DOI:
10.1039/D1RA06222K
(Paper)
RSC Adv., 2021,
11, 32505-32512
Off-line analysis in the manganese catalysed epoxidation of ethylene-propylene-diene rubber (EPDM) with hydrogen peroxide†
Received
17th August 2021
, Accepted 14th September 2021
First published on 4th October 2021
Abstract
The epoxidation of ethylene-propylene-diene rubber (EPDM) with 5-ethylidene-2-norbornene (ENB) as the diene to epoxidized EPDM (eEPDM) creates additional routes to cross-linking and reactive blending, as well as increasing the polarity and thereby the adhesion to polar materials, e.g., mineral fillers such as silica. The low solubility of apolar, high molecular weight polymers in the polar solvents constrains the catalytic method for epoxidation that can be applied. Here we have applied an in situ prepared catalyst comprising a manganese(II) salt, sodium picolinate and a ketone to the epoxidation of EPDM rubber with hydrogen peroxide (H2O2) as the oxidant in a solvent mixture, that balances the need for polymer and catalyst/oxidant miscibility and solubility. Specifically, a mixture of cyclohexane and cyclohexanone is used, where cyclohexanone functions as a co-solvent as well as the ketone reagent. Reaction progress was monitored off-line through a combination of Raman and ATR-FTIR spectroscopies, which revealed that the reaction profile and the dependence on the composition of the catalyst are similar to those observed with low molar mass alkene substrates, under similar reaction conditions. The combination of spectroscopies offers a reliable method for off-line reaction monitoring of both the extent of the conversion of unsaturation (Raman) and the extent of epoxidation (FTIR) as well as determining side reactions, such as epoxide ring opening and further, aerobic oxidation. The epoxidation of EPDM described, in contrast to currently available methods, uses a non-scarce manganese catalyst and H2O2, and avoids side reactions, such as those that can occur with peracids.
Introduction
Elastomers are amorphous polymers with little or no crystallinity and have a low glass transition temperature and, thus, they are soft and flexible materials. For industrial applications, rubber polymers are typically cross-linked to form 3D networks that are essential for elastic and insoluble products and enhanced tensile and tear strength, and abrasion and solvent resistance. Rubber polymers are often compounded with (reinforcing) fillers (typically carbon black and/or silica) and plasticizers to adjust desired properties, such as compound viscosity and vulcanisate hardness and strength.1 Rubbers are commonly cross-linked via sulphur vulcanization, which requires the presence of unsaturation,2 or by peroxide curing.3,4 Covalent crosslinking limits the recyclability of rubber waste, mainly because the cross-linked 3D network prevents processing via melt or solution.5,6
EPDM rubbers are versatile synthetic rubbers prepared from ethylene, propylene and a diene monomer (Fig. 1). In contrast to natural rubber, EPDM rubbers do not contain unsaturation in their polymer backbones, giving them good resistance to ozone, oxygen, and heat. Their apolar character provides good resistance to water and polar solvents. These features have resulted in the widespread use of EPDM rubber in applications, such as automotive sealing systems, roof sheeting, (waste) water seals, and radiator hoses. However, EPDM rubber performs poorly in contact with apolar solvents (e.g., petrol and oil) and adheres poorly to polar materials, both on a macroscopic (co-extrusion with polar polymers such as polyamides and polyesters) and on a microscopic level (composites with inorganic fillers and blends with polar polymers).7 The residual unsaturation in the side group of 5-ethylidene-2-norbornene (ENB) (Fig. 1) enables sulphur vulcanisation and enhances the peroxide crosslinking efficiency. Furthermore, the unsaturation opens opportunities to chemical modification that enable new routes for crosslinking and improving the adhesion to polar substrates and fillers. Apolar EPDM rubber can be compounded with polar silica fillers using bifunctional silanes as coupling agents, that react covalently with the filler surface as well as the rubber unsaturation.8–10 These coupling reagents have several drawbacks, e.g., extra costs, special mixing requirements and production of volatile organic by-products.11 Chemical modification of elastomers (e.g., hydrogenation, halogenation, and grafting with functional monomers) enables alteration and optimization of chemical and mechanical properties of rubbers.12,13 Epoxidation is a well-known modification of unsaturated elastomers,12 for example, epoxidized 1,2-polybutadiene shows improved adhesion to fillers, improved heat stability, and improved solvent resistance.14 Epoxidised natural and polybutadiene rubbers adhere better to silica, and, therefore, require lower amounts of coupling reagent during mixing in so-called green tyre compounds.7,11,15–17 Epoxidation of EPDM to eEPDM rubber is expected to improve the performance by allowing for alternative cross-linking methods, e.g., with diacids18,19 and (blocked) diamines, and reactive blending with polar substrates (mineral fillers, polycondensates).20,21
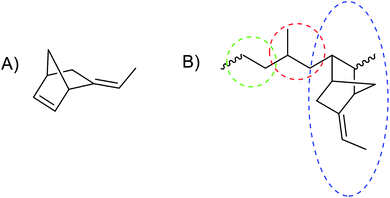 |
| Fig. 1 Chemical structures of (A) 5-ethylidene-2-ethylidene-2-norbornene (ENB); (B) ethylene-propylene-diene rubber (EPDM), a terpolymer with ethylene (green), propylene (red) and ENB (blue) monomers indicated. | |
EPDM and other types of unsaturated rubbers have been epoxidized over the past decades most commonly with peroxy acids (e.g., meta-chloroperbenzoic acid [mCPBA]).12,18,22–25 Performic acid generated in situ from hydrogen peroxide (H2O2) and formic acid has been used for the epoxidation of EPDM and other rubbers, because of the high reactivity of the performic acid and the simplicity of the system.18,21–30 Formic acid is corrosive and its acidity induces ring opening of the epoxide at high conversions, giving esters, ethers and alcohols as side products.12,23–25 Low-acid and acid-free routes towards eEPDM have been developed. Hay et al.31–33 used H2O2 in combination with a quaternary ammonium tetrakis(diperoxotungsto)phosphate catalyst to produce eEPDM without reported side reactions. Other methods for preparing eEPDM include using mixtures of molybdenum oxide with tert-butyl hydroperoxide34–36 or dimethyldioxirane (DMD) generated in situ from peroxymonosulphate and acetone.37–39 The extent of epoxidation has to be controlled in order to realise the full potential of eEPDM. Hence methods to determine the degree of epoxidation in the product are essential for quality control, as well as process control. Controlling the extent of epoxidation opens opportunities in various high-value applications.
