DOI:
10.1039/D0QM00549E
(Review Article)
Mater. Chem. Front., 2021,
5, 151-222
Recent advances and perspective on heterogeneous catalysis using metals and oxide nanocrystals
Received
29th July 2020
, Accepted 6th September 2020
First published on 7th September 2020
Abstract
Inorganic nanomaterials are widely used in heterogenous catalysis. With the development of nanoscience and nanotechnology, chemists can precisely control the size, morphology, and exposed facets of nanocrystals (NCs) in an elegant manner, further tailoring their catalytic performance towards diverse reactions. In this review, we focus on the design principles of high-performance catalysts using metal NCs and oxide NCs. Special attention is paid to the shape control and surface engineering of NCs. Some practically important heterogeneous catalytic reactions over nanocatalysts will be discussed. Finally, an outlook and perspective in nano-catalysis will be provided. The goal of this review is to discuss recent advances and perspective on heterogeneous catalysis using inorganic nanomaterials and motivate researchers to design efficient catalysts with high activity, selectivity and stability.
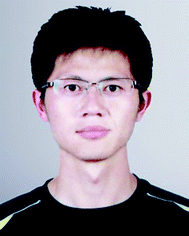
Yong Xu
| Yong Xu is currently a Professor at the School of Materials and Energy, Guangdong University of Technology. He obtained his PhD from the Department of Chemical Physics of University of Science and Technology of China in 2013. After being a Postdoctoral Fellow in Soochow University and Lawrence Berkeley National Laboratory, he joined Soochow University as an Associate Professor in 2017. His current research interests focus on the selective activation of hydrocarbons at the surface and interface of functional catalysts. |
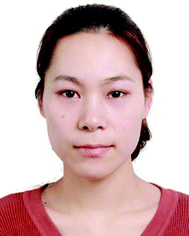
Muhan Cao
| Muhan Cao obtained her PhD degree in Environmental Science and Technology from Hohai University in 2015. Currently, she is an Assistant Research Fellow at Soochow University. Her current research interests focus on the design of metal and semiconductor nanocrystals and their applications in the optoelectronic field. |
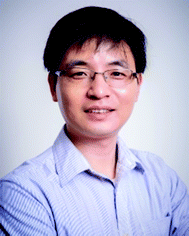
Qiao Zhang
| Qiao Zhang is a Professor in the Institute of Functional Nano & Soft Materials (FUNSOM), Soochow University, China. He received his PhD from the University of California Riverside (2012). After being a Postdoctoral Fellow in the Department of Chemistry, University of California Berkeley (2012–2014), he joined Soochow University in 2014. His main research field is molecular level studies of surface and heterogeneous catalysis, controllable synthesis of all-inorganic perovskites with tunable optical properties and their applications. |
1. Introduction
Heterogeneous catalysis plays a vital role in industry for the production of transportation fuels, lubricants, drugs, polymers, fibers, and other important high value-added chemicals. In heterogeneous catalysis, catalysts not only greatly accelerate the kinetics of reactions by reducing the activation energy, but also selectively form the desired products through the control of reaction pathways. It has been well accepted that the earliest report in catalysis can be traced back to the 18th century. Accordingly, with over 250 years of development, more than 90% of industrial chemicals are produced with the addition of catalysts. Generally, the majority of catalysts in industry are solid powders in which the active sites are dispersed in the form of very small nanoparticles and clusters.1 To obtain high-performance catalysts, the active elements need to be loaded on porous supports (e.g., Al2O3 and SiO2) to stabilize the active sites and add some promoters to avoid their deactivation.
It is well-known that nanostructures are more likely to exhibit much better catalytic performances due to the “nano-effect” originating from their small size.2 Due to the large ratio of surface atoms, these small nanoparticles can expose much more active sites than the bulk, leading to a significant increase in catalytic activity. Furthermore, small nanoparticles and clusters can bring new structural and electronic properties to enhance the catalytic performance. In addition, nanostructures provide an ideal platform for the fundamental investigation of the catalytic mechanism through precise surface engineering.3 With the development of nanoscience and nanotechnology, chemists have gained the ability to synthesize nanostructures with tunable morphologies and sizes.4–8 Over the past decades, various metal (Pt, Pd, Rh, Ru, etc.) and oxide nanostructures (NiO, FeOx, CoOx, CeO2, etc.) have been successfully synthesized as catalysts for diverse reactions including CO2 reduction,9–25 selective hydrogenation,26–33 CH4 activation,34–38 CO oxidation.39–44 that the catalytic performance of NCs is strongly dependent on their size, shape, composition and interfacial interactions. Recently, it has been gradually realized that compositing a single-component with another can significantly enhance the catalytic performance since the synergistic effects between the two components may bring additional properties to the composite catalyst. Consequently, tremendous effort has been devoted to the modification of NCs, leading to significant progress in nano-catalysis.
In this review, we discuss recent advances and perspective on heterogeneous catalysis using inorganic nanomaterials, with a specific focus on the design principle of high-performance catalysts using metal NCs and oxide NCs. Attention is paid to the shape control and surface engineering of NCs for achieving enhanced catalytic performances in some important heterogeneous catalytic reactions including CO2 reduction, selective hydrogenation, CH4 activation, CO oxidation, and oxygen reduction reaction (ORR). Finally, the outlook and perspective in nano-catalysis will be provided. The goal of this review is to motivate researchers to search for more efficient catalysts with high activity, selectivity and stability.
2. Metal NCs
Noble metals (Pt, Pd, Rh, Ru, Au, Ag, etc.) have been used as catalysts for diverse reactions due to their superior activities. Compared to non-noble catalysts, noble metal-based catalysts generally exhibit higher activity because their strong affinity to reactants. Thus, to achieve decent activity at a low cost, noble metals are generally dispersed on porous supports with a large surface area via the well-established wet-impregnation method. Indeed, catalyst preparation via the wet-impregnation method has a long history in industry, and it is still regarded as one of the most popular strategies nowadays. Scientists have empirically realized that the catalytic performance from supported catalysts is strongly dependent on the synthetic parameters, pre-treatment conditions, reduction temperature, and the support. With the progress in science, especially in characterization techniques, scientists have found that these noble metals exist as small nanoparticles, clusters and even isolated atoms. Thus, a variation in the synthesis, pre-treatment and reduction conditions will result in different sizes, morphologies, and geometry and coordination environment of the active sites. Many reports indicate that low-coordinated atoms exhibit much higher activity than that of full-coordinated atoms. For example, NCs with exposed high-index facets generally exhibit higher activity than that with low-index facets (e.g., (100) and (111) facets) because the surface atoms on high-index facets, especially at the edges and corners, are generally low-coordinated. However, NCs with high-index facets are unstable due to their high surface energy. Thus, the stabilization of these high-index facets in the synthetic process and catalytic process is critical to achieve superior catalytic performance in nano-catalysis. Therefore, tremendous effort has been devoted to the stabilization of NCs via surface engineering. In this section, we summarize the recent advances on the shape control and surface engineering of some typical noble metal-based NCs.
2.1 One-dimensional (1-D) metal NCs
Over the past decades, great progress has been achieved in the synthesis of 1-D metal NCs, including nanowires, nanorods and nanotubes. To date, chemists have empirically realized that the preferential protection of some specific facets can enable the anisotropic growth of metal nanoparticles. To obtain 1-D NCs, the anisotropic growth of NCs needs to be induced along some specific facets with the assistance of some specific capping agents. Although the detailed mechanism for the shape control of nanostructures is not completely understood to date, many strategies have been successfully developed for the preparation of 1-D metal NCs. In this section, we focus on this type of metal NCs which have been widely used as catalysts, such as Pt, Pd, and Rh.
2.1.1 Synthesis of 1-D Pt-based NCs.
Synthesis of 1-D Pt NCs.
Xia and co-workers synthesized Pt nanowires with a mean length and diameter of 100 nm and 5 nm, respectively, by reducing H2PtCl6 with ethylene glycol (EG) in the presence of poly(vinyl pyrrolidone) (PVP).45 A trace amount of Fe3+ or Fe2+ ions exhibited dual functions in the growth of the Pt nanowires as follows: (1) Fe3+ or Fe2+ ions can induce the aggregation of Pt nanoparticles into larger structures, which serve as nucleation sites and (2) Fe3+ or Fe2+ ions can greatly decrease the reaction rate and supersaturation level and further induce anisotropic growth. Subsequently, they described the synthesis of Pt single-crystal nanowires using the same precursor, reductant and capping agent on functional solid supports including Pt or W gauze,46,47 TiO2,48 SiO2,49 Ni(OH)2,50 Ti0.7Ru0.3O2 composite oxide,51 and sulfur-doped graphene.52 Sun et al. demonstrated a wet-chemical method for the growth of Pt single-crystalline nanowires on carbon nanospheres using H2PtCl6 and HCOOH as the precursor and reductant, respectively.53 They claimed that the anisotropic growth of the Pt nanowires along the (111) direction was strongly related to the slow reduction rate. Similarly, nitrogen-doped CNTs could also be used as a support for growing Pt nanowires. The obtained Pt nanowires had a mean diameter of 2.5 nm with a length of up to 100 nm.54 In addition to the support-induced synthetic method, atomic layer deposition (ALD) is a straightforward method to produce Pt nanowires, in which the obtained NCs are shaped by the support. For instance, Bent et al. prepared Pt nanowires on highly ordered pyrolytic graphite (HOPG) through ALD.55 It was shown that Pt was preferentially deposited only at the step edges of HOPG, leading to the formation of laterally aligned Pt nanowires. Shui and Li prepared ultralong Pt nanowires on the centimeter scale with a few nanometers in diameter via electrospinning. It was found that the parameters such as PVP concentration, water/ethanol ratio, feeding rate and electric field strength are critical for the formation of uniform Pt nanowires (Fig. 1).56 Ponrouch and co-workers obtained highly porous and preferentially oriented (100) Pt nanowires via electrodeposition. They highlighted that H2 plays a critical role in the growth of Pt nanowires because the surface free energy of the (100) facet in the presence of H2 is lower than that of the (111) facet, leading to the growth of predominantly exposed Pt(100) facets.57 Besides the success in the synthesis of Pt nanowires, the support also plays a critical role in the anisotropic growth of Pt nanowires, whose functions are not understood to date. On the other hand, the above-mentioned method cannot precisely tune the length and diameter of Pt nanowires, which has seriously impeded their practical application. Therefore, other synthetic methods have been developed to synthesize pure Pt nanowires in solution. For example, Teng and co-workers reported the synthesis of ultrathin Pt nanowires with a width of less than 2.5 nm and a length of over 30 nm via a phase-transfer method, in which inorganic Pt chloride was transferred to a mixture of octadecylamine and toluene in the presence of n-dodecyltrimethylammonium bromide (DTAB). After the addition of sodium tetrahydroborate (NaBH4) to the aqueous solution, the Pt cations were rapidly reduced and formed thermodynamically unstable elongated primary nanostructures, followed by an anisotropic growth along the (111) direction to form thread-like nanowires.58 Subsequently, the organic phase has been widely employed to produce Pt nanowires.59,60 In addition, the template-synthesis method has been reported for synthesizing Pt nanowires. Choi and co-workers prepared well-defined Pt nanowires with a diameter of 47 ± 9.8 nm and a length of 6 μm via a template-synthesis method by the electrodeposition of Pt within the pores of a track-etched polycarbonate membrane (Fig. 2a).61 Zhang et al. synthesized ordered porous Pt nanowires with controlled large mesopores (15–45 nm) using dual templates of porous anodic aluminum oxide (AAO) membranes and silica nanospheres self-assembled in the channels (Fig. 2b).62 Zhang and co-workers produced highly uniform single-crystal Pt nanowires with a diameter of about 1.8 nm and a superhigh aspect ratio of >104 using insulin amyloid fibrils as sacrificial templates (Fig. 2c and d). It was shown that these fibrils were critical for obtaining the ultralong Pt nanowires with preferential exposure of the low-energy crystal facets.63
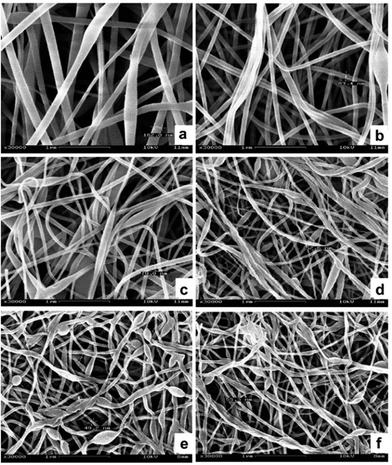 |
| Fig. 1 Morphology of electrospun Pt nanowires at different ratios of PVP/H2PtCl6: (a) PVP/H2PtCl6 = 33.1/10.6 mg mL−1 and (b) PVP/H2PtCl6 = 33.1/2.6 mg mL−1. Morphology of the nanowires with H2O/C2H5OH ratios of (c) 0.036 and (d) 0.075. Morphology of the electrospun nanowires at the feeding speeds of (e) 0.1 mL h−1 and (f) 0.2 mL h−1. Reprinted with permission from ref. 56. | |
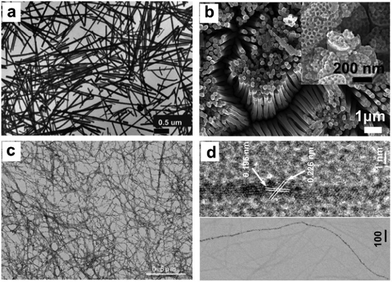 |
| Fig. 2 (a) Transmission electron microscopy (TEM) images of the Pt nanowires prepared from the track-etched polycarbonate membrane. Reprinted with permission from ref. 61. (b) Scanning electron microscopy (SEM) image of the mesoporous Pt nanowires and inset: high-magnification SEM image. Reprinted with permission from ref. 62. (c) Low-magnification TEM image of Pt nanowires and (d) high-resolution TEM (HRTEM) image of a single Pt nanowire. Reprinted with permission from ref. 63. | |
Synthesis of 1-D Pt/noble metal nanocomposites.
Despite the on successful synthesis of 1-D Pt nanowires in the above-mentioned reports, several disadvantages need to be overcome before their practical application: (1) a reduction in the amount of Pt in the catalysts due to its high cost; (2) pure Pt catalysts exhibit high activity, but suffer from low selectivity; and (3) pure Pt tends to rapidly deactivate due to sintering and poisoning. Therefore, it is necessary to modify pure 1-D Pt NCs prior to their utilization. A general strategy for modification is to composite Pt with other elements or compounds to form alloys, core@shell nanostructures and heterojunctions. Over the past decades, many strategies have been successfully developed to modify 1-D nanowires, which greatly promote their activity, selectivity and stability in heterogeneous catalysis. Teng and co-workers synthesized Au25Pt75 and Au48Pt52 ultrathin alloyed nanowires with an average width of less than 3 nm via a wet chemistry approach at room temperature.64 In these alloyed nanowires, the charge transfer between Au and Pt, especially d-charge depletion at the Au site and d-charge gain at the Pt site were observed, suggesting a strong interaction between Au and Pt. Hong et al. demonstrated that the synthesis of dendritic Au/Pt nanowires could be achieved through an epitaxial growth strategy.65 Zhong's group reported the synthesis of ultrathin Pt–Au alloy nanowires featuring a composition-tunable and (111) facet-dominant surface via a modified hydrothermal method (Fig. 3a–d).66 The authors emphasized that it was a surfactant-free method; however, the detailed mechanism for shape control was not discussed. Ag has been widely used to alloy with Pt to form Pt–Au nanowires. Cao and co-workers prepared uniform Pt–Ag nanowires via the co-reduction of AgNO3 and H2PtCl6 in a Teflon-lined autoclave at 220 °C for 20 h.67 Subsequently, they investigated the mechanism of the growth of Pt–Ag nanowires during the hydrothermal treatment. It was shown that the morphologies of the Pt–Ag NCs were strongly dependent on the amount of AgNO3 in the growth solution. Specifically, the morphology evolved from nanowires to nanotrees, and then nanochains with a decrease in the amount of AgNO3. By altering the concentration of AgNO3, uniform bimetallic Pt–Ag nanowires were obtained (Fig. 3e).68 Peng et al. demonstrated that Pt–Ag nanowires could be synthesized in oleylamine and oleic acid through oriented attachment (Fig. 3f). Mechanism studies indicated that the formation of nanowires through oriented attachment is driven by both thermodynamics (surface adsorption energy and potential energy) and kinetics (surface reconstruction). Consequently, the shape control of Pt–Ag NCs is plausible by altering the parameters to create synthetic conditions that meet both the thermodynamic and kinetic requirements.69 In addition, it has been reported that hollow Pt–Ag nanowires can be obtained by adding Ag nanowires to a solution of Pt4+. Because of the difference in the redox potentials, Pt4+ ions can be reduced by Ag nanowires via a galvanic reaction, leading to the formation of hollow Pt–Ag nanowires.70 The galvanic reaction can also be used to synthesize Pt–Au nanowires, in which Pt nanowires can reduce AuCl3 in the presence of DTAB.71 Other noble metals including Rh and Ru have also been used to modify 1-D Pt nanowires.72–77 For instance, Huang's group reported branched Rh–Pt bimetallic ultrathin nanowires through seed displacement and epitaxial growth in aqueous solution containing Rh nanocubes as seeds, K2PtCl6 and PVP.78 Another work by the same group showed that Rh–Pt nanowires could be obtained using Pt(acac)2 and Rh(acac)3 in the presence of oleic acid and oleylamine.79
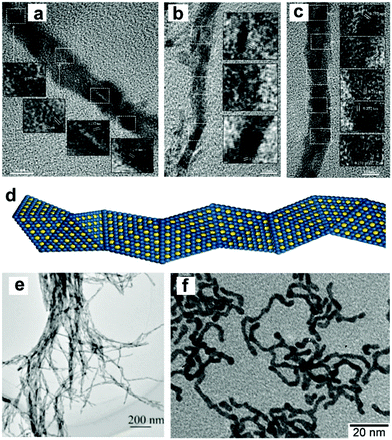 |
| Fig. 3 HRTEM images of (a–c) Pt72Au28 nanowires, where the inserts are the magnified views of areas for the determination of the lattice fringes, and (d) model illustrating the helix exhibited by an individual nanowire. Reprinted with permission from ref. 66. (e) TEM image of the as-prepared Pt0.8Ag0.2 nanowires. Reprinted with permission from ref. 68. (f) TEM images of Pt53Ag47 nanowires. Reprinted with permission from ref. 69. | |
Synthesis of 1-D Pt–Ni NCs.
In addition to noble metals, non-noble metals have attracted great attention in the modification of 1-D Pt nanowires. As one of the most important metals, Ni has been widely used to composite with Pt to improve its catalytic performance. Ma and co-workers reported a generic gas–solid method for the preparation of surfactant-free ultrathin Pt–Ni nanowires, in which H2 was essential for the formation of a unique 1-D morphology.80 Yang et al. fabricated multisegmented Pt–Ni nanowires via pulsed electrodeposition using porous AAO membranes as templates (Fig. 4a).81 It was shown that highly uniform wavy Pt–NiO hollow nanopeapods could be obtained by regulating the oxidation of Ni in the multisegmented Pt–Ni nanowires (Fig. 4b). Bu and co-workers demonstrated a protocol for the synthesis of twisted Pt–Ni nanowires using Pt(acac)2 and Ni(acac)2 as the precursors in the presence of hexadecyltrimethylammonium chloride (CTAC), glucose and oleylamine (Fig. 4c and d), in which three steps were involved: (1) formation of ultrathin Pt nanowires, (2) reduction of Ni species on the preformed nanowires, and (3) Pt diffusion into the Ni-rich 1-D nanowires.82 Another work from the same group studied the surface engineering of Pt–Ni nanowires through a post-treatment, in which the ratio of Ni and Pt significantly varied after treatment in air or H2 (Fig. 4e and f).83 Recently, it has been shown that the introduction of non-metallic elements into Pt–Ni nanowires can greatly enhance their catalytic performance. Wang et al. reported a two-step method for synthesizing Pt–Ni/NiS composite nanowires, in which segregated Pt–Ni nanowires were prepared in the first step and then reacted with sulfur in oleylamine (Fig. 5).84 Liu et al. achieved sulfur modification in aqueous solution with the introduction of sulfite (e.g., SO32− or HSO3−) in an acidic medium.85 Moreover, Xie and co-workers modified Pt–Ni nanowires by nitrogen through a high temperature treatment of as-obtained Pt–Ni nanowires (250 °C) in NH3. The final composite exhibited a structure of Pt–Ni/Ni4N nanowires after surface modification. Zhang and co-workers coated Pt–Ni nanowires with a metal–organic framework (MOF) to form a Pt–Ni@MOF composite, which could be used as an efficient catalyst for the chemoselective hydrogenation of cinnamaldehyde.{Zhang, 2018 #93}. It should be noted that modifying 1-D nanowires with non-metallic elements (e.g., N, S and C) may provide a novel and efficient strategy to promote their catalytic performance. However, the doping amounts should be carefully controlled since an excess amount may result in strong coordination between the metal and non-metallic elements (e.g., S), leading to the poisoning of the catalysts.
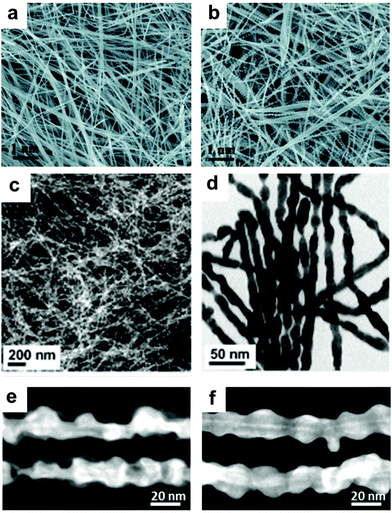 |
| Fig. 4 (a) SEM images of electrodeposited multisegmented Pt–Ni nanowires and (b) SEM images of the multisegmented Pt–Ni nanowires after annealing at 350 °C for 1 h in air. Reprinted with permission from ref. 81. (c) Scanning transmission electron microscopy (STEM) image and (d) TEM image of the 1-D Pt–Ni nanowires. Reprinted with permission from ref. 82. High angle circular dark field (HAADF)-STEM images of the treated Pt3Ni3 nanowires/C in (e) air and (f) H2. Reprinted with permission from ref. 83. | |
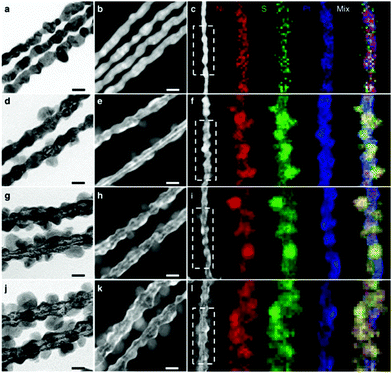 |
| Fig. 5 Representative (a, d, g and j) high-magnification TEM images, (b, e, h and k) HAADF-STEM images and (c, f, i and l) HAADF-STEM images, and corresponding energy dispersive X-ray spectrometry (EDS) elemental mappings (Ni in red, S in green and Pt in blue) of (a–c) Pt3Ni1 NWs–S, (d–f) Pt3Ni2 NWs–S, (g–i) Pt3Ni3 NWs–S and (j–l) Pt3Ni4 NWs–S. Scale bars: 20 nm. Reprinted with permission from ref. 84. | |
Synthesis of 1-D Pt–Fe NCs.
Introducing Fe into 1-D nanowires has been regarded another efficient way to enhance the catalytic performance of Pt NCs.86–89 Wang and co-workers synthesized Pt–Fe nanowires with diameters in the range of 2–3 nm in the presence of oleylamine and octadecene.90 By controlling the reduction of Pt(acac)2 and decomposition of Fe(CO)5, the length of the Pt–Fe nanowires could be tailored from 20 to 200 nm (Fig. 6a). Zhu et al. used a seed-induced method to synthesize Pt–Fe nanowires in the presence of oleylamine, oleic acid and 1-octadecene.43 It was reported that the diameter of the Pt–Fe nanowires could be systematically tuned through a secondary seeded growth step, in which the as-prepared Pt–Fe nanowires were used as seeds and Fe(CO)5 was used as the precursor.91 Kou's group prepared ultrafine Pt–Fe nanowires using Fe(Ac)2 as the precursor in the presence of W(CO)6, glucose, CTAC, oleylamine and 1-octadecene (Fig. 6b).92 Interestingly, when glucose in the growth solution was replaced by phloroglucinol (anhydrous), the obtained Pt–Fe nanowires exhibited a wicker-like morphology (Fig. 6c).93 They claimed that the smooth nanowires connected with each other and gradually grew into uneven interfacial nanowires with branch-rich exteriors. Moreover, Luo and co-workers used Fe(acac)3 as the precursor of Fe to synthesize zigzag-like Pt–Fe nanowires in the presence of Pt(acac)2, glucose, CTAC and oleylamine (Fig. 6d–f).94 Similarly, Bai et al. prepared zigzag-like Pt–Fe nanowires in organic solution using a different Fe precursor (e.g., Fe2(CO)9) and reductant (e.g., benzoin) (Fig. 6g–j).60 Thus, based on the above reports, it can be concluded that the changes in the types of precursor, reductants and surfactants in colloidal synthetic methods can systematically tune the final structures and morphologies.
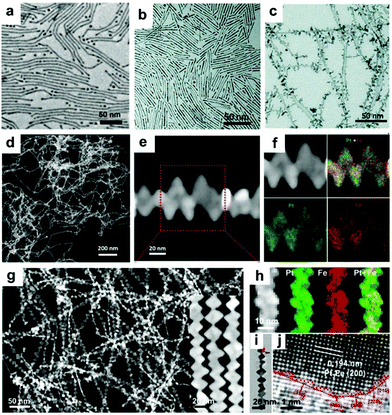 |
| Fig. 6 (a) TEM images of Fe55Pt45 nanowires with a length of 200 nm. Reprinted with permission from ref. 90. (b) TEM image of ultrafine Pt3Fe nanowires. Reprinted with permission from ref. 92. (c) TEM image of Pt3Fe nanowires. Reprinted with permission from ref. 93. (d) Low- and (e) high-magnification HAADF-STEM images and (f) STEM-EDS elemental mapping of Pt3Fe zigzag-like nanowires. Reprinted with permission from ref. 94. (g) HAADF-STEM image with low magnification and high magnification (inset), (h) HAADF-STEM image and elemental mappings, (i) TEM image and (j) HRTEM image of Pt–Fe nanowires. Reprinted with permission from ref. 60. | |
Synthesis of 1-D Pt–Co NCs.
Co, which is located in the same group in the periodic table, has also been widely used to composite with 1-D Pt NCs.95–100 It has been shown that the synthetic method for Pt–Co nanowires is similar to that of Pt–Ni nanowires by replacing the Ni precursor (e.g., NiCl2) with a Co precursor (e.g., CoCl2).80,85 Generally, CoCl·6H2O and Co(acac)3 are used as Co precursors, and H2PtCl6·6H2O and Pt(acac)2 are correspondingly used as Pt precursors for the preparation of Pt–Co nanowires. Based on the physicochemical properties of these precursors, Pt–Co nanowires can be obtained in both aqueous and organic solution. Owing to the low boiling point of water, the aqueous-phase synthesis of Pt–Co nanowires is performed in a pressed Teflon-lined stainless-steel autoclave to reach the desired temperature. By contrast, organic solvents, such as oleylamine, oleic acid and 1-octadecene, have a much higher boiling point than water. Therefore, the organic-phase synthesis of Pt–Co nanowires is performed in a glass reactor. Lu and co-workers synthesized Pt–Co nanowires via a hydrothermal method using H2PtCl6·6H2O and CoCl·6H2O as precursors in the presence of KOH, EG and dimethyl formamide (DMF) (Fig. 7a–e).101 The mechanism studies showed that small nanoparticles, elongated nanorods, and some nanochains were formed in the initial stage, and further assembled into a wire-like structure to reduce the surface energy under the solvothermal conditions, which is consistent with the typical oriented attachment mechanism. Bu et al. demonstrated a protocol for the synthesis of Pt–Co nanowires in the organic phase, in which Pt(acac)2 and Co(acac)3 were used as precursors, oleylamine as the solvent and surfactant, CTAC as the structure-directing agent, and glucose as a reducing agent (Fig. 7f–h).{Bu, 2016 #111} Guo et al. used a similar organic method to prepare Pt3Co nanowires for the electro-reduction of oxygen (Fig. 7i and j).102 Moreover, Bai and co-workers synthesized zigzag Pt4Co nanowires using Pt(acac)2 and Co(acac)3 as precursors in the presence of glucose, CTAC and oleylamine (Fig. 7k). It was shown that the zigzag Pt4Co nanowires with abundant steps/edges and Pt-rich surface could be used as highly efficient catalysts for the hydrogenation of CO2.103
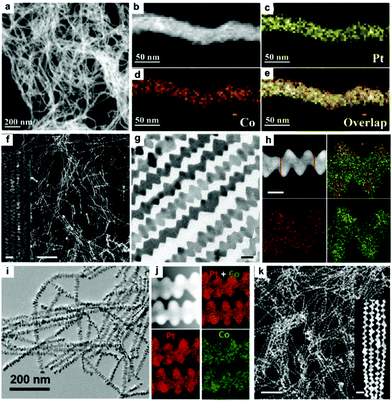 |
| Fig. 7 (a) HAADF-STEM images and (b–e) elemental mapping images of Pt95Co5 nanowires. Reprinted with permission from ref. 101. (f) STEM, (g) TEM and (h) STEM-ADF images and EDS elemental mappings of the hierarchical Pt3Co nanowires. Inset in (f) is an enlarged STEM image. The scale bars in (f), inset of (f), (g) and (h) are 200, 20, 10 and 10 nm, respectively. Reprinted with permission from ref. 104. (i) TEM image and (j) STEM-EDS elemental mapping of as-synthesized Pt3Co nanowires.102 (k) HAADF-STEM image of Pt4Co nanowires. Inset in (k) is an enlarged HAADF-STEM image. The scale bars in (k), inset of (a) are 100 and 20 nm, respectively. Reprinted with permission from ref. 103. | |
Synthesis of other 1-D Pt-based nanocomposites.
Yu et al. fabricated Pt–Cu nanowires using Pt(acac)2 and Cu(acac)2 in the presence of tetrabutylammonium bromide and oleylamine via a well-established oriented attachment process.105 Zhang and co-workers prepared screw thread-like Pt–Cu nanowires with high-index facets and controllable compositions in oleylamine via a colloidal synthesis method, in which Pt(acac)2 and CuCl2·2H2O were used as metal precursors, respectively (Fig. 8).106 Furthermore, Cao et al. synthesized Pt–Cu nanowires in aqueous solution using Na2PtCl6·6H2O and CuCl2·6H2O as the precursors via the classic hydrothermal method. The proposed mechanism can be briefly described as follows: (1) reduction of precursors by NaBH4 solution; (2) Pt and Cu atoms emerge, aggregate and fuse to form Pt–Cu nuclei, accompanied by the generation of abundant hydrogen bubbles from the hydrolysis and oxidation of NaBH4; and (3) Pt–Cu crystal nuclei anchor and then grow on the surfaces and interspaces of hydrogen the bubbles via self-assembly to form Pt–Cu nanowires.107 Similarly, Liao and co-workers obtained ultrathin (ca. 1 nm) and long Pt–Cu nanowires up to the micrometer scale using EG as the reductant (Fig. 9a and b).108 The above two cases indicate that the reduction kinetics may strongly influence the obtained morphologies of Pt–Cu nanowires. Compared to NaBH4, which can rapidly reduce the precursors, EG is a much weaker reductant and it can slow down the reduction rate, leading to the formation of long nanowires. In addition, the galvanic reaction can also be used for the synthesis of Pt–Cu nanowires due to the different redox potentials of Pt4+/Pt and Cu2+/Cu. Alia et al. synthesized Pt-coated Cu nanowires via the partial galvanic displacement of Cu nanowires. The obtained Pt–Cu nanowires possessed a mean diameter and length of 100 nm and 25–40 μm, respectively.109 The compositions of Pt–Cu nanowires can be tuned by controlling the degree of galvanic displacement, where complete displacement will lead to pure Pt nanowires.110 In addition, Xu and co-workers synthesized zigzag-like Pt–Zn alloy nanowires with high-index facets. In this synthetic protocol, Pt(acac)2 and Zn(acac)2 were used as precursors, glucose as a reductant, and CTAC/oleylamine as surfactants.111 However, compared to Pt–Co and Pt–Fe, reports on Pt–Zn nanowires are still limited, which may probably due to their moderate performance.
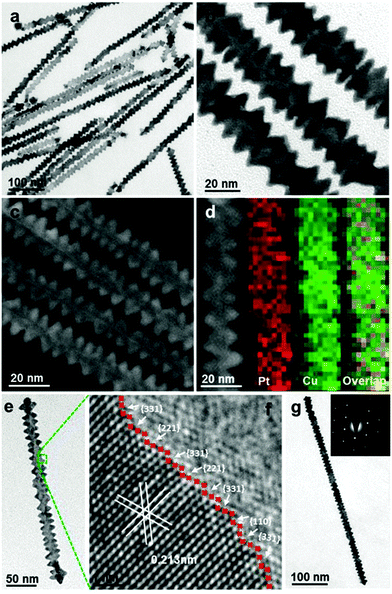 |
| Fig. 8 (a) Low-magnification TEM image, (b and e) high-magnification TEM images, (c) HAADF-STEM image, and (d) HAADF-STEM image and mapping images of PtCu1.8 nanowires. (f) HRTEM and (g) TEM image and corresponding selected-area-electron diffraction (SAED) (inset) of a single PtCu1.8 nanowire. Reprinted with permission from ref. 106. | |
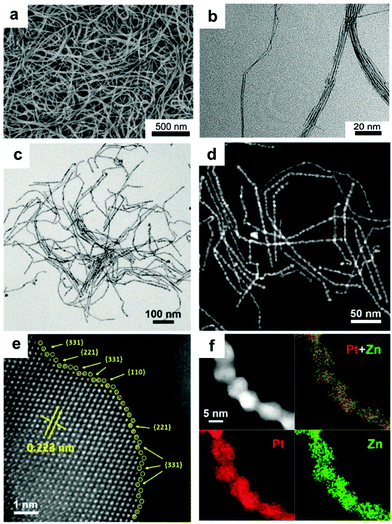 |
| Fig. 9 (a) Field emission SEM (FESEM) image and (b) TEM image of Pt32Cu68 nanowires. Reprinted with permission from ref. 108. (c) TEM image, (d) HAADF-STEM image, (e) aberration-corrected atomic-resolution STEM image and (f) STEM-EDS elemental mapping of as-prepared zigzag Pt–Zn nanowires. Reprinted with permission from ref. 111. | |
2.1.2 Synthesis of 1-D Pd-based NCs.
Synthesis of 1-D Pd NCs.
The solution-phase approach is regarded as a powerful and efficient protocol for the synthesis of Pd NCs. In general, the final morphologies of Pd NCs may be tuned by manipulating the thermodynamics or kinetics during their growth. In the thermodynamic mode, the obtained NCs tend to expose the facets with the lowest surface energy, in which surface capping agents play a vital role in shape control. In the kinetical mode, the shapes of Pd NCs can be tuned by adjusting the reduction kinetics.112,113 Template-assisted methods were used to synthesize Pd nanowires in earlier stages since the size and shape of NCs can be easily directed by templates. Lee et al. reported the preparation of Pd nanowires with a diameter of less than 10 nm using mesoporous silicate materials with different pore sizes and SBA-15 as templates.114 During the synthetic process, the Pd precursor was loaded into the template matrix via chemical vapor infiltration, followed by mild thermal decomposition to generate Pd nanowires inside the template. Finally, freestanding Pd nanowires were obtained by removing the silicate templates. Koenigsmann et al. reported the synthesis of Pd nanowires using polycarbonate or AAO membranes as a template.115 In addition to the hard template, some surfactants can act as soft templates for synthesizing Pd nanowires. Yu and co-workers used didodecyldimethylammonium chloride (DODAC) as a soft template to shape the morphology.116 It was shown that the double hydrophobic carbon chains of DODAC can make the mesophase more stable owing to the stronger hydrophobic interaction and effectively confine the crystalline growth of Pd nanostructures among the cylinders of a hexagonal micellar structure. Despite the great success in the template-assisted method for the synthesis of Pd nanowires, some disadvantages are still remaining. The key limitation of template-assisted methods is that they do not readily afford rational control over the diameter and length of the resulting nanowires. Therefore, other methods have been developed for the synthesis of Pd nanowires. Liang et al. developed a new template-assisted chemical process for the controllable synthesis of uniform Pd nanowires/nanotubes with an ultrahigh aspect ratio of 10
000, in which ultrathin Te nanowires were used as both a reducing agent and sacrificial template.117 To obtain uniform Pd nanowires, the reduction kinetics needs to be precisely controlled. Wang et al. systematically studied the relationship between the reaction kinetics and the obtained morphologies of Pd NCs. It was shown that two major parameters were critical for obtaining Pd nanowires, i.e., fast reaction kinetics during the nucleation stage and low surface charge of the small Pd particles generated in the early stage.118 Teng et al. developed a phase-transfer method for the synthesis of Pd nanowires, in which palladium nitride was transferred to a mixture of octadecylamine and toluene in the presence of DTAB, a phase-transfer agent.58 Huang and Zheng prepared 5-fold twinned Pd nanowires using PVP as the reductant in the presence of sodium iodide (Fig. 10a–f).119 It was shown that both PVP and I− were critical for the formation of the 5-fold twinned Pd nanowires. As one of the most famous shape-directing agents, PVP can also be used as a reductant during synthesis. I− can preferentially bind to the (100) facet, leading to the anisotropic growth of NCs. The above conclusion was further verified by Huang and co-workers, who synthesized penta-twinned Pd nanowires with diameters of less than 8 nm and aspect ratios of up to 100 in the presence of PVP and NaI (Fig. 10g–j). In this case, I− not only can coordinate with Pd (PdI42−) to slow the reaction rate, but also preferentially bind to the (100) facet, leading to the formation of penta-twinned nanowires.120 Moreover, Chen and co-workers used a seed-mediated synthesis process to prepare uniform Pd nanorods with average lengths of ∼200 and 300 nm with the addition of copper acetate. It was shown that copper acetate is critical for the formation of Pd nanorods since Cu has a similar but lower reduction potential than that of Pd, which results in the periodic deposition and reoxidation of the Cu atoms on the Pd nanorods and faceted particles, leading to the formation of nanorods and other shaped NCs.121 In addition to chemical methods, several techniques have also been employed for the preparation of Pd nanowires. Bhuvana and Kulkarni prepared Pd nanowires via direct-write electron beam lithography.122 On the other hand, Yoo et al. reported the growth of twin-free single-crystalline Pd nanowire arrays on an SrTiO3(110) substrate in a very high density. In particular, Pd powder was vaporized at 1100–1250 °C and transported to the lower temperature region by a carrier gas. Consequently, twin-free epitaxial Pd nanowires were formed on the substrate.123
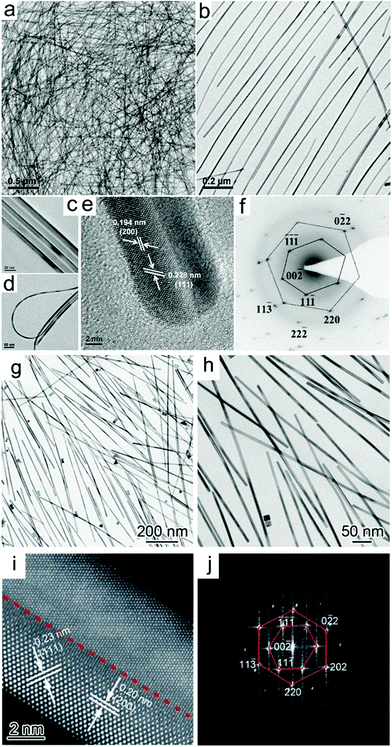 |
| Fig. 10 (a–d) TEM images of as-prepared Pd nanowires. (e and f) HRTEM image and SAED patterns of individual nanowires. Reprinted with permission from ref. 119. (g and h) TEM images at low and high magnifications, respectively, and (i) HRTEM image of as-prepared Pd nanowire. The red arrow and dotted line indicate the twin boundary along the long axis of the nanowire. (j) Fourier transform pattern derived from the lattice fringes in panel (i). Reprinted with permission from ref. 120. | |
Synthesis of 1-D Pd/noble metal nanocomposites.
Many physical and chemical methods, including the electrodeposition method,124,125 template-assisted synthesis,126–131 polyol-assisted synthesis,132,133 galvanic replacement reaction,134–136 hydrothermal and solvothermal treatment,137 seed-mediated synthesis,138 and chemical reduction,139–141 have been employed for the modification of Pd nanowires over the past decades. Jang et al. reported the synthetic of hollow Pd–Ag alloy nanowires via the electrodeposition of lithographically patterned Ag nanowires, followed by galvanic replacement reaction to form Pd. The relative atomic ratio between Pd and Ag could be controlled by controlling the reaction time of aligned Ag nanowires and Pd2+.125 Yang and co-workers prepared superlattice-structured Pd–Cu nanowires with random-gapped, screw-threaded and spiral shapes via electrodeposition on a template of AAO.125 Koenigsmann et al. developed a template-based technique for the preparation of a series of bimetallic Pd–Au and Pd–Pt nanowires with control over their composition and size without surfactants.129 Zhu et al. developed a facile method for the synthesis of Pd–Pt and Pd–Au nanowires, in which Te nanowires were employed as a sacrificial template and reducing agent (Fig. 11a).135 Moreover, Li and co-workers reported a scalable template-assisted method for the preparation of ultrathin and uniform Pd@Pt core@shell nanowires with a controllable composition and shell thickness, high aspect ratio, and smooth surface, in which Te NWs were employed as the sacrificial template and reductant (Fig. 11b–i).134 In another work from the same group, tri-metallic PdPtTe nanowires were produced with a similar method, in which the composition of the Pd–Pt–Te nanowires was controlled by the amount of Pt and Pd precursors in the growth solution.126 In addition to Te nanowires, Cu nanowires can also be used as a sacrificial template. For instance, Li and co-workers fabricated trimetallic Pt–Pd–Cu and bimetallic Pt–Cu nanotubes in dimethyl sulfoxide using Cu nanowires as templates.127 Teng and co-workers reported the synthesis of Pd–Au nanowires through the galvanic replacement reaction between Pd ultrathin nanowires and Au precursor (e.g., AuCl3), in which toluene, DTAB and octadecylamine were used as the solvent, phase transfer agent and capping agent, respectively.136 To obtain well-alloyed bimetallic Pd nanowires, the reduction rate of the different precursors in the growth solution needs to be precisely controlled. NaBH4 is one of the most common reductants in the colloidal synthesis of NCs, which can rapidly reduce noble metal ions in solution.142 Zhu et al. used NaBH4 to reduce Na2PdCl4 and HAuCl4 for the synthesis of twisted Pd–Au nanowires without any templates.143 It should be noted that the morphologies are determined by many other parameters in chemical reduction methods, such as solvent type, surfactant type, halide ion, and reaction temperature.142
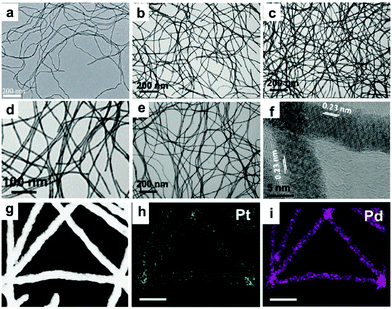 |
| Fig. 11 (a) TEM image of the obtained Pd80Pt20 nanowires. Reprinted with permission from ref. 135. TEM images of the Pd@Pt nanowires with Pt atomic ratios of (b) 6.0%, (c) 13.5%, (d) 21.2% and (e) 28.5%, (f) HRTEM image of Pd@Pt nanowires with a Pt atomic ratio of 21.2%. (g–i) EDS mapping analysis showing the elements in the Pd@Pt nanowires with a Pt atomic ratio of 21.2%. Reprinted with permission from ref. 134. | |
Synthesis of 1-D Pd/non-noble metal nanocomposites.
The modification of 1-D Pd NCs with non-noble metals has attracted great attention because it can greatly decrease the usage of noble metals and enhance the catalytic performance. As one of the most common non-noble metals, Fe has been widely used to composite with 1-D Pd NCs. Shui and co-workers synthesized Pd–Fe nanowires by electrospinning. Although the composition of the Pd–Fe nanowires was not uniform, the electrospinning method provides a simple strategy to obtain long nanowires up to millimeters in length (Fig. 12a).144 Wang et al. synthesized trimetallic PdPtFe nanowires using Pd(acac)2, Pt(acac)2 and Fe(CO)5 in the presence of oleylamine, 1-octadecene and sodium oleate (Fig. 12b). This method combined template-assisted synthesis and galvanic replacement reaction. Fe–Pt nanowires were pre-prepared as a template, and further reacted with a Pd precursor to form Pd–Pt–Fe nanowires through a galvanic replacement reaction (Fe + Pd2+ → Fe2+ + Pd).86 Oleylamine plays a vital role in the synthesis, which self-organizes into an elongated reverse-micelle-like structures to direct the growth of the Pt–Fe nanowires.90 Du and co-workers demonstrated the synthesis of Pd–Co nanowires with different Co contents via electrodeposition on AAO.128 As a template, AAO provides nanochannels for the electrodeposition of Pd and Co precursors, which can be removed to obtain uniform Pd–Co nanowires (Fig. 12c–k). On the other hand, Imura et al. used a template-assisted method for the synthesis of Pd–Ni nanowires in the presence of a long-chain amidoamine derivative. Different from hard templates, soft templates, such as some specific surfactants, can form micelles to direct the anisotropic growth of nanowires.145 Soft template-assisted methods have been widely used in the synthesis of 1-D Au NCs.146–150 In addition, other non-noble elements, such as Ce132 and Cu,125 were reported to composite with Pd nanowires.
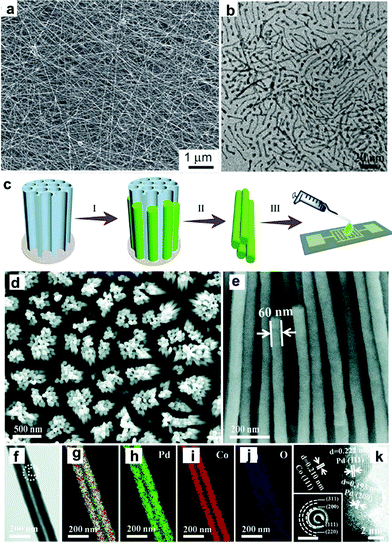 |
| Fig. 12 (a) SEM image of the obtained PdFe5 nanowires. Reprinted with permission from ref. 144. (b) TEM image of Pd–Pt–Fe nanowires. Reprinted with permission from ref. 86. (c) Schematic of the synthesis and integration of Pd–Co nanowires including electrodeposition, removal of AAO and integration. (d) Top-view and (e) side-view SEM images of Pd–Co nanowire arrays. (f) TEM image of Pd–Co NWs, and overlapped (g) and separated elemental mappings of (h) Pd, (i) Co and (j) O. (k) HRTEM image with the inset SAED pattern taken from the dashed rectangle and circle in (d), respectively. The scale bars in inset (k) are 1/(10 nm). Reprinted with permission from ref. 128. | |
2.1.3 Synthesis of other 1-D metal-based NCs.
Synthesis of 1-D Au NCs.
The synthesis of Au nanorods can be dated back to more than 30 years ago. Many review papers have been published with respect to the synthesis of Au nanorods.148,151–153 Thanks to the pioneering work from Murphy et al., seeded growth has been widely used for the synthesis of Au nanorods, in which CTAB and silver ions are used as the surfactant and directing agent, respectively.154,155 Three popular mechanisms were proposed for explaining the effects of CTAB and silver during the synthesis of Au nanorods: (1) silver deposits on the longitudinal faces of Au nanorods and enables the anisotropic growth of Au nanorods; (2) CTAB reacts with silver to form a complex of CTA–Br–Ag+, which can be used as a facet-specific capping agent for the growth of Au nanorods; and (3) the existence of silver can alter the shape of CTAB micelles from spherical to cylindrical shapes, which can be used as a soft template for the growth of Au nanorods.151 Ye et al. used a binary system including CTAB and sodium oleate for the synthesis of Au nanorods. It was found that the presence of sodium oleate could significantly improve the morphological yield of Au nanorods (>98%).156 Later, we used CTAC and sodium oleate as binary surfactants for revealing the mechanism for the synthesis of Au nanorods. In this work, it was found that sodium oleate could regulate the kinetics via the pre-reduction of Au3+ to Au+. On the other hand, the CTAC could react with Br− and Ag+ to form CTA–Br–Ag+, a key complex for the formation of Au nanorods (Fig. 13).149
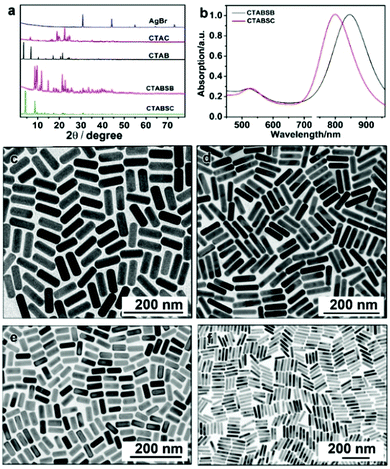 |
| Fig. 13 (a) Powder X-ray diffraction (XRD) patterns of different compounds: (from top to bottom) AgBr, CTAC, CTAB, CTA–Br–Ag–Br, and CTA–Br–Ag–Cl. (b) UV-vis spectra of Au nanorods prepared using CTA–Br–Ag–Cl (black curve) and CTA–Br–Ag–Br (red curve) as the ligands. (c and d) TEM images of Au nanorods prepared by using (c) CTA–Br–Ag–Cl and (d) CTA–Br–Ag–Br as the ligand. TEM images of Au nanorods prepared by dissolving AgBr crystals in (e) CTAC and (f) CTAB solution. Reprinted with permission from ref. 149. | |
Synthesis of 1-D Ag NCs.
The seeded growth method has also been used for the synthesis of Ag nanorods. Jana and co-workers reported a seed-mediated growth approach for the synthesis of Ag nanorods with various aspect ratios, in which nearly 4 nm spherical Ag nanoparticles were used as seeds.157 Similarly, Pietrobon et al. synthesized monodisperse size-controlled faceted Ag nanorods via the thermal regrowth of decahedral silver nanoparticles in the presence of citrate at 95 °C.158 It was found that the rod length could be varied precisely during the regrowth, while the width was determined by the choice of decahedra seeds since rod growth occurred exclusively along the five-fold axis. Rekha et al. prepared silver nanorods using a modified seed-mediated method. It was found that the aspect ratios of these nanorods could be regulated by controlling the amount of seed solution during the synthesis. Ni et al. studied the mechanism of the seeded growth method for the synthesis of Ag nanorods via a seed-mediated method.159 The wormlike micelles of cetyltrimethylammonium tosylate (CTAT) were characterized by HRTEM. Ag nanorods grew from multiply twinned decahedral seeds, and the blockage of circumferential growth led to an increase in the aspect ratio of the Ag nanorods. Mirkin's group demonstrated that Ag nanorods could be obtained via the plasmon excitation of Ag seed particles in the presence of Ag+ and trisodium citrate (Fig. 14). It was found that a red shift of the excitation wavelength of the Ag spherical seed particles reduced the rate of Ag+ reduction and led to the deposition of silver onto the tips of the growing nanorods compared to their sides, resulting in the generation of higher aspect ratio rods.160 On the other hand, Hu et al. reported a template-less and non-seed process for the synthesis of Ag nanorods and nanowires, in which silver nitrate was reduced by tri-sodium citrate in the presence of sodium dodecylsulfonate. Furthermore, the concentration of trisodium citrate was crucial for the synthesis of Ag nanocrystals, and sodium dodecylsulfonate acted an assistant in controlling the diameters and aspect ratios of the products.161
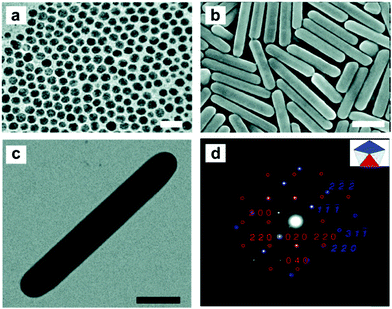 |
| Fig. 14 (a) TEM image of the silver seed nanoparticles. (b) SEM and (c) TEM images of silver nanorods synthesized with a bandpass filter centered at 600 ± 20 nm. (d) Selective-area electron diffraction (SAED) pattern of a single silver nanorod, showing the interpenetrating [100] (red) and [112] (blue) zone patterns. (Scale bars: 100 nm). Reprinted with permission from ref. 160. | |
In addition to above-mentioned cases, other 1-D metal-based NCs have been synthesized as catalysts. Fu and co-workers synthesized ultrathin wavy Rh nanowires using Na3RhCl6 and sodium ascorbate in the presence of PVP.162 Although the detailed mechanism was not mentioned, the halide ions (KI) played a critical role in the formation of the Rh nanowires. It was shown that NaI can also be used as an I− source for Rh nanowires, while the other parameters are similar to that in Fu's work.163 Mohamed and co-workers prepared Rh nanowires using a DNA template-assisted method. In this work, RhCl3 was used as a precursor, which could be reduced by an electrochemical method and NaBH4.164 Schoiswohl et al. modified Rh nanowires by decorating the steps of vicinal Rh(111) surfaces with Ni. After modification, the Rh–Ni nanowires exhibited much higher chemical reactivity towards oxygen than pure Rh nanowires.165 Liu and co-workers prepared single-crystalline RuO2 nanowires via a thermal evaporation method.166 It was shown that the diameter and length of the RuO2 nanowires could be tailored by altering the growth time.166 In addition, other 1-D metal NCs, including Fe, Co, and Ni, were synthesized.167–169 Compared to noble metal-based NCs, there are only a few reports on the synthesis of non-noble metal NCs, which may be attributed to the fact that noble metals exhibit much higher catalytic activity than non-noble metals.
2.2 Two-dimensional metal NCs
2.2.1 Synthesis of 2-D Pt-based nanocomposites.
Synthesis of 2-D Pt NCs.
