DOI:
10.1039/D0RA09699G
(Paper)
RSC Adv., 2021,
11, 1482-1492
Enhanced insect-resistance, UV protection, and antibacterial and antistatic properties exhibited by wool fabric treated with polyphenols extracted from mango seed kernel and feijoa peel†
Received
15th November 2020
, Accepted 18th December 2020
First published on 5th January 2021
Abstract
The synthetic dyes, antimicrobial and insect-resistant agents, UV radiation absorbents, and antistatic agents that are used to introduce multifunctional properties to textiles are not only toxic to the environment but also require multi-step treatments to achieve them. Toxic antimicrobials are responsible for the growth of drug-resistant bacteria. Nature-derived polyphenols, such as tannin, could be a viable green alternative. In this work, wool fabrics were treated with a commercial tannic acid (PP-1), and also with gallotannin-rich polyphenols extracted from feijoa fruit peel (PP-2) and mango seed kernel (PP-3) to introduce multifunctional properties, i.e. to make the fabric antistatic, insect-resistant, hydrophilic, and able to absorb harmful UV radiation. The effect of the treatment on the colour, colour intensity, surface resistivity, UV radiation absorption, antibacterial activity, and insect-repellence was systematically evaluated. It was found that PP-3-treated fabric exhibited excellent surface hydrophilicity, antibacterial activity against Staphylococcus aureus, Klebsiella pneumoniae, and Pseudomonas aeruginosa, and insect-resistant activity against the larvae of Tineola bisselliella. PP-3 treatment also provided comparable UV protection and antioxidant activity but was marginally inferior to the UV protection and antioxidant activity exhibited by the PP-1-treated fabric. The commercial tannic acid treated fabric provided the best antistatic properties but the lowest surface hydrophilicity. The developed treatment could provide a green and sustainable alternative to hazardous UV absorbing, antibacterial and insect-resistant agents used in the textile industry.
Introduction
Wool, a natural keratin protein fibre, is highly popular for the manufacture of interior textiles and apparel because of its various attributes, such as good fire retardancy, warmth, and biodegradability. However, as a protein fibre, it is prone to bacterial and insect attack. It is known that textiles are a carrier of microbes and therefore a vector for spreading diseases.1 Wool and other textile fibres also allow adherence and growth of different types of bacteria on their surface by providing the right environment, which may compromise the health and wellbeing of the wearer.2,3 The bacteria grown on textiles not only damage the fibre but may also produce an odour, making the apparel unpleasant.4,5 However, wool fibre-made fabrics are better compared to other fibres in this respect. Several insects, such as the larvae of carpet beetles (Anthrenus verbasci) and clothes moth (e.g. Tineola bisselliella) can digest keratin protein causing premature damage to wool-made fabrics.6,7 It is not the adult moths and carpet beetles, but their larvae that mainly eat the fibre and cause damage. Therefore, it is desirable to develop a sustainable but effective anti-bacterial and insect-resist treatment for wool. The apparel made of wool fabric cling to the body due to static charge build up, and the generated static charge may become a vector for fire at gas stations and may damage electronic components.
Not only to protect the textiles from damage and prevent them from being a vector for disease, but it is also helpful to prolong the hygienic conditions of textiles as modern consumers are quite busy and the frequent washing of textiles is expensive and time-consuming. Therefore, antibacterial treatments became quite desirable for textile finishing. A range of antimicrobial agents of synthetic and natural origin have been investigated to make wool fibres antibacterial. Of the synthetic antibacterial agents, various quaternary ammonium compounds,8 hydantoin-based,9 a conjugated polymer such as polyaniline and its sulfonated derivative,10,11 and polyhexa-methylene biguanide,12 have been investigated to make wool fabric antibacterial. In the case of quaternary ammonium compounds, the antibacterial actions depend on the chain length and the types of quaternary ammonium groups. The bacteria are killed due to the leakage of their cell membrane because of the interaction of the positively charged ammonium groups with the negatively charged cell membrane. The quaternary ammonium compounds are difficult to absorb into wool fibre because of the similar charge, they leach from the treated fibre quite quickly during washing, fibre-reactive versions are also not much reactive to wool, and also they make bacteria drug-resistant.13 Therefore, microencapsulation and modification with natural polymers have been investigated, which provided better durability compared to the traditional exhaustion treatment.14,15 Most of the synthetic antibacterial agents are responsible for the development of drug-resistant bacteria.16 Metallic nanoparticles, especially surface modified and unmodified silver, and TiO2 have been extensively investigated to make wool fabric antibacterial.17–19 However, the release of silver nanoparticles to the environment during the washing of treated textiles is becoming a concern. Natural polyphenols,20,21 and amino polysaccharides (e.g. chitosan),22 have been envisaged as an alternative to the synthetic toxic antibacterial agents. Tannic acid nanoparticles also have been used as an antibacterial agent for textiles.23
To protect the wool fabric from beetle and moth larvae attack, a range of treatment has been developed over the years. Synthetic pyrethroid (e.g. permethrin) is the most popular and effective insect-resist agent for wool.24,25 but the discharge of its effluent is restricted in many countries because of its toxicity. A range of alternative treatments such as treating wool fibres with antifeedant material, such as kaolinite, TiO2, and ZnO2 nanoparticles can be used instead.26–28 Recently, researchers looked back to nature and plant extracts of henna, and walnut hull also have been investigated as an alternative to synthetic pyrethroids.29
However, the concerns of textiles treated with synthetic dyes and chemicals because of their possible toxicity and implication on human health are driving the textile manufacturers to look for green alternatives. In this respect, nature-derived flavonoids have attracted attention as a viable alternative. Flavonoids are hydroxylated polyphenolic secondary metabolites found in plants and fruits. Flavonoids are known to have antioxidant and UV radiation absorption activities. Natural polyphenols are nature-derived macromolecules that have been investigated for the preservation of food as an antioxidant and antibacterial agent,30,31 and also for dyeing and antibacterial finishing of textiles.32 Biomasses including plant and crop residues and fruit wastes could be a cheap source of various polyphenols. It can be said that all polyphenols are not the same as they are made of multiples of phenolic structures (e.g. tannin, ellagitannin, gallic acid, resorcinol, pyrogallol, pyrocatechol, vanillin, cinnamic acid, ferulic acid, coumarin, etc.), therefore the composition may vary from plant to plant causing variation in their properties. Mango kernels and feijoa fruit peels are not eaten and become waste. Mango seed kernel is rich in tannin (20.7 mg/100 g), coumarin (12.6 mg/100 g), vanillin (20.2 mg/100 g), cinnamic acid (11.2 mg/100 g), ferulic acid (10.4 mg/100 g), gallic acid (6 mg/100 g), and 4.2 mg/100 g mangiferin.33 On the other hand, feijoa peel is rich in flavone, catechin, procyanidin B1, epicatechin, quercetin-3-galactoside, gallic acid, and quercetin.34 Mango seed kernel and feijoa peel extracts are known to be effective as an antibacterial agent,35 and they could be alternatives to synthetic toxic antimicrobial agents used in textiles. To the best of our knowledge, polyphenols (PPs) extracted from mango kernel and feijoa fruit peel were never studied for enhancing insect repellence, antistatic properties and surface hydrophilicity of wool fabric. In this work, wool fabrics were treated with the PPs extracted from mango seeds and feijoa peels, and their surface hydrophilicity, insect-resist, UV protection, and antistatic properties were assessed according to the standard methods.
