DOI:
10.1039/D0RA05300G
(Paper)
RSC Adv., 2020,
10, 29975-29982
A stable TiO2–graphene nanocomposite anode with high rate capability for lithium-ion batteries†
Received
16th June 2020
, Accepted 28th July 2020
First published on 13th August 2020
Abstract
A rapid microwave hydrothermal process is adopted for the synthesis of titanium dioxide and reduced graphene oxide nanocomposites as high-performance anode materials for Li-ion batteries. With the assistance of hydrazine hydrate as a reducing agent, graphene oxide was reduced while TiO2 nanoparticles were grown in situ on the nanosheets to obtain the nanocomposite material. The morphology of the nanocomposite obtained consisted of TiO2 particles with a size of ∼100 nm, uniformly distributed on the reduced graphene oxide nanosheets. The as-prepared TiO2–graphene nanocomposite was able to deliver a capacity of 250 mA h g−1 ± 5% at 0.2C for more than 200 cycles with remarkably stable cycle life during the Li+ insertion/extraction process. In terms of high rate capability performance, the nanocomposite delivered discharge capacity of ca. 100 mA h g−1 with >99% coulombic efficiency at C-rates of up to 20C. The enhanced electrochemical performance of the material in terms of high rate capability and cycling stability indicates that the as-developed TiO2–rGO nanocomposites are promising electrode materials for future Li-ion batteries.
Introduction
Li-ion batteries (LIBs) are considered to be the most attractive electrochemical energy storage technology among all technologies for portable devices and electric vehicles.1 With growing interest in developing green electrode materials for future LIBs, attention has also been given to TiO2 as a negative electrode material.2–4 TiO2 can be a viable electrode material because of its stable cycle life, low environmental impact, low cost, and abundance.5,6 The relatively higher working voltage of a TiO2 anode (≥1.5 V vs. Li+/Li) compromises the overall energy density of the cell but it can also effectively slows the growth of irreversible formation of an SEI layer, which consequently improves the coulombic efficiency compared to conventional carbon-based anode materials.7 However, the major challenge in its practical application for the anode in LIBs is its low electronic conductivity of TiO2 (∼10−12 S cm−1)8 which limits the rate capability and LIB performance.
To enhance the rate capability, extensive efforts have been deployed to increase the surface area of active material. Thus, the mobility of electrons and Li ions is facilitated by decreasing the diffusion path and controlling the stress mechanism. This was achieved by developing TiO2 nanotubes, nanowires, and altering the crystal structures of material through high temperature calcination.9–18 However, as discussed above the low electrical conductivity of TiO2 still limits its electrochemical performance for battery application.19 TiO2 composites with carbon and metal oxides have demonstrated improvements in electronic conductivity, but more work is required to achieve a material which can be of technical relevance.20–24 Compared to the traditional carbonaceous additives, graphene is considered promising to improve the electrochemical performances of various electrode materials due to its high electrical conductivity, superior mechanical strength and large surface area.25,26 These properties make graphene a suitable material for use in a TiO2 composite anode for LIBs.
The conventional methods to synthesize TiO2 nanostructures include sol–gel methods which can be utilized to develop TiO2–graphene nanocomposites.27,28 Nevertheless, these methods often require anhydrous alcohols as solvents and normally yield a mixture of rutile and anatase TiO2 phases instead of a pure single phase. The rutile TiO2 phase has been found to exhibit low rate performance when subjected to high current density during cycling.27 To address this challenge extensive studies such as template-assisted synthesis, electro-spinning, and anodization, have been carried out to obtain structures suitable for fast electron and Li+ mobility.29–33 In most cases an improved battery performance of TiO2–graphene nano-architectures was achieved by altering the synthesis conditions to control the particle size and phase of TiO2; however, the previously reported methods are time consuming and costly.6 There is thus a need for a rapid and cost-effective method for developing well-organized TiO2–graphene nanocomposites for application in LIBs. Herein, we report a swift and scalable method for in situ synthesis of TiO2 nanoparticles on rGO nanosheets via a microwave hydrothermal process to obtain a high-performance TiO2–rGO nanocomposite LIB anode material. These nanocomposites exhibit outstanding rate performance due to the fast mobility of electrons and Li+ diffusion during insertion/extraction. The improved electrochemical performance demonstrates the viability of this material as a high-rate negative electrode for advanced LIBs.
Experimental
The material synthesis, characterization and electrochemical testing methods used in this study are described below. The synthesis and electrochemical testing methods are also illustrated schematically in Fig. 1.
