DOI:
10.1039/D1RA02634H
(Paper)
RSC Adv., 2021,
11, 22278-22286
Copper nanoparticle anchored biguanidine-modified Zr-UiO-66 MOFs: a competent heterogeneous and reusable nanocatalyst in Buchwald–Hartwig and Ullmann type coupling reactions†
Received
3rd April 2021
, Accepted 18th June 2021
First published on 24th June 2021
Abstract
We have designed a functionalized metal–organic framework (MOF) of UiO topology as a support, with an extremely high surface area, adjustable pore sizes and stable crystalline coordination polymeric structure and implanted copper (Cu) nanoparticles thereon. The core three dimensional Zr-derived MOF (UiO-66-NH2) was modified with a biguanidine moiety following a covalent post-functionalization approach. The morphological and physicochemical features of the material were determined using analytical methods such as FT-IR, SEM, TEM, EDX, atomic mapping, XRD and ICP-OES. The SEM and XRD results justified the unaffected morphology of Zr-MOF after structural modifications. The as-synthesized UiO-66-biguanidine/Cu nanocomposite was catalytically explored in the aryl and heteroaryl Buchwald–Hartwig C–N and Ullmann type C–O cross coupling reactions with excellent yields. A library of biaryl amine and biaryl ethers was synthesized over the catalyst under mild and green conditions. Furthermore, the catalyst was isolated by centrifugation and recycled 11 times with no significant copper leaching or change in its activity.
1. Introduction
The transition metals (TMs) possess great affinity to form a broad range of complexes with various organic ligands based on their incompletely filled atomic orbitals. There are many reports of transition metal complexes in chelation with synthetically designed and suitably oriented novel organic ligands, which have otherwise numerous applications as homogeneous catalysts in different organic transformations.1–5 However, the catalyst isolation and reusability have been the major issue that restricts their use in view of eco-sustainability. Thereby, heterogenization of the TM complexes by immobilization over different solid supports like silica,6 magnetic nanoparticles,7 carbon nanotubes,8 mesoporous silica,9 zeolites10 and layered materials11 has been extensively explored in view of easy handling, thermal stability, facile isolation and reusability.12 Still, there remain problems like non-uniform distribution of catalysts and difficulty in characterizing such entities.13 This has prompted us to design functionalized metal–organic frameworks (MOFs) and subsequently anchor appropriate active sites into it. In the last few years MOFs have been come out as a significant group of porous materials having huge surface areas, high degree of tunability in terms of shape and dimensions of pore channels and pore sizes, defined and diverse crystal structures, uniformly distributed active sites in the whole network, adjustable active metal concentration and possess high compatibility in chemical functionalizations towards the secondary active metal chelations.14–16 Due to such unique features, different engineered MOFs find potential applications in separation, drug delivery, magnetism, gas storage, adsorption, water treatment, health-care applications, chemical sensing, non-linear optics, and as a nano reactor in catalysis.17–20 In this context, we wish to introduce a novel MOF based heterogeneous catalytic system, the Cu adorned biguanidine functionalized UiO-66-NH2 (UiO-66-biguanidine/Cu). The core skeleton is being synthesized with [Zr6O4(OH)4] octahedral secondary building units (SBU) and 2-amino-1,4-benzene dicarboxylate (BDC) ligands where each Zr6 cluster is three dimensionally coordinated to 12 BDC units forming a hierarchical framework.21–24 The biguanidine functionality, which is known to be an excellent chelating ligand, has been post-immobilized over it and subsequently Cu NPs have been anchored thereon as the active catalytic site (Scheme 1). In synthetic organic chemistry there are limited catalytic applications of post-synthetic modified MOFs via covalent surface functionalization with homodispersed co-operative active sites.25–29 Being encouraged by this and also in continuation to our ongoing endeavors on the development and synthetic utilizations of architectured heterogeneous nanocatalysts,30–38 we report the catalytic application of UiO-66-biguanidine/Cu in efficient C–N and C–O heterocoupling reactions (Scheme 1). These coupled products, especially those involving heterocycles, find extensive applications as important drugs and medicines, materials and also in biology.39–41 Earlier, a number of research groups have reported the C-heteroatom cross coupling reactions over Cu catalysts.42–48 However, most of the protocols involved various ligand based homogeneous catalysts or heterogeneous catalysts being synthesized using toxic and strong reducing agents. The procedure devised by us using UiO-66-biguanidine/Cu catalyst is the first report for an efficient, ligand free green synthesis of C-heteroatom coupled products with outstanding yields in quick intervals, making the overall procedure industrially and sustainably viable.
