DOI:
10.1039/D1SM00958C
(Review Article)
Soft Matter, 2021,
17, 9842-9858
Micro- and nanocelluloses from non-wood waste sources; processes and use in industrial applications
Received
28th June 2021
, Accepted 12th October 2021
First published on 13th October 2021
Abstract
In addition to renewability and abundance, nanocellulose materials have tremendous (and variable) properties for different applications, ranging from bulk applications, such as paper and packaging reinforcement, to emerging high added-value applications, such as substrates for optoelectronics. Lignocellulosic biomass from agricultural and industrial waste sources is readily available and shows great promise as an inexpensive and sustainable raw material for nanocellulose production. However, the understanding of the potential of using non-wood based biowaste sources is not established and systematic comparisons of versatile agricultural and industrial waste sources can elucidate this complex topic. Here we present an overview of the most studied and most promising sources from agro-industrial waste, the processes to convert them into nanocellulose, some of the established and emerging applications, and discuss the advancements that are still needed for large-scale production. Sugarcane bagasse and oil palm empty fruit bunch have been the most researched waste-based sources for nanocellulose production and demonstrate the most promise due to availability and access. Industrial sources seem to have advantages over agricultural sources in collectability and ease of access. This work gives insight on the potential and the challenges of nanocellulose production from waste sources and discusses how the criteria set for nanocellulose materials in different applications can be met, thus opening new routes for circular economy.
1 Introduction and definition of the key terms
Recent developments towards use of renewable resources have created a strong incentive to utilize cellulose as an alternative to many oil-based polymers in the form of nanocellulose.1 The main hindrance in commercialization of nanocellulose applications has been the lack of optimized industrial-scale production of nanocellulose.2 Other impediments include the lack of industrial-scale quality control and safety standards. Moreover, industrial production requires an abundant source of cellulose and, currently, wood is the most used source of cellulose production in the world.3 Hence, nanocellulose production is in inherent competition with current wood industries, such as pulp and paper, furniture, and construction. Moreover, using long high quality virgin fibre from wood just to chop it to small pieces in nanocellulose production could be considered an inefficient use of resources.
One way to bypass the issues related to wood as a raw material, is to use agricultural and industrial waste as a cellulose source for nanocellulose production.4,5 This could potentially gain both environmental and financial benefits as currently large amounts of biomass is burnt or tossed away as waste from agriculture and industry even in the developed countries.6 This would also pave the way for circular economy and resource-wise society. Biowastes are readily available independent of the climate zone, inexpensive, and renewable. Furthermore, the value added to otherwise unusable biomass could potentially be manifold and the bulk applications would benefit from not having to use expensive high quality virgin fibre from wood. Moreover, relatively recent progress in chemical and enzymatic pre-treatment has plummeted the price of nanocellulose. Consequently, previously extremely high energy consumption of mechanical disintegration has decreased and thus reduced the overall cost and increased sustainability.7,8
Cellulose, the main structural component in plants, is mostly located in the secondary cell wall of plants, and is composed of fibrils that are bundles a few microns thick.9 Each bundle is made of millions of microfibrils that are 10–50 nm in diameter.5 Microfibrils are made up of elementary fibrils that are 5 nm thick and semicrystalline.5 In addition to cellulose, plant biomass consists mostly of hemicellulose, lignin, and pectin, with some minor components like proteins and lipids. Hemicellulose acts as a matrix in cell wall and it is crosslinked by pectin in the outer primary cell wall and by lignin in the inner secondary cell wall providing strength to the structure.9 However, it is important to note that lignin is present only in vascular plants (tracheophytes).12Fig. 1 shows the structure of cellulose in plants. Depending on the plant, the composition of biomass and methods of cellulose isolation differ. Generally, wood has a higher overall cellulose content, but also more lignin, which makes isolation of cellulose more difficult, whereas softer industrial wastes, such as fruit pomace, contain more pectin and less lignin and cellulose, making isolation somewhat easier.13
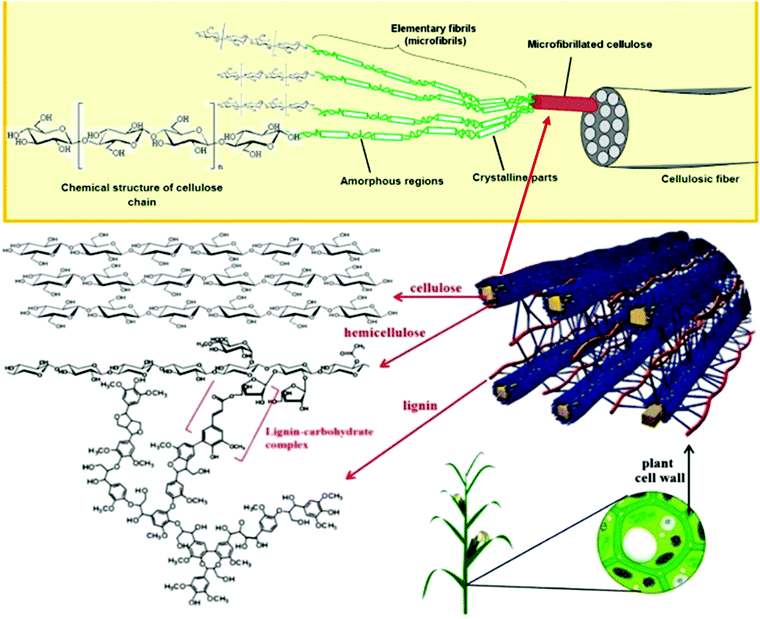 |
| Fig. 1 Figure shows structure of plants from cellular level down to structures of the chemical components. Figure is adapted and combined from two different sources10,11 with permission. Copyrights (2012) Elsevier and (2017) De Gruyte. | |
Nanocellulose literature is plagued by the nonunified terminology, which significantly imparts the comparison of different research articles. When talking in lay-terms nanocellulose is often defined as cellulose consisting of fibres or fibrils with at least one dimension in the nanoscale. It is now classified with ISO/TS 20477:2017 into three different categories having different functionalities and fabrication routes: cellulose nanofibers (CNF), cellulose nanocrystals (CNC), and bacterial cellulose (BC).2 The difference between CNC and CNF is illustrated in Fig. 2. Manufacturing of CNF traditionally consists of possible pre-treatment and mechanical grinding, even though it can be produced with only chemical treatment via TEMPO-mediated oxidation. Cellulose nanocrystals, which are isolated with acid treatment, are lower in aspect ratio and highly crystalline.5,8,14
 |
| Fig. 2 AFM pictures showing the fibril shape of MFC (a) and rod-like shape of CNC (b). Adapted with permission from ref. 15 Copyright (2018) Elsevier. | |
Cellulose nanofibrils often encompass a distribution of different fibril sizes ranging up to μm size fibril bundles. Even though the term microfibrillated cellulose (MFC) has an explicit reference to a μm-length scale, MFC has been used interchangeably with cellulose nanofibrils (CNF) or nanofibrillar cellulose (NFC)8 For the sake of clarity, the terms used in this article are MFC and CNC. With MFC, we mean an umbrella term to describe nanocellulose with high aspect ratio, length often being in microns and diameter on nanoscale. The exact length and diameter will always depend on the cellulose source and the manufacturing process.
This review maps the possibilities of nanocellulose production from agricultural and industrial waste and identifies the most promising material sources for large scale production of nanocellulose as well as the most potential applications with an industrial relevancy. In this contribution, we review the recent literature, which reports converting agricultural and industrial waste sources either to MFC or to CNC. These different raw materials are compared from the point of the view of prevalence in the literature, raw material availability, and ease of processing. As the most promising individual sources, sugarcane bagasse and oil palm empty fruit bunch emerged. Both are industrial sources that generate a lot of waste biomass concentrated at the processing mills, which was found to be highly beneficial. Waste biomass could also provide cheaper alternative to wood-based cellulose with improvements in process efficiency. Moreover, we will give an overview of the application prospects of these functional materials that have a huge potential to redeem the promise of circular economy in making these applications not only more cost-effective, but also significantly more sustainable.
2 Isolation of nanocellulose
Production of nanocellulose from lignocellulosic material is a two-step process. First step is purification of cellulosic material by removing lignin, hemicellulose, and other possible extractives, such as wax or pectin.16 It can be done with various cooking and bleaching methods that resemble the ones used in papermaking.8 Although MFC has been isolated directly from rice straw without any pre-treatment, the approach with traditional purification methods combined with separate nanocellulose isolation is more common.17
Second step is the isolation of nanocellulose that can be divided to two distinct categories, MFC isolation or CNC isolation. CNC isolation is a one-step process done with acid hydrolysis or with a strong oxidizer such as ammonium persulfate.17,18 The most used acids are sulfuric and hydrochloric acids, but due to environmental harm, corrosion of the equipment and difficulty of recovery of acid wastes, eco-friendlier alternatives, such as citric acid, are demonstrated.19 Acid hydrolysis removes the amorphous part of elemental fibrils, leaving the cellulosic material as rod-like highly crystalline nanoparticles with diameters around 3–35 nm and lengths of 200–500 nm, as illustrated in Fig. 2b.8Fig. 3 and 4 show the basic process steps of CNC and MFC isolation respectively.
 |
| Fig. 3 Flowchart presenting the CNC isolation process. | |
 |
| Fig. 4 MFC isolation process steps. Adapted from ref. 8. Copyright (2016) with permission from Elsevier. | |
MFC isolation is usually a multistep process, and it includes possible mechanical and chemical/biochemical pre-treatments, principal mechanical treatment, and optional post-treatments. The goal of the process is to fibrillate the fibril bundles to elementary fibrils or microfibrils 5–50 nm in diameter without reducing the length of the fibrils under micron range to achieve high aspect ratio.8 Due to the multitude of different preparation methods combined to the differences in the available raw material sources, the physical properties of the final MFC produced depends highly on the employed process, thus also rendering the comparison of publications reporting the same application but different MFC highly complicated.
3 Unique properties of nanocellulose and its applications
3.1 Established applications
Taken into account that a wide range of different physical properties can be achieved by varying the preparation process and the raw material source of nanocellulose, it is a promising materials family for multitude of applications. The connection between nanocellulose manufacturing processes and thus the composition of nanocellulose and exact specifications and requirements of proposed applications are not well established yet and more research is needed on the topic. This is especially pressing for emerging application areas, but also holds true for the most established applications of nanocellulose materials.
