DOI:
10.1039/D1MA00625H
(Review Article)
Mater. Adv., 2021,
2, 7277-7307
Surface functionalization of MXenes
Received
19th July 2021
, Accepted 20th September 2021
First published on 25th October 2021
Abstract
MXenes, a new family of two-dimensional (2D) transition metal carbides and nitrides, have received great research attention in diverse applications, including biomedicine, sensing, catalysis, energy storage and conversion, adsorption, and membrane-based separation, owing to their extraordinary physicochemical properties and various chemical compositions. In recent years, many surface functionalization strategies, such as surface-initiated polymerization and single heteroatom doping, have been cleverly developed to expand the potential of MXenes in different fields. This article reviews and puts into perspective the recent advances in MXene surface functionalization and various applications of the modified MXenes. The effect of surface functionalization on MXene properties (such as electronic, magnetic, mechanical, optical, and hydrophilicity/hydrophobicity) is discussed. Potential applications of pristine and functionalized MXenes in different fields are discussed. Finally, challenges and future directions in MXene surface modification are examined.
1. Introduction
In recent years, two-dimensional (2D) nanomaterials, such as MXenes, black phosphorus nanosheets, molybdenum disulfide, and graphene, have received considerable attention1–4 due to their unique structures and attractive chemical and physical properties. As such, they have shown potential for various applications in the fields of biomedicine, sensing, environment, and energy.5–8 In particular, MXenes have received considerable attention around the world.9,10 The first discovered MXene (Ti3C2) was synthesized by selective etching of Al elements using hydrofluoric acid (HF).11 The general chemical formula of MXenes is Mn+1XnTx (n = 1–4), where M, X, and T represent an early transition metal (including Mo, Nb, Cr, V, Ti, and Hf), carbon or nitrogen, and surface functional groups, respectively.10,12,13 The integer x is the number of functional groups.11 While many MXenes with various compositions have been proposed, only a limited number of them have been synthesized. The diversity of MXene compositions implies that a variety of MXenes with desired properties can be synthesized.14,15 The chemical formula of the reactant, the MAX phase (as a kind of ternary ceramic material), from which a MXene is synthesized, is Mn+1AXn, which has a layered hexagonal structure.16 The MAX phase is formed by covalent bonds between the M and X atoms, and the M–X layer is alternately ordered with an A atomic layer via a metallic bond between A and M, although M–A bonds are weaker compared to M–X bonds.17
Owing to their promising mechanical, chemical, and physical properties, and large surface area,18 MXenes are being applied in various applications such as adsorption,19–21 membrane separation,22–25 catalysis,26,27 energy storage,28–30 sensing,26,31–33 and biomedicine.34–36 Furthermore, the existence of many functional groups such as oxygen (–O), fluorine (–F), hydroxyl (–OH), and chloride (–Cl) on their surface allows for their surface functionalization, which increases their versatility further.37–40 For example, adsorption of metal ions was investigated using –O-containing composites of Ti3C2, which were produced by the conversion of –OH groups on their surface.41 Besides, because of their extraordinary biocompatibility,42 MXenes have shown great potential for biomedical applications.
Different methods of synthesizing MXenes have been introduced.43 They include (i) top-down methods (selective etching of MAX and non-MAX phases),44,45 (ii) bottom-up methods (chemical vapor deposition (CVD) and salt-templated growth), and (iii) chemical transformations. The single-layer and multilayer nanostructure of MXenes can be manufactured using these methods. On the other hand, poor stability in the presence of molecular oxygen, easy restacking, and low mechanical flexibility are the disadvantages of MXenes that have limited the applications of pristine MXenes.46–49 Despite the numerous merits of MXenes, they still lack properties needed in several fields.50 Additionally, pristine MXenes tend to precipitate and accumulate in water due to their poor water dispersibility.51 Hence, the surface functionalization and modification can substantially enhance their performance and stability.52
Generally, the surface properties of MXenes can be modified and improved by the type and fraction of the T group during the production process.53 Recently, functionalized MXenes have been synthesized by surface modification of pristine MXenes with covalent and non-covalent modifications. The non-covalent surface modification is obtained by a combination of van der Waals forces, hydrogen bonding, and electrostatic attraction.35,54–57 Covalent surface functionalization methods are classified into three groups:58–60 (i) those that involve small molecules such as alkali metal hydroxides, acid halide or acid anhydride, epoxy compounds, and organic amines,61–64 (ii) those that involve surface-initiated polymerization by macromolecules,65,66 and (iii) those that involve single heteroatoms.16
In this article, recent developments in the functionalization of MXenes are reviewed. First, strategies for MXene surface functionalization are reviewed and discussed. The properties of the surface modified MXenes and their potential applications in separation, biomedical, sensing, energy storage and conversion, and catalysis are discussed. Finally, the future perspective of functionalized MXenes, and challenges and opportunities in this field are highlighted.
2. Methods of surface functionalization
Plentiful –OH and –O containing groups on the surface of MXenes can be utilized as active sites for covalent binding by means of controlling the surface terminations, surface-active initiators, small molecules, and polymers.67–71 The performance of MXenes can be enhanced easily by suitable functional groups because of the hydrophilic nature of MXenes.16 Many have studied the chemical surface functionalization of MXenes. Table 1 lists the various modified MXenes and the surface-functionalization methods used to prepare them.
Table 1 Surface-modified MXenes and their methods of preparation
Surface functionalized 2D MXenes |
Sample |
Synthesis method |
Solvent or atmosphere reaction |
Temperature (°C) |
Ref. |
Functionalized MXenes by small molecules |
NaAlH4-modified Ti3C2 |
Ball milling |
Ar |
— |
72
|
FePc-modified Ti3C2 |
Self-assembly |
Dimethylformamide (DMF) |
— |
54
|
C12E6-modified Ti3C2 |
Sonication |
Water |
40 |
55
|
Et-modified Nb2C |
Hydrothermal approach |
Ethanol |
100 |
73
|
Functionalized MXenes by macromolecules |
Sodium alginate modified Ti3C2 |
Vacuum-assisted filtration |
Deionized water |
Room temperature |
74
|
PPy modified Ti3C2 |
In situ polymerization |
Deionized water |
Room temperature |
65
|
PS modified Ti3C2 |
Electrostatic assembly |
Deionized water |
50 |
75
|
PVA modified Ti3C2 |
Vacuum-assisted filtration |
Deionized water |
Room temperature |
76
|
PDDA modified Ti3C2 |
Vacuum-assisted filtration |
Deionized water |
Room temperature |
76
|
Functionalized MXenes by single heteroatoms |
V-Doped Ti3C2 |
Hydrothermal approach |
Water |
120 |
77
|
S-Doped Ti3C2 |
Solution blending |
Deionized water |
155 |
78
|
S-Doped Ti3C2 |
Heat and milling treatment |
Ar |
1650 |
79
|
N-Doped V4C3 |
Heat treatment |
Ammonia |
350–550 |
80
|
N-Doped Nb2C |
Hydrothermal approach |
Deionized water |
150 |
81
|
P-Doped V2C |
Heat treatment |
Ar |
300–500 |
82
|
2.1. Controlling surface terminations
The surface modification of MXenes through controlling the T groups allows for adjusting the physical properties of MXenes, including the concentrations and types of electrochemical active sites and electronic structures.83 –O and –F surface terminations can be easily achieved by conventional etching techniques such as fluoride-containing salts or HF. More importantly, the concentrations and types of surface terminations can be tuned by adjusting the etching time and the concentration of etchants, and using various post-treatments such as hydrazine and annealing in diverse atmospheres.84,85 For instance, Schultz et al. studied the effect of various surface terminations on the physical properties.86 Their measurement of the electronic structure indicated that Ti3C2 has a high (above 1 eV) dispersion due to its Ti–O bonds. Annealing at 380 °C in vacuum increases the work function from 3.9 to 4.8 eV, because of the desorption of –OH species, contaminants, and water. The work function decreased to 4.1 eV with fluorine desorption at higher temperatures from 500 to 750 °C. Moreover, density functional theory (DFT) has been used to evaluate the effect of surface terminations on the electronic conductivity.87 It was found that the Fermi level density of states (DOS) of an MXene is affected by surface terminations. The concentration of –F terminations decreased by annealing Ti3C2 from 300 to 775 °C, which was supported by measurements from in situ electron energy loss spectroscopy (Fig. 1a). The significant enhancement of electronic conductivity was ascribed to the decrease of –F terminations during annealing at 700–775 °C (Fig. 1b). Furthermore, Tang et al. investigated the saturation magnetization of Ti3C2 through Ti–C vacancy production under H2 annealing.88 They showed a similar level of –O concentration after annealing in H2 from 100 to 500 °C, while the C–Ti–OH functional groups transformed to O–Ti–O and C–Ti–O. The Ti–C vacancy with C and Ti vacancies formed in the annealing process (Fig. 1c). The fully terminated Ti3C2 MXenes were theoretically nonmagnetic, while the pristine Ti3C2 was ferromagnetic. The influence of Ti–C vacancy on the improvement of saturation magnetization was clearly confirmed from DFT calculations and magnetization enhancement (Fig. 1d).
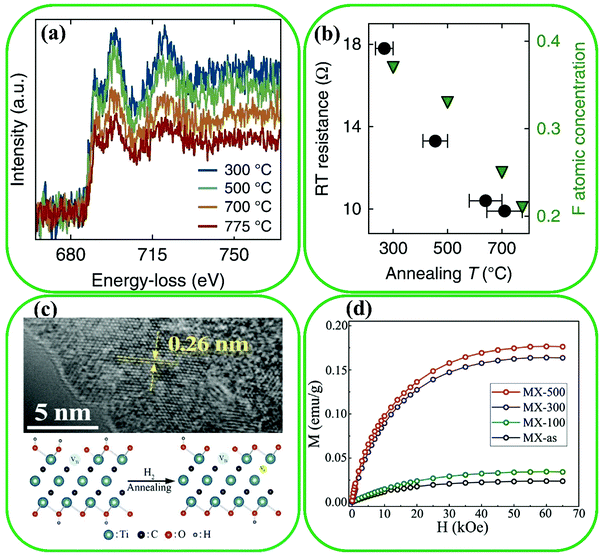 |
| Fig. 1 Effect of surface terminations on the conductivity of MXenes; (a) loss of –F terminations under annealing by in situ electron energy loss spectroscopy of Ti3C2, and (b) comparison of –F concentration (green triangles) and the post-anneal room temperature resistance of Ti3C2 (black circles). Reproduced with permission.87 Copyright 2019, Nature. (c) Representation scheme and high-resolution transmission electron microscopy of structural evolution after annealing in H2, and (d) indicating the comparison of magnetic properties as a function of the applied field H measured at 2 K. Reproduced with permission.88 Copyright 2020, Elsevier. | |
2.2. Small molecules
Performance characteristics of MXenes such as mechanical stability, electrical properties, and solution stability can be further enhanced by surface modification of MXenes with a variety of small molecules, which are easy to process and are inexpensive.61,63 To illustrate, Xia et al. introduced a non-ionic surfactant, hexaethylene glycol monododecyl ether (C12E6), on the surface of Ti3C2 MXenes (C12E6@Ti3C2) to improve molecular interactions, resulting in enhanced packing symmetry (Fig. 2a).55 In the C12E6@Ti3C2 composite, strong hydrogen bonds are formed between the –O or –F groups on the MXene's surface and the –OH groups of C12E6. A novel fan-like texture under an optical microscope was used to confirm the introduction of C12E6 between MXene nanosheets (Fig. 2b). In addition, a one-step direct reaction of Ti3C2 sheets with diazonium salt was reported by Lei et al. who prepared a sulfonic functionalized MXene, denoted as Ti3C2–SO3H.89 The results of SEM characterization demonstrated that the pristine Ti3C2 MXenes have packed stacked lamellar layered structures. By contrast, granular structures can be seen on the surface of Ti3C2–SO3H (Fig. 2c and d). Jin et al. used a simple solvothermal/hydrothermal method to modify the surface of Nb2C MXenes for developing the electromagnetic wave (EMW) absorbing performance.73 Deionized (DI) water or ethanol (Et) was used in the solvothermal treatment process instead of DMF. The results presented superior EMW performance for Et-treated Nb2C MXenes because of increased surface functional groups, enlarged interlayer spacing, and improved dielectric loss. Larger interlayer spacing can lead to multiple reflections between Nb2C sheets, resulting in enhanced EMW absorption. In addition, the functional groups on the edge and surface of Nb2C can act as polarization sites to attenuate the energy of EMW.
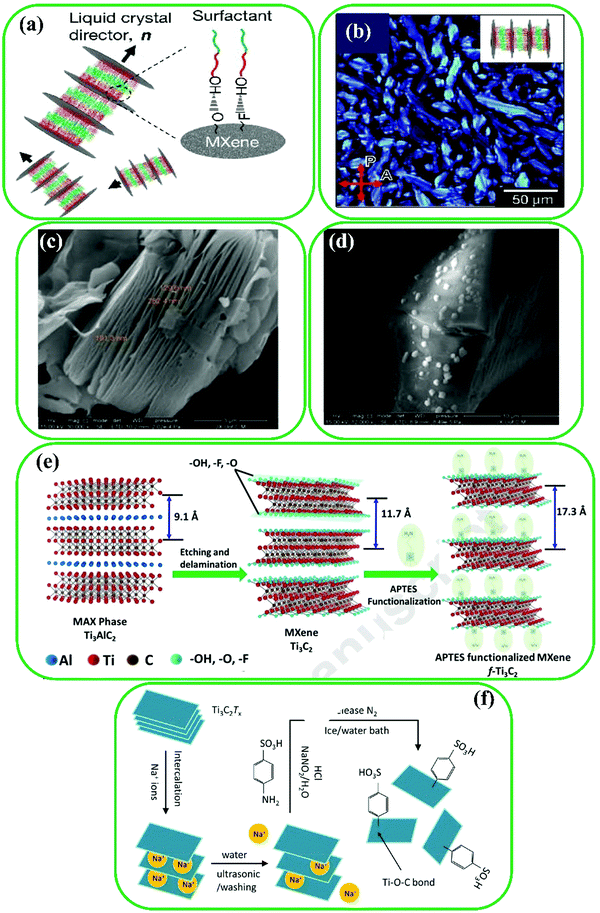 |
| Fig. 2 (a) Schematic illustration of the C12E6-improved lamellar structure of Ti3C2 MXenes. (b) The fan-like texture of the lamellar phase of Ti3C2 MXenes. Reproduced with permission.55 Copyright 2018, Nature. SEM images of (c) pristine Ti3C2 sheets and (d) Ti3C2–SO3H. Reproduced with permission.89 Copyright 2019, Elsevier. (e) Preparation of Ti3C2 MXenes by Al etching and surface modification of Ti3C2 MXenes. Reproduced with permission.90 Copyright 2018, Elsevier. (f) Surface modification of Ti3C2 MXene with diazonium ion. Reproduced with permission.91 Copyright 2018, Elsevier. | |
In addition, Yang et al. were able to increase the molecular interactions of MXene nanosheets using hexaethylene glycol monododecyl ether (C12E6) as a non-ionic surfactant.55 MXenes have also been functionalized using other small molecules such as bismuth ferrite (BiFeO3)92,93 and sodium aluminum hydride (NaAlH4).94 A chemical coupling method was applied to produce amino groups on the MXene's surface (Fig. 2e), and the resultant functionalized MXene nanosheets can be used as a platform to immobilize different biomolecules.90 To conduct large-scale delamination of MXenes, Wang et al. developed a method of diazonium surface chemistry,61 which weakens the M–X bonds and expands the interlayer spacing by the formation of aryl-surface linkage using diazonium and sulfanilic salts. In another study, diazonium ions were used for the in situ modification of the MXene's surface,91 as shown in Fig. 2f, where it is proven that the covalent grafting of C6H4SO3H groups on the surface of Ti3C2 improves the electrical properties. It should be noted that the –OH groups on the MXene's surface can react with trimesoyl chloride, epichlorohydrin, and silane agents to conduct etherification and esterification.95,96 During the production of MXene/cellulose hydrogels, epichlorohydrin served as a cross-linker between MXenes and cellulose via the formation of covalent bonds with the existing –OH groups on the surface of MXenes.
2.3. Surface-initiated polymerization
The numerous active functional groups on the surface of MXenes allow polymers to be ex situ blended or in situ polymerized.65,74,83,97–101 MXene/polymer composites are usually produced using an ex situ blending approach, which provides some merits such as well-defined polymer structures and tunable compositions. Hence, the interaction between polymers and MXenes can be efficiently improved by hydrogen bonding102 and electrostatic interactions.75,76 For instance, Sun et al. produced highly conductive MXene@polystyrene (PS) nanocomposites (MXene@PS) using the electrostatic assembling of positive PS and negative MXene nanosheets, followed by compression molding (Fig. 3a).75Fig. 3b shows the perfect and clean microstructure core–shell MXene@PS hybrid. The abundant functional groups (–F, –O, and –OH) on the surface of MXenes allow them to assemble on the PS by van der Waals forces, hydrogen bonding, and electrostatic interactions. At lower contents of Ti3C2 MXenes, assembling occurred through electrostatic interactions, whereas at higher contents, the van der Waals forces and hydrogen bonds are the main driving forces for the assembling of Ti3C2 MXenes on the surface of the PS. In addition, Ling et al. reported the fabrication of two Ti3C2/polymer composites: Ti3C2/polyvinyl alcohol (PVA) and Ti3C2/polydiallyldimethylammonium (PDDA) (Fig. 3c).76 A PVA/Ti3C2 composite can be easily obtained by hydrogen bonding owing to the abundant hydrogel groups on the structure of PVA. As Ti3C2 MXenes are negatively charged flakes and PDDA is a cationic polymer, the PDDA/Ti3C2 composite can be easily formed by electrostatic interactions. The TEM image of the PVA/Ti3C2 composite (Fig. 3e) clearly shows the intercalation of PVA layers, and Fig. 3d shows the orderly stacked layers of the PDDA/Ti3C2 composite formed by vacuum-assisted filtration.
