DOI:
10.1039/D0RA02254C
(Review Article)
RSC Adv., 2020,
10, 12653-12670
Ultrathin permselective membranes: the latent way for efficient gas separation
Received
10th March 2020
, Accepted 11th March 2020
First published on 27th March 2020
Abstract
Membrane gas separation has attracted the attention of chemical engineers for the selective separation of gases. Among the different types of membranes used, ultrathin membranes are recognized to break the trade-off between selectivity and permeance to provide ultimate separation. Such success has been associated with the ultrathin nature of the selective layer as well as their defect-free structure. These membrane features can be obtained from specific membrane preparation procedures used, in which the intrinsic properties of different nanostructured materials (e.g., polymers, zeolites, covalent–organic frameworks, metal–organic frameworks, and graphene and its derivatives) also play a crucial role. It is likely that such a concept of membranes will be explored in the coming years. Therefore, the goal of this review study is to give the latest insights into the use of ultrathin selective barriers, highlighting and describing the primary membrane preparation protocols applied, such as atomic layer deposition, in situ crystal formation, interfacial polymerization, Langmuir–Blodgett technique, facile filtration process, and gutter layer formation, to mention just a few. For this, the most recent approaches are addressed, with particular emphasis on the most relevant results in separating gas molecules. A brief overview of the fundamentals for the application of the techniques is given. Finally, by reviewing the ongoing development works, the concluding remarks and future trends are also provided.
1. Introduction: the overview of new membrane concepts
Membrane-based technologies are attracting considerable attention for different types of approaches in the field of chemical engineering. In particular, membrane gas separation (GS) has been recognized since decades ago for its ability in separating gas mixtures of diverse molecules, such as organic (CH4, C2H4, C2H6, C3H6, C3H8, C4H10, etc.) and inorganic gases (CO2, H2, CO, N2, SF6, O2, He, and Ar).1–3 Importantly, Baker4 has pointed out that the use of GS industrially comprises the separation of non-condensable gases, including nitrogen (N2) from air, carbon dioxide (CO2) from methane (CH4), and hydrogen (H2) from N2, argon, or CH4. The benefit of using this membrane process is that it has low-energy requirements and shows high selectivity, efficiency, and feasibility in terms of scale-up.5,6 It is important to highlight Baker's idea that GS applications require the development of new membranes and membrane processes.4 To date, several polymer-based membranes have been developed in the field; however, highly selective polymers do not demonstrate high permeation rates and highly permeable polymers are not selective enough.7,8 These perm-selectivity limitations do not allow particular polymer membranes (e.g., polyimides, poly(trimethylsilylpropyne), Teflon, polysulfone, cellulose acetate, and PDMS) to overcome the so-called Robeson trade-off, which was established to represent the relationship between permeability and selectivity towards specific gas pairs.7–9 Even if some pristine polymer membranes have shifted their performance (such as PIMs, thermally reduced polymers, Nafion®, Hyflon®, Viton®, Cytop™, and Teflon®AF) close to the upper bound relationship, their slope of the upper bound relationship has remained reasonably constant.8,10 Thereby, starting from the known separation features of the pristine polymers, several design concepts of new membranes have been developed, including cross-linked, polymer blending, annealed, composite, asymmetric and mixed matrix membranes (MMMs),11 and MMMs based on the copolymerization of organic macrocyclic molecules and microporous polymers.12–17 Among these types of membranes, the research community is looking for those involving nanostructured (inorganic, organic, or hybrid) materials, which once combined with polymer materials tend to result in a synergistic performance by combining the strengths of organic and inorganic materials. Nowadays, MMMs are likely the most explored membranes, often as a proof of concept for new porous fillers. In any event, the nanostructured materials used as fillers are contributing to the reduction in the drawbacks of polymer-based membranes, such as aging, plasticization phenomenon, and stability (e.g., physical, chemical, and thermal).18–21 However, the unsuitable merging, including poor compatibility at the interface as well as membrane preparation protocol, make the filler–polymer membranes show specific defects (see Fig. 1), e.g., new non-selective pathways for gas transport (case 3), which lead to an increase in the permeability but compromise on the selective properties.22 Of course, a good interface morphology (case 1) guarantees enhanced gas transport across the membranes, while other less favorable situations (cases 2 and 4) may compromise the expected increase in the performance of MMMs.
 |
| Fig. 1 General representation of different structures at the polymer–filler interface region in MMMs. | |
Compared with MMMs, ultrathin inorganic membranes from the corresponding nanosheets have been recognized as ideal candidates for obtaining superior performing membranes (see Fig. 2) and, importantly, using less amount of inorganic nanomaterials, which is in fact one of the main advantages of this type of membrane (see Table 1).
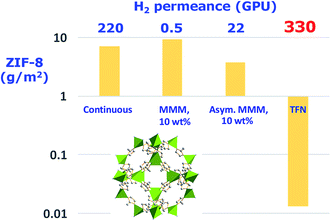 |
| Fig. 2 Amount of MOF ZIF-8 (ZIF-8 structure with the ZnN4 tetrahedra in green and carbon atoms from ligand molecules in grey. This structure was built with Diamond 3.2 using the corresponding crystallographic data,23 ref code: VELVOY01, CCDC: 602542) used in different types of gas selective membranes with their corresponding H2 permeance values. The thicknesses for continuous, MMMs (mixed matrix membrane), asymmetric MMMs, and TFN (thin film nanocomposite) membranes were 5 μm,24 106 μm,25 1 μm,26 and 100 nm (skin layer),27 respectively. | |
Table 1 Main advantages and drawbacks of ultrathin membranes compared to those of traditional ones
Advantages |
Drawbacks |
➢ Attractive separation performance |
➢ Specific devices for membrane preparation |
➢ Higher productivity (high permeances) |
➢ Hydrothermal stability issues on single-layered layers based on MOFs |
➢ Low amount of selective membrane-material |
➢ Challenging spatial distribution |
➢ Defect-free structure |
➢ Physical aging and plasticization in the polymer support and polymer-based layers |
➢ Less membrane area needed for a given separation |
➢ Limited preparation procedures at a large scale |
➢ Controlled grain size and thickness |
➢ Separation properties depending on precursors and ligands |
➢ Controllable tuning of the membrane pore size |
➢ Hydrothermal stability of ligand–metal bonds |
➢ Stable mechanical properties (e.g., graphene-based membranes) for potential large-scale applications |
|
➢ Atomically thin membranes |
|
➢ Materials, fabrication, and energy cost savings |
|
This is due to the fact that they can be synthesized with a defect-free morphology, obtained by means of specific procedures applied for their preparation, including atomic layer deposition (ALD), solvothermal crystallization, interfacial crystallization, electrophoretic deposition (ED), chemical vapor deposition (CVD), Langmuir–Blodgett (LB) deposition, facile filtration process, and gutter layer formation.28,29 The use of thin membranes of nanostructured materials, dealing with the concept of zeolite films, was realized in 1989 with the synthesis of a hydrophilic zeolite on top of a porous glass support, which was able to dehydrate an organic solvent.30 The first zeolite membranes had thicknesses of about several tens of microns; for example, Geus et al.31 reported a ca. 50 μm thick silicalite-1 membrane in the year 1992. One of the most relevant publications on the synthesis of zeolite membranes, from the point of view of zeolite layer thickness, was by Hedlund et al.32 In the year 2002, they produced a 500 nm thick silicalite-1 membrane on a commercially available and technologically suitable alpha-alumina tube with an N2 permeance of almost 40
000 GPU (gas permeation unit, 1 GPU being 3.35 × 10−10 mol m−2 s−1 Pa−1), which is useful for xylene isomer separation. In the year 2015, 100 nm thick silicalite-1 membranes were reported by Tsapatsis et al. with p-xylene permeance exceeding 1000 GPU and with the p-xylene/o-xylene separation factor reaching 1000.33 The development of unit cell-thick, highly crystalline zeolite nanosheets in the last decade is likely to allow the synthesis of thin zeolite membranes by a simple assembly in the near future.
It is important to point out that industrialized state-of-the-art technologies were used to fabricate reverse osmosis and nanofiltration membranes since the end seventies34 based on the interfacial polymerization (IP) of aromatic polyamides producing the so-called thin-film composite membranes (i.e., TFC and TFN membranes when incorporating fillers), which have endured two new evolutions. First, they have been recently applied for gas separation with good performance in H2/CO2 separation with H2 permeance in the range of 330–350 GPU.27,35 TFC membranes have controlling skin layers in the range of ca. 50 nm thickness and by special means, they can go down to ca. 10 nm,36 which explains their high permeances. Second, they have inspired the preparation of ultrathin films of porous coordination polymers by the same interfacial polymerization synthetic approach.37
Today, the use of ultrathin membranes provides some more advantages: (i) relatively small amounts of selective-layer materials, e.g., 1 m2 of a 100 nm dense and continuous layer of ZIF-8 (density 0.95 g cm−3), ZSM-5 (1.8 g cm−3), or graphite (2.2 g cm−3) would require 95, 180, or 220 mg of the material coated on top of the porous structures, representing a significant savings in material costs; (ii) it leads to an optimized membrane material and morphology in each layer, (iii) minimal limitations on the mechanical properties and processability of membrane materials as long as they can be formed or deposited as a thin layer on the top.38,39 As the membrane thickness decreases, both the membrane cost and permeance are favored. Permeability (the typical Barrer units, 1 Barrer = 10−10 cm3 (STP) cm cm−2 s−1 cmHg−1 = 3.35 × 10−16 mol mm−2 s−1 Pa−1) is the intrinsic transport parameter of a given membrane material. Thus, as Fig. 3 illustrates, for the same membrane material (e.g., polysulfone, Pebax® 1657, polyimide 6FDA-DAM, or PIM-1), permeance increases as the membrane thickness decreases (when the membrane thickness is 1 μm, a permeability of 1 Barrer corresponds to a permeance of 1 GPU). Fig. 3 suggests that even a slightly permeable material such as polysulfone, maintaining its selectivity properties, could become a technologically attractive material when prepared as an ultrathin membrane. Herein, the challenge is to choose the right preparation methodology able to produce defect-free ultrathin membranes. It is essential to mention that at least in some cases, the permeability may decrease when one reduces the membrane thickness, for example, PDMS permeability decreased 100-fold when the thickness was reduced from 1 mm to 200 nm.40
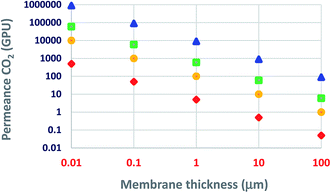 |
| Fig. 3 CO2 permeance as a function of membrane thickness: triangle, PIM-1; square, 6FDA-DAM; circle, Pebax® 1657; rhombus, polysulfone.29,41–43 | |
It still remains a big challenge to overcome such trade-off issues to reach high permeance and selectivity at the same time, i.e., to fabricate sub-1 μm thick membranes (even sub-100 nm) by using selective organic and inorganic materials44 such as polymers, zeolites, covalent–organic frameworks (COFs), metal–organic frameworks (MOFs), graphene, and carbon-based materials.38 Therefore, the goal of this review is to provide the latest insights into using ultrathin selective barriers, highlighting and describing the primary membrane preparation protocols used. Particular attention has been paid to the most relevant results in separating gas molecules. In addition, a brief overview of the fundamentals for the application of the techniques is given. Finally, by reviewing the ongoing development works, the concluding remarks and future perspectives are also addressed.
