DOI:
10.1039/D1QM01256H
(Research Article)
Mater. Chem. Front., 2022,
6, 78-85
Formamide-soluble solid-state ZnO as Zn source for synthesizing FeCo–NC with ultrahigh oxygen reduction reaction activity†
Received
11th September 2021
, Accepted 10th November 2021
First published on 11th November 2021
Abstract
The high-cost synthesis of highly dispersed non-noble metal–nitrogen–carbon (MNC) electrocatalysts hinders their practical applications. Here, we have developed a cost/time-efficient synthesis method for MNC electrocatalysts with highly dispersed metal sites, using the commercially available cheap ZnO as the Zn source, reducing the cost of Zn usage by over 80%. Our specially chosen solvent formamide can react with ZnO and allow the formation of nano-sized ZnFeCo–Nx complexes uniformly distributed in the formamide-derived high-N-doped carbon substrate. Further annealing the ZnFeCo–N–C precursor will produce a highly dispersed FeCo–NC target product. Electrochemical measurements show that the prepared FeCo–NC is an excellent electrocatalyst for alkaline oxygen reduction reaction (ORR), rendering superior onset and half-wave potentials of 1.05 and 0.92 V, respectively. The Al–air battery assembled using this also shows a high specific power (204.9 mW cm−2) and a large specific capacity (552 mA h g−1 at 10 mA cm−2), exceeding those of the 20 wt% Pt/C catalyst. Our method may inspire the scalable and low-cost production of highly dispersed MNC electrocatalysts and their wide range of practical applications.
Introduction
Nitrogen-doped carbon-supported atomic dispersed metal species have received considerable attention due to their precise atomic structures with 100% metal utilization, strong/adjustable metal–substrate interaction, and, more importantly, broad electrochemical energy conversion and storage applications.1–4 The synthesis of atomically dispersed metal–nitrogen–carbon (AD-MNC) materials has stimulated broad and extensive interest; many effective strategies have been developed to realize stabilized metal atoms on various types of nitrogen-doped carbons, including spatial confinement,5–7 atomic/molecule anchoring,8 defect capturing,9 space-constrained pyrolysis,10,11 and potential cycling.12–14 Among them, spatial confinement applying zinc species has demonstrated high effectiveness in dispersing and stabilizing active metal species nearly crossing the periodic table at the atomic scale.15,16 Owing to its high effectiveness in realizing atomic metal dispersion in carbon materials, the AD-MNC materials fabricated via Zn-assistance have been employed in a wide-range of electrochemical applications such as fuel cells,17 metal–air batteries,18 water electrolyzers,19 CO2/N2 value-added conversion,20 Li/Na plating,21 and S hosts for batteries.22
In general, Zn-assisted synthesis of AD-MNC materials uses high-purity ionic Zn salts such as ZnCl2 and Zn(NO3)2 as Zn sources to obtain organic M/Zn–Nx–C complex or framework precursors. The spatial confinement effect of Zn is reflected in the key step of inert annealing at elevated temperatures (such as 900 °C or higher). After the unstable Zn species and carbonaceous segments are removed, a stable and robust N-coordination with M is obtained. In some cases, Zn species were deliberately reserved to synergistically adjust the electronic structure of the main catalytic metal site and obtain enhanced overall catalytic performance;23,24 for instance, Gong et al. reported that the dual-site Zn/Co mode significantly affects the bonding strength of reaction intermediates compared to single-metal Co site, thereby optimizing the reaction pathway for catalyzing the reduction of CO2 to CO.25 Yet in most cases, the overwhelmingly used Zn species (usually Zn/Mx molar ratio > 9
:
1) were removed at high temperatures to gain pure M–Nx sites, and discarded as a waste without cycling.26–28 This drives us to explore alternative inexpensive Zn sources other than high-purity ZnCl2 and Zn(NO3)2 to achieve the low-cost fabrication of AD-MNC materials. Previously, solid-state metal-doped ZnO can react with gaseous organic N-containing ligands, leading to the formation of doped metal–organic framework (MOF) thin shells that can be further transformed into hollow structured AD-MNC materials,29,30 which has demonstrated the possibility of ZnO as an effective alternative Zn source.
Inspired by this design, we have developed an effective method for synthesizing highly dispersed FeCo–NC materials using commercial ZnO powder as a cheap Zn source. Compared with anhydrous ZnCl2 (Aladdin, 99.9% purity, a common Zn source for AD-MNC synthesis26), using ZnO (Aladdin, 99.8%) as the Zn source reduces the cost of Zn use by over 80% (cost can be further reduced by using bulk ZnO), which is a big saving for the mass production of AD-MNC materials. The typical synthesis of highly dispersed FeCo–NC includes two steps: (1) solvothermal treatment of ZnO and Fe/Co salts in formamide (FA) and (2) inert annealing of the ZnFeCo–NC precursor at elevated temperatures. Owing to the high reactivity of ZnO and FA, ZnO is completely converted into nano-sized Zn2Fe(CN)6 and uniformly dispersed in a FA-derived high-N-doped carbon substrate, providing a ZnFeCo–NC precursor with high-loadings of N (37.2 at%), Zn (7.8 at%), Fe (1.7 at%), and Co (0.6 at%). The FeCo–NC annealed at 900 °C shows no obvious signs of Fe and Co-related aggregates, when systematically characterized by using XRD, HRTEM, and XPS techniques, suggesting the highly dispersed Fe and Co in the FeCo–NC product. Electrochemical measurements reveal that the highly dispersed FeCo–NC exhibits a superior oxygen reduction reaction (ORR) performance in 0.1 M KOH, with the onset and half-wave potentials of 1.05 and 0.92 V, respectively. In addition, the Al–air battery assembled using this shows a specific power of 204.9 mW cm−2, and a very large specific capacity of 552 mA h g−1 at 10 mA cm−2, exceeding those of the 20 wt% Pt/C catalyst.
