DOI:
10.1039/D0SC00247J
(Edge Article)
Chem. Sci., 2020,
11, 6682-6689
A cobalt phosphide catalyst for the hydrogenation of nitriles†
Received
14th January 2020
, Accepted 4th June 2020
First published on 9th June 2020
Abstract
The study of metal phosphide catalysts for organic synthesis is rare. We present, for the first time, a well-defined nano-cobalt phosphide (nano-Co2P) that can serve as a new class of catalysts for the hydrogenation of nitriles to primary amines. While earth-abundant metal catalysts for nitrile hydrogenation generally suffer from air-instability (pyrophoricity), low activity and the need for harsh reaction conditions, nano-Co2P shows both air-stability and remarkably high activity for the hydrogenation of valeronitrile with an excellent turnover number exceeding 58000, which is over 20- to 500-fold greater than that of those previously reported. Moreover, nano-Co2P efficiently promotes the hydrogenation of a wide range of nitriles, which include di- and tetra-nitriles, to the corresponding primary amines even under just 1 bar of H2 pressure, far milder than the conventional reaction conditions. Detailed spectroscopic studies reveal that the high performance of nano-Co2P is attributed to its air-stable metallic nature and the increase of the d-electron density of Co near the Fermi level by the phosphidation of Co, which thus leads to the accelerated activation of both nitrile and H2. Such a phosphidation provides a promising method for the design of an advanced catalyst with high activity and stability in highly efficient and environmentally benign hydrogenations.
Introduction
The development of efficient, sustainable and cost-effective chemical processes is one of the ultimate goals of chemical research in both academia and industry. In this regard, the advance of catalytic hydrogenation processes of carboxylic acid derivatives is a major step towards developing green technology for producing numerous valuable chemicals and fuels.1,2 In particular, the hydrogenation of nitriles represents a significantly important and straightforward method with 100% atomic efficiency for the synthesis of primary amines, which are ubiquitous motifs and are widely used in industry as solvents, surfactants, polymer intermediates, dyes, and important building blocks for pharmaceuticals.3–5 In industrial nitrile hydrogenation processes, earth-abundant metal catalysts, Ni and Co-based sponge metals (RANEY® catalysts), have been mainly employed.6 However, these metallic (zero-valent) catalysts have the fatal issue of air instability (pyrophoricity), which results in the difficulty of catalyst handling,7 and thus makes the chemical processes complicated. Furthermore, these catalysts show low activity, requiring harsh reaction conditions such as high H2 pressures (200–400 bar) with limited substrate scope, and tend to significantly deactivate during storage.8
Hydrogenation of nitriles is facilitated by precious metal catalysts mainly based on Pt,9–11 Ru,12 Rh,13,14 Re15 and Ir.16 These catalysts are active under mild conditions; nevertheless, the constituent metals are expensive and rare. Alternatively, some improvements using homogeneous earth-abundant metal catalysts have been reported.17–26 However, these catalysts still require high H2 pressures and have practical drawbacks, such as difficulty of catalyst recovery and reuse, the need for synthetically complex ligands and the contamination risk of dissolved metals. Heterogeneous catalysts have numerous advantages over homogeneous catalysts, which include their high durability, facile separation from the reaction mixture and subsequent reusability. In recent studies on heterogeneous catalysts, surface modification of metal nanoparticles by pyrolysis, as a means to improve air stability, was successfully explored.27–31 The pyrolysis of metal–nitrogen complexes27–30 and metal–organic frameworks (MOFs)31 can provide Co and Ni nanoparticles with an N-doped carbon layer, which serve as air-stable and reusable catalysts for nitrile hydrogenation. However, owing to the shielding of surface active sites by the carbon coating, the air stability comes at the expense of activity, and these state-of-the-art catalysts still suffer from insufficient activity with a turnover number (TON) of less than 62.28 Therefore, earth-abundant metal heterogeneous catalysts with both high stability and activity have not yet been developed,32 and the establishment of a promising means to break the trade-off between air stability and activity remains a great challenge.
Herein, we show that the nano-sized cobalt phosphide (nano-Co2P) serves as a highly efficient heterogeneous catalyst for nitrile hydrogenation under mild conditions. The well-defined nano-Co2P catalyst has a unique metallic nature with air stability and shows a remarkably high activity with an excellent TON exceeding 58000. Moreover, nano-Co2P is shown, for the first time, to promote the ambient pressure hydrogenation of various aromatic and aliphatic nitriles, including di- and tetra-nitriles, which represents a breakthrough in overcoming the limitations of conventional catalysts. Metal phosphides are less common metals that extend beyond traditional metal (0) and metal oxide materials. Although metal phosphides have recently emerged as new electro- and photo-catalysts for the hydrogen evolution reaction33–37 and hydrotreatment catalysts in the petroleum industry,38–41 their catalysis for organic synthesis remains largely unexplored despite their unique characteristics.42–46 Therefore, nano-Co2P reported here can be categorized as a new class of catalyst for the hydrogenation of nitriles that is quite different from conventional catalysts of modified metal nanoparticles, sponge metals and metal complexes.
