DOI:
10.1039/D2PY00442A
(Paper)
Polym. Chem., 2022,
13, 2988-2998
Orthogonally grown polycarbonate and polyvinyl block copolymers from mechanistically distinct (co)polymerizations†
Received
6th April 2022
, Accepted 30th April 2022
First published on 11th May 2022
Abstract
Mechanistically distinct polymerization systems can afford unique block copolymers that would not be accessible by mere sequential polymerization. Herein we report a convenient one-pot synthesis of miscellaneous di- and triblock copolymers comprising CO2-based and polyvinyl blocks, obtained orthogonally through triethylborane (TEB)-mediated ring opening copolymerization (ROCOP) of CO2 with epoxides on the one hand and reversible addition fragmentation chain transfer (RAFT) polymerization of vinyl monomers on the other. 4-Cyano-4-[(dodecylsulfanylthiocarbonyl) sulfanyl] pentanoic acid (TTC-COOH), which carries a trithiocarbonate function and a carboxylic acid group, played the dual role of a chain transfer agent for RAFT polymerization and an initiator for the ROCOP of CO2/epoxide. Different bases such as tetrabutylammonium hydroxide, N-heterocyclic carbene (NHC), and tributylamine (TBA) were used for the deprotonation of TTC-COOH; in each case the compatibility of the generated carboxylic salts with trithiocarbonate functions was checked when they were utilized to copolymerize CO2 and epoxides. It was found that the salts produced in situ by the deprotonation of TTC-COOH using NHC and TBA did not harm trithiocarbonate functions. The two distinct polymerizations occurred as expected, affording a series of well-defined CO2-based AB and ABC block copolymers comprising one or two poly(vinyl) blocks, depending upon the choice of different combinations of epoxides and vinyl monomers. The thermal characterization of these AB and ABC block copolymers revealed either two or three glass transition temperatures indicative of phase-separated materials.
Introduction
Over the past decade, several examples of successful syntheses of aliphatic polycarbonates through metal-based catalytic systems,1–8 and more recently through metal free systems, have been disclosed.9–15 These chemistries described efficient ring-opening copolymerizations (ROCOP) of CO2 with epoxides, leveraging the direct utilization of over-emitted CO2 as a means to reduce carbon footprint and avoid fossil feedstock. However, applications derived from CO2-based polymers are still very limited due to their rather poor mechanical and thermal properties. Much effort has thus been dedicated to improve the properties of aliphatic polycarbonates through the incorporation of other types of blocks or segments along with CO2-based blocks in di- or triblock copolymers as a potential solution among various other reported strategies.4,5,16,17 As summarized by Coates et al.18 CO2-based block copolymers could be synthesized following three strategies: (1) sequential monomer addition or using a macroinitiator (macrotransfer agent), (2) resorting to a bifunctional initiator, or (3) kinetic resolution polymerization when one monomer is consumed faster than the other. Based on these strategies, CO2-containing block copolymers with different structures and compositions could be generated, as recently reviewed by Zhang and coworkers.4 Generally the block copolymers described were either all-polycarbonates,12,19–24 or polycarbonate-b-polyesters obtained through the ROCOP of CO2/epoxides and ROCOP of anhydrides/epoxides25–29 or ROP of cyclic esters.29–37 Due to the compatibility between polyester and polycarbonate blocks, these two blocks hardly phase separate unless the obtained block copolymers exhibit molar masses high enough to comply with the criterion of χN higher than 10.5, as recently demonstrated with the case of polycarbonate thermoplastic elastomers.20,38 In this context, CO2-based block copolymers comprising highly incompatible blocks are desirable, in particular in applications such as nanomaterials where phase separation is required.39–41 Following the first report by Lee and co-workers describing the synthesis of various CO2-based block copolymers through the immortal copolymerization of CO2 with PO,42 such block copolymers were mainly synthesized by a macroinitiator or macrotransfer agent strategy.40,41,43–45 Coates et al. described the synthesis of polyisoprene-b-polystyrene-b-poly(propylene carbonate) (PI-b-PS-b-PPC) triblock copolymers using PI-b-PS-OH as the macrotransfer agent which was obtained through anionic polymerization. These triblock terpolymers gave rise to ordered mesoporous templates after the orthogonal degradation of PI and PPC blocks in the self-assembled morphology.41 Our group on the other hand generated PS-b-PCHC and PI-b-PCHC diblocks by mere one-pot sequential anionic polymerization of styrene or dienes first and then of CO2 and CHO in the presence of trialkylaluminum.44 Wang and Xie reported a one-step synthesis of diblock copolymers including a CO2-based polycarbonate block and a polyvinyl block, both grown from a trithiocarbonate compound bearing a carboxylic group, TTC-COOH, that served a bifunctional transfer agent.43 Because the catalyst used to grow the polycarbonate block was inactive beyond 10 equivalents of TTC-COOH, this synthesis strategy afforded diblock copolymer samples contaminated with homopolymers and of relatively low molar mass. To address this issue, Wu and coworkers resorted to using a bifunctional compound based on a RAFT agent carrying a β-diiminate zinc complex and prepared a series of polyvinyl and polycarbonate block copolymers through the simultaneous ROCOP of CO2/epoxides and the RAFT polymerization of vinyl monomers.46 Recently, Wang and coworkers reported the synthesis of poly(vinyl acetate)-b-polycarbonate diblock copolymers mediated by (salen)Co(III)-R, using O2 to switch from the organometallic mediated radical polymerization (OMRP) of vinyl acetate to the ROCOP of CO2/epoxides.47 In view of the potential application of such copolymers as nanomaterials in the microelectronics field, the contamination by metallic residues in the above CO2-based block copolymers was viewed as an issue.