Results and discussion
A highly dispersed Fe/Co/N co-doped carbon material was realized by thermally driven conversion of pre-ZnFeCo–NC at a high temperature under N2 protection. As schematically illustrated in Fig. 1A, it involves two parts: (1) ball milling and solvothermal treatment of Co2+ and Fe3+ salts in formamide (FA) in the presence of commercially available ZnO at 180 °C (the resultant product was named pre-ZnFeCo–NC); and (2) inert annealing of pre-ZnFeCo–NC at 900 °C. In the first step, formamide reacts with ZnO and dissolves it into a FA-derived highly N-doped carbonaceous material,26 which also allows the Fe/Co species to be highly dispersed in the possible atomic structure of Fe(N3)–Co(N3) that is stabilized within the confinement of multiple N coordination, as previously investigated in related studies.26 The pre-ZnFeCo–NC (with a starting Fe
:
Co ratio of 1
:
1) was subjected to multiple characterizations. Fig. 1B shows the XRD profiles of pre-ZnFeCo–NC and the starting ZnO, revealing the complete dissolution of solid-state ZnO and formation of nanosized Zn2Fe(CN)6 after the solvothermal treatment. The texture of the resultant pre-ZnFeCo–NC was typical of amorphous carbon, as revealed by the presence of D (disorder) and G (graphitization) bands at 1388 and 1568 cm−1, respectively (Fig. 1C). The Raman bands ascribed to the Zn–O vibration at 442 and 580 cm−1 disappear,31 suggesting the complete reduction and dissolution of ZnO by FA and its derived N-containing complex. The HRTEM image (Fig. 1D) indicates that no apparent metallic aggregate is formed, implying the high-dispersion state of Zn, Fe, and Co. The HRTEM energy-dispersive spectroscopy (EDS) mapping images (Fig. 1E) confirm the uniform distribution of C, N, O, Fe, Co, and Zn elements; particularly, the N content of 37.2 at% is the key to stabilizing heavy metal species: Fe, Co, and Zn approach 1.7, 0.6, and 7.8 at%, respectively (Fig. 1F).
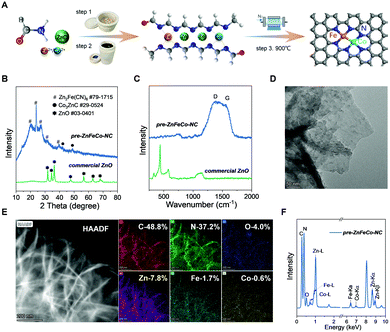 |
| Fig. 1 (A) Schematic diagram of the preparation of highly dispersed FeCo–NC using solid-state ZnO as the precursor. (B) XRD curves and (C) Raman spectra of pre-ZnFeCo–NC and starting ZnO. (D) HRTEM image, (E) HRTEM-HAADF image and element mapping images and (F) EDS spectra of pre-ZnFeCo–NC. | |
During inert annealing at 900 °C, the unstable N/C segments in pre-ZnFeCo–NC gradually decompose into gaseous byproducts,27 after annealing at 900 °C, about 34% of the initial weight is retained (Fig. S1, ESI†). This indicates the formation of a large number of micro-/mesopores that may help the enlargement of the electroactive surface area and the accessibility of the electrolyte and dissolved gases.32,33 The SEM images in Fig. S2 (ESI†) comparatively show that FeCo–NC and Fe–NC depict a flower-like structure while this structure is not formed in Co–NC; probably due to the formation of Zn2Fe(CN)6 and its directed growth of carbon precipitates.34 Similarly, the HRTEM image (Fig. 2A) of FeCo–NC clearly shows a thin-layer assembly texture, which can also be found in Fe–NC (Fig. S3A, ESI†), but not in Co–NC (Fig. S3C, ESI†). Further magnification of the HRTEM images (Fig. 2B and Fig. S3B, D, ESI†) reveals that all samples prepared using ZnO as Zn source merely contain amorphous carbon with short-range graphitic carbon islands, indicating that no small-sized Fe/Co-related aggregates are formed. HRTEM EDS mapping of the FeCo–NC sample, as shown in Fig. 2C and D, reveal the uniform distribution of highly dispersed Fe, Co, and Zn. The Fe and Co contents measured by EDS are 0.36 and 0.21 at%, respectively. Similarly, Fe or Co species are uniformly distributed throughout the carbon matrix of Fe–NC and Co–NC, respectively, which also indicates the successful manufacture of highly dispersed and uniform metal species in Fe–NC and Co–NC (Fig. S4 and S5, ESI†).
