DOI:
10.1039/D1RA00410G
(Paper)
RSC Adv., 2021,
11, 10699-10709
Preparation of superhydrophobic nylon-56/cotton-interwoven fabric with dopamine-assisted use of thiol–ene click chemistry
Received
17th January 2021
, Accepted 8th March 2021
First published on 11th March 2021
Abstract
With the help of dopamine, we constructed a hydroxyl-rich secondary reaction platform on a surface formed by interwoven nylon 56 and cotton fibres. Octadecyl mercaptan and vinyl trimethoxysilane (VTMS) are used for the click coupling preparation of superhydrophobic reagents, which are grafted onto polydopamine aggregates and successfully used to prepare superhydrophobic nylon 56/cotton-interwoven fabric. The static contact angle was 161° and the sliding angle was 8°. Note that the prepared superhydrophobic fabric can withstand corrosive liquids, water washing, ultraviolet radiation and mechanical abrasion, it has excellent superhydrophobic stability, and self-cleaning and oil–water-separation functionalities. This simple, fast and environmentally friendly method can be applied to other substrates and shows tremendous potential for expanding the field of superhydrophobic applications.
1. Introduction
Usually, superhydrophobic surfaces are defined as those with static water contact angles of >150° and sliding angles of <10°.1–4 Due to the superhydrophobicity, the water droplet can easily move down a tilted surface and it does not stick to the surface and also, it bounces when it is dropped on the surface from a height. Such surfaces exhibit unique wettability characteristics and have attracted considerable attention because of their potential applications, which include corrosion protection, anti-icing, self-cleaning,5 oil–water separation,6 antifouling,7 and microfluid transportation.8
There are two key points to consider when preparing superhydrophobic surfaces, namely, the construction of the micro–nano roughness and the use of materials with low surface energies.9–11 Scientists have developed multiple preparation methods, including nanoparticle loading,12 layer-by-layer assembly,13 and chemical vapour deposition.14 Using these methods, research institutions successfully created superhydrophobic surfaces on different substrates to meet various complex and changeable requirements.15–17 Unfortunately, certain superhydrophobic surfaces remain fragile and unstable at present and are easily affected by the external environment, resulting in a loss of their superhydrophobic properties. Moreover, there are certain problems with the manufacturing process, including its length, its high cost, and environmental pollution. Therefore, in this study, we provide a simple, fast, environmentally friendly, and pollution-free method for preparing durable superhydrophobic surfaces.
Cotton fibre, the world's most abundant plant fiber, is inexpensive and provides excellent comfort, reproducibility and biodegradability. Its primary component is cellulose. Because of the rich hydroxyl on the surface of the cellulose substrate, it absorbs water, and there it becomes wet and its durability reduces. Therefore, superhydrophobic properties must be present on the cotton fibre surface.18 Polyamide 56, commonly known as nylon 56, is amongst the most popular synthetic fibres; it has a wide range of applications because of its excellent durability, abrasion resistance, and corrosion resistance.19 By developing a micro–nano rough structure on nylon 56 fiber to give it superhydrophobic properties, it should be possible to broaden its field of applications.
Inspired by the excellent adhesion of marine mussels, a growing number of researchers are focusing on dopamine. As a surface modifier, dopamine plays an important role in multiple research fields, including biology,20 chemistry21 and medicine.22 For example, Chen et al. prepared a nickel/graphene/polydopamine-composite coating using dopamine-assisted electrodeposition technology. The durability and corrosion resistance of this composite coating were significantly improved, and it had hydrophobic properties.23 Based on the principle of self-polymerisation of dopamine and fluorescent polymer, Shi et al. prepared a yellow-green fluorescent–starch-based phosphor with high stability using an environmentally friendly method. This phosphor exhibited strong water dispersibility and high biocompatibility.24 The method for generating polydopamine through the oxidative polymerisation of dopamine is simple and easy to implement; polydopamine can be formed by self-polymerisation only under an aerobic weak base and can act with strong adhesion to almost any matrix. The surface of polymerized polydopamine coating is rich in hydroxyl, amino and other groups. In addition to modifying membrane materials25 and nanomaterials,26 it can be used to biomimic the surfaces of fibres and fabrics. By improving the surface properties of these materials, they can be made to provide a secondary reaction platform for subsequent experiments and see use in preparing functional textiles.27 Therefore, a series of superhydrophobic surfaces can be prepared with dopamine assistance.