Template-assisted methods have been widely used for the synthesis of 2-D Pt nanosheets or 149dendritic Pt nanosheets using multilamellar 1,2-dioctadecanoyl-sn-glycero-3-phosphocholine vesicles as templates in ascorbic acid solution. Under electron-beam irradiation, the dendritic nanosheets gradually evolved to metastable “holey” nanosheets, leading to an improved durability in electrocatalytic reactions due to their remarkable ripening resistance.170 Kijima and co-workers synthesized nanohole-structured single-crystalline Pt nanosheets via the reduction of a Pt precursor (e.g., Na2PtCl6) confined to the lyotropic liquid crystals of polyoxyethylene sorbitan monooleate.171 Furthermore, 2-D Pt nanosheets or nanoplates can be obtained by partially sacrificing the templates in bimetallic Pt-based nanoplates. For example, Chhetri et al. reported the synthesis of free-standing Pt nanosheets by the inducing mechanochemical transformation of Te template nanorods via galvanic displacement.172 Because Te is highly dissolvable in acid, it can be easily etched by chemical reaction. Feng et al. reported a protocol for the synthesis of porous Pt nanosheets, in which the Te in PtTe2 nanowires was removed by acetic acid.173 Liu and co-workers prepared ultrathin Pt nanoplates (2 nm) by etching the Ag templates from Ag@Pt core@shell nanoplates with concentrated nitric acid (Fig. 15).174 Moreover, Funatsu et al. reported the synthesis of monolayer Pt nanosheets with a homogeneous thickness via the exfoliation of layered Pt precursor materials with the addition of sodium dodecyl sulfate (SDS) during the electrochemical reduction.175
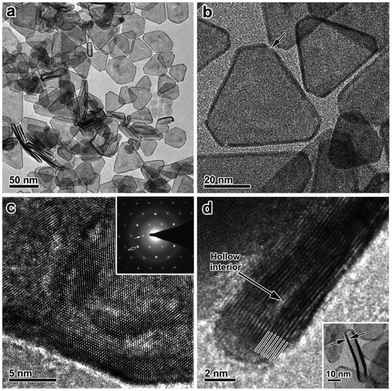 |
| Fig. 15 (a) Low-magnification TEM image of ultrathin Pt nanoplates. (b) TEM image of the ultrathin Pt nanoplates. The arrow indicates a defect. (c) HRTEM image of an individual ultrathin Pt nanoplate imaged with an electron beam perpendicular to the basal (111) facet. Inset: Typical SAED pattern. Black and white arrows indicate the (220) and the formally forbidden 1/3(422) diffractions, respectively. (d) HRTEM image of a vertically aligned ultrathin Pt nanoplate. Lines indicate the alignment of the atoms along the [111] direction. Inset: A low-magnification TEM image. Reprinted with permission from ref. 174. | |
Synthesis of 2-D Pt-based NCs.
Bi has been widely used to composite with Pt to form Pt–Bi nanoplates. Qin et al. synthesized Pt–Bi nanoplates using Pt(acac)2 and Bi(Ac)3 as precursors in the presence of NH4Br, 1-octadecene and oleylamine.176 Wang and co-workers obtained hexagonal Pt–Bi nanoplates in a mixture of PVP, CH3COOH and DMF, while Pt(acac)2 and Bi(Ac)3 were used as precursors.177 Zhang's group recently synthesized Pt–Bi nanoplates using Pt(acac)2 and bismuth neodecanoate as precursors in the presence of DEG and PVP. The detailed mechanism studies showed that Pt2+ ions were preferentially reduced in the initial stage, which acted as the seeds for the latter growth process.178 To achieve the anisotropic growth of Pt–Bi nanoplates, both precise control of the reduction kinetics and suppression of the growth along the (100) facet are necessary. Generally, the thickness of Pt–Bi nanoplates is related to the capping ability of the surfactant. Feng et al. revealed that the introduction of CO could act as both a reducing agent and capping agent during the synthesis of PtBi nanoplates.179 However, the effects of CO has not been discussed to date, which may be attributed to the strong adsorption of CO on the Pt surface. Similarly, Pt–Pb nanoplates were obtained when the Bi precursor was replaced by a Pb precursor.180 Sun et al. reported a synthetic protocol for Pt–Pb nanoplates by adding Pt(acac)2 and Pb(acac)2 to a mixture of L-ascorbic acid, oleylamine and 1-octadecene.181 Bu and co-workers synthesized hexagonal Pt–Pb@Pt core@shell nanoplates using Pt(acac)2 and Pb(acac)2 in the presence of L-ascorbic acid, oleylamine and 1-octadecene (Fig. 16). It was found that the edge-Pt and top (bottom)-Pt(110) facets underwent large tensile strain, which helped optimize the Pt–O bond strength, leading to a superior catalytic performance towards the ORR.182 Luo and co-workers fabricated intermetallic Pt45Sn25Bi30 nanoplates via a wet-chemistry method through the thermal decomposition of Pt(acac)2, SnCl2 and bismuth acetate [Bi(act)3] in a mixture of oleylamine and octadecene.183 The detailed characterizations revealed that the structure of Pt45Sn25Bi30 nanoplates consisted of the intermetallic (100) plane of Pt–Sn and Pt–Bi (Fig. 17). In addition, other metals, such as Co,184 Cu185 and Ag,186 were reported to composite with 2-D Pt nanoplates.
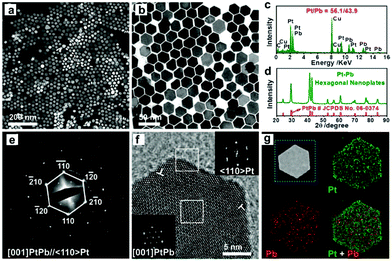 |
| Fig. 16 Morphology and structure characterization of Pt–Pb hexagonal nanoplates. Representative (a) HAADF-STEM image, (b) TEM image, (c) EDS, and (d) X-ray diffraction (XRD) pattern of Pt–Pb hexagonal nanoplates. (e) SAED and (f) HRTEM of a single hexagonal nanoplate. Insets of (f) are the fast Fourier transform (FFT) patterns from the white squares at the edge of and inside the nanoplate, respectively. (g) Elemental mapping of Pt–Pb hexagonal nanoplates: HAADF-STEM image, Pt mapping in green, Pb mapping in red, and integrated mapping of Pt and Pb. The compositional ratio between Pt/Pb is 55.9/44.1. Reprinted with permission from ref. 182. | |
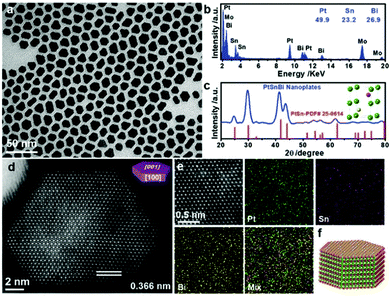 |
| Fig. 17 (a) TEM image, (b) EDS spectrum, and (c) XRD pattern of Pt45Sn25Bi30 nanoplates. The inset in (c) shows the unit cell of Pt50Sn25Bi25 intermetallic, in which green, purple, and yellow spheres represent Pt, Sn, and Bi atoms, respectively. (d) Aberration-corrected HAADF-STEM image of a typical hexagonal nanoplate. (e) High-resolution HAADF-STEM image and corresponding EDS mapping of the representative area in the nanoplate. (f) Schematic illustration of the atomic arrangement in the nanoplate. Reprinted with permission from ref. 183. | |
2.2.2 Synthesis of 2-D Pd-based NCs.
Synthesis of 2-D Pd NCs.
In 2009, Siril et al. reported a protocol for the production of ultrathin Pd nanosheets in emulsions formed by a ternary system (water/toluene containing Pd complexes/cetyltrimethylammonium bromide (CTAB)) and in quaternary hexagonal mesophases formed by water/toluene containing Pd complexes and CTAB/surfactant.187 They highlighted the critical effects of CO on the formation of Pd nanosheets. Subsequently, Huang and wo-workers modified this method by replacing the surfactant and solvent by PVP/CTAB and DMF, respectively, while CO was still used as a surface-confining agent.188 The freestanding hexagonal Pd nanosheets were as thin as 10 atomic layers, which exhibited a well-defined but tunable surface plasmon resonance peak in the near-infrared region (Fig. 18). The effects of CO on the formation of ultrathin Pd nanosheets were also highlighted in other reports.189–195 Li et al. demonstrated the shape-controlled synthesis of ultrathin Pd nanosheets by simply mixing a Pd carbonyl complex [Pd2(μ-CO)2Cl4]2− with H2O in the absence of any organic capping agents. The mechanism studies showed that the CO ligands in the complex serve as both a reductant and capping agent for the formation of Pd nanosheets.196 In another work from the same group, the authors demonstrated the face-to-face assembly of two-dimensional Pd nanosheets into one-dimensional Pd superlattice nanowires in the presence of trace amounts of Fe3+ and Al3+, in which the surfactant-free feature plays a critical role in the assembly of the Pd nanosheets into superlattice nanowires.197
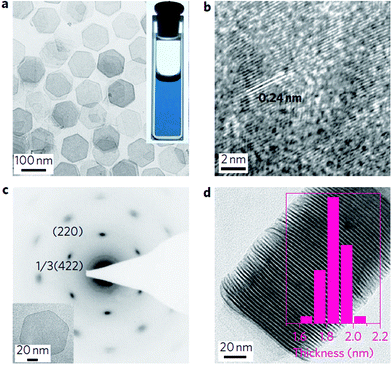 |
| Fig. 18 (a) TEM image of Pd nanosheets. Inset: Photograph of an ethanol dispersion of the as-prepared Pd nanosheets in a cuvette. (b) HRTEM image of a Pd nanosheet flat lying on the TEM grid. (c) SAED pattern of a single Pd nanosheet (shown in the inset). (d) TEM image of an assembly of Pd nanosheets perpendicular to the TEM grid. Inset: Thickness distribution of the Pd nanosheets. Reprinted with permission from ref. 188. | |
Synthesis of 2-D Pd nanocomposites.
2-D composite Pd-based nanosheets or nanoplates are generally synthesized via the direct co-reduction of precursors and epitaxial growth of other metals on Pd nanoplates. Yang and co-workers synthesized Pd–Cu nanosheets via the co-reduction of Pd(acac)2 and Cu(acac)2 in the presence of Mo(CO)6.198 Li et al. used Na2PdCl4 and CuCl2·2H2O as precursors to produce Pd–Cu nanoplates in the presence of W(CO)6, acetic acid, and DMF.199 Furthermore, the precursors of Na2PdCl4 and CuCl2 could be reduced by CO to form Pd–Cu nanoplates.200 As discussed before, CO not only serves as a reducing agent, but also can strongly confine the formation of ultrathin nanoplates or nanosheets. For example, Li et al. synthesized surfactant-free PdFe ultrathin nanosheets via a hydrothermal method. It was shown that CO played a vital role in the anisotropic growth of the nanosheets, which acted as a capping and reducing agent.201 Moreover, Cheong and co-workers obtained free-standing Pd–Ni alloy wavy nanosheets in a Teflon-lined high-pressure vessel by charging with 4 atm of CO.202 Other structure-directing agents, such as NH4Br, have been reported to direct the anisotropic growth 2-D nanoplates. Tang et al. synthesized Pd3Pb/Pd nanoplates in an organic solution of oleylamine/1-octadecene, in which Pd(acac)2 and Pb(HCOO)2 were used as the metal precursors, and glucose and NH4Br as the reducing agent and structure-directing agent, respectively (Fig. 19).203 Other Pd-based nanoplates (PdM, M = Ga, In, Sn, Pb, and Bi) have also been reported.204 In addition to non-noble metals, noble metals including Ag and Pt were also reported to alloy with Pd.205,206 Hong et al. reported the synthesis of Pd–Pt–Ag alloy nanosheets using K2PdCl4, K2PtCl4 and AgNO3 as precursors, in which the solution of precursors and ascorbic acid was sequentially injected into a CO-saturated aqueous solution of CTAC. It was shown that CO plays a vital role in the formation of ultrathin Pd–Pt–Ag ternary-alloy nanosheets with a thickness of approximately 3 nm.207 On the other hand, Pd nanoplates can be used as seeds or templates for the synthesis of bimetallic nanoplates via epitaxial growth and deposition. Yan and co-workers used Pd nanoplates as seeds for the synthesis of Pd@Pt nanoplates and multimetallic Pd@PtM (M = Ni, Rh, and Ru) nanoplates (Fig. 20).208 Chen et al. synthesized hexagonal Pd nanosheets, which were used as seeds for the formation of bimetallic Pd@Au nanoplates by chemically reducing AuPPh3Cl with hydrazine hydrate in DMF.209 Furthermore, Lim and co-workers prepared Pd@Pt core@shell nanoplates using a similar overgrowth method, in which hexagonal and triangular Pd nanoplates were employed as seeds.210
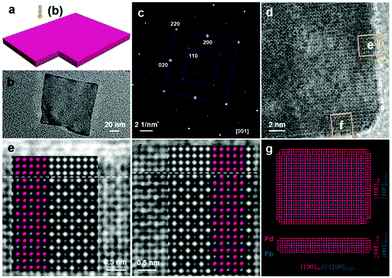 |
| Fig. 19 (a) Model, (b) TEM image from out-of-plate view, (c) SAED pattern, and (d) HRTEM image of a single nanosheet. (e and f) HRTEM images from the selected area in (d). Simulated HRTEM images as well as the atomic models in (e and f) are superimposed on the experimental images. (g) Atom models of the nanosheet showing the top interface [(100)Pd//(100)Pd3Pb] and the side interface [(001)Pd//(001)Pd3Pb]. Reprinted with permission from ref. 203. | |
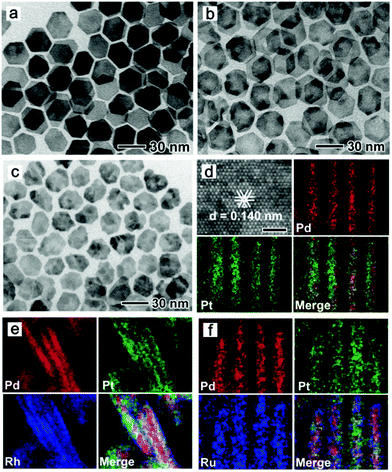 |
| Fig. 20 TEM and HAADF-STEM-EDS mapping images for (a and d) Pd@Pt nanoplates, (b and e) Pd@PtRh nanoplates, and (c and f) Pd@PtRu nanoplates, respectively, prepared using the standard procure, except for the different metal precursors. The scale bar in top, left part in panel d is 1 nm. Reprinted with permission from ref. 208. | |
2.2.3 Synthesis of 2-D Rh-based NCs.
Synthesis of 2-D Rh NCs.
Solvothermal treatment has been widely used for the synthesis of Rh nanoplates.211,212 Duan and co-workers obtained ultrathin Rh nanosheets in the presence of PVP via a solvothermal synthetic approach.213 The as-obtained Rh nanosheets were semi-transparent with an edge length of ca. 500–600 nm (Fig. 21a and b), which showed a superior catalytic performance towards the hydrogenation of phenol and hydroformylation of 1-octene.213 Using a similar solvothermal synthetic approach, Zhang et al. produced hierarchically-coiled ultrathin nanosheets by mixing RhCl3·3H2O, PVP and HCOONH4 in benzyl alcohol.214 Zhang et al. mixed RhCl3 with 1-octadecylamine in a Teflon-lined stainless-steel autoclave. Single-crystal hyperbranched Rh nanoplates were obtained after solvothermal treatment at 200 °C for 10 h.215 Zheng's group demonstrated a CO-confined growth strategy to prepare single-crystalline Rh nanosheets with atomic thickness and controllable size, in which CO was critical for the formation of nanosheets but did not vary the ratio of long edge to short edge of the different-sized Rh nanosheets (Fig. 21c). Jang and co-workers synthesized Rh nanoplates by dissolving [Rh(CO)2Cl]2 in oleylamine at 50 °C for 10 days (Fig. 21d). They emphasized that the solution must be left undisturbed.216 The mechanism studies showed that the coordinated oleylamine was located up and down the 1-D chains. The chains interact with each other via van der Waals interaction between alkyl groups to form a lamellar structure. The gradual reduction of Rh(I) to metallic Rh formed 2-D plates with shape evolution to triangle or quadrangle shapes.216
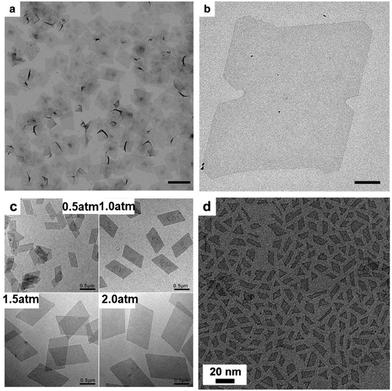 |
| Fig. 21 (a) Low-magnification TEM image of the PVP-capped Rh nanosheets. Scale bar, 1 μm. (b) High-magnification TEM image of the PVP-capped Rh nanosheets. Scale bar, 100 nm. Reprinted with permission from ref. 213. (c) TEM images of Rh nanosheets with a tunable size obtained under different CO pressures. Reprinted with permission from ref. 224. (d) TEM image of the top view of the prepared nanoplates. Reprinted with permission from ref. 216. | |
Synthesis of 2-D Rh nanocomposites.
Although there are many studies on Rh-based composite NCs,217–220 2-D Rh-based composite NCs have rarely been reported over the past decades. Köhler and co-workers reported the synthesis of bimetallic Bi–Rh nanoplates via a microwave-assisted polyol process. In this process, bismuth acetate and rhodium acetate dimer were used as metal precursors, and EG as the reducing agent. The average diameter and thickness of the Bi–Rh nanoplates were 60 nm and 20 nm, respectively.221 Compared to the ultrathin Rh nanosheets, these Bi–Rh nanoplates were much thicker, indicating the significance of the capping agents in the synthesis of 2-D NCs. Zhao et al. reported a cyanogel-reduction method for the synthesis of ultrathin Rh–Co alloy nanosheets, in which a (K3[Co(CN)6])–RhCl3 cyanogel was initially prepared and then reduced by HCHO at 240 °C for 6 h.222 Kang composited Rh nanosheets with reduced graphene oxide for achieving an enhanced methanol oxidation reaction performance.223
2.2.4 Synthesis of 2-D Au NCs.
The chemical reduction approach is a general method for the synthesis of 2-D Au NCs, which generally involves the reduction of an auric solution to form nanoplates in the presence of appropriate stabilizers (e.g., CTAB and PVP).225 The stabilizers are critical during the growth of the Au nanoplates since they can suppress the aggregation of nanoplates and control the growth process. Hence, the size of the prepared Au nanoplates can be tuned by varying in parameters involved in the synthesis, such as reagent concentration, solution temperature and reaction duration. In chemical reduction, the reductants are the key parameters for the synthesis of Au nanoplates. Sun's group reported the synthesis of morphology-controlled Au nanoplates in high yield and purity with a narrow size distribution via the chemical reduction of tetrachloroauric acid using trisodium citrate, which kinetically controlled the reaction pathway.226 The obtained Au nanoplates with two hexagonal shapes were highly [111] oriented with a flat top normal to the electron beam. The size of the nanoplates was determined by the relative amount of nuclei that were initially formed by the reduction by sodium citrate, leading to an increase in size with a decrease in the concentration of sodium citrate. Furthermore, they confirmed that the rate of the reaction can be controlled by sodium citrate, which proceeds in a two-step manner with self-seeding, resulting in the formation of planar nanocrystals or nanoplates with high yield and purity.
Chu and co-workers synthesized Au nanoplates via the reduction of HAuCl4 by trisodium citrate, and they claimed that the preheating of the HAuCl4 solution was quite important to control the size distribution of the nanoplates.227,228L-Ascorbic acid has been widely used for reducing tetrachloroauric acid in the seeded growth of Au nanorods.146,156,229–232 Yamamoto et al. reported a facile approach for the synthesis of star-shaped Au nanoplates via the reduction of HAuCl4 by L-ascorbic acid at room temperature in the presence of PVP.233 The obtained nanoplates were single-crystal nanoplates lying flat on their [111] planes with six symmetric hones extending to the [112] directions, but not the stacked two triangular plates or twin. Our group demonstrated a high morphology yield of gold nanoplates synthesized in the presence of CTAC and iodide ions.234 The kinetics of the growth could be controlled by fine-tuning the pH value using NaOH, resulting in the rapid growth of gold nanoplates in less than 10 min. Using the method, a high morphology yield (>90%) of triangular nanoplates with tunable edge lengths from about 45 nm to 120 nm were obtained (Fig. 22). Detailed investigations showed that the formation of the nanoplates was mainly determined by the selective binding of iodide ions, typically, the tri-iodide ions could facilitate the formation of nanoplates through selective binding on the Au(111) facets, and also formed I3− to selectively remove other shaped impurities in the early stage through chemical etching (Fig. 22g). This method was the first report on the rapid synthesis of small gold nanoplates with a high morphology yield of over 90% without any further purification steps, providing new insight to achieve cost-effective synthesis for practical applications.
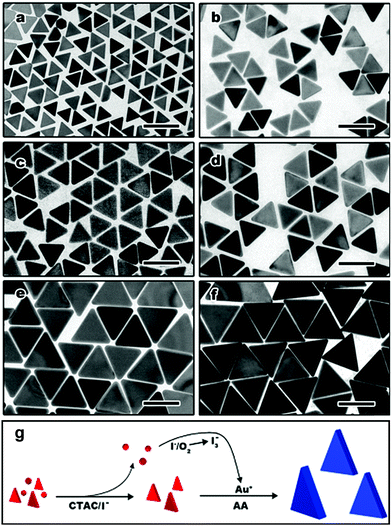 |
| Fig. 22 TEM images of Au nanoplates with tunable edge length. Average edge length of each sample is (a) 45.22 ± 3.38 nm; (b) 65.48 ± 2.92 nm; (c) 70.26 ± 3.07 nm; (d) 78.25 ± 3.16 nm; (e) 107.34 ± 8.01 nm; and (f) 117.29 ± 5.78 nm. The scale bars are 100 nm. (g) Proposed growth pathway of gold nanoplates through oxidative etching (gold nuclei with various crystal structures are produced in the early stage of nucleation. In the presence of oxygen and iodide, dominant gold nuclei with a planar twined structure are left and grow into nanoplates, while the other shaped nuclei are oxidized by tri-iodide ions). Reproduced with permission from ref. 234. | |
The seed-mediated approach is an effective procedure to obtain nanoparticles, which was originally developed for the synthesis of Au nanorods in 2001 by Murphy's group, in which CTAB and ascorbic acid are used as the shape-directing agent and reductant, respectively. Generally, seeds with a size in the range of 2–3 nm are prepared via the rapid reduction of auric solution by NaBH4.155,235 Owing to the high production yields, seeded growth methods have been widely used for generating nanoparticles including nanorods,146,230,236,237 bipyramids,238–242 and nanoplates.243–245 In 2004, Murphy's group reported that the shape of the Au nanoparticles could be controlled by systematically varying the experimental parameters in seeded growth. The growth solution contained CTAB, HAuCl4, L-ascorbic acid, and in some cases a small quantity of AgNO3, and the seed solution consisted of CTAB, HAuCl4 and NaBH4. The obtained shapes of the Au nanoparticles consisted of rod-like, hexagonal, cubic and triangular plates.246 Afterwards, Mirkin's group reported a procedure for generating Au nanoplates based on Murphy's seeded growth methods in 2005.247 All the obtained nanoplates with uniform edge lengths and thicknesses were triangular, while spherical nanoparticles were the major by-products (almost 50%). The obtained nanoplates possessed an average edge length and thickness of 144 and 7.8 nm, respectively, which were single crystalline with a [111] faceted flat top and bottom face according to the hexagonal electron diffraction pattern. To further tune the size of Au nanoplates, the subsequent work by Mirkin et al. reported an over-growth method for systematically controlling the edge length of Au nanoplates, in which seeds (Au nanoplates) were added into the growth solution containing a mixture of CTAB, HAuCl4, ascorbic acid and NaOH. They found that the edge length of the nanoplates could further grow from 100 nm to about 300 nm while preserving their original shape, crystal properties and thickness.248 The highly preferential growth of the side facets of the nanoplates over the triangular faces required the step-by-step injection of Au ions to avoid the formation of pseudospherical particles, which was attributed to the Gibbs-Thomson effect, indicating that a convex surface had a higher surface energy than a flat surface of the same material in the same phase.
Furthermore, Kim's group studied the tuning of both the edge length and thickness of triangular Au nanoplates using a modified seeded growth method.249 They claimed that multiple growth steps and the interval between multiple steps were critical for the preferential expansion of Au nanoplates. The edge length increased with an increase in the volume ratio between the isotropic growth solution and triangular Au nanoplates, ranging from 140 nm to about 260 nm, and the thickness correspondingly increased from 10 nm to 83 nm.249 Although the detailed mechanism was not mentioned, the procedure was similar to that of the conventional seeded growth methods, except for the addition of a certain amount of iodide ions, indicating that the iodide ions may play an important role in the formation of triangular nanoplates. Later, another work from Mirkin's group claimed that the morphologies of Au nanoparticles were strongly dependent on iodide ions.244 It was found that a high concentration of iodide ions (50 μM) favoured the formation of nanoplates in high yield (65% before purification), while a mixture of nanoparticle morphologies including nanorod, nanoprism, and nanosphere morphologies was observed at a lower iodide ion concentration of 10 μM. They claimed that the iodide ions were the dominant shape-directing agents, even more than the seed particles since nanorods, nanoprisms and nanospheres could be synthesized using the prepared seeds. This phenomenon was further confirmed by Sastry and co-workers, where they investigated the role of iodole ions on the morphology of gold nanotriangles in detail.250 The proposed mechanism could be understood based on the preferential adsorption of iodide on the [111] crystal facet of Au, which leads to a lack of preferential growth on the [111] facet.248,251,252
Besides, the seeded growth of Au nanoplates can also be performed on the surface. Akrajas and Munetaka reported the synthesis of two-dimensional Au nanoplates on the surface of indium tin oxide (ITO) through liquid-phase reduction from Au seed particles attached to the ITO surface in the presence of PVP. The obtained nanoplates were single crystalline in nature with [111] facets and the edge length of up to about 2 μm, which grew parallel to the surface of ITO. The concentration of PVP was the key factor to reduce the spherical or irregular-shaped nanoparticles and promote the growth of Au nanoplates on the surface of ITO.253 Zamborini and co-workers reported the growth of Au nanoplates directly on surfaces of glass and Si/SiOxvia a chemical seed-mediated growth method, in which involved purification by tape or sonication to improve the yield of Au nanoplates by up to 90%.254 A photochemical approach was reported by Jin et al. for generating Ag nanoplates in 2001.255 Zhu and co-workers reported the synthesis of Au plates via a photochemical approach using the ionic liquid 1-butyl-3-methylimidazolium tetrafluoroborate ([BMIM][BF4]) as the reaction medium, template, and capping agent.256 The proposed mechanism involved radical reactions photoexcited by UV light to reduce Au3+. As a template, the effects of [BMIM][BF4] were summarized as follows. Specifically, Au3+ ions were reduced to Au clusters by photoinduction, and the preferential adsorption of [BMIM][BF4] on the planes of Au crystals led to the formation of Au nanoplates. Ding's group developed a continuous method for generating Au nanoplates under UV irradiation in the presence of citric acid and PVP at room temperature. They claimed that the morphologies of the Au nanoparticles were strongly dependent on the concentration of PVP and the flow rate of the solution.257 Furthermore, Soejima and Kimizuka claimed that two processes were involved in the photo-assisted synthesis of Au nanoplates: (1) the growth of 2-D Au nanoplates via the photoreduction of Au(OH)4 complexes, and (2) the oxidative etching of Au nanoplates by dissolved molecular oxygen.258 NaBr plays multiple roles in terms of forming stable adlayers on Au surfaces and promoting the growth of 2-D nanoplates, and converting the oxidized Au(I) species to AuBr2− ions for the oxidative etching of gold nanocrystals. In addition, Pereira et al. developed a photocatalytic approach for the synthesis of triangular Au nanoplates in aqueous solution over a tin(IV) porphyrin photocatalyst, in which CTAB was used as stabilizer and triethanolamine as the final electron donor.259 The size of the Au nanoplates could be systematically tuned by varying the concentration of photocatalyst and CTAB. Specifically, tin(IV) porphyrin was photoexcited by light to form an intermediate with the electrons from triethanolamine, accompanied by the catalytic reduction of Au3+ over the intermediate to form Au nanoplates.
Synthesis of 2-D Au-based nanoplates.
Tsuji and co-workers investigated the shape-dependent evolution of Au@Ag core–shell nanocrystals using PVP-assisted N,N-dimethylformamide reduction. The final shapes of the Au@Ag core–shell nanostructures were determined by the shapes of the Au nanoplate seeds, and the edge length of the silver shells increased with an increase in the molar ratio of [AgNO3]/[HAuCl4].260 Besides, Park et al. demonstrated that the final shapes of the Ag shell on Au nanoplates could be tuned by the presence of iodide ions.261,262 It was found that the Ag shell was formed homogeneously over the entire surface of the flat Au nanoplates without iodide ions, whereas the presence of iodide ions induced the selective coating of the Ag shell in the direction perpendicular to the basal plane of the nanoplates, leading to the formation of Au@Ag core–shell hollow nanostructures via galvanic replacement reactions.
Mirkin et al.263 reported the plasmon-driven synthesis of triangular core–shell nanoplates from gold seeds, in which colloidal Au and Ag nanoparticles with diameters of 11 nm and 5 nm, respectively, were added to the aqueous solutions, followed by light irradiation with 550 nm light for 5 h. It was found that the edge length of the core–shell nanoplates was determined by the excitation wavelength, and long excitation wavelengths (600 nm) led to an increase in the average edge length (80 ± 7 nm). Zhang and co-workers synthesized hexagonal Au@Ag core–shell nanoplates on the (0002) face of ZnO nanorods via a two-step deposition-annealing method,264 in which high-quality ZnO nanorods with a flat (0002) face were grown via the chemical vapor deposition method. Au was firstly deposited by e-beam evaporation, and subsequently annealed at 700 °C for 60 s to enable the formation of a first layer of well-defined Au nanoplates, and then the prepared Au nanoplates underwent e-beam evaporation again for 1 nm Ag capping.
2.2.5 Synthesis of 2-D Ag NCs.
Jin and co-workers reported a photochemical approach for the preparation of 2-D Ag nanoplates in the presence of citrate and bis(p-sulfonatophenyl) phenylphosphine dihydrate dipotassium salt (BSPP).255 They revealed that this phenomenon disappeared in the dark even when the reaction time was over a two-month period, and the triangular shape silver nanoplates grew bigger with an increase in the radiation intensity. Thus, the synthesis of silver nanoplates could be simply controlled by turning on/off the light. The potential mechanism was that under the effect of BSPP, silver seeds were converted into small clusters through the photoinduced fragmentation of silver nanoparticles, and then to small nanoplates (edge lengths of 5–10 nm). The small nanoplates acted as seeds and grew at the expense of the small nanoparticles. Xia et al. demonstrated that citrate ions could promote the formation of nanoplates from spheres through a combination of chemical and photochemical methods.265 Another work presented by Maillard indicated that the silver nanoplates were formed in a solution of seed colloid and citrate, which grew through the reduction of silver ions induced by the incident beam.266
Mirkin et al. synthesized Ag nanoplates via dual-beam illumination (termed as the primary beam and secondary beam).267 It was shown that the excitation of a silver nanoparticle colloid with a single beam resulted in nanoplates with two size distributions, named Type 1 (edge length 70 ± 12 nm) and Type 2 (edge length 150 ± 16 nm). Although the size of the Type 2 nanoplates was almost twice that of the Type 1 nanoplates, their thickness was essentially the same, which may imply a mechanism that the triangular Type 2 nanoplates were assembled by three pieces of triangular Type 1 nanoplates. By contrast, only Type 1 nanoplates were formed when the solution was simultaneously excited via dual-beam with the wavelengths of 550 nm (dipole SPR excitation) and 450 nm (or 340 nm, quadrupole SPR excitation) light, and the edge lengths ranged from 40 to 120 nm with a variation in the length of the primary beam from 400 to 750 nm, which were also vividly shown in the TEM images (Fig. 23). The above results indicated that the fusion of the smaller nanoplates was inhibited by quadrupole or high energy excitation, indicating that it was feasible to control the edge length of the nanoplates.268 Another report by Markin's group demonstrated the mechanism of photo-mediated growth.269 They proposed that the growth of Ag nanoplates from nanoparticles may undergo several steps, i.e. plasmon excitation-initiated photo-reaction, shape transformation of spherical silver nanoparticles to small nanoplates, and growth from small nanoplate seeds to large nanoplates. They assumed that dipole and quadrupole plasmon excitation may play different roles in the shape control process. Dipole plasmon excitation favoured the growth of sharp corner nanoplates, while in-plane quadrupole excitation favoured the growth of truncated nanoplates.
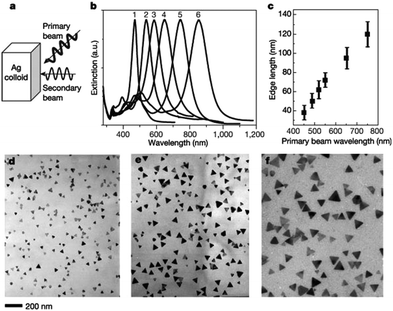 |
| Fig. 23 Unimodal growth of nanoplates. (a) Schematic diagram of dual-beam excitation. (b) Optical spectra (normalized) for six different-sized nanoplates (1–6 edge length: 38 ± 7 nm, 50 ± 7 nm, 62 ± 9 nm, 72 ± 8 nm, 95 ± 11 nm and 120 ± 14 nm) prepared by varying the primary excitation wavelength (central wavelength at 450, 490, 520, 550, 650 and 750 nm, respectively; width, 40 nm) coupled with a secondary wavelength (340 nm; width, 10 nm). (c) Edge length as a function of the primary excitation wavelength. (d–f) TEM images of Ag nanoplates with average edge lengths of (d) 38 ± 7 nm, (e) 72 ± 8 nm and (f) 120 ± 14 nm. Scale bar applies to panels d–f. Reprinted with permission from ref. 267. | |
In addition, the effects of incident light on the control of the morphology were further verified in other studies. Callegari and co-workers demonstrated that the shape could be controlled by choosing the wavelength of light used to drive the photochemical growth. Specifically, the edge length of the obtained triangular Ag nanoplates increased with an increase in the wavelength of the incident light.270 Liz-Marzán et al. reported that the later dimensions of the silver nanoplates could be controlled by illuminating pre-formed silver seeds under different illumination conditions.271 It was noted that although the later size of silver nanoplates increased with the wavelength of the incident light, the thickness was almost constant. Besides, the morphology of silver nanoplates could be tuned by altering other parameters (e.g., citrate, pH, and BSSP).272 Xue and Mirkin demonstrated a straightforward route for controlling the bimodal growth of silver nanoplates by simply adjusting the pH value of the solution based on the hypothesis that a variation in pH value can adjust the process of nanoplate fusion, thus affecting the growth pathways.273 It was shown that highly basic conditions were adverse for the formation of silver NCs since a passivating layer of AgOH likely formed on the surface of silver NCs and inhibited the photoreaction. However, a lower pH value may lead to the formation of nanoparticles with irregular shapes, and even further reduce the interplate repulsion. A subsequent work by Mirkin et al. investigated the effects of pH value and BSSP on the morphology and size of Ag NCs.274 It was found that a high pH value favoured the formation of bipyramids, whereas a low pH value favoured the formation of nanoplates, and the aspect ratio increased with an increase in the ratio of [BSPP]/[Ag+]. The proposed mechanism was that a fast reaction rate achieved by a high pH (10 or 11) and a relatively low [BSPP]/[Ag+] ratio (close to 1) favoured the growth of (100)-faceted right triangular bipyramids via the preferential deposition of Ag on the (111) facets compared to the (100) facets. By contrast, a slower reaction rate achieved by low pH value and high [BSPP]/[Ag+] ratio favoured the preferential deposition of Ag on the (100) facets, resulting in the formation of Ag NCs with a higher percentage of (111) facets (e.g., nanoplates). Zhang et al. reported that the morphology of the Ag nanoplates changed from thin triangular plates to thick round plates with the assistance of PVP through a UV-light-induced reconstruction process.275
In addition, the chemical reduction method, which is also named the thermal synthesis method, has been widely used for the synthesis of Ag nanoplates.276 As one of the most popular approaches for the synthesis of nanoplates, the chemical reduction method involves the gradual conversion of colloidal Ag nanoparticles into nanoplates.265,277–279 In principle, chemical reduction methods simply involve the reduction of metal ions by a specific chemical reducing agent with the help of a capping agent to form small nanoparticles, then grow into larger structures at an appropriate pH value and temperature.268 Zhang et al. demonstrated that various Ag sources could be directly converted into Ag nanoplates in H2O2 with the assistance of an appropriate capping ligand.280 Sun and Lei reported the conversion of Ag nanoplates into Au–Ag alloy nanoplates for enhancing their stability in catalytic applications, in which the Au–Ag nanoplates were formed by immersing a sample of Ag nanoplates into an aqueous solution of NaAuCl4 at room temperature.281 Sun and co-workers reported the synthesis of highly stable Ag–Au triangular nanoplates via galvanic reaction based on face-selective etching.282 The obtained alloy nanoplates exhibited tunable localized surface plasmon resonance and efficient two photon luminescence as well as high stability under the strong laser and tough ion-contained environment owing to the close match of the lattice spacing between Au and Ag. Moreover, galvanic displacement reactions have been applied for the synthesis of Ag–Pd nanoplates. Generally, Ag nanoplates are used as templates, and Ag–Pd nanoplates are obtained by sacrificing the Ag templates for the reduction of Pd2+ into Pd0via a galvanic displacement reaction. The properties of the obtained Ag–Pd alloy nanoplates were determined by the concentration of Pd2+ and the Ag templates. It has been reported that the size of the obtained alloy nanoplates could be tuned by altering the size of the Ag templates283 and the concentration of the Pd precursor.284–286 Moreover, this galvanic displacement method can be used to synthesize other Ag-based nanoplates, such as Ag–Pt nanoplates.287
2.2.6 Synthesis of other 2-D metal-based NCs.
Leng et al. reported the synthesis of single crystalline Ni nanosheets via the decomposition of Ni(COOH)2 with the aid of iron species.288 The edge lengths of the Ni nanosheets ranged from several tens to hundreds of nanometers, with the shapes of triangle and hexagon.288 In another work from the same group, they synthesized monodisperse fcc Ni nanoplates (Fig. 24) with a triangular shape and uniform sizes via a thermolysis method, in which oleic acid and oleylamine were used as the stabilizers. A plausible mechanism was proposed as follows: (1) small triangular nanoplates acted as the initial nuclei, and continued to grow within the (111) planes along the 〈110〉 direction by Ni atomic attachment, forming large triangular nanoplates and (2) some of the small nanoplates with the same size will be connected along the (110) lateral planes, leading to the formation of large triangular and hexagonal nanoplates.289 Another typical case for 2-D non-noble metal nanostructures is Cu nanoplates. Sun reported the synthesis of size- and shape-controlled planar Cu nanoplates in high yield via the reduction of a Cu(II)–tartrate complex using the mild reductant NaH2PO2 in the presence of PVP. The size of the Cu nanoplates could be systematically tuned from the nano-scale to submicron-scale by altering the type of complex agent or by adjusting the amount of tartrate complex.290 Pastoriza-Santos et al. synthesized single-crystalline Cu nanoplates with prominent surface plasmon bands through the reduction of copper salts (i.e., Cu(OAc)2) with hydrazine, using PVP as a stabilizer and without the need for an inert atmosphere.291 Moreover, Guo and co-workers reported the synthesis of hexagonal and triangular Ni–Cu alloy nanoplates with a well-defined twin structure via a one-pot non-aqueous synthetic approach in an Ar atmosphere. More importantly, the morphology of the Ni–Cu alloy nanoplates evolved from hexagon to triangle when dibenzyl ether was added to the growth solution. The mechanism was summarized as follows: (1) Ni(II) is reduced Ni(0) atoms, which then combined into crystal embryos; (2) Cu(II) will partially etch the surface Ni(0) into Ni(II) via galvanic replacement reactions in the presence of Cl−; and (3) the deposited Cu(0) on the surface of the Ni embryos will further catalyze the reduction of Ni(II) to form alloy nuclei. The reiteration of this oxidative etching and catalytic growth process enabled the alloy nuclei to grow into spherical seeds, which finally developed into alloy nanoplates.292 Bai and co-workers recently synthesized lichen-like Ru–Cu nanosheets via a solvothermal method.293 These lichen-like nanostructures with a thickness of about 3 nm exhibited a superior catalytic performance towards the direct oxidation of CH4. Compared to the noble metal-based NCs, non-noble metals, such as Ni, Cu, and Co, are less popular, mainly because they are prone to fast oxidation.291
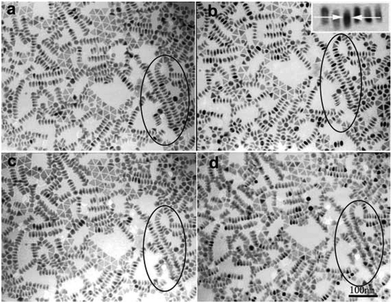 |
| Fig. 24 TEM images of the standing Ni nanoplates by tilting to confirm the self-assembled plate structure. Tilted TEM images obtained at (a) −10°, (b) 0°, (c) +10°, and (d) +25° tilt. The inset in (b) is the enlarged image of the standing edges of several triangular Ni nanoplates. Reprinted with permission from ref. 289. | |
2.3 Three-dimensional metal NCs
2.3.1 Synthesis of 3-D Pt-based NCs.
Synthesis of 3-D Pt NCs.
Based on previous reports, 3-D Pt NCs are generally enclosed by (100) and/or (111) facets. The first example is Pt nanocubes, which are enclosed by six (100) facets. Generally, Pt(acac)2 is used as a Pt source, and oleic acid and oleylamine are used as capping agents. In addition, some additives are needed to act as a shape-directing agent. Sun demonstrated the synthesis of Pt nanocubes by reducing Pt(acac)2 in the presence of oleic acid and oleylamine, in which Fe(CO)5 was employed as the shape-directing agent.294 Liu et al. reported that W(CO)6 could also be used as a shape-directing agent for the synthesis of Pt nanocubes.295 Loukrakpam and co-workers prepared Pt nanocubes via a chromium-assisted synthetic method in the presence of Cr(CO)6. The plausible mechanism suggests that Cr species can preferentially adsorb on Pt(111), leading to the effective blocking of the Pt(111) facet.296 In addition to metal hexacarbonyls (e.g., Fe(CO)5, W(CO)6, and Cr(CO)6), CO has been confirmed to direct the formation of Pt nanocubes.297,298 For Pt NCs enclosed by (111) facets, Kang et al. demonstrated that Mn2(CO)10 enabled the formation of Pt octahedrons (Fig. 25).299 Furthermore, they claimed that the obtained morphologies of the Pt NCs varied strongly by altering the ratio of Mn2(CO)10 and Pt(acac)2, as presented in Fig. 25. Liao et al. revealed the growth process in a liquid cell using TEM with high spatial and temporal resolution. It was shown that the growth rates of all the low index facets are similar until the (100) facets stop growing, while the continuous growth of the other facets leads to the formation of nanocubes.300 Discussing the effects of shape-directing agents on the morphologies of Pt NCs is critical for studying their mechanism; however, the mechanism is not completely understood to date. One popular explanation proposed by Kang et al. suggests that Mn from the decomposition of Mn2(CO)10 may selectively deposit on Pt(100) and then reduce Pt2+ to Pt, which takes the position occupied by the Mn atom.299 To determine the detailed mechanism, a more sensitive tool is necessary to unambiguously identify the efforts of shape-directing agents on the morphology control.
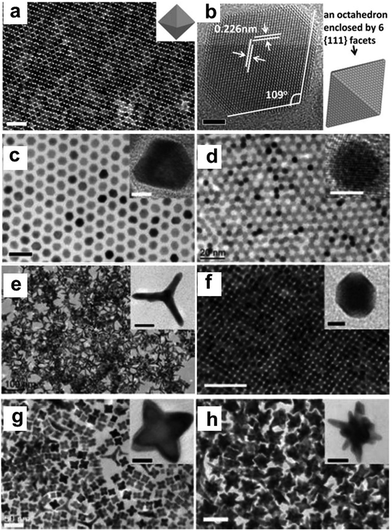 |
| Fig. 25 (a) TEM and (b) HRTEM images of Pt octahedra. Scale bars: (a) 50 nm and (b) 2 nm. TEM images of (c) Pt cuboctahedra, (d) Pt spheres, (e) Pt tetrapods, (f) Pt truncated cubes, (g) Pt star (octapods), and (h) Pt multipods. Scale bars: (c and d) 20 nm, (e) 100 nm, (f–h) 50 nm, insets of (c, d and f) 5 nm, insets of (e and h) 20 nm, and inset of (g) 10 nm. Reprinted with permission from ref. 299. | |
Pt NCs with concave surfaces are interesting in catalysis since their corners and edges generally exhibit higher catalytic activity than that of conventional Pt NCs. On the other hand, Pt NCs enclosed by high-index facets are much more active than NCs enclosed by low-index facets (e.g., (111) and (100) facets).301 However, Pt NCs with high-index facets generally have high surface energy, leading to instability during their synthesis and catalytic application.302 In principle, two strategies can be used for the synthesis of concave Pt NCs: (1) site-specific dissolution through etching and galvanic replacement and (2) directionally controlled overgrowth by facet-selective capping, kinetic control, and template-directed epitaxy.303 Zhang et al. summarized the most popular and common concave Pt NCs in previous works.303 Thus, here, we simply introduce some classic examples of the synthesis of Pt NCs enclosed by high-index facets. Zhang et al. presented the synthesis of Pt concave NCs with high-index facets in an aqueous solution via the reduction of H2PtCl6 in the presence of PVP and glycine, in which PVP acted as a surfactant, stabilizing agent and reductant, and glycine as a surface controller and co-reductant.304 Huang and co-workers synthesized concave Pt NCs enclosed by both high-index (411) and (100) facets via a solvothermal method (Fig. 26).305 It was shown that the amine played a vital role in the formation of the concave NCs. Zhang et al. reported the preparation of high-index facets of (211) and (411) via a solvothermal method using Pt(acac)2 as the Pt source, 1-octylamine as the solvent and capping agent, and formaldehyde as an additional surface structure regulator. The plausible mechanism suggests that amine can stabilize the monoatomic step edges, leading to the formation of the (211) facet. Formaldehyde decomposes into CO, and further leads to the formation of (411) surfaces by the additional adsorption of the CO on the (100) terraces.306 Moreover, an electrochemical method was employed to synthesize Pt NCs enclosed by high-index facets. Wei et al. reported the electrochemical synthesis of tetrahexahedral (THH) Pt NCs in deep eutectic solvents for the first time. The as-prepared THH Pt NCs were bound with (910) and vicinal high-index facets, which exhibited superior catalytic activity and stability for the electrooxidation of ethanol.307 In another work from the same group, the synthesis of a complex shape of Pt micro/nano-sized crystals was demonstrated, where a convex hexoctahedra enclosed with 48 (15 5 3) high-index facets were obtained via the electrochemical square-wave-potential method. It was realized that the shape of the Pt NCs with high-index facets evolved from THH to hexoctahedron (HOH), and then to trapezohedron (TPH) with an increase in the upper (EU) or lower potential (EL) (Fig. 27).308
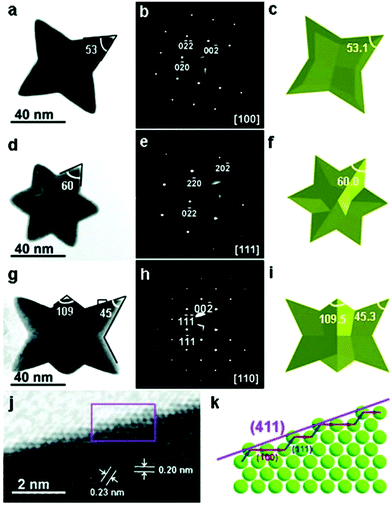 |
| Fig. 26 (a, d and g) TEM images, (b, e, and h) SAED patterns, and (c, f, and i) geometric models of individual concave Pt NCs oriented along the (a–c) [100], (d–f) [111], and (g–i) [110] directions. (j) HRTEM image of the region indicated by the box in (g). (k) Atomic model corresponding to the region indicated by the box in (j). Reprinted with permission from ref. 305. | |
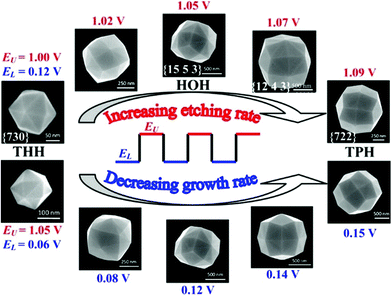 |
| Fig. 27 Shape evolution of Pt NCs from THH to TPH via HOH by increasing the EU or EL of the square-wave-potential. Increasing EU will increase the etching rate, and increasing EL will decrease growth rate of Pt NCs. Both approaches result in the same trend of shape evolution. Reprinted with permission from ref. 308. | |
Synthesis of 3-D Pt nanocomposites.
Among the composite Pt NCs,309–314 Pt3Ni nanostructures are some of the most popular catalysts in electrocatalysis over the past two decades.315–328 Zhang et al. synthesized monodisperse Pt3Ni nanoctahedra and nanocubes enclosed by (111) and (100) facets, respectively, via a high-temperature organic solution chemistry approach under an inert atmosphere. In this process, the precursors of Pt(acac)2 and Ni(acac)2 were dissolved in a mixture of oleylamine and oleic acid and then heated to 130 °C under an Ar gas flow. W(CO)6 was added as a shape-reducing agent, followed by heating to 230 °C for 40 min under vigorous agitation.317 Wu and co-workers presented a strategy for the synthesis of truncated-octahedral Pt3Ni catalysts with (111) facets. They claimed that short-alkane-chain amines appeared to favor the formation of (111) facets. When dodecylamine was used as the capping agent, only octahedra and truncated octahedra were obtained, while a certain of amount of cubes were observed when octadecylamine and hexadecylamine were used.316 In addition to the capping agent, the reduction kinetics may influence the final morphology of Pt3Ni NCs.318 Zhang et al. obtained Pt3Ni NCs with Pt skin and Ni-rich Pt3Ni NCs under thermal treatment.324 The different thermal stability of Pt and Ni may pull the Ni atoms to surface to decrease the surface energy. Shen and co-workers demonstrated the combinational use of multiple cutting-edge in situ techniques to study the growth process of octahedral Pt3Ni NCs. It was shown that Pt nuclei are formed in the initial stage, which further catalyze the reduction of Ni to form an alloy with moderate elemental segregation (Fig. 28a–e).329 To significantly expose more Pt atoms on the surface of Pt3Ni NCs, Huang et al. synthesized highly porous Pt3Ni NCs in the presence of PVP, DMF and phenol. They claimed that the selective use of phenol was critical for the formation of porous Pt3Ni NCs. PVP acted as a surfactant to prevent the aggregation of the NCs.320 Furthermore, the superstructure of octahedral Pt3Ni NCs, which was formed during the controlled evaporation of the solvents, was proven as an efficient strategy to reduce the surface ligands.319,323 As discussed above, it has been widely reported that the high-index facets of NCs may exhibit higher catalytic activity than that with low-index facets. Wang and co-workers demonstrated the synthesis of high-indexed Pt3Ni alloy THH nanoframes through preferential CO etching. In this process, PtNi4 THH NCs were prepared via the co-reduction of PtCl4 and NiCl2·6H2O in the presence of oleylamine, which were further subjected to sequential cleaning, carbon loading, CO-etching and annealing treatment to obtain the Pt3Ni alloy THH nanoframes (Fig. 28f–k).325 Huang et al. demonstrated the surface doping of Mo on Pt3Ni octahedrons on commercial carbon black without the use of any bulky capping agents, in which Mo(CO)6, Pt(acac)2 and Ni(acac)2 were added to a suspension of Pt3Ni/C in DMF and left to react at 170 °C for 48 h.322
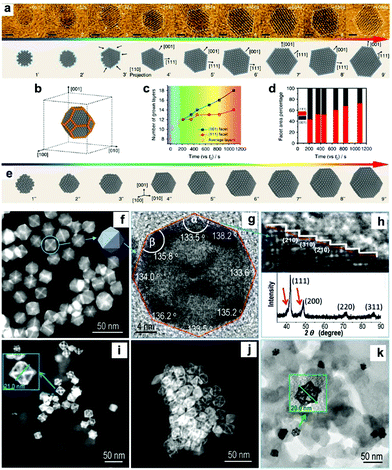 |
| Fig. 28 Shape evolution of Pt3Ni nanoparticle. (a) In situ STEM images of a growing Pt3Ni nanoparticle (upper row) and corresponding 2-D projection model (lower row), scale bar: 1 nm. (b) Representative atomic model (not to scale) of the nanoparticle during its growth. (c) Number of grown layers of the (001) and (111) facets and (d) their surface exposure ratio as function of experimental time. (e) 3-D model of the Pt3Ni growth process. The early stage model 1 was constructed to show a possible dynamical cluster structure. Reprinted with permission from ref. 329. (f) HAADF-STEM image of PtNi4 THH NCs (the inset is a THH model along the [001] zone). (g) HRTEM image of a single PtNi4 THH NC recorded along the [001] zone axis with the measured angles between surfaces. (h) HRTEM image zoomed from the boxed area in (g), displaying the surface atomic steps marked as (210) and (310) and XRD pattern of the obtained THH NCs, showing the alloy phase with the fcc structure. (i) HAADF-STEM image of THH nanoframes on carbon evolved by CO thermal annealing. (j) HAADF-STEM image of THH nanoframes on carbon obtained by annealing in the absence of air. (k) TEM image of generated nanoframes by annealing in air after 5000 electrochemical potential cycles from 0.6 to 1.0 V versus RHE at 0.5 V s−1 in 0.1 M HClO4, showing that the THH profile was perfectly preserved. Reprinted with permission from ref. 325. | |
2.3.2 Synthesis of 3-D Pd-based NCs.
Synthesis of 3-D Pd NCs.
Various Pd NCs have been synthesized over the past two decades. Zhang et al. summarized several typical shapes of Pd NCs in 2013.112 It was shown that most of the Pd NCs exposed their low-index facets including (100), (110) and (111) facets (Fig. 29). It is well known that the final shape of Pd NCs is determined by many parameters, such as capping agent, reduction kinetics and structure of the seeds. Xia's group reported that citrate ions could selectively stabilize the (111) facets, and thus favor the formation of Pd NCs enclosed by (111) facets.330 In contrast, halide ions (e.g., Br−) could selectively adsorb onto the (100) facets of Pd NCs, and thus stabilize these facets during growth, leading to the formation of Pd nanocubes enclosed by (100) facets.294 Further investigations revealed that halide ions (e.g., Br− and Cl−) may coordinate with Pd2+ to retard the reduction kinetics, leading to variable sizes of Pd nanocubes.40,331 Jin et al. demonstrated the synthesis of Pd NCs with controlled shapes and different proportions of (100) and (111) facets via the seeded growth method. By varying the ratio of precursor to seed, the shape of the Pd NCs evolved from cubes into truncated cubes, cuboctahedrons, truncated octahedrons, and octahedrons due to the faster growth along the 〈100〉 directions relative to the 〈111〉 directions (Fig. 30a–e).332 On the other hand, the seeded growth method was also used to prepare Pd concave nanocubes enclosed by 24 high-index facets through preferential overgrowth on Pd cubic seeds. In this process, Br− ions were added to reduce the reduction kinetics and stabilize the (100) facets.333 Huang and co-workers demonstrated the preparation of polyhedral concave Pd NCs with a tunable ratio of (111) and (110) facets in the presence of formaldehyde. They claimed that the aldehyde group (e.g., formaldehyde and benzaldehyde) was critical for the formation of concave Pd NCs, and the percentage of (110) of the NCs could be tuned by altering the amount of formaldehyde and the reaction temperature (Fig. 30f–i).334
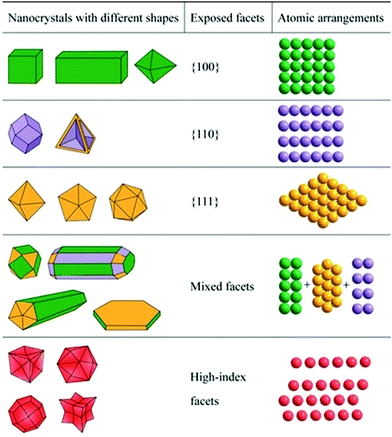 |
| Fig. 29 Typical Pd NCs with different shapes reported in the literature. Reprinted with permission from ref. 112. | |
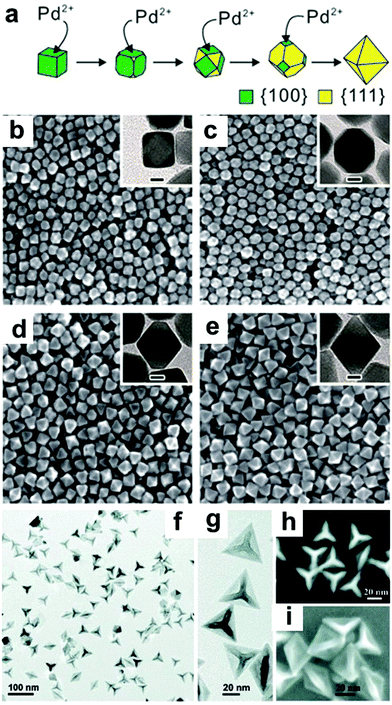 |
| Fig. 30 (a) Schematic illustration of how continuous growth on the (100) planes eventually leads to the transformation of a Pd cube bound by (100) facets into an octahedron enclosed by (111) facets, and (b–e) SEM images of Pd polyhedrons obtained by controlling the amount of Na2PdCl4 added to the reaction solution: (b) 5.8 mg, (c) 8.7 mg, (d) 17.4 mg, and (e) 29.0 mg. TEM images of the Pd polyhedrons are given in the insets (scale bars: 10 nm). The scale bars in (b–e) are 50 nm. Reprinted with permission from ref. 332. (f) Large-area and (g) enlarged TEM, (h) HAADF-STEM, and (i) SEM images of as-synthesized concave Pd NCs. Reprinted with permission from ref. 334. | |
Synthesis of 3-D Pd nanocomposites.