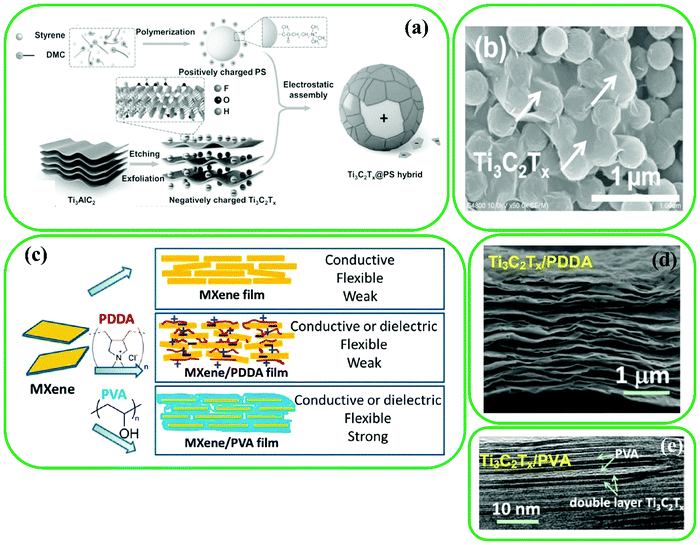 |
| Fig. 3 (a) Schematic representation of the synthesis of MXene@PS hybrid. (b) SEM image of MXene@PS hybrid. Reproduced with permission.75 Copyright 2017, Wiley. (c) MXene modification with charged PDDA and electrically neutral PVA, (d) cross-sectional image of PDDA/Ti3C2, and (e) high-resolution TEM image of PVA/Ti3C2 composite. Reproduced with permission.76 Copyright 2014, National Acad. Sciences. | |
Strong covalent bonds between MXenes and polymers can be formed via in situ polymerization with monomers such as ε-caprolaction103 and pyrrole.65,104 For example, Boota et al. developed a method for in situ polymerization of pyrrole between Ti3C2 layers65 (Fig. 4a). As shown in Fig. 4b, a periodic pattern was produced, which can be ascribed to the well-aligned polypyrrole (PPy) between Ti3C2 layers along with appropriate intercalation of PPy chains. In the case of PPy/Ti3C2 composites, the interaction between Ti3C2 and polymer chains is formed by hydrogen bonds between the –O groups on the surface of Ti3C2 and the H and N of PPy. Moreover, soybean phospholipid (SP) consists of biomacromolecules that are extensively used for surface functionalization due to their biocompatible characteristics.16 Lin et al. reported that surface functionalization of Ti3C2 with SP (Fig. 4c)35 improves blood circulation and biodistribution in tumors in physiological environments. Furthermore, enhanced stability of MXenes in physiological solutions was observed using poly(ethylene glycol) (PEG).105
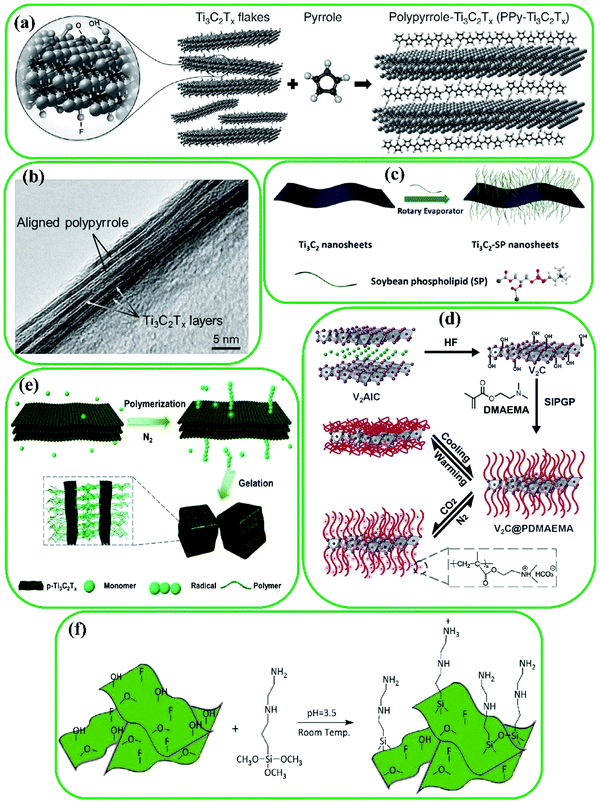 |
| Fig. 4 (a) In situ surface polymerization of Ti3C2 with pyrrole, and (b) cross-sectional image of PPy/Ti3C2 composites indicating well aligned PPy chains between Ti3C2 layers. Reproduced with permission.65 Copyright 2016, Wiley. (c) Illustration of surface functionalization of Ti3C2 with SP. Reproduced with permission.35 Copyright 2017, American Chemical Society. (d) Synthesis of V2C@PDMAEMA. Reproduced with permission.98 Copyright 2015, The Royal Society of Chemistry. (e) p-Ti3C2-initiated polymerization and alternative gelation. Reproduced with permission.106 Copyright 2019, The Royal Society of Chemistry. (f) Schematic illustration of Ti3C2 flake functionalization process with AEAPTMS (coupling agent). Reproduced with permission.13 Copyright 2020, Wiley. | |
Polydopamine (PDA) is another suitable agent for MXene surface modification, because there are abundant amino and catechol groups in its backbone, which can form non-covalent and covalent interactions with organic and inorganic surfaces.60,107 To produce a Ti3C2@carbon nanotube (CNT) composite, cobalt was adsorbed on the surface of Ti3C2, and CNTs were then formed after the formation of PDA layers on the surface of Ti3C2.16 The capacitive performance of Ti3C2 improved with PDA modification.108
Surface-initiated polymerization is another method for surface functionalization of MXenes. For instance, Fig. 4d illustrates the surface-initiated polymerization of V2C with poly(2-(dimethylamino)ethyl methacrylate) (PDMAEMA) using –OH groups as a photoactive site.98 Additionally, a peroxide decoration method was reported by Tao et al., where the –OH acts as an initiator for surface polymerization of monomers.106 Polymerization occurs by adding nitrogen to a mixture of an MXene and an acrylic monomer (Fig. 4e). The surface functionalization with macromolecules is a promising strategy to improve MXenes’ pristine properties tailored for various applications.
Furthermore, strong bonds between inorganic and organic groups can be made by silane reagents with different functional groups such as phenyl, chloro, vinyl, epoxy, methacrylate, amine, and diamine.13 Silanol groups can be obtained by the hydrolysis of alkoxy groups and the presence of water and moisture on the surface of nanomaterials, which can cause the formation of covalent bonds between the silanol groups and available –OH groups on the surface of nanomaterials by a dehydration reaction. Amino-silane functionalization of TiO2 was reported by Shamsabadi et al.,109 which inspired the amino-silane modification of Ti3C2 by the same group13 because of the similarity of –OH groups in TiO2 nanoparticles and Ti3C2. [3-(2-Aminoethylamino)propyl]trimethoxysilane (AEAPTMS) was grafted on the surface of Ti3C2via chemical reactions between the –OH groups of Ti3C2 and AEAPTMS: the amine group ends leading to electrostatic interactions, and the silanol group ends leading to covalent bonding (Fig. 4f). By amino functionalization of MXene materials, numerous opportunities of subsequent reactions are created. These include reactions with curing agents for epoxy resins and surface-initiated atom transfer radical polymerization due to the existence of free amine groups. These reactions make MXene materials suitable for use in energy-storage devices, electrochemical biosensors, fuel cells, catalysis, metal-ion batteries, antibacterial coating, drug delivery, and dye adsorbents.110–114
2.4. Single heteroatom method
The use of MXenes in Na-ion batteries (NIBs) and Li-ion batteries (LIBs) is still challenging115 because of their unfavorable electrochemical properties, which can be addressed by increasing the interlayer spacing of MXenes via single heteroatoms.116 Significant improvement in the electrochemical performance of MXenes has been obtained using P, S, and N doping approaches.81,82,117,118 For instance, N-doped Nb2C MXene was produced by Liu et al. by means of a hydrothermal method.81 The layered structure of N-doped Nb2C can be seen in Fig. 5a, where it can be concluded that the morphology of Nb2C does not change with N-doping, as confirmed by the uniform distribution of C, O, and Nb elements (Fig. 5b). Furthermore, p-doped V2C was synthesized by Yoon et al. using heat treatment via triphenylphosphine (TPP). p-Doped V2C with a large interlayer spacing (1.03 nm) was obtained, while pristine V2C had an interlayer spacing of 0.97 nm (Fig. 5c). Besides, N-doped V2C with different N contents was produced, as the heat treatment temperature was varied from 350 to 550 °C. The N-doped V2C was produced by annealing in an ammonia atmosphere, resulting in the uniform distribution of elements (such as N, C, and V). Other recent efforts to enhance the performance of MXenes include the syntheses of cation (NH4+, Al3+, Mg2+, Ca2+, and K+)-doped Ti3C2, germanium- and silicon-doped Sc2C(OH)2,119 boron-doped W2CO2 and Mo2CO2,120 and palladium/platinum-doped Nb2C.121
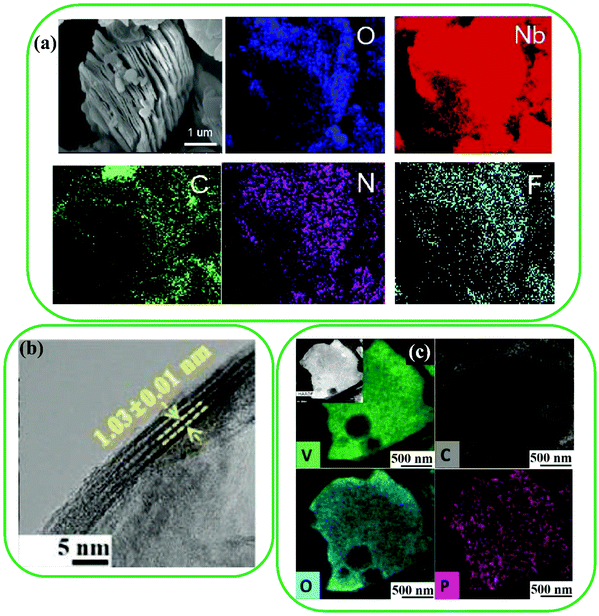 |
| Fig. 5 (a) A SEM image and corresponding EDS mapping images of N-doped Nb2C MXene. Reproduced with permission.81 Copyright 2019, Elsevier. (b) A TEM image and (c) EDS mapping images of P-doped V2C MXene. Reproduced with permission.82 Copyright 2019, Wiley. | |
3. Effects of surface functionalization on MXene properties
3.1. Electronic properties
MXenes have shown diverse electronic properties such as semiconductivity, metallicity, and topological insulativity, owing to their flexible thickness tunability, different surface functionalization possibilities, and various compositions.122,123 It should be noted that the electronic characteristics of MXenes can be improved by surface modification.124–126 However, as most MXenes are metallic,127 their electronic properties are mainly determined by the M atoms. As has been predicted, the Mo- and W-based MXenes are insulators.128,129 Some metallic MXenes may become semiconductors after surface modification.130 For instance, F- and I-terminated Ti3C2 have shown semiconductivity, while pristine Ti3C2131 has metallic properties.
Dong et al. reported Hf2VC2, Hf2MnC2, and Ti2MnC2 MXenes (Fig. 6a and b).132 Ti2MnC2 is metallic or a semiconductor based on the type of the functional groups. For example, it is a semiconductor with –O terminations. Moreover, Du et al. reported that some metallic MXenes with –OH and –O terminations (such as Nb4C3, Ti3C2, Nb2C, V2C, and Ti2C) have shown significant charge transfer,133 while Ti3CO2 exhibited semiconductor properties due to the generation of a large gap induced by the downshifting of the Fermi level (Fig. 6c). In TiCO2, by increasing the donation of electrons between carbon, oxygen, and titanium atoms, the Fermi level decreases. This phenomenon was confirmed by another study by Pandey et al. which evaluated the electronic properties of MnCn−1O2 MXenes (n = 2, 3, 4, and M = W, Ta, Hf, Mo, Nb, Zr, Y, Mn, Cr, V, Ti, Sc).134 Apart from several O-terminated MXenes, including Hf3C2O2, Hf2CO2, Zr3C3O2, ZrCO2, and TiCO2, other F- or OH-terminated MXenes were metallic. Furthermore, the electronic properties of i-MAX phases, such as (V2/3Zr1/3)2AlC, (W2/3Y1/3)2AlC, (W2/3Sc1/3)2AlC, (Mo2/3Y1/3)2AlC, and (Mo2/3Y1/3)2AlC, have been studied.135 The pristine MXenes synthesized from (Mo2/3Y1/3)2AlC and OH- and F-terminated of (Mo2/3Y1/3)2C are metallic, while the O-terminated sample becomes a semiconductor (Fig. 6d). Chen et al. investigated the conductivity properties of pristine Ti3C2 and Ti3C2/glycine hybrid.54 Their results (Fig. 6e) indicated that the conductivity of the hybrid diminished by increasing the amount of poor conductive glycine in the hybrid.
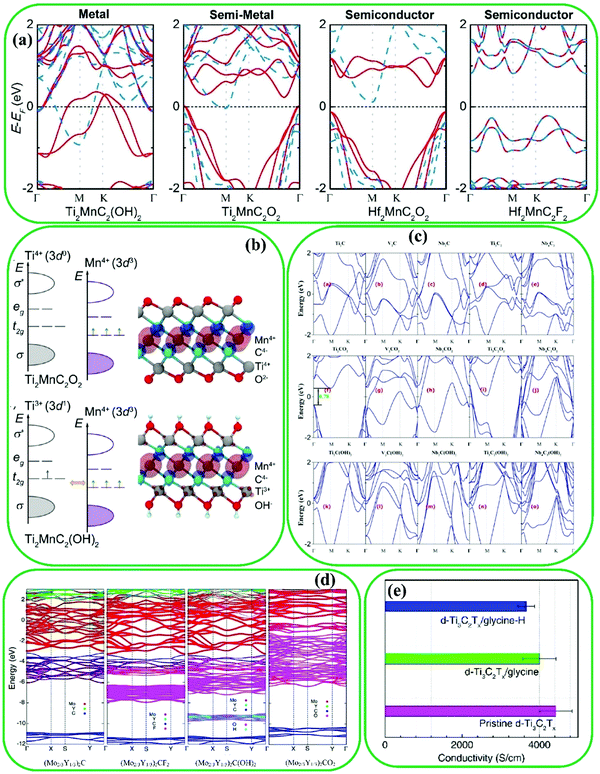 |
| Fig. 6 (a) Electronic band structures of different MXenes showing the effect of termination groups and transition metal elements on the MXene properties, (b) electronic band structures around the Fermi level (EF) for Ti2MnC2O2 and Ti2MnC2(OH)2. Reproduced with permission.132 Copyright 2017, American Chemical Society. (c) Electronic band structures of pristine MXenes (MnCn−1), O- and OH-terminated MXenes, where the Fermi level is zero. Reproduced with permission.133 Copyright 2017, American Chemical Society. (d) Electronic band structures of pristine (Mo2/3Y1/3)2C and the corresponding surface terminated MXenes. Reproduced with permission.135 Copyright 2018, American Physical Society. (e) The comparison of electrical conductivity between pristine Ti3C2 and Ti3C2/glycine hybrid. Reproduced with permission.54 Copyright 2018, The Royal Society of Chemistry. | |
In addition to experimental studies, theoretical studies have also been performed recently to assess the DOS, band structure, and electronic properties of pristine and functionalized MXenes.136 As examples, several MXenes such as Hf2CO2, Zr2CO2, Ti2CO2, and Sc2CTx (T = O, F, OH) were reported with a band gap ranging from 0.24 to 1.8 eV,130 which shows the remarkable effect of the surface groups of MXenes (Fig. 7a). The band structure of Sc2CO2 is different from those of Sc2CF2 and Sc2C(OH)2, and this remarkable effect can be ascribed to the fact that an –OH or –F group is stabilized by receiving an electron, while an –O group is stabilized by receiving two electrons. The electronic structures of pristine and functionalized MXenes were investigated to understand the mechanism of being semiconducting after the surface functionalization.130 From Fig. 7b and c, there is a tiny band gap between the p and d bands of X elements. Particularly, O terminations caused large downward shifting of the Fermi level energy resulting in the synthesis of the Ti2CO2 semiconductor, while F functionalization led to small downward shifting. These mechanisms are supported by DOS analysis (see Fig. 7).
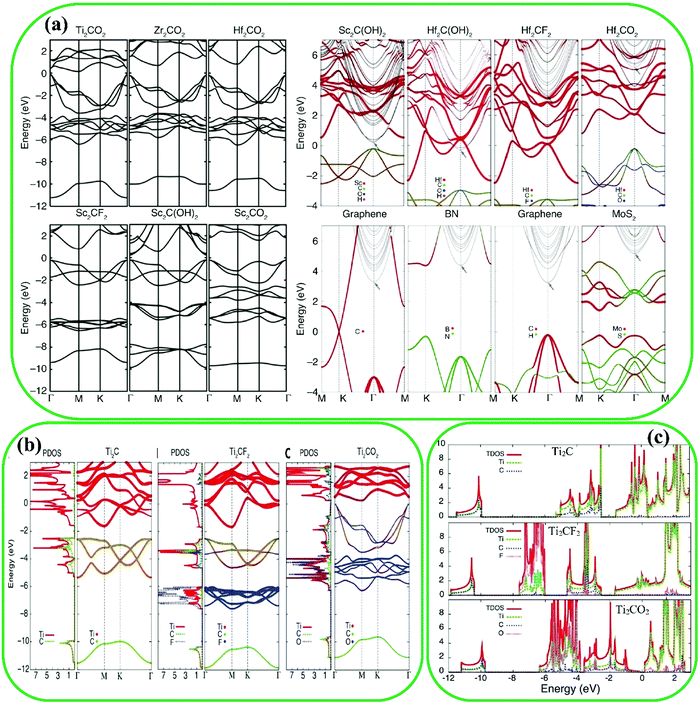 |
| Fig. 7 (a) Band structures of M2CT2 MXenes, showing the effect of T termination groups and M elements on the band structure and also their projected band structures. Reproduced with permission.130 Copyright 2013, Wiley. (b) Projected DOSs and band structures of pristine Ti2C, Ti2CF2, and Ti2CO2. Reproduced with permission.137 Copyright 2017, The Royal Society of Chemistry. (c) The DOS for pristine Ti2C, and F- and O-terminated MXenes. Reproduced with permission.130 Copyright 2013, Wiley. | |
3.2. Magnetic properties
The application of 2D materials in spintronics has been limited because 2D materials are mostly nonmagnetic.138 Hence, many studies have recently been carried out to improve the magnetic properties of MXenes. Fortunately, several MXenes such as Mn2C, Cr2N, Cr2C, Ti2N, and Ti2C are inherently magnetic. It has been found that Mn2C139 and Cr2N140 are antiferromagnetic, but Cr2C,141 Ti2N,142 and Ti2C140 are ferromagnetic. Recently, magnetic MXenes with half-metallic features have been studied, where one spin-channel is semiconducting, while the other one is metallic; thereby resulting in entirely spin-polarized electrons at the Fermi level.138 The band structure of Cr2C (a half-metallic MXene) is presented in Fig. 8a, which shows an insulating spin-down channel and a metallic spin-up channel.141
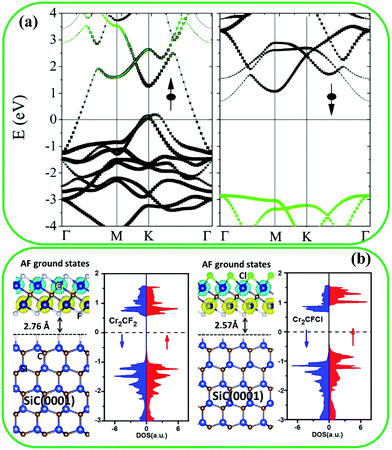 |
| Fig. 8 (a) Band structure of pristine Cr2C MXene. Reproduced with permission.141 Copyright 2015, American Chemical Society. (b) DOS of Cr2CFCl asymmetrically functionalized and Cr2CF2 symmetrically functionalized. Reproduced with permission.144 Copyright 2016, The Royal Society of Chemistry. | |
Surface modification can also affect the magnetic properties of MXenes. It can lead to a surface-functionalized MXene with poorer magnetic properties, which are induced by unpaired surface electrons of transition metal elements.138 For instance, modification with –Cl, –OH, –H, and –F groups changes the ferromagnetic half metal of pristine Cr2C to an antiferromagnetic semiconductor.143 However, modification with –O groups endows Cr2NO2 MXene with a ferromagnetic half metal feature.140 Furthermore, Mn2CCl2 MXene displays an antiferromagnetic insulator characteristic, while the pristine Mn2C is an antiferromagnetic metal. Interestingly, a ferromagnetic half metal of Mn2CF2 with a sizeable and half metallic gap, and a high Curie temperature, was fabricated.144 Moreover, as reported by Khazaei et al., functionalized Cr2N and Cr2C MXenes are ferromagnetic,130 and this could be related to the d orbitals of Cr, as it has been theoretically indicated that Cr atoms might have magnetic moments of (0.45μB/Cl) in MAX phases.145
The magnetic properties of functionalized MXenes with asymmetrical functionalization groups have been widely evaluated. As reported, Cr2CFOH, Cr2CHF, Cr2CHCl, Cr2CClBr, and Cr2CFCl are antiferromagnetic semiconductors with a Néel temperature of almost 400 K.144 Ferromagnetic or antiferromagnetic properties of asymmetrical functionalized Cr2C MXenes are similar to symmetrical functionalized materials.144Fig. 8b shows the DOS of Cr2CFCl and Cr2CF2, where Cr2CFCl exhibited bipolar magnetic semiconductor characteristics, indicating that the valence band maximum and the conductive band minimum show opposite spin polarization in comparison to Cr2CF2 with symmetrical functionalization groups.
