covalently incorporated by reaction with the unsaturated units in the organic components was assessed and quantified by a combination of DSC and fractionation studies.
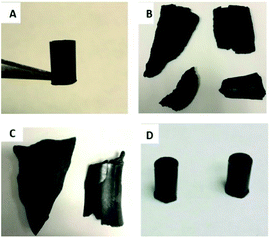 |
| Fig. 1 Photographs of CanBG90 (A), CanBG85 (B), SunBG90 (C), and SunBG85 (D). | |
Results and discussion
Preparation and composite composition
The brown grease used for this study was comprised primarily of triglycerides, with the balance comprised by 34.18% free fatty acids, 0.57% moisture, and 0.81% of unidentified impurities (from the supplier certificate of analysis). Further analysis by 1H NMR spectrometry allowed quantification of the total unsaturation content provided by the mixture of fatty acids and triglycerides (Fig. S10 in the ESI†). This analysis showed that the total olefin content of the brown grease was 3.24 mmol g−1.
Initial efforts to directly react sulfur with brown grease in several ratios led to visually heterogeneous, phase separated samples due to ineffective mixing of the brown grease and the sulfur at the reaction temperature (160–180 °C) despite high-speed mechanical stirring. This observation is not entirely surprising given the high free fatty acid content of the brown grease and previous reports that fatty acids and sulfur have poor miscibility.47 In previous work, the immiscibility of free fatty acids and sulfur for inverse vulcanization was overcome by the addition of ZnO. In those studies, it was hypothesized that Zn compatibilized the sulfur and fatty acids by coordination of S8 and the fatty acid carboxylates to the Zn. Such a mechanism has also been invoked in classic vulcanization of rubber in which stearic acid and Zn were added as compatibilizing agents.69
Efforts to similarly improve the miscibility of brown grease and sulfur by the addition of ZnO, however, was not fully effective in the case of reaction mixtures of sulfur and brown grease. Previous studies have demonstrated the compatibility of sulfur and triglycerides. Triglycerides are also known to be miscible with brown grease, so a blend of brown grease and a triglyceride-based plant oil was targeted for reaction with sulfur as a potentially more miscible comonomer blend. A 50
:
50 wt/wt blend of brown grease and plant oils proved to be fully miscible with sulfur at a reaction temperature of 180 °C when canola oil or sunflower oil was used in the blend. The resulting HSMs were composed of 90 wt% sulfur, 5 wt% brown grease, and 5 wt% canola oil (giving CanBG90) or 5 wt% sunflower oil (giving SunBG90).
The analogous reactions of sulfur with a higher brown grease to plant oil comonomer ratio was also performed. A blend of brown grease and plant oils (85
:
15% wt/wt) was fully miscible in sulfur at a reaction temperature of 180 °C yielding HSMs composed of 85 wt% sulfur, 10 wt% brown grease, and 5 wt% plant oils to yield CanBG85 and SunBG85 when canola oil or sunflower oil were used, respectively. All of the composites solidified as homogeneous materials upon cooling to room temperature to form black solids that could be readily remelted and poured onto surfaces to form sheets or into moulds to form shapes such as cylinders (Fig. 1).
Comparison of the infrared spectra of the plant-oils, brown grease and the CanBGx and SunBGx composites (Fig. S5 and S6 in the ESI†) showed a reduction of the cis-alkene C–H bending mode at around 720 cm−1 from the canola or sunflower oil in the composites, and a reduction in the C–H stretching vibration between 2846–2916 cm−1 of symmetrical and asymmetrical CH2 groups which indicate the consumption of the olefin units during the reaction. The composites also exhibited stretches between 1708–1728 cm−1 that can be attributed to C
O stretching of aliphatic esters. Additionally, the emergence of a peak at 794 cm−1 for the C–S stretch in the CanBGx and SunBGx composites confirmed the bond formation attributable to the inverse vulcanization process (Fig. S5 in the ESI†).
HSMs having a high sulfur content such as CanBGx and SunBGx are generally best described as composites because there is often some percentage of sulfur that is not covalently incorporated into the olefin/sulfur-catenate network. It was thus necessary to quantify the amount of sulfur entrapped as S8 rings versus that covalently-incorporated as catenates. Whereas free sulfur is quite soluble in CS2, sulfur that is covalently crosslinked into HSM networks is generally not soluble in CS2. This difference in solubility often allows fractionation of HSM composites by CS2-extractions as a tool to quantify free and covalently bound sulfur. In the current study, recursive CS2 extractions followed by elemental analysis of the resulting fraction confirmed that the CS2-soluble fractions were comprised of sulfur. The majority of sulfur in the brown grease-containing composites was stabilized as covalently-attached crosslinking catenates, with only 14–29 wt% extractable sulfur (Table 1). The ratio of sulfur to the total olefin units in the mixture of brown grease and canola oil/sunflower oil in the CS2-insoluble fractions allowed the quantification of the sulfur rank. The sulfur rank indicates the average length of sulfur chains per olefin unit. In the case of CanBGx and SunBGx, the sulfur rank varied from 32 to 60 sulfur atoms per olefin cross-linker and increased expectedly with increasing wt% S in the composites (Table 1).
