DOI:
10.1039/D1RA01328A
(Paper)
RSC Adv., 2021,
11, 19095-19105
Evaluating the potential of a novel hardwood biomass using a superbase ionic liquid†
Received
18th February 2021
, Accepted 10th May 2021
First published on 26th May 2021
Abstract
Lignocellulosic biomass, being ubiquitous and easily accessible, bears a huge potential for sustainable energy and other products. Fractionation, delignification, and subsequent utilization of hardwood biomass has been ever challenging for a bio-based refinery. Acacia nilotica (kikar in local language) is a hardwood tree commonly found in Pakistan, where its abundance owes to favorable and benign environmental conditions. Ionic liquids based on superbase “tetramethylguanidine (TMG)” are green solvents that are found to be good cellulose processing agents. Previously, TMG-based protic ionic liquids (PILs) have been used for cellulose processing and transformation into value-added products. In this study, an ionic liquid comprising a tetramethylguanidinium cation and a hydrogen sulfate anion was employed for the evaluation of the potential of acacia for fermentable sugars and lignin. Pretreatment was carried out at 100, 120, and 140 °C for 0.5, 1, 2 and 4 hours. The results indicate that [TMG][HSO4] is an efficient delignifying agent affording 81% lignin removal and 76% sugar yield by subsequent enzymatic hydrolysis. The evaluation of the efficiency of IL and the biomass was verified by compositional analysis, FT-IR, HSQC, and SEM analyses.
Introduction
Lignocellulosic material from agricultural and forest waste of plants has huge potential as a carbon neutral source of fuels, chemicals and materials. Chemically speaking, lignocellulosic material is formed of cellulose, hemicellulose and aromatic polyphenyl propanoid, i.e., lignin. These components make major portion of plant cell wall, the minor proportions being pectin and proteins. The chemical complexity of the plant cell wall hinders the utilization of this generous and the sustainable resource of green products. The major barrier in the conversion of cellulose into biofuel is lignin that tends to absorb enzymes, and thus inhibit their hydrolysis of cellulose-rich materials.1 To overcome this hurdle in attaining maximum conversion of cellulose into reducing sugars, several pretreatment technologies are being developed and optimized. The purpose of pretreatment is to alter the biomass compact structure by inhibiting their inter-unit covalent and non-covalent interactions.2 An effective pretreatment should remove maximum lignin content and reduce the crystallinity of the recovered cellulosic material, making it more prone to enzymatic hydrolysis into fermentable sugars. The greater the removal of lignin from raw biomass, the greater is the enzymatic efficiency towards ethanol production.3
In the field of biorefinery, ionic liquids (ILs) have drawn much attention as solvents for biomass processing due to some of their green properties such as negligible volatility, high thermal stability, low toxicity, and versatile solvating ability. These properties make them the solvents of choice for biomass processing.4 The focus of current research in the field of IL-based biorefinery is the identification of the best biomass sources and low-cost ILs. Protic ionic liquids (PILs) have proved promising in biomass processing. It has been found that anion and cation combination in IL greatly affects their performance in the pretreatment.5,6 PILs have been found to exhibit the exceptional capacity of lignin removal from biomass.7,8 PILs offer relatively mild biomass processing for the effective removal of lignin. Achhinivu et al. utilized pyrrolidinium acetate ([Pyrr][Ac]) protic ILs for the extraction of lignin from corn stover and achieved good lignin extraction (75%) at 90 °C for a pretreatment time of 24 hours.9 Hu et al. succeeded in the high lignin removal from coir and poplar biomass using [BMIM] [HSO4] in aqueous alcohols. As a result of pretreatment with this system, CRM (cellulose rich material) containing very low lignin content was obtained (0.95%). The extracted lignin was characterized with almost the same structure as that in milled wood from the above two biomass sources.10 Similarly, Gschwend et al., used ultra-low-cost PIL for highly efficient lignin removal (80%). In addition to high lignin removal, the ionic liquid was recovered (>99%) and reused successfully.11 PILs offer high biomass loading compromising the saccharification efficiency.12 Protic ionic liquids (PILs) based on the superbase tetramethylguanidine (TMG) cation have been shown to efficiently dissolve cellulose. For instance, Kuzmina reported a range of superbase-derived ionic liquids (SILs) including TMG for the dissolution of cellulose fibers and studied the effect on the properties of the recovered fibres.13 Similarly, Qu and coworkers used TMG-based ILs with different anions for the optimized conversion of microcrystalline cellulose (MCC) into 5-hydroxymethylfurfural in good yields.14 Carrera and coworkers prepared MCC gels in TMG IL and regenerated the MCC from gel at room temperature. They found out that regenerated MCC has reduced crystallinity.15 This shows the potential of TMG cations as promising for biomass pretreatment. It has been shown that HSO4-based ionic liquids are also good in biomass hydrolysis. Therefore, TMG IL with HSO4 was prepared and its potential in biomass processing was evaluated in this work. The high decomposition temperatures (250–300 °C) from thermos-physical studies demonstrate that the IL is stable under pretreatment conditions and is also suitable for high-temperature pretreatments.16 Furthermore, the strong acid–base combination in [TMG][HSO4] makes IL neutral and almost noncorrosive. As per our literature study, this ionic liquid has been used for cellulose alone and there is no study regarding the processing of any lignocellulosic biomass.
With the increase in the applications of ILs in the industry, their greenness has become a major concern. The ionic liquids' toxicity usually depends on the cation structure and side chains on cations, and therefore, different ionic liquids have different toxicities.17,18 TMG-based ILs have been reported to be safe and less toxic in the previous literature.19 In one such study, TMG-based ILs were found to be less toxic than choline-based ILs.20
Kikar (Acacia nilotica) belongs to an angiosperm class of plants that produce hard wood. It grows on a variety of soils and climate. It can withstand high temperatures (>50 °C) and conditions of drought. It can also withstand a moderate level of salinity and alkalinity in the soils with calcareous pans.21 The aforementioned properties make A. nilotica an abundant lignocellulosic biomass source in Pakistan. A. nilotica is extensively used as a timber and firewood material.22 The wood of A. nilotica is dark brown, strong, nearly twice as hard as teak, and is used for construction, tool handles, carts as well as firewood. During cutting sawing and construction of wood-based architecture, most of the wood goes wasted either as sawdust or wood chips and ends up in landfills,23 while a part of this wood waste is used for burning in domestic stoves and brick kilns. This causes higher emissions of NOx, SOx, soot, and volatile organic compounds (VOCs) during the incomplete combustion.24 Despite many reports on agricultural wastes and grasses, there are few reports on hardwood waste pretreatment using ionic liquids.25,26 These wood wastes can be an economic source of biorefinery products. The abundance of Acacia hardwood and its fast growing nature make wastes of this hardwood a viable candidate for biomass processing in countries like Pakistan.21
In this work, we evaluated the use of a PIL based on the superbase TMG for lignin removal from Acacia (commonly known as kikar in Pakistan), hardwood biomass. The ionic liquid exhibited efficient delignification (81%) of Acacia affording reasonable amounts of cellulose rich material at 140 °C. The cellulose-rich material (CRM) was subsequently subjected to enzymatic saccharification for sugar release. It revealed that Acacia holds huge potential for fine quality lignin as well as appreciably high percentage of sugars (76%).