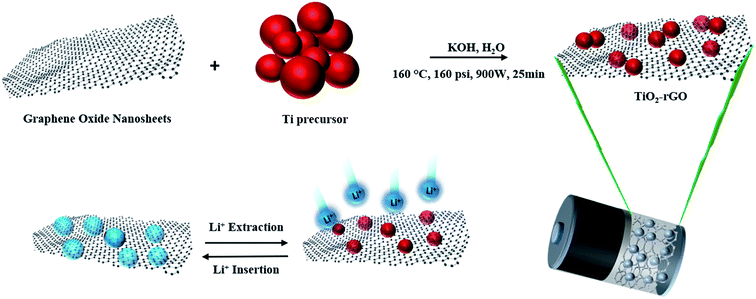 |
| Fig. 1 Schematic illustration of synthesis method of TiO2–rGO nanocomposite and Li insertion/extraction process. | |
(a) Synthesis of TiO2–rGO nanocomposite
GO was synthesized using the Hummers' method34 for which details are provided in ESI.† The resulting GO obtained was dried at 80 °C after washing with water several times. In the next step, to synthesize the desired TiO2–rGO nanocomposite, an aqueous solution containing 4 M of titanium(III) chloride precursor and 0.1 M of potassium hydroxide was prepared. Three different concentrations of wt% of rGO (1, 2 and 5) relative to the amount of TiO2 in the nanocomposite along with 50–100 μl of hydrazine hydrate (HH) reducing agent were added to the solution. The solution was transferred to a hydrothermal microwave (CEM MARS 5) at 160 °C, 160 psi, 900 W for 25 min. After hydrothermal microwave treatment, the product was washed in deionized water and ethanol several times and dried at 80 °C for 15 h. The as-prepared product was ground using a mortar and pestle prior to further study the physical and electrochemical properties. A more detailed description of the synthesis of TiO2–rGO nanocomposite is presented in the ESI.† Based on the wt% of rGO added to the TiO2 nanoparticles, these samples are named TiO2–pristine, TiO2–rGO 1%, TiO2–rGO 2%, TiO2–rGO 5% in the following discussion.
(b) Materials characterization
The structural characterization was performed using a Philips X'Pert MPD 3030 X-ray diffractometer equipped with Cu Kα radiation in the 2θ range of 20–60°. The morphological characterization of the composite was carried out by using field emission scanning electron microscopy (FESEM) and Jeol 2010F transmission electron microscopy (TEM) which was operated at 200 kV. Elemental mapping was obtained using energy-dispersive X-ray spectroscopy (EDS) using the same SEM. The nitrogen adsorption/desorption studies were performed using a Micromeritics ASAP 2020.
(c) Cell fabrication and electrochemical characterization
To explore electrochemical performance of TiO2–rGO nanocomposite, the working electrode was prepared by using the as-prepared TiO2–rGO nanocomposites with different amounts of rGO, polyvinylidene difluoride (PVDF) and Super P carbon black with a weight ratio of 8
:
1
:
1, respectively. The active material mass loading in the as-prepared electrodes was in range of 1.9 to 2.5 mg cm−2 for different experiments. Once the slurry was prepared, it was coated onto a copper foil and dried overnight. Lithium foil (purity 99.9%) served as the counter electrode, polypropylene (PP) membrane as a separator and 1 M lithium hexaflurophosphate (LiPF6) dissolved in ethylene carbonate (EC) and dimethyl carbonate (DMC) (1
:
1 in vol%) as the electrolyte. The 2032-type coin cells were assembled in an argon filled glovebox with O2 and H2O levels less than 0.1 ppm. Galvanostatic cycling and rate capability experiments were performed using multi-channel battery tester (LAND) with a potential range between 1 and 2.5 V at a range of current densities. An aging time of 12 h was used before starting the battery cycling. Cyclic voltammetry tests were carried out in a potential range of 0 to 3 V with a scan rate of 0.5 mV s−1. Electrochemical impedance spectroscopy (EIS) tests were conducted in a frequency range of 100 kHz to 10 mHz using a Biologic SP-300 potentiostat.
Results and discussion
The structural and morphological properties of TiO2-based nanocomposites are strongly dependent on the temperature and time of reaction which consequently affects the electrochemical response of nanocomposite in battery application.34–36 Although rutile is considered to be most stable TiO2 phase, it is not favorable for battery anode applications because of the limited Li+ diffusion along the c-axis channels only.33 It has been reported that anatase phase TiO2 with <200 nm particle size is thermodynamically stable.37–39 Thus, it is important to consider both the crystal structure as well as the particle size of TiO2 in order to achieve better electrochemical performance in LIB negative electrodes.
