DOI:
10.1039/D1RA07245E
(Paper)
RSC Adv., 2021,
11, 36439-36449
A novel electroactive plasticized polymer actuator based on chlorinated polyvinyl chloride gel
Received
29th September 2021
, Accepted 23rd October 2021
First published on 11th November 2021
Abstract
Plasticized poly (vinyl chloride) (PVC) gel is a promising electroactive polymer material for soft actuators and sensors, and it has attracted extensive attention and interest in multi-disciplinary fields. Chlorinated polyvinyl chloride (CPVC) has enhanced mechanical and chemical properties and shows a promising potential for fabricating gel materials for electroactive polymer gel actuators. Thus, we proposed a novel soft actuator based on CPVC gels. We studied the properties of CPVC gels with various technologies, such as Fourier transform infrared spectroscopy (FTIR), X-ray diffraction (XRD), scanning electron microscope (SEM) analysis, thermogravimetric analysis (TGA), etc. Furthermore, CPVC gel actuators were fabricated and the influence of membrane thickness and plasticizer content on the basic characteristics was investigated. The experimental results show that the CPVC gel actuator with a higher content of DBA has a better strain than that of the actuator with lower amount of DBA despite the membrane thickness. With the same ratio of DBA, the CPVC gel actuator has a better performance than the traditional PVC gel actuator under a low applied load. The maximum strain and stress of the CPVC gel (CPVC
:
DBA = 1
:
2.5) actuator are 9% and 0.12 MPa respectively at 400 V, which reaches the same level of the PVC gel actuator with higher content of DBA (PVC
:
DBA = 1
:
4). These results demonstrate a good potential of the proposed CPVC gel soft actuator for practical application.
1. Introduction
Recently, there has been an increasing interest in the field of soft robotic systems that deal with uncertain and dynamic tasks.1 Soft actuators, such as electroactive polymer (EAP) actuators are crucial in such robotic systems.2,3 Compared to traditional rigid actuators, they have many advantages, such as light weight, high flexibility, large actuation strain and/or stress, low noise and easy processing.4–6 Among EAPs, conducting polymer actuators (CPAs) are superior in strain, stress and driving voltage compared with other EAPs.7 For example, a polypyrrole (PPy) film actuator exhibits a large contraction strain of 40% and a stress of 49 MPa under a low operating voltage of several volts.8 However, it can be only actuated in solution. Similarly, ionic polymer–metal composite (IPMC) actuators show a big bending deformation under 1–3 volts, but with a relatively low response speed and limited lifetime.9 Dielectric elastomer actuators (DEAs) have been considered as a key power source for soft robots,10–12 due to their advantages of light weight, flexibility with non-geometric constraints, low cost and stable actuation in air, with huge strain (>300%), large stress (>3 MPa) and fast response. Nevertheless, they are still facing the challenge of a high driving voltage that is typically bigger than 2 kV. As a kind of electronic EAP actuator, PVC gel actuators have demonstrated equal strain, strength and speed to those of human muscle under a relatively low driving voltage (typically <0.4 kV), and have shown good stability and durability, which indicates a good potential as soft actuators.13,14 Therefore, it has attracted extensive attention and interest in multi-disciplinary fields. So far, many researches have been done on the actuation mechanism, materials characterization, structure design and application of PVC gel actuators.15–18
In our previous study, we have developed a human muscle-like contraction–expansion type multilayered soft actuator using PVC gels and stainless-steel mesh electrodes.15 At 400 V, the actuator demonstrated a contraction strain of 12%, an output stress of 90 kPa, a response rate of 9 Hz and a durability of over 5 million times (at 2 Hz) continuous actuation. The fabricated actuator can remain a stable operation for more than five years at room temperature in air with occasional operation (about 500 times per year) without bleeding out. And we have applied it to a motor brake,19 a wearable walking assist device20 and a soft gripper.21 However, for a practical application, the actuator is still facing the challenges of a notable weight, a big size and lack of strain and stress as compared to the biological muscle.22 On the other hand, CPVC is the product of PVC after chlorination.23,24 Fig. 1 shows the structural difference between PVC and CPVC. PVC has a stable head-tail structure (–CH2–CHCl–CH2–CHCl–). When chlorination begins, the amount of –CH2– plummets, and the content of –CHCl– and –CCl2– rises. When chlorine content reaches 70%, the original PVC structural unit is almost reduced to zero, and then CPVC is mainly composed of –CHCl– and –CCl2–. Since the molecular chains of –CHCl– and –CCl2– are not easy to decompose and dechlorinate hydrogen compared with –CH2–, the thermal stability of CPVC is higher than that of PVC. In addition, the irregularity of molecular chain arrangement and polarity increase after the chlorination, which increases the solubility and chemical stability of CPVC resin, and consequently improves the comprehensive performance (including the mechanical properties) of PVC resin.25 Thus, CPVC shows a promising potential for fabricating gel materials for electroactive polymer gel actuators. On this basis, we think that the CPVC gel would have a better performance than that of PVC gel. Therefore, to improve the performance of PVC gel actuator, we propose to construct a novel multilayered soft actuator based on CPVC gels. In this pilot study, we measured the basic properties of CPVC gels with varying content of plasticizer DBA, using Fourier transform infrared spectroscopy, X-ray diffraction (XRD), scanning electron microscope (SEM) analysis, etc. And we fabricated several types of CPVC gel actuators and investigated the influences of each component (e.g., membrane thickness and DBA content) of the actuator on the basic characteristics of the actuator. The comparison of the proposed CPVC gel actuator with traditional PVC gel actuator and other soft actuators is also discussed.
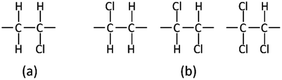 |
| Fig. 1 Molecular structure of two-carbon sequences for (a) PVC and (b) CPVC. | |
2. Experimental
2.1 Chemicals
CPVC powder is obtained from Lubrizol Specialty Chemicals Co., Ltd. (No. 88096, about 70% chlorination). PVC powder (CAS 9002-86-2, average Mw − 233
000), DBA plasticizer (CAS 105997, purity of 96%) and tetrahydrofuran (THF, CAS 109999, purity of 99.9%) were ordered from Sigma-Aldrich and used as received.
