DOI:
10.1039/D1RA04458C
(Paper)
RSC Adv., 2021,
11, 29939-29947
Highly efficient sorption of molybdenum from tungstate solution with modified D301 resin
Received
9th June 2021
, Accepted 16th August 2021
First published on 7th September 2021
Abstract
The separation of molybdenum (Mo) from tungstate solution is a bottleneck problem in tungsten (W) metallurgy, and it hinders the development of high-purity tungsten materials. In this research, a modified D301 resin was used to adsorb and separate molybdenum from tungstate solution. The maximum sorption capacity (Qe) of modified D301 for MoS42− was found to be 428 mg g−1 and the separation coefficient (β) was 108.9 when the contact time was 4 h and the reaction temperature was 25 °C and the pH value of the tungstate solution was 7.2. The sorption process conforms to Langmuir isotherm models and the quasi-second-order kinetic model. The sorption mechanism was also discussed, which was a single layered spontaneous sorption process. Theoretical calculations infer bonding behavior between the N atom on the resin and the S atom on the MoS42− molecule. The sorption energy is −7.67 eV, which indicated that the sorption process is stable chemical sorption. The desorption experiment showed that more than 90% molybdenum could be desorbed from the loaded resin when the concentration of sodium hydroxide solution was 5 w%. Finally, after three-stage sorption–desorption, almost all molybdenum in the solution was adsorbed, achieving better separation of tungsten and molybdenum.
1. Introduction
In recent years, the increasing growth of industrial waste has made the problem of environmental pollution more and more significant. Therefore, cleaner production and recycling are particularly important.1 For refractory metal resources such as tungsten and molybdenum contained in waste materials, the realization of clean extraction and recycling is a hot research topic.2,3 Tungsten, a national strategic resource, has a high hardness, high density, great melting point, low coefficient of thermal expansion, superb corrosion conflict, and safe processing performance, which is broadly expounded in the microelectronics, metallurgy, exosphere and other fields.4–6 With the increase in tungsten consumption, the number of years of tungsten ore mining remaining is decreasing year by year, so it is necessary to recover secondary resources of tungsten. The physicochemical properties (aqueous chemical behaviors, ionic extent) of molybdenum are quite akin to those of tungsten.5,7–9 So, molybdenum and tungsten easily coexist. However, the increasing needs aimed at high purity metallic tungsten and its mid product have become a severe task faced by the metallurgical engineer.10–12 Therefore, the separation of tungsten and molybdenum is an urgent problem in the recovery of tungsten secondary resources.
So far, many kinds of methods have been developed for the separation of W and Mo, such as precipitation, solvent extraction7,13 and ion exchange.14–17 A large amount of alkali was required to precipitate molybdenum from acidic solution to repeal the acid in solution, which may not only introduce other impurity ions but also costs much. Solvent extraction is inconvenient in commercial production.18–20 Trioctylamine (TOA) shows excellent extraction ability for Mo, and the loaded organic phase can be back-extracted with ammonium hydroxide solution. However, the separation of aqueous and organic phases is very difficult.21 During the past decade, various ion exchange resins have been used for the extraction of molybdenum from solution, and the method has already been confirmed the feasibility of extracting molybdenum.22 Fu et al. used D301 resin to directly extract Mo(VI) from the acid leaching solution of molybdenite.23 D301 shows excellent sorption capacity for Mo and Mo-loaded resin can be desorbed by ammonia hydroxide solution.
The ion exchange method is one of the environmentally friendly and easy to operate secondary resource recovery methods of tungsten and molybdenum.24 However, in existing literature, the sorption performance of resin on tungsten and molybdenum is almost the same. In order to develop new ion exchange resins for the separation of tungsten and molybdenum, we summarized the existing kinds of typical ion exchange resins. Tungsten and molybdenum are mostly in the form of anions in aqueous solutions, and anion exchange resins are often used for the recovery and separation of tungsten and molybdenum. This includes strong basic D201, which is the gel-type resin, and the microporous structure will slow diffusion. The other type is weak basic D301, which has a macroporous structure, and the pore structure will facilitate diffusion. Therefore, D301 is more suitable for recovery and separation of tungsten and molybdenum in solution.
Unfortunately, the existing ion-exchange method has some disadvantages, such as difficult desorption, low sorption capacity, and weak service resistance.23,25,26 Development of the new resins with high efficiency of selective sorption, desorption, and regeneration is the core of future separation technology.27,28 It is reported that some resin and extractant mixtures can greatly improve the sorption capacity and the selectivity of the resin.29 In addition, some heavy rare earth have been recovered with P227-impregnated resins system,17 Cr(vi) have been recovered with poly-epichlorohydrin-dimethylamine (EPIDMA) modified D301 resin.30
Hence, in order to improve the sorption efficiency of D301 resin, a mixture of D301 resin and TOA was explored to separate and recovery molybdenum from tungstate solution in the present study. The sorption dynamics and sorption mechanism were investigated. According to the quantum mechanical module of Materials Studio software, the Mulliken population was calculated, and the sorption mechanism by modified D301 was obtained. Besides, optimization of sorption process conditions was studied. Furthermore, desorption experiments were conducted to study the reusability of the modified D301 resin. Finally, separation and recovery of molybdenum from tungstate solution were achieved.