Currently, the most voluminous applications are: 1. paper, board, and packaging, 2. composites, and 3. filtration, with proportions of 36%, 25% and 19% of the market share, respectively.2 According to a recent review on nanocellulose from non-wood sources, the top research topics other than fundamental characterization were plastic nanocomposites, bionanocomposites, biomedical, electronic, adsorbent, and papermaking.20 Proportions of these research topics are shown in Fig. 5. Fig. 5b illustrates examples of nanocellulose and introduces the most important fields of the emerging applications. In following chapter, the potential and challenges of all these application areas will be briefly discussed to motivate further research of how to develop nanocellulose fabrication process from waste sources.
 |
| Fig. 5 (a) Shows proportions of the top research topics on nanocellulose. Reproduced with permission from ref. 20. Copyright (2019) Springer Nature. (b-i) Depict the various nanocellulose applications introduced in chapter 3. (b)–(d), (f) and (h) Reproduced with permission from http://www.pixabay.com. (e) Reproduced with permission from ref. 21. Copyright (2009) Elsevier. (g) Reproduced with permission from ref. 22. Copyright (2020) Royal Society of Chemistry. (i) Reproduced with permission from ref. 23. Copyright (2007) American Chemical Society. | |
3.1.1 Paper, board, and packaging.
Paper and board industry faces continuous pressure to produce better quality products with cost effective and more environmentally friendly processes. Inclusion of nanocellulose is seen as one of the options of improving the quality of the products in terms of strength and barrier properties.2 Nanocellulose has unique properties, such as high surface area, aspect ratio, mechanical strength, and stiffness. These properties combined with availability, biodegradability, and sustainability makes it desirable option compared to synthetic polymers such as polyolefins.24
The demand for cardboard has risen in recent years and it is often made up of recycled fibre. This generates a problem as the quality and the mechanical strength of the cardboard diminishes each time the fibres are reused.24 Nanocellulose has been proposed to be bio-based alternative to the synthetic reinforcing materials. Current use of nanocellulose in packaging is mostly as reinforcement in biodegradable packaging. The aim is to reduce the amount and quality of fibres needed while maintaining or improving the mechanical properties and it can be achieved with addition of low concentration of nanocellulose.25
Food packaging is an emerging application of nanocellulose that is pursued to achieve environmental benefits by moving away from oil-based polymers. Nanocellulose films have great barrier properties for many molecules due to their nanoscale dimensions, crystallinity, and their highly crosslinked network with small pores, which obstructs the molecules from passing through easily.26 Problems arise when films come to contact with water vapour, as nanocellulose is extremely hydrophilic and tends to swell and lose its structure. This has been combated by chemical modification and by high aspect ratio fillers to make nanocomposites with better qualities, but they affect the recyclability negatively.27
Paper, board, and packaging is a high-volume application with the largest market share and would thus benefit enormously from low-cost material in MFC or CNC production. In theory, in these applications the fibril size distribution could be wider, thus making the nanocellulose production processes easier. The role of non-wood based MFC could be as reinforcement fibres in cardboard or paper especially in countries without their own forest industry.28 High quality recycled paper and board products could be produced locally via utilizing available waste stream cellulosic feedstocks in the production.
3.1.2 Composites.
Nanocellulose is used in composites as reinforcement in the matrix. Its great mechanical properties, such as strength, stiffness, and high modulus of elasticity combined with low thermal coefficient, large specific surface area and renewability and sustainability makes it suitable for composites.29–32 Nanocellulose can be used as a filler fibre in relatively simple applications such as cement matrices, but also in biodegradable composites, that are being developed to reduce the consumption of oil-based plastics.30 The mechanical properties together with great modifiability and affinity with various materials makes nanocellulose suitable for more advanced materials and composites, opening possibilities for e.g., electronic, biomedical, and coating applications.31 The exact parameters for optimal mechanical properties are still unclear for nanocellulose composites, and more research on the systemic effects of different properties, such as charge density, aspect ratio, and fibre diameter is needed.29 Overall, the ecological benefits of nanocellulose use in composites could be substantial. The benefits of non-wood sources of nanocellulose could be big in high volume applications such as composites due to the lower energy consumption in production compared to wood.13 A specification window might be wider for nanocelluloses when used in composites meaning the production processes can be less controlled than in more specific applications.
3.1.3 Filtration.
Water purification is an important topic to research as there are still a lot of people in developing countries without access to clean water.33 Wastewater treatment could also benefit from advances in nanocellulose filtration technology, as membrane filtration, such as reverse osmosis and nanofiltration, provide a simple physical purification process even for the nanoscale contaminants that could challenge the traditional water treatment processes.34 Nanocellulose-based membranes have the advantage of great mechanical properties as they increase the durability and lifespan of the filters. Regarding filtration, the large specific surface area, high aspect ratio and vast opportunities for chemical modification are the most important strengths of nanocellulose. Nanocellulose membranes can be effective by themselves, but currently nanocellulose membranes combined with organic or inorganic components have been shown to perform the best.35 The motivation to use nanocellulose in filtration is mostly environmental and cost reduction, but it has been shown to have competitive qualities which make it a viable option for current market leaders such as synthetic polymers and coagulation/flocculation technique. MFC is more commonly used in filtration applications, but also CNC use has been experimented in composite filters. The high cost and low availability of low and uniform diameter nanocellulose still limits the commercial efficiency of nanocellulose filtration on large-scale. The use of agricultural and industrial wastes as nanocellulose source could be especially beneficial in countries where clean water is an issue and wood-based cellulose is not readily available.
3.2 Emerging applications
Some of the emerging applications will be introduced in this chapter. The current use of nanocellulose in these applications is not widespread, but they all show large potential and are intensively studied. Different applications require nanocelluloses with different physical qualities and especially some of the emerging applications require specific properties. For example, nanocellulose use in photovoltaic devices and textiles utilize completely different properties of nanocellulose, but both could benefit from its use. Instead of processing nanocellulose from conventional wood sources to fit the different parameters, it could be possible to utilize a waste source with properties already more fitting to the requirements. Due the differences in composition, plant morphology, and fibre morphology from different cellulose sources, the biomass selection is important step to optimize sustainability, material performance, and economic benefit.20
3.2.1 Electronics.
Nanocellulose composites can be used in electronic applications, especially in flexible electronics. The development of nanocellulose based flexible electronics could enable both lightweight and flexible basic electronic components and more advanced innovations.36 Replacing glass with nanocellulose films could be especially beneficial in lightweight and flexible electronics due to both ecology and properties nanocellulose.37 Nanocellulose itself is not conductive but it fits as a substrate for electronics as it has many desirable qualities compared to the commonly used substrates, metal foils, plastics, and glasses. In addition to the lightweight and renewability of nanocellulose, the architecture of nanocellulose allows modification and good affinity with various active materials such as gold and silver nanoparticles or metal oxides, which the commonly used alternatives lack.36 Different electronic applications with nanocellulose include basic components, such as electrodes, circuits, switches, and transistors, energy storage devices, nanogenerators, POC diagnostics, different kinds of sensors and photovoltaic devices.36,38,39 Overall electronics and photonics are expected to benefit remarkably both from the physical qualities that nanocellulose provides, and the ecological aspects.
3.2.2 Photonic structures and light management.
Emerging field of nanocellulose applications, photonic structures and light management includes applications such as light manipulation (photonic structural colours, transparency control etc.), photonic enabled chemical/physical sensing, and energy harvesting.40,41 The research of photonic applications of nanocellulose is very much in its beginning, and lots of development is needed to achieve the next generation photonic devices.40 Most of the photonic applications other than transparent films need a crystal structure and thus CNC is the preferred. The crystal structure must be precise to produce consistent colours and with nanocellulose based photonic structures achieving consistent results is a problem currently.40 In transparent films CNFs have the advantage of better mechanical strength. The transparency can be controlled with the diameter of the CNFs, but with better transparency comes worse mechanical strength.41 The ideal solution could be the mixture of CNF and CNC or different nanocomposites.41 Like electronics, photonic structures and light management could benefit both from physical qualities and ecological aspects.
3.2.3 Biomedical applications.
Nanocellulose is being studied for various biomedical application, ranging from drug delivery to biomimetic tissues and antibacterial materials.32,42 The potential in drug delivery applications is based on the high surface area, biocompatibility, availability, and surface modifiability of nanocellulose. These properties allow controlled and sustained release of drugs and provide solubility for poorly water-soluble drugs.43 Antibacterial applications rely on the ability of nanocellulose matrix to host different nanoparticles, such as Ag, TiO2, and ZnO.32 With its mechanical qualities combined with low toxicity and good biocompatibility, nanocellulose shows great potential for different biomedical applications but more research is still needed.
3.2.4 Coating, paint, stabilizer, and rheological applications.
Nanocellulose has shown its potential in coating, paint, stabilizer, and rheological applications.44–47 The ability to increase viscosity of solution even at relatively low solid contents due to the high specific surface area and crosslinking of nanocellulose makes it viable as a rheological modifier for different applications.46 Surface modifiability and great mechanical strength of nanocelluloses allow them to work as stabilizers in Pickering emulsions, which combined with the biocompatibility, makes them good for food additives and drug delivery, but also for painting and coating applications.47 The use of nanocellulose in Pickering emulsions could pave way towards novel biobased materials with easily scalable manufacturing due to mild and simple processing steps. Currently, the problem seems to be the lack of proper understanding of how multicomponent solvent systems affect the stability of Pickering emulsions.47 In rheology modifiers the surface chemistry seemed to play bigger part than the dimensions of the nanocellulose particles.46 Also, the role of nanocellulose from an interface stabilizer (Pickering emulsions etc.) to formation of continuous network is not simple, and its precise role is often disregarded in literature.45
3.2.5 Textile fibres.
As the world cotton production is closing on its maximum capacity, and the demand for textiles is not declining, man-made cellulosic fibres (MMCFs) are destined to fill the gap.48 Current market leaders in MMCFs, viscose and Lyocell, both require highly purified dissolved pulp or paper-grade pulp for the optimal production process. Additionally, both have environmental setbacks such as toxic chemicals and hazardous byproducts (viscose); and need for stabilizers to control the reaction (Lyocell).49 The use of ionic liquids with dry jet-wet spinning in a process termed Ioncell-F bypasses these restraints to produce MMCFs with an environment friendly process that tolerates low purity raw materials.49 The tolerance for waste cellulose sources, the absence of additional chemicals, and the possibility to reuse the ionic liquid in a continuous process could lead to a sustainable textile industry. Ionic liquids have also been used to manufacture nanocellulose from waste sources.50 Furthermore, in a similar dry jet-wet spinning ionic liquid manufacturing process, core shell filaments (CSF) with regenerated cellulose exterior and inner core of CNF have been fabricated from dissolved cellulose and TEMPO oxidized CNF hydrogel.51 These CSFs have been modified to function in e.g., wearable electronics, adsorbents, flame retardant fibers, and smart textiles.51 Overall, ionic liquids combined with waste cellulose sources could achieve more sustainable textile and smart textile industries.
4 MFC and CNC from waste sources
4.1 Agricultural waste as MFC source
Agricultural waste is one of the largest available biomass sources. Some of the waste is utilized actively as, for example, food for livestock or biomass for biofuel. Yet massive sources of biomass are still underutilized. Furthermore, they could be utilized as a material in high value applications such as production of nanocellulose. This chapter introduces different agricultural waste sources of biomass for fibre production in the order of hits in literature, and present ways of refining biomass to nanocellulose. Raw materials introduced in this chapter will be rice straw, wheat straw, corn stover, pineapple leaves, oil palm frond, cotton stalks and tobacco. They were the most researched agricultural waste sources for nanocellulose in Scopus database (see associated content for detailed description of the applied search method).