2.2 Preparation of gel membrane
2.2.1 Preparation of CPVC/DBA/THF mixed solutions. Firstly, CPVC powder was evenly scattered into THF solution by using a glass funnel. Secondly, DBA solution was poured into the CPVC/THF mixed solution and was then stirred by a centrifuge for 6 min at 3000 rpm to get a uniform mixture, as shown in Fig. 2(a). Finally, the CPVC gel solution was obtained after stirring with a magnetic stirrer at room temperature for about 24 h. Note that, the amount of solvent THF determines the viscosity of the final solution while the amount of plasticizer DBA effects the mechanical and electromechanical characteristics of the CPVC gel membranes. The weight ratio of CPVC and THF was adjusted to 1
:
4 and 1
:
8 for casting method and compression molding, respectively. To obtain the optimal amount of DBA, we adjusted the weight ratio of CPVC and DBA to 1
:
1, 1
:
1.5, 1
:
2 and 1
:
2.5, and the gels were denoted as CPVC10, CPVC15, CPVC20 and CPVC25, respectively. It is noteworthy that the CPVC gel is fragile and with poor mechanical properties when the weight ratio of CPVC and DBA is lower than 1
:
3.
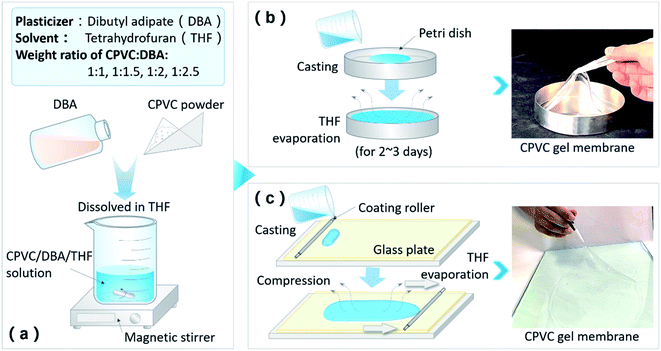 |
| Fig. 2 Fabrication of CPVC gel membranes. (a) Preparation of CPVC/DBA/THF mixed solutions, (b) fabrication by casting method, (c) fabrication by compression method. | |
2.2.2 Fabrication of CPVC gel membranes. As shown in Fig. 2, to obtain different thickness of CPVC gel membranes, we used two methods to fabricate the membranes, namely casting and compression molding. Casting is generally for the gel membrane with a thickness over two hundred of micrometers while compression molding is for the membrane which has a thickness under two hundred of micrometers. The thickness is adjusted by the solution amount adjustment in the Petri dish for the casting method (see Fig. 2(b)), while it is adjusted by the clearance adjustment between the roll and the slide plate for the compression molding method (see Fig. 2(c)). CPVC gel membranes are obtained after the THF evaporated at room temperature (about 24 °C, with a humidity of about 50%) for two to three days. The fabricated CPVC gel membrane is highly transparent, and generally can be deformed up to 350% by stretching.
2.3 Electromechanical deformation of CPVC gels
CPVC is the chlorination product of PVC. The main raw material for the CPVC resin is PVC resin. Therefore, similar to PVC gel, CPVC gel is also an electroactive polymer, exhibiting a creep-like deformation only at the anode side of electrodes in response to an electrical stimulus, as shown in Fig. 3(a). This may due to the accumulation of high-density negative charges in the portion of gel near the anode which generates a Maxwell force between the gel and anode electrodes and then causes the gel to deform asymmetrically between the electrodes. When the applied voltage is turned off, the CPVC gel returns to its original shape quickly due to its elasticity.
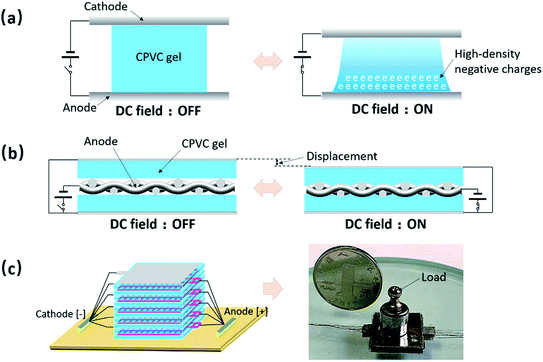 |
| Fig. 3 (a) Creep deformation of a CPVC gel membrane under a DC field (side view), (b) schematic of single-layer CPVC gel actuator and its contraction deformation (side view), (c) structure of 5-layer multilayered CPVC gel actuator (left side) and a sample of fabricated 5-layered multilayered CPVC gel actuator with a one-yuan coin (right side). | |
2.4 Construction and fabrication of CPVC gel actuators
Based on the unique creep deformation near the anode, we used meshed anode electrodes and stainless foil cathode electrodes to construct the CPVC actuator, which allows an expansion and contraction movement of the actuator. When the DC field is applied, the CPVC gel creeps into the mesh holes, and the actuator shrinks in the direction of thickness. And when the DC field is removed, it returns to its former shape by its elasticity (see Fig. 3(b)). Thus, it performs as an expansion–contraction deformation that similar to a human muscle. This deformation can be magnified by stacking up the single-layer structures, as illustrated in Fig. 3(c). The right side of Fig. 3(c) shows an example of fabricated 5-layer multilayered CPVC gel actuators, which is sandwiched by two glass slides at the top and bottom respectively. The height of the 5-layer actuator is about 2.875 mm and the weight is about 1.67 g.
