DOI:
10.1039/D2MA00600F
(Review Article)
Mater. Adv., 2022,
3, 8063-8080
Recent trends in covalent organic frameworks (COFs) for carbon dioxide reduction
Received
28th May 2022
, Accepted 20th September 2022
First published on 30th September 2022
Abstract
As the ultimate carbon emission product of the combustion process, carbon dioxide (CO2) is a serious environmental threat in increasing the global climate temperature through the greenhouse effect. Porous heterogeneous catalysts have attracted much attention for carbon capture and in the recent past; they have witnessed significant advancements in their design and implementation for the CO2 capture and conversion. In this context, covalent organic frameworks (COFs), a kind of porous crystalline polymeric material, are mainly constructed by organic module units connected with strong covalent bonds. COFs, possessing unique properties such as low-density, large specific surface area, high thermal stability, and developed pore-structure and the long-range order, good crystallinity, and excellent tunability of the monomer units find versatile applications ranging from adsorption and separation, sensing, catalysis, optoelectronics, energy storage, and mass transport. In this review article, we discuss the emerging developments in different types of covalent organic frameworks (COFs) as heterogeneous catalysts for CO2 reduction via photochemical, electrochemical, and photo coupled electrochemical pathways. The physicochemical properties of COFs and their influence on the efficiency, selectivity, and recyclability for CO2 reduction are enlightened systematically. This review provides a concise report on various types of COFs, current trends, their application in CO2 reduction for the synthesis of fuels and value-added fine chemicals, and future research directions for the deployment of COF catalysts in CO2 capture and reduction.
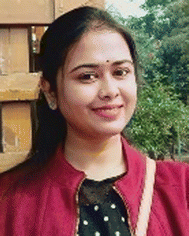
Priyanka Sarkar
| Ms Priyanka Sarkar is currently a PhD student at the University of Kalyani. She received her master's degree in science also from the University of Kalyani. Her current research focuses on the development of porous materials for CO2 fixation reactions and other organic transformations. |
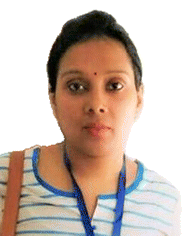
Ipsita Hazra Chowdhury
| Dr Ipsita Hazra Chowdhury is currently a research associate at the University of Kalyani. She received her PhD degree in Chemistry from CSIR-Central Glass and Ceramic Research Institute, Kolkata. She received her master's degree in science from IIEST, Shibpur. Her current research focuses on the development of porous polymers for the synthesis of valuable fine chemicals via CO2 fixation and reduction reactions. |
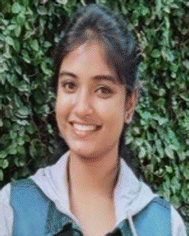
Surya Das
| Ms Surya Das is currently a PhD student at the University of Kalyani. She received her master's degree in science also from the University of Kalyani. Her current research focuses on the development of porous materials for CO2 reduction reactions and other organic transformations. |
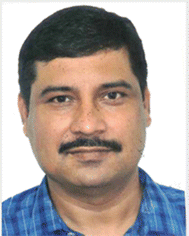
Sk. Manirul Islam
| Prof. Sk. Manirul Islam obtained his PhD degree from the Indian Institute of Technology Kharagpur in 1999 and carried out postdoctoral research at the State University of New York, USA, during 2000–2001. At present, he is serving as a Professor of Chemistry at the University of Kalyani, West Bengal, India. The present thrust of his research is to design and synthesize functionalized porous materials, such as COFs, MOFs, POPs, and their catalytic applications towards CO2 chemistry, CO2 fixation to value-added chemicals, in situ transformation of CO, catalytic conversion of CO into value-added chemicals, biofuel synthesis, CC/CN bond formation reactions, and multicomponent coupling reactions. |
1. Introduction
Currently, one of the greatest worldwide calamities is global warming caused by the continuously increasing concentration of CO2 in the atmosphere and ocean, which arises dramatically due to anthropogenic actions and the risk of ecosystem devastation.1 Population growth and industrial progress contribute significantly to enhancing excessive CO2 emissions unprecedentedly due to the escalating rate of carbon-based fuel consumption.2 Therefore, it is vital to diminish the accumulation of one of the main greenhouse gases, CO2, in the atmosphere using effectual technologies or tactics.3 To date, there are several ways to reduce emitted CO2 concentration in the atmosphere, for instance, decreasing the amount of produced carbon-dioxide, growing green carbon sinks e.g., plants, phytoplankton, and algae carrying chloroplasts, and capturing and storing up CO2. To tackle the hazardous problems of global climate change along with sustainable energy shortage, it would be a more advantageous approach to efficiently capture and transform atmospheric CO2 into useful carbon-based material or chemicals utilizing sustainable energy resources, forming a sustainable recycling system.4 CO2 is non-toxic, renewable, inexpensive, and most abundant raw C1 feedstocks and acts as a C1 building block for the synthesis of various valuable chemicals with added economic value.4 The proper resolution to pacify our present demand and future energy supply is the conversion of CO2 into valuable carbonaceous chemicals especially C1 and/or C2 products for example CO, CH4, CH3OH, C2H5OH, and other hydrocarbon compounds.5 For this purpose, numerous catalytic systems and methods such as hydrothermal, electrochemical, and photochemical methods have been explored for the conversion of CO2 to hydrocarbons having high catalytic efficiency, long-standing chemical stability, and non-toxicity, and low-cost materials. High temperature and pressure are required for the hydrothermal reduction process, which is energy intensive and expensive,6 hence photochemical and electrochemical methods are the most prominent and green methods for CO2 reduction, which shows a way for large-scale and long-lasting energy storage.7 Direct electrochemical CO2 reduction process is mainly achieved by changing parameters such as electrolytes and redox potential whereas the photocatalytic process is generally attributed to the slowest electron–hole recombination rate. In nature, the conversion of CO2 occurs daily through the photosynthesis process in green plants to balance the global carbon/oxygen cycle. To retain this cycle mimicking of the natural photosynthesis process, in 1979 a number of semiconductor materials (WO3, CdS, TiO2, GaP, ZnO, and SiC) were investigated for the photo-catalytic CO2 reduction in water to generate methanol, formic acid, formaldehyde and trace quantity of methane by Honda and his group.8 Then, modifying semiconductors a number of photo/electrocatalytic systems have been studied so far and the catalytic system having high CO2 adsorption capacity, good light absorbing ability, catalytic active sites, high selectivity, etc. are the main requirements for chemical reduction of CO2. To date emerging trends of heterogeneous porous materials, covalent organic frameworks (COFs) performed as a versatile material, which shows prominent contribution in the field of catalysis for photo/electrocatalytic CO2 reduction.9 COFs, a series of covalently connected porous networks, which exhibit high crystallinity, porosity and a greater degree of modularity than several porous compounds, are generally constructed using the dynamic covalent chemistry theory.10 A variety of methods have been involved in the preparation of COFs such as solvothermal,11 microwave-assisted,12 mechanochemical,13 and vapor-assisted conversion.14 However, in COF synthetic chemistry, the solvothermal method is the most well-known and usually utilized method. Owing to their ordered structure, highly accessible surface area, large pores, excellent thermal stability, predictable topologies, and tunable functionalities, it is predictable that COFs offer an ideal platform for adsorption, diffusion, and activation of CO2 molecules. Besides this, COFs ensure the uniform distribution and binding of single metal active sites throughout their networks.15 COFs have been employed in plentiful applications for instance sensors,16 gas storage,17 gas separation,18 catalysis,19 energy storage,20 photo-energy conversion,21 electronics and optoelectronics.22 Researchers have focused on developing materials for photocatalysis and electrocatalysis, and in this regard, COF materials for energy conversion and energy storage are in high demand by converting solar energy into chemical energy and fuel cells.23 Due to π-conjugation and coherent band structures, COF helps in light-harvesting, which promotes absorption and utilization of visible light during photocatalysis. Effective photo-induced charge carrier separation and transfer, which are crucial in photocatalysis, can be easily performed by adding functional groups to the skeletons of COFs. Additionally, to further improve the photocatalytic activity, COFs having a large surface area and suitable pore size can enhance mass transference and accommodate active molecules. COF-based materials for electrocatalysis can successfully resolve the conductivity and activity problems by adjustable molecular design and subsequent synthetic techniques where the building blocks can be connected via electron transmission channels, which can improve the efficiency of electrocatalysis. Also, electrocatalytic performances are enhanced by adding active sites, such as metal particles or functional groups to the COFs' frameworks. Therefore, crystalline COFs will be an idyllic model having outstanding potential for studying and understanding the highly effective electrocatalytic as well as photocatalytic CO2 reduction.
1.1. Covalent organic frameworks
Covalent organic frameworks (COFs) are one of the categories of crystalline porous polymers where the monomer units are linked by strong covalent bonds. So, by varying the monomer units during their synthesis, COFs with desired functionalities, such as different dimensions and properties, can be obtained. COFs have gained huge attention from researchers all over the world since their first discovery by Yaghi and his research group in 2005.11 The stability of COFs depends predominantly on the rigid covalent network of the systems. The arrangement and interaction between the layers of COFs are different for different dimensions. Thus, it is important for a researcher to understand the dimensions of the covalent organic framework. By understanding this, one can properly describe the properties of synthesized COFs. The dimensionality of COF depends on the geometry and connective patterns of the pioneers. Chemists have discovered the ability to form and control the covalent bonds in zero dimensions.24 Further extension of the dimension of COFs from zero-dimensional to one dimension was made possible by the polymer chemists. Dimensionality influences a lot of the functionalities of COFs, which change from one dimension to the other.
• Topologically, covalent organic frameworks can be classified into 3 following categories.
1.1.1. One-dimensional COFs.
One-dimensional (1D) COFs are mainly non-centrosymmetric linear crystalline polymers and can be synthesized by entropy-driven haphazard packing of organic chains, which mainly consist of one dimensionally-confined covalently bonded linkages, and mainly non-covalent interactions such as π–π interactions and hydrogen bonding. They show high degrees of freedom in molecular packing with enormously high anisotropy. A synthetic route for the preparation of novel 1D COF was recently depicted by Ziao Chen et al. with high surface area and thermal stability [Fig. 1b].25 Recently, Hai-Sen Xu et al. also successfully discovered a strategy to construct 1D conjugated polymer and introduced labile metal to this polymeric system, they constructed single-crystal-metallo-COFs [Fig. 1a].26 The linear chain of 1D COFs can also be transformed into 2D through chronological reversible-irreversible chemistries.27 In recent times, Li and his group successfully constructed the heterojunction composite of 1D β keto-enamine-based COF/2D g-C3N4.28 1D COF/2D g-C3N4 acted as an efficient photocatalyst where the photocatalytic activity was basically enhanced due to visible-light adsorption capability of 1D β keto-enamine-based COF. Recently, Wang et al. constructed an ultrathin self-standing 1D COF nanofluidic membrane (denoted as BDA-TAM) having the ability to build an efficient nanofluidic osmotic energy generator.29 As this, COF-based nanofluidic membrane, contains negative surface charges, it exhibits good selectivity towards cations and hence strong ionic conductance. Furthermore, the extraordinary stability of BDA-TAM extended across a wide range of saline solutions, temperatures, and pH values. This research broadens the area of utilization for self-standing 1D COF membranes, which can serve as a model for the fabrication of highly efficient osmotic energy generators.
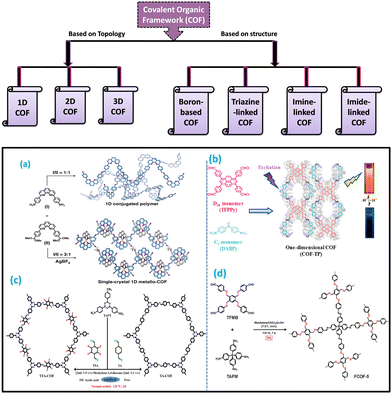 |
| Fig. 1 Examples of the formation of covalent organic frameworks in different dimensions. The schematic diagram for the production of (a) and (b) 1D covalent organic framework, (c) 2D COF, and (d) 3D COF. Adapted with permission from ref. 26. Copyright © 2020, The Author(s); ref. 25. Copyright © 2020 American Chemical Society; ref. 37. © 2020 Elsevier B.V. All rights reserved; and ref. 47. Copyright © 2021 American Chemical Society. | |
1.1.2. Two-dimensional COFs.
In 2014, the research group of Schlüter30 and King31 autonomously developed single crystals of 2D polymers. Two-dimensional COFs (2D COFs) consist of planar building blocks32 where the planar sheets are generally arranged in a face-to-face direction and the strong interaction of π–π stacking present between contiguous layers present in 2D COF helps mobilize charge throughout the layers.33 As such, it shows high electron delocalization and switchable band gap energy and that is why it plays a crucial role in electron conduction.34 They are visible light responsive and show potential applications in processes involving photocatalytic activity, e.g. H2 evolution,35 solar energy transformation, etc.36 2D COFs are highly crystalline, physically and thermally stable with high surface area porous polymers. In recent times, Yan et al. synthesized a newly designed fluorinated 2D COF having greater surface area and low band gap energy, which showed high photocatalytic activity towards H2 evolution, in comparison with non-fluorinated COF [Fig. 1c].37 Mateo-Alonso's group recently designed and synthesized a high π-stacking order and extremely crystalline wavy 2D COF (Marta-COF-2) and studied its structural properties to understand its charge transfer properties.38 Marta-COF-2 was constructed using distinctly shaped monomers such as 2,3,10,11,18,19-hexahydroxy-catahexabenzocoronene (HBC) and benzene-1,4-diboronic acid (BDBA) using the so-called solvothermal method, which gives rise to wavy chair-like honeycomb lattice structure [Fig. 2(I)]. Besides this, recently, Zhao and his group explored a new simplistic way to synthesize 2D vinylene-based COFs (named, BTH-1, 2, 3) with electron-withdrawing benzobisthiazoles units through a versatile Knoevenagel polycondensation reaction.39 Under this newly discovered reaction state, three novel completely sp2-conjugated COFs having high BET surface areas (644, 686, and 1140 m2 g−1 for BTH-1, BTH-2 and BTH-3, respectively) were constructed. These conjugated COFs served as acceptor moieties and showed semiconducting properties. It should be noted that under visible light irradiation, BTH-3 COF with electron-riched group benzotrithiophene demonstrated an impressive photocatalytic hydrogen evolution rate (HER), 15.1 mmol h−1 g−1, which is significantly higher than those of BTH-1 (HER = 10.5 mmol h−1 g−1) and BTH-2 (HER = 1.2 mmol h−1 g−1), because of the prolonged π-conjugation and well-organized donor–acceptor (D–A) structure. This study first offers a simple method for developing sp2-carbon conjugated COFs, secondly, the completely conjugated D–A type of COFs exhibit remarkable hydrogen evolution under the irradiation of light, which will unquestionably advance COFs in photocatalysis.
