DOI:
10.1039/D0RA01903H
(Paper)
RSC Adv., 2020,
10, 17816-17828
Synthesis, characterization and corrosion inhibition behavior of 2-aminofluorene bis-Schiff bases in circulating cooling water†
Received
28th February 2020
, Accepted 18th April 2020
First published on 7th May 2020
Abstract
In this work, two new bis-Schiff bases, namely 2-bromoisophthalaldehyde-2-aminofluorene (M1) and glutaraldehyde 2-aminofluorene (M2), were synthesized, and their structures were characterized and confirmed by infrared spectroscopy, Fourier transform mass spectrometry and UV-visible spectroscopy. Their corrosion inhibition performance on carbon steel in simulated circulating cooling water was investigated by weight loss measurements and electrochemical measurements. The potentiodynamic polarization curves confirmed that two bis-Schiff bases are anode-type inhibitors; electrochemical impedance spectroscopy tests showed that M1 and M2 possess the best inhibition efficiencies of 96.25% and 99.15% at the optimal concentration of 2.50 mmol L−1, respectively. The weight loss results showed that M1 and M2 exhibit maximum ηw values of 92.62% and 96.31%, respectively. Scanning electron microscopy showed that the inhibitors inhibited carbon steel corrosion. The adsorption isotherm measurements indicated that the two inhibitors exhibited physicochemisorption mechanisms and followed Langmuir adsorption isotherms. The relationships between the molecular structure and inhibition behavior of the inhibitors were explored by density functional theory, frontier molecular orbital studies, and Fukui index analysis, which affirmed that M2 possesses higher corrosion inhibition efficiency than M1.
1. Introduction
Metals are the most widely used engineering materials in modern society; however, metals tend to react with surrounding media, resulting in metal corrosion. In most cases, the metal corrosion starts from the surface and gradually extends to the interior and entirety of the metal. Metal corrosion not only seriously affects the national economy but also causes serious safety hazards and a series of environmental pollution problems.1–4 Increasing numbers of diverse anticorrosive measures are being studied for metal protection, such as alloy substitution, coating protection, electrochemical protection, and addition of inhibitors.5–8 Compared with other methods, addition of inhibitors to the corrosive medium is an anti-corrosion method with a simple process, low cost and remarkable effects. Although many inhibitors have good inhibition properties, they are unable to meet the needs of environmental protection and sustainable development strategies for various reasons (such as difficulty in degradation, toxicity or high temperature resistance). Stable, efficient and environmentally friendly inhibitors are the future direction of inhibitor development. There are many kinds of inhibitors, such as imidazolines,9 Mannich bases,10,11 quaternary ammonium salts,12,13 acetylene alcohols, pyridines,14 and Schiff bases.15,16 These inhibitors contain heteroatoms (N, S, O) or electron-rich chemical bonds (π bonds).17–20 The bis-Schiff base compounds contain N, O, and S heteroatoms and unsaturated C
N bonds, which can form strong and stable corrosion-inhibiting adsorption films on metal surfaces, exhibiting excellent inhibition effects. At the same time, Schiff base compounds have the characteristics of low cost, facile synthesis and purification, good water solubility, and non-toxicity, which are favored by researchers.21–23
Research on Schiff base inhibitors is prevalent; however, there are few studies on the application of Schiff base inhibitors in circulating cooling water. Circulating cooling water is a major item in industrial water. In the petrochemical electric power, steel, metallurgical and other industries, the amount of circulating cooling water accounts for 50–90% of the total water consumption of enterprises.24–27 There are many corrosive substances in circulating cooling water, such as chloride ions, sulfate ions, and microorganisms. When the cooling water is continuously circulated in the circulation system, the water temperature will rise and the water will evaporate; this will increase the concentration of the corrosive medium and erode the cooling equipment, leading to equipment corrosion and perforation and the formation of leaks, which create safety risks during industrial production. For equipment corrosion, inhibitors such as mercaptobenzothiazole (MBT) and benzotriazole (BTA) are usually added to the circulating cooling water.28–31 Inhibitors can form a corrosion-inhibiting film on the metal surface to inhibit the corrosion of metals by corrosive media. Because the inhibitor does not need to be added in a large amount, does not require special equipment, and does not need to be pre-treated, it is an economical metal corrosion protection technology. Therefore, the addition of an inhibitor to circulating cooling water is the preferred method to prevent harmful ions from corroding equipment.32–34 Currently, it is urgent to design and synthesize corrosion inhibitor molecules with higher corrosion inhibition efficiency.35,36 Therefore, research in the field of circulating cooling water inhibitors in industrial production plants is increasingly valued and favored by researchers. For different water quality and different test conditions, the following problems should be considered when synthesizing inhibitors: (a) increase in the concentration ratio of circulating cooling water by the inhibitor; (b) effective alleviation of the corrosion of metal pipes; (c) less environmental pollution.34
Herein, 2-bromoisophthalaldehyde-2-aminofluorene (M1) and glutaraldehyde 2-aminofluorene (M2) inhibitors were studied by electrochemical measurements, weight loss measurements, scanning electron microscopy and energy dispersive spectrometry in simulated circulating cooling water. Quantum chemical calculation studies were also used to study the corrosion inhibiting properties of the inhibitor molecules. Afterwards, the structural parameters of the inhibitors were also calculated by DFT, mainly including the electronegativity, HOMO, LUMO, chemical softness, chemical hardness, and maximum electron numbers transferred in the chemical reactions of the inhibitors. We also aimed to study the effects of the structural parameters of the inhibitors on their inhibitory effects through quantum chemical calculations and to study their adsorption mechanisms on the metal surface. We hoped to identify the inhibitor with the best corrosion inhibition performance between 2-bromoisohthalaldehyde-2-aminofluorene (M1) and glutaraldehyde 2-aminofluorene (M2) through these studies, which would be the most suitable for protecting circulating cooling water systems.
2. Experimental
2.1 Materials and solutions
In this study, all the required chemicals and solvents were analytical grade, such as 2-aminofluorene, 2-bromoisophthalaldehyde, glutaraldehyde, methanol, and acetonitrile; these were purchased from Aladdin and used without further purification. The composition of the carbon steel specimens (weight%) was 4.51% C, 0.37% Si, 26.37% O, 1.36% Cr and remainder Fe. The specimens were sanded with 400, 800, and 1200 emery paper until smooth, then cleaned with distilled water and ethanol37 and dried by cold air; then, the non-working surfaces were sealed with molten paraffin, wrapped in filter paper, and weighed three times before use to obtain the average value. Simulated circulating cooling water was prepared in the laboratory (according to the standards adopted by the American Society for Testing and Materials)38 for all studies; its properties are shown in Table 1.
Table 1 The composition of the simulated circulating cooling water
Composition |
NaCl |
MgCl2 |
Na2SO4 |
CaCl2 |
NaHCO3 |
KBr |
H3BO3 |
g L−1 |
29.06 ± 0.81 |
10.4 ± 0.24 |
8.18 ± 0.10 |
2.32 ± 0.18 |
0.402 ± 0.013 |
0.202 ± 0.011 |
0.054 ± 0.004 |
2.2 Synthesis of bis-Schiff base inhibitors
2-bromoisophthalaldehyde-2-aminofluorene (M1) and glutaraldehyde 2-aminofluorene (M2) were synthesized by solution methods.39–41 The raw materials were dissolved by ultrasonic vibration and refrigerated until use. To prepare M1, 2-aminofluorene (2.2 mM) and 2-bromoisophthalaldehyde (1.0 mM) were dissolved in 25 mL absolute ethanol and were placed in a three-necked flask (50 mL); then, 1 mL acetic acid was added. The three-necked flask was placed in a constant temperature water bath and magnetically stirred at a constant speed; the temperature was set to 45 °C, and nitrogen protection was performed. The products were washed three times with ethanol and dried in vacuum. Similarly, M2 was synthesized from 2-aminofluorene (2.2 mM) and glutaraldehyde (1.0 mM). The synthesis route and molecular structure of M1 and M2 are shown in Scheme 1.