2.5 Characterizations and measurements
2.5.1 Characterizations of CPVC gels. Fourier transform infrared spectroscopy (FTIR) (Nicolet 6700) was used to study the functional groups in CPVC gels. X-ray diffraction (XRD) analysis was carried out by X-ray diffractometer (D/mac 2500 VB2+/PC Rigaku) in the range of 2θ angle of 10–60° to study the crystallization of CPVC gels. The surface morphology of CPVC gel with different content of DBA was observed by scanning electron microscope (SEM). The mechanical properties of the gels were tested by electronic universal testing machine (CMT6103 MTS) at room temperature with a standard speed of 100 mm min−1. And thermogravimetric analysis (TGA) of the gels was analyzed using a synchronous thermal analyzer (TG-DSC). The temperature changes from 100 °C to 500 °C with a speed of 10 °C min−1.
2.5.2 Characteristics evaluation of CPVC gels actuators. We measured the basic characteristics of the proposed CPVC gel actuators, including the displacement and strain, output stress, current and response rate. To optimize the parameter of CPVC gel actuator, we investigated the displacement of the single-layer actuator with different applied voltages, different types of CPVC gels with varying thickness (from 0.05 to 0.25 mm) and weight ratio of CPVC/DBA (from 1
:
1 to 1
:
2.5). The basic parameters for CPVC gel actuators are shown in Table 1. A laser sensor (LK-H050, KEYENCE Corp.) was used for the displacement measurement. According to the results of the displacement, CPVC gel of CPVC25 with a thickness of 0.15 mm was selected for the multilayered CPVC gel actuator. We measured the relation between the displacement and output force of 5-layer multilayered CPVC gel actuators by using the method shown in Fig. 4. When a DC voltage is applied, the actuator shrinks in the thickness direction and brings a downward movement to the applied load. When the DC voltage is turned off, the actuator recovers to its original shape by its elasticity and consequently brings an upward movement to the external load. A preload of about 350 mN (about 1.1 kPa) was applied to eliminate the ununiformity of the multilayered actuator. The applied load was from 0.2 N to 50 N. Fig. 5 shows the method of current measurement of the actuators. We used a series resistor (1 kΩ) and a data logger (NI my RIO-1900) to measure the leakage current. Finally, the response rate was investigated by the frequency response of the displacement of CPVC actuator under different frequencies from 0.1 Hz to 10 Hz. The applied DC voltage for all the measurements above is from 100 V to 400 V.
Table 1 Structure parameters of CPVC/PVC gel actuators
|
CPVC gel (PVC gel) |
Anode |
Cathode |
Material |
CPVC : DBA = 1 : 1, 1 : 1.5, 1 : 2, 1 : 2.5 (PVC : DBA = 1 : 2.5) |
SUS304 stainless mesh: #100 (100 wires per inch) |
SUS304 stainless foil |
Size |
21 × 17 × 0.15 mm (21 × 17 × 0.15 mm) |
20 × 16 × 0.2 mm |
20 × 16 × 0.01 mm |
Number |
2 (2) for single-layer structure |
1 for single-layer structure |
2 for single-layer structure |
10 (10) for 5-layer structure |
5 for 5-layer structure |
6 for 5-layer structure |
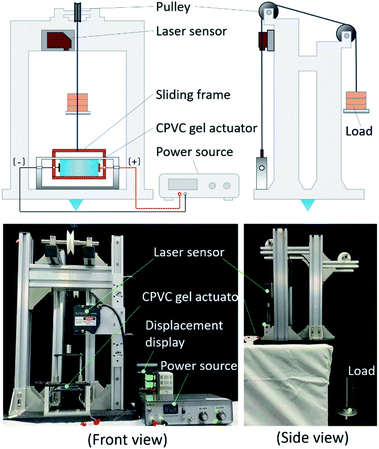 |
| Fig. 4 Displacement and output force measurement of CPVC/PVC gel actuators. | |
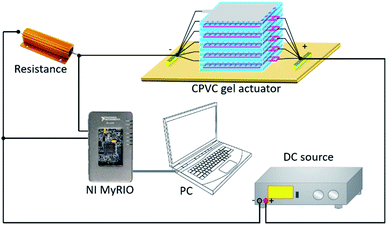 |
| Fig. 5 Current measurement of CPVC/PVC gel actuators. | |
As mentioned in Section 2.3, CPVC is chlorinated PVC with improved mechanical and chemical properties. We conducted experiments to compare the characteristics between CPVC gel actuators and PVC gel actuators. Since CPVC resin has several advantages over PVC resin, we have the hypotheses that the CPVC gel actuator has more positive properties than that of the PVC gel actuator. The PVC gel of PVC25 (PVC
:
DBA = 1
:
2.5) was used for fabricating 5-layer PVC gel actuators, with the same size of CPVC gel actuators (see Table 1). We investigated the displacement, output force, response rate and current of the PVC gel actuators and discussed the difference between the proposed CPVC gel actuator and the traditional PVC gel actuator.
3. Results and discussion
3.1 Functional groups and crystalline state of CPVC gel
The internal functional groups and molecular chain polarization of CPVC gel membranes with different contents of CPVC10, CPVC15, CPVC20 and CPVC25 were studied by FTIR, and the control group PVC25 was added for comparative analysis. As shown in Fig. 6(a), there are several main characteristic peaks in CPVC gel, including the peaks of C–H band (1427, 1257 cm−1), C–C vibration (968 cm−1) and C–Cl band (698, 636, 605 cm−1). The spectrum shows that the peak of carboxyl (C
O) band in 1732 cm−1 gel shows a strong characteristic peak, and the existence of the carbon group is one of the main functional groups for polymer polarization and plasticization.26 In addition, the functional group is mainly provided by plasticizer,27 which shows that CPVC and PVC molecules almost contain no carboxyl functional groups. In addition, by comparison, there was little difference between CPVC10 and CPVC25 in C–Cl band and PVC25. It can be seen from the Fourier transform spectrum that there is no significant difference in the functional groups of C
O and C–Cl for the five types of gel materials. They all show strong polarization characteristics. Besides, the CPVC resin obtained by chlorination of PVC resin shows no strong characteristic peak on the C–Cl functional group. In particular, the C
O band in the CPVC gel affects the solvent movement between the cathode and the anode under the applied field, and the dipole moment of the C–Cl band may lead to the alignment of molecules under the influence of polarizable solvents (THF was used as a solvent in this study).
