DOI:
10.1039/D1RA04057J
(Paper)
RSC Adv., 2021,
11, 27183-27192
Novel bio-based filler: hyperbranched polymer modified leather buffing dust and its influence on the porous structure and mechanical properties of polyurethane film
Received
24th May 2021
, Accepted 2nd August 2021
First published on 9th August 2021
Abstract
An amino-terminated hyperbranched polymer (A-HP) was employed to modify leather buffing dust (BD) to prepare functional filler, hyperbranched buffing dust (HBD). The structure and morphology of BD and HBD were characterized by XPS, DSC and SEM. Furthermore, HBD was added into the typical solvent type polyurethane (PU) to prepare a wetting PU film which was used as the coating for synthetic leather. By changing the dosage of HBD, the filler species, the properties of the porous structure and mechanical strength of the PU film were analyzed by SEM, DMA and so on. The experimental results indicated that with the increase of the dosage of HBD, the porous structure of the PU film increase. The content of the N element for BD increases from 4.27% to 7.29%. After modification and ball milling, the fineness of most fibers was in the range of 6.7–6.9 μm. The fiber dispersion state of HBD was more uniform. The Tg of the PU film with HBD is −8.67 °C, while for lignin is −8.41 °C, indicating that the wetting PU film filled with HBD has better flexibility at low temperature.
1. Introduction
Natural leather is widely used in the production of daily necessities and industrial products because of its excellent performances.1–3 However, with the growth of the world population, the demand for leather is growing significantly, and the limited amount of natural leather can't meet this demand. To solve this problem, scientists began to research and develop synthetic leather to make up for the shortage of natural leather. Synthetic leather is a kind of plastic product which simulates the composition and structure of natural leather and can be used as a substitute material. Synthetic leather has a smooth surface, and uniform thickness, color and strength. It is superior to natural leather in water resistance, acid and alkali resistance and microorganism resistance, but its air permeability, wear resistance and cold resistance are not as good as that of natural leather.4–6 The surface of synthetic leather is coated with microporous polyurethane (PU), and its base material is a non-woven fabric made of polyester, polypropylene and other synthetic fibers.7 In the field of synthetic leather, adding lower price fillers can not only reduce the cost, but also adjust the microporous structure of the PU film. The conventional fillers include light calcium carbonate, lignin and so on. Recently, cow hair powder has also been used as an environment-friendly filler for wet PU filling.8 However, calcium carbonate is an inorganic filler, which has poor compatibility with PU and readily causes problems such as aggregation, precipitation and uneven dispersion. There are interface defects between light CaCO3 and PU, which lead to the deterioration of machinability and mechanical properties of the material. Lignin can improve the moisture absorption and reduce the elasticity of the film, but it needs to consume wood resources. Although the use of cowhair powder can realize the recycling of waste cowhair resources, because it is keratin, it needs to use alkali sulfide when unhairing. And the recovered cowhair has sulfide residues. Accordingly, PU sizing will produce unpleasant smell when drying. Therefore, the development of new fillers is very important for the production and performance improvement of synthetic leather.
On the other hand, due to the non-uniform thickness of natural leather, it needs to be buffed. During this process, a large amount of buffing dust (BD) will be produced. According to statistic, about 2–6 kg of BD is liberated as a solid waste per ton of skin/hide processed.9 Actually, leather buffing dust is a kind of protein-based material, namely skin collagen, which contains a lot of hydrophilia groups such as –OH, –NH2, –COOH. Based on its characteristics of fine particle size structure, a large number of polar groups and low odor, the development of new filler using BD for synthetic leather has a bright application prospect. Unfortunately, there are only reports on the use of skin powders as fillers,10,11 and the research on the leather buffing dust is relatively less. In addition, after tanning, dyeing, fatliquoring and other processes of leather-making, the –COOH, –NH2 and other active groups on the leather combine with these chemicals, resulting in the reduction of the number of active groups. In order to increase the reaction sites, it is necessary to use hyperbranched polymers to modify the leather. At present, hydroxyl terminated hyperbranched polymers and amino terminated hyperbranched polymers (A-HP) are commonly used in modified skin collagen.12 Considering the high activity of amino group, especially the characteristic of easy to combine with anionic dyes, it can bring more bright coloring effect to the coating. In this study, A-HP was used to modify the leather buffing dust, and the modified BD was further used in the preparation of wet polyurethane coating to explore the possibility of using it as a filler for synthetic leather.
The purpose of this study is to realize the resource reuse of leather protein waste such as buffing dust, and find a more simple and easy application direction for the large number of BD. At the same time, it endows the synthetic leather with some characteristics of natural leathers, especially hygienic properties, such as hydrophilicity and moisture permeability.
2. Materials and methods
2.1 Materials
Light brown BD was supplied by Xinghao Leather Co., Ltd. (Dezhou, China). Diethylenetriamine (DETA), methyl acrylate, glutaraldehyde and methyl alcohol were purchased from Aladdin Biochemical Technology Co., Ltd. (Shanghai, China). Solvent type polyurethane, negative ion surfactant agent (OT-70), N,N-dimethylformamide (DMF), lignin, light CaCO3, were obtained from Luri Junda Leather Co., Ltd. (Jinan, China). Nonionic hyperbranched wetting agent13 and milled cowhair powder used in this study were prepared in laboratory.