Since the first discovery of ROCOP of CO2 with epoxides in the presence of triethylborane in 2016,15 the synthesis of polycarbonates could be achieved through a living anionic approach under metal-free conditions. As an illustration of the advances made, carboxylates were found to be reliable initiators for the ROCOP of CO2 with epoxides, exhibiting the same performance as the onium halides and onium alkoxides originally used.13 The wide availability of carboxylic acids and the ease with which they can be deprotonated and can generate carboxylate salts are major advantages for the design and synthesis of CO2-based macromolecules with different architectures. For instance, polycarbonate stars could be easily prepared using multifunctional carboxylic acid salts as the initiator.13 More recently, using a polycarbonate backbone carrying multiple tetrabutylammonium carboxylate salts as the initiator, well-defined all-polycarbonate graft copolymers could be obtained: in such a macromolecular structure all grafts were grown from each of the carboxylate sites of the backbone.10 In addition, the carboxylate groups serving as ROCOP initiating sites are generally compatible with other functional groups that are suitable for the initiation of other chain polymerizations. In this investigation, we describe the synthesis of di- and triblock copolymers using TTC-COOH in the dual role of an initiator for the ROCOP of epoxide/CO2 from its carboxylic acid group and of a transfer agent for the RAFT polymerization of vinyl monomers through its trithiocarbonate function (Scheme 1).48 The two distinct polymerizations were shown to proceed concomitantly in one pot, allowing the synthesis of AB diblock copolymers from a library of epoxides and vinyl monomers. Lastly, from the generated AB diblock copolymers, a third monomer such as ethylene oxide or cyclohexene oxide/CO2 could be subsequently copolymerized, leading to the formation of ABC triblock copolymers; a third block could also be grown on the RAFT side through controlled radical polymerization. With TTC-COOH playing the dual role of an initiator for ROCOP of CO2/epoxides and of a transfer agent for RAFT polymerization, well-defined miscellaneous triblock copolymers of high molar mass, comprising either two poly(vinyl) blocks and one CO2-based block or two CO2-based blocks and one poly(vinyl) block exhibiting phase separation, could be generated.
 |
| Scheme 1 Schematic representation for the one-pot synthesis of AB diblock and ABC triblock copolymers using TTC-COOH in a dual role of an initiator for the ROCOP of epoxide/CO2 and a transfer agent for the RAFT polymerization of vinyl monomers. | |
Results and discussion
Distinct polymerizations using TTC-COOH in a dual role of an initiator and a chain transfer agent
For our initial attempt at growing a polycarbonate block, we relied on our previous contributions where the use of carboxylate salts as initiators of the ROCOP of CO2/epoxides was described;9,10,13 we thus used 4-cyano-4-[(dodecylsulfanylthiocarbonyl) sulfanyl] pentanoic acid (TTC-COOH) playing a dual role as an initiator for the ROCOP of CO2/epoxides and a transfer agent for the RAFT polymerization of vinyl monomers (Scheme 1). The tetrabutylammonium carboxylate salt (TTC-COO−, Bu4N+) obtained after the deprotonation of TTC-COOH using tetrabutylammonium hydroxide was characterized by 1H NMR to check its structure (Fig. S1A†). TTC-COO−, Bu4N+ was subsequently evaluated as the initiator for the copolymerization of CO2 with propylene oxide (PO). The copolymerization of CO2 with PO did occur, but the polycarbonates obtained exhibited a bimodal distribution (entry 1, Table 1, Fig. S1C†), indicating the presence of difunctional protic impurities. Drying further TTC-COO−, Bu4N+ even worsened the results eventually obtained with a more pronounced bimodal distribution of molar masses (entry 2, Table 1, Fig. S1C†). In fact, freshly prepared yellow TTC-COO−, Bu4N+ became dark brown with time upon storage. Its characterization by 1H NMR (Fig. S1B†) just after generating the carboxylic salts and after 10 days of storage showed the disappearance of the peak at 2.40 ppm assigned to the four methylene protons next to the carboxylic group, suggesting the cleavage of trithiocarbonyl ester. In addition, the integral ratios of other peaks compared to freshly prepared TTC-COO−, Bu4N+ have changed, indicating the decomposition of this bifunctional initiator over time. The 13C NMR study also suggests that the peaks corresponding to carbon of CN at δ = 118 ppm and to the quaternary carbon next to the CN group at δ = 47 ppm are completely disappeared, indicating the decomposition of TTC-COO−, Bu4N+ (Fig. S2†).
Table 1 TEB-assisted copolymerization of propylene oxide and carbon dioxide with carboxylic acid neutralized by different basesa
Entry |
Initiator |
[M] : [I] : [TEB] : [B] |
Selectivityb (%) |
PCb (%) |
Yieldc (%) |
M
n(NMR) d kg mol−1 |
M
n(GPC) e kg mol−1/Đ |
Polymerizations were carried out in a 50 mL Parr reactor under 10 bar CO2 with stirring at 65 °C.
PC (polycarbonate content) and linear vs. cyclic selectivity were determined from the 1H NMR of the crude product.
Calculated by the gravimetric method.
M
n(NMR) was calculated based on NMR data: Mn (NMR) = [102 × (4Ia/Ie)] + 403 (Ia and Ie are integral values of peaks a and b as shown in Fig. 1A).
Determined by GPC with THF as the eluent and calibrated by a polystyrene standard.
The initiator was prepared and well dried before using for copolymerization (see Experimental).
|
1f |
TTC-COO−, Bu4N+ |
200 : 1 : 2 : 1 |
>99 |
75 |
78 |
— |
14.7/1.2 |
2f |
TTC-COO−, Bu4N+ |
200 : 1 : 2 : 1 |
>99 |
99 |
83 |
— |
17.3/1.2 |
3 |
TTC-COO−, NHCH+ |
20 : 1 : 2 : 0.9 |
96 |
99 |
83 |
1.8 |
1.9/1.2 |
4 |
SA(Bu3NH+)2 |
40 : 1 : 4 : 1 |
97 |
95 |
80 |
3.1 |
3.4/1.1 |
5 |
SA(Bu3NH+)2 |
40 : 1 : 4 : 0.4 |
98 |
96 |
82 |
3.1 |
3.3/1.1 |
6 |
TTC-COO−, Bu3NH+ |
40 : 1 : 2 : 0.2 |
98 |
96 |
82 |
3.5 |
3.9/1.1 |
To overcome the issues related to the attack of the trithiocarbonate group by the initiating carboxylate salt, we opted for the deprotonation of TTC-COOH by a weaker base such as N-heterocyclic carbenes (NHC). As NHCs can by themselves initiate the ROCOP of PO with CO2, iPr-NHC was used in these experiments in a 0.9
:
1 ratio with respect to TTC-COOH just to neutralize enough of TTC-COOH and generate carboxylate anions associated with imidazolium cations.49–51 The formation of anions of weaker nucleophilicity through the choice of a weaker base helped to preserve the integrity of the trithiocarbonate moiety of TTC-COOH as confirmed by 1H and 13C NMR characterization (Fig. S3 and S4†). As established in one of our previous reports carboxylate anions associated with imidazolium cations behave similarly to tetrabutylammonium carboxylates with respect to their ability to initiate the ROCOP of epoxides with CO2.52
After the deprotonation of TTC-COOH by 1,3-diisopropyl-imidazol-2-ylidene (iPr-NHC), the ROCOP of PO with CO2 was initiated in a Parr reactor under a CO2 pressure of 10 bar in the presence of TEB at 65 °C; at this temperature a high selectivity for linear polycarbonate vs. cyclic carbonate could be achieved during CO2/PO copolymerization. The polycarbonate obtained after purification was subsequently characterized (entry 3, Table 1). The GPC traces showed a unimodal symmetrical distribution indicating the integrity of the trithocarbonate moiety during copolymerization (Fig. S5A†). The 1H NMR spectrum of the obtained polycarbonate exhibits all the characteristic peaks for the latter polymer and for the trithiocarbonate moiety of TTC-COOH (Fig. S5B†). MALDI-TOF analysis results substantiate the incorporation of TTC-COOH in the polymer formed, confirming that the polycarbonates produced were initiated by TTC-COOH and not by iPr-NHC (Fig. S6†). Indeed, all the peaks from the main population satisfy well the following formula: m/z = 102.08n + 403.67 + 58.1 + 23, where 102.08, 403.67, 58.1 and 23 are, respectively, the molar mass of the propylene carbonate unit, TTC-COOH, PO and sodium.