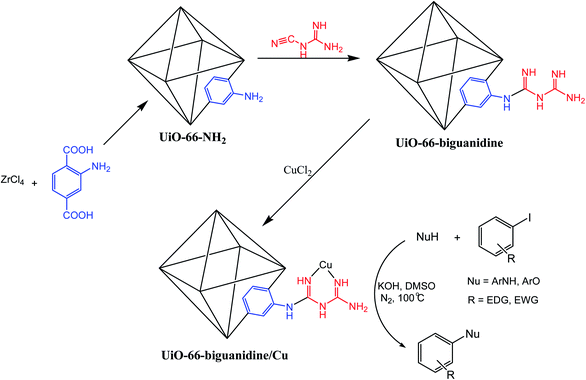 |
| Scheme 1 Schematic designing of UiO-66-biguanidine/Cu nanocomposite and its application in the C-heteroatom coupling reactions. | |
2. Experimental
2.1 Synthesis of UiO-66-NH2
1.166 g ZrCl4 (5 mmol) was dissolved in 2 mL DMF in presence of HCl (5 mL) under sonication for 20 min at ambient conditions. A solution of 2-aminobenzene-1,4-dicarboxylic acid (5 mmol, 0.9057 g) in DMF (30 mL) was then mixed to it and sonicated again for 20 min. The whole mixture was warmed at 80 °C for 6 h followed by heating at 100 °C for 24 h. On cooling the product was obtained as microcrystalline powder. It was isolated by centrifugation at 4000 rpm for 20 min and then washed thrice with DMF and EtOH (30 mL). Finally, UiO-66-NH2 was obtained as yellow powder (95%) on drying under vacuum at 100 °C for 24 h.
2.2 Synthesis of UiO-66-biguanidine
A 50 mL aqueous dispersion containing 0.5 g of UiO-66-NH2 was sonicated for 10 min and then an HCl solution (0.15 mol L−1, 50 mL) of 0.168 g dicyandiamide (2 mmol) was added to it. The mixture was heated at 100 °C for 24 h. It was cooled and worked up with 10% NaOH solution which resulted the UiO-66-biguanidine. The solid was collected by centrifugation at 4000 rpm for 20 min. It was washed thoroughly with 1
:
1 EtOH and dried as before.
2.3 Synthesis of UiO-66-biguanidine/Cu
0.5 g of UiO-66-biguanidine was sonicated well in H2O (50 mL) until a homogenous dispersion was obtained. Then an aqueous solution of CuCl2 (50 mL, 1 mg mL−1) was mixed to it as Cu source and the mixture was triturated at 12 h. The product was isolated by centrifuger and washed twice with 20 mL water followed by with 20 mL ethanol. It was dried under vacuum at 60 °C for 24 h. Cu content in UiO-66-biguanidine/Cu was found as 0.31 mmol g−1 by ICP-OES analysis.
2.4 UiO-66-biguanidine/Cu catalyzed C–N and C–O coupling
A mixture of N/O nucleophile (1 mmol), aryl halide (1.1 mmol) and KOH (1.5 mmol) were taken together in 3 mL dry DMF in presence of 0.8 mol% UiO-66-biguanidine/Cu catalyst at 100 °C under N2 atmosphere for requisite times. On completion (monitored by TLC), the reaction was brought to ambient conditions and the catalyst was separated by centrifugation. The reaction was worked up in 10 mL water and the product was extracted into EtOAc. The organic layer was washed with brine-water (10 mL), dried over Na2SO4, concentrated and finally purified by silica gel column chromatography.
3. Results and discussions
3.1 Catalyst characterization data analysis
On complete synthesis of the material following post-functionalization, we turned our attention to evaluate its structural and physicochemical characteristics using several analytical techniques like FT-IR, SEM, TEM, EDX, elemental mapping and XRD. Fig. S1† displays the comparative FT-IR spectra of UiO-66-NH2, UiO-66-biguanidine and UiO-66-biguanidine/Cu in order to understand the stepwise building of the material. In the spectrum of UiO-66-NH2 (Fig. S1a†), typical vibrations appeared at 1405 and 1571 cm−1 can be credited to the symmetric and asymmetric stretching vibrations of carboxylate groups from BDC. The H–N–H scissoring and the C–NH2 stretching vibrations of aromatic amines are observed at 1259 cm−1 and 1658 cm−1 respectively. The broad peaks at 3381 cm−1 and 3503 cm−1 are due to the N–H symmetric and asymmetric stretching vibrations respectively. On reaction of UiO-66-NH2 with dicyandiamide, it results the biguanidine/UiO-66 moiety, which was confirmed from the disappearance of all the free amine related peaks (1658, 3381, 3503 cm−1) while all other peaks remained unchanged (Fig. S1b†). However, no significant changes are observed in the spectrum of UiO-66-biguanidine/Cu from Fig. 1b, as the characteristic bands due to immobilization Cu on the biguanidine/Zr-MOF are very weak to be distinguished (Fig. S1c†).