Results and discussion
Preparation and characterization of nano-Co2P
A nano-Co2P was newly synthesized based on a previous report with some modifications.47 Briefly, CoCl2·6H2O was added to 1-octadecene in the presence of hexadecylamine and triphenylphosphite. The mixture was then stirred with increasing the temperature to 300 °C under an Ar atmosphere, which gave a black colloidal solution. The precipitate was collected by centrifugation and washed with acetone and chloroform, affording the nano-Co2P. Transmission electron microscope (TEM) images of the obtained nano-Co2P from the side view showed that nanorods with an average size of 20 × 9 nm (length × width) were regularly formed (Fig. 1a) and the hexagonal phase of nano-Co2P was observed from the top view (Fig. 1b). The rod-length of nano-Co2P is slightly shorter than the 33 nm length of Co2P previously reported.47 The high-resolution TEM (HRTEM) image further revealed that lattice fringes with a d-spacing of 0.22 nm corresponded to the (121) plane of the di-cobalt phosphide (Co2P) and the selected area electron diffraction (SAED) pattern (Fig. 1c inset) showed that the diffraction rings were indexed to (121), (002), (312) and (322) planes of the Co2P crystal, in agreement with the XRD pattern (Fig. S3a†).48 Scanning transmission electron microscope (STEM) with elemental mapping of nano-Co2P confirmed the presence of the constituent elements cobalt and phosphorus, which were distributed homogeneously within each nano-Co2P (Fig. 1d–f). The corresponding energy dispersive X-ray (EDX) spectrum also revealed that the atomic ratio between Co and P was close to 2
:
1. All these results strongly demonstrated the successful synthesis of a nano-sized Co2P. The fabricated nano-Co2P was stable and could be treated in air.
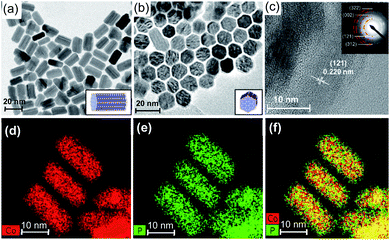 |
| Fig. 1 (a) Side view TEM image of nano-Co2P showing a nanorod morphology. (b) Top view TEM image of nano-Co2P showing the hexagonal phase structure. (c) HRTEM image of nano-Co2P with a SAED pattern (inset). Elemental mapping images of (d) Co and (e) P. (f) Composite overlay image formed from (d) and (e). | |
Catalytic performance of nano-Co2P in nitrile hydrogenation
The catalytic activity of various metal phosphides was investigated in the hydrogenation of valeronitrile (1a) as a model substrate in the presence of NH3 aq. under an H2 pressure of 40 bar at 130 °C without any catalyst treatment before the reaction. The results are shown in Fig. 2a. It is noted that nano-Co2P exhibited high catalytic activity, which produced the corresponding amine (1b) in high yield. Nano-cobalt phosphide with different compositions, nano-CoP also promoted the hydrogenation, giving a lower yield of 1b compared with nano-Co2P. In sharp contrast to CoxP (x = 1 or 2), other Ni-, Cu-, and Fe-based metal phosphides showed poor activity. Furthermore, the Co nanoparticles (NPs) without phosphidation, CoOx NP and bulk Co2P, were hardly active. These results clearly showed a specific behavior of nano-CoxP that was distinguished from the other metal phosphides and the conventional Co catalysts. This work is the first demonstration of a metal phosphide capable of the hydrogenation of carboxylic acid derivatives. The incorporation of phosphorus atoms into cobalt generated high catalytic activity for nitrile hydrogenation.
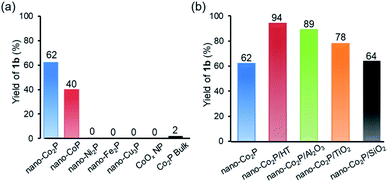 |
| Fig. 2 (a) Catalytic performance of various metal phosphides and Co oxide nanoparticles in the hydrogenation of 1a. (b) Catalytic performance of nano-Co2P and nano-Co2P on different supports. Reaction conditions: catalyst (metal: 4.2 mol%), 1a (0.5 mmol), 2-propanol (3 mL), NH3 aq. (1.2 mL), 130 °C, 40 bar H2, 1 h. | |
To evaluate the support effects of nano-Co2P with the highest activity, nano-Co2P supported on various materials was investigated in the hydrogenation of 1a (Fig. 2b). Co2P dispersed on supports all showed an improved activity from nano-Co2P itself in the yield of 1b owing to the increase of surface area of Co2P by dispersion. Hydrotalcite (HT: [Mg6Al2(OH)16]CO3·4H2O) was the best support among various materials.
With the optimized nano-Co2P/HT catalyst in hand, the catalytic performance was investigated under several reaction conditions. Remarkably, the high activity was demonstrated under much milder reaction conditions, with the hydrogenation of 1a proceeding to give a high yield of 1b even when the H2 pressure was decreased to just 1 bar (Scheme 1a). This is the first example of an earth-abundant metal catalyst promoting ambient pressure hydrogenation of nitriles. Furthermore, increasing the nitrile amounts to 5.0 g resulted in a high yield production of 1b with excellent TON exceeding 58000 based on the active surface Co atoms of nano-Co2P. This TON value is over 20- to 500-fold greater than those of the homogeneous and heterogeneous earth-abundant catalysts developed to date (Table S2†), which demonstrates the high activity and stability of this catalyst even under prolonged heating at elevated temperatures (Scheme 1b).
