Mapping the mechanical and electrical properties of commercial silicone elastomer formulations for stretchable transducers†
Received
14th September 2019
, Accepted 13th November 2019
First published on 14th November 2019
Abstract
Elastomers for fabricating soft and stretchable transducers primarily require high elongation at break, high dielectric permittivity, high breakdown strength and low leakage current. Commercial silicone elastomer formulations often do not encompass all of the properties necessary to function effectively as stretchable transducers, but they are nevertheless used out of familiarity. On a research level, Sylgard 184, Sylgard 186, Ecoflex 00-10, Ecoflex 00-30 and Ecoflex 00-50 are widely used for fabricating stretchable devices. We blend these commercial silicones with each other in various proportions, to make the blends most suitable for fabricating specific types of transducers. Furthermore, the properties of these blends, such as ultimate stress and strain, Young's modulus, dielectric permittivity, breakdown strength, viscosity, leakage current and optical transmittance, are investigated and mapped to identify those exhibiting the best-suited properties for fabricating soft and stretchable transducers. The elastomers obtained using the blending methods illustrated herein could act as a starting point for conceptualizing the feasibility of a product on a research level.
1. Introduction
The evolution of flexible and stretchable transducers as viable alternatives to conventional electromagnetic transducers has sparked unprecedented interest in transitioning from hard to soft equipment.1,2 Soft, stretchable and lightweight transducers that can generate motion and withstand wear and tear3,4 are beneficial for developing futuristic applications, for example soft robots,5 lifelike prosthetics,6,7 stretchable pressure sensors8 and intrinsic wearable biomedical devices.9 Sylgard 184, supplied by Dow, is a very popular elastomer for fabricating such devices, mainly due to its low viscosity and ease of processing. Sylgard 184 has been used to develop a wide range of products, such as shape memory composites,10 compliant graphite electrodes,11 microfluidic devices,12 super-stretch strain sensors,13 micro contact pressure sensors14 and tactile sensors.15 Though Sylgard 184 sets the benchmark for commercial silicone elastomers, our measurements show that it has limited extensibility (135%), a relatively high Young's modulus as for most commercial silicone elastomer compositions (2.4 MPa), relatively high leakage current (≈10−10 A) and a dielectric permittivity of ∼3.1 (1 Hz), which is not optimal for developing stretchable transducers, especially for high-voltage applications. Hence, in pursuit of better alternatives to Sylgard 184, we analyse the properties of Sylgard 186 and Ecoflex by Smooth-On, both of which have higher extensibility and a lower Young's modulus compared to Sylgard 184.16,17 Lately, Ecoflex has been used widely for fabricating soft, elastic, wearable pressure sensors/electronics.16,18 Exploiting the synergy between two formulations with contrasting properties is a simple way to formulate a silicone elastomer with desired properties when formulation expertise is not available.17,19 In previous studies by Russo et al.19 and Park et al.,17 an elastomer blend (Dragon Skin 00 20 + Sylgard 18419 and Dragon Skin 10 Slow + Sylgard 18417) was found to possess higher extensibility, better tear resistance and plasma bonding ability compared to pure Sylgard 184. In this work, five commercial silicone formulations (Sylgard 184 and 186, and Ecoflex 00-50, 00-30 and 00-10) are blended with each other. Some formulations (Sylgard 184 and 186) are also mixed at different stoichiometric ratios, in order to optimise their mechanical and electrical properties. Optically transparent formulations have been chosen, since optical transparency is extensively sought, especially for optics and “invisible” wearable sensors.20 The blends’ properties are mapped and compared to Sylgard 184, which is the current benchmark for stretchable electronics, as well as to Elastosil Film 2030 250/X, which recently has become a new benchmark for dielectric elastomer films, due to their commercial availability. Figures of merit for a dielectric elastomer actuator (Fom(DEA))20 and a dielectric elastomer generator (Fom(DEG)),21 respectively, are calculated to assess elastomer performance in the two respective operational modes.
2. Materials and sample preparation
Five different two-part (A and B) commercial Pt-curing silicone elastomers are used herein. Sylgard elastomers are purchased from Dow, Germany, Ecoflex elastomers purchased from FormX, Netherlands and Elastosil Films 2030 250/X, where, “X” denotes the thickness of the film (100 μm and 200 μm in thickness), provided by Wacker Chemie, Germany. From now on Elastosil Film 2030 250/X, will be denoted as Elastosil.