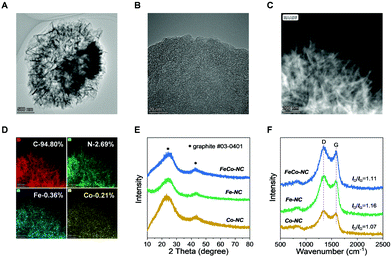 |
| Fig. 2 (A) TEM image, (B) HRTEM image, (C) HRTEM-HAADF image, and (D) HRTEM EDS mapping images of FeCo–NC. (E) XRD curves and (F) Raman spectra of FeCo–NC compared to those of Fe–NC and Co–NC. | |
XRD analysis (Fig. 2E) shows that all the synthetic MNC samples are amorphous carbon; no apparent peak can be identified as Fe or Co-related aggregates. The Raman spectra in Fig. 2F confirm the formation of a defect-rich graphitic carbon texture. The typical ID/IG ratio is about 1.1, which can be corelated with the process of thermally-driven Zn removal/activation by breaking down the Zn–Nx moiety.21,35 In addition, the BET measurements also confirm the formation of abundant micropores in three samples (Fig. 3A). FeCo–NC shows the largest hysteresis loop area and the largest specific surface area of 441 m2 g−1, followed by Co–NC (421 m2 g−1) and then by Fe–NC (340 m2 g−1). It is worth noting that from the pore distribution curves (Fig. 3B), the FeCo–NC and Fe–NC exhibit a similar pore structure distinct from Co–NC, which agrees with HRTEM characterization. At the same time, FeCo–NC shows a higher content of micropores with diameter <0.6 nm, indicating the occurrence of a stronger Zn activation process. All the MNC samples contain large content of mesopores, as indicated by the measured pore volume at pore size ranging from 2 to 20 nm, which is beneficial for electrolyte penetration.34
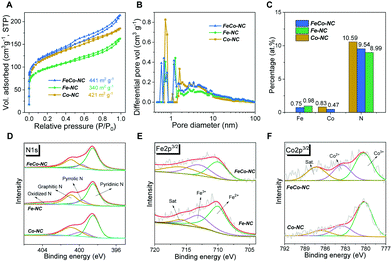 |
| Fig. 3 BET measurements of FeCo–NC compared to those of Fe–NC and Co–NC: (A) N2 isotherms and (B) pore distribution curves. XPS analysis results of FeCo–NC compared to those of Fe–NC and Co–NC: (C) element contents of Fe, Co, and N, (D) N1s spectra, (E) Fe2p3/2 spectra, and (F) Co 2p3/2 spectra. | |
According to XPS measurements (Fig. S6A, ESI†), the contents of Fe and Co in FeCo–NC are 0.75 and 0.47 at%, respectively (Fig. 3C and Table S1, ESI†), while Fe in Fe–NC is slightly higher, 0.98 at%, and Co in Co–NC is 0.83 at%. The exact Fe loadings in Fe–NC and FeCo–NC are 5.06 and 3.12 wt%, respectively, while Co contents in Co–NC and FeCo–NC are 1.82 and 1.05 wt%, respectively, as measured by ICP (Table S2, ESI†). It is worth noting that the N content of all the synthetic Fe/Co–NC samples fall in a range of 9 to 11 at%, the ultrahigh N content is key to stabilizing the high-content metal species in atomic dispersion.26 Fig. S6B (ESI†) shows the C1s spectra and their deconvolution, which depicts the largest contribution of heteroatom-containing functional groups from C–N species, which is consistent with the XPS elemental survey and HRTEM EDS mapping. As shown in Fig. 3D, all the synthesized Fe/Co–NC samples show the highest percentage of pyridinic N species and very minor presence of pyrrolic N species, which is probably due to the higher stability of the six-atom ringed structure of pyridinic N over pyrrolic N.36 Therefore, the less stable N form, i.e., pyrrolic N, would be more inclined to be removed or converted into stable N species,27 resulting in very low content of pyrrolic N species and a relatively high content of graphitic N for all three samples. Fig. 3E compares the Fe2p spectral deconvolutions of FeCo–NC and Fe–NC, revealing that Fe–NC contains more ferrous (Fe(II)/Fe(III) ratio = 1.75), while the Fe(II)/Fe(III) ratio in FeCo–NC is roughly 1.45. The above comparison suggests the strong coupling effect between Fe and Co.37 Accordingly, more Co2+ is seen presented in the Co2p spectra of FeCo–NC (Fig. 2F, Co(II)/Co(III) = 0.56).
Before the electrocatalytic measurements, the electrochemical double-layer capacitance (Cdl) was used as an indicator to compare the electrochemical specific areas (ECSAs) of all the synthetic Fe/Co–NC samples.38 As shown in Fig. S7 (ESI†), the calculated Cdl values of FeCo–NC, Fe–NC, and Co–NC at 1.035 V (vs. RHE) are 30.6, 30.5, and 29.6 mF cm−2, respectively, which indicates that their electrochemically accessible surface areas are comparable. To compare with Fe–NC, Co–NC, and commercial Pt/C, the ORR catalytic activity of FeCo–NC was evaluated in an O2-saturated 0.1 M KOH solution using a three-electrode setup. First, by using cyclic voltammetry (CV) to study the ORR performance at a scan rate of 20 mV s−1, the maximum ORR peak of FeCo–NC appears at about 0.86 V (Fig. S8, ESI†), which is the highest among all the samples, confirming its best ORR activity. The LSV polarization curves shown in Fig. 4A were obtained at a rotation speed of 1600 rpm. FeCo–NC shows the best ORR performance, rendering an onset potential (Eonset) of about 1.05 V, a half-wave potential (E1/2) of 0.92 V, and a limiting current density of about 5.70 mA cm−2 (data collected at U = 0.6 V, vs. RHE), which are superior to those of the commercial Pt/C catalyst (Eonset = 0.99 V and E1/2 = 0.89 V) and most of the currently reported metal–nitrogen–carbon (M–NC) materials.7,26,27,35,39–41 Meanwhile, Fe–NC and Co–NC also present very good ORR activity, exhibiting slightly lower onset potentials of 0.99 V and 0.95 V, respectively.