Table 1 Thermal and morphological properties of the plant oil–sulfur composites CanBG90, CanBG85, SunBG90, and SunBG85 with comparison to elemental sulfur
Materials |
Tda/°C |
Tmb/°C |
Tg,DSCc/°C |
Cold crystallization peaks/°C |
ΔHm/J g−1 |
ΔHcc/J g−1 |
Percent crystallinityd |
Sulfur ranke |
Percent insoluble fractionf |
The temperature at which the 5% mass loss was observed. The temperature at the peak maximum of the endothermic melting. Glass transition temperature. The reduction of percent crystallinity of each sample was calculated with respect to sulfur (normalized to 100%). Sulfur atoms per cross-link. Percent of non-extractable sulfur in each sample after CS2 extractions. |
CanBG90 |
226 |
116.2 |
−36.7 |
NA |
−39.3 |
NA |
12 |
60 |
86 |
CanBG85 |
223 |
116.9 |
NA |
14.3 |
−28.7 |
15.8 |
1 |
37 |
71 |
SunBG90 |
226 |
114.9 |
−36.7 |
NA |
−35.2 |
NA |
21 |
54 |
84 |
SunBG85 |
223 |
116.4 |
NA |
−1.8 |
−30.9 |
10.8 |
7 |
32 |
71 |
S8 |
229 |
118.5 |
NA |
NAb |
−44.8 |
NA |
100 |
NA |
NA |
Thermal/morphological properties of composites
The thermal and mechanical properties of HSMs are important considerations for their potential applications. The thermal stability of the composites was assessed by thermogravimetric analysis (TGA). Thermogravimetric analysis of the composites revealed the decomposition temperatures (Td, temperature at which 5% mass loss is observed upon heating under a N2 atmosphere). The Td values for CanBG90, CanBG85, SunBG90, SunBG85 were all between 223 and 226 °C (Table 1 and Fig. S3 in the ESI†), respectively, the typical range for HSMs. The Td for all the composites were similar to the Td of S8 (229 °C), which is not surprising given that the materials comprise 85–90 wt% sulfur. Other composites comprising similar wt% S, including the aforementioned triglyceride-sulfur composites CanS, SunS and LinS, showed similar Td values (226–227 °C). The char yield of the composites increased with higher wt% of the organic monomer incorporated in the materials. For instance, the char yield for both, SunBG90 and CanBG90, was 9%. In the case of SunBG85 and CanBG85, the char yields were 15 and 16%, respectively.68
Differential scanning calorimetry (DSC) confirmed thermal transitions associated with the presence of free and covalently bound sulfur in the HSMs. All of the composites exhibited the typical melting peak for sulfur between 114–116 °C (Fig. S1 in the ESI†). CanBG90 and SunBG90 exhibited glass transitions (Tg) at −37 °C, diagnostic for polymeric sulfur catenates. In the case of CanBG85 and SunBG85, no apparent Tg was observed, but cold crystallization peaks, often observed in HSMs with intermediate amounts of olefin crosslinker, were observed at 14.3 °C and −1.8 °C, respectively.
The percent crystallinity of the CanBGx and SunBGx composites relative to crystalline orthorhombic sulfur was calculated from the integration of the melting and cold crystallization enthalpies observed in the DSC data. From the integrations, it was concluded that composites with higher organic comonomer incorporation such as CanBG85 and SunBG85 had lower crystallinities (1% and 7%, respectively) and, in the case of CanBG90 and SunBG90, the crystallinities were higher, 12% and 21%, consistent with previous HSMs.39,57,68 Powder X-ray diffraction (PXRD) also corroborated that the primary crystalline domains were attributable to free sulfur present in CanBG90, CanBG85, SunBG90, and SunBG85 (Fig. S7 and S8 in the ESI†).