2.2 Preparation of HBD
The A-HP was prepared by polycondensation process.14 Then the glutaraldehyde was used as the crosslinking agent to graft the A-HP onto the surface of BD. Certain amount of BD was dispersed in distilled water (the pH was adjusted to 7). Then glutaraldehyde mixed with distilled water, and the mixture was added into the constant pressure drop funnel. Next, the A-HP was dissolved in distilled water and added into the constant pressure drop funnel, too. The reaction molar rate was nNH2 of A-HP
:
nglutaraldehyde
:
nNH2 of BD = 1
:
1.1
:
1, and the reaction last for 4 h under 45 °C. After that, the BD after modification was filtered by nylon fabric. Then wash filter with distilled water. The modified BD was collected and dried in the oven at 60–80 °C for 24 h.
The BD acted as an anchor to fix the molecular chain of A-HP. So, the A-HP can be retained in the PU film after multiple washing process. The structure diagram of modified buffing dust was shown in Fig. 1. The modified buffing dust was then grinded by wet ball-milling, freeze drying and dry milling process to prepare the functional filler HBD. The preparation process of HBD was shown in Fig. 2.
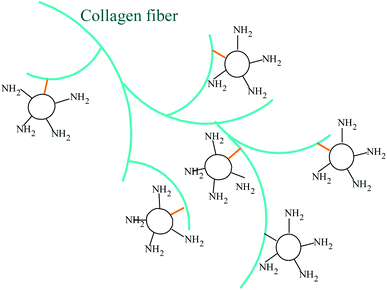 |
| Fig. 1 The structure diagram of HBD. | |
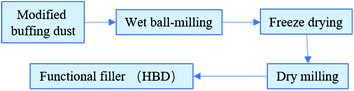 |
| Fig. 2 The preparation process of HBD. | |
2.3 Wetting film-forming process
The HBD, solvent type PU, nonionic hyperbranched wetting agent, OT-70 and DMF were used as the raw materials to prepare the wet PU sizing. Then the wet sizing was stay for overnight to deaeration. The applicator rolls with 0.7 mm thickness was employed to scarp the sizing on the glass. Then the glass was put into the prepared coagulation bath with a constant speed. The coagulation bath is consist by DMF solution with 35% mass fraction and temperature of the bath was 30 °C. After 25 min, the sizing on the glass changed to a solid film state.
The coagulation process of PU film is shown in Fig. 3. The film was transferred to gradient washing process under different temperature. The assignment procedure was as following: the film was firstly put into water with 40 °C for 20 min, then 50 °C for 15 min, at last, 60 °C for 15 min by manual scrubbing to remove the DMF in the porous structure in PU film. The washed film was then tack on the cardboard to dry and finalize the design in oven at 55 °C for 3 h. The PU film prepared under different conditions were obtained. In order to test the mechanical properties, the cutting shear with 4 cm × 50 cm size was employed to prepared the testing samples. Three samples were cut to test as the parallel and the average value was record.
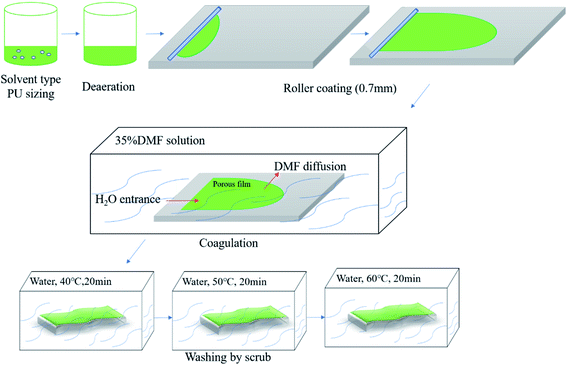 |
| Fig. 3 The film forming process. | |
In the coagulation process, the DMF and H2O are inter-miscible.15 The film forming mechanism is shown in Fig. 4. The coagulation process of PU film is a substitution process. The DMF in PU sizing enter into the coagulation solution, while the H2O in the coagulation solution access the PU/DMF system. The driving force of these two processes are both concentration difference, and the DMF as well as the H2O were moved from higher concentration to lower concentration solution.
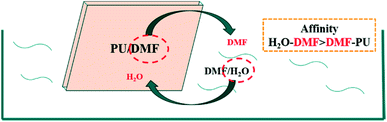 |
| Fig. 4 The generation of PU porous film. | |
At the same time, the affinity of H2O to DMF is higher than that of PU. The PU film changed from liquid state to gel state and then changed to solid state.16 Furthermore, the molecular structure of PU in DMF solution is stretching state. When it starts to coagulate, the molecular chain starts to shrink. So, the pore structure generates to replenish the volume decrement. At the same time, the pore structure enables the PU film with good air permeability and water vapor permeability.17 The existing of HBD actually provide more hydrophilic group, which means the exchanging site of H2O and DMF increased.