Throughout the manuscript the term ‘blend’ will refer to formulations obtained by combining two different commercial silicone systems. Sample compositions are shown in Table 1. Parts A and B of every silicone formulation are weighed according to the mixing ratio and mixed in a SpeedMixer DAC 150 FVZ-K for 2 minutes at 2000 rpm. Then, this well mixed formulation is blended with another well mixed formulation in the ratios specified in Table 1 for another 2 minutes at 2000 rpm, after which the blends are used to prepare samples. The manufacturer's recommended mixing ratio for Sylgard formulations is 10
:
1 (part A
:
part B) and for Ecoflex formulations the ratio is 1
:
1 (part A
:
part B). Films of different thicknesses are made for various measurements. To make these film samples, the formulations are doctor-bladed on polyester support film, provided by Pütz GmbH + Co. Folien KG, Germany. The blade gaps are 600 μm, 400 μm and 200 μm, respectively. After curing, film thicknesses are 450 ± 45 μm, 300 ± 30 μm and 100 ± 20 μm, respectively.22 The precise sample thickness is evaluated using optical microscope. Moreover, each composition is poured into a metal mold with 1 mm thick spacer and a metal cup in order to obtain samples with thicknesses of 1 ± 0.2 mm and 6.4 mm (or larger), respectively. All formulations are cured at 80 °C for 2 hours, and measurements are carried out in ambient conditions. The resulting elastomers do not adhere to any of the used supports, allowing for an easy peeling off. Swelling tests of prepared samples are performed and gel fraction is calculated as described in ESI.† Gel fractions (Table 1) show that all prepared samples are well cross-linked. For measurements on aged samples, the specimens are stored for 6 months at room temperature, with no exposure to sunlight. The properties of the stored samples are then re-measured and compared to the previous results. The methods for measuring the mechanical and electrical properties of the compositions are described in the ESI.†
Table 1 Sample names with their corresponding mixing ratios (part A and part B), blending ratios with other formulations and gel fraction of all formulations
No. |
Sample name |
Part Ia |
Ratio |
Part IIa |
Ratio |
Gel fraction, % |
Mixing weight ratios for part A and part B (A : B) of the respective silicone kits (in bracket).
The formulations of Sylgard 186 15 : 1 and 20 : 1 are not tested as these mixtures did not produce free-standing elastomers.
|
1 |
Sylgard 184 5 : 1 |
Sylgard 184 (5 : 1) |
— |
— |
— |
95.1 |
2 |
Sylgard 184 |
Sylgard 184 (10 : 1) |
— |
— |
— |
95.4 |
3 |
Sylgard 184 15 : 1 |
Sylgard 184 (15 : 1) |
— |
— |
— |
93.2 |
4 |
Sylgard 184 20 : 1 |
Sylgard 184 (20 : 1) |
— |
— |
— |
91.1 |
5 |
Sylgard 186 5 : 1 |
Sylgard 186 (5 : 1) |
— |
— |
— |
95.8 |
6 |
Sylgard 186b |
Sylgard 186 (10 : 1) |
— |
— |
— |
95.3 |
7 |
Sylgard MIX 1 : 3 |
