DOI:
10.1039/D0AY02069A
(Paper)
Anal. Methods, 2021,
13, 453-461
A spot test for direct quantification of acid green 16 adsorbed on a molecularly imprinted polymer through diffuse reflectance measurements†
Received
6th November 2020
, Accepted 15th December 2020
First published on 16th December 2020
Abstract
This work describes a novel technique for the direct quantification of Acid Green 16 (AG16) adsorbed on a molecularly imprinted polymer (MIP) through the application of diffuse reflectance spectrophotometry (DRS) directly in a solid material. The MIP was synthesized by a bulk method using 1-vinylimidazole as the functional monomer. To conduct DRS analysis, adsorption assays were performed through the application of the MIP in a solution containing different concentrations of AG16 for 120 minutes; subsequently, the MIP was left to dry and a certain quantity of the polymer was analyzed. Under optimized conditions, a linear concentration range of 1.0 μmol L−1 to 10.0 μmol L−1 and limits of detection and quantification of 0.3 μmol L−1 and 1.0 μmol L−1, respectively, were obtained. The repeatability and reproducibility of the method were evaluated and RSD values lower than 4% were obtained. Selectivity studies allowed finding imprinting factor values of 1.9, 2.6, 1.1, and 1.1 for AG16, Direct yellow 50, Acid Blue 1, and Brilliant Green, respectively. The proposed method was applied toward the analysis of river water and textile industry effluents. The advantage and novelty of the technique lie in the fact that the amount of the analyte adsorbed on the selective polymer is directly measured on the solid material for AG16 and not indirectly via the remaining solution as it has always been carried out in previous studies reported in the literature. The findings show that the proposed technique is relatively simple, novel and highly versatile for the quantification of analytes adsorbed on MIPs, as well as for the analysis of the material of interest and quantification of diverse analytes in different matrices.
1. Introduction
Synthetic dyes have been employed for a wide range of purposes in different areas (such as microbiology) and in diverse industries, including the textile, food, cosmetics, and pharmaceutical industries. The diverse applications of synthetic dyes in different sectors of the economy coupled with the huge popularity of these dyes among people worldwide have led to a dramatic rise in their production and consumption over the last few decades. Owing to their widespread use, there has been a sharp increase in the dumping of these dyes (regarded as emergent pollutants) into the environment. Annually, the textile industry currently produces between 700 thousand and 1 million tons of synthetic dyes worldwide; this corresponds to about 90% of the total production of dyes, and the amount of dyes produced tends to increase due to the growing interest in dyes of different colors. Synthetic dyes have a greater dyeing capacity, better performance and stability compared to natural dyes; these advantages have made them highly attractive and have contributed toward amplifying interest in research and development of more synthetic dyes on a large scale.1–4 Acid Green 16 (AG16; C.I. 44025) is an interesting dye known to be widely used in the textile industry mainly for the dyeing of wool and silk, as well as for photographic printing. AG16 is characterized by a dark green powder which dissolves in water (acquiring a blue-green color) and in ethanol (acquiring a green color).5,6 The widespread disposal of AG16-containing wastewater into the environment has become a serious environmental problem worldwide. In the textile industry, the presence of this dye in the effluents makes wastewater extremely toxic in addition to being carcinogenic and mutagenic, and this poses serious health risks to humans and other living beings, as well as to the environment as a whole.7,8 The control and reduction of the presence and effects of AG16 in wastewater are seen to be vital for the protection of the environment; this has led to the development of several methodologies for the detection and quantification of the dye in environmental samples.9 In this context, the search for efficient analytical techniques capable of sensitively and selectively detecting AG16 in different samples remains extremely crucial.10 Some studies published in the literature have employed techniques such as photocatalysis,11 photodegradation12 and chromatography for the determination and detection of AG16.2 The techniques based on spectroscopy in the UV-visible region have the advantages of being relatively fast; however, these techniques have been shown to have some limitations when it comes to detecting and measuring specific dyes in a mixture containing other interfering dyes. Spot tests are a sensitive and selective analytical technique that is applied to small volumes of samples containing the target analyte. The technique allows one to conduct satisfactory semi-micro and ultra micro tests using simple equipment in a short period of time. The procedure is as simple as possible with minimum physical and chemical operations, and the result of the spot test enables one to identify substances in a sample with the naked eye, either by the color change or by precipitate formation. The spot test technique is applicable to both inorganic and organic compounds. The outstanding advantages of this technique lie in the fact that the procedures are extremely simple and fast to perform, in addition to being relatively inexpensive. The major shortcoming of the technique is that it can handle only very small volumes of a given material and this limits its use when one needs to analyze huge volumes of a given material.13,14
In recent years, studies published in the literature have proposed the application of techniques based on the use of highly selective molecularly imprinted polymer (MIP) materials for the extraction and pre-concentration of various analytes. MIPs have been shown to have several advantages including selectivity, sensibility, durability, and cost-effectiveness; these polymers are able to specifically recognize analytes due to the formation of complementary cavities in a specific shape and size similar to the analytes of interest. In essence, one can say that MIPs are similar to an “antigen–antibody” system in which the analyte can be considered “the antigen” and the MIP the “antibody”. This is quite similar to biological systems of living organisms. Based on their characteristics, MIPs can be regarded as plastic antibodies or biomimetic polymers.15–17 Over the past few years, there has been growing interest in research on these polymers due to their capacity for selective recognition of different molecules and their wide variety of applications in different samples. Another outstanding merit of MIPs is that they can be stored for several years without losing their efficiency. MIPs can be synthesized in a variety of ways (solid particles, and core@shell, films, among others) and allow the direct measurements and determination of selective analytes without the need for sample pre-treatment.18–20 In addition, compared to biological systems (such as acidic or alkaline solution), MIPs are more resistant to different kinds of environments, as well as to high pressure and temperature.21 All these characteristics make MIPs suitable for detection analyses and help to explain the growing popularity of these materials and their diverse applications in different areas of research.
