DOI:
10.1039/D1GC03079E
(Communication)
Green Chem., 2021,
23, 9401-9405
OrganoSoxhlet: circular fractionation to produce pulp for textiles using CO2 as acid source†
Received
24th August 2021
, Accepted 5th November 2021
First published on 6th November 2021
Abstract
Organosolv pulping performed in a high-pressure Soxhlet extractor using carbon dioxide as a mild and recyclable acid is described. The system reached a liquid to wood ratio of 6.6 yielding 43 wt% of dissolving grade quality pulp from Populus trichocarpa. The set-up enabled to run reductive catalytic fractionation to yield a lipophilic lignin oil without affecting the performance nor the purity of the final pulp.
The constant population growth is causing a higher consumption rate of natural resources, demanding better exploitation of the ones already in use. Globally, about 35.5 million hectares of soil (2018) are cultivated for fibre production, of which 91% are currently planted with cotton. One hectare of cotton field is estimated to produce 2.1 tons of product per year of which 30 wt% would be fibre (0.7 tons), where the same amount of land could produce up to 4.0 tons of cereals.1 Moreover, more than 9000 tons of water are required for the manufacturing of 1 ton of cotton fabric.2 Therefore, a more efficient alternative to cotton for fibre fabrication is desired to liberate soil and thus enable an increase in food production. Synthetic fibres based on fossil-derived polymers have been used to fulfil the demand for textiles. However, due to the recent environmental concerns, e.g. climate change and microplastic pollution, fossil-based products will have to be synthesised from renewable feedstocks or replaced by green alternatives. Dissolving pulp originated from lignocellulose is widely considered as a valid alternative to cotton for fibre production.3,4 Short rotation forestry can provide the required amount of lignocellulose, greatly reducing the quantity of soil and resources needed.5–7 As a representative, the genotype 23.4 of Populus trichocarpa was selected. This particular clone of poplar has been recently developed to grow in regions with cold climates such as the Baltic Sea Region, showing a dry yield of 9.9 t of biomass per hectare per year.8 To obtain pulp as the final product, it needs to be liberated from the biomass.9 Nevertheless, the dissolving grade pulp consists of the glucan fraction of the lignocellulose where hemicellulose and lignin are considered impurities.9,10 Different pulping processes are industrially exploited, all of them utilise a large amount of chemicals, e.g. Kraft and sulphite pulping.11 To simplify the process, reduce the cost and the environmental impact of pulping, a technique only using solvents has been developed. This procedure, which is based on solvolysis and benign organic solvents, has been named Organosolv.12–15 Organosolv pulping can be achieved by using two different reaction technologies: batch autoclaves or flow-through reactors. A batch reactor has the advantage of requiring a relatively small amount of solvent. The current operating systems work averagely with a liquid to wood ratio of 10–20,16 where very rare scientific reports describing lower ratios can be found.17 However, solvent and substrate have to be mechanically stirred and the resulting liquors washed away from the pulp after the reaction, reducing the purity of the product and increasing the operational costs as well as the overall solvent consumption. Typically, an additional 3.3 of solvent to wood is required in this washing.18 However, a batch process could potentially reach optimal solvent to wood ratio if full solvent recycling and recirculation of washing liquids were developed. On the other hand, flow systems keep the substrate separated from the liquors by enclosing them into porous cartridges and letting the solvent flow through. Still, a major drawback is the large amount of solvent required to complete the reaction. These issues have been recently addressed by Deuss and coworkers.19 Other short-comings are non-homogeneous flows and difficulties in scaling-up. To overcome these issues we herein present an alternative type of pulping system based on Organosolv pulping