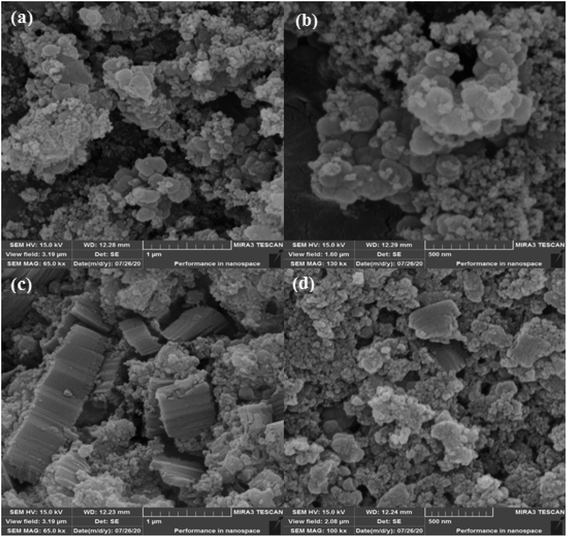 |
| Fig. 1 SEM images of UiO-66-NH2 (a and b); and UiO-66-biguanidine/Cu nanocomposite (c and d). | |
The particle size, shape and texture of UiO-66-NH2 and UiO-66-biguanidine/Cu was explored over SEM and represented in Fig. 1 at different magnifications. Both the samples have typical structure consisting of irregular intergrown microcrystalline polyhedra with a mean diameter of 50 to 90 nm. In a cross-sectional view, stacking units can be observed in Fig. 1c. No significant change in morphology is observed in the structure on post-functionalization or Cu attachment over it. The particles seem to be somewhat agglomerated due to high concentration during sample preparations.
Further justification of SEM investigation towards the detailed structural inherence regarding size and morphology was carried out through TEM analysis of the UiO-66-NH2 (Fig. 2) and UiO-66-biguanidine/Cu nanocomposite (Fig. 3). With comparison of these images, successful formation and immobilization of the copper monodispersed spherical shaped nanoparticles with a mean diameter of 20–40 nm could be confirmed in the Fig. 3. On close observation, stacking structural units of MOF can be observed.
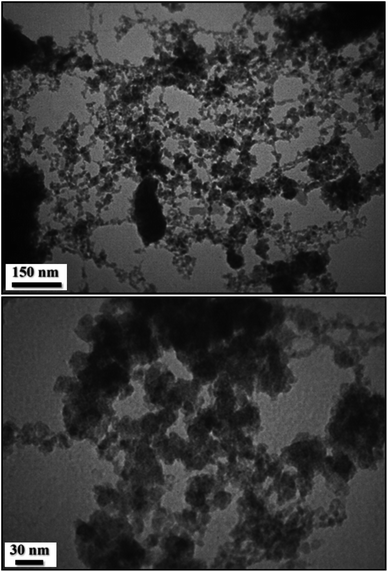 |
| Fig. 2 TEM images of UiO-66-NH2. | |
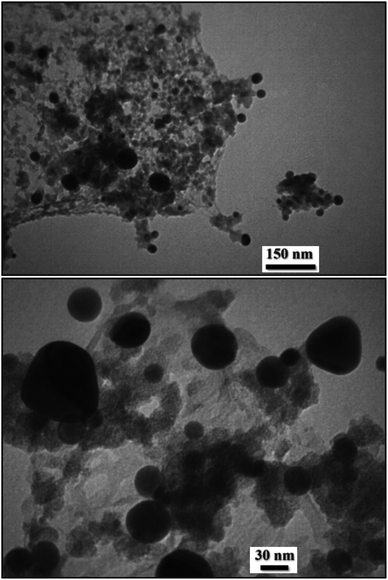 |
| Fig. 3 TEM images of UiO-66-biguanidine/Cu nanocomposite. | |
The chemical constitutions of both UiO-66-NH2 and UiO-66-biguanidine/Cu nanocomposite were established on EDX detector equipped with SEM instrument and represented in Fig. 4. The EDX spectrum of UiO-66-NH2 showed the peaks of Zr, C, N and O atoms which narrate the structural components being Zr as SBU and C, N, O signifying the BDC ligand (Fig. 4a). Fig. 4b exhibits the EDX profile of UiO-66-biguanidine/Cu, where it shows the Cu as element in addition to the previous elements signifying the attachment of Cu nanoparticles to UiO-66-biguanidine, a derivative of UiO-66-NH2.
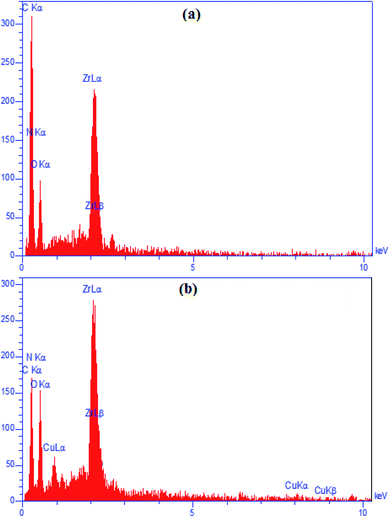 |
| Fig. 4 EDX spectra of UiO-66-NH2 (a); and Cu@bigua/UiO-66 nanocomposite (b). | |
The EDX data was further justified through X-ray atomic mapping and demonstrated in Fig. 5. Additionally, it shows the distribution of the constitutional elements in UiO-66-biguanidine/Cu nanocomposite. An X-ray sectional scanning of the surface displays the homogeneous dispersion of Zr, C, N and Cu atoms over the surface. Obviously, Zr and C display much higher density than other elements, as being the core component of the motif. The uniformity of active component definitely reasons for its excellent catalytic performances.