The present work reports the development and application of a selective MIP for AG16 determination. The MIP acts as an adsorbent material which selectively extracts the analyte while allowing its pre-concentration directly in complex samples; the analytical measurements are performed directly in the solid MIP material using diffuse reflectance via a spot test.
2. Experimental
2.1. Reagents and solutions
The synthesis of the MIP was performed using the procedure employed by Foguel et al.2 The experiments were conducted based on a bulk method using the following reagents: Acid Green 16 dye (Acid Green 16 – C27H25N2NaO6S2) as the template molecule, 1-vinylimidazole (1V) as the functional monomer, ethylene glycol-dimethacrylate (EGDMA) as the structural monomer, and 2-2′-azo-bis-(2-methylpropionitrile) (AIBN) as the radical initiator. All the reagents were acquired from Sigma-Aldrich®. Methanol (acquired from J.T. Baker®) was used as porogenic solvent and washing solvent (for cleaning and removing the analyte in the MIP) together with glacial acetic acid (Neon®). Deionized water was acquired from a Milli-Q ultra-pure water system (from Millipore®). Brilliant Green (BG), Acid Blue 1 (AB1), and Direct Yellow 50 (DY50) (all purchased from Sigma-Aldrich®) were used for the study of selectivity.
2.2. Equipment and apparatus
A UV/Vis spectrophotometer (from Agilent® Technologies model Cary 60) controlled by the Scan Cary WinUV® software was used to obtain reflectance spectra. Diffuse reflectance (DR) measurements conducted directly in the solid polymeric materials were performed under specific module (Barrelino®) using the aforementioned spectrophotometry equipment. A Unique® ultrasound equipment model USC-1850A and/or a sample homogenizer (the North Scientific® model NH 2200) were used for the homogenization of the solutions. For the synthesis of the imprinted polymers, a SOLAB® model SL 150/10 water bath was used. Nitrogen used in the reactions was supplied by Air Liquide®. pH was adjusted using a pH-meter (Sensoglass® model SP1800). The separation of the solid materials from the supernatant was performed with the aid of a Kasvi® model Speed ×1000 centrifuge. A high resolution field emission scanning electron microscope (FEG-SEM) – Jeol JSM 6330F, was used for the analysis of the surface morphology and characterization of the polymers.
2.3. Quantification of AG16 directly adsorbed on a MIP using diffuse reflectance spectrophotometry (DRS)
The synthesis of the MIP was performed by a bulk method based on a previously reported study conducted by our research group.2 After the synthesis, the polymers were washed in order to remove the analyte and other remaining reagents. The reaction was carried out initially in sealed flasks containing the following: 0.024 mmol of the template (Acid Green 16), 0.24 mmol of the functional monomer (1-vinylimidazole), and 4.0 mL of the porogenic methanol solvent. The mixture was subjected to an ultrasound bath for 10 minutes, and was then stirred for 2 hours using magnetic stirring. After that, the solution was subjected to a nitrogen gas flow for 10 minutes to remove all the oxygen dissolved in the solution. Subsequently, an amount of 2.7 mmol of the structural monomer (EGDMA) was added to the solution, and the solution was again subjected to a nitrogen gas flow for another 10 minutes. Afterwards, an amount of 0.061 mmol of the AIBN radical initiator was added to the mixture; the mixture was then subjected to additional 10 minutes of nitrogen flow. The system was completely sealed in order to avoid the escape of nitrogen and methanol vapor and to maintain anaerobic conditions without oxygen. Finally, the mixture was placed in a water bath at 60 °C under constant control and monitoring. The NIP was synthesized in the same manner, but without the presence of AG16. The average time employed for the synthesis of the polymers was about 60–90 minutes. After their syntheses, both the MIP and the NIP were washed using a Soxhlet system with a washing solution that consisted of methanol and acetic acid (applied in a ratio of 90
:
10 (v/v), respectively). Finally, the polymers were left to dry for 24 hours.