Mechanical properties of composites
Previous HSMs prepared from reaction sulfur with fatty acids triglycerides have shown a wide range of mechanical strengths. Although some HSMs have very low compressive strengths, several have compressive strength exceeding that of ordinary Portland cement. In the current study, one aim was to determine whether the crosslinking provided by the brown grease/plant oil mixture could endow their resultant composites with practically useful mechanical properties. Compressive test cylinders of the composites were readily prepared by melting the composites at 160 °C, pouring the liquid composite into a silicon mould and allowing the material to solidify. The test cylinders were cured for four days to allow for their direct comparison to previous triglyceride–sulfur composites that had also been cured for four days.68 The compressive strength of each composite was measured in triplicates by use of a mechanical test stand. The stress–strain curves resulting from these tests are provided in the ESI (Fig. S9†), while the compressive moduli and ultimate compressive strength at break are provided in Table 2 and Fig. 2 for comparison to some other fatty acid- and triglyceride-containing composite HSMs. The compressive strength of CanBG90, CanBG85, SunBG90, SunBG85 (32.0, 28.7, 35.9 and 33.2 MPa, respectively) proved to be higher than those of previously-reported fatty acid- or triglyceride-containing HSMs and in a comparable range to biomass-sulfur composites such as APS95, a composite made by inverse vulcanization of allyl-derivatized peanut shells.59,61
Table 2 Physical properties of the plant oil–sulfur composites CanBG90, SunBG90, CanBG85, and SunBG85
Materials |
Compressive strength (MPa) |
Compressive moduli (MPa) |
Flexural strength/modulus (MPa) |
Compressive strength (% of OPC) |
CanBG85 |
28.7 ± 1.0 |
110 |
8.5/700 |
170 |
CanBG90 |
32.0 ± 0.9 |
100 |
6.5/420 |
190 |
SunBG85 |
33.2 ± 0.2 |
110 |
7.7/560 |
200 |
SunBG90 |
35.9 ± 0.7 |
110 |
7.7/460 |
210 |
CanS (ref. 68) |
9.3 ± 1.0 |
74 |
NA |
55 |
SunS (ref. 68) |
17.8 ± 3.1 |
96 |
NA |
100 |
LinS (ref. 68) |
22.9 ± 3.5 |
110 |
NA |
140 |
Portland cement |
17.0 |
— |
3.7/580 |
100 |
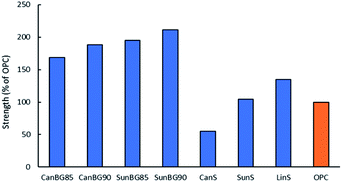 |
| Fig. 2 Compressive strengths for ordinary Portland cement (OPC) compared to those of plant oil–sulfur cements. | |
These HSMs were also subjected to dynamic mechanical analysis (DMA). Stress–strain testing of CanBG90, CanBG85, SunBG90, SunBG85 composites revealed that they have relatively high flexural strength and moduli at room temperature compared to other HSMs (Table 2 and Fig. S4 in the ESI†). In previous efforts, some fatty acid–sulfur HSMs composites reported flexural moduli that varied from 40–75 MPa, and flexural strengths between 1.0–2.0 MPa. In the case of CanBGx and SunBGx, these composites exhibited higher flexural strength and moduli. CanBG85 had the highest flexural strength (8.5 MPa) and the highest flexural modulus (700 MPa). The flexural strength of CanBG90 was 6.5 MPa and its flexural modulus was 420 MPa. In the case of both, SunBG85 and SunBG90, their flexural moduli were 7.7 MPa, however, SunBG85 had a higher flexural modulus (560 MPa) compared to SunBG90 (460 MPa). The flexural strength of CanBG85 represents 230% of the flexural strength of ordinary Portland cement (OPC). In fact, the flexural strengths, and moduli of CanBGx and SunBGx composites significantly exceed that of previously reported fatty acid–sulfur composites and traditional building materials such as Portland cement. The high flexural strength and compressive strength of brown grease-comprising composites is attributable to a higher cross-link density in the brown grease-plant oil composites afforded by the unsaturation number of the plant oils and the free fatty acids present in brown grease, which provide more potential sites for crosslinking in the CanBGx and SunBGx composites.
Conclusions
In conclusion, CanBGx and SunBGx composites were prepared from industrial by-product sulfur and a mixture of brown grease and plant oils (either canola or sunflower oil) as the organic monomer via the atom economical inverse vulcanization process. The thermal and mechanical properties of the composites were assessed. These composites exhibited impressive mechanical properties without the need of any aggregates. The compressive and flexural strengths of CanBGx and SunBGx composites were in comparable ranges to some biomass-sulfur composites and exceed that of Portland cement. These high sulfur content materials made from low-value animal sources represent an alternative to better utilize animal coproducts for value-added purposes. CanBGx and SunBGx composites show promising properties to be considered as high-strength sustainable structural materials. These first investigations on the use of brown grease as a component of structural materials reveals that this low value animal coproduct may be a useful component of structural materials for the replacement of traditional, less sustainable materials.