Experimental
Materials
Tetramethylguanidine (Sigma Aldrich) and sulfuric acid 72% (VWR) were used as received. All solvents used in this work were of analytical grade. Feedstock wood was taken from a local tree in Lahore (Pakistan) with unknown age. The moisture content of the ionic liquid was determined using a Karl Fischer Titrator (Mettler-Toledo V20). The acid–base ratio was determined using an acid–base titrator (Mettler-Toledo Compact Titrator G20S). The autoclave used was Sanyo Labo Autoclave ML5 3020 U. The incubator used for enzymatic hydrolysis was Stuart Orbital Incubator S150. The enzyme preparation used for enzymatic saccharification was enzyme mixture NS-22201 (Novozymes). All reagents used for the enzymatic study were purchased from Sigma Aldrich. A convection oven was used for all heating purposes (OMH60 Heratherm advanced protocol oven). A muffle furnace was used for ashing (Nabertherm + controller P 330).
Methods
Synthesis of [TMG][HSO4]
The ionic liquid was synthesized by following the procedure reported in the literature with some modification.27 In a round-bottomed flask, 115.18 g (1.00 mol) of TMG was cooled to maintain the temperature between 0 and 10 °C using an ice bath. Meanwhile, 136.11 g (1.00 mol) of cold 72% H2SO4 was added into TMG in a dropwise manner via a dripping funnel. The mixture was kept constantly stirred during the addition of the acid and continued for one more hour after complete addition. Since both acid and base used in the study are strong ones, even a small excess of any of the components can greatly affect the overall pH of IL. The acid–base ratio (1
:
1) was set using a titrator. Finally, the IL was characterized by proton-NMR and thermogravimetric analyses (TGA/DSC). Excess water was removed by evaporation and brought to 20%. The moisture content of the final IL mixture was confirmed by the Karl–Fischer titration in triplicate.
Preparation and characterization of biomass for pretreatment
The biomass (Acacia) wood chips were ground in a commercial mill (Retsch SM2000 smf/750 UpM) and sieved for particle size 180–800 μm using a mesh sieve (20 to 80 of US mesh scale). The ground biomass was left in the air for equilibration with air moisture for some time and stored in air-tight plastic bags. The moisture content of the biomass was determined as stated elsewhere.28
Pretreatment with [TMG][HSO4] was carried out according to a reported protocol.11 The IL/water mixture along with biomass was loaded in a pressure tube at temperatures of 100 °C, 120 °C and 140 °C for 0.5 hour, 1 hour, 2 hours and 4 hours. Ethanol was added to the pretreated mixture as an anti-solvent for the regeneration of the cellulosic pulp. The regenerated cellulosic material was separated from the IL and dissolved lignin mixture by centrifugation. The remaining IL–lignin mixture containing ethanol was evaporated to remove and recycle ethanol. Finally, lignin was separated from the IL by the addition of water to the IL–lignin mixture. The detailed process is presented in the ESI.†
Compositional analysis
Compositional analysis was carried out according to the protocol published by the NREL.29 A detailed description and relevant calculations along with equations used are given in the ESI.† The percent glucose and hemicellulose yields were calculated by comparing with the percentage of cellulose and hemicellulose contents in the original biomass. For each compositional analysis, 300 mg of air-dried and extractive-free samples were used. HPLC quantification of glucose and hemicellulose sugars was performed in the same way as for saccharification (ESI†).
Saccharification/enzymatic hydrolysis of the recovered pulp
The enzyme solution for saccharification was prepared by mixing 5 mL buffer solution (100 mM sodium citrate and citric acid, pH 4.8), 40 mL of a solution of tetracycline in ethanol (10 mg mL−1 of 70% ethanol) to avoid microbial growth, 30 μL cycloheximide solution in deionized water (10 mg mL−1), 50 μL enzyme mixture (Novozymes NS-22201) and 50 mL deionized water.
Saccharification assays were carried out as described in the NREL protocol.30 For this, 100 mg of untreated and recovered biomass was taken in a Sterilin tube and incubated at 50 °C for 7 days. The glucose released after 7 days was quantified using a HPLC system. The full detail of the procedure is given in the ESI.†
FTIR analysis
FTIR spectra of each of the recovered and untreated biomass were recorded using a Cary 630 FTIR (Agilent) with an ATR sampling module. The spectrum range was 600–4000 cm−1. For each sample, 32 background and 32 sample scans were run.
SEM analyses
For SEM images, 20 kV accelerating voltage was applied to visualize the untreated and pretreated Acacia samples using a Joel JSM5610LV microscope. For this purpose, the samples were mounted with a double-sided carbon tape on precut brass sample stubs and sputtered with approximately 30 Å of Au/Pd.
1D-1H and 2D-HSQC analysis
The 1H-NMR spectrum of the synthesized ionic liquid was recorded using a Bruker 600 MHz instrument. The dried IL (2 mg) was dissolved in DMSO-d6 for 1H-NMR acquisition. The HSQC spectra of treated lignin were recorded using a Bruker 600 MHz instrument equipped with an autosampler. For this, 65 mg of lignin was dissolved in 0.50 mL of DMSO-d6 and the solution was carefully transferred to an NMR tube. The axis width was set at 10 ppm in F2 (1H) with 2048 data points and at 160 ppm in F1 (13C) with 256 data points and one second interscan delay using pulse program hsqcedetgpsisp 2.3. Total 16 number of scans were run for a sample.
Results and discussions
Characterization of the ionic liquid
The synthesized IL was characterized by 1H NMR. For this purpose, the IL was first dried over a Schlenk line for 24 hours. The 1H-NMR spectrum of the ionic liquid is provided in the Fig. S1.† The spectrum shows a 12H-singlet of four methyl groups at 2.8 ppm and a solvent residual peak at 2.5 ppm (DMSO-d6). The
NH peak was identified at 5 ppm and the HSO4 peak at 8.06 ppm. The peak assignment was done according to the cited literature.16,31–33
The synthesized IL was characterized by thermogravimetric analyses (TGA/DSC), and the results were compared with the reported data for this IL. It was found that [TMG][HSO4] is stable up to 250 °C. The TGA/DSC plot of the ionic liquid is furnished in the ESI (Fig. S2†).