Sylgard 184 (10 : 1) |
1 |
Sylgard 186 (10 : 1) |
3 |
96.1 |
8 |
Sylgard MIX 1 : 1 |
Sylgard 184 (10 : 1) |
1 |
Sylgard 186 (10 : 1) |
1 |
95.8 |
9 |
Sylgard MIX 3 : 1 |
Sylgard 184 (10 : 1) |
3 |
Sylgard 186 (10 : 1) |
1 |
95.7 |
10 |
Ecoflex 00-50 |
Ecoflex 00-50 (1 : 1) |
— |
— |
— |
54.3 |
11 |
Eco MIX 00-50 1 : 3 |
Sylgard 184 (10 : 1) |
1 |
Ecoflex 00-50 (1 : 1) |
3 |
66.5 |
12 |
Eco MIX 00-50 1 : 1 |
Sylgard 184 (10 : 1) |
1 |
Ecoflex 00-50 (1 : 1) |
1 |
76.0 |
13 |
Eco MIX 00-50 3 : 1 |
Sylgard 184 (10 : 1) |
3 |
Ecoflex 00-50 (1 : 1) |
1 |
85.6 |
14 |
Ecoflex 00-30 |
Ecoflex 00-30 (1 : 1) |
— |
— |
— |
43.4 |
15 |
Eco MIX 00-30 1 : 3 |
Sylgard 184 (10 : 1) |
1 |
Ecoflex 00-30 (1 : 1) |
3 |
57.2 |
16 |
Eco MIX 00-30 1 : 1 |
Sylgard 184 (10 : 1) |
1 |
Ecoflex 00-30 (1 : 1) |
1 |
69.6 |
17 |
Eco MIX 00-30 3 : 1 |
Sylgard 184 (10 : 1) |
3 |
Ecoflex 00-30 (1 : 1) |
1 |
82.1 |
18 |
Ecoflex 00-10 |
Ecoflex 00-10 (1 : 1) |
— |
— |
— |
— |
19 |
Eco MIX 00-10 1 : 3 |
Sylgard 184 (10 : 1) |
1 |
Ecoflex 00-10 (1 : 1) |
3 |
60.7 |
20 |
Eco MIX 00-10 1 : 1 |
Sylgard 184 (10 : 1) |
1 |
Ecoflex 00-10 (1 : 1) |
1 |
72.7 |
21 |
Eco MIX 00-10 3 : 1 |
Sylgard 184 (10 : 1) |
3 |
Ecoflex 00-10 (1 : 1) |
1 |
83.1 |
3. Results and discussion
The properties of the different elastomers, i.e. elongation at break (εmax (%)), ultimate tensile strength (σmax (MPa)), viscosity (η (Pa s)), optical transmittance (T (%)), breakdown strength (EBD (V μm−1)), leakage current (ileak (A)) and ileak sensitivity to temperature (k (°C−1)), are plotted as functions of the Young's modulus (Y (MPa)) and shown in Fig. 1. The properties are plotted as functions of Y, since usually it is the primary specification for applications. All of the properties are also tabulated (Table 2). The Fom(DEA) and Fom(DEG) are plotted in Fig. 2. Mechanical and electrical properties are discussed further below. Plots for other properties, namely Shore hardness (Shard [A] and Shard [00]), dielectric permittivity (ε′) and T over the entire visible spectrum, are provided in the ESI.†
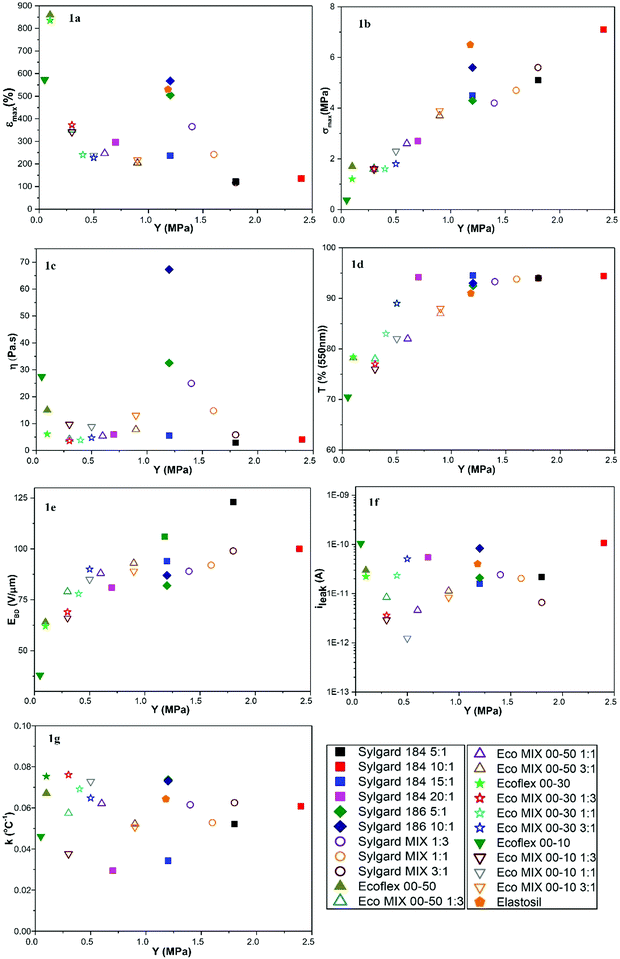 |
| Fig. 1 Various properties of the investigated silicone elastomers, plotted against the Young's modulus (Y). (a) Maximum strain. (b) Ultimate stress. (c) Viscosity@shear rate 0.1 s−1. (d) Transmittance at 0% pre-stretch at 550 nm. (e) Electrical breakdown strength. (f) ileak (applied electric field of 5 V μm−1) @ 25 °C and (g) sensitivity of ileak to temperature change. | |
Table 2 Properties of the different silicone elastomer formulations
|
Mechanical properties |
Electrical properties |
Sample name |
Y (MPa) |
ε
max (%) |
σ
max (MPa) |
σ
100% (MPa) |
η@shear rate 0.1 s−1 (Pa s) |
S
hard [A] |
S
hard [00] |
ε′ @1 Hz |
tan δ@1 Hz |
E
BD (V μm−1) |
i
leak@ 25 °C (×10−11, A) |
σ
AC @1 Hz (S cm−1) |
Measured at a shear rate of 0.524 s−1.
Too soft to be measured by this technique.
