DOI:
10.1039/D1NA00438G
(Paper)
Nanoscale Adv., 2021,
3, 5626-5635
Anionic/nonionic surfactants for controlled synthesis of highly concentrated sub-50 nm polystyrene spheres†
Received
13th June 2021
, Accepted 10th August 2021
First published on 10th August 2021
Abstract
Polystyrene nanospheres are of great importance in 3D hard templating along with many other fields like pharmaceuticals and coatings. Therefore, it is important to be able to prepare polystyrene beads with different sphere sizes that suit each application. In this work, the emulsion polymerization method was used to prepare monodispersed polystyrene (PS) spheres with an average size of 50 nm, using styrene monomer, sodium dodecyl sulfate (SDS) and polyvinylpyrrolidone (PVP) as surfactants, and potassium persulfate (KPS) as the initiator. The average size and size distribution of the PS spheres were controlled by optimizing the synthesis parameters such as the concentration of the monomer, initiator, and surfactant, the type of surfactant, and the time and temperature of polymerization. The shape, size, and size distribution of the prepared PS spheres were characterized using dynamic light scattering (DLS) and scanning electron microscopy (SEM). The preparation of perfectly spherical PS spheres as small as 50 nm with a narrow size distribution is obtained using 8% styrene with (5% SDS and 2% KPS of the styrene amount) at 90 °C, with the monomer and surfactant molar ratio and concentration and the polymerization temperature being the dominating factors that affect the PS bead size.
1. Introduction
Polymeric materials are relatively cheap and easy to make and can be made into different forms like thin films, spheres, and fibers. Polymers can be natural or synthetic.6 Polymer nanoparticles are important for many industrial applications like photonics, sensors, pollution control,1 environmental technology,2 smart drug delivery,3 and the preparation of colloidal crystal templates,4,5 which can be used to prepare three-dimensionally ordered nanoporous materials.
Polymer nanoparticles have been prepared using several methods like dispersion polymerization7 that is usually used to prepare micron sized particles, solvent evaporation,8 and salting out.9 Among several, the most commonly used method is emulsion polymerization (EmPoly) that includes traditional and surfactant-free emulsion polymerization10 and mini-emulsion polymerization.11
EmPoly got a lot of attention as it produces polymers in large quantities and is relatively simple, fast, reliable, and scalable at the same time. EmPoly is used today for most of the world's production of polymers and many variations of the original preparation method were proposed during the years.12 EmPoly is a radical polymerization process that involves the use of water as a solvent, a monomer of small organic molecules that can bond in long chains, an anionic, cationic, non-ionic, or amphoteric surfactant to lower the surface tension and form micelles that control the polymer final shape, and a radical initiator to start the polymerization process.13 In some cases, other ingredients like co-monomers are added to enhance the overall polymerization process and allow for more control over the final product.
Polystyrene (PS) is one of the most important polymers that could be easily made into different shapes or expanded as a foam,14 with applications ranging from the preparation of photonic crystals15 to drug delivery.16 PS nanoparticles were prepared using dispersion polymerization with a size range of 200 to 2000 nm.17 It was also prepared by EmPoly with a size range of 1.2 to 5 μm (ref. 18) and also with a size of almost 200 nm.19 Table S1† shows a comparison between the common methods used in polystyrene preparation.
One of the interesting uses of PS spheres is the preparation of three-dimensionally ordered macroporous materials.5,19–21 Materials/catalysts with a pore size of 50 to 100 nm are of great interest as the supply of reactants to the surface and removal of byproducts are enhanced, while maintaining the catalyst strength. Smaller PS spheres would give a larger surface area material, which is highly desired for surface dependent applications. However, the literature discussing the controlled synthesis of sub-50 nm PS spheres is not enough, and the experimental work that was re-tested did not provide controlled and reproducible results with the existence of agglomerates due to the use of very high surfactant concentrations and the need for filtration/centrifuging to get the final monodispersed spheres.22
In this work, the EmPoly method was used to prepare monodispersed polystyrene spheres with a size of 50 nm without the need for further filtration or separation. The effect of different preparation parameters on the size and size distribution of the PS spheres was studied to get a clear idea of the modification of the recipes that can produce a specific PS sphere size with a narrow size distribution.
2. Experimental
2.1. Materials
Styrene (99%, Sigma Aldrich), Polyvinylpyrrolidone (PVP, MW 40
000, Fluka), sodium dodecyl sulfate (SDS, Sigma Aldrich), potassium persulfate (KPS, Alfa), absolute ethanol, and acetone (99%) were used. All the chemicals were used as received without any further purification, and distilled water was used as the main solvent.
2.2. PS sphere preparation
All the polymerization reactions were conducted in a four-neck round bottom flask equipped with a digital thermometer, under nitrogen gas, and a reflux condenser, and the flask's fourth neck was used to add the reactants as shown in (Fig. 1). The following procedure was used to prepare all samples; at first, a specific amount of distilled water was added to the flask and heated to a certain temperature and nitrogen gas was bubbled into the water for 10 minutes to remove oxygen from the reaction medium. This is because oxygen can act as an initiator for the polymerization reaction, which would affect the process and start the polymerization randomly. Additionally, the presence of oxygen in radical polymerization could restrict the polymerization and decrease the yield or even terminate the formed radicals, which will interfere with the desired polymerization process for polystyrene preparation.23,24 A specific amount of the surfactant PVP or SDS was then added to the solution with magnetic stirring at 350–450 rpm and was left to stir at the desired temperature for 10 minutes. After that, the styrene monomer was added to the solution and the mixture was left to stir for another 20 minutes to ensure that most of the styrene droplets are in the SDS micelles or have been covered with PVP molecules. After that, the nitrogen gas tube is lifted from the solution and kept above the solution to keep the polymerization reaction going under an inert atmosphere, and then the initiator solution (specific weight of KPS in 25 ml of water) was added to the reaction mixture. Finally, the polymerization reaction is left to continue under magnetic stirring and heating for 24 hours, unless otherwise stated below.
