DOI:
10.1039/D0RA10667D
(Paper)
RSC Adv., 2021,
11, 8019-8024
Preparation of chemical staple fibers by plasticizing bleached coniferous pulps with 1-allyl-3-methylimidazolium chloride
Received
19th December 2020
, Accepted 8th February 2021
First published on 18th February 2021
Introduction
There is increasing environmental concern over petroleum-based polymers due to their ecological toxicity and non-renewable nature. Biopolymers have great potential to replace petroleum-originated polymers.1 These new biopolymers such as cellulose, starch, protein, lignin and so on,2 must be biodegradable, coming from a natural and renewable origin, with low-cost production and similar properties to conventional polymers.3
Among the most promising biopolymers, cellulose which consists of β-(1→4)-linked glucose repeating units4 is the most abundant natural polymer and has numerous applications in papermaking, film manufacturing, pharmaceuticals, textile and food industries.5–7 Due to the numerous inter- and intramolecular hydrogen bonds and amphiphilicity of repeat units,8 cellulose can neither dissolve in common solvents nor melt at elevated temperature even above the decomposition temperature, which makes this fantastic material difficult to process.9,10
So far, several solvents have been used for cellulose dissolution and film preparation, including ionic liquids (ILs), N-methylmorpholine-N-oxide, urea/NaOH, and ZnCl2. Among these solvents, ILs were essentially the most promising green solvent because of their negligible vapor pressure, low toxicity, easy recyclability, non-flammability, high chemical and thermal stability.11–14 Known as powerful solvents for cellulose and wood, ILs have been extensively studied for the plasticization of wood cell walls.15,16 Bulk wood samples treated with a small amount of ILs could achieve large deformations under low pressure without cell wall fracture.16 As early as in 2003, Mark P. Scott has regarded ILs as replacements for traditional plasticizers, with the potential to achieve materials that had better thermal stability, and a wider temperature range of flexible plastic behavior.17 As one of the ILs, 1-allyl-3-methylimidazolium chloride (AMIMCl) is a powerful non-derivatizing solvent for cellulose, and a solution containing 14.5 wt% cellulose can be prepared at 80 °Cwithout any pretreatment.18 It was first synthesized in Zhang's group in 2003.19
Cellulose content in cotton is nearly to 100%,20 which is the purest natural cellulose21 and widely used in the textile industry. We plasticized it and prepared chemical fibers successfully in our previous work,22 but it was rarely used in pulp and paper industry due to the price of cotton was higher than bleached coniferous pulps (BCPs). In terms of fiber length, BCPs are shorter than cotton. BCPs which main components are cellulose and a small amount of hemicellulose with the lignin removed in the process of bleaching are widely used in pulp and paper industry.23,24 It has superior quality of brightness, softness and cleanliness in comparison to unbleached pulps.25
In this study, we prepared chemical staple fibers (CSFs) by plasticizing BCPs with AMIMCl in a similar way to plasticize cotton under high temperature and pressure. The purpose of plasticizing was to reduce its melting point before it decomposed and achieved workability to a certain extent. There was no waste liquid in the process as the liquid ratio was small and the mass of AMIMCl was less than BCPs. Application of CSFs prepared by AMIMCl in papermaking was also discussed. Finally, in order to know whether the method of preparing CSFs with AMIMCl was universal, we chose 1-butyl-3-methylimidazolium chloride (BMIMCl) and 1-ethyl-3-methylimidazolium acetate (EMIMAc) for a simple experiment.
Experimental
Materials
BCPs were bleached kraft softwood pulps and provided by Nine Dragons Paper (Taicang) Co. Ltd, China. AMIMCl (98%, melting point 17 °C)19 was purchased from Shanghai Chengjie Chemical Co. Ltd, China.
Preparation of CSFs
The preparation process of CSFs was schematically shown in Fig. 1. BCPs were kneaded with AMIMCl at mass ratios of 1
:
5, 2
:
5, 3
:
5, 4
:
5 at room temperature, respectively. Then, the mixture was hot pressed for 1 minute at 160 °C, 2 MPa. It would be a piece of paper after hot-pressing when the mass ratios of AMIMCl to BCPs were 1
:
5, 2
:
5, 3
:
5. This process could only be hot pressed once and couldn't be repeated. However, it would be a piece of transparent paper after hot-pressing when the mass ratio of AMIMCl to BCPs was 4
:
5. Interestingly, it could be hot pressed into a new piece of transparent paper after the piece of transparent paper prepared above was torn to pieces and this process could be repeated several times.
