DOI:
10.1039/D0RA09704G
(Paper)
RSC Adv., 2021,
11, 6877-6884
Metal mobility and toxicity of reclaimed copper smelting fly ash and smelting slag†
Received
15th November 2020
, Accepted 9th January 2021
First published on 10th February 2021
Abstract
Copper is a nonferrous metal closely connected to humans. Approximately 40% of copper is produced by reclaimed copper smelting (RCS). Reclaimed copper smelting fly ash and smelting slag are generated during the RCS process, posing a serious threat to the ecosystem and environment as they contain many heavy metals, such as Cu and Zn. In this study, the metal mobility and toxicity of RCS fly ash and smelting slag were analyzed using standard leaching toxicity procedures, sequential extraction procedures, and bioavailability tests. The results showed that the main phases of RCS fly ash were Cu2(OH)3Cl, FeCl2·2H2O, CuS2, C, CuO, Cu, Ca2SiO4, ZnClO42, Zn(OH)2·0.5H2O, and KFeCl3, and those for smelting slag were SiO2, CaCO3, SiS2, CaAl2Si2O8·4H2O, Cu4O3, CuO, ZnO, NiSO4·6H2O, AlPO4, and Na3Mn(PO4)(CO)3. These two slags contain high contents of Cu, Zn and Fe and trace amounts of heavy metals, such as Ba, Be, Cd, Cr, Ni, As, Pb, Au, Se and Sb. RCS fly ash is classified as hazardous waste in both China and the USA as the toxic leaching concentrations of Pb and Cd exceed the thresholds of 5 and 1 mg L−1. Cu and Zn contained in these two slags can easily be released into the environment, although the residual fraction of Cu and Zn was found to be higher than 65%. Additionally, RCS fly ash and smelting slag also show significant biohazardous potential as the EDTA- and DTPA-extractable Zn, Cu and Se of these two residues are considerably high. The results described above could provide reclaimed copper smelting companies and governments with a better understanding of the risk of RCS fly ash and smelting slag, urging them to stop the slag from harming ecosystems and humans.
1. Introduction
Copper is a nonferrous metal strongly related to humans. It is widely used in the electrical, light, machinery manufacturing, construction, and national defense industries, as well as other fields.1 In 2019, the output of global copper mines was 20.69 million tons, and the output of refined copper production was 23.72 million tons. China is the world's largest refined copper producer, with an annual refined copper output of 9.784 million tons in 2019, accounting for 41.24% of the world's total. China is also the largest consumer of refined copper, accounting for approximately 48% of the world's total.2
Copper has an excellent recycling performance, and it is an important raw material for copper refining to directly utilize copper waste and indirect smelting of waste copper.3 Low energy consumption, material consumption, and waste discharge per unit of refined copper are produced from waste copper regeneration. They are also beneficial to energy conservation, emission reduction, and resource recycling compared with copper smelting.4 In 2019, the proportion of reclaimed copper production was very high according to data from the International Copper Research Organization (ICSG), among which the United States accounted for approximately 60%, Japan accounted for approximately 45%, and Germany accounted for approximately 80%, while China accounted for only 33.73%.
The most economical utilization method is determined by the composition of raw materials and different copper grades.5 The smelting process mainly includes one-stage and two-stage smelting.6 The one-stage smelting method is aimed at high-grade waste copper and miscellaneous copper. If the copper content is higher than 90%, it can be refined directly into anode copper through a fire refining furnace. The two-stage smelting process focuses on high-grade scrap copper and miscellaneous copper. If the copper content is lower than 90%, the smelting furnace first uses a melting furnace to remove impurities; if, after processing, the material has a copper content higher than 80%, a two-stage smelting method is adopted for direct input into the refining furnace for smelting anode copper. A three-stage smelting process is used if the copper content is lower than 80%.
Purple miscellaneous scrap copper is the primary reclaimed copper, including tin-plated steel waste, tin-bronze, brass, and various alloys.7 The copper content is higher than 95%, and the specific smelting process is shown in Fig. S1.† As presented in Fig. S1,† the flue gas produced in the melting furnace is mainly removed by the cloth bag dedusting process. The reclaimed copper smelting (RCS) fly ash and smelting slag contains many heavy metal ions because the purple miscellaneous scrap copper contains copper, lead, zinc, tin, protective iron, oxygen and other impurities. If RCS fly ash and smelting slag are piled up, they may contaminate the soil and water, effecting the growth of plants, and even endangering human health. The area of cultivated land polluted by heavy metals such as arsenic, cadmium, lead, and chromium accounts for about one fifth of the total area of cultivated land in China.8 As metal in farmland soil is the most important risk factor for carcinogenesis, with contribution rates of 99% in children and 98% in adults.9 Plants around mining areas are also severely contaminated by Sb, As, Cd and Pb. The edible parts of vegetables can take up 2.05 mg kg−1 of Sb, which has high risks for human ingestion, moreover, the metals of As and Pb in vegetables significantly exceed the standard guidelines.10 Direct discharge of RCS fly ash and smelting slag causes severe environmental pollution.
Researchers have performed a significant amount of research into the treatment and resource utilization of RCS fly ash and smelting slag to make it harmless.4,11,12 This research mainly includes water leaching,13 acid leaching,14–17 oxidation leaching,18,19 bioleaching,20,21 pressure oxidative leaching,14 chloride leaching,22 alkali leaching,1 controlling potential leaching,23 the leaching-extraction method and the leaching-blast furnace smelting method.24 The copper and zinc in RCS fly ash and smelting slag can be leached using water or dilute sulfuric acid, and the leaching solution and leach residue can be treated using other methods.25–27 However, limited information was found regarding the metal mobility and toxicity of RCS fly ash and smelting slag.