Pd–Au bimetallic NCs have recently attracted significant attention in heterogeneous catalysis due to their excellent catalytic performances. Accordingly, tremendous effort has been devoted to the controllable synthesis of Pd–Au bimetallic NCs with tailored shapes and sizes over the past decades. Generally, three major methods have been reported for the synthesis of Pd–Au bimetallic NCs, including seeded growth, template-assisted synthesis and one-pot synthesis.335 The seeded growth method has been regarded as an efficient and flexible strategy for the preparation of Pd–Au bimetallic NCs, in which the effect of the complicated nucleation process does not need to be considered. The final morphology of the NCs is determined by thermodynamic and kinetic parameters. Seeded growth methods have been widely used for the synthesis of different-shaped Pd–Au bimetallic NCs since Au seeds can be obtained easily. Li et al. reported that when spherical Au seeds were used, a number of morphologies including octahedrons, rectangular bars, cubes, and dendrites could be obtained.336 It has been reported that the final shapes of Pd–Au NCs are strongly related to the morphologies of the Au seeds. For example, Yang and co-workers prepared Au@Pd octahedrons, truncated octahedrons, cuboctahedrons and truncated cubes using octahedral Au seeds (Fig. 31a–e).337 Subsequently, chemists realized that kinetic control enabled the formation of NCs enclosed by high-index facets. Generally, the reduction kinetics can be controlled by changing the precursor concentration, reaction temperature, reducing agents and capping agents. Lee and co-workers demonstrated the synthesis of trioctahedral (TOH), hexoctahedral (HOH) and THH Au@Pd NCs using TOH Au seeds, in which the growth kinetics was tuned by altering the Pd/Au atomic ratio or the amount of introduced NaBr (Fig. 31f–i).338 In the growth solution with a low Pd/Au atomic ratio, Pd prefers to form a TOH shell via a layer-by-layer mode due to the template effect of Au seeds. With an increase in the Pd/Au ratio, the reduction kinetics becomes fast, leading to a fast growth rate in the 〈110〉 direction to form TOH NCs. Moreover, THH NCs will be obtained at much faster reduction kinetics.
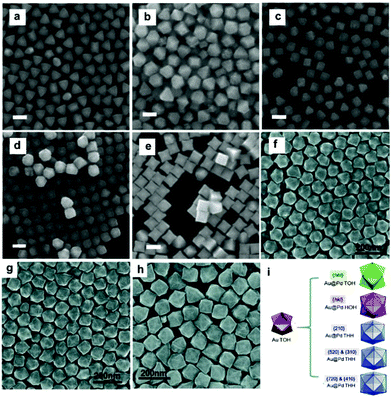 |
| Fig. 31 SEM images of the synthesized Au@Pd core@shell NCs with (a) octahedral, (b) truncated octahedral, (c) cuboctahedral, (d) truncated cubic, and (e) concave cubic shapes. All scale bars are 100 nm. Reprinted with permission from ref. 337. (f) SEM images of TOH Au@Pd NCs, (g) HOH Au@Pd NCs, and (h) THH Au@Pd NCs. (i) Schematic illustration of the reaction regions that form Au@Pd NCs with different polyhedral shapes and different high-index facets. Reprinted with permission from ref. 338. | |
The template-assisted method involves the epitaxial growth process. Generally, Au NCs with different shapes are used as a template, on which Pd atoms gradually grow to form Pd–Au NCs. Wang and co-workers prepared two types of Au@Pd NCs (e.g., TOH and THH) with high-index facets exposed through template synthesis, as shown in Fig. 32.339 Comparing the abovementioned two methods, one-pot synthesis is much more complicated since it needs precise control of the co-reduction of two different precursors. Lee et al. demonstrated the synthesis of Au@Pd octahedrons through the co-reduction of HAuCl4 and H2PdCl4 in the presence of CTAC.340 It was shown that CTAC was a weak reducing agent, and the final shape was controlled by thermodynamics. Consequently, the reaction was finished within 48 h, and Au@Pd octahedrons with low energy (111) facets were formed. In addition, Au@Pd NCs with high-index facets were prepared via a one-pot synthesis, such as truncated HOH Au@Pd NCs.341 Br− ions were added to the growth solution to form AuBr4− to control the reduction kinetics. It should be noted that the shape control and evolution of Pd–Au NCs have been well studied; however, it is still challenging to completely understand the detailed mechanism of this process.335
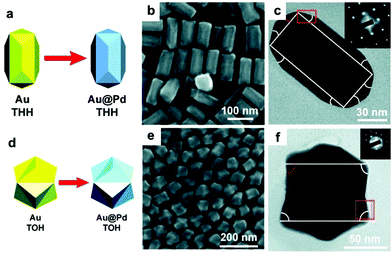 |
| Fig. 32 (a) Schematic showing the growth of THH Au@Pd core@shell NCs from THH Au NCs, (b) SEM image, (c) TEM image of a single core@shell NC viewed along the [00−1] axis. Inset: SAED pattern recorded on the NC, (d) schematic showing the growth of TOH Au@Pd core@shell NCs from TOH Au NCs, (e) SEM image, and (f) TEM image of a single Au@Pd core@shell NC viewed along the [−110] axis. Inset: SAED pattern recorded on the NC. Reprinted with permission from ref. 339. | |
Other metals have also been reported to composite with Pd NCs. Wang et al. demonstrated the synthesis of bimetallic Pd–Ni hollow nanoparticles via a modified galvanic replacement method using Ni nanoparticles as sacrificial templates in an aqueous medium. The Ni nanoparticles were synthesized via the re-reduction of NiCl2·6H2O by NaBH4 in the presence of sodium citrate. Afterwards, H2PdCl4 was added dropwise to the Ni particle/colloid for another 2 h to obtain Pd–Ni bimetallic nanoparticles (Fig. 33a).342 Fu and co-workers synthesized bimetallic Pd–Ag alloy networks on a large scale using a rapid and aqueous solution method at room temperature. Briefly, Pd(NO3)2·xH2O and AgNO3 were used as precursors, and NaBH4 solution was used the reducing agent.343 Luo et al. prepared concave Pd–Ag bimetallic NCs by introducing a Pd precursor (e.g., Na2PdCl4) in an aqueous suspension of Ag nanocubes in the presence of CTAC (Fig. 33b and c).344 A plausible mechanism was proposed. As illustrated in Fig. 33d, the Cl− ions from CTAC could preferentially bind to the (100) facets on the Ag nanocubes, making them more susceptible to oxidation and etching. On the other hand, Pd atoms grew on the Pd cubes through the galvanic replacement reaction to form concave NCs. Zhang et al. reported the fabrication of echinus-like Pd–Cu NCs via a one-step and template-free method. Experimentally, KBr and Pluronic F127 were first dissolved in distilled water. Subsequently, a certain amount of Na2PdCl4, CuCl2, HCl, and AA was added successively to the above solution at 90 °C for 2 h.345 Zhang et al. synthesized concave Pd–Cu NCs via a one-pot method, in which an Na2PdCl4 and CuCl2·2H2O solution was added to a mixture of PVP, decylamine, glucose and DMF (Fig. 33e).346 Li and co-workers synthesized Pd–Cu2O hybrid nanoconcaves via a seeded growth method. In the first step, octadecahedral Cu2O seeds were prepared and dispersed in hexane, which was added to a solution of Pd(acac)2 in 1-octadecene and oleylamine (Fig. 33f). Afterwards, the mixture was heated at 90 °C under agitation to evaporate the hexane, followed by a growth process in a capped 25 mL vial at 120 °C for 24 h.347 Xie et al. demonstrated the synthesis of Pd–Rh concave nanocubes via the site-specific overgrowth of Rh on Pd cubic seeds, as presented in Fig. 33g. It was shown that Pd could be etched in an acidic aqueous solution to generate Rh nanoframes.348
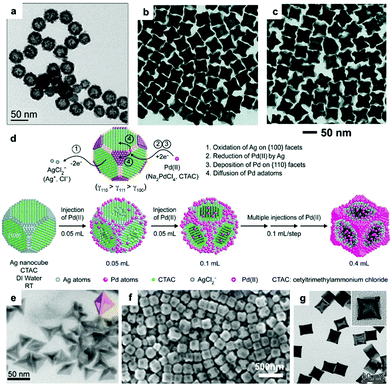 |
| Fig. 33 (a) TEM image of the hollow Pd–Ni NCs. Reprinted with permission from ref. 342. TEM images of concave NCs prepared by reacting Ag nanocubes with different volumes of Pd(II) precursor solution: (b) 0.3 mL and (c) 0.4 mL in the presence of CTAC. (d) Schematic illustration of the proposed mechanism for the oxidation of Ag on the (100) facets of a CTAC-capped Ag nanocube, the reduction of Pd(II) by Ag to generate Pd atoms for their deposition on the (110) facets, and the diffusion of the Pd atoms across the surface. (bottom) Illustration of the transformation of an Ag nanocube into an Ag–Pd nanocube and two subsequent concave NCs with different concavities on the side faces of the nanocubes with different volumes of Pd(II) precursor in the presence of CTAC. Reprinted with permission from ref. 344. (e) TEM image of the concave Pd–Cu NCs. Reprinted with permission from ref. 346. (f) SEM image of Pd–Cu2O nanoconcaves. Reprinted with permission from ref. 347. (g) TEM image of the Pd@Rh core@frame concave nanocubes. Reprinted with permission from ref. 348. | |
2.3.3 Synthesis of 3-D Rh-based NCs.
Synthesis of 3-D Rh NCs.
Rh has been widely used as a catalyst for a variety of chemical transformation processes. Thus, the shape control of Rh NCs offers an effective way to investigate the correlation between their catalytic performance and surface atomic structure.349 It is well known that the shape of Rh NCs is strongly related to the capping agents, reduction kinetics, etc.349 With the development of nanoscience, several protocols have been developed for the synthesis of Rh NCs. Zhang and co-workers synthesized Rh nanocubes with a mean size of 10 nm via a seedless polyol method. Their mechanism studies showed that the Br− ions from trimethyl(tetradecyl)ammonium bromide (TTAB) could selectively adsorb on the (100) faces, resulting in the formation of Rh nanocubes with (100) facets.350 Kim et al. demonstrated the synthesis of different-shaped Rh nanostructures including nanotetrahedrons, nanotetrapods, and hierarchical dendrites via a so-called assembly strategy.351 In the typical synthesis of Rh nanotetrahedrons, a solution of Rh(acac)3, 1,2-hexadecanediol, and stearic acid in 1-octadecene was placed in a flask under vacuum for 25 min at 100 °C under stirring, followed by heating to 245 °C at a rate of 5 °C min−1 in an O2/Ar flow. They claimed that O2 could oxidize the unstable side products (e.g., Rh nanoplates) into Rh ions (Fig. 34a–h). Chen et al. prepared Rh NCs with high-index facets via an oxidative etching process (Fig. 34i–l). HCl could etch the Rh NCs at 200 °C under hydrothermal conditions through two half-reactions: anode dissolution of Rh and cathode reduction of H+ ions. With an increase in the HCl concentration, the hydrogen electrode potential became more positive, leading to an increase in the dissolved corrosion rate of Rh simultaneously.352 Xie and co-workers etched Pd from Pd–Rh nanocubes with an Fe3+/Br− pair in the presence of HCl.287 The addition of HCl aimed to avoid the formation of insoluble Fe(OH)2. Consequently, cubic Rh nanoframes with a unique open structure were obtained after Pd etching. In addition to the chemical etching method, the solvothermal method has also been employed to synthesize Rh NCs with tunable sizes and shapes.292 Zhang et al. recently demonstrated the synthesis of different-shaped Rh NCs in the presence of oleylamine and 1-octadecene. It was shown that the morphology evolved from tetrahedron to concave tetrahedron, and to nanosheet when the volume ratios of oleylamine to 1-octadecene were changed (Fig. 34m–p).353
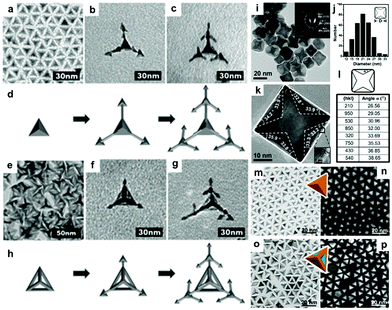 |
| Fig. 34 TEM images and schematic diagram of hierarchical Rh dendritic nanostructure (a–c) grown from a nanopyramid core and (e–g) grown from a nanoframe core. (d and h) Expanded schematic view of the nanodendrite with pertinent structural parameters. Reprinted with permission from ref. 351. (i) TEM image of Rh concave nanocubes. Inset: SAED pattern. (j) Size distribution of Rh concave nanocubes. (k) HRTEM image of an individual Rh concave nanocube projected along the [100] zone axis. The angles (α) between the concave facets and the (100) facets are marked. (l) Model of concave nanocube projected along the [100] zone axis and a table showing the calculated values for the angle α when the concave nanocube is bound by different high-index crystallographic facets. Reprinted with permission from ref. 352. Morphological and structural characterizations for (m and n) Rh tetrahedrons to (o and p) concave tetrahedrons. Reprinted with permission from ref. 353. | |
Synthesis of 3-D Rh-based nanocomposites.
Sneed and co-workers reported the synthesis of Rh–Pd nanoboxes through the control of metal migration in core@shell nanoparticles (Fig. 35a–h). They proposed that Pd atoms or ions could migrate from the particle cores via the small gaps between the Rh islands in the shell, which was further accelerated by Br− from CTAB in the growth solution.354 Similar Rh–Pd nanostructures were obtained by Ye et al. via the selective removal of the Pd cores from different Pd–Rh nanocubes. It was shown that HCHO played a vital role during the synthesis since it could alter the reaction kinetics and the growth behavior of Pd and Rh, leading to the formation of different nanocubes, which determined the following formation of hollow nanostructures, nanoframes or nanoboxes.355 Wang et al. demonstrated the one-pot shape-selective synthesis of Pd–Rh NCs with tunable compositions and morphologies, including hollow nanocubes, nanoicosahedrons, and truncated octahedrons via a facile hydrothermal approach (Fig. 35j–m). In this process, PVP was used as both the reductant and capping agent and halide anions (Br−/I−) as the shape control agents.356 Zhang et al. reported the synthesis of Ag@Rh core@frame nanocubes via the galvanic replacement reaction between Rh(III) and Ag nanocubes.357 Initially, the Rh atoms tended to nucleate and deposit at the edges of the Ag nanocubes when the amount of Rh(III) precursor was relatively low. With an increase in the amount of Rh(III) precursor, the galvanic replacement reaction between Rh(III) and the Ag nanocubes occurred to form Ag–Rh core-frame nanocubes (Fig. 35n–q). In addition to the abovementioned nanostructures, Rh–Pt nanocubes have also been prepared to improve the catalytic performance of Rh NCs.217,358,359
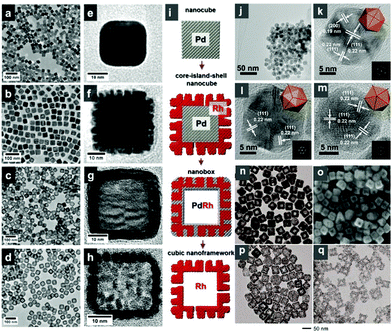 |
| Fig. 35 TEM images of (a and e) Pd nanocubes, (b and f) Pd@Rh core@island shell nanocubes, (c and g) Pd–Rh nanoboxes, and (d and h) Rh cubic nanoframeworks. Scheme in (i) shows models for the structural evolution from Pd nanocube to Rh cubic NCs. Reprinted with permission from ref. 354. (j) TEM image and (k–m) HRTEM images (insets are corresponding FFT patterns and geometrical models with 2-, 3-, and 5-fold symmetries, respectively). Reprinted with permission from ref. 356. (n) TEM and (o) SEM images of Ag–Rh hollow nanocubes. TEM images of (p) Ag–Rh nanoboxes and (q) Rh nanoboxes with highly porous walls. The Ag–Rh hollow nanocubes were prepared via the titration of 0.3 mL of Na3RhCl6 solution. The Ag–Rh and Rh nanoboxes were obtained by etching the Ag–Rh hollow nanocubes with H2O2 and Fe(NO3)3, respectively. Reprinted with permission from ref. 357. | |
2.3.4 Synthesis of other 3-D metal NCs.
Lee et al. synthesized concave rhombic dodecahedron Au NCs via a seeded growth method in the presence of 4-aminothiophenol (4-ATP). The obtained 3-D Au NCs were enclosed by stabilized facets of (331), (221), and (553). The mechanism studies revealed that the formation of Au–S between 4-ATP and Au NCs and the aromatic geometry of 4-ATP resulted in the excellent stability of the concave Au NCs even after rigorous electrochemical reactions.360 Moreover, the galvanic replacement reaction has also been used for the synthesis of Au NCs, in which Ag was used as the sacrificial seeds. Xia and co-workers described a method for the synthesis of Au nanocubes via the galvanic replacement reaction. In the first step, Ag nanocubes were prepared via the reduction of Ag(I) by ethylene glycol in the presence of PVP and a trace amount of Na2S, which served as sacrificial templates for the preparation of Au nanocages.361
To improve the stability and the catalytic performance of Au NCs, they are generally composited with other metals to form alloys or intermetallic compounds. Ma et al. reported the synthesis of Au–Ag core–shell nanocubes with edge lengths in the range of 13.4–50 nm via a seeded method, in which spherical single-crystal Au nanocrystals (11 nm), ascorbic acid, and CTAC were used as the seeds, reductant, and capping agent, respectively.362 Lu et al. developed a method for the synthesis of Au–Pd core–shell heterostructures with an unusual tetrahexahedral (THH) morphology enclosed by (730) facets using Au nanocubes as the structure-directing cores (Fig. 36).363 It was shown that the lattice mismatch between Au and Pd, chloride, oxygen, CTAC, and reaction temperature were the key factors for the formation of the THH core–shell nanocrystals. Consequently, the composite NCs exhibited a significantly enhanced catalytic performance toward the reduction of CO2. More information on the controllable synthesis of Au–Pd NCs was well summarized by Zhang et al.335 Other elements, such as Ni364 and Cu,365 have also been used to composite with Au to improve its stability.
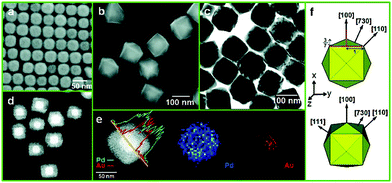 |
| Fig. 36 (a) SEM images of the cubic Au nanocrystals used as the cores. (b and c) SEM and TEM images of the THH Au–Pd core–shell nanocrystals. (d) HAADF-STEM image of the THH Au–Pd core–shell nanocrystals. (e) EDS line scan and elemental mapping image of a THH Au–Pd core–shell nanocrystal. (f) Schematic drawing of a THH nanocrystal viewed from different angles. The axes projecting along the [100], [110], [111], and [730] directions are also shown. Reprinted with permission from ref. 363. | |
2.4 Shape evolution of metal NCs
The final morphology of metal NCs is determined by many factors, such as the capping agent, reducing agent, reaction temperature, and kinetics. Therefore, changes in these parameters during the growth of metal NCs will lead to significant changes in the morphology of NCs. Specifically, the evolution of the morphology of metal NCs is determined by thermodynamics and kinetics in the steps of nucleation and growth. Langille et al. studied the roles of Ag+ and halides (Cl−, Br−, and I−) in the seed-mediated synthesis of Au NCs.366 They claimed that halides could adjust the reduction potential of Au3+ in solution and passivated the surface of Au NCs, leading to the control of growth kinetics, and thus the formation of Au NCs with different shapes. Moreover, Ag+ could be used as an underpotential deposition (UPD) agent to access a different set of particle shapes by controlling the growth of the resulting gold nanoparticles through surface passivation (Fig. 37). Xia and co-workers summarized the reaction pathway for the synthesis of metal NCs.367,368 During the nucleation process, the seeds may take a single-crystal, singly twinned, multiply twinned structure, or plate form. The inherent structures of seeds may lead to the growth of different seeds (Fig. 38). Generally, from single-crystal seeds, growth along the (111) and (100) will lead to the production of cubes, octahedrons, and cuboctahedrons,369 while the uniaxial growth of cuboctahedral and cubic seeds will result in the formation of octagonal rods and rectangular bars, respectively.368 Moreover, right bipyramids and nanobeams will be produced from singly twinned seeds,370,371 and icosahedrons, decahedrons, and pentagonal nanorods can be produced from multiply twinned seeds.229,372,373 Additionally, plates will be obtained when the seeds contain stacking faults.368
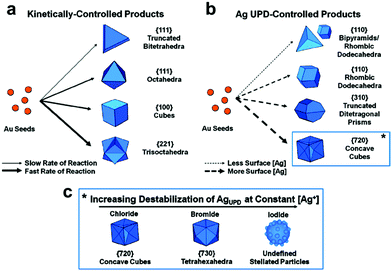 |
| Fig. 37 Scheme illustrating how halides and silver ions can be used to direct the growth of gold seeds in different growth pathways to yield different shaped products: (a) kinetically controlled products in the absence of silver ions; (b) Ag underpotential deposition-controlled products, where the interactions of silver with the particle surface dictate the product shape; and (c) effect of varying the stability of the Ag UPD layer with high concentrations of chloride, bromide, or iodide in the growth solution, yielding concave cubes, tetrahexahedra, and stellated particles, respectively. Reprinted with permission from ref. 366. | |
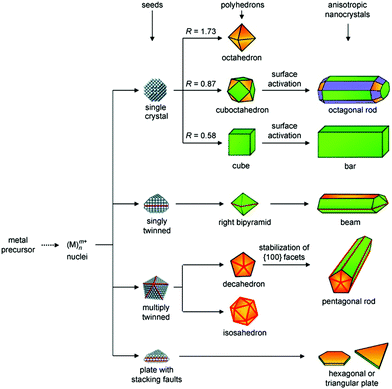 |
| Fig. 38 Schematic illustration of the reaction pathways that lead to Pd nanostructures with different shapes. Briefly, a palladium precursor is reduced to produce Pd atoms, which subsequently aggregate to form nuclei. Once the nuclei have grown past a certain size, they become seeds with a single-crystal, single-twinned, or multiple-twinned structure. If stacking faults are involved, the seeds will grow into plate-like nano-structures. The green, orange, and purple colors represent the (100), (111), and (110) facets, respectively. Twin planes are delineated in the figure with red lines. The parameter R is defined as the ratio between the growth rates along the 〈100〉 and 〈111〉 axes. Reprinted with permission from ref. 368. | |
3. Metal oxide NCs
Metal oxide NCs have attracted significant attention because of their outstanding structural flexibility combined with excellent properties and wide applications in diverse fields including piezoelectricity, chemical sensing, photodetection and catalysis. Compared to their bulk materials, metal oxide NCs may possess other unique properties associated with their highly anisotropic geometry and size confinement. Specifically, the “nano-effects” of NCs will lead to a variety of surface oxidation states, coordination numbers, symmetry, crystal-field stabilization, density, stoichiometry and acid–base surface properties, resulting in the significant electronic properties and crystal structures of metal oxides.374 Over the past decades, tremendous effort has been devoted to the development of metal oxide NCs. It has been well realized that metal oxide NCs exhibit significantly enhanced catalytic performances. For example, Zhou et al. reported that CeO2 nanorods exhibited much higher activity than their nanoparticle counterparts in the CO oxidation reaction.375 Xie and co-workers also demonstrated that Co3O4 nanorods with (110) planes favored the CO oxidation reaction at low temperature.376 Considering the wide variety of applications of metal oxide NCs, here, we focus on the design of metal oxide NCs for promoting their catalytic performance.
3.1 One-dimensional (1-D) oxide NCs
3.1.1 Synthesis of 1-D titanium oxide NCs.
There are four main polymorphs of TiO2 in nature, including anatase (tetragonal, space group I41/amd), rutile (tetragonal, space group P42/mnm), brookite (orthorhombic, space group Pbca), and TiO2(B) (monoclinic, space group C2/m).377 As an n-type semiconductor, TiO2 has been widely used in photocatalysis.378 The sol–gel method has also been widely used to prepare 1-D TiO2 NCs.379–381 Yun and co-workers reported the synthesis of TiO2 nanorods via the sol–gel method. Titanium tetraisopropoxide was added to an aqueous solution of triethanolamine. Afterwards, the resulting turbid white solution gradually turned transparent light yellow, followed by the addition of oleic acid, diethylamine, and diethylenetriamine aqueous solution to synthesize spherical and ellipsoidal TiO2 nanoparticles, respectively. Finally, the mixtures were added to Pyrex bottles and heated at 100 °C for 24 h, and then transferred to a Teflon-lined autoclave and heated at 250 °C for 72 h.382 Solvothermal methods are the most common and important methods for the synthesis of 1-D TiO2 NCs.383–388 Nian demonstrated the formation of single-crystalline anatase nanorods with a specific crystal-elongation direction through the hydrothermal treatment of titanate nanotube suspensions in an acidic environment. Before the hydrothermal treatment, the nanotube suspensions were prepared via treatment of TiO2 in NaOH, followed by mixing with HNO3 to achieve different pH values.389 Tahir et al. prepared monocrystalline rutile TiO2 nanorods via hydrothermal treatment at 150 °C using an aqueous TiCl4 solution under acidic conditions in the presence of dopamine.390 Yu et al. demonstrated the large-scale synthesis of single-crystalline anatase TiO2 nanorods via the hydrothermal treatment of H-titanate fibers. In this process, the pH value played an important role in the control of the shape and crystal structures.391 Liu reported a facile hydrothermal method for the growth of oriented single-crystalline rutile TiO2 nanorod films on transparent conductive fluorine-doped tin oxide (FTO) substrates (Fig. 39).392 It was shown that the epitaxial relation between the FTO substrate and rutile TiO2 with a small lattice mismatch played a key role in driving the nucleation and growth of the rutile TiO2 nanorods on FTO, and the sizes of the nanorods could be tuned by altering the parameters including growth time, temperature, reactant concentration, acidity, and additives. Bryan et al. demonstrated the preparation of Co2+- and Cr3+-doped TiO2 nanorods and NCs via a low-temperature hydrolytic route, which employed cobalt(II) acetate tetrahydrate and titanium(IV) tetraisopropoxide in the presence of trimethylamine N-oxide dehydrate and oleic acid.393 It has reported that AAO can be used as a hard template for the preparation of TiO2 nanorods, and the diameter of the TiO2 nanorods can be well controlled by tuning the pore size of AAO.394–396 In general, AAO is immersed into the sol solution of precursors, followed by high temperature treatment. TiO2 nanorods are obtained when AAO is removed in H3PO4 aqueous solution. The crystalline structure of the as-prepared TiO2 nanorods can be controlled by altering the calcination temperature. For example, a low temperature will lead to the formation of anatase TiO2 nanorods, while a high temperature favors the formation of rutile nanorods.
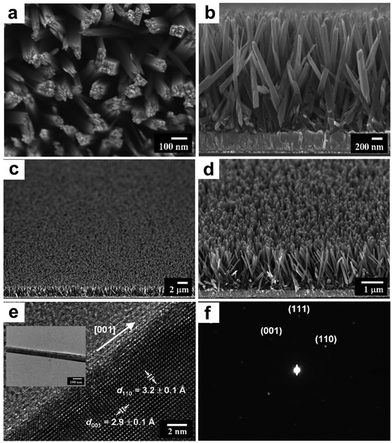 |
| Fig. 39 FESEM images of oriented rutile TiO2 nanorod film grown on FTO substrate. (a) Top view, (b) cross-sectional view, and (c and d) tilted cross-sectional views. (e) HRTEM image and SAED pattern of a single TiO2 nanorod shown in the inset of (f). Reprinted with permission from ref. 392. | |
TiO2 nanotubes are also important 1-D NCs with unique electronic properties including high electron mobility, high specific surface area, and high mechanical strength.397–401 Tian and co-workers reported the synthesis of large arrays of oriented TiO2-based nanotubes and continuous films via a one-pot protocol. Initially, a TiO2 suspension was prepared by dispersing P25 powder in water. Secondly, a titanium foil with TiO2 nanoparticles, which obtained through dip coating from the TiO2 suspension, reacted with an alkaline solution (NaOH) in a sealed Teflon reactor. Thirdly, the Ti foil was removed, and the products were soaked and washed with H2O, and dried in air.402 Anodization is widely employed for the preparation of regular TiO2 nanotubes.403–406 For instance, Albu et al. demonstrated the formation of free-standing TiO2 nanotubes via a three-step process: (1) preparation of a TiO2 nanotubular layer on Ti foil with a high aspect ratio; (2) selective dissolution of the metallic substrate; and (3) opening of the closed tube bottom by selective chemical etching. The TiO2 array consisted of regular tubes with a diameter of 160 ± 30 nm and a wall thickness of 20 ± 5 nm (Fig. 40a and b).407 Similarly, Jennings synthesized TiO2 nanotubes via anodization on 2.5 cm × 1.5 cm × 125 μm pieces of titanium foil (99.6% purity, Advent) in a nonaqueous fluoride-containing electrolyte (Fig. 40c and d).408 Macak et al. reported that a highly viscous glycerol electrolyte could suppress local concentration fluctuations and changes in pH during the anodization of titanium, leading to the formation of layers of smooth TiO2 nanotubes up to 7 μm thick with an average pore diameter of 40 nm (Fig. 40e).409 In another work by Macak et al., they synthesized TiO2 nanotubes by directly immersing a Cu clip into an electrolyte, which consisted of H2SO4/HF, Na2SO4/NaF and 1,2,3-propanetriol/NH4F. The size of the TiO2 nanotubes ranged from 500 nm to 4.5 μm.410 Kuang et al. synthesized highly ordered TiO2 nanotube arrays with a length of 5–14 μm via the electrochemical anodization of Ti foil.404 Sun and co-workers synthesized highly ordered TiO2 nanotube films via anodic oxidation in an NH4F organic electrolyte (Fig. 40f).411 Prior to anodization, the Ti foils were cleaned with ethanol and deionized water, followed by immersing the cleaned Ti foils into a 0.05% NH4F solution (in EG), and then they were subjected to a constant 60 V anodic potential for 20 h at room temperature in a two-electrode electrochemical cell connected to a DC power supply. After rinsing with deionized water and drying under N2, the obtained TiO2 nanotube arrays were annealed at 450 °C for 2 h with heating and cooling rates of 10 °C min−1 in O2. In addition, Perera et al. reported the synthesis of TiO2 nanotube/reduced graphene oxide composites via an alkaline hydrothermal process. They added TiO2 (P90) powder to a graphene oxide suspension under stirring for 1 h to ensure complete mixing. Subsequently, NaOH was added to the above system, and the mixture was transferred to a Teflon-lined autoclave. The hydrothermal process was performed at 120 °C for 24 h. The as-obtained TiO2 nanotubes with a small diameter of 9 nm exhibited promising activity towards the photocatalytic degradation of malachite green.412
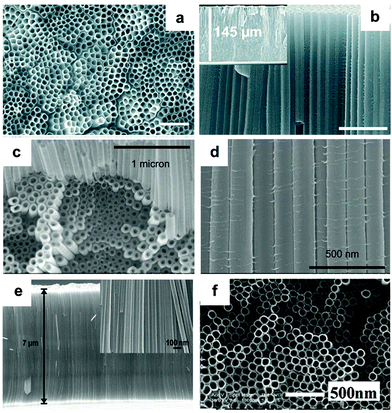 |
| Fig. 40 SEM images of the TiO2 nanotube layer obtained via anodization, (a) top view and (b) side view. Scale bar: 1 μm. Reprinted with permission from ref. 407. (c and d) Cross-section and oblique SEM images of TiO2 nanotube arrays used to fabricate dye-sensitized cells. Reprinted with permission from ref. 408. (e) Smooth TiO2 nanotubes 7 μm long produced in glycerol electrolyte with 0.5 wt% NH4F. The inset shows the walls of the nanotubes. Reprinted with permission from ref. 409. (f) Typical top view SEM image of the TiO2 nanotube array film. Reprinted with permission from ref. 411. | |
3.1.2 Synthesis of 1-D cerium oxide NCs.
CeO2 is one of the most important catalysts, which has recently attracted great attention in heterogeneous catalysis due to its high oxygen storage capacity (CeO2 → CeO2−x + 1/2O2). Numerous studies have shown that the oxygen vacancies in CeO2 can significantly promote the catalytic performance. Consequently, CeO2 has been widely used as a support, promoter and co-catalyst in industrial catalytic processes. A variety of shaped CeO2 NCs, such as CeO2 nanorods, CeO2 nanowires, CeO2 nanotubes, and CeO2 nanocubes have been synthesized, which have greatly prompted their application in catalysis.
1-D CeO2 nanorods are generally prepared via the hydrothermal method since this surfactant-free method can provide CeO2 nanorods with a clean surface for investigating their catalytic activity and mechanism.375,413–418 NaOH can also be used to synthesize CeO2 nanorods in the hydrothermal method. Liyanage and co-workers synthesized Y-doped CeO2 nanorods via the hydrothermal method, in which NaOH was used as a precipitant.418 Liu et al. mixed a CeCl3 aqueous solution with an NaOH aqueous solution under vigorous stirring. Subsequently, the mixed solution was transferred to a Teflon-lined stainless autoclave at 130 °C for 18 h.419 Mai and co-workers also used NaOH as a precipitant for the synthesis of CeO2 nanorods via the hydrothermal method.420 Yan et al. demonstrated the synthesis of uniform single-crystalline CeO2 nanorods via a hydrothermal process using Ce(NO3)3·6H2O and Na3PO4·6H2O as the cerium source and mineralizer, respectively. By altering the hydrothermal treatment time, the morphology of the CeO2 NCs evolved from nano-octahedrons to nanorods. Different from the reported cases using a strong base as the precipitant, such as NaOH, KOH and other organic alkalis, the use of Na3PO4 does not leave impurities in the hydrothermal reaction system and makes this process very simple to obtain and separate CeO2 nanorods.421 Ji and co-workers used a similar hydrothermal method for the synthesis of CeO2 nanorods. An aqueous solution of CeCl3·7H2O was vigorously mixed with Na3PO4 solution and then transferred to a Teflon-lined stainless-steel autoclave. Moreover, the as-prepared CeO2 nanorods were used as seeds to enable the growth of nanorods in length, but had a negligible influence on their diameter (Fig. 41).422 Bai and co-workers recently demonstrated the synthesis of CeO2 nanowires via a simple hydrothermal reaction by adding cerium chloride, sodium oleate, deionized water, and n-butylamine to a stainless reactor.423 The obtained CeO2 nanowires with a mean diameter of 6 nm and length of 300 nm can be used as an excellent support for Rh single atoms (SAs) due to the abundant vacancies on their surface.
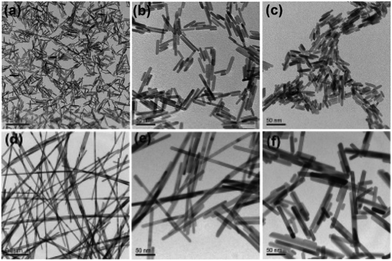 |
| Fig. 41 TEM images of CeO2 nanorods obtained from (a–c) primary and (d–f) secondary synthesis. When CeO2 nanorods obtained from primary synthesis using (a) 0.1 M, (b) 0.2 M, and (c) 0.4 M CeCl3 were used as seed crystals in a secondary hydrothermal treatment, CeO2 (d) nanowires and (e and f) nanorods were obtained, respectively. Both the primary and secondary syntheses were conducted at 220 °C. Reprinted with permission from ref. 422. | |
Soft template-assisted methods have also been reported for the synthesis of CeO2 nanorods. Vantomme and co-workers used CTAB as a surfactant for the preparation of CeO2 nanorods.424 Typically, this surfactant and CeCl3·7H2O with a molar ratio of 0.33 were dissolved in H2SO4 aqueous solution (pH = 2) at 40 °C under stirring for 1 h. Afterwards, 35 mL of ammonia solution (25 wt%) was added dropwise to the mixed solution to obtain a purple precipitation, which was transferring to a Teflon-lined autoclave. The CeO2 nanorods were obtained after hydrothermal treatment at 80 °C for 4 days under static conditions. Sun et al. demonstrated the synthesis of CeO2 nanorods via a solvothermal method using hydrated cerium(III) chloride as the cerium source, octadecylamine as the surfactant, and ethanol/water and ethylenediamine as the co-solvent. By altering the concentration of the precursors, the diameter and length could be tuned in the range of 40–50 nm and 0.3–2 μm, respectively. It was shown that ethylenediamine played a vital role because it acted both as a complexing agent to influence the ions competing in the complex reaction and a basic agent to influence the viscosity and adjust the pH value of the solution.425 In addition, Zhang and co-workers prepared polycrystalline CeO2 nanorods via an ultrasonication method, in which polyethylene glycol (PEG) was used as a structure-directing agent at room temperature. The obtained nanorods possessed a diameter and length in the range of 5–10 nm and 50–150 nm, respectively.426 In a typical synthesis, PEG600 was mixed with Ce(NO3)3 solution (PEG600: 1%) under ultrasonication at room temperature, followed by the addition of a certain amount of NaOH solution with vigorous stirring during ultrasonication for about 1 h. Afterwards, the precipitate was further sonicated for an additional 1 h to obtain the final products. It was shown that ultrasonication was critical for the formation of nanorods, where irregular nanoparticles were obtained without ultrasonication.
Han and co-workers reported the synthesis of well-crystalline CeO2−x nanotubes via a mild hydrothermal reaction route using cerium nitrate and ammonium hydroxide as reactants. More importantly, this hydrothermal method was conducted without high pressure and high temperature.427 Two successive steps were involved in the synthesis. Firstly, Ce(NO3)3·6H2O was added to deionized water and heated to 100 °C, followed by the addition of a certain amount of 5% ammonia hydroxide solution. Secondly, once the yellowish precipitates were formed, the products were aged for 3 min, and quickly cooled at 0 °C.427 Furthermore, Tang et al. produced CeO2 nanotubes through the thermal treatment of Ce(OH)3 nanotubes.428 Firstly, Ce(OH)3 nanotubes were prepared via a standard alkali thermal treatment process in a glove box under oxygen-free conditions as a hard template. In a typical process, anhydrate CeCl3 was added to an aqueous NaOH solution and placed in a Teflon-lined stainless-steel autoclave. Then, the autoclave was sealed and held at 120 °C for 72 h. Secondly, the as-synthesized Ce(OH)3 nanotubes were placed in a quartz tube after evacuation (10−2 Torr). Then, a gas flow of Ar/NH3 (20
:
1) was introduced at a flow rate of 500 sccm and gas pressure of 500 Torr. Finally, the samples were heated to 450 °C for 2 h at a heating rate of 50 °C h−1. Zhou and co-workers reported the formation CeO2 nanotubes with extended cavities via an oxidation–coordination-assisted dissolution process of partially oxidized 1-D Ce(OH)3 as follows:429 (1) 1-D Ce(OH)3 was exposed to air at room temperature for 24 h to partially oxidize Ce(OH)3; and (2) the partially oxidized Ce(OH)3 was dispersed in distilled water and H2O2, and treated under ultrasonication for 2 h. The mechanism studies showed that the partial oxidation of Ce(OH)3 and the addition of H2O2 are essential for the formation of CeO2 nanotubes (e.g., Ce3+ + OH− → Ce(OH)3; Ce(OH)3 + OH− → CeO2 + H2O).
3.1.3 Synthesis of 1-D copper oxide NCs.
Copper oxide has two typical compounds, cuprous oxide (Cu2O) and cupric oxide (CuO). Both of them are p-type semiconductors and used as promising candidate materials for the conversion of solar energy to electrical or chemical energy.374 Compared to Cu2O, CuO has a much a narrow band gap (1.2 eV vs. 2.17 eV), and thus has been widely used as a photocatalyst in many reactions.
Several methods have been reported for the synthesis of 1-D CuO NCs. Chen and co-workers demonstrated the synthesis of CuO nanorods with different surface areas. They simply mixed Cu(NO3)2·3H2O and NaOH in ethanol under stirring in a flask to obtain CuO nanorods. The surface area of the CuO nanorods could be systematically tuned upon further hydrothermal treatment in NaOH solution by altering the temperature in the range of 60–160 °C.430 Liu et al. used another Cu precursor, such as cupric dodecyl sulfate, to react with NaOH at 80 °C for the preparation of CuO nanorods. It was shown that the morphological yield of CuO nanorods was over 95%.431 Chang and co-worked systematically investigated the effects of the reaction parameters on the morphology and size of the CuO NCs. It was shown that single-crystalline CuO nanorods with a selected width of 5–15 nm could be obtained by simply altering the concentration of Cu(NO3)2 at low temperatures and atmospheric pressure. Long CuO nanorods/nanoribbons of up to 1 μm in length were produced via a two-step overgrowth process. A plausible mechanism for the overgrowth was proposed, where short nanorods in the growth solution can self-assemble into a two-dimensional netted structure with (001), (100) and (110) crystal planes.432 Shrestha et al. further verified the effects of the reaction parameters on the size and morphology by comparing three chemical combinations for the hydrothermal synthesis of CuO nanorods, including (1) copper nitrate, lactic acid/sodium hydroxide, (2) copper sulfate/sodium lactate/sodium hydroxide, and (3) copper nitrate/sodium hydroxide.433 Alammar and co-workers reported the ultrasound-assisted synthesis of CuO nanorods in a neat room-temperature ionic liquid (e.g., 1-butyl-3-ethylimidazoliumbis(trifluoromethylsulfonyl)imide).434 Gusain et al. further confirmed that the additional sonication of the as-prepared CuO nanorods with two different ionic liquids (e.g., 1-methylimidazole and tetrabutylammonium acetate) could guide the morphological changes of CuO nanorods with a high aspect ratio.435
Jia et al. demonstrated the direct synthesis of ultrathin CuO nanorods with high-index facets using oleylamine as both the solvent and the surface controller (Fig. 42a–c).436 It was shown that the growth of the CuO nanorods follows a classic oriented attachment mechanism. PEG can also be used as growth-directing agent for the synthesis of CuO nanorods. Chen and co-workers synthesized ultrathin CuO nanorods by adding PEG to a mixture of NaOH and CuCl2 solution (Fig. 42d). The control experiments showed that the length of the CuO nanorods decreased with an increase in the molecular weight of PEG.437 Wang et al. revealed the effects of PEG during the synthesis of CuO nanorods. As a nonionic surfactant, PEG monomer (CH2–CH2–O) can easily form chain structures in aqueous solution, which acts as a soft template for the growth of CuO nanorods.438 In addition to the soft template-assisted method, hard templates have also been employed for the synthesis of CuO nanorods. For instance, Wang et al. synthesized Cu(OH)2 from CuCl2 and NaOH, which was further subjected to calcination at 200–400 °C to obtain CuO nanorods.439 Porous CuO nanorods could be obtained by controlling the calcination temperature. Zhong et al. prepared CuO nanorods from a sacrificial Cu foil via naturally generated electrochemical corrosion. In particular, a wetted Cu foil was partially immersed in KOH solution (1 M) for 7 days. The CuO nanorods grew at the gas–liquid interfaces by sacrificing the Cu foil.440 Zhou and co-workers reported a similar method. Typically, a piece of Cu foil was immersed in a mixed solution of NaOH and (NH4)2S2O8 at 3 °C for serval min. Afterwards, the Cu(OH)2 product was cleaned with water, dried at 100 °C, and finally calcined at 400 °C in an N2 atmosphere to obtain Cu2O nanorods.441 Furthermore, Xia's group reported the synthesis of CuO nanorods through the chemical oxidation of Cu foil, in which the cleaned Cu foil was calcined in air at different temperatures (400–600 °C).442 The results showed that the lateral dimension of the CuO nanowires decreased from ∼100 to ∼30 nm when the calcination temperature was increased from 400 °C to 600 °C (Fig. 42e–g). A similar calcination process has been reported to prepare CuO nanorods.443
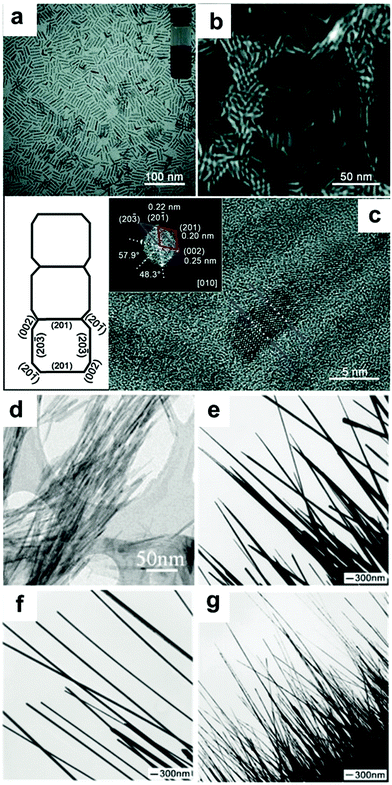 |
| Fig. 42 (a) TEM image and (b) HAADF-STEM image of ultrathin CuO nanorods. The inset in (a) shows a photograph of the as-prepared CuO nanorods dispersed in cyclohexane. (c) Typical HRTEM image of the individual nanorods projected from the [010] direction. The white dashed lines highlight the orientation between two parallel (201) facets. The blue arrows indicate the necking sites. The insets show the FFT patterns and the corresponding simulated two-dimensional shape of a nanorod. Small particles as “building blocks” attach with each other via the (201) facet to form a rod-like structure. Reprinted with permission from ref. 436. (d) TEM image of the CuO nanorods. Reprinted with permission from ref. 437. TEM images of CuO nanowires prepared by heating copper grids in air for 4 h at (e) 400 °C, (f) 500 °C and (g) 600 °C. Reprinted with permission from ref. 442. | |
Other methods such as seeded-mediated growth, solution combustion method, and directional aggregation method have been reported for the preparation of 1-D CuO NCs. Zhang and co-workers demonstrated the growth of a large-scale epitaxial array of CuO nanowires on the surface of a copper nanostructure via a seeded-mediated growth process.444 Yao et al. demonstrated the synthesis of uniform and monodisperse CuO nanorods through the directional aggregation and crystallization of tiny CuO nanoparticles. In this process, two steps are involved, i.e. the synthesis of CuO nanoparticles and aging of CuO nanoparticles to form CuO nanorods. The mechanism studies showed that these Cu nanoclusters were oxidized into CuO primary nanoparticles, which experienced a further self-aggregation and Ostwald ripening process to form CuO nanorods.445 Christy and co-workers reported a solution combustion method using citric acid as fuel for the preparation of CuO nanorods.446 In a typical synthetic process, a stoichiometric amount of citric acid was added to a Cu(NO3)2 aqueous solution. Then, the solution was kept in a furnace at 300 °C. CuO nanorods were obtained via the following chemical equation: Cu(NO3)2 + 0.611C6H8O7 → CuO + N2 + 3.66CO2 + 2.44H2O.
3.1.4 Synthesis of 1-D manganese oxide NCs.
MnO2 has several crystalline forms, such as α-, β-, γ- and δ-type MnO2.447–449 It is an important oxide and has been widely used in the magnetic field, electrochemistry, and catalysis.450–454 Based on the redox reactions of MnO4− and/or Mn2+, several methods have been developed for the synthesis of MnO2 NCs including thermal treatment,455 refluxing,456–458 hydrothermal,459 and sol–gel method.460–465
Li and co-workers synthesized single-crystal MnOOH nanorods with high aspect ratios via a simple hydrothermal using KMnO4 as the Mn precursor in the presence of PVP.466 The dimensions could be tuned by altering the hydrothermal temperature, reaction time and ratio of PVP/KMnO4. Further calcination of the as-prepared MnOOH nanorods led to the formation of MnO2 and Mn2O3 nanorods with high aspect ratios. Similarly, Zhang et al. prepared β-MnO2 nanorods through the thermal decomposition of a template precursor of MnOOH, which was obtained via the hydrothermal treatment of KMnO4 in an aqueous solution.467 Zhang et al. demonstrated a facile route for the synthesis of γ-MnO2 nanorods through the hydrothermal treatment of Mn3O4 nanoparticles, which were prepared by mixing an aqueous solution of MnSO4 and Na2CO3 (Fig. 43a and b).468
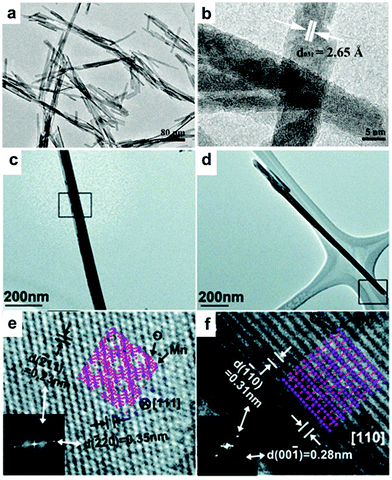 |
| Fig. 43 (a) TEM and (b) HRTEM images of the as-prepared γ-MnO2 nanorods. Reprinted with permission from ref. 468. Low magnification TEM images of a free standing (c) α-MnO2 nanorod and (d) β-MnO2 nanorod. Lattice-resolved HRTEM images of (e) α-MnO2 nanorod and (f) β-MnO2 nanorod. Left bottom inset images in (e and f) are the corresponding FFT patterns. The middle insets in (e and f) simulate the [111] projection of the tetragonal α-MnO2 crystal structure and the [110] projection of the tetragonal β-MnO2 crystal structure, respectively (Mn and O marked as purple and red in color, respectively). Reprinted with permission from ref. 471. | |
Liu and co-workers demonstrated the preparation of β-MnO2 nanorods via a refluxing route using MnSO4·H2O, Na2S2O8 and NaOH as precursors.469 In this process, MnSO4·H2O and Na2S2O8 were dissolved in deionized water, followed by the addition of a certain volume of NaOH aqueous solution under stirring for 30 min until a suspended liquid was formed. Afterwards, the suspended liquid was refluxed at 50 °C for 18 h, then refluxed at 80 °C for 5 h, and finally at 100 °C for 3 h. Wang et al. reported the formation of single-crystalline α-MnO2 nanorods with a diameter of 30–70 nm and length of 2 μm via the hydrothermal reaction of KMnO4 under acidic conditions.470 A plausible mechanism based on Ostwald ripening process was proposed. Firstly, KMnO4 decomposes into MnO2 and O2 in acidic conditions, and hydrothermal treatment may further enhance its decomposition. Secondly, the produced MnO2 colloids tend to form some larger agglomerates, and then small nanorods. When the KMnO4 is consumed completely, the whole system tends to be thermodynamically stable. Thirdly, the amorphous and poorly crystalline components in the agglomerates dissolve again and grow into nanorods through a dissolution–recrystallization process. Su and co-workers prepared α-MnO2 and β-MnO2 nanorods via the hydrothermal method (Fig. 43c–f).471 For the synthesis of α-MnO2 nanorods, 1.5 mmol KMnO4 and 5 mmol concentrated HCl were added to 15 mL deionized water with vigorous stirring until a transparent purple solution was formed, which was transferred to a Teflon-lined stainless steel autoclave and heated to 140 °C for 12 h. For the synthesis of β-MnO2 nanorods, 1 mmol (NH4)2S2O8 and MnSO4·H2O were dissolved in 20 mL deionized water. 0.2 g CTAB as a soft template was added into the solution and heated to 140 °C in a Teflon-lined autoclave for 12 h. Toufiq et al. investigated the effects of the hydrothermal dwell time on the dimensions of MnO2 nanorods.472 It was shown that the diameter of the MnO2 nanorods decreased from 460 nm to 250 nm with an increase in the hydrothermal reaction time from 5 h to 15 h. A plausible mechanism in the hydrothermal method was proposed, which involved two critical processes of oriented attachment and rolling-cum-phase.473 Tang et al. demonstrated a low-temperature sol–gel process associated with different surfactants (e.g., CTAB and PVP) in ethanol solvent for the preparation ultrafine MnO2 nanowires and nanorods. In a typical synthesis, 1.0 g surfactant was dissolved in 80 mL ethanol to form a transparent solution at room temperature, followed by the addition of 5 mL concentrated nitric acid and Mn(OAc)2·4H2O. After the mixture was sealed, vigorous stirring was performed for a few hours until (CH3COO)2Mn was completely dissolved. Finally, the mixed solution was dried at 80 °C to evaporate the solvent for 48 h, and the products were washed with water 5 times, and then dried in an oven at 80 °C overnight.
3.1.5 Synthesis of 1-D vanadium oxide NCs.
Vanadium oxides are well known as active catalysts for many hydrocarbon oxidation reactions. The research on vanadium oxides as catalysts can be dated back to the last century. It has been shown that the surface unsaturated coordinated V species can greatly promote their catalytic activity.474 Generally, vanadium oxides have several different valences, such as VO, V2O3, VO2, and V2O5. It should be noted that phase equilibria in the vanadium-oxygen system are rather complicated, which makes vanadium oxides display complex structural chemistry and structure-dependent catalytic performances.374 Among these oxides, the rutile phase VO2(R) is the most stable structure, and thus has recently attracted much attention.
Over the past decades, several methods have been developed for the synthesis of vanadium oxide NCs. Among them, hydrothermal treatment is one of the most important and common strategies for the preparation of 1-D VO2 nanorods.475–483 For instance, Gui and co-workers reported the synthesis of single-crystal VO2 hydrate nanorods via the hydrothermal reaction of KOH, V2O5, and hydrazine in a sealed autoclave at low temperature. They claimed that hydrazine played a key role in the control of the 1-D morphology.484 Chen et al. fabricated VO2 nanorods by reducing V2O5 with oxalic acid during the hydrothermal process.485 It was found that monoclinic phase VO2(B) was firstly formed and then transformed into the tetragonal VO2(A) phase with an increase in the system temperature or extended reaction time (Fig. 44). A plausible mechanism was proposed. Vanadium pentoxide was firstly dissolved and hydrated to form VO2+ and V10O26(OH)24−, which were further reduced by H2C2O4·2H2O to VO2+ under hydrothermal treatment. When the temperature was increased to 180 °C, VO2(B) nanobelts were formed from the VO2 nuclei through aggregation. Finally, the short VO2(B) nanobelts assembled into VO2(A) nanorods through crystallographic adjustment with an increase in the temperature from 180 °C to 230 °C. Ji et al. synthesized pure phase VO2(R) nanorods via the reduction of V2O5 by oxalic acid during a one-step hydrothermal treatment.476 It was shown that a lower temperature favored the formation of the VO2(B) phase, which gradually changed to the VO2(R) phase with an increase in temperature. They claimed that H2SO4 could affect the zeta potential and the crystallization-dissolution properties of VO2(R) in the solution as a result of the morphology control of the collected products.