Prior to conducting the DR measurements, the following procedures were executed: first, a mass of 8.0 mg of the MIP or NIP was placed in 2 mL Eppendorf. Next, 1.0 mL aqueous solution of the analyte was added to the polymer mass using the following concentrations: 0 (blank), 1.00, 2.00, 4.00, 6.00, 8.00 and 10.0 μmol L−1. Subsequently, the solutions containing the polymers were homogenized for 2 hours using an automatic homogenizer (incubation process). After this procedure, the vials were centrifuged to separate the supernatant (AG16 solution) and the precipitate (polymer). The supernatant solution was then discarded and the polymer was left to dry in an oven at a temperature of 60 °C for 24 hours. It is worth noting that the materials are required to be completely dry when carrying out reflectance measurements, since humidity interferes with the measurements.
After executing the aforementioned procedures, the samples were now ready to be applied in the spectrophotometer to perform attenuated total reflectance measurements. Equipment used for the diffuse reflectance measurements is shown in Fig. 1; as can be observed, the equipment consists of an accessory, which is connected to the spectrophotometer with an optical fiber. A lamp is inserted at the bottom of the equipment; the light from the lamp is used for performing the measurements and for obtaining the images of the samples. The equipment also possesses a plate-like structure upon which an amount of 1.0 mg of the sample is placed in the middle of a small hole (named the G point), where the lamp has been positioned to perform the DR measurements.
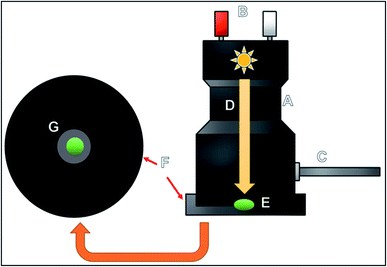 |
| Fig. 1 Illustrative description of how the device works: (A) device used for measurements; (B) buttons for turning on the lamp and for capturing images of the samples; (C) optical fiber cable connected to the spectrophotometer where the light passes; (D) two lamps are placed inside the device; one for photographing the sample, and the other one for performing diffuse reflectance measurements; (E) the sample is placed on a plate at the bottom where the lamp is inserted; (F) front and side views of the plate; (G) image of the sample from the front view of the plate. | |
2.4. Selectivity experiments
After the construction of the analytical curve, the experiments related to the study of the selectivity of the measurements were conducted using both the MIP and the NIP based on the procedures described in section 2.3.
The selectivity of the adsorption of AG16 and the other three compounds (BG, AB1 and DY50) on the polymers was evaluated using DR analysis. The solutions of these dyes were prepared using water as solvent. Each dye was analyzed at its specific wavelength relative to reflectance: BG at 625 nm, AB1 at 635 nm, and DY50 at 390 nm. All the analytical measurements were performed in triplicate.
2.5. Analysis in industrial residues and river samples
After the optimization and evaluation of the experiments, the proposed method was analyzed in real samples. The samples were collected from two rivers (Batalha and Jacaré-Guaçu) in the city of Araraquara, São Paulo state, Brazil, and from a textile industry located in the same city. The samples were spiked with AG16 in three different concentrations: 2.0, 4.0 and 6.0 μmol L−1. For the industrial effluent, one sample was measured after 50 times dilution and the other sample was used as collected without any pre-treatment.
3. Results and discussion
3.1. Morphological and FTIR characterization of the adsorbent materials, MIP and NIP
Fourier-transform infrared spectroscopy (FTIR) was used for the characterization of the functional groups present in the polymers, as well as the analyte and the reagents employed in the synthesis. The spectra of the MIP and NIP and the structural monomer (EDGMA) are shown in Fig. 2.
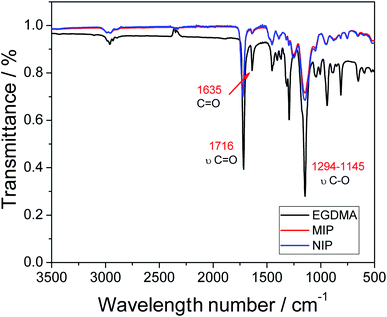 |
| Fig. 2 Infrared spectra of the MIP and NIP, and the structural monomer (EDGMA) along with its molecular structure (inset). | |
Looking at the FTIR profiles of the two polymers (MIP and NIP), one can observe the presence of two intense bands at 1716 cm−1, which are related to the ester group, and specifically to C
O stretching and bands between 1294 and 1145 cm−1, which correspond to C–O stretching and may also be associated with the ester group. The two bands are present in greater intensity in the EDGMA spectrum, and this shows that the polymers are composed mainly of this structural monomer, whose structure possesses the ester functional group. Further evidence pointing to the successful occurrence of the polymerization process is the complete disappearance of the band at 1635 cm−1; this band is associated with the double C
C bond,22–24 and although it can still be observed in the EDGMA spectrum, one can notice the drastic reduction of the intensity of the band in the spectrum of the polymers. The drastic reduction of the band intensity can be attributed to the breakage of the double C
C bond caused by the radical initiator, paving the way for the occurrence of the polymerization process.