In this study, typical RCS fly ash and smelting slag were collected and their metal levels, phases and morphologies were analyzed using X-ray diffractometry (XRD), X-ray fluorescence spectroscopy (XRF) and inductively coupled plasma optical emission spectroscopy (ICPOES). The metal mobility was examined using bioavailability tests and sequential extraction procedures; the leaching toxicity was classified according to the Identification Standards for Hazardous Waste-Leaching Toxicity (GB5085.3-2007) and the Toxicity Characteristic Leaching Procedure (TCLP). We expect that the results of this study will provide valuable information for managing and reusing RCS fly ash and smelting slag, in addition to reducing environmental risks.
2. Materials and method
2.1 Preparation of the materials
Reclaimed copper smelting fly ash and smelting slag were collected from an RCS factory in Sichuan province in China. RCS fly ash and smelting slag were dried at 80 °C for 24 h to achieve a constant weight. The carbon content of the RCS fly ash and smelting slag were 30.27% and 2.67%, respectively. The density of the RCS fly ash and smelting slag were 0.5769 and 1.0649 g cm−3, respectively. In this study, all the chemical reagents (HNO3, HCI, HF, H2SO4, CH3COOH, NaOH, NH4SCN, NH4Fe(SO4)2·12H2O, AgNO3, C15H15N3O2, NH3·H2O, CH3COONH4, HONH2HCl, H2O2, and EDTA–Na2) were purchased from Mianyang Xinjie Trading Co. Ltd, China (Analytical grade) and applied without further purification. Deionized water was provided using the Water Purification System (Advantage A10, Millipore, Burlington, MA, USA), and all experiments were carried out at room temperature.
2.2 Chemical composition
The chemical component of RCS fly ash and smelting slag were analyzed using XRF (Axios, PANalytical, Holland). In addition, these residues were digested and analyzed using ICPOES (OPTIMA 8000, PerkinElmer, U.S.) to quantify the concentrations of Al, Ba, Be, Cr, Cd, Cu, Fe, Ni, Pb, Sb, Sn, Tl, Zn, and Au. The chemical phase of the RCS fly ash and smelting slag were examined using XRD (D/MAX2500, Rigaku, Almelo, Holland).
2.3 Hazardous waste classification
The heavy metal leaching toxicities of RCS fly ash and smelting slag were examined using the Identification Standards for Hazardous Waste-Leaching toxicity (GB5085.3-2007, Ministry of Ecology and Environment of the People's Republic of China, 2007, Chinese standards) and the TCLP (US EPA 1992; American standards).28–30 The solid waste classifications of the RCS fly ash and smelting slag were examined using HJ/T 299-2007 (Solid waste-extraction for leaching toxicity, sulfuric and nitric acid method) and the TCLP (Method 1311; 40 CFR §261.24). Based on HJ/T 299-2007, only Al, As, Ba, Be, Cd, Cu, Ni, Pb, Sb, In, Se, Zn and Au were analyzed, while for TCLP, seven metals, Al, As, Ba, Be, Cd, Cr, Cu, Fe, Ni, Pb, Sb, In, Se and Zn were examined.
For HJ/T 299-2007, 10.00 g of RCS fly ash and 10.00 g smelting slag were placed into extraction bottles, respectively. 100 mL of sulfuric and nitric acid solution (the mass ratio of the concentrated sulfuric acids and nitric acids was 2
:
1) was used as the extraction liquid, and the pH of the extraction liquid was 3.20 ± 0.05. The bottles were fixed on a rotary extractor (extraction time, 18 ± 2 h; speed, 32 ± 2 rpm), and then the concentrations of heavy metals in the extraction liquid were analyzed using ICPOES after filtration through a 0.45 μm microporous membrane.
For the TCLP, 5 g RCS fly ash and 5 g smelting slag were placed into extraction bottles, respectively. Acetic acid was used as the extraction liquid, and the pH of the extraction liquid was 2.88 ± 0.05, when the solid–liquid ratio was 20
:
1 (kg L−1). The bottles were fixed on a rotary extractor (extraction time, 18 ± 2 h; speed, 32 ± 2 rpm), and then the concentrations of heavy metals in extraction liquid were analyzed using ICPOES after filtration through a 0.45 μm microporous membrane.
2.4 Metal chemical speciation and bioavailability
The chemical speciation of Al, Ba, Be, Cr, Cd, Cu, Fe, Ni, Pb, Sb, Sn, Tl and Zn in RCS fly ash and smelting slag were performed according to the three steps outlined in the Community Bureau of Reference (BCR) protocol of the European Standards Measurements and Testing Program, respectively.31 The details are shown in Table A in the ESI.† After each step, the suspensions were filtered using a 0.45 μm microporous membrane and tested using ICPOES. Metal bioavailability tests on RCS fly ash and smelting slag were tested using the Wear and Evans method, as well as the method proposed by Lindsay and Norvell. For the Wear and Evans method, 2.0 g of RCS fly ash and smelting slag were placed in a 50 mL centrifuge tube and mixed with 20 mL 0.05 mol L−1 EDTA at pH 7.0, respectively, as well as shaking the suspension in an oscillating device for 1 h. For the Lindsay and Norvell method, 10 g of the RCS fly ash and smelting slag were mixed in a 50 mL centrifuge tube and mixed with 20 mL 0.005 mol L−1 DTPA and 0.01 mol L−1 CaCl2 at pH 7.3, respectively,32,33 as well as shaking the suspension in a oscillating device for 2 h. After extraction, the suspensions were centrifuged at 3000 rpm for 20 min, and the suspensions were then filtered using a 0.45 μm microporous membrane and tested using ICPOES. All the tests were repeated three times, and the mean value of the three experiments was obtained without error bars in this study.