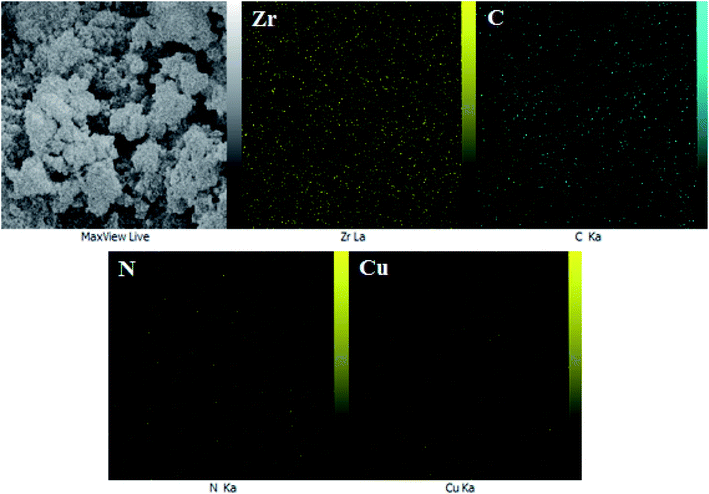 |
| Fig. 5 Elemental mapping of UiO-66-biguanidine/Cu nanocomposite. | |
The nitrogen adsorption–desorption isotherms of UiO-66-NH2, UiO-66-biguanidine and UiO-66-biguanidine/Cu are studied and the corresponding data are summarized in Table 1. It can be seen that the structures of each sample featured the type I isotherm. The Langmuir surface area of the UiO-66-NH2 was 1045 m2 g−1 with pore volume of 0.68 cm3 g−1. After the biguanidine modification, the Langmuir surface area decreased to 923 m2 g−1, while the pore volume decreased to 0.42 cm3 g−1, which indicates occupation of the internal channels by biguanidine moieties in Zr-MOF structure.49 The Langmuir surface area of UiO-66-biguanidine/Cu catalyst decreases to 810 m2 g−1 when the copper moiety is introduced.
Table 1 Nitrogen adsorption–desorption data for UiO-66-NH2, UiO-66-biguanidine and UiO-66-biguanidine/Cu
Entry |
Samples |
SBET (m2 g−1) |
Total pore volume (cm3 g−1) |
Mean pore diameter (nm) |
1 |
UiO-66-NH2 |
1045 |
0.68 |
0.62 |
2 |
UiO-66-biguanidine |
923 |
0.42 |
0.58 |
3 |
UiO-66-biguanidine/Cu |
810 |
0.22 |
0.53 |
The crystallinity and phase structure of UiO-66-NH2 and UiO-66-biguanidine/Cu nanocomposite were analyzed by XRD study (Fig. 6). Evidently, both the materials are poorly crystalline in nature. Three significant Braggs diffraction peaks of the UiO-66-NH2 are observed at 2θ = 7.32, 8.72 and 25.93° respectively, which are in close agreement with the literature. The UiO-66-biguanidine/Cu exhibits almost similar XRD pattern as the basic UiO-66-NH2 material, which indicates the unaltered framework even after surface modifications. There was no significant peak of Cu detected in the profile.
