DOI:
10.1039/D0EE03648J
(Review Article)
Energy Environ. Sci., 2021,
14, 4203-4227
The role of supercritical carbon dioxide for recovery of shale gas and sequestration in gas shale reservoirs†
Received
18th November 2020
, Accepted 16th April 2021
First published on 16th April 2021
Abstract
The development of hydraulic fracturing and horizontal drilling techniques has promoted the exploitation of shale gas resources. However, using water has several potential drawbacks including environmental issues, e.g., the contamination of groundwater, surface water, and soil. Supercritical carbon dioxide (SC-CO2), with its special physical properties, has shown potential to enhance shale gas recovery replacing water as the stimulation fluid. This review summarizes the current status of shale gas recovery, the potential role of SC-CO2 as a working fluid for shale gas recovery, and CO2 geological sequestration in shale reservoirs. SC-CO2 has a better rock-breaking capability than water, which is useful when drilling through shale formations. SC-CO2 fracturing creates rougher and more complex fracture networks than hydraulic fracturing, leading to higher permeabilities. Some of the injected CO2 for shale gas recovery could also be safely sequestered in shale reservoirs, thereby lowering carbon emissions and accessing CO2 tax credits. However, shale–CO2 or shale–water/brine–CO2 interactions during & after shale gas recovery and sequestration can affect reservoir properties. The implied shale–CO2 imbibition process from available data generally persists for several years, far more than the several days assumed for most laboratory tests. A more detailed understanding is required for SC-CO2 injection on the efficiency of shale gas recovery and the cost and environmental concerns of this technology. This will support the development of safe sequestration methods, supported by suitable laboratory and field tests, especially those focusing on geochemical, petrophysical, geomechanical and hydraulic properties.
Broader context
The production of shale gas has been drastically increased because of the development of hydraulic fracturing. Though shale gas is a much cleaner energy resource compared to coal and oil, hydraulic fracturing has potential environmental impacts, e.g., the large consumption of water and the contamination of groundwater and earth surface. Supercritical carbon dioxide (SC-CO2), with its special physical properties, has shown potential to enhance shale gas recovery replacing water as the stimulation fluid. This article summarizes the current status of shale gas development, the potential role of SC-CO2 as a working fluid for shale gas recovery, and CO2 geological sequestration in shale reservoirs. Meanwhile, the challenges of SC-CO2 fracturing in shale reservoirs are discussed in detail. Particularly, the concerns of SC-CO2 enhanced shale gas recovery are addressed which includes diffusion and adsorption of CO2 in shale gas reservoirs, the CO2–shale or CO2–water–shale interactions and related changes in shale properties, and further concerns such as the costs, environmental impacts, and life cycle assessments of using SC-CO2 for shale gas extraction. This review provides an overall understanding of the application of SC-CO2 in shale gas development and the feasibility of CO2 sequestration in shale reservoirs.
|
1 Introduction
The United States Energy Information Administration (EIA) world energy outlook (2019) predicted that world energy demand will rise nearly 50% between 2018 and 2050, and fossil fuel will still be the dominant energy source.1 As stated in the 2015 Paris Agreement as well as the Intergovernmental Panel on Climate Change (IPCC), the transition to consuming more environmentally friendly energy is being pursued as a matter of urgency by many counties to meet the 1.5 °C target.2 Compared to oil and coal, natural gas is a much cleaner energy source, producing only 45% of the carbon dioxide (CO2) of coal.3 Unconventional gas (e.g. shale gas or tight gas), which is known to be present in large resource quantities around the world, shows potential as a bridging fuel to transition to renewable energy sources. Natural gas from shale could adequately supply the continued growth in energy demand for developing economies in the next few decades and contribute significantly to the demand for decreasing CO2 emissions.4
The development of hydraulic fracturing and horizontal drilling techniques has promoted the rapid exploitation of shale gas resources, particularly in North America.3,5 In the US, shale gas production increased from 1990 billion cubic feet in 2007 to 23
550 billion cubic feet in 2018.6 In addition to the US and Canada, other countries like China and Argentina are making progress in commercial shale gas production. However, drilling, and hydraulic fracturing require large amounts of water. In the US, the amount of injected water per well is 10
000 to 50
000 cubic meters, only 9–34% of which returns to the surface after hydraulic fracturing.7–11
Based on the research from the World Resources Institute (WRI), eight of the top 20 countries with the largest shale gas resources face arid conditions or high to extremely high baseline water stress where the shale resources are located. China and India, which account for one-third of the world's population, are included in the eight countries. The widespread use of hydraulic fracturing will put more people at risk of water shortages and more pressure on existing water resources.12
The fracturing fluids are usually composed of water plus proppant (≥98%) and chemical additives (<2%).13 It has been estimated that about 14 types of chemicals are used in each well, such as gelling agents to improve the carrying ability of proppant, hydrochloric acid to open the fractures and dissolve carbonate minerals, friction reducers (slick water) to aid the penetration of the injected fluids and other substances.14–16 Some chemical additives are toxic and some toxic substances are produced during fracturing,13 although, over time, the toxic components historically used in fracturing fluids have been significantly reduced by most operators under pressure to reduce their environmental impacts. The residual fracturing fluids in the shale reservoirs and the disposal of flowback water potentially leads to the contamination of groundwater, surface water, and soil if not handled carefully.17–20 In addition, hydraulic fracturing can induce microseismic events.21 Based on the above drawbacks, Western Australia, New Brunswick, and California, as well as France, Ireland, and South Africa have banned hydraulic fracturing. Therefore, it is essential to explore new approaches for shale gas recovery which could reduce or even eliminate water consumption in fracture stimulation.22,23
With its attractive physical properties (e.g., liquid-like density, gas-like viscosity, no capillary force and good miscibility with hydrocarbons), supercritical carbon dioxide (SC-CO2) is now under consideration as a fracture stimulation fluid or component of energized fluids injected into unconventional shale or tight gas reservoirs to enhance gas recovery.24–27 Similar to slick water, the low viscosity of SC-CO2 can create complex, multi-orthogonal fracture networks allowing high flow rates.28 SC-CO2 has a lower value of chemical potential than methane,29 which offers a significant advantage over water in that methane can be easily desorbed by SC-CO2 as the adsorptive capacity of SC-CO2 in shale is about 2–3 times higher than methane.30 In addition, shale gas reservoirs have the potential to become targets for CO2 sequestration when using SC-CO2 as the fracturing fluid,31–33 The development of techniques for capturing CO2 from fossil-based power plants and the atmosphere will make it possible to offer sufficient CO2 for shale gas recovery.34–36 Meanwhile, obstacles like the current high costs of capturing, pressurizing, and transporting of CO2, the efficiency of shale gas recovery affected by CO2–shale interactions, and the reliability of long-term entrapment and safety of CO2 sequestration in shale reservoirs, remain uncertain. The IPCC report states that CO2 emission reduction targets can only be met if carbon capture and storage significantly contribute to the mitigation strategies. If implemented, CO2 will become available in significant amount, ultimately reducing costs for capturing.
This paper systematically summarizes the current status of shale gas exploitation, the geological utilization and sequestration of CO2, and the role of SC-CO2 in shale gas recovery including SC-CO2 used as a drilling fluid, SC-CO2-based fracturing, and CO2 storage in shale gas reservoirs. The advantages and drawbacks of these (SC-)CO2-related studies and applications in literature are discussed. Further, the concerns of SC-CO2 enhanced shale gas recovery are addressed which includes diffusion and adsorption of CO2 in shale gas reservoirs, the CO2–shale or CO2–water–shale interactions and related changes in shale properties, and further concerns such as the costs and the environmental impacts of SC-CO2 injection for shale gas recovery. Challenges and perspectives are presented to expand our understanding and verify the feasibility of SC-CO2 enhanced shale gas recovery and CO2 sequestration in shale gas reservoirs.
2 Shale gas and exploitation
2.1 Global shale gas resources and exploitation status
Based on the EIA findings in 2016, the world's technically recoverable shale gas resources are over 200 trillion cubic meters (TCM), which could support global natural gas consumption for more than six decades based on current gas consumption.37Fig. 1 shows the distribution of the global shale gas resources: China has the largest gas reserves of 36.1 TCM. However, in 2019, China's foreign dependence on oil and natural gas amounted to 72% and 43%, respectively.38 The US and Argentina have the second and third highest resources with 24.4 and 21.9 TCM, respectively. However, it should be noted that many countries and regions have yet to fully evaluate and quantify their shale gas resources; especially in the Middle East, Australia, North Africa, and Russia where large resources are expected. Though such evaluations could change over time as more data becomes available, the reserves of unconventional natural gas, e.g., shale gas, are widely considered to be significantly greater than conventional natural gas.
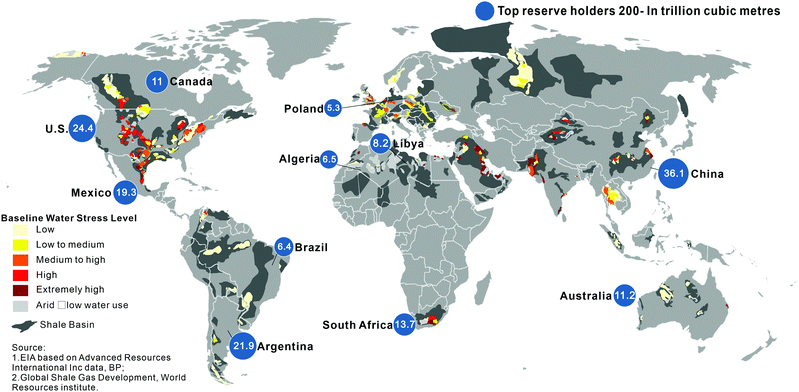 |
| Fig. 1 The global shale gas resources.12,39 | |
North America was the first region of the world to achieve commercial shale gas production. From 2007 to 2018, shale gas production increased by 702% to 0.6072 TCM per year,40 which is expected to increase until 2050. Texas’ Barnett shale was the first formation to commercially produce large quantities of shale gas and was the beginning or rapid technology development.41 The large-scale recovery of shale gas has helped the US to transform from an importer of natural gas into an exporter.3,42 Shale gas recovery has also rapidly developed in Canada. Although hydraulic fracturing is suspended or prohibited in the east of the country, shale gas production is expected to grow to annual values of 0.1926 TCM in 2050, mainly from western Canada.43 Commercial shale gas production in China commenced in 2010 and has grown continuously reaching annual volumes of 0.0154 TCM in 2019, making it the world's second-largest shale gas producer.
2.2 Overview of current gas recovery methods and fracturing fluids
Unconventional tight reservoirs, such as shale oil/gas, tight gas or coalbed methane, are characterized by their low permeability which is typically <1 mD.44,45 Therefore, advanced technologies such as horizontal drilling and multi-stage fracturing are required to commercially recover gas from such reservoirs.46–49
Shale formations are often characterized by laminated morphologies made up of multiple thin layers. Regionally, in broad basins the formations tend to be dominated by shallow dips, particularly in the deeply buried, thermally mature basin centers. In such conditions, horizontal wells can access much larger volumes of shale gas than vertical wells.50 When the vertical well reaches the shale formation, the drilling trajectories are adjusted by nearly 90 degree to a near-horizontal direction. One vertical well is likely to be branched into several lateral horizontal wells extending into the shale formation in different directions, like a radial net. The length of the horizontal well is commonly about 1 to 2 km.51 Horizontal drilling cannot on its own offer sufficient flow paths for gas moving from the adjacent shale formations into the wellbores. Therefore, hydraulic fracturing is needed to extract shale gas economically. Hydraulic fracturing is now widely used to enhance the production of unconventional oil and gas which are stored in tight reservoirs. During a hydraulic fracturing operation, high-pressure water is injected into a well and flows through the perforated zones. Fractures are created around and beyond the well. The hydraulic conductivity increases substantially following fracture stimulation, allowing more gas to be drained and flow into the wellbore.52 In order to maximize the fracturing efficiency, multi-stage hydraulic fracturing has become the standard stimulation technique applied to horizontal wellbores.53,54
There are various types of fracturing fluids employed for unconventional oil and gas recovery, which can be categorized as liquid-based fluids, foam-based fluids, and gas-based fluids, as shown in Table 1.
Table 1 The typical fracturing fluids used to stimulate tight gas and oil reservoirs
Liquid-based55–57 |
Foam-based58–60 |
Gas-based61,62 |
Water-based fluids |
Acid-based foams |
Air |
Acid-based fluids |
Liquid CO2-based foams |
CO2 |
Alcohol-based fluids |
Hydrocarbon-based foams |
N2 |
Emulsion-based fluid |
Alcohol-based foams |
|
Liquefied petroleum gas (LPG) fluids |
|
|
Water-based fluids were first used for hydraulic fracturing in Kansas in 1947.63 Slickwater, which is comprised of water-based fluids by 90 vol%, has the benefit of producing multi-fracture networks with high penetration depths, resulting in significantly enhanced permeabilities. Although such fluids are commonly the first choice for developing shale gas reservoirs, they have substantial drawbacks in certain locations and formations. Injecting large amounts of water typically results in a range of water–rock interactions, potentially causing formation damage.64 Mineral precipitation like carbonates can cause fracture closure and plugging of pore throats, thereby either decreasing fracture and/or matrix permeability or fully preventing accessibility to certain parts of the reservoir. The disposal of these vast amounts of back-produced fracturing fluids and formation waters requires huge capital expenses and, in some locations, the risk of impacting drinking water resources through aquifer contamination is given.65 To improve gas recovery from tight reservoirs, chemical additives are used in hydraulic fracturing fluids, which are increasingly recycled after back-production for reuse in subsequent stimulations. For example, polymer viscosifying agents are added in slickwater to improve its proppant-carrying ability. Hydrochloric or muriatic acid improves mineral dissolution which helps to enlarge fractures. However, some of these additives will produce toxic substances which, if not treated carefully, can lead to environmental contamination issues both above and below ground.20,66,67 Due to these issues and concerns about long-term effects associated with potential negative environmental impacts, the wide use of water-based fracturing fluids is contentious and a substantial number of countries and regions have enacted legislation to prohibit the use of hydraulic fracturing, at least temporarily while studies are conducted to better understand its impacts, and methods and materials are developed to mitigate its downside risks.68
The application of foam as a fracturing fluid has been investigated since the 1970s.69 Compared to water-based fluids, foam-based fluids present several desirable properties as potential fracturing fluids. Foams mainly consist of gas (60 to ∼95%, depending on the foam quality), reducing the consumption of water considerably. Foam has a high proppant-carrying and proppant-suspending capability, quick fluid recovery, low fluid loss into the formation and generally shows low formation damage.70,71 CO2 and N2 based foams are used most widely to replace water-based fracturing fluids.72 Compared to CO2 based foams, N2 based foams are generated at a low hydrostatic pressure, so that high surface pumping is necessary for most field applications, making this a relatively energy-intensive approach.58 On the other hand, CO2 transitions to its supercritical state when pumped into shale reservoirs.73 The behavior of SC-CO2 foam-based fluids is complicated because the multiphase flow includes a supercritical phase.74 To maintain the stability of fracturing fluids at high temperatures and pressures in shale reservoirs, surfactants and other chemicals are added during the process of foam generation at the surface.75 As with water-based fracturing fluids, the potential environmental impacts of these additives raise concerns about foam-based fracture stimulation fluid applications on a large scale.
Among the gas-based fracturing fluids, N2 has received more attention in research studies.76–80 Fracturing with N2-based foams consumes relatively little water and low quantities of chemical additives. Despite the easy accessibility, the large consumption of N2 in the stimulation of each well makes the fracturing process expensive. The low viscosity of N2 further limits its proppant suspension and transportation capability. N2-based fracturing can also induce self-propping fractures which contribute to fracture opening.81 However, this phenomenon is typically only induced on a meaningful scale in shallow wells. For shale reservoirs in China for example, most of which are deeper than 3000 m, self-propping typically only makes a minor contribution.
2.3 Drawbacks of hydraulic fracturing
2.3.1 Environmental concerns.
In general, environmental concerns associated with unconventional oil and gas development can be categorized into four main groups, including community issues (e.g., industrial noise and induced seismicity), water issues (e.g., groundwater and surface water contamination), land issues (e.g., ecosystem impacts), and atmospheric issues (e.g., air pollution).82–84 Recently, there is extensive research and debate in academia, industry, and society in general about the environmental impacts of unconventional reservoir development. In 2016, the US Environmental Protection Agency (EPA) reported the impacts of hydraulic fracturing water cycle on drinking water resources.85 It is widely recognized that the injection of water at high-pressure into subsurface formations can lead to pollution of the hydrosphere, biosphere, and atmosphere with serious consequences for flora and fauna and the quality of drinking waters. Another consequence is induced seismicity which may cause damage to surface structures, associated risks of personal injury, and potentially compromise the integrity of wellbores and other subsurface infrastructure (e.g., flowlines and pipelines).7,84,86–90 Among all above mentioned environmental risks, water issues, including water use and reuse, water contamination, and wastewater disposal, are the most direct and perhaps have the greatest negative impacts.