2. Experimental section
2.1 Materials
D301 resin used in this study is a weakly basic anion-exchange resin with tertiary ammonium as the fixed positive charge purchased from Shanghai Kaiping Chemical Co., Ltd., China. N,N-Dimethylformamide (DMF, purity ≥ 99%) and trioctylamine (TOA, purity ≥ 95%) were kindly provided by Shanghai Macklin Biochemistry Co., Ltd. The modified D301 resin can be obtained by assembling D301 and TOA by the dipping method. The specific process is shown in Scheme 1. At first, D301 resin was washed with distilled water until reach to neutral pH value. 10 g of the D301 resin was swelled in 40 mL of DMF (purity ≥ 99%) and aminated in 20 mL TOA at the reaction temperature of 65 °C to prepare the modified D301 resin, which was prepared for the following experiments. After modification, the amination strength in modified D301 resin increases. The increase in amine content can provide more sorption sites, thereby improving the sorption performance of the resin to Mo. The stock solution included tungsten molybdenum was prepared by dissolving Na2WO3 and Na2MoO3 (both purity > 99.9%) in deionized water. All other chemicals used in this study were analytical grade.
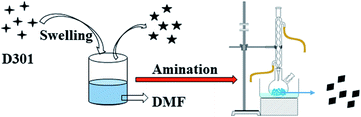 |
| Scheme 1 Flowcharts for the D301 resin modification reaction. | |
2.2 Preparation of metal solutions
Three different concentrations of Na2WO4·H2O solution containing molybdenum were dispensed (0.01 M W; 0.01 M Mo), (0.1 M W; 0.01 M Mo), (0.2 M W; 0.01 M Mo). Then the solution was vulcanized ([S]/[Mo] = 6). The vulcanization process of the three kinds of solutions is the same. The pH value of the solution was pre-adjusted to 7.12 and reacted for 2.5 h at 72 °C.
2.3 Sorption and desorption experiments
Typically, in sorption experiments, the solid/liquid ratio was 1 g L−1. 10 mg adsorbent was added to 10 mL solution with a certain concentration of Na2MoO4. In this study, all the sorption experiments were operated by shaking 0.02 g modified D301 with 20 mL the three different concentrations of mixed solution for 4 h. After solid–liquid separating, the aqueous phase was separated to wait for the determination of concentrations of metal elements. The effect of reaction conditions on the sorption process was studied such as reaction time, temperature and pH value. The desorption experiments were conducted by shaking the loaded modified D301 resin and 5 mL sodium hydroxide solution. And then the aqueous phase was collected. The concentration of W, Mo in the solution was tested using ICP-OES.
The removal of MoS42− was monitored by periodically taking aliquots of the solution and determining the Mo concentration using inductively coupled plasma-atomic emission spectrometry (ICP-AES; ICP-5110, Agilent, Americana). The sorption capacity of modified D301 to MoS42− can be expressed by Qe (mg g−1), which was calculated as
|
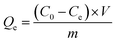 | (1) |
where
C0 is the initial concentration of Mo in the solution (g L
−1), and
Ce is the Mo concentration after modified D301 addition (g L
−1).
The separation effect of tungsten and molybdenum can be expressed by β, was calculated as
|
 | (2) |
where
DMo and
DW is the distribution ratio of molybdenum and tungsten, was calculated as
|
 | (3) |
2.4 Sorption isotherm models
The sorption isotherm process was studied based on the Langmuir and Freundlich isotherm models. These models are listed in eqn (4) and (5). In order to obtain the correlation coefficient R2 and compare the data points obtained by experiments more intuitively through the graphical, the relative parameters were calculated by nonlinear fitting.
Langmuir model:
|
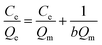 | (4) |
Freundlich model:
|
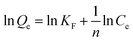 | (5) |
where
Ce is the Mo concentration after modified D301 addition (g L
−1);
Qe is the maximum quantities of Mo adsorbed (mg g
−1);
Qm is the quantities of Mo adsorbed at equilibrium (mg g
−1);
b,
KF and
n are the corresponding constant parameters of these models.
2.5 Sorption kinetics
The sorption kinetics were studied by nonlinear fitting, and two isothermal sorption models were used to fit the experimental data. These models are listed in eqn (6) and (7).
Lagergren-first-order model:
|
ln(Qe − Qt) = ln Qe − K1t
| (6) |
Pseudo-second-order model:
|
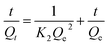 | (7) |
where
Qe is the quantities of Mo adsorbed at equilibrium (mg g
−1),
Qt is the quantities of Mo adsorbed at time
t, respectively (mg g
−1);
K1 is the rate constants of Lagergren-first-order model,
K2 is the rate constants of the second-order model.
2.6 Simulation analysis
Simulation analysis based on the density functional theory (DFT) has been widely used to explain experimental phenomena. In order to study the sorption mechanism, sorption energy and sorption configuration were calculated by Materials Studio 2020 (BIOVIA, American). The exchange correlation function of the calculation process selects the PBE function under the generalized gradient approximation (GGA).
3. Results and discussion
3.1 Preparation of materials
Firstly, the FT-IR spectra was used to illustrate the structural changes of D301 resin before and after modification. As shown in Fig. 1, a new vibration peak appears at the position of 1667.73 cm−1 after modification. And the vibration peak was considered as the tertiary amine functional group provided by the aminating agent TOA, indicating that the modified D301 resin was prepared successfully.