2.5 Analysis methods
The concentrations of heavy metals were determined via inductively coupled plasma optical emission spectrometer (ICP-OES; Thermo Fisher scientific, ICAP 6500, USA). pH value was measured by an ultra-trace sample volume-type pH electrode (PHS-3C, Shanghai, China). Samples and precipitates were analyzed by X-ray diffractometer (XRD; Japan D/max-IIIA), X-ray fluorescence (XRF; PANalytical B.V., Axios; Netherlands), Scanning Electron Microscopy (Slgma 300) and X-ray spectroscopy system (EDS; ΣIGMA+X-Max20, Zeiss, Germany).
3. Results and discussion
3.1 Chemical composition
The XRF chemical composition analysis of the RCS fly ash and smelting slag are shown in Table 1. As shown in Table 1, RCS fly ash mainly consists of CuO, Cl, ZnO, CaO, K2O and Fe2O3, all of which accounts for about 88.18% of the total composition, respectively. The main elements were composed primarily of their oxides (SiO2, CaO, CuO, Al2O3, Fe2O3 and MgO) and comprised 43.64%, 21.59%, 13.80%, 7.78%, 3.91% and 2.63% for smelting slag, respectively, as well as the oxides of Si, Ca, Al, Mg and Cu, which accounted for more than 90% of all the elements and are an order of magnitude higher than ZnO, Na2O, SO3, K2O and SnO2.
Table 1 Chemical composition of RCS fly ash and smelting slag obtained using XRF
RCS fly ash |
Oxide |
CuO |
Cl |
ZnO |
CaO |
K2O |
Fe2O3 |
SO3 |
PbO |
SiO2 |
Na2O |
Br |
SnO2 |
Wt% |
29.59 |
25.14 |
21.25 |
6.18 |
3.15 |
2.87 |
2.57 |
1.74 |
1.68 |
1.52 |
1.48 |
0.74 |
Oxide |
Cr2O3 |
Al2O3 |
MgO |
F |
P2O5 |
CdO |
I |
Sb2O3 |
Bi2O3 |
MoO3 |
SrO |
|
Wt% |
0.52 |
0.47 |
0.34 |
0.25 |
0.19 |
0.13 |
0.10 |
0.04 |
0.04 |
0.03 |
0.01 |
|
Smelting slag |
Oxide |
SiO2 |
CaO |
CuO |
Al2O3 |
Fe2O3 |
MgO |
ZnO |
Na2O |
SO3 |
K2O |
SnO2 |
Wt% |
43.64 |
21.59 |
13.80 |
7.78 |
3.91 |
2.63 |
1.74 |
1.07 |
0.74 |
0.62 |
0.54 |
Oxide |
I |
Cr2O3 |
TiO2 |
Cl |
P2O5 |
MnO |
Sb2O3 |
SrO |
ZrO2 |
NiO |
Others |
Wt% |
0.42 |
0.35 |
0.34 |
0.31 |
0.23 |
0.12 |
0.06 |
0.03 |
0.03 |
0.02 |
0.03 |
As shown in Table 2, both RCS fly ash and smelting slag contain valuable metallic resources. For example, the concentrations of Cu, Zn, Fe and Al in RCS fly ash and smelting slag were 172.24, 124.54, 21.66, and 6.00 mg g−1 and 11.47, 13.70, 19.73, and 17.20 mg g−1, respectively. The levels of Cu and Zn in RCS fly ash were found to be much higher than their corresponding ores,34,35 and can be used as resources for resource recovery. In addition, smelting slag can also be reused as a raw material for construction materials as it contains minerals of Si, Al, Fe and Ca. RCS fly ash and smelting slag are classified as hazardous waste by China owing to the high concentrations of copper and zinc in both residues. Other heavy metals such as Ba, Be, Cd, Cr, Ni, Pb, and Sb are also observed in Table 2. Therefore, when recycling valuable metals from RCS fly ash and smelting slag, the effect of heavy metals should also be considered. The results described above show that the elemental composition of RCS fly ash and smelting slag are different.