For the analysis of the morphology of the polymers, the images were recorded by field emission scanning electron microscopy (FE-SEM). The FE-SEM images presented in Fig. 3 show the morphological similarity of the polymers; this similarity was expected once the polymers were made of the same material. Here, it is worth pointing out that as the selective cavities of the MIP were formed at the molecular level, visualization by FE-SEM was not feasible;25 as such, SEM analysis was performed only for superficial characterization of the polymers.2 The Fig. 3 shows than the MIP was rougher than that of the NIP; this was clearly expected because the former possesses selective cavities in its structure.
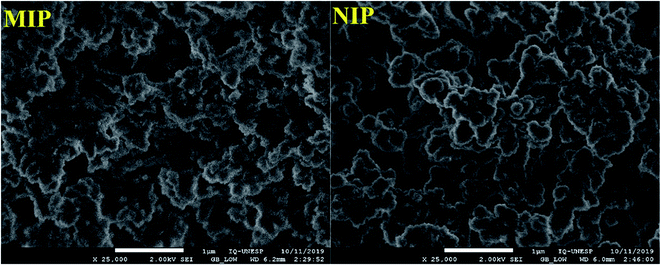 |
| Fig. 3 Scanning Electron Microscopy (SEM) images of the MIP and NIP. | |
3.2. DR profile for the AG16 adsorbed in the MIP
Diffuse reflectance spectrophotometry (DRS) is a widely applied contact sampling technique used for analyzing the surfaces of polymers; the technique is known for providing greater efficiency when it comes to the analysis of dense materials with high absorption. With these remarkable properties, DR is perfectly compatible to be used alongside imprinted polymers adsorbed with analytes such as dyes.
In diffuse reflectance, two types of reflection occur on the material surface: (i) regular or specular reflectance, and (ii) diffuse reflectance. Regular reflection occurs when there is parallelism between incidence and reflection rays, i.e., when their angles are equal. This type of phenomenon occurs on smooth and polished surfaces, such as mirrors. With regard to diffuse reflection, the reflection rays lose their parallelism, presenting different angles; this occurs on uneven surfaces and can be used in analytical methods.26,27 The two types of reflectance are illustrated in Fig. S1 (see the ESI†).
Diffuse reflectance occurs when there is a modification of light after it is reflected; the radiation is partially absorbed and the reflected light shows different values of intensity. During analysis, the presence of the analyte of interest (AG16) causes modification of the light. It is worth pointing out that each material has its own characteristics of absorbing/reflecting light at one or more wavelengths. The AG16 dye has a wavelength of maximum absorption at 640 nm; in other words, it is at this wavelength that the light intensity will be modified and the data obtained during the measurements will be collected.
The diffuse reflectance technique was employed aiming at developing a direct and simple method for quantifying the adsorption of AG16 in the synthesized polymers. A DR detector (Barrelino®), which is suitable for performing measurements on solid materials, was used to obtain the reflectance spectra (see Fig. 4).
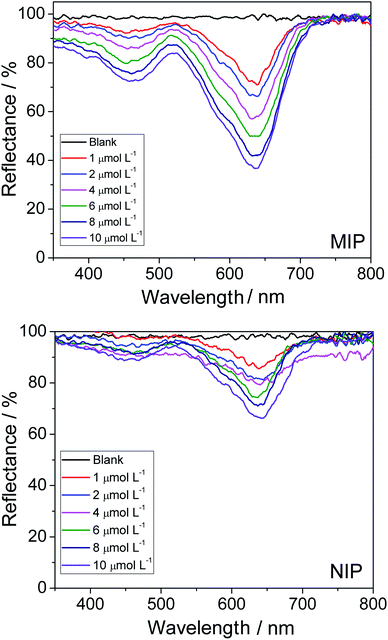 |
| Fig. 4 Reflectance spectra in the UV-Vis region for different concentrations of AG16 adsorbed on the surface of the polymers (applied under previously optimized conditions). One can observe that the reflectance is 100% for the blank material (this corresponds to each polymer without the analyte). | |
By analyzing the two graphs in Fig. 4, one can observe the occurrence of a greater variation in reflectance when the MIP is employed; this shows that the imprinted polymer adsorbed the analyte in a more efficient manner than the NIP (control polymer). Unsurprisingly, this result was expected because the MIP has selective cavities for the adsorption of the dye; this was totally different for the NIP, which is characterized by unspecific interactions. In addition, in the case of the MIP, there was an increase in analyte adsorption as the concentration of the dye was increased. This was manifested by the decrease in the value of diffuse reflectance (% R), since the absorbance of the material was found to increase when a greater amount of dye was adsorbed, which, consequently, resulted in a decrease in the reflectance value.
The spectra in Fig. 4 were used for the construction of analytical curves of % reflectance at 640 nm relative to the concentration of AG16 (Fig. 5). As can be observed in Fig. 5, the application of the MIP as an adsorbent material resulted in better linear adjustment and higher sensitivity (68% higher).
