DOI:
10.1039/D0MA00887G
(Review Article)
Mater. Adv., 2021,
2, 6519-6531
Effect of different parameters on caustic magnesia hydration and magnesium hydroxide rheology: a review
Received
15th November 2020
, Accepted 18th February 2021
First published on 17th August 2021
Abstract
Magnesium oxide and magnesium hydroxide are two compounds that show favorable properties, leading to their use in many industrial applications. This review discusses the methods of synthesizing magnesium oxide and magnesium hydroxide from dolomite, magnesite, brines and sea water using the conventional methods of precipitation and hydration. Nanoparticle preparation is via precipitation using sonochemical, sol–gel and electrochemical methods or via hydration using solvothermal and hydrothermal methods. Moreover, the application of both magnesium oxide and magnesium hydroxide is discussed in this review. This review article also provides extensive information on the hydration process of magnesium oxide and the effect of different parameters including the pH, temperature, surface area, particle size, hydrating agents, etc., which affect the rheological behavior of Mg(OH)2. This review is a source of scientific as well as practical information on the applications of Mg(OH)2 and MgO at the present time and on the methods of obtaining them, in the light of available and applied research techniques and discoveries made so far in the field of advanced powder technology.
Introduction
Magnesium hydroxide and magnesium oxide are commercial compounds that are readily available. Both Mg(OH)2 and MgO belong to a group of compounds with a unique nature, in view of their large number of favorable properties and possible practical applications. There are many ways to extract these powders traditionally. Due to their excellent properties for many industrial applications, they are commonly used as additives in the paper industry, as reinforcement powders in polymeric matrix composites1 used in flame retardants as well as in the purification of water pollutants.2
Magnesium oxide (MgO, or magnesia) can be described as white powdered material with a molar mass of 40.31 g mol−1 and a density of 3.58 g ml−1. Magnesia has a cubic crystal structure and melts at a high temperature of 2827 ± 30 °C. Magnesium hydroxide (Mg(OH)2) is also a white solid with a molar mass of 58.30 g mol−1 and a density of 2.40 g ml−1.3
Recently, micrometric and nanometric magnesium oxide and magnesium hydroxide have become key in high-rate technology development.2 Ultra-superfine magnesium hydroxide powder is used as a non-toxic flame-retardant filler in plastic matrix composites, rubber, and other halogen-free polymeric materials.3 Improvement of the mechanical properties of the material, such as a high thermal stability,4 high fire retardancy and very low toxicity, have been observed.5 The studies performed by Dong et al.6 have shown that nano-sized magnesium hydroxide can act as an antibacterial agent.7 The rate of hydration of magnesium oxide affects the size of the magnesium hydroxide aggregates. As the rate of hydration increases, the surface area of the hydroxide that is formed also increases.2
The basic point of reference for this literature review is research concerning the specific functions of Mg(OH)2 and MgO and the possibility of their application, as well as methods of obtaining those compounds. The aim of the research is to create possibilities for optimum and wide-ranging use of Mg(OH)2 and MgO in technological and biotechnological applications, particularly in environmental protection, construction, electrochemistry, pharmaceuticals, medicine, chemistry (organic, inorganic and hybrid materials) and biochemistry (Fig. 1).
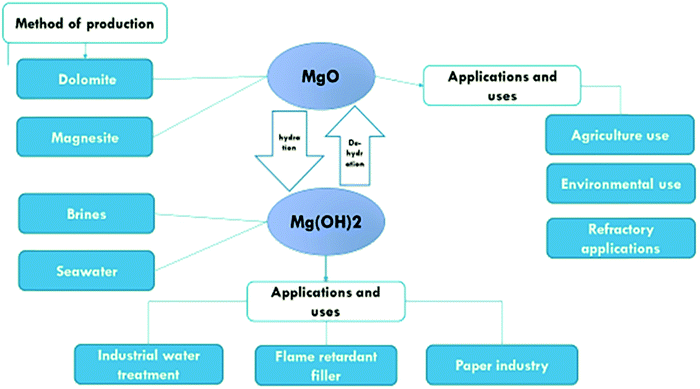 |
| Fig. 1 Schematic diagram of the synthesis and use of MgO and Mg(OH)2. | |
Magnesium oxide (MgO)
Magnesium oxide is an inorganic compound that occurs in nature in form of the mineral periclase. It can also be obtained through the heating of various forms of magnesium carbonate. The reactivity of magnesium oxide depends on the temperature and the duration of heat treatment of the magnesium compounds during its production. The reactivity of magnesium oxide determines the rate and extent of rehydration of the magnesium oxide sample when exposed to water. The methods used to produce magnesium hydroxide can also be used to produce magnesium oxide, following calcination.2,3
Methods for synthesizing magnesium oxide
Minerals for the production of magnesium oxide are mainly magnesium carbonate (also known as magnesite), and dolomite (CaMg(CO3)2), hydro-magnesite (Mg(CO3)·4H2O), brucite (Mg(OH)2), and serpentine (MgSiO10(OH)8). Sea water, and underground salt deposits of brines are also sources for magnesia production.
The calcination process8 is the process in which magnesite (magnesium carbonate) decomposes at a temperature ranging from 650 °C to 700 °C to form magnesium oxide and carbon dioxide:
MgCO3 (s) + heat → MgO (s) + CO2 (g). |
There are several grades of magnesium oxide MgO formed by applying heat, and different temperatures and times can result in the formation of different grades of magnesium oxide. Table 1 describes the grades of magnesium oxide (MgO), the reactivity of each type, the temperature ranges used, and their uses. These grades are light-burned also known as caustic calcined magnesia or medium reactive magnesia, hard-burned magnesia, and dead-burned magnesia.3
Table 1 Grades of magnesium oxide2
|
Light-burned magnesium oxide |
Hard-burned magnesium oxide |
Dead-burned magnesium oxide |
Temperature range |
700–1000 °C |
1000–1500 °C |
1500–2000 °C |
Reactivity |
High reactivity |
Narrow range of reactivity |
Reactivity has been eliminated |
Uses |
Plastics, rubber, paper and pulp processing, and adhesives |
Animal feeds and fertilizers |
Steel production and linings for equipment |
Applications of magnesium oxide
Light-burned magnesium oxide.
Light-burned magnesia is used in abrasives as a binder in grinding wheels, as a boiler additive to reduce the corrosion of steel pipes as well as for the purpose of preventing steam and sulfur emissions to get into the environment. It is also used in lubricating oils as an additive to neutralize acids, as a plastics filler, an acid acceptor, a thickener catalyst and in pigment enlargement, and in rubber compounding.9
Hard-burned magnesium oxide.
Hard-burned magnesium oxide is used in animal feed supplements as a source of magnesium ions for chickens, cattle, and other animals. It is also used in the chemical production of other magnesium salts, such as sulfate and nitrate, in fertilizers as a source of plant nutrition as well as in pharmaceutical uses of magnesium hydroxide, oxide and carbonate in antacids, cosmetics, toothpaste, and in constipation remedies.10
Dead-burned magnesium oxide.