3.3. Mechanical properties
Surface terminations of MXenes are considered as a main factor for their mechanical properties.146 Generally, O-terminated MXenes show higher stiffness compared to –OH and –F terminated MXenes.147 This phenomenon can be attributed to the various lattice properties of MXenes with diverse termination groups.148 For example, Guo et al. reported that the surface functionalization of Ti2C leads to increased flexibility,149 increased strain, but decreased Young's modulus.149 The critical strain increases, and the collapse of Ti layers decelerates, because the different functional groups on the surface of MXenes act as a delimiter under tensile deformation.
Another factor that influences the mechanical properties is the number of atomic layers of MXenes based on their chemical formula. In this regard, Borysiuk et al. found that the hardness and tensile strength of an Mn+1Xn MXene increase with decreased n.150 Furthermore, the mechanical properties of MXenes can be improved by incorporating CNTs and polymerizing with various types of polymers.146 It has been reported that MXene–polymer composites have higher compressive and tensile strengths, toughness, and flexibility, compared to pristine MXenes. For instance, the Ti3C2/PVA composite exhibited larger tensile strength compared to pristine Ti3C2.146 Additionally, Ti3C2/ultrahigh molecular weight polyethylene (UHMWPE)151 and Ti3C2/polyacrylamide (PAM)152 composites have higher yield strength and toughness compared to pristine Ti3C2.
3.4. Optical properties
Optical properties of MXenes, including refractive index, reflectivity, absorption, and transmittance are of importance in different applications. There have been a few experimental studies on the effect of surface functionalization on optical properties.153,154 For instance, pristine Ti3C2 showed 77% transmittance in visible light, while the 30% transmittance was observed for a thin Ti3AlC2 MAX phase.155,156 Ammonium bifluoride (NH4HF2) intercalated Ti3C2 thin films (Ti3C2.3O1.2F0.7N0.2) showed 90% transmittance.156 Optical properties such as reflection, absorption, and transmittance can be investigated theoretically by calculating the imaginary part of the dielectric function tensor at different photon wavelengths.147,157 Bai et al. reported the optical properties of pristine Ti2C and functionalized Ti2C with –O, –OH, and –F in both out-plane and in-plane directions (Fig. 9a). It can be seen obviously that the in-plane absorption coefficients of OH- and F-functionalized Ti2C MXenes are lower in comparison to pristine and O-functionalized Ti2C MXenes. Moreover, the white color indicates the OH- and F-functionalized Ti2C according to the refractivity results. Furthermore, the performance of MXenes in visible and UV light absorption is the key factor for the optoelectronic, photovoltaic, and photocatalytic properties, which are affected by the existence of functional groups (Fig. 9b).75,158,159 The same properties were observed for F- and OH-functionalized MXenes, in contrast to the performance of O-functionalized MXenes. Additionally, in the UV range, the reflectivity improved in comparison with pristine MXenes, while in the visible region, the F- and OH-functionalized MXenes decreased the reflectivity and absorption (Fig. 9c).
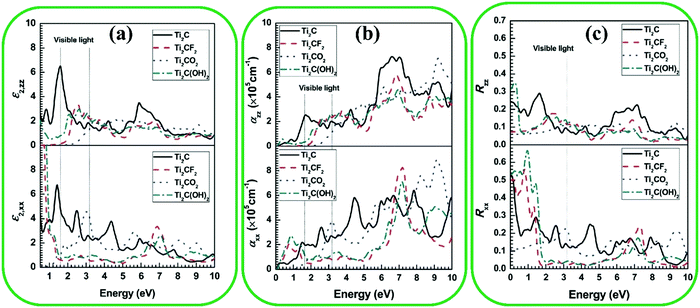 |
| Fig. 9 (a) Imaginary part (ε2), (b) adsorption coefficient (α), and (c) reflectivity (R) in the in-plane (XX) and out-plane (ZZ) as a function of photon frequency for surface-modified Ti2CT2 MXenes. Reproduced with permission.147 Copyright 2016, The Royal Society of Chemistry. | |
3.5. Hydrophilicity/hydrophobicity
As mentioned earlier, MXenes have shown superior performance in numerous applications.160–163 However, MXenes degrade in the presence of water and oxygen because of their hydrophilic nature induced by –O, –F, and –OH functional groups.164–168 The surface functionalization of MXenes has been reported as an efficient strategy to enhance their stability as well as their surface characteristics.169 For example, Ji et al. functionalized Ti3C2 with silylation reagents ((3-aminopropyl)triethoxysilane (APTES)) to tune its hydrophilicity (Fig. 10a).170 The stability of Ti3C2 improved by APTES functionalization by blocking the contact between water and MXenes. This improvement was also achieved for hexadecyltrimethoxysilane and 1H,1H,2H,2H-perfluorodecyltriethoxysilane (FOTS) (Fig. 10b). The results indicated the change of surface properties from hydrophilic to hydrophobic. Two superhydrophobic self-assembled monolayers (SAMs) [(3-chloropropyl)trimethoxysilane (CPTMS) and FOTS] were used for surface modification of MXenes via formation of covalent bonds between –OH and different surface functional groups (Fig. 10c).171,172 The water contact angle results (Fig. 10d) showed a superhydrophobicity of 156° and 96° for the fluorine-containing (Ti3C2-F) and chlorine-containing (Ti3C2-Cl) films, respectively, while the pristine Ti3C2 is basically hydrophilic due to its –O and –OH functional groups (a water contact angle of 33°). Hence, the functionalization of Ti3C2 with superhydrophobic reagents such as FOTS and CPTMS can be an effective approach to inhibit the degradation of MXene materials.
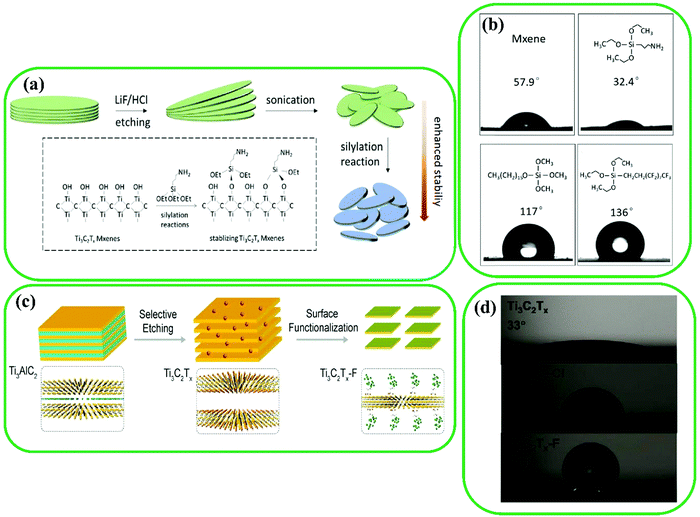 |
| Fig. 10 (a) Schematic representation of surface functionalization of Ti3C2 with silylation agents. (b) Water contact angle of various surface-modified Ti3C2. Reproduced with permission.170 Copyright 2019, Elsevier. (c) Modification process of Ti3C2 flakes. (d) Water contact measurements for pristine Ti3C2, Ti3C2-Cl, and Ti3C2-F. Reproduced with permission.173 Copyright 2020, American Chemical Society. | |
4. Applications
Because of their synergistic properties, functionalized MXenes have shown significantly better performances in comparison to pristine MXenes.6,174–177 To understand the effect of a specific functionalization on a MXene, the structural and application-specific properties of functionalized MXenes should be studied. To this end, herein, applications of surface-modified MXenes in fields such as biomedical application, sensors, catalysis, energy storage and conversion, and membrane-based separation are reviewed.
4.1. Biomedical applications
MXenes have been extensively used in biomedical applications owing to their outstanding properties such as magnetic, electronic, optical, etc. MXenes are typically non-toxic and biocompatible due to multiple compositions.42 The different functional groups (–F, –O, and –OH) on the surface of MXenes make them hydrophilic. Moreover, MXenes have excellent light absorption in the near-infrared (NIR) region, which allows their use in photoacoustic imaging (PAI) and photothermal therapy (PTT) applications.52 Additionally, the surface of MXenes can be easily modified by various approaches, providing new opportunities for further biomedical applications.36,99,178–180
4.1.1. Photoacoustic imaging.
Lin et al. reported that modified Ti3C2 MXenes with SP possesses enhanced the physiological stability, compared to pristine Ti3C2.35 The UV-vis-NIR absorption spectra of Ti3C2 demonstrated an absorption of around 750–850 nm at λ = 808 nm, and the absorption intensity remarkably increased by increasing the concentration of Ti3C2 (Fig. 11a). An extinction coefficient of 25.2 L g−1 cm−1 was achieved, and a linear relationship between the Ti3C2 concentration and the normalized adsorption intensity was observed. The photothermal performance of Ti3C2 was measured at various C concentrations at a power density of 1.5 W cm−2 (Fig. 11b), where the temperature of the solution (containing 72 ppm Ti3C2 MXenes) reached 57 °C, while the temperature of clean water had not changed, indicating the fast conversion of NIR light to thermal energy. Furthermore, the efficient effect of Ti3C2-SP MXene on the photothermal properties was confirmed under NIR laser irradiation, where by increasing the power density, more cells incubated with SP-modified Ti3C2 were killed compared to cells without Ti3C2-SP. TdT-mediated dUTP Nick-End labeling (TUNEL) and hematoxylin and eosin (H&E) staining indicated more necrosis of tumor cells after treatment with Ti3C2-SP under NIR laser irradiation than after treatment with other materials (Fig. 11c). Fig. 11d shows the strong effect of Ti3C2-SP under NIR laser irradiation on the in vivo proliferative activity of the Ki-67 antibody.
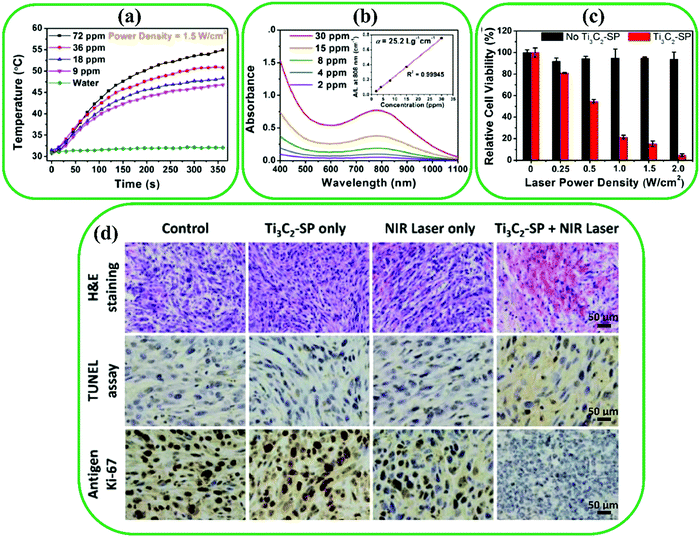 |
| Fig. 11 (a) Photothermal heating measurements of water and suspended Ti3C2 in water under a laser irradiation power of 1.5 W cm−2. (b) Absorbance spectra of suspended Ti3C2 in water at different concentrations. Inset: Normalized absorbance intensity at λ = 808 nm. (c) Relative cell viability of Ti3C2-SP at various laser power densities. (d) H&E, TUNEL, and antigen Ki-67 immunofluorescence staining for pathological changes in vivo, apoptosis in tumor, and cellular proliferation in tumor, respectively. Reproduced with permission.35 Copyright 2017, American Chemical Society. | |
4.1.2. Biosensing.
In addition, surface-functionalized MXenes have received a lot of attention in biosensing because of their outstanding biocompatibility, excellent electrical properties, and large surface area.181 For example, a new organ-like MXene-based material was prepared for biosensing applications to detect H2O2 in the range of 0.1–260 μM.182 Hereby, hemoglobin (Hb), as a protein, was utilized for the modification of the surface of Ti3C2 MXenes (Fig. 12a). The cyclic voltammogram (CVs) performances of Hb-functionalized Ti3C2 electrodes under the physiological condition of pH 7.0 are shown in Fig. 12b, where the Nafion/MXenes/glassy carbon (GC) electrode (curve a) did not show any redox peak, demonstrating its electro-inactive state in the potential window. Besides, two redox peaks can be observed at −0.327 V and −0.367 V vs. Ag/AgCl for the Nafion/Hb/MXenes/GC electrode (curve b), indicating that an appropriate microenvironment can be achieved for Hb to facilitate the reaction of electron transfer. A smaller redox peak is seen at the Nafion/Hb/GC electrode (curve c), which may be attributed to the unsuitable direct electron transfer (DET) between the electrode and the enzyme. It can be concluded that the DET process between the GC electrode and Hb molecules improved at the Nafion/Hb/MXene/GC electrode. Moreover, the Nafion/Hb/MXene/GC electrode exhibited good performance in detecting H2O2 by the measurement of amperometric responses (Fig. 12c and d). The nitrite biosensor and glucose biosensor based on MXenes have been reported in the literature.183,184 Hence, MXene-based materials have shown incredible potential for enzyme conjugation and biosensing applications.
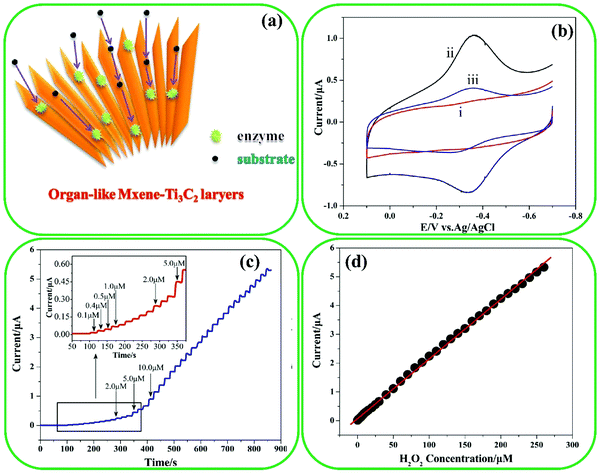 |
| Fig. 12 (a) Schematic presentation of organ-like Ti3C2 encapsulating hemoglobin. (b) Cyclic voltammograms with a scan rate of 0.1 V S−1 in 0.1 M of (i) Nafion/Ti3C2/GC electrode, (ii) Nafion/Hb/Ti3C2/GC electrode, and (iii) Nafion/Hb/GC electrode. (c) The current time response of the Nafion/Hb/Ti3C2/GC electrode to the addition of H2O2 under stirring conditions. (d) The steady state as a function of H2O2 concentration. Reproduced with permission.182 Copyright 2014, IOP Science. | |
4.1.3. Photothermal therapy and drug delivery system.
Cancer disease is a major cause of death worldwide.185 Recently, many operation treatments have been developed for cancer therapy, although most of them, such as radiotherapy and chemotherapy, not only do not remove cancer tumors completely, but also create side effects.186 Therefore, photothermal therapy (PTT) has emerged as a highly efficient strategy to prevent the growth of cancer tumors because PTT can transform NIR light to thermal energy.187 It should be noted that NIR light is classified into two sections, including first bio-window (750–1000 nm) and second bio-window (1000–1350 nm), where a few studies have utilized the second bio-window in PTT applications because there are no adequate materials with high-efficient photothermal conversion and tailored NIR light absorption.188 Interestingly, MXene-based materials have attracted tremendous attention for PTT applications owing to their high photothermal conversion and strong absorption. For instance, Lin et al. prepared poly(vinylpryrrolidone) (PVP)-functionalized Nb2C MXenes for using in the PTT of mice tumor xenografts, as depicted in Fig. 13a and b.99 At first glance, other treatment methods were applied on the tumor cells of mice, while the tumor cells are still large (Fig. 13c). Fig. 13d and e indicate that tumor regions entirely vanished once PTT was used by Nb2C-PVP + NIR-I and Nb2C-PVP + NIR-II. Fig. 13f depicts the comparison of survival curves for various treatment techniques, where it can be clearly seen that the recovered mice by Nb2C-PVP + NIR-I and Nb2C-PVP + NIR-II survived for more than 50 days.
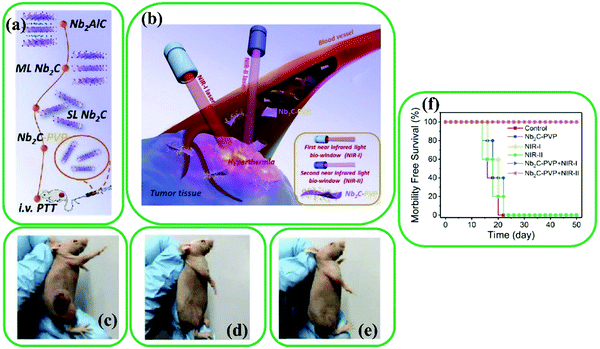 |
| Fig. 13 (a) and (b) Exhibition of surface functionalization of Nb2C with PVP for in vivo photothermal tumor ablation in NIR-I and NIR-II biowindows. (c)-(e) Images of tumor regions of mice after 16 days of different treatments; (c) control, (d) Nb2C-PVP + NIR-I, and (e) Nb2C-PVP + NIR-II. (f) Survival curves of mice after different treatments. Reproduced with permission.99 Copyright 2017, American Chemical Society. | |
MXene-based materials provide numerous opportunities to be anchored by therapeutic molecules, so they are widely applied for developing drug delivery systems.189 Recently, Han et al. synthesized Ti3C2 immobilized by SP for drug delivery of PTT and chemotherapy (Fig. 14a and b),37 which led to facile transport in blood vessels and superior water dispersibility.190 Afterward, electrostatic adsorption was used for the conjugation of anti-cancer drugs (Dox and doxorubicin) on the surface of Ti3C2-SP MXenes. The results showed that the photothermal conversion of Ti3C2-SP MXene led to a noticeable improvement of Dox release under laser irradiation. The red fluorescence (Fig. 14c–e) demonstrated more dead cells by combining laser irradiation and Dox@Ti3C2-SP MXenes compared with other groups (Ti3C2-SP + laser and Dox@Ti3C2-SP).
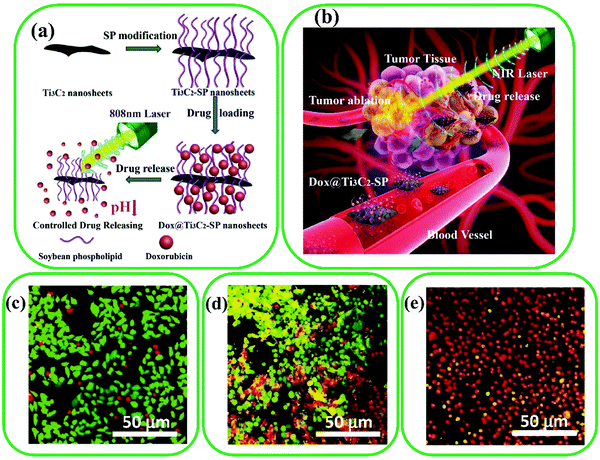 |
| Fig. 14 (a) Schematic illustration of Ti3C2 surface functionalization by SP, drug loading on the surface of the modified Ti3C2 MXenes, and stimuli-responsive drug release by inner and external irradiation. (b) Drug delivery scheme of surface-modified Ti3C2in vivo synergistic photothermal and chemotherapy of cancer, including transport in blood vessels, accumulation in tumor, drug release, and NIR laser ablation of tumor. CLSM images of cells after the treatment with (c) Dox@Ti3C2-SP, (d) Ti3C2-SP + laser, and (e) Dox@Ti3C2-SP + laser. The green and red fluorescence represent the live and dead cells, respectively. Reproduced with permission.37 Copyright 2018, Wiley. | |
4.2. Sensors
MXenes have been found to have promising potential in sensing applications, such as electrochemical sensors,33 strain sensors,191–193 biosensors,194–196 and gas sensors,31,197 due to their piezoelectric and thermoelectric response, rich surface groups, large surface area, and excellent anisotropy of conductivity. For instance, Shi et al. prepared layered Ti3C2–Ag nanowire-PDA/Ni2+ nanocomposite film-based strain sensors using a microscale “brick-and-mortar” architecture.192 They incorporated either Ni2+ or PDA into Ti3C2–Ag nanowires. As shown in Fig. 15a, the Ti3C2–Ag nanowire-PDA/Ni2+ nanocomposite exhibited superior performance of 83% stretchability compared to those of the pristine Ti3C2–Ag nanowire (32%), Ti3C2–Ag nanowire-Ni2+ (47%), and Ti3C2–Ag nanowire-PDA (75%). The output signals of Ti3C2–Ag nanowire-PDA/Ni2+ sensors were measured at various strains (Fig. 15b), and at a strain of 80%, the steady electrical responses of the sensors resulted in a strain rate of 1.2–8 mm S−1. Furthermore, the practical potential of the Ti3C2–Ag nanowire-PDA/Ni2+ strain sensor was verified by the attachment of two individual strain sensors on the skin of the knee and wrist joint of a volunteer (Fig. 15c). Fig. 15d shows the electrical signals generated by the strain sensor on the wrist when the volunteer is walking. The radial waves of a single heartbeat, including percussion (P), tidal (T), and diastolic (D), were isolated. The strain sensor detected motion signals in running, demonstrating the durability and reliability of the sensors (Fig. 15e).