The hydraulic fracturing fluid generally consists of three components:91 (i) the base fluid, which is the largest constituent (usually 98% or more) by volume and is typically water, (ii) the additives, which are generally a mixture of chemicals (as listed in Table 2), and (iii) the proppant, which is solid material designed to keep hydraulic fractures open. The chemical additives in the fracturing fluid and the products of their interaction with the organic matter and radioactive elements in the formation are initially released into the subsurface shale formation, some of which eventually flows back to the surface.92 The flow-back water may contaminate underground drinking water sources and the surface environment if not carefully handled.93,94 Of course, there has been a continuous effort to develop safer additives, and more importantly, there are no documented cases of propagation and contamination of fracturing fluid to shallow aquifers, though the potential for hydraulic fractures to propagate to the near-surface deserves special concern.85 Water contamination may occur especially in scenarios of shallow fracturing in the vicinity to aquifers and/or the regional groundwater levels, poorly cemented casing in the wellbores, and surface spills due to equipment failures or improper fluid-handling operations.66,95,96 In addition to the leakage of fracturing fluids, flow-back fluids and wastewater may perturbate the groundwater equilibrium and the stability of geochemical and hydrodynamic processes in the subsurface.88
Table 2 Common chemical additives in hydraulic fracturing fluids92
Additive type |
Example compounds |
Purpose |
Acid |
Hydrochloric acid |
Wellbore clean out, mineral dissolution, fracture initiation |
Friction reducer |
Polyacrylamide, petroleum distillate |
Minimize friction between fracturing fluid and wellbore pipe |
Corrosion inhibitor |
Isopropanol acetaldehyde |
Pipe corrosion prevention by diluted acid |
lron (Fe2+) control |
Citric acid, thioglycolic acid |
Prevent precipitation of metal oxides |
Biocide |
Glutaraldehyde, 2,2-dibromo-3-nitrilopropionamide (DBNPA) |
Bacterial control |
Gelling agent |
Guar/xantham gum or hydroxyethyl cellulose |
Thicken water to suspend proppants (e.g. sand) |
Crosslinker |
Borate salts |
Maximize fluid viscosity at high temperatures |
Breaker |
Ammonium persulfate, magnesium peroxide |
Promote breakdown of gel polymers |
Oxygen scavenger |
Ammonium bisulfite |
Remove oxygen from fluid to reduce pipe corrosion |
pH adjustment |
Potassium or sodium hydroxide or carbonate |
Maintain effectiveness of other compounds (such as crosslinker) |
Proppant |
Silica quartz sand |
Keep fractures open |
Scale inhibitor |
Ethylene glycol |
Reduce deposition on pipes |
Surfactant |
Ethanol, isopropyl alcohol,2-butoxyethanol |
Decrease surface tension to allow water recovery |
The development of shale gas plays can also lead to air pollution. Greenhouse gases, such as methane from fugitive emissions and carbon dioxide, and toxic gases like ozone and aromatic-rich vapors released from aromatic hydrocarbon liquids such as benzene, are produced regularly during fracture stimulation activities. The released greenhouse gases can degrade air quality and contribute to climate change. The toxic components can have negative health impacts and cause eco-system damage.97,98
2.3.2 Poor hydrocarbon recovery.
Shale is mostly water-wet and the initial water saturation is less than 100%.99,100 During the shale gas recovery process via hydraulic fracturing, water will imbibe into microfractures and shale pore system. Because of the capillary force, water will stay in the fractures or pores which narrows or even block the gas flow pathways.101 Therefore, the permeability of shale will decrease after water imbibition.102–104 The reduction of shale permeability will increase with the increase of water saturation.47,105
Injecting large amounts of water into shale reservoirs may cause specific water–shale interactions, potentially leading to reduced hydrocarbon recovery. Swelling clays, such as smectite, have the ability to take up water, leading to a volumetric expansion. If present in the shale reservoir, this can result in a reduction in pore and pore throat sizes.106 The swelling potential can be classified by the activity value which is a ratio of plasticity index and clay fraction.107Fig. 2 summarizes the swelling potential of several shales with different clay fractions.108–111 It can be seen that shales present appreciable swelling potential which increases with increased clay content. Even with clay content as low as 7%,112 the maximum free swelling percentage was about 1.6%. The swelling of shale can decrease the accessible specific surface area, ultimately reducing gas that could desorb and produced from the shale matrix.113 As water filtrates into cracks and pores, it tends to block the pore throats and trap hydrocarbons. The water-blocking effect leads to a decrease in permeability.102,114
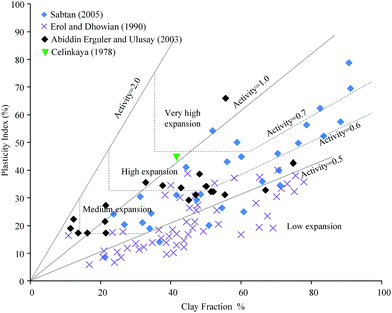 |
| Fig. 2 The swelling potential of shale with different clay fractions.108–111 | |
3 CO2 emissions and CO2 utilization, and storage
3.1 Anthropogenic CO2 emissions and global impacts
Present and future worldwide economic growth relies on the consumption of fossil fuels. Coal, oil and natural gas are responsible for a large amount of the global energy supply and similarly contribute to overall CO2 emission.115 In 2019, a total of 33.3 gigatons (Gt) of CO2 were emitted to the atmosphere globally, which is ∼60% higher than in 1990.116 In the US, more than 60% of the total stationary CO2 emissions are contributed by large stationary sources, like power plants, cement production plants, iron and steel manufacturing facilities, etc.117 It is important to note that different stationary sources have different CO2 quantities in their flue gases. Coal and natural gas-fired power plants, which are the major sources of CO2 with large flow rates, have flue gas compositions containing only 4–14% CO2. On the other hand, flue gas CO2 compositions of iron and steel production, agricultural processing and sugar production plants are often higher than 40%. The IPCC emphasizes that a 50% reductions of CO2 emission should be reached to limit the rise of global average temperature to 2–2.4 °C by 2050.118,119 How to limit the growth of CO2 emission has become a worldwide challenge and technically feasible and cost-effective solutions are not yet readily available.
In line with increasing CO2 emissions, atmospheric CO2 concentration have increased drastically at the same pace with the Earth's temperature (Fig. 3). This increasing trend is expected to continue due to forecasted global economic growth and industrial development.120 Consequently, global warming is generally expected to increasingly result in climate change which has significant impacts on all ecosystems.121 Consequently, CO2 emissions need to be limited to protect the environment for the benefit of all life on Earth.
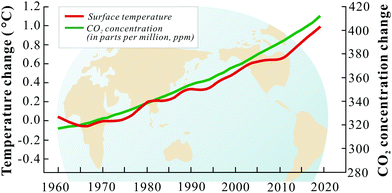 |
| Fig. 3 The variations of CO2 concentration/earth temperature with years.122,123 | |
3.2 CO2 utilization and sequestration in geoenergy exploitation
CO2 capture, utilization, and storage (CCUS) is considered a key requirement to limit CO2 emissions to the atmosphere, contributing at least one-sixth of global CO2 emission reductions by 2050.124 It is further estimated that CCUS will lead to a 14% reduction in cumulative emissions between 2015 and 2050 to achieve the targeted 2 °C scenario by 2050, and thereby reduce the overall costs required to mitigate the negative global impacts of climate change.124 The utilization and sequestration of CO2 in energy exploitation have shown promising potential to decrease the total CO2 emission.
3.2.1 CO2 utilization.
The utilization of CO2 can be divided into two types: physical utilization and chemical utilization.119 The physical utilization means CO2 is directly used without any conversion,125 while the chemical utilization involves CO2 being partially or totally converted to chemicals and fuels.126–128 Norhasyima and Mahlia129 have statistically analyzed the CO2 utilization methods from 3002 related patents searched from the Derwent Innovation. They found that, more than half of them were related to chemicals and fuel, a quarter d to enhanced oil (EOR) and enhanced coalbed methane (ECBM) recovery, 16.3% to biofuels from microalgae, mineral carbonation accounted for 3.4% and enhanced geothermal system (EGS) contributed 1.5%. The patent applications provide insight to the potential utilization of CO2 in geoenergy recovery.
3.2.1.1 CO2-EOR.
The primary oil recovery for conventional and unconventional formation is less than 20% and 10%, respectively.130,131 This means that large quantities of oil remain in the reservoir. The injection of CO2 has the potential to increase oil recovery by 5–15%.132–134 A schematic diagram for CO2 enhanced oil recovery is shown in Fig. 4. The potential additional oil recovery by secondary and tertiary recovery using carbonated (or CO2-saturated) water injection is 6.2–56.74% and 9–40.54%, respectively.135 The injection of CO2 increases the pressure of depleted oil formations and decreases the viscosity of oil, thereby creating high flow rates and mobility for additional recovery of oil. Meanwhile, CO2 especially under supercritical conditions, is a highly effective solvent that can decrease the viscosity of oil, allowing the oil to flow through the reservoir and into wellbores more easily.136–138 CO2 can penetrate into micropores and nanopores and dissolve the oil, leading to oil expansion. The increase in oil volume makes the oil easier to migrate in the reservoir and to the production well. Intermediate components of oil gradually form the miscible phase with CO2, reducing the oil and gas interfacial tension.139–141 Because of these benefits, CO2-EOR has been applied in many countries. As of 2019, there are more than 150 individual CO2-EOR projects around the world.142
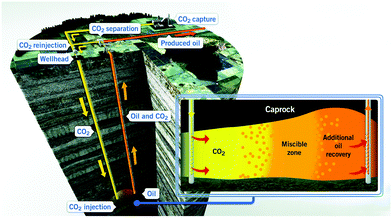 |
| Fig. 4 A schematic diagram for CO2-EOR.143 | |
3.2.1.2 CO2-ECBM.
In 2017, the proven coalbed methane reserves in the US were 11 TCF,144 with a recovery efficiency of 20–60%.145 Coalbed methane can be enhanced by CO2 injection as a secondary recovery mechanism.146,147 The injection of CO2 maintains the pressure of the coal seams and higher sorption ability promotes methane desorption from internal porous surfaces of coal. Then the desorbed methane migrates through the pore space or cleats (fractures in coal) to the production well.145,148–151 Several pilot and micro-pilot projects of CO2-ECBM have been applied in Australia, Canada, Japan, China, Poland and the US.150
3.2.1.3 Other utilization methods.
(1) Chemicals and fuel. In the chemical industry, CO2 is a suitable feedstock in fuel cells or hydrogen sources for electricity.152,153 CO2 can also be used to manufacture urea, salicylic acid, cyclic carbonates, formic acid and polycarbonates.154 However, current market demands for these products are relatively small. (2) Mineral carbonation. Some carbonates such as magnesium carbonate (MgCO3) and calcium carbonate (CaCO3), can be produced through CO2 mineralization processes.155 Feedstocks like natural silicate ores156 and alkaline solid wastes157,158 can be used in these processes. The mineralization is achieved by four methods: direct and indirect carbonation, carbonation curing, and electrochemical mineralization.159,160 (3) Enhanced geothermal systems (EGS). A typical EGS uses water or brine as the heat exchange fluid. Recent studies have shown that CO2 could be an alternative working fluid because of the following advantages: a poor solvent for the minerals, low viscosity which leads to high heat extraction rate, and large compressibility and expansibility which can generate favorable buoyancy forces.161–165 (4) Biological algae cultivation. Algae are among the oldest phototrophic organisms to evolve on Earth and they have the ability to utilize CO2 as a food source from the atmosphere, soluble carbonates, and discharged gases from heavy industry. Algae cultivation can be performed in an open or closed systems and controlled by various precursors.166 Certain algae offer the potential to efficiently manufacture biodiesel on a commercial scale.167
3.2.2 CO2 sequestration.
Generally, the approach adopted for CO2 sequestration is to capture CO2 emission point sources like coal fired power plants, to transport it to an injection site, and to then sequester it in subsurface formation over long periods of time.168,169 Considerable amounts of carbon dioxide will dissolve in formation waters, and might become mineralized (in the form of carbonates) over extended periods of time.170,171 Potential CO2 sequestration sites available are saline aquifers, depleted gas and oil reservoirs, unminable coal seams, and actively producing oil fields combined with enhanced recovery processes (see above).172–177
With more than 100 years of oil and gas exploitation, many oil and gas fields have already been depleted or are approaching the end of their commercially productive lives.133 Benefits of CO2 storage in depleted gas and oil reservoirs include:178 (1) the oil and/or gas already removed offers plenty of original CO2 storage capacity; (2) CO2 can be stored at pressures that are close to the original reservoir pressure prior to production which avoids the risk of long-term formation damage and potentially inducing man-made subsidence at the surface; (3) the favorable geological conditions that originally facilitated oil and gas entrapment decrease the risk of CO2 leakage through the primary caprock; (4) exiting wells and other infrastructure installed originally for oil and gas production purposes can be re-used for CO2 injection. Meanwhile, the depths of most hydrocarbon fields are greater than 800 m, which ensures that the CO2 would be stored in the supercritical phase.179
CO2 sequestration projects have been applied by many countries, as listed in the ESI.† By October 2019, there were 19 large-scale CCUS projects operating around the world storing ∼32 Mt of CO2 per year.‡
180 In the past 40 years, more than 1 billion tons of CO2 were injected for CO2-EOR operations in the US, and more than 99% of the injected CO2 remains safely trapped.181 The development of CO2 geological storage still needs supports from the government, such as the 45Q tax incentive in the US,182 and tools to better characterize and understand large-scale sequestration.183,184
4 Role of SC-CO2 in shale gas recovery and sequestration in shale gas reservoirs
When studying shale gas recovery, SC-CO2 has the potential to support three different key aspects: drilling, fracturing and long-term storage (Fig. 5). In this section, the potential of the three aspects are discussed.
4.1 SC-CO2 based drilling
The high-pressure water-jet technology has been widely used for drilling in the oil and gas industry since the 1950s. To further improve the drilling efficiency and rock cutting or breaking performance, structures and properties of the water jet have been optimized to develop various types of jets (e.g. abrasive, cavitating, rotary, pulsed non-circular nozzle).185–187 With the rapid development of deep resource exploration, more and more deep and ultra-deep vertical wells and long horizontal wells being used. This has intensified the demand for improving the rates of penetration (ROP) and minimizing the turn radius to reduce the cost of exploration and exploitation. The traditional high-pressure water jet offers few advantages for improving drilling efficiency because of the water-lock effect, the high threshold pressure for water jet erosion and the large pressure loss of coiled tubing.188,189 Air drilling fluids like foams and nitrogen can create satisfactory underbalanced drilling (UBD) conditions which in many subsurface conditions are beneficial for the improvement of ROP. However, their low density makes it difficult for such fluids to provide sufficient torque for bottom hole motors to operate efficiently.190 SC-CO2, which has liquid-like density, is an attractive choice by the drilling industry for certain sub-surface conditions. Above critical temperature and pressure for CO2, which is typically the case in shale gas reservoirs with horizontal wells, CO2 is in the supercritical phase.
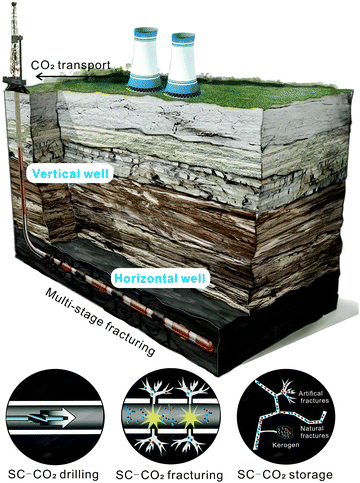 |
| Fig. 5 The role of SC-CO2 in shale gas recovery. | |
Kolle189 was the first to conduct laboratory tests to evaluate the SC-CO2 based drilling potential. The results show that the threshold erosion pressure for CO2 is ∼67% of water in the Sierra white granite and 44% of water in the Mancos shale. The specific energy for cutting granite with SC-CO2 is 42% of water and only 3% of water in shale. Since then, other studies have used additional experimental and numerical methods to further investigate the SC-CO2 jet. Gupta191 developed a circulation model to calculate the SC-CO2 jet impact force and the cuttings transport ratio. Results show the advantage of SC-CO2 drilling, specifically that its liquid-like density can turn the downhole motor and gas-like viscosity can maintain underbalanced conditions. Al-Adwani, et al.192 simulated the erosion rate of pure SC-CO2 in UBD operations, concluding that SC-CO2 is a viable UBD fluid.
In an experimental study using artificial rock cores, Du, et al.193 found that a SC-CO2 jet is able to achieve a higher rock-breaking depth than a water jet at the same pressure. Following these initial findings, a series of experimental and numerical studies were conducted to optimize the structure of nozzles which can improve the drilling ability of SC-CO2 jets.190,194–196 Meanwhile, further investigations were performed to analyze the flow field of SC-CO2 jets in wellbore conditions.197 It was found that the effects of pressurization,198 real gas behavior,199 and self-excited oscillations200 in SC-CO2 jets are beneficial for rock-breaking, while the stagnation effect201 has a detrimental impact on drilling (Table 3). Considering the low viscosity, the feasibility of SC-CO2 for carrying cuttings was experimentally and theoretically verified.202 The results showed that cuttings are difficult to transport when the well angle is between about 60° and 80°. Fortunately, the viscosity of SC-CO2 can easily be increased by adding additives such as the fluoroether disulfate telechelic ionomer, to improve its ability to effectively carry cuttings.203 A comparison of drilling ability between water and SC-CO2 is listed in Table 4.