Characterization of biomass
FTIR analyses. This is a first-hand technique for comparison of untreated and treated biomass in the IL. The pulps recovered under different conditions were analyzed for probable structural changes. The relative intensities of the peaks were compared by overlapping the IR spectra of treated samples with those of untreated ones (Fig. S3†). The cellulosic peaks at 3325, 2926 cm−1 are due to O–H and C–H stretching vibrations, respectively. A decrease in the intensity of these peaks accounts for the cleavage of inter-unit linkages between lignin and cellulosic materials in treated biomass.34 This decrease is prominent for the recovered pulp at 140 °C, where the OH stretching peak at around 3325 cm−1 was significantly reduced in intensity for the recovered biomass. Similarly, the peak at 898 cm−1 increased in intensity, which indicates the amorphous nature of regenerated biomass. The peak at 1430 cm−1, which is assigned to CH2 bending vibration and also known as a “crystallinity band”, becomes less intense after pretreatment with the IL. This is due to a reduction in crystallinity in regenerated cellulose.35 The cellulosic C–O–C ether bond vibration appears at 1029 cm−1. The peak at 1111 cm−1 is ascribed to C–H of the aromatic structure.36 The peak at 1725 cm−1 arises from the carbonyl group in hemicellulose, which is significant in untreated biomass and has almost vanished from the pretreated biomass at 100, 120 and 140 °C, indicating hydrolysis of hemicellulose–lignin bonds.37,38 According to Hou et.al., this band corresponds to the ester linkage between lignin and hemicellulose, and the disappearance of this peak indicated the cleavage of lignin–hemicellulose linkages.39The characteristic peaks of lignin in FTIR of treated and untreated biomass are 1030, 1508, 1601, and 1620 cm−1, which arise due to the aromatic structure of lignin. The broadband around 1230 cm−1 that originated from the C–O stretching vibration of the guaiacyl ring significantly decreased in the pretreated samples under all temperatures for 4 hours, indicating the effective removal of lignin. However, the characteristic lignin peaks at 1601 and 1508 cm−1 have gradually decreased in intensity as a result of the gradual removal of aromatic lignin from the pretreated biomass. This indicates that the removal of lignin is favored by higher temperatures. Overall efficient removal of lignin and reduced crystallinity in the regenerated biomass structure have occurred, which are some of the targets of a good pretreatment.40,41
Lignin recovered at 140 °C has been characterized by FTIR analysis (Fig. S4†). The IR spectrum of lignin shows all characteristic peaks of the lignin polymer. The vibration at 3400 cm−1 corresponds to OH, COOH, and H2O in lignin. The carboxylate group usually originates due to lignin oxidation at a high pretreatment temperature. The carbonyl peaks at 1700 cm−1 and 1664 cm−1 arise due to lignin oxidation into Hibbert ketones under an oxidative environment.42 Aromatic ring skeletal vibrations due to C
C bonds at 1605 and 1508 cm−1 and CH at 1460 and 1365 cm−1 are the most distinct peaks in the profile of the recovered lignin spectrum.43 The absence of these peaks in recovered biomass is indicative of the lignin removal as a result of pretreatment. Since hardwoods contain syringyl as well as guaiacyl subunits, the signals of the C–O groups at 1325 and 1110 cm−1 of ether bonds originate from the syringyl subunit.44 Similarly, the signals of the C–O groups at 1265 and 1030 cm−1 correspond to the guaiacyl subunits of the lignin macromolecule.
Pretreatment indices
The pretreatment reactions were run at 100, 120, and 140 °C. The time applied for pretreatment was 0.5, 1, 2, and 4 hours for each temperature. The cellulosic (cellulose + hemicellulose) and lignin contents of the untreated and recovered biomass were quantified by the methods reported in the literature.45 The extent of hemicellulose and lignin removal was estimated from the compositional data relative to the amounts in the original biomass using relevant formulae that have been taken from the literature.46,47 For the complete outcome of pretreatment in terms of lignin recovery/removal, hemicellulose removal and CRM recovery, see Table S1 (ESI).†
At 100 °C, the data show a very gradual decrease in the lignin content of biomass as a function of time. Maximum lignin removal was observed for 4 hours of treatment (42.67%) at 100 °C. Similarly, hemicellulose, which is less stable than cellulose, gradually decreased with an increase in pretreatment time. The hemicellulose removal is 5.67% after 0.5 hours and then it showed the peak removal (46%) after 4 hours. The gradual decrease in CRM (cellulose-rich material) could be due to the removal of glucose-containing hemicelluloses such as galactomannans and xyloglucans, rather than degradation of cellulose.48
A parallel relation between lignin and hemicellulose removal can be observed in Fig. 1. The penetration of IL into the biomass cell wall occurs by breaking the lignin–hemicellulose linkages.
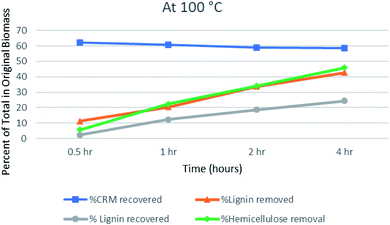 |
| Fig. 1 Different pretreatment indices affected by time at 100 °C. | |
The recovery of the cellulosic material at 120 °C decreased gradually from 54 to 41.67%, while going from 0.5 hours to 4 hours of pretreatment (Fig. 2). Researchers have reported that hemicellulose removal increases at higher temperatures and longer durations.45 In the case of hemicellulose and lignin, the removal reached 60.67 and 55% respectively after 4 hours. Labbé et al. have concluded that at high temperatures, an IL can cleave the acetyl groups covalently joining lignin and hemicellulose, causing the removal of hemicellulose and lignin as well.49
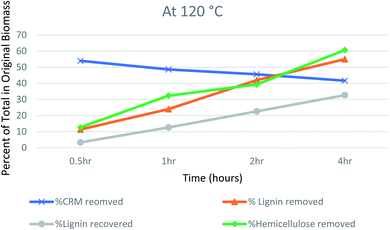 |
| Fig. 2 Different pretreatment indices affected by time at 120 °C. | |
The amount of recovered cellulose-rich material (CRM) at 140 °C decreased from 49.67 to 41.67% going from 0.5 hours to 4 hours (Fig. 3). This shows that maximum hemicellulose has been removed from biomass (92% compared to hemicellulose in untreated biomass). The lignin data showed continuous lignin removal even after 4 hours of treatment, where it reached 81% of the total lignin in the original biomass. This is in agreement with the literature reports that high temperature and longer periods favor significant lignin removal.50 However, no increase in lignin recovery was observed at a longer time of pretreatment. This shows more dissolution of lignin in the ionic liquid at elevated temperatures. Scientists have reported the formation of pseudo-lignin and its redeposition on biomass during pretreatments at elevated temperatures.11 In our case, no pseudo lignin formation or redisposition has been observed at 140 °C and 4 hours, rather the lignin content kept decreasing as a result of its removal.
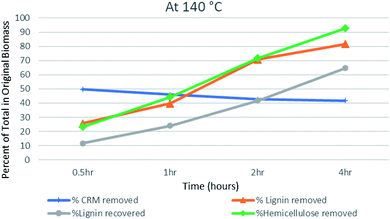 |
| Fig. 3 Different pretreatment indices affected by time at 140 °C. | |
Compositional analysis
Protic ILs have been proved to be efficient in biomass dissolution and delignification. The better the delignification, the better the subsequent enzymatic efficiency.3,51 For this purpose, compositional data collected for the recovered biomass after pretreatment with [TMG][HSO4], and the results are given in Fig. 5.
The compositional analysis of untreated biomass is depicted in Fig. 4, which indicates that the Acacia biomass used in the present study comprises 37.09 ± 0.23% of glucose, 20.07 ± 0.73% xylose, and 2.49 ± 0.04% arabinose as the collective cellulosic material and the acid-insoluble lignin or AIL and acid-soluble lignin or ASL make 23.46 ± 0.27% and 3.49 ± 0.45% of total original Acacia wood respectively.