4.1.1 Rice straws.
Rice is one of the largest crops in the world. 90% of the production is in Asia, and China and India alone account for approximately 50% of the total production. More than 660 million tonnes of rice is produced annually and over 800 million tonnes of dry agricultural residues, mainly rice straw, is formed in the process.52 Most of these residues are treated as waste which makes rice straws an appealing source to use for fibre production. It is composed mainly of cellulose and hemicellulose (around 33% and 28%) and of lignin (10%) and silica (12%).18,52 Other uses of waste rice straw include burning as fuel and feeding livestock, but no high-value large-scale applications are currently reported to be in use. Methods of nanocellulose isolation from rice straw and description of products found in literature are compiled in Table 1.
Table 1 Different processing methods of waste sources and dimensions of obtained nanocellulose products
Cellulose source |
Product type |
Different cellulose purification methods used |
Chemical or enzymatic treatments |
Physical treatments |
Diameters (nm) |
Lengths (nm) |
Ref. |
Rice straw |
MFC |
Toluene/ethanol |
Ammonium persulfate |
Ultrasonication supermass colloider |
7–370 |
Not available/1800 |
17
|
Bleaching |
Xylanase shear mixer |
Shear homogenizer sonication mixer high pressure homogenizer |
|
|
NaOH |
|
|
|
|
Valley beater |
|
|
|
|
Na2SO3 |
|
|
|
|
NaClO2 |
|
|
|
|
Rice straw |
CNC |
Hot water |
Acid hydrolysis H2SO4 H2O2/H2SO4 |
|
2–19 |
75–225 |
17,18,90,91
|
NaClO2 |
Ammonium persulfate |
|
|
|
3 : 1 H2O2/H2SO4 |
|
|
|
|
Bleaching |
|
|
|
|
Toluene/ethanol KOH |
|
|
|
|
NaOH |
|
|
|
|
Wheat straw |
MFC |
Active alkali |
TEMPO-mediated oxidation endoglucanase |
Homogenization microfluidizer supermasscolloi-der twin-screw extruder high-pressure homogenizer ultrafine friction grinder mixer |
4–40 |
103–5000/not available |
53,56,57,92,93
|
ClO2 |
|
|
|
|
NaOH |
|
|
|
|
Centrifugation |
|
|
|
|
HCl |
|
|
|
|
Sprout Bauer |
|
|
|
|
PFI beater acetone/H2O |
|
|
|
|
Acidic/alkali deep |
|
|
|
|
Eutectic solvent |
|
|
|
|
Ethanol |
|
|
|
|
Wheat straw |
CNC |
Isobutanol/KOH/ |
H2SO4 |
Centrifugation dialysis ultrasonication |
10–45 |
— |
94
|
H2O/hydrazine |
|
|
|
|
Acetic acid/H2O2 |
|
|
|
|
Corn stover |
MFC |
NaOH |
TEMPO-mediated oxidation |
High-pressure homogenization centrifugation |
5–50 |
103/not available |
95,96
|
NaCl |
|
|
|
|
Glacial acetic acid ethanolamine |
|
|
|
|
PFI mill |
|
|
|
|
Corn stover |
CNC |
NaOH |
Acid hydrolysis HCl |
Centrifugation |
7 |
360/not available |
62,97
|
NaClO NaOH NaClO2 |
|
|
|
|
Glacial acetic acid |
|
|
|
|
Pineapple leaves |
MFC |
NaOH |
TEMPO-mediated oxidation |
Ball milling steam explosion |
32–3000 |
103–93 000/not available |
65,98,99
|
HCl |
MMA modification lime juice hydrolysis |
|
|
|
NaClO2 |
|
|
|
|
Acetic acid |
|
|
|
|
Pineapple leaves |
CNC |
NaOH |
HCl |
High-shear homogenization ultrasonication |
15–70 |
88–1100/not available |
63,64
|
Acetic acid |
H2SO4 |
|
|
|
NaClO2 |
|
|
|
|
H2O2/NaOH |
|
|
|
|
Oil Palm Frond |
CNC |
Acetic acid |
H2SO4 |
Centrifugation dialysis |
7–23 |
95/not available |
68,70,100
|
NaClO2 |
|
|
|
|
NaOH |
|
|
|
|
High-pressure boiled |
|
|
|
|
Cotton stalks |
MFC |
NaOH/Na2SO4 |
— |
Masuko grinder |
41–115 |
200–2000 |
101
|
NaClO |
|
|
|
|
Cotton stalks |
CNC |
NaOH |
H2SO4 TEMPO-mediated oxidation |
Centrifugation dialysis ultrasonication |
3–50 |
10–500 |
73
|
HCl |
|
|
|
|
NaClO2 |
|
|
|
|
Tobacco |
MFC |
Solid–liquid extraction |
Formic acid |
Supermasscol-loider centrifugation homogenized |
5–70 |
— |
102,103
|
Steam explosion |
|
|
|
|
Bleaching ammonium sulfite |
|
|
|
|
H2O2/NaOh |
|
|
|
|
Tobacco |
CNC |
Benzene/ethane |
H2SO4 |
Centrifugation dialysis |
10 |
200 |
104
|
NaOH |
|
|
|
|
NaClO2 |
|
|
|
|
Sugarcane bagasse |
MFC |
Caustic soda method steam explosion |
Xylanase |
Ultra-micro mill, high-pressure homogenization high-speed blender ultrasonication centrifugation |
20–50 |
600–900/not available |
19,105,106
|
NaOH H2O2 |
NaOH |
|
|
|
|
Citric acid |
|
|
|
|
|
|
|
|
|
|
|
|
|
Sugarcane Bagasse |
CNC |
Ultrasonication |
H2SO4 |
Mechanical stirring & heating ultrasonication centrifugation |
3–30 |
160–600/not available |
19,79,107–109
|
Ethanol/water |
TEMPO-mediated oxidation H2O/adipic acid/H2SO4 citric acid |
|
|
|
NaOH/H2O2 |
|
|
|
|
NaOH/NaClO2 |
|
|
|
|
Empty Fruit Bunch |
MFC |
Ethanol/toluene |
Ni(NO3)2 |
Centrifugation dialysis ultrasonication nanogrinding |
18–40 |
>103/not available |
81,110
|
NaOH |
|
|
|
|
H2O2 |
|
|
|
|
Steam explosion NaClO2 |
|
|
|
|
Empty Fruit Bunch |
CNC |
ClO− |
Ammonium persulfate H2SO4 |
Centrifugation dialysis ultrasonication blending |
3–770 |
>100/not |
81,111–114
|
Acetic acid ethanol/toluene |
TEMPO-mediated oxidation |
|
|
available |
|
NaOH |
HCl |
|
|
|
H2O2 |
Phosphor-tungstic acid |
|
|
|
Bleached kraft pulp |
|
|
|
|
Pineapple waste |
CNC |
NaOH |
H2SO4 |
Centrifugation dialysis sonication |
15–40 |
190–250/not available |
63,84,115
|
H2O2/NaOH |
|
|
|
|
KOH |
|
|
|
|
Citrus pomace |
MFC |
NaOH |
Enzymatic hydrolysis |
Sonication high-shear homogenizer high-pressure homogenizer |
10–15 |
— |
89,116
|
NaClO2 |
|
|
|
|
Blender |
|
|
|
|
Cyclone mill |
|
|
|
|
Microwave |
|
|
|
|
Pressure cooker |
|
|
|
|
Centrifugation |
|
|
|
|
Citrus pomace |
CNC |
Toluene/ethanol |
HCl/H2SO4 ammonium persulfate TEMPO-mediated oxidation |
Centrifugation dialysis ultrasonication |
10–40 |
130–380/not available |
88,117,118
|
NaOH |
|
|
|
|
Sonification |
|
|
|
|
Ethanol |
|
|
|
|
4.1.2 Wheat straw.
Wheat is one of the largest crops globally and it generates 875 million tonnes of wheat straw as a byproduct53 Currently a fraction of the wheat straw is used as animal feed and the rest is mostly left on the fields, or burnt.54,55 Wheat straw is composed of approximately 40% of cellulose, 30% of hemicellulose and 18% of lignin.56,57 Wheat is produced in 115 countries54 and the most substantial producers are EU, China, India, Russia, and USA with 19%, 18%, 12%, 10%, and 8% shares of the production respectively.58 Methods of nanocellulose isolation from wheat straw and description of products found in literature are compiled in Table 1.
4.1.3 Corn stover.
Corn is one of the largest crops in the world with global production of 1100 million tonnes per year of which United States, China and Brazil produce most with 31%, 24% and 8% of the total respectively.58,59 Grain makes up half of the dry weight of corn while corn stover makes up the rest which leaves massive amount of lignocellulosic biomass available for utilization.60 Currently stover is used as feedstuff, as bedding for feedstock, in enriching soil, being burned as fuel and some of it is being converted to ethanol.61 Corn stover consist of stalks, leaves, husks, and cob, and the chemical composition is approximately 46% cellulose, 28% hemicellulose and 9% lignin, depending on the species.62 Methods of nanocellulose isolation from corn stover and description of products found in literature are compiled in Table 1.
4.1.4 Pineapple leaves.
Pineapple is one of the most popular tropical fruits with production of 19 million tonnes annually.63 Pineapple leaves weigh about 7% of the weight of the fruit.64 Pineapple leaves are very high on cellulose content with chemical composition of approximately 80% of cellulose, 12% of hemicellulose and 3% of lignin.64,65 Methods of nanocellulose isolation and description of products found in literature are compiled in Table 1.
4.1.5 Oil palm frond.
Palm oil production has grown in the recent years to become one of the most important commercial oil crops. Indonesia and Malaysia are the biggest producers of crude palm oil with 84% share of the global annual production of 72 million tonnes.66 With the production of tonne of palm oil, approximately 3.5 tonnes of waste oil palm frond (leaves of the palm, OPF) is formed.67,68 OPF is harvested regularly year around while pruning the palm trees, and while collecting the fruit bunches. Currently 75% of the frond waste is left to rot on the ground, while the rest is burnt.69 Dried OPF was found to contain 40% cellulose, 27% hemicellulose, and 20% lignin.70 Methods of nanocellulose isolation from OPF and description of products found in literature are compiled in Table 1.
4.1.6 Cotton stalks.
Cotton is an important crop worldwide mostly due to its use in textile products. The annual production of cotton is around 25 million tonnes and the largest producers are India, China, USA, Brazil, and Pakistan with combined share of 80% of the production.71 With the production of cotton, approximately 110 million tonnes of cotton stalk is left on the field after harvest.72 Currently most of the leftover stalk is burnt on the field causing considerable air pollution and leaving the stalks on the field leads to a pest problem.73 Dry cotton stalk contains approximately 66% of cellulose, 18% hemicellulose, and 15% lignin which combined with availability should make for appealing cellulose source.16 Methods of nanocellulose isolation from cotton stalk and description of products found in literature are compiled in Table 1.