Effects |
Key findings |
Pressurization effect195 |
The pressurization effect during SC-CO2 jet fracturing improves with an increase in pressure difference, ambient pressure, nozzle diameter, and fluid temperature; SC-CO2 jet fracturing achieves improved pressurization compared to a water jet in deep boreholes. |
Real gas effect198 |
Simulations covering the typical operating ranges (the liquid and supercritical regions) show that the Joule–Thompson throttling effects are much more prominent at higher inlet temperature and larger pressure drops. |
Self-excited oscillation effect199 |
The impinging peak pressure is higher than that of the continuous SC-CO2 jet; the frequency distribution is different from that of the self-excited oscillation pulsed water jet. |
Stagnation effect201 |
The increase of injection pressure presents a large increase of the stagnation pressure and a minor decrease of the ambient temperature; the stagnation temperature is mainly controlled by injection temperature. |
Table 4 The comparison of drilling ability between water and SC-CO2189,191–193,202
Factor |
Comparison between water and SC-CO2 |
Threshold erosion pressure |
SC-CO2 is 56% lower than water (same condition in the Mancos shale)189 |
Specific cutting energy |
SC-CO2 is 97% lower than water (same condition in the Mancos shale)189 |
Cuttings transport ratio |
SC-CO2 is better than water because SC-CO2 can maintain underbalanced conditions191 |
Erosion rate |
SC-CO2 is higher than water192 |
Rock-breaking depth |
SC-CO2 is deeper than water193 |
Cutting-carry ability |
Water is better than SC-CO2202 |
4.2 Using SC-CO2 as a fracturing fluid
SC-CO2 fracturing has been investigated through experimental and numerical methods.204–207 Due to its low viscosity and lack of surface tension, SC-CO2 used as a fracture stimulation fluid, has the potential to lower the formation breakdown pressure and create more irregular multiple fractures compared to liquid CO2 or water. Wang, et al.208 used the Niobrara shale to conduct fracturing experiments with gaseous and SC-CO2, as well as slickwater with the same confining pressures and temperature. They found that gaseous and SC-CO2 induced fracturing occurred at much lower pressures than slickwater fracturing, which were 6.6 MPa, 9.6 MPa and 11.0 MPa, respectively. In a numerical study, investigating the fracturing process with water, viscous oil and SC-CO2,209 it was demonstrated that SC-CO2 has the lowest and viscous oil the highest breakdown pressure. Fernandez, et al.165 used numerical and experimental methods to investigate the fracability of a CO2-reactive polymer (CO2 + nontoxic poly(allylamine)). They found that this nontoxic SC-CO2-based fracturing fluid could be used to fracture rock cores at lower net pressures, which was caused by the CO2-triggered volume expansion and the reduction in pore invasion pressure caused by the lower interfacial tension. Zhang, et al.210 found that SC-CO2 fracturing was more likely than hydraulic fracturing to create fractures, especially secondary fractures near the tail end of the transverse fractures that connect with natural fractures and bedding planes to form a more complex and interconnected fracture network. These results were confirmed by using coupled modelling to simulate shale fracturing using SC-CO2, liquid CO2, and water (Fig. 6).210,211 SC-CO2 fracturing can create rougher and more complex fracture surfaces than hydraulic fracturing, resulting in higher tortuosity of fractures created by SC-CO2 compared to freshwater (Fig. 7).212–215 While keeping the fracturing conditions the same, SC-CO2 induced an artificial fracture area, which was 60% higher than that induced by hydraulic fracturing.213 In addition, the fractal dimension of SC-CO2 induced fracture surface ranged from 2.2314 to 2.2660, higher than that of the water fractured surface (ranged from 2.0855 to 2.1058),215 indicating more complex rough surfaces. Generally, shale is an anisotropic sedimentary rock with geomechanics and transport properties varying significantly in the horizontal compared to the vertical direction. As such, the orientation of bedding related to the vertical load affects fracture propagation.77 It was found that the breakdown pressure with SC-CO2 fracturing was higher than that with freshwater fracturing when the bedding plane orientation varied from 0° to 90°.212 The reservoir stress and temperature, which also affect the fracturing characteristics, have been investigated by some researchers.78,216,217 The increase of temperature reduced the viscosity of SC-CO2 which can easily permeate into the microcrack tip and promote fracture propagation. The SC-CO2 flow in newly created void fractures will enhance fracturing because of the thermo-mechanical effects caused by the Joule-Thompson throttling process.218
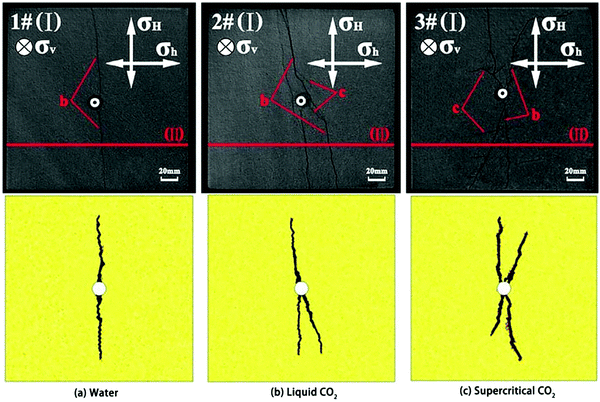 |
| Fig. 6 Fracture matrix created by different fracturing fluids. The upper images are CT scanning results for experimentally fractured Lower Silurian Longmaxi Formation shale cubes with sizes of 200 mm × 200 mm × 200 mm (σH (= 10 MPa) and σh (= 8 MPa) mean the horizontal principal stresses, σv (= 12 MPa) mean the vertical injected stress, b and c mean different types of fractures),210 the lower images are numerical results with the same boundary conditions.211 | |
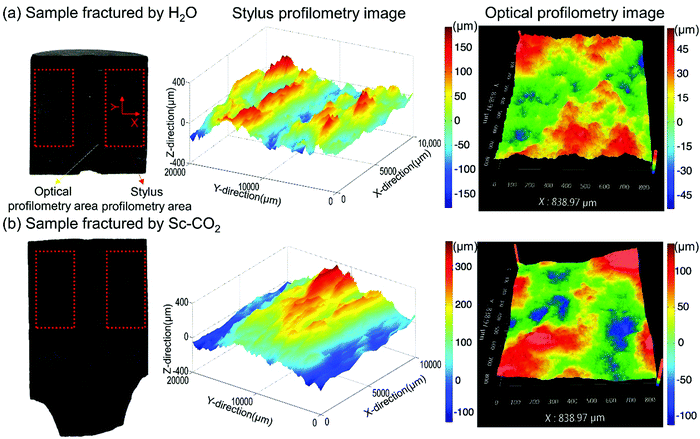 |
| Fig. 7 Surfaces of fractures created by water (a) and SC-CO2 (b).215 The stylus profilometry scan focused on an area of 20 mm × 10 mm (red line) and the optical profilometry scan focused on an area of 838.97 μm × 838.97 μm (yellow line). | |
Similar to N2, the low viscosity of SC-CO2 limits its transport capacity for proppants. However, SC-CO2 is a good solvent for synthetic polymers,219 which allows the viscosity to be modified by adding CO2-philic chemicals (e.g. fluoroether disulfate telechelic ionomer) to enhance proppant lifting, transport and delivery under borehole conditions.22,220,221 The composition of the natural gas in shale reservoirs, specifically its natural gas liquid concentrations, is also likely to impact the physical properties of SC-CO2 injected into gas-rich formations. For example, varying concentrations of methane, ethane, propane and nitrogen are known to impact the minimum miscibility of CO2-rich fluids with oil222 and are likely to impact SC-CO2 properties as it penetrates into a shale gas formation.
Field tests conducted in the Yan-2011 shale gas well in China showed that SC-CO2 fracturing was able to create a more complex fracture network than hydraulic fracturing.223 However, field tests for SC-CO2 fracturing are still limited. The microseismic response distributions after SC-CO2 fracturing need to be mapped and evaluated in more detail for a range of shale formations to better define the fracture network development potential SC-CO2 fracturing.21 Further field-scale studies are required to obtain additional information on actual shale gas recovery from real anisotropic shale formations, not just laboratory tests.
4.3 CO2 storage in shale gas reservoirs
When injected into shale gas reservoirs, CO2 is preferentially adsorbed over methane on organic and inorganic pore surfaces, resulting in methane desorption and CO2 storage within these formations. In addition, natural and induced fractures offer additional volumes for CO2 storage, in combination making shale gas reservoirs a potential sink for CO2 sequestration.
Godec, et al.32 estimated the theoretical CO2 storage capacity in the Marcellus shale in the Eastern US at >915 m depth. Considering reservoir properties (depth, thickness, total organic carbon, effective porosity, apparent gas saturation, CO2 and methane adsorption isotherms, and permeability), the adsorbed CO2 storage capacity is about 0.92 million tons per square kilometer (Mt per km2). Based on the statistical data from the US Energy Information Administration (EIA) which assesses the technically recoverable shale gas resource around the world,224 nearly 70 types of shale gas formations from 48 shale gas basins in 32 countries represented primary gas productions ranging from 20% to 35%. The reservoir characteristics of the Marcellus shale are similar to the shale gas basins with an average production of 25%. Assuming an additional 7% of shale gas production enhanced by CO2 injection, the total shale gas production for Marcellus shale is 32%.32 As such, it can be calculated that nearly 55 Gt of CO2 could potentially be sequestrated in the Marcellus shale. This CO2 storage capacity is 1.7 times larger than the world's CO2 emissions in 2019. In additional to the Marcellus shale, other shale formations such as the Barnett Shale in the US, the Montney Shale in Canada, and the Longmaxi shale in China which also show considerable technically recoverable shale gas resources, could potentially be used to sequestrate substantial quantities of CO2. It was therefore concluded that the potential of CO2 storage in shale gas reservoirs can fulfill the target of reducing 14% of CO2 which is and will be produced before 2050.124
The sustainability and safety of geological CO2 storage in shale reservoirs are the most important issues requiring careful assessments. The CO2 trapping mechanisms in saline aquifers are structural and/or stratigraphic trapping, residual (capillary) trapping, solubility trapping, and mineral trapping.225 However, adsorptive trapping plays a significant role in shale gas reservoirs due to their high clay and organic matter contents, providing significant internal surface area.226–228 simulated the feasibility of CO2 storage in the New Albany Shale and found that more than 95% of the injected CO2 was stored in the form of sorbed gas. As methane can be safely stored in the shale reservoir for long periods of time, the adsorption of CO2 is also expected to be safe and stable and CO2 has the potential to penetrate some of the nano-pores that hydrocarbon gases are unable to reach. This property is already exploited in gas adsorption studies to measure the nano-porosity distributions of shale. Liu, et al.229 solubility trapping and mineral trapping are more effective over longer timescales.230 However, the matrix swelling and mineral dissolution that cause permeability variations strongly affect the cap sealing performance.231–233 The risk that some shale reservoirs may not be sealed adequately to prevent long-term seepage of CO2 needs to be carefully evaluated in detail for each formation and potential trap. To date studies addressing long-term seepage of CO2 from shales are limited.
5 Concerns of SC-CO2 enhanced shale gas recovery and sequestration in shale gas reservoirs
5.1 Diffusion and adsorption of CO2 in shale gas reservoirs
5.1.1 Advective and diffusive flow in shale gas reservoirs.
The Knudsen number (Kn) is a commonly used parameter to classify flow regimes in porous media.234,235 It is a dimensionless parameter, which is defined as the ratio of the molecular mean free path of gas and the characteristic pore size. Accordingly, continuum, slip, transition, and Knudsen flow can be distinguished as summarized in Table 5.
Table 5 Flow-regime classifications based on Knudsen number236
Flow regime |
Knudsen number |
Description |
The details for Knudsen correction are provided in ref. 236.
The details for Knudsen correction are provided in ref. 237.
|
Continuum (viscous) flow |
Kn < 0.01 |
Darcy's equation for laminar flow, Navier–Stokes equations for turbulent flow |
Slip flow |
0.01 < Kn < 0.1 |
Darcy's equation with Klinkenberg correction |
Transition flow |
0.1 < Kn <10 |
Darcy's law with Knudsen correctiona |
Knudsen's (free molecular) flow |
Kn >10 |
Knudsen diffusion,b usually occurs in nanopores |
Typically, shale formations are multi-scale porous media, particularly thermally mature organic-rich shales. The space for gas storage and migration within shale reservoirs varies from meter scale to nanometer scale (Fig. 8). At the reservoir scale, gas moves through the reservoir (through the matrix and along connected fracture networks) and eventually flows into the wellbore due to pressure gradients. At the mesoscale, free gas in hydraulic fractures, natural fractures and macropores migrates following Darcy's law. At the microscale, the slippage effect and Knudsen diffusion become significant, because at that scale continuum assumptions for the pore space are partly invalid. At the nanoscale, gas adsorption and desorption and surface diffusion are primary mechanisms controlling gas migration.237,238 Certain gases such as CO2 and He, due to their molecular structure and size enter and move more easily than others at the nanopore scale. In adsorption tests on organic-rich shales with abundant nanopores, CO2 and CH4 penetrate the nanoscale pores more easily than N2.229
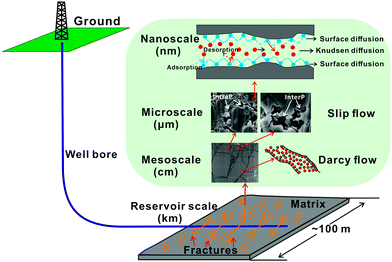 |
| Fig. 8 Gas storage and migration in shale reservoirs occurs at multiple pore scales with at least four distinct flow and gas movement mechanisms involved. | |
(1) Stress sensitivity effect.
During shale gas production, the effective stress of the formation will increase continuously due to a reduction in pore fluid pressure. At higher effective stresses, hydraulic fracture apertures decrease, resulting in a decrease in fracture transmissivity.239,240 Therefore, understanding the permeability variations of shale gas reservoirs in terms of effective stress is essential for long-term shale gas production, especially for stress-sensitive formations.241 To accurately estimate formation properties and shale gas production forecasts, various studies report permeability models coupled to mechanical effects.242–247 Liehui, et al.238 compared the different models and found that the Palmer and Mansoori248 model is suitable to describe permeability variations of a shale gas well over its entire production life span. Because of gas desorption in shale gas reservoirs, shale matrix shrinkage progressively occurs but particularly during the late production stage which can lead to an increase in permeability.238
(2) Slippage effect.
In conventional oil and gas reservoirs, fluid flow can be described according to Darcy's law where it is assumed that fluid flow occurs in an unimpeded continuum. However, in shale gas reservoirs, micropores and nanopores account for a non-negligible percentage of the total pore volume. At depth, gas flow paths in micropores are comparable to the gas mean free path length. Darcy's law, therefore, needs to be modified in such media because the continuity assumption is invalid.
According to the continuity assumption, the velocity of gas on the pore wall is zero. However, in micropores or nanopores, a non-zero molecular velocity should be considered at the pore wall, which is called the slippage or Klinkenberg effect. The slippage effect strongly affects the gas flow in shale reservoirs. Therefore, theoretical and experimental studies have been performed to describe the gas flow behaviors242,249–251 and a comprehensive summary is provided in Liehui, et al.238 There, it was pointed out that the two most commonly used methods for modeling gas flow including slippage are an empirical Klinkenberg correction and slippage modification based on slip boundary conditions. For the empirical Klinkenberg correction, the intrinsic permeability is corrected by an equation that includes pore pressure, the slippage factor, and apparent permeability.252 For the slip boundary conditions, the first order, second (or higher) order and Langmuir slip boundary conditions are used to describe the gas flow in a transitional flow regime.253,254
5.1.2 Sorption capacities and competitive adsorption of CO2versus CH4.
5.1.2.1 Shale gas sorption capacities.
Shale gas is commonly stored in reservoirs as dissolved gas, in the sorbed and in the free gas state. Sorbed gas accounts for 20 to 85% of the total shale gas storage capacity255 and is therefore important in the shale gas resource assessment. The gas sorption capacity of shales has been widely recognized as being closely related to moisture content, surface area, pore size distribution, total organic carbon (TOC) content, organic matter type and maturity, as well as clay mineralogy and clay content.256–262
TOC content is considered the most significant control on methane sorption capacity.263–265 Organic matter, typically quantified as TOC, is the source of the hydrocarbon gases present in a shale, while gas generation is mainly controlled by temperature and time during burial. Micropores in organic matter (<2 nm) provide high specific surface areas in comparison to macropores (>50 nm), particularly in thermally mature shales.261,266 Therefore, the methane sorption capacity correlates positively with TOC.259,267 Organic matter type and thermal maturity play complex roles in methane sorption capacity. For gas shales in the gas window, the sorption capacity shows a positive relationship with maturity because microporosity increases with maturity. Source rock organic matter can be classified in three types, which are found to generally show different sorption capacities, with Type I (lacustrine) < Type II (marine) < Type III (terrestrial).268 The micropores in clay minerals are also able to adsorb significant amounts of methane. For clay-rich shale, the methane sorption capacity can significantly contribute to the total sorption capacity.261,269–271 found that different types of clays have different sorption capacities: smectite ≫ mixed layer illite/smectite > kaolinite > chlorite > illite. Busch et al. found a similar relationship with smectite > illite > kaolinite > chlorite.226 It should be noted that although water has a negative effect on the sorption capacity,272 most sorption tests have been carried out on dry samples which are not representative of reservoir conditions and should be treated carefully.
5.1.2.2 Competitive adsorption of CO2versus CH4.
While injecting CO2 into shale reservoirs for gas recovery and CO2 sequestration, the sorption ability of CO2 in shales should be considered. Various studies investigated the CO2 adsorption capacity of shales and clay minerals.30,226,273–278 They all found that the sorption capacity of CO2 in shale samples was higher than for CH4. The CO2/CH4 sorption ratio ranges between 1.3 and 10 for dry shale samples (Fig. 9).276 The molecular diameter of CO2 (0.33 nm) is slightly smaller than for CH4 (0.38 nm), which allows access to narrower pores and therefore higher surface area. In addition, CO2 has a higher sorption enthalpy resulting in a higher sorption capacity of CO2 over CH4.227,279
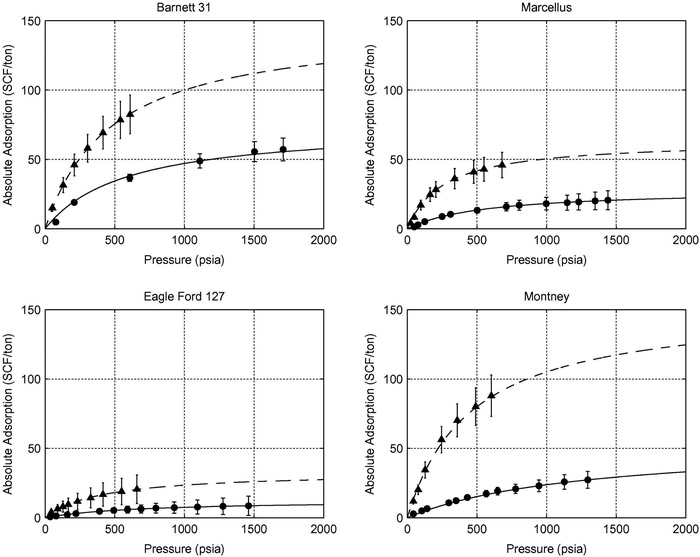 |
| Fig. 9 Methane and carbon dioxide adsorption isotherms on samples from the Barnett, Marcellus, Eagle Ford and Montney shale reservoirs (triangular point-CO2, dot-CH4, line-model fitting).30 | |
In the process of CO2-enhanced shale gas recovery, the competitive adsorption of CO2 and CH4 are essential to understand the efficiency of shale gas recovery and CO2 storage.30 Various studies report experimental CO2–CH4 competitive adsorption in shale samples.33,280–287 Here, shale samples are pressurized with CO2 and CH4 mixed gases at different molar ratios. With the increase in saturation pressure, the sorption volume of CO2 increases, while the sorption volume of CH4 decreases.281 As shown by nuclear magnetic resonance (NMR) studies, CO2 competitively sorbs over CH4.281 With an increase in reservoir pressure, CO2 shows better sorption ability than CH4.281,283,288 However, CO2 enhanced CH4 extraction exists in an optimal pressure range. In the study of Lee, et al.,289 the suggested pressure range was 7 to 9 MPa. Other factors such as pore volume and pore size distribution (PSD), also affect shale sorption capacity.283
5.2 CO2–shale or CO2–liquid–shale interactions
When CO2 is injected into shale gas reservoirs, geochemical CO2–water–rock interactions occur over a period of time. This might cause physical properties of shale to change, potentially affecting the shale gas recovery efficiency and CO2 storage process.