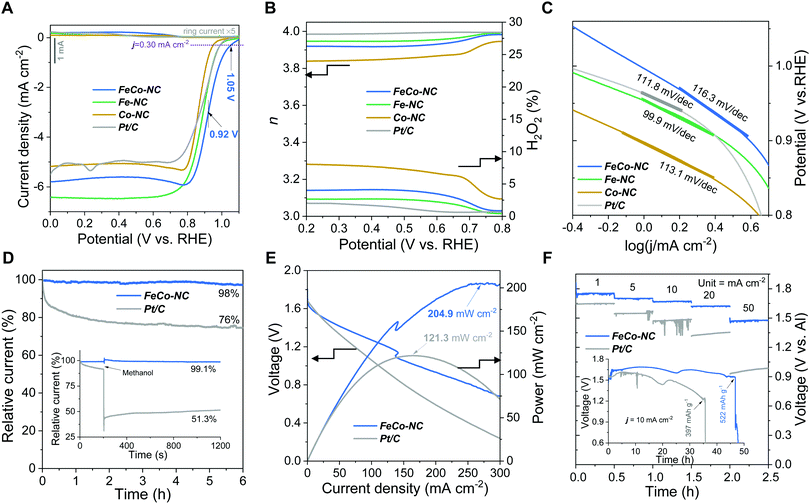 |
| Fig. 4 Electrochemical measurements of FeCo–NC compared to Fe–NC, and Co–NC, and Pt/C in O2-saturated 0.1 M KOH: (A) plots of disk current density and ring current versus applied potential; (B) calculated H2O2% and transfer electron number plots; (C) Tafel plots with slopes marked, and (D) long-term durability measurements; and inset of panel (D) shows the methanol crossover measurements. Al–air battery measurements of FeCo–NC compared with Pt/C in 6 M KOH containing additives such as Na2SnO3, In(OH)3 and ZnO; (E) plots of voltage and specific power versus applied current density, and (F) rate capability measurement at different current densities; inset of panel (F) shows the discharge profiles at 10.0 mA cm−2. | |
The transfer electron number (n) and the percentage of H2O2 were calculated using the disk and ring currents according to eqn (2) and (3) (Fig. 4B). The synthesized FeCo–NC, Fe–NC, and Pt/C show approximately 4 in a wide potential range of 0.2 to 0.8 V, while Co–NC exhibits a lower average n of 3.83. Accordingly, the H2O2 yield of FeCo–NC remains below 4% over a wide potential range of 0.2 to 0.8 V, compared to 2% for Pt/C, 3% for Fe–NC, and 8% for Co–NC (Fig. 4B). At the initial potential region controlled by electrochemical activity, the Tafel slope of FeCo–NC (approximately 116.3 mV dec−1) is lower than that of Pt/C (111.8 mV dec−1) (Fig. 4C), suggesting that the conversion of *O2 to *OOH is the a rate-determining step.42 Besides, the long-term working stability was evaluated using the chronoamperometry method. As shown in Fig. 4D, FeCo–NC exhibits a very high current retention of more than 98% after 6 h of continuous operation at 0.6 V, while Pt/C shows nearly 24% activity loss. In addition, FeCo–NC also shows a negligible activity decrease upon methanol crossover (inset of Fig. 4D), while Pt/C loses nearly half of its activity permanently upon methanol contamination.
The Al–air battery (AAB) measurements were performed using FeCo–NC or Pt/C-made air cathode by depositing the catalyst on a conductive carbon paper. An Al plate was used as the anode, and 6.0 mol L−1 KOH containing corrosion inhibiting additives such as Na2SnO3, In(OH)3, and ZnO was used as the electrolyte.43 FeCo–NC provides an increasing power in the wide current density range (0 to 270 mA cm−2) and manages the maximum power density of 204.9 mW cm−2 at a current density of 270 mA cm−2 relative to the Pt/C cathode at a current density of 121.3 mW cm−2 at 165.2 mA cm−2 (Fig. 4E). The discharge voltages of AAB fabricated using FeCo–NC or Pt/C at different current densities were measured, as shown in Fig. 4F. As measured using a multimeter, the FeCo–NC-assembled AAB exhibits an open circuit voltage (OCV) of 1.85 V (Fig. S9, ESI†). It is also observed that FeCo–NC achieves higher discharge voltages against Pt/C at all current densities of 1.0, 5.0, 10.0, 20.0, and 50.0 mA cm−2, reaching 1.75, 1.70, 1.67, 1.62, and 1. 47 V, respectively. It is noteworthy that the FeCo–NC-AAB still provides a very high discharge voltage of 1.47 V at 50 mA cm−2, which is 500 mV higher than that of Pt/C. The FeCo–NC-AAB was further subjected to long-term discharge with reference to Pt/C; the inset of Fig. 4F shows the discharge curves at a current density of 10 mA cm−2. The FeCo–NC-AAB initially shows a higher discharge voltage, which gradually decreases to the extent of Pt/C during the 11th to 16th hour time span and improves to the highest discharge voltage of 1.71 V until cell failure at the 47th hour, resulting in a remarkable specific capacity of 552 mA h g−1. In contrast, Pt/C-AAB shows a steady discharge voltage profile but reaches much earlier cell failure at the 36th hour, which results in a much lower specific capacity of 397 mA h g−1 implying that our developed FeCo–NC cathode significantly improved the discharge efficiency of AAB.
Conclusions
In summary, cheap ZnO instead of high-purity Zn salts was used as the Zn source to synthesize a highly dispersed FeCo–NC material, and a largely reduced cost of Zn was achieved, serving as a big saving for the mass production of AD-MNC materials. Thanks to the high reactivity between ZnO and FA, ZnO can be completely dissolved into ionic Zn, thereafter converted into nanosized Zn2Fe(CN)6, and further uniformly embedded in a FA-derived high-N-doped carbon substrate. This provides a unique ZnFeCo–NC precursor with heavy loadings of N (37.2 at%), Zn (7.8 at%), Fe (1.7 at%), and Co (0.6 at%). Subsequent inert annealing graphitized the ZnFeCo–NC precursor and enabled robust coordination by N ligand, while no obvious Fe and Co-related aggregates were observed, as thoroughly characterized by using XRD, HRTEM, and XPS techniques, which indicates that the Fe and Co species in the FeCo–NC product are in a state of high dispersion. Electrochemical measurements have proved the superior ORR performance of FeCo–NC in 0.1 M KOH, rendering the onset and half-wave potentials of 1.07 and 0.92 V, respectively. In addition, the Al–air battery assembled using this shows a specific power of 204.9 mW cm−2, and a very large specific capacity of 552 mA h g−1 at 10 mA cm−2, surpassing those of the 20 wt% Pt/C catalyst. Our work may contribute to the mass production of AD-MNC materials and their extensive electrochemical applications.