2. Fundamentals in membrane gas separation
In membrane gas separation, the membrane is certainly the primary tool for the separation of different gas molecules. To date, different gas transport mechanisms have been used to describe gas transport and thus, the separation mechanism in polymeric membranes, such as solution–diffusion transport, Knudsen-diffusion transport, surface diffusion, capillary condensation, viscous (Poiseuille) flow, and molecular sieving. Such mechanisms occur in membranes according to their structure (i.e., porous or non-porous). In the case of nanoporous membranes, several transport mechanisms can manifest at the same time. For example, activated transport (molecular sieving) from the nanopores but Knudsen-diffusion from the grain boundary defects and viscous transport from the pinholes. On the other hand, in non-porous membranes, so-called dense membranes, the mechanism is mainly governed by solution–diffusion transport.45 In general, mass transfer across a dense membrane involves three main steps: (i) adsorption of the gas molecules from the mixture to the membrane on the basis of its chemical affinity, (ii) diffusion of the gas molecules through the membrane as a result of the chemical potential (μi) and driving force, and (iii) desorption of the gas molecules at the permeate side of the membrane.46 The permeability (P) depends on the diffusivity (D) and solubility (S) of the transported molecules,45 as described by eqn (1). S is a thermodynamic parameter that provides insight into the amount of penetrant adsorbed by the membrane under equilibrium conditions, whereas D is a kinetic parameter that comprises the transport rate of the permeating molecules through the membrane.47 The two parameters can be denoted by the diffusion (D) and sorption (S) coefficients, respectively, and their product gives rise to permeability:where P is the permeability coefficient (cm3 (STP) cm cm−2 s−1 cmHg−1), in which Barrer (10−10 cm3 (STP) cm cm−2 s−1 cmHg−1) is the common unit. When the thickness of the active layer is not known, gas flows through the membrane can be determined by the gas permeation unit (GPU), which is expressed as 10−6 cm3 (STP) cm−2 s−1 cmHg−1 (see above for alternative IS units). To determine the selectivity of a membrane, the ideal selectivity (α) can be determined as a relationship of the permeability of one gas (A) over that of the other gas (B), as shown in eqn (2). Moreover, it can be defined as the ratio between the diffusivity coefficients, known as “diffusion selectivity”, and the ratio between sorption coefficients, named as “solubility selectivity”. |
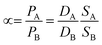 | (2) |
3. Preparation techniques of ultrathin organic/inorganic membranes: potential candidates for highly selective and permeable transport of gases
3.1 Advances in polymerization of ultrathin films
Today, the fabrication of an ultrathin selective layer onto a strong porous support is likely the most sought approach to develop next-generation high-performance membranes. In such an approach, the lamination of the layer generally employs the attachment of a previously prepared thin-film on top of a porous membrane support. Plasma polymerization protocol is a typical procedure that leads to the preparation of thin-film membranes,48,49 in which plasma polymers are coated on porous materials. Plasma polymerization is typically carried out within a vacuum system using helium or argon inert gases that induce plasma formation and, therefore, polymerization. This procedure possesses the advantage of forming an ultrathin defect-free film with thickness reaching a few nanometers, which is difficult to achieve by the conventional coating methods.38 On the contrary, such a technique finds its main drawback in the presence of many different reactive species (electrons, ions, radicals), which gives the possibility of multiple interactions of species. This makes it difficult to define the right chemical structure of the surface after exposure to a plasma.38 Fluorocarbon-based membranes have been prepared by such membrane preparation methods, which displayed a greater molecular sieving effect than those prepared by solution–diffusion separation.50 Recently, Fu et al.51 developed an ultrathin (∼100 nm) membrane with uniform thickness, which was able to facilitate high CO2 transport (i.e., CO2 permeance = 1260 GPU and CO2/N2 selectivity = 43). This breakthrough was achieved by continuous assembly technology via atom transfer radical polymerization (ATRP) for defect-free thin-film nanocomposites (TFC) based on cross-linked PDMS ultrathin dense layer (ca. 40 nm). Such an ultrathin selective layer was made of PEG-based cross-linkers polymerized on top of a functionalized PDMS layer with double function of polymerization initiator and gutter layer onto a microporous PAN support (see Fig. 4).
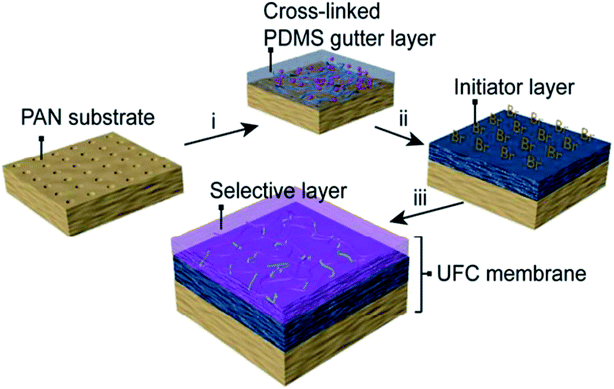 |
| Fig. 4 Schematic depiction of the ultra-TFC membranes developed by Fu et al.51 | |
Similarly, the preparation of a defect-free TFC membrane with a particular design has been documented by Xie et al.52 An ultrathin selective layer of about 30 nm was polymerized on a rough micro-scale MOF gutter layer. The polymer-on-MOF architecture provided impressive gas separation performance as well, for e.g., CO2 permeance = 3000 GPU and CO2/N2 selectivity = 34. These results were obtained due to the fact that the MOF layer was about 400 times more permeable than the PDMS layer. In particular, NH2-MIL-53(Al) was the MOF used as it possesses a number of amino groups that can be functionalized with an atom-transfer radical polymerization initiator and thus provides the ability to form a continuous porous layer. Importantly, MOFs are a category of crystalline porous materials based on metal ions or clusters interconnected by organic ligands via coordination bonds to form one-, two-, or three-dimensional periodic networks.13,53 According to the metal properties (e.g., polarizability, metal oxidation state, and ionic radius), the metal–ligand bond strength tends to vary.54 The synthetic route for forming MOF-based membranes on porous substrates is vastly different from that of MOF films on dense substrates. MOF membranes can be fabricated using various methods, including hydro/solvothermal synthesis, interfacial growth, CVD, ALD, and ED.55,56 The use of MOFs allows one to prepare ultrathin hybrid organic–inorganic selective membranes, for e.g., using [Zn2(benzimidazole)3(OH)(H2O)]n (hereafter abbreviated as Zn2(Bim)3) nanosheets.39 Herein, a modified soft physical exfoliation method was used to partially disintegrate a lamellar amphiprotic MOF into nanosheets. Afterwards, sub-10 nm-thick ultrathin membranes were successfully fabricated showing a suitable H2/CO2 separation performance, with a separation factor of 166 and with H2 permeance of up to 8 × 10−7 mol m−2 s−1 Pa−1 at elevated testing temperatures (200 °C), which is attributed to the size exclusion effect. In theory, H2 molecules (∼0.289 nm) can tightly pass through the apertures (∼0.29 nm) of the Zn2(Bim)3 nanosheets, while CO2 molecules (∼0.33 nm) and H2 can pass through the interlayer galleries. In fact, such molecular sieving mechanism was further proved by single permeation experiments through the nanosheet membranes; the experiments revealed a clear cut-off between H2 and other gas molecules having larger molecular diameters than the crystallographic pore size corresponding to Zn2(Bim)3 nanosheets.39
3.2 In situ growth and layer-by-layer (LBL) assembly
Very recently, Zhang et al.44 have reviewed emerging inorganic materials such as MOFs and COFs in the preparation of ultrathin membranes using advanced strategies such as contra-diffusion method, in situ growth, layer-by-layer (LBL) assembly, laminated assembly of MOF/COF nanosheets, metal-based precursor as the pre-functionalized layer, and interface-assisted strategy. To sum-up, the preparation of ultrathin membranes based on MOFs has been illustrated in Fig. 5. In particular, within the in situ growth protocol, the organic ligands and the metal ions are commonly mixed into one solution, in which the porous membrane support is immersed.44,57 At this point, the suitable selection of porous membrane supports should be taken into account in the MOF and even COF membranes due to the porous support surfaces (e.g., the ones based on α-Al2O3 porous supports) must display specific affinity to promote the nucleation and thus MOF/COF formation. For instance, α-Al2O3 possesses oxygen motifs including strong coordination interaction with metal ions to enhance the nucleation densities, thus satisfying several rugged reaction conditions of COFs (for e.g., polar solvents and high temperature). The drawbacks of in situ growth protocol are identified depending on the type of inorganic material, for e.g., the use of MOFs is challenging in terms of scale-up, fabrication procedures, and final production costs. As such, MOFs have been also recognized by their poor hydrothermal and chemical stability and durability.58 However, given the diversity of chemical compositions, structures, and stabilities, proper selection of the MOF is of paramount importance in order to obtain the best matching with other components of the membrane. Regarding COFs, the successful construction of a wide variety of such crystalline COFs materials greatly depends on the reversible reactions. But, in return, it produces drastic disadvantages related to their hydrolytic/chemical stability, for e.g., the presence of water during reversible COF formation may facilitate the backward reaction and thus the decomposition of COFs, making the use of COFs difficult in viable industrial approaches.59 To compensate in part for these drawbacks and as a counterpoint to what comes next regarding other membrane materials, MOFs and COFs can be prepared through alternative green methodologies that exclude solvents.60,61
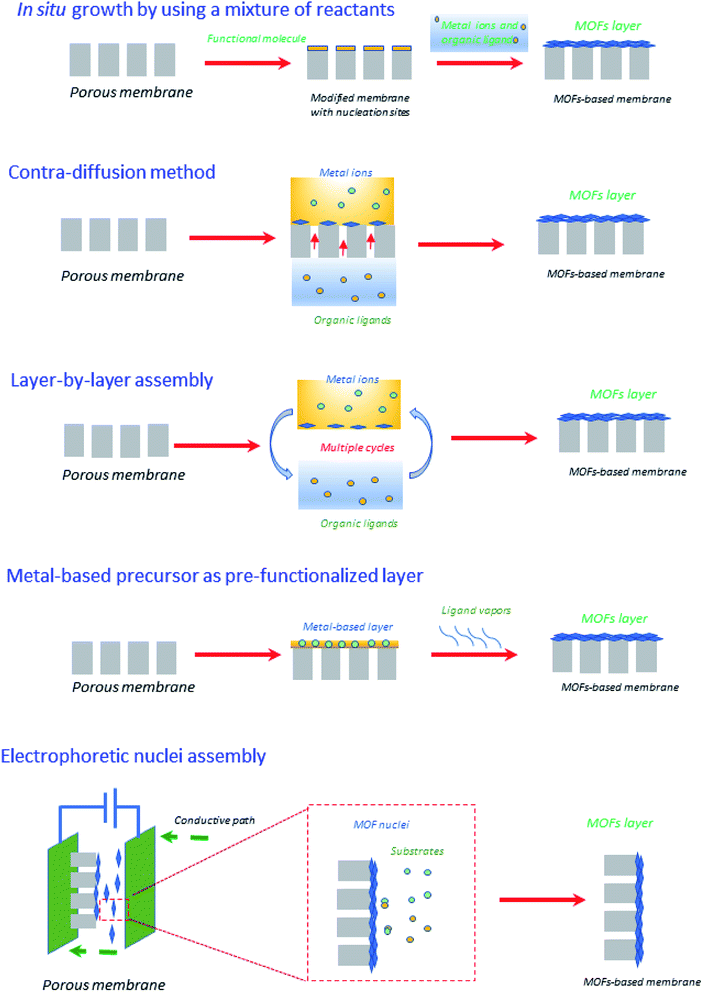 |
| Fig. 5 Graphical illustration of different strategies for creating ultrathin MOFs-based membranes.44 | |
In light of nucleation of MOFs, Knebel et al.62 developed a continuous ultrathin (ca. 200 nm) UiO-67 layer, which was designed by a high solvothermal process by mixing ZrCl4 and biphenyl-4,4′-dicarboxylic acid (BPDC) onto porous α-Al2O3. Such a membrane displayed acceptable separation factor values (in the range 5–29) towards different mixtures (e.g., H2/CO2, H2/N2, H2/CH4, H2/C2H6, and H2/C3H8). Importantly, this MOF tends to provide thinner membranes when compared with other types of MOFs, such as HKUST-1 and ZIF-8, which gave a thickness of ∼20 μm using a similar substrate and synthetic protocol.63,64 In this way, it is clear that the type of MOF (including their primary elements of formation) and the porous support property is highly important for such an in situ growth strategy.
