DOI:
10.1039/D0EE03382K
(Review Article)
Energy Environ. Sci., 2021,
14, 781-814
Electrochemical carbon dioxide capture to close the carbon cycle†
Received
24th October 2020
, Accepted 18th December 2020
First published on 18th December 2020
Abstract
Electrochemical CO2 capture technologies are gaining attention due to their flexibility, their ability to address decentralized emissions (e.g., ocean and atmosphere) and their fit in an electrified industry. In the present work, recent progress made in electrochemical CO2 capture is reviewed. The majority of these methods rely on the concept of “pH-swing” and the effect it has on the CO2 hydration/dehydration equilibrium. Through a pH-swing, CO2 can be captured and recovered by shifting the pH of a working fluid between acidic and basic pH. Such swing can be applied electrochemically through electrolysis, bipolar membrane electrodialysis, reversible redox reactions and capacitive deionization. In this review, we summarize main parameters governing these electrochemical pH-swing processes and put the concept in the framework of available worldwide capture technologies. We analyse the energy efficiency and consumption of such systems, and provide recommendations for further improvements. Although electrochemical CO2 capture technologies are rather costly compared to the amine based capture, they can be particularly interesting if more affordable renewable electricity and materials (e.g., electrode and membranes) become widely available. Furthermore, electrochemical methods have the ability to (directly) convert the captured CO2 to value added chemicals and fuels, and hence prepare for a fully electrified circular carbon economy.
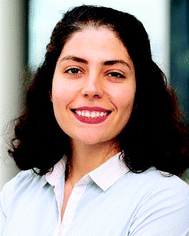
R. Sharifian
| Ir. Rezvan Sharifian is PhD candidate in the Vermaas group, Chemical Engineering department at Delft University of technology, and Wetsus, Centre of Excellence for Sustainable Water Technology, in the Netherlands. Her research focuses on new technologies for electrochemical CO2 capture via pH swing. As a recipient of the full TU Delft Energy Scholarship, she graduated her MSc with cum laude in petroleum engineering in the applied earth sciences faculty, in 2016. |
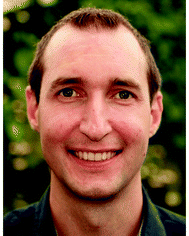
R. M. Wagterveld
| Dr Ir. R. Martijn Wagterveld is scientific project manager and theme coordinator Sensoring at Wetsus, European Centre of Excellence for Sustainable Water Technology, Netherlands. In this position, Dr Wagterveld is responsible for novel project definitions and guidance of academic research by PhD and postdoctoral researchers. His expertise is on water technology, primarily in the field of calcium carbonate crystallization, ion-exchange membranes, salinity gradient energy, separation technology, water quality sensors and data fusion. |
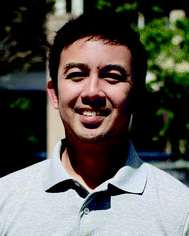
I. A. Digdaya
| Dr Ibadillah A. Digdaya received his BS in Engineering Physics from Bandung Institute of Technology in 2009 and completed a PhD from the Department of Chemical Engineering at Delft University of Technology with Professor Wilson A. Smith in 2018. He then joined the group of Dr Chengxiang Xiang as a research scientist in Joint Center for Artificial Synthesis at California Institute of Technology. Currently, his research interest includes design, fabrication, optimization of devices for CO2 capture and conversion using electrochemical and thermochemical processes. |
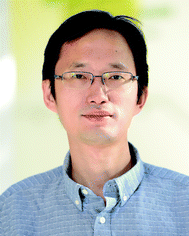
C. Xiang
| Dr Chengxiang (“CX”) Xiang is a Principal Investigator and Staff Scientist in Liquid Sunlight Alliance (LiSA) at California Institute of Technology. Dr Xiang leads a team of chemists, engineers and material scientists working on photoelectrochemical hydrogen generation, catalytic CO2 conversion and electrochemical CO2 capture from dilute sources. Dr Xiang received his PhD in Physics from University of California, Irvine in 2009. Dr Xiang research interests include design and fabrication of high efficiency solar-fuel prototypes, opto-electronic-catalytic modeling of advanced micro/nanostructured photoelectrochemical systems and multi-ion transport modeling in solution and polymer electrolytes. |
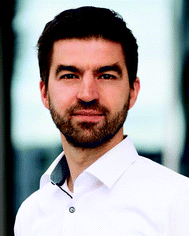
D. A. Vermaas
| David is an assistant professor at Delft University of Technology. He obtained his PhD in Chemical Engineering at University of Twente and Wetsus (2014), and started a research group on electrochemical flow systems at Delft in 2016. David's group currently hosts 15 researchers focusing on mass transport and membrane applications in electrochemical conversion, and collaborating in the e-refinery platform with industry and academics to innovate renewable energy technologies. Current projects include (bipolar) membranes for electrolysis, electrochemical CO2 capture, H2–Br2 redox flow batteries, and local transport near gas bubbles and membrane electrode assemblies. |
Broader context
The necessity of taking actions to achieve a net zero CO2 emission has brought up the question “how to achieve a circular carbon economy?”. To close the carbon cycle, sustainable CO2 capture and utilization are indispensable. Current technologies for CO2 capture rely dominantly on absorption of CO2 from flue gas, regenerated via energy-intensive temperature swings, which imply a huge energy consumption when expanding capture towards a net zero CO2 emission. When also realizing that approximately 40% of the CO2 emission is decentralized, which may even increase when power plants and industry are transitioning to renewable energy, we are facing a massive challenge for closing the carbon cycle. In that framework, electrochemical technologies for CO2 capture, from the atmosphere, ocean, and flue gas, can play an important role. The installed renewable electricity generation capacity is increasing each year, with more than 2300 GW in 2018. However, currently, most electrochemical methods are at early stages of development and are still energy intensive. In this contribution, we evaluate each of these technologies while focusing on the pH-swing approach. We establish the current state of the art, describe the major technical barriers and R&D needs, and discuss opportunities for improving electrochemical CO2 capture.
|
1 Introduction
To honour the Paris Agreement, a global net zero greenhouse gasses (GHG) emission needs to be realized by the end of this century.1–3 Among all GHG's, CO2(g) is accepted to be the main anthropogenic control knob on the climate and has been the focus of many studies.4,5 To achieve a net zero emission,6 reducing the total CO2 emission obtains most impact in the short term.7 The largest CO2 emission is due to combustion of fossil fuels and thus can be reduced through fossil fuels phase out. However, although ultimately fossil fuels phase out might be possible for the power industry and transportation sector (through substitution with renewable energy), many sectors (e.g., steel/cement production, intercontinental air transport or non electrical trains) do not have a suitable alternative for carbon based fuels. In addition, due to the current agriculture techniques, the net global deforestation and the growing demand for carbon as a resource, CO2 will be emitted due to many anthropogenic activities. Therefore, to achieve a net zero GHG's emission, in addition to emission reduction, CO2 capture and utilization is required in the long term. Also, as the long term CO2 emitters include decentralized emitters, direct capture from CO2 sinks (e.g., atmosphere and ocean, see Fig. 1 is necessary for effectively addressing the anthropogenic CO2 emissions.8,9
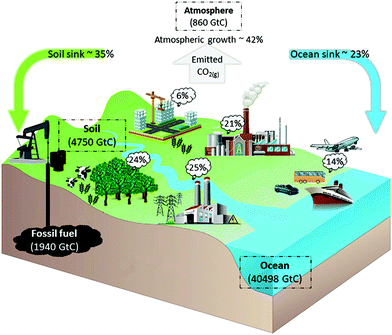 |
| Fig. 1 Schematic of the carbon cycle. The total carbon reserve is shown in gigatonnes of carbon (GtC). The global GHG emissions in CO2(eq) by economic sectors: 25% electricity and heat production, 24% agriculture, forestry and land use, 6% buildings, 14% transportation, 21% industry and 10% other energy usages. Data extracted from ref. 10–12. | |
The main challenge that currently available CO2 capture methods face is a high energy consumption.13–15 A few mature, non-electrochemical CO2 capture technologies e.g., absorption, adsorption, membrane separation and cryogenic capture are already available in industrial scales,16–25 Section 4. These methods often depend on the availability of thermal energy, which makes them less well suited for CO2 capture from dilute sources e.g., air and ocean. Furthermore, the cost of direct air capture via traditional technologies has been estimated in the literature from $100 to $1000 per tonne of captured CO2.3,26–28
Electrochemical processes have the potential to be rather energy efficient as they can target molecules directly (instead of the medium surrounding them).29,30 Using electrochemistry for CO2 capture dates back to the late 1960s, when molten carbonates as electrolyte were used for CO2 control in a manned spacecraft.31–34 Nowadays, electrochemical CO2 capture methods can be applied to all CO2 containing streams with any concentration. Direct capture from air,35 ocean8,36 and flue gas37–39 have been reported. Such capture units can be retrofitted as plug-and-play processes, allow small footprints and are geometrically flexible.39,40 They do not require external sources of heat or high pressures/vacuum for operation, nor degradation of sorbent material is expected.40 Although heat integration can be beneficial for power plants in reducing the need for energy, other industries (e.g., food and water sector) cannot integrate high heat, rising the need for technologies that can perform under low heat conditions from centralized emitters as well.14 In electrochemical systems, the electric potential gradient is the main driving force which can be controlled precisely to drive chemical reactions isothermally.29,30,41 A number of bench-scale capture demonstrations via electrochemical pH-swing have obtained CO2 capture and release at the promising value of ∼100 kJ mol−1 CO2.42,43
The added advantage of the electrochemical methods is their ability to integrate CO2 capture and utilization44 (Section 5). An example is the modular, sequential CO2 capture and conversion system that uses the pH-swing concept to produce CO electrochemically.45,46 In addition, reactive CO2 capture, in which the CO2 capturing medium pre-concentrates the dilute feed and produces favorable local micro-environments, has become an emerging field for integrated CO2 capture and conversion using electrochemical techniques.47,48
A wide variety of efforts to electrochemically capture CO2 has been demonstrated in the past 50 years, with an intensification of research activities in the last two decades. In this work we give an overview of such advances. The center of our scope are the electrochemical methods that use a pH-swing concept, as shown in Fig. 2a and b. The swing refers to (electrochemically) shifting the pH of a working fluid (continuously) between basic and acidic pH to influence the CO2 equilibrium to capture and recover CO2.
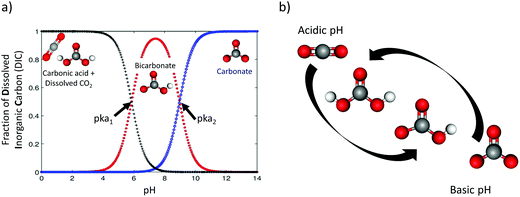 |
| Fig. 2 (a) Effect of pH on the CO2 equilibrium (for a closed system at temperature of 25 °C and salinity of 35 ppt). The solution is buffered around two pKa values. (b) Schematic of the pH-swing concept. | |
The pH-swing allows absorption and desorption at ambient temperature and does not require use of any special chemicals. Widely available, inexpensive, non toxic/non corrosive/non volatile salt solutions, such as NaCl, KCl, KHCO3 or even seawater can be used for the process. The pH-swing can be applied electrochemically using electrolysis, bipolar membrane electrodialysis (BPMED), capacitive deionization and reversible PCET agents as demonstrated in Fig. 3. In this work, after providing the required theoretical background in Section 2, each pH-swing route is explained and the research of this route is comprehensive reviewed in Section 3. In addition to a pH-swing approach, other electrochemical technologies involve using redox-active carriers49 (Section 3.3), molten carbonate cells and hybrid methods (Section 3.4) such as electrochemically enhanced absorption/adsorption.29,30 To enable comparison, we also briefly describe the main conventional capture methods, their drawbacks and advantages, and opportunities to improve these technologies with electrochemical methods, in Section 4. Finally, CO2 utilization and storage is discussed briefly in section to close the carbon cycle (Section 5).
 |
| Fig. 3 Summary of electrochemical CO2 capture methods. | |
2 Theory: pH-swing concept and involved reactions
The concept of CO2 capture via pH-swing leverages the responsiveness of the thermodynamic equilibrium of CO2 to pH changes. A pH-swing is also used for other resource recovery applications than CO2 capture, but the method is not always explicitly referred to as “pH-swing”. For instance, pH-swing is employed to recover ammonia electrochemically from urine50,51 and to remove phosphate from waste water streams.52
2.1 Carbonate equilibrium
The carbonate equilibrium can be described as open or closed based on the contact with an overlying gas and is explained in detail in ref. 53–56. In an open system, the total concentration of the dissolved inorganic carbon varies by changing in the pH; acidification results in CO2(g) out-gassing, while basification lead to more CO2(g) absorption, increasing the DIC. In a closed system (e.g., inside of an electrochemical cell), the total DIC remains constant regardless of any pH changes. If so, the dominant carbonic species alter by changing the pH as demonstrated in Fig. 2a. The equilibrium can be shown through reactions (1)–(4): |  | (2) |
|  | (3) |
|  | (4) |
Reaction (1) is dependent on the fugacity of CO2(g) and often described through Henry's law (see Section 2.3). It is often assumed to be really fast (i.e., 1010 s−1 in both directions) in a well-mixed scenario (i.e., only mass-transport limited).55,57,58 For experimental values of k1, k−1, k2, k−2 see ref. 57, 59 and 60. As the pH increases, reaction (3) pushes the equilibrium towards HCO3−, and it predominates reaction (2) above pH 8.5.59 See Section 2.2 for more discussion on the kinetics of the reactions. The total dissolved inorganic carbon, DIC, can be described as the summation of the concentration of all present carbonic species: | DIC = [H2CO3*] + [HCO3−] + [CO32−] | (5) |
where H2CO3* = H2CO3 + CO2(aq). In multi-ionic systems, additional carbonate species or complexes (e.g., NaCO3− and NaHCO3(aq)) are present in the definition of DIC, as well.61,62
2.2 Reactions kinetics and how to improve it
To capture and release CO2(g) through a pH-swing, both thermodynamics and kinetics play a role.57,59 Assuming thermodynamic equilibrium, the equilibrium ratio of
changes by a factor of more than 100 over when using a small pH-swing of only 2 pH-units, see Fig. 2a. However, although such a narrow pH-swing is thermodynamically favourable and enables lower energy consumption, it suffers from slow kinetics. At near neutral pH, the CO2 hydration rate is ∼2.9 × 10−2 s−1 and the (HCO3−) dehydration rate is ∼2 × 10−4 s−1.42,60 These reaction rates are a function of e.g. temperature and ionic strength of the system.63–65 To overcome the slow kinetics, (1) a wider range of pH-swing or (2) a reaction catalyst need to be applied. As for a wider pH-swing range, the base promoted hydration rate of the CO2/HCO3− system is reported to be ∼6 × 103 M−1 s−1 and the acid-promoted dehydration rate is increased to ∼4.1 × 104 M−1 s−1.42,59,60,65 Alternatively, the use of a catalyst such as the carbonic anhydrase (CA) enzyme66 is suggested for improving the kinetics.42,67,68 CA is reported to enhance both the CO2 hydration and dehydration reaction kinetics; hydration rate constant ∼105 s−1 and dehydration rate constant ∼106 s−1 near a neutral pH of 7 are reported.66 However, although initially effective, such enzyme is not stable, and is prone to enzyme loss, deactivation, or degradation. Investigation on improved catalysts is recommended, but until such catalysts are developed, to effectively capture and recover CO2, a wider range of pH-swing (pH < pKa1 and pKa2 < pH) is needed for capture application.
2.3 Inorganic carbon solubility
In equilibrium, the concentration of free CO2 in water (i.e., [CO2(aq)]) is proportional to its partial pressure in the gas phase; according to the Henrys law, [CO2(aq)] = K0 × fCO2(g) where K0 (in mol L−1 atm−1) is the solubility coefficient of CO2(g) and fCO2(g) stands for the gas fugacity (in atm), which is close to the partial pressure of CO2(g) (within 1%). Fig. 4a shows the solubility of CO2 as a function of temperature and CO2 partial pressure. At elevated alkalinity, the total solubility of CO2(g), and hence DIC (in eqn (5)) increases due to reaction (3) route. Fig. 4b shows the solubility of DIC as a function of the water pH and the partial pressure of CO2. See the ESI† for the used equations and references.
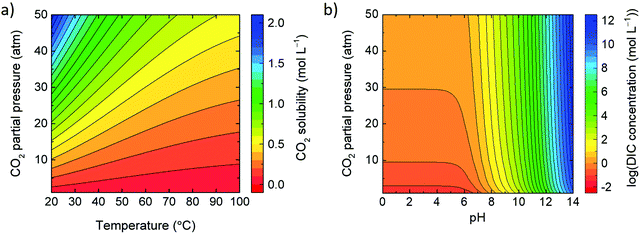 |
| Fig. 4 (a) CO2 solubility in water as a function of the temperature and CO2 partial pressure. (b) Logarithmic solubility of dissolved inorganic carbon (DIC) in water at 25 °C as a function of the water pH and CO2 partial pressure. | |
2.4 Inputs and metrics
Fig. 5 demonstrates input parameters and the metrics of electrochemical CO2 capture based on a pH-swing. The feed, cell, process and kinetics can be leveraged for the product/output. The main challenge such capture technologies are facing is their (estimated) high Capex, resulted from a high energy consumption and the immaturity of the technology.3 Data on Capex of electrochemical methods is still scarce, making the energy consumption (at high current density and capture efficiency) the most practical metric of comparison. Thankfully, despite the currently high energy consumption, optimization of the process and cell parameters can significantly decrease the energy loss involved in such processes as explained in Sections 3.2.1 and 3.5.
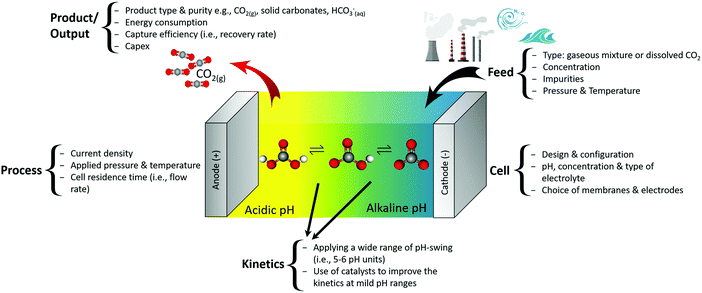 |
| Fig. 5 Input and metrics of electrochemical pH-swing based CO2 capture and the overall process concept. | |
3 Electrochemical pH-swing concepts
Electrochemically induced pH-swings for CO2 capture have been demonstrated through (membrane) electrolysis, bipolar membrane electrodialysis, reversible redox couples, capacitive deionization and hybrid processes that combine two or more methods as shown previously in Fig. 3. In this section we introduce each method separately and compare them in terms of feasibility, energy consumption, energy efficiency and technology readiness level (TRL).
3.1 Electrolysis
Electrolysis can enable the pH-swing in the vicinity of (two) electrodes as shown in Fig. 6. (Membrane) electrolysis for CO2 capture is used for alkali absorbent (re)generation38,69–73 or simultaneous H2 production.36,74–76 H2 production can (partially) offset the cost of CO2 capture and is possible when water electrolysis takes place. In the earliest work done by Stucki et al., CO2 is absorbed from a flue gas in an KOH absorbent, the resulted (bi)carbonate solution is fed into the electrolyser (for alkaline regeneration), where CO2 is recovered and H2 is produced via the following reaction: | 2H2O + K2CO3(aq) → 2KOH(aq) + CO2(g) + H2(g) + 0.5O2(g) | (6) |
The KOH can be used as absorbent for capturing CO2, turning into K2CO3(aq), which can be fed again to the electrolysis system.
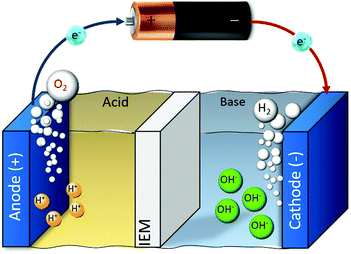 |
| Fig. 6 Schematic of water electrolysis. Depending on the catholyte/anolyte (air, water, etc.), applied voltage and the pH of the medium, different half reactions take place. | |
One downside in such systems is that the cell voltage has, in addition to 1.23 V for water splitting, a contribution from the pH difference between the anolyte and the catholyte, represented by Nernstian potential of Φ = 0.059ΔpH (in volts) at 25 °C, as shown in the Pourbaix diagram (Fig. 7).74 When using an extreme pH gradient (pH 0 at anode, pH 14 at cathode), this would imply a 2.06 V for balancing the free enthalpy of the reaction.
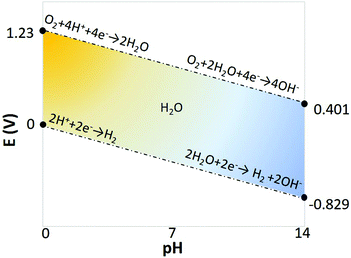 |
| Fig. 7 Pourbaix diagram of water electrolysis.77 | |
Using the pH-swing in electrolysis, the CO2 can be either released as (purified) gas (e.g., viareaction (6)), or as (bi)carbonate products in the work of Rau and Park et al.70,71,75,78 The latter has been demonstrated for Ca(HCO3)2(aq) (Fig. 8a) and71,75 solid carbonate mineral as shown in Fig. 8b.70 Natural (mined and crushed) carbonate minerals are used to provide Ca2+ in Fig. 8a. Through reaction (7), CO2 can be removed from an overlying gas mixture (e.g., air or flue gas). The produced Ca(HCO3)2(aq) can be diluted and stored in the ocean, water reservoirs or underground:
| 2H2O + CaCO3(s) + CO2(g) → Ca(HCO3)2(aq) + H2(g) + 0.5O2(g) | (7) |
Capture of 1 mole of CO
2(g) for each mole of CaCO
3viareaction (7) is possible, while 22 tonnes of CO
2 can be captured per tonne H
2 generated (assuming a 1
![[thin space (1/6-em)]](https://www.rsc.org/images/entities/char_2009.gif)
:
![[thin space (1/6-em)]](https://www.rsc.org/images/entities/char_2009.gif)
1 molar ratio).
71 This implies that, depending on CO
2 emission involved in the operation (
e.g., for supplying electricity and for limestone/carbonate mining, crushing and transport), the system has the potential of producing carbon-negative hydrogen.
79
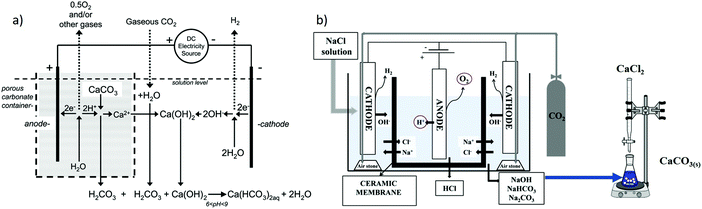 |
| Fig. 8 (a) H+ ions at the anode dissolve CaCO3(s), the resulted Ca2+ ions move towards the cathode, forming Ca(HCO3)2(aq). Reprinted (adapted) with permission from ref. 71; Copyright (2008) American Chemical Society. (b) NaCl electrolysis, where NaOH is used as the CO2(g) absorbent and CaCO3(s) is the final capture product, figure from ref. 70. Both approaches use the concept of placing the anode inside of a porous container. | |
The process efficiency in Fig. 8a can be enhanced e.g., by:
• Improving the mass transfer between the overlying gas and the absorbent (to improve CO2(g) dissolution).
• Introducing an ion selective membrane between the electrodes (to avoid unwanted secondary reactions).
Alternative to water electrolysis, salt electrolysis, such as NaCl69 and KCl38 can also be used for CO2 capture. If so, only an alkaline pH (at the cathode) is enabled, because at the anode e.g., the reaction 2Cl− → Cl2(g) + 2e− takes place instead of the oxygen evolution reaction (OER).70 The produced alkalinity at the cathode can then be utilized to sequestrate CO2 in the form of carbonate salts. When the capture product is CaCO3(s), no CO2(g) desorption step is required. Furthermore, CaCO3 is easier to transport and store compared to CO2(g). NaCl electrolysis for alkaline absorbent (re)generation follows reaction (8):69
| 2H2O + 2NaCl(aq) → 2NaOH(aq) + Cl2(g) + H2(g) | (8) |
Using salt electrolysis for CO
2 capture is especially interesting due to salt availability in the seawater, leveraging possible substitution of the electrolyte with abundant seawater.
69 The produced (toxic) Cl
2(g) at the anode can be treated by the produced NaOH solution using a scrubber, or can alternatively be utilized as a feedstock for the synthesis of HCl, Cl containing polymers and bleaching agents.