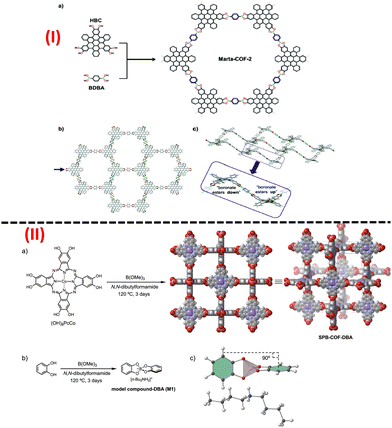 |
| Fig. 2 A schematic representation of the formation of (I) wavy 2D COF and (II) cubic 3D COF. Adapted with permission from ref. 38. Copyright © 2021 Royal Society of Chemistry; ref. 48. Copyright © 2021 The Authors. Published by American Chemical Society. | |
1.1.3. Three-dimensional COFs.
Three-dimensional (3D) COFs are periodic arrangements of tetrahedron building blocks.40 In 3D COFs, molecular building units are arranged three-dimensionally into the framework, which facilitates open sites in COFs.41 Noticeably, in comparison with 2D COFs, 3D COFs show much greater and highly accessible Brunauer–Emmett–Teller (BET) BET surface area, high crystallinity, thermal stability, a greater extent of active reaction sites, and photocatalytic activity, which has attracted a number of researchers recently. Based on these advantages, 3D COFs provide a significant advantages in gas storage and separation applications.42 Recently, Wang's group developed bipyridine-linked 3D covalent organic frameworks (COFs) produced by using a mixture of tetrakis(4-aminophenyl)methane (TAPM), 2,2′-bipyridine-5,5′-diamine (Bpy), and 4,4′-biphenyldicarboxaldehyde (BPDA) using the solvothermal method.43 Wang's research group depicted the preparation of 2D and 3D porphyrinic COF using same functional moieties and illustrated their different functionalities and properties and when compared with 2D porphyrinic COF, 3D COF showed better photocatalytic activity.44 They also in recent times reported the synthesis of a switchable 3D COF, which showed a reversible transformation in the framework through redox path maintaining its crystallinity and porosity.45 In recent times, 3D thioether-based covalent organic frameworks (JUC-570 and JUC-571) were developed by Zhang et al., which showed high Hg2+ uptake capacity from water.46 Recently, Wang's group reported the construction of a new highly crystalline porous 3D covalent organic framework (FCOF-5) by using flexible building blocks, which showed excellent breathing behavior, i.e., upon adsorption/desorption of vapors can undergo reversible expansion/contraction [Fig. 1d].47 Very recently, Cooper and his group developed a porous, crystalline and long-term ordered 3D COF (SPB-COF-DBA) by assembling simple and synthetically accessible square-planar cobalt(II) phthalocyanine (PcCo) units and tetrahedral spiroborate linkagesby[Fig. 2(II)].48 The SPB-COF-DBA exhibited everlasting porosity having cubic pores with a higher BET surface area (1726 m2 g−1). The majority of the reported lithium-ion-conducting COFs are 2D, in this regard, for the first time three kinds of poly(ethylene glycol) (PEG)-functionalized 3D COFs (3D-COF-PEG2, 3D-COF-PEG3 and 3D-COF-PEG6) with various lengths of PEG chains were effectively formed for ion transport in diverse directions by Zhang's group.49 By incorporating LiTFSI into the COFs, 3D-COF-PEG2-Li, 3D-COF-PEG3-Li, and 3D-COF-PEG6-Li were synthesized. Because the combining actions of the fragment of the PEG chain and Li-ions are taken into account, the LiTFSI incorporated 3D COF attained a high ion conductivity of 3.6 × 104 S cm−1 at 260 °C, which demonstrates that PEG-based COFs are extremely safe as Li-ion polyelectrolytes at high temperatures. This research added a novel approach to the development of highly effective PEG-based COFs for future-generation lithium-ion batteries.
• Based on structure, COFs are basically divided into the following four categories.
1.1.4. Boron-based COFs.
Boron-based COFs are the first category of COFs which were initially synthesized by Yaghi and his groups in 2005.11 COFs containing a huge number of B atoms are mainly constructed by boronate ester (C2O2B) or boroxine (B3O3) condensation. But these boron-containing COFs are not stable in moist air or in water and that is why their utility as a catalyst or for many long-standing uses became limited. Later, Zhang's group prepared boron-rich COFs having spiro-borate linkages, which displayed high thermal stability as well as hydrolytic and oxidative stabilities.50 Boron-based COFs show strong Lewis acidity that facilitates N2 adsorption.51 Yan and co-worker showed that electrochemical excitation of boron-rich COFs led to the catalyst accessibility to N2 and achieved NH3 synthesis by reduction under ambient conditions.52 Dong et al. reported porous boron-containing covalent organic frameworks, which exhibit strong ion adsorption ability and served as competent additives for Li+ ion transference number improvement of the polymer electrolyte.53 In recent times, Zhang's group prepared and immobilized Boron-based COF onto the surface of a capillary (COF-1@capillary column) and showed its application towards electro chromatographic separation [Fig. 3a].54
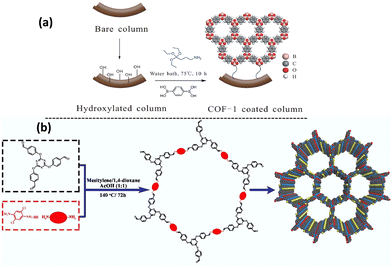 |
| Fig. 3 A schematic diagram for the development of (a) Boron-based COF and (b) Triazine-based COF. Adapted with permission from ref. 54. Copyright © 2021 Elsevier B.V. All rights reserved; ref. 62. © 2021 Elsevier Ltd. All rights reserved. | |
1.1.5. Triazine-based COFs.
Covalent organic framework (COF) is fabricated from triazine or nitrile-containing starting material via the formation of covalent bonding.55 1,3,5-substituted triazine-based COF is more stable compared with the 1,3,5 substituted benzene-based COF because of the greater electron affinity of triazine than the benzene ring.56 Chemically and thermally stable triazine-linked COFs show permanent tunable porosity, specific surface area, high N contents, high extraction efficiency towards some particular antibiotics, and also acts as an interesting adsorbents for organic pollutants57 and excellent photocatalysts in many chemical reactions.58 In 2021, Dinari et al. effectively developed a triazine-based MIL-101-NH2@COF for the elimination of dye-like acid blue 9 from the textile wastewater.59 By incorporating 2,4,6-triphenyl-1,3,5-triazine, Dai et al. recently formed organic frameworks (COFs) and established them as excellent photocathodes for H2 production.60 This work demonstrates that the crystalline donor–acceptor COFs exhibited considerable applications towards water splitting as highly efficient organic photoelectrodes. In 2020, Afshari et al. synthesized a novel porous triazine ring-based nanoneedle T-COF through a facile one-pot hydrothermal reaction, which showed super absorptivity (adsorption capacity of 1826 mg g−1), for the removal of the heavy metal ion Hg2+ from aqueous solutions61 and after that in recent times they also adopted a triazine-linked FT-COF via the solvothermal method to prosper the fire protection and mechanical characteristics of thermoplastic polyurethane (TPU) [Fig. 3b].62 In 2022, among the porous triazine COFs, COF (TS-COF) was synthesized and reported by Wang et al. employing the condensation of monomer units 1,3,5-tris-(4-aminophenyl)triazine (TAPT) and squaric acid (SA) under the solvothermal process. To study the electrochemical activity, Au nanoparticles were incorporated at the surface of TS-COF to develop AuNPs@TS-COF composite and further modification was carried out to constructAuNPs@TS-COF/RGO/GCE.63 It was found that the electrochemical performance was greatly enhanced from TS-COF to AuNPs@TS-COF and then to AuNPs@TS-COF/RGO/GCE as the electrochemical sensors and this opened a new way to use triazine-based COF for designing electrochemical sensors. At the same time, Kim et al. fabricated a rigid and planar triazine-based Covalent Organic Frameworks (TACOF1) by assembling the starting materials, 2,4,6-tris(4-formylphenyl)-1,3,5-triazine (TFPT) and hydrazine monohydrate.64 By direct carbonization of TACOF1 in a nitrogen atmosphere, they formed nitrogen-doped nanoporous carbon that contained a high surface area (1194 m2 g−1). The carbonized TACOF1 formed at 800 °C showed good capacitive ability owing to its nitrogen-riched porous framework structures. Liang et al. designed and prepared triazine-based porous crystalline covalent organic framework COF-SQ, which was further functionalized to generate quinoline-linked COF termed COF-SQ-Ph.65 Functionalized COF-SQ-Ph acted as a promising recipient and storage of sulphur and are being used as electrode materials in Li–S batteries due to their unique extended π-conjugated network. This study also promotes the large-scale synthesis of functionalized triazine-based COF material. Meanwhile, Zhang's group showed the application of allyl-riched COF (ART-COF) as a cathode host material for Li–S batteries.66 These studies suggested a reasonable approach toward the development of exceedingly stable and long-lasting Li–S batteries. Recently, the development of porous and highly efficient covalent organic frameworks (COFs) with large surface areas and low band gap energy have been achieved using the so-called solvothermal methodology by Liu's group.67 The synthesized COFs (designated as TTA-TTB and TAPB-TTB) possess donor–acceptor properties and thus serve as outstanding photo-cathodes for the production of H2 without using any sacrificial electron donor or cocatalyst. It was noticed that TAPB-TTB COF (110 A cm2) exhibit suggestively better visible-light-induced photocurrent responses compared to TTA-TTB COF (35 A cm2).
1.1.6. Imide-based COF.
Imide-linked COFs were first reported by Yan and his co-workers in 2014 through the imidization reaction [18]. Imide-based COF materials with their high-performance aromatic frameworks provide high thermal stability as well as high porosity and surface area and they exhibit wide applications in packing dye molecules and deliver drugs,68 energy storage,69 photocatalysis,70etc.
Recently, Nagai and his research group proposed a synthesis route of four redox-active mesoporous polyimide (PI) based COFs [Fig. 4a].71 DFT study and XRD analysis of the synthesized COFs revealed that the imide bonds form at an angle with one another, which minimizes the pore width and extends the pore walls. Recently, under a high-temperature solvothermal method, highly crystalline 2D imine-based COF was achieved with uniform porosity by Liu and co-workers.72 In this work, COF was used as a support for Ru3+ and the Cryst-2D-PMPI-Ru exhibited high electrocatalytic performance and stability. Recently, Zhao et al. reported the construction of two polyimide-based covalent organic frameworks in a green way without using any organic solvent and both COF (COF-1 and COF-2) showed outstanding fluorescence sensing properties for a variety of metal ions and distinctive antibiotics.73 Liu's group recently reported a 2D polyimide-based COF (PI-NT COF), which was prepared via a simplistic optimized solvothermal process on indium tin oxide-coated glass substrate.74 This PI-NT COF exhibited highly ordered crystalline, tunable thickness, and smooth surface, and owing to the inherent charge-transfer properties of 2D COF films, it showed excellent potential in high-performance data storage devices with low inaccuracy, high conformity, and stability. Maschita et al. proposed a new path for the synthesis of polyimide-linked COFs in 2020.75 In this work, they developed crystalline and porous COFs via the ionothermal process in ZnCl2 and eutectic salt mixtures and this method diminished the reaction time surprisingly compared to that of a typical solvothermal process and occurred without using any environmentally harmful solvents or catalyst. Recently, Maschita et al. prepared a series of stable, long-range crystalline porous imide-linked covalent organic frameworks (TAPA-PMDA-COF, TAPB PMDA-COF, and TAPE-PMDA-COF) following a green environmentally friendly approach using alcohol-supported hydrothermal polymerization method (aaHTP) permitted to obtain a new class of imide-based COFs by avoiding the toxic solvents.76 Synthesis of imide-linked TAPA-PMDA-COF, TAPB PMDA-COF, and TAPE-PMDA-COF was formed by the transformation of imine-linked COFs via linkage substitution. Additionally, Kim's group successfully synthesized porous crystalline polyimide-linked COFs (PICs) via geomimetic hydrothermal reaction conditions. They also established that the PICs possessed exceptional redox-active properties along with high surface area and served as a promising anode material in Li-ion batteries.77
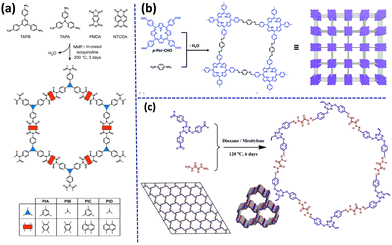 |
| Fig. 4 Schematic route of preparation of (a) polyimide-based COFs, (b) porphyrin-based imine-linked COF and (c) hydrazone-based imine-linked COF. Adapted with permission from ref. 71. Copyright © 2021 American Chemical Society; ref. 83. Copyright © 2021 Royal Society of Chemistry; ref. 87. © 2020 Elsevier B.V. All rights reserved. | |
1.1.7. Imine-linked COF.
In 2009, Yaghi and co-workers successfully constructed a different class of covalent organic framework based on the dynamic covalent chemistry that mainly contained distinct –C
N– bonds and acquired 3D five-fold interpenetrating diamond-like structure.78 Presently, the synthesis of imine-based COFs can be divided into two groups. One method is a condensation reaction between aldehyde and amine i.e., the Schiff base type of reaction79 and the other is a co-condensation reaction between an aldehyde and hydrazides.80 In other words, imine-based COFs gain much better crystallinity and structural regularity in comparison with other COFs as well as they possess much higher thermal and chemical stability compared to boron-based COFs. Also, 2D porous imine-linked COF membranes performed well in the C2H6/CH4 separation with high selectivity.81 Recently, Zamora and co-workers demonstrated a three-step process to prepare 2D imine-based COF aerogels having low densities and excellent porosities and showing outstanding adsorption capability.82
The study of the photocatalytic behavior of 2D imine-linked COFs has recently attracted much attention from researchers. Feng et al. reported the photocatalytic activity of porphyrin-based imine-linked COF (Por-COF) in the presence of (2,2,6,6-tetramethylpiperidin-1-yl)oxyl (TEMPO) [Fig. 4b].83 It was found that the presence of TEMPO enhanced the photocatalytic efficiency of Por-COF in the aerobic oxidation of sulfides selectively under visible light irradiation because of the supportive photocatalysis amongst Por-COF and the redox mediator, TEMPO. In the report of Chen's group, a porphyrin-based imine-linked covalent organic framework (TPE-Por-4) was constructed successfully by the condensation of the 5,10,15,20-tetra-(4-aminophenyl) porphyrin (Por-4) and 4,4′,4′′,4′′′-(ethane-1,1,2,2-tetrayl) tetrabenzaldehyde (TPE) monomers following solvothermal conditions.84 The suspension of the TPE-Por-4 exhibited exceptional fluorescence properties and a noticeable response to pH variations, ordering from 2 to 4 was observed. Imine-based covalent organic frameworks can act as a support material for metal ions through ‘N’ and ‘O’ sites present in it and the formed ‘metal ion-based COF’ can provide catalytic activity for a selective organic transformation. Gao's group recently developed Cu(I)-immobilized-COF TpBpy-Cu) wherein TpBpy is an imine-linked porous COF containing N, N, and N, O chelating sites.85 Cu(I)-TpBpyCOF proved to be an efficient catalyst because of the synergy effect between COF and Cu(I) sites for the terminal alkyne carboxylation reaction under 1 atmosphere of CO2 pressure and 60 °C. Four isostructural porphyrinic 2D COFs were constructed and characterized and their photocatalytic activity for H2 production from water was determined by Chen et al.86 Further, by the amalgamation of different metal ions at the surface of the COF's porphyrin units, photophysical and electronics properties of the COFs can be adjusted.