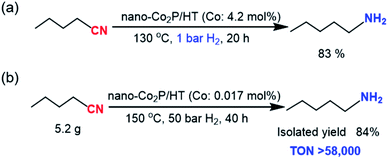 |
| Scheme 1 (a) Hydrogenation of 1a under ambient pressure of H2. (b) Gram scale experiment. | |
After the reaction, nano-Co2P/HT was easily recovered and proved to be reusable without any catalyst pre-treatment unlike previous reports29 and retained its high activity and selectivity even after the 7th reuse (Fig. 3a). The initial reaction rate was also maintained during the reuse experiments (Fig. S4†). Furthermore, the TEM image of the used nano-Co2P/HT showed that the rod-structure of nano-Co2P with an average size of 26 × 8 nm (length × width) was very similar to that of the fresh one, revealing the high durability of nano-Co2P (Fig. S1†). To determine whether the hydrogenation proceeded heterogeneously, nano-Co2P/HT was removed from the reaction mixture by filtration at 35% yield of 1b. The filtrate was again treated under hydrogen reaction conditions, and provided no formation of additional amine products, which clearly supported that the above hydrogenation occurred on the Co2P surface (Fig. 3b).
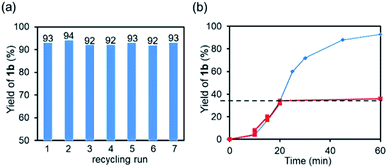 |
| Fig. 3 (a) Reuse experiments of nano-Co2P/HT in the hydrogenation of 1a to 1b. (b) Hot filtration experiment of nano-Co2P/HT in the hydrogenation of 1a to 1b. (blue line) In the presence of nano-Co2P/HT, and (red line) remove nano-Co2P/HT at 20 min. Reaction conditions: nano-Co2P/HT (0.1 g), 1a (0.5 mmol), 2-propanol (3 mL), NH3 aq. (0.8 mL), 130 °C, 40 bar H2, 1 h. | |
Next, the nano-Co2P/HT catalyst was examined for the hydrogenation of various nitriles. The results summarized in Table 1 demonstrate the remarkably wide scope of this catalyst: aliphatic (Table 1, entries 1–4) and aromatic nitriles (Table 1, entries 5–15), including benzonitriles having electron withdrawing or donating groups, were efficiently converted to the corresponding primary amines in high yields. Heteroaromatic nitriles, including nitrogen and oxygen atoms, were also good substrates and the desired amines were obtained in high yields (Table 1, entries 7–10). Furthermore, nano-Co2P was evaluated in the chemoselective hydrogenation of nitriles containing easily reducible functional groups, which is known as a highly challenging objective because of its low functional group tolerance.18 Notably, nano-Co2P showed high chemoselectivity: functional groups, such as ketone and ester moieties, were tolerant, and gave the corresponding amines in high yields (Table 1, entries 14 and 15).
Table 1 Hydrogenation of nitriles using the nano-Co2P/HT catalysta
Nano-Co2P/HT was also applicable to the hydrogenation of multinitriles (Scheme 2). Adiponitrile was hydrogenated to 1,6-hexamethylenediamine (16b), which is an important building block for the production of Nylon-6,6. Sebaconitrile, which can be obtained from biomass derivatives,49 was converted selectively to 1,10-diaminodecane (17b). Aromatic dinitriles, terephthalonitrile and isophthalonitrile sufficiently provided diamines (18b and 19b). A tetra-nitrile, 3,3′,3′′,3′′′-(butane-1,4-diyldinitrilo)tetrapropanenitrile, was also sufficiently transformed to its corresponding amine with all CN end groups hydrogenated (20b).
 |
| Scheme 2 Hydrogenation of multinitriles using the nano-Co2P catalyst. Reaction conditions: nano-Co2P/HT (0.1 g), substrate (0.5 mmol), 2-propanol (3 mL), NH3 aq. (1.2 mL), yield determined by GC using biphenyl as the standard. a Isolated yield as a hydrochloride salt. b NH3 aq. (0.6 mL), 4 h. c 4 h. d 10 h. e Substrate (0.07 mmol), 100 °C, 50 bar H2, 3 h and yield determined by NMR using biphenyl as the standard. | |
Moreover, various nitriles underwent an atmospheric pressure hydrogenation in the presence of nano-Co2P/HT, giving excellent yields of amines (Scheme 3), which demonstrated the generality and the high catalytic performance of nano-Co2P.