Experimental section
Materials
A plain-woven wool fabric of 225 g m−2 having 24.5 ends per cm and 23.5 picks per cm was used. PP-1, acetic acid, and acetone were purchased from Sigma-Aldrich Chemicals (USA). Sandozin MRN and Sandoclean PC were purchased from Arkema Chemicals, Switzerland. Albegal FFA was supplied by Huntsman Chemicals, USA. Softly®, a wool fibre washing detergent, was purchased from Pental Products Limited (Australia). Mango and feijoa fruits were purchased from a local supermarket. 2,2-Azino-bis(3-ethylbenzothiazoline-6-sulphonic acid) diammonium salt (ABTS), citric acid, disodium hydrogen phosphate, mono-potassium phosphate, and potassium persulphate were analytical grade reagents and they were purchased from Sigma-Aldrich Chemicals (USA).
Extraction of PPs from mango seeds and feijoa peels
In the case of extraction of PP from feijoa peel, the inside flesh of the feijoa fruits was removed by a spoon, the peels were fridge dried, and then grounded to powder by a cryogenic milling machine. This powdered feijoa peel was dispersed in a mixture of 80% acetone and 20% water at a consistency of 10%. The bottles were shaken at 220 rpm at 50 °C for 90 min, the liquid part was filtered, and the filtrate was concentrated by rotary evaporation. This concentrate was then freeze-dried to get feijoa peel PP (PP-2). In the case of mango seed kernel, the seed of the mango was removed and cleaned. The fibrous endocarps surrounding the mango kernels were discarded, the kernel was freeze-dried, and ground into fine powder by a milling machine. 50 g of dry powder was dispersed in water at a consistency of 10% in 500 mL Schott bottles. The bottles were shaken at 220 rpm at 50 °C for 90 min, their contents centrifuged (4000 rpm, 5 min, room temperature) and the supernatants removed by decanting. Then most of the water (water and acetone in the case of feijoa peel) was removed by a rotary evaporator at 35 °C and the concentrate was again freeze-dried to get PP powder of yellowish-brown colour mango seed PP (PP-3). The chemical structures of the main components of PP-2 and PP-3 are shown in Fig. 1. The dry PP powder was characterised by Fourier infra-red spectroscopy. A few milligrams of PP powders were mixed with KBr and a transparent disk was prepared by a hydraulic press. They were then scanned by a Nicolet Summit Pro Fourier-transform infrared (FTIR) spectrometer. 64 scans were signal-averaged.
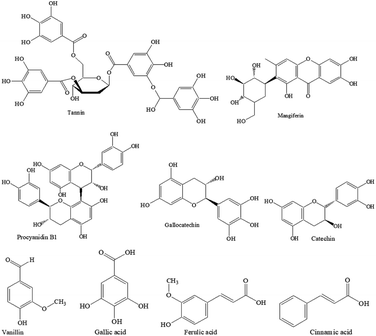 |
| Fig. 1 Chemical structures of components of mango seed kernel and feijoa peel extracts. | |
Treatment of wool fabric with PPs
The wool fabric was treated with a 2 g L−1 Sandoclean PC at 50 °C for 20 minutes to remove any processing oil and dirt remaining in the fabric. All the treatments were carried out in an Ahiba Turbomat laboratory dyeing machine (Model: 1000, Datacolor International, Switzerland) using tap water and a liquor ratio of 1
:
30. The stainless steel treatment vessel was filled with sufficient water, pre-dissolved PPs, 0.5 mL L−1 Sandozin MRN, 5 g L−1 sodium sulphate (as a levelling agent), and 1 g L−1 Albegal FFA. The pH of the bath was set at the required level and the wool fabric wrapped on a perforated carrier was introduced into the vessel and was run for 15 min. The pH was again adjusted to the required level, if any change in pH occurred, the temperature was then raised to 98 °C at 2 °C min−1 and held for 60 min. The dye bath was then cooled to 45 °C and the liquor was drained, and the dyed fabric was rinsed with cold water. The samples were then dried at 60 °C for 30 minutes. The treatment was carried out at different pHs and PP concentrations.
Assessment of antibacterial activity
The antibacterial properties of the untreated and natural PP treated wool fabric samples were measured according to the AATCC Test Method 147-1998 (antibacterial activity assessment of textile information: Parallel Streak Method) against Gram-positive Staphylococcus aureus and Gram-negative Klebsiella pneumoniae and Pseudomonas aeruginosa bacteria as they represent the most problematic pathogens. 1 mL of 24 h broth culture of bacteria was diluted with 9 mL of sterile distilled water and one loopful of diluted inoculum was transferred to the surface of the sterile agar plate by making 5 streaks of approximately 60 mm in length and spaced 10 mm apart covering the central area of a standard petri dish. Samples of fabric (25 mm × 50 mm) were gently pressed transversely across the inoculum streaks to ensure intimate contact with the agar plate containing bacterial streak and incubated at 37 ± 2 °C for 24 h. After which the interruption of bacterial growth along the streaks of inoculum under the specimen and zone of inhibition beyond its edge were examined. No growth of bacteria indicates antibacterial activity and the zone of inhibition indicates leaching of antibacterial agent to the inoculum surrounding the test specimens.
Assessment of insect-resist performance
The bioassays of wool fabrics treated with various PPs were conducted against Tineola bisselliella by following the Wools of New Zealand Test Method 25, which is based on ISO 3998-1977. The exposure period for the bioassay was 14 days. Test cages were plastic containers, 50 mm in diameter, and 18 mm high, with a fine stainless-steel mesh aperture in the lid. All test larvae were reared at the testing laboratory in the standard manner. After 14 days, the mortality of the larvae and the weight loss of the fabric were assessed. No mortality of the larvae and high weight loss of the fabric specimens indicate no insect-resistance. At least three samples were tested, and the averages are reported here. The statistical analysis of the data was carried out using ANOVA.