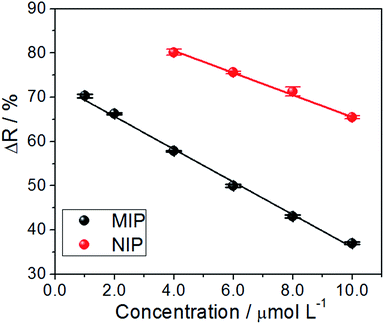 |
| Fig. 5 Analytical curve of reflectance versus the concentration at 640 nm (n = 3) based on the application of the MIP and NIP as adsorbents. | |
The analytical curves exhibited linearity, with a regression coefficient of R2 = 0.995 and R2 = 0.997 for the MIP and NIP, respectively, which, were linearly adjusted based on eqn (1) and (2) given below:
| YMIP = 73.0(±0.6) − 3.7(±0.1)xMIP | (1) |
| YNIP = 90.5(±0.8) − 2.5(±0.1)xNIP | (2) |
where
Y corresponds to the reflectance variation (%
R), and
x corresponds to the dye concentration in μmol L
−1. Based on the linear regression equations, one is able to calculate the values related to angular and linear coefficients for both polymers, as well as the method sensitivity and LOD (3 × SD/
m, where SD is the standard deviation for ten blank solution measurements (
n = 10) and
m is the analytical sensitivity).
28 All these values are shown in
Table 1 below.
Table 1 Parameter data obtained from the analytical curves of the MIP and NIP adsorbed with AG16
Parameters |
MIP |
NIP |
Response range (μmol L−1) |
1.0–10.0 |
4.0–10.0 |
Slope (sensibility) |
−3.68 |
−2.50 |
Intercept |
73.0 |
89.3 |
Limit of detection (μmol L−1) |
0.3 |
1.2 |
Limit of quantification (μmol L−1) |
1.0 |
4.0 |
A comparison of the two reflectance curves shows that the MIP adsorbed the analyte more efficiently than the NIP, as such, the MIP presented a much higher and stronger tendency to rebind with AG16. Although one is likely to arrive at the same conclusion via indirect measurements using the remaining liquid after the incubation process,29,30; the advantage of the proposed method lies in performing measurements directly on the solid material. Furthermore, once the adsorption process has taken place, it becomes advantageous to save time as this diminishes the pre-analysis steps, such as the centrifugation process. The approach helps avoid committing errors in the replicates due to the easy handling of the sample (with only one drying step) and, most importantly, the mechanism allows one to obtain the real adsorption isotherm. All these advantages make the proposed method (based on direct reflectance measurements of the MIP adsorbed with AG16) highly promising.
3.3. Validation parameters
The analysis of repeatability shows the agreement between the results obtained from the measurements made successively using the same method. The analysis of the repeatability of the measurements was performed using the same conditions, the same analyst and equipment/instrument, and the same parameters (including temperature, pH, time and the concentration).31 The results obtained from this analysis are shown in Table 2. Fig. S2 (see the ESI†) shows the graph related to reflectance curves as a function of concentration; the curve was constructed based on the average reflectance value obtained. With regard to relative standard deviations (RSD), the results showed that both the MIP and the NIP presented a RSD below 4%, with the MIP presenting a RSD less than 1%. This positive result shows that the MIP was relatively more efficient than the NIP. In addition, the fibers were found to have good repeatability.
Table 2 Calculated values from the reflectance average, standard deviation and relative standard deviation for n = 10 in repeatability studies
|
Concentration (μmol L−1) |
Reflectance (%) |
Standard error |
RSD |
MIP |
1.00 |
97.5 |
0.7 |
0.4% |
2.00 |
70.3 |
0.4 |
0.6% |
4.00 |
66.2 |
0.2 |
0.3% |
6.00 |
57.8 |
0.1 |
0.2% |
8.00 |
50.0 |
0.4 |
0.8% |
10.0 |
43.1 |
0.4 |
0.8% |
NIP |
1.00 |
97.5 |
1.0 |
1.0% |
2.00 |
85.9 |
0.7 |
0.8% |
4.00 |
82.0 |
2.7 |
3.3% |
6.00 |
80.1 |
0.7 |
0.9% |
8.00 |
75.5 |
0.2 |
0.3% |
10.0 |
71.2 |
1.0 |
1.4% |
Reproducibility is the degree of agreement between the results of measurements performed using a single sample under varying conditions (such as equipment, the material, the location, etc.).29 In this study, reproducibility was evaluated through the application of three MIPs and NIPs prepared in three separate syntheses using AG16 solution at the same concentration. The adsorption experiments were conducted under optimized conditions.
Table 3 shows the results obtained along with the average values and deviations. The graph related to average reflectance as a function of concentration is shown in Fig. S3 (see the ESI†).