The epoxidation of EPDM is preferably performed homogeneously with the polymer dissolved. The paradigm is to employ methods that use apolar solvents, e.g., toluene. Of the available methods used in the epoxidation of low molar mass alkene substrates, the requirement for an apolar medium favours those based on phase transfer catalysts (PTCs). However, from an environmental and toxicological perspective, a fully homogeneous method for the epoxidation of EPDM that avoids the use of PTCs is preferable.40,41 A solvent or solvent mixture that provides sufficient solubility of the EPDM polymer and is compatible with methods for alkene epoxidation, that provide high atom efficiency, high selectivity, use non-scarce catalysts, and limit the use of potentially corrosive, organic acids, is therefore needed.
Here we show that a catalyst system developed earlier by our group42,43 for the epoxidation of alkenes, has the required solvent scope to enable its application in the epoxidation of EPDM rubbers. The catalyst used in the present study is prepared in situ from pyridine-2-carboxylic acid (PCA), sodium acetate (NaOAc), manganese(II) perchlorate [or any other manganese(II) salt] and a ketone, either as solvent or sub-stoichiometrically, e.g., 2,3-butanedione (Scheme 1).43 The ketone's role is to establish an equilibrium with the oxidant H2O2 to form a gem-hydroxy-hydroperoxy species, which is essential to the generation of the active form of the catalyst but is also less polar and, therefore, can be taken up by the solvent mixture needed to solubilise EPDM (Scheme 1).43 The rate limiting step has been established to be the reaction of the gem-hydroxy-hydroperoxy species with the catalyst to form the oxygen-atom-transferring manganese complex and notably shows a zero order dependence on substrate (alkene) concentration. Quenching of the reaction by flash precipitation was followed by off-line analysis by Raman and attenuated total reflection Fourier-transform infrared (ATR-FTIR) spectroscopies. These data allow for the dependence of the reaction rate on several reaction parameters to be determined. Specifically, the combination of Raman and ATR-FTIR spectroscopies used to determine the conversion of the ENB unsaturation and the yield of the epoxide allows for verification that the kinetic behaviour of the catalytic system is retained under the conditions needed to solubilise high molar mass EPDM rubber. In this way, the extent of epoxidation can be controlled in a reliable manner.
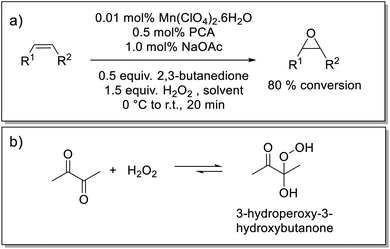 |
| Scheme 1 (a) Epoxidation of alkenes using an in situ prepared manganese(II)/PCA catalytic system that provides turnover frequencies of up to 40 s−1 with catalyst loadings of less than 0.01 mol% Mn(II), at room temperature (r.t.).42 (b) Equilibrium between H2O2/2,3-butanedione and 3-hydroperoxy-3-hydroxybutanone.43 | |
Experimental section
Materials
Fully amorphous and highly unsaturated EPDM (Keltan® 9950C with ethylene content of 44 wt% and ENB content of 9 wt%) and the low molar mass model compound 5-ethylidene-2-norbornane (ENBH; prepared via selective hydrogenation of ENB) were provided by ARLANXEO. Manganese(II) perchlorate hexahydrate, 2,3-butanedione, acetic acid (AcOH), hydrogen peroxide (50 wt% aqueous solution), CD3Cl, cyclohexane, cyclohexanone and 5-ethylidene-2-norbornene (ENB) were obtained from Sigma-Aldrich, and sodium picolinate was obtained from TCI Europe. All were used as received, unless stated otherwise.
Preparation of ethylidene norbornane epoxide
A solution of Mn(II)(ClO4)2·6H2O (0.02 mol%), picolinic acid (1.0 mol%) and sodium acetate (NaOAc) (2 mol%) was prepared in acetonitrile and stirred for 10 min. 2,3-Butanedione (0.125 M), acetic acid (25 mM) and ENBH (0.125 M) were added to the mixture, giving a total volume of 4 mL. 3.0 equivalent H2O2 (50%, aq.) was added dropwise. After 1 h at room temperature, the reaction solution was filtered over a silica-loaded glass pipette to remove non-volatile reaction components, followed by removal of the solvent in vacuo to obtain the volatile epoxide product. Samples for 1H NMR spectroscopy were prepared by withdrawing 4–5 drops of the reaction mixture, which were added to a mixture of 1 mL CDCl3/1 mL brine. The mixture was shaken well, the phases were separated, and the 1H NMR spectrum of the organic layer was recorded. Epoxidized ENBH was obtained with full conversion (Fig. S1†).