5.2.1 Carbonic acid in water + CO2.
The dissolution of gaseous CO2 in water creates a weak carbonic acid (H2CO3), which is in dynamic equilibrium with its dissociated forms (HCO3− and CO32−).290–293 The microsolvation of H2O and CO2 and the formation/decomposition of carbonic acid have been extensively studied by means of density functional theory (DFT), Hartree–Fock (HF), ab initio molecular dynamics, matrix isolation IR experiments, phase molecular beam, etc.293–298 However, the widely accepted reaction between H2O and CO2 in gaseous and aqueous conditions may be different in SC-CO2. The structural feature of SC-CO2 is that each CO2 molecule is surrounded by six other CO2 molecules configured in a distorted T-shaped configuration around the carbon.299 The reaction between H2O and CO2 to form H2CO3 in supercritical condition has a higher barrier than that of gaseous condition because H2O has to displace the surrounding CO2 molecule's out of their equatorial positions and align them with the reacting C.293,298 Glezakou, et al. used an ab initio molecular dynamics method to examine the structure, dynamics, and vibrational spectra of SC-CO2/(H2O)n (n = 0–4).298 They found that the strongest interactions between SC-CO2 and H2O occur in the case of monomeric water. The dynamic hydrogen bonds with the oxygens are mostly formed between the equatorial and polar coordinating CO2 molecules. For the decomposition of H2CO3, the enthalpy and entropy terms are similar in SC-CO2, but that is not the case for gaseous CO2. The formation of H2CO3 in SC-CO2 is thermodynamically unfavorable. Once formed, H2CO3 will probably be the undissociated form while the water is likely to remain unsaturated.293 The low solubility of water in SC-CO2 resulted in the water clustering when the water concentration in SC-CO2 was high. In the reservoir condition, the water usually contains brines like NaCl, the formation/decomposition of carbonic acid will be more complex and need further investigation.
5.2.2 Chemical reactions.
Although well-defined concepts in aqueous solutions such as mineral solubility and ion activity do not have corresponding thermodynamic meaning in water-based SC-CO2, McGrail, et al.171 demonstrated that water-based SC-CO2 can be reactive with different mineral phases. Many scholars have proved the mineral dissolution and precipitation in such acidic fluids.300–302 Busch, et al.226 investigated the CO2-shale interactions with temperatures between 45 °C and 50 °C and pressures up to 20 MPa. Minor geochemical reactions such as the dissolution of silicates and precipitation of carbonates were observed after sorption experiments. Alemu, et al.303 selected two caprock shale samples (a carbonate-rich and a clay-rich shale) to study the reactions between rocks and a mixture of brine and SC-CO2 (the pressure was 11 MPa, the temperature ranged from 80 to 250 °C). By analyzing fluid major element concentrations as well as SEM and XRD tests, they indicated dissolution and re-precipitation of carbonates, dissolution of plagioclase, illite, chlorite and the formation of smectite. When shale rocks are exposed to CO2–water mixtures, chemical reactions such as the dissolution of calcite, carbonates and clay minerals could be observed.304 If the imbibition time is long, quartz could also be dissolved.305 The geochemical reactions can potentially affect petrophysical properties which will be discussed below.
5.2.3 Physical changes.
Mineral dissolution creates additional porosity within rock formations, whereas precipitated minerals can block the connection of pores. These chemical processes can change the petrophysical properties of shales. Therefore, investigating shale properties following CO2–water–rock interaction can help predicting potential causes and consequences over long timescales, using advanced experimentation and reactive transport or batch modelling. This will promote the assessment of the suitability for CO2 enhanced shale gas recovery and CO2 sequestration of specific shale gas reservoirs. In the following, the macro and microscale changes of shale properties after reaction with CO2 and carbonated fluids are reviewed.
5.2.3.1 Macroscale variations.
Important macroscale properties of shales include mechanical (strength, brittleness, hardness/toughness) or petrophysical properties (permeability, porosity). Significant changes of these properties due to CO2–water–rock interactions might impact reservoir performance in terms of mechanical stability and recovery rates.
(1) Mechanical properties.
Strength is a fundamental mechanical property of a rock. Previous studies report uniaxial compressive strength (UCS) and tensile strength (TS) tests to determine the variation of a shale's strength after CO2–water–rock reaction. The experimental conditions and major results are shown in Table 6 and Fig. 10.306–312 It can be seen that CO2 and its saturated fluids decrease the strength of shale samples. With 30 days of imbibition, the strength of shales reacted with sub/supercritical CO2, sub/supercritical CO2 + water, and sub/supercritical CO2 + brine decreased by 20% and 30%, 56% and 66%, and 61% and 70%, respectively. Longer imbibition time leads to more extensive CO2–shale or CO2–water/brine–shale reactions and a higher reduction of stress. With a lower pH value than pure CO2, CO2 saturated water or brine yields conditions where chemical reactions are more violent.313 Therefore, the strength of shale samples with CO2 + water/brine imbibition is lower than that with CO2 imbibition. SC-CO2 has no capillary force and lower values of viscosity than subcritical CO2. With the same reaction time, SC-CO2 penetrates into shale samples and reduces their strength more than subcritical CO2. The trends of strength variation vary among shale types. Different shales have distinct anisotropy, mineral composition, and thermal evolution, which leads to differences in the mechanical changes caused by CO2 and CO2 + water/brine imbibition.
Table 6 Experimental studies of shale strength affected by imbibition of CO2 and CO2-based fluids subjected to different conditions and methods
Rock type |
Soaking fluids |
Soaking time |
Temperature and pressure |
Testing method |
Longmaxi shale306–308 |
CO2 |
10/20/30 days |
40 °C, 7 MPa |
UCS tests |
CO2 + water |
40 °C, 9 MPa |
CO2 + NaCl (20% wt) |
|
Longmaxi shale309 |
CO2 |
10 days |
38 °C, 4/6/8/12/16 MPa |
UCS tests |
Longmaxi shale310 |
CO2 |
7 days |
45 °C, 6 MPa |
UCS tests |
CO2 + NaCl (10% wt) |
45 °C, 12 MPa |
Longmaxi shale311 |
CO2 |
10/30/60 days |
40 °C, 10 MPa |
TS tests |
Longmaxi shale, Lujiaping shale312 |
CO2 + brine (KCl 2.0%, NaCl 5.5%, MgCl2 0.45%, CaCl2 0.55% wt) |
7 days |
80 °C, 20 MPa |
TS tests |
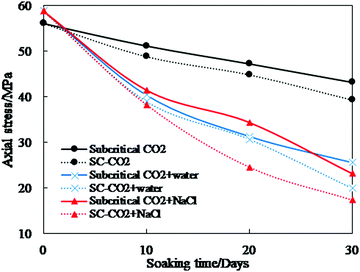 |
| Fig. 10 Compressive and tensile stress of shale samples after CO2 and CO2 saturated water or brine imbibition.306–308 | |
The shale–CO2 or shale–water/brine–CO2 interactions influence the brittleness index (BI) of shale. BI is usually used to characterize the potential of fracability, that is, a higher value BI means a better fracability, which is beneficial for reservoirs with re-fracturing treatment. Lyu, et al.314 used the energy-based method to calculate the BI values of shale samples with different soaking times in subcritical CO2, SC-CO2, subcritical CO2 + water, and SC-CO2 + water. The results showed that, with 30 days of imbibition, subcritical CO2 and SC-CO2 imbibition resulted in 13% increase of the BI values of shale, while samples with subcritical CO2 + water and SC-CO2 + water imbibition displayed 17% reduction of BI values. It can be deduced that CO2 imbibition enhances a shale's fracability, while CO2 + water imbibition lowers the fracability. The fracability can also be characterized by the variations of toughness and hardness. If the toughness decreases, the brittleness increases. A low value of hardness means fractures can be created more easily. Based on the study of Ilgen, et al.,315 with 7 days of CO2–brine imbibition, quartz-rich shales showed a small decrease, while dolomite- and muscovite-rich shales showed about 50% decrease in toughness and hardness. However, the fracability of shale reservoirs cannot be determined using BI, toughness, or hardness alone. As reported in Lyu, et al.306 and Lyu, et al.,307 samples soaked in CO2 + water were weakened more than those soaked in CO2. The weakening of shale which caused by imbibition induced cracks and pores also contributes to better fracability.
As discussed before, four types of gas flow should be considered when CO2 is injected into shale reservoirs: viscous flow, Knudsen diffusion, molecular diffusion, and surface diffusion.316–319 Shale–CO2 or shale–water/brine–CO2 reactions change the porosity and pore size distribution of shale, which potentially influence the dominant flow mechanisms in shale pores and alter the permeability.320,321 Kim, et al.322 simulated the SC-CO2 flooding and “huff and puff” process to elucidate the effects of CO2 injection for enhancing gas recovery and CO2 storage. The results showed that SC-CO2 injection enhances CH4 production because reactions with CO2 caused shale deformation and an increase in permeability. Zou, et al.312 tested the permeability variations of the Liujiaping (LJP) shale and Longmaxi (LMX) shale after soaking in CO2 + brine for different reaction time, temperature, and pressure. They found that the permeability of both shales increased with increasing reaction time, temperature, and pressure. This was caused by the dissolution of carbonates, which creates more pores and improved pore connectivity.
However, the experiments conducted by Zhou, et al.323 showed that CO2 adsorption leads to shale swelling and a decrease in permeability. The permeability reduction is more likely to occur in ultra-low permeability shales where fluids flow paths are more sensitive to CO2 sorption-induced swelling.324
The published experimental results, therefore, provide complex results suggesting that permeability of shale after CO2 and CO2 based fluids imbibition can either increase or decrease depending on shale properties and a range of factors. The complex trends are not just affected by the processes of adsorption/desorption and dissolution/precipitation. The composition of the samples and the bedding angles, testing methods, and imbibition conditions are also important factors. The salinity of the formation fluids and the temperature of the injected SC-CO2 fluids impact interfacial tension (IFT) of the shale–water/brine–CO2 solutions in the reservoir, which in turn impacts the relative permeability of the water/brine–CO2-rich phase versus the hydrocarbon-rich phase in the reservoir.325 More experimental and analytical studies are required to better quantify and rank the significance of these factors on permeability changes in a wide range of shales following SC-CO2 imbibition.
5.2.3.2 Microscale variations.
The macroscale changes of shale are accompanied by microscale variations. Pore sizes of microporous systems like gas shales are classified into three distinct groups: micropores (<2 nm), mesopores (2–50 nm), and macropores (>50 nm).326,327 CO2, with linear molecular geometry, can access a certain fraction of micropores that other naturally-occurring gases cannot access. Jiang, et al.328 experimentally investigated the microstructure of shales after treatment with SC-CO2 at different pressures (8–18 MPa), reaction times (0–5 days) and temperatures (40–90 °C). The specific surface area and porosity increased slightly with an increase in temperature and reaction time. Higher pressure significantly promoted an increase in specific surface area and porosity. Similarly, the increasing trends of porosity have also been observed in shales with SC-CO2 saturated brine imbibition.312 Pan, et al.329 used marine and terrestrial shale samples to conduct similar tests but increased the soaking time to 14 days. After SC-CO2 imbibition, the number of micropores and mesopores in the marine shale (with low clay contents) decreased, while the number of macropores increased, resulting in a higher porosity overall. However, the terrestrial shale with high clay content exhibited the opposite trend of porosity changes to the marine shale after SC-CO2 imbibition. This was interpreted to be mainly caused by clay swelling during imbibition.
The increase in porosity occurs mainly because of the chemical reactions between CO2/CO2-based fluids and shale minerals during the process of fracturing and sequestration. The dissolution of calcite, quartz, illite/smectite, and chlorite and the precipitation of iron-rich carbonate(siderite), illite, and smectite have been observed when shale samples are exposed to CO2.330–333
5.3 Further concerns
5.3.1 Costs of using SC-CO2 in shale gas recovery.
During the process of SC-CO2 enhanced shale gas recovery, the CO2-related costs are related to CO2 capture, transport, and storage. CO2 can be obtained from power plants and transported by pipelines, trucks or ships.334,335 Pipeline corrosion caused by CO2 can be prevented by surface coating and cathodic protection.336 CO2 should be compressed to a liquid phase which can be stored near the well. For SC-CO2 fracturing, CO2 will be compressed to a high pressure and injected into shale wells. The energy requirement for CO2 compression is about 1.2 to 1.5 kW h per t-CO2 per 1 MPa.337,338 The flowback gas which mixes with natural gas and CO2 need to be separated. The CO2 content in natural gas should be decreased to 2–5% to meet typical pipeline specifications.339 The major separation processes of CH4 and CO2 are chemical and physical adsorption, low temperature distillation, and membrane separation.340 Membrane separation represents commercial advantages and has become a major industrial application.341 The cost of the gas separation system is not a one-time investment, the operation and maintenance cost, the natural gas lost, and the gas processing cost should also be considered.342 The separated CO2 can be reused for fracturing. The cyclic injection process should be optimized based on the net present value (NPV).343
Currently, the investments required for SC-CO2 fracturing are significantly higher than for hydraulic fracturing. However, if the SC-CO2 fracturing process is combined with CO2 sequestration, costs can be lowered when the operation is part of a CO2 tax scheme. Shafeen, et al.344 calculated the investment of a CO2 sequestration project. A total of US$257 million dollars is needed for a project with 1 off shore platform, 10 injection wells, and 112 kilometers of pipelines, the CO2 capture costs ranging from US$30 per ton to US$60 per ton, are not included.345 For hydraulic fracturing, the total costs of disposal, basic separation, and desalination of flowback water range roughly between $78
000 and $1
460
000 for each well.346 The costs for groundwater and surface water cleanup add significant expenses to this operation.347 Till now, hydraulic fracturing is till the appropriate technique for shale gas recovery. The application of SC-CO2 fracturing together with CO2 sequestration relies on the supporting policy from the government, more capital channels, and the integration of social resources.
5.3.2 Induced seismicity and environmental impacts.
Similar to hydraulic fracturing, extracting hydrocarbons from low permeability shale formations through SC-CO2 fracturing may also cause environmental impacts and induce or trigger earthquakes. During the fracturing process, SC-CO2 can penetrate the unconnected micropores in the formation more easily than the water-based fracturing fluid, form a high pore pressure area around the wellbore, and may transfer the fluid pressure to the farther and deeper part of the formation. Numerous experimental studies and a few field tests have shown that SC-CO2 fracturing can generate more micro-fractures and microseismic events compared to hydraulic fracturing.210,348,349 In addition, characteristics of SC-CO2 under reservoir conditions may accelerate the reactivation of pre-existing faults, especially considering the potential phase changes. For instance, SC-CO2 will be converted to gaseous CO2 when the pressure decreases and suppress dilatancy hardening, which may promote the stable or aseismic slips along pre-existing faults.350 Besides, SC-CO2 fracturing tends to induce extensive three-dimensional cracking and shear dominant fracture due to the lower viscosity of SC-CO2 than water in this perspective. The risk of felt seismicity when using CO2 as a fracturing fluid or in CO2 sequestration might therefore be a considerable concern.
So far, studies investigating the environmental impacts of field SC-CO2 fracturing are still missing in the literature. CO2 is stable, non-flammable, and easy to be recycled. As an environmentally-friendly fluid, the use of (SC-)CO2 in shale gas recovery should lower environmental impacts (e.g., water contamination issues), especially considering the potential for CO2 sequestration both during and after the stimulation phase. However, CO2-based fracturing will definitely have an impact on the reservoir environment. Water in the formation will tend to dissolve in the SC-CO2, and the remaining brine will become supersaturated with dissolved salts and precipitation may occur.22 Precipitation of mineral salts could lead to the blocking of small pores in the reservoir and undesirably restrict subsequent extraction of the hydrocarbons.
5.3.3 Life cycle assessments of CO2-based fracturing.
Despite the concerns of costs and environmental impacts, life cycle assessments (LCA) of using SC-CO2 in shale gas recovery are necessary to quantify the challenges and opportunities that meet the industry and environmental protection goals. Wilkins, et al.351 systematically compared the life cycle energy use, greenhouse gas emissions, and water consumption of unconventional gas recovery between hydraulic fracturing fluid and CO2-based fracturing fluid. Because of the gas compression, separation, transportation, and energy losses for flaring, the net energy impact of CO2-based fracturing was 44% higher than that of water-based fracturing. While considering the increase of energy production, the net energy impact of CO2-based fracturing only accounted for two thirds of the water-based fracturing. It is worth noting that CO2-based fracturing achieved net carbon offsets as shale pores show considerable adsorption capacity of CO2. Water-based fracturing consumes large amount of water. The transfer to CO2-based fracturing avoids high-volume surface and groundwater extractions and further minimizes active fluid management over the well's lifetime, including produced water storage, transport, and treatment at the wellhead. CO2-based fracturing is region-specific. It is much more suitable for regions where the extractions and disposal of high volumes of water are constrained and CO2 sources are accessible.