3.3 Atomic layer deposition (ALD)
Atomic layer deposition (ALD) is likely one of the most used techniques in thin membrane preparation. ALD is recognized as a vapor phase technique that can produce thin films of plenty of materials. Such a technique offers multiple advantages including extraordinary conformality of high aspect ratio structures, thickness control at the angstrom range (0.1 nm), and tunable film composition.65 Fig. 6 briefly illustrates how such a technique works, which can be described as follows. The substrate surface (or porous membrane support) should either be natural or be functionalized (a). Typically, the precursor A is pulsed and therefore reacts with the surface (b). When there is excess precursor and reaction by-products, they are purged with an inert carrier gas (e.g., nitrogen or argon) (c). On the other hand, the precursor B is pulsed and reacts with the surface (d), and similarly, the remaining precursor and by-products are purged by using an inert gas (e). Finally, to reach the desired thickness, the stages (b–e) can be repeated. This technique gives the possibility of depositing several oxide precursor reactants by ALD (ZnO, TiO2, and Al2O3, among others) on diverse types of substrates (e.g., ceramics and polymers) and thus convert them on different MOF materials. The drawbacks of ALD technique are the time required for chemical reactions, high quantity of wasted material, high energy consumption, and possible nanoparticle emissions.66 For instance, ZnO layers, which correspond to 5–70 nm size, have been deposited onto α-Al2O3.67 Subsequently, the conversion to ZIF-8 using a 2-methylimidazole–methanol solution under solvothermal conditions was achieved.68 The ZIF-8/ZnO/α-Al2O3 nanocomposite membranes were found to be H2 selective (permeance up to 1.6 × 10−8 mol· m−2 s−1 Pa−1) towards equimolar H2/CO2 and H2/CH4 gas mixtures with selectivity values of 7.8 and 12.5, respectively. In a different study, some authors also produced HKUST-1 thin films via layer-by-layer growth on ALD-coated fiber mats; the average thickness was about 117 nm. Surprisingly, this methodology was able to create a MOF monolayer per cycle, in which the thickness/cycle was close to 2.6 nm. It is important to mention that the authors did not evaluate the ability of the HKUST-1 membranes in separating gases but they should be potentially tested towards CO2/N2, CO2/CH4, O2/N2, and H2/CH4 separations69,70 and some other selective pervaporation separations.71–73 Importantly, ultrathin membranes prepared via ALD are capable of separating saturated vapors of organic solvents, for e.g., Greil et al.74 evaluated the ability of ultrathin self-assembled block copolymer membrane (<50 nm) to separate acetone and ethyl acetate with the selectivity value of 7.
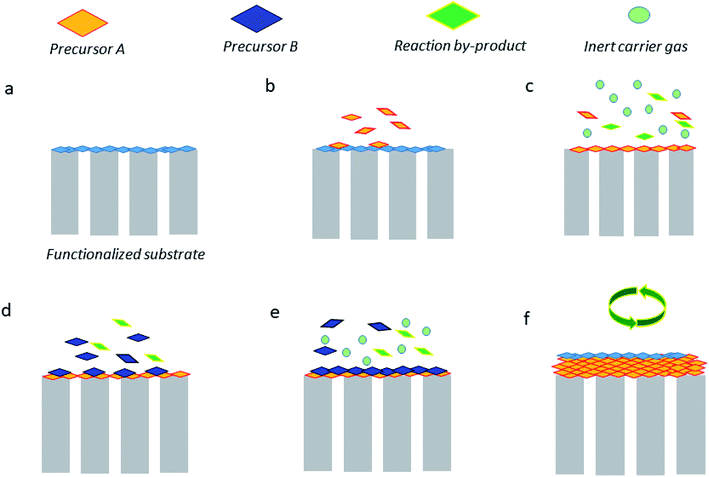 |
| Fig. 6 Graphical illustration of the most common stages of the ALD technique.65 (a) Functionalized support. (b) Precursor A reacts with the surface. (c) Purge of A and by-products. (d) Precursor B reacts with the surface. (e) Purge. (f) Repetition of (b–e) steps to achieve the target film thickness. | |
A similar approach was developed by Tran et al.,75 who performed the plasma-enhanced (by coupling with sol–gel method) ALD of titania (TiO2) on γ-Al2O3 porous support for its potential application as a H2-selective membrane. Using this methodology, after a number ALD cycles (280 cycles), a thin TiO2 layer with a thickness of ∼10 nm was obtained. Regarding gas permeation testing, the membrane presented a H2 permeance of approximately 12.5 × 10−8 mol m−2 s−1 Pa−1 and the H2/CO2 separation factor was about 5.8.
3.4 Chemical vapor deposition (CVD)
ALD is considered as a variant of chemical vapor deposition (CVD) in the deposition of thin films with highly precise thickness at the sub-monolayer level.76 The CVD technique has been recognized as advantageous compared to ALD due to ALD being a self-limiting layer-by-layer thin film deposition method. In particular, CVD employs the use of a substrate, which is exposed to one or more volatile precursors, reacting or decomposing on the substrate surface to produce the desired material. CVD usually guarantees excellent film quality and better control of film thickness.77 However, compared to ALD, the disadvantages of CVD are due to high temperatures required to decompose the precursor at the substrate surface, structurally defective material when synthetizing carbon nanotubes,78 possibility of producing gas by-products that are generally very toxic, uncontrollable thickness (when using graphene-based materials),79 and finally, similar to the other deposition techniques, CVD is also costly.66 Ultra-permeable poly[1-(trimethylsilyl)-1-propyne] (PTMSP) membranes have been proposed as supports to deposit metal–organic covalent networks, such as zinc(II) meso-tetraphenylporphyrin (ZnTPP), via CVD.80 In such ZnTPP–PTMSP membranes with a thickness of 150 nm, the gas permeances of larger gas molecules (such as N2 and CH4) were significantly diminished, while high permeances of smaller gas molecules (H2) were obtained. Towards the preparation of thin ZIF-8 layers, Li et al.81 combined sol–gel coating with vapor deposition for solvent-/modification-free and precursor-/time-saving synthesis on the PVDF hollow fiber support. The resulting layers possessed a thickness of about 17 nm, which certainly provided high permeable properties for H2 (up to 215 × 10−7 mol m−2 s−1 Pa−1). When dealing with the selectivity, the values were of 3400, 1030, and 70 for H2/C3H8, CO2/C3H8, and C3H6/C3H8, respectively. With such impressive performances, the membranes overcame the Robeson (2008) limit for polymeric membranes. Furthermore, they also revealed a permeation cut-off between CO2 (ca. 0.33 nm) and O2 (ca. 0.346 nm) based on the crystallographic aperture of ZIF-8 (ca. 0.34 nm), providing selectivity values of 4.6, 7.3, 8.9, 14, and 940 for CO2/O2, CO2/N2, CO2/CH4, CO2/C3H6, and CO2/C3H8, respectively. At this point, such thin membranes are among the thinnest membranes reported in literature and therefore, the study addresses a viable method as an alternative for the scalable and controllable production of ultrathin gas separation membranes with unique and promising molecular sieving properties.
3.5 Electrophoretic deposition
Electrophoretic deposition has been used for quite some time to deposit charged colloids on to a substrate with the help of an electric field (e.g., zeolite particles as seeds to growth a zeolite membrane)82 and has been recently demonstrated to synthesis sub-1 μm-thick high-performance MOF membranes.83–85 The flux of the colloids, N, is related to their concentration (c) and their velocity (v), as per eqn (3). v can be obtained from the mobility of colloid under the applied electric field, E (eqn (4)). |
 | (4) |
where ε0 and εr correspond to the permittivity of vacuum and dielectric constant of the medium, respectively. ζ corresponds to the zeta potential of charged particles and η refers to the viscosity of the medium.
The key advantage of using electrophoretic deposition for the synthesis of intergrown inorganic membranes is that one can carry out the synthesis directly from the precursor solution without the need for time-consuming separation of seed crystals. Further, this method can be optimized to deposit sub-100 nm-sized nuclei instead of large seed crystals. This has been demonstrated to promote intergrowth. Other advances include precise control on film deposition rate, high deposition rate, and prevention of agglomeration. The disadvantage of this approach is that the size and quality of the coating is limited by the electrode. For example, in the coating of reduced graphene oxide flakes, uncontrollable agglomeration of the flakes can be problematic.79 By applying an electric field in the early stage of crystallization, heterogeneous nucleation of the crystalline film can be precisely controlled. For example, He et al. could achieve a ZIF-8 nuclei (defined by ZIF-8 nanocrystals with particle size in the range of 10–20 nm) deposition rate of 30 nm min−1.84 The deposition of a 100 nm-thick nuclei film, followed by a short intergrowth step, gave rise to 500 nm-thick polycrystalline ZIF-8 films, which yielded extremely attractive performance in propene/propane separation (propylene permeance of 300 GPU and selectivity of 30). Interestingly, the synthesis of ZIF-8 membranes using fast-current-driven synthesis under an electric field can lead to sharpened molecular sieving performance, as shown recently by Zhou et al., achieving propene/propane selectivity of greater than 300.85
3.6 Facile vacuum filtration
Filtration has been recognized to be a useful protocol for assembling graphene and graphene oxide (GO)-based hybrid membranes due to the relatively facile procedure for creating controllable thickness and low-cost;86 however, the size and shape of the membranes are limited by the vacuum filtration device.79 These 2D materials, namely, graphene and GO, offer well-defined transport channels and atomic-thickness, giving extraordinary performance in gas separations (even for liquid separations).87–89 For instance, Kim et al.90 demonstrated that few- and several-layered graphene and GO sheets can be engineered to exhibit desired gas separation performance, for e.g., the membranes were fabricated by contacting the support membrane surface to the air liquid interface of a GO solution, followed by spin-coating. Such a procedure allowed to obtain layered (3- to 10 nanometer) GO membranes, which displayed tunable gas transport behavior dependent on the degree of interlocking within the GO stacking structure, for e.g., the CO2 permeability was ∼8500 Barrer, while the CO2/N2 selectivity was ∼20. Importantly, the authors also tested the gas permeance of these membranes (see Fig. 7), displaying gas permeance preference in the order CO2 > H2 ≥ He > CH4 > O2 > N2. Using the same 2D material, ultrathin molecular-sieving GO membranes for selective hydrogen separation were reported by Li et al.;91 in such a study, ultrathin GO membranes, with thickness approaching 1.8 nm, were prepared through a facile vacuum filtration process. These membranes displayed binary mixture separation selectivity values as high as 3400 and 900 for H2/CO2 and H2/N2 mixtures, respectively, through selective structural defects on GO. In particular, the authors found out that H2 and He permeances decreased exponentially as the membrane thickness was increased from 1.8 to 180 nm. Likewise, they speculated that the main gas transport pathway for these molecules was associated with selective structural defects within the GO flakes instead of d-spacing corresponding to the GO flakes.