Such results encouraged us to try tributylamine (N(Bu)3 or TBA), a weaker base that is cheaper and easier to handle than iPr-NHC to deprotonate TTC-COOH; in addition the tributylammonium cation formed after deprotonation possesses a structure similar to that of tetrabutylammonium. TTC-COOH neutralization by (TBA) was merely carried out by adding TBA to the solution of TTC-COOH in THF. The generated ammonium salt TTC-COO−, Bu3NH+ was analyzed by 1H and 13C NMR characterization and all the peaks corresponding to the moieties of TTC and TBA were found, indicating the formation of a stable initiator (Fig. S7 and S8†). Before using TTC-COO−, Bu3NH+ as the initiator for the ROCOP of PO with CO2, a control CO2/epoxide copolymerization was carried out using succinic acid (SA) as the difunctional initiator after partial neutralization by 0.5 eq. and 0.2 eq. of TBA (entries 4 and 5 Table 1). TBA was purposely used in less amount to avoid independent initiation by TBA. Indeed, recently Zhang and coworkers reported that tertiary amines combined with TEB can effectively initiate the CO2/PO copolymerization, a mechanism involving the quarternization of the tertiary amine and the formation of zwitterions.53 Succinic acid was purposely selected to easily distinguish populations of chains initiated by this initiator and putatively by TBA. Interestingly, monomodal and symmetrical GPC traces were found with an expected molar masses and narrow distribution with 0.5 eq. and 0.2 eq. equivalents of TBA (Fig. S9†); the amount of TBA added does not affect the polymerization results. The 1H NMR spectrum of the purified sample (entry 4, Table 1) shows the presence of the succinate peak and the absence of any tributyl ammonium peak, indicating that polycarbonate chains were all initiated by succinate salts and not by TBA (Fig. S10†): MALDI TOF analysis confirmed that only initiation by succinate anions occurred and also the absence of any TBA moiety (Fig. S11†). In the presence of carboxylic acid, tertiary amine thus serves to deprotonate succinic acid and generate tributylammonium cations and does not initiate CO2/PO ROCOP.53 After noticing the success of the control experiment, we then attempted to copolymerize CO2/PO using TTC-COOH after its deprotonation by TBA (entry 6, Table 1). 0.2 eq. of TBA to the TTC-COOH was charged along with other reactants. The characterization by 1H NMR of the obtained polycarbonates indicates the integrity of TTC-COO, all the characteristic proton peaks of TTC-COO moieties ‘d, e, f, h, and i’ and peaks for polycarbonates ‘a, b, and g’ being clearly detected as shown in Fig. 1A. The peak ‘e’ appearing at δ 2.50 ppm in Fig. 1A can be attributed to the two methylene groups of TTC-COO that are located next to the carboxylate group (–CH2–CH2–COO); the protons of these methylene groups then served to calculate the molar mass of the PPC sample formed. A monomodal and narrowly distributed population of chains revealed by GPC traces (Fig. S12†) and MALDI-TOF (Fig. 1B) results unambiguously confirm the initiation of copolymerization by TTC-COO−, Bu3NH+and the integrity of the trithiocarbonate moiety under the abovementioned polymerization conditions.
 |
| Fig. 1 (A) 1H NMR spectrum in CDCl3 and (B) MALDI-TOF mass spectrometry of PPC initiated by in situ generated TTC-COO−, Bu3NH+ (entry 6, Table 1). | |
After demonstrating that the CO2/epoxide copolymerization can be carried out using TTC-COOH as the initiator after deprotonation by iPr-NHC or TBA, we then attempted to polymerize methyl methacylate (MMA) by RAFT under conditions similar to those described above and in the absence of PO (entry 1, Table 2): TTC-COOH/AIBN/TEB/TBA/CO2 (10 bar) at 65 °C. The polymerization proceeded smoothly and results (expected molar mass and narrow polydispersity) similar to conventional RAFT polymerization were obtained under a CO2 atmosphere; the presence of TEB and TBA did not induce any side effect nor did it affect the radical polymerization. Besides 1H NMR and GPC characterization (Fig. S13†), the purified polymer was further characterized by MALDI-TOF. As shown in Fig. S14,† PMMA chains were all terminated by the trithiocarbonate group from TTC-COOH.
Table 2 Related data of CO2-based diblock copolymers prepared in one-pot through a bifunctional approacha
Entry |
Polymer designation |
Base (B) |
Feeding ratio |
Conv.b % |
PCb (%) |
M
n(NMR) c [kg mol−1] |
M
n(GPC) d [kg mol−1]/Đ |
Ep/VM/B/I |
Ep |
VM |
Polymerizations were carried out in a 50 mL Parr reactor under 10 bar CO2 with stirring at 65 °C.
Determined from the 1H NMR of the crude product.
M
n(NMR) was calculated based on NMR data.
Determined by GPC with THF as the eluent and calibrated by a polystyrene standard.