|
Sylgard 184 5 : 1 |
1.8 |
122 |
5.1 |
3.42 |
2.9
|
39 |
75 |
3.22 |
0.012 |
123
|
2.2 |
1.9 × 10−14 |
Sylgard 184
|
2.4
|
135
|
7.1
|
3.86
|
4
|
38
|
80
|
3.1
|
0.002
|
100
|
10.6
|
3.5 × 10
−15
|
Sylgard 184 15 : 1 |
1.2 |
237 |
4.5 |
0.77 |
5.5 |
28 |
72 |
3.2 |
0.008 |
94 |
1.6 |
1.3 × 10−14 |
Sylgard 184 20 : 1 |
0.7 |
296 |
2.7 |
0.39 |
6 |
18 |
68 |
3.1 |
0.013 |
81 |
5.5 |
2.2 × 10−14 |
Sylgard 186 5 : 1 |
1.2 |
505 |
4.3 |
0.49 |
32.5a |
26 |
75 |
3.5 |
0.002 |
82 |
2.1 |
4 × 10−15 |
Sylgard 186
|
1.2
|
567
|
5.6
|
0.48
|
67.3
|
24
|
73
|
3.4
|
0.001
|
87
|
8.3
|
1.6 × 10
−15
|
Sylgard MIX 1 : 3 |
1.4 |
365 |
4.2 |
0.60 |
24.9a |
38 |
75 |
3.5 |
0.002 |
89 |
2.4 |
2.3 × 10−15 |
Sylgard MIX 1 : 1 |
1.6 |
242 |
4.7 |
1.12 |
14.8a |
36 |
74 |
3.3 |
0.002 |
92 |
2 |
3.1 × 10−15 |
Sylgard MIX 3 : 1 |
1.8 |
117 |
5.6 |
2.45 |
5.8a |
34 |
73 |
3.3 |
0.003 |
99 |
6.6 |
4.4 × 10−15 |
Ecoflex 00-50
|
0.1
|
860
|
1.7
|
0.07
|
15
|
—
|
35
|
3.5
|
0.056
|
62
|
3
|
1 × 10
−13
|
Eco MIX 00-50 1 : 3 |
0.3 |
351 |
1.6 |
0.26 |
4.2 |
14 |
62 |
3.3 |
0.035 |
72 |
8.4 |
6.1 × 10−14 |
Eco MIX 00-50 1 : 1 |
0.6 |
247 |
2.6 |
0.62 |
5.4 |
23 |
67 |
3.3 |
0.027 |
88 |
4.6 |
4.5 × 10−14 |
Eco MIX 00-50 3 : 1 |
0.9 |
204 |
3.7 |
0.98 |
7.8 |
28 |
73 |
3.2 |
0.024 |
92 |
1.2 |
4 × 10−14 |
Ecoflex 00-30
|
0.1
|
835
|
1.2
|
0.05
|
6.1
|
—
|
23
|
3.4
|
0.040
|
59
|
2.2
|
8 × 10
−14
|
Eco MIX 00-30 1 : 3 |
0.3 |
373 |
1.6 |
0.23 |
3.6 |
10 |
53 |
3.4 |
0.035 |
66 |
0.4 |
6 × 10−14 |
Eco MIX 00-30 1 : 1 |
0.4 |
241 |
1.6 |
0.36 |
3.9 |
18 |
64 |
3.3 |
0.022 |
78 |
2.4 |
4.2 × 10−14 |
Eco MIX 00-30 3 : 1 |
0.5 |
228 |
1.8 |
0.43 |
4.7 |
28 |
73 |
3.2 |
0.016 |
87 |
5.1 |
2.7 × 10−14 |
Ecoflex 00-10
|
0.05
|
573
|
0.37
|
0.02
|
27.5
|
—
|
11
|
3.4
|
0.090
|
38
|
10.5
|
1.6 × 10
−13
|
Eco MIX 00-10 1 : 3 |
0.3 |
342 |
1.6 |
0.28 |
9.7 |
10 |
54 |
3.7 |
0.049 |
69 |
0.3 |
1 × 10−13 |
Eco MIX 00-10 1 : 1 |
0.5 |
238 |
2.3 |
0.63 |
8.9 |
24 |
66 |
3.5 |
0.061 |
94 |
0.12 |
1 × 10−13 |
Eco MIX 00-10 3 : 1 |
0.9 |
218 |
3.9 |
1.01 |
13.1 |
32 |
73 |
3.4 |
0.027 |
93 |
0.8 |
5 × 10−14 |
Elastosil |
1.18 |
530 |
6.5 |
0.68 |
— |
— |
— |
3.26 |
0.001 |
106 |
4 |
1.1 × 10−14 |
 |
| Fig. 2 Figures of merit (a) for actuator (Fom(DEA)) and (b) for generator (Fom(DEG)), both normalized with Sylgard 184. For the calculations, ε′ is measured at 1 Hz and φ calculated from hysteresis curves. | |
3.1. Mechanical properties
Sylgard 184 has the highest Y = 2.4 MPa and Ecoflex 00-10 the lowest Y = 0.05 MPa. Generally, for silicone elastomers, as the Y increases, σmax increases and εmax decreases. The low Y of Ecoflex 00-50, 00-30 and 00-10 (0.05 to 0.1 MPa) can be increased by blending with Sylgard 184, as shown by the Y values of Eco MIX 00-50, Eco MIX 00-30 and Eco MIX 00-10 (0.3 to 0.9 MPa). For soft and stretchable devices, extensibility (Fig. 1a) is a prominent parameter.23 Of all the formulations, Sylgard 184 5
:
1 has the lowest extensibility. By varying the mixing ratio of Sylgard 184, from 5
:
1 to 20
:
1, the εmax is doubled (122% to 296%). Sylgard 186 shows a high εmax of ∼568%. A blend of Sylgard 184 and 186 (i.e. Sylgard MIX 1
:
3) produces a higher εmax of 365%, which is a significant improvent compared to Sylgard 184. Ecoflex 00-50 and Ecoflex 00-30 have a high εmax of ∼ 800%, and their blends with Sylgard 184 (Eco MIX 00-50 and Eco MIX 00-30) show a εmax of ∼360%. The addition of a soft formulation to a hard one results in a composite with intermediate properties as expected. Sylgard 184 has the highest Shard [00] compared to the formulations tested (ESI†). The Sylgard 186 has a lower Shard [00] compared to Sylgard 184, whereas their blends (Sylgard MIX) show intermediate Shard [00]. Similarly, when the softer Ecoflex 00-10 with low Shard [00] is mixed with Sylgard 184, the resulting Eco MIX formulations have a much higher Shard [00] compared to the pure Ecoflex 00-10.