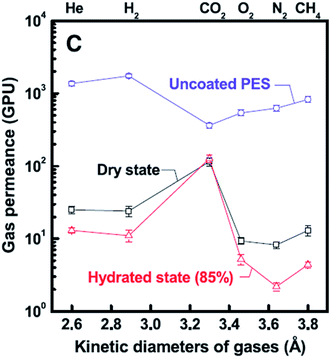 |
| Fig. 7 Gas transport behavior of ultrathin GO membranes prepared by Kim et al.90 | |
Unlike Kim's approach (CO2/N2 = 20),90 Liu et al.92 obtained higher CO2/N2 selective (about 30) but less CO2 permeable (∼2100 GPU) membranes. In general, ZnTCPP nanosheets (∼3–4 nm) were synthesized via a surfactant-assisted technique (using polyvinylpyrrolidone as the surfactant) and subsequently deposited onto a flexible porous PAN support by vacuum filtration. This produced an ultrathin (∼25 nm) layer, which was used as a highly permeable gutter layer with reduced gas resistance in comparison with conventional PDMS.
Wang et al.93 reported ultrathin single-layered molybdenum disulfide (MoS2) onto AAO (anodic aluminum oxide, 200 nm pore size) membranes with controlled thicknesses using a simple filtration technique. For example, the thickness of the MoS2 membranes were in the range of 17–60 nm and the one possessing 17 nm thickness certainly displayed the best separation performance (e.g., over 24
000 GPU for He and H2), which was governed by Knudsen gas transport mechanism (i.e., no relevant molecular sieving properties were achieved). This occurred within the regular space between the MoS2 flakes and the larger stacking space in the MoS2 membrane (e.g., 1.0 nm interlayer space). Finally, the highly permeable properties allowed to overcome the Robeson relationship even though the membranes had relatively low selectivity, i.e., H2/CO2 = 3.4.
This technique of filtration can also be applied to suspensions of nanosheets of zeolites94 and MOFs95,96 obtained upon exfoliation of the corresponding crystals. In particular, the results achieved by Peng et al.95 are outstanding, with H2/CO2 separation selectivity of 291 at 120 °C together with the H2 permeance of 3760 GPU.
3.7 Interfacial polymerization (IP)
When dealing with the synthesis of polymer-based nanofilms, i.e., the so-called thin film composite (TFC) or thin film nanocomposite (TFN) membranes, interfacial polymerization (IP) is a latent technique that provides highly crosslinked polymer films at nanoscale thickness. Typically, step-growth polymerization takes place at the interface between two immiscible phases (generally two liquids with a different monomer each), which results in a polymer that is constrained to the interface.97 In general, this procedure is not time-consuming (i.e., fast reaction) but, unfortunately, it provides low yield, high cost of some its reactants (e.g., acid chloride), and cannot run continuously. Also, there is a presence of remaining agents (e.g., reactants and solvents).98 In Livingston's group,99 ultrathin cross-linked polyacrylate nanofilms supported on PTMSP (∼20 nm) were formed in situ by interfacial polymerization (see Fig. 8). Such nano-sized membranes possessed enhanced microporosity and higher interconnectivity of intermolecular network voids, which revealed defined molecular sieving features, i.e., gas permeance decreased as He > H2 > CO2 > O2 > N2 ≈ CH4. Towards the overcoming of the so-called Robeson relationship, such nanomembranes clearly showed higher selectivity in comparison with typical polymer membranes with similar H2 permeability, positioning them near the trade-off (see Fig. 8). In any event, this performance has been recently overcome with analogous polyamide TFC membranes prepared on asymmetric polysulfone35 (H2/CO2 selectivity of 50 at 140 °C with a H2 permeance of 350 GPU) and polyimide27 (328 GPU of H2 and a H2/CO2 selectivity of 18.1 at 180 °C) supports.
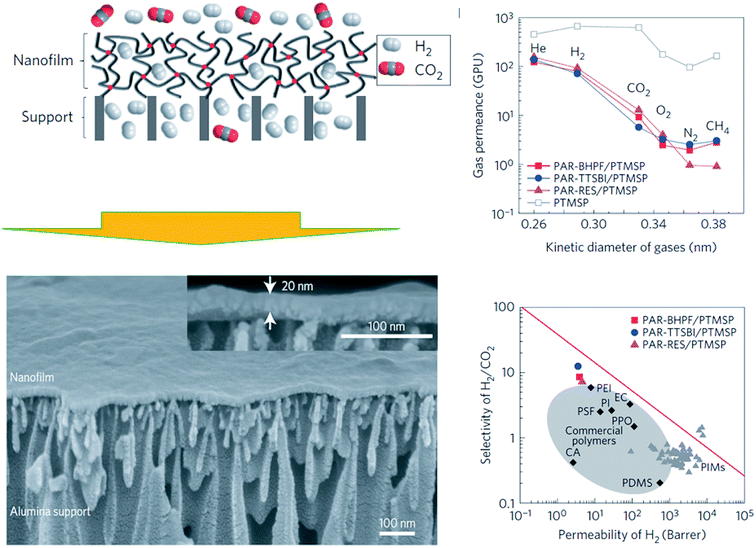 |
| Fig. 8 Interfacial polymerization of polyacrylate-based nanofilms and their gas separation performance. Adapted from Jimenez-Solomon et al.99 | |
Yuan et al.100 carried out IP using N-methyldiethanolamine (MEDA) and trimesoyl chloride (TMC) on crosslinked poly-dimethylsiloxane (PDMS) coated polysulfone support membrane. In general, the thickness of the PDMS skin-layer (between 49–308 nm) varied as a function of TMC content (from 0.0100 to 0.0750 mol L−1). In other words, TMC concentration governs the thickness of the membrane skin layer, in which higher TMC concentration promoted the formation of a more crosslinked membrane. In terms of permeance, higher TMC concentration (dealing with higher thickness) indeed contributed to less CO2 and N2 permeance values,100 for e.g., the highest CO2 (up to 3000 GPU) and N2 permeances (up to 90 GPU) were obtained at the lowest TMC content (0.0100 mol L−1). In particular, within the IP technique, the monomers in both aqueous and organic phases are crucial in determining the thickness of the skin layer of thin film composite membranes.101 Very recently, Yu et al.102 manufactured ultrathin microporous polyarylate membranes (thickness between 25–75 nm) via IP of 5,5,6,6-tetrahydroxy-3,3,3,3-tetramethylspirobisindane (TTSBI) and TMC. The membranes exhibited CO2 permeance in the range 100–2115 GPU with CO2/N2 selectivity of 45–21. Herein, a specific membrane preparation parameter, such as the pH, has been identified as important towards membrane thickness. For example, the authors stated that the thickness of the selective layer gradually decreases with increasing pH value. This is due to the fact that the number of reactive groups (i.e., –ONa) of TTSBI could differ under different pH values, which is obviously crucial to the IP method and membrane structure.103 Therefore, the pH value could remarkably affect the IP through hydrolysis of both TTSBI and TMC.
Two final remarks dealing with this technique are that: (i) filler nanoparticles can be incorporated during the IP process by maintaining the thickness of the membrane skin layer to an attractive value of ca. 100 nm (ref. 27) and is able to be operated up to 250 °C with H2/CO2 selectivity of 14.6 and a H2 permeance higher than 600 GPU; (ii) it can be applied to other polymer systems different from the typical polyamides used in the beginning of the development of the TFC membranes,34 as recently demonstrated by Shan et al.37 with the preparation of benzimidazole-linked polymer (BILPs) membranes with H2/CO2 selectivity up to 40 (at 24 GPU H2 permeance), high pressure resistance, and long-term stability (800 h in the presence of moisture).
3.8 Langmuir–Blodgett method
Langmuir–Blodgett (LB) is a technique generally used for the deposition of polymer-based monolayers on top of different types of membrane supports.104 Its disadvantages comprise equipment required for material processing, substrate size, film topology, and stability;105 however, the slow diffusion of substrates over the film and compressed floating films are typically obtained that are about one-fifth of the area of the trough, which restricts the quantity of the material that can be deposited onto a substrate in one batch. These features have, in fact, limited the commercial application of the LB technique.106 In general, several LB ultrathin membranes have been deposited onto PTMSP for enhancing the H2/CO2 and CO2/N2 separation. In this way, polymers of intrinsic microporosity (PIMs), as new kind of polymers with impressive gas separation performance (e.g., PCO2 > 1000 Barrer and PCO2/PN2 ∼ 20),107,108 have been used for the manufacture of ultrathin membranes thick monolayers supported on PTMSP, which displayed CO2 permeance up to 7 times higher than that of dense pristine PIM membranes using only 0.04% of the mass of PIM (PIM-EA-TB(H2)), without a significant decrease in CO2/N2 selectivity.29 It is important to note that when the transference of the monolayer was horizontal, as was the case here, instead of vertical, the name of the technique is Langmuir–Schaefer (LS).109 In the same line, the authors deposited monolayers of the 2D polymer PIM-TMN-Trip onto PTMSP,110 displaying a performance which varied as a function of the number of layers on the selective film, as shown in Fig. 9, where the highest CO2/N2 selectivity (>10) was obtained in membranes having 30 PIM layers, whereas the maximum CO2 permeance (>400 GPU) was obtained for less number of PIM monolayers. Compared to the study by Benito et al.,111 it is likely that the polyelectrolyte multilayers on PTMSP membranes (thickness 20–32 nm) proposed by Lin et al.112 are closer to the empirical “upper-bound”. Certainly, these breakthroughs provide clear insights that the smart design of new types of membranes, together with emerging membrane preparation protocols, may favor to break the performance trade-off limitations of existing materials. Here, as a main drawback, the manufacture of ultrathin membranes via LB technique generally results in membranes with poor mechanical properties, which leads to cracks or application of macroporous support layers that are tough to cover by LB film without defects.104 Finally, LS/LB may allow controlled filler positioning in a mixed matrix membrane, as demonstrated with MIL-101(Cr) based TFN membranes for nanofiltration.113
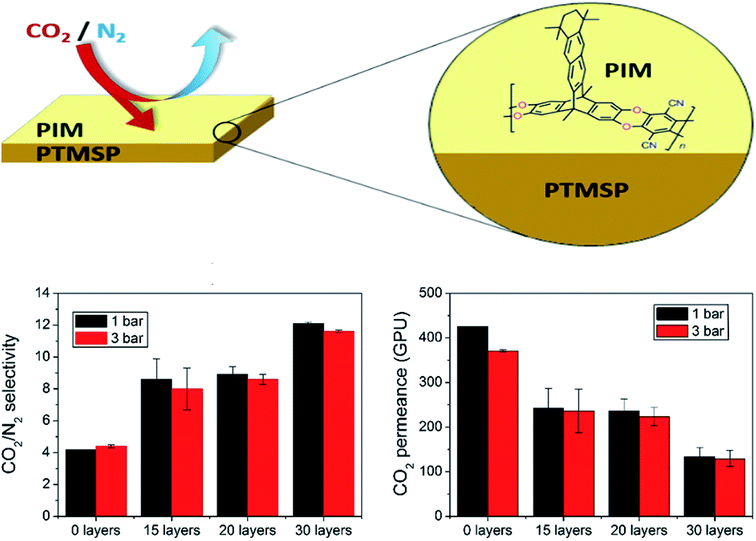 |
| Fig. 9 Separation performance of ultrathin PIM-PTMSP membranes as a function of number of PIM layers. Adapted from Benito et al.110 | |
3.9 Other emerging preparation protocols for the fabrication of ultrathin membranes
Recently, some other methods have been adopted in the preparation of ultrathin membranes towards successful gas separation. It is well known that selective layers, less than 100 nm thick, are highly desired for maximizing/optimizing the permeance of gas separation membranes for high energy efficiency. An extreme example of ultrathin selective layer is when the selective layer is only an atom thick, for e.g., in the case of single-layer graphene membranes.114,115 Since the discovery of graphene in 2004, rapid advances in this field have propelled the synthesis of single-layer graphene in a scalable way.116,117 Further advances have led to the synthesis of large-area graphene membranes, made possible by mechanically reinforcing the graphene layer. For example, Huang et al.118 reinforced the graphene layer by a nanoporous carbon film and could synthesize a 1 mm2 sized single-layer graphene film with H2/CH4 selectivity of 6–25 and H2 permeance of 100–1000 GPU with a low porosity of 0.03%. Very recently, by reinforcing graphene by a carbon nanotube mesh, large-area graphene membrane could be prepared.119 This could also allow the fabrication of a tubular membrane module from single-layer graphene membrane, which displayed salt rejection between 85.2–93.4% and water permeance of 97.7 L m−2 h−1 bar−1. The key to obtaining high-performance membrane is to etch the otherwise impermeable graphene lattice in a controlled way. A proof-of-principle study was reported by Koenig et al.,120 where by etching micromechanically exfoliated pristine graphene in UV/ozone, CO2/CH4 and CO2/N2 selectivities exceeding 1000 were achieved from pressurized graphene microbubbles. Further progress in controlled and tunable etching of CVD-derived large-area graphene has led to angstrom resolution in molecular differentiation with H2/C3H8 selectivity exceeding 200 and H2 permeance up to 6000 GPU.121 Single-layer graphene allows for guest–host chemistry and can be an ideal matrix to form hybrid membranes. For example, using molecular dynamics simulations, Tian et al.122 recently showed that by decorating graphene nanopores with ionic-liquid, one can create ion-gated transport leading to an attractive CO2/CH4 selectivity of about 42 with a CO2 permeance of 105 GPU. A similar concept was demonstrated by experiments, where He et al.123 functionalized single-layer graphene by CO2-selective polymer chains, achieving record high post-combustion carbon capture performance with CO2 permeance of 6180 GPU and CO2/N2 mixture separation factor over 22.5. Further developments in controlled etching of the graphene lattice, for example, by carbon gasification chemistry and functionalization of the lattice, is likely to allow a wide-range of industrially relevant gas separations from membranes based on single-layer graphene.