Purification of EPDM
Components (anti-oxidants) present in the EPDM as supplied were removed by dissolution in cyclohexane, followed by precipitation by addition of acetone. The removal of additives was verified by ATR-FTIR spectroscopy (Fig. S2†). The FTIR spectrum of EPDM, as received, shows spectral bands that indicate the presence of an ester (1015, 1045 and 1250 cm−1, from C–O stretches, and a band at 1740 cm−1 from C
O stretching). These features were absent after precipitation.
General procedure for epoxidation of EPDM (eEPDM)
3.5 mL of cyclohexanone and 5 mL of cyclohexane were heated in a 25 mL round-bottomed flask at 50 °C in a water bath. 400 mg EPDM rubber (30 mM in alkene units) was added in portions to the solvent mixture and allowed to dissolve fully (ca. 6 h). 1.08 mg Mn(II)(ClO4)2·6H2O (0.3 mM) was added to the reaction mixture to give a total volume of 10 mL and the mixture was stirred for 5 min. 2.2 mg sodium picolinate (1.5 mM) was added to the reaction mixture and the mixture was stirred for 5 min. 2,3-Butanedione (various concentrations) was added to the reaction mixture, followed by stirring for 5 min before addition of 17 μL of acetic acid (30 mM). The reaction was initiated by adding H2O2 (aq., 50 wt%) (various equivalents). After 1 to 4 h, the reaction was quenched through gentle addition of 5–10 mL acetone to precipitate the eEPDM. The remaining solution was discarded, and the recovered eEPDM was twice washed with acetone. A pincer was used to squeeze and sponge the rubber in acetone to facilitate removal of residual reagents. The rubber samples were air-dried for approximately 1 day before analysis. For 1H NMR spectral analysis, 0.5 mL of the reaction mixture was added to a mixture of 0.5 mL brine and 0.7 mL deuterated chloroform before and after the reaction. The solution was mixed and shaken and the organic layer (CDCl3) separated for analysis. The alkene conversion was dependent on the concentration of 2,3-butanedione and H2O2 added (see Results and discussion). Representative 1H NMR spectral data before and after epoxidation of EPDM rubber (2.5 mM in alkene units) with 0.25 M 2,3-butanedione, and 10 equiv. H2O2 show ≈90% conversion Fig. S3.†
Off-line analysis
Flash precipitation and washing of EPDM and eEPDM was used for off-line determination of conversion.25,36,37 0.5 mL aliquots were withdrawn from the reaction mixture at specified times and added to 5–10 mL acetone to precipitate the rubber. A pincer was used to squeeze the precipitated rubber to expel residual reagents. The rubber was dipped in water and then acetone and compressed several times, followed by standing in air to dry for several hours. Samples were analysed by Raman and ATR-FTIR spectroscopies. The averages of five Raman spectra or three ATR-FTIR spectra were used for the plots of conversions over time.
Spectroscopic methods
A JASCO 4000 series FT-IR spectrometer equipped with TGS detector and ATR accessory (germanium coated with diamond) was used for recording of infrared spectra with 32 accumulations and 8 cm−1 resolution. Raman spectra were recorded at 785 nm with either a BX51 upright microscope, equipped with a Shamrock 163 spectrograph with iVac-LCDD deep depletion CCD camera (Andor Technology) (10 accumulations of 10 s spectral acquisition) or a PerkinElmer RamanFlex spectrometer, equipped with Inphotonics reaction probe (spectra were typically 10 by 20 s acquisition). Where stated Raman spectra were recorded at 532 nm with a Shamrock 163 spectrograph with iDus 420 series deep depletion CCD camera (Andor Technology), 25 mW fiber coupled laser (Cobolt) and Inphotonics Raman probe. Normalizations, integrations and baseline corrections of Raman and FTIR spectra were performed using SpectraGryph 1.14 (ref. 44) and data visualisation was done in Python. 1H NMR (400.0 MHz) spectra were recorded on a Varian Avance 400 spectrometer in CDCl3.
Results and discussion
The EPDM rubber selected in the present study has ENB (Fig. 1) as diene monomer, which presents a tri-substituted alkene as a side group after polymerisation. Initial studies focused on the application of conditions for alkene epoxidation developed earlier42,43 in the epoxidation of the low molar mass ENBH model compound (Scheme 2). This model compound lacks the endocyclic C
C of the starting ENB diene, which is converted during polymerisation, so that only the exocyclic C
C is available for epoxidation. Direct analysis of the reaction mixture by 1H NMR spectroscopy shows complete conversion of the ENBH unsaturation with the disappearance of the 1H NMR signals of the –CH
CH2 alkene moiety at 5.0 and 5.2 ppm and the appearance of new signals at ca. 3.0 ppm, characteristic of the expected exo- and endo-epoxide products (Fig. S1†).