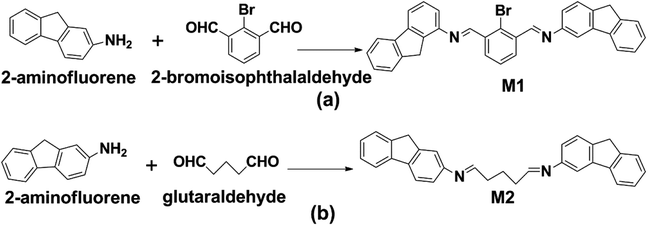 |
| Scheme 1 The synthesis routes of (a) 2-bromoisophthalaldehyde-2-aminofluorene (M1), (b) glutaraldehyde-2-aminofluorene (M2). | |
Next, M1 and M2 were characterized by elemental analysis, FTIR spectroscopy, FTMS and UV-vis spectroscopy.
For M1, yield: 78.36%, elemental analysis: anal. calcd: 75.55; H, 4.63; N, 5.18; found: C, 75.50; H, 4.58; N, 5.12%; characteristic IR peaks (KBr disk): ν C–H (aromatic) = 2919, ν C
O = 1616, ν C
N = 1458 cm−1 (ref. 42) (in Fig. S1†); FTMS M1 + H+: 539.11 amu in Fig. S2;† characteristic UV-vis peaks, C
O (n–π* transition) = 280, 363 nm in Fig. S3.†
For M2, yield: 82.51%, elemental analysis: anal. calcd: 89.39; H, 5.30; N, 5.31; found: C, 89.34; H, 5.27; N, 5.30%; characteristic IR peaks (KBr disk): ν C–H (aromatic) = 2933, ν C
O = 1592, ν C
N = 1454 cm−1 42 (in Fig. S1†); FTMS M1 + H +: 527.22 amu in Fig. S2;† characteristic UV-vis peaks, C
O (n–π* transition) = 315 nm in Fig. S3.†
2.3 Weight loss (WL) measurements
Treated carbon steel specimens were immersed in simulated circulating cooling water with and without addition of different concentrations of M1 and M2 for 48 h at 25 °C, respectively. Each concentration was tested three times in parallel, and the best results were chosen. The following equations were used to calculate the inhibition efficiency (ηw, %):43–45 |
 | (2) |
|
 | (3) |
where W0 and W1 are the average weight losses (g) of carbon steel sheets in simulated circulating cooling water without and with addition of M1 and M2, respectively.46–48 S is the total area of the carbon steel immersed in the simulated circulating cooling water (cm2), t is the immersing time (h), θ is the surface coverage, and iocorr and icorr are the corrosion rates (g cm−2 h−1) of the carbon steel sheet in the simulated circulating cooling water without and with addition of M1 and M2, respectively. Furthermore, in order to study the effects of temperature on the inhibition efficiency, the carbon steel sheet was immersed in simulated circulating cooling water containing 2.5 mmol L−1 inhibitor at different temperatures for 48 h.
2.4 Electrochemical measurements
The performance of the inhibitors was evaluated on a CHI860D electrochemical workstation with a classical three-electrode system.36 Before the experiment, the working electrode was plugged into simulated circulating cooling water for 25 min to obtain a stable open circuit potential (OCP); the scanning rate was 1 mV s−1 and the potential was ±400 mV for the potentiodynamic polarization (PDP) curves. The angular frequency range was 105 Hz to 102 Hz, and the sensitivity was automatically adjusted. Electrochemical impedance spectroscopy (EIS) was performed by a sine wave with 5 mV signal amplitude; the frequency range was 1 MHz to 100 kHz. Each concentration was tested three times in parallel.
The corrosion inhibition efficiency ηPDP (%) (calculated by the PDP parameters) and ηz (%) (calculated by the EIS parameters)49 were determined using the following equations, respectively:
|
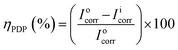 | (5) |
|
 | (6) |
where
Rct and
Roct are the charge transfer resistances of carbon steel with and without addition of
M1 and
M2 in simulated circulating cooling water, respectively;
Iicorr and
Iocorr are the corrosion current densities (μA cm
−2), respectively.
2.5 SEM and EDS studies
A scanning electron microscope (S4800) was used to observe the surface morphologies of the carbon steel specimens after immersion in simulated circulating cooling water with and without inhibitor for 24 h, and we compared the polished specimens to analyze the corrosion inhibition effects of the inhibitors. The test magnification was 1000 times and the acceleration voltage was 5.0 kV. A Bruker XFlash 6 | 10 energy spectrometer was used to perform elemental analysis on the surfaces of carbon steel samples immersed in simulated circulating cooling water containing the corrosion inhibitors.
2.6 Quantum chemical calculation studies
Due to its combination of chemistry and computation, the content of computational chemistry research is increasingly rich. Quantum chemical calculations are gaining increasing attention in the study of inhibition mechanisms.50–53 The molecular structures and electronic parameters of the inhibitors were studied to determine their adsorption behavior on carbon steel. Density functional theory (DFT) is a quantum chemical calculation method with high accuracy when calculating the molecular structure parameters of inhibitors,54 mainly including electronegativity, frontier orbitals (HOMO and LUMO), chemical softness, chemical hardness, maximum electron number transferred in the chemical reaction, etc.55 Through these structural parameters, the structure–activity relationships of inhibitors can be explored from the perspective of microscopic observation, the mechanisms of the inhibitors can be revealed, and theoretical guidance can be provided for the design and synthesis of new inhibitors. All the structural parameter calculations were derived from the Gaussian 09 program;56–58 the optimized molecular structures were mapped by the GaussView 05 program, the Fukui function was obtained from the Multiwfn program,59 and the Fukui function60,61 was visualized by the GaussView 05 program. All geometric configuration optimization and quantum chemical calculations were carried out in the gas phase using the B3LYP\6-311+G(d, p) method.62
The electronegativity (χ),63,64 chemical hardness (η),65 chemical softness (σ),66 and maximum electrons transferred were calculated by eqn (7)–(10), respectively:
|
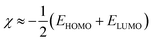 | (7) |
|
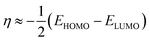 | (8) |
|
σ ≈ −2/(EHOMO − ELUMO)
| (9) |
|
 | (10) |
The Fukui function can be used to predict the active site of the inhibitor in an electrophilic substitution reaction. The Fukui function provides information about the sites in the molecule where atoms may be attacked by electrophiles and the sites in the molecule where atoms may be attacked by nucleophiles.
The Fukui functions of the inhibitor molecules were obtained from the following equations:
where
q is the electronic density of the molecule.
q(N+1),
qN and
q(N−1) are the atomic charges in a system with
N + 1,
N and
N − 1 electrons, respectively.
67
3. Results and discussion
3.1 Weight loss (WL) analysis
If a metal is corroded by corrosive media, it will lose weight. Circulating cooling water has a relatively high salt content, and it contains a large number of free chloride ions and corrosive substances which can cause metal equipment to lose weight due to corrosion. Therefore, the anti-corrosive behavior of the inhibitor molecules on carbon steel in simulated circulating cooling water was studied by WL measurements. Furthermore, the results obtained from the WL measurements are often in agreement with the results of electrochemical analysis.68 The corrosion inhibition efficiency ηw (%) and WL parameters are listed in Table 2. The weight loss of carbon steel decreased with increasing inhibitor concentration. When the inhibitor concentration was 2.50 mmol L−1, M1 and M2 exhibited maximum ηw (%) values of 92.62% and 96.31%, respectively. The corrosion inhibition efficiencies of M1 and M2 at different temperatures are listed in Table 3. If the adsorption mechanism of the corrosion inhibitor on the metal surface is physical adsorption, the inhibitor will gradually weaken or disappear as the temperature increases. However, the results showed that with increasing temperature, the corrosion rates did not decrease significantly; this indicates that the adsorption of the corrosion inhibitors onto the metal surface may occur by physicochemical adsorption (mainly chemical adsorption), which can effectively inhibit the corrosion of low-carbon steel.