The synthesis time to obtain the TiO2–rGO nanocomposite was only around 25 min. The simple process is a convenient synthesis route to prepare the nanocomposite in less time, with the desired morphology and the right crystal structure. Without adding rGO, the synthesized TiO2 materials (hereinafter referred to as TiO2–pristine) was found to have an anatase structure, confirmed by XRD analysis (Fig. 2a). The XRD patterns of samples with rGO 1, 2 and 5 wt% revealed that TiO2 retained this anatase crystalline structure. The anatase phase of the TiO2 nanoparticles was confirmed by the seven characteristic diffraction peaks (JCPDS 21-1272),40 while no evidence of rutile phase TiO2 was observed. The specific surface area and pore size distribution of the sample having maximum rGO content (TiO2–rGO 5%) was further explored by nitrogen adsorption/desorption studies, and the isotherms obtained are presented in Fig. 2b. The Brunauer–Emmett–Teller (BET) specific surface area of TiO2–rGO 5% was found to be ∼105 m2 g−1, much higher than that of TiO2–graphene nanoparticles previously reported.25,36 The high surface area can be attributed to the uniform distribution and relatively small size of the TiO2 nanoparticles, as well as the contribution of the graphene sheets in the nanocomposite. The differential pore volume in a plot calculated from the desorption isotherm by BET method (inset graph in Fig. 2b) represents mesopores having an average pore diameter of 7 nm in the nanocomposite. These mesopores in the nanocomposite are expected to be associated with the interparticle space.
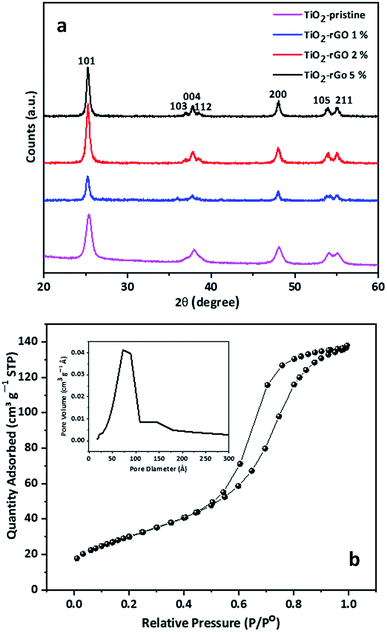 |
| Fig. 2 (a) XRD patterns of TiO2–pristine, TiO2–rGO 1%, TiO2–rGO 2%, TiO2–rGO 5%. Peaks at 2θ values of 25.3°, 36.9°, 37.8°, 38.5°, 48.0°, 53.8° and 55.0° correspond to the characteristic diffraction peaks of anatase TiO2 (JCPDS 21-1272).40 (b) Nitrogen adsorption/desorption isotherms TiO2–rGO 5%. The inset shows the pore-size distribution plot of the same sample. | |
Detailed morphological characterization was performed using FESEM and TEM. Fig. 3a shows an FESEM image of the TiO2–rGO 5% sample which reveals well dispersed TiO2 on GO nanosheets and connected to each other to form a well-defined nanocomposite. The TiO2 nanoparticles have a size in the range of ca. 100 nm. Fig. 3b shows EDS elemental mapping of the area shown in Fig. 3a, which indicates that all the major elements were homogenously present including carbon, titanium and oxygen. Fig. 3c and d present the bright-field TEM images of same sample at two different magnifications. The images confirm the homogenous distribution of TiO2 particles on sheet. This morphological characterization indicates that the TiO2 particle size is in the suitable size range for thermodynamic stability (<200 nm (ref. 37–39)), with appropriate pore size to achieve good electrochemical performance in LIBs.
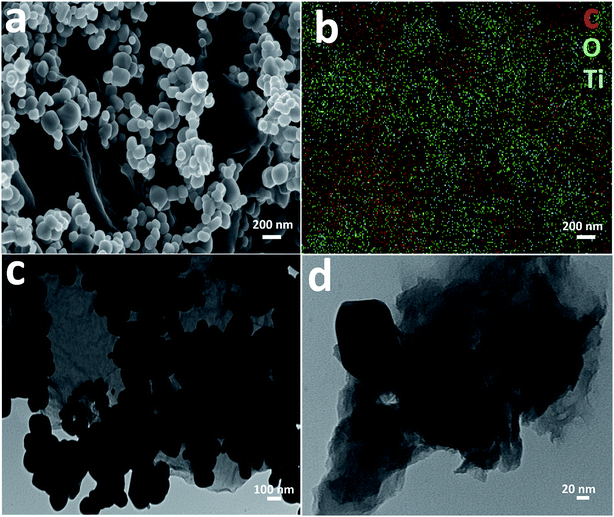 |
| Fig. 3 (a) FESEM image of TiO2–rGO 5%, (b) EDS elemental mapping of the area shown in (a), (c) bright-field TEM image of TiO2–rGO 5%, (d) bright-field TEM image at higher magnification. | |
The FESEM image and elemental mapping of TiO2–rGO 5% is presented in the ESI† along with EDS results Fig. S1 and S2.† Furthermore, the FESEM images of the pristine and samples with different rGO loadings are presented in ESI (Fig. S3).† When the rGO content was increased from 1% to 5%, no visible change was observed in the morphology. Therefore, differences in the electrochemical performance of these materials can be attributed to the rGO to TiO2 weight ratio rather than differences in the morphological structure, which was found to be independent of the composition ratio.