Table 3 Calculated values of the reflectance and their averages, standard deviation and relative standard deviation for n = 3 in reproducibility studiesa
|
Concentration (μmol L−1) |
Reflectances (%) |
RSD |
1° Rep. |
2° Rep. |
3° Rep. |
Average |
Rep.: Replicate.
|
MIP |
1.00 |
70.7 |
70.6 |
69.9 |
70.4 ± 0.5 |
0.7% |
2.00 |
66.3 |
66.1 |
67.2 |
66.5 ± 0.6 |
0.9% |
4.00 |
57.78 |
57.4 |
57.0 |
57.4 ± 0.4 |
0.7% |
6.00 |
49.7 |
48.6 |
49.0 |
49.1 ± 0.5 |
1.1% |
8.00 |
43.3 |
42.9 |
42.3 |
42.8 ± 0.5 |
1.2% |
10.0 |
37.1 |
36.7 |
36.7 |
36.8 ± 0.2 |
0.6% |
NIP |
1.00 |
85.6 |
85.8 |
85.9 |
85.8 ± 0.2 |
0.2% |
2.00 |
82.2 |
83.3 |
82.4 |
82.6 ± 0.6 |
0.7% |
4.00 |
80.1 |
80.6 |
80.6 |
80.4 ± 0.3 |
0.4% |
6.00 |
75.2 |
75.8 |
75.5 |
75.5 ± 0.3 |
0.4% |
8.00 |
71.2 |
71.6 |
71.4 |
71.4 ± 0.2 |
0.3% |
10.0 |
65.4 |
66.2 |
64.4 |
65.4 ± 0.9 |
1.4% |
The results obtained from the analysis of reproducibility were as satisfactory as those of the repeatability analysis. In the reproducibility analysis, RSDs of less than 1.5% were obtained for both the MIP and the NIP.
3.4. Selectivity studies
The selectivity of the proposed method (based on the application of the MIP as the adsorbent) was evaluated through its application in real samples. To perform this analysis, three different dyes (interfering molecules) with similar and different structures of AG16 were used: Bright Green (BG) and Acid Blue 1 (AB1) of the same triphenylmethane family, and Direct Yellow 50 (DY50), which belongs to a different structure. The analytical curve for each dye was obtained at its specific maximum absorption wavelength; the results are shown in Fig. S4 (see the ESI†) and 6.
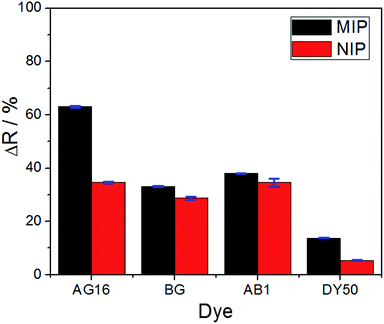 |
| Fig. 6 Comparison of reflectance variation between the MIP and the NIP for all the dyes under investigation (applied under 10.0 μmol L−1 concentration). | |
To evaluate the selectivity in numerical terms, the molecular imprinting factor (α) and the selectivity factor (β) were calculated using eqn (3) and (4) below. The equations were adapted from studies reported in the literature related to chemical sensors based on molecularly imprinted polymers, in which an evaluation was conducted regarding the analyte adsorption on the surface of the sensor.32–34
|  | (3) |
|  | (4) |
The results obtained were satisfactory in the sense that they showed a relatively greater detection of AG16 compared to other interfering dyes (Table 4). As can be noted in Table 4, the first three dyes displayed a similar chemical structure characterized by the presence of the central triphenylmethane group. Of all the chemical structures of these dyes, AB1 exhibited the chemical structure that was much more similar to that of AG16; this is in agreement with the results obtained from the selectivity analysis. Direct Yellow 50 (DY50), on the other hand, presented a structure found to be very different from that of the AG16; this explains its very low rebinding value with the imprinted polymer, which resulted in a relatively higher selectivity coefficient. In addition, the imprinting factor values close to 1 obtained for AB1 and BG indicate that the MIP and NIP were not selective for these two analytes; this lack of selectivity can be attributed to non-specific interactions. In the case of DY50, the value obtained for α (α = 2.6) shows that, unlike the NIP (which showed no selectivity for DY50), the MIP displayed selectivity for this dye; this can be confirmed by the high value obtained for the selectivity factor (β = 4.6) (see Table 4).
Table 4 Parameters related to the selectivity of the proposed method in comparison with the NIP in the presence of the main analyte AG16 and the possible interferents evaluated
Dye |
Structure |
Reflectance variation (Δ% R) |
Selectivity parameter |
MIP |
NIP |
α
(MIP, NIP)
|
β
(analyte, interferent)
|
AG 16 |
|
63.1 |
34.6 |
1.9 |
— |
BG |
|
33.0 |
28.7 |
1.1 |
1.9 |
AB1 |
|
38.0 |
34.6 |
1.1 |
1.7 |
DY50 |
|
13.8 |
5.4 |
2.6 |
4.6 |
Thus, considering the results obtained and the measurements of reflectance of AG16 adsorbed on the MIP, one can conclude that the proposed method demonstrated high selectivity; this can mainly be attributed to the selective characteristics of the imprinted polymer used as the adsorbent material.
3.5. Application of the proposed method in real samples
To measure the efficiency of the proposed method, AG16 was quantified in river and industrial wastewater samples. The samples were collected from two different rivers and from the effluents of a textile industry; the analyses were performed using raw samples from the water collected from the two rivers and the textile industry wastewater diluted 50 times. The samples were contaminated with known concentrations of the analyte (AG16) at three different concentration levels: 2.0, 4.0 and 6.0 μmol L−1, under optimized conditions. Based on the measurements conducted, the recovery rates (in percentage) were calculated using the MIP and NIP. The results obtained are shown in Table 5.