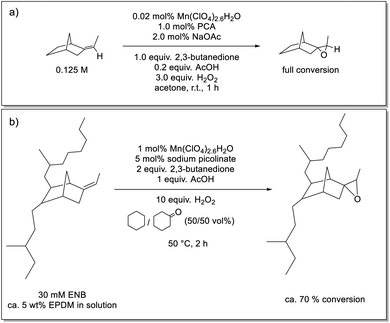 |
| Scheme 2 Epoxidation of 5-ethylidene-2-norbornane (ENBH) (a) and of ENB–EPDM rubber (b) with an in situ prepared manganese(II) catalyst and H2O2. mol% and equivalents are with respect to the C C concentration in the EPDM rubber. | |
The insolubility of EPDM in acetone means that the conditions used for the epoxidation of the ENBH model are unsuitable. Apolar solvents (e.g., alkanes or aromatic solvents) are required for the dissolution of high molar mass, apolar polymers, such as EPDM rubber. Methods available for the epoxidation of EPDM rubber use toluene as solvent.18,25,36,37 A primary requirement for the present catalytic system is that the reaction is fully homogenous and, hence, the solvent used should be sufficiently polar to solubilise the catalyst [Mn(II)/PCA], a base such as sodium acetate, and not undergo phase separation upon addition of aqueous H2O2. The good solvent tolerance of the Mn(II)-based method used here (e.g., acetone, ethanol, CH3CN etc.)43 means that conditions compatible with both EPDM dissolution and epoxidation are found in an equal mixture of cyclohexanone and cyclohexane. This solvent mixture is sufficiently apolar to solubilize the EPDM polymer and at the same time sufficiently polar to dissolve the catalyst components and oxidant. Furthermore, neither solvent is susceptible to oxidation (e.g. hydroxylation, Baeyer–Villiger) under these conditions.45
Under these modified conditions, the extent of conversion of the model compound ENBH was low, which was suspected to be due to precipitation of NaOAc upon its addition. This limitation was circumvented by using sodium picolinate, which is sufficiently soluble to achieve the concentrations required [3-fold excess with respect to the Mn(II) present] to ensure formation of an active catalyst.43 Sodium picolinate co-precipitates with the polymer, but is readily removed by washing the rubber residue with water (Fig. S4†). The extent of epoxidation of the EPDM rubber was 70% under these conditions (Scheme 2 and Fig. 2).
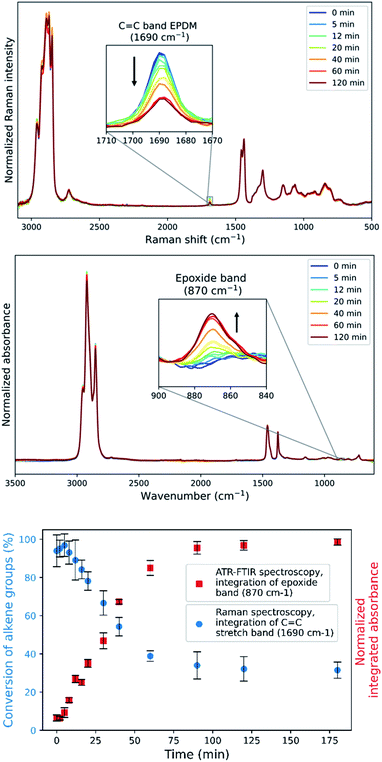 |
| Fig. 2 (Top) Raman spectra (λexc 785 nm) of ENB–EPDM rubber during epoxidation obtained following flash quenching at indicated reaction times, with expansion of the region around the alkene stretching band of the ENB unit at 1690 cm−1. (Middle) ATR-FTIR spectra of the same samples with expansion of the region around the epoxide band at 870 cm−1. (Bottom) Integrals of the Raman band at 1690 cm−1 and the FTIR absorption at 870 cm−1 with time, with standard deviations calculated from repeated measurements on each sample. Conditions: EPDM (30 mM in alkene), 0.3 mM Mn(II)(ClO4)2·6H2O, 1.5 mM sodium picolinate, 60 mM 2,3-butanedione, 30 mM acetic acid, and 300 mM H2O2 in cyclohexane/cyclohexanone (50/50 wt%) at 50 °C. Samples were withdrawn and quenched in acetone at the specified times. | |
An additional challenge is the viscosity of the EPDM-containing solutions. High concentrations of the rubber are desirable to reduce solvent demand. The increase in viscosity limits the concentrations that can be reached. At 50 °C, a 5 wt% solution of EPDM rubber could be achieved, which corresponds to a 30 mM in ‘ENB’ units, which is still compatible with the catalyst system used.43
On-line analysis of reaction progress
On-line analysis of the reaction progress is advantageous over off-line analysis for reaction optimisation, as the former does not require sampling and sample pretreatment.46 Facile on-line monitoring of alkene oxidation in situ with on-line Raman spectroscopy with the present catalytic system has been demonstrated earlier43 and initially a similar approach was investigated here for the epoxidation of the EPDM rubber. Two conditions that have to be met for this approach to be successful are: a sufficiently low viscosity (hence low concentration) of the EPDM rubber in the solvent mixture (cyclohexane/cyclohexanone, 50/50 v%) to allow dissolution of the other chemicals and good mixing, and a high enough concentration of the rubber to reach the spectroscopic limit of detection for the alkene units in the polymer. The maximum amount of EPDM rubber that could be dissolved in cyclohexane (to be still able to properly stir the solution) was about 100 mg in 2 mL cyclohexane (6.5 wt%). This concentration of EPDM rubber corresponds to a concentration of 37.5 mM of ENB monomer. ENB diene was used to determine the limit of detection of the alkene stretching band. Raman spectra, recorded at 532 nm of ENB in a 50/50 volume percent mixture of cyclohexane and cyclohexanone, show that neither the strongest band of ENB (exocyclic C
C stretching band at 1690 cm−1) nor any other band were above the limit of detection by Raman spectroscopy at concentrations of 30–100 mM (Fig. S5 and S6†). Furthermore, even if the concentration of ENB could be increased, the C
C stretching band of the ENB overlaps with the C
O stretching band of cyclohexanone. Hence, on-line monitoring of the conversion of the unsaturation in ENB–EPDM with Raman spectroscopy was concluded to be not feasible.
