DOI:
10.1039/D0RA09054A
(Paper)
RSC Adv., 2021,
11, 364-373
Hexamethylenetetramine-based ionic liquid/MIL-101(Cr) metal–organic framework composite: a novel and versatile tool for the preparation of pyrido[2,3-d:5,6-d′]dipyrimidines†
Received
23rd October 2020
, Accepted 8th December 2020
First published on 23rd December 2020
Abstract
In the current paper, a hexamethylenetetramine-based ionic liquid immobilized on the MIL-101(Cr) metal–organic framework was successfully synthesized as a novel, efficient, and recoverable catalyst for the synthesis of pyrido[2,3-d:5,6-d′]dipyrimidine derivatives via the reaction of barbituric acid derivatives, 6-aminouracil/6-amino-1,3-dimethyl uracil, and aromatic aldehydes under solvent-free conditions. Characterization of the catalyst was carried out using various methods such as field emission scanning electron microscopy (FE-SEM), energy-dispersive X-ray spectroscopy (EDS), X-ray diffraction (XRD), thermogravimetric analysis (TGA), Fourier transform infrared spectrophotometry (FT-IR), and Brunauer–Emmett–Teller (BET). Efficient transformation, short reaction times, excellent yields, easy product isolation, mild conditions, and the potential high recyclability of the organocatalyst are the main features of this protocol.
1. Introduction
Currently, inorganic clusters or metal ions (usually transition metal) are used to make solid compounds that are crystalline in structure, connecting to two or multifunctional organic elements for providing metal–organic frameworks (MOFs).1 Metal–organic frameworks have, in past years, been useful resources for their applications in preparing different catalysts, fuel cells, electronics, sensors, and extensive industrial products, together with their other use in drug delivery, selective separation, adsorption, and petrochemistry.2–4 High surface area and thermal stability are some benefits of these porous and nanoscopic materials.5–8 MIL-101 is one of the most promising porous materials for future energy and environmental applications, owing to its superior physicochemical properties including high hydrothermal/chemical stability and desirable textural properties.9 MIL-101 is a member of the large family of MOFs with the largest Langmuir surface area (4500 m2 g−1), pore size (29–34 Å), and cell volume (702.000 Å).10 Several probabilities to model the porous complexity of MOFs in a logical method have been offered by multivariate MOFs (MTV-MOFs), merging several nuclei, organic, and linker characteristics into a framework.11–13 Some other cases regarding carbon–carbon bond formation, oxidation reactions, and catalytic activity of MOFs have also been reported.14,15 The reusable rigid acid catalysts have recently been substantially replaced in industrial operations by dangerous homogeneous acid catalysts.16,17 By filtering or centrifuging, acidic heterogeneous catalyzing agents may be isolated efficiently from the reaction blend without a need for particular treatments, thus providing a promising ecological process and reducing the handling cost.18 The reusability is another advantage of the heterogeneous catalyst.19,20 Ionic liquids (ILs), consisting of ions, may have certain features; therefore, they are used broadly in different organic synthesis and catalytic reactions. ILs have further been allocated as a group of environmental materials owing to their non-flammable features, besides low vapor pressure.21 Cases of their uses as catalysts in Biginelli reaction have also recently been discussed, showing excellent catalytic activity.22,23 Although ample prospects are in using MOFs as solid supports of ILs, ILs/MOFs composites have revealed significant features due to the ILs nano sizing than the bulk ionic liquid, indicating the typical freezing or melting features.24 Therefore, preparing and exploring the use of chemically confinement ILs-MOFs for catalysis for the first time is very substantial. One of the most efficient strategies of synthesization of organic and medicinal chemistry products is multicomponent reactions (MCRs).25 A substantial group of annulated uracils is derivatives of pyridopyrimidine that, with a wide variety of medicinal, pharmacological, and biological features, have recently gained significant attention.26,27 Pyrido [2,3-d:6,5-d′]dipyrimidines is synthesized by various catalysts like piperidine,28 SBA-Pr-SO3H,29 P2O5 (ref. 30) and MWCNTs@L-His/Cu(II).31
These protocols have some advantages including high product yields, short reaction times, and mild reaction conditions while they have some drawbacks such as high production costs, low chemical and thermal stability, and tedious work-up. Therefore, there is a considerable attempt to build an appropriate catalytic system to synthesize pyrido[2,3-d:5,6-d′]dipyrimidine. Recently, we have reported various synthetic methods for the preparation of several heterocycle compounds using nanocatalysts.32–36 In experimental and industrial research, it is essential to decrease toxic waste and reaction process time to protect the environment.
In this research, we decided to investigate the application of HMTA-BAIL@MIL-101(Cr) as a novel Brønsted acidic ionic liquid, highly efficient and reusable catalyst for the synthesis of pyrido[2,3-d:5,6-d′]dipyrimidine derivatives via the one-pot three-component condensation reaction of 6-aminouracil or 6-amino-1,3-dimethyl uracil, barbituric acid derivatives and aromatic aldehydes under solvent-free conditions (Scheme 1).