performed in a Soxhlet extractor operated under high pressure. We studied its application in the production of dissolving grade pulp from short rotation forestry derived hardwood. In addition, the design of the reactor allowed us to involve a heterogeneous catalyst to achieve reductive catalytic fractionation on the lignin oil without contaminating the final product with the catalyst nor reducing the performance. The reactor discussed in this study consists of a 600 mL autoclave equipped with a gas valve, a thermowell and a cooling coil. A collecting cup (CC) and above this, an extraction cup (EC) equipped with a syphon which unloads directly into the CC are placed inside the autoclave (Fig. 1). Wood meal sawdust was chosen for the initial runs. Pulping attempts were performed by loading 5 g of biomass in the EC and filling the CC with 200 mL of EtOH
:
H2O mixture 1
:
1,20–22 setting the temperature at 220 °C and the cooling flow rate of 1 L min−1 which was the maximum allowed by our equipment. When running the OrganoSoxhlet under these conditions, carbonisation of both biomass and cotton containers was observed in the EC. Also, the liquors produced coke in approx. 5 wt%. The carbonisation of the substrate was confirmed after visual inspection of the residues associated with an abnormal mass loss of both wood and cotton bags (ESI, Fig. S6 and S7†), while the coke formation was evaluated by filtrating the liquors and weighing the solid residues. We assessed whether the carbonisation could be prevented by loading the liquors through the EC to soak the substrate already before the extraction. Carbonisation in the EC was avoided, however, coke formation was still observed in the CC. We argued that this was due to the complete evaporation of the liquors at the operating conditions, i.e. 13–15 barg at 220 °C. By adding 8 barg of inert nitrogen gas at room temperature, the system reached an operating pressure of approximately 25–30 barg at 220 °C. Under these conditions, water is just below its boiling point, resulting in more controlled evaporation of the solvent mixture. Therefore, when avoiding the complete evaporation of the liquors only negligible carbonisation in both EC and CC was observed (<1 wt%). However, pulping efficiency measured by loss of weight resulted in a poor 37.3 wt% from the aimed ∼50 wt%, which corresponds to the calculated weight of product from pulping considering 90% delignification, even after 4 hours. The analysis of the generated pulp showed that 15% of lignin and 10% hemicellulose were still present, disclosing an incomplete pulping. In common Organosolv procedures, an acid is used to promote the hydrolysis of hemicellulose and the release of lignin. The design of the OrganoSoxhlet reactor enabled us to use benign and easily recoverable carbon dioxide as the acid source. Therefore, we changed the atmosphere into CO2 aiming at a lower pH of the liquors by adding 8 barg at room temperature.23 A slightly acidic pH was found beneficial for lignocellulose delignification in our previous study.24 In the present system this effect is provided by the CO2 dissolved in the extracting liquors generating carbonic acid. By that, 54 wt% mass loss and high purity of the reacted wood were observed. Comparison of the results under N2 and CO2 atmospheres shows that CO2 has a beneficial impact on both delignification and removal of hemicellulose from the solid residues. This confirms that the lower pH obtained by the dissolution of CO2 into the liquors enhances the lignin carbohydrate complexes (LCCs) cleavage performance.25–29 The chemical analysis of the product obtained under the optimized conditions showed a high purity pulp containing 94 wt% of glucose and traces of lignin (3 wt%) and xylose (3 wt%), confirming the high selectivity of our system for cleavage of LCCs while preserving the glucan fraction of the biomass. The water content was screened and the optimal solvent composition was found to be 25 v/v% of EtOH in H2O (ESI, Fig. S4†). The low amount of alcohol needed, 50 mL, is due to the fact that the EC can only accommodate approximately 100 mL of solvent when the substrate is present in the containers. Therefore, the liquor composition in the