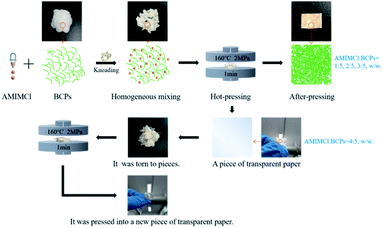 |
| Fig. 1 Schematic of preparation of CSFs. | |
Characterization
The morphologies of samples were observed by a field emission scanning electron microscope (FE-SEM, JSM-7600F, JEOL, Japan). XRD spectra were obtained using an X-ray refractometer (Ultima IV, Japan). The FT-IR spectra were obtained in a Fourier transform infrared spectroscopy spectrometer (Vertex80 V, Bruker, Germany). The thermal stabilities of the samples were determined via Thermogravimetric (TG) analyses using a gravimetric analyzer TGA (Q5000IR, TA instruments, USA). The glass transition temperature (Tg) of samples was obtained by DSC 214 F1 Phoenix (Netzsch, Germany).
Properties of paper made from BCPs and CSFs
Paper was prepared by a PTI paper machine (RK-2A 0529, Austria). Physical properties of paper, including tensile strength, burst strength, tear strength and folding strength were tested according to Chinese standard. Tensile strength was measured by tension meter (WZL-300, China). Burst strength was measured by burst tester (YQ-Z-23A, China). Tear strength was measured by tearing meter (J-SLY1000A, China). Folding strength was measured by folding tester (ZZD-25B, China).
Results and discussion
Morphologies of BCPs and CSFs
The morphologies of BCPs and CSFs were shown in Fig. 2. Fig. 2a showed the BCPs were intertwined in a random and fluffy way with a mean diameter of 21.72 μm. Fig. 2b showed the BCPs were blended with AMIMCl. Its mean diameter was 28.89 μm and it was larger than BCPs as the AMIMCl permeated the BCPs, resulting in limited swelling. We could see the surfaces of the BCPs were partially dissolved and became rough after blending with AMIMCl. It still retained fibrous form and fibers were randomly bonded together tightly after hot-pressing in Fig. 2c and d. It was a transparent paper after hot-pressing when the mass ratio of AMIMCl to BCPs was 4
:
5 due to the fact that BCPs were plasticized with the addition of AMIMCl gradually under high temperature and pressure.
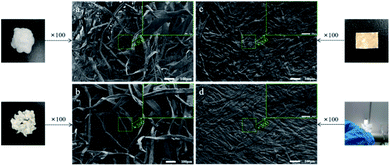 |
| Fig. 2 (a) SEM of BCPs. (b) SEM of BCPs blending with AMIMCl. (c) SEM of CSFs after hot-pressing when the mass ratios of AMIMCl to BCPs were 1 : 5, 2 : 5, 3 : 5. (d) SEM of the CSFs after hot-pressing when the mass ratio of AMIMCl to BCPs was 4 : 5. | |
The crystalline indices of BCPs and CSFs
Fig. 3 showed the X-ray diffraction spectrograms of BCPs and CSFs, indicating that the crystalline structure was cellulose I in all cases because of similar XRD patterns to those reported in the literature for cellulose I.26 The degrees of crystallinity calculated from the 2θ peaks at Iam and I200 were 34.6%, 39.6%, 47.1%, 52%, 56.3%, when the BCPs and the mass ratios of AMIMCl to BCPs were 1
:
5, 2
:
5, 3
:
5, 4
:
5, respectively. It was evident that the crystalline indices of the CSFs were higher than BCPs. The increase in crystallinity was attributed to the amorphous regions were dissolved by AMIMCl under high temperature and pressure. The more AMIMCl was added, the higher crystallinity was.