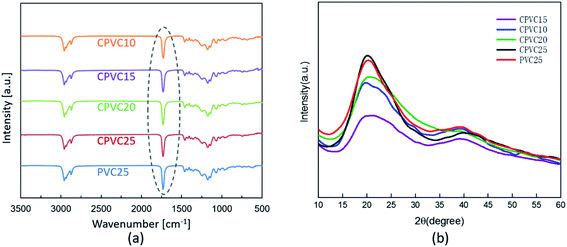 |
| Fig. 6 (a) The FTIR spectra and (b) XRD patterns of PVC25 and CPVC gels for varying CPVC/DBA ratios. | |
Fig. 6(b) shows the XRD pattern of the CPVC gel. Its wide halo represents an amorphous structure, indicating poor crystallization. The full width at half-maximum (FWHM) of the corresponding diffraction peaks of CPVC10, CPVC15, CPVC20, CPVC25 and PVC25 were 10.34°, 10.16°, 14.01°, 8.47° and 10.14°, respectively. The grain size can be obtained via the Scherrer equation:28
|
D = kλ/β cos θ
| (1) |
where
k is the Scheller constant, which is determined by the definition of ‘breadth’, the crystallite shape and the crystallite-size distribution.
29 Here,
k is assumed to be 1 for considering that the crystallites of the gel could be irregular in shape (for detailed discussion of
k, refer to ref.
29).
λ is the wavelength (
λ = 1.542 Å) of Cu Kα radiation,
β is the full width at half maximum (FWHM) of the line, and
θ is the diffraction angle. From the Scherrer equation, it is suggested that CPVC25 gel has a higher density (non-uniformity) microcrystalline network structure due to the large aggregation of polymer chains in the amorphous phase. However, the thin crystals induced by CPVC gel with low molecular weight are too weak to promote the physical interconnection network. Therefore, CPVC gel with reduced molecular weight after chlorination has low shape stability, poor mechanical strength and low elasticity. In addition, only two main broad peaks at about 22° and 40° were observed in the XRD pattern, indicating the uniformity of mixing of DBA and CPVC and the purity of the gel.
30
3.2 Thermal and mechanical properties of CPVC gel
Thermogravimetric analysis (TG) and derivative thermogravimetric analysis (DTG) were conducted to analyze the thermal degradation behavior of CPVC gels. As shown in Fig. 7(a), the weight loss in the first stage occurred at 73.4–255.22 °C (CPVC10), 73.4–263.13 °C (CPVC15), 73.4–248 °C (CPVC20) and 73.4–240 °C (CPVC25), respectively. And the corresponding weight loss is 47.71% (CPVC10), 59.20% (CPVC15), 67.54% (CPVC20) and 71.79% (CPVC25), respectively. The weight loss in this stage is mainly caused by the decomposition of DBA and the evaporation of solvent THF.31,32 It can be seen that the weight loss ratio in this stage increases with the increase of DBA content. The weight loss of PVC25 at this stage (73.4–256 °C) was 68.91%. Because its molecular weight was larger than that of CPVC, the content of DBA at the same weight was smaller, and the weight loss at the same stage was smaller than that of CPVC. The weight loss of the second stage occurred in 255.22–360 °C (CPVC10), 263.13–360 °C (CPVC15), 248–360 °C (CPVC20), 240–360 °C (CPVC25), respectively. At this stage, the weight loss may be due to the thermal decomposition of CPVC in CPVC gel into chlorine and other substances. Compared with PVC25 at 400–500 °C, there is a third stage of decomposition,33 and the final PVC25 is only 4.9%, which confirms that the thermal stability of CPVC after chlorination is higher than that of PVC.
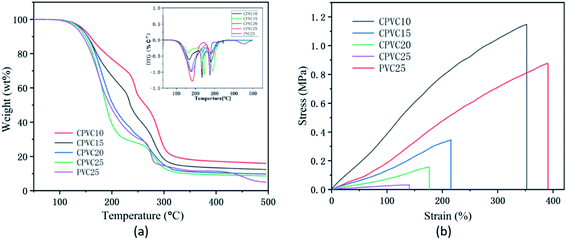 |
| Fig. 7 (a) The TGA and DTG thermograms and (b) stress–strain curves of PVC25 and CPVC gels for varying CPVC/DBA ratios. | |
The stress–strain behavior is an important characteristic for soft actuator materials. Fig. 7(b) shows the stress–strain curves of CPVC10, CPVC15, CPVC20 and CPVC25 gel samples, which were compared with those of PVC25 gels. At the same strain, the stress of CPVC gel decreases with the increase of DBA content, which is consistent with the relationship between the mechanical properties of PVC gel and the content of DBA in previous studies.30,34 The Young's modulus of CPVC gels were 0.42 MPa (CPVC10), 0.16 MPa (CPVC15), 0.09 MPa (CPVC20) and 0.06 MPa (CPVC25), respectively. The Young's modulus of PVC25 was 0.17 MPa. The mechanical properties of PVC25 are similar with CPVC10 in the elongation and tensile strength at break. With the same DBA content, the elongation at break of CPVC25 and PVC25 were 140% (CPVC25) and 380% (PVC25), and tensile strengths were 0.02 MPa (CPVC25) and 0.9 MPa (PVC25), respectively. The lower Young's modulus of CPVC gel will greatly affect the output force of CPVC gel actuators.