extraction cup, before being unloaded, is highly enriched in the solvent with the lower boiling point, which is EtOH. The reaction gave optimal results after 4 hours (ESI, Fig. S5†). Prolonged reaction time resulted in initial sugar degradation as the mass loss of the fabric cloth was found to be 14 wt%. Lower cooling flow rates were investigated. When setting the rate at 0.5 L min−1, the observed mass loss was 31 wt%, a sign of a slower condensation rate of the liquors and a consequent reduced pulping degree. When no cooling was involved the substrate and the containers were found partially carbonised after the treatment. Thus, 1 L min−1 was used as the cooling flow rate. The pulping degree was found to be independent of the loading of the substrate. This can be explained by the fact that the pulping liquors, which get in contact with the substrate, are always freshly distilled and therefore the substrate gets in contact with pure solvent at the beginning of every extraction cycle. The design of the extracting cup allowed us to increase the biomass loading to reach a maximum of 18.7 g of sawdust in one batch, still operating with 200 mL of solvent. The scale-up
gave comparable results in terms of pulping performance with 54.8 wt% mass loss and high purity of the residual pulp, glucose 94 wt%, lignin 4 wt% and xylose 3 wt%. Preliminary trials in the production of dissolving grade pulp with sawdust resulted in a too low viscosity material. To increase the quality of the final product, wood sticks were investigated as the substrate, which also have a more commercial relevance. Poplar wood sticks (approx. 35 × 2 × 2 mm) were treated under the same conditions optimized for sawdust and yielded 51.7 wt% of dry substance. (Table S1† entry 1). The lower mass loss compared to the sawdust-based reactions is probably because fewer small particles are produced during the treatment and passed through the cartridges since the purity of the reacted sticks is comparable to the reacted sawdust (glucose = 94 wt%). This was also confirmed by a lower coke formation observed in the collecting cup when using wood sticks. Due to the lower density of the sticks compared to the sawdust, the maximum loading of the reactor had to be lowered to 9.7 g per run. Nevertheless, we assessed the reduction in the amount of processable biomass by reducing solvent consumption. Recycling of the spent liquids was performed by running a series of subsequent reactions where the liquors were reused and the containers with treated sticks exchanged for ones carrying fresh substrate. The solvent system was recycled up to three times with a small refill to compensate for the loss due to the removal of the wet reacted wood bags (approx. 20 mL), always maintaining the operational volume of 200 mL (Table S1†). The yields in terms of delignification and hemicellulose removal were slightly lower but consistent with the previous runs. Thus, the treated solid material obtained from those three runs was collected together to be used in the next step. Therefore 30.1 g of poplar wood were treated with a mere 200 mL of solvent (50 mL of EtOH and 150 mL of water) reaching a liquid to wood ratio of 6.6 and an organic solvent to wood ratio of 1.66. To achieve the final product, the fibres contained in the delignified wood (Fig. 2B) needed to be released from each other. This was obtained by using an automatic disintegrator. The procedure yielded unbleached pulp (Fig. 2C) in 44 wt% yield compared to initial wood, 85 wt% yield from the previous step. During this step, the purity of the pulp further increased to reach the optimal 94 wt% of glucose (Fig. 2C). Consequently, elemental chlorine-free (ECF) bleaching was performed on the pulp by using a 1
:
1 ratio of sodium chlorite and a NaOH/AcOH buffer solution (see ESI†) to obtain 43 wt% of bleached pulp (Fig. 2D), 98 wt% yield from the unbleached pulp.30 A sheet made of bleached material was analysed by following the standard method ISO 2470-1 resulting in more than 91% of ISO-brightness. α-cellulose was quantified and a high value (90.58%) was found. The bleached material was further tested for viscosity (442 mL g−1) and DP (610) complying with the requirement for lyocell production.31–33 After the reaction, the liquors were collected, filtrated, and evaporated under vacuum to remove the solvents yielding an oil containing lignin as the product. In the attempt to valorise the lignin fraction, which is produced in the EC as a by-product of the solvolysis and constantly unloaded in low concentration in the CC, we considered involving a heterogeneous catalyst. The procedure of combining pulping with reductive catalysis is commonly known as reductive catalytic fractionation (RFC).34 The unique design of our pulping reactor allowed us to add a heterogeneous catalyst to the CC without contaminating the pulp which remains always confined in the EC. Indeed, this is a crucial achievement since in most of the lignin first approaches it is extremely challenging to obtain a final product with proper ISO brightness when the heterogeneous catalyst gets in contact with the pulp. The goal was to use the CC as a catalytic reactor in parallel with the pulping run in the EC while exploiting the same heat source. The organosolv liquor contains mono- and oligomeric fractions of lignin, which are highly reactive compounds prone to re-condensate. The heterogeneous catalyst under reducing conditions can transform these fragments into stable and valuable compounds through hydrodeoxygenation/reduction conditions.35 The ability of Pd to exploit sugars derived from the hemicellulose as a hydride donor has been already reported by our group.36 Therefore, commercially available Pd/C was selected as the heterogeneous catalyst, and no external source of hydrogen was added. The reaction with 4 mol% of Pd gave 17 wt% of upgraded lignin oil with respect to the initial biomass, in accordance with our previous report on poplar.36 The upgraded lignin oil was further analysed by GC-MS/FID and 2 wt% of monophenolic compounds in respect to the biomass were detected (ESI, Table S1†) while in the lignin oil collected in absence of the catalyst, in 27 wt% amount, no monomers were detected. While running the reaction under the optimized reaction conditions in a batch reactor, 4.4 wt% of monophenols were produced (ESI†). However, the reacted wood gave a mass loss of >66 wt% and severe contamination by the catalyst hindering further transformation into a bleached pulp. In this initial report, the RCF was not as efficient as other studies,37 mainly because of the heating supply configuration which led to condensation reactions. Further optimization of the catalytic step in the OrganoSoxhlet is required. Gratifyingly, the products that were originated from the reactions in presence of the catalyst under otherwise optimized conditions were not distinguishable from the ones reported without catalyst (Fig. 3).
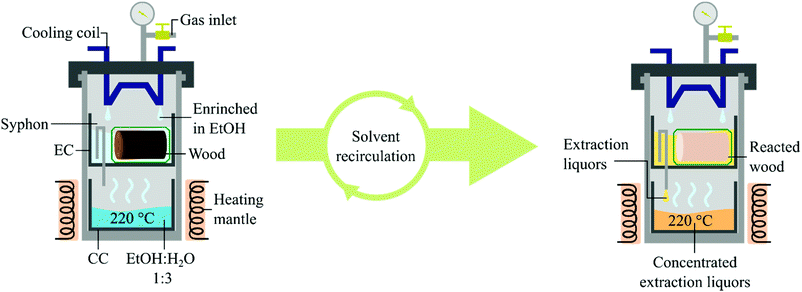 |
| Fig. 1 Schematic summary of the OrganoSoxhlet reactor over time. | |
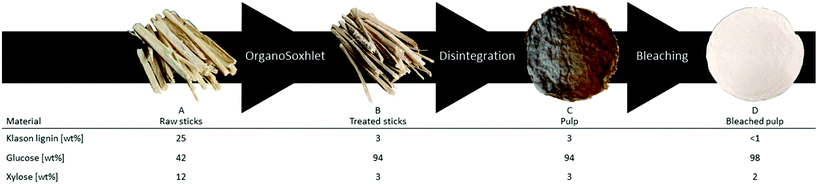 |
| Fig. 2 Poplar 23.4 composition over time, from sticks to bleached pulp. | |
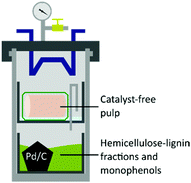 |
| Fig. 3 Catalytic OrganoSoxhlet. | |
Conclusions
An organosolv pulping performed in a high-pressure Soxhlet extractor has been developed. The reactor produced delignified pulp overcoming the need for any mineral acid, dewaxing, mechanical stirring, or late washing steps. Only a source of heat and a cooling flow under the CO2 atmosphere is required. The reported system can process up to 32.1 g of wood with only 200 mL of solvent (50 mL of which is ethanol) with a liquid to wood ratio of 6.6, yielding 13.8 g of dissolving grade quality pulp with an average delignification of 97% without any acidic pre-treatment. CO2 was found to have an active role in the pulping performance, due to the influence on the pH and consequently on the cleavage of LCCs. The resulting material was treated to yield bleached pulp with chemical and physical properties within the range of dissolving grade pulp, with a final yield of 43 wt% in respect to the initial biomass weight which is 99% of the theoretical maximum yield. By adding Pd/C to the reactor, reductive catalytic fractionation was operated on the lignin achieving an oil without affecting the quality of the final product nor the pulping performance of the system.