Infrared and 1H NMR spectroscopy have been applied for off-line analysis of eEPDM samples.18,25,31,36,37 The extent of epoxidation of EPDM rubber to eEPDM can be determined by 1H NMR spectroscopy (Fig. S3†).
For reaction progress monitoring and optimisation, off-line analysis with Raman and ATR-FTIR spectroscopy is more practical, as the Mn(II)-catalysed epoxidation reaction is quenched by dilution in acetone and minimal sample preparation is required (Fig. 2). The advantage of combining these two spectroscopies in the analysis of epoxidized EPDM rubber is that alkene conversion can be followed by the Raman band (alkene stretch) at 1690 cm−1 and epoxide formation through the IR absorption at 870 cm−1 (out-of-plane bending), with spectral normalization with the alkane bands at 1437 cm−1 and 1377 cm−1, respectively. Although transmission infrared analysis is possible with these rubbers,36 attenuated total reflection (ATR) infrared spectroscopy is preferred as it does not require sample preparation, specifically avoiding thermal damage (e.g., epoxide ring opening) during hot pressing of polymer sheets. The epoxide product is readily apparent in the ATR-FTIR spectra. However, whereas transmission FTIR allows for sample thickness to be adjusted to observe the alkene stretching band, alkene conversion cannot reasonably be determined by ATR methods due to the low molar absorptivity of the alkene stretching band.
Repeated measurements on each sample shows that the accuracy achieved by Raman spectroscopy is less than that by ATR-FTIR absorption spectroscopy (Fig. 2 Bottom and Fig. S7†), which is ascribed to the low density of the rubber which reduces the Raman scattering collected but has less effect on the sampling by ATR. A plot of the integrated intensity of the Raman band at 1690 cm−1 (alkene stretching) and absorbance at 870 cm−1 (epoxide o.o.p bending) shows an inverse correlation (R2 = 0.992) as expected for epoxidation (Fig. 3), showing that side products are not formed to a significant extent during the epoxidation reaction itself and indicating that both bands are reliable indicators of the extent of reaction.
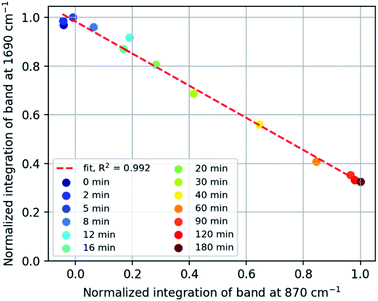 |
| Fig. 3 Normalized intensity of Raman ENB alkene band at 1690 cm−1 vs. FTIR epoxide absorption band at 870 cm−1. | |
The conversion of the ENB–EPDM unsaturation over time (Fig. 2) shows an initial, short lag period, followed by a linear decrease in the concentration of alkene. The zero order dependence on the alkene concentration is consistent with earlier studies in the epoxidation of low molecular weight alkenes,43 in which the lag period was shown to be due to the in situ formation of acetic acid from 2,3-butanedione.42,43 The zero-order dependence of the reaction on the concentration of EPDM unsaturation indicates that full conversion can be achieved by reducing its initial concentration and holding the concentrations of all other reaction components constant, as shown earlier for low molar mass alkenes. Indeed, reducing the concentration of EPDM rubber by half under similar reaction conditions shows already 90% conversion (Fig. S8†).
The factors that influence the reaction extent and its dependence on the concentration of ketone are of interest. Epoxidation of EPDM is less efficient than the epoxidation of analogous, low molar mass alkene substrates, e.g., ENBH. Even under these modified solvent conditions, reaction progress data (Fig. 2) indicate that the dependence of reaction rate on the concentrations of the reaction components is the same as for low molar mass substrates. The conversion after 2 h with various concentrations of 2,3-butanedione (45, 75, 60 and 150 mM) is approximately the same (ca. 70%) in all cases, while the conversion was ca. 90% with 225 and 300 mM 2,3-butanedione (Fig. S9†). Conversion is also observed in the absence of 2,3-butanedione (around 65% conversion, Fig. S10†), since the co-solvent cyclohexanone can also form the required hydroperoxide adduct with H2O2 (Fig. 4). It is of note that the initial report of this catalytic system used acetone (as solvent) alone,47 only with later studies showing the accelerating effect of 2,3-butanedione.42 The formation of the adduct between cyclohexanone and H2O2 was confirmed here by Raman spectroscopy with a decrease of the C
O stretching band of cyclohexanone and the appearance of an O–O stretching band of the adduct (Fig. S11†).
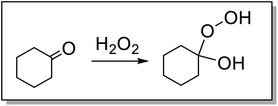 |
| Fig. 4 Formation of a hydroperoxide-adduct from cyclohexanone and H2O2. | |
The lower conversion of EPDM unsaturation in the absence of 2,3-butanedione is consistent with a reduced reaction rate as observed in acetone earlier. The data indicate that a minimum concentration of 2,3-butanedione (between 150 and 250 mM) is necessary for it to affect conversion, as it competes with cyclohexanone for formation of the hydroperoxide adduct.
Side reactions
Inspection of the fingerprint region of the ATR-FTIR spectra (Fig. 2) reveals changes in addition to those expected for epoxidation (Fig. 5). The band at 808 cm−1 assigned to the alkene o.o.p bending band of EPDM rubber decreases and has been frequently used to determine the conversion.25,36,37 However, the alkene band in the Raman spectrum at 1690 cm−1 is a more reliable measure of conversion in regard to signal to noise ratio and resolution (Fig. S12†) and thus has been used above. New bands also appear around 1000 and 950 cm−1 (Fig. 5), which are characteristic of C–O stretching bands, indicating the formation of ethers and esters as side products of the reaction.25 The absorption bands of these side products are weak compared to those of the epoxide product (Fig. 5). The extent of side reactions is low considering the correlation between alkene conversion and epoxide formation (Fig. 3).
