DOI:
10.1039/D0RA08230A
(Paper)
RSC Adv., 2021,
11, 781-797
Facile synthesis of superparamagnetic Fe3O4@noble metal core–shell nanoparticles by thermal decomposition and hydrothermal methods: comparative study and catalytic applications†
Received
25th September 2020
, Accepted 24th November 2020
First published on 24th December 2020
Abstract
Herein, we report on developing a facile synthetic route for reusable nanocatalysts based on a combination of the supermagnetic properties of magnetite with the unique optical and catalytic properties of noble metal hybrid nanomaterials. We compare two different synthetic methods, to find out which is best from synthetic and application points of view, for the synthesis of Fe3O4 and Fe3O4@M (M = Ag or Au) core–shell hybrid nanostructures. The two different single-step synthetic methods are: thermal decomposition and hydrothermal. The structural, morphological and magnetic properties of the obtained Fe3O4 and Fe3O4@M nanoparticles were characterized by various techniques. XRD of the Fe3O4 nanoparticles exhibited sharp and strong diffraction peaks, confirming the highly crystalline structure of the Fe3O4 particles synthesized by the hydrothermal method, while broad and weak peaks were observed on using the thermal decomposition method. Both Fe3O4@Ag and Fe3O4@Au core–shells obtained by the hydrothermal method showed the reflection planes of Fe3O4 and additional planes of Ag or Au. But on the formation of Fe3O4@Ag/Au by the thermal decomposition method the peak for Fe3O4 disappeared and only the diffraction peaks of Ag or Au appeared. According to TEM analysis there was a broad particle-size distribution, random near-spherical shapes and slight particle agglomeration for Fe3O4 synthesized by the thermal decomposition method. However, there was a moderate size distribution, spherical shapes and well-dispersed particles without large aggregations for the hydrothermal method. TEM images of the synthesized nanoparticles by the two methods used showed a pronounced difference in both size and morphological shape. The catalytic performance of the synthesized nanoparticles was examined for the reduction of Congo red dye in the presence of NaBH4. The Fe3O4 nanocatalyst maintained its catalytic activity for only one cycle. In the cases of Fe3O4@Au and Fe3O4@Ag, the catalytic activity was conserved for four and ten successive cycles, respectively. Based on the obtained results, it was concluded that the hydrothermal synthesis of Fe3O4, Fe3O4@Ag and Fe3O4@Au nanostructures is highly recommended due to their selectivity and merits.
1. Introduction
Core–shell hybrid nanoparticles formed from the combination of two or more types of nanoparticles are highly regarded by the scientific community. They have the potential to merge the unique physicochemical properties of two or more nanomaterials into one entity, leading to enormous advances by these structures towards various applications in the areas of catalysis, electronics, photonics, and biotechnology and environmental applications.1–7 Superparamagnetic Fe3O4 has found applications in medicine for drug transport as a local magnetic therapy, to diagnose and treat cancer using magnetic hyperthermia (ablation), for magnetic marking of cells (immunological separation) or for contrast strengthening in cell magnetic resonance imaging.8,9 Among these applications catalysis technologies are chosen to contribute to alleviation of the water pollution problem. It is a global issue and the world community is facing the worst effects of polluted water. One of the major sources of water pollution is the discharge of organic dyes as industrial waste. There is an urgent need to find an ideal remover that not only reduces these organic dyes but also achieves their selective separation and recovery to achieve a green chemistry concept. So, it is of utmost importance to develop new materials with tailored properties that can meet strong connections between eco-efficiency and performance, processing and manufacturing, recyclability, and costs. Actually, through nanocomposites with core–shell nanostructures, the catalytic properties can be enhanced to a great extent, which may not be achievable by the use of monometallic catalysts. Magnetic iron oxide nanoparticles (MIONPs) are ideal materials for industrial and biomedical applications because of their very low toxicity and biodegradability.10–15 Superparamagnetic iron oxide nanoparticles, such as magnetite nanoparticles (Fe3O4), are extremely attractive as a component of core–shell hybrid nanoparticles where the saturation magnetization value for the bulk material is 92 emu g−1, so they connect with external fields, providing them with the capability to be easily recovered and subsequently reused or else pulled by a magnetic bar.16,17 However, Fe3O4 nanoparticles have large specific surface areas; they are prone to oxidation and aggregation leading to low magnetism and poor dispersion. Recently, attempts have been made to apply certain facial modifications to Fe3O4 through the development of a wide range of hybrid nanoparticles.18 Distinct consideration is being paid now to the effect of noble metals, such as Ag and Au NPs, on the properties of Fe3O4, due to their specific characteristics like: (i) intense absorption in the optical region associated with localized surface plasmon resonance (LSPR),19 and (ii) their stability at high temperatures under conditions where base metals are rapidly oxidized.20 This was confirmed by an improvement in the stability of and an enhancement in the catalytic and antibacterial activities of the Fe3O4@noble metal hybrid nanoparticles, suggesting their importance for potential applications in water treatment and biomedicine.21–24 A wide variety of types of chemical processing can be used to synthesize hybrid nanoparticles, such as co-precipitation, thermal decomposition, electrodeposition, sol–gel, sonochemical and hydrothermal methods. Each technique used to produce hybrid nanoparticles has different characteristics and displays some advantages and disadvantages. The selection of a specific technique will be based on several factors, such as the kind of desired structure, the necessity for size control, time available to produce the particles, and the required interaction between both components. Thermal decomposition is a common method used in industry to synthesize narrow magnetic iron oxide nanoparticles (MIONPs). In this method, the iron precursor and reducing agent are injected into a solvent containing surfactant solution at a high temperature, which in turn decomposes the iron precursor in the presence of the surfactant that will coat and stabilize the formation of MIONPs. The thermal decomposition method is characterized by some advantages, in comparison with other methods: the process is non-toxic, inexpensive and achieves high crystallinity with a uniform size distribution, allowing a good amount of nanocrystals to be produced in a single reaction without a further size-sorting process.25 Hydrothermal synthesis of MIONPs in aqueous media is carried out in autoclaves/reactors at high temperature and pressure (above 200 °C and 13
790 kPa).26–31 Rapid nucleation and faster growth occur at high temperature and lead to the formation of MIONPs. The crystals formed by hydrothermal treatment are generally narrow with high purity and density. They do not aggregate due to the presence of stabilizing agents.
The main goal of the present study is to optimize a synthetic method for Fe3O4@M (M = Ag or Au) core–shell NPs. Herein, we applied two different single-step synthetic methods; (i) thermal decomposition and (ii) hydrothermal, to compare them to find which is better in terms of both synthetic and catalytic approaches. Different complementary analytical tools were used to characterize the synthesized nano-core–shells such as FTIR, XRD, TEM, EDX, UV-Vis, and magnetization. Congo red was selected as a target pollutant, due to its solubility in water and extensive use in the textile, paper, rubber and plastic industries. Congo red is a carcinogenic benzidine-based anionic diazo dye used for the coloration of paper products. The catalytic activities of Fe3O4@M core–shell NPs were utilized for the degradation of Congo red dye in aqueous solution using NaBH4 as a reducing agent. The effects of NaBH4, initial dye concentration and catalyst amount on the degradation process were also studied in detail.
2. Experimental
2.1 Materials and reagents
All chemicals were commercial grade and used without additional purification. They include ferric nitrate nonahydrate Fe(NO3)3·9H2O, silver nitrate AgNO3, tetrachloroauric acid HAuCl4·3H2O, tri-disodium citrate dihydrate C6H5O7Na3·2H2O, urea (CON2H4), polyacrylamide (PAM), sodium borohydride NaBH4 (99.0%) and Congo red. Deionized water was used for all synthesis and measurement procedures.
2.2 Methods for synthesis of Fe3O4, Fe3O4@Ag, and Fe3O4@Au NPs
2.2.1 Thermal decomposition method.
The thermal decomposition method is one of the best developed methods to tune the size and shape of modified iron oxide nanoparticles, MIONPs. Coordination compounds are used as precursors to increase the quality of MIONPs. In this method, an iron coordination compound containing a surfactant solution was injected into a solvent at high temperature, which in turn decomposed, giving an iron precursor in the presence of a surfactant. This coats and stabilizes the formed MIONPs.
2.2.1.1 Synthesis of magnetite nanoparticles (Fe3O4).
Magnetite nanoparticles were synthesized using an iron–urea complex, iron(III) hexaureatrinitrate [Fe(CON2H4)6](NO3)3, in the presence of sodium citrate as a stabilizing agent. This route was relatively environmentally-friendly because ferric nitrate and urea were the precursors for the iron complex. In a typical synthesis; 1 mmol Fe(NO3)3·9H2O, 6.2 mmol urea (CON2H4) and 3 mmol sodium citrate (C6H5O7Na3·2H2O) in 1
:
6.2
:
3 molar ratio were dissolved in about 15 mL of distilled water. The obtained light green colored precipitate was vigorously stirred for 1 h. Then 0.15 g of polyacrylamide (PAM) as a capping agent was added under continuous stirring until complete dissolution. The mixture was then taken in a round-bottom flask and refluxed with stirring in the air at 200 °C for about 12 h. After cooling down to room temperature, the precipitate was collected by magnetic separation, washed several times with ethanol, then with distilled water, and kept in an oven at 40 °C overnight for drying. The prepared sample was calcined at 600 °C in a muffle oven (heating rate = 2 °C min−1) under air atmosphere.