Sharpless, the winner of the 2001 Nobel Prize in Chemistry, proposed the concept of click chemistry.28 Thiol–ene click chemistry offers many advantages, including a high product yield, easy separation and purification, regiospecificity, stereospecificity, and mild reactions. Furthermore, it has a wide range of applications;29–31 e.g., Bao et al. prepared photochromic cotton fabrics with good durability based upon the principle of thiol–ene click chemistry. These fabrics have good resistance to ultraviolet rays and excellent fatigue resistance.32 Ning et al. adopted the thiol–ene click chemistry method to prepare a scratch-resistant coating with ultra-high adhesion on a styrene–butadiene rubber–elastomer matrix, thus making it superhydrophobic.33 These results indicate that thiol–ene click chemistry can be applied to the study of surface functional polymers and provide a new concept for preparing superhydrophobic surfaces.
In this work, we develop a simple, fast, environmentally friendly, and versatile method for preparing superhydrophobic nylon-56/cotton-interwoven fabrics (Fig. 1). With dopamine used to build a hydroxyl-rich secondary-reaction platform on the surface of nylon 56 and cotton fibres, octadecyl merthiol and vinyl trimethoxysilane were employed for click coupling to prepare superhydrophobic reagents and to graft them onto the polydopamine aggregate to form superhydrophobic textiles. In other existing superhydrophobic literature reports, some methods use fluorine-containing hydrophobizing agents as raw materials, However, despite their considerable hydrophobic effect, they contribute to environmental pollution. Dopamine is a non-toxic, environmentally friendly, and adaptable substance. Most organic materials can be modified by dopamine on its surface, so it can form a secondary reaction platform on the surface of nylon 56/cotton interwoven fabric. Some existing methods for preparing superhydrophobic surfaces take a long time. Using click chemistry to graft low surface energy substances, based on its advantages of fast reaction rate and modularity, we can prepare superhydrophobic fabrics in a short time. The superhydrophobic fabric prepared by this method possesses good anti-ultraviolet (UV) ageing, abrasion resistance, acid and alkali resistance, acetone solvent resistance, and oil–water separation performance.
 |
| Fig. 1 Formation mechanism of superhydrophobic textiles. | |
2. Experimental
2.1 Materials
Nylon 56/cotton-interwoven fabric containing 50% nylon-56 fibre and 50% cotton fibre was purchased from Jiangsu Lianfa Textile Co., Ltd.; dopamine hydrochloride (DA, 98.5%, AR) was purchased from Shanghai Yuanye Biotechnology Co., Ltd.; Tris(hydroxymethyl)methyl aminomethane THAM (Tris) and octadecyl mercaptan were obtained from Shanghai Jingchun Biochemical Technology Co., Ltd.; Vinyltrimethoxysilane (VTMS, 98%) was purchased from Shanghai Macleans Biochemical Technology Co., Ltd.; Tri(Hydroxymethyl) amino methane hydrochloride (Tris–HCl) was provided by Suzhou Great Pharmaceutical Technology Co., Ltd.; 2,2-dimethoxy-2-phenylacetophenone (DMPA), pure ethanol, and ethyl acetate were purchased from China Sinopharm Chemical Reagent Co., Ltd.
2.2 Preparation of dopamine-modified nylon 56/cotton interwoven fabric
For adjusting the solubility pH of the liquid to 8.5, 0.4 g of dopamine are dissolved in 200 mL of deionised water in an Erlenmeyer flask, with Tris and Tris–HCl. The original nylon-56/cotton-interwoven fabric (4 cm × 4 cm) is then placed in the flask, which is then placed in a low-noise oscillating dyeing machine (temperature 45 °C) and shaken for 18 h. The treated fabric is ultrasonically vibrated with pure ethyl alcohol to remove the poly dopamine with a weak binding force; then, it is dried in an oven at 60 °C for 0.5 h to obtain dopamine-modified nylon-56/cotton-interwoven fabric.
2.3 Preparation of superhydrophobic nylon 56/cotton interwoven fabric
The dopamine-modified nylon-56/cotton-interwoven fabric (4 cm × 4 cm) is then dipped in a solution comprising 100 mL of ethyl acetate. Octadecyl mercaptan (0.56 g), vinyl trimethoxysilane (0.3 g) and 2,2-dimethoxy-2-phenylacetophenone (0.25 g) are then added to the solution. The reaction system is sealed and irradiated under a UV lamp (250 W, λ = 365 nm) for 0.5 h, and the fabric is placed 15 cm away from the light source. Furthermore, 15 min after the start of the reaction, the fabric is turned over; eventually, it is washed with pure ethanol to remove the remaining reactants and dried in an oven at 80 °C for 1 h to obtain a superhydrophobic nylon-56/cotton-interwoven fabric.