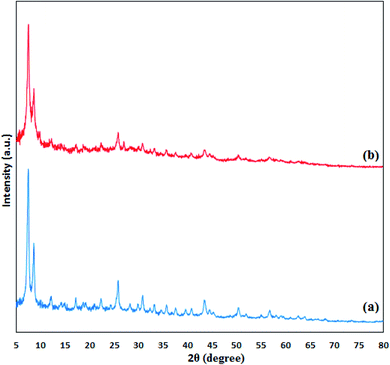 |
| Fig. 6 XRD patterns of UiO-66-NH2 (a); and UiO-66-biguanidine/Cu nanocomposite (b). | |
3.2 Catalytic applications of UiO-66-biguanidine/Cu nanocomposite
After the complete characterizations of the as-synthesized final material, we paid attention on the catalytic applications. We inspected the performance of UiO-66-biguanidine/Cu nanocomposite in the Buchwald–Hartwig (C–N) and Ullmann (C–O) type coupling reactions. Several iodobenzene derivatives were coupled to various N and O nucleophiles in presence of an additive base over our catalyst, following a simplistic clean protocol. After completion, the catalyst was retrieved by centrifuge and recycled in consecutive runs. However, prior to general studies, optimization of the reaction conditions seemed quite significant and hence, a reaction between indole and iodobenzene was selected as a model and an array of screening experiments were conducted applying diverse conditions like catalyst load, solvent, base and temperature. The outcomes are shown in Table 2. In the absence of catalyst, there was absolutely no product at all and a poor yield was obtained in the lack of external base, which signifies their importance in the reaction (Table 2, entries 10 and 11). In presence of catalyst and a base, the reaction yield gradually increases and we got the best output over 0.8 mol% Cu loaded catalyst and KOH as base at 100 °C in DMF solvent (Table 2, entry 8). A moderate yield was obtained at lower temperatures (Table 2, entries 5 and 6). While screening the reaction in different solvents like EtOH, DMF, toluene, DMSO, CH2Cl2 and CH3CN, we got the best result in DMF (Table 2, entries 1–6). As the external base was significant in the reaction, we also studied the influence of various bases like KOH, NaHCO3, Et3N, Na2CO3 and K2CO3, when the first one afforded the best yield while the others resulted moderate to good yields (entries 8–14). Optimizing the reaction conditions with N-nucleophile, the same were applied using phenol as an O-nucleophile in the reaction which also produced 90% yield. This justifies the authenticity of the said stabilized conditions. Additionally, we carried out the variation of catalysts with the stabilized conditions over the probe reaction which has been shown separately in Table 3. Different precursors and intermediates of the final catalyst were involved in the catalysis in order to identify and investigate the role of active site. The reaction was absolutely failed over UiO-66 and UiO-biguanidine as catalyst which indicates there is definitely a role of Cu in the reaction. Now, to get a deeper insight we involved the Cu(II) impregnated UiO-66 (UiO-66/Cu) composite in the reaction where it afforded a moderate 72% yield. This result is very interesting signifying the role of biguanidine, which has an important role in stabilizing the Cu NP and also to prevent the metal to leach. Moreover, biguanidine also protects the Cu NPs to agglomerate.
Table 2 Optimization of reaction condition for UiO-66-biguanidine/Cu catalyzed cross coupling of indole/phenol with iodobenzenea

|
Entry |
NuH |
Cat. (mol%) |
Base |
Solvent |
T (°C) |
t (h) |
Yieldb (%) |
Reaction conditions: N/O nucleophile (1.0 mmol), iodobenzene (1.1 mmol), UiO-66-biguanidine/Cu, base (1.5 mmol), solvent (3.0 mL), N2 atmosphere. Isolated yield. |
1 |
Indole |
0.3 |
KOH |
EtOH |
80 |
10 |
55 |
2 |
Indole |
0.3 |
KOH |
DMF |
100 |
10 |
75 |
3 |
Indole |
0.3 |
KOH |
Toluene |
100 |
10 |
65 |
4 |
Indole |
0.3 |
KOH |
DMSO |
100 |
10 |
65 |
5 |
Indole |
0.3 |
KOH |
CH2Cl2 |
60 |
24 |
40 |
6 |
Indole |
0.3 |
KOH |
CH3CN |
70 |
24 |
50 |
7 |
Indole |
0.6 |
KOH |
DMF |
100 |
10 |
90 |
8 |
Indole |
0.8 |
KOH |
DMF |
100 |
10 |
96 |
9 |
Indole |
0.8 |
— |
DMF |
100 |
24 |
Trace |
10 |
Indole |
— |
KOH |
DMF |
100 |
24 |
0 |
11 |
Indole |
0.8 |
K2CO3 |
DMF |
100 |
12 |
75 |
12 |
Indole |
0.8 |
Na2CO3 |
DMF |
100 |
12 |
60 |
13 |
Indole |
0.8 |
Et3N |
DMF |
100 |
10 |
85 |
14 |
Indole |
0.8 |
NaHCO3 |
DMF |
100 |
10 |
60 |
15 |
Indole |
0.8 |
KOH |
DMF |
80 |
10 |
75 |
16 |
Indole |
0.8 |
KOH |
DMF |
25 |
10 |
30 |
17 |
Phenol |
0.8 |
KOH |
DMF |
100 |
10 |
90 |
Table 3 Variation of catalysts in the cross coupling of indole with iodobenzenea
Entry |
Catalyst |
Time (h) |
Yieldb (%) |
Reaction conditions: indole (1.0 mmol), iodobenzene (1.1 mmol), KOH (1.5 mmol), DMF (3.0 mL), 100 °C, N2 atmosphere. Isolated yield. |
1 |
UiO-66 |
24 |
0 |
2 |
UiO-66-biguanidine |
24 |
0 |
3 |
UiO-66-Cu |
10 |
72 |
4 |
UiO-66-biguanidine/Cu |
10 |
96 |
On stabilizing the optimum conditions, the investigations were extended in search for their generalizations through substrate variations. A wide range of biaryl amine and biaryl ether derivatives were synthesized by coupling of diverse aryl iodides and aryl/heteroaryl amines or phenols under the optimized conditions (Table 4). Among the N-nucleophiles (Table 4, entries 1–15), aniline reacted much faster (4–5 h) as compared to indole or imidazole (10–12 h) towards the N-coupled products, whereas, the aryl iodides were highly reactive irrespective of their substitutions, being electron donating (CH3, OCH3) or electron withdrawing (NO2). In most of the cases excellent yields were obtained (>90%). Similarly, different phenols and their derivatives were also equally compatible with various aryl iodides resulting very good productivity (entries 16–24). All the products are known, as given in the references, being justified from 1H NMR data.