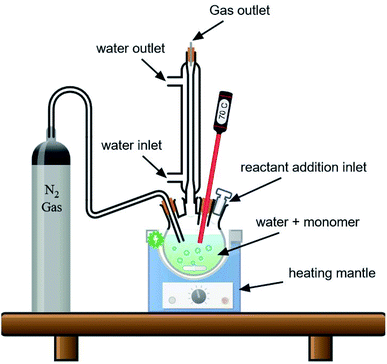 |
| Fig. 1 Setup for the preparation of PS spheres using the emulsion polymerization process under a nitrogen atmosphere. | |
2.3. Characterization
The prepared PS spheres were characterized by dynamic light scattering (DLS) using a Zetasizer Nano ZS90 (Malvern Panalytical), which gave information about the size and size distribution of the prepared spheres. To do so, 1 ml of the polymer solution was taken and diluted with distilled water until a transparent solution was obtained and analyzed to get the average size and size distribution using three measurements with 40 runs each.
The shape and size of the PS spheres were verified by scanning electron microscopy (SEM) using Carl Zeiss, SUPRA 55 Field Emission Scanning Electron Microscopes (FESEM). To do so, 1 ml of the polymer solution was put on a glass slide and left to dry at room temperature and then the dried PS over the slide was coated with a layer of gold using a “Hummer 8.0 Sputter System” at a current of 15 mA for two minutes.
3. Results and discussion
The size of the prepared PS spheres ranged between 40 and 250 nm and the change of each of the following parameters gave different sizes and size distributions. All experiments were conducted multiple times to verify the reproducibility of the results, and the final recipe was used to prepare more than ten batches with different batch sizes to make sure that the results were reliable.
3.1. The effect of surfactant concentration
The surfactant concentration is one of the parameters that affect the EmPoly process the most, as experimental results indicate. Upon addition of the surfactant, the surfactant molecules adsorb on the solution surface, causing a surface tension decrease until the critical micelle concentration (CMC) is reached. This leads to micelle formation inside the solution. Any further increase in the surfactant concentration, above the CMC, will have a minimal effect on the surface tension but will continue to decrease the interfacial tension. Even though the solution surface will remain covered by the surfactant molecules after reaching the CMC, the hydrophobic parts of the surfactant will start to orient themselves inside the micelles to lower their interaction with the water molecules. In the case of ionic surfactants, increasing the surfactant concentration above the CMC usually leads to an increase in the number of micelles, which in turn reduces the size of the micelles down due to electrostatic repulsion. Meanwhile in the case of nonionic surfactants, the continuous addition of surfactants will increase the steric effect, making it harder for the monomer molecules to approach each other, which will eventually lead to the formation of small size particles. The increase in the number of micelles affords a high number of active centers in the polymerization initiation step, resulting in higher monomer conversion rates and smaller size particles.25,26
In the case of PVP (MW 40
000), even though increasing the concentration of the surfactant from 12 to 35% did not result in decreasing the size of the PS spheres, with the size maintained in the range of 160–170 nm, it resulted in a very narrow size distribution according to the dynamic light scattering (DLS) measurements that are shown in Table 1. In this PVP concentration range, increasing the PVP concentration just increases the PVP steric effect, and the stabilization of the monomer takes place as soon as PVP is added to the solution. However, at a high concentration (50%) of PVP (MW = 40
000), a white precipitate was formed especially when temperatures above 90 °C were used, and the DLS measurements showed multiple peaks, as Table 1 shows, with a wide size distribution. This was also noticed in the case of PVP (MW = 360
000) at much lower concentrations (12%) at 70, 80, and 90 °C. In the case of high concentrations of PVP (MW = 40
000), a significant amount of PVP is not expected to be involved in the stabilization of the styrene monomer and will form insoluble compounds when heated between 70 and 90 °C due to the presence of persulfate and styrene. This behavior of PVP (MW = 40
000 and 360
000) is reported in the presence of persulfate and vinyl acetate.27 This effect is also noticed at lower concentrations of PVP with a high molecular weight (MW = 360
000). Moreover, it is expected that in some experiments the white precipitate was due to the cloud point and it is a known phenomenon in nonionic surfactants that depends on its concentration, the reaction temperature, and the existence of salts and other additives in the solution especially SDS where insoluble clusters are formed.28,29 The effects of the PVP concentration and molecular weight were studied and the results showed a high dependency of the PS spheres on the PVP concentration.30
Table 1 Recipes for the surfactant concentration effect on the PS sphere size
Recipe |
% of styrene |
Particle size (nm) |
SD |
RSD% |
PDI |
PVP |
SDS |
S1 |
12 |
— |
163 |
11.74 |
7.20 |
0.08 |
S2 |
17 |
— |
176 |
8.94 |
5.07 |
0.068 |
S3 |
25 |
— |
167 |
13.4 |
8.02 |
0.02 |
S4 |
35 |
— |
171 |
5.65 |
3.30 |
0.026 |
S5 |
50 |
— |
122–584 & precipitate |
— |
— |
0.49 |
S6 |
— |
2 |
172 |
4.497 |
2.61 |
0.038 |
S7 |
— |
5 |
50 |
2.198 |
4.39 |
0.036 |
S8 |
— |
8 |
41 |
1.59 |
3.87 |
0.102 |
S9 |
— |
12.5 |
76.18–4208 |
— |
— |
0.244 |
S10 |
— |
25 |
49–214 & precipitate |
— |
— |
0.752 |
Temperature 90 °C; water 125 ml; styrene: 8%; KPS: 2% of styrene |
In the case of SDS, the increase in the concentration from 2 to 8% (relative to the styrene amount) had a higher impact on the size of the PS spheres than PVP, as shown in Table 1, with the size going down from 170 to 40 nm. The DLS results of the S07 sample in Fig. 2 showed a sharp peak, indicating a narrow size distribution and small PDI values (Table 1). The anionic surfactants such as SDS are known to result in particles with a smaller size than the nonionic surfactants such as PVP. Even though the size dropped to 40 nm when an SDS concentration of 8% was used, the PDI increased and reached 0.1. At higher SDS concentrations, the DLS measurements showed higher particle sizes,31 multiple peaks, and/or a very wide size distribution (Fig. 2), similar to what was observed in the case of PVP. At high SDS concentrations, a white participant was formed, which can be the result of SDS hydrolysis at high temperatures into dodecanol.32 A proposed mechanism of the EmPoly process in the presence of SDS and PVP surfactants is illustrated in Fig. 3a and b, respectively. In both cases, the surfactant molecules behave the same way, lowering the surface and interfacial tension and then forming micelles. The difference is in the stabilizing mechanism of each surfactant, where SDS micelles are stabilized by electrostatic repulsion, while PVP micelles are stabilized by the steric effect which forms a bundle of surfactant molecules that surround the monomer by multiple layers.