2.4 Analysis of film forming conditions
Different kinds of filler, light CaCO3, lignin, milled cowhair powder and HBD were used to prepare the PU film to observe the porous structure. Furthermore, through changing the type of fillers and the dosage of HBD, a series of PU films were prepared.
2.4.1 The dosage of HBD. The mass ratio of PU and DMF was 2.5
:
1. The dosage of nonionic hyperbranched wetting agent and OT-70 was 1.3% and 0.66% of PU resin respectively. And the dosage of HBD was 0%, 1%, 2%, 3% and 4% of PU resin respectively.
2.4.2 Different filler. The formula of the wet PU sizing was as following: the ratio of PU and DMF was 2.5
:
1. The dosage of nonionic hyperbranched wetting agent, OT-70 and different filler (light CaCO3, lignin, milled cowhair powder and HBD) were 1.3%, 0.66% and 2% (mass fraction) of PU, and the coagulation time was 20 min.
2.5 Characterization
2.5.1 Characterization of BD and HBD. The thermo Scientific ESCALAB Xi + XPS analysis meter was used to determine the element content of BD and HBD. The TA DSC-25 was used for DSC analysis of BD and HBD. The analysis temperature was raised from 30 °C to 140 °C. The rising speed of temperature was 10 °C min−1. The table scanning electron microscope (EM 30 plus+, Korea COXEM) as well as the ultra-depth microscope (Leica DVM6 Digital Versatile Microscope) were employed to observe the surface structure of different filler.
2.5.2 Characterization of PU film. The AI-3000 Gotech multi-function tension machine was employed to test the mechanical properties of PU film. The American Thermal DMA Q800 was used to analysis dynamic mechanical properties18 of PU film. The viscosity of the sizing is measured by Brookfield DV2T viscometer. The water contact angle is determined by Krüss DSA25 (Germany). The determination method of moisture permeability of PU film is followed the ref. 19. The table scanning electron microscope (EM 30 plus+, Korea COXEM) were employed to observe the cross section of PU film.
3. Results and discussion
3.1 Characterization and micro morphology analysis of BD and HBD
3.1.1 Determination of the content of amino groups. The amino contents of A-HP, BD and HBD were determined according to the alicylaldehyde20 method, respectively. The experimental results indicated that the amino content of A-HP, BD and HBD were 9.67%, 8.62% and 9.06%. The amino content of BD increased by 5.1% after modification.
3.1.2 XPS. The XPS spectrum and the surface element determination by XPS of pristine BD and HBD were shown in Fig. 5 and Table 1. The content of N element increases from 4.27% to 7.29%, which indicates the –NH2 groups on the HBD was increased compared with the BD. It can be attributed to the large amount of –NH2 contained on the hyperbranched polymer which was introduced to BD by the crosslinking function of glutaraldehyde.
 |
| Fig. 5 The XPS spectrum of BD and HBD. | |
Table 1 Surface element determination by XPS
Name |
Atomic/% |
BD |
HBD |
C 1s |
72.02 |
71.62 |
O 1s |
18.39 |
15.6 |
N 1s |
4.27 |
7.29 |
Si 2p |
4.55 |
4.78 |
S 2p |
0.77 |
0.72 |
3.1.3 DSC. The denaturation temperature is a way to reflect the natural helical structure of collagen protein.21 When the temperature of system increased to denaturation temperature, the extending structure of collagen protein changed to random curl.22 The DSC analysis results of BD and HBD were shown in Fig. 6. The BD is tanned fiber, due to its tiny structure of collagen fiber, the first peak corresponding to the distortion temperature was 55.6 °C. While for the HBD, the distortion temperature increased to 56.3 °C. The slight increase in the thermal stability of modified BD may be due to the crosslinking effect of glutaraldehyde. In addition, the glutaraldehyde acted as a bridging agent between BD and hyperbranched polymer. Glutaraldehyde has tanning effect on skin protein. The two aldehyde groups on the glutaraldehyde crosslinked the amino groups on the peptide chain of BD as well as the amino group on the A-HP. The peak at 130.7 °C appeared in the spectrum of HBD was the Tm of A-HP.