3.2. Viscosity and pot life
Viscosities are plotted in Fig. 1c and tabulated in Table 2. Formulations with low viscosity are preferred, as they result in easier processing. Generally, Ecoflex 00-50, Ecoflex 00-30, Ecoflex 00-10, Eco MIX 00-50, Eco MIX 00-30 and Eco MIX 00-10 possess low η compared to Sylgard 186 and Sylgard MIX, whilst Sylgard 186 has a higher premix η compared to Sylgard 184. Formulations with a η ∼ 5–10 Pa s are relatively easy to process, while higher η formulations typically require extra solvent or flow control agents, which in turn might compromise dielectric and/or mechanical properties.22 The pot life of Sylgard 184 and 186 is generally more than 1 h at room temperature. Ecoflex 00-50, 00-30 and 00-10 have a pot life ∼20 min only, which leaves very little time for processing. Interestingly, the blends of Ecoflex and Sylgard 184 have a pot life of ∼1 h, which is a significant improvement over the original Ecoflex formulations. The pot life data for all formulations are available in the ESI.†
3.3. Optical transmittance
T values (at 550 nm24 and 0% pre-stretch) are plotted in Fig. 1d. The data indicate that Sylgard 184, Sylgard 186, Sylgard MIX and Elastosil have better optical transparency compared to all of the Ecoflex and Eco MIX samples. It is noteworthy that Ecoflex shows a higher ε′ and a low T compared to Sylgard 184, which indicates the presence of substances other than organosilicon compounds. Sylgard 186 has a slightly lower T compared to Sylgard 184. If one needs transparent elastomers, then Ecoflex should be avoided or used in minimal amounts in blends. The T of the film samples varies over the entire visible spectrum (380–740 nm) and is also affected by pre-stretching (data in ESI†): as the pre-stretch increases, the T of the films decreases (data in ESI†).
3.4. Electrical properties
Of all the tested commercial formulations, Sylgard 184 shows the highest EBD of 100 V μm−1 (Fig. 1e). By varying the mixing ratio of Sylgard 184 from 10
:
1 to 5
:
1, the EBD increases to 123 V μm−1. Generally, silicone formulations with a higher Y show a higher EBD as well. By changing the mixing ratio of Sylgard 186 from 10
:
1 to 5
:
1, a higher ε′ of 3.5 can be achieved (ESI†). Ecoflex 00-50, 00-30 and 00-10 have a lower EBD compared to Sylgard 184 and 186, and the blends resulting from the amalgamation of these formulations, namely Eco MIX 00-50, Eco MIX 00-30 and Eco MIX 00-10, benefit from being moderately reinforced by the relatively high ε′ of Ecoflex 00-50, Ecoflex 00-30 and Ecoflex 00-10, and the high EBD of Sylgard 184. An efficient and quick way to include a higher ε′ and EBD in silicone formulations is by fabricating such blends instead of using high dielectric constant fillers (e.g. titanium dioxide), which require tedious processing.25,26 Furthermore, it is observed that all of the investigated elastomers break down electrically in similar ways by creating silica as a solid residue.27,28 The dielectric loss tangent for all elastomers at 1 Hz is much lower than 1. Ecoflex 00-50 and Eco MIX 00-10 1
:
1 show the highest loss of approximately 0.06, due to their capacitive nature, which is still in the range suitable for performing as dielectric transducers.29 Conductivity at 1 Hz (Table 2) for the elastomers is very low, and this is ideal for their performance as dielectric transducers.
3.5. Leakage current
The ileak should be ideally lower than ∼10−15 A for an elastomer to function as a reliable transducer,30 and it affects the actuation efficiency and the lifetime of the transducer, especially in high-voltage operations.31,32 In this work, ileak is measured at an applied electric field of 5 V μm−1. Measurements show that Sylgard 184 exhibits a relatively high ileak of ∼10−10 A at 25 °C. Sylgard 186 shows the highest ileak of ≈10−9 A at 60 °C. The ileak of the elastomers at 25 °C is plotted and shown in Fig. 1f, and all the ileak data at 25 °C, 40 °C and 60 °C are tabulated in the ESI.†ileak becomes significant with an increasing electric field and generates undesirable heat in the transducer.33 Also, as the operating temperature increases, ileak increases – as shown by our measurements. The sensitivity of ileak (k (°C−1)) to operating temperatures is plotted in Fig. 1g, which shows that Ecoflex 00-30, EcoMIX 00-10 1
:
3, Sylgard 186 5
:
1 and Sylgard 186 have higher sensitivity compared to the remaining elastomers. Apart from Sylgard 184 and 186, and Ecoflex 00-10, all samples show ileak ≤ 10 −11 A at all three operating temperatures.