The electrochemical performance of TiO2–rGO nanocomposites prepared with 1, 2 and 5 wt% GO as anode materials was evaluated in Li half-cells. A schematic of the coin cell assembly is shown in Fig. S4.† The first galvanostatic discharge/charge voltage profiles of the four samples tested at 0.2C with a voltage window of 1.0–2.5 V are presented in Fig. 4a. With this voltage window no contribution from rGO is anticipated because LiC6 formation only takes place at potentials lower than 1.0 V. In these samples, all the cells display characteristic discharge and charge voltage plateaus at 1.75 V and 1.85 V, respectively, associated with anatase-TiO2.27 The initial discharge and charge capacities of all the three samples were between 125 mA h g−1 (based on the mass of the TiO2–rGO nanocomposite) and 255 mA h g−1 with excellent first cycle coulombic efficiencies. These high coulombic efficiencies (>90%) demonstrate that formation of SEI in case of TiO2 anodes is notably less than for conventional carbon negative electrode materials.24,41
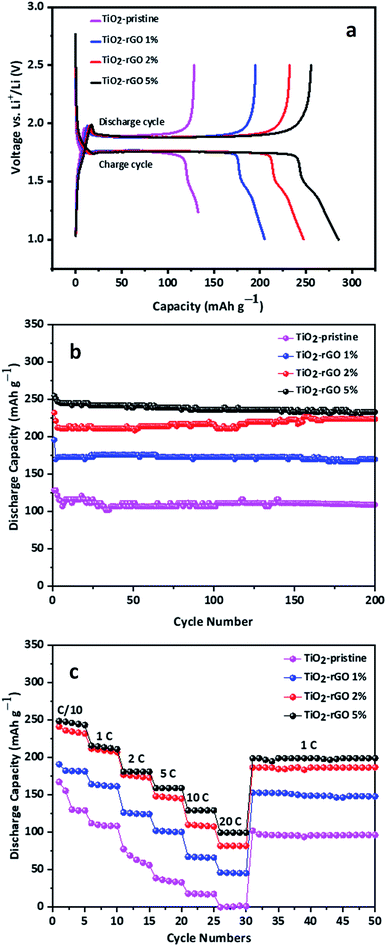 |
| Fig. 4 Electrochemical characteristics of TiO2–pristine, TiO2–rGO 1%, TiO2–rGO 2%, TiO2–rGO 5%: (a) voltage profiles for the first cycle, (b) cycle performances at a rate of 0.2C (c) rate capability performance at a range of current densities. | |
The TiO2–rGO 5% nanocomposite showed the highest first discharge capacity of mA h g−1 among all tested samples. The nanocomposite prepared using 2% rGO is comparable to 5%, however, the capacity shown by sample TiO2–rGO 1% and TiO2–pristine is significantly lower which is attributed to the low rGO content in the nanocomposite, and thus its relatively low conductivity. Increasing the rGO content from 2 wt% to 5 wt% led to only a small increase in electrochemical performance, suggesting that the percolation threshold of the nanocomposite had been reached and thus the increase in the conductivity was relatively small. Furthermore, 5% graphene content is reported to be the most favorable composition ratio with TiO2 to achieve best C-rate performance.26 Adding more than 5% rGO could result in re-stacking of rGO nanosheets, which in turn will limit the diffusion of Li+. However, further experimental studies could be conducted with higher amounts of rGO to determine the optimum. TiO2–rGO 5% is expected to have the highest content of rGO and thus will have the highest conductivity. The longest voltage plateau for the TiO2–rGO 5% confirms that the rGO enhances the discharge capacity. The shorter and similar terminal voltage slope in all the samples show that the capacitive behavior and its contribution in the discharge capacity of these electrodes is negligible.
The TiO2–rGO 5% shows remarkable cycling stability with superior discharge capacity. The cyclic stability is one of the key features of TiO2 based anodes which is apparent in the experimental results presented in Fig. 4b. All the cells retained about 90% of their initial capacity after 200 cycles at 0.2C. The average fade in capacity was lower than 1% each cycle while the coulombic efficiency was above 99% for each cycle after first few formation cycles.