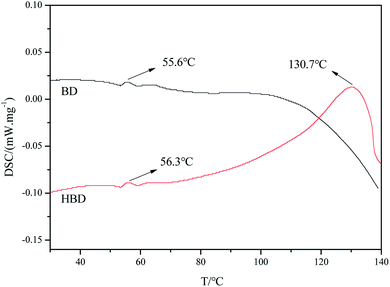 |
| Fig. 6 DSC curves of BD and HBD. | |
3.1.4 The ultra-depth electron microscope observation. The surface structures of BD and HBD observed by Leica DVM6 Digital Versatile Microscope were shown in Fig. 7. According to the analysis, the diameter of dispersive single fiber for HBD (Fig. 7(b)) was in the range of 5.32–8.17 μm. There are some tiny fibers existed in the field of view. But the fineness of most fiber was about 6.7–6.9 μm. The dispersion of the fiber is uniformly. While for the BD (Fig. 7(a)), the fineness of the collagen fiber is 7.3–11.46 μm. Meantime, the collagen fiber in BD was bonding with each other. After modification and wet/dry milling, the collagen bundle was dispersed. That might attribute to the grafting of the hyperbranched polymer. Hyperbranched polymer23 is a kind of three-dimensional structure polymer, when it was grafted onto the collagen fiber, the gap of the fiber was enlarged. Then the HBD changed to fibrous structure. What's more, in the experimental process, we observed that the BD is hardly dissolved in the water at first, after 10 min stirring, it can be wetted. While for the HBD, it can be dispersed in water as soon as it contacted with water. Hence, the hydrophilia property HBD is better than BD.
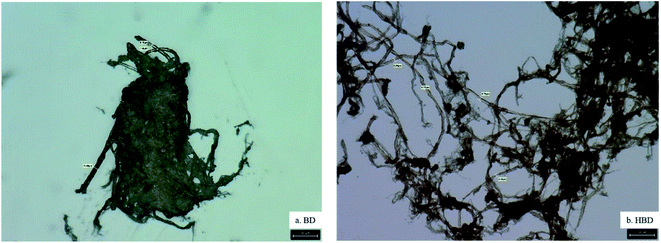 |
| Fig. 7 The ultra-depth electron microscope picture of BD (a) and HBD (b) (×1000). | |
3.1.5 SEM analysis. The appearances of different filler observed by SEM were shown in Fig. 8. Including the light CaCO3, lignin, milled cowhair powder and HBD. The size of light CaCO3, lignin and milled cowhair powder are dispersed bulk structure. While for the milled HBD, it's fibrous structure.
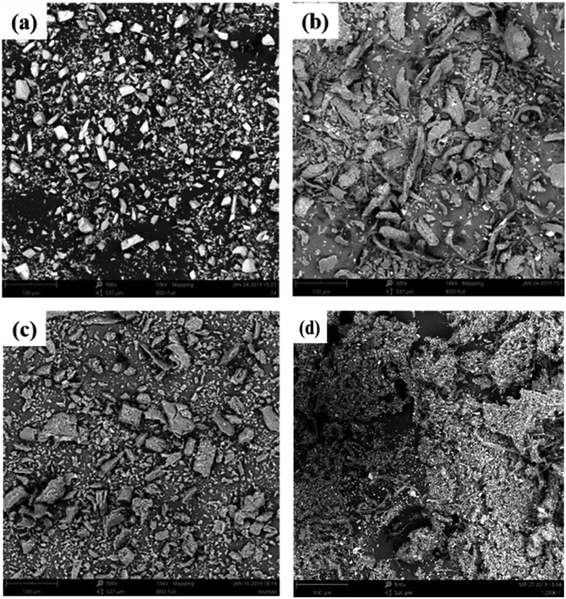 |
| Fig. 8 The SEM picture (×500) of different filler ((a) light CaCO3, (b) lignin, (c) milled cowhair powder, (d) HBD). | |
3.2 Performance analysis of PU film with HBD as the filler
3.2.1 SEM observation. The SEM pictures of PU film with different dosage of HBD were shown in Fig. 9. According to the pictures, when there is no filler in the film, the pore is less. With the increase of the dosage of HBD, the porous structure in the film was increased. Especially when the dosage of buffing dust is 2%, the distribution of the pore is more uniform. The pore size is round. This might attribute to the existence of terminated amino group, the coagulation points increased.24 When the dosage of HBD was further increased to 3%, the pore amount decreased. The possible reason is that too much HBD absorbed part of the polar solvent DMF, resulting in the decrease of DMF concentration in PU sizing and the increase of viscosity of sizing, which reduced the DMF concentration difference between coagulation bath and PU sizing. At the same time, the larger viscosity system hindered the mass transfer rate of H2O and DMF. Generally speaking, in the wet process, the lower the DMF concentration of PU sizing, the slower the diffusion speed to the coagulation bath, and the slower solidification rate of PU film, resulting in the increase of density of PU film. And the corresponding number of large pores decreased significantly, while the honeycomb micropores dominated. This phenomenon can be observed from Fig. 9(d). Considering that the larger porosity is beneficial to the water vapor permeability of the coating, the amount of HBD in PU coating should not exceed 2%.