Hydrazone-linked COFs show structural variety, are synthetically accessible and extremely high thermal and chemical stability, and contain a copious number of N atoms, which facilitates the adsorption of gas molecules. A recent report by Amini and co-workers provided a synthetic route for the formation of hydrazone-based 2D COF by a condensation reaction between 2,4,6-tris(p-formylphenoxy)-1,3,5-triazine and oxalyl dihydrazide under the solvothermal approach [Fig. 4c].87 This obtained imine-linked hydrazone-based COF was highly stable in boiling water or even in a strongly acidic medium and provides a large BET surface area with high CO2 uptake ability. Recently, Ahmed et al. illustrated the construction of a novel hydrazone based highly crystalline, and chemically stable covalent organic framework (TFPB–DHTH COF) via solvothermal analysis using 1,3,5-tris(4-formylphenyl)benzene (TFPB) and 2,5-dihydroxyterephthalohydrazide (DHTH) as starting materials.88 Recently, Zhang and co-workers similarly established the synthesis of a new stable covalent organic framework (Tfpa–Mth COF) via the condensation (Schiff base) reaction involving tris(4-formylphenyl) amine (Tfpa) and a chiral hydrazide (Mth).89 Tfpa–Mth COF achieved fluorescence property due to its uniformly distributed surface and thick films and acted as a potential fluorescent sensor for the recognition of Fe (III) ions. A recent finding from S. Wu et al. showed that a well-ordered two-dimensional hydrazone-linked crystalline porphyrinic COF, Por-DETH-COF, was congregated from 5,10,15,20-tetrakis (4-benzaldehyde) porphyrin (p-Por-CHO) and 2,5-diethoxyterephthalohydrazide (DETH), followed by a study of its excellent photocatalytic activity assessed with the oxidation of benzyl amines to the selectively for imines in the presence of air and red-light irradiation.90 Along this line C. Zhang, Y. Dong, and co-workers utilized a quintessential bicarbazoleusing as the major building block units and hydrazone as the linkers to synthesize a 2D COF (CZ-DHZ-COF) and showed that CZ-DHZ-COF generates intense cyan colour emission in its solid state.91 The as-synthesized powder-like CZ-DHZ-COF exhibited fast fluorescence response with weak and red-shifted fluorescence towards acid vapor; besides this, the liquid obtained by suspending CZ-DHZ-COF showed precise identification for Fe(III) ions with excellent fluorescence quenching. Hence, CZ-DHZ-COF would act as a decent applicant for fluorescence sensing to distinguish Fe(III) ions and acid vapor, also used in versatile applications for fluorescence sensing.
Amide-based COFs show vast potential in diverse practical applications because of their high stability and crystallinity of the porous polyamide structural moiety. But due to the lack of proper synthetic approaches, very few amide-linked COFs have been reported till now. Yaghi and his co-workers, first in 2016, reported two amide-based COFs via the oxidation of the imine linkages of the imine-based COF using an oxidizing agent, sodium chlorite.92 Just a while ago, similar to that one reported by Yaghi's group, amide-linked highly porous crystalline COF was synthesized using KHSO3 as an oxidant by rapid conversion from the imine-linked framework into amide-linked framework under green reaction condition.93 Later in 2020, Yan's group designed and constructed an irreversible amine-based COF termed as JNU-1, which exhibited good stability, excellent selectivity, extraordinary fast kinetics and high-absorbance capacity for gold recovery.94 The building block exchange (BBE) tactic was involved for the construction of JNU-1 COF. Due to its intrinsic linkage and the presence of functional groups, COF is irreversible and hence leads to the ultrafast recovery of gold selectively. Far ahead, Yang and his group synthesized a novel 2D amide-linked covalent organic framework (COF-TM), wherein COF acted as a support for Pd(II) ion in Pd@COF-TM.95 The synthesized Pd@COF-TM showed outstanding catalytic activity for Suzuki-Miyaura coupling reaction, it also was demonstrated that the heterogeneous catalyst Pd@COF-TM exhibited high durability and high recyclability up to nine consecutive cycles. In recent times, Ma et al. synthesized amide-linked 2D COF (COF-JLU19) with electron donor-acceptor structural properties with inherent porosity, high specific BET surface area, good stability along with brilliant photoelectric property [Fig. 5(I)].96 COF-JLU19 showed excellent photocatalytic activity and good recyclability using water as a medium under metal-free conditions and visible light irradiation. They also prepared an amide-linked COF-JLU19 electrospinning membrane and photocatalytic activity with recyclability towards the photodegradation action of Rhodamine B (RhB) in H2O under sunlight irradiation was studied. Das et al. recently applied the strategy of incorporating new functional groups like amide and hydrazide into the COF material in order to improve their porosity, stability, and crystallinity by the formation of inter and intralayer H-bonding.97 Thus, they effectively constructed three triazine-based amide-hydrazide linked COFs named as CON, CONN, and CONNCO and also showed that these COFs have luminescent properties with fascinating fluorescence on-off different pH-responsive for scavenging of protons from an aqueous solution.
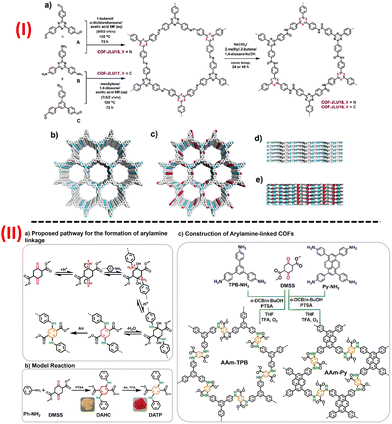 |
| Fig. 5 A schematic representation for the construction of (I) amide-based COFs, (II) aryl amine-based imine-linked COF. Adapted with permission from ref. 96. Copyright © 2021 Dalian Institute of Chemical Physics, the Chinese Academy of Sciences. Published by Elsevier B.V. All rights reserved; ref. 99. © 2021 Wiley-VCH GmbH. | |
Again, another triazine-based two new photoactive 2D COFs of imine and amide-linkages (COF-JLU32 and COF-JLU33) have been recently reported by Liu's group and their photocatalytic experiment for the preparation of α-trifluoromethylated ketones was tested.98 Mainly, amide-linked COF-JLU33, a metal-free catalyst, exhibited efficient photocatalytic activity as well as good recyclability related to the other reported heterogeneous catalysts.
For the first time, Chen and his group recently evaluated an efficient strategy to develop a new aryl amine-linkage for the synthesis of COFs, which enriched the COFs with other tailored characteristics along with the present building blocks, and thus modified the COFs with required functions [Fig. 5b].99 The group successfully prepared two aryl-linked COFS AAm-TPB and AAm-Py having hcb and sql topologies, respectively, with better stability as well as a highly conjugated network and they also explored their pseudocapacitive energy storage capacity and AAm-TPB COF exceptionally exhibited the highest capacitance of 271 F g−1 among the other reported COF-based electrode material.
The variation in physical properties with the structure of the COF is illustrated in Table 1, from which we can observe that using triazine as a monomer unit, the textural property of the COF is enhanced. Moreover, due to the presence of more N atoms in the structure, it has been established that highly polar and N-rich Lewis-base groups can facilitate the adsorption and activation of carbon dioxide. On the other hand, from Table 2, it is easy to notice that the majority of reports found in the literature dedicated to COF-based catalytic CO2RR are based on the formation of hybrid materials in which the semiconductor COF is combined with a different metal or other conductive materials. As a result, fine-tuning of various parameters like appropriate monomer units for the hybrid materials, the physical hetero-junction created between both hybrid materials, relative molar ratios, or the specific location of the dopant onto the catalyst, involved in the formation of a heterogeneous nanohybrid, could have an impact on the electronic structure of the COF and also on its active sites and thus different catalytic properties of the materials has been noticed.
Table 1 Relationship between structure and physical properties of COFs
Type of COF |
Monomer units |
Synthesis process |
Physical properties |
Ref. |
Boron based COFs |
1,4-Benzene diboronic acid (BDBA) |
Static solvothermal method |
S-COF-1: SBET = 690 m2 g−1, Vtotal = 0.47 cm3 g−1 |
53
|
Solvothermal method |
H-COF-1@5: SBET = 717 m2 g−1, Vtotal = 0.46 cm3 g−1 |
H-COF-1@10: SBET = 812 m2 g−1, Vtotal = 0.48 cm3 g−1 |
Ionic conductivity (H-COF-1@10 > H-COF-1@5 > S-COF-1) |
Crystallinity (S-COF-1 > H-COF-1@5 > H-COF-1@10) |
Triazine-based COFs |
4,4′,4′′-(1,3,5-triazine-2,4,6-triyl)trianiline (TTA) and 4,4′,4′′-(1,3,5-triazine-2,4,6-triyl)tribenzaldehyde (TTB) |
Solvothermal method |
TTA-TTB COF: SBET = 1592 m2 g−1, pore size = 2.2 nm, Vtotal = 1.08 cm3 g−1, band gap = 2.67 eV |
67
|
1,3,5-tris(4-aminophenyl)benzene (TAPB) and 4,4′,4′′-(1,3,5-triazine-2,4,6-triyl)tribenzaldehyde (TTB) |
Solvothermal method |
TAPB-TTB COF: SBET = 932 m2 g−1, pore size = 2.19 nm, Vtotal = 0.65 cm3 g−1, band gap = 2.43 eV |
Imidebased COF |
2,4,6-tris(4-aminophenyl)-benzene (TAPB) and perylene-3,4,9,10-tetracarboxylic dianhydride (PTCDA) |
Ionothermal method |
TAPB-PTCDA-COF: SBET = 1250 m2 g−1, Pore width = 31 Å, highly crystalline |
75
|
2,4,6-tris(4-aminophenyl)-benzene (TAPB) and pyromellitic dianhydride (PMDA) |
Ionothermal method |
TAPB-PMDA-COF: SBET = 460 m2 g−1, pore width = 29 Å, highly crystalline |
Imine linked COF |
1,3,5-triformylphloroglucinol (Tp) and 2,2′-bipyridine-5,5′-diamine (Bpyda) |
Solvothermal method |
TpBpy: SBET = 1480 m2 g−1, CO2 adsorption capacity = 66.8 cm3 g−1 |
85
|
TpBpy-Cu: SBET = 460 m2 g−1, CO2 adsorption capacity = 47.2 cm3 g−1 |
Crystallinity (TpBpy > TpBpy-Cu) |
Hydrazone-linked COF |
2,4,6-tris(p-formylphenoxy)-1,3,5-triazine and oxalyl dihydrazide |
Solvothermal method |
TPT/OH COF: SBET = 424 m2 g−1, CO2 capture capacity = 0.9 mmol g−1, highly chemically stable |
87
|
Triazine-based imine linked COFs |
1,3,5-tris-(4-aminophenyl)triazine (TAPT) and benzo[1,2-b:3,4-b′:5,6-b′′]trithiophene-2,5,8-tricarbaldehyde (BTT) |
Solvothermal method |
COF-JLU32: SBET = 1501 m2 g−1, Vtotal = 0.707 cm3 g−1, highly crystalline, optical band gap energy (Eg) = 2.46 eV |
98
|
Triazine-based amide linked COFs |
TPT/OH COF (imine-linked COF) |
Irreversible conversion from the imine-linked framework into an amide-linked framework |
COF-JLU33: SBET = 1148 m2 g−1, Vtotal = 0.701 cm3 g−1, highly crystalline, optical band gap energy (Eg) = 2.37 eV |
98
|
Crystallinity (COF-JLU 33 > COF-JLU32) |
Table 2 COFs and their composites for CO2 reduction
Catalyst |
Surface area (m2 g−1) |
Process |
Product |
Yield |
Ref. |
COF |
432 |
Photo-reduction |
Carbon monoxide (CO) |
18.7 (TON) |
102
|
COF |
521 |
Photo-reduction |
CO & O2 (trace amount CH4, H2) |
102.7 mol g−1 h−1 (CO) & 51.3 μmol g−1 h−1 (O2) |
103
|
COF |
421.64 |
Photo-reduction |
HCOOH and HCHO |
0.027 mole HCOOH, 0.96 mole HCHO |
104
|
COF |
571.6 |
Photo-reduction |
CO |
54 (TON)/17.93 mmol g−1 |
105
|
COF |
843.8 |
Photo-reduction |
CO, H2, O2 |
295.2 μmol g−1 |
106
|
DQTP COF-Co |
195.92 |
Photo-reduction |
CO |
1.02 × 103 μmol h−1 g−1 |
107
|
DQTP COF-Zn |
345.57 |
Photo-reduction |
HCOOH |
152.5 μmol h−1 g−1 |
107
|
COF/[Ir-ppy] |
137.9 |
Photo-reduction |
CO |
88.6 μmol h−1 g−1 |
108
|
Re-Bpy-sp2c-COF |
323 |
Photo-reduction |
CO |
1400 mmol g−1 h−1 |
109
|
PdIn@N3-COF |
100.46 |
Photo-reduction |
MeOH (74%), CH3CH2OH (26%) |
798 μmol g−1 |
110
|
COF-3 |
1010 |
Photo-reduction |
Formic acid (HCOOH) |
170 μmol |
111
|
COF-4 |
1660 |
Photo-reduction |
HCOOH |
226.3 μmol |
111
|
3.0 wt.% Ru/TpPa-1 |
385 |
Photo-reduction |
Formic acid (HCOOH) |
108.8 μmol g−1 h−1 |
112
|
TpBD-H2 |
535 |
Photo-reduction |
Formic acid (HCOOH) |
45.7 μmol g−1 h−1 |
113
|
TpBD-(CH3)2 |
406 |
Photo-reduction |
Formic acid (HCOOH) |
86.3 μmol g−1 h−1 |
113
|
TpBD-(OCH3)2 |
388 |
Photo-reduction |
Formic acid (HCOOH) |
108.3 μmol g−1 h−1 |
113
|
TpBD-(NO2)2 |
259 |
Photo-reduction |
Formic acid (HCOOH) |
22.2 μmol g−1 h−1 |
113
|
COF-TVBT-PA |
198.4 |
Photo-reduction |
CO |
70.8 μmol g−1 |
114
|
COFbpyMn |
1601 |
Electro-reduction |
Carbon monoxide (CO) |
TON = 5800 |
115
|
Co-mNCCOF |
1985 |
Electro-reduction |
Carbon monoxide (CO) |
FECO = 81% |
116
|
Fe-mNCCOF |
— |
Electro-reduction |
CO |
FECO = >90% |
116
|
Ni-mNCCOF |
— |
Electro-reduction |
CO |
FECO = >95% |
116
|
AAn-COF-Cu (NF) |
161 |
Electro-reduction |
CH4 |
FECH4 = 77% |
117
|
OH-AAn-COF-Cu (HT) |
470 |
Electro-reduction |
CH4 |
FECH4 = 61% |
117
|
2D TT-Por(Co)-COF |
748 |
Electro-reduction |
CO |
FECO = 91.4% |
118
|
NiPc-COF |
358 |
Electro-reduction |
CO |
FECO = 99.1% |
119
|
TTF-Por(Co)-COF |
888 |
Electro-reduction |
CO |
FECO = 95% |
120
|
Co-TTCOF |
481 |
Electro-reduction |
CO |
FECO = 99.7% |
121
|
CoPc-PI-COF-1 |
181 |
Electro-reduction |
CO |
FECO = 97% |
122
|
CoPc-PI-COF-2 |
291 |
Electro-reduction |
CO |
FECO = 96% |
122
|
TAPP(Co)-B18C6-COF |
942 |
Electro-reduction |
CO |
FECO = 93.3% TOF = 1267 h−1 |
123
|
TAPP(H2)-B18C6- COF |
906 |
Electro-reduction |
CO |
FECO = 86% |
123
|
CoPc-PDQ-COF |
762 |
Electro-reduction |
CO |
TOF= 11 412 h−1 |
124
|
COF-366-(OMe)2Co@CNT |
196 |
Electro-reduction |
CO |
FECO = 93.6% |
125
|
NiPc/CoPc-TFPN COF |
252.375 |
Electro-reduction |
CO |
FECO = 99.8% |
126
|
NiPc/CoPc-TFPN COF |
252.375 |
Photo-electroreduction |
CO |
FECO ∼ 100% |
126
|
Cu@[OH]-H2P-COF/CF |
895 |
Photo-electroreduction |
CH3OH, CH3CH2OH, CH3OCH3, CH3CH(OH)2 |
5352 μM g−1 h−1 |
127
|
NAHN-Tp |
137.9 |
Photo-reduction |
CO |
88.6 μmol h−1 |
128
|
CoPc-PI-COF-1 |
181 |
Electro-reduction |
CO |
FECO = 97% |
129
|
CoPc-PI-COF-1 |
291 |
Electro-reduction |
CO |
FECO = 96% |
129
|
CoPc-PI-COF-3 |
415 |
Electro-reduction |
CO |
FECO = 96% |
130
|
H2Pc-PI-COF-3 |
320 |
Electro-reduction |
CO |
FECO = 21% |
130
|
3D-Por (Co/H)-COF |
922 |
Electro-reduction |
CO |
FECO = 92.4% TOF = 4610 h−1 |
131
|
Re-TpBpy |
— |
Photo-reduction |
CO |
19.6 μmol g−1 h−1 |
132
|
MWCNT-Por-COF-Co |
— |
Electro-reduction |
CO |
FECO = 99.3% |
133
|
MWCNT-Por-COF-Cu |
— |
Electro-reduction |
CH4 |
FECH4 = 71.2% |
134
|
2. Application
2.1. CO2 reduction
The reactions involved in the CO2 reduction process are shown below:
CO2 + 2H+ + 2e− → CO + H2O |
CO2 + 4H+ + 4e− → C + 2H2O |
CO2 + 4H+ + 4e− → HCHO + H2O |
CO2 + 6H+ + 6e− → CH3OH + H2O |
CO2 + 8H+ + 8e− → CH4 + 2H2O |
2CO2 + 8H2O + 12e− → C2H4 + 12OH− |
2CO2 + 9H2O + 12e− → C2H5OH + 12OH− |
2.1.1. Electrocatalytic CO2 reduction (ECR).
The electroreduction of CO2 using different types of COF catalysts is shown in Table 2. Generally, a wide range of metal particles and metal oxide-based catalysts are used for the reduction of carbon dioxide.100 Electrochemical Reduction of CO2 using heterogeneous solid catalysts is affected by the interaction between the adsorbed CO2 molecule at the surface of catalysts, electrons, and protons. Mainly three fundamental steps are involved in the electro-catalytic CO2 reduction reaction: (i) CO2 molecule adsorption at the surface of catalyst; (ii) sharing of electron and proton between catalyst and CO2; (iii) the desorption of products (Fig. 6). The first step is the most crucial step for operating the whole reaction and achieving products. By sharing electrons, CO2 is transformed into CO2.-radical anion species. Depending on the type of the catalyst, different types of reaction pathways or grouping of two or more reaction steps can lead to the formation of a wide range of products by CO2 reduction. Electrochemical reactions occur in the liquid phase, so protons remain free to react. If the catalyst has a weak capability of absorbing CO intermediate, then CO is obtained as a major product via the formation of the COOH* intermediate followed by the addition of one electron and proton. Catalysts with pi electrons can improve the absorption of CO2˙− radical and thus inhibit further reduction of CO2˙−, consequential in the formation of formate through the protonation method. The production of the liquid fuel CH3OH is mainly achieved via the CH3O intermediate from CO2 followed by protonation. Under the electrochemical environment dimerization of two carbon radical anions give rise to the synthesis of C2 products (such as C2H4, and C2H5OH). The production of hydrocarbons, as well as CH4 and C2H4, is achieved due to the transformation of the adsorbed CO to *CHO via the hydrogenation process and further hydrogenation is not possible because CHOH is thermodynamically unstable.101 Formations of CH4 from CO2 are generally 8 electron processes and occur at high potential. Therefore, a variety of side products e.g., ethane, hydrogen, CO, formate, etc. are obtained because of the applied high potential, and thus selectivity of CH4 synthesis becomes low. From Table 2, based on the reported literature, it is observed that metal-based (e.g., Fe, Cu, and Co) COFs are more efficient for the electrocatalytic reduction of CO2, and selectively CH4 or CO is obtained as a product, i.e., the efficiency of electrocatalytic reactions is increased significantly in the presence of metal particles.
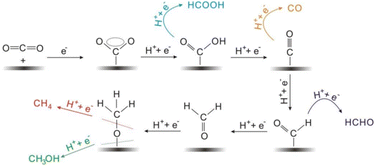 |
| Fig. 6 The proposed reaction mechanism of production of mainly C1 products by electrochemical CO2 reduction. Adapted from ref. 100. © 2017 Wiley-VCH Verlag GmbH & Co. KGaA, Weinheim. | |
2.1.2. Photocatalytic CO2 reduction (PCR).
The photoreduction of CO2 involving a variety of COF-based catalysts is illustrated in Table 2, from which it can be observed that the noble metal Re-complex combined with COF materials proved to be an excellent photocatalyst and exhibited outstanding efficiency in the photocatalytic reduction of CO2. Re-Bpy-sp2c-COF catalyst prepared by Cooper's group in 2019, showed 1400 mmol g−1 h−1 CO production from CO2 with up to 86% selectivity.109 They demonstrated that tethering molecular catalysts—a complex of rhenium, [Re(bpy)(CO)3Cl] along with a crystalline covalent organic framework (COF) offered a heterogeneous photocatalyst, which exhibited strong absorption of light in the visible region, a high-affinity CO2-binding and eventually an enhanced catalytic performance beyond its homogeneous Re counterpart. The bipyridine sites on the COF permitted the Re complex to be ligated into a completely p-conjugated backbone, which is chemically stable and promotes light harvesting.
For the photocatalytic reduction of CO2, metal-impregnated COF-based materials and hybrid COF catalyst systems coupled with homogeneous metal-complex possess better activity compared to pure COFs. This activity enrichment was mainly endorsed by the presence of transition-metal elements, which usually facilitate excellent CO2 adsorption with high-catalytic capability or have the capacity to significantly intensify photo-induced charge generation and enhance the charge-transfer process. It is noticeable from the preceding existing literature, that both only COF and metal-based COFs are reported for the reduction of CO2 to C1 as well as C2 products based on the physical and chemical properties of different types of COFs (Table 2).
In 2019, the group created the world's first metalated COF material for heterogeneous photocatalytic CO2 reduction.107 DMA (N,N-dimethylacetamide)/1,3,5-trimethylbenze/acetic acid mixed solvent was mixed with 2,6-diaminoanthraquinone (DQ) and 2,4,6-triformylphloroglucinol (TP), which was then heated at 120 °C/72 h. CO and HCOOH were synthesized using the metalated COFs. Fig. 7 depicts the reaction mechanism schematically. Metal coordinating sites via anthraquinone O atoms were abundant in the as-prepared 2D-anthraquinone-based DQTP-COF. To incorporate the Co(II) ion into the COF structure, the aqueous solution was sonicated, followed by heating with cobalt salt. Under visible-light irradiation (λ ≥ 420 nm) sensitized by Ru(II) salt and employing TEOA as a sacrificial electron donor, the as-prepared DQTP-COF-Co catalyst demonstrated promising CO2 reduction capability. The as-prepared metalated catalyst produced CO at a rate of 1.02 × 103 μmol g−1 h−1, which was significantly greater than non-metalated DQTP-COF, DQTP-Ni-COF, and DQTP-Zn-COF samples. CO had moderate selectivity over H2 (59.4 percent). When the Zn(II) ion was loaded into the DQTP-COF structure, however, HCOOH was produced with a selectivity of up to 90% and a formation rate of 152.5 μmol g−1 h−1. For this distinguishing selectivity, the scientists postulated a “two-pathway” mechanism. The two pathways forming either HCOOH or CO share the same intermediate, i.e., M-COOH. When the coordination environment for COOH was electron-rich, the C–O bond was prone to cleavage, forming CO product, whereas when the coordination environment was electron-deficient, HCOOH formation was facilitated via the proton-coupled-electron-transfer process (PCET), which bypassed the C–O cleavage pathway. CO was the predominant product because CO is an excellent-electron donor, whereas the – electron acceptor metal centre in Zn-based COF would encourage the synthesis of HCOOH. The generation rates of CO and HCOOH were nearly comparable for Ni-COF, which was neither electron-rich nor deficient. Lan's research was the first to use metalated-COF as a heterogeneous photocatalyst for the reduction of CO2.
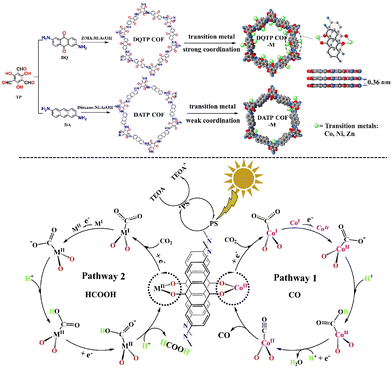 |
| Fig. 7 Synthesis and metallization process of DQTP COF and DATP COF and proposed mechanism for the photocatalytic reduction of CO2 with DQTP-COF-M (M = Zn, Ni, and Co). Adapted from ref. 107. © 2019 Elsevier B.V. All rights reserved. | |
Huang et al. applied a viable strategy for the conversion of CO2 into C1/C2 alcohols, expanding the field of artificial photosynthesis.110 Different composites of PdxIny@N3-COF where x
:
y = 1
:
0, 0
:
1, 1
:
2, 1
:
1, 2
:
1 were easily constructed using bimetallic PdIn nanoclusters enclosed in a photoactive COF (N3-COF). The resultant PdIn@N3-COF showed remarkable photoactivity for CO2 reduction along with H2O oxidation into CH3OH (74%) and CH3CH2OH (26%) with a total yield of 798 mol g−1. The synergy in both the bimetallic NCs and the cluster@N3-COF assisted significantly in the interfacial charge transfer and C–C coupling, resulting in good photoactivity for CO2 reduction to C1/C2 alcohols. In order to better understand the C–C coupling, in situ FTIR studies were performed during the photoreduction of CO2 and a possible reaction mechanism was also predicted by predicting the surface molecules produced during photocatalysis.
You et al. demonstrated a heterogeneous photocatalytic system based on an iridium complex (Ir-ppy) and hydrazone-based COF (NAHN-Tp), which acts as a photosensitizer and can absorb visible light energy.128 The formed 2D hydrazone-based COF synthesized from 1,3,5-triformylphloroglucinol (Tp) and N-amino-4-hydrazino-1,8-naphthalimide (NAHN) and combined with NAHN-Tp(Ir-ppy) took part in the photochemical CO2 reduction to CO [Fig. 8].
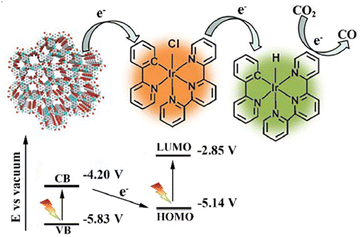 |
| Fig. 8 Z-scheme electron transfer during CO2 reduction using a NAHN-Tp and [Ir-ppy]. Adapted from ref. 128. © 2020 Published by Elsevier Inc. | |
2.1.3. Photo-electrocatalytic CO2 reduction (PCER).
For the first time, Lan's group published dioxin-linked metallophthalocyanine covalent organic frameworks as photo-coupled CO2 reduction electrocatalysts in 2020.126 In this study, they designed a series of crystalline and stable dioxin-linked metallophthalocyanine covalent organic frameworks (MPc-TFPN COF, M = Ni, Co, Zn), among which NiPc/CoPc-TFPN COF showed excellent activity for CO2 reduction when coupled with light compared to a dark environment. The reaction mechanism was also studied by DFT, which revealed that an external light field can improve the electron transfer to the adsorbed CO2 in phthalocyanine COFs leading to the favorable CO2. DFT calculation results indicated that in the COF systems, the N atom in the phthalocyanine ligand plays a major role in adsorbing and activating CO2. The free energy change for CO2 adsorption on the central metal in the NiPc-TFPN COF and CoPc-TFPN COF is substantially higher than the N site (NM, which means N in MPc, which is highlighted with blue background in Fig. 9a). Hence, according to the minimum energy principle, CO2 molecules have a tendency to be adsorbed as well as activated on NM atoms in the first step of ECR i.e. (* + CO2 + 2H+ + 2e− → *CO2 + 2H+ + 2e−) on these two catalysts. To understand the effect of light on the ECR, the electronic properties of S1 and T1 excited states for the COF catalysts were examined. The NiPc-TFPN COF was first excited from S0 to S1 state upon light irradiation, followed by transforming to T1 state through intersystem crossing (Fig. 9c). The energy gap between S0 and S1 was found to be 2.05 eV, and the optical transition energy of the T1 state was discovered to be 0.80 eV (vs. ground state), showing that the phthalocyanine COF catalysts will be driven to a higher energy-excited state under light irradiation. The free energy change is reduced from the T1 excited state to the active centre compared to the ground state, which leads to the beneficial activation of CO2 to *COOH. This is how they explained the inherent reason why NiPc-TFPN COF showed better PECR activity than ECR. Some of the studies on photo-electrochemical reduction of CO2 are shown in Table 2.