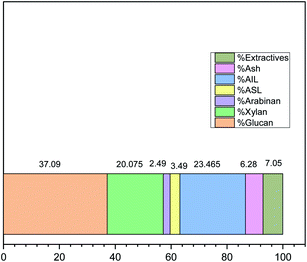 |
| Fig. 4 Composition of Acacia wood used in this study. | |
The compositional analyses performed on all the recovered pulps after pretreatment (Table S2, ESI†) indicate an increase in hemicellulose removal with an increase in the pretreatment time for a given temperature (Fig. 5). Hemicellulose fraction reduced more gradually at 120 °C concerning time and almost complete removal of hemicellulose at 140 °C. This is confirmed by the compositional analysis of pulp, where hemicellulose has been reduced to 1.92% in recovered Acacia at 140 °C for 4 hours. It has been reported by da Silva that on varying the temperature for pretreatment, the hemicellulose recovery shows an irregular trend and almost complete removal of hemicellulose occurs at around 140 °C.52 Similarly, the composition of biomass recovered at longer durations and temperatures showed increased mass loss that could be due to degradation of hemicellulose into other hydrolysis products like HMF.53
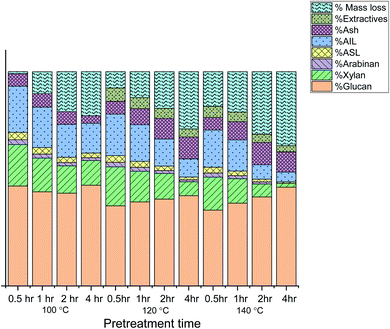 |
| Fig. 5 Composition of pulps recovered at 100, 120, and 140 °C for different time periods. | |
A gradual increase in lignin removal can be observed with time and temperature.4,54 The acidity of the ionic liquid and the temperature of the pretreatment have been reported to be key factors in delignification.55,56 It can be observed in the present study that delignification increased at higher temperatures and longer durations (140 °C and 4 hours). Moreover, the percent mass loss has increased with the increase in temperature and time. Gschwend reported that ionic liquids which are neither acidic nor basic require >100 °C to actively delignify the pulp and enhance saccharification. Since [TMG][HSO4] is also a neutral IL, good delignification is exhibited at high temperatures.57
The lignin fraction left in the recovered biomass indicates maximum lignin removal at 140 °C and 4 hours starting from 26.93% (maximum theoretical lignin in original biomass) to only 5.18% in recovered pulp (% ASL + % AIL).
The percent mass loss was calculated for each condition and maximum mass loss was observed for 140 °C for 4 hours; however, this mass loss is due to lignin and hemicellulose removal. The percentage of glucans in the biomass pretreated at 140 °C and 4 hours (46.07%) shows only a marginal decrease as compared with the biomass pretreated at 100 °C and 4 hours (47.00%). This indicates that the cellulose is stable towards IL-induced hydrolysis and chemical transformation.
Effect of time and temperature on saccharification yields
The major goal of pretreatment is to get cellulosic pulp rich for bioethanol production. The saccharification efficiency largely depends on a reduction in lignin content and disruption of the microfibril structure of the cell wall.58,59 As reported in previous studies, the results indicate a direct relationship between time, temperature, lignin removal, and saccharification efficiency. The higher the temperature, the better the lignin removal. In addition, more lignin removal leads to an escalation in the saccharification yield. This is because lignin acts as an enzyme inhibitor by absorbing the hydrolyzing enzymes and making them unavailable for hydrolysis.60 To assess the optimum condition of pretreatment that produces the most suitable pulp for bioethanol production, we compared the time and temperature conditions of Acacia pretreatment with glucose release, and the results are given in Fig. 6, 7 and 8. The results indicate that high temperatures and prolonged pretreatment produce better pulp for saccharification. In the present study, the saccharification of the pulp treated at 140 °C for 4 hours released 75.80 ± 0.13% of glucose for ethanol production. This is interesting to note that despite a decrease in recovered CRM with time at 140 °C, the saccharification yield kept increasing, i.e., from 49.62% for 0.5 hours to 75.8 for 4 hours. This can be explained in two ways: first, the cellulose at 140 °C and 4 hours might have become much less crystalline and more prone to saccharification.45,61 The other reason is that significant removal of lignin, which is the major barrier towards saccharification, makes cellulose more exposed to enzymes and hydrolysable.39,62
 |
| Fig. 6 Sugar yields from cellulose-rich material (CRM) after pretreatment at 100 °C. | |
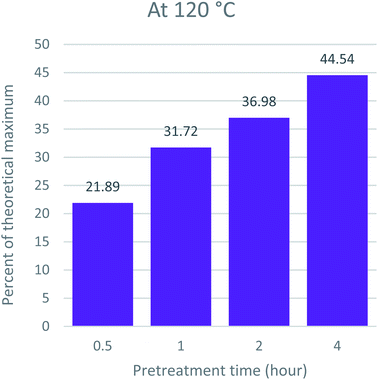 |
| Fig. 7 Sugar yields from cellulose-rich material (CRM) after pretreatment at 120 °C. | |
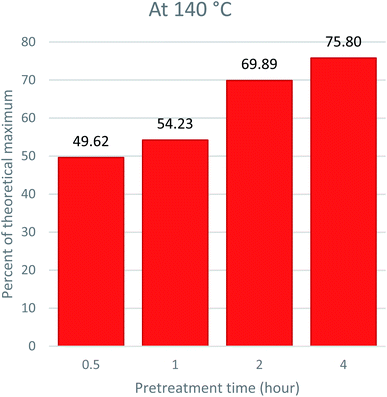 |
| Fig. 8 Sugar yields from cellulose-rich material (CRM) after pretreatment at 140 °C. | |
SEM analysis of the recovered pulp
The morphological changes on the biomass surface arise due to pretreatment and pave the way to enzyme accessibility to cellulosic fibers. To view the changes in the biomass structure as a result of pretreatment, the pretreated samples of cellulosic material (CRM) were visualized using a scanning electron microscope (SEM). The SEM micrographs thus obtained are provided in Fig. 9. The untreated biomass (Fig. 9a) has a compact and intact surface at 2000× magnification, indicating the original morphology of untreated Acacia biomass.63 The pretreated wood at 100 °C for 4 hours shows minor changes to the lignocellulosic surface structure magnified at 1000× (Fig. 9b). This is due to the mild pretreatment conditions and adamant nature of lignocellulose towards chemical changes. The regenerated biomass at 120 °C (Fig. 9c) shows distinct changes in the biomass surface even at low resolution (500×). This indicates the effective penetration of the IL into the biomass. This is also in agreement with the pretreatment indices, indicating partial removal of hemicellulose from biomass. Fig. 9d shows the more ruptured structure of biomass exhibiting a conglomerate structure.36,64 This rough surface of regenerated biomass reveals the removal of lignin and a decrease in the crystallinity of biomass as a result of deep penetration of [TMG][HSO4] at higher temperatures (140 °C) as well as longer durations (four hours).