Conflicts of interest
There are no conflicts to declare.
Acknowledgements
We thank the Swedish Energy Agency for funding our research, Igor Lebedev (Comvics) for the technical support, and Drs Anneli Adler and Almir Karacic (SLU) for donation of poplar sample.
Notes and references
- FAOSTAT, http://www.fao.org/faostat/en/#data/QC, (accessed 21 December 2020).
- A. K. Chapagain, A. Y. Hoekstra, H. H. G. Savenije and R. Gautam, Ecol. Econ., 2006, 60, 186–203 CrossRef.
- Cellulose (dissolving pulp) manufacturing processes and properties, https://bioresources.cnr.ncsu.edu/, (accessed 21 December 2020).
-
H. Sixta, in Handbook of Pulp, John Wiley & Sons, Ltd, 2006, pp. 1009–1067 Search PubMed.
- I. Dimitriou and B. Mola-Yudego, For. Ecol. Manag., 2017, 383, 99–107 CrossRef.
- B. Mola-Yudego, O. Díaz-Yáñez and I. Dimitriou, BioEnergy Res., 2015, 8, 1769–1777 CrossRef.
- S. Y. Dillen, S. N. Djomo, N. Al Afas, S. Vanbeveren and R. Ceulemans, Biomass Bioenergy, 2013, 56, 157–165 CrossRef.
- A. Adler, A. Karacic, A.-C. R. Wästljung, U. Johansson, K. Liepins, A. Gradeckas and L. Christersson, BioEnergy Res., 2021, 14, 426–444 CrossRef CAS.
- H. Kumar and L. P. Christopher, Cellulose, 2017, 24, 2347–2365 CrossRef CAS.
- P. Sannigrahi, A. J. Ragauskas and G. A. Tuskan, Biofuels, Bioprod. Biorefin., 2010, 4, 209–226 CrossRef CAS.
-
R. Alén, in Industrial Biorefineries & White Biotechnology, ed. A. Pandey, R. Höfer, M. Taherzadeh, K. M. Nampoothiri and C. Larroche, Elsevier, Amsterdam, 2015, pp. 91–126 Search PubMed.
-
United States, US3585104A, 1971 Search PubMed.
- D. W. K. Chin, S. Lim, Y. L. Pang and M. K. Lam, Biofuels, Bioprod. Biorefin., 2020, 14, 808–829 CrossRef.
- T. Kleinert and K. v Tayenthal, Angew. Chem., 1931, 44, 788–791 CrossRef CAS.
-
H. L. Hergert
, Enviromentally Friendly Technol. Pulp Pap Ind.
- M. N. Borand and F. Karaosmanoğlu, J. Renewable Sustainable Energy, 2018, 10, 033104 CrossRef.
- S. V. den Bosch, W. Schutyser, S.-F. Koelewijn, T. Renders, C. M. Courtin and B. F. Sels, Chem. Commun., 2015, 51, 13158–13161 RSC.
- J. Kautto, M. J. Realff and A. J. Ragauskas, Biomass Convers. Biorefin., 2013, 3, 199–212 CrossRef CAS.
- D. S. Zijlstra, J. de Korte, E. P. C. de Vries, L. Hameleers, E. Wilbers, E. Jurak and P. J. Deuss, Front. Chem., 2021, 9, 329 Search PubMed.