Follow up studies on evaluating the long-term stability of these brown-grease sulfur composites are currently underway.
Experimental
General considerations
Fourier transform infrared spectra were obtained using an IR instrument (Shimadzu IRAffinity-1S) with an ATR attachment. Scans were collected over the range 400–4000 cm−1 at ambient temperature with a resolution of 8 cm−1. TGA was recorded (Mettler Toledo TGA 2 STARe System) over the range 20–800 °C with a heating rate of 10 °C min−1 under a flow of N2 (100 mL min−1). Each measurement was acquired in duplicate and presented results represent an average value. DSC was acquired (Mettler Toledo DSC 3 STARe System) over the range −60 to 140 °C with a heating rate of 10 °C min−1 under a flow of N2 (200 mL min−1). Each DSC measurement was carried out over three heat–cool cycles.
Carbon disulfide extractions were performed by suspending 0.6 g of finely ground material in 20 mL of CS2, allowing the solid to settle for 30 minutes, pipetting off the supernatant into a separate vial, and adding another 20 mL of CS2. This process was repeated an additional three times so that a total of five washes was performed. The residual CS2 was evaporated under a flow of N2 and each vial was weighed to determine the fraction that was soluble (collected as supernatant) or insoluble (remained in the initial vial).
Compressional analysis was performed on a Mark-10 ES30 test stand equipped with a M3-200 force gauge (1 kN maximum force with ±1 N resolution) with an applied force rate of 3–4 N s−1. Compression cylinders were cast from silicone resin moulds (Smooth-On Oomoo® 30 tin-cure) with diameters of approximately 6 mm and heights of approximately 10 mm. Samples were manually sanded to ensure uniform dimensions and measured with a digital calliper with ±0.01 mm resolution. Compressional analysis was performed in triplicate and results were averaged.
Dynamic Mechanical Analysis (DMA) was performed using a Mettler Toledo DMA 1 STARe System in single cantilever mode. DMA samples were cast from silicone resin moulds (Smooth-On Oomoo® 30 tin-cure). The sample dimensions were 1.2 × 10.4 × 5.0 mm. Clamping force was 1 cN m and the temperature was 25 °C. The samples were tested in duplicates and the results were averaged.
For percent crystallinity calculations, Tm, ΔHm and ΔHcc, the data was taken from the first heat/cool cycles. Melting enthalpies and the cold crystallization enthalpies were calculated using DSC data. The reduction of the percent crystallinity of the composites CanBGx and SunBGx with respect to sulfur was calculated using the following equation.
Δχc – change of percentage crystallinity with respect to sulfur.
ΔHm(CanBGx) – melting enthalpy of composite materials (CanBGx or SunBGx).
ΔHcc(CanBGx) – cold crystallization enthalpy of composite materials.
ΔHm(S) – melting enthalpy of sulfur.
ΔHcc(S) – cold crystallization enthalpy of sulfur.
Materials and methods
Brown grease was supplied by industrial partners. All materials were used as received: canola oil (Crisco), sunflower oil (Maple Holistics), and sulfur (Dugas Diesel) and used without further purification. Plant-oil–sulfur composite materials were aged for 4 d prior to compressive and flexural strength testing.
General synthesis of CanBGx and SunBGx
Caution: heating elemental sulfur with organics can result in the formation of H2S gas. H2S is toxic, foul smelling, and corrosive. Although we did not observe any mass loss attributable to gas generation, temperature must be carefully controlled to prevent thermal spikes, which contribute to the potential for H2S evolution. Rapid stirring shortened heating times, and very slow addition of reagents can help prevent unforeseen temperature spikes.
Syntheses proceeded by heating the given amounts of reagents with rapid mechanical stirring to give the target composite in essentially quantitative yield. A small amount (∼1–4%) of mass loss in each case occurs as a result of sulfur sublimation during heating. Sublimed sulfur is visually observed at the top of the reaction vessel and is removed by scraping prior to collection of the bulk material.
Synthesis of CanBG90
Preparation of CanBG90 involved reaction of canola oil (2.5 g, 5 wt%), brown grease (2.5 g, 5 wt%) and sulfur (45.0 g, 0.17 mol, 90 wt%). Sulfur was first melted in an oil bath at 160 °C with rapid mechanical stirring. Then, the temperature was heated further to 180 °C, where sulfur exists primarily as polymeric diradicals. Once the temperature was stable, brown grease was slowly added to the sulfur while stirring. Once the brown grease was added, the canola oil was added dropwise to the brown grease–sulfur mixture. The reaction mixture was stirred for 24 h at 180 °C. Within 24 h of the reaction time, the desired product, a homogeneous solution was produced. Upon cooling to room temperature, the material solidified to a black solid composite. Elemental analysis calculated: C 3.00, H 1.00, S 90.00; found: C 5.63, H 0.34, S 92.99.