Thermal stability and antioxidant activity
The thermal stability of PP-3 treated and untreated wool fabrics was assessed by thermo-gravimetric (TG) analysis carried out on a Shimadzu Thermo-gravimetric Analyser (Model: TGA-50H, Shimadzu Corporation, Japan) from room temperature to 600 °C at a heating rate of 10 °C min−1 under the nitrogen atmosphere. At least three samples were tested for each treatment. The antioxidant activity of the wool fabrics treated with various PPs was measured by the ABTS decolourisation assay according to the method published in the literature.37
Surface characterisations
The characterisation of various PPs and examination of surface morphologies of wool fabric samples treated with various PPs were carried out by a Hitachi scanning electron microscope (Model: TM 3030 Plus, Hitachi Corporation, Tokyo, Japan). The elemental analysis of C, O, N, and S was carried out by an energy dispersive X-ray (EDX) using the same SEM equipped with Quantax75 energy dispersive X-ray attachment. The Fourier transform infrared (FTIR) spectra were recorded by a spectrometer (Model: Nicolet Summit Pro, ThermoFisher Scientific, USA) equipped with an attenuated total reflectance (ATR) attachment at a resolution of 2 cm−1 in the range from 650 to 3600 cm−1 by using a diamond crystal and 64 scans were signal-averaged. The contact angle of the untreated and treated wool fabrics were measured at 10 places of face and back surfaces by a KSV Contact Angle Measurement Apparatus (Model: CAM 100, KSV Instruments, Finland) and the average contact angle has been reported. The surface resistance of the fabrics preconditioned at 20 ± 2 °C and 65 ± 2% relative humidity for 48 h was measured by a surface/volume resistance meter equipped with a concentric ring probe (Model 152-1, Trek, Inc., Lockport, USA) at 10 positions with an applied voltage of 100 V, and the average surface resistance is reported.
Results and discussion
FTIR characterisation of various PPs
Fig. 2 shows the FTIR spectra of PP-1, PP-2, and PP-3. The spectra of all PPs show similar IR bands except PP-3 which shows new bands at 820, 2850 and 2916 cm−1. The spectrum of commercial tannic acid (PP-1) shows characteristics of tannic acid IR bands at 754, 867, 1086, 1191, 1328, 1452, 1614, 1718, 2730, and 3354 cm−1. The strong and wide band at 3354 cm−1 available in the spectra of all three PPs is associated with the stretching vibrations of hydroxyl groups and hydrogen bonding between hydroxyl groups, but its intensity increased from PP1 to PP3. The spectrum of PP-3 shows a sharp peak at 2927 cm−1 and a small shoulder at 2860 cm−1 which can be associated with the symmetric and asymmetric stretching vibrations of CH2 and CH3 groups associated to ferulic acid and vanillin present in mango seed kernel extract. These bands are absent in the spectra of the other two PPs. The small band at 2730 cm−1 available in the spectra of all three PPs is associated with the CH stretching vibrations. The strong and sharp band at 1716 cm−1 suggests the presence of carbonyl groups in these PPs as this band is associated with the IR band of carbonyl (C
O) groups. At 754 cm−1 shows the resulting distortion vibration of C
C in benzene rings and at around 1452 cm−1 stretching vibrations of –C–Caromatic groups respectively.36
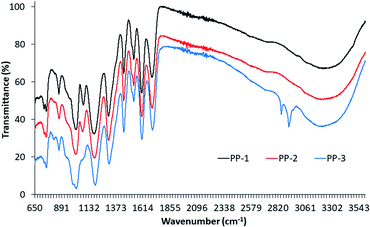 |
| Fig. 2 FTIR spectra of PP-1, PP-2, and PP3. | |
Effect of pH and concentrations of PPs on UV light transmission
Fig. 3 shows the effect of treatment pH on the UV light transmission through the wool fabric treated with various PPs at the dosage of 3% owf. The solar radiation that comes to the earth's atmosphere can be categorised into three radiation ranges, namely UV-A (320–400 nm), UV-B (280–320 nm), and UV-C (200–280 nm). Of them, the most damaging UV-C does not reach the earth's atmosphere as it is absorbed by the ozone layer. Of the UV radiation that reaches the earth, only 6% is UV-B and the rest 94% is UV-A. Therefore, the UV transmission through the fabric at 290 and 340 nm is the determining factor of fabric to protect the wearer from sun exposure. All the treatments considerably reduced the UV light transmission through the fabric at 290 and 340 nm compared to the untreated fabric. The control fabric transmitted 10.20 and 1.92% UV-A and UV-B respectively, i.e. poor UV-A protection but good UV-B protection. The treatment pH showed a considerable effect on the UV light transmission through the fabric treated with various PPs. For all the PPs, the UV light transmission through the fabric decreased with an increase in the treatment pH, which may suggest that the absorption of PP increases with an increase in the treatment pH. Usually, a fabric that transmits less than 2.5% UV is considered as a good UV radiation protective fabric.37 The UV light transmission through the wool fabric treated with PP-1, PP-2, and PP-3, the UV-A and UV-B transmission decreased to 1.43% and 0.76%, 2.10% and 0.98%, 2.38%, and 0.94%, respectively. Of the fabric treated with various PPs, the wool fabric treated with the commercial tannin (PP-1) showed the best UV radiation protection, but the fabrics treated with other PPs also showed very good UV protection. The results suggest that the adsorption of PPs into wool fabric increased with an increase in treatment pH.
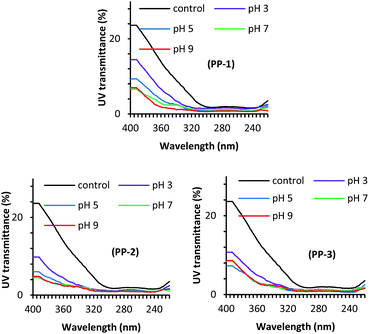 |
| Fig. 3 Effect of treatment pH on the UV transmission of wool fabrics treated with various PPs. | |
Fig. 4 shows the effect of the PP dosage on the UV protection performance of wool fabric treated at pH 5. As expected, the increase in the dosage of PP decreased UV transmission through the fabric. For the wool fabric treated with PP-1, the UV-A and UV-B transmission decreased from 3.30% and 1.06% to 2.22% and 0.93%, respectively when the applied dosage of PP-1 increased from 1% owf to 5% owf. Similarly, for the wool fabrics treated with PP-2 and PP-3, the UV light transmission through the fabric decreased from 3.91% and 1.24%, and 4.51% and 1.15% to 2.08 and 0.60, 2.08%, and 0.80%, respectively when the applied dosage of PPs was increased from 1% owf to 5% owf. Overall, all the PP-treated wool fabrics showed excellent UV radiation protection capability. The UV protection capability could be associated with the PPs absorbed by the wool fabric and the colour intensity of the treated fabric should be correlated UV protection performance of treated wool fabrics. Therefore, we measured the colour intensity of wool fabrics treated with various PPs at different treatment conditions. It was reported that the textiles treated with polyphenols derived from various natural plants showed enhanced UV radiation absorption as the phenolic groups absorb UV radiation.38,39 Therefore, wool fabric treated with tannic acid and other PPs showed excellent UV radiation absorption.