Table 4 UiO-66-biguanidine/Cu catalyzed coupling of amines and phenols with aryl iodidesa
Entry |
Substrate |
Aryl iodide |
Time (h) |
Yieldb (%) |
Ref.c |
Reaction conditions: amines/phenols (1.0 mmol), iodobenzene (1.1 mmol), UiO-66-biguanidine/Cu (0.8 mol%), KOH (1.5 mmol), DMF (3.0 mL), stirring, nitrogen atmosphere, 100 °C. Isolated yield. Known product. |
1 |
Indole |
C6H5I |
10 |
96 |
50 |
2 |
Indole |
p-CH3C6H4I |
10 |
95 |
51 |
3 |
Indole |
p-ClC6H4I |
10 |
95 |
50 |
4 |
Indole |
p-CH3OC6H4I |
10 |
90 |
50 |
5 |
Indole |
p-NO2C6H4I |
10 |
92 |
50 |
6 |
Indole |
o-CH3OC6H4I |
12 |
90 |
50 |
7 |
Aniline |
C6H5I |
5 |
96 |
52 |
8 |
Aniline |
p-CH3C6H4I |
4 |
95 |
53 |
9 |
Aniline |
p-ClC6H4I |
5 |
90 |
53 |
10 |
Aniline |
p-CH3OC6H4I |
5 |
90 |
54 |
11 |
Aniline |
p-NO2C6H4I |
4 |
95 |
52 |
12 |
Aniline |
o-CH3OC6H4I |
5 |
90 |
55 |
13 |
Imidazole |
C6H5I |
12 |
88 |
53 |
14 |
Imidazole |
p-CH3C6H4I |
12 |
85 |
56 |
15 |
Imidazole |
p-CH3OC6H4I |
12 |
70 |
57 |
16 |
Pyrrole |
C6H5I |
10 |
91 |
53 |
17 |
Benzimidazole |
C6H5I |
12 |
86 |
53 |
18 |
Phenol |
C6H5I |
10 |
90 |
58 |
19 |
Phenol |
p-CH3C6H4I |
10 |
90 |
59 |
20 |
Phenol |
p-ClC6H4I |
10 |
88 |
55 |
21 |
Phenol |
p-CH3OC6H4I |
10 |
92 |
55 |
22 |
Phenol |
p-NO2C6H4I |
8 |
92 |
55 |
23 |
Phenol |
o-CH3OC6H4I |
12 |
75 |
60 |
24 |
4-Methylphenol |
C6H5I |
12 |
80 |
60 |
25 |
4-Methoxylphenol |
C6H5I |
12 |
92 |
60 |
26 |
2-Methylphenol |
C6H5I |
24 |
85 |
60 |
3.3 Reusability study of catalyst
In order to validate the catalytic sustainability and green chemical methodology, the study of reusability is an utmost important criterion. After completion of the fresh cycle of the reaction between indole and iodobenzene, the catalyst was recollected by centrifuger and thoroughly washed with aqueous EtOH. It was regenerated by drying and used in the successive runs. The UiO-66-biguanidine/Cu nanocomposite showed significant reactivity upto 11 successive cycles with only a nominal change in yields. The yield was slightly decreased after 8th run probably due to agglomeration of catalysts. The outcome has been displayed in Fig. 7. Also the ICP-AES analysis of the catalyst after 8 runs was shown that amount of Cu loaded on the catalyst is 0.30 mmol g−1, that was shown a slight change in amount of Cu (0.31 to 0.30 mmol g−1). It can be concluded that the catalyst has good stability and the leaching of Cu from the catalyst surface is low.
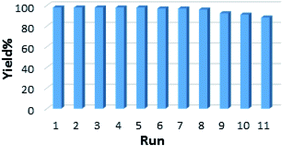 |
| Fig. 7 Recycling of the UiO-66-biguanidine/Cu nanocomposite catalyst in the reaction between indole with iodobenzene. | |
4. Conclusion
In summary, we demonstrate a Cu nanoparticle embedded and biguanidine modified Zr-UiO-66 MOF as a novel heterogeneous nanocomposite catalyst. A covalent post-synthetic modification approach was followed in this synthesis to immobilize the Cu NPs than the conventional deposition over the MOF. The strong chelating ability of biguanidine has been used to immobilize Cu NPs over it. The morphological structure was evaluated through different analytical methods. Thereafter, the nanocatalyst was explored in the Buchwald–Hartwig C–N and Ullmann type C–O cross coupling reactions for the synthesis of diverse range of diaryl amine and ethers under mild and green conditions affording outstanding yields. The material has been proved to be sufficiently rigid to be recycled for consecutive 11 cycles with only a slight decrease in activity after 8 runs.