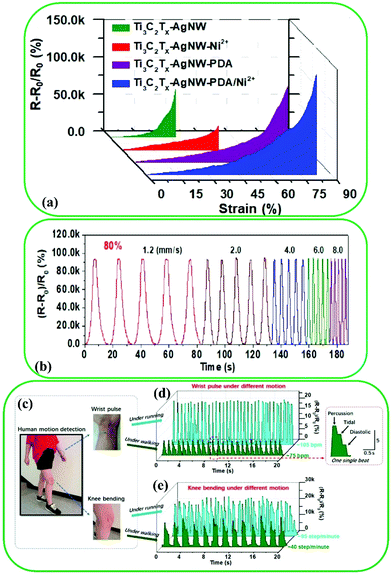 |
| Fig. 15 (a) Typical relative resistance change vs. applied strain for the Ti3C2–AgNW, Ti3C2–AgNW–PDA, Ti3C2–AgNW–Ni2+, Ti3C2–AgNW–PDA/Ni2 sensors. (b) Relative resistance variation of the Ti3C2–AgNW–PDA/Ni2+ strain sensor under incremental strain rates cycling from 0 to 80%. Monitoring human body (knee bonding and wrist pulse) under running and walking conditions by means of Ti3C2–AgNW–PDA/Ni2+ strain sensors. (c) Images of wearable strain sensors attached to the wrist and knee. (d) Relative resistance variation of a wrist pulse. (e) Relative resistance change of knee bending. Reproduced with permission.192 Copyright 2018, American Chemical Society. | |
Kumar et al. reported a biofunctionalized Ti3C2 (f-Ti3C2) via APTES for the detection of cancer.90 Besides, the deposition of TiO2 nanoparticles on the surface of MXenes may offer further advantages for the detection of H2O2.198 Therefore, the shielding microenvironment for increasing the stability and activity of enzymes can be achieved by loading TiO2 with exceptional biocompatibility on the surface of MXenes. The active sites of enzyme adsorption significantly increased for TiO2–Ti3C2 compared with pristine Ti3C2. Moreover, Chen et al. reported that the dispersion of MXenes could be adjusted by varying the temperature and CO2 concentration, which changes the conductivity and transmittance of V2C,98 where PDMAEMA was used to modify the surface of V2C by self-initiated photografting and photopolymerization. By increasing the temperature of the solution above the lower critical solution temperature (LCST), the hydrophilic nature of PDMAEMA changes to hydrophobic, resulting in the enhancement of the transmittance of V2C@PDMAEMA. Besides, when CO2 was added to water to form charged ammonium bicarbonate, the conductivity of V2C@PDMAEMA increased because of the CO2 responsive characteristic of V2C@PDMAEMA, demonstrating that V2C@PDMAEMA is sensitive to CO2 and temperature.
4.3. Catalysis
Recently, the utilization of MXene-based materials in catalysis applications has received considerable attention. This is due to the appealing properties of MXenes such as (i) the abundant active sites and rich surface groups, (ii) the adjustable band gap of MXenes by the arrangement of surface chemistries, and (iii) the exceptional carrier mobility of MXene-based materials, which can lead to improving the migration and separation of photogenerated electron–hole pairs.161,199,200 For example, Ramalingam et al. reported the coordination interactions between Ti3C2 and ruthenium single atoms (RuSA) through the S and N heteroatom doping method.201 The polarization curves of the hydrogen evolution reaction (HER) of MXene-based materials (including RuSA-N-S-Ti3C2, RuSA-Ti3C2, N-S-Ti3C2, Ti3C2, and carbon paper) (Fig. 16a) revealed that RuSA, N, and S co-doped Ti3C2 have great potential for electrocatalytic HER performance; they showed approximately remarkable zero onset potential and the smallest overpotential of 76 and 237 mV to reach 10 and 100 mA cm−2, respectively. The HER baseline of RuSA-doped Ti3C2 and RuSA, N, and S co-doped Ti3C2 catalysts are not at zero potential; this may be due to the underpotential hydrogen adsorption effect of Ru and the capacitance effect of the nanocarbons of Ti3C2 MXenes.202 The slope of Tafel plots was calculated to evaluate the reaction kinetics of the catalysts in the HER process (Fig. 16b), where this slope for the RuSA, N, and S co-doped Ti3C2 catalysts was about 90 mV dec−1, demonstrating that the Volmer–Heyrovsky mechanism is followed by these electrocatalysts which includes two steps: (i) fast initial discharge reaction (reaction (I)) and (ii) slow electrochemical desorption reaction (reaction (II)).203,204 | H3O+ + e− → Hads + H2O | (I) |
| Hads + H3O+ + e− → Hads + H2O | (II) |
Additionally, the significant activity of the RuSA, N, and S co-doped Ti3C2 electrocatalysts was confirmed by the measurements of turnover frequency (ToF), showing the exceptional performance of these electrocatalysts compared to other RuSA-based electrocatalysts.
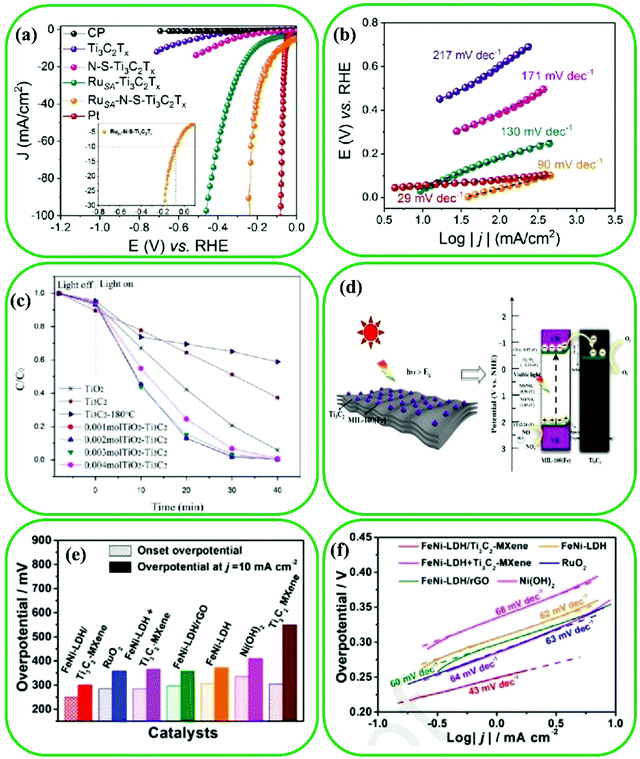 |
| Fig. 16 Electrocatalysis HER performance of the RuSA-N-S-Ti3C2 catalyst. (a) The HER polarization curves in 0.5 M H2O2 for bare carbon paper, pristine Ti3C2, N-S-Ti3C2, RuSA-Ti3C2, and RuSA-N-S-Ti3C2 catalysts. Inset: The magnified HER polarization curve of RuSA-N-S-Ti3C2. (b) The Tafel plots relating to part (a). Reproduced with permission.201 Copyright 2019, Wiley. (c) The curves of photocatalytic degradation rate for catalysts. Reproduced with permission.208 Copyright 2015, Elsevier. (d) Proposed mechanism for photocatalytic oxidation of NO by the M/T-3 Schottky catalyst under visible light. Reproduced with permission.210 Copyright 2019, American Chemical Society. (e) A comparison of FeNi-LDH/Ti3C2-MXene, RuO2, FeNi-LDH + Ti3C2-MXene, FeNi-LDH/rGO, FeNi-LDH, Ni(OH)2, and Ti3C2-MXene catalysts at overpotential and onset overpotential required to achieve a current density of 10 mA cm2. (f) Tafel plots of the reported catalysts. Reproduced with permission.211 Copyright 2017, Elsevier. | |
Interfacial engineering of MXene-based materials can be easily coupled with other nano-materials by the combination of large exposed basal plane and good flexibility of two phases, resulting in the formation of highly active catalysts.205 Besides, the reaction kinetics can be improved via the change in the electronic structure of MXenes.205 Recently, many studies have been performed on the effect of the interfacial structure of Ti3C2 MXene and TiO2 nanoparticles on the photocatalytic reactions,88,206,207 where the TiO2/Ti3C2 was prepared by the in situ growth of TiO2 on the surface of Ti3C2 by a hydrothermal strategy.208 As Fig. 16c shows, the TiO2/Ti3C2 exhibited superior photocatalytic degradation (almost 98%) compared to pristine TiO2 (42%) in 30 min; this can be related to the effective electron–hole separation. In addition, a mild oxidation method has been applied for the homogeneous growth of Nb2O5 on the surface of Nb2C MXenes in order for the HER.209 Charge carriers were generated at the interface of Nb2O5/Nb2C due to the contact between conductive Nb2O5 and Nb2C. Wang et al. formed a Schottky barrier in MIL-100(Fe)/Ti3C2 (Fig. 16d).210 The efficient visible light photocatalytic properties obtained for MIL-100(Fe)/Ti3C2 were three and four times higher than those for pristine MIL-100 and Ti3C2, respectively.
Moreover, FeNi-LDH nanoplates were interfacially coupled on the surface of Ti3C2,211 leading to an increase in the positive charge of FeNi-LDH/Ti3C2 owing to the strong electronic junction between the Ti3C2 MXenes and FeNi-LDH. This indicated the significant improvement of the oxygen evolution reaction (OER) performance, as the Tafel slope decreased from 62 to 43 mV dec−1 in comparison to FeNi-LDH (Fig. 16e and f). The HER activity of Nb-doped Ti3C2 was enhanced by surface modification with an Ni/Co alloy, which led to the weakening of the M–H affinity.212 DFT calculations showed that better catalysts can be fabricated by replacing Ti with Co or Ni, which can be attributed to the synergistic effect of Ni/Co@Nb-doped Ti3C2.
MXene-based materials have also found applications in photocatalytic water splitting, a novel technology of clean energy conversion.138 Traditional catalysts such as precious metal-based oxides have shown low efficiency due to their high cost and scarcity.213,214 However, recently MXene-based materials have been widely utilized in photocatalytic water splitting technology because of their rich exposed metal sites, suitable hydrophilicity, and excellent electronic conductivity. The OER is considered as a key reaction in water splitting because it allows the production of highly pure O2. The high catalytic performance of MXene-based materials can be obtained by adjusting their geometric properties.205 It was found that N-doped Ti3C2 (denoted as Ti3C1.6N0.4) possessed high electrical conductivity in comparison to pristine Ti3C2 (Fig. 17b).215 The smaller contact angle with the KOH electrolyte can be seen for the prepared film of Ti3C1.6N0.4 MXene, confirming its suitability as an electrolyte for the OER (Fig. 17a). As depicted in Fig. 17c and d, the Tafel slope and onset potential of the Ti3C1.6N0.4 film were 216.4 mV dec−1 and 245.8 mV, respectively, showing better electrocatalytic properties compared to the pristine Ti3C2. Furthermore, the surface structures of Mo2C were tuned by incorporating isolated cobalt atoms into the lattice of Mo2C MXenes, leading to a lower overpotential.216 Moreover, using an electrodeposition approach, Pt atoms were anchored on the surface of Mo2TiC2. The resulting material showed high HER performance, which can be ascribed to the efficient active site of Pt atoms for the HER.217 DFT calculations exhibited strong atomic interactions in Mo2TiC2–PtSA, resulting in the enhancement of d-electron domination near the Fermi level and also conductivity, and consequently, leading to improved catalytic activity. Besides, the strong bonding between the Mo2TiC2 and Pt atoms led to improved stability properties.
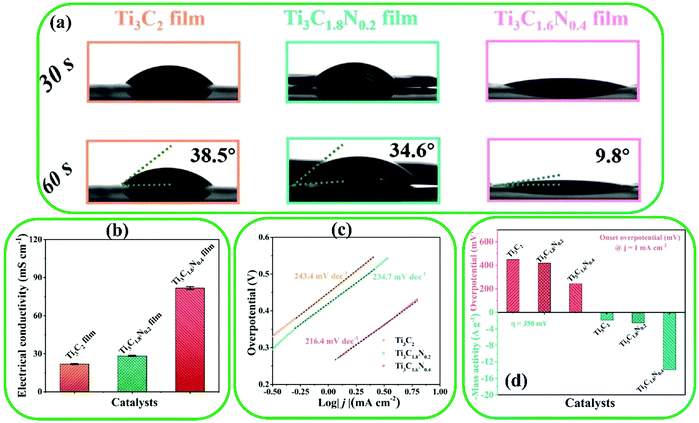 |
| Fig. 17 (a) The contact angle measurements of Ti3C2, Ti3C1.8N0.2, and Ti3C1.6N0.4 films in a 1M KOH electrolyte. (b) Electrical conductivity of the three films. (c) Tafel plots of the three electrocatalysts. (d) Comparison of the Ti3C2, Ti3C1.8N0.2, and Ti3C1.6N0.4 electrocatalysts at an onset overpotential of 1.0 mA cm−2 and a mass activity of 350 mV. Reproduced with permission.215 Copyright 2020, The Royal Society of Chemistry. | |
4.4. Energy storage and conversion
4.4.1. Energy storage.
MXene-based materials have great potential for energy storage and conversion applications, because of their appropriate mechanical stability, metallic conductivity, and good hydrophilic surface.6,115 The low capacity and tendency of restacking of pristine MXenes have restricted their applications in energy storage and conversion, which can be overcome by surface functionalization of MXenes.26 In the case of battery performance, the volume variation of charge and discharge cycles can be substantially diminished, while modified MXenes have exhibited improved performance.218,219 For instance, a melamine formaldehyde template method was employed to fabricate N-doped Ti3C2 for lithium (Li)–sulfur (S) chemistry, as a highly efficient electrocatalyst.220 The process of conversion and capture of lithium polysulfides (LiPSs) by porous N-doped Ti3C2 MXenes has been depicted in Fig. 18a, where numerous active sites are provided for the conversion and adsorption of LiPSs because MXenes have high electrical conductivity, large surface area, and porous structure. Besides, the interfacial interactions between the porous N-doped Ti3C2 MXenes and the Li2S cluster were improved by the N doping process, which led to the degradation of the Li2S dissociation barrier on the porous N-doped Ti3C2 MXenes and as well as the acceleration of the nucleation kinetics of Li2S, thereby the decomposition reaction of Li2S increases. Moreover, the sulfur redox kinetics are notably facilitated by the low diffusion barrier of Li atoms on the porous N-doped Ti3C2. The results showed that the prepared S-porous N-doped Ti3C2 cathode has higher capacities compared to the S/Ti3C2 cathode and pristine S cathode (Fig. 18b). Fig. 18c shows the initial capacity and coulombic efficiency, where S-porous N-doped Ti3C2 MXenes exhibited superior performance at 0.5 C in comparison to those of S/Ti3C2 and pristine S cathode.220
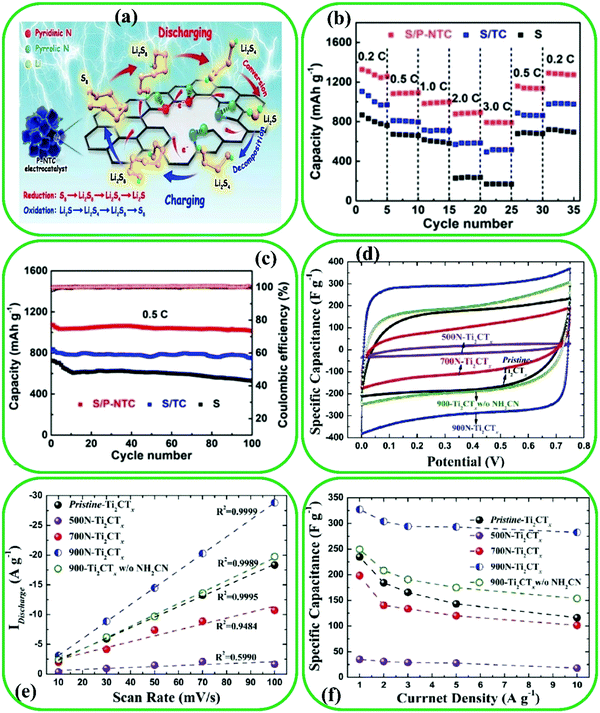 |
| Fig. 18 (a) Schematic exhibition of the role of N-doped Ti3C2 in the Li-S cell. (b) Performance of the bare S cathode, pristine Ti3C2, and N-doped Ti3C2. (c) Cycling performance of S/N-doped Ti3C2 at 0.5 C. Reproduced with permission.220 Copyright 2020, Elsevier. Electrochemical properties of pristine Ti3C2, 500N-Ti3C2, 700N-Ti3C2, 900N-Ti3C2, and 900N-Ti3C2 without NH2CN electrodes with 6M KOH as the electrolyte; (d) comparison of cyclic voltammetry curves at a scan rate of 100 mV S−1. (e) Discharge current densities as a function of scan rate. (f) Gravimetric specific capacitance at different current densities. Reproduced with permission.118 Copyright 2018, Willey. | |
4.4.1.1. Electrochemical capacitors.
Electrochemical capacitors have attracted great interest because of their high power densities, long cycle life, and fast charge/discharge capabilities.221 Among the various materials, MXene-based materials have received considerable attention owing to their superior electrical conductivity, excellent intercalation effects, and electrochemical energy storage characteristics.159,222 It should be noted that the capacitive performance can be significantly affected by surface modification.223 For example, an N-doped Ti2C MXene with various contents of N doping was prepared by carbon nitride decomposition and sequential intercalation via exfoliation and thermal annealing approach.118 The capacitance performance of all pristine Ti2C and N-doped Ti2C demonstrated that as the annealing temperature increases, the cyclic voltammetry (CV) curve shape becomes more and more rectangular and the related surface areas increase (Fig. 18d). Indeed, the largest area observed for N-doped Ti2C MXene at 900° suggests the high efficiency of the doping strategy. The discharge current densities of N-doped Ti2C exhibit an approximately linear relationship with the scan rate, indicating that the fast electrochemical reaction occurred on the entire surface of the electrode (Fig. 18e). The highest specific capacitance of the N-doped Ti2C electrode can attain 327 ± 1 F g−1 at 900 °C which is higher than those of the pristine Ti2C and other N-doped-based MXene electrodes at different temperatures (Fig. 18f).