4.1.7 Tobacco.
Tobacco is economically important crop as global production of cigarettes and it was worth 665 billion US dollars in 2010.74 It generates approximately 8 million tonnes of tobacco stalk waste, which is currently either burned on the fields or used for indoor combustion.75 In addition to stalk waste, portion of the leaves processed become waste as the stems are not used in cigarettes due to their higher cellulose content of 20%. Tobacco stalk contains 45% cellulose, 30% hemicellulose and 25% lignin.16 China, Brazil, and India are the biggest producers of tobacco of which China leads the production with portion of 40% of the global production.75 Methods of nanocellulose isolation from tobacco and description of products found in literature are compiled in Table 1.
4.2 Industrial waste as MFC source
Industrial waste streams are an important source for biomass. Less biomass is available from industrial sources than from agricultural sources. However, no extra steps of gathering the wastes are needed, as the biomass is concentrated in the processing plants. Currently the waste biomass amassed in processing plants are mostly used as fuel, feed for animals, or fertilizer.76,77 This chapter introduces potential industrial waste sources in the order of literature hits and present ways of refining biomass to nanocellulose found in literature. Raw materials introduced in this chapter are sugarcane bagasse, empty fruit bunch and processed pineapple waste. They were the most researched industrial waste sources regarding nanocellulose production in Scopus database (see associated content for detailed description.)
4.2.1 Sugarcane bagasse.
Sugarcane production amounts to 22.4% of total agricultural production worldwide by weight with 1683 million metric tonnes produced in 2009.78 Sugarcane is crushed to extract its juice in sugar mills and one third of the sugarcane's mass is left as a residue, bagasse.79 Currently 9% of the bagasse is used in ethanol production, 6% is discarded and 85% is burnt as fuel in sugar mills even though bagasse has low caloric power and burning it produces air pollution due to the quality of smoke released in the atmosphere.80 Furthermore, dry bagasse is generally composed of around 45% of cellulose, 26% of hemicellulose and 24% of lignin, which combined with availability makes it an appealing source for cellulose fibres.108 Methods of nanocellulose isolation from sugarcane bagasse and description of products found in literature are compiled in Table 1.
4.2.2 Oil palm empty fruit bunch.
Palm oil production has grown in the recent years to become one of the most important commercial oil crops. Indonesia and Malaysia are the biggest producers of crude palm oil with 84% share of the global annual production of 72 million tonnes.66 With every tonne of crude palm oil produced, 1.1 tonnes of waste empty fruit bunch (EFB) is left behind in the mills.81 Currently it is mostly burnt which leads to bad air quality, or used as organic fertilizer which through improper methods leads to negative effect on environment.76 Palm oil EFB contains approximately 50% of cellulose, 30% of hemicellulose and 15% of lignin which makes it suitable for fibre extraction.67,81 Methods of nanocellulose isolation from EBF and description of products found in literature are compiled in Table 1.
4.2.3 Processed pineapple waste.
Pineapple is one of the most popular tropical fruits with production of 19 million tonnes annually.63 Third of the production is used to make canned pineapple.82 where peel and core of the pineapple are disposed. Peel and core make up 44% and 15% of the mass respectively and after processing 34% of the raw material is fibrous waste.83 Currently the fibrous waste is mostly used as feed-stock or composted.84 Chemical compositions of pineapple peel and core are 23% and 17% of cellulose, 14% and 12% hemicellulose, and 5% and 2% lignin.83 Methods of nanocellulose isolation and description of products found in literature are compiled in Table 1.
4.2.4 Citrus waste.
Citruses are the largest fruit crop in the world with production of 120 million tonnes annually.85 Almost third of the production is industrially processed for juice production where half of the fruit ends up as waste, mainly the peel, pulp, and seeds.86 The three most grown categories of citrus are orange, citrus and lemon, and tangerines, oranges taking up about half of the global production. The biggest producers are Brazil, China, USA, Mexico, India, and Spain.87 Currently the solid waste of juice production is either disposed in landfills causing considerable pollution while untreated, burnt or sold as pellets for cattle without profit.88 Dry citrus waste contains approximately 15 to 20% cellulose, 6 to 18% hemicellulose, 18 to 24% pectin, depending on the source.88,89 Methods of nanocellulose isolation and description of products found in literature are compiled in Table 1.
5 Discussion
In order to identify the most promising material sources for large scale nanocellulose production, this chapter will discuss and compare the potential of the raw materials introduced. Comparisons will focus firstly on prevalence in literature, secondly on availability of the biomass, thirdly on difficulty of processing and environmental impact of the, and finally on the potential applications. These factors were chosen as they give a simple but comprehensive picture about the interest and the potential of the raw materials regarding industrial production of nanocellulose.
5.1 Prevalence in literature
The prevalence of the raw materials in literature links directly to the trends in scientific research, which might give insight about the potential of the raw material. The most studied materials have some obvious advantages that make them more attractive to researchers. According to the search method used sugarcane bagasse, empty fruit bunch, and rice straw emerged as the most researched agricultural and industrial raw materials for nanocellulose production. The fibre sources and their frequency in the Scopus database in the order of the frequency are presented in Table 2. It should be noted that several review articles regarding nanocellulose production from non-wood sources were used to find the most studied fibre sources,5,6,8,16 Thus the results for the most studied sources should be reasonably accurate.
Table 2 Frequency of nanocellulose related studies of waste materials in Scopus database using uniform search phrase
Raw material |
Hits overall |
Hits 2018–2020 |
Industrial sources on grey, agricultural sources on white. |
Sugarcane bagasse |
96 |
61 |
Empty fruit bunch |
86 |
55 |
Rice straw |
68 |
33 |
Wheat straw |
44 |
18 |
Corn stover |
37 |
18 |
Pineapple leaves |
33 |
23 |
Processed pineapple waste |
14 |
11 |
Oil palm frond |
14 |
8 |
Citrus waste |
10 |
6 |
Cotton stalks |
6 |
— |
Tobacco stalks |
3 |
2 |
5.2 Availability of biomass
An important factor while considering future nanocellulose sources, is the amount of biomass from the source. Absolute amounts of waste biomass per source are shown in Table 3. Furthermore, the availability and ease of access to the biomass should also be considered. For example, the two most researched waste materials for nanocellulose production, sugarcane bagasse and empty fruit bunch, are both collected at processing mills as waste product thus being readily available compared to agricultural waste that must be collected from the fields in a separate process52,60 Moreover, agricultural wastes have differences in collectability. According to Wang, Bi & Gao (2010), the cultivation system used and the need for returning the wastes to the field as fertilizer affect the collectability, but the most important factor is method of harvesting. In the same study, collectability coefficient ranging from 0 to 1 was determined with data from field surveys. Coefficient for cotton stalks and tobacco was found to be 0.90, 0.83 for rice straws, and 0.60 for vegetable vine and residue.119 Graham et al. (2007) found that only 28% of corn stover produced in US could be sustainably collected at farm gate at the cost lower than $33 per tonne with current practises.60 Wastes have different costs of collecting and this should be considered while choosing the cellulose source. Moreover, the harvesting method of the source should be optimized for efficient production.
Table 3 Absolute amounts of waste biomass per source
Raw material |
Waste biomass (million tonnes) |
Industrial sources on grey, agricultural on white. |
Corn stover59 |
1100 |
Wheat straw53 |
875 |
Rice straw52 |
800 |
Sugarcane bagasse78 |
600 |
Oil palm frond66 |
250 |
Cotton stalks72 |
110 |
Empty fruit bunch66,81 |
80 |
Citrus waste85,86 |
20 |
Tobacco stalks75 |
8 |
Processed pineapple waste63,82,83 |
4 |
Pineapple leaves63 |
1 |
Another factor to consider, while choosing suitable cellulose source, is seasonality of the waste biomass. Most of the waste is produced upon harvest and the possible storage costs and other problems like spoilage must be acknowledged. Some sources, such as oil palm frond are available around year due to pruning.69 Competition must be taken into consideration when comparing the availabilities of materials. Bioethanol production is the biggest competitor regarding waste lignocellulosic material but as it is a low-value product compared to nanocellulose, it probably will not be a problem if nanocellulose production takes off.
5.3 Processing
The structure of nanocellulose is dependent not only on the production method, but also on the cellulose source.120 The source also dictates the difficulty of treating the biomass. Treatability is mainly determined by lignin and hemicellulose content, crystallinity, and degree of polymerization of cellulose, and the fibre strength, porosity, and coarseness of the raw material.16 Thus, the production process must not only take desired product into consideration but also the source. Chemical compositions of materials presented are shown in Table 4. Lignin content is one of the easiest ways of approximating the treatability of the lignocellulosic mass, as the lignin binds cellulose together and makes the source “woodier”.13,16 Lower lignin content facilitates easier access to other components, allowing the use of lower processing times and milder chemicals thus reducing the economic and environmental costs of nanocellulose production.13 It should be noted that components other than cellulose, such as lignin or pectin, can be also extracted and utilized, if the processes are made suitable.
Table 4 Chemical compositions of source materials in the order of hits in literature
Raw material |
Cellulose (%) |
Hemicellulose (%) |
Lignin (%) |
Industrial sources on grey, agricultural on white. |
Sugarcane bagasse108 |
45 |
26 |
24 |
Empty fruit bunch67,81 |
50 |
30 |
15 |
Rice straw18,52 |
33 |
28 |
10 |
Wheat straw56,57 |
40 |
30 |
18 |
Corn stover62 |
46 |
28 |
9 |
Pineapple leaves64,65 |
80 |
12 |
3 |
Processed pineapple waste83 |
20 |
13 |
4 |
Oil palm frond70 |
40 |
27 |
20 |
Citrus waste88,89 |
15 |
18 |
<1 |
Cotton stalks16 |
66 |
18 |
15 |
Tobacco stalks16 |
45 |
30 |
25 |
Since the industrial nanocellulose production is still in its beginnings, no consensus has been found for the best CNC or MFC production methods. Therefore, comparing the production processes of different cellulose sources on a deeper level is difficult especially since most of the materials were treated with variety of methods, and the characterisation methods of nanocellulose are still not able to describe behaviour and properties very well.121 Similar process steps were used on most of the materials and when the most popular methods have not been used once on a material, it is probably due to lack of trying. Comparison of the effect of the same chemical and physical treatments on different raw materials is not feasible based on current literature, due to differences in the applied reaction times (and other details), differences in reporting, and the lack of standardized analytical methods.
Simple but efficient processing methods would be better for large-scale applications. Generally, CNC production requires less and simpler steps than MFC. On the other hand, especially in CNC production the effluent waters should be taken into consideration and currently CNC production requires also higher capital investment for same production capacity.122 It should be noted that new more environmentally safe and sustainable methods of producing nanocellulose are being developed. Ammonium persulfate has been shown to work as a more environmentally safer option for CNC production, while in MFC production the fibrillation process is still the most energy consuming and thus the most non-eco-friendly step in the process.17,114 Also, deep eutectic solvents were shown to be good at delignification as an eco-friendlier option.53 During processing, also the nanosafety aspect has to be considered while designing nanocellulose manufacturing processes. The pulmonary exposure to airborne nanocellulose during processing, especially when working with dry materials, is the likeliest health risk for human health that nanocellulose poses.124,125 Another safety aspect to be considered when working dry organic material is the possibility of dust explosion, and proper measures should be carried out to avoid these occupational hazards.