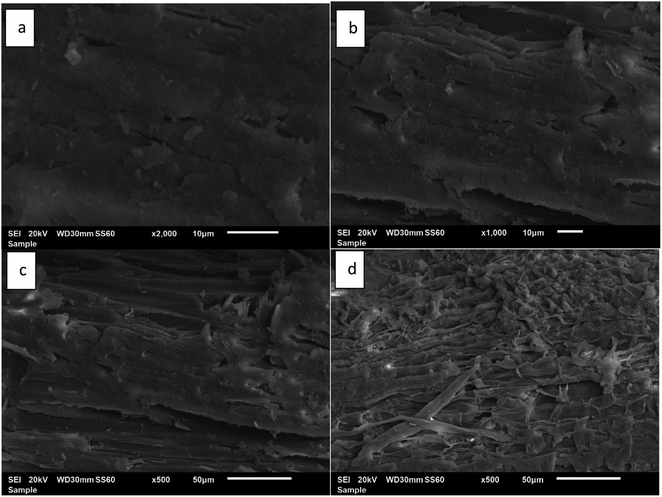 |
| Fig. 9 SEM images of (a) untreated acacia biomass, (b) recovered pulp at 100 °C, (c) at 120 °C, and (d) at 140 °C for 4 hours of pretreatment. | |
HSQC NMR analysis of recovered lignin
Lignin is a complex heterogenous polyphenolic polymer composed of phenylpropanoid (C9) units. Acacia wood in the present study belongs to an angiosperm class of plants having considerable S, H and G type units in its lignin structure and has a more linear structure than that of softwood lignin that is mainly made of guaiacyl units. This makes hardwood lignin easy to remove from the biomass.65 The HSQC revealed that lignin has considerable amounts of S and G units. This is evident from the HSQC spectrum of lignin extracted from Acacia lignin recovered after pretreatment at 140 °C for 4 hours (Fig. 10). The aromatic region (80–140/6–8 ppm) shows characteristic peaks of all representative phenylpropanoids, namely, guaiacyl (G), syringyl (S), and p-hydroxyphenyl (H) (Fig. S5 ESI†). The peaks have been assigned following literature reports.43,66 During higher temperature pretreatment conditions, the recovered lignin has a relatively more condensed structure as evidenced by the lower C2/H2 and C6/H6 correlation signal intensities of the G unit and the presence of G2 condensed signal (Fig. 10). C2,6–H2,6 correlations in the S unit were defined at δC/δH 103.8/6.68 ppm, while the signals for the Cα-oxidized S-units (S′) were observed at δC/δH 106.3/7.21 (Fig. S5†).
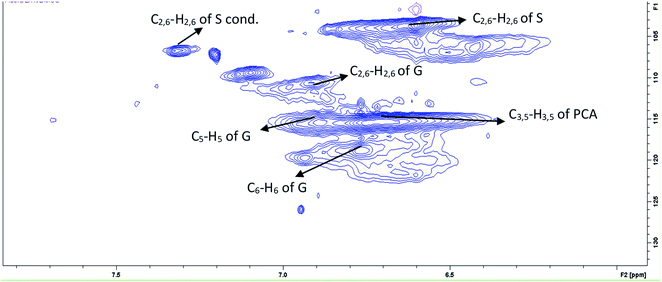 |
| Fig. 10 HSQC spectrum of the aromatic region of lignin recovered at 140 °C and 4 hours. | |
In the aliphatic region of the spectrum (30–80/2–6 ppm, Fig. 11), the most prominent peak was methoxy peak at δC/δH 56.4/3.70 ppm. The cross-peak at δC/δH 83.5/5.28 ppm was assigned to Cβ–Hβ in β-O-4 moieties of S-type with α-carbonyl.67 The signals of the Cγ–Hγ correlation in H type units were observed at 61.9/4.12 ppm. From the HSQC spectrum, the β-O-aryl ether linkage in lignin was confirmed by the cross peaks at δC/δH 72.0/4.8 and 86.0/4.2 ppm for α and β of C–H side-chain correlations, respectively. The low signal intensity of the β-O-4 linkage indicates that in situ lignin depolymerization has also occurred.68 The structural changes in lignin macromolecule that occur during pretreatment have been reported by Dutta and coworkers43 and state that β-O-4 bond is the weakest bond in the lignin structure and lignin cleavage occurs mostly from this bond. The cross peaks at δC/δH 87.4/5.5 and 53.2/3.5 ppm are attributed to α and β-carbon correlations respectively for the H unit. The hardwood lignin usually has more S subunits than H units.65 This is also very clear from the low signal intensity for the H subunit. The same is true for the signals of most abundant β-O-4 linkages. The lower signal intensities could be attributed to the cleavage of lignin chain from these bonds.44 The lignin condensation during pretreatment is depicted from the resinol units, which were also detected due to the presence of Cα–Hα correlations at δC/δH 85.7/4.6 ppm.69 This indicates the probable condensation of lignin that occurs at high temperature pretreatments.
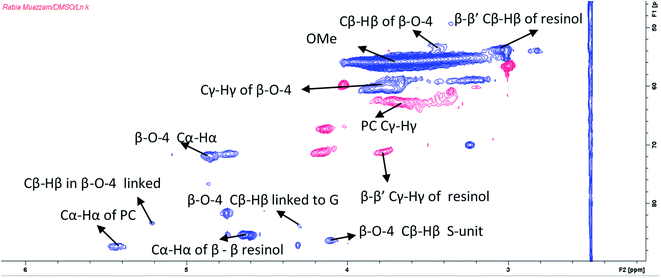 |
| Fig. 11 HSQC spectrum of the aliphatic region of lignin recovered at 140 °C and 4 hours. | |
Conclusion
The progressive investigation into the field of IL-assisted biomass processing aimed to find a most suitable IL for biomass processing that should be benign toward the environment. Previous reports on TMG-based ILs have identified it as green. Therefore, we reported for the first time a protic IL tetramethylguanidinium hydrogen sulfate [TMG][HSO4]–based ionoSolv fractionation of Acacia nilotica, a hardwood biomass from timber industry, into cellulose- and lignin-rich fractions at different temperatures and time periods of pretreatment. The time range studied for pretreatment is from 0.5 hour to 4 hours and temperature from 100 to 140 °C. The optimum treatment condition has been found to be 140 °C and 4 hours that have afforded maximum lignin removal and sugar release. Under this condition, 81% of the total lignin was removed from the biomass. The compositional and FT-IR analyses of recovered biomass showed appreciable lignin removal, which was further validated by the lignin yields. The recovered lignin was identified by HSQC and FT-IR and compared with the reported data about hard wood-lignin.
The compositional analysis of the pulp recovered at 140 °C and 4 hours showed 92.66% hemicellulose removal and the saccharification of the pretreated pulp afforded 75% glucose as reducing sugar. Since only glucose has been considered as the saccharification product, the total reducing sugars (xylose, mannose etc.) from the recovered biomass would have been far more than this value.
The lignin recovered after pretreatment shows similar contents of S and G subunits based on their HSQC signal intensity. This hard wood lignin can further be converted into valuable chemicals. Conclusively, Acacia nilotica, being a hardwood, has shown great potential for lignin and fermentable sugars after being fractionated by the ionic liquid [TMG][HSO4]. This implies the potential of [TMG][HSO4] as a good delignifying agent for the hardwood.
Conflicts of interest
The authors declare no conflict of interest.
Acknowledgements
This work was financially supported by the Higher Education Commission (HEC) Pakistan, project numbers: 8639/Punjab/NRPU/R&D/HEC/2017 and TDF-03/294. School of Chemistry, University of the Punjab is acknowledged for its support for this project. A part of experimental work was performed at the Chemical Engineering Department, Imperial College London; we pay our utmost gratitude for the facilities and substantial support provided there.
References
- A. Zanchetta, A. C. F. dos Santos, E. Ximenes, C. da Costa Carreira Nunes, M. Boscolo, E. Gomes and M. R. Ladisch, Temperature Dependent Cellulase Adsorption on Lignin from Sugarcane Bagasse, Bioresour. Technol., 2018, 252, 143–149, DOI:10.1016/j.biortech.2017.12.061.
- J. S. Moulthrop, R. P. Swatloski, G. Moyna and R. D. Rogers, High-Resolution 13C NMR Studies of Cellulose and Cellulose Oligomers in Ionic Liquid Solutions, Chem. Commun., 2005,(12), 1557–1559, 10.1039/b417745b.