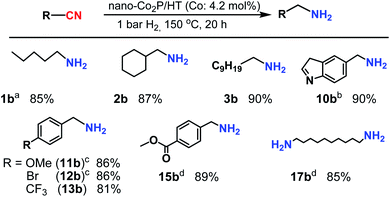 |
| Scheme 3 Hydrogenation of nitriles using the nano-Co2P catalyst under ambient pressure of H2. Reaction conditions: nano-Co2P/HT (0.1 g), substrate (0.5 mmol), 2-propanol (3 mL), NH3 aq. (1.2 mL) and yield determined by GC using biphenyl as the standard. a 130 °C. b NH3 aq. (0.6 mL). c 16 h. d Nano-Co2P/HT (0.2 g), NH3 aq. (0.6 mL). | |
To investigate the origin of the unique catalytic properties of nano-Co2P, X-ray absorption fine structure (XAFS) analysis was carried out under an air atmosphere. The Co K-edge X-ray absorption near edge structure (XANES) spectra of nano-CoP and nano-Co2P exposed in air are depicted in Fig. 4a. The absorption edge energies were much lower than that of CoO and very similar to that of Co foil, which suggested that the Co species in nano-CoP and nano-Co2P represented metallic states even under atmospheric conditions.50 Fourier transformation (FT) of the k3-weighted extended X-ray adsorption fine structure (EXAFS) data of nano-CoP and nano-Co2P showed two main peaks around 1.8 and 2.3 Å, which were attributed to Co–P and Co–Co scattering,51 respectively (Fig. 4b). A metallic nature with hydrogenation ability of nano-Co2P can be derived from the construction of the metal–metal bond.52 The higher peak intensity of the Co–Co bond of nano-Co2P than nano-CoP may account for the superior activity of nano-Co2P to nano-CoP in the nitrile hydrogenation.53
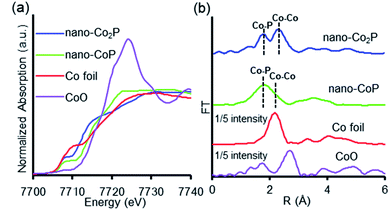 |
| Fig. 4 (a) Co K-edge XANES spectra of nano-Co2P, nano-CoP, Co foil, and CoO. (b) Fourier transformation of the k3-weighted EXAFS of nano-Co2P, nano-CoP, Co foil, and CoO. | |
The electronic state of surface Co in nano-Co2P was also investigated by X-ray photoelectron spectroscopy (XPS). The Co 2p spectrum of nano-Co2P showed a typical pair of Co 2p3/2 and Co 2p1/2 (Fig. 5a). The Co 2p3/2 and 2p1/2 binding energy peaks were located dominantly at 777.7 eV and 792.9 eV, respectively, which were very close to those of metallic Co 2p3/2 (777.9 eV) and 2p1/2 (793.5 eV). Thus, there were reduced Co species in the nano-Co2P surface that were partially negatively charged (Coδ−). These data are consistent with the XANES results (Fig. 4a).54 The XPS spectrum of P 2p showed an asymmetric peak, which could be split into two peaks located at 129.0 and 130.0 eV attributed to P 2p3/2 and P 2p1/2 in Co2P,55 and another peak that split into two peaks located at 133.3 and 134.4 eV, which represented the phosphate species due to the surface oxidation (Fig. S5†).56
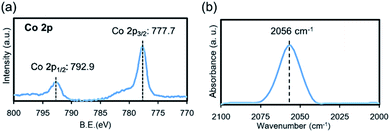 |
| Fig. 5 (a) Co 2p XPS spectrum of nano-Co2P. (b) In situ FT-IR spectroscopy of CO adsorption on nano-Co2P. | |
FT-IR spectroscopy of CO adsorption is another important tool to investigate the electronic state of Co. Fig. 5b shows the FT-IR spectrum of CO chemisorption on nano-Co2P. An absorption band was observed at 2056 cm−1, which lay at lower frequencies than that of gaseous CO (2143 cm−1) owing to the back-donation of electrons to the 2π* antibonding molecular orbital of CO. This red-shift was attributed to CO linearly adsorbed on an electron-populated cobalt center.57
Taken as a whole, these results clearly showed that nano-Co2P has an air-stable metallic nature (Coδ−) much different from the conventional earth-abundant metals (0) with air instability. Therefore, nano-Co2P enables easy catalyst handling with a safety in air and no requirement for pre-treatment with H2 at high temperatures before the hydrogenation.
Finally, the structure–activity relationship of nano-Co2P was investigated by the density functional theory (DFT) calculations (see the ESI† for DFT calculation details). Fig. 6a and b show the projected density of states (PDOS) of Co d-orbitals in bulk Co, bulk Co2P, and Co2P (0001) surfaces, and their differences, respectively. It is noted that Co atoms at the Co2P surface exhibited larger amplitudes of the d-orbital PDOS around the Fermi level compared with the Co atoms both in the bulk Co and in bulk Co2P.58 This increase of the d-electrons around the Fermi level favors the donation of the electrons to the lowest unoccupied molecular orbital (LUMO) of nitrile, which dissociates the C
N bond.59 We also investigated H2 dissociation around the Co atoms at the Co2P surface. The H2 molecule at the hollow site of the Co2P was dissociated, where the distance between two H atoms was increased from 0.79 Å to 2.02 Å (Fig. 6d). The dissociative adsorption energy of H2 on the Co2P surface was calculated to be 26 kcal mol−1, which was larger than that on the Co surface.60 This indicated that Co2P enhanced the H2 dissociation compared with Co metal through the electron transfer from Co2P to the σ* orbital of H2. These calculation results well support the high activity of nano-Co2P in the hydrogenation of nitriles, where the increase of the d-electrons in nano-Co2P would enhance the back-donation to the π* orbital of nitrile, which weakens the C
N bond. The activated C
N bond may easily be hydrogenated by the dissociatively adsorbed hydrogen at the Co site.