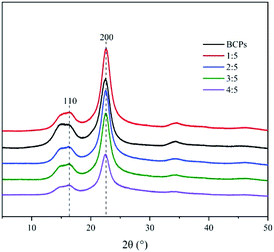 |
| Fig. 3 X-ray diffraction patterns of BCPs and CSFs. | |
Chemical structures of BCPs and CSFs
The FT-IR spectra of BCPs and CSFs were shown in Fig. 4. The dominant peaks in the region 3750 to 3000 cm−1 were attributed to O–H groups which were associated with the stretching vibrations in cellulose from inter-molecular and intra-molecular hydrogen bonds26 and C–H which was an unsaturated carbon in the molecular structure of AMIMCl.27 The peaks in the region 3000 to 2700 cm−1 were due to the stretching vibrations of C–H which was saturated carbon in cellulose and AMIMCl. The peaks in the region 1690 to 1500 cm−1 were due to the stretching vibration of C
C in the molecular structure of AMIMCl. That at 1370 cm−1 showed C–H asymmetric deformations.26 Additionally, absorption peaks caused by C–O were observed near 1100 cm−1, 1050 cm−1 and 990 cm−1, these were typical absorption bands of cellulose.28 The results of FT-IR analysis indicated that no new chemical structures occurred, only initial characteristics were observed in the CSFs, and proved that there was no chemical reaction between AMIMCl and BCPs.
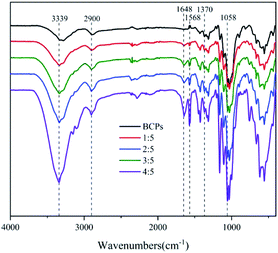 |
| Fig. 4 FT-IR spectra of BCPs and CSFs. | |
Thermal stabilities of BCPs and CSFs
As shown in Fig. 5, BCPs began to degrade at about 227 °C. The initial decomposition temperature of CSFs was approximately 192 °C when the mass ratios of AMIMCl to BCPs were 1
:
5, 2
:
5, 3
:
5, 4
:
5.
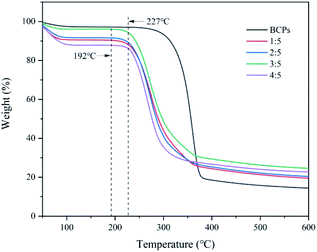 |
| Fig. 5 TG curves of BCPs and CSFs. | |
Fig. 6 presented the derivative thermogravimetric (DTG) curves of the samples. The temperatures corresponding to the maximum decomposition rates of BCPs were 360.17 °C and CSFs were 273.70 °C (AMIMCl to BCPs was 1
:
5, w/w), 273.21 °C (2
:
5), 273.71 °C (3
:
5), 267.45 °C (4
:
5), respectively; although thermal stability of CSFs was lower than BCPs, the temperatures corresponding to the maximum decomposition rates of CSFs were almost the same with the addition of AMIMCl.
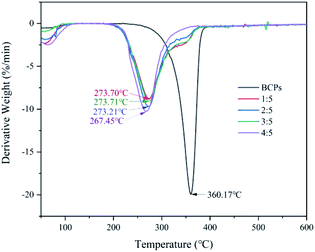 |
| Fig. 6 DTG curves of BCPs and CSFs. | |
In brief, AMIMCl had large effect on the thermal stability of BCPs in the beginning, then, the CSFs were very stable with the addition of AMIMCl.
The glass transitions of CSFs
In terms of molecular structure, the Tg is a relaxation phenomenon of the amorphous part of the polymer from freezing to thawing.29 Below the Tg, the polymer is in a glassy state, the molecular chain and the chain segment cannot move, but the atoms (or groups) which constitute the molecule vibrate in its equilibrium position.30 Above the Tg, although the molecular chain cannot move, the chain segment starts to move, showing high elastic properties.31 If the temperature continues to rise, the entire molecular chain will move and show viscous flow properties.32,33 We can further confirm BCPs are plasticized by AMIMCl through it.
DSC curves of CSFs were shown in Fig. 7. There were no exothermic peak of BCPs and CSFs when the mass ratios of AMIMCl to BCPs were 1
:
5, 2
:
5, 3
:
5. However, the exothermic peak occurred when the mass ratio of AMIMCl to BCPs was 4
:
5 and the corresponding temperature was 149 °C, which was lower than the initial decomposition temperatures of CSFs in Fig. 5, therefore, CSFs could achieve workability to a certain extent. It was the same to the phenomenon in Fig. 1.