Table 2 Weight loss parameters of carbon steel corrosion in simulated circulating cooling water for 48 h without and with different concentrations of M1 and M2 at 25 °C
Inhibitor |
C (mmol L−1) |
ΔW (g) |
A (g m−2 h−1) |
θ |
ηw (%) |
Blank |
0 |
0.514 ± 0.014 |
25.73 ± 0.43 |
— |
— |
M1 |
0.05 |
0.189 ± 0.013 |
7.35 ± 0.16 |
0.6322 |
63.22 |
0.10 |
0.128 ± 0.010 |
6.40 ± 0.08 |
0.7512 |
75.12 |
0.50 |
0.088 ± 0.009 |
4.40 ± 0.10 |
0.8289 |
82.89 |
1.00 |
0.056 ± 0.005 |
2.05 ± 0.06 |
0.8912 |
89.12 |
2.50 |
0.038 ± 0.005 |
1.90 ± 0.04 |
0.9262 |
92.62 |
M2 |
0.05 |
0.195 ± 0.015 |
7.70 ± 0.19 |
0.6206 |
62.06 |
0.10 |
0.125 ± 0.012 |
6.25 ± 0.11 |
0.7571 |
75.71 |
0.50 |
0.061 ± 0.010 |
3.05 ± 0.06 |
0.8815 |
88.15 |
1.00 |
0.045 ± 0.009 |
2.25 ± 0.04 |
0.9125 |
91.25 |
2.50 |
0.019 ± 0.005 |
0.95 ± 0.03 |
0.9631 |
96.31 |
Table 3 Corrosion inhibition behavior of carbon steel in simulated circulating cooling water for 48 h with 2.50 mmol L−1 M1 and M2 at different temperatures
Inhibitor |
A (g m−2 h−1) |
ηw (%) |
25 °C |
35 °C |
45 °C |
55 °C |
25 °C |
35 °C |
45 °C |
55 °C |
Blank |
25.73 ± 0.13 |
28.67 ± 0.19 |
44.67 ± 0.38 |
63.62 ± 0.51 |
|
|
|
|
M1 |
1.89 ± 0.05 |
3.14 ± 0.09 |
5.69 ± 0.11 |
9.06 ± 0.22 |
92.62 |
89.04 |
87.26 |
85.75 |
M2 |
0.95 ± 0.04 |
2.10 ± 0.06 |
4.55 ± 0.12 |
7.87 ± 0.18 |
96.31 |
92.68 |
89.81 |
87.63 |
The weight loss experiment results showed that M2 possesses better corrosion inhibition performance. This may be because the M2 structure has good planarity and the structure contains fewer hydrophobic benzene rings; thus, M2 is more soluble and more easily adsorbed on the carbon steel surface.
3.2 Potentiodynamic polarization curve analysis
The corrosion process of carbon steel mainly involves anodic dissolution and cathodic reduction.69 The PDP curves for carbon steel without and with addition of M1 and M2 in simulated circulating cooling water at 25 °C are displayed in Fig. 1. The potentiodynamic polarization curves show that M1 and M2 have the same trend as the polarization curves of the blank group (without inhibitor); this reveals that addition of the inhibitors does not change the corrosion mechanism of carbon steel.70 Both inhibitors have the same corrosion inhibition process. Compared with the blank group, the current densities of the anode and the cathode of the specimens with the inhibitors were low, showing the inhibitory effect. The dynamic potential parameters obtained from the experiments, including the Tafel slopes of the anode and cathode (βa and βc) and the calculated corrosion inhibition rates (ηPDP, %), are shown in Table 4. When the inhibitors were added, the ηPDP (%) increased, and the highest ηPDP (%) values were 83.14% and 85.94% at the maximum concentration (2.50 mol L−1) for M1 and M2, respectively. It can be clearly seen from Table 4 that the changes of βa and βc are not obvious when compared with the blank group data; this indicates that the inhibitor molecules are adsorbed on the surface of carbon steel to reduce the number of active centers of the metal surface rather than by changing the anode and cathode mechanism to inhibit corrosion.48,71
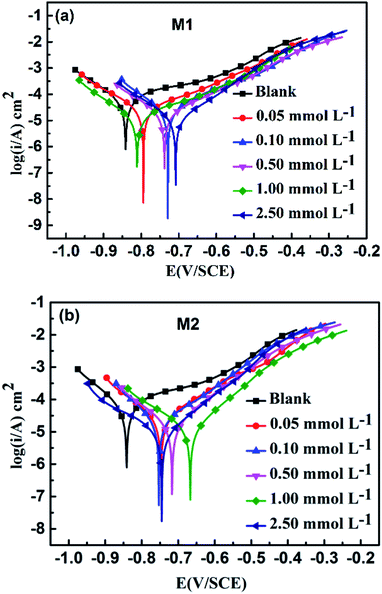 |
| Fig. 1 Potentiodynamic polarization curves for carbon steel in simulated circulating cooling water in the absence and presence of different concentrations of M1 (a) and M2 (b). | |
Table 4 Potentiodynamic polarization curve (PDP) parameters for carbon steel in simulated circulating cooling water without and with different concentrations of M1 and M2 at 25 °C
Inhibitor |
Conc. (mmol L−1) |
−Ecorr (mV)/SCE |
Icorr (μA cm−2) |
βa (mV dec−1) |
−βc (mV dec−1) |
η (%) (PDP) |
Blank |
0 |
841 ± 27 |
74.2 ± 8.4 |
3.43 ± 0.50 |
9.09 ± 0.52 |
— |
M1 |
0.05 |
794 ± 22 |
34.9 ± 4.1 |
4.73 ± 0.51 |
7.59 ± 0.48 |
52.93 |
0.10 |
729 ± 24 |
24.7 ± 2.1 |
6.71 ± 0.82 |
10.18 ± 0.59 |
66.72 |
0.50 |
738 ± 21 |
20.1 ± 2.2 |
6.46 ± 0.91 |
8.77 ± 0.53 |
72.99 |
1.00 |
811 ± 25 |
15.5 ± 1.1 |
4.43 ± 0.63 |
9.40 ± 0.59 |
79.09 |
2.50 |
708 ± 21 |
12.5 ± 1.0 |
8.59 ± 0.70 |
9.04 ± 0.60 |
83.14 |
M2 |
0.05 |
747 ± 23 |
28.2 ± 2.3 |
6.82 ± 0.62 |
8.14 ± 0.55 |
61.98 |
0.10 |
753 ± 19 |
21.5 ± 1.7 |
6.78 ± 0.84 |
10.66 ± 0.64 |
71.05 |
0.50 |
717 ± 24 |
16.8 ± 1.3 |
8.10 ± 0.71 |
8.85 ± 0.58 |
77.38 |
1.00 |
667 ± 20 |
13.4 ± 1.3 |
6.80 ± 0.57 |
9.47 ± 0.51 |
81.91 |
2.50 |
745 ± 22 |
10.4 ± 1.1 |
5.65 ± 0.51 |
9.07 ± 0.59 |
85.94 |
3.3 EIS analysis
EIS was used to explore the electrode process dynamics and surface phenomena at the metal-solution interface.35 The Nyquist and Bode diagrams obtained from EIS studies of carbon steel with different concentrations of M1 and M2 at 25 °C are displayed in Fig. 2. The generation of the capacitive anti-arc is the result of the formation of an adsorption film on the carbon steel surface by the inhibitor and the resistance of the charge transfer.49 The Nyquist diagrams show that in the simulated circulating cooling water, the diameters of the capacity arcs of the specimens with the inhibitors were larger than that of the carbon steel without inhibitor, which indicates that the corrosion reaction was inhibited. The corrosion inhibition efficiency was affected by the corrosion inhibitor concentration. The concentration of the inhibitor in the simulated circulating cooling water can affect the formation rate of the adsorption film layer; therefore, the corresponding capacitive loop and radius increase with increasing concentration. The formation of the time constant at the intermediate frequency can be observed from the angular phase. According to Fig. 2(c)–(f), one time constant for the curve without inhibitor was observed in the Bode plots. However, the angle phase plot shows the formation of two time constants when the inhibitor was added to simulated circulating cooling water. This is due to the film resistance (RF) of the corrosion inhibitor formed on the surface of the carbon steel. In Fig. 2(d), the phase angles for uninhibited and inhibited solutions of M1 were 27.37° at 1.212 Hz, 24.20° at 0.026 Hz, 29.75° at 0.038 Hz, 30.04° at 0.121 Hz, 24.05° at 0.032 Hz, and 51.08° at 0.010 Hz, respectively. In Fig. 2(f), the phase angles for uninhibited and inhibited solutions of M2 were 27.37° at 1.212 Hz, 27.22° at 0.056 Hz, 20.97° at 0.178 Hz, 23.78° at 0.026 Hz, 45.47° at 0.010 Hz, and 34.55° at 0.010 Hz, respectively.