The public concerns of hydraulic fracturing focus on the large amount of water consumption, drinking water contamination, fugitive methane emissions, seismic events, noise pollution, and truck traffic.7,352 Although CO2-based fracturing avoids water consumption and contamination, the increase of total truck trips (100% higher than water-based fracturing) will lead to high public health risks. The construction of CO2 pipelines can help to reduce the risks and increase the fluid transport efficiency. Depleted shale well can be used for CO2 sequestration. A design of collocated parallel pipelines for both CO2 and natural gas transport is beneficial for CO2 fracturing/sequestration and natural gas supply.353 The advanced pipeline strategy requires the coordination between CO2 sources, field services suppliers, and producers. Although CO2-based fracturing shows advantages for shale gas recovery, the effective large-scale deployment of this technique should consider social, technical, and environmental trade-offs.
5.3.4 Further investigations.
5.3.4.1 Laboratory study.
Previous work has shown some advantages of SC-CO2 enhanced shale gas recovery. However, the changes to shale properties, fracturing results, and drilling ability after imbibition with CO2 or CO2-based fluids are complex. Generalization of established trends is not yet possible using information from studies published to date. This is because the laboratory tests are limited by several factors:
(a) Sample anisotropy. With the process of deposition, burial, and lithification, shale can be divided into three types: marine shale, continental (lacustrine) shale, and transitional facies shale. The mineral composition and porosity of the three types of shales are different, which results in variable adsorption abilities.261,354 Even for one type of shale, the clay minerals assemblage can vary by location. The methane adsorption ability of each clay mineral assemblage tends to be different (e.g., where smectite ≫ illite compared to smectite mixed layers > kaolinite > chlorite > illite).355 Therefore, it is necessary to determine the types of shale and characterize its clay mineralogy and heterogeneity before imbibition tests.
(b) Sample Size effect. The mechanical properties of rocks are closely related to the size (diameter, height-diameter ratio) of samples.356 The bedding angles of shale formations also affects rock properties.357 More importantly, the size scale of samples used in laboratory tests is typically too small to reliably represent the real reservoir conditions. Therefore, comparisons of reaction results between samples with different sizes are necessary. Despite the difficulty of sample preparation, large shale samples are suggested for conducting robust SC-CO2 imbibition tests.
(c) Reaction conditions. The CO2 injection and release rate, the heating rate, and the pressure/temperature stabilization in the imbibition process affect the actual sample test results. The soaking time in most published studies was less than 30 days. According to some published research,358,359 30 days of imbibition is not long enough to affect the porosity of shale or coal. A shale gas well might remain productive for 5 to 40 years, and CO2 sequestration needs to be stable for thousands of years. While the diffusion of CO2 in shale rocks is as slow as millimeters per year. Therefore, to better understand the effects of SC-CO2 on shale reservoirs, longer soaking times in laboratory tests are required.
5.3.4.2 Field tests.
Previous studies mainly focus on the laboratory tests of the possibility of using SC-CO2 for shale gas recovery. Field tests for SC-CO2 fracturing are still limited. More investigations should be conducted by field tests to promote the application of SC-CO2 enhanced shale gas recovery. (a) Drilling. Laboratory tests have demonstrated the feasibility of SC-CO2 based drilling. However, in the real condition of application, the drilling ability should consider both the fluids flow in the wellbore and the cutting-carry ability of fragments. The physical properties of SC-CO2 is sensitive to the pressure and temperature that are related to the CO2 injection, injection pressure and temperature, depth of the well, and the roughness of the well surface.360,361 The change of physical properties will directly affect the drilling ability of SC-CO2. Some researchers have investigated the SC-CO2 flow by simplified models.191,362,363 However, these models have not been validated by field tests. To increase the drilling efficiency, the fragments produced by drilling need be cleaned immediately. The cutting-carry ability of SC-CO2 was studied by laboratory experiments with a meter-scale. While a well for shale gas recovery is usually composed of a vertical well with hundreds of meters to several kilometers and several horizontal wells with more than one kilometer. The cutting-carry ability of SC-CO2 at a kilometer-scale remains unknow. (2) Proppant-carry in fractures. Like hydraulic fracturing, SC-CO2 fracturing also needs the proppants to hold the fractures open. However, SC-CO2 has good diffusion ability, the filtrate loss is larger than using water. Thereby the proppant-carry ability decreases with a decrease in turbulence intensity in fractures. Meanwhile, the particle-fluid multiphase flow is also affected by temperature and pressure variations caused by the heat transfer between shale rocks and SC-CO2.364,365 (3) Fracturing equipment. Before fracturing, sands should be continuously be added to the liquid CO2. It is very difficult to control the high-pressure sand-CO2 mixing process. Sands in the well can block perforation nozzles resulting in overpressure of the fracturing equipment.349,366 Therefore, a sand-adding equipment is necessary to fulfil the demand of large-scale SC-CO2 fracturing.
6 Conclusions, challenges, and perspectives
Based on the review of the current literature, we conclude that it is feasible to use SC-CO2 to enhance shale gas recovery instead of using conventional water-based fracturing fluids. SC-CO2 might be applied with three distinct objectives: (1) Drilling. The rock-breaking threshold pressure and cutting energy required for SC-CO2 jets are lower than those of water jets. However, the capacity of SC-CO2 to carry cuttings still needs to be improved. (2) Fracturing. SC-CO2 fracturing can create more irregular multiple fractures and rougher and more complex fracture surfaces than liquid CO2 or water. (3) Sequestration. Shale gas reservoirs have substantial potential for CO2 sequestration. CO2 injected into reservoirs could be safely and stably stored by solubility, adsorption, and mineral trapping. Considering the large quantities of CO2 consumed during each SC-CO2 fracture stimulation operation, the large-scale application of SC-CO2 enhanced shale gas recovery is restricted by the high expense of CO2 capture and transportation to supply CO2 to many injection sites.
Although SC-CO2 shows significant benefits in enhancing shale gas recovery, there are still some challenges that need to be addressed. Firstly, CO2–shale or CO2–water/brine–shale interactions strongly affect the properties of shale. The direct and indirect effects of these interactions on the recovery of shale gas and CO2 sequestration are still unknown. More work is required to better quantify and model such effects. Secondly, the mechanism of SC-CO2 fracturing is still unclear. The fracturing process is affected by the variations in pressure and temperature, the physical properties of SC-CO2, the leak-off of SC-CO2 and the physical and chemical reactions between shale and SC-CO2. It is totally different from hydraulic fracturing. The numerical simulation methods such as the extended finite element method, boundary element method and other advanced methods can be used together with delicate laboratory tests to reveal the mechanism of fracture initiation and propagation during SC-CO2 fracturing. Thirdly, more data from field tests is necessary to demonstrate the feasibility of SC-CO2 enhanced shale gas recovery and CO2 sequestration in a wide range of potential shale gas reservoirs. The proppant-carry and sand-carry abilities of SC-CO2 are poor. Proppant and sand could therefore potentially accumulate in the wellbore or the tips of cracks which would be detrimental to perforation and fracturing. The flow resistance of SC-CO2 in the wellbore and the bit nozzles is very high. To fulfill the injection volume, a higher pumping pressure is therefore needed. This risks causing overpressure in the surface equipment.349 Moreover, induced-seismicity monitoring is required. This involves multi-disciplinary inputs from geophysics, geology, and reservoir engineering, which are required for advanced identification, processing, and interpretation of induced seismicity. Such monitoring and recorded signal interpretations are essential to ensure the safe and effective production and sequestration of shale gas over long time periods.
Author contributions
Jingqiang Tan conceived the idea and organized writing. Qiao Lyu, Jingqiang Tan, and Yiwen Ju led the preparation of the manuscript. Lei Li, Andreas Busch, David A. Wood, Pathegama Gamage Ranjith, and Richard Middleton helped to revise and edit the article. Biao Shu and Qiao Lyu conducted a literature review of CO2 emissions and CO2 capture, utilization, and storage. Chenger Hu helped to summarize the costs of using SC-CO2 in shale gas recovery and field tests. Zhanghu Wang and Ruining Hu drew and improved some of the figures. All authors contributed to the study with valuable discussions.
Conflicts of interest
There are no conflicts to declare.
Acknowledgements
The authors are grateful for financial support from the National Natural Science Foundation of China (Grant No. 72088101, 41530315, 41872151, 41872160, 42002160, and 42004115), the Strategic Priority Research Program of the Chinese Academy of Sciences (Grant No. XDA05030100) and the Innovation-Driven Project of Central South University (Grant no.: 502501005).
Notes and references
- EIA, International Energy Outlook, 2019, https://www.eia.gov/outlooks/ieo/pdf/ieo2019.pdf.
- I. P. o. C. C. (IPCC), Climate change and land: An IPCC special report on climate change, desertification, land degradation, sustainable land management, food security, and greenhouse gas fluxes in terrestrial ecosystems, 2019.
- R. A. Kerr, Science, 2010, 328, 1624–1626 Search PubMed.
- H. Yang and J. R. Thompson, Nature, 2014, 513, 315 Search PubMed.
- J. Yuan, D. Luo and L. Feng, Appl. Energy, 2015, 148, 49–65 Search PubMed.
-
E. I. Administration, U.S. Natural Gas Gross Withdrawals and Production, DOI: https://www.eia.gov/dnav/ng/ng_prod_sum_dc_NUS_mmcf_a.htm.
- A. Vengosh, R. B. Jackson, N. Warner, T. H. Darrah and A. Kondash, Environ. Sci. Technol., 2014, 48, 8334–8348 Search PubMed.
-
D. Alleman, Hydraulic Fracturing of the Marcellus Shale, 2011 Search PubMed.
- D. M. Kargbo, R. G. Wilhelm and D. J. Campbell, Environ. Sci. Technol., 2010, 44, 5679–5684 Search PubMed.
- J. Wang, M. Liu, Y. Bentley, L. Feng and C. Zhang, J. Environ. Manage., 2018, 226, 13–21 Search PubMed.
- J. P. Nicot and B. R. Scanlon, Environ. Sci. Technol., 2012, 46, 3580–3586 Search PubMed.
-
P. Reig, T. Luo and J. N. Proctor, Global shale gas development: water availability and business risks, World Resources Institute, 2014 Search PubMed.
- W. T. Stringfellow, J. K. Domen, M. K. Camarillo, W. L. Sandelin and S. Borglin, J. Hazard. Mater., 2014, 275, 37–54 Search PubMed.
- R. Jackson, A. Gorody, B. Mayer, J. Roy, M. Ryan and D. Van Stempvoort, Groundwater, 2013, 51, 488–510 Search PubMed.
- K. B. Gregory, R. D. Vidic and D. A. Dzombak, Elements, 2011, 7, 181–186 Search PubMed.
- H. Chen and K. E. Carter, J. Environ. Manage., 2017, 200, 312–324 Search PubMed.
-
E. Rester and S. D. Warner, in Environmental and Health Issues in Unconventional Oil and Gas Development, ed. D. Kaden and T. Rose, Elsevier, 2016, pp. 49–60 DOI:10.1016/B978-0-12-804111-6.00004-2.
- D. C. DiGiulio and R. B. Jackson, Environ. Sci. Technol., 2016, 50, 4524–4536 Search PubMed.
- E. E. Yost, J. Stanek and L. D. Burgoon, Sci. Total Environ, 2017, 574, 1544–1558 Search PubMed.
- G. A. Kahrilas, J. Blotevogel, P. S. Stewart and T. Borch, Environ. Sci. Technol., 2015, 49, 16–32 Search PubMed.
- L. Li, J. Tan, D. A. Wood, Z. Zhao, D. Becker, Q. Lyu, B. Shu and H. Chen, Fuel, 2019, 242, 195–210 Search PubMed.
- R. S. Middleton, J. W. Carey, R. P. Currier, J. D. Hyman, Q. Kang, S. Karra, J. Jiménez-Martínez, M. L. Porter and H. S. Viswanathan, Appl. Energy, 2015, 147, 500–509 Search PubMed.
- C. Fu and N. Liu, J. Nat. Gas Sci. Eng., 2019, 67, 214–224 Search PubMed.
-
D. V. S. Gupta and T. T. Leshchyshyn, presented in part at the SPE Latin American and Caribbean Petroleum Engineering Conference, Rio de Janeiro, Brazil, 2005/1/1/, 2005.
- Gupta and Bobier, presented in part at the SPE Gas Technology Symposium, Calgary, Alberta, Canada, 1998/1/1/, 1998.
-
S. Meng, H. Liu, J. Xu, Y. Duan, Q. Yang and Z. Yao, presented in part at the SPE Asia Pacific Oil & Gas Conference and Exhibition, Perth, Australia, 2016/10/25/, 2016.
- Y. Fang, C. Wang, D. Elsworth and T. Ishibashi, Geomech. Geophys. Geo-Energy Geo-Resources, 2017, 3, 189–198 Search PubMed.
-
M. K. Fisher, C. A. Wright, B. M. Davidson, A. Goodwin, E. Fielder, W. Buckler and N. Steinsberger, SPE Annual Technical Conference and Exhibition, San Antonio, Texas, 2002 Search PubMed.
-
V. I. Likhtman, E. D. Shchukin and P. A. Rebinder, Physicochemical mechanics of metals: adsorption phenomena in the process of deformation and failure of metals, 1964 Search PubMed.
- R. Heller and M. Zoback, J. Unconv. Oil Gas Resour., 2014, 8, 14–24 Search PubMed.
- P. Huo, D. Zhang, Z. Yang, W. Li, J. Zhang and S. Jia, Int. J. Greenhouse Gas Control, 2017, 66, 48–59 Search PubMed.
- M. Godec, G. Koperna, R. Petrusak and A. Oudinot, Int. J. Coal Geol., 2013, 118, 95–104 Search PubMed.
- L. Huang, Z. Ning, Q. Wang, W. Zhang, Z. Cheng, X. Wu and H. Qin, Appl. Energy, 2018, 210, 28–43 Search PubMed.
- D. W. Keith, G. Holmes, D. St. Angelo and K. Heidel, Joule, 2018, 2, 1573–1594 Search PubMed.
- J. Bao, W. Lu, J. Zhao and X. T. Bi, Carbon Resour. Convers., 2018, 1, 183–190 Search PubMed.
- R. S. Middleton, G. N. Keating, H. S. Viswanathan, P. H. Stauffer and R. J. Pawar, Int. J. Greenhouse Gas Control, 2012, 8, 132–142 Search PubMed.
- UNCTAD, Journal, 2018.
- BP Statistical Review of World Energy, https://www.bp.com/en/global/corporate/energy-economics/statistical-review-of-world-energy.html.
- EIA, Technically Recoverable Shale Oil and Shale Gas Resources, https://www.eia.gov/analysis/studies/worldshalegas/.
- EIA, Journal, 2019, 2019-010-01.
- R. S. Middleton, R. Gupta, J. D. Hyman and H. S. Viswanathan, Appl. Energy, 2017, 199, 88–95 Search PubMed.
- D. Malakoff, Science, 2014, 344, 1464–1467 Search PubMed.
- M. Thomas, N. Pidgeon, D. Evensen, T. Partridge, A. Hasell, C. Enders, B. Herr Harthorn and M. Bradshaw, Wiley Interdiscip. Rev. Clim. Change, 2017, 8, e450 Search PubMed.
- W. A. M. Wanniarachchi, P. G. Ranjith and M. S. A. Perera, Environ. Earth Sci., 2017, 76, 91 Search PubMed.
- L. Wang, Y. Tian, X. Yu, C. Wang, B. Yao, S. Wang, P. H. Winterfeld, X. Wang, Z. Yang, Y. Wang, J. Cui and Y.-S. Wu, Fuel, 2017, 210, 425–445 Search PubMed.
- B. Hou, R. Zhang, Y. Zeng, W. Fu, Y. Muhadasi and M. Chen, J. Pet. Sci. Eng., 2018, 170, 231–243 Search PubMed.
- Z. Zhou, H. Abass, X. Li and T. Teklu, J. Nat. Gas Sci. Eng., 2016, 29, 413–430 Search PubMed.
- P. Tan, Y. Jin, K. Han, B. Hou, M. Chen, X. Guo and J. Gao, Fuel, 2017, 206, 482–493 Search PubMed.
- W. A. M. Wanniarachchi, P. G. Ranjith, M. S. A. Perera, T. D. Rathnaweera, D. C. Zhang and C. Zhang, Eng. Fract. Mech., 2018, 194, 117–135 Search PubMed.
- A. Kotsakis, Rev. Eur. Community Int. Environ. Law, 2012, 21, 282–290 Search PubMed.
- S. Bilgen and İ. Sarıkaya, J. Nat. Gas Sci. Eng., 2016, 35, 637–645 Search PubMed.
- T. G. Burton, H. S. Rifai, Z. L. Hildenbrand, D. D. Carlton, B. E. Fontenot and K. A. Schug, Sci. Total Environ, 2016, 545-546, 114–126 Search PubMed.
- M. Vishkai and I. Gates, J. Pet. Sci. Eng., 2019, 174, 1127–1141 Search PubMed.
- Z. Lian, H. Yu, T. Lin and J. Guo, J. Nat. Gas Sci. Eng., 2015, 23, 538–546 Search PubMed.
-
L. Gandossi, Eur. Commisison Jt. Res. Cent. Tech. Reports, 2013, 26347.
- F. Gao, C. Cai and Y. Yang, Results Phys., 2018, 9, 252–262 Search PubMed.