4.4.1.2. Metal-ion batteries.
In the area of metal-ion batteries, including LIBs and SIBs, MXene-based materials have received considerable attention due to their kinetics and thermodynamics of metal-ion diffusion and intercalation in the lamellar space of MXenes. However, there are still unknowns such as the storage mechanism of metal ions, appropriate surface functional groups, and optimal MXene/metal ratios.224,225
The specific capacities of MXene-based materials are much lower than those of other electrode materials.226 Hence, surface modification is a promising method to enhance the performance in SIBs and LIBs via combining the advantages of active sites and the conductivity of MXenes. For instance, the rate capability and the specific capacity of MXenes have been improved via surface modification through hydrothermal oxidation of TiO2;227–229 a specific capacity of 291 mA h g−1 for LIBs after 2000 cycles at a current density of 100 mA g−1
230 was achieved. Liu et al. synthesized a novel N-doped Nb2C MXene via a thermal reaction with urea.81 Their N-doped Nb2C MXene presented superior cycling stability and an excellent capacity of 360 mA h g−1 due to the improved specific surface area and electrical conductivity caused by the extension of the c-lattice parameter. Moreover, the surface chemistry of MXenes can be adjusted by cation modification.29 The ion capacity of Sn4+ decorated V2C MXenes was boosted to 1284 mA h g−1 at a density of 0.1 A g−1, and the cycling stability reached a remarkable value of 1262.9 mA h g−1 after 90 cycles at the same density.231 These improvements can be ascribed to the V–O–Sn bond and enlarged interlayer space, resulting in the fast charge transfer and interface ionic diffusion. Moreover, Guo et al. fabricated a 2D phosphorene/MXene hybrid anode with an in situ formed fluorinated interphase for LIB applications.232 Their theoretical and experimental investigations showed that the combination of Ti3C2 and the 2D phosphorene heterostructure not only enhances the sodium diffusion but also alleviates the volume change of phosphorene. Furthermore, an in-depth X-ray photoelectron spectroscopy analysis demonstrated that the –F terminated MXene could enhance the Coulombic efficiencies and cyclic performances of the phosphorene/MXene hybrid anode by forming fluorine-rich compounds. As a result, the phosphorene/Ti3C2F2 presented excellent cycling performance (343 mA h g−1 after 1000 cycles at 1 A g−1) and a superior reversible capacity of 535 mA h g−1 at 0.1 A g−1 compared to the fluorine-free electrolyte. Natu et al. reported that Ti3AlC2 can be etched and delaminated in various organic solvents in the presence of NH4HF2.233 They found that the electrode capacity of the Ti3C2 etched in propylene carbonate (PC) was almost two times more than the same MXene synthesized in water when tested in NIB and that Ti3C2 rich in –F terminations can be synthesized using NH4HF2-containing polar organic solvents in the etching process.
Chen et al. investigated the experimental and theoretical influence of glycine functionalization of Ti3C2O2 MXenes on charge storage because organic molecules can lead to enhanced interlayer space and hinder restacking.54 The strong chemical reaction between glycine and Ti3C2O2 MXenes was ascribed to the formation of the Ti–N bond via shared electrons between them. The interlayer spacing of pristine Ti3C2O2 increased from 10.16 to 14.06 Å by surface functionalization (Fig. 19a and b), which leads to enhanced cycling performance, improved charging rate, and better ion accessibility. Surface functionalization of Ti3C2O2 led to a high capacitance of 324 F g−1 at a scan rate of 10 mV s−1 (Fig. 19c), and also to an improved retention capacitance of 140 F g−1 for Ti3C2O2/glycine electrodes, which is double the value for pristine Ti3C2O2.
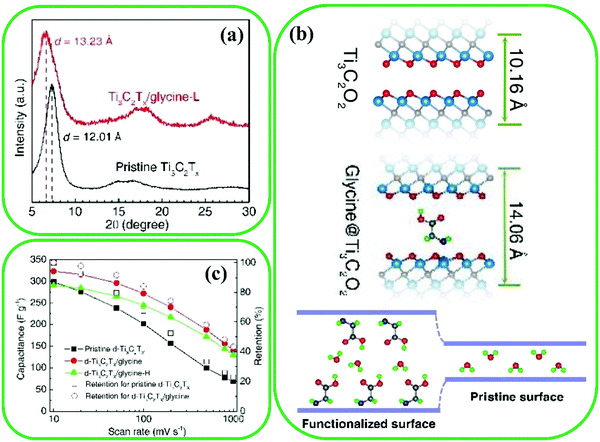 |
| Fig. 19 (a) XRD patterns for pristine Ti3C2 and Ti3C2/glycine films. (b) Predicted interlayer spacing and schematic diagrams for pristine and glycine functionalized Ti3C2O2. (c) Rate performance and capacitance retention for pristine and glycine functionalized Ti3C2O2. Reproduced with permission.54 Copyright 2018, The Royal Society of Chemistry. | |
4.4.2. Energy conversion.
The use of abundant solar energy allows the existing challenges in energy and environmental pollution to be addressed.234 Solar energy can be directly converted to heat energy using 2D materials such as MXenes.235 Photothermal energy conversion is extensively used in self-heating textiles,236 seawater desalination,237 and tumor treatment.238 For instance, Yang et al. prepared PPy-modified Ti3C2 MXenes by in situ polymerization on the surface of Ti3C2 to enhance the antioxidant capacity and performance of photothermal energy conversion.239 They then sprayed the PPy-modified MXenes (MXene@PPy) on a transparent film heater. Superior photothermal conversion of MXene@PPy can be obtained because of the synergistic effect of Ti3C2 and PPy. A comparison of the photothermal energy conversion performances of the pristine MXene and MXene@PPy films (Fig. 20a and b) indicated that under 200 mW cm−2 irradiation, the pristine MXene film showed tiny light-to-heat conversion along with a negligible increment in the temperature. In contrast, MXene@PPy was able to convert light to thermal energy more efficiently. The surface temperature increased from 25 to 61 °C. This enhancement in temperature confirmed the efficient photothermal conversion ability of MXene@PPy compared to the pristine MXene. After grafting PPy onto the MXene surface, the photothermal conversion performance is stable for approximately 7 months in air atmosphere. Du et al. synthesized a polymerized PDA-decorated MXene (Ti3C2@PDA) by in situ grafting of PDA on the surface of Ti3C2.240Fig. 20c illustrates the solar-thermal conversion performance of Ti3C2@PDA by calculation of the temperature evolution curves under 250 mW cm−2 irradiation. The solar-thermal efficiencies of a pristine film and an MXene-based film with 2%wt content of Ti3C2@PDA were reported to be 64.2% and 90.1%, respectively. It is obvious that the solar-thermal conversion performance of the organic phase change materials (PMCs) enhanced with the incorporation of Ti3C2@PDA. Furthermore, Fan et al. reported the introduction of silver nanoparticles (AgNPs) onto the surface of MXene for transparent device applications.241 The obtained AgNP@MXene hybrid demonstrated a substantial temperature gain of 111 and 148 °C under the irradiation of 600 and 800 mW cm−2, respectively. The effect of surface modification was evaluated by measuring the surface temperature of pristine MXene and AgNP@MXene hybrid at different time instants under vis-IR light (Fig. 20d). The significant discrepancy in the temperature of the AgNP@MXene hybrid shows the efficient conversion of light to thermal energy owing to the thermal conductivity and photothermal effect of MXenes with the plasmonic properties of AgNPs in conjunction.
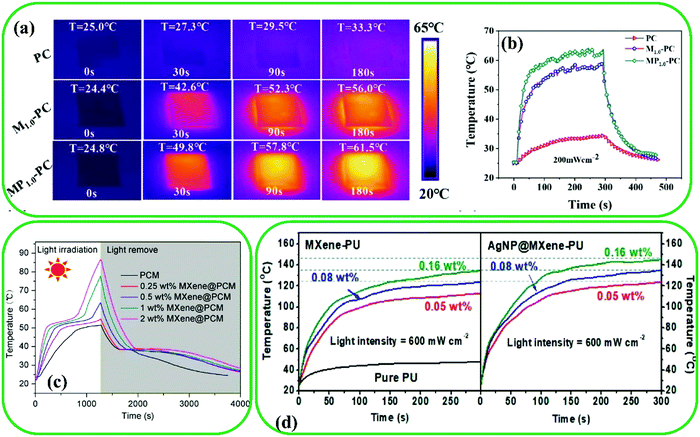 |
| Fig. 20 (a) IR thermal images and (b) surface temperature evolution curves of different MXene@PPy-based films under 200 mW cm−2. Reproduced with permission.239 Copyright 2021, American Chemical Society. (c) Temperature evolution curves of pristine PCM and MXene@PCM at different concentrations of Ti3C2. Reproduced with permission.240 Copyright 2020, American Chemical Society. (d) Temperature changes as a function of time for MXene-PU (left) and AgNP@MXene-PU (right) under 600 mW cm−2. Reproduced with permission.241 Copyright 2019, American Chemical Society. | |
4.5. Membrane-based separation
In the past few decades, many conventional techniques, including filtration, condensation, crystallization, and distillation, have been widely utilized in separation. However, membrane-based processes have emerged as a promising candidate for use in different applications such as water and wastewater treatment, and pharmaceutical and chemical industries.242,243 Recently, MXene-based materials have been employed in membrane-based separation with high separation performance because of their large surface area, superior flexibility, and abundant surface functional groups.13,244,245 This section reviews the effect of MXene-based materials on the separation performance of membranes and puts the advances into perspective.
4.5.1. Pervaporation.
Membrane-based separation processes have attracted much attention in solvent dehydration because of their high energy efficiency and simplicity.246,247 MXene-based materials have shown excellent separation performance, due to their good mechanical strength and excellent metallic conductivity.248,249 It should be noted that enough care should be taken to achieve a defect-free layered structure for MXene-based membranes along with highly efficient solvent dehydration. Liu et al. prepared an ordered laminar structure of Ti3C2 MXene membrane by introducing positively charged polyelectrolytes (including PDDA, polyallylamine hydrochloride (PAH), and polyethylene (PEI)) to create electrostatic interactions with negatively charged Ti3C2 nanosheets (Fig. 21a) for pervaporation dehydration of isopropanol.250 The lowest value of water contact angle for MXene–PDDA indicated that it can absorb more water molecules and facilitate the transport pathway of water, showing better separation performance compared to those of pristine MXene, MXene-PAH, and MXene–PEI membranes. As revealed in Fig. 21b, the MXene-PDDA membrane showed water content of ∼99.5 wt%, while it was ∼57, ∼63, and ∼18.9 wt% for the MXene–PAH, MXene–PEI, and pristine MXene membranes, respectively. The separation mechanism of the pervaporation process was described according to solution–diffusion;251 the diffusion selectivity improved by the formation of regular packing of MXenes induced by PDDA introduction and the enhancement of water content may be related to the improvement of adsorption selectivity toward the water. Moreover, water flux decreased when the PDDA concentrations increased from 0 to 0.36 mg mL−1, suggesting an increase of transport resistance due to the occupation of transport pathways and enhanced membrane thickness.252 However, the separation factor first increased and then decreased because of the promotion of selective diffusion and preferential sorption of water rather than isopropanol caused by the improvement of either the packing order of MXenes or hydrophilicity.
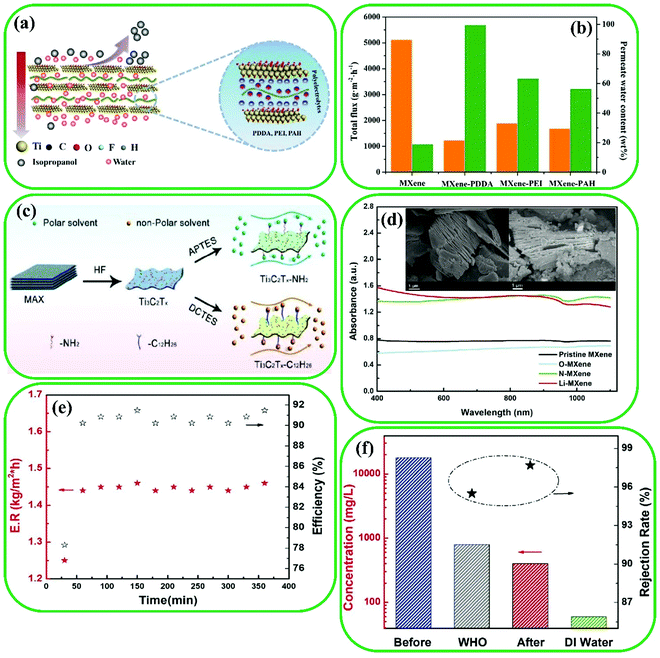 |
| Fig. 21 (a) Schematic illustration of Ti3C2 laminar membranes functionalized via polyelectrolytes. (b) Effects of polyelectrolytes on MXene-based membranes for pervaporation dehydration of 90 wt% isopropanol/water at 50 °C. Reproduced with permission.250 Copyright 2020, American Chemical Society. (c) Synthesis process of pristine Ti3C2 and functionalized Ti3C2 composites. Reproduced with permission.253 Copyright 2017, Elsevier. (d) UV-vis absorbance spectrum of various powders. Inset: SEM images of MXene flakes, pristine MXene (left) and Li-MXene (right). (e) Energy conversion efficiency evaluation during continuous 6 h illumination. (f) Salt rejection rate revealed by ion concentration comparison before and after desalination showing the capability to produce drinking water. Reproduced with permission.254 Copyright 2020, Wiley. | |
4.5.2. Nanofiltration.
In another study, functionalized Ti3C2 MXenes were employed in thin-film nanocomposite membranes (TFNs) to improve selectivity and flux for alcohol-based solvents.253 Four modifiers – APTES, (dodecyl)triethoxysilane (DCTES), (methyl aniline)triethoxysilane (MATES) and (γ-methacryloxypropyl)trimethoxysilane (MPTMS) – were employed to prepare functionalized Ti3C2–NH2, Ti3C2–C12H26, Ti3C2–C6H6, and Ti3C2–COOR, respectively (Fig. 21c). The area swelling and solvent uptake of the prepared TFN membranes were evaluated with polar solvents (ethyl acetate and isopropanol) and non-polar solvents (n-heptane and toluene). As a result, the incorporation of Ti3C2 MXene led to the reduction of area swellings and solvent uptakes except for isopropanol due to its non-swelling characteristics. However, the storage and adsorption of isopropanol were promoted by the –OH groups on Ti3C2 through H-interaction. For the same reason, Ti3C2–COOR and Ti3C2–NH2 embedded TFN membranes demonstrated higher area swelling and solvent uptakes for polar solvents, while Ti3C2–C6H6 and Ti3C2–C12H26 exhibited higher area swelling and solvent uptakes toward non-polar solvents. All Ti3C2-M incorporated TFN membranes improved the affinity for a specific solvent based on the polarity properties of solvents and functional groups. This phenomenon can be ascribed to the fact that each of the four functional groups acts as a carrier and facilitates molecular transport through the TFN membranes. The affinity of Ti3C2–NH2 and Ti3C2–COOR incorporated membranes can be improved towards polar solvents. For example, –NH2 can facilitate the transport of isopropanol molecules by acting as carrier sites. Similarly, embedding Ti3C2–C12H26 and Ti3C2–C6H6 enhances the transport of non-polar solvents. Adding a Ti3C2–M into the polymer matrix improves the rejection ability, and this could be related to the Ti3C2 and Ti3C2-M blocking the transport of molecules.
4.5.3. Desalination.
MXene-based materials have provided a great opportunity to prepare membranes for seawater desalination.255,256 MXene-based membranes have been synthesized to separate salts according to ionic charges and the hydration radius,257 where the interlayer spacing can play a key role in salt separation. The surface modification of MXene nanosheets enhances the interlayer spacing, resulting in the improvement of selective separation.258 Furthermore, it has been predicted that MXenes can show significant performance as a photothermal material along with the conversion of photo-to-thermal characteristics,259 due to their rich surface chemistry and unique layered structure. For instance, Fei et al. prepared a novel solar steam generator with a highly efficient photothermal conversion of a cellulose acetate–MXene (CAM) membrane, which was synthesized by introducing the modified MXenes into the polymeric network of cellulose acetate.254 Li-intercalated MXene (denoted as Li-MXene) possesses a high absorption rate (Fig. 21d) with high structural similarity to the pristine MXene. This may be attributed to the high photon absorption of Li-MXene in its structure and also to its black color, where lower lights are reflected. Measurement of the mass change demonstrated a remarkable enhancement of steam generation by the CAM membrane, which are ascribed to the superior photothermal characteristics of Li-MXene. Fig. 21e shows the energy conversion of the CAM membrane, where an efficiency of 92.1% was obtained after 11 cycles. In addition, a salt rejection of 97.7% was achieved for high salinity synthesized seawater (Na+ concentration of 18
000 mg L−1) (Fig. 21f). These results showed that CAM membranes are good candidates for solar desalination applications because of their excellent robustness, scalability, and effectiveness.
4.5.4. Dye removal.
Dyes are the major pollutants of discharged wastewater from industries, which can threaten human health issues because of their high carcinogenicity.260 Therefore, the removal of dyes from wastewater should be considered as a major priority from an environmental viewpoint. Functionalized MXene-based membranes have exhibited promising potential for the removal of dyes from water and wastewater.261,262 In this area, the interlayer spacing of MXenes plays a vital role in pressure-driven membrane processes because molecules larger than the interlayer spacing are rejected, and solvents are facilely penetrated.22 Pandey et al. synthesized Ag@MXene membranes by grafting Ag on the surface of MXenes to enhance the interlayer spacing.263 Accordingly, water flux increased by introducing Ag nanoparticles on the MXene surface compared to the pristine MXene-based membrane. This promotion can be due to the interlayer voids of additional nanochannels by the presence of Ag nanoparticles, leading to facile water pathways. Besides, the Ag@MXene membranes exhibited high rejection of 100%, 92%, and 79.9% for bovine serum albumin (BSA), methyl green (MG), and rhodamine, respectively (Fig. 22a and b). Flux recovery of membranes needs to be evaluated to understand the membrane fouling properties. The Ag@MXene membranes after exposure to BSA and MG indicated 91% and 97% of flux recovery compared to 81% and 86% for the pristine MXene membrane.
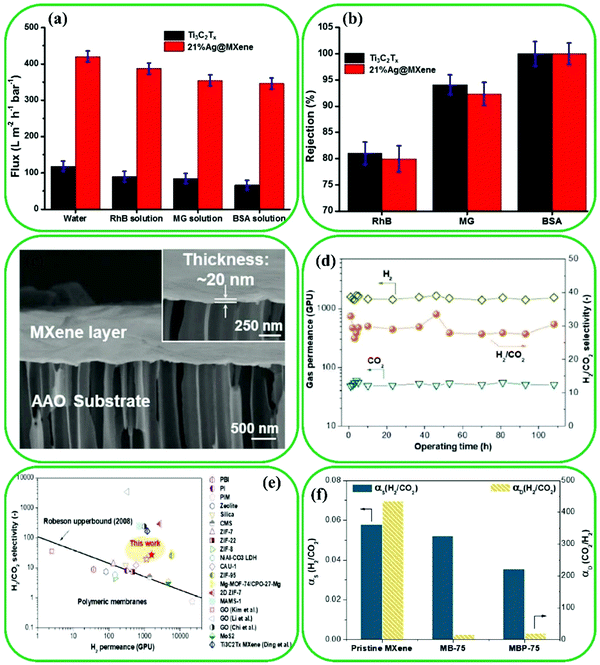 |
| Fig. 22 Comparison of the performance of the pristine Ti3C2 and 21%Ag@Ti3C2 membranes for the separation of RhB, MG, and BSA molecules at 25 °C: (a) flux and (b) rejection. Reproduced with permission.263 Copyright 2018, The Royal Society of Chemistry. (c) Cross-section SEM image of MXene nanofilms. (d) Long-term gas transport properties of H2-selective MXene nanofilms. (e) H2/CO2 separation compared with state-of-the-art gas separation membranes. (f) Sorption selectivity (αs) as well as diffusion selectivity (αD) of H2/CO2 for various MXene-based nanofilms. Reproduced with permission.264 Copyright 2018, Wiley. | |
4.5.5. Gas separation.
Another field that MXene-based materials have impacted is the area of membrane-based gas separation, which is growing due to the low energy consumption and high efficiency of these processes.265 Different kinds of 2D materials, such as metal–organic frameworks (MOFs),266,267 covalent-organic frameworks (COFs),268 zeolites,269 and graphene,270 have been extensively employed for improving the gas separation performance of membranes by surpassing the trade-off relationship between permeability and selectivity.271 MXene-based materials are attractive to further improve the gas separation performance by tuning the interlayer spacing, as gas molecules larger than the interlayer spacing are prevented from passing through.272 The extraordinary separation performance of MXene-based membranes, such as favorable mechanical stability and good reproducibility due to the existence of ordered channels in lamellar MXene membranes, has been reported.272 The surface modification of MXene nanosheets can improve the interlayer space, resulting in enhanced selective molecular separation. Shen et al. prepared a MXene-based nanofilm on an anodic aluminum oxide (AAO) substrate for H2/CO2 separation (Fig. 22c).264 The pristine MXene nanofilm with 20 nm thickness showed high permeance of 1584 GPU and H2/CO2 selectivity of 27, which exceeded the Robeson upper-bound. Besides, it is worth noting that this kind of membrane exhibited stable performance during 100 h of continuous long-term operation (Fig. 22d). Borate and polyethylenimine (PEI) were introduced between the MXene nanosheets to assess the gas transport behavior of CO2 capture. Borate can not only facilitate the transport of CO2 molecules with reversible reactions for the enhancement of CO2 permeance, but can also crosslink with the –O groups on MXenes to decrease the interlayer spacing for promoting the selectivity of CO2/N2 and CO2/CH4. Furthermore, strong electrostatic interactions can be formed between the positively charged PEI and negatively charged MXene with the possible reaction of Ti suboxides and amine groups on PEI. Excellent gas separation was obtained for functionalized MXene nanofilms (Fig. 22e). The investigation of gas separation mechanism of pristine and functionalized MXene nanofilms demonstrated that pristine MXene membranes are diffusion-controlled, while borate and PEI functionalized MXene nanofilms indicated CO2 selective separation (Fig. 22f) because of the CO2-philic nature of borate and PEI.