3.3 Surface and internal morphological analysis of CPVC gel
Fig. 8 shows the microscopic images of CPVC gels under SEM. Fig. 8(a)–(h) shows the microstructure and cross-sectional images of CPVC10, CPVC15, CPVC20, CPVC25 gel surface formed naturally. It can be seen in CPVC10 image that the surface and cross section of the gel are almost flat, indicating that a small amount of plasticizer does not affect the uniformity of CPVC molecular chain distribution. It is noteworthy that there is still a small amount of CPVC particles in the image (within the red circle), indicating that the plasticizer DBA does not dissolve all the CPVC particles at this ratio. With the increase of DBA content, the plasticizer increased the adhesion between the molecular chains,32 and promoted the aggregation of the gel in the solidification process to form independent peaks and grooves. The existence of these peaks and grooves will greatly affect the mechanical properties of the gel, and reduce its elongation at break and elasticity. The surface morphology of PVC25 and CPVC25 is almost the same, indicating that the effect of DBA on the surface forming is consistent. However, the larger molecular weight of PVC may make the molecular chain have more entanglement in both longitudinal and transverse directions,35,36 thus ensuring a certain mechanical strength.
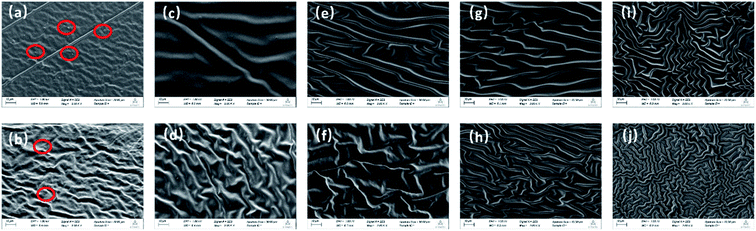 |
| Fig. 8 SEM micrographs of (a) CPVC10, (b) CPVC10 (cross section), (c) CPVC15, (d) CPVC15 (cross section), (e) CPVC20, (f) CPVC20 (cross section), (g) CPVC25, (h) CPVC25 (cross section), (i) PVC25, (j) PVC25 (cross section). | |
3.4 Characterizations of the proposed CPVC gel soft actuator
3.4.1 Displacement. We investigated the influence of the thickness of the gel and the content of DBA on the displacement of the single-layer CPVC gel actuator. It can be seen from Fig. 9 that the maximum displacement and strain of the actuator increases with the increase of the applied voltage. When the voltage is 400 V, the displacement and strain of the single-layer CPVC25 gel actuator is about 33.4 μm and 8%, respectively. At the same applied voltage, the displacement of the actuator increases with the increase of the thickness of CPVC gel. Besides, the displacement and strain of the actuator increases with the increase of the amount of plasticizer DBA. This shows that the deformation principle of CPVC gel actuator is similar to that of PVC gel actuator, that is due to the movement of DBA molecules in CPVC molecular chain. However, for the gel thickness within a range from 50 μm to 250 μm, there is no significant difference in the strain (the dashed lines) of the actuators with different gel thickness, which is consistent with the phenomenon that observed in the PVC gel actuator. As presented by K. Asaka et al.37 that the deformation of PVC gel is generated by the static force between the S–R layer (with high space-charge density) of PVC gel and the surface of the anode electrode. And the estimated thickness of the S–R layer was from several micrometers to several tens of micrometers, finding no significant change from the thickness of 0.3 mm to 0.8 mm. Therefore, these results indicate that it would be an effective approach to construct the CPVC gel actuator with thinner CPVC gels (<0.3 mm) and higher DBA content to obtain a large displacement.
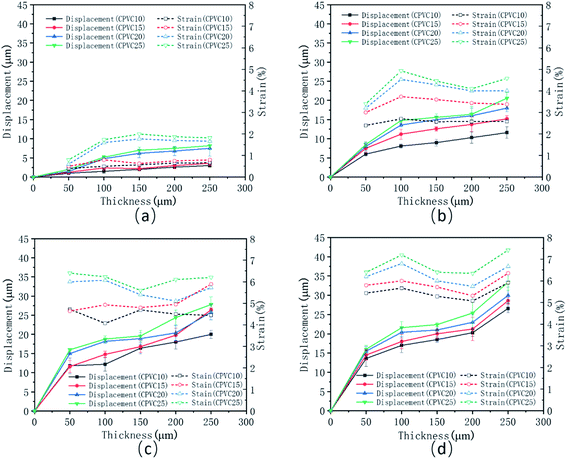 |
| Fig. 9 Displacement and strain of single-layer CPVC gel actuators with different gel membrane thicknesses. (a) At 100 V, (b) at 200 V, (c) at 300 V, (d) at 400 V. | |
3.4.2 Output force measurement. Since the displacement of the single-layer actuator is too small to measure the output force of the actuator, we used 5-layer multilayered CPVC gel actuators for the output force measurement. CPVC25 with a thickness of 0.15 mm was selected for the multilayered CPVC gel actuator. And we conducted experiments to compare the characteristics between CPVC gel actuators and the traditional PVC gel actuators using PVC25 gel (PVC
:
DBA = 1
:
2.5) actuator.As shown in Fig. 10(a), the displacement of the actuator increases with the increase of the applied voltage while it decreases with the increase of the applied load. When the output force is plotted as a function of the displacement, the output force is inversely proportional to the displacement (see Fig. 10(b)). At the same applied voltage, with the increase of the output stress, the displacement decreases. While the output force increases with the increase of the applied voltage. This nonlinear relation can be modeled by using Hill's muscle model,38 with a good agreement with the experimental results. The simulated maximum output force of CPVC was about 41 N (115 kPa) at 400 V. Fig. 11 shows the results of the relation between the output force and displacement of the CPVC gel (CPVC25) actuators compared with that of PVC gel (PVC25) actuators. It can be seen that the CPVC gel actuator has a bigger output force when the displacement is in the range of 72%, 78%, 66% and 72% of the maximum displacement of the actuator at 400 V, 300 V, 200 V and 100 V, respectively (the output force is not higher than 3.7 N, 4.4 N, 2.7 N and 3.1 N, respectively). This indicates that under the same load, the displacement of the soft actuator based on CPVC gel is better than that of the soft actuator based on PVC gel that with the same ratio of DBA. This might due to the CPVC gel actuator has a bigger contraction strain (about 9%) than that of PVC gel actuator (about 7%) with an initial load of 0.35 N, as shown in Fig. 12. However, the displacement of CPVC gel actuators is dramatically decreases with further increases of the output force. At a higher output force, the stroke of CPVC gel actuator is significantly less than that of PVC gel actuator with the same ratio of DBA due to the mechanical properties of the CPVC25 gel itself is far less than that of PVC25 gel.