Table 2 Chemical composition of RCS fly ash and smelting slag obtained using ICPOES (mg g−1)
Metals |
Cu |
Zn |
Fe |
Al |
Ba |
Be |
Cd |
As |
RCS fly ash |
172.24 |
124.54 |
21.66 |
6.00 |
0.76 |
0.42 |
0.72 |
0.65 |
Smelting slag |
11.47 |
13.70 |
19.73 |
17.196 |
0.79 |
0.21 |
0.01 |
0.23 |
Metals |
Cr |
Ni |
Pb |
Sb |
Sn |
Tl |
Au |
Se |
RCS fly ash |
ND |
0.26 |
4.35 |
0.92 |
4.20 |
3.58 |
0.46 |
0.46 |
Smelting slag |
0.42 |
0.33 |
1.22 |
2.40 |
ND |
2.01 |
0.23 |
0.33 |
The XRD phase analysis of RCS fly ash and smelting slag are shown in Fig. 1. As shown in Fig. 1, RCS fly ash and smelting slag have completely different phases. In Fig. 1a, the main mineralogical components of RCS fly ash are Cu2(OH)3Cl (clinoatacamite), FeCl2·2H2O (lawrencite), CuS2 (villamaninite), C (graphite), CuO (copper oxide), Cu, Ca2SiO4 (calcium silicate), Zn(ClO4)2 (zinc chlorate), Zn(OH)2·0.5H2O (zinc hydroxide) and KFeCl3 (potassium iron chloride). Fig. 1b shows that SiO2 (quartz), CaCO3 (calcite), SiS2 (silicon sulfide), CaAl2Si2O8·4H2O (gismondine), Cu4O3 (papamelaconite), CuO (tenorite), ZnO (zincite), NiSO4·6H2O (retgersite), AlPO4 (berlinite) and Na3Mn(PO4)(CO3) (sidorenkite) were identified in the smelting slag. The chemical composition of Pb, Cu and Bi in copper ash accounted for about 32.23%, 8.56% and 2.56% in the available literature, respectively.36 The chemical composition of copper smelting slag was mainly Fe, Mg, Si, Zn, Cu, Pb, all of which account for about 41.33%, 9.3%, 3%, 2%, 1% and 1%, respectively.37 The above results show that the main components of RCS fly ash and smelting slag produced by different processes are quite different. The primary phases of RCS fly ash are Cu2(OH)3Cl, C, FeCl2·2H2O and CuS2 owing to the smelting of copper scrap. Graphite mainly comes from the charcoal used in the reduction process. Copper in the RCS fly ash is in the phase of Cu2(OH)3Cl, CuO and Cu. As shown in Fig. 1b, the peak intensity of SiO2, CaCO3 and CaAl2Si2O8·4H2O were observed in smelting slag, because part of the firebrick fell off at the bottom of the furnace. Copper in the smelting slag is in the phase of Cu4O3 and CuO.
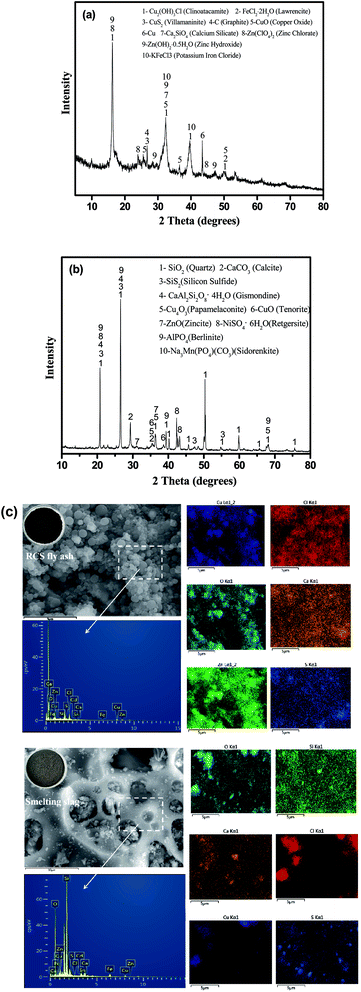 |
| Fig. 1 XRD patterns of samples (a) RCS fly ash; and (b) smelting slag. (c) Appearance of SME and EDX mapping of the RCS fly ash and smelting slag. | |
The microstructure and compositional distribution of the RCS fly ash and smelting slag were further investigated using SEM and energy dispersive X-ray analysis (EDX) mapping. In Fig. 1c, the SEM images of RCS fly ash showed spherical particles of uneven sizes piled up together. EDX analysis showed that the surface of the spherical particles mainly contains C, Ca, O, Zn, Fe, Cu, S, Si and Cl. The EDX elemental maps reveals that the compositional distributions of the five elements (Cu, O, Zn, S, Ca and Al) in RCS fly ash are uniform, suggesting a mixed mineral structure. In Fig. 1c, SEM images of the smelting slag showed a lumpy structure of unequal size with rounded grooves of unequal size on the surface. EDX analysis showed that the surface of the spherical particles mainly contain Si, O, Ca, Zn, Fe, Cd, Cu, S and Cl. The EDX elemental maps further reveal that the compositional distributions of the three elements (Cu, O and Ca) in the smelting slag are uniform, suggesting a mixed mineral structure.
3.2 Hazardous waste assessment
Leachates from RCS fly ash and smelting slag according to HJ/T 299-2007 are shown in Table 3. As shown in Table 3, the concentrations of Cd, Pb and Zn in RCS fly ash were 12.13, 6.46 and 1373.0 mg L−1, respectively. All concentrations exceeded the threshold values of 1.0, 5.0 and 100 mg L−1 for Cd, Pb and Zn, respectively. The most significant leaching toxicity was Zn which was orders of magnitude higher than Pb and Cd, as well as Al, Be, In and Se, which were not detected in RCS fly ash. The concentrations of metal ions in smelting slag were lower than the threshold. The results showed that both RCS fly ash types are classified as hazardous waste because of the Cd, Zn and Pb contamination. Furthermore, the result also suggests that the smelting industry and government should focus on hazardous elements other than Zn when recycling RCS fly ash.