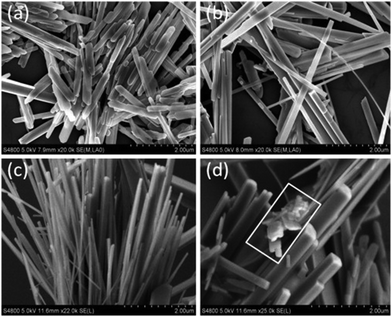 |
| Fig. 44 SEM images of VO2 nanorods formed at different temperatures for 24 h with a filling ratio of 0.4: (a) 180 °C, (b) 210 °C, (c) 230 °C, and (d) 250 °C. Reprinted with permission from ref. 485. | |
V2O5 has been considered as one of the most attractive candidates for cathodes due to its fascinating merits such as abundance, low cost, and extraordinarily high theoretical capacity.486–488 Pinna and co-workers reported the preparation γ-V2O5 nanorods and nanowires via a reverse micelle technique. In a mixture of sodium bis(ethyl-2-hexyl)sulfosuccinate Na(AOT)/isooctane/H2O, the ratio of [H2O]/[AOT] was kept constant at 10. Reverse micelles were formed under these conditions. A solution of alkoxide VO(OR)3 (5 × 10−3 M) with RCH(CH3)2 in isooctane was then rapidly added to the micellar solution. When the reaction time was extended from 24 h to 100 days, the short γ-V2O5 nanorods evolved into long nanowires, as shown in Fig. 45a and b.489 Ostermann et al. demonstrated the synthesis of single-crystal V2O5 nanorods on electrospun rutile nanofibers by carefully calcining composite nanofibers consisting of amorphous V2O5, amorphous TiO2, and PVP (Fig. 45c and d).490 Detailed experiments indicated that the shape and size of the obtained V2O5 nanorods could be controlled by the content of TiO2 and calcination conditions. In the initial stage, the TiO2 networks in the composite fibers favored the formation of small nuclei at low temperature, resulting in the formation of thin and long nanorods. On the other hand, the presence of TiO2 may influence the crystallization and diffusion rates of V2O5 and further promote the growth of V2O5 nanorods. Glushenkov and co-workers demonstrated the preparation of V2O5 nanorods via a solid-state, mass-quantity transformation from V2O5 powder.491 Two steps were involved in the synthetic process, i.e., controlled nanoscale growth from the nanocrystals and ball milling treatment along the [010] direction.
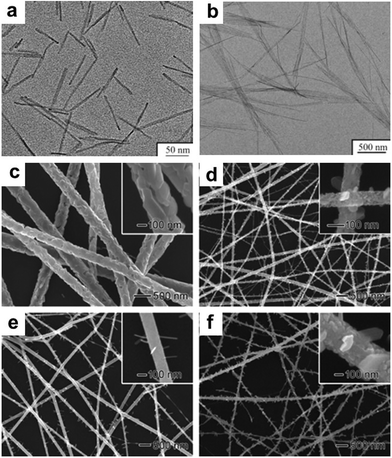 |
| Fig. 45 TEM images of V2O5 nanorods synthesized in reverse micelles observed after (a) 24 h and (b) 100 days. Reprinted with permission from ref. 489 SEM images of V2O5–TiO2 nanofibers prepared by electrospinning from a solution of 2-propanol containing different ratios (r) of VO(OiPr)3 to Ti(OiPr)4 and then calcination at various temperatures (T): (c) r = 1 : 0, T = 475 °C, (d) r = 4 : 1, T = 475 °C, (e) r = 1 : 1, T = 425 °C, and (f) r = 1 : 1, T = 525 °C. Reprinted with permission from ref. 490. | |
3.1.6 Synthesis of 1-D gallium oxide NCs.
Ga2O3 has recently attracted significant attention due to its promising catalytic activity towards alkane dehydrogenation.474 The calcination of gallium oxide hydrate (GaOOH) nanorods is a straightforward strategy for the synthesis of Ga2O3 nanorods. Zhang and co-workers synthesized GaOOH via a facile large-scale hydrothermal process from a mixed solution of GaCl3, H2O and NaOH under suitable pH conditions. After calcination at 900 °C, GaOOH could be transformed into β-Ga2O3 crystals with a similar morphology. In our recent work, GaOOH nanorods were prepared via a hydrothermal process from Ga(NO3)3 and NaOH without any surfactant, which could be further converted into Ga2O3 nanorods after calcination at 600 °C for 2 h.492 It was shown that the length of the GaOOH rods was strongly related to the concentration of NaOH. More specifically, a high concentration of NaOH led to the formation of GaOOH rods with a short length. Kumar et al. synthesized β-Ga2O3 nanorods through the ultrasonic irradiation of molten gallium in warm water to form α-GaOOH. β-Ga2O3 was formed after the calcination of α-GaOOH in air at 600 °C for 3 h.493
Li et al. demonstrated the production of β-Ga2O3 nanorods with diameters in the range of 10–60 nm through a simple gas reaction method.494 In a typical process, a substrate of single-crystal LaAlO3 (8 mm × 8 mm × 0.5 mm) was quickly dipped into a Co(NO3)2 ethanol solution (0.01 M). Then, 2 g of Ga metal and substrate were put in the center of a horizontal quartz tube with a distance of about 6 mm after drying. Afterwards, the quartz tube was evacuated for 30 min, and then heated to 780 °C. Finally, and the quartz tube was ventilated by air at a rate of 26 cm3 min−1. The final Ga2O3 nanorods were collected on the substrate after cooling to room temperature. Shi et al. prepared Ga2O3 nanorods on an Si(111) substrate via magnetron sputtering through ammoniating Ga2O3 thin films.495 It was shown the ammoniating time affected the crystallinity of the Ga2O3 nanorods. Girija and co-workers demonstrated the preparation of pure monoclinic phase of single crystalline β-Ga2O3 nanorods through a facile reflux condensation process.496 In a typical synthetic process, a stoichiometric amount of CTAB was added to Ga(NO3)3 solution under magnetic stirring for 30 min. The solution was heated and refluxed with continuous stirring at 90 °C for 12 h in a two-neck refluxing pot. Afterwards, the reaction system was cooled to room temperature, and the collected white precipitate was washed with ethanol and distilled water. Finally, the product was dried at 100 °C and calcined at 900 °C for 3 h to obtain pure β-Ga2O3 nanorods.
In addition to the above-mentioned 1-D oxide NCs, other 1-D NCs, including ZnO nanorods,497–501 In2O3 nanorods,502–507 SnO2 nanorods,508–517 WO3 nanorods and nanowires,518–523 and ZrO2 nanorods,524–526 have also been synthesized in the literature. However, herein, we are not going to give a detailed review of them due to the following two reasons: (1) these oxides are generally not used as active components but as promoters in catalysis and (2) their synthetic protocols are similar to that of the oxides mentioned in Section 3.1. Thus, readers may refer the corresponding literature for more information.
3.2 Two-dimensional (2-D) oxide NCs
3.2.1 Synthesis of 2-D titanium oxide NCs.
Sofianou and co-workers synthesized anatase TiO2 nanoplates with exposed (001) facets via a solvothermal process.527 In a typical protocol, Ti(C3H7O)4 was dissolved in ethanol under vigorous stirring at room temperature. Subsequently, hydrofluoric acid (HF 40%) was added to the above solution as a capping agent, which was further transferred to a Teflon-lined autoclave. The reaction was operated in an oven at 180 °C for 24 h. The as-synthesized product was collected via centrifugation. Zhang et al. demonstrated a similar hydrothermal method for the synthesis of black hydrogenated/N-doped anatase TiO2 nanoplates with a flower-like hierarchical architecture, which involved two steps of hydrothermal synthesis and hydrogenation.528 In the hydrothermal step, a Ti(OC4H9)4 solution was added dropwise to methanol with vigorous stirring for 30 min. Subsequently, tripolycyanamide was added to the above solution with vigorous stirring for 2 h and subsequent ultrasonication for 20 min. Then, the suspension was transferred to a 50 mL Teflon-lined stainless-steel autoclave and heated to 180 °C for 12 h. In the hydrogenation step, after drying at 60 °C for 3 h, this dry gel was then calcined at 600 °C for 4 h to obtain flower-like hierarchical N-doped TiO2 anatase, which was further subjected to an additional hydrogenation process at 600 °C in a continuous H2 flow (100 mL min−1) for 3 h to obtain the final nanoplates. Sun and co-workers demonstrated a fluorine-free solvothermal synthetic method for the preparation of rhombic TiO2 nanoplates with (010) facets in non-aqueous solvent.529 In this process, tetrabutyl titanate was used as a precursor, and acetic acid and DMF were employed as capping agents. They claimed that carboxylic acids tended to bind on the anatase (001) facets, while amide preferred the (101) facets. Consequently, the selective binding on different facets of TiO2 restricted the crystal growth in the corresponding [001] and [101] direction, leading to the formation of rhombic-shaped TiO2 nanoplates.
Furthermore, Katoch and co-workers demonstrated the fabrication of polyaniline/TiO2 hybrid nanoplates via a sol–gel chemical method by adding TiO2 NCs with a size of 3–5 nm in the process of the chemical polymerization of aniline. It was shown that the morphology evolved from a plate-like structure to an aggregate structure with an increase in the amount of TiO2.530 Song et al. reported the synthesis of 2-D anatase TiO2 hollow nanoplates via a templates-assisted route using α-Fe2O3 nanoplates.531 α-Fe2O3 nanosheets were dispersed in ethanol with sonication for 6 h, followed by the addition of tetrabutyl titanate to the suspension under stirring. After the addition of ammonia solution (28 wt%), the mixture was transferred to an ultrasound bath for 4 h to obtain α-Fe2O3@amorphous TiO2 nanoplates. After washing and drying, these Fe2O3@amorphous TiO2 nanoplates were calcined at different temperatures (350 °C, 450 °C, and 600 °C) in air for 2 h at a heating rate of 1 °C min−1 to promote the crystallization of the TiO2 nanoplates. Hu and co-workers prepared NH4TiOF3 nanoplates with a thickness of 100 nm via a solvent-free low-heating solid-state chemical method in the absence of a template. Moreover, the NH4TiOF3 nanoplates could be converted into TiO2 nanoplates with exposed (001) facets after calcination in the temperature range of 200–800 °C.532 Specifically, when the calcination temperature was below 800 °C, smooth TiO2 nanoplates with a thickness of 50 nm were obtained, as shown in Fig. 46. However, when the calcination temperature was over than 800 °C, the nanoplates disappeared under high temperature calcination, with the presence of big particles.
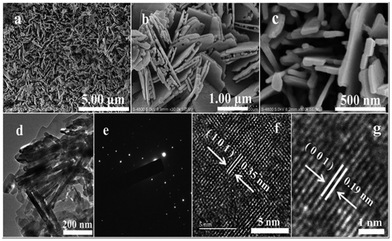 |
| Fig. 46 TiO2 nanoplates calcined at 800 °C: (a–c) SEM images, (d) TEM image, (e) SAED pattern and (f and g) HRTEM images. Reprinted with permission from ref. 532. | |
3.2.2 Synthesis of 2-D cerium oxide NCs.
Pan et al. fabricated CeO2 nanoplates via the hydrothermal treatment of Ce(NO3)3·6H2O, CTAB, and NH3·H2O at 100–160 °C. It was shown that the controlled conversion of nanoplates into nanotubes and nanorods could be achieved by altering the reaction time, temperature and CTAB/Ce3+ ratio. They claimed that CTAB could strongly protect the growth along (111) facet. When the concentration of CTAB is low, the insufficient protection may lead to the formation of nanorods. With an increase in the concentration of CTAB, the capping ability of CTAB increased significantly, leading to a significant restriction in the formation of nanoplates.533 Lin and co-workers demonstrated the synthesis of CeO2 nanoplates via the thermal decomposition of a mixture of cerium acetate, oleic acid, oleylamine and 1-octadecene.534 They claimed that when oleylamine was added to the mixed solution together with oleic acid in a one-step process, the final product was CeO2 nanoplates. By contrast, only CeO2 nanorods could be obtained when oleylamine was added in a separate step (Fig. 47a and b). Furthermore, Zhang and co-workers presented a hydrothermal approach for preparing single-crystal CeO2 nanoplates with new hexagonal unit cells via a disproportionation–reduction–oxidation process of Ce(III)–Ce(IV)–Ce(III) species (Fig. 47c).535 A plausible mechanism was proposed for revealing the formation process of the CeO2 nanoplates as follows: (1) the formation of CeO2 small nanocubes from polyhedra; (2) the subsequent self-assembly of nanocubes into hexagonal stacks; and (3) the formation of CeO2 nanoplates from CeO2 nanocubes and rearrangement of the CeO2 lattices via oriented attachment. On the other hand, Hu and co-workers prepared CuO–CeO2 binary oxide nanoplates via a solvothermal method (Fig. 47d and e).536 In a typical procedure, an aqueous solution of Cu(NO3)2·3H2O, Ce(NO3)3·6H2O and PEG were prepared, followed by the dropwise addition of NaOH solution under magnetic stirring at room temperature. After aging for 2 h, the products were collected by filtering and washing with deionized water and ethanol. Subsequently, the as-obtained gel was dispersed in 500 mL ethanol by sonication and then transferred to an autoclave. After reaction at 260 °C for 2 h, the resultant powder was cooled to room temperature under a continuous Ar flow. Finally, the powder was calcined in air at 400 °C for 4 h.
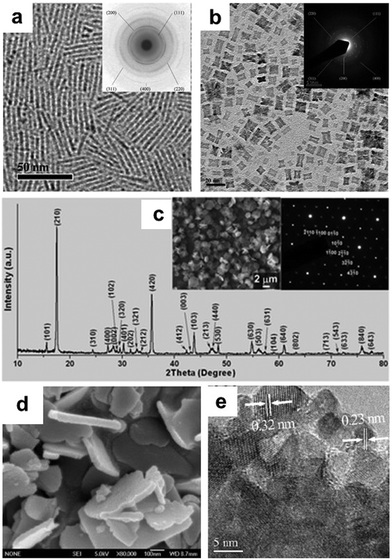 |
| Fig. 47 TEM images of the as-prepared CeO2 (a) nanorods and (b) nanoplates. The insets are the corresponding SAED patterns. Reprinted with permission from ref. 534. (c) XRD pattern recorded from the hexagonal CeO2 nanoplates. The left and right insets show the SEM image and SAED pattern of the CeO2 nanoplates, respectively. Reprinted with permission from ref. 535. (d) TEM and (e) HRTEM images of the as-prepared CuO–CeO2 nanoplates. Reprinted with permission from ref. 536. | |
3.2.3 Synthesis of other 2-D oxide NCs.
Other 2-D oxide nanoplates have also been synthesized, such as NiO, CuO, MnO2, ZnO, and WO3 nanoplates. Behm and co-workers synthesized NiO nanoplates through the calcination of Ni(OH)2 nanoplates, which were prepared by mixing NiCl2·6H2O, ammonium hydroxide, and hexadecyltrimethylammonium bromide in H2O (Fig. 48a).537 Cao et al. demonstrated the synthesis of CuO nanoplates via a hydrothermal reaction from Cu(NO3)·3H2O (Fig. 48b).538 Ai and co-workers synthesized MnO2 nanoplates via a microwave irradiation method in aqueous solution in the absence of any templates, catalysts or organic reagents (Fig. 48c).539 Also, Jin et al. used a microwave-assisted method for the production of ZnO nanoplates (Fig. 48d).540 Zheng and co-workers fabricated WO3 nanoplates via the hydrothermal method, in which L-lactic acid was used as a capping agent in the hydrothermal process for the preparation of rectangular WO3 nanoplates (Fig. 48e).541
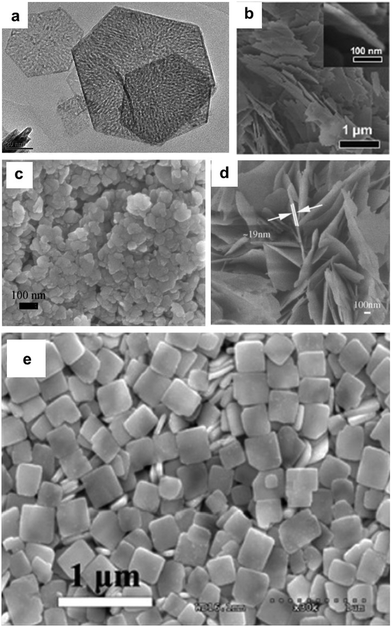 |
| Fig. 48 (a) TEM image of NiO nanoplates. Reprinted with permission from ref. 537. (b) SEM image of CuO nanoplates. Reprinted with permission from ref. 538. (c) SEM image of MnO2 nanoplates. Reprinted with permission from ref. 539. (d) SEM image of ZnO nanoplates. Reprinted with permission from ref. 540. (e) SEM image of WO3 nanoplates. Reprinted with permission from ref. 541. | |
3.3 Three-dimensional (3-D) oxide NCs
3.3.1 Synthesis of 3-D titanium oxide NCs.
Many studies have focused on the preparation of 3-D TiO2 structures. Although the overall size of these 3-D TiO2 structures are on the micrometer scale, all of them consist of nano units. For example, Zhou and co-workers synthesized 3-D TiO2 nanostructures with various microstructures via hydrothermal methods.542 It was shown that the solvent used in hydrothermal treatment strongly influenced the microstructures of the TiO2 nanostructures. Typically, 3-D dandelion-like TiO2 structures self-assembled from nanorods were obtained in a non-polar solvent based on the water–non-polar solvent interface. By contrast, 3-D microspheres were obtained when n-hexane was used as the solvent. Zhu et al. demonstrated the fabrication of flower-like anatase TiO2 nanostructures via a one-step template-free hydrothermal method using titanocene dichloride as the precursor and ethylenediamine as the chelating agent in aqueous solution.543 Liu and co-workers reported the synthesis of flower-like TiO2 nanostructures with exposed (001) facets via a low-temperature hydrothermal process from Ti powder (Fig. 49a and b). It was shown that HF acted as a critical shape-directing agent, which could react with Ti under hydrothermal conditions. On the other hand, F− could reduce the surface energy of (001) facets, leading to the formation of flower-like TiO2 nanostructures with exposed (001) facets.544 Sun and co-workers demonstrated a hydrothermal method for the preparation of 3-D TiO2 nanostructures with different morphologies by adjusting the precursor hydrolysis rate and the surfactant aggregation (Fig. 49c–k).545 Detailed experimental data showed that the final morphologies are strongly determined by the hydrolysis rate. Specifically, a rapid hydrolysis rate cause the nano-units surrounding the TiO2 nuclei to grow in the form of nanorods. By contrast, the nano-units tend to become nanoribbons when EG is introduced since EG can retard the hydrolysis rate in this reaction system.
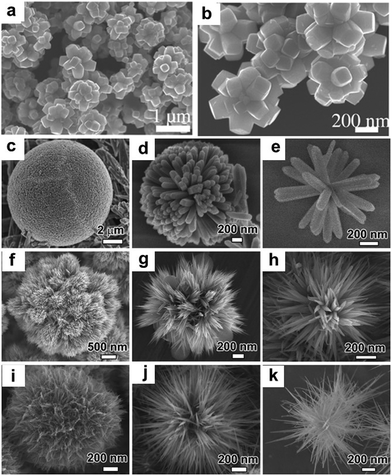 |
| Fig. 49 (a and b) SEM images of the as-prepared flower-like TiO2 nanostructures at low and high magnifications, respectively. Reprinted with permission from ref. 544. (c–k) Typical SEM images of 3-D dendritic TiO2 nanostructures with different morphologies. Reprinted with permission from ref. 545. | |
3.3.2 Synthesis of 3-D cerium oxide NCs.
CeO2 nanocubes enclosed by six (200) planes were prepared through a facile one-pot method with the assistance of solvothermal treatment. Typically, 15 mL toluene, 1.5 mL oleic acid and 0.15 mL tert-butylamine were added to a solution of cerium(III) nitrate aqueous in a Teflon-lined stainless-steel autoclave without stirring (Fig. 50a and b). After the autoclave was capped, it was put in an oven and heated to 180 °C for 24 h. It was shown that the shape and size of the CeO2 NCs were related to the concentration of the reactants, the amount of stabilizing agents, and the water/toluene ratio in the reaction system.546 Dang and co-workers reported a similar method for the preparation of CeO2 nanocubes using toluene, oleic acid, tert-butylamine and cerium(III) nitrate. They revealed the shape evolution from polyhedral particles to nanocubes with a prolonged reaction time (Fig. 50c and d). Detailed studies showed that the growth of the [100] direction of CeO2 is dominant because the (111) face has a lower surface energy, leading to the formation of octahedron or truncated octahedron in the aqueous solution. In contrast, OLA prefers to bind to the (100) face with a high surface energy and limits the growth of the [100] direction in the oil phase, resulting in the formation of CeO2 nanocubes.547 The synthesis of CeO2 nanocubes at the liquid–liquid interface has also been reported.548 On the other hand, it has been reported that CeO2 nanocubes can be produced via the hydrothermal reaction of Ce(NO3)3 and NaOH. For instance, Zhang et al. demonstrated the synthesis of CeO2 nanocubes by mixing 0.1 M Ce(NO3)3 solution and 0.3 M NaOH (Fig. 50e and f).549 After stirring for 6 h, the precursor was centrifuged and washed several times with distilled water. Afterwards, 2.5 mL of the above precursor was transferred to a stainless-steel autoclave, followed by the addition of an appropriate amount of decanoic acid. After the autoclave was capped, the reaction was performed in the reactor at 400 °C for 10 min and terminated by submerging the reactor in a water bath at room temperature. Wu et al. discussed two different precursors in detail, including cerium(III) chloride and cerium(III) nitrate, for the synthesis of CeO2 nanocubes. Moreover, the CeO2 nanorods could be converted into nanocubes with the assistance of NO3− ions. Other ions such as Br−, I−, Cl− and SO42− can lead to the formation of CeO2 nanorods.550 Also, Qian and co-workers demonstrated the synthesis of cubic-like CeO2 NCs via a solvothermal process using hexadecylamine as a capping agent and CeCl3 as the precursor at 180 °C for 24 h. It was found that both the shape and size of the CeO2 NCs can be systematically tuned by altering the amount of water, the concentration of ligand and different types of aliphatic amine.551 In addition to nanocubes, flower-like CeO2 NCs were synthesized.552–556
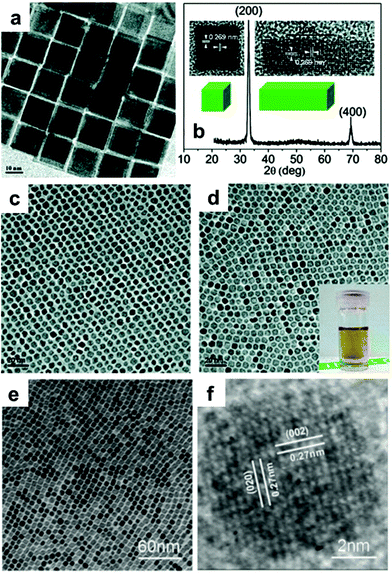 |
| Fig. 50 (a) TEM image and (b) XRD pattern of the as-prepared CeO2 nanocubes. Insets of (b) HRTEM images. Reprinted with permission from ref. 546. TEM images of (c) CeO2 polyhedral particles and (d) CeO2 nanocubes. Reprinted with permission from ref. 547. (e) TEM and (f) HRTEM images of the as-prepared CeO2 nanocubes. Reprinted with permission from ref. 549. | |
3.3.3 Synthesis of 3-D copper oxide NCs.
Huang and co-workers demonstrated the synthesis of Cu2O NCs by mixing an aqueous solution of CuCl2, SDS, NaOH, and NH2OH·HCl reductant.557 It was shown that the shapes could systematically evolve from cubic to face-raised cubic, edge- and corner-truncated octahedral, all-corner-truncated rhombic dodecahedral, (100)-truncated rhombic dodecahedral, and rhombic dodecahedral structures with an increase in the NH2OH·HCl concentration (Fig. 51). In another work from the same group, Kuo and co-workers synthesized monodisperse Cu2O truncated cubic, cuboctahedral, truncated octahedral, and octahedral NCs using CuCl2, SDS, hydroxylamine and NaOH, respectively.558 It was shown that the morphologies of the Cu2O NCs were strongly related to SDS, while their sizes were controlled by the amount of NaOH. Yao et al. synthesized Cu2O nanocubes and dodecahedra using 1-hexadecylamine and copper(II) acetate monohydrate. For the synthesis of Cu2O nanocubes, copper(II) acetate monohydrate and warm 1-hexadecylamine were added to a 100 mL flask. For the synthesis of Cu2O dodecahedra, copper(II) acetate monohydrate, warm HDA and undecane were added to a 100 mL flask. The above mixtures were preheated to 90 °C and kept for 10 min under vigorous stirring, followed by a rapid heating to 160–220 °C for 15–90 min.559 Susman and co-workers described the fabrication of Cu2O NCs on substrates through chemical deposition. In the absence of additives, the morphologies could be well controlled. Through the chemical deposition of Cu2O NCs on Au-seeded substrates in citrate-based solutions, the morphologies of Cu2O NCs could be precisely controlled from cubes to octahedra.560
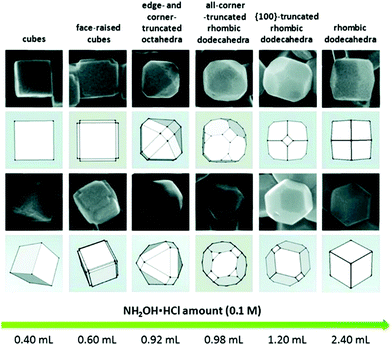 |
| Fig. 51 SEM images and the corresponding schematic drawings of the Cu2O NCs synthesized with morphology evolution from cubes to rhombic dodecahedra upon increasing the amount of NH2OH·HCl. Two orientations are shown for each particle shape. Reprinted with permission from ref. 557. | |
The synthesis of hollow Cu2O NCs was also reported using the hydrothermal method. Kuo and co-workers demonstrated the fabrication of Cu2O nanocages and nanoframes possessing an unusual truncated rhombic dodecahedral structure.561 The growth solution consisted of CuCl2, SDS, NH2OH·HCl, HCl, and NaOH. This protocol was quite similar to that for the synthesis of Cu2O NCs in Fig. 52, except for the addition of HCl. In a typical synthetic process, 0.087 g SDS was added to 0.1 mL CuCl2 solution (0.1 M) under vigorous stirring. Subsequently, 0.45 mL NH2OH·HCl (0.2 M) and 0.09 mL of HCl (2 M) were added with slight shaking by hand, followed by the rapid injection of 0.25 mL 1 M NaOH with additional shaking for 10 s. Type-I nanoframes and nanocages were obtained after aging for 45 min and 2 h, respectively, while ethanol was added under sonication for the formation of type-II nanoframes (Fig. 52).
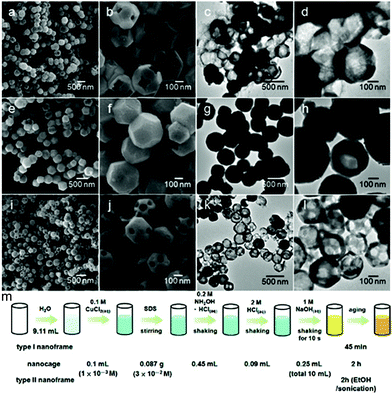 |
| Fig. 52 SEM and TEM images of the truncated rhombic dodecahedral Cu2O nanoparticles: (a–d) type-I nanoframes, (e–h) nanocages, and (i–l) type-II nanoframes. The magnified images clearly show the hollow structures of the nanoparticles. (m) Schematic illustration of the procedure for the synthesis of Cu2O nanocages and nanoframes. Reprinted with permission from ref. 561. | |
3.3.4 Synthesis of other 3-D oxide NCs.
Wang and co-workers prepared 3-D hierarchical WO3 nanostructures with a novel nanosheet-assembled morphology through the acidification of Na2WO4·2H2O and HCl.562 After mixing Na2WO4·2H2O with HCl, a yellow precipitate was formed, which was washed with deionized water and ethanol, and then dried at 80 °C for 10 h. Finally, the precipitates were sintered at 500 °C to obtain the WO3 sample. A work from Huang et al. claimed that the Ostwald ripening process was involved the formation of 3-D WO3 nanostructure.563 Qiu et al. prepared flower-like WO3 nanostructures via a solvothermal method using H2WO4 as the precursor. An additional treatment of H2WO4 with H2O2 was highlighted (Fig. 53a).564 In a typical process, H2O2 (50 wt%) was added to an aqueous solution of H2WO4 under stirring on a hot plate (95 °C). Subsequently, a mixture of the treated H2WO4 solution, oxalic acid, urea, HClO4 and acetonitrile in a certain ratio was sealed in a Teflon-lined stainless steel autoclave and maintained at 180 °C for 10 h. Wang and co-workers demonstrated the synthesis of flower-like WO3 structures via the simple calcination of W18O49 nanowires. Initially, W18O49 nanowires were prepared via a microwave-assisted solvothermal method using WCl6 as a precursor. Different from the reported solvothermal systems, this system was heated by microwave at 200 °C for 2 h.565 Zhang and co-workers demonstrated that BF4− could be added to the autoclave as a guiding agent, which led to the formation of orthorhombic WO3 NCs with a tunable percentage of (001) facets.566 Ma et al. prepared uniform flower-like hierarchical Co3O4 nanostructures via a surfactant-free hydrothermal process at low temperature using CoCl2, NaCl and C6H12N4 (Fig. 53b).567 Also, the hydrothermal method has been used for the synthesis of other flower-like nanostructures, such as MoO3–In2O3 (Fig. 53c)568 and SnO2 (Fig. 53d).569
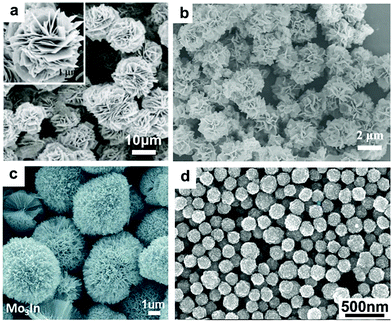 |
| Fig. 53 (a) SEM image of flower-like WO3 nanostructures. Inset: High magnification SEM image. Reprinted with permission from ref. 564. (b) SEM image of flower-like Co3O4 nanostructures. Reprinted with permission from ref. 567. (c) SEM image of flower-like MoO3–In2O3 nanostructures. Reprinted with permission from ref. 568. (d) SEM image of flower-like SnO2 nanostructures. Reprinted with permission from ref. 569. | |
4. Catalytic applications
4.1 CH4 oxidation
CH4 is among the most important and attractive feedstocks in the chemical industry due to its large reserves in the Earth.423 Thus, the production of high value-added products from CH4 is highly important, not only because it can alleviate the oil crisis, but also reduce the emission of greenhouse gas.570–572 Indeed, the oxidation of CH4 has been widely investigated over the past decades for the production of methanol, olefins and aromatics.573–582 However, these existing processes suffer from the disadvantages of high operating temperature and/or high pressure, leading to high cost. Generally, NCs with specific shapes, sizes and structures cannot bear these harsh conditions. Consequently, chemists have attempted to disperse metals on a support to prevent them from sintering under high temperature. Recently, the selective oxidation of CH4 to produce methanol has attracted significant attention in the chemical industry, which has been regarded as a dream reaction. Despite the huge challenges arise from the strong C–H bonds in CH4, a low operating temperature is beneficial for nanocatalysts with tailored morphologies and sizes. Over the past decade, great effort has been devoted to the direct oxidation of CH4 to CH3OH; however several critical points need to be overcome as follows: (1) the existing catalytic systems use H2O2 as an oxidant or a co-oxidant, and the high cost of H2O2 seriously impedes the practical application of this type of catalytic process and (2) the balance of CH4 conversion and methanol selectivity still requires further investigation. Therefore, recent reports aimed to design efficient catalysts for reducing the concentration of H2O2 and/or replacing H2O2 by O2 for the direct oxidation of CH4 to CH3OH.
Rahim and co-workers reported that H2O2 could be used as an efficient oxidant for CH4 conversion to CH3OH under mild conditions.583 With the assistance of electron paramagnetic resonance (EPR), ˙CH3 and ˙OH were observed in the reaction system, indicating that the oxidation of CH4 was triggered by radicals. Moreover, they compared the performance of TiO2-supported Au–Pd nanoparticles and Au–Pd/TiO2 prepared via the conventional impregnation method. It was shown that Au–Pd/TiO2 exhibited a much lower yield than TiO2-supported Au–Pd nanoparticles. Detailed experiments showed that Au–Pd/TiO2 prepared via a conventional impregnation method tended to decompose H2O2 to form H2O besides ˙OH, while Au–Pd nanoparticles could suppress the decomposition of H2O2, leading to a significant increase in CH3OH yield. Subsequently, another work from the same group demonstrated the production of CH3OH through the direct oxidation of CH4 with H2O2 and O2 at 50 °C on colloidal Au–Pd nanoparticles.37 They claimed that the presence of H2O2 can trigger the oxidation of CH4via a radical process. These PVP-stabilized Au–Pd nanoparticles can strongly suppress the degradation of H2O2 to form H2O, leading to a significant increase of the CH3OH yield. The yield of CH3OH and CH3OOH reached about 53.6 mol kgcat.−1 h−1 at a total selectivity of 88% H2O2 (Table 1). Furthermore, to reduce the usage of H2O2, O2 was added as a co-oxidant. Detailed experiments showed that the PVP-stabilized Au–Pd nanoparticles not only promoted the formation of radicals and CH4 activation, but also suppressed the degradation of H2O2. Isotope experiments were performed to further reveal the mechanism using H216O2 and 18O2. The appearance of 16O in the products suggests that ˙CH3 may react with ˙16O16OH or 16O2 (from H216O2). When 10 mmol of H2O2 and 5 bar of 18O2 pressure were employed, the primary products contained 70% 18O and 30% 16O. Consequently, a plausible mechanism was proposed, where H2O2 can produce ˙OH, which can activate CH4 to form ˙CH3. Moreover, ˙CH3 will further react with ˙OOH or O2 to form CH3OOH.
Table 1 Comparison of the catalytic activity of supported and unsupported colloidal Au-only, Pd-only, and Au–Pd catalysts for the liquid phase oxidation of CH4 using H2O2. Test conditions: reaction time = 0.5 h; stirring speed = 1500 rpm; CH4 pressure = 30 bar; reaction temperature = 50 °C; and stirred heating ramp rate = 2.25 °C min−1. Dash indicates not applicable. Reprinted with permission from ref. 37
Entry |
Catalyst |
H2O2 amount (μmol) |
O2 pressure (bar) |
Amount of product (μmol) |
Primary oxygenate selectivity (%) |
Oxygenate productivity (mol kgcatalyst−1 hour−1) |
H2O2 consumed (%) |
Gain factor |
CH3OOH |
CH3OH |
HCOOH |
CO2 |
Entry 1: sol-immobilized solid catalyst, 100 mg (6.6 μmol of metal in 10 mL of water).
Entries 2 to 7: colloidal catalysts (10 mL, 6.6 μmol of metal).
Entries 8 and 9: homogeneous metal precursor solutions (6.6 μmol of metal in 10 mL of water).
|
1a |
1%Au–Pd/TiO2 |
1000 |
0 |
0.0 |
0.4 |
0.00 |
1.2 |
26 |
0.03 |
73 |
2 × 10−3 |
2b |
Au–Pd colloid |
1000 |
0 |
11.8 |
3.3 |
0.6 |
1.1 |
90 |
29.4 |
38 |
3 × 10−2 |
3b |
Au–Pd colloid |
1000 |
5 |
17.4 |
7.6 |
1.8 |
1.5 |
88 |
53.6 |
27 |
9 × 10−2 |
4b |
Au–Pd colloid |
0 |
5 |
0 |
0 |
0 |
0.2 |
0 |
0 |
0 |
— |
5b |
Au–Pd colloid |
50 |
5 |
15.7 |
2.8 |
1.2 |
0.3 |
92 |
39.4 |
44 |
1.2 |
6b |
Pd colloid |
50 |
5 |
0 |
0 |
0 |
0.7 |
0 |
0 |
22 |
0 |
7b |
Au colloid |
50 |
5 |
0 |
0 |
0 |
0.1 |
0 |
0 |
12 |
0 |
8c |
PdCl2 |
50 |
5 |
0 |
0 |
0 |
0.3 |
0 |
0 |
5 |
0 |
9c |
HAuCl4 |
50 |
5 |
0 |
0 |
0 |
0.2 |
0 |
0 |
10 |
0 |
Based on the above two cases, two critical points should be highlighted as follows: (1) only one C–H bond should be activated in CH4 to increase the selectivity of CH3OH. Sometimes, highly dispersed metal atoms may over-activate C–H to form the products of COx and (2) H2O2 is a very important chemical, which is much more expensive than CH3OH, and thus this dream process of CH4 oxidation with H2O2 may be seriously impeded in industry. Thus, to overcome these problems, recent studies focused on the surface modification of metals to balance their activity and selectivity, and the reduction of the amount of H2O2 used in reaction. For example, Bai and co-workers modified Pd nanoparticles with Cu to boost the selective oxidation of CH4 to CH3OH and CH3OOH.584 It was shown that the interface of CuPdO2/CuO, which was formed by calcining Pd–Cu nanoparticles in air, could efficiently activate and convert CH4 to CH3OH using H2O2 or O2 as an oxidant under mild conditions. By altering the amount of Pd and Cu in these nanoparticles, different ratios of CuPdO2 and CuO were observed, leading to a variable oxygenate yield. The optimized catalyst gave a yield of oxygenates of 4076.5 μmol g−1 h−1 and a selectivity of 93.9% (Fig. 54). Bai et al. further tuned the Ru4+ ratio at the interface of Ru–Cu lichen-like nanoparticles.293 It was shown that the composition-dependent synergistic effects between Ru and Cu in these nanoparticles, which is related to the ratio of Ru4+ on the surface of the catalysts, can significantly promote the selective oxidation of CH4 to form CH3OH. To further demonstrate the role of Ru4+ species, they calcinated these lichen-like nanoparticles at different temperatures. High temperature calcination led to a high ratio of Ru4+ as a result of the stronger synergy at the interface and higher oxygenate yield. Although high temperature calcination will result in the sintering of Ru–Cu nanoparticles, surface engineering of composite catalysts indeed affects their catalytic performance strongly. They proposed a radical trigger mechanism for the selective oxidation of CH4 by detecting ˙CH3 and ˙OH radicals in the reaction system. This work highlighted the significance of interface modification on the selective oxidation of CH4. More importantly, the amount of H2O2 was as low as 10 μmol, while the oxygenate yield was 3241.6 μmol g−1 h−1 with a total selectivity of 93.8%.
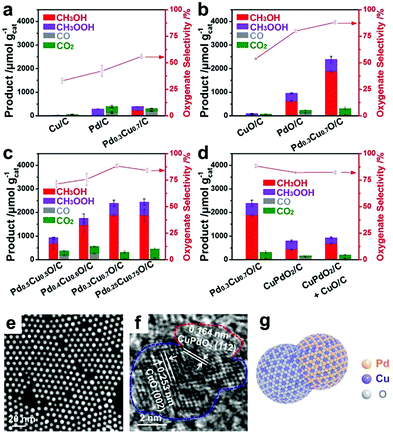 |
| Fig. 54 Product yields and oxygenate selectivity of (a) Cu/C, Pd/C, and Pd0.3Cu0.7/C, (b) CuO/C, PdO/C, and Pd0.3Cu0.7O/C, (c) PdxCu1−xO/C and (d) Pd0.3Cu0.7O/C, CuPdO2/C, and CuPdO2/C + CuO/C. Reaction conditions: 10 mg of catalyst, 0.5 MPa CH4, 20 mL of 1 mol L−1 H2O2, and 50 °C, 1 h. (e) HAADF-STEM image of Pd0.3Cu0.7 nanoparticles. (f) HRTEM image and (g) atomic model of Pd0.3Cu0.7O/C. Reprinted with permission from ref. 584. | |
To achieve the selective activation of C–H bonds in CH4, Bai et al. recently demonstrated that the cooperation of CeO2 nanowires and Rh SAs can efficiently catalyze the selective oxidation of CH4 to CH3OH.423 It was shown that the abundant vacancies on CeO2 nanowires can well anchor isolated Pt atoms. A plausible mechanism was proposed, where H2O2 can be decomposed into ˙OH on two neighboring Ce(III) atoms with vacancies and into ˙OOH on Ce(IV) atoms. CH4 will be adsorbed and activated on Rh SAs to form ˙CH3 with the assistance of radicals. ˙CH3 further reacts with ˙OH and ˙OOH to form CH3OH and CH3OOH. The over-oxidation of ˙CH3 is suppressed on Rh SAs based on density functional theory (DFT) calculations. By contrast, CH4 activation with H2O2 on Rh clusters is different from that on Rh SAs. ˙CH3 and CH3OOH can be oxidized into *CH2 and then to HCOOH by ˙OH on Rh clusters. Finally, HCOOH will react with ˙OH to form CO and CO2. The vacancies can be compensated by H2O2via a revisable process of Ce(III) ↔ Ce(IV). Different from the existing systems, CeO2 is involved in the selective oxidation of CH4 by promoting the formation of ˙OH, leading to a significant increase in the oxygenate yield in comparison to Rh clusters on CeO2 nanowires (Fig. 55).
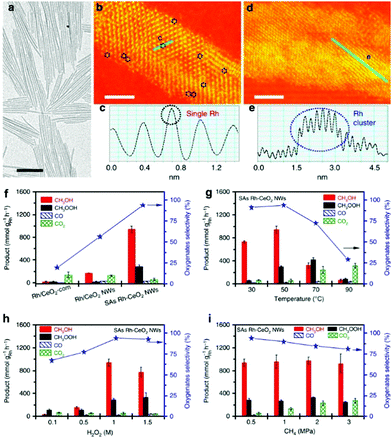 |
| Fig. 55 (a) TEM image of the SAs Rh–CeO2 nanowires. (b) Aberration-corrected (AC)-HAADF-STEM image in temperature color of the SA Rh–CeO2 nanowires. The isolated Rh atoms are marked with black circles. (c) Intensity profile recorded from the line in (b). (d) AC-HAADF-STEM image in temperature color of the Rh/CeO2 NWs. The Rh cluster is marked with blue line. (e) Intensity profile recorded from the line in panel (d). (f) Yield and selectivity of oxygenates from Rh/CeO2-com, Rh/CeO2 nanowires, and SAs Rh–CeO2 nanowires. Reaction conditions: PCH4: 0.5 MPa, H2O2: 20 mL (1 M), T: 50 °C, reaction time: 1 h, and catalyst weight: 10 mg. (g) Catalytic performance at different temperatures over SA Rh–CeO2 nanowires. Reaction conditions: PCH4: 0.5 MPa, H2O2: 20 mL (1 M), T: 30–90 °C, reaction time: 1 h, and catalyst weight: 10 mg. (h) Catalytic performance with different H2O2 concentrations over SA Rh–CeO2 nanowires. Reaction conditions: PCH4: 0.5 MPa, H2O2: 20 mL (0.1–1.5 M), T: 50 °C, reaction time: 1 h, and catalyst weight: 10 mg. (i) Catalytic performance at different CH4 partial pressures over SA Rh–CeO2 nanowires. Reaction conditions: PCH4: 0.5–3 MPa, H2O2: 20 mL (1 M), T: 50 °C, reaction time: 1 h, and catalyst weight: 10 mg. The error bars represent the standard deviation of three experiments. Reprinted with permission from ref. 423. | |
Despite the promising activity of CH4 conversion in the presence of H2O2, the high cost of H2O2 is the main problem for the practicability of this process. Accordingly, because H2O2 can be directly produced from H2 and O2, a feasible process by converting CH4 with H2 and O2 to CH3OH was proposed. To achieve this process, one should well balance the formation of H2O2 and the activation of CH4 because H2O2 production from H2 and O2 is generally operated at a low temperature (e.g., 0 °C),585,586 while CH4 activation requires a high temperature. Another challenge is that H2O2 tends to rapidly decompose to H2O and O2, leading to a very low amount of H2O2 and low CH4 conversion. Thus, to solve these problems, Jin and co-workers recently reported a strategy for the in situ formation of peroxide in the CH4 oxidation process to CH3OH.35 They loaded Au–Pd alloy nanoparticles in aluminosilicate zeolite crystals and modified the external surface of the zeolite with organosilanes. The silanes allowed the diffusion of H2, O2 and CH4 molecules in the Au–Pd nanoparticle, but suppressed the desorption of formed H2O2, leading to a great enhancement in the reaction activity. The optimized catalyst gave a methane conversion of 17.3% at a methanol selectivity of 92%, as shown in Fig. 56. The concept of a molecular fence was further verified by testing the catalysts in the presence of H2O2. Compared to the high CH3OH yield from the conventional ZSM-5-supported Au–Pd catalyst, the capped Au–Pd nanoparticles exhibited much lower activity, indicating that silanes can inhibit the diffusion of H2O2 from the solution to the catalyst surface. Similarly, the silanes will also prohibit the desorption of H2O2 in the solution as a result of the high CH4 conversion.
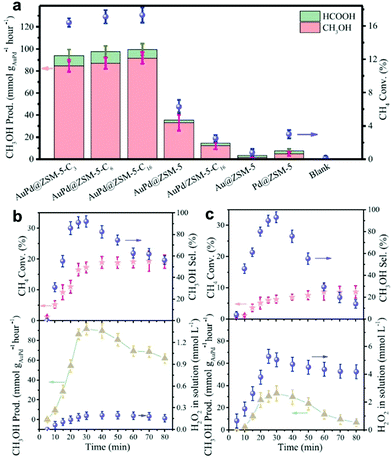 |
| Fig. 56 (a) Oxidation of CH4 with H2 and O2 over various catalysts. Reaction conditions: 10 mL water, 30 min, 70 °C, 27 mg of catalyst, and feed gas at 3.0 MPa with 3.3% H2/6.6% O2/1.6% CH4/61.7% Ar/26.8% He, and 1200 revolutions per minute (rpm). (b and c) Dependence of the methane conversion (Conv.), methanol selectivity (Sel.), methanol productivity (Prod.), and H2O2 concentration in water solution on the reaction time over (b) Au–Pd@ZSM-5-C16 and (c) Au–Pd@ZSM-5 catalysts. Reaction conditions: 10 mL of water, 70 °C, 27 mg of catalyst, feed gas at 3.0 MPa with 3.3% H2/6.6% O2/1.6% CH4/61.7% Ar/26.8% He, and 1200 rpm. Each reaction was tested eight times to obtain the error bars. Reprinted with permission from ref. 35. | |
4.2 CO2 reduction
CO2 reduction is another hot topic in catalysis, which has attracted great attention in chemical industry. Generally, different types of catalytic processes have been reported for the reduction of CO2, such as thermal catalysis, electrocatalytic process, and photocatalysis. For the conventional thermal catalytic process, CO2 can be converted into high value-added products, such as methanol, ethanol and olefins, through hydrogenation. For an electrochemical process, CO2 can be converted into CO, CH4, and alcohols. For a photocatalytic process, CO2 can be reduced into CO, CH4 and other chemicals. The thermal catalytic CO2 reduction has been studied for several decades; however, it still requires further investigation to increase its conversion and selectivity. Compared to CO oxidation, thermal catalytic CO2 reduction is much more difficult due to the chemical inertness of CO2. Thus, a common strategy for improving the CO2 reduction is to increase the reaction temperature. However, a high temperature will lead to an increase in the energy consumption and bring great difficulty in the control of selectivity. On the other hand, a high temperature may result in the aggregation of nanocrystals. Thus based on these issues, electrochemical and photocatalytic CO2 reduction under mild conditions have become a hot topic in the chemical industry. Although the progress in nanomaterials has significantly improved their catalytic performance, the electrochemical and photocatalytic reduction of CO2 still suffer from the disadvantages of poor activity and low selectivity. To achieve high-efficiency electrochemical CO2 reduction, one needs to design efficient and robust nanocatalysts that can balance the activation of CO2 and coupling of C-C bonds to form value-added products. The main challenges for photocatalytic CO2 reduction are the low activity and poor selectivity for the product, especially poor selectivity for C2+ products. Therefore, the design of efficient catalysts is highly necessary for the efficient reduction of CO2.
4.2.1 Thermal catalytic CO2 reduction.
Zhang and co-workers reported that the d-band center and negative charge density of Rh are dependent on the dimensions and structures of NCs.587 They alloyed Rh with W to form RhW nanosheets and nanoparticles for the hydrogenation of CO2 to methanol. The experimental results showed that the activity of the Rh75W25 nanosheets is 5.9, 4.0, and 1.7 times higher than that that of Rh nanoparticles, Rh nanosheets, and Rh73W27 nanoparticles, as shown in Fig. 57a and b. Two factors were considered to explain this enhancement in activity. The addition of W into Rh nanosheets can promote the charge transfer from W to Rh, leading to a high d-band center. On the other hand, the quantum confinement on the nanosheets will also strengthen the d-band center of Rh in comparison to nanoparticles, resulting in the stronger adsorption of CO2 on Rh. A high density of electrons on active sites can promote CO2 adsorption. In addition to alloying with another element to increase the electron density via charge transfer, some specific morphologies may favor the accumulation of electrons. Khan et al. synthesized Pt3Co octapods, Pt3Co nanocubes, Pt octapods, and Pt nanocubes for the hydrogenation of CO2 to methanol.588 It was shown that the vertices in the Pt3Co octapods are more negatively charged than that in the other three NCs due to the sharp-tip and alloy effects. Consequently, the CO2 conversion was 2.2, 6.1, and 6.6 times higher than that of Pt3Co nanocubes, Pt octapods, and Pt nanocubes (Fig. 57c and d). Bai et al. demonstrated that ordered PdCu nanoparticles can promote *CO hydrogenation to *HCO, the rate-determining step for the hydrogenation of CO2 to ethanol, leading to a TOF value of 359.0 h−1 at a high ethanol selectivity of 92.0% (Fig. 57e–h).589 X-ray photoelectron spectroscopy (XPS) measurements also confirmed that the electrons transfer from Cu to Pd, leading to a significant increase in ethanol selectivity.
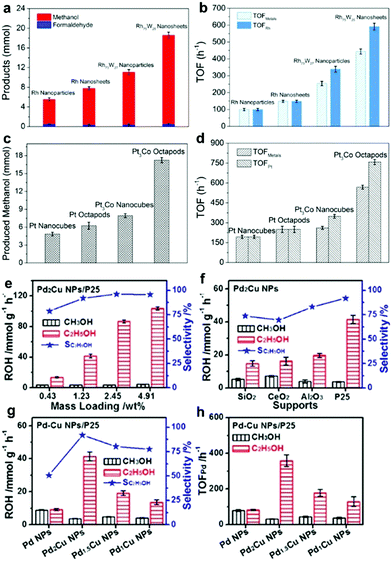 |
| Fig. 57 (a) Products of CO2 hydrogenation over Rh nanoparticles, Rh nanosheets, Rh73W27 nanoparticles, and Rh75W25 nanosheets at 150 °C after 5 h. (b) Comparison of TOFmetals and TOFRh for different catalysts. Reprinted with permission from ref. 587. (c) Product yields achieved on Pt nanocubes, Pt octapods, Pt3Co nanocubes, and Pt3Co octapods (20 mg, 5% mass loading) in the hydrogenation of CO2 at 150 °C for 5 h. (d) Comparison of the TOFMetal and TOFPt numbers of different catalysts. Reprinted with permission from ref. 588. Achieved product yields of CH3OH and C2H5OH (ROH) and selectivity of C2H5OH of Pd2Cu nanoparticles with different loadings on (e) P25 and (f) over different supports in the hydrogenation of CO2 at 200 °C for 5 h. (g) Achieved product yields of ROHs and selectivity of C2H5OH and (h) comparison of the TOFPd values of Pd–Cu NPs/P25. Error bars correspond to deviations from three independent experiments. Reprinted with permission from ref. 589. | |
Other non-noble metals have been widely used for CO2 hydrogenation. With the development of nanoscience, chemists can synthesize non-noble NCs with desired shapes to investigate the mechanism of catalytic performance on different-shaped NCs. Liao and co-workers presented the shape effect of ZnO NCs on their interaction with Cu in the synthesis of methanol from the hydrogenation of CO2. It was shown that the interface of Cu–ZnO facilitated the reduction of ZnO via surface Cu oxides by spilled hydrogen at a much lower temperature.590 Rungtaweevoranit et al. composited Cu nanoparticles with a Zr-based metal–organic framework (MOF) (UIO-66) for the hydrogenation of CO2.591 It was shown that the strong interaction between the Cu nanoparticles and Zr oxide [Zr6O4(OH)4(–CO2)12] secondary building units of the MOF could strongly promote the catalytic performance. The performance of optimized catalyst exceeded the benchmark Cu/ZnO/Al2O3 catalyst and gives a steady 8-fold enhanced yield and 100% selectivity for methanol.
4.2.2 Electrocatalytic CO2 reduction.
The electrocatalytic reduction of CO2 is a promising process to convert CO2 into useful products. Compared with other conversion methods, the electrocatalytic reduction of CO2 does not require H2 as a feedstock since it is intrinsically coupled with the electrocatalytic splitting of H2O.592 However, the electrocatalytic reduction of CO2 suffers from the disadvantages of high overpotential (about −1.0 V) and low selectivity for desirable products.593 It has been reported that both the activity and selectivity depend on the sizes and shapes of Cu NCs. Loiudice and co-workers demonstrated the non-monotonic size dependence of the selectivity in cubic Cu NCs in the electrocatalytic reduction of CO2.594 They prepared Cu nanocubes with sizes of 24 nm, 44 nm and 63 nm. It was shown that the cubes with a 44 nm edge length gave the highest selectivity towards the electrocatalytic reduction of CO2 and faradaic efficiency for ethylene (Fig. 58a). Manthiram et al. demonstrated that Cu nanoparticles supported on glassy carbon (n-Cu/C) exhibited 4 times greater methanation current densities compared to high-purity copper foil electrodes in the electrocatalytic reduction of CO2 (Fig. 58b and c).595 Moreover, Baturina and co-workers reported that Cu nanoparticles exhibited much higher C2H4 selectivity than smooth Cu films (Fig. 58d).596 The selectivity of C2H4 increased with a decrease in the size of the Cu nanoparticles, which may be attributed to the increase of under-coordinated sites, such as corners, edges, and defects in Cu nanoparticles with small sizes. A similar correlation between particle size and catalytic performance was reported on other metals, such as Au,597,598 Ag599 and Pd nanoparticles.600 For example, it was shown that the electrocatalytic activity significantly increased when the size of Au nanoparticles was lower than 5 nm, which may be attributed to the significant increase in low-coordinated Au atoms on the surface of small nanoparticles.601
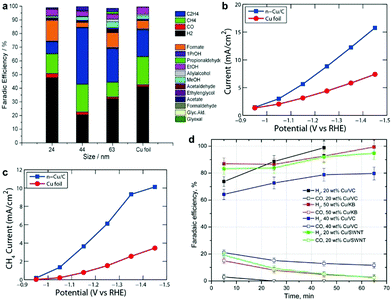 |
| Fig. 58 (a) Bar graph reporting the faradaic efficiencies for each product in Cu nanocubes with different sizes and Cu foil at −1.1 V vs. RHE. The glassy carbon signal was subtracted. Reprinted with permission from ref. 594. (b) Total current density, demonstrating that n-Cu/C has greater overall reduction activity than copper foil. (c) Methanation current density, in which the combined effect of the improved current density and faradaic efficiency on n-Cu/C is apparent. Reprinted with permission from ref. 595. (d) Faradaic efficiency vs. time for the generation of H2 (solid squares) and CO (open squares) on different thin films held at −1.2 V. CO2-Purged 0.1 M KHCO3 solutions at pH = 6.8, 1600 rpm, and 20 μg Cu cm−2 Cu loading. Reprinted with permission from ref. 596. | |
Furthermore, it has been found that the electrocatalytic performance of Cu NCs is strongly related to their shape. Wang and co-worked discussed the electrocatalytic performance for the reduction of CO2 on different facets of Cu NCs. They used Cu nanocubes with (100) facets as a starting model to create high energy surface of (110) via a chemical etching process. It was shown that the etched NCs exhibited much higher catalytic activities in comparison to Cu nanocubes.602 Roberts and co-workers compared the catalytic performance on different facets of Cu NCs, including Cu(100), Cu(211) and Cu(111).603 It was shown that Cu(100) exhibited the highest selectivity for the production of ethylene, while Cu(111) gave the worst ethylene selectivity (Fig. 59). They claimed that the single-crystal studies failed to explain the formation of methane. Despite the highest ethylene selectivity on Cu (100), the (100) facet generates a significant amount of methane. On the other hand, compared to bulk foil, the local pH value of Cu NCs is much higher, leading to an improvement in the selectivity for ethylene.