69 Alternatively, using water electrolysis and by inserting two ion exchange membranes (IEMs) between the electrodes (
Fig. 9), produces H
2 simultaneous acidifies seawater to recover CO
2(g).
36,80,81 The use of two IEMs avoids the production of Cl
2(g) and electrode contamination.
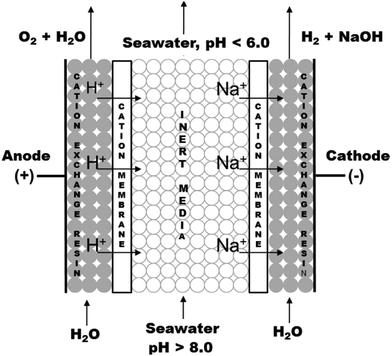 |
| Fig. 9 CO2 capture and H2 production via sea water acidification and water electrolysis. In the middle compartment, cation exchange resins are used. Reprinted (adapted) with permission from ref. 81; Copyright (2014) American Chemical Society. | |
When applying electrolysis using a reversible redox reaction – thus no net gas production – saves energy. For example, the production of O2(g) (or Cl2(g)) can be avoided by recirculating the produced H2(g) from the cathode to the anode compartment.72,73 Alternatively, H2 production can be avoided if O2 reduction takes place on the cathode, instead of the H2O reduction.82 At the cathode, depending on availability of O2 or H2, two possible reactions may exist for OH− production:
| 2H2O + O2 + 4e− → 4OH− (E0 = 0.401 V vs. SHE) | (9) |
| 4H2O + 4e− → 2H2(g) + 4OH− (E0 = −0.83 V vs. SHE) | (10) |
When sufficient O
2 is available at the cathode, or sufficient H
2 at the anode, the H
+/OH
− generation can take place in a practical cell voltage range of 1.3 V to 2.2 V through
reaction (9). The supply of sufficient gas to the opposing electrode can be assisted by using gas diffusion electrodes.
83 Without recirculating the gaseous products, the cell voltage is typically >2.2 V.
82
From a thermodynamic point of view, the use of (net) water electrolysis requires a significant thermodynamic minimum energy (1.23 V for water splitting), in addition to the potential required for generating a pH difference (see Fig. 7).77,84 Considering the necessity of a wide pH-swing to enhance the carbon equilibrium kinetics, and using pH 0 and 14 to favour electrolyte conductivity, a minimum of 2.06 V is required, corresponding to 199 kJ mol−1 CO2. Furthermore, in almost all demonstrated devices/systems, the rate of CO2 capture is locked with the rate of H2 or O2 generation, which sometimes may not be desirable and present additional challenges for multi-stack development of the system. These drawbacks can be addressed using bipolar membrane electrodialysis as explained in the following section.
3.2 Bipolar membrane electrodialysis (BPMED)
A bipolar membrane (BPM) consists of an anion (AEL) and a cation (CEL) exchange layers, laminated together. When a sufficient electric field is applied, the BPM dissociates water into OH− and H+, producing a controllable ΔpH over the membrane as shown in Fig. 10a and b.85–90 Using a bipolar membrane, the thermodynamic minimum voltage required for this water dissociation is 0.829 volts for a produced ΔpH = 14. That is 2.5 times lower than that of water electrolysis at the same ΔpH = 14 (1.23 + 0.829 at minimum), as no gas evolution takes place using a bipolar membrane.85 The thermodynamic voltages over the BPM are even lower for smaller ΔpH over the membrane.84,88 The feasibility of using bipolar membrane electrodialysis for pH-swing based CO2 capture is shown in early studies in 1995;91 alkaline KOH and acidic H2SO4 were regenerated in a two compartment BPMED cell, containing a BPM and a cation exchange membrane. After CO2 from air is captured in KOH absorbent, it can be recovered through acidification. The produced K2SO4 is treated in the BPMED cell to regenerate the desired acid and base again. CO2 capture via BPMED has been further explored by others, and these works are addressed in more details in next sections.
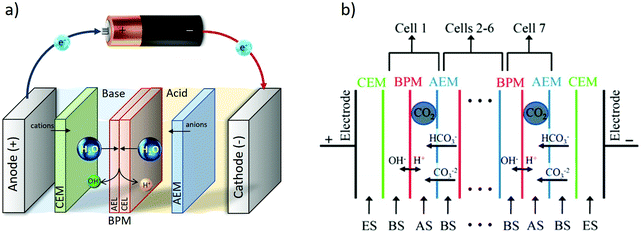 |
| Fig. 10 (a) BPMED schematic. (b) BPMED for CO2 recovery in ref. 92. (ES) electrode solution = KOH, (AS) acid solution of KH2PO4 + H3PO4, (BS) base solution of six different mixtures of KHCO3, K2CO3 and KOH. Figure adapted from ref. 92. | |
3.2.1 Energy consumption and capture efficiency.
In BPMED, a trade off between the energy consumption and the process rate, determined by the applied current density, exists. Operating at very low current densities is not effective due to the higher salt ion leakage through the BPM and hence the lower water dissociation rate.92 On the other hand, at high current densities, the ohmic voltage losses increase, leading to an undesirable higher energy consumption (see ESI†). As an example, Fig. 11a shows the minimum energy consumption for CO2(g) recovery from 0.125 M K2CO3-rich solution via BPMED at a current density around 10 mA cm−2.3 However, although the energy consumption is the lowest at that current density, production rate favours higher current densities as shown in Fig. 11c. The experimentally measured current efficiency (i.e., faradaic efficiency) in Fig. 11b shows – in addition to its low values at i < 10 mA cm−2 due to salt cross-over – a slight decreases at i > 20 mA cm−2. It is hypothesized that current densities above the optimum value, reduce the BPM's permselectivity93 or enhance the water splitting reaction in the AEM's,94,95 leading to a lower efficiency.92 The current efficiency also decreases if the current is carried by an undesired ion through the membranes. For example, in Fig. 10b, the (bi)carbonate ions are the desired current carriers. However, if (as a result of high pH) OH− ions become the main charge carrier through the AEM, the current efficiency decreases. On the other hand, when capturing CO2(g) from flue gas or in DAC, a high pH (i.e., high [OH−]) is favoured in the outlet of the same compartment, because CO2(g) absorption capacity and rate increase in a solution with high pH. Adopting monovalent-ion-selective AEM's that favour the transport of HCO3− ions over OH− ions then could improve the efficiency when such process is intended.3,96
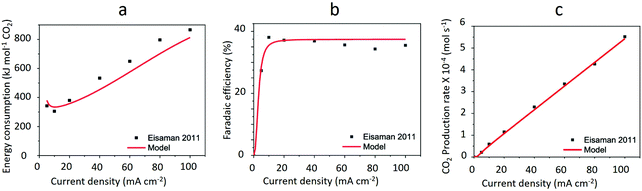 |
| Fig. 11 Trend of energy consumption, faradaic efficiency and CO2 production rate vs. current density in CO2(g) recovery from 0.125 M K2CO3-rich solution via BPMED. The black squares are experimentally measured data by ref. 92 while the red lines show the calculated values performed by ref. 3. Reprinted (adapted) with permission from ref. 3; Copyright (2020) American Chemical Society. | |
As opposed to what is shown in Fig. 11b, the current efficiency of BPMED can reach as high as 95% if e.g., a 0.5 M KHCO3 is used instead of the 0.125 M K2CO3 for CO2(g) recovery through acidification. In fact, both in BPMED and (membrane) electrolysis, in addition to the current density, the anolyte and catholyte concentrations and the operation temperature affect the current efficiency, as demonstrated in Fig. 1238 and summarized in Table 1.
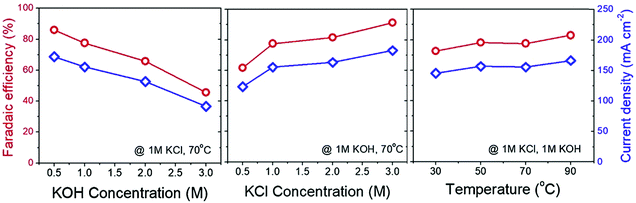 |
| Fig. 12 Change of the measured current density (blue diamond line) and faradaic efficiency (red circle line) with regards to the change in catholyte concentration, anolyte concentration and the applied temperature in an electrochemical KOH (absorbent) production via KCl electrolyser. Reprinted from ref. 38, Copyright (2019), with permission from Elsevier. | |
Table 1 Electrochemical CO2 capture
Capture method |
Feed |
Energy-consumptiona (kJ mol−1 CO2) |
Current-efficiency |
Product |
Current-density (mA cm−2) |
Remarks |
Only for the electrochemical step, defined as in eqn (11).
For KOH electrochemical regeneration.
Although the theoretical work requirement for the reaction is only 266 kJ mol−1 CO2.
Calculated from data on energy consumption for KOH production, assuming 2 moles KOH delivers 1 mole CaCO3.
Plus 200 for CO2(g) capture into hydroxide solutions.193
Only for the production of HCl and NaOH, not for CO2 capture and recovery.
Calculated based on data from ref. 76: R = 0.5–1.8 Ω, i = 20.4–61.2 mA cm−2 and recovered CO2 rate of 0.004 mol min−1.
Only for the CO2 desorption step.
|
Fuel-cell
35
|
Air + H2 |
350 |
23% |
CO2(g) |
0.5 |
Upscaling unfeasible (low current-density) |
Electrolysis74
|
Air |
290–350 (kJ mol−1 KOH) |
>95%b |
CO2(g) + H2(g) |
100 |
KOH/K2CO3 electrolysis at 70 °C |
Electrolysis
71
|
Air + mined CaCO3(s) |
1 267 200c |
Not reported |
H2(g) + CO2(g) |
Not reported |
Water electrolysis. Fig. 8a |
Electrolysis
38
|
Synthetic flue gas + cement kiln dust |
>634–1276 (kJ mol−1 CaCO3)d |
60–90%b |
CaCO3(s) |
100–200 |
KCl electrolysis. Fig. 12 |
BPMED
91
|
K2SO4 |
∼308 |
Not reported |
CO2(g) |
50 |
Produces KOH + H2SO4 |
BPMED
106
|
NaHCO3/NaOH |
160–500 |
65–80% |
CO2(g) |
5–20 |
|
BPMED
92
|
KHCO3/K2CO3 |
100–450e |
95% (KHCO3), 50% (K2CO3) |
CO2(g) |
5–100 |
Fig. 10b for cell design & Fig. 11 for cell performance |
BPMED
43
|
KHCO3 |
200–500 |
70–90% |
CO2(g) |
22–139 |
High pressure BPMED enables 30% energy win. See Section 3.2.3 |
BPMED
113
|
Artificial seawater |
250–400 |
<70% |
CO2(g) |
1–3 |
59% of DIC from seawater was removed using ca. 242 kJ mol−1 CO2 |
BPMED
8
|
Artificial seawater + NaCl |
390–640 |
60–95%f |
CO2(g) or CaCO3(s) |
100 |
Cost of membrane contactors is avoided via the base route |
BPMED
107
|
Artificial seawater + CO2(g) |
1080–2880 (kJ mol−1 CaCO3) |
Not reported |
CaCO3(s) |
Not reported |
CO2(g) absorption in basified seawater followed by crystallization |
EDI + BPMED
42
|
Synthetic flue gas |
Not reported |
Not reported |
CO2(g) |
2–16 |
At near neutral pH, the slow kinetics can be enhanced using CA enzyme |
EDI + electrolysis
36,76,81,194
|
Natural seawater |
2775–6940g |
Not reported |
CO2(g)/H2(g) |
20–61 |
Fig. 9
|
MCDI
156
|
Synthetic flue gas |
40–50 |
60–80% |
CO2(g) |
0.02–0.06 |
Using IEM's improve efficiency37 |
Redox-active carriers + pH-swing
140
|
Synthetic flue gas |
106h |
90% |
CO2(g) |
18 |
Aqueous tiron (Na2Q) is used as pH mediator/active carrier to capture CO2 |
Redox-active carriers
147
|
Synthetic flue gas |
56 |
>75% |
CO2(g) |
0.5 |
|
The (slightly) positive effect of temperature on improving the faradaic efficiency of electrochemical methods has been reported.38,69 Higher temperatures improve the electrochemical reaction rates. In the case of BPMED, the kinetics of water dissociation in BPM is also enhanced at elevated temperatures.97,98 However, in addition to the extra energy needed for heating up the electrolytes, the thermal stability of the ion exchange membranes poses a limitation on high temperature processes. For instance, the commercial bipolar membranes are cannot withstand temperatures higher than 40–60 °C for a long duration.99 Moreover, CO2 solubility decrease at higher temperatures (up to 100 °C).100–102 This means that operating at high temperature is not yet practical.
A breakdown of energy consumption and comparison for (membrane) electrolysis and BPMED is provided in Section 3.5 and the ESI.†
3.2.2 Cell configuration.
The cell configuration defines the number of membranes, membrane cell pair arrangement, electrolyte flow path and the thickness of the compartment/membrane. The design of the cell is the most important factor to minimize the cell resistance.74 As opposed to the BPMED for traditional acid and base production (i.e., BPM–CEM–AEM–BPM), the pH-swing process for CO2 capture allows a simplified membrane sequence due to the limited pH-range (i.e., pH 3–9 instead of 0–14).
In choosing the optimised configuration, the (co-)ionic leakage of the membranes is crucial. When using multi-ionic CO2 feed, such as seawater, carbonic species should be rejected to obtain a maximum capture efficiency. Carbonic species are neutral (e.g., CO2(aq) and H2CO3) or negatively charged and hence are rejected better by a CEM than by an AEM. In addition to higher selectivity, the use of CEM's instead of AEM's have proven to increase conductivity and mechanical stability in a BPMED cell for CO2 capture72).103
For further reducing co-ionic cross-over, a trade off between the permselectivity of IEM's and their resistance should be considered, which is controlled by the membrane thickness. In general, thicker membranes have higher resistivity but show a better selectivity.72 Applying a reinforced structure to a thinner membrane can improve its selectivity while maintaining its resistivity to a certain extent.72,104
Depending on the charge carriers in the cell, the flow mode (i.e., one-way pass vs. batch mode) and feed concentration, each BPMED process asks for a different cell configuration. While BPM–CEM might be the choice of some researchers for CO2 recovery from carbonate solutions,105,106 others chose a BPM–AEM43,92 for the same purpose. That is while novel configurations as BPM–AEM–AEM are also emerging for minimizing BPM fouling when extracting CaCO3 from seawater,107 see Section 3.2.4.
3.2.3 High pressure BPMED.
In a closed system (such as the one created inside of an electrochemical cell), acidification increases the concentration of dissolved CO2. This concentration can lead to the formation of CO2(g) bubbles inside of the cell. Theoretical models, suggest the trapped CO2 in the acid solution dominate the cell resistance and increase the energy consumption.108 Trapped gas bubbles lower the effective membrane surface area, cause high voltages and shorten the membrane lifetime (due to localized “hot spots” of high current density). To avoid gas production inside of the cell, Eisaman et al.43 proposed a high pressure BPMED process using a similar cell as shown in Fig. 10b where the entire stack is kept at high pressure, i.e., there is no pressure difference across the membranes in the stack. The authors observed that by increasing the pressure, the total cell voltage decreases due to the avoided CO2 gas bubbles production in the cell; the electrochemical energy required at 6 atm (333 kJ mol−1 CO2) was seen to be 29% less than that of 1.5 atm (471 kJ mol−1 CO2) at a current density of 139 mA cm−2.
3.2.4 BPMED for CO2 extraction from seawater.
The ocean is a massive sink for CO2.11,109,110 The higher carbon content of the oceans compared to that of the atmosphere8,54,111 makes the ocean an interesting source for CO2 capture.109 Moreover, as opposed to the separation of CO2 from a gas mixture that involves two steps (i.e., capture and release), in CO2 capture from seawater, a separate CO2(g) adsorption/absorption step is not required, because the ocean already acts as CO2 absorbent leveraging its gigantic surface. The ocean contain DIC of ∼2.3–2.5 mM, mainly in the form of HCO3− ions, in normal seawater of pH ∼ 8.1.
The product of seawater CO2 capture can be (1) gaseous CO2,8 (2) solid carbonates,107 or (3) dissolved bicarbonates and carbonates ions (to be subsequently stored in the ocean).71,75,78,112 To extract the CO2 as gas, the bi-/carbonate ions present in the seawater can be converted into H2CO3* in the acidic compartments adjacent to the BPM.113 Subsequently, through vacuum stripping of the acidified stream using membrane contactors, CO2(g) can then be produced.8,113 Alternatively, at alkaline pH > pKa2, HCO3− converts to CO32− and can subsequently precipitate through reaction with dissolved Mg2+ or Ca2+.8,107 When the partial pressure of CO2 remains unchanged, the pH determines which mineral is obtained e.g., the precipitation of CaCO3 (in synthetic seawater) is favoured in 9.3 < pH < 9.6.8,114 Considering that the Ca2+ and Mg2+ concentrations in seawater are respectively ×4 and ×25 higher than that of DIC, mineralization has the potential to remove all DIC, theoretically.115 In addition, mineralization eliminates the expenses of using a membrane contactor.116,117 In the third option, converting CO2 to dissolved alkaline bicarbonates and carbonates enables carbon sequestration. This is a long-term carbon storage which also helps against ocean acidification by increasing the ocean alkalinity.71,75,78,112 However, further research is required for understanding the full range and capacity of such approach.
The main bottlenecks in using in situ BPMED for this mineral crystallization are the risk of membrane contamination (i.e., fouling) in the stack and the slow kinetics of the carbonate precipitation. To avoid the fouling, pure NaCl (instead of seawater) can be used in the BPMED for NaOH and HCl production.8 The produced NaOH is then added to the seawater stream in a controlled crystallizer to initiate the precipitation. In order to improve the kinetics of the precipitation, use of a seeded crystallizer unit is suggested.107,118 Although seawater CO2 capture through mineralization is shown feasible, debates on the environmental impacts of reducing Ca2+/Mg2+ concentration of the ocean are in progress.115,119
3.2.5 Electrodeionization (EDI).
Electrodeionization (EDI) combines ion exchange membranes technology with ion exchange resins.120–125 Ion exchange resins are solid cross-linked polymers that contain fixed charged groups typically based on acrylic or styrene monomers. When filling the flow compartments with beads or 3D structures of ion exchange resins, the polymer–electrolyte interface area is increased.126 The combination can help overcome the concentration polarization losses associated with electrodialysis and electrolysis. The major application of electrodeionization (EDI) includes the removal/recovery of heavy metals and organic acids for pure water production.127–131 The combination of BPMED with resin wafer electrodeionization (RW-EDI) is demonstrated in the lab-scale, where porous, solid matrix of ion-exchange resin beads are incorporated in between of the CEM's and BPM's in the cell.42 However, unfortunately, data on the energy consumption and current efficiency of the system is not reported. The combination of electrodeionization (EDI) with electrolysis is shown feasible as demonstrated in Fig. 9.76,81 However, as shown in Table 1, the process still requires further optimization (in terms of production of H2(g) and cost/stability of resins) to decrease its significant energy consumption. Furthermore, the (bio)fouling of the resin beads due to the contact with seawater decreases the overall efficiency of the method and needs yet to be addressed.
The pH-swing based EDI application for CO2 capture has only been explored at a basic level.127 More work has been done on the use of amine based ion exchange resins as adsorbent for CO2 capture, through thermal swing. Such resins are reported to show good stability after repetitive adsorption–desorption cycles with only a small reduction in capture capacity, and require relatively mild desorption conditions.126,132,133 Recently, wafer enhanced electrodeionization for conversion of CO2 into HCO3− feed for algae cultured photobioreactors is reported.134 Suggestions for further research on EDI technology are producing inexpensive ion exchange resins, reducing possibility of resin fouling (e.g., for the case of seawater feed76), and maintaining long-term resin stability.127
3.3 Redox-active carriers and electrode reactions
An alternative to BPMED and electrolysis for CO2 capture, is the more classical electrochemically-mediated separation strategies that perform absorber/desorber cycles using specific redox-active sorbent carriers.39,49 These redox-active carriers can be used for separation of CO2(g) from a gas mixture through (1) binding route Fig. 13a and (2) pH-swing route Fig. 13b. Both routes have been demonstrated feasible in the lab-scale.135,136
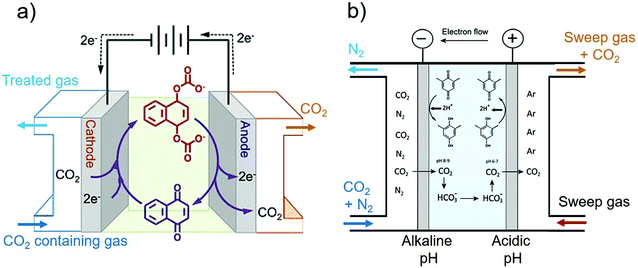 |
| Fig. 13 (a) Electrochemical CO2 separation using gas diffusion electrodes (GDE) through binding with quinone redox-active carrier (i.e., no pH-swing is created). Reprinted (adapted) with permission from ref. 144; Copyright (2015) American Chemical Society. (b) Combination of pH-swing with the chemistry of redox active carriers through (PCET) reaction using mixture of hydroquinone, quinone, and sodium bicarbonate. Reprinted (adapted) with permission from ref. 136; Copyright (2015) American Chemical Society. | |
As for the “binding route”, the suitable carrier is activated at the cathode and can bind with the target species at its reduced state. The target species in this case is the CO2 molecule. Subsequently, the captured CO2 can be released at the anode through oxidation of the carrier while the carrier is regenerated. This process is also referred to as “electrochemical CO2 pumping”,135,137 see Fig. 13a. The cycle can be broken down into four steps:41
• Sorbent activation through oxidation or reduction.
• CO2(g) capture on the activated sorbent.
• Sorbent deactivation through the reverse electrochemical process.
• CO2(g) release.
Alternatively, in order to decrease the required electrical energy, these steps could be integrated in a two or three-stage process40,41 by e.g., enabling CO2 capture or release to be performed simultaneously with electrochemical reduction or oxidation of the carrier.
In order to improve the kinetics of CO2 capture and release, the “pH-swing route” can be integrated, where the chemistry of redox-active carriers are designed to undergo proton coupled electron transfer (PCET) reactions,135,136,138,139 as shown in Fig. 13b.135,136,140 If so, an “electrochemical H+ pumping” takes place that enables an acidic and a basic pH on the anode and the cathode, respectively.
Although redox-active systems have yet to achieve industrial utility, they have the potential of producing a pure CO2 stream even from dilute gas mixtures, such as air.141 Among different classes of redox-active compounds that have been explored, such as bipyridines,142,143 disulfides49 and copper/amine systems,29,30 the quinone species141,144–146 are of particular interest,40 owing their strong binding affinity for CO2 in their reduced form compared to that of their neutral state.39,147 Quinones are organic compounds derived from aromatics, through conversion of an even number of –CH
groups into –C(
O)– groups.148 Quinones have also gained great interest as potential ideal candidates for PCET mechanism138,139,149–153 inspired by their role in biological systems.154 These redox reactions are (ideally) reversible, and can operate within the water splitting window.135
The choice of catalysts on the surface of the electrodes to facilitate the electron transfer together with the type and concentration of the electrolyte are important in determining the process efficiency in terms of capture, transport and release of CO2, and kinetics.136 Furthermore, the local pH shown in Fig. 13b is not the same as the bulk pH.155 While the high pH at the cathode determines the CO2 absorption and the lower pH at the anode drives CO2 desorption, only the bulk pH can be controlled in a practical process. That makes the choice of an appropriate average pH that enhances both reactions, challenging. Alternatively, the local pH can be maintained by inserting (1) an anion-exchange membrane (AEM) or (2) an extra salt compartment sandwiched between an AEM and a cation-exchange membrane (CEM) between the electrodes.147
Despite its progress in the lab-scale, CO2 separation using redox active carriers is not yet practically implemented because of the limitation it faces in terms of both solvents and carriers. It is difficult to find a solvent that is inexpensive, safe, electrochemically stable and allows high solubility of the redox species.49,147 Possible improvements in terms of solvents can be achieved by using ionic liquids as electrolytes39,144 or using salt-concentrated aqueous electrolytes.147 As for the carriers, the solubility, chemical stability and kinetics of the redox molecule can pose limitations on the process.49 To address these drawbacks, electrochemically mediated amine regeneration can be employed, using a similar concept, but by employing amines rather than quinones as described in Section 4.1.3. Alternative to using dissolved carriers in an electrolyte – where the transport of both the electrolyte and the carrier molecules between the two electrodes is required, the active carriers can be immobilized between the opposite electrodes.39 The latter is explained further in Section 4.2.1. Recently, solid polymerized quinone (formed into a composite with carbon nanotubes to confer electronic conductivity) is employed.39 This so called “electro-swing” process exhibits a high faradaic efficiency and a low energy consumption (40–90 kJ mol−1 CO2 captured) compared to the thermal or pressure swings for sorbent regeneration. However, it needs to be improved in terms of capacity and kinetics.