Experiment section
Chemicals and reagents
Ferric chloride (FeCl3, A.R. grade) and cobaltous chloride (CoCl2, A.R. grade) were bought from Shanghai Macklin Biochemical Co., Ltd. Formamide (CH3NO, purity > 99%) was brought from Tianjin Damao Chemical Factory. ZnO (99.8%, 50 ± 10 nm, A.R. grade) was purchased from Aladdin Co., Ltd. Absolute ethanol was purchased from Sinopharm Chemical Reagent Co. Ltd. Nafion solution (5.0 wt%, Dupont) and commercial Pt/C (20.0 wt%) were bought from Shanghai Hesen Electric Co., Ltd. Carbon black (BP2000) was purchased from Nanjing Xianfeng Nanomaterial Technology Co., Ltd. All reagents were used as received without further purification.
Preparation of FeCo–NC materials
First, a mixture of 0.2 mmol FeCl2, 0.2 mmol CoCl2, 1.00 g of ZnO, and 40 mL of formamide was placed in a 50 mL-packed ZrO2 jar and ball-milled at 300 Hz for 2 hours. Then, the as-obtained slurry was submitted to solvothermal treatment at 180 °C for 12 hours to make pre-FeCo–NC. In this step, the solid-state ZnO was completely converted into organic Zn–N frameworks and played the role of fencing the active metals of Fe and Co in atom dispersion. Subsequently, the obtained black-colored pre-FeCo–NC was washed with absolute ethanol 2–3 times and dried at 60 °C overnight. Then the dried precursor was ground in a quartz mortar and heated to 900 °C for 1 h at a heating rate of 5 °C min−1 under N2 flow protection. The control samples of Fe–NC and Co–NC were synthesized with the addition of only Fe (0.4 mmol) or Co (0.4 mmol). The rest of the steps were the same as those for the synthesis of FeCo–NC.
Materials characterization
Powder X-ray diffraction (XRD) was performed using a Brüker D8 Advance diffractometer at 40 kV and 40 mA using Cu Kα radiation (λ = 0.15406 nm). Scanning electron microscopy (SEM) was performed using an Apreo S HiVac scanning electron microscope at an acceleration voltage of 15 kV. Transmission electron microscopy (TEM), high-resolution TEM (HRTEM) images, high-angle annular dark-field scanning transmission electron microscopy (HAADF-STEM) images, and EDS mapping images were obtained using a FEI Talos 200S high-resolution transmission electron microscope at an acceleration voltage of 200 kV. Raman spectra were obtained using a DXR2 Raman Microscope (Thermo Fisher) with a 532 nm line of Ar laser as the excitation source. Brunauer–Emmett–Teller (BET) N2 adsorption–desorption isotherms were performed using a Micromeritics-ASAP2460 for obtaining the specific surface area (SSA) of all samples at 77 K, degassed at 300 °C before measurement. The pore size distribution plot was determined by using the density-functional theory (DFT) method. The thermogravimetric analysis (TGA, STA449F5) was operated under an N2 atmosphere at a heating rate of 5 °C min−1. Elemental analysis of Fe and Co in the solid samples was performed using an inductively coupled plasma optical emission spectrometry (ICP-OES, Agilent 720es). X-ray photoelectron spectrum (XPS) analysis was performed using a PHI 5000 Versaprobe system using monochromatic Al Kα radiation (1486.6 eV). All binding energies were referenced to the C1s peak at 284.6 eV.
Electrochemical measurements
ORR measurements were performed on a typical three-electrode system using a CHI 760e electrochemical station (Shanghai Chenhua Co., China) at room temperature. A glassy carbon electrode (GCE), a saturated calomel electrode (SCE), and a graphite rod electrode were used as the working electrode, reference electrode, and counter electrode, respectively. Catalyst ink was prepared by ultrasonically mixing 5.0 mg of the catalyst, 1.0 mg of carbon black and 10.0 μL of Nafion solution (5 wt%) in 500 μL of absolute ethanol. Then, the well-dispersed catalyst ink was drop-casted on the glassy carbon electrode (RDE) or glassy carbon rotating ring-disk electrode (RRDE) with 0.25 mg cm−2 loading for all samples. 0.1 mol L−1 KOH aqueous solution was used as the electrolyte. Before ORR measurements, the O2 gas was purged into the electrolyte for at least 30 min to achieve O2 saturation. Before data collection, all the working electrodes were pretreated by repeated cyclic voltammetry scans at a scan rate of 50 mV s−1 to fully activate the electrochemically assessable surface. The linear sweep voltammetry (LSV) polarization curves were obtained at a scan rate of 5.0 mV s−1 in 0.1 mol L−1 KOH aqueous solution. All the potentials were converted to the potential vs the reversible hydrogen electrode (RHE) according to eqn (1). | E(RHE) = E(SCE) + 0.241 + 0.059 × pH | (1) |
The ORR polarization curves obtained using RRDE for the transferred electron number (n) and the hydrogen peroxide yield (H2O2%) were collected at a rotating speed of 1600 rpm at a scan rate of 5 mV s−1. The ring electrode potential was set at 0.2 V vs. RHE in the KOH electrolyte. The hydrogen peroxide yield (H2O2%) and the transferred electron number (n) were determined using the following equations:27
| 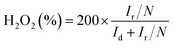 | (2) |
| 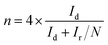 | (3) |
where
Id is the disk current,
Ir is the ring current, and the current collection efficiency of the Pt ring (N) is 0.37. Long-term stability tests were recorded by chronoamperometric measurement at a constant overpotential of 0.2 V. The methanol crossover tests were performed by adding 3.0 mL of methanol at ∼300 s.