Pushing the thickness limit of conventional materials, Zhang et al.124 created a shear-aligned GO filled Pebax® 1657 hollow fiber membrane onto a porous polyvinylidene fluoride (PVDF) support by means of facile dip-coating technique. Particularly, the embedding of 0.1 wt% aligned GO laminates significantly enhanced the original Pebax® CO2 permeance properties from 220 up to 410 GPU, without compromising the selectivity properties towards CO2/N2 (∼45). This can be attributed to the defined GO d-spacing of ∼0.7 nm (intergallery distance of ∼0.35 nm), which is in the range of the kinetic diameters of the molecules (e.g., CO2 = 0.33 nm and N2 = 0.36 nm). In addition to this, the composite membrane presented good operational stability and enhanced mechanical characteristics. It is important to note that a gutter layer based on PTMSP, as a highly permeable polymer, was applied to the PVDF support in order to skip the possible penetration of the coating layer into PVDF pores, favoring the creation of a true and effective ultrathin membrane. The use of a thin gutter layer was also proposed by Yoo et al.125 to prevent pore penetration in the selective layers. However, such a layer may provoke a decrease in the selectivity unless the gutter layer can be well designed. Based on this, Yoo et al.125 described a gutter material (e.g., Teflon AF2400) that displayed six-folds higher CO2 permeance than PDMS (the most common gutter material). The membranes with ultrathin gutter (e.g., 75 nm) and selective layers (e.g., 70 nm) were tested for CO2/N2 separation, revealing a CO2 permeance >1455 GPU and selectivity of 68.1.
In a different approach, ethylenediamine (EDA)-functionalized GO flakes were used for the preparation of 28 nm EDA–GO membrane layer126 by deposition onto the inner surface of PES hollow fibers. Here, a vacuum-assisted coating method, consisting of seeding and coating steps, was applied. In terms of gas testing, such membranes displayed a high CO2 permeance of 660 GPU and a CO2/N2 selectivity of about 500. Moreover, it was reported that these functionalized membranes also presented selective water transport over gases and impressive water permeance >15
000 GPU.
A new route for the fast in situ growth of ZIF-8 membrane with the use of 2D graphitic carbon nitride (g-C3N4) was reported by Hou et al.127 In practice, 2-methylimidazole was used as a ligand solution for subsequent spin coating. The support (porous anodic aluminum oxide) was covered with Zn2+/g-C3N4 nanosheets and the ligand solution via cyclical spin coating. The obtained membranes displayed a thickness of about 200 nm that can be considered as thin, which is a result of the inhibition effect of the 2D nanosheets to avoid the growth of larger ZIF-8 particles.127 For instance, Table 2 enlists some other membranes based on ZIF-8 obtained using other methodologies and conditions, where it can be seen that spin coating meets the requirements of preparing ultrathin membranes. Similar to the study by Hou et al.,127 ultrathin ZIF-8 membranes with a thickness of about 200 nm were synthesized via chemical vapor modification of surface chemistry and nanopores of an asymmetric bromomethylated poly(2,6-dimethyl-1,4-phenylene oxide) (BPPO) substrate.128 Such membranes showed excellent H2 permeance (2.05 × 10−6 mol m−2 s−1 Pa−1) with acceptable H2/N2 and H2/CO2 selectivity values (9.7 and 12.8, respectively). For different types of separation (i.e., propylene/propane), relatively thicker ZIF-8 hollow fiber membranes (thickness ∼800 nm) were designed by Joo et al.129 Basically, ZIF-8 membranes were supported on porous Matrimid® polymer hollow fibers by means of microwave-assisted seeding and microfluidic secondary growth. The authors packed densely ZIF-8 layers on hollow fibers under microwave heating. The ZIF-8 layers were then secondarily grown into well-intergrown ZIF-8 membranes under continuous flow of the growth solution. Likewise, the membranes exhibited a propylene/propane separation factor of ∼46 and propylene permeance of ∼55 GPU (permeability ∼ 49.4 Barrer). According to the authors' insights, these membranes are commercially attractive as they can overcome the upper bound of this separation and therefore, are located in the desired region. Besides, microfluidics can be used to access the interior of a hollow fiber support for proper synthesis of the active membrane material130 and to produce bilayered MOF membranes or to functionalize previously prepared MOF membranes by sequential pumping of the needed reactants.131
Table 2 Thin ZIF-8 membranes obtained with different techniques and synthetic conditions
Membrane |
Technique |
Time (h) |
Temperature (°C) |
Thickness (nm) |
Reference |
ZIF-8/g-C3N4 |
Spin coating |
0.5 |
25 |
200 |
127 |
ZIF-8/PTSC |
Counter-diffusion |
48 |
25 |
620 |
132 |
ZIF-8/GO |
Counter-diffusion |
6 |
25 |
100 |
133 |
ZIF-8–MBPPO |
Immersion |
16 |
25 |
200 |
128 |
ZIF-8 |
Counter-diffusion |
4 |
120 |
1500 |
134 |
ZIF-8@BPPO–EDA |
Counter-diffusion |
2 |
25 |
2000 |
135 |
ZIF-8 |
Secondary growth with seeding |
6 |
30 |
2200 |
136 |
Nowadays, carbon molecular sieves (CMS) have emerged as highly promising membrane materials. CMS are typically have disordered packing of aromatic carbon strands, which are derived from the pyrolysis of a polymeric precursor.137 Such materials offer the possibility of being synthetized with a narrow pore-size-distribution, producing attractive sieving performances. Specific pores have been reported with a sub-angstrom resolution, displaying excellent molecular differentiation towards C2H4/C2H6 (ref. 138) and N2/CH4 (ref. 139) separations. In the framework of ultrathin CMS membranes, Huang et al.140 reported two fabrication ways, namely, transfer and masking techniques, allowing the preparation of CMS films of the order of 100 nm, providing attractive gas-sieving performances with H2 permeance reaching up to 3060 GPU and selectivity values between 18 and 24 for H2/CH4.
Highly permeable and oriented pseudozeolite aluminophosphate AlPO-18 membranes were prepared on the inner surface of tubular asymmetric alumina supports using directly synthesized nanosheets.141 In principle, AlPO-18 presented a thin sheet-like and hexagonal-prism morphology with a length of approximately 600 nm and thickness of only 30 nm. However, after the membrane preparation procedure, the coated layer grew into a continuous AlPO-18 layer and a thickness of approximately 1 μm was obtained. Regardless of the thicker layer of the membrane, the membranes gave a CO2 permeance as high as 3.6 × 10−6 mol m−2 s−1 Pa−1 (∼10
500 GPU), while the CO2/CH4 selectivity was about 91.5 at equimolar CO2/CH4 mixture.
PDMS/copper hydroxide nanofibers/(polyacrylonitrile) PAN ultrathin membrane layers (≈100 nm) were evaluated for CO2 capture applications (e.g., CO2/N2 separation).142 Such composite layers were appropriately designed using generic interface-decoration-layer strategy. This generally involves molecular-scale organic–inorganic hybridization in the selective layer to obtain a high-performance ultrathin film composite. Such a membrane provided a 2.5-fold increase in the gas permeance up to 2860 GPU. Interestingly, the organic part of the composite material contributed to facilitate CO2-selective adsorption (e.g., CO2/N2 selectivity of 28.2); on the other hand, the inorganic part helped to maintain a robust membrane structure.142 Therefore, a remarkable enhancement in the selective properties towards CO2 was obtained based on the synergistic effect of merging both inorganic and organic membranes.
Using atom transfer radical polymerization, Kim et al.143 developed ultrathin MMMs by merging bio-inspired iron(III)–dopamine nanoparticles into a cross-linked selective layer (∼45 nm) of PEG macrocross-linker. Such a MMM selective layer was deposited on the top of the porous PAN substrate previously treated with a PDMS gutter layer. The CO2 permeance was about 1200 GPU, whereas the CO2/N2 selectivity was over 35. In such a study, the authors evaluated the performance of membranes in the presence of common gas contaminants, revealing that the CO2/N2 selective properties were still maintained over 4 months, while the CO2 permeance experienced a slight increase, which could be associated with the dissociation of coordinate bond between Fe3+ and dopamine in dry conditions.144 This might reduce the volume occupied by the nanoparticles, allowing the increase in the free volume and therefore, the enhanced CO2 and N2 permeances.