Currently, there is a need for studies to understand how factors such as gas mixture composition, the size of MXene nanosheets, the interaction between MXene nanosheets and gas molecules, and various surface terminations affect gas selectivity and permeability.
5. Conclusion and perspective
In the past decade, MXenes have received considerable attention because of their appealing properties such as physicochemical, mechanical, magnetic and electronic characteristics, abundant surface terminations, and great surface area. As such, they have found applications in many areas such as biomedicine, sensing, catalysis, energy storage and conversion, and membrane-based separation. Surface functionalization of MXenes allows the alteration of various properties of MXenes, further increasing their versatility and enabling their weaknesses such as poor stability in the presence of water and molecular oxygen, facile restacking, and low flexibility to be addressed. This article reviewed the recent advances in MXene surface functionalization methods, MXene-affected properties, and the practical applications of the resulting surface-modified MXenes. Surface-modified MXenes have demonstrated great potential for use in different applications. Previous studies indicate that for every specific application, a modified MXene that outperforms the pristine MXene can be fabricated. In spite of many reported studies on surface functionalization of MXenes, there are still challenges and opportunities in this area. Examples are as follows:
1. An MXene with desired concentrations of termination groups and interlayer spacing is essential to prepare surface-modified MXene materials for different applications.
2. In catalysis, the exact mechanisms via which pristine and surface-modified MXenes promote reactions and the role of active sites on their surface are not well understood. Hence, computational and experimental studies are needed to improve the understanding, allowing the invention of novel catalysts.
3. In biomedical applications, MXene-based materials have shown great potential and low toxicity. However, the effect of toxicity of pristine and surface-modified MXenes on humans and the environment has not been investigated yet.
4. The water dispersity of MXenes can be improved via surface modification with hydrophilic polymers. However, these surface-modified MXenes are not stable adequately under some excessive conditions. Thus, better functionalization approaches are needed to form covalent and dynamic bonds. Besides, the effect of surface functionalization on biocompatibility needs to be explored further.
5. For application in sensors and photodetectors, performances of pristine and surface functionalized MXenes such as sensitivity and responsivity are still limited. Furthermore, the weight and size of pristine and surface functionalized MXene-based sensors need to be reduced for practical applications, especially for biomedical sensors. Therefore, energy-efficient, highly sensitive, super-small, and intelligent sensors and photodetectors should be developed.
6. It has been demonstrated that the interlayer spacing and surface functional groups of pristine and surface-modified MXenes have a great influence on their performance and structure. However, the impact of every single functional group on the performance of supercapacitors and batteries has not been studied; the relationship between the physicochemical characteristics and every single termination group is very important to understand.
7. For LIBs, the first cycle coulombic efficiency should be adequately enhanced by either modifying the anode/electrode interface or developing the surface chemistry of MXenes. The interface functionalization can be performed by providing an artificial layer of solid electrolyte interface on the MXene electrode, which leads to hindering undesirable reactions and does not prevent the Li+ ion diffusion.
8. Pristine and surface-modified MXenes are promising candidates for separation applications due to their outstanding features. However, easy tuning of the interlayer spacing and reducing the degradation of MXenes materials should be addressed.
9. It is essential to master tailoring of the surface chemistry of MXenes by post-etch processing, which facilitates the surface modification of MXenes and enhances MXene properties. The effect of individual functional group in each application needs to be investigated further via ex situ and in situ characterization studies.
Conflicts of interest
There are no conflicts to declare.
Acknowledgements
M. Soroush acknowledges financial support from the U.S. National Science Foundation under Grant No. CBET–1804285. Any opinions, findings, and conclusions or recommendations expressed in this material are those of the authors and do not necessarily reflect the views of the National Science Foundation.
References
- S. Stankovich, D. A. Dikin, G. H. Dommett, K. M. Kohlhaas, E. J. Zimney, E. A. Stach, R. D. Piner, S. T. Nguyen and R. S. Ruoff, Nature, 2006, 442, 282–286 CrossRef CAS PubMed.
- E. Benavente, M. Santa Ana, F. Mendizábal and G. González, Coord. Chem. Rev., 2002, 224, 87–109 CrossRef CAS.
- W. Chen, J. Ouyang, H. Liu, M. Chen, K. Zeng, J. Sheng, Z. Liu, Y. Han, L. Wang and J. Li, Adv. Mater., 2017, 29, 1603864 CrossRef PubMed.
- C. R. Martin, Science, 1994, 266, 1961–1966 CrossRef CAS PubMed.
- A. Shahzad, K. Rasool, M. Nawaz, W. Miran, J. Jang, M. Moztahida, K. A. Mahmoud and D. S. Lee, Chem. Eng. J., 2018, 349, 748–755 CrossRef CAS.
- Y. Wu, P. Nie, L. Wu, H. Dou and X. Zhang, Chem. Eng. J., 2018, 334, 932–938 CrossRef CAS.
- S. Sun, C. Liao, A. M. Hafez, H. Zhu and S. Wu, Chem. Eng. J., 2018, 338, 27–45 CrossRef CAS.
- C. Ding, J. Liang, Z. Zhou, Y. Li, W. Peng, G. Zhang, F. Zhang and X. Fan, Chem. Eng. J., 2019, 378, 122205 CrossRef CAS.
-
Z. Xiao, S. Ruan, L. B. Kong, W. Que, K. Zhou, Y. Liu and T. Zhang, Springer Nature, 2020 Search PubMed.
- M. Naguib, V. N. Mochalin, M. W. Barsoum and Y. Gogotsi, Adv. Mater., 2014, 26, 992–1005 CrossRef CAS PubMed.
- M. Naguib, M. Kurtoglu, V. Presser, J. Lu, J. Niu, M. Heon, L. Hultman, Y. Gogotsi and M. W. Barsoum, Adv. Mater., 2011, 23, 4248–4253 CrossRef CAS PubMed.
-
M. W. Barsoum, MAX phases: properties of machinable ternary carbides and nitrides, John Wiley & Sons, 2013 Search PubMed.
- H. Riazi, M. Anayee, K. Hantanasirisakul, A. A. Shamsabadi, B. Anasori, Y. Gogotsi and M. Soroush, Adv. Mater. Interfaces, 2020, 7, 1902008 CrossRef CAS.
- X. Wu, X. Cui, W. Wu, J. Wang, Y. Li and Z. Jiang, Angew. Chem., Int. Ed., 2019, 58, 18524–18529 CrossRef CAS PubMed.
- L. Verger, V. Natu, M. Carey and M. W. Barsoum, Trends Chem., 2019, 1, 656–669 CrossRef CAS.
- J. Chen, Q. Huang, H. Huang, L. Mao, M. Liu, X. Zhang and Y. Wei, Nanoscale, 2020, 12, 3574–3592 RSC.
- M. Magnuson, J. Halim and L.-Å. Näslund, J. Electron Spectrosc. Relat. Phenom., 2018, 224, 27–32 CrossRef CAS.
- H. Lin, L. Chen, X. Lu, H. Yao, Y. Chen and J. Shi, Sci. China: Mater., 2019, 62, 662–670 CrossRef CAS.
- S. Zhang, H. Zhuo, S. Li, Z. Bao, S. Deng, G. Zhuang, X. Zhong, Z. Wei, Z. Yao and J.-G. Wang, Catal. Today, 2021, 368, 187–195 CrossRef CAS.
- A. Shahzad, M. Nawaz, M. Moztahida, J. Jang, K. Tahir, J. Kim, Y. Lim, V. S. Vassiliadis, S. H. Woo and D. S. Lee, Chem. Eng. J., 2019, 368, 400–408 CrossRef CAS.
- C. Peng, P. Wei, X. Chen, Y. Zhang, F. Zhu, Y. Cao, H. Wang, H. Yu and F. Peng, Ceram. Int., 2018, 44, 18886–18893 CrossRef CAS.
- J. Li, X. Li and B. Van der Bruggen, Environ. Sci.: Nano, 2020, 7, 1289–1304 RSC.
- H. E. Karahan, K. Goh, C. Zhang, E. Yang, C. Yıldırım, C. Y. Chuah, M. G. Ahunbay, J. Lee, Ş. B. Tantekin-Ersolmaz and Y. Chen, Adv. Mater., 2020, 32, 1906697 CrossRef CAS PubMed.
- Y. A. J. Al-Hamadani, B.-M. Jun, M. Yoon, N. Taheri-Qazvini, S. A. Snyder, M. Jang, J. Heo and Y. Yoon, Chemosphere, 2020, 254, 126821 CrossRef CAS PubMed.
- L. Gao, C. Li, W. Huang, S. Mei, H. Lin, Q. Ou, Y. Zhang, J. Guo, F. Zhang and S. Xu, Chem. Mater., 2020, 32, 1703–1747 CrossRef CAS.
- W. Huang, L. Hu, Y. Tang, Z. Xie and H. Zhang, Adv. Funct. Mater., 2020, 30, 2005223 CrossRef CAS.
- S. Cao, B. Shen, T. Tong, J. Fu and J. Yu, Adv. Funct. Mater., 2018, 28, 1800136 CrossRef.
- X. Zhang, Z. Zhang and Z. Zhou, J. Energy Chem., 2018, 27, 73–85 CrossRef.
- X. Hui, X. Ge, R. Zhao, Z. Li and L. Yin, Adv. Funct. Mater., 2020, 30, 2005190 CrossRef CAS.
- E. Pomerantseva and Y. Gogotsi, Nat. Energy, 2017, 2, 1–6 Search PubMed.
- S. J. Kim, H.-J. Koh, C. E. Ren, O. Kwon, K. Maleski, S.-Y. Cho, B. Anasori, C.-K. Kim, Y.-K. Choi and J. Kim, ACS Nano, 2018, 12, 986–993 CrossRef CAS PubMed.
- H. L. Chia, C. C. Mayorga-Martinez, N. Antonatos, Z. K. Sofer, J. J. Gonzalez-Julian, R. D. Webster and M. Pumera, Anal. Chem., 2020, 92, 2452–2459 CrossRef CAS PubMed.
- F. Shahzad, A. Iqbal, S. A. Zaidi, S.-W. Hwang and C. M. Koo, J. Ind. Eng. Chem., 2019, 79, 338–344 CrossRef CAS.
- S. M. George and B. Kandasubramanian, Ceram. Int., 2020, 46, 8522–8535 CrossRef CAS.
- H. Lin, X. Wang, L. Yu, Y. Chen and J. Shi, Nano Lett., 2017, 17, 384–391 CrossRef CAS PubMed.
- K. Huang, Z. Li, J. Lin, G. Han and P. Huang, Chem. Soc. Rev., 2018, 47, 5109–5124 RSC.
- X. Han, J. Huang, H. Lin, Z. Wang, P. Li and Y. Chen, Adv. Healthcare Mater., 2018, 7, 1701394 CrossRef PubMed.
- H. Ouyang, M. Zhou, Y. Guo, M. He, H. Huang, X. Ye, Y. Feng, X. Zhou and S. Yang, Fitoterapia, 2014, 96, 152–158 CrossRef CAS PubMed.
- X. Zhang, J. Li, B. Xie, B. Wu, S. Lei, Y. Yao, M. He, H. Ouyang, Y. Feng and W. Xu, Front. Pharmacol., 2018, 9, 282 CrossRef PubMed.
- X. Zhang, M. He, S. Lei, B. Wu, T. Tan, H. Ouyang, W. Xu and Y. Feng, J. Pharm. Biomed. Anal., 2018, 156, 221–231 CrossRef CAS PubMed.
- Y. Xie, M. Naguib, V. N. Mochalin, M. W. Barsoum, Y. Gogotsi, X. Yu, K.-W. Nam, X.-Q. Yang, A. I. Kolesnikov and P. R. Kent, J. Am. Chem. Soc., 2014, 136, 6385–6394 CrossRef CAS PubMed.
- K. Chen, N. Qiu, Q. Deng, M.-H. Kang, H. Yang, J.-U. Baek, Y.-H. Koh, S. Du, Q. Huang and H.-E. Kim, ACS Biomater. Sci. Eng., 2017, 3, 2293–2301 CrossRef CAS PubMed.
- M. Mozafari, A. Arabi Shamsabadi, A. Rahimpour and M. Soroush, Adv. Mater. Technol., 2021, 2001189 CrossRef.
- M. Alhabeb, K. Maleski, B. Anasori, P. Lelyukh, L. Clark, S. Sin and Y. Gogotsi, Chem. Mater., 2017, 29, 7633–7644 CrossRef CAS.
- J. Jeon, Y. Park, S. Choi, J. Lee, S. S. Lim, B. H. Lee, Y. J. Song, J. H. Cho, Y. H. Jang and S. Lee, ACS Nano, 2018, 12, 338–346 CrossRef CAS PubMed.
- O. Mashtalir, K. M. Cook, V. N. Mochalin, M. Crowe, M. W. Barsoum and Y. Gogotsi, J. Mater. Chem. A, 2014, 2, 14334–14338 RSC.
- X.-H. Zha, Q. Huang, J. He, H. He, J. Zhai, J. S. Francisco and S. Du, Sci. Rep., 2016, 6, 1–10 CrossRef PubMed.
- C. J. Zhang, S. Pinilla, N. McEvoy, C. P. Cullen, B. Anasori, E. Long, S.-H. Park, A. S. Seral-Ascaso, A. Shmeliov and D. Krishnan, Chem. Mater., 2017, 29, 4848–4856 CrossRef CAS.
- A. Rozmysłowska, T. Wojciechowski, W. Ziemkowska, L. Chlubny, A. Olszyna, S. Poźniak, K. Tomkiewicz and A. Jastrzębska, Int. J. Electrochem. Sci., 2018, 13, 10837–10847 CrossRef.
- H. Lin, Y. Wang, S. Gao, Y. Chen and J. Shi, Adv. Mater., 2018, 30, 1703284 CrossRef PubMed.
- Z. Friedman, K. H. Marks, M. J. Maisels, R. Thorson and R. Naeye, Pediatrics, 1978, 61, 694–698 CrossRef CAS PubMed.
- S. Wang, Y. Liu, Q.-F. Lü and H. Zhuang, J. Mol. Liq., 2020, 297, 111810 CrossRef CAS.
- A. C. Rajan, A. Mishra, S. Satsangi, R. Vaish, H. Mizuseki, K.-R. Lee and A. K. Singh, Chem. Mater., 2018, 30, 4031–4038 CrossRef CAS.
- Z. Li, Z. Zhuang, F. Lv, H. Zhu, L. Zhou, M. Luo, J. Zhu, Z. Lang, S. Feng and W. Chen, Adv. Mater., 2018, 30, 1803220 CrossRef PubMed.
- Y. Xia, T. S. Mathis, M.-Q. Zhao, B. Anasori, A. Dang, Z. Zhou, H. Cho, Y. Gogotsi and S. Yang, Nature, 2018, 557, 409–412 CrossRef CAS PubMed.
- Z. Huang, S. Wang, S. Kota, Q. Pan, M. W. Barsoum and C. Y. Li, Polymer, 2016, 102, 119–126 CrossRef CAS.
- W. Shao, M. Tebyetekerwa, I. Marriam, W. Li, Y. Wu, S. Peng, S. Ramakrishna, S. Yang and M. Zhu, J. Power Sources, 2018, 396, 683–690 CrossRef CAS.
- J. Chen, M. Liu, H. Huang, F. Deng, L. Mao, Y. Wen, L. Huang, J. Tian, X. Zhang and Y. Wei, J. Mol. Liq., 2018, 259, 179–185 CrossRef CAS.
- X. Zhang, K. Wang, M. Liu, X. Zhang, L. Tao, Y. Chen and Y. Wei, Nanoscale, 2015, 7, 11486–11508 RSC.
- M. Liu, G. Zeng, K. Wang, Q. Wan, L. Tao, X. Zhang and Y. Wei, Nanoscale, 2016, 8, 16819–16840 RSC.
- H. Wang, J. Zhang, Y. Wu, H. Huang, G. Li, X. Zhang and Z. Wang, Appl. Surf. Sci., 2016, 384, 287–293 CrossRef CAS.
- X. Zhu, B. Liu, H. Hou, Z. Huang, K. M. Zeinu, L. Huang, X. Yuan, D. Guo, J. Hu and J. Yang, Electrochim. Acta, 2017, 248, 46–57 CrossRef CAS.
- Y. Tian, W. Que, Y. Luo, C. Yang, X. Yin and L. B. Kong, J. Mater. Chem. A, 2019, 7, 5416–5425 RSC.
- P. Liu, W. Ding, J. Liu, L. Shen, F. Jiang, P. Liu, Z. Zhu, G. Zhang, C. Liu and J. Xu, J. Alloys Compd., 2020, 829, 154634 CrossRef CAS.
- M. Boota, B. Anasori, C. Voigt, M. Q. Zhao, M. W. Barsoum and Y. Gogotsi, Adv. Mater., 2016, 28, 1517–1522 CrossRef CAS PubMed.
- L. Qin, Q. Tao, X. Liu, M. Fahlman, J. Halim, P. O. Persson, J. Rosen and F. Zhang, Nano Energy, 2019, 60, 734–742 CrossRef CAS.
- R. Jiang, M. Liu, H. Huang, L. Mao, Q. Huang, Y. Wen, Q.-Y. Cao, J. Tian, X. Zhang and Y. Wei, Dyes Pigm., 2018, 153, 99–105 CrossRef CAS.
- Z. Long, M. Liu, R. Jiang, Q. Wan, L. Mao, Y. Wan, F. Deng, X. Zhang and Y. Wei, Chem. Eng.
J., 2017, 308, 527–534 CrossRef CAS.
- Q. Wan, Q. Huang, M. Liu, D. Xu, H. Huang, X. Zhang and Y. Wei, Appl. Mater. Today, 2017, 9, 145–160 CrossRef.
- R. Jiang, M. Liu, C. Li, Q. Huang, H. Huang, Q. Wan, Y. Wen, Q.-Y. Cao, X. Zhang and Y. Wei, Mater. Sci. Eng., C, 2017, 80, 708–714 CrossRef CAS PubMed.
- L. Huang, S. Yang, J. Chen, J. Tian, Q. Huang, H. Huang, Y. Wen, F. Deng, X. Zhang and Y. Wei, Mater. Sci. Eng., C, 2019, 94, 270–278 CrossRef CAS PubMed.