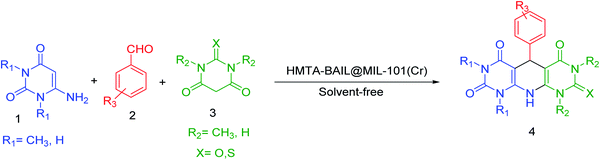 |
| Scheme 1 Synthesis of pyrido[2,3-d:5,6-d′]dipyrimidine derivatives using HMTA-BAIL@MIL-101(Cr) under solvent-free conditions. | |
2. Experimental
2.1 Materials and instrumentation
The high purities chemicals were bought from Sigma-Aldrich and Merck. The substances with the commercial reagent grades were utilized with no more purifying. The melting point was unmodified and defined in a capillary tube over a melting point microscope (Boetius). 1H NMR and 13C NMR spectra were attained on Bruker 250 MHz spectrometer with DMSO-d6 as a solvent and utilizing TMS as an internal standard. Recording FT-IR spectra was performed on Magna-IR, spectrometer 550. The elemental analyses (H, C, N) were conducted using a Carlo ERBA Model EA 1108 analyzer. Powder XRD (X-ray diffraction) was performed on a Philips diffractometer (X'pert Co.) with Cu Kα mono chromatized radiation (λ = 1.5406 Å). The microscopic morphology of the products was observed through SEM (LEO, 1455VP). Recording the mass spectra was based on a Joel D-30 tool at an ionizing potential of 70 eV. The energy dispersive analysis of X-ray was used to perform compositional analysis (EDX, Kevex, Delta Class 1). A Mettler Toledo TGA was considered to perform thermogravimetric analysis (TGA), under argon and heating was performed to 825 °C from room temperature. A Belsorp mini automatic adsorption tool was used to measure nitrogen adsorption–desorption isotherms at 196 °C followed by degassing the specimens for 5 h at 150 °C. The sample weight was estimated as 10 mg in the TG test with heating at 10 °C per minute.
2.2 Preparation of MIL-101(Cr)
Scheme 2 illustrates the synthesis procedure of the MIL-101(Cr), which was performed under hydrothermal conditions based on a previously used procedure with minor modification.37 To this end, a combination of 5.4 g of Cr(NO3)3·9H2O, 1.5 g of terephthalic acid (BDC), 45 mL of deionized water, and 0.6 mL of hydrofluoric acid (5 mol L−1) was sonicated for 10 min and then the mixture was transferred to a Teflon-lined stainless steel autoclave for 8 h at 220 °C. Subsequent to cooling down the autoclave to ambient temperature, the reaction mixture was subjected to filtration and washing by distilled water. The resultant solid was dehydrated in an 80 °C oven nightlong and denoted as crude MIL-101(Cr) crystals.
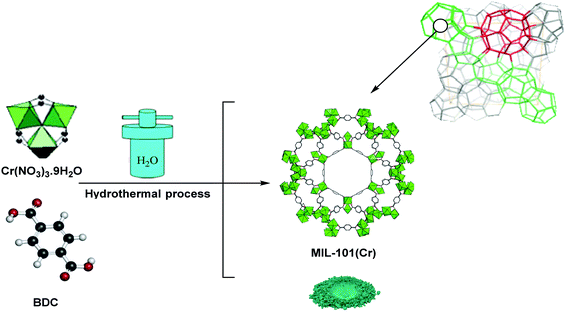 |
| Scheme 2 Preparation of MIL-101(Cr). | |
2.3 Preparation of HMTA-BAIL
HMTA-BAIL was prepared based on the previous method with a slight modification.38 A mixture of hexamethylenetetramine (0.01 mol) and 1,4-butane sultone (0.08 mol) was stirred at room temperature for 72 h under solvent-free conditions. The produced white solid zwitterion (HMTA-BAIL precursor) was filtered out and washed repeatedly by diethyl ether. An ionic liquid was formed through adding a stoichiometric quantity of sulfuric acid to the zwitterion and then stirring the produced admixture at 90 °C for 8 h. Lastly, washing the BAIL phase was performed for different times by diethyl ether and toluene for removing non-ionic remains, and then dehydrating was performed at 100 °C under vacuum (Scheme 3).
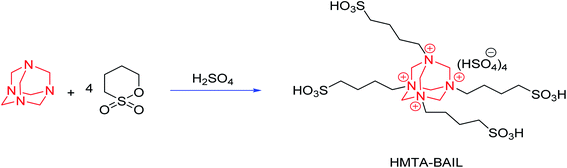 |
| Scheme 3 Preparation of HMTA-BAIL. | |
2.4 Preparation of HMTA-BAIL@MIL-101(Cr)
Scheme 4 displays the preparing procedure of the new and vigorous Brönsted acidic ionic liquid functionalized MIL-101(Cr) MOF. In brief, dehydration of MIL-101(Cr) (1.0 g) was done under vacuum at 110 °C for 12 h. A suspension of MIL-101(Cr) in anhydrous toluene (30 mL) was prepared in a round bottom flask, and hexamethylenetetramine (5 mmol) was added afterward. The reaction combinations were refluxed through stirring for 12 h at 80 °C. To separate the solvent, it was filtrated upon the termination of the reaction, and then washed by toluene to remove the extra hexamethylenetetramine. Thereafter, the product was dissipated in 30 mL of anhydrous toluene. Throughout stirring vigorously, an equal molar ratio 1,4-butane sultone (5 mmol) was incorporated into the solution, followed by refluxing the admixture for 12 h at 80 °C. Finally, the solid was harvested via filtration and dehydrated under vacuum for 3 h at 110 °C. A suspension of the solid was then made in 20 mL of ethanol simultaneously an equivalent amount of concentrated H2SO4 (98%) was added dropwise for 24 h at 50 °C. In the end, the catalyst was isolated by filtration and desiccated under vacuum for 12 h at 50 °C.