Dead-burned magnesium oxide has a very high resistance to thermal shock so it can be used as a refractory material and in ceramics as it is the basic ingredient in product formulations for the steel industry. It is also used in the steel industry annealing process as a coating for grain-oriented silicon steel used in electrical transformers, in oil and gas drilling, and in specialist glass manufacture.11
Magnesium hydroxide Mg(OH)2
Magnesium hydroxide is also known as the mineral brucite. It is usually found as a low-temperature, hydrothermal vein mineral associated with calcite, aragonite, talc, or magnesite. It appears as a decomposition product of magnesium silicates associated with serpentine, dolomite, magnesite, and chromite. Brucite also occurs as a hydrated form of periclase and is found in serpentine, marble, and chlorite. Magnesium hydroxide can be prepared using either physical or chemical methods. Examples of chemical methods are direct precipitation method, hydrothermal method and hydration method.3,11–13
The magnesium hydroxide suspension must have a high solid loading and be reasonably stable with adequate fluidity to prevent the aggregation and sedimentation of particles over a broad range of solid loadings.14 To produce a pumpable slurry, the addition of a dispersant is typically required to lower the slurry viscosity. Unless the suspension is stable, the solid will have the tendency to settle to the bottom of the storage vessel, although the settled solids can be easily resuspended and do not form a hard cake at the bottom of the container. Magnesium hydroxide has many characteristics, such as its low water solubility. Its alkaline character is released slowly when heated, and it can absorb heat and decompose,15 and produce water. This is accompanied by good adsorption properties and high reaction activity. Hence, it is used in wastewater treatment instead of caustic soda and lime, in flue gas desulfurization, in flame resistant materials, and in other fields.10 There are many methods of extracting magnesium hydroxide, and other methods used to prepare it in the laboratory are described in detail in the next section.
Traditional methods of synthesizing magnesium hydroxide
Several traditional methods are used to synthesize magnesium hydroxide, such as the precipitation method from sea water or brines, and the hydration method “dissolution–precipitation process”16 as well as modern techniques.17
Precipitation methods of magnesium hydroxide
There have been many studies on the precipitation of magnesium hydroxide from brines or sea water with an alkali. The precipitation of magnesium hydroxide from brines or sea water occurs according to the following stages:2
1. Magnesium ion precipitates by mixing brine with an alkaline medium such as calcium hydroxide or sodium hydroxide.
2. In order to precipitate further amounts of magnesium oxide, mixing fresh brine or sea water in a single stage is recommended, where each amount is separately added to the alkaline suspension.
3. The precipitated magnesium hydroxide is then washed using an alkaline solution, e.g., with sodium hydroxide or calcium hydroxide several times, then filtered.
The reactions for production of magnesium hydroxide can be written as follows:18
• Calcination process:
| CaMg(CO3)2 → CaO·MgO + 2CO2 (g) | (1) |
• Slaking process:
| CaO·MgO + 2H2O (l) → Ca(OH)2 + Mg(OH)2 | (2) |
• Precipitation of magnesium hydroxide (Mg(OH)2):
| Ca(OH)2 + Mg(OH)2 + MgCl2 → 2Mg(OH)2 + CaC12 | (3) |
The most common chemical precipitation technique describes the use of ancestors of magnesium inorganic salts like MgCl2, MgSO4 and Mg(NO3)2, while organic compounds of magnesium, such as Mg(CH3CO2)2,19,20 are used occasionally. In the precipitation method, the reaction takes place in which the synthesis of magnesium hydroxide Mg(OH)2 from a magnesium salt and NH4OH with direct functionalization with polyethylene glycol is precipitated from solutions of salts using a precipitating agent, such as a strong base like ammonia.21
For this reason, many research groups are studying experiments focused on determining the reaction conditions that will have the most favorable effect on the course of the reaction, and consequently on the specific properties of the product,2
Hydration of magnesium oxide to Mg(OH)2
The hydration process is the most desirable method for preparing magnesium hydroxide because this product can be easily handled, transported, stored and pumped. The suspensions of magnesium hydroxide should be at a high solid loading level to minimize transportation and storage costs. However, there is a disadvantage with this process that sedimentation and hard-cake formation at the bottom of the container may occur due to the absence of agitation; this occurs when the magnesium hydroxide solid content in the suspension exceeds 45 wt%, such that the viscosity becomes very high.2
Magnesium hydroxide is usually synthesized by the hydration of magnesium oxide in water and the following reaction mechanism has been proposed by Feitknecht and Braun:22
• A liquid layer is formed on the surface of the solid as a result of adsorbed water vapor.
• Then water reacts with magnesia forming magnesium hydroxide on the surface layer.
• This leads to magnesium hydroxide dissolving in the water layer.
• When water solution becomes saturated with magnesium hydroxide particles, precipitation occurs.
The reaction of magnesium oxide in water occurs according to the reaction in eqn (4)
| MgO (s) + H2O (l) → Mg(OH)2(s) | (4) |
The effect of different parameters on the hydration of magnesium oxide (MgO) plays an important role in modifying the hydration process. The main factors are temperature, pH, hydrating agents and other factors.
Two-phase reaction systems such as gas–solid, liquid–solid or liquid–liquid hydration reaction systems are most studied for the preparation of magnesia. Recently, other studies have reported the advantages of a three-phase, namely, gas–liquid–solid, hydration reaction system.13 This study showed that a three-phase reaction is better than a two-phase reaction. The two-phase reaction is considered to proceed via a common dissolution–precipitation mechanism, while the three-phase reaction system differs in that the initial stage is like the dissolution–precipitation process, where magnesium hydroxide is formed and covers the surfaces and pores of magnesium oxide (MgO) particles. The steam applied in a three-phase reaction causes cracking and peeling off of the Mg(OH)2 layer from the magnesia particles. Finally, the fresh magnesium oxide (MgO) surface that is left behind by peeling-off the Mg(OH)2 is attacked by water again. It can be concluded that the peeling-off process exclusively causes a higher hydration rate and efficiency.13,23
Also, a multi-rate model has been proposed to describe the mechanism of magnesium oxide hydration.24
Synthesizing nanoparticles of magnesium hydroxide
The same traditional methods, such as precipitation and hydration, are used to produce nanoparticles of magnesium hydroxide, but these methods are carried out different media and under different conditions. For precipitation, there are many methods used to produce nanoparticles of magnesium hydroxide, such as sonochemical, sol–gel, and electrochemical methods. For hydration, there are solvothermal and hydrothermal methods, which are discussed briefly in the next section.
Precipitation of magnesium hydroxide
Sonochemical method.
This method produces very finely powdered magnesium hydroxide, and takes place under extreme conditions to synthesize the very small particle diameters and a more homogeneous structure. Many studies and research centers have shown that sonochemical methods may be used to synthesize nanoparticles of magnesium hydroxide successfully.2 The sol–gel method is a hydrolysis process that is based on the alkoxides reactive metal precursors, and has been used for the preparation of metal oxides of nanometre size.25 This method results in the production of the desired metal hydroxide and an alcohol. The condensation of molecules accompanied by the removal of water molecules, leading to the formation of a structural network in the form of a dense, porous gel.
Electrochemical method.
This method is used to produce nanoparticles of hydroxides, but it is a rarely used technique, due to relatively high costs of production and the low quality of the final products, which may occur with the production of agglomerates and impurities.26 There are not many studies and literature reports about this method, but it remains the focus of attention for many researchers.