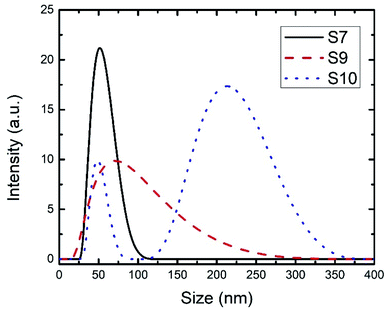 |
| Fig. 2 DLS curves for the SDS-S7, SDS-S9, and SDS-S10 recipes, with 8% SDS relative to the monomer concentration. | |
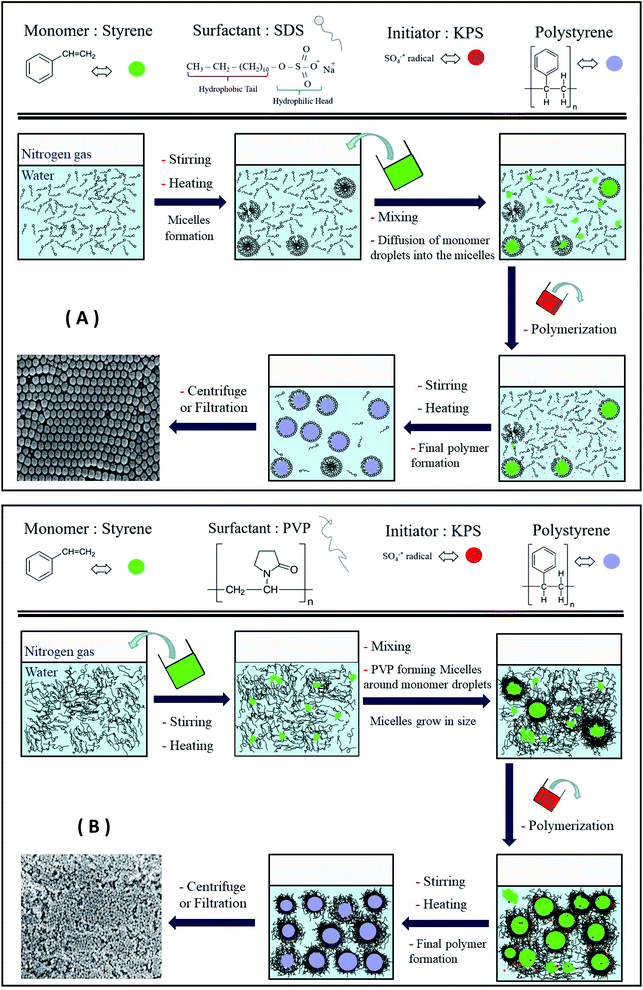 |
| Fig. 3 Polymerization process mechanism using: (A) SDS; (B) PVP. | |
3.2. The effect of surfactant type
Aiming to investigate the effect of adding SDS to PVP to verify whether smaller and more uniformed PS spheres than those obtained in the presence of PVP could be formed, several mixtures of PVP and SDS were tested with different ratios and with a low monomer concentration of 1% as shown in Table 2. As demonstrated by the results above, the anionic SDS surfactant gave smaller PS spheres than non-ionic PVP, while the size distribution was narrow in both cases. Anionic surfactants always give a smaller particle size than non-ionic ones,33 which is because the electrostatic repulsion between the anionic surfactant molecules is much stronger than the steric repulsion between the non-ionic surfactant molecules (Fig. 3a).