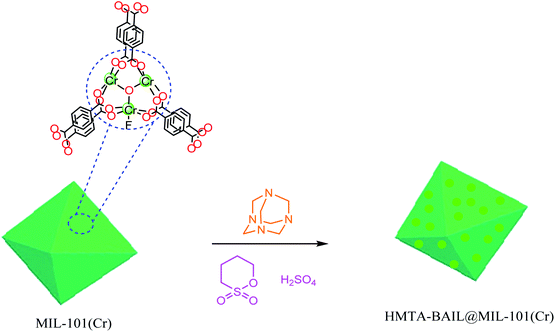 |
| Scheme 4 Preparation of HMTA-BAIL@MIL-101(Cr). | |
2.5 General procedure for the synthesis of pyrido[2,3-d:5,6-d′]dipyrimidine(4a–4p)
A combination of 6-aminouracil/6-amino-1,3-dimethyl uracil (1 mmol), barbituric acid derivatives (1 mmol), aldehyde (1 mmol), and HMTA-BAIL@MIL-101(Cr) (0.008 g) was heated at 80 °C for 10–15 min. Followed by completing the reaction based on the TLC (hexane/ethyl acetate, 4
:
1) (thin layer chromatography), cooling the reaction combination was performed to room temperature and the achieved solid was dissolved within dichloromethane. Then, the catalyst was not soluble in CH2Cl2 and was separated through simple filtration. Evaporating the solvent was performed and recrystallizing the residue from ethanol was performed to obtain the pure product.
Spectral data of the new products are given below.
5-(5-Bromo-2-hydroxyphenyl)-7,9-dimethyl-8-thioxo-5,8,9,10-tetrahydropyrido[2,3-d:6,5-d′]dipyrimidine-2,4,6(1H,3H,7H)-trione (4o). White solid; mp: >300 °C. 1H NMR (250 MHz, DMSO-d6) δ: 3.01 (s, 3H, CH3), 3.66 (s, 3H, CH3), 4.22 (s, 1H, CH), 6.96–6.99 (d, 1H, J = 7.4 Hz, ArH), 7.07 (s, 1H, ArH), 7.30–7.33 (d, 1H, J = 7.8 Hz, ArH), 9.27 (s, 1H, OH), 10.40 (s, 1H, NH), 10.64 (s, 1H, NH), 11.58 (s, 1H, NH); 13C NMR (62.9 MHz, DMSO-d6) δ: 27.49, 31.76, 50.39, 82.52, 97.14, 114.97, 118.79, 123.66, 129.29, 131.61, 135.34, 146.33, 150.33, 151.57, 152.85, 157.33, 162.33. FT-IR (KBr): 3365, 3172, 3051, 1705, 1674, 1591 cm−1; anal. calcd. For C17H14BrN5O4S: C 50.80, H 3.62, Br 7.50, N 17.77, O 13.53, S 6.78. Found C 50.76, H 3.61, Br 7.53, N 17.74, O 13.46, S 6.64.; MS (EI) (m/z): 462.99 (M+).
5-(2-Hydroxy-5-nitrophenyl)-1,3-dimethyl-8-thioxo-5,8,9,10-tetrahydropyrido[2,3-d:6,5-d′]dipyrimidine-2,4,6(1H,3H,7H)-trione (4p). White solid; mp: >300 °C.·1H NMR (250 MHz, DMSO-d6) δ: 3.09 (s, 3H, CH3), 3.22 (s, 3H, CH3), 4.13 (s, 1H, CH), 6.73 (d, 1H, J = 7.4 Hz, ArH), 7.11 (d, 1H, J = 7.7 Hz, ArH), 7.19 (d, 1H, J = 7.8 Hz, ArH), 9.12 (s, 1H, OH); 9.18 (s, 1H, NH), 10.28 (s, 1H, NH), 11.12 (s, 1H, NH); 13C NMR (62.9 MHz, DMSO-d6) δ: 27.64, 33.24, 50.53, 82.52, 97.68, 116.51, 121.32, 123.53, 126.94, 128.65, 135.82, 146.86, 150.74, 151.57, 152.43, 157.24, 162.45. FT-IR (KBr): 3456, 3444, 3107, 2951, 1693, 1668, 1597 cm−1; anal. calcd. For C17H14N6O6S: C 47.44, H 3.28, N 19.53, O 22.30, S 7.45. Found C 47.42, H 3.31, N 19.51, O 22.32, S 7.42.; MS (EI) (m/z): 430.07 (M+).
3. Results and discussion
The prepared catalyst was analyzed through some characterization methods such as EDS, FE-SEM, XRD, FT-IR, BET, and TGA.