Hydration of magnesium hydroxide
Hydrothermal method.
This is a process that uses chemical reactions, taking place in aqueous solutions under pressure and at a temperature above boiling point, to crystallize materials. Key advantages of the hydrothermal method include the low probability of forming agglomerates in the powder in addition to excellent control over the size and morphology of the crystallites. The products of the hydrothermal method usually improve homogeneity and solubility and enhance the kinetics of the chemical reactions and crystallization. The hydrothermal method enables the synthesis of magnesium hydroxide (Mg(OH)2) crystallites with very small sizes and surface areas.2,27
The solvothermal method is a process in which aqueous solutions are replaced by other solutions under critical conditions. The solvothermal method is often used because it reduces the impurities28 that appear in materials produced using the hydrothermal method. An analysis was made of how the properties of the hydroxide depended on the magnesium precursors, the solvents, and the process conditions. Using the hydrothermal process it is possible to control the morphology of magnesium hydroxide (Mg(OH)2) particles by controlling pH of the process, leading to the formation of many different shapes, such as nanoflowers, needles, platelets, and regular and irregular spherical particles.29
Application and uses of magnesium hydroxide
Applications of magnesium hydroxide include its capability as an antibacterial agent,30 as a neutralizer of acidic water pollutants, liquid wastes and gases, as a filler in the paper industry, as a neutralizing agent in pharmaceuticals, as a fertilizer additive, as a precursor for the production of magnesium oxide and as a new-generation flame retardant.2
Industrial wastewater treatment
Magnesium hydroxide is used in the treatment of industrial wastewater. The white solid suspension of magnesium hydroxide is added to raise the pH of acidic solutions in an environmentally acceptable manner. It is not a harmful alkali like caustic soda or lime neutralizing compounds.18 Magnesium hydroxide is safe and non-hazardous and does not cause chemical burns as do caustic soda or lime.31 Magnesium hydroxide can neutralize wastewater without exceeding the limit of acidity above pH of 9–10.2
Flame-retardant filler
Magnesium hydroxide can be used as a flame-retardant additive in polymer production.32 It is more environmentally friendly than flame retardants based on antimony metal or halogenated compounds because it contains neither halogens nor heavy metals.33–35 Magnesium hydroxide hydrated from magnesite can be used as a flame retardant, which is more cost effective than magnesium hydroxide hydrated from commercial magnesia, for which purification is needed before use.3
Magnesium hydroxide as a paper preservative
One of the most important uses of magnesium hydroxide is in the preservation of paper. Papers are subjected to many changes in their physical, chemical and mechanical properties as a result of their storage and use. Due to the morphological dispersion and homogeneity of magnesium hydroxide, it can be best used in paper preservatives.2,3
The effect of different parameters on the hydration of MgO
MgO hydration is dependent on many parameters. Fig. 2 shows an overview of these factors, which are discussed in detail in the next sections.
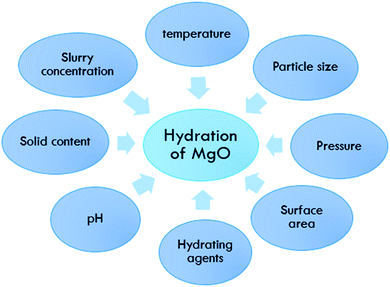 |
| Fig. 2 Schematic of the factors affecting the hydration of MgO. | |
Effect of temperature
Temperature is one of the main factors affecting the hydration of MgO, as it affects the degree of hydration of magnesia and the amount of magnesium hydroxide formed, thus influencing the homogeneity of the suspension.3,36 Kurama et al. discussed how the temperature affects the product weight. The author compared different samples of calcined and un-calcined magnesia at three different temperatures (40, 60, and 80 °C) finding that the higher weight measured for the calcined sample clearly indicated the importance of the calcination step before the hydration process, as shown in Fig. 3. Kurama et al.36 showed that TG curves can be used to discuss the mass loss % difference due to the change in temperature in calcined and uncalcined magnesia samples. There is a huge mass loss % in both samples, but when the temperature was increased to 600 °C the mass loss % of the calcined sample dropped to 78%, which was less than in the uncalcined sample which dropped to 83%.
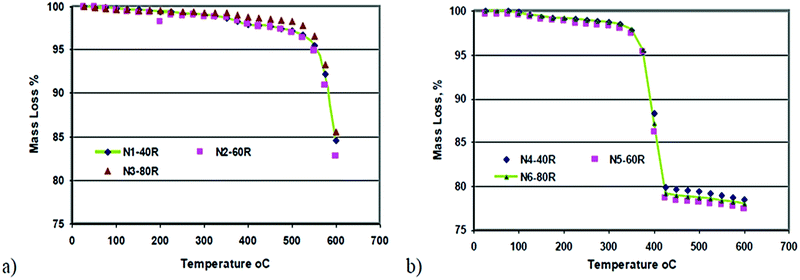 |
| Fig. 3 TG results of samples: (a) uncalcined and (b) calcined magnesia.36 | |
Effect of hydrating agent
According to the literature, the degree of hydration depends on the use of different hydrating agents.
Kgabo et al. studied the influence of each hydrating agent on the hydration of magnesium oxide and carried out a study concluding that there was no significant difference in the hydration behavior of the hydrating agents up to 50 °C, where less than 10% of magnesium hydroxide was formed. The amount of hydroxide increased at temperatures above 60 °C. When compared with hydration in water, all the hydrating agents, except for sodium acetate, showed a significant increase in the degree of hydration. Kgabo et al. used hydrating agents such as aqueous solutions of ammonium chloride, magnesium acetate, magnesium nitrate, nitric acid, acetic acid, magnesium chloride, sodium acetate and hydrochloric acid, with distilled water as the control. The results indicate that the degree of hydration is very sensitive to the hydration temperature. The optimum amount of magnesium hydroxide formed at higher temperatures is because of the high solubility of MgO at higher temperatures and thus the precipitation of magnesium hydroxide is high, as shown in Fig. 4.37
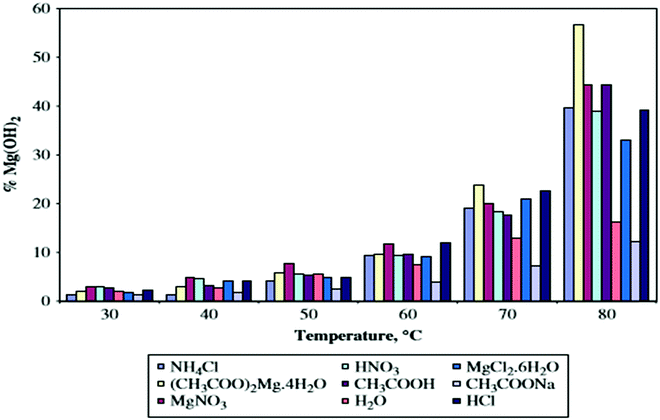 |
| Fig. 4 Degree of hydration as a function of temperature for the different hydrating agents.19 | |
As shown in Fig. 4, sodium acetate formed the lowest amount of magnesium hydroxide, ranging between 1.2 and 12.2% magnesium hydroxide, while the largest percentage is 56.7% of magnesium hydroxide formed from hydration in magnesium acetate at 80 °C. The increased degree of hydration in magnesium acetate can be attributed to the presence of acetate ions.37 This result has been verified in more recent studies as well.38 The three-phase reaction system showed a significantly higher degree of hydration than that of a two-phase reaction system. The hydration rate was determined by the rate of magnesia dissolution and the precipitation of magnesium hydroxide.