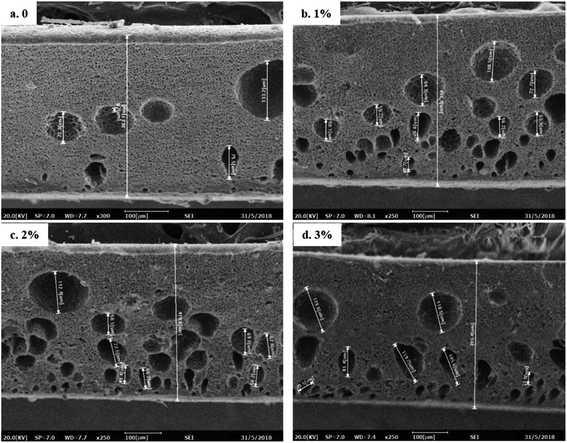 |
| Fig. 9 The SEM pictures (×250) of film with different dosage of HBD ((a) 0, (b) 1%, (c) 2%, (d) 3%). | |
3.2.2 The mechanical property of PU film. The influence of dosage to the mechanical property of film was shown in Fig. 10. With the increase of dosage of buffing dust, the tensile strength as well as elongation at break decreased. The decrease of tensile strength of PU film is in accordance with the increase of pore amounts in the PU film which revealed by SEM pictures. Generally, it is considered that the effect of the pore on the whole material is equivalent to the crack, which mainly plays a negative role in splitting the matrix and destroying the strength. The more pores, that is, the more defects, the more obvious the damage effect on the material, and the more the strength decreases. Therefore, when the amount of HBD increases from 0% to 2%, the increase of the number of pores in the coating is the main reason for the decrease of tensile strength of PU film. When the amount of HBD increased to 3% or 4%, the mechanical properties of PU films were further decreased due to the large and uneven pore distribution.
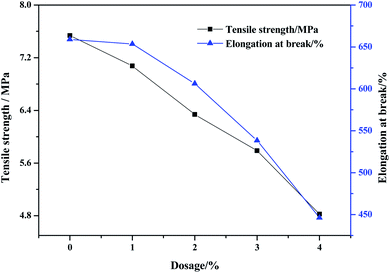 |
| Fig. 10 The influence of HBD dosage to the mechanical properties of PU film. | |
3.3 Performance evaluation of PU film with different filler
3.3.2 SEM-EDS analysis. The cross-section SEM of PU film obtained by wet coagulation process was observed to analysis the distribution of various filler powder in coating. The cross section of PU films with different filler inside the film were shown in Fig. 11.
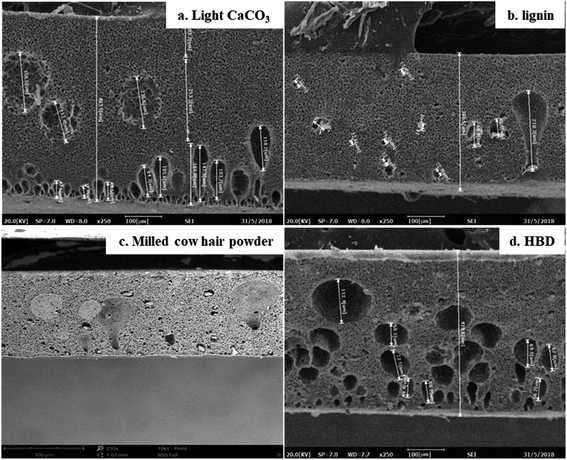 |
| Fig. 11 The SEM picture (×250) of cross section of PU film with different filler ((a) light CaCO3, (b) lignin, (c) milled cowhair powder, (d) HBD). | |
Fig. 11(a) is the PU film used the light CaCO3 as the filler. What we can see from the Fig. 11(a) is that the pore mainly focused on the side contact with the water, some pore with finger shape is existed on the upper side. According to the Fig. 11(b) which use the lignin as the filler, the pore in the film was very small, and the distribution of pore is not uniform. The pore structure is quite small.25,26
In the Fig. 11(c), the milled cowhair powder was distributed dispersively in the cross section of the film. The milled cowhair powder provides the coagulation site when it occurred. Many hydrophilic groups existed in the structure of the milled cowhair powder, such as the hydroxyl groups,27 disulfide bond, amino bond. While the pore distribution in the film was not uniform. The milled cowhair powder existed in the upper part of the pore. So, the powder act as the coagulation cell. When the film was entering into the water, the exchanging process between the DMF and H2O was occurred near the milled cowhair powder.
As can be seen from Fig. 11(d), the PU film filled with HBD has a large number of round pores. The reason was that in addition to large amounts of protein polar hydrophilic groups, HBD also introduced additional amino groups, which accelerated the displacement speed of DMF in PU sizing and H2O in coagulation bath, resulting in accelerated coagulation rate of PU, large shrinkage stress and large number of tearing points. PU polymer didn't have sufficient strain time, and the supplementary strain was not enough to fully cope with the generated stress. When the stress developed to a certain extent, it would crack and form pores in the vulnerable area. So as to increase the volume to deal with the generated stress and make it reach the balance, resulting in more pores. In other words, the formation of these pores were the result of stress (volume shrinkage) and strain.
The EDS spectrum of cross section of PU films were shown in Fig. 12. The PU film mainly consist by C, N, O, when light CaCO3 was added as the filler, the Ca in the cross section of PU was detected and the content of Ca was 0.17%. The N contents of PU films with HBD and milled cowhair powder were around 11%, but the N content of HBD was slightly higher than that of cattle hair. Because all proteins contain nitrogen, and the N content of each protein is very close, with an average of 16%, the PU film filled with amino terminated HBD has more N content.