Polymerization was carried out in a 50 mL Parr reactor under 10 bar CO2 with stirring at 70 °C. Ep: epoxide, VM: vinyl monomer, B: Base, I: TTC-COOH, PC: polycarbonate, TBA: tributylamine, NHC: 1,3-diisopropylimidazol-2-ylidene, PPC: poly(propylene carbonate), PCHC: poly(cyclohexene carbonate), PEC: poly(ethylene carbonate), PMMA: poly(methyl methacrylate), PS: polystyrene, PDMA: poly(N,N-dimethyl acrylamide).
|
1 |
PMMA38 |
TBA |
0/50/0.2/1 |
— |
76 |
— |
3.8 |
5.7/1.1 |
2 |
PPC105-b-PMMA28 |
TBA |
100/50/0.2/1 |
99 |
60 |
97 |
13.4 |
11.3/1.04 |
3 |
PPC100-b-PMMA82 |
TBA |
100/100/0.2/1 |
99 |
82 |
98 |
18.5 |
16.5/1.04 |
4 |
PPC78-b-PMMA150 |
TBA |
100/200/0.2/1 |
78 |
75 |
98 |
22.5 |
18.2/1.06 |
5 |
PCHC46-b-PMMA98 |
TBA |
50/100/0.2/1 |
90 |
99 |
99 |
16.1 |
13.9/1.08 |
6e |
PPC69-b-PS19 |
TBA |
100/50/0.2/1 |
69 |
38 |
97 |
9.2 |
7.8/1.08 |
7 |
PPC42-b-PDMA32 |
TBA |
50/40/0.2/1 |
84 |
64 |
97 |
8.2 |
7.2/1.06 |
8 |
PEC89-b-PMMA29 |
TBA |
100/50/0.2/1 |
89 |
60 |
68 |
9.9 |
11.1/1.2 |
9 |
PPC66-b-PMMA72 |
NHC |
100/100/0.9/1 |
66 |
72 |
98 |
14.0 |
11.6/1.07 |
10 |
PPC127-b-PMMA80 |
NHC |
200/100/0.9/1 |
51 |
78 |
98 |
21.2 |
15.2/1.1 |
One pot orthogonal CO2/epoxide ROCOP and RAFT polymerization of vinyl monomers
AB diblock copolymers.
After successfully demonstrating that CO2/PO ROCOP and MMA RAFT polymerizations can be separately carried out from TTC-COOH serving as an initiator or a chain transfer agent, we turned our attention towards their simultaneous polymerizations. Our initial interest was to prepare block copolymers made of PPC and PMMA. Block copolymers made of PPC and PMMA are of special interest as PPC is degradable and PMMA is recyclable. PPC blocks can be easily depolymerized into five membered cyclic propylene carbonate in the presence of a base or at higher temperature. On the other hand PMMA is the only vinyl based polymer prepared by a radical mechanism that can be degraded back to the MMA monomer upon heating the polymer above 400 °C.54,55 All monomers, MMA, PO along with the bifunctional initiator TTC-COOH, TEB, TBA and AIBN were charged into a Parr reactor filled with 10 bar of CO2 and brought to 65 °C for 12 h. To avoid the cleavage of the thiocarbonylthio group at the polymer chain ends that may occur in the presence of O2, the polymerization was stopped and quenched under an inert atmosphere.56 The GPC traces exhibited a monomodal and narrow distribution with molar mass 11.3 kg mol−1 and a polydispersity index of 1.04 (entry 2, Table 2, Fig. S24†). As shown by the 1H NMR characterization of the copolymer formed (Fig. 2), the characteristic peaks due to two blocks of PPC and PMMA were clearly detected. In addition, the peak ‘f’ appearing at δ 2.50 ppm corresponds to two methylene groups next to the carboxylic group (–CH2–CH2–COOH) and peak ‘e’ at δ 3.32 ppm corresponds to methylene protons next to the sulfur atom (C11H23–CH2–S–) of TTC-COOH, indicating the incorporation of the TTC-COO moiety within the copolymer formed. The following diffusion-ordered spectroscopy (DOSY, Fig. 2B) analysis of this copolymer sample shows a single diffusion coefficient, further confirming the formation of a block copolymer containing PPC and PMMA. With the peak f at δ 2.50 ppm serving as the reference, the composition and degree of polymerization of each block could be calculated; for instance, entry 2 in Table 2 corresponds to PPC105-b-PMMA28. Varying the feeding ratio of PO to MMA, PPC-b-PMMA block copolymers with different compositions and molar masses could be easily obtained. In all cases, the block polymers obtained exhibited the expected molar masses and narrow distributions, and high carbonate contents in the PPC block (entries 2–4, Table 2). In addition to PO and MMA as the monomer combination, some other epoxides and vinyl monomers could also be (co)polymerized orthogonally. As shown in entries 5–8 of Table 2, after the copolymerization of CO2 /epoxides such as cyclohexene oxide (CHO) and ethylene oxide (EO) was carried out simultaneously with the RAFT polymerization of MMA, styrene and N,N-dimethyl acrylate (DMA) were also polymerized by RAFT, leading to well-defined PCHC-b-PMMA, PEC-b-PMMA, PPC-b-PSt and PPC-b-PDMA diblock copolymers (Fig. S15–S22†). Access to diblock copolymers with different block combinations of hard, soft, hydrophilic and hydrophobic natures was thus possible through the choice of various epoxides and vinyl monomers. The criteria to consider when choosing epoxide and vinyl monomers for orthogonal polymerization were the polymerization temperature and compatibility between monomers with respect to their reaction mechanisms: too high a polymerization temperature for epoxide/CO2 may for instance increase the formation of cyclics. In a control experiment, we showed that iPr-NHC functions like TBA in these one-pot polymerizations, allowing the successful synthesis of diblock copolymers (entries 9 and 10, Table 2, Fig. S21 and 22†).
 |
| Fig. 2
1H NMR spectrum (A) and (B) DOSY NMR spectra of the PPC-b-PMMA diblock copolymer in CDCl3 (entry 2 in Table 2). | |
In particular we checked the compatibility of the RAFT polymerization of DMA in the presence of TEB that may be prone to interact with the amide function of DMA, which may in turn disrupt the ROCOP of CO2 with PO. Actually, both ROCOP and RAFT polymerization proceeded as expected without interference resulting in high linear/cyclic polycarbonate selectivity and a high carbonate content of the PPC block, affording a well-defined amphiphilic diblock copolymer (Fig. S19†). Amide groups of DMA were thus found not to affect the activity of Lewis acid TEB during terpolymerization. A 0.1 wt% aqueous solution of PPC42-b-PDMA32 was prepared and the self-assembly of this diblock copolymer was characterized by DLS measurements. Micelles of an average size of 59 nm were formed (Fig. S23†). Such block copolymers prepared from metal free reaction conditions may serve as promising candidates for drug delivery applications.57
ABC triblock copolymers.