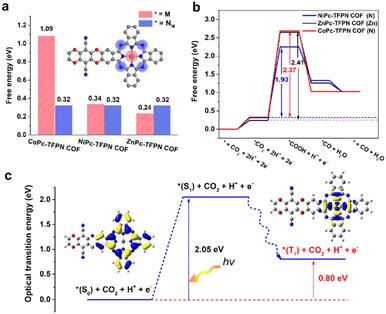 |
| Fig. 9 (a) Mechanism and DFT calculations. (a) A comparison of the relative adsorption energy for the first step of ECR (* + CO2 + 2H+ + 2e− → *CO2 + 2H+ + 2e−) on the metal site (red) and nitrogen site (blue) on MPc-TFPN COF, (b) the free energy diagrams for CO2 reduction to CO on MPc-TFPN COF (Note that the symbols in brackets represent the reaction sites). The rate-determining step and the corresponding free energy on each COFs are indicated, (c) schematic representation of the excited states of NiPc-TFPN COF. Adapted from ref. 126. © 2020 Wiley-VCH GmbH. | |
A while back, Jing's group first demonstrated Cu@porphyrin-COFs nanorods by a solvothermal technique, which served as an effective photoelectrocatalyst for producing C1–C3 products such as CH3OH, CH3CH2OH, CH3CH(OH)2 and CH3COCH3 with apparent faradaic efficiency (AFE) of 452.75% by CO2 reduction.127 The incorporation of Cu by electrodeposition on the surface of porphyrin-COFs is believed to considerably boost the rate of charge transfer by protons harvesting and outstanding absorption of light, thus favoring the C–C coupling process. Besides this, the presence of organic linkers bearing –OH groups would increase the stability of COFs by benefiting the development of intermolecular hydrogen bonds that enhance the reaction activity of CO2 reduction. However, some of the studies on photo-electrochemical CO2 reduction are shown in Table 2, which suggests that these findings pave the path for designing innovative and highly active photoelectrocatalysts for effective PEC CO2 reduction. PCER can explore a new strategy toward the reduction of CO2 in the near future as there are hardly any reported experiments explored in this field yet.
3. Shortcomings of COFs
The synthesis of a broad range of COFs mainly depends on the involved reversible reactions, which generate a significant drawback associated with the chemical stability of the COFs. During this reversible COF formation process, water is produced as a by-product, which boosts the reaction in the backward direction. As a result, the decomposition of COFs occurs, which restricts the employment of COFs in rational industrial applications along with other spacious utilizations such as gas storage, sensors, and catalysis. Hence, the development of COFs having greater stability in aqueous and organic conditions serves as a driving factor in this field of research. In order to develop stable COFs, many academic disciplines give huge efforts to rational design and synthesis of COFs, which can maintain their porosity and crystallinity under harsh environmental conditions.134 For the production of stable COFs, two methods have been established until now, firstly, using stable organic linkers and the second one is to form intramolecular and interlayer hydrogen bonds.135
One of the main disadvantages of COFs for electrochemical applications is their poor electrical conductivity even though COFs exhibit a large surface area. Considering the existence of active sites present in the COF framework, a specific charge-transport route is required for effective electrocatalytic activities. By using the right building blocks and synthetic methods or by the assimilation of extremely conductive units (such as thiophene and thieno-thiophene derivatives) into the COF framework, this intrinsic drawback can be overcome.136
4. Future scope and conclusions
In conclusion, covalent organic frameworks (COFs) are particularly promising CO2 reduction catalysts for next-generation applications. They have multiple advantages over traditional heterogeneous catalysts such as metal-oxide, noble-metal plasmonic inorganic semiconductors, and inorganic–organic hybrid MOF-based catalysts. COFs are composed of organic moieties and non-metal elements; therefore, the COF's monomer units are low-cost and more readily available than metal-containing inorganic catalysts and MOFs. The electronic and steric factors in COF can be tuned conveniently using different monomer units, which allow us to modify the structure of COF, which are more suitable for CO2 adsorption and reduction reactions. As shown in Table 2, most of the reported literature dedicated to COF-based catalytic CO2RR is focused on the development of hybrid materials, which combine semiconductor COF with various metals or other conductive materials. In this way, fine-tuning the various parameters involved in the construction of a heterogeneous nanohybrid, for instance, heterojunction formed between both molecular units, their corresponding molar ratios, or the precise site of the dopant on the catalyst, could have an impact on both the electronic structure of the COF and its active sites, and thus, are the important factors in determining the catalytic properties. Comparatively, low reaction yields that presently impede more advancements in this arena can be improved through the logical regulation of such factors. Even though COFs as CO2 reduction catalysts have multiple advantages, there are still many spaces to address some challenges, which need to be resolved in this area of research. Primarily, the use of the SARS in the photocatalytic CO2 reduction reaction is severely constrained by the ambiguity of the COF structure. Secondly, the significant difficulty in generating a great sufficient 2D COF single-crystal for typical X-ray single-crystal diffraction characterization continues to limit the construction of 2D COFs for a variety of applications, including catalytic CO2 reduction. In spite of the fact that photo-coupled electrochemical reduction is a promising method for CO2 reduction, the PCER method is poorly explored using COFs as heterogeneous catalysts. On the other hand, the major issue is the reaction mechanism, which must be decoded soon so that we could design more effective COFs for CO2 reduction. Therefore, if the above-addressed issues are properly addressed COFs-based materials can contribute immensely as CO2 reduction catalysts to achieve sustainable energy and environment in the future.
Conflicts of interest
There are no conflicts to declare.
Acknowledgements
SMI acknowledges the Department of Science and Technology DST-SERB (project reference no. CRG/2020/000244), New Delhi, Govt. of India and Council of Scientific and Industrial and Research, CSIR (project reference no. 02(0453)/21/EMR-II dated 08/06/2021), New Delhi, Govt. of India and Board of Research in Nuclear Sciences (BRNS), Govt. of India, (project reference no. 58/14/15/2022-BRNS/37077) for providing financial support. PS is thankful to CSIR, India (09/106(0178)/2018-EMR-I) for her fellowship. I. H. C. is thankful to CSIR, India (09/106(0181)/2019-EMR-I) for her fellowship. SD is thankful to SVMCM, Govt. of West Bengal for her fellowship. We acknowledge the DST for providing a grant to the Department of Chemistry by FIST and PURSE grant.
Notes and references
-
(a) W.-H. Wang, Y. Himeda, J. T. Muckerman, G. F. Manbeck and E. Fujita, Chem. Rev., 2015, 115, 12936–12973 CrossRef;
(b) J. C. Zachos, G. R. Dickens and R. E. Zeebe, Nature, 2008, 451, 279–283 CrossRef PubMed.
- Y. Izumi, Coord. Chem. Rev., 2013, 257, 171–186 CrossRef.
-
A. Gore, An Inconvenient Truth, The Wylie Agency, London, UK, 2006, p. 66 Search PubMed.
-
(a) A. Kubacka, M. Fernández-García and G. Colón, Chem. Rev., 2012, 112, 1555–1614 CrossRef PubMed;
(b) S. Wang and X. Wang, Appl. Catal., B, 2015, 162, 494–500 CrossRef;
(c) I. H. Chowdhury, A. H. Chowdhury, P. Sarkar and S. M. Islam, ChemNanoMat, 2021, 7, 580–591 CrossRef;
(d) A. H. Chowdhury, I. H. Chowdhury, S. Biswas and S. M. Islam, Mol. Catal., 2020, 493, 111050 CrossRef;
(e) A. H. Chowdhury, I. H. Chowdhury and S. M. Islam, Ind. Eng. Chem. Res., 2019, 58, 11779–11786 CrossRef CAS;
(f) A. H. Chowdhury, A. Das, S. Riyajuddin, K. Ghosh and S. M. Islam, Catal. Sci. Tech., 2019, 9, 6566–6569 RSC;
(g) I. H. Chowdhury, A. H. Chowdhury, P. Sarkar and S. M. Islam, ChemNanoMat, 2021, 7, 580–591 CrossRef;
(h) A. H. Chowdhury, I. H. Chowdhury, S. Biswas and S. M. Islam, Mol. Catal., 2020, 493, 111050 CrossRef;
(i) A. H. Chowdhury, I. H. Chowdhury and S. M. Islam, Ind. Eng. Chem. Res., 2019, 58, 11779–11786 CrossRef CAS;
(j) S. Ghosh, R. A. Molla, U. Kayal, A. Bhaumik and S. M. Islam, Dalton Trans., 2019, 48, 4657–4666 RSC;
(k) S. M. Islam, A. S. Roy, P. Mondal and N. Salam, J. Mol. Catal. A: Chem., 2012, 358, 38–48 CrossRef CAS;
(l) N. Haque, S. Biswas, P. Basu, I. H. Biswas, R. Khatun, A. Khan and S. M. Islam, New J. Chem., 2020, 44, 15446–15458 RSC;
(m) A. Sahoo, A. H. Chowdhury, P. Singha, A. Banerjee, S. M. Islam and T. Bala, Mol. Catal., 2020, 493, 111070 CrossRef CAS;
(n) P. Bhanja, K. Ghosh, S. S. Islam, A. K. Patra, S. M. Islam and A. Bhaumik, ACS Sustainable Chem. Eng., 2016, 4(12), 7147–7157 CrossRef CAS;
(o) S. Roy, P. Bhanja, S. S. Islam, A. Bhaumik and S. M. Islam, Chem. Commun., 2016, 52, 1871 RSC;
(p) S. Roy, B. Banerjee, A. Bhaumik and S. M. Islam, RSC Adv., 2016, 6, 31153–31160 RSC;
(q) S. Bhunia, R. A. Molla, V. Kumari, S. M. Islam and A. Bhaumik, Chem. Commun., 2015, 51, 15732 RSC;
(r) S. Roy, T. Chatterjee, B. Banerjee, N. Salam, A. Bhaumik and S. M. Islam, RSC Adv, 2014, 4(86), 46075–46083 RSC;
(s) R. A. Molla, K. Ghosh, K. Tuhina and S. M. Islam, New J. Chem., 2015, 39(2), 921–930 RSC;
(t) S. M. Islam, A. S. Roy, P. Mondal, S. Paul and N. Salam, Inorg. Chem. Commun., 2012, 24, 170–176 CrossRef CAS;
(u) S. M. Islam, D. Mal, B. K. Palit and C. R. Saha, J. Mol. Catal. A: Chem., 1999, 142(2), 169–181 CrossRef CAS;
(v) S. M. Islam, N. Salam, P. Mondal, A. S. Roy, K. Ghosh and K. Tuhina, J. Mol. Catal. A: Chem., 2014, 387, 7–19 CrossRef CAS;
(w) S. Roy, B. Banerjee, N. Salam, A. Bhaumik and S. M. Islam, ChemCatChem, 2015, 7(17), 2689–2697 CrossRef CAS;
(x) S. M. Islam, R. A. Molla, A. S. Roy and K. Ghosh, RSC Adv., 2014, 4(50), 26181–26192 RSC;
(y) S. M. Islam, R. A. Molla, A. S. Roy and K. Ghosh, RSC Adv., 2014, 4(50), 26181–26192 RSC;
(z) A. H. Chowdhury, S. Ghosh and S. M. Islam, New J. Chem., 2018, 42(17), 14194–14202 RSC.
-
(a) G. Centi, E. A. Quadrelli and S. Perathoner, Energy Environ. Sci., 2013, 6, 1711–1731 RSC;
(b) W. Wang, S. Wang, X. Ma and J. Gong, Chem. Soc. Rev., 2011, 40, 3703–3727 RSC;
(c) P. Sarkar, A. H. Chowdhury, S. Riyajuddin, S. Biswas, K. Ghosh and S. M. Islam, New J. Chem., 2020, 44, 744–752 RSC;
(d) P. Chakrabortty, A. Das, A. H. Chowdhury, S. Ghosh, A. Khan and S. M. Islam, New J. Chem., 2021, 45, 4738–4745 RSC;
(e) P. Sarkar, A. H. Chowdhury, S. Biswas, A. Khan and S. M. Islam, Mater. Today Chem., 2021, 21, 100509 CrossRef CAS;
(f) S. Das, I. H. Chowdhury, A. Chakraborty, M. K. Naskar, M. Sarkar and S. M. Islam, Mater. Adv., 2022, 3, 3165–3173 RSC;
(g) R. Khatun, S. Biswas, S. Islam, I. H. Biswas, S. Riyajuddin, K. Ghosh and S. M. Islam, ChemCatChem, 2019, 11(4), 1303–1312 CrossRef;
(h) A. H. Chowdhury, S. Ghosh and S. M. Islam, New J. Chem., 2018, 42(17), 14194–14202 RSC;
(i) R. Khatun, P. Bhanja, P. Mondal, A. Bhaumik, D. Das and S. M. Islam, New J. Chem., 2017, 41(21), 12937–12946 RSC;
(j) R. A. Molla, M. A. Iqubal, K. Ghosh and S. M. Islam, Green Chem., 2016, 18(17), 4649–4656 RSC;
(k) R. Khatun, S. Biswas, I. H. Biswas, S. Riyajuddin, N. Haque and K. Ghosh, J. CO2 Util., 2020, 40, 101180 CrossRef;
(l) P. Sarkar, S. Riyajuddin, A. Das, A. H. Chowdhury, K. Ghosh and S. M. Islam, Mol. Catal., 2020, 484, 110730 CrossRef;
(m) S. Sarkar, S. Ghosh and S. M. Islam, Org. Biomol. Chem., 2022, 20(8), 1707–1722 RSC;
(n) U. Mandi, A. S. Roy, S. K. Kundu, S. Roy, A. Bhaumik and S. M. Islam, J. Colloid Interface Sci., 2016, 472, 202–209 CrossRef;
(o) R. A. Molla, A. S. Roy, K. Ghosh, N. Salam, M. A. Iqubal, K. Tuhina and S. M. Islam, J. Organomet. Chem., 2014, 776, 170–179 CrossRef;
(p) U. Mandi, A. S. Roy, B. Banerjee and S. M. Islam, RSC Adv., 2014, 4(80), 42670–42681 RSC;
(q) R. Khatun, P. Bhanja, R. A. Molla, S. Ghosh, A. Bhaumik and S. M. Islam, Mol. Catal., 2017, 434, 25–31 CrossRef;
(r) I. H. Biswas, S. Biswas, M. S. Islam, S. Riyajuddin, P. Sarkar and K. Ghosh, New J. Chem., 2019, 43(36), 14643–14652 RSC;
(s) T. K. Dey, K. Ghosh, P. Basu, R. A. Molla and S. M. Islam, New J. Chem., 2018, 42(11), 9168–9176 RSC;
(t) N. Salam, P. Paul, S. Ghosh, U. Mandi, A. Khan, S. M. Alam, D. Das and S. M. Islam, New J. Chem., 2020, 44(14), 5448–5456 RSC;
(u) R. K. Mondal, S. Riyajuddin, A. Ghosh, S. Ghosh, K. Ghosh and S. M. Islam, J. Organomet. Chem., 2019, 880, 322–332 CrossRef;
(v) S. Das, P. Mondal, S. Ghosh, B. Satpati, S. Deka, S. M. Islam and T. Bala, New J. Chem., 2018, 42(9), 7314–7325 RSC;
(w) S. Sarkar, S. Ghosh, J. Mondal and S. M. Islam, Chem. Commun., 2020, 56(81), 12202–12205 RSC;
(x) N. Haque, S. Biswas, P. Basu, I. H. Biswas, R. Khatun, A. Khan and S. M. Islam, New J. Chem., 2020, 44(36), 15446–15458 RSC;
(y) I. H. Chowdhury, A. H. Chowdhury, A. Das, A. Khan and S. M. Islam, New J. Chem., 2020, 44(27), 11720–11726 RSC;
(z) M. Islam, A. S. Roy and S. Islam, Catal. Lett., 2016, 146(6), 1128–1138 CrossRef CAS.