The comparison of the hydration degree under three-phase and two-phase reaction systems at a hydration time of 0.5 h was further discussed in the literature. A higher degree of hydration was obtained under a three-phase reaction system in the same solution when compared with a two-phase reaction system because of the pressure. Aphane studied the effect of varying the Mg(CH3COO)2 concentration between 0 and 0.2 M. Table 2 shows the results of the percentage mass loss and the percentage Mg(OH)2 formed from MgO hydrated in magnesium acetate solutions ranging from 0 and 0.2 M, using 15 g of MgO in 100 ml of solution. The percentage of magnesium hydroxide in the samples was determined via TG analysis and was calculated using the experimental mass loss obtained for the sample and the theoretical mass loss of magnesium hydroxide (30.9%).39
Table 2 Influence of magnesium acetate concentration (0–0.2 M) on the hydration of magnesia39
[MgAc]/(M) |
Mass loss % |
Mg(OH)2% |
Untreated |
0.50 |
1.6 |
0.005 |
9.60 |
31.1 |
0.01 |
10.03 |
32.4 |
0.05 |
10.40 |
33.7 |
0.1 |
12.69 |
41.1 |
0.15 |
13.39 |
43.3 |
0.20 |
14.73 |
47.7 |
As shown in the results of Table 2, the optimum concentration was found to be 0.2 M. The hydration temperature affected the solubility of magnesium oxide and magnesium acetate, resulting in a higher concentration of magnesium ions in solution, which precipitates out as magnesium hydroxide.
Effect of surface area
Normally the surface areas of the products produced from hydration decreased slightly at a hydration temperature of 80 °C, except for magnesium acetate and acetic acid. Magnesium acetate and acetic acid showed an increase in the product surface areas with increasing temperature. The products formed from hydration in water had surface areas close to those obtained from hydration in ammonium chloride, magnesium nitrate, hydrochloric acid, sodium acetate and magnesium chloride.37 Magnesium acetate was the hydrating agent that showed the strongest temperature dependence, with the highest product surface areas. Due to the rapid hydration of magnesium oxide, relatively small hydroxide particles with high surface areas are formed. This can explain the higher surface areas of products formed via hydration in magnesium acetate and acetic acid. It seems that the products were formed at a rate that decreased the possibility of crystal formation or agglomeration.3,12
Effect of particle size
The particle size of magnesia powder affects the hydration rate. The hydration rate increases with temperature and with decreasing mean particle size. Magnesia powders with different parameters were selected, and their composition, particle size and the activity of citric acid were discussed. To make a comparative study between the size of the powder particle, as shown in Table 3, the first and third samples of magnesia powder were selected with a similar activity but with different particle sizes with a control pressure of 0.20 MPa.13
Table 3 Chemical compostion of different purities and mesh sizes of magnesia13
Item |
LOI |
MgO |
Al2O3 |
Fe2O3 |
Particle size |
Activity |
% |
Mesh size |
s |
1 |
1.73 |
95.38 |
0.01 |
0.31 |
300 |
55 |
2 |
1.88 |
95.21 |
0.01 |
0.31 |
80 |
81 |
3 |
2.09 |
92.45 |
0.21 |
0.45 |
80 |
54 |
4 |
2.87 |
90.40 |
0.21 |
0.45 |
80 |
99 |
Magnesia with a smaller particle size has a larger specific surface area; correspondingly, the contact area with water is larger, and therefore the hydration rate is higher. In the hydration process, magnesia powder dissolves and forms magnesium hydroxide on the surface of the parent particles. According to previous research, high pressure steam can gradually dissolve some products in the three-phase hydration reaction system. Therefore, as the reaction proceeds, the larger particles of magnesia are dissolved, and the particle size is gradually reduced until the steam stripping ability is insufficient to reduce the particle diameter. For the two kinds of magnesia powder with different initial particle sizes, the magnesia hydration rates are consistent with the results of Ohira et al.13,40
Effect of pressure
One of the important factors affecting hydration and the degree of hydration of MgO is pressure. It is challenging to apply pressure to the system as it demands high-efficiency equipment to be installed. Tang et al. decided to apply three reaction pressures, 0.1 MPa, 0.15 MPa and 0.2 MPa, with a control precision of ±0.01 MPa. They prepared a slurry with a concentration of 10 wt% using MgO with a particle mesh size of 300 with 95% purity. Fig. 5 shows the relationship between the degree of hydration under different reaction pressures with time.13
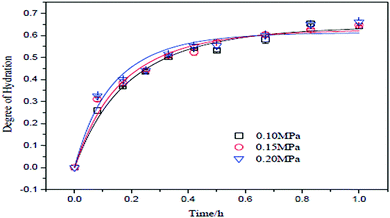 |
| Fig. 5 Relationship between reaction pressure and degree of hydration.13 | |
According to Fig. 5, the degree of hydration is directly proportional to the reaction pressure and time. The highest degree of hydration was obtained with a hydration pressure of 0.2 MPa. The curve shows that at a pressure of 0.2 MPa, 0.15 MPa and 0.10 MPa, the rate was 0.571, 0.569 and 0.533, respectively. The reaction temperature corresponding to the reaction pressure was 120, 110 and 100 °C, respectively.
Tang et al. prepared Mg(OH)2via MgO hydration under a gas–liquid–solid (three-phase) reaction system. Fig. 6 shows a comparison between the degree of hydration of MgO of the three-phase reaction system and the two-phase reaction with time. It was found that the degree of hydration of MgO of the three-phase hydration reaction system is significantly higher than that of the two-phase hydration reaction system.13
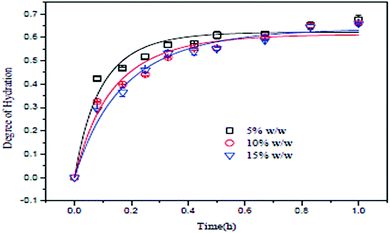 |
| Fig. 6 Relationship between MgO concentration and the degree of hydration.13 | |
Yimin et al. reported on an invention to prepare a magnesium hydroxide slurry stably and efficiently by reacting magnesium oxide with an aqueous vapor via controlling the pressure and temperature. The hydration ratio was discussed where magnesium oxide accounts for 5–15% of the total weight, where the pressure was controlled to be 0.2–0.5 MPa as the temperature reaches 90–150 °C and circulating for 10–35 min. Table 4 shows the 6 samples under different conditions used to reveal the hydration ratio.41
Table 4 Six examples under different conditions41
Embodiment |
MgO% by weight (%) |
Pressure (MPa) |
Temperature (°C) |
Circulation flow(L min−1) |
Hydration degree (%) |
1 |
5 |
0.2–0.3 |
90–120 |
1.95 |
59.1 |
2 |
5 |
0.3–0.5 |
120–150 |
1.55 |
59.4 |
3 |
10 |
0.2–0.3 |
90–120 |
1.2 |
83.4 |
4 |
10 |
0.3–0.5 |
120–150 |
2.9 |
82.1 |
5 |
15 |
0.2–0.3 |
90–120 |
3.1 |
92.4 |
6 |
15 |
0.3–0.5 |
120–150 |
2.75 |
95.1 |
This patent compared the traditional method (two-phase) and the invented method (three-phase) with an applied pressure of 0.2–0.3 MPa. The comparison concluded that the invented method, compared with the traditional method, had the remarkable advantage of being quick and efficient. Because of a shortened reaction ratio, the occupied area of the device disclosed by the invented method was greatly reduced compared with that of a traditional device, as shown in Table 5.