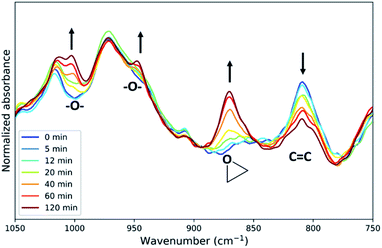 |
| Fig. 5 Fingerprint regions of the ATR-FTIR spectra from samples taken at various times over 2 h in the epoxidation of ENB–EPDM rubber. See Fig. 2 for details. | |
Another side reaction occurs concomitant with epoxidation. In the absence of H2O2 but in the presence of all other reagents, the ENB–EPDM unsaturation converts slowly to a product (≈35% conversion over 24 h), which is manifested in a sharp ATR-FTIR absorption band at ≈1710 cm−1 (Fig. 6, Bottom), indicating the formation of carbonyl groups as in carboxylic acid or ketone. The Raman spectrum shows the formation of the carbonyl product also with the intensity of the alkene stretching band decreasing (Fig. 6, Top). This side reaction may proceed by an auto-oxidative pathway where Mn(II) ions trigger the activation of oxygen.48 Alternatively, the oxidative side reaction may be due to the combination of 2,3-butanedione and Mn(II)(ClO4)2·6H2O, which generates a reactive species, e.g., inorganic peroxyl radical and a consequence of removal of the stabilisers (anti-oxidants) from the as-supplied rubber.
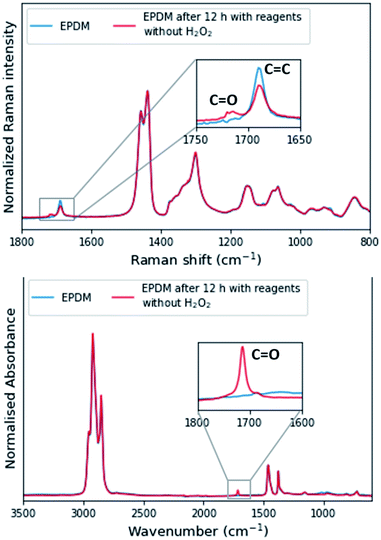 |
| Fig. 6 Spectroscopic evidence for side reactions in EPDM rubber in the absence of H2O2. Raman and ATR-FTIR spectra of original EPDM and eEPDM after 12 h. Conditions: 30 mM ENB from EPDM, 0.3 mM Mn(II)(ClO4)2·6H2O, 1.5 mM sodium picolinate, 150 mM 2,3-butanedione, 30 mM acetic acid in 50/50 wt% cyclohexane/cyclohexanone. | |
Ageing and cross-linking of eEPDM
As mentioned earlier epoxidation of EPDM with formic acid/H2O2 leads to epoxide ring-opening with longer reaction times, limiting the conversion that could be achieved.25 In the present study ring-opening was not observed during the required reaction time, however, the eEPDM prepared undergoes ageing on standing in the acetone-quenched mixture as well as after isolation under ambient conditions, apparent from Raman and ATR-FTIR spectral analysis of eEPDM rubber after several weeks (Fig. 7). The epoxidation with the present catalyst was incomplete, as manifested in the observation of residual alkene stretching bands of the eEPDM rubber obtained. Within one week this alkene stretch band was no longer apparent and was replaced by bands at 1720 and 1660 cm−1 indicating the formation of carbonyl moieties. Oxidative ageing of EPDM has been shown earlier,49–51 and it is concluded that for the present case, the eEPDM rubber samples age with a similar mechanism even under moderate conditions, as prior and during epoxidation, as anti-degradants (present inside the raw EPDM rubber sample before purification in cyclohexane, but not after, see Fig. S2†) are removed.
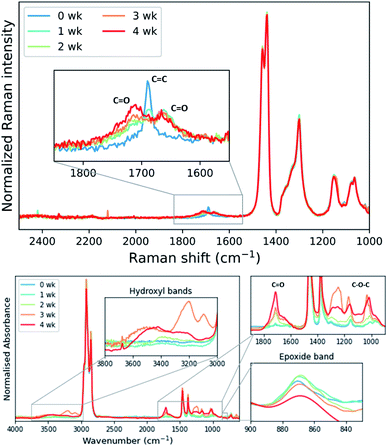 |
| Fig. 7 Raman spectra (785 nm) (top) and ATR-FTIR spectra (bottom) of eEPDM rubber samples at specified times (wk = week) after isolation and storage. | |
Infrared spectra indicate the presence of C–O–C moieties (between 1300–1000 cm−1, from ethers and/or esters), hydroxyl groups (between 3600–3000 cm−1), and a decrease in the absorption of the epoxide band at 870 cm−1. These observations can be explained by ring-opening of the epoxide and subsequent cross-linking of a ring-opened epoxide and a second epoxide group (Fig. 8). Hydroxyl bands are formed upon ring-opening and remain after cross-linking, when formation of C–O–C units has taken place also. Cross-linking is manifested by the insolubility of the final rubber samples in cyclohexane. Thus, it is essential that analysis of the eEPDM reaction products immediately after recovery from the epoxidation in order to obtain useful data for correlating alkene conversion with epoxide formation as in Fig. 3.