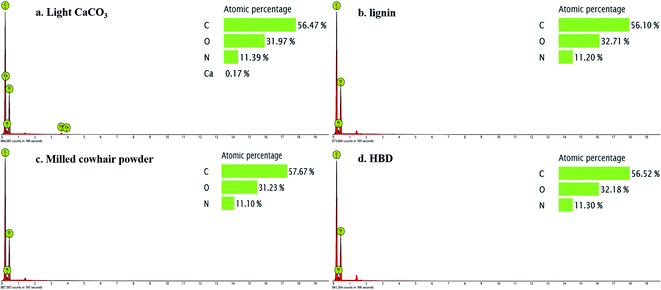 |
| Fig. 12 The EDS spectrum of cross section of PU film with different fillers ((a) light CaCO3, (b) lignin, (c) milled cowhair powder, (d) HBD). | |
3.3.3 The mechanical property of PU film with different filler. The mechanical properties of the PU film with different kind of fillers were shown in Fig. 13. Among the four PU films, the tensile strength of PU film with lignin filler was the highest, which was 7.7 MPa. The tensile strength of PU film with Light CaCO3, HBD and milled cowhair powder is in the range of 6.2–6.7 MPa. This is because that a large number of hydroxyl groups in the molecular structure of lignin form hydrogen bonds with the carbamate bonds of PU. Since the hydrogen bonds are secondary crosslinking and have strong force, they will greatly improve the compatibility between the filler and the PU resin, thus improving the binding force between lignin and PU as well as the film strength. However, the compatibility between CaCO3 and PU is poor, and the interface is difficult to form a good bond. So, the inorganic filler almost has no strengthening effect, and is mainly used as a filler to reduce the manufacturing cost. Its excessive addition will cause a significant reduction in the mechanical properties of PU. Therefore, the mechanical strength of PU film filled with CaCO3 is the lowest. In addition, it can be seen from the figure that the tensile strength of PU films with cowhair and HBD as fillers is medium. It mainly because they belong to protein and contain polar groups which are easy to form hydrogen bonds with PU molecular chain, which has a certain reinforcing effect. However, due to the uneven distribution of pore in coating, the mechanical properties of the membrane are reduced.
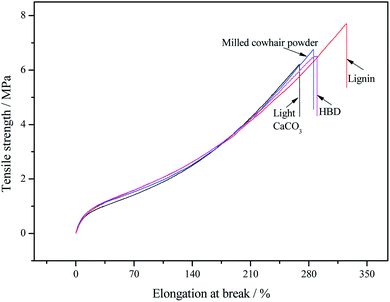 |
| Fig. 13 The mechanical properties of PU film with different filler. | |
3.3.4 DMA analysis. In the process of wet film-forming of synthetic leather, lignin is the most commonly used filler, which belongs to plant fiber, while HBD is collagen fiber. Therefore, the dynamic mechanical properties of PU films modified by fibrous fillers, namely lignin and HBD (2%) were further tested. The DMA analysis results were shown in Fig. 12. From Fig. 12(a), after the addition of lignin, the storage modulus of PU film was increased, this might attribute to the rigid structure of lignin and the hydrogen-bond interaction between lignin and polyurethane. In the control sample, the arrangement of polyurethane is regular, so it can generate the intact crystal region, the storage modulus is relatively high.28 In general, the higher the storage modulus, the greater the rigidity of the material. Due to more pores of HBD modified PU, the coating is soft, so the storage modulus is the lowest. As for the lignin modified PU with higher storage modulus, it may be due to the formation of a large number of hydrogen bonds between the hydroxyl groups on the lignin and PU. At the same time, because of its rod-shaped fiber structure, it plays a certain role in connecting the PU coating, so the PU film is difficult to deform and has higher hardness with bigger storage modulus.In the tan
δ curves (Fig. 14(b)), the α slack loss peak appeared, which indicated that the sticky elastic behavior of the elastomer in the vitrification transition region. The PU film with different filler have different glass transition temperature (Tg). The peak of energy consumption factor (tan
δ)29 corresponding to the Tg of PU. The Tg of PU film without filler was −8.18 °C, after the addition of filler, the Tg of the PU film decreased. The PU film using HBD as the filler was −8.67 °C, while for the lignin is −8.41 °C. This might due to the decrease of crystallinity area of PU molecular chain. The move of PU polymer chain was easy, and the Tg decreased.