-
R. Myers, presented in part at the SPE/AAPG Eastern Regional Meeting, Pittsburgh, Pennsylvania, USA, 2018/10/5/, 2018.
- W. A. M. Wanniarachchi, P. G. Ranjith, M. S. A. Perera, A. Lashin, N. Al Arifi and J. C. Li, Geomech. Geophys. Geo-Energy Geo-Resources, 2015, 1, 121–134 Search PubMed.
- Z. Jing, C. Feng, S. Wang, D. Xu and G. Xu, J. Pet. Sci. Eng., 2017, 159, 710–716 Search PubMed.
-
G. Beck, C. Nolen, K. Hoopes, C. Krouse, M. Poerner, A. Phatak and S. Verma, presented in part at the SPE Annual Technical Conference and Exhibition, San Antonio, Texas, USA, 2017/10/9/, 2017.
- X. Zhao, B. Huang and J. Xu, Fuel, 2019, 236, 1496–1504 Search PubMed.
- P. Hou, F. Gao, Y. Gao, Y. Yang and C. Cai, Int. J. Rock Mech. Min. Sci., 2018, 109, 84–90 Search PubMed.
- C. T. Montgomery and M. B. Smith, J. Pet. Technol., 2010, 62, 26–40 Search PubMed.
- B. Yuan and D. A. Wood, Fuel, 2018, 227, 99–110 Search PubMed.
- R. M. Buono, B. Mayor and E. López-Gunn, Environ. Sci. Policy, 2018, 90, 193–200 Search PubMed.
- J. L. Luek and M. Gonsior, Water Res., 2017, 123, 536–548 Search PubMed.
- A. Kondash and A. Vengosh, Environ. Sci. Technol. Lett., 2015, 2, 276–280 Search PubMed.
-
D. Jolly, The New York Times, 2013, vol. 11 Search PubMed.
-
R. E. Blauer and C. A. Kohlhaas, presented in part at the Fall Meeting of the Society of Petroleum Engineers of AIME, Houston, Texas, 1974/1/1/, 1974.
-
X. Kong, J. McAndrew and P. Cisternas, presented in part at the Abu Dhabi International Petroleum Exhibition & Conference, Abu Dhabi, UAE, 2016/11/7/, 2016.
-
L. H. Burke, G. W. Nevison and W. E. Peters, presented in part at the SPE Eastern Regional Meeting, Columbus, Ohio, USA, 2011/1/1/, 2011.
-
M. M. Reynolds, R. C. Bachman and W. E. Peters, presented in part at the SPE Hydraulic Fracturing Technology Conference, The Woodlands, Texas, USA, 2014/2/4/, 2014.
- X. Sun, X. Liang, S. Wang and Y. Lu, J. Pet. Sci. Eng., 2014, 119, 104–111 Search PubMed.
-
Y. Chen, T. L. Pope and J. C. Lee, presented in part at the SPE European Formation Damage Conference, Sheveningen, The Netherlands, 2005/1/1/, 2005.
- A. Verma, G. Chauhan and K. Ojha, Asia-Pac. J. Chem. Eng., 2017, 12, 872–883 Search PubMed.
- S. A. Faroughi, A. J.-C.
J. Pruvot and J. McAndrew, J. Pet. Sci. Eng., 2018, 163, 243–263 Search PubMed.
- Y. Zhang, J. He, X. Li and C. Lin, J. Pet. Sci. Eng., 2019, 173, 932–940 Search PubMed.
- D. Zhou, G. Zhang, M. Prasad and P. Wang, Fuel, 2019, 247, 126–134 Search PubMed.
- L. Wang, B. Yao, M. Cha, N. B. Alqahtani, T. W. Patterson, T. J. Kneafsey, J. L. Miskimins, X. Yin and Y.-S. Wu, J. Nat. Gas Sci. Eng., 2016, 35, 160–174 Search PubMed.
- T. Ishida, K. Aoyagi, T. Niwa, Y. Chen, S. Murata, Q. Chen and Y. Nakayama, Geophys. Res. Lett., 2012, 39, 1–6 Search PubMed.
- A. Rogala, M. Bernaciak, J. Krzysiek and H. Jan, Physicochem. Probl. Miner. Process., 2012, 49, 313–322 Search PubMed.
- M. D. Zoback and D. J. Arent, Elements, 2014, 10, 251–253 Search PubMed.
-
M. Zoback, S. Kitasei and B. Copithorne, Addressing the environmental risks from shale gas development, Worldwatch Institute, Washington, DC, 2010 Search PubMed.
- A. Vengosh, N. Warner, R. Jackson and T. Darrah, Procedia Earth Planet. Sci., 2013, 7, 863–866 Search PubMed.
- U. S. EPA, Hydraulic Fracturing for Oil and Gas: Impacts from the Hydraulic Fracturing Water Cycle on Drinking Water Resources in the United States.
- D. Zhang and T. Yang, Pet. Explor. Dev., 2015, 42, 876–883 Search PubMed.
- J. Currie, M. Greenstone and K. Meckel, Sci. Adv., 2017, 3, e1603021 Search PubMed.
-
D. Kaden and T. Rose, Environmental and health issues in unconventional oil and gas development, Elsevier, Amsterdam, Boston, 2016 Search PubMed.
- M. Schimmel, W. Liu and E. Worrell, Earth-Sci. Rev., 2019, 194, 455–471 Search PubMed.
- D. Elsworth, C. J. Spiers and A. R. Niemeijer, Science, 2016, 354, 1380 Search PubMed.
- U. S. EPA, U.S. Environmental Protection Agency, 2015, EPA/600/R-615/047.
- R. D. Vidic, S. L. Brantley, J. M. Vandenbossche, D. Yoxtheimer and J. D. Abad, Science, 2013, 340, 1235009 Search PubMed.
- N. R. Warner, R. B. Jackson, T. H. Darrah, S. G. Osborn, A. Down, K. Zhao, A. White and A. Vengosh, Proc. Natl. Acad. Sci. U. S. A., 2012, 109, 11961–11966 Search PubMed.
- T. Engelder, Proc. Natl. Acad. Sci. U. S. A., 2012, 109, E3625 Search PubMed.
- G. T. Llewellyn, F. Dorman, J. L. Westland, D. Yoxtheimer, P. Grieve, T. Sowers, E. Humston-Fulmer and S. L. Brantley, Proc. Natl. Acad. Sci. U. S. A., 2015, 112, 6325–6330 Search PubMed.
- P. A. Hammond, T. Wen, S. L. Brantley and T. Engelder, Hydrogeol. J., 2020, 28, 1481–1502 Search PubMed.
- R. D. Vidic, S. L. Brantley, J. M. Vandenbossche, D. Yoxtheimer and J. D. Abad, Science, 2013, 340, 1235009 Search PubMed.
- S. G. Osborn, A. Vengosh, N. R. Warner and R. B. Jackson, Proc. Natl. Acad. Sci. U. S. A., 2011, 108, 8172 Search PubMed.
- M. A. Q. Siddiqui, S. Ali, H. Fei and H. Roshan, Earth-Sci. Rev., 2018, 181, 1–11 Search PubMed.
- Z. Gao, Y. Fan, Q. Hu, Z. Jiang, Y. Cheng and Q. Xuan, Mar. Pet. Geol., 2019, 109, 330–338 Search PubMed.
- P. Mohammadmoradi and A. Kantzas, Can. J. Chem. Eng., 2019, 97, 1627–1642 Search PubMed.
- Y. Shen, H. Ge, M. Meng, Z. Jiang and X. Yang, Energy Fuels, 2017, 31, 4973–4980 Search PubMed.
- T. Liang, X. Luo, Q. Nguyen and D. A. DiCarlo, Spe J., 2018, 23, 762–771 Search PubMed.
- T. Liang, F. Zhou, J. Lu, D. DiCarlo and Q. Nguyen, Fuel, 2017, 209, 650–660 Search PubMed.
- Y. Shen, H. Ge, C. Li, X. Yang, K. Ren, Z. Yang and S. Su, J. Nat. Gas Sci. Eng., 2016, 35, 1121–1128 Search PubMed.
- A. Zolfaghari, H. Dehghanpour and J. Holyk, Int. J. Coal Geol., 2017, 179, 130–138 Search PubMed.
- A. Skempton, Selected Papers on Soil Mechanics, 1953, 106–118 Search PubMed.
- A. A. Sabtan, J. Asian Earth Sci., 2005, 25, 747–757 Search PubMed.
- A. O. Erol and A. Dhowian, Q. J. Eng. Geol. Hydrogeol., 1990, 23, 243–254 Search PubMed.
- Z. Abiddin Erguler and R. Ulusay, Eng. Geol., 2003, 67, 331–352 Search PubMed.
- L. t. Johnson and D. Snethen, ASTM Geotech. Test. J., 1978, 1, 1–8 Search PubMed.
- Q. Lyu, P. Ranjith, X. Long, Y. Kang and M. Huang, J. Nat. Gas Sci. Eng., 2015, 27, 1421–1431 Search PubMed.
- D. Feng, X. Li, X. Wang, J. Li, F. Sun, Z. Sun, T. Zhang, P. Li, Y. Chen and X. Zhang, Appl. Clay Sci., 2018, 155, 126–138 Search PubMed.
- R. A. Longoria, T. Liang, U. T. Huynh, Q. P. Nguyen and D. A. DiCarlo, Spe J., 2017, 22, 1393–1401 Search PubMed.
- BP, Statistical Review of World Energy, https://www.bp.com/content/dam/bp/business-sites/en/global/corporate/pdfs/energy-economics/statistical-review/bp-stats-review-2019-full-report.pdf.
- Global CO2 emissions in 2019, https://www.iea.org/articles/global-co2-emissions-in-2019.
- M. M. F. Hasan, E. L. First, F. Boukouvala and C. A. Floudas, Comput. Chem. Eng., 2015, 81, 2–21 Search PubMed.
- T. Skodvin and K. H. Alfsen, The Intergovernmental Panel on Climate Change (IPCC): Outline of an assessment, 2010 Search PubMed.
- P. Markewitz, W. Kuckshinrichs, W. Leitner, J. Linssen, P. Zapp, R. Bongartz, A. Schreiber and T. E. Müller, Energy Environ. Sci., 2012, 5, 7281–7305 Search PubMed.
- G. P. Peters, G. Marland, C. Le Quéré, T. Boden, J. G. Canadell and M. R. Raupach, Nat. Clim. Change, 2012, 2, 2–4 Search PubMed.
- R. Afroz, M. N. Hassan and N. A. Ibrahim, Environ. Res., 2003, 92, 71–77 Search PubMed.
- T. H. Oh, Renewable Sustainable Energy Rev., 2010, 14, 2697–2709 Search PubMed.
- Scripps CO2 Program: CO2 concentration at Mauna Loa Observatory, Hawaii, http://scrippsco2.ucsd.edu.
- R. M. Cuéllar-Franca and A. Azapagic, J. CO2 Util., 2015, 9, 82–102 Search PubMed.
- Z. Dai, R. Middleton, H. Viswanathan, J. Fessenden-Rahn, J. Bauman, R. Pawar, S.-Y. Lee and B. McPherson, Environ. Sci. Technol. Lett., 2014, 1, 49–54 Search PubMed.
-
M. Aresta, Utilization of Dense Carbon Dioxide as an Inert Solvent for Chemical Syntheses, Wiley-VCH, 2010 Search PubMed.
- E. Alper and O. Yuksel Orhan, Petroleum, 2017, 3, 109–126 Search PubMed.
- H. B. Jung, K. C. Carroll, S. Kabilan, D. J. Heldebrant, D. Hoyt, L. Zhong, T. Varga, S. Stephens, L. Adams, A. Bonneville, A. Kuprat and C. A. Fernandez, Green Chem., 2015, 17, 2799–2812 Search PubMed.
- R. S. Norhasyima and T. M. I. Mahlia, J. CO2 Util., 2018, 26, 323–335 Search PubMed.
- F. I. Stalkup Jr, J. Pet. Technol., 1983, 35, 815–826 Search PubMed.
- J. J. Sheng, J. Pet. Sci. Eng., 2017, 159, 654–665 Search PubMed.
- M. K. Verma, Fundamentals of carbon dioxide-enhanced oil recovery (CO2-EOR): a supporting document of the assessment methodology for hydrocarbon recovery using CO2-EOR associated with carbon sequestration, 2015 Search PubMed.
-
J. Davidson, P. Freund and A. Smith, Putting Carbon Back in the Ground, IEA, 2001 Search PubMed.
- S. Bachu, Energy Convers. Manage., 2000, 41, 953–970 Search PubMed.
- M. Salehpour, M. Riazi, M. R. Malayeri and M. Seyyedi, J. Pet. Sci. Eng., 2020, 195, 107663 Search PubMed.
-
V. A. Kuuskraa and T. Malone, presented in part at the Offshore Technology Conference, Houston, Texas, USA, 2016/5/2/, 2016.
-
B. Chen and R. Pawar, presented in part at the SPE Annual Technical Conference and Exhibition, Dallas, Texas, USA, 2018/9/24/, 2018.
-
D. Merchant, presented in part at the Carbon Management Technology Conference, Houston, Texas, USA, 2019/11/13/, 2019.
- A. Hemmati-Sarapardeh, S. Ayatollahi, M.-H. Ghazanfari and M. Masihi, J. Chem. Eng. Data, 2014, 59, 61–69 Search PubMed.
- M. Lashkarbolooki and S. Ayatollahi, Chin. J. Chem. Eng., 2018, 26, 373–379 Search PubMed.
- Z. Song, Y. Song, Y. Li, B. Bai, K. Song and J. Hou, Fuel, 2020, 276, 118006 Search PubMed.
- Carbon Capture, Use, and Storage (CCUS) Report, National Petroleum Council, U.S., 2019.
- M. Bui, C. S. Adjiman, A. Bardow, E. J. Anthony, A. Boston, S. Brown, P. S. Fennell, S. Fuss, A. Galindo, L. A. Hackett, J. P. Hallett, H. J. Herzog, G. Jackson, J. Kemper, S. Krevor, G. C. Maitland, M. Matuszewski, I. S. Metcalfe, C. Petit, G. Puxty, J. Reimer, D. M. Reiner, E. S. Rubin, S. A. Scott, N. Shah, B. Smit, J. P. M. Trusler, P. Webley, J. Wilcox and N. Mac Dowell, Energy Environ. Sci., 2018, 11, 1062–1176 Search PubMed.
- EIA, U.S. Coalbed Methane Proved Reserves, https://www.eia.gov/dnav/ng/ng_enr_coalbed_a_EPG0_R51_Bcf_a.htm.
- M. Mukherjee and S. Misra, Earth-Sci. Rev., 2018, 179, 392–410 Search PubMed.
- R. Sander, L. D. Connell, Z. Pan, M. Camilleri, D. Heryanto and N. Lupton, Int. J. Coal Geol., 2014, 131, 113–125 Search PubMed.
- W. B. Fei, Q. Li, X. C. Wei, R. R. Song, M. Jing and X. C. Li, Eng. Geol., 2015, 196, 194–209 Search PubMed.
-
G. J. Koperna and D. E. Riestenberg, presented in part at the SPE International Conference on CO2 Capture, Storage, and Utilization, San Diego, California, USA, 2009/1/1/, 2009.
-
C. Temizel, D. J. Betancourt, A. Tiwari, M. Zhang, S. S. Aktas and F. Quiros, presented in part at the SPE Argentina Exploration and Production of Unconventional Resources Symposium, Buenos Aires, Argentina, 2016/6/1/, 2016.
- M. Mazzotti, R. Pini and G. Storti, J. Supercrit. Fluids, 2009, 47, 619–627 Search PubMed.
- A. Busch and Y. Gensterblum, Int. J. Coal Geol., 2011, 87, 49–71 Search PubMed.
- O. Ola, M. Mercedes Maroto-Valer and S. Mackintosh, Energy Procedia, 2013, 37, 6704–6709 Search PubMed.
- F. D. Meylan, V. Moreau and S. Erkman, J. CO2 Util., 2015, 12, 101–108 Search PubMed.
- A. Dibenedetto, A. Angelini and P. Stufano, J. Chem. Technol. Biotechnol., 2014, 89, 334–353 Search PubMed.
- A. A. Olajire, J. Pet. Sci. Eng., 2013, 109, 364–392 Search PubMed.
- S. J. Gerdemann, W. K. O'Connor, D. C. Dahlin, L. R. Penner and H. Rush, Environ. Sci. Technol., 2007, 41, 2587–2593 Search PubMed.
- S.-Y. Pan, P.-C. Chiang, W. Pan and H. Kim, Crit. Rev. Environ. Sci. Technol., 2018, 48, 471–534 Search PubMed.
- E. Georgakopoulos, R. M. Santos, Y. W. Chiang and V. Manovic, Greenhouse Gases: Sci. Technol., 2016, 6, 470–491 Search PubMed.
- S.-L. Pei, S.-Y. Pan, Y.-M. Li and P.-C. Chiang, Environ. Sci. Technol., 2017, 51, 10674–10681 Search PubMed.
- H. Xie, H. Yue, J. Zhu, B. Liang, C. Li, Y. Wang, L. Xie and X. Zhou, Engineering, 2015, 1, 150–157 Search PubMed.
- A. F. Esteves, F. M. Santos and J. C. Magalhães Pires, Renewable Sustainable Energy Rev., 2019, 114, 109331 Search PubMed.
- C. Pan, O. Chávez, C. E. Romero, E. K. Levy, A. Aguilar Corona and C. Rubio-Maya, Energy, 2016, 102, 148–160 Search PubMed.
- C. Xu, P. Dowd and Q. Li, J. Rock Mech. Geotech. Eng., 2016, 8, 50–59 Search PubMed.