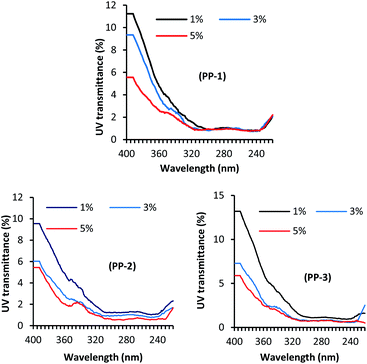 |
| Fig. 4 Effect of concentrations of PP-1, PP-2, and PP-3 on the UV transmission of wool fabrics treated with various PPs. | |
Fig. S1(a) (ESI†) shows the effect of pH on the colour intensity of wool fabrics treated with various PPs. It is evident that the treatment pH had a considerable effect on the colour intensity of the fabric treated with PPs. PP-2 treated wool fabric produced the highest colour strength and the PP-3 treated fabric the lowest. The colour intensity increased with an increase in the pH for the wool fabrics treated with PP-1 and PP-2 but for the PP-3 the highest colour strength showed by the fabric treated at pH 5 and the second highest by the fabric treated with pH 7. Overall, the colour strength produced by the treatment with various PP was quite poor as the highest colour strength produced by the fabric treated with 3% PP-2 owf at pH 9 was only 2.03 and the lowest colour strength was produce by the fabric treated with PP-1 (tannic acid) at pH 3 was only 0.99. The results are consistent with the UV transmission data shown in Fig. 3 except for the fabric treated with PP-3.
PPs are weakly anionic and therefore the highest absorption by wool fabric should be at pH 3 as the cationic charge of wool fabric increases with a decrease in pH from the isoelectric point of wool fibre in the aqueous medium (pH 4.5–5.0). The increase in pH should increase the anionic charge of wool fibre and therefore the absorption of PP should decrease with an increase of pH, but the absorption of UV increased with an increase in the pH suggesting the absorption of PP increased with an increase of pH. Polyphenols are high-molecular-weight polymer and at pH 3 the affinity of PP towards wool fibre is the highest and therefore many PP molecules tried to enter the wool fibre at the same time, blocking the pores of wool fibre and limiting their absorption. The increase in pH slowed down the affinity and therefore more controlled transportation of PP molecules occurred into the fibre at higher pH. PPs are stable at pH 3–6 but at alkaline conditions, they are hydrolysed and release gallic acid, which is oxidised producing yellow colour.40,41 The hydrolysis reduced the molecular weight of PPs and therefore the adsorption of PP further increased at the alkaline side of the pH. The UV transmission data shows that the adsorption of PP-3 by wool increased with an increase in pH up to 9 but the colour intensity produced by the fabric at pH 9 was lower than the fabric treated at pH 7. Probably the absorption of PP-3 was high, but the colour intensity decreased due to the overoxidation of some components of PP. However, it was observed that the leftover dyebath of the fabrics treated with PPs at acidic pH was colourless but the PPs treated at pH 7 and 8 produced brown coloured liquor whose colour intensity increased with an increase in pH, suggesting greater absorption in acidic pH than the alkaline pH.
Fig. S1(b) (ESI†) shows the effect of the applied dosage of PP on the colour intensity of the treated wool fabrics at pH 5.0. For all the PPs, the colour intensity gradually increased with an increase in the pH. At 1% owf, PP-2 treated fabric produced the greater colour strength compared to the fabrics treated with the other two PPs but 5% applied dosage, wool fabric treated with all PPs showed similar colour intensity.
Surface resistance
The effect of treatment pH on the surface resistance of wool fabrics treated with various PPs at an applied dosage of 3% owf is shown in Fig. 5 (top). The fabric sample treated with PP-1 showed the lowest surface resistance (125.6 × 109 ohm per cm) at all the pHs except pH 9 and the highest by the fabric sample treated with PP-3. For all PPs, the fabric samples treated at pH 3 showed the lowest surface resistance, which increased with an increase in the treatment pH up to pH 7, beyond that pH the surface resistance started decreasing. Therefore, pH 3 is the optimum pH to achieve the lowest surface resistance.
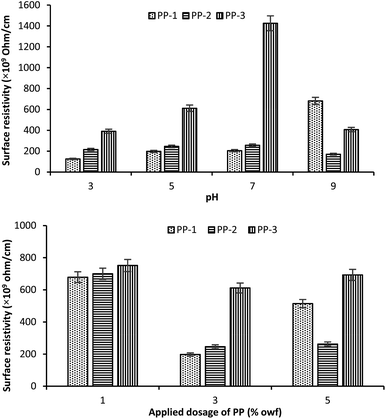 |
| Fig. 5 Effect of treatment pH (top) and the applied dosage of PPs (bottom) on the surface resistance of the treated wool fabric. | |
The effect of the applied dosage of PP on the surface resistance of wool fabric treated with various PPs at pH 5 is shown in Fig. 5 (bottom). The untreated fabric showed quite a high surface resistance, 8.7 × 1012 ohm per cm. For all PPs investigated, the surface resistance of the fabric decreased with an increase in the applied dosage of PP until 3% owf, after which the surface resistance started increasing. The lowest surface resistance was shown by the wool fabric treated with 3% owf PP-1, which was 197.7 × 109 ohm per cm. The surface resistance of wool fabric decreased from 8.7 × 1012 ohm per cm for the untreated to 197.7 × 109 ohm per cm for the fabric treated with 3% PP-1 at pH 5, i.e. from electric insulator, the wool fabric became antistatic.
Antibacterial properties
Table 1 shows the antibacterial activity of wool fabric treated with 3% owf various PPs at pH 5 against Staphylococcus aureus, Klebsiella pneumoniae and Pseudomonas aeruginosa bacteria. The control fabric did not show antibacterial activity and also any zone of inhibition as the growth of bacteria was observed up to the edge of the fabric specimens.