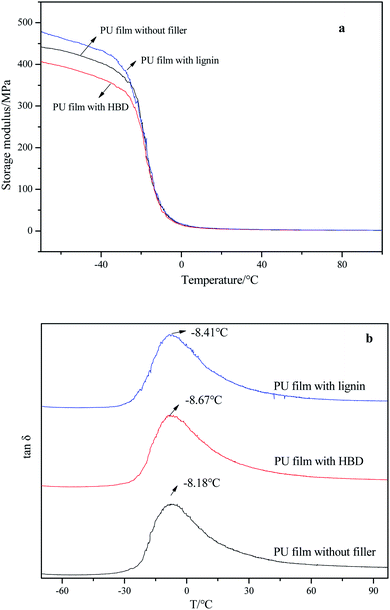 |
| Fig. 14 The DMA curves of PU films with different fillers ((a) storage modulus, (b) tan δ). | |
3.3.5 The moisture permeability of PU film. The moisture permeability determination results of PU film with lignin and HBD were further shown in Table 3. It can be seen from Table 3 that the PU film added HBD has a higher water vapor permeability, while it is poor for blank PU sample. Generally speaking, the moisture permeability of PU film is not only related to the hydrophilic groups of the membrane itself, but also related to the number of pores in the film. In contrast, both lignin and HBD have hydrophilic groups such as hydroxyl and amino groups, so their vapor permeability is much higher than that of PU film without fillers. More importantly, the previous SEM images clearly showed that HBD modified PU film also has a lot of pore structure, which leads to the best moisture permeability.
Table 3 The moisture permeability determination of PU film
Sample |
Blank |
Lignin |
HBD |
Moisture permeability (mg cm−2 h−1) |
146.726 |
442.577 |
464.403 |
4. Conclusion
In this paper, the amino-terminated hyperbranched polymer was used to modify the waste protein biomass resource, BD, so as to increase the hydrophilic active sites of BD, to improve the defect of poor hygienic performance of PU coating of traditional synthetic leather, and recycle the solid waste. The results of salicylaldehyde titration, XPS and DSC showed that the modified HBD had more amino groups, higher N content and better thermal stability. Morphological observation displayed that HBD had typical fibrous structure and fine fibers. The application test of HBD filler indicated that with the increase of HBD dosage (0–2%), the number of pores in PU film first increased and then decreased (>3%), while the strength decreased continuously. Compared with other fillers such as lignin, light calcium carbonate and milled cowhair powder, HBD has a significant thickening effect to PU sizing. The wet PU film filled with HBD has more pores and better moisture permeability, but its mechanical property is lower than that of conventional lignin filler and better than that of light calcium carbonate. Our research revealed that the amino functional buffing dust can be used as an excellent biomass functional filler to improve the hygienic property of synthetic leather, and provide a novel way for the treatment and disposal of leather buffing waste.
Conflicts of interest
There are no conflicts to declare.
Acknowledgements
This work was supported by the Key R&D Plan of the 13th Five Year Plan (CN) [grant number 2017YFB0308600]; a Project of Shandong Province Higher Educational Science and Technology Program [grant number J18KA114].
References
- S. Saravanabhavan, P. Thanikaivelan, J. R. Rao, B. U. Nair and T. Ramasami, Natural leathers from natural materials: progressing toward a new arena in leather processing, Environ. Sci. Technol., 2004, 38(3), 871–879 CrossRef CAS PubMed.
- J. Kanagaraj, R. C. Panda and M. V. Kumar, Trends and advancements in sustainable leather processing: Future directions and challenges–A review, J. Environ. Chem. Eng., 2020, 8(5), 104379 CrossRef.
- J. D. Wegene and P. Thanikaivelan, Conducting leathers for smart product applications, Ind. Eng. Chem. Res., 2014, 53(47), 18209–18215 CrossRef CAS.
- R. W. Liu, Y. Chen and H. J. Fan, Design, characterization, dyeing properties, and application of acid-dyeable polyurethane in the manufacture of microfiber synthetic leather, Fibers Polym., 2015, 16(9), 1970–1980 CrossRef CAS.
- L. G. Hole and R. E. Whittaker, Structure and properties of natural and artificial leathers, J. Mater. Sci., 1971, 6(1), 1–15 CrossRef CAS.
- E. K. Roh, Mechanical properties and preferences of natural and artificial leathers, and their classification with a focus on leather for bags, J. Eng. Fiber. Farb., 2020, 15, 1–10 Search PubMed.
- M. Meyer, S. Dietrich, H. Schulz and A. Mondschein, Comparison of the Technical Performance of Leather, Artificial Leather, and Trendy Alternatives, Coatings, 2021, 11(2), 226 CrossRef CAS.
- J. Liu, F. F. Zhang, X. D. Xu, X. S. Li and Z. C. Liu, A preparation method of cowhair powder filler modified polyurethane wet base, Chinese Pat., CN 108360269A, 2020 Search PubMed.
- G. Sekaran, K. A. Shanmugasundaram and M. Mariappan, Characterization and utilisation of buffing dust generated by the leather industry, J. Hazard. Mater., 1998, 63(1), 53–68 CrossRef CAS.
- X. M. Luo, W. J. Hu, X. C. Wang, J. Y. Feng, Y. W. Hu and S. X. Huang, Application of Ultrafine Skin Powder in Synthetic Leather Wet Base, Leather Sci. Eng., 2019, 29(3), 42–46 Search PubMed.