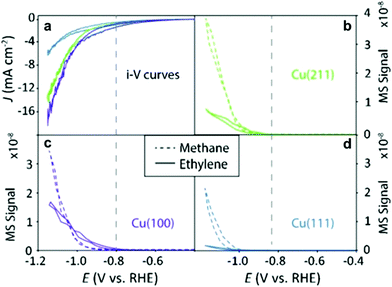 |
| Fig. 59 (a) Comparison of cyclic voltammograms (CVs) in 0.1 M KHCO3. Methane and ethylene formation on (b) Cu(211), (c) Cu(100), and (d) Cu(111). Reprinted with permission from ref. 603. | |
4.2.3 Photocatalytic CO2 reduction.
The photocatalytic reduction of CO2 has attracted increasing attention recently since it is regarded as a clean and renewable process for simultaneously capturing this major greenhouse gas and solving the shortage of sustainable energy. Thus, many reviews regarding the photocatalytic reduction of CO2 have been published over the past decade. They discussed the fundamental concept, catalyst design and modification and mechanism about photocatalysis in detail.604–617 Hence, here, we focus on the shape-dependent photocatalytic performance.
Yu and co-workers demonstrated the correlation of photocatalytic CO2 reduction activity and exposed surface of anatase TiO2.618 It was shown that the yield of CH4 was strongly dependent on the ratio of (001) and (101) facets. The optimized catalyst has a (001) ratio of 58% (Fig. 60a). A plausible mechanism was proposed. Most of electrons and holes are mainly accumulated on the (101) facets due to the low percentage of (001) facets. The charge carriers easily recombine with holes and only a small fraction of electrons and holes are separated, leading to a poor photocatalytic performance. Once an optimal ratio of (001) facet and (101) facet was achieved, the electron and hole pairs could be separated, since the electrons would migrate to (101) facet, while holes would migrate to (001) facet. Consequently, an improved photocatalytic performance was achieved. Moreover, Liu and co-workers compared the photocatalytic performance on different phases of TiO2 NCs.619 It was shown that the densities of surface oxygen vacancies were different on the TiO2 NCs after He pre-treatment. Consequently, Ti3+ sites were observed on anatase and brookite but not on rutile. These oxygen vacancies can significantly promote the formation of CO and CH4 from the photocatalytic reduction of CO2 (Fig. 60b). Liu et al. also claimed that the co-existence of (001) and (101) facets could greatly promote the formation of oxygen vacancies, leading to a significant enhancement in photocatalytic efficiency (Fig. 60c and d).620 The synergistic effects associated with the co-existence of (001) and (101) facets enabled a 4-fold enhancement in CO2 reduction in comparison to TiO2 with a single (001) plane or (101) plane and P25. Truong and co-workers demonstrated that branched TiO2 NCs with (331) facets exhibited much higher activity than rods with exposed (110) facets in the photocatalytic reduction of CO2.621 It was shown this high-index facet could not only provide more active sites such as edge and corner sites, but also promote the separation of electron–hole pairs. The presence of defects, such as oxygen vacancies and uncoordinated Ti atoms, can greatly enhance the photocatalytic performance for the reduction of CO2. Kong and co-workers demonstrated that both surface and bulk defects in TiO2 NCs could strongly influence the performance for the photocatalytic reduction of CO2.622 It was shown that a decrease in the relative concentration ratio of bulk defects to surface defects could significantly promote the separation of electron and hole pairs, leading to a sharp increase in activity.
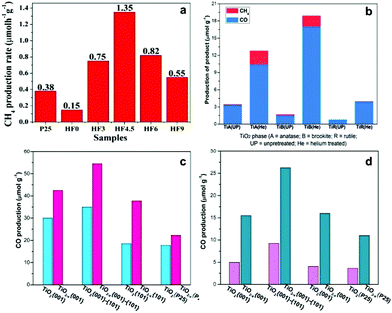 |
| Fig. 60 (a) Comparison of the photocatalytic CH4-production activity of P25 and TiO2 samples prepared by varying the HF content. Reprinted with permission from ref. 618. (b) Production of CO and CH4 on the three unpretreated and He pre-treated TiO2 polymorphs under 6 h illumination. Reprinted with permission from ref. 619. CO production over TiO2 and TiO2–x NCs with different exposed facets under (c) UV-vis light (200–700 nm) and (d) visible light (400–700 nm) irradiation. Reprinted with permission from ref. 620. | |
4.3 Selective hydrogenation
Selective hydrogenation is one of the most important processes in the chemical industry, which requires catalysts that can selectively catalyze the desired reaction paths but suppress side reactions.623–629 To achieve selective hydrogenation, one needs to precisely control the surface properties of catalysts to promote the formation of desired products, but suppress the generation of by-products. Conventional strategies such as increasing the dispersity of metals and exposing more active sites can significantly increase the activity. However, selective hydrogenation generally requires the suppression of the activity to some extent since a high dispersity of active sites may favor the formation of by-products. For example, the selective hydrogenation of light alkynes (e.g., acetylene and propyne) to relative alkenes (e.g. ethylene and propylene) is a critical process to remove trace amounts of alkynes the alkenes before polymerization since the presence of alkynes can poison the catalyst. To remove trace amount alkynes, one needs to selectively convert alkynes to alkenes rather than alkanes. Noble metal-based catalysts (e.g., Pd) are active for hydrogenation; however, they favor over-hydrogenation. Another important case is the compounds with co-existing C
C and C
O bonds. The selective hydrogenation of C
O is a very important process in the chemical industry. However, the C
C bond is much more active than the C
O bond, which is generally preferentially converted. Specifically, selective hydrogenation requires activity to be partially sacrificed for selectivity. With the development of nanoscience and nanotechnology, chemists achieved control of the morphology and composition of nanocrystals, and thus can regulate the surface properties of catalysts for selectively adsorbing/desorbing the reactant/intermediate/product.
Chung and co-workers demonstrated that Pd nanocubes enclosed by (100) facets exhibited much higher alkene selectivity (>90%) than a commercial Pd/C catalyst in the selective hydrogenation of 5-decyne, 2-butyne-1,4-diol, and phenylacetylene.630 They claimed that the enhancement in selectivity was caused by the large adsorption energy of the carbon–carbon triple bond on the (100) facets of the Pd nanocubes. However, the detailed mechanism should be further studied since the strong adsorption of the carbon–carbon triple bond on (100) facet is insufficient for explaining the high selectivity of alkenes. Crespo-Quesada et al. investigated the catalytic performance of the selective hydrogenation of acetylene on Pd NCs enclosed by (100) and (111) facets. They considered Pd–C as the active sites for the selective hydrogenation of acetylene. Pd cubes with (100) facets reacted with acetylene to form a PdC0.13 phase at a rate roughly 6-fold higher than that of Pd octahedrons with (111) facets. Consequently, the Pd nanocubes exhibited higher activity than Pd octahedrons towards the selective hydrogenation of acetylene.631 Niu and co-workers claimed that poisoning the Pd surface with Pb could significantly promote the selective hydrogenation of alkyne.632 They found that the addition of Pb influenced the morphologies of Pd–Pb NCs. However, only octahedrons exhibited high selectivity for the hydrogenation of phenylacetylene (Fig. 61). The poisoning effects of Pb have also been reported by Zhang and co-workers.633 They indicated that Pd–Pb NCs exhibited much higher styrene selectivity than that of Pd-C catalysts. Moreover, they found that the concave shape of Pd–Pb nanocubes gave much higher activity at a comparable styrene selectivity (Fig. 62).
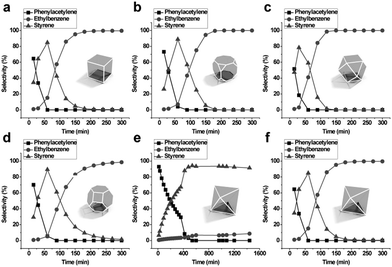 |
| Fig. 61 Hydrogenation of phenylacetylene on Pd–Pb NCs with different shapes and Pb surface compositions: (a) cubes, 0%; (b) cuboctahedra, 0.2%; (c) truncated octahedra, 2.1%; (d) slightly truncated octahedra, 13.8%; (e) octahedra, 27.0%; and (f) octahedra, 0%. Reprinted with permission from ref. 632. | |
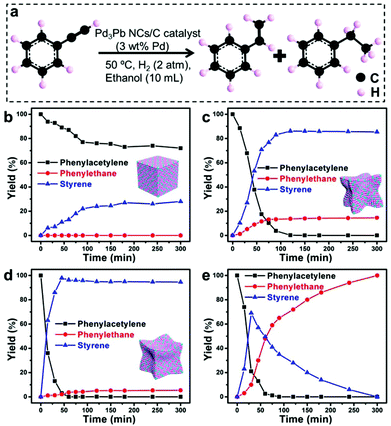 |
| Fig. 62 (a) Hydrogenation of phenylacetylene over different concave degree Pd–Pb catalysts and a benchmark catalyst: (b) Pd3Pb nanocubes, (c) Pd3Pb concave NCs, (d) Pd3Pb concave NCs and (e) Pd/C. Reaction conditions: phenylacetylene (0.1 mmol), ethanol (10 mL), H2 (2 atm), 50 °C, and catalyst (5 mg; 10% Pd/C, 5 mg). Reprinted with permission from ref. 633. | |
Our recent work indicated that Pd octahedrons enclosed by (111) facets could be used as highly active, selective and stable catalysts for the selective hydrogenation of propyne.634 By contrast, Pd nanocubes enclosed by (100) facets favored the over-hydrogenation of propyne. Different from these existing reports that claimed Pd carbides are the active sites for the selective hydrogenation of alkyne, we found that both the (111) and (100) facets tended to over-hydrogenate propyne; however, the apexes of cubes and octahedrons are the active sites since propyne prefers to adsorb at the apexes. Theoretical calculations further confirmed that propyne molecules can be easily converted into propylene. However, over-hydrogenation is kinetically suppressed because the formed propylene tends to desorb from the apexes other than over-hydrogenate into propane. To further confirm the theoretical calculations, more control experiments were performed. For example, FeCl3 solution was used to etch the apexes of Pd octahedrons. It was found that the apexes were gradually etched with an increase in time, which completely evolved into spherical Pd nanoparticles. The selectivity of propylene correspondingly decreased from about 96% to 50% after the apexes were etched (Fig. 63).
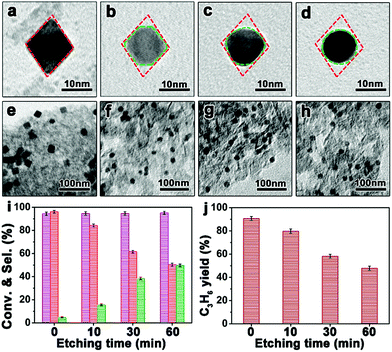 |
| Fig. 63 TEM images of etched Pd octahedrons (∼19 nm) and their catalytic performance for the hydrogenation of propyne. TEM images of Pd octahedrons and SIRAL40-supported Pd nanoparticles after etching by FeCl3 solution for different times: (a and e) 0 min; (b and f) 10 min; (c and g) 30 min; and (d and h) 60 min. (i) Propyne conversion, propylene selectivity, and propane selectivity of SIRAL40-supported Pd nanoparticles etched by FeCl3 for propyne hydrogenation: purple, propyne conversion; red, propylene selectivity; and green, propane selectivity. (j) Propylene yield of SIRAL40-supported Pd nanoparticles etched by FeCl3 for propyne hydrogenation. Conditions for etching: 1 mL FeCl3 solution (1 M) was added to 5 mL Pd octahedron solution with moderate stirring (600 rpm) at 45 °C. Conditions for hydrogenation: T = 35 °C, Ptotal = 0.1 MPa, C3H4/H2/N2 = 6/12/32 mL min−1, weight of supported catalyst 0.2 g. Reprinted with permission from ref. 634. | |
The selective hydrogenation of α,β-unsaturated ketones and aldehydes to unsaturated alcohols is a very important process in the petrochemical, biological and chemical industries.635–647 As mentioned above, α,β-unsaturated ketones and aldehydes have an unsaturated C
C and C
O bond; however, the C
C bond is thermodynamically preferred during hydrogenation. Thus, highly efficient catalysts with high selectivity for the hydrogenation of the C
O bond need to be designed.
Zhu and co-workers reported that ultrasmall Au25(SR)18 (25 and 18 represent the number of Au atoms and ligands, respectively) nanoparticles could achieve 100% chemoselectivity for the unsaturated alcohol in the selective hydrogenation of α,β-unsaturated ketones (e.g. benzalacetone).648 A plausible mechanism was proposed that Au25 possessed low-coordinated Au atoms, which could be used as active sites for C
O activation. To further reveal the mechanism, Ouyang and Jiang simulated the catalytic process using first-principles DFT calculations. It was shown that that H2 and benzalacetone were co-adsorbed on Au25(SR)18 clusters. When H2 was cleaved into two H atoms on the surface of Au, one of them diffused from the Au atom to the adsorbed benzalacetone. The energy barrier for the hydrogenation of C
O and C
C is 0.99 and 1.12 eV, respectively, indicating that the hydrogenation of C
O is preferred. Moreover, ethanol was found to further stabilize the partially hydrogenated intermediate in the hydrogenation of C
O via a hydrogen bond, leading to a smaller H2 cleavage energy (0.90 eV).649 Wu et al. demonstrated that alkylamine-capped Pt3Co alloy NCs could be used as highly selective catalysts for the chemoselective hydrogenation of cinnamaldehyde and citral.650 It was shown that the selectivity for unsaturated alcohols gradually deceased with the shortening of the amine chain length, which was coated on the Pt3Co NCs, as presented in Fig. 64a and b. The plausible mechanism suggests that an amine with a long chain length can retard the adsorption of the reactants on Pt3Co alloy NCs, leading to a slow reaction rate, but a high selectivity for unsaturated alcohol. Serrano-Ruiz and co-workers studied the surface structure and shape of Pt NCs in the selective hydrogenation of crotonaldehyde and cinnamaldehyde.651 It was reported that the Pt(111) facet showed higher selectivity for unsaturated alcohol than the Pt(100) facet but a much slower reaction rate. It seems that sacrificing activity is a general strategy to increase the selectivity of unsaturated alcohols in many cases. This is consistent with the conclusion that the adsorption of H2 or α,β-unsaturated ketones/aldehydes should be weakened on the surface of catalysts to further tune the selectivity via kinetic control. This contradiction may be solved by compositing active sites with other active elements, such as Fe. The synergistic effects between different active sites can significantly increase the selectivity of unsaturated alcohols. For example, Bai et al. used PtFe zigzag nanowires as selective catalysts for the selective hydrogenation of cinnamaldehyde.60 Compared to the pure Pt zigzag nanowires, the PtFe zigzag nanowires exhibited both higher activity and selectivity for cinnamyl alcohol (Fig. 64c and d). They claimed that the high selectivity can be attributed to the lower electron density of Pt owing to the electronic interaction between Fe and Pt.
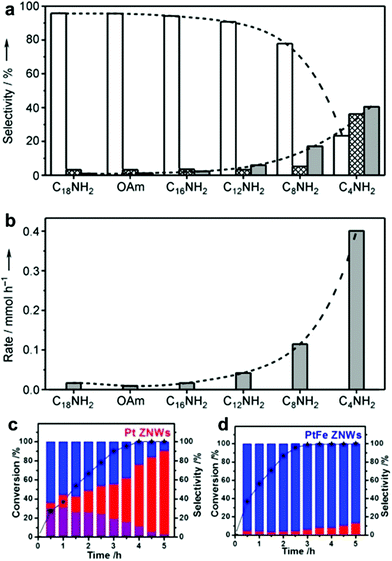 |
| Fig. 64 Histograms of (a) selectivity for cinnamyl alcohol (white), hydrocinnamaldehyde (cross-hatch), and hydrocinnamyl alcohol (gray) at nearly 100% conversion in the hydrogenation of cinnamaldehyde with different amine-capped Pt3Co catalysts. (b) Rates of hydrocinnamyl alcohol production after complete conversion of cinnamaldehyde with different amine-capped Pt3Co nanocatalysts. Conditions: Pt3Co nanocatalysts (11 mg), n-butanol (10 mL), cinnamaldehyde (3 mmol), nonane (1 mmol), H2 (1.5 atm), and 25 °C. Reprinted with permission from ref. 650. Cinnamaldehyde hydrogenation performances of (c) Pt ZNWs and (d) PtFe ZNWs. Reprinted with permission from ref. 60. | |
4.4 CO oxidation
The low-temperature oxidation of CO is one of the most extensively studied reactions in heterogeneous catalysis, which has attracted increasing attention in the context of cleaning the air and lowering automotive emissions.39,41,376,652–661 This reaction is also fundamentally important for investigating the mechanism of catalysts as a model reaction. An ideal catalyst should be capable increasing the activity and reducing the reaction temperature. The advances in precise surface/interface engineering have enabled chemists to carefully investigate the correlation between structure and activity. It has been reported that the catalytic performance for the oxidation of CO is dependent on the size and structure of metal NCs. For example, Jin and co-workers demonstrated that the activity for the oxidation of CO increased by a factor of 10 when the size of Pd nanoparticles decreased from 18 nm to 6 nm.40 The decrease in size can largely increase the content of surface atoms, leading to a significant enhancement in activity. However, something must be overlooked since the increased activity is not exactly linear with an increase in the content of atoms. Specifically, the activity on every single exposed atom is different, which may strongly be related to their coordination environment. For example, the atom arrangements differ on different facets, which means that the electronic properties are different, leading to different activity. On the other hand, alloying with another metal or depositing on an oxide can also change the coordination environment of atoms, resulting in different catalytic performances.662 For example, Zhang and co-workers synthesized different Rh NCs with (100) and (111) facets. It was shown that the Rh(111) facet exhibited higher activity than Rh(100) facet towards the oxidation of CO. Choi et al. reported that octahedral and cubic Pd@Rh NCs gave higher activity compared with the Rh/C catalyst towards the oxidation of CO.44 However, they claimed that only slight differences were observed on octahedral and cubic Pd@Rh NCs.
Najafishirtari and co-workers demonstrated that the synergistic effects between different metals could largely boost the oxidation of CO.42 When Au–Cu nanoparticles were treated at high temperature (e.g., 350 °C), the occurrence of segregation between Au and Cu led to a weak interaction and low activity. Moreover, when the sample was further reduced at 350 °C, Au and Cu re-alloyed to form an fcc phase NC. Furthermore, George and co-workers reported the interaction between metal-based nanoparticles and an oxide support could significantly promote their activity towards the oxidation of CO.663 They compared the CO oxidation performance of two different nanostructures, i.e. Au0.80Pd0.20–FexOy dumbbell NCs and Au0.75Pd0.25 NCs, on Al2O3. It was shown that the Au0.80Pd0.20–FexOy dumbbell NCs exhibited higher activity, indicating that the strong interaction between the metal alloy and oxide could highly enhance the CO oxidation.
Strong interaction between metals and oxides can be achieved via the formation of a metal-oxide interface on an oxide with abundant O vacancies, such as CeO2. It should be noted that the vacancies in CeO2 can greatly promote the activity of metals. Carrettin et al. demonstrated that depositing Au on nanocrystalline particles of CeO2 resulted in an enhancement in activity by two orders of magnitude in comparison to that of the Au catalyst deposited on a regular CeO2 support.664 They highlighted that the vacancies, which could be produced by H2 treatment, greatly promoted the oxidation of CO. Guzman et al. provided spectroscopic evidence of the enhancement from the active O vacancies in a CeO2-supported Au catalyst.656 Kim and co-workers further confirmed the effects of vacancies in CeO2 on the oxidation of CO through theoretical calculations.665 Other oxides, such as FeOx,39 MgO,666 and Co3O4,376 can also been used to promote the activity of metal atoms through strong M–O–M interaction. For instance, Xie and co-workers demonstrated that Co3O4 nanorods exhibited superior catalytic performance towards the oxidation of CO at temperatures as low as −77 °C.376 Detailed characterization indicated that more active Co3+ species were observed on the (111) planes of the Co3O4 nanorods, leading to a significantly higher reaction rate (Fig. 65a). Kinetics studies showed that the reaction order of CO and O2 over the Co3O4 nanorods was 0.12 and 0.28, respectively. At low temperature (e.g. −77 °C), the adsorbed CO and O2 on Co3O4 nanorods can usually exceed the rate of surface reaction, leading to the occurrence of CO oxidation on the Co3+ sites (Fig. 65b). On the other hand, the similar apparent activation energy of CO oxidation on the Co3O4 nanorods (22 kJ mol−1) and Co3O4 nanoparticles (21 kJ mol−1) indicated that Co3+ could be assigned as the active sites (Fig. 65c).
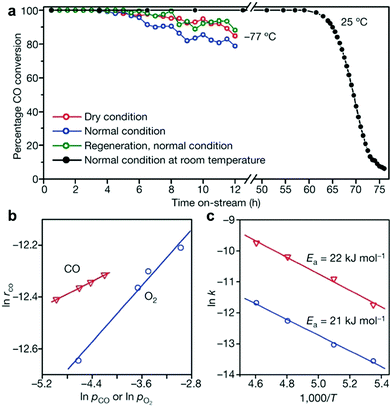 |
| Fig. 65 (a) Effects of moisture content, regeneration and temperature on the oxidation of CO over Co3O4 nanorods. CO oxidation with a feed gas of 1.0 vol% CO/2.5 vol% O2/He under normal (moisture 3–10 ppm, blue symbols) and dry (moisture <1 ppm, red symbols) conditions at −77 °C. The used sample was regenerated with a 20 vol% O2/He mixture at 450 °C for 30 min and then tested for CO oxidation under normal conditions (green symbols) at −77 °C. CO oxidation at 25 °C (black symbols) was tested with the normal feed gas. Reaction kinetics of CO oxidation. (b) Reaction rates (rCO) as a function of CO or O2 concentration over Co3O4 nanorods: (triangle symbols) CO and (circle symbols) O2. The reaction rates were measured at −77 °C and the concentrations of CO and O2 were in the range of 0.5–1.2 vol% and 1.0–5.1 vol%, respectively. PCO and PO2, partial pressures. (c) Arrhenius plots for the reaction rate constants (activation energies, Ea) on Co3O4 nanorods (triangle symbols) and nanoparticles (circle symbols) in the temperature (T) range of −86 °C to −56 °C with a feed gas of 1.0 vol% CO/2.5 vol% O2/He. Reprinted with permission from ref. 376. | |
4.5 Oxygen reduction
The ORR is of utmost importance in advanced electrochemical energy conversion technologies. However, the ORR suffers from the disadvantages of sluggish kinetics.667–674 Pt has been regarded as promising catalyst for the ORR; however, the high cost and poor activity of Pt seriously impede its practical application.599 Over the past decades, many strategies have been developed for designing efficient Pt-based catalysts by compositing with non-noble metals, such as Ni and Co. On the other hand, many shaped Pt-based NCs with high-index facets and/or low coordinated atoms were synthesized for achieving high ORR activity. The use of a non-noble component in catalysts can significantly increase their ORR activity and reduce their cost; however, maintaining the durability of catalysts during such long-term harsh working conditions is another key point.
Pt–Ni alloys have been widely reported as promising ORR catalyst over the past decade. Wu and co-workers synthesized Pt3Ni NCs for the ORR.254 The carbon-supported Pt3Ni catalysts exhibited an area-specific activity of 850 μA cmPt−2 at 0.9 V, which is ∼4 times higher than that of the commercial Pt/C catalyst (∼0.2 mA cmPt−2 at 0.9 V). Huang et al. prepared highly porous Pt3Ni NCs for the ORR. It was shown that the porous Pt3Ni NCs exhibited a much better ORR performance that commercial Pt black and commercial Pt/C catalyst.320 The current density and mass activity of Pt3Ni NCs were 5 times and 6 times higher than that of the commercial Pt catalyst. Moreover, the porous Pt3Ni NCs exhibited better stability in 6000 potential sweeps. Zhang and co-workers demonstrated that the composition evolution of the Pt3Ni NCs influenced their ORR performance. For example, it was shown that Pt3Ni NCs with an Ni-rich surface gave a 300% increase in mass activity towards to HCOOH oxidation compared with the commercial Pt/C catalyst, while Pt3Ni NCs with a Pt-rich surface showed a 300% increase in mass activity towards the ORR in comparison to a commercial ORR catalyst.324 Gong and co-workers synthesized 1 nm-thick Pt3Ni bimetallic alloy nanowires for the ORR.267 It was shown that the Pt3Ni nanowires exhibited a significant enhancement in mass activity in comparison to the commercial Pt/C catalyst (0.546 vs. 0.135 A mgPt−1). Also, Pt3Ni nanowires exhibited better durability than Pt nanowires and the commercial Pt/C catalyst, as shown in Fig. 66. Huang and co-workers demonstrated that the addition of a transition metal can significantly enhance the ORR performance of Pt3Ni octahedra.322 Among the transition metals, Mo resulted in the highest increase in ORR activity. The Mo-doped Pt3Ni/C exhibited the best ORR performance with a specific activity of 10.3 mA cm−2 and mass activity of 6.98 A mgPt−1, which are 81- and 73-fold enhancements compared with the commercial Pt/C catalyst (0.127 mA cm−2 and 0.096 A mgPt−1), respectively (Fig. 67).
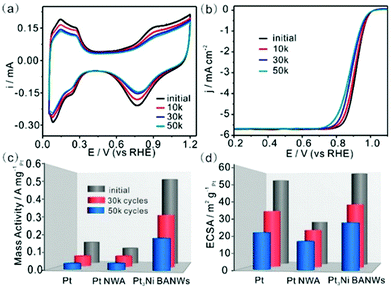 |
| Fig. 66 Electrocatalytic durability measurements: (a) CVs curves and (b) positive-going linear sweep voltammetry (LSV) curves of Pt3Ni nanowires during accelerated durability test. (c) Mass activity and (d) electrochemical surface area (ECSA) comparison of Pt and Pt nanowires, and Pt3Ni nanowires at different cycles. Reprinted with permission from ref. 267. | |
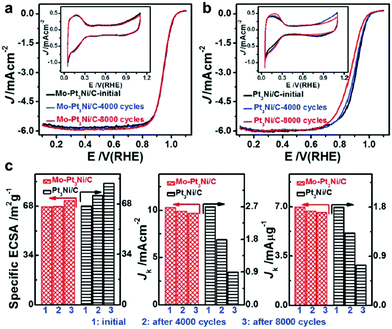 |
| Fig. 67 Electrochemical durability of the high-performance octahedral Mo–Pt3NiCo/C catalyst and octahedral Pt3Ni/C catalyst. (a and b) ORR polarization curves and (inset) corresponding CVs of (a) octahedral Mo–Pt3Ni/C catalyst and (b) octahedral Pt3Ni/C catalyst before and after 4000, and after 8000 potential cycles between 0.6 and 1.1 V versus RHE. (c) Changes in the ECSA (left), specific activity (middle), and mass activity (right) of the octahedral Mo–Pt3Ni/C catalyst and octahedral Pt3Ni/C catalyst before and after 4000, and after 8000 potential cycles. The durability tests were carried out at room temperature in O2-saturated 0.1 M HClO4 at a scan rate of 50 mV s−1. Reprinted with permission from ref. 322. | |
5. Summary and outlook
In this review, we discussed the controllable synthesis of metal and oxide NCs with tailored shapes, sizes and compositions. Special attention was paid to the fabrication, stabilization and modification of the typical metals and oxides that are regarded as promising catalysts. Finally, we summarized some typical and popular processes, such as CH4 selective oxidation, CO2 reduction, selective hydrogenation, CO oxidation and ORR, to elucidate the importance of shape, size and composition on catalytic performance. This review aimed to summarize the correlation of structure–activity of metal and oxide NCs.
Despite the tremendous progress in the controllable synthesis of metals and oxides and their catalytic application, some challenges remain. With the development of nanoscience and nanotechnology over the past decades, chemists have gained the ability to fabricate metal NCs. Many methods including seeded growth, polyol method, hydrothermal method, solvothermal method, and templated-assisted method have been developed for the preparation of nanostructures. The successful experience has been applied for the synthesis of oxide NCs, such as CeO2, Co3O4, and TiO2 nanostructures, which significantly promoted their promising application in both thermal-catalysis and photocatalysis. However, the detailed mechanism for their growth has not been completely understood to date. Some principles have been proposed for interpreting the morphology control. For example, thermodynamics shows that the obtained NCs will expose the most stable facets (lowest surface energy). To obtain high-index facets with high surface energy, precise control of the growth kinetics is necessary. During the control of the kinetics, some capping agents are required, such as PVP, oleylamine, and oleic acid, to selectively protect the facets. In some cases, halide ions are used to tune the shapes of NCs via selective etching in the presence of capping agents. However, the intrinsic mechanism of these capping agents is unclear, leading to the unrepeatable synthesis of NCs. Thus, some advanced technologies should be developed for revealing the growth process of nanocrystals. For instance, the advances on liquid TEM measurement allow chemists to observe the growth process of nanocrystals and monitor the growth rate of different positions of the seeds. Some other surface technologies are essential for investigating the effects of surface ligands on the growth of nanocrystals.
Another challenge is the stability of shaped NCs. As discussed before, thermodynamics principles suggest that NCs tend to aggregate or expose low-index facets to decrease their surface energy. Some capping agents are used for obtaining metal and oxide NCs with tailored morphologies and sizes. However, the presence of capping agents will retard the adsorption of reactant molecules on the metal surface, leading to a decrease in catalytic performance. The removal of capping agents from NCs can favor an increase in exposed active sites on their surface; however, these NCs will suffer from aggregation and/or shape evolution without the protection of a capping agent. It is widely accepted that the apex, edge, terrace and low-coordinated atoms are the most active. Thus, it is still challenging to apply NCs with high-index facets in industry unless this contradiction is solved. One probable strategy for improving the stability is the surface modification of nanocrystals with other elements. (1) Surface modification with metals to form alloys or intermetallics will lead to significantly enhanced stability and activity. (2) Surface modification with non-metal elements, such as N and C, can also promote the activity and improve the stability of catalysts. Metal-free catalysts have recently become a hot topic in catalysis, such as C3N4. These metal-free catalysts are generally produced under harsh conditions, which may exhibit better stability than metal-based catalysts under the same conditions.
Thirdly, catalysis is a systematic and complicated process. The catalytic performance is strongly related to the surface properties of catalysts. However, is impossible for the surface of a catalyst to be invariable. Specifically, the chemical environment of surface atoms strongly varies after the adsorption of reactant molecules. This variation in the chemical environment of the surface atoms will further influence their electronic properties, and thus their catalytic performance. Specifically, one probable situation is that the highlighted active sites from high-index facets or terraces may not actually exist during the catalytic reaction. With the development of science and technology, more advanced in situ techniques may greatly help scientists to reveal the real mechanism on the surface of catalysts.
Finally, heterogeneous catalysis requires a good balance between activity and selectivity. For most catalytic reactions in the chemical industry, there are at least two different pathways, and only one of them is preferred. Sometimes, selectivity is more important than activity in industry because unreacted raw materials can be recycled into other reactants for further conversion. To achieve actual industrial application, catalysts should exhibit high selectivity, high activity, excellent stability and low cost. Accordingly, it is still a long way for chemists to pursue more efficient and economical catalytic processes. On the other hand, more attention should be devoted to renewable and eco-friendly processes, such as photocatalysis.
In summary, we attempted to review the recent advances on thermal catalysis, photocatalysis and electrocatalysis using metal and oxide nanostructures. We hope that this review can help readers better understand the correlation of structure–activity, and inspire researchers to design highly active, selective and stable catalysts.
Conflicts of interest
There are no conflicts to declare.
Acknowledgements
This work is supported National Natural Science Foundation of China (21673150, 51802206, 21703146, 51922073) and Natural Science Foundation of Jiangsu Province (BK20180846, BK20180097). We acknowledge the financial support from the 111 Project, Collaborative Innovation Center of Suzhou Nano Science and Technology (NANO-CIC) and the Priority Academic Program Development of Jiangsu Higher Education Institutions (PAPD).
Notes and references
- A. T. Bell, The Impact of Nanoscience on Heterogeneous Catalysis, Science, 2003, 299, 1688–1691 CrossRef CAS
.
- Y. Xu, L. Chen, X. Wang, W. Yao and Q. Zhang, Recent advances in noble metal based composite nanocatalysts: colloidal synthesis, properties, and catalytic applications, Nanoscale, 2015, 7, 10559–10583 RSC
.
- C. Cui and S. Yu, Engineering interface and surface of noble metal nanoparticle nanotubes toward enhanced catalytic activity for fuel cell applications, Acc. Chem. Res., 2013, 46, 1427–1437 CrossRef CAS
.
- C. Tan, X. Cao, X. J. Wu, Q. He, J. Yang, X. Zhang, J. Chen, W. Zhao, S. Han, G. H. Nam, M. Sindoro and H. Zhang, Recent advances in ultrathin two-dimensional nanomaterials, Chem. Rev., 2017, 117, 6225–6331 CrossRef CAS
.
- H. Lv, D. Li, D. Strmcnik, A. P. Paulikas, N. M. Markovic and V. R. Stamenkovic, Recent advances in the design of tailored nanomaterials for efficient oxygen reduction reaction, Nano Energy, 2016, 29, 149–165 CrossRef CAS
.
- B. L. Cushing, V. L. Kolesnichenko and C. J. O'Connor, Recent advances in the liquid-phase syntheses of inorganic nanoparticles, Chem. Rev., 2004, 104, 3893–3946 CrossRef CAS
.
- Y. Xu and B. Zhang, Recent advances in porous Pt-based nanostructures: synthesis and electrochemical applications, Chem. Soc. Rev., 2014, 43, 2439–2450 RSC
.
- V. S. Balachandran, S. R. Jadhav, P. K. Vemula and G. John, Recent advances in cardanol chemistry in a nutshell: from a nut to nanomaterials, Chem. Soc. Rev., 2013, 42, 427–438 RSC
.
- M. Gattrell, N. Gupta and A. Co, A review of the aqueous electrochemical reduction of CO2 to hydrocarbons at copper, J. Electroanal. Chem., 2006, 594, 1–19 CrossRef CAS
.
- Y. Chen, C. W. Li and M. W. Kanan, Aqueous CO2 reduction at very low overpotential on oxide-derived Au nanoparticles, J. Am. Chem. Soc., 2012, 134, 19969–19972 CrossRef CAS
.
- Y. Fu, D. Sun, Y. Chen, R. Huang, Z. Ding, X. Fu and Z. Li, An amine-functionalized titanium metal–organic framework photocatalyst with visible-light-induced activity for CO2 reduction, Angew. Chem., Int. Ed., 2012, 51, 3364–3367 CrossRef CAS
.
- C. W. Li and M. W. Kanan, CO2 reduction at low overpotential on cu electrodes resulting from the reduction of thick Cu2O films, J. Am. Chem. Soc., 2012, 134, 7231–7234 CrossRef CAS
.
- S. Lin, C. S. Diercks, Y. B. Zhang, N. Kornienko, E. M. Nichols, Y. Zhao, A. R. Paris, D. Kim, P. Yang, O. M. Yaghi and C. J. Chang, Covalent organic frameworks comprising cobalt porphyrins for catalytic CO2 reduction in water, Science, 2015, 349, 1208–1213 CrossRef CAS
.
- K. Jiang, R. B. Sandberg, A. J. Akey, X. Liu, D. C. Bell, J. K. Norskov, K. Chan and H. Wang, Metal ion cycling of Cu foil for selective C–C coupling in electrochemical CO2 reduction, Nat. Catal., 2018, 1, 111–119 CrossRef CAS
.
- C. G. Morales-Guio, E. R. Cave, S. A. Nitopi, J. T. Feaster, L. Wang, K. P. Kuhl, A. Jackson, N. C. Johnson, D. N. Abram, T. Hatsukade, C. Hahn and T. F. Jaramillo, Improved CO2 reduction activity towards C2+ alcohols on a tandem gold on copper electrocatalyst, Nat. Catal., 2018, 1, 764–771 CrossRef CAS
.
- K. Tran and Z. W. Ulissi, Active learning across intermetallics to guide discovery of electrocatalysts for CO2 reduction and H2 evolution, Nat. Catal., 2018, 1, 696–703 CrossRef CAS
.
- Z. Guo, G. Chen, C. Cometto, B. Ma, H. Zhao, T. Groizard, L. Chen, H. Fan, W. L. Man, S. M. Yiu, K. C. Lau, T. C. Lau and M. Robert, Selectivity control of CO versus HCOO− production in the visible-light-driven catalytic reduction of CO2 with two cooperative metal sites, Nat. Catal., 2019, 2, 801–808 CrossRef CAS
.
- J. J. Leung, J. Warnan, K. H. Ly, N. Heidary, N. D. Heon, M. F. Kuehneh and E. Reisner, Solar-driven reduction of aqueous CO2 with a cobalt bis(terpyridine)-based photocathode, Nat. Catal., 2019, 2, 354–365 CrossRef CAS
.
- Y. Lum and J. W. Ager, Evidence for product-specific active sites on oxide-derived Cu catalysts for electrochemical CO2 reduction, Nat. Catal., 2019, 2, 86–93 CrossRef CAS
.
- C. Qian, W. Sun, D. L. H. Hung, C. Qiu, M. Makaremi, S. G. H. Kumar, L. Wan, M. Ghoussoub, T. E. Wood, M. Xia, A. A. Tountas, Y. F. Li, L. Wang, Y. Dong, I. Gourevich, C. V. Singh and G. A. Ozin, Catalytic CO2 reduction by palladium-decorated silicon-hydride nanosheets, Nat. Catal., 2019, 2, 46–54 CrossRef CAS
.
- R. M. Rodrigues, X. Guan, J. A. Iniguez, D. A. Estabrook, J. O. Chapman, S. Huang, E. M. Sletten and C. Liu, Perfluorocarbon nanoemulsion promotes the delivery of reducing equivalents for electricity-driven microbial CO2 reduction, Nat. Catal., 2019, 2, 407–414 CrossRef CAS
.
- B. M. Tackett, E. Gomez and J. G. Chen, Net reduction of CO2via its thermocatalytic and electrocatalytic transformation reactions in standard and hybrid processes, Nat. Catal., 2019, 2, 381–386 CrossRef CAS
.
- B. M. Tackett, E. Gomez and J. G. Chen, Net reduction of CO2via its thermocatalytic and electrocatalytic transformation reactions in standard and hybrid processes, Nat. Catal., 2019, 2, 466 CrossRef
.
- Y. Dong, S. Chertopalov, K. Maleski, B. Anasori, L. Hu, S. Bhattacharya, A. M. Rao, Y. Gogotsi, V. N. Mochalin and R. Podila, Saturable absorption in 2D Ti3C2 mxene thin films for passive photonic diodes, Adv. Mater., 2018, 30, 1705714 CrossRef
.
- Z. Guo, G. Chen, C. Cometto, B. Ma, H. Zhao, T. Groizard, L. Chen, H. Fan, W. L. Man, S. M. Yiu, K. C. Lau, T. C. Lau and M. Robert, Selectivity control of CO versus HCOO− production in the visible-light-driven catalytic reduction of CO2 with two cooperative metal sites, Nat. Catal., 2019, 2, 801–808 CrossRef CAS
.
- R. Noyori and T. Ohkuma, Asymmetric catalysis by architectural and functional molecular engineering: practical chemo- and stereoselective hydrogenation of ketones, Angew. Chem., Int. Ed., 2001, 40, 40–73 CrossRef CAS
.
- W. Tang and X. Zhang, New chiral phosphorus ligands for enantioselective hydrogenation, Chem. Rev., 2003, 103, 3029–3069 CrossRef CAS
.
- A. Corma and P. Serna, Chemoselective hydrogenation of nitro compounds with supported gold catalysts, Science, 2006, 313, 332–334 CrossRef CAS
.
- D. C. Elias, R. R. Nair, T. M. G. Mohiuddin, S. V. Morozov, P. Blake, M. P. Halsall, A. C. Ferrari, D. W. Boukhvalov, M. I. Katsnelson, A. K. Geim and K. S. Novoselov, Control of graphene's properties by reversible hydrogenation: evidence for graphane, Science, 2009, 323, 610–613 CrossRef CAS
.
- W. Wang, S. Wang, X. Ma and J. Gong, Recent advances in catalytic hydrogenation of carbon
dioxide, Chem. Soc. Rev., 2011, 40, 3703–3727 RSC
.
- H. Zhao, J. Miao, L. Zhang, Y. Rong, J. Chen, J. Deng, R. Yu, J. Cao, H. Wang and X. Xing, Lattice distortion and orbital hybridization in NdFeO3–PbTiO3 ferroelectric thin films, Dalton Trans., 2016, 45, 1554–1559 RSC
.
- S. Kattel, P. J. Ramirez, J. G. Chen, J. A. Rodriguez and P. Liu, Catalysis active sites for CO2 hydrogenation to methanol on Cu/ZnO catalysts, Science, 2017, 355, 1296–1299 CrossRef CAS
.
- S. Li, Y. Xu, Y. Chen, W. Li, L. Lin, M. Li, Y. Deng, X. Wang, B. Ge, C. Yang, S. Yao, J. Xie, Y. Li, X. Liu and D. Ma, Tuning the selectivity of catalytic carbon dioxide hydrogenation over iridium/cerium oxide catalysts with a strong metal-support interaction, Angew. Chem., Int. Ed., 2017, 56, 10761–10765 CrossRef CAS
.
- R. A. Periana, D. J. Taube, S. Gamble, H. Taube, T. Satoh and H. Fujii, Platinum catalysts for the high-yield oxidation of methane to a methanol derivative, Science, 1998, 280, 560–564 CrossRef CAS
.
- Z. Jin, L. Wang, E. Zuidema, K. Mondal, M. Zhang, J. Zhang, C. Wang, X. Meng, H. Yang, C. Mesters and F. S. Xiao, Hydrophobic zeolite modification for in situ peroxide formation in methane oxidation to methanol, Science, 2020, 367, 193–197 CAS
.
- V. L. Sushkevich, D. Palagin, M. Ranocchiari and J. A. van Bokhoven, Selective anaerobic oxidation of methane enables direct synthesis of methanol, Science, 2017, 356, 523–527 CrossRef CAS
.
- N. Agarwal, S. J. Freakley, R. U. McVicker, S. M. Althahban, N. Dimitratos, Q. He, D. J. Morgan, R. L. Jenkins, D. J. Willock, S. H. Taylor, C. J. Kiely and G. J. Hutchings, Aqueous Au–Pd colloids catalyze selective CH4 oxidation to CH3OH with O2 under mild conditions, Science, 2017, 358, 223–227 CrossRef CAS
.
- R. A. Periana, O. Mironov, D. Taube, G. Bhalla and C. J. Jones, Catalytic, Oxidative Condensation of CH4 to CH3COOH in one step via CH activation, Science, 2003, 301, 814–818 CrossRef CAS
.
- A. A. Herzing, C. J. Kiely, A. F. Carley, P. Landon and G. J. Hutchings, Identification of active gold nanoclusters on iron oxide supports for CO oxidation, Science, 2008, 321, 1331–1335 CrossRef CAS
.
- M. Jin, H. Liu, H. Zhang, Z. Xie, J. Liu and Y. Xia, Synthesis of Pd nanocrystals enclosed by {100} facets and with sizes <10 nm for application in CO oxidation, Nano Res., 2011, 4, 83–91 CrossRef CAS
.
- B. Qiao, A. Wang, X. Yang, L. F. Allard, Z. Jiang, Y. Cui, J. Liu, J. Li and T. Zhang, Single-atom catalysis of CO oxidation using Pt-1/FeOx, Nat. Chem., 2011, 3, 634–641 CrossRef CAS
.
- S. Najafishirtari, R. Brescia, P. Guardia, S. Marras, L. Manna and M. Colombo, Nanoscale transformations of alumina-supported AuCu ordered phase nanocrystals and their activity in CO oxidation, ACS Catal., 2015, 5, 2154–2163 CrossRef CAS
.
- H. Zhu, Z. Wu, D. Su, G. M. Veith, H. Lu, P. Zhang, S. H. Chai and S. Dai, Constructing hierarchical interfaces: TiO2-supported PtFe–FeOx nanowires for room temperature CO oxidation, J. Am. Chem. Soc., 2015, 137, 10156–10159 CrossRef CAS
.
- S. I. Choi, A. Young, S. R. Lee, C. Ma, M. Luo, M. Chi, C.-K. Tsung and Y. Xia, Pd@Rh core–shell nanocrystals with well-defined facets and their enhanced catalytic performance towards CO oxidation, Nanoscale Horiz., 2019, 4, 1232–1238 RSC
.
- J. Y. Chen, T. Herricks, M. Geissler and Y. N. Xia, Single-crystal nanowires of platinum can be synthesized by controlling the reaction rate of a polyol process, J. Am. Chem. Soc., 2004, 126, 10854–10855 CrossRef CAS
.
- E. P. Lee, Z. Peng, D. M. Cate, H. Yang, C. T. Campbell and Y. Xia, Growing Pt nanowires as a densely packed array on metal gauze, J. Am. Chem. Soc., 2007, 129, 10634–10635 CrossRef CAS
.
- E. P. Lee, Z. Peng, W. Chen, S. Chen, H. Yang and Y. Xia, Electrocatalytic properties of Pt nanowires supported on Pt and W gauzes, ACS Nano, 2008, 2, 2167–2173 CrossRef CAS
.
- E. Formo, E. Lee, D. Campbell and Y. Xia, Functionalization of electrospun TiO2 nanofibers with Pt nanoparticles and nanowires for catalytic applications, Nano Lett., 2008, 8, 668–672 CrossRef CAS
.
- E. P. Lee and Y. Xia, Growth and patterning of Pt Nanowires on silicon substrates, Nano Res., 2008, 1, 129–137 CrossRef CAS
.
- H. Yin, S. Zhao, K. Zhao, A. Muqsit, H. Tang, L. Chang, H. Zhao, Y. Gao and Z. Tang, Ultrathin platinum nanowires grown on single-layered nickel hydroxide with high hydrogen evolution activity, Nat. Commun., 2015, 6, 6430 CrossRef CAS
.
- H. Van Thi Thanh, N. Nam Giang, C. J. Pan, J. H. Cheng, J. Rick, W. N. Su, J. F. Lee, H. S. Sheu and B. J. Hwang, Advanced nanoelectrocatalyst for methanol oxidation and oxygen reduction reaction, fabricated as one-dimensional pt nanowires on nanostructured robust Ti0.7Ru0.3O2 support, Nano Energy, 2012, 1, 687–695 CrossRef
.
- M. A. Hoque, F. M. Hassan, D. Higgins, J. Y. Choi, M. Pritzker, S. Knights, S. Ye and Z. Chen, Multigrain platinum nanowires consisting of oriented nanoparticles anchored on sulfur-doped graphene as a highly active and durable oxygen reduction electrocatalyst, Adv. Mater., 2015, 27, 1229–1234 CrossRef CAS
.
- S. Sun, F. Jaouen and J. P. Dodelet, Controlled growth of Pt nanowires on carbon nanospheres and their enhanced performance as electrocatalysts in PEM fuel cells, Adv. Mater., 2008, 20, 3900–3904 CrossRef CAS
.
- S. Sun, G. Zhang, Y. Zhong, H. Liu, R. Li, X. Zhou and X. Sun, Ultrathin single crystal Pt nanowires grown on N–doped carbon nanotubes, Chem. Commun., 2009, 7048–7050 RSC
.
- H. B. R. Lee, S. H. Baeck, T. F. Jaramillo and S. F. Bent, Growth of Pt nanowires by atomic layer deposition on highly ordered pyrolytic graphite, Nano Lett., 2013, 13, 457–463 CrossRef CAS
.
- J. Shui and J. C. M. Li, Platinum nanowires produced by electrospinning, Nano Lett., 2009, 9, 1307–1314 CrossRef CAS
.
- A. Ponrouch, S. Garbarino, E. Bertin, C. Andrei, G. A. Botton and D. Guay, Highly porous and preferentially oriented {100} platinum nanowires and thin films, Adv. Funct. Mater., 2012, 22, 4172–4181 CrossRef CAS
.
- X. Teng, W. Han, W. Ku and M. Huecker, Synthesis of ultrathin palladium and platinum nanowires and a study of their magnetic properties, Angew. Chem., Int. Ed., 2008, 47, 2055–2058 CrossRef CAS
.
- F. Kong, M. N. Banis, L. Du, L. Zhang, L. Zhang, J. Li, K. Doyle-Davis, J. Liang, Q. Liu, X. Yang, R. Li, C. Du, G. Yin and X. Sun, Highly stable one-dimensional Pt nanowires with modulated structural disorder towards the oxygen reduction reaction, J. Mater. Chem. A, 2019, 7, 24830–24836 RSC
.
- S. Bai, L. Bu, Q. Shao, X. Zhu and X. Huang, Multicomponent Pt-based zigzag nanowires as selectivity controllers for selective hydrogenation reactions, J. Am. Chem. Soc., 2018, 140, 8384–8387 CrossRef CAS
.
- S. M. Choi, J. H. Kim, J. Y. Jung, E. Y. Yoon and W. B. Kim, Pt nanowires prepared via a polymer template method: its promise toward high Pt-loaded electrocatalysts for methanol oxidation, Electrochim. Acta, 2008, 53, 5804–5811 CrossRef CAS
.
- C. Zhang, L. Xu, Y. Yan and J. Chen, Controlled synthesis of Pt nanowires with ordered large mesopores for methanol oxidation reaction, Sci. Rep., 2016, 6, 31440 CrossRef CAS
.
- L. Zhang, N. Li, F. Gao, L. Hou and Z. Xu, Insulin amyloid fibrils: an excellent platform for controlled synthesis of ultrathin superlong platinum nanowires with high electrocatalytic activity, J. Am. Chem. Soc., 2012, 134, 11326–11329 CrossRef CAS
.
- X. Teng, M. Feygenson, Q. Wang, J. He, W. Du, A. I. Frenkel, W. Han and M. Aronson, Electronic and magnetic properties of ultrathin Au/Pt nanowires, Nano Lett., 2009, 9, 3177–3184 CrossRef CAS
.
- W. Hong, J. Wang and E. Wang, Dendritic Au/Pt and Au/PtCu nanowires with enhanced electrocatalytic activity for methanol electrooxidation, Small, 2014, 10, 3262–3265 CrossRef CAS
.
- F. Chang, S. Shan, V. Petkov, Z. Skeete, A. Lu, J. Ravid, J. Wu, J. Luo, G. Yu, Y. Ren and C. J. Zhong, Composition tunability and (111)-dominant facets of ultrathin platinum–gold alloy nanowires toward enhanced electrocatalysis, J. Am. Chem. Soc., 2016, 138, 12166–12175 CrossRef CAS
.
- X. Cao, Y. Han, C. Gao, X. Huang, Y. Xu and N. Wang, PtAg nanowires: facile synthesis and their applications as excellent oxygen reduction electrocatalysts for label-free electrochemical immunoassay, J. Mater. Chem. A, 2013, 1, 14904–14909 RSC
.
- X. Cao, N. Wang, Y. Han, C. Gao, Y. Xu, M. Li and Y. Shao, PtAg bimetallic nanowires: facile synthesis and their use as excellent electrocatalysts toward low-cost fuel cells, Nano Energy, 2015, 12, 105–114 CrossRef CAS
.
- Z. Peng, H. You and H. Yang, Composition-dependent formation of platinum silver nanowires, ACS Nano, 2010, 4, 1501–1510 CrossRef CAS
.
- F. Liu, P. Qi, X. Liang, W. Chen, B. Li, L. Zhang, Y. Yang and S. Huang, Tuning ion complexing to rapidly prepare hollow Ag–Pt nanowires with high activity toward the methanol oxidization reaction, Chem. – Eur. J., 2018, 24, 17345–17355 CrossRef CAS
.
- X. Teng, W. Han, Q. Wang, L. Li, A. I. Frenkel and J. C. Yang, Hybrid Pt/Au nanowires: synthesis and electronic structure, J. Phys. Chem. C, 2008, 112, 14696–14701 CrossRef CAS
.
- H. Huang, K. Li, Z. Chen, L. Luo, Y. Gu, D. Zhang, C. Ma, R. Si, J. Yang, Z. Peng and J. Zeng, Achieving remarkable activity and durability toward oxygen reduction reaction based on ultrathin Rh-doped Pt nanowires, J. Am. Chem. Soc., 2017, 139, 8152–8159 CrossRef CAS
.
- Y. Shen, B. Gong, K. Xiao and L. Wang,
In situ assembly
of ultrathin ptrh nanowires to graphene nanosheets as highly efficient electrocatalysts for the oxidation of ethanol, ACS Appl. Mater. Interfaces, 2017, 9, 3535–3543 CrossRef CAS
.
- G. Y. Zhao, C. L. Xu, D. J. Guo, H. Li and H. L. Li, Template preparation of Pt–Ru and Pt nanowire array electrodes on a Ti/Si substrate for methanol electro-oxidation, J. Power Sources, 2006, 162, 492–496 CrossRef CAS
.
- Y. S. Kim, S. H. Nam, H. S. Shim, H. J. Ahn, M. Anand and W. B. Kim, Electrospun bimetallic nanowires of PtRh and PtRu with compositional variation for methanol electrooxidation, Electrochem. Commun., 2008, 10, 1016–1019 CrossRef CAS
.
- B. Li, D. C. Higgins, S. Zhu, H. Li, H. Wang, J. Ma and Z. Chen, Highly active Pt-Ru nanowire network catalysts for the methanol oxidation reaction, Catal. Commun., 2012, 18, 51–54 CrossRef CAS
.
- J. Zheng, D. A. Cullen, R. V. Forest, J. A. Wittkopft, Z. Zhuang, W. Sheng, J. G. Chen and Y. Yan, Platinum-ruthenium nanotubes and platinum-ruthenium coated copper nanowires as efficient catalysts for electro-oxidation of methanol, ACS Catal., 2015, 5, 1468–1474 CrossRef CAS
.