Table 5 Comparison between the traditional method (a) and the invented method (b)41
(a) |
|
|
|
|
MgO% by weight |
Temp. (°C) |
Stirring rate (rpm) |
Time (min) |
Hydration degree |
Traditional method |
10% |
90 |
900 |
120 |
77.7% |
(b) |
MgO% by weight |
Temp. (°C) |
Circulation flow (L min−1) |
Time (min) |
Hydration degree |
Invented method |
|
|
|
|
10% |
90 – 120 |
1.2 |
10 |
82.5% |
Effect of slurry concentration
The slurry concentration has a significant effect on the degree of hydration of MgO. Tang et al. investigated the degree of hydration of MgO using three different slurry concentrations under a constant pressure of 0.2 MPa. The slurry concentrations were 5 wt%, 10 wt% and 15 wt%, using MgO particles of mesh size 300 with 95% purity. As shown in Fig. 7, the degree of hydration of MgO is inversely proportional to the slurry concentration. The degree of hydration (about 60%) was better when the slurry concentration was 5 wt%. However, after 30 min, the degree of hydration for the three slurry concentrations did not change further.13
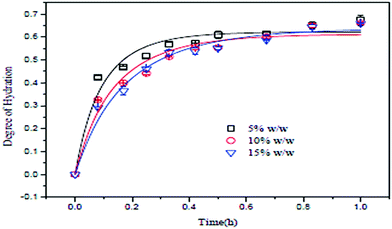 |
| Fig. 7 Relationship between MgO concentration and the degree of hydration.13 | |
Effect of pH
The hydration process was found to depend on the hydrating solution and its pH value. Matabola et al. investigated the influence of different hydrating agents on the pH of hydrating solutions, the degree of hydration of MgO and the product surface area as a function of temperature. As shown in Fig. 8, a decrease in the solution pH was observed when the hydration temperature was increased. Similar trends were observed for hydration studies performed with most of the other hydrating agents.37
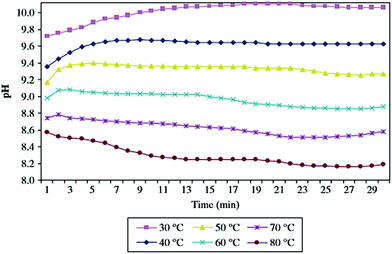 |
| Fig. 8 Variation of pH with temperature for the hydration of MgO in magnesium acetate.19 | |
Tang et al. examined the effect of hydrating agents on the degree of hydration of MgO in a three-phase reaction system. The initial pH value was measured before MgO was added to the solution. The effect of pH with hydration time is shown in Fig. 9, where the pH of all the solutions increased with time except for Mg(CH3COO)2. The pH increases as large amounts of OH ions are released. As for Mg(CH3COO)2, large amounts of Mg2+ and OH− ions are in solution already, thus there is no increase but an obvious decrease in the pH.42
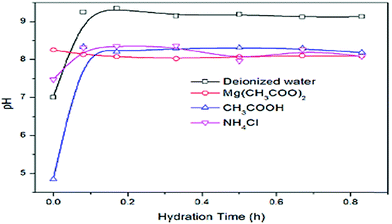 |
| Fig. 9 Variation of pH with hydration time under a three-phase reaction system.42 | |
Kurama and Hosgun studied the hydration behavior of MgO waste, both calcined and uncalcined, as the reactivity of MgO determined the degree of hydration of the sample. The hydration experiments were carried out at temperatures ranging from 30 °C to 80 °C. As shown in Fig. 10, the pH value of the solution was inversely proportional to the time and the temperature, but higher pH values were obtained for calcined samples.36
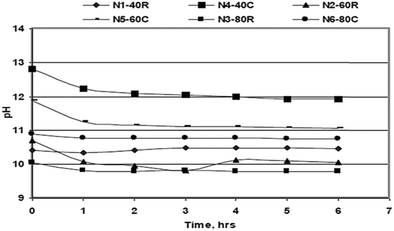 |
| Fig. 10 Variation of the solution pH during the hydration process.18 | |
Rheological behavior of Mg(OH)2
The rheological behavior of a Mg(OH)2 suspension is influenced by many factors, such as the solid loading, the dosage of dispersants, the shear rate and the temperature, as shown in Fig. 11. The effect of these factors on the stability and the rheological behavior of Mg(OH)2 was investigated by means of viscosity and sedimentation measurements.
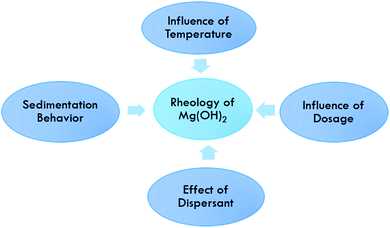 |
| Fig. 11 Schematic of the rheological behavior of magnesium hydroxide. | |
Effect of dispersant
A dispersant, or a dispersing agent, or a surface-active substance is usually added to a suspension of Mg(OH)2 to improve the separation of particles and to prevent settling or clumping.43 Dispersants consist normally of one or more surfactants. Recent studies have reported on the effect of dispersants on the rheology of Mg(OH)2 hydration.44 Furthermore, the effect of NaPA on the rheological behavior and stability of Mg(OH)2 suspensions was investigated. The influence of NaPA on the viscosity of Mg(OH)2 suspensions was examined. As the dispersant dosage increases, the viscosity decreases, and the viscosity reached a minimum when the dispersant dosage exceeded 0.6 wt% and generated a lower sedimentation height. However, flocculation will occur in the presence of excess or an insufficient NaPA concentration.45
The effect of comb-like polyelectrolyte NaPAA-PEO on the rheological behavior and stability of Mg(OH)2 suspensions was also studied. The influence of NaPAA-PEO on the viscosity was examined; the viscosity decreases with an increase in the NaPAA-PEO dosage accompanied by a remarkable shear thinning behavior with the increase in solid loading. As sufficient stabilization was successfully induced at 0.6 wt% of NaPAA-PEO, a reduction in the viscosity was effectively obtained with 40 wt% Mg(OH)2 suspensions, although the sedimentation height decreased with an increase in the NaPAA-PEO dosage.45
Influence of solid loading
The solid loading of Mg(OH)2 suspensions, with 0.6 wt% NaPA added to all the samples to facilitate the viscosity measurements, was studied. The influence of solid loading on the shear dependent behavior is illustrated in Fig. 12; as the viscosity increases, the shear rate decreases. When the solid loading of the suspensions was less than 30 wt%, there was only a slight shear thinning. When it exceeded 40 wt%, there was noticeable shear-thinning behavior, indicating the presence of direct contacts between the particles.45
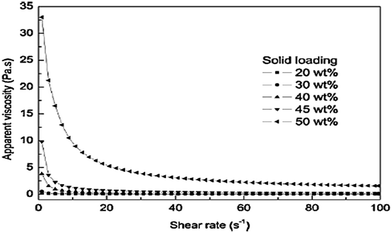 |
| Fig. 12 Effect of solid loading on the viscosity for suspensions dispersed with 0.6 wt% NaPA.45 | |
Furthermore, the rheological behavior and stability of aqueous magnesium hydroxide suspensions in the presence of a comb-like polyelectrolyte was studied, namely, sodium salts of poly(acrylic acid)-poly(ethylene oxide) (NaPAA-PEO), at a high ionic strength of 0.9 wt% NaPAA-PEO to facilitate the viscosity measurements. The influence of the solid loading on the rheological behavior of Mg (OH)2 suspensions is illustrated in Fig. 13; as the viscosity increases, the shear rate decreases. When the solid loading of the suspensions was less than 50 wt%, there was only slight shear thinning. When it exceeded 50 wt%, there was noticeable shear-thinning behavior, indicating the presence of particle packing in the suspensions. As shown in Fig. 14, as the shear rate is increased, the flocs were gradually destroyed and a higher particle packing density was obtained.46