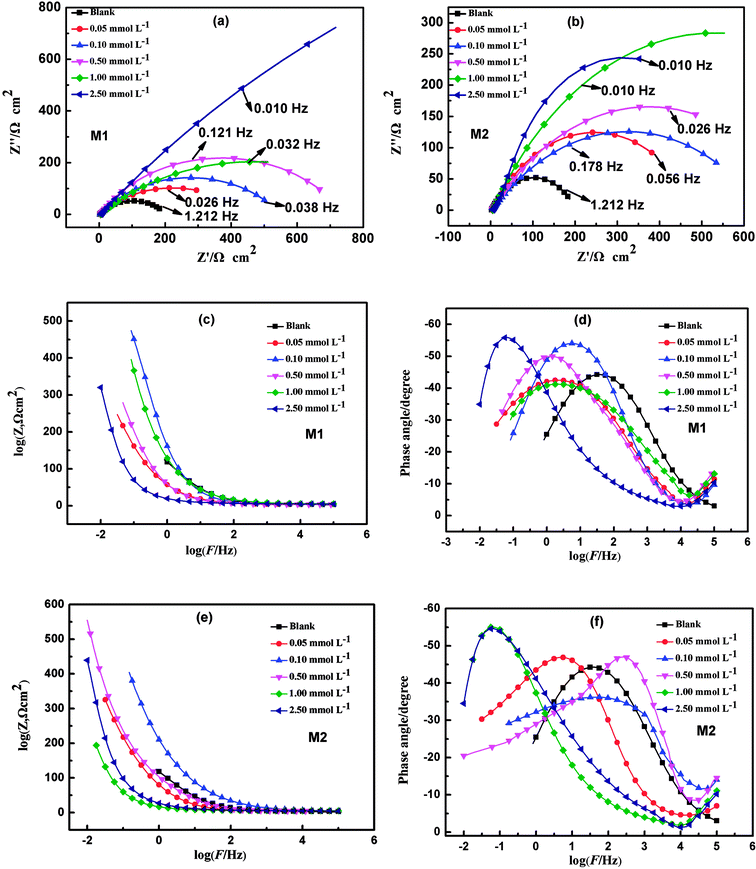 |
| Fig. 2 Nyquist (a and b), Bode (c and e) and phase angle diagrams (d and f) for carbon steel in simulated circulating cooling water in the absence and presence of different concentrations of M1 and M2. | |
The electrochemical equivalent circuit that was used to fit the interface electrochemical reaction is shown in Fig. 3, where Rct is the charge transfer resistance, Rf is the film resistance, Rdl is the diffuse layer resistance, CPE is the constant phase element, and Rs is the solution resistance.35 Rp is the polarization resistance (Rp = Rct + Rf + Rdl) of carbon steel in the absence of inhibitor. It is worth noting that when the simulated circulating cooling water contained no inhibitor, the values of RF and CPEF were approximately equal to 0. Typically, the Rp value is affected by the electron transfer between the metal and the inhibitor; therefore, the Rp value is associated with corrosion inhibition efficiency.72,73 For better fitting, a CPE was introduced instead of double-layer capacitors (Cdl). The CPE can be defined as follows:74,75
where
Y0 refers to the proportionality constant of the CPE, j is the imaginary unit,
ω is the angular frequency and
n is the phase shift.
35 Cdl is equated as below:
|
 | (14) |
where

represents the angular frequency of impedance.
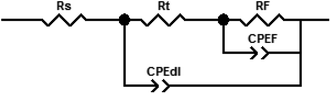 |
| Fig. 3 Electrical equivalent circuit used to fit the EIS data. | |
The electrochemical impedance spectroscopy parameters and the calculated inhibition rate ηz (%) are shown in Table 5. The data analysis shows that the value of Rp increased with increasing inhibitor concentration. This is because increasing the concentration of inhibitor can increase the coverage of the inhibitor on the metal surface. However, as the concentration of inhibitor increases, the CPE value decreases, which indicates that the thickness of Cdl increased and the dielectric constant decreased; this indicates that the inhibitor was successfully adsorbed on the carbon steel surface and improved the properties of the electric double layer. The ηz (%) value of M2 is greater than that of M1; therefore, the anti-corrosive effect of M2 on carbon steel is better than that of M1, which is consistent with the potentiodynamic polarization curve and the weight loss measurement results. This may be because the planar structure of the M2 molecule is smoother, and M2 is thus more easily adsorbed on the surface of the carbon steel than M1. In addition to the difference in raw materials, the solubility of M2 in the simulated circulating cooling water is stronger than that of M1, and a denser protective film is formed on the surface of the carbon steel; this can disrupt electrons and form a closed loop between the metal and the corrosive medium, effectively protecting the metal from corrosion.