3.1 EDS analysis
Fig. 1 illustrates the elemental analysis of the MIL-101(Cr) and HMTA-BAIL@MIL-101(Cr) obtained from EDS. The results confirmed the existence of C, O, Cr, F and N as the only elementary components of MIL-101(Cr) MOF (Fig. 1a). In EDS spectrum of HMTA-BAIL@MIL-101(Cr), C, O, Cr, F, N and S elements were observed (Fig. 1b). The presence of the S element in the Fig. 1b confirmed the successful functionalization of the ionic liquid.
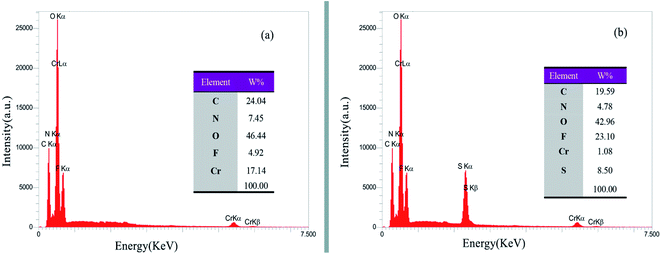 |
| Fig. 1 The EDS spectra of MIL-101(Cr) (a) and HMTA-BAIL@MIL-101(Cr) (b). | |
3.2 FE-SEM analysis
To distinguish the particle size and surface morphology of the synthesized HMTA-BAIL@MIL-101(Cr) SEM was studied. Fig. 2a and b show an FE-SEM micrograph of the as-synthesized MIL-101(Cr) and HMTA-BAIL@MIL-101(Cr) representing a characteristic octahedral shape form.
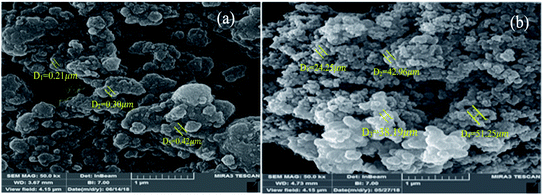 |
| Fig. 2 FE-SEM images of MIL-101(Cr) (a) and HMTA-BAIL@MIL-101(Cr) (b). | |
3.3 Powder X-ray diffraction
The PXRD (powder X-ray diffraction) patterns of the BAIL functionalized MIL-101(Cr) substances represent nearly all the main diffraction peaks regarding the pure MIL-101(Cr) and simulated pattern (Fig. 3). Such findings showed that the MIL-101(Cr) materials' crystalline structures were unaffected and remained intact over the BAIL functionalization procedure. The reflection planes equivalent to the Miller indices (201), (311), (440), (402), (333), (531), (606), (753), (666), and (600) are indexed for the MIL-101 consistent with the reported values.37,39 It is found that there is a good consistency between the representative peaks of the synthesized HMTA-BAIL@MIL-101(Cr) materials and MIL-101(Cr). There is also an agreement between the observations and the one reported in the studies.40
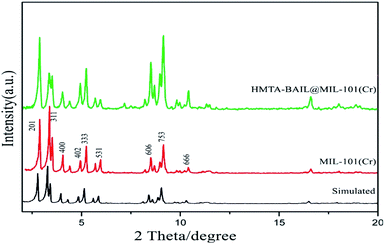 |
| Fig. 3 XRD patterns of MIL-101(Cr) and HMTA-BAIL@MIL-101(Cr). | |
3.4 Infrared spectroscopy
The FT-IR spectra of the BAIL-functionalized MIL-101(Cr) and bare MIL-101(Cr) nanostructure are represented in Fig. 4. FT-IR spectrum of MIL-101(Cr) shows the absorption bands at 1381 and 1663 cm−1 related to symmetric and asymmetric stretching vibrations of COO–.41 Moreover, Cr–O bonds are appeared around 550 and 663 cm−1. In addition, the contribution of HMTA-BAIL in the HMTA-BAIL@MIL-101(Cr) composite was verified with the existence of the absorption bands corresponding to hexamethylenetetramine ring and sulfonyl groups. As indicated in FT-IR spectrum of HMTA-BAIL@MIL-101(Cr), the absorption bands at 1155 and 1185 cm−1 are corresponding to stretching vibrations of S–O and C–N bonds, respectively. Moreover, the stretching vibrations of O
S
O is appeared at 1452 cm−1 confirming that the incorporation of HMTA-BAIL into the MIL-101(Cr).
 |
| Fig. 4 The FT-IR spectra of MIL-101(Cr) and HMTA-BAIL@MIL-101(Cr). | |
3.5 BET analysis
The N2 adsorption–desorption isotherm of MIL-101(Cr) and HMTA-BAIL@MIL-101(Cr) was shown in Fig. 5. For the bare MIL-101(Cr) an overall pore volume and BET surface area were 1.42 cm3 g−1 and 2473 m2 g−1, these values are close to the reported values (pore volume and BET surface area were 1.19 cm3 g−1 and 2338 m2 g−1, respectively) for MIL-101(Cr).42 The HMTA-BAIL@MIL-101(Cr) exhibited corresponding values (pore volume and BET surface area) of 1.06 cm3 g−1 and 1921 m2 g−1. The reduced porosity for HMTA-BAIL@MIL-101(Cr) in comparison with MIL-101(Cr) may be related to the pore blockage of MIL-101(Cr) via the BAIL groups.
 |
| Fig. 5 The N2 adsorption–desorption isotherms at 77 K of MIL-101(Cr) and HMTA-BAIL@MIL-101(Cr). | |
3.6 TGA analysis
The thermogravimetric analysis curves for MIL-101(Cr) and HMTA-BAIL@MIL-101(Cr) show two-step weight losses at 30 to 100 °C and >300 °C to 400 °C, respectively (Fig. 6). The first loss can be related to the solvent loss in the framework. The subsequent loss can be attributed to decomposing the immobilized ionic liquid moieties into the MIL-101(Cr) nanocages, causing the collapse of frameworks.