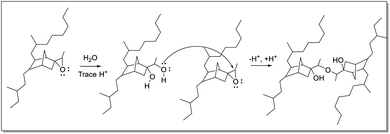 |
| Fig. 8 Ring-opening and subsequent cross-linking of epoxide groups of eEPDM, forming an ether linkage between the polymer backbones. | |
Conclusions
The epoxidation of ENB–EPDM rubber using an in situ prepared manganese catalyst and H2O2 is shown to be effective under solvent conditions compatible with polymer dissolution. The method uses non-toxic reagents and the extent of epoxidation can be controlled to allow for variation in rubber properties. Although in-line reaction monitoring is unfeasible due to the poor rubber solubility and, thus, the low EPDM alkene concentration, reaction optimization is facilitated by off-line analysis combining ATR-FTIR with Raman spectroscopies and with validation by 1H NMR spectroscopy.18,25,31,36,37 This combined spectroscopic approach allows for the reliable monitoring the formation of the epoxide as well as the conversion of the alkene of the EPDM rubber. Furthermore, the approach allows for the determination of the extent of further oxidation and ring opening of the epoxide units in the recovered eEPDM products also. The reported method is like suitable for a wide range of other, alkene-containing rubbers.
Author contributions
All authors contributed equally.
Conflicts of interest
There are no conflicts to declare.
Acknowledgements
The work was supported by The Netherlands Ministry of Education, Culture and Science (WRB, Gravity Program 024.001.035) and the European Research Council (StgG 279549, WRB, FM).
Notes and references
- A. bin Samsuri, in Natural Rubber Materials, Vol. 2. Composites and Nanocomposites, 2013, pp. 73–111 Search PubMed.
- L. Imbernon, E. K. Oikonomou, S. Norvez and L. Leibler, Polym. Chem., 2015, 6, 4271–4278 RSC.
- R. Winters, W. Heinen, M. A. L. Verbruggen, J. Lugtenburg, M. Van Duin and H. J. M. De Groot, Macromolecules, 2002, 35, 1958–1966 CrossRef CAS.
- R. A. Orza, P. C. M. M. Magusin, V. M. Litvinov, M. Van Duin and M. A. J. Michel, Macromolecules, 2009, 42, 8914–8924 CrossRef CAS.
- D. J. Fortman, J. P. Brutman, G. X. De Hoe, R. L. Snyder, W. R. Dichtel and M. A. Hillmyer, ACS Sustainable Chem. Eng., 2018, 6, 11145–11159 CrossRef CAS.
- V. P. Swapna and R. Stephen, in Recycling of Polymers, Wiley-VCH Verlag GmbH & Co. KGaA, Weinheim, Germany, 2016, pp. 141–161 Search PubMed.
- K. Sengloyluan, K. Sahakaro, W. K. Dierkes and J. W. M. Noordermeer, Eur. Polym. J., 2014, 51, 69–79 CrossRef CAS.
- J. W. ten Brinke, S. C. Debnath, L. A. E. M. Reuvekamp and J. W. M. Noordermeer, Compos. Sci. Technol., 2003, 63, 1165–1174 CrossRef CAS.
- A. Das, D. Basu and G. Heinrich, in Encyclopedia of Polymeric Nanomaterials, ed. S. Kobayashi and K. Müllen, Springer Berlin Heidelberg, Berlin, Heidelberg, 2014, pp. 1–5 Search PubMed.
- J. W. Brinke, Silica Reinforced Tyre Rubbers, PhD thesis, University of Twente, Enschede, 2002.
- V. K. Srivastava, G. C. Basak, M. Maiti and R. V. Jasra, Int. J. Ind. Chem., 2017, 8, 411–424 CrossRef CAS.
- D. N. Schulz, S. R. Turner and M. A. Golub, Rubber Chem. Technol., 1982, 55, 809–859 CrossRef CAS.
- D. N. Schulz and A. O. Patil, in Handbook of elastomers, ed. A. K. Bhowmick and H. L. Stephens, Marcel Dekker, Inc, 2nd edn, 2000, pp. 107–130 Search PubMed.
- H. L. Stephens and A. K. Bhowmick, Handbook of Elastomers, CRC Press, New York, 2001 Search PubMed.
- W. Kaewsakul, Silica-reinforced natural rubber for low rolling, energy-saving tires, Twente University Press, University of Twente, Enschede, The Netherlands, 2013 Search PubMed.
- A. K. Manna, A. K. Bhattacharyya, P. P. De, D. K. Tripathy, S. K. De and D. G. Peiffer, Polymer, 1998, 39, 7113–7117 CrossRef CAS.
- A. K. Manna, D. K. Tripathy, P. P. De, S. K. De, M. K. Chatterjee and D. G. Peiffer, J. Appl. Polym. Sci., 1999, 72, 1895–1903 CrossRef.
- G. Zhang, X. Zhou, K. Liang, B. Guo, X. Li, Z. Wang and L. Zhang, ACS Sustainable Chem. Eng., 2019, 7, 11712–11720 CrossRef.
- M. Pire, C. Lorthioir, E. K. Oikonomou, S. Norvez, I. Iliopoulos, B. Le Rossignol and L. Leibler, Polym. Chem., 2012, 3, 946 RSC.
- M. van Duin and R. J. M. Borggreve, Reactive Modifiers for Polymers, Blackie Academic & Professional, London, 1997 Search PubMed.
- M. Vadivel, M. S. C. Kumar, J. A. Mohaideen, M. Alagar, M. Sankarganesh and J. D. Raja, Polym. Polym. Compos., 2019, 28, 589–597 Search PubMed.