- Q. Yuan, Z. Zhou, J. Zhuang and X. Wang, Seed displacement, epitaxial synthesis of Rh/Pt bimetallic ultrathin nanowires for highly selective oxidizing ethanol to CO2, Chem. Mater., 2010, 22, 2395–2402 CrossRef CAS
.
- K. Jiang, L. Bu, P. Wang, S. Guo and X. Huang, Trimetallic PtSnRh wavy nanowires as efficient nanoelectrocatalysts for alcohol electrooxidation, ACS Appl. Mater. Interfaces, 2015, 7, 15061–15067 CrossRef CAS
.
- Y. Ma, W. Gao, H. Shan, W. Chen, W. Shang, P. Tao, C. Song, C. Addiego, T. Deng, X. Pan and J. Wu, Platinum-based nanowires as active catalysts toward oxygen reduction reaction: in situ observation of surface-diffusion-assisted, solid-state oriented attachment, Adv. Mater., 2017, 29, 1703460 CrossRef
.
- Y. Yang, L. Liu, F. Gueder, A. Berger, R. Scholz, O. Albrecht and M. Zacharias, Regulated oxidation of nickel in multisegmented nickel-platinum nanowires: an entry to wavy nanopeapods, Angew. Chem., Int. Ed., 2011, 50, 10855–10858 CrossRef CAS
.
- L. Bu, J. Ding, S. Guo, X. Zhang, D. Su, X. Zhu, J. Yao, J. Guo, G. Lu and X. Huang, A general method for multimetallic platinum alloy nanowires as highly active and stable oxygen reduction catalysts, Adv. Mater., 2015, 27, 7204–7212 CrossRef CAS
.
- P. Wang, K. Jiang, G. Wang, J. Yao and X. Huang, Phase and interface engineering of platinum-nickel nanowires for efficient electrochemical hydrogen evolution, Angew. Chem., Int. Ed., 2016, 55, 12859–12863 CrossRef CAS
.
- P. Wang, X. Zhang, J. Zhang, S. Wan, S. Guo, G. Lu, J. Yao and X. Huang, Precise tuning in platinum-nickel/nickel sulfide interface nanowires for synergistic hydrogen evolution catalysis, Nat. Commun., 2017, 8, 14580 CrossRef CAS
.
- N. Zhang, Q. Shao, P. Wang, X. Zhu and X. Huang, Porous Pt–Ni nanowires within in situ generated metal–organic frameworks for highly chemoselective cinnamaldehyde hydrogenation, Small, 2018, 14, 1704318 CrossRef
.
- S. Guo, S. Zhang, X. Sun and S. Sun, Synthesis of ultrathin FePtPd nanowires and their use as catalysts for methanol oxidation reaction, J. Am. Chem. Soc., 2011, 133, 15354–15357 CrossRef CAS
.
- Y. Xu, A. V. Ruban and M. Mavrikakis, Adsorption and dissociation of O2 on Pt–Co and Pt–Fe alloys, J. Am. Chem. Soc., 2004, 126, 4717–4725 CrossRef CAS
.
- H. Chen, R. Wang, R. Huang, C. Zhao, Y. Li, Z. Gong, Y. Yao, Y. Cui, F. Yang and X. Bao, Surface and subsurface structures of the Pt–Fe Surface alloy on Pt(111), J. Phys. Chem. C, 2019, 123, 17225–17231 CrossRef CAS
.
- S. Bai, B. Huang, Q. Shao and X. Huang, Universal strategy for ultrathin Pt–M (M = Fe, Co, Ni) nanowires for efficient catalytic hydrogen generation, ACS Appl. Mater. Interfaces, 2018, 10, 22257–22263 CrossRef CAS
.
- C. Wang, Y. Hou, J. Kim and S. Sun, A general strategy for synthesizing FePt nanowires and nanorods, Angew. Chem., Int. Ed., 2007, 46, 6333–6335 CrossRef CAS
.
- S. Guo, D. Li, H. Zhu, S. Zhang, N. M. Markovic, V. R. Stamenkovic and S. Sun, FePt and CoPt nanowires as efficient catalysts for the oxygen reduction reaction, Angew. Chem., Int. Ed., 2013, 52, 3465–3468 CrossRef CAS
.
- P. Song, H. Xu, J. Wang, Y. Zhang, F. Gao, J. Guo, Y. Shiraishi and Y. Du, 1D alloy ultrafine Pt–Fe nanowires as efficient electrocatalysts for alcohol electrooxidation in alkaline media, Nanoscale, 2018, 10, 16468–16473 RSC
.
- Y. Zhang, F. Gao, T. Song, C. Wang, C. Chen and Y. Du, Novel networked wicker-like PtFe nanowires with branch-rich exteriors for efficient electrocatalysis, Nanoscale, 2019, 11, 15561–15566 RSC
.
- M. Luo, Y. Sun, X. Zhang, Y. Qin, M. Li, Y. Li, C. Li, Y. Yang, L. Wang, P. Gao, G. Lu and S. Guo, Stable high-index faceted pt skin on zigzag-like PtFe nanowires enhances oxygen reduction catalysis, Adv. Mater., 2018, 30, 1705515 CrossRef
.
- J. X. Feng, S. Y. Tong, Y. X. Tong and G. R. Li, Pt-like hydrogen evolution electrocatalysis on PANI/CoP hybrid nanowires by weakening the shackles of hydrogen ions on the surfaces of catalysts, J. Am. Chem. Soc., 2018, 140, 5118–5126 CrossRef CAS
.
- S. M. Alia, S. Pylypenko, K. C. Neyerlin, D. A. Cullen, S. S. Kocha and B. S. Pivovar, Platinum-coated cobalt nanowires as oxygen reduction reaction electrocatalysts, ACS Catal., 2014, 4, 2680–2686 CrossRef CAS
.
- B. Xia, H. Wu, N. Li, Y. Yan, X. Lou and X. Wang, One-pot synthesis of Pt–Co alloy nanowire assemblies with tunable composition and enhanced electrocatalytic properties, Angew. Chem., Int. Ed., 2015, 54, 3797–3801 CrossRef CAS
.
- D. C. Higgins, R. Wang, M. A. Hoque, P. Zamani, S. Abureden and Z. Chen, Morphology and composition controlled platinum–cobalt alloy nanowires prepared by electrospinning as oxygen reduction catalyst, Nano Energy, 2014, 10, 135–143 CrossRef CAS
.
- Z. Wang, X. Ren, Y. Luo, L. Wang, G. Cui, F. Xie, H. Wang, Y. Xie and X. Sun, An ultrafine platinum–cobalt alloy decorated cobalt nanowire array with superb activity toward alkaline hydrogen evolution, Nanoscale, 2018, 10, 12302–12307 RSC
.
- L. Liu, E. Pippel, R. Scholz and U. Goesele, Nanoporous Pt–Co alloy nanowires: fabrication, characterization, and electrocatalytic properties, Nano Lett., 2009, 9, 4352–4358 CrossRef CAS
.
- Q. Lu, L. Sun, X. Zhao, J. Huang, C. Han and X. Yang, One-pot synthesis of interconnected Pt95Co5 nanowires with enhanced electrocatalytic performance for methanol oxidation reaction, Nano Res., 2018, 11, 2562–2572 CrossRef CAS
.
- M. Luo, Y. Sun, Y. Qin, S. Chen, Y. Li, C. Li, Y. Yang, D. Wu, N. Xu, Y. Xing, L. Wang, P. Gao and S. Guo, Surface and near-surface engineering of PtCo nanowires at atomic scale for enhanced electrochemical sensing and catalysis, Chem. Mater., 2018, 30, 6660–6667 CrossRef CAS
.
- S. Bai, Q. Shao, Y. Feng, L. Bu and X. Huang, Highly efficient carbon dioxide hydrogenation to methanol catalyzed by zigzag platinum–cobalt nanowires, Small, 2017, 13, 1604311 CrossRef
.
- L. Bu, S. Guo, X. Zhang, X. Shen, D. Su, G. Lu, X. Zhu, J. Yao, J. Guo and X. Huang, Surface engineering of hierarchical platinum-cobalt nanowires for efficient electrocatalysis, Nat. Commun., 2016, 7, 11850 CrossRef CAS
.
- X. Yu, D. Wang, Q. Peng and Y. Li, Pt–M (M = Cu, Co, Ni, Fe) Nanocrystals: From Small Nanoparticles to Wormlike Nanowires by Oriented Attachment, Chem. – Eur. J., 2013, 19, 233–239 CrossRef CAS
.
- N. Zhang, L. Bu, S. Guo, J. Guo and X. Huang, Screw thread-like platinum–copper nanowires bounded with high-index facets for efficient electrocatalysis, Nano Lett., 2016, 16, 5037–5043 CrossRef CAS
.
- J. Cao, Y. Du, M. Dong, Z. Chen and J. Xu, Template-free synthesis of chain-like PtCu nanowires and their superior performance for oxygen reduction and methanol oxidation reaction, J. Alloys Compd., 2018, 747, 124–130 CrossRef CAS
.
- Y. Liao, G. Yu, Y. Zhang, T. Guo, F. Chang and C. J. Zhong, Composition-tunable PtCu alloy nanowires and electrocatalytic synergy for methanol oxidation reaction, J. Phys. Chem. C, 2016, 120, 10476–10484 CrossRef CAS
.
- S. M. Alia, B. S. Pivovar and Y. Yan, Platinum-coated copper nanowires with high activity for hydrogen oxidation reaction in base, J. Am. Chem. Soc., 2013, 135, 13473–13478 CrossRef CAS
.
- S. M. Alia, K. Jensen, C. Contreras, F. Garzon, B. Pivovar and Y. Yan, Platinum coated copper nanowires and platinum nanotubes as oxygen reduction electrocatalysts, ACS Catal., 2013, 3, 358–362 CrossRef CAS
.
- Y. Xu, X. Cui, S. Wei, Q. Zhang, L. Gu, F. Meng, J. Fan and W. Zheng, Highly active zigzag-like Pt–Zn alloy nanowires with high-index facets for alcohol electrooxidation, Nano Res., 2019, 12, 1173–1179 CrossRef CAS
.
- H. Zhang, M. Jin, Y. Xiong, B. Lim and Y. Xia, Shape-controlled synthesis of Pd nanocrystals and their catalytic applications, Acc. Chem. Res., 2013, 46, 1783–1794 CrossRef CAS
.
- B. Lim, M. Jiang, J. Tao, P. H. C. Camargo, Y. Zhu and Y. Xia, Shape-controlled synthesis of pd nanocrystals in aqueous solutions, Adv. Funct. Mater., 2009, 19, 189–200 CrossRef CAS
.
- K. B. Lee, S. M. Lee and J. Cheon, Size-controlled synthesis of Pd nanowires using a mesoporous silica template via chemical vapor infiltration, Adv. Mater., 2001, 13, 517–520 CrossRef CAS
.
- C. Koenigsmann, A. C. Santulli, E. Sutter and S. S. Wong, Ambient surfactant less synthesis, growth mechanism, and size-dependent electrocatalytic behavior of high-quality, single crystalline palladium nanowires, ACS Nano, 2011, 5, 7471–7487 CrossRef CAS
.
- D. Xu, X. Liu, M. Han and J. Bao, Facile synthesis of ultrathin single-crystalline palladium nanowires with enhanced electrocatalytic activities, Chem. Commun., 2016, 52, 12996–12999 RSC
.
- H. Liang, S. Liu, J. Gong, S. Wang, L. Wang and S. Yu, Ultrathin Te nanowires: an excellent platform for controlled synthesis of ultrathin platinum and palladium nanowires/nanotubes with very high aspect ratio, Adv. Mater., 2009, 21, 1850–1854 CrossRef CAS
.
- Y. Wang, S. I. Choi, X. Zhao, S. Xie, H. Peng, M. Chi, C. Huang and Y. Xia, Polyol synthesis of ultrathin Pd nanowires via attachment-based growth and their enhanced activity towards formic acid oxidation, Adv. Funct. Mater., 2014, 24, 131–139 CrossRef CAS
.
- X. Huang and N. Zheng, One-pot, high-yield synthesis of 5-fold twinned Pd nanowires and nanorods, J. Am. Chem. Soc., 2009, 131, 4602–4603 CrossRef CAS
.
- H. Huang, A. Ruditskiy, S. I. Choi, L. Zhang, J. Liu, Z. Ye and Y. Xia, One-pot synthesis of penta-twinned palladium nanowires and their enhanced electrocatalytic properties, ACS Appl. Mater. Interfaces, 2017, 9, 31203–31212 CrossRef CAS
.
- Y. Chen, H. Hung and M. Huang, Seed-mediated synthesis of palladium nanorods and branched nanocrystals and their use as recyclable Suzuki coupling reaction catalysts, J. Am. Chem. Soc., 2009, 131, 9114–9121 CrossRef CAS
.
- T. Bhuvana and G. U. Kulkarni, Highly conducting patterned Pd nanowires by direct-write electron beam lithography, ACS Nano, 2008, 2, 457–462 CrossRef CAS
.
- Y. Yoo, I. Yoon, H. Lee, J. Ahn, J. P. Ahn and B. Kim, Pattern-selective epitaxial growth of twin-free Pd nanowires from supported nanocrystal seeds, ACS Nano, 2010, 4, 2919–2927 CrossRef CAS
.
- J. S. Jang, S. Qiao, S. J. Cho, G. Jha, A. F. Ogata, W. T. Koo, D. H. Kim, I. D. Kim and R. M. Penner, Hollow Pd–Ag composite nanowires for fast responding and transparent hydrogen sensors, ACS Appl. Mater. Interfaces, 2017, 9, 39464–39474 CrossRef CAS
.
- D. Yang, J. Carpena-Nunez, L. F. Fonseca, A. Biaggi-Labiosa and G. W. Hunter, Shape-controlled synthesis of palladium and copper superlattice nanowires for high-stability hydrogen sensors, Sci. Rep., 2014, 4, 3773 CrossRef
.
- H. Li, S. Zhao, M. Gong, C. Cui, D. He, H. Liang, L. Wu and S. Yu, Ultrathin PtPdTe nanowires as superior catalysts for methanol electrooxidation, Angew. Chem., Int. Ed., 2013, 52, 7472–7476 CrossRef CAS
.
- H. Li, C. Cui, S. Zhao, H. Yao, M. Gao, F. Fan and S. Yu, Mixed-PtPd-shell PtPdCu nanoparticle nanotubes templated from copper nanowires as efficient and highly durable electrocatalysts, Adv. Energy Mater., 2012, 2, 1182–1187 CrossRef CAS
.
- L. Du, D. Feng, X. Xing, Y. Fu, L. F. Fonseca and D. Yang, Palladium/cobalt nanowires with improved hydrogen sensing stability at ultra-low temperatures, Nanoscale, 2019, 11, 21074–21080 RSC
.
- C. Koenigsmann, E. Sutter, T. A. Chiesa, R. R. Adzic and S. S. Wong, Highly enhanced electrocatalytic oxygen reduction performance observed in bimetallic palladium-based nanowires prepared under ambient, surfactantless conditions, Nano Lett., 2012, 12, 2013–2020 CrossRef CAS
.
- X. Zeng, Y. Wang, H. Deng, M. L. Latimer, Z. Xiao, J. Pearson, T. Xu, H. Wang, U. Welp, G. W. Crabtree and W. K. Kwok, Networks of ultrasmall Pd/Cr nanowires as high performance hydrogen sensors, ACS Nano, 2011, 5, 7443–7452 CrossRef CAS
.
- C. Koenigsmann and S. S. Wong, Tailoring chemical composition to achieve enhanced methanol oxidation reaction and methanol-tolerant oxygen reduction reaction performance in palladium-based nanowire systems, ACS Catal., 2013, 3, 2031–2040 CrossRef CAS
.
- H. Peng, C. Rao, N. Zhang, X. Wang, W. Liu, W. Mao, L. Han, P. Zhang and S. Dai, Confined ultrathin Pd–Ce nanowires with outstanding moisture and SO2 tolerance
in methane combustion, Angew. Chem., Int. Ed., 2018, 57, 8953–8957 CrossRef CAS
.
- Y. Sun, Z. Tao, J. Chen, T. Herricks and Y. Xia, Ag nanowires coated with Ag/Pd alloy sheaths and their use as substrates for reversible absorption and desorption of hydrogen, J. Am. Chem. Soc., 2004, 126, 5940–5941 CrossRef CAS
.
- H. H. Li, S. Y. Ma, Q. Q. Fu, X. J. Liu, L. Wu and S. H. Yu, Scalable bromide-triggered synthesis of Pd@Pt core–shell ultrathin nanowires with enhanced electrocatalytic performance toward oxygen reduction reaction, J. Am. Chem. Soc., 2015, 137, 7862–7868 CrossRef CAS
.
- C. Zhu, S. Guo and S. Dong, PdM (M = Pt, Au) bimetallic alloy nanowires with enhanced electrocatalytic activity for electro-oxidation of small molecules, Adv. Mater., 2012, 24, 2326–2331 CrossRef CAS
.
- X. Teng, Q. Wang, P. Liu, W. Han, A. Frenkel, W. Wen, N. Marinkovic, J. C. Hanson and J. A. Rodriguez, Formation of Pd/Au nanostructures from Pd nanowires via galvanic replacement reaction, J. Am. Chem. Soc., 2008, 130, 1093–1101 CrossRef CAS
.
- B. Yan, H. Xu, K. Zhang, S. Li, J. Wang, Y. Shi and Y. Du, Cu assisted synthesis of self-supported PdCu alloy nanowires with enhanced performances toward ethylene glycol electrooxidation, Appl. Surf. Sci., 2018, 434, 701–710 CrossRef CAS
.
- S. Guo, S. Zhang, D. Su and S. Sun, Seed-mediated synthesis of core/shell FePtM/FePt (M = Pd, Au) nanowires and their electrocatalysis for oxygen reduction reaction, J. Am. Chem. Soc., 2013, 135, 13879–13884 CrossRef CAS
.
- S. Zhu, Q. Wang, X. Qin, M. Gu, R. Tao, B. P. Lee, L. Zhang, Y. Yao, T. Li and M. Shao, Tuning structural and compositional effects in Pd–Au nanowires for highly selective and active CO2 electrochemical reduction reaction, Adv. Energy Mater., 2018, 8, 1802238 CrossRef
.
- J. Lv, Z. Wang, J. Feng, R. Qiu, A. Wang and X. Xu, Facile synthesis of highly active Pd–Cu nanowires catalyst through a simple wet-chemical strategy for ligand-free Suzuki cross coupling reaction, Appl. Catal., A, 2016, 522, 188–193 CrossRef CAS
.
- H. Liu, R. R. Adzic and S. S. Wong, Multifunctional ultrathin PdxCu1−x and PtPdxCu1−x one-dimensional nanowire motifs for various small molecule oxidation reactions, ACS Appl. Mater. Interfaces, 2015, 7, 26145–26157 CrossRef CAS
.
- A. Kumar, M. M. Mohammadi and M. T. Swihart, Synthesis, growth mechanisms, and applications of palladium-based nanowires and other one-dimensional nanostructures, Nanoscale, 2019, 11, 19058–19085 RSC
.
- S. Zhu, Q. Wang, X. Qin, M. Gu, R. Tao, B. P. Lee, L. Zhang, Y. Yao, T. Li and M. Shao, Tuning structural and compositional effects in Pd–Au nanowires for highly selective and active CO2 electrochemical reduction reaction, Adv. Energy Mater., 2018, 8, 1802238 CrossRef
.
- J.l. Shui, C. Chen and J. C. M. Li, Evolution of nanoporous Pt–Fe alloy nanowires by dealloying and their catalytic property for oxygen reduction reaction, Adv. Funct. Mater., 2011, 21, 3357–3362 CrossRef CAS
.
- Y. Imura, K. Tsujimoto, C. Morita and T. Kawai, Preparation and catalytic activity of Pd and bimetallic Pd–Ni nanowires, Langmuir, 2014, 30, 5026–5030 CrossRef CAS
.
- B. Nikoobakht and M. A. El-Sayed, Preparation and growth mechanism of gold nanorods (NRs) using seed-mediated growth method, Chem. Mater., 2003, 15, 1957–1962 CrossRef CAS
.
- X. Huang, S. Neretina and M. A. El-Sayed, Gold nanorods: from synthesis and properties to biological and biomedical applications, Adv. Mater., 2009, 21, 4880–4910 CrossRef CAS
.
- H. Chen, L. Shao, Q. Li and J. Wang, Gold nanorods and their plasmonic properties, Chem. Soc. Rev., 2013, 42, 2679–2724 RSC
.
- Y. Xu, L. Chen, X. Ye, X. Wang, J. Yu, Y. Zhao, M. Cao, Z. Xia, B. Sun and Q. Zhang, Cooperative interactions among CTA+, Br− and Ag+ during seeded growth of gold nanorods, Nano Res., 2017, 10, 2146–2155 CrossRef CAS
.
- Y. Xu, X. Wang, L. Chen, Y. Zhao, L. He, P. Yang, H. Wu, F. Bao and Q. Zhang, High-yield synthesis of gold nanoribbons by using binary surfactants, J. Mater. Chem. C, 2015, 3, 1447–1451 RSC
.
- S. E. Lohse and C. J. Murphy, The quest for shape control: a history of gold nanorod synthesis, Chem. Mater., 2013, 25, 1250–1261 CrossRef CAS
.
- J. Pérez-Juste, I. Pastoriza-Santos, L. M. Liz-Marzán and P. Mulvaney, Gold nanorods: synthesis, characterization and applications, Coord. Chem. Rev., 2005, 249, 1870–1901 CrossRef
.
- N. Li, P. Zhao and D. Astruc, Anisotropic gold nanoparticles: synthesis, properties, applications, and toxicity, Angew. Chem., Int. Ed., 2014, 53, 1756–1789 CrossRef CAS
.
- N. R. Jana, L. Gearheart and C. J. Murphy, Seed-mediated growth approach for shape-controlled synthesis of spheroidal and rod-like gold nanoparticles using a surfactant template, Adv. Mater., 2001, 13, 1389–1393 CrossRef CAS
.
- N. R. Jana, L. Gearheart and C. J. Murphy, Wet chemical synthesis of high aspect ratio cylindrical gold nanorods, J. Phys. Chem. B, 2001, 105, 4065–4067 CrossRef CAS
.
- X. Ye, C. Zheng, J. Chen, Y. Gao and C. B. Murray, Using binary surfactant mixtures to simultaneously improve the dimensional tunability and monodispersity in the seeded growth of gold nanorods, Nano Lett., 2013, 13, 765–771 CrossRef CAS
.
- N. R. Jana, L. Gearheart and C. J. Murphy, Wet chemical synthesis of silver nanorods and nanowires of controllable aspect ratio, Chem. Commun., 2001, 617–618 RSC
.
- B. Pietrobon, M. McEachran and V. Kitaev, Synthesis of size-controlled faceted pentagonal silver nanorods with tunable plasmonic properties and self-assembly of these nanorods, ACS Nano, 2009, 3, 21–26 CrossRef CAS
.
- C. Ni, P. A. Hassan and E. W. Kaler, Structural characteristics and growth of pentagonal silver nanorods prepared by a surfactant method, Langmuir, 2005, 21, 3334–3337 CrossRef CAS
.
- J. Zhang, M. R. Langille and C. A. Mirkin, Synthesis of silver nanorods by low energy excitation of spherical plasmonic seeds, Nano Lett., 2011, 11, 2495–2498 CrossRef CAS
.
- J. Hu, Q. Chen, Z. Xie, G. Han, R. Wang, B. Ren, Y. Zhang, Z. Yang and Z. Tian, A simple and effective route for the synthesis of crystalline silver nanorods and nanowires, Adv. Funct. Mater., 2004, 14, 183–189 CrossRef CAS
.
- X. Fu, Z. Zhao, C. Wan, Y. Wang, Z. Fan, F. Song, B. Cao, M. Li, W. Xue, Y. Huang and X. Duan, Ultrathin wavy Rh nanowires as highly effective electrocatalysts for methanol oxidation reaction with ultrahigh ECSA, Nano Res., 2019, 12, 211–215 CrossRef CAS
.
- K. Liu, W. Wang, P. Guo, J. Ye, Y. Wang, P. Li, Z. Lyu, Y. Geng, M. Liu and S. Xie, Replicating the defect structures on ultrathin Rh nanowires with Pt to achieve superior electrocatalytic activity toward ethanol oxidation, Adv. Funct. Mater., 2019, 29, 1806300 CrossRef
.
- H. D. A. Mohamed, S. M. D. Watson, B. R. Horrocks and A. Houlton, Chemical and electrochemical routes to DNA-templated rhodium nanowires, J. Mater. Chem. C, 2015, 3, 438–446 RSC
.
- J. Schoiswohl, F. Mittendorfer, S. Surnev, M. G. Ramsey, J. N. Andersen and F. P. Netzer, Chemical reactivity of Ni–Rh nanowires, Phys. Rev. Lett., 2006, 97, 126102 CrossRef CAS
.
- Y. Liu, Z. Wu, K. Lin, J. Huang, F. Chen, J. Kai, Y. Lin, W. Jian and J. Lin, Growth of single-crystalline RuO2 nanowires with one- and two-nanocontact electrical characterizations, Appl. Phys. Lett., 2007, 90, 013105 CrossRef
.
- S. Zhang and H. C. Zeng, Solution-based epitaxial growth of magnetically responsive Cu@Ni nanowires, Chem. Mater., 2010, 22, 1282–1284 CrossRef CAS
.
- P. M. Paulus, F. Luis, M. Kröll, G. Schmid and L. J. de Jongh, Low-temperature study of the magnetization reversal and magnetic anisotropy of Fe, Ni, and Co nanowires, J. Magn. Magn. Mater., 2001, 224, 180–196 CrossRef CAS
.
- H. Pan, B. Liu, J. Yi, C. Poh, S. Lim, J. Ding, Y. Feng, C. H. A. Huan and J. Lin, Growth of single-crystalline ni and co nanowires via electrochemical deposition and their magnetic properties, J. Phys. Chem. B, 2005, 109, 3094–3098 CrossRef CAS
.
- Y. Song, M. A. Hickner, S. R. Challa, R. M. Dorin, R. M. Garcia, H. Wang, Y. B. Jiang, P. Li, Y. Qiu, F. van Swol, C. J. Medforth, J. E. Miller, T. Nwoga, K. Kawahara, W. Li and J. A. Shelnutt, Evolution of dendritic platinum nanosheets into ripening-resistant holey sheets, Nano Lett., 2009, 9, 1534–1539 CrossRef CAS
.
- T. Kijima, Y. Nagatomo, H. Takemoto, M. Uota, D. Fujikawa, Y. Sekiya, T. Kishishita, M. Shimoda, T. Yoshimura, H. Kawasaki and G. Sakai, Synthesis of nanohole-structured single-crystalline platinum nanosheets using surfactant-liquid-crystals and their electrochemical characterization, Adv. Funct. Mater., 2009, 19, 545–553 CrossRef CAS
.
- M. Chhetri, M. Rana, B. Loukya, P. K. Patil, R. Datta and U. K. Gautam, Mechanochemical synthesis of free-standing platinum nanosheets and their electrocatalytic properties, Adv. Mater., 2015, 27, 4430–4437 CrossRef CAS
.
- Y. Feng, B. Huang, C. Yang, Q. Shao and X. Huang, Platinum porous nanosheets with high surface distortion and Pt utilization for enhanced oxygen reduction catalysis, Adv. Funct. Mater., 2019, 29, 1904429 CrossRef CAS
.
- H. Liu, P. Zhong, K. Liu, L. Han, H. Zheng, Y. Yin and C. Gao, Synthesis of ultrathin platinum nanoplates for enhanced oxygen reduction activity, Chem. Sci., 2018, 9, 398–404 RSC
.
- A. Funatsu, H. Tateishi, K. Hatakeyama, Y. Fukunaga, T. Taniguchi, M. Koinuma, H. Matsuura and Y. Matsumoto, Synthesis of monolayer platinum nanosheets, Chem. Commun., 2014, 50, 8503–8506 RSC
.
- Y. Qin, M. Luo, Y. Sun, C. Li, B. Huang, Y. Yang, Y. Li, L. Wang and S. Guo, Intermetallic hcp-PtBi/fcc-Pt core/shell nanoplates enable efficient bifunctional oxygen reduction and methanol oxidation electrocatalysis, ACS Catal., 2018, 8, 5581–5590 CrossRef CAS
.
- C. Wang, Z. Yu, G. Li, Q. Song, G. Li, C. Luo, S. Yin, B. Lu, C. Xiao, B. Xu, Z. Zhou, N. Tian and S. Sun, Intermetallic PtBi nanoplates with high catalytic activity towards electro-oxidation of formic acid and glycerol, ChemElectroChem, 2020, 7, 239–245 CrossRef CAS
.
- X. Yuan, X. Jiang, M. Cao, L. Chen, K. Nie, Y. Zhang, Y. Xu, X. Sun, Y. Li and Q. Zhang, Intermetallic PtBi core/ultrathin Pt shell nanoplates for efficient and stable methanol and ethanol electro-oxidization, Nano Res., 2019, 12, 429–436 CrossRef CAS
.
- Y. Feng, Q. Shao, F. Lv, L. Bu, J. Guo, S. Guo and X. Huang, Intermetallic PtBi nanoplates boost oxygen reduction catalysis with superior tolerance over chemical fuels, Adv. Sci., 2020, 7, 1800178 CrossRef CAS
.
- Y. Liang, Y. Sun, X. Wang, E. Fu, J. Zhang, J. Du, X. Wen and S. Guo, High electrocatalytic performance inspired by crystalline/amorphous interface in PtPb nanoplate, Nanoscale, 2018, 10, 11357–11364 RSC
.
- Y. Sun, Y. Liang, M. Luo, F. Lv, Y. Qin, L. Wang, C. Xu, E. Fu and S. Guo, Defects and interfaces on PtPb nanoplates boost fuel cell electrocatalysis, Small, 2018, 14, 1702259 CrossRef
.
- L. Bu, N. Zhang, S. Guo, X. Zhang, J. Li, J. Yao, T. Wu, G. Lu, J. Y. Ma, D. Su and X. Huang, Biaxially strained PtPb/Pt core/shell nanoplate boosts oxygen reduction catalysis, Science, 2016, 354, 1410–1414 CrossRef CAS
.
- S. Luo, W. Chen, Y. Cheng, X. Song, Q. Wu, L. Li, X. Wu, T. Wu, M. Li, Q. Yang, K. Deng and Z. Quan, Trimetallic synergy in intermetallic PtSnBi nanoplates boosts formic acid oxidation, Adv. Mater., 2019, 31, 1903683 CrossRef CAS
.
- M. Lokanathan, I. M. Patil, P. Mukherjee, A. Swami and B. Kakade, Molten-salt synthesis of Pt3Co binary alloy nanoplates as excellent and durable electrocatalysts toward oxygen electroreduction, ACS Sustainable Chem. Eng., 2020, 8, 986–993 CrossRef CAS
.
- F. Saleem, Z. Zhang, B. Xu, X. Xu, P. He and X. Wang, Ultrathin Pt–Cu nanosheets and nanocones, J. Am. Chem. Soc., 2013, 135, 18304–18307 CrossRef CAS
.
- C. L. Lee and C. M. Tseng, Ag–Pt nanoplates: galvanic displacement preparation and their applications as electrocatalysts, J. Phys. Chem. C, 2008, 112, 13342–13345 CrossRef CAS
.
- P. F. Siril, L. Ramos, P. Beaunier, P. Archirel, A. Etcheberry and H. Remita, Synthesis of ultrathin hexagonal palladium nanosheets, Chem. Mater., 2009, 21, 5170–5175 CrossRef CAS
.
- X. Huang, S. Tang, X. Mu, Y. Dai, G. Chen, Z. Zhou, F. Ruan, Z. Yang and N. Zheng, Freestanding palladium nanosheets with plasmonic and catalytic properties, Nat. Nanotechnol., 2011, 6, 28–32 CrossRef CAS
.
- Q. Feng, S. Zhao, Y. Wang, J. Dong, W. Chen, D. He, D. Wang, J. Yang, Y. Zhu, H. Zhu, L. Gu, Z. Li, Y. Liu, R. Yu, J. Li and Y. Li, Isolated single-atom Pd sites in intermetallic nanostructures: high catalytic selectivity for semihydrogenation of alkynes, J. Am. Chem. Soc., 2017, 139, 7294–7301 CrossRef CAS
.
- S. Tang, M. Chen and N. Zheng, Multifunctional ultrasmall Pd nanosheets
for enhanced near-infrared photothermal therapy and chemotherapy of cancer, Nano Res., 2015, 8, 165–174 CrossRef CAS
.
- W. Fang, S. Tang, P. Liu, X. Fang, J. Gong and N. Zheng, Pd nanosheet-covered hollow mesoporous silica nanoparticles as a platform for the chemo-photothermal treatment of cancer cells, Small, 2012, 8, 3816–3822 CrossRef CAS
.
- S. Tang, X. Huang and N. Zheng, Silica coating improves the efficacy of Pd nanosheets for photothermal therapy of cancer cells using near infrared laser, Chem. Commun., 2011, 47, 3948–3950 RSC
.
- S. Tang, M. Chen and N. Zheng, Sub-10 nm Pd nanosheets with renal clearance for efficient near-infrared photothermal cancer therapy, Small, 2014, 10, 3139–3144 CrossRef CAS
.
- Y. Pan, X. Yin, K. S. Kwok and H. Yang, Higher-order nanostructures of two-dimensional palladium nanosheets for fast hydrogen sensing, Nano Lett., 2014, 14, 5953–5959 CrossRef CAS
.
- X. Yin, X. Liu, Y. T. Pan, K. A. Walsh and H. Yang, Hanoi tower-like multi layered ultrathin palladium nanosheets, Nano Lett., 2014, 14, 7188–7194 CrossRef CAS
.
- H. Li, G. Chen, H. Yang, X. Wang, J. Liang, P. Liu, M. Chen and N. Zheng, Shape-controlled synthesis of surface-clean ultrathin palladium nanosheets by simply mixing a dinuclear Pd–I carbonyl chloride complex with H2O, Angew. Chem., Int. Ed., 2013, 52, 8368–8372 CrossRef CAS
.
- C. Hu, K. Lin, X. Wang, S. Liu, J. Yi, Y. Tian, B. Wu, G. Chen, H. Yang, Y. Dai, H. Li and N. Zheng, Electrostatic self-assembling formation of Pd superlattice nanowires from surfactant-free ultrathin Pd nanosheets, J. Am. Chem. Soc., 2014, 136, 12856–12859 CrossRef CAS
.
- N. Yang, Z. Zhang, B. Chen, Y. Huang, J. Chen, Z. Lai, Y. Chen, M. Sindoro, A. L. Wang, H. Cheng, Z. Fan, X. Liu, B. Li, Y. Zong, L. Gu and H. Zhang, Synthesis of ultrathin PdCu alloy nanosheets used as a highly efficient electrocatalyst for formic acid oxidation, Adv. Mater., 2017, 29, 1700769 CrossRef
.
- L. Jin, H. Xu, C. Chen, H. Shang, Y. Wang, C. Wang and Y. Du, Three-dimensional PdCuM (M = Ru, Rh, Ir) trimetallic alloy nanosheets for enhancing methanol oxidation electrocatalysis, ACS Appl. Mater. Interfaces, 2019, 11, 42123–42130 CrossRef CAS
.
- X. Zhao, L. Dai, Q. Qin, F. Pei, C. Hu and N. Zheng, Self-supported 3D PdCu alloy nanosheets as a bifunctional catalyst for electrochemical reforming of ethanol, Small, 2017, 13, 1602970 CrossRef
.
- S. Li, T. Wang, R. Yue, H. Wang, Q. Bai, H. Xiao, N. Sui, L. Wang, M. Liu and W. W. Yu, PdFe ultrathin nanosheets for highly sensitive detection of nitrite, Electroanalysis, 2019, 32, 931–938 CrossRef
.
- W. C. Cheong, C. Liu, M. Jiang, H. Duan, D. Wang, C. Chen and Y. Li, Free-standing palladium-nickel alloy wavy nanosheets, Nano Res., 2016, 9, 2244–2250 CrossRef CAS
.
- C. Tang, N. Zhang, Y. Ji, Q. Shao, Y. Li, X. Xiao and X. Huang, Fully tensile strained Pd3Pb/Pd tetragonal nanosheets enhance oxygen reduction catalysis, Nano Lett., 2019, 19, 1336–1342 CrossRef
.
- H. Shang, H. Xu, C. Wang, L. Jin, C. Chen, G. Zhou, Y. Wang and Y. Du, General synthesis of Pd–pm (pm = Ga, In, Sn, Pb, Bi) alloy nanosheet assemblies for advanced electrocatalysis, Nanoscale, 2020, 12, 3411–3417 RSC
.
- C. Hu, X. Mu, J. Fan, H. Ma, X. Zhao, G. Chen, Z. Zhou and N. Zheng, Interfacial effects in PdAg bimetallic nanosheets for selective dehydrogenation of formic acid, ChemNanoMat, 2016, 2, 28–32 CrossRef CAS
.
- Q. Yang, L. Shi, B. Yu, J. Xu, C. Wei, Y. Wang and H. Chen, Facile synthesis of ultrathin Pt–Pd nanosheets for enhanced formic acid oxidation and oxygen reduction reaction, J. Mater. Chem. A, 2019, 7, 18846–18851 RSC
.
- J. W. Hong, Y. Kim, D. H. Wi, S. Lee, S. U. Lee, Y. W. Lee, S. I. Choi and S. W. Han, Ultrathin free-standing ternary-alloy nanosheets, Angew. Chem., Int. Ed., 2016, 55, 2753–2758 CrossRef CAS
.
- Y. Yan, H. Shan, G. Li, F. Xiao, Y. Jiang, Y. Yan, C. Jin, H. Zhang, J. Wu and D. Yang, Epitaxial growth of multimetallic Pd@PtM (M = Ni, Rh, Ru) core–shell nanoplates realized by in situ-produced CO from interfacial catalytic reactions, Nano Lett., 2016, 16, 7999–8004 CrossRef CAS
.
- M. Chen, S. Tang, Z. Guo, X. Wang, S. Mo, X. Huang, G. Liu and N. Zheng, Core–shell Pd@Au nanoplates as theranostic agents for in-vivo photoacoustic imaging, CT imaging, and photothermal therapy, Adv. Mater., 2014, 26, 8210–8216 CrossRef CAS
.
- B. Lim, J. Wang, P. H. C. Camargo, M. Jiang, M. J. Kim and Y. Xia, Facile synthesis of bimetallic nanoplates consisting of Pd cores and Pt shells through seeded epitaxial growth, Nano Lett., 2008, 8, 2535–2540 CrossRef CAS
.
- Y. Zhao, S. Xing, X. Meng, J. Zeng, S. Yin, X. Li and Y. Chen, Ultrathin Rh nanosheets as a highly efficient bifunctional electrocatalyst for isopropanol-assisted overall water splitting, Nanoscale, 2019, 11, 9319–9326 RSC
.
- J. Bai, G. R. Xu, S. H. Xing, J. H. Zeng, J. X. Jiang and Y. Chen, Hydrothermal synthesis and catalytic application of ultrathin rhodium nanosheet nanoassemblies, ACS Appl. Mater. Interfaces, 2016, 8, 33635–33641 CrossRef CAS
.
- H. Duan, N. Yan, R. Yu, C. R. Chang, G. Zhou, H. S. Hu, H. Rong, Z. Niu, J. Mao, H. Asakura, T. Tanaka, P. J. Dyson, J. Li and Y. Li, Ultrathin rhodium nanosheets, Nat. Commun., 2014, 5, 3093 CrossRef
.
- Z. Zhang, X. Wang, K. Yuan, W. Zhu, T. Zhang, Y. Wang, J. Ke, X. Zheng, C. Yan and Y. Zhang, Free-standing iridium and rhodium-based hierarchically-coiled ultrathin nanosheets for highly selective reduction of nitrobenzene to azoxybenzene under ambient conditions, Nanoscale, 2016, 8, 15744–15752 RSC
.
- J. Zhang, M. Chen, J. Chen, H. Li, S. Wang, Q. Kuang, Z. Cao and Z. Xie, Synthesis of single-crystal hyperbranched rhodium nanoplates with remarkable catalytic properties, Sci. China Mater., 2017, 60, 685–696 CrossRef CAS
.
- K. Jang, H. J. Kim and S. U. Son, Low-temperature synthesis of ultrathin rhodium nanoplates via molecular orbital symmetry interaction between rhodium precursors, Chem. Mater., 2010, 22, 1273–1275 CrossRef CAS
.
- J. Y. Park, Y. Zhang, M. Grass, T. Zhang and G. A. Somorjai, Tuning of catalytic CO oxidation by changing composition of Rh–Pt bimetallic nanoparticles, Nano Lett., 2008, 8, 673–677 CrossRef CAS
.
- B. Yoon and C. M. Wai, Microemulsion-templated synthesis of carbon nanotube-supported Pd and Rh nanoparticles for catalytic applications, J. Am. Chem. Soc., 2005, 127, 17174–17175 CrossRef CAS
.
- W. Zhan, Q. Zhu, S. Dang, Z. Liu, M. Kitta, K. Suenaga, L. Zheng and Q. Xu, Synthesis of highly active sub-nanometer Pt@Rh core–shell nanocatalyst via a photochemical route: porous titania nanoplates as a superior photoactive support, Small, 2017, 13, 1603879 CrossRef
.
- I. Nakamula, Y. Yamanoi, T. Imaoka, K. Yamamoto and H. Nishihara, A uniform bimetallic rhodium/iron nanoparticle catalyst for the hydrogenation of olefins and nitroarenes, Angew. Chem., Int. Ed., 2011, 50, 5830–5833 CrossRef CAS
.
- D. Köhler, M. Heise, A. I. Baranov, Y. Luo, D. Geiger, M. Ruck and M. Armbrüster, Synthesis of BiRh nanoplates with superior catalytic performance in the semihydrogenation of acetylene, Chem. Mater., 2012, 24, 1639–1644 CrossRef
.
- Y. Zhao, J. Bai, X. Wu, P. Chen, P. Jin, H. Yao and Y. Chen, Atomically ultrathin RhCo alloy nanosheet aggregates for efficient water electrolysis in broad pH range, J. Mater. Chem. A, 2019, 7, 16437–16446 RSC
.
- Y. Kang, Q. Xue, P. Jin, J. Jiang, J. Zeng and Y. Chen, Rhodium nanosheets-reduced graphene oxide hybrids: a highly active platinum-alternative electrocatalyst for the methanol oxidation reaction in alkaline media, ACS Sustainable Chem. Eng., 2017, 5, 10156–10162 CrossRef CAS
.
- L. Zhao, C. Xu, H. Su, J. Liang, S. Lin, L. Gu, X. Wang, M. Chen and N. Zheng, Single-crystalline rhodium nanosheets with atomic thickness, Adv. Sci., 2015, 2, 1500100 CrossRef
.
- M. E. Stewart, C. R. Anderton, L. B. Thompson, J. Maria, S. K. Gray, J. A. Rogers and R. G. Nuzzo, Nanostructured plasmonic sensors, Chem. Rev., 2008, 108, 494–521 CrossRef CAS
.
- C. S. Ah, Y. J. Yun, H. J. Park, W. J. Kim, D. H. Ha and W. S. Yun, Size-controlled synthesis of machinable single crystalline gold nanoplates, Chem. Mater., 2005, 17, 5558–5561 CrossRef CAS
.
- H. Chu, C. Kuo and M. Huang, Thermal aqueous solution approach for the synthesis of triangular and hexagonal gold nanoplates with three different size ranges, Inorg. Chem., 2006, 45, 808–813 CrossRef CAS
.
- W. Huang, C. Chen and M. Huang, Investigation of the growth process of gold nanoplates formed by thermal aqueous solution approach and the synthesis of ultra-small gold nanoplates, J. Phys. Chem. C, 2007, 111, 2533–2538 CrossRef CAS
.
- C. J. Murphy and N. R. Jana, Controlling the aspect ratio of inorganic nanorods and nanowires, Adv. Mater., 2002, 14, 80–82 CrossRef CAS
.
- A. Gole and C. J. Murphy, Seed-mediated synthesis of gold nanorods: role of the size and nature of the seed, Chem. Mater., 2004, 16, 3633–3640 CrossRef CAS
.
- C. J. Johnson, E. Dujardin, S. A. Davis, C. J. Murphy and S. Mann, Growth and form of gold nanorods prepared by seed-mediated, surfactant-directed synthesis, J. Mater. Chem., 2002, 12, 1765–1770 RSC
.
- X. Ye, Y. Gao, J. Chen, D. C. Reifsnyder, C. Zheng and C. B. Murray, Seeded growth of monodisperse gold nanorods using bromide-free surfactant mixtures, Nano Lett., 2013, 13, 2163–2171 CrossRef CAS
.
- M. Yamamoto, Y. Kashiwagi, T. Sakata, H. Mori and M. Nakamoto, Synthesis and morphology of star-shaped gold nanoplates protected by poly (N-vinyl-2-pyrrolidone), Chem. Mater., 2005, 17, 5391–5393 CrossRef CAS
.
- L. Chen, F. Ji, Y. Xu, L. He, Y. Mi, F. Bao, B. Sun, X. Zhang and Q. Zhang, High-Yield Seedless Synthesis of Triangular Gold Nanoplates through Oxidative Etching, Nano Lett., 2014, 14, 7201–7206 CrossRef CAS
.
- N. R. Jana, L. Gearheart and C. J. Murphy, Seeding growth for size control of 5–40 nm diameter gold nanoparticles, Langmuir, 2001, 17, 6782–6786 CrossRef CAS
.
- S. E. Habas, H. Lee, V. Radmilovic, G. A. Somorjai and P. Yang, Shaping binary metal nanocrystals through epitaxial seeded growth, Nat. Mater., 2007, 6, 692–697 CrossRef CAS
.
- T. K. Sau and C. J. Murphy, Seeded high yield synthesis of short Au nanorods in aqueous solution, Langmuir, 2004, 20, 6414–6420 CrossRef CAS
.
- H. L. Wu, C. H. Chen and M. H. Huang, Seed-mediated synthesis of branched gold nanocrystals derived from the side growth of pentagonal bipyramids and the formation of gold nanostars, Chem. Mater., 2008, 21, 110–114 CrossRef
.
- M. Liu and P. Guyot-Sionnest, Mechanism of silver(I)-assisted growth of gold nanorods and bipyramids, J. Phys. Chem. B, 2005, 109, 22192–22200 CrossRef CAS
.
- X. Kou, S. Zhang, C. K. Tsung, M. H. Yeung, Q. Shi, G. D. Stucky, L. Sun, J. Wang and C. Yan, Growth of gold nanorods and bipyramids using CTEAB surfactant, J. Phys. Chem. B, 2006, 110, 16377–16383 CrossRef CAS
.
- X. Kou, W. Ni, C. K. Tsung, K. Chan, H. Q. Lin, G. D. Stucky and J. Wang, Growth of gold bipyramids with improved yield and their curvature-directed oxidation, Small, 2007, 3, 2103–2113 CrossRef CAS
.
- M. L. Personick, M. R. Langille, J. Zhang, N. Harris, G. C. Schatz and C. A. Mirkin, Synthesis and isolation of {110}-faceted gold bipyramids and rhombic dodecahedra, J. Am. Chem. Soc., 2011, 133, 6170–6173 CrossRef CAS
.
- J. Zeng, X. Xia, M. Rycenga, P. Henneghan, Q. Li and Y. Xia, Successive deposition of silver on silver nanoplates: lateral versus vertical growth, Angew. Chem., Int. Ed., 2011, 50, 244–249 CrossRef CAS
.
- J. E. Millstone, W. Wei, M. R. Jones, H. Yoo and C. A. Mirkin, Iodide ions control seed-mediated growth of anisotropic gold nanoparticles, Nano Lett., 2008, 8, 2526–2529 CrossRef CAS
.
- K. Aslan, J. R. Lakowicz and C. D. Geddes, Rapid deposition of triangular silver nanoplates on planar surfaces: application to metal-enhanced fluorescence, J. Phys. Chem. B, 2005, 109, 6247–6251 CrossRef CAS
.
- T. K. Sau and C. J. Murphy, Room temperature, high-yield synthesis of multiple shapes of gold nanoparticles in aqueous solution, J. Am. Chem. Soc., 2004, 126, 8648–8649 CrossRef CAS
.
- J. E. Millstone, S. Park, K. L. Shuford, L. Qin, G. C. Schatz and C. A. Mirkin, Observation of a quadrupole plasmon mode for a colloidal solution of gold nanoprisms, J. Am. Chem. Soc., 2005, 127, 5312–5313 CrossRef CAS
.
- J. E. Millstone, G. S. Métraux and C. A. Mirkin, Controlling the edge length of gold nanoprisms via a seed-mediated approach, Adv. Funct. Mater., 2006, 16, 1209–1214 CrossRef CAS
.
- A. Rahim Ferhan, High-yield synthesis of triangular gold nanoplates with improved shape uniformity, tunable edge length and thickness, Nanoscale, 2014, 6, 6496–6500 RSC
.
- A. Rai, A. Singh, A. Ahmad and M. Sastry, Role of halide ions and temperature on the morphology of biologically synthesized gold nanotriangles, Langmuir, 2006, 22, 736–741 CrossRef CAS
.
- O. M. Magnussen, Ordered anion adlayers on metal electrode surfaces, Chem. Rev., 2002, 102, 679–726 CrossRef CAS
.
- T. H. Ha, H. J. Koo and B. H. Chung, Shape-controlled syntheses of gold nanoprisms and nanorods influenced by specific adsorption of halide ions, J. Phys. Chem. C, 2007, 111, 1123–1130 CrossRef CAS
.
- A. Ali Umar and M. Oyama, Formation of gold nanoplates on indium tin oxide surface: two-dimensional crystal growth from gold nanoseed particles in the presence of poly (vinylpyrrolidone), Cryst. Growth Des., 2006, 6, 818–821 CrossRef
.
- S. R. Beeram and F. P. Zamborini, Purification of gold nanoplates grown directly on surfaces for enhanced localized surface plasmon resonance biosensing, ACS Nano, 2010, 4, 3633–3646 CrossRef CAS
.
- R. Jin, Y. Cao, C. A. Mirkin, K. L. Kelly, G. C. Schatz and J. G. Zheng, Photoinduced conversion of silver nanospheres to nanoprisms, Science, 2001, 294, 1901–1903 CrossRef CAS
.
- J. Zhu, Y. Shen, A. Xie, L. Qiu, Q. Zhang and S. Zhang, Photoinduced synthesis of anisotropic gold nanoparticles in room-temperature ionic liquid, J. Phys. Chem. C, 2007, 111, 7629–7633 CrossRef CAS
.
- S. Yang, T. Zhang, L. Zhang, S. Wang, Z. Yang and B. Ding, Continuous synthesis of gold nanoparticles and nanoplates with controlled size and shape under UV irradiation, Colloids Surf., A, 2007, 296, 37–44 CrossRef CAS
.
- T. Soejima and N. Kimizuka, One-pot room-temperature synthesis of single-crystalline gold nanocorolla in water, J. Am. Chem. Soc., 2009, 131, 14407–14412 CrossRef CAS
.
- A. Miranda, E. Malheiro, E. Skiba, P. Quaresma, P. A. Carvalho, P. Eaton, B. de Castro, J. A. Shelnutt and E. Pereira, One-pot synthesis of triangular gold nanoplates allowing broad and fine tuning of edge length, Nanoscale, 2010, 2, 2209–2216 RSC
.
- M. Tsuji, R. Matsuo, P. Jiang, N. Miyamae, D. Ueyama, M. Nishio, S. Hikino, H. Kumagae, K. S. N. Kamarudin and X. L. Tang, Shape-dependent evolution of Au@Ag core–shell nanocrystals by PVP-assisted N,N-dimethylformamide reduction, Cryst. Growth Des., 2008, 8, 2528–2536 CrossRef CAS
.
- J. Kim, S. Hong, H. J. Jang, Y. Choi and S. Park, Influence of iodide ions on morphology of silver growth on gold hexagonal nanoplates, J. Colloid Interface Sci., 2013, 389, 71–76 CrossRef CAS
.
- S. Hong, Y. Choi and S. Park, Shape control of Ag shell growth on Au nanodisks, Chem. Mater., 2011, 23, 5375–5378 CrossRef CAS
.
- C. Xue, J. E. Millstone, S. Li and C. A. Mirkin, Plasmon-driven synthesis of triangular core–shell nanoprisms from gold seeds, Angew. Chem., Int. Ed., 2007, 46, 8436–8439 CrossRef CAS
.
- J. M. Zhang, B. Y. Lai, Z. X. Chen, S. Chu, G. Chu and R. F. Peng, Hexagonal core–shell and alloy Au/Ag nanodisks on ZnO nanorods and their optical enhancement effect, Nanoscale Res. Lett., 2014, 9, 237 CrossRef
.
- Y. Sun and Y. Xia, Triangular nanoplates of silver: synthesis, characterization, and use as sacrificial templates for generating triangular nanorings of gold, Adv. Mater., 2003, 15, 695–699 CrossRef CAS
.
- M. Maillard, P. Huang and L. Brus, Silver nanodisk growth by surface plasmon enhanced photoreduction of adsorbed [Ag+], Nano Lett., 2003, 3, 1611–1615 CrossRef CAS
.
- R. Jin, Y. C. Cao, E. Hao, G. S. Metraux, G. C. Schatz and C. A. Mirkin, Controlling anisotropic nanoparticle growth through plasmon excitation, Nature, 2003, 425, 487–490 CrossRef CAS
.
- J. E. Millstone, S. J. Hurst, G. S. Métraux, J. I. Cutler and C. A. Mirkin, Colloidal gold and silver triangular nanoprisms, Small, 2009, 5, 646–664 CrossRef CAS
.
- C. Xue, G. S. Métraux, J. E. Millstone and C. A. Mirkin, Mechanistic study of photomediated triangular silver nanoprism growth, J. Am. Chem. Soc., 2008, 130, 8337–8344 CrossRef CAS
.
- A. Callegari, D. Tonti and M. Chergui, Photochemically grown silver nanoparticles with wavelength-controlled size and shape, Nano Lett., 2003, 3, 1565–1568 CrossRef CAS
.
- V. Bastys, I. Pastoriza-Santos, B. Rodríguez-González, R. Vaisnoras and L. M. Liz-Marzán, Formation of silver nanoprisms with surface plasmons at communication wavelengths, Adv. Funct. Mater., 2006, 16, 766–773 CrossRef CAS
.
- B. Tang, S. Xu, J. An, B. Zhao and W. Xu, Photoinduced shape conversion and reconstruction of silver nanoprisms, J. Phys. Chem. C, 2009, 113, 7025–7030 CrossRef CAS
.
- C. Xue and C. A. Mirkin, pH-switchable silver nanoprism growth pathways, Angew. Chem., Int. Ed., 2007, 46, 2036–2038 CrossRef CAS
.
- J. Zhang, M. R. Langille and C. A. Mirkin, Photomediated synthesis of silver triangular bipyramids and prisms: the effect of pH and BSPP, J. Am. Chem. Soc., 2010, 132, 12502–12510 CrossRef CAS
.
- Q. Zhang, J. Ge, T. Pham, J. Goebl, Y. Hu, Z. Lu and Y. Yin, Reconstruction of silver nanoplates by uv irradiation: tailored optical properties and enhanced stability, Angew. Chem., Int. Ed., 2009, 48, 3516–3519 CrossRef CAS
.