2.4 Characterisation
A scanning electron microscope (SEM) (Hitachi S-4800) is used to observe the surface structure and morphology of the superhydrophobic textile, and a Thermo Fisher instrument (NEXSA, USA) and an AlKα X-ray source (1486.6 eV) are used to perform X-ray photoelectron spectroscopy (XPS). The energy-dispersive spectrometer (EDS) attached to the Hitachi TM3030 SEM (Japan) is employed for elemental composition analysis, and the Nicolet 5700 Fourier Transform Infrared Spectrometer (American Thermoelectric Company) is used for Fourier transform infrared (FTIR) spectroscopy. The static and dynamic contact angle wetting characteristics of the treated interwoven fabric are measured via KrüssDSA 100 (Krüss, Germany) equipment. Note that 6 μL of water droplets are used for the static contact angle (CA) and sliding angle (SA) measurements. In the tensile stability test, the breaking strength and breaking elongation of the original fabric and the superhydrophobic fabric were tested with the INSTRON-3365 material testing machine (American NSTRON Company, Norwood, MA, USA) according to the standard ISO 13934-1-2013. The tests were carried out in warp and weft directions respectively and the average value was obtained.
To evaluate chemical stability, the modified fabric is immersed in solutions with different pH values (1, 3, 5, 7, 9, 11, and 13) for 48 h and in acetone for various durations (4, 8, 12, 16, 20, and 24 h). The UV resistance of the modified fabric is determined by radiation under UV light for 4, 8, 12, and 16 h. An SWB-12A washing machine is used to determine the washing durability according to the standard AATCC Test Method 61-2003 No. 1A. For the sandpaper abrasion test, a 100 g weight is placed on the modified fabric sample and its surface is rubbed against sandpaper (1000 CW) and moved for 15 cm. After each of the aforementioned processes, the samples are cleaned with deionised water and dried at 70 °C to measure both CA and SA. Self-cleaning and oil–water-separation tests are then performed (Sections 3.6 and 3.7 for specific steps).
3. Results and discussions
3.1 Brief formation mechanism of superhydrophobic nylon-56/cotton-interwoven fabric
Dopamine is first oxidized to benzoquinone and then undergoes intramolecular cyclization, generates 5,6-dihydroxyindole through intramolecular rearrangement reactions and finally forms a polydopamine coating with irreversible high-strength covalent bonds on the substrate. The formed polydopamine coating is rich in hydroxyl functional groups. Vinyltrimethoxysilane is hydrolysed to form silanol, which undergoes a condensation reaction with the hydroxyl groups in polydopamine to form hydrogen bonds. Octadecyl mercaptan is then assisted by the photoinitiator click reaction with vinyl trimethoxy silane to form a micro–nanoscale rough structure on the substrate, thereby preparing the super hydrophobic textile.
3.2 Surface morphology and composition of the superhydrophobic nylon-56/cotton-interwoven fabric
Fig. 2 shows scanning electron images of the original nylon-56/cotton-interwoven fabric, the dopamine-modified nylon-56/cotton-interwoven fabric and the superhydrophobic nylon-56/cotton-interwoven fabric. From Fig. 2a and b, we can see that the original nylon-56/cotton fibres show relatively smooth surfaces with a clean appearance and no other substances attached. Fig. 2c and d show that after the dopamine-modification treatment, the surfaces of these fibres are covered with polydopamine aggregates, thus building a secondary reaction platform rich in hydroxyl groups. Fig. 2e and f illustrate that the surface morphologies of the nylon 56 and cotton fibres have significantly changed and that a large number of granular block polymers have appeared; this is attributed to silane is hydrolysed and condenses with the hydroxyl group in polydopamine to form a hydrogen bond, after which it forms a polymer through click reactions with thiol under UV light; these nano-scale particles increase the roughness of the fibre surface, thus lending the fabric superhydrophobic properties.