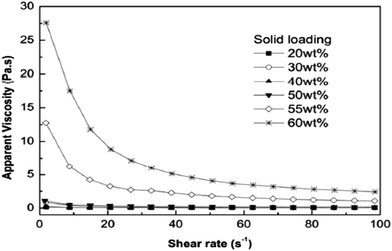 |
| Fig. 13 Effect of solid loading on the apparent viscosity of Mg(OH)2 suspensions.46 | |
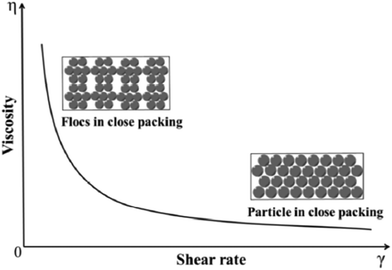 |
| Fig. 14 Schematic of particle packing in suspensions with increasing shear rate.46 | |
Influence of dosage
The dosage of dispersants influences the preparation of Mg(OH)2 suspensions and affects the rheological behavior of the suspensions. The specific dosage of dispersant facilitates the stability and fluidity of the suspensions of particles. As shown in Fig. 15, the effect of NaPA dosage on the viscosity of Mg(OH)2 suspensions with a 40 wt% solid loading was examined. As the NaPA dosage is increased, the viscosity decreases and the shear rate increases, where the optimum dosage is 0.6 wt%.45
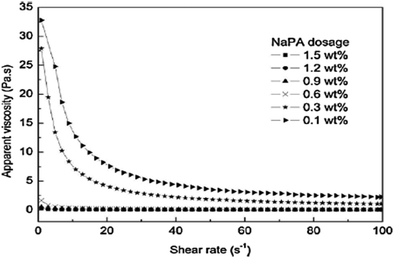 |
| Fig. 15 Apparent viscosity of 40 wt% Mg(OH)2 suspensions with different NaPA dosage.45 | |
The effect of NaPAA-PEO dosage on the rheological behavior of Mg(OH)2 suspensions with 40 wt% solid loading was examined. As shown in Fig. 16, as the NaPAA-PEO dosage is increased, the viscosity decreases and shear rate increases. From 0.6 wt% to 1.2 wt%, NaPAA-PEO dosage, the surface coverage of the particles is sufficient to generate a platform, thus the suspensions are well dispersed and exhibit Newtonian behavior.46
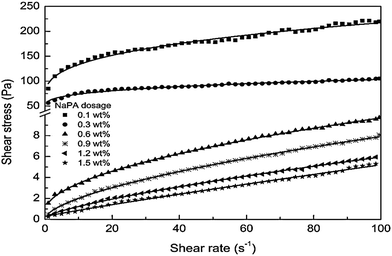 |
| Fig. 16 Shear stress of 40 wt% Mg(OH)2 suspensions with different NaPA dosage. | |
Influence of temperature
The effect of temperature on the rheological behavior of 40 wt% Mg(OH)2 suspensions with 0.6 wt% NaPA dosage has been reported. As shown in Fig. 17, shear-thinning behavior was observed in all the suspensions within the shear rate range, and the apparent viscosity decreased as the temperature was increased. This is attributed to the fact that the increase in temperature causes activation of the adsorption of NaPA, resulting in a thicker adsorbed layer.45
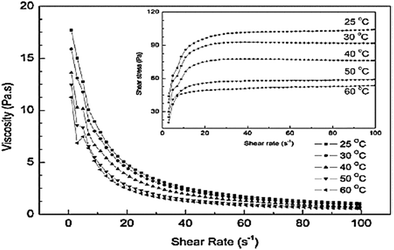 |
| Fig. 17 Effect of temperature on the rheological behavior of 40 wt% Mg(OH)2 suspensions with 0.6 wt% NaPA dosage.45 | |
Sedimentation behavior
The sedimentation behavior with different dosages of NaPA and ionic strengths in Mg(OH)2 suspensions was studied. After 7 days, the sedimentation heights of Mg(OH)2 suspension were measured for several dosages. As shown in Fig. 18, the higher NaPA dosage generated a lower sedimentation height and a stable suspension. As shown in Fig. 19, in the absence of KNO3 the sedimentation height decreases as the NaPA dosage is increased, and a more stable suspension including a cloudy supernatant and low sedimentation can be obtained. However, an excess of KNO3 in the suspension causes the cloudy supernatant to become clear at high NaPA dosages, as shown in Fig. 20.45
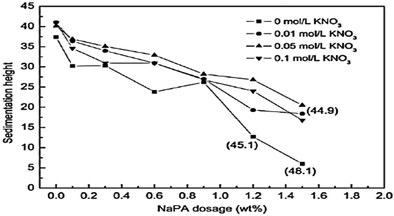 |
| Fig. 18 Effect of NaPA amount and ionic strength on the sedimentation height of Mg(OH)2 suspensions. Period, 7 days; solid loading, 10 wt%. The numbers in parentheses refer to the rough height at the interface of the cloudy and clear supernatant.45 | |
 |
| Fig. 19 Sedimentation of the suspensions with different concentrations of NaPA. Period, 7 days; solid loading, 10 wt%.45 | |
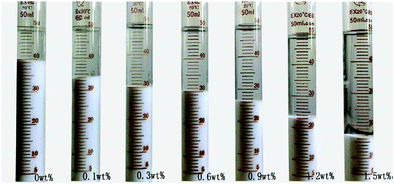 |
| Fig. 20 Sedimentation of the suspensions with different concentrations of NaPA. Period, 7 days; solid loading, 10 wt%; ionic strength, 0.1 mol L−1 KNO3.45 | |
The sedimentation behavior with different dosages of NaPAA-PEO and counter-ions (K+, Mg2+ and Ca2+) in Mg(OH)2 suspension was investigated. After 7 days, the sedimentation heights of the Mg(OH)2 suspensions were measured for several dosages, as shown in Fig. 21. As the NaPAA-PEO dosage increases, the sedimentation decreases and Mg(OH)2 particles were well dispersed. The suspensions with NaPAA-PEO also exhibited excellent salt-tolerance for monovalent K+ ions and divalent Ca2+ and Mg2+ ions.46
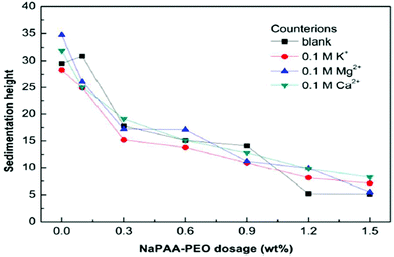 |
| Fig. 21 Effect of NaPAA-PEO dosage and counterions on the sedimentation height of Mg(OH)2.46 | |
Conclusions
A large number of scientific reports published on the study of Mg(OH)2 and MgO provides evidence of the constantly growing level of interest in these materials, and will undoubtedly lead to the spread of knowledge about both compounds and the development of new opportunities for their use. Currently, magnesium hydroxide is most renowned as a flame retardant, used not only in combination with polymeric materials but it is also known as an antibacterial agent and a neutralizer of pollutants in freshwater and wastewater. Moreover, attention is frequently drawn to magnesium oxide's surface reactivity, porosity and high specific surface area, which favor the use of the compound in adsorptive and catalytic processes. This review gives an overview of the possibility of producing magnesium hydroxide with a high solid content with increasing reaction pressures. It is speculated that the main reason for the success of the three-phase hydration reaction system in improving the hydration rate is the spalling effect caused by a high-pressure steam blast, which contributes to the product layer being peeled off from the parent particles, so that the exposed MgO can continue to react with water. Magnesium acetate as a hydrating agent increases the solid content produced due to a large number of acetate ions at high temperatures. The rheological behavior and stability of Mg(OH)2 suspensions are found to be affected strongly by the solid loading, polyelectrolyte concentration, temperature and ionic strength. The apparent viscosity of concentrated Mg(OH)2 suspensions decreased pronouncedly as the dispersant dosage was increased.