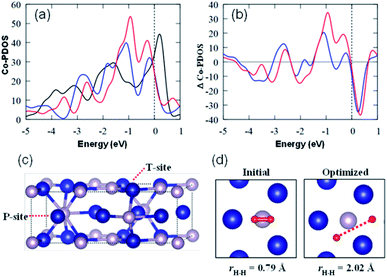 |
| Fig. 6 (a) Projected density of states of the Co atom (Co-PDOS) in bulk Co (black), bulk Co2P (blue) and on the Co2P surface (red). (b) Differences of Co-PDOSs (ΔCo-PDOS) between bulk Co and bulk Co2P (blue) and between the bulk Co and Co2P surface (red). (c) Simulated unit cell of bulk Co2P (Co in blue and P in pink). Co sites have tetrahedral (T) and pyramidal (P) geometries in the hexagonal Co2P, and the DOSs of the Co atoms at T-site are shown in (a) and (b) (the others are in the ESI†). Fermi level is set to be zero. (d) Initial and optimized structures of the H2 molecules on Co2P (0001) T-site surface with the height of 1.2 Å and the distances between the hydrogen atoms (rH–H). Several other structures are presented in the ESI.† | |
Conclusions
We report a new, general and green sustainable methodology for producing primary amines from nitriles by developing a well-defined nano-Co2P catalyst. The fabricated nano-Co2P uniquely has air stability and high catalytic activity for a wide range of nitriles to the corresponding primary amines under mild conditions. Typically, the catalyst could be operated under an H2 pressure of just 1 bar, far milder than the conventional harsh reaction conditions, which represents the first example of an earth-abundant metal catalyst for ambient pressure hydrogenation of nitriles. XAFS and DFT calculations reveal that the nano-Co2P catalyst originally has a metallic nature with a high d-electron density of Co, which leads to high activity with air stability through the accelerated activation of both nitrile and H2. Our findings not only provide a new category of nitrile hydrogenation catalysts, but also represent the first attempt to use metal phosphides as air-stable heterogeneous catalysts for the hydrogenation of carboxylic acid derivatives, which might lead to a new paradigm in the development of efficient, sustainable and cost-effective hydrogenation of various compounds, especially other carboxylic acid derivatives.
Experimental
Materials
All precursors and solvents were used as received, without further purification. CoCl2·6H2O and 1-octadecene (technical grade 90%) were purchased from Nacalai Tesque, Inc., and Sigma-Aldrich. Co. Hexadecylamine and triphenyl phosphite were purchased from Tokyo Chemical Industry Co., Ltd. Hydrotalcite (AD 500NS) was purchased from Tomita Pharmaceutical Co., Ltd. Al2O3 was purchased from Sumitomo Chemical. TiO2 (JRC TIO-9) was provided by the Catalysis Society of Japan as a reference catalyst. SiO2 (Q-9) was purchased from Fuji Silysia Chemicals Ltd. All nitriles were commercially available. Tokyo Chemical Industry Co., Ltd.: valeronitrile (>98%), decanenitrile (>98%), phenylacetonitrile (>98%), anisonitrile (>98%), 4-(trifluoromethyl)benzonitrile (>98%), methyl-4-cyanobenzoate (>98%), adiponitrile (>98%), sebaconitrile (98%), and isophthalonitrile (>98%). FUJIFILM Wako Pure Chemical: 1-adamantanecarbonitrile (97%), benzonitrile (>98%), 3-cyanopridine (>98%), 4-cyanopridine (>98%), 2-furancarbonitrile (98%), 5-cyanopridine (96%), 4-acetylbenzonitrile (>98%), and terephthalonitrile (>95%). Sigma-Aldrich: cyclohexanecarbonitrile (98%) and 4-bromobenzonitrile (99%).
Synthesis of nano-metal phosphides
All reactions were carried out under an argon atmosphere using standard Schlenk line techniques. In a typical synthesis, CoCl2·6H2O (1.0 mmol) and 2.4 g (10 mmol) of hexadecylamine were combined with 10.0 mL of 1-octadecene and 2.6 mL (10 mmol) of triphenyl phosphite in a Schlenk flask. The mixture was heated to 150 °C under an argon flow and maintained for 1 h. The temperature was then increased to 300 °C and kept at this temperature for 2 h, which yielded a black colloidal solution. The mixture was then cooled in air to room temperature. The obtained colloid was isolated by precipitation with acetone, and the redispersion and precipitation cycles continued using a chloroform and acetone mixed solvent (chloroform
:
acetone = 1
:
1) until the supernatant liquid was transparent. The obtained powder was dried in vacuum overnight at room temperature to give nano-Co2P. The other nano-sized metal phosphides were prepared in a similar way to nano-Co2P by using the corresponding metal precursors (Ni: NiCl2·6H2O, Cu: CuCl2·2H2O, and Fe: Fe(CO)5).
Preparation of the nano-Co2P/support
Typically, nano-Co2P (0.04 g) was dispersed in hexane (50 mL) and stirred with hydrotalcite (1.0 g) for 2 h at room temperature. The obtained powder was dried in a vacuum overnight at room temperature to give nano-Co2P/HT as a gray powder. The same procedure was used to prepare other nano-Co2P/support catalysts (support = Al2O3, TiO2 and SiO2).
Synthesis of nano-CoP
In a typical synthesis, under a flow of argon, Co(acac)2 (1 mmol), 1-octadecene (5 mL, 15.6 mmol) and oleylamine (10 mL, 30.4 mmol) were placed in a Schlenk flask. The mixture was stirred and heated to 120 °C and kept at this temperature for 1 h. Then, triphenylphosphine (5 mL, 11 mmol) was added to the above solution and heated to 340 °C for 4 h. Afterwards, the mixture was allowed to cool in air to room temperature. To remove as much organics as possible, redispersion and precipitation cycles continued until the supernatant liquid was transparent using a hexane and ethanol mixed solvent (hexane
:
ethanol = 1
:
1). The obtained powder was dried at room temperature in a vacuum overnight. The corresponding EDX spectrum revealed that the atomic ratio between Co and P was close to 1
:
1.