Synthesis of CanBG85
Preparation of CanBG85 involved reaction of canola oil (2.5 g, 5 wt%), brown grease (5.0 g, 10 wt%) and sulfur (42.5 g, 0.16 mol, 90 wt%). Sulfur was first melted in an oil bath at 160 °C with rapid mechanical stirring. Then, the temperature was heated further to 180 °C, where sulfur exists primarily as polymeric diradicals. Once the temperature was stable, brown grease was slowly added to the sulfur while stirring. Once the brown grease was added, the canola oil was added dropwise to the brown grease–sulfur mixture. The reaction mixture was stirred for 24 h at 180 °C. Within 24 h of the reaction time, the desired product, a homogeneous solution was produced. Upon cooling to room temperature, the material solidified to a black solid composite. Elemental analysis calculated: C 3.00, H 1.00, S 85.00; found: C 11.14, H 0.81, S 87.73.
Synthesis of SunBG90
Preparation of SunBG90 involved reaction of sunflower oil (2.5 g, 5 wt%), brown grease (2.5 g, 5 wt%) and sulfur (45.1 g, 0.17 mol, 90 wt%). Sulfur was first melted in an oil bath at 160 °C with rapid mechanical stirring. Then, the temperature was heated further to 180 °C, where sulfur exists primarily as polymeric diradicals. Once the temperature was stable, brown grease was slowly added to the sulfur while stirring. Once the brown grease was added, the canola oil was added dropwise to the brown grease–sulfur mixture. The reaction mixture was stirred for 24 h at 180 °C. Within 24 h of the reaction time, the desired product, a homogeneous solution was produced. Upon cooling to room temperature, the material solidified to a black solid composite. Elemental analysis calculated: C 3.85, H 1.00, S 90.00; found: C 5.17, H 0.40, S 92.33.
Synthesis of SunBG85
Preparation of SunBG85 involved reaction of sunflower oil (2.5 g, 5 wt%), brown grease (5.0 g, 10 wt%) and sulfur (42.7 g, 0.16 mol, 90 wt%). Sulfur was first melted in an oil bath at 160 °C with rapid mechanical stirring. Then, the temperature was heated further to 180 °C, where sulfur exists primarily as polymeric diradicals. Once the temperature was stable, brown grease was slowly added to the sulfur while stirring. Once the brown grease was added, the canola oil was added dropwise to the brown grease–sulfur mixture. The reaction mixture was stirred for 24 h at 180 °C. Within 24 h of the reaction time, the desired product, a homogeneous solution was produced. Upon cooling to room temperature, the material solidified to a black solid composite. Elemental analysis calculated: C 3.00, H 1.00, S 85.00; found: C 14.59, H 1.03, S 81.35.
Conflicts of interest
There are no conflicts to declare.
Acknowledgements
We thank the Animal Coproducts Research and Education Center and the National Science Foundation (CHE-1708844) for financial support. CVL thanks the Call Me Doctor Program for fellowship support.
Notes and references
- W. J. Chung, J. J. Griebel, E. T. Kim, H. Yoon, A. G. Simmonds, H. J. Ji, P. T. Dirlam, R. S. Glass, J. J. Wie, N. A. Nguyen, B. W. Guralnick, J. Park, A. Somogyi, P. Theato, M. E. Mackay, Y.-E. Sung, K. Char and J. Pyun, Nat. Chem., 2013, 5, 518–524 CrossRef CAS PubMed.
- Y. Zhang, R. S. Glass, K. Char and J. Pyun, Polym. Chem., 2019, 10, 4078–4105 RSC.
- T. S. Kleine, R. S. Glass, D. L. Lichtenberger, M. E. MacKay, K. Char, R. A. Norwood and J. Pyun, ACS Macro Lett., 2020, 9, 245–259 CrossRef CAS.
- P. Yan, W. Zhao, B. Zhang, L. Jiang, S. Petcher, J. A. Smith, D. J. Parker, A. I. Cooper, J. Lei and T. Hasell, Angew. Chem., Int. Ed., 2020, 59, 13371–13378 CrossRef CAS PubMed.
- M. J. H. Worthington, R. L. Kucera and J. M. Chalker, Green Chem., 2017, 19, 2748–2761 RSC.
- J. M. Chalker, M. J. H. Worthington, N. A. Lundquist and L. J. Esdaile, Top. Curr. Chem., 2019, 377, 1–27 CrossRef CAS PubMed.