- N. Malikova, I. Pastoriza-Santos, M. Schierhorn, N. A. Kotov and L. M. Liz-Marzán, Layer-by-layer assembled mixed spherical and planar gold nanoparticles: control of interparticle interactions, Langmuir, 2002, 18, 3694–3697 CrossRef CAS
.
- Y. Sun, B. Mayers and Y. Xia, Transformation of silver nanospheres into nanobelts and triangular nanoplates through a thermal process, Nano Lett., 2003, 3, 675–679 CrossRef CAS
.
- S. Chen and D. L. Carroll, Synthesis and characterization of truncated triangular silver nanoplates, Nano Lett., 2002, 2, 1003–1007 CrossRef CAS
.
- S. Chen and D. L. Carroll, Silver nanoplates: size control in two dimensions and formation mechanisms, J. Phys. Chem. B, 2004, 108, 5500–5506 CrossRef CAS
.
- Q. Zhang, N. Li, J. Goebl, Z. Lu and Y. Yin, A systematic study of the synthesis of silver nanoplates: is citrate a “magic” reagent?, J. Am. Chem. Soc., 2011, 133, 18931–18939 CrossRef CAS
.
- Y. Sun and C. Lei, Synthesis of Out-of-Substrate Au–Ag Nanoplates with Enhanced Stability for Catalysis, Angew. Chem., 2009, 121, 6956–6959 CrossRef
.
- J. Sun, X. Wang, J. Liu, P. Wan, Q. Liao, F. Wang, L. Luo and X. Sun, Highly stable Ag–Au nanoplates and nanoframes for two-photon luminescence, RSC Adv., 2014, 4, 35263–35267 RSC
.
- L. Liang, T. Ming, W. Bing and Y. Long, Hollow Ag/Pd triangular nanoplate: a novel activator for electroless nickel deposition, Nanotechnology, 2008, 19, 215709 CrossRef
.
- C. L. Lee, H. P. Chiou, C. M. Syu, C. R. Liu, C. C. Yang and C. C. Syu, Displacement triangular Ag/Pd nanoplate as methanol-tolerant electrocatalyst in oxygen reduction reaction, Int. J. Hydrogen Energy, 2011, 36, 12706–12714 CrossRef CAS
.
- C. L. Lee, C. M. Tseng and R. B. Wu, Triangular Ag/Pd nanoplates with sawtooth edges: displacement synthesis and optical and catalytic properties, Electrochem. Commun., 2009, 11, 627–630 CrossRef CAS
.
- C. L. Lee, C. M. Tseng, R. B. Wu, C. C. Wu and C. M. Syu, Porous Ag–Pd triangle nanoplates with tunable alloy ratio for catalyzing electroless copper deposition, Colloids Surf., A, 2009, 352, 84–87 CrossRef CAS
.
- C. L. Lee, C. M. Syu, C. H. Huang, H. P. Chiou, Y. J. Chao and C. C. Yang, Cornered silver and silverplatinum nanodisks: preparation and promising activity for alkaline oxygen reduction catalysis, Appl. Catal., B, 2013, 132–133, 229–236 CrossRef CAS
.
- Y. Leng, Y. Zhang, T. Liu, M. Suzuki and X. Li, Synthesis of single crystalline triangular and hexagonal Ni nanosheets with enhanced magnetic properties, Nanotechnology, 2006, 17, 1797–1800 CrossRef CAS
.
- Y. Leng, Y. Li, X. Li and S. Takahashi, Improved magnetic anisotropy of monodispersed triangular nickel nanoplates, J. Phys. Chem. C, 2007, 111, 6630–6633 CrossRef CAS
.
- Y. Sun, L. Xu, Z. Yin and X. Song, Synthesis of copper submicro/nanoplates with high stability and their recyclable superior catalytic activity towards 4-nitrophenol reduction, J. Mater. Chem. A, 2013, 1, 12361–12370 RSC
.
- I. Pastoriza-Santos, A. Sánchez-Iglesias, B. Rodríguez-González and L. M. Liz-Marzán, Aerobic synthesis of Cu nanoplates with intense plasmon resonances, Small, 2009, 5, 440–443 CrossRef CAS
.
- H. Guo, Y. Chen, H. Ping, L. Wang and D. L. Peng, One-pot synthesis of hexagonal and triangular nickel–copper alloy nanoplates and their magnetic and catalytic properties, J. Mater. Chem., 2012, 22, 8336–8344 RSC
.
- S. Bai, Q. Yao, Y. Xu, K. Cao and X. Huang, Strong synergy in a lichen-like RuCu nanosheet boosts the direct methane oxidation to methanol, Nano Energy, 2020, 71, 104566 CrossRef CAS
.
- Y. Xiong, H. Cai, B. J. Wiley, J. Wang, M. J. Kim and Y. Xia, Synthesis and mechanistic study of palladium nanobars and nanorods, J. Am. Chem. Soc., 2007, 129, 3665–3675 CrossRef CAS
.
- R. Li, K. Bian, Y. Wang, H. Xu, J. A. Hollingsworth, T. Hanrath, J. Fang and Z. Wang, An obtuse rhombohedral superlattice assembled by Pt nanocubes, Nano Lett., 2015, 15, 6254–6260 CrossRef CAS
.
- R. Loukrakpam, P. Chang, J. Luo, B. Fang, D. Mott, I. T. Bae, H. R. Naslund, M. H. Engelhard and C. J. Zhong, Chromium-assisted synthesis of platinum nanocube electrocatalysts, Chem. Commun., 2010, 46, 7184–7186 RSC
.
- G. Chen, Y. Tan, B. Wu, G. Fu and N. Zheng, Carbon monoxide-controlled synthesis of surface-clean Pt nanocubes with high electrocatalytic activity, Chem. Commun., 2012, 48, 2758–2760 RSC
.
- B. Wu, N. Zheng and G. Fu, Small molecules control the formation of Pt nanocrystals: a key role of carbon monoxide in the synthesis of Pt nanocubes, Chem. Commun., 2011, 47, 1039–1041 RSC
.
- Y. Kang, J. B. Pyo, X. Ye, R. E. Diaz, T. R. Gordon, E. A. Stach and C. B. Murray, Shape-controlled synthesis of Pt nanocrystals: the role of metal carbonyls, ACS Nano, 2013, 7, 645–653 CrossRef CAS
.
- H. G. Liao, D. Zherebetskyy, H. Xin, C. Czarnik, P. Ercius, H. Elmlund, M. Pan, L. W. Wang and H. Zheng, Facet development during platinum nanocube growth, Science, 2014, 345, 916 CrossRef CAS
.
- R. Huang, Y. H. Wen, Z. Z. Zhu and S. G. Sun, Structure and stability of platinum nanocrystals: from low-index to high-index facets, J. Mater. Chem., 2011, 21, 11578–11584 RSC
.
- Y. Xiong, B. J. Wiley and Y. Xia, Nanocrystals with unconventional shapes—a class of promising catalysts, Angew. Chem., Int. Ed., 2007, 46, 7157–7159 CrossRef CAS
.
- H. Zhang, M. Jin and Y. Xia, Noble-metal nanocrystals with concave surfaces: synthesis and applications, Angew. Chem., Int. Ed., 2012, 51, 7656–7673 CrossRef CAS
.
- Z. C. Zhang, J. F. Hui, Z. C. Liu, X. Zhang, J. Zhuang and X. Wang, Glycine-mediated syntheses of Pt concave nanocubes with high-index {hk0} facets and their enhanced electrocatalytic activities, Langmuir, 2012, 28, 14845–14848 CrossRef CAS
.
- X. Huang, Z. Zhao, J. Fan, Y. Tan and N. Zheng, Amine-assisted synthesis of concave polyhedral platinum nanocrystals having {411} high-index facets, J. Am. Chem. Soc., 2011, 133, 4718–4721 CrossRef CAS
.
- L. Zhang, D. Chen, Z. Jiang, J. Zhang, S. Xie, Q. Kuang, Z. Xie and L. Zheng, Facile syntheses and enhanced electrocatalytic activities of Pt nanocrystals with {hkk} high-index surfaces, Nano Res., 2012, 5, 181–189 CrossRef CAS
.
- L. Wei, Y. J. Fan, N. Tian, Z. Y. Zhou, X. Q. Zhao, B. W. Mao and S. G. Sun, Electrochemically shape-controlled synthesis in deep eutectic solvents—a new route to prepare Pt nanocrystals enclosed by high-index facets with high catalytic activity, J. Phys. Chem. C, 2012, 116, 2040–2044 CrossRef CAS
.
- J. Xiao, S. Liu, N. Tian, Z. Y. Zhou, H. X. Liu, B. B. Xu and S. G. Sun, Synthesis of convex hexoctahedral Pt micro/nanocrystals with high-index facets and electrochemistry-mediated shape evolution, J. Am. Chem. Soc., 2013, 135, 18754–18757 CrossRef CAS
.
- R. Easterday, O. Sanchez-Felix, B. D. Stein, D. G. Morgan, M. Pink, Y. Losovyj and L. M. Bronstein, Structural study of Pt–Fe nanoparticles: new insights into Pt bimetallic nanoparticle formation with oxidized Fe species, J. Phys. Chem. C, 2014, 118, 24769–24775 CrossRef CAS
.
- S. Prabhudev, M. Bugnet, G. Z. Zhu, C. Bock and G. A. Botton, Surface segregation of Fe in Pt–Fe alloy nanoparticles: its precedence and effect on the ordered-phase evolution during thermal annealing, ChemCatChem, 2015, 7, 3655–3664 CrossRef CAS
.
- S. Wang, Q. Luo, Y. Zhu, S. Tang and Y. Du, Facile Synthesis of Quaternary Structurally Ordered L1(2)–Pt(Fe, Co, Ni)(3) Nanoparticles with Low Content of Platinum as Efficient Oxygen Reduction Reaction Electrocatalysts, ACS Omega, 2019, 4, 17894–17902 CrossRef CAS
.
- Q. Yue, K. Zhang, X. Chen, L. Wang, J. Zhao, J. Liu and J. Jia, Generation of OH radicals in oxygen reduction reaction at Pt–Co nanoparticles supported on graphene in alkaline solutions, Chem. Commun., 2010, 46, 3369–3371 RSC
.
- H. L. L. Xin, S. Alayoglu, R. Tao, A. Genc, C. Wang, L. Kovarik, E. A. Stach, L. Wang, M. Salmeron, G. A. Somorjai and H. Zheng, Revealing the atomic restructuring of Pt–Co nanoparticles, Nano Lett., 2014, 14, 3203–3207 CrossRef CAS
.
- D. S. Choi, A. W. Robertson, J. H. Warner, S. O. Kim and H. Kim, Low-temperature chemical vapor deposition synthesis of Pt–Co alloyed nanoparticles with enhanced oxygen reduction reaction catalysis, Adv. Mater., 2016, 28, 7115–7122 CrossRef CAS
.
- V. R. Stamenkovic, B. Fowler, B. S. Mun, G. Wang, P. N. Ross, C. A. Lucas and N. M. Markovic, Improved oxygen reduction activity on Pt3Ni(111) via increased surface site availability, Science, 2007, 315, 493–497 CrossRef CAS
.
- J. Wu, J. Zhang, Z. Peng, S. Yang, F. T. Wagner and H. Yang, Truncated octahedral Pt3Ni oxygen reduction reaction electrocatalysts, J. Am. Chem. Soc., 2010, 132, 4984–4985 CrossRef CAS
.
- J. Zhang, H. Yang, J. Fang and S. Zou, Synthesis and oxygen reduction activity of shape-controlled Pt3Ni nanopolyhedra, Nano Lett., 2010, 10, 638–644 CrossRef CAS
.
- J. Wu and H. Yang, Synthesis and electrocatalytic oxygen reduction properties of truncated octahedral Pt3Ni nanoparticles, Nano Res., 2011, 4, 72–82 CrossRef CAS
.
- J. Zhang, Z. Luo, Z. Quan, Y. Wang, A. Kumbhar, D. M. Smilgies and J. Fang, Low packing density self-assembled superstructure of octahedral Pt3Ni nanocrystals, Nano Lett., 2011, 11, 2912–2918 CrossRef CAS
.
- X. Huang, E. Zhu, Y. Chen, Y. Li, C. Y. Chiu, Y. Xu, Z. Lin, X. Duan and Y. Huang, A facile strategy to Pt3Ni nanocrystals with highly porous features as an enhanced oxygen reduction reaction catalyst, Adv. Mater., 2013, 25, 2974–2979 CrossRef CAS
.
- N. Becknell, Y. Kang, C. Chen, J. Resasco, N. Kornienko, J. Guo, N. M. Markovic, G. A. Somorjai, V. R. Stamenkovic and P. Yang, Atomic structure of Pt3Ni nanoframe electrocatalysts by in situ X-ray absorption spectroscopy, J. Am. Chem. Soc., 2015, 137, 15817–15824 CrossRef CAS
.
- X. Huang, Z. Zhao, L. Cao, Y. Chen, E. Zhu, Z. Lin, M. Li, A. Yan, A. Zettl, Y. M. Wang, X. Duan, T. Mueller and Y. Huang, High-performance transition metal-doped Pt3Ni octahedra for oxygen reduction reaction, Science, 2015, 348, 1230–1234 CrossRef CAS
.
- R. Li, J. Zhang, R. Tan, F. Gerdes, Z. Luo, H. Xu, J. A. Hollingsworth, C. Klinke, O. Chen and Z. Wang, Competing interactions between various entropic forces toward assembly of Pt3Ni octahedra into a body-centered cubic superlattice, Nano Lett., 2016, 16, 2792–2799 CrossRef CAS
.
- B. W. Zhang, Z. C. Zhang, H. G. Liao, Y. Gong, L. Gu, X. M. Qu, L. X. You, S. Liu, L. Huang, X. C. Tian, R. Huang, F. C. Zhu, T. Liu, Y. X. Jiang, Z. Y. Zhou and S. G. Sun, Tuning Pt-skin to Ni-rich surface of Pt3Ni catalysts supported on porous carbon for enhanced oxygen reduction reaction and formic electro-oxidation, Nano Energy, 2016, 19, 198–209 CrossRef CAS
.
- C. Wang, L. Zhang, H. Yang, J. Pan, J. Liu, C. Dotse, Y. Luan, R. Gao, C. Lin, J. Zhang, J. P. Kilcrease, X. Wen, S. Zou and J. Fang, High-Indexed Pt3Ni alloy tetrahexahedral nanoframes evolved through preferential CO etching, Nano Lett., 2017, 17, 2204–2210 CrossRef CAS
.
- M. Gong, Z. Deng, D. Xiao, L. Han, T. Zhao, Y. Lu, T. Shen, X. Liu, R. Lin, T. Huang, G. Zhou, H. Xin and D. Wang, One-nanometer-thick Pt3Ni bimetallic alloy nanowires advanced oxygen reduction reaction: integrating multiple advantages into one catalyst, ACS Catal., 2019, 9, 4488–4494 CrossRef CAS
.
- J. Kim, W. H. Park, W. H. Doh, S. W. Lee, M. C. Noh, J. J. Gallet, F. Bournel, H. Kondoh, K. Mases, Y. Jung, B. S. Mun and J. Y. Park, Adsorbate-driven reactive interfacial Pt–NiO1−x nanostructure formation on the Pt3Ni(111) alloy surface, Sci. Adv., 2018, 4, eaat3151 CrossRef
.
- P. Wang, Q. Shao, X. Cui, X. Zhu and X. Huang, Hydroxide-membrane-coated Pt3Ni nanowires as highly efficient catalysts for selective hydrogenation
reaction, Adv. Funct. Mater., 2018, 28, 1705918 CrossRef
.
- X. Shen, C. Zhang, S. Zhang, S. Dai, G. Zhang, M. Ge, Y. Pan, S. M. Sharkey, G. W. Graham, A. Hunt, I. Waluyo, J. T. Miller, X. Pan and Z. Peng, Deconvolution of octahedral Pt3Ni nanoparticle growth pathway from in situ characterizations, Nat. Commun., 2018, 9, 4485 CrossRef
.
- B. Lim, Y. Xiong and Y. Xia, A water-based synthesis of octahedral, decahedral, and icosahedral Pd nanocrystals, Angew. Chem., Int. Ed., 2007, 46, 9279–9282 CrossRef CAS
.
- B. Lim, H. Kobayashi, P. H. C. Camargo, L. F. Allard, J. Liu and Y. Xia, New insights into the growth mechanism and surface structure of palladium nanocrystals, Nano Res., 2010, 3, 180–188 CrossRef CAS
.
- M. S. Jin, H. Zhang, Z. Xie and Y. Xia, Palladium nanocrystals enclosed by {100} and {111} facets in controlled proportions and their catalytic activities for formic acid oxidation, Energy Environ. Sci., 2012, 5, 6352–6357 RSC
.
- M. Jin, H. Zhang, Z. Xie and Y. Xia, Palladium concave nanocubes with high-index facets and their enhanced catalytic properties, Angew. Chem., Int. Ed., 2011, 50, 7850–7854 CrossRef CAS
.
- X. Huang, S. Tang, H. Zhang, Z. Zhou and N. Zheng, Controlled formation of concave tetrahedral/trigonal bipyramidal palladium nanocrystals, J. Am. Chem. Soc., 2009, 131, 13916–13917 CrossRef CAS
.
- L. Zhang, Z. Xie and J. Gong, Shape-controlled synthesis of Au–Pd bimetallic nanocrystals for catalytic applications, Chem. Soc. Rev., 2016, 45, 3916–3934 RSC
.
- J. Li, Y. Zheng, J. Zeng and Y. Xia, Controlling the size and morphology of Au@Pd core–shell nanocrystals by manipulating the kinetics of seeded growth, Chem. – Eur. J., 2012, 18, 8150–8156 CrossRef CAS
.
- C. W. Yang, K. Chanda, P. H. Lin, Y. N. Wang, C. W. Liao and M. H. Huang, Fabrication of Au–Pd core–shell heterostructures with systematic shape evolution using octahedral nanocrystal cores and their catalytic activity, J. Am. Chem. Soc., 2011, 133, 19993–20000 CrossRef CAS
.
- Y. Yu, Q. Zhang, B. Liu and J. Y. Lee, Synthesis of nanocrystals with variable high-index Pd facets through the controlled heteroepitaxial growth of trisoctahedral Au templates, J. Am. Chem. Soc., 2010, 132, 18258–18265 CrossRef CAS
.
- F. Wang, C. Li, L. D. Sun, H. Wu, T. Ming, J. Wang, J. C. Yu and C. H. Yan, Heteroepitaxial growth of high-index-faceted palladium nanoshells and their catalytic performance, J. Am. Chem. Soc., 2011, 133, 1106–1111 CrossRef CAS
.
- Y. W. Lee, M. Kim, Z. H. Kim and S. W. Han, One-step synthesis of Au@Pd core–shell nanooctahedron, J. Am. Chem. Soc., 2009, 131, 17036–17037 CrossRef CAS
.
- Y. Park, Y. W. Lee, S. W. Kang and S. W. Han, One-pot synthesis of Au@Pd core–shell nanocrystals with multiple high- and low-index facets and their high electrocatalytic performance, Nanoscale, 2014, 6, 9798–9805 RSC
.
- M. Wang, W. Zhang, J. Wang, D. Wexler, S. D. Poynton, R. C. T. Slade, H. Liu, B. Winther-Jensen, R. Kerr, D. Shi and J. Chen, PdNi hollow nanoparticles for improved electrocatalytic oxygen reduction in alkaline environments, ACS Appl. Mater. Interfaces, 2013, 5, 12708–12715 CrossRef CAS
.
- S. Fu, C. Zhu, D. Du and Y. Lin, Facile one-step synthesis of three-dimensional Pd–Ag bimetallic alloy networks and their electrocatalytic activity toward ethanol oxidation, ACS Appl. Mater. Interfaces, 2015, 7, 13842–13848 CrossRef CAS
.
- Z. Luo, J. Ahn and D. Qin, Fabrication of Ag–Pd concave nanocrystals through facet-selective oxidation of Ag atoms, Nanoscale, 2019, 11, 6710–6718 RSC
.
- Z. Zhang, G. Ren, Y. Liu, Y. Liang, M. Wang, S. Wu and J. Shen, Facile synthesis of PdCu echinus-like nanocrystals as robust electrocatalysts for methanol oxidation reaction, Chem. – Asian J., 2019, 14, 4217–4222 CrossRef CAS
.
- L. Zhang, H. Su, M. Sun, Y. Wang, W. Wu, T. Yu and J. Zeng, Concave Cu–Pd bimetallic nanocrystals: ligand-based Co-reduction and mechanistic study, Nano Res., 2015, 8, 2415–2430 CrossRef CAS
.
- L. Li, X. Chen, Y. Wu, D. Wang, Q. Peng, G. Zhou and Y. Li, Pd–Cu2O and Ag–Cu2O hybrid concave nanomaterials for an effective synergistic catalyst, Angew. Chem., Int. Ed., 2013, 52, 11049–11053 CrossRef CAS
.
- S. Xie, N. Lu, Z. Xie, J. Wang, M. J. Kim and Y. Xia, Synthesis of Pd–Rh core-frame concave nanocubes and their conversion to Rh cubic nanoframes by selective etching of the Pd cores, Angew. Chem., Int. Ed., 2012, 51, 10266–10270 CrossRef CAS
.
- S. Xie, X. Y. Liu and Y. Xia, Shape-controlled syntheses of rhodium nanocrystals for the enhancement of their catalytic properties, Nano Res., 2015, 8, 82–96 CrossRef CAS
.
- Y. Zhang, M. E. Grass, J. N. Kuhn, F. Tao, S. E. Habas, W. Huang, P. Yang and G. A. Somorjai, Highly selective synthesis of catalytically active monodisperse rhodium nanocubes, J. Am. Chem. Soc., 2008, 130, 5868–5869 CrossRef CAS
.
- H. Kim, K. Nguyen Tien, J. Yoon, H. Yang, Y. Chae, H. Baik, H. Lee, J. H. Sohn and K. Lee, Fabrication of hierarchical Rh nanostructures by understanding the growth kinetics of facet-controlled Rh nanocrystals, Chem. Commun., 2013, 49, 2225–2227 RSC
.
- Y. Chen, Q. Chen, S. Peng, Z. Wang, G. Lu and G. Guo, Manipulating the concavity of rhodium nanocubes enclosed by high-index facets via site-selective etching, Chem. Commun., 2014, 50, 1662–1664 RSC
.
- N. Zhang, Q. Shao, Y. Pi, J. Guo and X. Huang, Solvent-mediated shape tuning of well-defined rhodium nanocrystals for efficient electrochemical water splitting, Chem. Mater., 2017, 29, 5009–5015 CrossRef CAS
.
- B. T. Sneed, C. N. Brodsky, C. Kuo, L. K. Lamontagne, Y. Jiang, Y. Wang, F. Tao, W. Huang and C. K. Tsung, Nanoscale-phase-separated Pd–Rh boxes synthesized via metal migration: an archetype for studying lattice strain and composition effects in electrocatalysis, J. Am. Chem. Soc., 2013, 135, 14691–14700 CrossRef CAS
.
- W. Ye, S. Kou, X. Guo, F. Xie, H. Sun, H. Lu and J. Yang, Controlled synthesis of bimetallic Pd–Rh nanoframes and nanoboxes with high catalytic performances, Nanoscale, 2015, 7, 9558–9562 RSC
.
- S. Wang, W. Zhu, J. Ke, M. Lin and Y. Zhang, Pd–Rh nanocrystals with tunable morphologies and compositions as efficient catalysts toward Suzuki cross-coupling reactions, ACS Catal., 2014, 4, 2298–2306 CrossRef CAS
.
- Y. Zhang, J. Ahn, J. Liu and D. Qin, Syntheses, plasmonic properties, and catalytic applications of Ag–Rh core-frame nanocubes and Rh nanoboxes with highly porous walls, Chem. Mater., 2018, 30, 2151–2159 CrossRef CAS
.
- E. W. Harak, K. M. Koczkur, D. W. Harak, P. Patton and S. E. Skrabalak, Designing efficient catalysts through bimetallic architecture: Rh@Pt nanocubes as a case study, ChemNanoMat, 2017, 3, 815–821 CrossRef CAS
.
- F. Gao, Y. Zhang, P. Song, J. Wang, T. Song, C. Wang, L. Song, Y. Shiraishi and Y. Du, Precursor-mediated size tuning of monodisperse PtRh nanocubes as efficient electrocatalysts for ethylene glycol oxidation, J. Mater. Chem. A, 2019, 7, 7891–7896 RSC
.
- H. E. Lee, K. D. Yang, S. M. Yoon, H. Y. Ahn, Y. Y. Lee, H. Chang, D. H. Jeong, Y. S. Lee, M. Y. Kim and K. T. Nam, Concave rhombic dodecahedral Au nanocatalyst with multiple high-index facets for CO2 reduction, ACS Nano, 2015, 9, 8384–8393 CrossRef CAS
.
- S. E. Skrabalak, L. Au, X. Li and Y. Xia, Facile synthesis of Ag nanocubes and Au nanocages, Nat. Protoc., 2007, 2, 2182–2190 CrossRef CAS
.
- Y. Ma, W. Li, E. C. Cho, Z. Li, T. Yu, J. Zeng, Z. Xie and Y. Xia, Au@Ag core–shell nanocubes with finely tuned and well-controlled sizes, shell thicknesses, and optical properties, ACS Nano, 2010, 4, 6725–6734 CrossRef CAS
.
- C. L. Lu, K. S. Prasad, H. Wu, J. A. A. Ho and M. Huang, Au nanocube-directed fabrication of Au–Pd core–shell nanocrystals with tetrahexahedral, concave octahedral, and octahedral structures and their electrocatalytic activity, J. Am. Chem. Soc., 2010, 132, 14546–14553 CrossRef CAS
.
- S. Duan and R. Wang, Au/Ni12P5 core/shell nanocrystals from bimetallic heterostructures: in situ synthesis, evolution and supercapacitor properties, NPG Asia Mater., 2014, 6, e122 CrossRef CAS
.
- C. Wang, J. Li, Y. Lou, C. Kan, Y. Zhu, X. Feng, Y. Ni, H. Xu, D. Shi and X. Wei, Facile synthesis and heteroepitaxial growth mechanism of Au@Cu core–shell bimetallic nanocubes probed by first-principles studies, CrystEngComm, 2017, 19, 7287–7297 RSC
.
- M. R. Langille, M. L. Personick, J. Zhang and C. A. Mirkin, Defining rules for the shape evolution of gold nanoparticles, J. Am. Chem. Soc., 2012, 134, 14542–14554 CrossRef CAS
.
- Y. Xia, Y. Xiong, B. Lim and S. E. Skrabalak, Shape-controlled synthesis of metal nanocrystals: simple chemistry meets complex physics?, Angew. Chem., Int. Ed., 2009, 48, 60–103 CrossRef CAS
.
- Y. Xiong and Y. Xia, Shape-controlled synthesis of metal nanostructures: the case of palladium, Adv. Mater., 2007, 19, 3385–3391 CrossRef CAS
.
- Z. Wang, Transmission Electron Microscopy of Shape-Controlled Nanocrystals and Their Assemblies, J. Phys. Chem. B, 2000, 104, 1153–1175 CrossRef CAS
.
- B. J. Wiley, Z. Wang, J. Wei, Y. Yin, D. H. Cobden and Y. Xia, Synthesis and electrical characterization of silver nanobeams, Nano Lett., 2006, 6, 2273–2278 CrossRef CAS
.
- B. J. Wiley, Y. Xiong, Z. Y. Li, Y. Yin and Y. Xia, Right bipyramids of silver: a new shape derived from single twinned seeds, Nano Lett., 2006, 6, 765–768 CrossRef CAS
.
- B. Wiley, Y. Sun, B. Mayers and Y. Xia, Shape-controlled synthesis of metal nanostructures: the case of silver, Chem. – Eur. J., 2005, 11, 454–463 CrossRef CAS
.
- B. Wiley, Y. Sun and Y. Xia, Synthesis of silver nanostructures with controlled shapes and properties, Acc. Chem. Res., 2007, 40, 1067–1076 CrossRef CAS
.
- Y. Li, X. Y. Yang, Y. Feng, Z. Y. Yuan and B. L. Su, One-dimensional metal oxide nanotubes, nanowires, nanoribbons, and nanorods: synthesis, characterizations, properties and applications, Crit. Rev. Solid State Mater. Sci., 2012, 37, 1–74 CrossRef
.
- K. Zhou, X. Wang, X. M. Sun, Q. Peng and Y. Li, Enhanced catalytic activity of ceria nanorods from well-defined reactive crystal planes, J. Catal., 2005, 229, 206–212 CrossRef CAS
.
- X. Xie, Y. Li, Z. Liu, M. Haruta and W. Shen, Low-temperature oxidation of CO catalysed by Co3O4 nanorods, Nature, 2009, 458, 746–749 CrossRef CAS
.
- S. Bakardjieva, V. Stengl, L. Szatmary, J. Subrt, J. Lukac, N. Murafa, D. Niznansky, K. Cizek, J. Jirkovsky and N. Petrova, Transformation of brookite-type TiO2 nanocrystals to rutile: correlation between microstructure and photoactivity, J. Mater. Chem., 2006, 16, 1709–1716 RSC
.
- M. Cao, Z. Tang, Q. Liu, Y. Xu, M. Chen, H. Lin, Y. Li, E. Gross and Q. Zhang, The synergy between metal facet and oxide support facet for enhanced catalytic performance: the case of Pd–TiO2, Nano Lett., 2016, 16, 5298–5302 CrossRef CAS
.
- J. Liu, H. Bai, Y. Wang, Z. Liu, X. Zhang and D. Sun, Self-assembling TiO2 nanorods on large graphene oxide sheets at a two-phase interface and their anti-recombination in photocatalytic applications, Adv. Funct. Mater., 2010, 20, 4175–4181 CrossRef CAS
.
- L. Pan, X. Zhu, X. Xie and Y. Liu, Smart hybridization of TiO2 nanorods and Fe3O4 nanoparticles with pristine graphene nanosheets: hierarchically nanoengineered ternary heterostructures for high-rate lithium storage, Adv. Funct. Mater., 2015, 25, 3341–3350 CrossRef CAS
.
- M. Zhang, Y. Bando and K. Wada, Sol–gel template preparation of TiO2 nanotubes and nanorods, J. Mater. Sci. Lett., 2001, 20, 167–170 CrossRef CAS
.
- H. J. Yun, H. Lee, J. B. Joo, W. Kim and J. Yi, Influence of aspect ratio of TiO2 nanorods on the photocatalytic decomposition of formic acid, J. Phys. Chem. C, 2009, 113, 3050–3055 CrossRef CAS
.
- P. D. Cozzoli, R. Comparelli, E. Fanizza, M. L. Curri, A. Agostiano and D. Laub, Photocatalytic synthesis of silver nanoparticles stabilized by TiO2 nanorods: a semiconductor/metal nanocomposite in homogeneous nonpolar solution, J. Am. Chem. Soc., 2004, 126, 3868–3879 CrossRef CAS
.
- Z. Liu, X. Zhang, S. Nishimoto, M. Jin, D. A. Tryk, T. Murakami and A. Fujishima, Anatase TiO2 nanoparticles on rutile TiO2 nanorods: a heterogeneous nanostructure via layer-by-layer assembly, Langmuir, 2007, 23, 10916–10919 CrossRef CAS
.
- J. Li and D. Xu, Tetragonal faceted-nanorods of anatase TiO2 single crystals with a large percentage of active {100} facets, Chem. Commun., 2010, 46, 2301–2303 RSC
.
- I. S. Cho, Z. Chen, A. J. Forman, D. R. Kim, P. M. Rao, T. F. Jaramillo and X. Zheng, Branched TiO2 nanorods for photoelectrochemical hydrogen production, Nano Lett., 2011, 11, 4978–4984 CrossRef CAS
.
- Z. Zhao, X. Zhang, G. Zhang, Z. Liu, D. Qu, X. Miao, P. Feng and Z. Sun, Effect of defects on photocatalytic activity of rutile TiO2 nanorods, Nano Res., 2015, 8, 4061–4071 CrossRef CAS
.
- A. Fakharuddin, F. Di Giacomo, A. L. Palma, F. Matteocci, I. Ahmed, S. Razza, A. D'Epifanio, S. Licoccia, J. Ismail, A. Di Carlo, T. M. Brown and R. Jose, Vertical TiO2 nanorods as a medium for stable and high-efficiency perovskite solar modules, ACS Nano, 2015, 9, 8420–8429 CrossRef CAS
.
- J. Nian and H. Teng, Hydrothermal synthesis of single-crystalline anatase TiO2 nanorods with nanotubes as the precursor, J. Phys. Chem. B, 2006, 110, 4193–4198 CrossRef CAS
.
- M. N. Tahir, P. Theato, P. Oberle, G. Melnyk, S. Faiss, U. Kolb, A. Janshoff, M. Stepputat and W. Tremel, Facile synthesis and characterization of functionalized, monocrystalline rutile TiO2 nanorods, Langmuir, 2006, 22, 5209–5212 CrossRef CAS
.
- Y. Yu and D. Xu, Single-crystalline TiO2 nanorods: highly active and easily recycled photocatalysts, Appl. Catal., B, 2007, 73, 166–171 CrossRef CAS
.
- B. Liu and E. S. Aydil, Growth of oriented single-crystalline rutile TiO2 nanorods on transparent conducting substrates for dye-sensitized solar cells, J. Am. Chem. Soc., 2009, 131, 3985–3990 CrossRef CAS
.
- J. D. Bryan, S. A. Santangelo, S. C. Keveren and D. R. Gamelin, Activation of high-T-c ferromagnetism in Co2+: TiO2 and Cr3+: TiO2 nanorods and nanocrystals by grain boundary defects, J. Am. Chem. Soc., 2005, 127, 15568–15574 CrossRef CAS
.
- L. Miao, S. Tanemura, S. Toh, K. Kaneko and M. Tanemura, Fabrication, characterization and Raman study of anatase TiO2 nanorods by a heating-sol–gel template process, J. Cryst. Growth, 2004, 264, 246–252 CrossRef CAS
.
- L. Miao, S. Tanemura, S. Toh, K. Kaneko and M. Tanemura, Heating-sol–gel template process for the growth of TiO2 nanorods with rutile and anatase structure, Appl. Surf. Sci., 2004, 238, 175–179 CrossRef CAS
.
- Z. Luo, W. Yang, A. Peng, Y. Zeng and J. Yao, The fabrication of TiO2 nanorods from TiO2 nanoparticles by organic protection assisted template method, Nanotechnology, 2009, 20, 345601 CrossRef
.
- P. Roy, S. Berger and P. Schmuki, TiO2 nanotubes: synthesis and applications, Angew. Chem., Int. Ed., 2011, 50, 2904–2939 CrossRef CAS
.
- K. Zhu, N. R. Neale, A. Miedaner and A. J. Frank, Enhanced charge-collection efficiencies and light scattering in dye-sensitized solar cells using oriented TiO2 nanotubes arrays, Nano Lett., 2007, 7, 69–74 CrossRef CAS
.
- G. K. Mor, K. Shankar, M. Paulose, O. K. Varghese and C. A. Grimes, Use of highly-ordered TiO2 nanotube arrays in dye-sensitized solar cells, Nano Lett., 2006, 6, 215–218 CrossRef CAS
.
- J. H. Park, S. Kim and A. J. Bard, Novel carbon-doped TiO2 nanotube arrays with high aspect ratios for efficient solar water splitting, Nano Lett., 2006, 6, 24–28 CrossRef CAS
.
- K. Woan, G. Pyrgiotakis and W. Sigmund, Photocatalytic carbon-nanotube–TiO2 composites, Adv. Mater., 2009, 21, 2233–2239 CrossRef CAS
.
- Z. R. Tian, J. A. Voigt, J. Liu, B. McKenzie and H. Xu, Large oriented arrays and continuous films of TiO2-based nanotubes, J. Am. Chem. Soc., 2003, 125, 12384–12385 CrossRef CAS
.
- J. M. Macák, H. Tsuchiya and P. Schmuki, High-aspect-ratio TiO2 nanotubes by anodization of titanium, Angew. Chem., Int. Ed., 2005, 44, 2100–2102 CrossRef
.
- D. Kuang, J. Brillet, P. Chen, M. Takata, S. Uchida, H. Miura, K. Sumioka, S. M. Zakeeruddin and M. Grätzel, Application of highly ordered TiO2 nanotube arrays in flexible dye-sensitized solar cells, ACS Nano, 2008, 2, 1113–1116 CrossRef CAS
.
- J. Park, S. Bauer, K. von der Mark and P. Schmuki, Nanosize and vitality: TiO2 nanotube diameter directs cell fate, Nano Lett., 2007, 7, 1686–1691 CrossRef CAS
.
- X. Lu, G. Wang, T. Zhai, M. Yu, J. Gan, Y. Tong and Y. Li, Hydrogenated TiO2 nanotube arrays for supercapacitors, Nano Lett., 2012, 12, 1690–1696 CrossRef CAS
.
- S. P. Albu, A. Ghicov, J. M. Macak, R. Hahn and P. Schmuki, Self-organized, free-standing TiO2 nanotube membrane for flow-through photocatalytic applications, Nano Lett., 2007, 7, 1286–1289 CrossRef CAS
.
- J. R. Jennings, A. Ghicov, L. M. Peter, P. Schmuki and A. B. Walker, Dye-sensitized solar cells based on oriented TiO2 nanotube arrays: transport, trapping, and transfer of electrons, J. Am. Chem. Soc., 2008, 130, 13364–13372 CrossRef CAS
.
- J. M. Macak, H. Tsuchiya, L. Taveira, S. Aldabergerova and P. Schmuki, Smooth anodic TiO2 nanotubes, Angew. Chem., Int. Ed., 2005, 44, 7463–7465 CrossRef CAS
.
- J. M. Macak, M. Zlamal, J. Krysa and P. Schmuki, Self-organized TiO2 nanotube layers as highly efficient photocatalysts, Small, 2007, 3, 300–304 CrossRef CAS
.
- W. Sun, Y. Yu, H. Pan, X. Gao, Q. Chen and L. Peng, CdS quantum dots sensitized TiO2 nanotube-array photoelectrodes, J. Am. Chem. Soc., 2008, 130, 1124–1125 CrossRef CAS
.
- S. D. Perera, R. G. Mariano, K. Vu, N. Nour, O. Seitz, Y. Chabal and K. J. Balkus, Hydrothermal synthesis of graphene-TiO2 nanotube composites with enhanced photocatalytic activity, ACS Catal., 2012, 2, 949–956 CrossRef CAS
.
- R. Si and M. Flytzani-Stephanopoulos, Shape and crystal-plane effects of nanoscale ceria on the activity of Au–CeO2 catalysts for the water–gas shift reaction, Angew. Chem., Int. Ed., 2008, 47, 2884–2887 CrossRef CAS
.
- Tana, M. Zhang, J. Li, H. Li, Y. Li and W. Shen, Morphology-dependent redox and catalytic properties of CeO2 nanostructures: nanowires, nanorods and nanoparticles, Catal. Today, 2009, 148, 179–183 CrossRef CAS
.
- N. Ta, J. Liu, S. Chenna, P. A. Crozier, Y. Li, A. Chen and W. Shen, Stabilized gold nanoparticles on ceria nanorods by strong interfacial anchoring, J. Am. Chem. Soc., 2012, 134, 20585–20588 CrossRef CAS
.
- Q. Xu, W. Lei, X. Li, X. Qi, J. Yu, G. Liu, J. Wang and P. Zhang, Efficient removal of formaldehyde by nanosized gold on well-defined CeO2 nanorods at room temperature, Environ. Sci. Technol., 2014, 48, 9702–9708 CrossRef CAS
.
- S. Zhang, C. R. Chang, Z. Q. Huang, J. Li, Z. Wu, Y. Ma, Z. Zhang, Y. Wang and Y. Qu, High catalytic activity and chemoselectivity of sub-nanometric Pd clusters on porous nanorods of CeO2 for hydrogenation of nitroarenes, J. Am. Chem. Soc., 2016, 138, 2629–2637 CrossRef CAS
.
- A. D. Liyanage, S. D. Perera, K. Tan, Y. Chabal and K. J. Balkus, Jr., Synthesis, characterization, and photocatalytic activity of Y-doped CeO2 nanorods, ACS Catal., 2014, 4, 577–584 CrossRef CAS
.
- X. Liu, K. Zhou, L. Wang, B. Wang and Y. Li, Oxygen vacancy clusters promoting reducibility and activity of ceria nanorods, J. Am. Chem. Soc., 2009, 131, 3140–3141 CrossRef CAS
.
- H. X. Mai, L. D. Sun, Y. W. Zhang, R. Si, W. Feng, H. P. Zhang, H. C. Liu and C. H. Yan, Shape-selective synthesis and oxygen storage behavior of ceria nanopolyhedra, nanorods, and nanocubes, J. Phys. Chem. B, 2005, 109, 24380–24385 CrossRef CAS
.
- L. Yan, R. Yu, J. Chen and X. Xing, Template-free hydrothermal synthesis of CeO2 nano-octahedrons and nanorods: investigation of the morpholog evolution, Cryst. Growth Des., 2008, 8, 1474–1477 CrossRef CAS
.
- Z. Ji, X. Wang, H. Zhang, S. Lin, H. Meng, B. Sun, S. George, T. Xia, A. E. Nel and J. I. Zink, Designed synthesis of CeO2 nanorods and nanowires for studying toxicological effects of high aspect ratio nanomaterials, ACS Nano, 2012, 6, 5366–5380 CrossRef CAS
.
- S. Bai, F. Liu, B. Huang, F. Li, H. Lin, T. Wu, M. Sun, J. Wu, Q. Shao, Y. Xu and X. Huang, High-efficiency direct methane conversion to oxygenates on a cerium dioxide nanowires supported rhodium single-atom catalyst, Nat. Commun., 2020, 11, 954 CrossRef CAS
.
- A. Vantomme, Z. Yuan, G. Du and B. Su, Surfactant-assisted large-scale preparation of crystalline CeO2 nanorods, Langmuir, 2005, 21, 1132–1135 CrossRef CAS
.
- C. Sun, H. Li, H. Zhang, Z. Wang and L. Chen, Controlled synthesis of CeO2 nanorods by a solvothermal method, Nanotechnology, 2005, 16, 1454–1463 CrossRef CAS
.
- D. Zhang, H. Fu, L. Shi, C. Pan, Q. Li, Y. Chu and W. Yu, Synthesis of CeO2 nanorods via ultrasonication assisted by polyethylene glycol, Inorg. Chem., 2007, 46, 2446–2451 CrossRef CAS
.
- W. Q. Han, L. J. Wu and Y. M. Zhu, Formation and oxidation state of CeO2−x nanotubes, J. Am. Chem. Soc., 2005, 127, 12814–12815 CrossRef CAS
.
- C. Tang, Y. Bando, B. Liu and D. Golberg, Cerium oxide nanotubes prepared from cerium hydroxide nanotubes, Adv. Mater., 2005, 17, 3005–3009 CrossRef CAS
.
- K. Zhou, Z. Yang and S. Yang, Highly reducible CeO2 nanotubes, Chem. Mater., 2007, 19, 1215–1217 CrossRef CAS
.
- L. Chen, L. Li and G. Li, Synthesis of CuO nanorods and their catalytic activity in the thermal decomposition of ammonium Perchlorate, J. Alloys Compd., 2008, 464, 532–536 CrossRef CAS
.
- Q. Liu, Y. Liang, H. Liu, J. Hong and Z. Xu, Solution phase synthesis of CuO nanorods, Mater. Chem. Phys., 2006, 98, 519–522 CrossRef CAS
.
- Y. Chang and H. Zeng, Controlled synthesis and. self-assembly of single-crystalline CuO nanorods and nanoribbons, Cryst. Growth Des., 2004, 4, 397–402 CrossRef CAS
.
- K. M. Shrestha, C. M. Sorensen and K. J. Klabunde, Synthesis of CuO nanorods, reduction of CuO into Cu nanorods, and diffuse reflectance measurements of CuO and Cu nanomaterials in the near infrared region, J. Phys. Chem. C, 2010, 114, 14368–14376 CrossRef CAS
.
- T. Alammar, A. Birkner and A. V. Mudring, Ultrasound-assisted synthesis of CuO nanorods in a neat room-temperature ionic liquid, Eur. J. Inorg. Chem., 2009, 2765–2768 CrossRef CAS
.
- R. Gusain and O. P. Khatri, Ultrasound assisted shape regulation of CuO nanorods in ionic liquids and their use as energy efficient lubricant additives, J. Mater. Chem. A, 2013, 1, 5612–5619 RSC
.
- W. Jia, Y. Liu, P. Hu, R. Yu, Y. Wang, L. Ma, D. Wang and Y. Li, Ultrathin CuO nanorods: controllable synthesis and superior catalytic properties in styrene epoxidation, Chem. Commun., 2015, 51, 8817–8820 RSC
.
- H. Chen, G. Zhao and Y. Liu, Low-temperature solution synthesis of CuO nanorods with thin diameter, Mater. Lett., 2013, 93, 60–63 CrossRef CAS
.
- W. Wang, Z. Liu, Y. Liu, C. Xu, C. Zheng and G. Wang, A simple wet-chemical synthesis and characterization of CuO nanorods, Appl. Phys. A: Mater. Sci. Process., 2003, 76, 417–420 CrossRef CAS
.
- L. Wang, H. Gong, C. Wang, D. Wang, K. Tang and Y. Qian, Facile synthesis of novel tunable highly porous CuO nanorods for high rate lithium battery anodes with realized long cycle life and high reversible capacity, Nanoscale, 2012, 4, 6850–6855 RSC
.
- K. Zhong, J. Xue, Y. Mao, C. Wang, T. Zhai, P. Liu, X. Xia, H. Li and Y. Tong, Facile synthesis of CuO nanorods with abundant adsorbed oxygen concomitant with high surface oxidation states for CO oxidation, RSC Adv., 2012, 2, 11520–11528 RSC
.
- J. Zhou, Y. Li, L. Yu, Z. Li, D. Xie, Y. Zhao and Y. Yu, Facile in situ fabrication of Cu2O@Cu metal-semiconductor heterostructured nanorods for efficient visible-light driven CO2 reduction, Chem. Eng. J., 2020, 385, 123940 CrossRef
.
- X. C. Jiang, T. Herricks and Y. N. Xia, CuO nanowires can be synthesized by heating copper substrates in air, Nano Lett., 2002, 2, 1333–1338 CrossRef CAS
.
- J. Chen, F. Zhang, J. Wang, G. Zhang, B. Miao, X. Fan, D. Yan and P. Yan, CuO nanowires synthesized by thermal oxidation route, J. Alloys Compd., 2008, 454, 268–273 CrossRef CAS
.
- X. Zhang, G. Wang, W. Zhang, N. Hu, H. Wu and B. Fang, Seed-mediated growth method for epitaxial array of CuO nanowires on surface of Cu nanostructures and its application as a glucose sensor, J. Phys. Chem. C, 2008, 112, 8856–8862 CrossRef CAS
.
- W. Yao, S. Yu, Y. Zhou, J. Jiang, Q. Wu and L. Zhang, Formation of uniform CuO nanorods by spontaneous aggregation: selective synthesis of CuO, Cu2O, and Cu nanoparticles by a solid–liquid phase arc discharge process, J. Phys. Chem. B, 2005, 109, 14011–14016 CrossRef CAS
.
- A. J. Christy, L. C. Nehru and M. Umadevi, A novel combustion method to prepare CuO nanorods and its antimicrobial and photocatalytic activities, Powder Technol., 2013, 235, 783–786 CrossRef CAS
.
- L. M. Housel, L. Wang, A. Abraham, J. Huang, G. D. Renderos, C. D. Quilty, A. B. Brady, A. C. Marschilok, K. J. Takeuchi and E. S. Takeuchi, Investigation of alpha-MnO2 tunneled structures as model cation hosts for energy storage, Acc. Chem. Res., 2018, 51, 575–582 CrossRef CAS
.
- H. Hu, L. Wu, Y. Tan, Q. Zhong, M. Chen, Y. Qiu, D. Yang, B. Sun, Q. Zhang and Y. Yin, Interfacial Synthesis of Highly Stable CsPbX3/Oxide Janus Nanoparticles, J. Am. Chem. Soc., 2018, 140, 406–412 CrossRef CAS
.
- W. Guo, C. Yu, S. Li, Z. Wang, J. Yu, H. Huang and J. Qiu, Strategies and insights towards the intrinsic capacitive properties of MnO2 for supercapacitors: challenges and perspectives, Nano Energy, 2019, 57, 459–472 CrossRef CAS
.
- L. Cheng, J. Wang, C. Zhang, B. Jin and Y. Men, Boosting acetone oxidation efficiency over MnO2 nanorods by tailoring crystal phases, New J. Chem., 2019, 43, 19126–19136 RSC
.
- L. Wang, Q. Wu, A. Abraham, P. J. West, L. M. Housel, G. Singh, N. Sadique, C. D. Quilty, D. Wu, E. S. Takeuchi, A. C. Marschilok and K. J. Takeuchi, Silver-containing alpha-MnO2 nanorods: electrochemistry in rechargeable aqueous Zn-MnO2 batteries, J. Electrochem. Soc., 2019, 166, A3575–A3584 CrossRef CAS
.
- X. Hu, J. Chen, S. Li, Y. Chen, W. Qu, Z. Ma and X. Tang, The promotional effect of copper in catalytic oxidation by Cu-doped alpha-MnO2 nanorods, J. Phys. Chem. C, 2020, 124, 701–708 CrossRef CAS
.
- C. Cui, G. Du, K. Zhang, T. An, B. Li, X. Liu and Z. Liu, Co3O4 nanoparticles anchored in MnO2 nanorods as efficient oxygen reduction reaction catalyst for metal–air batteries, J. Alloys Compd., 2020, 814, 152239 CrossRef CAS
.
- D. Gangwar and C. Rath, Electrochemical and magnetic properties of alpha-MnO2:Dy nanorods, J. Magn. Magn. Mater., 2020, 497, 166074 CrossRef CAS
.
- Y. Muraoka, H. Chiba, T. Atou, M. Kikuchi, K. Hiraga, Y. Syono, S. Sugiyama, S. Yamamoto and J. C. Grenier, Preparation of α-MnO2 with an open tunnel, J. Solid State Chem., 1999, 144, 136–142 CrossRef CAS
.
- N. Kijima, H. Yasuda, T. Sato and Y. Yoshimura, Preparation and characterization of open tunnel oxide α-MnO2 precipitated by ozone oxidation, J. Solid State Chem., 2001, 159, 94–102 CrossRef CAS
.
- T. Xiao, E. R. Strutt, M. Benaissa, H. Chen and B. H. Kear, Synthesis of high active-site density nanofibrous MnO2-base materials with enhanced permeabilities, Nanostruct. Mater., 1998, 10, 1051–1061 CrossRef CAS
.
- R. N. DeGuzman, Y. Shen, E. J. Neth, S. L. Suib, C. L. O'Young, S. Levine and J. M. Newsam, Synthesis and characterization of octahedral molecular sieves (OMS-2) having the hollandite structure, Chem. Mater., 1994, 6, 815–821 CrossRef CAS
.
- Y. Shen, R. P. Zerger, R. N. DeGuzman, S. L. Suib, L. McCurdy, D. I. Potter and C. L. Young, Manganese oxide octahedral molecular sieves: preparation, characterization, and applications, Science, 1993, 260, 511 CrossRef CAS
.
- R. N. Reddy and R. G. Reddy, Sol–gel MnO2 as an electrode material for electrochemical capacitors, J. Power Sources, 2003, 124, 330–337 CrossRef CAS
.
- X. Wang, W. Huang, P. J. Sebastian and S. Gamboa, Sol–gel template synthesis of highly ordered MnO2 nanowire arrays, J. Power Sources, 2005, 140, 211–215 CrossRef CAS
.
- K. Shimamoto, K. Tadanaga and M. Tatsumisago, All-solid-state electrochemical capacitors using MnO2 electrode/SiO2-Nafion electrolyte composite prepared by the sol–gel process, J. Power Sources, 2014, 248, 396–399 CrossRef CAS
.
- W. Tang, X. Shan, S. Li, H. Liu, X. Wu and Y. Chen, Sol–gel process for the synthesis of ultrafine MnO2 nanowires and nanorods, Mater. Lett., 2014, 132, 317–321 CrossRef CAS
.
- P. V. M. Dixini, B. B. Carvalho, G. R. Goncalves, V. C. B. Pegoretti and M. B. J. G. Freitas, Sol–gel synthesis of manganese oxide supercapacitor from manganese recycled from spent Zn-MnO2 batteries using organic acid as a leaching agent, Ionics, 2019, 25, 4381–4392 CrossRef CAS
.
- D. Shin, H. Hwang, T. Yeo, S. Park, T. Kim, J. Lee and W. Choi, Sol–gel-driven combustion wave for scalable transformation of Mn(NO3)2 precursors into MnO2−x/MWCNT supercapacitor electrodes capable of electrochemical activation, Carbon, 2019, 152, 746–754 CrossRef CAS
.
- Z. Li, S. Chen, C. Dong, X. Chen and Q. Zhou, Facile hydrothermal synthesis of ultra-long manganese oxyhydroxide nanorods and their transformation into MnO2 and Mn2O3 nanorods, Micro Nano Lett., 2013, 8, 325–329 CrossRef CAS
.
- W. Zhang, Z. Yang, X. Wang, Y. Zhang, X. Wen and S. Yang, Large-scale synthesis of β-MnO2 nanorods and their rapid and efficient catalytic oxidation of methylene blue dye, Catal. Commun., 2006, 7, 408–412 CrossRef CAS
.
- X. Zhang, P. Yu, D. Zhang, H. Zhang, X. Sun and Y. Ma, Room temperature synthesis of Mn3O4 nanoparticles: characterization, electrochemical properties and hydrothermal transformation to γ-MnO2 nanorods, Mater. Lett., 2013, 92, 401–404 CrossRef CAS
.
- X. Liu, S. Fu and C. Huang, Synthesis, characterization and magnetic properties of β-MnO2 nanorods, Powder Technol., 2005, 154, 120–124 CrossRef CAS
.
- H. Wang, Z. Lu, D. Qian, Y. Li and W. Zhang, Single-crystal α-MnO2 nanorods: synthesis and electrochemical properties, Nanotechnology, 2007, 18, 115616 CrossRef
.
- D. Su, H. J. Ahn and G. Wang, Hydrothermal synthesis of α-MnO2 and β-MnO2 nanorods as high capacity cathode materials for sodium ion batteries, J. Mater. Chem. A, 2013, 1, 4845–4850 RSC
.
- A. M. Toufiq, F. Wang, Q. U. A. Javed and Y. Li, Effect of hydrothermal dwell time on the diameter-controlled synthesis and magnetic property of MnO2 nanorods, Mod. Phys. Lett. B, 2014, 28, 1450045 CrossRef
.
- X. Zhang, B. Li, X. Li, Q. Chu, M. Yang, X. Wang, H. Chen, L. Peng and X. Liu, Morphology-controlled synthesis and growth mechanisms of branched α-MnO2 nanorods via facile microwave-assisted hydrothermal method, J. Mater. Sci.: Mater. Electron., 2014, 25, 906–913 CrossRef CAS
.
- J. J. H. B. Sattler, J. Ruiz-Martinez, E. Santillan-Jimenez and B. M. Weckhuysen, Catalytic dehydrogenation of light alkanes on metals and metal oxides, Chem. Rev., 2014, 114, 10613–10653 CrossRef CAS
.