Table 2 Recipes for the surfactant type effect on the PS sphere size
Recipe |
% of styrene |
Particle size (nm) |
SD |
RSD% |
PDI |
PVP |
SDS |
SP0 |
25 |
0 |
133 |
12.723 |
9.56 |
0.055 |
SP1 |
25 |
1 |
71 |
4.21 |
5.92 |
0.013 |
SP2 |
25 |
2 |
229 |
9.744 |
4.25 |
0.095 |
SP3 |
25 |
3 |
>400 |
— |
— |
0.407 |
SP4 |
10 |
2 |
72 |
3.252 |
4.51 |
0.015 |
SP5 |
0 |
5 |
152 |
7.29 |
4.79 |
0.042 |
SP6 |
0 |
10 |
128 |
7.64 |
5.96 |
0.051 |
Temperature 70 °C, water 125 ml; styrene: 1%; KPS: 2% of styrene |
When a mixture of both surfactants was used by adding small amounts of SDS with a specific concentration of PVP (25%), it was found that the polymerization could only take place at temperatures up to 75 °C. Any higher temperatures at this PVP concentration and any SDS concentration led to the formation of a white precipitate, which consists of SDS micelles that agglomerate along the PVP strands to form different sizes of SDS/PVP aggregates and this is expected as SDS is known to interact with PVP polymer34–36 especially at high temperatures due to the cloud point effect discussed above, which is affected by the addition of SDS and the temperature change. This would lead to a polydispersed product containing the PS spheres and those aggregates. Moreover, when the SDS amount in the surfactant mixture was raised to 2% or above as shown in Table 2, even at low temperatures (70 °C), precipitation has occurred due to the interactions between SDS and PVP triggered by the high concentration of SDS. The smallest PS sphere size obtained using these mixtures was 71 nm using (25% PVP + 1% SDS of the styrene amount) or (10% PVP + 2% SDS of the styrene amount) with a PDI of 0.013. The results showed that using PVP only as a surfactant, using 25% PVP to styrene, gave a sphere size of 133 nm, which means that the addition of 1% SDS to the recipe reduced the size by 62 nm, which is almost around half its original value.
3.3. The effect of monomer concentration
The monomer concentration was changed between 1 and 10% of the total mixture and the results are demonstrated in Table 4. It is reported by many studies37,38 that when all the other parameters are constant in emulsion polymerization, the size of PS spheres increases with increasing the monomer concertation, as more monomer molecules would be present in solution. After the addition of the initiator, the first nucleation sites are formed when the water-soluble initiator diffuses inside the micelles, and then these sites would start to attract more monomer molecules from the solution. Therefore, the increase in the initial monomer concentration means more chance for the particle size to be enlarged and this is in agreement with most of the literature discussing the effect of the monomer concentration on the size of polymer nanoparticles. In the case of both SDS and PVP, when the concentration of the surfactant was fixed, an increase in the monomer concentration caused an increase in the PS sphere size. In the case of PVP, when the surfactant concentration was changed as a specific percentage, 25%, of the monomer concentration, an increase in the monomer concentration caused an increase in the PS sphere size as well. Table 3 shows that after the monomer concentration was decreased to 0.75%, no major change in the size or size distribution was noticed with any further decrease in the concentration. These results indicate that the lowest size that can be obtained using PVP under these conditions is around 100 nm.
Table 3 Recipes for the monomer concentration effect on the PS sphere size
Recipe |
Styrene% |
Particle size (nm) |
SD |
RSD% |
PDI |
M1 |
8 |
167 |
— |
— |
0.02 |
M2 |
4 |
161 |
— |
— |
0.07 |
M3 |
2 |
155 |
— |
— |
0.12 |
M4 |
1 |
125 |
— |
— |
0.115 |
M5 |
0.75 |
100 |
13.24 |
13.24 |
0.016 |
M6 |
0.5 |
102 |
— |
— |
0.053 |
M7 |
0.25 |
105 |
— |
— |
0.03 |
Temperature 90 °C; water 125 ml; PVP: 25% of styrene; KPS: 2% of styrene |
M8 |
10 |
44 |
1.249 |
2.83 |
0.07 |
M9 |
8 |
50 |
2.198 |
4.39 |
0.036 |
M10 |
6 |
78 |
7.727 |
9.90 |
0.032 |
M11 |
4 |
121 |
— |
— |
0.01 |
M12 |
2 |
133 |
— |
— |
0.002 |
M13 |
1 |
140 |
— |
— |
0.024 |
Temperature 90 °C; water 125 ml; SDS: 5% of styrene; KPS: 2% of styrene |
Table 4 Effect of the polymerization time on the PS sphere size
Recipe |
Time |
Particle size (nm) |
PDI |
T1 |
3 |
49 |
0.092 |
T2 |
6 |
47 |
0.051 |
T3 |
9 |
51 |
0.081 |
T3 |
12 |
51 |
0.042 |
T3 |
15 |
50 |
0.057 |
T4 |
20 |
51 |
0.037 |
T5 |
24 |
50 |
0.036 |
Temperature 90 °C; water 125 ml; styrene: 8%; (SDS: 5%; KPS: 2% of styrene) |
Fig. 4 shows the shape of the PS spheres for the M2, M9, M11, and M12 recipes. The images clearly show the formation of PS spheres with different sizes, while the SEM image of recipe S5 shows non-uniform PS formation with aggregates and large size particles due to the high PVP concentration. As expected, a small decrease in the size is noticed in these SEM images in comparison to the DLS reported sizes. For example, in the case of the M9 recipe, the particle size for randomly selected 40 particles is measured using ImageJ software and is found to be 50.2 ± 1.7 nm, as shown in Fig. S1,† which is very similar to the DLS results (Table 3). In the case of the PVP/SDS mixture, the dependence of the PS sphere size on the monomer concentration was very similar to that of PVP alone.