Table 1 Antibacterial performance of wool fabric treated with polyphenols extracted from various plants against various bacteria
Treatments |
Antibacterial performance against |
Pseudomonas aeruginosa |
Staphylococcus aureus |
Klebsiella pneumoniae |
Control |
No zone of inhibition was seen around the fabric. Strong growth of bacteria directly under the fabric was observed |
No zone of inhibition was seen around the fabric. Strong growth of bacteria directly under the fabric was observed |
No zone of inhibition was seen around the fabric. Strong growth of bacteria directly under the fabric was observed |
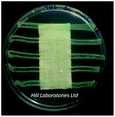 |
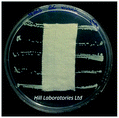 |
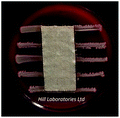 |
PP1-1 |
No zone of inhibition was seen around the fabric. Weak growth of bacteria under the fabric was observed |
No zone of inhibition was seen around the fabric. Strong growth of bacteria under the fabric was observed |
No zone of inhibition was seen around the fabric. No growth of bacteria under the fabric was observed |
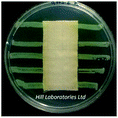 |
 |
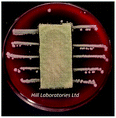 |
PP-2 |
No zone of inhibition was seen around the fabric. No growth of bacteria under the fabric |
No zone of inhibition was seen around the fabric. Strong growth of bacteria under the fabric |
No zone of inhibition was seen around the fabric. No growth of bacteria under the fabric |
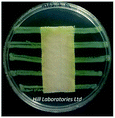 |
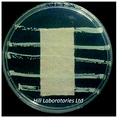 |
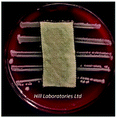 |
PP-3 |
No zone of inhibition was seen around the fabric. No growth of bacteria under the fabric |
No zone of inhibition was seen around the fabric. No growth of bacteria under the fabric |
No zone of inhibition was seen around the fabric. No growth of bacteria under the fabric |
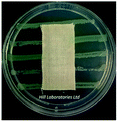 |
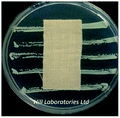 |
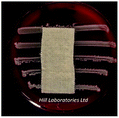 |
The tannic acid (PP-1)-treated fabric showed very good antibacterial activity only against Klebsiella pneumoniae and some level of activity against Pseudomonas aeruginosa (the growth of bacteria was weakened) but no antibacterial activity against Staphylococcus aureus as strong growth of bacteria was observed directly under the test specimens, i.e. failed to suppress the growth of Staphylococcus aureus. No zone of inhibition was observed for any type of bacteria. The fabric treated with PP-2 produced strong antibacterial activity against Klebsiella pneumoniae and Pseudomonas aeruginosa as the growth of bacteria was completely hindered directly under the test specimens but no antibacterial activity was observed against Staphylococcus aureus. The treated fabric also did not show any zone of inhibition. The fabric treated with PP-3 showed excellent antibacterial activity against all three types of bacteria but did not show any zone of inhibition indicating no release of PPs occurred to the surrounding moist agar medium from the test specimens. It is not surprising as PPs irreversibly bind to proteins, such as wool keratin.42 The antibacterial activities observed are consistent with the antibacterial activities of textiles treated with non-leaching antibacterial agents. Considering all the results, the fabric treated with PP-3 produced the best antibacterial activity and the fabric treated with tannic acid (PP-1) showed the poorest antibacterial performance. The mechanism of antibacterial activity provided by mango seed kernel (PP-3) is due to the iron-chelating ability of gallotannins with steric effects making the smaller gallotannins more effective than the larger ones, and mangeferin (a trihydroxyxanthone glucoside) also worked synergistically with gallotannins.43,44
The durability of the antibacterial treatment was only tested for the fabric treated with PP-3 for up to 10 IWS 7A washing (equivalent to at least 30 domestic washing), which is enough as wool garments are less frequently washed compared to the garments made with other natural fibres. The results are presented in Table S1 (ESI†). It is evident that the washed fabric slightly lost its antibacterial activity but still showed excellent antibacterial activity against Klebsiella pneumoniae and Pseudomonas aeruginosa but the antibacterial activity against Staphylococcus aureus slightly deteriorated as very faint growth of bacteria was observed directly under the test specimen. Overall, the wool fabric treated with PP-3 showed excellent antibacterial activity.
Insect-resist properties
Table 2 shows the insect-resist activity of wool fabric treated with various PPs at various applied dosages against Tineola bisselliella larvae. The untreated fabric showed little insect-resist activity as the mortality of the larvae was zero and the mean mass loss was very high, 59.3 mg (89.5% mass loss). Wool fabrics treated with all PPs even at the lowest concentrations showed quite good insect-rest activity, which increased with an increase in the applied concentrations. In the case of wool fabric treated with PP-1, the mean mortality of larvae was 33.9% for the applied dosage of 1% owf, which increased to 58.3% for the applied dosage of 5% owf. The mean mass loss decreased from 22.3% to 7.7%. Of the PPs investigated, the fabric treated with PP-3 showed the greatest insect-resist activity and the maximum mortality of larvae was 67.6% for the 5% owf applied dosage of PP-3 and the lowest mass loss was 2.7% only. None of the treatments showed 100% mortality but considerably reduced the damage to wool fibre. The PP-treated fabrics showed insect repellence rather than killing the larvae showed by nanoparticle-treated fabrics observed by other researchers.26,27
Table 2 Bioassay of wool fabric treated with various PPs against Tineola bisseliella
Treatment |
Mean mortality (%) |
Mean pupation (%) |
Mean mass loss (mg) |
Mean mass loss (%) |
Visual assessment (2 & 3) |
Pass (p), fail (f) or borderline (b) |
Control |
0 |
00 |
59.3 ± 0.9 |
89.5 |
4D |
f |
1% PP-1 |
33.9 |
00 |
13.2 ± 0.3 |
22.3 |
3C |
p |
3% PP-1 |
50.0 |
00 |
5 ± 0.4 |
8.5 |
1A |
p |
5% PP-1 |
58.3 |
00 |
3.6 ± 0.4 |
7.7 |
1A |
p |
1% PP-2 |
34.3 |
00 |
12.9 ± 0.2 |
21.7 |
3C |
p |
3% PP-2 |
52.1 |
00 |
4.8 ± 0.3 |
8.2 |
1A |
p |
5% PP-2 |
62.8 |
00 |
3.7 ± 0.4 |
6.4 |
1A |
p |
1% PP-3 |
37.5 |
00 |
11.2 ± 0.3 |
21.3 |
3C |
p |
3% PP-3 |
55.7 |
00 |
4.6 ± 0.4 |
7.6 |
1A |
p |
5% PP-3 |
67.6 |
00 |
2.7 ± 0.4 |
6.3 |
1A |
p |
Surface morphologies and contact angle
The surface of wool fabrics treated with various PPs was characterised by SEM, and contact angle measurement. SEM scanning was carried out to observe the surface coverage of wool fibres by PPs. Fig. 6 shows the SEM images of wool fabrics treated with 5% owf PP-1, PP-2, and PP-3 at pH 5. The surface of untreated or control wool fabric shows a typical scaly structure of the wool fibre. The surface of the untreated fabric looks quite clean, and the scales are clearly visible. The fabric samples treated with PPs show uniform deposition of PPs on the surface of the fabric. The surface of fabric treated with PP-2 shows less deposition of PP on the fibre surface than the surface of fibres treated with other two PPs and some scales are visible. However, the colour strength presented in Fig. S1 (ESI†) showed that the fabric treated with all PPs showed similar colour strength suggesting that most of the PP-2 absorbed into the wool fibres and the molecular weight of the PP-2 probably was the lowest compared to the other two PPs. The fabric treated with PP-3 produced the most uniform coating on the fabric suggesting most of the PPs deposited on the surface of the fibres and the molecular weight were the highest of the three PPs.