Table 5 EIS parameters for carbon steel in simulated circulating cooling water without and with different concentrations of M1 and M2 at 25 °C
Inhibitor |
C (mmol L−1) |
Rs (Ω cm2) |
Rp (Ω cm2) |
CPE |
Cdl (×10−6 sn Ω−1 cm−2) |
ηz (%) |
Y0 (×10−6 sn Ω−1 cm−2) |
n |
Blank |
0 |
2.711 ± 0.071 |
199.6 ± 3.8 |
1515.6 ± 4.8 |
0.81 ± 0.03 |
686 ± 5 |
— |
M1 |
0.05 |
3.057 ± 0.085 |
441.7 ± 4.7 |
5988.1 ± 22.7 |
0.55 ± 0.02 |
12 365 ± 17 |
54.81 |
0.10 |
3.212 ± 0.101 |
546.3 ± 5.2 |
5260.3 ± 18.8 |
0.61 ± 0.02 |
10 447 ± 19 |
63.46 |
0.50 |
4.643 ± 0.109 |
735.5 ± 8.8 |
1680.0 ± 5.1 |
0.53 ± 0.02 |
1754 ± 9 |
72.86 |
1.00 |
5.016 ± 0.106 |
927.7 ± 10.3 |
2647.6 ± 4.9 |
0.53 ± 0.03 |
6230 ± 10 |
78.48 |
2.50 |
5.329 ± 0.111 |
5329 ± 82.1 |
18 499.0 ± 61.8 |
0.60 ± 0.02 |
55 338 ± 43 |
96.25 |
M2 |
0.05 |
4.196 ± 0.100 |
484.0 ± 4.4 |
3991.2 ± 11.7 |
0.60 ± 0.04 |
3230 ± 11 |
58.76 |
0.10 |
3.925 ± 0.087 |
639.5 ± 7.1 |
1452.4 ± 6.8 |
0.48 ± 0.02 |
1370 ± 7 |
68.79 |
0.50 |
3.640 ± 0.073 |
742.8 ± 10.7 |
3527.0 ± 9.2 |
0.53 ± 0.02 |
8200 ± 17 |
73.13 |
1.00 |
5.657 ± 0.102 |
1046.0 ± 13.8 |
21 994.0 ± 68.8 |
0.63 ± 0.04 |
110 409 ± 85 |
80.92 |
2.50 |
5.430 ± 0.108 |
23 552 ± 111.3 |
12 988.0 ± 44.1 |
0.58 ± 0.02 |
41 534 ± 31 |
99.15 |
3.4 Adsorption isotherm and thermodynamics analysis
Electrochemical studies have confirmed that inhibitor molecules can effectively inhibit the corrosion of carbon steel in simulated circulating cooling water.35 Through fitting to determine the adsorption isotherm, then choosing the closest r2 value, the mechanism of the adsorption process of an inhibitor on metal can also be determined. The surface coverage (θ) and concentration (C) of inhibitor molecules on the surface of carbon steel are used to calculate the adsorption constant (Kads), and small changes in coverage can affect the inhibition efficiency. The Langmuir adsorption isotherm is expressed as below:76,77 |
 | (15) |
The Langmuir adsorption isotherms of M1 and M2 on the surface of carbon steel at various concentrations are shown in Fig. 4. The correlation coefficient (r2),78 adsorption constant (Kads), and thermodynamic parameters (ΔGoads, ΔHoads, ΔSoads)79,80 of the adsorption isotherms are shown in Table 6. The following equation correlates Kads and ΔGoads as follows (16)–(18):
|
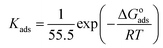 | (16) |
|
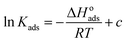 | (17) |
|
ΔGoads = ΔHoads − TΔSoads
| (18) |
where
R,
c, and
T are the ideal gas constant, integral constant, and absolute temperature (K), respectively. 55.5 is the molar concentration of water (mol L
−1).
 |
| Fig. 4 Langmuir adsorption plots for carbon steel in simulated circulating cooling water containing different concentrations of M1 and M2. | |
Table 6 Thermodynamic parameters and adsorption parameters of carbon steel in simulated circulating cooling water with M1 and M2 at 298 K.
Inhibitor |
Temperature (K) |
r2 |
Slope |
Kads (kJ mol−1) |
ΔGoads (kJ mol−1) |
ΔHoads (kJ mol−1) |
ΔSoads (J mol−1 K−1) |
M1 |
298 |
0.99955 |
1.067 |
937.21 |
−26.90 |
−16.95 |
33.39 |
M2 |
298 |
0.99958 |
1.026 |
974.66 |
−27.02 |
−17.05 |
33.46 |
From Table 6, the r2 and slope values of inhibitors M1 and M2 are very close to 1; this indicates that the adsorption of M1 and M2 on the carbon steel surface follows the Langmuir isotherm, and the adsorption type is single-layer.81,82 If the absolute value of ΔGoads ≥ 20 kJ mol−1, the inhibitor molecule experiences electrostatic interactions with the metal surface through physisorption. If the absolute value of ΔGoads ≤ 40 kJ mol−1, the inhibitor transfers electrons to the metal surface through chemisorption.83,84 The ΔGoads values of M1 and M2 are −26.90 kJ mol−1 and −27.02 kJ mol−1, respectively. This indicates that the inhibitor adsorbs on the steel surface in simulated circulating cooling water by a spontaneous physicochemisorption process.85,86 Moreover, the negative values for ΔHoads of M1 and M2 indicated that the adsorption is exothermic; therefore, increasing the temperature can reduce the adsorption capacity of the inhibitor molecules on carbon steel.87 The ΔSoads values are positive for M1 and M2, which indicates that the inhibitors replace the water molecules adsorbed on the carbon steel surface, increase the chaos of the system, and improve the stability of the protective film.
3.5 SEM and EDS investigations
The morphological information of the carbon steel surface was obtained by SEM analysis. The SEM of carbon steel after 24 h immersion in the simulated circulating cooling water is shown in Fig. 5. The surface of the polished carbon steel was smooth, and the entire surface had some negligible roughness and scratches which were caused by sanding the prepared test piece, as shown in Fig. 5(a). It can be observed that the carbon steel surface (without inhibitor) was severely corroded and oxidized and that corrosion pits appeared, as shown in Fig. 5(b). However, as shown in Fig. 5(c) and (d), when the inhibitor (2.50 mmol L−1) was added to the simulated circulating cooling water, the carbon steel surface become smoother and cleaner because a protective film formed on the carbon steel surface; this can effectively inhibit the corrosion of carbon steel by simulated circulating cooling water. Moreover, the carbon steel in Fig. 5(d) is smoother and flatter than that in Fig. 5(c), which indicates that M2 possesses better corrosion inhibition ability.
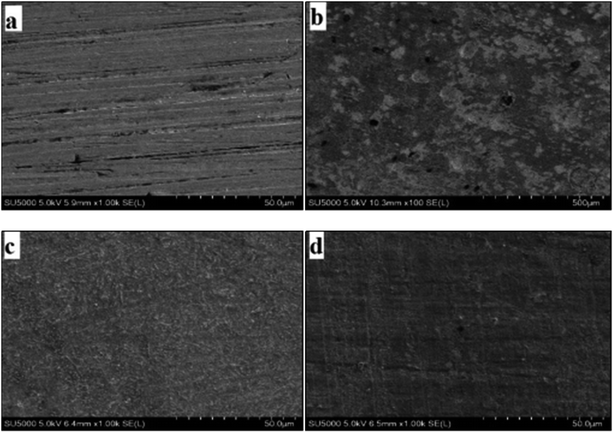 |
| Fig. 5 SEM images of carbon steel surfaces: polished (a) and after 24 h immersion in simulated circulating cooling water without inhibitor (b), with 2.50 mmol L−1 M1 (c) and with 2.50 mmol L−1 M2 (d). | |
The EDS data of mild steel immersed in simulated circulating cooling water in the presence of M1 and M2 are listed in Table 7. The presence of nitrogen on the surface of the carbon steel indicates that the corrosion inhibitor was adsorbed on the surface of the carbon steel. A large number of Cl− ions are present in the simulated circulating cooling water, but only a small amount exists on the surface of the carbon steel; this can be explained by the existence of the etching film layer, which effectively blocks erosion of the carbon steel surface by Cl− ions.