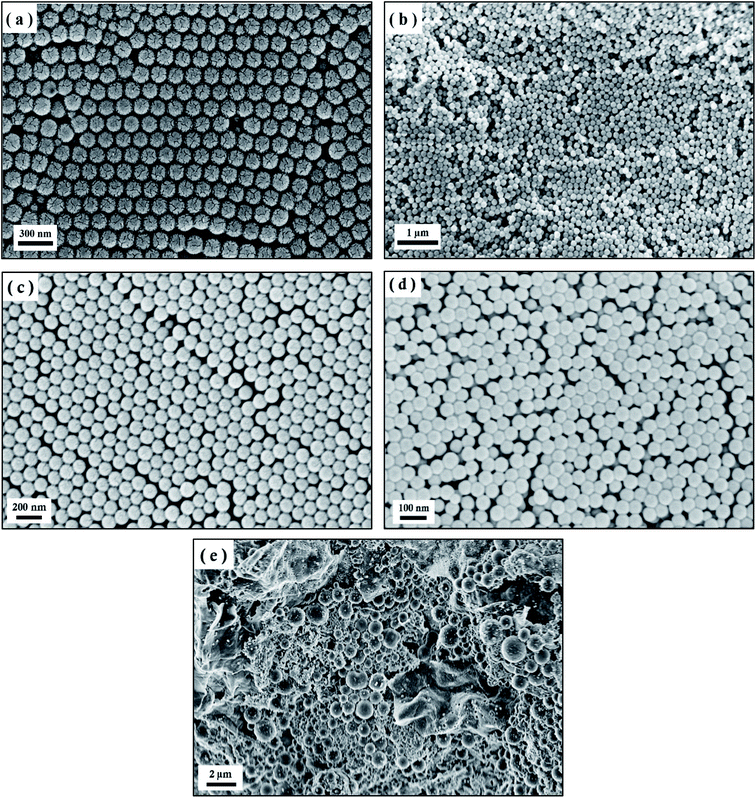 |
| Fig. 4 SEM images for (a) PVP-M2 with 4% monomer concentration, (b) SDS-M12 recipe with 2% monomer concentration, (c) SDS-M11 recipe with 4% monomer concentration, (d) SDS-M9 recipe with 8% monomer concentration (for imaging the solution was diluted 20 times, drop-cast, and dried), and (e) PVP-S5 recipe with 50% PVP of the styrene concentration. | |
Opposite to nonionic surfactants such as PVP, in the case of SDS, increasing the monomer concentration, while changing the SDS concentration at a fixed percentage of the monomer (5%), caused a decrease in the PS sphere size. As the amount of SDS was fixed at 5% of the amount of styrene, with increasing the styrene from 1 to 8%, the amount of SDS would increase 8 fold. Therefore, due to the SDS anionic nature, increasing the SDS concentration significantly increased the repulsion between the SDS molecules and led to the formation of a large number of small micelles.
Moreover, with the increase in the monomer concentration and the number of micelles, it would be easier for the initiator to diffuse and reach the monomer inside the micelles as mentioned above. This would give a large number of nucleation sites at the beginning of the initiation step leaving a small amount of styrene in the solution and leading to the formation of small size PS spheres. This means that a higher concentration of styrene could be used to give smaller size PS spheres in large numbers instead of using only low concentrations like 1% or 2% and this would be more convenient to lower the number of preparation batches for any application.
3.4. The effect of initiator concentration
The initiator is the main component in emulsion polymerization as it starts the first stage, which controls the whole process and the working mechanism of the initiator is discussed in detail in the literature.12
The KPS initiator used in this study is an anionic water-soluble initiator that decomposes thermally to give free radicals, which diffuse into the micelles and start the polymerization process. During the initiation step, the formed free radicals act as nucleation sites that attract styrene molecules from the monomer droplets, which exist outside the surfactant micelles in the reaction medium. The initiator decomposition and radical formation rates are directly proportional to their rate constants, the initiator efficiency, and the initiator concentration. Increasing the decomposition rate of the initiator increases the formation of the radicals, which in turn increases the rate of the polymerization reaction and decreases the final particle size due to the increased number of formed nuclei.10
At low concentrations of the initiator, a few KPS free radicals will form and accordingly a small number of nuclei. This would leave a large amount of the styrene monomer in the solution that will eventually increase the final PS sphere size during the growth stage of polymerization. Increasing the initiator concentration leads to a large number of free radicals that will, in turn, form a large number of nucleation sites, leaving a small amount of the styrene monomer in the solution to be incorporated in the growth of those nuclei and leading to the formation of small PS spheres. However, after a certain KPS concentration, the increase in the number of KPS radicals would have a limited effect on the PS sphere size, as the number of nuclei is already at maximum.
In this research, the KPS concentration was varied from 0.5 to 6% of the styrene, while fixing the monomer and surfactant concentration at 8% and 5% of styrene, respectively. Increasing the KPS concentration caused a decrease in the PS sphere size when SDS or PVP was used as a surfactant. However, no further significant decrease in the size of the PS sphere was observed when the KPS concentration reached 2% of the monomer concentration. The PS sphere size changed from 184 to 153 nm in the case of PVP and went down from 62 to 48 nm using SDS.
3.5. The effect of polymerization time
The optimal recipe for the smallest size obtained using SDS (styrene: 8%; SDS: 5% of styrene; KPS: 2% of styrene) was used to study the effect of polymerization time on the PS sphere size and size distribution. Samples were taken from the polymerization mixture every three hours for 24 hours and the size was checked using DLS (Table 4). Over this time, the size changed from 47 to 51 nm and the PDI changed from 0.1 to 0.036. As could be observed, the size was almost constant in all samples but the size distribution is improved with increasing the polymerization time as a longer time allows the spheres to grow uniformly under the reaction conditions. Meanwhile at short polymerization times, the spheres would not be entirely uniform as most of the styrene would still be in the droplets and did not join the polymeric chains inside the micelles. The high concentration of surfactant used in those experiments increased the number of micelles, yielding a high conversion rate which explains the minor change in the particle size with time.25
Samples collected at 15 hours and above were found to be almost identical and this period would allow for full conversion of the styrene monomer to polystyrene as most literature on polystyrene preparation mentions that the reaction time needs to be between 15 and 24 hours to ensure full monomer conversion.18,21,38,39 In this research, the optimal polymerization time was found to be 15 hours but the polymerization process can be allowed to continue for 24 hours just to improve the size distribution and the yield.