As a futuristic outlook, it is expected that researchers will develop new methods for the synthesis of magnesium hydroxide and magnesium oxide from the perspective of producing materials with better physicochemical and utility properties. A very important and innovative step will certainly be the combination of magnesium hydroxide and oxide with widespread biopolymers, among others lignin and its derivatives, cellulose, chitin, and other materials. This will give multifunctional hybrid materials for specific applications.
Conflicts of interest
The authors declare that there is no conflict of interest.
References
- S. P. Jozić, D. Jozić, J. Jakić and B. Andričić, Preparation and characterization of PLA composites with modified magnesium hydroxide obtained from seawater, J. Therm. Anal. Calorim., 2020, 142, 1877–1889 CrossRef.
- A. A. Pilarska, Ł Klapiszewski and T. Jesionowski, Recent development in the synthesis, modification and application of Mg(OH)2 and MgO: A review, Powder Technol., 2017, 319, 373–407 CrossRef CAS.
- E. Aphane, E. Merwe and C. Strydom, Influence of hydration time on the hydration of MgO in water and in a magnesium acetate solution, J. Therm. Anal. Calorim., 2009, 96(6), 987–992 CrossRef.
- A. Sierra-Fernández, L. S. Gomez-Villalba, O. Milosevic, R. Fort and M. E. Rabanal, Synthesis and morpho-structural characterization of nanostructured magnesium hydroxide obtained by a hydrothermal method, Ceram. Int., 2014, 40, 12285–12292 CrossRef.
- X. Li, T. Shi, P. Chang, H. Hu, J. Xie and Y. Liu, Preparation of magnesium hydroxide flame retardant from light calcined powder by ammonia circulation method, Powder Technol., 2014, 260, 98–104 CrossRef CAS.
- C. Dong, D. Song, J. Cairney, O. L. Maddan, G. He and Y. Deng, Antibacterial study of Mg (OH)2 nanoplatelets, Mater. Res. Bull., 2011, 46, 576–582 CrossRef CAS.
- A. F. Halbus, T. S. Horozov and V. N. Paunov, Controlling the Antimicrobial Action of Surface Modified Magnesium Hydroxide Nanoparticles, Biomimetics, 2019, 4(2), 41 CrossRef CAS PubMed.
- X. Li, Y. Zhang, Y. Zhang, J. Ze, P. Chang and Y. Liu, Preparation of active magnesium oxide with caustic calcined magnesia by ammonia circulation method, Adv. Powder Technol., 2016, 27(4), 1109–1114 CrossRef CAS.
- C. K. Chau and Z. Li, Accelerated Reactivity Assessment of Light Burnt Magnesium Oxide, J. Am. Ceram. Soc., 2008, 91(5), 1640–1645 CrossRef CAS.
-
M. A. Shand, The Chemistry and Technology of Magnesia, John Wiley & Sons, Inc, Canada, 2006 Search PubMed.
- C. A. Strydom, E. M. Merwe and M. E. Aphane, The effect of calcining conditions on the rehydration of dead burnt magnesium oxide using magnesium acetate as a hydrating agent, J. Therm. Anal. Calorim., 2005, 80(6), 659–662 CrossRef CAS.
- D. Filippou, N. Katiforis, N. Papassiopi and K. Adam, On the Kinetics of Magnesia Hydration in Magnesium Acetate Solutions, J. Chem. Technol. Biotechnol., 1999, 74(4), 322–328 CrossRef CAS.
- X. Tang, Q. Lv, L. Yin, Y. Nie, Q. Jin, Y. Ji and Y. Zhu, Pilot scale experiments of magnesia hydration under gas–liquid–solid (three-phase) reaction system, AIP Conf. Proc., 2017, 1864, 020004 CrossRef.
-
S. R. Punnamaraju, The Evaluation of the Sedimentation Behavior of Magnesium Hydroxide in the Never Dried State, The University of Toledo, Ohio, 2012 Search PubMed.
- S. Iwasaki, S. Kodani and N. Koga, Physico-Geometrical Kinetic Modeling of the Thermal Decomposition of Magnesium Hydroxide, J. Phys. Chem. C, 2020, 124(4), 2458–2471 CrossRef CAS.
- A. Alamdari, M. Rahimpour, N. Esfandiari and E. Nourafkan, Kinetics of magnesium hydroxide precipitation from sea bittern, Chem. Eng. Process., 2008, 47, 215–221 CrossRef CAS.
- A. Jarosinski, P. Radomski, L. Lelek and J. Kulczycka, New Production Route of Magnesium Hydroxide and Related Environmental Impact, Sustainability, 2020, 12, 8822 CrossRef CAS.
- S. D. F. Rocha, M. B. Mansur and V. S. T. Ciminelli, Kinetics and mechanistic analysis of caustic magnesia hydration, J. Chem. Technol. Biotechnol., 2004, 79, 816–821 CrossRef CAS.
- E. Alvarado, L. M. Torres-Martinez, A. F. Fuentes and P. Quintana, Preparation and characterization of MgO powders obtained from different magnesium salts and the mineral dolomite, Polyhedron, 2000, 19, 2345–2351 CrossRef CAS.
- H. Guo, Y. Pei, Z. Wang, Y. Yang, K. Wang, J. Xie and Y. Liu, Preparation of Mg(OH)2 with caustic calcined magnesia through ammonium acetate circulation, Hydrometallurgy, 2015, 152, 13–19 CrossRef CAS.