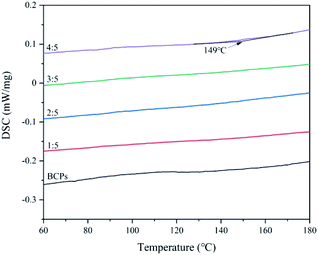 |
| Fig. 7 DSC curves of BCPs and CSFs. | |
Application of CSFs in papermaking
We should have prepared plasticized paper with CSFs, but water was needed in the process of papermaking, which would lead to the loss of AMIMCl, affecting the later plasticizing effect. In order to test the physical properties of plasticized paper made from CSFs, we adopted another method, which was schematically shown in Fig. 8. Firstly, we prepared paper with BCPs (beating degree was 15). Secondly, we coated paper evenly with AMIMCl which was uniformly dispersed in a small amount of water according to the above mass ratios. Thirdly, paper was dried in an oven. Finally, plasticized paper was prepared under hot-pressing. It wouldn't be a new piece of paper after hot-pressing when the mass ratios of AMIMCl to paper were 1
:
5, 2
:
5, 3
:
5. It would be a new piece of transparent paper after hot-pressing when the mass ratio of AMIMCl to paper was 4
:
5. This was the same as the phenomenon in Fig. 1 and 7, confirming that the paper was indeed plasticized by AMIMCl. For better comparison, unplasticized paper made from BCPs was also hot pressed under the same conditions.
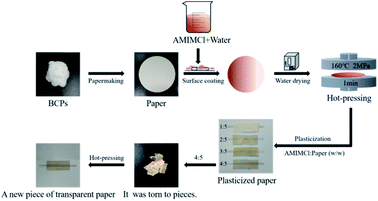 |
| Fig. 8 Schematic of preparation of plasticized paper. | |
The physical properties of paper and plasticized paper could be seen in Table 1. The grammage of all dried paper was 100 g m−2 and the density was about 0.67 g cm−3. The tensile index increased with the increase of the mass proportion of AMIMCl. The burst index increased continuously from sample 1 to sample 3 and then tended to be stable. The reason for this phenomenon was that the fibers of BCPs were initially bonded by hydrogen bonds. The bonding between fibers was enhanced due to the interaction between the melt formed by melting after BCPs were plasticized into CSFs. AMIMCl had little effect on the tear index, but great effect on the folding strength. The folding strength increased with the increase of the mass proportion of AMIMCl, especially for sample 5, which increased significantly, further indicating the plasticizing effect of AMIMCl on BCPs.
Table 1 Physical properties of paper and plasticized paper
Sample |
AMIMCl : paper (w/w) |
Grammage of dried paper [g m−2] |
Density [g cm−3] |
Tensile index [N m g−1] |
Burst index [kPa·m2 g−1] |
Tear index [mN·m2 g−1] |
Folding strength |
1 |
0 |
100 |
0.63 |
9.044 |
0.40 |
0.22 |
5 |
2 |
1 : 5 |
100 |
0.65 |
9.629 |
0.75 |
0.30 |
8 |
3 |
2 : 5 |
100 |
0.67 |
12.66 |
1.20 |
0.23 |
29 |
4 |
3 : 5 |
100 |
0.71 |
14.25 |
1.20 |
0.25 |
33 |
5 |
4 : 5 |
100 |
0.67 |
16.06 |
1.18 |
0.25 |
60 |
Plasticizing effects of other ILs on BCPs
In order to know whether the method of preparing CSFs with AMIMCl was universal, we chose BMIMCl and EMIMAc for a simple experiment. They were all purchased from Shanghai Chengjie Chemical Co. Ltd, China. The plasticizing effects of two ILs on BCPs were shown in Fig. 9 and Fig. 11. The mass ratio of IL to BCPs we chose was 4
:
5, which was the best plasticizing mass ratio for AMIMCl. BMIMCl (melting point was 70 °C) was solid at room temperature, so we adopted the method shown in Fig. 9. Both BMIMCl and EMIMAc plasticized BCPs could be hot pressed into a piece of paper and then hot pressed for a second time, which was similar to the effect in Fig. 1. DSC curves of CSFs prepared by BMIMCl and EMIMAc were shown in Fig. 11. Tg was 169 °C and 143 °C respectively with the appearance of exothermic peaks, which was lower than the initial decomposition temperatures in Fig. 10 and directly confirmed that BCPs were plasticized by two ILs. In short, the above results indicated that the preparation method of CSFs was applicable not only to AMIMCl but also to other ILs.