3.3.1 Electrode induced pH-swing.
Another electrochemical based CO2 capture concept utilizing local pH near electrodes is the (membrane) capacitive deionization (MCDI) method.37,156 Capacitive deionization is mainly used for water treatment, but its application has recently expanded to energy harvesting and CO2 capture.157–165 The motivation to capture CO2via such system is that deionized water can be used without the need of any other chemicals, using inexpensive carbon based electrodes.37,156
MCDI cells consist of activated carbon electrodes and ion-exchange membranes. When a current is applied in the charging step of MCDI, HCO3− and H+ ions are adsorbed into the porous electrodes inside of the cell (causing a local low pH at the cathode and increasing pH in the bulk). As the electrolyte is being depleted from ions, more CO2(g) can be absorbed in the deionized water due to the shift in the CO2 equilibrium, to make up for the depletion. It has been proposed to use a gas–liquid contactor spiral glass tube outside of the cell for in situ absorption. When the current direction is reversed (i.e., discharging step), the subsequent desorption of H+ and HCO3− (plus a small amount of CO32−) ions from the carbon electrodes drives the chemical equilibrium in the opposite direction. As the concentration of H2CO3* will exceed the solubility, CO2(g) is formed from the electrolyte. CO2(g) absorption and desorption can be controlled through shifting the current direction. CDI can also be used in combination with NH3-based CO2 capture.166
In addition to the carbon based capacitive electrodes, other metals can also be used. For example, CO2 can be captured through intercalation/deintercalation of protons on the manganese dioxide (MnO2) based electrodes. The electrodes can host protons (i.e., intercalation) during reduction and release them (i.e., deintercalation) during oxidation, creating the required pH-swing for CO2 absorption and desorption, respectively.167 In such methods, periodic electrode polarity and the switching fluid flows ensure a continuous process.
3.4 Molten carbonate cells and hybrid electrochemical capture methods
Electrochemical methods can benefit from a pH-swing approach but are not limited to it. Examples are using (high temperature) molten carbonate cells or the hybrid methods that integrate CO2 capture and conversion.
High-temperature molten carbonate cells are early electrochemical CO2 capture examples.32,168 In such process, a CO2 containing (flue) gas is fed to the cathode side of an electrochemical cell, where electricity is used to drive CO2 and O2 (in form of CO32−) across a molten carbonate salts electrolyte (sandwiched between ceramic membranes in contact with the electrodes). At the anode, carbonate ion will be reduced to CO2 and O2 again. An alternative design enables a molten carbonate fuel cell, where CO2 is captured while H2 is produced.169–171 Involved challenges are difficult operating conditions due to the high temperatures, corrosion and sensitivity to the presence of SOx in the gaseous mixture.20,24,172 Research for developing dense molten carbonate CO2 selective membranes at high temperatures (>723 K) is still in progress.173–175
Examples of electrochemical hybrid capture and utilization is the electrochemical seawater battery system,176 the alkali metal-based CO2 batteries (e.g., lithium–CO2 batteries177,178) and electrochemical CO2 capture and conversion combinations.25,179–183 The absence of pH-swings, and the lack of further development of these proposed electrochemical capture routes, categorizes these concepts beyond the scope of this review. The broader context in terms of CO2 utilization is discussed in Section 5.
3.5 Which electrochemical method to use?
A comparison of the metrics of electrochemical pH-swing based CO2 capture methods is given in Table 1. These capture methods have often energy consumption >300 kJ mol−1 CO2. As a comparison with conventional methods, the energy consumption of CO2 capture (from flue gas) via aqueous monoethanolamine (MEA) using a thermal swing, currently the most mature capture method, is between ∼170–300 kJ mol−1 CO2.184–190 Approximately ∼80% of this energy is the contribution of the thermal regeneration,13 included in the reboiler heat duty.191 Most conventional and electrochemical captures are energy intensive, when compared to the combustion energy of various fuels and the emitted CO2 per mole of the fuel. From an economic point of view, CO2 capture is only interesting if the energy consumption of the capture is <66 kJ mol−1 CO2.42,192
Renewable sources would be preferred over fossil fuels for driving electrochemical CO2 capture to (1) maximize the reduction in net carbon emission and (2) leverage the advantage of electrifying the CO2 capture process. At the same time, the absence of flue gas from power plants in renewable sources would make diffused CO2 sources (e.g., atmosphere and seawater) the most logical feed for electrochemical CO2 capture technologies. This is also reflected in Table 1, where most research has focused on capture from air, seawater or (low concentrated) bi(carbonate) solutions.
At present, (membrane) electrolysis and BPMED are the most studied electrochemical capture approaches. Fig. 14a shows the estimated energy consumption of both methods (see ESI† for calculations). This electrical energy consumption, E (in kJ mol−1 CO2), is calculated via:
|  | (11) |
where
i is the current density (A m
−2),
A is effective area of the electrodes (m
2),
V is the total cell voltage (volts) and
rCO2 is the recovery rate of the captured CO
2(g) in mol s
−1. To put the energy consumption of
Fig. 14a in perspective, the energy produced per mole of fuel (through combustion) and the associated emitted CO
2 are shown in
Fig. 14b. This emphasizes the energy-intensive nature of the capture process: capturing 1 mole of CO
2via BPMED consumes 25–60% of the energy obtained from combustion of hydrocarbon fuel per mole of CO
2, dependent on the fuel type. For conventional methods and electrochemical capture
via electrolysis, this figure is even larger.
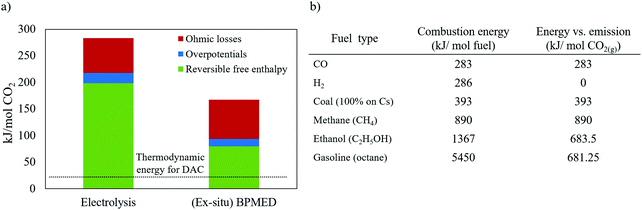 |
| Fig. 14 (a) Electrical energy consumption for direct air capture (DAC) through (membrane) electrolysis. Current density of 20 mA cm−2 and ΔpH = 14 is assumed for both cases. See Section S2 of the ESI† for detailed calculations. The thermodynamic work required for DAC (assuming 400 ppm CO2(g)) is 20 kJ mol−1 CO2.15 (b) The combustion heat of common fuels and their CO2(g) emission, obtained from ref. 195 and stoichiometric combustion reactions. | |
Fig. 14a shows that the ohmic losses cover a significant part of the energy losses,77 and bring in a lever to reduce E. In electrochemical cells, such losses can appear as e.g., heat and/or unwanted chemical byproducts. For example, losses caused by product recombination, such as recombination of produced H+ and OH− in BPMED or the recombination of O2(g) and H2(g) in water electrolysis to form water again. Membrane co-ion leakage is another common loss often involved in membrane based electrochemical processes.93 The limitations and areas of improvements of each electrochemical CO2 capture method can be summarized as:
(1) It is obvious from Fig. 14a that the energy consumption for BPMED is lower than that of electrolysis when targeting CO2 capture. In case hydrogen is an aimed product as well, the energy difference between these two methods (which is equivalent to 1.23 V) can be justified, and can be lower than the energy for two separate systems making acid/base and hydrogen. However, in more detail, the combination of these two products in electrolysis complicates the optimal current density, which is not necessarily the same for hydrogen and acid/base production. Moreover, most hydrogen catalysts are geared towards acidic environments, and earth abundant oxygen catalyst are available for alkaline environments, while the opposite environments are present in the combined electrolysis/acid–base production.196 That limits the options for electrocatalytic material (e.g., platinum and ruthenium), which can pose resource limitations as a relatively large electrode area is required. On the contrary, up scaling can be done easily for BPMED capture method by repeating multiple cell pairs within a single electrode pair.
(2) When using BPMED, despite its uncomplicated up scaling, the typical energy consumption in Table 1 is still 2–3 times more than theoretically expected in Fig. 14a. These losses are due to the involved non-idealities in charged membranes (e.g., high resistivity, co-ion leakage, low chemical stability), the high over potential of water dissociation in BPM, or carbonate feed (requiring 2 H+ per molecule to acidify to H2CO3) instead of bicarbonate. Thankfully, achieving a lower energy consumption is possible both through process optimization and material engineering. Process optimizations can be done by e.g., controlling the applied current density (i), feed flow rate (residence time in the cell), electrolyte conductivity/pH, cell configuration, flow path/mode, and operation pressure/temperature, while water dissociation can be improved through material engineering.197,198 The current minimum economic cost of BPMED is at least twice of the cost of the wet-scrubbing rival.3 However, the cost can significantly decrease if improvements in the cost of renewable energies, cost and availability of ion exchange membrane, membrane life time and membrane selectivity is achieved. Finally, the total capture cost does not only depend on the method, but also on the source of the capture. For example, depending on the pumping facilities and plant location, indirect ocean capture (IOC) can be economically favored relative to direct air capture (DAC), or vice versa.199
(3) The reversible free enthalpy in Fig. 14a is based on a ΔpH = 14. Using lower ΔpH, a lower reversible free enthalpy is involved.84 Although it is theoretically possible to perform a pH swing between pH 4–7, potentially reducing the energy consumption to values close to the thermodynamic limits, this low energy consumption is not obtained in practical BPMED at medium to high current density.
(4) Membrane capacitive deionization (MCDI) is recently demonstrated to capture CO2 from a CO2(g) + N2(g) mixture, using only demineralized water37,156 with the lowest capture energy among other methods (∼40–50 kJ mol−1 CO2), see Table 1. However, the obtained current density is extremely low (∼0.02–0.06 mA cm−2) and there is a long way to go before (M)CDI becomes a competitive means of CO2 capture as the stability and performance of the large-scale CDI applications are yet unknown. Future work is suggested to investigate the physical and chemical effects of weak electrolyte solutions in CDI.156
(5) Only a few works on CO2 capture through electrodeionization (EDI) show lab scale feasibility76,121,200 as summarized in Table 1. However, no data on the energy consumption of those systems is available. CO2 capture through EDI is limited due to the cost of ion exchange resins, their poor stability and their sensitivity to fouling.127
(6) Electrochemical methods that use redox-active carriers are shown to be less energy intensive (∼100 kJ mol−1 CO2). However, these results have been only obtained using synthetic flue gas. Quinones, used as binding agents for CO2, are highly sensitive to water and oxygen, making the applications for real flue gas (or direct air capture) impractical. Moreover, most redox carriers need organic solvents electrolytes that suffer from a low ionic conductivity which limit the current density. When using quinones as carriers, the total CO2 carrying capacity is limited by the solubility of quinone in the solvent, the applied electrode potentials, evaporative solvent losses and consequent drying of the electrodes.144 Luckily, the efficiency of the CO2 absorption and desorption in such systems can be increased by combining a pH-swing through electrochemical reactions,136 where proton coupled electron transfer (PCET) takes place. However, the practicality of this approach still awaits the improvement of electrochemical redox kinetics. The low solubility of PCET organics limits its capture capacity.135 Furthermore, PCET carriers are also very sensitive to gasses such as O2 and sulfur, posing again challenges for (real) gas CO2 capture application.135 Upscaling can be done by using a larger electrode surface area.
All electrochemical CO2 capture methods are still under development (TRL 5 to 6), although they enable high CO2 recovery rate (>80%). In order to provide a framework of comparison between these methods and the conventional (non-electrochemical) processes – which have already been commercialized – the conventional processes are described further in the next section.
4 Combining electrochemical methods with conventional capture technologies
Conventionally, the capture industry only targeted CO2 capture from centralized CO2 emitters such as fossil fueled power plants, iron, steel, and cement industries. However, this approach is impotent to achieve a net zero CO2 emission because, as shown in Table 2, decentralized sources still constitute a large part of the total emission (total GHG emission of 55 Gt CO2eq in 2019
201). Therefore, currently DAC and IOC are gaining attention (Table 3). For achieving climate targets, CO2 removal within a gigaton order of magnitude is needed.202,203
Table 2 Thermodynamically required energy, properties and the scale of main capture feeds
Source |
Thermodynamic properties & required energy |
Emission & capture scale |
Centralized
|
• Flue gas: |
• >58% of total emission, see Fig. 1 |
– 150 < T < 1200 °C, pCO2 ∼ 0.03–0.15 atm204,205 |
• Current post-combustion capture >2.4 Mt CO2 per year207 |
– 7 kJ mol−1 CO2 for 13% flue gas206 |
|
|
Decentralized
|
• Direct air capture (DAC): |
• <42% of total emission, see Fig. 1 |
– Ambient T, pCO2 ∼ 0.0004 atm (∼400 ppm) |
• Current DAC capture shown in Table 3, but no large scale IOC, yet209 |
– 20 kJ mol−1 CO215,206,208 |
|
• Indirect ocean capture (IOC): |
|
– 5 < T < 35 °C, pCO2 ∼ 0.072 atm (∼2.5 mM DIC) |
|
– Same thermodynamically required energy as DAC199 |
|
Table 3 Large scale DAC companies
Company |
Process mechanism |
Capacity (tonne CO2 per year) |
Carbon Engineering
210
|
(KOH) absorption + high temperature calcination |
1 000 000 |
Global Thermostat
211
|
(Amine based) adsorption + thermal & pressure swing regeneration |
4000 |
Climeworks
212,213
|
(Amine based) adsorption + thermal swing regeneration |
900 |
The (centralized) capture technologies are often grouped in main categories of;18 (1) oxy-fuel combustion, (2) pre-combustion, (3) post-combustion and (4) chemical looping (combustion) as discussed in Table 4. In addition, capture by algae,214–220 biochar221–226 and charcoal227 are recently demonstrated. While there are many CO2 capture methods, introducing all of them are out of scope of this work and we refer the reader to various available literature on this topic.13,17–25,228,229 For an overview of the current state-of-the-art of CO2 capture, transport, utilisation and storage see ref. 230. Among the available methods, most research focus has been given to the post-combustion methods as they can be retrofitted more easily to the existing industrial units, compared to the oxy-fuel and pre-combustion methods.229 Traditional post-combustion capture methods are absorption,18,19,231–236 adsorption,13,18,237–239 membrane gas separation,240–246 calcium looping19,247–249 and mineral carbonation,110,250–260 see Table 4. These methods are combined with thermal swing, pressure swing or vacuum swing for CO2 desorption.
Table 4 Dominant non-electrochemical CO2 capture methods (continued)
Capture method |
Process mechanism |
Challenges |
Oxy-fuel
261–263
|
Instead of air, pure O2(g) or a CO2(g)/O2(g) mixture is used for fuel combustion. 75–80% CO2 is produced as opposed to combustion in normal air where 3–15% CO2 is produced |
• High oxygen production energy costs (ca. 200–220 kW h per tonne of oxygen generated by cryogenic air separation263) |
• High sensitivity to air leakage into the system |
• Although an efficient capture method,264 difficult to retrofit compared to post-combustion method |
• Special materials are needed to resist the high flame temperature (ca. 3500 °C). Although, the recycled CO2 can be used to moderate this temperature18 |
|
Pre-combustion
265–268
|
CO2 is separated from H2-rich fuel before combustion. For example, synthetic gas is produced from fossil fuel by adding steam or pure oxygen at high temperature and pressure (1400 °C and 25–55 atm) and a subsequent water–gas shift reaction. |
• Retrofit to existing plants is costly and more difficult compared to oxy-fuel and post-combustion |
• Reaction CO + steam ↔ CO2 + H2 produces 15–40% CO2 at 14–40 atm. The produced H2 can be used for power generation, but CO2 needs to be removed using a subsequent separation technique |
|
Post-combustion: |
Absorption18,19,231–236 |
CO2(g) (from flue gas or air) is absorbed (i.e., chemically or physically) in an absorbent. Pure CO2(g) is subsequently recovered through temperature swing desorption while the absorbent will be regenerated. Currently, amine based capture is the most mature method for CO2 capture |
• Limited CO2 absorbing capacity resulted from the reaction stoichiometry and dependent on the absorbent type (e.g., low capacity as 0.4 kg CO2 per kg-MEA or higher as 1.2 kg CO2 per kg-NH318,269) |
• High absorbent regeneration (i.e., CO2 desorption) energy |
• Solvent losses caused by volatility or thermal/chemical degradation, the subsequent equipment corrosion & negative environmental impacts of solvent emissions |
• High sensitivity to flue gas temperature, pressure and presence of impurities, such as NOx, SOx and oxygen (i.e., oxidative degradation)270 |
|
Adsorption13,18,237–239 |
CO2(g) is adsorbed on solid materials and will be recovered through temperature, pressure or vacuum swing desorption |
• When used for flue gas, pre-treatments to remove impurities, such as NOx, SOx and H2O and to decrease gas temperature are needed |
• Possible loss in the adsorption capacity of the adsorbent after desorption step (e.g., 4–9% loss for amine immobilized onto solid silica) |
• Sorbent degradation in cyclic operation |
|
Membrane gas separation13,240,241,244,246,271,272 |
Process is driven by partial pressure difference of the gas molecules to be separated. Gas molecules permeate according to their size, diffusivity, or solubility through the membrane. |
• Not feasible for streams with low CO2 partial pressure and concentration |
• To accommodate the high flow rate of industrial flue gas, high membrane surface area is required |
• Sensitivity to presence of moisture (i.e., lower selectivity) |
• On-going research on new membranes with high selectivity and permeability273–275 |
|
Calcium looping13,248,276 |
A variant of chemical looping (combustion) that involves carbonation and calcination. Metal oxides e.g., CuO, Mn2O3, NiO, and Fe2O3 are used instead of O2(g) in oxy-fuel combustion |
• Rapid decrease in the limestone (i.e., sorbent) capacity after a number of cycles of reaction with CO2 |
• Environmental concerns caused by limestone mining, the waste from Ca-looping (i.e., the spent CaO) and the need for high temperatures for the operation |
• Need for air separation unit to obtain pure O2 for calcination |
The conventional absorption and adsorption based captures can be combined with electrochemical methods to decrease (or eliminate) the required thermal energy for the regeneration step as discussed in Sections 4.1.3 and 4.2.1. No available work have been found on electrochemical enhancement of the other conventional methods.
4.1 Absorption (wet scrubbing)
CO2 is a weak acid. Therefore, substrates that contain basic moieties such as amine groups (e.g., alkanolamines) are efficient absorbents for CO2 capture.277 Amines are derivatives of ammonia (NH3), containing a basic nitrogen atom, where one (R–NH2) or more hydrogen atoms have been replaced by a substituent. Amines act as a nucleophiles (i.e., electron pair donors also known as Lewis bases), reacting with CO2 at the electrophilic (i.e., electron pair acceptor) carbon center to form a carbamate (derivatives of carbamic acid H2NCOOH where one or more hydrogens are replaced by other organic functional groups).49,167,278 Although the amine capture processes are extensively studied, the reaction mechanism is not yet fully understood. For a detailed description see ref. 279.
The post-combustion CO2 capture is dominated by amine-based absorption, using aqueous solutions of mono-, di-, tri-ethanolamine or hindered amines to absorb CO2 in gas form.232,278,280–283 Aqueous solutions are often used in order to control the density, viscosity, surface tension, and the thermal expansion coefficient of the pure amines.284–286 This is while. the energy consumption for solvent regeneration decreases substantially with increasing the amine concentration (due to an improved CO2 reaction rate and absorption capacity287). However, such high concentrations also increase the degradation rate, viscosity and the involved environmental concerns, posing challenges on the overall capture process.285,287 In addition to aqueous solutions, both non- and low-aqueous solvents (i.e., water–lean solvent) are viable.284,288,289 These alternatives are not well studied yet although they have gained interests recently. All currently assessed water–lean solvents have shown lower CO2 solubilities than aqueous monoethanolamine (MEA). However, because the heat of absorption is not much affected, solvents with the lower volatility than water could potentially offer opportunities for processes with overall less reboiler heat duties than that of ordinary aqueous MEA.284
Amines have been used for CO2 capture since 1930.278 Monoethanolamine (MEA) scrubbing technology is seen as a benchmark technology for CO2 capture from flue gas of large-scale power plants.187,190,290,291 In this method, CO2(g) is chemically absorbed at low temperatures (∼40 to 60 °C) in the absorbent and is extracted in a desorber column later, generally via a temperature swing at high temperatures (∼120 °C), where the absorbent is also regenerated.186,292 The energy consumption of CO2 capture (from flue gas) via aqueous monoethanolamine (MEA) thermal swing is between ∼170–300 kJ mol−1 CO2.184–190
To address the drawbacks discussed in Table 4, for CO2 capture via chemical absorption, other inorganic solvents, such as aqueous potassium and sodium carbonate,167 ammonia solution and alkali hydroxide solution have been investigated.293,294 When using alkaline or carbonate based solution, hydration of CO2 takes place rather than carbamate formation.167 However, CO2 absorption in carbonate is very slow compared to that of amines.270 Increasing the absorbent pH (i.e., applying a wide range pH-swing), can enhance the kinetics substantially.
4.1.1 pH-swing vs. thermal swing.
All available large-scale CO2 capture processes rely on heating or using a combination of heat and vacuum to release the captured CO2.27,294 Given the initial focus was to capture CO2 from flue gas of fossil fuel power stations, heat integration is relatively straightforward. However, as an alternative to this thermal swing, an (electrochemical) pH-swing approach can be applied for CO2 recovery and absorbent regeneration.3
In a thermal swing absorption process, the energy performance is dominated by (1) absorbent absorption capacity, (2) absorption rate, (3) heat of absorption and (4) thermal degradation.270 The required thermal energy is often exacerbated due to use of aqueous solutions in which the capturing agent is contained (e.g., water for the case of MEA270).49 Furthermore, the required heat is normally generated from combustion of fossil fuels, decreasing the net captured CO2 in the conventional processes.108
Alternatively a pH-swing can be used, to absorb and desorb CO2. The cost of absorbent regeneration through pH-swing via BPMED in wet scrubbing (using KOH absorbent) is estimated to be ∼773 $ per tonne CO2. That is more than three times of the cost of the thermal swing rival. However, the cost can significantly decrease if the cost of renewable energy decreases (e.g., from 0.06 to 0.018 $ per kW h), cost of membrane decreases (to lower than 100 $ m−2), membrane life time increases from around 3 years295 to 15 years and the process is optimized.3
4.1.2 Physical absorption.
The advantage of the physical absorption to chemical absorption explained above is its lower heat consumption in the solvent regeneration step.21,22 Solvents, such as methanol, poly(ethylene glycol) and dimethyl ether can be used to absorb CO2(g) physically. Recently, ionic liquids have been proposed as alternatives to the conventional absorption solvents.296–298 Ionic liquids are molten salts that exist as liquids near room temperature, often composed of an organic cation with an inorganic or organic anion and featuring polar properties.25 Ionic liquids are referred to as green solvents due to their low volatility, exceptional thermal stability, non-flammability and environmentally benign character.299 The capture using ionic liquids is often based on physisorption although some ionic liquids react with CO2 in a chemisorption mechanism.22
4.1.3 Electrochemical enhancement of amine based absorption.
Electrochemical methods provide alternative routes to the conventional thermal regeneration step in absorption based capture. Such electrochemical enhancements are shown feasible through (1) pre-concentrating the CO2 rich amine stream, (2) substituting CO2 with suitable metallic species or (3) pH-swing. These three routes are explained below.
For pre-concentrating the CO2 rich amine stream, a capacitive deionization unit (CDI) can be used. Inside the CDI cell, when current is applied, ionic species (i.e., MEAH+ and MEACOO− in case of monoethanolamine absorption) are adsorbed at the electrodes, creating an ion-free solution (mainly water270) that can be sent back to the absorber column without the need to undergo the thermal desorption step. Subsequently, when power is switched off or reversed, the adsorbed ions will be released back from the porous electrodes, creating a carbon rich stream that can then be sent to the stripper column. When applying thermal regeneration, the concentrated solution from the CDI unit then requires 50% lower solvent regeneration heat energy because of its high CO2 loading.300
As an alternative approach, the conventional temperature swing step in the amine absorption process can be replaced by metal ion substitution in an electrochemical cell.29,30,301 Such a cell consists of multiple anode and cathode chambers made of copper. At the anode, Cu2+ reacts with the amines, displacing the CO2 as shown in Fig. 15. CO2 is subsequently removed in flash tanks after the anode chambers and the amines are regenerated by subsequent reduction of the Cu2+ to Cu in the cathodes. The process allows for higher CO2 desorption pressures, smaller absorber columns and lower energy demands.