The rate capability performance of an anode material is one of the most important parameters for practical application.30 To evaluate the as-prepared samples for rate capability performance, all the cells were subjected to current densities ranging from 0.1 to 20C with identical discharge and charge current density and five charge/discharge cycles at each current density. The results presented in Fig. 4c show that at a current density of 0.1C, both TiO2–rGO 5% and TiO2–rGO 2% possess a noticeably higher capacity than TiO2–rGO 1%, which is also higher than TiO2–pristine. As the C-rate was increased from 1 to 20C, the capacities of TiO2–pristine sample declined from 167 mA h g−1 to almost zero. At up to 2C the capacities for TiO2–rGO 5% and TiO2–rGO 2% remained comparable, but at 5C and above the TiO2–rGO 5% anode showed the highest capacity, achieving 100 mA h g−1 or above at current densities as high as 20C. At 20C, the TiO2–rGO 5% anode retained 40% of the capacity recorded at 0.1C. When returned to 1C after cycling at 20C, the samples retained their capacities nicely and remained stable for the next 20 cycles. TiO2-based anodes have been studies previously, including at even higher C-rates; however, the achievable discharge capacity remained in the range of ca. 100 mA h g−1.42 Stable discharge capacities of ca. 161 mA h g−1 at 5C, ca. 129 mA h g−1 at 10C, and ca. 100 mA h g−1 at 20C, were obtained for the TiO2–rGO 5% anode. These capacities demonstrate that the rGO contributed significantly to enhanced electrochemical performance in comparison to other recent studies of TiO2 based anodes.43
Cyclic voltammetry (CV) is a useful electrochemical technique to evaluate redox potentials of reversible systems. CV results for the TiO2 nanocomposite samples were recorded using a potential window 0.0 to 3.0 V vs. Li+/Li are shown in Fig. 5a. The CV results show no significant change in the redox potentials, but differences in the magnitude of the cathodic and anodic peak currents were observed. A higher amplitude in the cathodic and anodic peak currents (at around 1.45 V and 1.5 V respectively) was observed for TiO2–rGO 5%, indicating higher redox activity in terms of current for this sample. It is evident from the results that beside the characteristic pair of current peaks from the anatase TiO2, broad peaks were also recorded in the lower voltage range around 0.1 V. These cathodic and anodic peaks can be attributed to additional electrochemical processes including formation of an SEI layer taking place due to the presence of rGO and Super P carbon black in the electrode. However, further studies are required to understand the impact of carbon in the TiO2 electrodes.
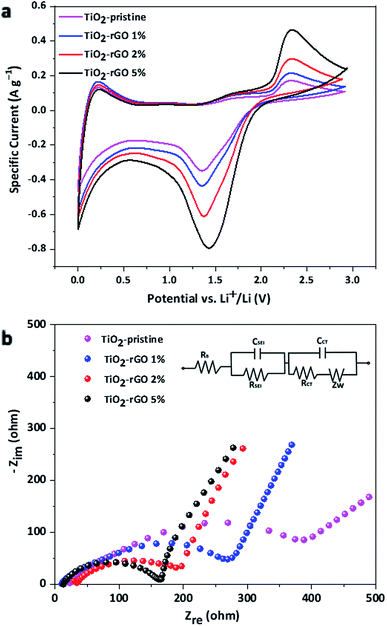 |
| Fig. 5 (a) Representative cyclic voltammograms of TiO2–pristine, TiO2–rGO 1%, TiO2–rGO 2%, TiO2–rGO 5% at a scan rate of 0.5 mV s−1 between 0 V and 3 V; (b) EIS Nyquist plots of the same samples, along with the equivalent circuit (RB is the bulk resistance, RSEI and CSEI are the resistance and capacitance of the solid electrolyte interface, RCT and CCT are the charge transfer resistance and capacitance, and ZW is the Warburg impedance). | |
Electrochemical impedance spectroscopy (EIS) was conducted to investigate the electrode resistance and active material-current collector interfacial resistance. The results of EIS study is illustrated using the Nyquist spectra shown in Fig. 5b. The shape of the impedance arc (depressed or distinct) depends on the total resistance offered by the cell. In the case of the four different samples the contact resistance was strongly dependent on the amount of GO present in the composite due to differences in the electron mobility in the nanocomposites. For the TiO2–pristine, the poor electrical contact hindered the electron flow from the Cu current collector to the active materials, consistent with previous studies.41,44,45 The high contact resistance for the TiO2–pristine led to a large overall resistance of ∼387 Ω, calculated from the x-intercept of impedance arc. The total resistance for TiO2–rGO 5% was ∼164 Ω, which is about 60% decrease in overall resistance of the pristine cell. From the EIS results it is evident that the TiO2–rGO 2% and 5% nanocomposite anodes have low surface resistance, enabling the high capacity and rate capability of the half-cell using these materials.