- X. Pan, J. F. Kadla, K. Ehara, N. Gilkes and J. N. Saddler, J. Agric. Food Chem., 2006, 54, 5806–5813 CrossRef CAS PubMed.
- M. E. Vallejos, M. D. Zambon, M. C. Area and A. A. da S. Curvelo, Ind. Crops Prod., 2015, 65, 349–353 CrossRef CAS.
- L. Yao, C. Chen, C. G. Yoo, X. Meng, M. Li, Y. Pu, A. J. Ragauskas, C. Dong and H. Yang, ACS Sustainable Chem. Eng., 2018, 6, 14767–14773 CrossRef CAS.
- I. Dalmolin, E. Skovroinski, A. Biasi, M. L. Corazza, C. Dariva and J. V. Oliveira, Fluid Phase Equilib., 2006, 245, 193–200 CrossRef CAS.
- S. Rautiainen, D. Di Francesco, S. N. Katea, G. Westin, D. N. Tungasmita and J. S. M. Samec, ChemSusChem, 2019, 12, 404–408 CrossRef CAS PubMed.
- R. B. Santos, P. Hart, H. Jameel and H. Chang, BioResources, 2013, 8, 1456–1477 Search PubMed.
- E. Jasiukaitytė-Grojzdek, M. Huš, M. Grilc and B. Likozar, Sci. Rep., 2020, 10, 11037 CrossRef PubMed.
- Y. Zhang, Q. Hou, W. Xu, M. Qin, Y. Fu, Z. Wang, S. Willför and C. Xu, Ind. Crops Prod., 2017, 108, 864–871 CrossRef CAS.
- E. I. Evstigneyev and S. M. Shevchenko, Wood Sci. Technol., 2020, 54, 787–820 CrossRef CAS.
- A. C. Lindsay, S. Kudo and J. Sperry, Org. Biomol. Chem., 2019, 17, 7408–7415 RSC.
- S. Boufi and A. Gandini, RSC Adv., 2014, 5, 3141–3151 RSC.
- H. Kirci and M. Akgül, Turk. J. Agric. For., 2002, 26, 239–245 CAS.
- S. Zhang, C. Chen, C. Duan, H. Hu, H. Li, J. Li, Y. Liu, X. Ma, J. Stavik and Y. Ni, BioResources, 2018, 13, 4577–4592 Search PubMed.
- D. Ingildeev, F. Effenberger, K. Bredereck and F. Hermanutz, J. Appl. Polym. Sci., 2013, 128, 4141–4150 CrossRef CAS.
- M. M. Abu-Omar, K. Barta, G. T. Beckham, J. S. Luterbacher, J. Ralph, R. Rinaldi, Y. Román-Leshkov, J. S. M. Samec, B. F. Sels and F. Wang, Energy Environ. Sci., 2021, 14, 262–292 RSC.
- T. Renders, G. Van den Bossche, T. Vangeel, K. Van Aelst and B. Sels, Curr. Opin. Biotechnol., 2019, 56, 193–201 CrossRef CAS PubMed.
- M. V. Galkin, A. T. Smit, E. Subbotina, K. A. Artemenko, J. Bergquist, W. J. J. Huijgen and J. S. M. Samec, ChemSusChem, 2016, 9, 3280–3287 CrossRef CAS PubMed.
- D. G. Brandner, J. S. Kruger, N. E. Thornburg, G. G. Facas, J. K. Kenny, R. J. Dreiling, A. R. C. Morais, T. Renders, N. S. Cleveland, R. M. Happs, R. Katahira, T. B. Vinzant, D. G. Wilcox, Y. Román-Leshkov and G. T. Beckham, Green Chem., 2021, 23, 5437–5441 RSC.
Footnote |
† Electronic supplementary information (ESI) available: DETAILS. See DOI: 10.1039/d1gc03079e |
|
This journal is © The Royal Society of Chemistry 2021 |
Click here to see how this site uses Cookies. View our privacy policy here.