Al–air battery (AAB) measurements
The measurements of AAB were performed on home-built electrochemical cells with a sandwich structure. Typically, for the fabrication of the gas-diffusion electrode (GDE), 5.0 mg of the catalyst was initially dispersed into a mixed solution of 500 μL of ethanol and 10 μL of 5% Nafion to prepare the catalyst ink. The as-made catalyst was then coated on a conductive carbon paper to reach a mass loading of 1.0 mg cm−2; the gas-diffusible area was controlled in 1.0 cm2. A polished 0.8 mm-thick Al plate was used as the anode. The electrolyte is 6.0 M KOH containing Na2SnO3, In(OH)3 and ZnO.43 The rate performance of AAB was evaluated by performing galvanostatic discharge at various current densities: 0, 1, 5, 10, 20, and 50 mA cm−2.
Author contributions
Y. Sun and G. Zhang conceived the project and designed the experiments. Y. Sun, Z. Li, and Y. Wu conducted the experiments. Y. Sun, Z. Li, Y. Wu, and J. Tian jointly analyzed the data. G. Zhang and Y. Sun co-wrote the manuscript, Y. Wang, M. Yang, and G. Zhang revised the manuscript. M. Yang and G. Zhang obtained the funding sources. All authors have approved the final version of the manuscript.
Conflicts of interest
There are no conflicts to declare.
Acknowledgements
This work was financially supported by the National Natural Science Foundation of China (NSFC, 22071137).
References
- C. X. Zhao, B. Q. Li, J. N. Liu and Q. Zhang, Intrinsic Electrocatalytic Activity Regulation of M–N–C Single-Atom Catalysts for the Oxygen Reduction Reaction, Angew. Chem., Int. Ed., 2021, 60, 4448–4463 CrossRef CAS PubMed.
- G. Meng, J. Zhang, X. Li, D. Wang and Y. Li, Electronic structure regulations of single-atom site catalysts and their effects on the electrocatalytic performances, Appl. Phys. Rev., 2021, 8, 021321 CAS.
- X.-F. Yang, A. Wang, B. Qiao, J. Li, J. Liu and T. Zhang, Single-Atom Catalysts: a New Frontier in Heterogeneous Catalysis, Acc. Chem. Res., 2013, 46, 1740–1748 CrossRef CAS.
- F. D. Speck, J. H. Kim, G. Bae, S. H. Joo, K. J. J. Mayrhofer, C. H. Choi and S. Cherevko, Single-Atom Catalysts: a Perspective toward Application in Electrochemical Energy Conversion, JACS Au, 2021, 1, 1086–1100 CrossRef CAS.
- Y. Zhou, X. Tao, G. Chen, R. Lu, D. Wang, M.-X. Chen, E. Jin, J. Yang, H.-W. Liang, Y. Zhao, X. Feng, A. Narita and K. Müllen, Multilayer stabilization for fabricating high-loading single-atom catalysts, Nat. Commun., 2020, 11, 5892 CrossRef CAS.
- H. Zhang, H. T. Chung, D. A. Cullen, S. Wagner, U. I. Kramm, K. L. More, P. Zelenay and G. Wu, High-performance fuel cell cathodes exclusively containing atomically dispersed iron active sites, Energy Environ. Sci., 2019, 12, 2548–2558 RSC.
- L. Gong, H. Zhang, Y. Wang, E. Luo, K. Li, L. Gao, Y. Wang, Z. Wu, Z. Jin, J. Ge, Z. Jiang, C. Liu and W. Xing, Bridge Bonded Oxygen Ligands between Approximated FeN4 Sites Confer Catalysts with High ORR Performance, Angew. Chem., Int. Ed., 2020, 59, 13923–13928 CrossRef CAS.
- L. Wang, M.-X. Chen, Q.-Q. Yan, S.-L. Xu, S.-Q. Chu, P. Chen, Y. Lin and H.-W. Liang, A sulfur-tethering synthesis strategy toward high-loading atomically dispersed noble metal catalysts, Sci. Adv., 2019, 5, eaax6322 CrossRef CAS PubMed.
- L. Zhang, Y. Jia, G. Gao, X. Yan, N. Chen, J. Chen, M. T. Soo, B. Wood, D. Yang, A. Du and X. Yao, Graphene Defects Trap Atomic Ni Species for Hydrogen and Oxygen Evolution Reactions, Chemistry, 2018, 4, 285–297 CrossRef CAS.
- L. Jiao, R. Zhang, G. Wan, W. Yang, X. Wan, H. Zhou, J. Shui, S.-H. Yu and H.-L. Jiang, Nanocasting SiO2 into metal–organic frameworks imparts dual protection to high-loading Fe single-atom electrocatalysts, Nat. Commun., 2020, 11, 2831 CrossRef CAS.
- X. Wan, X. Liu, Y. Li, R. Yu, L. Zheng, W. Yan, H. Wang, M. Xu and J. Shui, Fe–N–C electrocatalyst with dense active sites and efficient mass transport for high-performance proton exchange membrane fuel cells, Nat. Catal., 2019, 2, 259–268 CrossRef CAS.