 |
| Fig. 2 SEM images of (a) original nylon-56 fibre; (b) original cotton fibre; (c) dopamine-modified nylon-56 fibre; (d) dopamine-modified cotton fibre; (e) superhydrophobic nylon-56 fibre; (f) superhydrophobic cotton fibre. | |
Fig. 3 and 4 show the EDS energy spectra of the nylon-56 and cotton fibres before and after finishing, respectively. Fig. 3b shows that the dopamine-modified nylon-56 fibre comprises 65.555% C, 19.075% O, and 15.370% N. This shows a change in the content ratios of C, O, and N compared to Fig. 3a, indicating that polydopamine aggregates are attached to the surfaces of nylon 56 fibres. Two new elements (S and Si) appear, revealing that a click reaction occurred and that the hydrophobic reagent was successfully grafted on the nylon 56 fibre surface. Fig. 3c indicates that S accounts for 1.2% of the content on the superhydrophobic nylon 56 fibre while Si accounts for 2.350%. Fig. 3f shows a nitrogen content of 8.047% in dopamine-modified cotton fibre. Compared with Fig. 3e, the appearance of N shows that polydopamine aggregates are successfully arranged on the surface of the cotton fibre; Fig. 3f indicates that S accounts for 3.192% of the superhydrophobic cotton fibre while Si accounts for 4.197%. Fig. 4g and h shows the distribution of S and Si on the surface of the modified fabric; the elements were evenly distributed.
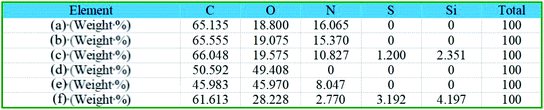 |
| Fig. 3 Element composition content of (a) original nylon-56 fibre, (b) dopamine-modified nylon-56 fibre and (c) superhydrophobic nylon-56 fibre, (d) original cotton fibre, (e) dopamine-modified cotton fibre, (f) superhydrophobic cotton fibre. | |
 |
| Fig. 4 EDS spectra of (a) original nylon-56 fibre, (b) dopamine-modified nylon-56 fibre and (c) superhydrophobic nylon-56 fibre, (d) original cotton fibre, (e) dopamine-modified cotton fibre, (f) superhydrophobic cotton fibre. (g) Element mapping of superhydrophobic nylon-56 fibre, (h) Element mapping of superhydrophobic cotton fibre. | |
Fig. 5 shows the infrared spectra (ATR) of the original nylon-56/cotton-interwoven fabric, the dopamine-modified nylon-56/cotton-interwoven fabric and the superhydrophobic nylon-56/cotton-interwoven fabric. The vibration peak at 1420 cm−1 is attributed to the pulling of the aromatic ring. The extensional vibrations show that dopamine successfully forms a polydopamine coating on the surface of the interwoven fabric. The vibrational peaks appearing at 2818 cm−1 and 2850 cm−1 are attributed to the symmetrical and asymmetrical vibrations of the –CH2 group in the long alkyl chain. Si–C-bending vibration peaks appear at 1260 cm−1. The vibration peak at 798 cm−1 is attributed to the tensile vibration of Si–O–Si. The above characteristic peaks indicate that the thiol–ene click–chemistry reaction has successfully occurred on the polydopamine coating.
 |
| Fig. 5 Infrared spectra of original nylon-56/cotton-interwoven fabric, dopamine-modified nylon-56/cotton-interwoven fabric and superhydrophobic nylon-56/cotton-interwoven fabric. | |
To validate the hydrophobisation process, an XPS test is performed. The XPS measurement spectrum presented in Fig. 6a shows that the nitrogen characteristic-peak area (at 398.4 eV) of the dopamine-modified nylon 56 fibre has changed compared with the original nylon 56 fibre. Fig. 6b shows a comparison with the original cotton fibre. The characteristic peak of nitrogen (at 398.4 eV) appears on the dopamine-modified cotton fibre, thereby confirming that dopamine successfully forms a polydopamine coating on the surfaces of nylon 56 and cotton fibres. Moreover, the area of the characteristic peak (at 284.8 eV) of carbon dramatically increases for the superhydrophobic textile, which can be attributed to the effect of the long-chain alkyl of octadecyl thiol. For superhydrophobic fibres, we can clearly observe four new peaks in Fig. 6a and b; these occur at 150.5 eV (Si 2s), 100.1 eV (Si 2p), 229.0 eV (S 2s) and 164.0 eV (S 2p). This shows that the superhydrophobic reagent prepared by click coupling with octadecyl mercaptan and vinyl trimethoxysilane is successfully grafted on the polydopamine aggregates.