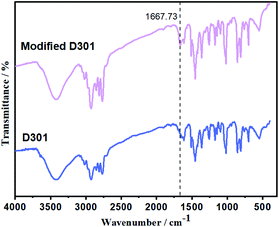 |
| Fig. 1 FT-IR spectra of D301 resin and modified D301 resin. | |
In the aqueous system of W–Mo–H2O, most tungsten and molybdenum are exit in the form of polymeric anions, and the two exist in very similar forms, which makes their separation difficult. However, in the W–Mo–S–H2O aqueous system, molybdenum will preferentially combine with sulfur to form Mo–S polymer ions, and W will still exist in the form of W–O anions. This makes the tungsten and molybdenum ions in the solution form an ionic difference, which increases the possibility of separation of tungsten and molybdenum ions in the solution. Therefore, in order to better separate and recover the tungsten and molybdenum solution, we first sulfide the tungsten and molybdenum solution. Fig. 2(a) showed the structures of chemical structures of NaWO4, NaMoO4 and Na2S. The molar ratio of NaWO4 and NaMoO4 was 1
:
1, 10
:
1, 20
:
1 and all of the molar ratio of NaMoO4 was 0.01 mol L−1. The photographs of these solution are shown in listed in Fig. 2(b). After vulcanization treatment, the colors of the solutions are obviously different. MoO42− in the solution is colorless, and the MoS42− in the solution is orange, combined with Fig. 2(b), we can find that, after the vulcanization treatment, the color of the solution has changed, which reflects MoO42− in the solution was successfully converted into MoS42− through a thiolation reaction. Among them, when the tungsten concentration is 0.2 mol L−1, the solution color is lightest after vulcanization. Besides, Fig. 2(c) shows the pH changes of the three solutions before and after vulcanization treatment. It can be clearly seen that the pH of the solution is very different when the concentration of tungsten in the solution is different. As the molar ratio of tungsten increased, the pH of the solution gradually increased. The initial pH of the solution after vulcanization treatment was 12.67, 12.19 and 7.69.
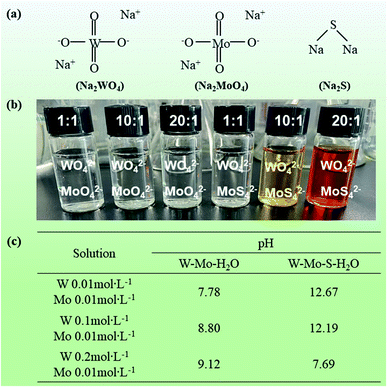 |
| Fig. 2 (a) The molecular structure of used in this work, (b) photograph of prepared solution, (c) pH of three solutions before and after vulcanization treatment. | |
In order to further confirm the combination of molybdenum and sulfur in the solution, Fig. 3 shows the Raman spectra of the solution before and after vulcanization. It can be seen from Fig. 3(a) that the Mo–O bond peak appears at 322 cm−1 and W–O bond appears at 931 cm−1 for the three solutions before vulcanization, and the peak intensity increases as the concentration of tungsten in the solution increase. After vulcanization, Mo–S bonds appear at the position of 473 cm−1, but there is no W–S peak detected.
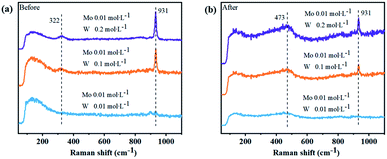 |
| Fig. 3 Raman spectra of prepared solution (a) before and (b) after vulcanization. | |
3.2 Sorption experiment
3.2.1 Effect of pH value. The main factor affecting Mo removal performance is pH value, which normally affects the characteristics of Mo in the solution.3 To better improve the feasibility of practical separation processes, the species change of molybdenum and tungsten in the S–Mo–W–H2O system at pH 0–14 were investigated by thermodynamic analysis. Take the total amount of molybdenum c(Mo) = 0.01 mol L−1, the total amount of tungsten c(W) = 0.01–0.2 mol L−1, and the total amount of sulphate c(S) = 0.06 mol L−1, calculate the equilibrium concentration fraction of each ion for different pH values to examine them. The ion distribution changes with pH, and the results are shown in Fig. 4.
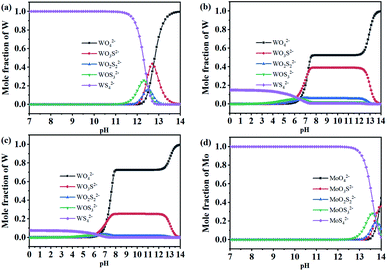 |
| Fig. 4 The species of Mo–W–S–H2O system ([Mo]T = 0.01 mol L−1, [S]T = 0.06 mol L−1), (a) W ([W]T = 0.01 mol L−1); (b) W ([W]T = 0.1 mol L−1); (c) W ([W]T = 0.2 mol L−1); (d) Mo species. | |
As shown in Fig. 4, as the pH value increases, the anions of molybdenum and tungsten change in different forms. When the pH value is more than 11, the tungsten ions in the solution are almost all WO42− form exists, and in the solution of c(W) = 0.1 mol L−1, c(W) = 0.2 mol L−1, WS42− in the solution is almost 0. However, Mo will combine with S to form anionic species as Mo–S compound. The distribution of MoO42−, MoO3S2−, MoO2S22−, MoO3S2−, MoS42− with the change of pH value in the solution was shown in Fig. 4(d). When the pH value is less than 12, molybdenum mainly exists in the form of MoS42−. It is found in Fig. 4 that in the weakly alkaline or weakly acidic tungstate solution, controlling the initial pH of the solution and increasing the W concentration can make MoO42− preferentially vulcanized, but WO42− hardly vulcanized. The difference in the affinity of tungsten and molybdenum for sulfur can effectively separate tungsten and molybdenum. Therefore, the range of pH value 4–12 was chosen as the research range to conduct sorption optimization experiments.