Conclusions
In this study, rGO was investigated as an additive to enhance the conductivity of TiO2 anodes. TiO2–rGO nanocomposites were synthesized by a simple and rapid in situ method. The experimental results demonstrated that TiO2 nanoparticles homogenously dispersed on rGO nanosheets could be obtained. The electrochemical results demonstrate that high rate capability and cycle stability could be achieved with the developed TiO2–rGO electrode. The well-integrated rGO nano-filler enhanced the electrode conductivity enabling the increased rate capability of the TiO2-electrodes. The as-prepared TiO2–rGO nanocomposite showed potential for use as a viable anode material in advanced Li-ion battery applications which require high power.
Conflicts of interest
There are no conflicts to declare.
Acknowledgements
The authors acknowledge the financial support from Natural Sciences and Engineering Research Council of Canada (NSERC). This work contributes to the research performed at CELEST (Center for Electrochemical Energy Storage Ulm-Karlsruhe).
References
- M. Armand, Nature Lithium Battery, Nature, 2001, 414, 359–367 CrossRef PubMed
. - E. Ferg, R. J. Gummow, A. D. Kock and M. M. Thackeray, Spinel anodes for lithium-ion batteries, J. Electrochem. Soc., 1994, 141(11), L147–L150 CrossRef CAS
. - A. R. Armstrong, G. Armstrong, J. Canales, R. García and P. G. Bruce, Lithium-ion intercalation into TiO2-B nanowires, Adv. Mater., 2005, 17(7), 862–865 CrossRef CAS
. - C. Arrouvel, S. C. Parker and M. S. Islam, Lithium Insertion and Transport in the TiO2−B Anode Material: A Computational Study, Chem. Mater., 2009, 21(20), 4778–4783 CrossRef CAS
. - M. B. Vazquez-Santos, P. Tartaj, E. Morales and J. M. Amarilla, TiO2 Nanostructures as Anode Materials for Li/Na-Ion Batteries, Chem. Rec., 2018, 18(7), 1178–1191 CrossRef CAS PubMed
. - M. Madian, A. Eychmüller and L. Giebeler, Current advances in TiO2-based nanostructure electrodes for high performance lithium ion batteries, Batteries, 2018, 4(1), 7 CrossRef
. - P. Li, P. Li, X. Guo, S. Wang, R. Zang, X. Li, Z. Man, S. Liu, Y. Wu and G. Wang, Two-dimensional Sb@TiO2−X nanoplates as a high-performance anode material for sodium-ion batteries, J. Mater. Chem. A, 2019, 7(6), 2553–2559 RSC
. - D. Deng, M. G. Kim, J. Y. Lee and J. Cho, Green energy storage materials: nanostructured TiO2 and Sn-based anodes for lithium-ion batteries, Energy Environ. Sci., 2009, 2(8), 818–837 RSC
. - J. Zhang, X. Yan, J. Zhang, W. Cai, Z. Wu and Z. Zhang, Preparation and electrochemical performance of TiO2/C composite nanotubes as anode materials of lithium-ion batteries, J. Power Sources, 2012, 198, 223–228 CrossRef CAS
. - J. Y. Cheong, C. Kim, J. W. Jung, T. G. Yun, D. Y. Youn, S. H. Cho, K. R. Yoon, H. Y. Jang, S. W. Song and I. D. Kim, Incorporation of amorphous TiO2 into one-dimensional SnO2 nanostructures as superior anodes for lithium-ion batteries, J. Power Sources, 2018, 400, 485–492 CrossRef CAS
. - T. Song and U. Paik, TiO2 as an active or supplemental material for lithium batteries, J. Mater. Chem. A, 2015, 4(1), 14–31 RSC
. - Y. Liu, J. Liu, D. Bin, M. Hou, A. G. Tamirat, Y. Wang and Y. Xia, Ultrasmall TiO2-Coated Reduced Graphene Oxide Composite as a High-Rate and Long-Cycle-Life Anode Material for Sodium-Ion Batteries, ACS Appl. Mater. Interfaces, 2018, 10(17), 14818–14826 CrossRef CAS PubMed
. - S. Nagpure, Q. Zhang, M. A. Khan, S. Z. Islam, J. Xu, J. Strzalka, Y. T. Cheng, B. L. Knutson and S. E. Rankin, Layer-by-Layer Synthesis of Thick Mesoporous TiO2 Films with Vertically Oriented Accessible Nanopores and Their Application for Lithium-Ion Battery Negative Electrodes, Adv. Funct. Mater., 2018, 28(37), 1–10 CrossRef