- A. G. Simmonds, J. J. Griebel, J. Park, K. R. Kim, W. J. Chung, V. P. Oleshko, J. Kim, E. T. Kim, R. S. Glass, C. L. Soles, Y.-E. Sung, K. Char and J. Pyun, ACS Macro Lett., 2014, 3, 229–232 CrossRef CAS.
- I. Gomez, O. Leonet, J. A. Blazquez and D. Mecerreyes, ChemSusChem, 2016, 9, 3419–3425 CrossRef CAS PubMed.
- A. Hoefling, D. T. Nguyen, Y. J. Lee, S.-W. Song and P. Theato, Mater. Chem. Front., 2017, 1, 1818–1822 RSC.
- S. Zeng, L. Li, L. Xie, D. Zhao, N. Wang and S. Chen, ChemSusChem, 2017, 10, 3378–3386 CrossRef CAS PubMed.
- Y. Zhang, J. J. Griebel, P. T. Dirlam, N. A. Nguyen, R. S. Glass, M. E. MacKay, K. Char and J. Pyun, J. Polym. Sci., Part A: Polym. Chem., 2017, 55, 107–116 CrossRef CAS.
- P. Dong, K. S. Han, J.-I. Lee, X. Zhang, Y. Cha and M.-K. Song, ACS Appl. Mater. Interfaces, 2018, 10, 29565–29573 CrossRef CAS PubMed.
- Q. Jiang, Y. Li, X. Zhao, P. Xiong, X. Yu, Y. Xu and L. Chen, J. Mater. Chem. A, 2018, 6, 17977–17981 RSC.
- F. Zhao, Y. Li and W. Feng, Small Methods, 2018, 2, 1–34 CAS.
- T. S. Sahu, S. Choi, P. Jaumaux, J. Zhang, C. Wang, D. Zhou and G. Wang, Polyhedron, 2019, 162, 147–154 CrossRef CAS.
- J. J. Griebel, S. Namnabat, E. T. Kim, R. Himmelhuber, D. H. Moronta, W. J. Chung, A. G. Simmonds, K.-J. Kim, J. van der Laan, N. A. Nguyen, E. L. Dereniak, M. E. MacKay, K. Char, R. S. Glass, R. A. Norwood and J. Pyun, Adv. Mater., 2014, 26, 3014–3018 CrossRef CAS PubMed.
- S. Namnabat, J. J. Gabriel, J. Pyun and R. A. Norwood, Proc. SPIE, 2014, 8983, 89830D/89831–89830D/89838 Search PubMed.
- S. Namnabat, J. J. Gabriel, J. Pyun, R. A. Norwood, E. L. Dereniak and J. van der Laan, Proc. SPIE, 2014, 9070, 90702H/90701–90702H/90707 Search PubMed.
- J. J. Griebel, N. A. Nguyen, S. Namnabat, L. E. Anderson, R. S. Glass, R. A. Norwood, M. E. MacKay, K. Char and J. Pyun, ACS Macro Lett., 2015, 4, 862–866 CrossRef CAS.
- L. E. Anderson, T. S. Kleine, Y. Zhang, D. D. Phan, S. Namnabat, E. A. LaVilla, K. M. Konopka, L. Ruiz Diaz, M. S. Manchester, J. Schwiegerling, R. S. Glass, M. E. Mackay, K. Char, R. A. Norwood and J. Pyun, ACS Macro Lett., 2017, 6, 500–504 CrossRef CAS.
- T. S. Kleine, T. Lee, K. J. Carothers, M. O. Hamilton, L. E. Anderson, L. Ruiz Diaz, N. P. Lyons, K. R. Coasey, W. O. Parker Jr, L. Borghi, M. E. MacKay, K. Char, R. S. Glass, D. L. Lichtenberger, R. A. Norwood and J. Pyun, Angew. Chem., Int. Ed., 2019, 58, 17656–17660 CrossRef CAS PubMed.
- J. Kuwabara, K. Oi, M. M. Watanabe, T. Fukuda and T. Kanbara, ACS Appl. Polym. Mater., 2020, 2, 5173–5178 CrossRef CAS.
- T. Hasell, D. J. Parker, H. A. Jones, T. McAllister and S. M. Howdle, Chem. Commun., 2016, 52, 5383–5386 RSC.
- M. W. Thielke, L. A. Bultema, D. D. Brauer, P. Theato, B. Richter and M. Fischer, Polymers, 2016, 8, 1–9 CrossRef PubMed.
- D. J. Parker, H. A. Jones, S. Petcher, L. Cervini, J. M. Griffin, R. Akhtar and T. Hasell, J. Mater. Chem. A, 2017, 5, 11682–11692 RSC.