The sorption performance of Mo with modified D301 at different pH values was studied at 25 °C, the contact time is 4 h. The influence of pH values on the Q and separation factor of modified D301 was investigated, the experimental data was shown in Fig. 5, respectively. It could be found that the calculated value of QMo was increased firstly and then decreased with the increase of pH value. When the pH value was 7.2, QMo = 428 mg g−1, the maximum separation factor β was 108.9. This is mainly because MoO42− will release OH− during the vulcanization process, which can be expressed as eqn (8)–(11). When increasing the pH value of the solution will also introduce OH−, which hinders the vulcanization of MoO42−, thereby reducing the separation factor. Then, if only the influence of OH− is considered, the overall separation coefficient should decrease as the pH value increases. But under acidic conditions, low concentrations of OH− may no longer be the main influencing factor. Because under acidic conditions, tungsten and molybdenum mostly exist in the form of heteropoly acid. The heteropoly acid is a macromolecular structure that will cause considerable steric hindrance, thereby reducing the sorption capacity and sorption selectivity of the resin. In summary, when the pH value is 7.2, the modified resin has the largest sorption capacity.
|
MoO42− + S2− + H+ = MoO3S2− + OH−
| (8) |
|
MoO3S− + S2− + H+ = MoO2S22− + OH−
| (9) |
|
MoO2S22− + S2− + H+ = MoO1S32− + OH−
| (10) |
|
MoO1S32− + S2− + H+ = MoS42− + OH−
| (11) |
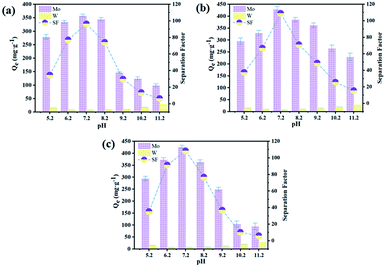 |
| Fig. 5 Effect of different pH on QMo, QW and separation factor ([Mo]T = 0.01 mol L−1), (a) W ([W]T = 0.01 mol L−1); (b) W ([W]T = 0.1 mol L−1); (c) W ([W]T = 0.2 mol L−1). | |
3.2.2 Effect of temperature. The molybdenum sorption capacity of modified D301 with different temperatures under sulfide solutions was tested, the results were shown in Fig. 6. As shown in Fig. 6, with an exaltation temperature from 25 °C to 75 °C, both the sorption capacity and the separation factor of modified D301 for Mo slowly decreased. It illustrated that the sorption action of Mo is an exothermic process. The temperature of 25 °C was considered the most suitable. It can also be seen from Fig. 6, with the increase in the amount of W associated with an increase in separation factor and sorption capacity. The events explained the sorption capacity was significantly elevated with the addition of tungsten percentage in the feed solution. It is also reported in the literature that the percentage of W can influence the sorption capacity of resin, with a higher separation rate for higher W content in the solution.31 Also, the amount of W can influence its sorption capacity.32 Furthermore, the Q increases as the increase of the initial W concentration, for the reason that towards a certain amount of adsorbent, the higher the W percentage in the solution, the greater the concentration slope, the easier the Mo to be adsorbed.
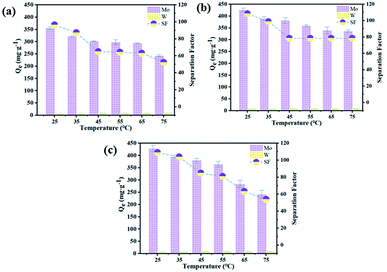 |
| Fig. 6 Effect of different temperature on QMo, QW and separation factor ([Mo]T = 0.01 mol L−1), (a) W ([W]T = 0.01 mol L−1); (b) W ([W]T = 0.1 mol L−1); (c) W ([W]T = 0.2 mol L−1) at pH 7.2, 240 min. | |
Finally, as shown in Table 1, we summarized some typical molybdenum adsorbents.33–36 Obviously, compared with other molybdenum adsorbents materials, the maximum sorption capacity (Qe) of modified D301 have unique advantages. The maximum sorption capacity of modified D301 for MoS42− was found to be 428 mg g−1, which is much higher than that of D301 resin. The sorption capacity increased by 2.7 times and it can greatly improve the sorption efficiency when using the same amount of resin.