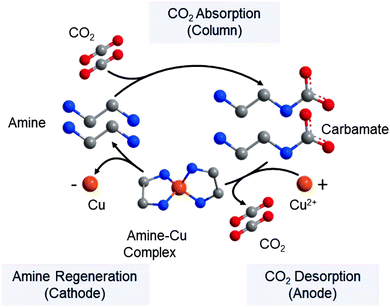 |
| Fig. 15 Electrochemically-mediated amine regeneration (EMAR) using copper. Reprinted from ref. 302, Copyright (2019), with permission from Elsevier. The conventional thermal swing is replaced with an electrochemical step. In addition to Cu/Cu2+, many possible chemistries can be utilized in such separation processes as discussed further in ref. 29, 30 and 301. | |
There are few works available on using a pH-swing to regenerate amine based absorbents; The early work of Zabolotskii et al. shows the feasibility of a low-temperature BPMED for regeneration of aqueous monoethanolamine (MEA) sorbent.303 Huang et al. demonstrated a pH-swing for amine based absorbents, doing so electrochemically (for flue gas desulfurization)304 and Feng et al. by simply adding a (weak) acid to the rich amine stream (for CO2 capture).236 Such addition of acid is reported to have the potential to increase the volume of the released CO2 and to decrease the absorbent regeneration heat energy. Both contributing to a higher energy efficiency.236
4.2 Adsorption
CO2 can be adsorbed on solid porous materials, where CO2(g) is subsequently recovered and the adsorbent is regenerated through a temperature, pressure,305 vacuum306–315 or electric swing desorption.316 Previous work has shown CO2 adsorption on metal–organic frameworks (MOF's), silica, zeolites, immobilized amine, alumina, polymeric resins, molecular sieves and activated carbon. Adsorption is possible through both physical (e.g., on zeolite, graphene, MOF's, silica) and chemical (e.g., amine and calcium based materials) bonding with CO2.
An advantage of adsorption based capture is that using solid adsorbents (instead of the mature aqueous monoethanolamine (MEA) technology) in capturing systems reduce the regeneration heat (due to the much lower heat capacity of solid adsorbents and the avoidance of water evaporation in the regenerator).187 The (calculated) regeneration heat for polyethyleneimine (PEI)/silica adsorbent based capture is reported to be around 2.46 GJ per tonne CO2, which is much lower than the value of 3.3–3.9 GJ per tonne CO2 for a typical aqueous MEA system.187 In general, adsorption also has higher CO2 adsorption capacity compared to that of absorption e.g., ca. 88–176 kg CO2 per kg adsorbent305vs. 0.4–1.2 kg CO2 per kg absorbent.18,269,317
4.2.1 Electrochemical enhancement of adsorption.
Similar to absorbents, the CO2 capture and recovery of recent adsorbents has been assessed via electrochemical swings instead of the conventional pressure or temperature swings.39,318 As an example, the redox active carriers described in Section 3.3 can be employed as solid adsorbents, immobilized on surface of electrodes. Such electro-swing systems normally operate in charge/discharge cycles where changing the cell polarity regulates the activation and deactivation of the carrier.39 The significant advantage of the electro-swing process with respect to pressure swing adsorption (PSA) and temperature swing adsorption (TSA) is that the CO2 capacity of these solid adsorbents does not depend on the feed concentration, making them suitable for CO2 capture even from very dilute streams.39 Moreover, up-scaling is easily achievable in electro-swing adsorption by using multiple anode and cathode chambers repeating within one cell.
Alternative to the electrochemical electro swing approach described above and in ref. 39, the electrochemical process can induce a temperature swing. In that case, a low voltage passes through a conductor to change the sorbent temperature via Joule heating (i.e., resistance turning electric energy into heat).318–322
5 CO2 utilization
After CO2 is captured, it can be stored or utilized, see Fig. 16. CO2 is an inexpensive, non-toxic, renewable commodity.323,324 The market for CO2 use is projected to grow from 0.23 gigatonnes (Gt) per year today to 7 Gt per year by 2030.325
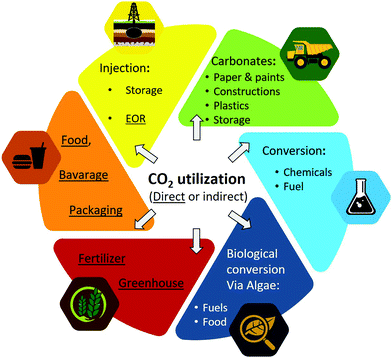 |
| Fig. 16 Schematic of direct and indirect (i.e., via conversion) utilization of CO2. Alternative to gaseous CO2, carbonate minerals (e.g., CaCO3) can be utilized326 in paper industry, coating, plastics,327 paints, adhesive/sealants, rubber, cement and construction materials.328 | |
In addition to fuels, chemicals such as ethylene, alcohols, formic acid (or formate), syngas, urea and other organic materials can be produced from CO2, electrochemically, thermo-chemically or by other approaches.323,329–337 Such organic chemicals are often more expensive than fuels and may offer advantages in the techno-economic analysis. However, the global demand for them are much lower than fuels as shown in Fig. 17. For instance, the global demand for one of the largest chemical markets, ethylene, is 184 Mt per year.338 Ethylene manufacture also stands as the prime contributor for CO2 emissions among carbon-based chemicals, with a CO2 emissions rate of 184.3–213 Mt in 2015, which could reach 1.34 Gt per year by 2030.339
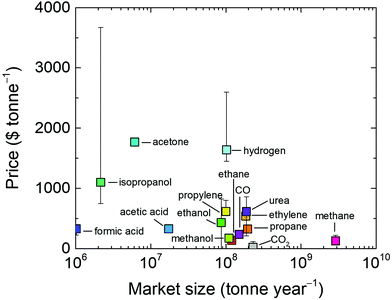 |
| Fig. 17 Average price of CO2 utilization products as a function of their market size. Error bars indicate anomalies in some regions (see the ESI,† Table S1 for values). CO2 and H2 are included for reference. | |
Production of synthetic hydrocarbon fuels and chemicals often requires high purity CO2 feeds. Many CO2 capture facilities using centralized sources simultaneously capture sulfur containing compounds, such as hydrogen sulfide (H2S) that must be removed upstream to avoid catalyst poisoning.340 The process of desulfurization typically involves liquid phase oxidation to promote H2S oxidation to sulfur, followed by sulfur separation from the gas stream.341 Chemical adsorption using high surface area ZnO-based adsorbents may be used in sequence to further eliminate H2S prior to pipeline transmission.342,343 Alternatively, CO2 conversion can take place via biocatalytic routes with both natural and engineered microorganisms344,345 that generally have higher tolerance for impurities.346 CO2 capture from dilute sources, such as from air and seawater, usually contains non-negligible amount of O2 and N2.28,45 While N2 is an inert gas and may not negatively impact the CO2 conversion, a trace amount of O2 may lower the catalytic turnover through the unwanted reaction with hydrogen in the thermochemical process,347 or through the preferential reaction of oxygen reduction in the electrochemical process.45 Strategies for O2 removal from CO2 stream include catalytic oxidation of hydrogen348 or methane349 on noble metal catalysts such as Pt or Pd,350 chemical adsorption of O2 on Cu surfaces at elevated temperatures,348 and electrochemical reduction of O2 on Ag catalysts.45
A pressurized CO2(aq) stream is beneficial for a subsequent CO2 conversion step. In a CO2 electrolyser for methanol production, when the produced CO2 remains dissolved due to an applied pressure, the avoided typical gas regeneration step and CO(g) compression step save more than 150 kJ mol−1 CO2.46 High pressure electrolyser (up to 40 bar) is also reported to increase the current efficiency of CO2 reduction to formic acid/formate.351,352 Moreover, a high pressure CO2(g) is required for the transportation in the pipes, enhanced oil recovery or geological CO2 sequestration for underground injection. Supercritical CO2 (above its critical temperature 31.0 °C and pressure 72.8 atm) with its low density and viscosity plays a significant role in the extraction of oil.353–355 Furthermore, supercritical CO2 can be used in the enhanced geothermal system for heat exchange.247,356
The electrochemical CO2 conversion lacks studies that demonstrate the capability of the technology at scales large enough for industrial implementation.357 As an alternative, CO2 can be converted biologically to organic carbon in plants or microalgae, through photosynthesis, resulting in various products, such as biofuel or animal feed.358,359
Gaseous CO2 can be stored (i.e., sequestrated) in deep geological layers or in the ocean.19,360–362 In 2019, from the 19 in operation large-scale carbon capture & storage (CCS) facilities, 33.2 Mt per year of CO2 were captured and stored363 (i.e., less than 0.1% of the total global emissions).364 By addition of the already in constructions facilities, this value is estimated to be doubled, within the coming years. Most of this storage is done through enhanced oil recovery (EOR) application (i.e., over 260 Mt of anthropogenic CO2 by 2019).363
As an alternative to sequestration of gaseous CO2, CO2(g) can first be converted to bicarbonate ion and, subsequently, be stored as already abundant forms of ocean alkalinity, through electrogeochemistry.71,75,78,112
There are social concerns associated with the gas sequestration including fear of CO2 leakages, lack of suitable locations, required site monitoring, unknown impacts on living organisms and limitations involved with CO2 transportation and injection to storage sites. Alternatively, solid (carbonates) storage can be used. Such mineral carbonate sequestration is permanent, safe, has a large worldwide storage capacity and is less subject to social opposition.328,365,366
6 Conclusions
Electrochemical CO2 capture methods are undergoing a renaissance as their applications expand due to their higher energy efficiency, flexibility and sustainability compared to the conventional approaches. Electrochemical CO2 capture is classified into four categories; (1) methods that apply a pH-swing to capture and recover the CO2, (2) methods that rely on the binding affinity of CO2 molecules to redox-active species, (3) molten carbonate cells and (4) hybrid electrochemical processes that combine CO2 capture and e.g., direct conversion. Among the electrochemical capture methods, pH-swing based approaches, leveraging the carbonate equilibrium, are most widely studied, due to their straightforward operation and the absence of toxic or expensive chemicals. In theory, a mild pH-swing over ca. 2–3 pH units would allow to capture >98% of the CO2. However, in practice, to improve the slow kinetics associated with such a mild swing, either a wider pH range (ca. 5–6 pH units) or catalytic enzymes (e.g., carbonic anhydrase) need to be applied.
An electrochemical pH-swing is induced via electrolysis, bipolar membrane electrodialysis (BPMED), redox active molecules that undergo proton coupled electron transfer (PCET) or capacitive deionization. Among all, electrolysis is the earliest method (used for alkaline absorbent regeneration), but is still rather energy intensive due to the intrinsic irreversibility of the gas evolution redox reactions. However, the produced H2(g) (through water electrolysis) can be used to offset the total energy consumption. Capture via PCET active agents enable high current efficiencies, but are at the moment limited by slow electrode kinetics, low solubility of PCET organics and the sensitivity of the process to impurities in the flue gas such as O2, water and sulfur. Using (membrane) capacitive deionization (MCDI) enables capture with an electrical energy consumption as low as 40 kJ mol−1 using only deionized water. However, (M)CDI capture is so far only applied at very low current densities, is still in the very early stage of the lab-scale research (TRL of 3) and its large scale applications await more performance studies. All electrochemical capture methods can be used easily as plug-and-play units. Among the four technology for electrochemical pH-swing, BPMED has the advantage of keeping a small footprint upon up scaling. At present, the cost of using BPMED for CO2 desorption and alkaline (re)generation in alkaline wet scrubbing is estimated to be 2–3 times more than the conventional thermal swing desorption rival. However, the cost can significantly decrease if improvements in the cost of renewable energies and ion exchange membranes, membrane life time and their permselectivity and resistivity are achieved.
Despite of the successful lab-scale demonstrations, both CO2 capture via electrolysis and BPMED have achieved TRL of 5–6 and are not yet commercialized. This is while, the conventional post-combustion CO2 capture methods, such as absorption, adsorption, membrane separation and chemical looping have found their way to industrial applications. As opposed to the electrochemical captures, conventional methods are mainly designed to capture CO2 from centralized emitters such as fossil fueled power plants. These methods have a larger footprint and are not geared for efficient decentralised emitted CO2. However, in the last decade, to benefit from the high efficiency and selectivity of the electrochemical processes, conventional methods are also promoted to be combined with electrochemical process. Substituting the temperature or pressure swings with an electrochemical swing in an amine based absorption capture is shown to halve the energy consumption of the CO2 desorption step while decreasing the footprint of the unit. The framework established in this paper can be the basis for future studies on the energetics of electrochemical CO2 capture processes, not only for flue gas separations, but also for a range of other applications, such as seawater CO2 capture and direct air capture.
Conflicts of interest
There are no conflicts to declare.
Acknowledgements
This work was performed in the NWO-cooperation framework of Wetsus, Centre of Excellence for Sustainable Water Technology (http://www.wetsus.nl). Wetsus is funded by the Dutch Ministry of Economic Affairs, the European Union Regional Development Fund, the Province of Fryslân, the City of Leeuwarden and the EZ/Kompas program of the “Samenwerkingsverband Noord-Nederland”. The authors like to thank the participants of the research theme “Concentrates” in Wetsus and research group “Transport phenomena” in faculty of applied sciences at TU Delft for the discussions and their (financial) support. This research received funding from the Netherlands Organization for Scientific Research (NWO) in the framework of the project ALW.2016.004. The work on aqueous carbonate equilibrium and CO2 utilization is based on work performed by the Liquid Sunlight Alliance, which is supported by the U.S. Department of Energy, Office of Science, Office of Basic Energy Sciences, Fuels from Sunlight Hub under Award Number DE-SC0021266. The authors also thank the support from SoCalGas.
References
-
M. Fajardy, A. Köberle, N. Mac Dowell and A. Fantuzzi, BECCS-deployment: a-reality-check, 2018 Search PubMed
.
- J. P. Mulligan, Carbon Dioxide Emissions, Nova Science, 2010 Search PubMed
.
- F. Sabatino, M. Mehta, A. Grimm, M. Gazzani, F. Gallucci, G. J. Kramer and M. van Sint Annaland, Evaluation of a Direct Air Capture Process Combining Wet Scrubbing and Bipolar Membrane Electrodialysis, Ind. Eng. Chem. Res., 2020, 59(15), 7007–7020, DOI:10.1021/acs.iecr.9b05641
.
- S. Nanda, S. N. Reddy, S. K. Mitra and J. A. Kozinski, The progressive routes for carbon capture and sequestration, Energy Sci. Eng., 2016, 4(2), 99–122, DOI:10.1002/ese3.117
.
-
IPCC, in Summary for Policymakers, ed. T. Stocker, et al., Cambridge University Press, Cambridge, United Kingdom and New York, NY, USA, 2013, ch. SPM, pp. 1–30 DOI:10.1017/CBO9781107415324.004, URL: http://www.climatechange2013.org, ISBN: 978-1-107-66182-0
.
- C. Fernández-Dacosta, V. Stojcheva and A. Ramirez, Closing carbon cycles: Evaluating the performance of multi-product CO2 utilisation and storage configurations in a refinery, J. CO2 Util., 2018, 23, 128–142, DOI:10.1016/j.jcou.2017.11.008
, URL: http://www.sciencedirect.com/science/article/pii/S2212982017305589, ISSN: 2212-9820.
- A. Fane, A grand challenge for membrane desalination: More water, less carbon, Desalination, 2018, 426, 155–163, DOI:10.1016/j.desal.2017.11.002
, URL: http://www.sciencedirect.com/science/article/pii/S0011916417320866, ISSN: 0011-9164.
- C.-F. de Lannoy, M. D. Eisaman, A. Jose, S. D. Karnitz, R. W. DeVaul, K. Hannun and J. L. Rivest, Indirect ocean capture of atmospheric CO2: Part I. Prototype of a negative emissions technology, Int. J. Greenhouse Gas Control, 2018, 70, 243–253, DOI:10.1016/j.ijggc.2017.10.007
, URL: http://www.sciencedirect.com/science/article/pii/S1750583617304322, ISSN: 1750-5836.
- S. E. Tanzer and A. Ramírez, When are negative emissions negative emissions?, Energy Environ. Sci., 2019, 12, 1210–1218, 10.1039/C8EE03338B
.
-
O. Edenhofer, Climate change 2014: mitigation of climate change, Cambridge University Press, 2015, vol. 3 Search PubMed
.
- C. Le Quéré,
et al., Global Carbon Budget 2018, Earth Syst. Sci. Data, 2018, 10(4), 2141–2194, DOI:10.5194/essd-10-2141-2018
, URL: https://www.earth-syst-sci-data.net/10/2141/2018/.
- A. Alonso, J. Moral-Vico, A. A. Markeb, M. Busquets-Fité, D. Komilis, V. Puntes, A. Sánchez and X. Font, Critical review of existing nanomaterial adsorbents to capture carbon dioxide and methane, Sci. Total Environ, 2017, 595, 51–62 CrossRef CAS
.
- C. Song, Q. Liu, N. Ji, S. Deng, J. Zhao, Y. Li, Y. Song and H. Li, Alternative pathways for efficient CO2 capture by hybrid processes—A review, Renewable Sustainable Energy Rev., 2018, 82, 215–231, DOI:10.1016/j.rser.2017.09.040
, URL: http://www.sciencedirect.com/science/article/pii/S1364032117312947, ISSN: 1364-0321.
- A. Al-Mamoori, A. Krishnamurthy, A. A. Rownaghi and F. Rezaei, Carbon Capture and Utilization Update, Energy Technol., 2017, 5(6), 834–849, DOI:10.1002/ente.201600747
, URL: https://onlinelibrary.wiley.com/doi/abs/10.1002/ente.201600747.
- K. Z. House, A. C. Baclig, M. Ranjan, E. A. van Nierop, J. Wilcox and H. J. Herzog, Economic and energetic analysis of capturing CO2 from ambient air, Proc. Natl. Acad. Sci. U. S. A., 2011, 108(51), 20428–20433, DOI:10.1073/pnas.1012253108
.
- J. Míguez, J. Porteiro, R. Pérez-Orozco, D. Patiño and S. Rodríguez, Evolution of CO2 capture technology between 2007 and 2017 through the study of patent activity, Appl. Energy, 2018, 211, 1282–1296, DOI:10.1016/j.apenergy.2017.11.107
, URL: http://www.sciencedirect.com/science/article/pii/S0306261917317087, ISSN: 0306-2619.
- R. S. Haszeldine, Carbon Capture and Storage: How Green Can Black Be?”, Science, 2009, 325(5948), 1647–1652, DOI:10.1126/science.1172246
, URL: https://science.sciencemag.org/content/325/5948/1647.
- B. P. Spigarelli and S. K. Kawatra, Opportunities and challenges in carbon dioxide capture, J. CO2 Util., 2013, 1, 69–87, DOI:10.1016/j.jcou.2013.03.002
, URL: http://www.sciencedirect.com/science/article/pii/S221298201300005X, ISSN: 2212-9820.
- D. Y. Leung, G. Caramanna and M. M. Maroto-Valer, An overview of current status of carbon dioxide capture and storage technologies, Renewable Sustainable Energy Rev., 2014, 39, 426–443, DOI:10.1016/j.rser.2014.07.093
, URL: http://www.sciencedirect.com/science/article/pii/S1364032114005450, ISSN: 1364-0321.
- E. J. Granite and T. O’Brien, Review of novel methods for carbon dioxide separation from flue and fuel gases, Fuel Process. Technol., 2005, 86(14), 1423–1434, DOI:10.1016/j.fuproc.2005.01.001
, URL: http://www.sciencedirect.com/science/article/pii/S0378382005000123, ISSN: 0378-3820.
- M. M. Abu-Khader, Recent Progress in CO2 Capture/Sequestration: A Review, Energy Sources, Part A, 2006, 28(14), 1261–1279, DOI:10.1080/009083190933825
.
- D. M. D’Alessandro, B. Smit and J. R. Long, Carbon Dioxide Capture: Prospects for New Materials, Angew. Chem., Int. Ed., 2010, 49(35), 6058–6082, DOI:10.1002/anie.201000431
.
-
Y. Surampalli Rao, Environmental and Water Resources Institute (U.S.) and Carbon Capture and Storage Task Committee, English, Reston, Virginia: American Society of Civil Engineers, 2015, URL: https://app.knovel.com/web/toc.v/cid:kpCCSPCBM8/viewerType:toc/root_slug:carbon-capture-storage.
- M. Songolzadeh, M. Soleimani, M. T. Ravanchi and R. Songolzadeh, Carbon Dioxide Separation from Flue Gases: A Technological Review Emphasizing Reduction in Greenhouse Gas Emissions, Sci. World J., 2014, 2014, 1–34, DOI:10.1155/2014/828131
.
- A. S. R. Machado and M. N. da Ponte, CO2 capture and electrochemical conversion, Curr. Opin. Green Sustainable Chem., 2018, 11, 86–90, DOI:10.1016/j.cogsc.2018.05.009
, URL: http://www.sciencedirect.com/science/article/pii/S2452223617301207, ISSN: 2452-2236.
- Y. Ishimoto, M. Sugiyama, E. Kato, R. Moriyama, K. Tsuzuki and A. Kurosawa, Putting Costs of Direct Air Capture in Context, SSRN Electron. J., 2017 DOI:10.2139/ssrn.2982422
, URL: https://papers.ssrn.com/sol3/papers.cfm?abstract_id=2982422.
- National Academies of Sciences, Engineering and Medicine, Negative Emissions Technologies and Reliable Sequestration: A Research Agenda, The National Academies Press, Washington, DC, 2019, ISBN: 978-0-309-48452-7, DOI: 10.17226/25259, URL: https://www.nap.edu/catalog/25259/negative-emissionstechnologies-and-reliable-sequestration-a-research-agenda.
- D. W. Keith, G. Holmes, D. S. Angelo and K. Heidel, A Process for Capturing CO2 from the Atmosphere, Joule, 2018, 2(8), 1573–1594, DOI:10.1016/j.joule.2018.05.006
, URL: http://www.sciencedirect.com/science/article/pii/S2542435118302253, ISSN: 2542-4351.
- M. C. Stern, F. Simeon, H. Herzog and T. A. Hatton, Post-combustion carbon dioxide capture using electrochemically mediated amine regeneration, Energy Environ. Sci., 2013, 6, 2505–2517, 10.1039/C3EE41165F
.
- M. Wang, H. J. Herzog and T. A. Hatton, CO2 Capture Using Electrochemically Mediated Amine Regeneration, Ind. Eng. Chem. Res., 2020, 59(15), 7087–7096, DOI:10.1021/acs.iecr.9b05307
.
- H. Rg and A. Babinsky, Electrochemical concentration and separation of carbon dioxide for advanced life support systems-carbonation cell system, SAE Trans., 1969, 78, 151 Search PubMed
.
- M. P. Kang and J. Winnick, Concentration of carbon dioxide by a high-temperature electrochemical membrane cell, J. Appl. Electrochem., 1985, 15(3), 431–439, DOI:10.1007/BF00615996
, ISSN: 1572-8838.
- L. Walke, K. Atkinson, D. Clark, D. Scardaville and J. Winnick, Recovery of CO2 from flue gas using an electrochemical membrane, Gas Sep. Purif., 1988, 2(2), 72–76, DOI:10.1016/0950-4214(88)80015-X
, URL: http://www.sciencedirect.com/science/article/pii/095042148880015X, ISSN: 0950-4214.
-
J. Winnick, Electrochemical membrane gas separation, 1990 Search PubMed
.
-
M. Eisaman, D. E. Schwartz, S. Amic, D. Larner, J. Zesch, F. Torres and K. Littau, Energy-efficient electrochemical CO2 capture from the atmosphere, Technical Proceedings of the 2009 Clean Technology Conference and Trade Show, 2009.
-
F. F. Dimascio, H. Willauer, D. Hardy, K. Lewis and F. Williams, Extraction of Carbon Dioxide from Seawater by an Electrochemical Acidification Cell, Part 1 – Initial Feasibility Studies, 2010, vol. 25.
- L. Legrand, O. Schaetzle, R. C. F. de Kler and H. V. M. Hamelers, Solvent-Free CO2 Capture Using Membrane Capacitive Deionization, Environ. Sci. Technol., 2018, 52(16), 9478–9485, DOI:10.1021/acs.est.8b00980
, PMID: 29993236.
- M. H. Youn,
et al., Carbon dioxide sequestration process for the cement industry, J. CO2 Util., 2019, 34, 325–334, DOI:10.1016/j.jcou.2019.07.023
, URL: http://www.sciencedirect.com/science/article/pii/S221298201930410X, ISSN: 2212-9820.