The main problems in commercial MFC production are energy efficiency and the difficulty of producing a dry product due to agglomeration, which leads to loss of dispersability and rheological properties.8,123 The inability to ship a dried product means low solid content and thus high transportation costs. Despite these challenges in industrial scale production, there are companies with commercial or pilot scale MFC production (Borregaard, OJI Holdings, Nippon Paper Group, UPM, Stora Enso, etc.). The current commercially available MFC products include rheology modifiers in different applications (Exilva by Borregaard, Aurovisco by OJI Holdings), paper and board product additives (Stora Enso MFC, Nippon Paper Group CNF), and higher value applications such as UPM's 3D cell culture GrowDex. The applications and future trends are discussed more in 5.4.
The production seems to be divided to two categories: 1. Manufacturing MFC in separate mills to sell to others as a product. 2. Manufacturing it onsite for companies’ own products (mostly as paper and board additives) which circumvents the drying and transport problems but requires big investments. There are currently 10 companies producing CNC at industrial scale, with production rates of over 10 tonnes per year.132 Unlike MFC, CNC can be shipped as a dry powder as the most prominent CNC producer CelluForce does, thus removing some of the biggest problems that current MFC industry faces.133 Sulfuric acid hydrolysis has been the most successful production method, but acid free oxidative routes are rising as sustainable alternatives by pioneering companies like Anomera Inc. and Blue Goose Biorefiniries.132
Concerning methods of fibrillation, extrusion seems to be promising for MFC production.8 Extrusion has the advantages of continuous production with high solid content and lower energy demand.126,127 According to Debiagi et al. (2020), extrusion can be modified into reactive extrusion, where extruder is used as a continuous chemical reactor. 118Using reactive extrusion lowers the energy demand even more, it requires significantly lower quantity of reagents, and it produces less effluents and it is quicker, when comparing to conventional methods.126,128 Reactive extrusion can also be done in a relatively simple process, with one-step extrusion after bleaching. The use of reactive extrusion in nanocellulose production seems to be very promising, but currently quite few papers have been published about it and it needs to be researched more thoroughly.
5.4 Applications
The three biggest current nanocellulose applications are: 1. Paper, board, and packaging, 2. Composites, and 3. Filtration, with respective percentages of 36%, 25% and 19% of the market share.2 The two biggest application streams have quite similar purposes for nanocellulose use. Paper, board, and packaging, as well as composites are both potential large-scale applications motivated by cost reduction, ecological benefits, and by the mechanical properties that nanocellulose provides. Cost reduction is a huge factor considering the massive scale of the market size, as even small reduction in cost would have considerable effect overall. Furthermore, pulp was found to be taking up to 60% of the manufacturing cost, while using market pulp.122 The possibility of utilizing low quality fibres to produce nanocellulose and using it in applications, such as water filtration, cardboard recycling, or as paper additives is promising.129 It could decrease the reliance of developing countries on imports, reduce environmental load, and facilitate economic growth.
For many others of the applications (lightweight electronics, photovoltaic devices, etc.) introduced here, the interest relies more on the technical opportunities that nanocellulose provides. However, the sustainability aspect is still one of the key qualities of nanocellulose. In addition to the sustainability and easier processability provided by waste source nanocellulose discussed earlier, the possibility of turning low value waste into high quality products through nanocellulose use could be financially favourable.
To assure the safety of commercial nanocellulose applications, more research is needed.124,125 The biggest safety concern is related to nanoscale products. ECHA(European Chemical Agency) defies nanomaterials as having over 50% of particles between 1–100 nm. Currently, inconsistent results and unrealistic doses in mice tests have handicapped the studies and caused contradictions about nanocellulose's safety.124 According to a review on potential health hazards of nanocellulose by Stoudmann et al. (2020), more systematic information about nanocellulose's biopersistence, effects of dermal exposure, nanocellulose induced inflammation, and the effects of surface modification to nanosafety are called for, especially in realistic low dose, long exposure scenarios. It is also noteworthy that a lot of safety data collected as a part of commercialization of CNC and MFC products is not publicly available.
As discussed earlier, the application determines the quality requirements expected from the nanocellulose. Currently, the use of MFC seems more common in the established applications, as the properties of MFC match the requirements of high-volume applications better. Some bulk applications, such as composites, might be more lenient towards irregularities in the nanocellulose morphology, compared to for example photonic structural colours, where a precise organisation of the building blocks is required to achieve the desired effect. The difficulties in producing and characterising homogeneous nanocellulose are still inhibiting the industrial potential of nanocellulose applications. However, nanocellulose is already in commercial use, and for some of the more established applications, such as paper, board and packaging, the hindrance seems to be mostly the current high price. Thus, reduction of the price could lead to larger market adaptation.
6 Conclusions and outlook
This work sums up knowledge about the most researched and promising agricultural and industrial waste sources for nanocellulose production. The most promising individual waste-based material sources were found to be sugarcane bagasse and oil palm empty fruit bunch. Both are side streams of industrial processes that generate a lot of waste biomass concentrated at the processing mills with nearly continuous supply.130,131 Although no distinctive advantages were found in the processability of sugarcane bagasse and empty fruit bunch, they were the most researched sources and showed great potential in accessibility. Overall, the most important factor in selection of waste biomass was found to be the accessibility of the waste. When the waste biomass sources are vast, the usability and ease of access of the biomass are likely to emerge as bottlenecks. Seasonality has also a big effect in choice of source, as it can make the continuous and homogenous production of nanocellulose difficult. Biorefineries could be built together with sugar mills etc. to take advantage of waste biomass amassed in mills and produce nanocellulose possibly together with lignin, pectin, and hemi-cellulose.
Regarding processes of nanocellulose production, the waste source does not affect the core process steps markedly. The principles stay the same for all waste sources, although the process parameters should be optimized for each source separately as the composition and structure of the raw material influence the treatability. Processes could be made environmentally safer for delignification and cellulose extraction by using fewer organic solvents and strong alkalis or acids with the help of deep eutectic solvents. CNC hydrolysis could be done with ammonium persulfate, or some other alternative found suitable in the future. For MFC production environmental benefits are best accomplished with reduction of energy used in fibrillation. Reactive extrusion seems promising for this purpose, but more research is needed to reach a uniform conclusion on this.
There are various different categories of nanocellulose applications. Some high-volume applications, such as paper, board and packaging, have already established commercial use of nanocellulose. Employment of nanocellulose in these applications is motivated by the cost reduction and sustainability aspects, whereas many emerging applications, such as photovoltaic devices, light weight electronics, etc., rely on the unique technical possibilities that nanocellulose provides. Since a variety of properties can be created via modifications of nanocellulose, very diverse applications can benefit from this. Waste sources seem to be most advantageous in large-scale applications, where reducing pulp cost can significantly lower the overall costs. Furthermore, waste-sourced nanocellulose could decrease the reliance of imports for various specialty chemicals, synthetic polymers, and forest products, as they could be replaced by locally sourced nanocellulose alternatives, enhancing both environmental and social sustainability by diversifying the local economies.
Future research should be concentrated on optimizing process parameters for promising sources. For CNC production, finding best suited chemicals for hydrolysis step is important. For MFC production, the fibrillation step is the most important to finetune. Also, the potential of using wastes produced in the forest industry should be studied further. Furthermore, nanocellulose production overall would benefit greatly from more efficient and standardized characterisation methods that would make the quality and comparisons of different studies and their products easier and better. Even with these imperfections commercial nanocellulose production exists already, and waste biomass sources are waiting to be utilised better. The environmental and economic benefits make great argument for taking advantage of these wastes, and the technology and knowledge required is already mostly available.
Methodology section
Description of the applied methodology: scopus was the main database used in this research. Several review articles regarding nanocellulose production from non-wood sources were used to find the most studied fibre sources,5,6,8,16 Same structure for search phrase was used for each raw material: ““name of raw material” AND nanocellulose OR mfc OR cnc OR cnf OR nfc”. Some additional search terms were added in cases, where more accurate ruling out was needed due to identical abbreviations used in other literature. The number of relevant documents found with each search and the portion of recent studies are showcased in the introduction of each potential raw material. Google scholar was used to acquire supporting information.
Author contributions
The manuscript was written through contributions of all authors.
Funding sources
J. V. acknowledges generous funding from Academy of Finland (SUBSTAINABLE project, decision number 334818), as well as Flagship Programme under Projects No. 318890 and 318891 (Competence Center for Materials Bioeconomy, FinnCERES).
Abbreviations
BC | Bacterial cellulose |
CNC | Cellulose nanocrystals |
CNF | Cellulose nanofibril |
CSF | Core shell filament |
EFB | Empty fruit bunch |
MFC | Microfibrillated cellulose |
MMCF | Man-made cellulosic fiber |
NFC | Nanofibrillar cellulose |
OPF | Oil palm frond |
Conflicts of interest
There are no conflicts of interest to declare.
References
- H. Shaghaleh, X. Xu and S. Wang, Current progress in production of biopolymeric materials based on cellulose, cellulose nanofibers, and cellulose derivatives, RSC Adv., 2018, 8, 825–842 RSC.
- A. Balea, E. Fuente, M. C. Monte, N. Merayo, C. Campano, C. Negro and A. Blanco, Industrial Application of Nanocelluloses in Papermaking: A Review of Challenges, Technical Solutions, and Market Perspectives, Molecules, 2020, 25, 526 CrossRef CAS PubMed.
- A. Rodríguez, A. Moral, L. Serrano, J. Labidi and L. Jiménez, Rice straw pulp obtained by using various methods, Bioresour. Technol., 2008, 99, 2881–2886 CrossRef PubMed.
- E. Abraham, B. Deepa, L. A. Pothan, M. Jacob, S. Thomas, U. Cvelbar and R. Anandjiwala, Extraction of nanocellulose fibrils from lignocellulosic fibres: A novel approach, Carbohydr. Polym., 2011, 86, 1468–1475 CrossRef CAS.
- M. Rajinipriya, M. Nagalakshmaiah, M. Robert and S. Elkoun, Importance of Agricultural and Industrial Waste in the Field of Nanocellulose and Recent Industrial Developments of Wood Based Nanocellulose: A Review, ACS Sustainable Chem. Eng., 2018, 6, 2807–2828 CrossRef CAS.
- Z. Anwar, M. Gulfraz and M. Irshad, Agro-industrial lignocellulosic biomass a key to unlock the future bio-energy: A brief review, J. Radiat. Res. Appl. Sci., 2014, 7, 163–173 CrossRef CAS.
- M. Pääkkö, M. Ankerfors, H. Kosonen, A. Nykänen, S. Ahola, M. Österberg, J. Ruokolainen, J. Laine, P. T. Larsson, O. Ikkala and T. Lindström, Enzymatic Hydrolysis Combined with Mechanical Shearing and High-Pressure Homogenization for Nanoscale Cellulose Fibrils and Strong Gels, Biomacromolecules, 2007, 8, 1934–1941 CrossRef PubMed.
- O. Nechyporchuk, M. N. Belgacem and J. Bras, Production of cellulose nanofibrils: A review of recent advances, Ind. Crops Prod., 2016, 93, 2–25 CrossRef CAS.