- D. G. S. M. Cavalcante, A. S. Gomes, R. J. Santos, L. E. Kerche-Silva, C. S. Danna, E. Yoshihara and A. E. Job, Composites produced from natural rubber and chrome-tanned leather wastes: evaluation of their in vitro toxicological effects for application in footwear and textile industries, J. Polym. Environ., 2018, 26(3), 980–988 CrossRef CAS.
- X. C. Wang, J. B. Zhu, X. H. Liu, H. J. Zhang and X. Zhu, Novel Gelatin-based Eco-friendly Adhesive with a Hyperbranched Cross-linked Structure, Ind. Eng. Chem. Res., 2020, 59(13), 5500–5511 CrossRef CAS.
- J. Liu, F. F. Zhang, Y. H. Song, K. Lv, N. Zhang and Y. C. Li, The Synthesis of Nonionic Hyperbranched Organosilicone Surfactant and Characterization of Its Wetting Ability, Coatings, 2021, 11, 32 CrossRef CAS.
- F. F. Zhang, Study On Preparation and Adsorption Property of Hyperbranched Polymer Modified Collagen Fiber, Shaanxi University of Science and Technology, Xi’an, China, 2015 Search PubMed.
- J. B. Qu, Synthetic Leather Materials and Technology, Chemical Industry Press, China, 2015 Search PubMed.
- N. Athir, S. A. A. Shah, F. K. Shehzad, J. Cheng, J. Y. Zhang and L. Shi, Rutile TiO2 integrated zwitterion polyurethane composite films as an efficient photostable food packaging material, React. Funct. Polym., 2020, 157, 104733 CrossRef CAS.
- S. Członka, M. F. Bertino and K. Strzelec, Rigid polyurethane foams reinforced with industrial potato protein, Polym. Test., 2018, 68, 135–145 CrossRef.
- B. Naureen, A. S. M. A. Haseeb, W. J. Basirun and F. Muhamad, Recent advances in tissue engineering scaffolds based on polyurethane and modified polyurethane, Mater. Sci. Eng. C, 2021, 118, 111228 CrossRef CAS PubMed.
- The Determination Method For Permeability of Leather, Standard For Light Industry of The People's Republic of China, QB/T 1811-1993 Search PubMed.
- Z. X. Zhang and R. G. Zhang, Quantitative
Analysis of Organic Functional Groups, Chemical Industry Press, Beijing, 1990 Search PubMed.
- M. Zhang, F. Song, X. L. Wang and Y. Z. Wang, Development of soy protein isolate/waterborne polyurethane blend films with improved properties, Colloids Surf., B, 2012, 100, 16–21 CrossRef CAS.
- M. Liu, J. L. Li, N. H. Dan and W. H. Dan, Extraction and Characterization of Collagen Fiber from Bovine Tendon, China Leather, 2013, 42(1), 19–22 CrossRef CAS.
- C. Yang, X. Y. Wen, Y. W. Wang, H. R. Song, Z. Li, Y. N. Cui and C. P. Li, Preparation of hyper-crosslinked polymers with hierarchical porous structure from hyperbranched polymers for adsorption of naphthalene and 1-naphthylamine, Sep. Purif. Technol., 2021, 266, 118542 CrossRef.
- Z. Cheng, Q. T. Li, Z. Yan, G. F. Liao, B. X. Zhang, Y. M. Yu, C. F. Yi and Z. S. Xu, Design and synthesis of novel aminosiloxane crosslinked linseed oil-based waterborne polyurethane composites and its physicochemical properties, Prog. Org. Coat., 2019, 127, 194–201 CrossRef CAS.
- A. Kobyliukh, K. Olszowska, U. Szeluga and S. Pusz, Iron oxides/graphene hybrid structures – Preparation, modification, and application as fillers of polymer composites, Adv. Colloid Interface Sci., 2020, 285, 102285 CrossRef CAS PubMed.
- F. Zia, K. M. Zia, Z. I. H. Nazli, S. Tabasum, M. K. Khosa and M. Zuber, Preparation of hydroxyethyl cellulose/halloysite nanotubes graft polylactic acid-based polyurethane bionanocomposites, Int. J. Biol. Macromol., 2020, 153, 591–599 CrossRef CAS.
- H. F. Tian, Y. X. Wang, L. Zhang, C. Y. Quan and X. Z. Zhang, Improved flexibility and water resistance of soy protein thermoplastics containing waterborne polyurethane, Ind. Crops Prod., 2010, 32(1), 13–20 CrossRef CAS.
- N. Sukhawipat, N. Saetung, P. Pasetto, J. F. Pilard, S. Bistac and A. Saetung, A novel high adhesion cationic waterborne polyurethane for green coating applications, Prog. Org. Coat., 2020, 148, 105854 CrossRef CAS.
- Q. Zhao and K. L. Yan, Preparation and Viscoelastic Properties of Waterborne Polyurethane/Cellulose Nanocrystals Composites, Adv. Mater. Res., 2013, 771, 105–108 Search PubMed.
|
This journal is © The Royal Society of Chemistry 2021 |
Click here to see how this site uses Cookies. View our privacy policy here.