- S. Voskian and T. A. Hatton, Faradaic electro-swing reactive adsorption for CO2 capture, Energy Environ. Sci., 2019, 12, 3530–3547, 10.1039/C9EE02412C
.
- R. A. Shaw and T. A. Hatton, Electrochemical CO2 capture thermodynamics, Int. J. Greenhouse Gas Control, 2020, 95, 102878, DOI:10.1016/j.ijggc.2019.102878
, URL: http://www.sciencedirect.com/science/article/pii/S175058361930427X, ISSN: 1750-5836.
-
M. C. Stern, F. Simeon, T. Hammer, H. Landes, H. J. Herzog and T. A. Hatton, Electrochemically mediated separation for carbon capture, Energy Procedia 4, 10th International Conference on Greenhouse Gas Control Technologies, 2011, pp. 860–867, ISSN: 1876-6102, DOI: http://10.1016/j.egypro.2011.01.130, URL: http://www.sciencedirect.com/science/article/pii/S1876610211001329.
- S. Datta,
et al., Electrochemical CO2 Capture Using Resin-Wafer Electrodeionization, Ind. Eng. Chem. Res., 2013, 52(43), 15177–15186, DOI:10.1021/ie402538d
.
- M. D. Eisaman, L. Alvarado, D. Larner, P. Wang and K. A. Littau, CO2 desorption using high-pressure bipolar membrane electrodialysis, Energy Environ. Sci., 2011, 4, 4031–4037, 10.1039/C1EE01336J
.
- B. Mot, J. Hereijgers, M. Duarte and T. Breugelmans, Influence of flow and pressure distribution inside a gas diffusion electrode on the performance of a flow-by CO2 electrolyzer, Chem. Eng. J., 2019, 378, 122224, DOI:10.1016/j.cej.2019.122224
, URL: http://www.sciencedirect.com/science/article/pii/S1385894719316183, ISSN: 1385-8947.
- I. A. Digdaya, I. Sullivan, M. Lin, L. Han, W.-H. Cheng, H. A. Atwater and C. Xiang, A direct coupled electrochemical system for capture and conversion of CO2 from oceanwater, Nat. Commun., 2020, 11(1), 1–10 CrossRef
.
- W. A. Smith, T. Burdyny, D. A. Vermaas and H. Geerlings, Pathways to Industrial-Scale Fuel Out of Thin Air from CO2 Electrolysis, Joule, 2019, 3(8), 1822–1834, DOI:10.1016/j.joule.2019.07.009
, URL: http://www.sciencedirect.com/science/article/pii/S2542435119303538, ISSN: 2542-4351.
- T. Li, E. W. Lees, M. Goldman, D. A. Salvatore, D. M. Weekes and C. P. Berlinguette, Electrolytic Conversion of Bicarbonate into CO in a Flow Cell, Joule, 2019, 3(6), 1487–1497, DOI:10.1016/j.joule.2019.05.021
, URL: http://www.sciencedirect.com/science/article/pii/S2542435119302648, ISSN: 2542-4351.
- E. W. Lees, M. Goldman, A. G. Fink, D. J. Dvorak, D. A. Salvatore, Z. Zhang, N. W. X. Loo and C. P. Berlinguette, Electrodes Designed for Converting Bicarbonate into CO, ACS Energy Lett., 2020, 5(7), 2165–2173, DOI:10.1021/acsenergylett.0c00898
.
- J. H. Rheinhardt, P. Singh, P. Tarakeshwar and D. A. Buttry, Electrochemical Capture and Release of Carbon Dioxide, ACS Energy Lett., 2017, 2(2), 454–461, DOI:10.1021/acsenergylett.6b00608
.
- P. Kuntke, M. Rodríguez Arredondo, L. Widyakristi, A. ter Heijne, T. H. J. A. Sleutels, H. V. M. Hamelers and C. J. N. Buisman, Hydrogen Gas Recycling for Energy Efficient Ammonia Recovery in Electrochemical Systems, Environ. Sci. Technol., 2017, 51(5), 3110–3116, DOI:10.1021/acs.est.6b06097
.
- P. Kuntke, M. Rodrigues, T. Sleutels, M. Saakes, H. V. M. Hamelers and C. J. N. Buisman, Energy-Efficient Ammonia Recovery in an Up-Scaled Hydrogen Gas Recycling Electrochemical System, ACS Sustainable Chem. Eng., 2018, 6(6), 7638–7644, DOI:10.1021/acssuschemeng.8b00457
.
- Y. Lei, S. Narsing, M. Saakes, R. D. van der Weijden and C. J. N. Buisman, Calcium Carbonate Packed Electrochemical Precipitation Column: New Concept of Phosphate Removal and Recovery, Environ. Sci. Technol., 2019, 53(18), 10774–10780, DOI:10.1021/acs.est.9b03795.0
.
-
V. L. Snoeyink and D. Jenkins, Water chemistry, John Wiley & Sons, Ltd, 1980 Search PubMed
.
-
J. Butler, Carbon dioxide equilibria and their applications, 1982 Search PubMed
.
-
J. J. Morgan and W. Stumm, Aquatic chemistry: chemical equilibria and rates in natural waters, Wiley, 1996 Search PubMed
.
-
J. W. Murray, Ocean Carbonate Chemistry: The Aquatic Chemistry Fundamentals, in The Ocean Carbon Cycle and Climate, ed. M. Follows and T. Oguz, Springer Netherlands, Dordrecht, 2004, pp. 1–29 Search PubMed
.
- M. J. Mitchell, O. E. Jensen, K. A. Cliffe and M. M. Maroto-Valer, A model of carbon dioxide dissolution and mineral carbonation kinetics, Proc. R. Soc. A, 2010, 466(2117), 1265–1290 CrossRef CAS
, URL: http://www.jstor.org/stable/25661496, ISSN: 13645021.
-
C. A. Rochelle, I. Czernichowski-Lauriol and A. E. Milodowski, The impact of chemical reactions on CO2 storage in geological formations: a brief review, Geological Society, London, 2004, Special Publications, vol. 233(issue 1), pp. 87–106 DOI:10.1144/GSL.SP.2004.233.01.07, eprint: https://sp.lyellcollection.org/content/233/1/87.full.pdf, ISSN: 0305-8719
.
- X. Wang, W. Conway, R. Burns, N. McCann and M. Maeder, Comprehensive study of the hydration and dehydration reactions of carbon dioxide in aqueous solution, J. Phys. Chem. A, 2010, 114(4), 1734–1740, DOI:10.1021/jp909019u
, ISSN: 1089-5639.
- Y. Pocker and D. W. Bjorkquist, Stopped-Flow Studies of Carbon Dioxide Hydration and Bicarbonate Dehydration in H2O and D2O. Acid–Base and Metal Ion Catalysis, J. Am. Chem. Soc., 1977, 99(20), 6537–6543, DOI:10.1021/ja00462a012
, ISSN: 15205126.
-
A. G. Dickson, C. L. Sabine and J. R. Christian, Guide to best practices for ocean CO2 measurements, North Pacific Marine Science Organization, 2007 Search PubMed
.
-
R. Zeebe and D. Wolf-Gladrow, CO2 in Seawater: Equilibrium, Kinetics, Isotopes, 2001 Search PubMed
.
- F. J. Millero, The thermodynamics of the carbonate system in seawater, Geochim. Cosmochim. Acta, 1979, 43(10), 1651–1661, DOI:10.1016/0016-7037(79)90184-4
, ISSN: 0016-7037.
- A. Dickson and J. Riley, The estimation of acid dissociation constants in seawater media from potentionmetric titrations with strong base. I. The ionic product of water—Kw, Mar. Chem., 1979, 7(2), 89–99, DOI:10.1016/0304-4203(79)90001-X
, URL: http://www.sciencedirect.com/science/article/pii/030442037990001X, ISSN: 0304-4203.
- K. Schulz, U. Riebesell, B. Rost, S. Thoms and R. Zeebe, Determination of the rate constants for the carbon dioxide to bicarbonate inter-conversion in pH-buffered seawater systems, Mar. Chem., 2006, 100(1), 53–65, DOI:10.1016/j.marchem.2005.11.001
, URL: http://www.sciencedirect.com/science/article/pii/S0304420305001684, ISSN: 0304-4203.
- S. Lindskog, The catalytic mechanism of carbonic anhydrase, Inorg. Chim. Acta, 1983, 79, 36, DOI:10.1016/S0020-1693(00)95058-8
, URL: http://www.sciencedirect.com/science/article/pii/S0020169300950588, ISSN: 0020-1693.
- J. da Costa Ores, L. Sala, G. P. Cerveira and S. J. Kalil, Purification of carbonic anhydrase from bovine erythrocytes and its application in the enzymic capture of carbon dioxide, Chemosphere, 2012, 88(2), 255–259 CrossRef CAS
.
- I. M. Power, A. L. Harrison, G. M. Dipple and G. Southam, Carbon sequestration via carbonic anhydrase facilitated magnesium carbonate precipitation, Int. J. Greenhouse Gas Control, 2013, 16, 145–155, DOI:10.1016/j.ijggc.2013.03.011
, URL: http://www.sciencedirect.com/science/article/pii/S175058361300131X, ISSN: 1750-5836.
- H. Yun, Y. E. Kim, W. Lee, M. H. Youn, S. K. Jeong, K. T. Park and K. B. Lee, Simultaneous Sodium Hydroxide Production by Membrane Electrolysis and Carbon Dioxide Capture, Chem. Eng. Technol., 2017, 40(12), 2204–2211, DOI:10.1002/ceat.201700151
.
- H. Park, J. S. Lee, J. Han, S. Park, J. Park and B. Min, CO Fixation by Membrane Separated NaCl Electrolysis, Energies, 2015, 8, 8704–8715, DOI:10.3390/en8088704
.
- G. H. Rau, Electrochemical Splitting of Calcium Carbonate to Increase Solution Alkalinity: Implications for Mitigation of Carbon Dioxide and Ocean Acidity, Environ. Sci. Technol., 2008, 42(23), 8935–8940, DOI:10.1021/es800366q
, PMID: 19192821.
- A. Mehmood, M. I. Iqbal, J.-Y. Lee, J. Hwang, K.-D. Jung and H. Y. Ha, A novel high performance configuration of electrochemical cell to produce alkali for sequestration of carbon dioxide, Electrochim. Acta, 2016, 219, 655–663, DOI:10.1016/j.electacta.2016.09.123
, URL: http://www.sciencedirect.com/science/article/pii/S0013468616320436, ISSN: 0013-4686.
- J. Way,
et al., Low-Voltage Electrochemical Process for Direct Carbon Dioxide Sequestration, J. Electrochem. Soc., 2012, 159, B627–B628, DOI:10.1149/2.033206jes
.
- S. Stucki, A. Schuler and M. Constantinescu, Coupled CO2 recovery from the atmosphere and water electrolysis: Feasibility of a new process for hydrogen storage, Int. J. Hydrogen Energy, 1995, 20(8), 653–663, DOI:10.1016/0360-3199(95)00007-Z
, URL: http://www.sciencedirect.com/science/article/pii/036031999500007Z, ISSN: 0360-3199.
- G. H. Rau, Electrochemical CO2 capture and storage with hydrogen generation, Energy Procedia, 2009, 1(1), 823–828, DOI:10.1016/j.egypro.2009.01.109
, URL: http://www.sciencedirect.com/science/article/pii/S1876610209001106, ISSN: 1876-6102.
-
H. D. Willauer, F. DiMascio and D. R. Hardy, Extraction of Carbon Dioxide and Hydrogen from Seawater By an Electrolytic Cation Exchange Module (E-CEM) Part 5: E-CEM Effluent Discharge Composition as a Function of Electrode Water Composition, Tech. Rep. Naval Research Lab, Washington D.C., USA, 2017.
-
A. Bard and L. Faulkner, Electrochemical Methods: Fundamentals and Applications, Wiley Textbooks, 2nd edn, 2000, ISBN: 9781118312803, URL: https://books.google.nl/books?id=hQocAAAAQBAJ Search PubMed
.
- G. H. Rau, CO2 Mitigation via Capture and Chemical Conversion in Seawater, Environ. Sci. Technol., 2011, 45(3), 1088–1092, DOI:10.1021/es102671x
, PMID: 21189009.
-
National Research Council and National Academy of Engineering, The Hydrogen Economy: Opportunities, Costs, Barriers, and R&D Needs, The National Academies Press, Washington, DC, 2004 DOI:10.17226/10922, URL: https://www.nap.edu/catalog/10922/the-hydrogen-economyopportunities-costs-barriers-and-rd-needs, ISBN: 978-0-309-09163-3
.
- H. D. Willauer, F. DiMascio, D. R. Hardy, M. K. Lewis and F. W. Williams, Development of an Electrochemical Acidification Cell for the Recovery of CO2 and H2 from Seawater II. Evaluation of the Cell by Natural Seawater, Ind. Eng. Chem. Res., 2012, 51(34), 11254–11260, DOI:10.1021/ie301006y
.
- H. D. Willauer, F. DiMascio, D. R. Hardy and F. W. Williams, Feasibility of CO2 Extraction from Seawater and Simultaneous Hydrogen Gas Generation Using a Novel and Robust Electrolytic Cation Exchange Module Based on Continuous Electrodeionization Technology, Ind. Eng. Chem. Res., 2014, 53(31), 12192–12200, DOI:10.1021/ie502128x
.
- C. Wang, H. Liu, X. Li and L. Zheng, Importance of Ambient O2 for Electrochemical Enrichment of Atmospheric CO2, Ind. Eng. Chem. Res., 2013, 52(7), 2470–2476, DOI:10.1021/ie302991y
.
- H. W. Pennline, E. J. Granite, D. R. Luebke, J. R. Kitchin, J. Landon and L. M. Weiland, Separation of CO2 from flue gas using electrochemical cells, Fuel, 2010, 89(6), 1307–1314, DOI:10.1016/j.fuel.2009.11.036
, URL: http://www.sciencedirect.com/science/article/pii/S0016236109005584, ISSN: 0016-2361.
- S. Z. Oener, S. Ardo and S. W. Boettcher, Ionic Processes in Water Electrolysis: The Role of Ion-Selective Membranes, ACS Energy Lett., 2017, 2(11), 2625–2634, DOI:10.1021/acsenergylett.7b00764
.
- H. Strathmann, J. Krol, H.-J. Rapp and G. Eigenberger, Limiting current density and water dissociation in bipolar membranes, J. Membr. Sci., 1997, 125(1), 123–142, DOI:10.1016/S0376-7388(96)00185-8
, URL: http://www.sciencedirect.com/science/article/pii/S0376738896001858, ISSN: 0376-7388.
- T. Xu, W. Yang and B. He, Water dissociation phenomena in a bipolar membrane, Sci. China, Ser. B: Chem., 1999, 42(6), 589–598, DOI:10.1007/BF02874323
, ISSN: 1862-2771.
- D. A. Vermaas and W. A. Smith, Synergistic Electrochemical CO2 Reduction and Water Oxidation with a Bipolar Membrane, ACS Energy Lett., 2016, 1(6), 1143–1148, DOI:10.1021/acsenergylett.6b00557
.
- D. A. Vermaas, S. Wiegman, T. Nagaki and W. A. Smith, Ion transport mechanisms in bipolar membranes for (photo)electrochemical water splitting, Sustainable Energy Fuels, 2018, 2, 2006–2015, 10.1039/C8SE00118A
.
- W. J. van Egmond, M. Saakes, I. Noor, S. Porada, C. J. N. Buisman and H. Hamelers, Performance of an environmentally benign acid base flow battery at high energy density, Int. J. Energy Res., 2018, 42(4), 1524–1535, DOI:10.1002/er.3941
.
- J.-H. Han,
et al., Reverse electrodialysis (RED) using a bipolar membrane to suppress inorganic fouling around the cathode, Water Res., 2019, 115078, DOI:10.1016/j.watres.2019.115078
, URL: http://www.sciencedirect.com/science/article/pii/S0043135419308528, ISSN: 0043-1354.
- A. Bandi, M. Specht, T. Weimer and K. Schaber, CO2 recycling for hydrogen storage and transportation—Electrochemical CO2 removal and fixation, Energy Convers. Manage., 1995, 36(6), 899–902, DOI:10.1016/0196-8904(95)00148-7
, URL: http://www.sciencedirect.com/science/article/pii/0196890495001487, ISSN: 0196-8904.
- M. D. Eisaman, L. Alvarado, D. Larner, P. Wang, B. Garg and K. A. Littau, CO2 separation using bipolar membrane electrodialysis, Energy Environ. Sci., 2011, 4, 1319–1328, 10.1039/C0EE00303D
.
- R. E. Moussaoui, G. Pourcelly, M. Maeck, H. D. Hurwitz and C. Gavach, Co-ion leakage through bipolar membranes Influence on I–V responses and water-splitting efficiency, J. Membr. Sci., 1994, 90(3), 283–292, DOI:10.1016/0376-7388(94)80078-2
, URL: http://www.sciencedirect.com/science/article/pii/0376738894800782, ISSN: 0376-7388.
- Y. Tanaka, Acceleration of water dissociation generated in an ion exchange membrane, J. Membr. Sci., 2007, 303(1), 234–243, DOI:10.1016/j.memsci.2007.07.020
, URL: http://www.sciencedirect.com/science/article/pii/S037673880700484X, ISSN: 0376-7388.
- Y. Tanaka, Water dissociation reaction generated in an ion exchange membrane, J. Membr. Sci., 2010, 350(1), 347–360, DOI:10.1016/j.memsci.2010.01.010
, URL: http://www.sciencedirect.com/science/article/pii/S0376738810000190, ISSN: 0376-7388.
- T. Luo, S. Abdu and M. Wessling, Selectivity of ion exchange membranes: A review, J. Membr. Sci., 2018, 555, 429–454, DOI:10.1016/j.memsci.2018.03.051
, URL: http://www.sciencedirect.com/science/article/pii/S0376738817335779, ISSN: 0376-7388.
- A. Alcaraz, P. Ramírez, J. Manzanares and S. Mafé, Conductive and Capacitive Properties of the Bipolar Membrane Junction Studied by AC Impedance Spectroscopy, J. Phys. Chem. B, 2001, 105, 11669, DOI:10.1021/jp011581x
.
- P. Ramírez, V. Aguilella, J. Manzanares and S. Mafé, Effects of temperature and ion transport on water splitting in bipolar membranes, J. Membr. Sci., 1992, 73(2), 191–201, DOI:10.1016/0376-7388(92)80129-8
, URL: http://www.sciencedirect.com/science/article/pii/0376738892801298, ISSN: 0376-7388.
- R. Pärnamäe, S. Mareev, V. Nikonenko, S. Melnikov, N. Sheldeshov, V. Zabolotskii, H. Hamelers and M. Tedesco, Bipolar membranes: A review on principles, latest developments, and applications, J. Membr. Sci., 2021, 617, 118538, DOI:10.1016/j.memsci.2020.118538
, URL: http://www.sciencedirect.com/science/article/pii/S0376738820311157, ISSN: 0376-7388.
- R. Wiebe and V. L. Gaddy, The Solubility of Carbon Dioxide in Water at Various Temperatures from 12 to 40° and at Pressures to 500 Atmospheres. Critical Phenomena, J. Am. Chem. Soc., 1940, 62(4), 815–817, DOI:10.1021/ja01861a033
.
- L. Diamond and N. Akinfiev, Solubility of CO2 in water from −1.5 to 100 °C and from 0.1 to 100 MPa: Evaluation of literature data and thermodynamic modelling, Fluid Phase Equilib., 2003, 208, 265–290, DOI:10.1016/S0378-3812(03)00041-4
.
-
S. Hangx, Behaviour of the CO2-H2O system and preliminary mineralisation model and experiments, CATO Workpackage WP 4.1, 2005, pp. 1–43 Search PubMed
.
- M. Vandiver, B. Caire, J. Carver, K. Waldrop, M. Hibbs, J. Varcoe, A. Herring and M. Liberatore, Mechanical Characterization of Anion Exchange Membranes by Extensional Rheology under Controlled Hydration, J. Electrochem. Soc., 2014, 161, H677–H683, DOI:10.1149/2.0971410jes
.
- J. Peron,
et al., Properties of Nafion® NR-211 membranes for PEMFCs, J. Membr. Sci., 2010, 356(1), 44–51, DOI:10.1016/j.memsci.2010.03.025
, URL: http://www.sciencedirect.com/science/article/pii/S0376738810002437, ISSN: 0376-7388.
- H. Nagasawa, A. Yamasaki, A. Iizuka, K. Kumagai and Y. Yanagisawa, A New Recovery Process of Carbon Dioxide from Alkaline Carbonate Solution via Electrodialysis, AIChE J., 2009, 55, 3286–3293, DOI:10.1002/aic.11907
.
- A. Iizuka, K. Hashimoto, H. Nagasawa, K. Kumagai, Y. Yanagisawa and A. Yamasaki, Carbon dioxide recovery from carbonate solutions using bipolar membrane electrodialysis, Sep. Purif. Technol., 2012, 101, 49–59, DOI:10.1016/j.seppur.2012.09.016
.
- Y. Zhao, J. Wang, Z. Ji, J. Liu, X. Guo and J. Yuan, A novel technology of carbon dioxide adsorption and mineralization via seawater decalcification by bipolar membrane electrodialysis system with a crystallizer, Chem. Eng. J., 2020, 381, 122542, DOI:10.1016/j.cej.2019.122542
, URL: http://www.sciencedirect.com/science/article/pii/S138589471931945X, ISSN: 1385-8947.
- C. Jiang, S. Li, D. Zhang, Z. Yang, D. Yu, X. Chen, Y. Wang and T. Xu, Mathematical modelling and experimental investigation of CO2 absorber recovery using an electro-acidification method, Chem. Eng. J., 2019, 360, 654–664, DOI:10.1016/j.cej.2018.12.006
, URL: http://www.sciencedirect.com/science/article/pii/S1385894718324781, ISSN: 1385-8947.
- H. Li, Z. Tang, X. Xing, D. Guo, L. Cui and X.-z. Mao, Study of CO2 capture by seawater and its reinforcement, Energy, 2018, 164, 1135–1144, DOI:10.1016/j.energy.2018.09.066
, URL: http://www.sciencedirect.com/science/article/pii/S0360544218318309, ISSN: 0360-5442.
-
S. A. Rackley, 10-Mineral carbonation, Carbon Capture and Storage, ed. S. A. Rackley, Butterworth-Heinemann, Boston, 2nd edn, 2017, pp. 253–282 DOI:10.1016/B978-0-12-812041-5.00010-6, URL: http://www.sciencedirect.com/science/article/pii/B9780128120415000106, ISBN: 978-0-12-812041-5
.
-
T. Coffey, D. R. Hardy, G. E. Besenbruch, K. R. Schultz, L. C. Brown and J. P. Dahlburg, Hydrogen as a Fuel for DOD, Defense Horizons, 2003, p. 1 Search PubMed
.
- G. H. Rau, H. D. Willauer and Z. J. Ren, The global potential for converting renewable electricity to negative-CO2-emissions hydrogen, Nat. Clim. Change, 2018, 8(7), 621–625 CrossRef
.
- M. D. Eisaman, K. Parajuly, A. Tuganov, C. Eldershaw, N. Chang and K. A. Littau, CO2 extraction from seawater using bipolar membrane electrodialysis, Energy Environ. Sci., 2012, 5, 7346–7352, 10.1039/C2EE03393C
.
- M. L. Druckenmiller and M. M. Maroto-Valer, Carbon sequestration using brine of adjusted pH to form mineral carbonates, Fuel Process. Technol., 2005, 86(14–15), 1599–1614 CrossRef CAS
.
- W. Wang, M. Hu, Y. Zheng, P. Wang and C. Ma, CO2 Fixation in Ca2+-/Mg2+-Rich Aqueous Solutions through Enhanced Carbonate Precipitation, Ind. Eng. Chem. Res., 2011, 50(13), 8333–8339, DOI:10.1021/ie1025419
.
- D. Desai,
et al., Electrochemical Desalination of Seawater and Hypersaline Brines with Coupled Electricity Storage, ACS Energy Lett., 2018, 3(2), 375–379, DOI:10.1021/acsenergylett.407b01220
.
- M. D. Eisaman, J. L. Rivest, S. D. Karnitz, C.-F. de Lannoy, A. Jose, R. W. DeVaul and K. Hannun, Indirect ocean capture of atmospheric CO2: Part II. Understanding the cost of negative emissions, Int. J. Greenhouse Gas Control, 2018, 70, 254–261, DOI:10.1016/j.ijggc.2018.02.020
, URL: http://www.sciencedirect.com/science/article/pii/S175058361730436X, ISSN: 1750-5836.