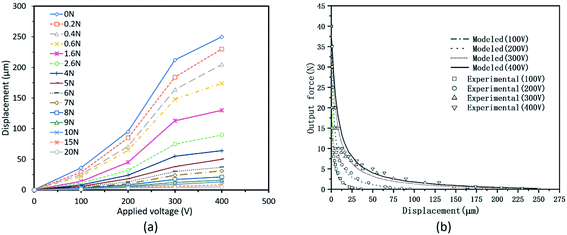 |
| Fig. 10 (a) The contraction strain change vs. the applied DC voltage for CPVC gel actuators with varying applied loads. (b) Output stress vs. strain for CPVC gel actuators with varying applied DC voltages. | |
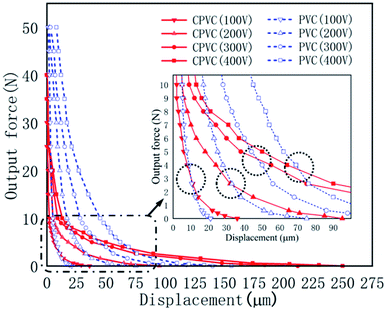 |
| Fig. 11 Comparison of the results of the relationship between the output force and displacement of CPVC25 and PVC25 gel actuators. | |
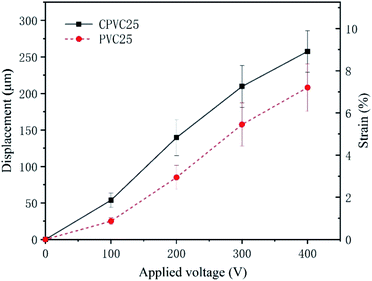 |
| Fig. 12 Comparison of displacement and strain of CPVC25 and PVC25 gel actuators under an initial applied load of 0.35 N. | |
3.4.3 Current measurement. The current is an important parameter to evaluate the power consumption of soft actuators. Due to the complex equivalent circuit of the gel actuator, it is difficult to directly measure the current of the actuator. Therefore, we measured the current of the actuator by measuring the voltage of a series 1 kΩ resistor (see Fig. 5).Since the resistance of the actuator can reach several megahertz, the error caused by a 1 kΩ resistor in series to the current of the entire circuit is within an allowable range. We applied a 300 V rectangular voltage wave with a frequency of about 1 Hz to the 5-layer CPVC25 gel and PVC25 gel actuators, and the current variation is shown in Fig. 13.
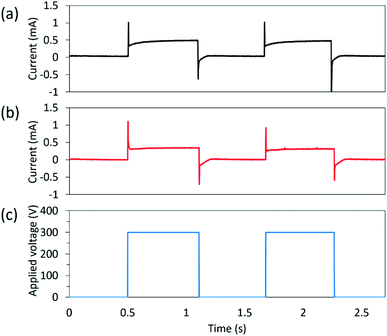 |
| Fig. 13 Current variation of (a) the 5-layer CPVC25 gel and (b) PVC25 gel actuators under (c) an applied voltage of 300 V. | |
It can be seen that when the DC field is turned on, there is an instantaneous inrush current occurs and rapidly decrease to a stable state, and a negative instantaneous inrush current occurs and decrease to zero quickly when the DC field is turned off, both for CPVC gel and PVC gel actuators. This is due to the charging and discharging behavior of the capacitance of the gel actuator, which indicates that CPVC gel actuators have a similar equivalent circuit of PVC gel actuators reported in prior literature.39 The average leakage current of CPVC25 gel actuator (about 0.5 mA) is bigger than that of PVC25 gel actuator (about 0.3 mA). It is speculated that the reason is that more chloride ions in CPVC gel increases the leakage current.
3.4.4 Response rate measurement. The response rate of the actuator is studied by frequency response method. Rectangular voltage pulse signals with frequencies from 0.1 Hz to 10 Hz and an amplitude of 300 volt. The Bode diagrams of the displacement of the two types of actuators are shown in Fig. 14.
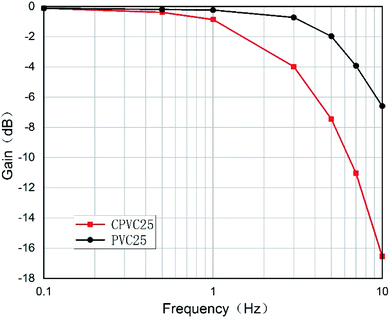 |
| Fig. 14 Bode diagram of displacement for CPVC25 and PVC25 gel actuators. | |
The bandwidth of CPVC25 gel actuator (−3dB) is about 2.4 Hz, while PVC25 gel actuator is about 6 Hz. The response speed of the actuator is related to the elasticity of the gel. The difference of elasticity between CPVC gel and PVC gel under the same ratio can be reflected by the difference of response rate.