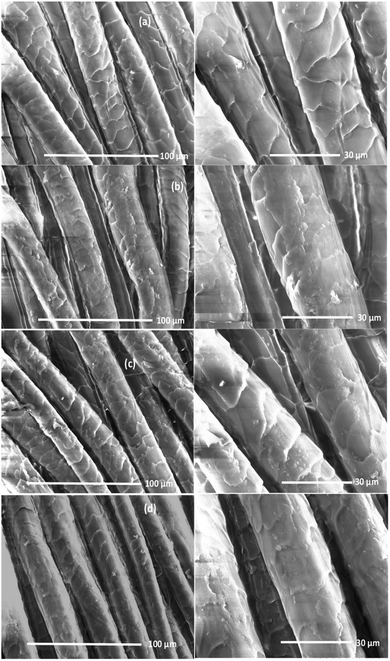 |
| Fig. 6 Surface morphologies of untreated (a) and wool fabrics treated with 5% owf PP-1 (b), PP-2 (c) and PP-3 (d). | |
Dynamic contact angle
Table 3 shows the dynamic contact angle of surface of wool fabrics treated with various PPs and optical images of water droplets at various times are shown in Fig. S2 (ESI†). The surface contact angle at 0 s shown by the untreated wool fabric was 121.9 ± 0.5° and decreased to 110.5 ± 1.3° after 120 s, which is consistent with previously published results.11,45 The untreated fabrics showed some level of hydrophobicity. However, wool fabrics treated with PPs showed quite a hydrophilicity. Of them, the fabric treated with PP-1 showed the lowest contact angle at 0 s (96.3 ± 1.8°) but the fabric treated with PP-2 showed the highest contact angle (121.3 ± 1.2°). In the case of wool fabric treated with PP-1, the contact angle decreased to 28.1 ± 0.9° at 120 s, but for the fabric treated with PP-2 and PP-3, the contact angle became zero after 90 and 60 s respectively. The contact angle shown by various treated fabric at 0 s, is consistent with the surface resistance shown in Fig. 5(a), i.e. the surface resistance is related to the surface hydrophilicity of wool fabrics.
Table 3 Dynamic contact angle of surfaces of untreated wool fabric, and also wool fabric treated with 3% owf of various PPs at pH 5
Sample ID |
Contact angle (°) at |
0 s |
30 s |
60 s |
90 s |
120 s |
Untreated |
121.9 ± 0.5 |
117.0 ± 0.3 |
114.7 ± 0.7 |
112.0 ± 1.1 |
110.5 ± 1.3 |
PP-1 |
96.3 ± 1.8 |
88.8 ± 1.4 |
57.8 ± 1.5 |
46.0 ± 1.1 |
28.1 ± 0.9 |
PP-2 |
121.3 ± 1.2 |
101.7 ± 0.7 |
79.2 ± 1.1 |
39.9 ± 0.8 |
0 |
PP-3 |
117.3 ± 2.2 |
30.3 ± 1.5 |
0 |
0 |
0 |
Elemental analysis
Fig. 7 shows the EDX spectra and elemental analysis results of C, N, O, and S elements of untreated and the wool fabric samples treated with various PPs. The elemental mapping is presented in Fig. S4 (ESI†), which shows that all the elements are uniformly distributed on the surface of fibres of the various treated fabrics. The C, N, O, and S content of the untreated wool fabric was 50.14, 20.76, 26.36, and 2.74 respectively, which is consistent with our previous findings.18 All the fabric samples treated with PPs showed higher oxygen content due to the abundant hydroxyl groups present in the PPs. The fabric treated with PP-1 had more O but less C, N, and S than the control. The sulphur content varied in the fabric samples treated with various PPs compared to the control due to the addition of PPs as no PP had sulphur in their chemical structure. The change in the elemental content of wool fabric suggests the presence of PPs in the treated fabrics.
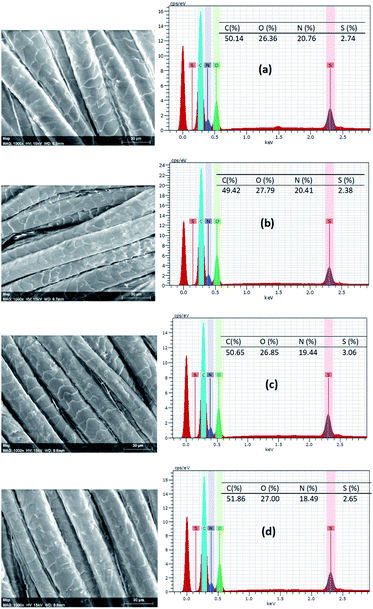 |
| Fig. 7 EDX spectra of untreated (a) and wool fabrics treated with 5% owf PP1 (b), PP2 (c), and PP3 (d). | |
ATR-FTIR
The ATR-FTIR spectra of wool fabrics treated with various PPs at 5% owf dosage are shown in Fig. S3 (ESI†). The spectrum of control wool fibre shows wool keratin-related IR bands of amide III, amide II, and amide I peak at 1227, 1350, 1540, and 1635 cm−1, respectively.46 The peak at 1506 cm−1 could be attributed to the C–N stretching and also to the N–H in-plane bending vibrations (amide II). The IR band at 2860, 2927, and 2960 cm−1 could be attributed to the symmetric and asymmetric vibration of methyl groups.11 The broad IR band at 3264 cm−1 could be attributed to the hydroxyl groups of wool fibre. The band at 1040 cm−1 could be attributed to the Bunte-salt groups of wool fibre. Conversely, the wool fabric treated with various PPs also showed similar bands except for the intensity of the IR bands increased, and shape of the bands changed. In the case of control wool fabric, the IR band at 1230 cm−1 was quite sharp but for the fabrics treated with various PPs, a shoulder was formed at 1203 cm−1 suggesting interaction of PPs with wool fibres. In the case of PP-3, the intensity of IR bands at 2860 and 2927 cm−1 increased compared untreated and treated wool fabrics and these bands are also associated with the ferulic acid and vanillin present in PP-3. The change in the intensity and shape of the IR bands suggest interaction of wool keratin with PPs.
Antioxidant activity and thermal stability
Fig. 8 shows the antioxidant activity of wool fabric treated with various PPs at different concentrations. The untreated wool fabric exhibited very poor antioxidant activity (only 16.7%). Conversely, wool fabric treated with all PPs showed excellent antioxidant activity as the ABTS solution in contact with fabric samples treated with PPs became colourless demonstrating their high antioxidant activity. The antioxidant activity increased with an increase in the applied dosage of PPs. Of them, PP-1 showed the greatest activity, even at 1% owf dosage, the antioxidant activity reached 88.5%. PP-2 showed comparatively poor activity and even at the highest applied dosage (5% owf), the antioxidant activity only reached 79.9%. On the other hand, at lower dosage PP-3 showed antioxidant activity lower than the activity showed by the PP-1, but at 5% applied dosage the antioxidant activity reached 94.6%, almost similar to the antioxidant activity exhibited by the PP-1. It can be concluded that PP-3 was highly effective as an antioxidant.