-
(a) J. Mao, T. Peng, X. Zhang, K. Li and L. Zan, Catal. Commun., 2012, 28, 38–41 CrossRef CAS;
(b) M. Tahir and N. S. Amin, Energy Convers. Manag., 2013, 76, 194–214 CrossRef CAS;
(c) H. Yang, J. Yan, Z. Lu, X. Cheng and Y. Tang, J. Alloys Compd., 2009, 476, 715–719 CrossRef CAS.
-
(a) P. De Luna, R. Quintero-Bermudez, C.-T. Dinh, M. B. Ross, O. S. Bushuyev, P. Todorović, T. Regier, S. O. Kelley, P. Yang and E. H. Sargent, Nat. Catal., 2018, 1, 103–110 CrossRef CAS;
(b) P. De Luna, C. Hahn, D. Higgins, S. A. Jaffer, T. F. Jaramillo and E. H. Sargent, Science, 2019, 364, eaav 3506 CrossRef CAS;
(c) V. S. Thoi, N. Kornienko, C. G. Margarit, P. D. Yang and C. J. Chang, J. Am. Chem. Soc., 2013, 135, 14413–14424 CrossRef CAS;
(d) E. E. Barton, D. M. Rampulla and A. B. Bocarsly, J. Am. Chem. Soc., 2008, 130, 6342–6344 CrossRef CAS.
- T. Inoue, A. Fujishima, S. Konishi and K. Honda, Nature, 1979, 277, 637–638 CrossRef CAS.
-
(a) S. Yang, W. Hu, X. Zhang, P. He, B. Pattengale, C. Liu, M. Cendejas, I. Hermans, X. Zhang, J. Zhang and J. Huang, J. Am. Chem. Soc., 2018, 140, 14614–14618 CrossRef CAS PubMed;
(b) P. Sarkar, S. Riyajuddin, A. Das, A. H. Chowdhury, K. Ghosh and S. M. Islam, Mol. Catal., 2020, 484, 110730 CrossRef CAS;
(c) N. Huang, P. Wang and D. Jiang, Nat. Rev. Mater., 2016, 1, 1–19 Search PubMed;
(d) M. S. Lohse and T. Bein, Adv. Funct. Mater., 2018, 28, 1705553 CrossRef;
(e) C. S. Diercks and O. M. Yaghi, Science, 2017, 355, eaal1585 CrossRef PubMed;
(f) S. L. Cai, W. G. Zhang, R. N. Zuckermann, Z. T. Li, X. Zhao and Y. Liu, Adv. Mater., 2015, 27, 5762–5770 CrossRef PubMed;
(g) Y. Song, Q. Sun, B. Aguila and S. Ma, Adv. Sci., 2019, 6, 1801410 CrossRef;
(h) I. Omae, Coord. Chem. Rev., 2012, 256, 1384–1405 CrossRef;
(i) S. Ghosh, S. Riyajuddin, S. Sarkar, K. Ghosh and S. M. Islam, ChemNanoMat, 2020, 6, 160–172 CrossRef;
(j) S. Ghosh, P. Mondal, D. Das, K. Tuhina and S. M. Islam, J. Organomet. Chem., 2018, 866, 1–12 CrossRef;
(k) N. Salam, P. Paul, S. Ghosh, U. Mandi, A. Khan, S. M. Alam, D. Das and S. M. Islam, New J. Chem., 2020, 44, 5448–5456 RSC;
(l) S. S. Islam, N. Salam, R. A. Molla, S. Riyajuddin, N. Yasmin, D. Das and K. Ghosh, Mol. Catal., 2019, 477, 110541 CrossRef;
(m) R. K. Mondal, S. Riyajuddin, A. Ghosh, S. Ghosh, K. Ghosh and S. M. Islam, J. Organomet. Chem., 2019, 880, 322–332 CrossRef;
(n) S. Biswas, D. Roy, S. Ghosh and S. M. Islam, J. Organomet. Chem., 2019, 898, 120877 CrossRef;
(o) A. Das, R. K. Mondal, P. Chakrabortty, S. Riyajuddin and A. H. Chowdhury, Mol. Catal., 2021, 499, 111253 CrossRef CAS;
(p) S. M. Islam, A. S. Roy, P. Mondal, S. Paul and N. Salam, Inorg. Chem. Commun., 2012, 24, 170–1762012 CrossRef CAS;
(q) S. M. Islam, D. Mal, B. K. Palit and C. R. Saha, J. Mol. Catal. A: Chem., 1999, 142(2), 169–181 CrossRef;
(r) R. A. Molla, K. Ghosh, K. Tuhina and S. M. Islam, New J. Chem., 2015, 39(2), 921–930 RSC;
(s) S. Ghosh, P. Bhanja, N. Salam, R. Khatun, A. Bhaumik and S. M. Islam, Catal. Today, 2018, 309, 253–262 CrossRef;
(t) R. Khatun, P. Bhanja, R. A. Molla, S. Ghosh, A. Bhaumik and S. M. Islam, Mol. Catal., 2017, 434, 25–31 CrossRef CAS;
(u) I. H. Biswas, S. Biswas, M. S. Islam, S. Riyajuddin, P. Sarkar and K. Ghosh, New J. Chem., 2019, 43(36), 14643–14652 RSC;
(v) S. Biswas, R. Khatun, M. Dolai, I. H. Biswas, N. Haque, M. Sengupta and M. S. Islam, New J. Chem., 2020, 44(1), 141–151 RSC;
(w) S. Biswas, D. Roy, S. Ghosh and S. M. Islam, J. Organomet. Chem., 2019, 898, 120877 CrossRef;
(x) S. Ghosh, A. Ghosh, S. Riyajuddin, S. Sarkar, A. H. Chowdhury and K. Ghosh, ChemCatChem, 2020, 12(4), 1055–1067 CrossRef CAS;
(y) S. Ghosh, S. Riyajuddin, S. Sarkar, K. Ghosh and S. M. Islam, ChemNanoMat, 2020, 6(1), 160–172 CrossRef CAS;
(z) S. M. Islam, A. S. Roy, P. Mondal, S. Paul and N. Salam, Inorg. Chem. Commun., 2012, 24, 170–176 CrossRef CAS.
-
(a) H. M. El-Kaderi, J. R. Hunt, J. L. Mendoza-Cortes, A. P. Cote, R. E. Taylor, M. O'Keeffe and O. M. Yaghi, Science, 2007, 316, 268–272 CrossRef CAS PubMed;
(b) R. A. Molla, M. A. Iqubal, K. Ghosh and S. M. Islam, Green Chem., 2016, 18, 4649–4656 RSC;
(c) R. Khatun, S. Biswas, I. H. Biswas, S. Riyajuddin, N. Haque and K. Ghosh, J. CO2 Util., 2020, 40, 101180 CrossRef CAS;
(d) R. Khatun, P. Bhanja, R. A. Molla, S. Ghosh, A. Bhaumik and S. M. Islam, Mol. Catal., 2017, 434, 25–31 CrossRef CAS;
(e) S. Biswas, R. Khatun, M. Dolai, I. H. Biswas, N. Haque, M. Sengupta and S. M. Islam, New J. Chem., 2020, 44, 141–151 RSC;
(f) I. H. Biswas, S. Biswas, M. S. Islam, S. Riyajuddin, P. Sarkar and K. Ghosh, New J. Chem., 2019, 43, 14643–14652 RSC;
(g) S. Ghosh, A. Ghosh, S. Riyajuddin, S. Sarkar, A. H. Chowdhury and K. Ghosh, ChemCatChem, 2020, 12, 1055–1067 CrossRef CAS;
(h) S. Sarkar, S. Ghosh, J. Mondal and S. M. Islam, Chem. Commun., 2020, 56, 12202–12205 RSC;
(i) T. K. Dey, P. Bhanja, P. Basu, A. Ghosh and S. M. Islam, ChemistrySelect, 2019, 4, 14315–14328 CrossRef CAS;
(j) S. Ghosh, A. Ghosh, S. Biswas, M. Sengupta, D. Roy and S. M. Islam, ChemistrySelect, 2019, 4, 3961–3972 CrossRef CAS;
(k) S. S. Islam, S. Biswas, R. Ali Molla, N. Yasmin and S. M. Islam, ChemNanoMat, 2020, 6, 1386–1397 CrossRef CAS;
(l) P. Basu, T. K. Dey, S. Riyajuddin, S. Biswas, K. Ghosh and S. M. Islam, New J. Chem., 2020, 44, 12680–126919 RSC;
(m) R. Khatun, S. Biswas, S. Islam, I. H. Biswas, S. Riyajuddin, K. Ghosh and S. M. Islam, ChemCatChem, 2019, 11, 1303–1312 CrossRef;
(n) M. Sengupta, A. Bag, S. Ghosh, P. Mondal, A. Bordoloi and S. M. Islam, J. CO2 Util., 2019, 34, 533–542 CrossRef;
(o) A. H. Chowdhury, S. Ghosh and S. M. Islam, New J. Chem., 2018, 42, 14194–14202 RSC;
(p) R. Khatun, P. Bhanja, P. Mondal, A. Bhaumik, D. Das and S. M. Islam, New J. Chem., 2017, 41, 12937–12946 RSC;
(q) A. H. Chowdhury, U. Kayal, I. H. Chowdhury, S. Ghosh and S. M. Islam, ChemistrySelect, 2019, 4, 1069–1077 CrossRef;
(r) S. Ghosh, P. Bhanja, N. Salam, R. Khatun, A. Bhaumik and S. M. Islam, Catal. Today, 2018, 309, 253–262 CrossRef;
(s) R. A. Molla, K. Ghosh, K. Tuhina and S. M. Islam, New J. Chem., 2015, 39(2), 921–930 RSC;
(t) M. Islam, A. S. Roy and S. Islam, Cat. Lett., 2016, 146(6), 1128–1138 CrossRef CAS;
(u) S. M. Islam, N. Salam, P. Mondal, A. S. Roy, K. Ghosh and K. Tuhina, J. Mol. Catal. A: Chem., 2014, 387, 7–19 CrossRef CAS;
(v) S. Roy, B. Banerjee, N. Salam, A. Bhaumik and S. M. Islam, ChemCatChem, 2015, 7(17), 2689–2697 CrossRef CAS;
(w) S. M. Islam, R. A. Molla, A. S. Roy and K. Ghosh, RSC Adv., 2014, 4(50), 26181–26192 RSC;
(x) S. Roy, T. Chatterjee, B. Banerjee, N. Salam, A. Bhaumik and S. M. Islam, RSC Adv., 2014, 4(86), 46075–46083 RSC;
(y) S. Ghosh, T. S. Khan, A. Ghosh, A. H. Chowdhury, M. A. Haider and A. Khan, ACS Sustainable Chem. Eng., 2020, 8(14), 5495–5513 CrossRef CAS;
(z) R. Khatun, P. Bhanja, P. Mondal, A. Bhaumik, D. Das and S. M. Islam, New J. Chem., 2017, 41(21), 12937–12946 RSC.
- A. P. Cote, A. I. Benin, N. W. Ockwig, M. O'Keeffe, A. J. Matzger and O. M. Yaghi, Science, 2005, 310, 1166–1170 CrossRef CAS.
- N. L. Campbell, R. Clowes, L. K. Ritchie and A. I. Cooper, Chem. Mater., 2009, 21, 204–206 CrossRef CAS.
- B. P. Biswal, S. Chandra, S. Kandambeth, B. Lukose, T. Heine and R. Banerjee, J. Am. Chem. Soc., 2013, 135, 5328–5331 CrossRef CAS PubMed.
- D. D. Medina, J. M. Rotter, Y. Hu, M. Dogru, V. Werner, F. Auras, J. T. Markiewicz, P. Knochel and T. Bein, J. Am. Chem. Soc., 2015, 137, 1016–1019 CrossRef CAS PubMed.
- S. B. Kalidindi, H. Oh, M. Hirscher, D. Esken, C. Wiktor, S. Turner, G. Van Tendeloo and R. A. Fischer, Chem. – Eur. J., 2012, 18, 10848–10856 CrossRef CAS.
- T. Ben and S. Qiu, CrstEngComm, 2013, 15, 17–26 RSC.
- S. Y. Ding and W. Wang, Chem. Soc. Rev., 2013, 42, 548–568 RSC.
- Q. Fang, Z. Zhuang, S. Gu, R. B. Kaspar, J. Zheng, J. Wang, S. Qiu and Y. Yan, Nat. Commun., 2014, 5, 1–8 Search PubMed.