4. Discussion and future work
CPVC resin is chlorinated by PVC resin, with enhanced mechanical and chemical properties which show a promising potential for fabricating gel materials for electroactive polymer gel actuators. Therefore, we proposed a novel soft actuator based on CPVC gels. We prepared four types of CPVC gels with different ratio of CPVC
:
DBA, as CPVC10, CPVC15, CPVC20 and CPVC25. And we investigated the characteristics of the corresponding CPVC gel actuators. The experimental results show that the maximum strain of the CPVC gel actuator at 400 V is about 9%, which is higher than that of the PVC gel actuator (7%) with the same ratio of DBA and close to that of the PVC gel actuator with a high content of DBA (PVC
:
DBA = 1
:
4).15 In addition, the displacement of the CPVC gel actuator is bigger than that of the PVC gel actuator when there is an external applied load of not more than 3.7 N at 400 V. However, with the further increase of the applied load, the displacement of CPVC gel was gradually exceeded by PVC gel due to its insufficient elasticity. Due to the lack of elasticity, the bandwidth of CPVC gel actuator is only 2.4 Hz, which is lower than 6 Hz of PVC gel actuator and 10 Hz of natural muscle. It is noteworthy that, the content of plasticizer DBA mainly affects the performance of the gel actuators.40 Within a certain range, the higher the content of DBA, the better the performance of the gel actuators. Though CPVC25 gel actuators have an advantage over PVC25 gel actuators in the aspects of displacement and output force, the performance of PVC gel actuators with higher DBA content (i.e. PVC
:
DBA = 1
:
4) is better than that of CPVC gel actuators based on lower DBA content (i.e., CPVC
:
DBA = 1
:
2.5). While it is difficult for CPVC resin to form a gel membrane with a notable mechanical property when the content of DBA is larger than 70% due to the high solubility of the CPVC resin, which might be the challenge of constructing a CPVC gel actuator with high performance for practical applications.
Table 2 shows the comparison of CPVC gel actuator with other soft actuators. As can be seen that, CPVC actuators can be stably actuated in air under a low electric field, with an intermediate strain and a relative fast response speed, but a low output force. CPVC resin is still in the development stage. Further researches should be focused on the characteristic optimization of CPVC gel actuators, in the aspects of investing the influence of different CPVC resins with varying degree of chlorination and different molecular weight on the performance of the actuator, optimizing the parameters of the gels and electrodes and improving the structure of the actuator.
Table 2 Comparison of proposed CPVC gel actuator and other soft actuator technologies
Actuator type |
Function |
Operating voltage (V) |
DC field strength (V μm−1) |
Maximum strain (%) |
Maximum stress (MPa) |
Relative speed (full cycle) |
Cycle life |
The shape memory polymer and coiled nylon actuators are typically driven by thermal stimulation, with a typical temperature of over 100 °C. |
CPVC gel actuators (CPGAs) (meshed electrodes based structure) |
Contractile |
100–400 |
0.67–2.67 |
9 |
>0.12 |
Fast (<0.4 s) |
— |
PVC gel actuators (PGAs) (meshed electrodes based structure)15 |
Contractile |
80–400 |
0.4–2 |
11 |
>0.09 |
Fast (<0.1 s) |
Long (>5 million) |
PVC gel actuators (PGAs) (soft planer electrodes based structure)41 |
Contractile, bending |
50–2400 |
0.5–41 |
76 |
>0.6 |
Fast (<0.2 s) |
Long (>1 million) |
Ionic polymer–metal composites (IPMCs)9 |
Bending (in liquids) |
1–3 |
0.25 |
3 |
30 |
Slow (>2 s) |
Low (8000) |
Conducting polymer actuators (CPAs) (polypyrrole)8 |
Contractile (in liquids) |
1–2 |
0.05 |
40 |
49 |
Slow (>2 s) |
Low |
Dielectric elastomer actuators (DEAs) (acrylic)10 |
Contractile |
>1000 |
>200 |
380 |
7.2 |
Medium (∼2 s) |
— |
Dielectric elastomer actuators (DEAs) (silicone)42 |
Contractile |
>1000 |
>300 |
120 |
3 |
Fast |
— |
Shape memory polymers (SMPs)43 |
Contractile, bending |
a |
— |
100 |
4 |
Slow (>5 s) |
Low |
Coiled nylon actuators (CNAs)44 |
Contractile |
a |
— |
49 |
>140 |
Slow (>5 s) |
Long (>1 million) |
Natural muscle22 |
Contractile |
— |
— |
20–40 |
0.35 |
Fast (0.1 s) |
Long |
5. Conclusions
We have proposed a novel soft actuator based on CPVC gel and meshed electrodes. Fourier transform spectroscopy, XRD, SEM analysis, tensile test and TGA were conducted to study the property of CPVC gel. The results showed that the internal deformation mechanism and molecular chain crosslinking mechanism of CPVC gel were supposed to be the same as those of PVC gel. However, CPVC gel shows a lower mechanical property than PVC gel with the same content of DBA. Furthermore, we investigated the influences of the applied voltage, membrane thickness and plasticizer content on the basic characteristics of the CPVC actuators compared with the PVC gel actuator with the same ratio of DBA. It was found that the CPVC gel actuator has a favorable performance under a low external applied load (about 4 N) compared with the traditional PVC gel actuator. The maximum strain and stress of CPVC gel actuator are 9% and 0.12 MPa respectively, which reaches the same level of the PVC gel actuator with higher content of DBA. In the future work, we should focus on the characteristic optimization of CPVC gel actuators, in the aspects of CPVC resin materials and the structure of the actuators so as to realize a soft actuator with high performance under low driving voltages.
Conflicts of interest
There are no conflicts to declare.
Acknowledgements
This work was supported by the National Natural Science Foundation of China (Grant No. 51805482 and 51975523).