Based on the success of AB diblock copolymer synthesis, the synthesis of ABC triblock copolymers was also attempted with a focus on the synthesis of copolymer samples of high molar mass. Due to the versatility of the TEB/onium initiating system,9,38 as shown in Scheme 1, more than one block could be grown by the ROCOP of CO2/epoxide or by the ROP of a cyclic monomer. A similar observation can be made about the RAFT trithiocarbonate chain transfer agent which also allows the controlled growth of more than one poly(vinyl) block. We have decided to first grow three blocks made of one poly(vinyl) block obtained through the RAFT polymerization of MMA, and two blocks obtained by the ROCOP of CO2/PO and the ROP of EO. After obtaining the PPC105-b-PMMA28 diblock copolymer (entry 2, Table 2), EO was sequentially charged in the same reactor after the release of CO2 and full conversion of PO: the growth of the PEO block afforded an amphiphilic PMMA-b-PPC-b-PEO triblock copolymer (entry 1, Table 3). A complete shift in the GPC overlay was observed after EO polymerization (Fig. S24†). 1H NMR characterization showed the presence of new peaks at δ 3.65 ppm corresponding to the methylene protons of ethylene oxide units (Fig. S25†). On the other hand, after the simultaneous ROCOP of PO/CO2 under low pressure (∼1 bar) of CO2 and the RAFT polymerization of MMA producing the poly(ether-carbonate)-b-PMMA diblock copolymer, an alternating polycarbonate block was grown through the ROCOP of CHO/CO2 under 10 bar of CO2: in the latter case PMMA-b-P(PPO-r-PPC)-b-PCHC triblock copolymers comprising two hard blocks at the end and a soft central poly(ether-carbonate) block were obtained (entry 2, Table 3) (Fig. S26†). Similarly the versatility of our polymerization system was utilized to grow two poly(vinyl) blocks by RAFT polymerization and one block by ROCOP. A PCHC-b-PLMA diblock copolymer was prepared in one-pot by the simultaneous ROCOP of CHO with CO2 and the RAFT polymerization of (lauryl methacrylate) (LMA) at 65 °C and 10 bar CO2 pressure. After releasing CO2 RAFT polymerization was carried on upon the addition of MMA; in the latter case a triblock copolymer PMMA-b-PLMA-b-PCHC (entry 3, Table 3) was obtained (Fig. S27 and S28†). All these three triblock copolymers exhibited unimodal and narrow distributions of molar masses, with peaks characteristic of each block in the 1H NMR spectra, confirming the triblock nature of the generated copolymers.
Table 3 One-pot preparation of triblock copolymers through the sequential addition of epoxide or vinyl monomers using TTC-COOH for the ROCOP of epoxide with CO2 and the RAFT polymerization of vinyl monomersa
Polymer designation |
Base (B) |
Conv.b % |
PC % |
M
n(NMR) c (kg mol−1) |
M
n(GPC) d (kg mol−1)/Đ |
Ep1/Ep2 |
VM |
PC1/PC2 |
Polymerizations were first carried out in a 50 mL Parr reactor under initially 10 bar CO2 with stirring at 65 °C, then the second monomer was sequentially added and polymerized after the release of CO2.
Determined from the 1H NMR of the crude product. For entry 1, Ep1 = PO and Ep2 = EO; for entry 2, Ep1 = PO and Ep2 = CHO.
M
n(NMR) was calculated based on NMR data.
Determined by GPC with THF as the eluent and calibrated by a polystyrene standard.
PO/CO2/MMA polymerization was initially carried out at 1 bar of CO2 in a 50 mL Parr reactor, then CO2 was raised to 10 bar after the addition of CHO.
|
PMMA28-PPC105-PEO58 |
TBA |
99/98 |
— |
99/0 |
16.0 |
13.8/1.04 |
PMMA208-(PPO404-r-PPC77)-PCHC180e |
TBA |
90/99 |
99 |
16/99 |
77.5 |
57.1/1.1 |
PMMA140-PLMA310-PCHC60 |
TBA |
99 |
99 |
100 |
101.6 |
52.4/1.1 |
Thermal analysis.
The block copolymers prepared were characterized by thermal analysis using differential scanning calorimetry (DSC). Due to the distinct nature of the composed blocks, two different Tgs corresponding to the polycarbonate block and the vinyl polymer block were detected. As shown in Fig. 3A, PPC-b-PMMA (entry 3, Table 2) diblock copolymers show two distinct Tg values around 33.9 °C and 96.4 °C corresponding to the PPC block and the PMMA block; the two other diblock copolymer samples PPC-b-PS and PCHC-b-PMMA also exhibit two Tgs appearing at 20.8 °C, 95.1 °C and 97.8 °C, 121.9 °C, respectively. In the case of triblock PMMA-b-PPC-PEO due to the compatibility between PEO and PPC blocks only two Tgs were observed at 6.5 °C for the PEO-b-PPC block and 94.3 °C for the PMMA block. The PMMA-b-(PPC-r-PPO)-b-PCHC (entry 2, Table 3) ABC triblock copolymer with three distinct blocks made up of PMMA and PCHC as hard blocks and polypropylene ether carbonate as a middle soft block with 16% carbonate content exhibits three different Tgs corresponding to the three distinct blocks. Here a low carbonate content is the key factor to obtain phase separation between poly(propylene ether carbonate) and the PCHC block. Similarly ABC triblock PMMA-b-PLMA-b-PCHC (entry 3, Table 3) also exhibits three different Tgs corresponding to three different blocks (Fig. 3B).
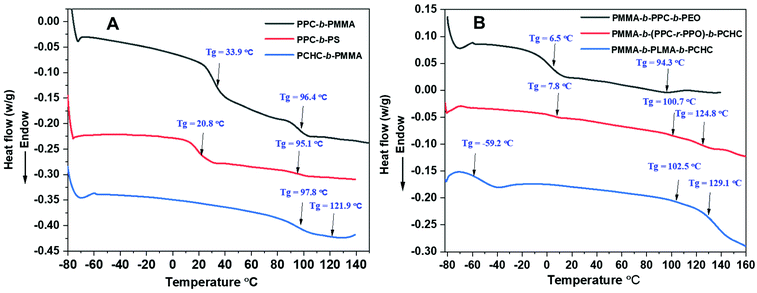 |
| Fig. 3 DSC graph showing different Tgs for diblock copolymers (A) PPC-b-PMMA (entry 3, Table 2), PPC-b-PS (entry 6, Table 2), PCHC-b-PMMA (entry 5, Table 2); and triblock copolymers (B) PMMA-b-PPC-b-PEO (entry 1, Table 3), PMMA-b-(PPC-r-PPO)-b-PCHC (entry 2, Table 3), PMMA-b-PLMA-b-PCHC (entry 3, Table 3). | |
Conclusion
We have demonstrated a convenient process for the one-pot synthesis of di and triblock copolymers obtained through the orthogonal ROCOP of CO2/epoxides and the RAFT polymerization of vinyl monomers. Using in situ produced TTC-COO−, Bu3NH+ salts obtained by the deprotonation of TTC-COOH with TBA these two distinct (co)polymerizations could be carried out without interference to produce miscellaneous pure diblock AB and triblock ABC copolymers exhibiting a well-defined structure and phase separation. In a subsequent investigation the mechanical behavior of these phase separated triblock copolymers will be disclosed and discussed. Considering the versatility of RAFT polymerization for vinyl monomers and the TEB/onium initiating system for the ROCOP of epoxides with CO2 and more generally for oxygenated monomers, the described process can be used to produce block copolymers with a wide range of block compositions and structures. In addition, the produced polymers are metal-free and therefore could be resourceful in bio-medical, microelectronic and lithographic areas.