2.2.1.2 Synthesis of core–shell hybrid nanoparticles of Fe3O4@M (M = Ag or Au).
The preparation of Fe3O4@M core–shell nanoparticles was carried out following the same procedures as in Section 2.2.1.1, with only one additional step, where 0.5 mmol AgNO3 was used for the synthesis Fe3O4@Ag, and 0.5 mmol HAuCl4·3H2O for the synthesis Fe3O4@Au, where each of these additives was dissolved in 5 mL of distilled water, then dropped slowly into the former solution until it dissolved completely. The molar ratio of the noble metal precursor to that of iron was 1
:
2. The remaining steps were followed exactly until the required product was obtained.
2.2.2 Hydrothermal method.
This technique is relatively simple, inexpensive and rapid. It provides highly crystalline Fe3O4 nanoparticles with good magnetic properties and high monodispersity,32,33 because it exploits the solubility of inorganic substances at certain temperatures and high pressures. To achieve a real comparison between this method and the thermal decomposition method, the same reactants were used in the same order, so that the only difference in the resulting product is due to the effect of the method used.
2.2.2.1 Synthesis of magnetite nanoparticles (Fe3O4).
Fe(NO3)3·9H2O (1 mmol), urea (CON2H4) (6.2 mmol), and sodium citrate (C6H5O7Na3·2H2O) (3 mmol) were dissolved in about 15 mL of distilled water followed by intensive stirring for 1 h until the reactants were completely converted to a light green precipitate. Then, 0.15 g of polyacrylamide (PAM) was slowly added under vigorous stirring until complete dissolution of all the materials. The solution was subsequently transferred to a 50 mL Teflon-lined autoclave. The autoclave was then sealed and subsequently put into an oven at 200 °C for 12 h. After the autoclave had cooled down to room temperature, the black precipitate was collected by an external magnet, washed alternately with absolute ethanol and distilled water several times, and dried in the oven at 50 °C overnight.
2.2.2.2 Synthesis of core–shell hybrid nanoparticles of Fe3O4@M (M = Ag or Au).
Fe3O4@M core–shell nanoparticles synthesized by the hydrothermal method were achieved by following the same procedures as in Section 2.2.2.1. Then 5 mL of 0.5 mmol aqueous AgNO3 0.5 mmol HAuCl4·3H2O, for the synthesis of Fe3O4@Ag or Fe3O4@Au, respectively, were dropped slowly into the formed solution until it had totally dissolved. The same molar ratio of noble metal precursor to iron precursor was taken into account, which was 1
:
2. The remaining steps were followed exactly as previously.
The chemical steps for the synthesis of Fe3O4@Ag and Fe3O4@Au core–shell nanoparticles by the two investigated methods are shown in Scheme 1.
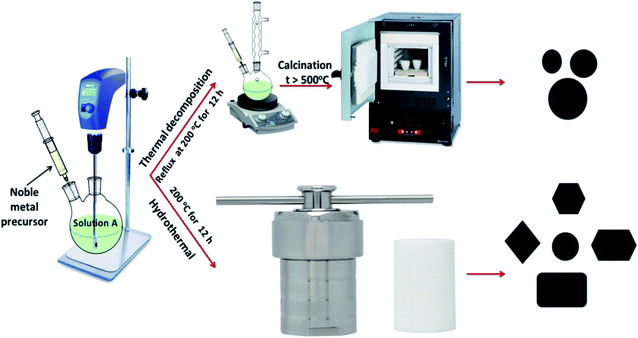 |
| Scheme 1 Schematic representation of the procedures for the synthesis of Fe3O4@Ag and Fe3O4@Au core–shell NPs by the two methods. | |
2.3 Catalytic performance of the synthesized NPs
The catalytic behavior of all synthesized nanostructures has been demonstrated toward the reduction of Congo red dye, CR. CR was not reduced readily in aqueous media by addition of NaBH4 as a reducing agent and the reaction was not kinetically feasible. The reaction mixture consisted of 0.5 mL of dye solution of 1 × 10−3 mol L−1, 5 mL of aqueous solution of 0.05 mol L−1 NaBH4 and the solution mixture was brought up to 10 mL using distilled water and then finally 20 mg of nanocatalyst was added. The time-dependent UV/Vis absorption spectra were recorded at 496 nm immediately after the addition of the nanocatalyst into the reaction mixture to follow the reduction process. The decrease in the absorbance of unreduced CR was recorded, until the steady-state was reached.
To follow the progress of CR dye degradation under these conditions, the efficiency percentage was calculated as a function of time. The degradation efficiency was calculated as;34
where,
A0 and
At are the absorbance of the free CR dye and at time
t, respectively.
2.4 Instrumentation
An FT-IR-4100 (JASCO, Japan) spectrophotometer was used to record the FT-IR spectra within the range 4000–400 cm−1 with a resolution of 2 cm−1 using KBr pellets. The crystalline structure of all synthesized nanostructures was analyzed by X-ray powder diffraction (XRD) with a GNR APD 2000 PRO diffractometer in the angular range 2θ = 5°–90° at 293 K using nickel-filtered Cu Kα (λ = 1.5405 Å) radiation operating at 40 kV and 30 mA. The morphology was examined by transmission electronic microscopy (TEM) measurements using a JEOL (Jem-2100) electron microscope (HT 200 eV; resolution 0.1432 nm; option 1.5 million). An energy-dispersive X-ray spectrometer (EDX) IT100LA operating at an accelerating voltage of 20.00 keV was attached to a transmission electron microscope (TEM). Magnetic properties were measured by a vibrating sample magnetometer (VSM, Lake Shore, 7410 model) at room temperature. The thermal analysis, TGA, was carried out in the range 30–800 °C using a Shimadzu TG-50 thermogravimetric analyzer under a nitrogen atmosphere with a heating rate of 20 °C min−1. The UV-Vis absorption spectra were recorded using a Shimadzu double beam UV-Vis Scanning Spectrophotometer (UV-3101 PC), using matched quartz cuvettes.
3. Results and discussion
3.1 Mechanism of formation of Fe3O4@M core–shell nanostructures
A possible mechanism for the formation of the Fe3O4@M core–shell from the iron–urea complex is depicted in Schemes 2 and 3. It was proposed that cyanuric acid is formed along with iron oxide nanoparticles on the thermal decomposition of the iron–urea complex.35 The cyanuric acid molecules present on the surface of the iron oxide nanoparticles are hydrogen-bonded to sodium citrate molecules and coat them completely. Citrate and PAM play important roles in the formation of well-defined Fe3O4@M core–shell NPs. The polymer, PAM, played two roles in the synthetic route. Firstly, PAM with abundant amide groups is considered to be an efficient chelating agent for the preparation of supported Ag NPs through the coordination of N and O atoms with Ag+ ions.36 Secondly, it worked as a capping agent and stabilizer.37 Due to the large amount of amide ligands, PAM could be adsorbed on the surface of the product, consequently stabilizing the primary formed particles. The increased viscosity slows down the reaction rate as well as the rate of movement of the primary nanoparticles.38 Slowing down the rate allows primary nanoparticles to have enough time to aggregate into regular spheres.
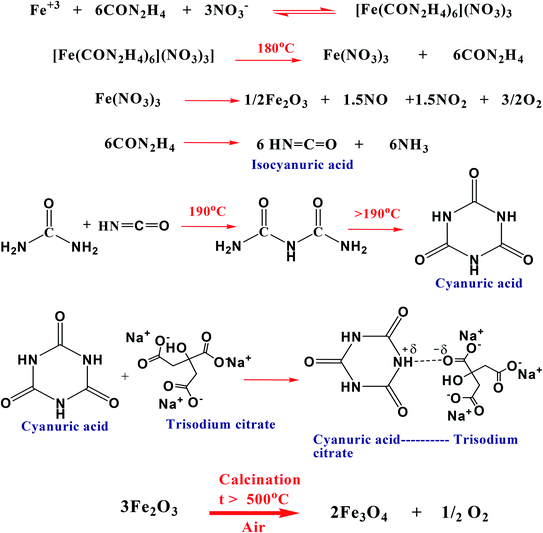 |
| Scheme 2 Possible reactions involved in the formation of Fe3O4 by the thermal decomposition method. | |
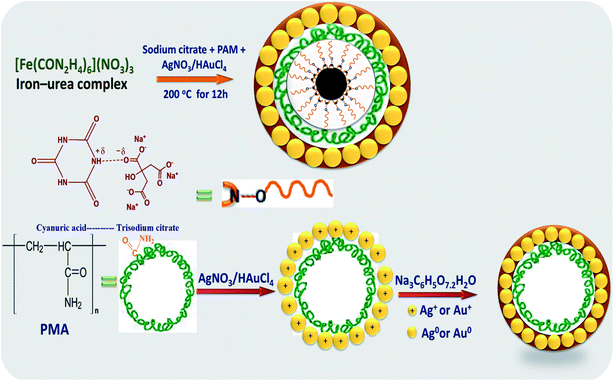 |
| Scheme 3 The suggested mechanism for the formation of Fe3O4@M core–shell. | |
3.2 Structural characterization of the synthesized nanostructures
Different spectroscopic techniques were utilized to characterize and confirm the structure of the investigated nanostructured materials, Fe3O4, Fe3O4@Ag and Fe3O4@Au synthesized by the two methods.