. - H. Han, T. Song, J. Y. Bae, L. F. Nazar, H. Kim and U. Paik, Nitridated TiO2 hollow nanofibers as an anode material for high power lithium ion batteries, Energy Environ. Sci., 2011, 4(11), 4532–4536 RSC
. - K. Hwang, H. Sohn and S. Yoon, Mesostructured niobium-doped titanium oxide-carbon (Nb-TiO2-C) composite as an anode for high-performance lithium-ion batteries, J. Power Sources, 2018, 378, 225–234 CrossRef CAS
. - W. Song, J. Chen, X. Ji, X. Zhang, F. Xie and D. J. Riley, Dandelion-shaped TiO2/multi-layer graphene composed of TiO2(B) fibrils and anatase TiO2 pappi utilizing triphase
boundaries for lithium storage, J. Mater. Chem. A, 2016, 4(22), 8762–8768 RSC
. - W. Zheng, Z. Yan, Y. Dai, N. Du, X. Jiang, H. Dai, X. Li and G. He, Interpenetrated Networks between Graphitic Carbon Infilling and Ultrafine TiO2 Nanocrystals with Patterned Macroporous Structure for High-Performance Lithium Ion Batteries, ACS Appl. Mater. Interfaces, 2017, 9(24), 20491–20500 CrossRef CAS PubMed
. - I. Moriguchi, R. Hidaka, H. Yamada, T. Kudo, H. Murakami and N. Nakashima, A mesoporous nanocomposite of TiO2 and carbon nanotubes as a high-rate Li-intercalation electrode material, Adv. Mater., 2006, 18(1), 69–73 CrossRef CAS
. - S. Pervez, D. Kim, C. H. Doh, U. Farooq, A. Yaqub, J. H. Choi, Y. J. Lee and M. Saleem, High areal capacity for battery anode using rapidly growing self-ordered TiO2 nanotubes with a high aspect ratio, Mater. Lett., 2014, 137, 347–350 CrossRef CAS
. - Z. Li, H. Zhao, P. Lv, Z. Zhang, Y. Zhang, Z. Du, Y. Teng, L. Zhao and Z. Zhu, Watermelon-Like Structured SiOx–TiO2@C Nanocomposite as a High-Performance Lithium-Ion Battery Anode, Adv. Funct. Mater., 2018, 28(31), 1–11 Search PubMed
. - V. Aravindan, Y. S. Lee, R. Yazami and S. Madhavi, TiO2 polymorphs in “rocking-chair” Li-ion batteries, Mater. Today, 2015, 18(6), 345–351 CrossRef CAS
. - X. Gao, X. Sun, Z. Jiang, Q. Wang, N. Gao, H. Li, H. Zhang, K. Yu and C. Su, Introducing nanodiamond into TiO2-based anode for improving the performance of lithium-ion batteries, New J. Chem., 2019, 43(9), 3707–3712 RSC
. - S. Bashir, P. Hanumandla, H. Y. Huang and J. L. Liu, Nanostructured materials for advanced energy conversion and storage devices: safety implications at end-of-life disposal. Nanostructured Mater. Next-Generation Energy Storage Convers, Fuel Cells, 2018, 4, 517–542 Search PubMed
. - S. Jiang, R. Wang, M. Pang, H. Wang, S. Zeng, X. Yue, L. Ni, Y. Yu, J. Dai, S. Qiu and Z. Zhang, Assembling porous carbon-coated TiO2(B)/anatase nanosheets on reduced graphene oxide for high performance lithium-ion batteries, Electrochim. Acta, 2015, 182, 406–415 CrossRef CAS
. - A. Mondal, S. Maiti, K. Singha, S. Mahanty and A. B. Panda, TiO2-rGO nanocomposite hollow spheres: large scale synthesis and application as an efficient anode material for lithium-ion batteries, J. Mater. Chem. A, 2017, 5(45), 23853–23862 RSC
. - B. Zhang, Y. Yu, Y. Liu, Z. D. Huang, Y. B. He and J. K. Kim, Percolation threshold of graphene nanosheets as conductive additives in Li4Ti5O12 anodes of Li-ion batteries, Nanoscale, 2013, 5(5), 2100–2106 RSC
. - E. Lim, H. Shim, S. Fleischmann and V. Presser, Fast and stable lithium-ion storage kinetics of anatase titanium dioxide/carbon onion hybrid electrodes, J. Mater. Chem. A, 2018, 6(20), 9480–9488 RSC
. - T. Kogure and T. Umezawa, Formation of TiO2 (B) Nanocrystallites in Sol-Gel-Derived SiO2-TiO2 Film, J. Am. Ceram. Soc., 1999, 50, 3248–3250 Search PubMed
. - M. Pfanzelt, Development of TiO2 Rutile as Negative Electrode Material for Lithium Ion Batteries, PhD Dissertation, Ulm University, 2012