Experimental section
Materials and characterization
All chemicals were purchased from Aldrich chemicals and used as received unless otherwise mentioned. PO, CHO, MMA, styrene, DMA, tributyl amine (TBA) were stirred over CaH2 and distilled under reduced pressure. TTC-COOH was freeze-dried in dioxane. iPr-NHC was prepared from 1,3-diisopropyl imidazolium chloride following a reported procedure.58 A 1 M solution of iPr-NHC was prepared in THF and stored under argon in a freezer. Tetrahydrofuran (THF) was dried over sodium metal and distilled under reduced pressure. CO2 (99.995%), purchased from Abdullah Hashim Industrial & Gas Co., was further purified by passing through a CO2 purifier (VICI Co., US). All 1H and 13C NMR spectra were recorded on a Bruker AVANCE III-400 Hz, 500 Hz and 600 Hz instrument. GPC traces were recorded by VISCOTEK VE2001 equipped with Styragel HR2 THF and Styragel HR4 THF using THF (1 mL min−1) as the eluent. Narrow Mw polystyrene standards were used to calibrate the instrument. MALDI-TOF MS experiments were carried out by using trans-2-[3-(4-t-butyl-phenyl)-2-methyl2-propenylidene] malononitrile (DCTB) as the matrix in THF at a loading of 1
:
5 with sodium trifluoroacetate as an ionizing agent. DSC measurements were performed with a Mettler Toledo DSC1/TC250 under nitrogen. The samples were first heated from 25 °C to 120 °C to erase the thermal history, then cooled to −80 °C, and heated again to 140 °C at a heating rate of 5 °C min−1 for block copolymers. Dynamic Light Scattering (DLS) measurements were carried out by preparing 0.1 wt% aqueous solution on a Malvern Zetasizer Nano ZS instrument with a 30 mW He–Ne laser light source with emission wavelength 632.8 nm at a scattering angle of 90°.
Initiator synthesis: synthesis of TTC-COO-, Bu4N+
In a 100 mL round bottom flask equipped with a magnetic stirring bar, 4-cyano-4-[(dodecyl sulfanyl thiocarbonyl) sulfanyl] pentanoic acid (TTC-COOH) (2.02 g, 5.0 mmol) was dissolved in 5 mL of THF. A 55 wt% aqueous solution of tetrabutyl ammonium hydroxide (2.45 mL, 5 mmol) was added and stirred for 1 h. The organic volatiles were removed using a rotary evaporator. The reaction mixture was further diluted with distilled water. The aqueous solution was lyophilized to obtain dried tetrabutylammonium salt TTC-COO−, Bu4N+.
Synthesis of the AB diblock copolymer
A typical experimental procedure for one-pot polymerization, represented by entry 2 in Table 2 as an example is described below. A well dried 50 mL Parr reactor in an oven at 120 °C with a magnetic stir bar and a small glass vial inside was immediately transferred into a glovebox under an argon atmosphere. The reactor was cooled to 25 °C and then TTC-COOH (0.1 g, 0.25 mmol) dissolved in 1.5 mL of THF, and TBA (0.012 mL, 0.049 mmol) and TEB (0.49 mL, 1 M solution in THF, 0.49 mmol) were sequentially charged and well mixed. AIBN (0.08 g, 0.049 mmol) and MMA (1.32 mL, 12.4 mmol) were added into the reactor, while propylene oxide (1.74 mL, 24.8 mmol) was added into a glass vial inside the reactor. The reactor was quickly sealed and taken out from the glovebox. After charging CO2 to a pressure of 10 bar, the reactor was vigorously shaken and polymerization was carried out at 65 °C for 14 h with stirring. The reactor was cooled, the unreacted CO2 was slowly released, and the polymer solution was quenched inside the glovebox with 1 M HCl solution in THF. The crude product was diluted with THF and purified by precipitation in methanol. The product was collected and dried in a vacuum at 40 °C.
Synthesis of triblock copolymers
Synthesis of ABC triblock copolymer PMMA-b-PPC-b-PEO.
Following the above reaction procedure for preparing the PPC-b-PMMA diblock copolymer (0.125 mmol), EO was charged (0.372 mL, 7.4 mmol) after the release of CO2 and the reactor was sealed and stirred at 25 °C for 1 h. The polymer solution was quenched inside the glovebox with 1 M HCl solution in THF and purified by precipitation in methanol and dried under vacuum at 40 °C for 48 h.
Synthesis of PMMA-b-(PPC-r-PPO)-b-PCHC, ABC tri-block copolymer.
Step 1: one pot synthesis of PMMA-b-(PPC-r-PO)
The first step for the synthesis of the diblock copolymer is carried out upon modifying the above procedure of synthesis of the AB diblock copolymer. To a well dried reactor, TTC-COOH (0.05 g, 0.124 mmol), TBA (0.012 mL, 0.025 mmol), TEB (0.248 mL, 1 M solution in THF), MMA (0.372 mL, 3.72 mmol), AIBN (3.8 mg, 0.024 mmol) and 2 mL of THF were charged under argon. The reactor was sealed and charged with CO2 to ensure the reaction occurred under a CO2 atmosphere and then PO (4.3 mL, 62 mmol) was injected through a syringe and the reactor was connected to a CO2 line with 1.0 bar continuous pressure. The reaction mixture was stirred at 65 °C for 24 h to ensure the complete consumption of PO.
Step-2: synthesis of PMMA-(PPC-r-PPO)-b-PCHC by sequential addition
Cyclohexene oxide (0.375 mL, 3.72 mmol) was injected into the reactor and CO2 was re-filled to 10 bar. The reaction was carried at 65 °C for another 14 h, then the reactor was cooled and excess CO2 was released. The polymerization was quenched inside the glovebox with 1 M HCl solution in THF, and the mixture was diluted with THF and precipitated in methanol. The precipitation procedure was repeated three times. The obtained polymer was dried in a vacuum at 40 °C.