- S. H. Lee, T. V. Doherty, R. J. Linhardt and J. S. Dordick, Ionic Liquid-Mediated Selective Extraction of Lignin from Wood Leading to Enhanced Enzymatic Cellulose Hydrolysis, Biotechnol. Bioeng., 2009, 102(5), 1368–1376, DOI:10.1002/bit.22179..
- J. Luo, M. Cai and T. Gu, Pretreatment of Lignocellulosic Biomass Using Green Ionic Liquids, in Green Biomass Pretreatment for Biofuels Production, ed. T. Gu, Springer Briefs in Molecular Science; Springer Netherlands, Dordrecht, 2013, pp. 127–153. DOI:10.1007/978-94-007-6052-3_6.
- J. Bernardo, F. Gírio and R. Łukasik, The Effect of the Chemical Character of Ionic Liquids on Biomass Pre-Treatment and Posterior Enzymatic Hydrolysis, Molecules, 2019, 24(4), 808–824, DOI:10.3390/molecules24040808.
- Y. Li, J. Wang, X. Liu and S. Zhang, Towards a Molecular Understanding of Cellulose Dissolution in Ionic Liquids: Anion/Cation Effect, Synergistic Mechanism and Physicochemical Aspects, Chem. Sci., 2018, 9(17), 4027–4043, 10.1039/c7sc05392d.
- A. M. Asim, M. Uroos, S. Naz, M. Sultan, G. Griffin, N. Muhammad and A. S. Khan, Acidic Ionic Liquids: Promising and Cost-Effective Solvents for Processing of Lignocellulosic Biomass, J. Mol. Liq., 2019, 287, 110943–111958, DOI:10.1016/j.molliq.2019.110943.
- A. Brandt, J. P. Hallett, D. J. Leak, R. J. Murphy and T. Welton, The Effect of the Ionic Liquid Anion in the Pretreatment of Pine Wood Chips, Green Chem., 2010, 12(4), 672–679, 10.1039/b918787a.
- E. C. Achinivu, R. M. Howard, G. Li, H. Gracz and W. A. Henderson, Lignin Extraction from Biomass with Protic Ionic Liquids, Green Chem., 2014, 16(3), 1114–1119, 10.1039/c3gc42306a.
- F. Cheng, X. Zhao and Y. Hu, Lignocellulosic Biomass Delignification Using Aqueous Alcohol Solutions with the Catalysis of Acidic Ionic Liquids: A Comparison Study of Solvents, Bioresour. Technol., 2018, 249, 969–975, DOI:10.1016/j.biortech.2017.10.089.
- F. J. V. Gschwend, F. Malaret, S. Shinde, A. Brandt-Talbot and J. P. Hallett, Rapid Pretreatment of Miscanthus Using the Low-Cost Ionic Liquid Triethylammonium Hydrogen Sulfate at Elevated Temperatures, Green Chem., 2018, 20(15), 3486–3498, 10.1039/c8gc00837j.
- P. Weerachanchai and J.-M. Lee, Effect of Organic Solvent in Ionic Liquid on Biomass Pretreatment, ACS Sustainable Chem. Eng., 2013, 1(8), 894–902, DOI:10.1021/sc300147f.
- O. Kuzmina, J. Bhardwaj, S. R. Vincent, N. D. Wanasekara, L. M. Kalossaka, J. Griffith, A. Potthast, S. Rahatekar, S. J. Eichhorn and T. Welton, Superbase Ionic Liquids for Effective Cellulose Processing from Dissolution to Carbonisation, Green Chem., 2017, 19(24), 5949–5957, 10.1039/c7gc02671d.
- Y. Qu, Q. Wei, H. Li, P. Oleskowicz-Popiel, C. Huang and J. Xu, Microwave-Assisted Conversion of Microcrystalline Cellulose to 5-Hydroxymethylfurfural Catalyzed by Ionic Liquids, Bioresour. Technol., 2014, 162, 358–364, DOI:10.1016/j.biortech.2014.03.081.
- G. V. S. M. Carrera, A. Raymundo, F. M. B. Fernandes, N. Jordão, I. Sousa, M. N. da Ponte and L. C. Branco, Tetramethylguanidine-Based Gels
and Colloids of Cellulose, Carbohydr. Polym., 2017, 169, 58–64, DOI:10.1016/j.carbpol.2017.03.084.
- S. Kumar, R. K. Singh and S. L. Jain, 1,1,3,3-Tetramethylguanidinium Hydrogen Sulphate (TMG·HSO4) Ionic Liquid in Carbon Dioxide Enriched Water: A Highly Efficient Acidic Catalytic System for the Hydrolysis of Cellulose, RSC Adv., 2014, 4(102), 58238–58242, 10.1039/c4ra11906a.
- C.-W. Cho, T. Phuong Thuy Pham, Y.-C. Jeon and Y.-S. Yun, Influence of Anions on the Toxic Effects of Ionic Liquids to a Phytoplankton Selenastrum capricornutum, Green Chem., 2008, 10(1), 67–72, 10.1039/b705520j.
- D. J. Couling, R. J. Bernot, K. M. Docherty, J. K. Dixon and E. J. Maginn, Assessing the Factors Responsible for Ionic Liquid Toxicity to Aquatic Organisms via Quantitative Structure–Property Relationship Modeling, Green Chem., 2006, 8(1), 82–90, 10.1039/b511333d.
- A. Pratap Singh, D. Sithambaram, R. Sanghavi, P. Kumar Gupta, R. Shanker Verma, M. Doble, R. L. Gardas and S. Senapati, Environmentally Benign Tetramethylguanidinium Cation Based Ionic Liquids, New J. Chem., 2017, 41(20), 12268–12277, 10.1039/c7nj03167j.
- A. H. Rantamäki, S.-K. Ruokonen, E. Sklavounos, L. Kyllönen, A. W. T. King and S. K. Wiedmer, Impact of Surface-Active Guanidinium-, Tetramethylguanidinium-, and Cholinium-Based Ionic Liquids on Vibrio fischeri Cells and Dipalmitoylphosphatidylcholine Liposomes, Sci. Rep., 2017, 7(1), 46673–46684, DOI:10.1038/srep46673.
- N. Wulijarni-Soetjipto and J. S. Siemonsma, Plant Resources of South-East Asia, No. 3: Dye and Tannin-Producing Plants, PROSEA Foundation, Bogor, 1991 Search PubMed.
- R. K. Gupta, Resource Survey of Gummiferous acacias in Western Rajasthan, Trop. Ecol., 1970, 11(2), 148–161 Search PubMed.
- S. Singh, J. P. Chakraborty and M. K. Mondal, Torrefaction of Woody Biomass (Acacia nilotica): Investigation of Fuel and Flow Properties to Study Its Suitability as a Good Quality Solid Fuel, Renewable Energy, 2020, 153, 711–724, DOI:10.1016/j.renene.2020.02.037.
- S. N. A. Tahir, M. Rafique and A. S. Alaamer, Biomass Fuel Burning and Its Implications: Deforestation and Greenhouse Gases Emissions in Pakistan, Environ. Pollut., 2010, 158(7), 2490–2495, DOI:10.1016/j.envpol.2010.03.017.
- V. Rigual, A. Ovejero-Pérez, S. Rivas, J. C. Domínguez, M. V. Alonso, M. Oliet and F. Rodriguez, Protic, Aprotic, and Choline-Derived Ionic Liquids: Toward Enhancing the Accessibility of Hardwood and Softwood, ACS Sustainable Chem. Eng., 2020, 8(3), 1362–1370, DOI:10.1021/acssuschemeng.9b04443.