 |
| Fig. 6 (a) XPS spectra of the original nylon-56 fibre, dopamine-modified nylon-56 fibre and superhydrophobic nylon-56 fibre; (b) XPS spectra of raw cotton fibre, dopamine-modified cotton fibre and superhydrophobic cotton fibre. | |
3.3 The effect of UV-irradiation time and reactant ratio on the superhydrophobic finishing of nylon-56/cotton-interwoven fabric
Fig. 7a displays the changes in the CA and SA of the superhydrophobic fabric under different UV irradiation times. For an illumination time of 30 min, the CA reaches 156.38° and the SA is <10°. The change in CA increases with illumination time and finally stabilises, which may be attributed to the completion of click reaction. The results show that the best illumination time is 30 min.
 |
| Fig. 7 (a) Changes in CA and SA with reaction time. (b) Changes in CA and SA with the ratio of vinyltrimethoxysilane to octadecyl mercaptan. | |
Vinyl trimethoxy silane and octadecyl mercaptan are used to generate polymers through the thiol–ene click reaction in which mercaptan and vinyl functional groups are almost equally consumed. Here, vinyl trimethoxy silane is hydrophobic and octadecyl mercaptan contains hydrophobic groups; hence, the ratio of vinyltrimethoxysilane to octadecyl mercaptan is crucial for determining surface wettability. Fig. 7b shows that CA and SA change with the molar-mass ratio; when the molar-mass ratio of vinyltrimethoxysilane and octadecyl mercaptan is 1
:
2, CA reaches 161°, SA reaches 8° and the nylon-56/cotton-interwoven fabric becomes superhydrophobic.
The degree of hysteresis of the contact angle represents how easy it is for the liquid to detach from the solid surface. The greater the difference between the advancing contact angle and the receding contact angle, the less likely it is for the liquid to move on the surface of the fabric. As shown in Fig. 8, the contact angle hysteresis of the samples is almost all less than 10°, indicating that the droplets are easy to fall off the surface of the superhydrophobic fabric.
 |
| Fig. 8 The data of the sample's advancing contact angle, receding contact angle and contact angle hysteresis. | |
3.4 Mechanical stability of superhydrophobic nylon-56/cotton-interwoven fabric
The mechanical stability of superhydrophobic fabrics should be considered for real-life applications because this largely determines their durability. Thus, we conducted a simple sandpaper-abrasion test. As shown in Fig. 9a, the fabric is placed on 1000-CW sandpaper, pressed with a weight of 100 g, and pulled 15 cm along the ruler. The CA of water was recorded after every five wear cycles to show the change in the fabric surface's wettability (Fig. 9b). The CA of the fabric remained >150° over 25 abrasion cycles; this may be attributed to the excellent adhesion of polydopamine. The nano aggregates on the fibre did not significantly fall off, resulting in stable and excellent hydrophobic properties. The mechanical stability of superhydrophobic fabrics also includes tensile stability, which is mainly characterized by testing mechanical strength. The test results are shown in the Fig. 10. Compared with the original fabric, the breaking strength and breaking elongation of the superhydrophobic fabric in the warp direction have not changed significantly, while the breaking strength and breaking elongation in the weft direction have been improved. The experimental finishing method not only caused no damage to the fabric, but also improved its mechanical properties. In summary, it shows that the superhydrophobic fabric has good mechanical stability, thereby improving the potential for superhydrophobic textile applications.
 |
| Fig. 9 (a) Picture of sandpaper-abrasion test. (b) CA and SA changes of the superhydrophobic nylon-56/cotton-interwoven fabric after 25 abrasion cycles. | |
 |
| Fig. 10 Tensile test of original fabric and superhydrophobic fabric. | |
3.5 Chemical stability and durability of superhydrophobic nylon-56/cotton-interwoven fabric
In the course of daily life, fabrics will be exposed to harsh and complex environments such as strong acids or bases, organic solvents, washing and ultraviolet radiation; therefore, it is necessary to improve the chemical stability and durability of superhydrophobic fabrics. To test the effects of ultraviolet radiation, our fabric sample is exposed to UV light. The fabric is situated 15 cm away from the light source. Each light cycle lasts 4 h, after which the CA and SA of the fabric are tested (Fig. 11a). From the figure, it can be seen that, after four photoperiods, the CA of the fabric gradually decreases with UV irradiation time, although it remains above 150°; the SA, moreover, increases slightly. Good hydrophobic properties are therefore observed, indicating that superhydrophobic fabric exhibits UV resistance. To test the effect of organic solvents on such fabrics, fabric samples are immersed in acetone every 4 h for a certain time period and then rinsed with deionised water and dried at 70 °C. As shown in Fig. 11b, after the fabric is soaked in acetone for 24 h, the CA remains above 155°, indicating that the fabric has good durability against acetone; this may be attributed to the chemical polymer grafted onto the polydopamine coating has good resistance to corrosion by organic