Synthesis of ABC triblock copolymer PMMA-b-PLMA-b-PCHC.
Step 1: one pot synthesis of PCHC-b-PLMA
The first step of diblock copolymer synthesis was carried out upon modifying the above procedure of synthesis of the AB diblock copolymer. The procedure followed for entry 2 in Table 3 is described as an example: to a well dried reactor, TTC-COOH (0.05 g, 0.124 mmol), TBA (0.012 mL, 0.025 mmol), TEB (0.248 mL, 1 M solution in THF), CHO (0.75 mL, 7.44), LMA (10.9 mL, 37.2 mmol), AIBN (3.8 mg, 0.024 mmol) and 2 mL of THF were charged under argon. The reactor was sealed and charged with 10 bar CO2. The reaction mixture was stirred at 65 °C for 24 h to ensure the complete consumption of monomers, the unreacted CO2 was released and the reactor was moved to a glovebox.
Step-2: synthesis of PMMA-b-PLMA-b-PCHC by sequential addition
MMA (1.5 mL, 15.0 mmol) was then charged to the reactor and the reaction was carried at 65 °C for another 24 h, then the reactor was cooled and the polymerization was quenched with 1 M HCl solution in THF, the mixture was diluted with THF and precipitated in methanol. The precipitation procedure was repeated three times. The obtained polymer was dried in a vacuum at 40 °C.
Conflicts of interest
The authors declare no competing financial interest.
Acknowledgements
This research work is supported by KAUST under baseline funding (BAS/1/1374-01-01).
References
- A. C. Deacy, E. Moreby, A. Phanopoulos and C. K. Williams, J. Am. Chem. Soc., 2020, 142, 19150–19160 CrossRef CAS PubMed.
- K. A. Andrea, H. Plommer and F. M. Kerton, Eur. Polym. J., 2019, 120, 109202 CrossRef CAS.
- M. Mandal, J. Organomet. Chem., 2020, 907, 121067 CrossRef CAS.
- Y. Li, Y.-Y. Zhang, L.-F. Hu, X.-H. Zhang, B.-Y. Du and J.-T. Xu, Prog. Polym. Sci., 2018, 82, 120–157 CrossRef CAS.
- Y. Xu, L. Lin, M. Xiao, S. Wang, A. T. Smith, L. Sun and Y. Meng, Prog. Polym. Sci., 2018, 80, 163–182 CrossRef CAS.
- Y. Wang and D. J. Darensbourg, Coord. Chem. Rev., 2018, 372, 85–100 CrossRef CAS.
- D. J. Darensbourg, Chem. Rev., 2007, 107, 2388–2410 CrossRef CAS PubMed.
- G. W. Coates and D. R. Moore, Angew. Chem., Int. Ed., 2004, 43, 6618–6639 CrossRef CAS PubMed.
- M. Jia, D. Zhang, Y. Gnanou and X. Feng, ACS Sustainable Chem. Eng., 2021, 9, 10370–10380 CrossRef CAS.
- P. Alagi, G. Zapsas, N. Hadjichristidis, S. C. Hong, Y. Gnanou and X. S. Feng, Macromolecules, 2021, 54, 6144–6152 CrossRef CAS.
- C.-J. Zhang, S.-Q. Wu, S. Boopathi, X.-H. Zhang, X. Hong, Y. Gnanou and X.-S. Feng, ACS Sustainable Chem. Eng., 2020, 8, 13056–13063 CrossRef CAS.
- M. Jia, D. Zhang, G. W. de Kort, C. Wilsens, S. Rastogi, N. Hadjichristidis, Y. Gnanou and X. Feng, Macromolecules, 2020, 53, 5297–5307 CrossRef CAS PubMed.
- N. G. Patil, S. K. Boopathi, P. Alagi, N. Hadjichristidis, Y. Gnanou and X. Feng, Macromolecules, 2019, 52, 2431–2438 CrossRef CAS.
- S. K. Boopathi, N. Hadjichristidis, Y. Gnanou and X. Feng, Nat. Commun., 2019, 10, 293 CrossRef PubMed.
- D. Zhang, S. K. Boopathi, N. Hadjichristidis, Y. Gnanou and X. Feng, J. Am. Chem. Soc., 2016, 138, 11117–11120 CrossRef CAS PubMed.
- A. C. Deacy, G. L. Gregory, G. S. Sulley, T. T. D. Chen and C. K. Williams, J. Am. Chem. Soc., 2021, 143, 10021–10040 CrossRef CAS PubMed.
- Y.-Y. Zhang, G.-P. Wu and D. J. Darensbourg, Trends Chem., 2020, 2, 750–763 CrossRef CAS.
- R. C. Jeske, J. M. Rowley and G. W. Coates, Angew. Chem., Int. Ed., 2008, 47, 6041–6044 CrossRef CAS PubMed.
- G.-W. Yang and G.-P. Wu, ACS Sustainable Chem. Eng., 2019, 7, 1372–1380 CrossRef CAS.
- G. S. Sulley, G. L. Gregory, T. T. D. Chen, L. Pena Carrodeguas, G. Trott, A. Santmarti, K. Y. Lee, N. J. Terrill and C. K. Williams, J. Am. Chem. Soc., 2020, 142, 4367–4378 CrossRef CAS PubMed.
- M. Jia, N. Hadjichristidis, Y. Gnanou and X. Feng, ACS Macro Lett., 2019, 8, 1594–1598 CrossRef CAS.
- Y. Wang, J. Fan and D. J. Darensbourg, Angew. Chem., Int. Ed., 2015, 54, 10206–10210 CrossRef CAS PubMed.
- J. G. Kim, C. D. Cowman, A. M. LaPointe, U. Wiesner and G. W. Coates, Macromolecules, 2011, 44, 1110–1113 CrossRef CAS.
- D. J. Darensbourg, M. Ulusoy, O. Karroonnirum, R. R. Poland, J. H. Reibenspies and B. Çetinkaya, Macromolecules, 2009, 42, 6992–6998 CrossRef CAS.
- Y. Liu, K. Huang, D. Peng and H. Wu, Polymer, 2006, 47, 8453–8461 CrossRef CAS.
- J. Zhang, L. Wang, S. Liu, X. Kang and Z. Li, Macromolecules, 2021, 54, 763–772 CrossRef CAS.
- V. K. Chidara, S. K. Boopathi, N. Hadjichristidis, Y. Gnanou and X. Feng, Macromolecules, 2021, 54, 2711–2719 CrossRef CAS.
- S. Ye, W. Wang, J. Liang, S. Wang, M. Xiao and Y. Meng, ACS Sustainable Chem. Eng., 2020, 8, 17860–17867 CrossRef CAS.