- L. J. Gibson, The hierarchical structure and mechanics of plant materials, J. R. Soc., Interface, 2012, 9, 2749–2766 CrossRef CAS PubMed.
- N. Lavoine, I. Desloges, A. Dufresne and J. Bras, Microfibrillated cellulose – Its barrier properties and applications in cellulosic materials: A review, Carbohydr. Polym., 2012, 90, 735–764 CrossRef CAS PubMed.
- B. Volynets, F. Ein-Mozaffari and Y. Dahman, Biomass processing into ethanol: pretreatment, enzymatic hydrolysis, fermentation, rheology, and mixing, Green Process. Synth., 2017, 6, 1–22 CAS.
- J. Weng and C. Chapple, The origin and evolution of lignin biosynthesis, New Phytol., 2010, 187, 273–285 CrossRef CAS PubMed.
- M. Szymańska-Chargot, M. Chylińska, K. Gdula, A. Kozioł and A. Zdunek, Isolation and Characterization of Cellulose from Different Fruit and Vegetable Pomaces, Polymers, 2017, 9, 495 CrossRef PubMed.
- M. T. Islam, M. M. Alam, A. Patrucco, A. Montarsolo and M. Zoccola, Preparation of Nanocellulose: A Review, AATCC J. Res., 2014, 1, 17–23 CrossRef.
- O. Nechyporchuk, K. Kolman, A. Bridarolli, M. Odlyha, L. Bozec, M. Oriola, G. Campo-Francés, M. Persson, K. Holmberg and R. Bordes, On the potential of using nanocellulose for consolidation of painting canvases, Carbohydr. Polym., 2018, 194(161–169), 0144–8617 Search PubMed.
- A. García, A. Gandini, J. Labidi, N. Belgacem and J. Bras, Industrial and crop wastes: a new source for nanocellulose biorefinery, Ind. Crops Prod., 2016, 93, 26–38 CrossRef.
- A. A. Oun and J. Rhim, Isolation of oxidized nanocellulose from rice straw using the ammonium persulfate method, Cellulose, 2018, 25, 2143–2149 CrossRef CAS.
- M. Thakur, A. Sharma, V. Ahlawat, M. Bhattacharya and S. Goswami, Process optimization for the production of cellulose nanocrystals from rice straw derived α-cellulose, Mater. Sci. Energy Technol., 2020, 3, 328–334 CAS.
- H. Ji, Z. Xiang, H. Qi, T. Han, A. Pranovich and T. Song, Strategy towards one-step preparation of carboxylic cellulose nanocrystals and nanofibrils with high yield, carboxylation and highly stable dispersibility using innocuous citric acid, Green Chem., 2019, 21, 1956–1964 RSC.
- J. Pennells, I. D. Godwin, N. Amiralian and D. J. Martin, Trends in the production of cellulose nanofibers from non-wood sources, Cellulose, 2020, 27, 575–593 CrossRef CAS.
- Y. Okahisa, A. Yoshida, S. Miyaguchi and H. Yano, Optically transparent wood–cellulose nanocomposite as a base substrate for flexible organic light-emitting diode displays, Composites Sci. Technol., 2009, 69, 1958–1961 CrossRef CAS.
- G. Chu, D. Qu, A. Camposeo, D. Pisignano and E. Zussman, When nanocellulose meets diffraction grating: freestanding photonic paper with programmable optical coupling, Mater. Horiz., 2020, 7, 511–519 RSC.
- W. K. Czaja, D. J. Young, M. Kawecki and R. M. Brown, The Future Prospects of Microbial Cellulose in Biomedical Applications, Biomacromolecules, 2007, 8, 1–12 CrossRef CAS PubMed.
- V. A. Barbash and O. V. Yashchenko, Preparation and application of nanocellulose from non-wood plants to improve the quality of paper and cardboard, Appl. Nanosci., 2020, 10, 2705–2716 CrossRef CAS.
- O. Laitinen, T. Suopajärvi and H. Liimatainen, Enhancing packaging board properties using micro- and nanofibers prepared from recycled board, Cellulose, 2020, 27, 7215–7225 CrossRef CAS.
- S. S. Nair, J. Zhu and Y. Deng,
et al., High performance green barriers based on nanocellulose, Sustain. Chem Process, 2014, 2, 23 CrossRef.
- P. Tyagi, L. A. Lucia, M. A. Hubbe and L. Pal, Nanocellulose-based multilayer barrier coatings for gas, oil, and grease resistance, Carbohydr. Polym., 2019, 206, 281–288 CrossRef CAS PubMed.
- A. M. Adel, A. A. El-Gendy, M. A. Diab, R. E. Abou-Zeid, W. K. El-Zawawy and A. Dufresne, Microfibrillated cellulose from agricultural residues. Part I: Papermaking application, Ind. Crops Products, 2016, 93, 161–174 CrossRef CAS.
- A. J. Benítez and A. Walther, Cellulose nanofibril nanopapers and bioinspired nanocomposites: a review to understand the mechanical property space, J. Mater. Chem. A, 2017, 5, 16003–16024 RSC.
- C. Zinge and B. Kandasubramanian, Nanocellulose based biodegradable polymers, Eur. Polym. J., 2020, 133, 109758 CrossRef CAS.
- A. Sharma, M. Thakur, M. Bhattacharya, T. Mandal and S. Goswami, Commercial application of cellulose nano-composites – A review, Biotechnol. Rep., 2019, 21, e00316 CrossRef PubMed.
- Q. Zhang, L. Zhang, W. Wu and H. Xiao, Methods and applications of nanocellulose loaded with inorganic nanomaterials: a review, Carbohydr. Polym., 2020, 229, 115454 CrossRef CAS PubMed.
- P. R. Sharma, S. K. Sharma, T. Lindström and B. S. Hsiao, Nanocellulose-Enabled Membranes for Water Purification: Perspectives, Adv. Sustainable Syst., 2020, 4, 1900114 CrossRef CAS.
- H. Tan, B. S. Ooi and C. P. Leo, Future perspectives of nanocellulose-based membrane for water treatment, J. Water Process Eng., 2020, 37, 101502 CrossRef.
- H. Tan, B. S. Ooi and C. P. Leo, Future perspectives of nanocellulose-based membrane for water treatment, J. Water Process Eng., 2020, 37, 101502 CrossRef.
- Y. Zhang, L. Zhang, K. Cui, S. Ge, X. Cheng, M. Yan, J. Yu and H. Liu, Flexible Electronics Based on Micro/Nanostructured Paper, Adv. Mater., 2018, 30, 1801588 CrossRef PubMed.
- A. W. Lang, A. M. Österholm and J. R. Reynolds, Paper-Based Electrochromic Devices Enabled by Nanocellulose-Coated Substrates, Adv. Funct. Mater., 2019, 29, 1903487 CrossRef.
- D. Zhao, Y. Zhu, W. Cheng, W. Chen, Y. Wu and H. Yu, Cellulose-Based Flexible Functional Materials for Emerging Intelligent Electronics, Adv. Mater., 2020, n/a, 2000619 Search PubMed.
- E. Kontturi, P. Laaksonen, M. B. Linder, Nonappa, A. H. Gröschel, O. J. Rojas and O. Ikkala, Advanced Materials through Assembly of Nanocelluloses, Adv. Mater., 2018, 30, 1703779 CrossRef PubMed.
- R. Xiong, J. Luan, S. Kang, C. Ye, S. Singamaneni and V. V. Tsukruk, Biopolymeric photonic structures: design, fabrication, and emerging applications, Chem. Soc. Rev., 2020, 49, 983–1031 RSC.
- G. Jacucci, L. Schertel, Y. Zhang, H. Yang and S. Vignolini, Light Management with Natural Materials: From Whiteness to Transparency, Adv. Mater., 2020, n/a, 2001215 Search PubMed.
- J. Si, Z. Cui, Q. Wang, Q. Liu and C. Liu, Biomimetic composite scaffolds based on mineralization of hydroxyapatite on electrospun poly(ε-caprolactone)/nanocellulose fibers, Carbohydr. Polym., 2016, 143, 270–278 CrossRef CAS PubMed.
- S. Salimi, R. Sotudeh-Gharebagh, R. Zarghami, S. Y. Chan and K. H. Yuen, Production of Nanocellulose and Its Applications in Drug Delivery: A Critical Review, ACS Sustainable Chem. Eng., 2019, 7, 15800–15827 CrossRef CAS.
- P. Thomas, T. Duolikun, N. P. Rumjit, S. Moosavi, C. W. Lai, M. R. Bin Johan and L. B. Fen, Comprehensive review on nanocellulose: recent developments, challenges and future prospects, J. Mech. Behav. Biomed. Mater., 2020, 110, 103884 CrossRef CAS PubMed.
- S. A. Kedzior, V. A. Gabriel, M. A. Dubé and E. D. Cranston, Nanocellulose in Emulsions and Heterogeneous Water-Based Polymer Systems: A Review, Adv. Mater., 2020, n/a, 2002404 Search PubMed.
- C. Liu, H. Du, L. Dong, X. Wang, Y. Zhang, G. Yu, B. Li, X. Mu, H. Peng and H. Liu, Properties of Nanocelluloses and Their Application as Rheology Modifier in Paper Coating, Ind. Eng. Chem. Res., 2017, 56, 8264–8273 CrossRef CAS.
- S. Fujisawa, E. Togawa and K. Kuroda, Nanocellulose-stabilized Pickering emulsions and their applications, Sci. Technol. Adv. Mater., 2017, 18, 959–971 CrossRef CAS PubMed.
- A. Michud, M. Tanttu, S. Asaadi, Y. Ma, E. Netti, P. Kääriainen, A. Persson, A. Berntsson, M. Hummel and H. Sixta, Ioncell-F: ionic liquid-based cellulosic textile fibers as an alternative to viscose and Lyocell, Text. Res. J., 2016, 86, 543–552 CrossRef.
- Y. Ma, M. Hummel, I. Kontro and H. Sixta, High performance man-made cellulosic fibres from recycled newsprint, Green Chem., 2018, 20, 160–169 RSC.
- H. S. Onkarappa, G. K. Prakash, G. H. Pujar, C. R. Rajith Kumar, M. S. Radha Latha and V. S. Betageri, Synthesis and characterization of nanocellulose using renewable resources through Ionic liquid medium, Adv. Nat. Sci.: Nanosci. Nanotechnol., 2020, 11, 035001 CAS.
- G. Reyes, M. J. Lundahl, S. Alejandro-Martín, L. E. Arteaga-Pérez, C. Oviedo, A. W. T. King and O. J. Rojas, Coaxial Spinning of All-Cellulose Systems for Enhanced Toughness: Filaments of Oxidized Nanofibrils Sheathed in Cellulose II Regenerated from a Protic Ionic Liquid, Biomacromolecules, 2020, 21, 878–891 CrossRef CAS PubMed.
- L. Domínguez-Escribá and M. Porcar, Rice straw management: the big waste, Biofuels, Bioprod. Bioref., 2010, 4, 154–159 CrossRef.