-
(a) M. Wu, G. Chen, P. Liu, W. Zhou and Q. Jia, Analyst, 2016, 141, 243–250 RSC;
(b) A. Das, R. K. Mondal, P. Chakrabortty, S. Riyajuddin, A. H. Chowdhury, S. Ghosh, A. Khan, K. Ghosh and S. M. Islam, Mol. Catal., 2021, 499, 111253 CrossRef CAS;
(c) M. Sengupta, A. Bag, S. Ghosh, P. Mondal, A. Bordoloi and S. M. Islam, J. CO2 Util., 2019, 34, 533–542 CrossRef CAS;
(d) S. S. Islam, S. Biswas, R. A. Molla, N. Yasmin and S. M. Islam, ChemNanoMat, 2020, 6, 1386–1397 CrossRef CAS;
(e) M. Islam, A. S. Roy and S. Islam, Catal. Lett., 2016, 146(6), 1128–1138 CrossRef;
(f) N. Haque, S. Biswas, S. Ghosh, A. H. Chowdhury, A. Khan and S. M. Islam, ACS Appl. Nano Mater., 2021, 4, 7663–7674 CrossRef;
(g) S. Sarkar, S. Ghosh, J. Mondal and S. M. Islam, Chem. Commun., 2020, 56, 12202–12205 RSC;
(h) S. Sarkar, S. Ghosh and S. M. Islam, Org. Biomol. Chem., 2022, 20, 1707–1722 RSC;
(i) P. Sarkar, A. H. Chowdhury, S. Riyajuddin, S. Biswas, K. Ghosh and S. M. Islam, New J. Chem., 2020, 44, 744–752 RSC;
(j) P. Chakrabortty, A. Das, A. H. Chowdhury, S. Ghosh, A. Khan and S. M. Islam, New J. Chem., 2021, 45, 4738–4745 RSC;
(k) P. Sarkar, A. H. Chowdhury, S. Biswas, A. Khan and S. M. Islam, Mater. Today Chem., 2021, 21, 100509 CrossRef CAS;
(l) S. Biswas, R. Khatun, M. Sengupta and S. M. Islam, Mol. Catal., 2018, 452, 129–137 CrossRef CAS;
(m) S. Roy, B. Banerjee, A. Bhaumik and S. M. Islam, RSC Adv., 2016, 6, 31153–31160 RSC;
(n) S. Ghosh, P. Bhanja, R. A. Molla, R. Khatun and S. M. Islam, ChemistrySelect, 2017, 2, 2159–2165 CrossRef CAS;
(o) I. H. Chowdhury, A. H. Chowdhury, A. Das, A. Khan and S. M. Islam, New J. Chem., 2020, 44, 11720–11726 RSC;
(p) P. Sarkar, S. Riyajuddin, A. Das, A. H. Chowdhury, K. Ghosh and S. M. Islam, Mol. Catal., 2020, 484, 110730 CrossRef CAS;
(q) S. M. Islam, N. Salam, P. Mondal and A. S. Roy, J. Mol. Catal. A: Chem., 2013, 366, 321–332 CrossRef CAS;
(r) S. M. Islam, P. Mondal, S. Mukherjee, A. S. Roy and A. Bhaumik, Polym. Adv. Technol., 2011, 22(6), 933–941 CrossRef CAS;
(s) M. Sengupta, A. Bag, S. Ghosh, P. Mondal, A. Bordoloi and S. M. Islam, J. CO2 Util., 2019, 34, 533–542 CrossRef;
(t) A. H. Chowdhury, S. Ghosh and S. M. Islam, New J. Chem., 2018, 42(17), 14194–14202 RSC;
(u) S. M. Islam, P. Mondal, S. Mukherjee, A. S. Roy and A. Bhaumik, Polym. Adv. Technol., 2011, 22(6), 933–941 CrossRef;
(v) S. M. Islam, A. Bose, B. K. Palit and C. R. Saha, J. Catal., 1998, 173(2), 268–281 CrossRef;
(w) S. Roy, T. Chatterjee, B. Banerjee, N. Salam, A. Bhaumik and S. M. Islam, RSC Adv., 2014, 4(86), 46075–46083 RSC;
(x) S. K. Das, B. K. Chandra, R. A. Molla, M. Sengupta, S. M. Islam and A. Majee, Mol. Catal., 2020, 480, 110650 CrossRef;
(y) P. Basu, P. Bhanja, N. Salam, T. K. Dey, A. Bhaumik, D. Das and S. M. Islam, Mol. Catal., 2017, 439, 31–40 CrossRef;
(z) N. Salam, P. Mondal, J. Mondal, A. S. Roy, A. Bhaumik and S. M. Islam, RSC Adv., 2012, 2(16), 6464–6477 RSC.
- A. Shahvar, R. Soltani, M. Saraji, M. Dinari and S. Alijani, J. Chromatogr. A, 2018, 1565, 48–56 CrossRef CAS PubMed.
- T. Sick, A. G. Hufnagel, J. Kampmann, I. Kondofersky, M. Calik, J. M. Rotter, A. Evans, M. Döblinger, S. Herbert, K. Peters, D. Böhm, P. Knochel, D. D. Medina, D. Fattakhova-Rohlfing and T. Bein, J. Am. Chem. Soc., 2018, 140, 2085–2092 CrossRef CAS.
- L. Ma, S. Wang, X. Feng and B. Wang, Chin. Chem. Lett., 2016, 27, 1383–1394 CrossRef CAS.
-
(a) V. Hasija, S. Patial, P. Raizada, A. A. P. Khan, A. M. Asiri, Q. Van Le, V. H. Nguyen and P. Singh, Coord. Chem. Rev., 2022, 452, 214298 CrossRef CAS;
(b) H. Wang, H. Wang, Z. Wang, L. Tang, G. Zeng, P. Xu, M. Chen, T. Xiong, C. Zhou, X. Liand and D. Huang, Chem. Soc. Rev., 2020, 49, 4135–4165 RSC;
(c) D. G. Wang, T. Qiu, W. Guo, Z. Liang, H. Tabassum, D. Xiaand and R. Zou, Energy Environ. Sci., 2021, 14, 688–728 RSC;
(d) J. You, Y. Zhao, L. Wangand and W. Bao, J. Cleaner Prod., 2021, 291, 125822 CrossRef CAS.
-
(a) R. B. Woodward, Pure Appl. Chem., 1973, 33, 145–177 CAS;
(b) E. J. Corey, Chem. Soc. Rev., 1988, 17, 111–133 RSC.
- Z. Chen, K. Wang, X. Hu, P. Shi, Z. Guo and H. Zhan, ACS Appl. Mater. Interfaces, 2020, 13, 1145–1151 CrossRef.
- H. S. Xu, Y. Luo, X. Li, P. Z. See, Z. Chen, T. Ma, L. Liang, K. Leng, I. Abdelwahab, L. Wang, R. Li, X. Shi, Y. Zhou, X. F. Lu, X. Zhao, C. Liu, J. Sun and K. P. Loh, Nat. Commun., 2020, 11, 1434 CrossRef CAS PubMed.
- D. Zhu, X. Li, Y. Li, M. Barnes, C. P. Tseng, S. Khalil, M. M. Rahman, P. M. Ajayan and R. Verduzco, Chem. Mater., 2021, 33, 413–419 CrossRef CAS.
- Y. Xing, L. Yin, Y. Zhao, Z. Du, H. Q. Tan, X. Qin, W. Ho, T. Qiu and Y. G. Li, Appl. Mater. Interfaces, 2020, 12, 51555–51562 CrossRef CAS.
- C. Wang, J. Tang, L. Li, J. Wan, Y. Ma, Y. Jin, J. Liu, H. Wangand and Q. Zhang, Adv. Funct. Mater., 2022, 2204068 CrossRef CAS.
- M. J. Kory, M. Wörle, T. Weber, P. Payamyar, S. W. van de Poll, J. Dshemuchadse, N. Trapp and A. D. Schlüter, Nat. Chem., 2014, 6, 779–784 CrossRef CAS.
- P. Kissel, D. J. Murray, W. J. Wulftange, V. J. Catalano and B. T. King, Nat. Chem., 2014, 6, 774–778 CrossRef CAS.
- E. Vitaku and W. R. Dichtel, J. Am. Chem. Soc., 2017, 139, 12911–12914 CrossRef CAS.
- S. Wan, F. Gandara, A. Asano, H. Furukawa, A. Saeki, S. K. Dey, L. Liao, M. W. Ambrogo, Y. Y. Botros and X. Duan, Chem. Mater., 2011, 23, 4094–4097 CrossRef CAS.
- Z. Lei, Q. Yang, Y. Xu, S. Guo, W. Sun, H. Liu, L.-P. Lv, Y. Zhang and Y. Wang, Nat. Commun., 2018, 9, 1–13 CrossRef.
- J. A. Ming, A. Liu, J. W. Zhao, P. Zhang, H. W. Huang, H. Lin, Z. T. Xu, X. M. Zhang, X. X. Wang, J. Hofkens, M. B. J. Roeffaers and J. L. Long, Angew. Chem., Int. Ed., 2019, 58, 18290–18294 CrossRef.
- D. G. Wang, T. Qiu, W. Guo, Z. Liang, H. Tabassum, D. Xia and R. Zou, Energy Environ. Sci., 2021, 14, 688–728 RSC.
- C. Liu, Y. Xiao, Q. Yang, Y. Wang, R. Lu, Y. Chen, C. Wang and H. Yan, Appl. Surf. Sci., 2021, 537, 148082 CrossRef CAS.
- M. Martínez-Abadía, K. Strutyński, C. T. Stoppiello, B. L. Berlanga, C. Martí-Gastaldo, A. N. Khlobystov, A. Saeki, M. Melle-Franco and A. Mateo-Alonso, Nanoscale, 2021, 13, 6829–6833 RSC.
- Y. Wang, W. Hao, H. Liu, R. Chen, Q. Pan, Z. Liand and Y. Zhao, Nat. Commun., 2022, 13, 1–7 Search PubMed.
- Y. Chen, Z.-L. Shi, L. Wei, B. Zhou, J. Tan, H.-L. Zhou and Y.-B. Zhang, J. Am. Chem. Soc., 2019, 141, 3298–3303 CrossRef CAS PubMed.
- H. Ding, J. Li, G. Xie, G. Lin, R. Chen, Z. Peng, C. Yang, B. Wang, J. Sun and C. Wang, Nat. Commun., 2018, 9, 1–7 CrossRef CAS.
- M. Zhang, J. Li, C. Zhang, Z. Wu, Y. Yang, J. Li, F. Fu and Z. Lin, J. Chromatogr. A, 2020, 1615, 460773–460783 CrossRef CAS.
- L. Wang, Y. Chen, Z. Zhang, Y. Chen, Q. Deng and S. Wang, Microchim. Acta, 2021, 188, 1–9 CrossRef.
- Y. Meng, Y. Luo, J. L. Shi, H. Ding, X. Lang, W. Chen, A. Zheng, J. Sun and C. Wang, Angew. Chem., Int. Ed., 2020, 59, 3624–3629 CrossRef CAS.
- C. Gao, J. Li, S. Yin, J. Sun and C. Wang, Nat. Commun., 2020, 11, 1–8 CrossRef.
- Y. Zhang, H. Li, J. Chang, X. Guan, L. Tang, Q. Fang, V. Valtchev, Y. Yan and S. Qiu, Small, 2021, 17, 2006112 CrossRef CAS.
- X. Liu, J. Li, B. Gui, G. Lin, Q. Fu, S. Yin, X. Liu, J. Sun and C. Wang, J. Am. Chem. Soc., 2021, 143, 2123–2129 CrossRef CAS PubMed.
- X. Wang, M. Bahri, Z. Fu, M. A. Little, L. Liu, H. Niu, N. D. Browning, S. Y. Chong, L. Chen, J. W. Ward and A. I. Cooper, J. Am. Chem. Soc., 2021, 143, 15011–15016 CrossRef CAS.
- M. Wu, H. Huang, B. Xu and G. Zhang, RSC Adv., 2022, 12, 16354–16357 RSC.
- Y. Du, H. Yang, J. M. Whiteley, S. Wan, Y. Jin, S. H. Lee and W. Zhang, Angew. Chem., 2016, 128, 1769–1773 CrossRef.
- Y. Song, Q. Sun, B. Aguila and S. Ma, Adv. Sci., 2018, 5, 1801410 Search PubMed.
- S. Liu, M. Wang, T. Qian, H. Ji, J. Liu and C. Yan, Nat. Commun., 2019, 10, 3898 CrossRef PubMed.
- D. Dong, H. Zhang, B. Zhou, Y. Sun, H. Zhang, M. Cao, J. Li, H. Zhou, H. Qian, Z. Lin and H. Chen, Chem. Commun., 2019, 55, 1458–1461 RSC.
- T. Bao, S. Wang, N. Zhang and J. Zhang, J. Chromatogr. A, 2021, 1645, 462130 CrossRef CAS PubMed.
- P. Puthiaraj, Y. R. Lee, S. Zhang and W. S. Ahn, J. Mater. Chem. A, 2016, 4, 16288–16311 RSC.
- J. Huo, B. Luo and Y. Chen, ACS Omega, 2019, 4, 22504–22513 CrossRef CAS PubMed.
- G. Wang, T. Zhou and Y. Lei, RSC Adv., 2020, 10, 11557–11564 RSC.
- Y. Yang, H. Niu, L. Xu, H. Zhang and Y. Cai, Appl. Catal., B, 2020, 269, 118799 CrossRef CAS.
- M. Dinari and F. Jamshidian, Polymer, 2021, 215, 123383 CrossRef CAS.
- C. Dai, T. He, L. Zhong, X. Liu, W. Zhen, C. Xue, S. Li, D. Jiang and B. Liu, Adv. Mater. Interfaces, 2021, 8, 2002191 CrossRef.
- M. Afshari, M. Dinari, K. Zargoosh and H. Moradi, Ind. Eng. Chem. Res., 2020, 59, 9116–9126 CrossRef.
- M. Afshari and M. Dinari, Composites, Part A, 2021, 147, 106453 CrossRef.
- M. Wang, H. Guo, N. Wu, J. Zhang, T. Zhang, B. Liu, Z. Pan, L. Peng and W. Yang, Colloids Surf., A, 2022, 634, 127928 CrossRef.
- G. Kim, T. Shiraki and T. Fujigaya, Bull. Chem. Soc. Jpn., 2020, 93, 414–420 CrossRef.
- Y. Liang, M. Xia, Y. Zhao, D. Wang, Y. Li, Z. Sui, J. Xiao and Q. Chen, J. Colloid Interface Sci., 2022, 608, 652–661 CrossRef.
- M. Li, Y. Wang, S. Sun, Y. Yang, G. Gu and Z. Zhang, Chem. Eng. J., 2022, 429, 132254 CrossRef.
- C. Dai, T. He, L. Zhong, X. Liu, W. Zhen, C. Xue, S. Li, D. Jiang and B. Liu, Adv. Mater. Interfaces, 2021, 8, 2002191 CrossRef CAS.
- Q. Fang, J. Wang, S. Gu, R. B. Kaspar, Z. Zhuang, J. Zheng, H. Guo, S. Qiu and Y. Yan, J. Am. Chem. Soc., 2015, 137, 8352–8355 CrossRef CAS.
- Z. Wang, B. Zhang, H. Yu, L. Sun, C. Jiao and W. Liu, Chem. Commun., 2010, 46, 7730–7732 RSC.
- J. Zhou, Y. Lei, C. Ma, W. Lv, N. Li, Y. Wang, H. Xu and Z. Zou, Chem. Commun., 2017, 53, 10536–10539 RSC.