Preparation of CoOx
All reactions were carried out under an argon atmosphere using standard Schlenk line techniques. Tri-n-octylphosphine oxide (0.1 g) and 0.09 g (0.32 mmol) of oleic acid were dissolved with 12 mL of 1,2-dichlorobenzene in a Schlenk flask. The mixture was heated to 180 °C under an argon flow and maintained for 10 min. 0.52 g (1.52 mmol) of Co2(CO)8 dissolved in 4 mL of 1,2-dichlorobenzene was quickly injected and stirred for 4 min. Afterwards, the mixture was allowed to cool in air to room temperature. The obtained powder was purified by using ethanol and centrifuged. Then the supernatant was removed and the powder was redispersed in hexane. The precipitation/redispersion process was performed twice overall.
Procedure for catalytic hydrogenation
A typical reaction procedure for the hydrogenation of nitrile using nano-Co2P/HT was as follows. Nano-Co2P/HT powder (0.1 g) was placed in a 50 mL stainless-steel autoclave with a Teflon inner cylinder, followed by addition of nitrile (0.5 mmol), 2-propanol (3 mL) and NH3 aq. (25%, 1.2 mL). The reaction mixture was stirred vigorously at 130 °C under 40 bar of H2. After the reaction, the reaction solution was analyzed by GC to determine the conversion and the yield using biphenyl as an internal standard. After reaction, to obtain the hydrochloride salts, the crude reaction mixture was filtered to remove the catalyst and the ammonia was removed under vacuum conditions. The mixture was then added to a hydrogen chloride solution (1.25 M, 1,4-dioxane). The solvent was removed leaving behind the corresponding salt, giving the pure hydrochloride salts, which were subjected to NMR analysis.
Characterization
Gas chromatography (GC-FID) and GC-mass spectrometry (GC-MS) were performed using a Shimadzu GC-2014 instrument equipped with an InertCap for amines (30 m × 0.32 mm i.d.) and a GCMS-QP2010 SE instrument equipped with an InertCap WAX-HT capillary column (30 m × 0.25 mm i.d.). The oven temperature was programmed as follows: 120 °C starting temperature, kept for 3 min, temperature ramp at 10 °C min−1 to 260 °C, then at −20 °C min−1 to 120 °C. Other conditions were as follows: 2.44 mL min−1 column flow rate, 10.0 split ratio; vaporization chamber temperature of 250 °C; detector temperature of 260 °C. 1H and 13C nuclear magnetic resonance (NMR) spectra were recorded using a JEOL JNM-ESC400 spectrometer. Transmission electron microscopy (TEM) observations were carried out using a JEM-ARM200F instrument operated at 200 kV. Scanning transmission electron microscopy (STEM) images with elemental maps were collected using a FEI Titan Cubed G2 60-300 instrument operated at 300 kV, and equipped with a Super-X energy-dispersive X-ray spectroscopy (EDX) detector. Elemental mapping based on quantification analysis of EDX spectra was carried out using Esprit. The TEM sample and STEM sample were deposed without any pretreatment on a holey carbon supported Cu-grid (167 mesh. 30 μm thickness) and transferred to a microscope. Co K-edge X-ray absorption spectra were recorded at room temperature at the BL01B1 and BL14B2 lines, using a Si (311) or Si (111) monochromator, at SPring-8, Japan Synchrotron Radiation Research Institute (JASRI), Harima, Japan. Data analysis was performed using the REX 2000 program, ver. 2.5.7 (Rigaku). Fourier-transform infrared (FT-IR) spectra were recorded using a JASCO FT-IR 4100 spectrometer equipped with a mercury cadmium telluride detector. X-ray photoelectron spectroscopy (XPS) analyses were performed on an ESCA1700R system equipped with a dual Mg/Al X-ray source and a hemispherical analyzer operating in a fixed analyzer transmission mode. Spectra were obtained using a pass energy of 58.7 eV; an Al Kα X-ray source was operated at 350 W and 14 kV. Excess charges on the samples were neutralized by argon ion sputtering. The analysis area was 0.8 × 2 mm. The working pressure in the analyzing chamber was less than 1 × 10−7 Pa. Spectra were acquired in the Co 2p, P 2p, O 1s, C 1s, and Si 2p regions. The C 1s peak at a binding energy (BE) of 285 eV was taken as an internal reference.
Conflicts of interest
There are no conflicts to declare.
Acknowledgements
This work was supported by JSPS KAKENHI Grant Nos 26289303, 26105003, 24246129, 17H05224, 18H01790 and 20H02523. This study was partially supported by the Cooperative Research Program of Institute for Catalysis, Hokkaido University (19A1002 and 20B1027). A part of this work was supported by the “Nanotechnology Platform Program” at Hokkaido University (A-19-HK-0039) and Nanotechnology Open Facilities in Osaka University (A-19-OS-0060), Ministry of Education, Culture, Sports, Science and Technology (MEXT), Japan. The TEM experiments were performed at the Research Center for Ultra-high Voltage Electron Microscopy, Osaka University. The DFT calculations were performed on the Numerical Materials Simulator at NIMS and the computer resource offered under the category of General Projects by Research Institute for Information Technology, Kyushu University. We thank Dr. Ina (SPring-8) for XAFS measurements (2019A1390, 2019A1649 and 2019B1560) and R. Ota of Hokkaido University for STEM analysis. We express our thanks to Prof. Nakajima in Hokkaido University for useful discussion.
Notes and references
-
A. P. G. Kieboom, F. van Rantwijk and H. van Bekkum, Hydrogenation and Hydrogenolysis in Synthetic Organic Chemistry, Delft University Press, Delft, 1977 Search PubMed.
- J. Pritchard, G. Filonenko, R. Putten, E. Hensen and E. Pidko, Chem. Soc. Rev., 2015, 44, 3808–3833 RSC.