4. Concluding remarks and future trends
Even if the idea of ultrathin membrane is obvious (as the membrane thickness decreases both the membrane cost and permeance), there have been important technical limitations in realizing them over the past years. Throughout this study, we have reviewed the most applied and new techniques used by the research community aimed at the fabrication of ultrathin membranes for a synergic gas separation performance. Herein, we have identified that the most desired membranes are those that possess a thickness less than 100 nm. Nevertheless, according to the polymer and inorganic and hybrid materials, in addition to their design, relatively thicker membranes (let us say with thicknesses of selective layers below ca. 1 μm) may meet good separation performance and robustness as well. By reviewing the literature, it has been found that specific ultrathin preparation techniques (e.g., chemical vapor deposition and facile vacuum filtration) are able to provide extremely thin membranes (ca. 17 nm) with highly permeable features (H2 permeance and good selectivities towards H2/CO2), which mostly surpass the Robeson trade-off. In fact, these values reveal that some procedures, even if highly promising, still need improvement to meet both high permeance and selectivity. In addition, three important suggestions for future research in the field can be noted: (i) evaluate the performance of thin membranes in long term operation. This could be useful in realizing the real potentiality of such a concept of membranes for real application and also, if there exists a limitation for the membrane stability as a function of membrane thickness for the same active material. (ii) The research community should start the testing of those membranes using complex gas mixtures that may contain real contaminants or some other organic components, as well as simulated close operating conditions. (iii) Towards successful industrialization, the fabrication of large-area membranes is also needed. However, the manufacture of membrane modules is still quite challenging since large-scale membranes with defect-free structures are difficult to obtain, which obligates resorting to healing techniques usually based on coating with elastomers such as PDMS.145 In addition to this, it is important to note that most of the approaches based on ultrathin membranes have been mainly focused on the preparation of flat-sheet membranes; therefore, if we seek commercialization and industrial consolidation, hollow fiber membrane modules are more attractive since they display less fouling and larger effective surface area, which can be translated to high productivities. Thereby, hollow fiber membranes seem to be the most feasible configurations and should be further explored, considering the high separation performance of some hollow fiber concepts, such as PIM-1/Matrimid,146 crosslinked PDMS,147,148 poly trimethyl phenylene ether sulfone,149 PIM/PDMS/PAN multi-layer composites,150 and those based on the crystallization of continuous MOF layers on these kind of supports130,151 and on the use of MOF based mixed matrix membranes.152 Several nano-materials have been tested in the preparation of thin layers; it is quite possible that 2D materials and COFs will be widely explored in the field. While the progress in applications of ultrathin-MOF membranes finds its main bottleneck due to the structural, chemical, and hydrothermal (acidic/basic) stability of the ligand–metal bonds, they are the dominant challenges to be faced in industrial applications. Moreover, it is time to explore new polymeric materials (e.g., Teflon AF2400)125 as alternatives of traditional gutter layers (e.g., PTMSP) onto porous substrates, which attempts the prevention of the coating layer into the pores of the substrates. Finally, it seems logic that particles of nanoporous materials with a high aspect ratio, e.g., nanosheets, should be available with proper stability to create ultrathin membranes claimed in this review, particularly as mixed matrix membranes. In the particular case of MOFs (but this applies to all the materials described here), these nanosheets can be prepared by either exfoliation top-down approach95,96 or direct synthesis bottom-up approach.153,154 In any event, nanoporous nanosheets will most likely be the building blocks in creating a new generation of ultimate gas selective membranes.
To date, ALD technique has been likely the most used and explored technique since it can overcome many of the main drawbacks of conventional deposition techniques and it can be even be used to coat particles within ultrathin layers. Moreover, it allows to control the thickness (in the angstrom range, 0.1 nm) and tunable film composition. However, ALD is an analog of the CVD technique, which is most appropriate for binary compounds since a binary CVD reaction can easily be separated into two half-reactions.79 While other new techniques, such as electrophoretic deposition, have provided good insights into the fabrication of membranes but they still have limitations. It is clear that there is a growing trend in the development of ultrathin membranes in the future and the need to manufacture membranes in an eco-friendly manner (e.g., electrophoretic deposition, electrochemical based techniques, and self-assembly). In summary, to select the right preparation protocol is a difficult task since it will depend on the type of membrane as well as its desired features, type of material (type of polymer and its physicochemical properties), type of inorganic phase (e.g., size, shape, physicochemical properties, and stability of the nanomaterial), the cost incurred during the fabrication protocol, among others. Therefore, this paper has identified and provided to the readers the key advantages and drawbacks of each technique, providing a good guideline for the selection of a suitable ultrathin preparation technique according to their necessities.
Nomenclature
AAO | Anodic aluminum oxide |
AlPO | Aluminophosphate |
ALD | Atomic layer deposition |
ATRP | Atom transfer radical polymerization |
BILP | Benzimidazole-linked polymer |
BPPO | Bromomethylated poly(2,6-dimethyl-1,4-phenylene oxide) |
CVD | Chemical vapor deposition |
CMS | Carbon molecular sieve |
COF | Covalent–organic framework |
ED | Electrophoretic deposition |
EDA | Ethylenediamine |
D | Diffusivity |
GO | Graphene oxide |
GPU | Gas permeation unit |
GS | Gas separation |
IP | Interfacial polymerization |
LBL | Layer-by-layer |
LB | Langmuir–Blodgett |
LS | Langmuir–Schaefer |
MOF | Metal–organic framework |
MEDA | N-Methyl diethanolamine |
MMM | Mixed matrix membrane |
P | Permeability |
PAN | Polyacrylonitrile |
PTMSP | Poly[1-(trimethylsilyl)-1-propyne] |
PDMS | Poly-dimethylsiloxane |
PES | Polyethersulfone |
PEG | Polyethylene glycol |
PVDF | Porous polyvinylidene fluoride |
PIM | Polymer of intrinsic microporosity |
S | Solubility |
TFC | Thin-film composite |
TFN | Thin-film nanocomposite |
TMC | Trimesoyl chloride |
TTSBI | Tetramethylspirobisindane |
ZnTPP | Zinc(II) meso-tetraphenylporphyrin |
Conflicts of interest
The authors declare no conflict of interest.
Acknowledgements
R. Castro-Muñoz acknowledges the School of Science and Engineering and the FEMSA-Biotechnology Center at Tecnológico de Monterrey for their support through the Bioprocess (0020209I13) Focus Group. Financial support from the Spanish Ministry of Science, Innovation and Universities and FEDER (MAT2016-77290-R), the Aragón Government (T43-17R) and the ESF is also gratefully acknowledged. K. V. Agrawal acknowledges support from Swiss National Science Foundation (SNSF) Assistant Professor energy grant (PYAPP2_173645) and European Research Council (ERC) starting grant (805437 Ultimate Membranes).
References
- A. Brunetti, F. Scura, G. Barbieri and E. Drioli, J. Membr. Sci., 2010, 359, 115–125 CrossRef CAS
. - M. Al-Juaied and W. J. Koros, J. Membr. Sci., 2006, 274, 227–243 CrossRef CAS
. - R. Castro-Muñoz, V. Fíla and C. T. Dung, Chem. Eng. Commun., 2017, 204, 295–309 CrossRef
. - R. W. Baker, Ind. Eng. Chem. Res., 2002, 41, 1393–1411 CrossRef CAS
. - R. W. Baker and B. T. Low, Macromolecules, 2014, 47, 6999–7013 CrossRef CAS
. - D. Jansen, M. Gazzani, G. Manzolini, E. Van Dijk and M. Carbo, Int. J. Greenhouse Gas Control, 2015, 40, 167–187 CrossRef CAS
. - B. W. Rowe, L. M. Robeson, B. D. Freeman and D. R. Paul, J. Membr. Sci., 2010, 360, 58–69 CrossRef CAS
. - L. M. Robeson, J. Membr. Sci., 2008, 320, 390–400 CrossRef CAS
. - L. M. Robeson, J. Membr. Sci., 1991, 62, 165–185 CrossRef CAS