- W. Omar, J. Chen and J. Ulrich, Application of seeded batch crystallization methods for reduction of the scaling tendency of seawater–A study of growth kinetics of calcium carbonate in seawater, Cryst. Res. Technol., 2009, 44(5), 469–476 CrossRef CAS
.
- A. Kirchofer, A. Brandt, S. Krevor, V. Prigiobbe and J. Wilcox, Impact of alkalinity sources on the life-cycle energy efficiency of mineral carbonation technologies, Energy Environ. Sci., 2012, 5, 8631–8641, 10.1039/C2EE22180B
.
- G. C. Ganzi, J. H. Wood and C. S. Griffin, Water purification and recycling using the CDI process, Environ. Prog., 1992, 11(1), 49–53, DOI:10.1002/ep.670110117
, URL: https://aiche.onlinelibrary.wiley.com/doi/abs/10.1002/ep.670110117.
-
R. Datta, Y. Lin, D. Burke and S.-P. Tsai, Electrodeionization substrate, and device for electrodeionization treatment, 2002 Search PubMed
.
-
Y. J. Lin, M. P. Henry and S. W. Snyder, Electronically and ionically conductive porous material and method for manufacture of resin wafers therefrom, 2011 Search PubMed
.
- S.-Y. Pan, S. W. Snyder, H.-W. Ma, Y. J. Lin and P.-C. Chiang, Development of a Resin Wafer Electrodeionization Process for Impaired Water Desalination with High Energy Efficiency and Productivity, ACS Sustainable Chem. Eng., 2017, 5(4), 2942–2948, DOI:10.1021/acssuschemeng.6b02455
.
-
I. N. Widiasa, P. D. Sutrisna and I. Wenten, Performance of a novel electrodeionization technique during citric acid recovery, 2004 Search PubMed
.
- L. Alvarado and A. Chen, Electrodeionization: Principles, Strategies and Applications, Electrochim. Acta, 2014, 132, 583–597, DOI:10.1016/j.electacta.2014.03.165
, ISSN: 0013-4686.
- M. Parvazinia, S. Garcia and M. Maroto-Valer, CO2 capture by ion exchange resins as amine functionalized adsorbents, Chem. Eng. J., 2018, 331, 335–342, DOI:10.1016/j.cej.2017.08.087
, URL: http://www.sciencedirect.com/science/article/pii/S1385894717314316, ISSN: 1385-8947.
- G. Zeng, J. Ye and M. Yan, Application of Electrodeionization Process for Bioproduct Recovery
and CO2 Capture and Storage, Curr. Org. Chem., 2016, 20, 1, DOI:10.2174/1385272820666160513153326
.
- J. Wang, S. Wang and M. Jin, A study of the electrodeionization process—high-purity water production with a RO/EDI system, Desalination, 2000, 132(1), 349–352, DOI:10.1016/S0011-9164(00)00171-5
, URL: http://www.sciencedirect.com/science/article/pii/S0011916400001715, ISSN: 0011-9164.
- K. H. Yeon, J. H. Seong, S. Rengaraj and S. H. Moon, Electrochemical Characterization of Ion-Exchange Resin Beds and Removal of Cobalt by Electrodeionization for High Purity Water Production, Sep. Sci. Technol., 2003, 38(2), 443–462, DOI:10.1081/SS-120016584
.
- Ö. Arar, Ü. Yüksel, N. Kabay and M. Yüksel, Various applications of electrodeionization (EDI) method for water treatment—A short review, Desalination, 2014, 342, 16–22, DOI:10.1016/j.desal.2014.01.028
, URL: http://www.sciencedirect.com/science/article/pii/S0011916414000745, ISSN: 0011-9164.
- R. N. Gurram, S. Datta, Y. J. Lin, S. W. Snyder and T. J. Menkhaus, Removal of enzymatic and fermentation inhibitory compounds from biomass slurries for enhanced biorefinery process efficiencies, Bioresour. Technol., 2011, 102(17), 7850–7859, DOI:10.1016/j.biortech.2011.05.043
, URL: http://www.sciencedirect.com/science/article/pii/S0960852411007036, ISSN: 0960-8524.
- W. R. Alesi and J. R. Kitchin, Evaluation of a Primary Amine-Functionalized Ion-Exchange Resin for CO2 Capture, Ind. Eng. Chem. Res., 2012, 51(19), 6907–6915, DOI:10.1021/ie300452c
.
- R. Veneman, N. Frigka, W. Zhao, Z. Li, S. Kersten and W. Brilman, Adsorption of H2O and CO2 on supported amine sorbents, Int. J. Greenhouse Gas Control, 2015, 41, 268–275, DOI:10.1016/j.ijggc.2015.07.014
, URL: http://www.sciencedirect.com/science/article/pii/S1750583615300219, ISSN: 1750-5836.
-
K. Afrasiabi, Wafer Enhanced Electrodeionization for Conversion of CO2 into Bicarbonate Feed for Algae Cultured Photobioreactors, 2018 Search PubMed
.
- H. Xie, Y. Wu, T. Liu, F. Wang, B. Chen and B. Liang, Low-energy-consumption electrochemical CO2 capture driven by biomimetic phenazine derivatives redox medium, Appl. Energy, 2020, 259, 114119, DOI:10.1016/j.apenergy.2019.114119
, URL: http://www.sciencedirect.com/science/article/pii/S0306261919318069, ISSN: 0306-2619.
- J. D. Watkins, N. S. Siefert, X. Zhou, C. R. Myers, J. R. Kitchin, D. P. Hopkinson and H. B. Nulwala, Redox-Mediated Separation of Carbon Dioxide from Flue Gas, Energy Fuels, 2015, 29(11), 7508–7515, DOI:10.1021/acs.energyfuels.5b01807
.
-
B. P. Sullivan, K. Krist and H. Guard, Electrochemical and electrocatalytic reactions of carbon dioxide, Elsevier, 2012 Search PubMed
.
- M. Robert, Proton-coupled electron transfer, Energy Environ. Sci., 2012, 5, 7695, 10.1039/C2EE90013K
.
- C. Costentin, Electrochemical Approach to the Mechanistic Study of Proton-Coupled Electron Transfer, Chem. Rev., 2008, 108(7), 2145–2179, DOI:10.1021/cr068065t
.
- C. Huang, C. Liu, K. Wu, H. Yue, S. Tang, H. Lu and B. Liang, CO2 Capture from Flue Gas Using an Electrochemically Reversible Hydroquinone/Quinone Solution, Energy Fuels, 2019, 33(4), 3380–3389, DOI:10.1021/acs.energyfuels.8b04419
.
- P. Scovazzo, J. Poshusta, D. DuBois, C. Koval and R. Noble, Electrochemical Separation and Concentration of 1% Carbon Dioxide from Nitrogen, J. Electrochem. Soc., 2003, 150(5), D91, DOI:10.1149/1.1566962
.
- H. Ishida, T. Ohba, T. Yamaguchi and K. Ohkubo, Interaction between CO2 and Electrochemically Reduced Species of N-propyl-4,4-bipyridinium Cation, Chem. Lett., 1994, 23(5), 905–908, DOI:10.1246/cl.1994.905
.
- R. Ranjan, J. Olson, P. Singh, E. D. Lorance, D. A. Buttry and I. R. Gould, Reversible electrochemical trapping of carbon dioxide using 4,4-bipyridine that does not require thermal activation, J. Phys. Chem. Lett., 2015, 6(24), 4943–4946 CrossRef CAS
.
- B. Gurkan, F. Simeon and T. A. Hatton, Quinone Reduction in Ionic Liquids for Electrochemical CO2 Separation, ACS Sustainable Chem. Eng., 2015, 3(7), 1394–1405, DOI:10.1021/acssuschemeng.5b00116
.
- D. H. Apaydin, E. D. Głowacki, E. Portenkirchner and N. S. Sariciftci, Direct Electrochemical Capture and Release of Carbon Dioxide Using an Industrial Organic Pigment: Quinacridone, Angew. Chem., Int. Ed., 2014, 53(26), 6819–6822, DOI:10.1002/anie.201403618
.
- M. Mizen and M. Wrighton, Reductive Addition of CO2 to 9,10-Phenanthrenequinone, J. Electrochem. Soc., 1989, 136, 941 CrossRef CAS
, URL: http://jes.ecsdl.org/content/136/4/941.abstract.
- Y. Liu, H.-Z. Ye, K. Diederichsen, T. Voorhis and T. Hatton, Electrochemically mediated carbon dioxide separation with quinone chemistry in salt-concentrated aqueous media, Nat. Commun., 2020, 11, 2278, DOI:10.1038/s41467-020-16150-7
.
- G. P. Moss, P. A. S. Smith and D. Tavernier, Glossary of class names of organic compounds and reactivity intermediates based on structure (IUPAC Recommendations 1995), Pure Appl. Chem., 1995, 67(8–9), 1307–1375 Search PubMed
, URL: https://www.degruyter.com/view/journals/pac/67/8-9/article-p1307.xml.
- P. S. Guin, S. Das and P. C. Mandal, Electrochemical Reduction of Quinones in Different Media: A Review, Int. J. Electrochem., 2011, 2011, 816202, DOI:10.4061/2011/816202
.
- L. F. Fieser, The Tautomerism of Hydroxy Quinones, J. Am. Chem. Soc., 1928, 50(2), 439–465, DOI:10.1021/ja01389a033
.
- E. Laviron, Electrochemical reactions with protonations at equilibrium: Part XII. The 2e, 2H+ homogeneous isotopic electron exchange reaction (nine-member square scheme), J. Electroanal. Chem. Interfacial Electrochem., 1984, 169(1), 29–46, DOI:10.1016/0022-0728(84)80071-6
, URL: http://www.sciencedirect.com/science/article/pii/0022072884800716.
- M. Quan, D. Sanchez, M. F. Wasylkiw and D. K. Smith, Voltammetry of Quinones in Unbuffered Aqueous Solution: Reassessing the Roles of Proton Transfer and Hydrogen Bonding in the Aqueous Electrochemistry of Quinones, J. Am. Chem. Soc., 2007, 129(42), 12847–12856, DOI:10.1021/ja0743083
.
- D. R. Weinberg,
et al., Proton-Coupled Electron Transfer, Chem. Rev., 2012, 112(7), 4016–4093, DOI:10.1021/cr200177j
.
- B. Trumpower, The protonmotive Q cycle. Energy transduction by coupling of proton translocation to electron transfer by the cytochrome bc1 complex, J. Biol. Chem., 1990, 265(20), 11409–11412 CrossRef CAS
.
- Y. Lei, B. Song, R. D. van der Weijden, M. Saakes and C. J. N. Buisman, Electrochemical Induced Calcium Phosphate Precipitation: Importance of Local pH, Environ. Sci. Technol., 2017, 51(19), 11156–11164, DOI:10.1021/acs.est.7b03909
, PMID: 28872838.
- L. Legrand, Q. Shu, M. Tedesco, J. Dykstra and H. Hamelers, Role of ion exchange membranes and capacitive electrodes in membrane capacitive deionization (MCDI) for CO2 capture, J. Colloid Interface Sci., 2020, 564, 478–490, DOI:10.1016/j.jcis.2019.12.039
, URL: http://www.sciencedirect.com/science/article/pii/S0021979719314985, ISSN: 0021-9797.
- W. Xing,
et al., Versatile applications of capacitive deionization (CDI)-based technologies, Desalination, 2020, 482, 114390, DOI:10.1016/j.desal.2020.114390
, URL: http://www.sciencedirect.com/science/article/pii/S0011916419322519, ISSN: 0011-9164.
- D. Vermaas, M. Saakes and K. Nijmeijer, Capacitive Electrodes for Energy Generation by Reverse Electrodialysis, Procedia Eng., 2012, 44, 496–497, DOI:10.1016/j.proeng.2012.08.463
, URL: http://www.sciencedirect.com/science/article/pii/S1877705812034753, ISSN: 1877-7058.
- Z.-H. Huang, Z. Yang, F. Kang and M. Inagaki, Carbon electrodes for capacitive deionization, J. Mater. Chem. A, 2017, 5, 470–496, 10.1039/C6TA06733F
.
- P. Ratajczak, M. E. Suss, F. Kaasik and F. Béguin, Carbon electrodes for capacitive technologies, Energy Storage Mater., 2019, 16, 126–145, DOI:10.1016/j.ensm.2018.04.031
, URL: http://www.sciencedirect.com/science/article/pii/S2405829717307171, ISSN: 2405-8297.
- K. Singh, Z. Qian, P. Biesheuvel, H. Zuilhof, S. Porada and L. C. Smet, Nickel hexacyanoferrate electrodes for high mono/divalent ion-selectivity in capacitive deionization, Desalination, 2020, 481, 114346, DOI:10.1016/j.desal.2020.114346
, URL: http://www.sciencedirect.com/science/article/pii/S0011916419321538, ISSN: 0011-9164.
- P. Biesheuvel, R. Zhao, S. Porada and A. van der Wal, Theory of membrane capacitive deionization including the effect of the electrode pore space, J. Colloid Interface Sci., 2011, 360(1), 239–248, DOI:10.1016/j.jcis.2011.04.049
, URL: http://www.sciencedirect.com/science/article/pii/S0021979711004796, ISSN: 0021-9797.
- R. Zhao, P. M. Biesheuvel and A. van der Wal, Energy consumption and constant current operation in membrane capacitive deionization, Energy Environ. Sci., 2012, 5, 9520–9527, 10.1039/C2EE21737F
.
- P. Długołęcki and A. van der Wal, Energy Recovery in Membrane Capacitive Deionization, Environ. Sci. Technol., 2013, 47(9), 4904–4910, DOI:10.1021/es3053202
, PMID: 23477563.
- S. Porada, R. Zhao, A. van der Wal, V. Presser and P. Biesheuvel, Review on the science and technology of water desalination by capacitive deionization, Prog. Mater. Sci., 2013, 58(8), 1388–1442, DOI:10.1016/j.pmatsci.2013.03.005
, URL: http://www.sciencedirect.com/science/article/pii/S0079642513000340, ISSN: 0079-6425.
- A. Ullah, M. W. Saleem and W.-S. Kim, Performance and energy cost evaluation of an integrated NH3-based CO2 capture-capacitive deionization process, Int. J. Greenhouse Gas Control, 2017, 66, 85–96, DOI:10.1016/j.ijggc.2017.09.013
, URL: http://www.sciencedirect.com/science/article/pii/S1750583617303699, ISSN: 1750-5836.
- M. Rahimi, G. Catalini, S. Hariharan, M. Wang, M. Puccini and T. A. Hatton, Carbon Dioxide Capture Using an Electrochemically Driven Proton Concentration Process, Cell. Rep. Phys. Sci., 2020, 100033, DOI:10.1016/j.xcrp.2020.100033
, URL: http://www.sciencedirect.com/science/article/pii/S2666386420300230, ISSN: 2666-3864.
- J. Winnick, H. Toghiani and P. Quattrone, Carbon dioxide concentration for manned spacecraft using a molten carbonate electrochemical cell, AIChE J., 1982, 28(1), 103–111 CrossRef CAS
.
- J. Rosen,
et al., Molten Carbonate Fuel Cell Performance for CO2 Capture from Natural Gas Combined Cycle Flue Gas, J. Electrochem. Soc., 2020, 167(6), 064505, DOI:10.1149/1945-7111/ab7a9f
.
- M. Spinelli, D. Bona, M. Gatti, E. Martelli, F. Viganò and S. Consonni, Assessing the potential of molten carbonate fuel cell-based schemes for carbon capture in natural gas-fired combined cycle power plants, J. Power Sources, 2020, 448, 227223, DOI:10.1016/j.jpowsour.2019.227223
, URL: http://www.sciencedirect.com/science/article/pii/S0378775319312169, ISSN: 0378-7753.
- P. Greppi, B. Bosio and E. Arato, Membranes and Molten Carbonate Fuel Cells to Capture CO2 and Increase Energy Production in Natural Gas Power Plants, Ind. Eng. Chem. Res., 2013, 52(26), 8755–8764, DOI:10.1021/ie302725a
.
- K. Sugiura, K. Takei, K. Tanimoto and Y. Miyazaki, The carbon dioxide concentrator by using MCFC, J. Power Sources, 2003, 118(1), 218–227, DOI:10.1016/S0378-7753(03)00084-3
, URL: http://www.sciencedirect.com/science/article/pii/S0378775303000843, ISSN: 0378-7753.
-
D. Shekhawat, D. R. Luebke and H. W. Pennline, A Review of Carbon Dioxide Selective Membranes: A Topical Report, 2003, DOI:10.2172/819990, URL: https://www.osti.gov/biblio/819990.
- Z. Rui, M. Anderson, Y. Lin and Y. Li, Modeling and analysis of carbon dioxide permeation through ceramic-carbonate dual-phase membranes, J. Membr. Sci., 2009, 345(1), 110–118, DOI:10.1016/j.memsci.2009.08.034
, URL: http://www.sciencedirect.com/science/article/pii/S0376738809006310, ISSN: 0376-7388.
- Z. Rui, H. Ji and Y. Lin, Modeling and analysis of ceramic–carbonate dual-phase membrane reactor for carbon dioxide reforming with methane, Int. J. Hydrogen Energy, 2011, 36(14), 8292–8300, DOI:10.1016/j.ijhydene.2011.02.110
, URL: http://www.sciencedirect.com/science/article/pii/S0360319911004678, ISSN: 0360-3199.
- H. Bae, J.-S. Park, S. Senthilkumar, S. M. Hwang and Y. Kim, Hybrid seawater desalination-carbon capture using modified seawater battery system, J. Power Sources, 2019, 410–411, 99–105, DOI:10.1016/j.jpowsour.2018.11.009
, URL: https://linkinghub.elsevier.com/retrieve/pii/S0378775318312382.
- A. Khurram, M. He and B. M. Gallant, Tailoring the Discharge Reaction in Li-CO2 Batteries through Incorporation of CO2 Capture Chemistry, Joule, 2018, 2(12), 2649–2666, DOI:10.1016/j.joule.2018.09.002
, URL: http://www.sciencedirect.com/science/article/pii/S2542435118304057, ISSN: 2542-4351.
- Y. Li, A. Khurram and B. M. Gallant, A High-Capacity Lithium–Gas Battery Based on Sulfur Fluoride Conversion, J. Phys. Chem. C, 2018, 122(13), 7128–7138, DOI:10.1021/acs.jpcc.8b00569
.
- H. Yin, X. Mao, D. Tang, W. Xiao, L. Xing, H. Zhu, D. Wang and D. R. Sadoway, Capture and electrochemical conversion of CO2 to value-added carbon and oxygen by molten salt electrolysis, Energy Environ. Sci., 2013, 6, 1538–1545, 10.1039/C3EE24132G
.
- N. Hollingsworth, S. F. R. Taylor, M. T. Galante, J. Jacquemin, C. Longo, K. B. Holt, N. H. de Leeuw and C. Hardacre, CO2 capture and electrochemical conversion using superbasic [P66614][124Triz], Faraday Discuss., 2015, 183, 389–400, 10.1039/C5FD00091B
.
- S. Kar, A. Goeppert and G. K. S. Prakash, Integrated CO2 Capture and Conversion to Formate and Methanol: Connecting Two Threads, Acc. Chem. Res., 2019, 52(10), 2892–2903, DOI:10.1021/acs.accounts.9b00324
, PMID: 31487145.
-
P. Zhang, J. Tong and K. Huang, Electrochemical CO2 Capture and Conversion, Materials and Processes for CO2 Capture, Conversion, and Sequestration, John Wiley Sons, Ltd, 2018, ch. 5, pp. 213–266 DOI:10.1002/9781119231059.ch5, URL: https://onlinelibrary.wiley.com/doi/abs/10.1002/9781119231059.ch5, ISBN: 9781119231059
.
- N. Li, X. Chen, W.-J. Ong, D. R. MacFarlane, X. Zhao, A. K. Cheetham and C. Sun, Understanding of Electrochemical Mechanisms for CO2 Capture and Conversion into Hydrocarbon Fuels in Transition-Metal Carbides (MXenes), ACS Nano, 2017, 11(11), 10825–10833, DOI:10.1021/acsnano.7b03738
, PMID: 28892617.
- J. Choi, H. Cho, S. Yun, M.-G. Jang, S.-Y. Oh, M. Binns and J.-K. Kim, Process design and optimization of MEA-based CO2 capture processes for non-power industries, Energy, 2019, 185, 971–980, DOI:10.1016/j.energy.2019.07.092
, URL: http://www.sciencedirect.com/science/article/pii/S0360544219314331, ISSN: 0360-5442.
- R. Notz, H. P. Mangalapally and H. Hasse, Post combustion CO2 capture by reactive absorption: Pilot plant description and results of systematic studies with MEA, Int. J. Greenhouse Gas Control, 2012, 6, 84–112 CrossRef CAS
.
- T. Yokoyama, Analysis of reboiler heat duty in MEA process for CO2 capture using equilibrium-staged model, Sep. Purif. Technol., 2012, 94, 97–103, DOI:10.1016/j.seppur.2011.12.029
, URL: http://www.sciencedirect.com/science/article/pii/S1383586611007398, ISSN: 1383-5866.
- W. Zhang, H. Liu, Y. Sun, J. Cakstins, C. Sun and C. E. Snape, Parametric study on the regeneration heat requirement of an amine-based solid adsorbent process for post-combustion carbon capture, Appl.
Energy, 2016, 168, 394–405, DOI:10.1016/j.apenergy.2016.01.049
, URL: http://www.sciencedirect.com/science/article/pii/S0306261916300290, ISSN: 0306-2619.
- H. P. Mangalapally, R. Notz, S. Hoch, N. Asprion, G. Sieder, H. Garcia and H. Hasse, Pilot plant experimental studies of post combustion CO2 capture by reactive absorption with MEA and new solvents, Energy Procedia, 2009, 1(1), 963–970 CrossRef CAS
.
- S.-Y. Oh, M. Binns, H. Cho and J.-K. Kim, Energy minimization of MEA-based CO2 capture process, Appl. Energy, 2016, 169, 353–362, DOI:10.1016/j.apenergy.2016.02.046
, URL: http://www.sciencedirect.com/science/article/pii/S0306261916301696, ISSN: 0306-2619.
- M. R. Abu-Zahra, L. H. Schneiders, J. P. Niederer, P. H. Feron and G. F. Versteeg, CO2 capture from power plants: Part I. A parametric study of the technical performance based on monoethanolamine, Int. J. Greenhouse Gas Control, 2007, 1(1), 37–46 CrossRef CAS
.
-
J. Thomas and W. Echt, The evolution of performance solvents for gas treating, Petroenergy Conference, 1989, vol. 24.
- M. Clausse, J. Merel and F. Meunier, Numerical parametric study on CO2 capture by indirect thermal swing adsorption, Int. J. Greenhouse Gas Control, 2011, 5(5), 1206–1213 CrossRef CAS
.
- J. K. Stolaroff, D. W. Keith and G. V. Lowry, Carbon Dioxide Capture from Atmospheric Air Using Sodium Hydroxide Spray, Environ. Sci. Technol., 2008, 42(8), 2728–2735, DOI:10.1021/es702607w
.
- H. D. Willauer, F. Dimascio, D. R. Hardy, M. K. Lewis and F. W. Williams, Development of an electrochemical acidification cell for the recovery of CO2 and H2 from seawater, Ind. Eng. Chem. Res., 2011, 50(17), 9876–9882, DOI:10.1021/ie2008136
, ISSN: 08885885.
-
E. ToolBox, Heat of combustion [online], https://www.engineeringtoolbox.com/standard-heatof-combustion-energy-content-d_1987.html, 2017.
- C. C. L. McCrory, S. Jung, I. M. Ferrer, S. M. Chatman, J. C. Peters and T. F. Jaramillo, Benchmarking Hydrogen Evolving Reaction and Oxygen Evolving Reaction Electrocatalysts for Solar Water Splitting Devices, J. Am. Chem. Soc., 2015, 137(13), 4347–4357, DOI:10.1021/ja510442p
, PMID: 25668483.
- S. Z. Oener, M. J. Foster and S. W. Boettcher, Accelerating water dissociation in bipolar membranes and for electrocatalysis, Science, 2020, 369(6507), 1099–1103, DOI:10.1126/science.aaz1487
, URL: https://science.sciencemag.org/content/369/6507/1099, ISSN: 0036-8075.
- M. L. Jordan, L. Valentino, N. Nazyrynbekova, V. M. Palakkal, S. Kole, D. Bhattacharya, Y. J. Lin and C. G. Arges, Promoting water-splitting in Janus bipolar ion-exchange resin wafers for electrodeionization, Mol. Syst. Des. Eng., 2020, 5, 922–935, 10.1039/C9ME00179D
.