solvents. To test the influence of the acid–base environment on the superhydrophobic fabric, the fabric samples are immersed in solutions of different pH (pH = 1, 3, 5, 7, 9, 11 and 13) for 48 h. Fig. 11c shows the CA; although there is a slight change, it still remains at >150°. The results show that the acid–base environment has a certain effect upon the superhydrophobic properties of the fabric, but that the fabric still maintains a high hydrophobicity. Therefore, superhydrophobic fabric has a certain resistance to acidic and alkaline environments. This may be because the air trapped upon the fabric's surface can inhibit acid or alkali corrosion. To test the effect of washing on superhydrophobic fabrics, washing durability is tested with reference to the standard washing-machine procedure outlined in the AATCC Test Method 61-2003 Test No. 1A. The washing times are set to 0, 45, 90, 135, 180, 225, and 270 min. As shown in Fig. 11d, the CA and SA of the fabric change with the washing time; however, the former remains above 155° while the latter remains below 10°. This may be attributed to the super adsorption of polydopamine, which makes it difficult for low-surface-energy substances to fall off of the surface of the substrate. Therefore, superhydrophobic fabric exhibits excellent UV resistance, solvent resistance, acid and alkali resistance, and water-washing resistance, all of which is conducive to industrial production.
 |
| Fig. 11 The changes in the CA and SA of superhydrophobic nylon-56/cotton-interwoven fabric under the following conditions: (a) UV irradiation over various times; (b) soaking in acetone over various times; (c) soaking in various-pH solutions over 48 hours; (d) washing over various times. | |
3.6 Self-cleaning performance of the superhydrophobic nylon-56/cotton-interwoven fabric
In this work, a reactive blue dye was used as a contaminant for self-cleaning tests; as shown in Fig. 12a and b, when water droplets fall, we can clearly see the difference between the original fabric and the superhydrophobic fabric. The surface of the original fabric is completely wetted and contaminated with dye; however, on the superhydrophobic fabric, this dye is removed by water droplets to ensure the surface is clean. To demonstrate the water-repellent characteristics of the superhydrophobic fabric, it, in addition to the original fabric, was completely immersed in water. The original fabric was reported to sink in water after being released while the superhydrophobic fabric floated (Fig. 13a). In practical applications, fabrics will come into contact with liquids commonly used in daily life; here, we use salt water, coffee, milk, dyed water, cola and tea. As shown in Fig. 13b and c, the original fabric was wetted and contaminated by these liquids; however, the surface of the superhydrophobic fabric showed spherical droplets and no contamination occurred. Fig. 14a and b show that when the droplets contact the original fabric, the fabric is completely penetrated. However, the droplets on the superhydrophobic fabric are in a spherical form. The results indicate that the permeability of the fabric is significantly reduced. This may be the hydrophobic agent grafted on the fiber surface achieves super hydrophobic effect. These results indicate that the superhydrophobic fabric has excellent self-cleaning and antifouling properties that are suitable for use in daily life.
 |
| Fig. 12 Self-cleaning test of nylon-56/cotton-interwoven fabric: (a) original fabric, (b) superhydrophobic fabric. | |
 |
| Fig. 13 (a) Water soaking of the original nylon-56/cotton-interwoven fabric and the superhydrophobic nylon-56/cotton-interwoven fabric; (b) the state of different droplets on the original nylon-56/cotton-interwoven fabric; (c) the state of different droplets on the superhydrophobic nylon-56/cotton-interwoven fabric. | |
 |
| Fig. 14 (a) Penetration effect of original fabric, (b) penetration effect of superhydrophobic fabric. | |
3.7 Oil–water-separation performance of superhydrophobic nylon-56/cotton-interwoven fabric
As industrialisation progresses, a large amount of oily wastewater will be generated during manufacturing processes. A superhydrophobic fabric can be used for oil–water separation, which is beneficial for environmental protection. Fig. 15a and b display methylene chloride and carbon tetrachloride stained with Oil Red O. The results illustrate that the superhydrophobic fabric can adsorb dichloromethane and carbon tetrachloride. Fig. 15c presents a schematic of an oil–water-separation test using a superhydrophobic fabric. Dichloromethane is dyed red with Oil Red O and water is dyed blue with methyl blue. The oil/water mixture (with both oil and water having volumes of 100 mL) is poured into an oil–water separation device. The oil quickly penetrates the fabric while the water is left on top; it can be seen that the oil–water separation performance of the superhydrophobic fabric is relatively excellent. Regardless of the density of the oil, the superhydrophobic fabric can selectively absorb oil. And based on the excellent durability, abrasion resistance and corrosion resistance of nylon 56, the super-hydrophobic fabric can be used in harsh environments, broadening the application in the field of oil–water separation.