3.2.1 FT-IR analysis.
Analysis of the surface components of the investigated nanostructures was performed with FTIR. FTIR spectra of Fe3O4 and core–shell nanospheres formed by the two methods are shown in Fig. 1(a–c). Both FTIR spectra of Fe3O4 obtained by the two methods showed a broad peak at 3435 cm−1 assigned to the characteristic NH2 group of PAM and the peak at 1640 cm−1 assigned to the characteristic O
C–NH amide group, proving that an amount of –NH2 is embedded on the surface of Fe3O4 NPs. The characteristic absorption peaks at 1590 (sh) and 1455 cm−1 were assigned to the asymmetric and symmetric vibrations of the carboxylate ion COO− in trisodium citrate molecules. The two bands appearing around 590 and 440 cm−1 correspond to the Fe–O stretching vibrational mode in the tetrahedral site and the Fe–O stretching vibrational mode in an octahedral environment, which confirm the formation of the mixed Fe3O4 oxide. Actually, the characteristic IR peaks of Fe3O4 synthesized by the two methods shown in Fig. 1(a) are very similar. Fig. 1(b and c) illustrate the FTIR spectra of the Fe3O4@Ag core–shell obtained by the two methods and Fe3O4@Au by the hydrothermal method. By comparing Fig. 1(b and c) with Fig. 1(a), it was found that there is not much difference between them. The spectra of Fe3O4@M (M = Ag or Au) display the well-defined characteristic bands that appeared in the spectrum of Fe3O4. The bands were slightly shifted with different relative intensities.
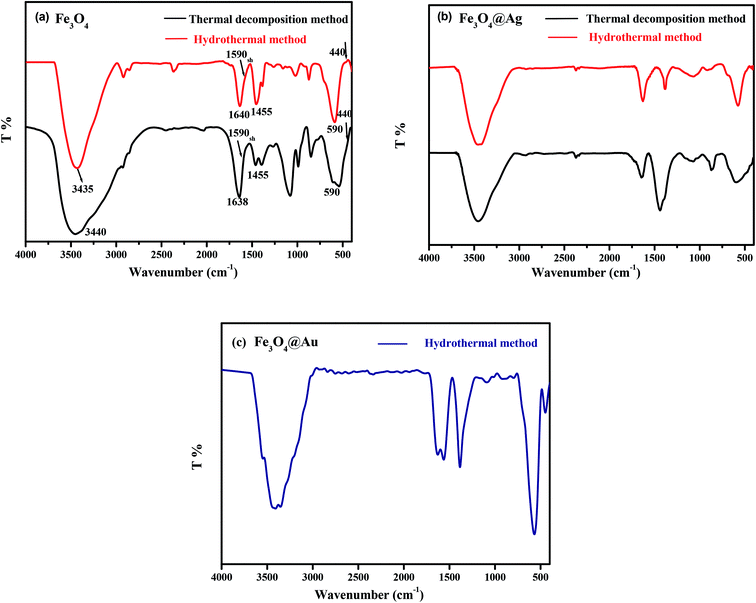 |
| Fig. 1 FT-IR spectra of (a) Fe3O4, (b) Fe3O4@Ag and (c) Fe3O4@Au synthesized by the investigated methods. | |
3.2.2 XRD measurements.
The phase composition of the prepared nanocatalysts was determined by X-ray powder diffraction. Fig. 2(a–c) show the X-ray diffraction patterns of Fe3O4, Fe3O4@Ag and Fe3O4@Au NPs. The X-ray diffraction pattern of the Fe3O4 nanoparticles exhibited peaks at 2θ = 18.8°, 30.52°, 35.54°, 43.59°, 53.91°, 57.11°, and 62.89° fully indexed to diffraction from the (111), (220), (311), (400), (422), (511) and (440) planes of the magnetite phases. The sharp and strong diffraction peaks confirm the crystalline nature of the Fe3O4 particles synthesized by the hydrothermal method. But on using the thermal decomposition method, the X-ray diffraction pattern of the Fe3O4 NPs showed broad and weak peaks at phases (220), (311), (400) only, indicating the amorphous structure of the synthesized Fe3O4. It was observed that the peaks of the synthesized Fe3O4 are in agreement with the data of the face centered cubic structure for the reference magnetite in ICDD no. 19:629.39 The X-ray diffraction pattern of the as-prepared Fe3O4@Ag shows the reflection planes (111), (220), (311), (422) and (511) of Fe3O4 and an additional four diffraction peaks at 2θ = 38.1, 44.3, 64.4 and 77.4 corresponding to the (111), (200), (220) and (511) planes of silver, respectively, indicating the face-centered cubic structure of the nanosilver. But on formation of Fe3O4@Ag by the thermal decomposition method, the peak of Fe3O4 disappeared completely and only the diffraction peaks of Ag appear. The presence or absence of magnetite peaks in the X-ray diffraction patterns of the Fe3O4@Ag core–shell depends on the shell thickness. When the shell has a large thickness, the signal from the core is shielded and becomes invisible in the X-ray diffraction pattern, which was elucidated from measurement of the particle diameter obtained from TEM measurements. The X-ray diffraction pattern of Fe3O4@Au core–shell NPs obtained by the hydrothermal method shows two phases of the Fe3O4 core and the Au shell. It shows a characteristic diffraction peak at (311) for Fe3O4, in addition to four diffraction peaks at 38.1, 44.3, 64.4 and 77.4, corresponding to the (111), (200), (220) and (311) planes of the face-centered cubic structure of Au, respectively.
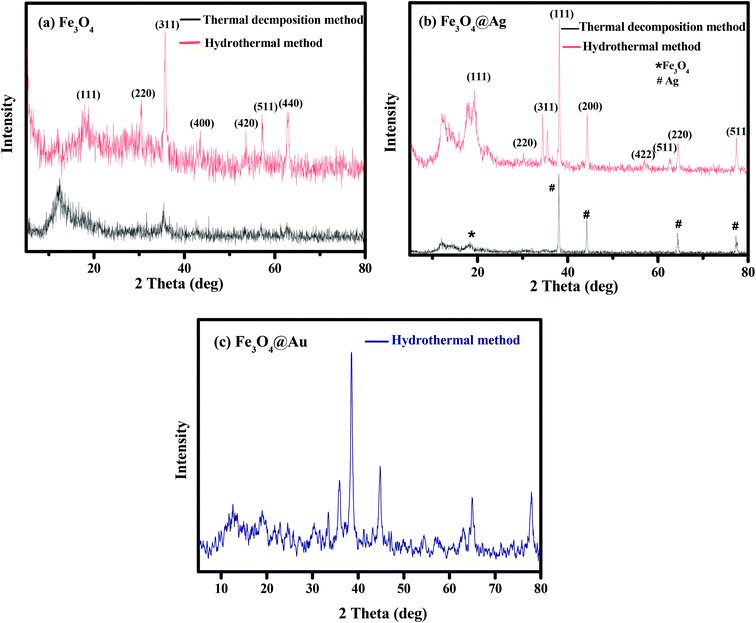 |
| Fig. 2 XRD patterns of (a) Fe3O4, (b) Fe3O4@Ag and (c) Fe3O4@Au synthesized by the investigated methods. | |
The crystal size of the synthesized nanoparticles was determined from the width of the X-ray diffraction peaks using the Debye–Scherrer equation for the most intense diffraction peaks for the (220), (311), (400) faces of Fe3O4.40
where
D is the particle size (nm),
λ is the wavelength (0.15406 nm for the X-ray source),
β is the full width at half maximum intensity (FWHM) of the peak (radians), and
θ is the diffraction angle (radians). Then the average crystalline particle size of Fe
3O
4 was calculated as:
d(average) =
D1 +
D2 +
D3.
The calculated average crystalline sizes of Fe3O4 NPs synthesized by thermal decomposition and hydrothermal methods were found to be 27.75 and 16.02 nm, respectively. While for Fe3O4@Ag, they were 69.82 and 29.19 nm for the two previous methods, respectively. The calculated particle size of Fe3O4@Au synthesized by the hydrothermal method was found to be 46.93 nm.