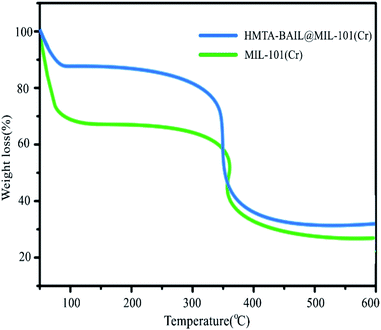 |
| Fig. 6 TGA curves of the MIL-101(Cr) and HMTA-BAIL@MIL-101(Cr) under Ar atmosphere. | |
In the next step of our research, we decided to evaluate the catalytic activity of the prepared novel catalyst for synthesizing pyrido[2,3-d:5,6-d′]dipyrimidines. For achieving this purpose, the reaction conditions (solvent, catalyst, and amount of catalyst) were first optimized, while selecting the reaction between 6-aminouracil, barbituric acid, and 4-chlorobenzaldehyde as a model reaction (Scheme 5).
 |
| Scheme 5 The model reaction for the synthesis pyrido[2,3-d:5,6-d′]dipyrimidine 4j. | |
To discover the effects of solvent in preparing pyrido[2,3-d:5,6-d′]dipyrimidine 4j, we conducted the model reaction using HMTA-BAIL@MIL-101(Cr) by different solvents as well as solvent-free conditions at various temperatures. As illustrated in Fig. 7, it concluded that solvent-free conditions with high temperatures have great effects on the reaction accelerating. The best findings (98% yield within 10 min) were attained without using any toxic solvent at 80 °C for this multicomponent reaction. A temperature increase in this reaction represented no significant impacts on time and product yield.
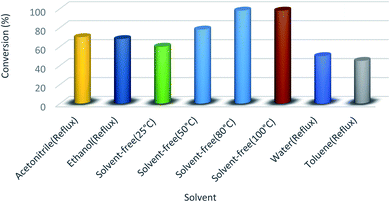 |
| Fig. 7 The optimization of the solvent in the model study. | |
Furthermore, to assess the effects of diverse catalysts, the catalytic performance of seven types of catalysts like KOH, CaO, MgO, ZnO, HMTA, MIL-101(Cr), HMTA-BAIL@CaO and HMTA-BAIL@MIL-101(Cr) was examined on the model reaction under solvent-free conditions (Fig. 8). The results of this study exhibited that HMTA-BAIL@MIL-101(Cr) was afforded pyrido[2,3-d:5,6-d′]dipyrimidine 4j in superior yield within short reaction time compared to the other catalysts.
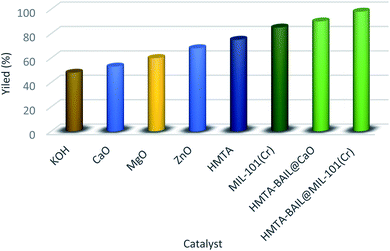 |
| Fig. 8 The effect of various catalysts on model reaction. | |
To continue our study, we ran the reaction of 6-aminouracil, barbituric acid, and 4-chlorobenzaldehyde using different amounts of HMTA-BAIL@MIL-101(Cr) nanocatalyst under solvent-free conditions. According to Fig. 9, the optimum concentration of HMTA-BAIL@MIL-101(Cr) was attained at 0.008 g. The time and yield of the reaction are not altered by a value of higher than 0.008 g.
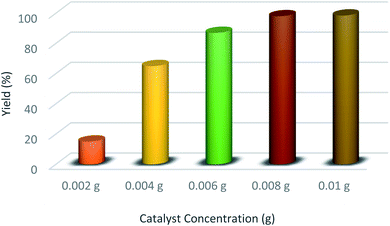 |
| Fig. 9 The effect of catalyst amount on the model reaction. | |
After examining different conditions on the reaction progress, we found the general applicability of the HMTA-BAIL@MIL-101(Cr) catalyst with aryl aldehydes comprising electron withdrawing or donating substituents, barbituric acid/thiobarbituric acid/1,3-dimethylbarbituric acid and 6-aminouracil or 6-amino-1,3-dimethyl uracil. According to Table 1, all of the derivatives with electron withdrawing or donating groups were afforded the products in good to the superior yields. The total HMTA-BAIL@MIL-101(Cr) was made to be a highly efficient nanostructure for the synthesis of pyrido[2,3-d:5,6-d′]dipyrimidines.