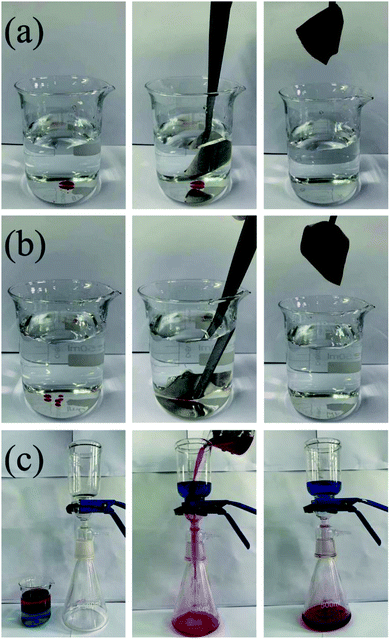 |
| Fig. 15 (a and b) The selective adsorption of superhydrophobic nylon-56/cotton-interwoven fabric to methylene chloride (dyed with Oil Red O) and carbon tetrachloride in water (dyed with Oil Red O); (c) oil–water-separation test of superhydrophobic nylon-56/cotton-interwoven fabric. | |
4. Conclusion
We oxidised and polymerised dopamine to form a polydopamine coating, built a secondary reaction platform rich in hydroxyl on the surface of cotton and nylon 56 fibres and grafted a superhydrophobic reagent onto the polydopamine aggregate via the click coupling of octadecyl mercaptan and vinyl trimethoxysilane; this not only improved the fabric's surface roughness but also reduced its surface energy. Thus, we successfully manufactured superhydrophobic textiles. The CA and SA of the superhydrophobic textiles are 161° and 8°, respectively. These textiles can withstand acidic and alkaline environments, organic solvents, washing with water, UV irradiation and mechanical wear. Moreover, they have excellent superhydrophobic stability and functionality for self-cleaning and oil–water separation. Our method is simple, rapid, environmentally friendly and universally applicable and can be applied to endow other substrates with high hydrophobicity. Thus, our technique shows good prospects for superhydrophobic applications.
Conflicts of interest
There are no conflicts to declare.
Acknowledgements
This work was supported by the Key R & D plan of Jiangsu Province (BE2019001), National Natural Science Foundation of China (519731441) and the Major Program of Natural Science Research of Jiangsu Higher Education Institutions of China (18KJA540002).
References
- M. Zhang, C. Guo and J. Hu, Surf Coat Tech, 2020, 400, 126155 CrossRef CAS.
- Y. Li, S. P. Zhao, W. H. Hu, X. Zhang, L. Pei and Z. Wang, Appl. Surf. Sci., 2019, 481, 374 CrossRef.
- A. Bake, N. Merah, A. Matin, M. Gondal, T. Qahtan and N. Abu-Dheir, Prog. Org. Coat., 2018, 122, 170 CrossRef.
- Q. Shang, J. Q. Chen, C. G. Liu, Y. Hu, L. H. Hu, X. H. Yang and Y. H. Zhou, Prog. Org. Coat., 2019, 137, 105346 CrossRef CAS.
- G. Pawar, R. Xing, R. C. Kambale, A. MadhanKumard, S. H. Liu and S. Latthe, Prog. Org. Coat., 2017, 105, 235 CrossRef.
- N. Wang and Z. W. Deng, Synthesis of magnetic, Mater. Res. Bull., 2019, 115, 19 CrossRef CAS.
- Y. He, P. Cao, F. Tian, X. Q. Bai and C. Q. Yuan, Surf Coat Tech, 2019, 357, 180 CrossRef.
- I. Vinogradova and A. L. Dubov, Mendeleev Commun., 2012, 22, 229 CrossRef.
- Y. Zhu and X. F. Hu, Surf Coat Tech, 2017, 313, 294 CrossRef.
- Y. Long, S. Peng, W. S. Deng, X. J. Yang, K. Miao, N. Wen, X. R. Miao and W. L. Deng, J. Colloid Interface Sci., 2017, 508, 18 CrossRef PubMed.
- Y. Liu, Q. Y. Wang, X. Q. Zhu, F. Yang, M. Y. Akrama and J. Nie, Mater. Lett., 2017, 190, 48 CrossRef CAS.