- Z. Liu, S. Li, J. Yang, X. Tan, C. Yu, C. Zhao, X. Han, H. Huang, G. Wan, Y. Liu, K. Tschulik and J. Qiu, Ultrafast Construction of Oxygen-Containing Scaffold over Graphite for Trapping Ni2+ into Single Atom Catalysts, ACS Nano, 2020, 14, 11662–11669 CrossRef CAS PubMed.
- B. Yan, H. Song and G. Yang, A facile and green large-scale fabrication of single atom catalysts for high photocatalytic H2 evolution activity, Chem. Eng. J., 2022, 427, 131795 CrossRef CAS.
- L. Zhang, L. Han, H. Liu, X. Liu and J. Luo, Potential-Cycling Synthesis of Single Platinum Atoms for Efficient Hydrogen Evolution in Neutral Media, Angew. Chem., Int. Ed., 2017, 56, 13694–13698 CrossRef CAS PubMed.
- S. Mitchell and J. Pérez-Ramírez, Single atom catalysis: a decade of stunning progress and the promise for a bright future, Nat. Commun., 2020, 11, 4302 CrossRef CAS PubMed.
- S. Ji, Y. Chen, X. Wang, Z. Zhang, D. Wang and Y. Li, Chemical Synthesis of Single Atomic Site Catalysts, Chem. Rev., 2020, 120, 11900–11955 CrossRef CAS.
- L. Chen, X. Liu, L. Zheng, Y. Li, X. Guo, X. Wan, Q. Liu, J. Shang and J. Shui, Insights into the role of active site density in the fuel cell performance of Co–N–C catalysts, Appl. Catal., B, 2019, 256, 117849 CrossRef CAS.
- X. Liu, L. Wang, G. Zhang, F. Sun, G. Xing, C. Tian and H. Fu, Zinc assisted epitaxial growth of N-doped CNTs-based zeolitic imidazole frameworks derivative for high efficient oxygen reduction reaction in Zn–air battery, Chem. Eng. J., 2021, 414, 127569 CrossRef CAS.
- R. Liu, Z. Gong, J. Liu, J. Dong, J. Liao, H. Liu, H. Huang, J. Liu, M. Yan, K. Huang, H. Gong, J. Zhu, C. Cui, G. Ye and H. Fei, Design of Aligned Porous Carbon Films with Single-Atom Co–N–C Sites for High-Current-Density Hydrogen Generation, Adv. Mater., 2021, 2103533 CrossRef CAS.
- J. Han, P. An, S. Liu, X. Zhang, D. Wang, Y. Yuan, J. Guo, X. Qiu, K. Hou, L. Shi, Y. Zhang, S. Zhao, C. Long and Z. Tang, Reordering d Orbital Energies of Single-Site Catalysts for CO2 Electroreduction, Angew. Chem., Int. Ed., 2019, 58, 12711–12716 CrossRef CAS PubMed.
- C.-C. Hou, Y. Wang, L. Zou, M. Wang, H. Liu, Z. Liu, H.-F. Wang, C. Li and Q. Xu, A Gas-Steamed MOF Route to P-Doped Open Carbon Cages with Enhanced Zn-Ion Energy Storage Capability and Ultrastability, Adv. Mater., 2021, 33, 2101698 CrossRef CAS PubMed.
- Z. Du, X. Chen, W. Hu, C. Chuang, S. Xie, A. Hu, W. Yan, X. Kong, X. Wu, H. Ji and L.-J. Wan, Cobalt in Nitrogen-Doped Graphene as Single-Atom Catalyst for High-Sulfur Content Lithium–Sulfur Batteries, J. Am. Chem. Soc., 2019, 141, 3977–3985 CrossRef CAS.
- Y. Li, R. Hu, Z. Chen, X. Wan, J.-X. Shang, F.-H. Wang and J. Shui, Effect of Zn atom in Fe–N–C catalysts for electro-catalytic reactions: theoretical considerations, Nano Res., 2021, 14, 611–619 CrossRef CAS.
- L. Cao, Y. Shao, H. Pan and Z. Lu, Designing Efficient Dual-Metal Single-Atom Electrocatalyst TMZnN6 (TM = Mn, Fe, Co, Ni, Cu, Zn) for Oxygen Reduction Reaction, J. Phys. Chem. C, 2020, 124, 11301–11307 CrossRef CAS.
- W. Zhu, L. Zhang, S. Liu, A. Li, X. Yuan, C. Hu, G. Zhang, W. Deng, K. Zang, J. Luo, Y. Zhu, M. Gu, Z.-J. Zhao and J. Gong, Enhanced CO2 Electroreduction on Neighboring Zn/Co Monomers by Electronic Effect, Angew. Chem., Int. Ed., 2020, 59, 12664–12668 CrossRef CAS PubMed.
- G. Zhang, Y. Jia, C. Zhang, X. Xiong, K. Sun, R. Chen, W. Chen, Y. Kuang, L. Zheng, H. Tang, W. Liu, J. Liu, X. Sun, W.-F. Lin and H. Dai, A general route via formamide condensation to prepare atomically dispersed metal–nitrogen–carbon electrocatalysts for energy technologies, Energy Environ. Sci., 2019, 12, 1317–1325 RSC.
- M. Ma, A. Kumar, D. Wang, Y. Wang, Y. Jia, Y. Zhang, G. Zhang, Z. Yan and X. Sun, Boosting the bifunctional oxygen electrocatalytic performance of atomically dispersed Fe site via atomic Ni neighboring, Appl. Catal., B, 2020, 274, 119091 CrossRef CAS.
- D. Zhao, Z. Zhuang, X. Cao, C. Zhang, Q. Peng, C. Chen and Y. Li, Atomic site electrocatalysts for water splitting, oxygen reduction and selective oxidation, Chem. Soc. Rev., 2020, 49, 2215–2264 RSC.