3.6. The effect of polymerization temperature
The polymerization temperature was one of the parameters that had an obvious effect on the PS sphere size. When solutions of 8% styrene, 5% SDS to styrene and 2% KPS to styrene were used to synthesize PS spheres at different temperatures (60 to 90 °C) (Table 5), the smallest sphere size was obtained at 90 °C for both surfactants. At high temperatures, the decomposition rate of KPS increases (KPS decomposes between 50 and 60 °C),40 and hence more KPS free radicals exist at the initial stage of the polymerization process causing more nuclei sites to form. Accordingly, smaller particle sizes and a narrower size distribution were observed as mentioned.41 This can also be noticed from the solution color, as the samples prepared at 60 and 70 °C remained transparent after the addition of the initiator and it took more than three hours for the solution to turn fully milky white, which means that there is an induction period before nucleation and polymerization occur. Meanwhile the samples at 80 and 90 °C tuned milky white very soon after the initiator was added to the solution indicating that the polymerization process started immediately and PS spheres started to form in the flask.
Table 5 Effect of the polymerization temperature on the PS sphere size
Recipe |
Temperature °C |
Particle size (nm) |
SD |
RSD% |
PDI |
C1 |
60 |
60 |
11.79 |
19.65 |
0.063 |
C2 |
70 |
56 |
9.81 |
14.51 |
0.050 |
C3 |
80 |
54 |
4.37 |
8.09 |
0.053 |
C3 |
90 |
49 |
2.94 |
6 |
0.036 |
Water 125 ml; styrene: 8%; SDS: 5% of styrene; KPS: 2% of styrene |
Further testing showed that the samples prepared at 60 °C did not produce PS polymer spheres. According to the DLS measurements, the sample has a wide size distribution which could be explained by the slow initiation step that allows for the formation of a small number of nuclei that grow in size, while new KPS radicals initiated new nucleation sites forming polydisperse PS spheres. However, when the samples were dried and analyzed by SEM, no PS spheres were obtained and the dried powder was a resin-like brown residue at the bottom of the flask. This means that the DLS measurements did not measure stable PS spheres that can be used for further analysis.
In the case of PVP, the effect of the polymerization temperature was noticeable at all monomer concentrations with a size difference of around 35 nm between 70 and 90 °C. However, after a certain temperature and depending on the PVP concentration and other factors mentioned above, the high temperature will increase the dehydration of the nonionic surfactant making it hydrophobic, which promotes separation at the cloud point. Meanwhile in the case of SDS, the change of the size with the polymerization temperature was higher at low concentrations of styrene as the SDS micelle size is decreased by increasing the temperature.42 When 2% concentration of styrene was used, the size decreased from 168 nm at 70 °C to 131 nm at 90 °C but at high concentrations of 8% and 10%, and the effect of the polymerization temperature became low because the high concentration of the surfactant produced small spheres even at 70 °C as shown by the results in Table 5. Additionally, the increase in temperature would decrease the solution surface tension43 and it would increase the solubility of the monomer, which leads to the formation of smaller size particles as discussed.
The standard deviation (SD) and relative standard deviation (RSD%) were calculated for all recipes prepared at least three times and the values obtained are shown in the tables next to each recipe while the standard errors are illustrated in Fig. S2.† Finally, the polymerization yield was calculated for all samples that had no precipitation after the experimental time ended (usually 24 hours). The solution was poured into a Petri dish and heated in an oven at 80 °C overnight to evaporate the solvent. Then the dried powder was washed with ethanol several times and left to dry and then the weight of the starting monomer was divided by the weight of the dried polymer. As most of the experiments were conducted at 90 °C, the yield ranged between 87% and 92% and even the experiments conducted at lower temperatures (70 and 80 °C) gave a yield of at least 85% after 24 hours of polymerization. The C1 sample prepared at 60 °C was the only experiment to give a yield of 72%.
4. Conclusion
The results obtained by recipes M8 and M9 indicated that no agglomeration occurred and that the resulting emulsion did not need any filtration or centrifuging to get the final highly monodispersed 50 nm and smaller spheres. It was also found that using PVP on its own gave a final sphere size of 100 nm with high monodispersity. The obtained results showed that the surfactant and monomer concentration and the polymerization temperature are the parameters that control the final size the most. When using a mixture of SDS and PVP, the ratio between the two and the polymerization temperature is of great importance to get an emulsion with high monodispersity and without any agglomerates.
Conflicts of interest
There are no conflicts to declare.
Acknowledgements
The authors are thankful to the American University in Cairo for supporting this work.
References
- Q. Zhang and K. T. Chuang, Adsorption of Organic Pollutants from Effluents of a Kraft Pulp Mill on Activated Carbon and Polymer Resin, Adv. Environ. Res., 2001, 5(3), 251–258, DOI:10.1016/S1093-0191(00)00059-9.
- S. Mallakpour and V. Behranvand, Polymeric Nanoparticles: Recent Development in Synthesis and Application, eXPRESS Polym. Lett., 2016, 10(11), 895–913, DOI:10.3144/expresspolymlett.2016.84.
-
D. Bennet and S. KimPolymer Nanoparticles for Smart Drug Delivery, in Application of Nanotechnology in Drug Delivery, ed. A. D. Sezer, InTech, 2014, DOI:10.5772/58422.
- X. Wang, C. J. Summers and Z. L. Wang, Large-Scale Hexagonal-Patterned Growth of Aligned ZnO Nanorods for Nano-Optoelectronics and Nanosensor Arrays, Nano Lett., 2004, 4(3), 423–426, DOI:10.1021/nl035102c.
- S. Li, J. Zheng, Y. Zhao and Y. Liu, Preparation of a Three-Dimensional Ordered Macroporous Titanium Dioxide Material with Polystyrene Colloid Crystal as a Template, J. Appl. Polym. Sci., 2008, 107(6), 3903–3908, DOI:10.1002/app.27433.