- T. Suopajärvi, P. Ricci, V. Karvonen, G. Ottolina and H. Liimatainen, Acidic and alkaline deep eutectic solvents in delignification and nanofibrillation of corn stalk, wheat straw, and rapeseed stem residues, Ind. Crops Prod., 2020, 145, 111956 CrossRef.
- F. Talebnia, D. Karakashev and I. Angelidaki, Production of bioethanol from wheat straw: An overview on pretreatment, hydrolysis and fermentation, Bioresour. Technol., 2010, 101, 4744–4753 CrossRef CAS PubMed.
- M. Z. Farooq, M. Zeeshan, S. Iqbal, N. Ahmed and S. A. Y. Shah, Influence of waste tire addition on wheat straw pyrolysis yield and oil quality, Energy, 2018, 144, 200–206 CrossRef CAS.
- S. R. Djafari Petroudy, J. Ranjbar and E. Rasooly Garmaroody, Eco-friendly superabsorbent polymers based on carboxymethyl cellulose strengthened by TEMPO-mediated oxidation wheat straw cellulose nanofiber, Carbohydr. Polym, 2018, 197, 565–575 CrossRef CAS PubMed.
- E. Espinosa, F. Rol, J. Bras and A. Rodríguez, Use of multi-factorial analysis to determine the quality of cellulose nanofibers: effect of nanofibrillation treatment and residual lignin content, Cellulose, 2020, 27, 10689–10705 CrossRef CAS.
- United States Department of Agriculture Foreign Agricultural Service Grain: World Markets and Trade. United States Department of Agriculture 2020, 1-21.
- P. Ranum, J. P. Peña-Rosas and M. Garcia-Casal, Global maize production, utilization, and consumption, Ann. N. Y. Acad. Sci., 2014, 1312, 105–112 CrossRef PubMed.
- R. L. Graham, R. Nelson, J. Sheehan, R. D. Perlack and L. L. Wright, Current and Potential U.S. Corn Stover Supplies, Agron. J., 2007, 99, 1–11 CrossRef.
- M. Delgado-Aguilar, F. Vilaseca, Q. Tarrés, F. Julián, P. Mutjé and F. X. Espinach, Extending the value chain of corn agriculture by evaluating technical feasibility and the quality of the interphase of chemo-thermomechanical fiber from corn stover reinforced polypropylene biocomposites, Composites, Part B, 2018, 137, 16–22 CrossRef CAS.
- L. A. S. Costa, D. D. J. Assis, G. V. P. Gomes, J. B. A. D. Silva, A. F. Fonsêca and J. I. Druzian, Extraction and Characterization of Nanocellulose from Corn Stover, Mater. Today: Proc., 2015, 2, 287–294 Search PubMed.
- H. Dai, S. Ou, Y. Huang and H. Huang, Utilization of pineapple peel for production of nanocellulose and film application, Cellulose, 2018, 25, 1743–1756 CrossRef CAS.
- M. Mahardika, Production of nanocellulose from pineapple leaf fibers via high-shear homogenization and ultrasonication, Fibers, 2018, 6, 28 CrossRef.
- S. Tanpichai, S. Witayakran and A. Boonmahitthisud, Study on structural and thermal properties of cellulose microfibers isolated from pineapple leaves using steam explosion, J. Environ. Chem. Eng., 2019, 7, 102836 CrossRef.
- United States Department of Agriculture Foreign Agricultural Service Oilseeds: World Markets and Trade. Foreign Agricultural Service United States Department of Agriculture 2020, 1–39.
- B. Shanmugarajah, I. M. Chew, N. M. Mubarak, T. S. Choong, C. Yoo and K. Tan, Valorization of palm oil agro-waste into cellulose biosorbents for highly effective textile effluent remediation, J. Clean. Prod., 2019, 210, 697–709 CrossRef CAS.
- F. N. N. M. Hussin, N. Attan and R. A. Wahab, Extraction and Characterization of Nanocellulose from Raw Oil Palm Leaves (Elaeis guineensis), Arabian J. Sci. Eng., 2020, 45, 175–186 CrossRef CAS.
- M. F. Awalludin, O. Sulaiman and R. Hashim, Nadhari, Wan Noor Aidawati Wan An overview of the oil palm industry in Malaysia and its waste utilization through thermochemical conversion, specifically via liquefaction, Renewable Sustainable Energy Rev., 2015, 50, 1469–1484 CrossRef CAS.
- N. F. S. M. Azani, M. K. M. Haafiz, A. Zahari, S. Poinsignon, N. Brosse and M. H. Hussin, Preparation and characterizations of oil palm fronds cellulose nanocrystal (OPF-CNC) as reinforcing filler in epoxy-Zn rich coating for mild steel corrosion protection, Int. J. Biol. Macromol., 2020, 153, 385–398 CrossRef CAS PubMed.
- United States Department
of Agriculture, Foreign Agricultural Service Cotton: World Markets and Trade. United States Department of Agricultulture 2020, 1-30.
- S. A. Y. Shah, M. Zeeshan, M. Z. Farooq, N. Ahmed and N. Iqbal, Co-pyrolysis of cotton stalk and waste tire with a focus on liquid yield quantity and quality, Renewable Energy, 2019, 130, 238–244 CrossRef CAS.
- B. Soni, E. B. Hassan and B. Mahmoud, Chemical isolation and characterization of different cellulose nanofibers from cotton stalks, Carbohydr. Polym., 2015, 134, 581–589 CrossRef CAS PubMed.
- V. Strezov, E. Popovic, R. V. Filkoski, P. Shah and T. Evans, Assessment of the Thermal Processing Behavior of Tobacco Waste, Energy Fuels, 2012, 26, 5930–5935 CrossRef CAS.
- Z. Qin, M. Sun, X. Luo, H. Zhang, J. Xie, H. Chen, L. Yang and L. Shi, Life-cycle assessment of tobacco stalk utilization, Bioresour. Technol., 2018, 265, 119–127 CrossRef CAS PubMed.
-
N. Muna; A. A. N. Fauzi; D. Setyaningsih and S. Yuliani Isolation of Microfibrilated Cellulose from Oil Palm Empty Fruit Bunches (EFB) Through Peracetic Acid Delignification and Enzyme Hydrolysis. IOP Conference Series: Earth and Environmental Science 2019, 309, 012063.
- A. Hideno, K. Abe and H. Yano, Preparation using Pectinase and Characterization of Nanofibers from Orange Peel Waste in Juice Factories, J. Food Sci., 2014, 79, N1218–N1224 CrossRef CAS PubMed.
- M. K. Chauhan, Varun, S. Chaudhary, S. Kumar and Samar, Life cycle assessment of sugar industry: a review, Renewable Sustainable Energy Rev., 2011, 15, 3445–3453 CrossRef.
- L. O. Pinto, J. S. Bernardes and C. A. Rezende, Low-energy preparation of cellulose nanofibers from sugarcane bagasse by modulating the surface charge density, Carbohydr. Polym., 2019, 218, 145–153 CrossRef CAS PubMed.
- D. Verma, P. C. Gope, M. K. Maheshwari and R. K. Sharma, Bagasse fiber composites-A review, J. Mater. Environ. Sci., 2012, 3, 1079–1092 Search PubMed.
- M. Yahya, Y. W. Chen, H. V. Lee, C. C. Hock and W. H. W. Hassan, A New Protocol for Efficient and High Yield Preparation of Nanocellulose from Elaeis guineensis Biomass: A Response Surface Methodology (RSM) Study, J. Polym. Environ., 2019, 27, 678–702 CrossRef CAS.
- O. K. Lun, T. B. Wai and L. S. Ling, Pineapple cannery waste as a potential substrate for microbial biotranformation to produce vanillic acid and vanillin, Int. Food Res. J., 2014, 21, 953–958 CAS.
- V. Sukruansuwan and S. C. Napathorn, Use of agro-industrial residue from the canned pineapple industry for polyhydroxybutyrate production by Cupriavidus necator strain A-04, Biotechnol. Biofuels, 2018, 11, 202 CrossRef PubMed.
- K. S. Prado and M. A. S. Spinacé, Isolation and characterization of cellulose nanocrystals from pineapple crown waste and their potential uses, Int. J. Biol. Macromol., 2019, 122, 410–416 CrossRef CAS PubMed.
- S. Dubey, J. Singh and R. P. Singh, Biotransformation of sweet lime pulp waste into high-quality nanocellulose with an excellent productivity using Komagataeibacter europaeus SGP37 under static intermittent fed-batch cultivation, Bioresour. Technol., 2018, 247, 73–80 CrossRef CAS PubMed.
- A. Mohammadshirazi, A. Akram, S. Rafiee, S. H. Mousavi Avval and E. Bagheri Kalhor, An analysis of energy use and relation between energy inputs and yield in tangerine production, Renewable Sustainable Energy Rev., 2012, 16, 4515–4521 CrossRef.
- D. A. Zema, P. S. Calabrò, A. Folino, V. Tamburino, G. Zappia and S. M. Zimbone, Valorisation of citrus processing waste: a review, Waste Manage., 2018, 80, 252–273 CrossRef CAS PubMed.
- D. Z. Cypriano, L. L. da Silva and L. Tasic, High value-added products from the orange juice industry waste, Waste Manage., 2018, 79, 71–78 CrossRef CAS PubMed.
- M. Mariño, L. L. d. Silva, N. Duran and L. Tasic, Enhanced Materials from Nature: Nanocellulose from Citrus Waste, Molecules, 2015, 20, 5908–5923 CrossRef PubMed.
- L. Q. Dien, T. D. Cuong, N. T. Minh Phuong, P. H. Hoang, D. N. Truyen and N. T. Minh Nguyet, Nanocellulose fabrication from Oryza sativa L. rice straw using combined treatment by hydrogen peroxide and dilute sulfuric acid solution, Energy Sources, Part A, 2019, 1–10 Search PubMed.
- G. Zhao, J. Du, W. Chen, M. Pan and D. Chen, Preparation and thermostability of cellulose nanocrystals and nanofibrils from two sources of biomass: rice straw and poplar wood, Cellulose, 2019, 26, 8625–8643 CrossRef CAS.
- A. Sinclair, L. Jiang, D. Bajwa, S. Bajwa, S. Tangpong and X. Wang, Cellulose nanofibers produced from various agricultural residues and their reinforcement effects in polymer nanocomposites, J. Appl. Polym. Sci., 2018, 135, 46304 CrossRef.
- E. Espinosa, F. Rol, J. Bras and A. Rodríguez, Production of lignocellulose nanofibers from wheat straw by different fibrillation methods. Comparison of its viability in cardboard recycling process, J. Clean. Prod, 2019, 239, 118083 CrossRef CAS.
- V. A. Barbash and O. V. Yashchenko, Preparation and application of nanocellulose from non-wood plants to improve the quality of paper and cardboard, Appl. Nanosci., 2020, 10, 2705–2716 CrossRef CAS.
- J. Xu, E. F. Krietemeyer, V. M. Boddu, S. X. Liu and W. Liu, Production and characterization of cellulose nanofibril (CNF) from agricultural waste corn stover, Carbohydr. Polym., 2018, 192, 202–207 CrossRef CAS PubMed.