- D. Swern, G. N. Billen, T. W. Findley and J. T. Scanlan, J. Am. Chem. Soc., 1945, 67, 1786–1789 CrossRef CAS.
- K. Udipi, J. Appl. Polym. Sci., 1979, 23, 3311–3321 CrossRef CAS.
- K. Udipi, J. Appl. Polym. Sci., 1979, 23, 3301–3309 CrossRef CAS.
- X. Wang and H. Zhang, Polymer, 1997, 38, 5407–5410 CrossRef CAS.
- Y. H. Ao, S. L. Sun, Z. Y. Tan, C. Zhou and H. X. Zhang, J. Appl. Polym. Sci., 2006, 102, 3949–3954 CrossRef CAS.
- O. R. Obanla, J. D. Udonne, O. O. Ajani, M. E. Ojewumi, O. J. Omodara and B. A. Oni, J. Phys.: Conf. Ser., 2019, 1378, 022025 CrossRef CAS.
- N. V. Bac, L. Terlemezyan and M. Mihailov, J. Appl. Polym. Sci., 1991, 42, 2965–2973 CrossRef.
- M. Vadivel, IOSR J. Appl. Chem., 2012, 1, 40–46 CrossRef.
- S. Roy, B. R. Gupta and B. R. Maiti, J. Elastomers Plast., 1990, 22, 280–294 CrossRef CAS.
- X. Jian and A. S. Hay, J. Polym. Sci., Part C: Polym. Lett., 1990, 28, 285–288 CrossRef.
- X. Jian and A. S. Hay, J. Polym. Sci., Part A: Polym. Chem., 1991, 29, 1183–1189 CrossRef.
- X. Jian and A. S. Hay, J. Polym. Sci., Part A: Polym. Chem., 1991, 29, 547–553 CrossRef.
- Y. Zhang, X. Chen, Y. Zhang and Y. Zhang, Macromol. Mater. Eng., 2001, 286, 443–448 CrossRef.
- Y. Zhang, X. Z. Chen, Y. Zhang and Y. X. Zhang, J. Appl. Polym. Sci., 2001, 81, 2987–2992 CrossRef CAS.
- Y. Zhang, Y. Zhang, X. Z. Chen and Y. Zhang, React. Funct. Polym., 2001, 47, 93–99 CrossRef CAS.
- M. M. A. Nikje, S. Motahari, M. Haghshenas and R. K. Sanami, J. Macromol. Sci., Part A: Pure Appl. Chem., 2006, 43, 1205–1214 CrossRef.
- M. M. A. Nikje and Z. Mozaffari, Des. Monomers Polym., 2008, 11, 271–281 CrossRef.
- F. H. Rajabi, M. M. A. Nikje and T. Taslimipour, Des. Monomers Polym., 2010, 13, 535–546 CrossRef CAS.
- B. S. Lane and K. Burgess, Chem. Rev., 2003, 103, 2457–2473 CrossRef CAS PubMed.
- G. Grigoropoulou, J. H. Clark and J. A. Elings, Green Chem., 2003, 5, 1–7 RSC.
- J. J. Dong, P. Saisaha, T. G. Meinds, P. L. Alsters, E. G. Ijpeij, R. P. Van Summeren, B. Mao, M. Fañanás-Mastral, J. W. De Boer, R. Hage, B. L. Feringa and W. R. Browne, ACS Catal., 2012, 2, 1087–1096 CrossRef.
- P. Saisaha, J. J. Dong, T. G. Meinds, J. W. De Boer, R. Hage, F. Mecozzi, J. B. Kasper and W. R. Browne, ACS Catal., 2016, 6, 3486–3495 CrossRef.
- F. Menges, Spectragryph - optical spectroscopy software, Version 1.2.14, 2019 Search PubMed.
- J. J. Dong, D. Unjaroen, F. Mecozzi, E. C. Harvey, P. Saisaha, D. Pijper, J. W. De Boer, P. Alsters, B. L. Feringa and W. R. Browne, ChemSusChem, 2013, 6, 1774–1778 CrossRef PubMed.
- L. Dagge, K. Harr, M. Paul and G. Schnedl, Cem. Int., 2009, 7, 2–9 Search PubMed.
- P. Saisaha, D. Pijper, R. P. van Summeren, R. Hoen, C. Smit, J. W. de Boer, R. Hage, P. L. Alsters, B. L. Feringa and W. R. Browne, Org. Biomol. Chem., 2010, 8, 4444 RSC.
- C. Deville, S. K. Padamati, J. Sundberg, V. McKee, W. R. Browne and C. J. McKenzie, Angew. Chem., Int. Ed., 2016, 55, 545–549 CrossRef CAS PubMed.
- H. Schnecko and J. S. Walker, Eur. Polym. J., 1971, 7, 1047–1056 CrossRef CAS.
- F. Delor-Jestin, J. Lacoste, N. Barrois-Oudin, C. Cardinet and J. Lemaire, Polym. Degrad. Stab., 2000, 67, 469–477 CrossRef CAS.
- F. Delor, G. Teissedre, M. Baba and J. Lacoste, Polym. Degrad. Stab., 1998, 60, 321–331 CrossRef CAS.
Footnotes |
† Electronic supplementary information (ESI) available: Additional spectral data. See DOI: 10.1039/d1ra06222k |
‡ Current address: Faculty of Science and Engineering, Manchester Metropolitan University, John Dalton Building, Chester Street, Manchester M1 5GD, UK. |
|
This journal is © The Royal Society of Chemistry 2021 |
Click here to see how this site uses Cookies. View our privacy policy here.