3.6. Figure of merit
The Fom(DEA)20 and Fom(DEG),21 which take into account the most important relevant parameters (ε′, EBD, Y and strain energy (φ))34,35 of dielectric elastomers, help in reviewing their theoretical performance as transducers. However, the Fom does not take into account current leakage or dielectric and mechanical losses.36
The Fom(DEA) is derived by Sommer–Larsen and Larsen,20 and Fom(DEG) is derived by McKay et al.21 as:
| 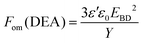 | (1) |
| 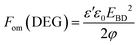 | (2) |
Here,
ε0 is the permittivity of free space (8.854 × 10
−12 F m
−1), and
φ is the strain energy function of the elastomer.
Fom(DEG) is comprehensive only when the strain energy function of the elastomer is considered, though data on this function are usually scarce. The
φ of the elastomers is calculated from their hysteresis curves, the details of which can be found in ESI.
†37 The
Fom(DEA) and
Fom(DEG) are normalised with the Sylgard 184 benchmark and plotted in
Fig. 2 as a function of Y. Upon analysing the
Fom(DEA) and
Fom(DEG), it can be concluded that pure Ecoflex formulations are the best candidates for performing as actuators and by far exceed the Sylgard 184 benchmark, albeit they exhibit lower
Fom(DEG) compared to Sylgard 184. Alternatively, Sylgard 184 5
![[thin space (1/6-em)]](https://www.rsc.org/images/entities/char_2009.gif)
:
![[thin space (1/6-em)]](https://www.rsc.org/images/entities/char_2009.gif)
1 and Elastosil qualify as better materials to perform as generators in comparison to Sylgard 184. From
Fig. 2, it is evident that softer elastomers perform well as actuators, and hard elastomers are good candidates for generators. In comparison to Sylgard 184, the following blends, namely Sylgard MIX 3
![[thin space (1/6-em)]](https://www.rsc.org/images/entities/char_2009.gif)
:
![[thin space (1/6-em)]](https://www.rsc.org/images/entities/char_2009.gif)
1, Eco MIX 00-50 3
![[thin space (1/6-em)]](https://www.rsc.org/images/entities/char_2009.gif)
:
![[thin space (1/6-em)]](https://www.rsc.org/images/entities/char_2009.gif)
1, Eco MIX 00-10 3
![[thin space (1/6-em)]](https://www.rsc.org/images/entities/char_2009.gif)
:
![[thin space (1/6-em)]](https://www.rsc.org/images/entities/char_2009.gif)
1 and Elastosil, show a higher
Fom(DEA) and
Fom(DEG) compared to Sylgard 184.
Hence, for transducer applications, the above blends and Elastosil would perform better than the benchmark. Another issue to consider when transitioning from research to commercialisation is a product's lifetime. Research on this crucial topic is emerging and holds great promise for the transducer technology.38–43 Of all the properties considered for Fom, the EBD, though ideally an intrinsic material property, is often compromised as a result of elastomer processing, electrode geometry and transducer operating conditions.44–46
3.7. Ageing
Properties of the aged samples (6 months) are remeasured to examine how ageing influences the properties of the film samples (tabulated in the ESI†). Sylgard 184 5
:
1, Sylgard 186, Sylgard MIX 1
:
3, Sylgard MIX 3
:
1, EcoMIX 00-50 1
:
3 and Eco MIX 00-30 3
:
1 show a higher Y with age, which is due to post-curing.47 Post-curing may be an effect of residual hydride groups condensing with water and then subsequently crosslinking,47 as well as sterically hindered reactive groups being given time enough to react. Generally for silicone elastomers, as Y increases in post-curing, σmax increases and εmax decreases. The εmax of most of the samples depriciated with age. Sylgard 184, Sylgard 184 15
:
1, Sylgard MIX 3
:
1 display a higher εmax with age, due to relaxation processes taking place in the network, which is also manifested by the decreasing Y with age as the elastomers soften. The EBD of Sylgard 184 15
:
1, Sylgard 186, Sylgard MIX, EcoMIX 00-50, EcoMIX 00-30 and EcoMIX 00-10 increased with age, which is commonly observed for silicone elastomers that harden while post-curing.38
The Shard [00] of the samples shows an overall decreasing trend with age except for Sylgard 184 15
:
1, Sylgard 184 20
:
1, Sylgard 186, Sylgard MIX 3
:
1, Ecoflex 00-30, Ecoflex 00-10, Eco MIX 30 1
:
3 and Eco MIX 10 3
:
1. With regards to T, the aged samples of Eco MIX 00-50 1
:
3, Eco MIX 00-50 1
:
1 and Eco MIX 00-10 1
:
3 show higher optical transparency. The rest of the aged samples show a similar or slightly reduced T compared to the fresh samples. If curing conditions are optimised, the impact of post-curing on elastomer properties can be diminished to a great extent.