- M. D. Eisaman, Negative Emissions Technologies: The Tradeoffs of Air-Capture Economics, Joule, 2020, 4(3), 516–520, DOI:10.1016/j.joule.2020.02.007
, URL: http://www.sciencedirect.com/science/article/pii/S2542435120300854, ISSN: 2542-4351.
- M. L. Jordan, L. Valentino, N. Nazyrynbekova, V. M. Palakkal, S. Kole, D. Bhattacharya, Y. J. Lin and C. G. Arges, Promoting water-splitting in Janus bipolar ion-exchange resin wafers for electrodeionization, Mol. Syst. Des. Eng., 2020, 5(5), 922–935, 10.1039/C9ME00179D
, URL: http://dx.doi.org/10.1039/C9ME00179D.
- J. G. J. Olivier and J. A. H. W. Peters, Trends in global CO2 and total greenhouse gas emissions 2019 Report, PBL Netherlands Environmental Assessment Agency, 2020.
- G. Realmonte, L. Drouet, A. Gambhir, J. Glynn, A. Hawkes, A. C. Köberle and M. Tavoni, An inter-model assessment of the role of direct air capture in deep mitigation pathways, Nat. Commun., 2019, 10(1), 1–12 CrossRef
.
- C. Beuttler, L. Charles and J. Wurzbacher, The Role of Direct Air Capture in Mitigation of Anthropogenic Greenhouse Gas Emissions, Front. Clim., 2019, 1, 10, DOI:10.3389/fclim.2019.00010
, URL: https://www.frontiersin.org/article/10.3389/fclim.2019.00010, ISSN: 2624-9553.
- G. Reiter and J. Lindorfer, Evaluating CO2 sources for power-to-gas applications–A case study for Austria, J. CO2 Util., 2015, 10, 40–49 CrossRef CAS
.
- E. I. Koytsoumpa, C. Bergins and E. Kakaras, The CO2 economy: Review of CO2 capture and reuse technologies, J. Supercrit. Fluids, 2018, 132, 3–16, DOI:10.1016/j.supflu.2017.07.029
, URL: http://www.sciencedirect.com/science/article/pii/S0896844617300694, ISSN:0896- 8446.
- K. S. Lackner, The thermodynamics of direct air capture of carbon dioxide, Energy, 2013, 50, 38–46 CrossRef CAS
.
-
I. Paris, The role of CCUS in low-carbon power systems, 2020, URL: https://www.iea.org/reports/the-role-of-ccus-in-low-carbon-power-systems.
- C. Pritchard, A. Yang, P. Holmes and M. Wilkinson, Thermodynamics, economics and systems thinking: What role for air capture of CO2?, Process Saf. Environ. Prot., 2015, 94, 188–195, DOI:10.1016/j.psep.2014.06.011
, URL: http://www.sciencedirect.com/science/article/pii/S0957582014000913, ISSN: 0957-5820.
-
I. Paris, Direct Air Capture, 2020, https://www.iea.org/reports/direct-air-capture.
-
K. Heidel, D. Keith, A. Singh and G. Holmes, Process design and costing of an air-contactor for air-capture, Energy Procedia 4, 10th International Conference on Greenhouse Gas Control Technologies, 2011, pp. 2861–2868, DOI: http://10.1016/j.egypro.2011.02.192, URL: http://www.sciencedirect.com/science/article/pii/S1876610211003894, ISSN: 1876-6102.
- G. Thermostat and M. I. New, Global Thermostat, 2018.
-
J. Wurzbacher, Capturing CO2 from air, Internationaler Motorenkongress 2017, Springer, 2017, pp. 499–511 Search PubMed
.
- A. Kiani, K. Jiang and P. Feron, Techno-Economic Assessment for CO2 Capture From Air Using a Conventional Liquid-Based Absorption Process, Front. Energy Res., 2020, 8, 92, DOI:10.3389/fenrg.2020.00092
, URL: https://www.frontiersin.org/article/10.3389/fenrg.2020.00092, ISSN: 2296-598X.
- D. Moreira and J. C. Pires, Atmospheric CO2 capture by algae: negative carbon dioxide emission path, Bioresour. Technol., 2016, 215, 371–379 CrossRef CAS
.
- D. D.-W. Tsai, P. H. Chen and R. Ramaraj, The potential of carbon dioxide capture and sequestration with algae, Ecol. Eng., 2017, 98, 17–23 CrossRef
.
- M. K. Lam, K. T. Lee and A. R. Mohamed, Current status and challenges on microalgae-based carbon capture, Int. J. Greenhouse Gas Control, 2012, 10, 456–469 CrossRef CAS
.
- A. Ghorbani, H. R. Rahimpour, Y. Ghasemi, S. Zoughi and M. R. Rahimpour, A review of carbon capture and sequestration in Iran: microalgal biofixation potential in Iran, Renewable Sustainable Energy Rev., 2014, 35, 73–100 CrossRef CAS
.
- A. Ghosh and B. Kiran, Carbon concentration in algae: reducing CO2 from exhaust gas, Trends Biotechnol., 2017, 35(9), 806–808 CrossRef CAS
.
- W. Zhou,
et al., Bio-mitigation of carbon dioxide using microalgal systems: advances and perspectives, Renewable Sustainable Energy Rev., 2017, 76, 1163–1175 CrossRef CAS
.
- K. Zhou, S. Chaemchuen and F. Verpoort, Alternative materials in technologies for Biogas upgrading via CO2 capture, Renewable Sustainable Energy Rev., 2017, 79, 1414–1441 CrossRef CAS
.
- M. Waqas, A. Aburiazaiza, R. Miandad, M. Rehan, M. Barakat and A. Nizami, Development of biochar as fuel and catalyst in energy recovery technologies, J. Cleaner Prod., 2018, 188, 477–488 CrossRef CAS
.
- X.-f. Tan,
et al., Biochar-based nano-composites for the decontamination of wastewater: a review, Bioresour. Technol., 2016, 212, 318–333 CrossRef CAS
.
- N. A. Qambrani, M. M. Rahman, S. Won, S. Shim and C. Ra, Biochar properties and
eco-friendly applications for climate change mitigation, waste management, and wastewater treatment: A review, Renewable Sustainable Energy Rev., 2017, 79, 255–273 CrossRef CAS
.
- A. E. Creamer, B. Gao and S. Wang, Carbon dioxide capture using various metal oxyhydroxide–biochar composites, Chem. Eng. J., 2016, 283, 826–832 CrossRef CAS
.
- S. P. Galinato, J. K. Yoder and D. Granatstein, The economic value of biochar in crop production and carbon sequestration, Energy Policy, 2011, 39(10), 6344–6350 CrossRef
.
- S. Gupta, H. W. Kua and C. Y. Low, Use of biochar as carbon sequestering additive in cement mortar, Cem. Concr. Compos., 2018, 87, 110–129 CrossRef CAS
.
- P.-H. Huang, H.-H. Cheng and S.-H. Lin, Adsorption of carbon dioxide onto activated carbon prepared from coconut shells, J. Chem., 2015, 2015, 1–10, DOI:10.1155/2015/106590
.
- M. Asif, M. Suleman, I. Haq and S. A. Jamal, Post-combustion CO2 capture with chemical absorption and hybrid system: current status and challenges, Greenhouse Gases: Sci. Technol., 2018, 8(6), 998–1031, DOI:10.1002/ghg.1823
, URL: https://onlinelibrary.wiley.com/doi/abs/10.1002/ghg.1823.
- B. Dutcher, M. Fan and A. G. Russell, Amine-Based CO2 Capture Technology Development from the Beginning of 2013—A Review, ACS Appl. Mater. Interfaces, 2015, 7(4), 2137–2148, DOI:10.1021/am507465f
.
- M. Bui,
et al., Carbon capture and storage (CCS): the way forward, Energy Environ. Sci., 2018, 11(5), 1062–1176, 10.1039/C7EE02342A
.
- I. Sreedhar, T. Nahar, A. Venugopal and B. Srinivas, Carbon capture by absorption–path covered and ahead, Renewable Sustainable Energy Rev., 2017, 76, 1080–1107 CrossRef CAS
.
- J. T. Yeh, H. W. Pennline and K. P. Resnik, Study of CO2 Absorption and Desorption in a Packed Column, Energy Fuels, 2001, 15(2), 274–278, DOI:10.1021/ef0002389
.
- V. Nikulshina, D. Hirsch, M. Mazzotti and A. Steinfeld, CO2 capture from air and co-production of H2 via the Ca(OH)2–CaCO3 cycle using concentrated solar power–Thermodynamic analysis, Energy, 2006, 31(12), 1715–1725, DOI:10.1016/j.energy.2005.09.014
, URL: http://www.sciencedirect.com/science/article/pii/S0360544205001891, ISSN: 0360-5442.
- V. Nikulshina, M. Gálvez and A. Steinfeld, Kinetic analysis of the carbonation reactions for the capture of CO2 from air via the Ca(OH)2–CaCO3–CaO solar thermochemical cycle, Chem. Eng. J., 2007, 129(1), 75–83, DOI:10.1016/j.cej.2006.11.003
, URL: http://www.sciencedirect.com/science/article/pii/S1385894706004955, ISSN: 1385-8947.
- V. Nikulshina, N. Ayesa, M. Gálvez and A. Steinfeld, Feasibility of Na-based thermochemical cycles for the capture of CO2 from air—Thermodynamic and thermogravimetric analyses, Chem. Eng. J., 2008, 140(1), 62–70, DOI:10.1016/j.cej.2007.09.007
, URL: http://www.sciencedirect.com/science/article/pii/S1385894707006134, ISSN: 1385-8947.
- B. Feng, M. Du, T. J. Dennis, K. Anthony and M. J. Perumal, Reduction of Energy Requirement of CO2 Desorption by Adding Acid into CO2-Loaded Solvent, Energy Fuels, 2010, 24(1), 213–219, DOI:10.1021/ef900564x
.
- A. Samanta, A. Zhao, G. K. H. Shimizu, P. Sarkar and R. Gupta, Post-Combustion CO2 Capture Using Solid Sorbents: A Review, Ind. Eng. Chem. Res., 2012, 51(4), 1438–1463, DOI:10.1021/ie200686q
.
- Q. Cen, M. Fang, T. Wang, I. Majchrzak-Kucęba, D. Wawrzyńczak and Z. Luo, Thermodynamics and regeneration studies of CO2 adsorption on activated carbon, Greenhouse Gases: Sci. Technol., 2016, 6(6), 787–796, DOI:10.1002/ghg.1621
, URL: https://onlinelibrary.wiley.com/doi/abs/10.1002/ghg.1621.
- S. Choi, J. H. Drese and C. W. Jones, Adsorbent
Materials for Carbon Dioxide Capture from Large Anthropogenic Point Sources, ChemSusChem, 2009, 2(9), 796–854, DOI:10.1002/cssc.200900036
.
- P. Pandey and R. Chauhan, Membranes for gas separation, Prog. Polym. Sci., 2001, 26(6), 853–893, DOI:10.1016/S0079-6700(01)00009-0
, URL: http://www.sciencedirect.com/science/article/pii/S0079670001000090, ISSN: 0079-6700.
- P. Bernardo, E. Drioli and G. Golemme, Membrane Gas Separation: A Review/State of the Art, Ind. Eng. Chem. Res., 2009, 48(10), 4638–4663, DOI:10.1021/ie8019032
.
- T. C. Merkel, H. Lin, X. Wei and R. Baker, Power plant post-combustion carbon dioxide capture: An opportunity for membranes, J. Membr. Sci., 2010, 359(1), 126–139, DOI:10.1016/j.memsci.2009.10.041
, URL: http://www.sciencedirect.com/science/article/pii/S0376738809007832, ISSN: 0376-7388.
- T. C. Merkel, X. Wei, Z. He, L. S. White, J. G. Wijmans and R. W. Baker, Selective Exhaust Gas Recycle with Membranes for CO2 Capture from Natural Gas Combined Cycle Power Plants, Ind. Eng. Chem. Res., 2013, 52(3), 1150–1159, DOI:10.1021/ie302110z
.
- G. Russo, G. Prpich, E. J. Anthony, F. Montagnaro, N. Jurado, G. D. Lorenzo and H. G. Darabkhani, Selective-exhaust gas recirculation for CO2 capture using membrane technology, J. Membr. Sci., 2018, 549, 649–659, DOI:10.1016/j.memsci.2017.10.052
, URL: http://www.sciencedirect.com/science/article/pii/S0376738817308505, ISSN: 0376-7388.
- X. Feng and J. Ivory, Development of hollow fiber membrane systems for nitrogen generation from combustion exhaust gas: Part I. Effects of module configurations, J. Membr. Sci., 2000, 176(2), 197–207, DOI:10.1016/S0376-7388(00)00445-2
, URL: http://www.sciencedirect.com/science/article/pii/S0376738800004452, ISSN: 0376-7388.
- U. W. Siagian, A. Raksajati, N. F. Himma, K. Khoiruddin and I. Wenten, Membrane-based carbon capture technologies: Membrane gas separation vs. membrane contactor, J. Nat. Gas Sci. Eng., 2019, 67, 172–195, DOI:10.1016/j.jngse.2019.04.008
, URL: http://www.sciencedirect.com/science/article/pii/S1875510019301039, ISSN: 1875-5100.
- M. Anwar,
et al., CO2 capture and storage: A way forward for sustainable environment, J. Environ. Manage., 2018, 226, 131–144, DOI:10.1016/j.jenvman.2018.08.009
, URL: http://www.sciencedirect.com/science/article/pii/S0301479718308788, ISSN: 0301-4797.
- J. Blamey, E. Anthony, J. Wang and P. Fennell, The calcium looping cycle for large-scale CO2 capture, Prog. Energy Combust. Sci., 2010, 36(2), 260–279, DOI:10.1016/j.pecs.2009.10.001
, URL: http://www.sciencedirect.com/science/article/pii/S0360128509000574, ISSN: 0360-1285.
- M. Erans, V. Manovic and E. J. Anthony, Calcium looping sorbents for CO2 capture, Appl. Energy, 2016, 180, 722–742, DOI:10.1016/j.apenergy.2016.07.074
, URL: http://www.sciencedirect.com/science/article/pii/S0306261916310157, ISSN: 0306-2619.
- P. R. Jeon, J. Choi, T. S. Yun and C.-H. Lee, Sorption equilibrium and kinetics of CO2 on clay minerals from subcritical to supercritical conditions: CO2 sequestration at nanoscale interfaces, Chem. Eng. J., 2014, 255, 705–715, DOI:10.1016/j.cej.2014.06.090
, URL: http://www.sciencedirect.com/science/article/pii/S1385894714008390.
- A. A. Olajire, A review of mineral carbonation technology in sequestration of CO2, J. Pet. Sci. Eng., 2013, 109, 364–392, DOI:10.1016/j.petrol.2013.03.013
, URL: http://www.sciencedirect.com/science/article/pii/S0920410513000673.
- A.-H. A. Park and L.-S. Fan, CO2 mineral sequestration: physically activated dissolution of serpentine and pH swing process, Chem. Eng. Sci., 2004, 59(22), 5241–5247, DOI:10.1016/j.ces.2004.09.008
, URL: http://www.sciencedirect.com/science/article/pii/S0009250904006773, ISSN: 0009-2509.
- S. Kodama, T. Nishimoto, N. Yamamoto, K. Yogo and K. Yamada, Development of a new pH-swing CO2 mineralization process with a recyclable reaction solution, Energy, 2008, 33(5), 776–784, DOI:10.1016/j.energy.2008.01.005
, URL: http://www.sciencedirect.com/science/article/pii/S0360544208000273, ISSN: 0360-5442.
- S. Eloneva, A. Said, C.-J. Fogelholm and R. Zevenhoven, Preliminary assessment of a method utilizing carbon dioxide and steelmaking slags to produce precipitated calcium carbonate, Appl. Energy, 2012, 90(1), 329–334, DOI:10.1016/j.apenergy.2011.05.045
, URL: http://www.sciencedirect.com/science/article/pii/S0306261911003400, ISSN: 0306-2619.
- A. Sanna, M. Dri and M. Maroto-Valer, Carbon dioxide capture and storage by pH swing aqueous mineralisation using a mixture of ammonium salts and antigorite source, Fuel, 2013, 114, 153–161, DOI:10.1016/j.fuel.2012.08.014
, URL: http://www.sciencedirect.com/science/article/pii/S0016236112006503, ISSN: 0016-2361.
- A. Azdarpour, M. Asadullah, E. Mohammadian, H. Hamidi, R. Junin and M. A. Karaei, A review on carbon dioxide mineral carbonation through pH-swing process, Chem. Eng. J., 2015, 279, 615–630, DOI:10.1016/j.cej.2015.05.064
, URL: http://www.sciencedirect.com/science/article/pii/S1385894715007408, ISSN: 1385-8947.
- V. Prigiobbe, M. Hänchen, M. Werner, R. Baciocchi and M. Mazzotti, Mineral carbonation process for CO2 sequestration, Energy Procedia, 2009, 1(1), 4885–4890, DOI:10.1016/j.egypro.2009.02.318
, URL: http://www.sciencedirect.com/science/article/pii/S1876610209009618, ISSN: 1876-6102.
- S. J. Gerdemann, W. K. O’Connor, D. C. Dahlin, L. R. Penner and H. Rush,
Ex Situ Aqueous Mineral Carbonation, Environ. Sci. Technol., 2007, 41(7), 2587–2593, DOI:10.1021/es0619253
.
- A. Azdarpour, M. Asadullah, E. Mohammadian, R. Junin, H. Hamidi, M. Manan and A. R. M. Daud, Mineral carbonation of red gypsum via pH-swing process: Effect of CO2 pressure on the efficiency and products characteristics, Chem. Eng. J., 2015, 264, 425–436, DOI:10.1016/j.cej.2014.11.125
, URL: http://www.sciencedirect.com/science/article/pii/S1385894714015939, ISSN: 1385-8947.
- G. L. A. Ferrufino, S. Okamoto, J. C. Santos, J. A. Carvalho, I. Avila, C. M. Luna and T. S. Neto, CO2 sequestration by pH-swing mineral carbonation based on HCl/NH4OH system using iron-rich lizardite 1T, J. CO2 Util., 2018, 24, 164–173, DOI:10.1016/j.jcou.2018.01.001
, URL: http://www.sciencedirect.com/science/article/pii/S221298201730272X, ISSN: 2212-9820.
- R. Stanger,
et al., Oxyfuel combustion for CO2 capture in power plants, Int. J. Greenhouse Gas Control, 2015, 40, 55–125, DOI:10.1016/j.ijggc.2015.06.010
, URL: http://www.sciencedirect.com/science/article/pii/S1750583615002637, ISSN: 1750-5836.
- G. Scheffknecht, L. Al-Makhadmeh, U. Schnell and J. Maier, Oxy-fuel coal combustion—A review of the current state-of-the-art, Int. J. Greenhouse Gas Control, 2011, 5, S16–S35, DOI:10.1016/j.ijggc.2011.05.020
, URL: http://www.sciencedirect.com/science/article/pii/S1750583611000806, ISSN: 1750-5836.
-
L. Zheng, 1-Overview of oxy-fuel combustion technology for carbon dioxide (CO2) capture, in Oxy-Fuel Combustion for Power Generation and Carbon Dioxide (CO2) Capture, ed. L. Zheng, Woodhead Publishing Series in Energy, Woodhead Publishing, 2011, pp. 1–13 DOI:10.1533/9780857090980.1, URL: http://www.sciencedirect.com/science/article/pii/B9781845696719500016, ISBN: 978-1-84569-671-9
.
-
B. Metz, O. Davidson, H. De Coninck, M. Loos and L. Meyer, IPCC special report on carbon dioxide capture and storage, Tech. Rep., Intergovernmental Panel on Climate Change, Geneva (Switzerland), 2005.
- C. F. Song, Y. Kitamura and S. H. Li, Evaluation of Stirling cooler system for cryogenic CO2 capture, Appl. Energy, 2012, 98, 491–501 CrossRef CAS
.
- T. F. Wall, Combustion processes for carbon capture, Proc. Combust. Inst., 2007, 31(1), 31–47 CrossRef
.
-
R. Pardemann and B. Meyer, Pre-Combustion Carbon Capture, Handbook of Clean Energy Systems, American Cancer Society, 2015 DOI:10.1002/9781118991978.hces061, URL: https://onlinelibrary.wiley.com/doi/abs/10.1002/9781118991978.hces061, ISBN: 9781118991978
.
- O. d. Q. F. Araújo and J. L. de Medeiros, Carbon capture and storage technologies: present scenario and drivers of innovation, Curr. Opin. Chem. Eng., 2017, 17, 22–34 CrossRef
.
- A. C. Yeh and H. Bai, Comparison of ammonia and monoethanolamine solvents to reduce CO2 greenhouse gas emissions, Sci. Total Environ., 1999, 228(2), 121–133, DOI:10.1016/S0048-9697(99)00025-X
, URL: http://www.sciencedirect.com/science/article/pii/S004896979900025X, ISSN: 0048-9697.
-
G. Rochelle, 3-Conventional amine scrubbing for CO2 capture, in Absorption-Based Post-combustion Capture of Carbon Dioxide, ed. P. H. Feron, Woodhead Publishing, 2016, pp. 35–67 DOI:10.1016/B978-0-08-100514-9.00003-2, URL: http://www.sciencedirect.com/science/article/pii/B9780081005149000032, ISBN: 978-0-08-100514-9
.
- M. T. Ho, G. W. Allinson and D. E. Wiley, Reducing the Cost of CO2 Capture from Flue Gases Using Membrane Technology, Ind. Eng. Chem. Res., 2008, 47(5), 1562–1568, DOI:10.1021/ie070541y
, URL: https://doi.org/10.1021/ie070541y.
- C. E. Powell and G. G. Qiao, Polymeric CO2/N2 gas separation membranes for the capture of carbon dioxide from power plant flue gases, J. Membr. Sci., 2006, 279(1), 1–49, DOI:10.1016/j.memsci.2005.12.062
, URL: http://www.sciencedirect.com/science/article/pii/S0376738806000068, ISSN: 0376-7388.
- Y. Peng, Y. Li, Y. Ban and W. Yang, Two-Dimensional Metal–Organic Framework Nanosheets for Membrane-Based Gas Separation, Angew. Chem., Int. Ed., 2017, 56(33), 9757–9761, DOI:10.1002/anie.201703959
.
- X. Zou and G. Zhu, Microporous Organic Materials for Membrane-Based Gas Separation, Adv. Mater., 2018, 30(3), 1700750, DOI:10.1002/adma.201700750
.
- J. Wang, J. Luo, S. Feng, H. Li, Y. Wan and X. Zhang, Recent development of ionic liquid membranes, Green Energy Environ., 2016, 1(1), 43–61, DOI:10.1016/j.gee.2016.05.002
, URL: http://www.sciencedirect.com/science/article/pii/S246802571630022X, ISSN: 2468-0257.
- A. Perejón, L. M. Romeo, Y. Lara, P. Lisbona, A. Martínez and J. M. Valverde, The Calcium-Looping technology for CO2 capture: On the important roles of energy integration and sorbent behavior, Appl. Energy, 2016, 162, 787–807, DOI:10.1016/j.apenergy.2015.10.121
, URL: http://www.sciencedirect.com/science/article/pii/S0306261915013616, ISSN: 0306-2619.
- C. Verma and E. E. Ebenso, Ionic liquid-mediated functionalization of graphene-based materials for versatile applications: a review, Graphene Technol., 2019, 4(1–2), 1–15 Search PubMed
.
- G. T. Rochelle, Amine Scrubbing for CO2 Capture, Science, 2009, 325(5948), 1652–1654, DOI:10.1126/science.1176731
, URL: http://science.sciencemag.org/content/325/5948/1652, ISSN: 0036-8075.
- S. Kim, H. Shi and J. Y. Lee, CO2 absorption mechanism in amine solvents and enhancement of CO2 capture capability in blended amine solvent, Int. J. Greenhouse Gas Control, 2016, 45, 181–188, DOI:10.1016/j.ijggc.2015.12.024
, URL: http://www.sciencedirect.com/science/article/pii/S1750583615301675, ISSN: 1750-5836.
- G. Sartori and D. W. Savage, Sterically hindered amines for carbon dioxide removal from gases, Ind. Eng. Chem. Fundam., 1983, 22(2), 239–249, DOI:10.1021/i100010a016
.
- A. Dibenedetto, M. Aresta, C. Fragale and M. Narracci, Reaction of silylalkylmono- and silylalkyldiamines with carbon dioxide: evidence of formation of inter- and intra-molecular ammonium carbamates and their conversion into organic carbamates of industrial interest under carbon dioxide catalysis, Green Chem., 2002, 4, 439–443, 10.1039/B205319P
.