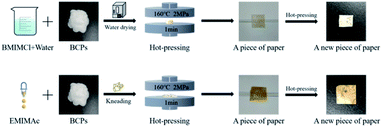 |
| Fig. 9 Plasticizing effects of BMIMCl and EMIMAc on BCPs. | |
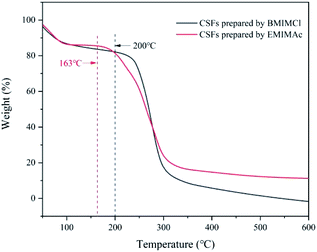 |
| Fig. 10 TG curves of CSFs prepared by BMIMCl and EMIMAc. | |
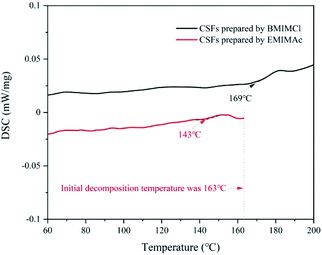 |
| Fig. 11 DSC curves of CSFs prepared by BMIMCl and EMIMAc. | |
Conclusions
CSFs were successfully prepared in this work. The morphologies of fibers showed that BCPs could be plasticized with AMIMCl. The crystallinity of CSFs increased as the amorphous regions were dissolved by AMIMCl under high temperature and pressure. The results of FT-IR analysis indicated that no new chemical structures occurred and BCPs were just physically plasticized in this process. TG and DTG showed that AMIMCl had large effect on the thermal stability of BCPs in the beginning, but the CSFs were very stable with the addition of AMIMCl. The Tg occurred in CSFs when the mass ratio of AMIMCl to BCPs was 4
:
5 and the corresponding temperature was 149 °C, which was lower than the initial decomposition temperature, therefore, CSFs could achieve workability to a certain extent. The plasticizing effect of AMIMCl on BCPs was further verified by testing the properties of paper. The plasticizing effects of BMIMCl and EMIMAc on BCPs showed the universality of the method of preparing CSFs with AMIMCl.
Author contributions
Xiaolong Qiao: writing – original draft, software, methodology, formal analysis; Hailong Lu: resources, software; Hui Cai: resources, formal analysis; Shuzhen Ni: writing – review & editing; Xiaofan Zhou: conceptualization, supervision, writing – review & editing.
Conflicts of interest
There are no conflicts to declare.
Acknowledgements
The authors acknowledge the financial support from the Natural Science Foundation of Jiangsu Provincial University (16KJA220005) and the State Key Laboratory of Biobased Material and Green Papermaking Foundation of Qilu University of Technology (ZZ20200103).
References
- M. A. Haq, Y. Habu, K. Yamamoto, A. Takada and J. Kadokawa, Carbohydr. Polym., 2019, 223, 115058 CrossRef CAS.
- K. Wilpiszewska and T. Spychaj, Carbohydr. Polym., 2011, 86, 424–428 CrossRef CAS.
- M. R. Area, M. Rico, B. Montero, L. Barral, R. Bouza, J. López and C. Ramírez, Carbohydr. Polym., 2019, 206, 726–733 CrossRef CAS.
- L. Feng and Z. Chen, J. Mol. Liq., 2008, 142, 1–5 CrossRef.
- K. Xu, Y. Xiao, Y. Cao, S. Peng, M. Fan and K. Wang, Carbohydr. Polym., 2019, 209, 382–388 CrossRef CAS.
- R. D. Gupta and N. Raghav, Int. J. Biol. Macromol., 2020, 147, 921–930 CrossRef CAS.
- D.-F. Hou, Z.-Y. Liu, L. Zhou, H. Tan, W. Yang and M.-B. Yang, Int. J. Biol. Macromol., 2020, 161, 177–186 CrossRef CAS.
- Y. Fourati, A. Magnin, J.-L. Putaux and S. Boufi, Carbohydr. Polym., 2020, 229, 115554 CrossRef CAS.