3.2.3 Energy dispersive X-ray spectroscopic analysis of synthesized NPs.
The energy dispersive X-ray signals provide information about the sample and its composition. EDX spectra measured from the samples imaged by TEM for the synthesized Fe3O4@Ag and Fe3O4@Au core–shell NPs are shown in Fig. 3(a and b) and their tentative data are collected in Table 1. The EDX analysis has demonstrated that Fe, O, C and Ag are the major elements in Fe3O4@Ag, while Fe, O, C and Au are the major elements in Fe3O4@Au. These results show that the source of the C element was the trisodium citrate dehydrate coating the Ag or Au NPs. EDX analysis indicated the presence of O and Fe in mass% close to the chemical composition of Fe3O4. The mass% of Ag metal is 21.25% which is greater than that of Au which is 19.74%. According to the EDX feedback, it was concluded that each individually synthesized material is consistent with its elements, which further supports the XRD results.
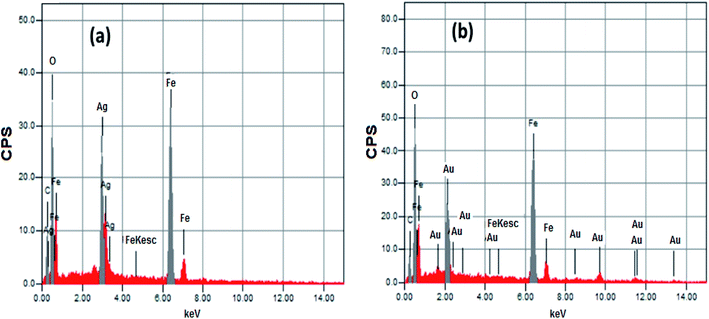 |
| Fig. 3 EDX of (a) Fe3O4@Ag and (b) Fe3O4@Au core–shell NPs. | |
Table 1 EDX analysis of synthesized core–shell NPs and mass percentage of each element
Core–shell |
Element mass% |
C |
O |
Fe |
Ag |
Au |
Fe3O4@Ag |
9.18 |
32.84 |
36.73 |
21.25 |
— |
Fe3O4@Au |
8.99 |
31.10 |
40.17 |
— |
19.74 |
3.2.4 TEM analysis of Fe3O4@Ag and Fe3O4@Au NPs.
Transmission electron microscopy (TEM) was used to analyze the morphology, structure and size of the samples prepared by thermal decomposition and hydrothermal methods. Fig. 4(a–f) show the TEM micrographs of Fe3O4, Fe3O4@Ag and Fe3O4@Au nanoparticles. As can observed from the images, the size and morphology of the synthesized NPs are significantly different. Starting with Fe3O4, there was a broad random size distribution, near-spherical shapes and slight particle agglomeration (Fig. 4(a)). This is due to the higher magnetostatic coupling between the particles obtained by the thermal decomposition method. In contrast, there was a narrow size distribution, spherical shapes and well-dispersed particles without any agglomeration for the particles formed by the hydrothermal method (Fig. 4(b)). The average size of the Fe3O4 nanoparticles synthesized by thermal decomposition is 46.5 nm, while for nanoparticles synthesized by the hydrothermal method it is 21.3 nm, which is nearly half that formed by the other method. Fig. 4(c) shows that Fe3O4 nanoparticles were successfully coated with a thick shell of Ag, leading to a spherical core–shell structure for Fe3O4@Ag with an average size ≈72.8 nm in the case of the thermal decomposition method, but in the case of the hydrothermal method, there was a thin shell layer of Ag coated magnetite (average size ≈ 27.8 nm) in a prismatic shape, in addition to the spherical shape (Fig. 4(d)). Also, Fe3O4@Ag NPs synthesized by the hydrothermal method were more dispersed in nature than those synthesized by thermal decomposition. Based on these observations we decided to use the hydrothermal method for coating Fe3O4 with Au. Fe3O4@Au NPs exhibited different shapes like rhombic, spherical and square, demonstrating a well-defined core–shell structure of average size ≈ 48.9 nm (Fig. 4(e and f)). The average sizes of all synthesized NPs agreed well with the values calculated from XRD using the Debye–Scherrer equation.
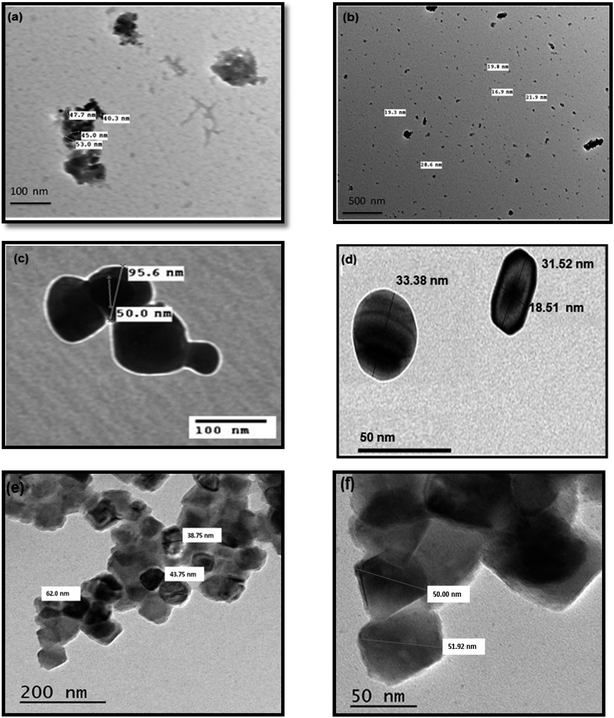 |
| Fig. 4 TEM images of Fe3O4 synthesized by (a) thermal decomposition method, (b) hydrothermal method. Fe3O4@Ag synthesized by (c) thermal decomposition method, (d) hydrothermal method. (e and f) Fe3O4@Au obtained by the hydrothermal method. | |
3.2.5 Magnetization of Fe3O4, Fe3O4@Ag and Fe3O4@Au NPs.
The magnetization properties of Fe3O4, Fe3O4@Ag and Fe3O4@Au NPs synthesized by the two methods were measured by VSM. The relationship between particle size and the magnetic properties of Fe3O4 NPs has been reported.41 The critical size value of Fe3O4 NPs indicates the transition from a single-domain to a multi-domain structure. This value depends on the crystal structure whether it is spherical or cubic, or has multiple phases. The critical size for a multi-domain structure has been theoretically estimated to be 128 nm for spherical Fe3O4 NPs.42,43
Fig. 5(a–c) depict the hysteresis loop of the nanocatalysts measured under a magnetic field varying from −8000 to 8000 Oe at room temperature. Generally, the saturation magnetization, Mg, values of magnetized Fe3O4, and Fe3O4@Ag nanoparticles decreased from 6.82, and 3.55 emu g−1 to 3.9, and 1.99 emu g−1 for the nanocatalysts synthesized by the thermal decomposition and hydrothermal methods, respectively. However, the saturation magnetization value of hydrothermal magnetized Fe3O4@Au was found to be 6.88 emu g−1. Obviously, the decrease in Ms in the case of Fe3O4@Ag relative to Fe3O4 is due to the shielding effect of nonmagnetic Ag NPs. However, the saturation magnetization value of Fe3O4@Au was greater than that of Fe3O4@Ag. This may be due to the liberation of Au NPs from their core–shell, leaving Fe3O4 NPs with the same value for its individual case, as will be discussed later in Section 3.3. Also, Fe3O4@Ag and Fe3O4@Au NPs could be magnetically separated easily from aqueous solution by an external magnet and re-dispersed in water, as shown in the images in Fig. 5(b and c). The outstanding magnetic properties of Fe3O4@Ag NPs rendered them economic and reusable for various applications, especially for treatment of wastewater.
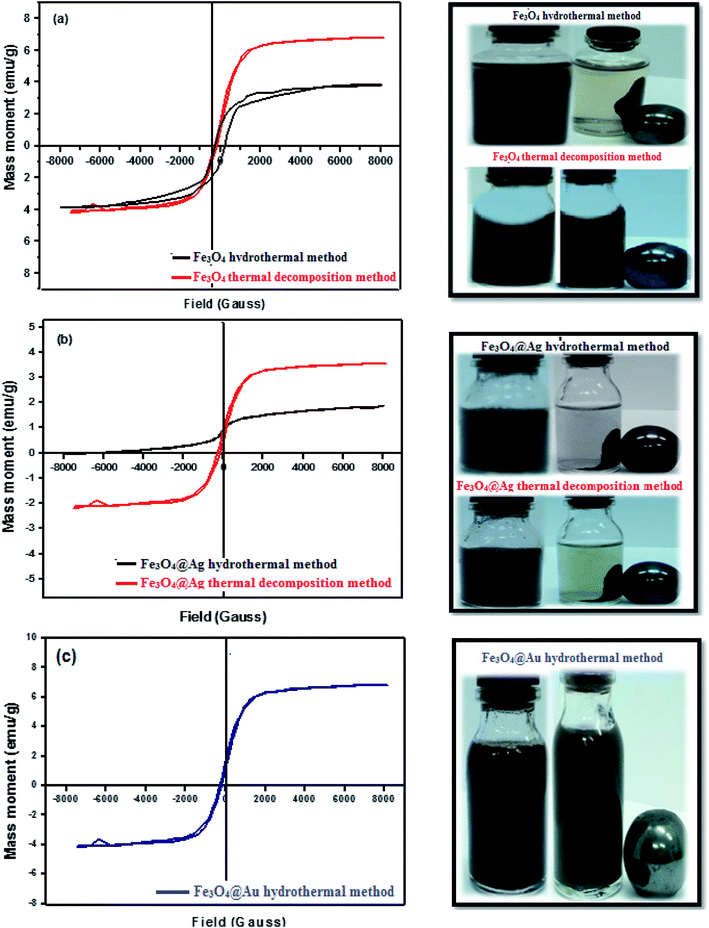 |
| Fig. 5 VSM analysis of (a) Fe3O4, (b) Fe3O4@Ag obtained by the two investigated methods and (c) Fe3O4@Au obtained by the hydrothermal method. Pictures of them dispersed in water: without a magnet, and being attracted by a magnet. | |