Table 3 Leachates from RCS fly ash and smelting slag according to HJ/T 299-2007 (mg L−1)a
|
Al |
As |
Ba |
Be |
Cd |
Cu |
Fe |
Ni |
Pb |
Sb |
Zn |
Au |
In |
Se |
ND = not detected. * No provisions. |
RCS fly ash |
ND |
0.234 |
0.38 |
ND |
12.13 |
27.06 |
ND |
0.191 |
6.456 |
0.231 |
1373.0 |
0.034 |
ND |
ND |
Smelting slag |
2.842 |
ND |
0.756 |
0.01 |
0.021 |
0.251 |
ND |
0.01 |
0.672 |
ND |
2.031 |
0.016 |
0.016 |
ND |
Threshold |
* |
5 |
100 |
0.02 |
1 |
100 |
* |
5 |
5 |
5 |
100 |
* |
* |
1 |
Table 4 presents leachates from RCS fly ash and smelting slag according to the TCLP. As shown in Table 4, RCS fly ash is identified as hazardous waste owing to the excessive levels of Cd and Pb. The TCLP leaching concentrations of Ba, Cd, Cu, Pb and Zn for RCS fly ash are 1.6, 13.35, 554.6, 211.35 and 3644.5 mg L−1, respectively, and the concentrations of metal ions in smelting slag were lower than the threshold. Cd, Zn, Pb and Cu showed the most significant leaching toxicity, and Al, As, Ba, Be, Cr, Fe, Ni, Sb and Se were not detected in RCS fly ash. Tables 3 and 4 demonstrate that the concentrations of Cd, Pb, Cu and Zn by HJ/T 299-2007 in RCS fly ash were lower than those obtained using the TCLP. The results confirmed that TCLP is much stricter than HJ/T 299-2007, suggesting that China should consider stricter regulation protocols for identifying hazardous waste when considering the environment and human health.
Table 4 Leachates from RCS fly ash and smelting slag according to the TCLP (mg L−1)a
|
Al |
As |
Ba |
Be |
Cd |
Cr |
Cu |
Fe |
Ni |
Pb |
Sb |
Zn |
Au |
In |
Se |
ND = not detected. * No provisions. |
RCS fly ash |
ND |
ND |
ND |
ND |
13.35 |
ND |
554.6 |
ND |
ND |
211.35 |
ND |
3644.5 |
0.054 |
0.02 |
ND |
Smelting slag |
ND |
ND |
1.6 |
0.15 |
ND |
0.67 |
6.451 |
ND |
0.08 |
0.264 |
0.323 |
11.27 |
0.043 |
ND |
ND |
Threshold |
* |
5 |
100 |
* |
1 |
5 |
* |
* |
* |
5 |
* |
* |
* |
* |
1 |
3.3 Chemical speciation analysis
Fig. 2 presents the metal chemical speciation values of RCS fly ash and smelting slag, and Table B in the ESI† provides detailed data. As shown in Fig. 2a, the residual fraction of Sn and Fe in RCS fly ash was almost 100%, while the fractions of Ba, Pb, Cu and Be were 90.97%, 75.51%, 71.78% and 56.36%, respectively.38 The contents of Ba, Cd, Au, Se, Ni, Sb and Be were less than 1‰, as displayed in Table 2. Therefore, the risks associated with these seven metals in RCS fly ash are insignificant. The contents of Cu and Zn are higher than 10% in Table 2. Cu poses significant environmental and human health risks, although its residual fraction was 71.78%. The copper concentration in RCS fly ash is relatively high, and its exchangeable and soluble fractions are approximately 8.10%. Zn poses a significant risk as the sum of exchangeable and soluble fractions and reducible and oxidizable fractions surpasses 67.4%. Therefore, the risks associated with Cu and Zn metals in RCS fly ash are significant. Pb poses the highest risk as the sum of its exchangeable and soluble fractions and reducible and oxidizable fractions is approaching 24.5%. Both levels are consistent with the TCLP results. Data from Tables 3 and 4 and Fig. 1a and 2b indicate that Cu, Pb, Cr and Zn are also the primary concerns when dealing with RCS fly ash.
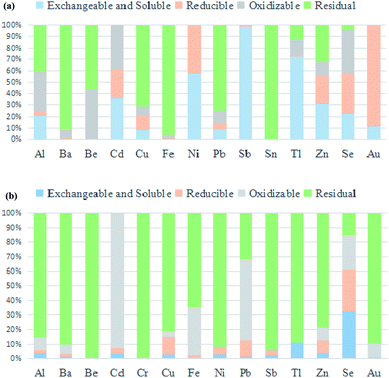 |
| Fig. 2 Fractions of metals contained in RCS fly ash (a) and smelting slag (b) obtained using the BCR. | |
For smelting slag (Fig. 2b), most metals are more stable than in RCS fly ash as their residual fractions are higher, with the exception of Fe and Pb. The contents of Cu and Zn are higher than 1% in Table 2. The residual fraction of Zn in RCS fly ash was only 32.60% but this increased significantly to 78.63% in smelting slag. Metal mobility increases in the following sequence: exchangeable and soluble < reducible < oxidizable < residual,39,40 indicating that the mobility of Zn in RCS fly ash is much higher than that in smelting slag. Conversely, the residual fraction of Fe in RCS fly ash significantly exceeds that in smelting slag (96.4% vs. 64.78%). The contents of Cr, Ni, Pb, Sb, Sn, Tl, Au, Se, Ba, Be and Cd were less than 3%, as shown in Table 2. Therefore, the hazards associated with these 11 metals in RCS smelting slag are insignificant.