- A. M. Abraham, S. V. Kumar and S. M. Alhassan, Chem. Eng. J., 2018, 332, 1–7 CrossRef CAS.
- H.-K. Lin, Y.-S. Lai and Y.-L. Liu, ACS Sustainable Chem. Eng., 2019, 7, 4515–4522 CrossRef CAS.
- Y. Chen, A. Yasin, Y. Zhang, X. Zan, Y. Liu and L. Zhang, Materials, 2020, 13, 632 CrossRef CAS PubMed.
- A. D. Tikoalu, N. A. Lundquist and J. M. Chalker, Adv. Sustainable Syst., 2020, 4, 1900111 CrossRef CAS.
- C. R. Westerman and C. L. Jenkins, Macromolecules, 2018, 51, 7233–7238 CrossRef CAS.
- C. Herrera, K. J. Ysinga and C. L. Jenkins, ACS Appl. Mater. Interfaces, 2019, 11, 35312–35318 CrossRef CAS PubMed.
- K. Orme, A. H. Fistrovich and C. L. Jenkins, Macromolecules, 2020, 53, 9353–9361 CrossRef CAS.
- X. Wu, J. A. Smith, S. Petcher, B. Zhang, D. J. Parker, J. M. Griffin and T. Hasell, Nat. Commun., 2019, 10, 10035–10044 Search PubMed.
- B. Zhang, S. Petcher and T. Hasell, Chem. Commun., 2019, 55, 10681–10684 RSC.
- B. Zhang, H. Gao, P. Yan, S. Petcher and T. Hasell, Mater. Chem. Front., 2020, 4, 669–675 RSC.
- N. A. Lundquist, A. D. Tikoalu, M. J. H. Worthington, R. Shapter, S. J. Tonkin, F. Stojcevski, M. Mann, C. T. Gibson, J. R. Gascooke, A. Karton, L. C. Henderson, L. J. Esdaile and J. M. Chalker, Chem.–Eur. J., 2020, 26, 10035–10044 CrossRef CAS PubMed.
- S. J. Tonkin, C. T. Gibson, J. A. Campbell, D. A. Lewis, A. Karton, T. Hasell and J. M. Chalker, Chem. Sci., 2020, 11, 5537–5546 RSC.
- B. Meyer, Chem. Rev., 1964, 64, 429–451 CrossRef CAS.
- M. S. Karunarathna, A. G. Tennyson and R. C. Smith, J. Mater. Chem. A, 2020, 8, 548–553 RSC.
- T. Thiounn, M. S. Karunarathna, L. M. Slann, M. K. Lauer and R. C. Smith, J. Polym. Sci., 2020, 58, 1347–1364 CrossRef CAS.
- M. S. Karunarathna, M. K. Lauer and R. C. Smith, J. Mater. Chem. A, 2020, 8, 20318–20322 RSC.
- T. Thiounn, M. K. Lauer, M. S. Karunarathna, A. G. Tennyson and R. C. Smith, Sustainable Chem., 2020, 1, 183–197 CrossRef.
- T. Thiounn and R. C. Smith, J. Polym. Sci., 2020, 58, 1347–1364 CrossRef CAS.
- S. J. Tonkin, C. T. Gibson, J. A. Campbell, D. A. Lewis, A. Karton, T. Hasell and J. M. Chalker, Chem. Sci., 2020, 11, 5537–5546 RSC.
- L. J. Dodd, O. Omar, X. Wu and T. Hasell, ACS Catal., 2021, 11, 4441–4455 CrossRef CAS.
- S. Petcher, B. Zhang and T. Hasell, Chem. Commun., 2021, 57, 5059–5062 RSC.
- A. D. Smith, T. Thiounn, E. W. Lyles, E. K. Kibler, R. C. Smith and A. G. Tennyson, J. Polym. Sci., Part A: Polym. Chem., 2019, 57, 1704–1710 CrossRef CAS.
- A. D. Smith, C. D. McMillin, R. C. Smith and A. G. Tennyson, J. Polym. Sci., 2020, 58, 438–445 CrossRef CAS.
- A. D. Smith, R. C. Smith and A. G. Tennyson, Sustainable Chem., 2020, 1, 209–237 CrossRef.
- M. K. Lauer, A. G. Tennyson and R. C. Smith, ACS Appl. Polym. Mater., 2020, 2, 3761–3765 CrossRef CAS.
- C. P. Maladeniya, M. S. Karunarathna, M. K. Lauer, C. V. Lopez, T. Thiounn and R. C. Smith, Mater. Adv., 2020, 1, 1665–1674 RSC.