3.2.6 TGA analysis of Fe3O4, Fe3O4@Ag and Fe3O4@Au NPs.
Fig. 6(a) shows the TGA thermogram of the Fe3O4 NPs formed by the two investigated methods, to evaluate the mass percentage of PAM and trisodium citrate on the surface of Fe3O4 NPs. The first decomposition stage occurred within the 30–113 °C temperature range for Fe3O4 obtained by thermal decomposition and between 30 and 122 °C for that obtained by the hydrothermal method. Steep weight losses of 21.9% and 15.6% were calculated for the NPs obtained from the two methods, respectively, owing to the release of any remaining water and alcohol on the particle surface. The second stage shows weight losses of 12% and 10% over a wide range of temperature, 113–650 °C and 122–685 °C for the nanocatalysts synthesized by the two methods, respectively. This weight loss is due to the PAM decomposition of the thin layer of PAM coating the surface of the Fe3O4 NPs in both cases. In the temperature range of 650–800 °C, PAM and the rest of any organic carbon from the citrate were completely decomposed, resulting in weight losses of about 9% and 5%, respectively, for the two methods. Then no further weight loss is observed because of the high thermal stability of Fe3O4. From these findings, we concluded that Fe3O4 NPs synthesized by the hydrothermal method are more thermally stable than those synthesized by thermal decomposition. For Fe3O4@Ag and Fe3O4@Au core–shell NPs, the thermogravimetric curves (Fig. 6(b and c)) followed the same decomposition profile as Fe3O4 NPs but with greater thermal stability, due to the intervention of the noble metals Ag or Au. In fact, the Fe3O4@Ag core–shell reflects higher thermal stability than the Fe3O4@Au core–shell.
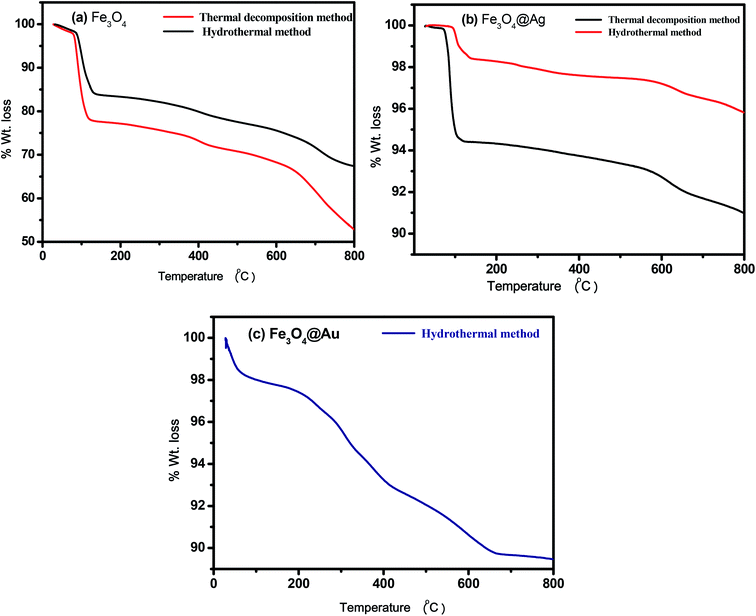 |
| Fig. 6 TGA of (a) Fe3O4 formed by hydrothermal and thermal decomposition methods, (b) Fe3O4@Ag obtained by hydrothermal and thermal decomposition methods, and (c) Fe3O4@Au synthesized by the hydrothermal method. | |
3.3 Kinetics of reductive degradation of the investigated dye
3.3.1 Catalytic degradation of Congo red in water.
Herein, the catalytic performance of the Fe3O4, Fe3O4@Ag and Fe3O4@Au core–shell nanocatalysts with NaBH4 as a reducing agent, toward the degradation of CR dye was investigated under ambient conditions. Firstly, the effect of NaBH4 on the degradation of CR was tested, where it was found that NaBH4 alone could not degrade the dye even after 24 h. Similarly, in the absence of NaBH4, the nanocatalyst itself showed no degradation efficiency. This suggested that neither NaBH4 nor the nanocatalyst alone is viable for catalyzing the degradation of CR, and the reaction could be finished quickly only when both the nanocatalyst and NaBH4 were used together. This is due to the fact that the nanocatalyst efficiently catalyzed the reduction of CR by inducing the relay of electrons from BH4− species to the CR dye.
The kinetics of the catalytic reduction of CR using the investigated Fe3O4, Fe3O4@Ag and Fe3O4@Au core–shell nanoparticles was studied using UV-Vis spectroscopy by following the disappearance of the absorbance of CR at λmax = 496 nm (Fig. 7). The absorption spectra indicated that in the presence of NaBH4, Fe3O4, Fe3O4@Ag and Fe3O4@Au core–shell nanoparticles reduce the intensity of the absorption bands of CR over time intervals, where the band disappeared completely within 35, 16, and 26 min for the mentioned nanocatalysts, respectively. The breakage of the azo group of the CR dye leads to the formation of aromatic amine products (Scheme 4).
 |
| Fig. 7 Absorption spectra of Congo red under the optimum conditions, [CR] = 5 × 10−5 M, [NaBH4] = 2.5 × 10−2 M, and the amount of nanocatalysts = 20 mg, recorded at different time intervals. | |
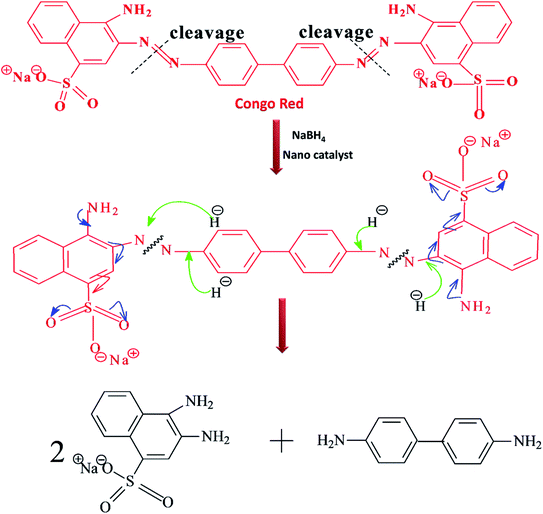 |
| Scheme 4 Proposed mechanism for the reduction of Congo red by NaBH4 catalyzed by the synthesized nanocatalyst. | |
An interesting phenomenon occurred when tracking the degradation of the CR using Fe3O4@Au, where a bathochromic shift of the absorption band of CR dye by 36 nm was observed on increasing the reaction time, with the formation of an isopiestic point at 593 nm. This was assigned to the liberation of Au NPs in the solution, which has a high plasmonic band and leads to a noticeable overlap in the absorption spectra with increasing time. This observation confirms the higher value of saturation magnetization of Fe3O4@Au, as represented in Fig. 5(c).
The efficiencies of removal of CR were found to be 84.2, 96.2, and 91.2% within 35, 16, and 26 min in the presence of Fe3O4, Fe3O4@Ag and Fe3O4@Au NPs, respectively. This clearly shows the higher efficiency of Fe3O4@Ag core–shell NPs over those of Fe3O4 and Fe3O4@Au NPs.
The kinetics of the catalytic reaction were adapted to the pseudo-first-order reaction model, which was used to determine the catalytic rate constant, as expressed by the following equation;
where
A0 and
At, are the absorbance of the free CR dye and that at different time intervals;
k and
t are the catalytic rate constant and the time taken for CR removal in the presence of NaBH
4 and the mentioned nanocatalyst. The semi-logarithmic plots are straight lines with a good linear correlation (
r ≈ 0.99) (Fig. S1
†). This confirmed that the degradation reaction follows pseudo-first-order kinetics with respect to the CR dye concentration. The rate constants of degradation of CR dye in the presence of NaBH
4 and the nanocatalysts, Fe
3O
4, Fe
3O
4@Ag and Fe
3O
4@Au, were determined from the slopes, and found to be 0.045, 0.16, and 0.09 min
−1, respectively. This indicated the highly efficient catalysis of Fe
3O
4@Ag NPs compared to Fe
3O
4@Au and Fe
3O
4 NPs.
Examining the obtained results, it was found that the core–shells, Fe3O4@Ag and Fe3O4@Au were the most efficient nanocatalysts for the degradation of CR dye over Fe3O4 nanoparticles. So the reaction conditions, such as the initial concentration of the dye, the concentration of NaBH4, and the amount of catalyst have been studied considering the two nanocatalysts: Fe3O4@Ag and Fe3O4@Au core–shells.