- A. Pilarska, I. Linda, M. Wysokowski, D. Paukszta and T. Jesionowski, Synthesis of Mg(OH)2 from magnesium salts and NH4OH by direct functionalisation with poly(ethylene glycols), Physicochem. Probl. Miner. Process., 2012, 48, 631–643 CAS.
- W. Feitknecht and H. Braun, Der Mechanisms der Hydratation von Magnesiumoxid mit Wasserdampf, Helv. Chim. Acta, 1967, 50(10), 2040–2053 CrossRef CAS.
- X. Tang, L. Guo, C. Chen, Q. Liu, T. Li and Y. Zhu, The analysis of magnesium oxide hydration in three-phase reaction system, J. Solid State Chem., 2014, 213, 32–37 CrossRef CAS.
- Z. Xing, L. Bai, Y. Ma, D. Wang and M. Li, Mechanism of Magnesium Oxide Hydration Based on the Multi-Rate Model, Materials, 2018, 11(10), 1835 CrossRef PubMed.
- Y. Cai, D. Wu, X. Zhu, W. Wang, F. Tan, J. Chen, X. Qiao and X. Qiu, Sol–gel preparation of Ag-doped MgO nanoparticles with high efficiency for bacterial inactivation, Ceram. Int., 2017, 43, 1066–1072 CrossRef CAS.
- S. Gehringer, C. Luckeneder, F. Hrach and H. Flachberger, Processing of Caustic Calcined Magnesite (Magnesium Oxide) by the Use of Triboelectrostatic Belt Separation, Berg- Huettenmaenn. Monatsh., 2019, 164, 303–309 CrossRef CAS.
- K. Byrappa and T. Adschiri, Hydrothermal technology for nanotechnology, Prog. Cryst. Growth Charact. Mater., 2007, 53, 117–166 CrossRef CAS.
- C. M. F. Santos, A. F. B. Andrade and S. D. F. Rocha, The effect of caustic magnesia natural impurities on magnesium oxide hydroxylation, J. Nanotechnol. Mater. Sci., 2017, 45–54 CAS.
- Z. Zhao, H. Dai, Y. Du, J. Deng, L. Zhang and F. Shi, Solvo- or hydrothermal fabrication and excellent carbon dioxide adsorption behaviors of magnesium oxides with multiple morphologies and porous structures, Mater. Chem. Phys., 2011, 128, 348–356 CrossRef CAS.
- S. G. Al Attas, F. Al-Hazmi, R. Alwafi, A. A. Alahmadi, D. A. Al-Quwaie, A. Bahieldin and S. Edris, Bactericidal Efficacy of New Types of Magnesium Hydroxide and Calcium Carbonate Nanoparticles, Mol. Genet., 2019, vol. 34, 252–262 Search PubMed.
- V.-T. Luong, R. Amal, S. Jason, S. Ehrenberger and T. Tran, A comparison of carbon footprints of magnesium oxide and magnesium hydroxide produced from conventional processes, J. Cleaner Prod., 2018, 202, 1035–1044 CrossRef CAS.
- F. Laoutid, V. Duriez, L. Brison, S. Aouadi, H. Vahabi and P. Dubois, Synergistic flame-retardant effect between lignin and magnesium hydroxide in poly(ethylene-co-vinyl acetate), Flame Retardancy and Thermal Stability of Materials, 2019, 2, 9–18 Search PubMed.
- T. S. Rötting, J. Cama, C. Ayora, J.-L. Cortina and J. De Pablo, Use of Caustic Magnesia To Remove Cadmium, Nickel, and Cobalt from Water in Passive Treatment Systems:
Column Experiments, Environ. Sci. Technol., 2006, 40(20), 6438–6443 CrossRef PubMed.
- J.-L. Cortina, I. Lagreca, J. De Pablo, J. Cama and C. Ayora, Passive In Situ Remediation of Metal-Polluted Water with Caustic Magnesia:
Evidence from Column Experiments, Environ. Sci. Technol., 2003, 37(9), 1971–1977 CrossRef CAS PubMed.
- J. M. Chimenos, A. I. Fernández, L. Haurie and M. Calaf, Trace metal partitioning in caustic calcined magnesia produced from natural magnesite, J. Environ. Sci. Health, Part A: Toxic/Hazard. Subst. Environ. Eng., 2012, 47(1), 93–100 CrossRef CAS PubMed.
- H. Kurama and H. L. Hosgun, Magnesium hydroxide recovery from magnesia waste by calcinations and hydration processes, Physicochem. Probl. Miner. Process., 2015, 51(1), 233–245 Search PubMed.
- K. P. Matabola, E. M. Merwe, C. A. Strydom and F. J. W. Labuschagne, The influence of hydrating agents on the hydration of industrial magnesium oxide, J. Chem. Technol. Biotechnol., 2010, 85, 1569–1574 CrossRef CAS.
- F. von Hoessle, R. Farid, M. Mohamed, R. M. Hammouda, F. E. Kühn and G. Bassioni, The Effect of Different Hydration Media on Magnesia, Discover Materials, 2021 DOI:10.1007/s43939-021-00017-9.
-
M. E. Aphane, The hydration of magnesium oxide with different reactivities by water and magnesium acetate, 2009 Search PubMed.
- Y. Ohira and E. Obata, Effect of Particle Size on Hydration Rate of Magnesium Oxide, Kagaku Kogaku Ronbunshu, 2009, 35, 543–547 CrossRef CAS.
-
Y. Zhu, T. A. N. G. Xiaojia, L. Guo, Q. Liu, C. Chen and T. Li, Preparation method and device for efficiently preparing magnesium hydroxide, US Pat., US9776882B2, 2017.
- X. Tang, Y. Ji, Y. Nie, L. Guo, Q. Liu, J. Zhao, T. Li and Y. Zhu, Three-phase hydration of magnesium oxide using hydration agents, Cryst. Res. Technol., 2017, 52, 1600393 CrossRef.
- Y. Ding, J. Zhao, L. Wei, W. Li and Y. Chi, Effects of Mixing Conditions on Floc Properties in Magnesium Hydroxide Continuous Coagulation Process, Appl. Sci., 2019, 9(5), 973 CrossRef CAS.
- F. von Hoessle, M. Mohamed, R. Farid, R. M. Hammouda, F. E. Kühn and G. Bassioni, Interfacial phenomena of Magnesium hydroxide micro phases, Ain Shams Eng. J., 2021 DOI:10.1016/j.asej.2021.01.020.
- K. Tong, X. Song, S. Sun, Y. Xu and J. Yu, The rheological behavior and stability of Mg(OH)2 aqueous suspensions in the presence of sodium polyacrylate, Colloids Surf., A, 2013, 436, 1111–1120 CrossRef CAS.
- K. Tong, X. Song, G. Xiao and J. Yu, Improvement in Salt-Tolerance of Aqueous Magnesium Hydroxide Suspensions by Comb-Like Polyelectrolyte, Ind. Eng. Chem. Res., 2015, 54, 6115–6122 CrossRef CAS.
|
This journal is © The Royal Society of Chemistry 2021 |
Click here to see how this site uses Cookies. View our privacy policy here.