- M. P. Crockett, A. M. Evans, M. J. H. Worthington, I. S. Albuquerque, A. D. Slattery, C. T. Gibson, J. A. Campbell, D. A. Lewis, G. J. L. Bernardes and J. M. Chalker, Angew. Chem., Int. Ed., 2016, 55, 1714–1718 CrossRef CAS PubMed.
- F. Wu, S. Chen, V. Srot, Y. Huang, S. K. Sinha, P. A. van Aken, J. Maier and Y. Yu, Adv. Mater., 2018, 30, 1706643 CrossRef PubMed.
- J. A. Smith, S. J. Green, S. Petcher, D. J. Parker, B. Zhang, M. J. H. Worthington, X. Wu, C. A. Kelly, T. Baker, C. T. Gibson, J. A. Campbell, D. A. Lewis, M. J. Jenkins, H. Willcock, J. M. Chalker and T. Hasell, Chem.–Eur. J., 2019, 25, 10433–10440 CrossRef CAS PubMed.
- M. K. Lauer and R. C. Smith, Compr. Rev. Food Sci. Food Saf., 2020, 1–53, DOI:10.1111/1541-4337.12627.
- M. K. Lauer, A. G. Tennyson and R. C. Smith, Mater. Adv., 2021, 2, 2391–2397 RSC.
- M. S. Karunarathna, M. K. Lauer, T. Thiounn, R. C. Smith and A. G. Tennyson, J. Mater. Chem. A, 2019, 7, 15683–15690 RSC.
- M. S. Karunarathna and R. C. Smith, Sustainability, 2020, 12, 734–748 CrossRef CAS.
- M. K. Lauer, M. S. Karunarathna, A. G. Tennyson and R. C. Smith, Mater. Adv., 2020, 1, 2271–2278 RSC.
- M. K. Lauer, T. A. Estrada-Mendoza, C. D. McMillen, G. Chumanov, A. G. Tennyson and R. C. Smith, Adv. Sustainable Syst., 2019, 3, 1900062 CrossRef CAS.
- M. K. Lauer, M. S. Karunarathna, A. G. Tennyson and R. C. Smith, Mater. Adv., 2020, 1, 590–594 RSC.
- I. Bu Najmah, N. A. Lundquist, M. K. Stanfield, F. Stojcevski, J. A. Campbell, L. J. Esdaile, C. T. Gibson, D. A. Lewis, L. C. Henderson, T. Hasell and J. M. Chalker, ChemSusChem, 2021, 14, 2352–2359 CrossRef CAS PubMed.
- N. Israa Bu, L. Nicholas, S. K. Melissa, S. Filip, C. A. Jonathan, E. Louisa, G. T. Christopher, L. A. David, H. C. Luke, H. Tom and C. Justin, Insulating Composites Made from Sulfur, Canola Oil, and Wool, 2020 Search PubMed.
- C. Pastore, A. Lopez and G. Mascolo, Bioresour. Technol., 2014, 155, 91–97 CrossRef CAS PubMed.
- Y.-L. Sim, N. Meyappan, N. S. Yen, S. Kamala a/p Subramaniam, C. H. Khoo, W. L. Cheah, D. St. Hilaire, T. Pinnock, B. Bacolod, Z. B. Cai, D. Gurung, R. Hasnat, J. Strothers, C. T. Remy, P. K. Gentles, S. Groveman, M. Vittadello, J. Kim and L. M. Pratt, Fuel, 2017, 207, 274–282 CrossRef CAS.
- J. Strothers, R. B. Matthews, A. Toney, M. R. Cobham, S. Cox, W. Ford, S. Joseph, W. Joyette, S. Khadka, S. Pinnock, M. Burns, M. Noel, M. G. Tamang, D. Saint Hilaire, J.-H. Kim and L. M. Pratt, Fuel, 2019, 239, 573–578 CrossRef CAS.
- A. D. Smith, R. C. Smith and A. G. Tennyson, Sustainable Chem. Pharm., 2020, 16, 100249 CrossRef.
- C. V. Lopez, M. S. Karunarathna, M. K. Lauer, C. P. Maladeniya, T. Thiounn, E. D. Ackley and R. C. Smith, J. Polym. Sci., 2020, 58, 2259–2266 CrossRef CAS.
- M. Akiba and A. S. Hashim, Prog. Polym. Sci., 1997, 22, 475–521 CrossRef CAS.
Footnote |
† Electronic supplementary information (ESI) available: Proton NMR spectral data, FTIR spectra, TGA curves, DSC curves, DMA curves, powder XRD and stress–strain plots. See DOI: 10.1039/d1ra06264f |
|
This journal is © The Royal Society of Chemistry 2022 |
Click here to see how this site uses Cookies. View our privacy policy here.