Table 1 Comparison of the sorption capacity of some typical sorbents
Some typical sorbents |
Qe (mg g−1) |
Ref. |
TVEX-TOPO resin |
17.5 |
33 |
D290 resin |
76.3 |
34 |
D201 resin |
85 |
35 |
Montmorillonite resin |
162 |
36 |
D301 resin |
157 |
This work |
Modified D301 resin |
428 |
This work |
3.3 Sorption models
Like other sorption reactions, the sorption equilibrium of modified D301 was characterized by sorption models. With the help of Langmuir model37,38 and Freundlich model39 the sorption process of molybdenum by modified D301 resin was described. These two models can be expressed by eqn (4) and (5). Fig. 7 shows the sorption isotherm of molybdenum, and the correlation coefficient data is shown in Table 2. It can be seen from Fig. 7 that when the equilibrium concentration of molybdenum increases from 0 to 7.2 g L−1, and the sorption capacity can reach 2707 mg g−1 at the highest. Then the correlation coefficient R2 were obtained by nonlinear fitting. The correlation coefficient R2 of the Langmuir model is 0.987 larger than that of the Freundlich model, these show that sorption progress was fitted better with the Langmuir model. So the sorption process of molybdenum is a single layered spontaneous sorption process.40
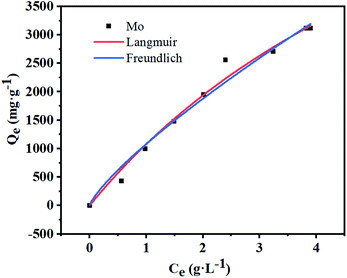 |
| Fig. 7 Langmuir model and Freundlich model of Mo on modified D301 resin. | |
Table 2 The model parameters for sorption at 25 °C
Component |
Equilibrium equation |
R2 |
Mo |
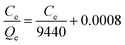 |
0.987 |
ln Qe = 0.8 ln Ce + 6.9 |
0.971 |
3.4 Sorption kinetics
To explore the sorption reaction, sorption kinetics was adopted. Kinetic behavior of Mo sorption by modified D301 was evaluated at two experiential kinetic models, the Lagergren-first-order model (eqn (6)) and the pseudo-second-order model (eqn (7)), to mathematically picture the intrinsic kinetic sorption constant.41,42 To investigate the sorption kinetics of Mo with the modified D301, sorption experiments with different contact time were conducted. The sorption capacity of modified D301 was performed in Fig. 8. As shown in Fig. 8, the points in the figure represent the experimental data before nonlinear curve fitting, the solid line represents the pseudo-second-order kinetic model, and the dashed line represents the Lagergren-first-order kinetic model. The Q of modified D301 to Mo increased along with the increase of operational time, suggesting a beneficial effect of the contact time on the sorption of Mo. The process reached equilibrium at about 4 h. With the accumulation of Mo, the sorption capacity increases slightly until it inclines to equilibrium, respectively. With the reaction proceeds, the molar ratio between modified D301 and Mo rise obviously, the driving force for Mo transfer decreases, therefore, a slowly increase in the sorption capacity, and then the sorption equilibrium is bit by bit reached.
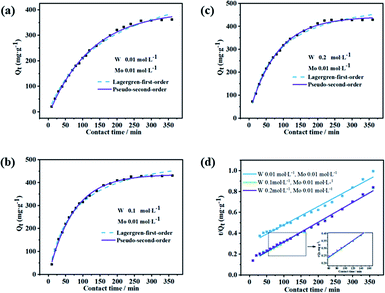 |
| Fig. 8 Effect of different contact time on QMo and separation factor ([Mo]T = 0.01 mol L−1). (a) W ([W]T = 0.01 mol L−1); (b) W ([W]T = 0.1 mol L−1); (c) W ([W]T = 0.2 mol L−1) at pH 7.2, 25 °C; (d) linearization of the pseudo-second-order model. | |
The linear regression curve of different models at 25 °C is shown in Fig. 8(d). The calculated parameters are presented in Table 3. R2 figures of Lagergren-first-order kinetic model was lower than that of the pseudo-second-order kinetic model. Accordingly, the sorption kinetics were better referred to as the pseudo-second-order model, illustrating that the procedure of Mo taken up by modified D301 was chemical behavior.30
Table 3 The linear regression data of different models at 25 °C
Solution (mol L−1) |
R2 |
Lagergren-first-order |
Pseudo-second-order |
t/Qt − t |
W 0.01 |
0.992 |
0.998 |
0.983 |
Mo 0.01 |
W 0.1 |
0.992 |
0.998 |
0.994 |
Mo 0.01 |
W 0.2 |
0.992 |
0.998 |
0.996 |
Mo 0.01 |
3.5 Sorption mechanism
In order to further clarify the sorption mechanism, a molecular model of modified D301 and MoS42− was constructed by Materials Studio software, and the sorption reaction was simulated. As shown in Fig. 9, one MoS42− molecular close to modified D301, and the other two move away. The S atom in MoS42− and the N atom in the N–C bond of modified D301 are close to each other. By measuring the distance between the center radii of two atoms, d1 = 168.2 pm < rS(1.02 pm) + rN(0.75 pm), d2 = 4.055 pm > rS(1.02 pm) + rN(0.75 pm), d3 = 3.967 pm > rS(1.02 pm) + rN(0.75 pm). Meanwhile, the sorption energy can get is −7.67 eV, sorption energy is less than 0, which indicates that the sorption process is stable chemical sorption. The results of theoretical calculation can infer the bonding behavior between the N atom on the resin and the S atom on the MoS42− molecule.
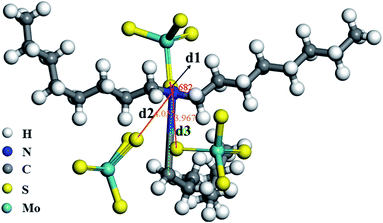 |
| Fig. 9 The molecular models of modified D301 and MoS42−. | |
In order to understand the sorption process of Mo by modified D301 resin, Fig. 10 shows the SEM images and EDS analyses of adsorbed resins in different solutions at 240 min. It can be seen that the spherical morphology of the resin has not changed after sorption, indicating that the mechanical properties of the resin are good, which is conducive to the repeated use of the resin. In order to present the element changes after the sorption process, EDS tests were performed. EDS results demonstrate that after sorption MoS42−, Mo in the resin is progressively appears. With the sorption proceeding, the MoS42− ions are gradually distributed into the resin particles. When sorption action was completed, the particles were all filled with molybdenum ions, Zhao et al. in their study on the separation of tungsten and molybdenum obtained the content of W adsorbed in the exterior is lower than that in the interior, while for Mo, the result is the opposite.31 Because Mo ions with rapid spread rate are masterly adsorbed in the internal layer, while W ions are adsorbed few in the external layer. It can also be seen from EDS that the higher the tungsten concentration in the solution, the larger the proportion of molybdenum adsorbed in the resin, which is consistent with the sorption experimental data.