. - H. B. Park, J. Kamcev, L. M. Robeson, M. Elimelech and B. D. Freeman, Science, 2017, 356, 1138–1148 CrossRef PubMed
. - X. Guo, Z. Qiao, D. Liu and C. Zhong, J. Mater. Chem. A, 2019, 7, 24738–24759 RSC
. - R. Castro-Muñoz, V. Martin-Gil, M. Z. Ahmad and V. Fíla, Chem. Eng. Commun., 2018, 205, 161–196 CrossRef
. - B. Seoane, J. Coronas, I. Gascon, M. E. Benavides, O. Karvan, J. Caro, F. Kapteijn and J. Gascon, Chem. Soc. Rev., 2015, 44, 2421–2454 RSC
. - J. Dechnik, J. Gascon, C. J. Doonan, C. Janiak and C. J. Sumby, Angew. Chem., Int. Ed., 2017, 56, 9292–9310 CrossRef CAS PubMed
. - M. Z. Ahmad, H. Pelletier, V. Martin-Gil, R. Castro-Muñoz and V. Fila, Membranes, 2018, 8, 1–16 CrossRef PubMed
. - F. Cacho-Bailo, G. Caro, M. Etxeberria, O. Karvan, C. Tellez and J. Coronas, RSC Adv., 2016, 5881–5889 RSC
. - J. Wu, J. Liu and T.-S. Chung, Adv. Sustainable Syst., 2018, 2, 1800044 CrossRef
. - C. H. Lau, P. T. Nguyen, M. R. Hill, A. W. Thornton, K. Konstas, C. M. Doherty, R. J. Mulder, L. Bourgeois, A. C. Y. Liu, D. J. Sprouster, J. P. Sullivan, T. J. Bastow, A. J. Hill, D. L. Gin and R. D. Noble, Angew. Chem., Int. Ed., 2014, 53, 5322–5326 CrossRef CAS PubMed
. - A. Ebadi Amooghin, M. Omidkhah, H. Sanaeepur and A. Kargari, J. Energy Chem., 2016, 25, 450–462 CrossRef
. - B. W. Rowe, B. D. Freeman and D. R. Paul, Polymer, 2009, 50, 5565–5575 CrossRef CAS
. - J. K. Adewole and A. L. Ahmad, J. Polym. Res., 2017, 24, 70 CrossRef
. - S. Shu, S. Husain and W. J. Koros, J. Phys. Chem. C, 2007, 111, 652–657 CrossRef CAS
. - K. S. Park, Z. Ni, A. P. Côté, J. Y. Choi, R. Huang, F. J. Uribe-Romo, H. K. Chae, M. O'Keeffe and O. M. Yaghi, Proc. Natl. Acad. Sci. U. S. A., 2006, 103, 10186–10191 CrossRef CAS PubMed
. - S. Friebe, A. Mundstock, D. Schneider and J. Caro, Chemistry, 2017, 27, 6522–6526 CrossRef PubMed
. - J. Sánchez-Laínez, B. Zornoza, S. Friebe, J. Caro, S. Cao, A. Sabetghadam, B. Seoane, J. Gascon, F. Kapteijn, C. Le Guillouzer, G. Clet, M. Daturi, C. Téllez and J. Coronas, J. Membr. Sci., 2016, 515, 45–53 CrossRef
. - J. Sánchez-laínez, B. Zornoza, C. Téllez and J. Coronas, J. Membr. Sci., 2018, 563, 427–434 CrossRef
. - J. Sanchez-Lainez, L. Paseta, M. Navarro, B. Zornoza, C. Tellez and J. Coronas, Adv. Mater. Interfaces, 2018, 15, 1800647 CrossRef
. - J. K. J. Yong, G. W. Stevens, F. Caruso and S. E. Kentish, J. Membr. Sci., 2016, 514, 556–565 CrossRef CAS
. - J. Benito, J. Sánchez-Lainez, B. Zornoza, S. Martín, M. Carta, R. Malpass-Evans, C. Téllez, N. Mckeown, J. Coronas and I. Gascón, ChemSusChem, 2017, 10, 4014–4017 CrossRef CAS PubMed
. - A. Ishikawa, T. Chiang and F. Toda, J. Chem. Soc., Chem. Commun., 1989, 12, 764–765 RSC
. - E. Geus, H. van Bekkum, W. J. W. Bakker and J. Moulijn, J. Membr. Sci., 1993, 1, 131–147 CAS
. - J. Hedlund, J. Sterte, M. Anthonis, A. Bons, B. Carstensen, N. Corcoran, D. Cox, H. Deckman, W. De Gijnst, P. De Moor, F. Lai and J. Mchenry, Microporous Mesoporous Mater., 2002, 52, 179–189 CrossRef CAS
. - K. V. Agrawal, B. Topuz, T. C. T. Pham, T. H. Nguyen, N. Sauer, N. Rangnekar, H. Zhang, K. Narasimharao, S. N. Basahel, L. F. Francis, C. W. Macosko, S. Al-Thabaiti, M. Tsapatsis and K. B. Yoon, Adv. Mater., 2015, 27, 3243–3249 CrossRef CAS PubMed
. - J. Cadotte, R. King, R. Majerle and R. Petersen, J. Macromol. Sci., Part A: Pure Appl.Chem., 1981, 15, 727–755 CrossRef
. - Z. Ali, F. Pacheco, E. Litwiller, Y. Wang, Y. Han and I. Pinnau, J. Mater. Chem. A, 2018, 6, 30–35 RSC
. - S. Karan, Z. Jiang and A. Livingston, Science, 2015, 348, 1347–1351 CrossRef CAS PubMed
. - M. Shan, X. Liu, X. Wang, B. Seoane, F. Kapteijn and J. Gascon, Sci. Adv., 2018, 4, 1698 CrossRef PubMed
. - C. Z. Liang, T. S. Chung and J. Y. Lai, Prog. Polym. Sci., 2019, 97, 101141 CrossRef CAS
. - Y. Peng, Y. Li, Y. Ban and W. Yang, Angew. Chem., Int. Ed., 2017, 56, 9757–9761 CrossRef CAS PubMed
. - G. Firpo, E. Angeli, L. Repetto and U. Valbusa, J. Membr. Sci., 2015, 481, 1–8 CrossRef CAS
. - M. Z. Ahmad, M. Navarro, M. Lhotka, B. Zornoza, C. Téllez, W. M. De Vos, N. E. Benes, N. M. Konnertz, T. Visser, R. Semino, G. Maurin, V. Fila and J. Coronas, J. Membr. Sci., 2018, 558, 64–77 CrossRef CAS
. - B. Zornoza, C. Téllez and J. Coronas, J. Membr. Sci., 2011, 368, 100–109 CrossRef CAS
. - J. Sanchez-Lainez, I. Gracia-Guillen, B. Zornoza, C. Tellez and J. Coronas, New J. Chem., 2019, 43, 312–319 RSC
. - C. Zhang, B. Wu, M. Ma, Z. Wang and Z. Xu, Chem. Soc. Rev., 2019, 48, 3811 RSC
. - J. G. Wijmans and R. W. Baker, J. Membr. Sci., 1995, 107, 1–21 CrossRef CAS
. - R. W. Baker, Membrane Technology and Applications, John Wiley & Sons, Ltd, Chichester, UK, 2012 Search PubMed
. - R. D. Noble, J. Membr. Sci., 2011, 378, 393–397 CrossRef CAS
. - O. Kylián, A. Choukourov and H. Biederman, Thin Solid Films, 2013, 548, 1–17 CrossRef
. - H. Yasuda, J. Membr. Sci., 1984, 18, 273–284 CrossRef CAS
. - H. Nomura, P. Kramer and H. Yasuda, Thin Solid Films, 1984, 118, 187–195 CrossRef CAS
. - Q. Fu, J. Kim, P. Gurr, J. Scofield, S. Kentish and G. Qiao, Energy Environ. Sci., 2016, 9, 434–440 RSC
. - K. Xie, Q. Fu, C. Xu, H. Lu and Q. Zhao, Energy Environ. Sci., 2018, 11, 544–550 RSC
. - S. Sorribas, P. Gorgojo, C. Téllez, J. Coronas and A. G. Livingston, J. Am. Chem. Soc., 2013, 135, 15201–15208 CrossRef CAS PubMed
. - R. Castro-Muñoz, Ó. De La Iglesia, V. Fila, C. Téllez and J. Coronas, Ind. Eng. Chem. Res., 2018, 57, 15998–16011 CrossRef
. - R. Seetharaj, P. V. Vandana, P. Arya and S. Mathew, Arabian J. Chem., 2019, 12, 295–315 CrossRef CAS
. - F. Cacho-Bailo, I. Matito-Martos, J. Perez-Carbajo, M. Etxeberria-Benavides, O. Karvan, V. Sebastian, S. Calero, C. Tellez and J. Coronas, Chem. Sci., 2017, 8, 325–333 RSC
. - X. Wang, Q. Cheng, Y. Yu and X. Zhang, Angew. Chem., Int. Ed., 2018, 57, 7836–7840 CrossRef CAS PubMed
. - O. Shekhah, V. Chernikova, Y. Belmabkhout and M. Eddaoudi, Crystals, 2018, 8, 412 CrossRef
. - S. Yuan, X. Li, J. Zhu, G. Zhang, P. Van Puyvelde and B. Van Der Bruggen, Chem. Soc. Rev., 2019, 48, 2665–2681 RSC
. - S. Tanaka, K. Kida, T. Nagaoka, T. Ota and Y. Miyake, Chem. Commun., 2013, 49, 7884–7886 RSC
. - L. Paseta, G. Potier, S. Sorribas and J. Coronas, ACS Sustainable Chem. Eng., 2016, 4, 3780–3785 CrossRef CAS
. - A. Knebel, L. Sundermann, A. Mohmeyer, I. Strauß, S. Friebe, P. Behrens and J. Caro, Chem. Mater., 2017, 29, 3111–3117 CrossRef CAS
. - X. Ma, S. Peng, W. Li, H. Liu and Y. Chen, CrystEngComm, 2018, 20, 407–411 RSC
. - Q. Liu, N. Wang, J. Caro and A. Huang, J. Am. Chem. Soc., 2013, 135, 17679–17682 CrossRef CAS PubMed
. - R. W. Johnson, A. Hultqvist and S. F. Bent, Mater. Today, 2014, 17, 236–246 CrossRef CAS
. - P. O. Oviroh, R. Akbarzadeh, D. Pan, R. A. M. Coetzee and T.-C. Jen, Sci. Technol. Adv. Mater., 2019, 20, 465–496 CrossRef PubMed
. - X. Ma, P. Kumar, N. Mittal, A. Khlyustova, P. Daoutidis, K. Andre Mkhoyan and M. Tsapatsis, Science, 2018, 361, 1008–1011 CrossRef CAS PubMed
. - M. Drobek, M. Bechelany, C. Vallicari, A. A. Chaaya, C. Charmette, C. Salvador-levehang, P. Miele and A. Julbe, J. Membr. Sci., 2015, 475, 39–46 CrossRef CAS
. - B. Zornoza, B. Seoane, J. M. Zamaro and C. Tøllez, ChemPhysChem, 2011, 12, 2781–2785 CrossRef CAS PubMed
. - H. B. Tanh Jeazet, C. Staudt and C. Janiak, Dalton Trans., 2012, 41, 14003 RSC
. - S. Sorribas, A. Kudasheva, E. Almendro, B. Zornoza, Ó. De, C. Téllez and J. Coronas, Chem. Eng. Sci., 2015, 124, 37–44 CrossRef CAS
. - R. Castro-Muñoz, J. Food Eng., 2019, 253, 27–39 CrossRef
. - R. Castro-Muñoz, M. Z. Ahmad and V. Fíla, Front. Chem., 2020, 7, 1–14 RSC
. - S. Greil, A. Rahman, M. Liu and C. Black, Chem. Mater., 2017, 21, 9572–9578 CrossRef
. - T. H. Y. Tran, W. G. Haije, V. Longo, W. M. M. Kessels and J. Schoonman, J. Membr. Sci., 2011, 378, 438–443 CrossRef CAS
. - S. M. George, Chem. Rev., 2010, 110, 111–131 CrossRef CAS PubMed
. - G. Xomeritakis and Y. S. Lin, J. Membr. Sci., 1996, 120, 261–272 CrossRef CAS
. - Y. M. Manawi, Ihsanullah, A. Samara, T. Al-Ansari and M. A. Atieh, Materials, 2018, 11, 822 CrossRef PubMed
. - X. Zhao, P. Zhang, Y. Chen, Z. Su and G. Wei, Nanoscale, 2015, 7, 5080–5093 RSC
. - N. D. Boscher, M. Wang, A. Perrotta, K. Heinze, M. Creatore and K. K. Gleason, Adv. Mater., 2016, 28, 7479–7485 CrossRef CAS PubMed
. - W. Li, P. Su, Z. Li, Z. Xu, F. Wang, H. Ou, J. Zhang, G. Zhang and E. Zeng, Nat. Commun., 2017, 8, 1–8 CrossRef PubMed
. - T. Seike, M. Matsuda and M. Miyake, J. Mater. Chem., 2002, 12, 366–368 RSC
. - D. J. Babu, G. He, J. Hao, M. T. Vahdat, P. A. Schouwink, M. Mensi and K. Agrawal, Adv. Mater., 2019, 31, 1900855 CrossRef PubMed
. - G. He, M. Dakhchoune, J. Zhao, S. Huang and K. V. Agrawal, Adv. Funct. Mater., 2018, 28, 1–8 Search PubMed