4. Conclusion
After examining the results, it is notable that the properties of commercial elastomer formulations can be manipulated, by either mixing them at different stoichiometric ratios or by blending two formulations with each other. From the present study, it can also be concluded that blending is a quick method to make reliable soft networks with mechanical integrity, as opposed to varying the stoichiometry, which, if done inappropriately, often leads to the formation of weak networks.23 A mixture of two formulations with contrasting properties often results in a blend that is reinforced with the properties that are intermediate to both formulations. The properties of the blends always fall within limits, defined by the parent formulations. Appropriate curing conditions should be employed for these blends, to ensure that their properties remain constant over time. The pure Ecoflex formulations show much higher Fom(DEA) and very poor Fom(DEG), compared to the Sylgard 184 benchmark. The blends Sylgard MIX 3
:
1, EcoMIX 00-50 3
:
1, EcoMIX 00-10 3
:
1 and Elastosil show a higher Fom(DEG) and Fom(DEA) compared to the Sylgard 184 benchmark, and so they qualify as better candidates compared to Sylgard 184 in terms of fabricating transducers. It is thereby demonstrated that a blend of two formulations with different properties can be advantageous. Moreover, such blends can act as a good starting point for developing advanced hi-tech, versatile and stretchable devices.
Conflicts of interest
There are no conflicts to declare.
Acknowledgements
The authors acknowledge funding from the Independent Research Fund Denmark.
References
- S. Bauer, S. Bauer-Gogonea, I. Graz, M. Kaltenbrunner, C. Keplinger and R. Schwödiauer, Adv. Mater., 2014, 26, 149–162 CrossRef CAS.
- R. Herbert, J. Kim, Y. S. Kim, H. M. Lee and W. Yeo, Materials, 2018, 11, 1–33 CrossRef.
- I. A. Anderson, T. A. Gisby, T. G. Mckay, B. M. O. Brien and E. P. Calius, J. Appl. Phys., 2012, 112, 041101 CrossRef.
- J. D. Madden, Science, 2007, 318, 1094–1098 CrossRef CAS.
- D. Rus and M. T. Tolley, Nature, 2015, 521, 467–475 CrossRef CAS.
- S. Park, H. Kim, M. Vosgueritchian, S. Cheon, H. Kim, J. H. Koo, T. R. Kim, S. Lee, G. Schwartz, H. Chang and Z. Bao, Adv. Mater., 2014, 26, 7324–7332 CrossRef CAS PubMed.
- X. Wang, Y. Gu, Z. Xiong, Z. Cui and T. Zhang, Adv. Mater., 2014, 26, 1336–1342 CrossRef CAS PubMed.
- C. Choong, M. Shim, B. Lee, S. Jeon, D. Ko, T. Kang, J. Bae, S. H. Lee, K. Byun, J. Im, Y. J. Jeong, C. E. Park, J. Park and U. Chung, Adv. Mater., 2014, 26, 3451–3458 CrossRef CAS.
- S. Jung, J. H. Kim, J. Kim, S. Choi, J. Lee, I. Park, T. Hyeon and D. Kim, Adv. Mater., 2014, 26, 4825–4830 CrossRef CAS.
- X. Luo and P. T. Mather, Macromolecules, 2009, 42, 7251 CrossRef CAS.
- M. Kujawski, J. D. Pearse and E. Smela, Carbon, 2010, 48, 2409–2417 CrossRef CAS.
- I. D. Johnston, D. K. McCluskey, C. K. L. Tan and M. C. Tracey, J. Micromech. Microeng., 2014, 24, 035017 CrossRef.
- L. Cai, L. Song, P. Luan, Q. Zhang, N. Zhang, Q. Gao and D. Zhao, Sci. Rep., 2013, 3, 1–9 Search PubMed.
- S. Woo, J. Kong, D. Kim and J. Kim, J. Mater. Chem. C, 2014, 2, 4415–4422 RSC.
- H. Lee, S. Chang and E. Yoon, J. Microelectromech. Syst., 2006, 15, 1681–1686 CAS.
- Kenry, J. C. Yeo and C. T. Lim, Microsyst. Nanoeng., 2016, 2, 1–19 Search PubMed.
- S. Park, K. Mondal, R. M. Treadway, V. Kumar, S. Ma, J. D. Holbery and M. D. Dickey, ACS Appl. Mater. Interfaces, 2018, 10, 11261–11268 CrossRef CAS.
- D. Kwon, T. Lee, J. Shim, S. Ryu, M. S. Kim, S. Kim, T. Kim and I. Park, ACS Appl. Mater. Interfaces, 2016, 8, 16922–16931 CrossRef CAS.
-
S. Russo, T. Ranzani, J. Gafford, C. J. Walsh and R. J. Wood, Proceedings – IEEE International Conference on Robotics and Automation, 2016, pp. 750–757.