- F. Zhou, X. Zhao, H. Xu and C. Yuan, Hydrothermal synthesis of metastable VO2 nanorods as cathode materials for lithium ion batteries, Chem. Lett., 2006, 35, 1280–1281 CrossRef CAS
.
- S. Ji, Y. Zhao, F. Zhang and P. Jin, Direct formation of single crystal VO2(R) nanorods by one-step hydrothermal treatment, J. Cryst. Growth, 2010, 312, 282–286 CrossRef CAS
.
- C. Wu, X. Zhang, J. Dai, J. Yang, Z. Wu, S. Wei and Y. Xie, Direct hydrothermal synthesis of monoclinic VO2(M) single-domain nanorods on large scale displaying magnetocaloric effect, J. Mater. Chem., 2011, 21, 4509–4517 RSC
.
- P. Liu, K. Zhu, Y. Gao, Q. Wu, J. Liu, J. Qiu, Q. Gu and H. Zheng, Ultra-long VO2 (A) nanorods using the high-temperature mixing method under hydrothermal conditions: synthesis, evolution and thermochromic properties, CrystEngComm, 2013, 15, 2753–2760 RSC
.
- Y. Zhang, X. Zhang, Y. Huang, M. Xiao, F. Niu, C. Huang, C. Meng and W. Wu, Active functional group-coated VO2 (B) nanorods: facile one-pot hydrothermal synthesis and conversion to V2O3, Chem. Lett., 2014, 43, 337–339 CrossRef CAS
.
- J. Zheng, Y. Zhang, Q. Wang, H. Jiang, Y. Liu, T. Lv and C. Meng, Hydrothermal encapsulation of VO2(A) nanorods in amorphous carbon by carbonization of glucose for energy storage devices, Dalton Trans., 2018, 47, 452–464 RSC
.
- X. Li, X. Chen, X. Chen, C. Han and C. Shi, Hydrothermal synthesis and characterization of VO2 (B) nanorods array, J. Cryst. Growth, 2007, 309, 43–47 CrossRef CAS
.
- S. Liang, Q. Shi, H. Zhu, B. Peng and W. Huang, One-step hydrothermal synthesis of W-Doped VO2(M) nanorods with a tunable phase-transition temperature for infrared smart windows, ACS Omega, 2016, 1, 1139–1148 CrossRef CAS
.
- S. Song, Q. Huang and W. Zhu, Hydrothermal route to VO2 (B) nanorods: controlled synthesis and characterization, J. Nanopart. Res., 2017, 19, 353 CrossRef
.
- Z. Gui, R. Fan, W. Mo, X. Chen, L. Yang, S. Zhang, Y. Hu, Z. Wang and W. Fan, Precursor morphology controlled formation
of rutile VO2 nanorods and their self-assembled structure, Chem. Mater., 2002, 14, 5053–5056 CrossRef CAS
.
- X. Cheng, H. Xu, Z. Wang, K. Zhu, G. Li and S. Jin, Synthesis, characterization and formation mechanism of metastable phase VO2(A) nanorods, Mater. Res. Bull., 2013, 48, 3383–3388 CrossRef CAS
.
- S. Ayyaru, S. Mahalingam and Y. H. Ahn, A non-noble V2O5 nanorods as an alternative cathode catalyst for microbial fuel cell applications, Int. J. Hydrogen Energy, 2019, 44, 4974–4984 CrossRef CAS
.
- S. Islam, M. H. Alfaruqi, D. Y. Putro, V. Soundharrajan, B. Sambandam, J. Jo, S. Park, S. Lee, V. Mathew and J. Kim, K+ intercalated V2O5 nanorods with exposed facets as advanced cathodes for high energy and high rate zinc-ion batteries, J. Mater. Chem. A, 2019, 7, 20335–20347 RSC
.
- D. Yan, X. Zhu, K. Wang, X. Gao, Y. Feng, K. Sun and Y. Liu, Facile and elegant self-organization of Ag nanoparticles and TiO2 nanorods on V2O5 nanosheets as a superior cathode material for lithium-ion batteries, J. Mater. Chem. A, 2016, 4, 4900–4907 RSC
.
- N. Pinna, M. Willinger, K. Weiss, J. Urban and R. Schlögl, Local structure of nanoscopic materials: V2O5 nanorods and nanowires, Nano Lett., 2003, 3, 1131–1134 CrossRef CAS
.
- R. Ostermann, D. Li, Y. Yin, J. T. McCann and Y. Xia, V2O5 nanorods on TiO2 nanofibers: a new class of hierarchical nanostructures enabled by electrospinning and calcination, Nano Lett., 2006, 6, 1297–1302 CrossRef CAS
.
- A. M. Glushenkov, V. I. Stukachev, M. F. Hassan, G. G. Kuvshinov, H. Liu and Y. Chen, A novel approach for real mass transformation from V2O5 particles to nanorods, Cryst. Growth Des., 2008, 8, 3661–3665 CrossRef CAS
.
- Y. Xu, J. Chen, X. Yuan, Y. Zhang, J. Yu, H. Liu, M. Cao, X. Fan, H. Lin and Q. Zhang, Sintering-resistant Pt on Ga2O3 rods for propane dehydrogenation: the morphology matters, Ind. Eng. Chem. Res., 2018, 57, 13087–13093 CrossRef CAS
.
- V. B. Kumar, R. K. Mishra, I. N. Pulidindi, Z. E. Porat, J. H. T. Luong and A. Gedanken, Preparation and catalytic activity of thermosensitive Ga2O3 nanorods, Energy Fuels, 2016, 30, 7419–7427 CrossRef CAS
.
- J. Li, Z. Qiao, X. Chen, L. Chen, Y. Cao, M. He, H. Li, Z. Cao and Z. Zhang, Synthesis of β-Ga2O3 nanorods, J. Alloys Compd., 2000, 306, 300–302 CrossRef CAS
.
- F. Shi, S. Zhang and C. Xue, Influence of annealing time on microstructure of one-dimensional Ga2O3 nanorods, J. Alloys Compd., 2010, 498, 77–80 CrossRef CAS
.
- K. Girija, S. Thirumalairajan and D. Mangalaraj, Morphology controllable synthesis of parallely arranged single-crystalline β-Ga2O3 nanorods for photocatalytic and antimicrobial activities, Chem. Eng. J., 2014, 236, 181–190 CrossRef CAS
.
- C. Pacholski, A. Kornowski and H. Weller, Self-assembly of ZnO: from nanodots, to nanorods, Angew. Chem., Int. Ed., 2002, 41, 1188–1191 CrossRef CAS
.
- J. Wu and S. Liu, Low-temperature growth of well-aligned ZnO nanorods by chemical vapor deposition, Adv. Mater., 2002, 14, 215–218 CrossRef CAS
.
- B. Liu and H. Zeng, Hydrothermal synthesis of ZnO nanorods in the diameter regime of 50 nm, J. Am. Chem. Soc., 2003, 125, 4430–4431 CrossRef CAS
.
- L. Vayssieres, Growth of arrayed nanorods and nanowires of ZnO from aqueous solutions, Adv. Mater., 2003, 15, 464–466 CrossRef CAS
.
- X. Wang, C. J. Summers and Z. Wang, Large-scale hexagonal-patterned growth of aligned ZnO nanorods for nano-optoelectronics and nanosensor arrays, Nano Lett., 2004, 4, 423–426 CrossRef CAS
.
- Z. Cheng, X. Dong, Q. Pan, J. Zhang and X. Dong, Preparation and characterization of In2O3 nanorods, Mater. Lett., 2006, 60, 3137–3140 CrossRef CAS
.
- X. Lai, D. Wang, N. Han, J. Du, J. Li, C. Xing, Y. Chen and X. Li, Ordered arrays of bead-chain-like In2O3 nanorods and their enhanced sensing performance for formaldehyde, Chem. Mater., 2010, 22, 3033–3042 CrossRef CAS
.
- J. Gan, X. Lu, T. Zhai, Y. Zhao, S. Xie, Y. Mao, Y. Zhang, Y. Yang and Y. Tong, Vertically aligned In2O3 nanorods on FTO substrates for photoelectrochemical applications, J. Mater. Chem., 2011, 21, 14685–14692 RSC
.
- S. Park, S. Kim, G. Sun and C. Lee, Synthesis, structure, and ethanol gas sensing properties of In2O3 nanorods decorated with Bi2O3 nanoparticles, ACS Appl. Mater. Interfaces, 2015, 7, 8138–8146 CrossRef CAS
.
- J. Xu, Y. Chen, Q. Pan, Q. Xiang, Z. Cheng and X. Dong, A new route for preparing corundum-type In2O3 nanorods used as gas-sensing materials, Nanotechnology, 2007, 18, 115615 CrossRef
.
- Y. Yan, Y. Zhang, H. Zeng, J. Zhang, X. Cao and L. Zhang, Tunable synthesis of In2O3 nanowires, nanoarrows and nanorods, Nanotechnology, 2007, 18, 175601 CrossRef
.
- Y. Liu, C. Zheng, W. Wang, C. Yin and G. Wang, Synthesis and characterization of rutile SnO2 nanorods, Adv. Mater., 2001, 13, 1883–1887 CrossRef CAS
.
- D. Zhang, L. Sun, J. Yin and C. Yan, Low-temperature fabrication of highly crystalline SnO2 nanorods, Adv. Mater., 2003, 15, 1022–1025 CrossRef CAS
.
- B. Cheng, J. M. Russell, W. Shi, L. Zhang and E. T. Samulski, Large-scale, solution-phase growth of single-crystalline SnO2 nanorods, J. Am. Chem. Soc., 2004, 126, 5972–5973 CrossRef CAS
.
- J. He, T. Wu, C. Hsin, K. Li, L. Chen, Y. Chueh, L. Chou and Z. Wang, Beaklike SnO2 nanorods with strong photoluminescent and field-emission properties, Small, 2006, 2, 116–120 CrossRef
.
- X. Xue, L. Xing, Y. Chen, S. Shi, Y. Wang and T. Wang, Synthesis and H2S sensing properties of CuO–SnO2 core/shell PN-junction nanorods, J. Phys. Chem. C, 2008, 112, 12157–12160 CrossRef CAS
.
- G. Xi and J. Ye, Ultrathin SnO2 nanorods: template- and surfactant-free solution phase synthesis, growth mechanism, optical, gas-sensing, and surface adsorption properties, Inorg. Chem., 2010, 49, 2302–2309 CrossRef CAS
.
- A. Kar, S. Kundu and A. Patra, Surface defect-related luminescence properties of SnO2 nanorods and nanoparticles, J. Phys. Chem. C, 2011, 115, 118–124 CrossRef CAS
.
- Z. Zhang, R. Zou, G. Song, L. Yu, Z. Chen and J. Hu, Highly aligned SnO2 nanorods on graphene sheets for gas sensors, J. Mater. Chem., 2011, 21, 17360–17365 RSC
.
- C. Xu, J. Sun and L. Gao, Direct growth of monodisperse SnO2 nanorods on graphene as high capacity anode materials for lithium ion batteries, J. Mater. Chem., 2012, 22, 975–979 RSC
.
- Y. Chen, X. Xue, Y. Wang and T. Wang, Synthesis and ethanol sensing characteristics of single crystalline SnO2 nanorods, Appl. Phys. Lett., 2005, 87, 233503 CrossRef
.
- M. R. S. Joice, T. M. David and P. Wilson, WO3 nanorods supported on mesoporous TiO2 nanotubes as one-dimensional nanocomposites for rapid degradation of methylene blue under visible light irradiation, J. Phys. Chem. C, 2019, 123, 27448–27464 CrossRef
.
- J. H. Kim, D. H. Kim, J. W. Yoon, Z. Dai and J. H. Lee, Rational design of branched WO3 nanorods decorated with BiVO4 Nanoparticles By All-Solution Processing For Efficient Photoelectrochemical Water Splitting, ACS Appl. Energy Mater., 2019, 2, 4535–4543 CrossRef CAS
.
- A. V. Salkar, R. X. Fernandes, S. V. Bhosale and P. P. Morajkar, NH- and CH-substituted ureas as self-assembly directing motifs for facile synthesis and electrocapacitive applications of advanced WO3−x one-dimensional nanorods, ACS Appl. Energy Mater., 2019, 2, 8724–8736 CrossRef CAS
.
- Y. Li, Z. Liu, M. Ruan, Z. Guo and X. Li, 1D WO3 Nanorods/2D WO3−x nanoflakes homojunction structure for enhanced charge separation and transfer towards efficient photoelectrochemical performance, ChemSusChem, 2019, 12, 5282–5290 CrossRef CAS
.
- B. Paul, S. Sharma, D. D. Purkayastha, S. S. Dhar and R. Bal, Facile synthesis of size-controlled Ag supported on WO3 nanorods and their application as novel and active catalyst in oxidant-free dehydrogenation of benzyl alcohols, Catal. Commun., 2019, 132, 105804 CrossRef
.
- Y. Huang, R. Lu, M. Wang, J. Sakamoto and P. F. P. Poudeu, Hexagonal-WO3 nanorods encapsulated in nitrogen and sulfur co-doped reduced graphene oxide as a high-performance anode material for lithium ion batteries, J. Solid State Chem., 2020, 282, 121068 CrossRef CAS
.
- Y. Lu, Z. Wang, S. Yuan, L. Shi, Y. Zhao and W. Deng, Microwave-hydrothermal synthesis and humidity sensing behavior of ZrO2 nanorods, RSC Adv., 2013, 3, 11707–11714 RSC
.
- S. A. Khan, Z. Fu, W. Wang, H. Wang and M. Asif, Hierarchical m-ZrO2 nanorods template-free synthesis by hydrothermal method, Int. J. Appl. Ceram. Technol., 2014, 11, 590–593 CrossRef CAS
.
- G. H. Kwon, T. W. Kim, H. I. Lee, W. C. Cho and H. Kim, Synthesis of ZrO2 nanorods and their application as membrane materials, J. Korean Ceram. Soc., 2019, 56, 541–548 CrossRef CAS
.
- M. V. Sofianou, V. Psycharis, N. Boukos, T. Vaimakis, J. Yu, R. Dillert, D. Bahnemann and C. Trapalis, Tuning the photocatalytic selectivity of TiO2 anatase nanoplates by altering the exposed crystal facets content, Appl. Catal., B, 2013, 142–143, 761–768 CrossRef CAS
.
- K. Zhang, W. Zhou, L. Chi, X. Zhang, W. Hu, B. Jiang, K. Pan, G. Tian and Z. Jiang, Black N/H-TiO2 nanoplates with a flower-like hierarchical architecture for photocatalytic hydrogen evolution, ChemSusChem, 2016, 9, 2841–2848 CrossRef CAS
.
- W. Sun, H. Liu, J. Hu and J. Li, Controllable synthesis and morphology-dependent photocatalytic performance of anatase TiO2 nanoplates, RSC Adv., 2015, 5, 513–520 RSC
.
- A. Katoch, M. Burkhart, T. Hwang and S. S. Kim, Synthesis of polyaniline/TiO2 hybrid nanoplates via a sol–gel chemical method, Chem. Eng. J., 2012, 192, 262–268 CrossRef CAS
.
- C. Song, L. Wang, F. Gao and Q. Lu, Two-dimensional hollow TiO2 nanoplates with enhanced photocatalytic activity, Chem. – Eur. J., 2016, 22, 6368–6373 CrossRef CAS
.
- J. Hu, Y. Cao, K. Wang and D. Jia, Green solid-state synthesis and photocatalytic hydrogen production activity of anatase TiO2 nanoplates with super heat-stability, RSC Adv., 2017, 7, 11827–11833 RSC
.
- C. Pan, D. Zhang and L. Shi, CTAB assisted hydrothermal synthesis, controlled conversion and CO oxidation properties of CeO2 nanoplates, nanotubes, and nanorods, J. Solid State Chem., 2008, 181, 1298–1306 CrossRef CAS
.
- H. Lin, C. Wu and R. Chiang, Facile synthesis of CeO2 nanoplates and nanorods by [100] oriented growth, J. Colloid Interface Sci., 2010, 341, 12–17 CrossRef CAS
.
- Y. Zhang, F. Hou and Y. Tan, CeO2 nanoplates with a hexagonal structure and their catalytic applications in highly selective hydrogenation of substituted nitroaromatics, Chem. Commun., 2012, 48, 2391–2393 RSC
.
- C. Hu, Q. Zhu, L. Chen and R. Wu, CuO–CeO2 binary oxide nanoplates: synthesis, characterization, and catalytic performance for benzene oxidation, Mater. Res. Bull., 2009, 44, 2174–2180 CrossRef CAS
.
- N. Behm, D. Brokaw, C. Overson, D. Peloquin and J. C. Poler, High-throughput microwave synthesis and characterization of NiO nanoplates for supercapacitor devices, J. Mater. Sci., 2013, 48, 1711–1716 CrossRef CAS
.
- K. Cao, H. Liu, W. Li, Q. Han, Z. Zhang, K. Huang, Q. Jing and L. Jiao, CuO nanoplates for high-performance potassium-ion batteries, Small, 2019, 15, 1901775 CrossRef
.
- Z. Ai, L. Zhang, F. Kong, H. Liu, W. Xing and J. Qiu, Microwave-assisted green synthesis of MnO2 nanoplates with environmental catalytic activity, Mater. Chem. Phys., 2008, 111, 162–167 CrossRef CAS
.
- Z. Jing and J. Zhan, Fabrication and gas-sensing properties of porous ZnO nanoplates, Adv. Mater., 2008, 20, 4547–4551 CrossRef CAS
.
- J. Zheng, G. Song, J. Hong, T. K. Van, A. U. Pawar, D. Y. Kim, C. W. Kim, Z. Haider and Y. Kang, Facile fabrication of WO3 nanoplates thin films with dominant crystal facet of (002) for water splitting, Cryst. Growth Des., 2014, 14, 6057–6066 CrossRef CAS
.
- J. Zhou, G. Zhao, B. Song and G. Han, Solvent-controlled synthesis of three-dimensional TiO2 nanostructures via a one-step solvothermal route, CrystEngComm, 2011, 13, 2294–2302 RSC
.
- T. Zhu, J. Li and Q. Wu, Construction of TiO2 hierarchical nanostructures from nanocrystals and their photocatalytic properties, ACS Appl. Mater. Interfaces, 2011, 3, 3448–3453 CrossRef CAS
.
- M. Liu, L. Piao, W. Lu, S. Ju, L. Zhao, C. Zhou, H. Li and W. Wang, Flower-like TiO2 nanostructures with exposed {001} facets: facile synthesis and enhanced photocatalysis, Nanoscale, 2010, 2, 1115–1117 RSC
.
- Z. Sun, J. H. Kim, Y. Zhao, F. Bijarbooneh, V. Malgras, Y. Lee, Y. M. Kang and S. X. Dou, Rational design of 3D dendritic TiO2 nanostructures with favorable architectures, J. Am. Chem. Soc., 2011, 133, 19314–19317 CrossRef CAS
.
- S. Yang and L. Gao, Controlled synthesis and self-assembly of CeO2 nanocubes, J. Am. Chem. Soc., 2006, 128, 9330–9331 CrossRef CAS
.
- F. Dang, K. Kato, H. Imai, S. Wada, H. Haneda and M. Kuwabara, Characteristics of CeO2 nanocubes and related polyhedra prepared by using a liquid–liquid interface, Cryst. Growth Des., 2010, 10, 4537–4541 CrossRef CAS
.
- Y. Zhang, M. Lei, K. Huang, C. Liang, Y. Wang, S. Ding, R. Zhang, D. Y. Fan, H. Yang and Y. Wang, A facile route to mono-dispersed CeO2 nanocubes and their enhanced photocatalytic properties, Mater. Lett., 2014, 116, 46–49 CrossRef CAS
.
- J. Zhang, S. Ohara, M. Umetsu, T. Naka, Y. Hatakeyama and T. Adschiri, Colloidal ceria nanocrystals: a tailor-made crystal morphology in supercritical water, Adv. Mater., 2007, 19, 203–206 CrossRef CAS
.
- Q. Wu, F. Zhang, P. Xiao, H. Tao, X. Wang, Z. Hu and Y. Lü, Great influence of anions for controllable synthesis of CeO2 nanostructures: from nanorods to nanocubes, J. Phys. Chem. C, 2008, 112, 17076–17080 CrossRef CAS
.
- L. Qian, J. Zhu, W. Du and X. Qian, Solvothermal synthesis, electrochemical and photocatalytic properties of monodispersed CeO2 nanocubes, Mater. Chem. Phys., 2009, 115, 835–840 CrossRef CAS
.
- R. Yu, L. Yan, P. Zheng, J. Chen and X. Xing, Controlled synthesis of CeO2 flower-like and well-aligned nanorod hierarchical architectures by a phosphate-assisted hydrothermal route, J. Phys. Chem. C, 2008, 112, 19896–19900 CrossRef CAS
.
- H. Li, G. Lu, Q. Dai, Y. Wang, Y. Guo and Y. Guo, Efficient low-temperature catalytic combustion of trichloroethylene over flower-like mesoporous Mn-doped CeO2 microspheres, Appl. Catal., B, 2011, 102, 475–483 CrossRef CAS
.
- A. Xie, W. Liu, S. Wang, X. Liu, J. Zhang and Y. Yang, Template-free hydrothermal synthesis and CO oxidation properties of flower-like CeO2 nanostructures, Mater. Res. Bull., 2014, 59, 18–24 CrossRef CAS
.
- B. Zong, Facile hydrothermal synthesis and optical properties of flower-like CeO2 composed of numerous porous nanorods, J. Mater. Sci.: Mater. Electron., 2017, 28, 2458–2461 CrossRef CAS
.
- L. Liu, J. Shi, X. Zhang and J. Liu, Flower-like Mn-doped CeO2 microstructures: synthesis, characterizations, and catalytic properties, J. Chem., 2015, 24, 1–11 Search PubMed
.
- W. Huang, L. Lyu, Y. Yang and M. Huang, Synthesis of Cu2O nanocrystals from cubic to rhombic dodecahedral structures and their comparative photocatalytic activity, J. Am. Chem. Soc., 2012, 134, 1261–1267 CrossRef CAS
.
- C. Kuo and M. Huang, Facile synthesis of Cu2O nanocrystals with systematic shape evolution from cubic to octahedral structures, J. Phys. Chem. C, 2008, 112, 18355–18360 CrossRef CAS
.
- K. Yao, X. Yin, T. Wang and H. Zeng, Synthesis, self-assembly, disassembly, and reassembly of two types of Cu2O nanocrystals unifaceted with {001} or {110} planes, J. Am. Chem. Soc., 2010, 132, 6131–6144 CrossRef CAS
.
- M. D. Susman, Y. Feldman, A. Vaskevich and I. Rubinstein, Chemical deposition of Cu2O nanocrystals with precise morphology control, ACS Nano, 2014, 8, 162–174 CrossRef CAS
.
- C. Kuo and M. Huang, Fabrication of truncated rhombic dodecahedral Cu2O nanocages and nanoframes by particle aggregation and acidic etching, J. Am. Chem. Soc., 2008, 130, 12815–12820 CrossRef CAS
.
- C. Wang, X. Li, C. Feng, Y. Sun and G. Lu, Nanosheets assembled hierarchical flower-like WO3 nanostructures: synthesis, characterization, and their gas sensing properties, Sens. Actuators, B, 2015, 210, 75–81 CrossRef CAS
.
- J. Huang, X. Xu, C. Gu, G. Fu, W. Wang and J. Liu, Flower-like and hollow sphere-like WO3 porous nanostructures: selective synthesis and their photocatalysis property, Mater. Res. Bull., 2012, 47, 3224–3232 CrossRef CAS
.
- Y. Qiu, G. Xu, Q. Kuang, S. Sun and S. Yang, Hierarchical WO3 flowers comprising porous single-crystalline nanoplates show enhanced lithium storage and photocatalysis, Nano Res., 2012, 5, 826–832 CrossRef CAS
.
- Z. Wang, P. Sun, T. Yang, Y. Gao, X. Li, G. Lu and Y. Du, Flower-like WO3 architectures synthesized via a microwave-assisted method and their gas sensing properties, Sens. Actuators, B, 2013, 186, 734–740 CrossRef CAS
.
- D. Zhang, S. Wang, J. Zhu, H. Li and Y. Lu, WO3 nanocrystals with tunable percentage of (001)-facet exposure, Appl. Catal., B, 2012, 123–124, 398–404 CrossRef CAS
.
- J. Ma, X. Wang, W. Cao, C. Han, H. Yang, J. Yuan and M. Cao, A facile fabrication and highly tunable microwave absorption of 3D flower-like Co3O4-rGO hybrid-architectures, Chem. Eng. J., 2018, 339, 487–498 CrossRef CAS
.
- J. Hu, X. Wang, M. Zhang, Y. Sun, P. Li, W. Zhang, K. Lian, L. Chen and Y. Chen, Synthesis and characterization of flower-like MoO3/In2O3 microstructures for highly sensitive ethanol detection, RSC Adv., 2017, 7, 23478–23485 RSC
.
- H. Wang, Q. Liang, W. Wang, Y. An, J. Li and L. Guo, Preparation of flower-like SnO2 nanostructures and their applications in gas-sensing and lithium storage, Cryst. Growth Des., 2011, 11, 2942–2947 CrossRef CAS
.
- H. D. Gesser, N. R. Hunter and C. B. Prakash, The direct conversion of methane to methanol by controlled oxidation, Chem. Rev., 1985, 85, 235–244 CrossRef CAS
.
- D. Wang, J. H. Lunsford and M. P. Rosynek, Characterization of a Mo/ZSM-5 catalyst for the conversion of methane to benzene, J. Catal., 1997, 169, 347–358 CrossRef CAS
.
- J. H. Lunsford, Catalytic conversion of methane to more useful chemicals and fuels: a challenge for the 21st century, Catal. Today, 2000, 63, 165–174 CrossRef CAS
.
- R. A. Periana, D. J. Taube, E. R. Evitt, D. G. Loffler, P. R. Wentrcek, G. Voss and T. Masuda, A mercury-catalyzed, high-yield system for the oxidation of methane to methanol, Science, 1993, 259, 340–343 CrossRef CAS
.
- R. A. Periana, D. J. Taube, S. Gamble, H. Taube, T. Satoh and H. Fujii, Platinum catalysts for the high-yield oxidation of methane to a methanol derivative, Science, 1998, 280, 560–564 CrossRef CAS
.
- R. Palkovits, M. Antonietti, P. Kuhn, A. Thomas and F. Schueth, Solid catalysts for the selective low-temperature oxidation of methane to methanol, Angew. Chem., Int. Ed., 2009, 48, 6909–6912 CrossRef CAS
.
- C. Hammond, M. M. Forde, M. H. Ab Rahim, A. Thetford, Q. He, R. L. Jenkins, N. Dimitratos, J. A. Lopez-Sanchez, N. F. Dummer, D. M. Murphy, A. F. Carley, S. H. Taylor, D. J. Willock, E. E. Stangland, J. Kang, H. Hagen, C. J. Kiely and G. J. Hutchings, Direct catalytic conversion of methane to methanol in an aqueous medium by using copper-promoted Fe-ZSM-5, Angew. Chem., Int. Ed., 2012, 51, 5129–5133 CrossRef CAS
.
- K. P. Kuhl, T. Hatsukade, E. R. Cave, D. N. Abram, J. Kibsgaard and T. F. Jaramillo, Electrocatalytic conversion of carbon dioxide to methane and methanol on transition metal surfaces, J. Am. Chem. Soc., 2014, 136, 14107–14113 CrossRef CAS
.
- X. Guo, G. Fang, G. Li, H. Ma, H. Fan, L. Yu, C. Ma, X. Wu, D. Deng, M. Wei, D. Tan, R. Si, S. Zhang, J. Li, L. Sun, Z. Tang, X. Pan and X. Bao, Direct, nonoxidative conversion of methane to ethylene, aromatics, and hydrogen, Science, 2014, 344, 616–619 CrossRef CAS
.
- S. H. Morejudo, R. Zanon, S. Escolastico, I. Yuste-Tirados, H. Malerod-Fjeld, P. K. Vestre, W. G. Coors, A. Martinez, T. Norby, J. M. Serra and C. Kjolseth, Direct conversion of methane to aromatics in a catalytic co-ionic membrane reactor, Science, 2016, 353, 563–566 CrossRef CAS
.
- Y. Jiang, I. V. Yentekakis and C. G. Vayenas, Methane to ethylene with 85-percent yield in a gas recycle electrocatalytic reactor-separator, Science, 1994, 264, 1563–1566 CrossRef CAS
.
- L. Chen, L. Lin, Z. Xu, X. Li and T. Zhang, Dehydro-oligomerization of methane to ethylene and aromatics over molybdenum/HZSM-5 catalyst, J. Catal., 1995, 157, 190–200 CrossRef CAS
.
- S. Grundner, M. A. C. Markovits, G. Li, M. Tromp, E. A. Pidko, E. J. M. Hensen, A. Jentys, M. Sanchez-Sanchez and J. A. Lercher, Single-site trinuclear copper oxygen clusters in mordenite for selective conversion of methane to methanol, Nat. Commun., 2015, 6, 7546 CrossRef
.
- M. H. Ab Rahim, M. M. Forde, R. L. Jenkins, C. Hammond, Q. He, N. Dimitratos, J. A. Lopez-Sanchez, A. F. Carley, S. H. Taylor, D. J. Willock, D. M. Murphy, C. J. Kiely and G. J. Hutchings, Oxidation of methane to methanol with hydrogen peroxide using supported gold–palladium alloy nanoparticles, Angew. Chem., Int. Ed., 2013, 52, 1280–1284 CrossRef CAS
.
- S. Bai, Y. Xu, P. Wang, Q. Shao and X. Huang, Activating and converting CH4 to CH3OH via the CuPdO2/CuO nanointerface, ACS Catal., 2019, 9, 6938–6944 CrossRef CAS
.
- Y. Han, Z. Zhong, K. Ramesh, F. Chen, L. Chen, T. White, Q. Tay, S. N. Yaakub and Z. Wang, Au promotional effects on the synthesis of H2O2 directly from H2 and O2 on supported Pd–Au alloy catalysts, J. Phys. Chem. C, 2007, 111, 8410–8413 CrossRef CAS
.
- Q. Liu, J. C. Bauer, R. E. Schaak and J. H. Lunsford, Supported palladium nanoparticles: an efficient catalyst for the direct formation of H2O2 from H2 and O2, Angew. Chem., Int. Ed., 2008, 47, 6221–6224 CrossRef CAS
.
- W. Zhang, L. Wang, H. Liu, Y. Hao, H. Li, M. U. Khan and J. Zeng, Integration of quantum confinement and alloy effect to modulate electronic properties of RhW nanocrystals for improved catalytic performance toward CO2 hydrogenation, Nano Lett., 2017, 17, 788–793 CrossRef CAS
.
- M. U. Khan, L. Wang, Z. Liu, Z. Gao, S. Wang, H. Li, W. Zhang, M. Wang, Z. Wang, C. Ma and J. Zeng, Pt3Co octapods as superior catalysts of CO2 hydrogenation, Angew. Chem., Int. Ed., 2016, 55, 9548–9552 CrossRef
.
- S. Bai, Q. Shao, P. Wang, Q. Dai, X. Wang and X. Huang, Highly active and selective hydrogenation of CO2 to ethanol by ordered Pd–Cu nanoparticles, J. Am. Chem. Soc., 2017, 139, 6827–6830 CrossRef CAS
.
- F. Liao, Y. Huang, J. Ge, W. Zheng, K. Tedsree, P. Collier, X. Hong and S. C. Tsang, Morphology-dependent interactions of ZnO with Cu nanoparticles at the materials’ interface in selective hydrogenation of CO2 to CH3OH, Angew. Chem., Int. Ed., 2011, 50, 2162–2165 CrossRef CAS
.
- B. Rungtaweevoranit, J. Baek, J. R. Araujo, B. S. Archanjo, K. M. Choi, O. M. Yaghi and G. A. Somorjai, Copper nanocrystals encapsulated in Zr-based metal–organic frameworks for highly selective CO2 hydrogenation to methanol, Nano Lett., 2016, 16, 7645–7649 CrossRef CAS
.
- H. Mistry, A. S. Varela, S. Kuhl, P. Strasser and B. R. Cuenya, Nanostructured electrocatalysts with
tunable activity and selectivity, Nat. Rev. Mater., 2016, 1, 16009 CrossRef CAS
.
- L. Zhang, Z. Zhao and J. Gong, Nanostructured materials for heterogeneous electrocatalytic CO2 reduction and their related reaction mechanisms, Angew. Chem., Int. Ed., 2017, 56, 11326–11353 CrossRef CAS
.
- A. Loiudice, P. Lobaccaro, E. A. Kamali, T. Thao, B. Huang, J. W. Ager and R. Buonsanti, Tailoring copper nanocrystals towards C2 products in electrochemical CO2 reduction, Angew. Chem., Int. Ed., 2016, 55, 5789–5792 CrossRef CAS
.
- K. Manthiram, B. J. Beberwyck and A. P. Alivisatos, Enhanced electrochemical methanation of carbon dioxide with a dispersible nanoscale copper catalyst, J. Am. Chem. Soc., 2014, 136, 13319–13325 CrossRef CAS
.
- O. A. Baturina, Q. Lu, M. A. Padilla, L. Xin, W. Li, A. Serov, K. Artyushkova, P. Atanassov, F. Xu, A. Epshteyn, T. Brintlinger, M. Schuette and G. E. Collins, CO2 electroreduction to hydrocarbons on carbon-supported Cu nanoparticles, ACS Catal., 2014, 4, 3682–3695 CrossRef CAS
.
- W. Zhu, Y. J. Zhang, H. Zhang, H. Lv, Q. Li, R. Michalsky, A. A. Peterson and S. Sun, Active and selective conversion of CO2 to CO on ultrathin Au nanowires, J. Am. Chem. Soc., 2014, 136, 16132–16135 CrossRef CAS
.
- W. Zhu, R. Michalsky, Ö. Metin, H. Lv, S. Guo, C. J. Wright, X. Sun, A. A. Peterson and S. Sun, Monodisperse Au nanoparticles for selective electrocatalytic reduction of CO2 to CO, J. Am. Chem. Soc., 2013, 135, 16833–16836 CrossRef CAS
.
- S. Back, M. S. Yeom and Y. Jung, Active sites of Au and Ag nanoparticle catalysts for CO2 electroreduction to CO, ACS Catal., 2015, 5, 5089–5096 CrossRef CAS
.
- D. Gao, H. Zhou, J. Wang, S. Miao, F. Yang, G. Wang, J. Wang and X. Bao, Size-dependent electrocatalytic reduction of CO2 over Pd nanoparticles, J. Am. Chem. Soc., 2015, 137, 4288–4291 CrossRef CAS
.
- H. Mistry, R. Reske, Z. Zeng, Z. Zhao, J. Greeley, P. Strasser and B. R. Cuenya, Exceptional size-dependent activity enhancement in the electroreduction of CO2 over Au nanoparticles, J. Am. Chem. Soc., 2014, 136, 16473–16476 CrossRef CAS
.
- Z. Wang, G. Yang, Z. Zhang, M. Jin and Y. Yin, Selectivity on etching: creation of high-energy facets on copper nanocrystals for CO2 electrochemical reduction, ACS Nano, 2016, 10, 4559–4564 CrossRef CAS
.
- F. S. Roberts, K. P. Kuhl and A. Nilsson, High selectivity for ethylene from carbon dioxide reduction over copper nanocube electrocatalysts, Angew. Chem., Int. Ed., 2015, 54, 5179–5182 CrossRef CAS
.
- X. Chang, T. Wang and J. Gong, CO2 photo-reduction: insights into CO2 activation and reaction on surfaces of photocatalysts, Energy Environ. Sci., 2016, 9, 2177–2196 RSC
.
- C. Wu, Y. Zhou and Z. Zou, Research progress in photocatalytic conversion of CO2 to hydrocarbons, Chin. J. Catal., 2011, 32, 1565–1572 CAS
.
- E. V. Kondratenko, G. Mul, J. Baltrusaitis, G. O. Larrazabal and J. Perez-Ramirez, Status and perspectives of CO2 conversion into fuels and chemicals by catalytic, photocatalytic and electrocatalytic processes, Energy Environ. Sci., 2013, 6, 3112–3135 RSC
.
- B. Lan and H. Shi, Review of systems for photocatalytic conversion of CO2 to hydrocarbon fuels, Acta Phys.-Chim. Sin., 2014, 30, 2177–2196 CAS
.
- W. Tu, Y. Zhou and Z. Zou, Photocatalytic conversion
of CO2 into renewable hydrocarbon fuels: state-of-the-art accomplishment, challenges, and prospects, Adv. Mater., 2014, 26, 4607–4626 CrossRef CAS
.
- M. Marszewski, S. Cao, J. Yu and M. Jaroniec, Semiconductor-based photocatalytic CO2 conversion, Mater. Horiz., 2015, 2, 261–278 RSC
.
- K. Li, B. Peng and T. Peng, Recent advances in heterogeneous photocatalytic CO2 conversion to solar fuels, ACS Catal., 2016, 6, 7485–7527 CrossRef CAS
.
- M. Yang and Y. Xu, Photocatalytic conversion of CO2 over graphene-based composites: current status and future perspective, Nanoscale Horiz., 2016, 1, 185–200 RSC
.
- Y. Y. Lee, H. S. Jung and Y. T. Kang, A review: effect of nanostructures on photocatalytic CO2 conversion over metal oxides and compound semiconductors, J. CO2 Util., 2017, 20, 163–177 CrossRef CAS
.
- Y. Ma, Z. Wang, X. Xu and J. Wang, Review on porous nanomaterials for adsorption and photocatalytic conversion of CO2, Chin. J. Catal., 2017, 38, 1956–1969 CrossRef CAS
.
- Y. Fang and X. Wang, Photocatalytic CO2 conversion by polymeric carbon nitrides, Chem. Commun., 2018, 54, 5674–5687 RSC
.
- M. Khalil, J. Gunlazuardi, T. A. Ivandini and A. Umar, Photocatalytic conversion of CO2 using earth-abundant catalysts: a review on mechanism and catalytic performance, Renewable Sustainable Energy Rev., 2019, 113, 109246 CrossRef CAS
.
- A. Razzaq, and S.I. In, TiO2 based nanostructures for photocatalytic CO2 conversion to valuable chemicals, Micromachines, 2019, 10, 326 CrossRef
.
- I. Lee, W. J. Kim and D. C. Lee, Design of metallic cocatalysts in heterostructured nanoparticles for photocatalytic CO2-to-hydrocarbon conversion, J. Phys. D: Appl. Phys., 2020, 53, 123001 CrossRef CAS
.
- J. Yu, J. Low, W. Xiao, P. Zhou and M. Jaroniec, Enhanced photocatalytic CO2-reduction activity of anatase TiO2 by coexposed {001} and {101} facets, J. Am. Chem. Soc., 2014, 136, 8839–8842 CrossRef CAS
.
- L. Liu, H. Zhao, J. M. Andino and Y. Li, Photocatalytic CO2 reduction with H2O on TiO2 nanocrystals: comparison of anatase, rutile, and brookite polymorphs and exploration of surface chemistry, ACS Catal., 2012, 2, 1817–1828 CrossRef CAS
.
- L. Liu, Y. Jiang, H. Zhao, J. Chen, J. Cheng, K. Yang and Y. Li, Engineering coexposed {001} and {101} facets in oxygen-deficient TiO2 nanocrystals for enhanced CO2 photoreduction under visible light, ACS Catal., 2016, 6, 1097–1108 CrossRef CAS
.
- Z. Xiong, Z. Lei, X. Chen, B. Gong, Y. Zhao, J. Zhang, C. Zheng and J. C. S. Wu, CO2 photocatalytic reduction over Pt deposited TiO2 nanocrystals with coexposed {101} and {001} facets: effect of deposition method and Pt precursors, Catal. Commun., 2017, 96, 1–5 CrossRef CAS
.
- M. Kong, Y. Li, X. Chen, T. Tian, P. Fang, F. Zheng and X. Zhao, Tuning the relative concentration ratio of bulk defects to surface defects in TiO2 nanocrystals leads to high photocatalytic efficiency, J. Am. Chem. Soc., 2011, 133, 16414–16417 CrossRef CAS
.
- R. Shen, T. Chen, Y. Zhao, R. Qiu, Y. Zhou, S. Yin, X. Wang, M. Goto and L. Han, Facile regio- and stereoselective hydrometalation of alkynes with a combination of carboxylic acids and group 10 transition metal complexes: selective hydrogenation of alkynes with formic acid, J. Am. Chem. Soc., 2011, 133, 17037–17044 CrossRef CAS
.
- D. Srimani, Y. Diskin-Posner, Y. Ben-David and D. Milstein, Iron pincer complex catalyzed, environmentally benign, E-selective semi-hydrogenation of alkynes, Angew. Chem., Int. Ed., 2013, 52, 14131–14134 CrossRef CAS
.
- M. K. Karunananda and N. P. Mankad,
E-selective semi-hydrogenation of alkynes by heterobimetallic catalysis, J. Am. Chem. Soc., 2015, 137, 14598–14601 CrossRef CAS
.
- J. Chen, M. Chu, F. Lyu, J. Gong, L. Wu, L. Liu, Y. Xu and Q. Zhang, Strong synergy between Ti3C2 and N-Doped Co nanoparticles boosts the selective hydrogenation of propyne, Ind. Eng. Chem. Res., 2019, 58, 21413–21418 CrossRef CAS
.
- F. P. da Silva, J. L. Fiorio, R. V. Goncalves, E. Teixeira-Neto and L. M. Rossi, Synergic effect of copper and palladium for selective hydrogenation of alkynes, Ind. Eng. Chem. Res., 2018, 57, 16209–16216 CrossRef CAS
.
- M. Cordoba, F. Coloma-Pascual, M. E. Quiroga and C. R. Lederhos, Olefin purification and selective hydrogenation of alkynes with low loaded Pd nanoparticle catalysts, Ind. Eng. Chem. Res., 2019, 58, 17182–17194 CrossRef CAS
.
- T. Kojima, S. Kameoka, S. Fujii, S. Ueda and A. P. Tsai, Catalysis-tunable Heusler alloys in selective hydrogenation of alkynes: a new potential for old materials, Sci. Adv., 2018, 4, eaat6063 CrossRef CAS
.
- J. Chung, C. Kim, H. Jeong, T. Yu, D. H. Binh, J. Jang, J. Lee, B. M. Kim and B. Lim, Selective semihydrogenation of alkynes on shape-controlled palladium nanocrystals, Chem. – Asian J., 2013, 8, 919–925 CrossRef CAS
.
- M. Crespo-Quesada, S. Yoon, M. Jin, A. Prestianni, R. Cortese, F. Cárdenas-Lizana, D. Duca, A. Weidenkaff and L. Kiwi-Minsker, Shape-dependence of Pd nanocrystal carburization during acetylene hydrogenation, J. Phys. Chem. C, 2015, 119, 1101–1107 CrossRef CAS
.
- W. Niu, Y. Gao, W. Zhang, N. Yan and X. Lu, Pd–Pb alloy nanocrystals with tailored composition for semihydrogenation: taking advantage of catalyst poisoning, Angew. Chem., Int. Ed., 2015, 54, 8271–8274 CrossRef CAS
.
- J. Zhang, W. Xu, L. Xu, Q. Shao and X. Huang, Concavity tuning of intermetallic Pd–Pb nanocubes for selective semihydrogenation catalysis, Chem. Mater., 2018, 30, 6338–6345 CrossRef CAS
.
- Y. Xu, W. Bian, Q. Pan, M. Chu, M. Cao, Y. Li, Z. Gong, R. Wang, Y. Cui, H. Lin and Q. Zhang, Revealing the active sites of Pd nanocrystals for propyne semihydrogenation: from theory to experiment, ACS Catal., 2019, 9, 8471–8480 CrossRef CAS
.
- C. H. Hao, X.-N. Guo, Y. T. Pan, S. Chen, Z. F. Jiao, H. Yang and X. Y. Guo, Visible-light-driven selective photocatalytic hydrogenation of cinnamaldehyde over Au/SiC catalysts, J. Am. Chem. Soc., 2016, 138, 9361–9364 CrossRef CAS
.
- S. Chen, L. Meng, B. Chen, W. Chen, X. Duan, X. Huang, B. Zhang, H. Fu and Y. Wan, Poison tolerance to the selective hydrogenation of cinnamaldehyde in water over an ordered mesoporous carbonaceous composite supported Pd catalyst, ACS Catal., 2017, 7, 2074–2087 CrossRef CAS
.
- S. Wei, Y. Zhao, G. Fan, L. Yang and F. Li, Structure-dependent selective hydrogenation of cinnamaldehyde over high-surface-area CeO2-ZrO2 composites supported Pt nanoparticles, Chem. Eng. J., 2017, 322, 234–245 CrossRef CAS
.
- R. Li, W. Yao, Y. Jin, W. Jia, X. Chen, J. Chen, J. Zheng, Y. Hu, D. Han and J. Zhao, Selective hydrogenation of the C
C bond in cinnamaldehyde over an ultra-small Pd–Ag alloy catalyst, Chem. Eng. J., 2018, 351, 995–1005 CrossRef CAS
.
- Z. Weng and F. Zaera, Sub-monolayer control of mixed-oxide support composition in catalysts via atomic layer deposition: selective hydrogenation of cinnamaldehyde promoted by (SiO2-ALD)–Pt/Al2O3, ACS Catal., 2018, 8, 8513–8524 CrossRef CAS
.
- Y. Yang, D. Rao, Y. Chen, S. Dong, B. Wang, X. Zhang and M. Wei, Selective hydrogenation of cinnamaldehyde over Co-based intermetallic compounds derived from layered double hydroxides, ACS Catal., 2018, 8, 11749–11760 CrossRef CAS
.
- K. Yuan, T. Song, D. Wang, X. Zhang, X. Gao, Y. Zou, H. Dong, Z. Tang and W. Hu, Effective and selective catalysts for cinnamaldehyde hydrogenation: hydrophobic hybrids of metal–organic frameworks, metal nanoparticles, and micro- and mesoporous polymers, Angew. Chem., Int. Ed., 2018, 57, 5708–5713 CrossRef CAS
.
- S. Bewana, M. J. Ndolomingo, E. Carleschi, B. P. Doyle, R. Meijboom and N. Bingwa, Inorganic perovskite-lnduced synergy on highly selective Pd-catalyzed hydrogenation of cinnamaldehyde, ACS Appl. Mater. Interfaces, 2019, 11, 32994–33005 CrossRef CAS
.
- X. Huang, L. Zhang, C. Li, L. Tan and Z. Wei, High selective electrochemical hydrogenation of cinnamaldehyde to cinnamyl alcohol on RuO2–SnO2–TiO2/Ti electrode, ACS Catal., 2019, 9, 11307–11316 CrossRef CAS
.
- Z. Weng and F. Zaera, Atomic layer deposition (ALD) as a way to prepare new mixed-oxide catalyst supports: the case of alumina addition to silica-supported platinum for the selective hydrogenation of cinnamaldehyde, Top. Catal., 2019, 62, 838–848 CrossRef CAS
.
- H. Xin, Y. Xue, W. Zhang, P. Wu and X. Li, CoxFe1−xAl2O4 composite oxides supported Pt nanoparticles as efficient and recyclable catalysts for the liquid-phase selective hydrogenation of cinnamaldehyde, J. Catal., 2019, 380, 254–266 CrossRef CAS
.
- J. Zhu, X. Ding, D. Li, M. Dou, M. Lu, Y. Li and F. Luo, Graphene oxide-supported catalyst with thermoresponsive smart surface for selective hydrogenation of cinnamaldehyde, ACS Appl. Mater. Interfaces, 2019, 11, 16443–16451 CrossRef CAS
.
- X. Gao, H. Dai, L. Peng, D. Lu, X. Wan, C. Zhou, J. Zheng, Y. Dai, H. Wang and Y. Yang, Effect of hydrotalcites interlayer water on Pt-catalyzed aqueous-phase selective hydrogenation of cinnamaldehyde, ACS Appl. Mater. Interfaces, 2020, 12, 2516–2524 CrossRef CAS
.
- Y. Zhu, H. Qian, B. A. Drake and R. Jin, Atomically Precise Au25(SR)18 nanoparticles as catalysts for the selective hydrogenation of α,β-unsaturated ketones and aldehydes, Angew. Chem., Int. Ed., 2010, 49, 1295–1298 CrossRef CAS
.
- R. Ouyang and D. E. Jiang, Understanding selective hydrogenation of α,β-unsaturated ketones to unsaturated alcohols on the Au25(SR)18 cluster, ACS Catal., 2015, 5, 6624–6629 CrossRef CAS
.
- B. Wu, H. Huang, J. Yang, N. Zheng and G. Fu, Selective hydrogenation of α,β-unsaturated aldehydes catalyzed by amine-capped platinum-cobalt nanocrystals, Angew. Chem., Int. Ed., 2012, 51, 3440–3443 CrossRef CAS
.
- J. C. Serrano-Ruiz, A. López-Cudero, J. Solla-Gullón, A. Sepúlveda-Escribano, A. Aldaz and F. Rodríguez-Reinoso, Hydrogenation of α, β unsaturated aldehydes over polycrystalline, (111) and (100) preferentially oriented Pt nanoparticles supported on carbon, J. Catal., 2008, 253, 159–166 CrossRef CAS
.
- J. D. Grunwaldt, C. Kiener, C. Wogerbauer and A. Baiker, Preparation of supported gold catalysts for low-temperature CO oxidation via “size-controlled” gold colloids, J. Catal., 1999, 181, 223–232 CrossRef CAS
.
- M. M. Schubert, S. Hackenberg, A. C. van Veen, M. Muhler, V. Plzak and R. J. Behm, CO oxidation over supported gold catalysts-“inert” and “active” support materials and their role for the oxygen supply during reaction, J. Catal., 2001, 197, 113–122 CrossRef CAS
.
- N. Lopez and J. K. Norskov, Catalytic CO oxidation by a gold nanoparticle:
a density functional study, J. Am. Chem. Soc., 2002, 124, 11262–11263 CrossRef CAS
.
- N. Lopez, T. V. W. Janssens, B. S. Clausen, Y. Xu, M. Mavrikakis, T. Bligaard and J. K. Norskov, On the origin of the catalytic activity of gold nanoparticles for low-temperature CO oxidation, J. Catal., 2004, 223, 232–235 CrossRef CAS
.
- J. Guzman, S. Carrettin and A. Corma, Spectroscopic evidence for the supply of reactive oxygen during CO oxidation catalyzed by gold supported on nanocrystalline CeO2, J. Am. Chem. Soc., 2005, 127, 3286–3287 CrossRef CAS
.
- B. Yoon, H. Hakkinen, U. Landman, A. S. Worz, J. M. Antonietti, S. Abbet, K. Judai and U. Heiz, Charging effects on bonding and catalyzed oxidation of CO on Au8 clusters on MgO, Science, 2005, 307, 403–407 CrossRef CAS
.
- M. Comotti, W. Li, B. Spliethoff and F. Schuth, Support effect in high activity gold catalysts for CO oxidation, J. Am. Chem. Soc., 2006, 128, 917–924 CrossRef CAS
.
- C. Xu, J. Su, X. Xu, P. Liu, H. Zhao, F. Tian and Y. Ding, Low temperature CO oxidation over unsupported nanoporous gold, J. Am. Chem. Soc., 2007, 129, 42–43 CrossRef CAS
.
- H. Jiang, B. Liu, T. Akita, M. Haruta, H. Sakurai and Q. Xu, Au@ZIF-8: CO oxidation over gold nanoparticles deposited to metal–organic framework, J. Am. Chem. Soc., 2009, 131, 11302–11303 CrossRef CAS
.
- I. X. Green, W. Tang, M. Neurock and J. T. Yates, Jr., Spectroscopic observation of dual catalytic sites during oxidation of CO on a Au/TiO2 catalyst, Science, 2011, 333, 736–739 CrossRef CAS
.
- Y. Zhang, M. E. Grass, W. Huang and G. A. Somorjai, Seedless polyol synthesis and CO oxidation activity of monodisperse (111)- and (100)-oriented rhodium nanocrystals in sub-10 nm sizes, Langmuir, 2010, 26, 16463–16468 CrossRef CAS
.
- C. George, A. Genovese, A. Casu, M. Prato, M. Povia, L. Manna and T. Montanari, CO oxidation on colloidal Au0.80Pd0.20–FexOy dumbbell nanocrystals, Nano Lett., 2013, 13, 752–757 CrossRef CAS
.
- S. Carrettin, P. Concepción, A. Corma, J. M. López Nieto and V. F. Puntes, Nanocrystalline CeO2 increases the activity of Au for CO oxidation by two orders of magnitude, Angew. Chem., Int. Ed., 2004, 43, 2538–2540 CrossRef CAS
.
- H. Y. Kim, H. M. Lee and G. Henkelman, CO oxidation mechanism on CeO2-supported Au nanoparticles, J. Am. Chem. Soc., 2012, 134, 1560–1570 CrossRef CAS
.
- B. Yoon, H. Häkkinen, U. Landman, A. S. Wörz, J. M. Antonietti, S. Abbet, K. Judai and U. Heiz, Charging Effects on Bonding and Catalyzed Oxidation of CO on Au8 Clusters on MgO, Science, 2005, 307, 403–407 CrossRef CAS
.
- L. Dai, Y. Xue, L. Qu, H. J. Choi and J. B. Baek, Metal-free catalysts for oxygen reduction reaction, Chem. Rev., 2015, 115, 4823–4892 CrossRef CAS
.
- F. Jaouen, E. Proietti, M. Lefevre, R. Chenitz, J. P. Dodelet, G. Wu, H. T. Chung, C. M. Johnston and P. Zelenay, Recent advances in non-precious metal catalysis for oxygen-reduction reaction in polymer electrolyte fuel cells, Energy Environ. Sci., 2011, 4, 114–130 RSC
.
- L. Lai, J. R. Potts, D. Zhan, L. Wang, C. K. Poh, C. Tang, H. Gong, Z. Shen, J. Lin and R. S. Ruoff, Exploration of the active center structure of nitrogen-doped graphene-based catalysts for oxygen
reduction reaction, Energy Environ. Sci., 2012, 5, 7936–7942 RSC
.
- G. Wu and P. Zelenay, Nanostructured nonprecious metal catalysts for oxygen reduction reaction, Acc. Chem. Res., 2013, 46, 1878–1889 CrossRef CAS
.
- Y. Nie, L. Li and Z. Wei, Recent advancements in Pt and Pt-free catalysts for oxygen reduction reaction, Chem. Soc. Rev., 2015, 44, 2168–2201 RSC
.
- J. Zhang, Z. Zhao, Z. Xia and L. Dai, A metal-free bifunctional electrocatalyst for oxygen reduction and oxygen evolution reactions, Nat. Nanotechnol., 2015, 10, 444–452 CrossRef CAS
.
- D. Guo, R. Shibuya, C. Akiba, S. Saji, T. Kondo and J. Nakamura, Active sites of nitrogen-doped carbon materials for oxygen reduction reaction clarified using model catalysts, Science, 2016, 351, 361–365 CrossRef CAS
.
- M. Shao, Q. Chang, J. P. Dodelet and R. Chenitz, Recent advances in electrocatalysts for oxygen reduction reaction, Chem. Rev., 2016, 116, 3594–3657 CrossRef CAS
.
Footnote |
† Yong Xu and Muhan Cao contributed equally. |
|
This journal is © the Partner Organisations 2021 |
Click here to see how this site uses Cookies. View our privacy policy here.