Table 5 Results obtained in recovery tests using water of two different rivers and an industrial effluent (raw and diluted) obtained in the city of Araraquara (SP)
Concentration (μmol L−1) |
Recuperation (%) |
Jacaré-Guaçu |
Batalha |
Gross residue |
Diluted 50× residue |
MIP |
NIP |
MIP |
NIP |
MIP |
NIP |
MIP |
NIP |
2.0 |
93.3 |
42.5 |
93.4 |
36.6 |
67.3 |
20.8 |
98.2 |
65.5 |
4.0 |
98.8 |
35.4 |
98.2 |
69.5 |
72.1 |
28.2 |
97.0 |
66.0 |
6.0 |
96.6 |
55.8 |
97.3 |
56.9 |
71.0 |
34.4 |
98.3 |
66.4 |
As can be observed in Table 5, the application of the MIP resulted in higher recovery rates. This points to the efficiency of the proposed method in terms of rebinding/extraction of AG16 in complex samples, especially in the raw sample collected from the textile industry, which is really complex and dark. The results obtained essentially show that the proposed method for dye detection has applicability potential with good degree of accuracy when it comes to the analysis of real samples.
4. Conclusions
This work reported the development and application of a rapid spot test technique for measuring reflectance on the surfaces of molecularly imprinted polymers. The results obtained from the application of the technique for the analysis of acid green dye 16 were found to be satisfactory; the technique promoted good adsorption of the analyte in the selective cavities of the MIP in the presence of other interfering dyes. Under optimized conditions, the proposed technique presented limits of detection and quantification of 0.3 μmol L−1 and 1.0 μmol L−1, respectively, with good repeatability and reproducibility (RSD of less than 4%). The results obtained from the calculations of selectivity parameters α and β showed that the technique has a high degree of selectivity. The proposed MIP-based methodology was successfully applied in real samples where it presented an excellent recovery rate without the need for complex pre-treatment of the samples.
Conflicts of interest
The authors declare that they have no known competing financial interests or personal relationships that could have appeared to influence the work reported in this paper.
Acknowledgements
FAPESP (grants #2014/50945–4 and #2019/00677-7) and CNPq (grants #465571/2014–0, #408050/2018-7 and #301728/2019-4). BM would like to thank CAPES for the scholarship granted during the master's degree and AW is thankfulfor PROJ. AUX/PE/PROEX No 0674/2018 CAPES.
References
- T. Robinson, G. McMullan, R. Marchant and P. Nigam, Bioresour. Technol., 2001, 77(3), 247–255, DOI:10.1016/S0960-8524(00)00080-8.
- M. V. Foguel, N. T. B. Pedro, A. Wong, S. Khan, M. V. B. Zanoni and M. del P. T. Sotomayor, Talanta, 2017, 170, 244–251, DOI:10.1016/j.talanta.2017.04.013.
- S. Khan, A. Wong, M. V. B. Zanoni and M. D. P. T. Sotomayor, Mater. Sci. Eng., C, 2019, 103, 109825, DOI:10.1016/j.msec.2019.109825.
- V. V. C. Lima, F. B. Dalla Nora, E. C. Peres, G. S. Reis, É. C. Lima, M. L. S. Oliveira and G. L. Dotto, J. Environ. Chem. Eng., 2019, 7(5), 103410, DOI:10.1016/j.jece.2019.103410.
-
N. Sekar, Acyd Dyes Handbook of Textile and Industrial Dyeing: Principles, Processes and Types of Dyes, Woodhead Publishing Limited, 2011, vol. 1, ch. 15, pp. 486–514 Search PubMed.
- P. K. Brahman, N. Pandey, S. N. Topkaya and R. Singhai, Talanta, 2015, 134, 554–559, DOI:10.1016/j.talanta.2014.10.054.
- T. Ito, Y. Adachi, Y. Yamanashi and Y. Shimada, Water Res., 2016, 100, 458–465, DOI:10.1016/j.watres.2016.05.050.
- A. de O. Martins, V. M. Canalli, C. M. N. Azevedo and M. Pires, Dyes Pigm., 2006, 68(2–3), 227–234, DOI:10.1016/j.dyepig.2005.02.002.
- T. Wrońska-Nofer, J. Wiśniewska-Knypl, K. Wyszyńska and E. Dziubałtowska, Mutat. Res., Genet. Toxicol. Environ. Mutagen., 1997, 392(3), 229–235, DOI:10.1016/S1383-5718(97)00067-3.
- A. R. Firooz, A. A. Ensafi, N. Kazemifard and R. Khalifeh, Sens. Actuators, B, 2013, 176, 598–604, DOI:10.1016/j.snb.2012.10.045.
- S. Sakthivel, B. Neppolian, M. Palanichamy, B. Arabindoo and V. Murugesan, Indian J. Chem. Technol., 1999, 6, 161–165 CAS.