3.3.2 Effect of dye concentration.
The effect of CR concentration on the degradation rate was investigated at various concentrations (3.0, 4.5, 5.0 and 10.0 × 10−5 M), with the NaBH4 concentration fixed at 2.5 × 10−2 M, and the amount of the nanocatalysts fixed at 20 mg for Fe3O4@Ag and Fe3O4@Au core–shells. The concentration of NaBH4 was 250–833 times greater than that of CR dye to ensure that the reaction proceeded following pseudo-first-order conditions with respect to the CR dye. The semi-logarithmic plots of the absorbance of CR dye against time are straight lines (Fig. 8), confirming that the catalytic reaction is pseudo-first-order type. The rate constants of the reaction were determined from the slope of the straight lines and were found to be 0.018, 0.035, 0.056, 0.18 min−1 for Fe3O4@Ag and 0.08, 0.063, 0.048, 0.037 for Fe3O4@Au, corresponding to dye concentrations of 3.0, 4.5, 5.0 and 10.0 × 10−5 M, respectively.
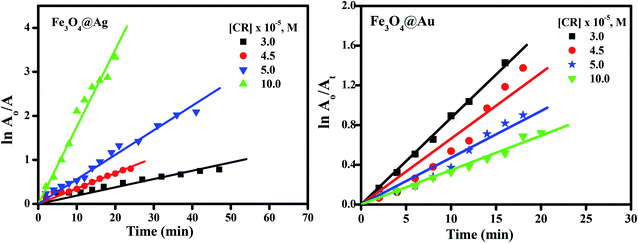 |
| Fig. 8 Pseudo-first-order kinetic plot of ln A0/Atvs. time for the catalytic degradation of CR dye (3.0–10.0 × 10−5 M), in the presence of NaBH4 (2.5 × 10−2 M), and the nanocatalysts (20 mg for Fe3O4@Ag and Fe3O4@Au nanoparticles). | |
It is clear from Fig. 9(a) that the reaction rate increases with an increase in the dye concentration in the presence of Fe3O4@Ag as a nanocatalyst, reaching a maximum value of 0.17 min−1 at a dye concentration of 1 × 10−4 M. The increase in rate is due to an enhancement of the electron transfer process on the surface of the nanocatalyst, by the generation of electrons as a result of oxidation of Ag0 to Ag+ ions, in addition to the electrons of the NaBH4 which leads to an enrichment of the electrons on the surface of the nanocatalysts, and an enhancement in the degradation of CR dye.
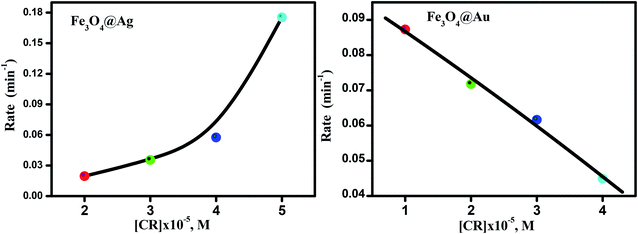 |
| Fig. 9 The effect of dye concentrations on reaction rate, [NaBH4] = 2.5 × 10−2 M, and the amount of catalyst = 20 mg. | |
However, in the presence of Fe3O4@Au as a nanocatalyst, the reaction rate decreases with an increase in the dye concentration, reaching a minimum value of about 0.044 min−1 at a dye concentration of 1 × 10−4 M (Fig. 9(b)). The decrease in the rate of catalytic reaction upon increasing the concentration of CR dye may be due to competition between the reaction products or the generated intermediates and the free dye molecules which attach to the catalyst surface. Such interference of reaction products or intermediates will render the catalyst surface poisoned and consequently the dye degradation will ultimately be retarded. A further explanation of this phenomenon is that, when the initial concentration of the dye is increased, more and more dye molecules are adsorbed on the surface of the nanocatalysts. The existence of large amounts of adsorbed dye resulted in the lack of any direct contact with the active sites, thus causing an inhibition effect on the dye degradation.44
3.3.3 Effect of NaBH4 concentration.
It is known that the concentration of NaBH4, as a reducing agent, influences the catalytic degradation of dye substances. So, the concentration of NaBH4 was varied in the range (1.0–2.5) × 10−2 M, while the concentration of CR dye was kept constant at 5 × 10−5 M, and the amount of nanocatalyst was also kept constant at 20 mg. It was found that the extent of degradation increases upon increasing the NaBH4 concentration, where complete degradation was observed in the presence of 2.5 × 10−5 M NaBH4 at the prescribed reaction time. This observation suggests that an appropriate concentration of BH4− ions is imperative for achieving the best catalytic efficiency of the Fe3O4@Ag and Fe3O4@Au core–shells. The plots of ln(At/A0) vs. time for CR degradation within the range of NaBH4 concentrations are presented in Fig. 10. As can be seen from Fig. S2,† the rate of the reaction increases with an increase in the concentration of NaBH4, due to enhanced electron transfer from BH4− ions to the dye molecules upon raising the concentration of NaBH4.
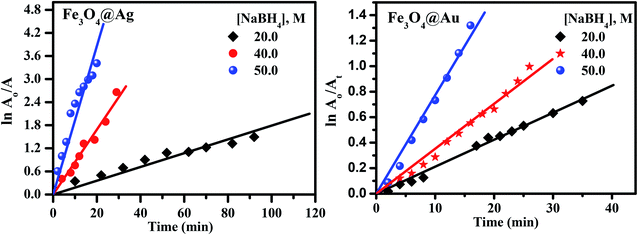 |
| Fig. 10 Pseudo-first-order kinetic plots of ln A0/Atvs. time for the catalytic degradation of CR dye (5.0 × 10−5 M), with varying concentrations of NaBH4 (1.0–2.5 × 10−2 M), keeping the amount of nanocatalysts constant (20 mg). | |
3.3.4 Effect of the amount of Fe3O4@Ag and Fe3O4@Au nanocatalysts.
In order to investigate the effect of nanocatalyst dose on the degradation of CR, the amount of Fe3O4@Ag and Fe3O4@Au nanocatalysts was varied from 10 to 20 mg, keeping the other two reaction parameters constant. The degradation profiles of 5.0 × 10−5 M aqueous CR solution over the different amounts of nanocatalyst along with NaBH4 (2.5 × 10−2 M) were investigated. It was found that the degradation efficiency increases as the amount of nanocatalyst increases. This is attributed to the higher availability of surface active sites for the adsorption of BH4− ions and dye molecules. The rate constants were calculated from the slope of the plots of ln(At/A0) vs. time (Fig. 11). The overall results showed an increase in the rate constants with nanocatalyst dose (Fig. S3†). Such an increase was attributed to the increased number of active sites generated with a larger amount of the nanocatalyst. These active sites act as mediators45 for the electron transfer from the donor to the acceptor molecules, which renders their interaction feasible enough to form the reduction products.
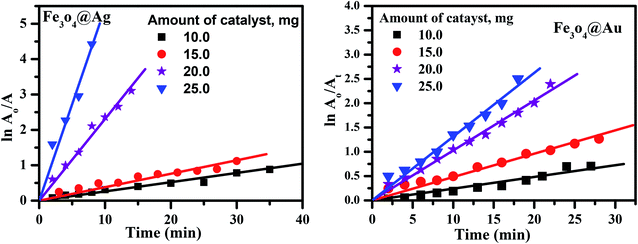 |
| Fig. 11 Pseudo-first-order kinetic plot of ln A0/Atvs. time (in min) for the catalytic degradation of CR dye (5.0 × 10−5 M), the concentrations of NaBH4 (2.5 × 10−2 M), with a changing amount of nanocatalysts (10–20 mg). | |
3.3.5 Recycling of Fe3O4, Fe3O4@Ag, and Fe3O4@Au nanocatalysts.
The reusability of Fe3O4, Fe3O4@Ag, and Fe3O4@Au nanocatalysts was investigated for the reduction of CR under the optimum reaction conditions which are: [CR] = 5.0 × 10−5 M, and [NaBH4] = 2.5 × 10−2 M at 27 °C. It was found that the Fe3O4 nanocatalyst maintained its catalytic activity for one cycle, while the reusability of Fe3O4@Ag was evaluated for ten cycles. On the other hand, the catalytic reductive capacity of the Fe3O4@Au nanocatalyst was retained for four successive cycles. After every cycle, the nanocatalyst was recovered from the reaction mixture by centrifugation and washed well with ethanol and water. The as-obtained sample was thereafter dried and reused for the next cycle. The relation between the efficiency% and the number of cycles for the catalytic degradation of CR using the prepared nanocatalysts is presented in Fig. 12. It was found that the efficiency% of CR reduction by the regenerated Fe3O4@Au nanocatalyst was nearly equal to that of the fresh nanocatalyst even after the repetition of four cycles. However, the Fe3O4@Ag nanocatalyst showed a slight loss in its capacity after the fifth cycle, as indicated by the small decrease in the catalytic efficiency. After the sixth cycle, a dramatic decrease in the catalytic efficiency was observed. The decrease in the efficiency is due to the loss of catalyst during separation, so the number of reactive surface sites for adsorption of CR and BH4− decreases.