- V. Rigual, T. M. Santos, J. C. Domínguez, M. V. Alonso, M. Oliet and F. Rodriguez, Evaluation of Hardwood and Softwood Fractionation Using Autohydrolysis and Ionic Liquid Microwave Pretreatment, Biomass Bioenergy, 2018, 117, 190–197, DOI:10.1016/j.biombioe.2018.07.014.
- H. Gao, B. Han, J. Li, T. Jiang, Z. Liu, W. Wu, Y. Chang and J. Zhang, Preparation of Room-Temperature Ionic Liquids by Neutralization of 1,1,3,3-Tetramethylguanidine with Acids and Their Use as Media for Mannich Reaction, Synth. Commun., 2004, 34(17), 3083–3089, DOI:10.1081/SCC-200028532.
- F. J. V. Gschwend, A. Brandt, C. L. Chambon, W.-C. Tu, L. Weigand and J. P. Hallett, Pretreatment of Lignocellulosic Biomass with Low-Cost Ionic Liquids, JoVE, 2016, 114, 54246–54251, DOI:10.3791/54246.
- A. Sluiter, Determination of Structural Carbohydrates and Lignin in Biomass, Laboratory Analytical Procedure (LAP), 2008, 1617(1), 1–16 Search PubMed.
- A. Sluiter, B. Hames, R. Ruiz, C. Scarlata, J. Sluiter, D. Templeton and D. Crocker, Determination of Structural Carbohydrates and Lignin in Biomass, Laboratory Analytical Procedure, 2008, 1617(1), 1–16 Search PubMed.
- X. Du, J. Zhang, Y. Wang and Y. Qu, Conversion of Carbohydrates into Platform Chemicals Catalyzed by Alkaline Ionic Liquids, Catalysts, 2017, 7(9), 245–255, DOI:10.3390/catal7090245.
- A. M. Asim, M. Uroos, S. Naz and N. Muhammad, Pyridinium Protic Ionic Liquids: Effective Solvents for Delignification of Wheat Straw, J. Mol. Liq., 2021, 325, 115013–115023, DOI:10.1016/j.molliq.2020.115013.
- M. V. Reddy, K. R. Valasani, K. T. Lim and Y. T. Jeong, Tetramethylguanidiniumchlorosulfonate Ionic Liquid (TMG IL): An Efficient Reusable Catalyst for the Synthesis of Tetrahydro-1H-Benzo[a]Chromeno[2,3-c]Phenazin-1-Ones under Solvent-Free Conditions and Evaluation for Their in Vitro Bioassay Activity, New J. Chem., 2015, 39(12), 9931–9941, 10.1039/c5nj01866h.
- S. Saher, H. Saleem, A. M. Asim, M. Uroos and N. Muhammad, Pyridinium Based Ionic Liquid: A Pretreatment Solvent and Reaction Medium for Catalytic Conversion of Cellulose to Total Reducing Sugars (TRS), J. Mol. Liq., 2018, 272, 330–336, DOI:10.1016/j.molliq.2018.09.099.
- R. S. Orozco, P. B. Hernández, G. R. Morales, F. U. Núñez, J. O. Villafuerte, V. L. Lugo, N. F. Ramírez, C. E. B. Díaz and P. C. Vázquez, Characterization of Lignocellulosic Fruit Waste as an Alternative Feedstock for Bioethanol Production, Bioresources, 2014, 9(2), 1873–1885 Search PubMed.
- T. N. Ang, G. C. Ngoh, A. S. M. Chua and M. G. Lee, Elucidation of the Effect of Ionic Liquid Pretreatment on Rice Husk via Structural Analyses, Biotechnol. Biofuels, 2012, 5(1), 67–76, DOI:10.1186/1754-6834-5-67.
- I. S. Azmi, A. Azizan and R. Mohd Salleh, Pretreatment of Oil Palm Frond (OPF) with Ionic Liquid, IOP Conf. Ser.: Mater. Sci. Eng., 2018, 358, 012071–012080, DOI:10.1088/1757-899X/358/1/012071.
- S. Y. Oh, D. I. Yoo, Y. Shin and G. Seo, FTIR Analysis of Cellulose Treated with Sodium Hydroxide and Carbon Dioxide, Carbohydr. Res., 2005, 340(3), 417–428, DOI:10.1016/j.carres.2004.11.027.
- X.-D. Hou, T. J. Smith, N. Li and M.-H. Zong, Novel Renewable Ionic Liquids as Highly Effective Solvents for Pretreatment of Rice Straw Biomass by Selective Removal of Lignin, Biotechnol. Bioeng., 2012, 109(10), 2484–2493, DOI:10.1002/bit.24522.
- J. Bian, F. Peng, X.-P. Peng, X. Xiao, P. Peng, F. Xu and R.-C. Sun, Effect of [Emim]Ac Pretreatment on the Structure and Enzymatic Hydrolysis of Sugarcane Bagasse Cellulose, Carbohydr. Polym., 2014, 100, 211–217, DOI:10.1016/j.carbpol.2013.02.059.
- S. Sun, S. Sun, X. Cao and R. Sun, The Role of Pretreatment in Improving the Enzymatic Hydrolysis of Lignocellulosic Materials, Bioresour. Technol., 2016, 199, 49–58, DOI:10.1016/j.biortech.2015.08.061.
- B. Shrestha, Y. le Brech, T. Ghislain, S. Leclerc, V. Carré, F. Aubriet, S. Hoppe, P. Marchal, S. Pontvianne, N. Brosse and A. Dufour, A Multitechnique Characterization of Lignin Softening and Pyrolysis, ACS Sustainable Chem. Eng., 2017, 5(8), 6940–6949, DOI:10.1021/acssuschemeng.7b01130.
- T. Dutta, N. G. Isern, J. Sun, E. Wang, S. Hull, J. R. Cort, B. A. Simmons and S. Singh, Survey of Lignin-Structure Changes and Depolymerization during Ionic Liquid Pretreatment, ACS Sustainable Chem. Eng., 2017, 5(11), 10116–10127, DOI:10.1021/acssuschemeng.7b02123.
- Y.-X. An, N. Li, H. Wu, W.-Y. Lou and M.-H. Zong, Changes in the Structure and the Thermal Properties of Kraft Lignin during Its Dissolution in Cholinium Ionic Liquids, ACS Sustainable Chem. Eng., 2015, 3(11), 2951–2958, DOI:10.1021/acssuschemeng.5b00915.
- F. J. V. Gschwend, C. L. Chambon, M. Biedka, A. Brandt-Talbot, P. S. Fennell and J. P. Hallett, Quantitative Glucose Release from Softwood after Pretreatment with Low-Cost Ionic Liquids, Green Chem., 2019, 21(3), 692–703, 10.1039/c8gc02155d.
- A. R. Abouelela, S. Tan, G. H. Kelsall and J. P. Hallett, Toward a Circular Economy: Decontamination and Valorization of Postconsumer Waste Wood Using the IonoSolv Process, ACS Sustainable Chem. Eng., 2020, 8(38), 14441–14461, DOI:10.1021/acssuschemeng.0c04365.