- C. Romain, Y. Zhu, P. Dingwall, S. Paul, H. S. Rzepa, A. Buchard and C. K. Williams, J. Am. Chem. Soc., 2016, 138, 4120–4131 CrossRef CAS PubMed.
- X. Li, C. Hu, X. Pang, R. Duan and X. Chen, Catal. Sci. Technol., 2018, 8, 6452–6457 RSC.
- Y. Li, J. Hong, R. Wei, Y. Zhang, Z. Tong, X. Zhang, B. Du, J. Xu and Z. Fan, Chem. Sci., 2015, 6, 1530–1536 RSC.
- S. Kernbichl, M. Reiter, F. Adams, S. Vagin and B. Rieger, J. Am. Chem. Soc., 2017, 139, 6787–6790 CrossRef CAS PubMed.
- G.-P. Wu, D. J. Darensbourg and X.-B. Lu, J. Am. Chem. Soc., 2012, 134, 17739–17745 CrossRef CAS PubMed.
- S. Paul, C. Romain, J. Shaw and C. K. Williams, Macromolecules, 2015, 48, 6047–6056 CrossRef CAS.
- M. R. Kember, J. Copley, A. Buchard and C. K. Williams, Polym. Chem., 2012, 3, 1196–1201 RSC.
- M. Li, Y. Tao, J. Tang, Y. Wang, X. Zhang, Y. Tao and X. Wang, J. Am. Chem. Soc., 2019, 141, 281–289 CrossRef CAS PubMed.
- M. Li, S. Zhang, X. Zhang, Y. Wang, J. Chen, Y. Tao and X. Wang, Angew. Chem., Int. Ed., 2021, 60, 6003–6012 CrossRef CAS.
- M. Jia, D. Zhang, G. W. de Kort, C. Wilsens, S. Rastogi, N. Hadjichristidis, Y. Gnanou and X. Feng, Macromolecules, 2020, 53, 5297–5307 CrossRef CAS PubMed.
- G.-W. Yang, G.-P. Wu, X. Chen, S. Xiong, C. G. Arges, S. Ji, P. F. Nealey, X.-B. Lu, D. J. Darensbourg and Z.-K. Xu, Nano Lett., 2017, 17, 1233–1239 CrossRef CAS PubMed.
- Y.-Y. Zhang, G.-W. Yang, Y. Wang, X.-Y. Lu, G.-P. Wu, Z.-S. Zhang, K. Wang, R.-Y. Zhang, P. F. Nealey, D. J. Darensbourg and Z.-K. Xu, Macromolecules, 2018, 51, 791–800 CrossRef CAS.
- C. D. Cowman, E. Padgett, K. W. Tan, R. Hovden, Y. Gu, N. Andrejevic, D. Muller, G. W. Coates and U. Wiesner, J. Am. Chem. Soc., 2015, 137, 6026–6033 CrossRef CAS PubMed.
- A. Cyriac, S. H. Lee, J. K. Varghese, E. S. Park, J. H. Park and B. Y. Lee, Macromolecules, 2010, 43, 7398–7401 CrossRef CAS.
- Y. Wang, Y. Zhao, Y. Ye, H. Peng, X. Zhou, X. Xie, X. Wang and F. Wang, Angew. Chem., Int. Ed., 2018, 57, 3593–3597 CrossRef CAS PubMed.
- D. Zhang, H. Zhang, N. Hadjichristidis, Y. Gnanou and X. Feng, Macromolecules, 2016, 49, 2484–2492 CrossRef CAS.
- M. Reiter, A. Kronast, S. Kissling and B. Rieger, ACS Macro Lett., 2016, 5, 419–423 CrossRef CAS.
- Y.-Y. Zhang, G.-W. Yang and G.-P. Wu, Macromolecules, 2018, 51, 3640–3646 CrossRef CAS.
- Y. Zhao, Y. Wang, X. Zhou, Z. Xue, X. Wang, X. Xie and R. Poli, Angew. Chem., Int. Ed., 2019, 58, 14311–14318 CrossRef CAS PubMed.
- G. Moad, E. Rizzardo and S. H. Thang, Aust. J. Chem., 2005, 58, 379–410 CrossRef CAS.
- Y. Zhang, R. Liu, H. Jin, W. Song, R. Augustine and I. Kim, Commun. Chem., 2018, 1, 40 CrossRef.
- S. Csihony, D. A. Culkin, A. C. Sentman, A. P. Dove, R. M. Waymouth and J. L. Hedrick, J. Am. Chem. Soc., 2005, 127, 9079–9084 CrossRef CAS PubMed.
- G. W. Nyce, T. Glauser, E. F. Connor, A. Möck, R. M. Waymouth and J. L. Hedrick, J. Am. Chem. Soc., 2003, 125, 3046–3056 CrossRef CAS PubMed.
- N. Patil, S. Bhoopathi, V. Chidara, N. Hadjichristidis, Y. Gnanou and X. Feng, ChemSusChem, 2020, 13, 5080–5087 CrossRef CAS PubMed.
- Y. Wang, J.-Y. Zhang, J.-L. Yang, H.-K. Zhang, J. Kiriratnikom, C.-J. Zhang, K.-L. Chen, X.-H. Cao, L.-F. Hu, X.-H. Zhang and B. Z. Tang, Macromolecules, 2021, 54, 2178–2186 CrossRef CAS.
- B.-S. Kang, S. G. Kim and J.-S. Kim, J. Anal. Appl. Pyrolysis, 2008, 81, 7–13 CrossRef CAS.
- W. Kaminsky and J. Franck, J. Anal. Appl. Pyrolysis, 1991, 19, 311–318 CrossRef CAS.
- P. Alagi, N. Hadjichristidis, Y. Gnanou and X. S. Feng, ACS Macro Lett., 2019, 8, 664–669 CrossRef.
- M. Gregori, D. Bertani, E. Cazzaniga, A. Orlando, M. Mauri, A. Bianchi, F. Re, S. Sesana, S. Minniti, M. Francolini, A. Cagnotto, M. Salmona, L. Nardo, D. Salerno, F. Mantegazza, M. Masserini and R. Simonutti, Macromol. Biosci., 2015, 15, 1687–1697 CrossRef CAS PubMed.
- A. J. Arduengo, H. V. R. Dias, R. L. Harlow and M. Kline, J. Am. Chem. Soc., 1992, 114, 5530–5534 CrossRef CAS.
|
This journal is © The Royal Society of Chemistry 2022 |
Click here to see how this site uses Cookies. View our privacy policy here.