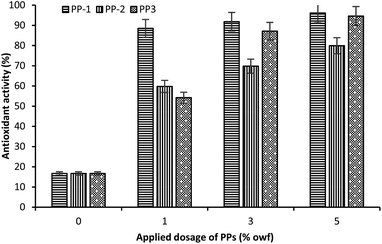 |
| Fig. 8 Effect of applied dosage of PP on the antioxidant activity of wool fabric treated with various PPs. | |
It was reported that the catechol moiety and hydroxyl groups of flavonoids are responsible for antioxidant activity.47 It was also reported that tannin procyanidin B1, epicatechin, gallic acid, and gallocatechin, the main components of PP-2 and PP-3, possess high antioxidant activity.47–49 Therefore, it is not unexpected that wool fabric treated with PPs extracted from mango seed kernel and feijoa fruit peel showed excellent antioxidant activity.
The thermogravimetric curves of untreated and wool fabrics treated with 3 and 5% owf PP-1 is presented in Fig. S5 (ESI†). The treatment with PP-1 hardly affected the thermal stability of wool, even at 5% owf dosage but the char yield increased with an increase in the concentration of PP-1. The ash content increased from approx. 14% to 20% with an increase of the applied dosage of PP-1 from 0 to 5% owf, which is consistent with our previous finding.50 It is known that the treatment of fibres with nitrogen (N) and phosphorous (P) containing organic compounds and polymers enhances the thermal stability of the treated fibre but the PPs do not have N or P in their chemical structure, and therefore the archived results are not unexpected.
Discussion
The wool fabric treated with PP-3 showed the best antibacterial properties, insect-repellence, and surface hydrophilicity but the fabric treated with PP-1 exhibited slightly better antioxidant activity, UV radiation absorption and antistatic properties. It is known that the introduction of hydrophilic groups on the surface of fibre enhances its antistatic properties through the reduction of surface electrical resistance.51 The tannin has many phenolic groups that are responsible for the high antioxidant and UV radiation absorption properties exhibited by the fabric treated with PP-1. On the other hand, PP-2 has procyanidin B1, epicatechin, quercetin-3-galactoside, gallic acid, and quercetin, rich in hydrophilic polyphenolic and carboxyl (more hydrophilic than hydroxyl groups) groups.34 Therefore, the fabric treated with PP-2 showed better hydrophilicity but lower UV radiation absorption and antioxidant activity as these properties are associated with the phenolic groups. The antibacterial activity of tannins depends on the individual microorganism, but they affect the cell wall membrane of the microorganisms and also deprive iron.52 PP-2 provided slightly better antibacterial activity than the PP-1 as it has quercetin and epicatechin that are known to be able to bind to peptidoglycan of bacterial cell walls jeopardizing their viability and also can from complex with iron.53 The PP-3 not only has tannin and mangiferin but also carboxyl groups containing gallic, cinnamic and ferulic acids providing the treated fabric most hydrophilicity but affected the antioxidant and UV radiation absorption properties because of the decreased phenolic groups than the PP-1. The fabric treated with PP-3 showed the best antibacterial properties as it has a potent antibacterial agent, mangiferin, which shows activity against both Gram-positive and Gram-negative bacteria.54
Conclusions
This work has demonstrated that PPs extracted from mango seed kernel (PP-3) not only work as an antibacterial agent but also can replace synthetic pyrethroids used in wool industry as an insecticide. The treatment with PP-3 also enhanced UV radiation protection ability of wool fabric and also made the fabric antistatic, antioxidant, and hydrophilic. The pH and the concentration of PPs showed a considerable effect on the absorption of PPs by wool fabric, and also showed an effect on various functional properties of the treated wool fabrics. The fabrics treated with various PPs not only showed excellent antibacterial and UV radiation absorption properties but also showed excellent insect repellence. Of the PPs investigated, PP-3 provided the best antibacterial properties against various Gram-positive and Gram-negative bacteria and insect repellence against Tineola bisselliella larvae, considerably better than the antibacterial properties and insect repellence provided by the untreated and commercial tannic acid (PP-1) treated fabrics. Although PP-1 treatment provided the best UV protection, PP-3 treatment showed only marginally inferior UV absorption and antioxidant activity. The treatment with various PPs made the fabric surface hydrophilic and made them antistatic. The surface resistance of the fabric decreased from 8.7 × 1012 ohm per cm for the untreated to 125.6 × 109 ohm per cm for the fabric treated with 3% PP-1 at pH 3. The developed single treatment can be used in the textile industry as an alternative to the hazardous and multi-step treatments using toxic antibacterial, antistatic, insect-resist and UV absorbents to make natural polyamide fibres multi-functional.
Conflicts of interest
There are no conflicts to declare.
Acknowledgements
The authors acknowledge the financial support received from the Ministry of Business Innovation and Employment (MBIE) of the New Zealand Government through Grant #C10X0824. The author would like to thank Rouke Bakker of AsureQuality for insect-resist performance, and Barbara Müller of R. J. Hill Laboratories for the antibacterial performance assessment.
Notes and references
- S. A. Sattar, S. Springthorpe and S. Mani, J. Appl. Microbiol., 2001, 90, 962–970 CrossRef CAS.
- R. A. Macqueen, R. M. Laing, H. J. L. Brooks and B. E. Niven, Text. Res. J., 2007, 77, 449–456 CrossRef.
- L. Teufel, A. Pipal, K. C. Schuster, T. Staudinger and B. Redl, J. Appl. Microbiol., 2010, 108, 4450–4461 CrossRef.
- C. Callewaert, E. De Maeseneire, F.-M. Kerckhof, A. Verliefde, T. Van de Wiele and N. Boon, Appl. Environ. Microbiol., 2014, 80, 6611–6619 CrossRef.
- M. M. Hassan, Antimicrobial coatings for textiles, in Handbook of Antimicrobial Coatings, ed. A. Tiwari, Elsevier, Amsterdam, 2018, pp. 321–355 Search PubMed.
- R. F. Powning and H. Irzykiewicz, J. Insect Physiol., 1962, 8, 275–284 CrossRef CAS.
- P. Trematerra and D. Pinniger, Museum Pests–Cultural Heritage Pests, in Recent Advances in Stored Product Protection, ed. C.G. Athanassiou and F. H. Arthur, Springer-Verlag GmbH, Berlin, 2018, pp. 229–260 Search PubMed.
- P. Zhu and G. Sun, J. Appl. Polym. Sci., 2004, 93, 1037–1042 CrossRef CAS.
- G. Sun, X.-G. Xu, J. R. Bickett and J. F. Williams, Ind. Eng. Chem. Res., 2001, 40, 1016–1021 CrossRef CAS.
- J. Yu, Z.-G. Pang, J. Zhang, H.-M. Zhu and Q. Wei, Colloids Surf., A, 2018, 548, 117–124 CrossRef CAS.
- M. M. Hassan, RSC Adv., 2020, 10, 17515–17523 RSC.