- R. Jiang, X. Xiao, J. Zheng, M. Chen and L. Chen, Mater. Chem. Phys., 2020, 242, 122529 CrossRef CAS.
- Z. Jin, Y. Fang, X. Wang, G. Xu, S. Wei, C. Zhou, Y. Zhang and Y. Xu, J. Colloid Interface Sci., 2019, 537, 306–315 CrossRef CAS PubMed.
- F. Shahzad, M. Alhabeb, C. B. Hatter, B. Anasori, S. M. Hong, C. M. Koo and Y. Gogotsi, Science, 2016, 353, 1137–1140 CrossRef CAS PubMed.
- R. Sun, H. B. Zhang, J. Liu, X. Xie, R. Yang, Y. Li, S. Hong and Z. Z. Yu, Adv. Funct. Mater., 2017, 27, 1702807 CrossRef.
- Z. Ling, C. E. Ren, M.-Q. Zhao, J. Yang, J. M. Giammarco, J. Qiu, M. W. Barsoum and Y. Gogotsi, Proc. Natl. Acad. Sci. U. S. A., 2014, 111, 16676–16681 CrossRef CAS PubMed.
- Z. W. Gao, W. Zheng and L. Y. S. Lee, Small, 2019, 15, 1902649 CrossRef PubMed.
- X. Liang, A. Garsuch and L. F. Nazar, Angew. Chem., 2015, 127, 3979–3983 CrossRef.
- W. Bao, C. E. Shuck, W. Zhang, X. Guo, Y. Gogotsi and G. Wang, ACS Nano, 2019, 13, 11500–11509 CrossRef CAS PubMed.
- H. Li, X. Wang, H. Li, S. Lin, B. Zhao, J. Dai, W. Song, X. Zhu and Y. Sun, J. Alloys Compd., 2019, 784, 923–930 CrossRef CAS.
- R. Liu, W. Cao, D. Han, Y. Mo, H. Zeng, H. Yang and W. Li, J. Alloys Compd., 2019, 793, 505–511 CrossRef CAS.
- Y. Yoon, A. P. Tiwari, M. Choi, T. G. Novak, W. Song, H. Chang, T. Zyung, S. S. Lee, S. Jeon and K. S. An, Adv. Funct. Mater., 2019, 29, 1903443 CrossRef.
- C. Wang, S. Chen and L. Song, Adv. Funct. Mater., 2020, 30, 2000869 CrossRef CAS.
- R. Thakur, A. VahidMohammadi, J. Moncada, W. R. Adams, M. Chi, B. Tatarchuk, M. Beidaghi and C. A. Carrero, Nanoscale, 2019, 11, 10716–10726 RSC.
- O. Mashtalir, M. Naguib, B. Dyatkin, Y. Gogotsi and M. W. Barsoum, Mater. Chem. Phys., 2013, 139, 147–152 CrossRef CAS.
- T. Schultz, N. C. Frey, K. Hantanasirisakul, S. Park, S. J. May, V. B. Shenoy, Y. Gogotsi and N. Koch, Chem. Mater., 2019, 31, 6590–6597 CrossRef CAS.
- J. L. Hart, K. Hantanasirisakul, A. C. Lang, B. Anasori, D. Pinto, Y. Pivak, J. T. van Omme, S. J. May, Y. Gogotsi and M. L. Taheri, Nat. Commun., 2019, 10, 1–10 CrossRef CAS PubMed.
- D. Zhang, S. Wang, R. Hu, J. Gu, Y. Cui, B. Li, W. Chen, C. Liu, J. Shang and S. Yang, Adv. Funct. Mater., 2020, 30, 2002471 CrossRef CAS.
- Y. Lei, Y. Cui, Q. Huang, J. Dou, D. Gan, F. Deng, M. Liu, X. Li, X. Zhang and Y. Wei, Ceram. Int., 2019, 45, 17653–17661 CrossRef CAS.
- S. Kumar, Y. Lei, N. H. Alshareef, M. Quevedo-Lopez and K. N. Salama, Biosens. Bioelectron., 2018, 121, 243–249 CrossRef CAS PubMed.
- H. Wang, J. Zhang, Y. Wu, H. Huang and Q. Jiang, J. Phys. Chem. Solids, 2018, 115, 172–179 CrossRef CAS.
- M. A. Iqbal, S. I. Ali, F. Amin, A. Tariq, M. Z. Iqbal and S. Rizwan, ACS Omega, 2019, 4, 8661–8668 CrossRef CAS PubMed.
- A. Tariq, S. I. Ali, D. Akinwande and S. Rizwan, ACS Omega, 2018, 3, 13828–13836 CrossRef CAS PubMed.
- R. Wu, H. Du, Z. Wang, M. Gao, H. Pan and Y. Liu, J. Power Sources, 2016, 327, 519–525 CrossRef CAS.
- X. Wu, L. Hao, J. Zhang, X. Zhang, J. Wang and J. Liu, J. Membr. Sci., 2016, 515, 175–188 CrossRef CAS.
- Y. Jiang, X. Xie, Y. Chen, Y. Liu, R. Yang and G. Sui, J. Mater. Chem. C, 2018, 6, 8679–8687 RSC.
- W.-T. Cao, F.-F. Chen, Y.-J. Zhu, Y.-G. Zhang, Y.-Y. Jiang, M.-G. Ma and F. Chen, ACS Nano, 2018, 12, 4583–4593 CrossRef CAS PubMed.
- J. Chen, K. Chen, D. Tong, Y. Huang, J. Zhang, J. Xue, Q. Huang and T. Chen, Chem. Commun., 2015, 51, 314–317 RSC.
- C. Chen, M. Boota, X. Xie, M. Zhao, B. Anasori, C. E. Ren, L. Miao, J. Jiang and Y. Gogotsi, J. Mater. Chem. A, 2017, 5, 5260–5265 RSC.
- Z. Zhang, S. Yang, P. Zhang, J. Zhang, G. Chen and X. Feng, Nat. Commun., 2019, 10, 1–9 CrossRef PubMed.
- G. S. Gund, J. H. Park, R. Harpalsinh, M. Kota, J. H. Shin, T.-I. Kim, Y. Gogotsi and H. S. Park, Joule, 2019, 3, 164–176 CrossRef CAS.
- S. Tu, Q. Jiang, X. Zhang and H. N. Alshareef, ACS Nano, 2018, 12, 3369–3377 CrossRef CAS PubMed.
- M. Carey, Z. Hinton, M. Sokol, N. J. Alvarez and M. W. Barsoum, ACS Appl. Mater. Interfaces, 2019, 11, 20425–20436 CrossRef CAS PubMed.
- Q. W. Wang, H. B. Zhang, J. Liu, S. Zhao, X. Xie, L. Liu, R. Yang, N. Koratkar and Z. Z. Yu, Adv. Funct. Mater., 2019, 29, 1806819 CrossRef.
- J. Xuan, Z. Wang, Y. Chen, D. Liang, L. Cheng, X. Yang, Z. Liu, R. Ma, T. Sasaki and F. Geng, Angew. Chem., 2016, 128, 14789–14794 CrossRef.
- N. Tao, D. Zhang, X. Li, D. Lou, X. Sun, C. Wei, J. Li, J. Yang and Y.-N. Liu, Chem. Sci., 2019, 10, 10765–10771 RSC.
- X. Li, J. Zhu, L. Wang, W. Wu and Y. Fang, Electrochim. Acta, 2017, 258, 291–301 CrossRef CAS.
- H. Wang, L. Li, C. Zhu, S. Lin, J. Wen, Q. Jin and X. Zhang, J. Alloys Compd., 2019, 778, 858–865 CrossRef CAS.
- A. A. Shamsabadi, F. Seidi, E. Salehi, M. Nozari, A. Rahimpour and M. Soroush, J. Mater. Chem. A, 2017, 5, 4011–4025 RSC.
- Z. Nie, A. Petukhova and E. Kumacheva, Nat. Nanotechnol., 2010, 5, 15–25 CrossRef CAS PubMed.
- L. Fu, Z. Yan, Q. Zhao and H. Yang, Adv. Mater. Interfaces, 2018, 5, 1801094 CrossRef.
- S. B. Ambade, R. B. Ambade, W. Eom, S. H. Noh, S. H. Kim and T. H. Han, Adv. Mater. Interfaces, 2018, 5, 1801361 CrossRef.
- A. Ali, K. Hantanasirisakul, A. Abdala, P. Urbankowski, M.-Q. Zhao, B. Anasori, Y. Gogotsi, B. Aïssa and K. A. Mahmoud, Langmuir, 2018, 34, 11325–11334 CrossRef CAS PubMed.
- A. VahidMohammadi, J. Moncada, H. Chen, E. Kayali, J. Orangi, C. A. Carrero and M. Beidaghi, J. Mater. Chem. A, 2018, 6, 22123–22133 RSC.
- J. Li, D. Yan, S. Hou, Y. Li, T. Lu, Y. Yao and L. Pan, J. Mater. Chem. A, 2018, 6, 1234–1243 RSC.
- C. Lu, L. Yang, B. Yan, L. Sun, P. Zhang, W. Zhang and Z. Sun, Adv. Funct. Mater., 2020, 30, 2000852 CrossRef CAS.
- L. Yu, Z. Fan, Y. Shao, Z. Tian, J. Sun and Z. Liu, Adv. Energy Mater., 2019, 9, 1901839 CrossRef.
- Y. Yoon, M. Lee, S. K. Kim, G. Bae, W. Song, S. Myung, J. Lim, S. S. Lee, T. Zyung and K. S. An, Adv. Energy Mater., 2018, 8, 1703173 CrossRef.
- E. Balcı, Ü. Ö. Akkuş and S. Berber, J. Condens. Matter Phys., 2018, 30, 155501 CrossRef PubMed.
- S. Zheng, S. Li, Z. Mei, Z. Hu, M. Chu, J. Liu, X. Chen and F. Pan, J. Phys. Chem. Lett., 2019, 10, 6984–6989 CrossRef CAS PubMed.
- D. Kan, D. Wang, X. Zhang, R. Lian, J. Xu, G. Chen and Y. Wei, J. Mater. Chem. A, 2020, 8, 3097–3108 RSC.
- Y. Liu, H. Xiao and W. A. Goddard III, J. Am. Chem. Soc., 2016, 138, 15853–15856 CrossRef CAS PubMed.
- M. Khazaei, M. Arai, T. Sasaki, A. Ranjbar, Y. Liang and S. Yunoki, Phys. Rev. B: Condens. Matter Mater. Phys., 2015, 92, 075411 CrossRef.
- M. Naguib, J. Halim, J. Lu, K. M. Cook, L. Hultman, Y. Gogotsi and M. W. Barsoum, J. Am. Chem. Soc., 2013, 135, 15966–15969 CrossRef CAS PubMed.
- J. Halim, S. Kota, M. R. Lukatskaya, M. Naguib, M. Q. Zhao, E. J. Moon, J. Pitock, J. Nanda, S. J. May and Y. Gogotsi, Adv. Funct. Mater., 2016, 26, 3118–3127 CrossRef CAS.
- B. Anasori, C. Shi, E. J. Moon, Y. Xie, C. A. Voigt, P. R. Kent, S. J. May, S. J. Billinge, M. W. Barsoum and Y. Gogotsi, Nanoscale Horiz., 2016, 1, 227–234 RSC.
-
Z. Xiao, S. Ruan, L. B. Kong, W. Que, K. Zhou, Y. Liu and T. Zhang, MXenes and MXenes-based Composites: Processing and Applications, Springer Nature, 2020 Search PubMed.
- H. Weng, A. Ranjbar, Y. Liang, Z. Song, M. Khazaei, S. Yunoki, M. Arai, Y. Kawazoe, Z. Fang and X. Dai, Phys. Rev. B: Condens. Matter Mater. Phys., 2015, 92, 075436 CrossRef.
- M. Khazaei, A. Ranjbar, M. Arai and S. Yunoki, Phys. Rev. B, 2016, 94, 125152 CrossRef.
- M. Khazaei, M. Arai, T. Sasaki, C. Y. Chung, N. S. Venkataramanan, M. Estili, Y. Sakka and Y. Kawazoe, Adv. Funct. Mater., 2013, 23, 2185–2192 CrossRef CAS.
- Q. Tang, Z. Zhou and P. Shen, J. Am. Chem. Soc., 2012, 134, 16909–16916 CrossRef CAS PubMed.
- L. Dong, H. Kumar, B. Anasori, Y. Gogotsi and V. B. Shenoy, J. Phys. Chem. Lett., 2017, 8, 422–428 CrossRef CAS PubMed.
- G. Gao, A. P. O’Mullane and A. Du, ACS Catal., 2017, 7, 494–500 CrossRef CAS.
- M. Pandey and K. S. Thygesen, J. Phys. Chem. C, 2017, 121, 13593–13598 CrossRef CAS.
- M. Khazaei, V. Wang, C. Sevik, A. Ranjbar, M. Arai and S. Yunoki, Phys. Rev. Mater., 2018, 2, 074002 CrossRef CAS.
- Y. Wang, Y. Xu, M. Hu, H. Ling and X. Zhu, Nanophotonics, 2020, 9, 1601–1620 CrossRef CAS.
- M. Khazaei, A. Ranjbar, M. Arai, T. Sasaki and S. Yunoki, J. Mater. Chem. C, 2017, 5, 2488–2503 RSC.
- X. Zhan, C. Si, J. Zhou and Z. Sun, Nanoscale Horiz., 2020, 5, 235–258 RSC.
- L. Hu, X. Wu and J. Yang, Nanoscale, 2016, 8, 12939–12945 RSC.
- G. Wang, J. Phys. Chem. C, 2016, 120, 18850–18857 CrossRef CAS.
- C. Si, J. Zhou and Z. Sun, ACS Appl. Mater. Interfaces, 2015, 7, 17510–17515 CrossRef CAS PubMed.
- G. Gao, G. Ding, J. Li, K. Yao, M. Wu and M. Qian, Nanoscale, 2016, 8, 8986–8994 RSC.
- D. Xiong, X. Li, Z. Bai and S. Lu, Small, 2018, 14, 1703419 CrossRef PubMed.
- J. He, P. Lyu and P. Nachtigall, J. Mater. Chem. C, 2016, 4, 11143–11149 RSC.
-
W. Luo, C. Fang and R. Ahuja, Condensed Matter Theories: Volume 23, World Scientific, 2009, pp. 207–211 Search PubMed.
- M. Naguib, T. Saito, S. Lai, M. S. Rager, T. Aytug, M. P. Paranthaman, M.-Q. Zhao and Y. Gogotsi, RSC Adv., 2016, 6, 72069–72073 RSC.
- Y. Bai, K. Zhou, N. Srikanth, J. H. L. Pang, X. He and R. Wang, RSC Adv., 2016, 6, 35731–35739 RSC.
- X.-H. Zha, K. Luo, Q. Li, Q. Huang, J. He, X. Wen and S. Du, EPL, 2015, 111, 26007 CrossRef.
- Z. Guo, J. Zhou, C. Si and Z. Sun, Phys. Chem. Chem. Phys., 2015, 17, 15348–15354 RSC.
- V. N. Borysiuk, V. N. Mochalin and Y. Gogotsi, Nanotechnology, 2015, 26, 265705 CrossRef PubMed.
- E. A. Mayerberger, O. Urbanek, R. M. McDaniel, R. M. Street, M. W. Barsoum and C. L. Schauer, J. Appl. Polym. Sci., 2017, 134, 45295 CrossRef.
- H. Zhang, L. Wang, Q. Chen, P. Li, A. Zhou, X. Cao and Q. Hu, Mater. Des., 2016, 92, 682–689 CrossRef CAS.
- M. Khazaei, A. Mishra, N. S. Venkataramanan, A. K. Singh and S. Yunoki, Curr. Opin. Solid State Mater. Sci., 2019, 23, 164–178 CrossRef CAS.
- X. Jiang, A. V. Kuklin, A. Baev, Y. Ge, H. Ågren, H. Zhang and P. N. Prasad, Phys. Rep., 2020, 848, 1–58 CrossRef CAS.
- M. Mariano, O. Mashtalir, F. Q. Antonio, W.-H. Ryu, B. Deng, F. Xia, Y. Gogotsi and A. D. Taylor, Nanoscale, 2016, 8, 16371–16378 RSC.
- J. Halim, M. R. Lukatskaya, K. M. Cook, J. Lu, C. R. Smith, L.-Å. Näslund, S. J. May, L. Hultman, Y. Gogotsi, P. Eklund and M. W. Barsoum, Chem. Mater., 2014, 26, 2374–2381 CrossRef CAS PubMed.
- H. Lashgari, M. Abolhassani, A. Boochani, S. Elahi and J. Khodadadi, Solid State Commun., 2014, 195, 61–69 CrossRef CAS.
- G. R. Berdiyorov, AIP Adv., 2016, 6, 055105 CrossRef.
- K. Hantanasirisakul, M. Q. Zhao, P. Urbankowski, J. Halim, B. Anasori, S. Kota, C. E. Ren, M. W. Barsoum and Y. Gogotsi, Adv. Electron. Mater., 2016, 2, 1600050 CrossRef.
- J. Luo, X. Tao, J. Zhang, Y. Xia, H. Huang, L. Zhang, Y. Gan, C. Liang and W. Zhang, ACS Nano, 2016, 10, 2491–2499 CrossRef CAS PubMed.
- J. Ran, G. Gao, F.-T. Li, T.-Y. Ma, A. Du and S.-Z. Qiao, Nat. Commun., 2017, 8, 13907 CrossRef CAS PubMed.
- B. Anasori, Y. Xie, M. Beidaghi, J. Lu, B. C. Hosler, L. Hultman, P. R. Kent, Y. Gogotsi and M. W. Barsoum, ACS Nano, 2015, 9, 9507–9516 CrossRef CAS PubMed.
- K. Hantanasirisakul and Y. Gogotsi, Adv. Mater., 2018, 30, 1804779 CrossRef PubMed.
- Y. Chae, S. J. Kim, S.-Y. Cho, J. Choi, K. Maleski, B.-J. Lee, H.-T. Jung, Y. Gogotsi, Y. Lee and C. W. Ahn, Nanoscale, 2019, 11, 8387–8393 RSC.
- T. Habib, X. Zhao, S. A. Shah, Y. Chen, W. Sun, H. An, J. L. Lutkenhaus, M. Radovic and M. J. Green, NPJ 2D Mater. Appl., 2019, 3, 1–6 CrossRef.
- Y. T. Liu, P. Zhang, N. Sun, B. Anasori, Q. Z. Zhu, H. Liu, Y. Gogotsi and B. Xu, Adv. Mater., 2018, 30, 1707334 CrossRef PubMed.
- X. Zhao, A. Vashisth, E. Prehn, W. Sun, S. A. Shah, T. Habib, Y. Chen, Z. Tan, J. L. Lutkenhaus and M. Radovic, Matter, 2019, 1, 513–526 CrossRef.
- J. Liu, H. B. Zhang, R. Sun, Y. Liu, Z. Liu, A. Zhou and Z. Z. Yu, Adv. Mater., 2017, 29, 1702367 CrossRef PubMed.
- D. Chen, Y. Zou and S. Wang, Mater. Today Energy, 2019, 12, 250–268 CrossRef.
- J. Ji, L. Zhao, Y. Shen, S. Liu and Y. Zhang, FlatChem, 2019, 17, 100128 CrossRef CAS.
- D. Yoo, Y. Kim, M. Min, G. H. Ahn, D.-H. Lien, J. Jang, H. Jeong, Y. Song, S. Chung and A. Javey, ACS Nano, 2018, 12, 11062–11069 CrossRef CAS PubMed.
- Y. Lee, S. Bae, B. Hwang, M. Schroeder, Y. Lee and S. Baik, J. Mater. Chem. C, 2019, 7, 12297–12305 RSC.