. - H. Han, T. Song, E. K. Lee, A. Devadoss, Y. Jeon, J. Ha, Y. C. Chung, Y. M. Choi, Y. G. Jung and U. Paik, Dominant factors governing the rate capability of a TiO2 nanotube anode for high power lithium ion batteries, ACS Nano, 2012, 6(9), 8308–8315 CrossRef CAS PubMed
. - D. Dambournet, I. Belharouak and K. Amine, Tailored preparation methods of TiO2 anatase, rutile, brookite: mechanism of formation and electrochemical properties, Chem. Mater., 2010, 22(3), 1173–1179 CrossRef CAS
. - V. Mathew, J. Gim, M. H. Alfaruqi, S. Kim, J. Song, J. P. Baboo, S. Kim, S. Park, D. Kim and J. Kim, A porous TiO2 electrode prepared by an energy efficient pyro-synthesis for advanced lithium-ion batteries, J. Electrochem. Soc., 2015, 162(7), A1220–A1226 CrossRef CAS
. - X. Xin, X. Zhou, J. Wu, X. Yao and Z. Liu, Scalable synthesis of TiO2/graphene nanostructured composite with high-rate performance for lithium ion batteries, ACS Nano, 2012, 6(12), 11035–11043 CrossRef CAS PubMed
. - W. S. Hummers and R. E. Offeman, Preparation of Graphitic Oxide, J. Am. Chem. Soc., 1958, 80(6), 1339 CrossRef CAS
. - V. Augustyn, J. Come, M. A. Lowe, J. W. Kim, P. L. Taberna, S. H. Tolbert, H. D. Abruña, P. Simon and B. Dunn, High-rate electrochemical energy storage through Li+ intercalation pseudocapacitance, Nat. Mater., 2013, 12(6), 518–522 CrossRef CAS PubMed
. - H. E. Wang, H. Cheng, C. Liu, X. Chen, Q. Jiang, Z. Lu, Y. Y. Li, C. Y. Chung, W. Zhang, J. A. Zapien, L. Martinu and I. Bello, Facile synthesis and electrochemical characterization of porous and dense TiO2 nanospheres for lithium-ion battery applications, J. Power Sources, 2011, 196(15), 6394–6399 CrossRef CAS
. - M. C. Yang, Y. Y. Lee, B. Xu, K. Powers and Y. S. Meng, TiO2 flakes as anode materials for Li-ion-batteries, J. Power Sources, 2012, 207, 166–172 CrossRef CAS
. - J. Y. Hwang, H. L. Du, B. N. Yun, M. G. Jeong, J. S. Kim, H. Kim, H. G. Jung and Y. K. Sun, Carbon-Free TiO2 Microspheres as Anode Materials for Sodium Ion Batteries, ACS Energy Lett., 2019, 4(2), 494–501 CrossRef CAS
. - U. Lafont, D. Carta, G. Mountjoy, A. V. Chadwick and E. M. Kelder, In situ structural changes upon electrochemical lithium insertion in nanosized anatase TiO2, J. Phys. Chem. C, 2010, 114(2), 1372–1378 CrossRef CAS
. - M. G. Choi, Y. G. Lee, S. W. Song and K. M. Kim, Anode properties of titanium oxide nanotube and graphite composites for lithium-ion batteries, J. Power Sources, 2010, 195(24), 8289–8296 CrossRef CAS
. - M. Mao, F. Yan, C. Cui, J. Ma, M. Zhang, T. Wang and C. Wang, Pipe-wire TiO2-Sn@carbon nanofibers paper anodes for lithium and sodium ion batteries, Nano Lett., 2017, 17(6), 3830–3836 CrossRef CAS PubMed
. - J. H. Jeong, M. S. Kim, Y. H. Kim, K. C. Roh and K. B. Kim, High-rate Li4Ti5O12/N-doped reduced graphene oxide composite using cyanamide both as nanospacer and a nitrogen doping source, J. Power Sources, 2016, 336, 376–384 CrossRef CAS
. - D. P. Opra, S. V. Gnedenkov and S. L. Sinebryukhov, Recent efforts in design of TiO2(B) anodes for high-rate lithium-ion batteries: a review, J. Power Sources, 2019, 442, 227225 CrossRef CAS
. - M. Wagemaker, A. P. M. Kentjens and F. M. Mulder, Equilibrium lithium transport between nanocrystalline phases in intercalated TiO2 anatase, Nature, 2002, 418(6896), 397–399 CrossRef CAS PubMed
. - Y. Liu, Y. K. Tzeng, D. Lin, A. Pei, H. Lu, N. A. Melosh, Z. X. Shen, S. Chu and Y. Cui, An Ultrastrong Double-Layer Nanodiamond Interface for Stable Lithium Metal Anodes, Joule, 2018, 2(8), 1595–1609 CrossRef CAS
.
Footnote |
† Electronic supplementary information (ESI) available. See DOI: 10.1039/d0ra05300g |
|
This journal is © The Royal Society of Chemistry 2020 |
Click here to see how this site uses Cookies. View our privacy policy here.