- M. Chen, F. Malaret, A. E. J. Firth, P. Verdía, A. R. Abouelela, Y. Chen and J. P. Hallett, Design of a Combined Ionosolv-Organosolv Biomass Fractionation Process for Biofuel Production and High Value-Added Lignin Valorisation, Green Chem., 2020, 22(15), 5161–5178, 10.1039/d0gc01143f.
- P. Mäki-Arvela, T. Salmi, B. Holmbom, S. Willför and D. Yu. Murzin, Synthesis of Sugars by Hydrolysis of Hemicelluloses- A Review, Chem. Rev., 2011, 111(9), 5638–5666, DOI:10.1021/cr2000042.
- N. Labbé, L. M. Kline, L. Moens, K. Kim, P. C. Kim and D. G. Hayes, Activation of Lignocellulosic Biomass by Ionic Liquid for Biorefinery Fractionation, Bioresour. Technol., 2012, 104, 701–707, DOI:10.1016/j.biortech.2011.10.062.
- W. Li, N. Sun, B. Stoner, X. Jiang, X. Lu and R. D. Rogers, Rapid Dissolution of Lignocellulosic Biomass in Ionic Liquids Using Temperatures above the Glass Transition of Lignin, Green Chem., 2011, 13(8), 2038–2047, 10.1039/c1gc15522a.
- C. Huang, J. He, D. Min, C. Lai and Q. Yong, Understanding the Nonproductive Enzyme Adsorption and Physicochemical Properties of Residual Lignins in Moso Bamboo Pretreated with Sulfuric Acid and Kraft Pulping, Appl. Biochem. Biotechnol., 2016, 180(8), 1508–1523, DOI:10.1007/s12010-016-2183-8.
- S. P. Magalhães da Silva, A. M. da Costa Lopes, L. B. Roseiro and R. Bogel-Łukasik, Novel Pre-Treatment and Fractionation Method for Lignocellulosic Biomass Using Ionic Liquids, RSC Adv., 2013, 3(36), 16040–16050, 10.1039/c3ra43091j.
- L. Weigand, S. Mostame, A. Brandt-Talbot, T. Welton and J. P. Hallett, Effect of Pretreatment Severity on the Cellulose and Lignin Isolated from Salix Using IonoSolv Pretreatment, Faraday Discuss., 2017, 202, 331–349, 10.1039/c7fd00059f.
- A. Brandt, M. J. Ray, T. Q. To, D. J. Leak, R. J. Murphy and T. Welton, Ionic Liquid Pretreatment of Lignocellulosic Biomass with Ionic Liquid–Water Mixtures, Green Chem., 2011, 13(9), 2489–2499, 10.1039/c1gc15374a.
- L. D. Tolesa, B. S. Gupta and M.-J. Lee, Treatment of Coffee Husk with Ammonium-Based Ionic Liquids: Lignin Extraction, Degradation, and Characterization, ACS Omega, 2018, 3(9), 10866–10876, DOI:10.1021/acsomega.8b01447.
- A. Brandt, J. Gräsvik, J. P. Hallett and T. Welton, Deconstruction of Lignocellulosic Biomass with Ionic Liquids, Green Chem., 2013, 15(3), 550–583, 10.1039/c2gc36364j.
- F. J. Gschwend, J. P. Hallett and A. Brandt-Talbot, Exploring the Effect of Water Content and Anion on the Pretreatment of Poplar with Three 1-Ethyl-3-Methylimidazolium Ionic Liquids, Molecules, 2020, 25(10), 2318–2331, DOI:10.3390/molecules25102318.
- A. Brandt-Talbot, F. J. V. Gschwend, P. S. Fennell, T. M. Lammens, B. Tan, J. Weale and J. P. Hallett, An Economically Viable Ionic Liquid for the Fractionation of Lignocellulosic Biomass, Green Chem., 2017, 19(13), 3078–3102, 10.1039/c7gc00705a.
- C. Zhang, W. Xu, P. Yan, X. Liu and Z. C. Zhang, Overcome the Recalcitrance of Eucalyptus Bark to Enzymatic Hydrolysis by Concerted Ionic Liquid
Pretreatment, Process Biochem., 2015, 50(12), 2208–2214 CrossRef CAS.
- L. Kumar, V. Arantes, R. Chandra and J. Saddler, The Lignin Present in Steam Pretreated Softwood Binds Enzymes and Limits Cellulose Accessibility, Bioresour. Technol., 2012, 103(1), 201–208, DOI:10.1016/j.biortech.2011.09.091.
- H. Wang, G. Gurau and R. D. Rogers, Ionic Liquid Processing of Cellulose, Chem. Soc. Rev., 2012, 41(4), 1519–1537, 10.1039/c2cs15311d.
- D. Fu, G. Mazza and Y. Tamaki, Lignin Extraction from Straw by Ionic Liquids and Enzymatic Hydrolysis of the Cellulosic Residues, J. Agric. Food Chem., 2010, 58(5), 2915–2922, DOI:10.1021/jf903616y.
- A. M. Asim, M. Uroos and N. Muhammad, Extraction of Lignin and Quantitative Sugar Release from Biomass Using Efficient and Cost-Effective Pyridinium Protic Ionic Liquids, RSC Adv., 2020, 10(72), 44003–44014, 10.1039/d0ra09098k.
- S. Naz, M. Uroos, A. M. Asim, N. Muhammad and F. U. Shah, One-Pot Deconstruction and Conversion of Lignocellulose into Reducing Sugars by Pyridinium-Based Ionic Liquid–Metal Salt System, Front. Chem., 2020, 8, 236–246, DOI:10.3389/fchem.2020.00236.
- D. S. Nawawi, W. Syafii, I. Tomoda, Y. Uchida, T. Akiyama, T. Yokoyama and Y. Matsumoto, Characteristics and Reactivity of Lignin in Acacia and Eucalyptus Woods, J. Wood Chem. Technol., 2017, 37(4), 273–282, DOI:10.1080/02773813.2017.1291684.
- M. V. Bule, A. H. Gao, B. Hiscox and S. Chen, Structural Modification of Lignin and Characterization of Pretreated Wheat Straw by Ozonation, J. Agric. Food Chem., 2013, 61(16), 3916–3925, DOI:10.1021/jf4001988.
- R. Martin-Sampedro, E. A. Capanema, I. Hoeger, J. C. Villar and O. J. Rojas, Lignin Changes after Steam Explosion and Laccase-Mediator Treatment of Eucalyptus Wood Chips, J. Agric. Food Chem., 2011, 59(16), 8761–8769, DOI:10.1021/jf201605f.
- J.-L. Wen, T.-Q. Yuan, S.-L. Sun, F. Xu and R.-C. Sun, Understanding the Chemical Transformations of Lignin during Ionic Liquid Pretreatment, Green Chem., 2014, 16(1), 181–190, 10.1039/c3gc41752b.
- R. Samuel, M. Foston, N. Jaing, S. Cao, L. Allison, M. Studer, C. Wyman and A. J. Ragauskas, HSQC (Heteronuclear Single Quantum Coherence) 13C–1H Correlation Spectra of Whole Biomass in Perdeuterated Pyridinium Chloride–DMSO System: An Effective Tool for Evaluating Pretreatment, Fuel, 2011, 90(9), 2836–2842, DOI:10.1016/j.fuel.2011.04.021.
Footnote |
† Electronic supplementary information (ESI) available. See DOI: 10.1039/d1ra01328a |
|
This journal is © The Royal Society of Chemistry 2021 |
Click here to see how this site uses Cookies. View our privacy policy here.