- J. Meng, J. Li, J. Liu, X. Zhang, G. Jiang, L. Ma, Z.-Y. Hu, S. Xi, Y. Zhao, M. Yan, P. Wang, X. Liu, Q. Li, J. Z. Liu, T. Wu and L. Mai, Universal Approach to Fabricating Graphene-Supported Single-Atom Catalysts from Doped ZnO Solid Solutions, ACS Cent. Sci., 2020, 6, 1431–1440 CrossRef CAS PubMed.
- S. Liu, M. Wang, X. Yang, Q. Shi, Z. Qiao, M. Lucero, Q. Ma, K. L. More, D. A. Cullen, Z. Feng and G. Wu, Chemical Vapor Deposition for Atomically Dispersed and Nitrogen Coordinated Single Metal Site Catalysts, Angew. Chem., Int. Ed., 2020, 59, 21698–21705 CrossRef CAS PubMed.
- H. Yang, Z. Chang, Y. Qiao, H. Deng, X. Mu, P. He and H. Zhou, Constructing a Super-Saturated Electrolyte Front Surface for Stable Rechargeable Aqueous Zinc Batteries, Angew. Chem., Int. Ed., 2020, 59, 9377–9381 CrossRef CAS.
- Y. Wang, Z. Li, P. Zhang, Y. Pan, Y. Zhang, Q. Cai, S. R. P. Silva, J. Liu, G. Zhang, X. Sun and Z. Yan, Flexible carbon nanofiber film with diatomic Fe–Co sites for efficient oxygen reduction and evolution reactions in wearable zinc–air batteries, Nano Energy, 2021, 87, 106147 CrossRef CAS.
- J. Kim, J. Lee, J. Yun, S. H. Choi, S. A. Han, J. Moon, J. H. Kim, J.-W. Lee and M.-S. Park, Functionality of Dual-Phase Lithium Storage in a Porous Carbon Host for Lithium–Metal Anode, Adv. Funct. Mater., 2020, 30, 1910538 CrossRef CAS.
- D. Wang, Y. Wu, Z. Li, H. Pan, Y. Wang, M. Yang and G. Zhang, N-doped carbon nanoflower-supported Fe–N4 motifs for high-efficiency reduction of oxygen in both alkaline and acid, Chem. Eng. J., 2021, 424, 130401 CrossRef CAS.
- Y. Wang, A. Kumar, M. Ma, Y. Jia, Y. Wang, Y. Zhang, G. Zhang, X. Sun and Z. Yan, Hierarchical peony-like FeCo–NC with conductive network and highly active sites as efficient electrocatalyst for rechargeable Zn–air battery, Nano Res., 2020, 13, 1090–1099 CrossRef CAS.
- D. Malko, A. Kucernak and T. Lopes, In situ electrochemical quantification of active sites in Fe–N/C non-precious metal catalysts, Nat. Commun., 2016, 7, 13285 CrossRef CAS PubMed.
- L. Chen, Y. Zhang, L. Dong, W. Yang, X. Liu, L. Long, C. Liu, S. Dong and J. Jia, Synergistic effect between atomically dispersed Fe and Co metal sites for enhanced oxygen reduction reaction, J. Mater. Chem. A, 2020, 8, 4369–4375 RSC.
- Y. Hao, Y. Xu, N. Han, J. Liu and X. Sun, Boosting the bifunctional electrocatalytic oxygen activities of CoOx nanoarrays with a porous N-doped carbon coating and their application in Zn–air batteries, J. Mater. Chem. A, 2017, 5, 17804–17810 RSC.
- X. Han, Z. Zheng, J. Chen, Y. Xue, H. Li, J. Zheng, Z. Xie, Q. Kuang and L. Zheng, Efficient oxygen reduction on sandwich-like metal@N–C composites with ultrafine Fe nanoparticles embedded in N-doped carbon nanotubes grafted on graphene sheets, Nanoscale, 2019, 11, 12610–12618 RSC.
- Y. Guan, N. Li, Y. Li, L. Sun, Y. Gao, Q. Zhang, C. He, J. Liu and X. Ren, Two dimensional ZIF-derived ultra-thin Cu–N/C nanosheets as high performance oxygen reduction electrocatalysts for high-performance Zn–air batteries, Nanoscale, 2020, 12, 14259–14266 RSC.
- H. Luo, W.-J. Jiang, C. Lin, W. Dong, S. Niu, L.-B. Huang, X. Zhang, Z. Wei and J.-S. Hu, Scalable solid-state synthesis of coralline-like nanostructured Co@CoNC electrocatalyst for Zn–air batteries, Chem. Commun., 2018, 54, 8190–8193 RSC.
- G. Zhang, H. Luo, H. Li, L. Wang, B. Han, H. Zhang, Y. Li, Z. Chang, Y. Kuang and X. Sun, ZnO-promoted dechlorination for hierarchically nanoporous carbon as superior oxygen reduction electrocatalyst, Nano Energy, 2016, 26, 241–247 CrossRef CAS.
- Y. Wang, G. Zhang, M. Ma, Y. Wang, Y. Zhang, X. Sun and Z. Yan, Sacrificial carbon nitride-templated hollow FeCo–NC material for highly efficient oxygen reduction reaction and Al–air battery, Electrochim. Acta, 2020, 341, 136066 CrossRef CAS.
Footnote |
† Electronic supplementary information (ESI) available: TGA profile of precursors, additional SEM and HRTEM images of M-NCs, XPS survey and C1s spectra of M-NCs, and addition electrochemical measurements. See DOI: 10.1039/d1qm01256h |
|
This journal is © the Partner Organisations 2022 |
Click here to see how this site uses Cookies. View our privacy policy here.