- H. Shao, S. Kabilan, S. Stephens, N. Suresh, A. N. Beck, T. Varga, P. F. Martin, A. Kuprat, H. B. Jung, W. Um, A. Bonneville, D. J. Heldebrant, K. C. Carroll, J. Moore and C. A. Fernandez, Geothermics, 2015, 58, 22–31 Search PubMed.
- C. A. Fernandez, V. Gupta, G. L. Dai, A. P. Kuprat, A. Bonneville, D. Appriou, J. A. Horner, P. F. Martin and J. A. Burghardt, ACS Sustainable Chem. Eng., 2019, 7, 19660–19668 Search PubMed.
- D. Chiaramonti, M. Prussi, D. Casini, M. R. Tredici, L. Rodolfi, N. Bassi, G. C. Zittelli and P. Bondioli, Appl. Energy, 2013, 102, 101–111 Search PubMed.
-
E. Sadatshojaei, D. A. Wood and D. Mowla, in Sustainable Green Chemical Processes and their Allied Applications, ed. Inamuddin and A. Asiri, Springer International Publishing, Cham, 2020, pp. 575–588 DOI:10.1007/978-3-030-42284-4_21.
- J. D. Figueroa, T. Fout, S. Plasynski, H. McIlvried and R. D. Srivastava, Int. J. Greenhouse Gas Control, 2008, 2, 9–20 Search PubMed.
- R. S. Middleton, G. N. Keating, P. H. Stauffer, A. B. Jordan, H. S. Viswanathan, Q. J. Kang, J. W. Carey, M. L. Mulkey, E. J. Sullivan, S. P. Chu, R. Esposito and T. A. Meckel, Energy Environ. Sci., 2012, 5, 7328–7345 Search PubMed.
- Developments and Innovation in Carbon Dioxide (CO2) Capture and Storage Technology: Carbon Dioxide (CO2) Storage and Utilisation, Elsevier, 2010.
- B. P. McGrail, H. T. Schaef, V. A. Glezakou, L. X. Dang and A. T. Owen, Energy Procedia, 2009, 1, 3415–3419 Search PubMed.
- M. E. Boot-Handford, J. C. Abanades, E. J. Anthony, M. J. Blunt, S. Brandani, N. Mac Dowell, J. R. Fernández, M.-C. Ferrari, R. Gross, J. P. Hallett, R. S. Haszeldine, P. Heptonstall, A. Lyngfelt, Z. Makuch, E. Mangano, R. T. J. Porter, M. Pourkashanian, G. T. Rochelle, N. Shah, J. G. Yao and P. S. Fennell, Energy Environ. Sci., 2014, 7, 130–189 Search PubMed.
- K. S. Lackner, Science, 2003, 300, 1677 Search PubMed.
- Z. Li, M. Dong, S. Li and S. Huang, Energy Convers. Manage., 2006, 47, 1372–1382 Search PubMed.
- H. T. Schaef, C. L. Davidson, A. T. Owen, Q. R. S. Miller, J. S. Loring, C. J. Thompson, D. H. Bacon, V. A. Glezakou and B. P. McGrail, Energy Procedia, 2014, 63, 7844–7851 Search PubMed.
- Y. W. Liwei Zhang, X. Miao, M. Gan and X. Li, Adv. Geo-Energy Res., 2019, 3, 304–313 Search PubMed.
- C. D. Wallace, R. Ershadnia and M. R. Soltanian, Adv. Geo-Energy Res., 2020, 4, 392–405 Search PubMed.
- D. A. Voormeij and G. J. Simandl, Geoscience Canada, 2004, 31, 265–275 Search PubMed.
-
L. G. H. van der Meer, in Greenhouse Gas Control Technologies - 6th International Conference, ed. J. Gale and Y. Kaya, Pergamon, Oxford, 2003, pp. 201–206 DOI:10.1016/B978-008044276-1/50032-5.
- Carbon Capture, Use, and Storage (CCUS) Report, National Petroleum Council, U.S., 2019.
- ISO, Journal, 2019, 27916:2019.
- S. M. Benson and J. Deutch, Joule, 2018, 2, 1386–1389 Search PubMed.
- R. S. Middleton, B. Chen, D. R. Harp, R. M. Kammer, J. D. Ogland-Hand, J. M. Bielicki, A. F. Clarens, R. P. Currier, K. M. Ellett, B. A. Hoover, D. N. McFarlane, R. J. Pawar, P. H. Stauffer, H. S. Viswanathan and S. P. Yaw, Appl. Comput. Geosci., 2020, 7, 100035 Search PubMed.
- R. S. Middleton, J. D. Ogland-Hand, B. Chen, J. M. Bielicki, K. M. Ellett, D. R. Harp and R. M. Kammer, Energy Environ. Sci., 2020, 13, 5000–5016 Search PubMed.
- Y. Lu, J. Tang, Z. Ge, B. Xia and Y. Liu, Int. J. Rock Mech. Min. Sci., 2013, 60, 47–56 Search PubMed.
- K. Peng, S. Tian, G. Li, Z. Huang, R. Yang and Z. Guo, Pet. Explor. Dev., 2018, 45, 343–350 Search PubMed.
- R. Wang, W. Zhou, Z. Shen and Y. Yang, China Safety Science Journal, 1999, 9, 1–5 Search PubMed.
- X. Li, Z. Feng, G. Han, D. Elsworth, C. Marone, D. Saffer and D. S. Cheon, Geomech. Geophys. Geo-Energy Geo-Resources, 2016, 2, 63–76 Search PubMed.
-
J. J. Kolle, CIM International Conference on Horizontal Well Technology, Calgary, Alberta, Canada, 2000 Search PubMed.
- S. Tian, Z. He, G. Li, H. Wang, Z. Shen and Q. Liu, J. Nat. Gas Sci. Eng., 2016, 29, 232–242 Search PubMed.
-
A. P. Gupta, A. Gupta and J. Langlinais, presented in part at the SPE Annual Technical Conference and Exhibition, Dallas, Texas, 2005/1/1/, 2005.
- F. A. Al-Adwani, J. Langlinais and R. G. Hughes, SPE Drill. Completion, 2009, 24, 599–610 Search PubMed.
- Y. Du, R. Wang, H. Ni, M. Li, W. Song and H. Song, J. Hydrodyn., Ser. B, 2012, 24, 554–560 Search PubMed.
- Y. Du, R. Wang, H. Ni, Z. Huang and M. Li, J. Hydrodyn., Ser. B, 2013, 25, 528–534 Search PubMed.
- M. Huang, Y. Kang, X. Wang, Y. Hu, D. Li, C. Cai and Y. Liu, Exp. Therm. Fluid Sci., 2018, 94, 304–315 Search PubMed.
- R. H. Wang, H. J. Huo, Z. Y. Huang, H. F. Song and H. J. Ni, J. Hydrodyn., 2014, 26, 226–233 Search PubMed.
- Y. Hu, Y. Kang, X. Wang, X. Li, M. Huang and M. Zhang, J. Nat. Gas Sci. Eng., 2016, 36, 108–116 Search PubMed.
- Z. He, S. Tian, G. Li, H. Wang, Z. Shen and Z. Xu, J. Nat. Gas Sci. Eng., 2015, 27, 842–851 Search PubMed.
- X. Long, Q. Liu, X. Ruan, Y. Kang and Q. Lyu, J. Nat. Gas Sci. Eng., 2016, 34, 1044–1053 Search PubMed.
- M. Huang, Y. Kang, X. Wang, Y. Hu, C. Cai, Y. Liu and H. Chen, Appl. Therm. Eng., 2018, 139, 445–455 Search PubMed.
- X. Sun, H. Ni, R. Wang, Z. Shen and M. Zhao, J. Pet. Sci. Eng., 2018, 162, 532–538 Search PubMed.
- H. Huo, R. Wang, H. Ni, Y. Li, C. Tan and S. Xue, J. CO2 Util., 2017, 20, 105–112 Search PubMed.
-
R. M. Enick and J. Ammer, Website of the National Energy Technology Laboratory, 1998.
- P. Peng, Y. Ju, Y. Wang, S. Wang and F. Gao, Int. J. Numer. Anal. Methods, 2017, 41, 1992–2013 Search PubMed.
- P. Pei, K. Ling, J. He and Z. Liu, J. Nat. Gas Sci. Eng., 2015, 26, 1595–1606 Search PubMed.
- T. Ishida, Y. Chen, Z. Bennour, H. Yamashita, S. Inui, Y. Nagaya, M. Naoi, Q. Chen, Y. Nakayama and Y. Nagano, J. Geophys. Res.: Solid Earth, 2016, 121, 8080–8098 Search PubMed.
- X. Zhang, J. G. Wang, F. Gao and Y. Ju, J. Nat. Gas Sci. Eng., 2017, 45, 291–306 Search PubMed.
- L. Wang, B. Yao, H. Xie, P. H. Winterfeld, T. J. Kneafsey, X. Yin and Y.-S. Wu, Energy, 2017, 139, 1094–1110 Search PubMed.
- J. Wang, D. Elsworth, Y. Wu, J. Liu, W. Zhu and Y. Liu, Rock Mech. Rock Eng., 2018, 51, 299–313 Search PubMed.
- X. Zhang, Y. Lu, J. Tang, Z. Zhou and Y. Liao, Fuel, 2017, 190, 370–378 Search PubMed.
- L. Liu, W. Zhu, C. Wei, D. Elsworth and J. Wang, J. Pet. Sci. Eng., 2018, 164, 91–102 Search PubMed.
- J. He, L. O. Afolagboye, C. Lin and X. Wan, Energies, 2018, 11, 557 Search PubMed.
- S. Li and D. Zhang, Spe J., 2019, 24, 857–876 Search PubMed.
- X. Song, Y. Guo, J. Zhang, N. Sun, G. Shen, X. Chang, W. Yu, Z. Tang, W. Chen, W. Wei, L. Wang, J. Zhou, X. Li, X. Li, J. Zhou and Z. Xue, Joule, 2019, 3, 1913–1926 Search PubMed.
- Y. Jia, Y. Lu, D. Elsworth, Y. Fang and J. Tang, J. Pet. Sci. Eng., 2018, 165, 284–297 Search PubMed.
- Y. Jiang, C. Qin, Z. Kang, J. Zhou, Y. Li, H. Liu and X. Song, J. Nat. Gas Sci. Eng., 2018, 55, 382–394 Search PubMed.
-
X. Li, G. Li, W. Yu, H. Wang, K. Sepehrnoori, Z. Chen, H. Sun and S. Zhang, in Unconventional Resources Technology Conference, Austin, Texas, 24-26 July 2017, Society of Exploration Geophysicists, American Association of Petroleum Geologists, Society of Petroleum Engineers, 2017, pp. 2129–2144 DOI:10.15530/urtec-2017-2687198.
-
Q. Lv, X. Long, Y. Kang, L. Xiao and W. Wu, presented in part at the 6th International Conference on Pumps and Fans with Compressors and Wind Turbines, Beijing, China, 2013.
- J. J. Watkins and T. J. McCarthy, Chem. Mater., 1995, 7, 1991–1994 Search PubMed.
- M. Raje, K. Asghari, S. Vossoughi, D. W. Green and G. P. Willhite, SPE Reservoir Eval. Eng., 1999, 2, 205–210 Search PubMed.
- C. Shi, Z. Huang, S. Kilic, J. Xu, R. M. Enick, E. J. Beckman, A. J. Carr, R. E. Melendez and A. D. Hamilton, Science, 1999, 286, 1540 Search PubMed.
- A. Choubineh, A. Helalizadeh and D. Awood, Pet. Sci., 2019, 117–126 Search PubMed.
- J. Zhou, N. Hu, X. Xian, L. Zhou, J. Tang, Y. Kang and H. Wang, Adv. Geo-Energy Res., 2019, 3, 207–224 Search PubMed.
-
E. I. Administration and V. Kuuskraa, World shale gas resources: an initial assessment of 14 regions outside the United States, US Department of Energy, USA, 2011 Search PubMed.
-
S. M. Benson, P. Cook, J. Anderson, S. H. Bachu, B. Nimir, B. Basu, J. Bradshaw, G. Deguchi, J. Gale and G. von-Goerne, Underground Geological Storage, Cambridge, England, 2005 Search PubMed.
- A. Busch, S. Alles, Y. Gensterblum, D. Prinz, D. N. Dewhurst, M. D. Raven, H. Stanjek and B. M. Krooss, Int. J. Greenhouse Gas Control, 2008, 2, 297–308 Search PubMed.
- S. M. Kang, E. Fathi, R. J. Ambrose, I. Y. Akkutlu and R. F. Sigal, Spe J., 2011, 16, 842–855 Search PubMed.
- F. Liu, K. Ellett, Y. Xiao and J. A. Rupp, Int. J. Greenhouse Gas Control, 2013, 17, 111–126 Search PubMed.
- B. Hazra, D. A. Wood, V. Vishal and A. K. Singh, Energy Fuels, 2018, 32, 8175–8186 Search PubMed.
- S. J. Altman, B. Aminzadeh, M. T. Balhoff, P. C. Bennett, S. L. Bryant, M. B. Cardenas, K. Chaudhary, R. T. Cygan, W. Deng, T. Dewers, D. A. DiCarlo, P. Eichhubl, M. A. Hesse, C. Huh, E. N. Matteo, Y. Mehmani, C. M. Tenney and H. Yoon, J. Phys. Chem. C, 2014, 118, 15103–15113 Search PubMed.
- I. Okamoto, X. Li and T. Ohsumi, Energy, 2005, 30, 2344–2351 Search PubMed.
-
D. B. Bennion and S. Bachu, presented in part at the EUROPEC/EAGE Conference and Exhibition, London, UK, 2007/1/1/, 2007.
- B. Bennion and S. Bachu, SPE Reservoir Eval. Eng., 2008, 11, 487–496 Search PubMed.
- F. Civan, AIP Conf. Proc., 2010, 1254, 53–58 Search PubMed.
- A. Sakhaee-Pour and S. Bryant, SPE Reservoir Eval. Eng., 2012, 15, 401–409 Search PubMed.
- A. S. Ziarani and R. Aguilera, Transp. Porous Media, 2012, 91, 239–260 Search PubMed.
- W. Shen, L. Zheng, C. M. Oldenburg, A. Cihan, J. Wan and T. K. Tokunaga, Transp. Porous Media, 2018, 123, 521–531 Search PubMed.
- Z. Liehui, S. Baochao, Z. Yulong and G. Zhaoli, Int. J. Heat Mass Transfer, 2019, 139, 144–179 Search PubMed.
- M. Gutierrez, L. E. Øino and R. Nygård, Mar. Pet. Geol., 2000, 17, 895–907 Search PubMed.
- T. Phillips, N. Kampman, K. Bisdom, N. D. Forbes Inskip, S. A. M. den Hartog, V. Cnudde and A. Busch, Earth-Sci. Rev., 2020, 211, 103390 Search PubMed.
-
R. M. Bustin, A. M. M. Bustin, A. Cui, D. Ross and V. M. Pathi, presented in part at the SPE Shale Gas Production Conference, Fort Worth, Texas, USA, 2008/1/1/, 2008.
- F. O. Jones and W. W. Owens, J. Pet. Technol., 1980, 32, 1631–1640 Search PubMed.
- J. Zhang, S. Huang, L. Cheng, W. Xu, H. Liu, Y. Yang and Y. Xue, J. Nat. Gas Sci. Eng., 2015, 24, 291–301 Search PubMed.
-
R. Raghavan and L. Y. Chin, presented in part at the SPE Annual Technical Conference and Exhibition, San Antonio, Texas, 2002/1/1/, 2002.
- A. F. Gangi, Int. J. Rock Mech. Min. Sci. Geomech. Abstr., 1978, 15, 249–257 Search PubMed.
- A. Wasaki and I. Y. Akkutlu, Spe J., 2015, 20, 1384–1396 Search PubMed.
- S. Wang, J. Shi, K. Wang, Z. Sun and Z. Zhao, Energy Fuels, 2017, 31, 13545–13557 Search PubMed.
-
I. Palmer and J. Mansoori, presented in part at the SPE Annual Technical Conference and Exhibition, Denver, Colorado, 1996/1/1/, 1996.
-
J. A. Rushing, K. E. Newsham, P. M. Lasswell, J. C. Cox and T. A. Blasingame, presented in part at the SPE Annual Technical Conference and Exhibition, Houston, Texas, 2004/1/1/, 2004.
-
E. Fathi, A. Tinni and I. Y. Akkutlu, Shale Gas Correction to Klinkenberg Slip Theory, 2012 Search PubMed.
- D. A. Lockerby, J. M. Reese and M. A. Gallis, AIAA J., 2005, 43, 1391–1393 Search PubMed.
-
L. J. Klinkenberg, presented in part at the Drilling and Production Practice, New York, New York, 1941/1/1/, 1941.
- R. W. Barber and D. R. Emerson, Heat Transfer Eng., 2006, 27, 3–12 Search PubMed.
- H. Singh and F. Javadpour, Fuel, 2016, 164, 28–37 Search PubMed.
- J. B. Curtis, AAPG Bull., 2002, 86, 1921–1938 Search PubMed.
- F. Javadpour, D. Fisher and M. Unsworth, J. Can. Pet. Technol., 2007, 46, 55–61 Search PubMed.
-
R. J. Ambrose, R. C. Hartman, M. Diaz Campos, I. Y. Akkutlu and C. Sondergeld, SPE unconventional gas conference, 2010 Search PubMed.
- G. R. Chalmers and R. M. Bustin, Bull. Can. Pet. Geol., 2008, 56, 22–61 Search PubMed.
- R. J. Hill, E. Zhang, B. J. Katz and Y. Tang, AAPG Bull., 2007, 91, 501–521 Search PubMed.
- D. J. Ross and R. M. Bustin, AAPG Bull., 2008, 92, 87–125 Search PubMed.
- D. J. K. Ross and R. Marc Bustin, Mar. Pet. Geol., 2009, 26, 916–927 Search PubMed.
- M. Gasparik, P. Bertier, Y. Gensterblum, A. Ghanizadeh, B. M. Krooss and R. Littke, Int. J. Coal Geol., 2014, 123, 34–51 Search PubMed.