- G. Puxty, R. Rowland, A. Allport, Q. Yang, M. Bown, R. Burns, M. Maeder and M. Attalla, Carbon Dioxide Postcombustion Capture: A Novel Screening Study of the Carbon Dioxide Absorption Performance of 76 Amines, Environ. Sci. Technol., 2009, 43(16), 6427–6433, DOI:10.1021/es901376a
.
- H. Ahn, M. Luberti, Z. Liu and S. Brandani, Process configuration studies of the amine capture process for coal-fired power plants, Int. J. Greenhouse Gas Control, 2013, 16, 29–40, DOI:10.1016/j.ijggc.2013.03.002
, URL: http://www.sciencedirect.com/science/article/pii/S1750583613001229, ISSN: 1750-5836.
- R. R. Wanderley, D. D. Pinto and H. K. Knuutila, Investigating opportunities for water–lean solvents in CO2 capture: VLE and heat of absorption in water–lean solvents containing MEA, Sep. Purif. Technol., 2020, 231, 115883, DOI:10.1016/j.seppur.2019.115883
, URL: http://www.sciencedirect.com/science/article/pii/S1383586619327583, ISSN: 1383-5866.
- H. Karunarathne, D. Eimer and L. Øi, Physical Properties of MEA + Water + CO2 Mixtures in Postcombustion CO2 Capture: A Review of Correlations and Experimental Studies, J. Eng., 2020, 2020, 1–17, DOI:10.1155/2020/7051368
.
- P. Luis, Use of monoethanolamine (MEA) for CO2 capture in a global scenario: Consequences and alternatives, Desalination, 2016, 380, 93–99, DOI:10.1016/j.desal.2015.08.004
, URL: http://www.sciencedirect.com/science/article/pii/S001191641500418X, ISSN: 0011-9164.
- K. Li, A. Cousins, H. Yu, P. Feron, M. Tade, W. Luo and J. Chen, Systematic study of aqueous monoethanolamine based CO2 capture process: model development and process improvement, Energy Sci. Eng., 2016, 4(1), 23–39, DOI:10.1002/ese3.101
.
- I. M. Bernhardsen and H. K. Knuutila, A review of potential amine solvents for CO2 absorption process: Absorption capacity, cyclic capacity and pKa, Int. J. Greenhouse Gas Control, 2017, 61, 27–48 CrossRef CAS
.
- S. Singto, T. Supap, R. Idem, P. Tontiwachwuthikul and S. Tantayanon, The effect of chemical structure of newly synthesized tertiary amines used for the post combustion capture process on carbon dioxide (CO2): Kinetics of CO2 absorption using the stopped-flow apparatus and regeneration, and heat input of CO2 regeneration, Energy Procedia, 2017, 114, 852–859 CrossRef CAS
.
- M. K. Mondal, H. K. Balsora and P. Varshney, Progress and trends in CO2 capture/separation technologies: a review, Energy, 2012, 46(1), 431–441 CrossRef CAS
.
- C. Han, K. Graves, J. Neathery and K. Liu, Simulation of the Energy Consumption of CO2 Capture by Aqueous Monoethanolamine in Pilot Plant, Energy Environ. Res., 2011, 1(1), 67 Search PubMed
.
- F. A. Chowdhury, H. Yamada, T. Higashii, K. Goto and M. Onoda, CO2 Capture by Tertiary Amine Absorbents: A Performance Comparison Study, Ind. Eng. Chem. Res., 2013, 52(24), 8323–8331, DOI:10.1021/ie400825u
.
- M. Mahmoudkhani and D. W. Keith, Low-energy sodium hydroxide recovery for CO2 capture from atmospheric air—Thermodynamic analysis, Int. J. Greenhouse Gas Control, 2009, 3(4), 376–384, DOI:10.1016/j.ijggc.2009.02.003
, URL: http://www.sciencedirect.com/science/article/pii/S1750583609000176, ISSN: 1750-5836.
- F. Zeman, Energy and Material Balance of CO2 Capture from Ambient Air, Environ. Sci. Technol., 2007, 41(21), 7558–7563, DOI:10.1021/es070874m
.
-
Y. Tanaka, 17-Bipolar Membrane Electrodialysis, in Ion Exchange Membranes, ed. Y. Tanaka, Elsevier, Amsterdam, 2nd edn, 2015, pp. 369–392 DOI:10.1016/B978-0-444-63319-4.00017-1, URL: http://www.sciencedirect.com/science/article/pii/B9780444633194000171, ISBN: 978-0-444-63319-4
.
- E. D. Bates, R. D. Mayton, I. Ntai and J. H. Davis, CO2 Capture by a Task-Specific Ionic Liquid, J. Am. Chem. Soc., 2002, 124(6), 926–927, DOI:10.1021/ja017593d
, PMID: 11829599.
- M. Ramdin, T. W. de Loos and T. J. Vlugt, State-of-the-Art of CO2 Capture with Ionic Liquids, Ind. Eng. Chem. Res., 2012, 51(24), 8149–8177, DOI:10.1021/ie3003705
.
- K. Huang, F.-F. Chen, D.-J. Tao and S. Dai, Ionic liquid–formulated hybrid solvents for CO2 capture, Curr. Opin. Green Sustainable Chem., 2017, 5, 67–73, DOI:10.1016/j.cogsc.2017.03.016
, URL: http://www.sciencedirect.com/science/article/pii/S2452223616300931, ISSN: 2452-2236.
- M. Smiglak, A. Metlen and R. D. Rogers, The Second Evolution of Ionic Liquids: From Solvents and Separations to Advanced Materials—Energetic Examples from the Ionic Liquid Cookbook, Acc. Chem. Res., 2007, 40(11), 1182–1192, DOI:10.1021/ar7001304
, PMID: 17979252.
- Y. A. C. Jande, M. Asif, S. M. Shim and W. S. Kim, Energy minimization in monoethanolamine based CO2 capture using capacitive deionization, Int. J. Energy Res., 2014, 38(12), 1531–1540, DOI:10.1002/er.3168
.
- M. C. Stern, F. Simeon, H. Herzog and T. A. Hatton, An Electrochemically-mediated Gas Separation Process for Carbon Abatement, Energy Procedia, 2013, 37, 1172–1179, DOI:10.1016/j.egypro.2013.05.214
, URL: http://www.sciencedirect.com/science/article/pii/S1876610213002245, ISSN: 1876-6102.
- M. Wang, M. Rahimi, A. Kumar, S. Hariharan, W. Choi and T. A. Hatton, Flue gas CO2 capture via electrochemically mediated amine regeneration: System design and performance, Appl. Energy, 2019, 255, 113879, DOI:10.1016/j.apenergy.2019.113879
, URL: http://www.sciencedirect.com/science/article/pii/S0306261919315661, ISSN: 0306-2619.
- V. I. Zabolotskii, L. F. El’nikova, N. P. Gnusin and Y. N. Omel’chenko, Regeneration of monoethanolaminebased sorbents of carbon dioxide by electrodialysis with bipolar membranes, J. Appl. Chem. USSR (Engl. Transl.), 1986, 58(10 Pt 2) Search PubMed
, https://www.osti.gov/biblio/6848071.
- C. Huang, T. Xu and X. Yang, Regenerating Fuel-Gas Desulfurizing Agents by Using Bipolar Membrane Electrodialysis (BMED): Effect of Molecular Structure of Alkanolamines on the Regeneration Performance, Environ. Sci. Technol., 2007, 41(3), 984–989, DOI:10.1021/es061918e
.
- M. T. Ho, G. W. Allinson and D. E. Wiley, Reducing the Cost of CO2 Capture from Flue Gases Using Pressure Swing Adsorption, Ind. Eng. Chem. Res., 2008, 47(14), 4883–4890, DOI:10.1021/ie070831e
.
-
R. T. Yang, Cyclic Gas Separation Processes, Gas Separation by Adsorption Processes, ed. R. T. Yang, Butterworth-Heinemann, 1987, ch. 6, pp. 201–235 DOI:10.1016/B978-0-409-90004-0.50009-X, URL: http://www.sciencedirect.com/science/article/pii/B978040990004050009X, ISBN: 978-0-409-90004-0
.
- E. S. Kikkinides and R. T. Yang, Concentration and Recovery of CO2 from Flue Gas by Pressure Swing Adsorption (PSA), Ind. Eng. Chem. Res., 1993, 32, 2714 CrossRef CAS
.
- K. T. Chue, J. N. Kim, Y. J. Yoo, S. H. Cho and R. T. Yang, Comparison of Activated Carbon and Zeolite 13X for CO2 Recovery from Flue Gas by Pressure Swing Adsorption, Ind. Eng. Chem. Res., 1995, 34, 591 CrossRef CAS
.
- S. J. Doong and R. T. Yang, Bulk Separation of Multicomponent Gas Mixtures by Pressure Swing Adsorption: Pore Surface Diffusion and Equilibrium Models, AIChE J., 1986, 32, 397 CrossRef CAS
.
- D. Ko, R. Siriwardane and L. Biegler, Optimization of Pressure Swing Adsorption and Fractionated Vacuum Pressure Swing Adsorption Processes for CO2 Sequestration, Ind. Eng. Chem. Res., 2005, 44, 8084 CrossRef CAS
.
- D. Ko, R. Siriwardane and L. Biegler, Optimization of Pressure Swing Adsorption Process Using Zeolite 13X for CO2 Sequestration, Ind. Eng. Chem. Res., 2003, 42, 339 CrossRef CAS
.
- C. Chou and C. Chen, Carbon Dioxide Recovery by Vacuum Swing Adsorption, J. Chin. Inst. Chem. Eng., 2003, 34, 135 Search PubMed
.
- W. K. Choi, T. I. Kwon, Y. K. Yeo, H. Lee, B. K. Na and H. K. Song, Optimal Operation of the Pressure Swing Adsorption Process for CO2 Recovery, Korean J. Chem. Eng., 2003, 20, 617 CrossRef CAS
.
- J. Zhang, P. A. Webley and P. Xiao, Effect of Process Parameters on the Power Requirements of Vacuum Swing Adsorption Technology for CO2 Capture from Flue Gas, Energy Convers. Manage., 2008, 49, 346 CrossRef CAS
.
- A. Kapoor and R. T. Yang, Kinetic Separation of Methane–Carbon Dioxide Mixture by Adsorption on Molecular Sieve Carbon, Chem. Eng. Sci., 1989, 44, 1723 CrossRef CAS
.
- C.-H. Yu, C.-H. Huang and C.-S. Tan, A Review of CO2 Capture by Absorption and Adsorption, Aerosol Air Qual. Res., 2012, 12(5), 745–769, DOI:10.4209/aaqr.2012.05.0132
, URL: https://doi.org/10.4209%2Faaqr.2012.05.0132, ISSN: 1750-5836.
- J. Huertas and J. Garzon, CO2 Absorbing Capacity of MEA, J. Chem., 2015, 2015, 1–7, DOI:10.1155/2015/965015
, URL: https://doi.org/10.4209%2Faaqr.2012.05.0132.
- C. A. Grande and A. E. Rodrigues, Electric Swing Adsorption for CO2 removal from flue gases, Int. J. Greenhouse Gas Control, 2008, 2(2), 194–202, DOI:10.1016/S1750-5836(07)00116-8
, URL: http://www.sciencedirect.com/science/article/pii/S1750583607001168, ISSN: 1750-5836.
- H. An, B. Feng and S. Su, CO2 capture by electrothermal swing adsorption with activated carbon fibre materials, Int. J. Greenhouse Gas Control, 2011, 5(1), 16–25, DOI:10.1016/j.ijggc.2010.03.007
, URL: http://www.sciencedirect.com/science/article/pii/S1750583610000447, ISSN: 1750-5836.
- N. Tlili, G. Grévillot, A. Latifi and C. Vallières, Electrical Swing Adsorption Using New Mixed Matrix Adsorbents for CO2 Capture and Recovery: Experiments and Modeling, Ind. Eng. Chem. Res., 2012, 51(48), 15729–15737, DOI:10.1021/ie3016818
.
- M. Petkovska, D. Tondeur, G. Grevillot, J. Granger and M. Mitrović, Temperature-Swing Gas Separation with Electrothermal Desorption Step, Sep. Sci. Technol., 1991, 26(3), 425–444, DOI:10.1080/01496399108050482
.
- M. Rahimi, J. K. Singh and F. Müller-Plathe, CO2 Adsorption on Charged Carbon Nanotube Arrays: A Possible Functional Material for Electric Swing Adsorption, J. Phys. Chem. C, 2015, 119(27), 15232–15239, DOI:10.1021/acs.jpcc.5b02874
.
- R. M. Cuéllar-Franca and A. Azapagic, Carbon capture, storage and utilisation technologies: A critical analysis and comparison of their life cycle environmental impacts, J. CO2 Util., 2015, 9, 82–102, DOI:10.1016/j.jcou.2014.12.001
, URL: http://www.sciencedirect.com/science/article/pii/S2212982014000626, ISSN: 2212-9820.
- K. M. K. Yu, I. Curcic, J. Gabriel and S. C. E. Tsang, Recent Advances in CO2 Capture and Utilization, ChemSusChem, 2008, 1(11), 893–899, DOI:10.1002/cssc.200800169
.
-
I. Paris, Putting CO2 to use – Creating value from emissions, 2019, URL: https://www.iea.org/reports/putting-co2-to-use.
- C. M. Woodall, N. McQueen, H. Pilorgé and J. Wilcox, Utilization of mineral carbonation products: current state and potential, Greenhouse Gases: Sci. Technol., 2019, 9(6), 1096–1113, DOI:10.1002/ghg.1940
.
- J. van Heek, K. Arning and M. Ziefle, Reduce, reuse, recycle: Acceptance of CO2-utilization for plastic products, Energy Policy, 2017, 105, 53–66, DOI:10.1016/j.enpol.2017.02.016
, URL: http://www.sciencedirect.com/science/article/pii/S0301421517300915, ISSN: 0301-4215.
- R. Chang, S. Kim, S. Lee, S. Choi, M. Kim and Y. Park, Calcium Carbonate Precipitation for CO2 Storage and Utilization: A Review of the Carbonate Crystallization and Polymorphism, Front. Energy Res., 2017, 5, 17, DOI:10.3389/fenrg.2017.00017
.
- M. Ramdin,
et al., High Pressure Electrochemical Reduction of CO2 to Formic Acid/Formate: A Comparison between Bipolar Membranes and Cation Exchange Membranes, Ind. Eng. Chem. Res., 2019, 58(5), 1834–1847, DOI:10.1021/acs.iecr.8b04944
.
- A. Adamu, F. Russo-Abegão and K. Boodhoo, Process intensification technologies for CO2 capture and conversion – a review, BMC Chem. Eng., 2020, 2(1), 1–18, DOI:10.1186/s42480-019-0026-4
.
- H. Hashiba, L.-C. Weng, Y. Chen, H. K. Sato, S. Yotsuhashi, C. Xiang and A. Z. Weber, Effects of Electrolyte Buffer Capacity on Surface Reactant
Species and the Reaction Rate of CO2 in Electrochemical CO2 Reduction, J. Phys. Chem. C, 2018, 122(7), 3719–3726, DOI:10.1021/acs.jpcc.7b11316
.
- Y. Hori, K. Kikuchi and S. Suzuki, Production of CO and CH4 in electrochemical reduction of CO2 at metal electrodes in aqueous hydrogencarbonate solution, Chem. Lett., 1985, 1695–1698, DOI:10.1246/cl.1985.1695
.
- K. P. Kuhl, E. R. Cave, D. N. Abram and T. F. Jaramillo, New insights into the electrochemical reduction of carbon dioxide on metallic copper surfaces, Energy Environ. Sci., 2012, 5, 7050–7059, 10.1039/C2EE21234J
.
- Y. Song,
et al., High-Selectivity Electrochemical Conversion of CO2 to Ethanol using a Copper Nanoparticle/N-Doped Graphene Electrode, ChemistrySelect, 2016, 1(19), 6055–6061, DOI:10.1002/slct.201601169
.
- Y. C. Li,
et al., CO2 Electroreduction from Carbonate Electrolyte, ACS Energy Lett., 2019, 4(6), 1427–1431, DOI:10.1021/acsenergylett.9b00975
.
- J. Lee, J. Lim, C.-W. Roh, H. S. Whang and H. Lee, Electrochemical CO2 reduction using alkaline membrane electrode assembly on various metal electrodes, J. CO2 Util., 2019, 31, 244–250, DOI:10.1016/j.jcou.2019.03.022
, URL: http://www.sciencedirect.com/science/article/pii/S2212982019300216, ISSN: 2212-9820.
-
J. Qiao, Y. Liu and J. Zhang, Electrochemical reduction of carbon dioxide: fundamentals and technologies, CRC Press, Boca Raton, 2016 Search PubMed
.
-
D. Knuth, Rapid changes in the ethylene capacity world order, 2019, URL: https://www.woodmac.com/news/opinion/rapid-changes-in-the-ethylene-capacity-world-order/, August 2020.
-
L. A. Hamilton, et al., Plastic & Climate: The Hidden Costs of a Plastic Planet, Center for International Environmental Law (CIEL), 2019 Search PubMed
.
- D. Méndez-Mateos, V. L. Barrio, J. M. Requies and J. F. Cambra, A study of deactivation by H2S and regeneration of a Ni catalyst supported on Al2O3, during methanation of CO2. Effect of the promoters Co, Cr, Fe and Mo, RSC Adv., 2020, 10(28), 16551–16564 RSC
.
- X. Zhang, Y. Tang, S. Qu, J. Da and Z. Hao, H2S-selective catalytic oxidation: catalysts and processes, ACS Catal., 2015, 5(2), 1053–1067 CrossRef CAS
.
- M. Davidson, C. H. Lawrie and K. Sohail, Kinetics of the absorption of hydrogen sulfide by high purity and doped high surface area zinc oxide, Ind. Eng. Chem. Res., 1995, 34(9), 2981–2989 CrossRef
.
-
P. Spath, A. Aden, T. Eggeman, M. Ringer, B. Wallace and J. Jechura, Biomass to hydrogen production detailed design and economics utilizing the Battelle Columbus Laboratory indirectly-heated gasifier, Tech. Rep., National Renewable Energy Lab., Golden, CO (US), 2005.
- J. C. Liao, L. Mi, S. Pontrelli and S. Luo, Fuelling the future: microbial engineering for the production of sustainable biofuels, Nat. Rev. Microbiol., 2016, 14(5), 288–304 CrossRef CAS
.
- T. Haas, R. Krause, R. Weber, M. Demler and G. Schmid, Technical photosynthesis involving CO2 electrolysis and fermentation, Nat. Catal., 2018, 1(1), 32–39 CrossRef CAS
.
- M. Götz, J. Lefebvre, F. Mörs, A. M. Koch, F. Graf, S. Bajohr, R. Reimert and T. Kolb, Renewable Power-to-Gas: A technological and economic review, Renewable Energy, 2016, 85, 1371–1390 CrossRef
.
- K. Müller, M. Fleige, F. Rachow and D. Schmeißer, Sabatier based CO2-methanation of flue gas emitted by conventional power plants, Energy Procedia, 2013, 40, 240–248 CrossRef
.
- Z. Abbas, T. Mezher and M. R. Abu-Zahra, Evaluation of CO2 purification requirements and the selection of processes for impurities deep removal from the CO2 product stream, Energy Procedia, 2013, 37, 2389–2396 CrossRef CAS
.
- Q. Zheng, S. Zhou, M. Lail and K. Amato, Oxygen removal from oxy-combustion flue gas for CO2 purification via catalytic methane oxidation, Ind. Eng. Chem. Res., 2018, 57(6), 1954–1960 CrossRef CAS
.
-
N. Chambron, A. Darde, R. Dubettier-Grenier and M. Leclerc, Method and unit for removing oxygen from a gas flow comprising CO2, US Pat., 14/438,309, 2015 Search PubMed
.
- M. Ramdin,
et al., High-Pressure Electrochemical Reduction of CO2 to Formic Acid/Formate: Effect of pH on the Downstream Separation Process and Economics, Ind. Eng. Chem. Res., 2019, 58(51), 22718–22740, DOI:10.1021/acs.iecr.9b03970
.
- M. Ramdin,
et al., High Pressure Electrochemical Reduction of CO2 to Formic Acid/Formate: A Comparison between Bipolar Membranes and Cation Exchange Membranes, Ind. Eng. Chem. Res., 2019, 58(5), 1834–1847, DOI:10.1021/acs.iecr.8b04944
.
- Z. Zhang and D. Huisingh, Carbon dioxide storage schemes: technology, assessment and deployment, J. Cleaner Prod., 2017, 142, 1055–1064 CrossRef CAS
.
- R. C. Ferguson, C. Nichols, T. V. Leeuwen and V. A. Kuuskraa, Storing CO2 with enhanced oil recovery, Energy Procedia, 2009, 1(1), 1989–1996, DOI:10.1016/j.egypro.2009.01.259
, URL: http://www.sciencedirect.com/science/article/pii/S1876610209002604, ISSN: 1876-6102.
-
S. Lee and S. Kam, Enhanced Oil Recovery by Using CO2 Foams: Fundamentals and Field Applications, in Enhanced Oil Recovery Field Case Studies, ed. J. J. Sheng, Gulf Professional Publishing, Boston, 2013, ch. 2, pp. 23–61 DOI:10.1016/B978-0-12-386545-8.00002-6, URL: http://www.sciencedirect.com/science/article/pii/B9780123865458000026, ISBN: 978-0-12-386545-8
.
- C. Xu, P. Dowd and Q. Li, Carbon sequestration potential of the Habanero reservoir when carbon dioxide is used as the heat exchange fluid, J. Rock Mech. Geotech. Eng., 2016, 8(1), 50–59 CrossRef
.
- J. Durst,
et al., Electrochemical CO2 reduction–a critical view on fundamentals, materials and applications, Chimia Int. J. Chem., 2015, 69(12), 769–776 CrossRef CAS
.
- L. Brennan and P. Owende, Biofuels from microalgae—A review of technologies for production, processing, and extractions of biofuels and co-products, Renewable Sustainable Energy Rev., 2010, 14(2), 557–577, DOI:10.1016/j.rser.2009.10.009
, URL: http://www.sciencedirect.com/science/article/pii/S1364032109002408, ISSN: 1364-0321.
-
P. Styring, D. Jansen, H. De Coninck, H. Reith and K. Armstrong, Carbon Capture and Utilisation in the green economy, Centre for Low Carbon Futures, New York, 2011 Search PubMed
.
- K. Michael, A. Golab, V. Shulakova, J. Ennis-King, G. Allinson, S. Sharma and T. Aiken, Geological storage of CO2 in saline aquifers–A review of the experience from existing storage operations, Int. J. Greenhouse Gas Control, 2010, 4(4), 659–667, DOI:10.1016/j.ijggc.2009.12.011
, URL: http://www.sciencedirect.com/science/article/pii/S1750583610000071 ISSN: 1750-5836.
- F. Yang, B. Bai, D. Tang, D.-N. Shari and W. David, Characteristics of CO2 sequestration in saline aquifers, Pet. Sci., 2010, 7(1), 83–92, DOI:10.1007/s12182-010-0010-3
, ISSN: 1995-8226.
- K. Asghari, A. Al-Dliwe and N. Mahinpey, Effect of Operational Parameters on Carbon Dioxide Storage Capacity in a Heterogeneous Oil Reservoir: A Case Study, Ind. Eng. Chem. Res., 2006, 45(8), 2452–2456, DOI:10.1021/ie050572y
.
- G. C. Institute, Global status of CCS 2019, 2019, URL: https://www.globalccsinstitute.com/resources/global-status-report/.
- R. G. Grim, Z. Huang, M. T. Guarnieri, J. R. Ferrell, L. Tao and J. A. Schaidle, Transforming the carbon economy: challenges and opportunities in the convergence of low-cost electricity and reductive CO2 utilization, Energy Environ. Sci., 2020, 13, 472–494, 10.1039/C9EE02410G
.
- A. Sanna, M. Uibu, G. Caramanna, R. Kuusik and M. M. Maroto-Valer, A review of mineral carbonation technologies to sequester CO2, Chem. Soc. Rev., 2014, 43, 8049–8080, 10.1039/C4CS00035H
.
-
B. Smit, J. A. Reimer, C. M. Oldenburg and I. C. Bourg, Introduction to Carbon Capture and Sequestration, Imperial College Press, 2014 DOI:10.1142/p911, URL: https://www.worldscientific.com/doi/abs/10.1142/p911
.
Footnote |
† Electronic supplementary information (ESI) available. See DOI: 10.1039/d0ee03382k |
|
This journal is © The Royal Society of Chemistry 2021 |