- C. Cho, C. Wan, C. Jian, Y. S. Hsiao, K. C. Lee and J. H. Huang, J. Taiwan Inst. Chem. Eng., 2016, 67, 476 CrossRef.
- D. Jiang, H. Zhou, S. Wan, G. Y. Cai and Z. H. Dong, Surf Coat Tech, 2018, 339, 155 CrossRef CAS.
- W. Sun, L. D. Wang, Z. Q. Yang, S. J. Li, T. T. Wu and G. C. Liu, Corros. Sci., 2017, 128, 176 CrossRef CAS.
- A. Liu, X. L. Yang, G. B. Pang, F. Zhang, Y. Q. Han, X. Y. Wang, X. Liu and L. Xue, Surf Coat Tech, 2019, 375, 527 CrossRef.
- A. Liu, F. Zhang, Y. Chen, H. Zhang, Y. Q. Han, J. Y. Liu, L. Huang and X. Liu, Colloids Surf., A, 2019, 572, 317 CrossRef.
- W. Zeng, Z. L. Qin, Q. H. Hua, Y. L. Min and Q. J. Xu, Surf Coat Tech, 2019, 362, 62 CrossRef.
- S. Lei, Z. Q. Shi, J. F. Ou, F. J. Wang, M. S. Xue, W. Li, G. J. Qiao, X. H. Guan and J. Zhang, Colloids Surf., A, 2017, 533, 249 CrossRef CAS.
- Q. Jia, M. Herrera-Alonso and T. McCarthy, Polymer, 2006, 47, 4916 CrossRef.
- B. Zhang, G. Tang, H. Q. Dong, Q. Q. Geng, J. F. Niu, J. Y. Tang, J. L. Yang, H. Huo and Y. S. Cao, Colloids Surf., B, 2019, 178, 153 CrossRef.
- N. Wanga, Z. G. Zhang, J. R. Huang and Y. X. Hu, Chem. Eng. Sci., 2019, 203, 312 CrossRef.
- J. Carey and J. L. Carey, Pharmacol., Biochem. Behav., 2017, 163, 36 CrossRef.
- F. Chen, J. T. Zhang, M. J. Hu, Z. Q. Zheng, K. D. Wang and X. B Li, Surf Coat Tech, 2018, 353, 1 CrossRef.
- G. Shi, D. Z. Xu, M. Y. Liu, L. H. Fu, Q. Wan, L. C. Mao, Y. F. Dai, Y. Q. Wen, X. Y. Zhang and Y. Wei, Mater. Sci. Eng., C, 2018, 82, 204 CrossRef PubMed.
- R. Zhou, R. B. Jia, Y. L. Wang, S. H. Sun, X. D. Xin, M. Q. Wang, Q. H. Zhao and H. H. Zhu, Sep. Purif. Technol., 2020, 234, 116099 CrossRef.
- J. Song, Y. J. Zhang, Y. C. Wang, M. H. Huang, S. Gul and H. Q. Jiang, Sep. Purif. Technol., 2020, 242, 116816 CrossRef.
- D. Zhang, G. L. Zheng, C. Zheng, Y. H. Wu and Z. Long, Prog. Org. Coat., 2019, 134, 226 CrossRef.
- C. Kolb and K. B. Sharpless, Drug Discovery Today, 2003, 8, 1128 CrossRef.
- A. Bassam, B. Noorullah, S. Suchetha, A. M. Saleh and A. S. Fakhreia, Polymer, 2018, 154, 233 CrossRef.
- L. Yu, Z. Zhang, Y. Z. You and C. Y. Hong, Eur. Polym. J., 2018, 103, 80 CrossRef CAS.
- X. Zhou, Y. M. Liu, T. F. Jiao, R. R. Xing, Z. Q. Yang, J. Z. Fan, J. Z. Liu, B. B. Li and Q. M. Peng, Colloids Surf., A, 2018, 538, 7 CrossRef.
- W. Bao, S. A. Bai, J. Fan, J. H. Su, W. Wang and D. Yu, Dyes Pigm., 2019, 171, 107778 CrossRef.
- Y. Ning, S. Wang, Z. T. Zhang, Z. B. Feng, Z. P. Zheng, B. Yu, M. Tian and L. Q. Zhang, Chem. Eng. J., 2019, 373, 318 CrossRef.
|
This journal is © The Royal Society of Chemistry 2021 |
Click here to see how this site uses Cookies. View our privacy policy here.