- B. V. N. Nagavarma, H. Yadav, A. Ayaz, L. Vasudha and H. Shivakumar, Different techniques for preparation of polymeric nanoparticles – a review, Asian J. Pharm. Clin. Res., 2012, 5(3), 16–23 CAS.
-
S. Kawaguchi and K. Ito, Dispersion Polymerization, in Polymer Particles, ed M. Okubo, Advances in Polymer Science, Springer Berlin Heidelberg, Berlin, Heidelberg, 2005, vol. 175, pp. 299–328, DOI:10.1007/b100118.
- L. T. M. Hoa, N. T. Chi, L. H. Nguyen and D. M. Chien, Preparation and Characterisation of Nanoparticles Containing Ketoprofen and Acrylic Polymers Prepared by Emulsion Solvent Evaporation Method, J. Exp. Nanosci., 2012, 7(2), 189–197, DOI:10.1080/17458080.2010.515247.
- J. P. Rao and K. E. Geckeler, Polymer Nanoparticles: Preparation Techniques and Size-Control Parameters, Prog. Polym. Sci., 2011, 36(7), 887–913, DOI:10.1016/j.progpolymsci.2011.01.001.
-
A. N. M. B. El-hoshoudy, Emulsion Polymerization Mechanism, in Recent Research in Polymerization, ed. N. Cankaya, InTech, 2018, DOI:10.5772/intechopen.72143.
- D. Crespy and K. Landfester, Miniemulsion Polymerization as a Versatile Tool for the Synthesis of Functionalized Polymers, Beilstein J. Org. Chem., 2010, 6, 1132–1148, DOI:10.3762/bjoc.6.130.
-
H. Berber
Emulsion Polymerization: Effects of Polymerization Variables on the Properties of Vinyl Acetate Based Emulsion Polymers, in Polymer Science, ed. F. Ylmaz, InTech, 2013, DOI:10.5772/51498.
-
Introduction to Surfactant Analysis, ed. D. C. Cullum, Springer Netherlands, Dordrecht, 1994, DOI:10.1007/978-94-011-1316-8.
-
J. R. Wunsch, Rapra Technology Limited. Polystyrene: Synthesis, Production and Applications, Rapra Technology Ltd: Shawbury, Shrewsbury, Shropshire, UK, 2000 Search PubMed.
- F. Di Stasio, L. Berti, S. O. McDonnell, V. Robbiano, H. L. Anderson, D. Comoretto and F. Cacialli, Fluorescent Polystyrene Photonic Crystals Self-Assembled with Water-Soluble Conjugated Polyrotaxanes, APL Mater., 2013, 1(4), 042116, DOI:10.1063/1.4826544.
- C. Canal, R. M. Aparicio, A. Vilchez, J. Esquena and M. J. García-Celma, Drug Delivery Properties of Macroporous Polystyrene Solid Foams, J. Pharm. Pharm. Sci., 2012, 15(1), 197, DOI:10.18433/J3X884.
- S. T. Ha, O. O. Park and S. H. Im, Size Control of Highly Monodisperse Polystyrene Particles by Modified Dispersion Polymerization, Macromol. Res., 2010, 18(10), 935–943, DOI:10.1007/s13233-010-1008-9.
- S. Y. Yoon, Y. S. Park and J. S. Lee, Controlled Synthesis of Spherical Polystyrene Beads and Their Template-Assisted Manual Assembly, Bull. Korean Chem. Soc., 2014, 35(8), 2281–2284, DOI:10.5012/BKCS.2014.35.8.2281.
- G. Lui, G. Li, X. Wang, G. Jiang, E. Lin, M. Fowler, A. Yu and Z. Chen, Flexible, Three-Dimensional Ordered Macroporous TiO2 Electrode with Enhanced Electrode–Electrolyte Interaction
in High-Power Li-Ion Batteries, Nano Energy, 2016, 24, 72–77, DOI:10.1016/j.nanoen.2016.03.019.
- W. Cui, H. Liu, C. Wang and Y. Xia, Highly Ordered Three-Dimensional Macroporous FePO4 as Cathode Materials for Lithium-Ion Batteries, Electrochem. Commun., 2008, 10(10), 1587–1589, DOI:10.1016/j.elecom.2008.08.037.
- F. He, K. Zhao, Z. Huang, X. Li, G. Wei and H. Li, Synthesis of Three-Dimensionally Ordered Macroporous LaFeO3 Perovskites and Their Performance for Chemical-Looping Reforming of Methane, Chin. J. Catal., 2013, 34(6), 1242–1249, DOI:10.1016/S1872-2067(12)60563-4.
- H. Wutzel and W. M. Samhaber, Exploring the Limits of Emulsion Polymerization of Styrene for the Synthesis of Polymer Nanoparticles, Monatsh. Chem., 2007, 138(4), 357–361, DOI:10.1007/s00706-007-0605-6.
-
G. G. Odian, Principles of Polymerization, Wiley-Interscience, Hoboken, N.J, 4th edn, 2004 Search PubMed.
- V. A. Bhanu and K. Kishore, Role of Oxygen in Polymerization Reactions, Chem. Rev., 1991, 91(2), 99–117, DOI:10.1021/cr00002a001.
- S. Krishnan, A. Klein, M. S. El-Aasser and E. D. Sudol, Effect of Surfactant Concentration on Particle Nucleation in Emulsion Polymerization of n-Butyl Methacrylate, Macromolecules, 2003, 36(9), 3152–3159, DOI:10.1021/ma021120p.
- I. S. Altarawneh, V. G. Gomes and M. H. Srour, Polymer Chain Extension in Semibatch Emulsion Polymerization with RAFT-Based Transfer Agent: The Influence of Reaction Conditions on Polymerization Rate and Product Properties, J. Appl. Polym. Sci., 2009, 114(4), 2356–2372, DOI:10.1002/app.30752.