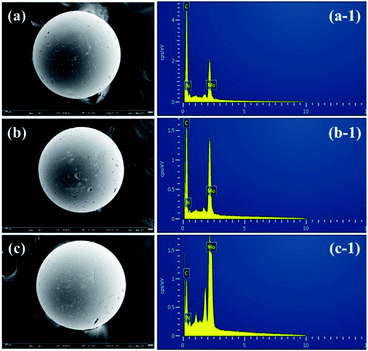 |
| Fig. 10 SEM images and EDS analyses of adsorbed resins in (a) ([Mo]T = 0.01 mol L−1, [W]T = 0.01 mol L−1); (b) ([Mo]T = 0.01 mol L−1, [W]T = 0.1 mol L−1); (c) ([Mo]T = 0.01 mol L−1, [W]T = 0.2 mol L−1) at pH 7.2, 240 min. | |
3.6 Desorption and reusability experiments
Desorption is a necessary factor to evaluate the ion exchange system. Therefore, the desorption behavior of Mo from the loaded resin by sodium hydroxide solution was investigated, the results were shown in Fig. 11. In Fig. 11(a), different concentrations of sodium hydroxide solutions were used as eluent, and the desorption rates are all above 90%. NaOH (1–5 w%) base media was found successful reagent. Considering comprehensively, we choose 5 w% concentration of sodium hydroxide solution as the eluent. As shown in Fig. 11(b), in the 1st to 5th cycles of the sorption–desorption process, the sorption capacity of Mo with modified D301 was maintained to be high. These results indicated that the desorption capacity of sodium hydroxide solutions was high, and modified D301 could repeatedly be used for the sorption–desorption process.
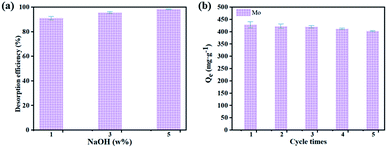 |
| Fig. 11 (a) Desorption and (b) reusability of modified D301. | |
3.7 Proposed flow sheet of separating W and Mo
On the basis of the above experimental results, a flow sheet of separating W and Mo from the tungstate solution was proposed as shown in Fig. 12. In this process, molybdate was vulcanized and separated from tungstate solution by modified D301. Moreover, modified D301 was regenerated by sodium hydroxide solutions for cycling sorption. The concentrations of three feed solution are different (0.01 M W; 0.01 M Mo), (0.1 M W; 0.01 M Mo), (0.2 M W; 0.01 M Mo). After three-stage sorption–desorption, almost all Mo in the solution can be removed. And the tungsten loss is less than 2%. The molybdenum-loaded resin was desorbed by 5 w% sodium hydroxide solution. The molybdenum in the desorption solution and tungsten in the effluent can be used as a raw material for molybdenum deep-processing products.
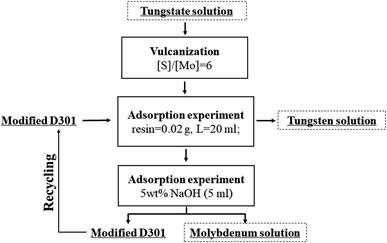 |
| Fig. 12 Flowchart of separating W and Mo by modified D301. | |
4. Conclusions
This study proposed a sorption system of modified D301 resin, for separation and recovery of molybdenum from tungstate solution. In brief, modified D301 resin had high sorption efficiency of MoS42− and the separation factors. In sulfur medium, when the pH value is less than 10, molybdenum mainly exists in the form of MoS42−, tungsten mainly exists in the form of WO42−. The maximum sorption capacity of modified D301 for MoS42− was found to be 428 mg g−1 and the separation coefficient (β) is 108.9 when the reaction time was 4 h and reaction temperature was 25 °C and the pH value of tungstate solution was 7.2. The sorption process conforms to the quasi-second-order kinetic model.
The sorption mechanism was speculated by simulation analysis, the N atom in the resin and the S atom of MoS42− can form an N–S bond during the sorption process. Besides, the desorption characteristic of MoS42− with sodium hydroxide solution was investigated. When sodium hydroxide solution concentration was 5 w%, the desorption efficiency is 98.3%. After three-stage sorption–desorption, almost all molybdenum in the solution was adsorbed, achieving better separation of tungsten and molybdenum.
Conflicts of interest
There are no conflicts to declare.
Acknowledgements
This work was supported by National Key R&D Program of China (2018YFC1901700), National Natural Science Foundation of China (51621003).
References
- A. B. Cueva Sola, P. K. Parhi, J.-Y. Lee, H. N. Kang and R. K. Jyothi, Environmentally friendly approach to recover vanadium and tungsten from spent SCR catalyst leach liquors using Aliquat 336, RSC Adv., 2020, 10, 19736–19746 RSC.
- Q. He and H. Chen, Increased efficiency of butanol production from spent sulfite liquor by removal of fermentation inhibitors, J. Cleaner Prod., 2020, 263, 121356 CrossRef CAS.
- J. Du, J. Li, D. He, M. Xu, G. Zhang, Z. Cao and S. Wu, Green separation and recovery of molybdenum from tungstate solution achieved by using a recyclable vulcanizing agent, J. Cleaner Prod., 2021, 278, 123930 CrossRef CAS.
- W. Jin and Y. Zhang, Sustainable Electrochemical Extraction of Metal Resources from Waste Streams: From Removal to Recovery, ACS Sustainable Chem. Eng., 2020, 8, 4693–4707 CrossRef CAS.