- W. Y. Chen, S.-N. Lai, C.-C. Yen, X. Jiang, D. Peroulis and L. A. Stanciu, ACS Nano, 2020, 14, 11490–11501 CrossRef CAS PubMed.
- X. Wang, H. Li, H. Li, S. Lin, W. Ding, X. Zhu, Z. Sheng, H. Wang, X. Zhu and Y. Sun, Adv. Funct. Mater., 2020, 30, 0190302 CrossRef CAS.
- H. Zhang, M. Li, J. Cao, Q. Tang, P. Kang, C. Zhu and M. Ma, Ceram. Int., 2018, 44, 19958–19962 CrossRef CAS.
- P. Kuang, M. He, B. Zhu, J. Yu, K. Fan and M. Jaroniec, J. Catal., 2019, 375, 8–20 CrossRef CAS.
- J. Qin, X. Hu, X. Li, Z. Yin, B. Liu and K.-H. Lam, Nano Energy, 2019, 61, 27–35 CrossRef CAS.
- C. Xing, S. Chen, M. Qiu, X. Liang, Q. Liu, Q. Zou, Z. Li, Z. Xie, D. Wang and B. Dong, Adv. Healthcare Mater., 2018, 7, 1870030 CrossRef.
- C. Dai, Y. Chen, X. Jing, L. Xiang, D. Yang, H. Lin, Z. Liu, X. Han and R. Wu, ACS Nano, 2017, 11, 12696–12712 CrossRef CAS PubMed.
- W. Tang, Z. Dong, R. Zhang, X. Yi, K. Yang, M. Jin, C. Yuan, Z. Xiao, Z. Liu and L. Cheng, ACS Nano, 2018, 13, 284–294 CrossRef PubMed.
- Y. Jiang, X. Zhang, L. Pei, S. Yue, L. Ma, L. Zhou, Z. Huang, Y. He and J. Gao, Chem. Eng. J., 2018, 339, 547–556 CrossRef CAS.
- F. Wang, C. Yang, C. Duan, D. Xiao, Y. Tang and J. Zhu, J. Electrochem. Soc., 2014, 162, B16 CrossRef.
- H. Liu, C. Duan, C. Yang, W. Shen, F. Wang and Z. Zhu, Sens. Actuators, B, 2015, 218, 60–66 CrossRef CAS.
- R. Rakhi, P. Nayak, C. Xia and H. N. Alshareef, Sci. Rep., 2016, 6, 1–10 CrossRef PubMed.
- K. S. Naunheim, P. J. Petruska, T. S. Roy, C. H. Andrus, F. E. Johnson, J. M. Schlueter and A. E. Baue, J. Thorac. Cardiovasc. Surg., 1992, 103, 887–895 CrossRef CAS PubMed.
- M. S. Piver, J. J. Barlow, F. T. Lee and V. Vongtama, Am. J. Obstet. Gynecol., 1975, 122, 355–357 CrossRef CAS PubMed.
- J. T. Robinson, S. M. Tabakman, Y. Liang, H. Wang, H. Sanchez Casalongue, D. Vinh and H. Dai, J. Am. Chem. Soc., 2011, 133, 6825–6831 CrossRef CAS PubMed.
- A. Bashkatov, E. Genina, V. Kochubey and V. Tuchin, J. Phys. D: Appl. Phys., 2005, 38, 2543 CrossRef CAS.
- D. J. Slamon, B. Leyland-Jones, S. Shak, H. Fuchs, V. Paton, A. Bajamonde, T. Fleming, W. Eiermann, J. Wolter and M. Pegram, N. Engl. J. Med., 2001, 344, 783–792 CrossRef CAS PubMed.
- T. Ide, S. Hirabayashi, S. Kano and M. Sugano, Biochim. Biophys. Acta, Lipids Lipid Metab., 1992, 1124, 163–170 CrossRef CAS.
- Y.-Z. Zhang, K. H. Lee, D. H. Anjum, R. Sougrat, Q. Jiang, H. Kim and H. N. Alshareef, Sci. Adv., 2018, 4, eaat0098 CrossRef PubMed.
- X. Shi, H. Wang, X. Xie, Q. Xue, J. Zhang, S. Kang, C. Wang, J. Liang and Y. Chen, ACS Nano, 2018, 13, 649–659 CrossRef PubMed.
- Y. Cai, J. Shen, G. Ge, Y. Zhang, W. Jin, W. Huang, J. Shao, J. Yang and X. Dong, ACS Nano, 2018, 12, 56–62 CrossRef CAS PubMed.
- L. Lorencova, V. Gajdosova, S. Hroncekova, T. Bertok, J. Blahutova, A. Vikartovska, L. Parrakova, P. Gemeiner, P. Kasak and J. Tkac, Electroanalysis, 2019, 31, 1833–1844 CrossRef CAS.
- X. Chen, J. Li, G. Pan, W. Xu, J. Zhu, D. Zhou, D. Li, C. Chen, G. Lu and H. Song, Sens. Actuators, B, 2019, 289, 131–137 CrossRef CAS.
- J. Liu, X. Jiang, R. Zhang, Y. Zhang, L. Wu, W. Lu, J. Li, Y. Li and H. Zhang, Adv. Funct. Mater., 2019, 29, 1807326 CrossRef.
- W. Yuan, K. Yang, H. Peng, F. Li and F. Yin, J. Mater. Chem. A, 2018, 6, 18116–18124 RSC.
- F. Wang, C. Yang, M. Duan, Y. Tang and J. Zhu, Biosens. Bioelectron., 2015, 74, 1022–1028 CrossRef CAS PubMed.
- B. Shao, J. Wang, Z. Liu, G. Zeng, L. Tang, Q. Liang, Q. He, T. Wu, Y. Liu and X. Yuan, J. Mater. Chem. A, 2020, 8, 5171–5185 RSC.
- H. Wang, Y. Wu, T. Xiao, X. Yuan, G. Zeng, W. Tu, S. Wu, H. Y. Lee, Y. Z. Tan and J. W. Chew, Appl. Catal., B, 2018, 233, 213–225 CrossRef CAS.
- V. Ramalingam, P. Varadhan, H. C. Fu, H. Kim, D. Zhang, S. Chen, L. Song, D. Ma, Y. Wang and H. N. Alshareef, Adv. Mater., 2019, 31, 1903841 CrossRef CAS PubMed.
- Y. Zheng, Y. Jiao, Y. Zhu, L. H. Li, Y. Han, Y. Chen, M. Jaroniec and S.-Z. Qiao, J. Am. Chem. Soc., 2016, 138, 16174–16181 CrossRef CAS PubMed.
- J. Kibsgaard, T. F. Jaramillo and F. Besenbacher, Nat. Chem., 2014, 6, 248 CrossRef CAS PubMed.
- W. Yuan, L. Cheng, Y. An, H. Wu, N. Yao, X. Fan and X. Guo, ACS Sustainable Chem. Eng., 2018, 6, 8976–8982 CrossRef CAS.
- Q. Zhu, Y. Cui, Y. Zhang, Z. Cao, Y. Shi, J. Gu, Z. Du, B. Li and S. Yang, Mater. Today Nano, 2021, 13, 100104 CrossRef.
- J. Zhang, L. Yang, H. Wang, G. Zhu, H. Wen, H. Feng, X. Sun, X. Guan, J. Wen and Y. Yao, Inorg. Chem., 2019, 58, 5414–5418 CrossRef CAS PubMed.
- J. Low, L. Zhang, T. Tong, B. Shen and J. Yu, J. Catal., 2018, 361, 255–266 CrossRef CAS.
- Y. Gao, L. Wang, A. Zhou, Z. Li, J. Chen, H. Bala, Q. Hu and X. Cao, Mater. Lett., 2015, 150, 62–64 CrossRef CAS.
- T. Su, R. Peng, Z. D. Hood, M. Naguib, I. N. Ivanov, J. K. Keum, Z. Qin, Z. Guo and Z. Wu, ChemSusChem, 2018, 11, 688–699 CrossRef CAS PubMed.
- H. Wang, R. Zhao, J. Qin, H. Hu, X. Fan, X. Cao and D. Wang, ACS Appl. Mater. Interfaces, 2019, 11, 44249–44262 CrossRef CAS PubMed.
- M. Yu, S. Zhou, Z. Wang, J. Zhao and J. Qiu, Nano Energy, 2018, 44, 181–190 CrossRef CAS.
- C. F. Du, X. Sun, H. Yu, Q. Liang, K. N. Dinh, Y. Zheng, Y. Luo, Z. Wang and Q. Yan, Adv. Sci., 2019, 6, 1900116 CrossRef PubMed.
- B.-Z. Zhan, M. A. White, T.-K. Sham, J. A. Pincock, R. J. Doucet, K. R. Rao, K. N. Robertson and T. S. Cameron, J. Am. Chem. Soc., 2003, 125, 2195–2199 CrossRef CAS PubMed.
- S. Cheng, H. Liu and B. E. Logan, Environ. Sci. Technol., 2006, 40, 364–369 CrossRef CAS PubMed.
- Y. Tang, C. Yang, Y. Tian, Y. Luo, X. Yin and W. Que, Nanoscale Adv., 2020, 2, 1187–1194 RSC.
- D. A. Kuznetsov, Z. Chen, P. V. Kumar, A. Tsoukalou, A. Kierzkowska, P. M. Abdala, O. V. Safonova, A. Fedorov and C. R. Müller, J. Am. Chem. Soc., 2019, 141, 17809–17816 CrossRef CAS PubMed.
- J. Zhang, Y. Zhao, X. Guo, C. Chen, C.-L. Dong, R.-S. Liu, C.-P. Han, Y. Li, Y. Gogotsi and G. Wang, Nat. Catal., 2018, 1, 985–992 CrossRef CAS.
- M. Naguib, J. Come, B. Dyatkin, V. Presser, P.-L. Taberna, P. Simon, M. W. Barsoum and Y. Gogotsi, Electrochem. Commun., 2012, 16, 61–64 CrossRef CAS.
- Y.-Y. Peng, B. Akuzum, N. Kurra, M.-Q. Zhao, M. Alhabeb, B. Anasori, E. C. Kumbur, H. N. Alshareef, M.-D. Ger and Y. Gogotsi, Energy Environ. Sci., 2016, 9, 2847–2854 RSC.
- Y. Song, Z. Sun, Z. Fan, W. Cai, Y. Shao, G. Sheng, M. Wang, L. Song, Z. Liu and Q. Zhang, Nano Energy, 2020, 70, 104555 CrossRef CAS.
- H. Yu, Y. Wang, Y. Jing, J. Ma, C.-F. Du and Q. Yan, Small, 2019, 15, 1901503 CrossRef PubMed.
- M. Ghidiu, J. Halim, S. Kota, D. Bish, Y. Gogotsi and M. W. Barsoum, Chem. Mater., 2016, 28, 3507–3514 CrossRef CAS.
- M. Ghidiu, M. R. Lukatskaya, M.-Q. Zhao, Y. Gogotsi and M. W. Barsoum, Nature, 2014, 516, 78–81 CrossRef CAS PubMed.
- X. Tang, X. Guo, W. Wu and G. Wang, Adv. Energy Mater., 2018, 8, 1801897 CrossRef.
- C. Eames and M. S. Islam, J. Am. Chem. Soc., 2014, 136, 16270–16276 CrossRef CAS PubMed.
- V. Etacheri, R. Marom, R. Elazari, G. Salitra and D. Aurbach, Energy Environ. Sci., 2011, 4, 3243–3262 RSC.
- J. Huang, R. Meng, L. Zu, Z. Wang, N. Feng, Z. Yang, Y. Yu and J. Yang, Nano Energy, 2018, 46, 20–28 CrossRef CAS.
- B. Ahmed, D. H. Anjum, M. N. Hedhili, Y. Gogotsi and H. N. Alshareef, Nanoscale, 2016, 8, 7580–7587 RSC.
- W. Lv, J. Zhu, F. Wang and Y. Fang, J. Mater. Sci.: Mater. Electron., 2018, 29, 4881–4887 CrossRef CAS.
- C. Yang, Y. Liu, X. Sun, Y. Zhang, L. Hou, Q. Zhang and C. Yuan, Electrochim. Acta, 2018, 271, 165–172 CrossRef CAS.
- C. Wang, S. Chen, H. Xie, S. Wei, C. Wu and L. Song, Adv. Energy Mater., 2019, 9, 1802977 CrossRef.
- X. Guo, W. Zhang, J. Zhang, D. Zhou, X. Tang, X. Xu, B. Li, H. Liu and G. Wang, ACS Nano, 2020, 14, 3651–3659 CrossRef CAS PubMed.
- V. Natu, R. Pai, M. Sokol, M. Carey, V. Kalra and M. W. Barsoum, Chem, 2020, 6, 616–630 CAS.
- A. Uihlein and D. Magagna, Renewable Sustainable Energy Rev., 2016, 58, 1070–1081 CrossRef.
- C. S. Ponseca Jr, P. Chabera, J. Uhlig, P. Persson and V. Sundstrom, Chem. Rev., 2017, 117, 10940–11024 CrossRef PubMed.
- X. Liu, X. Jin, L. Li, J. Wang, Y. Yang, Y. Cao and W. Wang, J. Mater. Chem. A, 2020, 8, 12526–12537 RSC.
- Y. Yang, R. Zhao, T. Zhang, K. Zhao, P. Xiao, Y. Ma, P. M. Ajayan, G. Shi and Y. Chen, ACS Nano, 2018, 12, 829–835 CrossRef CAS PubMed.
- Z. Zha, X. Yue, Q. Ren and Z. Dai, Adv. Mater., 2013, 25, 777–782 CrossRef CAS PubMed.
- D. Yang, B. Zhou, G. Han, Y. Feng, J. Ma, J. Han, C. Liu and C. Shen, ACS Appl. Mater. Interfaces, 2021, 13, 8909–8918 CrossRef CAS PubMed.
- X. Du, J. Qiu, S. Deng, Z. Du, X. Cheng and H. Wang, ACS Sustainable Chem. Eng., 2020, 8, 5799–5806 CrossRef CAS.
- X. Fan, Y. Ding, Y. Liu, J. Liang and Y. Chen, ACS Nano, 2019, 13, 8124–8134 CrossRef CAS PubMed.
- Y. A. Al-Hamadani, B.-M. Jun, M. Yoon, N. Taheri-Qazvini, S. A. Snyder, M. Jang, J. Heo and Y. Yoon, Chemosphere, 2020, 126821 CrossRef CAS PubMed.
- X. Li, Y. Liu, J. Wang, J. Gascon, J. Li and B. Van der Bruggen, Chem. Soc. Rev., 2017, 46, 7124–7144 RSC.
- A. Sinha, H. Zhao, Y. Huang, X. Lu, J. Chen and R. Jain, TrAC, Trends Anal. Chem., 2018, 105, 424–435 CrossRef CAS.
- A. Arabi Shamsabadi, M. Sharifian Gh, B. Anasori and M. Soroush, ACS Sustainable Chem. Eng., 2018, 6, 16586–16596 CrossRef CAS.
- H. B. Park, J. Kamcev, L. M. Robeson, M. Elimelech and B. D. Freeman, Science, 2017, 356, 1138–1148 CrossRef PubMed.
- K. Guan, F. Liang, H. Zhu, J. Zhao and W. Jin, ACS Appl. Mater. Interfaces, 2018, 10, 13903–13913 CrossRef CAS PubMed.
- L. Ding, Y. Wei, Y. Wang, H. Chen, J. Caro and H. Wang, Angew. Chem., Int. Ed., 2017, 56, 1825–1829 CrossRef CAS PubMed.
- M. Naguib, M. Kurtoglu, V. Presser, J. Lu, J. Niu, M. Heon, L. Hultman, Y. Gogotsi and M. W. Barsoum, Adv. Mater., 2011, 23, 4248–4253 CrossRef CAS PubMed.
- G. Liu, S. Liu, K. Ma, H. Wang, X. Wang, G. Liu and W. Jin, Ind. Eng. Chem. Res., 2020, 59, 4732–4741 CrossRef CAS.
- J. G. Wijmans and R. W. Baker, J. Membr. Sci., 1995, 107, 1–21 CrossRef CAS.
- C. S. Lee, M. k. Choi, Y. Y. Hwang, H. Kim, M. K. Kim and Y. J. Lee, Adv. Mater., 2018, 30, 1705944 CrossRef PubMed.
- L. Hao, H. Zhang, X. Wu, J. Zhang, J. Wang and Y. Li, Composites, Part A, 2017, 100, 139–149 CrossRef CAS.
- J. Fei, S. W. Koh, W. Tu, J. Ge, H. Rezaeyan, S. Hou, H. Duan, Y. C. Lam and H. Li, Adv. Sustainable Syst., 2020, 4, 2000102 CrossRef CAS.
- L. Ding, L. Li, Y. Liu, Y. Wu, Z. Lu, J. Deng, Y. Wei, J. Caro and H. Wang, Nat. Sustainable, 2020, 3, 296–302 CrossRef.
- I. Ihsanullah, Nano-Micro Lett., 2020, 12, 1–20 CrossRef PubMed.
- C. E. Ren, K. B. Hatzell, M. Alhabeb, Z. Ling, K. A. Mahmoud and Y. Gogotsi, J. Phys. Chem. Lett., 2015, 6, 4026–4031 CrossRef CAS PubMed.
- M. Rezakazemi, A. A. Shamsabadi, H. Lin, P. Luis, S. Ramakrishna and T. M. Aminabhavi, Renewable Sustainable Energy Rev., 2021, 143, 110878 CrossRef CAS.
- R. Li, L. Zhang, L. Shi and P. Wang, ACS Nano, 2017, 11, 3752–3759 CrossRef CAS PubMed.
- K. Vikrant, B. S. Giri, N. Raza, K. Roy, K.-H. Kim, B. N. Rai and R. S. Singh, Bioresour. Technol., 2018, 253, 355–367 CrossRef CAS PubMed.
- B.-M. Jun, N. Her, C. M. Park and Y. Yoon, Environ. Sci.: Water Res. Technol., 2020, 6, 173–180 RSC.
- Y. Du, B. Yu, L. Wei, Y. Wang, X. Zhang and S. Ye, J. Mater. Sci., 2019, 54, 13283–13297 CrossRef CAS.
- R. P. Pandey, K. Rasool, V. E. Madhavan, B. Aïssa, Y. Gogotsi and K. A. Mahmoud, J. Mater. Chem. A, 2018, 6, 3522–3533 RSC.
- J. Shen, G. Liu, Y. Ji, Q. Liu, L. Cheng, K. Guan, M. Zhang, G. Liu, J. Xiong and J. Yang, Adv. Funct. Mater., 2018, 28, 1801511 CrossRef.
- C. Ma and J. J. Urban, Proc. Natl. Res. Soc., 2018, 2, 2002 CrossRef.
- M. Mozafari, R. Abedini and A. Rahimpour, J. Mater. Chem. A, 2018, 6, 12380–12392 RSC.
- M. Mozafari, A. Rahimpour and R. Abedini, J. Ind. Eng. Chem., 2020, 85, 102–110 CrossRef CAS.
- S. Yuan, X. Li, J. Zhu, G. Zhang, P. Van Puyvelde and B. Van der Bruggen, Chem. Soc. Rev., 2019, 48, 2665–2681 RSC.
- C. Y. Chuah, J. Lee, Y. Bao, J. Song and T.-H. Bae, J. Membr. Sci., 2021, 622, 119031 CrossRef CAS.
- N. Nidamanuri, Y. Li, Q. Li and M. Dong, Eng. Sci., 2020, 9, 3–16 CAS.
- J. Zhu, J. Hou, A. Uliana, Y. Zhang, M. Tian and B. Van der Bruggen, J. Mater. Chem. A, 2018, 6, 3773–3792 RSC.
- L. Ding, Y. Wei, L. Li, T. Zhang, H. Wang, J. Xue, L.-X. Ding, S. Wang, J. Caro and Y. Gogotsi, Nat. Commun., 2018, 9, 1–7 CrossRef PubMed.
|
This journal is © The Royal Society of Chemistry 2021 |