Conflicts of interest
The authors declare that they have no known competing financial interests or personal relationships that could have appeared to influence the work reported in this paper.
Acknowledgements
We are thankful to Payame Noor University (PNU), Tehran, Iran for financial supports and Gobardanga Hindu College for providing research facilities.
References
- H. Veisi, S. Hemmati and P. Safarimehr, J. Catal., 2019, 365, 204 CrossRef.
- H. Veisi, M. Pirhayati and A. Kakanejadifard, Tetrahedron Lett., 2017, 58, 4269 CrossRef CAS.
- M. Kazemnejadi and A. R. Sardarian, RSC Adv., 2016, 6, 91999 RSC.
- A. Dewaele, F. Verpoort and B. Sels, ChemCatChem, 2016, 8, 3010 CrossRef CAS.
- H. Keypour, S. G. Saremi, H. Veisi and R. Azadbakht, RSC Adv., 2016, 6, 77020 RSC.
- X. Qiu, S. Han, Y. Hu, M. Gao and H. Wang, J. Mater. Chem. A, 2014, 2, 1493 RSC.
- L. Chen, B. Li and D. Liu, Catal. Lett., 2014, 144, 1053 CrossRef CAS.
- M. Navidi, B. Movassagh and S. Rayati, Appl. Organomet. Chem., 2013, 452, 24 CAS.
- V. Ganesan, M. Pal and M. Tiwari, Bull. Mater. Sci., 2014, 37, 623 CrossRef CAS.
- G. R. Reddy, S. Balasubramanian and K. Chennakesavulu, J. Mater. Chem. A, 2014, 2, 15598 RSC.
- S. Eyele-Mezui, E. Delahaye, G. Rogez and P. Rabu, Eur. J. Inorg. Chem., 2012, 2012, 5225 CrossRef CAS.
- S. Hemmati, M. Hekmati, D. Salamat, M. Yousefi, B. Karmakar and H. Veisi, Polyhedron, 2020, 179, 114359 CrossRef CAS.
- N. C. Thacker, Z. Lin, T. Zhang, J. C. Gilhula, C. W. Abney and W. Lin, J. Am. Chem. Soc., 2016, 138, 3501 CrossRef CAS PubMed.
- A. Dhakshinamoorthy, A. M. Asiri and H. Garcia, Chem. Commun., 2014, 50, 12800 RSC.
- W. J. Cui, G. Y. Zhang, T. L. Hu and X. H. Bu, Coord. Chem. Rev., 2019, 387, 79 CrossRef CAS.
- B. Gole, U. Sanyal, R. Banerjee and P. S. Mukherjee, Inorg. Chem., 2016, 55, 2345 CrossRef CAS.
- Y.-B. Huang, J. Liang, X.-S. Wang and R. Cao, Chem. Soc. Rev., 2017, 46, 126 RSC.
- H. C. Zhou and S. Kitagawa, Chem. Soc. Rev., 2014, 43, 5415 RSC.
- V. Pascanu, G. G. Miera, A. K. Inge and B. M. Matute, J. Am. Chem. Soc., 2019, 141, 7223 CrossRef CAS PubMed.
- Q. Yang, Q. Xu and H. L. Jiang, Chem. Soc. Rev., 2017, 46, 4774 RSC.
- V. R. Bakuru, D. Davis and S. B. Kalidindi, Dalton Trans., 2019, 48, 8573 RSC.
- M. Nasrabadi, M. A. Ghasemzadeh and M. R. Z. Monfared, New J. Chem., 2019, 43, 16033 RSC.
- H. Lv, Y. Zhang, P. Chen, J. Xue, X. Jia and J. Chen, Langmuir, 2020, 36, 4025 CrossRef CAS PubMed.
- Y.-Z. Chen and H.-L. Jiang, Chem. Mater., 2016, 28, 6698 CrossRef CAS.
- Y. Luan, H. Gao, R. S. Andriamitantsoa, N. Zheng and G. Wang, J. Mater. Chem. A, 2015, 3, 17320 RSC.
- H. Konnerth, B. M. Matsagar, S. S. Chen, M. H. G. Prechtl, F.-K. Shieh and K. C.-W. Wu, Coord. Chem. Rev., 2020, 416, 213319 CrossRef CAS.
- L. Zhu, X.-Q. Liu, H.-L. Jiang and L.-B. Sun, Chem. Rev., 2017, 117, 8129 CrossRef CAS PubMed.
- S. Koushik and S. Velmathi, Chem.–Eur. J., 2019, 25, 16451 CrossRef PubMed.
- P. Li, S. Regati, H. C. Huang, H. D. Arman and B. L. Chen, Chin. Chem. Lett., 2015, 26, 6 CrossRef CAS.
- T. Tamoradi, H. Veisi and B. Karmakar, ChemistrySelect, 2019, 4, 10953 CrossRef CAS.