- L. Huang, M. Li, Y. Pan, Y. Shi, X. Quan and G. Li Puma, Efficient W and Mo deposition and separation with simultaneous hydrogen production in stacked bioelectrochemical systems, Chem. Eng. J., 2017, 327, 584–596 CrossRef CAS.
- F. Ogata, T. Nakamura, E. Ueta, E. Nagahashi, Y. Kobayashi and N. Kawasaki, Adsorption of tungsten ion with a novel Fe-Mg type hydrotalcite prepared at different Mg2+/Fe3+ ratios, J. Environ. Chem. Eng., 2017, 5, 3083–3090 CrossRef CAS.
- H. Fu, Y. Li, G. Cao and Z. Zhao, Separation of Tungsten from Phosphorus-Containing Molybdate Solution Using Solvent Extraction with Primary Amine N1923, Jom, 2018, 70(12), 2864–2868 CrossRef CAS.
- J. Yang, X. Chen, X. Liu, Z. Zhao, W. Wang and W. Peng, Separating W(VI) and Mo(VI) by two-step acid decomposition, Hydrometallurgy, 2018, 179, 20–24 CrossRef CAS.
- F. Ogata, T. Nakamura and N. Kawasaki, Adsorption capability of virgin and calcined wheat bran for molybdenum present in aqueous solution and elucidating the adsorption mechanism by adsorption isotherms, kinetics, and regeneration, J. Environ. Chem. Eng., 2018, 6, 4459–4466 CrossRef CAS.
- W. Fu, G. Ji, H. Chen, S. Yang, B. Guo, H. Yang and Z. Huang, Molybdenum sulphide modified chelating resin for toxic metal adsorption from acid mine wastewater, Sep. Purif. Technol., 2020, 251, 117407 CrossRef CAS.
- D. Gong, K. Zhou, J. Li, C. Peng and W. Chen, Rapid Leaching of Synthetic Scheelite by a Resin-in-Pulp Process, JOM, 2018, 70, 2846–2855 CrossRef CAS.
- J. Tang, Y. Liu, J. W. Ye, Z. N. Cao, S. Q. Ma and X. J. Yang, Microstructure and mechanical properties improvements in cemented carbides by (Cr,Mo,Ta)2(C,N) inhibitors, Rare Met., 2020, 679–686 Search PubMed.
- T. H. Nguyen and M. S. Lee, Separation of molybdenum(VI) and tungsten(VI) from sulfate solutions by solvent extraction with LIX 63 and PC 88A, Hydrometallurgy, 2015, 155, 51–55 CrossRef CAS.
- M. F. Hamza, K. A. M. Salih, A. A. H. Abdel-Rahman, Y. E. Zayed, Y. Wei, J. Liang and E. Guibal, Sulfonic-functionalized algal/PEI beads for scandium, cerium and holmium sorption from aqueous solutions (synthetic and industrial samples), Chem. Eng. J., 2021, 403, 126399 CrossRef CAS.
- F. Liu, R. Hua, F. Zhang, H. Liu, C.-P. Lee, H. Liu and B. Xu, Adsorption and separation of Re(VII) using trimethylamine-functionalized strong base anion exchange resin, J. Radioanal. Nucl. Chem., 2020, 326, 445–454 CrossRef CAS.
- W. Wang, A. Maimaiti, H. Shi, R. Wu, R. Wang, Z. Li, D. Qi, G. Yu and S. Deng, Adsorption behavior and mechanism of emerging perfluoro-2-propoxypropanoic acid (GenX) on activated carbons and resins, Chem. Eng. J., 2019, 364, 132–138 CrossRef CAS.
- B. Yang, S. Wu, X. Liu, Z. Yan, Y. Liu, Q. Li, F. Yu and J. Wang, Solid-phase extraction and separation of heavy rare earths from chloride media using P227-impregnated resins, Rare Met., 2020, 40, 2633–2644 CrossRef.
- Y. Song, Y. Tsuchida, M. Matsumiya, Y. Uchino and I. Yanagi, Separation of tungsten and cobalt from WC-Co hard metal wastes using ion-exchange and solvent extraction with ionic liquid, Miner. Eng., 2018, 128, 224–229 CrossRef CAS.
- S. Van Roosendael, M. Regadío, J. Roosen and K. Binnemans, Selective recovery of indium from iron-rich solutions using an Aliquat 336 iodide supported ionic liquid phase (SILP), Sep. Purif. Technol., 2019, 212, 843–853 CrossRef CAS.
- X. Wu, G. Zhang, L. Zeng, W. Guan, S. Wu, Z. Li, Q. Zhou, D. Zhang, J. Qing, Y. Long, J. Li, Q. Li, Z. Cao and L. Xiao, Continuous solvent extraction operations for the removal of molybdenum from ammonium tungstate solution with quaternary ammonium salt extractant, Hydrometallurgy, 2020, 195, 105401 CrossRef CAS.
- M. Ghadiri, S. N. Ashrafizadeh and M. Taghizadeh, Study of molybdenum extraction by trioctylamine and tributylphosphate and stripping by ammonium solutions, Hydrometallurgy, 2014, 144, 151–155 CrossRef.
- A. Daud, G. Gray, C. D. Lynch, N. H. F. Wilson and I. R. Blum, A randomised controlled study on the use of finishing and polishing systems on different resin composites using 3D contact optical profilometry and scanning electron microscopy, J. Dent., 2018, 71, 25–30 CrossRef CAS PubMed.
- Y. Fu, Q. Xiao, Y. Gao, P. Ning, H. Xu and Y. Zhang, Direct extraction of Mo(VI) from acidic leach solution of molybdenite ore by ion exchange resin: Batch and column adsorption studies, Trans. Nonferrous Met. Soc. China, 2018, 28, 1660–1669 CrossRef CAS.