References
- D. H. Kim, Y. Lee and H. Park, Soft robotics, 2021 DOI:10.1089/soro.2020.0167
. - Soft Actuators – Materials, Modeling, Applications and Future Perspectives, ed. K. Asaka and H. Okuzaki, Springer, Japan, 2014 Search PubMed
. - Electromechanically Active Polymers – A Concise Reference, ed. F. Carpi, Springer, Berlin, 2016 Search PubMed
. - J. H. Youn, S. M. Jeong, G. Hwang, H. Kim, K. Hyeon, J. Park and K. U. Kyung, Appl. Sci., 2020, 2, 640 CrossRef
. - B. C. Yoseph and A. A. lain, Mechanics of soft materials, 2019, 1, p. 5 Search PubMed
. - B. T. Mirfakhraia, J. D. W. Maddena and R. H. Baughman, Mater. Today, 2007, 10, 30 CrossRef
. - K. Kaneto, J. Phys.: Conf. Ser., 2016, 704, 012004 CrossRef
. - T. Zama, S. Hara, W. Takashima and K. Kaneto, Smart Mater. Struct., 2005, 14, 1501–1510 CrossRef
. - C. Jo, D. Pugal, I.-K. Oh, K. J. Kim and K. Asaka, Prog. Polym. Sci., 2013, 7, 1037 CrossRef
. - R. Pelrine, R. Kornbluh, Q. Pei and J. Joseph, Science, 2000, 287, 836 CrossRef CAS PubMed
. - B. Paul and P. Qibing, Macromol. Rapid Commun., 2010, 1, 10 Search PubMed
. - G. Y. Gu, Z. Jian, L. M. Zhu and X. Y. Zhu, Bioinspiration Biomimetics, 2017, 12, 011003 CrossRef PubMed
. - M. Yamano, N. Ogawa, M. Hashimoto, M. Takasaki and T. Hirai, 2008 IEEE International Conference on Robotics and Biomimetics, IEEE, 2009, p. 745 Search PubMed
. - Y. Li, M. F. Guo and Y. B. Li, J. Mater. Chem. C, 2019, 7, 12991 RSC
. - Y. Li and M. Hashimoto, Sens. Actuators, A, 2015, 233, 246 CrossRef CAS
. - H. Xia and T. Hirai, J. Phys. Chem. B, 2010, 114, 10756 CrossRef CAS
. - W. H. Park, E. J. Shin, S. Yun and S. Y. Kim, IEEE Trans. Haptics, 2018, 11, 22 Search PubMed
. - B. Jin, D. S. Choi, I. H. Han and S. Y. Kim, ACS Appl. Mater. Interfaces, 2021, 13, 10397–10408 CrossRef PubMed
. - M. Shibagaki, T. Matsuki and M. Hashimoto, Proceedings of the 2010 IEEE International Conference on Mechatronics and Automation, IEEE, 2010, p. 39 Search PubMed
. - Y. Li and M. Hashimoto, Smart Mater. Struct., 2017, 26, 125003 CrossRef
. - Y. Li, B. Sun, T. M. Chen, B. W. Hu, M. F. Guo and Y. B. Li, Jpn. J. Appl. Phys., 2021, 60, 087001 CrossRef CAS
. - R. H. Baughman, Science, 2005, 308, 63 CrossRef CAS
. - N. Merah, F. Saghir, Z. Khan and A. Bazoune, Eng. Fract. Mech., 2005, 11, 1691 CrossRef
. - A. Mukherjee, Trans. Inst. Met. Finish., 1998, 8, 41 CrossRef
. - L. Wei, C. Tengfei, W. Qi and C. Yi, Plasma Processes Polym., 2011, 2, 94 Search PubMed
. - L. Coltro, J. B. Pitta and E. Madaleno, Polym. Test., 2013, 32, 272 CrossRef CAS
. - T. Hwang, Z. Frank, J. Neubauer and K. J. Kim, Sci. Rep., 2019, 9, 1 CAS
. - M. Kahouli, A. Barhoumi, A. Bouzid, A. Al-Hajry and S. Guermazi, Superlattices Microstruct., 2015, 85, 7–23 CrossRef CAS
. - J. I. Langford and A. J. C. Wilson, Scherrer after sixty years: a survey and some new results in the determination of crystallite size, J. Appl. Crystallogr., 1978, 11, 102–113 CrossRef CAS
. - X. Hong, T. Ueki and T. Hirai, Multi-Functional Materials and Structures II, Adv. Mater. Res., 2009, 2063 Search PubMed
, Pts 1 and 2.. - H. Gaabour and K. A. Hamam, Silicon, 2018, 4, 1403 CrossRef
. - S. Foghmoes, F. Teocoli, K. Brodersen, T. Klemensø and M. D. Negra, J. Eur. Ceram. Soc., 2016, 14, 3441 CrossRef
. - T. Hwang, Z. Frank, J. Neubauer and K. J. Kim, Sci. Rep., 2019, 9, 1 CAS
. - P. N. Nikam and V. D. Deshpande, Mater. Today: Proc., 2018, 1, 2254 Search PubMed
. - W. Q. Xu and C. R. Zheng, Mod. Plast. Process. Appl., 1992, 1, 54 Search PubMed
. (in Chinese).. - L. J. Fetters, D. J. Lohse and W. W. Graessley, J. Polym. Sci., Part B: Polym. Phys., 1999, 10, 1023 CrossRef
. - K. Asaka and M. Hashimoto, Sens. Actuators, B, 2018, 273, 1246 CrossRef CAS
. - A. V. Hill, Proc. Royal Soc. B, 1938, 126, 136 Search PubMed
. - M. Shibagaki, N. Ogawa and M. Hashimoto, 2010 IEEE International Conference on Robotics and Biomimetics (ROBIO), 2010, p. 1434 Search PubMed
. - M. Ali, T. Ueki, D. Tsurumi and T. Hirai, Langmuir, 2011, 27, 7902–7908 CrossRef CAS PubMed
. - Y. Li, Y. Li and M. Hashimoto, Sens. Actuators, B, 2019, 282, 482 CrossRef CAS
. - D. Chen and Q. Pei, Chem. Rev., 2017, 117, 11239 CrossRef CAS
. - J. Leng, X. Lan, Y. Liu and S. Du, Prog. Mater. Sci., 2011, 56, 1077 CrossRef CAS
. - S. Haines, M. D. Lima, N. Li, G. M. Spinks, J. Foroughi, J. D. W. Madden, S. H. Kim, S. L. Fang, M. J. de Andrade, F. Goktepe, O. Goktepe, S. M. Mirvakili, S. Naficy, X. Lepro, J. Y. Oh, M. E. Kozlov, S. J. Kim, X. R. Xu, B. J. Swedlove, G. G. Wallace and R. H. Baughman, Science, 2014, 6173, 868 CrossRef PubMed
.
|
This journal is © The Royal Society of Chemistry 2021 |
Click here to see how this site uses Cookies. View our privacy policy here.