-
P. Sommer-Larsen and A. L. Larsen, Proceedings of SPIE: Electroactive Polymer Actuators and Devices (EAPAD), 2004, vol. 5385, pp. 68–77.
-
T. G. Mckay, E. Calius and I. A. Anderson, Proceedings of SPIE: Electroactive Polymer Actuators and Devices (EAPAD), 2009, vol. 7287, p. 72870P.
- P. Mazurek, S. Vudayagiri and A. L. Skov, Chem. Soc. Rev., 2019, 48, 1448–1464 RSC.
- J. S. Noh, Polymers, 2016, 8, 1–19 CrossRef.
- Y. Li, G. Xu, C. Cui and Y. Li, Adv. Energy Mater., 2018, 8, 1–28 Search PubMed.
- L. Yu and A. L. Skov, Int. J. Smart Nano Mater., 2015, 6, 268–289 CrossRef CAS.
- L. Yu and A. L. Skov, RSC Adv., 2017, 7, 45784–45791 RSC.
- A. L. Skov and L. Yu, Adv. Eng. Mater., 2018, 20, 1–21 CrossRef.
- L. Yu, F. B. Madsen and A. L. Skov, Int. J. Smart Nano Mater., 2017, 9, 1–16 Search PubMed.
- L. Yu, F. B. Madsen, S. Hvilsted and A. L. Skov, RSC Adv., 2015, 5, 49739–49747 RSC.
- F. B. Madsen, A. E. Daugaard, S. Hvilsted and A. L. Skov, Macromol. Rapid Commun., 2016, 37, 378–413 CrossRef CAS.
- P. Caspari, S. J. Du, F. A. Nu and D. M. Opris, J. Mater. Chem. C, 2018, 6, 2043–2053 RSC.
-
T. Töpper, B. Osmani, S. Lörcher, B. Müller, T. Töpper, B. Osmani, S. Lörcher and B. Müller, Proceedings of SPIE: Electroactive Polymer Actuators and Devices (EAPAD), 2017, vol. 10163, p. 101631F.
- T. Lu, Z. Shi, Z. Chen, H. Huang and T. J. Wang, Appl. Phys. Lett., 2015, 107, 152901 CrossRef.
- A. M. Freudenthal and M. Shinozuka, J. Appl. Polym. Sci., 1965, 9, 2565–2579 CrossRef.
- R. S. Rivlin and K. N. Sawyers, Trans. Soc. Rheol., 1976, 20, 545–557 CAS.
- S. Vudayagiri, S. Zakaria, L. Yu, S. S. Hassouneh, M. Benslimane and A. L. Skov, Smart Mater. Struct., 2014, 23, 1–15 CrossRef.
- C. T. Lachowicz, Int. J. Fatigue, 2001, 23, 643–652 CrossRef.
- F. B. Madsen, S. Zakaria, L. Yu and A. L. Skov, Adv. Eng. Mater., 2016, 18, 1154–1165 CrossRef CAS.
- S. Zakaria, L. Yu, G. Kofod and A. L. Skov, Mater. Today Commun., 2015, 4, 204–213 CrossRef CAS.
- S. Zakaria, P. H. F. Morshuis, M. Y. Benslimane, L. Yu and A. L. Skov, Smart Mater. Struct., 2015, 24, 055009 CrossRef.
-
A. Iannarelli and M. G. Niasar, Proceedings of SPIE: Electroactive Polymer Actuators and Devices (EAPAD), 2017, vol. 10163, p. 1016326.
-
P. Lotz, M. Matysek and H. F. Schlaak, Proceedings of SPIE: Electroactive Polymer Actuators and Devices (EAPAD), 2011, vol. 7976, p. 79760P.
- T. Köckritz, R. Luther, G. Paschew, I. Jansen, A. Richter, O. Jost, A. Schönecker and E. Beyer, Micromachines, 2016, 7, 1–15 CrossRef PubMed.
-
R. Valentina, R. V. Mateiu, L. Yu and A. L. Skov, Proceedings of SPIE: Electroactive Polymer Actuators and Devices (EAPAD), 2017, vol. 10163, p. 1016328.
- S. Jin, A. Koh, T. Li, J. Zhou, X. Zhao, W. Hong, J. Zhu and Z. Suo, J. Polym. Sci., Part B: Polym. Phys., 2011, 49, 504–515 CrossRef.
- A. Trols, A. Kogler, R. Baumgartner, R. Kaltseis, C. Keplinger, R. Schwodiauer, I. Graz and S. Bauer, Smart Mater. Struct., 2013, 22, 104012 CrossRef.
- S. Zakaria, F. B. Madsen and A. L. Skov, Polym.-Plast. Technol. Eng., 2017, 56, 83–95 CrossRef CAS.
Footnote |
† Electronic supplementary information (ESI) available. See DOI: 10.1039/c9tc05072h |
|
This journal is © The Royal Society of Chemistry 2020 |
Click here to see how this site uses Cookies. View our privacy policy here.