Table 1 Synthesis of pyrido[2,3-d:5,6-d′]dipyrimidines using HMTA-BAIL@MIL-101(Cr) catalyst
Entry |
R1 |
R2 |
R3 |
X |
Product |
Time(min) |
Yielda (%) |
Mp °C |
Lit. Mp °C |
Isolated yield. New products. |
1 |
CH3 |
H |
H |
O |
4a |
20 |
91 |
>300 °C |
>300 °C28 |
2 |
CH3 |
H |
4-Cl |
O |
4b |
14 |
95 |
>300 °C |
>300 °C28 |
3 |
CH3 |
H |
4-NO2 |
O |
4c |
15 |
97 |
>300 °C |
>300 °C28 |
4 |
CH3 |
H |
4-CH3 |
O |
4d |
16 |
88 |
>300 °C |
>300 °C28 |
5 |
H |
CH3 |
H |
O |
4e |
12 |
92 |
>300 °C |
>300 °C28 |
6 |
H |
CH3 |
4-Cl |
O |
4f |
20 |
87 |
>300 °C |
>300 °C28 |
7 |
H |
CH3 |
4-NO2 |
O |
4g |
10 |
90 |
>300 °C |
>300 °C28 |
8 |
H |
CH3 |
4-CH3 |
O |
4h |
18 |
89 |
>300 °C |
>300 °C28 |
9 |
H |
H |
H |
O |
4i |
17 |
93 |
>300 °C |
>300 °C28 |
10 |
H |
H |
4-Cl |
O |
4j |
10 |
98 |
>300 °C |
>300 °C28 |
11 |
H |
H |
H |
S |
4k |
14 |
93 |
>300 °C |
>300 °C28 |
12 |
H |
H |
4-Cl |
S |
4l |
16 |
96 |
>300 °C |
>300 °C28 |
13 |
H |
CH3 |
H |
S |
4m |
13 |
91 |
>300 °C |
>300 °C28 |
14 |
H |
H |
4-Cl |
S |
4n |
15 |
93 |
>300 °C |
>300 °C28 |
15 |
H |
CH3 |
5-Br, 2-OH |
S |
4o |
17 |
95 |
>300 °C |
—b |
16 |
CH3 |
H |
2-OH, 5-NO2 |
S |
4p |
19 |
89 |
>300 °C |
—b |
The catalytic performance and efficiency of HMTA-BAIL@MIL-101(Cr) were compared with several previous approaches to synthesize the pyrido[2,3-d:5,6-d′]dipyrimidines, presented in Table 2. As indicated, HMTA-BAIL@MIL-101(Cr) nanocomposite is greater based on the reported catalysts regarding reaction time, yield, and conditions. Our method has the advantages of short reaction time, mild conditions, and good to superior yields (Table 2).
Table 2 Comparison on the efficiency of HMTA-BAIL@MIL-101(Cr) for the synthesis of pyrido[2,3-d:5,6-d′]dipyrimidinesa
Entry |
Catalyst |
Conditions |
Time/yield (%) |
References |
Based on the three-component reaction of 6-aminouracil, barbituric acid, 4-chlorobenzaldehyde. |
1 |
Piperidine |
H2O/60 °C/U. S. |
1 h/81–91 |
28 |
2 |
SBA-Pr-SO3H |
Solvent-free/140 °C |
1.5 h/65–90 |
29 |
3 |
P2O5 |
EtOH/reflux |
2 h/80–88 |
30 |
4 |
MWCNTs@L-His/Cu(II) |
EtOH/reflux |
1 h/78–92 |
31 |
5 |
HMTA-BAIL@MIL-101(Cr) |
Solvent-free, 80 °C |
10 min/87–98 |
This work |
3.7 Recycling and reusing of the catalyst
The recovery and recyclability of the HMTA-BAIL@MIL-101(Cr) were also controlled by taking the condensation reaction for the model reaction. Followed by completing the reaction (based on TLC), dissolving the residues was performed in CH2Cl2, while filtering the catalyst. According to Fig. 10, this catalyst could be reused over six runs with no considerable loss of its catalytic activity.
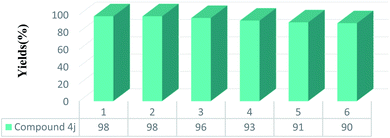 |
| Fig. 10 Reusability of the HMTA-BAIL@MIL-101(Cr) catalyst. | |
The chemical structure of recovered HMTA-BAIL@MIL-101(Cr) was verified using XRD pattern and FT-IR spectrum. There is no significant difference between the XRD and FT-IR of the fresh and recovered nanocomposite (Fig. 11(a and b)). Also, the acid sites (1.23 mmol g−1) of the catalyst after 6 times reused had no dramatic changes based on the acid–base titration measurement, in comparison with acid sites of the fresh HMTA-BAIL@MIL-101(Cr) nanocomposite (1.26 mmol g−1). These facts prove that the efficiency, appearance and structure of HMTA-BAIL@MIL-101(Cr) catalyst remained intact in recycles and there was no considerable deformation or leaching after 6 runs.