- G. R. Chalmers and R. M. Bustin, Int. J. Coal Geol., 2007, 70, 223–239 Search PubMed.
- S. Wang, Z. Song, T. Cao and X. Song, Mar. Pet. Geol., 2013, 44, 112–119 Search PubMed.
- J. Tan, P. Weniger, B. Krooss, A. Merkel, B. Horsfield, J. Zhang, C. J. Boreham, G. V. Graas and B. A. Tocher, Fuel, 2014, 129, 204–218 Search PubMed.
-
M. M. Dubinin, in Progress in Surface and Membrane Science, ed. D. A. Cadenhead, J. F. Danielli and M. D. Rosenberg, Elsevier, 1975, vol. 9, pp. 1–70 Search PubMed.
- A. Miceli Romero and R. P. Philp, AAPG Bull., 2012, 96, 493–517 Search PubMed.
- T. Zhang, G. S. Ellis, S. C. Ruppel, K. Milliken and R. Yang, Org. Geochem., 2012, 47, 120–131 Search PubMed.
- X. Lu, F. Li and A. T. Watson, SPE Form. Eval., 1995, 10, 109–113 Search PubMed.
- M. Gasparik, A. Ghanizadeh, P. Bertier, Y. Gensterblum, S. Bouw and B. M. Krooss, Energy Fuels, 2012, 26, 4995–5004 Search PubMed.
- L. Ji, T. Zhang, K. L. Milliken, J. Qu and X. Zhang, Appl. Geochem., 2012, 27, 2533–2545 Search PubMed.
- A. Merkel, R. Fink and R. Littke, Int. J. Coal Geol., 2015, 147–148, 1–8 Search PubMed.
- X. Luo, S. Wang, Z. Wang, Z. Jing, M. Lv, Z. Zhai and T. Han, Int. J. Coal Geol., 2015, 150–151, 210–223 Search PubMed.
- D. S. Berawala and P. Ø. Andersen, SPE Reservoir Eval. Eng., 2020, 17 Search PubMed , preprint.
- A. Bemani, A. Baghban, A. H. Mohammadi and P. Ø. Andersen, J. Nat. Gas Sci. Eng., 2020, 76, 103204 Search PubMed.
- I. Klewiah, D. S. Berawala, H. C. Alexander Walker, P. Ø. Andersen and P. H. Nadeau, J. Nat. Gas Sci. Eng., 2020, 73, 103045 Search PubMed.
-
B. C. Nuttal, C. Eble, R. M. Bustin and J. A. Drahovzal, in Greenhouse Gas Control Technologies 7, ed. E. S. Rubin, D. W. Keith, C. F. Gilboy, M. Wilson, T. Morris, J. Gale and K. Thambimuthu, Elsevier Science Ltd, Oxford, 2005, pp. 2225–2228 DOI:10.1016/B978-008044704-9/50306-2.
- P. Weniger, W. Kalkreuth, A. Busch and B. M. Krooss, Int. J. Coal Geol., 2010, 84, 190–205 Search PubMed.
- S. Duan, M. Gu, X. Du and X. Xian, Energy Fuels, 2016, 30, 2248–2256 Search PubMed.
- J. Zhou, S. Xie, Y. Jiang, X. Xian, Q. Liu, Z. Lu and Q. Lyu, Energy Fuels, 2018, 32, 6073–6089 Search PubMed.
- J. Liu, L. Xie, D. Elsworth and Q. Gan, Environ. Sci. Technol., 2019, 53, 9328–9336 Search PubMed.
- Y. Wang, T. T. Tsotsis and K. Jessen, Ind. Eng. Chem. Res., 2015, 54, 12187–12195 Search PubMed.
- M. Gu, X. Xian, S. Duan and X. Du, J. Nat. Gas Sci. Eng., 2017, 46, 296–306 Search PubMed.
- T. Wang, S. Tian, G. Li and M. Sheng, J. Nat. Gas Sci. Eng., 2018, 50, 181–188 Search PubMed.
- X.-D. Du, M. Gu, S. Duan and X.-F. Xian, J. Energy Resour. Technol., 2016, 139, 1–9 Search PubMed.
- Y. Ma, C. Yue, S. Li, X. Xu and Y. Niu, Carbon Resour. Convers., 2019, 2, 35–42 Search PubMed.
- B. Liu, C. Qi, T. Mai, J. Zhang, K. Zhan, Z. Zhang and J. He, J. Nat. Gas Sci. Eng., 2018, 53, 329–336 Search PubMed.
- W. Zhou, H. Wang, Y. Yan and X. Liu, Energy Fuels, 2019, 33, 6542–6551 Search PubMed.
- M.-S. Lee, B. P. McGrail, R. Rousseau and V.-A. Glezakou, J. Phys. Chem. C, 2018, 122, 1125–1134 Search PubMed.
- D. Pines, J. Ditkovich, T. Mukra, Y. Miller, P. M. Kiefer, S. Daschakraborty, J. T. Hynes and E. Pines, J. Phys. Chem. B, 2016, 120, 2440–2451 Search PubMed.
- A. Stirling and I. Pápai, J. Phys. Chem. B, 2010, 114, 16854–16859 Search PubMed.
- K. Adamczyk, M. Prémont-Schwarz, D. Pines, E. Pines and E. T. J. Nibbering, Science, 2009, 326, 1690 Search PubMed.
- D. Polino, E. Grifoni, R. Rousseau, M. Parrinello and V.-A. Glezakou, J. Phys. Chem. A, 2020, 124, 3963–3975 Search PubMed.
- T. Loerting and J. Bernard, ChemPhysChem, 2010, 11, 2305–2309 Search PubMed.
- M. T. Nguyen, M. H. Matus, V. E. Jackson, V. T. Ngan, J. R. Rustad and D. A. Dixon, J. Phys. Chem. A, 2008, 112, 10386–10398 Search PubMed.
- N. R. Jena and P. C. Mishra, Theor. Chem. Acc., 2005, 114, 189–199 Search PubMed.
- P. P. Kumar, A. G. Kalinichev and R. J. Kirkpatrick, J. Chem. Phys., 2007, 126, 204315 Search PubMed.
- V.-A. Glezakou, R. Rousseau, L. X. Dang and B. P. McGrail, Phys. Chem. Chem. Phys., 2010, 12, 8759–8771 Search PubMed.
- M. Saharay and S. Balasubramanian, J. Phys. Chem. B, 2007, 111, 387–392 Search PubMed.
- I. Gaus, Int. J. Greenhouse Gas Control, 2010, 4, 73–89 Search PubMed.
- S. Farquhar, J. Pearce, G. Dawson, A. Golab, S. Sommacal, D. Kirste, D. Biddle and S. Golding, Chem. Geol., 2015, 399, 98–122 Search PubMed.
-
M. Watson, CO2CRC Publication Number RPT06-0098, 2006.
- B. L. Alemu, P. Aagaard, I. A. Munz and E. Skurtveit, Appl. Geochem., 2011, 26, 1975–1989 Search PubMed.
- J. Zhou, K. Yang, S. Tian, L. Zhou, X. Xian, Y. Jiang, M. Liu and J. Cai, Fuel, 2020, 263, 116642 Search PubMed.
- F. K. Crundwell, Hydrometallurgy, 2014, 149, 265–275 Search PubMed.
- Q. Lyu, X. Long, P. G. Ranjith, J. Tan, Y. Kang and Z. Wang, Energy, 2018, 147, 1288–1298 Search PubMed.
- Q. Lyu, P. Ranjith, X. Long and B. Ji, Materials, 2016, 9, 663 Search PubMed.
- Q. Lyu, X. Long, P. G. Ranjith, J. Tan, J. Zhou, Z. Wang and W. Luo, Geomech. Geophys. Geo-Energy Geo-Resources, 2018, 4, 141–156 Search PubMed.
- H. Yin, J. Zhou, X. Xian, Y. Jiang, Z. Lu, J. Tan and G. Liu, Energy, 2017, 132, 84–95 Search PubMed.
- S. Zhang, X. Xian, J. Zhou and L. Zhang, RSC Adv., 2017, 7, 42946–42955 Search PubMed.
- G. Feng, Y. Kang, Z.-D. Sun, X.-C. Wang and Y.-Q. Hu, Energy, 2019, 173, 870–882 Search PubMed.
- Y. Zou, S. Li, X. Ma, S. Zhang, N. Li and M. Chen, J. Nat. Gas Sci. Eng., 2018, 49, 157–168 Search PubMed.
- K. L. Toews, R. M. Shroll, C. M. Wai and N. G. Smart, Anal. Chem., 1995, 67, 4040–4043 Search PubMed.
- Q. Lyu, J. Tan, J. M. Dick, Q. Liu, R. Pathegama Gamage, L. Li, Z. Wang and C. Hu, Rock Mech. Rock Eng., 2018, 52, 2039–2052 Search PubMed.
- A. G. Ilgen, M. Aman, D. N. Espinoza, M. A. Rodriguez, J. M. Griego, T. A. Dewers, J. D. Feldman, T. A. Stewart, R. C. Choens and J. Wilson, Int. J. Greenhouse Gas Control, 2018, 78, 244–253 Search PubMed.
-
C. K. Ho and S. W. Webb, Gas Transport in Porous Media, Springer, Netherlands, 2006 Search PubMed.
- P. Billemont, B. Coasne and G. De Weireld, Langmuir, 2013, 29, 3328–3338 Search PubMed.
- E. Fathi and I. Y. Akkutlu, Int. J. Coal Geol., 2014, 123, 52–61 Search PubMed.
- X. Li, J. Fan, H. Yu, Y. Zhu and H. Wu, Int. J. Heat Mass Transfer, 2018, 122, 1210–1221 Search PubMed.
- Y. Lan, Z. Yang, P. Wang, Y. Yan, L. Zhang and J. Ran, Fuel, 2019, 238, 412–424 Search PubMed.
- Q. Lyu, K. Wang, W. A. M. Wanniarachchi, C. Hu and J. Shi, Geomech. Geophys. Geo-Energy Geo-Resources, 2020, 6, 69 Search PubMed.
- T. H. Kim, J. Cho and K. S. Lee, Appl. Energy, 2017, 190, 1195–1206 Search PubMed.
- J. Zhou, G. Liu, Y. Jiang, X. Xian, Q. Liu, D. Zhang and J. Tan, J. Nat. Gas Sci. Eng., 2016, 36, 369–377 Search PubMed.
- W. Wu, M. D. Zoback and A. H. Kohli, Fuel, 2017, 203, 179–186 Search PubMed.
- A. H. Hosseini, H. Ghadery-Fahliyany, D. Wood and A. Choubineh, Gas Process. J., 2020, 8, 83–92 Search PubMed.
- H. Zhu, Y. Ju, C. Huang, K. Han, Y. Qi, M. Shi, K. Yu, H. Feng, W. Li, L. Ju and J. Qian, Fuel, 2019, 241, 914–932 Search PubMed.
- Y. Ju, C. Huang, Y. Sun, Q. Wan, X. Lu, S. Lu, H. He, X. Wang, C. Zou, J. Wu, H. Liu, L. Shao, X. Wu, H. Chao, Q. Liu, J. Qiu, M. Wang, J. Cai, G. Wang and Y. Sun, J. Nanosci. Nanotechnol., 2017, 17, 5930–5965 Search PubMed.
- Y. Jiang, Y. Luo, Y. Lu, C. Qin and H. Liu, Energy, 2016, 97, 173–181 Search PubMed.
- Y. Pan, D. Hui, P. Luo, Y. Zhang, L. Zhang and L. Sun, J. CO2 Util., 2018, 28, 152–167 Search PubMed.
- K. M. Mouzakis, A. K. Navarre-Sitchler, G. Rother, J. L. Bañuelos, X. Wang, J. P. Kaszuba, J. E. Heath, Q. R. S. Miller, V. Alvarado and J. E. McCray, Environ. Eng. Sci., 2016, 33, 725–735 Search PubMed.
- J. P. Kaszuba, D. R. Janecky and M. G. Snow, Chem. Geol., 2005, 217, 277–293 Search PubMed.
- S. Carroll, W. McNab, S. Torres, M. Singleton and P. Zhao, Energy Procedia, 2011, 4, 5186–5194 Search PubMed.
- H. Yin, J. Zhou, Y. Jiang, X. Xian and Q. Liu, Fuel, 2016, 184, 289–303 Search PubMed.
- K. Goto, K. Yogo and T. Higashii, Appl. Energy, 2013, 111, 710–720 Search PubMed.
- A. B. Rao and E. S. Rubin, Environ. Sci. Technol., 2002, 36, 4467–4475 Search PubMed.
- O. Yevtushenko, D. Bettge, R. Bäßler and S. Bohraus, Mater. Corros., 2015, 66, 334–341 Search PubMed.
- O. Bolland and H. Undrum, Adv. Environ. Res., 2003, 7, 901–911 Search PubMed.
- M. Lucquiaud and J. Gibbins, Chem. Eng. Res. Des., 2011, 89, 1553–1571 Search PubMed.
- A. K. Datta and P. K. Sen, J. Membr. Sci., 2006, 283, 291–300 Search PubMed.
- F. Ahmad, K. K. Lau, A. M. Shariff and G. Murshid, Comput. Chem. Eng., 2012, 36, 119–128 Search PubMed.
-
R. W. Baker, Membrane Technology and Applications, John Wiley & Sons, Chichester, UK, 2nd edn, 2004 Search PubMed.
- J. Hao, P. A. Rice and S. A. Stern, J. Membr. Sci., 2008, 320, 108–122 Search PubMed.
- B. Jia, J.-S. Tsau and R. Barati, Fuel, 2019, 236, 404–427 Search PubMed.
- A. Shafeen, E. Croiset, P. L. Douglas and I. Chatzis, Energy Convers. Manage., 2004, 45, 3207–3217 Search PubMed.
- D. Singh, E. Croiset, P. L. Douglas and M. A. Douglas, Energy Convers. Manage., 2003, 44, 3073–3091 Search PubMed.
- E. Mohammad-Pajooh, D. Weichgrebe, G. Cuff, B. M. Tosarkani and K.-H. Rosenwinkel, Chemosphere, 2018, 212, 898–914 Search PubMed.
- R. B. Jackson, A. Vengosh, J. W. Carey, R. J. Davies, T. H. Darrah, F. O'Sullivan and G. Pétron, Annu. Rev. Environ. Resour., 2014, 39, 327–362 Search PubMed.
- J. Zhou, G. Liu, Y. Jiang, X. Xian, Q. Liu, D. Zhang and J. Tan, J. Nat. Gas Sci. Eng., 2016, 36, 369–377 Search PubMed.
- H. Wang, G. Li, Y. Zheng, S. Kamy, Z. Shen, B. Yang and L. Shi, Acta Pet. Sin., 2020, 41, 116–126 Search PubMed.
- X. Lei, T. Tamagawa, K. Tezuka and M. Takahashi, Geophys. Res. Lett., 2011, 38, 1–5 Search PubMed.
- R. Wilkins, A. H. Menefee and A. F. Clarens, Environ. Sci. Technol., 2016, 50, 13134–13141 Search PubMed.
- D. J. Soeder, S. Sharma, N. Pekney, L. Hopkinson, R. Dilmore, B. Kutchko, B. Stewart, K. Carter, A. Hakala and R. Capo, Int. J. Coal Geol., 2014, 126, 4–19 Search PubMed.
- P. Noothout, F. Wiersma, O. Hurtado, D. Macdonald, J. Kemper and K. van Alphen, Energy Procedia, 2014, 63, 2481–2492 Search PubMed.
- M. J. Kennedy, D. R. Pevear and R. J. Hill, Science, 2002, 295, 657 Search PubMed.
- J. Liming, Q. Junli, Z. Tongwei and X. Yanqing, Earth Sci., 2012, 37, 1043–1050 Search PubMed.
- Z. T. Bieniawski, Int. J. Rock Mech. Min. Sci. Geomech. Abstr., 1968, 5, 325–335 Search PubMed.
- Q. Lyu, P. Ranjith, X. Long, Y. Kang and M. Huang, Arabian J. Geosci., 2015, 8, 10289–10299 Search PubMed.
- R. Lahann, M. Mastalerz, J. A. Rupp and A. Drobniak, Int. J. Coal Geol., 2013, 108, 2–9 Search PubMed.
- M. Mastalerz, A. Drobniak and J. Rupp, Energy Fuels, 2008, 22, 4049–4061 Search PubMed.
- L.-P. Yi, X.-G. Li, Z.-Z. Yang and J. Sun, Int. J. Heat Mass Transfer, 2018, 121, 680–690 Search PubMed.
- H. Wang, X. Li, K. Sepehrnoori, Y. Zheng and W. Yan, Int. J. Heat Mass Transfer, 2019, 139, 10–16 Search PubMed.
- J. Wang, B. Sun, H. Li, X. Wang, Z. Wang and X. Sun, Int. J. Heat Mass Transfer, 2018, 118, 1012–1021 Search PubMed.
- G. Linga and H. Lund, Int. J. Greenhouse Gas Control, 2016, 51, 71–80 Search PubMed.
- B. Sun, J. Wang, Z. Wang, Y. Gao and J. Xu, J. Pet. Sci. Eng., 2018, 166, 420–432 Search PubMed.
- L. Hou, B. Sun, Z. Wang and Q. Li, J. Supercrit. Fluids, 2015, 100, 121–128 Search PubMed.
- Z. Shuli, H. Zengping and P. Jiadong, China Petroleum Machinery, 2016, 44, 79–84 Search PubMed.
Footnotes |
† Electronic supplementary information (ESI) available. See DOI: 10.1039/d0ee03648j |
‡ Large-scale projects are defined as those integrated projects that store at least 80 000 tons of CO2 per year from a coal-based facility or at least 400 000 tons of CO2 per year from other sources. |
|
This journal is © The Royal Society of Chemistry 2021 |