- S. Sakthivel, B. Neppolian, B. Arabindoo, M. Palanichamy and V. Murugesan, J. Sci. Ind. Res., 2000, 59(7), 556–562 CAS . http://nopr.niscair.res.in/handle/123456789/26591.
- A. E. Zeraik, F. S. Souza, O. Fatibello-Filho and O. D. Leite, Quim. Nova, 2008, 31(4), 731–734, DOI:10.1590/S0100-40422008000400003.
-
E. Jungreis, Encyclopedia of Analytical Chemistry, 2006, pp. 1–19, DOI:10.1002/9780470027318.a8111.
- S. Khan, M. M. D. C. Vila and M. Tubino, Food Addit. Contam., Part A, 2012, 29(8), 1256–1262, DOI:10.1080/19440049.2012.692486.
- M. Luna Quinto, S. Khan, G. Picasso and M. D. P. Taboada Sotomayor, J. Hazard. Mater., 2019, 384, 121374, DOI:10.1016/j.jhazmat.2019.121374.
- K. Haupt and K. Mosbach, Biochem. Soc. Trans., 1999, 27(2), 344–350, DOI:10.1042/bst0270344.
- T. A. Sergeyeva, O. O. Brovko, E. V. Piletska, S. A. Piletsky, L. A. Goncharova, L. V. Karabanova, L. M. Sergeyeva and A. V. El’skaya, Anal. Chim. Acta, 2007, 582(2), 311–319, DOI:10.1016/j.aca.2006.09.011.
- A. Pietrzyk-Le, W. Kutner, R. Chitta, M. E. Zandler, F. D'Souza, F. Sannicolò and P. R. Mussini, Anal. Chem., 2009, 81(24), 10061–10070, DOI:10.1021/ac9020352.
- S. R. Carter and S. Rimmer, Adv. Funct. Mater., 2004, 14(6), 553–561, DOI:10.1002/adfm.200305069.
- C. R. T. Tarley, M. D. P. T. Sotomayor and L. T. Kubota, Quim. Nova, 2005, 28(6), 1076–1086, DOI:10.1590/S0100-40422005000600024.
- C. Berthomieu and R. Hienerwadel, Photosynth. Res., 2009, 101(2–3), 157–170, DOI:10.1007/s11120-009-9439-x.
- R. Ginzburg-Turgeman and D. Mandler, Phys. Chem. Chem. Phys., 2010, 12, 11041–11050, 10.1039/B927478B.
- Yanti, T. Nurhayati, I. Royani, Widayani and Khairurrijal, J. Phys.: Conf. Ser., 2016, 739, 19–20, DOI:10.1088/1742-6596/739/1/012143.
-
M. V. Foguel, Doctoral Dissertation, Universidade Estadual Paulista (UNESP), 2015 Search PubMed.
- P. T. Sotomayor, I. M. Raimundo, G. De Oliveira Neto, J. J. R. Rohwedder and G. Oliveira Neto, Ecletica Quim., 2010, 35(2), 33–43, DOI:10.26850/1678-4618eqj.v35.2.2010.p33-43.
- P. T. Sotomayor, I. M. Raimundo, G. De Oliveira Neto and L. T. Kubota, Anal. Chim. Acta, 2001, 447(1–2), 33–40, DOI:10.1016/S0003-2670(01)01291-0.
- D. A. Armbruster and T. Pry, Limit of Blank, Clin. Biochem. Rev., 2008, 29(Suppl. 1), 49–52 Search PubMed . https://www.ncbi.nlm.nih.gov/pmc/articles/PMC2556583/.
- R. R. Pupin, M. V. Foguel, L. M. Gonçalves and P. T. Sotomayor, J. Appl. Polym. Sci., 2019, 137(13), 48496, DOI:10.1002/app.48496.
- S. Khan, S. Hussain, A. Wong, M. V. Foguel, L. M. Gonçalves, M. I. P. Gurgo and M. D. P. T. Sotomayor, React. Funct. Polym., 2018, 122, 175–182, DOI:10.1016/j.reactfunctpolym.2017.11.002.
- M. Ribani, C. B. G. Bottoli, C. H. Collins, I. C. S. F. Jardim and L. Melo, Quim. Nova, 2004, 27(5), 771–780, DOI:10.1590/S0100-40422004000500017.
- P. T. Sotomayor, I. M. Raimundo, G. De Oliveira Neto and W. A. De Oliveiira, Sens. Actuators, B, 1998, 51(1–3), 382–390, DOI:10.1016/S0925-4005(98)00225-1.
- L. D. Marestoni, A. Wong, G. T. Feliciano, M. R. R. Marchi, C. R. T. Tarley and M. D. P. T. Sotomayor, Talanta, 2017, 170(1), 244–251, DOI:10.1016/j.talanta.2017.04.013.
- D. A. Spivak, Adv. Drug Delivery Rev., 2005, 57(12), 1779–1794, DOI:10.1016/j.addr.2005.07.012.
Footnote |
† Electronic supplementary information (ESI) available. See DOI: 10.1039/d0ay02069a |
|
This journal is © The Royal Society of Chemistry 2021 |
Click here to see how this site uses Cookies. View our privacy policy here.