- H. MacKeown, J. A. Gyamfi, M. Delaporte, K. V. K. M. Schoutteten, L. Verdickt, B. Ouddane and J. Criquet, Removal of disinfection by-product precursors by ion exchange resins, J. Environ. Chem. Eng., 2021, 9, 20–24 Search PubMed.
- Y. Cao, Q. Guo, Z. Shu, C. Jiao, L. Luo, W. Guo, Q. Zhao and Z. Yin, Tungstate removal from aqueous solution by nanocrystalline iowaite: An iron-bearing layered double hydroxide, Environ. Pollut., 2019, 247, 118–127 CrossRef CAS PubMed.
- N. Reynier, L. Coudert, J. F. Blais, G. Mercier and S. Besner, Treatment of contaminated soil leachate by precipitation, adsorption and ion exchange, J. Environ. Chem. Eng., 2015, 3, 977–985 CrossRef CAS.
- R. Li, N. Liang, X. Ma, B. Chen and F. Huang, Study on the adsorption behavior of glycerin from fatty acid methyl esters by a tertiary amine-type anion exchange resin, J. Chromatogr. A, 2019, 1586, 62–71 CrossRef CAS PubMed.
- R. V. Xikhongelo, F. M. Mtunzi, P. N. Diagboya, B. I. Olu-Owolabi and R.-A. Düring, Polyamidoamine-Functionalized Graphene Oxide–SBA-15 Mesoporous Composite: Adsorbent for Aqueous Arsenite, Cadmium, Ciprofloxacin, Ivermectin, and Tetracycline, Ind. Eng. Chem. Res., 2021, 60, 3957–3968 CrossRef CAS.
- F. Q. An, Y. Wang, X.-Y. Xue, T.-P. Hu, J.-F. Gao and B.-J. Gao, Design and application of thiourea modified D301 resin for the effective removal of toxic heavy metal ions, Chem. Eng. Res. Des., 2018, 130, 78–86 CrossRef CAS.
- Y. Zang, Q. Yue, Y. Kan, L. Zhang and B. Gao, Research on adsorption of Cr(VI) by Poly-epichlorohydrin-dimethylamine (EPIDMA) modified weakly basic anion exchange resin D301, Ecotoxicol. Environ. Saf., 2018, 161, 467–473 CrossRef CAS PubMed.
- Z. Zhao, J. Zhang, X. Chen, X. Liu, J. Li and W. Zhang, Separation of tungsten and molybdenum using macroporous resin: Equilibrium adsorption for single and binary systems, Hydrometallurgy, 2013, 140, 120–127 CrossRef CAS.
- X. z. Zhu, G. s. Huo, J. Ni and Q. Song, Removal of tungsten and vanadium from molybdate solutions using ion exchange resin, Trans. Nonferrous Met. Soc. China, 2017, 27, 2727–2732 CrossRef CAS.
- B. A. Masry and J. A. Daoud, Sorption behavior of tungsten and molybdenum on TVEX-TOPO resin from nitric acid solution, J. Chem. Technol. Biotechnol., 2021, 1399–1410 CrossRef CAS.
- L. S. Xiao, Q. X. Zhang, B. F. Gong and S. Y. Huang, Separation of molybdenum from tungstate solution by a combination of moving packed bed and fluid bed ion-exchange techniques, Int. J. Refract. Met. Hard Mater., 2001, 19, 145–148 CrossRef CAS.
- Z. Zheng, Q. Jia, X. Xie, X. Zheng, C. Yao, C. Xiong and J. Jiang, Removal and Recovery of Mo(IV) from Aqueous Solutions by D201 Resin: Adsorption and Column Studies, Asian J. Chem., 2014, 26, 393–395 CrossRef CAS.
- M. Tuchowska, B. Muir, M. Kowalik, R. P. Socha and T. Bajda, Sorption of Molybdates and Tungstates on Functionalized Montmorillonites: Structural and Textural Features, Materials, 2019, 12, 2253 CrossRef CAS PubMed.
- I. Langmuir, The constitution and fundamental properties of solids and liquids, J. Am. Chem. Soc., 1916, 38, 2221–2295 CrossRef CAS.
- X. Chen, Z. Tian, H. Cheng, G. Xu and H. Zhou, Adsorption process and mechanism of heavy metal ions by different components of cells, using yeast (Pichia pastoris) and Cu2+ as biosorption models, RSC Adv., 2021, 11, 17080–17091 RSC.
- A. W. Adamson and A. P. Gast, Physical chemistry of surfaces, Interscience Publishers New York, 1967, vol. 150 Search PubMed.
- S. Hassanpour and M. Taghizadeh, Rapid and selective separation of molybdenum ions using a novel magnetic Mo(VI) ion imprinted polymer: a study of the adsorption properties, RSC Adv., 2016, 6, 100248–100261 RSC.
- J. P. Simonin, On the comparison of pseudo-first order and pseudo-second order rate laws in the modeling of adsorption kinetics, Chem. Eng. J., 2016, 300, 254–263 CrossRef CAS.
- I. A. Tan, A. L. Ahmad and B. H. Hameed, Adsorption of basic dye on high-surface-area activated carbon prepared from coconut husk: equilibrium, kinetic and thermodynamic studies, J. Hazard. Mater., 2008, 154, 337–346 CrossRef CAS PubMed.
|
This journal is © The Royal Society of Chemistry 2021 |
Click here to see how this site uses Cookies. View our privacy policy here.