Table 7 The EDS data of mild steel immersed in simulated circulating cooling water in the presence of M1 and M2
Inhibitor |
Elemental analysis |
Atomic number |
Net value (%) |
Quality (%) |
Normalized quality (%) |
Atomic percentage (%) |
M1 |
Oxygen |
8 |
191 120 |
26.37 |
27.44 |
49.67 |
Iron |
6 |
224 270 |
57.93 |
60.28 |
31.26 |
Carbon |
6 |
11 230 |
4.51 |
4.69 |
11.31 |
Sodium |
9 |
9689 |
3.15 |
3.28 |
4.13 |
Chromium |
24 |
10 048 |
1.36 |
1.42 |
0.79 |
Chlorine |
17 |
14 128 |
0.88 |
0.91 |
0.75 |
Magnesium |
12 |
6075 |
0.59 |
0.61 |
0.73 |
Sulfur |
16 |
8697 |
0.52 |
0.54 |
0.49 |
Silicon |
14 |
5671 |
0.37 |
0.38 |
0.40 |
Nitrogen |
7 |
556 |
0.18 |
0.19 |
0.39 |
Bromine |
35 |
2084 |
0.25 |
0.26 |
0.09 |
Manganese |
25 |
2572 |
0.80 |
0.79 |
0.35 |
M2 |
Oxygen |
8 |
117 555 |
29.02 |
29.78 |
51.42 |
Iron |
26 |
120 001 |
54.90 |
56.34 |
27.87 |
Carbon |
6 |
8570 |
5.90 |
6.05 |
13.93 |
Sodium |
8 |
9784 |
2.34 |
2.40 |
2.88 |
Chromium |
24 |
6284 |
1.48 |
1.52 |
0.81 |
Chlorine |
17 |
9037 |
0.98 |
1.01 |
0.79 |
Magnesium |
12 |
3373 |
0.53 |
0.55 |
0.62 |
Sulfur |
16 |
5830 |
0.61 |
0.62 |
0.54 |
Manganese |
25 |
2731 |
0.91 |
0.93 |
0.47 |
Nitrogen |
7 |
265 |
0.15 |
0.16 |
0.31 |
Silicon |
14 |
2150 |
0.23 |
0.24 |
0.23 |
Bromine |
35 |
1975 |
0.39 |
0.40 |
0.14 |
3.6 Quantum chemical calculation analysis
3.6.1 Optimal geometrical structures. The optimal geometries and planar structures of M1 and M2 are shown in Fig. 6. The two anthracene rings of the M2 molecule are coplanar with the glutaraldehyde skeleton, which is related to the fact that the skeleton contains a free-rotating fluorene single bond. The two fluorene rings of the M1 molecule are in the meta position on the benzene ring; there is large steric hindrance, resulting in non-coplanarity with the benzene ring. In organic chemistry, especially for aromatic compounds, determining the relative activity of each atomic position in an electrophilic or nucleophilic substitution reaction according to front-line orbital theory is an important issue.
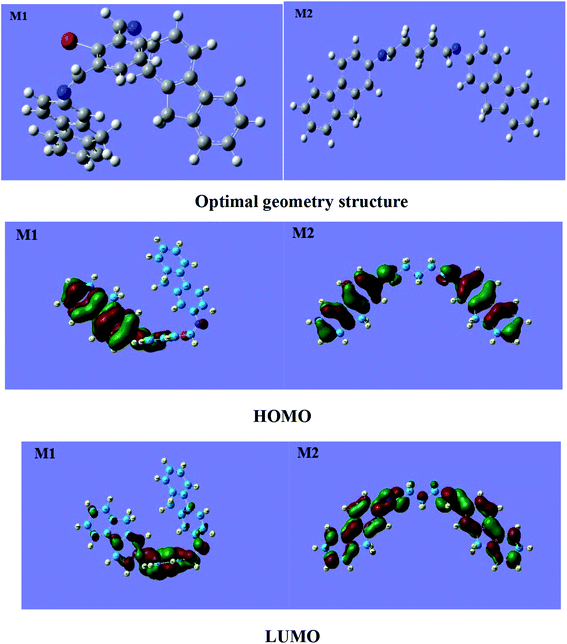 |
| Fig. 6 The optimal geometry structures and HOMO and LUMO orbitals of M1 and M2. | |
In organic chemistry, especially for aromatic compounds, frontier orbital theory (FMO) can be used to determine the relative activity of each atomic position in electrophilic or nucleophilic substitution reactions.35 The HOMO and LUMO distributions of M1 and M2 are shown in Fig. 6. The HOMO of M1 is mainly distributed on one side of the annulus and the other side of the anthracene ring and is less distributed the intermediate benzene rings; the HOMO of M2 is mainly distributed on the anthracene rings on both sides and is less distributed the intermediate benzene ring and glutaraldehyde skeleton. HOMOs with high density distributions may become sites for electrophilic attack, which can provide electrons to interact with metallic iron. The LUMO of M1 is mainly distributed in the middle benzene ring; however, that of M2 is mainly distributed on the ankle rings on both sides. Regions with large LUMO distributions are likely to be sites for nucleophilic attack, which can enable electrons to interact with metallic iron. However, the electronic donation capacity of M2 is greater than that of M1.
The better corrosion inhibition performance of M2 than of M1 may be due to the flatter molecular structure, better symmetry, and higher density distribution of the HOMO and LUMO of M2, which enable it to more readily form a protective film on the surface of carbon steel.
3.6.2 Correlation analysis between the structural parameters and corrosion inhibition efficiency. The quantum chemical parameters of the M1 and M2 molecules are listed in Table 8. Previous studies have shown that structural parameters such as the EHOMO, ELUMO, and dipole moment (μ) can be used to explain the adsorption ability of inhibitors on a metal surface.88,89 As shown in Table 8, the ELUMO value of M1 is larger than that of M2. The greater the ELUMO value, the weaker the ability of the inhibitor to provide an empty orbital to accept d orbital electrons from metallic iron. Therefore, M2 has higher electron accepting ability and more readily adsorbs on metal surfaces. The gap energy of M1 is larger than that of M2, which indicates that M2 with a higher inhibition rate can better provide electrons to the empty orbitals of metallic iron. The dipole moment is related to the covalent bond polarity and electron distribution. An inhibitor with a larger μ value is more easily adsorbed on a metal surface. The trend of the dipole moment μ is M2 > M1, which indicates that M2 has relatively high inhibition efficiency. An inhibitor molecule with greater chemical hardness (η) has greater resistance to charge transfer; the smaller the chemical softness (σ) of the inhibitor molecule, the stronger its ability to accept electrons. The order of the σ values is M2 > M1, and the trend of η is opposite to that of σ. This shows that electron transfer occurs more readily between M2 and metallic iron than between M1 and iron. The higher the chemical transfer maximum electron transfer number (ΔNmax) of an inhibitor molecule, the higher its tendency to bind to a metal surface. The order of the ΔNmax value is M2 > M1; therefore, M2 has stronger ability to bind to the metal surface than M1. Through the analysis of the above structural parameters, it is confirmed that M2 has greater corrosion inhibition efficiency.
Table 8 Molecular structure parameters of M1 and M2
Inhibitor |
Quantum chemical parameter |
EHOMO (eV) |
ELUMO (eV) |
ΔE (eV) |
χ |
η (eV) |
σ (eV) |
ΔNmax (eV) |
M1 |
−6.12 |
−4.97 |
1.15 |
5.55 |
0.575 |
1.74 |
4.81 |
M2 |
−6.63 |
−5.86 |
0.77 |
6.25 |
0.385 |
2.60 |
8.12 |
3.6.3 Fukui function analysis. The Fukui function distributions of M1 and M2 are shown in Fig. 7. The orange area is the electronic distribution area; the darker the orange, the greater the density of the electron distribution, and the lighter the orange, the smaller the density of the electron distribution. In the molecular structure of M1, the f− function is mostly distributed on the benzene ring and the surrounding N atom. In the molecular structure of M2, most of the f− functions are distributed on the ankle rings on both sides. The f− function distribution is basically consistent with the molecular orbital distribution of the front lines, as shown in Fig. 7. From the above analysis, it was found that the preferred active sites of M1 and M2 interacting with the metal surface are the aromatic heterocyclic π system and the C
N functional group, respectively.