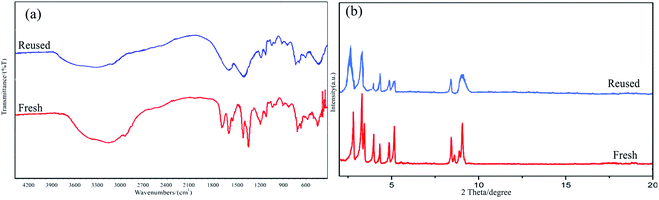 |
| Fig. 11 FT-IR spectrum (a) and XRD pattern (b) of the recovered HMTA-BAIL@MIL-101(Cr) after 6 runs. | |
A plausible mechanism for the synthesis of pyrido[2,3-d:5,6-d′]dipyrimidines utilizing HMTA-BAIL@MIL-101(Cr) as the catalyst is represented in Scheme 6. The findings were experimentally studied based on the literature.29,30 It is likely that HMTA-BAIL@MIL-101(Cr) acts as a Brønsted acid and increments the carbonyl group's electrophilicity on the aldehyde by release proton. Firstly, barbituric acid 3 has a reaction with aromatic aldehydes 2 to create standard Knoevenagel condensation product I. The succeeding Michael-type adding of the 6-aminouracil 1 with Knoevenagel product I after cyclization provides the intermediate II giving desired product 4 on dehydration.
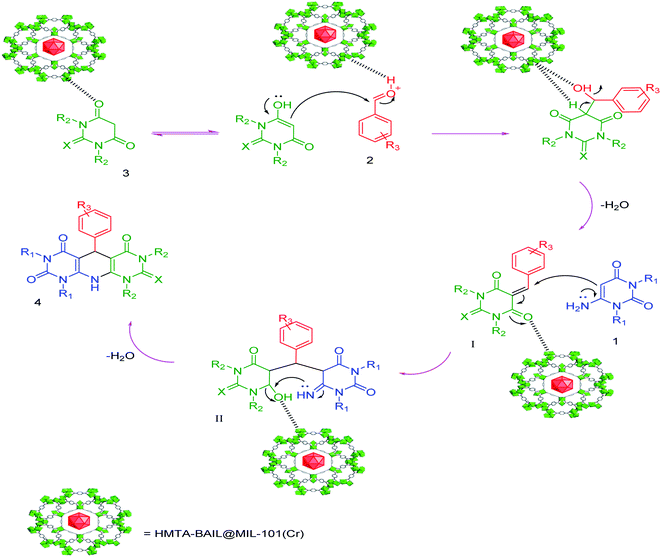 |
| Scheme 6 Proposed mechanism for the synthesis of pyrido[2,3-d:5,6-d′]dipyrimidines. | |
4. Conclusions
In conclusion, we have reported a new Brönsted acidic ionic liquid immobilized on MIL-101(Cr) MOF as an efficient nanoporous and heterogeneous catalyst for the synthesis of pyrido[2,3-d:5,6-d′]dipyrimidine derivatives under solvent-free conditions. The new catalyst was characterized by EDS, SEM, XRD, FT-IR, BET and TGA. The main benefits of this work are the short reaction time, facile workup, reusability of the catalyst, and high yield of products. The highly reactive and heterogeneity nature of this catalyst offers a wide application in heterocyclic synthesis and medicinal chemistry applications.
Conflicts of interest
There are no conflicts to declare.
Acknowledgements
The author gratefully acknowledges the financial support of this work by the Research Affairs Office of the Islamic Azad University, Qom Branch, Qom, I. R. Iran [grant number 2019-2898] and Department of Chemistry, North Tehran Branch, Islamic Azad University, Tehran, Iran.
References
- Z. Hong-Cai, J. R. Long and O. M. Yaghi, Chem. Rev., 2012, 112, 673–674 CrossRef.
- M. E. Davis, Nature, 2002, 417, 813–821 CrossRef CAS.
- K. Ariga, A. Vinu, Y. Yamauchi, Q. Ji and J. P. Hill, Bull. Chem. Soc. Jpn., 2012, 85, 1–11 CrossRef CAS.
- Y. Yamauchi, N. Suzuki, L. Radhakrishnan and L. Wang, Chem. Rec., 2009, 9, 321–339 CrossRef CAS.
- M. A. Ghasemzadeh, B. Mirhosseini-Eshkevari, M. Tavakoli and F. Zamani, Green Chem., 2020, 22, 7265–7300 RSC.
- H. M. A. Hassan, M. A. Betiha, S. K. Mohamed, E. A. El-Sharkawy and E. A. Ahmed, J. Mol. Liq., 2017, 236, 385–394 CrossRef CAS.
- M. Samy El-Shall, V. Abdelsayed, A. El R. S. Khder, H. M. A. Hassan, H. M. El-Kaderi and E. T. Reich, J. Mater. Chem., 2009, 19, 7625–7631 RSC.
- H. M. A. Hassan, M. A. Betiha, S. K. Mohamed, E. A. El-Sharkawy and E. A. Ahmed, Appl. Surf. Sci., 2017, 412, 394–404 CrossRef CAS.
- V. I. Isaeva and L. M. Kustov, Pet. Chem., 2010, 50, 167–180 CrossRef.
- P. D. Du, H. T. M. Thanh, T. C. To, H. S. Thang, M. X. Tinh, T. N. Tuyen, T. T. Hoa and D. Q. Khieu, J. Nanomater., 2019, 2019, 1–15 CrossRef.
- T. B. Faust and D. M. D'Alessandro, RSC Adv., 2014, 4, 17498–17512 RSC.
- F. Wei, Q. Ren and Z. Liang, ChemistrySelect, 2019, 4, 5755–5762 CrossRef CAS.
- M. Nasrabadi, M. A. Ghasemzadeh and M. R. Zand Monfared, New J. Chem., 2019, 43, 16033–16040 RSC.