- Y. Gao and R. Cranston, J. Appl. Polym. Sci., 2020, 117, 2882–2887 Search PubMed.
- K. Hegstad, S. Langsrud, B. T. Lunestad, A. A. Scheie, M. Sunde and S. P. Yazdankhah, Microb. Drug Resist., 2010, 16, 91–104 CrossRef CAS.
- M. M. Hassan, RSC Adv., 2015, 5, 35497–35505 RSC.
- M. M. Hassan and M. Sunderland, Prog. Org. Coat., 2015, 85, 221–229 CrossRef CAS.
- J. Davies and D. Davies, Microbiol. Mol. Biol. Rev., 2010, 74, 417–433 CrossRef CAS.
- M. M. Hassan, ChemistrySelect, 2017, 2, 504–512 CrossRef CAS.
- M. M. Hassan, Colloids Surf., A, 2020, 581, 123819 CrossRef.
- M. Zahid, E. L. Papadopoulou, G. Suarato, V. D. Binas, G. Kiriakidis, I. Gounaki, O. Moira, D. Venieri, I. S. Bayer and A. Athanassiou, ACS Appl. Bio Mater., 2018, 1, 1154–1164 CrossRef CAS.
- K. H. Hong, Fibers Polym., 2015, 16, 565–571 CrossRef CAS.
- K. H. Hong, Cellulose, 2015, 22, 2129–2136 CrossRef CAS.
- S.-H. Hsieh, Z. K. Huang, Z. Z. Huang and Z. S. Tseng, J. Appl. Polym. Sci., 2004, 94, 1999–2007 CrossRef CAS.
- I. Perelshtein, E. Ruderman, A. Francesko, M. M. Fernandes, T. Tzanov and A. Gedanken, Ultrason. Sonochem., 2014, 21, 1916–1920 CrossRef CAS.
- J. M. Wimbush, Color. Technol., 1990, 106, 241–244 CrossRef CAS.
- T. Shaw, Water Environ. J., 1994, 8, 393–398 CrossRef CAS.
- A. Nazari, M. Montazer and M. Dehghani-Zahedani, Ind. Eng. Chem. Res., 2013, 52, 1365–1371 CrossRef CAS.
- A. Nazari, M. Montazer and M. Dehghani-Zahedani, J. Ind. Eng. Chem., 2014, 20, 4207–4214 CrossRef CAS.
- S. Jose, S. Nachimuthu, S. Das and A. Kumar, J. Text. Inst., 2018, 109, 225–231 CrossRef CAS.
- A. Nazari, J. Text. Inst., 2017, 108, 755–765 CrossRef CAS.
- I. Gutiérrez-del-Río, J. Fernández and F. Lombó, Int. J. Antimicrob. Agents, 2018, 52, 309–315 CrossRef.
- L. Bouarab Chibane, P. Degraeve, H. Ferhout, J. Bouajila and N. Oulahal, J. Sci. Food Agric., 2019, 99, 1457–1474 CrossRef CAS.
- D. S. Morais, R. M. Guedes and M. A. Lopes, Materials, 2016, 9, 498 CrossRef.
- A. Ahmed, D. Saeid, A. Eman and E. Reham, Food Chem., 2007, 103, 1141–1152 CrossRef.
- Y.-Y. Peng, K. S. Bishop and S. Y. Quek, Antioxidants, 2019, 8, 141 CrossRef CAS.
- P. Widsten, B. B. Mesic, C. D. Cruz, G. C. Fletcher and M. A. Chycka, J. Food Sci. Technol., 2017, 54, 2379–2386 CrossRef CAS.
- G. Socrates, Infrared and Raman Characteristics Group Frequencies, Tables and Chart. 3a, John Wiley & Sons, Inc., USA, 2001, pp. 125–142 Search PubMed.
- G. Reinert, E. Schmidt and R. Hilfiker, Melliand Textilberichte Eng. Ed., 1994, 7–8, E151–E153 Search PubMed.
- Y. Zhou and R.-C. Tang, ACS Sustainable Chem. Eng., 2017, 5, 10518–10526 CrossRef CAS.
- M. Á. Bonet-Aracil, P. Díaz-García, E. Bou-Belda, N. Sebastiá, A. Montoro and R. Rodrigo, UV protection from cotton fabrics dyed with different tea extracts, Dyes Pigm., 2016, 134, 448–452 CrossRef.
- C.-C. Wang, H.-F. Chen, J.-Y. Wu and L.-G. Chen, Molecules, 2019, 24, 365 CrossRef.
- R. Osawa and T. P. Walsh, J. Agric. Food Chem., 1993, 41, 704–707 CrossRef CAS.
- K. J. Siebert, N. V. Troukhanova and P. Y. Lynn, J. Agric. Food Chem., 1996, 44, 80–85 CrossRef CAS.
- C. Engels, M. G. Gäzle and A. Schieber, J. Agric. Food Chem., 2010, 58, 775–780 CrossRef CAS.
- A. Matkowski, P. Kus, E. Goralska and D. Wozniak, Mini-Rev. Med. Chem., 2013, 13, 439–455 CAS.
- M. M. Hassan and J. R. McLaughlin, ACS Appl. Mater. Interfaces, 2013, 5, 1548–1555 CrossRef CAS.
- K. Lemańska, H. Szymusiak, B. Tyrakowska, R. Zieliński, A. E. Soffers and I. M. Rietjens, Free Radical Biol. Med., 2001, 31, 869–881 CrossRef.
- P. Pedrielli, G. F. Pedulli and L. H. Skibsted, J. Agric. Food Chem., 2001, 49, 3034–3040 CrossRef CAS.
- M. Nikoo, J. M. Regenstein and H. A. Gavlighi, Compr. Rev. Food Sci. Food Saf., 2018, 17, 732–753 CrossRef CAS.
- L. C. Schwingel, G. O. Schwingel, N. Storch, F. Barreto and V. L. Bassani, Ind. Crops Prod., 2014, 55, 56–62 CrossRef CAS.
- M. M. Hassan, L. Schiermeister and M. P. Staiger, RSC Adv., 2015, 5, 55353–55362 RSC.
- X.-H. Kuang, J.-P. Guan, R.-C. Tang and G.-Q. Chen, Mater. Res. Express, 2017, 4, 095302 CrossRef.
- A. Scalbert, Phytochemistry, 1991, 30, 3875–3883 CrossRef CAS.
- C. Papuc, G. V. Goran, C. N. Predescu, V. Nicorescu and G. Stefan, Compr. Rev. Food Sci. Food Saf., 2017, 16, 1243–1268 CrossRef CAS.
- M. Masibo and Q. He, Compr. Rev. Food Sci. Food Saf., 2008, 7, 309–319 CrossRef.
Footnote |
† Electronic supplementary information (ESI) available. See DOI: 10.1039/d0ra09699g |
|
This journal is © The Royal Society of Chemistry 2021 |
Click here to see how this site uses Cookies. View our privacy policy here.