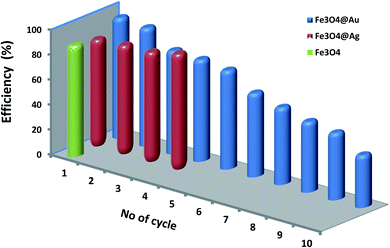 |
| Fig. 12 The relation between catalytic efficiency of Fe3O4, Fe3O4@Ag, and Fe3O4@Au nanocatalysts and the number of cycles of CR dye reduction. | |
A quick review of the literature relevant to the degradation of CR by different methods is summarized in Table 2. This reveals that degradation of CR dye is carried out using Fe3O4 based nanocomposites in different systems, such as catalytic reduction, photo-degradation and adsorption using Fe3O4@Ag hydrothermally synthesized in the present study. As shown from this review, an excellent catalytic degradation for CR dye with fantastic recyclability reaching 10 cycles without any considerable loss of the catalyst efficiency was achieved using our catalyst.
Table 2 Catalytic parameters of Fe3O4-based nanocatalysts for the degradation of Congo red
Catalyst |
Method |
Reaction time (min) |
Efficiency% |
Weight |
No. of cycles |
Reference |
Fe3O4@PANI@Au |
Reduction NaBH4 |
20 |
100 |
10 mg |
5 |
46
|
Fe3O4/MgAl-LDH |
Adsorption |
30 |
100 |
80 mg |
— |
47
|
Fe3O4–PbS |
UV-photo degradation |
120 |
80 |
— |
— |
48
|
Fe3O4@BTCA |
Adsorption |
20 |
97 |
20 mg |
5 |
49
|
1,2,4,5-Benzenetetracarboxylic acid |
|
|
|
|
|
|
BTCA |
|
|
|
|
|
|
Fe3O4–Ag nanoalloys |
Adsorption |
4 |
92 |
30 μg |
— |
46
|
Fe3O4@Ag (present work) |
Reduction NaBH4 |
16 |
96 |
20 mg |
10 |
— |
4. Conclusion
Herein, highly efficient and reusable nanocatalysts, Fe3O4@Ag and Fe3O4@Au, have been synthesized by utilizing a facile and economic synthesis using a hydrothermal method which showed excellent CR dye reduction ability in the presence of NaBH4 as a reducing agent via an electron-relaying process. The reduction followed pseudo-first-order kinetics and the rate of the reaction depends greatly on the concentration of the dye, NaBH4 and the nanocatalyst. The excellent catalytic activity and good reusability suggest that the Fe3O4@Ag, and Fe3O4@Au nanocatalysts could be used as potential candidates for the treatment of industrially discharged wastewater.
Conflicts of interest
There are no conflicts to declare.
Acknowledgements
The authors are grateful to the Scientific Research Fund at Tanta University, Egypt for funding this work through research project code TU:02-19-03.
References
- B. J. Kim, T. Park, H. C. Moon, S.-Y. Park, D. Hong, E. H. Ko, J. Y. Kim, J. W. Hong, P. S. Woo, Y.-G. Kim and I. S. Choi, Cytoprotective Alginate/Polydopamine Core/Shell Microcapsules in Microbial Encapsulation, Angew. Chem., Int. Ed., 2014, 53, 14443–14446, DOI:10.1002/anie.201408454.
- T. Ozel, G. R. Bourret, A. L. Schmucker, K. A. Brown and C. A. Mirkin, Hybrid semiconductor core-shell nanowires with tunable plasmonic nanoantennas, Adv. Mater., 2013, 25, 4515–4520, DOI:10.1002/adma.201301367.
- Z. Shan, D. Clayton, S. Pan, P. S. Archana and A. Gupta, Visible Light Driven Photoelectrochemical Properties of Ti@TiO2 Nanowire Electrodes Sensitized with Core–Shell Ag@Ag2S Nanoparticles, J. Phys. Chem. B, 2014, 118, 14037–14046, DOI:10.1021/jp504346k.
- C. R. Ghosh and S. Paria, Core/shell nanoparticles: classes, properties, synthesis mechanisms, characterization, and applications, Chem. Rev., 2012, 112, 2373–2433, DOI:10.1021/cr100449n.
- L. Yang, W. Luo and G. Cheng, Graphene-Supported Ag-Based Core–Shell Nanoparticles for Hydrogen Generation in Hydrolysis of Ammonia Borane and Methylamine Borane, ACS Appl. Mater. Interfaces, 2013, 5, 8231–8240, DOI:10.1021/am402373p.
- M. B. Gawande, A. Goswami, T. Asefa, H. Guo, A. V. Biradar, D.-L. Peng, R. Zboril and R. S. Varma, Core-shell nanoparticles: synthesis and applications in catalysis and electrocatalysis, Chem. Soc. Rev., 2015, 44, 7540–7590, 10.1039/c5cs00343a.
- R. Liu and R. D. Priestley, Rational design and fabrication of core–shell nanoparticles through a one-step/pot strategy, J. Mater. Chem. A, 2016, 4, 6680–6692, 10.1039/C5TA09607C.
- A. K. Gupta and M. Guptab, Synthesis and surface engineering of iron oxide nanoparticles for biomedical applications, Biomaterials, 2005, 26, 3995–4021, DOI:10.1016/j.biomaterials.2004.10.012.
- W. Fang, J. Zheng, C. Chen, H. Zhang, Y. Lu, L. Mac and G. Chen, One-pot synthesis of porous Fe3O4 shell/silver core nanocomposites used as recyclable magnetic antibac-terial agents, J. Magn. Magn. Mater., 2014, 357, 1–6, DOI:10.1016/j.jmmm.2014.01.024.
-
S. E. Lyshevski, Dekker encyclopedia of nanoscience and nanotechnology, CRC Press, Boca Raton, 3rd edn, 2014, p. 7 Search PubMed.
- L. R. Harivardhan, J. L. Arias, J. Nicolas and P. Couvreur, Magnetic Nanoparticles: Design andCharacterization, Toxicity and Biocompatibility, Pharmaceutical and Biomedical Applications., Chem. Rev., 2012, 112, 5818–5878, DOI:10.1021/cr300068p.
- K. Ulbrich, K. Hol, V. Subr, A. Bakandritsos, J. Tucek and R. Zboril, Magnetic Nanoparticles: Design and Characterization, Toxicity and Biocompatibility, Pharmaceutical and Biomedical Applications, Chem. Rev., 2016, 116, 5338–5431, DOI:10.1021/acs.chemrev.5b00589.
-
S. Laurent, L. Vander Elst and R. N. Muller, Superparamagnetic iron oxide nanoparticles for MRI, The chemistry of contrast agents in medical magnetic resonance imaging, 2013, vol. 10, pp. 427–447 Search PubMed.
- S. Laurent, D. Forge, M. Port, A. Roch, C. Robic, L. E. Vander and R. N. Muller, Magnetic Iron Oxide Nanoparticles: Synthesis, Stabilization, Vectorization, Physicochemical Characterizations, and Biological Applications, Chem. Rev., 2008, 108, 2064–2110, DOI:10.1021/cr068445e.
- H. Shokrollahi, Structure, synthetic methods, magnetic properties and biomedical applications of ferrofluids, Mater. Sci. Eng., C, 2013, 33, 2476–2487, DOI:10.1016/j.msec.2013.03.028.
- J.-M. Li, A. C. H. Huan, L. Wang, Y.-W. Du and D. Feng, Interface effects on magnetoresistance and magnetic-field-reduced Raman scattering in magnetite, Phys. Rev. B: Condens. Matter Mater. Phys., 2000, 61, 6876, DOI:10.1103/PhysRevB.61.6876.
- R. R. Castillo and M. Vallet-Regí, Functional Mesoporous Silica Nanocomposites: Biomedical Applications and Biosafety, Int. J. Mol. Sci., 2019, 20, 929, DOI:10.3390/ijms20040929.
- J.-M. Li, X.-L. Zeng and Z.-A. Xu, Partial cationic inversion-induced magnetic hardening of densely packed 23-nm-sized nanocrystallite-interacting nickel ferrite electrospun nanowires, Appl. Phys. Lett., 2013, 103, 232410, DOI:10.1063/1.4840320.
-
C. F. Bohren and D. R. Huffman, Absorption and scattering of light by small particles, Wiley-VCH, 2008 Search PubMed.
- M. Rai, A. P. Ingle, S. Birla, A. Yadav and C. A. Dos Santos, Strategic role of selected noble metal nanoparticles in medicine, Crit. Rev. Microbiol., 2016, 42, 696–719, DOI:10.3109/1040841x.2015.1018131.
- P. Gong, H. Li, X. He, K. Wang, J. Hu, W. Tan, S. Zhang and X. Yang, Nanotechnology Preparation and antibacterial activity of Fe3O4@Ag nanoparticles, Nanotechnology, 2007, 18, 285604, DOI:10.1088/0957-4484/18/28/285604.