-
H.-J. Muller, D. Wang and A. Kumar, Cross linking treatment of polymer membranes, US Pat., 2008/0214687A1, 2008, https://patents.google.com/patent/US20080214687A1/en Search PubMed.
- A. Dan, S. Ghosh and S. P. Moulik, The Solution Behavior of Poly(Vinylpyrrolidone): Its Clouding in Salt Solution, Solvation by Water and Isopropanol, and Interaction with Sodium Dodecyl Sulfate, J. Phys. Chem. B, 2008, 112(12), 3617–3624, DOI:10.1021/jp077733r.
- J. Hierrezuelo, J. Molina-Bolívar and C. Ruiz, An Energetic Analysis of the Phase Separation in Non-Ionic Surfactant Mixtures: The Role of the Headgroup Structure, Entropy, 2014, 16(8), 4375–4391, DOI:10.3390/e16084375.
- X. Du and J. He, Facile Size-Controllable Syntheses of Highly Monodisperse Polystyrene Nano- and Microspheres by Polyvinylpyrrolidone-Mediated Emulsifier-Free Emulsion Polymerization, J. Appl. Polym. Sci., 2008, 108(3), 1755–1760, DOI:10.1002/app.27774.
- C. Zhao, R. Sugimoto and Y. Naruoka, A Simple Method for Synthesizing Ultra-High-Molecular-Weight Polystyrene through Emulsion Polymerization Using Alkyl-9-BBN as an Initiator, Chin. J. Polym. Sci., 2018, 36(5), 592–597, DOI:10.1007/s10118-018-2064-4.
- A. Javadi, N. Mucic, D. Vollhardt, V. B. Fainerman and R. Miller, Effects of Dodecanol on the Adsorption Kinetics of SDS at the Water–Hexane Interface, J. Colloid Interface Sci., 2010, 351(2), 537–541, DOI:10.1016/j.jcis.2010.07.033.
- A. M. Fernandez and L. Jebbanema, The effect of surfactant selection on emulsion polymer properties, Paint Coat. Ind., 2007, 23, 62–68 Search PubMed.
- M. Prasad, R. Palepu and S. P. Moulik, Interaction between Sodium Dodecyl Sulfate (SDS) and Polyvinylpyrrolidone (PVP) Investigated with Forward and Reverse Component Addition Protocols Employing Tensiometric, Conductometric, Microcalorimetric, Electrokinetic, and DLS Techniques, Colloid Polym. Sci., 2006, 284(8), 871–878, DOI:10.1007/s00396-005-1453-8.
- S. Badoga, S. K. Pattanayek, A. Kumar and L. M. Pandey, Effect of Polymer-Surfactant Structure on Its Solution Viscosity, Asia-Pac. J. Chem. Eng., 2011, 6(1), 78–84, DOI:10.1002/apj.461.
- B. Mandal, S. P. Moulik and S. Ghosh, Influence of Aquo-Organic Solvent Media on the Self-Aggregation of Sodium Dodecyl Sulfate (SDS) and Its Interaction with Polyvinylpyrrolidone (PVP), Colloid Polym. Sci., 2014, 292(10), 2485–2495, DOI:10.1007/s00396-014-3273-1.
- Y.-S. Cho, S. Ji and Y. S. Kim, Synthesis of Polymeric Nanoparticles by Emulsion Polymerization for Particle Self-Assembly Applications, J. Nanosci. Nanotechnol., 2019, 19(10), 6398–6407, DOI:10.1166/jnn.2019.17032.
- Y.-S. Cho, Synthesis of Latex Particles with Surface Functional Groups and Their Applications for the Fabrication of Porous Materials, J. Dispersion Sci. Technol., 2015, 36(9), 1237–1246, DOI:10.1080/01932691.2014.966310.
- G. M. Claro, F. R. Bencomo, L. P. Delgado, M. Lasa, E. G. Aznar, O. O. Alfaro, R. Acevedo, N. B. Rivero, Y. A. Ramírez, D. Z. Silva and T. M. Medina, Polystyrene Latex Synthesis and Application in Neisseria meningitidis Serogroup W Serotyping, Rev. Cubana Invest. Biomed., 2017, 36, 1 Search PubMed.
- N. M. Beylerian, L. R. Vardanyan, R. S. Harutyunyan and R. L. Vardanyan, Kinetics and Mechanism of Potassium Persulfate Decomposition in Aqueous Solutions Studied by a Gasometric Method, Macromol. Chem. Phys., 2002, 203(1), 212 CrossRef CAS.
- C.-S. Chern, S.-Y. Lin and T. J. Hsu, Effects of Temperature on Styrene Emulsion Polymerization Kinetics, Polym. J., 1999, 31(6), 516–523, DOI:10.1295/polymj.31.516.
- B. Hammouda, Temperature Effect on the Nanostructure of SDS Micelles in Water, J. Res. Natl. Inst. Stand. Technol., 2013, 118, 151, DOI:10.6028/jres.118.008.
- V. I. Kovalchuk, G. Loglio, A. G. Bykov, M. Ferrari, J. Krägel, L. Liggieri, R. Miller, O. Yu. Milyaeva, B. A. Noskov, F. Ravera, E. Santini and E. Schneck, Effect of Temperature on the Dynamic Properties of Mixed Surfactant Adsorbed Layers at the Water/Hexane Interface under Low-Gravity Conditions, Colloids Interfaces, 2020, 4(3), 27, DOI:10.3390/colloids4030027.
Footnote |
† Electronic supplementary information (ESI) available. See DOI: 10.1039/d1na00438g |
|
This journal is © The Royal Society of Chemistry 2021 |