3.4 Bioavailability assessment
The method of EDTA- and/or DTPA-extractions was applied to examine the metal bioavailability of RCS fly ash and smelting slag.41 As shown in Table 5, Al, Cr, Fe, Ni, Sn and TI were not detected by either EDTA or DTPA in either residue. Metal levels from the EDTA extraction for RCS fly ash and smelting slag were Zn > Cu > Pb > Se > Cd > Au > Sb > Ba > Be and Cu > Zn > Se > Pb > Au > Cd > Ba, respectively. Metal levels from DTPA extractions for both residues were Zn > Cu > Se > Cd > As > Pb > Au > Ba > Be and Cu > Se > Zn > As > Au > Pb > Cd > Be, respectively. Cu and Zn are considered to be the most significant bio-hazards. Cu EDTA extractions for both RCS fly ash and smelting slag produce as much as 7085 and 3563 mg kg−1, respectively, while for Zn the EDTA extractions obtained were 18
495 and 301.5 mg kg−1, respectively. The Cu and Zn bio-hazards of RCS fly ash are much higher than smelting slag regardless of the extraction methodology, EDTA or DPTA. In addition, EDTA extractable Zn and Cu exceeded the DTPA extractable Zn and Cu (Table 5). The bio-hazards of Cd and Se also cause concern because EDTA and DTPA extractable concentrations of RCS fly ash and smelting slag were the third highest values obtained. Meanwhile, the levels of EDTA and DTPA extractable Ba, Be, As, Cr, Ni, Sb and Au in RCS fly ash and smelting slag were also low; for example, DTPA extractable As from RCS fly ash was only 8 mg kg−1. The above described results suggest that Cu and Zn in RCS fly ash and smelting slag pose significant bio-hazardous risks and directly impact the vegetation that surrounds the stacks.
Table 5 EDTA- and DTPA-extractable metals in RCS fly ash and smelting slag (mg kg−1)a
|
Al |
As |
Ba |
Be |
Cd |
Cr |
Cu |
Fe |
Ni |
Pb |
Sb |
Sn |
Tl |
Zn |
Au |
Se |
ND = not detected. |
EDTA |
RCS fly ash |
ND |
ND |
4.5 |
1.5 |
82.5 |
ND |
7085 |
ND |
ND |
1001 |
34.5 |
ND |
ND |
18 495 |
40 |
106.5 |
Smelting slag |
ND |
ND |
ND |
1.5 |
6 |
ND |
3563 |
ND |
ND |
65.5 |
ND |
ND |
ND |
301.5 |
25 |
176 |
![[thin space (1/6-em)]](https://www.rsc.org/images/entities/char_2009.gif) |
DTPA |
RCS fly ash |
ND |
8 |
0.5 |
0.3 |
62 |
ND |
2391 |
ND |
ND |
5.9 |
0.6 |
ND |
ND |
8933 |
3.3 |
95.8 |
Smelting slag |
ND |
13.2 |
ND |
0.3 |
0.8 |
ND |
571.9 |
ND |
ND |
2.2 |
ND |
ND |
ND |
22.2 |
3.2 |
55.6 |
4. Conclusions
Reclaimed copper smelting fly ash and smelting slag are generated during the reclaimed copper smelting process and contain a large amount of valuable metals such as Cu and Zn, which have a certain recovery value. In this study, the metal mobility and toxicity of RCS fly ash and smelting slag were analyzed. The results showed that RCS fly ash and smelting slag contain high contents of Cu, Zn and Fe and trace amounts of heavy metals, such as Ba, Be, Cd, Cr, Ni, As, Pb, Au, Se and Sb. RCS fly ash is classified as hazardous waste in both China and the USA as the toxic leaching concentrations of Pb and Cd exceed the thresholds of 5 and 1 mg L−1. Cu and Zn contained in these two slags can easily be released into the environment. Additionally, RCS fly ash and smelting slag also show significant biohazardous potential as the EDTA- and DTPA-extractable Zn, Cu and Se of these two residues are considerably high. The above described results not only provide a certain reference basis for the field of RCS fly ash and smelting slag, but will also enable recycled copper smelting enterprises and government departments to better understand RCS fly ash and smelting slag and the associated levels of risk. Recycling copper smelting enterprises should consider the leaching toxicity and bioavailability when stacking RCS fly ash and smelting slag.
Conflicts of interest
There are no conflicts to declare.
Acknowledgements
This work was supported by ‘Sichuan Province Science and Technology plan-Key Research and Development’ (19ZDYF0911), the ‘National Natural Science Foundation of China’ (21806132), the ‘National Key R&D Program of China’ (2018YFC1903500), the ‘Science and Technology Program of Guizhou Province-China’ ([2019]2863), the ‘Key R & D Program of Guangxi Province’ (AB18126088), and the ‘Science and Technology Project of Mianyang City, Sichuan Province (2019YFZJ014)’.
References
- Y. H. Zhang, X. Y. Feng and B. J. Jin, An effective separation process of arsenic, lead, and zinc from high arsenic-containing copper smelting ashes by alkali leaching followed by sulfide precipitation, Waste Manage. Res., 2020, 38, 1214–1221 CrossRef CAS.
- Q. M. Wang, Z. C. Li, D. Li, Q. H. Tian, X. Y. Guo, Z. S. Yuan, B. J. Zhao, Z. Wang, Y. J. Wang, S. L. Qu, J. Yan and G. M. Peng, A Method of High-quality Silica Preparation from Copper Smelting Slag, JOM, 2020, 72, 2676–2685 CrossRef CAS.
- J. P. Wang and U. Erdenebold, A Study on Reduction of Copper Smelting Slag by Carbon for Recycling into Metal Values and Cement Raw Material, Sustainability, 2020, 12, 1421 CrossRef CAS.