- J. L. Legras, G. Chuzel, A. Arnaud and P. Galzy, World J. Microbiol. Biotechnol., 1990, 6, 83–108 CrossRef CAS PubMed.
-
S. A. Lawrence, Amines: Synthesis Properties, and Application, Cambridge University Press, Cambridge, 2006 Search PubMed.
- S. D. Roughley and A. M. Jordan, J. Med. Chem., 2011, 54, 3451–3479 CrossRef CAS PubMed.
-
S. Nishimura, Handbook of Heterogeneous Catalytic Hydrogenation for Organic Synthesis, Wiley-VCH, New York, 2001 Search PubMed.
-
G. Ertl, H. Knözinger and J. Weitkamp, Preparation of Solid Catalysts, Wiley-VCH, New York, 1999 Search PubMed.
-
P. Roose, K. Eller, E. Henkes, R. Rossbacher and H. Höke, Amines, Aliphatic. Ullmann's Encyclopedia of Industrial Chemistry, Wiley-VCH, New York, 2015 Search PubMed.
- L. Hegedűs and T. Máthé, Appl. Catal., A, 2005, 296, 209–215 CrossRef.
- M. Chatterjee, H. Kawanami, M. Sato, T. Ishizaka, T. Yokoyama and T. Suzuki, Green Chem., 2010, 12, 87–93 RSC.
- M. Yoshimura, A. Komatsu, M. Niimura, Y. Takagi, T. Takahashi, S. Ueda, T. Ichikawa, Y. Kobayashi, Y. Monguchi and H. Sajiki, Adv. Synth. Catal., 2018, 360, 1726–1732 CrossRef CAS.
- D. Bagal and B. Bhanage, Adv. Synth. Catal., 2015, 357, 883–900 CrossRef CAS.
- R. Reguillo, M. Grellier, N. Vautravers, L. Vendier and S. Sabo-Etienne, J. Am. Chem. Soc., 2010, 132, 7854–7855 CrossRef CAS PubMed.
- M. Chatterjee, M. Sato, H. Kawanami, T. Yokoyama, T. Suzuki and T. Ishizaka, Adv. Synth. Catal., 2010, 352, 2394–2398 CrossRef CAS.
- K. Rajesh, B. Dudle, O. Blacque and H. Berke, Adv. Synth. Catal., 2011, 353, 1479–1484 CrossRef CAS.
- C. Chin and B. Lee, Catal. Lett., 1992, 14, 135 CrossRef CAS.
- C. Bornschein, S. Werkmeister, B. Wendt, H. Jiao, E. Alberico, W. Baumann, H. Junge and M. Beller, Nat. Commun., 2014, 5, 4111 CrossRef CAS PubMed.
- S. Chakraborty, G. Leitus and D. Milstein, Chem. Commun., 2016, 52, 1812–1815 RSC.
- S. Lange, S. Elangovan, C. Cordes, A. Spannenberg, H. Jiao, H. Junge, S. Bachmann, M. Scalone, C. Topf, K. Junge and M. Beller, Catal. Sci. Technol., 2016, 6, 4768–4772 RSC.
- R. Adam, C. Bheeter, J. Cabrero-Antonino, K. Junge, R. Jackstell and M. Beller, ChemSusChem, 2017, 10, 842–846 CrossRef CAS PubMed.
- A. Mukherjee, D. Srimani, S. Chakraborty, Y. Ben-David and D. Milstein, J. Am. Chem. Soc., 2015, 137, 8888–8891 CrossRef CAS PubMed.
- S. Elangovan, C. Topf, S. Fischer, H. Jiao, A. Spannenberg, W. Baumann, R. Ludwig, K. Junge and M. Beller, J. Am. Chem. Soc., 2016, 138, 8809–8814 CrossRef CAS.
- K. Tokmic, B. Jackson, A. Salazar, T. Woods and A. Fout, J. Am. Chem. Soc., 2017, 139, 13554–13561 CrossRef CAS PubMed.
- H. Dai and H. Guan, ACS Catal., 2018, 8, 9125–9130 CrossRef CAS.
- J. Garduño and J. García, ACS Catal., 2019, 9, 392–401 CrossRef.
- S. Weber, B. Stöger and K. Kirchner, Org. Lett., 2018, 20, 7212–7215 CrossRef CAS PubMed.
- F. Chen, C. Topf, J. Radnik, C. Kreyenschulte, H. Lund, M. Schneider, A. Surkus, L. He, K. Junge and M. Beller, J. Am. Chem. Soc., 2016, 138, 8781–8788 CrossRef CAS.
- R. Ferraccioli, D. Borovika, A. Surkus, C. Kreyenschulte, C. Topf and M. Beller, Catal. Sci. Technol., 2018, 8, 499–507 RSC.
- Y. Zhang, H. Yang, Q. Chi and Z. Zhang, ChemSusChem, 2019, 12, 1–11 CrossRef.
- P. Ryabchuk, G. Agostini, M. Pohl, H. Lund, A. Agapova, H. Junge, K. Junge and M. Beller, Sci. Adv., 2018, 4, eaat0761 CrossRef PubMed.
- K. Murugesan, T. Senthamarai, M. Sohail, A. Alshammari, M. Pohl, M. Beller and R. Jagadeesh, Chem. Sci., 2018, 9, 8553–8560 RSC.
- J. Wang, Q. Tang, S. Jin, Y. Wang, Z. Yuan, Q. Chi and Z. Zhang, New J. Chem., 2020, 44, 549–555 RSC.