. - S. Zhou, Y. Wei, L. Li, Y. Duan, Q. Hou, L. Zhang, L. X. Ding, J. Xue, H. Wang and J. Caro, Sci. Adv., 2018, 4, 1–8 Search PubMed
. - S. K. Alen, S. W. Nam and S. A. Dastgheib, Int. J. Mol. Sci., 2019, 20, 5609 CrossRef PubMed
. - G. Liu, W. Jin and N. Xu, Angew. Chem., Int. Ed., 2016, 55, 2–16 CrossRef
. - R. Castro-Muñoz, J. Buera-Gonzalez, O. de la Iglesia, F. Galiano, V. Fíla, M. Malankowska, C. Rubio, A. Figoli, C. Tellez and J. Coronas, J. Membr. Sci., 2019, 582, 423–434 CrossRef
. - R. R. Nair, H. A. Wu, P. N. Jayaram, I. V. Grigorieva and A. K. Geim, Science, 2012, 335, 442–445 CrossRef CAS PubMed
. - H. W. Kim and E. Al, Science, 2014, 342, 91–95 CrossRef PubMed
. - H. Li, Z. Song, X. Zhang, Y. Huang, S. Li, Y. Mao, H. Ploehn, Y. Bao and M. Yu, Science, 2013, 342, 95–98 CrossRef CAS PubMed
. - M. Liu, K. Xie, M. Nothling, P. Gurr, S. Tan, Q. Fu, P. Webley and G. Qiao, ACS Nano, 2018, 12, 11591–11599 CrossRef CAS PubMed
. - D. Wang, Z. Wang, L. Wang, L. Hu and J. Jin, Nanoscale, 2015, 7, 17649–17652 RSC
. - K. Varoon, X. Zhang, B. Elyassi, D. D. Brewer, M. Gettel, S. Kumar, J. Lee, S. Maheshwari, A. Mittal, C. Sung, M. Cococcioni, L. Franxis, A. McCormick, K. Mkhoyan and M. Tsapatsis, Science, 2011, 334, 72–75 CrossRef CAS PubMed
. - Y. Peng, Y. S. Li, Y. J. Ban, H. Jin, W. M. Jiao, X. L. Liu and W. S. Yang, Science, 2014, 346, 1356–1359 CrossRef CAS PubMed
. - A. Perea-Cachero, J. Sánchez-Laínez, B. Zornoza, E. Romero-Pascual and C. T. J. Coronas, Dalton Trans., 2019, 48, 3392–3403 RSC
. - Y. Song, J. Fan, S. Wang and J. Fan, Mater. Chem. Front., 2017, 1, 1028–1040 RSC
. - M. Adamczak, G. Kamińska and J. Bohdziewicz, Int. J. Polym. Sci., 2019, 2019, 1–13 CrossRef
. - M. F. Jimenez-Solomon, Q. Song, K. E. Jelfs, M. Munoz-Ibanez and A. G. Livingston, Nat. Mater., 2016, 15, 760–767 CrossRef CAS PubMed
. - F. Yuan, Z. Wang, S. Li, J. Wang and S. Wang, J. Membr. Sci., 2012, 421–422, 327–341 CrossRef CAS
. - Y. Liu, B. He, J. Li, R. D. Sanderson, L. Li and S. Zhang, J. Membr. Sci., 2011, 373, 98–106 CrossRef CAS
. - S. Yu, S. Li, Y. Liu, S. Cui and X. Shen, J. Membr. Sci., 2019, 573, 425–438 CrossRef CAS
. - L. Li, S. Zhang and X. Zhang, J. Membr. Sci., 2009, 335, 133–139 CrossRef CAS
. - M. Marek, E. Brynda, Z. Pientka and L. Brozova, Macromol. Rapid Commun., 1998, 57, 53–57 CrossRef
. - A. Kausar, Polym.-Plast. Technol. Eng., 2017, 56, 932–945 CrossRef CAS
. - L. Xu, A. R. Tetreault, H. H. Khaligh, I. A. Goldthorpe, S. D. Wettig and M. A. Pope, Langmuir, 2019, 35, 51–59 CrossRef CAS PubMed
. - P. M. Budd, K. J. Msayib, C. E. Tattershall, B. S. Ghanem, K. J. Reynolds, N. B. McKeown and D. Fritsch, J. Membr. Sci., 2005, 251, 263–269 CrossRef CAS
. - P. M. Budd and N. B. Mckeown, Polym. Chem., 2010, 9, 63–68 RSC
. - J. Liu and J. Conboy, Langmuir, 2005, 21, 9091–9097 CrossRef CAS PubMed
. - J. Benito, J. Vidal, J. Sánchez-laínez, B. Zornoza, C. Téllez, S. Martín, K. J. Msayib, B. Comesaña-gándara, N. B. Mckeown, J. Coronas and I. Gascón, J. Colloid Interface Sci., 2019, 536, 474–482 CrossRef CAS PubMed
. - J. Benito, M. Fenero, S. Sorribas, B. Zornoza, K. J. Msayib, N. B. Mckeown, C. Téllez, J. Coronas and I. Gascón, Colloids Surf., A, 2015, 470, 161–170 CrossRef CAS
. - C. Lin, Q. Chen, S. Yi, M. Wang and S. L. Regen, Langmuir, 2014, 30, 687–691 CrossRef CAS PubMed
. - M. Navarro, J. Benito, L. Paseta, I. Gascon, J. Coronas and C. Tellez, ACS Appl. Mater. Interfaces, 2018, 10, 1278–1287 CrossRef CAS PubMed
. - A. Kaplan, Z. Yuan, J. D. Benck, A. Govind Rajan, X. S. Chu, Q. H. Wang and M. S. Strano, Chem. Soc. Rev., 2017, 46, 4530–4571 RSC
. - L. Wang, M. S. H. Boutilier, P. R. Kidambi, D. Jang, N. G. Hadjiconstantinou and R. Karnik, Nat. Nanotechnol., 2017, 12, 509–522 CrossRef CAS PubMed
. - X. Li, W. Cai, J. An, S. Kim, J. Nah, D. Yang, R. Piner, A. Velamakanni, I. Jung, E. Tutuc, S. Banerjee, L. Colombo and R. Ruoff, Science, 2009, 324, 1312–1314 CrossRef CAS PubMed
. - S. Bae, H. R. Kim, Y. Lee, X. Xu, J.-S. Park, Y. Zheng, J. Balakrishnan, T. Lei, H. Ri Kim, Y. I. Song, Y.-J. Kim, K. S. Kim, B. Ozyilmaz, J.-H. Ahn, B. H. Hong and S. Iijima, Nat. Nanotechnol., 2010, 5, 574–578 CrossRef CAS PubMed
. - S. Huang, M. Dakhchoune, W. Luo, E. Oveisi, G. He, M. Rezaei, J. Zhao, D. T. L. Alexander, A. Züttel, M. S. Strano and K. V. Agrawal, Nat. Commun., 2018, 9, 1–11 CrossRef PubMed
. - Y. Yang, X. Yang, L. Liang, Y. Gao, H. Cheng, X. Li, M. Zou, R. Ma, Q. Yuan and X. Duan, Science, 2019, 364, 1057–1062 CrossRef CAS PubMed
. - S. P. Koenig, L. Wang, J. Pellegrino and J. S. Bunch, Nat. Nanotechnol., 2012, 7, 728–732 CrossRef CAS PubMed
. - J. Zhao, G. He, S. Huang, L. F. Villalobos, M. Dakhchoune, H. Bassas and K. V. Agrawal, Sci. Adv., 2019, 5, 1–10 CAS
. - Z. Tian, S. M. Mahurin, S. Dai and D. Jiang, Nano Lett., 2017, 17, 1802–1807 CrossRef CAS PubMed
. - G. He, S. Huang, L. F. Villalobos, J. Zhao, M. Mensi, E. Oveisi, M. Rezaei and K. V. Agrawal, Energy Environ. Sci., 2019, 12–16 Search PubMed
. - Y. Zhang, Q. Shen, J. Hou, P. Sutrisna and V. Chen, J. Mater. Chem. A, 2017, 5, 7732–7737 RSC
. - M. Jin Yoo, K. Hyun, J. Hyeok, T. Woo and C. Wook, J. Membr. Sci., 2018, 566, 336–345 CrossRef
. - F. Zhou, H. Ngoc, Q. Dong, W. L. Xu, H. Li and S. Li, J. Membr. Sci., 2019, 573, 184–191 CrossRef CAS
. - J. Hou, Y. Wei, S. Zhou, Y. Wang and H. Wang, Chem. Eng. Sci., 2018, 182, 180–188 CrossRef CAS
. - E. Shamsaei, Z. Low, X. Lin, A. Mayahi, H. Liu, X. Zhang, J. Liu and H. Wang, Chem. Commun., 2015, 51, 11474–11477 RSC
. - M. Joo, M. Rezi, A. Hamid, J. Lee and J. Sung, J. Membr. Sci., 2018, 559, 28–34 CrossRef
. - A. J. Brown, N. A. Brunelli, K. Eum, F. Rashidi, J. R. Johnson, W. J. Koros, C. W. Jones and S. Nair, Science, 2014, 345, 72–75 CrossRef CAS PubMed
. - C. Echaide-Gorriz, F. Cacho-Bailo, C. Tellez and J. Coronas, J. Mater. Chem. A, 2018, 6, 5485–5506 RSC
. - E. Barankova, X. Tan, L. Villalobos, E. Litwiller and K. Peinemann, Angew. Chem., Int. Ed., 2017, 56, 2965–2968 CrossRef CAS PubMed
. - Y. Hu, J. Wei, Y. Liang, H. Zhang, X. Zhang, W. Shen and H. Wang, Angew. Chem., Int. Ed., 2016, 3800, 2048–2052 CrossRef PubMed
. - H. Kwon and H. Jeong, J. Am. Chem. Soc., 2013, 135, 10763–10768 CrossRef CAS PubMed
. - E. Shamsaei, X. Lin, Z. Low, Z. Abbasi, Y. Hu, J. Liu and H. Wang, ACS Appl. Mater. Interfaces, 2016, 8, 6236–6244 CrossRef CAS PubMed
. - Y. Pan, T. Li, G. Lestari and Z. Lai, J. Membr. Sci., 2012, 390–391, 93–98 CrossRef CAS
. - A. Singh-Ghosal and W. J. Koros, J. Membr. Sci., 2000, 174, 177–188 CrossRef CAS
. - M. Rungta, L. Xu and W. J. Koros, Carbon, 2012, 50, 1488–1502 CrossRef CAS
. - C. Zhang and W. Koros, Adv. Mater., 2017, 29, 1–6 Search PubMed
. - S. Huang, L. Villalobos, D. Babu, G. He, M. Li, A. Zuttel and K. Agrawal, ACS Appl. Mater. Interfaces, 2019, 11, 16729–16736 CrossRef CAS PubMed
. - B. Wang, F. Gao, F. Zhang, W. Xing and R. Zhou, J. Mater. Chem. A, 2019, 7, 13164–13172 RSC
. - Y. Ji, M. Zhang, K. Guan, J. Zhao, G. Liu and W. Jin, Adv. Funct. Mater., 2019, 15, 1–9 Search PubMed
. - J. Kim, Q. Fu, J. Scofield, S. Kentish and G. Qiao, Nanoscale, 2016, 8, 8312–8323 RSC
. - N. Xia, X. Xiong, J. Wang, M. Rong and M. Zhang, Chem. Sci., 2016, 7, 2736–2742 RSC
. - L. Y. Jiang, T. S. Chung and S. Kulprathipanja, J. Membr. Sci., 2006, 276, 113–125 CrossRef CAS
. - W. F. Yong, F. Y. Li, Y. C. Xiao, T. S. Chung and Y. W. Tong, J. Membr. Sci., 2013, 443, 156–169 CrossRef CAS
. - C. Z. Liang, W. F. Yong and T. S. Chung, J. Membr. Sci., 2017, 541, 367–377 CrossRef CAS
. - C. Z. Liang and T. S. Chung, Macromol. Rapid Commun., 2018, 39, 1–7 CrossRef PubMed
. - W. F. Yong, T. S. Chung, M. Weber and C. Maletzko, J. Membr. Sci., 2018, 552, 305–314 CrossRef CAS
. - C. Z. Liang, J. T. Liu, J. Y. Lai and T. S. Chung, J. Membr. Sci., 2018, 563, 93–106 CrossRef CAS
. - F. Cacho-Bailo, S. Catalán-Aguirre, M. Etxeberría-Benavides, O. Karvan, V. Sebastian, C. Téllez and J. Coronas, J. Membr. Sci., 2015, 476, 277–285 CrossRef CAS
. - Y. Dai, J. R. Johnson, O. Karvan, D. S. Sholl and W. J. Koros, J. Membr. Sci., 2012, 401–402, 76–82 CrossRef CAS
. - A. Pustovarenko, M. Goesten, S. Sachdeva, M. Shan, Z. Amghouz, Y. Belmabkhout, A. Dikhtiarenko, T. Rodenas, D. Keskin, I. Voets, B. Weckhuysen, M. Eddaoudi, L. de Smet, E. Sudholter, F. Kapteijn, B. Seoane and J. Gascon, Adv. Mater., 2018, 30, 1707234 CrossRef PubMed
. - T. Rodenas, I. Luz, G. Prieto, B. Seoane, H. Miro, A. Corma, F. Kapteijn, F. Xamena and J. Gascon, Nat. Mater., 2015, 14, 48–55 CrossRef CAS PubMed
.
|
This journal is © The Royal Society of Chemistry 2020 |
Click here to see how this site uses Cookies. View our privacy policy here.