- R. Ghorbani-Vaghei, H. Veisi, M. H. Aliani, P. Mohammadi and B. Karmakar, J. Mol. Liq., 2021, 327, 114868 CrossRef CAS.
- H. Veisi, S. Najafi and S. Hemmati, Int. J. Biol. Macromol., 2018, 113, 186 CrossRef CAS.
- H. Veisi, T. Tamoradi, A. Rashtiani, S. Hemmati and B. Karmakar, J. Ind. Eng. Chem., 2020, 90, 379 CrossRef CAS.
- S. Hemmati, M. M. Heravi, B. Karmakar and H. Veisi, J. Mol. Liq., 2020, 319, 114302 CrossRef CAS.
- H. Veisi, S. Azizi and P. Mohammadi, J. Cleaner Prod., 2018, 170, 1536 CrossRef CAS.
- H. Veisi, T. Tamoradi, B. Karmakar, P. Mohammadi and S. Hemmati, Mater. Sci. Eng., C, 2019, 104, 109919 CrossRef CAS.
- T. Tamoradi, M. Daraie, M. M. Heravi and B. Karmakar, New J. Chem., 2020, 44, 11049 RSC.
- H. Veisi, T. Tamoradi, B. Karmakar and S. Hemmati, J. Phys. Chem. Solids, 2020, 138, 109256 CrossRef CAS.
- G. Evano, N. Blanchard and M. Toumi, Chem. Rev., 2008, 108, 3054 CrossRef CAS PubMed.
- J. P. Corbet and G. Mignani, Chem. Rev., 2006, 106, 2651 CrossRef CAS PubMed.
- L. Luza, A. Gual and J. Dupont, ChemCatChem, 2014, 6, 702 CrossRef CAS.
- H. Weingarten, J. Org. Chem., 1964, 29, 3624 CrossRef CAS.
- J. C. Antilla, A. Klapars and S. L. Buchwald, J. Am. Chem. Soc., 2002, 124, 11684 CrossRef CAS PubMed.
- D. Toummini, A. Tlili, J. Berges, F. Ouazanni and M. Taillefer, Chem.–Eur. J., 2014, 20, 14619 CrossRef CAS PubMed.
- F. Monnier and M. Taillefer, Angew. Chem., Int. Ed., 2008, 47, 3096 CrossRef CAS PubMed.
- F. Monnier and M. Taillefer, Angew. Chem., Int. Ed., 2009, 48, 6954 CrossRef CAS PubMed.
- S. Bhunia, G. G. Pawar, S. Vijay Kumar, Y. Jiang and D. Ma, Angew. Chem., Int. Ed., 2017, 56, 16136 CrossRef CAS PubMed.
- S. Pradhan, P. B. De and T. Punniyamurthy, J. Org. Chem., 2017, 82, 4883 CrossRef CAS PubMed.
- M. Servalli, M. Ranocchiari and J. A. Van Bokhoven, Chem. Commun., 2012, 48, 1904–1906 RSC.
- H. Veisi, Y. Metghalchi, M. Hekmati and S. Samadzadeh, Appl. Organomet. Chem., 2017, 17, 3676 CrossRef.
- Y. Z. Huang, J. Gao, H. Ma, H. Miao and J. Xu, Tetrahedron Lett., 2008, 49, 948 CrossRef CAS.
- M. L. Kantam, R. Roy, S. Roy, B. Sreedhar and R. L. De, Catal. Commun., 2008, 9, 2226 CrossRef CAS.
- N. R. Jogdand, B. B. Shingate and M. S. Shingare, Tetrahedron Lett., 2009, 50, 4019 CrossRef CAS.
- S. Jammi, S. Sakthivel, L. Rout, T. Mukherjee, S. Mandal, R. Mitra, P. Saha and T. Punniyamurthy, J. Org. Chem., 2009, 74, 1971 CrossRef CAS PubMed.
- R. Ghorbani-Vaghei, S. Hemmati and H. Veisi, Tetrahedron Lett., 2013, 54, 7095 CrossRef CAS.
- J. B. Zhu, L. Cheng, Y. Zhang, R. G. Xie and J. S. You, J. Org. Chem., 2007, 72, 2737 CrossRef PubMed.
- M. Akhavan, S. Hemmati, M. Hekmati and H. Veisi, New J. Chem., 2018, 42, 2782 RSC.
- M. Tao and W. Lei, Tetrahedron Lett., 2007, 48, 95 CrossRef.
- S. M. Islam, S. Mondal, P. Mondal, S. Singh Roy, K. Tuhina, N. Salam and M. Mobarak, J. Organomet. Chem., 2012, 696, 4264 CrossRef CAS.
- H. Veisi, M. Hamelian, S. Hemmati and A. Dalvand, Tetrahedron Lett., 2017, 58, 4440 CrossRef CAS.
Footnote |
† Electronic supplementary information (ESI) available. See DOI: 10.1039/d1ra02634h |
|
This journal is © The Royal Society of Chemistry 2021 |
Click here to see how this site uses Cookies. View our privacy policy here.