- E. Popczun, J. McKone, C. Read, A. Biacchi, A. Wiltrout, N. Lewis and R. Schaak, J. Am. Chem. Soc., 2013, 135, 9267–9270 CrossRef CAS PubMed.
- S. Cao, Y. Chen, C. Wang, P. He and W. Fu, Chem. Commun., 2014, 50, 10427–10429 RSC.
- Y. Shi and B. Zhang, Chem. Soc. Rev., 2016, 45, 1529–1541 RSC.
- P. Liu and J. Rodriguez, J. Am. Chem. Soc., 2005, 127, 14871–14878 CrossRef CAS PubMed.
- T. Liu, D. Liu, F. Qu, D. Wang, L. Zhang, R. Ge, S. Hao, Y. Ma, G. Du, A. Asiri, L. Chen and X. Sun, Adv. Energy Mater., 2017, 7, 1700020 CrossRef.
- S. T. Oyama, J. Catal., 2003, 216, 343–352 CrossRef CAS.
- Y. Lee and S. T. Oyama, Appl. Catal., A, 2017, 548, 103–113 CrossRef CAS.
- P. Bui, S. T. Oyama, A. Takagaki, B. Carrow and K. Nozaki, ACS Catal., 2016, 6, 4549–4558 CrossRef CAS.
- A. Berenguer, T. M. Sankaranarayanan, G. Gómez, I. Moreno, J. M. Coronado, P. Pizarro and D. P. Serrano, Green Chem., 2016, 18, 1938–1951 RSC.
- S. Yang, L. Peng, E. Oveisi, S. Bulut, D. Sun, M. Asgari, O. Trukhina and W. Queen, Chem.Eur. J., 2018, 24, 4234–4238 CrossRef CAS PubMed.
- K. Liu, Y. Wang, P. Chen, W. Zhong, Q. Liu, M. Li, Y. Wang, W. Wang, Z. Lu and D. Wang, Appl. Catal., B, 2016, 196, 223–231 CrossRef CAS.
- R. Gao, L. Pan, H. Wang, X. Zhang, L. Wang and J. Zou, ACS Catal., 2018, 8, 8420–8429 CrossRef CAS.
- S. Carenco, A. Leyva-Pérez, P. Concepción and A. Corma, Nano Today, 2012, 7, 21–28 CrossRef CAS.
- H. Feng, X. Li, H. Qian, Y. Zhang, D. Zhang, D. Zhao, S. Hong and N. Zhang, Green Chem., 2019, 21, 1743–1756 RSC.
- J. Liu, Z. Wang, J. David, J. Llorca and A. Cabot, J. Mater. Chem. A, 2018, 6, 11453–11462 RSC.
- J. Liu, M. Meyns, T. Zhang, J. Arbiol, A. Cabot and A. Shavel, Chem. Mater., 2018, 30, 1799–1807 CrossRef CAS.
- A. Corma, S. Iborra and A. Velty, Chem. Rev., 2007, 107, 2411–2502 CrossRef CAS PubMed.
- K. Liu, C. Zhang, Y. Sun, G. Zhang, X. Shen, F. Zou, H. Zhang, Z. Wu, E. Wegener, C. Taubert, J. Miller, Z. Peng and Y. Zhu, ACS Nano, 2018, 12, 158–167 CrossRef CAS PubMed.
- L. Zhou, C. Zhu, L. Edmonds, H. Yang, W. Cui and B. Li, RSC Adv., 2014, 4, 43220–43226 RSC.
-
F. A. G. Cotton, Progress in Inorganic Chemistry: Metal–Metal Bonds in Transition Metal Compounds, Wiley-VCH, New York, 1968 Search PubMed.
- Y. Chen, C. Li, J. Zhou, S. Zhang, D. Rao, S. He, M. Wei, D. Evans and X. Duan, ACS Catal., 2015, 10, 5756–5765 CrossRef.
-
C. D. Wagner, W. M. Riggs, L. E. Davis, J. F. Moulder and G. E. Muilenberg, Handbook of X-Ray Photoelectron Spectroscopy, Perkin-Elmer, Eden Prairie, 1979 Search PubMed.
- S. Cao, Y. Chen, C. Hou, X. Lv and W. Fu, J. Mater. Chem. A, 2015, 3, 6096–6101 RSC.
- J. Wang, L. Zhu, G. Dharan and G. Ho, J. Mater. Chem. A, 2017, 5, 16580–16584 RSC.
- A. Khassin, T. Yurieva, V. Kaichev, V. Bukhtiyarov, A. Budneva, E. Paukshtis and V. Parmon, J. Mol. Catal. A: Chem., 2001, 175, 189–204 CrossRef CAS.
- Z. Liang, X. Zhong, T. Li, M. Chen and G. Feng, ChemElectroChem, 2019, 6, 260–267 CrossRef CAS.
- H. La Pierre, J. Arnold, R. Bergman and F. Dean Toste, Inorg. Chem., 2012, 51, 13334–13344 CrossRef CAS PubMed.
- Q. Chen, I.-H. Svenum, L. Gavrilovic, D. Chen and E. A. Blekkan, Surf. Sci., 2019, 681, 24–31 CrossRef CAS.
Footnote |
† Electronic supplementary information (ESI) available. See DOI: 10.1039/d0sc00247j |
|
This journal is © The Royal Society of Chemistry 2020 |
Click here to see how this site uses Cookies. View our privacy policy here.