- A. Balea, N. Merayo, E. Fuente, M. Delgado-Aguilar, P. Mutje, A. Blanco and C. Negro, Valorization of corn stalk by the production of cellulose nanofibers to improve recycled paper properties, BioResources, 2016, 11, 3416–3431 CAS.
- M. Krstic, Z. Maksimovic, S. Ibric, T. Bakic, J. Prodanovic and S. Razic, Lignocellulosic biomass as a source of microcrystalline cellulose – chemical and technological characterization and future perspectives, Cellul. Chem. Technol., 2018, 52, 577–588 CAS.
- Y. F. Shih, Highly transparent and impact-resistant PMMA nanocomposites reinforced by cellulose nanofibers of pineapple leaves modified by eco-friendly methods, eXPRESS Polym. Lett., 2018, 12, 844–854 CrossRef CAS.
- L. Ravindran, M. S. Sreekala and S. Thomas, Novel processing parameters for the extraction of cellulose nanofibres (CNF) from environmentally benign pineapple leaf fibres (PALF): Structure-property relationships, Int. J. Biol. Macromol., 2019, 131, 858–870 CrossRef CAS PubMed.
- N. Elias, S. Chandren, N. Attan, N. A. Mahat, F. I. A. Razak, J. Jamalis and R. A. Wahab, Structure and properties of oil palm-based nanocellulose reinforced chitosan nanocomposite for efficient synthesis of butyl butyrate, Carbohydr. Polym., 2017, 176, 281–292 CrossRef CAS PubMed.
- A. M. Adel, A. A. El-Gendy, M. A. Diab, R. E. Abou-Zeid, W. K. El-Zawawy and A. Dufresne, Microfibrillated cellulose from agricultural residues. Part I: Papermaking application, Ind. Crops Prod., 2016, 93, 161–174 CrossRef CAS.
- G. Tuzzin, M. Godinho, A. Dettmer and A. J. Zattera, Nanofibrillated cellulose from tobacco industry wastes, Carbohydr. Polym., 2016, 148, 69–77 CrossRef CAS PubMed.
- Q. Wang, H. Du, F. Zhang, Y. Zhang, M. Wu, G. Yu, C. Liu, B. Li and H. Peng, Flexible cellulose nanopaper with high wet tensile strength, high toughness and tunable ultraviolet blocking ability fabricated from tobacco stalk via a sustainable method, J. Mater. Chem. A, 2018, 6, 13021–13030 RSC.
- J. Shi, W. Liu, X. Jiang and W. Liu, Preparation of cellulose nanocrystal from tobacco-stem and its application in ethyl cellulose film as a reinforcing agent, Cellulose, 2020, 27, 1393–1406 CrossRef CAS.
- S. Nie, C. Zhang, Q. Zhang, K. Zhang, Y. Zhang, P. Tao and S. Wang, Enzymatic and cold alkaline pretreatments of sugarcane bagasse pulp to produce
cellulose nanofibrils using a mechanical method, Ind. Crops Prod., 2018, 124, 435–441 CrossRef CAS.
- Y. Feng, T. Cheng, W. Yang, P. Ma, H. He, X. Yin and X. Yu, Characteristics and environmentally friendly extraction of cellulose nanofibrils from sugarcane bagasse, Ind. Crops Prod., 2018, 111, 285–291 CrossRef CAS.
- J. de Aguiar, T. J. Bondancia, P. I. C. Claro, L. H. C. Mattoso, C. S. Farinas and J. M. Marconcini, Enzymatic Deconstruction of Sugarcane Bagasse and Straw to Obtain Cellulose Nanomaterials, ACS Sustainable Chem. Eng., 2020, 8, 2287–2299 CrossRef CAS.
- F. V. Ferreira, M. Mariano, S. C. Rabelo, R. F. Gouveia and L. M. F. Lona, Isolation and surface modification of cellulose nanocrystals from sugarcane bagasse waste: From a micro- to a nano-scale view, Appl. Surf. Sci., 2018, 436, 1113–1122 CrossRef CAS.
- Z. Kassab, H. Ben youcef, H. Hannache and M. El Achaby, Isolation of Cellulose Nanocrystals from Various Lignocellulosic Materials: Physico-chemical characterization and Application in Polymer Composites Development, Mater. Today: Proc., 2019, 13, 964–973 CAS.
- M. A. F. Supian, K. N. M. Amin, S. S. Jamari and S. Mohamad, Production of cellulose nanofiber (CNF) from empty fruit bunch (EFB) via mechanical method, J. Environ. Chem. Eng., 2020, 8, 103024 CrossRef CAS.
- A. Wibowo, H. Madani, H. Judawisastra, E. Restiawaty, C. Lazarus and Y. W. Budhi, An eco-friendly preparation of cellulose nano crystals from oil palm empty fruit bunches, IOP Conf. Series: Earth Environ. Sci., 2018, 105, 012059 CrossRef.
- N. Hastuti, K. Kanomata and T. Kitaoka, Characteristics of TEMPO-Oxidized Cellulose Nanofibers from Oil Palm Empty Fruit Bunches Produced by Different Amounts of Oxidant, IOP Conf. Series: Earth Environ. Sci., 2019, 359, 012008 CrossRef.
- N. Hastuti, K. Kanomata and T. Kitaoka, Hydrochloric Acid Hydrolysis of Pulps from Oil Palm Empty Fruit Bunches to Produce Cellulose Nanocrystals, J. Polym. Environ., 2018, 26, 3698–3709 CrossRef CAS.
- Y. W. Budhi, M. Fakhrudin, N. T. U. Culsum, V. Suendo and F. Iskandar, Preparation of cellulose nanocrystals from empty fruit bunch of palm oil by using phosphotungstic acid, IOP Conf. Series: Earth Environ. Sci., 2018, 105, 012063 CrossRef.
- P. H. F. Pereira, H. L. Ornaghi Júnior, L. V. Coutinho, B. Duchemin and M. O. H. Cioffi, Obtaining cellulose nanocrystals from pineapple crown fibers by free-chlorite hydrolysis with sulfuric acid: physical, chemical and structural characterization, Cellulose, 2020, 27, 5745–5756 CrossRef CAS.
- T. Impoolsup, N. Chiewchan and S. Devahastin, On the use of microwave pretreatment to assist zero-waste chemical-free production process of nanofibrillated cellulose from lime residue, Carbohydr. Polym., 2020, 230, 115630 CrossRef CAS PubMed.
- N. Sania, A. Naveed, A. Javeed, M. A. Nasir, A. Attarad and Z. Muhammad, Management of citrus waste by switching the production of nanocellulose, IET Nanobiotechnol., 2016, 10, 395–399 CrossRef PubMed.
- H. Zhang, Y. Chen, S. Wang, L. Ma, Y. Yu, H. Dai and Y. Zhang, Extraction and comparison of cellulose nanocrystals from lemon (Citrus limon) seeds using sulfuric acid hydrolysis and oxidation methods, Carbohydr. Polym., 2020, 238, 116180 CrossRef CAS PubMed.
- Y. Wang, Y. Bi and C. Gao, The Assessment and Utilization of Straw Resources in China, Agric. Sci. China, 2010, 9, 1807–1815 CrossRef.
- M. Szymańska-Chargot, M. Chylińska, P. M. Pieczywek and A. Zdunek, Tailored nanocellulose structure depending on the origin. Example of apple parenchyma and carrot root celluloses, Carbohydr. Polym., 2019, 210, 186–195 CrossRef PubMed.
- A. Dufresne, Nanocellulose Processing Properties and Potential Applications, Curr. Forestry Rep., 2019, 5, 76–89 CrossRef.
- C. A. de Assis, M. C. Iglesias, M. Bilodeau, D. Johnson, R. Phillips, M. S. Peresin, E. M. Bilek, O. J. Rojas, R. Venditti and R. Gonzalez, Cellulose micro- and nanofibrils (CMNF) manufacturing - financial and risk assessment, Biofuels, Bioprod. Bioref., 2018, 12, 251–264 CrossRef CAS.
- E. J. Foster, R. J. Moon, U. P. Agarwal, M. J. Bortner, J. Bras, S. Camarero-Espinosa, K. J. Chan, M. J. D. Clift, E. D. Cranston, S. J. Eichhorn, D. M. Fox, W. Y. Hamad, L. Heux, B. Jean, M. Korey, W. Nieh, K. J. Ong, M. S. Reid, S. Renneckar, R. Roberts, J. A. Shatkin, J. Simonsen, K. Stinson-Bagby, N. Wanasekara and J. Youngblood, Current characterization methods for cellulose nanomaterials, Chem. Soc. Rev., 2018, 47, 2609–2679 RSC.
- P. Thomas, T. Duolikun, N. P. Rumjit, S. Moosavi, C. W. Lai, M. R. Bin Johan and L. B. Fen, Comprehensive review on nanocellulose: Recent developments, challenges and future prospects, J. Mech. Behav. Biomed. Mater., 2020, 110, 103884 CrossRef CAS PubMed.
- N. Stoudmann, M. Schmutz, C. Hirsch, B. Nowack and C. Som, Human hazard potential of nanocellulose: quantitative insights from the literature, Nanotoxicology, 2020, 14, 1241–1257 CrossRef CAS PubMed.
- F. Debiagi, P. Faria-Tischer and S. Mali, Nanofibrillated cellulose obtained from soybean hull using simple and eco-friendly processes based on reactive extrusion, Cellulose, 2020, 27, 1975–1988 CrossRef CAS.
- R. Baati, A. Magnin and S. Boufi, High Solid Content Production of Nanofibrillar Cellulose via Continuous Extrusion, ACS Sustainable Chem. Eng., 2017, 5, 2350–2359 CrossRef CAS.
- A. Merci, A. Urbano, M. V. E. Grossmann, C. A. Tischer and S. Mali, Properties of microcrystalline cellulose extracted from soybean hulls by reactive extrusion, Food Res. Int., 2015, 73, 38–43 CrossRef CAS.
- A. M. Adel, E. O. Ahmed, M. M. Ibrahim, W. K. El-Zawawy and A. Dufresne, Microfibrillated cellulose from agricultural residues. Part II: Strategic evaluation and market analysis for MFCE30, Ind. Crops Prod., 2016, 93, 175–185 CrossRef CAS.
- United Nations Environment Programme Converting Waste Agricultural Biomass into a Resource-Compendium of Technologies, 2009.
- R. Abdullah, An analysis of crude palm oil production in Malaysia, Oil Palm Industry Economic J., 2012, 12, 36–43 Search PubMed.
- G. Delepierre, O. Vanderfleet, E. Niinivaara, B. Zakani and E. Cranston, Benchmarking Cellulose Nanocrystals Part II: New Industrially Produced Materials, Langmuir, 2021, 37(28), 8393–8409 CrossRef CAS PubMed.
- E. Foster and R. Moon,
et al., Current characterization methods for cellulose nanomaterials, Chem. Soc. Rev., 2018, 47, 2609 RSC.
|
This journal is © The Royal Society of Chemistry 2021 |
Click here to see how this site uses Cookies. View our privacy policy here.