- A. A. Komkov and R. I. Kamkin, Mechanism for the Reduction of Oxides in Copper-Smelting Slag under Blowing with CO-CO2 Gas Mixtures, Russ. J. Non-Ferrous Met., 2020, 61, 57–64 CrossRef.
- L. Klemettinen, K. Avarmaa, H. O’Brien, P. Taskinen and A. Jokilaakso, Behavior of Tin and Antimony in Secondary Copper Smelting Process, Minerals, 2019, 9, 39 CrossRef CAS.
- E. M. Kharchenko, K. Z. Zhumashev and E. N. Selivanov, Development of Technology for Recycling Copper Smelting Production Waste, Metallurgist, 2019, 62, 1250–1254 CrossRef CAS.
- Y. Y. Shao and F. Shao, Optimization of operating mode in Copper Flash Smelting process, Adv. Mater. Res., 2014, 1046, 43–53 Search PubMed.
- M. Dong and Y. LI, Analysis of soil heavy metal pollution and prevention and remediation, Agric. Technol., 2020, 40, 125–127 Search PubMed.
- F. Chen, G. Yu, J. W. Hou, Z. Y. Zhou, L. L. Yang, Y. S. Li and H. Q. Wu, Risk assessment of heavy metals in farmland soils on both sides of the slag transportation road, J. Southwest Univ., 2020, 42, 9–21 Search PubMed.
- C. Yuan, H. Z. Zhang, T. Chi, F. Yu, J. Song and L. H. Wu, Heavy metal and metalloid pollution of soils and plants in typical antimony mining area of central-south China, Soil, 2015, 47, 960–964 CAS.
- H. Y. Cao, L. Zhang, C. G. Wang, N. X. Fu, Z. T. Sui and N. X. Feng, Study on Selectively Separating Iron Constituents in Copper Smelting Slags, EPD Congr., 2009, 939–941 CAS.
- J. Zhang, Y. H. Qi, D. L. Yan, X. L. Cheng and P. He, Characteristics and Mechanism of Reduction and Smelting-separation Process of Copper Slag, J. Iron Steel Res. Int., 2015, 22, 121–127 CrossRef CAS.
- M. D. Dimitrijevic, D. M. Urosevic, Z. D. Jankovic and S. M. Milic, Recovery of Copper from Smelting Slag by Sulphation Roasting and Water Leaching, Physicochem. Probl. Miner. Process., 2016, 52, 409–421 CAS.
- G. C. Shi, Y. L. Liao, B. W. Su, Y. Zhang, W. Wang and J. J. Xi, Kinetics of copper extraction from copper smelting slag by pressure oxidative leaching with sulfuric acid, Sep. Purif. Technol., 2020, 241, 116699 CrossRef CAS.
- K. Gargul, B. Boryczko, A. Bukowska, P. Jarosz and S. Malecki, Leaching of lead and copper from flash smelting slag by citric acid, Arch. Civ. Mech. Eng., 2019, 19, 648–656 CrossRef.
- K. A. Karimov, S. S. Naboichenko, A. V. Kritskii, M. A. Tret'yak and A. A. Kovyazin, Oxidation Sulfuric Acid Autoclave Leaching of Copper Smelting Production Fine Dust, Metallurgist, 2019, 62, 1244–1249 CrossRef CAS.
- K. A. Karimov and S. S. Naboichenko, Sulfuric Acid Leaching of High-Arsenic Dust from Copper Smelting, Metallurgist, 2016, 60, 456–459 CrossRef CAS.
- M. S. Chen, X. M. Zhu, Z. R. Han, P. Ning and Y. X. Ma, Copper from Copper Smelting Slag by Oxidation
Leaching, Appl. Mech. Mater., 2014, 477–478, 1413–1418 CAS.
- P. Gautam, S. Kumar and S. Lokhandwala, Advanced Oxidation Processes for Treatment of Leachate from Hazardous Waste Landfill: A Critical Review, J. Cleaner Prod., 2019, 237, 117639 CrossRef CAS.
- V. Manyapu, A. Mandpe and S. Kumar, Synergistic effect of fly ash in- vessel-composting of biomass and kitchen waste, Bioresour. Technol., 2017, 251, 114–120 CrossRef.
- A. H. Kaksonen, L. Lavonen, M. Kuusenaho, A. Kolli, H. Narhi, E. Vestola, J. A. Puhakka and O. H. Tuovinen, Bioleaching and recovery of metals from final slag waste of the copper smelting industry, Miner. Eng., 2011, 24, 1113–1121 CrossRef CAS.
- M. Dimitrijevic, D. Urosevic, S. Milic, M. Sokic and R. Markovic, Dissolution of Copper from Smelting Slag by Leaching in Chloride Media, J. Min. Metall., Sect. B, 2017, 53, 407–412 CrossRef CAS.
- W. F. Liu, X. X. Fu, T. Z. Yang, D. C. Zhang and L. Chen, Oxidation leaching of copper smelting dust by controlling potential, Trans. Nonferrous Met. Soc. China, 2018, 28, 1854–1861 CrossRef CAS.
- P. Shao and L. P. Jiang, Flow and Mixing Behavior in a New Bottom Blown Copper Smelting Furnace, Int. J. Mol. Sci., 2019, 20, 5757 CrossRef CAS.