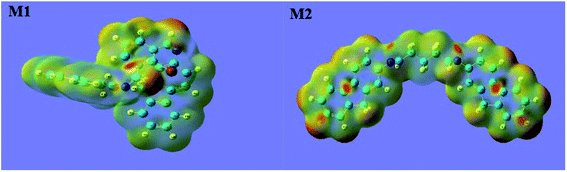 |
| Fig. 7 Fukui function density distribution maps. | |
3.7 Anticorrosion mechanism analysis
Both these bis-Schiff bases contain two unsaturated –C
N– bonds and heterocyclic functional groups, which provide more adsorption sites and stronger coordination capabilities. The above research shows that the inhibitors M1 and M2 have good corrosion inhibition performance for carbon steel in simulated circulating cooling water, which may be due to the physical and chemical adsorption between the inhibitor molecules and the carbon steel surface. The adsorption of corrosion inhibitors on metal surfaces can be summarized as follows: firstly, the corrosion inhibition efficiencies of M1 and M2 can be attributed to the existence of electron-rich N atoms and heterocyclic rings in their structures.90 The unsaturated –C
N– bond in the neutral M1 and M2 molecular structures contains a lone pair of electrons, which can form a stable covalent bond with the empty orbital of the Fe atom in the carbon steel; thus, the inhibitors can be absorbed on the surface of the carbon steel. The heterocyclic rings in the compounds have abundant shared π electrons and can interact with the metal surface through polycentric adsorption to form a dense protective film on the carbon steel surface.91 The simulated circulating cooling water has high salt content, and unsaturated –C
N– bonds can chemically react with metal ions, reducing the substitution reaction between the carbon steel surface and other active metal ions. Secondly, because the simulated circulating cooling water contains a certain amount of H+, H+ is adsorbed on the carbon steel surface and is positively charged; under the action of Coulomb forces, anions such as Cl− are preferentially adsorbed on the carbon steel surface. Hence, the adsorption of the carbon steel surface is selectively converted from negative charge to positive charge,48 and the adsorption of protonated M1, M2 molecules on the carbon steel surface is promoted by electrostatic action. In summary, M1 and M2 molecules are adsorbed on the carbon steel surface by physical and chemical interactions to form a dense protective film in the simulated circulating cooling water, thereby effectively preventing the corrosion of the carbon steel by the corrosive medium.
4. Conclusions
In this paper, two new 2-aminofluorene bis-Schiff base compounds, M1 and M2, were designed, successfully synthesized, and characterized.
The weight loss and electrochemical measurement results showed that M1 and M2 exhibit maximum inhibition efficiency at concentrations of 2.50 mmol L−1 at 25 °C.
The SEM studies confirmed that M1 and M2 successfully formed films on the surface of carbon steel.
The negative values of ΔGoads confirmed that the adsorption processes for M1 and M2 are spontaneous physicochemisorption processes that obey Langmuir adsorption isotherms.
All experimental and theoretical results supported that the bis-Schiff base inhibitor M2 possesses higher corrosion inhibition efficiency than M1.
Conflicts of interest
There are no conflicts of interest to declare.
Acknowledgements
We thank the National Nature Science Foundation of China (61661014), Nature Science Foundation of Guangxi Province (No. 2018GXNSFAA281198, 2018GXNSFBA281135, 2018GXNSFAA294042) and Guangxi Zhuang Autonomous Region and the special funding for distinguished expert, Guangxi One Thousand Young and Middle-aged College and University Backbone Teachers Cultivation Program and Guangxi Science and Technology Base and Talents Special Project (2018AD09002).
References
- M. V. Biezma and J. R. S. CristãBal, Corros. Eng. Sci. Technol., 2013, 40, 344–352 CrossRef.
- T. Miroshnikova and N. Kuchugin, Procedia Economics and Finance, 2015, 24, 426–434 CrossRef.
- S. Shahabi, S. Hamidi and J. B. Ghasemi, J. Mol. Liq., 2019, 285, 626–639 CrossRef CAS.
- Y. M. Panchenko and A. I. Marshakov, Corros. Sci., 2016, 109, 217–229 CrossRef CAS.
- D. J. Carbonell, A. García-Casas and J. Izquierdo, Corros. Sci., 2016, 111, 625–636 CrossRef CAS.
- H. R. Bhat, U. P. Singh and P. Gahtori, RSC Adv., 2013, 3, 2942 RSC.
- S. Chimenti, J. M. Vega and M. Aguirre, J. Coat. Technol. Res., 2017, 14, 829–839 CrossRef.
- H. B. Choe, H. S. Lee and J. H. Shin, Materials, 2014, 7, 7722–7736 CrossRef PubMed.
- P. Han, C. Chen and W. Li, J. Colloid Interface Sci., 2018, 516, 398–406 CrossRef PubMed.
- I. Ahamad, R. Prasad and M. A. Quraishi, Corros. Sci., 2010, 52, 1472–1481 CrossRef.
- L. Fu, Y. Fei and Z. Bo, Russ. J. Appl. Chem., 2018, 91, 499–509 CrossRef.
- X. Luo, X. Pan and Y. Song, Corros. Sci., 2017, 125, 139–151 CrossRef.
- H. Peng, C. Chen and H. Yu, Corros. Sci., 2016, 112, 128–137 CrossRef.
- A. A. Golovanov, S. A. Dan'Kov and S. A. Sokov, Chem. Heterocycl. Compd., 2019, 55, 1–4 CrossRef.
- S. Vikneshvaran and S. Velmathi, Mater. Corros., 2018, 69, 1084–1094 CrossRef CAS.
- M. Abdel-Shakour, W. A. El-Said and I. M. Abdellah, J. Mater. Sci.: Mater. Electron., 2019, 30, 5081–5091 CrossRef CAS.
- N. Kovačević and A. Kokalj, Mater. Chem. Phys., 2012, 137, 331–339 CrossRef.
- M. Goyal, S. Kumar and I. Bahadur, J. Mol. Liq., 2018, 256, 565–573 CrossRef CAS.
- M. J. Garciaramirez, G. F. Dominguez Patiño and J. G. Gonzalezrodriguez, Adv. Mater. Phys. Chem., 2016, 6, 9–20 CrossRef CAS.
- C. Verma, J. Haque and E. E. Ebenso, Results Phys., 2018, 9, 100–112 CrossRef.
- N. M. E. Basiony, A. Elgendy and H. A. Nady, RSC Adv., 2019, 9, 10473–10485 RSC.
- X. Yang, F. Li and W. Zhang, RSC Adv., 2019, 9, 10454–10464 RSC.
- C. Küstü, K. C. Emregül and O. Atakol, Corros. Sci., 2007, 49, 2800–2814 CrossRef.
- P. Roy, A. Pal and D. Sukul, RSC Adv., 2014, 4, 10607 RSC.
- M. A. Deyab, Electrochim. Acta, 2016, 202, 262–268 CrossRef CAS.
- L. Fang, L. ü. Yucui and J. Guofei, China Pet. Process. Petrochem. Technol., 2017, 19, 21–32 Search PubMed.
- R. Liang, J. Li and M. Liu, Colloids Surf., B, 2018, 172, 1–9 CrossRef CAS.
- G. Petkova, E. Sokolova and S. Raicheva, Br. Corros. J., 1996, 31, 55–60 CrossRef CAS.
- K. Rahmani, Appl. Therm. Eng., 2017, 114, 849–856 CrossRef CAS.
- Y. M. Chen, C. X. Sun and H. W. Xu, Adv. Mater. Res., 2014, 881–883, 604–609 Search PubMed.
- A. C. Balaskas, M. Curioni and G. E. Thompson, Surf. Interface Anal., 2015, 47, 1029–1039 CrossRef CAS.
- Y. Liu, Y. Zhang and J. Yuan, Eng. Failure Anal., 2014, 45, 225–233 CrossRef CAS.
- J. Kao and R. Chen, Curr. Nanosci., 2012, 8, 1–2 CrossRef.
- X. Sang, Z. Wang and J. Li, ChemistrySelect, 2018, 3, 7358–7362 CrossRef CAS.
- M. Murmu, K. S. Saha and C. N. Murmu, Corros. Sci., 2019, 146, 134–151 CrossRef CAS.
- S. S. Chen, A. Singh and Y. Q. Wang, Int. J. Electrochem. Sci., 2017, 12, 782–796 CrossRef CAS.
- D. B. Celepci, N. Korkmaz and S. T. Astley, J. Struct. Chem., 2019, 60, 151–158 CrossRef.
- L. Fang, L. Xianhui and Y. Wei, Desalination, 2013, 313, 18–27 CrossRef.
- Y. J. Yu, D. S. Byeon and Y. J. Shin, CrystEngComm, 2017, 19, 6731–6735 RSC.