- J. Wu, J. Bai, Z. Xue, Y. Liao, X. Zhou and X. Xie, Cellulose, 2015, 22, 89–99 CrossRef CAS.
- T. Lu, M. Jiang, Z. Jiang, D. Hui, Z. Wang and Z. Zhou, Composites, Part B, 2013, 51, 28–34 CrossRef CAS.
- X. Zheng, F. Huang, L. Chen, L. Huang, S. Cao and X. Ma, Carbohydr. Polym., 2019, 203, 214–218 CrossRef CAS.
- J. Zhang, H. Kitayama, Y. Gotoh, A. Potthast and T. Rosenau, Carbohydr. Polym., 2019, 226, 115258 CrossRef.
- X. Y. Tan, S. B. Abd Hamid and C. W. Lai, Biomass Bioenergy, 2015, 81, 584–591 CrossRef CAS.
- J. Zhang, J. Wu, Y. Cao, S. Sang, J. Zhang and J. He, Cellulose, 2009, 16, 299–308 CrossRef CAS.
- J. Chen, X. Chen, M. Su, J. Ye, J. Hong and Z. Yang, Chem. Eng. J., 2015, 279, 136–142 CrossRef CAS.
- R. Ou, Y. Xie, Q. Wang, S. Sui and M. P. Wolcott, Holzforschung, 2014, 68(5), 555–566 CAS.
- M. P. Scott, M. Rahman and C. S. Brazel, Eur. Polym. J., 2003, 39, 1947–1953 CrossRef CAS.
- Y. Zhang, A. Xu, B. Lu, Z. Li and J. Wang, Carbohydr. Polym., 2015, 117, 666–672 CrossRef CAS.
- H. Zhang, J. Wu, J. Zhang and J. He, Macromolecules, 2005, 38, 8272–8277 CrossRef CAS.
- C. Zhao, H. Okada and R. Sugimoto, Polym. J., 2019, 51, 1023–1028 CrossRef CAS.
- H. N. Cheng and A. Biswas, Carbohydr. Polym., 2011, 84, 1004–1010 CrossRef CAS.
- X. Qiao, S. Ni, H. Lu, X. Wang and X. Zhou, Int. J. Biol. Macromol., 2021, 166, 1508–1512 CrossRef CAS.
- P. Bajpai, Green
Chemistry and Sustainability in Pulp and Paper Industry, Springer International Publishing, Cham, 2015 Search PubMed.
- A. L. Macfarlane, J. F. Kadla and R. J. Kerekes, Ind. Eng. Chem. Res., 2012, 51, 10702–10711 CrossRef CAS.
- N. Sharma, N. K. Bhardwaj and R. B. P. Singh, J. Clean. Prod., 2020, 256, 120338 CrossRef CAS.
- H. Lu, L. Zhang, C. Liu, Z. He, X. Zhou and Y. Ni, Cellulose, 2018, 25, 7043–7051 CrossRef CAS.
- D. Zhao, C. Wang, X. Luo, X. Fu, H. Liu and L. Yu, Int. J. Biol. Macromol., 2015, 78, 304–312 CrossRef CAS.
- X. Wang, H. Bian, S. Ni, S. Sun, L. Jiao and H. Dai, Int. J. Biol. Macromol., 2020, 157, 259–266 CrossRef CAS.
- A. L. Holmberg, N. A. Nguyen, M. G. Karavolias, K. H. Reno, R. P. Wool and T. H. Epps, Macromolecules, 2016, 49, 1286–1295 CrossRef CAS.
- Y. Fourati, A. Magnin, J.-L. Putaux and S. Boufi, Carbohydr. Polym., 2020, 229, 115554 CrossRef CAS.
- S. Ismail, N. Mansor and Z. Man, Procedia Eng., 2017, 184, 567–572 CrossRef CAS.
- Y. Xu, Y. Xu, C. Sun, L. Zou and J. He, Eur. Polym. J., 2020, 133, 109768 CrossRef CAS.
- C. Wang, H. Gao, X. Chen, S. Ni, N. Liu and H. Dai, Journal of Qilu University of Technology, 2020, 34(4), 28–34 Search PubMed.
|
This journal is © The Royal Society of Chemistry 2021 |
Click here to see how this site uses Cookies. View our privacy policy here.