- M. B. Vukmirovic, R. R. Adzic and R. Akolkar, Copper Electrodeposition from Deep Eutectic Solvents-Voltammetric Studies Providing Insights into the Role of Substrate: Platinum vs Glassy Carbon, J. Phys. Chem. B, 2020, 124, 5465–5475 CrossRef CAS.
- W. C. He, Z. N. Shi, F. G. Liu and S. Yang, Electrodeposition of Copper Metal from the 1-Ethyl-3-methylimidazolium Fluoride ([EMIM]F)-urea-H2O System Containing Cu2O, Electrochemistry, 2020, 88, 253–255 CrossRef CAS.
- A. Kuleyin and H. E. Uysal, Recovery of Copper Ions from Industrial Wastewater by Electrodeposition, Int. J. Electrochem. Sci., 2020, 15, 1474–1485 CrossRef CAS.
- D. Golui, S. P. Datta, B. S. Dwivedi, M. C. Meena, V. K. Trivedi, S. Jaggi and K. K. Bandyopadhya, Effectiveness of Toxicity Characteristics Leaching Procedure for Assessing Metal Hazards of Polluted Soils in Relation to Human Health, Soil Sediment Contam., 2020, 29, 304–321 CrossRef CAS.
- V. Intrakamhaeng, K. A. Clavier and T. G. Townsend, Initiatives to reduce lead from electronic devices: evidence of success from the toxicity characteristic leaching procedure, J. Air Waste Manage., 2019, 69, 1116–1121 CrossRef CAS.
- B. Cherif, M. Karim, H. Abdelkader and A. Chahinez, Modeling and Evaluation of the Performance of the Stabilization/Solidification Process of Hazardous Compound Pbo by Toxicity Characteristic Leaching Procedure Test, Rev. Rom. Mater., 2018, 48, 260–267 CAS.
- L. Z. Tong, J. Y. He, F. Wang, Y. Wang, L. Wang, D. C. W. Tsang, Q. Hu, B. Hu and Y. Tang, Evaluation of the BCR sequential extraction scheme for trace metal fractionation of alkaline municipal solid waste incineration fly ash, Chemosphere, 2020, 249, 126115 CrossRef CAS.
- L. Xiao, M. H. Li, J. Dai, M. Motelica-Heino, X. F. Chen, J. L. Wu, L. F. Zhao, K. X. Liu and C. Zhang, Assessment of earthworm activity on Cu, Cd, Pb and Zn bioavailability in contaminated soils using biota to soil accumulation factor and DTPA extraction, Ecotoxicol. Environ. Saf., 2020, 195, 110513 CrossRef CAS.
- J. L. Santos, J. L. Malvar, J. Martin, I. Aparicio and E. Alonso, Distribution of metals in sediments of the Guadiamar river basin 20 years after the Aznalcollar mine spill: Bioavailability and risk assessment, J. Environ. Manage., 2020, 260, 110146 CrossRef CAS.
- M. Chen, K. Avarmaa, L. Klemettinen, H. O'brien, D. Sukhomlinov, J. Shi, P. Taskinen and A. Jokilaakso, Recovery of Precious Metals (Au, Ag, Pt, and Pd) from Urban Mining Through Copper Smelting, Metall.
Mater. Trans. B, 2020, 51, 1495–1508 CrossRef CAS.
- K. Avarmaa, H. O'Brien, L. Klemettinen and P. Taskinen, Precious metal recoveries in secondary copper smelting with high-alumina slags, J. Mater. Cycles Waste Manage., 2020, 22, 642–655 CrossRef CAS.
- E. Y. Zhang, X. W. Lu, D. L. Gong, A. J. Ma and G. Y. Cao, Study on copper ash treatment with ammonium carbonate solution, Min. Metall. Eng., 2013, 33, 68–70 CrossRef CAS.
- Y. H. Ran, Z. Zhang, Q. Guo, X. Y. Han, L. Zou and Y. P. Li, Mineral processing technology test of copper recovery from copper smelting slag, Min. Res. Dev., 2019, 39, 63–66 Search PubMed.
- V. D. Trinta, P. D. Padilha, S. Petronilho, R. E. Santelli, B. F. Braz, A. S. Freire, C. Saunders, H. F. da Rocha, A. Sanz-Medel and M. L. Fernandez-Sanchez, Total metal content and chemical speciation analysis of iron, copper, zinc and iodine in human breast milk using high-performance liquid chromatography separation and inductively coupled plasma mass spectrometry detection, Food Chem., 2020, 326, 126978 CrossRef CAS.
- M. Amde, Y. G. Yin, D. Zhang and J. F. Liu, Methods and recent advances in speciation analysis of mercury chemical species in environmental samples: a review, Chem. Speciation Bioavailability, 2016, 28, 51–65 CrossRef CAS.
- H. Drossman, Chemical speciation analysis of sports drinks by acid-base Titrimetry and ion chromatography: A challenging beverage formulation project, J. Chem. Educ., 2007, 84, 124–127 CrossRef CAS.
- N. Zheng, S. N. Hou, S. J. Wang, S. Y. Sun, Q. R. An, P. Y. Li and X. Q. Li, Health risk assessment of heavy metals in street dust around a zinc smelting plant in China based on bioavailability and bioaccessibility, Ecotoxicol. Environ. Saf., 2020, 197, 110617 CrossRef CAS.
Footnote |
† Electronic supplementary information (ESI) available. See DOI: 10.1039/d0ra09704g |
|
This journal is © The Royal Society of Chemistry 2021 |
Click here to see how this site uses Cookies. View our privacy policy here.