- H. Matsubara, K. Mizuno and Y. Takeuchi, Jpn. J. Appl. Phys., 2013, 52, 08JE17 CrossRef.
- G. Georg, L. Alberto and J. Rafael Sendra, J. Comput. Appl. Math., 2016, 300, 119–133 CrossRef.
- B. Stuart, Infrared Spectroscopy: Fundamentals and Applications, Wiley, 2004, ISBN no. 978-0-470-85428-0 Search PubMed.
- M. Beniken, M. Driouch and M. Sfaira, J. Bio. Tribo-Corros., 2018, 4, 38–51 CrossRef.
- H. M. Abd Ellateef, V. M. Abbasov and L. I. Aliyeva, J. Surface. Interfac. Mater, 2013, 1, 4–14 CrossRef.
- N. Al-Baker, R. Shawabkeh and R. Rihan, Br. Corros. J., 2013, 46, 767–776 Search PubMed.
- V. V. Torres, R. S. Amado and C. F. D. Sá, Corros. Sci., 2011, 53, 2385–2392 CrossRef CAS.
- G. Liang, X. Peng and X. Luyao, J. Mater. Eng. Perform., 2013, 22, 3043–3048 CrossRef CAS.
- C. X. Liang, Z. Liu and Q. Q. Liang, J. Mol. Liq., 2019, 277, 330–340 CrossRef CAS.
- K. V. Rybalka, L. A. Beketaeva and A. D. Davydov, Russ. J. Electrochem., 2018, 54, 456–458 CrossRef CAS.
- S. Yesudass, L. O. Olasunkanmi and I. Bahadur, J. Taiwan Inst. Chem. Eng., 2016, 64, 252–268 CrossRef CAS.
- H. Lgaz, K. S. Bhat and R. Salghi, J. Mol. Liq., 2017, 238, 71–83 CrossRef CAS.
- A. Ehsani, M. G. Mahjani and R. Moshrefi, RSC Adv., 2014, 4, 20031 RSC.
- S. Issaadi, T. Douadi and A. Zouaoui, Corros. Sci., 2011, 53, 1484–1488 CrossRef CAS.
- S. Shirin and N. Parviz, Int. J. Electrochem. Sci., 2017, 12, 2628–2646 Search PubMed.
- T. Peme, L. Olasunkanmi and I. Bahadur, Molecules, 2015, 20, 16004–16029 CrossRef CAS.
- H. E. Yi, Y. Q. Zhou and R. R. Yang, Mod. Chem. Ind., 2016, 15, 37–42 Search PubMed.
- E. M. Zayed, A. M. M. Hindy and G. G. Mohamed, Appl. Organomet. Chem., 2018, 32, 3952–3968 CrossRef.
- F. Cuenú, J. Londoñosalazar and J. E. Torres, J. Mol. Struct., 2018, 1152, 163–176 CrossRef.
- M. M. A. El-Sukkary, I. Aiad and A. Deeb, Liq. Fuels Technol., 2010, 28, 1158–1169 CAS.
- Z. Demircioğlu, C. A. Kastas and O. Büyükgüngör, Spectrochim. Acta, Part A, 2015, 139, 539–548 CrossRef PubMed.
- Y. Ma, L. Jin and D. Zhao, RSC Adv., 2014, 4, 17262–17264 RSC.
- C. L. Murulana, M. M. Kabanda and E. E. Ebenso, J. Mol. Liq., 2016, 215, 763–779 CrossRef.
- A. Miodek, E. Regan and N. Bhalla, Sensors, 2015, 15, 25015–25032 CrossRef PubMed.
- P. Tsakiropoulos, Materials, 2018, 11(1), 69 CrossRef PubMed.
- M. Franco-Pérez, J. L. Gázquez and P. W. Ayers, J. Chem. Phys., 2015, 143, 154103 CrossRef PubMed.
- K. Ansari, M. Quraishi and A. Singh, Corros. Sci., 2014, 79, 5–15 CrossRef CAS.
- J. Jennane, M. E. Touhami and S. Zehra, Mater. Chem. Phys., 2019, 227, 200–210 CrossRef CAS.
- D. S. Carvalho, C. J. B. Joia and O. R. Mattos, Corros. Sci., 2005, 47, 2974–2986 CrossRef CAS.
- D. I. Zhukhovitskii, O. F. Petrov and T. W. Hyde, New J. Phys., 2015, 17, 846–861 CrossRef.
- W. Yang and W. J. Mortier, J. Am. Chem. Soc., 1986, 108, 5708–5711 CrossRef CAS PubMed.
- M. Migahed, A. Al-Sabagh, E. Khamis and E. Zaki, J. Mol. Liq., 2015, 212, 360–371 CrossRef CAS.
- T. C. Liu, Q. Y. Hu and X. H. Li, J. Mater. Chem. A, 2019, 7, 20911–20918 RSC.
- H. Han, S. J. Park and J. S. Jang, et al., ACS Appl. Mater. Interfaces, 2013, 5, 3441–3448 CrossRef CAS PubMed.
- P. Thiraviyam and K. Kannan, Arabian J. Sci. Eng., 2013, 38, 1757–1767 CrossRef CAS.
- J. H. Shim, S. J. Lee and H. Gim, Mol. Med. Rep., 2016, 14, 3908–3916 CrossRef CAS.
- C. H. Hsu and F. Mansfeld, Corros. Sci., 2001, 57, 747–753 CrossRef CAS.
- L. O. Olasunkanmi, B. P. Moloto and I. O. Obot, J. Mol. Liq., 2018, 252, 62–74 CrossRef CAS.
- S. M. A. Hosseini and M. J. Bahrami, Mater. Corros., 2015, 86, 166–871 Search PubMed.
- M. V. Ozhukil, M. Roopesh and S. Alwarappan, Langmuir, 2018, 34, 5374–5380 CrossRef PubMed.
- Z. Cui, J. Zhang and Y. Xue, Langmuir, 2018, 34, 3197–3206 CrossRef CAS PubMed.
- Y. P. Khodyrev, E. S. Batyeva and E. K. Badeeva, Corros. Sci., 2011, 53, 976–983 CrossRef CAS.
- H. T. Dang, M. D. S. Dias and A. Liebsch, Phys. Rev. B, 2016, 93, 115–123 CrossRef.
- X. Q. Hu and C. H. Liang, Mater. Chem. Phys., 2008, 110, 285–290 CrossRef CAS.
- P. Thanapackiam, S. Rameshkumar and S. S. Subramanian, Mater. Chem. Phys., 2016, 174, 129–137 CrossRef CAS.
- P. C. Okafor and Y. Zheng, Corros. Sci., 2009, 51, 850–859 CrossRef CAS.
- P. Roy, S. K. Saha, P. Banerjee, S. Dey and D. Sukul, Res. Chem. Intermed., 2017, 43, 4423–4444 CrossRef CAS.
- L. C. Murulana, M. M. Kabanda and E. E. Ebenso, J. Mol. Liq., 2016, 215, 763–779 CrossRef CAS.
- A. Döner, R. Solmaz and M. Özcan, Corros. Sci., 2011, 53, 2902–2913 CrossRef.
- F. J. Rodríguez-Gómez, M. P. Valdelamar and A. E. Vazquez, J. Mol. Struct., 2019, 1183, 168–181 CrossRef.
- P. Muthukrishnan, B. Jeyaprabha, P. Tharmaraj and P. Prakash, Res. Chem. Intermed., 2015, 41, 5961–5984 CrossRef CAS.
- S. P. Fakrudeen, H. C. A. Murthy and V. B. Raju, J. Chil. Chem. Soc., 2012, 57, 1364–1371 CrossRef CAS.
Footnote |
† Electronic supplementary information (ESI) available. See DOI: 10.1039/d0ra01903h |
|
This journal is © The Royal Society of Chemistry 2020 |
Click here to see how this site uses Cookies. View our privacy policy here.