- W. Chaikittisilp, K. Ariga and Y. Yamauchi, J. Mater. Chem., 2013, 1, 14–19 RSC.
- N. L. Torad, M. Hu, Sh. Ishihara, H. Sukegawa, A. A. Belik, M. Imura, K. Ariga, Y. Sakka and Y. Yamauchi, Small, 2014, 10, 2096–2107 CrossRef CAS.
- S. A. Hassan, A. M. Al-Sabagh, N. H. Shalaby, S. A. Hanafi and H. A. Hassan, Egypt. J. Pet., 2013, 22, 179–188 CrossRef.
- H. M. Hassan, M. A. Betiha, S. K. Mohamed, E. El-Sharkawy and E. A. Ahmed, Appl. Surf. Sci., 2017, 412, 394–404 CrossRef CAS.
- Y. C. Sharma, B. Singh and J. Korstad, Biofuels, Bioprod. Biorefin., 2011, 5, 69–92 CrossRef CAS.
- H. C. Zhou, J. R. Long and O. M. Yaghi, Chem. Rev., 2012, 112, 673–674 CrossRef CAS.
- H. M. Hassan, M. A. Betiha, S. K. Abd El Rahman, M. Mostafa and M. Gallab, J. Porous Mater., 2016, 23, 1339–1351 CrossRef CAS.
- W. R. Mohamed, S. S. Metwally, H. A. Ibrahim, E. A. El-Sherief, H. S. Mekhamer, I. M. Moustafa and E. M. Mabrouk, J. Mol. Liq., 2017, 236, 9–17 CrossRef CAS.
- H. M. Savanur, R. G. Kalkhambkar, G. Aridoss and K. K. Laali, Tetrahedron Lett., 2016, 57, 3029–3035 CrossRef CAS.
- R. Kore and R. Srivastava, J. Mol. Catal. A: Chem., 2011, 345, 117–126 CrossRef CAS.
- R. L. Vekariya, J. Mol. Liq., 2017, 227, 44–60 CrossRef CAS.
- A. Dömling and I. Ugi, Chem. Eng. [Int. Ed.], 2000, 39, 3168–3210 Search PubMed.
- D. A. Ibrahim and A. M. El-Metwally, Eur. J. Med. Chem., 2010, 45, 1158–1166 CrossRef CAS.
- M. J. Aliaga, D. J. Ramon and M. Yus, Org. Biomol. Chem., 2010, 8, 43–46 RSC.
- M. H. Mosslemin and M. R. Nateghi, Ultrason. Sonochem., 2010, 17, 162–167 CrossRef CAS.
- G. M. Ziarani, P. Ghlamzadeh, A. Badiei, S. H. Asadi and A. A. Soorki, J. Chil. Chem. Soc., 2015, 60, 2975–2978 CrossRef CAS.
- K. T. Patil, P. P. Warekar, P. T. Patil, S. S. Undare, G. B. Kolekar and P. V. Anbhule, J. Heterocycl. Chem., 2018, 55, 154–160 CrossRef CAS.
- H. Saeidiroshan and L. Moradi, J. Organomet. Chem., 2019, 893, 1–10 CrossRef CAS.
- I. Yavari and M. Esnaashari, Synthesis, 2005, 7, 1049–1051 CrossRef.
- M. A. Ghasemzadeh, M. H. Abdollahi-Basr and B. Mirhosseini-Eshkevari, Green Chem. Lett. Rev., 2018, 11, 47–53 CrossRef CAS.
- M. A. Ghasemzadeh, B. Mirhosseini-Eshkevari and M. H. Abdollahi-Basr, Appl. Organomet. Chem., 2018, 33, 4679–4687 CrossRef.
- B. Mirhosseini-Eshkevari, M. A. Ghasemzadeh and J. Safaei-Ghomi, Res. Chem. Intermed., 2015, 41, 7703–7715 CrossRef CAS.
- M. A. Ghasemzadeh, M. Azimi-Nasrabad, S. Farhadi and B. Mirhosseini-Eshkevari, J. Organomet. Chem., 2019, 900, 120935–120942 CrossRef.
- C. Férey, C. Mellot-Draznieks, F. Serre, J. Millange, S. S. Dutour and I. A Margiolaki, Science, 2005, 309, 2040–2042 CrossRef.
- X. Liang and J. Yang, Green Chem., 2010, 12, 201–204 RSC.
- H. Wei, B. Teo, A. Chakraborty and S. Kayal, Appl. Therm. Eng., 2016, 101, 891–900 Search PubMed.
- T. Hu, Q. Jia, S. He, S. Shan, H. Su, Y. Zhi and L. He, J. Alloys Compd., 2017, 727, 114–122 CrossRef CAS.
- C. P. Cabello, G. Berlier, G. Magnacca, P. Rumori and G. T. Palomino, CrystEngComm, 2015, 17, 430–437 RSC.
- X. Huang, Q. Hu, L. Gao, Q. Hao, P. Wang and D. Qin, RSC Adv., 2018, 8, 27623–27630 RSC.
Footnote |
† Electronic supplementary information (ESI) available. See DOI: 10.1039/d0ra09054a |
|
This journal is © The Royal Society of Chemistry 2021 |
Click here to see how this site uses Cookies. View our privacy policy here.