- R. Van Der Jagt, A. Vasileiadis, H. Veldhuizen, P. Shao, X. Feng, S. Ganapathy, N. C. Habisreutinger, M. A. Van Der Veen, C. Wang, M. Wagemaker, S. Van Der Zwaag and A. Nagai, Chem. Mater., 2021, 33, 818–833 CrossRef CAS.
- R. Pan, J. Wu, W. Wang, C. Cheng and X. Liu, Colloids Surf., A, 2021, 621, 126511 CrossRef.
- N. Zhao, J. M. Liu, F. E. Yang, S. W. Lv, J. Wang and S. Wang, ACS Appl. Bio Mater., 2021, 4, 995–1002 CrossRef.
- B. Sun, X. Li, T. Feng, S. Cai, T. Chen, C. Zhu, J. Zhang, D. Wang and Y. Liu, ACS Appl. Mater. Interfaces, 2020, 12, 51837–51845 CrossRef PubMed.
- J. Maschita, T. Banerjee, G. Savasci, F. Haase, C. Ochsenfeld and B. V. Lotsch, Angew. Chem., Int. Ed., 2020, 59, 15750–15758 CrossRef.
- J. Maschita, T. Banerjee and B. V. Lotsch, Chem. Mater., 2022, 34(5), 2249–2258 CrossRef PubMed.
- T. Kim, S. H. Joo, J. Gong, S. Choi, J. H. Min, Y. Kim, G. Lee, E. Lee, S. Park, S. K. Kwak and H. S. Lee, Angew. Chem., 2022, 134, 202113780 Search PubMed.
- F. J. Uribe-Romo, J. R. Hunt, H. Furukawa, C. Klöck, M. O. Keeffe and O. M. Yaghi, J. Am. Chem. Soc., 2009, 131, 4570–4571 CrossRef.
- X. Liu, J. Li, B. Gui, G. Lin, Q. Fu, S. Yin, X. Liu, J. Sun and C. Wang, J. Am. Chem. Soc., 2021, 143, 2123–2129 CrossRef CAS.
- N. Bagherian, A. R. Karimi and A. Amini, Colloids Surf., A, 2021, 613, 126078 CrossRef.
- H. Wang, D. Wang, Y. Liu, Z. Wang, C. Li, S. Sun, Q. Lyu and S. Hu, Appl. Surf. Sci., 2022, 152601 CrossRef.
- J. Á. Martín-Illán, D. Rodríguez-San-Miguel, O. Castillo, G. Beobide, J. Perez-Carvajal, I. Imaz, D. Maspoch and F. Zamora, Angew. Chem., Int. Ed., 2021, 60, 13969–13977 CrossRef.
- K. Feng, H. Hao, F. Huang, X. Lang and C. Wang, Mater. Chem. Front., 2021, 5, 2255–2260 RSC.
- X. Wu, X. Zhang, Y. Li, B. Wang, Y. Li and L. Chen, J. Mater. Sci., 2021, 56, 2717–2724 CrossRef.
- R. Bu, L. Zhang, L. L. Gao, W. J. Sun, S. L. Yang and E. Q. Gao, J. Mol. Catal., 2021, 499, 111319 CrossRef.
- R. Chen, Y. Wang, Y. Ma, A. Mal, X. Y. Gao, L. Gao, L. Qiao, X. B. Li, L. Z. Wu and C. Wang, Nat. Commun., 2021, 12, 1–9 CrossRef PubMed.
- N. Bagherian, A. R. Karimi and A. Amini, Colloids Surf., A, 2021, 613, 126078 CrossRef CAS.
- L. R. Ahmed, A. F. EL-Mahdy, C. T. Pan and S. W. Kuo, Adv. Mater., 2021, 2, 4617–4629 RSC.
- D. M. Li, S. Y. Zhang, J. Y. Wan, W. Q. Zhang, Y. L. Yan, X. H. Tang, S. R. Zheng, S. L. Cai and W. G. Zhang, CrystEngComm, 2021, 23, 3594–3601 RSC.
- S. Wu, Y. F. Zhang, H. Ding, X. Li and X. Lang, J. Colloid Interface Sci., 2022, 610, 446–454 CrossRef CAS PubMed.
- W. Gong, C. Liu, H. Shi, M. Yin, W. Li, Q. Song, Y. Dong and C. Zhang, J. Mater. Chem. C, 2022, 10, 3553–3559 RSC.
- P. J. Waller, S. J. Lyle, T. M. Osborn Popp, C. S. Diercks, J. A. Reimer and O. M. Yaghi, J. Am. Chem. Soc., 2016, 138, 15519–15522 CrossRef CAS PubMed.
- Z. B. Zhou, X. H. Han, Q. Y. Qi, S. X. Gan, D. L. Ma and X. Zhao, J. Am. Chem. Soc., 2022, 144, 1138 CrossRef CAS.
- H. L. Qian, F. L. Meng, C. X. Yang and X. P. Yan, Angew. Chem., Int. Ed., 2020, 59, 17607–17613 CrossRef CAS PubMed.
- S. Wu, N. Ding, P. Jiang, L. Wu, Q. Feng, L. Zhao, Y. Wang, Q. Su, H. Zhang and Q. Yang, Tetrahedron Lett., 2020, 61, 152656 CrossRef.
- S. Ma, Z. Li, J. Jia, Z. Zhang, H. Xia, H. Li, X. Chen, Y. Xu and X. Liu, Chin. J. Catal., 2021, 42, 2010–2019 CrossRef.
- P. Das and S. K. Mandal, ACS Appl. Mater. Interfaces, 2021, 13, 14160–14168 CrossRef.
- Z. Li, J. A. Wang, S. Ma, Z. Zhang, Y. Zhi, F. Zhang, H. Xia, G. Henkelman and X. Liu, Appl. Catal., B, 2022, 310, 121335 CrossRef.
- Z. Yang, J. Liu, Y. Li, G. Zhang, G. Xing and L. Chen, Angew. Chem., Int. Ed., 2021, 60, 20754–20759 CrossRef PubMed.
- L. Zhang, Z. J. Zhao and J. Gong, Angew. Chem., Int. Ed., 2017, 56, 11326–11353 CrossRef.
- K. J. P. Schouten, Y. Kwon, C. J. M. van der Ham, Z. Qin and M. T. M. Koper, Chem. Sci., 2011, 2, 1902–1909 RSC.
- Z. Fu, X. Wang, A. M. Gardner, X. Wang, S. Y. Chong, G. Neri, A. J. Cowan, L. Liu, X. Li, A. Vogel and R. Clowes, Chem. Sci., 2020, 11, 543–550 RSC.
- K. Lei, D. Wang, L. Ye, M. Kou, Y. Deng, Z. Ma, L. Wang and Y. Kong, ChemSusChem, 2020, 13, 1725–1729 CrossRef PubMed.
- I. H. Chowdhury, A. H. Chowdhury, A. Das, A. Khan and S. M. Islam, New J. Chem., 2020, 44, 11720–11726 RSC.
- Y. Xiang, W. Dong, P. Wang, S. Wang, X. Ding, F. Ichihara, Z. Wang, Y. Wada, S. Jin, Y. Weng and H. Chen, Appl. Catal., B, 2020, 274, 119096 CrossRef.
- L. J. Wang, R. L. Wang, X. Zhang, J. L. Mu, Z. Y. Zhou and Z. M. Su, ChemSusChem, 2020, 13, 2973–2980 CrossRef.
- M. Lu, Q. Li, J. Liu, F. M. Zhang, L. Zhang, J. L. Wang, Z. H. Kang and Y. Q. Lan, Appl. Catal., B, 2019, 254, 624–633 CrossRef.
- S. Q. You, J. Zhou, M. M. Chen, C. Y. Sun, X. J. Qi, A. Yousaf, X. L. Wang and Z. M. Su, J. Catal., 2020, 392, 49–55 CrossRef.
- Z. Fu, X. Wang, A. M. Gardner, X. Wang, S. Y. Chong, G. Neri, A. J. Cowan, L. Liu, X. Li, A. Vogel, R. Clowes, M. Bilton, L. Chen, R. S. Sprick and A. I. Cooper, Chem. Sci., 2020, 11, 543–550 RSC.
- Y. Huang, P. Du, W. X. Shi, Y. Wang, S. Yao, Z. M. Zhang, T. B. Lu and X. Lu, Appl. Catal., B, 2021, 288, 120001 CrossRef.
- N. Singh, D. Yadav, S. V. Mulay, J. Y. Kim, N. J. Park and J. O. Baeg, ACS Appl. Mater. Interfaces, 2021, 13, 14122–14131 CrossRef PubMed.
- K. Guo, X. Zhu, L. Peng, Y. Fu, R. Ma, X. Lu, F. Zhang, W. Zhu and M. Fan, Chem. Eng., 2021, 405, 127011 CrossRef.
- L. Peng, S. Chang, Z. Liu, Y. Fu, R. Ma, X. Lu, F. Zhang, W. Zhu, L. Kong and M. Fan, Catal. Sci. Technol., 2021, 11, 1717–1724 RSC.
- M. Fernández, A. Shamsabadi and V. Chudasama, Chem. Commun., 2020, 56, 1125–1128 RSC.
- G. C. D. Bandomo, S. S. Mondal, F. Franco, A. Bucci, V. Martin-Diaconescu, M. A. Ortuño, P. H. van Langevelde, A. Shar, N. López and J. Lloret-Fillol, ACS Catal., 2021, 11, 7210–7222 CrossRef.
- Y. Zhao, L. Hao, J. Ning, H. Zhu, A. Vijayakumar, C. Wang and G. G. Wallace, Appl. Catal., B, 2021, 291, 119915 CrossRef.
- M. Liu, Y. R. Wang, H. M. Ding, M. Lu, G. K. Gao, L. Z. Dong, Q. Li, Y. Chen, S. L. Li and Y. Q. Lan, Sci. Bull., 2021, 66, 1659–1668 CrossRef.
- Q. Wu, M. J. Mao, Q. J. Wu, J. Liang, Y. B. Huang and R. Cao, Small, 2021, 17, 2004933 CrossRef.
- M. D. Zhang, D. H. Si, J. D. Yi, S. S. Zhao, Y. B. Huang and R. Cao, Small, 2020, 16, 2005254 CrossRef PubMed.
- Q. Wu, R. K. Xie, M. J. Mao, G. L. Chai, J. D. Yi, S. S. Zhao, Y. B. Huang and R. Cao, ACS Energy Lett., 2020, 5, 1005–1012 CrossRef.
- H. J. Zhu, M. Lu, Y. R. Wang, S. J. Yao, M. Zhang, Y. H. Kan, J. Liu, Y. Chen, S. L. Li and Y. Q. Lan, Nat. Commun., 2020, 11, 1–10 CrossRef PubMed.
- B. Han, X. Ding, B. Yu, H. Wu, W. Zhou, W. Liu, C. Wei, B. Chen, D. Qi, H. Wang and K. Wang, J. Am. Chem. Soc., 2021, 143, 7104–7113 CrossRef.
- S. An, C. Lu, Q. Xu, C. Lian, C. Peng, J. Hu, X. Zhuang and H. Liu, ACS Energy Lett., 2021, 6, 3496–3502 CrossRef.
- J. Huang and K. Pu, Angew. Chem., Int. Ed., 2020, 132, 11813–11827 CrossRef.
- Y. Lu, J. Zhang, W. Wei, D. D. Ma, X. T. Wu and Q. L. Zhu, ACS Appl. Mater. Interfaces, 2020, 12, 37986–37992 CrossRef.
- M. Lu, M. Zhang, C. G. Liu, J. Liu, L. J. Shang, M. Wang, J. N. Chang, S. L. Li and Y. Q. Lan, Angew. Chem., Int. Ed., 2021, 133, 4914–4921 CrossRef.
- B. Wang, F. Yang, Y. Dong, Y. Cao, J. Wang, B. Yang, Y. Wei, W. Wan, J. Chen and H. Jing, Chem. Eng., 2020, 396, 125255 CrossRef CAS.
- S. Q. You, J. Zhou, M. M. Chen, C. Y. Sun, X. J. Qi, A. Yousaf, X. L. Wang and Z. M. Su, J. Catal., 2020, 392, 49–55 CrossRef CAS.
- B. Han, X. Ding, B. Yu, H. Wu, W. Zhou, W. Liu, C. Wei, B. Chen, D. Qi, H. Wang and K. Wang, J. Am. Chem. Soc., 2021, 143, 7104–7113 CrossRef CAS PubMed.
- B. Han, Y. Jin, B. Chen, W. Zhou, B. Yu, C. Wei, H. Wang, K. Wang, Y. Chen, B. Chen and J. Jiang, Angew. Chem., 2022, 134, e202114244 Search PubMed.
- S. Y. Chi, Q. Chen, S. S. Zhao, D. H. Si, Q. J. Wu, Y. B. Huang and R. Cao, J. Mater. Chem. A, 2022, 10, 4653–4659 RSC.
- Q. Pan, M. Abdellah, Y. Cao, W. Lin, Y. Liu, J. Meng, Q. Zhou, Q. Zhao, X. Yan, Z. Liand and H. Cui, Nat. Commun., 2022, 13, 1–13 Search PubMed.
- H. Dong, M. Lu, Y. Wang, H. L. Tang, D. Wu, X. Sunand and F. M. Zhang, Appl. Catal., B, 2022, 303, 120897 CrossRef CAS.
-
(a) S. Kandambeth, D. B. Shinde, M. K. Panda, B. Lukose, T. Heine and R. Banerjee, Angew. Chem., Int. Ed., 2013, 52, 13052–13056 CrossRef CAS;
(b) H. Xu, J. Gao and D. Jiang, Nat. Chem., 2015, 7, 905 CrossRef CAS.
-
(a) M. S. Lohse and T. Bein, Adv. Funct. Mater., 2018, 28, 1705553 CrossRef;
(b) F. J. Uribe-Romo, C. J. Doonan, H. Furukawa, K. Oisaki and O. M. Yaghi, J. Am. Chem. Soc., 2011, 133, 11478–11481 CrossRef CAS;
(c) S. Kandambeth, A. Mallick, B. Lukose, M. V. Mane, T. Heine and R. Banerjee, J. Am. Chem. Soc., 2012, 134, 19524–19527 CrossRef CAS PubMed;
(d) Z. Li, Y. Zhang, H. Xia, Y. Mu and X. Liu, Chem. Commun., 2016, 52, 6613–6616 RSC.
- J. Guo, Y. Xu, S. Jin, L. Chen, T. Kaji, Y. Honsho, M. A. Addicoat, J. Kim, A. Saeki, H. Ihee, S. Seki, S. Irle, M. Hiramoto, J. Gao and D. Jiang, Nat. Commun., 2013, 4, 2736 CrossRef.
|
This journal is © The Royal Society of Chemistry 2022 |
Click here to see how this site uses Cookies. View our privacy policy here.