- B. Chudasama, A. K. Vala, N. Andhariya, R. V. Upadhyay and R. V. Mehta, Enhanced antibacterial activity of bifunctional Fe3O4-Ag core-shell nanostructures, Nano Res., 2009, 2, 955–965, DOI:10.1007/s12274-009-9098-4.
- A. Amarjargal, L. D. Tijing, I. T. Im and C. S. Kim, Simultaneous preparation of Ag/Fe3O4 core–shell nanocomposites with enhanced magnetic moment and strong antibacterial and catalytic properties, Chem. Eng. J., 2013, 226, 243–254, DOI:10.1016/j.cej.2013.04.054.
- W. Q. Jiang, Y. F. Zhou, Y. L. Zhang, S. H. Xuan and X. L. Gong, Superparamagnetic Ag@Fe3O4core-shell nanospheres: fabrication, characterization and application as reusable nanocatalysts, Dalton Trans., 2012, 41, 4594–4601, 10.1039/c2dt12307j.
- J. Park, K. An, Y. Hwang, J.-G. Park, H.-J. Noh, J.-Y. Kim, J.-H. Park, N.-M. Hwang and T. Hyeon, Ultra-large-scale syntheses of monodisperse nanocrystals, Nat. Mater., 2004, 3, 891–895, DOI:10.1038/nmat1251.
- J. S. Salazar, L. Perez, O. D. Abril, L. P. Truong, D. Ihiawakrim, M. Vazquez, G. Jean-Marc, S. Begin-Colin and G. Pourroy, Magnetic Iron Oxide Nanoparticles in 10−40 nm Range: Composition in Terms of Magnetite/Maghemite Ratio and Effect on the Magnetic Properties, Chem. Mater., 2011, 23, 1379–1386, DOI:10.1021/cm103188a.
- S. Ge, X. Shi, K. Sun, C. Li, C. Uher, J. R. Baker, M. M. BanaszakHoll and B. G. Orr, Facile hydrothermal synthesis of iron oxide nanoparticles with tunable magnetic properties, J. Phys. Chem. C, 2009, 113, 13593–13599, DOI:10.1021/jp902953t.
- H. Cai, X. An, C. Jun, J. Li, S. Wen, K. Li, M. Shen, L. Zheng, G. Zhang and X. Shi, Facile hydrothermal synthesis and surface functionalization of polyethyleneimine-coated iron oxide nanoparticles for biomedical applications., ACS Appl. Mater. Interfaces, 2013, 5, 1722–1731, DOI:10.1021/am302883m.
- Y. B. Khollam, S. R. Dhage, H. S. Potdar, S. B. Deshpande, P. P. Bakare, S. D. Kulkarni and S. K. Date, Microwave hydrothermal preparation of submicron-sized spherical magnetite (Fe3O4) powders, Mater. Lett., 2002, 56, 571–577, DOI:10.1016/S0167-577X(02)00554-2.
- J. Li, X. Shi and M. Shen, Hydrothermal Synthesis and Functionalization of Iron Oxide Nanoparticles for MR Imaging Applications, Part. Part. Syst. Charact., 2014, 31, 1223–1237, DOI:10.1002/ppsc.201400087.
- S. A. M. Khawja Ansari, F. Eleonora, R. F. Alessandro, S. Ilaria, A. Monica, A. Ornella, C. Roberta, G. Caterina and D. Federico, Magnetic Iron Oxide Nanoparticles: Synthesis, Characterization and Functionalization for Biomedical Applications in the Central Nervous System, Materials, 2019, 12, 465, DOI:10.3390/ma12030465.
- Á. D. Jesús Ruz-Baltazar, Green synthesis assisted by sonochemical activation of Fe3O-Ag nano-alloys: Structural characterization and studies of sorption of cationic dyes, Inorg. Chem. Commun., 2020, 120, 108148, DOI:10.1016/j.inoche.2020.108148.
- N. Mizutani, T. Iwasaki and S. Watano, Response Surface Methodology Study on Magnetite Nanoparticle Formation under Hydrothermal Conditions, Nanomater. Nanotechnol., 2015, 5, 1–7, DOI:10.5772/60649.
- W. Wu, Z. Wu, T. Yu, C. Jiang and W. S. Kim, Recent progress on magnetic iron oxide nanoparticles: synthesis, surface functional strategies and biomedical applications, Sci. Technol. Adv. Mater., 2015, 16, 023501, DOI:10.1088/1468-6996/16/2/023501.
- G. Sharma and P. Jeevanandam, Synthesis of self-assembled prismatic iron oxide nanoparticles by a novel thermal decomposition route, RSC Adv., 2013, 3, 189, 10.1039/C2RA22004K.
- Y. Zhu, Y. Qian, X. Li and M. Zhang, A nonaqueous solution route to synthesis of polyacrylamide-silver nanocomposites at room temperature, Nanostruct. Mater., 1998, 10, 673–678, DOI:10.1016/S0965-9773(98)00096-8.
- Y. Peng, A. W. Xu, B. Deng, M. Antonietti and H. Colfen, Polymer-controlled crystallization of zinc oxide hexagonal nanorings and disks, J. Phys. Chem. B, 2006, 110, 2988–2993, DOI:10.1021/jp056246d.
- G. Z. Wang, R. Saeterli, P. M. Rorvik, A. T. J. van Helvoort, R. Holmestad, T. Grande and M. A. Einarsrud, Self-Assembled Growth of PbTiO3 Nanoparticles into Microspheres and Bur-like Structures, Chem. Mater., 2007, 19, 2213, DOI:10.1021/cm063047d.
- M. Yamaura and D. A. Fungaro, Synthesis and characterization of magnetic adsorbent preparedby magnetite nanoparticles and zeolite from coal fly ash, J. Mater. Sci., 2013, 48, 5093–5101, DOI:10.1007/s10853-013-7297-6.
- S.-J. Cho, J.-C. Idrobo, J. Olamit, K. Liu, N. D. Browning and S. M. Kauzlarich, Growth Mechanisms and Oxidation-Resistance of Gold-Coated Iron Nanoparticles, Chem. Mater., 2005, 17, 3181–3186, DOI:10.1021/cm0500713.
- Q. Li, C. W. Kartikowati, S. Horie, T. Ogi, T. Iwaki and K. Okuyama, Correlation between particle size/domain structure and magnetic properties of highly crystalline Fe3O4 nanoparticles, Sci. Rep., 2017, 7, 9894, DOI:10.1038/s41598-017-09897-5.
- R. F. Butler and S. K. Banerjee, Theoretical single-domain grain-size range in magnetite and titanomagnetite, J. Geophys. Res., 1975, 80, 4049–4058, DOI:10.1029/JB080i029p04049.
- D. L. Leslie-Pelecky and R. D. Rieke, Magnetic Properties of Nanostructured Materials, Chem. Mater., 1996, 8, 1770–1783, DOI:10.1021/cm960077f.
- N. Shimizu, C. Ogino, M. F. Dadjour and T. Murata, Sonocatalytic degradation of methylene blue with TiO2 pellets in water, Ultrason. Sonochem., 2007, 14, 184–190, DOI:10.1016/j.ultsonch.2006.04.002.
- S. Gupta, C. Giordano, M. Gradzielski and S. K. Mehta, Microwave-assisted synthesis of small Ru nanoparticles and their role in degradation of congo red, J. Colloid Interface Sci., 2013, 411, 173–181, DOI:10.1016/j.jcis.2013.08.030.
- M. Chen, P. Liu, C. Wang, W. Ren and G. W. Diao, Fast catalytic reduction of an azo dye by recoverable and reusable Fe3O4@PANI@Au magnetic composites, New J. Chem., 2014, 38, 4566–4573, 10.1039/C4NJ00806E.
- R. Shan, L. Yan, K. Yang, S. Yu, Y. Hao, H. Yu and B. Du, Magnetic Fe3O4/MgAl-LDH composite for effective removal of three red dyes from aqueous solution, Chem. Eng. J., 2014, 15, 38–46, DOI:10.1016/j.cej.2014.04.105.
- K. Hedayati, M. Goodarzi and M. Kord, Green and facile synthesis of Fe3O4-PbS magnetic nanocomposites applicable for the degradation of toxic organic dyes, Main Group Met. Chem., 2016, 39, 183–194, DOI:10.1515/mgmc-2016-0027.
- S. Chatterjee, N. Guha, S. Krishnan, A. K. Singh, P. Mathur and D. K. Rai, Selective and Recyclable Congo Red Dye Adsorption by Spherical Fe3O4 Nanoparticles Functionalized with 1,2,4,5-Benzenetetracarboxylic Acid, Sci. Rep., 2020, 10, 111, DOI:10.1038/s41598-019-57017-2.
Footnote |
† Electronic supplementary information (ESI) available. See DOI: 10.1039/d0ra08230a |
|
This journal is © The Royal Society of Chemistry 2021 |
Click here to see how this site uses Cookies. View our privacy policy here.